Углеволокно — это… Что такое Углеволокно?
Углеродное волокно
История
Впервые получение и применение углеродных волокон (УВ) (точнее, нитей) было предложено и запатентовано известным американским изобретателем — Томасом Алва Эдисоном в 1880 г. в качестве нитей накаливания в электрических лампах. Эти волокна получались в результате пиролиза хлопкового или вискозного волокна и отличались хрупкостью и высокой пористостью и впоследствии были заменены вольфрамовыми нитями. В течение последующих 20 лет он же предложил получать углеродные и графитированные волокна на основе различных природных волокон. Вторично интерес к углеродным волокнам появился в середине XX в., когда велись поиски материалов, пригодных для использования в качестве компонентов композитов для изготовления ракетных двигателей. УВ по своим качествам оказались одними из наиболее подходящих для такой роли армирующими материалами, поскольку они обладают высокой термостойкостью, хорошими теплоизоляционными свойствами, коррозионной стойкостью к воздействию газовых и жидких сред, высокими удельными прочностью и жесткостью.

Получение
Рис. 1. Структуры, образующиеся при окислении ПАН-волокна
УВ обычно получают термической обработкой химических или природных органических волокон, при которой в материале волокна остаются главным образом атомы углерода. Температурная обработка состоит из нескольких этапов. Первый из них представляет собой окисление исходного (полиакрилонитрильного, вискозного) волокна на воздухе при температуре 250 °C в течение 24 часов. В результате окисления образуются лестничные структуры, представленные на рис. 1. После окисления следует стадия карбонизации — нагрева волокна в среде азота или аргона при температурах от 800 до 1500 °C. В результате карбонизации происходит образование графитоподобных структур. Процесс термической обработки заканчивается графитизацией при температуре 1600-3000°С, которая также проходит в инертной среде. В результате графитизации количество углерода в волокне доводится до 99 %. Помимо обычных органических волокон (чаще всего вискозных и полиакрилонитрильных), для получения У. в. могут быть использованы специальные волокна из фенольных смол, лигнина, каменноугольных и нефтяных пеков.
Дополнительная переработка УВ
Углеродные волокна могут выпускаться в разнообразном виде: штапелированные (резаные, короткие) нити, непрерывные нити, тканые и нетканые материалы. Наиболее распространенный вид продукции — жгуты, пряжа, ровинги, нетканые холсты. Изготовление всех видов текстильной продукции производится по обычным технологиям, так же как для других видов волокон. Вид текстильной продукции определяется предполагаемым способом использования УВ в композиционном материале, точно так же, как и сам метод получения композита. Основные методы получения композитов, армированных углеродными волокнами, являются обычными для волокнистых материалов: выкладка, литье под давлением, пултрузия и другие. В настоящее время выпускается ряд видов УВ и УВМ, основные из которых перечислены ниже. На основе вискозных нитей и волокон: • нити, ленты, ткани — Урал®; • нетканый материал — Карбопон®; • активированные сорбирующие ткани — Бусофит®,САУТ-1С, АУТ-М; • активированные сорбирующие нетканые материалы — Карбопон-Актив®. На основе вискозных штапельных волокон: • волокна и нетканые материалы: карбонизованые — Углен® (технология восстановлена на Светлогорском ПО «Химволокно») и графитированые — Грален®; На основе ПАН-нитей и жгутов: • ленты и ткани — ЛУ®, УКН®, Кулон®, Элур®.
До 2007 г. в СНГ углеродные волокна производятся на двух предприятиях: «Аргон» (г. Балаково, Россия) — производство на основе ПАН (полиакрилонитрила) и РУП «Светлогорское ПО Химволокно» (г. Светлогорск, Беларусь, www.sohim.by) — производство на основе вискозы. Оба предприятия обладают собственными мощностями по производству прекурсора. Предприятие в Беларуси — крупнейший мировой производитель углеволокна из вискозы (http://www.promvest.info/354/5338/). По некоторым данным, продолжают работать обе линии НПО «Химволокно» в г. Мытищи. Существовавшие во времена СССР в г.
Компания ОАО «НПК «Химпроминжиниринг» (входит в структуру Росатома) является единственным в России производителем углеродных волокон и одним из не многих производителей ПАН-прекурсоров, которые выпускаются на ее дочерних предприятиях – ООО «Аргон» (г. Балаково Саратовской области), ООО «Завод углеродных и композиционных материалов» http://zukm.ru/ (г. Челябинск) и ООО «СНВ» (г. Саратов). Так же ПАН-прекурсоры (нить, жгут) выпускает ФГУП «ВНИИСВ» (г.Тверь).Основными потребителями углеродных волокон являются предприятия атомной отрасли, а также авиационные предприятия и предприятия военно-промышленного комплекса. ОАО «НПК «Химпроминжиниринг» планирует к 2020 году выйти на объем производства не менее 3000 тонн углеродных волокон в год.
Свойства
УВ имеют исключительно высокую теплостойкость: при тепловом воздействии вплоть до 1600—2000 °С в отсутствии кислорода механические показатели волокна не изменяются. Это предопределяет возможность применения УВ в качестве тепловых экранов и теплоизоляционного материала в высокотемпературной технике. На основе УВ изготавливают углерод-углеродные композиты, которые отличаются высокой абляционной стойкостью. УВ устойчивы к агрессивным химическим средам, однако окисляются при нагревании в присутствии кислорода. Их предельная температура эксплуатации в воздушной среде составляет 300—350°С. Нанесение на УВ тонкого слоя карбидов, в частности SiC, или нитрида бора позволяет в значительной мере устранить этот недостаток. Благодаря высокой химической стойкости УВ применяют для фильтрации агрессивных сред, очистки газов, изготовления защитных костюмов и др. Изменяя условия термообработки, можно получить УВ с различными электрофизическими свойствами (удельное объёмное электрическое сопротивление от 2·10^-3 до 10^6 ом/см) и использовать их в качестве разнообразных по назначению электронагревательных элементов, для изготовления термопар и др.
Активацией УВ получают материалы с большой активной поверхностью (300—1500 м²/г), являющиеся прекрасными сорбентами. Нанесение на волокно катализаторов позволяет создавать каталитические системы с развитой поверхностью.
Обычно УВ имеют прочность порядка 0,5—1 Гн/м² и модуль 20—70 Гн/м², а подвергнутые ориентационной вытяжке — прочность 2,5—3,5 Гн/м² и модуль 200—450 Гн/м². Благодаря низкой плотности (1,7—1,9 г/м³) по удельному значению (отношение прочности и модуля к плотности) механических свойств УВ превосходят все известные жаростойкие волокнистые материалы. На основе высокопрочных и высокомодульных УВ с использованием полимерных связующих получают конструкционные углеродопласты. Разработаны композиционные материалы на основе УВ и керамических связующих, УВ и углеродной матрицы, а также УВ и металлов, способные выдерживать более жесткие температурные воздействия, чем обычные пластики.
Применение
УВ применяют для армирования композиционных, теплозащитных, хемостойких в качестве наполнителей в различных видах углепластиков. Наиболее емкий рынок для УВ в настоящее время — производство первичных и вторичных структур в самолетах «Боинг» и «Аэробус» (до 30тн на одно изделие). По причине резко возросшего спроса в 2004-2006г.г. на рынке наблюдался большой дефицит волокна, что привело к его резкому удорожанию.
Из УВМ изготовляют электроды, термопары, экраны, поглощающие электромагнитное излучение, изделия для электро- и радиотехники. На основе УВ получают жесткие и гибкие электронагреватели, в том числе ставшие полулярными т.н. «карбоновые нагреватели», обогреваемую одежду и обувь. Углеродный войлок — единственно возможная термоизоляция в вакуумных печах, работающих при температуре 1100 С и выше. Благодаря химической инертности углеволокнистые материалы используют в качестве фильтрующих слоев для очистки агрессивных жидкостей и газов от дисперсных примесей, а также в качестве уплотнителей и сальниковых набивок. УВА и углеволокнистые ионообменники служат для очистки воздуха, а также технологических газов и жидкостей, выделения из последних ценных компонентов, изготовления средств индивидуальной защиты органов дыхания. Широкое применение находят УВА (в частности, актилен) в медицине для очистки крови и других биологических жидкостей. В специальных салфетках для лечения гнойных ран, ожогов и диабетических язв — незаменима ткань АУТ-М, разработанная в начале 80-х годов и опробованная в Афганистане (http://www.health-ua.com/articles/2291.html). Как лекарственное средство применяют при отравлениях (благодаря высокой способности сорбировать яды. Например препарат «Белосорб», или АУТ-МИ на основе светлогорского сорбента), как носители лекарственных и биологически активных веществ. УВ катализаторы используют в высокотемпературных процессах неорганических и органических синтеза, а также для окисления содержащихся в газах примесей (СО до CO2, SO2 до SO3 и др.).
Ссылки
[1] К. Перепелкин, «Текстиль» 2 (4), 2003
[2] С. Симамура. Углеродные волокна. М.: «Мир», 1987 г.
[3] Конкин А. А., Углеродные и другие жаростойкие волокнистые материалы, М., 1974.
Wikimedia Foundation. 2010.
Углеродное волокно: технологии в области строительства набирают силу
Главная страница » Углеродное волокно: технологии в области строительства набирают силу
Инновационные применения технологии углеродного волокна в строительстве оцениваются специалистами в плане полезности и экологической безопасности оптимальным выбором. Теперь продавцы недвижимости главным критерием продаж называют вес жилого дома. Поэтому запрос на углеродное волокно в строительстве видится вполне актуальным, судя по конструкции проекта «Dymaxion».
СОДЕРЖИМОЕ ПУБЛИКАЦИИ :
Аргументы для технологий современного строительства
Проект состоит из легкой алюминиевой обшивки листовым металлом. Обшивку держит только одна центральная мачта. Масса такой постройки составляет всего 1,5 тонны (примерно 10% веса стандартного проекта жилого дома средней величины).
