Ремонт коленчатых валов и подшипников дизелей
Страница 19 из 75
После вскрытия люков картера во время профилактического осмотра проверяют состояние вала, подшипников и маслопроводов. Обращают внимание на отсутствие баббита вблизи подшипников. У дизелей типа Д100 через один М2 проверяют «провисание» 1, 2, 3, 4, 5, 6 и 7-й коренных шеек нижнего коленчатого вала.
Дополнительно при М3 проверяют зазор «на масло» у коренных подшипников дизелей типа Д100 и у всех подшипников дизелей типа Д50. У этого дизеля измеряют расхождение щек колена шестого цилиндра. Большой периодический ремонт предусматривает съемку у дизелей типа Д100 верхнего вала и его коренных подшипников, шатунных подшипников обоих валов, коренных подшипников 4, 8, 10 и 12 шеек нижнего вала. Измеряют износ 1-й коренной шейки верхнего вала и 8-й нижнего вала. Определяют ступенчатость («провисание») положения шеек валов на опорах.
При М5 у дизелей различного типа осматривают все подшипники, измеряют их толщину, валы осматривают, проверяют дефектоскопом и измеряют износ у наиболее изнашиваемых шеек.
На заводе шейки коленчатых валов обрабатывают под ремонтные размеры, отличающиеся друг от друга по диаметру на 0,5 мм. Соответственно градационные размеры установлены и для вкладышей по толщине, которая изменяется за счет основной (бронзовой части), но не фрикционного сплава.
Рис. 57. Подрезка и накатка шеек валов дизелей типа Д100 на токарном станке ДИП-500: 1-патрон-люлька; 2— люнет; 3 — головка для подрезки; 4 — суппорт; 5 — гидроусилитель; 6 — головка для накатки; 7 — кольцо градационное: 8 — втулка; 9 — люнет концевой; 10— манометр
Восстановление цилиндрической формы шеек коленчатых валов.
Перед обработкой шеек на шлифовальных станках валы очищают и проверяют магнитным седлообразным дефектоскопом (стальные) и ультразвуком (чугунные), шейка которых имеет канавку у галтели глубиной не более 0,7 мм. Затем определяют при помощи микрометра, с какими градационными размерами шеек вал поступил на завод.
Стальные валы передают на станок для шлифования шатунных, а затем и коренных шеек, а чугунные (дизель Д100) — на токарный станок для проточки и накатки галтелей, далее на шлифовальные станки для шлифования шатунных и коренных шеек.
При установке вала дизелей типа Д100 на токарный станок типа ДИП-500 предварительно на его концы надевают сменные кольца 7 (рис. 57), подобранные по диаметру градационных размеров шеек и втулки 8. Вал со сменными втулками укладывают в патрон-люльку 1 станка и концевой люнет 9 со стороны задней бабки. Поджимают конец вала центром задней бабки.
Рис. 58. Схема управления процессом проточки и накатки шеек коленчатых валов: 1— манометр 60 кГ/см2, 2 и 10— пневмогидравлические цилиндры; 3 — электропневматический вентиль включения ВР-1; 4— манометр 10 кГ/см2; 5 — регулятор давления; 6 — масленка; 7 — воздухоочиститель; 8— запорный кран; 9— 4-ходовой пневмокран; 11— маслопроводы; 12, 15 — дроссели; 13 — головка для проточки галтелей шатунных шеек; 14 — головка для проточки галтелей коренных шеек; 16 — головка для накатывания галтелей шатунных шеек; 17—головка для накатывания галтелей коренных шеек
Проточку и накатку производят одновременно у пары шеек (шатунных и коренных) устройством, устанавливаемым на суппорте 4 станка. Проточка головками 3 и накатка головками 6 ведутся при восьми оборотах вала в минуту, за 12— 15 оборотов на глубину 0,7—1,2 мм. Резцы устанавливают по длине шейки по приспособлению с ограничивающими роликами.
Усилие накатки на каждую пару роликов, опирающихся на две противоположные галтели одной шейки, 3000 кГ, что соответствует показанию манометра 35 кГ/см2.
В процессе накатывания упрочняемая поверхность смазывается машинным маслом. Чистота поверхности после накатывания должна соответствовать не ниже 6.

Шейки коленчатых валов обрабатывают на шлифовальных станках типа ХШ-335 (коренные шейки) и типа 3Α428Η13 (шатунные шейки). Перемещение стола и изменение числа оборотов шлифуемого вала у станков осуществляются бесступенчато.
