Способы измерения твёрдости металла, резины, бетона
Первоисточник статьи — https://vostok-7.ru/articles/tverdost/
Единого общепринятого определения термина «ТВЁРДОСТЬ» не существует поскольку методы определения этой метрологической величины настолько разнообразны, что нет возможности их объединить в одной фразе или описании. При этом даже для одного типа материала (напр. металлов) методов определения твердости существует более 5… Также именно по этой причине приборы для измерения твёрдости именуются не только твердомерами, но и другими названиями, указывающими на метод или материал измерения: дюрометр (для резин), склерометр (для минералов) и т.д.
Лаборатория НТЦ «Эксперт» оказывает услуги по измерению твердости различных деталей. Лаборатория укомплектована твердомерами различных типов и имеет аттестованных специалистов II уровня. По результатам измерений выдается заключение лаборатории неразрушающего контроля или заключение метрологической службы по выбору заказчика. Мы работаем с юридическими и физическими лицами. Проведение работ возможно как лабораторно, так и с выездом.
Твёрдость минералов
Шкала твёрдости минералов Мооса (склерометры царапающие) – метод определения твёрдости минералов путём царапания одного минерала другим минералом для сравнительной диагностики твёрдости минералов между собой по системе мягче-твёрже. Испытываемый минерал либо не царапается другим минералом (эталоном Мооса или склерометром) и тогда его твёрдость по Моосу выше, либо царапается — и тогда его твёрдость по Моосу ниже.
Типы исследуемых материалов:
- минералы (природные и искусственные), в т.ч. измеряется твёрдость камней горных пород
- бетон и другие строительные материалы: твёрдость искусственных камней, плитки, стекла и др.
Молотки Шмидта (склерометры-молотки) – метод определения твёрдости и прочности на сжатие без разрушения строительный материалов: бетона, кирпичей, строительного раствора и пр. Оценка материалов происходит по предварительно установленной градуировочной зависимости между прочностью эталонных образцов и значением отскока бойка молотка Шмидта от поверхности материала.
Типы исследуемых материалов:
- бетон
- кирпич
- строительный раствор
- природные камни и горные породы
Твёрдость металлов
Твёрдость металлов – наиболее глубоко изученное и стандартизированное международной практикой измерение твёрдости. Наиболее распространены следующие методы:
Измерение твёрдости металлов по Бринеллю (твердомеры)
Один из старейших методов, твёрдость определяется по диаметру отпечатка, оставляемому металлическим шариком, вдавливаемым в поверхность. Обозначается HB, где H — Hardness (твёрдость, англ.), B — Brinell (Бринелль, англ.)
Измерение твёрдости металлов по Роквеллу (твердомеры)
Это самый распространённый из методов начала XX века, твёрдость определяется по относительной глубине вдавливания металлического шарика или алмазного конуса в поверхность тестируемого материала. Обозначается HR, где H — Hardness (твёрдость, англ.), R — Rockwell (Роквелл, англ.), а 3-й буквой идёт обозначение типа шкалы, напр. HRA, HRB, HRC и т.д.
Измерение твёрдости металлов по Виккерсу (твердомеры и микротвердомеры)
Самая широкая по охвату шкала, твёрдость определяется по площади отпечатка, оставляемого четырёхгранной алмазной пирамидкой, вдавливаемой в поверхность. Обозначается HV, где H — Hardness (твёрдость, англ.), V — Vickers (Виккерс, англ.).
Измерение твёрдости металлов по Шору (твердомеры и склероскопы)
Данный метод крайне редко используется, твёрдость определяется по высоте отскока бойка от поверхности. Обозначается HS, где H — Hardness (твёрдость, англ.), S — Shore (Шор, англ.), а 3-й буквой идёт обозначение типа шкалы, напр. HSD
Измерение твёрдости металлов по Либу (твердомеры)
Это самый широко применяемый на сегодня метод в мире, твёрдость определяется как отношение скоростей до и после отскока бойка от поверхности. Обозначается HL, где H — Hardness (твёрдость, англ.), L — Leeb (Либ, англ.), а 3-й буквой идёт обозначение типа датчика, напр. HLD, HLC и т. д.
Твёрдость резины
Определить твердость резины сегодня можно несколькими методами:
Измерение твёрдости резины по Шору (твердомеры и дюрометры)
Самый широко применяемый на сегодня метод в мире, твёрдость резины определяется по глубине проникновения в материал специальной закаленной стальной иглы (индентора) под действием калиброванной пружины. Твёрдость резины обозначается в международной практике как H, где H — Hardness (твёрдость, англ.), а 2-й буквой идёт обозначение типа шкалы, напр. HA, HB, HC, HD и т.д., в практике России пишется как «твёрдость по Шору тип А» или «твёрдость по Шору тип D».
Измерение твёрдости по Аскеру (твердомеры и дюрометры)
Это национальный японский метод, сходный с методом измерения твёрдости резины по Шору, но отличающийся от него типом инденторов, пружин и пр. Твёрдость резины обозначается в международной практике как Asker (Аскер, англ.), а далее идёт обозначение типа шкалы, напр. Asker С, Asker D и т.д. В России не применяется.
Измерение твёрдости по Роквеллу (твердомеры)
В этом случае используется стандартный твердомер Роквелла для измерения твёрдости металлов, но вместо индентора-конуса используются инденторы со стальными шариками. Твёрдость резины обозначается HR, где H — Hardness (твёрдость, англ.), R — Rockwell (Роквелл, англ.), а 3-й буквой идёт обозначение типа шкалы, напр. HRP, HRL, HRM или HRE.