Акцентирование на массе строительных конструкций становится важным аспектом современности, учитывая постоянно растущее воздействие на окружающую среду транспортировки сырья и обработанных материалов по всей планете.
Автомобильная и аэрокосмическая промышленность достигли значительных успехов, применяя стратегию «облегчения», используя новые и более лёгкие материалы, уменьшая тем самым вес компонентов. Инновационный подход позволил авиакомпаниям значительно увеличить эффективность использования топлива (на 125% за период 1978-2017 гг.).
Углеродное волокно всё чаще используется для изготовления различных сверхлёгких конструкций, начиная от кузовов автомобилей «Формулы-1», завершая велосипедными рамами.
Изготовленные из углеродных нитей, обычно вплетаемых в ткань, углеродное волокно часто покрывают смолой или термопластами для создания композитов, обладающих высоким отношением прочности к весу. В результате получается материал:
- в пять раз прочнее,
- в пять раз легче,
- в два раза жёстче,
традиционной стали, материал, сравнительно легко переносящий воздействия тепла и коррозии. Эти рабочие свойства делают углеродное волокно идеальным материалом для применения в экстремальных условиях.
Углеродное волокно под строительство зданий разного типа
Несмотря на относительно высокую стоимость углеродного волокна, архитекторы и строительные инженеры стараются активно использовать углеродное волокно под строительство зданий, а также различных инфраструктурных проектов.
КАРБОН
Павильон «BUGA 2019» — одна из демонстрационных современных конструкций, созданная на основе инновационного строительного материала – волокнистого углепластикаНапример, специалисты Института вычислительного проектирования и строительства, принадлежащего университету Штутгарта, использовали углеродное волокно в качестве основного строительного материала одной из последних работ. Речь идёт о проекте волоконно-оптического павильона «BUGA 2019» года в Германии, где купол созданный:
- из рёбер,
- из стекла,
- из углеродного волокна,
заключенных в прозрачную мембрану ЭТФЕ (сополимер этилен/тетрафторэтилен).
Сооружение структуры выполнялось запрограммированными роботами, которыми осуществлялась доставка более 150 000 волокнистых нитей в пространственном расположении. Применяя разный тип и плотность волокна, строители получили возможность вариаций в зависимости от структурных нагрузок.
Разработанные для имитации биологических систем, углеродные волокна окружают прозрачные стеклянные волокна, образуя связанные элементы структуры, напоминающие изогнутые мышечные ткани.
Примеры прочности конструкций на углеродном волокне
По словам специалистов, один волокнистый компонент способен выдерживать около 25 тонн веса – массу примерно 15 автомобилей. Купол, имеющий свободный пролёт около 23 метров, укрывающий площадь пола 1312 м2, состоит из 60 таких компонентов, каждый из которых несёт массу не более 5 кг/м2.
Несмотря на тот момент, что работа принимает форму демонстраций на заказ, другая исследовательская группа широко внедряет углеродное волокно в общественной инфраструктуре.
Так, центром перспективных конструкций и композитов Университета штата Мэн разработана система композитных арочных мостов из углеродного волокна, армированного бетоном.
Предназначенная для однопролётных мостов длиной до 20 метров, система содержит серию труб из углепластика, заполненных бетоном непосредственно на месте, а затем покрытых железобетонным настилом.
ИНСТРУМЕНТ
Система «Bridge-in-a-Backpack»: 1 – композитный настил; 2 – гравийная засыпка; 3 – композитная арка; 4 – бетонное основание; 5 – боковая стена; 6 – композитный экзоскелет; 7 – бетонное ядроПодобно надувным плотам, трубы из углепластика транспортируются на площадку в компактном сложенном состоянии — отсюда и название проекта «Bridge-in-a-Backpack» («Мост в рюкзаке).
Согласно информации центра университета, арки легко транспортируются, быстро разворачиваются и не требуют тяжёлого оборудования или крупных бригад строителей, привлекаемых в условиях обычного строительства.
Свойство лёгкости – главное преимущество нового материала
Помимо свойства лёгкости, трубы из углепластика служат бетонной опалубкой, чем устраняется необходимость в дополнительных материалах. Углепластиковые трубы также выполняют функцию коррозионного армирования бетона, обладая явным преимуществом перед сталью, которая подвержена ржавчине.
Основываясь на этих многочисленных преимуществах, система на данный момент использовалась для создания уже 23 мостов.
Отмеченные примеры демонстрируют, насколько свойство лёгкости, помимо прочих свойств материала, даёт углеродному волокну преимущество в строительстве. Но как работает это свойство лёгкости, когда проект, кроме всего прочего, требует повышения устойчивости?
Специалисты исследовательского центра Института перспективных инноваций в Ноксвилле штата Теннеси отвечают на вопрос неоднозначно. Углеродное волокно обладает ярко выраженным потенциалом лёгкого веса, но при этом требует массу энергии.
Согласно исследованию, проведенному Министерством энергетики США и специалистами Национальной лаборатории, для типичного композита углепластика требуется в среднем 800 МДж/кг. Для сравнения: сталь требует 50 МДж/кг, что приводит к получению соотношений экономии 1:16 и 1:22, соответственно.
ТКАННОЕ
Полиакрилонитриловые нити – материал, массово являющийся компонентом современных углепластиков – продукт производства нефтехимической промышленностиКроме того, на каждую тонну произведенного углеродного волокна выбрасывается 20 тонн углекислого газа. Углеродное волокно также тесно связано с ископаемым топливом, поскольку наиболее распространенным сырьём является полиакрилонитрил, материал-прекурсор, производимый в нефтехимической промышленности.
Химически активированные смолы или полимеры, обычно используемые для получения углепластика, также являются производными нефти.
Энергетические потребности при транспортировке
Однако для конкретных применений углеродное волокно находит компромисс между эксплуатационной и внедрённой площадью. Углеродное волокно – материал, способный привести к значительному сокращению энергетических потребностей при транспортировке.
Так, если конструкция кузова автомобиля на 30% легче благодаря использованию углеродного волокна, выброс 50 тонн углекислого газа сокращается примерно до 1 тонны за 10 лет эксплуатации.
Если конструкция фюзеляжа самолета на 20% легче за счёт использования углеродного волокна, при тех же условиях эксплуатации ожидается сокращение углекислого газа на 1400 тонн.
КАРБОН
Что-то в этом роде можно представить, если рассматривать концепцию карбонового фюзеляжа и других компонентов современного самолётаТак имеет ли материал экологический смысл для неподвижных зданий? Уменьшение массы и объема материала может оказать положительное влияние на большинстве этапов жизненного цикла здания, поскольку для транспортировки, установки и возможной разборки требуется меньше топлива и тяжелой техники.
Тем не менее, рабочий аргумент в пользу углеродного волокна является более сложным аргументом для зданий в отношении экономии энергии. Правда, устойчивость материала к чрезмерному нагреву и деградации окружающей среды — критерии продления срока службы здания и сокращения объёмов технического обслуживания.
Использование углеродного волокна и строительная архитектура
Чтобы принять обоснованное решение о том, использовать ли углеродное волокно в архитектуре, проектная группа должна провести всестороннюю оценку воплощенных и эксплуатационных воздействий в течение ожидаемого срока службы здания. Другое критическое соображение, которое здесь не затронуто — конечная стоимость.
С точки зрения экологии, характеристики материала должны улучшаться:
- за счёт более широкого использования сырья на биологической основе,
- более эффективных производственных процессов,
- растущих темпов переработки.
Поскольку углеродное волокно рассматривается всё чаще экологически более выгодным строительным материалом, мечта относительно замены тяжеловесных зданий сверхлёгкой архитектурой постепенно приближается к реальности.
При помощи информации: ArchitectMagazine
Углеродное волокно – восстановление здоровья или одно из самых эффективных лечений современности
Что такое углеродное волокно и за счёт чего оно может лечить и восстанавливать здоровье ? За счет чего углеродная ткань обладает такой уникальной целительной силой?
Для некоторых, углеродная ткань не представляет никакой ценности, в силу отсутствия каких-либо знаний об этом материале и его уникальных свойствах.
Углеродный текстильный материал на самом деле может помочь вашему организму задействовать свои природные возможности по регенерации и восстановлению больных, поврежденных органов и тканей.
В народе иногда данный текстильный материал называю «черный подорожник» отождествляя его с природным целительным растением.
Вся его ценность кроется в том, из чего его производят и каким образом.
Углеродное волокно получают термической обработкой химических полимерных (ПАН) или природных органических волокон (вискозных) за счет их поэтапной высокотемпературной обработки (до 3000°C). Содержание углерода в готовом волокне составляет 92-99,99 %.
Если при производстве углеродного волокна полиакрилонитрил (ПАН) используется в большей степени как композит конструкционный, где определяющим является прочность, то вискозное волокно в высокотемпературных процессах дополняет и замещает графит. Поэтому, вискозное углеродное волокно и применяется в первую очередь, как углеродный материал, а не как сверхпрочный конструкционный.
Само же по себе исходное вискозное волокно (белое) — это искусственное химическое волокно из гидратцеллюлозы, полученное в свою очередь из природной целлюлозы в процессе многоступенчатой щелочной обработки. Гидратцеллюлоза характеризуется высокими сорбционными свойствами, гигроскопичностью и большей способностью к гидролизу, этерификации и окислению. Поэтому в основу лечебных свойств углеродного волокна и ткани заложено именно вискозное волокно.
Упрощённо схему получения вискозного материала (основного сырья для углеродного материала) можно представить следующим образом:
Далее готовое вискозное волокно в виде ткани или нити передается на высокотемпературную обработку, где уже формируется само углеродное волокно:
Углеродный волокнистый сорбент производится на основе пиролиза (разложения органических природных соединений при недостатке кислорода) с последующей активацией волокон на основе вискозы. Такой материал характеризуются микропористой структурой, предназначенной для сорбции вредных веществ. Изменяя условия процесса активации можно улучшать сорбционные свойства материала за счет увеличения объема микропор. Углеродный волокнистый материал обладает отличными сорбционными свойствами (1 гр. может поглотить до 50 гамм нефтепродуктов).
