Принцип работы турбины. Турбонаддув в автомобиле, плюсы.
Для более ясного представления о том, как работает турбина в автомобиле, прежде всего необходимо ознакомится с принципом работы двигателя внутреннего сгорания. Сегодня, основная масса грузовых и легковых автомобилей оснащаются 4-х тактными силовыми агрегатами, работа которых контролируется впускными и выпускными клапанами.
Каждый из рабочих циклов такого двигателя состоит из 4 тактов, при которых коленвал делает 2 полных оборота.
Впуск — при этом такте осуществляется движение поршня вниз, при этом в камеру сгорания поступает смесь топлива и воздуха (если это бензиновый двигатель) или только воздуха в случае если это дизельный агрегат.
Компрессия — при этом такте происходит сжатие горючей смеси.
Расширение — на этом этапе происходит воспламенение горючей смеси при помощи искры, вырабатываемой свечами.
Выпуск — поршень двигается вверх, при этом освобождаются выхлопные газы.
Такой принцип работы двигателя определяет следующие способы повышения его эффективности:
— Установка турбонаддува
— Увеличение рабочего объёма двигателя
— Увеличение числа оборотов коленчатого вала двигателя
Как работает турбина в автомобиле?
Увеличение рабочего объёма двигателя
Увеличение объёма двигателя возможно двумя путями: либо увеличением объема камер сгорания, либо — увеличением количества цилиндров в силовом агрегате. Однако такой способ повышения мощности не совсем оправдан, так как имеет ряд недостатков, среди которых: повышенный расход топлива.
Увеличение числа оборотов коленчатого вала двигателя
Еще один возможный способ повышения производительности двигателя заключается в увеличении числа оборотов коленчатого вала.
Турбонаддув
В двух предыдущих способах двигатель использует воздух, который поступает благодаря собственному нагнетанию. При использовании турбокомпрессора в цилиндр поступает тот же объем воздуха но с предварительным его сжатием. Это дает возможность поступлению большего количества воздуха в цилиндр, благодаря чему появляется возможность сжигания большего объема топлива. При использовании такой технологии, мощность двигателя возрастает по отношению к количеству потребляемого топлива и объему двигателя.
Охлаждение воздуха
В процессе компрессии воздух может нагреваться вплоть до 180 С. Однако воздух имеет свойство увеличения плотности при охлаждении, что дает возможность значительно увеличить объем воздуха, попадающего в цилиндр. Кроме этого, увеличение плотности воздуха существенно снижает расход топлива и количество выбросов продуктов сгорания.
Также существует два разных типа турбонаддува: турбокомпрессор, основанный на использовании энергии выхлопных газов и турбонагнетатель с механическим приводом.
Турбонагнетатель с механическим приводом
В случае использования такого типа компрессии, воздух сжимается благодаря специальному компрессору, который работает от привода двигателя. Но такой метод имеет один большой недостаток. Все дело в том, что при использовании механического турбокомпрессора часть мощность двигателя уходит на обеспечение работы самого компрессора, по этому двигатель, оборудован таким нагнетателем, имеет больший расход топлива чем обычный двигатель такой же мощности.
Турбокомпрессор основанный на использовании энергии выхлопных газов
Такой метод основан на использовании энергии выхлопных газов, которая направлена на привод турбины. При использовании такого способа отсутствует механическое соединение с двигателем, благодаря чему потери мощности не происходит.
Плюсы и минусы турбонаддува
Как уже известно читателю, турбина в автомобиле не имеет жесткой связи с коленчатым валом двигателя. По логике, подобное решение должно нивелировать зависимость оборотов турбины от частоты вращения последнего.
Тем не менее, в реальности эффективность работы турбины находится в прямой зависимости от оборотов мотора. Чем сильнее открыта дроссельная заслонка, чем больше обороты мотора, тем выше энергия выхлопных газов, вращающих турбину и, как результат, больше объем воздуха, нагнетаемого компрессором в цилиндры силового агрегата.
Собственно говоря, «опосредованная» связь между оборотами и частотой вращения турбины не через коленвал, а через выхлопные газы, приводит к «хроническим» недостаткам турбонаддувов.
Среди них – задержка роста мощности мотора при резком нажатии на педаль «газа», ведь турбине нужно раскрутиться, а компрессору – дать цилиндрам достаточную порцию сжатого воздуха. Подобное явление называют «турбоямой», то есть моментом, когда отдача мотора минимальна.
Исходя из этого недостатка сразу исходит и второй – резкий скачок давления после того, как двигатель преодолевает «турбояму». Это явление получило название «турбоподхвата».
И главной задачей инженеров-мотористов, создающих наддувные двигатели, является «выравнивание» этих явлений для обеспечения равномерной тяги. Ведь «турбояма», по своей сути, обуславливается высокой инерционностью системы турбонаддува, ведь для приведения наддува «в полную готовность» требуется определенное время.
В результате потребность в мощности со стороны водителя в конкретной ситуации приводит к том
как работает, устройство, признаки поломки и эксплуатация
На сегодняшний день современный автопром активно внедрил технологию использования турбинных двигателей, и теперь без них представить современный автомобиль уже немыслимо.
Но не все имеют полное представление о том как работает турбина у авто, преимуществах турбины, рациональности установки и использования.
Итак, рассмотрим принцип действия турбины:
Двигатель состоит из цилиндров, в которых сгорает топливо того или иного вида. Мощность прямо пропорционально зависит от количества цилиндров.
Турбина предназначена для ускорения подачи топлива в камеру сгорания, чем больше будет его сгорать, тем больше потребуется воздуха. Этого можно достичь с помощью такой конструкции как у турбин – улиткооборазной.
Максимальные обороты агрегата составляют 240000 оборотов в минуту, а двигатель, к примеру, развивает только 10000. Чем больше нагнетается воздуха, тем больше сгорает горючей смеси и увеличивается мощность, что приводит к увеличению скорости.
Как правильно эксплуатировать изделие:
• Монтаж катализатора осуществляется очень тщательно, во избежание появления трещин от механического воздействия;
• Необходимо систематическая замена фильтрующих элементов, с целью недопущения прямого попадания пыли, песка, грязи;
• Не рекомендуется длительное время ездить на повышенных оборотах, с целью недопущения перегрева и выхода со строя;
• Не допускать агрессивное использование турбины на дорогах городского значения, уберегая себя и других участников от дорожно-транспортных происшествий.
Новинкой стало использование двух турбин на одном двигателе, а моторы стали битурбированными. Сила «железного коня» увеличится вдвое, но есть и неприятный исход, так как при остановке нагнетателя, коленвал до полной остановки вращается без смазочной жидкости, что может привести в ускоренному износу.
Катализаторы устанавливаются абсолютно на все транспортные средства, и без того достаточно мощны. Владелец машины может в любой момент демонтировать ускоритель на любом сервисном центре.
Положительная сторона турбин:
• Быстрота ускорения и набора скорости, приёмистость;
• Уникальность звучания катализатора;
• Возможность самовыражения в кругу знакомых.
Отрицательная сторона:
• Повышенное потребление топлива;
• При отсутствии опыта шансы совершить аварию увеличиваются в несколько раз;
• За лихачество на дорогах существенные штрафные санкции.
Турбинный механизм состоит из: крыльчатки-турбины, вала, непосредственно корпуса. Инженеры часто употребляют такое слово как турболаг – это период (яма) между моментом нажатия на акселератор и нагнетанием воздуха турбиной.
С данной проблемой на сегодняшний день успешно борются путём монтажа в ускоритель двух клапанов: для нагнетания воздуха и для выпуска отработанных газов.
Ограниченный ресурс службы был продлён с помощью замены материала для изготовления шариков подшипника на керамику, способную выдерживать перепады температурных режимов, огромную частоту вращения, общая масса изделия снижена на 20 %.
С целью достижения максимального использования нагнетающегося воздуха, специалистами разработано устройство под названием интеркулер, задача которого состоит в том, чтобы охлаждать нагнетаемый воздух, тем самым повышая эффективность работы компрессора.
Автопрому известны компрессоры трёх видов: центробежный, роторный, двухвинтовой, которые отличаются системой подачи воздуха в мотор. Кулачковый вал применяется роторным и двухвинтовым компрессоры, а центробежный – крыльчатку.
Роторный компрессор имеет огромные габариты, и как правило размещён над двигателем, выступая за капот. Фанаты дрэгстеров и роддеров приобретают такие установки.
Двухвинтовой нагнетатель более практичен и компактен, но ввиду своей конструкции цена выше, чем у «братьев».
Центробежный катализатор эффективен и востребован, по сравнению с родственниками. Лёгок, компактен, практичен в установке в передней части мотора, заставляющий прохожих оборачиваться слыша такой прекрасный свист.
Признаки поломки агрегата:
Наличие белого дыма в выхлопной трубе автомобиля, резкое падение мощности, существенное потребление моторного масла двигателем – это первые симптомы, свидетельствующие о необходимости поездки на сертифицированный сервис технического обслуживания для устранения поломки и предотвращения появления новых.
Могут подлежать замене или профилактике: подшипники и уплотнительные кольца, пропускающие потоки масла, преобразующиеся в белый дым. Осуществлять демонтаж следует очень аккуратно и только всю турбину в сборе.
Подводя итог, следует отметить, что устанавливать или нет турбину решать конечно только собственнику транспорта, но учитывать указанные в статье рекомендации необходимо каждому, с целью недопущения возникновения ошибок и аварийности на дорогах.
Предназначение турбонаддува, его устройство и как он работает
Турбонаддув – это такой способ агрегатного наддува, при котором подача воздуха в цилиндры двигателя происходит под давлением, нагнетаемым действием энергии отработавших газов. Сегодня такой метод – самый эффективный, призванный увеличивать мощность двигателя, не повышая объёма его цилиндров и частоты вращения коленчатого вала.
Кроме этого, использование турбонаддува даёт экономию топлива в соотношении расхода к мощности и уменьшает токсичность отработавших газов, осуществляя более полное сгорание топлива.
Применение турбонаддува
Применение система турбонаддува находит на обоих типах двигателей – и на бензиновых, и на дизельных. Однако на последних она гораздо эффективнее за счёт их более высокой степени сжатия и сравнительно небольшой частоты вращения коленчатого вала.
Использование же турбонаддува для бензиновых двигателей ограничено, во-первых, вероятностью наступления детонации, обусловленной значительным увеличением оборотов двигателя, а во-вторых, перегревом турбонагнетателя из-за повышенной температуры отработавших газов – около 1000°С, в то время как у дизелей она составляет порядка 600°С.
Устройство
Основная часть компонентов турбонаддува – это типовые элементы впускной системы. Присутствие же в системе турбокомпрессора, интеркулера и конструктивно новых элементов управления становится отличительной особенностью именно турбонаддува.
Хотя конструкции отдельных систем турбонаддува и различаются, можно обозначить их общие компоненты. Помимо вышеперечисленных турбокомпрессора, интеркулера и элементов управления это воздухозаборник с воздушным фильтром, дроссельная заслонка, впускной коллектор, напорные шланги и соединительные патрубки, а в некоторых системах ещё и впускные заслонки.
Турбокомпрессор или турбонагнетатель — главный конструктивный компонент системы турбонаддува. Он нагнетает воздух во впускную систему.
Его устройство выглядит следующим образом:
Устройство турбонагнетателя:
1 — корпус компрессора; 2 — вал ротора; 3 — корпус турбины; 4 — турбинное колесо; 5 — уплотнительные кольца; 6 — подшипники скольжения; 7 — корпус подшипников; 8 — компрессорное колесо.
Турбинное колесо, находясь в специальном теплоустойчивом корпусе, превращает энергию потока отработавших газов в энергию вращения и перенаправляет её на компрессорное колесо. С его помощью воздух всасывается, сжимается и подаётся в цилиндры двигателя. Оба эти колеса жёстко закреплены на роторном валу, вращающемся на подшипниках скольжения плавающего вида. Интеркулер является радиатором жидкостного или воздушного типа. Он охлаждает сжатый воздух, увеличивая его плотность и давление.
Главный элемент управления системой турбонаддува – это регулятор давления наддува, он, по сути, является перепускным клапаном (wastegate). Его задача – ограничивать энергию отработавших газов и направлять часть их потока в обход турбинного колеса. Таким образом, достигается оптимальная величина давления наддува. Привод перепускного клапана – электрический или пневматический. Для его срабатывания система управления двигателем подаёт сигнал от датчика давления наддува.
Как работает турбонаддув
Принцип работы турбонаддува берёт за основу использование энергии отработавших газов. Их струя заставляет вращаться турбинное колесо, передающее вращение через роторный вал компрессорному колесу. С помощью последнего происходит сжатие воздуха и его нагнетание в систему.
Принцип работы турбонаддува
Интеркулер охлаждает воздух, нагретый при сжатии, после чего тот подаётся в цилиндры двигателя.
Принцип работы турбины двигателя автомобиля
Окт 26 2014
Термин «турбо» практически у всех на слуху. Свистит турбина, ревёт прямоток. Хоть единожды в жизни любому автолюбителю приходила в голову идея заиметь «турбомонстрика».
Любому хочется увеличить поголовье «коняшек» под капотом. Но чаще всего приходится отказываться от мечты по причине мнимой дороговизны и непрактичности. Соответствует ли это реальности? Давайте разберёмся, как работает турбина, принцип действия турбины, обратившись к теории.
Мощность движка напрямую зависит от рабочего объёма цилиндров, от количества подаваемой воздушно-топливной смеси, от эффективности её сгорания, а также от энергетической части топлива.
Назначение турбины — увеличить подачу воздушно-топливной смеси. Мощность мотора повышается пропорционально увеличению количества сжигаемого за единицу времени топлива. Но для горения бензина необходим недюжинный запас воздуха в моторе.
То есть, чем больше сжигаем бензина, тем большее количество воздуха нужно, которое необходимо «впихнуть» в мотор (именно, «впихнуть», так как сам мотор не справится с забором такого количества воздуха, и фильтры нулевого сопротивления в этом ему не помощники). Вот тут и выходит на сцену устрашающая маленькая деталь турбина.
У турбины нагнетатель-крыльчатка размещён на едином валу с турбиной-крыльчаткой, встроенной в выпускной коллектор, и приводимой в движение вращения с помощью отработанных газов. Величина частоты вращения часто выше 200 тыс. об/мин.
И здесь проявляется один минус: при резком нажатии газа, надо ждать увеличение оборотов мотора, увеличение давления выхлопных газов, раскрутку турбины, и загонку воздуха. Это явление называется turbo-lag (турбо-яма), и сегодня его умеют укрощать, справляться с данным эффектом.
Для этих целей применяются два клапана. Один для перепускания излишнего воздуха в компрессор через трубопровод из двигательного коллектора. Другой клапан для отработанных газов.
Конструкция турбины | ТурбоМастер
Дата публикации: 2015-04-10
Содержание
Конструкция и основные функции турбокомпрессора (ТК) не претерпели принципиальных изменений с момента его изобретения швейцарским инженером Альфредом Бюхи, предложившим идею турбонаддува в 1905 году. Турбокомпрессор, как и следует из его названия, состоит из турбины и компрессора, соединенных общим валом. Турбина, приводимая в действие отработавшими газами (ОГ), передает энергию вращения на компрессор.
В автотехнике наиболее популярны центробежные компрессоры и радиально-осевые (центростремительные) турбины, которые и являются основой большинства современных ТК.
Компрессор
Входящий в состав турбокомпрессора центробежный компрессор состоит из трех основных компонентов: колеса компрессора, диффузора и корпуса. Вращающимся колесом поток воздуха всасывается в осевом направлении, разгоняется до большой скорости и затем вытесняется в радиальном направлении. Диффузор замедляет высокоскоростной поток воздуха практически без потерь, так что и его давление, и температура возрастают. Диффузор сформирован опорным диском компрессора и частью спирального корпуса (улитки). Последний, в свою очередь, собирает истекающий поток и еще больше замедляет его до выхода из компрессора.
Основные компоненты компрессора: крыльчатка (колесо компрессора), диффузор и спиралевидный корпус. Диффузор — узкий канал, сформированный опорным диском компрессора и частью корпуса.
Характеристики компрессора
Рабочие характеристики компрессора определяются картой режимов, которая отражает зависимость между степенью повышения давления и объемным или массовым расходом. Для удобства сравнения объемный и массовый расход компрессора соотносят со стандартными условиями на входе в компрессор. Рабочая область карты для центробежных компрессоров ограничивается зонами неустойчивых режимов (слева – линией помпажа, справа – линией насыщения), а также максимально допустимой частотой вращения. Компрессор для автомобильного применения должен устойчиво работать при изменении расхода воздуха в большом диапазоне. Поэтому он должен иметь карту режимов с широкой рабочей областью.
Область помпажа
Автомобильный турбокомпрессор — агрегат, состоящий из центробежного компрессора и радиально-осевой турбины, соединенных общим валом.
Карта режимов слева ограничена линией помпажа. По сути, помпаж – это срыв потока воздуха на входе в компрессор. При слишком малом объемном расходе и слишком высокой степени повышения давления поток отрывается от входных плоскостей лопаток и нормальный процесс нагнетания нарушается. Поток воздуха через компрессор реверсируется до тех пор пока перепад давления не стабилизируется. Направление потока вновь становится нормальным, давление наддува восстанавливается и цикл повторяется. Эта нестабильность потока продолжается с фиксированной частотой. Возникающий из-за этого акустический шум известен как помпаж.
Линию помпажа смещают в область меньших объемных расходов путем применения лопаток с загнутыми назад кромками, так что рабочий диапазон расходов компрессора увеличивается. Обратный изгиб лопаток приводит к образованию длинных, постепенно расширяющихся каналов. Они замедляют скорость потока и производят меньше пограничных расслоений, чем в случае лопаток с радиальными кромками.
«Улитка» собирает высокоскоростной поток и замедляет его, что приводит к росту температуры и давления.
Ширина диффузора также оказывает позитивный эффект на расположение линии помпажа. В общем случае компрессоры с диффузорами узкой конфигурации имеют более стабильную карту режимов.
Линия насыщения
Максимальный объемный расход центробежного компрессора обычно ограничивается величиной сечения на входе. Когда скорость потока на входе в колесо достигает скорости звука, дальнейшее увеличение расхода становится невозможным. Линию насыщения можно определить по круто снижающимся кривым максимальной частоты вращения компрессора в правой части карты режимов. Входное сечение компрессора может быть увеличено, а линия насыщения сдвинута в область больших расходов путем смещения передней кромки каждой второй лопатки (так называемые сплиттерные лопатки).
Когда увеличивается входной диаметр компрессора, возрастает так называемое хаб отношение ( hub ratio) — отношение между входным диаметром и диаметром колеса. Это приводит к росту максимального расхода. Из-за требований к прочности деталей и по соображениям аэродинамики увеличение хаб отношения возможно примерно до 0,8. По той же причине такие большие хаб отношения позволяют получить только относительно низкие значения степени повышения давления, которые требуются в пассажирских автомобилях.
Утоньшение лопаток и уменьшение их количества увеличивает площадь поперечного сечения на входе в колесо, так что линия насыщения отодвигается в сторону больших объемных расходов воздуха. Минимальная толщина лопаток лимитируется технологией литья и прочностными требованиями. Однако когда количество лопаток сокращается, степень повышения давления также уменьшается.
Таким образом, компрессорные колеса турбокомпрессоров пассажирских автомобилей характеризуются высоким хаб отношением и уменьшенным количеством тонких лопаток с сильным обратным загибом. Компрессор — «холодная» часть ТК, функция которой — повысить давление, а, вместе с этим, и плотность воздуха, поступающего в двигатель.
Корпуса компрессоров для коммерческих дизелей, где требуются и высокая степень повышения давления, и широкая карта режимов, часто изготавливают с рециркуляционными каналами. По каналам часть всасываемого воздуха возвращается из компрессора в основной поток на входе в него. Благодаря возникающей рециркуляции течение стабилизируется и линия помпажа смещается в сторону меньших объемных расходов. Более того, тем же путем воздух можно подвести к колесу в зоне позади ограничивающего входного сечения, так что линия насыщения сдвигается в область больших расходов.
Предельная частота вращения
Частота вращения колеса компрессора ограничивается нагрузками, которые испытывают его компоненты. Максимальная частота вращения определяется допустимой скоростью кончиков лопаток и наружным диаметром колеса. Допустимая скорость кромок лопаток обычно составляет около 520 м/с. Если не принимаются никакие меры для снижения нагрузок, увеличение скорости оборачивается сокращением срока службы.
Турбина
Турбина турбокомпрессора (ТК) состоит из турбинного колеса и корпуса. Она преобразует энергию отработавших газов (ОГ) в механическую энергию для привода компрессора. Поток ОГ несет энергию в форме высокого давления и температуры. После прохождения через турбину энергия газов (давление и температура) уменьшается. Перепад давления и температуры газов между входом и выходом из турбины преобразуется в кинетическую энергию вращения турбинного колеса.
Существуют два основных вида турбин: с осевым и радиальным потоком. В случае колес диаметром до 160 мм используются только радиальные турбины. КПД маленьких радиальных турбин выше, а стоимость изготовления при больших объемах производства существенно ниже, чем осевых. Поэтому они обычно применяются в пассажирских и коммерческих дизелях, а также в индустриальных силовых агрегатах.
В улитке радиальных (центростремительных) турбин давление ОГ преобразуется в кинетическую энергию и они с постоянной скоростью направляются с периферии на турбинное колесо. Трансформация кинетической энергии в мощность на валу происходит в турбинном колесе. Оно спроектировано так, чтобы почти вся кинетическая энергия газа преобразовалась к моменту, когда он выходит из крыльчатки.
Рабочие характеристики
Устройство крыльчатки компрессора. Сплиттерные лопатки увеличивают входное сечение компрессора. Обратный изгиб лопаток на выходе из компрессорного колеса — способ борьбы с помпажем.Мощность турбины возрастает по мере роста перепада давления между ее входом и выходом, то есть, когда перед турбиной скапливается больше отработавших газов (ОГ). Это происходит в результате повышения оборотов двигателя или увеличения температуры газов вследствие их большей энергии.
Поведение турбинной характеристики определяется относительным сечением проточной части. Чем меньше относительное сечение, тем больше газов скапливается на входе в турбину (повышается давление перед турбиной). В результате увеличения перепада давления производительность турбины возрастает. Таким образом, с уменьшением относительного сечения давление наддува увеличивается.
Относительное сечение турбины можно легко варьировать путем замены ее корпуса. Большинство производителей турбокомпрессоров (ТК) для каждого типа турбины предлагает корпуса разных размеров. Это позволяет в широких пределах изменять давление наддува путем подбора нужного относительного сечения проточной части турбинного корпуса.
Помимо относительного сечения на массовый расход газов через турбину также оказывает влияние площадь отверстия на выходе из колеса. Механическая обработка литого турбинного колеса по контуру — трим (trim) — дает возможность регулировать площадь сечения а, следовательно, и давление наддува. Увеличение контура колеса выливается в большее проходное сечение для потока. В рамках одной серии ТК производители предлагают колеса турбин с разным тримом, которые изготовлены из одних литьевых заготовок.
В турбинах с изменяемой геометрией проходное сечение потока между каналом улитки и выходом из колеса варьируется. На входе в турбинное колесо оно изменяется с помощью подвижных управляемых лопаток или скользящего кольца, частично перекрывающего сечение.
На практике рабочие характеристики турбины ТК описываются картами, показывающими зависимость параметров потока ОГ от перепада давления на турбине. На карте турбины показаны кривые массового расхода и КПД турбины для разных частот вращения. Для упрощения карты зависимости расхода и эффективности могут быть представлены в виде усредненных кривых.
Материалы турбин
Поскольку при работе двигателя и после его останова турбина подвергается действию очень высоких температур, колесо и корпус турбины изготавливаются из материалов, обладающих высокой жаропрочностью. В общем случае крыльчатки турбин делают из сплавов на основе никеля, таких как Inconel 713 и GMR 235. Основные компоненты этих сплавов – никель и хром. В то время как GMR 235 работает в условиях температуры отработавших газов (ОГ) на входе в турбину до 850°С, Inconel 713 (73% никеля, 13% хрома) применяется при температурах свыше 1000°С.
Выбор материала для корпуса турбины также зависит от температуры. Сегодня серый чугун GGG40 со сферическим графитом (до 680°С) применяется реже. Для большинства дизельных агрегатов используется кремниево-молибденовый чугун GGG SiMo 5. 1 (до 760°С) или GGV SiMo 4.5 0.6 (до 850 °С). Реже для температур ОГ до 850 °С используется высоколегированный никель-хромовый чугун GGG NiCrSi 20 2 2 (Niresist D2).
В большинстве турбокомпрессоров для бензиновых двигателей с температурами ОГ до 970°С применяется сплав GGG NiCrSi 35 5 2 (Niresist D5). Для самых высоких температур до 1050 °С, что потребуется в бензиновых двигателях ближайшего будущего, используется жаростойкая литьевая аустенитная сталь.
Турбины с двойным входом
Давление истекающих из двигателя отработавших газов (ОГ) не постоянное — оно пульсирует в соответствии с чередованием тактов выпуска в разных цилиндрах. Импульсные системы наддува используют пульсации давления ОГ, позволяющие кратковременно увеличить перепад давления на турбине. За счет роста перепада давления увеличивается КПД турбины, улучшая ее работу до тех пор пока через нее не пойдет большой, эффективный поток газов. В результате более полного использования энергии ОГ улучшаются характеристики давления наддува и, соответственно, поведение кривой крутящего момента, особенно на низких оборотах двигателя.
Для предотвращения взаимного влияния цилиндров при разных тактах впуска-выпуска они делятся на две независимые группы. Каждая группа объединяется в свой выпускной коллектор, который транслирует ОГ непосредственно на вход в турбину. В этом случае турбина с двойным входом позволяет утилизировать ОГ из двух групп цилиндров отдельно. В двигателях пассажирских автомобилей чаще используются неразделенные коллекторы и турбины с «однозаходным» корпусом. Это позволяет сделать коллектор компактнее и расположить турбину ближе к головке блока. Поскольку здесь сечение и длина газоподводящих каналов меньше, преимущества импульсного наддува нивелируются.
И все же в отдельных случаях турбины с двойным входом применяются в бензиновых моторах пассажирских автомобилей. Их преимущество — хорошая характеристика крутящего момента при низком давлении ОГ. В то же время им свойственны и недостатки – высокая термическая нагрузка разделяющей перегородки и дорогое производство маленьких корпусов с интегрированным байпасом, особенно, если в качестве материала нужно использовать литьевую сталь из-за больших температур.
Отклик
Для двигателей пассажирских автомобилей жизненно важную роль играют инерционные характеристики турбокомпрессора (ТК). Замедленная реакция на изменение положения педали акселератора, которую также называют «турбояма», часто воспринимается как фактор, снижающий управляемость автомобиля. В последние годы этот негативный эффект компенсирован применением ТК меньшего размера. У них меньше сечение проточной части и ниже инерция ротора как результат применения колес меньшего диаметра. Таким образом, при увеличении частоты вращения турбокомпрессора приходится раскручивать ротор меньшей массы. Момент инерции турбинного колеса также может быть снижен путем удаления сегментов опорного диска между лопатками. В еще большей степени динамические характеристики ТК могут быть улучшены применением турбин с изменяемой геометрией проточной части.
Оптимальные условия для потока и низкие потери тепла достигаются в интегрированных системах наддува с отлитыми заодно выпускным коллектором и корпусом турбины, что оборачивается улучшенными характеристиками отклика. Прочие аргументы за применение таких систем – сокращение веса до 1 кг, а также увеличение свободного пространства между двигателем и пассажирской кабиной, что часто жизненно необходимо по соображениям безопасности.
Керамические колеса турбин
В сравнении с металлическими колесами керамические турбинные колеса существенно легче, что улучшает характеристики отклика (чувствительность) турбокомпрессора. Современные керамические материалы позволили разработать такие колеса, пригодные для массового производства. Однако керамические материалы очень хрупкие и могут быть легко разрушены при попадании посторонних частиц. Более того, лопатки таких турбин толще и поэтому их эффективность ниже, так что они редко используются в автотехнике.
Алюминид титана имеет такую же плотность как керамика. Этот материал сравнительно менее подвержен разрушению, а лопатки такие же тонкие как металлические. Его недостаток – низкая температурная стойкость (максимум 700°С).
Типовая карта режимов компрессора. Рабочая область карты режимов ограничена линиями помпажа, насыщения и предельно допустимой частоты вращения.
Водоохлаждаемые корпуса
При разработке турбокомпрессоров (ТК) также должны учитываться аспекты безопасности. Например, в судовых моторных отсеках следует избегать горячих поверхностей из-за опасности пожара. Поэтому корпуса турбин ТК для морского применения изготавливаются с водяным охлаждением или с покрытием изолирующими материалами.
Система управления
Тяговые характеристики современных турбодвигателей должны отвечать таким же высоким требованиям, как и характеристики атмосферных моторов с идентичными мощностными параметрами. Это означает, что полное давление наддува должно быть доступно, начиная с минимально возможных частот вращения двигателя. Это, в свою очередь, может быть достигнуто только путем управления турбокомпрессором на турбинной стороне.
Байпасное регулирование на турбинной стороне
Установка байпасного клапана в турбинной части турбокомпрессора (ТК) – самый простой способ контроля давления наддува.
Геометрические параметры турбины выбирают таким образом, чтобы обеспечить характеристику крутящего момента на низких оборотах, необходимую для достижения заданных динамических показателей автомобиля. При такой конструкции ТК уже незадолго до достижения максимального крутящего момента на турбину начинает поступать избыточное количество отработавших газов. Таким образом, как только номинальное давление наддува достигнуто, избыток отработавших газов направляется по байпасному каналу в обход турбинного колеса. Клапан «вейстгейт», который открывает и закрывает байпас, обычно приводится в действие пневматической камерой с подпружиненной диафрагмой, реагирующей на давление наддува. Так по мере дальнейшего увеличения оборотов двигателя давление наддува остается на неизменном уровне.
В этом, очень экономичном, решении на диафрагму камеры управления, предварительно нагруженную спиральной пружиной, воздействует давление наддува. Как только давление наддува преодолеет силу предварительного сжатия пружины, шток через рычаг открывает тарелку байпасного клапана и ОГ начинают перетекать вокруг турбины в систему выпуска.
В современных бензиновых и дизельных двигателях все чаще применяются электронно управляемые системы контроля наддувочного давления. В сравнении с чисто пневматическим регулированием, которое действует только как ограничитель давления на полной нагрузке, гибкое управление позволяет устанавливать оптимальное давление наддува в режимах частичной нагрузки. Электронное регулирование работает в соответствии с различными параметрами, такими как температура наддувочного воздуха, качество топлива и параметры опережения впрыска (зажигания). Также становится возможным кратковременный «перенаддув» при интенсивном ускорении.
Механический привод байпасной заслонки действует так же как и в описанном выше случае. Вместо полного давления наддува на диафрагму камеры управления подается модулированное управляющее давление. Оно меньше полного давления наддува и вырабатывается так называемым пропорциональным клапаном. Этим достигается то, что на диафрагму воздействует комбинация давления наддува и давления на выходе из компрессора в изменяющейся пропорции.
Пропорциональный клапан управляется электроникой двигателя и срабатывает с частотой от 10 до 15 Гц. В сравнение с обычной системой управления усилие предварительного сжатия пружины существенно ниже, что позволяет осуществлять регулирование также и на режимах частичной нагрузки, то есть, при меньшем давлении наддува.
В электронных системах управления турбокомпрессоров дизельных двигателей пневмокамеры регулируются вакуумом.
Турбины с изменяемой геометрией
Байпасные системы регулирования управляют мощностью турбины, направляя часть отработавших газов (ОГ) в обход нее. Таким образом, «дармовая» энергия газов используется не полностью. Турбины с изменяемой геометрией позволяют варьировать сечение проточной части турбины в зависимости от режима работы двигателя. Это дает возможность полностью утилизировать энергию ОГ, оптимизируя конфигурацию канала, по которому ОГ попадают на турбинное колесо, для данного режима двигателя. Как результат, эффективность турбокомпрессора (ТК) и, соответственно, двигателя выше тех, что удается достичь при байпасном регулировании.
Сегодня турбины с РСА в виде подвижных направляющих лопаток (VNT, VTG, VGT) – самое передовое решение для современных легковых дизельных автомобилей. В результате непрерывной адаптации проходного сечения турбинного канала к рабочему режиму двигателя сокращаются потребление топлива и вредные выбросы. Высокий крутящий момент уже на низких оборотах и адекватная стратегия управления обеспечивают существенное улучшение динамических характеристик.
Подвижные направляющие лопатки между корпусом улитки и турбинным колесом влияют на протекание процесса восстановления давления и, таким образом, на выходные характеристики турбины. Это позволяет варьировать поток газов через турбину в диапазоне 1:3 при хороших уровнях эффективности. На низких оборотах сечение проточной части турбины уменьшается путем закрытия направляющих лопаток. Давление наддува и, следовательно, крутящий момент двигателя возрастают как результат увеличения перепада давления на входе и выходе из турбины. С повышением оборотов двигателя управляемые лопатки постепенно открываются.
Требуемое давление наддува достигается при низком перепаде давления на турбине — так достигается сокращение расхода топлива. При ускорении машины с низкой скорости (оборотов двигателя) управляемые лопатки закрываются для получения максимальной энергии от ОГ. По мере увеличения скорости лопатки открываются и адаптируются к соответствующему рабочему режиму.