В качестве примера рассмотрим технологию шлифования коренных шеек нижнего коленчатого вала дизеля типа Д100. Вал (рис. 60) зачаливают за IV и IX шейки и устанавливают на станок, используя для привода поводок со стороны шейки 1, а в качестве опор — шесть люнетов. К шейкам 1 и 12 подводят люнеты на неизношенные поверхности и вал центрируют, используя центровочный шарик и щуп.
Рис. 59. Головки для накатки шеек валов
Зазор между шариком и центровой пробкой 0,05 мм. Люнеты № 2, 3, 4 и 5 не должны касаться шеек. Затем вал окончательно центрируют, используя индикаторные упоры. Размеры проверяют в вертикальной и горизонтальной плоскостях от мерительных платиков, определяя градацию шеек. Шлифуют шейку 7 предварительно без люнета № 4 при скорости вращения вала 20 об/мин до выведения выработки. Окончательно шлифуют шейку 7 с люнетом № 4 до градационного размера и чистотой поверхности V8. После окончательного шлифования на люнет кладут войлок и смазывают машинным маслом.
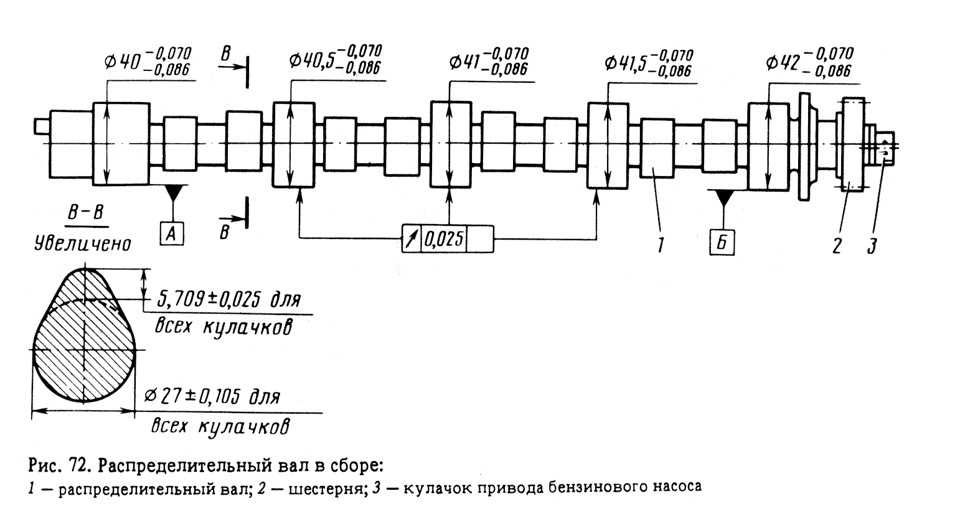
Рис. 60. Шлифование коренных шеек нижнего коленчатого вала дизеля типа Д100:
1—12 — коренные шейки; I—X — шатунные шейки
В процессе обработки размеры шеек проверяют микрометром в поясах. Обработанный вал должен иметь следующую характеристику: овальность и конусность шеек не более 0,02 мм, биение 5, 6 7 и 8 коренных шеек не более 0,1 мм, а для остальных не более 0,05 мм. Корсетность, бочкообразность и рифленость не допускаются. Чистота обработки шеек не ниже 8.
Шлифованный вал дизелей типа Д100 на некоторых заводах «облагораживают» стеклянной шкуркой с зерном 3 мк, закладываемой в хомуты, а затем полируют (на всех заводах) на специальном станке типа ТК401-61 конструкции ПКБ ЦТВР. Размеры шеек одного вала не должны отличаться между собой более чем на одну ремонтную градацию.
Повышение чистоты поверхности шеек коленчатого вала улучшает работу трущейся пары и увеличивает срок службы ее деталей, поэтому целесообразно применение суперфиниширования. Для коленчатых валов, отлитых из высокопрочного магниевого чугуна, оптимальный режим при использовании специального станка следующий. При 55 об/мин коленчатого вала колебания головки 650 двойных ходов/мин в течение 30—120 сек. Для предварительной обработки используют бруски К35СМ2К размерами 20 х 20 χ 74 мм и 20 х 20 х 35 мм для коренных шеек и 20 х 20 х 94 мм и 20 х 20 х 45 мм для шатунных шеек с давлением на бруски 1 кГ/см2. Окончательную обработку ведут брусками КЗМ14СМ1К с теми же размерами при 105 об/мин вала, частоте 650 двойных ходов/мин, давлении 0,3—0,5 кГ/см
После механической обработки коленчатый вал устанавливают на контрольную плиту (двигатели разного типа) или на стенд типа Р9570-2151 (двигатель типа Д100), где проверяют: размеры шеек по диаметру, величину биения, овальности и конусности — микрометром, отсутствие рифлености — набором шаблонов, смазываемых краской («утюжки»), а также расхождение щек (у валов двигателей типа Д50) и ступенчатость коренных шеек при помощи оптических приборов (2Д100).
