2.2 Погрузка и выгрузка грузов из вагонов собственными силами и собственными или арендуемыми средствами хозяйства, механизация этих работ за год
Росстатом сообщено (Информация от 24.12.2021), что изменения, внесенные Приказом Росстата от 17.12.2021 N 925, вступают в силу с 1 января 2022 года.
2.2 Погрузка и выгрузка грузов из вагонов собственными
силами и собственными или арендуемыми средствами
хозяйства, механизация этих работ за год
13. Данные по подразделу заполняются хозяйством по всем работам, выполняемым собственными силами и собственными или арендуемыми средствами, независимо от места осуществления погрузки и выгрузки вагонов, а также по работам, выполненным предприятиями, эксплуатирующими подъездной путь и не составляющими отчета.
14. Раздел составляется на основании актов и нарядов на выполнение работ.
В подразделе отражаются погрузка и выгрузка вагонов, выполненные грузчиками и механизмами как железнодорожного (транспортного) цеха, так и других производственных цехов отчитывающегося хозяйства.
Погрузка и выгрузка вагонов, выполненные для хозяйства сторонними хозяйствами (т.е. их силами и их или арендуемыми ими средствами), в раздел 2 не включаются.
15. Под комплексной механизацией погрузочно-разгрузочных работ следует понимать такую механизированную переработку грузов, при которой основные операции (подъем и перемещение грузов) от начала до конца операции выполняются машинами и механизмами, а труд людей сведен к управлению этими машинами или к выполнению вспомогательных операций без применения ручного труда на основных операциях.
К вспомогательным операциям при комплексной механизированной переработке грузов относятся:
застропка и отстропка грузов;
открывание и закрывание люков, дверей вагонов, бортов платформ и автомобилей;
зачистка вагонов после выгрузки от остатков груза;
установка и снятие стоек прокладок, щитов и решеток, крепление грузов на подвижном составе;
подача сигналов управления;
подноска и уборка инвентаря, приспособлений.
16. В объем работ, выполненных комплексно-механизированным способом, включаются погрузочно-разгрузочные работы, произведенные с помощью различных типов подъемно-транспортного оборудования — транспортеров, кранов, автопогрузчиков, экскаваторов, а также выгрузка, осуществляемая из саморазгружающегося подвижного состава (саморазгружающиеся полувагоны, думпкары; при помощи специальных приспособлений — на повышенных путях).
17. Погрузочно-разгрузочные работы, выполняемые при помощи механизмов и приспособлений, приводимых в действие вручную (например, тачки, тележки, блоки, лебедки), а также выгрузка грузов из полувагонов и специального подвижного состава на неповышенных путях без участия погрузочно-разгрузочных машин к комплексно-механизированным работам не относятся.
Погрузочно-разгрузочные работы, выполненные в связи с внутрицеховыми перевозками, а также в связи с штабелировкой и перевалкой грузов на складах, базах или территории хозяйства, в отчет не включаются.
Правила погрузки и выгрузки вагонов, полувагонов и железнодорожных платформ.

ОТВЕТ:
Организация производства работ по погрузке и разгрузке транспортных средств (полувагонов, автомашин).
