Основные детали двигателей внутреннего сгорания
Фундаментная рама является основанием двигателя и состоит из двух продольных балок коробчатого или двутаврового сечения, на которые устанавливаются стойки и станины, и нескольких поперечных балок необходимой формы для установки рамовых подшипников. Фундаментные рамы могут быть сварными или литыми (стальными, чугунными). Они бывают закрытые и открытые, цельные и составные. Нижняя часть закрытой фундаментной рамы, т. е. поддон, выполнена за одно целое с продольными балками. Между поперечными балками вращаются кривошипы (мотыли) коленчатого вала, поэтому пространства между ними и продольными балками называют мотылевыми колодцами. Поперечные балки в нижней части имеют отверстия для перетекания масла из одного мотылевого колодца в другой. В быстроходных и легких двигателях применяют так называемые картерные рамы, позволяющие устанавливать блок цилиндров непосредственно на раме, в результате чего отпадает необходимость в станине. На рис. 55 показан общий вид фундаментной рамы. По блокам рамы по всей длине имеются горизонтальные полки с приливами, в которых сделаны отверстия для болтов, крепящих фундаментную раму к судовому фундаменту.
Рис. 55. Общий вид фундаментной рамы двигателя.
Станина двигателя устанавливается на фундаментную раму и соединяется с ней болтами. Станины бывают цельными и составными и могут иметь различную конструкцию. Некоторые двигатели большой мощности имеют станины открытого типа в виде соединенных между собой вверху и внизу колонн. Сверху на колонны устанавливают цилиндры двигателя.
На рис. 56 показана литая станина 3 мощного двигателя, которая так называемыми анкерными связями — длинными стяжными шпильками 1 — соединяется с рубашками цилиндров 2 и фундаментной рамой 4 в одно целое.
Рис. 56. Литая станина мощного двигателя.
Рабочие цилиндры изготовляют каждый в отдельности или в виде блочной конструкции. Конструкция отдельного цилиндра четырехтактного двигателя показана на рис. 57. Цилиндр состоит из рубашки 1 (или блока цилиндров) и рабочей втулки 2, запрессованной в расточку рубашки и опирающейся буртиком 9 на верхний кольцевой выступ рубашки. Между рубашкой и втулкой образуется замкнутая полость — зарубашечное пространство, куда непрерывно нагнетается насосом циркулирующая охлаждающая вода; через отверстие 3 вода вначале попадает в нижнюю часть зарубашечного пространства, а затем поднимается и переходит через отверстие 8 в полость охлаждения крышки цилиндра. Рубашка имеет фланец 4, которым цилиндр соединен со станиной двигателя. В нижней части рубашки расположен поясок 6 для фиксирования положения втулки. В пояске делают кольцевую выточку, в которую укладывают резиновые кольца 5 круглого сечения, что обеспечивает плотность соединения, т. е. предотвращает проникновение охлаждающей воды из зарубашечного пространства в картер двигателя. Для очистки и осмотра зарубашечного пространства в наружной рубашке предусмотрены горловины 7, плотно закрываемые крышками. Если рубашки цилиндров выполнены за одно целое, то такая общая конструкция называется блоком цилиндров.
Рис. 57. Цилиндр четырехтактного двигателя.
Рабочие цилиндры двухтактных двигателей отличаются от рабочих цилиндров четырехтактных тем, что имеют окна для подвода продувочного воздуха и удаления отработавших газов. Это приводит к необходимости обеспечивать уплотнение между втулкой и рубашкой не только в нижней ее части, но и в районе окон. В канавки, прилегающие к окнам, закладывают медные кольца, а в остальные канавки— резиновые кольца.
Крышка цилиндра — наиболее ответственная и сложная по конфигурации деталь двигателя. Она должна выдерживать высокое давление и температуру. Если две или более крышек выполнены за одно целое, то такая деталь называется головкой блока. Самой сложной по конфигурации является крышка четырехтактного двигателя, где кроме отверстий для форсунки и клапанов имеются канал для подвода воздуха к пусковому клапану и каналы для газообмена между цилиндром и атмоферой.
Простейшая конструкция крышки цилиндра двухтактного двигателя показана на рис. 58. Крышка имеет центральное отверстие в котором устанавливают объединенные в одном корпусе форсунку и пусковой клапан. В кольцевом пространстве 2 циркулирует охлаждающая вода. Крышка крепится к цилиндру при помощи шпилек 3. Для увеличения жесткости во внутренних полостях крышки имеются ребра 4. Уплотнение крышки осуществляется при помощи буртика 5, входящего в кольцевую выточку фланца цилиндра. В выточку для уплотнения устанавливают медное отожженное кольцо.
Рис. 58. Простейшая конструкция крышки цилиндра двухтактного двигателя.
Поршень тронкового двигателя, выполняющий дополнительно функции ползуна, имеет сравнительно длинную направляющую часть, называемую «юбкой» или тронком. Поршень тронкового двигателя соединен с шатуном шарнирно — при помощи поршневого пальца. На рис. 59 показано устройство тронкового поршня, у которого головка 3 и тронк 1 отлиты за одно целое. Применяется наиболее часто такой способ установки поршневого пальца 5 в бобышках направляющей части поршня, когда он может свободно проворачиваться вокруг своей оси, но лишен возможности передвигаться вдоль оси. Такой палец называется плавающим. В верхних канавках 4 поршня установлены уплотнительные поршневые кольца 2, а в нижней части — маслосъемные кольца 6.
Рис. 59. Поршень тронкового двигателя.
На рис. 60 показана конструкция поршня крейцкопфного двигателя. Вогнутое днище 1 поршня подкреплено ребрами 2. В верхних канавках поршня установлены уплотнительные кольца 3, а в нижней части — маслосъемные кольца 4. Поршень соединен со штоком 6 при помощи шпилек 5 фланцем 7. Диск 8 закрывает внутреннюю полость поршня, охлаждаемую водой.
Рис. 60. Поршень крейцкопфного двигателя.
Поршневые кольца обеспечивают не только уплотнение цилиндра от прорыва газов и воздуха, но и передачу теплоты от головки поршня к стенкам втулки цилиндра. Кольца выполняют самопружинящими. Для надевания на поршень они снабжены косым или ступенчатым разрезом, который называют замком. Разрезные кольца хорошо пружинят и при движении поршня плотно прижимаются к стенкам цилиндра. В четырехтактных двигателях поршневые кольца в канавках обычно не фиксируют. В двухтактных двигателях кольца приходится фиксировать, если имеется опасность попадания их замков в зону продувочных или выпускных окон. Если такую фиксацию не предусмотреть, кольца могут сломаться.
Маслосъемные кольца имеют обычно скос на наружной поверхности. Благодаря этому при ходе поршня вниз маслосъемные кольца удаляют с поверхности цилиндра излишки смазочного масла, а при ходе вверх свободно проскальзывают по масляному слою.
Поршневой шток крейцкопфного двигателя соединен с поперечиной крейцкопфа фланцем или конусным соединением. Для уменьшения массы шток часто выполняют полым.
Крейцкопф состоит из поперечины и присоединенных к ней башмаков (ползунов). Поперечина имеет две цапфы для соединения с вилкой шатуна. Рабочую поверхность башмаков заливают баббитом. Крейцкопфы реверсивных двигателей имеют башмаки с обеих сторон. Для соединения с поршневым штоком поперечина имеет конусное отверстие, соответствующее конусу поршневого штока, или пятку для соединения с фланцем штока.
Шатун двигателя передает усилие от поршня коленчатому валу двигателя. На рис. 61 показан шатун тронкового двигателя. Он состоит из трех основных частей — нижней головки с мотылевым подшипником, стержня и верхней головки с головным подшипником. В неразрезной верхней головке устанавливают путем запрессовки головной подшипник 12, имеющий вид втулки. Эта втулка может фиксироваться шпонкой и пластиной 11 для обеспечения неизменного положения в головке. Стержень шатуна имеет центральное отверстие 10 для подачи под давлением смазки к головному подшипнику. Мотылевый подшипник состоит из двух половин 2 и 4, рабочая поверхность которых залита антифрикционным сплавом. Выступ 1 разгружает винты 7 от срезывающих усилий и служит также для центровки стержня с мотылевым подшипником. Изменяя толщину прокладки 9, установленной между пяткой шатуна и верхней половиной мотылевого подшипника, можно регулировать объем камеры сгорания. Набор прокладок 3 в разъеме мотылевого подшипника служит для установки и регулирования масляного зазора между мотылевой шейкой коленчатого вала и подшипником; прокладки фиксируют шпильками 8 и винтами 7. Обе половины мотылевого подшипника стягиваются двумя шатунными болтами 6, которые имеют три посадочных пояска и крепятся корончатыми гайками 5. У быстроходных дизелей наличие прокладок в разъеме мотылевого подшипника не допускается.
Рис. 61. Шатун тронкового двигателя.
Шатуны крейцкопфного двигателя отличаются от шатунов тронкового тем, что имеют два головных подшипника, соединяющихся с цапфами поперечины крейцкопфа, если шатун имеет вильчатую форму.
Коленчатый вал — одна из самых ответственных и дорогостоящих деталей двигателя. Валы изготовляют из высококачественной стали, а также отливают из модифицированного и легированного чугуна. В зависимости от конструкции и числа цилиндров коленчатый вал может иметь разное число колен (кривошипов). Кривошипы вала развертывают по отношению друг к другу на определенный угол, который зависит от числа цилиндров и от тактности двигателя. Коленчатые валы чаще всего бывают цельноковаными и реже сборными, состоящими из двух-трех отдельных частей, соединенных между собой фланцами.
Основными элементами коленчатого вала (рис. 62, а) являются рамовые или коренные шейки 1, мотылевые или шатунные шейки 2 и щеки 3, соединяющие шейки между собой. Иногда для уравновешивания сил инерции вращающихся масс к щекам 1 крепят противовесы 2 (рис. 62, б). Мотылевые шейки коленчатого вала охвачены подшипником нижней головки шатуна, а рамовые шейки опираются на рамовые подшипники, установленные в фундаментной раме двигателя. Смазка шеек осуществляется так: к рамовым шейкам масло подается под давлением через отверстие в крышке подшипника и верхнем вкладыше, а затем через сверление в щеке (рис. 62, в) направляется к мотылевой шейке.