Методы измерения твердости металлов
Разработано и произведено в Украине
Внимание! В связи с войной в нашей стране и нестабильным курсом доллара актуальность цен уточняйте, пожалуйста, по телефону или электронной почте.
Методы измерения твердости металлов
Все методы измерения твердости металлов можно условно разделить на две группы: прямые и косвенные.
1.

Это классические методы измерения твердости по Бринеллю, по Роквеллу, по Виккерсу, по Шору, по Супер-Роквеллу. Твердость металлов измеряется или оценивается в единицах твердости. Принцип измерения твердости всеми прямыми методами вытекает из определения твердости – способности материала сопротивляться внедрению другого, более твердого тела. В качестве более твердого тела используются инденторы, изготавливаемые, например, из алмаза или карбида вольфрама и имеющие определенную форму –шарик, конус, пирамида.
Приборы для измерения твердости прямыми методами являются стационарными установками, где к индентору, внедряющемуся в изделие или образец, прикладывается определенная нагрузка. Например, стационарный твердомер Роквелла NOVOTEST ТС-Р комплектуется двумя инденторами – шарик с диаметром 1.5875 мм и алмазная конусная пирамидка с углом 120°, прилагаемые испытательные нагрузки 60,100 и 150 кг.
После приложения нагрузки на поверхности образца остается отпечаток. Для каждого прямого метода определения твердости сформулирована зависимость для вычисления значения твердости по известным значениям приложенного усилия и определенным геометрическим параметрам отпечатка. Для метода Роквелла, к примеру, регистрируется глубина отпечатка.
Из достоинств прямых методов измерения твердости стоит отметить универсальность в отношении материала испытываемого образца. Стационарные твердомеры изначально готовы к измерению твердости любых металлов и сплавов без дополнительной калибровки. Недостатки – отсутствие мобильности, ограничение по размерам измеряемых изделии, наличие достаточно большого отпечатка, невысокий темп проведения замеров.
2. Косвенные методы
Косвенных методов всего два – ультразвуковой и динамический. Эти методы не напрямую измеряют твердость, а лишь оценивают значение твердости металла в зависимости от других физических свойств.
2.1. Измерение твердости ультразвуком заключается в фиксации степени изменения (затухания) частоты колебаний стержня с закрепленным на конце индентором при внедрении в поверхность образца. Чем мягче металл, тем больше глубина проникновения индентора и, соответственно, площадь его контакта с металлом, тем выше степень затухания частоты колебаний (в ультразвуковом диапазоне). Метод практически не имеет ограничений по массе и размерам испытуемых изделий, оставляет едва заметный отпечаток, применим для измерения твердости поверхностно упрочненных слоев и изделий со сложной конструкцией (шестерни, подшипники, метизы и т.д.). Ограниченно применяется на изделиях с крупнозернистой структурой.
2.2. Динамический метод реализует зависимость скорости отскока твердого тела от твердости на поверхности соударения. Чем мягче металл, тем больше энергии удара уходит на формирование отпечатка (пластическая деформация) и тем меньше скорость отскока бойка с твердосплавным шариком. Динамический метод применим для крупных, массивных изделий с весом не менее 5 кг и толщиной стенки не менее 10 мм. Подходит для измерения твердости, в том числе и на литых изделиях. Менее чувствителен к качеству поверхности, чем ультразвуковой метод.
2.3. Оба косвенных метода получили распространение в виде портативных, электронных приборов. Измерение твердости переносным твердомером основано на правильном выборе метода контроля (ультразвук или динамика) и использовании корректной калибровки прибора. Обычно портативные твердомеры изначально откалиброваны по стали на стальных мерах твердости и имеют возможность пользовательской калибровки на других металлах и сплавах при наличии образцов с известной твердостью.
Преимущества переносных твердомеров NOVOTEST очевидны: мобильность, портативность, автономность, высокая скорость проведения измерений. Также стоит отметить наличие в электронных приборах возможности измерения твердости по нескольким шкалам, архивации и статистической обработки данных, связи с компьютером.
3. Меры твердости
Используются для настройки и проверки как портативных, так и стационарных твердомеров. Выпускаются по каждой шкале твердости отдельно и имеют уникальные размеры и номиналы в
единицах твердости в соответствии с нормативно-технической документацией.
Автор: Сергей Погорелов
Измерение твердости металлов | Статьи
Одной из наиболее распространенных характеристик, определяющих качество металлов и сплавов, возможность их применения в различных конструкциях и при различных условиях работы, является твёрдость. Твёрдость – свойство материала сопротивляться проникновению в него другого, более твёрдого тела — индентора. Обычно испытания на твердость производятся чаще, чем определение других механических характеристик металлов: деформации, прочности, относительного удлинения, пластичности и прочее.
Твердостью материала называют способность оказывать сопротивление механическому проникновению в его поверхностный слой другого твердого тела. Для определения твердости в поверхность материала с определённой силой вдавливается тело (индентор*), выполненное в виде стального шарика, алмазного конуса, пирамиды или иглы. По размерам получаемого на поверхности отпечатка судят о твердости материала. Таким образом, под твердостью понимают сопротивление материала местной пластической деформации, возникающей при внедрении в него более твердого тела – индентора. В зависимости от способа измерения твердости материала, количественно ее характеризуют числами твердости по Бринеллю (НВ), Роквеллу (HRC) или Виккерсу(HV).