9.5.18 е) погрузочно-разгрузочные работы и складирование грузов кранами на базах, складах, площадках должны выполняться по технологическим картам, разработанным с учетом требований ГОСТ 12.3.009 и утвержденным в установленном порядке;
ж) не разрешается опускать груз на автомашину, а также поднимать груз при нахождении людей в кузове или кабине автомашины. В местах постоянной погрузки и разгрузки автомашин и полувагонов должны быть установлены стационарные эстакады или навесные площадки для стропальщиков. Погрузка и разгрузка полувагонов крюковыми кранами должны производиться по технологии, утвержденной производителем работ, в которой должны быть определены места нахождения стропальщиков при перемещении грузов, а также возможность выхода их на эстакады и навесные площадки. Нахождение людей в полувагонах при подъеме и опускании грузов краном не допускается;
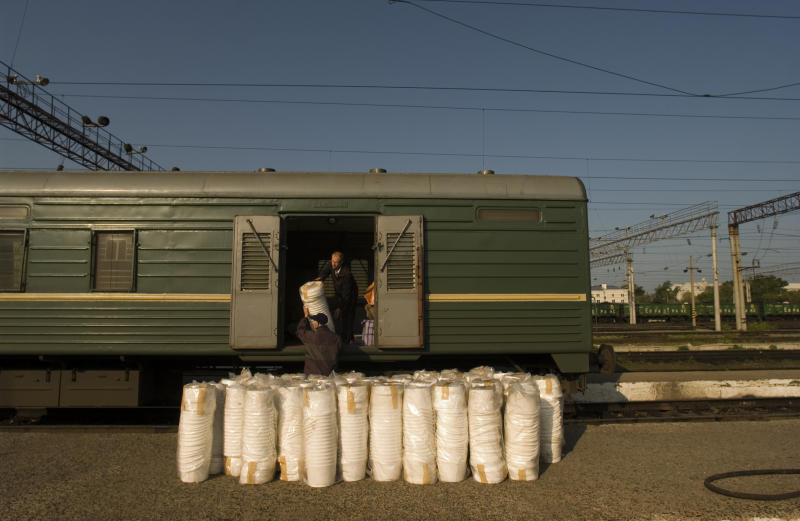
1. Технологическая карта, схемы строповок.
2. Полувагоны — лицо, отв. по ст.9.4.4.
3. П/в — башмаки, локомотив.
4. А/м — тормоза и отсутствие людей в кабине.
5. Отсутствие стропальщиков в п/в и кузове при подъеме или опускании груза.
6. Эстакады, навесные площадки, лестницы.
7. Пронос груза над кабиной запрещен.
8. Укладка и разборка груза равномерно без нарушения равновесия транспортных средств.Предъявляемый
к перевозке груз должен быть подготовлен
к перевозке таким образом, чтобы в
процессе перевозки были обеспечены
безопасность движения поездов, сохранность
груза, вагонов и контейнеров. С этой
целью грузоотправителем должны быть
обеспечены: –
прочность узлов и деталей груза,
предназначенных для установки средств
крепления. При необходимости груз должен
быть оборудован приспособлениями для
его крепления;
– надежное
закрепление груза внутри упаковки;
–
подготовка автотракторной техники
и сельскохозяйственных машин к перевозке
в порядке, установленном соответствующими
правилами перевозок железнодорожным
транспортом;
– перед
погрузкой грузов, содержащих мелкие
фракции, дополнительные меры по уплотнению
зазоров кузова вагона, поверхность
груза после погрузки на открытый
подвижной состав должна быть разровнена,
а при необходимости и уплотнена.
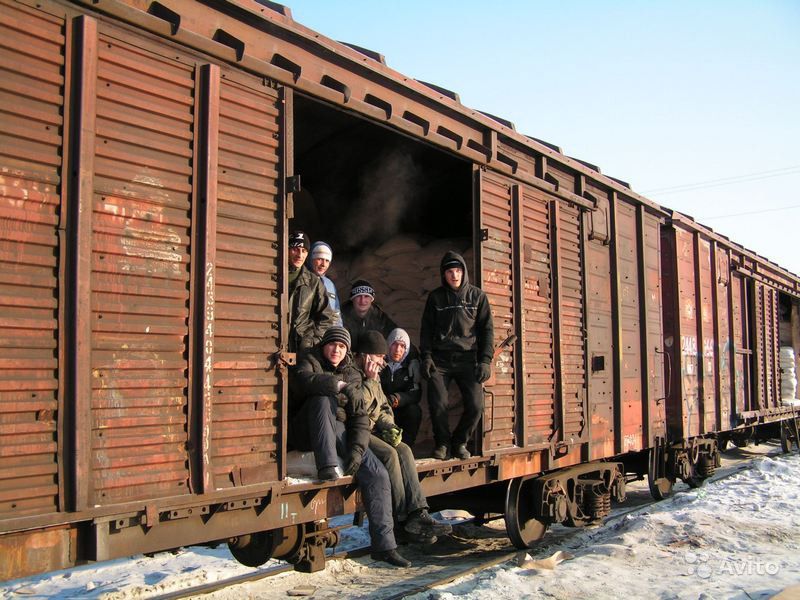

Погрузка и разгрузка железнодорожных вагонов. Современные решения для смешанного вагонного парка.