Рис. 62. Коленчатый вал двигателя.
В коленчатых валах с полыми шейками масло поступает на рабочие поверхности мотылевых шеек через полости рамовых шеек и радиальные отверстия, выполненные в мотылевых шейках. Для предотвращения утечки масла из полостей шеек последние с торцов закрыты заглушками, стянутыми болтами или шпильками.
www.stroitelstvo-new.ru
Детали ДВС: основы основ
Страницы: 1 2
Все двигатели от прошлых до современных моделей включают в себя: кривошипно-шатунный механизм; механизм газораспределения; систему охлаждения; смазочную систему; систему питания; систему зажигания (у карбюраторных двигателей).
Детали, составляющие двигатель, можно разделить на две группы: подвижные и неподвижные. К неподвижным деталям относятся блок цилиндров, цилиндры, головка блока цилиндров, поддон картера.
Цилиндры двигателя выполнены или установлены в массивном жестком корпусе, называемом блоком цилиндров двигателя. Блок изготавливается из чугуна или алюминиевого сплава. Между цилиндрами в нем выполнены каналы для охлаждающей жидкости, служащей для отвода теплоты от сильно нагревающихся деталей. Сверху на блоке закреплена головка блока цилиндров. Снизу к блоку цилиндров прикреплен поддон картера, служащий емкостью для масла, необходимого для смазывания деталей двигателя во время его работы.
Кривошипно-шатунный механизм. Преобразует прямолинейное (возвратно-поступательное) движение поршня во вращательное движение коленчатого вала. Включает в себя следующие детали, имеющие определенное назначение.
Поршень (рис. 7) изготовлен из алюминиевого сплава и имеет сложную форму. Он состоит из днища, уплотняющей и направляющей частей. На уплотняющей части поршня выполнены кольцевые канавки под поршневые кольца — компрессионные и маслосъемные.
Компрессионные кольца 2 препятствуют проникновению газов из камеры сгорания в зазор между цилиндром и поршнем. Маслосъемные кольца 1 снимают излишки масла со стенок цилиндра. Кольца разрезные, при установке поршня в цилиндр они пружинят и плотно прижимаются к его стенке.
Поршневой палец 3 соединяет поршень с шатуном. Поршневой палец может быть запрессован в теле поршня, при этом он свободно вращается в верхней головке шатуна. Другая конструкция предполагает свободное вращение пальца в бобышках (утолщениях) поршня и запрессовку его в верхнюю головку шатуна. От осевого перемещения в поршне палец удерживается стопорными кольцами 4, установленными в проточках бобышек поршня.
Шатун штампуется из стали. Он состоит из стержня, верхней и нижней головок. В верхнюю головку шатуна запрессована втулка 8, в которой вращается (или запрессован) поршневой палец. Нижняя головка выполнена разъемной и имеет проточки для установки шатунных вкладышей. Части нижней головки соединены между собой специальными шатунными болтами 6.
Коленчатый вал изготавливают из стали или чугуна. Коленчатый вал четырехцилиндрового двигателя состоит из пяти опорных (коренных) шеек, расположенных по одной оси, и четырех шатунных шеек, попарно направленных в противоположные стороны. Коренные шейки вращаются в подшипниках (в виде двух половин вкладышей). Для разгрузки коренных подшипников от действия центробежных сил служат противовесы 10.
На переднем конце вала устанавливается звездочка, шкив или шестерня привода распределительного вала. В торец переднего конца вала ввертывают храповик или болт для проворачивания коленчатого вала вручную при техническом обслуживании. В торце заднего конца вала помещен подшипник первичного вала коробки передач. В задней же части коленчатого вала имеется фланец, к которому прикреплен маховик. На его обод напрессован стальной зубчатый венец, с которым соединяется шестерня стартера при пуске двигателя.
Страницы: 1 2
Порекомендуйте статью друзьям: |
www.car-tales.ru
Автомобильный двигатель: основные детали и принцип работы AutoRemka

Мотор автомобиля работает на бензине или на каком-либо другом горючем, которое легко воспламеняется. Двигатель машины чаще называют двигателем внутреннего сгорания, так как внутри цилиндра происходит процесс горения топлива.
Детали мотора
Коленчатый вал четырехцилиндрового мотора представляет собой круглые точеные элементы, на которых крепятся шатуны и поршни.
Две головки шатуна – это верхний и нижний подшипники, благодаря которым шатун подвижно крепит меж собой коленчатый вал и поршень.
Поршень – это цилиндрическое тело в двигателя, на которое оказывают воздействия действие газы. Специальные пружинящие кольца служат для того, чтобы удержать внутри газы большого давления. Они устанавливаются в выступах поршня, и называются поршневыми шашками.
В цилиндре мотора автомобиля происходит процесс сгорания топлива и воздуха. Следует отметить, что при этом вырабатывается высокая температура, которая довольно вредно воздействует на цилиндр, поэтому автомобильные цилиндры оборудованы водным охладителем. Для данного действия в верхней части цилиндра имеется двойная стенка, по которой циркулирует вода.
Нужно отметить, что цилиндры мотора машины закрепляются болтами на картере, который одновременно является разъемной коробкой, имеющей посередине коленчатый вал. На нем укреплены прибор зажигания, охлаждения и смазки мотора.
Внутри цилиндра поршень двигается вверх и вниз, вдоль оси, при этом коленчатый вал крутится подшипниками; при помощи шатуна, от поршня движение передается к коленчатому валу. Предназначение клапанов мотора состоит в запуске свежего газа в цилиндр и выпуска из него перегоревшего. Поднятие клапанов происходит с помощью толкателей, которые движутся кулачковыми валиками и связанными с коленчатым валом цилиндрическими шестернями.
В моторе машины происходит сжигание смеси паров бензина (или другого горючего) и воздуха. Отметим, что данная смесь воспламеняется электрической искрой, при этом сама смесь должна хорошо сгорать. Число горючего и воздуха должно составлять около 15 кг кислорода на 1 кг топлива, при этом горючее должно полностью испариться и смещаться с воздухом. Для этого в двигателе имеется карбюратор. К нему по особой трубке из бака поступает топливо, которое, в свою очередь, внутри карбюратора распыляется и смешивается с воздухом в четком количестве.
Чтобы элементы мотора имели меж собой малое трение, в моторе имеется специальный масляный насос, с помощью которого масло подается к трущимся деталям.
Особенности работы двигателя
Итак, мы рассмотрели основные детали двигатели и узнали, что мотор работает за счет внутреннего сгорания горючего в цилиндрах, а также за счет тепла, которое выделяется в процессе этого.
Следовательно, работа двигателя – это общность процессов, а именно: заполнение цилиндра двигателя рабочим раствором, сгорание которого и чистит цилиндр от остатков продуктов сгорания.
Обычно, двигатель машины имеет от двух до двенадцати цилиндров, однако рабочие процессы в них всегда одинаковы. При обороте коленчатого вала вправо, движущийся поршень создает в цилиндре давление газа меньше внешнего. Вал расположен так, что позволяет под толкателем открывать всасывающий клапан. В цилиндр через клапан засасывается консистенция бензина и воздуха, которая образовалась в карбюраторе.
Процесс всасывания необходим для того, чтобы зарядить цилиндр новой рабочей смесью и является первый шагом к запуску мотора. За этот период поршень сделает один ход, а коленчатый вал пройдет половину оборота.
Вал, вращаясь, приводит поршень из нижнего положения в верхнее, а кулачковые валики не подходят к толкателям клапанов, поэтому они остаются прикрытыми, когда поршень движется вверх. В этот момент полость цилиндра не соприкасается с воздухом и внутри цилиндра совершается сокращение консистенции. При верхнем положении поршня сокращение является максимальным, не менее 6—6,5 атмосфер. Это второй шаг рабочего процесса мотора.
Поршень двигается вверх и сжимает рабочую смесь, затем на короткий промежуток времени останавливается в верхнем положении. В этот момент через свечу проходит электрическая искра, которая и воспламеняет смесь. Горючая смесь быстро сгорает, повышая ее температуру и давление до 25—30 атмосфер.
Далее поршень движется вниз под давлением газов, заставляя поворачиваться коленчатый вал. При этом возрастает размер полости цилиндра, и давление газа уменьшается. При нижнем положении поршня давление падает до 4—5 атмосфер.
Процедура расширения перегоревших газов и передачи их на коленчатый вал двигателя считается третьим шагом в работе мотора.
Тогда, когда поршень будет приближаться к нижней точке расположения, кулачковый вал развернется так, что его кулачок поднимет выпускной клапан и газы начнут извергаться вовне. Потом клапан остается раскрытым во время всех движений поршня вверх, через него будет выталкиваться с цилиндра перегоревшее топливо.
Эта процедура очистки цилиндра от перегоревшего топлива является четвертым тактом рабочего хода мотора.
Во время того, как поршень за процедуру выталкивания дойдет до собственного верхнего состояния, выпускной клапан прикрывается, так как кулачок уже минует толкач клапана. Кулачок валика к этому времени дойдет к толкателю всасывающего клапана и приоткроет последний, после чего все процессы начнутся сначала, и будут меняться друг за другом — всасывание, сжатие, расширение и выталкивание.
Тут же клапаны открываются по 1 разу, следовательно, за 2 оборота вала кулачки приблизятся по 1 разу к толкателям всасывающего и выпускного клапанов.
