дефектация — это… Что такое дефектация?
дефектация — Определение потребного ремонта [http://slovarionline.ru/anglo russkiy slovar neftegazovoy promyishlennosti/] Тематики нефтегазовая промышленность EN repair determination … Справочник технического переводчика
Дефектация — процесс выявления неисправностей в агрегатах и деталях военной техники для определения их технического состояния н пригодности к дальнейшему использованию … Словарь военных терминов
дефектация — (лат. defectus кемістік, ақау) әскери техниканың агрегаттары мен бөлшектерінің бұзылған жерін табу, олардың техникалық жағдайын және одан әрі қолдануға жарамдылығын айқындау процесі. Жөндеу кезінде Д дан бұрын, әдетте, алдымен бұйымдар… … Казахский толковый терминологический словарь по военному делу
дефектация судна — Определение вида технического состояния судна, состава и объема операций, обеспечивающих восстановление после ремонта значений технико эксплуатационных характеристик судна до заданных.
дефектация ЖРД — Разборка и исследование технического состояния ЖРД после испытания с целью обнаружения дефектов. [ГОСТ 17655 89] Тематики двигатели ракетные жидкостные … Справочник технического переводчика
Дефектация судна — 27. Дефектация судна D. Schiffsdefektentdeckung Е. Ship defects discovering F. Mise en évidence des défauts du navire Определение вида технического состояния судна, состава и объема операций, обеспечивающих восстановление после ремонта значений… … Словарь-справочник терминов нормативно-технической документации
ГОСТ 24166-80: Система технического обслуживания и ремонта судов. Ремонт судов. Термины и определения
— Терминология ГОСТ 24166 80: Система технического обслуживания и ремонта судов. Ремонт судов. Термины и определения оригинал документа: 15. Аварийный ремонт судна D.
ГОСТ 23346-78: Эксплуатация транспортного морского флота техническая. Термины и определения — Терминология ГОСТ 23346 78: Эксплуатация транспортного морского флота техническая. Термины и определения оригинал документа: 4. Ввод судна в эксплуатацию D. Inbetriebsetzung des Schiffes E. Ship entering in exploitation F. Mise du navire en… … Словарь-справочник терминов нормативно-технической документации
РЕМОНТ судна — комплекс работ по восстановлению работоспособного состояния судна. Р. выполняют по планово предупредит. сист. (ППС), предусматривающей плановые ремонты определ. видов, производимые с заданными последовательностью и периодичностью. К осн. видам… … Морской энциклопедический справочник
Ахтубинский ССРЗ — ЗАО «Ахтубинский судостроительно судоремонтный завод» Тип Закрытое акционерное общество Год основания 1910 Расположение … Википедия
РЕМОНТ ТЕХНИКИ — в сельском хозяйстве, совокупность органи зац. и технич. мероприятий, осуществляемых с целью восстановления исправности или работоспособности технич. средств. В зависимости от конструктивных особенностей, характера повреждений и степени износа… … Сельско-хозяйственный энциклопедический словарь
Дефектация деталей
Очищенные детали подвергают дефектации с целью оценки их технического состояния, выявления дефектов и установления возможности дальнейшего использования, необходимости ремонта или замены. При дефектации выявляют: износы рабочих поверхностей в виде изменений размеров и геометрической формы детали; наличие выкрошиваний, трещин, сколов, пробоин, царапин, рисок, задиров и т. п.; остаточные деформации в виде изгиба, скручивания, коробления; изменение физико-механических свойств в результате воздействия теплоты или среды. Способы выявления дефектов:
1. Внешний осмотр. Позволяет определить значительную часть дефектов: пробоины, вмятины, явные трещины, сколы, значительные изгибы и скручивания, сорванные резьбы, нарушение сварных, паяных и клеевых соединений, выкрошивания в подшипниках и зубчатых колесах, коррозию и др.
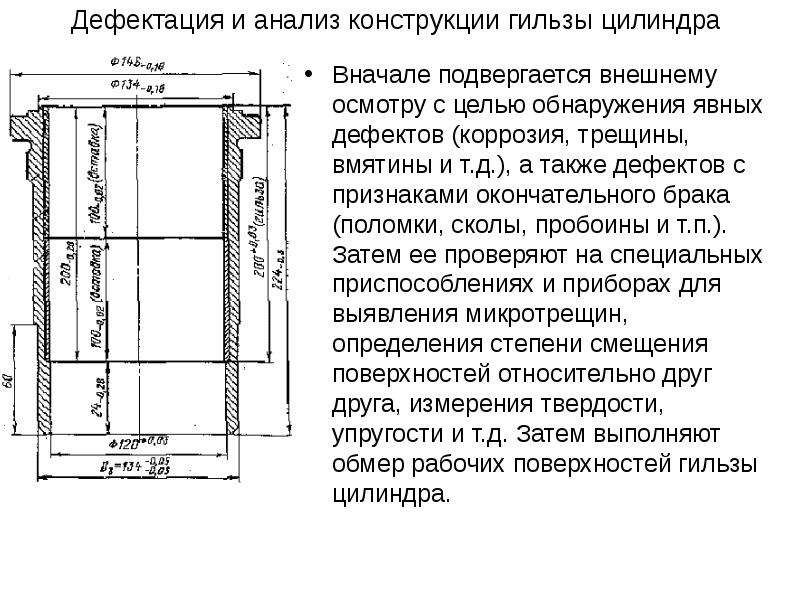
2. Проверка на ощупь. Определяется износ и смятие резьбы на деталях, легкость проворота подшипников качения и цапф вала в подшипниках скольжения, легкость перемещения шестерен по шлицам вала, наличие и относительная величина зазоров сопряженных деталей, плотность неподвижных соединений.
4. Керосиновая проба. Проводится с целью обнаружения трещины и ее концов. Деталь либо погружают на 15-20 мин в керосин, либо предполагаемое дефектное место смазывают керосином. Затем тщательно протирают и покрывают мелом. Выступающий из трещины керосин увлажнит мел и четко проявит границы трещины.
5. Измерение. С помощью измерительных инструментов и средств определяется величина износа и зазора в сопряженных деталях, отклонение от заданного размера, погрешности формы и расположения поверхностей.
6. Проверка твердости. По результатам замера твердости поверхности детали обнаруживаются изменения, произошедшие в материале детали в процессе ее эксплуатации.
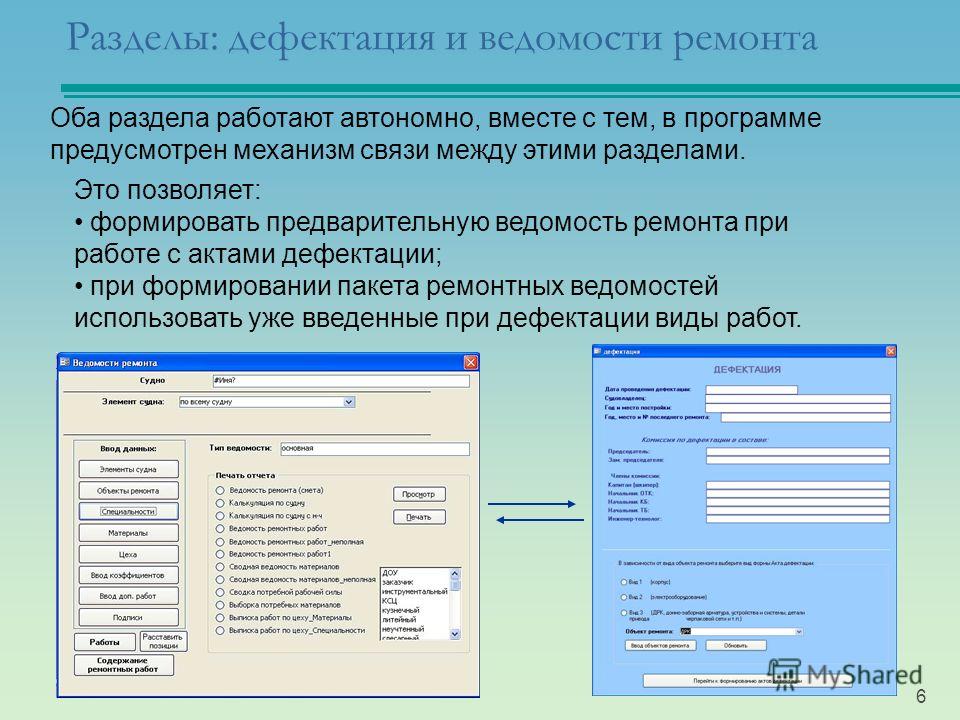
7. Гидравлическое (пневматическое) испытание. Служит для обнаружения трещин и раковин в корпусных деталях. С этой целью в корпусе заглушают все отверстия, кроме одного, через которое нагнетают жидкость под давлением 0,2-6,3 МПа. Течь или запотевание стенок укажет на наличие трещины. Возможно также нагнетание воздуха в корпус, погруженный в воду. Наличие пузырьков воздуха укажет на имеющуюся неплотность.
8. Магнитный способ. Основан на изменении величины и направления магнитного потока, проходящего через деталь, в местах с дефектами. Это изменение регистрируется нанесением на испытуемую деталь ферромагнитного порошка в сухом или взвешенном в керосине (трансформаторном масле) виде: порошок оседает но кромкам трещины. Способ используется для обнаружения скрытых трещин и раковин в стальных и чугунных деталях. Применяются стационарные и переносные (для крупных деталей) магнитные дефектоскопы.
9. Ультразвуковой способ. Основан на свойстве ультразвуковых волн отражаться от границы двух сред (металла и пустоты в виде трещины, раковины, непровара).
