Углеволокно. Свойства и применение. Виды заготовок и особенности
Углеволокно (УВ) – специализированный прочный материал, состоящий из тонких нитей толщиной от 5 до 10 мкм, сформированных атомами углерода. Обычно они в дальнейшем собираются для изготовления особой пряжи. Особенность данного материала в химической инертности, малом удельном весе, а также высокой прочностью к растяжению.
Углеволокно отличается высокой стоимостью, так как технология его производства достаточно затратная и сложная. В качестве исходного сырья для получения углеволокна применяются органические волокна. Задача производителя – удалить из них все лишнее, кроме атомов углерода.
Чтобы получить углеродное волокно, исходное сырье окисляют на воздухе, долго воздействуя на него при температуре 250°C. Длительность этого процесса может доходить до 1 суток. Температура способствует строению в волокнах особенных лестничных структур атомов.
На следующем производственном этапе выполняется постепенный нагрев до температуры 800°C, а затем ее повышением до 1500°C. Это происходит уже в среде азота или аргона. Данный процесс называется карбонизация. Он заканчивается образованием графитовой структуры.
Финальная стадия производства называется графитизация. Это очень ресурсозатратный сложный процесс, который подразумевает прогрев формируемого волокна до 3000°C. В итоге в нем остается не более 1% примесей, основную же структуру занимают именно атомы углерода.
Полученные волокна в разы тоньше человеческого волоса. В итоге они собираются пучками, после чего из них обычно сплетается подобие ткани. Такой материал в основном применяется для изготовления различных изделий методом соединения слоями с использованием в качестве связующего полимерных смол.
Виды полуфабрикатного сырья из углеволокнаВолокна перерабатываются в различные материалы, используемые как полуфабрикат для получения других изделий. Производители предлагают свое сырье в таком виде:
- Резаные нити.
- Непрерывные нити.
- Тканые и нетканые материалы.
- Ленты.
- Жгуты.
- Пряжа.
Вся эта продукция применяется в композитных материалах, где углеволокно служит армирующим слоем. В качестве же связующего, может использовать смола, бетон и т.д. Также существуют варианты применения углеродных волокон в чистом виде, однако в этом случае они ценятся не за прочность, а к примеру адсорбирующие качества.
Свойства углеродного волокнаМатериал имеет выдающиеся качества, за счет чего является незаменимым во многих направлениях. К главным техническим параметрам углеродного волокна можно отнести:
- Температурную стойкость.
- Химическую нейтральность.
- Высокую удельную прочность.
- Повышенные теплофизические характеристики.
Материал способен выносить нагрев вплоть до 1600-2000°С без изменения качеств, при условии нахождения в бескислородной среде. Данное свойство углеволокна дает возможность его использовать как тепловой экран в различных устройствах, эксплуатируемых в условиях повышенных экстремальных температур.
Углеволокно способно переносить контакт практически с любыми химическими веществами. Но все же оно не идеальное, так как окисляется в кислородной среде при сильном нагреве. В итоге реально использовать углеродное волокно на воздухе можно только при условии нагрева не более, чем 370°С. Это все же не так плохо. Нужно отметить, что обычно материал находится в композите, где не контактирует с воздухом. Если связующий компонент композита способен держать большую температуру чем 370°С, то и для углеволокна предел будет ограничен только стойкостью внешней оболочки. Пока последняя не разрушится, волокно будет работать без изменения рабочих качеств.
Удельная прочность углеволокна доходит до 2,5-3,5 ГПа при воздействии на разрыв. Это один из самых крепких материалов. При этом он гибкий и очень легкий. Изделия из углеволокна в разы превосходят возможности пластиков, дерева и т.д. Благодаря этому из них делают облегченные сверхмощные рамы для велосипедов, мотоциклов и даже детали обшивки гоночных автомобилей, космических аппаратов, самолетов.
При пропускании через углеволокно электрического тока, оно сильно разогревается. Именно это изначально и являлось основным ценным свойством материала. Его изобретатель Т.Эдисон разработал технологию получения волокон из углерода именно благодаря тому, что тот при пропускании тока греется. Ученый использовал УВ в качестве нити накаливания для своих электрических ламп освещения. В дальнейшем такое применение было прекращено, так как использование вольфрама более практичное. Сейчас токопроводимостью углеволокна пользуются в электронике.
Где используетсяУглеродное волокно применяется в самых разнообразных сферах и областях, так как ценится за легкость и прочность.
Углеволокно используется в таких направлениях производства:
- Спортивного инвентаря.
- Авиационной промышленности.
- Космонавтике.
- Ветроэнергетике.
- Машиностроении.
- Строительстве.
- Системах фильтрации.
В больших объемах УВ расходуется в строительной сфере. В своем большинстве он нужен для реставрации старинных архитектурных сооружений. Одним из примеров такого применения является углебетон. Это композитный материал, представляющий собой по составу обычный бетон, в который слоями вложено углеволокно. Он намного прочнее прочих бетонов, к тому же не боится коррозии, так как не имеет стальной арматуры. Также углеволокном, с применением полимерных смол, укрепляют различные поврежденные поверхности, чтобы вернуть их монолитность перед оштукатуриванием, не создавая слишком толстый слой штукатурки.