В готовом виде углеродное волокно состоит из микро нитей диаметром до 15 микрон, полученных в основном атомами углерода. Атомы углерода объединены в микро- кристаллы, выстроенные параллельно друг другу в виде слоев графита. При нагреве и вытяжке угловое расположение этих слоев может значительно изменяться. Ориентация углеродных слоев становится более совершенной при увеличении температуры термообработки. Поры волокна сориентированы вдоль своей оси. Их объемная доля увеличивается с повышением температуры и уменьшается при вытяжке.
Регулируя процесс термообработки, можно получить углеродное волокно с различными электрофизическими свойствами.
Исходя из сложной морфологической структуры элементарного углеволокна, данный материал обладает способностью образовывать стабильные цепи, обеспечивающие разнообразие органических соединений. Углеродная ткань уникальна и тем, что воздух проходя через ее волокна насыщается отрицательными ионами, что благотворно влияет на весь организм, исцеляя его от многих болезней.
Исходя из природных свойств исходного сырья, самой технологии его переработки и рождаются полезные свойства этого материала, который может быть представлен в виде углеродных салфеток, повязок, жгутов и других текстильных и трикотажных изделий.
Уникальность углеродной ткани, как средства для восстановления здоровья заключается в его :
- высоких сорбционных свойствах
- способности сохранять инфракрасное излучение, исходящее от самого источника
Высокие сорбционные свойства углеродного волокна способствуют эффективному снятию воспалительных процессов, повреждений различной этиологии и стимуляции роста жизнеспособных грануляций. Восстановление поврежденных тканей и органов происходит в 2 раза быстрее по сравнению с обычными методами лечения.
Сложная структура углеродной ткани, её волокнистость и одновременно токопроводность, обеспечивают применение материала в качестве экрана от электромагнитных излучений.
В свою очередь данное свойство может позитивно влиять и на здоровье — способствовать регенерации и стимуляции иммунной системы человека за счет возможности возврата этого излучения тем клеткам, органам и системам, которые они излучают сами на тех же частотах.
Кроме электромагнитного излучения такой углеродной ткани свойствены нейтральность к воде, высокой температуре, агрессивным средам и она обладает высокой поглощаемостью запахов. Свойство переотражения инфракрасного излучения способствует созданию эффекта сухого тепла, направленного на регенерацию и восстановление поврежденных органов и тканей, стимуляцию иммунной системы.
Процесс регенерации и восстановления органов является сегодня одной из актуальных тем биологии и современной медицины. Ученые всего мира до конца не могут понять, почему у одних живых организмов процесс восстановления тканей присущ (пресмыкающиеся и тому подобные), а для других нет. Загадка кроется в этапе эмбрионального начала развития организма, когда этот процесс вполне осуществим, за счет пиковой активности регенерирующей функции организма. И все усилия сводятся к тому, чтобы разбудить мозг и заставить вспомнить этот этап и активировать эту природную возможность.
Конечно, современная медицина в своем идеале имеет определенные подходы в решении такой проблемы. Есть утверждения, что процесс регенерации тканей живого организма возможен только с помощью стволовых клеток, которых во взрослом организме очень ограниченное количество. Именно с детородной функции образуются первые стволовые клетки, с которых начинается развитие органов и тканей человека. Поэтому целью современной науки и является поиск методов и способов активизации организма к воспроизводству этих, уникальных своего рода, клеток.
Пытаясь раскрыть тайну регенерации тканей и проводя исследования над организмами, обладающими такими способностями (ящерицы, моллюски, саламандра), учёные Австралийского института регенеративной медицины сделали заявление, что в основе регенерационной способности организма лежат клетки иммунной системы, которые предназначены переваривать отмершие клетки, грибки и бактерии, отторгнутые организмом и способствовать созданию на их основе здоровых, в прямом смысле этого слова.
Долгие эксперименты на саламандрах позволили специалистам сделать заключение, что именно клетки иммунной системы формируют особые химические вещества, которые создают основу регенеративного процесса. Активировать регенерационные процессы, в человеческом организме, возможно только добавив в него определенные специальные компоненты или пробудив саму иммунную систему выполнять свои врожденные функции.
Вот в этом как раз и проявляются лечебные свойства углеродной ткани, как источника инфракрасного излучения от тех же органов, которые его излучают, пробуждая тем самым иммунную систему человека на восстановление больных клеток, органов и систем!
Для этих целей успешно используется текстильный углеродный сорбент медицинского назначения в виде углеродных салфеток, повязок, жгутов, поясов, шорт, нарукавников, наколенников, масок для сна и углеродных вкладышей для постельного белья.
В заключение хотелось бы отметить, что углеродное волокно на вискозной основе представляет из себя сложной морфологической структуры продукт на природной основе, созданный в процессе его высокотехнологичной обработки.
Из-за своей уникальности и относительной дороговизны, данный материал ограничен объемами своего производства в мировых масштабах. Учитывая свою техническую и социальную значимость, данный материал является дефицитным продуктом.
Углеволокно — что это такое
Материал из тончайших нитей (от 3 до 15 микрон), основу которых составляют атомы углерода, сгруппированные в малюсенькие кристаллы и находящиеся параллельно один к другому, называется углеродным волокном. Благодаря тому, что кристаллы строго выравнены, волокно весьма плохо растягивается.
Углеволокно бренда fibarm и любого другого, инертно к химическим веществам, обладает малым удельным весом, способно хорошо натягиваться, с низким коэффициентом температурного расширения, термической стойкостью.
Из чего складывается цена
Кто хоть раз интересовался стоимостью углеволокна, знает, что она весьма высокая. Объясняется это необходимостью больших затрат электроэнергии при его производстве.
Однако полученный продукт с лихвой компенсирует такой «недостаток» своими великолепными технико-физическими данными.
В качестве сырья берут химические волокна органического происхождения или природные. После специальной их обработки под воздействием очень высокой температуры от них остаются только атомы углерода.
Термообработка проводится в несколько стадий:
- Сначала при +250 градусах первичная структура окисляется.
- Далее исходное вещество нагревают при 1500 градусов в азотной среде, чтобы они карбонизировались. После этого они приобретают структуру, похожую на графит.
- В завершении проводится графитизация при температуре 3000 градусов. В этот период волокна становятся на 99% чисто углеродными.
Использование
Углеродное волокно с успехом применяют в производстве карбонов (carbone переводится как «углерод»), то есть карбонопластиков, который также называют углепластиком. Эти композиционные материалы представляют собой переплетенные нити рассматриваемого волокна, помещенные в эпоксидную или сделанную из других полимерных смол матрицу.
Данные продукты отличаются малым весом, прочностью выше стали, жесткостью. Они применяются в таких сферах:
- энергетика;
- строительство – материалы с композитами;
- машиностроение;
- производство товаров народного потребления, бытовых приборов, электротехники, спортинвентаря;
- авиационная и космическая промышленность;
- медицина (электроды) и т.д.
Скорее всего, со временем область применения углеволокна станет еще шире. С каждым днем все больше производств используют этот материал в своей деятельности и это далеко не предел, так как он превосходит многие в силу своих характеристик.
Углеродное волокно 101: понимание переплетений и тканей
После того, как углеродные волокна были изготовлены и проклеены по размеру, они часто вплетаются в ткани. Чтобы начать создавать ткани, производители создают пучки углеродных волокон, называемые жгутом. Жгуты оцениваются в соответствии с их содержанием волокна или нити, обычно обозначаются как 3k, 6k, 12k и 15k. Буква k означает «тысяча», что означает, что жгут длиной 3k состоит из 3000 углеродных нитей. Так как одна прядь углеродного волокна имеет толщину всего около 5-10 микрон, жгут 3k может быть только около.125 дюймов толщиной. Тогда жгут 6k будет примерно в два раза толще, чем жгут 3k, 12k в четыре раза толще и так далее. Большое количество прочных углеродных волокон в таком компактном пространстве — вот что придает материалам из углеродного волокна невероятную прочность.
Плетение из углеродного волокна
Катушки из углеродного волокна вплетаются в ткань на ткацком станке. Наиболее распространены полотняное переплетение, саржа и жгут из атласа.
Ткань полотняного переплетения или 1×1 из углеродного волокна симметрична и напоминает шахматную доску.Жгуты тканы по узору сверху / снизу, что дает плотно переплетенные волокна, которые обладают высокой стабильностью. Стабильность ткани означает способность материала сохранять ориентацию волокон и угол переплетения. Углеродная ткань с полотняным переплетением из-за высокой прочности не подходит для сложных контуров, поскольку она не особенно гибкая. Однако с ним проще обращаться, не создавая искажений на ткани. Поэтому он хорошо подходит для плоских листов, труб и двумерных кривых.
Обжим — это кривизна одиночного волокна в переплетении, а ткань из углеродного волокна с полотняным переплетением имеет резкий изгиб из-за плотных переплетений в жгутах. Этот резкий обжим может создать стрессовые ситуации, которые со временем вызовут слабые места.
Саржевое переплетение состоит из рисунка 2×2 или 4×4 и является наиболее широко признанным типом углеродного волокна. В переплетении 2×2 каждая буксировка проходит через две буксиры, а затем — через две. Таким образом, очевидно, что переплетение 4×4 состоит из того, что каждый буксир проходит через четыре буксира, а затем через четыре буксира. Это переплетение с пере / недоразвитием создает отчетливый диагональный рисунок. Расстояние между переплетениями жгута при саржевом переплетении больше, чем при полотняном переплетении. Следовательно, происходит меньше изгибов, что снижает вероятность возникновения точек напряжения.