В настоящее время управление лопатками преимущественно электронное, с помощью вакуумно-регулируемой камеры управления и пропорционального клапана. В будущем все чаще будут применяться электрические приводы с положительной обратной связью, позволяющие реализовать точное и чрезвычайно гибкое управление давлением наддува.
Температура ОГ современных высокоэффективных дизельных двигателей может достигать 830°С. Точная и надежная работа управляющих лопаток в потоке горячих газов предъявляет высокие требования к материалам и точности допусков в конструкции турбины. Независимо от типоразмера турбокомпрессора направляющие лопатки должны иметь минимальные зазоры для обеспечения надежной работы в течение всего срока службы автомобиля.
С уменьшением размера ТК относительные потери потока через турбину возрастают и ее эффективность падает. Поэтому цель многих разработок – отодвинуть эти ограничения области применения технологии VTG как можно дальше в сторону ТК малых размеров.
Альтернативное решение – турбины с регулирующим механизмом в виде подвижного (скользящего) кольца (VST-variable sliding turbine). Простота конструкции и исполнение многих функций небольшим количеством компонентов – преимущества для маленьких турбин или там, где требуется работа в условиях высоких температур ОГ. Это особенно применимо в компактных дизельных двигателях с рабочим объемом менее 1,4 л. Преимущества – высокая эффективность, низкая цена и сокращение установочных размеров. Для бензиновых моторов с высокой температурой ОГ технология VST – надежная возможность управления давлением наддува путем изменения геометрии проточной части турбины.
Прочный механизм VST противостоит высоким температурам ОГ значительно лучше, чем VTG с направляющими лопатками.
Байпас, который для бензиновых двигателей необходим даже в ТК с изменяемой геометрией из-за большого диапазона изменения расхода, интегрирован в механизм управления.
Корпус турбины аналогичен турбинам с двойной улиткой (с двухканальным направляющим аппаратом). Перегородка, разделяющая каналы, не выходит на впускной фланец, а начинается внутри улитки. На низких оборотах двигателя открыт только один канал. Второй канал, который закрыт скользящим кольцом, постепенно открывается по мере увеличения оборотов. Затем скользящее кольцо приоткрывает и байпасный канал, ведущий от входа в турбину по внешнему контуру скользящего кольца к выходу из турбины. Это дополнительно увеличивает расход газов через турбину. Для регулирования сечения проточной части и открытия байпасного канала требуется всего один управляющий механизм. Могут быть использованы как пневматический, так и электронный приводы.
Узел подшипников
Ротор турбокомпрессора (ТК) вращается с частотой до 300 000 мин -1. Срок службы ТК должен соответствовать ресурсу двигателя, который может составлять 1 000 000 км пробега для коммерческого автомобиля. Только специально разработанные для ТК подшипники скольжения могут соответствовать таким жестким требованиям при приемлемой стоимости.
Опорные подшипники
В подшипнике скольжения вал вращается практически без трения на масляной пленке внутри втулки подшипника.
Масло подается в турбокомпрессор (ТК) от системы смазки двигателя. Подшипниковый узел спроектирован так, что между неподвижным корпусом и вращающимся валом расположены «плавающие» бронзовые подшипниковые втулки. Они вращаются с частотой, вдвое меньшей частоты вращения вала. Это позволяет высокоскоростным подшипникам адаптироваться таким образом, что на любых режимах работы ТК нет прямого контакта «металл-металл» между валом и подшипниками.
Кроме функции смазки масляная пленка в зазорах подшипника играет роль демпфера, который способствует стабилизации вала и турбинного колеса. Гидродинамическая несущая способность пленки и демпфирующие характеристики подшипника оптимизируются величиной зазоров. Таким образом, толщина смазывающей пленки для внутренних зазоров выбирается исходя из нагрузки на подшипник, в то время как толщина внешних зазоров определяется с учетом демпфирования подшипника. Зазоры в подшипниках составляют несколько сотых долей миллиметра. Увеличение зазоров приведет к более мягкому демпфированию и, одновременно, к снижению несущей способности подшипника.
Так называемый патрон — специальный вид опорного подшипника скольжения. Вал вращается в неподвижной целиковой втулке, снаружи которой прокачивается масло. Внешний зазор выбирается исключительно из условия демпфирования подшипника, так как патрон не проворачивается. Вытекающая из этого меньшая ширина подшипника позволяет создать более компактный ТК.
Упорный подшипник
Ни один из рассмотренных типов опорных подшипников, ни свободно плавающие втулки, ни фиксированный плавающий патрон, не воспринимают нагрузки в осевом направлении. Поскольку газы воздействуют на компрессорное и турбинное колеса в осевом направлении с разной силой, ротор турбокомпрессора (ТК) испытывает осевую нагрузку. Она воспринимается упорным подшипником скольжения с конической плоскостью (рабочей поверхностью). Два маленьких диска, закрепленных на валу, служат контактными поверхностями. Упорный подшипник фиксируется в центральном корпусе подшипников. Маслоотражающая пластина предотвращает попадание масла в зону уплотнения вала.
Слив масла
Масло подается в турбокомпрессор (ТК) при давлении примерно 4 бар. Поскольку масло сливается из турбины при меньшем давлении (самотеком), диаметр трубки для слива значительно больше, чем маслоподающей трубки. Проток масла через корпус подшипников должен быть по возможности вертикальным, сверху вниз. Сливная трубка должна выходить в картер выше уровня масла. Любое препятствие на пути слива масла оборачивается увеличением противодавления в корпусе подшипников. В этом случае масло начинает просачиваться сквозь уплотнительные кольца в компрессор и турбину.
Уплотнения
Центральный корпус подшипников должен быть уплотнен от прорыва в него горячих отработавших газов из турбины и от утечек масла из корпуса. Для этого в канавки на валу ротора, со стороны компрессора и турбины установлены разрезные кольца, аналогичные поршневым. Кольца не вращаются, а неподвижно расклинены в центральном корпусе. Это бесконтактное уплотнение, один из видов лабиринтного уплотнения. Благодаря многочисленным резким изменениям направления движения потока оно затрудняет утечку масла и пропускает в картер лишь небольшое количество отработавших газов.
Тепловая нагрузка на подшипники
Учитывая небольшое расстояние между центральным корпусом и горячим корпусом турбины, тепло может проникать в центральный корпус и нагревать масло до температуры коксования. Тогда масляный кокс мог бы осаждаться в зазорах и на поверхностях, засорять масляные каналы и нарушать работу подшипников и уплотнений. Большое количество углеводородных отложений может вызвать дефицит смазки и граничное трение, приводящие к ускоренному износу системы подшипников.
Тепловой экран и охлаждение разбрызгиванием масла<
Тепловой экран, расположенный позади опорного диска турбинного колеса, предотвращает контакт горячих отработавших газов с центральным корпусом. В некоторых конструкциях при работе двигателя масло распыляется на вал ротора через маленькое распылительное отверстие в опоре подшипника с турбинной стороны, охлаждая вал и уменьшая риск коксования.
Наивысшие температуры в центральном корпусе достигаются вскоре после останова двигателя. Горячий турбинный корпус нагревает систему подшипников, которая больше не охлаждается моторным маслом.
Термическая развязка
В расчете на термическую развязку правой подшипниковой опоры передача тепла от корпуса турбины к системе подшипников сокращается даже после того как двигатель был заглушен. Для этого систему подшипников располагают ниже точки подачи масла, так же как силовой агрегат размещают под крылом самолета. Правая подшипниковая опора больше не контактирует с горячей стенкой центрального корпуса, значит, передача тепла к системе подшипников ограничивается.
Водяное охлаждение
Бензиновые двигатели, у которых температура отработавших газов на 200-300°С выше чем у дизелей, обычно оснащаются турбокомпрессорами с охлаждаемыми центральными корпусами. При работе двигателя центральный корпус интегрируется в его контур охлаждения. После выключения двигателя остаточное тепло снимается посредством малого кольца циркуляции, которое задействуется электрическим насосом с термостатом.
Рециркуляционный клапан
В бензиновых турбодвигателях дроссельная заслонка, которая управляет нагрузкой двигателя, располагается после компрессора, во впускном коллекторе. В момент внезапного сброса газа заслонка закрывается, а компрессор из-за своей инерционности продолжает нагнетать воздух в почти замкнутый объем. Вследствие этого начался бы помпаж компрессора. Частота вращения турбокомпрессора (ТК) быстро упала бы.
Начиная с определенного давления, открывается подпружиненный клапан и направляет воздух обратно на вход в компрессор, ограничивая рост давления и исключая помпаж. Частота вращения ТК остается высокой, и давление наддува появится, как только будет задействован акселератор.
Принцип работы турбореактивного двигателя самолёта
Совершая полет в самолете в большинстве случаев люди никогда не задумываются о том, как работает его двигатель. Но на самом деле о работе двигателя и реактивной тяги с помощью, которой работает сам двигатель, знали ее в Античное время. Но применить эти знания на практике смогли не так давно, так как раньше не технологии не позволяли никому достичь его исправной работы. Гонка вооружения между Англией и Германией стала толчком к созданию ТРД (турбореактивного двигателя).
В работе ТРД самолета нет никаких сложностей, принцип его работы может понять почти каждый человек. Но данный двигатель имеет несколько нюансов, их соблюдение контролируется под строгим присмотром руководства. Для того чтобы авиалайнер смог держаться в небе, необходима идеальная работа двигателя. Так как от работы двигателя напрямую зависят жизни пассажиров находящихся на борту авиатранспорта.
Принцип работы реактивного двигателя
За работу двигателя отвечает реактивная тяга. Для создания реактивной тяги необходима определенная жидкость, которая подается из задней части двигателя и по ходу ее продвижения увеличивается ее скорость движения вперед. Работу тяги отлично объясняет один из законов Ньютона, звучит он так «Любое действия вызывает равное противодействие».
Вместо жидкости в ТРД используется горючая смесь (газы и воздух со сгоревшими частичками топлива). Благодаря этой смеси самолет толкает вперед и позволяет ему лететь дальше.
Разработки таких двигателей начались в тридцатых годах. Первыми кто начал разрабатывать двигатели такого типа стали немцы и англичане. Но в гонке вооружений одержали победу ученные из Германии, так как они выпустили самый первый в мире самолет с ТРД под названием «Ласточка», данный самолет впервые взлетел в небеса над Люфтваффом. Спустя некоторое время появился и Английский самолет «Глостерский метеор»
Также сверхзвуковые двигатели принято считать турбореактивными, но они отличаются более совершенными модификациями, в отличие от ТРД.
Устройство двигателя имеет четыре главные детали, а именно:
- Компрессор.
- Камера горения.
- Турбина.
- Выхлоп.
Компрессор
В компрессоре находиться несколько турбин, с помощью которых происходит засасывание и сжатие воздуха. Во время сжатия воздуха, его давление и температура начинает нагнетаться и расти.
Камера горения
После того как воздух проходит турбину и его сжимает до необходимых размеров. Часть сжатого воздуха поступает в камеру горения, где воздух начинает смешиваться с топливом, после чего его поджигают. Благодаря этому увеличивается тепловая энергия воздуха. После смесь выходит из камеры с большой скорости и расширяется.
Турбина
После выхода эта смесь снова попадает в турбину, с помощью высокой энергии газа лопасти в турбине начинают свое вращение. Турбина тесно связанна с компрессором, который находиться в начале двигателя. Благодаря этому турбина начинает свою работу. Остатки воздуха выходят в выхлоп. В момент выхода смеси температура достигает рекордных размеров. Но она продолжает повышать свою температуру с помощью эффекта Дросселирования. После того как температура воздуха доходит до своего пика, она начинает идти на спад и выходит из турбины.
Принцип работы турбореактивного двигателя
В отличие от реактивного двигателя, который пользуется спросом почти у всех самолетов, турбореактивный двигатель больше подходит для пассажирских авиалайнеров. Так как для работы реактивного двигателя необходимо не только топливо, но и окислитель.
Благодаря своему строению окислитель поступает вместе с топливом из бака. А в случаи с ТРД окислитесь, поступает напрямую из атмосферы. А в остальном их работа совершенно идентична и не отличается друг от друга.
У турбореактивного двигателя главной деталью является лопасть турбины, так как от ее исправной работы напрямую зависит мощность двигателя. Благодаря этим лопастям и образуется тяга, которая необходима для поддержания скорости самолета. Если сравнить одну лопасть с автомобильным двигателем, то она сможет обеспечить мощностью целых десять машин.
Лопасти устанавливаются за камерой сгорания, так как там нагнетается самое высокое давления, также температура воздуха в данной части двигателя может доходить до 1400 градусов Цельсия.
В целях улучшения прочности и устойчивости лопасти перед различными факторами их монокристаллизируют, благодаря этому они могут держать высокую температуру и давление. Прежде чем установить такой двигатель на самолет его тестируют на полном тяговом усилителе. Также двигатель должен получить сертификат от Европейского совета по безопасности.
Атомный двигатель
В период холодной войны в мире были попытки создания атомного двигателя, за основу был взят турбореактивный двигатель. Главной задумкой ученых было создание двигателя, основанного не на химической реакции радиоактивных веществ, а на вырабатываемом тепле от ядерного реактора. Он должен был находиться на месте камеры сгорания.
В теории воздух должен был проходить через работающую зону реактора, благодаря этому реактор должен был остужаться, а температура воздуха наоборот возрастать. После чело воздух должен был расширяться и выходить через сопла (выхлоп) на этот момент скорость воздуха должна была превышать скорость полета самолета.
В Советском союзе были попытки проведения испытаний подобного двигателя, также ученные в соединенных штатах Америки, вели разработку данного двигателя, и их работа почти подходила к тестам двигателя на настоящем самолете.
Но по ряду причин разработки этого двигателя было решено закрыть. Так как у двигателя было множество недостатков, а именно:
- Пилоты были подвержены постоянному радиоактивному облучению на протяжении всего полета.
- Вместе с воздухом через сопла выходили и частички радиоактивного элемента в атмосферу.
- В том случае если самолет терпел крушение, был очень большой шанс взрыва радиоактивного реактора, что влекло за собой радиоактивное отравление на довольно большой площади.
Турбина Каплан — ее составные части, работа и применение
Турбина Каплан работает по принципу реакции осевого потока. В турбинах с осевым потоком вода течет через бегунок в направлении, параллельном оси вращения рабочего колеса. Вода на входе в турбину обладает как кинетической энергией, так и энергией давления для эффективного вращения лопастей гидроэлектростанции.
Рис. 1: Турбина Каплана.
В 1913 году австрийский профессор Виктор Каплан, который разработал эту турбину, объединил автоматически регулируемые лопасти гребного винта с автоматически регулируемыми заслонками калитки для достижения эффективности в широком диапазоне расхода и уровня воды.Она также называется пропеллерной турбиной и произошла от турбины Фрэнсиса. Он способен очень эффективно работать при низком напоре и высоких расходах, что невозможно с турбиной Фрэнсиса.
В этой статье рассматривается порядок работы, основные компоненты и их применение.
Основные компоненты турбины Каплана
Основные части турбины Каплан,
1. Спиральный кожух
Это спиральный кожух с уменьшающейся площадью поперечного сечения.Вода из затворов попадает в корпус спирали, а затем движется к направляющим лопастям, где вода поворачивается на 90 ° и течет в осевом направлении через желоб. Он защищает рабочее колесо, направляющие лопатки рабочих лопаток и другие внутренние части турбины от внешних повреждений.
Рис. 2: Основные компоненты турбины Каплана.
2. Механизм направляющей лопасти
Это единственная управляющая часть всей турбины, которая открывается и закрывается в зависимости от потребности в мощности.Если требуется большая выходная мощность, он открывается шире, чтобы больше воды попадало на лопасти ротора, а когда требуется низкая выходная мощность, он закрывается, чтобы прекратить поток воды. При отсутствии направляющих лопаток турбина не может работать эффективно и ее КПД снижается.
3. Трубка отсасывающая
Давление на выходе из рабочего колеса реакционной турбины обычно ниже атмосферного. Вода на выходе не может напрямую сбрасываться в хвостовую часть.Труба или труба с постепенно увеличивающейся площадью используется для отвода воды от выхода турбины до хвостовой части. Эта трубка с увеличивающейся площадью называется вытяжной трубкой. Один конец трубки подсоединен к выпускному отверстию бегунка, а другой конец погружен ниже уровня воды в хвостовой части.
4. Лезвия рабочего колеса
Сердцем компонента в турбине Каплана являются рабочие лопатки, так как это вращающаяся часть, которая помогает в производстве электроэнергии. Вал соединен с валом генератора.Рабочее колесо этой турбины имеет большой выступ, на котором крепятся его лопасти, а лопасти рабочего колеса регулируются под оптимальным углом атаки для максимальной выходной мощности. Лопатки турбины Каплана имеют закрутку по длине.
Рис. 3. Рабочие лопатки турбины Каплана.
Рабочий процесс турбины Каплана
Вода, поступающая из загона, попадает в кожух спирали. Корпус спирали выполнен такой формы, чтобы не терять давление потока.Направляющие лопатки направляют воду к лопастям рабочего колеса. Лопасти регулируются и могут регулироваться в зависимости от скорости потока. Вода поворачивается на 90 градусов, поэтому направление воды является осевым по отношению к лопастям бегунка.
Лопасти бегунка начинают вращаться при ударе воды из-за силы реакции воды. Лезвия бегунка имеют изгиб по всей длине, чтобы всегда иметь оптимальный угол атаки для всего поперечного сечения лезвий для достижения большей эффективности.
Из лопастей рабочего колеса вода поступает в вытяжную трубу, где ее энергия давления и кинетическая энергия уменьшаются. Кинетическая энергия преобразуется в энергию давления, что приводит к увеличению давления воды.
Вращение турбины используется для вращения вала генератора для производства электроэнергии.
Применение турбины Каплана
- Турбины Каплана широко используются во всем мире для производства электроэнергии.
- Может работать более эффективно при низком напоре воды и высоком расходе по сравнению с другими типами турбин.
- Он меньше по размеру и прост в сборке.
- КПД турбины Каплана очень высок по сравнению с другими гидравлическими турбинами.
Недостаток турбины Каплана
- Единственным недостатком турбины Каплана является кавитация, возникающая из-за падения давления в отсасывающей трубе. Использование вытяжной трубы и подходящего материала, как правило, из нержавеющей стали для лопастей рабочего колеса, может в большей степени уменьшить проблему кавитации.
Турбина | Британника
Турбина , любое из различных устройств, преобразующих энергию потока жидкости в механическую энергию. Преобразование обычно осуществляется путем пропускания жидкости через систему неподвижных каналов или лопаток, которые чередуются с каналами, состоящими из лопастей, похожих на ребра, прикрепленных к ротору. За счет организации потока так, чтобы на лопасти ротора действовала касательная сила или крутящий момент, ротор вращается, и работа извлекается.
Ветровые турбины около Техачапи, Калифорния
© Грег Рэндлс / Shutterstock.com Турбины можно разделить на четыре основных типа в зависимости от используемых жидкостей: вода, пар, газ и ветер. Хотя одни и те же принципы применимы ко всем турбинам, их конкретные конструкции достаточно различаются, чтобы заслужить отдельное описание.
Гидравлическая турбина использует потенциальную энергию, возникающую в результате разницы в высоте между верхним водным резервуаром и уровнем воды на выходе из турбины (отводом) для преобразования этого так называемого напора в работу.Водяные турбины — современные преемники простых водяных колес, которым около 2000 лет. Сегодня гидротурбины в основном используются для производства электроэнергии.
Однако наибольшее количество электроэнергии вырабатывается паровыми турбинами, соединенными с электрогенераторами. Турбины приводятся в действие паром, вырабатываемым либо в генераторе, работающем на ископаемом топливе, либо в атомном генераторе. Энергию, которую можно извлечь из пара, удобно выражать через изменение энтальпии в турбине.Энтальпия отражает формы как тепловой, так и механической энергии в процессе потока и определяется суммой внутренней тепловой энергии и произведением давления на объем. Доступное изменение энтальпии через паровую турбину увеличивается с увеличением температуры и давления парогенератора и с уменьшением давления на выходе из турбины.
Оформите подписку Britannica Premium и получите доступ к эксклюзивному контенту.
Подпишитесь сейчас Для газовых турбин энергия, извлекаемая из текучей среды, также может быть выражена через изменение энтальпии, которое для газа почти пропорционально перепаду температуры в турбине.В газовых турбинах рабочим телом является воздух, смешанный с газообразными продуктами сгорания. Большинство газотурбинных двигателей включает, по крайней мере, компрессор, камеру сгорания и турбину. Обычно они монтируются как единое целое и работают как законченный первичный двигатель в так называемом открытом цикле, когда воздух всасывается из атмосферы, а продукты сгорания, наконец, снова выбрасываются в атмосферу. Поскольку успешная работа зависит от интеграции всех компонентов, важно рассматривать устройство в целом, которое фактически является двигателем внутреннего сгорания, а не только турбиной.По этой причине газовые турбины рассматриваются в статье двигатель внутреннего сгорания.
Энергия ветра может быть извлечена ветровой турбиной для производства электроэнергии или для откачки воды из колодцев. Ветряные турбины являются преемниками ветряных мельниц, которые были важными источниками энергии с позднего средневековья до 19 века.
Фред Лэндис Водяные турбины обычно делятся на две категории: (1) импульсные турбины, используемые для высокого напора воды и низкого расхода, и (2) реактивные турбины, обычно используемые для напора ниже примерно 450 метров и среднего или высокого расхода.Эти два класса включают в себя основные типы, обычно используемые, а именно импульсные турбины Пелтона и реактивные турбины типа Фрэнсиса, пропеллера, Каплана и Дериаза. Турбины могут иметь горизонтальный или, чаще, вертикальный вал. Для каждого типа возможны широкие вариации конструкции для соответствия конкретным местным гидравлическим условиям. Сегодня большинство гидравлических турбин используются для выработки электроэнергии на гидроэлектростанциях.
Импульсные турбины
В импульсной турбине потенциальная энергия или напор воды сначала преобразуется в кинетическую энергию путем выпуска воды через сопло тщательно продуманной формы.Струя, выбрасываемая в воздух, направляется на изогнутые ковши, закрепленные на периферии бегунка, для извлечения энергии воды и преобразования ее в полезную работу.
Современные импульсные турбины основаны на конструкции, запатентованной в 1889 году американским инженером Лестером Алленом Пелтоном. Свободная водная струя попадает в лопатки турбины по касательной. Каждый ковш имеет высокий центральный гребень, так что поток разделяется, оставляя желоб с обеих сторон. Колеса Пелтона подходят для высоких напоров, обычно выше 450 метров при относительно низком расходе воды.Для максимальной эффективности скорость конца рабочего колеса должна составлять примерно половину скорости ударной струи. КПД (работа, производимая турбиной, деленная на кинетическую энергию свободной струи) может превышать 91 процент при работе с 60–80 процентами полной нагрузки.
Мощность одного колеса можно увеличить, используя более одного жиклера. Для горизонтальных валов характерны двухструйные устройства. Иногда на одном валу устанавливаются два отдельных бегунка, приводящих в движение один электрогенератор. Агрегаты с вертикальным валом могут иметь четыре или более отдельных форсунок.
Если электрическая нагрузка на турбину изменяется, ее выходная мощность должна быть быстро отрегулирована в соответствии с потребностями. Это требует изменения расхода воды, чтобы поддерживать постоянную скорость генератора. Скорость потока через каждое сопло регулируется расположенным в центре наконечником или иглой аккуратной формы, которая скользит вперед или назад под управлением гидравлического серводвигателя.
Правильная конструкция иглы гарантирует, что скорость воды, выходящей из сопла, остается практически неизменной независимо от отверстия, обеспечивая почти постоянную эффективность в большей части рабочего диапазона.Нецелесообразно внезапно уменьшать поток воды, чтобы соответствовать уменьшению нагрузки. Это может привести к разрушительному скачку давления (гидроудару) в подающем трубопроводе или водопроводе. Таких скачков можно избежать, добавив временное сопло для разлива, которое открывается при закрытии основного сопла, или, что чаще, частично вставляя отражающую пластину между струей и колесом, отклоняя и рассеивая часть энергии при медленном закрытии иглы.
Другой тип импульсной турбины — турбина турго.Струя падает под косым углом на бегунок с одной стороны и продолжает двигаться по единственному пути, выбрасывая его с другой стороны. Этот тип турбины использовался в установках среднего размера с умеренно высоким напором.
Реакционные турбины
В реакционной турбине силы, приводящие в движение ротор, достигаются за счет реакции ускоряющегося потока воды в рабочем колесе при падении давления. Принцип реакции можно наблюдать в роторном оросителе для газонов, где выходящая струя вращает ротор в противоположном направлении.Из-за большого разнообразия возможных конструкций рабочего колеса реактивные турбины могут использоваться в гораздо большем диапазоне напоров и расходов, чем импульсные турбины. Реакционные турбины обычно имеют спиральный впускной кожух, который включает регулирующие заслонки для регулирования потока воды. На входе часть потенциальной энергии воды может быть преобразована в кинетическую энергию по мере ускорения потока. Впоследствии энергия воды отбирается в роторе.
Как отмечалось выше, широко используются четыре основных типа реактивных турбин: турбины Каплана, Фрэнсиса, Дериаза и пропеллерные.В турбинах Каплана с неподвижными лопастями и с регулируемыми лопастями (названными в честь австрийского изобретателя Виктора Каплана), по существу, существует осевой поток через машину. Турбины типа Фрэнсиса и Дериаза (в честь американского изобретателя британского происхождения Джеймса Б. Фрэнсиса и швейцарского инженера Поля Дериаза, соответственно) используют «смешанный поток», когда вода поступает радиально внутрь и выпускается в осевом направлении. Рабочие лопасти на турбинах Фрэнсиса и пропеллера состоят из неподвижных лопастей, в то время как в турбинах Каплана и Дериаза лопасти могут вращаться вокруг своей оси, которая находится под прямым углом к главному валу.
Объяснение 9 различных стратегий
Профилактическое обслуживание и корректирующее обслуживание
На верхнем уровне я вижу профилактическое или корректирующее обслуживание:
- Когда мы выполняем профилактическое обслуживание , мы выполняем задачу до того, как произойдет сбой . Эта задача может быть направлена на предотвращение отказа, минимизацию последствий отказа или оценку риска возникновения отказа.
- Когда мы проводим корректирующее обслуживание , произошел сбой , и мы в основном восстанавливаем работоспособность оборудования. Чтобы было ясно, корректирующее обслуживание может быть результатом преднамеренной стратегии безотказной работы.
Профилактическое обслуживание
Профилактическое обслуживание можно определить как «стратегию обслуживания оборудования, основанную на замене или восстановлении актива через фиксированные интервалы времени, независимо от его состояния. Запланированные задачи восстановления и задачи замены являются примерами задач профилактического обслуживания ».
Профилактическое обслуживание (или профилактическое обслуживание) в основном представляет собой тип обслуживания, который выполняется через регулярные промежутки времени, пока оборудование все еще функционирует, с целью предотвращения отказа или снижения вероятности отказа.
Профилактическое обслуживание может проводиться по времени, т.е. каждую неделю, каждый месяц или каждые три месяца. Но профилактическое обслуживание также может быть основано на использовании e.г. каждые 150 циклов, каждые 10 000 часов или как ваш автомобиль: обслуживание каждые 10 000 км.
Помимо регулярного интервального обслуживания (обслуживания по времени), существуют также другие виды обслуживания, которые подпадают под категорию профилактического обслуживания:
В следующих параграфах я более подробно рассмотрю каждый из этих типов обслуживания, в том числе, когда вам следует рассмотреть возможность их использования.
Обслуживание по времени (TBM)
Временное обслуживание относится к замене или обновлению элемента для восстановления его надежности в фиксированное время, интервал или использование независимо от его состояния.Это то, что Мубрей называет задачами запланированного восстановления или запланированного удаления в своей книге RCMII.
Я ограничиваю использование этой фразы, так как по какой-то причине люди приходят к выводу, что другое техническое обслуживание не запланировано. Хотя на самом деле, конечно, все техническое обслуживание следует планировать в соответствии с нашим недельным расписанием. Единственным исключением может быть экстренное обслуживание, которое по самой своей природе требует немедленного внимания и не может быть запланировано.
Цель обслуживания по времени — защитить себя от выхода из строя известных изнашиваемых деталей, которые имеют предсказуемое среднее время наработки на отказ (MTBF) i.е. Техническое обслуживание по времени предполагает, что отказ связан с возрастом и может быть определен точный срок службы. Или что просто не стоит прилагать усилия для оценки состояния, а замена по времени более экономична и все же (в разумной степени) эффективна.
Time Based Maintenance никогда не сможет эффективно управлять режимами отказов, не связанными с возрастом, и поэтому должно составлять лишь небольшую часть вашей общей программы технического обслуживания, поскольку> 70% режимов отказа на вашем предприятии не связаны с возрастом (см. Статью 9 Принципы Современное обслуживание).
Важно понимать, что во многих отраслях компании действительно должны выполнять определенные задачи для соответствия нормативным требованиям, и они, как правило, выполняются в фиксированный интервал времени, то есть техобслуживание на основе времени. Но даже при обслуживании, связанном с соблюдением требований, часто есть возможности привлечь регулирующий орган и рассмотреть возможность перехода, например, к подходам, основанным на оценке риска. Хорошим примером этого может быть принятие инспекции на основе рисков (RBI) для инспекций судов вместо e.г. Внутренние осмотры судов каждые 4 года.
Поиск неисправностей (FFM)
Поиск отказов Задачи обслуживания направлены на обнаружение скрытых отказов, обычно связанных с защитными функциями. Подумайте о предохранительных клапанах давления, датчиках отключения и тому подобном.
Оборудование этого типа не будет работать, пока не выйдет из строя что-то еще. Это означает, что при нормальных условиях эксплуатации вы не узнаете, работает ли это оборудование i.е. режимы отказа скрыты.
И поскольку эти сбои скрыты, вам нужно будет найти их, прежде чем вы будете полагаться на это оборудование для защиты.
Действительно просто.
Важно понимать, что задачи технического обслуживания по поиску отказов не предотвращают отказ, а просто обнаруживают его. И после обнаружения вам придется устранить обнаруженную неисправность. Обнаружение отказов Техническое обслуживание проводится через фиксированные интервалы времени, обычно определяемые законодательством или подходами, основанными на оценке риска.
Техническое обслуживание с учетом рисков (RBM)
Техническое обслуживание на основе рисков (RBM) — это когда вы используете методологию оценки рисков для распределения ваших скудных ресурсов на техническое обслуживание тем активам, которые несут наибольший риск в случае отказа (помня, что риск = вероятность x последствия).
В результате оборудование с более высоким риском и очень высокой вероятностью отказа будет подвергаться более частому техническому обслуживанию и осмотру. Оборудование с низким уровнем риска может обслуживаться с гораздо меньшей частотой и, возможно, с гораздо меньшим объемом работ.
При эффективном внедрении процесса обслуживания с учетом рисков вы должны снизить общий риск отказа всего предприятия наиболее экономичным способом.
Risk-Based Maintenance — это, по сути, профилактическое обслуживание, при котором частота и объем работ по техническому обслуживанию постоянно оптимизируются на основе результатов тестирования или инспекции и тщательной оценки рисков. Примерами технического обслуживания на основе рисков могут быть проверки на основе рисков применительно к статическому оборудованию, такому как сосуды и трубопроводы, или даже предохранительные клапаны.
Техническое обслуживание по условию (CBM)
Большинство видов отказов не связаны с возрастом. Тем не менее, большинство режимов отказа действительно выдают какое-то предупреждение о том, что они происходят или вот-вот произойдут.
Если можно найти доказательства того, что что-то находится на ранних стадиях отказа, можно принять меры для предотвращения полного отказа и / или во избежание последствий отказа. Таким образом, техническое обслуживание по состоянию в качестве стратегии ищет физические доказательства того, что отказ происходит или вот-вот произойдет.Такой подход к CBM показывает его более широкие применения за пределами методов мониторинга состояния, часто связанных только с вращающимся оборудованием.
Важной концепцией технического обслуживания по состоянию является кривая P-F, показанная на рисунке ниже:
Кривая показывает, что по мере того, как сбой начинает проявляться, оборудование изнашивается до точки, в которой его можно обнаружить (точка «P»).
Если отказ не обнаружен и не устранен, он продолжается до тех пор, пока не произойдет функциональный отказ (точка «F»).Временной диапазон между P и F, обычно называемый интервалом P-F, представляет собой окно возможностей, в течение которого инспекция, возможно, может обнаружить неминуемый отказ и дать вам время для его устранения.
Важно понимать, что CBM как стратегия технического обслуживания не снижает вероятность отказа, возникающего в результате обновления срока службы, а вместо этого направлена на вмешательство до того, как произойдет отказ, исходя из того, что это более экономично и должно иметь меньше влияние на доступность.
Другими словами: мониторинг состояния не исправляет машины, а мониторинг состояния не останавливает отказы. Мониторинг состояния позволяет обнаруживать проблемы только до того, как они перерастут в отказ.
Общее практическое правило состоит в том, что интервал между задачами CBM должен составлять половину или одну треть интервала P-F.
Насколько эффективнее CBM выше аварийного обслуживания, зависит от продолжительности интервала P-F. При наличии большого количества предупреждений можно запланировать исправление, мобилизовать материалы и ресурсы и предотвратить поломку (хотя производство все еще останавливается на время технического обслуживания).Когда интервал P-F составляет всего несколько дней, в результате организационные действия и действия на рабочем месте очень похожи на поломку, и ценность CBM в значительной степени теряется.