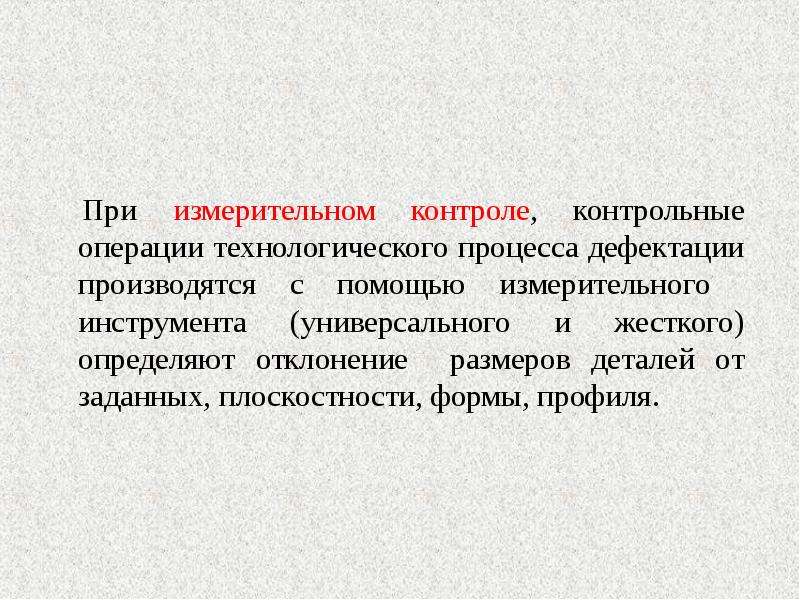
10. Люминесцентный способ. Основан на свойстве некоторых веществ светиться в ультрафиолетовых лучах. На поверхность детали кисточкой или погружением в ванну наносят флюоресцирующий раствор. Через 10—15 мин поверхность протирают, просушивают сжатым воздухом и наносят на нее тонкий слой порошка (углекислого магния, талька, силикагеля), впитывающего жидкость из трещин или пор. После этого деталь осматривают в затемненном помещении в ультрафиолетовых лучах. Свечение люминофора укажет расположение трещины. Используются стационарные и переносные дефектоскопы. Способ применяется в основном для деталей из цветных металлов и неметаллических материалов, так как их контроль магнитным способом невозможен.
По результатам дефектоскопии, детали сортируют на три группы: годные, требующие ремонта и негодные. После сортировки детали маркируют по группам, например, краской разного цвета. Отнесение деталей к той или иной группе определяется величиной износа, технологическими и экономическими соображениями.
Результаты дефектации деталей заносят в ведомость дефектов, являющуюся основным документом для определения объема ремонтно-восстановительных работ и потребности в новых деталях, запасных частях, материалах. Таким образом определяется стоимость ремонта машины.
Контроль и анализ технического состояния ЭТО ТЭС | Уровень (подуровень) квалификации | ||||
Происхождение трудовой функции | Заимствовано из оригинала | ||||
Код оригинала | Регистрационный номер профессионального стандарта | ||||
Трудовые действия | Разработка планов технического диагностирования и технического освидетельствования ЭТО | ||||
Организация ведения учета и проведение анализа результатов испытаний и измерений ЭТО | |||||
Проведение дефектации ЭТО при подготовке к ремонту | |||||
Контроль учета и проведение анализа дефектов на ЭТО, подготовка рекомендаций по их устранению | |||||
Формирование исполнительной документации по дефектации и обоснование дополнительного объема ремонтных работ | |||||
Ведение учета и паспортизации технических и технологических данных ЭТО | |||||
Анализ причин нарушений нормальной работы ЭТО | |||||
Составление планов размещения ЭТО, технического оснащения и организации рабочих мест | |||||
Подготовка рекламаций на ЭТО для направления организациям-изготовителям | |||||
Контроль исправного состояния и использования поверочных и проверочных установок и приборов, предназначенных для проведения технического обслуживания и ремонта ЭТО | |||||
Необходимые умения | Анализировать информацию, полученную по результатам контроля параметров работы и технического обследования ЭТО, для оценки состояния оборудования | ||||
Обосновывать необходимость проведения ремонтных работ | |||||
Определять причины неисправностей и отказов ЭТО | |||||
Анализировать, систематизировать и интерпретировать техническую документацию, данные диагностики и мониторинга ЭТО | |||||
Использовать технические средства для измерения основных параметров работы оборудования | |||||
Разрабатывать предложения по результатам анализа дефектов (несоответствий) оборудования | |||||
Оценивать безопасность условий труда на рабочем месте | |||||
Вести деловую переписку | |||||
Использовать информационные ресурсы для создания, актуализации и анализа базы данных основных параметров работы оборудования | |||||
Необходимые знания | Методы обработки информации с применением технических средств, коммуникаций и связи, вычислительной техники | ||||
Методы энергосбережения и энергоэффективности | |||||
Назначение, конструкция, технические характеристики, конструктивные особенности, принципы работы и правила технической эксплуатации ЭТО, установленного на ТЭС | |||||
Основные технологические и электрические схемы ТЭС | |||||
Основы механики, электротехники и электроники | |||||
Основы технологического процесса производства электрической энергии и мощности | |||||
Правила оформления технической и технологической документации | |||||
Правила технической эксплуатации электростанций и сетей | |||||
Правила устройства электроустановок | |||||
Требования охраны труда при эксплуатации электроустановок | |||||
Система планово-предупредительного ремонта, рациональной эксплуатации ЭТО | |||||
Схемы, конструктивное выполнение электрических машин постоянного тока ремонтируемых серий | |||||
Территориальное расположение обслуживаемого ЭТО | |||||
Технический регламент, межгосударственные, национальные, отраслевые стандарты ЭТО электростанции | |||||
Технологии эксплуатации, диагностики состояния ЭТО | |||||
Ведомственные и межотраслевые нормативные правовые акты, регламентирующие вопросы ремонта ЭТО | |||||
Локальные нормативные акты организации, регламентирующие вопросы ремонта ЭТО | |||||
Требования охраны труда, промышленной и пожарной безопасности, производственной санитарии и противопожарной защиты, регламентирующие деятельность по трудовой функции | |||||
Другие характеристики |
ОЦЕНКА СОСТОЯНИЯ КОРПУСА СУДОВ И КОРАБЛЕЙ
Корпус судна – первичная основа его живучести. Поэтому оценка его состояния – регламентируемая операция, которую время от времени должно проходить каждое плавающее средство.
Дефектация
Оценка состояния корпуса судна или корабля называется дефектацией. Это – многотрудная операция, обусловленная размерами объекта, сложностью доступа к подводной части и обрастанием.
Впечатляет даже объем работ дефектации корпуса судна в сухом доке
Полная дефектация должна выполняться в сухом доке, где корпус очищают от всего постороннего, в том числе — от остатков старой краски и других слоев. Поступление судна в док используется не только для дефектации корпуса, но и для всех необходимых обследований и работ:
- Визуальный осмотр корпуса в сопоставлении с его конструкцией
- Более тщательная визуальная и инструментальная проверка качества обшивки корпуса и его несущих конструкций
- При необходимости – демонтаж фрагментов обшивки.
Операции с корпусом судна проводят в комплексе с другими видами контроля с внутренней стороны.
- Осмотр
- Контроль
- Испытания.
Сочетания всех методов и приемов оценки качества корпуса обеспечивают полную и достоверную картину, важную для эксплуатации таких дорогостоящих средств водного транспорта.
Обнаружение основных дефектов корпуса судна
Основные дефекты корпуса судна обусловлены коррозией и действием нагрузок. Вот некоторые из них:
- Отклонения от требуемой геометрии корпуса
- Повреждения от коррозии
- Повреждения от нагрузок
- Дефекты от аварийного механического воздействия (столкновений).
Обнаружение таких отклонения и дефектов выполняются наиболее пригодными методами. Предполагается, что исполнитель дефектации, обладает всей необходимой аппаратурой или заказывает некоторые операции контроля привлеченным профильным специалистам.
Для современных судов проведение дефектации облегчается наличием проектной и исполнительной документации, в том числе – рекомендаций строителя судна.
В дефектоскопии задействованы все основные группы аппаратуры:
- Рентгеновская
- Ультразвуковая
- Тепловизионная
- Магнитно-резонансная и другие.
Ни одно обследование корпусов судов и кораблей не обходится без простого, наглядного и точного капиллярного метода, прежде всего в его традиционном и старинном варианте – в виде керосиновой пробы.
Ремонт корпуса судна
На основании дефектации принимаются проектные решения о составе ремонта. Методы ремонта корпуса традиционны:
- Рихтовка обшивки и остова
- Замена листов обшивки
- Выполнение сварных швов и заклепочных соединений.
Все работы по корпусу увязываются с другими операциями, а это — способ применить рациональные технологии и интенсифицировать ремонт. Очередность и содержание операций должны определяться проектом. К примеру, демонтаж фрагментов обшивки корпуса можно использовать для облегчения доступа к внутренним объемам судна.
Одна из финальных стадий ремонта корпуса – проверка качества ремонтных работ. Этой проверке подлежат сварные швы и заклепочные соединения, а также – герметичность корпуса.