Саржевое переплетение податливо и может формировать сложные контуры, сохраняя при этом хорошую стабильность. С ней нужно обращаться более осторожно, чем с тканью полотняного переплетения, чтобы не допустить искажения переплетения. Плетение 4×4 легче сформировать, чем плетение 2×2, но оно также имеет меньшую устойчивость ткани.
Атласное переплетение использовалось на протяжении тысячелетий для придания шелковой ткани прекрасного драпирующего качества, оставляя ткань гладкой и бесшовной. При использовании в композитах из углеродного волокна атласное переплетение дает возможность легко формировать сложные контуры. Очевидно, это означает, что атласные переплетения также обладают меньшей стабильностью, чем другие переплетения.
Самыми распространенными типами атласного переплетения для жгутов являются четыре сатиновых жгута (4HS), пять сатиновых жгутов (5HS) и восемь атласных жгутов (8HS).Число указывает на общее количество пропущенных и пропущенных буксиров. Например, переплетение 4HS состоит из трех пропущенных жгутов и одной пропущенной снизу. Для 5HS четыре буксира пропущены, а затем одна ниже, а 8HS — это семь буксиров, пропущенных сверху и одна ниже. Чем выше номер атласного переплетения, тем он более пластичный и менее устойчивый.
Существует ряд других переплетений, которые можно использовать для создания тканей из углеродного волокна. К ним относятся плетение рыбы, жгут, косы, однонаправленное плетение и нестандартное плетение.Каждое переплетение обладает уникальными свойствами, благодаря которым оно отлично подходит для одних дизайнов и не подходит для других. При определении того, какое плетение из углеродного волокна следует использовать для той или иной функции, необходимо учитывать множество факторов. Эти факторы включают прочность, формуемость, стабильность и обжатие. Производители углеродного волокна знают, какую ткань использовать для какого дизайна.
Практическое применение решений из углеродного волокна
Композиты из углеродного волокна DragonPlate ™ имеют удивительные характеристики, которые делают их привлекательными для широкого круга клиентов.Среди его многочисленных приложений перечислены ниже.
Промышленная автоматизация и робототехника
Промышленная автоматизация и робототехника — это область, в которой начинают осознавать преимущества конструкций из углеродного волокна. Для многих приложений способность уменьшить вес и повысить жесткость конструкции напрямую отражается на более быстром времени отклика и уменьшении нагрузок на двигатель и привод. Это, в свою очередь, приводит к повышению производительности и увеличению продолжительности циклов технического обслуживания. В сфере автоматизации, где машины часто работают с максимальной скоростью 24 часа в сутки, 7 дней в неделю, снижение инерционных нагрузок за счет замены компонентов из тяжелого металла на оптимизированные конструкции из углеродного волокна может, в свою очередь, сократить время изготовления деталей, что значительно увеличивает рентабельность.В таких случаях окупаемость инвестиций из-за увеличения стоимости материалов, связанных с углеродным волокном, часто бывает очень короткой.
DragonPlate трубы большого диаметра, косынки и листы из углеродного волокна могут быть легко собраны в каркасы для самых разных роботизированных приложений. Для применений, где нагрузки и прогибы имеют большое значение, DragonPlate также может настроить укладку или размеры углеродного волокна в соответствии со спецификациями заказчика.
Один из недавних примеров материалов из углеродного волокна DragonPlate — из мира коммерческих роботов.Компания International Climbing Machines создала революционного робота для лазания по стенам, шасси которого почти полностью изготовлено из углеродного волокна DragonPlate. Этот робот используется в атомной промышленности, при проверке самолетов и во многих других областях, где окружающая среда либо чрезвычайно сурова для людей, либо способность подниматься боком и вверх ногами приведет к значительному сокращению рабочего времени (как в случае проверки фюзеляж или крыло самолета). Заменив оригинальную металлическую конструкцию на конструкцию из DragonPlate, компания ICM смогла значительно повысить производительность робота и способность переносить полезную нагрузку.
Натяжные ролики из углеродного волокна
Dragonplate производит широкий спектр труб из углеродного волокна, используемых для промежуточных роликов, от стандартных труб с модулем упругости с жесткостью, сравнимой с алюминием, до труб со сверхвысоким модулем, более жестких, чем сталь.
БПЛА и дроны
От любителя до профессионала Dragonplate предлагает строительные материалы, которые понадобятся вам для создания практически любого дрона. Наша серийная линия плоских листов из углеродного волокна, плетеных и свернутых в рулон трубок, уголков и широкого спектра пултрузионных материалов обеспечивает все необходимое. Наша запатентованная система соединителей для пултрузионных труб, а также наши модульные соединители для труб в оплетке и рулонах обеспечивают идеальный метод изготовления рам, особенно для многороторных вертолетов. Для сборки также доступны различные конструкционные эпоксидные смолы и крепежные детали.
Подробнее об использовании композитов из углеродного волокна DragonPlate для создания БПЛА и дронов
БПЛА и дронов
Углеродное волокно для внутренней отделки морских судов и самолетов
Dragonplate предлагает широкий выбор готовых продуктов и услуг по изготовлению на заказ для поддержки индустрия роскошных интерьеров яхт и самолетов.Будь то частный, корпоративный или государственный заказчик, композиты из углеродного волокна могут принести пользу вашим проектам двумя способами: уменьшением веса и уникальностью высоких технологий. Это особенно верно при проектировании интерьера для самолета, поскольку каждый сэкономленный фунт означает повышение эффективности и дополнительную полезную нагрузку в других частях транспортного средства. Вес и баланс также важны для больших яхт, где также может помочь снижение веса над ватерлинией.
Узнать больше о внутренней отделке судов и самолетов из углеродного волокна
Внутренние части для судов и самолетов
Инструменты и производственные приспособления для аэрокосмической отрасли
Проблема с большими инструментами, особенно с инструментами для производства самолетов, заключается в том, что они могут быть очень большими, а значит, тяжелыми и сложными двигаться.Dragonplate регулярно помогает клиентам снизить вес инструмента на 50% и более. Используя расчеты FEA, в некоторых случаях возможно снижение веса до 75% по сравнению со старыми алюминиевыми и стальными инструментами и приспособлениями.
Корпуса для электроники из углеродного волокна
Легкие корпуса для электроники из углеродного волокна обладают несколькими преимуществами. Основная причина, по которой наши клиенты выбирают углеродное волокно для этих целей, — это снижение веса. В дополнение к уменьшенному весу и увеличению собственной частоты корпуса для электроники из углеродного волокна сохраняют допуски на размеры в гораздо более широком диапазоне температур, чем пластиковые или металлические корпуса.Коэффициент теплового расширения (КТР) углеродного волокна примерно такой же, как у инвара, что значительно снижает тепловые проблемы для чувствительной электроники, лазера, зеркал и датчиков.
Композитные радиолокационные системы
Dragonplate строит радиолокационные системы для военных целей более десяти лет. Преимущество углеродного волокна, стекловолокна и кевлара в таком устройстве очевидно, если учесть проблемы перемещения оборудования в удаленные места. Легкие композиты из углеродного волокна могут означать разницу между тем, что переносят, и системой, которую необходимо перемещать на автомобиле.И даже радарные системы, устанавливаемые на транспортных средствах и самолетах, значительно выигрывают от снижения веса.
Приложения для медицинской визуализации, рентгеновского и гамма-излучения
Углеродное волокно быстро стало одним из основных материалов, используемых в медицинских устройствах для получения изображений, рентгеновского и гамма-излучения. В частности, углеродное волокно обеспечивает рентгенопрозрачный материал, обладающий достаточной прочностью и жесткостью, чтобы сохранять критические размеры под нагрузкой, и не разрушается с течением времени даже после высоких доз рентгеновского и гамма-излучения.
Метрология и научное оборудование
Углеродное волокно быстро становится одним из лучших материалов в области метрологии из-за его высокой стабильности и низкого теплового расширения. В приложениях, где тепловые изменения будут вывести сопоставимые металлические инструменты для измерения и центровки за пределы допуска из-за расширения или сжатия материала, углеродное волокно останется практически неизменным в широком диапазоне температур.
Tactical Military и SWAT Gear
Dragonplate регулярно сотрудничает как с военными, так и с полицией SWAT для разработки новых и инновационных решений тактических проблем.Ключевым примером является наша запатентованная система лестниц из углеродного волокна, которая началась с того, что члены сообщества спецназа запросили оборудование, которое было бы легче, портативнее и прочнее, чем существующие телескопические и складные лестницы, которые у них были. Сотрудничество между Dragonplate и солдатами включало в себя оценку и отзывы о ранних моделях, что позволило нашей команде создать продукт, специально разработанный для удовлетворения требований морских пехотинцев и спецназа армии и флота, с которыми мы работали.
Предметы роскоши и корпоративные подарки из углеродного волокна
Dragonplate предлагает широкий спектр композитных материалов, которые можно использовать в корпоративных и исполнительных подарках, индивидуальных наградах, трофеях, медалях и других подобных приложениях. Углеродное волокно придаст вашему проекту высокотехнологичный и стильный вид. Dragonplate тесно сотрудничает с компаниями, занимающимися индивидуальными наградами и корпоративными подарками, чтобы эти продукты выделялись среди других.
Углеродное волокно для выставок и дизайна интерьера
Углеродное волокно все чаще используется при строительстве выставочных стендов и в более общем контексте дизайна интерьера, как для снижения веса, так и для высоких технологий, связанных с углеродом композиты. DragonPlate предлагает широкий ассортимент готовой продукции для создания высококлассных кабин или интерьеров.