Для того, чтобы CBM была эффективной как стратегия, необходимо раннее вмешательство. Это требует действенного и действенного процесса сбора данных, анализа данных, принятия решений и, наконец, вмешательства.
Для режимов отказа, где интервал P-F показывает большую изменчивость, мониторинг состояния не является эффективной стратегией.
Если вам интересно узнать больше о том, как лучше всего управлять режимами отказа, не забудьте прочитать мою статью Техническое обслуживание, ориентированное на надежность — 9 принципов современного технического обслуживания.
Принцип работы (кратко). Принцип действия реактивного двигателя
Под реактивным понимается движение, при котором от тела с определенной скоростью отделяется одна из его частей. Сила, возникающая в результате такого процесса, действует сама по себе. Другими словами, у нее нет даже малейшего контакта с внешними телами.
Реактивное движение в природе
Во время летнего отдыха на юге почти все мы, купаясь в море, встречались с медузами. Но мало кто думал, что эти животные движутся так же, как реактивный двигатель. Принцип действия в природе такого агрегата можно наблюдать при перемещении определенных видов морского планктона и личинок стрекоз. Причем эффективность этих беспозвоночных зачастую выше, чем у технических средств.
Кто еще может наглядно продемонстрировать, какой из реактивных двигателей работает? Кальмары, осьминоги и каракатицы.Подобное движение совершают многие другие морские моллюски. Возьмем, например, каракатицу. Она втягивает воду в свою жаберную полость и энергично выбрасывает ее через воронку, которая направляется назад или в сторону. При этом моллюск способен совершать движения в нужную сторону.
Принцип действия реактивного двигателя можно наблюдать и при перемещении барабана. Это морское животное берет воду в широкой впадине. После этого мышцы его тела сокращаются, выталкивая жидкость через отверстие, которое находится позади.Реакция образовавшейся струи позволяет саженцу двигаться вперед.
Sea Missiles
Но наибольшего совершенства в реактивной навигации достиг все тот же кальмар. Даже форма самой ракеты словно скопирована с этого морского обитателя. При движении с небольшой скоростью кальмар периодически выгибает ромбовидный плавник. Но для быстрого броска ему приходится использовать собственный «реактивный двигатель». Принцип работы всех его мышц и тела стоит рассмотреть подробнее.
Кальмар имеет своеобразную мантию.Это мышечная ткань, которая окружает его тело со всех сторон. Во время движения животное засасывает в эту мантию большой объем воды, резко выбрасывая струю через специальную узкую насадку. Такие действия позволяют кальмарам двигаться назад со скоростью до семидесяти километров в час. Во время движения животное собирает в пучок все свои десять щупалец, что придает телу обтекаемую форму. На насадке есть специальный клапан. Его поворачивает животное сокращением мышц. Это позволяет моряку менять направление.Роль штурвала при передвижении кальмара выполняют его щупальца. Он направляет их влево или вправо, вниз или вверх, легко уворачиваясь от столкновений с различными препятствиями.
Существует разновидность кальмаров (stenoteutis), относящаяся к званию лучшего пилота среди моллюсков. Опишите принцип работы реактивного двигателя — и вы поймете, почему, преследуя рыбу, это животное иногда выпрыгивает из воды, даже попадая на палубы кораблей, плывущих по океану. Как это произошло? Пилот-кальмар, находясь в водной стихии, развивает для себя максимальную реактивную тягу.Это позволяет ему летать над волнами на расстоянии до пятидесяти метров.
Если мы рассмотрим реактивный двигатель, принцип Какое животное работает, мы можем упомянуть еще? Это, на первый взгляд, мешковатый осьминог. Пловцы не так быстры, как кальмары, но в случае опасности их скорости могут позавидовать даже лучшие спринтеры. Биологи, изучавшие миграцию осьминогов, выяснили, что они движутся по принципу действия реактивного двигателя.
Животное при каждой струе воды, выбрасываемой из воронки, делает рывок на два или даже два с половиной метра.При этом плывет осьминог своеобразным образом — задом наперед.
Другие примеры реактивного движения
В мире растений есть ракеты. Принцип действия реактивного двигателя можно наблюдать, когда даже при очень легком прикосновении «бешеный огурец» с большой скоростью отскакивает от ножки, отталкивая при этом липкую жидкость с семенами. При этом сам плод летит на значительное расстояние (до 12 м) в обратном направлении.
Принцип работы реактивного двигателя можно наблюдать и в лодке.Если с него в определенном направлении бросить в воду тяжелые камни, то он будет двигаться в противоположном направлении. Ракетно-реактивный двигатель имеет такой же принцип работы. Только там вместо камней используются газы. Они создают реактивную силу, которая обеспечивает движение как в воздухе, так и в разряженном пространстве.
Фантастическое путешествие
Человечество давно мечтает о космических полетах. Об этом свидетельствуют произведения писателей-фантастов, которые для достижения этой цели предлагали самые разные средства.Например, герой рассказа французского писателя Эркюля Савинена Сирано де Бержерак достиг Луны на железной повозке, на которую постоянно бросался мощный магнит. Знаменитый Мюнхгаузен тоже достиг той же планеты. Гигантский стебель фасоли помог ему совершить путешествие.
Реактивный двигатель использовался в Китае еще в первом тысячелетии до нашей эры. Бамбуковые трубы, набитые порохом, служили своеобразными ракетами для развлечения. Кстати, проект первой машины на нашей планете, созданный Ньютоном, тоже был с реактивным двигателем.
История RD
Только в XIX в. мечта человечества о космосе стала приобретать конкретные черты. Ведь именно в этом веке русский революционер Н.И. Кибальчич создал первый в мире проект самолета с реактивным двигателем. Все бумаги были составлены Народным освободителем в тюрьме, куда он попал после покушения на Александра. Но, к сожалению, 04.03.1881 Кибальчич был казнен, а его идея не нашла практического воплощения.
В начале 20 в. Идея использования ракет для космических полетов была выдвинута русским ученым К.Е. Циолковский. Впервые его работа, содержащая описание движения тела переменной массы в виде математического уравнения, была опубликована в 1903 году. Позже ученый разработал саму схему реактивного двигателя, работающего на жидком топливе.
Также Циолковским была изобретена многоступенчатая ракета и выдвинута идея создания настоящих космических городов на низкой околоземной орбите.Циолковский убедительно доказал, что единственное средство для полета в космос — это ракета. То есть аппарат, оснащенный реактивным двигателем, заправляемый горючим и окислителем. Только такая ракета способна преодолеть силу тяжести и вылететь за пределы атмосферы Земли.
Освоение космоса
Статья Циолковского, опубликованная в журнале «Научное обозрение», подтвердила для ученых репутацию мечтателя. Никто не принимал всерьез его аргументы.
Идея Циолковского была реализована советскими учеными.Под руководством Сергея Павловича Королева они запустили первый искусственный спутник Земли. 4 октября 1957 года это устройство было доставлено на орбиту ракетой с реактивным двигателем. Работа РД была основана на преобразовании химической энергии, которая передается топливом газовой струе, превращаясь в кинетическую энергию. В этом случае ракета движется в обратном направлении.
Реактивный двигатель, принцип действия которого используется много лет, находит свое применение не только в космосе, но и в авиации.Но больше всего он используется для запуска ракет. Ведь только RD может перемещать аппарат в пространстве, в котором отсутствует какая-либо среда.
Жидкостный реактивный двигатель
Тот, кто стрелял из огнестрельного оружия или просто наблюдал за этим процессом со стороны, знает, что существует сила, которая непременно оттолкнет ствол назад. А при большей сумме заряда отдача обязательно увеличится.
Система управления
Тяговые характеристики современных турбодвигателей должны отвечать таким же высоким требованиям, как и характеристики атмосферных моторов с идентичными мощностными параметрами. Это означает, что полное давление наддува должно быть доступно, начиная с минимально возможных частот вращения двигателя. Это, в свою очередь, может быть достигнуто только путем управления турбокомпрессором на турбинной стороне.
Байпасное регулирование на турбинной стороне
Установка байпасного клапана в турбинной части турбокомпрессора (ТК) – самый простой способ контроля давления наддува.
Геометрические параметры турбины выбирают таким образом, чтобы обеспечить характеристику крутящего момента на низких оборотах, необходимую для достижения заданных динамических показателей автомобиля. При такой конструкции ТК уже незадолго до достижения максимального крутящего момента на турбину начинает поступать избыточное количество отработавших газов. Таким образом, как только номинальное давление наддува достигнуто, избыток отработавших газов направляется по байпасному каналу в обход турбинного колеса. Клапан «вейстгейт», который открывает и закрывает байпас, обычно приводится в действие пневматической камерой с подпружиненной диафрагмой, реагирующей на давление наддува. Так по мере дальнейшего увеличения оборотов двигателя давление наддува остается на неизменном уровне.
В этом, очень экономичном, решении на диафрагму камеры управления, предварительно нагруженную спиральной пружиной, воздействует давление наддува. Как только давление наддува преодолеет силу предварительного сжатия пружины, шток через рычаг открывает тарелку байпасного клапана и ОГ начинают перетекать вокруг турбины в систему выпуска.
В современных бензиновых и дизельных двигателях все чаще применяются электронно управляемые системы контроля наддувочного давления. В сравнении с чисто пневматическим регулированием, которое действует только как ограничитель давления на полной нагрузке, гибкое управление позволяет устанавливать оптимальное давление наддува в режимах частичной нагрузки. Электронное регулирование работает в соответствии с различными параметрами, такими как температура наддувочного воздуха, качество топлива и параметры опережения впрыска (зажигания). Также становится возможным кратковременный «перенаддув» при интенсивном ускорении.
Механический привод байпасной заслонки действует так же как и в описанном выше случае. Вместо полного давления наддува на диафрагму камеры управления подается модулированное управляющее давление. Оно меньше полного давления наддува и вырабатывается так называемым пропорциональным клапаном. Этим достигается то, что на диафрагму воздействует комбинация давления наддува и давления на выходе из компрессора в изменяющейся пропорции.
Пропорциональный клапан управляется электроникой двигателя и срабатывает с частотой от 10 до 15 Гц. В сравнение с обычной системой управления усилие предварительного сжатия пружины существенно ниже, что позволяет осуществлять регулирование также и на режимах частичной нагрузки, то есть, при меньшем давлении наддува.
В электронных системах управления турбокомпрессоров дизельных двигателей пневмокамеры регулируются вакуумом.
Турбины с изменяемой геометрией
Байпасные системы регулирования управляют мощностью турбины, направляя часть отработавших газов (ОГ) в обход нее. Таким образом, «дармовая» энергия газов используется не полностью. Турбины с изменяемой геометрией позволяют варьировать сечение проточной части турбины в зависимости от режима работы двигателя. Это дает возможность полностью утилизировать энергию ОГ, оптимизируя конфигурацию канала, по которому ОГ попадают на турбинное колесо, для данного режима двигателя. Как результат, эффективность турбокомпрессора (ТК) и, соответственно, двигателя выше тех, что удается достичь при байпасном регулировании.
Сегодня турбины с РСА в виде подвижных направляющих лопаток (VNT, VTG, VGT) – самое передовое решение для современных легковых дизельных автомобилей. В результате непрерывной адаптации проходного сечения турбинного канала к рабочему режиму двигателя сокращаются потребление топлива и вредные выбросы. Высокий крутящий момент уже на низких оборотах и адекватная стратегия управления обеспечивают существенное улучшение динамических характеристик.
Подвижные направляющие лопатки между корпусом улитки и турбинным колесом влияют на протекание процесса восстановления давления и, таким образом, на выходные характеристики турбины. Это позволяет варьировать поток газов через турбину в диапазоне 1:3 при хороших уровнях эффективности. На низких оборотах сечение проточной части турбины уменьшается путем закрытия направляющих лопаток. Давление наддува и, следовательно, крутящий момент двигателя возрастают как результат увеличения перепада давления на входе и выходе из турбины. С повышением оборотов двигателя управляемые лопатки постепенно открываются.
Требуемое давление наддува достигается при низком перепаде давления на турбине — так достигается сокращение расхода топлива. При ускорении машины с низкой скорости (оборотов двигателя) управляемые лопатки закрываются для получения максимальной энергии от ОГ. По мере увеличения скорости лопатки открываются и адаптируются к соответствующему рабочему режиму.
В настоящее время управление лопатками преимущественно электронное, с помощью вакуумно-регулируемой камеры управления и пропорционального клапана. В будущем все чаще будут применяться электрические приводы с положительной обратной связью, позволяющие реализовать точное и чрезвычайно гибкое управление давлением наддува.
Температура ОГ современных высокоэффективных дизельных двигателей может достигать 830°С. Точная и надежная работа управляющих лопаток в потоке горячих газов предъявляет высокие требования к материалам и точности допусков в конструкции турбины. Независимо от типоразмера турбокомпрессора направляющие лопатки должны иметь минимальные зазоры для обеспечения надежной работы в течение всего срока службы автомобиля.
С уменьшением размера ТК относительные потери потока через турбину возрастают и ее эффективность падает. Поэтому цель многих разработок – отодвинуть эти ограничения области применения технологии VTG как можно дальше в сторону ТК малых размеров.
Альтернативное решение – турбины с регулирующим механизмом в виде подвижного (скользящего) кольца (VST-variable sliding turbine). Простота конструкции и исполнение многих функций небольшим количеством компонентов – преимущества для маленьких турбин или там, где требуется работа в условиях высоких температур ОГ. Это особенно применимо в компактных дизельных двигателях с рабочим объемом менее 1,4 л. Преимущества – высокая эффективность, низкая цена и сокращение установочных размеров. Для бензиновых моторов с высокой температурой ОГ технология VST – надежная возможность управления давлением наддува путем изменения геометрии проточной части турбины.
Прочный механизм VST противостоит высоким температурам ОГ значительно лучше, чем VTG с направляющими лопатками.
Байпас, который для бензиновых двигателей необходим даже в ТК с изменяемой геометрией из-за большого диапазона изменения расхода, интегрирован в механизм управления.
Корпус турбины аналогичен турбинам с двойной улиткой (с двухканальным направляющим аппаратом). Перегородка, разделяющая каналы, не выходит на впускной фланец, а начинается внутри улитки. На низких оборотах двигателя открыт только один канал. Второй канал, который закрыт скользящим кольцом, постепенно открывается по мере увеличения оборотов. Затем скользящее кольцо приоткрывает и байпасный канал, ведущий от входа в турбину по внешнему контуру скользящего кольца к выходу из турбины. Это дополнительно увеличивает расход газов через турбину. Для регулирования сечения проточной части и открытия байпасного канала требуется всего один управляющий механизм. Могут быть использованы как пневматический, так и электронный приводы.
Узел подшипников
Ротор турбокомпрессора (ТК) вращается с частотой до 300 000 мин -1. Срок службы ТК должен соответствовать ресурсу двигателя, который может составлять 1 000 000 км пробега для коммерческого автомобиля. Только специально разработанные для ТК подшипники скольжения могут соответствовать таким жестким требованиям при приемлемой стоимости.
Опорные подшипники
В подшипнике скольжения вал вращается практически без трения на масляной пленке внутри втулки подшипника.
Масло подается в турбокомпрессор (ТК) от системы смазки двигателя. Подшипниковый узел спроектирован так, что между неподвижным корпусом и вращающимся валом расположены «плавающие» бронзовые подшипниковые втулки. Они вращаются с частотой, вдвое меньшей частоты вращения вала. Это позволяет высокоскоростным подшипникам адаптироваться таким образом, что на любых режимах работы ТК нет прямого контакта «металл-металл» между валом и подшипниками.
Кроме функции смазки масляная пленка в зазорах подшипника играет роль демпфера, который способствует стабилизации вала и турбинного колеса. Гидродинамическая несущая способность пленки и демпфирующие характеристики подшипника оптимизируются величиной зазоров. Таким образом, толщина смазывающей пленки для внутренних зазоров выбирается исходя из нагрузки на подшипник, в то время как толщина внешних зазоров определяется с учетом демпфирования подшипника. Зазоры в подшипниках составляют несколько сотых долей миллиметра. Увеличение зазоров приведет к более мягкому демпфированию и, одновременно, к снижению несущей способности подшипника.
Так называемый патрон — специальный вид опорного подшипника скольжения. Вал вращается в неподвижной целиковой втулке, снаружи которой прокачивается масло. Внешний зазор выбирается исключительно из условия демпфирования подшипника, так как патрон не проворачивается. Вытекающая из этого меньшая ширина подшипника позволяет создать более компактный ТК.
Упорный подшипник
Ни один из рассмотренных типов опорных подшипников, ни свободно плавающие втулки, ни фиксированный плавающий патрон, не воспринимают нагрузки в осевом направлении. Поскольку газы воздействуют на компрессорное и турбинное колеса в осевом направлении с разной силой, ротор турбокомпрессора (ТК) испытывает осевую нагрузку. Она воспринимается упорным подшипником скольжения с конической плоскостью (рабочей поверхностью). Два маленьких диска, закрепленных на валу, служат контактными поверхностями. Упорный подшипник фиксируется в центральном корпусе подшипников. Маслоотражающая пластина предотвращает попадание масла в зону уплотнения вала.
Слив масла
Масло подается в турбокомпрессор (ТК) при давлении примерно 4 бар. Поскольку масло сливается из турбины при меньшем давлении (самотеком), диаметр трубки для слива значительно больше, чем маслоподающей трубки. Проток масла через корпус подшипников должен быть по возможности вертикальным, сверху вниз. Сливная трубка должна выходить в картер выше уровня масла. Любое препятствие на пути слива масла оборачивается увеличением противодавления в корпусе подшипников. В этом случае масло начинает просачиваться сквозь уплотнительные кольца в компрессор и турбину.
Уплотнения
Центральный корпус подшипников должен быть уплотнен от прорыва в него горячих отработавших газов из турбины и от утечек масла из корпуса. Для этого в канавки на валу ротора, со стороны компрессора и турбины установлены разрезные кольца, аналогичные поршневым. Кольца не вращаются, а неподвижно расклинены в центральном корпусе. Это бесконтактное уплотнение, один из видов лабиринтного уплотнения. Благодаря многочисленным резким изменениям направления движения потока оно затрудняет утечку масла и пропускает в картер лишь небольшое количество отработавших газов.
Тепловая нагрузка на подшипники
Учитывая небольшое расстояние между центральным корпусом и горячим корпусом турбины, тепло может проникать в центральный корпус и нагревать масло до температуры коксования. Тогда масляный кокс мог бы осаждаться в зазорах и на поверхностях, засорять масляные каналы и нарушать работу подшипников и уплотнений. Большое количество углеводородных отложений может вызвать дефицит смазки и граничное трение, приводящие к ускоренному износу системы подшипников.
Тепловой экран и охлаждение разбрызгиванием масла<
Тепловой экран, расположенный позади опорного диска турбинного колеса, предотвращает контакт горячих отработавших газов с центральным корпусом. В некоторых конструкциях при работе двигателя масло распыляется на вал ротора через маленькое распылительное отверстие в опоре подшипника с турбинной стороны, охлаждая вал и уменьшая риск коксования.
Наивысшие температуры в центральном корпусе достигаются вскоре после останова двигателя. Горячий турбинный корпус нагревает систему подшипников, которая больше не охлаждается моторным маслом.
Термическая развязка
В расчете на термическую развязку правой подшипниковой опоры передача тепла от корпуса турбины к системе подшипников сокращается даже после того как двигатель был заглушен. Для этого систему подшипников располагают ниже точки подачи масла, так же как силовой агрегат размещают под крылом самолета. Правая подшипниковая опора больше не контактирует с горячей стенкой центрального корпуса, значит, передача тепла к системе подшипников ограничивается.
Водяное охлаждение
Бензиновые двигатели, у которых температура отработавших газов на 200-300°С выше чем у дизелей, обычно оснащаются турбокомпрессорами с охлаждаемыми центральными корпусами. При работе двигателя центральный корпус интегрируется в его контур охлаждения. После выключения двигателя остаточное тепло снимается посредством малого кольца циркуляции, которое задействуется электрическим насосом с термостатом.
Рециркуляционный клапан
В бензиновых турбодвигателях дроссельная заслонка, которая управляет нагрузкой двигателя, располагается после компрессора, во впускном коллекторе. В момент внезапного сброса газа заслонка закрывается, а компрессор из-за своей инерционности продолжает нагнетать воздух в почти замкнутый объем. Вследствие этого начался бы помпаж компрессора. Частота вращения турбокомпрессора (ТК) быстро упала бы.
Начиная с определенного давления, открывается подпружиненный клапан и направляет воздух обратно на вход в компрессор, ограничивая рост давления и исключая помпаж. Частота вращения ТК остается высокой, и давление наддува появится, как только будет задействован акселератор.
Принцип работы турбореактивного двигателя самолёта
Совершая полет в самолете в большинстве случаев люди никогда не задумываются о том, как работает его двигатель. Но на самом деле о работе двигателя и реактивной тяги с помощью, которой работает сам двигатель, знали ее в Античное время. Но применить эти знания на практике смогли не так давно, так как раньше не технологии не позволяли никому достичь его исправной работы. Гонка вооружения между Англией и Германией стала толчком к созданию ТРД (турбореактивного двигателя).
В работе ТРД самолета нет никаких сложностей, принцип его работы может понять почти каждый человек. Но данный двигатель имеет несколько нюансов, их соблюдение контролируется под строгим присмотром руководства. Для того чтобы авиалайнер смог держаться в небе, необходима идеальная работа двигателя. Так как от работы двигателя напрямую зависят жизни пассажиров находящихся на борту авиатранспорта.
Принцип работы реактивного двигателя
За работу двигателя отвечает реактивная тяга. Для создания реактивной тяги необходима определенная жидкость, которая подается из задней части двигателя и по ходу ее продвижения увеличивается ее скорость движения вперед. Работу тяги отлично объясняет один из законов Ньютона, звучит он так «Любое действия вызывает равное противодействие».
Вместо жидкости в ТРД используется горючая смесь (газы и воздух со сгоревшими частичками топлива). Благодаря этой смеси самолет толкает вперед и позволяет ему лететь дальше.
Разработки таких двигателей начались в тридцатых годах. Первыми кто начал разрабатывать двигатели такого типа стали немцы и англичане. Но в гонке вооружений одержали победу ученные из Германии, так как они выпустили самый первый в мире самолет с ТРД под названием «Ласточка», данный самолет впервые взлетел в небеса над Люфтваффом. Спустя некоторое время появился и Английский самолет «Глостерский метеор»
Также сверхзвуковые двигатели принято считать турбореактивными, но они отличаются более совершенными модификациями, в отличие от ТРД.
Устройство двигателя имеет четыре главные детали, а именно:
- Компрессор.
- Камера горения.
- Турбина.
- Выхлоп.
Компрессор
В компрессоре находиться несколько турбин, с помощью которых происходит засасывание и сжатие воздуха. Во время сжатия воздуха, его давление и температура начинает нагнетаться и расти.
Камера горения
После того как воздух проходит турбину и его сжимает до необходимых размеров. Часть сжатого воздуха поступает в камеру горения, где воздух начинает смешиваться с топливом, после чего его поджигают. Благодаря этому увеличивается тепловая энергия воздуха. После смесь выходит из камеры с большой скорости и расширяется.
Турбина
После выхода эта смесь снова попадает в турбину, с помощью высокой энергии газа лопасти в турбине начинают свое вращение. Турбина тесно связанна с компрессором, который находиться в начале двигателя. Благодаря этому турбина начинает свою работу. Остатки воздуха выходят в выхлоп. В момент выхода смеси температура достигает рекордных размеров. Но она продолжает повышать свою температуру с помощью эффекта Дросселирования. После того как температура воздуха доходит до своего пика, она начинает идти на спад и выходит из турбины.
Принцип работы турбореактивного двигателя
В отличие от реактивного двигателя, который пользуется спросом почти у всех самолетов, турбореактивный двигатель больше подходит для пассажирских авиалайнеров. Так как для работы реактивного двигателя необходимо не только топливо, но и окислитель.
Благодаря своему строению окислитель поступает вместе с топливом из бака. А в случаи с ТРД окислитесь, поступает напрямую из атмосферы. А в остальном их работа совершенно идентична и не отличается друг от друга.
У турбореактивного двигателя главной деталью является лопасть турбины, так как от ее исправной работы напрямую зависит мощность двигателя. Благодаря этим лопастям и образуется тяга, которая необходима для поддержания скорости самолета. Если сравнить одну лопасть с автомобильным двигателем, то она сможет обеспечить мощностью целых десять машин.
Лопасти устанавливаются за камерой сгорания, так как там нагнетается самое высокое давления, также температура воздуха в данной части двигателя может доходить до 1400 градусов Цельсия.
В целях улучшения прочности и устойчивости лопасти перед различными факторами их монокристаллизируют, благодаря этому они могут держать высокую температуру и давление. Прежде чем установить такой двигатель на самолет его тестируют на полном тяговом усилителе. Также двигатель должен получить сертификат от Европейского совета по безопасности.
Атомный двигатель
В период холодной войны в мире были попытки создания атомного двигателя, за основу был взят турбореактивный двигатель. Главной задумкой ученых было создание двигателя, основанного не на химической реакции радиоактивных веществ, а на вырабатываемом тепле от ядерного реактора. Он должен был находиться на месте камеры сгорания.
В теории воздух должен был проходить через работающую зону реактора, благодаря этому реактор должен был остужаться, а температура воздуха наоборот возрастать. После чело воздух должен был расширяться и выходить через сопла (выхлоп) на этот момент скорость воздуха должна была превышать скорость полета самолета.
В Советском союзе были попытки проведения испытаний подобного двигателя, также ученные в соединенных штатах Америки, вели разработку данного двигателя, и их работа почти подходила к тестам двигателя на настоящем самолете.
Но по ряду причин разработки этого двигателя было решено закрыть. Так как у двигателя было множество недостатков, а именно:
- Пилоты были подвержены постоянному радиоактивному облучению на протяжении всего полета.
- Вместе с воздухом через сопла выходили и частички радиоактивного элемента в атмосферу.
- В том случае если самолет терпел крушение, был очень большой шанс взрыва радиоактивного реактора, что влекло за собой радиоактивное отравление на довольно большой площади.
Турбина Каплан — ее составные части, работа и применение
Турбина Каплан работает по принципу реакции осевого потока. В турбинах с осевым потоком вода течет через бегунок в направлении, параллельном оси вращения рабочего колеса. Вода на входе в турбину обладает как кинетической энергией, так и энергией давления для эффективного вращения лопастей гидроэлектростанции.
Рис. 1: Турбина Каплана.
В 1913 году австрийский профессор Виктор Каплан, который разработал эту турбину, объединил автоматически регулируемые лопасти гребного винта с автоматически регулируемыми заслонками калитки для достижения эффективности в широком диапазоне расхода и уровня воды.Она также называется пропеллерной турбиной и произошла от турбины Фрэнсиса. Он способен очень эффективно работать при низком напоре и высоких расходах, что невозможно с турбиной Фрэнсиса.
В этой статье рассматривается порядок работы, основные компоненты и их применение.
Основные компоненты турбины Каплана
Основные части турбины Каплан,
1. Спиральный кожух
Это спиральный кожух с уменьшающейся площадью поперечного сечения.Вода из затворов попадает в корпус спирали, а затем движется к направляющим лопастям, где вода поворачивается на 90 ° и течет в осевом направлении через желоб. Он защищает рабочее колесо, направляющие лопатки рабочих лопаток и другие внутренние части турбины от внешних повреждений.
Рис. 2: Основные компоненты турбины Каплана.
2. Механизм направляющей лопасти
Это единственная управляющая часть всей турбины, которая открывается и закрывается в зависимости от потребности в мощности.Если требуется большая выходная мощность, он открывается шире, чтобы больше воды попадало на лопасти ротора, а когда требуется низкая выходная мощность, он закрывается, чтобы прекратить поток воды. При отсутствии направляющих лопаток турбина не может работать эффективно и ее КПД снижается.
3. Трубка отсасывающая
Давление на выходе из рабочего колеса реакционной турбины обычно ниже атмосферного. Вода на выходе не может напрямую сбрасываться в хвостовую часть.Труба или труба с постепенно увеличивающейся площадью используется для отвода воды от выхода турбины до хвостовой части. Эта трубка с увеличивающейся площадью называется вытяжной трубкой. Один конец трубки подсоединен к выпускному отверстию бегунка, а другой конец погружен ниже уровня воды в хвостовой части.
4. Лезвия рабочего колеса
Сердцем компонента в турбине Каплана являются рабочие лопатки, так как это вращающаяся часть, которая помогает в производстве электроэнергии. Вал соединен с валом генератора.Рабочее колесо этой турбины имеет большой выступ, на котором крепятся его лопасти, а лопасти рабочего колеса регулируются под оптимальным углом атаки для максимальной выходной мощности. Лопатки турбины Каплана имеют закрутку по длине.
Рис. 3. Рабочие лопатки турбины Каплана.
Рабочий процесс турбины Каплана
Вода, поступающая из загона, попадает в кожух спирали. Корпус спирали выполнен такой формы, чтобы не терять давление потока.Направляющие лопатки направляют воду к лопастям рабочего колеса. Лопасти регулируются и могут регулироваться в зависимости от скорости потока. Вода поворачивается на 90 градусов, поэтому направление воды является осевым по отношению к лопастям бегунка.
Лопасти бегунка начинают вращаться при ударе воды из-за силы реакции воды. Лезвия бегунка имеют изгиб по всей длине, чтобы всегда иметь оптимальный угол атаки для всего поперечного сечения лезвий для достижения большей эффективности.
Из лопастей рабочего колеса вода поступает в вытяжную трубу, где ее энергия давления и кинетическая энергия уменьшаются. Кинетическая энергия преобразуется в энергию давления, что приводит к увеличению давления воды.
Вращение турбины используется для вращения вала генератора для производства электроэнергии.
Применение турбины Каплана
- Турбины Каплана широко используются во всем мире для производства электроэнергии.
- Может работать более эффективно при низком напоре воды и высоком расходе по сравнению с другими типами турбин.
- Он меньше по размеру и прост в сборке.
- КПД турбины Каплана очень высок по сравнению с другими гидравлическими турбинами.
Недостаток турбины Каплана
- Единственным недостатком турбины Каплана является кавитация, возникающая из-за падения давления в отсасывающей трубе. Использование вытяжной трубы и подходящего материала, как правило, из нержавеющей стали для лопастей рабочего колеса, может в большей степени уменьшить проблему кавитации.
Турбина | Британника
Турбина , любое из различных устройств, преобразующих энергию потока жидкости в механическую энергию. Преобразование обычно осуществляется путем пропускания жидкости через систему неподвижных каналов или лопаток, которые чередуются с каналами, состоящими из лопастей, похожих на ребра, прикрепленных к ротору. За счет организации потока так, чтобы на лопасти ротора действовала касательная сила или крутящий момент, ротор вращается, и работа извлекается.
Ветровые турбины около Техачапи, Калифорния
© Грег Рэндлс / Shutterstock.com Турбины можно разделить на четыре основных типа в зависимости от используемых жидкостей: вода, пар, газ и ветер. Хотя одни и те же принципы применимы ко всем турбинам, их конкретные конструкции достаточно различаются, чтобы заслужить отдельное описание.
Гидравлическая турбина использует потенциальную энергию, возникающую в результате разницы в высоте между верхним водным резервуаром и уровнем воды на выходе из турбины (отводом) для преобразования этого так называемого напора в работу.Водяные турбины — современные преемники простых водяных колес, которым около 2000 лет. Сегодня гидротурбины в основном используются для производства электроэнергии.
Однако наибольшее количество электроэнергии вырабатывается паровыми турбинами, соединенными с электрогенераторами. Турбины приводятся в действие паром, вырабатываемым либо в генераторе, работающем на ископаемом топливе, либо в атомном генераторе. Энергию, которую можно извлечь из пара, удобно выражать через изменение энтальпии в турбине.Энтальпия отражает формы как тепловой, так и механической энергии в процессе потока и определяется суммой внутренней тепловой энергии и произведением давления на объем. Доступное изменение энтальпии через паровую турбину увеличивается с увеличением температуры и давления парогенератора и с уменьшением давления на выходе из турбины.
Оформите подписку Britannica Premium и получите доступ к эксклюзивному контенту.
Подпишитесь сейчас Для газовых турбин энергия, извлекаемая из текучей среды, также может быть выражена через изменение энтальпии, которое для газа почти пропорционально перепаду температуры в турбине.В газовых турбинах рабочим телом является воздух, смешанный с газообразными продуктами сгорания. Большинство газотурбинных двигателей включает, по крайней мере, компрессор, камеру сгорания и турбину. Обычно они монтируются как единое целое и работают как законченный первичный двигатель в так называемом открытом цикле, когда воздух всасывается из атмосферы, а продукты сгорания, наконец, снова выбрасываются в атмосферу. Поскольку успешная работа зависит от интеграции всех компонентов, важно рассматривать устройство в целом, которое фактически является двигателем внутреннего сгорания, а не только турбиной.По этой причине газовые турбины рассматриваются в статье двигатель внутреннего сгорания.
Энергия ветра может быть извлечена ветровой турбиной для производства электроэнергии или для откачки воды из колодцев. Ветряные турбины являются преемниками ветряных мельниц, которые были важными источниками энергии с позднего средневековья до 19 века.