Карта дефектаций — Справочник химика 21
Карты дефектации (дефектные ведомости) являются основным техническим документом, на основании которого проводятся осмотр, измерение, а при необходимости испытание деталей и сопряжений с последующей сортировкой их на три группы 1) детали, годные в сопряжении с новыми деталями 2) детали, подле-240 [c.240] Дефектация необходима для оценки технического состояния деталей и определения их пригодности к дальнейшему использованию. При дефектации руководствуются техническими требованиями, которые составляются для каждой детали в виде карт (табл. 7.7). [c.96]
Карты дефектации (дефектные ведомости) являются основным техническим документом, на основании которого осуществляются осмотр, измерение, а при необходимости испытание деталей и сопряжений с последующей сортировкой их на три группы 1) детали, годные в сопряжении с новыми деталями 2) детали, подлежащие ремонту 3) детали, непригодные для дальнейшего использования. [c.225]
Ступенчатость гнезда коренных подшипников проверяют в дву. взаимно перпендикулярных плоскостях в плоскости, проходящей через оси цилиндров, и в плоскости разъема подщипников. Способ измерения ступенчатости гнезд зависит от длины рамы. Возможны измерения оптическими способами, с помощью технологического вала и пластинок щупа, индикатором на точной поверочной плите. При проверке вторым способом технологический вал укладывают в гнезда подшипников, а затем пластинками щупа измеряют зазоры между шейками вала и гнездами (с обоих концов) в точках Д, В и С (рис. 133). Измерения в точках А и С следует проводить, отступая на 10—20 мм от плоскости разъема подшипника. Результаты измерений записывают в карту дефектации. Сопоставление зазоров в точках В каждого гнезда позволяет установить ступенчатость гнезд в плоскости, проходящей через оси цилиндров, а сопоставление зазоров в точках Л и С всех гнезд — ступенчатость в плоскости разъема подшипников (практически в параллельной плоскости). [c.202]
Сортируют детали на годные, требующие ремонта и негодные на основании чертежей и карт дефектации, которые являются частью технической ремонтной документации. [c.187]
Технические требования на дефектацию и ремонт. Дефектация деталей проводится на специальном рабочем месте, оснащенном картами дефектации и необходимым комплектом приборов и измерительных инструментов. [c.225]
Предварительная дефектация имеет своей целью выяснение наи более вероятных очагов нарушений правильности сопряжений деталей между собой, одновременно анализируются записи в ремонтных журналах или в ремонтных картах, в которых зафиксированы результаты предыдущего ремонта и данные межремонтных осмотров. [c.116]
На каждую деталь или узел составляется отдельная технологическая карта технических условий на дефектацию и ремонт. [c.187]
Цель предварительной дефектации — выяснение наиболее вероятных мест нарушения правильности сопряжения сборочных единиц и деталей между собой. При этом анализируются записи в ремонтных журналах и ремонтных картах. При предварительной дефектации проводится наблюдение за фактическими функциональными показателями работоспособности машины или аппарата, проверка температуры нагрева узлов трения, проверка вибраций, ударов, характера стуков и т. п. [c.39]
Технические уеловия на ремонт узлов. Дефектация узлов (сборочных единиц) машин производится на основании технических условий на их ремонт, сборку и испытание, которыё разрабатываются, как и дефектовочные карты, проектными организациями или ремонтными предприятиями и содержат сборочный чертеж узла карту зазоров (натягов) в сопряжениях по чертежу и допустимых без ремонта сведения о допусках на соосность отдельных деталей, групп, подгрупп способы определения правильного положения и взаимодействия деталей признаки исправного действия узла в целом способы проверки качества работы или производительности. [c.265]
Дефектовочные ведомости и карты. Сортировка деталей на годные, требующие ремонта и негодные производится на основании ведомостей или карт дефектации. [c.265]
Ремонты и Р2 выполняет эксплуатационный персонал КС. Без таких ремонтов невозможна длительная и бесперебойная работа турбокомпрессора и всей системы газотурбинного наддува. Ремонт Рз выполняют специализированные мастерские или завод после 1500—2000 ч работы турбокомпрессора. К наиболее характерным причинам, вызывающим проведение капитального ремонта турбокомпрессора, относят поломку рабочих лопаток газовой турбины, изменение поверхностей или заклинивание ротора, разрушение корпуса газовой турбины и др. Дефектация и ремонт турбокомпрессоров включают в себя разборочно-дефектовочные, ремонтно-восстановительные и сборочные работы, а также испытание собранных узлов и отремонтированного турбокомпрессора в целом. По результатам дефектации и контроля на все детали должны быть составлены карты дефектации, являющиеся основным руководящим документом при ремонте турбокомпрессора. До начала разборки на турбокомпрессоре необходимо отметить мелом или краской места подтеков воды, масла, утечки воздуха или газов, а также проверить состояние корпусов с точки зрения перегрева. Эту операцию желательно проводить на работающем агрегате. На сопряженные детали, взаимное положение которых регламентировано, керном необходимо нанести контрольные метки для облегчения сборки узлов турбокомпрессора после ремонта. Турбокомпрессор следует разбирать с помощью специальных инструментов и присиособлений, поставляемых заводом-изготовителем. Разборку следует осуществлять в определенной последовательности снять концевые крышки опорных подшипников, глушитель (если он есть), демонтировать опорный подшипник со стороны компрессора, спиральную камеру диффузора компрессора, ротор, корпус и сопловой аппарат газовой турбины, разобрать теплоизоляционную вставку. [c.246]
Дефектацня деталей. После разборки компрессора все детали делят на детали, годные к дальнейшему использованию детали, подлежащие ремонту и восстановлению детали, непригодные к дальнейшему использованию и неподлежащие ремонту и восстановлению. Сортировку деталей производяг на основании карт дефектации, которые являются частью ремонтной технической документации и разрабатывают для каждого вида оборудования. В карте дефектации указывают возможные дефекты, способы определения дефекта и измерительный инструмент, номинальные и допустимые при данном виде ремонта размеры, величину предельного износа, указывают способ устранения дефекта или условие выбраковки. [c.295]
Технологическая карта контроля (Te hnologi al ard of Inspe tion) Описание в установленной форме процедуры контроля данного объекта объема, способа, класса чувствительности, используемых материалов и технологии контроля, указание на нормативные и руководящие документы по контролю, дефектации объекта, по оформлению заключения на контроль, а также других требований проектной и технологической документации [c.573]
Анализируя существующие технологические карты на капитальный ремонт каландров, можно установить, что до 35% всей трудоемкости составляет шабровка вкладышей подшипников и пригонка узлов валок-подшипники в направляющих станины для обеспечения параллельности осей и заданной геометрии зазоров между валками. На такую пригонку затрачивается свыше 400 час. (при ремонте пятивального каландра), так как каждый валок ставится и вынимается из станин по б—8 раз. Применяя в данном случае правильные методы дефектации при первичной разборке можно было [c.300]
Карты на дефектацпю и ремонт являются одним из основных технических документов для ремонта. В них излагаются указания по дефектации деталей. Карты располагаются в порядке возрастания нумерации сборочных единиц и деталей или по конструктивной последовательности расположения сборочных единиц. [c.41]
Проверка и диагностика складских стеллажей по ГОСТ
Современные складские комплексы ежегодные увеличивают объемы и скорости логистических процессов. В процессе эксплуатации стеллажного оборудования неизбежно происходят повреждения несущих элементов. Безопасная эксплуатация оборудования — это залог его долговременной работы. Дефектовка элементов стеллажей — это наиболее доступный способ идентифицировать повреждения и предотвратить полное разрушение стеллажной системы.
Идентификация поврежденных элементов
Идентификацию поврежденных элементов стеллажей проводят в соответствии со значениями деформаций по ГОСТу, указанными на рисунке.
При этом в случае соответствия деформации элемента значению, указанному на рисунке, эксплуатация элемента стеллажей допускается. В случае превышения значения деформации эксплуатация стеллажей не допускается, при этом должна быть проведена незамедлительная замена поврежденного элемента (при отсутствии других указаний со стороны предприятия-изготовителя).
На территории Москвы и МО дефектовка элементов стеллажей производится бесплатно |
Преимущества работы с нашей компанией
- Многолетний опыт работы наших специалистов во всех направлениях сервисных работ.
- Несколько штатных бригад.
- Наличие профильных разрешительных документов на весь персонал.
- Высокая скорость и качественная организация выполняемых работ.
- Возможность проведения работ 24/7.
- Скидки для постоянных клиентов.
- Успешно проводим проверку и испытание стеллажей более 10 лет.
- Гибкие условия оплаты с возможностью отсрочки платежей.
Компания ООО «Новейшие Технологии ЛС» оказывает профессиональные услуги по комплексному оснащению складских помещений. Опытная бригада наших специалистов оперативно произведет любые виды требуемых работы на всей территории РФ, в том числе проверку стеллажей (диагностику) и дефектацию поврежденных элементов. Для размещения заказа пишите: [email protected] или [email protected] или звоните по тел.: 8 (495) 662-92-73, 8 (999) 599-250-01.
Акт о выявленных дефектах (о дефектации) оборудования: образец, форма ОС-16, заполнение
Современные условия производства диктуют необходимость интенсивной эксплуатации оборудования, что может привести к его поломкам задолго до окончания гарантированного срока его использования. В этом случае техника отправляется в ремонт, а для фиксации неисправности составляют акт дефектации.
Что такое акт дефектации оборудования
Это первичный документ, который подтверждает обоснованность ремонта. Его цель – определить объем ремонтных работ, необходимых для восстановления работоспособности оборудования. Суть состоит в следующем – зафиксировать все дефекты и неисправности, имеющиеся в данном агрегате, что достигается так:
- Проводится внешний осмотр неисправной техники и ее производственных параметров. Это называется предварительная дефектация.
- Затем следует поузловая, при которой осматривают узлы машины с их возможным демонтажем.
- И в заключении – подетальная дефектация с определением с определением конкретных причин поломки и масштаба ремонта.
- По итогам осмотра составляется акт, в котором обозначаются неисправные детали и суть их поломки.
Какими нормативными актами регулируется
Составление данного акта будет основанием для последующего ремонта и сопутствующих ему затрат, поэтому документ не может быть произвольным. При его заполнении надо учитывать положения:
- Закона №129.
- Закона №402 (новая редакция).
- Постановления Госкомстата, утверждающего форму акта ОС-16 (дефектации).
Соотношение с актом списания
И не надо акт дефектации путать с актом списания. Это разные документы, хотя и схожи между собой. Их главное различие состоит в том, что:
- Акт дефектации указывает на возникшие поломки и необходимость или способ их ремонта.
- Акт на списание утверждает необходимость полного вывода оборудования из эксплуатации и его списания.
Поэтому в нем отражается:
Кто составляет и где используется
Составляется и подписывается данный акт комиссией, состав которой должен быть утвержден приказом руководителя компании. Стандартный состав комиссии следующий:
Дефиктационный акт нужен для проведения ремонта неисправного оборудования. Он является основанием для:
- Составления сметы на ремонт.
- Разработки технической документации (при необходимости).
- Заявки на необходимые для восстановления материалы или детали.
Образец дефектного акта ОС-16
Как составляется
Форма
Для акта дефектовки применяется форма ОС-16. В ней обязательно должно быть озвучено:
- Наименование компании владельца.
- Наименование и тип оборудования.
- Его маркировка или паспортный номер.
- Дата его изготовления.
- Дата покупки или внедрения в производство.
- Описание выявленных дефектов.
- Рекомендации по их устранению.
Это видео содержит полезную информацию в том числе по теме актов дефектации оборудования:
Пример заполнения
Унифицированный акт заполняется так:
- Вверху – название и реквизиты компании.
- Далее, ниже слова «Акт» — местонахождение оборудования.
Затем по необходимости указываются:
- Изготовитель.
- Поставщик.
- Грузоотправитель.
- Перевозчик.
- Монтажная фирма.
После чего переходим непосредственно к обнаруженным дефектам:
И затем идет главная часть акта – таблица дефектов, в которой на каждую позицию выдается следующая информация:
- Наименование.
- Маркировка.
- Тип или марка.
- Изготовитель.
- Время изготовления.
- Дата прихода.
- Описание дефекта.
И в заключение рекомендации и подписи комиссии.
Особые случаи
В конкретных случаях при заполнении акта возможны варианты. Так изготовитель и поставщик указывается в актах дефектации на:
А в актах дефектации на:
- Кондиционеры.
- Котлы.