Существует несколько способов измерения твердости, различающихся по характеру воздействия наконечника. Твердость можно измерять вдавливанием индентора (способ вдавливания), ударом или же по отскоку наконечника – шарика. Твердость, определенная царапаньем, характеризует сопротивление разрушению, по отскоку – упругие свойства, вдавливанием — сопротивление пластической деформации. Перспективным и высокоточным методом является метод непрерывного вдавливания, при котором записывается диаграмма перемещения, возникающего при внедрении индентора, с одновременной регистрацией усилий. В зависимости от скорости приложения нагрузки на индентор твердость различают статическую (нагрузка прикладывается плавно) и динамическую (нагрузка прикладывается ударом).
Таблица 1 – Особенности различных методов измерения твердости.
Далее, мы кратко рассмотрим классические методы измерения твердости металлов:
Твердость по методу Бринелля
Для измерения твердости по методу Бринелля, в нашем каталоге представлен современный стационарный твердомер TH-600 и HB-3000B— более улучшенный твердомер, может быть использован для определения твердости закаленных и незакаленных сталей, чугуна, цветных сплавов, мягких материалов для вкладышей подшипников.

Твердость по методу Роквелла — твердость, определяемая разностью между условной максимальной глубиной проникновения индентора и остаточной глубиной его внедрения под действием основной нагрузки, после снятия этой нагрузки, но при сохранении предварительной нагрузки. При этом методе индентором является алмазный конус или стальной закаленный шарик. В отличие от измерений по методу Бринелля твердость определяют по глубине отпечатка, а не по его площади. Глубина отпечатка измеряется в самом процессе вдавливания, что значительно упрощает испытания. Нагрузка прилагается последовательно в две стадии (ГОСТ 9013-59): сначала предварительная, обычно равная 10 кгс (для устранения влияния упругой деформации и различной степени шероховатости), а затем основная.
Твердомер Роквелла TH-320 измеряет разность между глубиной отпечатков, полученных от вдавливания наконечника под действием основной и предварительной нагрузок.
При измерении твердости методом Роквелла необходимо, чтобы на поверхности образца не было окалины, трещин, выбоин и др. Необходимо контролировать перпендикулярность приложения нагрузки и поверхности образца и устойчивость его положения на столике прибора. Расстояние отпечатка должно быть не менее 1,5 мм при вдавливании конуса и не менее 4мм при вдавливании шарика. Толщина образца должна не менее чем в 10 раз превышать глубину внедрения наконечника после снятия основной нагрузки. Твердость следует измерять не менее 3 раз на одном образце, усредняя полученные результаты.
Твердость по методу Виккерса в поверхность материала вдавливается алмазная четырехгранная пирамида с углом при вершине равным 136 градусов. После снятия нагрузки вдавливания измеряется диагональ отпечатка. Число твердости по Виккерсу HV подсчитывается как отношение нагрузки к измеренному значению диагонали отпечатка:

При измерении твердости по Виккерсу должны быть соблюдены следующие условия:
• плавное возрастание нагрузки до необходимого значения;
• обеспечение перпендикулярности приложения действующего усилия к испытуемой поверхности;
• поверхность испытуемого образца должна иметь шероховатость не более 0,16 мкм;
• поддержание постоянства приложенной нагрузки в течение установленного времени;
• расстояние между центром отпечатка и краем образца или соседнего отпечатка должно быть не менее 2,5 длины диагонали отпечатка;
Преимущество метода Виккерса по сравнению с методом Бринелля заключается в том, что методом Виккерса можно испытывать материалы более высокой твердости из-за применения алмазной пирамиды.
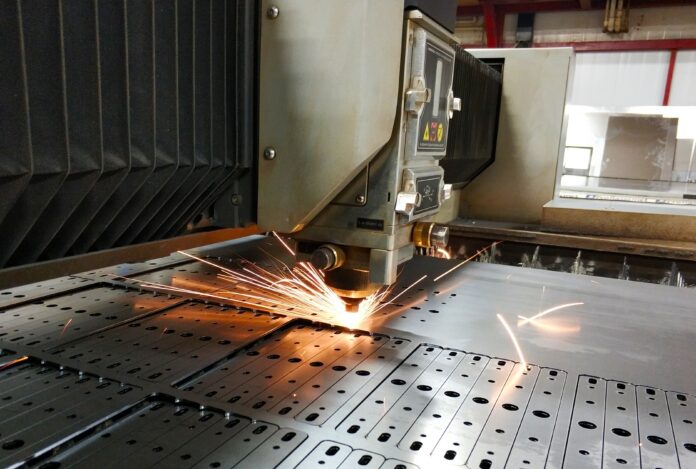
В нашем каталоге представлена целая линейка стационарных твердомеров по методу Виккерса: HV-10, HV-30 и HV-50.
Твердомеры серии HV представляют собой механические твердомеры, обладающие высокой точностью и удобством в эксплуатации и обслуживании. Данные твердомеры широко применяются на производстве, в научно-исследовательских институтах и лабораториях. Уникальное устройство преобразования и микро окулярное устройство считывания измерений, позволяющие сочетать в приборе легкость использования и высокую точность измерений.
*Индентор (англ. indenter от indent — вдавливать) — изготовленный из алмаза, твёрдого сплава или закаленной стали наконечник прибора, используемого для измерения твёрдости. Иногда инденторами (Nanoindenter) называют сами приборы для измерения нанотвердости.
Методы измерения твердости
- Блог: Термическая обработка и другие идеи, индукционная термообработка
Закалка металла — это процедура термообработки, позволяющая упрочнить внешний слой металла, в то время как сердцевина остается мягкой. Затвердевший слой материала известен как «корпус».