Фред Лэндис Водяные турбины обычно делятся на две категории: (1) импульсные турбины, используемые для высокого напора воды и низкого расхода, и (2) реактивные турбины, обычно используемые для напора ниже примерно 450 метров и среднего или высокого расхода.Эти два класса включают в себя основные типы, обычно используемые, а именно импульсные турбины Пелтона и реактивные турбины типа Фрэнсиса, пропеллера, Каплана и Дериаза. Турбины могут иметь горизонтальный или, чаще, вертикальный вал. Для каждого типа возможны широкие вариации конструкции для соответствия конкретным местным гидравлическим условиям. Сегодня большинство гидравлических турбин используются для выработки электроэнергии на гидроэлектростанциях.
Импульсные турбины
В импульсной турбине потенциальная энергия или напор воды сначала преобразуется в кинетическую энергию путем выпуска воды через сопло тщательно продуманной формы.Струя, выбрасываемая в воздух, направляется на изогнутые ковши, закрепленные на периферии бегунка, для извлечения энергии воды и преобразования ее в полезную работу.
Современные импульсные турбины основаны на конструкции, запатентованной в 1889 году американским инженером Лестером Алленом Пелтоном. Свободная водная струя попадает в лопатки турбины по касательной. Каждый ковш имеет высокий центральный гребень, так что поток разделяется, оставляя желоб с обеих сторон. Колеса Пелтона подходят для высоких напоров, обычно выше 450 метров при относительно низком расходе воды.Для максимальной эффективности скорость конца рабочего колеса должна составлять примерно половину скорости ударной струи. КПД (работа, производимая турбиной, деленная на кинетическую энергию свободной струи) может превышать 91 процент при работе с 60–80 процентами полной нагрузки.
Мощность одного колеса можно увеличить, используя более одного жиклера. Для горизонтальных валов характерны двухструйные устройства. Иногда на одном валу устанавливаются два отдельных бегунка, приводящих в движение один электрогенератор. Агрегаты с вертикальным валом могут иметь четыре или более отдельных форсунок.
Если электрическая нагрузка на турбину изменяется, ее выходная мощность должна быть быстро отрегулирована в соответствии с потребностями. Это требует изменения расхода воды, чтобы поддерживать постоянную скорость генератора. Скорость потока через каждое сопло регулируется расположенным в центре наконечником или иглой аккуратной формы, которая скользит вперед или назад под управлением гидравлического серводвигателя.
Правильная конструкция иглы гарантирует, что скорость воды, выходящей из сопла, остается практически неизменной независимо от отверстия, обеспечивая почти постоянную эффективность в большей части рабочего диапазона.Нецелесообразно внезапно уменьшать поток воды, чтобы соответствовать уменьшению нагрузки. Это может привести к разрушительному скачку давления (гидроудару) в подающем трубопроводе или водопроводе. Таких скачков можно избежать, добавив временное сопло для разлива, которое открывается при закрытии основного сопла, или, что чаще, частично вставляя отражающую пластину между струей и колесом, отклоняя и рассеивая часть энергии при медленном закрытии иглы.
Другой тип импульсной турбины — турбина турго.Струя падает под косым углом на бегунок с одной стороны и продолжает двигаться по единственному пути, выбрасывая его с другой стороны. Этот тип турбины использовался в установках среднего размера с умеренно высоким напором.
Реакционные турбины
В реакционной турбине силы, приводящие в движение ротор, достигаются за счет реакции ускоряющегося потока воды в рабочем колесе при падении давления. Принцип реакции можно наблюдать в роторном оросителе для газонов, где выходящая струя вращает ротор в противоположном направлении.Из-за большого разнообразия возможных конструкций рабочего колеса реактивные турбины могут использоваться в гораздо большем диапазоне напоров и расходов, чем импульсные турбины. Реакционные турбины обычно имеют спиральный впускной кожух, который включает регулирующие заслонки для регулирования потока воды. На входе часть потенциальной энергии воды может быть преобразована в кинетическую энергию по мере ускорения потока. Впоследствии энергия воды отбирается в роторе.
Как отмечалось выше, широко используются четыре основных типа реактивных турбин: турбины Каплана, Фрэнсиса, Дериаза и пропеллерные.В турбинах Каплана с неподвижными лопастями и с регулируемыми лопастями (названными в честь австрийского изобретателя Виктора Каплана), по существу, существует осевой поток через машину. Турбины типа Фрэнсиса и Дериаза (в честь американского изобретателя британского происхождения Джеймса Б. Фрэнсиса и швейцарского инженера Поля Дериаза, соответственно) используют «смешанный поток», когда вода поступает радиально внутрь и выпускается в осевом направлении. Рабочие лопасти на турбинах Фрэнсиса и пропеллера состоят из неподвижных лопастей, в то время как в турбинах Каплана и Дериаза лопасти могут вращаться вокруг своей оси, которая находится под прямым углом к главному валу.
Объяснение 9 различных стратегий
Профилактическое обслуживание и корректирующее обслуживание
На верхнем уровне я вижу профилактическое или корректирующее обслуживание:
- Когда мы выполняем профилактическое обслуживание , мы выполняем задачу до того, как произойдет сбой . Эта задача может быть направлена на предотвращение отказа, минимизацию последствий отказа или оценку риска возникновения отказа.
- Когда мы проводим корректирующее обслуживание , произошел сбой , и мы в основном восстанавливаем работоспособность оборудования. Чтобы было ясно, корректирующее обслуживание может быть результатом преднамеренной стратегии безотказной работы.
Профилактическое обслуживание
Профилактическое обслуживание можно определить как «стратегию обслуживания оборудования, основанную на замене или восстановлении актива через фиксированные интервалы времени, независимо от его состояния. Запланированные задачи восстановления и задачи замены являются примерами задач профилактического обслуживания ».
Профилактическое обслуживание (или профилактическое обслуживание) в основном представляет собой тип обслуживания, который выполняется через регулярные промежутки времени, пока оборудование все еще функционирует, с целью предотвращения отказа или снижения вероятности отказа.
Профилактическое обслуживание может проводиться по времени, т.е. каждую неделю, каждый месяц или каждые три месяца. Но профилактическое обслуживание также может быть основано на использовании e.г. каждые 150 циклов, каждые 10 000 часов или как ваш автомобиль: обслуживание каждые 10 000 км.
Помимо регулярного интервального обслуживания (обслуживания по времени), существуют также другие виды обслуживания, которые подпадают под категорию профилактического обслуживания:
В следующих параграфах я более подробно рассмотрю каждый из этих типов обслуживания, в том числе, когда вам следует рассмотреть возможность их использования.
Обслуживание по времени (TBM)
Временное обслуживание относится к замене или обновлению элемента для восстановления его надежности в фиксированное время, интервал или использование независимо от его состояния.Это то, что Мубрей называет задачами запланированного восстановления или запланированного удаления в своей книге RCMII.
Я ограничиваю использование этой фразы, так как по какой-то причине люди приходят к выводу, что другое техническое обслуживание не запланировано. Хотя на самом деле, конечно, все техническое обслуживание следует планировать в соответствии с нашим недельным расписанием. Единственным исключением может быть экстренное обслуживание, которое по самой своей природе требует немедленного внимания и не может быть запланировано.
Цель обслуживания по времени — защитить себя от выхода из строя известных изнашиваемых деталей, которые имеют предсказуемое среднее время наработки на отказ (MTBF) i.е. Техническое обслуживание по времени предполагает, что отказ связан с возрастом и может быть определен точный срок службы. Или что просто не стоит прилагать усилия для оценки состояния, а замена по времени более экономична и все же (в разумной степени) эффективна.
Time Based Maintenance никогда не сможет эффективно управлять режимами отказов, не связанными с возрастом, и поэтому должно составлять лишь небольшую часть вашей общей программы технического обслуживания, поскольку> 70% режимов отказа на вашем предприятии не связаны с возрастом (см. Статью 9 Принципы Современное обслуживание).
Важно понимать, что во многих отраслях компании действительно должны выполнять определенные задачи для соответствия нормативным требованиям, и они, как правило, выполняются в фиксированный интервал времени, то есть техобслуживание на основе времени. Но даже при обслуживании, связанном с соблюдением требований, часто есть возможности привлечь регулирующий орган и рассмотреть возможность перехода, например, к подходам, основанным на оценке риска. Хорошим примером этого может быть принятие инспекции на основе рисков (RBI) для инспекций судов вместо e.г. Внутренние осмотры судов каждые 4 года.
Поиск неисправностей (FFM)
Поиск отказов Задачи обслуживания направлены на обнаружение скрытых отказов, обычно связанных с защитными функциями. Подумайте о предохранительных клапанах давления, датчиках отключения и тому подобном.
Оборудование этого типа не будет работать, пока не выйдет из строя что-то еще. Это означает, что при нормальных условиях эксплуатации вы не узнаете, работает ли это оборудование i.е. режимы отказа скрыты.
И поскольку эти сбои скрыты, вам нужно будет найти их, прежде чем вы будете полагаться на это оборудование для защиты.
Действительно просто.
Важно понимать, что задачи технического обслуживания по поиску отказов не предотвращают отказ, а просто обнаруживают его. И после обнаружения вам придется устранить обнаруженную неисправность. Обнаружение отказов Техническое обслуживание проводится через фиксированные интервалы времени, обычно определяемые законодательством или подходами, основанными на оценке риска.
Техническое обслуживание с учетом рисков (RBM)
Техническое обслуживание на основе рисков (RBM) — это когда вы используете методологию оценки рисков для распределения ваших скудных ресурсов на техническое обслуживание тем активам, которые несут наибольший риск в случае отказа (помня, что риск = вероятность x последствия).
В результате оборудование с более высоким риском и очень высокой вероятностью отказа будет подвергаться более частому техническому обслуживанию и осмотру. Оборудование с низким уровнем риска может обслуживаться с гораздо меньшей частотой и, возможно, с гораздо меньшим объемом работ.
При эффективном внедрении процесса обслуживания с учетом рисков вы должны снизить общий риск отказа всего предприятия наиболее экономичным способом.
Risk-Based Maintenance — это, по сути, профилактическое обслуживание, при котором частота и объем работ по техническому обслуживанию постоянно оптимизируются на основе результатов тестирования или инспекции и тщательной оценки рисков. Примерами технического обслуживания на основе рисков могут быть проверки на основе рисков применительно к статическому оборудованию, такому как сосуды и трубопроводы, или даже предохранительные клапаны.
Техническое обслуживание по условию (CBM)
Большинство видов отказов не связаны с возрастом. Тем не менее, большинство режимов отказа действительно выдают какое-то предупреждение о том, что они происходят или вот-вот произойдут.
Если можно найти доказательства того, что что-то находится на ранних стадиях отказа, можно принять меры для предотвращения полного отказа и / или во избежание последствий отказа. Таким образом, техническое обслуживание по состоянию в качестве стратегии ищет физические доказательства того, что отказ происходит или вот-вот произойдет.Такой подход к CBM показывает его более широкие применения за пределами методов мониторинга состояния, часто связанных только с вращающимся оборудованием.
Важной концепцией технического обслуживания по состоянию является кривая P-F, показанная на рисунке ниже:
Кривая показывает, что по мере того, как сбой начинает проявляться, оборудование изнашивается до точки, в которой его можно обнаружить (точка «P»).
Если отказ не обнаружен и не устранен, он продолжается до тех пор, пока не произойдет функциональный отказ (точка «F»).Временной диапазон между P и F, обычно называемый интервалом P-F, представляет собой окно возможностей, в течение которого инспекция, возможно, может обнаружить неминуемый отказ и дать вам время для его устранения.
Важно понимать, что CBM как стратегия технического обслуживания не снижает вероятность отказа, возникающего в результате обновления срока службы, а вместо этого направлена на вмешательство до того, как произойдет отказ, исходя из того, что это более экономично и должно иметь меньше влияние на доступность.
Другими словами: мониторинг состояния не исправляет машины, а мониторинг состояния не останавливает отказы. Мониторинг состояния позволяет обнаруживать проблемы только до того, как они перерастут в отказ.
Общее практическое правило состоит в том, что интервал между задачами CBM должен составлять половину или одну треть интервала P-F.
Насколько эффективнее CBM выше аварийного обслуживания, зависит от продолжительности интервала P-F. При наличии большого количества предупреждений можно запланировать исправление, мобилизовать материалы и ресурсы и предотвратить поломку (хотя производство все еще останавливается на время технического обслуживания).Когда интервал P-F составляет всего несколько дней, в результате организационные действия и действия на рабочем месте очень похожи на поломку, и ценность CBM в значительной степени теряется.
Для того, чтобы CBM была эффективной как стратегия, необходимо раннее вмешательство. Это требует действенного и действенного процесса сбора данных, анализа данных, принятия решений и, наконец, вмешательства.
Для режимов отказа, где интервал P-F показывает большую изменчивость, мониторинг состояния не является эффективной стратегией.
Если вам интересно узнать больше о том, как лучше всего управлять режимами отказа, не забудьте прочитать мою статью Техническое обслуживание, ориентированное на надежность — 9 принципов современного технического обслуживания.
Принцип работы (кратко). Принцип действия реактивного двигателя
Под реактивным понимается движение, при котором от тела с определенной скоростью отделяется одна из его частей. Сила, возникающая в результате такого процесса, действует сама по себе. Другими словами, у нее нет даже малейшего контакта с внешними телами.
Реактивное движение в природе
Во время летнего отдыха на юге почти все мы, купаясь в море, встречались с медузами. Но мало кто думал, что эти животные движутся так же, как реактивный двигатель. Принцип действия в природе такого агрегата можно наблюдать при перемещении определенных видов морского планктона и личинок стрекоз. Причем эффективность этих беспозвоночных зачастую выше, чем у технических средств.
Кто еще может наглядно продемонстрировать, какой из реактивных двигателей работает? Кальмары, осьминоги и каракатицы.Подобное движение совершают многие другие морские моллюски. Возьмем, например, каракатицу. Она втягивает воду в свою жаберную полость и энергично выбрасывает ее через воронку, которая направляется назад или в сторону. При этом моллюск способен совершать движения в нужную сторону.
Принцип действия реактивного двигателя можно наблюдать и при перемещении барабана. Это морское животное берет воду в широкой впадине. После этого мышцы его тела сокращаются, выталкивая жидкость через отверстие, которое находится позади.Реакция образовавшейся струи позволяет саженцу двигаться вперед.
Sea Missiles
Но наибольшего совершенства в реактивной навигации достиг все тот же кальмар. Даже форма самой ракеты словно скопирована с этого морского обитателя. При движении с небольшой скоростью кальмар периодически выгибает ромбовидный плавник. Но для быстрого броска ему приходится использовать собственный «реактивный двигатель». Принцип работы всех его мышц и тела стоит рассмотреть подробнее.
Кальмар имеет своеобразную мантию.Это мышечная ткань, которая окружает его тело со всех сторон. Во время движения животное засасывает в эту мантию большой объем воды, резко выбрасывая струю через специальную узкую насадку. Такие действия позволяют кальмарам двигаться назад со скоростью до семидесяти километров в час. Во время движения животное собирает в пучок все свои десять щупалец, что придает телу обтекаемую форму. На насадке есть специальный клапан. Его поворачивает животное сокращением мышц. Это позволяет моряку менять направление.Роль штурвала при передвижении кальмара выполняют его щупальца. Он направляет их влево или вправо, вниз или вверх, легко уворачиваясь от столкновений с различными препятствиями.
Существует разновидность кальмаров (stenoteutis), относящаяся к званию лучшего пилота среди моллюсков. Опишите принцип работы реактивного двигателя — и вы поймете, почему, преследуя рыбу, это животное иногда выпрыгивает из воды, даже попадая на палубы кораблей, плывущих по океану. Как это произошло? Пилот-кальмар, находясь в водной стихии, развивает для себя максимальную реактивную тягу.Это позволяет ему летать над волнами на расстоянии до пятидесяти метров.
Если мы рассмотрим реактивный двигатель, принцип Какое животное работает, мы можем упомянуть еще? Это, на первый взгляд, мешковатый осьминог. Пловцы не так быстры, как кальмары, но в случае опасности их скорости могут позавидовать даже лучшие спринтеры. Биологи, изучавшие миграцию осьминогов, выяснили, что они движутся по принципу действия реактивного двигателя.
Животное при каждой струе воды, выбрасываемой из воронки, делает рывок на два или даже два с половиной метра.При этом плывет осьминог своеобразным образом — задом наперед.
Другие примеры реактивного движения
В мире растений есть ракеты. Принцип действия реактивного двигателя можно наблюдать, когда даже при очень легком прикосновении «бешеный огурец» с большой скоростью отскакивает от ножки, отталкивая при этом липкую жидкость с семенами. При этом сам плод летит на значительное расстояние (до 12 м) в обратном направлении.
Принцип работы реактивного двигателя можно наблюдать и в лодке.Если с него в определенном направлении бросить в воду тяжелые камни, то он будет двигаться в противоположном направлении. Ракетно-реактивный двигатель имеет такой же принцип работы. Только там вместо камней используются газы. Они создают реактивную силу, которая обеспечивает движение как в воздухе, так и в разряженном пространстве.
Фантастическое путешествие
Человечество давно мечтает о космических полетах. Об этом свидетельствуют произведения писателей-фантастов, которые для достижения этой цели предлагали самые разные средства.Например, герой рассказа французского писателя Эркюля Савинена Сирано де Бержерак достиг Луны на железной повозке, на которую постоянно бросался мощный магнит. Знаменитый Мюнхгаузен тоже достиг той же планеты. Гигантский стебель фасоли помог ему совершить путешествие.
Реактивный двигатель использовался в Китае еще в первом тысячелетии до нашей эры. Бамбуковые трубы, набитые порохом, служили своеобразными ракетами для развлечения. Кстати, проект первой машины на нашей планете, созданный Ньютоном, тоже был с реактивным двигателем.
История RD
Только в XIX в. мечта человечества о космосе стала приобретать конкретные черты. Ведь именно в этом веке русский революционер Н.И. Кибальчич создал первый в мире проект самолета с реактивным двигателем. Все бумаги были составлены Народным освободителем в тюрьме, куда он попал после покушения на Александра. Но, к сожалению, 04.03.1881 Кибальчич был казнен, а его идея не нашла практического воплощения.
В начале 20 в. Идея использования ракет для космических полетов была выдвинута русским ученым К.Е. Циолковский. Впервые его работа, содержащая описание движения тела переменной массы в виде математического уравнения, была опубликована в 1903 году. Позже ученый разработал саму схему реактивного двигателя, работающего на жидком топливе.
Также Циолковским была изобретена многоступенчатая ракета и выдвинута идея создания настоящих космических городов на низкой околоземной орбите.Циолковский убедительно доказал, что единственное средство для полета в космос — это ракета. То есть аппарат, оснащенный реактивным двигателем, заправляемый горючим и окислителем. Только такая ракета способна преодолеть силу тяжести и вылететь за пределы атмосферы Земли.
Освоение космоса
Статья Циолковского, опубликованная в журнале «Научное обозрение», подтвердила для ученых репутацию мечтателя. Никто не принимал всерьез его аргументы.
Идея Циолковского была реализована советскими учеными.Под руководством Сергея Павловича Королева они запустили первый искусственный спутник Земли. 4 октября 1957 года это устройство было доставлено на орбиту ракетой с реактивным двигателем. Работа РД была основана на преобразовании химической энергии, которая передается топливом газовой струе, превращаясь в кинетическую энергию. В этом случае ракета движется в обратном направлении.
Реактивный двигатель, принцип действия которого используется много лет, находит свое применение не только в космосе, но и в авиации.Но больше всего он используется для запуска ракет. Ведь только RD может перемещать аппарат в пространстве, в котором отсутствует какая-либо среда.
Жидкостный реактивный двигатель
Тот, кто стрелял из огнестрельного оружия или просто наблюдал за этим процессом со стороны, знает, что существует сила, которая непременно оттолкнет ствол назад. А при большей сумме заряда отдача обязательно увеличится.




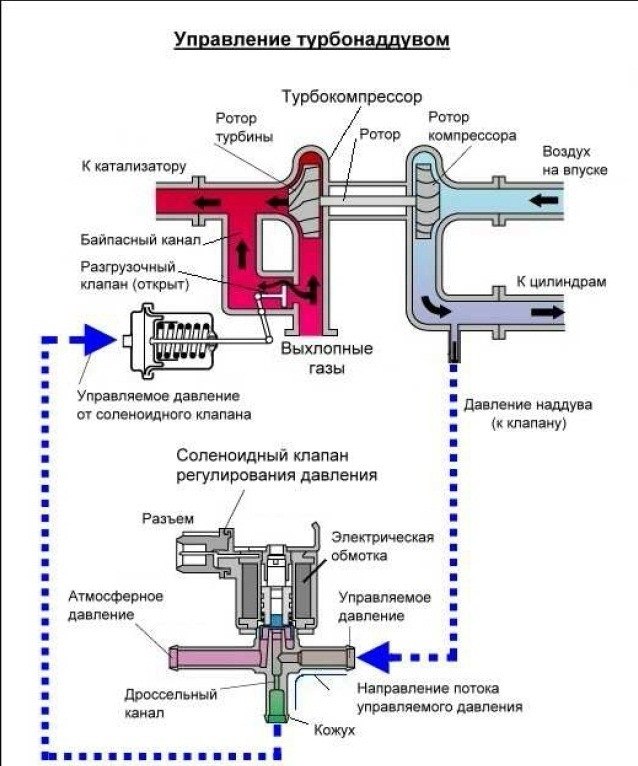


Узел подшипников
Ротор турбокомпрессора (ТК) вращается с частотой до 300 000 мин -1. Срок службы ТК должен соответствовать ресурсу двигателя, который может составлять 1 000 000 км пробега для коммерческого автомобиля. Только специально разработанные для ТК подшипники скольжения могут соответствовать таким жестким требованиям при приемлемой стоимости.
Опорные подшипники
В подшипнике скольжения вал вращается практически без трения на масляной пленке внутри втулки подшипника.
Масло подается в турбокомпрессор (ТК) от системы смазки двигателя. Подшипниковый узел спроектирован так, что между неподвижным корпусом и вращающимся валом расположены «плавающие» бронзовые подшипниковые втулки. Они вращаются с частотой, вдвое меньшей частоты вращения вала. Это позволяет высокоскоростным подшипникам адаптироваться таким образом, что на любых режимах работы ТК нет прямого контакта «металл-металл» между валом и подшипниками.
Кроме функции смазки масляная пленка в зазорах подшипника играет роль демпфера, который способствует стабилизации вала и турбинного колеса. Гидродинамическая несущая способность пленки и демпфирующие характеристики подшипника оптимизируются величиной зазоров. Таким образом, толщина смазывающей пленки для внутренних зазоров выбирается исходя из нагрузки на подшипник, в то время как толщина внешних зазоров определяется с учетом демпфирования подшипника. Зазоры в подшипниках составляют несколько сотых долей миллиметра. Увеличение зазоров приведет к более мягкому демпфированию и, одновременно, к снижению несущей способности подшипника.
Так называемый патрон — специальный вид опорного подшипника скольжения. Вал вращается в неподвижной целиковой втулке, снаружи которой прокачивается масло. Внешний зазор выбирается исключительно из условия демпфирования подшипника, так как патрон не проворачивается. Вытекающая из этого меньшая ширина подшипника позволяет создать более компактный ТК.
Упорный подшипник
Ни один из рассмотренных типов опорных подшипников, ни свободно плавающие втулки, ни фиксированный плавающий патрон, не воспринимают нагрузки в осевом направлении. Поскольку газы воздействуют на компрессорное и турбинное колеса в осевом направлении с разной силой, ротор турбокомпрессора (ТК) испытывает осевую нагрузку. Она воспринимается упорным подшипником скольжения с конической плоскостью (рабочей поверхностью). Два маленьких диска, закрепленных на валу, служат контактными поверхностями. Упорный подшипник фиксируется в центральном корпусе подшипников. Маслоотражающая пластина предотвращает попадание масла в зону уплотнения вала.
Слив масла
Масло подается в турбокомпрессор (ТК) при давлении примерно 4 бар. Поскольку масло сливается из турбины при меньшем давлении (самотеком), диаметр трубки для слива значительно больше, чем маслоподающей трубки. Проток масла через корпус подшипников должен быть по возможности вертикальным, сверху вниз. Сливная трубка должна выходить в картер выше уровня масла. Любое препятствие на пути слива масла оборачивается увеличением противодавления в корпусе подшипников. В этом случае масло начинает просачиваться сквозь уплотнительные кольца в компрессор и турбину.
Уплотнения
Центральный корпус подшипников должен быть уплотнен от прорыва в него горячих отработавших газов из турбины и от утечек масла из корпуса. Для этого в канавки на валу ротора, со стороны компрессора и турбины установлены разрезные кольца, аналогичные поршневым. Кольца не вращаются, а неподвижно расклинены в центральном корпусе. Это бесконтактное уплотнение, один из видов лабиринтного уплотнения. Благодаря многочисленным резким изменениям направления движения потока оно затрудняет утечку масла и пропускает в картер лишь небольшое количество отработавших газов.
Тепловая нагрузка на подшипники
Учитывая небольшое расстояние между центральным корпусом и горячим корпусом турбины, тепло может проникать в центральный корпус и нагревать масло до температуры коксования. Тогда масляный кокс мог бы осаждаться в зазорах и на поверхностях, засорять масляные каналы и нарушать работу подшипников и уплотнений. Большое количество углеводородных отложений может вызвать дефицит смазки и граничное трение, приводящие к ускоренному износу системы подшипников.
Тепловой экран и охлаждение разбрызгиванием масла<
Тепловой экран, расположенный позади опорного диска турбинного колеса, предотвращает контакт горячих отработавших газов с центральным корпусом. В некоторых конструкциях при работе двигателя масло распыляется на вал ротора через маленькое распылительное отверстие в опоре подшипника с турбинной стороны, охлаждая вал и уменьшая риск коксования.
Наивысшие температуры в центральном корпусе достигаются вскоре после останова двигателя. Горячий турбинный корпус нагревает систему подшипников, которая больше не охлаждается моторным маслом.
Термическая развязка
В расчете на термическую развязку правой подшипниковой опоры передача тепла от корпуса турбины к системе подшипников сокращается даже после того как двигатель был заглушен. Для этого систему подшипников располагают ниже точки подачи масла, так же как силовой агрегат размещают под крылом самолета. Правая подшипниковая опора больше не контактирует с горячей стенкой центрального корпуса, значит, передача тепла к системе подшипников ограничивается.
Водяное охлаждение
Бензиновые двигатели, у которых температура отработавших газов на 200-300°С выше чем у дизелей, обычно оснащаются турбокомпрессорами с охлаждаемыми центральными корпусами. При работе двигателя центральный корпус интегрируется в его контур охлаждения. После выключения двигателя остаточное тепло снимается посредством малого кольца циркуляции, которое задействуется электрическим насосом с термостатом.
Рециркуляционный клапан
В бензиновых турбодвигателях дроссельная заслонка, которая управляет нагрузкой двигателя, располагается после компрессора, во впускном коллекторе. В момент внезапного сброса газа заслонка закрывается, а компрессор из-за своей инерционности продолжает нагнетать воздух в почти замкнутый объем. Вследствие этого начался бы помпаж компрессора. Частота вращения турбокомпрессора (ТК) быстро упала бы.
Начиная с определенного давления, открывается подпружиненный клапан и направляет воздух обратно на вход в компрессор, ограничивая рост давления и исключая помпаж. Частота вращения ТК остается высокой, и давление наддува появится, как только будет задействован акселератор.
Принцип работы турбореактивного двигателя самолёта
Совершая полет в самолете в большинстве случаев люди никогда не задумываются о том, как работает его двигатель. Но на самом деле о работе двигателя и реактивной тяги с помощью, которой работает сам двигатель, знали ее в Античное время. Но применить эти знания на практике смогли не так давно, так как раньше не технологии не позволяли никому достичь его исправной работы. Гонка вооружения между Англией и Германией стала толчком к созданию ТРД (турбореактивного двигателя).
В работе ТРД самолета нет никаких сложностей, принцип его работы может понять почти каждый человек. Но данный двигатель имеет несколько нюансов, их соблюдение контролируется под строгим присмотром руководства. Для того чтобы авиалайнер смог держаться в небе, необходима идеальная работа двигателя. Так как от работы двигателя напрямую зависят жизни пассажиров находящихся на борту авиатранспорта.
Принцип работы реактивного двигателя
За работу двигателя отвечает реактивная тяга. Для создания реактивной тяги необходима определенная жидкость, которая подается из задней части двигателя и по ходу ее продвижения увеличивается ее скорость движения вперед. Работу тяги отлично объясняет один из законов Ньютона, звучит он так «Любое действия вызывает равное противодействие».
Вместо жидкости в ТРД используется горючая смесь (газы и воздух со сгоревшими частичками топлива). Благодаря этой смеси самолет толкает вперед и позволяет ему лететь дальше.
Разработки таких двигателей начались в тридцатых годах. Первыми кто начал разрабатывать двигатели такого типа стали немцы и англичане. Но в гонке вооружений одержали победу ученные из Германии, так как они выпустили самый первый в мире самолет с ТРД под названием «Ласточка», данный самолет впервые взлетел в небеса над Люфтваффом. Спустя некоторое время появился и Английский самолет «Глостерский метеор»
Также сверхзвуковые двигатели принято считать турбореактивными, но они отличаются более совершенными модификациями, в отличие от ТРД.
Устройство двигателя имеет четыре главные детали, а именно:
- Компрессор.
- Камера горения.
- Турбина.
- Выхлоп.
Компрессор
В компрессоре находиться несколько турбин, с помощью которых происходит засасывание и сжатие воздуха. Во время сжатия воздуха, его давление и температура начинает нагнетаться и расти.
Камера горения
После того как воздух проходит турбину и его сжимает до необходимых размеров. Часть сжатого воздуха поступает в камеру горения, где воздух начинает смешиваться с топливом, после чего его поджигают. Благодаря этому увеличивается тепловая энергия воздуха. После смесь выходит из камеры с большой скорости и расширяется.
Турбина
После выхода эта смесь снова попадает в турбину, с помощью высокой энергии газа лопасти в турбине начинают свое вращение. Турбина тесно связанна с компрессором, который находиться в начале двигателя. Благодаря этому турбина начинает свою работу. Остатки воздуха выходят в выхлоп. В момент выхода смеси температура достигает рекордных размеров. Но она продолжает повышать свою температуру с помощью эффекта Дросселирования. После того как температура воздуха доходит до своего пика, она начинает идти на спад и выходит из турбины.
Принцип работы турбореактивного двигателя
В отличие от реактивного двигателя, который пользуется спросом почти у всех самолетов, турбореактивный двигатель больше подходит для пассажирских авиалайнеров. Так как для работы реактивного двигателя необходимо не только топливо, но и окислитель.
Благодаря своему строению окислитель поступает вместе с топливом из бака. А в случаи с ТРД окислитесь, поступает напрямую из атмосферы. А в остальном их работа совершенно идентична и не отличается друг от друга.
У турбореактивного двигателя главной деталью является лопасть турбины, так как от ее исправной работы напрямую зависит мощность двигателя. Благодаря этим лопастям и образуется тяга, которая необходима для поддержания скорости самолета. Если сравнить одну лопасть с автомобильным двигателем, то она сможет обеспечить мощностью целых десять машин.
Лопасти устанавливаются за камерой сгорания, так как там нагнетается самое высокое давления, также температура воздуха в данной части двигателя может доходить до 1400 градусов Цельсия.
В целях улучшения прочности и устойчивости лопасти перед различными факторами их монокристаллизируют, благодаря этому они могут держать высокую температуру и давление. Прежде чем установить такой двигатель на самолет его тестируют на полном тяговом усилителе. Также двигатель должен получить сертификат от Европейского совета по безопасности.
Атомный двигатель
В период холодной войны в мире были попытки создания атомного двигателя, за основу был взят турбореактивный двигатель. Главной задумкой ученых было создание двигателя, основанного не на химической реакции радиоактивных веществ, а на вырабатываемом тепле от ядерного реактора. Он должен был находиться на месте камеры сгорания.
В теории воздух должен был проходить через работающую зону реактора, благодаря этому реактор должен был остужаться, а температура воздуха наоборот возрастать. После чело воздух должен был расширяться и выходить через сопла (выхлоп) на этот момент скорость воздуха должна была превышать скорость полета самолета.
В Советском союзе были попытки проведения испытаний подобного двигателя, также ученные в соединенных штатах Америки, вели разработку данного двигателя, и их работа почти подходила к тестам двигателя на настоящем самолете.
Но по ряду причин разработки этого двигателя было решено закрыть. Так как у двигателя было множество недостатков, а именно:
- Пилоты были подвержены постоянному радиоактивному облучению на протяжении всего полета.
- Вместе с воздухом через сопла выходили и частички радиоактивного элемента в атмосферу.
- В том случае если самолет терпел крушение, был очень большой шанс взрыва радиоактивного реактора, что влекло за собой радиоактивное отравление на довольно большой площади.
Турбина Каплан — ее составные части, работа и применение
Турбина Каплан работает по принципу реакции осевого потока. В турбинах с осевым потоком вода течет через бегунок в направлении, параллельном оси вращения рабочего колеса. Вода на входе в турбину обладает как кинетической энергией, так и энергией давления для эффективного вращения лопастей гидроэлектростанции.
Рис. 1: Турбина Каплана.