УВ применяется также для изготовления систем фильтрации. Оно обладает очень выраженными абсорбирующими качествами. Это позволяет фильтрам на его основе удалять органические и хлорорганические соединения. Считается, что они позволяют убрать из питьевой воды сторонние вкус и запахи. Само УВ при этом является полностью безопасным для человека, так как не выделяет никаких опасных компонентов в жидкость.
Что такое карбонОдним их самых известных материалов, получаемых из углеволокна, является карбон. Он изготавливается из хаотично расположенных волокон, из которых формируются пучки. Последние переплетаются по схожей технологии, что применяется при изготовлении тканей. Количество ниток в пучках исчисляется тысячами. Чем их больше, тем толще карбон. В связи с этим в его названии применяется маркировка, указывающая на количество волокон. Так, если толщина обозначена как 2.5K, то это говорит, что в карбон вплетено 2,5 тыс. волокон. Встречается материал разной толщины: 6K, 12K и даже 24 К.
Стоит отметить, что карбон толщиной в 12К настолько прочный, что преимущественно применяется в военной промышленности. Из него делают головки баллистических ракет, и даже лопасти для вертолетов. Углеволокно в карбоне такой толщины способно выносить колоссальные нагрузки, от которых обычный металл просто изогнется. При этом это очень легкий материал.
Что такое углепластикМногие знают об углепластике, который также содержит в себе УВ. Для его формирования применяются 3 технологии:
- Мокрая.
- Прессование.
- Намотка.
При использовании мокрого способа, углеродное волокно укладывается слоями в формы, между ними наносится смола. Чаще всего применяется эпоксидная, или полиэфирная. В итоге сделанное таким образом изделие высушивается до полимеризации связующего, после чего извлекается из формы.
Также распространенным методом является прессование. Для этого исходное сырье пропитываться смолой, затем спрессовывается. В итоге во время сжатия полимер затвердевает, и на выходе получается готовое изделие. Оно отличается от получаемых другими методами тем, что имеет ребристую поверхность. Особенность этой технологии в том, что возможно делать в итоге предмет практически любой объемной формы.
Также из углеволокна можно изготавливать трубы методом намотки. Для этого применяется только тканый или нетканый материал в виде холста. Он наматывается на цилиндр нужного диаметра, с нанесением между слоями смолы. В итоге достаточно быстро формируются трубки. Обычно их используют для изготовления легких лыжных палок, удилищ. Аналогичным методом делают и облегченные рамы для спортивных велосипедов.
У углеволокна имеются и недостатки. В целом это хороший материал, но композиты на его основе далеко не идеальные. Они имеют ряд слабых сторон:
- Слабо держат точечные удары.
- Сложны в изготовлении.
Сами по себе композитные материалы на основе углеволокна отличаются превосходной стойкостью. При этом они плохо переносят точечные удары. В итоге от такого воздействия на них могут образовываться сколы. Конечно проблема здесь не в самом углеволокне, а смоле. Волокно служит внутренней арматурой, а сама смола выполняет силовую скрепляющую функцию. Так что при ударах скалывается именно она.
Сложно изготовить как само углеволокно, так и в дальнейшем изделия из него. Нужно укладывать его слой за слоем, и промазывать связывающим полимером. К примеру, чтобы сформировать лист углепластика толщиной 1 мм, нужно уложить 4 слоя углеволокна. То есть сам процесс достаточно длительный и кропотливый.
Очень часто под видом изделий из углеволокна продают стеклопластик и подобные композиты. Внешне они могут быть похожи, но являются менее прочными. Так что не всегда, если заявлено что изделие содержит УВ, это на самом деле так, и оно отличается повышенной прочностью.
Похожие темы:
- Каучук. Виды и применение. Свойства и особенности
- Стекловолокно. Виды и применение. Производство и особенности
- Стеклоткань. Свойства и применение. Плюсы и минусы. Особенности
- Стекломат. Назначение и применение. Плюсы и особенности
- Синтепон. Свойства и применение. Плюсы и минусы. Особенности
- Латекс. Виды и свойства. Применение и особенности
- Композит. Виды и применение. Плюсы и минусы. Особенности
Углеводородное волокно, карбоновая нить, производство полимерных материалов и карбона, углеволокно цена
Углеродное волокно — материал, состоящий из тонких нитей диаметром от 3 до 15 микрон, образованных преимущественно атомами углерода. Атомы углерода объединены в микроскопические кристаллы, выровненные параллельно друг другу. Выравнивание кристаллов придает волокну большую прочность на растяжение. Углеродные волокна характеризуются высокой силой натяжения, низким удельным весом, низким коэффициентом температурного расширения и химической инертностью.
Производством углеродного волокна в России занимается компания ООО «Композит-Волокно», входящее в холдинг «Композит»
Углеродное волокно является основой для производства углепластиков (или карбона, карбонопластиков, от «carbon», «carbone» — углерод). Углепластики — полимерные композиционные материалы из переплетенных нитей углеродного волокна, расположенных в матрице из полимерных (чаще эпоксидных) смол.