Музыкальные инструменты
Полосы из углеродного волокна служат во многих сферах применения при изготовлении музыкальных инструментов, где такие свойства материала, как малая масса и высокая жесткость, делают их идеальным выбором. Полосы из углеродного волокна или наша D-образная трубка, на которую подана заявка на патент, могут использоваться в различных конфигурациях для усиления горловины в деревянных шейках. Короткие полосы можно использовать для усиления шарнира головной бабки.Полосы из углеродного волокна могут быть использованы для крепления гитары, где его можно использовать в сочетании с бальзой или елью в качестве придающего жесткость ламината. Полосы могут использоваться в решетчатых опорных связях верхней пластины, чтобы обеспечить большее утонение и усиление отклика. Некоторые производители нашли другие творческие применения в использовании полос из углеродного волокна в качестве продольных внутренних опор для снижения нагрузки на верхние звуковые пластины. Благодаря своей высокой прочности на сжатие / растяжение и малой массе, а также отличному сцеплению с эпоксидными и цианоакрилатными клеями, углеродное волокно является дверью для приборостроения нового поколения.
Одним из наиболее распространенных способов использования углеродного волокна при изготовлении и ремонте струнных инструментов является армирование грифа. Справа приведен пример того, как углеродное волокно может быть использовано для большей устойчивости шеи и уменьшения скручивания. Это поперечное сечение грифа показывает один из возможных способов установки углеродного волокна. Ориентация полос из углеродного волокна определяется размерами поперечного сечения вашей шеи.
Мебель из углеродного волокна
Углеродное волокно все чаще используется в производстве мебели.Производители мебели используют углеродное волокно из-за его легкого веса, прочности и внешнего вида. Углеродное волокно может придать мебели вид «высокотехнологичного» или «элитного», уменьшив при этом ее общий вес.
Композиты из углеродного волокна: свойства | методы производства
Большинство композитов из углеродного волокна обладают устойчивостью к температуре 70-120 o C. Для обеспечения долговременной устойчивости к температуре до 150-250 o C требуются некоторые специально разработанные смолы, а композит из углеродного волокна должен подвергаться отверждение при высокой температуре в течение многих часов.Это недостаток композитов из углеродного волокна по сравнению с металлами, устойчивыми к высоким температурам.
В случае композитов из углеродного волокна требуются некоторые дорогостоящие материалы (например, фенольные препреги) для обеспечения устойчивости к высоким температурам, а также к высокотемпературному отверждению композита.
Хотя металлы имеют высокую температуру плавления, на практике предполагается, что металлы изменяют свои свойства при температуре ~ 300 ° ° C в случае алюминия, 750 ° ° C в случае стали и 860 o C в случае титана. Инженер-конструктор может получить материал, который обладает всеми необходимыми свойствами, которые дают металлам преимущество — и никакой дополнительной обработки в производственном процессе не требуется.
Ориентация волокна — отсутствие изотропного материала
В отличие от металлов композиты из углеродного волокна являются анизотропными материалами.
Следовательно, такие свойства композита, как жесткость, зависят от ориентации волокон. В случае металлов свойства всегда одинаковы, независимо от ориентации, и эти материалы называются изотропными.Это существенная разница между композитами из углеродного волокна и металлами. Композиты из углеродного волокна похожи на древесину, прочность и жесткость которой зависят от текстуры и рисунка колец .
При производстве элементов из углеродного волокна принимается решение относительно ориентации углеродных волокон и типа ткани. Существуют, например, однонаправленные ткани (UD), двунаправленные ткани (например, однотонные или саржевые), а также ткани, изготовленные из некоторых различно ориентированных тканей UD — e. г. двухосный, трехосный. Этот производственный процесс позволяет получить оптимальный композит, а именно обеспечить большее количество тканей в местах, подверженных высокой нагрузке, и уменьшить количество тканей в местах, где нагрузка ограничена.
Кроме того, помимо контроля количества тканей и толщины элемента, этот процесс также обеспечивает контроль ориентации ткани в зависимости от нагрузки на практике. Таким образом, вы можете значительно уменьшить вес элемента по сравнению с металлическим.Однако это требует определенных знаний и опыта от инженеров-конструкторов.
Если для данного элемента требуется прочность в каком-либо конкретном направлении, углеродная ткань должна быть равномерно ориентирована под углом 0, -45, + 45, 90 градусов, чтобы обеспечить квазиизотропную структуру, аналогичную той, которая встречается в металлах.
КОМПОЗИТЫ ИЗ УГЛЕРОДНОГО ВОЛОКНА — МЕТОДЫ ПРОИЗВОДСТВА
В зависимости от объема производства, конструкции элемента, размера и требуемых свойств, а также эстетики, существует несколько методов производства композитов из углеродного волокна.
Ручное ламинирование
Это очень простой метод производства композитов из углеродного волокна, который часто используется для производства композитов из стекловолокна. Эта технология используется для деталей простого дизайна без особых эстетических и конструктивных требований, которые изготавливаются вручную с помощью валика и кисти. Некоторые недостатки, связанные с этим методом, включают плохую повторяемость, воздушные пустоты внутри углеродного композита и повреждение плетения. Этот метод производства не требует дорогостоящего оборудования, такого как автоклавы или термопрессы.
Вакуумная упаковка
Технология, использующая вакуумный мешок, была разработана на основе ручного ламинирования. Начальные шаги идентичны ручному ламинированию, когда смола наносится вручную с помощью валика или кисти, а затем размещаются слои ткани из углеродного волокна. Разница связана с использованием вакуумного мешка на заключительном этапе. Как следует из названия, вакуумный мешок обеспечивает герметизацию вокруг формы для удаления воздуха с помощью вакуумного насоса. Создаваемый вакуум обеспечивает адгезию углеродных волокон к поверхности и давление на форму.
Несмотря на некоторые теоретические преимущества, связанные с уплотненным ламинатом, производство с вакуумным мешком не предотвращает образование воздушных пустот, которые очень распространены в этом методе, поэтому он иногда используется для производства деталей и деталей из углеродного волокна. Если высокое качество не требуется, используется ручное производство, тогда как если высокое качество является приоритетом, то предпочтительны инфузия смолы, препрег или технология горячего прессования.
Настой смолы
В отличие от предыдущих методов, технология инфузии смолы связана с наложением сухих тканей e.г. 5 слоев по 200 гр вес. На эти ткани нанесен специальный клей, обеспечивающий идеальное прилегание к форме и переплетению. Затем укладывается специальная сетка для правильного распределения смолы. Вся заклеена пленкой и бутиловой лентой. С одной стороны подсоединен вакуумный насос, который сначала всасывает воздух с помощью вакуума, а вакуумный мешок обеспечивает прижимание ткани к форме. Затем с другой стороны откроется клапан на подающем трубопроводе из бака со смолой. Благодаря вакууму, смола автоматически подается через сетку и каналы, размещенные ранее, чтобы обеспечить пропитку сухих тканей из углеродного волокна.
RTM
Этот метод используется для крупносерийного производства композитов из углеродного волокна, которые обычно окончательно окрашиваются краской (не прозрачным лаком) . Обычно используются стальные или алюминиевые формы, охватываемые и охватываемые. Сначала внутрь формы помещаются сухие ткани. Затем формы прижимаются друг к другу, и вокруг форм и между ними обеспечивается уплотнение. При этой технологии впрыск смолы следует под высоким давлением (10-20 бар).Процесс пропитки и отверждения занимает 30-60 минут. RTM высокого давления следует при давлении до 100-120 бар, и весь производственный процесс занимает всего 10 минут.
Основное преимущество этого метода — гладкая поверхность (с обеих сторон) и относительно короткий производственный цикл . К недостаткам можно отнести высокую стоимость внедрения процесса и производства композитов из углеродного волокна, предназначенных для окраски. На самом деле этот метод не гарантирует идеального размещения углеродных визуальных тканей и не подчеркивает структуру углеродного волокна, когда наносится только прозрачный верхний слой.
Этот метод использовался в крупносерийном производстве компанией Dodge при производстве Viper (2005). В настоящее время по этой технологии производятся некоторые детали, а также кузов BMW i3 и BMW i8 или крыша гоночных автомобилей BMW M3 и M6.
RTM Легкий
Разница между RTM и Light RTM в основном связана с давлением. В случае первого метода давление вливания смолы составляет 20-120 бар, тогда как в Light RTM оно составляет всего 1,2 бар, и весь процесс использует отрицательное давление. Этот процесс позволяет разработать контрформс с малым весом, в основном из композитного материала, отсюда и название «Light» RTM. Давление настаивания смолы составляет ок. 1,2 бар, отрицательное давление 0,7 бар.
Инфузия смолы следует с одной стороны при низком отрицательном давлении 1,2 бар, а экстракция следует с другой стороны (как в случае инфузии смолы) при отрицательном давлении 0,7 бар. Перепад давления приводит к пропитке тканей внутри. Этот метод редко используется для производства композитов из углеродного волокна, поскольку он предлагает низкое качество и эстетику по сравнению с RTM.
Композиты для автоклавов Prepreg
Метод препрега с автоклавом широко используется для производства углеродных композитов для гоночных автомобилей F1, моноблоков, диффузоров, передних крыльев, а также спойлеров. Эта технология обеспечивает высочайшее качество и эстетичный внешний вид композитов из углеродного волокна. , но она сопряжена с высокими затратами из-за использования дорогостоящего оборудования — автоклавов — и умеренного производственного цикла (по сравнению с горячим прессом (HP) или RTM.
Технология автоклавирования Prepreg обеспечивает высочайшее качество и эстетичный внешний вид композитов из углеродного волокна.
Автоклав — это устройство, которое создает одновременно высокое давление ~ 8 бар и высокую температуру ~ 120-150 ° C .Этот метод включает использование препрегов, а именно углеродных тканей, которые предварительно пропитаны смолой. Следовательно, материал — ткань из углеродного волокна с предварительной пропиткой смолой — поставляется в рулонах длиной 30-50 м и хранится в холодильнике для предотвращения случайного затвердевания. Отверждение углеродных тканей, предварительно пропитанных смолой, происходит при высокой температуре> 90 ° C , и, следовательно, их срок службы после извлечения из холодильника составляет 20-40 дней при температуре окружающей среды в зависимости от типа материала.На практике после извлечения рулона препрега из холодильника нужно подождать 2-3 часа, чтобы материал стал мягким и можно было разрезать. Затем, после разворачивания, материал помещается на плоттер и выполняется резка в соответствии с производственными потребностями. Затем остаток рулона убирают в холодильник. Материал можно хранить в холодильнике 4-8 месяцев .