В 1913 году австрийский профессор Виктор Каплан, который разработал эту турбину, объединил автоматически регулируемые лопасти гребного винта с автоматически регулируемыми заслонками калитки для достижения эффективности в широком диапазоне расхода и уровня воды.Она также называется пропеллерной турбиной и произошла от турбины Фрэнсиса. Он способен очень эффективно работать при низком напоре и высоких расходах, что невозможно с турбиной Фрэнсиса.
В этой статье рассматривается порядок работы, основные компоненты и их применение.
Основные компоненты турбины Каплана
Основные части турбины Каплан,
1. Спиральный кожух
Это спиральный кожух с уменьшающейся площадью поперечного сечения.Вода из затворов попадает в корпус спирали, а затем движется к направляющим лопастям, где вода поворачивается на 90 ° и течет в осевом направлении через желоб. Он защищает рабочее колесо, направляющие лопатки рабочих лопаток и другие внутренние части турбины от внешних повреждений.
Рис. 2: Основные компоненты турбины Каплана.
2. Механизм направляющей лопасти
Это единственная управляющая часть всей турбины, которая открывается и закрывается в зависимости от потребности в мощности.Если требуется большая выходная мощность, он открывается шире, чтобы больше воды попадало на лопасти ротора, а когда требуется низкая выходная мощность, он закрывается, чтобы прекратить поток воды. При отсутствии направляющих лопаток турбина не может работать эффективно и ее КПД снижается.
3. Трубка отсасывающая
Давление на выходе из рабочего колеса реакционной турбины обычно ниже атмосферного. Вода на выходе не может напрямую сбрасываться в хвостовую часть.Труба или труба с постепенно увеличивающейся площадью используется для отвода воды от выхода турбины до хвостовой части. Эта трубка с увеличивающейся площадью называется вытяжной трубкой. Один конец трубки подсоединен к выпускному отверстию бегунка, а другой конец погружен ниже уровня воды в хвостовой части.
4. Лезвия рабочего колеса
Сердцем компонента в турбине Каплана являются рабочие лопатки, так как это вращающаяся часть, которая помогает в производстве электроэнергии. Вал соединен с валом генератора.Рабочее колесо этой турбины имеет большой выступ, на котором крепятся его лопасти, а лопасти рабочего колеса регулируются под оптимальным углом атаки для максимальной выходной мощности. Лопатки турбины Каплана имеют закрутку по длине.
Рис. 3. Рабочие лопатки турбины Каплана.
Рабочий процесс турбины Каплана
Вода, поступающая из загона, попадает в кожух спирали. Корпус спирали выполнен такой формы, чтобы не терять давление потока.Направляющие лопатки направляют воду к лопастям рабочего колеса. Лопасти регулируются и могут регулироваться в зависимости от скорости потока. Вода поворачивается на 90 градусов, поэтому направление воды является осевым по отношению к лопастям бегунка.
Лопасти бегунка начинают вращаться при ударе воды из-за силы реакции воды. Лезвия бегунка имеют изгиб по всей длине, чтобы всегда иметь оптимальный угол атаки для всего поперечного сечения лезвий для достижения большей эффективности.
Из лопастей рабочего колеса вода поступает в вытяжную трубу, где ее энергия давления и кинетическая энергия уменьшаются. Кинетическая энергия преобразуется в энергию давления, что приводит к увеличению давления воды.
Вращение турбины используется для вращения вала генератора для производства электроэнергии.
Применение турбины Каплана
- Турбины Каплана широко используются во всем мире для производства электроэнергии.
- Может работать более эффективно при низком напоре воды и высоком расходе по сравнению с другими типами турбин.
- Он меньше по размеру и прост в сборке.
- КПД турбины Каплана очень высок по сравнению с другими гидравлическими турбинами.
Недостаток турбины Каплана
- Единственным недостатком турбины Каплана является кавитация, возникающая из-за падения давления в отсасывающей трубе. Использование вытяжной трубы и подходящего материала, как правило, из нержавеющей стали для лопастей рабочего колеса, может в большей степени уменьшить проблему кавитации.
Турбина | Британника
Турбина , любое из различных устройств, преобразующих энергию потока жидкости в механическую энергию. Преобразование обычно осуществляется путем пропускания жидкости через систему неподвижных каналов или лопаток, которые чередуются с каналами, состоящими из лопастей, похожих на ребра, прикрепленных к ротору. За счет организации потока так, чтобы на лопасти ротора действовала касательная сила или крутящий момент, ротор вращается, и работа извлекается.
Ветровые турбины около Техачапи, Калифорния
© Грег Рэндлс / Shutterstock.com Турбины можно разделить на четыре основных типа в зависимости от используемых жидкостей: вода, пар, газ и ветер. Хотя одни и те же принципы применимы ко всем турбинам, их конкретные конструкции достаточно различаются, чтобы заслужить отдельное описание.
Гидравлическая турбина использует потенциальную энергию, возникающую в результате разницы в высоте между верхним водным резервуаром и уровнем воды на выходе из турбины (отводом) для преобразования этого так называемого напора в работу.Водяные турбины — современные преемники простых водяных колес, которым около 2000 лет. Сегодня гидротурбины в основном используются для производства электроэнергии.
Однако наибольшее количество электроэнергии вырабатывается паровыми турбинами, соединенными с электрогенераторами. Турбины приводятся в действие паром, вырабатываемым либо в генераторе, работающем на ископаемом топливе, либо в атомном генераторе. Энергию, которую можно извлечь из пара, удобно выражать через изменение энтальпии в турбине.Энтальпия отражает формы как тепловой, так и механической энергии в процессе потока и определяется суммой внутренней тепловой энергии и произведением давления на объем. Доступное изменение энтальпии через паровую турбину увеличивается с увеличением температуры и давления парогенератора и с уменьшением давления на выходе из турбины.
Оформите подписку Britannica Premium и получите доступ к эксклюзивному контенту.
Подпишитесь сейчас Для газовых турбин энергия, извлекаемая из текучей среды, также может быть выражена через изменение энтальпии, которое для газа почти пропорционально перепаду температуры в турбине.В газовых турбинах рабочим телом является воздух, смешанный с газообразными продуктами сгорания. Большинство газотурбинных двигателей включает, по крайней мере, компрессор, камеру сгорания и турбину. Обычно они монтируются как единое целое и работают как законченный первичный двигатель в так называемом открытом цикле, когда воздух всасывается из атмосферы, а продукты сгорания, наконец, снова выбрасываются в атмосферу. Поскольку успешная работа зависит от интеграции всех компонентов, важно рассматривать устройство в целом, которое фактически является двигателем внутреннего сгорания, а не только турбиной.По этой причине газовые турбины рассматриваются в статье двигатель внутреннего сгорания.
Энергия ветра может быть извлечена ветровой турбиной для производства электроэнергии или для откачки воды из колодцев. Ветряные турбины являются преемниками ветряных мельниц, которые были важными источниками энергии с позднего средневековья до 19 века.
Фред Лэндис Водяные турбины обычно делятся на две категории: (1) импульсные турбины, используемые для высокого напора воды и низкого расхода, и (2) реактивные турбины, обычно используемые для напора ниже примерно 450 метров и среднего или высокого расхода.Эти два класса включают в себя основные типы, обычно используемые, а именно импульсные турбины Пелтона и реактивные турбины типа Фрэнсиса, пропеллера, Каплана и Дериаза. Турбины могут иметь горизонтальный или, чаще, вертикальный вал. Для каждого типа возможны широкие вариации конструкции для соответствия конкретным местным гидравлическим условиям. Сегодня большинство гидравлических турбин используются для выработки электроэнергии на гидроэлектростанциях.
Импульсные турбины
В импульсной турбине потенциальная энергия или напор воды сначала преобразуется в кинетическую энергию путем выпуска воды через сопло тщательно продуманной формы.Струя, выбрасываемая в воздух, направляется на изогнутые ковши, закрепленные на периферии бегунка, для извлечения энергии воды и преобразования ее в полезную работу.
Современные импульсные турбины основаны на конструкции, запатентованной в 1889 году американским инженером Лестером Алленом Пелтоном. Свободная водная струя попадает в лопатки турбины по касательной. Каждый ковш имеет высокий центральный гребень, так что поток разделяется, оставляя желоб с обеих сторон. Колеса Пелтона подходят для высоких напоров, обычно выше 450 метров при относительно низком расходе воды.Для максимальной эффективности скорость конца рабочего колеса должна составлять примерно половину скорости ударной струи. КПД (работа, производимая турбиной, деленная на кинетическую энергию свободной струи) может превышать 91 процент при работе с 60–80 процентами полной нагрузки.
Мощность одного колеса можно увеличить, используя более одного жиклера. Для горизонтальных валов характерны двухструйные устройства. Иногда на одном валу устанавливаются два отдельных бегунка, приводящих в движение один электрогенератор. Агрегаты с вертикальным валом могут иметь четыре или более отдельных форсунок.
Если электрическая нагрузка на турбину изменяется, ее выходная мощность должна быть быстро отрегулирована в соответствии с потребностями. Это требует изменения расхода воды, чтобы поддерживать постоянную скорость генератора. Скорость потока через каждое сопло регулируется расположенным в центре наконечником или иглой аккуратной формы, которая скользит вперед или назад под управлением гидравлического серводвигателя.
Правильная конструкция иглы гарантирует, что скорость воды, выходящей из сопла, остается практически неизменной независимо от отверстия, обеспечивая почти постоянную эффективность в большей части рабочего диапазона.Нецелесообразно внезапно уменьшать поток воды, чтобы соответствовать уменьшению нагрузки. Это может привести к разрушительному скачку давления (гидроудару) в подающем трубопроводе или водопроводе. Таких скачков можно избежать, добавив временное сопло для разлива, которое открывается при закрытии основного сопла, или, что чаще, частично вставляя отражающую пластину между струей и колесом, отклоняя и рассеивая часть энергии при медленном закрытии иглы.
Другой тип импульсной турбины — турбина турго.Струя падает под косым углом на бегунок с одной стороны и продолжает двигаться по единственному пути, выбрасывая его с другой стороны. Этот тип турбины использовался в установках среднего размера с умеренно высоким напором.
Реакционные турбины
В реакционной турбине силы, приводящие в движение ротор, достигаются за счет реакции ускоряющегося потока воды в рабочем колесе при падении давления. Принцип реакции можно наблюдать в роторном оросителе для газонов, где выходящая струя вращает ротор в противоположном направлении.Из-за большого разнообразия возможных конструкций рабочего колеса реактивные турбины могут использоваться в гораздо большем диапазоне напоров и расходов, чем импульсные турбины. Реакционные турбины обычно имеют спиральный впускной кожух, который включает регулирующие заслонки для регулирования потока воды. На входе часть потенциальной энергии воды может быть преобразована в кинетическую энергию по мере ускорения потока. Впоследствии энергия воды отбирается в роторе.
Как отмечалось выше, широко используются четыре основных типа реактивных турбин: турбины Каплана, Фрэнсиса, Дериаза и пропеллерные.В турбинах Каплана с неподвижными лопастями и с регулируемыми лопастями (названными в честь австрийского изобретателя Виктора Каплана), по существу, существует осевой поток через машину. Турбины типа Фрэнсиса и Дериаза (в честь американского изобретателя британского происхождения Джеймса Б. Фрэнсиса и швейцарского инженера Поля Дериаза, соответственно) используют «смешанный поток», когда вода поступает радиально внутрь и выпускается в осевом направлении. Рабочие лопасти на турбинах Фрэнсиса и пропеллера состоят из неподвижных лопастей, в то время как в турбинах Каплана и Дериаза лопасти могут вращаться вокруг своей оси, которая находится под прямым углом к главному валу.
Объяснение 9 различных стратегий
Профилактическое обслуживание и корректирующее обслуживание
На верхнем уровне я вижу профилактическое или корректирующее обслуживание:
- Когда мы выполняем профилактическое обслуживание , мы выполняем задачу до того, как произойдет сбой . Эта задача может быть направлена на предотвращение отказа, минимизацию последствий отказа или оценку риска возникновения отказа.
- Когда мы проводим корректирующее обслуживание , произошел сбой , и мы в основном восстанавливаем работоспособность оборудования. Чтобы было ясно, корректирующее обслуживание может быть результатом преднамеренной стратегии безотказной работы.
Профилактическое обслуживание
Профилактическое обслуживание можно определить как «стратегию обслуживания оборудования, основанную на замене или восстановлении актива через фиксированные интервалы времени, независимо от его состояния. Запланированные задачи восстановления и задачи замены являются примерами задач профилактического обслуживания ».
Профилактическое обслуживание (или профилактическое обслуживание) в основном представляет собой тип обслуживания, который выполняется через регулярные промежутки времени, пока оборудование все еще функционирует, с целью предотвращения отказа или снижения вероятности отказа.
Профилактическое обслуживание может проводиться по времени, т.е. каждую неделю, каждый месяц или каждые три месяца. Но профилактическое обслуживание также может быть основано на использовании e.г. каждые 150 циклов, каждые 10 000 часов или как ваш автомобиль: обслуживание каждые 10 000 км.
Помимо регулярного интервального обслуживания (обслуживания по времени), существуют также другие виды обслуживания, которые подпадают под категорию профилактического обслуживания:
В следующих параграфах я более подробно рассмотрю каждый из этих типов обслуживания, в том числе, когда вам следует рассмотреть возможность их использования.
Обслуживание по времени (TBM)
Временное обслуживание относится к замене или обновлению элемента для восстановления его надежности в фиксированное время, интервал или использование независимо от его состояния.Это то, что Мубрей называет задачами запланированного восстановления или запланированного удаления в своей книге RCMII.
Я ограничиваю использование этой фразы, так как по какой-то причине люди приходят к выводу, что другое техническое обслуживание не запланировано. Хотя на самом деле, конечно, все техническое обслуживание следует планировать в соответствии с нашим недельным расписанием. Единственным исключением может быть экстренное обслуживание, которое по самой своей природе требует немедленного внимания и не может быть запланировано.
Цель обслуживания по времени — защитить себя от выхода из строя известных изнашиваемых деталей, которые имеют предсказуемое среднее время наработки на отказ (MTBF) i.е. Техническое обслуживание по времени предполагает, что отказ связан с возрастом и может быть определен точный срок службы. Или что просто не стоит прилагать усилия для оценки состояния, а замена по времени более экономична и все же (в разумной степени) эффективна.
Time Based Maintenance никогда не сможет эффективно управлять режимами отказов, не связанными с возрастом, и поэтому должно составлять лишь небольшую часть вашей общей программы технического обслуживания, поскольку> 70% режимов отказа на вашем предприятии не связаны с возрастом (см. Статью 9 Принципы Современное обслуживание).
Важно понимать, что во многих отраслях компании действительно должны выполнять определенные задачи для соответствия нормативным требованиям, и они, как правило, выполняются в фиксированный интервал времени, то есть техобслуживание на основе времени. Но даже при обслуживании, связанном с соблюдением требований, часто есть возможности привлечь регулирующий орган и рассмотреть возможность перехода, например, к подходам, основанным на оценке риска. Хорошим примером этого может быть принятие инспекции на основе рисков (RBI) для инспекций судов вместо e.г. Внутренние осмотры судов каждые 4 года.
Поиск неисправностей (FFM)
Поиск отказов Задачи обслуживания направлены на обнаружение скрытых отказов, обычно связанных с защитными функциями. Подумайте о предохранительных клапанах давления, датчиках отключения и тому подобном.
Оборудование этого типа не будет работать, пока не выйдет из строя что-то еще. Это означает, что при нормальных условиях эксплуатации вы не узнаете, работает ли это оборудование i.е. режимы отказа скрыты.
И поскольку эти сбои скрыты, вам нужно будет найти их, прежде чем вы будете полагаться на это оборудование для защиты.
Действительно просто.
Важно понимать, что задачи технического обслуживания по поиску отказов не предотвращают отказ, а просто обнаруживают его. И после обнаружения вам придется устранить обнаруженную неисправность. Обнаружение отказов Техническое обслуживание проводится через фиксированные интервалы времени, обычно определяемые законодательством или подходами, основанными на оценке риска.
Техническое обслуживание с учетом рисков (RBM)
Техническое обслуживание на основе рисков (RBM) — это когда вы используете методологию оценки рисков для распределения ваших скудных ресурсов на техническое обслуживание тем активам, которые несут наибольший риск в случае отказа (помня, что риск = вероятность x последствия).
В результате оборудование с более высоким риском и очень высокой вероятностью отказа будет подвергаться более частому техническому обслуживанию и осмотру. Оборудование с низким уровнем риска может обслуживаться с гораздо меньшей частотой и, возможно, с гораздо меньшим объемом работ.
При эффективном внедрении процесса обслуживания с учетом рисков вы должны снизить общий риск отказа всего предприятия наиболее экономичным способом.
Risk-Based Maintenance — это, по сути, профилактическое обслуживание, при котором частота и объем работ по техническому обслуживанию постоянно оптимизируются на основе результатов тестирования или инспекции и тщательной оценки рисков. Примерами технического обслуживания на основе рисков могут быть проверки на основе рисков применительно к статическому оборудованию, такому как сосуды и трубопроводы, или даже предохранительные клапаны.
Техническое обслуживание по условию (CBM)
Большинство видов отказов не связаны с возрастом. Тем не менее, большинство режимов отказа действительно выдают какое-то предупреждение о том, что они происходят или вот-вот произойдут.
Если можно найти доказательства того, что что-то находится на ранних стадиях отказа, можно принять меры для предотвращения полного отказа и / или во избежание последствий отказа. Таким образом, техническое обслуживание по состоянию в качестве стратегии ищет физические доказательства того, что отказ происходит или вот-вот произойдет.Такой подход к CBM показывает его более широкие применения за пределами методов мониторинга состояния, часто связанных только с вращающимся оборудованием.
Важной концепцией технического обслуживания по состоянию является кривая P-F, показанная на рисунке ниже:
Кривая показывает, что по мере того, как сбой начинает проявляться, оборудование изнашивается до точки, в которой его можно обнаружить (точка «P»).
Если отказ не обнаружен и не устранен, он продолжается до тех пор, пока не произойдет функциональный отказ (точка «F»).Временной диапазон между P и F, обычно называемый интервалом P-F, представляет собой окно возможностей, в течение которого инспекция, возможно, может обнаружить неминуемый отказ и дать вам время для его устранения.
Важно понимать, что CBM как стратегия технического обслуживания не снижает вероятность отказа, возникающего в результате обновления срока службы, а вместо этого направлена на вмешательство до того, как произойдет отказ, исходя из того, что это более экономично и должно иметь меньше влияние на доступность.
Другими словами: мониторинг состояния не исправляет машины, а мониторинг состояния не останавливает отказы. Мониторинг состояния позволяет обнаруживать проблемы только до того, как они перерастут в отказ.
Общее практическое правило состоит в том, что интервал между задачами CBM должен составлять половину или одну треть интервала P-F.
Насколько эффективнее CBM выше аварийного обслуживания, зависит от продолжительности интервала P-F. При наличии большого количества предупреждений можно запланировать исправление, мобилизовать материалы и ресурсы и предотвратить поломку (хотя производство все еще останавливается на время технического обслуживания).Когда интервал P-F составляет всего несколько дней, в результате организационные действия и действия на рабочем месте очень похожи на поломку, и ценность CBM в значительной степени теряется.
Для того, чтобы CBM была эффективной как стратегия, необходимо раннее вмешательство. Это требует действенного и действенного процесса сбора данных, анализа данных, принятия решений и, наконец, вмешательства.
Для режимов отказа, где интервал P-F показывает большую изменчивость, мониторинг состояния не является эффективной стратегией.
Если вам интересно узнать больше о том, как лучше всего управлять режимами отказа, не забудьте прочитать мою статью Техническое обслуживание, ориентированное на надежность — 9 принципов современного технического обслуживания.
Принцип работы (кратко). Принцип действия реактивного двигателя
Под реактивным понимается движение, при котором от тела с определенной скоростью отделяется одна из его частей. Сила, возникающая в результате такого процесса, действует сама по себе. Другими словами, у нее нет даже малейшего контакта с внешними телами.
Реактивное движение в природе
Во время летнего отдыха на юге почти все мы, купаясь в море, встречались с медузами. Но мало кто думал, что эти животные движутся так же, как реактивный двигатель. Принцип действия в природе такого агрегата можно наблюдать при перемещении определенных видов морского планктона и личинок стрекоз. Причем эффективность этих беспозвоночных зачастую выше, чем у технических средств.
Кто еще может наглядно продемонстрировать, какой из реактивных двигателей работает? Кальмары, осьминоги и каракатицы.Подобное движение совершают многие другие морские моллюски. Возьмем, например, каракатицу. Она втягивает воду в свою жаберную полость и энергично выбрасывает ее через воронку, которая направляется назад или в сторону. При этом моллюск способен совершать движения в нужную сторону.
Принцип действия реактивного двигателя можно наблюдать и при перемещении барабана. Это морское животное берет воду в широкой впадине. После этого мышцы его тела сокращаются, выталкивая жидкость через отверстие, которое находится позади.Реакция образовавшейся струи позволяет саженцу двигаться вперед.
Sea Missiles
Но наибольшего совершенства в реактивной навигации достиг все тот же кальмар. Даже форма самой ракеты словно скопирована с этого морского обитателя. При движении с небольшой скоростью кальмар периодически выгибает ромбовидный плавник. Но для быстрого броска ему приходится использовать собственный «реактивный двигатель». Принцип работы всех его мышц и тела стоит рассмотреть подробнее.
Кальмар имеет своеобразную мантию.Это мышечная ткань, которая окружает его тело со всех сторон. Во время движения животное засасывает в эту мантию большой объем воды, резко выбрасывая струю через специальную узкую насадку. Такие действия позволяют кальмарам двигаться назад со скоростью до семидесяти километров в час. Во время движения животное собирает в пучок все свои десять щупалец, что придает телу обтекаемую форму. На насадке есть специальный клапан. Его поворачивает животное сокращением мышц. Это позволяет моряку менять направление.Роль штурвала при передвижении кальмара выполняют его щупальца. Он направляет их влево или вправо, вниз или вверх, легко уворачиваясь от столкновений с различными препятствиями.
Существует разновидность кальмаров (stenoteutis), относящаяся к званию лучшего пилота среди моллюсков. Опишите принцип работы реактивного двигателя — и вы поймете, почему, преследуя рыбу, это животное иногда выпрыгивает из воды, даже попадая на палубы кораблей, плывущих по океану. Как это произошло? Пилот-кальмар, находясь в водной стихии, развивает для себя максимальную реактивную тягу.Это позволяет ему летать над волнами на расстоянии до пятидесяти метров.
Если мы рассмотрим реактивный двигатель, принцип Какое животное работает, мы можем упомянуть еще? Это, на первый взгляд, мешковатый осьминог. Пловцы не так быстры, как кальмары, но в случае опасности их скорости могут позавидовать даже лучшие спринтеры. Биологи, изучавшие миграцию осьминогов, выяснили, что они движутся по принципу действия реактивного двигателя.
Животное при каждой струе воды, выбрасываемой из воронки, делает рывок на два или даже два с половиной метра.При этом плывет осьминог своеобразным образом — задом наперед.
Другие примеры реактивного движения
В мире растений есть ракеты. Принцип действия реактивного двигателя можно наблюдать, когда даже при очень легком прикосновении «бешеный огурец» с большой скоростью отскакивает от ножки, отталкивая при этом липкую жидкость с семенами. При этом сам плод летит на значительное расстояние (до 12 м) в обратном направлении.
Принцип работы реактивного двигателя можно наблюдать и в лодке.Если с него в определенном направлении бросить в воду тяжелые камни, то он будет двигаться в противоположном направлении. Ракетно-реактивный двигатель имеет такой же принцип работы. Только там вместо камней используются газы. Они создают реактивную силу, которая обеспечивает движение как в воздухе, так и в разряженном пространстве.
Фантастическое путешествие
Человечество давно мечтает о космических полетах. Об этом свидетельствуют произведения писателей-фантастов, которые для достижения этой цели предлагали самые разные средства.Например, герой рассказа французского писателя Эркюля Савинена Сирано де Бержерак достиг Луны на железной повозке, на которую постоянно бросался мощный магнит. Знаменитый Мюнхгаузен тоже достиг той же планеты. Гигантский стебель фасоли помог ему совершить путешествие.
Реактивный двигатель использовался в Китае еще в первом тысячелетии до нашей эры. Бамбуковые трубы, набитые порохом, служили своеобразными ракетами для развлечения. Кстати, проект первой машины на нашей планете, созданный Ньютоном, тоже был с реактивным двигателем.
История RD
Только в XIX в. мечта человечества о космосе стала приобретать конкретные черты. Ведь именно в этом веке русский революционер Н.И. Кибальчич создал первый в мире проект самолета с реактивным двигателем. Все бумаги были составлены Народным освободителем в тюрьме, куда он попал после покушения на Александра. Но, к сожалению, 04.03.1881 Кибальчич был казнен, а его идея не нашла практического воплощения.
В начале 20 в. Идея использования ракет для космических полетов была выдвинута русским ученым К.Е. Циолковский. Впервые его работа, содержащая описание движения тела переменной массы в виде математического уравнения, была опубликована в 1903 году. Позже ученый разработал саму схему реактивного двигателя, работающего на жидком топливе.
Также Циолковским была изобретена многоступенчатая ракета и выдвинута идея создания настоящих космических городов на низкой околоземной орбите.Циолковский убедительно доказал, что единственное средство для полета в космос — это ракета. То есть аппарат, оснащенный реактивным двигателем, заправляемый горючим и окислителем. Только такая ракета способна преодолеть силу тяжести и вылететь за пределы атмосферы Земли.
Освоение космоса
Статья Циолковского, опубликованная в журнале «Научное обозрение», подтвердила для ученых репутацию мечтателя. Никто не принимал всерьез его аргументы.
Идея Циолковского была реализована советскими учеными.Под руководством Сергея Павловича Королева они запустили первый искусственный спутник Земли. 4 октября 1957 года это устройство было доставлено на орбиту ракетой с реактивным двигателем. Работа РД была основана на преобразовании химической энергии, которая передается топливом газовой струе, превращаясь в кинетическую энергию. В этом случае ракета движется в обратном направлении.
Реактивный двигатель, принцип действия которого используется много лет, находит свое применение не только в космосе, но и в авиации.Но больше всего он используется для запуска ракет. Ведь только RD может перемещать аппарат в пространстве, в котором отсутствует какая-либо среда.
Жидкостный реактивный двигатель
Тот, кто стрелял из огнестрельного оружия или просто наблюдал за этим процессом со стороны, знает, что существует сила, которая непременно оттолкнет ствол назад. А при большей сумме заряда отдача обязательно увеличится.
Упорный подшипник
Ни один из рассмотренных типов опорных подшипников, ни свободно плавающие втулки, ни фиксированный плавающий патрон, не воспринимают нагрузки в осевом направлении. Поскольку газы воздействуют на компрессорное и турбинное колеса в осевом направлении с разной силой, ротор турбокомпрессора (ТК) испытывает осевую нагрузку. Она воспринимается упорным подшипником скольжения с конической плоскостью (рабочей поверхностью). Два маленьких диска, закрепленных на валу, служат контактными поверхностями. Упорный подшипник фиксируется в центральном корпусе подшипников. Маслоотражающая пластина предотвращает попадание масла в зону уплотнения вала.
Слив масла
Масло подается в турбокомпрессор (ТК) при давлении примерно 4 бар. Поскольку масло сливается из турбины при меньшем давлении (самотеком), диаметр трубки для слива значительно больше, чем маслоподающей трубки. Проток масла через корпус подшипников должен быть по возможности вертикальным, сверху вниз. Сливная трубка должна выходить в картер выше уровня масла. Любое препятствие на пути слива масла оборачивается увеличением противодавления в корпусе подшипников. В этом случае масло начинает просачиваться сквозь уплотнительные кольца в компрессор и турбину.
Уплотнения
Центральный корпус подшипников должен быть уплотнен от прорыва в него горячих отработавших газов из турбины и от утечек масла из корпуса. Для этого в канавки на валу ротора, со стороны компрессора и турбины установлены разрезные кольца, аналогичные поршневым. Кольца не вращаются, а неподвижно расклинены в центральном корпусе. Это бесконтактное уплотнение, один из видов лабиринтного уплотнения. Благодаря многочисленным резким изменениям направления движения потока оно затрудняет утечку масла и пропускает в картер лишь небольшое количество отработавших газов.
Тепловая нагрузка на подшипники
Учитывая небольшое расстояние между центральным корпусом и горячим корпусом турбины, тепло может проникать в центральный корпус и нагревать масло до температуры коксования. Тогда масляный кокс мог бы осаждаться в зазорах и на поверхностях, засорять масляные каналы и нарушать работу подшипников и уплотнений. Большое количество углеводородных отложений может вызвать дефицит смазки и граничное трение, приводящие к ускоренному износу системы подшипников.
Тепловой экран и охлаждение разбрызгиванием масла<
Тепловой экран, расположенный позади опорного диска турбинного колеса, предотвращает контакт горячих отработавших газов с центральным корпусом. В некоторых конструкциях при работе двигателя масло распыляется на вал ротора через маленькое распылительное отверстие в опоре подшипника с турбинной стороны, охлаждая вал и уменьшая риск коксования.
Наивысшие температуры в центральном корпусе достигаются вскоре после останова двигателя. Горячий турбинный корпус нагревает систему подшипников, которая больше не охлаждается моторным маслом.
Термическая развязка
В расчете на термическую развязку правой подшипниковой опоры передача тепла от корпуса турбины к системе подшипников сокращается даже после того как двигатель был заглушен. Для этого систему подшипников располагают ниже точки подачи масла, так же как силовой агрегат размещают под крылом самолета. Правая подшипниковая опора больше не контактирует с горячей стенкой центрального корпуса, значит, передача тепла к системе подшипников ограничивается.
Водяное охлаждение
Бензиновые двигатели, у которых температура отработавших газов на 200-300°С выше чем у дизелей, обычно оснащаются турбокомпрессорами с охлаждаемыми центральными корпусами. При работе двигателя центральный корпус интегрируется в его контур охлаждения. После выключения двигателя остаточное тепло снимается посредством малого кольца циркуляции, которое задействуется электрическим насосом с термостатом.
Рециркуляционный клапан
В бензиновых турбодвигателях дроссельная заслонка, которая управляет нагрузкой двигателя, располагается после компрессора, во впускном коллекторе. В момент внезапного сброса газа заслонка закрывается, а компрессор из-за своей инерционности продолжает нагнетать воздух в почти замкнутый объем. Вследствие этого начался бы помпаж компрессора. Частота вращения турбокомпрессора (ТК) быстро упала бы.
Начиная с определенного давления, открывается подпружиненный клапан и направляет воздух обратно на вход в компрессор, ограничивая рост давления и исключая помпаж. Частота вращения ТК остается высокой, и давление наддува появится, как только будет задействован акселератор.
Принцип работы турбореактивного двигателя самолёта
Совершая полет в самолете в большинстве случаев люди никогда не задумываются о том, как работает его двигатель. Но на самом деле о работе двигателя и реактивной тяги с помощью, которой работает сам двигатель, знали ее в Античное время. Но применить эти знания на практике смогли не так давно, так как раньше не технологии не позволяли никому достичь его исправной работы. Гонка вооружения между Англией и Германией стала толчком к созданию ТРД (турбореактивного двигателя).
В работе ТРД самолета нет никаких сложностей, принцип его работы может понять почти каждый человек. Но данный двигатель имеет несколько нюансов, их соблюдение контролируется под строгим присмотром руководства. Для того чтобы авиалайнер смог держаться в небе, необходима идеальная работа двигателя. Так как от работы двигателя напрямую зависят жизни пассажиров находящихся на борту авиатранспорта.
Принцип работы реактивного двигателя
За работу двигателя отвечает реактивная тяга. Для создания реактивной тяги необходима определенная жидкость, которая подается из задней части двигателя и по ходу ее продвижения увеличивается ее скорость движения вперед. Работу тяги отлично объясняет один из законов Ньютона, звучит он так «Любое действия вызывает равное противодействие».
Вместо жидкости в ТРД используется горючая смесь (газы и воздух со сгоревшими частичками топлива). Благодаря этой смеси самолет толкает вперед и позволяет ему лететь дальше.
Разработки таких двигателей начались в тридцатых годах. Первыми кто начал разрабатывать двигатели такого типа стали немцы и англичане. Но в гонке вооружений одержали победу ученные из Германии, так как они выпустили самый первый в мире самолет с ТРД под названием «Ласточка», данный самолет впервые взлетел в небеса над Люфтваффом. Спустя некоторое время появился и Английский самолет «Глостерский метеор»
Также сверхзвуковые двигатели принято считать турбореактивными, но они отличаются более совершенными модификациями, в отличие от ТРД.
Устройство двигателя имеет четыре главные детали, а именно:
- Компрессор.
- Камера горения.
- Турбина.
- Выхлоп.
Компрессор
В компрессоре находиться несколько турбин, с помощью которых происходит засасывание и сжатие воздуха. Во время сжатия воздуха, его давление и температура начинает нагнетаться и расти.
Камера горения
После того как воздух проходит турбину и его сжимает до необходимых размеров. Часть сжатого воздуха поступает в камеру горения, где воздух начинает смешиваться с топливом, после чего его поджигают. Благодаря этому увеличивается тепловая энергия воздуха. После смесь выходит из камеры с большой скорости и расширяется.