Индукционная закалка имеет много преимуществ, в том числе дополнительную прочность, ударную вязкость и возможность выборочного применения поверхностной твердости к частям материала. Хотя эти преимущества влияют на закаленную поверхность, сердцевина остается гибкой.
После завершения процесса необходимо проверить металл, чтобы убедиться, что в процессе индукционной термообработки был достигнут надлежащий уровень твердости. Тестирование необходимо для проверки того, что детали достигли нужной твердости, необходимой для использования в тех условиях, для которых они предназначены. Способы измерения твердости и методы испытаний различаются.
Как измеряется твердость металла?
Существует несколько различных методов измерения твердости металла. Наиболее распространенные тесты на твердость материала включают удар по металлу с последующим измерением уровня сопротивления вдавливанию или размера вмятины.
Двумя распространенными методами испытаний являются микро- и макро-испытания на твердость. Основное различие между двумя типами испытаний заключается в том, что микротвердость измеряет размер вмятины для определения твердости на микроскопическом уровне. Испытания на макротвердость, такие как тест Роквелла, измеряют сопротивление вдавливанию, а не размер вмятины.
Испытание состоит из использования фиксированной силы или нагрузки и индентора. Тест проникает в металл, а твердость рассчитывается по сопротивлению металла вдавливанию или размеру вмятины.
В каждом методе тестирования используется свой пенетратор. К ним относятся пенетраторы, изготовленные как из закаленной стали или алмаза, так и в форме шара, конуса или пирамиды.
Показатели твердости выражаются в индексе, основанном либо на глубине вмятины после испытания, либо в величине вмятины. За цифрой твердости следует код, идентифицирующий метод испытания.
Соответствующие тесты должны быть проведены в зависимости от материала, обработки поверхности, твердости и других факторов, таких как плотность, геометрия и глубина твердости, чтобы определить, какие тесты лучше подходят для проверки качества конкретных приложений.
Существует множество различных методов испытаний, но наиболее часто используемыми инструментами для испытаний являются твердомеры Роквелла, Бринелля и твердомеры по Виккерсу.
Макроизмерение твердости
Метод определения твердости по Роквеллу
Испытание по Роквеллу является наиболее часто применяемым методом определения твердости. Относительно простая в использовании и точная шкала Роквелла представляет собой тест на макротвердость, поскольку для определения твердости не требуется микроскопическая оценка. Испытательное оборудование доступно как в ручном, так и в полуавтоматическом режимах.
Испытание заключается в приложении двух нагрузок к металлу инденторами, изготовленными либо из шарика из карбида вольфрама, либо из алмаза в форме пирамиды.
Тест Роквелла можно использовать практически для всех типов металлов. Это испытание может оказаться неподходящим, если на индентор будут воздействовать слишком большие вариации поверхности или структуры испытуемого материала или если отпечаток будет слишком большим для применения.
После подготовки поверхности испытуемого металла к индентору прикладывают небольшую нагрузку или усилие, обычно в пределах от 3 до 5 кгс (килограмм-сила), создавая контрольную точку для измерения. Затем в течение определенного периода времени прикладывают большую силу (от 15 до 150 кгс, в зависимости от прочности испытуемого материала).
Наконец, большая сила снимается, а легкая остается на месте. Измерение числа твердости по Роквеллу рассчитывается с использованием разницы в глубине проникновения между двумя более легкими нагрузками как до, так и после приложения более тяжелой нагрузки.
Метод определения твердости по Бринеллю
Еще один распространенный тест на макротвердость, метод Бринелля, в основном используется для металлов, которые слишком грубы или шероховаты для измерения другими методами испытаний, таких как отливки или кованые материалы.
Испытательная нагрузка или сила очень велика, от 500 до 3000 кгс и более, а индентор намного больше, чем при других испытаниях (например, твердосплавный шарик диаметром 10 мм).
Испытание заключается в приложении нагрузки к индентору и удерживании ее на закаленном металле в течение определенного периода времени перед снятием. После удаления измеряется размер углубления. Расчет числа твердости по Бринеллю состоит из нагрузки, деленной на площадь поверхности отпечатка.
Испытание на микротвердость
Метод определения твердости по Виккерсу
Испытание на определение твердости по Виккерсу также называется определением микротвердости, поскольку оно определяется путем наблюдения за размером отпечатка под микроскопом и обычно используется на более мелких деталях и деталях, тонком материале или корпусах или для точного измерения глубины корпуса. Тестовые материалы должны быть отполированы, чтобы должным образом поддерживать и измерять более мелкие отпечатки, сделанные с помощью этого метода.
Индентор представляет собой алмаз в виде квадратной пирамиды, а нагрузки, используемые для испытаний, очень малы по сравнению с испытаниями на макротвердость, часто от 10 г до 1 кгс. Благодаря более легкой силе и методу определения другие материалы, не являющиеся металлами, такие как глиняные или керамические детали, могут быть проверены с помощью метода Виккерса.
Метод Виккерса основан на оптической системе измерения и из-за его небольшого размера требует микроскопа для точных измерений меньших отпечатков, сделанных индентором. Часто необходимо разделить тестовый материал, чтобы он поместился внутри тестера.
Испытания на твердость в Zion
В Zion мы используем различные методы испытаний для определения твердости в зависимости от материала и спецификаций заказчика. Как правило, мы используем тест Роквелла для общего измерения твердости поверхности материала в процессе производства и некоторых определений глубины слоя. Тест на микротвердость по Виккерсу используется для приложений, требующих этого конкретного теста, и для более точного определения глубины слоя.
