Дефектовка и ремонт оборудования
Дефектовка и ремонт оборудования
Услуги дефектовки станков на данный момент являются востребованными множеством производственных предприятий. Благодаря данной процедуре появляется возможность определить неисправности и техническое состояние промышленного оборудования. Конечный результат дефектовки – выявление поломок и неисправностей.
Этапы дефектовки
Дефектация в нашей компании происходит в несколько основных этапов:
- Предварительная дефектовка. Процедура производится путём визуального поверхностного осмотра технологической линии на предмет визуальных повреждений. Производится замер основных показателей производительности, нагревания техники при запуске и основных параметров функционирования оборудования.
- Поузловая дефектовка оборудования. На этом этапе производится разбор оборудования на основные составляющие элементы, их осмотр и анализ пригодности.
- Подетальная дефектовка.
Вас приятно удивит скорость выполнения услуг и потрясающее качество. Специалисты нашей компании так же могут подобрать готовое оборудование, создать его по вашим индивидуальным требованиям, провести балансировку и помочь ввести в эксплуатацию технику.
В компании Апрель можно приобрести специальное оборудование для работы с пластиком или металлом. Мы работаем в Москве и Новосибирске. Если вам нужны станки или услуги по их настройке и ремонту, то звоните к нам и мы удовлетворим запросы вашего предприятия.
Преимущества дефектовки промышленного оборудования в компании Апрель:
- профессиональный подход;
- высокая скорость выполнения услуги;
- доступная стоимость на дефектовку;
- точность в определении поломок и прочих неисправностей.
Дефектовка изношенных деталей машин и оборудования и определение маршрутов восстановления деталей
Категория:
Практика ремонта машин
Публикация:
Дефектовка изношенных деталей машин и оборудования и определение маршрутов восстановления деталей
Читать далее:
Дефектовка изношенных деталей машин и оборудования и определение маршрутов восстановления деталей
Цель работы.
1. Освоить методику определения дефектов и их сочетаний на деталях.
2. Определить маршруты восстановления деталей по сочетаниям дефектов.
3. Освоить методику составления дефектных ведомостей.
Задание.
1. Ознакомиться с оборудованием рабочего места.
2. Изучить характерные дефекты на основных деталях машин, их характер, места расположения, форму, допустимые и предельные размеры.
3. Провести дефектовку деталей, подлежащих ремонту, и заполнить карту дефектовки.
4. Определить варианты сочетаний дефектов в дефектуе-мой детали путем обработки цифровых данных в карте дефектовки.
5. Установить маршруты восстановления детали.
Оснащение рабочего места. Автотракторные детали 6—8 наименований с 3—5 дефектами (по 140—150 деталей каждого наименования), контрольно-измерительный инструмент; бланки карт дефектовки деталей.
Рекламные предложения на основе ваших интересов:
Содержание и порядок выполнения работы. Дефектовкой называется процесс технического контроля (осмотра, измерения и при необходимости испытания) деталей и сопряжений с последующей их сортировкой. В зависимости от величины износа, вида и характера повреждений детали при дефектовке сортируют на годные без ремонта, требующие ремонта и негодные. Контроль (сортировка) деталей проводится в соответствии с техническими условиями, составленными ГОСНИТИ по каждой марке тракторов и их деталей.
Все детали, подлежащие дефектовке, должны быть чистыми и сухими. Детали измеряют при помощи универсальных или специальных контрольно-измерительных инструментов и приборов (измерительных линеек, штангенциркулей, микрометров, индикаторов, нутромеров индикаторных, дефектоскопов и др.).
Дефектовка деталей в зависимости от специализации ремонтного предприятия и принятого метода ремонта машин может быть обезличенной или индивидуальной. В первом случае все детали предварительно группируются по методам измерения и применяемым инструментам. Клапаны, валы, пружины, болты, шпильки и т. д. При индивидуальной дефектовке все детали данного узла или агрегата контролируются комплектно и годные детали в специальной таре отправляются в комплектовочное отделение.
Дефектовщик при контроле деталей в первую очередь проверяет наличие дефектов, при которых данная деталь считается негодной, и только после этого проверяет остальные возможные дефекты. Каждый дефектовщик должен знать все возможные дефекты на деталях ремонтируемых машин, определять их характер и величину, уметь пользоваться контрольно-измерительным инструментом и приборами и знать сочетания дефектов по технологическим маршру-
Варианты сочетаний дефектов в деталях изучаются путем дефектовки достаточного количества деталей одного наименования.
В результате проведенной работы студенты должны убедиться в том, что износные дефекты на деталях машин встречаются в определенных сочетаниях.
Для выполнения данной работы группа студентов делится на звенья по 3—5 человек, каждому из которых вручается бланк карты дефектовки той детали, на которую будет составлять маршрутную технологию данное звено. В качестве образца приводится форма карты дефектовки опорного катка трактора ДТ-75. Замеры следует проводить в местах наибольшего износа детали.
При записи дефектов в карту дефектовки необходимо учесть, что один и тот же дефект, устраняемый в зависимости от его размера разными технологическими методами, указывается столько раз, сколькими методами он устраняется. Например, износ клапанных гнезд головки цилиндров в зависимости от его величины устраняется фрезерованием или путем постановки колец; при износе внутренней резьбы применяется перенарезание ее на ремонтный размер или постановка ввертышей, а для наружной резьбы — нарезание резьбы ремонтного размера или наплавка с последующей нарезкой новой резьбы номинального размера.
Каждый студент звена должен продефектовать 25—30 деталей и данные замера записать в карту дефектовки.
Затем обрабатывают данные всех карт, заполненных студентами звена, и определяют сочетание дефектов в данной детали. Для этого звену вручается форма таблицы, в которой по вертикали записывают обнаруженные сочетания дефектов, а по горизонтали номера дефектов по карте дефектовки и данные их обработки. Так, из всех карт выбирают детали, имеющие одинаковое сочетание дефектов, определяют их количество (в штуках и процентах к общему количеству замеренных деталей) и составляют форму.
В результате обработки карт дефектов деталей обнаруживается очень большое количество различных вариантов сочетаний дефектов, для каждого из которых составлять отдельный технологический процесс нецелесообразно.
Под маршрутом восстановления деталей машин понимается содержание работ по устранению комплекса сочетаний дефектов на детали единым технологическим процессом.
Поэтому варианты сочетаний дефектов, отличающиеся между собой наличием или отсутствием одного незначительного дефекта, объединяются в один маршрут.
Кроме того, некоторые варианты сочетаний дефектов объединяются в один маршрут по технологическим соображениям, например восстановление соосных поверхностей, посадочного места, шпоночной канавки и др.
В один маршрут также включают варианты сочетания дефектов, отличающиеся от основных вариантов, куда входит большее количество деталей, отсутствием только одного дефекта и охватывающие при этом сравнительно небольшое количество деталей.
В одном маршруте можно объединить варианты сочетаний, включающие различные дефекты, которые устраняют одинаковым технологическим методом с приблизительно одинаковой трудоемкостью (трещины в разных местах детали, небольшие изломы и сколы, деформации различного характера и величины и др.).
Таким подбором значительно сокращается количество маршрутов, на каждый из которых составляется единый технологический процесс.
Отчет о работе.
1. Представляют карту дефектовки установленного количества одноименных деталей (например, опорного катка).
2. Совместно со студентами звена представляют обнаруженные сочетания дефектов.
Рекламные предложения:
Читать далее: Восстановление изношенных сопряжений машин способом ремонтных размеров
Категория: — Практика ремонта машин
Главная → Справочник → Статьи → Форум
31604348892 Диагностика (дефектовка) и ремонт бензопил и воздуходувок.