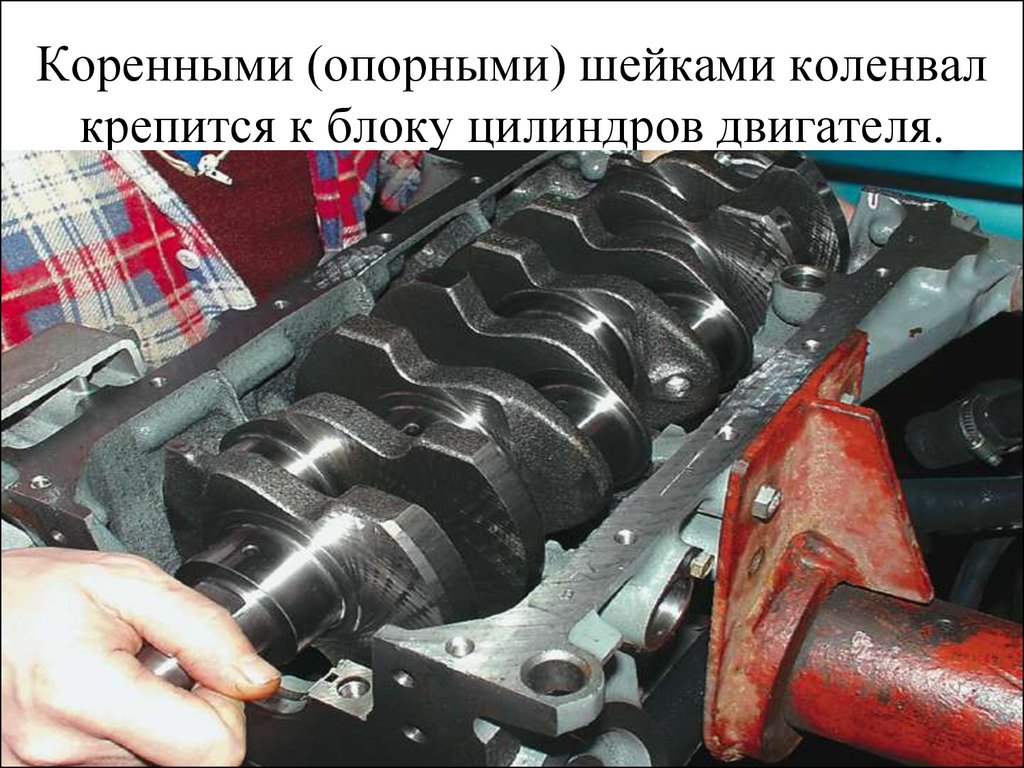
В основу оптического метода измерений положен принцип «висящей нити». Вал укладывают на две опоры (рис. 61), имеющих V-образную форму. На опорные губки укладывают плитки 3 и 4 шириной 15—20 мм, изготовленные из меди. Автоколлиматор 1 устанавливают у конца вала, а шаговый мостик 2 — на первую пару коренных шеек. Положение автоколлиматора корректируют по взаиморасположению окулярного и отраженного перекрестия. Далее шаговый мостик переставляют на следующие опоры. Одиннадцать отсчетов по горизонтальному лимбу автоколлиматора переводятся в микроны и составляется таблица. Затем вал поворачивают на 90° и производят такие же измерения и записи. По полученным данным строят графики. Большие из полученных измерений принимаются за общую кривизну вала.
Рис. 61. Схема измерения несоосности коренных шеек вала дизеля типа Д100 автоколлиматором: а — схема расположения вала на опорах и приборов; б — совмещенные отраженное и окулярное перекрестия; в — несовмещенные перекрестия; 1 — автоколлиматор; 2 — шаговый мостик; 3 и 4 — плитки медные; 5 — боковые поверхности шеек
Рис. 62. Схема правки вала наклепом щек:
a’b’ — c’d’ — положение оси коренных шеек до правки, ab—cd — положение оси коренных шеек после правки
Правка вала.