Турбина
После выхода эта смесь снова попадает в турбину, с помощью высокой энергии газа лопасти в турбине начинают свое вращение. Турбина тесно связанна с компрессором, который находиться в начале двигателя. Благодаря этому турбина начинает свою работу. Остатки воздуха выходят в выхлоп. В момент выхода смеси температура достигает рекордных размеров. Но она продолжает повышать свою температуру с помощью эффекта Дросселирования. После того как температура воздуха доходит до своего пика, она начинает идти на спад и выходит из турбины.
Принцип работы турбореактивного двигателя
В отличие от реактивного двигателя, который пользуется спросом почти у всех самолетов, турбореактивный двигатель больше подходит для пассажирских авиалайнеров. Так как для работы реактивного двигателя необходимо не только топливо, но и окислитель.
Благодаря своему строению окислитель поступает вместе с топливом из бака. А в случаи с ТРД окислитесь, поступает напрямую из атмосферы. А в остальном их работа совершенно идентична и не отличается друг от друга.
У турбореактивного двигателя главной деталью является лопасть турбины, так как от ее исправной работы напрямую зависит мощность двигателя. Благодаря этим лопастям и образуется тяга, которая необходима для поддержания скорости самолета. Если сравнить одну лопасть с автомобильным двигателем, то она сможет обеспечить мощностью целых десять машин.
Лопасти устанавливаются за камерой сгорания, так как там нагнетается самое высокое давления, также температура воздуха в данной части двигателя может доходить до 1400 градусов Цельсия.
В целях улучшения прочности и устойчивости лопасти перед различными факторами их монокристаллизируют, благодаря этому они могут держать высокую температуру и давление. Прежде чем установить такой двигатель на самолет его тестируют на полном тяговом усилителе. Также двигатель должен получить сертификат от Европейского совета по безопасности.
Атомный двигатель
В период холодной войны в мире были попытки создания атомного двигателя, за основу был взят турбореактивный двигатель. Главной задумкой ученых было создание двигателя, основанного не на химической реакции радиоактивных веществ, а на вырабатываемом тепле от ядерного реактора. Он должен был находиться на месте камеры сгорания.
В теории воздух должен был проходить через работающую зону реактора, благодаря этому реактор должен был остужаться, а температура воздуха наоборот возрастать. После чело воздух должен был расширяться и выходить через сопла (выхлоп) на этот момент скорость воздуха должна была превышать скорость полета самолета.
В Советском союзе были попытки проведения испытаний подобного двигателя, также ученные в соединенных штатах Америки, вели разработку данного двигателя, и их работа почти подходила к тестам двигателя на настоящем самолете.
Но по ряду причин разработки этого двигателя было решено закрыть. Так как у двигателя было множество недостатков, а именно:
- Пилоты были подвержены постоянному радиоактивному облучению на протяжении всего полета.
- Вместе с воздухом через сопла выходили и частички радиоактивного элемента в атмосферу.
- В том случае если самолет терпел крушение, был очень большой шанс взрыва радиоактивного реактора, что влекло за собой радиоактивное отравление на довольно большой площади.
Турбина Каплан — ее составные части, работа и применение
Турбина Каплан работает по принципу реакции осевого потока. В турбинах с осевым потоком вода течет через бегунок в направлении, параллельном оси вращения рабочего колеса. Вода на входе в турбину обладает как кинетической энергией, так и энергией давления для эффективного вращения лопастей гидроэлектростанции.
Рис. 1: Турбина Каплана.
В 1913 году австрийский профессор Виктор Каплан, который разработал эту турбину, объединил автоматически регулируемые лопасти гребного винта с автоматически регулируемыми заслонками калитки для достижения эффективности в широком диапазоне расхода и уровня воды.Она также называется пропеллерной турбиной и произошла от турбины Фрэнсиса. Он способен очень эффективно работать при низком напоре и высоких расходах, что невозможно с турбиной Фрэнсиса.
В этой статье рассматривается порядок работы, основные компоненты и их применение.
Основные компоненты турбины Каплана
Основные части турбины Каплан,
1. Спиральный кожух
Это спиральный кожух с уменьшающейся площадью поперечного сечения.Вода из затворов попадает в корпус спирали, а затем движется к направляющим лопастям, где вода поворачивается на 90 ° и течет в осевом направлении через желоб. Он защищает рабочее колесо, направляющие лопатки рабочих лопаток и другие внутренние части турбины от внешних повреждений.
Рис. 2: Основные компоненты турбины Каплана.
2. Механизм направляющей лопасти
Это единственная управляющая часть всей турбины, которая открывается и закрывается в зависимости от потребности в мощности.Если требуется большая выходная мощность, он открывается шире, чтобы больше воды попадало на лопасти ротора, а когда требуется низкая выходная мощность, он закрывается, чтобы прекратить поток воды. При отсутствии направляющих лопаток турбина не может работать эффективно и ее КПД снижается.
3. Трубка отсасывающая
Давление на выходе из рабочего колеса реакционной турбины обычно ниже атмосферного. Вода на выходе не может напрямую сбрасываться в хвостовую часть.Труба или труба с постепенно увеличивающейся площадью используется для отвода воды от выхода турбины до хвостовой части. Эта трубка с увеличивающейся площадью называется вытяжной трубкой. Один конец трубки подсоединен к выпускному отверстию бегунка, а другой конец погружен ниже уровня воды в хвостовой части.
4. Лезвия рабочего колеса
Сердцем компонента в турбине Каплана являются рабочие лопатки, так как это вращающаяся часть, которая помогает в производстве электроэнергии. Вал соединен с валом генератора.Рабочее колесо этой турбины имеет большой выступ, на котором крепятся его лопасти, а лопасти рабочего колеса регулируются под оптимальным углом атаки для максимальной выходной мощности. Лопатки турбины Каплана имеют закрутку по длине.
Рис. 3. Рабочие лопатки турбины Каплана.
Рабочий процесс турбины Каплана
Вода, поступающая из загона, попадает в кожух спирали. Корпус спирали выполнен такой формы, чтобы не терять давление потока.Направляющие лопатки направляют воду к лопастям рабочего колеса. Лопасти регулируются и могут регулироваться в зависимости от скорости потока. Вода поворачивается на 90 градусов, поэтому направление воды является осевым по отношению к лопастям бегунка.
Лопасти бегунка начинают вращаться при ударе воды из-за силы реакции воды. Лезвия бегунка имеют изгиб по всей длине, чтобы всегда иметь оптимальный угол атаки для всего поперечного сечения лезвий для достижения большей эффективности.
Из лопастей рабочего колеса вода поступает в вытяжную трубу, где ее энергия давления и кинетическая энергия уменьшаются. Кинетическая энергия преобразуется в энергию давления, что приводит к увеличению давления воды.
Вращение турбины используется для вращения вала генератора для производства электроэнергии.
Применение турбины Каплана
- Турбины Каплана широко используются во всем мире для производства электроэнергии.
- Может работать более эффективно при низком напоре воды и высоком расходе по сравнению с другими типами турбин.
- Он меньше по размеру и прост в сборке.
- КПД турбины Каплана очень высок по сравнению с другими гидравлическими турбинами.
Недостаток турбины Каплана
- Единственным недостатком турбины Каплана является кавитация, возникающая из-за падения давления в отсасывающей трубе. Использование вытяжной трубы и подходящего материала, как правило, из нержавеющей стали для лопастей рабочего колеса, может в большей степени уменьшить проблему кавитации.
Турбина | Британника
Турбина , любое из различных устройств, преобразующих энергию потока жидкости в механическую энергию. Преобразование обычно осуществляется путем пропускания жидкости через систему неподвижных каналов или лопаток, которые чередуются с каналами, состоящими из лопастей, похожих на ребра, прикрепленных к ротору. За счет организации потока так, чтобы на лопасти ротора действовала касательная сила или крутящий момент, ротор вращается, и работа извлекается.
Ветровые турбины около Техачапи, Калифорния
© Грег Рэндлс / Shutterstock.com Турбины можно разделить на четыре основных типа в зависимости от используемых жидкостей: вода, пар, газ и ветер. Хотя одни и те же принципы применимы ко всем турбинам, их конкретные конструкции достаточно различаются, чтобы заслужить отдельное описание.
Гидравлическая турбина использует потенциальную энергию, возникающую в результате разницы в высоте между верхним водным резервуаром и уровнем воды на выходе из турбины (отводом) для преобразования этого так называемого напора в работу.Водяные турбины — современные преемники простых водяных колес, которым около 2000 лет. Сегодня гидротурбины в основном используются для производства электроэнергии.
Однако наибольшее количество электроэнергии вырабатывается паровыми турбинами, соединенными с электрогенераторами. Турбины приводятся в действие паром, вырабатываемым либо в генераторе, работающем на ископаемом топливе, либо в атомном генераторе. Энергию, которую можно извлечь из пара, удобно выражать через изменение энтальпии в турбине.Энтальпия отражает формы как тепловой, так и механической энергии в процессе потока и определяется суммой внутренней тепловой энергии и произведением давления на объем. Доступное изменение энтальпии через паровую турбину увеличивается с увеличением температуры и давления парогенератора и с уменьшением давления на выходе из турбины.
Оформите подписку Britannica Premium и получите доступ к эксклюзивному контенту.
Подпишитесь сейчас Для газовых турбин энергия, извлекаемая из текучей среды, также может быть выражена через изменение энтальпии, которое для газа почти пропорционально перепаду температуры в турбине.В газовых турбинах рабочим телом является воздух, смешанный с газообразными продуктами сгорания. Большинство газотурбинных двигателей включает, по крайней мере, компрессор, камеру сгорания и турбину. Обычно они монтируются как единое целое и работают как законченный первичный двигатель в так называемом открытом цикле, когда воздух всасывается из атмосферы, а продукты сгорания, наконец, снова выбрасываются в атмосферу. Поскольку успешная работа зависит от интеграции всех компонентов, важно рассматривать устройство в целом, которое фактически является двигателем внутреннего сгорания, а не только турбиной.По этой причине газовые турбины рассматриваются в статье двигатель внутреннего сгорания.
Энергия ветра может быть извлечена ветровой турбиной для производства электроэнергии или для откачки воды из колодцев. Ветряные турбины являются преемниками ветряных мельниц, которые были важными источниками энергии с позднего средневековья до 19 века.
Фред Лэндис Водяные турбины обычно делятся на две категории: (1) импульсные турбины, используемые для высокого напора воды и низкого расхода, и (2) реактивные турбины, обычно используемые для напора ниже примерно 450 метров и среднего или высокого расхода.Эти два класса включают в себя основные типы, обычно используемые, а именно импульсные турбины Пелтона и реактивные турбины типа Фрэнсиса, пропеллера, Каплана и Дериаза. Турбины могут иметь горизонтальный или, чаще, вертикальный вал. Для каждого типа возможны широкие вариации конструкции для соответствия конкретным местным гидравлическим условиям. Сегодня большинство гидравлических турбин используются для выработки электроэнергии на гидроэлектростанциях.
Импульсные турбины
В импульсной турбине потенциальная энергия или напор воды сначала преобразуется в кинетическую энергию путем выпуска воды через сопло тщательно продуманной формы.Струя, выбрасываемая в воздух, направляется на изогнутые ковши, закрепленные на периферии бегунка, для извлечения энергии воды и преобразования ее в полезную работу.
Современные импульсные турбины основаны на конструкции, запатентованной в 1889 году американским инженером Лестером Алленом Пелтоном. Свободная водная струя попадает в лопатки турбины по касательной. Каждый ковш имеет высокий центральный гребень, так что поток разделяется, оставляя желоб с обеих сторон. Колеса Пелтона подходят для высоких напоров, обычно выше 450 метров при относительно низком расходе воды.Для максимальной эффективности скорость конца рабочего колеса должна составлять примерно половину скорости ударной струи. КПД (работа, производимая турбиной, деленная на кинетическую энергию свободной струи) может превышать 91 процент при работе с 60–80 процентами полной нагрузки.
Мощность одного колеса можно увеличить, используя более одного жиклера. Для горизонтальных валов характерны двухструйные устройства. Иногда на одном валу устанавливаются два отдельных бегунка, приводящих в движение один электрогенератор. Агрегаты с вертикальным валом могут иметь четыре или более отдельных форсунок.
Если электрическая нагрузка на турбину изменяется, ее выходная мощность должна быть быстро отрегулирована в соответствии с потребностями. Это требует изменения расхода воды, чтобы поддерживать постоянную скорость генератора. Скорость потока через каждое сопло регулируется расположенным в центре наконечником или иглой аккуратной формы, которая скользит вперед или назад под управлением гидравлического серводвигателя.
Правильная конструкция иглы гарантирует, что скорость воды, выходящей из сопла, остается практически неизменной независимо от отверстия, обеспечивая почти постоянную эффективность в большей части рабочего диапазона.Нецелесообразно внезапно уменьшать поток воды, чтобы соответствовать уменьшению нагрузки. Это может привести к разрушительному скачку давления (гидроудару) в подающем трубопроводе или водопроводе. Таких скачков можно избежать, добавив временное сопло для разлива, которое открывается при закрытии основного сопла, или, что чаще, частично вставляя отражающую пластину между струей и колесом, отклоняя и рассеивая часть энергии при медленном закрытии иглы.
Другой тип импульсной турбины — турбина турго.Струя падает под косым углом на бегунок с одной стороны и продолжает двигаться по единственному пути, выбрасывая его с другой стороны. Этот тип турбины использовался в установках среднего размера с умеренно высоким напором.
Реакционные турбины
В реакционной турбине силы, приводящие в движение ротор, достигаются за счет реакции ускоряющегося потока воды в рабочем колесе при падении давления. Принцип реакции можно наблюдать в роторном оросителе для газонов, где выходящая струя вращает ротор в противоположном направлении.Из-за большого разнообразия возможных конструкций рабочего колеса реактивные турбины могут использоваться в гораздо большем диапазоне напоров и расходов, чем импульсные турбины. Реакционные турбины обычно имеют спиральный впускной кожух, который включает регулирующие заслонки для регулирования потока воды. На входе часть потенциальной энергии воды может быть преобразована в кинетическую энергию по мере ускорения потока. Впоследствии энергия воды отбирается в роторе.
Как отмечалось выше, широко используются четыре основных типа реактивных турбин: турбины Каплана, Фрэнсиса, Дериаза и пропеллерные.В турбинах Каплана с неподвижными лопастями и с регулируемыми лопастями (названными в честь австрийского изобретателя Виктора Каплана), по существу, существует осевой поток через машину. Турбины типа Фрэнсиса и Дериаза (в честь американского изобретателя британского происхождения Джеймса Б. Фрэнсиса и швейцарского инженера Поля Дериаза, соответственно) используют «смешанный поток», когда вода поступает радиально внутрь и выпускается в осевом направлении. Рабочие лопасти на турбинах Фрэнсиса и пропеллера состоят из неподвижных лопастей, в то время как в турбинах Каплана и Дериаза лопасти могут вращаться вокруг своей оси, которая находится под прямым углом к главному валу.
Объяснение 9 различных стратегий
Профилактическое обслуживание и корректирующее обслуживание
На верхнем уровне я вижу профилактическое или корректирующее обслуживание:
- Когда мы выполняем профилактическое обслуживание , мы выполняем задачу до того, как произойдет сбой . Эта задача может быть направлена на предотвращение отказа, минимизацию последствий отказа или оценку риска возникновения отказа.
- Когда мы проводим корректирующее обслуживание , произошел сбой , и мы в основном восстанавливаем работоспособность оборудования. Чтобы было ясно, корректирующее обслуживание может быть результатом преднамеренной стратегии безотказной работы.
Профилактическое обслуживание
Профилактическое обслуживание можно определить как «стратегию обслуживания оборудования, основанную на замене или восстановлении актива через фиксированные интервалы времени, независимо от его состояния. Запланированные задачи восстановления и задачи замены являются примерами задач профилактического обслуживания ».
Профилактическое обслуживание (или профилактическое обслуживание) в основном представляет собой тип обслуживания, который выполняется через регулярные промежутки времени, пока оборудование все еще функционирует, с целью предотвращения отказа или снижения вероятности отказа.
Профилактическое обслуживание может проводиться по времени, т.е. каждую неделю, каждый месяц или каждые три месяца. Но профилактическое обслуживание также может быть основано на использовании e.г. каждые 150 циклов, каждые 10 000 часов или как ваш автомобиль: обслуживание каждые 10 000 км.
Помимо регулярного интервального обслуживания (обслуживания по времени), существуют также другие виды обслуживания, которые подпадают под категорию профилактического обслуживания:
В следующих параграфах я более подробно рассмотрю каждый из этих типов обслуживания, в том числе, когда вам следует рассмотреть возможность их использования.
Обслуживание по времени (TBM)
Временное обслуживание относится к замене или обновлению элемента для восстановления его надежности в фиксированное время, интервал или использование независимо от его состояния.Это то, что Мубрей называет задачами запланированного восстановления или запланированного удаления в своей книге RCMII.
Я ограничиваю использование этой фразы, так как по какой-то причине люди приходят к выводу, что другое техническое обслуживание не запланировано. Хотя на самом деле, конечно, все техническое обслуживание следует планировать в соответствии с нашим недельным расписанием. Единственным исключением может быть экстренное обслуживание, которое по самой своей природе требует немедленного внимания и не может быть запланировано.
Цель обслуживания по времени — защитить себя от выхода из строя известных изнашиваемых деталей, которые имеют предсказуемое среднее время наработки на отказ (MTBF) i.е. Техническое обслуживание по времени предполагает, что отказ связан с возрастом и может быть определен точный срок службы. Или что просто не стоит прилагать усилия для оценки состояния, а замена по времени более экономична и все же (в разумной степени) эффективна.
Time Based Maintenance никогда не сможет эффективно управлять режимами отказов, не связанными с возрастом, и поэтому должно составлять лишь небольшую часть вашей общей программы технического обслуживания, поскольку> 70% режимов отказа на вашем предприятии не связаны с возрастом (см. Статью 9 Принципы Современное обслуживание).
Важно понимать, что во многих отраслях компании действительно должны выполнять определенные задачи для соответствия нормативным требованиям, и они, как правило, выполняются в фиксированный интервал времени, то есть техобслуживание на основе времени. Но даже при обслуживании, связанном с соблюдением требований, часто есть возможности привлечь регулирующий орган и рассмотреть возможность перехода, например, к подходам, основанным на оценке риска. Хорошим примером этого может быть принятие инспекции на основе рисков (RBI) для инспекций судов вместо e.г. Внутренние осмотры судов каждые 4 года.
Поиск неисправностей (FFM)
Поиск отказов Задачи обслуживания направлены на обнаружение скрытых отказов, обычно связанных с защитными функциями. Подумайте о предохранительных клапанах давления, датчиках отключения и тому подобном.
Оборудование этого типа не будет работать, пока не выйдет из строя что-то еще. Это означает, что при нормальных условиях эксплуатации вы не узнаете, работает ли это оборудование i.е. режимы отказа скрыты.
И поскольку эти сбои скрыты, вам нужно будет найти их, прежде чем вы будете полагаться на это оборудование для защиты.
Действительно просто.
Важно понимать, что задачи технического обслуживания по поиску отказов не предотвращают отказ, а просто обнаруживают его. И после обнаружения вам придется устранить обнаруженную неисправность. Обнаружение отказов Техническое обслуживание проводится через фиксированные интервалы времени, обычно определяемые законодательством или подходами, основанными на оценке риска.
Техническое обслуживание с учетом рисков (RBM)
Техническое обслуживание на основе рисков (RBM) — это когда вы используете методологию оценки рисков для распределения ваших скудных ресурсов на техническое обслуживание тем активам, которые несут наибольший риск в случае отказа (помня, что риск = вероятность x последствия).
В результате оборудование с более высоким риском и очень высокой вероятностью отказа будет подвергаться более частому техническому обслуживанию и осмотру. Оборудование с низким уровнем риска может обслуживаться с гораздо меньшей частотой и, возможно, с гораздо меньшим объемом работ.
При эффективном внедрении процесса обслуживания с учетом рисков вы должны снизить общий риск отказа всего предприятия наиболее экономичным способом.
Risk-Based Maintenance — это, по сути, профилактическое обслуживание, при котором частота и объем работ по техническому обслуживанию постоянно оптимизируются на основе результатов тестирования или инспекции и тщательной оценки рисков. Примерами технического обслуживания на основе рисков могут быть проверки на основе рисков применительно к статическому оборудованию, такому как сосуды и трубопроводы, или даже предохранительные клапаны.
Техническое обслуживание по условию (CBM)
Большинство видов отказов не связаны с возрастом. Тем не менее, большинство режимов отказа действительно выдают какое-то предупреждение о том, что они происходят или вот-вот произойдут.
Если можно найти доказательства того, что что-то находится на ранних стадиях отказа, можно принять меры для предотвращения полного отказа и / или во избежание последствий отказа. Таким образом, техническое обслуживание по состоянию в качестве стратегии ищет физические доказательства того, что отказ происходит или вот-вот произойдет.Такой подход к CBM показывает его более широкие применения за пределами методов мониторинга состояния, часто связанных только с вращающимся оборудованием.
Важной концепцией технического обслуживания по состоянию является кривая P-F, показанная на рисунке ниже:
Кривая показывает, что по мере того, как сбой начинает проявляться, оборудование изнашивается до точки, в которой его можно обнаружить (точка «P»).
Если отказ не обнаружен и не устранен, он продолжается до тех пор, пока не произойдет функциональный отказ (точка «F»).Временной диапазон между P и F, обычно называемый интервалом P-F, представляет собой окно возможностей, в течение которого инспекция, возможно, может обнаружить неминуемый отказ и дать вам время для его устранения.
Важно понимать, что CBM как стратегия технического обслуживания не снижает вероятность отказа, возникающего в результате обновления срока службы, а вместо этого направлена на вмешательство до того, как произойдет отказ, исходя из того, что это более экономично и должно иметь меньше влияние на доступность.
Другими словами: мониторинг состояния не исправляет машины, а мониторинг состояния не останавливает отказы. Мониторинг состояния позволяет обнаруживать проблемы только до того, как они перерастут в отказ.
Общее практическое правило состоит в том, что интервал между задачами CBM должен составлять половину или одну треть интервала P-F.
Насколько эффективнее CBM выше аварийного обслуживания, зависит от продолжительности интервала P-F. При наличии большого количества предупреждений можно запланировать исправление, мобилизовать материалы и ресурсы и предотвратить поломку (хотя производство все еще останавливается на время технического обслуживания).Когда интервал P-F составляет всего несколько дней, в результате организационные действия и действия на рабочем месте очень похожи на поломку, и ценность CBM в значительной степени теряется.
Для того, чтобы CBM была эффективной как стратегия, необходимо раннее вмешательство. Это требует действенного и действенного процесса сбора данных, анализа данных, принятия решений и, наконец, вмешательства.
Для режимов отказа, где интервал P-F показывает большую изменчивость, мониторинг состояния не является эффективной стратегией.
Если вам интересно узнать больше о том, как лучше всего управлять режимами отказа, не забудьте прочитать мою статью Техническое обслуживание, ориентированное на надежность — 9 принципов современного технического обслуживания.
Принцип работы (кратко). Принцип действия реактивного двигателя
Под реактивным понимается движение, при котором от тела с определенной скоростью отделяется одна из его частей. Сила, возникающая в результате такого процесса, действует сама по себе. Другими словами, у нее нет даже малейшего контакта с внешними телами.
Реактивное движение в природе
Во время летнего отдыха на юге почти все мы, купаясь в море, встречались с медузами. Но мало кто думал, что эти животные движутся так же, как реактивный двигатель. Принцип действия в природе такого агрегата можно наблюдать при перемещении определенных видов морского планктона и личинок стрекоз. Причем эффективность этих беспозвоночных зачастую выше, чем у технических средств.
Кто еще может наглядно продемонстрировать, какой из реактивных двигателей работает? Кальмары, осьминоги и каракатицы.Подобное движение совершают многие другие морские моллюски. Возьмем, например, каракатицу. Она втягивает воду в свою жаберную полость и энергично выбрасывает ее через воронку, которая направляется назад или в сторону. При этом моллюск способен совершать движения в нужную сторону.
Принцип действия реактивного двигателя можно наблюдать и при перемещении барабана. Это морское животное берет воду в широкой впадине. После этого мышцы его тела сокращаются, выталкивая жидкость через отверстие, которое находится позади.Реакция образовавшейся струи позволяет саженцу двигаться вперед.
Sea Missiles
Но наибольшего совершенства в реактивной навигации достиг все тот же кальмар. Даже форма самой ракеты словно скопирована с этого морского обитателя. При движении с небольшой скоростью кальмар периодически выгибает ромбовидный плавник. Но для быстрого броска ему приходится использовать собственный «реактивный двигатель». Принцип работы всех его мышц и тела стоит рассмотреть подробнее.
Кальмар имеет своеобразную мантию.Это мышечная ткань, которая окружает его тело со всех сторон. Во время движения животное засасывает в эту мантию большой объем воды, резко выбрасывая струю через специальную узкую насадку. Такие действия позволяют кальмарам двигаться назад со скоростью до семидесяти километров в час. Во время движения животное собирает в пучок все свои десять щупалец, что придает телу обтекаемую форму. На насадке есть специальный клапан. Его поворачивает животное сокращением мышц. Это позволяет моряку менять направление.Роль штурвала при передвижении кальмара выполняют его щупальца. Он направляет их влево или вправо, вниз или вверх, легко уворачиваясь от столкновений с различными препятствиями.
Существует разновидность кальмаров (stenoteutis), относящаяся к званию лучшего пилота среди моллюсков. Опишите принцип работы реактивного двигателя — и вы поймете, почему, преследуя рыбу, это животное иногда выпрыгивает из воды, даже попадая на палубы кораблей, плывущих по океану. Как это произошло? Пилот-кальмар, находясь в водной стихии, развивает для себя максимальную реактивную тягу.Это позволяет ему летать над волнами на расстоянии до пятидесяти метров.
Если мы рассмотрим реактивный двигатель, принцип Какое животное работает, мы можем упомянуть еще? Это, на первый взгляд, мешковатый осьминог. Пловцы не так быстры, как кальмары, но в случае опасности их скорости могут позавидовать даже лучшие спринтеры. Биологи, изучавшие миграцию осьминогов, выяснили, что они движутся по принципу действия реактивного двигателя.
Животное при каждой струе воды, выбрасываемой из воронки, делает рывок на два или даже два с половиной метра.При этом плывет осьминог своеобразным образом — задом наперед.
Другие примеры реактивного движения
В мире растений есть ракеты. Принцип действия реактивного двигателя можно наблюдать, когда даже при очень легком прикосновении «бешеный огурец» с большой скоростью отскакивает от ножки, отталкивая при этом липкую жидкость с семенами. При этом сам плод летит на значительное расстояние (до 12 м) в обратном направлении.
Принцип работы реактивного двигателя можно наблюдать и в лодке.Если с него в определенном направлении бросить в воду тяжелые камни, то он будет двигаться в противоположном направлении. Ракетно-реактивный двигатель имеет такой же принцип работы. Только там вместо камней используются газы. Они создают реактивную силу, которая обеспечивает движение как в воздухе, так и в разряженном пространстве.
Фантастическое путешествие
Человечество давно мечтает о космических полетах. Об этом свидетельствуют произведения писателей-фантастов, которые для достижения этой цели предлагали самые разные средства.Например, герой рассказа французского писателя Эркюля Савинена Сирано де Бержерак достиг Луны на железной повозке, на которую постоянно бросался мощный магнит. Знаменитый Мюнхгаузен тоже достиг той же планеты. Гигантский стебель фасоли помог ему совершить путешествие.
Реактивный двигатель использовался в Китае еще в первом тысячелетии до нашей эры. Бамбуковые трубы, набитые порохом, служили своеобразными ракетами для развлечения. Кстати, проект первой машины на нашей планете, созданный Ньютоном, тоже был с реактивным двигателем.
История RD
Только в XIX в. мечта человечества о космосе стала приобретать конкретные черты. Ведь именно в этом веке русский революционер Н.И. Кибальчич создал первый в мире проект самолета с реактивным двигателем. Все бумаги были составлены Народным освободителем в тюрьме, куда он попал после покушения на Александра. Но, к сожалению, 04.03.1881 Кибальчич был казнен, а его идея не нашла практического воплощения.
В начале 20 в. Идея использования ракет для космических полетов была выдвинута русским ученым К.Е. Циолковский. Впервые его работа, содержащая описание движения тела переменной массы в виде математического уравнения, была опубликована в 1903 году. Позже ученый разработал саму схему реактивного двигателя, работающего на жидком топливе.
Также Циолковским была изобретена многоступенчатая ракета и выдвинута идея создания настоящих космических городов на низкой околоземной орбите.Циолковский убедительно доказал, что единственное средство для полета в космос — это ракета. То есть аппарат, оснащенный реактивным двигателем, заправляемый горючим и окислителем. Только такая ракета способна преодолеть силу тяжести и вылететь за пределы атмосферы Земли.
Освоение космоса
Статья Циолковского, опубликованная в журнале «Научное обозрение», подтвердила для ученых репутацию мечтателя. Никто не принимал всерьез его аргументы.
Идея Циолковского была реализована советскими учеными.Под руководством Сергея Павловича Королева они запустили первый искусственный спутник Земли. 4 октября 1957 года это устройство было доставлено на орбиту ракетой с реактивным двигателем. Работа РД была основана на преобразовании химической энергии, которая передается топливом газовой струе, превращаясь в кинетическую энергию. В этом случае ракета движется в обратном направлении.
Реактивный двигатель, принцип действия которого используется много лет, находит свое применение не только в космосе, но и в авиации.Но больше всего он используется для запуска ракет. Ведь только RD может перемещать аппарат в пространстве, в котором отсутствует какая-либо среда.
Жидкостный реактивный двигатель
Тот, кто стрелял из огнестрельного оружия или просто наблюдал за этим процессом со стороны, знает, что существует сила, которая непременно оттолкнет ствол назад. А при большей сумме заряда отдача обязательно увеличится.
Уплотнения
Центральный корпус подшипников должен быть уплотнен от прорыва в него горячих отработавших газов из турбины и от утечек масла из корпуса. Для этого в канавки на валу ротора, со стороны компрессора и турбины установлены разрезные кольца, аналогичные поршневым. Кольца не вращаются, а неподвижно расклинены в центральном корпусе. Это бесконтактное уплотнение, один из видов лабиринтного уплотнения. Благодаря многочисленным резким изменениям направления движения потока оно затрудняет утечку масла и пропускает в картер лишь небольшое количество отработавших газов.
Тепловая нагрузка на подшипники
Учитывая небольшое расстояние между центральным корпусом и горячим корпусом турбины, тепло может проникать в центральный корпус и нагревать масло до температуры коксования. Тогда масляный кокс мог бы осаждаться в зазорах и на поверхностях, засорять масляные каналы и нарушать работу подшипников и уплотнений. Большое количество углеводородных отложений может вызвать дефицит смазки и граничное трение, приводящие к ускоренному износу системы подшипников.
Тепловой экран и охлаждение разбрызгиванием масла<
Тепловой экран, расположенный позади опорного диска турбинного колеса, предотвращает контакт горячих отработавших газов с центральным корпусом. В некоторых конструкциях при работе двигателя масло распыляется на вал ротора через маленькое распылительное отверстие в опоре подшипника с турбинной стороны, охлаждая вал и уменьшая риск коксования.
Наивысшие температуры в центральном корпусе достигаются вскоре после останова двигателя. Горячий турбинный корпус нагревает систему подшипников, которая больше не охлаждается моторным маслом.
Термическая развязка
В расчете на термическую развязку правой подшипниковой опоры передача тепла от корпуса турбины к системе подшипников сокращается даже после того как двигатель был заглушен. Для этого систему подшипников располагают ниже точки подачи масла, так же как силовой агрегат размещают под крылом самолета. Правая подшипниковая опора больше не контактирует с горячей стенкой центрального корпуса, значит, передача тепла к системе подшипников ограничивается.
Водяное охлаждение
Бензиновые двигатели, у которых температура отработавших газов на 200-300°С выше чем у дизелей, обычно оснащаются турбокомпрессорами с охлаждаемыми центральными корпусами. При работе двигателя центральный корпус интегрируется в его контур охлаждения. После выключения двигателя остаточное тепло снимается посредством малого кольца циркуляции, которое задействуется электрическим насосом с термостатом.
Рециркуляционный клапан
В бензиновых турбодвигателях дроссельная заслонка, которая управляет нагрузкой двигателя, располагается после компрессора, во впускном коллекторе. В момент внезапного сброса газа заслонка закрывается, а компрессор из-за своей инерционности продолжает нагнетать воздух в почти замкнутый объем. Вследствие этого начался бы помпаж компрессора. Частота вращения турбокомпрессора (ТК) быстро упала бы.
Начиная с определенного давления, открывается подпружиненный клапан и направляет воздух обратно на вход в компрессор, ограничивая рост давления и исключая помпаж. Частота вращения ТК остается высокой, и давление наддува появится, как только будет задействован акселератор.
Принцип работы турбореактивного двигателя самолёта
Совершая полет в самолете в большинстве случаев люди никогда не задумываются о том, как работает его двигатель. Но на самом деле о работе двигателя и реактивной тяги с помощью, которой работает сам двигатель, знали ее в Античное время. Но применить эти знания на практике смогли не так давно, так как раньше не технологии не позволяли никому достичь его исправной работы. Гонка вооружения между Англией и Германией стала толчком к созданию ТРД (турбореактивного двигателя).