Углеродные композиционные материалы отличаются высокой прочностью, жесткостью и малой массой, часто прочнее стали, но гораздо легче.
Наше предложение
Производство полимерных материалов требует значительного опыта. Для достижения принятых стандартов качества необходимы не только квалифицированные сотрудники, но и налаженная технология изготовления изделий. По этим причинам все представленные позиции в каталоге имеют высокое качество, гарантируют достижение поставленных перед ними задач и обладают регулярными положительными отзывами.
В каталоге вы сможете подобрать изделия для таких сфер:
- машиностроение;
- космическая и авиационная промышленность;
- ветроэнергетика;
- строительство;
- спортивный инвентарь;
- товары народного потребления
Наше производство изделий из полимерных материалов
может обеспечить вас тем количеством изделий, которое вам будет необходимо. Отсутствуют ограничения по объему заказа. При этом вы можете рассчитывать на полную консультацию от профессионалов и оперативное выполнение поставленных задач. Производство полимерных материалов в России, которое мы осуществляем, дает возможность приобретения необходимых единиц каталога по оптовой системе. Изучите наш каталог, а также, если у вас остались какие-либо вопросы — не откладывайте их на потом и обращайтесь прямо сейчас в нашу службу поддержки.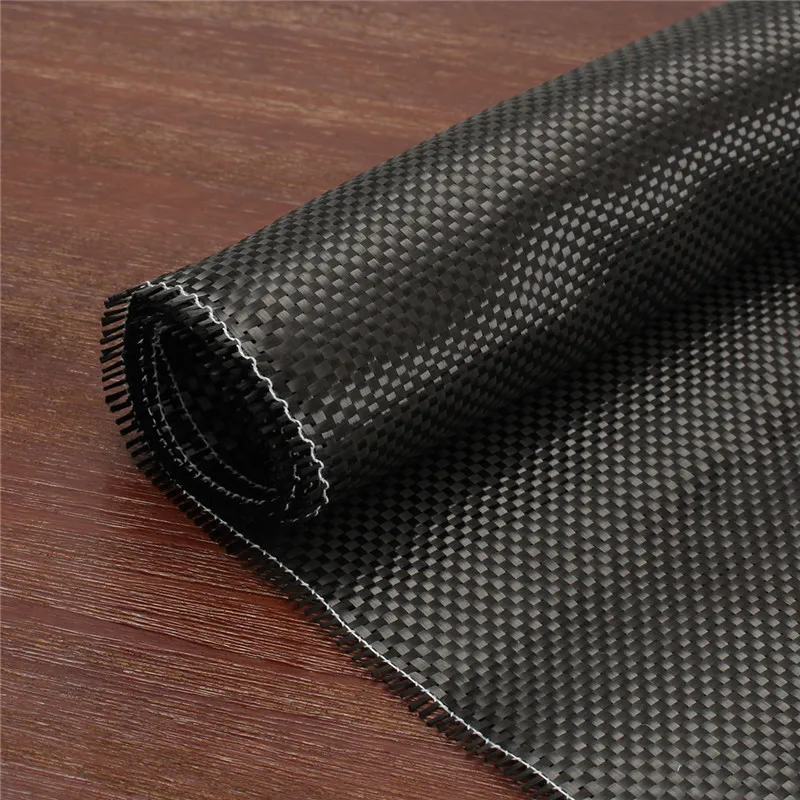
Почему цена на углеволокно так высока?
Большие затраты энергии — основная причина высокой себестоимости углеродного волокна. Впрочем, это с лихвой компенсируется впечатляющим результатом. Даже не верится, что все начиналось с «мягкого и пушистого» материала, содержащегося в довольно прозаических вещах и известных не только сотрудникам химических лабораторий. Белые волокна — так называемые сополимеры полиакрилонитрила — широко используются в текстильной промышленности. Они входят в состав плательных, костюмных и трикотажных тканей, ковров, брезента, обивочных и фильтрующих материалов. Иными словами, сополимеры полиакрилонитрила присутствуют везде, где на прилагающейся этикетке упомянуто акриловое волокно. Некоторые из них «несут службу» в качестве пластмасс. Наиболее распространенный среди таковых — АБС-пластик. Вот и получается, что «двоюродных родственников» у карбона полным-полно.
Карбоновая нить имеет впечатляющие показатели по усилию на разрыв, но ее способность «держать удар» на изгиб «подкачала».
Что такое карбоновая ткань?
Для изготовления карбоновых деталей применяется как просто углеродное волокно с хаотично расположенными и заполняющими весь объем материала нитями, так и ткань (Carbon Fabric). Существуют десятки видов плетений. Наиболее распространены Plain, Twill, Satin. Иногда плетение условно — лента из продольно расположенных волокон «прихвачена» редкими поперечными стежками только для того, чтобы не рассыпаться.
Плотность ткани, или удельная масса, выраженная в г/м2, помимо типа плетения зависит от толщины волокна, которая определяется количеством угленитей. Данная характеристика кратна тысячи. Так, аббревиатура 1К означает тысячу нитей в волокне. Чаще всего в автоспорте и тюнинге применяются ткани плетения Plain и Twill плотностью 150–600 г/м2, с толщиной волокон 1K, 2.5K, 3К, 6K, 12K и 24К. Ткань 12К широко используется и в изделиях военного назначения (корпуса и головки баллистических ракет, лопасти винтов вертолетов и подводных лодок, и пр.), то есть там, где детали испытывают колоссальные нагрузки.