В случае искривления стального вала его правят одним из следующих способов: термическим, термомеханическим, релаксационным и механическим с наклепом. Термический способ рекомендуется при прогибах в пределах 0,5—1 мм, термомеханический — 0,7—1,3 мм, релаксационный (кольцевой нагрев) при прогибах свыше 1,3 мм, а также при прогибах, сопровождающихся значительными повреждениями поверхности вала при выходе из строя вкладышей. Способ термической правки заключается в быстром местном нагреве выпуклого участка вала, при котором нагретый слой металла вала испытывает напряжения выше предела текучести. Комбинированная термомеханическая правка отличается от термической тем, что до начала нагрева участка вала, установленного выпуклой стороной вверх, в нем заранее создают напряжения при помощи механического нажима (хомутом или траверсой).
Правка с использованием явлений релаксации напряжений заключается в том, что вал нагревают до температуры 600—650° С на участке искривления по всей окружности, а затем прогибают его при помощи нажимного приспособления в сторону, противоположную прогибу. После правки этим способом остаточные внутренние напряжения отсутствуют, что создает стабильность формы вала.
Для правки валов двигателей небольшой и средней мощности используют комбинированный способ механического нажима и поверхностного наклепа. После определения места прогиба вала на призмах его правят под прессом, доводя величину прогиба до 0,3 мм, а затем наклепом доводят ее до 0,15 мм, после чего ведут обработку шеек.
Поверхности щек справа и слева от шейки наклепывают молотком с таким расчетом, чтобы при возникающей после этого деформации щеки получалось
необходимое смещение оси вала (рис. 62). Для правки способом наклепа используют ручные молотки с шаровой головкой или чеканки.
Способы повышения износостойкости шеек коленчатых валов.
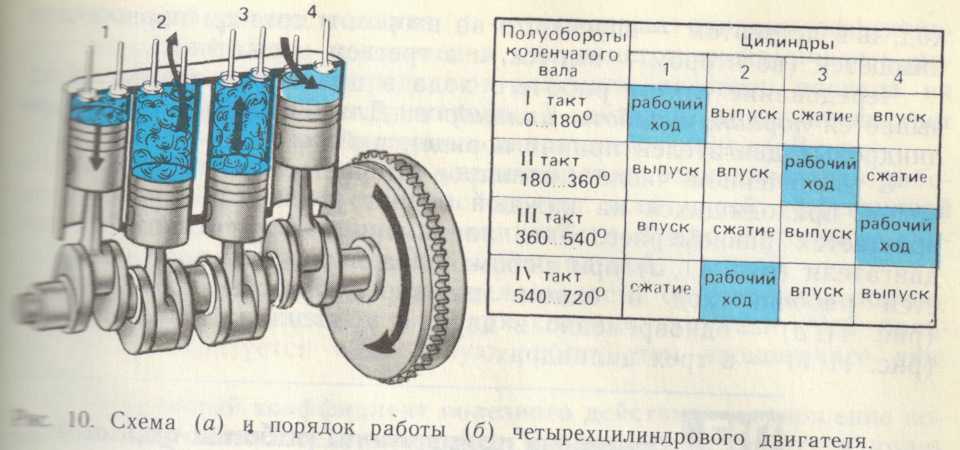
Повысить износостойкость шеек валов можно: хромированием, поверхностной электрозакалкой, закалкой после нагрева кислородно-ацетиленовым пламенем и азотированием. Валы дизелей М750 после термической обработки азотируют при температуре 490—500° С на глубину 0,15— 0,4 мм. Длительность выдержки составляет 34—35 ч, в результате чего шейки приобретают твердость не ниже НV = 600.
Первую и вторую шейки двигателей типа Д50, как наиболее изнашиваемые, покрывают молочным хромом, что повышает их износоустойчивость по сравнению с не хромированными шейками в 2—3 раза; соответственно улучшаются условия работы вкладышей, замена которых при текущем ремонте сокращается примерно в 2 раза. Шейки коленчатых валов двигателей типа Д50 хромируют по следующему технологическому процессу: а) обезводороживание в масле, нагретом до 200° С в течение 4,5 ч с последующим остыванием в этой среде до температуры помещения; б) обезжиривание авиационным бензином; в) обезжиривание в электролите двумя ступенями в течение 4 мин на катоде и 1 мин на аноде при плотности тока 7,5 а/дм2 и температуре ванны 70+5° С; г) промывка в теплой проточной воде; д) нанесение защитных покрытий на нехромируемые поверхности с применением полихлорвиниловых смол и пластикатов, кислотоупорных эмалей и цапон-лаков; е) окончательное обезжиривание венской известью с последующей промывкой холодной водой, а затем спиртом; ж) хромирование при температуре 50 — 51° С в электролите, содержащем 180 г/л хромового ангидрида и 1,8 г/л концентрированной серной кислоты; з) промывка в холодной проточной воде; и) обезводороживание по режиму пункта «а». После хромирования вал обрабатывают при помощи разъемных притиров с использованием пасты типа СУ-М20. Процесс хромирования идет по следующему циклу: предварительное декапирование, хромирование с силой тока 12 а/дм2 в течение 12—15 мин, затем с силой тока 35 а/дм2 в течение 5,5—6 ч. В результате получается слой хрома с твердостью HY = 9004- 980 толщиной 130—140 мк с мелкодисперсным подслоем.