Для того, чтобы снизить колебания скорости оборотов коленчатого вала за рабочий процесс мотора, на коленчатый вал прикрепляется большой элемент — маховик. Чем он массивнее, тем правильнее ход двигателя и тем лучше он работает. В многоцилиндровом моторе за 2 оборота коленчатого вала такое количество рабочих ходов равно количеству цилиндров. Иными словами, чем больше имеется цилиндров у мотора, тем плавнее движется автомобиль.
autoremka.ru
Вкладыши для двигателя – детали критические
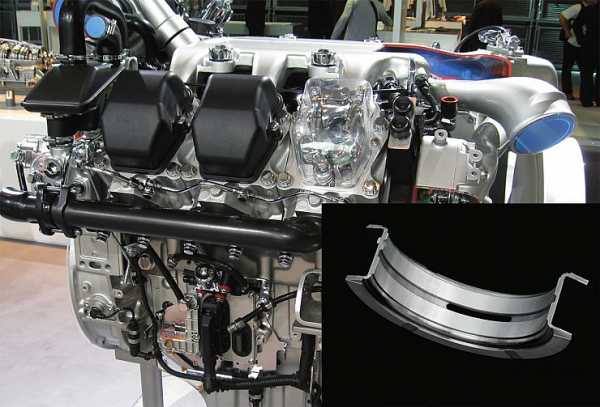
На первый взгляд вкладыши – это просто штамповка. Но впечатление обманчиво: подшипники скольжения представляют собой высокотехнологические изделия из сложного композитного материала, имеющие специфическую геометрию и точные размеры. И, что немаловажно – они являются критическими деталями двигателя, отказ которых ведет к его остановке и очень дорогому ремонту…
Функции подшипников
Вращающиеся компоненты двигателей внутреннего сгорания оборудованы подшипниками скольжения, которые выполняют разные функции:
• коренные вкладыши поддерживают коленчатый вал и обеспечивают его вращение. Устанавливаются в блоке цилиндров. Каждый вкладыш состоит из верхней и нижней половин. На внутренней поверхности верхней половины, как правило, есть канавка для смазки и отверстие для подачи масла.
• шатунные вкладыши обеспечивают вращение шейки шатуна, который, в свою очередь, вращает коленвал. Устанавливаются в нижней головке шатуна.
• упорные кольца предотвращают осевое движение вала. Часто упорные кольца являются частью одного из коренных вкладышей – такие комбинированные подшипники называются буртовыми или фланцевыми вкладышами.
• втулки верхней головки шатуна обеспечивают вращение поршневого пальца, соединяющего поршень с шатуном.
• вкладыши распредвала поддерживают распредвал и обеспечивают его вращение. Устанавливаются в верхней части головки блока цилиндров (или в блоке цилиндров – у двигателей с нижним расположением распредвала).
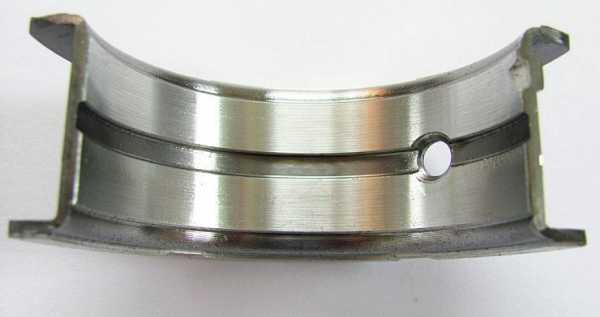


Подшипники скольжения смазываются моторным маслом, постоянно подающимся к их поверхности и обеспечивающим гидродинамический режим трения.
Непосредственный контакт между трущимися в гидродинамическом режиме поверхностями отсутствует – благодаря масляной пленке, которая образуется в сходящемся зазоре (масляном клине) между поверхностями подшипника и вала.
Условия работы подшипников скольжения
Масляная пленка предотвращает локальную концентрацию нагрузки. Однако при определенных условиях гидродинамический режим трения сменяется на смешанный. Это происходит, если имеются:
• недостаточный поток масла;
• высокие нагрузки;
• низкая вязкость масла;
• перегрев масла, дополнительно снижающий его вязкость;
• высокая шероховатость поверхностей подшипника и вала;
• загрязнение масла;
• деформация и геометрические дефекты подшипника, его гнезда или вала.
В смешанном режиме трения возникает непосредственный физический контакт поверхностей, чередующийся с гидродинамическим трением. А это может привести к задирам, повышенному износу подшипника и даже к схватыванию с валом.
ДВС характеризуются циклическими нагрузками подшипников, обусловленными переменным давлением в цилиндрах и инерционными силами, вызванными движущимися частями. И эти циклические нагрузки на подшипник могут привести к его разрушению. Отсюда – высочайшие требования к материалам, из которого он производится.

Материалы подшипников скольжения
Материалы, из которых делают подшипники, должны обладать многими, иногда противоречивыми, свойствами.
• Усталостная прочность (максимальная нагрузка) – максимальная циклическая нагрузка, которую подшипник выдерживает в течение неограниченного числа циклов. Превышение этой нагрузки приводит к образованию усталостных трещин в материале.
• Сопротивление схватыванию (совместимость) – способность материала подшипника сопротивляться свариванию с материалом вала во время прямого физического контакта между ними.
• Износостойкость – способность материала подшипника сохранять свои размеры несмотря на присутствие абразивных частиц в масле, а также в условиях механического контакта с валом.
• Прирабатываемость – способность материала подшипника компенсировать небольшие геометрические дефекты вала и гнезда за счет незначительного локального износа или пластической деформации.
• Абсорбционная способность – способность материала подшипника захватывать мелкие чужеродные частицы, циркулирующие с маслом.
• Коррозионная стойкость – способность материала подшипника сопротивляться химическим воздействиям окисленных или загрязненных масел.
• Кавитационная стойкость – способность материала подшипника выдерживать ударные нагрузки, производимые схлопывающимися кавитационными пузырьками (пузырьки образуются в результате резкого падения давления в текущем масле).
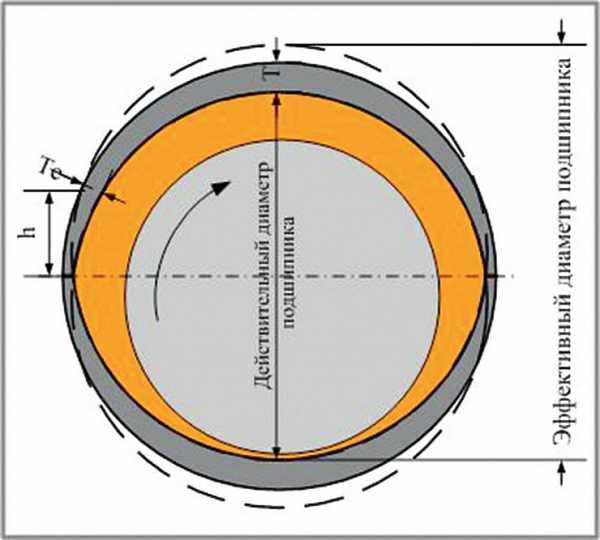
Соответственно длительная и надежная работа подшипника скольжения достигается соединением высокой прочности (усталостной прочности, износостойкости, кавитационной стойкости) с мягкостью (прирабатываемостью, сопротивлением схватыванию, абсорбционной способностью).
То есть материал должен быть одновременно и прочным, и мягким. Это звучит парадоксально, однако существующие подшипниковые материалы соединяют эти противоположные свойства – правда, с определенным компромиссом.
Для достижения этого компромисса используются композитные структуры, которые могут быть или слоистыми (мягкое покрытие, нанесенное на прочное основание) или дисперсными (мягкие частички, распределенные внутри прочной матрицы).
Биметаллические подшипники имеют стальное основание, обеспечивающее жесткость и натяг в тяжелых условиях повышенной температуры и циклических нагрузок.
Второй слой материала состоит из антифрикционного сплава. Его толщина относительно велика: она составляет около 0,3 мм. Толщина антифрикционного слоя – важная характеристика биметаллических подшипников, способных прирабатываться и приспосабливаться к относительно большим геометрическим дефектам. Биметаллический подшипник также обладает хорошей абсорбционной способностью, поглощая как мелкие, так и крупные включения в масле.
Обычно рабочий слой делают из алюминия, содержащего 6–20% олова в качестве твердого смазочного материала: именно олово обеспечивает антифрикционные свойства. Кроме этого, сплав часто содержит 2–4% кремния в виде мелких включений, распределенных в алюминии. Твердый кремний упрочняет сплав и обладает способностью полировать поверхность вала – поэтому его присутствие особенно важно при работе с валами из ковкого чугуна. Сплав может быть дополнительно упрочнен небольшими добавками меди, никеля, марганца, ванадия и других элементов.
Триметаллические подшипники, помимо стального основания, имеют промежуточный слой из медного сплава, содержащего 20–25% свинца в качестве твердой смазки и 2–5% олова для упрочнения меди.
Третий слой представляет собой покрытие на основе свинца, которое также содержит около 10% олова, повышающего коррозионную стойкость сплава и несколько процентов меди для упрочнения. Толщина покрытия составляет всего 12–20 мкм. Низкая толщина покрытия повышает его усталостную прочность, однако снижает антифрикционные свойства (прирабатываемость, абсорбционную способность, сопротивление схватыванию), особенно если мягкое покрытие было подвергнуто износу. Между промежуточным слоем и свинцовистым покрытием наносится очень тонкий (1–2 мкм) слой никеля, служащий барьером, предотвращающим диффузию олова из покрытия в промежуточный слой.
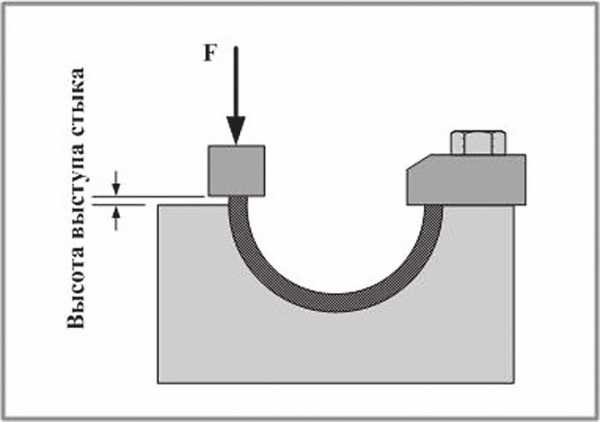
Инновационные материалы для подшипников скольжения постоянно разрабатываются производителями подшипников. Это новые материалы, способные работать в тяжело нагруженных двигателях (дизельные двигатели с непосредственным впрыском топлива, двигатели с турбонаддувом), а также в гибридных и старт-стоп двигателях, в том числе:
• высокопрочные алюминиевые биметаллические материалы;
• прочные металлические покрытия для триметаллических подшипников;
• полимерные композитные покрытия, содержащие частицы твердых смазочных материалов;
• бессвинцовые экологически чистые безвредные материалы.
Свойства подшипниковых материалов
Свойства материалов подшипников, характеризующие прочность и мягкость, сочетаются в различных пропорциях у разных материалов.