Размещение завершено
Участники и результаты
Диагностика (дефектовка) и ремонт бензопил и воздуходувок
Публичное акционерное общество «Новороссийский Морской Торговый Порт»
ИНН 2315004404 КПП 231501001
- Место поставки
-
г. Новороссийск, территория ПАО «НМТП»
Преимущества
Участниками закупки могут быть только субъекты малого и среднего предпринимательства
Требования к участникам
Требование к отсутствию участников закупки в реестре недобросовестных поставщиков
Закупка иного способа размещения признана несостоявшейся:
В связи с тем, что на лот была подана/допущена одна заявка на участие
Участник | Цена, ₽ | Рассмотрение заявок |
---|---|---|
░░░ ░░░░░░░ |
░░░░░ |
Дефектовка (диагностика) компрессорного оборудования в Екатеринбурге
ДЕФЕКТОВКА (ДИАГНОСТИКА) КОМПРЕССОРНОГО ОБОРУДОВАНИЯ
Компрессор как и любое оборудование имеет свой определенный ресурс работоспособности заложенный в него заводом изготовителем. Рано или поздно наступает момент, когда оборудование выходит из строя. Современный компрессор это достаточно сложная машина со множеством узлов и агрегатов. Человеку без должной подготовки очень сложно найти и выяснить причину выхода из строя компрессора, на практике начинают менять разные детали компрессора не имеющие отношения к проблеме и тратя значительные денежные средства.
Наши специалисты каждый день сталкиваются с различными ситуациями связанными с поломками компрессоров. Мы проходим обучения на предприятиях производителях компрессорной техники, тщательно разбираем каждый случай аварии и сохраняем его в нашей базе. За время нашей работы мы получили огромный опыт по ремонту компрессоров различных марок. Сервисные инженеры Уральской компрессорной Компании имеют в своем распоряжении специальное оборудование и инструменты для выявления и устранения неисправностей.
Для точного определения причины выхода из строя компрессора мы предлагаем услугу по дефектовке (диагностике) компрессорного оборудования.
В случае выхода из строя компрессора сервисный инженер прибудет к Вам на предприятие и произведет комплекс работ по диагностике и дефектовке компрессора, после чего выдаст заключение с указанием вышедших из строя деталей, рекомендаций по дальнейшему ремонту и эксплуатации компрессора.
На практике во время проведения дефектовки довольно часто сервисному инженеру получается восстановить компрессор либо обеспечить его временную работоспособность до момента проведения ремонта, но все зависит от каждого конкретного случая.
Обратившись в Уральскую Компрессорную Компанию для проведения дефектовки (диагностики) компрессора, Вы получите квалифицированную помощь и сэкономите значительные средства, нежели при самостоятельном поиске неисправности и замене лишних деталей компрессора.
Отправить запросРемонт, то, сервисное обслуживание, дефектовка промышленного оборудования в Краснодаре — гарантийное и постгарантийное обслуживание — сроки и цены
«ВПК Конкордия» занимает ведущие позиции на рынке ремонта промышленного электрооборудования.
Наш приоритет — установка долгосрочных партнерских отношений с заказчиком. Добиваться этой цели нам помогает профессионализм наших специалистов и ответственный подход к каждой задаче. Мы постоянно держим руку на пульсе, оперативно внедряя современные методы в реализацию наших проектов. Благодаря накопленному опыту и непрерывному процессу обучения мы способны решать задачи любой сложности.
Своевременное обслуживание — гарантия от простоев
Даже самое надежное оборудование от регулярной эксплуатации может со временем выйти из строя. При работе с заказчиком мы берем на себя обязательства по обслуживанию электростанций и обеспечению их бесперебойной службы. Специалисты «ВПК Конкордия» своевременно выполнят весь необходимый комплекс работ, предотвратив возникновение простоев в эксплуатации техники.

Для правильной диагностики и выявления даже мелких неисправностей мы используем высокоточные приборы, а также весь опыт и накопленный нашими специалистами багаж знаний. Это не только позволяет увеличить срок эксплуатации оборудования в долгосрочной перспективе, но и избежать финансовых потерь из-за внезапных аварий и последующего ремонта.
Ремонт от А до Я
Главная особенность предлагаемых нами услуг заключается в комплексном подходе к ремонту техники.
В этом процессе можно выделить следующие этапы:
- Визуальный осмотр и диагностика.
- Локализация неисправности и определение причины ее возникновения.
- Ремонтно-восстановительные процедуры.
- Запуск и тестирование.
- винтовые компрессоры;
- поршневые компрессоры;
- передвижные компрессоры с ДВС;
- винтовые блоки компрессоров;
- ротационные воздуходувки;
- дизельные электростанции;
- электростанции на газу;
- бензиновые генераторы;
- сварочные аппараты и генераторы;
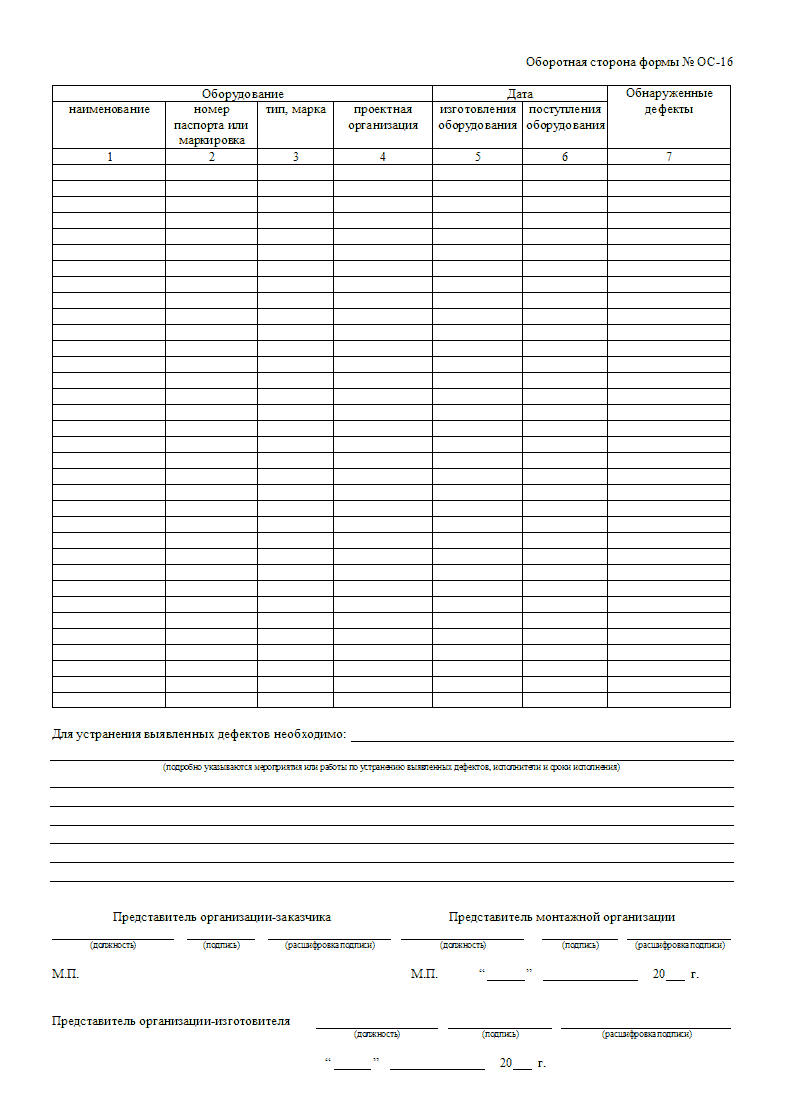
«ВПК Конкордия» работает только с сертифицированными поставщиками запасных частей и расходных материалов. Наряду с соблюдением технологий ремонта и обслуживания мы уделяем особое внимание качеству комплектующих.
Почему стоит обратиться в «ВПК Конкордия»?