- Назад
- Вперёд
Дефектовка коленчатого вала
28.10.2014 / 25.04.2018 • 51709 / 27819 Если блок цилиндров является «базой» автомобильного двигателя, то коленчатый вал Состоящий из одного или нескольких колен и нескольких соосных коренных шеек, опирающихся на подшипники. Каждое колено К. в. имеет две щеки и одну шейку для присоединения шатуна. Оси шатунных шеек смещены относительно оси вращения К. в.. выполняет другую важнейшую функцию — именно с него снимается полезная мощность на трансмиссию и навесные агрегаты. То есть собственно то, ради чего и нужен мотор. Если коленвал выйдет из строя, то неизбежна полная разборка двигателя для ремонта. Причём, в исключительных случаях, поломка коленвала приводит к тяжелейшим последствиям — вплоть до разрушения блока. Грамотная дефектовка коленчатого вала поможет не только определить причины поломок, но и сбережёт немало времени и сил при ремонте.
Дефект 1. Сильный износ и задиры на поверхностях коренных и шатунных шеек коленчатого вала.
Причины:
- Недостаточное давление в системе смазки.
- Недостаточный уровень масла в картере.
- Некачественное масло.
- Сильный перегрев, приводящий к разжижению масла.
- Попадание в масло топлива (бензина или дизтоплива), приводящее к разжижению масла.
- Засорённый масляный фильтр.
- Работа двигателя на грязном масле.
Действия:
- Капитальный ремонт двигателя. Шлифовка шеек коленвала в ремонтный размер и установка утолщённых (ремонтного размера) вкладышей.
В некоторых случаях — замена вала. Проверьте посадочные места под вкладыши коленчатого вала в блоке цилиндров и нижних головок шатунов, системы смазки и масляного насоса и при необходимости отремонтируйте или замените масляный насос. Прочистите, промойте и продуйте масляные каналы блока цилиндров и колен чатого вала. Проверьте системы охлаждения, при необходимости отремонтируйте её. Проверьте, при необходимости отремонтируйте системы питания.
Дефект 2. Сильный износ торцевых поверхностей под упорные полукольца коленчатого вала.
Причины:
- Неисправность привода выключения сцепления.
- Стоянка на месте с работающим двигателем и с выжатым сцеплением.
- Движение с неполностью отпущенной педалью сцепления.
Действия:
- При наличии подобных повреждений коленчатый вал, как правило, ремонтируется обработкой упорных фланцев в ремонтный размер с дальнейшей установкой утолщённых (ремонтного размера) полуколец. В некоторых случаях требуется замена коленчатого вала.
Проверьте при вод выключения сцепления и в случае неисправности отремонтируйте его. Не держите без необходимости ногу на педали сцепления.
Дефект 3. Царапины на поверхности коренных и шатунных шеек коленчатого вала
Причины:
- Большой пробег двигателя.
- Попадание посторонних частиц в моторное масло.
Действия:
- Проверьте исправность системы смазки.
- Применяйте моторное масло надлежащего качества и регулярно, в предписанные производителем сроки, меняйте моторное масло и фильтр. При наличии подобных повреждений коленчатый вал, как правило, ремонтируется шлифовкой шеек в следующий ремонтный размер.
Примечание. Подобные следы являются косвенным признаком износа шеек коленчатого вала. Проверку износа, эллипсности и конусности каждой шейки следует выполнять так: с помощью микрометра промеряем каждую шейку в двух взаимноперпендикулярных плоскостях и сравниваем полученные данные с размерами, предписанными производителем.Если полученный размер выходит за пределы указанных допусков, вал ремонтируется шлифовкой шеек в следующий ремонтный размер.
Дефект 4. Прогиб коленчатого вала.
Обязательно проверьте изгиб коленчатого вала. Особенно важна эта процедура для двигателей тяжёлых грузовиков и строительной техники. Вал укладывается на призмы, установленные на металлической плите. С помощью стрелочного индикатора, установленного на стойке, проверяем прогиб оси коленвала, вращая коленвал. Изгиб не должен превышать: для легковых моторов 0,05 мм; для грузовых моторов 0,1 мм. При необходимости произведите правку («выпрямление») коленчатого вала. Данная операция поможет выявить наличие трещин.