Для получения дополнительной информации о наших процессах и процедурах позвоните нам по телефону 330-483-4650 или свяжитесь с нами, чтобы узнать больше о том, как наш опыт в области индукционного нагрева может улучшить ваш бизнес.
Полное руководство – Изготовление из металла
Долгое время я думал, что единственный способ правильно проверить твердость металла – это использовать подходящую испытательную машину Rockwell. К счастью, за эти годы я изучил несколько других методов и приемов, которые действительно сделали это более выполнимым без машины стоимостью более 2500 долларов.
На самом деле, есть несколько разных способов сделать это, хотя результаты точности и практичности будут различаться. В этой статье я рассмотрю некоторые из этих методов, плюсы и минусы, и как их успешно реализовать. Используйте оглавление, если вас интересует конкретный метод.
Оглавление
Испытательная машина Rockwell
Вероятно, это наиболее распространенный способ профессионально и точно проверить твердость металлов. Закругленный стальной шарик или конический алмазный наконечник вдавливается в металл, и машина измеряет глубину вмятины.
Машина использует малую нагрузку и большую нагрузку, чтобы обеспечить точность показаний. Вы задаете незначительную нагрузку, и деталь правильно сядет между пенетратором и наковальней. Затем вы нажимаете кнопку или дергаете рычаг (в зависимости от машины), и тестер прикладывает основную нагрузку. Машина считывает разницу в расстоянии между грузами и дает точные показания.
Плюсы:
- Сверхточная, достаточно простая проверка работы в пределах +/- 1 HRC или лучше, в зависимости от станка и того, насколько хорошо вы можете поддерживать заготовку наковальней
- Обычно они используются в механическом цехе, так что вы не потеряете их (по крайней мере, я надеюсь, что нет) и с меньшей вероятностью повредите их
- Обычно подготовка поверхности не требуется или почти не требуется реально шероховатый, как из песчаника)
Минусы:
- Машины дорогие! Хотя и не так дорого, как некоторые другие профессиональные системы
- Большие или неплоские детали может быть очень трудно (если не невозможно) проверить
- Он оставляет острую небольшую выемку на детали
- Не позволяет точно измерить тонкие детали
- Деталь должна иметь хорошую плоскую поверхность между наковальней и алмазным наконечником.
В качестве альтернативы круглые детали могут быть установлены в V-образный блок, но в любом случае металл должен иметь очень хорошую опору.
В целом, это золотой стандарт для тех, кто хочет проверить твердость металла. Это быстро и легко, если вы знаете, как пользоваться машиной.
Чаще всего используется для проверки твердости стали, прошедшей термообработку. Вот процесс:
Как пользоваться испытательной машиной Rockwell
- Выньте пенетратор. Обычно для мягких материалов, таких как мягкая сталь 1018, используется шкала Роквелла B, в которой используется закругленный стальной пенетратор 1/16 дюйма с основной нагрузкой 100 кг. Для закаленной или легированной стали будет использоваться шкала Роквелла C, в которой используется V-образный пенетратор с алмазным наконечником и основная нагрузка 150 кг. Как правило, в мастерских просто оставляют алмазный наконечник в станке, поскольку мало кто заботится о твердости мягкой стали.
- Хорошей практикой является проверка калибровки с использованием сертифицированной тестовой шайбы, чтобы убедиться, что установка работает, а затем проверить деталь, которую необходимо измерить.
- Поместите соответствующую наковальню в тестер. Используйте плоскую пятку для плоских деталей и V-образную пятку для круглых деталей.
- Загрузите начальную силу. Обычно это делается путем поднятия нижней наковальни с помощью маховика до тех пор, пока индикатор не совпадет с отметкой на циферблате (обычно это маленькая красная точка). Вы также можете выполнить точную настройку на циферблате, чтобы он идеально выровнялся на 0,9.0004
- Загрузить основную силу. Обычно это делается либо нажатием кнопки, либо нажатием рычага. Дайте ему несколько секунд, чтобы успокоиться и перестать двигаться.
- Отпустите основную нагрузку. Машина оставит незначительную нагрузку на индентор. Измерение твердости отобразится на циферблате.
Проделав это один или два раза, вы поймете, что это очень простое измерение, если у вас хорошая и стабильная установка.
Минимальная толщина для испытания на твердость по Роквеллу
Поскольку при испытании по Роквеллу необходимо сделать вмятину на испытательном образце, существует минимальная толщина, связанная с испытанием. Если материал слишком тонкий, вы будете измерять твердость опорной наковальни в большей степени, чем твердость испытуемого образца.
Вот небольшая таблица минимальной толщины материала по шкале Роквелла в зависимости от твердости:
Минимальная толщина | Твердость С по Роквеллу | Твердость по Роквеллу В |
0.022″ | 69 | – |
0.024″ | 67 | 94 |
0.026″ | 65 | 87 |
0.028″ | 62 | 80 |
0.030 ″ | 57 | 71 |
0.032″ | 52 | 62 |
0.034″ | 45 | 52 |
0.036″ | 37 | 40 |
0.038″ | 28 | 28 |
0.040″ | 20 | – |
So what does this mean? Вы не можете использовать метод Роквелла для проверки твердости прокладок 0,020″, если предполагается, что она составляет 60 HRC. Просто имейте в виду, что минимальная толщина находится в диапазоне 0,040 дюйма и меньше, поэтому вы можете найти ссылку, если вам когда-нибудь понадобится.