Наши преимущества, которые уже отметили наши постоянные клиенты:
- сервисные центры по всей России;
- огромный склад запчастей;
- ремонт с выездом на объект;
- гарантия на работы и запчасти;
- наличные и безналичные формы оплаты;
- строгое соблюдение сроков ремонта.

Ремонтируем и обслуживаем все модели
Ниже представлен список моделей, которые мы чаще всего ремонтируем:Дефектация деталей и сопряжений — лекция
Страница 1 из 2
РМО.
Тема: Лекция о дефектации деталей и сопряжений.
План:
1.Сущность и основные задачи дефектации.
2. Классификация дефектов типовых деталей.
3. Методы дефектации. Оборудование и инструмент для дефектации.
4.Обнаружение скрытых дефектов.
1.Сущность, задачи и методы дефектации.
Дефектация — это процесс выявления состояния деталей и сопряжений путем сравнения фактических показателей с данными технической документации, где приведены нормальные, допустимые и предельные значения размеров деталей, зазоров и натягов сопряжений, а также отклонения от нормы и от взаимного расположения поверхностей деталей и другие параметры их состояния.
Основная задача дефектовочных работ – не пропустить на сборку детали, ресурс которых исчерпан или меньше планового межремонтного срока, и не выбраковать годные без ремонта детали.
Организация работ по дефектации.
В достаточно крупных и специализированных ремонтных предприятиях для выполнения работ по дефектации создаются специальные участки.
Например:
Рис. 1. План размещения оборудования в отделении дефектовки деталей специализированного ремонтного предприятия (годовая программа ремонта 400—500 тракторов):
/ — рольганг; 2 — стол для дефектовки средних и мелких деталей; 3 — стол для дефектовки крупных деталей; 4 — ящик для утиля; 5 — стеллаж; 6 — шкаф для инструмента; 7 — конторский стол; 8 — кран-балка; 9 — стол для комплектования узлов.
Как видно из плана, отделение дефектовки включено в поточную технологическую линию (конвейер). Детали поступают из разборочно-моечного отделения и после дефектации направляются в отделение комплектования.
Рабочие места в отделениях дефектовки, по мере необходимости, оснащаются специальным оборудованием и инструментом. Примерный перечень оборудования приведен в таблице 1.
Таблица 1.Обобрудование участка дефектации.
Оборудование |
Тип, чертежная модель |
Габаритные размеры в плане, мм |
Стол для дефектации деталей |
ОРГ — 1468-0 1-090А |
2400X800 |
Стол для дефектации металлоизделий (метизов) |
70-7825-1505 |
1160X695 |
Стол монтажный металлический |
ОРГ — 1468-0 1-080 А |
1200X800 |
Шкаф с набором универсаль-ных инструментов |
ОРГ-1661 |
615X750 |
Шкаф для материалов и измерительного инструмента |
ОРГ — 1468-07 |
860X360 |
Подставка для корпусных деталей |
— |
966X636 |
Контейнер для выбракованных Деталей |
ОРГ-1598 |
885Х 865 |
Контейнер для выбракован-ных подшипников |
— |
700Х 570 |
Стол для поверочной плиты |
3702-08А |
966X636 |
Автоматическая справочная установка |
АСУ-50 |
1000X900 |
Центры универсальные для проверки валов |
2ЖМ-00-00 |
1566X666 |
Дефектоскоп магнитный |
УМД-Э-2500 или МД-50П или ПМД-70 |
1800X700 1000X780 620Х 500 |
Стенд для испытания на герметичность головок блоков цилиндров ДВС. |
КИ-1040 |
1080X900 |
Создание специальных отделений и специализированных рабочих мест позволяет увеличить производительность труда и улучшить качество работы. Пример рабочего места для дефектации крепежных деталей приведен на рисунке 2.
Рис. 2. Столы для дефектовки крепежных деталей
Рабочие места для дефектовки деталей оснащаются набором измерительного инструмента, контрольных приспособлений и приборов.
В мастерских общего назначения (в мастерских аграрных предприятий) годовая программа ремонта (годовой объем ремонтно-технических работ) недостаточен для создания поточных технологических линий. В таких мастерских дефектовка выполняется на тех рабочих местах, где производится ремонт агрегатов или восстановление деталей. При этом, необходимый для дефектации инструмент, приспособления и приборы могут постоянно находиться на данном рабочем месте, например на участках ремонта топливной аппаратуры, электрооборудования, двигателей и т. п., или в инструментальной кладовой, например инструмент, необходимый для дефектовки деталей трансмиссии, ходовой части и других агрегатов, ремонт которых выполняется в ремонтно-монтажном отделении.
В процессе дефектации все детали разделяют на Пять групп и Маркируют их краской Определенного цвета:
— годные, параметры которых находятся в пределах, допускаемых для использования с деталями, бывшими в эксплуатации или новыми;
— годные, параметры которых находятся в пределах,
допускаемых для работы только с новыми деталями;
— утратившие работоспособность, которую можно восстановить в условиях данного предприятия;
— утратившие работоспособность, ремонт и восстановление которых возможны только на специализированных предприятиях;
— те, которые по своему состоянию не могут быть использованы в дальнейшем; их сдают во «Вторчермет».
Методы дефектации Могут быть классифицированы в соответствии со схемой, изображенной на рисунке 3.
Рис. Методы дефектации деталей и сопряжений.
Осмотр — наиболее распространенный метод дефектации для выявления наружных повреждений деталей:
— деформации, трещины, обломы, выкрашивание, прогар;
— отложения, раковины, задиры, царапины, повреждение покрытий, коррозия;
— негерметичность и др.
Осмотр возможен как Невооруженным глазом, так и с помощью Оптических средств: простых и бинокулярных луп, микроскопов.
Простукивание — используется для определения Плотности посадки шпилек, нарушения сплошности (целостности) деталей.
Метод основан на изменении тона звучания детали при нанесении по ней легкого удара молотком.
Звучание чистое — посадка плотная и деталь сплошная.
Звук глухой, дребезжащий – целостность детали нарушена.
Опробование вручную и проверка на ощупь – позволяет определить:
— наличие зазора,
— плавность вращения,
— перемещение детали,
— свободный ход рычагов,
— эластичность резинотехнических деталей,
— наличие местного износа.
Органолептические методы в большинстве случаев не позволяют сделать окончательный вывод о состоянии детали, поскольку имеют Субъективный характер.
Измерение размеров.
Порядок измерения, применяемый инструмент и приспособления, место и число замеров оговаривается в соответствующих технологических картах.
Для выполнения измерений используются универсальные и специальные измерительные инструменты и приспособления, а так же контрольные средства.
Например:
— универсальные инструменты: штангенциркуль (рис.4.), микрометр (рис.5.) , нутромер и т. п.;
— специальные – штангенрейсмус, штангензубомер (рис. 6), и др.;
— контрольные средства – калибры, шаблоны, щупы, поверочные плиты, угольники и др. (рис.7 — 15).
Калибры для контроля шлицевых соединений.
Калибры для контроля отверстий.
Калибры для контроля валов.
Калибры для контроля конусных поверхностей.
Калибры для контроля длин.
Калибры для контроля расположения отверстий.
Рис. Калибры для контроля соосности отверстий.
Рис. Регулируемые калибры-скобы для контроля болтов.
Рис. 15. Использование калибров.
Капиллярные методы — основаны на способности некоторых жидкостей с хорошей смачиваемостью проникать в мельчайшие трещины.
К этим методам относятся люминесцентная и цветная дефектоскопии (метод красок), применяемые для выявления поверхностных трещин в деталях, изготовленных из магнитных и немагнитных материалов.
Магнитная дефектоскопия применяется для обнаружения наружных скрытых дефектов (трещин) в деталях, изготовленных из стали и серого чугуна. Метод основан на появлении магнитного поля рассеивания вокруг дефекта при прохождении магнитно-силовых линий через деталь и концентрации ферромагнитного порошка по краям дефектного участка.