Препреги похожи на липкую клеенку.Этот материал легко прилипает к стенкам формы и, следовательно, можно формировать сложные формы . После укладки слоев препрега формы заклеиваются пленкой и бутиловой лентой. Затем следует прижимание к форме с помощью вакуума, который удаляет воздух из продукта. Позже форма, включая запечатанный продукт, помещается внутрь автоклава, который создает давление до 8 бар, чтобы прижать угольные препреги к стенкам формы, чтобы удалить воздух и обеспечить уплотнение структуры.
Наконец, после отверждения обычно в течение 1-2 часов при 120 градусах, вы можете сбросить давление в автоклаве, выключить нагреватели и удалить готовый композит из углеродного волокна.
Преимущества изготовления препрегов автоклавированных композитов из углеродного волокна:
- Возможна закалка любого количества в течение одного производственного цикла (например, 50 идентично сформированных деталей).
- Наивысший эстетический вид композита — отсутствие воздушных пустот и повреждений ткани.
- Возможно изготовление деталей сложной формы и использование комбинированных, составных форм.
Недостатки изготовления препрегов автоклавированных композитов из углеродного волокна :
- Высокая стоимость оборудования — автоклава.
- Средне трудоемкий процесс (короче, чем инфузия смолы, и дольше, чем горячее прессование).
- Требуются формы, устойчивые к высоким температурам — чаще всего дорогостоящие углеродные препег-формы или алюминиевые, изготавливаемые методом фрезерования.
Горячий пресс / термоформование
Этот способ обычно используется для крупносерийного производства изделий и деталей простой конструкции и обычно небольших размеров.
В этом методе, как и в автоклаве, используются угольные препреги. Разница касается пресса, который используется для обеспечения прижатия слоев препрега к форме, а не давления воздуха, как в случае автоклава. Обе формы прессуются нагревательным прессом, который обеспечивает быстрый нагрев.Чаще всего следует горячее прессование, с препрегами с коротким временем затвердевания всего 5-10 минут.
Преимущества производства композитов из углеродного волокна с горячей штамповкой:
- Высокое содержание углеродного волокна до ~ 70% в композите, аналогично автоклавному методу.
- Устойчивость к высоким температурам.
- Короткий производственный цикл.
Недостатки производства углепластика методом горячего прессования:
- Высокие затраты на внедрение продукции.
- Трудно изготовить элементы с так называемыми отрицательными углами
Молдинг мочевого пузыря
В технологии формования баллонов используются угольные препреги, как и в случае производства угольного композита с использованием горячего пресса и автоклава.
- Препреги помещают внутрь обеих форм (охватываемой и охватывающей) и вокруг мочевого пузыря.
- Баллон помещается внутрь формы, форма закрывается и фиксируется.
- Перекачивание следует внутри баллона для обеспечения давления, необходимого для получения поверхности желаемого качества.Создаваемое давление, например 4 стержня прижимают препреги к стенкам формы, чтобы удалить воздух и обеспечить укрепление структуры углеродного композита.
- Нагрев формы — внутри пресса, печи или автоклава.
- При отверждении композита давление снижается. После разборки баллон снимается. Мочевой пузырь — деталь многоразового использования.
Когда используется формовка мочевого пузыря?
Данная технология используется для производства сложных длинномерных деталей малого диаметра эл.г. рама велосипеда.
КОМПОЗИТЫ УГЛЕРОДНОГО ВОЛОКНА — ПРЕИМУЩЕСТВА И НЕДОСТАТКИ
Композиты из углеродного волокна обладают как преимуществами, так и недостатками.
Преимущества композитов из углеродного волокна:
- Композиты из углеродного волокна имеют малый вес — ок. На 40-50% легче алюминия, а жесткость улучшена в 4-5 раз по сравнению со сталью и алюминием того же веса. Этот материал широко используется для производства деталей кузова гоночных автомобилей (F1), сверхлегких велосипедов, удочек, деталей автоматизированных машин, дронов или военной продукции.
Композиты из углеродного волокна обладают малой массой и экономят энергию транспортных средств (BMW i3) Малый вес композитов из углеродного волокна способствует экономии энергии, поскольку более легкие автомобили потребляют меньше топлива . Предполагается, что снижение веса автомобиля на 10% приведет к снижению расхода топлива на 6-8%. Поэтому электромобили, такие как BMW i3 или i8, имеют шасси из углеродного волокна, что увеличивает запас хода. - Композиты из углеродного волокна обладают уникальными свойствами, в том числе очень низким тепловым расширением .
Например, композит из углеродного волокна имеет тепловое расширение в 5,5 раз ниже, чем у стали, в 8,5 раз ниже, чем у нержавеющей стали и на 11,5 раз меньше, чем у алюминия . Таким образом, благодаря практически нулевому тепловому расширению композиты из углеродного волокна используются в оптике — для производства 3D-сканеров и в военных целях, например. производство высокоточных спутниковых дисков.
- Еще одно преимущество композитов из углеродного волокна связано с совместимостью с рентгеновским излучением. Композиты из углеродного волокна не блокируют рентгеновские лучи и поэтому широко используются для производства систем рентгеновского сканирования.
- Благодаря своему уникальному и оригинальному эстетическому виду композиты из углеродного волокна используются в автомобильной промышленности и в целях проектирования . На самом деле это материал, связанный с продуктами премиум-класса, поскольку он используется производителями гоночных автомобилей, а также поставщиками досок для серфинга, каяков, защитных шлемов, громкоговорителей, кофемашин и многих других продуктов премиум-класса.
Недостатки композитов из углеродного волокна:
- Самый большой недостаток композитов из углеродного волокна связан с производственными затратами . Композиты из углеродного волокна в основном производятся путем ручной укладки нескольких слоев углеродной ткани. Весь процесс требует времени и требует определенных затрат . Дополнительные использованные материалы () стоят года, такие как углеродная ткань, смола, препреги. Квадратный метр углепластика стоит ок. 30-50 евро, а, например, для изготовления композита толщиной 2 мм требуется 4-5 слоев. Обработка композитов из углеродного волокна с последующей 3- или 5-осевой обработкой углеродного волокна с ЧПУ, и обычно на него наносят несколько слоев верхнего покрытия, что приводит к высоким производственным затратам.
Когда дело доходит до передового производства, такого как производство композитов из углеродного волокна в автоклаве, требуется дорогое оборудование, например стоимость автоклавов ок.
~ 500000 долларов США.
Следовательно, конечный продукт стоит в несколько раз больше, чем изготовленный из алюминия, например . - Другой недостаток связан с некоторыми ограничениями на этапе проектирования . Не каждая деталь, которая может быть достигнута при фрезеровании алюминия, может быть изготовлена с использованием углеродного волокна, и некоторые детали необходимо адаптировать особым образом.
- Хотя углеродное волокно имеет много преимуществ в отношении своих свойств, обратите внимание, что углеродный композит предлагает плохую / умеренную устойчивость к ударам , что делает его хрупким по сравнению со сталью или алюминием. Поэтому детали или части, подверженные ударам, изготавливаются из композитов из углеродного стекловолокна, углерод-арамидных композитов, углеродных композитов, включая алюминиевые соты, или их комбинации.
- Углеродное волокно — это материал, который проводит электрический ток в меньшей степени, чем металлы.
- Металлические элементы внутри углеродного волокна (например, резьбовая втулка) должны быть изолированы смолой или клеем для обеспечения защиты от коррозии.
- К другим недостаткам относится ремонт композитов из углеродного волокна — например. сломанная рама велосипеда. Эти детали часто не подлежат ремонту или ремонт сложен и требует больших затрат.
- В отличие от металлических деталей, композиты из углеродного волокна горючие, что означает, что они могут воспламениться и загореться при воздействии открытого огня в течение определенного периода времени.
9 СЕКРЕТОВ О СОСТАВЕ УГЛЕРОДНОГО ВОЛОКНА:
- Углеродный композит имеет прочность до 5 раз больше, чем сталь (вес к весу).
- Углеродное волокно , используемое для производства автомобилей Формулы 1 и других гоночных автомобилей (называемых «pre-pregs»), стоит столько же, сколько 60 долларов США за метр.
2 .
- Углеродный композит с умеренной проводимостью (меньше, чем у металлов).
- Карбон — черный , который обеспечивает уникальный узор.Композиты любого другого цвета могут быть поддельными углеродным волокном — стекловолокном или кевларом.
- Углеродное волокно — очень жесткий материал, с модулем Юнга 230 ГПа (Toray T300, наряду с волокном). Чем выше модуль Юнга, тем выше жесткость материала. Углеродное волокно с высоким модулем упругости (повышенной прочности) обычно имеет модуль Юнга вместе с волокном 500-880 ГПа (пример волокна 880 ГПа — Granoc XN 90 Nippon). Для сравнения, сталь обычно имеет модуль Юнга около 200 ГПа.
- Углеродный композит демонстрирует низкое тепловое расширение — он расширяется при высокой температуре и сжимается при низкой температуре намного меньше, чем такие материалы, как сталь и алюминий.
- Карбон более устойчив к усталости материала.
— элементы из углеродного волокна обеспечивают большую прочность при работе в тяжелых условиях.
- Карбон, как и другие композиты, позволяет определять прочность любой области элемента — в любом направлении . Например, рама велосипеда из углеродного волокна будет иметь много слоев ткани в местах, подверженных высокой нагрузке, тогда как будет минимальное количество слоев в местах, которые не передают нагрузку.Такая конструкция оптимизирует и снижает вес композита.
- Углеродное волокно также имеет некоторые недостатки — например, средняя ударная вязкость . В случае элементов, подверженных ударам (например, панели под двигателем автомобилей WRC), часто используется арамидное волокно (называемое кевларом).