Испытание на твердость по Бринеллю
Возможно, вы слышали об этом в школе, что вы можете взять шарикоподшипник, ударить его молотком по куску металла с известной твердостью, а затем ударить им по рассматриваемому куску металла, сравните диаметры отпечатков и по результатам определите твердость металла.
Звучит удивительно просто, не правда ли?
На самом деле, люди, которые могут успешно справиться с этим, — вымирающий вид. И под умирающей породой я подразумеваю, что я еще не встречал ни одной живой.
Слишком много переменных, чтобы делать это вручную. Дважды подряд ударить молотком по чему-либо с одинаковой силой — это само по себе искусство легенды.
Более современный способ сделать это — использовать машину, которая нагружает индентор контролируемым усилием. Затем оператор с помощью специального микроскопа проверяет диаметр.
Тем не менее, точность этого метода в целом неоднозначна. Довольно редко можно найти одну из этих машин (кроме литейных заводов) просто потому, что обычно есть лучшие способы проверки твердости.
Плюсы:
- Если у вас есть только молоток и шарик из закаленной стали, это может дать вам общее представление о твердости отливки, где твердость будет варьироваться. Диаметр шарика будет соприкасаться с большей площадью поверхности детали и даст большую среднюю твердость
Минусы:
- Супер устаревшая технология. Это действительно непоследовательно даже среди профессионалов, и, как правило, есть лучшие способы проверки твердости. практично для твердой стали
Справедливости ради следует отметить, что существуют машины, которые автоматически определяют размер отпечатка без микроскопа оператора. Однако они делают это на основе измеренной глубины индентора. Это процесс, который использует Rockwell. Почему бы просто не использовать машину Роквелла?
Суть в том, что, если не считать применения неоднородных материалов (таких как отливки), у вас просто не будет особых причин для выбора этого метода.
Определение микротвердости
Это действительно интересно. Наиболее распространены микротвердости по Виккерсу и Кнупу. В реальной жизни я гораздо чаще сталкивался с Виккерсом.
Я сосредоточусь на Виккерсе, так как он мне больше знаком.
Концепция похожа на гибрид теста Роквелла и теста Бринелля. Пирамидальный индентор вдавливается в заготовку с небольшим усилием (менее 2 фунтов), после чего отпечаток измеряется по диагонали.
Квадратная выемка намного четче и ее легче измерить, чем круглая выемка Бринелля, но она также намного меньше. Нужен хороший микроскоп.
Плюсы:
- Можно точно измерить очень тонкие детали
- Можно измерить очень мягкие и гораздо более твердые образцы – процесс имеет превосходный диапазон, и один и тот же индентор используется для всех испытаний
- такой маленький, что процесс вряд ли повлияет на часть
Минусы:
- Поверхность образца необходимо отшлифовать и отполировать для точного измерения – требования для теста Виккерса намного строже, чем для теста Роквелла
- Процесс медленный – требуется от 30 до 60 секунд на сам тест, но подготовка заготовки может быть утомительной
- Система дорогая, так как вам также нужна оптическая измерительная система в дополнение к индентору
- Это тест, который действительно должен быть выполнен в чистой лаборатории вместо этого цеха (как у Rockwell) – рекомендуются даже виброустойчивые столы
Тем не менее метод Виккерса становится все более популярным благодаря своей точности и универсальности, несмотря на то, что требует много времени. Маловероятно, что вы будете часто видеть их в своем обычном механическом цехе, но они становятся основным продуктом на специализированных объектах, таких как мастерские по производству и ремонту турбин и медицинские производственные предприятия.
Вот несколько заметок о тесте Кнупа. В принципе очень похоже на Виккерс, за следующими исключениями:
- Индентор имеет ромбовидную форму
- Глубина отпечатка составляет половину глубины Виккерса, поэтому чрезвычайно тонкие детали могут быть осмотрены. Пример: алюминиевая фольга
- Он особенно подходит для измерения очень твердых и хрупких материалов, таких как стекло и керамика, так как при этом методе испытаний меньше трещин -достойно (хотя Роквелл самый обычный для автомастерских). Теперь давайте перейдем к некоторым действительно доступным и простым решениям, которые часто достаточно хороши и имеют некоторые действительно примечательные преимущества.
Склероскоп или Либ (тест на отскок)
Когда я впервые увидел эту штуку, я подумал, что это самая нелепая идея.
Затем я попробовал его несколько раз и понял, что это действительно не так уж и плохо. Он предназначен для очень портативной проверки твердости.
Для ясности: я бы не стал полагаться на этот метод для критических деталей. Тем не менее, это очень просто и просто хороший инструмент для справки.
Собственно, и в одной ремонтной мастерской, где я работал, всем продавцам выдавали по одному из таких тестеров. Таким образом, когда они смотрели на ремонтную работу, они могли быстро выяснить, была ли деталь твердой или нет, чтобы они могли правильно настроить ожидания клиентов с места в карьер.
Итак, у этого теста есть два варианта: старый способ и удобная, более современная карманная версия (Leeb). Честно говоря, сегодня они не так популярны, но о них приятно знать.
Метод старой школы был настоящей маленькой машиной. Магнит будет удерживать груз с алмазным наконечником, называемый молотком, и машина будет отображать высоту отскока молотка, когда он будет брошен с фиксированного места.
Чем тверже материал, тем выше отскок.