- Генераторы.
Необходимо упоминание и на монтажной организации.
Полезная информация
Если при написании акта дефектовки у компании не имелось в распоряжении форы ОС-16, то акт можно составлять и не на бланке. Главное что придерживаться таких требований:
- Форма не должна выходить за рамки нормативных требований.
- Обнаруженные дефекты должны быть описаны достаточно подробно и обстоятельно.
Правильно составленный акт позволит:
- Определить возможность и объем ремонта.
- Выявить виновных в поломке.
Обнаружение и диагностика отказов — обзор
4.3.2 Обнаружение и диагностика отказов
Обнаружение и диагностика отказов (FDD) сосредотачиваются на аномальных ситуациях, а не на одномерных сигналах тревоги, что важно для поддержания благоприятных рабочих условий и прогнозирования рисков химических процессов. Venkatasubramanian, Rengaswamy, Yin и Kavuri (2003) классифицировали методы FDD на две категории: основанные на модели и основанные на истории процессов, причем последние также называются основанными на данных. Методы, основанные на моделях, обычно разрабатываются на основе некоторого фундаментального понимания физики процесса, которые нелегко реализовать из-за сложности химического процесса. Методы, основанные на данных, стали более доступными для FDD. Многие усилия позволили разобраться в соответствующей работе в области FDD, управляемой данными, и провели несколько обзоров с анализом и сравнением (Alauddin, Khan, Imtiaz, & Ahmed, 2018; Ge, 2017; Jiang, Yan, & Huang, 2019; Ming & Zhao). , 2017). Многомерные статистические методы широко использовались для мониторинга процессов, представленных в разделе 3.1, и более подробное применение MSPM можно найти в обзоре Wang, Si, et al. (2018).
Выгоды от сильных классификационных способностей, методы искусственного интеллекта показывают захватывающие перспективы в области FDD химических процессов.Экспертная система — это самый ранний метод искусственного интеллекта, применявшийся к FDD химического процесса (Рамеш, Шум и Дэвис, 1988; Рич и Венкатасубраманян, 1987). Основные компоненты экспертной системы для FDD включают: получение знаний, выбор представления знаний, кодирование знаний в базе знаний, разработку процедур вывода для диагностических рассуждений и разработку интерфейсов ввода-вывода (Venkatasubramanian, Rengaswamy, Kavuri , & Инь, 2003). Однако из-за системных знаний для разработки экспертных систем сценарии применения моделей FDD весьма ограничены, что затрудняет их применение в химической промышленности.
ИНС — это самый популярный метод искусственного интеллекта для FDD, а нейронная сеть с обратным распространением (BPNN) — наиболее подходящий тип ИНС. Однако, ограниченные возможностью сбора данных в химических процессах и низкой производительностью решения проблем сложных систем, традиционные методы ИНС используются для академических исследований, но не для промышленных приложений. С популяризацией построения информации на химических предприятиях и развитием методов глубокого обучения исследования FDD на основе ИИ открыли еще один кульминационный момент, такой как RBM, CNN и Deep Belief Network (DBN) (Gupta, 2018; Shu, Ming , Cheng, Zhang, & Zhao, 2016; Wu & Zhao, 2018a; Zhang & Zhao, 2017).
Являясь очень успешным методом обнаружения и распознавания объектов в области компьютерного зрения, преимущество извлечения признаков делает методы CNN подходящими для FDD химических процессов. Ву и Чжао (2018a) предложили метод диагностики неисправностей на основе глубокой сверточной нейронной сети (DCNN) для сложных химических процессов, как показано на рис. 11. Его процедуры диагностики, включая этапы офлайн и онлайн, в то время как необработанные данные процесса преобразуются в am × n матрица с изменяющимися во времени функциями, где m представляет продолжительность выборки, а n представляет количество переменных.
Рис. 11. Структура метода диагностики неисправностей на основе DCNN (Wu & amp; Zhao, 2018a).
Большинство методов FDD на основе AI отслеживают сбои процесса только в статическом состоянии. Учитывая изменяющиеся во времени особенности данных о неисправностях и данных в переходных состояниях, динамическая искусственная иммунная система (DAIS) предлагается для FDD химических процессов (Dai & Zhao, 2011). В отличие от традиционных методов AIS, антитела и антигены представлены матрицами данных с временной выборкой в DAIS.Преимущества, заключающиеся в высокой способности адаптации и независимости от количества обучающих выборок, FDD на основе DAIS можно использовать для полных рабочих циклов химических процессов (Zhao, Shu, Zhu, & Dai, 2014). Для решения проблем практических промышленных приложений. , такие как крупномасштабные переменные процесса и несколько исторических выборок неисправностей, алгоритм выбора признаков (Ming & Zhao, 2018) и метод трансплантации вакцины (Shu & Zhao, 2016) были предложены для улучшения метода DAIS.
И DBN, и DCNN, и DAIS относятся к контролируемым методам обучения. Однако по разным причинам почти сейчас можно найти записи после инцидента или опасного происшествия. Кроме того, многие исторические данные с большим смыслом, которые могут быть полезны для FDD, не помечены. В качестве алгоритма обучения методы на основе автоэнкодера демонстрируют большое преимущество в промышленных приложениях. Недавно вариационный автокодировщик (VAE) был предложен в качестве подхода глубокого генеративного моделирования, при котором набор данных, взятый из любого распределения, может быть сгенерирован с помощью набора скрытых переменных и отображать их с помощью достаточно сложной функции, что означает, что VAE может естественным образом обрабатывать нелинейность в данных ( Kingma & Welling, 2013). Вариационный рекуррентный автоэнкодер (VRAE) использует рекуррентную нейронную сеть для извлечения мониторов временных характеристик и отрицательной вариационной оценки (NVS) в вероятностном пространстве, которое больше подходит для химических процессов (Cheng, He, & Zhao, 2019). Основанные на методах методы состоят в том, чтобы сначала оценить условную плотность вероятности скрытых переменных с помощью структуры оптимизации VRAE, а затем оценить оцененную NVS отдельных измерений для обнаружения неисправностей. Структура методов на основе VRAE представлена на рис.12.
Рис. 12. Структура системы мониторинга процессов на основе VRAE (Cheng et al., 2019).
(PDF) Методы обнаружения неисправностей: обзор литературы.
MIPRO 2011 / CTS 115
структуры процесса, динамики процесса, доступного процесса
сигналов, сложности процесса, доступного количества процесса
данных ввода-вывода и пригодности процесса для описания в терминах правил
. Самый простой подход — это прямая проверка предела измеряемой переменной
.Крупномасштабные процессы (например, химические
заводы) могут выиграть от многомерного статистического анализа, особенно
PCA. Некоторые процессы генерируют периодические или
стохастические сигналы, которые могут использоваться для обнаружения сбоев, если
изменений в моделях сигналов вызваны сбоями процесса.
Когда можно получить большой объем данных ввода-вывода процесса
, но структура процесса неизвестна или слишком сложна для моделирования
, можно использовать методы распознавания образов (нейронные сети
и k-NN).
Обнаружение сбоя на основе модели процесса включает динамику процесса и неизмеримые
переменных состояния, но требует точных моделей и его проще
применять для четко определенных процессов, таких как электрические и
механические, чем для термических и химических процессов. Если известно
, основная взаимосвязь между неисправностями и симптомами
в виде правил, основанных на знаниях, является выбором.
ЛИТЕРАТУРА
[1] R.Isermann, Fault-Diagnosis Systems, Springer, Berlin, 2006
[2] Р. Изерманн, «Обнаружение и диагностика неисправностей на основе модели
и приложения», Annual Reviews in Control, Vol. 29, Ис. 1, 2005
[3] Р. Изерманн, «Обнаружение сбоев в процессе на основе моделирования и методов оценки
— обзор», Automatica, Vol. 20, No. 4, 1984
[4] I. Castillo and T. Эдгар, «Обнаружение неисправностей на основе моделей и диагностика
», Конференция TWCCC, весна 2008 г., Остин, Техас
[5] V.Венкатасубраманян, Р. Ренгасвами, С. Н. Кавури и К.
Инь, «Обзор обнаружения и диагностики сбоев в процессе, часть I:
Методы, основанные на количественных моделях», Компьютеры и химия
Engineering, № 27, 2003, стр. 293-311
[6] В. Венкатасубраманян, Р. Ренгасвами и С. Н. Кавури, «Обзор
обнаружения и диагностики технологических сбоев, Часть II: Качественные модели
и стратегии поиска», Компьютеры и химия
Engineering, Нет. 27, 2003, стр. 313-326
[7] В. Венкатасубраманян, Р. Ренгасвами, С. Н. Кавури и К.
Инь, «Обзор обнаружения и диагностики сбоев процесса, часть III,
Методы, основанные на истории процесса» , Computers and Chemical
Engineering, No. 27, 2003, стр. 327-346
[8] С. Катипамула и М.Р. Брамбли, «Методы обнаружения неисправностей,
Диагностика и прогнозирование строительных систем — обзор»,
Часть I », HVAC & R Research, Vol.11, No. 1, January 2005
[9] С. Катипамула и М. Р. Брамбли, «Методы обнаружения неисправностей,
Диагностика и прогнозирование строительных систем — Обзор,
Часть II», HVAC & R Research, Vol. 11, No. 2, April 2005
[10] A. S. Willsky, «Обзор методов проектирования для обнаружения отказов
в динамических системах», Automatica, Vol. 12, pp. 601-611, 1976
[11] Л. Х. Чанг, Э. Л. Рассел и Р. Д. Браатц, Обнаружение неисправностей и диагностика
в промышленных системах, Springer-Verlag, Лондон, Великобритания, 2001
[12] P. М. Франк, «Диагностика отказов в динамических системах с использованием
аналитического и основанного на знаниях резервирования, обзор и около
новых результатов», Automatica, Vol. 26, No. 3, pp. 459-474, 1990, UK
[13] С. Веррон, Т. Типлика и А. Коби, Обнаружение ошибок одномерных
негауссовских данных с байесовской сетью, IEEE International
Конференция по промышленной технологии (ICIT’10), 2010
[14] Ю. Тарро, Г. Муро, Дж. Раго и Д.Макин, «Обнаружение неисправностей
и изоляция с помощью надежного анализа главных компонентов», Int. J.