Отличные мягкие антифрикционные свойства триметалла ограничены толщиной покрытия (12 мкм). Если геометрический дефект или чужеродные частицы превышают толщину покрытия, ее антифрикционные свойства резко падают.
Мягкие свойства биметалла несколько ниже, чем у триметалла, однако они не ограничены толщиной покрытия, поэтому биметаллические подшипники способны прирабатываться к относительно крупным несоосностям и другим геометрическим дефектам. С другой стороны, усталостная прочность (максимальная нагрузка) биметаллических подшипников ниже (40–50 МПа), чем у триметаллических материалов (60–70 МПа). Также биметаллические подшипники без кремния хуже работают с чугунным валом.
Геометрические характеристики подшипников скольжения
Масляный зазор – это основной геометрический параметр подшипников скольжения. Он равняется разнице между внутренним диаметром подшипника и диаметром вала (внутренний диаметр подшипника измеряется под углом 90° к линии, разделяющей верхний и нижний вкладыши).
Величина масляного зазора – очень важный показатель. Большой зазор приводит к увеличению потока масла, что снижает его нагрев в подшипнике, однако вызывает неоднородное распределение нагрузки (она концентрируется на меньшей площади поверхности и увеличивает вероятность разрушения вследствие усталости). Также большой зазор производит значительную вибрацию и шум. А слишком маленький зазор вызывает перегрев масла и резкое падение его вязкости.
Типичные величины масляного зазора С: для пассажирских автомобилей Cмин = 0,0005D, Cмакс = 0,001D, для гоночных автомобилей Cмин = 0,00075D, Cмакс = 0,0015D (где D – диаметр вала).
Эксцентриситет является мерой, определяющей некруглость подшипника. Действительно, внутренняя поверхность подшипника не является абсолютно круглой. Она имеет форму, напоминающую лежащий на боку лимон. Это достигается за счет переменной толщины стенки подшипника, имеющей максимальное значение (Т) в центральной части и постепенно уменьшающейся в направлении стыка.
Принято измерять минимальное значение толщины (Te) на определенной высоте h для того, чтобы исключить зону выборки в области стыка. Разница между максимальным и минимальным значениями толщины называется эксцентриситетом: Т – Те.
Эксцентриситет, образованный переменной толщиной стенки вкладыша, добавляется к эксцентриситету, вызванному смещением вала относительно центра подшипника. Наличие эксцентриситета позволяет стабилизировать гидродинамический режим смазки за счет создания масляного клина с большим углом схождения. Рекомендуемые величины эксцентриситета: для пассажирских автомобилей 5–20 мкм, для гоночных автомобилей 15–30 мкм.
Посадочный натяг необходим для обеспечения надежной посадки подшипника в гнезде. Прочно посаженный подшипник имеет равномерный контакт с поверхностью гнезда – это предотвращает смещение подшипника во время работы, обеспечивает максимальный отвод тепла из области трения и увеличивает жесткость гнезда. Поэтому наружный диаметр подшипника и его периметр всегда больше диаметра гнезда и его периметра.
Поскольку прямое измерение наружного периметра подшипника – трудная задача, обычно измеряется другой параметр: высота выступа стыка (выступание). Высота выступа стыка равна разнице между наружным периметром половины подшипника и периметром половины гнезда.
Проверяемый вкладыш устанавливают в измерительный блок и прижимают с определенным усилием F, величина которого пропорциональна площади сечения стенки подшипника. Оптимальная величина высоты выступа стыка зависит от диаметра подшипника, жесткости и теплового расширения гнезда и температуры. Типичные значения высоты выступа стыка для подшипников диаметром 40–65 мм: для пассажирских автомобилей 25–50 мкм, для гоночных автомобилей 50–100 мкм.
Несмотря на самые совершенные конструкцию, материалы и технологии, в эксплуатации ДВС встречаются случаи износов и повреждений подшипников. Чтобы найти и устранить их причины, знание конструкции подшипников необходимо, но недостаточно. Об этом – в следующей статье.
Дмитрий Копелиович
abs-magazine.ru
Подвижные детали двигателя
Строительные машины и оборудование, справочник
Подвижные детали двигателяКатегория:
Дизельные двигатели
Подвижные детали двигателя
Кривошипно-шатунный механизм воспринимает давление газов и преобразует прямолинейное возвратно-поступательное движение поршня во вращательное движение коленчатого вала.
В зависимости от типа и размера двигателя детали кривошипно-шатунного механизма отличаются большим разнообразием конструкций. Однако все они рассчитаны на такие условия работы, которые связаны с необходимостью воспринимать и передавать большие нагрузки, вызывающие высокие напряжения в металле, в результате чего они подвержены более значительному износу, чем неподвижные детали.
Для изготовления деталей тихоходных и средней быстроходности дизелей в основном используется углеродистая качественная сталь (ГОСТ 1050—60). Поршневые пальцы, кулачные шайбы и валики изготовляются из стали с малым содержанием углерода (до 0,2%) с цементацией и закалкой рабочих поверхностей.
Поршень воспринимает давление расширяющихся газов и передает его коленчатому валу через шатун. Поршень обычно изготовляют из серого чугуна (марки СЧ 24-44, ГОСТ 1412—70) или из алюминиевых сплавов, обеспечивающих достаточную прочность при работе в условиях высоких температур.
В поршне различают головку, канавки для поршневых колец, юбку, канавку для стопорного кольца и бобышки. Днище поршня имеет толщину 10—30 мм и с внутренней стороны укрепляется ребрами. Верхняя часть боковых стенок делается такой же толщины, как и днище, а нижняя часть (юбка) — несколько тоньше, но достаточно жесткой. В средней цилиндрической части поршня имеются приливы (бобышки) с отверстиями для установки поршневого пальца 6. Чтобы при тепловом расширении поршень передвигался свободно, он устанавливается в цилиндре с зазором.
На наружной поверхности поршень имеет проточенные канавки для колец: верхние — для компрессионных (газоуплотнительных), а нижние — для маслосъемных. Маслосъемные кольца располагаются одно выше, а другое ниже поршневого пальца. В канавках для маслосъемных колец просверлены сквозные отверстия, через которые масло стекает внутрь поршня.
При работе двигателя поршень у днища нагревается сильнее и, следовательно, больше расширяется, чем у нижней направляющей части. Поэтому для обеспечения необходимого зазора поверхность поршня от оси пальца до днища обработана на конус: с меньшим диаметром у донышка и большим — у пальца. При такой обработке во время работы двигателя форма поршня приближается к цилиндрической, что обеспечивает нормальный зазор между рабочей поверхностью втулки цилиндра и поршнем. У поршней быстроходных двигателей нижняя часть имеет фаску, в которой собирается масло при поступательном движении поршня вниз и затем равномерно распределяется по рабочей поверхности втулки цилиндра, обеспечивая тем самым хорошую его смазку.
Рис. 1. Детали кривошипно-шатунногомеханизма дизеля:
Рис. 2. Поршень. 1 — поршень; 2 — поршневый палец; 3 — шатун; 4 — коленчатый вал
В настоящее время много внимания уделяется качеству материала поршней и их конструкции. Поршни из алюминиевого сплава имеют меньший вес по сравнению с чугунными, следовательно, и меньшие величины сил инерции, вызывающих в двигателях дополнительные напряжения.
Теплопроводность алюминия в 2,0—2,5 раза больше, чем чугуна, а теплоотдача от газов к алюминиевому днищу поршня на 30% меньше, чем к чугунному, т. е. днище алюминиевого поршня имеет более низкую температуру и меньшие температурные напряжения по сравнению с днищем чугунных поршней.
Так как коэффициент линейного расширения алюминия в 2,0— 2,5 раза больше, чем чугуна, во избежание заеданий поршня при расширении его вследствие нагрева зазоры между поршнем и втулкой рабочего цилиндра необходимо делать значительных размеров. С повышением температуры механические качества алюминия резко понижаются, что приводит к быстрой разработке канавок для колец и отверстий в бобышке для пальца поршня. В том случае, когда поршень чугунный, зазор между поршнем и рабочей поверхностью цилиндра, их износ, а также утечка газа не столь значительны. Поэтому при повышении мощности двигателей, вызывающем повышение тепловой и механической нагрузки, приходится отказываться от поршней из алюминиевых сплавов и переходить на чугунные или составные из чугуна и стали и применять внутреннее охлаждение поршня водой или маслом.
Величина монтажного зазора между поршнем и втулкой цилиндра зависит от технологических условий обработки деталей, чистоты обработки их поверхностей, тщательности их пригонки и монтажа двигателя в целом. Особенно большое влияние оказывают неточности при расточке отверстий для поршневых пальцев в приливах поршня. При обмерах поршней необходимо иметь в виду, что на точность обмера оказывает влияние посадка поршневого пальца. При изготовлении поршня окончательная шлифовка до заданного размера производится со вставленным поршневым пальцем. В связи с этим обмеры поршня необходимо также производить с установленным пальцем.
Большое распространение получили поршни, верхняя часть которых выполнена из кованой стали, а нижняя — из чугуна, с охлаждением верхней части маслом (двигатели «Зульцер», МАН, «Гета-веркен» и др.). У некоторых двигателей тронковые поршни снабжены в верхней части медным пояском, чтобы уменьшить зазор и возможность заедания (двигатель МАН). Иногда такой поясок ставится и внизу поршня (двигатель «Зульцер»).
Рис. 3. Поршень дизеля 18Д: 1 — поршень; 2 — компрессионное кольцо; 3 — втулка; 4 — штифт; 5 —заглушка; 6 — палец
Вместо поршней обычной конструкции с бобышками для пальца, ставляемого через боковые отверстия, применяются поршни, в ко-орых палец крепится к приливам (без сквозного отверстия в поршне) что облегчает выемку поршня из цилиндра без шатуна (двигатель «Нордберг»).
На рис. 3 изображен поршень двигателя 18Д, у которого палец может поворачиваться во втулках, запрессованных в бобышки поршня. Втулки предохраняют отверстия бобышек от износа, а потому исключается необходимость их расточки при ремонте или смене поршневого пальца.