Бывает ли цветной карбон? Желтый карбон бывает?
Часто от производителей тюнинговых деталей и, как следствие, от заказчиков можно услышать про «серебристый» или «цветной» карбон. «Серебряный» или «алюминиевый» цвет — всего лишь краска или металлизированное покрытие на стеклоткани. И называть карбоном такой материал неуместно — это стеклопластик. Отрадно, что и в данной области продолжают появляться новые идеи, но по характеристикам стеклу с углем углеродным никак не сравниться. Цветные же ткани чаще всего выполнены из кевлара. Хотя некоторые производители и здесь применяют стекловолокно; встречается даже окрашенные вискоза и полиэтилен.
Что такое кевлар и какие у него свойства?
По весовым, прочностным и температурным свойствам кевлар уступает углеволокну. Способность же кевлара воспринимать изгибающие нагрузки существенно выше. Именно с этим связано появление гибридных тканей, в которых карбон и кевлар содержатся примерно поровну. Детали с угольно-арамидными волокнами воспринимают упругую деформацию лучше, чем карбоновые изделия. Однако есть у них и минусы. Карбон-кевларовый композит менее прочен. Кроме того, он тяжелее и «боится» воды. Арамидные волокна склонны впитывать влагу, от которой страдают и они сами, и большинство смол. Дело не только в том, что «эпоксидка» постепенно разрушается водно-солевым раствором на химическом уровне. Нагреваясь и охлаждаясь, а зимой вообще замерзая, вода механически расшатывает материал детали изнутри. И еще два замечания. Кевлар разлагается под воздействием ультрафиолета, а формованный материал в смоле утрачивает часть своих замечательных качеств. Высокое сопротивление разрыву и порезам отличают кевларовую ткань только в «сухом» виде. Потому свои лучшие свойства арамиды проявляют в других областях. Маты, сшитые из нескольких слоев таких материалов, — основной компонент для производства легких бронежилетов и прочих средств безопасности. Из нитей кевлара плетут тонкие и прочные корабельные канаты, делают корд в шинах, используют в приводных ремнях механизмов и ремнях безопасности на автомобилях.
А можно обклеить деталь карбоном?
Непреодолимое желание иметь в своей машине детали в черно-черную или черно-цветную клетку привели к появлению диковинных суррогатов карбона. Тюнинговые салоны обклеивают деревянные и пластмассовые панели салонов углеродной тканью и заливают бесчисленными слоями лака, с промежуточной ошкуриванием. На каждую деталь уходят килограммы материалов и масса рабочего времени. Перед трудолюбием мастеров можно преклоняться, но такой путь никуда не ведет. Выполненные в подобной технике «украшения» порой не выдерживают температурных перепадов. Со временем появляется паутина трещин, детали расслаиваются. Новые же детали неохотно встают на штатные места из-за большой толщины лакового слоя.
Как производятся карбоновые и/или композитные изделия?
Технология производства настоящих карбоновых изделий основывается на особенностях применяемых смол. Компаундов, так правильно называют смолы, великое множество. Наиболее распространены среди изготовителей стеклопластиковых обвесов полиэфирная и эпоксидная смолы холодного отверждения, однако они не способны полностью выявить все преимущества углеволокна. Прежде всего, по причине слабой прочности этих связующих компаундов. Если же добавить к этому плохую стойкость к воздействию повышенных температур и ультрафиолетовых лучей, то перспектива применения большинства распространенных марок весьма сомнительна. Сделанный из таких материалов карбоновый капот в течение одного жаркого летнего месяца успеет пожелтеть и потерять форму. Кстати, ультрафиолет не любят и «горячие» смолы, поэтому, для сохранности, детали стоит покрывать хотя бы прозрачным автомобильным лаком.
Компаунды холодного твердения.
«Холодные» технологии мелкосерийного выпуска малоответственных деталей не позволяют развернуться, поскольку имеют и другие серьезные недостатки. Вакуумные способы изготовления композитов (смола подается в закрытую матрицу, из которой откачан воздух) требуют продолжительной подготовки оснастки. Добавим к этому и перемешивание компонентов смолы, «убивающее» массу времени, что тоже не способствует производительности. Говорить о ручной выклейке вообще не стоит. Метод же напыления рубленого волокна в матрицу не позволяет использовать ткани. Собственно, все идентично стеклопластиковому производству. Просто вместо стекла применяется уголь. Даже самый автоматизированный из процессов, который к тому же позволяет работать с высокотемпературными смолами (метод намотки), годится для узкого перечня деталей замкнутого сечения и требует очень дорогого оборудования.
Эпоксидные смолы горячего отверждения прочнее, что позволяет выявить качества карбонов в полной мере. У некоторых «горячих» смол механизм полимеризации при «комнатной» температуре запускается очень медленно. На чем, собственно, и основана так называемая технология препрегов, предполагающая нанесение готовой смолы на углеткань или углеволокно задолго до процесса формования. Приготовленные материалы просто ждут своего часа на складах.