Для намагничивания деталей применяют стационарные и переносные магнитные дефектоскопы (М-217, 77МД-1, 77МД-ЗМ).
Трансформатор. Схема магнитного дефектоскопа.
Ультразвуковая дефектоскопия основана на способности ультра-звуковых колебаний распространяться в материале на большую глубину в виде направленных пучков и отражаться от дефектного участка вследствие разного изменения акустического сопротивления среды. В практике ремонтного производства используются дефектоскопы, работающие по теневому методу и методу отражения.
Рис. Схема ультразвукового дефектоскопа:
А — работающего по теневому методу:
1— ультразвуковой генератор; 2 — излучатель; 3 — деталь;
4 — Ультразвуковые волны; 5 — приемник; 6 — дефект; 7 — индикатор;
Б — Работающего по методу отражения: 1— контролируемое изделие; 2 — приемная пластина; 3 — Элемент; 4 — усилитель; 5 — электронно-лучевая трубка; 6 —генератор; 7— генератор развертки; 8 — дефект; А — начальный импульс; В — отраженный импульс; С — Донный сигнал.
%d0%b4%d0%b5%d1%84%d0%b5%d0%ba%d1%82%d0%be%d0%b2%d0%ba%d0%b0 — со всех языков на все языки
Все языкиАнглийскийРусскийКитайскийНемецкийФранцузскийИспанскийШведскийИтальянскийЛатинскийФинскийКазахскийГреческийУзбекскийВаллийскийАрабскийБелорусскийСуахилиИвритНорвежскийПортугальскийВенгерскийТурецкийИндонезийскийПольскийКомиЭстонскийЛатышскийНидерландскийДатскийАлбанскийХорватскийНауатльАрмянскийУкраинскийЯпонскийСанскритТайскийИрландскийТатарскийСловацкийСловенскийТувинскийУрдуФарерскийИдишМакедонскийКаталанскийБашкирскийЧешскийКорейскийГрузинскийРумынский, МолдавскийЯкутскийКиргизскийТибетскийИсландскийБолгарскийСербскийВьетнамскийАзербайджанскийБаскскийХиндиМаориКечуаАканАймараГаитянскийМонгольскийПалиМайяЛитовскийШорскийКрымскотатарскийЭсперантоИнгушскийСеверносаамскийВерхнелужицкийЧеченскийШумерскийГэльскийОсетинскийЧеркесскийАдыгейскийПерсидскийАйнский языкКхмерскийДревнерусский языкЦерковнославянский (Старославянский)МикенскийКвеньяЮпийскийАфрикаансПапьяментоПенджабскийТагальскийМокшанскийКриВарайскийКурдскийЭльзасскийАбхазскийАрагонскийАрумынскийАстурийскийЭрзянскийКомиМарийскийЧувашскийСефардскийУдмурдскийВепсскийАлтайскийДолганскийКарачаевскийКумыкскийНогайскийОсманскийТофаларскийТуркменскийУйгурскийУрумскийМаньчжурскийБурятскийОрокскийЭвенкийскийГуараниТаджикскийИнупиакМалайскийТвиЛингалаБагобоЙорубаСилезскийЛюксембургскийЧерокиШайенскогоКлингонский
Все языкиРусскийАнглийскийДатскийТатарскийНемецкийЛатинскийКазахскийУкраинскийВенгерскийТурецкийТаджикскийПерсидскийИспанскийИвритНорвежскийКитайскийФранцузскийИтальянскийПортугальскийАрабскийПольскийСуахилиНидерландскийХорватскийКаталанскийГалисийскийГрузинскийБелорусскийАлбанскийКурдскийГреческийСловенскийИндонезийскийБолгарскийВьетнамскийМаориТагальскийУрдуИсландскийХиндиИрландскийФарерскийЛатышскийЛитовскийФинскийМонгольскийШведскийТайскийПалиЯпонскийМакедонскийКорейскийЭстонскийРумынский, МолдавскийЧеченскийКарачаевскийСловацкийЧешскийСербскийАрмянскийАзербайджанскийУзбекскийКечуаГаитянскийМайяАймараШорскийЭсперантоКрымскотатарскийОсетинскийАдыгейскийЯкутскийАйнский языкКхмерскийДревнерусский языкЦерковнославянский (Старославянский)ТамильскийКвеньяАварскийАфрикаансПапьяментоМокшанскийЙорубаЭльзасскийИдишАбхазскийЭрзянскийИнгушскийИжорскийМарийскийЧувашскийУдмурдскийВодскийВепсскийАлтайскийКумыкскийТуркменскийУйгурскийУрумскийЭвенкийскийЛожбанБашкирскийМалайскийМальтийскийЛингалаПенджабскийЧерокиЧаморроКлингонскийБаскскийПушту
При поиске неисправностей в оборудовании важно первое впечатление
При поиске и устранении неисправностей оборудования, будь то необычная проблема с вибрацией или отказ компонента, такого как подшипник или уплотнение, очень важны первые впечатления от первоначального осмотра оборудования. Любое мероприятие по поиску и устранению неисправностей должно начинаться с тщательного изучения истории машины — процесса, конструкции, эксплуатации, обслуживания и всех доступных деталей машины. Эти первые впечатления необходимы, чтобы убедиться, что группа устранения неполадок полностью вооружена важными данными и минимизировать вероятность ошибочного диагноза.
Многие люди, плохо знакомые с процессом устранения неполадок, имеют тенденцию немедленно брать инструменты и начинать работу. Лучше отложить инструменты и собрать первые впечатления. Хотя они могут не сразу выявить проблему, они могут выявить ряд проблем, влияющих на общую надежность. Рекомендации для этих первоначальных проверок включают:
- Общая чистота: Хорошая уборка часто показывает, что методы обслуживания оборудования соответствуют более высоким стандартам.Обратите внимание не только на пыль, но и на состояние основания и фундамента, опор трубопроводов, утечки через уплотнения и т.
Д., Чтобы получить доказательства того, что методы технического обслуживания или факторы окружающей среды отрицательно влияют на надежность. Каковы ожидания того, что ремонт в полевых условиях можно будет провести без попадания загрязняющих веществ, которые сократят срок службы запасных частей?
- Более подробный осмотр машины: Начните с основания машины и найдите явные признаки разрушения или неправильного крепления.Поднимитесь к опорам и осмотрите прокладки и прижимные болты. Плохая работа на базе часто свидетельствует о некачественном ремонте. Переместитесь к валу и приводу (то есть к муфтам, ремням и т. Д.) И найдите доказательства повреждения вала, неправильной сборки муфты и неправильной длины шпонки. Хотя проблемы с этими областями могут не быть причиной текущей проблемы, улучшения, внесенные с помощью необходимого ремонта, повысят надежность оборудования.
- При работе выполните базовую проверку вибрации: Используйте простой инструмент, например монету с зазубренными краями, чтобы получить впечатление относительного движения машины, если машина все еще работает.
В то время как измерения вибрации, как правило, сосредоточены на подшипниках, с монетой в руке, начинают с основания и продвигаются к местам расположения подшипников, чтобы почувствовать необычное движение. Обратите особое внимание на границы и соединения, такие как основание к фундаменту, опоры машины к основанию, а также все трубопроводы и кабелепровод. Простое условие, такое как ослабление болта основания, может серьезно повлиять на машину.
- Сохраняйте подробные записи о первых впечатлениях: Они предоставят исчерпывающий и профессиональный отчет об улучшениях, которые повлияют на срок службы и надежность машины.Находясь на строительной площадке, осмотрите другое оборудование поблизости на предмет аналогичных проблем и внимательно представьте эту информацию заинтересованным сторонам. Хотя никому не нравится раскрывать свои недостатки, хорошая презентация шагов, которые можно предпринять для положительного воздействия на оборудование, будет хорошо принята.