Поршень двигателя типа Д6, изготовленный горячей штамповкой из алюминиевого сплава, показан на рис. 4. Для облегчения с наружной стороны бобышек сделаны выемки. В нижней части поршня просверлены отверстия для стока масла. Форма днища образована по контуру струй топлива, впрыскиваемого в цилиндр двигателя. Для увеличения жесткости и лучшего отвода тепла, которое передается воздуху картера, нижняя поверхность днища выполнена ребристой. Для того чтобы впускные и выпускные клапаны свободно открывались и закрывались, на головке поршня сделаны соответствующие выемки. Относительно малая высота поршня позволяет сделать рабочие втулки небольшой длины и в целом уменьшить высоту двигателя.
Рис. 4. Поршень дизеля Дб: 1 — поршень; 2 — палец; 3 — компрессионное кольцо; 4 — маслосъемное кольцо
На рис. 5 показан поршень дизеля Д-54 с плоским днищем, на котором вдоль оси поршневого пальца выфрезерованы выточки для свободного открывания впускного и выпускного клапанов.
Чтобы придать ему большую жесткость и обеспечить интенсивный отвод тепла от головки поршня, с внутренней стороны сделаны восемь радиальных и одно кольцевое ребро. Поршневой палец пустотелый, с плотной посадкой в бобышках поршня.
Рис. 5. Поршень тракторного дизеля Д-54:
Рис. 6. Поршень дизеля 6БК-43: 1 – поршень; 2 – компрессионное кольцо; 3 – палец; 4 – стопор; 5 – шпонка
Рис. 7. Пояса и направления обмеров поршня
Так же замеряют наружный диаметр пальца.
Наружный диаметр тронка поршня замеряют в трех поясах и в двух направлениях (аа и 66). Первый пояс расположен на расстоянии 10 мм от верхней кромки поршня, второй — между верхним краем отверстия бобышки и нижним поршневым кольцом головки поршня, а третий — на расстоянии 10 мм от нижнего края поршня. Данные этого замера использует механик для подсчета зазора втулка — поршень. Высоту канавок для колец записывают по результатам замеров в соответствующие графы.
Поршневые кольца служат для уплотнения поршня в цилиндре, предотвращения попадания масла в камеру сгорания и отвода тепла от поршня в стенку цилиндра. Материалом для изготовления поршневых колец служит чугун, соответствующий маркам СЧ21-40 и СЧ24-44 с повышенным содержанием фосфора (до 0,5— 0-9%) и с присадкой хрома, никеля или других легирующих элементов. Механические качества материала должны удовлетворять требованиям, предъявляемым к кольцам (твердость, упругость и т. д.).
Твердость колец обычно не превышает 190—230 НВ. Готовые кольца подбирают к цилиндрам с допуском единиц по отношению к твердости втулки цилиндра. Если твердость колец несколько превышает твердость втулки, это нельзя считать недостатком. В отношении износа поршневые кольца находятся в худших условиях, чем втулка, так как работа трения, отнесенная к единице поверхности кольца, всегда больше, чем у втулки. Для колец, изготовляемых из модифицированного чугуна и работающих в паре с втулками высокой твердости, задают твердость 220—250 НВ и выше. Иногда при стальных азотированных втулках применяют кольца повышенной твердости порядка 350—400 НВ при сохранении первоначальной прочности.
Для ускорения приработки колец и повышения износостойкости широко применяются разнообразные покрытия: лужение, свинцевание, фосфатирование, оксидирование. Иногда в кольцах предусматривают канавки для антифрикционного материала, например за-вальцовывают в них бронзовые пояски или заполняют канавки массой, содержащей графит, которую затем спекают. Благодаря своей упругости поршневые кольца прижимаются к стенкам цилиндра и создают необходимую плотность соединения.
Поршневые кольца четырехтактных двигателей при движении поршня вниз, во время такта впуска (всасывания воздуха), прижимаются к верхней торцовой поверхности канавки, а во время хода поршня вверх (при сжатии) — к нижней поверхности. Такое перемещение колец в канавках создает насосное действие, способствующее попаданию масла в камеру сгорания. Для того чтобы уменьшить это вредное явление, необходимо стремиться к минимальным зазорам между кольцом и торцовой поверхностью канавки по высоте. У двухтактных двигателей поршневые кольца все время нагружены сверху и прижаты к нижней торцовой поверхности канавки поршня; здесь насосное действие кольца отсутствует.
По назначению они подразделяются на компрессион-н ы е (газоуплотнительные) и маслосъемные. Компрессионные кольца имеют прямоугольное сечение. Число компрессионных колец зависит от давления газов и диаметра цилиндра и обычно составляет 3—5 у быстроходных двигателей и 6—7 У тихоходных.
Маслосъемные кольца служат для удаления избыточного масла со стенок цилиндра и не допускают его попадания в камеру сгорания.
Кольца ставят по одному вверху под компрессионными и внизу тронковой части поршня.
В свободном состоянии наружный диаметр поршневого кольца несколько больше диаметра цилиндра. Чтобы кольцо не заело при нагревании, в замке, образованном разрезом кольца, устанавливается небольшой зазор.
У хромированию. Износ поршневых колец зависит от скорости движения поршня, температуры рабочей среды, нагрузки и режима работы двигателя и степени загрязнения смазочного масла. Они выходят из строя не одновременно: сперва — верхние, а затем —средние и нижние. При одинаковой мощности износ колец в быстроходном дизеле выше, чем в тихоходном.
Очень большое влияние на износ поршней и колец имеют нагрузка и температура двигателя. Высокая температура внутри цилиндра затрудняет смазку его поверхностей, а низкая обычно является причиной ускоренного износа поршней и поршневых колец вследствие коррозии. Попадание пыли из воздуха также является причиной значительного изнашивания поршневых колец. Поэтому необходимо содержать фильтры в исправности и обеспечивать полную герметичность в соединениях.
Рис. 9. Схема насосного Действия поршневых колец
Рис. 10. Замки поршневых колец: а — прямой; б — косой; в — ступенчатый
Наибольшему износу подвержены два верхних поршневых кольца, поэтому для повышения износостойкости их подвергают пористо-
Измерение величины зазора между поршневым кольцом и опорной поверхностью канавки в поршне производится по всей окружности щупом при надетом на поршень кольце.
Износ поршневых колец сверх допустимых размеров наступает значительно раньше предельного износа цилиндра. Поэтому предельный износ поршневых колец определяет сроки профилактического ремонта двигателей. Перед тем как ставить на поршень новые кольца, их концы следует подогнать под соответствующий нормам размер. Суммарная длина просветов между кольцом и втулкой не должна превышать длины дуги 90°, величина просвета должна быть не более 0,05 мм. Во время работы двигателя изнашиваются также торцовые поверхности поршневых колец и канавок поршня. Пригорают поршневые кольца у двухтактных двигателей, работающих при высокой температуре.
Значительные износы колец (увеличение зазоров в стыках), а также пригорание их вызывают ухудшение пусковых качеств двигателя, проникновение отработавших газов в картер, увеличение дымности выпускных газов и удельного расхода топлива и понижение развиваемой двигателем мощности.
Поршневой палец служит для шарнирного сочленения поршня с шатуном. Он воспринимает силу давления газов, действующую на поршень, и передает ее шатуну. Поршневые пальцы для тихоходных двигателей изготовляют из мягкой углеродистой стали, а для быстроходных — из хромоникелевой стали 12ХНЗА. Для повышения прочности и износостойкости поверхность пальцев цементируют на глу-бнну 0,75—1,0 мм и закаляют. Часто поверхность пальцев хромируют.
В зависимости от характера посадки в бобышках поршня пальцы бывают неподвижные и плавающие. Плавающие пальцы, поворачиваясь относительно своей оси при работе двигателя, способствуют уменьшению износа и устраняют возможность односторонней выработки. Для предотвращения осевого перемещения пальцы в бобышке фиксируют пружинными кольцами или алюминиевыми заглушками со сферической головкой. При этом радиус сфер головок несколько меньше диаметра цилиндра. В заглушке просверлено отверстие, через которое выходит воздух из полости пальца при работе двигателя. Если бы отверстия не было, оставшийся внутри пальца воздух при нагреве, расширяясь, прижимал бы заглушку к рабочей поверхности втулки цилиндра, что вызывало бы ее местный износ.
Рис. 11. Плавающий поршневой палец
Рис. 12. Неподвижный поршневой палец
На рис. 12 изображен поршневой палец с неподвижной посадкой в поршне. От проворачивания он удерживается шпонкой, а от осевого перемещения — коническим штифтом. Такое крепление обеспечивает свободное удлинение пальца в одну сторону при нагревании, не вызывая деформации в теле поршня. Чтобы легче было ставить палец на место и вынимать при разборке, он сделан ступенчатым с большим диаметром со стороны шпонки, средним — в месте соединения с шатуном и меньшим — со стороны конического штифта. Поэтому вынимать палец можно только в сторону шпонки.
Учитывая, что поршневые пальцы работают в условиях больших давлений и высоких температур, их, в целях уменьшения износа, шлифуют и полируют с чистотой отделки поверхности 0,1—0,2 мк. Рабочую поверхность пальцев часто хромируют. Внешний диаметр пальца обычно составляет 0,25—0,3 диаметра поршня, а длина вкладыша верхней головки шатуна должна быть максимально возможной с тем, чтобы создать достаточную опорную поверхность.
Втулка верхней головки шатуна, в которой работает палец, должна всегда иметь достаточное количество смазки, которая у большинства дизелей поступает от коленчатого вала — через шатун или разбрызгиванием.
Выработку поршневого пальца и втулки верхней головки шатуна определяет механик, измеряя зазор между поверхностью пальца и втулкой и обмеряя сам палец.
Карта обмера узла «палец — втулка» должна отражать результаты контроля за изменением размеров поршневого пальца и втулки верхней головки шатуна при каждом ремонте двигателя. Техническое состояние головного сочленения определяется изношенностью пальца, втулки верхней головки шатуна и величиной зазора между ними.
Пояса II и III втулки и пальца находятся в одной плоскости замера. Это позволяет определить величину зазора «втулка — палец» вычитанием из замеренного диаметра втулки наружного диаметра пальца. После замеров, проведенных при ремонте двигателя, механик пишет «Заключение о состоянии и необходимом ремонте» (замена, обработка по ремонтным размерам и т. д.) по каждому головному сочленению.