Заяв. Математика. Comput. Наук, 2008, т. 18, No. 4, 429–442
[15] Д. Гарсиа-Альварес, «Обнаружение неисправностей с использованием анализа главного компонента
(PCA) в очистных сооружениях (КОС)», 62-й
Int. Студенческая научная конференция, Санкт-Петербург, 13-17 апреля 2009 г.
[16] Г. Кланчар, «Обнаружение и изоляция неисправностей с помощью компонентного анализа принципала
», семинар для аспирантов, сен. 2000, Марианска, Чехия
[17] Т. Кохонен, «Самоорганизующиеся карты», 2nd.Ed., Springer, 1997
[18] MJ Fuente и C. Represa, «Сравнительное исследование нейронных сетей
» Основанный подход к обнаружению неисправностей », 3-й симпозиум IFAC
, Кингстон-апон-Халл, Великобритания, 26-28 августа 1997 г.
[19] М.А. Хусейн, CRC Hassan, KS Loh и KW Mah,
« Применение методов искусственного интеллекта в процессе. Ошибка
Диагностика», Журнал технических наук и технологий, Vol.
2, № 3, 2007, 260-270
[20] А. Саксена и А. Саад, «Диагностика неисправностей в вращающихся механических системах
с использованием самоорганизующихся карт», ANNIE 04, 2004, Сент-Луис, Мисс
[21] MROthman, MWAli и MZ Камсах, «Обнаружение сбоев процесса
с использованием стратегии диагностики иерархической искусственной нейронной сети
», Jurnal Teknologi, 46 (F), июнь 2007: 11–26, Малайзия
[22] PM Frank и X. Ding, «Обзор надежных остаточная генерация
и методы оценки в системах обнаружения неисправностей на основе наблюдателя
», Дж.Proc. Com., Vol. 7, No. 6, pp. 403-424, 1997
[23] А. Шварте и Р. Изерманн, «Приложения нейронных сетей для
Обнаружение неисправностей на основе моделей с помощью уравнений четности», 2002 IFAC
15-й Всемирный конгресс, проводимый раз в три года. , Барселона, Испания
[24] К. Анджели и А. Хатциниколау, «Обнаружение сбоев в сети
Методы для технических систем: обзор», Международный журнал
of Computer Science & Applications, Vol. Я нет.1, стр. 12–30
[25] К. Агнели, Диагностические экспертные системы: от экспертных знаний
к системам реального времени, Электронная книга TMRF, основанные на передовых знаниях
Системы: модель, приложения и исследования, Том . 1, стр. 50–73, 2010
[26] AT Azar (Ed.), Fuzzy Systems, Intech Publishing, Indiana 2010
[27] М. Кулкарни, «Обнаружение неисправностей в гидравлической системе с использованием нечеткой логики
» , Proc. Всемирного конгресса по технике и компьютерам
Science 2009, Vol.II, WCECS 2009, октябрь 2009 г., Сан-Франциско, США
[28] С.К. Ядав и П.К. Калра, «Автоматическая диагностика неисправностей двигателя внутреннего сгорания
на основе спектрограммы и искусственной нейронной сети
», Proc.10th WSEAS, Ноябрь 2008, Бухарест, Румыния
[29] Л. Цзяньминь и К. Синьюн, «Метод диагностики неисправности цилиндра
двигателя на основе искусственной нейронной сети»,
Proc. 2008 CSSE, 12-14 декабря 2008 г., Ухань, Китай
[30] J.Чжу, «Мониторинг состояния судового дизельного двигателя с помощью нейронной сети BP
», Proc. IMESC 2009, март 2009 г., Гонконг
[31] Л.Чен и Л.Као, «Диагностика неисправностей двигателя с помощью объединения данных», Proc.
Четвертого китайско-японского международного семинара по Интернету
Технологии и приложения управления Хунань, октябрь 2005 г., Китай
[32] К.С. Гаид и Х.А.Ф. Мохамед, «Диагностика и отказоустойчивость
Техника управления асинхронными двигателями a Обзор », AJBAS
февраль 2010 г., стр.227-246
[33] Р. Зуари, С. Зиг-Зиеба и М. Сидахмед, «Система обнаружения неисправностей
для центробежных насосов с использованием нейронных сетей и
нейро-нечетких методов», CMSM 2005, март 2005, Тунис
[34] Г. Чжао, Д. Цзян, Дж. Диао и Л. Цянь, «Применение частотно-временного анализа
при диагностике неисправностей для паровой турбины
», Surveillance 5 CETIM, 11-13 окт. 2004, Санлис, Франция
[35] G.Вердье и Ариан Феррейра, «Адаптивное расстояние Махаланобиса
и правило k-ближайшего соседа для обнаружения неисправностей в производстве полупроводников
», EMSE-CMP WP 2009/14
[36] А.Н. Вишванат Рао, «Применение автоассоциативной нейронной сети
» Сетьдля обнаружения неисправностей датчика системы управления авиационным двигателем,
Изоляция и размещение », DRDO Sci.Spec., March 3009, стр. 12-15
[37] Дж. Л. Аравена и Ф. Н. Чоудхури,« Обнаружение неисправностей рейса
Критическое. Системы », DASC.20-я конференция, октябрь 2001 г., Дейтона, Флорида,
[38] Х. Лонг и Х. М. Ван, «Диагностическая неисправность топливной системы самолета
, обнаружениес помощью экспертной системы», 25-й Международный конгресс
авиационных наук, сентябрь 2006, Гамбург, Германия
[39] Ф. Киммих и Р. Изерманн, «Обнаружение неисправностей на основе модели для
: впрыск, сгорание и двигатель-трансмиссия», 15-я Международная федерация бухгалтеров (IFAC),
21–26 июля 2002 г., Барселона, Испания
[40] X.Дж. Дин и Т.К. Мей, «Обнаружение неисправностей подвески
на основе системного динамического взаимодействия», CONTROL 2008, UK
[41] Дж. Шейн и С.Т. Бушби, «Метод обнаружения и диагностики неисправностей
на основе иерархических правил и диагностики для систем отопления, вентиляции и кондиционирования воздуха» , HVAC & R
Research, Vol. 12, № 1, январь 2006 г., стр. 111-125
[42] Сайед Азхар Сайед Аб. Рахман, «Применение искусственной нейронной сети
в исследовании обнаружения неисправностей процесса пакетной этерификации
», Int.J. of Eng. & Tech., IJENS, Том 10, № 03; Июнь 2010 г.
[43] Л. Сальваторе, Б. Пирес, MCM Campos и MBA Де Соуза младший
МБ, «Гибридный подход к обнаружению и диагностике неисправностей в процессе гидроочистки дизельного топлива
», Всемирная академия наук,
Engineering and Technology, Issue 12, December 2005
Тенденции в диагностике неисправностей датчиков
В последнее время широко востребована автоматизация процессов. Многие отрасли стремятся оптимизировать время производства, затраты или отходы.Здесь можно рассмотреть только несколько высокоавтоматизированных отраслей, таких как производство силиконовых чипов, управление отходами и водными ресурсами, а также транспортировка жидкостей, но в связи с недавней пандемией также есть другие преимущества в автоматическом управлении. Однако для полного использования его потенциала необходимо надежное и быстрое обнаружение неисправностей (либо для профилактического обслуживания, либо для отказоустойчивого управления). В этом специальном выпуске «Датчики » предпринята попытка описать современные тенденции в диагностике неисправностей в промышленных приложениях. Основными причинами его создания послужили широкий охват отраслей, а также множество последних разработок.Начиная с обнаружения неисправностей для пневматических клапанов, через сенсорные сети, автономные транспортные средства (наземные или воздушные), водопроводы и заканчивая гораздо более распространенными коробками передач, подшипниками качения или тормозами. Все эти захватывающие темы освещаются в этом специальном выпуске, во всех случаях открывая новые перспективы для приложений диагностики неисправностей.
Авторы [1] включают авторегрессионную нейронную сеть с экзогенными входами для поведенческого прогнозирования при обнаружении неисправностей и диагностике пневматических клапанов.ИТ позволяет создавать матрицу сигнатур и дерево решений. Использование методов мягких вычислений приносит все более удовлетворительные результаты, поскольку качество методов растет параллельно с вычислительной мощностью, необходимой в процессе. Метод Кинсмана также используется в [2] для обнаружения неисправностей и отказоустойчивого управления магнитной тормозной системой. Однако в этом случае нейронная сеть используется для настройки модели системы в пространстве состояний, повышая качество более традиционного механизма обнаружения неисправностей на основе остаточных ошибок, работающего с контроллером обратной связи.Кроме того, [3] включает неглубокую искусственную нейронную сеть для сканирования цепочек (с использованием векторов признаков отказа). В упомянутых статьях используются неглубокие сети, тогда как в [4] авторы реализуют глубокую сеть в виде составного автокодера для диагностики неисправностей подшипников качения. Точно так же в [5] авторы представляют сверточную глубокую нейронную сеть для классификации потенциальных неисправностей. Некоторые подходы, основанные на аналитических моделях, также представляют интерес в этой области. Более пристальное рассмотрение [6], а также [7] может привести читателя к выводу, что особенно линейные модели заслуживают изучения.В случае [6] это простая, но эффективная линеаризация вокруг рабочей точки, тогда как в [7] авторы предлагают нечеткую модель Такаги – Сугено, состоящую из ряда линейных подмоделей. Хотя подходы к моделированию схожи, в обеих документах диагностика неисправностей рассматривается немного по-разному. Авторы первого используют хорошо известные фильтры Калмана, а авторы последнего реализуют вид модифицированного наблюдателя Люенбергера. Вышеупомянутые подходы имеют некоторые общие черты и, следовательно, преимущества и недостатки, но также во многом отличаются.Необходимо тщательно изучить и то, и другое, чтобы выбрать подходящее решение или идею и адаптировать их для своих собственных преимуществ.
В отличие от вышеизложенного, авторы [8] сосредотачивают свои усилия на повышении качества частотных методов диагностики неисправностей. Они предлагают улучшение данных для последующего вейвлет-преобразования. Затем неисправность обнаруживается классификатором SVM. Основная идея обнаружения неисправностей и прогнозирования снижения производительности в [9] также основана на машине опорных векторов.Однако авторы предложили сильно модифицированный алгоритм в виде гибрида с функцией ядра, оптимизированного для стада криля. Здесь, как и в [8], методы применяются в частотной области. Вышеупомянутый SVM также является частью метода диагностики неисправностей, предложенного в [10], где машина векторов поддержки мультиклассов один-против-один получает сигнал с шумом, уменьшенным с помощью метода адаптивной фильтрации шума. Метод шумоподавления основан на LMS-фильтре с генератором опорного гауссовского шума.Этот очень интересный метод применяется в частотной области.