В работе ТРД самолета нет никаких сложностей, принцип его работы может понять почти каждый человек. Но данный двигатель имеет несколько нюансов, их соблюдение контролируется под строгим присмотром руководства. Для того чтобы авиалайнер смог держаться в небе, необходима идеальная работа двигателя. Так как от работы двигателя напрямую зависят жизни пассажиров находящихся на борту авиатранспорта.
Принцип работы реактивного двигателя
За работу двигателя отвечает реактивная тяга. Для создания реактивной тяги необходима определенная жидкость, которая подается из задней части двигателя и по ходу ее продвижения увеличивается ее скорость движения вперед. Работу тяги отлично объясняет один из законов Ньютона, звучит он так «Любое действия вызывает равное противодействие».
Вместо жидкости в ТРД используется горючая смесь (газы и воздух со сгоревшими частичками топлива). Благодаря этой смеси самолет толкает вперед и позволяет ему лететь дальше.
Разработки таких двигателей начались в тридцатых годах. Первыми кто начал разрабатывать двигатели такого типа стали немцы и англичане. Но в гонке вооружений одержали победу ученные из Германии, так как они выпустили самый первый в мире самолет с ТРД под названием «Ласточка», данный самолет впервые взлетел в небеса над Люфтваффом. Спустя некоторое время появился и Английский самолет «Глостерский метеор»
Также сверхзвуковые двигатели принято считать турбореактивными, но они отличаются более совершенными модификациями, в отличие от ТРД.
Устройство двигателя имеет четыре главные детали, а именно:
- Компрессор.
- Камера горения.
- Турбина.
- Выхлоп.
Компрессор
В компрессоре находиться несколько турбин, с помощью которых происходит засасывание и сжатие воздуха. Во время сжатия воздуха, его давление и температура начинает нагнетаться и расти.
Камера горения
После того как воздух проходит турбину и его сжимает до необходимых размеров. Часть сжатого воздуха поступает в камеру горения, где воздух начинает смешиваться с топливом, после чего его поджигают. Благодаря этому увеличивается тепловая энергия воздуха. После смесь выходит из камеры с большой скорости и расширяется.
Турбина
После выхода эта смесь снова попадает в турбину, с помощью высокой энергии газа лопасти в турбине начинают свое вращение. Турбина тесно связанна с компрессором, который находиться в начале двигателя. Благодаря этому турбина начинает свою работу. Остатки воздуха выходят в выхлоп. В момент выхода смеси температура достигает рекордных размеров. Но она продолжает повышать свою температуру с помощью эффекта Дросселирования. После того как температура воздуха доходит до своего пика, она начинает идти на спад и выходит из турбины.
Принцип работы турбореактивного двигателя
В отличие от реактивного двигателя, который пользуется спросом почти у всех самолетов, турбореактивный двигатель больше подходит для пассажирских авиалайнеров. Так как для работы реактивного двигателя необходимо не только топливо, но и окислитель.
Благодаря своему строению окислитель поступает вместе с топливом из бака. А в случаи с ТРД окислитесь, поступает напрямую из атмосферы. А в остальном их работа совершенно идентична и не отличается друг от друга.
У турбореактивного двигателя главной деталью является лопасть турбины, так как от ее исправной работы напрямую зависит мощность двигателя. Благодаря этим лопастям и образуется тяга, которая необходима для поддержания скорости самолета. Если сравнить одну лопасть с автомобильным двигателем, то она сможет обеспечить мощностью целых десять машин.
Лопасти устанавливаются за камерой сгорания, так как там нагнетается самое высокое давления, также температура воздуха в данной части двигателя может доходить до 1400 градусов Цельсия.
В целях улучшения прочности и устойчивости лопасти перед различными факторами их монокристаллизируют, благодаря этому они могут держать высокую температуру и давление. Прежде чем установить такой двигатель на самолет его тестируют на полном тяговом усилителе. Также двигатель должен получить сертификат от Европейского совета по безопасности.
Атомный двигатель
В период холодной войны в мире были попытки создания атомного двигателя, за основу был взят турбореактивный двигатель. Главной задумкой ученых было создание двигателя, основанного не на химической реакции радиоактивных веществ, а на вырабатываемом тепле от ядерного реактора. Он должен был находиться на месте камеры сгорания.
В теории воздух должен был проходить через работающую зону реактора, благодаря этому реактор должен был остужаться, а температура воздуха наоборот возрастать. После чело воздух должен был расширяться и выходить через сопла (выхлоп) на этот момент скорость воздуха должна была превышать скорость полета самолета.
В Советском союзе были попытки проведения испытаний подобного двигателя, также ученные в соединенных штатах Америки, вели разработку данного двигателя, и их работа почти подходила к тестам двигателя на настоящем самолете.
Но по ряду причин разработки этого двигателя было решено закрыть. Так как у двигателя было множество недостатков, а именно:
- Пилоты были подвержены постоянному радиоактивному облучению на протяжении всего полета.
- Вместе с воздухом через сопла выходили и частички радиоактивного элемента в атмосферу.
- В том случае если самолет терпел крушение, был очень большой шанс взрыва радиоактивного реактора, что влекло за собой радиоактивное отравление на довольно большой площади.
Турбина Каплан — ее составные части, работа и применение
Турбина Каплан работает по принципу реакции осевого потока. В турбинах с осевым потоком вода течет через бегунок в направлении, параллельном оси вращения рабочего колеса. Вода на входе в турбину обладает как кинетической энергией, так и энергией давления для эффективного вращения лопастей гидроэлектростанции.
Рис. 1: Турбина Каплана.
В 1913 году австрийский профессор Виктор Каплан, который разработал эту турбину, объединил автоматически регулируемые лопасти гребного винта с автоматически регулируемыми заслонками калитки для достижения эффективности в широком диапазоне расхода и уровня воды.Она также называется пропеллерной турбиной и произошла от турбины Фрэнсиса. Он способен очень эффективно работать при низком напоре и высоких расходах, что невозможно с турбиной Фрэнсиса.
В этой статье рассматривается порядок работы, основные компоненты и их применение.
Основные компоненты турбины Каплана
Основные части турбины Каплан,
1. Спиральный кожух
Это спиральный кожух с уменьшающейся площадью поперечного сечения.Вода из затворов попадает в корпус спирали, а затем движется к направляющим лопастям, где вода поворачивается на 90 ° и течет в осевом направлении через желоб. Он защищает рабочее колесо, направляющие лопатки рабочих лопаток и другие внутренние части турбины от внешних повреждений.
Рис. 2: Основные компоненты турбины Каплана.
2. Механизм направляющей лопасти
Это единственная управляющая часть всей турбины, которая открывается и закрывается в зависимости от потребности в мощности.Если требуется большая выходная мощность, он открывается шире, чтобы больше воды попадало на лопасти ротора, а когда требуется низкая выходная мощность, он закрывается, чтобы прекратить поток воды. При отсутствии направляющих лопаток турбина не может работать эффективно и ее КПД снижается.
3. Трубка отсасывающая
Давление на выходе из рабочего колеса реакционной турбины обычно ниже атмосферного. Вода на выходе не может напрямую сбрасываться в хвостовую часть.Труба или труба с постепенно увеличивающейся площадью используется для отвода воды от выхода турбины до хвостовой части. Эта трубка с увеличивающейся площадью называется вытяжной трубкой. Один конец трубки подсоединен к выпускному отверстию бегунка, а другой конец погружен ниже уровня воды в хвостовой части.
4. Лезвия рабочего колеса
Сердцем компонента в турбине Каплана являются рабочие лопатки, так как это вращающаяся часть, которая помогает в производстве электроэнергии. Вал соединен с валом генератора.Рабочее колесо этой турбины имеет большой выступ, на котором крепятся его лопасти, а лопасти рабочего колеса регулируются под оптимальным углом атаки для максимальной выходной мощности. Лопатки турбины Каплана имеют закрутку по длине.
Рис. 3. Рабочие лопатки турбины Каплана.
Рабочий процесс турбины Каплана
Вода, поступающая из загона, попадает в кожух спирали. Корпус спирали выполнен такой формы, чтобы не терять давление потока.Направляющие лопатки направляют воду к лопастям рабочего колеса. Лопасти регулируются и могут регулироваться в зависимости от скорости потока. Вода поворачивается на 90 градусов, поэтому направление воды является осевым по отношению к лопастям бегунка.
Лопасти бегунка начинают вращаться при ударе воды из-за силы реакции воды. Лезвия бегунка имеют изгиб по всей длине, чтобы всегда иметь оптимальный угол атаки для всего поперечного сечения лезвий для достижения большей эффективности.
Из лопастей рабочего колеса вода поступает в вытяжную трубу, где ее энергия давления и кинетическая энергия уменьшаются. Кинетическая энергия преобразуется в энергию давления, что приводит к увеличению давления воды.
Вращение турбины используется для вращения вала генератора для производства электроэнергии.
Применение турбины Каплана
- Турбины Каплана широко используются во всем мире для производства электроэнергии.
- Может работать более эффективно при низком напоре воды и высоком расходе по сравнению с другими типами турбин.
- Он меньше по размеру и прост в сборке.
- КПД турбины Каплана очень высок по сравнению с другими гидравлическими турбинами.
Недостаток турбины Каплана
- Единственным недостатком турбины Каплана является кавитация, возникающая из-за падения давления в отсасывающей трубе. Использование вытяжной трубы и подходящего материала, как правило, из нержавеющей стали для лопастей рабочего колеса, может в большей степени уменьшить проблему кавитации.
Турбина | Британника
Турбина , любое из различных устройств, преобразующих энергию потока жидкости в механическую энергию. Преобразование обычно осуществляется путем пропускания жидкости через систему неподвижных каналов или лопаток, которые чередуются с каналами, состоящими из лопастей, похожих на ребра, прикрепленных к ротору. За счет организации потока так, чтобы на лопасти ротора действовала касательная сила или крутящий момент, ротор вращается, и работа извлекается.
Ветровые турбины около Техачапи, Калифорния
© Грег Рэндлс / Shutterstock.com Турбины можно разделить на четыре основных типа в зависимости от используемых жидкостей: вода, пар, газ и ветер. Хотя одни и те же принципы применимы ко всем турбинам, их конкретные конструкции достаточно различаются, чтобы заслужить отдельное описание.
Гидравлическая турбина использует потенциальную энергию, возникающую в результате разницы в высоте между верхним водным резервуаром и уровнем воды на выходе из турбины (отводом) для преобразования этого так называемого напора в работу.Водяные турбины — современные преемники простых водяных колес, которым около 2000 лет. Сегодня гидротурбины в основном используются для производства электроэнергии.
Однако наибольшее количество электроэнергии вырабатывается паровыми турбинами, соединенными с электрогенераторами. Турбины приводятся в действие паром, вырабатываемым либо в генераторе, работающем на ископаемом топливе, либо в атомном генераторе. Энергию, которую можно извлечь из пара, удобно выражать через изменение энтальпии в турбине.Энтальпия отражает формы как тепловой, так и механической энергии в процессе потока и определяется суммой внутренней тепловой энергии и произведением давления на объем. Доступное изменение энтальпии через паровую турбину увеличивается с увеличением температуры и давления парогенератора и с уменьшением давления на выходе из турбины.
Оформите подписку Britannica Premium и получите доступ к эксклюзивному контенту.
Подпишитесь сейчас Для газовых турбин энергия, извлекаемая из текучей среды, также может быть выражена через изменение энтальпии, которое для газа почти пропорционально перепаду температуры в турбине.В газовых турбинах рабочим телом является воздух, смешанный с газообразными продуктами сгорания. Большинство газотурбинных двигателей включает, по крайней мере, компрессор, камеру сгорания и турбину. Обычно они монтируются как единое целое и работают как законченный первичный двигатель в так называемом открытом цикле, когда воздух всасывается из атмосферы, а продукты сгорания, наконец, снова выбрасываются в атмосферу. Поскольку успешная работа зависит от интеграции всех компонентов, важно рассматривать устройство в целом, которое фактически является двигателем внутреннего сгорания, а не только турбиной.По этой причине газовые турбины рассматриваются в статье двигатель внутреннего сгорания.
Энергия ветра может быть извлечена ветровой турбиной для производства электроэнергии или для откачки воды из колодцев. Ветряные турбины являются преемниками ветряных мельниц, которые были важными источниками энергии с позднего средневековья до 19 века.
Фред Лэндис Водяные турбины обычно делятся на две категории: (1) импульсные турбины, используемые для высокого напора воды и низкого расхода, и (2) реактивные турбины, обычно используемые для напора ниже примерно 450 метров и среднего или высокого расхода.Эти два класса включают в себя основные типы, обычно используемые, а именно импульсные турбины Пелтона и реактивные турбины типа Фрэнсиса, пропеллера, Каплана и Дериаза. Турбины могут иметь горизонтальный или, чаще, вертикальный вал. Для каждого типа возможны широкие вариации конструкции для соответствия конкретным местным гидравлическим условиям. Сегодня большинство гидравлических турбин используются для выработки электроэнергии на гидроэлектростанциях.
Импульсные турбины
В импульсной турбине потенциальная энергия или напор воды сначала преобразуется в кинетическую энергию путем выпуска воды через сопло тщательно продуманной формы.Струя, выбрасываемая в воздух, направляется на изогнутые ковши, закрепленные на периферии бегунка, для извлечения энергии воды и преобразования ее в полезную работу.
Современные импульсные турбины основаны на конструкции, запатентованной в 1889 году американским инженером Лестером Алленом Пелтоном. Свободная водная струя попадает в лопатки турбины по касательной. Каждый ковш имеет высокий центральный гребень, так что поток разделяется, оставляя желоб с обеих сторон. Колеса Пелтона подходят для высоких напоров, обычно выше 450 метров при относительно низком расходе воды.Для максимальной эффективности скорость конца рабочего колеса должна составлять примерно половину скорости ударной струи. КПД (работа, производимая турбиной, деленная на кинетическую энергию свободной струи) может превышать 91 процент при работе с 60–80 процентами полной нагрузки.
Мощность одного колеса можно увеличить, используя более одного жиклера. Для горизонтальных валов характерны двухструйные устройства. Иногда на одном валу устанавливаются два отдельных бегунка, приводящих в движение один электрогенератор. Агрегаты с вертикальным валом могут иметь четыре или более отдельных форсунок.
Если электрическая нагрузка на турбину изменяется, ее выходная мощность должна быть быстро отрегулирована в соответствии с потребностями. Это требует изменения расхода воды, чтобы поддерживать постоянную скорость генератора. Скорость потока через каждое сопло регулируется расположенным в центре наконечником или иглой аккуратной формы, которая скользит вперед или назад под управлением гидравлического серводвигателя.
Правильная конструкция иглы гарантирует, что скорость воды, выходящей из сопла, остается практически неизменной независимо от отверстия, обеспечивая почти постоянную эффективность в большей части рабочего диапазона.Нецелесообразно внезапно уменьшать поток воды, чтобы соответствовать уменьшению нагрузки. Это может привести к разрушительному скачку давления (гидроудару) в подающем трубопроводе или водопроводе. Таких скачков можно избежать, добавив временное сопло для разлива, которое открывается при закрытии основного сопла, или, что чаще, частично вставляя отражающую пластину между струей и колесом, отклоняя и рассеивая часть энергии при медленном закрытии иглы.
Другой тип импульсной турбины — турбина турго.Струя падает под косым углом на бегунок с одной стороны и продолжает двигаться по единственному пути, выбрасывая его с другой стороны. Этот тип турбины использовался в установках среднего размера с умеренно высоким напором.
Реакционные турбины
В реакционной турбине силы, приводящие в движение ротор, достигаются за счет реакции ускоряющегося потока воды в рабочем колесе при падении давления. Принцип реакции можно наблюдать в роторном оросителе для газонов, где выходящая струя вращает ротор в противоположном направлении.Из-за большого разнообразия возможных конструкций рабочего колеса реактивные турбины могут использоваться в гораздо большем диапазоне напоров и расходов, чем импульсные турбины. Реакционные турбины обычно имеют спиральный впускной кожух, который включает регулирующие заслонки для регулирования потока воды. На входе часть потенциальной энергии воды может быть преобразована в кинетическую энергию по мере ускорения потока. Впоследствии энергия воды отбирается в роторе.
Как отмечалось выше, широко используются четыре основных типа реактивных турбин: турбины Каплана, Фрэнсиса, Дериаза и пропеллерные.В турбинах Каплана с неподвижными лопастями и с регулируемыми лопастями (названными в честь австрийского изобретателя Виктора Каплана), по существу, существует осевой поток через машину. Турбины типа Фрэнсиса и Дериаза (в честь американского изобретателя британского происхождения Джеймса Б. Фрэнсиса и швейцарского инженера Поля Дериаза, соответственно) используют «смешанный поток», когда вода поступает радиально внутрь и выпускается в осевом направлении. Рабочие лопасти на турбинах Фрэнсиса и пропеллера состоят из неподвижных лопастей, в то время как в турбинах Каплана и Дериаза лопасти могут вращаться вокруг своей оси, которая находится под прямым углом к главному валу.
Объяснение 9 различных стратегий
Профилактическое обслуживание и корректирующее обслуживание
На верхнем уровне я вижу профилактическое или корректирующее обслуживание:
- Когда мы выполняем профилактическое обслуживание , мы выполняем задачу до того, как произойдет сбой . Эта задача может быть направлена на предотвращение отказа, минимизацию последствий отказа или оценку риска возникновения отказа.
- Когда мы проводим корректирующее обслуживание , произошел сбой , и мы в основном восстанавливаем работоспособность оборудования. Чтобы было ясно, корректирующее обслуживание может быть результатом преднамеренной стратегии безотказной работы.
Профилактическое обслуживание
Профилактическое обслуживание можно определить как «стратегию обслуживания оборудования, основанную на замене или восстановлении актива через фиксированные интервалы времени, независимо от его состояния. Запланированные задачи восстановления и задачи замены являются примерами задач профилактического обслуживания ».
Профилактическое обслуживание (или профилактическое обслуживание) в основном представляет собой тип обслуживания, который выполняется через регулярные промежутки времени, пока оборудование все еще функционирует, с целью предотвращения отказа или снижения вероятности отказа.
Профилактическое обслуживание может проводиться по времени, т.е. каждую неделю, каждый месяц или каждые три месяца. Но профилактическое обслуживание также может быть основано на использовании e.г. каждые 150 циклов, каждые 10 000 часов или как ваш автомобиль: обслуживание каждые 10 000 км.
Помимо регулярного интервального обслуживания (обслуживания по времени), существуют также другие виды обслуживания, которые подпадают под категорию профилактического обслуживания:
В следующих параграфах я более подробно рассмотрю каждый из этих типов обслуживания, в том числе, когда вам следует рассмотреть возможность их использования.
Обслуживание по времени (TBM)
Временное обслуживание относится к замене или обновлению элемента для восстановления его надежности в фиксированное время, интервал или использование независимо от его состояния.Это то, что Мубрей называет задачами запланированного восстановления или запланированного удаления в своей книге RCMII.
Я ограничиваю использование этой фразы, так как по какой-то причине люди приходят к выводу, что другое техническое обслуживание не запланировано. Хотя на самом деле, конечно, все техническое обслуживание следует планировать в соответствии с нашим недельным расписанием. Единственным исключением может быть экстренное обслуживание, которое по самой своей природе требует немедленного внимания и не может быть запланировано.
Цель обслуживания по времени — защитить себя от выхода из строя известных изнашиваемых деталей, которые имеют предсказуемое среднее время наработки на отказ (MTBF) i.е. Техническое обслуживание по времени предполагает, что отказ связан с возрастом и может быть определен точный срок службы. Или что просто не стоит прилагать усилия для оценки состояния, а замена по времени более экономична и все же (в разумной степени) эффективна.
Time Based Maintenance никогда не сможет эффективно управлять режимами отказов, не связанными с возрастом, и поэтому должно составлять лишь небольшую часть вашей общей программы технического обслуживания, поскольку> 70% режимов отказа на вашем предприятии не связаны с возрастом (см. Статью 9 Принципы Современное обслуживание).
Важно понимать, что во многих отраслях компании действительно должны выполнять определенные задачи для соответствия нормативным требованиям, и они, как правило, выполняются в фиксированный интервал времени, то есть техобслуживание на основе времени. Но даже при обслуживании, связанном с соблюдением требований, часто есть возможности привлечь регулирующий орган и рассмотреть возможность перехода, например, к подходам, основанным на оценке риска. Хорошим примером этого может быть принятие инспекции на основе рисков (RBI) для инспекций судов вместо e.г. Внутренние осмотры судов каждые 4 года.
Поиск неисправностей (FFM)
Поиск отказов Задачи обслуживания направлены на обнаружение скрытых отказов, обычно связанных с защитными функциями. Подумайте о предохранительных клапанах давления, датчиках отключения и тому подобном.
Оборудование этого типа не будет работать, пока не выйдет из строя что-то еще. Это означает, что при нормальных условиях эксплуатации вы не узнаете, работает ли это оборудование i.е. режимы отказа скрыты.
И поскольку эти сбои скрыты, вам нужно будет найти их, прежде чем вы будете полагаться на это оборудование для защиты.
Действительно просто.
Важно понимать, что задачи технического обслуживания по поиску отказов не предотвращают отказ, а просто обнаруживают его. И после обнаружения вам придется устранить обнаруженную неисправность. Обнаружение отказов Техническое обслуживание проводится через фиксированные интервалы времени, обычно определяемые законодательством или подходами, основанными на оценке риска.
Техническое обслуживание с учетом рисков (RBM)
Техническое обслуживание на основе рисков (RBM) — это когда вы используете методологию оценки рисков для распределения ваших скудных ресурсов на техническое обслуживание тем активам, которые несут наибольший риск в случае отказа (помня, что риск = вероятность x последствия).
В результате оборудование с более высоким риском и очень высокой вероятностью отказа будет подвергаться более частому техническому обслуживанию и осмотру. Оборудование с низким уровнем риска может обслуживаться с гораздо меньшей частотой и, возможно, с гораздо меньшим объемом работ.
При эффективном внедрении процесса обслуживания с учетом рисков вы должны снизить общий риск отказа всего предприятия наиболее экономичным способом.
Risk-Based Maintenance — это, по сути, профилактическое обслуживание, при котором частота и объем работ по техническому обслуживанию постоянно оптимизируются на основе результатов тестирования или инспекции и тщательной оценки рисков. Примерами технического обслуживания на основе рисков могут быть проверки на основе рисков применительно к статическому оборудованию, такому как сосуды и трубопроводы, или даже предохранительные клапаны.
Техническое обслуживание по условию (CBM)
Большинство видов отказов не связаны с возрастом. Тем не менее, большинство режимов отказа действительно выдают какое-то предупреждение о том, что они происходят или вот-вот произойдут.
Если можно найти доказательства того, что что-то находится на ранних стадиях отказа, можно принять меры для предотвращения полного отказа и / или во избежание последствий отказа. Таким образом, техническое обслуживание по состоянию в качестве стратегии ищет физические доказательства того, что отказ происходит или вот-вот произойдет.Такой подход к CBM показывает его более широкие применения за пределами методов мониторинга состояния, часто связанных только с вращающимся оборудованием.
Важной концепцией технического обслуживания по состоянию является кривая P-F, показанная на рисунке ниже:
Кривая показывает, что по мере того, как сбой начинает проявляться, оборудование изнашивается до точки, в которой его можно обнаружить (точка «P»).
Если отказ не обнаружен и не устранен, он продолжается до тех пор, пока не произойдет функциональный отказ (точка «F»).Временной диапазон между P и F, обычно называемый интервалом P-F, представляет собой окно возможностей, в течение которого инспекция, возможно, может обнаружить неминуемый отказ и дать вам время для его устранения.
Важно понимать, что CBM как стратегия технического обслуживания не снижает вероятность отказа, возникающего в результате обновления срока службы, а вместо этого направлена на вмешательство до того, как произойдет отказ, исходя из того, что это более экономично и должно иметь меньше влияние на доступность.
Другими словами: мониторинг состояния не исправляет машины, а мониторинг состояния не останавливает отказы. Мониторинг состояния позволяет обнаруживать проблемы только до того, как они перерастут в отказ.
Общее практическое правило состоит в том, что интервал между задачами CBM должен составлять половину или одну треть интервала P-F.
Насколько эффективнее CBM выше аварийного обслуживания, зависит от продолжительности интервала P-F. При наличии большого количества предупреждений можно запланировать исправление, мобилизовать материалы и ресурсы и предотвратить поломку (хотя производство все еще останавливается на время технического обслуживания).Когда интервал P-F составляет всего несколько дней, в результате организационные действия и действия на рабочем месте очень похожи на поломку, и ценность CBM в значительной степени теряется.
Для того, чтобы CBM была эффективной как стратегия, необходимо раннее вмешательство. Это требует действенного и действенного процесса сбора данных, анализа данных, принятия решений и, наконец, вмешательства.
Для режимов отказа, где интервал P-F показывает большую изменчивость, мониторинг состояния не является эффективной стратегией.
Если вам интересно узнать больше о том, как лучше всего управлять режимами отказа, не забудьте прочитать мою статью Техническое обслуживание, ориентированное на надежность — 9 принципов современного технического обслуживания.
Принцип работы (кратко). Принцип действия реактивного двигателя
Под реактивным понимается движение, при котором от тела с определенной скоростью отделяется одна из его частей. Сила, возникающая в результате такого процесса, действует сама по себе. Другими словами, у нее нет даже малейшего контакта с внешними телами.
Реактивное движение в природе
Во время летнего отдыха на юге почти все мы, купаясь в море, встречались с медузами. Но мало кто думал, что эти животные движутся так же, как реактивный двигатель. Принцип действия в природе такого агрегата можно наблюдать при перемещении определенных видов морского планктона и личинок стрекоз. Причем эффективность этих беспозвоночных зачастую выше, чем у технических средств.
Кто еще может наглядно продемонстрировать, какой из реактивных двигателей работает? Кальмары, осьминоги и каракатицы.Подобное движение совершают многие другие морские моллюски. Возьмем, например, каракатицу. Она втягивает воду в свою жаберную полость и энергично выбрасывает ее через воронку, которая направляется назад или в сторону. При этом моллюск способен совершать движения в нужную сторону.
Принцип действия реактивного двигателя можно наблюдать и при перемещении барабана. Это морское животное берет воду в широкой впадине. После этого мышцы его тела сокращаются, выталкивая жидкость через отверстие, которое находится позади.Реакция образовавшейся струи позволяет саженцу двигаться вперед.
Sea Missiles
Но наибольшего совершенства в реактивной навигации достиг все тот же кальмар. Даже форма самой ракеты словно скопирована с этого морского обитателя. При движении с небольшой скоростью кальмар периодически выгибает ромбовидный плавник. Но для быстрого броска ему приходится использовать собственный «реактивный двигатель». Принцип работы всех его мышц и тела стоит рассмотреть подробнее.
Кальмар имеет своеобразную мантию.Это мышечная ткань, которая окружает его тело со всех сторон. Во время движения животное засасывает в эту мантию большой объем воды, резко выбрасывая струю через специальную узкую насадку. Такие действия позволяют кальмарам двигаться назад со скоростью до семидесяти километров в час. Во время движения животное собирает в пучок все свои десять щупалец, что придает телу обтекаемую форму. На насадке есть специальный клапан. Его поворачивает животное сокращением мышц. Это позволяет моряку менять направление.Роль штурвала при передвижении кальмара выполняют его щупальца. Он направляет их влево или вправо, вниз или вверх, легко уворачиваясь от столкновений с различными препятствиями.
Существует разновидность кальмаров (stenoteutis), относящаяся к званию лучшего пилота среди моллюсков. Опишите принцип работы реактивного двигателя — и вы поймете, почему, преследуя рыбу, это животное иногда выпрыгивает из воды, даже попадая на палубы кораблей, плывущих по океану. Как это произошло? Пилот-кальмар, находясь в водной стихии, развивает для себя максимальную реактивную тягу.Это позволяет ему летать над волнами на расстоянии до пятидесяти метров.
Если мы рассмотрим реактивный двигатель, принцип Какое животное работает, мы можем упомянуть еще? Это, на первый взгляд, мешковатый осьминог. Пловцы не так быстры, как кальмары, но в случае опасности их скорости могут позавидовать даже лучшие спринтеры. Биологи, изучавшие миграцию осьминогов, выяснили, что они движутся по принципу действия реактивного двигателя.
Животное при каждой струе воды, выбрасываемой из воронки, делает рывок на два или даже два с половиной метра.При этом плывет осьминог своеобразным образом — задом наперед.
Другие примеры реактивного движения
В мире растений есть ракеты. Принцип действия реактивного двигателя можно наблюдать, когда даже при очень легком прикосновении «бешеный огурец» с большой скоростью отскакивает от ножки, отталкивая при этом липкую жидкость с семенами. При этом сам плод летит на значительное расстояние (до 12 м) в обратном направлении.
Принцип работы реактивного двигателя можно наблюдать и в лодке.Если с него в определенном направлении бросить в воду тяжелые камни, то он будет двигаться в противоположном направлении. Ракетно-реактивный двигатель имеет такой же принцип работы. Только там вместо камней используются газы. Они создают реактивную силу, которая обеспечивает движение как в воздухе, так и в разряженном пространстве.
Фантастическое путешествие
Человечество давно мечтает о космических полетах. Об этом свидетельствуют произведения писателей-фантастов, которые для достижения этой цели предлагали самые разные средства.Например, герой рассказа французского писателя Эркюля Савинена Сирано де Бержерак достиг Луны на железной повозке, на которую постоянно бросался мощный магнит. Знаменитый Мюнхгаузен тоже достиг той же планеты. Гигантский стебель фасоли помог ему совершить путешествие.
Реактивный двигатель использовался в Китае еще в первом тысячелетии до нашей эры. Бамбуковые трубы, набитые порохом, служили своеобразными ракетами для развлечения. Кстати, проект первой машины на нашей планете, созданный Ньютоном, тоже был с реактивным двигателем.
История RD
Только в XIX в. мечта человечества о космосе стала приобретать конкретные черты. Ведь именно в этом веке русский революционер Н.И. Кибальчич создал первый в мире проект самолета с реактивным двигателем. Все бумаги были составлены Народным освободителем в тюрьме, куда он попал после покушения на Александра. Но, к сожалению, 04.03.1881 Кибальчич был казнен, а его идея не нашла практического воплощения.
В начале 20 в. Идея использования ракет для космических полетов была выдвинута русским ученым К.Е. Циолковский. Впервые его работа, содержащая описание движения тела переменной массы в виде математического уравнения, была опубликована в 1903 году. Позже ученый разработал саму схему реактивного двигателя, работающего на жидком топливе.
Также Циолковским была изобретена многоступенчатая ракета и выдвинута идея создания настоящих космических городов на низкой околоземной орбите.Циолковский убедительно доказал, что единственное средство для полета в космос — это ракета. То есть аппарат, оснащенный реактивным двигателем, заправляемый горючим и окислителем. Только такая ракета способна преодолеть силу тяжести и вылететь за пределы атмосферы Земли.
Освоение космоса
Статья Циолковского, опубликованная в журнале «Научное обозрение», подтвердила для ученых репутацию мечтателя. Никто не принимал всерьез его аргументы.
Идея Циолковского была реализована советскими учеными.Под руководством Сергея Павловича Королева они запустили первый искусственный спутник Земли. 4 октября 1957 года это устройство было доставлено на орбиту ракетой с реактивным двигателем. Работа РД была основана на преобразовании химической энергии, которая передается топливом газовой струе, превращаясь в кинетическую энергию. В этом случае ракета движется в обратном направлении.
Реактивный двигатель, принцип действия которого используется много лет, находит свое применение не только в космосе, но и в авиации.Но больше всего он используется для запуска ракет. Ведь только RD может перемещать аппарат в пространстве, в котором отсутствует какая-либо среда.
Жидкостный реактивный двигатель
Тот, кто стрелял из огнестрельного оружия или просто наблюдал за этим процессом со стороны, знает, что существует сила, которая непременно оттолкнет ствол назад. А при большей сумме заряда отдача обязательно увеличится.
Тепловой экран и охлаждение разбрызгиванием масла<
Тепловой экран, расположенный позади опорного диска турбинного колеса, предотвращает контакт горячих отработавших газов с центральным корпусом. В некоторых конструкциях при работе двигателя масло распыляется на вал ротора через маленькое распылительное отверстие в опоре подшипника с турбинной стороны, охлаждая вал и уменьшая риск коксования.
Наивысшие температуры в центральном корпусе достигаются вскоре после останова двигателя. Горячий турбинный корпус нагревает систему подшипников, которая больше не охлаждается моторным маслом.
Термическая развязка
В расчете на термическую развязку правой подшипниковой опоры передача тепла от корпуса турбины к системе подшипников сокращается даже после того как двигатель был заглушен. Для этого систему подшипников располагают ниже точки подачи масла, так же как силовой агрегат размещают под крылом самолета. Правая подшипниковая опора больше не контактирует с горячей стенкой центрального корпуса, значит, передача тепла к системе подшипников ограничивается.
Водяное охлаждение
Бензиновые двигатели, у которых температура отработавших газов на 200-300°С выше чем у дизелей, обычно оснащаются турбокомпрессорами с охлаждаемыми центральными корпусами. При работе двигателя центральный корпус интегрируется в его контур охлаждения. После выключения двигателя остаточное тепло снимается посредством малого кольца циркуляции, которое задействуется электрическим насосом с термостатом.