Рис. 13. Пояса обмера деталей головного соединения (поршневого пальца и головной втулки)
Шатун — основная деталь шатунно-кривошипного механизма, преобразующего возвратно-поступательное прямолинейное движение поршня во вращательное движение коленчатого вала. Шатуны изготовляют штамповкой или поковкой из углеродистой стали высокого качества. В малооборотных двигателях применяют главным образом углеродистые стали: для стержней — сталь 35, для головок — сталь 25, 35; для шатунных болтов — сталь 30, а иногда и легированные стали. В многооборотных двигателях в зависимости от степени напряжения для стержней и крышек при меняют углеродистую сталь 45 , легированные стали 40Х, 45Х, 30ХМА,40ХНМА и, наконец, 18Х2Н4ВА, отличающуюся особо высокими показателями прочности и ударной вязкости; для шатунных болтов — сталь 20ХНВА и 18Х2Н4ВА.
Шатуны делают обычно круглого сечения, а в быстроходных двигателях (с целью облегчения) — двутавровыми. Шатун состоит из трех частей: верхней головки, стержня и нижней головки. Верхняя головка
неразъемная. В нее запрессовывается бронзовая втулка с канавками на рабочей поверхности, по которым подводится смазочное масло к средней части поршневого пальца. Втулки верхней головки изготовляются из бронзы. В настоящее время все больше применяются биметаллические втулки, состоящие из слоя бронзы, залитой в стальную втулку. Это объясняется их небольшой стоимостью и возможностью посадки в отверстие с большим натягом.
Нижняя головка шатуна, соединяющая его с шейкой вала, разъемная. Крышка нижней головки шатуна прикрепляется к телу шатуна через установленные в стыках прокладки двумя или четырьмя шатунными болтами с гайками из высококачественной стали. Внутренние поверхности нижней головки шатуна залиты баббитом. Трущиеся поверхности баббита имеют канавки, которые обеспечивают равномерное распределение смазки по мотылевой шейке вала. Прилегание вкладыша нижней головки к шейке коленчатого вала по мере выработки баббита регулируется уменьшением количества прокладок в разъеме подшипника.
Рис. 14. Шатун с круглым сечением стержня: 1 — верхняя головка; 2 — стержень; 3— маслоподводящий канал; 4 — нижняя головка; 5 — крышка подшипника
Стяжные болты нижней головки шатуна подвержены растяжению и разрыву, поэтому по истечении установленного заводом срока их необходимо заменить новыми, даже при отсутствии дефектов.
В V-образных быстроходных двигателях применяют два типа шатунов. В первом случае оба шатуна нижними головками соединяются непосредственно с мотылевой шейкой коленчатого вала; во втором — один шатун (главный) соединяется непосредственно с мотылевой шейкой, а второй (дополнительный) — с проушиной главного шатуна.
Рис. 15. Шатуны с двутавровым сечением стержня с прямым разъемом нижней головки: 1— верхняя головка; 2—головная втулка; 3— стержень; 4 — маслоподводящий канал; 5 — нижняя головка; 6—вкладыш подшипника; 7 — крышка подшипника
Рис. 16. Шатун с двутавровым сечением стержня и с косым разъемом нижней головки: 1 —верхняя головка; 2 — головная втулка; 3 — стержень; 4 — нижняя головка; 5 — вкладыш подшипника; 6 — шатунный болт
Коленчатый вал—наиболее ответственная и сложная по конструкции деталь, срок службы которой часто определяет долговечность двигателя. При работе двигателя коленчатый вал подвергается действию периодически изменяющихся сил давления газов, сил инерции возвратно-поступательно движущихся деталей и центробежных сил вращающихся деталей. Все они вызывают деформации вала (изгиб, скручивание, сжатие и растяжение). Длительная работа коленчатого вала может быть обеспечена только при услозии правильного его положения в подшипниках, исключающих недопустимый прогиб вала при работе. У тихоходных двигателей коленчатые валы чаще всего изготовляют из углеродистой стали, а у быстроходных—из легированной; они состоят из коренных и шатунных шеек, соединенных щеками.
Коленчатые валы характеризуются парностью колен, углом между ними и порядком работы цилиндров. Число колен вала зависит от числа цилиндров. Небольшие валы изготовляют цельными, крупные — составными из двух или трех частей. В шейках вала и щеках просверлены отверстия, по которым к подшипникам подводится смазка.
При выборе угла между коленами исходят из условия необходимости обеспечения наиболее равномерного вращения вала двигателя. Для этого воспламенение топлива в отдельных цилиндрах должно происходить через определенные углы поворота вала и одинаковые промежутки времени. Угол между соседними мотылями определяется числом тактов двигателя и числом его цилиндров и равен количеству градусов поворота вала за весь цикл, разделенному на число цилиндров. Для четырехцилиндрового четырехтактного двигателя угол ф = 720 : 4 = 180°, т. е. все мотыли располагаются в одной плоскости. Для шестицилиндрового двухтактного двигателя Ф = 360 : 6 = 60°.
Его колена расположены относительно друг друга под углом 720 : 6 = 120° и в определенной последовательности (согласно порядку работы цилиндров). Наиболее распространенные порядки работы цилиндров шестицилиндрового двигателя следующие: 1—5—3—6—2—4, 1—4—2—6—3—5, 1—2—3—6—5—4.
Рис. 17. Главный и прицепной шатуны: 1 — главный шатун; 2 — заглушка; 3 — поршневой палец; 4 — поршень; 5 — прицепной шатун; 6 — палец для крепления шатуна; 7 — винт; 8 — шайба; 9 — проушина для крепления прицепного шатуна; 10 — крышка; 11 — вкладыш
Один конец вала имеет фланец для крепления маховика двигателя. На другом конце крепятся шестерни привода компрессора, водяного и масляных насосов.
Рис. 18. Конструкции коленчатых валов: а — прямоугольная форма мотыли; б, «, г —эллиптическая форма мотыля; д,е — со скосами углов мотыля; ж, з— круглая форма мотыля
Для уравновешивания центробежных сил, с которыми вращающиеся массы действуют на подшипники, щеки мотылей снабжены противовесами.
Хорошая жесткость вала достигается при овальной или круглой форме щек мотыля. Для уменьшения износа шейки подвергаются цементации, азотированию или поверхностной закалке токами высокой частоты.
Причиной изнашивания коленчатого вала является, в первую очередь, трение шеек в подшипниках, а также наличие механических примесей в смазочном масле. В результате выработки сечение шейки делается овальным (эллиптичным), а сама шейка — конусовидной. Овальность, или эллиптичность, определяется разностью двух взаимно перпендикулярных диаметров сечения шейки, а конусность — разностью диаметров двух сечений шейки, при условии, что эти диаметры лежат в одной плоскости, проходящей через ось конуса.
Рис. 19. Коленчатый вал шестицилиндрового дизеля
Для свободного вращения шеек коленчатого вала в рамовых подшипниках и для размещения слоя масла необходимой толщины между трущимися поверхностями во вкладышах устанавливаются зазоры определенного размера. Зазоры в подшипниках при работе двигателя не остаются постоянными, особенно в первые часы работы двигателя после ремонта, т. е. в период приработки подшипников. После обкатки двигателя производится подтяжка подшипников с доведением величин монтажных зазоров до эксплуатационных.
В двигателях, не имеющих прокладок в разъемах вкладышей подшипников, монтажные и эксплуатационные зазоры одинаковы.
Зазоры замеряют до и после каждого ремонта двигателя и подтяжки подшипника, раскепы — еще чаще. Эллиптичность и биение рамовых шеек замеряют перед каждым заводским ремонтом двигателя, а уменьшение диаметра шеек — перед капитальным ремонтом.
Диаметр рамовых шеек замеряют микрометром с ценой деления 0,01 мм в двух поясах и в двух взаимно перпендикулярных направлениях, располагаемых по осям ближайшей щеки.
Рис. 20. Коленчатый вал дизеля 24 10,5/13: 1 — шестерня; 2 — болт крепления противовеса; 3—противовес; 4 — заглушка со стяжным болтом; 5 — шейка вала; 6 — шестерня привода распределительного вала; 7 — шпонка; 8 — масляная трубка
Кроме того, при втором заводском (капитальном) ремонте биение рамовых шеек вала обязательно проверяют на стенке, для чего вал предварительно устанавливают по центровой линии. Гнездо рамового подшипника замеряют без крышки в двух поясах (I и II) на расстоянии 1/4 длины гнезда от его края.
Рис. 21. Обмер рамовых шеек коленчатого вала
Рис. 22. Измерение зазора в рамовом подшипнике: 1 — перемычка фундаментной рамы; 2— нижняя половинка вкладыша рамового подшипника; 3 — шейка коленчатого вала: 4 — прутки свинцовой проволоки
Монтажный зазор замеряют при сборке двигателя после ремонта или изготовления, а эксплуатационный — после приработки подшипников и регулировки зазора путем удаления или замены части прокладок. Эллиптичность шеек вала для каждого пояса определяется разностью размеров наибольшего и наименьшего диаметров вала, замеряемых в направлениях аа и бб.
Диаметры мотылевых шеек замеряют микрометром в двух поясах (I и II) и двух взаимно перпендикулярных направлениях (аа и бб). Для четырехтактных двигателей направление аа смещено от оси цилиндра на 10—15° в сторону вращения кривошипа, для двухтактных — против вращения кривошипа. Эллиптичность шеек вала для каждого пояса определяется разностью размеров наибольшего и наименьшего диаметров вала, замеренных в направлениях аа и бб. Внутренний диаметр мотылевого подшипника замеряют микрометрическим или индикаторным нутромером, установленным по микрометру, в двух поясах (I и II) и одном направлении (аа).
Зазор между подшипником и шейкой вала определяют как разность замеров внутреннего диаметра подшипника и диаметра моты-левой шейки либо посредством выжимки свинцовой проволоки. Монтажный зазор замеряют при сборке двигателя после ремонта или изготовления, а эксплуатационный — после приработки подшипников и регулировки зазора путем удаления или замены части прокладок.
зависящие от величины вращающих моментов, сил упругости вала и сил инерции, вызывающих колебания. При совпадении частот и направлений собственных и вынужденных колебаний наступает так называемое состояние резонанса, вызывающее возрастание внутренних напряжений вала. Число оборотов коленчатого вала, при котором наступает явление резонанса, называется критическим, а колебания при этом — критическими колебаниями.
Критические числа оборотов и напряжения, возникающие при них в вале, определяются расчетом и проверяются при помощи специального прибора, называемого торсиографом.