Наконец, [11] сравнивает множество подходов к обнаружению, изоляции, идентификации и даже восстановлению неисправностей для автомобильных датчиков, таких как LIDAR. Авторы сравнивают 120 работ за последние 15 лет и дают исчерпывающее представление о рассматриваемой теме. Авторы четко классифицируют неисправности датчиков восприятия на семь категорий, предоставляют примерные методы их устранения и анализируют. Дополнительно рассматриваются некоторые подклассы.Одним из интересных результатов этого исследования является вывод о том, что в последнее время большинство исследователей сосредоточено на экологических неисправностях, таких как дождь, туман или снег. Это кажется верным и разумным для выяснения того, являются ли погодные условия наиболее частым источником неисправностей и шумов, поскольку ими нельзя управлять.
Сравнивая предложенные подходы, становится ясно, что не существует универсального решения для всех проблем диагностики неисправностей; скорее, решение должно быть адаптировано к конкретному случаю.Все упомянутые статьи ясно показывают, что это лучший подход. Рассматривая аналитические методы или методы мягких вычислений, нужно сначала глубоко понять лежащую в основе систему и выбрать наиболее подходящий метод. Редактор глубоко надеется, что этот небольшой специальный выпуск о диагностике неисправностей датчиков поможет многим читателям выбрать свой путь и найти решения, соответствующие их потребностям.
Разработка системы обнаружения и устранения неисправностей для интеллектуальной системы навигации транспортного средства
В этом документе рассматривается разработка системы обнаружения и устранения неисправностей (FDI) для интеллектуального транспортного средства, транспортного средства, оборудованного усовершенствованной системой помощи водителю (ADAS).ADAS оснащены датчиками для получения различной информации о транспортном средстве и его окрестностях. Поскольку эти датчики чувствительны к сбоям, следует разработать эффективную систему прямых иностранных инвестиций. Разработанная система FDI состоит из трех частей: части обнаружения, части принятия решений и части управления неисправностями. Часть обнаружения применяет обобщенную схему наблюдателя (GOS). В GOS имеется набор расширенных фильтров Калмана (EKF), каждый из которых возбуждается всеми измерениями, кроме одного датчика. Таким образом, остаток, генерируемый обновлением измерений каждого EKF, чувствителен ко всем сбоям датчика, кроме одной.Таким образом, шаблон чувствительности остатка к неисправности позволяет обнаружить неисправность и определить местонахождение неисправного датчика. Разработанная система FDI была внедрена и протестирована в автономном режиме на реальных экспериментальных данных. Хорошие результаты были получены при диагностике неисправностей отдельных датчиков и выдаче исправных состояний автомобиля.
1. Введение
В настоящее время в исследованиях автомобильных перевозок делается упор на разработку систем ADAS, которые помогают водителю управлять транспортным средством.Эти автомобильные мехатронные системы оснащены датчиками, такими как радары, одометры и акселерометры, для получения различной информации о транспортном средстве и его окрестностях. Поскольку эти датчики чувствительны к сбоям, следует разработать эффективную систему FDI, чтобы на основе измерений датчиков можно было обнаруживать и изолировать сбои датчиков в режиме онлайн, тем самым обеспечивая правильную работу ADAS.
Датчик считается неисправным, если он показывает результат измерения, который значительно отличается от характеристик.Это отклонение может проявляться в нескольких формах, а именно в смещении, дрейфе, полном отказе и ухудшении точности. Система FDI содержит систему обнаружения неисправностей, за которой следует система изоляции неисправностей. Определение обнаружения неисправности состоит в том, чтобы принять решение: произойдет ли неисправность или нет. Определение локализации неисправности состоит в том, чтобы точно определить место неисправности, например, какой датчик вышел из строя. Поскольку можно построить надежную модель транспортного средства, особое внимание будет уделено обсуждению основанных на моделях стратегий ПИИ.Кроме того, в отношении неисправности датчика, которая может произойти, можно сделать следующие предположения. (1) Одновременно может присутствовать только одна неисправность. (2) Все датчики могут иметь частичные или полные неисправности. (3) Полные неисправности могут быть рассматривается как аддитивная неисправность, размер которой равен отрицательному значению реального сигнала датчика. (4) Обычно неисправности бывают аддитивными и переходными (т. е. они исчезают через некоторое время).
ПИИ на основе моделей — это метод определения неисправностей системы на основе сравнения доступных системных измерений с априорной информацией, представленной математической моделью системы.Структуру FDI на основе модели можно увидеть на рисунке 1, где остаток является сигналом, указывающим на неисправность, а принятие решения заключается в проверке остатка на предмет вероятности неисправностей [1].
С начала 1970-х годов было разработано множество подходов к моделированию ПИИ, и доступная литература весьма обширна. Обзорные статьи, дающие исчерпывающий обзор доступных методов для ПИИ, — это [2–7]. В течение 1990-х годов особенно быстро увеличивалось количество применений ПИИ, основанных на моделях.Приложения к автомобильным системам управления можно найти в [8–17]. Исследование прямых иностранных инвестиций для ADAS в основном проводилось Калифорнийской PATH. В различных публикациях рассматривается применение различных подходов к ПИИ и обсуждаются экспериментальные результаты.
Ниже приводится краткое описание широко используемых стратегий ПИИ на основе моделей. Наблюдатели состояния [3, 18] в основном включают специальных наблюдателей (детерминированная система) и инновационный подход (стохастическая система) для процессов с множеством выходов.(1) Наблюдатель, возбуждаемый одним выходом: из этого выхода можно реконструировать другие выходы и сравнивать с соответствующими измерениями (обнаружение неисправности одного датчика). (2) Один фильтр Калмана (KF), управляемый всеми выходами: изменение стохастические инновации, указывающие на изменения во внутренних состояниях процесса. (3) Банк наблюдателей, возбуждаемых всеми выходами: это подходит, если неисправности вызывают изменения во внутренних состояниях процесса. (4) Банк наблюдателей, каждый из которых возбуждается другой выход (схема выделенного наблюдателя, DOS): его можно использовать для диагностики неисправности одного датчика или нескольких неисправностей датчиков.(5) Банк наблюдателей, каждый из которых возбуждается всеми выходами, кроме одного (обобщенная схема наблюдателя, GOS): этот метод повышает надежность системы FDI, но может диагностировать только одну неисправность датчика.
Основанные на моделях схемы ПИИ были успешно применены к сложной модели динамики транспортных средств и достигли устойчивости к неопределенностям модели. В [19] разработан специальный наблюдатель. Скорость рыскания и поперечное ускорение можно восстановить и сравнить с соответствующими измерениями гироскопа и акселерометра.Этот метод точно обнаруживает и изолирует одиночную неисправность в одном из этих датчиков. Авторы в [20] используют одиночный KF, управляемый полным выходным вектором, и используют тот факт, что остаточный сигнал представляет собой белый шум с нулевым средним значением, когда не происходит сбоев. Возникновение неисправности отслеживается с помощью статистических инновационных тестов белизны, среднего и ковариантности. Применение GOS можно найти в [3], где для построения GOS применяется банк наблюдателей или KF. Каждый наблюдатель управляется всеми входами и всеми выходами, кроме одного, для диагностики неисправности датчика.
Кроме того, в недавней работе [21–23] EKF используется для вычисления распределения вероятностей измерения положения интеллектуального транспортного средства для нелинейных моделей, управляемых гауссовым шумом. Используя распределение вероятностей нововведений, полученное от EKF, можно проверить, соответствуют ли измеренные данные моделям. Когда произойдет сбой датчика, модели не будут действительными и новинка не будет гауссовой и белой.
Основным вкладом этой работы является то, что, в отличие от предыдущих исследований, в этой работе особое внимание будет уделяться следующему: для обеспечения надлежащего функционирования ADAS на интеллектуальном транспортном средстве система FDI на основе модели предназначена для диагностики неисправности одного датчика. с учетом помех в системе и шума.Детали вкладов заключаются в том, чтобы (1) улучшить остаточную генерацию с использованием метода на основе наблюдателя, (2) повысить устойчивость основанных на модели FDI к возмущениям и шумам, (3) построить аналитическую избыточность для обеспечения надежной оценки неисправного датчика. сигнал, так что производительность ADAS по-прежнему может быть гарантирована. Обзор разработанной системы FDI показан на рисунке 2.
Этот документ организован следующим образом. Раздел 2 описывает измерения датчика. В разделе 3 представлена стратегия оценки состояния автомобиля.Раздел 4 посвящен проектированию системы обнаружения и изоляции неисправностей. В разделе 5 показаны экспериментальные результаты. Заключение и будущая работа обсуждаются в Разделе 6.
2. Технические условия на измерения датчиков
Испытательное транспортное средство представляет собой интеллектуальное транспортное средство, которое представляет собой небольшое 2-дверное транспортное средство с автоматической коробкой передач. Smart имеет привод от задних колес, а двигатель расположен посередине автомобиля. Для этой работы Smart оснащен необходимыми датчиками GPS и INS: акселерометром, одометром и гироскопом.Взаимодействие датчиков Smart осуществляется с помощью комбинации сети контроллеров (CAN) и ноутбука. В таблице 1 описаны дисперсия, смещение и дрейф каждого измерения датчика, полученные из таблицы данных продукта или рассчитанные на основе необработанных данных.
|
Для оценки глобального положения использовался приемник дифференциальной глобальной системы позиционирования Trimble Lassen (DGPS).В нашем эксперименте используются следующие сигналы GPS: качество, точность горизонтального разбавления (HDOP), количество спутников, время, продольное / поперечное положение, направление и скорость. Основываясь на техническом описании продукта, мы знаем, что частота обновления DGPS составляет 1 Гц, а точность составляет ± 5 м.
Два акселерометра использовались для регистрации поперечного и продольного ускорения автомобиля. Сигналы акселерометра имеют частоту обновления 50 Гц и смещены. Это смещение — это всегда присутствующий в акселерометре низкочастотный сигнал.Скорость рыскания, измеренная гироскопом, имеет диапазон 100 градусов / с, а его отклонение составляет менее 2 градусов / час. В нашем эксперименте одометры используются для измерения скорости колес транспортного средства.