В зависимости от марки смолы время жидкого состояния обычно длится от нескольких часов до нескольких недель. Для продления сроков жизнеспособности, приготовленные препреги, иногда хранят в холодильных камерах. Некоторые марки смол «живут» годами в готовом виде. Прежде чем добавить отвердитель, смолы разогревают до 50–60 C, после чего, перемешав, наносят посредством специального оборудования на ткань. Затем ткань прокладывают полиэтиленовой пленкой, сворачивают в рулоны и охлаждают до 20–25 C. В таком виде материал будет храниться очень долго. Причем остывшая смола высыхает и становится практически не заметной на поверхности ткани. Непосредственно при изготовлении детали нагретое связующее вещество становится жидким как вода, благодаря чему растекается, заполняя весь объем рабочей формы и процесс полимеризации ускоряется.
Компаунды горячего твердения.
«Горячих» компаундов великое множество, при этом у каждой собственные температурные и временные режимы отверждения. Обычно, чем выше требуемые показания термометра в процессе формовки, тем прочнее и устойчивее к нагреву готовое изделие. Исходя из возможностей имеющегося оборудования и требуемых характеристик конечного продукта, можно не только выбирать подходящие смолы, но делать их на заказ.
Препреги как нельзя лучше подходят для производства карбона в автоклавах. Перед загрузкой в рабочую камеру нужное количество материала тщательно укладывается в матрице и накрывается вакуумным мешком на специальных распорках. Правильное расположение всех компонентов очень важно, иначе не избежать нежелательных складок, образующихся под давлением. Исправить ошибку впоследствии будет невозможно. Если бы подготовка велась с жидким связующим, то стала бы настоящим испытанием для нервной системы рабочих с неясными перспективами успеха операции.
Процессы, происходящие внутри установки, незатейливы. Высокая температура расплавляет связующее и «включает» полимеризацию, вакуумный мешок удаляет воздух и излишки смолы, а повышенное давление в камере прижимает все слои ткани к матрице. Причем происходит все одновременно.
С одной стороны, одни преимущества. Прочность такого углепластика практически максимальна, объекты самой затейливой формы делаются за один «присест». Сами матрицы не монументальны, поскольку давление распределено равномерно во всех направлениях и не нарушает геометрию оснастки. Что означает быструю подготовку новых проектов. С другой стороны, нагрев до нескольких сотен градусов и давление, порой доходящее до 20 атм., делают автоклав очень дорогостоящим сооружением. В зависимости от его габаритов цены на оборудование колеблются от нескольких сотен тысяч до нескольких миллионов долларов. Прибавим к этому нещадное потребление электроэнергии и трудоемкость производственного цикла. Результат — высокая себестоимость продукции. Есть, впрочем, технологии подороже и посложнее, чьи результаты впечатляют еще больше. Углерод-углеродные композиционные материалы (УУКМ) в тормозных дисках на болидах Формулы-1 и в соплах ракетных двигателей выдерживают чудовищные нагрузки при температурах эксплуатации, достигающих 3000 C. Эту разновидность карбона получают путем графитизации термореактивной смолы, которой пропитывают спрессованное углеродное волокно заготовки.
Если решение найдено, оно выглядит настолько простым, что удивляешься: «Что же мешало додуматься раньше?». Тем не менее, идея разделить процессы, происходящие в автоклаве, возникла спустя годы поиска. Так появилась и стала набирать обороты технология, сделавшая горячее формование карбона похожим на штамповку. Препрег готовится в виде сэндвича. После нанесения смолы ткань с обеих сторон покрывается либо полиэтиленовой, либо более термостойкой пленкой. «Бутерброд» пропускается между двух валов, прижатых друг к другу. При этом лишняя смола и нежелательный воздух удаляются, примерно так же, как и при отжиме белья в стиральных машинах образца 1960-х годов. В матрицу препрег вдавливается пуансоном, который фиксируется резьбовыми соединениями.
Тюнинговые фирмы изготавливают матрицы из того же карбона и даже прочных марок алебастра. Гипсовые рабочие формы, правда, недолговечны, но пара-тройка изделий им вполне по силам. Более «продвинутые» матрицы делаются из металла и иногда оснащаются встроенными нагревательными элементами. В серийном производстве они оптимальны. Кстати, метод подходит и для некоторых деталей замкнутого сечения. В этом случае легкий пуансон из вспененного материала остается внутри готового изделия. Антикрыло Mitsubishi Evo — пример такого рода.
Механические усилия заставляют думать о прочности оснастки, да и система матрица — пуансон требует либо 3D-моделирования, либо модельщика экстра-класса. Но это, все же, в сотни раз дешевле технологии с автоклавом.
Алексей Романов редактор журнала «ТЮНИНГ Автомобилей»
- Твитнуть
Углеродное волокно — Войлочные велосипеды
Углеродное волокно — Войлочные велосипедыЧТО ТАКОЕ УГЛЕРОДНОЕ ВОЛОКНО?