Рециркуляционный клапан
В бензиновых турбодвигателях дроссельная заслонка, которая управляет нагрузкой двигателя, располагается после компрессора, во впускном коллекторе. В момент внезапного сброса газа заслонка закрывается, а компрессор из-за своей инерционности продолжает нагнетать воздух в почти замкнутый объем. Вследствие этого начался бы помпаж компрессора. Частота вращения турбокомпрессора (ТК) быстро упала бы.
Начиная с определенного давления, открывается подпружиненный клапан и направляет воздух обратно на вход в компрессор, ограничивая рост давления и исключая помпаж. Частота вращения ТК остается высокой, и давление наддува появится, как только будет задействован акселератор.
Принцип работы турбореактивного двигателя самолёта
Совершая полет в самолете в большинстве случаев люди никогда не задумываются о том, как работает его двигатель. Но на самом деле о работе двигателя и реактивной тяги с помощью, которой работает сам двигатель, знали ее в Античное время. Но применить эти знания на практике смогли не так давно, так как раньше не технологии не позволяли никому достичь его исправной работы. Гонка вооружения между Англией и Германией стала толчком к созданию ТРД (турбореактивного двигателя).
В работе ТРД самолета нет никаких сложностей, принцип его работы может понять почти каждый человек. Но данный двигатель имеет несколько нюансов, их соблюдение контролируется под строгим присмотром руководства. Для того чтобы авиалайнер смог держаться в небе, необходима идеальная работа двигателя. Так как от работы двигателя напрямую зависят жизни пассажиров находящихся на борту авиатранспорта.
Принцип работы реактивного двигателя
За работу двигателя отвечает реактивная тяга. Для создания реактивной тяги необходима определенная жидкость, которая подается из задней части двигателя и по ходу ее продвижения увеличивается ее скорость движения вперед. Работу тяги отлично объясняет один из законов Ньютона, звучит он так «Любое действия вызывает равное противодействие».
Вместо жидкости в ТРД используется горючая смесь (газы и воздух со сгоревшими частичками топлива). Благодаря этой смеси самолет толкает вперед и позволяет ему лететь дальше.
Разработки таких двигателей начались в тридцатых годах. Первыми кто начал разрабатывать двигатели такого типа стали немцы и англичане. Но в гонке вооружений одержали победу ученные из Германии, так как они выпустили самый первый в мире самолет с ТРД под названием «Ласточка», данный самолет впервые взлетел в небеса над Люфтваффом. Спустя некоторое время появился и Английский самолет «Глостерский метеор»
Также сверхзвуковые двигатели принято считать турбореактивными, но они отличаются более совершенными модификациями, в отличие от ТРД.
Устройство двигателя имеет четыре главные детали, а именно:
- Компрессор.
- Камера горения.
- Турбина.
- Выхлоп.
Компрессор
В компрессоре находиться несколько турбин, с помощью которых происходит засасывание и сжатие воздуха. Во время сжатия воздуха, его давление и температура начинает нагнетаться и расти.
Камера горения
После того как воздух проходит турбину и его сжимает до необходимых размеров. Часть сжатого воздуха поступает в камеру горения, где воздух начинает смешиваться с топливом, после чего его поджигают. Благодаря этому увеличивается тепловая энергия воздуха. После смесь выходит из камеры с большой скорости и расширяется.
Турбина
После выхода эта смесь снова попадает в турбину, с помощью высокой энергии газа лопасти в турбине начинают свое вращение. Турбина тесно связанна с компрессором, который находиться в начале двигателя. Благодаря этому турбина начинает свою работу. Остатки воздуха выходят в выхлоп. В момент выхода смеси температура достигает рекордных размеров. Но она продолжает повышать свою температуру с помощью эффекта Дросселирования. После того как температура воздуха доходит до своего пика, она начинает идти на спад и выходит из турбины.
Принцип работы турбореактивного двигателя
В отличие от реактивного двигателя, который пользуется спросом почти у всех самолетов, турбореактивный двигатель больше подходит для пассажирских авиалайнеров. Так как для работы реактивного двигателя необходимо не только топливо, но и окислитель.
Благодаря своему строению окислитель поступает вместе с топливом из бака. А в случаи с ТРД окислитесь, поступает напрямую из атмосферы. А в остальном их работа совершенно идентична и не отличается друг от друга.
У турбореактивного двигателя главной деталью является лопасть турбины, так как от ее исправной работы напрямую зависит мощность двигателя. Благодаря этим лопастям и образуется тяга, которая необходима для поддержания скорости самолета. Если сравнить одну лопасть с автомобильным двигателем, то она сможет обеспечить мощностью целых десять машин.
Лопасти устанавливаются за камерой сгорания, так как там нагнетается самое высокое давления, также температура воздуха в данной части двигателя может доходить до 1400 градусов Цельсия.
В целях улучшения прочности и устойчивости лопасти перед различными факторами их монокристаллизируют, благодаря этому они могут держать высокую температуру и давление. Прежде чем установить такой двигатель на самолет его тестируют на полном тяговом усилителе. Также двигатель должен получить сертификат от Европейского совета по безопасности.
Атомный двигатель
В период холодной войны в мире были попытки создания атомного двигателя, за основу был взят турбореактивный двигатель. Главной задумкой ученых было создание двигателя, основанного не на химической реакции радиоактивных веществ, а на вырабатываемом тепле от ядерного реактора. Он должен был находиться на месте камеры сгорания.
В теории воздух должен был проходить через работающую зону реактора, благодаря этому реактор должен был остужаться, а температура воздуха наоборот возрастать. После чело воздух должен был расширяться и выходить через сопла (выхлоп) на этот момент скорость воздуха должна была превышать скорость полета самолета.
В Советском союзе были попытки проведения испытаний подобного двигателя, также ученные в соединенных штатах Америки, вели разработку данного двигателя, и их работа почти подходила к тестам двигателя на настоящем самолете.
Но по ряду причин разработки этого двигателя было решено закрыть. Так как у двигателя было множество недостатков, а именно:
- Пилоты были подвержены постоянному радиоактивному облучению на протяжении всего полета.
- Вместе с воздухом через сопла выходили и частички радиоактивного элемента в атмосферу.
- В том случае если самолет терпел крушение, был очень большой шанс взрыва радиоактивного реактора, что влекло за собой радиоактивное отравление на довольно большой площади.
Турбина Каплан — ее составные части, работа и применение
Турбина Каплан работает по принципу реакции осевого потока. В турбинах с осевым потоком вода течет через бегунок в направлении, параллельном оси вращения рабочего колеса. Вода на входе в турбину обладает как кинетической энергией, так и энергией давления для эффективного вращения лопастей гидроэлектростанции.
Рис. 1: Турбина Каплана.
В 1913 году австрийский профессор Виктор Каплан, который разработал эту турбину, объединил автоматически регулируемые лопасти гребного винта с автоматически регулируемыми заслонками калитки для достижения эффективности в широком диапазоне расхода и уровня воды.Она также называется пропеллерной турбиной и произошла от турбины Фрэнсиса. Он способен очень эффективно работать при низком напоре и высоких расходах, что невозможно с турбиной Фрэнсиса.
В этой статье рассматривается порядок работы, основные компоненты и их применение.
Основные компоненты турбины Каплана
Основные части турбины Каплан,
1. Спиральный кожух
Это спиральный кожух с уменьшающейся площадью поперечного сечения.Вода из затворов попадает в корпус спирали, а затем движется к направляющим лопастям, где вода поворачивается на 90 ° и течет в осевом направлении через желоб. Он защищает рабочее колесо, направляющие лопатки рабочих лопаток и другие внутренние части турбины от внешних повреждений.
Рис. 2: Основные компоненты турбины Каплана.
2. Механизм направляющей лопасти
Это единственная управляющая часть всей турбины, которая открывается и закрывается в зависимости от потребности в мощности.Если требуется большая выходная мощность, он открывается шире, чтобы больше воды попадало на лопасти ротора, а когда требуется низкая выходная мощность, он закрывается, чтобы прекратить поток воды. При отсутствии направляющих лопаток турбина не может работать эффективно и ее КПД снижается.
3. Трубка отсасывающая
Давление на выходе из рабочего колеса реакционной турбины обычно ниже атмосферного. Вода на выходе не может напрямую сбрасываться в хвостовую часть.Труба или труба с постепенно увеличивающейся площадью используется для отвода воды от выхода турбины до хвостовой части. Эта трубка с увеличивающейся площадью называется вытяжной трубкой. Один конец трубки подсоединен к выпускному отверстию бегунка, а другой конец погружен ниже уровня воды в хвостовой части.
4. Лезвия рабочего колеса
Сердцем компонента в турбине Каплана являются рабочие лопатки, так как это вращающаяся часть, которая помогает в производстве электроэнергии. Вал соединен с валом генератора.Рабочее колесо этой турбины имеет большой выступ, на котором крепятся его лопасти, а лопасти рабочего колеса регулируются под оптимальным углом атаки для максимальной выходной мощности. Лопатки турбины Каплана имеют закрутку по длине.
Рис. 3. Рабочие лопатки турбины Каплана.
Рабочий процесс турбины Каплана
Вода, поступающая из загона, попадает в кожух спирали. Корпус спирали выполнен такой формы, чтобы не терять давление потока.Направляющие лопатки направляют воду к лопастям рабочего колеса. Лопасти регулируются и могут регулироваться в зависимости от скорости потока. Вода поворачивается на 90 градусов, поэтому направление воды является осевым по отношению к лопастям бегунка.
Лопасти бегунка начинают вращаться при ударе воды из-за силы реакции воды. Лезвия бегунка имеют изгиб по всей длине, чтобы всегда иметь оптимальный угол атаки для всего поперечного сечения лезвий для достижения большей эффективности.
Из лопастей рабочего колеса вода поступает в вытяжную трубу, где ее энергия давления и кинетическая энергия уменьшаются. Кинетическая энергия преобразуется в энергию давления, что приводит к увеличению давления воды.
Вращение турбины используется для вращения вала генератора для производства электроэнергии.
Применение турбины Каплана
- Турбины Каплана широко используются во всем мире для производства электроэнергии.
- Может работать более эффективно при низком напоре воды и высоком расходе по сравнению с другими типами турбин.
- Он меньше по размеру и прост в сборке.
- КПД турбины Каплана очень высок по сравнению с другими гидравлическими турбинами.
Недостаток турбины Каплана
- Единственным недостатком турбины Каплана является кавитация, возникающая из-за падения давления в отсасывающей трубе. Использование вытяжной трубы и подходящего материала, как правило, из нержавеющей стали для лопастей рабочего колеса, может в большей степени уменьшить проблему кавитации.
Турбина | Британника
Турбина , любое из различных устройств, преобразующих энергию потока жидкости в механическую энергию. Преобразование обычно осуществляется путем пропускания жидкости через систему неподвижных каналов или лопаток, которые чередуются с каналами, состоящими из лопастей, похожих на ребра, прикрепленных к ротору. За счет организации потока так, чтобы на лопасти ротора действовала касательная сила или крутящий момент, ротор вращается, и работа извлекается.
Ветровые турбины около Техачапи, Калифорния
© Грег Рэндлс / Shutterstock.com Турбины можно разделить на четыре основных типа в зависимости от используемых жидкостей: вода, пар, газ и ветер. Хотя одни и те же принципы применимы ко всем турбинам, их конкретные конструкции достаточно различаются, чтобы заслужить отдельное описание.
Гидравлическая турбина использует потенциальную энергию, возникающую в результате разницы в высоте между верхним водным резервуаром и уровнем воды на выходе из турбины (отводом) для преобразования этого так называемого напора в работу.Водяные турбины — современные преемники простых водяных колес, которым около 2000 лет. Сегодня гидротурбины в основном используются для производства электроэнергии.
Однако наибольшее количество электроэнергии вырабатывается паровыми турбинами, соединенными с электрогенераторами. Турбины приводятся в действие паром, вырабатываемым либо в генераторе, работающем на ископаемом топливе, либо в атомном генераторе. Энергию, которую можно извлечь из пара, удобно выражать через изменение энтальпии в турбине.Энтальпия отражает формы как тепловой, так и механической энергии в процессе потока и определяется суммой внутренней тепловой энергии и произведением давления на объем. Доступное изменение энтальпии через паровую турбину увеличивается с увеличением температуры и давления парогенератора и с уменьшением давления на выходе из турбины.
Оформите подписку Britannica Premium и получите доступ к эксклюзивному контенту.
Подпишитесь сейчас Для газовых турбин энергия, извлекаемая из текучей среды, также может быть выражена через изменение энтальпии, которое для газа почти пропорционально перепаду температуры в турбине.В газовых турбинах рабочим телом является воздух, смешанный с газообразными продуктами сгорания. Большинство газотурбинных двигателей включает, по крайней мере, компрессор, камеру сгорания и турбину. Обычно они монтируются как единое целое и работают как законченный первичный двигатель в так называемом открытом цикле, когда воздух всасывается из атмосферы, а продукты сгорания, наконец, снова выбрасываются в атмосферу. Поскольку успешная работа зависит от интеграции всех компонентов, важно рассматривать устройство в целом, которое фактически является двигателем внутреннего сгорания, а не только турбиной.По этой причине газовые турбины рассматриваются в статье двигатель внутреннего сгорания.
Энергия ветра может быть извлечена ветровой турбиной для производства электроэнергии или для откачки воды из колодцев. Ветряные турбины являются преемниками ветряных мельниц, которые были важными источниками энергии с позднего средневековья до 19 века.
Фред Лэндис Водяные турбины обычно делятся на две категории: (1) импульсные турбины, используемые для высокого напора воды и низкого расхода, и (2) реактивные турбины, обычно используемые для напора ниже примерно 450 метров и среднего или высокого расхода.Эти два класса включают в себя основные типы, обычно используемые, а именно импульсные турбины Пелтона и реактивные турбины типа Фрэнсиса, пропеллера, Каплана и Дериаза. Турбины могут иметь горизонтальный или, чаще, вертикальный вал. Для каждого типа возможны широкие вариации конструкции для соответствия конкретным местным гидравлическим условиям. Сегодня большинство гидравлических турбин используются для выработки электроэнергии на гидроэлектростанциях.
Импульсные турбины
В импульсной турбине потенциальная энергия или напор воды сначала преобразуется в кинетическую энергию путем выпуска воды через сопло тщательно продуманной формы.Струя, выбрасываемая в воздух, направляется на изогнутые ковши, закрепленные на периферии бегунка, для извлечения энергии воды и преобразования ее в полезную работу.
Современные импульсные турбины основаны на конструкции, запатентованной в 1889 году американским инженером Лестером Алленом Пелтоном. Свободная водная струя попадает в лопатки турбины по касательной. Каждый ковш имеет высокий центральный гребень, так что поток разделяется, оставляя желоб с обеих сторон. Колеса Пелтона подходят для высоких напоров, обычно выше 450 метров при относительно низком расходе воды.Для максимальной эффективности скорость конца рабочего колеса должна составлять примерно половину скорости ударной струи. КПД (работа, производимая турбиной, деленная на кинетическую энергию свободной струи) может превышать 91 процент при работе с 60–80 процентами полной нагрузки.
Мощность одного колеса можно увеличить, используя более одного жиклера. Для горизонтальных валов характерны двухструйные устройства. Иногда на одном валу устанавливаются два отдельных бегунка, приводящих в движение один электрогенератор. Агрегаты с вертикальным валом могут иметь четыре или более отдельных форсунок.
Если электрическая нагрузка на турбину изменяется, ее выходная мощность должна быть быстро отрегулирована в соответствии с потребностями. Это требует изменения расхода воды, чтобы поддерживать постоянную скорость генератора. Скорость потока через каждое сопло регулируется расположенным в центре наконечником или иглой аккуратной формы, которая скользит вперед или назад под управлением гидравлического серводвигателя.
Правильная конструкция иглы гарантирует, что скорость воды, выходящей из сопла, остается практически неизменной независимо от отверстия, обеспечивая почти постоянную эффективность в большей части рабочего диапазона.Нецелесообразно внезапно уменьшать поток воды, чтобы соответствовать уменьшению нагрузки. Это может привести к разрушительному скачку давления (гидроудару) в подающем трубопроводе или водопроводе. Таких скачков можно избежать, добавив временное сопло для разлива, которое открывается при закрытии основного сопла, или, что чаще, частично вставляя отражающую пластину между струей и колесом, отклоняя и рассеивая часть энергии при медленном закрытии иглы.
Другой тип импульсной турбины — турбина турго.Струя падает под косым углом на бегунок с одной стороны и продолжает двигаться по единственному пути, выбрасывая его с другой стороны. Этот тип турбины использовался в установках среднего размера с умеренно высоким напором.
Реакционные турбины
В реакционной турбине силы, приводящие в движение ротор, достигаются за счет реакции ускоряющегося потока воды в рабочем колесе при падении давления. Принцип реакции можно наблюдать в роторном оросителе для газонов, где выходящая струя вращает ротор в противоположном направлении.Из-за большого разнообразия возможных конструкций рабочего колеса реактивные турбины могут использоваться в гораздо большем диапазоне напоров и расходов, чем импульсные турбины. Реакционные турбины обычно имеют спиральный впускной кожух, который включает регулирующие заслонки для регулирования потока воды. На входе часть потенциальной энергии воды может быть преобразована в кинетическую энергию по мере ускорения потока. Впоследствии энергия воды отбирается в роторе.
Как отмечалось выше, широко используются четыре основных типа реактивных турбин: турбины Каплана, Фрэнсиса, Дериаза и пропеллерные.В турбинах Каплана с неподвижными лопастями и с регулируемыми лопастями (названными в честь австрийского изобретателя Виктора Каплана), по существу, существует осевой поток через машину. Турбины типа Фрэнсиса и Дериаза (в честь американского изобретателя британского происхождения Джеймса Б. Фрэнсиса и швейцарского инженера Поля Дериаза, соответственно) используют «смешанный поток», когда вода поступает радиально внутрь и выпускается в осевом направлении. Рабочие лопасти на турбинах Фрэнсиса и пропеллера состоят из неподвижных лопастей, в то время как в турбинах Каплана и Дериаза лопасти могут вращаться вокруг своей оси, которая находится под прямым углом к главному валу.
Объяснение 9 различных стратегий
Профилактическое обслуживание и корректирующее обслуживание
На верхнем уровне я вижу профилактическое или корректирующее обслуживание:
- Когда мы выполняем профилактическое обслуживание , мы выполняем задачу до того, как произойдет сбой . Эта задача может быть направлена на предотвращение отказа, минимизацию последствий отказа или оценку риска возникновения отказа.
- Когда мы проводим корректирующее обслуживание , произошел сбой , и мы в основном восстанавливаем работоспособность оборудования. Чтобы было ясно, корректирующее обслуживание может быть результатом преднамеренной стратегии безотказной работы.
Профилактическое обслуживание
Профилактическое обслуживание можно определить как «стратегию обслуживания оборудования, основанную на замене или восстановлении актива через фиксированные интервалы времени, независимо от его состояния. Запланированные задачи восстановления и задачи замены являются примерами задач профилактического обслуживания ».
Профилактическое обслуживание (или профилактическое обслуживание) в основном представляет собой тип обслуживания, который выполняется через регулярные промежутки времени, пока оборудование все еще функционирует, с целью предотвращения отказа или снижения вероятности отказа.
Профилактическое обслуживание может проводиться по времени, т.е. каждую неделю, каждый месяц или каждые три месяца. Но профилактическое обслуживание также может быть основано на использовании e.г. каждые 150 циклов, каждые 10 000 часов или как ваш автомобиль: обслуживание каждые 10 000 км.
Помимо регулярного интервального обслуживания (обслуживания по времени), существуют также другие виды обслуживания, которые подпадают под категорию профилактического обслуживания:
В следующих параграфах я более подробно рассмотрю каждый из этих типов обслуживания, в том числе, когда вам следует рассмотреть возможность их использования.
Обслуживание по времени (TBM)
Временное обслуживание относится к замене или обновлению элемента для восстановления его надежности в фиксированное время, интервал или использование независимо от его состояния.Это то, что Мубрей называет задачами запланированного восстановления или запланированного удаления в своей книге RCMII.
Я ограничиваю использование этой фразы, так как по какой-то причине люди приходят к выводу, что другое техническое обслуживание не запланировано. Хотя на самом деле, конечно, все техническое обслуживание следует планировать в соответствии с нашим недельным расписанием. Единственным исключением может быть экстренное обслуживание, которое по самой своей природе требует немедленного внимания и не может быть запланировано.
Цель обслуживания по времени — защитить себя от выхода из строя известных изнашиваемых деталей, которые имеют предсказуемое среднее время наработки на отказ (MTBF) i.е. Техническое обслуживание по времени предполагает, что отказ связан с возрастом и может быть определен точный срок службы. Или что просто не стоит прилагать усилия для оценки состояния, а замена по времени более экономична и все же (в разумной степени) эффективна.
Time Based Maintenance никогда не сможет эффективно управлять режимами отказов, не связанными с возрастом, и поэтому должно составлять лишь небольшую часть вашей общей программы технического обслуживания, поскольку> 70% режимов отказа на вашем предприятии не связаны с возрастом (см. Статью 9 Принципы Современное обслуживание).
Важно понимать, что во многих отраслях компании действительно должны выполнять определенные задачи для соответствия нормативным требованиям, и они, как правило, выполняются в фиксированный интервал времени, то есть техобслуживание на основе времени. Но даже при обслуживании, связанном с соблюдением требований, часто есть возможности привлечь регулирующий орган и рассмотреть возможность перехода, например, к подходам, основанным на оценке риска. Хорошим примером этого может быть принятие инспекции на основе рисков (RBI) для инспекций судов вместо e.г. Внутренние осмотры судов каждые 4 года.
Поиск неисправностей (FFM)
Поиск отказов Задачи обслуживания направлены на обнаружение скрытых отказов, обычно связанных с защитными функциями. Подумайте о предохранительных клапанах давления, датчиках отключения и тому подобном.
Оборудование этого типа не будет работать, пока не выйдет из строя что-то еще. Это означает, что при нормальных условиях эксплуатации вы не узнаете, работает ли это оборудование i.е. режимы отказа скрыты.
И поскольку эти сбои скрыты, вам нужно будет найти их, прежде чем вы будете полагаться на это оборудование для защиты.
Действительно просто.
Важно понимать, что задачи технического обслуживания по поиску отказов не предотвращают отказ, а просто обнаруживают его. И после обнаружения вам придется устранить обнаруженную неисправность. Обнаружение отказов Техническое обслуживание проводится через фиксированные интервалы времени, обычно определяемые законодательством или подходами, основанными на оценке риска.
Техническое обслуживание с учетом рисков (RBM)
Техническое обслуживание на основе рисков (RBM) — это когда вы используете методологию оценки рисков для распределения ваших скудных ресурсов на техническое обслуживание тем активам, которые несут наибольший риск в случае отказа (помня, что риск = вероятность x последствия).
В результате оборудование с более высоким риском и очень высокой вероятностью отказа будет подвергаться более частому техническому обслуживанию и осмотру. Оборудование с низким уровнем риска может обслуживаться с гораздо меньшей частотой и, возможно, с гораздо меньшим объемом работ.
При эффективном внедрении процесса обслуживания с учетом рисков вы должны снизить общий риск отказа всего предприятия наиболее экономичным способом.
Risk-Based Maintenance — это, по сути, профилактическое обслуживание, при котором частота и объем работ по техническому обслуживанию постоянно оптимизируются на основе результатов тестирования или инспекции и тщательной оценки рисков. Примерами технического обслуживания на основе рисков могут быть проверки на основе рисков применительно к статическому оборудованию, такому как сосуды и трубопроводы, или даже предохранительные клапаны.
Техническое обслуживание по условию (CBM)
Большинство видов отказов не связаны с возрастом. Тем не менее, большинство режимов отказа действительно выдают какое-то предупреждение о том, что они происходят или вот-вот произойдут.
Если можно найти доказательства того, что что-то находится на ранних стадиях отказа, можно принять меры для предотвращения полного отказа и / или во избежание последствий отказа. Таким образом, техническое обслуживание по состоянию в качестве стратегии ищет физические доказательства того, что отказ происходит или вот-вот произойдет.Такой подход к CBM показывает его более широкие применения за пределами методов мониторинга состояния, часто связанных только с вращающимся оборудованием.
Важной концепцией технического обслуживания по состоянию является кривая P-F, показанная на рисунке ниже:
Кривая показывает, что по мере того, как сбой начинает проявляться, оборудование изнашивается до точки, в которой его можно обнаружить (точка «P»).
Если отказ не обнаружен и не устранен, он продолжается до тех пор, пока не произойдет функциональный отказ (точка «F»).Временной диапазон между P и F, обычно называемый интервалом P-F, представляет собой окно возможностей, в течение которого инспекция, возможно, может обнаружить неминуемый отказ и дать вам время для его устранения.
Важно понимать, что CBM как стратегия технического обслуживания не снижает вероятность отказа, возникающего в результате обновления срока службы, а вместо этого направлена на вмешательство до того, как произойдет отказ, исходя из того, что это более экономично и должно иметь меньше влияние на доступность.
Другими словами: мониторинг состояния не исправляет машины, а мониторинг состояния не останавливает отказы. Мониторинг состояния позволяет обнаруживать проблемы только до того, как они перерастут в отказ.
Общее практическое правило состоит в том, что интервал между задачами CBM должен составлять половину или одну треть интервала P-F.
Насколько эффективнее CBM выше аварийного обслуживания, зависит от продолжительности интервала P-F. При наличии большого количества предупреждений можно запланировать исправление, мобилизовать материалы и ресурсы и предотвратить поломку (хотя производство все еще останавливается на время технического обслуживания).Когда интервал P-F составляет всего несколько дней, в результате организационные действия и действия на рабочем месте очень похожи на поломку, и ценность CBM в значительной степени теряется.
Для того, чтобы CBM была эффективной как стратегия, необходимо раннее вмешательство. Это требует действенного и действенного процесса сбора данных, анализа данных, принятия решений и, наконец, вмешательства.
Для режимов отказа, где интервал P-F показывает большую изменчивость, мониторинг состояния не является эффективной стратегией.
Если вам интересно узнать больше о том, как лучше всего управлять режимами отказа, не забудьте прочитать мою статью Техническое обслуживание, ориентированное на надежность — 9 принципов современного технического обслуживания.
Принцип работы (кратко). Принцип действия реактивного двигателя
Под реактивным понимается движение, при котором от тела с определенной скоростью отделяется одна из его частей. Сила, возникающая в результате такого процесса, действует сама по себе. Другими словами, у нее нет даже малейшего контакта с внешними телами.
Реактивное движение в природе
Во время летнего отдыха на юге почти все мы, купаясь в море, встречались с медузами. Но мало кто думал, что эти животные движутся так же, как реактивный двигатель. Принцип действия в природе такого агрегата можно наблюдать при перемещении определенных видов морского планктона и личинок стрекоз. Причем эффективность этих беспозвоночных зачастую выше, чем у технических средств.
Кто еще может наглядно продемонстрировать, какой из реактивных двигателей работает? Кальмары, осьминоги и каракатицы.Подобное движение совершают многие другие морские моллюски. Возьмем, например, каракатицу. Она втягивает воду в свою жаберную полость и энергично выбрасывает ее через воронку, которая направляется назад или в сторону. При этом моллюск способен совершать движения в нужную сторону.
Принцип действия реактивного двигателя можно наблюдать и при перемещении барабана. Это морское животное берет воду в широкой впадине. После этого мышцы его тела сокращаются, выталкивая жидкость через отверстие, которое находится позади.Реакция образовавшейся струи позволяет саженцу двигаться вперед.
Sea Missiles
Но наибольшего совершенства в реактивной навигации достиг все тот же кальмар. Даже форма самой ракеты словно скопирована с этого морского обитателя. При движении с небольшой скоростью кальмар периодически выгибает ромбовидный плавник. Но для быстрого броска ему приходится использовать собственный «реактивный двигатель». Принцип работы всех его мышц и тела стоит рассмотреть подробнее.
Кальмар имеет своеобразную мантию.Это мышечная ткань, которая окружает его тело со всех сторон. Во время движения животное засасывает в эту мантию большой объем воды, резко выбрасывая струю через специальную узкую насадку. Такие действия позволяют кальмарам двигаться назад со скоростью до семидесяти километров в час. Во время движения животное собирает в пучок все свои десять щупалец, что придает телу обтекаемую форму. На насадке есть специальный клапан. Его поворачивает животное сокращением мышц. Это позволяет моряку менять направление.Роль штурвала при передвижении кальмара выполняют его щупальца. Он направляет их влево или вправо, вниз или вверх, легко уворачиваясь от столкновений с различными препятствиями.
Существует разновидность кальмаров (stenoteutis), относящаяся к званию лучшего пилота среди моллюсков. Опишите принцип работы реактивного двигателя — и вы поймете, почему, преследуя рыбу, это животное иногда выпрыгивает из воды, даже попадая на палубы кораблей, плывущих по океану. Как это произошло? Пилот-кальмар, находясь в водной стихии, развивает для себя максимальную реактивную тягу.Это позволяет ему летать над волнами на расстоянии до пятидесяти метров.
Если мы рассмотрим реактивный двигатель, принцип Какое животное работает, мы можем упомянуть еще? Это, на первый взгляд, мешковатый осьминог. Пловцы не так быстры, как кальмары, но в случае опасности их скорости могут позавидовать даже лучшие спринтеры. Биологи, изучавшие миграцию осьминогов, выяснили, что они движутся по принципу действия реактивного двигателя.
Животное при каждой струе воды, выбрасываемой из воронки, делает рывок на два или даже два с половиной метра.При этом плывет осьминог своеобразным образом — задом наперед.
Другие примеры реактивного движения
В мире растений есть ракеты. Принцип действия реактивного двигателя можно наблюдать, когда даже при очень легком прикосновении «бешеный огурец» с большой скоростью отскакивает от ножки, отталкивая при этом липкую жидкость с семенами. При этом сам плод летит на значительное расстояние (до 12 м) в обратном направлении.
Принцип работы реактивного двигателя можно наблюдать и в лодке.Если с него в определенном направлении бросить в воду тяжелые камни, то он будет двигаться в противоположном направлении. Ракетно-реактивный двигатель имеет такой же принцип работы. Только там вместо камней используются газы. Они создают реактивную силу, которая обеспечивает движение как в воздухе, так и в разряженном пространстве.
Фантастическое путешествие
Человечество давно мечтает о космических полетах. Об этом свидетельствуют произведения писателей-фантастов, которые для достижения этой цели предлагали самые разные средства.Например, герой рассказа французского писателя Эркюля Савинена Сирано де Бержерак достиг Луны на железной повозке, на которую постоянно бросался мощный магнит. Знаменитый Мюнхгаузен тоже достиг той же планеты. Гигантский стебель фасоли помог ему совершить путешествие.
Реактивный двигатель использовался в Китае еще в первом тысячелетии до нашей эры. Бамбуковые трубы, набитые порохом, служили своеобразными ракетами для развлечения. Кстати, проект первой машины на нашей планете, созданный Ньютоном, тоже был с реактивным двигателем.
История RD
Только в XIX в. мечта человечества о космосе стала приобретать конкретные черты. Ведь именно в этом веке русский революционер Н.И. Кибальчич создал первый в мире проект самолета с реактивным двигателем. Все бумаги были составлены Народным освободителем в тюрьме, куда он попал после покушения на Александра. Но, к сожалению, 04.03.1881 Кибальчич был казнен, а его идея не нашла практического воплощения.
В начале 20 в. Идея использования ракет для космических полетов была выдвинута русским ученым К.Е. Циолковский. Впервые его работа, содержащая описание движения тела переменной массы в виде математического уравнения, была опубликована в 1903 году. Позже ученый разработал саму схему реактивного двигателя, работающего на жидком топливе.
Также Циолковским была изобретена многоступенчатая ракета и выдвинута идея создания настоящих космических городов на низкой околоземной орбите.Циолковский убедительно доказал, что единственное средство для полета в космос — это ракета. То есть аппарат, оснащенный реактивным двигателем, заправляемый горючим и окислителем. Только такая ракета способна преодолеть силу тяжести и вылететь за пределы атмосферы Земли.
Освоение космоса
Статья Циолковского, опубликованная в журнале «Научное обозрение», подтвердила для ученых репутацию мечтателя. Никто не принимал всерьез его аргументы.
Идея Циолковского была реализована советскими учеными.Под руководством Сергея Павловича Королева они запустили первый искусственный спутник Земли. 4 октября 1957 года это устройство было доставлено на орбиту ракетой с реактивным двигателем. Работа РД была основана на преобразовании химической энергии, которая передается топливом газовой струе, превращаясь в кинетическую энергию. В этом случае ракета движется в обратном направлении.
Реактивный двигатель, принцип действия которого используется много лет, находит свое применение не только в космосе, но и в авиации.Но больше всего он используется для запуска ракет. Ведь только RD может перемещать аппарат в пространстве, в котором отсутствует какая-либо среда.
Жидкостный реактивный двигатель
Тот, кто стрелял из огнестрельного оружия или просто наблюдал за этим процессом со стороны, знает, что существует сила, которая непременно оттолкнет ствол назад. А при большей сумме заряда отдача обязательно увеличится.
Водяное охлаждение
Бензиновые двигатели, у которых температура отработавших газов на 200-300°С выше чем у дизелей, обычно оснащаются турбокомпрессорами с охлаждаемыми центральными корпусами. При работе двигателя центральный корпус интегрируется в его контур охлаждения. После выключения двигателя остаточное тепло снимается посредством малого кольца циркуляции, которое задействуется электрическим насосом с термостатом.