Устранение неисправностей машин — жизненно важный, но постоянно сокращающийся навык в отрасли
Текущие новости
Новости 2020 г.
Новости за 2019 год
Новости за 2018 год
Новости за 2017 год
Новости за 2016 год
Новости за 2015 год
Новости за 2014 год
Новости за 2013 год
Новости за 2012 год
- Amatrol объявляет о выпуске справочников для студентов
Новости за 2011 год
Новости 2010 г.
Устранение неисправностей машин — жизненно важный, но постоянно сокращающийся навык в отрасли
Специалисты по устранению неполадок — это высококвалифицированные работники, но, к сожалению, они становятся все более редкой породой в рабочей силе. Я сел с менеджерами нескольких крупных производителей, чтобы обсудить проблему поиска квалифицированных специалистов по устранению неполадок, и они объяснили, что в прошлом на учебных курсах преподавались только основы, в то время как реальные навыки устранения неполадок приобретались на рабочем месте в течение длительного периода времени. слежка за высококвалифицированным, опытным обслуживающим персоналом. К сожалению, большинство этих высококвалифицированных рабочих покидают штат и отправляются на заслуженную пенсию, и недостаточное количество новых ремонтных рабочих обладает этим ценным набором навыков.
Настоящая проблема заключается в том, что эффективное устранение неполадок важно для любого производителя, чтобы оставаться конкурентоспособным на сегодняшних жестких рынках. Быстрый и эффективный поиск и устранение неисправностей машин жизненно важен для того, чтобы тонкая, как бумага, прибыль не упала в минус. Это возлагает на технических инструкторов огромную ответственность за подготовку рабочих к работе в первый же день. Давно прошли те времена, когда машина долгое время простаивала, в то время как специалисты по устранению неполадок заменяли один компонент за другим, основываясь на своем личном опыте или предположениях.
Поскольку позволить перспективным молодым специалистам по устранению неполадок тратить годы на приобретение навыков устранения неполадок на работе, невозможно, обучение этим навыкам в классе имеет важное значение. Будущие технические специалисты и операторы должны получить реальный опыт устранения неполадок, прежде чем они попадут в производственный цех. Следовательно, учреждения, такие как общественные колледжи и учебные центры компаний, должны иметь возможность создавать проблемы с оборудованием во многих комбинациях, чтобы накопить опыт устранения неполадок. Использование учебного оборудования с возможностью вставки в систему широкого спектра реалистичных неисправностей имеет решающее значение, чтобы работники могли получить практический опыт диагностики и устранения широкого спектра проблем, встречающихся в реальном мире. Более того, чтобы обеспечить обучение правильным процедурам устранения неполадок, в программе обучения устранению неполадок следует использовать проверенный в отрасли учебный план, обеспечивающий согласованность результатов каждого работника.
Общественные колледжи и промышленные учебные центры прилагают все усилия, чтобы решить эту проблему, предлагая программы, специально предназначенные для обучения навыкам поиска и устранения неисправностей. Хотя эти программы могут различаться по методам обучения, для эффективного устранения неполадок, независимо от конкретной технологии, необходимо выполнить пять основных шагов.
- Шаг 1. Определите симптомы
- Шаг 2: Определите проблему с конкретным компонентом
- Шаг 3. Проверьте подозреваемый компонент
- Шаг 4: Отремонтируйте или замените компонент
- Шаг 5: Протестируйте систему
Выявление симптомов неисправной машины является абсолютно важным, потому что это может сократить процесс поиска и устранения неисправностей, сосредоточив внимание только на тех компонентах, которые могут вызвать эти конкретные проблемы. Очень важно научить будущих специалистов по устранению неполадок сначала попросить оператора определить любые наблюдаемые симптомы неисправной машины.Давайте посмотрим правде в глаза; Независимо от того, насколько хорошо обучен специалист по устранению неполадок, оператор, который ежедневно запускает и контролирует эту конкретную машину, гораздо лучше знаком с ее работой, чем кто-либо другой, и их вклад на данном этапе имеет решающее значение. Слишком часто неопытные специалисты по устранению неполадок предполагают, что знают ответ, хотя на самом деле не понимают вопроса. При обучении специалистов по устранению неполадок важно научить их не упускать из виду этот чрезвычайно ценный ресурс. После того, как оператор определил специфические симптомы машины, сделать полезные выводы относительно неисправности, вызвавшей проблему, будет намного проще.
Классификация вероятной неисправности на основе симптомов позволяет сосредоточить усилия специалиста по устранению неполадок на значительно меньшей области, что экономит драгоценное время и деньги. Например, хорошо обученный специалист по устранению неполадок должен уметь быстро разделить проблему на последовательность машин, производительность машины или проблемы, связанные с системой.
Машинная последовательность | Относится к порядку, в котором происходят события, включая движения привода, изменения давления или изменения скорости |
Производительность машины | Относится к характеристикам движения или выходной мощности привода, например, скорости или выходному усилию. |
Связанные с системой | Обозначает общие характеристики системы, такие как вибрация, температура жидкости, общее давление в системе, утечки жидкости и т. Д. |
Например, давайте рассмотрим гидросистему, чтобы увидеть, насколько полезна категоризация неисправности. Сбои в работе машины указывают на проблемы с компонентами, которые управляют движением, такими как датчики, гидрораспределители или контроллер ПЛК. И наоборот, сбои в работе машины обычно вызваны выходными компонентами или компонентами, которые влияют на выход, такими как редукционные клапаны, предохранительные клапаны или насосы. Симптомы, которые попадают в эти две категории, могут быстро сузить поиск и устранение неисправностей до конкретных участков и деталей машины.Когда сообщается о связанных с системой сбоях, таких как утечки, они указывают на проблемы, которые могут вызвать сбой машины. В некоторых случаях сбои, связанные с системой, сопровождают сбой в последовательности или производительности и являются полезными индикаторами того, что может быть причиной проблемы. Такой систематический подход позволяет специалисту по устранению неполадок быстро решить проблему.
После того, как проблема классифицирована, следует использовать методологию тестирования для правильного определения отказавшего компонента.
Ружье | Проверяет каждый компонент или соединение в пораженной области, пока не будет обнаружена проблема движения, изменения давления или изменения скорости |
Полуразъем | Непрерывно проверяет точку на полпути между заведомо хорошей тестовой точкой и заведомо плохой тестовой точкой, пока не будет выявлена проблема |
Выход-Назад | Начинает тестирование выходов системы и систематически возвращается к входам, пока не будет обнаружена проблема |
Признак и причина | Изоляет проблему в зависимости от того, может ли компонент вызывать наблюдаемые симптомы |
Многие высококвалифицированные специалисты по устранению неполадок рекомендуют метод «Симптомы и причины» как наиболее эффективный. Обучение специалистов по устранению неполадок сосредоточению внимания только на тех компонентах, которые могут вызывать наблюдаемые симптомы, экономит время, поэтому правильное определение симптомов машины имеет решающее значение. Чтобы этот метод был эффективным, специалисты по устранению неполадок должны понимать не только функцию компонента, но и то, как он работает внутри для достижения этой функции. После того, как неисправный компонент будет идентифицирован посредством внутрисхемного тестирования, его следует протестировать вне цепи, чтобы убедиться в его отказе. Один производитель запчастей заявил, что почти 70% возвращенных им запчастей не были дефектными.Тестирование вне цепи изолирует компонент от остальной системы и может предотвратить потерю времени на замену неправильного компонента.