Когда-то углеродное волокно использовалось только в аэрокосмической промышленности и на вершинах соревнований по автоспорту, но на протяжении нескольких десятилетий оно было предпочтительным материалом для высокопроизводительных велосипедов, колес и других велосипедных компонентов. Углеродное волокно дает велосипедным инженерам возможность создать опыт вождения, который предлагает непревзойденное сочетание комфорта, жесткости, прочности и эффективности. Благодаря невероятно высокому соотношению прочности к весу и пластичности углеродное волокно не имеет себе равных при создании лучших в мире велосипедов. В необработанном виде углеродное волокно представляет собой соединение тонких прочных волокон. Эти волокна бывают разных сортов в зависимости от общей прочности и модуля.
Чем выше модуль, тем он жестче и легче — проще говоря, «модуль» — это термин, обозначающий жесткость данного материала. Однако это не означает, что лучшие велосипеды полностью изготовлены из высокомодульного углеродного волокна. Напротив, ключом к созданию велосипедов является смешивание различных типов углеродных волокон, чтобы найти идеальный баланс между жесткостью, прочностью и весом. Кроме того, ни один велосипед не изготавливается только из углеродного волокна — оно используется в сочетании со смолой, которая действует как связующее вещество, скрепляющее конструкцию. Создать велосипед из углеродного волокна, который не только хорошо ездит, но и может обойти конкурентов, — сложная головоломка. Но точно так же, как лучшие пищевые ингредиенты требуют навыков шеф-повара, чтобы приготовить действительно изысканное блюдо, материалы для велосипедных рам требуют инженерных знаний для производства действительно великолепного велосипеда.
«Ключ к созданию велосипедов — смешивать и сочетать различные типы углеродных волокон, чтобы найти идеальный баланс между жесткостью, прочностью и весом».
ВСЕ О ОДНОНАПРАВЛЕННОМ
Однонаправленное углеродное волокно является наиболее распространенным типом углеродного волокна, используемого в производстве велосипедов. Как следует из названия, лист однонаправленного углерода имеет волокна, ориентированные в одном направлении или параллельно (например, «в одном направлении»). Чтобы помочь визуализировать характеристики из однонаправленного углеродного волокна, подумайте о бокале вина. Если вы уроните его на твердый пол, он разобьется, потому что он такой тонкий, жесткий и ломкий. Теперь подумайте о пластиковом стакане. Вы можете уронить его, и ничего не произойдет из-за его гибких свойств. Углерод следует аналогичным правилам. По мере увеличения модуля волокна становятся более жесткими и хрупкими. А если пойти в другом направлении, то волокна не такие жесткие, но более податливые и прочные. Таким образом, не существует велосипедной рамы, полностью изготовленной из высокомодульного углеродного волокна, по крайней мере такой, на которой было бы безопасно или приятно ездить.
Скорее всего, он развалится, как только вы впервые попадете в достаточно большую выбоину. С высокомодульным углеродным волокном может быть сложно работать, и должен быть баланс между жесткостью, весом, прочностью и долговечностью. Также помните, что не все однонаправленные углеродные волокна созданы одинаковыми — существует бесчисленное множество разновидностей и версий, созданных различными производителями композитов по всему миру, каждая из которых имеет разный вес, долговечность, виброустойчивость и другие характеристики, которые могут сильно повлиять на то, как будет выглядеть готовая конструкция. выполнять. Думайте о различных типах углерода, как о бумаге: простые белые листы бумаги предназначены для компьютерных принтеров; более толстая цветная плотная бумага идеальна для поделок; а толстая, эластичная и прочная бумага лучше всего подходит для архивной печати и бухгалтерского учета. Каждый тип имеет свои уникальные свойства и идеальное использование.
Вплетены в микс
В дополнение к однонаправленному углеродному волокну, тканое углеродное волокно также очень часто используется в конструкции велосипедов. Как следует из названия, тканый углерод состоит из относительно узких нитей однонаправленного углеродного волокна, сплетенных вместе, как если бы это был текстиль на ткацком станке. Поскольку углеродное волокно является таким уникальным универсальным материалом, но имеет врожденные недостатки, когда дело доходит до ориентации его нитей, переплетение углеродных нитей вместе дает специалистам по композитам и инженерам больше возможностей манипулировать структурой, которую они проектируют. Но, как и в случае с однонаправленным углеродным волокном, не все тканые углеродные волокна одинаковы. Все они имеют свои уникальные свойства. Одним из самых лучших типов углеродного волокна, которое мы давно используем для повышения производительности наших велосипедов, является TeXtreme. Читайте дальше, чтобы узнать, что делает TeXtreme таким особенным.
ЧТО ДЕЛАЕТ TEXTREME ТАКИМ ОСОБЕННЫМ?
Поскольку Felt Bicycles была первой компанией в велосипедной индустрии, которая использовала TeXtreme в своих продуктах, многие велосипедисты считают, что это тип углерода, созданный Felt или уникальный для него. Тем не менее, это не так. TeXtreme — это тип тканого углеродного волокна, созданный шведской компанией Oxeon, производящей материалы, которая делает его доступным для десятков брендов в самых разных отраслях, включая аэрокосмическую промышленность и автоспорт. Тем не менее, это все еще редкий материал в велосипедостроении из-за его высокой стоимости. Тем не менее, в соответствии с нашей миссией предоставить всем велосипедистам наилучшие впечатления от вождения, мы готовы взять на себя денежный удар, чтобы создать самые лучшие велосипеды в мире. Так что же делает TeXtreme идеальным для использования на велосипедах? Прочность и вес.