Погрузка и разгрузка вагонов являются звеньями одной цепи.
Компания «ТТС» специализируется на конвейерном оборудовании для обработки сыпучих грузов на морских терминалах, складах и заводах.
Большинство крупных проектов морских терминалов связаны с доставкой грузов в порт по железной дороге. Когда годовой объем перевалки достигает миллионов тонн, железнодорожный транспорт является единственным способом доставки сыпучих грузов с точки зрения рентабельности и сроков. По железной дороге перевозят уголь, руду, минеральные удобрения, зерно, цемент и многие другие виды сыпучих грузов. Для перевозки используются различные виды железнодорожных вагонов, как специальных, так и многоцелевых. В данной статье мы рассмотрим перспективные технологические решения, направленные на оптимизацию погрузки и разгрузки вагонов-хопперов, используемых для перевозки минерального сырья по железнодорожным путям колеи 1520 мм.
Проблема.
Заказчик ТТС контролирует как добычу железной и апатитовой руды, так и транспортировку и отгрузку продукции на портовом терминале. Добыча полезных ископаемых ведется в Мурманской области, а погрузка судов осуществляется в Морском торговом порту. Расстояние между местами погрузки и разгрузки около 300 км. Для столь короткого расстояния перевозки большую роль играет скорость погрузки и разгрузки вагонов (оборот). Технология погрузки и разгрузки не менялась более 30 лет, однако развитие компании направлено на значительное увеличение добычи и объема производства. С ростом интенсивности отгрузки ГОК столкнулся со следующими трудностями:
— достигнут предел пропускной способности существующей станции погрузки вагонов. В настоящее время пропускная способность составляет 900-1000 т/ч на двух железнодорожных путях.
— проблемы со скоростью разгрузки буферного силоса, расположенного над железнодорожным полотном — груз склонен к слеживанию и выгибанию.
— сложно выполнить требования по точной загрузке вагонов. Максимальный вес строго ограничен вагоновладельцами и владельцами железных дорог. Износ железнодорожных путей и инфраструктуры не позволяет доставлять перегруженные вагоны. Недогрузка вагонов приводит к убыткам, так как стоимость аренды не зависит от веса груза.
— парк вагонов очень разнообразен. В одном поезде могут находиться вагоны 6-8 разных моделей. Это связано с дефицитом специализированных вагонов для полезных ископаемых на 1520 путей. В связи с этим используются вагоны различной вместимости, длины и расположения загрузочных люков.
— потеря груза из-за запыления и связанных с этим тяжелых условий труда операторов.
Решение проблемы.
Расположение станции погрузки относительно производственных линий горно-обогатительного комбината и складов, а также конфигурация железнодорожных путей не позволяли решить проблему роста грузоподъемности простым увеличением количества одновременно загружаемых рельсов легковые автомобили. Места просто не было, а инвестиции в расширение станции и строительство новых путей и буферных бункеров были слишком велики.
Наша команда дизайнеров всегда начинает свою работу с изучения текущей ситуации и сбора данных. Инженеры компании ТТС много часов замеряли время цикла погрузки и регистрировали все операции и работу персонала. Анализ данных показал, что основным фактором потери времени является проблема заполнения вагонов до их максимальной грузоподъемности. Из-за разного количества вагонов и расположения верхних люков приходилось их сдвигать при погрузке. Загрузочные горловины, через которые материал подавался из буферного силоса, имели фиксированное положение и не совпадали с загрузочными люками вагонов разного типа. Перемещение вагона под погрузку через другой люк привело к невозможности взвешивания вагона. Вагон соскользнул с весовой платформы. Поэтому дозагрузка производилась операторами «на глазок». Часто вагоны уходили недогруженными, так как критичнее был перевес.
После обработки данной информации специалисты ТТС провели проектные работы и моделирование процессов реконструкции станции налива вагонов, а также решили все задачи заказчика на стадии проектирования, поэтому сейчас проект находится на стадии реализации.