3. Оценка состояния транспортного средства
Для нелинейных систем общее стохастическое разностное уравнение для дискретных систем определяется следующим образом: где — нелинейная функция. В этой работе для вывода разностного уравнения используется метод численного интегрирования Эйлера с фиксированным шагом по времени.На практике значения шумов и неизвестны и также установлены равными нулю, поскольку в предлагаемой системе нет управляющего входа; поэтому векторы состояния и измерения должны быть аппроксимированы где — оценка состояния на основе измерения (апостериори).
Предполагается, что переменные и являются гауссовыми с нулевым средним и представлены их ковариационными матрицами и. представляет собой нормальное распределение: Можно определить два вида ошибок оценки: ошибка априорной оценки и ошибка апостериорной оценки .Их описывают где — априорная оценка состояния, основанная на знании процесса до шага, и — апостериорное состояние, основанное на измерении. Ковариации ошибок оценивания определяются следующим образом: где — ковариация ошибки априорной оценки и — ковариация ошибки апостериорной оценки.
Алгоритм EKF состоит из двух этапов: обновления времени и обновления измерения [24]. Различные этапы этапа обновления времени: где — якобиан уравнений модели системы.
На этапе обновления результатов измерения следующие этапы: где — коэффициент Калмана, который минимизирует ковариацию ошибки апостериорной оценки, и — якобиан функции измерения.
Хотя предполагается, что переменные и в (1) являются гауссовыми с нулевым средним, предположение гауссовости часто не выполняется на практике. Следовательно, матрицы и нельзя рассматривать как ковариационные матрицы, а как параметры настройки высокого уровня, ведущие к неоптимальным решениям.Кроме того, линеаризация в EKF может привести к снижению производительности и расхождению фильтра для сильно нелинейных задач. Усовершенствованием EKF являются некоторые локальные нелинейные оценщики, фильтр разделенных разностей, фильтр Калмана без запаха (UKF) и т. Д. UKF аппроксимирует плотность вероятности, полученную в результате нелинейного преобразования случайной величины, вместо аппроксимации нелинейных функций разложением в ряд Тейлора. UKF имеет несколько оптимальные характеристики по сравнению с EKF при использовании в системе оценки состояния навигации транспортного средства.Однако, поскольку низкая динамика транспортного средства делает потенциальные ошибки линеаризации EKF незначительными, а время вычисления UKF намного больше, чем время вычисления EKF, EKF по-прежнему выбирается в этой работе для оценки состояния транспортного средства [25 ].
3.1. Стратегия объединения датчиков
На основе измерений датчиков, перечисленных в таблице 1, и кинематической модели транспортного средства можно разработать EKF для оценки некоторых важных состояний Smart. Обзор конфигурации датчика для Smart показан на рисунке 3.В этой конфигурации измерения INS также используются для обновления предполагаемого местоположения и курса транспортного средства, когда обновление DGPS недоступно.
3.2. Конструкция расширенных фильтров Калмана для интеллектуального автомобиля
Движение транспортного средства будет называться навигационной рамкой, которая описывается системой правой ортогональной оси () на Земле. Вторая опорная рамка (базовая рама), закрепленная в транспортном средстве, описывается осями (), закрепленными вдоль центральных главных осей транспортного средства.Взаимосвязь между навигацией и базовой рамкой можно увидеть на Рисунке 4.
Измерения датчика будут назначены в разные рамки. Продольное, поперечное положение и курс DGPS отображаются в навигационной рамке. Ускорение и скорость колеса, измеренные с помощью INS, находятся в базовой раме. Чтобы получить траекторию в навигационном кадре, необходимо преобразовать инерционные сигналы из базового кадра в навигационный кадр, где мы предполагаем, что дорога ровная, а затем пренебрегаем осями и.Это можно сделать с помощью следующей матрицы (упрощенная форма матрицы прямого косинуса):
3.2.1. Модель автомобиля с четырьмя колесами
В этом разделе разработан EKF на основе кинематической модели четырехколесного автомобиля, показанной на рисунке 5. Предполагается, что испытательный трек, по которому движется Smart, является плоским.
Чтобы воспроизвести траекторию, по которой следует транспортное средство, кинематические правила для модели были использованы для описания движения транспортного средства.Кинематическая модель транспортного средства может быть разработана как где и — продольное и поперечное положение в навигационной раме и указывают продольную и поперечную скорости в базовой раме. Кроме того, для каждой скорости колеса у нас есть
где — скорость вращения колес, измеренная от переднего левого, переднего правого, заднего левого и заднего правого колес, — скорость рыскания, — длина от передней и задней осей до Smart COG, и — длина передней и задней гусеницы.Уравнения (12) и (13) выводятся из условия, что задние колеса не являются управляемыми и их углы поворота равны нулю.
Все состояния модели описаны в таблице 2, где состояния смещения моделируются как случайные блуждания. Используя модель случайного блуждания, можно отразить рост неопределенности истинного значения смещения и скорости его изменения [26]. Кроме того, измерения EKF указаны в таблице 3.
|
|
Используя метод Эйлера с шагом по времени, уравнения состояния с дискретным временем могут быть записаны как Кроме того, уравнения измерения могут быть указаны следующим образом:
3.2.2. Наблюдаемость системы
Говорят, что динамическая система является наблюдаемой, если возможно однозначно восстановить информацию о состоянии на основе модели системы с учетом входов и выходов системы. Нелинейная модель для автомобиля Smart: где = col ():.
Хотя эта модель является нелинейной, она каждый раз линеаризуется для EKF. Матрица наблюдаемости вычисляется для каждой линеаризации в прогоне EKF. Если имеет полный ранг при каждом запуске, то линеаризованная модель является локально наблюдаемой.В этом проекте матрица наблюдаемости накапливается на всем временном шаге от начального до конечного в качестве глобальной проверки [27]. Поскольку в этой работе используется модель с дискретным временем в пространстве состояний, переходное событие не изучается, а затем не учитывается при проверке наблюдаемости.
Модель локально наблюдаема во время движения автомобиля; когда транспортное средство стоит на месте и измеренная скорость рыскания равна нулю, расчетные продольные / поперечные скорости центра тяжести / и состояния смещения для передних / задних одометров, и становятся ненаблюдаемыми.Это связано с тем, что, когда транспортное средство стоит на месте, информация о скорости не поступает от кодировщиков колес, поэтому ничего нельзя сказать об ошибке в вычислении скорости.
4. Проектирование системы обнаружения и устранения неисправностей
Обобщенная схема наблюдателя (GOS) предусматривает, что блок оценки, предназначенный для определенного датчика, управляется всеми выходами, кроме выходного сигнала соответствующего датчика. Эта схема позволяет обнаруживать и изолировать только одну неисправность в любом из датчиков, однако с повышенной надежностью по отношению к неизвестным входам.
GOS подходит для обнаружения одной неисправности за раз в одном из датчиков системы. Наблюдатель () управляется всеми, кроме измеряемой переменной (т. Е.). Следовательно, каждый остаток от наблюдателя будет чувствителен ко всем, кроме неисправности датчика. не используется в наблюдателе, поскольку предполагается, что он поврежден из-за сбоя и, следовательно, не несет полезной информации о системе [3].
Уравнения нелинейной системы включают неисправности датчиков и неизвестные возмущения. где = col ():.- -мерный вектор состояния. — -мерный вектор измерений. Более того, модель подвержена как сигналу неисправности, так и неизвестному сигналу возмущения. Величина неисправности — это произвольная скалярная функция времени, которая равна нулю, когда неисправности нет.
GOS может быть спроектирован для датчика FDI, где есть EKF, каждый из которых использует все измерения, кроме измерения датчика. Для каждого EKF его остаток может быть сгенерирован на этапе обновления измерений как Поскольку каждый EKF возбуждается всеми выходными сигналами датчика, кроме одного, при отказе датчика в датчике остаточный сигнал будет удовлетворять следующей логике изоляции: где () — пороги изоляции [28].Такая схема GOS показана на рисунке 6.
Банк EKF GOS устойчив к ошибкам моделирования системы и неизвестным возмущениям в реальной среде. Это связано с тем, что в GOS, только если все невязки в (28) должны пропускать зажигание, может быть принято неверное решение о неисправности.
Здесь приведен пример, чтобы проиллюстрировать, как GOS может точно диагностировать неисправность одного датчика в системе, как показано на рисунке 6. В таблице 4 каждая строка представляет неисправность, где число 1 в позиции строки и столбца означает, что неисправность влияет на остаток.Как указывалось ранее, каждый остаток, сгенерированный из GOS, чувствителен ко всем отказам датчика, кроме одного, и, следовательно, для возникновения каждого отказа существует уникальная комбинация остаточного отклика, которая, как можно заметить, называется обобщенным остаточным набором. в каждой строке таблицы 4. С помощью такой остаточной таблицы любая неисправность отдельного датчика, если она произойдет, может быть однозначно обнаружена и изолирована.
4.1. Общая схема системы FDI
Базовая схема системы FDI указана на рисунке 7, где система обнаружения неисправностей должна идентифицировать возникшую неисправность, а система изоляции неисправностей может определить место неисправности.Дополнительная система управления отказами используется для распознавания и обработки отказа, которая содержит систему выбора состояния.
4.2. EKF в GOS
В автомобиле Smart установлено восемь датчиков: DGPS, продольные / поперечные акселерометры, гироскоп и датчик скорости вращения колеса на каждом колесе автомобиля. Для обнаружения единственной неисправности в этих датчиках разработан банк EKF GOS, состоящий из восьми EKF. В случае неисправности датчика выход из блока остаточной оценки (диагностическая информация) будет указывать, какая неисправность происходит, и впоследствии выбрать состояние, оцененное из EKF, используя все измерения датчика, кроме ошибочного, в качестве выхода без ошибок, который показано на рисунке 8.На рисунке видно, что остатки и состояния, сгенерированные из каждого EKF, вводятся в систему оценки остатков и управления отказами, соответственно. Далее будет оцениваться каждый EKF (в GOS) для оценки состояния транспортного средства, где EKF 0 использует все измерения датчиков (номинальный EKF).
EKF 1: На основе всех измерений, кроме DGPS . Он использует все данные, кроме данных DGPS. В случае сбоя DGPS будут применяться оценочные состояния из этого EKF.
EKF 2: На основе всех измерений, кроме продольного акселерометра .Все измерения, кроме продольного ускорения, используются EKF 2. Если продольный акселерометр неисправен, EKF 2 будет применяться для оценки состояния. На рисунке 9 можно увидеть, что расчетное продольное ускорение является надежным аналитическим резервом для замены ошибочного измерения акселерометра.