Проверка работы системы после «устранения» проблемы является последним шагом перед подписанием заявки на выполнение работ и уходом от ремонта машины. Следующий пример иллюстрирует важность этого шага. Был заменен главный предохранительный клапан гидравлической системы, и система начала проверку на утечку. Однако, как только обслуживающий персонал ушел, оператор машины попытался отрегулировать клапан на нужное давление в системе только для того, чтобы обнаружить, что они не могут этого сделать, потому что был установлен неправильный запасной клапан.Это привело к увеличению времени простоя и увеличению затрат на ремонт почти вдвое.
Промышленности требуется гораздо больше средств устранения неполадок, чем существует сегодня. Поскольку производители стремятся создавать качественные продукты в более короткие сроки, чем когда-либо, они сталкиваются с острой необходимостью в этих квалифицированных рабочих. Сегодня этим навыкам обучают в местных колледжах и отраслевых учебных центрах — нам просто нужно гораздо больше, чем доступно сейчас.
Создано для Amatrol Ларри Уэйд и Кимберли Перкинс. Amatrol® © разрабатывает и производит системы технического обучения для образовательных и производственных учебных заведений по всему миру. www.amatrol.com
методов поиска и устранения неисправностей | Стайлз Машиностроение
Опыт ничем не заменим. Как наиболее квалифицированный персонал приобретает опыт и совершенствует свои навыки поиска и устранения неисправностей? Эти навыки приобретаются за счет нескольких часов крови, пота и слез, интенсивных тренировок и умения решать проблемы поиска и устранения неисправностей методическим способом.Доказано, что есть методы, которые можно использовать для развития навыков устранения неполадок и повышения квалификации в диагностике проблем.
Этот метод не предназначен для использования в качестве контрольного списка, а скорее как мыслительный процесс для подхода к решению проблем.
В чем проблема?
Звучит достаточно просто. Так что подумайте на мгновение и подумайте, что произошло. Это процесс сбора информации, для которого оператор станка должен быть вашим самым полезным источником.Не забывайте здравый смысл. Часто здравый смысл игнорируется, и проблема становится намного серьезнее, чем есть на самом деле.
После того, как проблемная зона изолирована, важно обеспечить вашу безопасность и безопасность окружающих, прежде чем пытаться манипулировать машиной. Хорошо обученный оператор может сыграть ключевую роль в помощи вам в управлении.
Определите проблему
Теперь возьмите собранную информацию и рассмотрите три переменные. Является ли проблема механической, электрической, пневматической / гидравлической или комбинацией всех трех? Остерегайтесь ложных индикаторов, которые могут ввести в заблуждение.Например, неправильное использование тестового оборудования или невозможность считывания отпечатков приведет к неправильным выводам при проверке электрических цепей. Чтобы определить, какая из трех переменных на самом деле вызывает проблемы, требуется понимание системы и приложения.
Использовать доступные ресурсы
Возможно, доступно больше вариантов, чем предполагалось изначально. Первый важный ресурс, который у вас есть, — это другие сотрудники, которые, возможно, уже исправили такие проблемы. Эти закаленные «старожилы» имеют большой опыт и могут помочь подтвердить ваши наблюдения.
Другой доступный ресурс — это машинная документация. Это должно включать электрические схемы, пневматические схемы, инструкции по эксплуатации и списки деталей. Эти документы следует изучить до того, как возникнет проблема, чтобы вы знали, как организованы руководства и где найти конкретную информацию.
Существует также очень полезный ресурс, который находится на расстоянии одного телефонного звонка, техническая поддержка.Чтобы наилучшим образом воспользоваться этой услугой, вам следует провести исследование до того, как сделать первый звонок. Это включает в себя состояние машины, входы и выходы, измерения напряжения и т. Д. Наличие этой информации позволит персоналу службы технической поддержки помочь с диагностикой проблемы быстрее и может очень сильно повлиять на определение проблемы при первом обращении. .
Сформулируйте теорию
Развивайте понимание того, что на самом деле произошло, а что именно не удалось. Настоятельно рекомендуется установить факты как можно более дипломатично с оператором и другими лицами. При правильном подходе будет раскрыто гораздо больше деталей о будущих проблемах.
Установление этой теории может занять больше времени, если вы не знакомы с системой или оборудованием. Но при этом следует спросить: «Возникла ли проблема из-за отсутствия профилактического обслуживания, ошибки оператора или неправильного использования оборудования?» Если ответ — отсутствие профилактического обслуживания, следует инициировать программу, которая поможет предотвратить повторение проблемы в будущем.Если ответ — ошибка оператора или неправильное использование оборудования, может потребоваться дополнительное обучение персонала.
После утверждения теории убедитесь, что проблема заключается в том, во что вы верите. Это станет намного проще, если вы сможете воссоздать проблему с помощью собранной информации. Без проверки детали и / или компоненты могут быть заменены без необходимости, что приведет к дополнительным затратам времени и средств.
Сделать необходимый ремонт
На этом этапе должно быть очевидно, в чем проблема и какие действия необходимы для правильного ремонта системного оборудования.
Протестируйте машину, чтобы убедиться, что проблема устранена
Проверка ремонта так же важна, как и сам ремонт. Без тестирования, чтобы убедиться, что проблема была устранена, невозможно узнать, что ремонт был успешным. Убедитесь, что защитные ограждения и компоненты машины возвращены в исходное состояние.
Задокументируйте свои действия и ремонт
Чаще всего, когда задача завершена, к обслуживающему персоналу предъявляются другие требования.Задокументировав проблему, шаги по ее решению и выполненный ремонт послужат ценными справочными материалами, если такая же проблема возникнет в будущем.
Практикуя эти методы, время простоя наверняка сократится. При поиске и устранении неисправностей любой конкретной системы всегда будет возникать вопрос «а что, если», но, применяя логический подход время от времени, обслуживающий персонал может начать оттачивать свои навыки.
Хотите узнать больше?
Stiles University предлагает курсы по техническому обслуживанию и поиску и устранению неисправностей на самых разных машинах.Доступны полные описания курса. Позвоните нам по телефону 616.698.7500 для получения дополнительной информации или для регистрации!
6 советов и методов поиска и устранения неисправностей Техническое обслуживание
Полное руководство по поиску и устранению неисправностей при техническом обслуживании и советы по улучшению ваших навыков поиска и устранения неисправностей для повышения эффективности всей вашей операции.
Устранение неисправностей при техническом обслуживании может быть одновременно искусством и наукой. Проблема в том, что искусство может быть красивым, но оно не известно своей эффективностью. При переходе на следующий уровень поиск и устранение неисправностей может избавиться от прозвища методом проб и ошибок и превратиться в чисто научное мероприятие. Это помогает техническим специалистам быстрее находить нужные проблемы и решения. Если устранение неполадок выполнено правильно, вся ваша операция по техническому обслуживанию может намного более эффективно преодолеть отставание, потери производства и проблемы с соблюдением требований.
Давайте посмотрим, что на самом деле представляет собой устранение неполадок, почему это важно для специалистов по обслуживанию и как ваша команда может оптимизировать свой подход.
Что такое устранение неполадок?
Системы выходят из строя — это просто факт жизни. Будь то конвейерная лента или промышленная дрель, мы все сталкиваемся с оборудованием, которое не отвечает, неисправно или работает ненормально без всякой причины.Это может быть совершенно неприятно.
Устранение неполадок — это процесс определения того, что не так с этими неисправными системами, когда проблема не сразу очевидна. Устранение неполадок обычно следует систематическому, четырехэтапному подходу; определить проблему, спланировать ответ, протестировать решение и устранить проблему. Шаги с первого по третий часто повторяются несколько раз, прежде чем будет достигнуто разрешение.
Определите проблему
Запланировать ответ
Проверить решение
Повторяйте, пока проблема не будет решена
Подумайте об этом так: когда конвейерная лента выходит из строя, вы можете попробовать несколько различных методов, чтобы исправить это.Во-первых, вы определяете, какая часть конвейерной ленты не работает. После того, как вы определили проблемную область, вы планируете ответ и тестируете его, например, перенастраивайте или смазывайте деталь. Если это не решит проблему, вы можете заменить деталь, что заставит конвейерную ленту снова работать. Это устранение неполадок.