Рис. 23. Пояса и направления обмеров мотылевых шеек
Коленчатый вал и присоединенные к нему валы, передающие крутящий момент к гребному винту, представляют собой упругую систему, способную под действием внешних периодически изменяющихся нагрузок колебаться. Колебания, продолжающиеся и после того, как вызвавшие их силы или моменты сил перестали действовать, называются собственными колебаниями. Характер собственных колебаний и скорость их затухания зависят от внутренних сопротивлений материала вала, внешнего сопротивления окружающей среды и трения в подшипниках. При затухании частота колебаний остается постоянной, а амплитуда колебаний уменьшается.
Колебания, вызванные периодически изменяющимися вращательными моментами, называются вынужденными колебаниями, причем сила скручивания вала непрерывно изменяется на протяжении полного оборота.
Во время работы двигателя собственные колебания практически затухают. Остаются лишь вынужденные крутильные колебания.
Возникновение резонанса при соответствующих ему критических числах оборотов вала сопровождается значительным шумом, сильной вибрацией дизеля и стуками в соединениях подвижных частей. Происходящее при этом скручивание вала приводит к на-рушению балансировки двигателя и регулировки газораспределительных органов.
Дополнительные напряжения вала, возникающие в диапазоне резонансных колебаний, обычно значительно превышают величину тех крутильных напряжений, на которые рассчитан коленчатый вал. В результате может наступить разрушение вала. При этом излом происходит вблизи так называемого вибрационного узла, т. е. у предпоследнего или последнего колена вала, расположенного у маховика. Излом в таких случаях имеет характер повреждения, возникшего от усталости металла.
В двигателях с большим количеством цилиндров и широким диапазоном чисел оборотов при эксплуатации невозможно избежать резонансных колебаний. В этом случае некоторые числа оборотов следует исключить (быстрым переключением). Ширина запрещенного диапазона обычно составляет около 10% от номинального числа оборотов. Если резонанс наступает при номинальном числе оборотов двигателя, то в этом случае иногда приходится изменять размеры промежуточного вала или гребного винта с целью смещения зоны критических чисел оборотов.
Если же интервал критических чисел оборотов невозможно исключить из рабочего диапазона чисел оборотов двигателя, на носке коленчатого вала двигателя закрепляется демпфер (успокоитель колебаний). Работа демпфера заключается в том, что при возникновении колебаний вала дополнительная масса демпфера, вращающаяся вместе с валом, воспринимает часть энергии возмущающих сил, что способствует затуханию колебаний.
Маховик предназначен для накопления энергии во время рабочего хода, когда давление газов на поршень достигает наибольшей величины, и отдачи ее во время нерабочих ходов. Благодаря этому достигается равномерное вращение вала в условиях периодически меняющихся давлений на поршень. Маховик дает также возможность выводить коленчатый вал из мертвых точек и облегчает пуск двигателя. Отливают маховики обычно из стали или чугуна и после обработки проверяют балансировкой. Маховик обычно крепится на фланце коленчатого вала призонными болтами.
Реклама:
Читать далее: Газораспределительный механизм двигателя
Категория: — Дизельные двигатели
Главная → Справочник → Статьи → Форум
stroy-technics.ru
Основные детали двигателя
Камера сгорания
Камера сгорания образуется днищем (верхней частью) поршня, нижней частью головки блока цилиндров и стенками цилиндра. В этой замкнутой камере каждый час происходит процесс, равносильный взрыву 32 шашек динамита. Для надежной работы двигателя необходимы точность и прочность деталей.
Поршни и поршневые кольца
Поршень образует нижний край камеры сгорания и передает усилие от сгорания топлива на коленчатый вал (коленвал) посредством шатуна. Поршни бывают различных видов и конструкций. Виды могут отличаться по конструкции юбки поршня, по конструкции головки поршня, по технологическому процессу изготовления поршня и по сорту используемого металла.
Поршневые кольца устанавливаются вокруг верхней части поршня. Они образуют окружность чуть большего диаметра, чем окружность поршня. Когда концы дуги (окружности) встречаются внутри цилиндра, то образуется уплотнение, и это уплотнение удерживает отработанные газы от попадания в картер двигателя, а масло из картера — от попадания в камеру сгорания.
Конструкция юбки
Для поршней используются две основные конструкции юбки. Более старые поршни в двигателях с невысоким числом оборотов имеют полноценные юбки. Эта полноценная юбка увеличивает движущуюся инертность и движущуюся массу двигателя.
Когда коленвалы приобрели противовесы, а обороты двигателя увеличились выше уровня, имеющегося в косилках для газонов, на поршнях появились частичные (облегченные) юбки. Такая частичная юбка уменьшила вес поршня и обеспечила пространство для противовесов коленвала. Почти все современные двигатели используют поршни с частичными юбками. Уменьшенная движущаяся масса поршня с частичной юбкой позволяет увеличить максимальное число оборотов двигателя.
Конструкция головки блока цилиндров
У стандартных поршней обычно плоская головка (днище). Многие высокофорсированные двигатели, особенно предназначенные для гонок, используют поршни с выпуклым днищем. Во многих случаях установка этих выпуклых поршней не является преимуществом, так как они препятствуют распространению фронта пламени в камере сгорания. Когда поршень идет вверх в такте сжатия, выпуклость днища заполняет часть камеры сгорания в головке блока цилиндров. Это увеличивает степень сжатия. Хотя увеличение степени сжатия увеличивает потенциальную мощность двигателя, при этом есть тенденция увеличения температуры сгорания. Когда температура в камере сгорания превышает значение 1380*С, кислород и азот в камере сгорания образуют окись азота. Эти соединения являются одними из самых токсичных и тщательно контролируются экологическими нормами. Если вы решили двигатель, то проверьте, соответствуют ли выбранные вами поршни необходимым требованиям.
Процесс производства
Поршни могут быть литыми или кованными. Кованые поршни являются более прочными, более точно изготовленными, но и более дорогими. По этим причинам они используются в форсированных двигателях высокой мощности.
Металлургия
Поршни двигателей старых автомобилей изготавливались из литого чугуна. Поршни из чугуна соответствуют ненормальной движущейся массе. Эта масса отбирает у двигателя часть мощности и снижает его максимальные обороты.
В 1950-е — 60-е годы в массовом производстве автомобильных двигателей стали использоваться поршни из алюминия. Это позволило повысить максимальные обороты двигателя и уменьшить паразитные потери мощности за счет возвратно-поступательного движения массы поршня.
Типичный поршень не является идеально круглым, как отверстие цилиндра. Он имеет форму эллипса с про-дольной осью, называемой опорной осью, которая перпендикулярна короткой оси, называемой осью поршневого пальца. Такая конструкция поршня называется кулачковой шлифовкой (притиркой) и позволяет термическое расширение поршня вдоль оси поршневого пальца. Кроме этого, такая конструкция позволяет сжатие опорной оси поршня при такте рабочего хода. Когда выполняются измерения на поршне в процессе разборки, особенности конструкции следует учитывать.
Днище поршня может иметь различные конструкции. Каждая конструкция служит для решения определенных проблем. Для большинства ремонтных операций на двигателе вполне подходит поршень с гладким днищем. Поршни с выпуклым днищем очень популярны на форсированных двигателях. Выпуклость, однако, влияет на движение фронта пламени и увеличивает степень сжатия. Двигатели с высокой степенью сжатия обычно не очень хорошо работают на стандартном бензине, который предназначен для обычных автомобилей выпуска 90-х годов.
Шатуны
Шатун передает вертикальное усилие, получаемое от сгорания топлива в камере сгорания, и действующее | на поршень, на коленчатый вал. Хотя эти шатуны должны быть прочными, они должны передавать на коленвал как можно меньше своего собственного веса. Проще говоря, шатунам нужно быть легкими и прочными. Эту комбинацию легко оптимизировать; уровень оптимизации увеличивается вместе с ценой шатуна.
Процесс производства
Подобно поршням, шатуны могут быть литыми или кованными. Кованые шатуны более прочные и изготовлены точнее, следовательно, они обычно применяются для форсированных двигателей.
Металлургия
Шатуны для обычных автомобилей сделаны из литого чугуна. Такие шатуны соответствуют ненормальной I движущейся массе. Эта масса отбирает у двигателя мощность и максимальные обороты. Гоночные двигатели и 1 другие высокофорсированные двигатели используют алюминиевые шатуны.
В 1950-е — 60-е годы появились алюминиевые I шатуны на форсированных двигателях. Это позволило I повысить максимальное число оборотов и уменьшить! паразитные потери мощности из-за возвратно-поступательного движения шатунов большой массы.
У каждого шатуна есть большой конец и малый конец. Малый конец устанавливается в поршень в том месте, где мощность передается от поршня к шатуну через поршневой палец. Поршневой палец может быть запрессован в шатун и иметь плавающую посадку в поршне или может быть запрессован в поршень и иметь плавающую посадку в конце шатуна, или же может иметь полную плавающую посадку, т.е. плавающая посадка имеется как в поршне, так и в шатуне.
Большой конец шатуна соединен с коленвалом. По внутренней стороне большого конца шатуна расположены сменные вкладыши. Из-за большой нагрузки, приходящейся на вкладыши, они принадлежат к тем деталям двигателя, которые более всего склонны к повреждениям.
Коленчатый вал
Мощность, развиваемая двигателем, передается на трансмиссию с помощью коленчатого вала (коленвала). Можно сказать, что коленвал преобразует возвратно-поступательное движение поршней в цилиндрах во вращательное движение, требуемое для вращения колес авто-мобиля.
Вес около 2000 кг или даже 8000 кг (грузовик) передвигается через металлическую деталь диаметром около 10 см.
Коленвал может быть кованным или литым из различных сплавов. Хотя кованый коленвал обычно прочнее, он и дороже. Литой коленвал более чем подходящий для большинства обычных (не гоночных) применений.
После отливки или ковки поверхности подшипников обрабатываются, а затем шлифуются и полируются. На современных коленвалах используются противовесы, которые балансируют их с весом поршней и шатунов. Дальнейшая балансировка осуществляется с помощью удаления металла с противовесов.