Наша компания является поставщиком композитов из углеродного волокна
Поставляем серию изделий из углеродного волокна. В зависимости от требуемой прочности производственный процесс может включать технологию препрега , инфузию смолы, вакуумный мешок или ручное ламинирование.
Расположение: Польша (Европа), Доставка по всему миру.
Свяжитесь с нами: Dexcraft Composites, www.dexcraft.com, [email protected], тел. +48 797-775-826, +48 505-555-524
В чем разница между Kevlar® и углеродным волокном?
Как кевлар®, так и углеродное волокно имеют интересную историю, демонстрирующую исследования материалов и инновации.В Markforged мы любим изучать материалы и их комбинации, раскрывать новый потенциал и возглавлять разработку инноваций в индустрии аддитивного производства. Мы являемся лидером в области 3D-печати непрерывных волоконных нитей с помощью нашего запатентованного процесса CFF (Continuous Filament Fabrication), который укладывает непрерывные волокна в детали из оникса FFF для эффективного усиления пластиковых деталей металлической прочностью. Это значительно увеличивает долговечность и срок службы детали, а также оптимизирует профиль прочности детали за счет добавления волокон там, где прочность больше всего необходима.
Прочтите разницу между стекловолокном и углеродным волокном
Давайте подробнее рассмотрим наше понимание кевлара.
Кевлар
О чем вы думаете, когда слышите название кевлар? Большинство людей думают о пуленепробиваемых жилетах. Вы можете не подумать DuPont ™, но этот материал был разработан DuPont ™ еще в 1964 году польско-американским химиком Стефани Кволек.
Знаете ли вы, что кевлар может применяться по-разному в разных отраслях? Вы можете найти его для повседневного использования, например:
- Шины для автомобилей и велосипедов
- Пластины для грузов
- Паруса и трос
- Перчатки, носки и багаж
- Рабочие ботинки
- Тормозные колодки
- Защитное снаряжение
- Герметики
Кевлар — это синтетическое волокно, которое относится к группе термостойких арамидных волокон.Кевлар и Номекс входят в эту группу. Синтетические волокна — это волокна, синтезированные путем химического синтеза, в отличие от натуральных волокон, полученных из живых организмов. Синтетические волокна получают путем выдавливания волокнообразующего материала через фильеры, формирующие волокна.
Кевлар представляет собой высокомодульный тип, используемый в основном в волоконно-оптических кабелях, обработке текстиля, тросах, кабелях, армировании пластика и композитных материалах для аэрокосмической, автомобильной, оборонной, энергетической, бытовой, электронной, медицинской и тяжелой промышленности. несколько.Инженерное командование военно-морских сооружений изучило возможности использования кевларового каната в океанотехнике и строительстве, в результате чего были разработаны инновационные конструкции и приложения, обеспечиваемые невероятной прочностью на растяжение и плавучестью кевлара. Кевларовое волокно имеет прочность на разрыв, сравнимую с прочностью углеродного волокна, модуль упругости между стекловолокном и углеродным волокном и более низкую плотность, чем оба.
Кевларовый арамид используется для высокопроизводительных композитных материалов, где важны легкий вес, высокая прочность и жесткость, устойчивость к повреждениям, а также устойчивость к усталости и разрушению под напряжением.Markforged находит, что усиление оникса, оникса FR и даже белого нейлона кевларом позволяет инженерам и проектировщикам деталей создавать чрезвычайно универсальные детали. Кевлар может претерпевать значительные изменения в низкотемпературных средах, до 320 ° F (-196 ° C) и не проявлять хрупкости или разрушения, а также в средах с электронным излучением, поскольку электронное излучение не вредно для кевлара. Однако кевлар чувствителен к УФ (ультрафиолетовому) свету.
Дизайнеры могут разработать детали, которые будут безопасными, прочными, жесткими, легкими и устойчивыми к окружающей среде, условиям применения и нагрузкам, печатая с использованием непрерывных волокон.Создавая детали с использованием процесса CFF (производство непрерывных волокон), разработчики могут использовать прочность кевлара на растяжение (растяжение или растяжение), которая более чем в восемь раз превышает прочность стальной проволоки.
Markforged Kevalr filament
Армирование CFF позволяет любому проектировщику создавать композитные детали с прочностью металла, увеличивать их долговечность (срок службы) и оптимизировать прочность детали там, где это больше всего необходимо. Кевлар также имеет очень большой диапазон пластической деформации, и когда он выходит из строя, он делает это по одной нити за раз и даже сгибается или падает вместо того, чтобы сломаться.Он имеет гораздо более предсказуемый и простительный режим отказа по сравнению с другими волокнами, такими как углеродное волокно.
Посмотрите видео: детали из ABS (синий), PLA (красный) и армированного кевларом оникса (черный), удары молотком
Посмотрите видео: медленное движение кевлара в машине Instron выходит из строя, начало @ 2: 00 минут (Science Channel, 2017).
Уникальные свойства кевларовых волокон:
- Очень низкое растяжение
- Высокая прочность на разрыв
- Очень высокое отношение прочности к массе
- Отличная усталостная прочность
- Хорошие характеристики в широком диапазоне температур
- Не плавится; разлагается при 800 ° F — 900 ° F (от 427 ° C до 482 ° C)
- Низкая ползучесть
- Без усадки
- Хорошая химическая стабильность
- Высокая стойкость к истиранию
- Слабая прочность в поперечном направлении (слабая прочность на сжатие )
- Режим наименьшего катастрофического разрушения всех нитей Markforged
Ударопрочность
Кевлар в 8 раз более устойчив к ударам, чем ABS, но при этом остается на 15-20% легче, чем другие армирующие волокна.
Прочность на изгиб
При трехточечном изгибе кевлар, напечатанный на 3D-принтере, в 3 раза прочнее, чем ABS, и в 6 раз прочнее, чем нейлон.
Жесткость на изгиб
Кевлар, напечатанный на 3D-принтере, в 12 раз жестче, чем ABS, и в 30 раз жестче, чем нейлон.
Кевлар обладает превосходной прочностью, что делает его оптимальным для деталей, которые подвергаются повторяющимся и внезапным нагрузкам. Такая жесткая, как стекловолокно, и гораздо более пластичная, она может использоваться в самых разных областях, связанных с аддитивным производством, таких как:
- Спортивная обувь
- Робототехника и люльки
- Концевые эффекторы / захваты
- Чехлы для смартфонов, личные электроника
- Детали, предназначенные для привода от гидравлики или пневматики
- Защитное снаряжение, каски; боевой, мотоцикл
- Тормозные рычаги, зажимы, крепления
- Крепления, инструменты, зажимы, мягкие губки
- Шестерни, ключи, дроны
- Спортивные товары и аксессуары, карабины
- Части конечного использования, товары народного потребления и т.
..
Захваты клапанов Dixon напечатаны ониксом и усилены кевларом. Материал должен быть достаточно прочным, чтобы передавать зажимное усилие, долговечным при повторяющихся циклах нагрузки и не допускать повреждений клапанов.
композиты в 3D печати воспользоваться прочности на сжатие пластиковой матрицы — несущей конструкции, которая содержит большую часть объема часть — и предел прочности на разрыв встроенных волокон. Эти два материала взаимозависимы: без волокна прочность пластмассовой детали определяется степенью адгезии внутри и между экструдированными пластиковыми нитями.Без матрицы волокно не имеет структуры и поэтому не может сохранять свою форму. Матрица создает пространство, поэтому волокно имеет рычаг для стабилизации нагрузки. В сочетании они взаимодействуют друг с другом, образуя композит с большей прочностью как на сжатие, так и на растяжение, чем каждый из них может предложить по отдельности. Это верно для всех наших волокон; Кевлар, углеродное волокно, стекловолокно и стекловолокно HSHT.
А теперь давайте подробнее рассмотрим наше понимание углеродного волокна.
Углеродное волокно
Нить из углеродного волокна
Нить из углеродного волокна состоит из атомов углерода, организованных в кристаллическую структуру.Благодаря очень высокой жесткости и прочности он широко используется в аэрокосмической и автомобильной промышленности. У него одно из самых высоких соотношений прочности к весу — выше, чем у стали и титана.
Прочтите наше бесплатное руководство по проектированию композитов
Отношение прочности к массе
По сравнению с алюминием 6061, углеродное волокно, напечатанное на 3D-принтере, имеет на 50% более высокое отношение прочности к массе при изгибе и на 300% при растяжении .
Прочность на изгиб
При трехточечном изгибе наше углеродное волокно, напечатанное на 3D-принтере, в 8 раз прочнее, чем АБС, и на 20% прочнее алюминия.
Жесткость при изгибе
Углеродная нить, напечатанная на 3D-принтере, в 25 раз жестче, чем ABS, и в 2 раза жестче, чем остальные армирующие волокна Markforged.
Характеристики материала углеродного волокна:
- Углеродное волокно Markforged, напечатанное на 3D-принтере, равно пределу текучести 6061 алюминия
- Оно выходит из строя при том же напряжении, при котором алюминий начинает пластически деформироваться.
- Углеродное волокно вернется к своей исходной форме после снятия нагрузки, в то время как алюминий пластически деформируется
- Высокая жесткость и высокая удельная масса
- Электропроводность
- Коррозионно-термостойкость
- Жесткость до разрушения резкая и непредсказуемая)
- Идеальная нагрузка постоянная — постоянная поддержка известной силы.
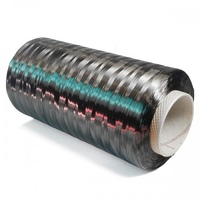
позволяют использовать его в качестве замены металла там, где важна экономия веса. Теперь у каждой отрасли есть возможность использовать CFF с углеродным волокном и печатать невероятно прочные детали. Генеративный дизайн также предлагает преимущества в сочетании с Markforged CFF, который позволяет дизайнерам исследовать несколько оптимизированных решений и иметь возможность выбирать лучший дизайн, адаптированный для его использования, как с точки зрения дизайна, так и с точки зрения прочности.