Дефект 5. Трещины коленвала.
Причины:
- Причины перечислены ранее, в пункте 1. К появлению трещин в коленвале может также привести разрушение поршня и шатуна в результате гидроудара или попадания в цилиндр посторонних предметов.
Действия:
- Коленчатый вал ремонту не подлежит.
Примечание. Определить наличие трещин и их размеры можно визуально или с помощью небольшого молотка. При ударе молотком должен раздаваться чистый, а не дребезжащий звук.
Дефект 6. Выработка и царапины на поверхности под сальники коленчатого вала
Причины:
- Длительная работа двигателя.
- Попадание посторонних частиц в моторное масло.
- Неаккуратное обращение с коленчатым валом при замене сальников на двигателе.
Действия:
- Замена коленчатого вала. При наличии незначительных царапин возможна шлифовка поверхностей под сальники. При незначительной выработке возможна установка новых сальников с небольшим осевым смещением.
Дефект 7. Разрушение шпоночных пазов и посадочных мест под штифты и втулки.
Причины:
- Неправильная затяжка болтов, крепящих шкивы и маховики. Биение шкивов.
- Последствия аварии, при которой произошла деформация моторного отсека.
Действия:
- Замена коленчатого вала.
В некоторых случаях возможно прорезание нового шпоночного паза или посадочного места под штифт или втулку. При сборке мотора с таким коленвалом требуется особое внимание при совмещении меток на шкивах или шестернях ГРМ.
Дефект 8. Разрушение резьбы в крепёжных отверстиях.
Причины:
- Неправильная затяжка крепёжных болтов.
Действия:
- Замена коленчатого вала. В исключительных случаях возможно нарезание резьбы большего диаметра.
Необходимо помнить: после ремонта коленчатый вал должен быть тщательно промыт и продут сжатым воздухом для удаления загрязнений.
Ремонт коленчатого вала большого четырехтактного дизельного двигателя
Ремонт на месте на Карибском острове
Компания n-situ Machining Solutions (UK) Ltd успешно завершила капитальный ремонт коленчатого вала большого четырехтактного дизельного двигателя, расположенного на Карибском острове. Удаление коленчатого вала было бы полной катастрофой с точки зрения затрат и простоя двигателя.
Работа заключалась в ремонте диаметров шатунных и коренных подшипников после того, как двигатель сильно заклинил во время работы, что привело к искусственному упрочнению (650 HB), вызванному интенсивным трением между вкладышами подшипников и диаметрами шеек.
После обширной калибровки шейки было решено совместно с OEM уменьшить диаметр шатунной шейки на 16 мм, а коренной подшипник на 7 мм, чтобы устранить возникшее искусственное затвердевание. Услуга калибровки состояла из полного измерения, теста на твердость, MPI с помощью магнитопорошкового процесса и проверки соосности коленчатого вала, чтобы установить, не произошел ли какой-либо изгиб из-за отказа двигателя.
Ремонт шатунных/шатунных подшипников
Компания In-situ Machining Solutions (UK) Ltd располагает серией токарных/суперфинишных/полировальных станков для очень эффективного решения подобных проблем.
Для шатунных шеек используются орбитальные токарные станки для быстрого уменьшения диаметра поврежденных шатунных шеек. Они предназначены для вращения на коленчатом валу в пределах радиуса закругления шатунной шейки и являются гораздо более эффективными, чем методы шлифования, используемые некоторыми нашими конкурентами.
В случаях, когда радиусы галтелей повреждены или эксцентричны по отношению к оси коленчатого вала, как в случае с этим конкретным двигателем, у компании есть уникальные средства ремонта с использованием орбитального токарного станка, установленного на муляже или системе ложных шеек, для повторной нарезки. радиусы скругления.
Из этой шатунной шейки было выточено 16 мм, чтобы удалить зону индукционной закалки, и, наконец, суперобработано и отполировано до Ø374 мм. Радиусы галтелей и масляные отверстия были преобразованы в соответствии с процедурой OEM и совмещены с вновь обработанным диаметром меньшего размера.
После завершения плоскостность штифта была проверена линейкой и инженерным синим, 90% контакта зафиксировано в нескольких положениях вокруг цапфы.
Параллельность шатунной шейки относительно осевой линии коленчатого вала была откалибрована и записана в пределах 0,09/1000 мм с помощью прецизионного микроуровня и проверено в четырех положениях вокруг шатунной шейки.