EKF 3: На основе всех измерений, кроме бокового акселерометра . EKF 3 управляется любым сигналом, кроме бокового ускорения. В момент сбоя бокового акселерометра будут применяться состояния, оцененные по EKF 3.
EKF 4: На основе всех измерений, кроме гироскопа . Этот EKF использует все измерения, кроме гироскопа. В случае неисправности гироскопа для оценки состояния автомобиля будет использоваться EKF 4.
EKF 5/6/7/8: Управляется всеми измерениями, кроме каждого датчика скорости колеса . EKF 5 приводится в действие всеми сигналами скорости вращения переднего левого колеса. Когда происходит эта неисправность датчика, оценочные состояния EKF 5 все еще безошибочные. EKF 6–8 используют все, кроме трех других сигналов скорости вращения колес, соответственно, и могут достигать почти тех же результатов оценок, что и EKF 5.Поэтому подробное описание этих трех EKF опускается. В случае, если какой-либо из этих датчиков скорости вращения колеса неисправен, соответствующий EKF будет применен к оценке состояния.
4.3. Обнаружение и обнаруживаемость неисправностей датчика
В GOS в идеале существует невязка, генерируемая каждым EKF, которая чувствительна ко всем неисправностям датчика, кроме одного. С этой целью нам необходимо проверить в каждом EKF, обнаруживаются ли эти неисправности датчиков по отношению к сгенерированной невязке. Это требует, чтобы передаточные функции от этих неисправностей датчиков к остаточной не равнялись нулю.
4.3.1. Неисправности датчика Описание
Система FDI для Smart предназначена для диагностики восьми неисправностей датчиков, которые перечислены в таблице 5. Моделирование неисправности датчика можно увидеть в (26), где соответствует каждому измерению датчика.
|
4.3.2. Остаточная генерация
В этом разделе обсуждаются несколько возможностей остаточной генерации из каждого EKF. После сравнения выбирается наиболее перспективный. Вначале сделаны остаточные обозначения, которые будут применяться на протяжении всей работы. Остаток — это остаток, созданный из EKF в GOS. Поскольку в GOS восемь EKF, у нас есть. Между тем, поскольку семь уравнений измерения применяются в EKF 0, семь остатков могут быть сгенерированы из GOS. Чтобы сделать четкое обозначение, порядок этих семи остатков фиксирован как остаток, сгенерированный в результате обновления измерения: DGPS, -ускорение, -ускорение, скорость рыскания, скорость переднего левого колеса, скорость переднего правого колеса и средняя скорость заднего колеса}.
Сигналы DGPS могут блокироваться зданиями, деревьями, мостами и т. Д. В этой работе отказ DGPS просто обнаруживается с помощью следующей логики. (1) Число спутников упало ниже 4. (2) Значение HDOP больше 10, когда позиционные измерения должны использоваться только для указания очень приблизительная оценка текущего местоположения.
Для проектирования системы INS FDI в качестве примера взята остаточная генерация в EKF 1. Поскольку не используются только измерения DGPS, этот EKF может генерировать остатки из всех обновлений измерений INS.Сгенерированные остатки до перечислены в Таблице 6, где — скорость рыскания, — это расчетная скорость центра тяжести, — это длина Smart track и — длина от Smart COG до передней оси. Следует отметить, что хотя EKF 1 управляется всеми семью измерениями INS, могут быть сгенерированы только шесть остатков. Причина в том, что средняя скорость заднего колеса вместо двух отдельных скоростей используется в обновлении измерений EKF 1, что можно увидеть в (23).
|
Таким образом, в каждом EKF, который содержит весь сгенерированный вектор EKF, эти шесть остатков, кроме одного.Чтобы построить GOS, из каждого EKF необходимо сгенерировать векторную или скалярную невязку, на которую влияют все неисправности датчика, кроме одной.
В работе рассматриваются скалярные остатки. Что касается INS FDI, скалярная невязка должна быть выбрана среди до, на которую влияет как можно больше отказов датчика. Как видно из таблицы 6, существует больше состояний, участвующих в генерации остатков и. Таким образом, любой или может быть применен к конструкции системы датчиков FDI. Далее будет проверяться обнаруживаемость каждой неисправности INS по отношению к остаточной ошибке.
4.3.3. Теория проверки возможности обнаружения неисправностей
Когда в контролируемом процессе возникают неисправности, остаточный вектор откликается на где определяется как матрица переноса неисправностей, которая представляет отношение между остатком и неисправностями, является столбцом и является компонентом. Если, обнаруживается в остатке. Это определяется как условие обнаруживаемости неисправности невязки [28].
Модель транспортного средства, применяемая в этом проекте, является нелинейной и линеаризуется на каждом временном шаге для EKF.Для вывода линеаризованного уравнения используется метод численного интегрирования Эйлера с фиксированным шагом по времени. Поэтому мы предлагаем проверять локальную обнаруживаемость неисправности датчика на каждом временном шаге для линеаризованной модели с дискретным временем. Модель представлена следующим образом: В этой системе уравнение обновления измерений фильтра Калмана с дискретным временем может быть записано как где — коэффициент Калмана, — оператор сдвига в модели с дискретным временем. Из (31) передаточная функция от вектора состояния к вектору измерения может быть представлена как Следовательно, в нормальных условиях где нижний индекс означает нормальное состояние, а нижний индекс в нижеследующем означает неисправное состояние.Теперь, если измерение нарушено вектором неисправности, Тогда из (34) оценка состояния принимает вид Нормальный остаток фильтра можно определить как а невязка в условиях неисправности равна Ясно, что неисправность датчика обнаруживается относительно остаточной последовательности, когда член не равен нулю [28, 29].
4.3.4. Проверка возможности обнаружения неисправностей в GOS
Поскольку используемая модель является нелинейной, но линеаризуется каждый раз для EKF, матрица обнаруживаемости рассчитывается для каждой линеаризации в некоторых прогонах EKF.Если при каждом запуске ненулевое значение, то неисправность обнаруживается локально.
В следующем тесте линейная модель транспортного средства строится в рабочей точке, где транспортное средство движется прямо с курсом 0,02 радиана. Линеаризация выполняется со скоростью 10 метров в секунду. Необходимо учитывать возможность обнаружения всех отказов INS по отношению к каждой сгенерированной остаточной ошибке. Здесь в качестве примера взята оценка обнаруживаемости неисправностей INS по невязкам EKF 1. Возможность обнаружения неисправности в этой рабочей точке проверяется численно и будет подтверждена на практике при других условиях эксплуатации.Точно так же такой метод проверки можно применить к другим EKF. После линеаризации матрица пространства состояний в EKF 1 вычисляется как
Матрица перехода от неисправностей к остаткам может быть представлена как, где и / может обозначаться как в таблицах 5 и 6. После описания как ошибок, так и ошибок , мы знаем, что это матрица передачи с семью строками и семью столбцами. Семь передаточных функций в определенной строке представляют собой отношение между каждой неисправностью датчика и определенной невязкой.Далее будет проверяться возможность обнаружения неисправностей от каждой неисправности датчика до остаточной ошибки путем вычисления соответствующих передаточных функций.
Обнаружение неисправностей относительно остаточного . Каждую передаточную функцию в пятой строке матрицы можно вычислить. Функции используются для представления всех передаточных функций в строке матрицы, которые описаны в таблице 7. Далее представлена диаграмма Боде для каждой функции, которую можно применить для анализа обнаруживаемости каждого отказа датчика до остатка. (чтобы показать частотную характеристику остатка для каждой неисправности датчика).
|
Диаграмма Боде передаточной функции от продольного отказа акселерометра до показана на рисунке 10 (а), где учитывается только высокочастотный диапазон.Поскольку неисправности датчика считаются временными, они всегда являются высокочастотными сигналами. На этой частоте запас по усилению составляет около -20 дБ, и, таким образом, можно передать десять процентов величины неисправности. Эта неисправность обнаруживается при применении небольшого порога. Диаграмму Боде можно увидеть на рисунке 10 (б). На высокой частоте запас по усилению составляет около -70 дБ, поэтому эта неисправность практически не обнаруживается. Диаграмма Боде, передаточная функция от неисправности гироскопа до, показана на рисунке 10 (c).На высокой частоте запас по усилению превышает 0 дБ, и поэтому сто процентов величины неисправности может передаваться на остаточную величину. Таким образом, эта неисправность обнаруживается в. Передаточная функция должна быть равна единице. Кроме того, если посмотреть на диаграммы Боде и, все неисправности датчика скорости переднего правого и заднего колеса можно обнаружить в отношении.
Обнаружение неисправностей датчика в других рабочих ситуациях . Поскольку используемая модель линеаризуется каждый раз для EKF 1, матрица обнаруживаемости вычисляется для каждой линеаризации в некоторых прогонах EKF 1 для локальной проверки.Кроме того, мы показываем эффективность этого остатка в ответ на возникновение каждой неисправности датчика, то есть постоянной аддитивной неисправности. Таким образом, выполняется шесть отдельных автономных тестов, каждый раз срабатывающих с разными ошибками датчика. Описание этих неисправностей можно увидеть в Таблице 8, где размеры неисправностей выбраны эмпирически, за которыми следует реальный размер неисправности датчика. Аналогичным образом можно провести тесты для других GOS EKF.
|
Это видно на рисунках 11, 12, на рисунках и 13, что при возникновении всех неисправностей датчиков в любой рабочей точке остаток имеет очевидное и постоянное изменение.Кроме того, величина при номинальных условиях составляет около 0,1 м, что можно увидеть в нижней части рисунка 11. В случае, если происходит сбой одного датчика с разумным размером, указанным в таблице 8, изменение намного больше, чем номинальная остаточная величина. Таким образом, выбрав фиксированный порог, можно обнаружить это изменение.
4.3.5. Генерация остатков GOS
Для всех INS на первом этапе рассматривается создание остатка для обнаружения всех неисправностей, кроме бокового датчика акселерометра.Обнаружение сбоя бокового акселерометра может быть достигнуто с помощью простой стратегии, то есть проверки разницы между исходным и расчетным ускорением, генерируемым только EKF 3, который управляется всеми измерениями, кроме бокового акселерометра. Таким образом, все остатки, сгенерированные для проектирования системы ПИИ, классифицированы и перечислены в таблице 9. Формульные представления этих остаточных поколений можно увидеть в таблице 6.