Markforged Composites Material Datasheet
Углеродное волокно может использоваться для самых разных применений; аэрокосмическая промышленность, автомобилестроение, архитектура и строительство, товары народного потребления, медицина, энергетика, оборона, электроника, промышленное оборудование и т. д., адаптированные для аддитивного производства, и этому списку нет конца, поэтому вот лишь некоторые из них:
- Робототехника и робототехника рычаги
- Концевые эффекторы, захваты и мягкие губки
- Контрольные приспособления, приспособления для сварки и приспособления для КИМ
- Формовочные инструменты
- Велосипеды и их компоненты
- Высококачественные приложения для автоспорта
Взгляните на Haddington Dynamics Пример использования: роботизированная рука, напечатанная на 3D-принтере, армированная непрерывной нитью из углеродного волокна, достаточно жесткая и легкая, чтобы роботизированная рука имела точность 50 микрон.Используя 3D-принтер из углеродного волокна, компания смогла сократить количество деталей с 800 до менее 70.
Ссылка: 12,5 кг (27,5 фунта) подвешены как на 7-граммовом образце оникса, армированном углеродным волокном (слева), так и на 12-граммовый образец алюминия (справа)
Обращайтесь к нам за дополнительной помощью или советом по выбору армирующего волокна, наиболее подходящего для вашего применения. Закажите сегодня образец кевлара или углеродного волокна.
Производство углеродного волокна в велосипедах
Версия этой статьи была первоначально опубликована в журнале Triathlete Magazine
В первой части этой серии был представлен обзор наиболее распространенных производственных процессов, используемых в производстве велосипедов и компонентов из углеродного волокна.Во второй части мы обсудим сырье (ингредиенты), из которого делают препрег из углеродного волокна, который чаще всего используется при производстве продуктов из углеродного волокна, и его связь с некоторыми из общих терминов, используемых в велосипедном маркетинге.
Наиболее распространенной формой исходного композитного материала, используемого при производстве углеродного волокна в велосипедной промышленности, является «препрег» — нити из углеродного волокна (или других материалов, таких как стекло или бор), пропитанные смолой для создания однонаправленной ленты или тканого материала.В то время как тканые ткани из препрега образуют косметические узоры, которые большинство людей ассоциируют с углеродным волокном, обычно это нетканая однонаправленная лента (часто скрытая под тканым слоем), которая формирует основную несущую структуру конструкции.
Костная система препрега — это сырое волокно. Как и пряжа, необработанное / сухое углеродное волокно поступает на катушки из переплетенных углеродных нитей, называемых «паклей». Жгуты жгутов бывают разных размеров, которые подразделяются на количество волокон (от 1000 до 50 000) в жгуте.Результатом стали обычные монишеры «3K» (3000 прядей) и «12K» (12000 прядей), которые прикрепляются ко многим изделиям из углеродного волокна. Чем выше «К», тем больше физический размер жгута и (в случае тканого препрега) больше косметический клетчатый узор плетения. Однако, за исключением всех препрегов, кроме самых тонких, размер жгута («K») практически не влияет на качество используемого угля. Тип волокна имеет значение, поскольку он напрямую влияет на важные механические свойства, такие как прочность на разрыв (прочность на разрыв), модуль (насколько материал прогибается под нагрузкой) и скорость деформации (удлинение волокна до разрушения).Таким образом, упоминание «K» больше связано с эстетикой рамы или компонента, в то время как модуль упругости (стандартный, средний или высокий) волокна напрямую связан с его жесткостью.
Смола — другая часть препрега. Подобно соединительной ткани, смола скрепляет скелетную систему волокон и должна быть правильно спроектирована, чтобы позволить ей правильно функционировать в процессе производства. Смолы — это термочувствительные смеси, полученные путем комбинирования определенных соотношений жидкостей и твердых веществ в нагретом смесителе.С того момента, как смесь смол станет катализатором, ее необходимо хранить в холодной (ниже точки замерзания), иначе она преждевременно застынет. Хотя смола редко упоминается в потребительском маркетинге («смола 301» звучит не так броско, как «12K»), очень важно, чтобы используемая смола соответствовала требованиям конечного продукта, для которого будет использоваться препрег.
После смешивания смола точно переносится на рулон разделительной бумаги (например, Fruit Roll-Ups) с помощью машины, называемой разливочной машиной. Полученные рулоны полимерной бумаги устанавливают на машину для препрега, где большой ткацкий станок формирует и подает до нескольких сотен жгутов пучков волокон на полимерную бумагу в указанном порядке.Когда полимерная бумага загружается жгутом, она нагревается и уплотняется роликами, которые помогают теплой смоле проникать в волокна. Затем полученные листы препрега охлаждают, прокатывают и готовят к использованию в производстве. На протяжении всего процесса строгое соблюдение процедур контроля качества и надлежащая документация гарантирует, что конечный результат соответствует спецификации.
Листы препрега из углеродного волокна производятся в большом количестве комбинаций, и каждый лист препрега классифицируется по коду, который включает в себя все: от названия производителя до типа используемого волокна (модуля), содержания волокна и смолы в препрег.Содержание волокна выражается в «поверхностном весе волокна» (Faw) и представляет собой просто количество (в граммах) волокна на один квадратный метр препрега. Если велосипедная компания продает свой продукт как «110», «120», «150», это, вероятно, означает, что препрег, используемый в ее конструкции, имеет этот Faw. Чем ниже Faw, тем тоньше и легче препрег и тем выше модуль углеродного волокна, необходимый для сохранения жесткости. «Rc» — это содержание смолы в одном квадратном метре препрега, выраженное в процентах.Когда компания ссылается на соотношение волокна к смоле 70/30 или 65/35, они говорят о процентном соотношении волокна к его Rc.
Помимо размера связки («3K», «12K»…), Faw («110», «120»…) и Rc (70/30), некоторые производители ссылаются на сорт углерода, который они используют, по допустимой нагрузке на растяжение. . Например, «800 фунтов на квадратный дюйм» (обратите внимание на маленький «k») означает, что волокно может выдерживать давление 800 000 фунтов на квадратный дюйм, прежде чем оно разорвется. Другие компании используют свою собственную систему «рейтинга», которая указывает, насколько жестким и / или легким является углеродное волокно, по относительной шкале (10.5, 8.5…). Хотя некоторые из этих чисел более информативны, чем другие, каждое отдельное число отражает лишь небольшую часть реальной истории, поскольку качество однонаправленного препрега представляет собой комбинацию типа волокна (модуля), Faw и Rc. Многие каркасы сегодня также трудно поддаются количественной оценке, поскольку в них используются многомодульные схемы укладки, в которых сочетаются многие типы препрега, чтобы максимально соответствовать конечным целям продукта и конструкции.
Прочность рамы определяется ее самым слабым звеном, и металл, используемый в конструкции, также является важным элементом.Металл приклеен к большому количеству рам из углеродного волокна в местах контакта подшипников, резьбы и колес (каретка, гарнитура, дропауты). Алюминий — наиболее часто используемый металл при изготовлении карбонового каркаса, поскольку он легкий и недорогой. Однако алюминий может подвергаться гальванической коррозии и требует, чтобы строитель обернул его таким материалом, как стекловолокно, чтобы минимизировать вероятность коррозии. В некоторых из углеродных оправ самого лучшего качества используется титан, потому что он очень прочный, устойчивый к коррозии, легкий и один из самых чистых металлов для сцепления.
Итак, если большая часть маркетинговой номенклатуры не относится напрямую к общему качеству углерода, как вы можете определить, какое место в спектре опций занимает велосипед? Как упоминалось в первой части, цена часто является одним из наиболее точных индикаторов. Что касается материалов, никто в велосипедной индустрии не может покупать материалы по настолько значительно более низкой цене, чем все остальные, что они могут подорвать рынок, предлагая продукт более высокого качества по гораздо более низкой цене.Чем выше качество используемого карбона и металла, тем выше цена велосипеда, но при этом тем больше требуется ручной работы, и тем более гибкой и надежной будет поездка. Короче говоря, с углеродным волокном вы почти всегда получаете то, за что платите.
В части 3 мы рассмотрим четыре различных типа компаний, предлагающих продукцию из углеродного волокна для велосипедной индустрии, и их отношение к методам производства и уровням качества, обсуждаемым в частях 1 и 2.
Наслаждайтесь поездкой и тренируйтесь усердно и умно!
Ян
Спасибо Майку Лопесу, директору по разработке и производству композитов компании Serotta Cycles, за его вклад в эту статью.
Первоначально опубликовано в журнале Triathlete Magazine Октябрь 2008 г. / Copyright © 2008
Тип изделий из углеродного волокна и их особенности
Углеродные волокна, обладающие превосходными характеристиками, находят широкое применение. Используя различное сырье и применяя различные производственные процессы, поставщики могут предоставить широкий спектр волокон с различными характеристиками. Ниже представлены различные типы волокон и соответствующие характеристики.
Два типа по сырью
Тип PAN Углеродное волокно
Тип волокна, производимого карбонизацией прекурсора PAN (PAN: полиакрилонитрил), обладающего высокой прочностью на разрыв и высоким модулем упругости, широко применяемого в композиционных материалах конструкционных материалов в аэрокосмической и промышленной сфере, а также в товарах для спорта и отдыха.
Тип шага Углеродное волокно
Другой тип волокна, полученный карбонизацией предшественника нефтяного / угольного пека, обладает обширными свойствами от низкого модуля упругости до сверхвысокого модуля упругости.Волокна со сверхвысоким модулем упругости широко используются в компонентах с высокой жесткостью и для различных целей, например, для использования с высокой теплопроводностью и / или электропроводностью.
Типы по механическим свойствам
Тип со сверхвысоким модулем упругости (UHM)
Модуль упругости при растяжении: 600 ГПа или выше
Предел прочности на разрыв: 2500 МПа или выше.