БОЛЬШЕ, ЧЕМ КАЖЕТСЯ НА ГЛАЗ
TeXtreme отличается уникальным составом, который Oxeon называет технологией «Spread Tow». «Жгут» — это термин, который относится к определенному типу нити, используемой для плетения листов из углеродного волокна. Конструкция TeXtreme Spread Tow обеспечивает прочность двух слоев однонаправленного углерода при весе примерно вдвое меньше. Кроме того, для TeXtreme требуется меньше смолы, чем для сопоставимой комбинации волокон, что еще больше снижает общий вес готовой конструкции. В качестве дополнительного бонуса, широкий «шахматный» рисунок TeXtreme также весьма эстетичен. Вы можете узнать больше о TeXtreme на веб-сайте Oxeon. Но важно помнить, что TeXtreme — это всего лишь один из ингредиентов для создания велосипеда Felt, который включает в себя несколько других типов углеродных волокон, искусно уложенных мастерами по сложным графикам укладки, разработанным лучшими велосипедными инженерами мира. «Но подождите», — скажете вы. «Какой график простоя?» Мы вас прикрыли — продолжайте читать.
«Важно помнить, что TeXtreme — это всего лишь один из ингредиентов для создания велосипеда Felt».
ЧТО ТАКОЕ ПРОСТАВКИ И РАСПИСАНИЯ?
Термин «укладка» или «график укладки» относится к общему рецепту того, как различные типы и формы листов углеродного волокна соединяются вместе (или «укладываются» в форму перед добавлением смолы). в процессе изготовления велосипедной рамы. Список часто состоит из списков, диаграмм, диаграмм или их комбинации, в которой подробно описаны различные размеры, модули, ориентация волокон и содержание смолы для каждой детали. Вместе эта информация представляет собой дорожную карту, ведущую к готовому кадру. Каждая модель велосипеда может содержать сотни таких записей. Многие люди думают, что все карбоновые конструкции велосипедов одинаковы. И, конечно же, каждый производитель велосипедов может изменить ориентацию слоев и материалы, а также использовать различные смолы, чтобы скрепить все вместе. Но если вы не потратите время на этапе проектирования, чтобы по-настоящему понять структурные взаимосвязи, вы просто создадите обычные велосипеды.
РАЗРАБОТКА РАМЫ И СПЕЦИФИКА РАЗМЕРА
Благодаря обширному автоматизированному проектированию (CAD), анализу методом конечных элементов (FEA) и испытаниям прототипов профессиональными гонщиками Felt наши инженеры могут определить, какие типы волокон использовать. Цель состоит в том, чтобы точно расположить каждую деталь на раме, чтобы максимально использовать ее специфические свойства. В некоторых областях мы можем использовать материал с промежуточным модулем, потому что он может предложить идеальный баланс жесткости и прочности. В других областях мы выбираем высокомодульный материал для дополнительной жесткости. TeXtreme также используется во многих моделях, часто как способ повысить прочность и долговечность без чрезмерного веса. Каждый дизайн рамы ведет себя по-разному, и каждый размер рамы требует уникальной укладки. Вот почему мы десятилетиями создавали рамы определенного размера, чтобы у каждого велосипедиста был одинаковый опыт вождения.
Смешивание этих материалов может сильно различаться. Например, более жесткие слои волокна обычно используются в областях, требующих максимальной производительности, таких как каретка и нижняя труба. Более прочное волокно лучше всего подходит для областей, более подверженных ударам. То же самое внимание уделяется изменениям размера кадра. По мере изменения диаметра труб и пересечения меняются ориентация слоев и характеристики материалов. Эти решения занимают месяцы, а то и годы, чтобы принять окончательное решение с учетом всех вариантов. После того, как будет определено идеальное сочетание материалов и ориентации слоев, составляется график укладки, в котором описываются все детали процесса строительства. Затем рама изготавливается на заводе и готовится к испытаниям в реальных условиях, прежде чем поступит в массовое производство для продажи.
ПОНИМАНИЕ НАШЕЙ ТЕРМИНОЛОГИИ
Если вы просматривали технические детали различных моделей велосипедов на нашем веб-сайте, вы, вероятно, видели такие фразы, как «UHC Ultimate + TeXtreme», «UHC Advanced + TeXtreme» и «UHC Performance» и другие. Эти фразы являются нашими обозначениями уникальных типов карбоновых накладок, используемых на различных моделях велосипедов. Так что именно они означают? Ну, во-первых, «UHC» означает «ультрагибридный углерод», и это наш термин, который мы использовали в течение многих лет, чтобы указать, что наши карбоновые рамы используют сложные графики укладки, состоящие из различных типов компонентов из углеродного волокна, все кропотливо ориентированы на получение характеристик производительности, к которым мы стремимся, когда речь идет о каждом велосипеде.