Головка блока цилиндров имеет несколько функций. Она содержит камеры сгорания и обеспечивает подвод для топливовоздушной смеси в камеру сгорания. Кроме этого, головка обеспечивает отвод выхлопных га-зов из камеры сгорания в выпускной коллектор. Каналы для газов открываются и закрываются клапанами. Со времен второй мировой войны эти клапаны располагаются в головке блока цилиндров.
Клапаны и привод клапанов
Клапаны управляют потоками топливовоздушной (рабочей) смеси и выхлопных газов в камеру сгорания и из нее. Впускной клапан открывается всякий раз, когда поршень идет вниз, чтобы втянуть топливо и воздух в камеру сгорания. Выпускной клапан открывается при движении поршня вверх, чтобы отработанные газы были вытеснены из камеры сгорания.
У большинства двигателей всего лишь два клапана на каждый цилиндр: один впускной и один выпускной. В попытках улучшить поток газов через камеру сгорания многие двигатели последних моделей используют по два или даже больше впускных или выпускных клапанов, или обоих видов клапанов в каждом цилиндре. Хотя, на первый взгляд, это делает двигатель более сложным, на самом деле это означает всего лишь большее количество деталей, но не увеличившуюся сложность.
Открывание клапанов на многих двигателях про-изводится с помощью толкателей (штанг) и коромысел. Как можно видеть по старым двигателям времен первой мировой войны, это старый метод, но он остается очень функциональным.
Обычно клапан большего размера является впускным клапаном. Впускной клапан открывается, чтобы впустить воздух и топливо в камеру сгорания. Клапан меньшего размера, называемый выпускным, открывается для выпуска газов после окончания процесса сгорания.
Распределительный вал (распредвал)
Распределительный вал состоит из серии яйцеобразных кулачков, ответственных за открывание и закрывание впускных и выпускных клапанов. В некоторых двигателях распредвал расположен внутри блока цилиндров. Связь между распредвалом и клапанами осуществляется толкателями и штангами.
Многие двигатели имеют распредвал, расположенный поверх клапанов. Распредвал более-менее непосредственно воздействует на клапаны. В таких двигателях единственными деталями, находящимися между распредвалом и клапаном, являются рокер (коромысло). Это исключает необходимость использования толкателей и штанг. Во многих двигателях нет даже рокеров. Исключение толкателей и штанг сокращает количество деталей двигателя, которые склонны к износу. Кроме этого, возможны более высокие обороты, так как отсутствие штанг исключает потенциальные отрицательные эффекты, которые могут повлиять на приемистость двигателя.
Распредвал приводится в движение от коленвала и синхронизирован с ним. Кулачки распредвала перемещают толкатели вверх и вниз, толкатели перемещают штанги, а штанги приводят в движение коромысла для открывания клапанов. Вообще говоря, чем больше подъем кулачков распредвала, тем большее количество воздуха под действием атмосферного давления может попасть в цилиндр, и чем больше продолжительность открывания, тем больше времени воздух поступает в цилиндр.
Конфигурации распредвала и газораспределительного механизма
Когда гонщик Чак Егер преодолел звуковой барьер на автомобиле в 1947 году, мысли конструкторов двигались вокруг плоских головок блоков цилиндров двигателей. В такой конфигурации клапаны расположены в блоке цилиндров. В 50-е годы в массовое производство было запущено серьезное новшество: двигатель с верхнерасположенными клапанами. Движение клапанов в головке блока цилиндров означает улучшение потоков впускных и выхлопных газов через камеру сгорания.
Хотя двигатели со штангами выпускаются уже очень долго и хотя они очень надежны, новые приоритеты и требования к автомобильным двигателям медленно вытесняют эту конструкцию.
Двигатель с верхнерасположенным распредвалом был разработан в 20-е годы XX века. Исключение штанг обеспечивает лучшее управление клапанами и меньшую инерционность внутри двигателя. Такая конфигурация известна под названием верхнерасположенного распредвала (ОНС). Некоторые более сложные конструкции двигателей используют отдельные верхнерасположенные распредвалы для впускных и выпускных клапанов. Эта конструкция называется двойным верхнерасположенным распредвалом (DOHC).
Шестерни газораспределительного механизма, цепи и зубчатые ремни
Цепь привода газораспределительного механизма (ГРМ) соединяет распредвал и коленвал и синхронизирует их работу. Показанная здесь цепь имеет обычную конструкцию. Специальные цепи (для форсированных двигателей) имеют роликовую конструкцию. Многие дорогие европейские двигатели использовали роликовые цепи в качестве стандартного оборудования. Звездочка большего размера является звездочкой распредвала; звездочка меньшего размера является звездочкой коленвала. Смещенная от центра круглая ступица на большой звездочке служит для привода топливного насоса. Такого привода нет на большинстве двигателей с впрыском топлива, так как они используют электрический топливный насос.
Многие двигатели с верхним распределительным валом используют цепь для соединения распредвала и коленвала, но в большинстве двигателей используется зубчатый ремень. Эксплуатация и старение стремятся осла-бить резиновые зубцы ремня, что может привести к повреждениям. Разрыв зубчатого ремня может привести к серьезным повреждениям поршней и деталей привода клапанов, если двигатель работает на высоких оборотах, а на некоторых двигателях — даже на холостом ходу.
Если открытые клапаны имеют отрицательный зазор с поршнем в положении верхней мертвой точки (ВМТ), и если система привода газораспределительного механизма (шестерни/цепь/зубчатый ремень) не обеспечивает правильную синхронизацию распредвала и коленвала (это может случиться при обрыве цепи и ремня), то могут произойти различные повреждения. Когда поршни встречаются с клапанами, то клапаны гнутся. Если вам повезло, то это все, что случится. Если же вам не повезло, то повреждение зубчатого ремня или приводной цепи выведет из строя головку блока цилиндров, клапаны, поршни и, возможно, блок цилиндров.
Из сказанного следует простой вывод: новый зубчатый ремень и несколько часов работы стоят намного дешевле, чем новый двигатель. Если руководство по ремонту вашего автомобиля рекомендует замену зубчатого ремня с определенной периодичностью (по пробегу или по времени), то следуйте неукоснительно этим рекомендациям.
Смотрите так же
qrx.com.ua
Основная деталь — двигатель — Большая Энциклопедия Нефти и Газа, статья, страница 1
Основная деталь — двигатель
Cтраница 1
Сейчас основные детали двигателей обрабатываются на автоматических линиях. Только в цехах механосборочного производства действует 36 автоматических линий, на которых обрабатываются блоки цилиндров, головки блоков, коленва-лы, картеры, крышки, валы коробок передач. [1]
Основные детали двигателя внутреннего сгорания при работе испытывают большую напряженность, вследствие чего узлы трения необходимо смазывать, а также отводить теплоту от нагревающихся деталей. При введении слоя масла между трущимися поверхностями уменьшаются работа трения и механические потери, предотвращается заедание деталей и устраняется их чрезмерный износ. Кроме того, смазка защищает детали двигателя от коррозии и способствует уплотнению поршневыми кольцами рабочей полости цилиндра. [3]
Основной деталью двигателя является цельнолитой блок 6 ( фиг. Внутри блока расположены детали кривошипно-шатунного механизма: коленчатый вал 1, поршень 8 с шатуном 25, распределительный вал 3 с деталями, механизм декомпрессора, а также главный маслопровод. [4]
Основными деталями двигателей, изменение износа которых можно ожидать при переходе на топлинно-водяную эмульсию, являются цилиндрово-поршвевые группы и плунжерные пары топливных насосов. Износ остальных трущихся поверхностей определяется главным образом рабочим процессом дизеля и старением смазочного масла. Как показали исследования, рабочий процесс дизеля ( жесткость работы, величина Рг) не претерпевает заметного изменения при переходе на топливную эмульсию. [5]
Какие основные детали двигателя относятся к кривошипно-шатунному механизму. Какие силовые и тепловые нагрузки испытывают поршень, цилиндр, шатун, коленчатый вал. Для чего поршню придают конусную и эллипсную форму сечений. Какую функцию выполняют разрезы на юбках поршней. [6]
Износ основных деталей двигателя 14 — 10 5 / 13 после 500 час. [7]
Перед сборкой основные детали двигателей были подвергнуты микрометрированию. [8]
Обработка всех основных деталей двигателя автомобиля ЗИЛ-130 выполняется на автоматических линиях. Всего цех V-образных двигателей завода ЗИЛ имеет до 40 автоматических линий. На первом Государственном подшипниковом заводе ( 1ГПЗ) действуют уже три автоматических цеха по производству массовых типов подшипников. [9]
Блок цилиндров — основная деталь двигателя, поэтому износостойкости цилиндров придается особое значение. Износ таких цилиндров в верхней части составляет примерно 10 — 20 мк на 1000 км пробега. Лучший результат дает применение вставных гильз из высоколегированного чугуна с высоким содержанием никеля или хрома. Чугун с содержанием никеля до 15 % широко применяется для двигателей ГАЗ, МЗМА, ЗИЛ в виде коротких сухих гильз, устанавливаемых в верхней части цилиндра, наиболее подвержен ной влиянию коррозирующего действия продуктов сгорания. Характерной особенностью этого чугуна является высокая сопротивляемость коррозийному износу в сочетании с хорошей обрабаты ваемостью. Износ таких цилиндров при эксплуатации двигателя в условиях малой запыленности воздуха будет в 3 — 4 раза меньше, чем износ цилиндров из обычного серого чугуна. [10]
Если картер и основные детали двигателя не очищаются перед заливом свежего масла, то оставшиеся в двигателе продукты окисления будут являться катализаторами, ускоряющими реакцию взаимодействия кислорода воздуха с углеводородами свежего масла. [11]
Безопасный ресурс таких основных деталей двигателя, как диски ротора, на стадии проектирования определяется расчетом и в дальнейшем обязательно подтверждается натурными испытаниями двигателя или дисков. [12]
Лучшими расчетами на усталость основных деталей двигателя ( шатун, коленчатый вал и др.) нужно считать расчеты, данные акад. [13]
В результате общий износ основных деталей двигателя возрастает более чем в 2 раза по сравнению с маслом, эксплуатационные свойства которого отвечают требованиям стандартов. Таким образом, использование масел, у которых при хранении выпала часть присадок, недопустимо, так как резко сокращается долговечность двигателей из-за повышения интенсивности износа, особенно коррозионного. [14]
Страницы: 1 2 3 4
www.ngpedia.ru