Шероховатость поверхности шатунной шейки по завершению составила 0,2 Ra мкм, что находится в пределах ограничений OEM, поэтому показания твердости и растрескивания поверхности не зарегистрированы.
Циферблатная индикация прилегания коренных подшипников к поврежденной шатунной шейке при вращении коленчатого вала валоповоротным механизмом двигателя оказалась в пределах допусков завода-изготовителя.
Ремонт коренных подшипников
В отличие от работ с шатунными шейками, этот ремонт не может быть выполнен с использованием оборудования для орбитальной обработки из-за чрезвычайно ограниченного доступа, всего 8 мм, между диаметром основного подшипника и корпусом отверстия основного подшипника этого подвесного двигателя.
Так как данный ремонт никогда не проводился на этом конкретном двигателе, инженеры In-situ Machining (UK) Ltd спроектировали и изготовили шлифовальную систему для выполнения этого ремонта.
Станок предназначен для размещения в области, которая обычно занята крышкой коренного подшипника, и состоит из опорных кронштейнов, системы линейных направляющих и сверхмощной пневматической шлифовальной головки, которая проходит через коренной подшипник в виде серии разрезов, как коленчатый вал. вращается валоповоротной системой двигателя.
Радиусы галтелей подшипника также отшлифованы с использованием дополнительной насадки, они были сформированы в соответствии с процедурами OEM и объединены с вновь обработанным уменьшенным диаметром 7 мм, также как и радиусы отверстий для смазки. Был оставлен небольшой припуск на диаметр коренного подшипника, чтобы обеспечить окончательную суперфинишную обработку и полировку до Ø443 мм.
Плоскостность коренного подшипника, твердость и обнаружение поверхности и трещин были проверены и были аналогичны таковым для работы коленчатого вала и соответствовали рекомендациям OEM в отношении пределов и посадок.
Все измерения проводились с использованием калиброванного оборудования, в том числе специального наружного микрометра, который необходимо было изготовить для доступа к 8-миллиметровому зазору между коренным подшипником и гнездом коренного подшипника.
Работы, связанные с шатунной шейкой и коренным подшипником, были проверены инженерами заказчика и представителем страховой компании.
По отзывам заказчика и OEM-производителя, двигатель успешно работает при нормальной рабочей температуре подшипников более 12 месяцев.
Electro Motive Diesel 645-20 Ремонт коленчатого вала в США
Electro Motive Diesel EMD
Осмотр коленчатого вала и подготовка к хромированию
Сначала ваш картер двигателя обрабатывают горячей щелочью, чтобы удалить все посторонние вещества. Затем он очищается паром, чтобы заделать все крошечные отверстия и щели. Также удаляются любые противовесы, временный ремонт или заглушки. Теперь коленчатый вал намагничивается, а затем опрыскивается растворителем, содержащим мелкие частицы железа. Они показывают флуоресцентный свет для проверки каждой несущей поверхности, шпоночного паза, лямки и радиуса.
Дополнительные проверки от магнитопорошковой до ультразвуковой проводятся периодически по мере необходимости на протяжении всего процесса. Готовится полный письменный отчет, который прикрепляется к вашему коленчатому валу. Это сравнивает вал с оригинальным O.E.M. стандарты и отчет сопровождает ваш коленчатый вал во время восстановления. Отчет проверяется на каждом этапе каждым руководителем работ и трижды проверяется инспекторами по обеспечению качества вплоть до завершения утилизации и восстановления.
После завершения осмотра коленчатый вал готов к предварительному шлифованию для хромирования с соблюдением радиуса коленчатого вала, чтобы не потерять прочность основного материала. Уменьшение размера коленчатого вала перед хромированием зависит от области применения коленчатого вала и условий эксплуатации, в которых будет использоваться коленчатый вал. То есть сварные валы подвергаются дробеструйной обработке ДВАЖДЫ. Это перестраивает молекулярную структуру и улучшает прочность на растяжение, усталостную прочность и теплостойкость поковки. Вал очищается от любых загрязнений. Затем идет хромирование.
БОЛЬШИЕ КОЛЕНВАЛЫ. ИЗ-ЗА ОСОБОЙ НЕОБХОДИМОСТИ И НАТЯЖЕНИЯ БОЛЬШИХ ВАЛОВ ДЛИНОЙ ДО 28 ФУТОВ В КОМПАНИИ COASTAL PLATING БЫЛИ РАЗРАБОТАНЫ ВРАЩАЮЩИЕСЯ ОПОРЫ, КОТОРЫЕ ГАРАНТИРУЮТ, ЧТО НЕЗАВИСИМО ОТ РАЗМЕРА, ВЕСА ИЛИ КОНФИГУРАЦИИ КОЛЕНЧАТЫЙ ВАЛ БУДЕТ ВОССТАНОВЛЕН В ОРИГИНАЛЬНЫЙ O.