Почему нам важно это отметить? Проще говоря, не все бренды прилагают усилия для создания таких сложных творений. Действительно, даже компании в других отраслях, таких как аэрокосмическая, полагаются исключительно на простые конструкции, состоящие, например, из однонаправленного углеродного волокна. «UHC» представляет нашу приверженность поиску самых лучших качеств из самых современных доступных материалов. Посмотрите на диаграмму ниже, чтобы узнать больше о нашей терминологии и о том, что делает каждое из наших творений из углеродного волокна уникальным.
Прошлое, настоящее и будущее углеродного волокна
При мысли о самом прочном, надежном и универсальном материале почти сразу возникает ссылка на один конкретный вид: углеродное волокно.
Углеродное волокно — это одновременно прочный и легкий полимер, используемый в самых разных областях: от аэрокосмической и авиационной промышленности до производства игрушек, клюшек для гольфа и рукояток для ножей. Он в пять раз прочнее стали, но весит всего одну треть ее веса.
Сегодня углеродное волокно является уникальным и необходимым компонентом во многих отраслях промышленности. Хотя нынешние формы и использование углеродного волокна представляют особый интерес, стоит рассмотреть впечатляющую историю этого материала и его предполагаемое будущее. Давайте взглянем на прошлое углеродного волокна, его блестящее настоящее и светлое будущее.
Углеродное волокно: его удивительное начало
Углеродное волокно было впервые изобретено еще в 1860 году человеком по имени сэр Джозеф Уилсон Свон. Свон был английским изобретателем, физиком и химиком, одним из первых независимых разработчиков первой лампы накаливания.
Свон изобрел углеродное волокно, чтобы использовать его в ранней версии нити накала лампы накаливания. Он использовал углеродное волокно, потому что его высокая теплостойкость была идеальной, что делало его превосходным электрическим проводником. Его процесс создания углеродных волокон для своих нитей был настолько тщательным и впечатляющим, что химики-полимерщики до сих пор используют его.
Лампочка Свона с нитью из углеродного волокна была использована в качестве основы для запатентованной лампочки Томаса Эдисона двадцать лет спустя. Эдисон создал свою лампочку, затем запатентовал ее в Соединенных Штатах и рекламировал, что он был изобретателем, по сути, изобретения Свона. В конце концов они пошли на компромисс: в Англии они учредили «Edison & Swan Electric Light Company» (она же «Ediswan»), а в США Эдисону были переданы права на производство электрического освещения.
Однако в конце концов углеродное волокно в этих нитях было заменено вольфрамом, и углеродное волокно устарело на следующие пятьдесят лет. Только в 1950-х годах, когда Union Carbide начала экспериментировать с применением углеродного волокна, особенно для военных, она стала популярной. С 1950-х по 1970-е годы материал видоизменялся и формовался, чтобы сделать его гораздо более полезным.
Углеродное волокно сегодня
Сегодня углеродное волокно в его многочисленных формах используется во множестве продуктов, больших и малых, и различных применений по всему миру. 9Например, чешуйки из углеродного волокна 0077 используются в качестве основного материала в рукоятках ножей. Листы из углеродного волокна используются во многих отраслях промышленности, таких как автомобили, самолеты, робототехника, медицина, дроны и потребительские товары.
Ткани из углеродного волокна также бывают различных переплетений, что влияет на их внешний вид и функциональность. Ткань 3k, например, состоит из 3000 нитей ткани из углеродного волокна. Листы из углеродного волокна (или композиты) создаются из этих тканей.
Чешуйки из углеродного волокна , листы, ткани и другие варианты обеспечивают бесчисленные преимущества всего продукта, в котором они используются. Он исключительно легкий по сравнению с его уровнем прочности, имеет низкое тепловое расширение, устойчив к коррозии, электропроводен (как и при первом изобретении) и даже устойчив к ультрафиолетовому излучению.
Сегодня углеродное волокно используется в бесчисленном количестве продуктов, некоторые из которых мы используем ежедневно, а некоторые — в особых случаях. Углеродное волокно содержится в таких предметах, как велосипеды, клюшки для гольфа, софтбольные и бейсбольные биты, космические корабли, лопасти ветряных турбин, транспортные средства (даже гоночные автомобили), зонтики, электронные устройства, чехлы для мобильных телефонов — список можно продолжать и продолжать.
Что ждет углеродное волокно в будущем?
Будущее углеродного волокна захватывающее и постоянно развивается. Углеродное волокно, несомненно, является удивительно универсальным материалом, который при правильных условиях может служить всю жизнь. Тем не менее, есть некоторые текущие проблемы с углеродным волокном, которые, как ожидается, будут изменены в будущем для нашего улучшения.
Одной из самых серьезных проблем, с которыми приходится сталкиваться углеродному волокну, является стоимость его производства. На самом деле, это один из самых дорогих и долговечных материалов. Тем не менее, в этом отношении есть надежда на углеродное волокно в будущем, поскольку цена на него резко снизилась только за последние пять лет, поскольку популярность углеродного волокна во всех его формах возросла.
Следующие несколько десятилетий, в частности, должны обеспечить нас углеродным волокном, которое будет легко доступным, более экономичным и при этом чрезвычайно надежным, прочным и легким.