Как обычно выполняется поиск и устранение неисправностей при техническом обслуживании?
Остановите нас, если вы слышали эту историю раньше. Актив выходит из строя, и никто не знает почему. Вы разговариваете с оператором, читаете руководства и проверяете свои записи об активе.Вы пытаетесь запустить машину и снова работать безуспешно. Прежде чем вы сможете попробовать третье или четвертое возможное решение, вас вызовут в другую чрезвычайную ситуацию, а актив все еще не работает.
Это часто происходит при поиске и устранении неисправностей при техническом обслуживании, особенно когда предприятие полагается на бумажные записи или таблицы Excel. Процесс основан на сборе максимально возможного количества информации из максимально возможного количества источников для определения наиболее вероятной причины поломки.Вы никогда не ошибетесь при сборе информации, но именно способ сбора информации может превратить устранение неполадок из необходимости в кошмар.
Почему при техническом обслуживании важно устранение неисправностей?
Неожиданный отказ оборудования — единственная причина, по которой существует устранение неисправностей. Если активы никогда не выходят из строя без явных признаков неминуемой поломки, устранять проблему не нужно. Но мы знаем, что это не так.
Неисправность актива не всегда происходит по предсказуемой схеме.Да, группы технического обслуживания могут использовать профилактическое обслуживание и техническое обслуживание по состоянию, чтобы снизить вероятность незапланированных простоев. Однако полностью устранить это невозможно. Что вы можете сделать, так это внедрить процессы, чтобы максимально уменьшить количество сбоев и исправить их как можно скорее, когда они все же возникнут. Вот где пригодятся сильные методы устранения неполадок.
Поскольку устранение неисправностей всегда будет частью уравнения технического обслуживания, люди также всегда будут играть свою роль.Технология обслуживания не отменяет необходимости вмешательства человека при поиске и устранении неисправностей; это просто делает процесс намного более эффективным. Если устранение неполадок не усовершенствовано, это может привести к потере времени на отслеживание информации, значительным потерям в производстве, небезопасной рабочей среде и более частым сбоям. Короче говоря, знание некоторых передовых методов устранения неполадок может быть разницей между огромным количеством невыполненных работ и стабильной программой обслуживания.
Советы по поиску и устранению неисправностей при техническом обслуживании
Ниже приведены лишь несколько способов, с помощью которых ваше предприятие может улучшить свои возможности по устранению неполадок, чтобы преодолеть хаос и взять под контроль его обслуживание.
Оцените эффективность активов и поймите, как использовать результаты
Это, вероятно, само собой разумеется, но чем глубже вы знаете актив, тем лучше вы будете готовы диагностировать проблему. Годы работы с определенным активом могут помочь вам распознать, когда он работает неправильно. Но исключительное устранение неполадок — это не просто знание обычных звуков, скорости или запаха конкретной машины. Вместо этого речь идет о том, как анализировать эффективность активов на более глубоком уровне, и именно здесь важна расширенная отчетность.
Ознакомьтесь с передовыми методами отслеживания и использования данных об активах
Подробнее
Когда операторы и технические специалисты полагаются исключительно на свой прошлый опыт работы с оборудованием, у них остаются огромные пробелы в знаниях, которые затрудняют процесс поиска и устранения неисправностей. Например, это оставляет слишком много места для предвзятости новизны, чтобы повлиять на принятие решений, а это означает, что технические специалисты, скорее всего, попробуют последнее, что решило конкретную проблему, не рассматривая другие варианты или углубляясь в основную причину.Кроме того, если поиск и устранение неисправностей опирается на собственные знания нескольких технических специалистов, это означает, что для ремонта придется подождать, пока этот конкретный персонал не появится в наличии.
Обслуживающий персонал должен обладать ноу-хау для проведения глубокого анализа производительности актива. Например, технические специалисты должны понимать, как составлять отчеты, и понимать ключевые показатели эффективности для критически важного оборудования, такие как среднее время наработки на отказ и общая эффективность оборудования. При использовании технического обслуживания на основе состояния группа технического обслуживания также должна знать кривую P-F для каждого объекта и значение различных показаний датчиков.Когда технические специалисты получат более глубокое представление об активе, им будет легче определить, где возникла проблема и как ее исправить, как в краткосрочной, так и в долгосрочной перспективе.
Создание подробной истории активов
Информация — это топливо, которое способствует исключительному поиску и устранению неисправностей при техническом обслуживании. Знание того, как конкретный актив работал и отказал сотням других, — хорошее место для начала ремонта. Вот почему руководства — полезный инструмент при поиске и устранении неисправностей. Однако каждый актив, объект и операция индивидуальны, а это означает, что сбой актива не всегда следует сценарию.Подробные записи об истории актива могут открыть тупик и привести вас к решению гораздо быстрее.
Подробная история активов может дать вам преимущество при поиске и устранении неисправностей различными способами. Он предлагает простой метод сопоставления симптомов текущей проблемы с элементами прошлых проблем. Например, технический специалист может увидеть, обрабатывалась ли машина с определенным типом материала или были ли какие-либо ранние предупреждающие признаки, идентифицированные для предыдущего отказа. Чем больше нынешняя ситуация согласуется с прошлым сценарием, тем больше вероятность того, что потребуется такое же исправление.Таким образом можно определить приоритеты решений, что приведет к меньшему количеству промахов, меньшему времени простоя, меньшему количеству ненужных запчастей и многому другому.
Если устранение неполадок выполнено правильно, вся ваша операция по техническому обслуживанию может намного более эффективно преодолеть отставание, потери производства и проблемы с соблюдением нормативных требований.
При создании подробных историй активов для устранения неполадок (а также профилактического обслуживания) важно включать как можно больше информации. Обязательно записывайте время и даты любых заметных действий, предпринятых с активом или частью оборудования.Это могут быть поломки, ТО, осмотры, замена деталей, производственные графики и ненормальное поведение, такое как дым или необычные звуки. Затем задокументируйте шаги, предпринятые во время технического обслуживания, включая PM или ремонт. Наконец, выделите успешное решение и то, что требовалось для его выполнения, например, необходимые детали, рабочую силу и оборудование для обеспечения безопасности. Не забудьте также добавить в историю активов все соответствующие показатели и отчеты.
Один из способов собрать всю эту информацию в одном месте — создать хорошо продуманный журнал обслуживания оборудования, например:
Загрузите собственный шаблон журнала обслуживания оборудования здесь
Использовать анализ первопричин и коды ошибок
Эффективный поиск и устранение неисправностей при техническом обслуживании начинается с устранения двусмысленности и краткосрочных решений.Быстрое обнаружение корня проблемы, ее эффективное решение и обеспечение того, чтобы она оставалась решенной, — вот формула успеха. Анализ первопричин и коды сбоев — это пара инструментов, которые помогут вам в достижении этой цели.
Анализ первопричин — это метод, позволяющий точно определить причину сбоя. Метод состоит в том, чтобы спрашивать «почему», пока вы не дойдете до сути проблемы. Например:
- Почему вышло из строя оборудование ?: Изношен подшипник
- Почему износился подшипник ?: Из-за смещения муфты
- Почему муфта не соосна ?: Потому что недавно не обслуживалась.
- Почему муфта не обслуживалась ?: Потому что техническое обслуживание не было запланировано.
- Почему не было запланировано техническое обслуживание ?: Потому что мы не знали, как часто его следует проводить.
Проведите следующий анализ первопричин с помощью этого шаблона RCA
У этого процесса есть два преимущества при поиске и устранении неисправностей при техническом обслуживании. Во-первых, это позволяет определить непосредственную причину сбоя и быстро устранить ее. Во-вторых, это подводит вас к сути проблемы и к долгосрочному решению.В приведенном выше примере ясно, что требуется более совершенная программа профилактического обслуживания, чтобы улучшить управление активами и сократить незапланированные простои.