В целом, это не очень точно, но это достойный способ получить приблизительное представление. Машина была изобретена в 1907 году, но она никогда не пользовалась таким успехом, как метод Роквелла (по очевидным причинам). В 1975 году процесс был улучшен благодаря изобретению теста Лееба
Хорошо, маловероятно, что вы увидите устройства старой школы, которые все еще используются сегодня, но вы можете увидеть более современные «карманные эталонные» устройства, которые на самом деле делать больше или меньше работы.
Честно говоря, большинство этих устройств на самом деле предназначены для других материалов, таких как бетон (так называемые резиометры), но есть несколько устройств для металла, например этот. Они на самом деле не очень дешевые (самые экономичные, которые я нашел, стоят около 400 долларов, а более красивые могут стоить около 1000 долларов), но это намного дешевле, чем 2500 долларов за машину Rockwell, и она значительно более портативна.
Я также видел парней, у которых есть очень простой механический, который представляет собой трубку со шкалой и шариковым подшипником с магнитным освобождением. Тем не менее, они довольно похожи по цене. Обычно больше 250 долларов. Для того, который я использовал, я смог получить показания в пределах +/- 3-5 HRC.
Проверка напильником
Это классический и простой способ, которым кузнецы проверяют эффективность термообработки. Сама концепция очень проста:
Если режущий инструмент тверже материала, он будет резать. Если мягче, то нет.
Таким образом, если вы царапаете напильником кусок металла, он впивается в него, если металл мягче напильника, и скользит по заготовке, если он тверже. На самом деле не требуется никаких навыков или «чувства», чтобы сделать это правильно — это совершенно очевидно, когда напильник вгрызается.
Так что это хорошая стандартная проверка да/нет, чтобы увидеть, имеет ли сталь твердость около 60 HRC или нет. Это не будет стоить вам ничего, чего у вас еще нет, и это просто работает.
Но что, если вам нужно проверить что-то, что должно иметь твердость 50 HRC? или 40 HRC? Большинство парней думают, что для этого вам нужен тестер Rockwell. Вот набор инструментов стоимостью менее 100 долларов, который сильно облегчит вам жизнь:
Вы можете купить наборы напильников для проверки различных твердостей. Напильники проходят термообработку с шагом 5 HRC, поэтому вы можете начать с самого твердого напильника и постепенно уменьшать его, пока не получите тот, который скользит, а не кусается.
У меня есть один из них в моем ящике с инструментами, и я буквально использую его все время. Это не очень точно, так как вы можете проверить только шаг 5 HRC, но он работает точно так, как задумано, и это отличный способ получить примерное значение. И, для протокола, я проверил это на машине Роквелла, и я еще не ошибся.
Я купил свой на Amazon. Вот ссылка, чтобы вы могли убедиться в этом сами. Если вы работаете с закаленной сталью, это действительно полезно иметь в своем наборе инструментов.
Он также отлично подходит для больших или непризматических (причудливой формы) деталей, которые не помещаются в машину Роквелла.
В целом, вы, наверное, догадались, какие методы тестирования я предпочитаю: Rockwell для точного тестирования и наборы файлов для быстрой, мобильной приблизительной проверки. Конечно, всегда будут обстоятельства, при которых другой тип теста будет более подходящим, но с этими двумя в вашем распоряжении вы будете хорошо подготовлены для выполнения подавляющего большинства возникающих заданий.
Как проверить твердость металлов
Проверка твердости металловИзображение предоставлено: Shutterstock/Thaweesak Thipphamon
Существует несколько различных методов испытаний и шкал, которые используются для измерения относительной твердости таких материалов, как металлы. Ниже приводится краткое изложение наиболее распространенных из этих методологий.
Испытание на твердость по Бринеллю
Испытание по Бринеллю для определения твердости металлических материалов заключается в приложении известной нагрузки к поверхности испытуемого материала через закаленный стальной шарик известного диаметра.
Измеряют диаметр полученного постоянного отпечатка в металле, а затем рассчитывают число твердости по Бринеллю (BHN) по следующей формуле, в которой D = диаметр шарика в миллиметрах, d = измеренный диаметр по краю отпечатка в миллиметрах, и P = приложенная нагрузка в килограммах.
Если бы стальной шарик не деформировался под действием приложенной нагрузки и если бы отпечаток был действительно сферическим, то предыдущая формула была бы общей, и можно было бы использовать любую комбинацию приложенной нагрузки и размера шарика. Отпечаток, однако, не совсем сферическая поверхность, потому что всегда должна быть некоторая деформация стального шарика и некоторое восстановление формы металла в отпечатке; следовательно, для стандартного теста Бринелля размер и характеристики мяча, а также величина приложенной нагрузки должны быть стандартизированы. В стандартной пробе Бринелля используется мяч диаметром 10 мм и нагрузка 3000, 1500 или 500 кг. Желательно, хотя и не обязательно, чтобы испытательная нагрузка была такой величины, чтобы диаметр отпечатка находился в диапазоне от 2,50 до 4,75 мм.
Следующие испытательные нагрузки и приблизительные числа Бринелля для этого диапазона диаметров оттисков составляют: 3000 кг, от 160 до 600 BHN; 1500 кг, от 80 до 300 BHN; 500 кг, от 26 до 100 руб. При проведении теста Бринелля нагрузку следует прикладывать постоянно и без рывков в течение не менее 15 с для железа и стали и не менее 30 с при испытании других металлов. Минимальный период 2 минуты, например, рекомендуется для магния и магниевых сплавов. (Для более мягких металлов иногда используются нагрузки 250, 125 или 100 кг.)
В соответствии со стандартом E10-66 Американского общества по испытаниям и материалам стальной шарик можно использовать для материала с BHN не более 450, шар Hultgren — для материала не более 500 или карбидный шарик — для материала не более 630. Испытание на твердость по Бринеллю не рекомендуется для материалов с BHN выше 630.