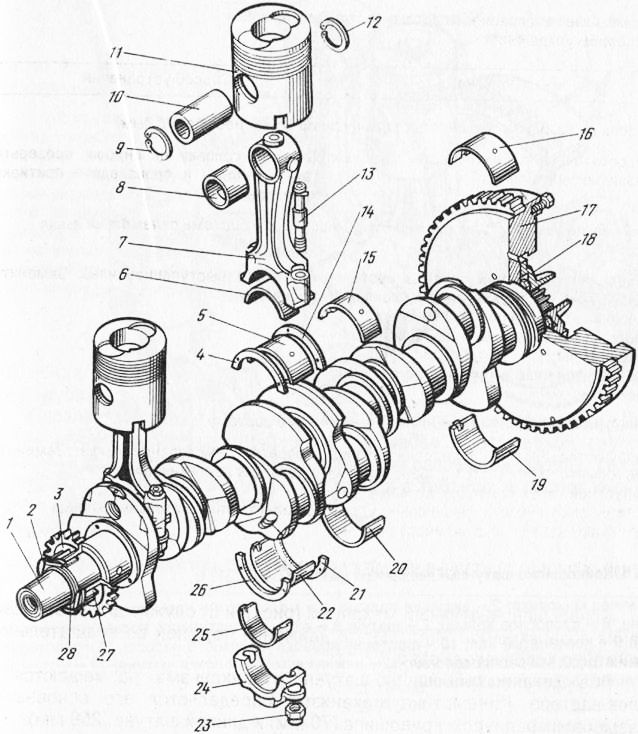
ШЛИФОВКА И БАЛАНСИРОВКА Коленчатых валов
После хромирования каждая поверхность отдельно шлифуется, чтобы привести ее в точное соответствие с письменными спецификациями и O.E.M. стандарты. Оборудование Coastal Plating — большая часть которого импортируется из Италии — позволяет шлифовать поверхности подшипников и шейки с точностью до 0,0002 дюйма.
После шлифовки проводится окончательный осмотр Magnaflux, чтобы убедиться в отсутствии дефектов на какой-либо части коленчатого вала. Затем вал подвергается динамической балансировке, поэтому он будет работать плавно, без вибрации и ударов на ВСЕХ рабочих скоростях. Кроме того, после шлифовки хромированные поверхности притираются и полируются, чтобы убедиться, что все шейки, шкивы и шестерни, а также отверстия под болты идеальны и соответствуют заводским стандартам. Проводится окончательная проверка, и письменный отчет лично проверяется Coastal Plating Management.
Когда отремонтированный коленчатый вал проходит окончательную проверку, он немедленно окрашивается антикоррозийным составом для защиты при транспортировке или хранении и подготавливается к отправке обратно на рабочую площадку. Компания Coastal Plating осознает, насколько важно правильно отремонтировать коленчатый вал с первого раза, чтобы вы могли заново собрать двигатель и снова приступить к работе. По этой причине ни мастер, ни механизатор, ни надзиратель не позволят продолжать процесс реставрации до тех пор, пока каждый этап изготовления не станет ИДЕАЛЬНЫМ.
Процесс сварки коленчатого вала
Если шейки прогорели и на них появились трещины, они будут отремонтированы с помощью дуговой сварки под флюсом. Каждый радиус, точка напряжения, упорная поверхность и шейка тщательно проверяются. Каждая трещина шлифуется и заваривается. Мы не завариваем трещины, какими бы маленькими они ни были.
БОЛЬШИЕ КОЛЕНВАЛЫ. ИЗ-ЗА ОСОБОЙ ТРЕБОВАНИЯ И НАТЯЖЕНИЯ БОЛЬШИХ ВАЛОВ ДО 40 ФУТОВ В ДЛИНЕ, КОМПАНИЯ COASTAL PLATING РАЗРАБОТАЛА ВРАЩАЮЩИЕСЯ ОПОРЫ, КОТОРЫЕ ГАРАНТИРУЮТ, ЧТО НЕЗАВИСИМО ОТ РАЗМЕРА, ВЕСА ИЛИ КОНФИГУРАЦИИ КОЛЕНВАЛ БУДЕТ ВОССТАНОВЛЕН В ОРИГИНАЛЬНОМ O.E.M. СТАНДАРТЫ.
Термическая обработка коленчатого вала
Плакировка береговой термической обработкой коленчатого вала для снятия любого напряжения, существующего в поковке.