Вот что предлагалось изменить:
1. Буферные силосы будут оборудованы виброприводами и системой пневматического дробления материала для предотвращения выгибания материала и ускорения его выгрузки.
2. Фиксированные загрузочные горлышки заменены на телескопические загрузочные лотки с позиционерами, позволяющими перемещать загрузочный лоток вдоль оси железнодорожного пути и достигать любого загрузочного люка без движения вагона. Телескопический загрузочный желоб со встроенной системой аспирации также решил вопросы запыления груза – теперь соединение рукава и вагонного люка является герметичным для вагона любой высоты.
3. Модернизация системы взвешивания вагонов позволила интегрировать ее в современный автоматизированный комплекс погрузки. В настоящее время точность загрузки составляет 50 кг. Вот как это работает. Система видеонаблюдения, регистрирующая номера вагонов, определяет максимальную грузоподъемность вагона и дает команду на начало загрузки. Операция загрузки осуществляется по показаниям весов без участия оператора. Для точной дозировки груза используются специальные задвижки с малым временем срабатывания. Единственная задача оператора — открывать и закрывать люки вагонов, а также позиционировать телескопический загрузочный желоб с помощью простого пульта управления. После загрузки транспортные документы выдаются автоматически на основании считанных номеров и весов.
Эти простые шаги позволяют решить все поставленные задачи без больших вложений и остановки работы станции. Проект предполагает модернизацию без остановки производственного процесса. Расчетная производительность погрузки увеличена до 1800 т/час. Также решена проблема с недогрузкой вагонов. Потери груза от запыления должны снизиться на 90%. Кроме того, процесс модернизации будет заключаться в сокращении числа операторов и улучшении условий их труда.
Погрузка и разгрузка рельсов — Telestack Ltd
- Продукция
- Материалы
- Промышленность
- Видео
- Послепродажное обслуживание
- Тематические исследования
- Карьера
- Новости
- События
- О нас
- Контакт
- Поддержка
Мобильные системы Telestack предназначены для целого ряда применений, при этом операторы значительно выигрывают от устранения двойной обработки сыпучих материалов за счет выгрузки непосредственно из грузовиков, колесных погрузчиков и грейферов в железнодорожные вагоны. Эти мобильные решения обеспечивают высокую скорость загрузки и меньшее воздействие на окружающую среду.
Рельсовые системы разгрузки Telestack учитывают ряд различных методов разгрузки вагонов, используемых в отрасли, в том числе боковое опрокидывание, подземную разгрузку, разгрузку «брюхом» и многие другие. Telestack настраивает эти системы в соответствии с потребностями каждого приложения.
Радиальный телескопический штабелер является одним из самых экономичных и эффективных способов складирования материала на рынке. Уменьшение сегрегации, деградации, загрязнения и уплотнения при складировании обеспечивает материал «соответствующий спецификации» для любого применения. Они предлагают на 30% больше складской емкости при той же занимаемой площади по сравнению со стандартными штабелерами.
Компания Telestack производит гусеничные складские конвейеры, гусеничные радиальные складские конвейеры и гусеничные телескопические конвейеры, которые уменьшают потребность в транспортировке на месте и идеально подходят для дробления и сортировки.
Приемные питатели Titan (мобильные устройства разгрузки грузовиков) позволяют оператору напрямую разгружать грузовики, чтобы исключить двойную обработку материала.
Ассортимент передвижных загрузочных бункеров позволяет оператору напрямую производить разгрузку из колесных погрузчиков/грейферных кранов, чтобы исключить двойную обработку материала на месте. Полностью мобильные блоки используются для «контролируемой» подачи материала в другое оборудование Telestack или вспомогательные блоки
.Передвижные звеньевые конвейеры Telestack предлагают полный спектр конвейерных систем, позволяющих уменьшить или устранить необходимость в транспортировке грузов грузовиками/колесными погрузчиками на месте. Звенья конвейера могут быть либо на гусеничном ходу, либо с полностью автоматическим приводом, либо на колесах/на буксируемых колесах
Ассортимент передвижных бункеров для регенерации позволяет оператору напрямую осуществлять регенерацию с помощью колесных погрузчиков на наземных конвейерах/системах штабелеров-реклаймеров.