Испытание на твердость по Роквеллу
Твердомер по Роквеллу представляет собой прибор, который измеряет твердость путем определения глубины проникновения пенетратора в образец при определенных фиксированных условиях испытания.
Пенетратор может представлять собой стальной шарик или алмазный сфероконический пенетратор. Число твердости связано с глубиной вдавливания, и число выше, чем тверже материал. Сначала прикладывается небольшая нагрузка в 10 кг, вызывающая начальное проникновение; циферблат устанавливается на ноль на черно-цифровой шкале, и прикладывается основная нагрузка. Эта основная нагрузка обычно составляет 60 или 100 кг, когда в качестве пенетратора используется стальной шар, но при необходимости могут использоваться и другие нагрузки. Шаровой пенетратор обычно имеет диаметр 1 дюйм, но для мягких металлов можно использовать другие пенетраторы большего диаметра, например 18 дюймов. При использовании алмазного сфероконического пенетратора нагрузка обычно составляет 150 кг. Опыт определяет наилучшее сочетание нагрузки и пенетратора для использования. После того, как большая нагрузка приложена и снята, в соответствии со стандартной процедурой, показания снимаются, пока еще действует второстепенная нагрузка.
Шкала твердости по Роквеллу
Различные шкалы Роквелла и их применение показаны в следующей таблице. Тип пенетратора и нагрузка, используемая с каждым из них, показаны в таблицах 5 и 6, в которых приведены сравнительные значения твердости для различных шкал твердости.
Там, где желателен неглубокий отпечаток или небольшая площадь для материалов, более мягких, чем закаленная сталь.
Склероскоп Шора
Склероскоп — это инструмент, который измеряет твердость работы с точки зрения эластичности. Молоток с алмазным наконечником падает с известной высоты на испытуемый металл. Когда этот молоток ударяет по металлу, он отскакивает, и чем тверже металл, тем сильнее отскок. Записывается предельная высота отскока, и среднее число показаний, снятых на одном изделии, даст хорошее представление о твердости работы. Гладкость поверхности работы влияет на показания прибора. На показания также влияют контур и масса изделия и глубина гильзы, а в науглероженном изделии мягкий сердечник малоглубинного науглероживания, пакетной закалки или цианидной закалки, поглощающий силу удара молотка.
и уменьшая отскок. Молоток весит около 40 гран, высота отскока закаленной стали составляет около 100 по шкале, или около 614 дюймов (158,8 мм), а общее падение составляет около 10 дюймов или 255 миллиметров.
Испытание на твердость по Виккерсу
Критерий Виккерса в принципе аналогичен критерию Бринелля. Стандартный пенетратор Виккерса представляет собой алмазную пирамиду с квадратным основанием, имеющую угол при вершине 136 градусов. Числовое значение числа твердости равно приложенной нагрузке в килограммах, деленной на площадь пирамидального вдавления. Требуется гладкая, прочно поддерживаемая, плоская поверхность. Нагрузка, которую обычно прикладывают в течение 30 секунд, может составлять 5, 10, 20, 30, 50 или 120 килограммов. 50-килограммовая нагрузка – самая обычная. Число твердости основано на длине диагонали квадратного отпечатка. Тест Виккерса считается очень точным и может применяться как к тонким листам, так и к более крупным профилям при надлежащем регулировании нагрузки.
Числа твердости по Кнупу
Испытание на твердость по Кнупу применимо к чрезвычайно тонким металлам, поверхностям с покрытием, исключительно твердым и хрупким материалам, очень мелким науглероженным или азотированным поверхностям, а также в тех случаях, когда прикладываемая нагрузка должна быть ниже 3600 граммов. Индентор Кнупа представляет собой алмаз, отшлифованный до вытянутой пирамидальной формы, и он производит отпечаток, имеющий длинные и короткие диагонали с соотношением примерно 7 к 1. Продольный угол индентора составляет 172 градуса, 30 минут, а поперечный угол 130 градусов. . Прибор Tukon Tester, в котором используется индентор Кнупа, является полностью автоматическим с электронным управлением. Число твердости по Кнупу равно нагрузке в килограммах, деленной на проектируемую площадь вмятины в квадратных миллиметрах. Число отпечатков, соответствующее длинной диагонали и заданной нагрузке, можно определить по таблице, рассчитанной для теоретически идеального индентора.
Нагрузку, которая может варьироваться от 25 до 3600 грамм, прикладывают в течение определенного времени и всегда перпендикулярно испытуемой поверхности. Необходимы притертые плоские поверхности без царапин.
Индикатор твердости Monotron
С помощью этого инструмента импрессорный наконечник с алмазным шариком диаметром 34 мм вдавливается в материал на глубину 95000 дюймов; давление, необходимое для создания этого постоянного отпечатка, указывает на твердость. Один из двух циферблатов показывает давление в килограммах и фунтах, а другой — глубину отпечатка в миллиметрах и дюймах. Показания в числах Бринелля можно получить с помощью шкалы, обозначенной как М-1.
Тест Крепости
С помощью этого устройства стандартное стальное сверло делает определенное число оборотов, прижимая его со стандартной силой к испытуемому образцу. Твердость автоматически записывается на диаграмме, на которой совершенно мягкий материал дает горизонтальную линию, а материал, такой же твердый, как само сверло, дает вертикальную линию, промежуточная твердость представлена соответствующим углом между 0 и 90 градусами.