Коды отказов предоставляют единообразный метод описания причин отказа актива. Коды ошибок состоят из трех действий: перечисление всех возможных проблем, всех возможных причин и всех возможных решений. В этом процессе регистрируются ключевые аспекты отказа в соответствии с заранее определенными категориями, например, несоосность или коррозия.
Коды отказовполезны при поиске и устранении неисправностей при техническом обслуживании, потому что технические специалисты могут сразу видеть общие коды неисправностей, определять лучшее решение и быстро его внедрять.Коды отказов также можно использовать для выявления общей проблемы среди группы активов и определения долгосрочного решения.
Создавайте потрясающие коды ошибок с помощью этого бесплатного шаблона FMEA
Создание подробных списков задач
Исключительное устранение неисправностей требует твердого планирования и предвидения. Четкие процессы представляют собой план для технических специалистов, чтобы они могли быстро выявлять проблемы и внедрять более эффективные решения. Создание подробных списков задач — один из способов укрепить ваше планирование и избежать головной боли в будущем.
Список задач содержит ряд задач, которые необходимо выполнить, чтобы завершить более крупную работу. Они гарантируют, что важные шаги не будут упущены при проведении инспекций, аудитов или PM. Например, более крупная работа может заключаться в регулярном осмотре дефибрилляторов вашего учреждения. Эта работа разбита на список более мелких задач, таких как «Проверка установки батареи» и «Проверка внешних компонентов на предмет трещин».
Технология обслуживания не устраняет необходимость вмешательства человека при поиске и устранении неисправностей; это просто делает процесс намного более эффективным.
Подробные списки задач чрезвычайно важны при поиске и устранении неисправностей при техническом обслуживании. Они действуют как руководство при тестировании возможных решений, чтобы технические специалисты могли как можно быстрее решить проблему или аннулировать диагноз. Чем яснее список задач, тем тщательнее работа и тем меньше вероятность того, что технический специалист совершит ошибку. Исчерпывающие списки задач также могут предоставить ценные данные при возникновении сбоя. Они дают представление о типе недавно проделанной работы с активом, чтобы вы могли определить, были ли пропущены какие-либо действия и было ли это источником проблемы.
Есть несколько рекомендаций по созданию подробных списков задач. Во-первых, включите все отдельные действия, составляющие задачу. Например, вместо того, чтобы инструктировать кого-то «Осмотреть охлаждающий вентилятор», включите в него шаги, составляющие этот осмотр, такие как «Проверить на наличие видимых трещин» и «Осмотреть на предмет незакрепленных деталей». Организуйте все шаги в том порядке, в котором они должны выполняться. Наконец, включите любую дополнительную информацию, которая может быть полезна при выполнении задач, включая необходимые материалы, ресурсы (т. Е.руководства) и СИЗ.
Создавайте контрольные списки PM мирового класса с помощью этого бесплатного шаблона
Сделайте дополнительную информацию доступной
Мы уже говорили это раньше и повторим еще раз; отличное устранение неполадок часто является результатом хорошей информации. Однако, если к этой информации трудно получить доступ, вы потеряете все преимущества, которые она дает. Вот почему для вашего предприятия крайне важно не только создать большой ресурсный центр, но и сделать его очень доступным.Это расширит ваши возможности по устранению неполадок и быстрее вернет ваши активы в оперативный режим в случае незапланированного простоя.
Начнем с элементов отличного информационного центра. Мы говорили о важности отчетов, историй активов, кодов сбоев и списков задач при устранении неполадок при техническом обслуживании. Некоторые другие ключевые ресурсы включают диаграммы, стандартные рабочие процедуры (СОП), обучающие видеоролики и руководства. Все они должны быть включены и организованы по активам. Если технический специалист заходит в тупик при устранении проблемы, эти инструменты могут предложить решение, которое могло быть упущено при первоначальном анализе.
Теперь, когда вы собрали все свои документы, пора сделать их легко доступными для всей группы обслуживания. Если ресурсы заперты в картотеке, в электронной таблице или в голове отдельного человека, они не принесут много пользы техническому специалисту. Их можно потерять, потерять и их трудно найти — не говоря уже о неэффективности, связанной с необходимостью идти от актива до офиса, чтобы просто взять руководство. Один из способов обойти это препятствие — создать центр цифровых знаний с программным обеспечением для обслуживания.Делая все ваши ресурсы доступными через мобильное устройство, технические специалисты могут получить доступ к любому инструменту, который им нужен для устранения проблемы. Вместо того, чтобы просматривать бумажные файлы в поисках истории активов или диаграммы, они могут получить доступ к той же информации в любом месте и в любое время.
Все, что вам нужно знать о показателях обслуживания
Подробнее
Использование программного обеспечения для обслуживания для поиска и устранения неисправностей
Если вам кажется, что собрать, систематизировать, проанализировать и распространить всю информацию, необходимую для успешного устранения неполадок, потребуется много работы, вы не ошиблись.Без надлежащих инструментов этот процесс может стать тяжелым испытанием для перегруженных бригад технического обслуживания. Программное обеспечение для обслуживания — это инструмент, который может помочь облегчить нагрузку на каждом этапе пути. Цифровая платформа, такая как CMMS, берет на себя обработку чисел, систематизирует данные и делает их доступными где угодно и когда угодно, поэтому вы можете сосредоточиться на использовании этой информации для принятия правильных решений и более эффективного устранения неполадок.
Например, при построении подробной истории актива важно документировать каждую встречу с частью оборудования.Это большая работа для техника, спешащего с одной работы на другую, и ее трудно уследить постфактум. Инвестиции в программное обеспечение для обслуживания помогут вам преодолеть эти препятствия. Это достигается за счет того, что технические специалисты могут использовать заранее определенный набор вопросов для создания и извлечения заметок в режиме реального времени с помощью нескольких щелчков мышью.
То же самое и с кодами ошибок. Ключ к их эффективному использованию — правильная организация и доступность. Без этих двух ключевых ингредиентов коды отказов становятся скорее помехой, чем помощью.Один из способов добиться этого — использовать программное обеспечение для обслуживания. Цифровая платформа может систематизировать коды отказов лучше, чем любой картотечный шкаф или электронная таблица Excel, и упростить для технических специалистов их быструю сортировку и определение соответствующих кодов с места поломки.
Итог
Устранение неисправностей всегда будет присутствовать в обслуживании. Вы никогда не будете на 100 процентов уверены на 100 процентов при диагностике причины сбоя. Что вы можете сделать, так это предпринять шаги к более эффективному процессу устранения неполадок, чтобы обеспечить быстрый и эффективный ремонт оборудования.Объединив хорошее понимание метрик обслуживания с подробной историей активов, кодами отказов, списками задач и другими ресурсами активов, а также сделав всю эту информацию доступной, вы можете перейти от поиска и устранения неисправностей к более научному подходу.
Основы поиска и устранения неисправностей оборудованияEquifactor® — Анализ первопричин TapRooT®
22 июня 2020 г. | Кен РидДавайте вернемся к основам. Я хотел бы описать, как предназначен модуль устранения неполадок оборудования Equifactor® системы анализа первопричин TapRooT®.
Equifactor® разработан для того, чтобы помочь специалистам по техобслуживанию и надёжности вашего оборудования выявить основные причины отказов механического или электрического оборудования.
Что такое устранение неисправностей оборудования Equifactor®?При выполнении анализа первопричин с помощью TapRooT® очень важно собрать правильную информацию о проблеме. Это может быть информация по технике безопасности, экологические процедуры, политики и рабочие инструкции для конкретной задачи и т. Д.Обычно довольно очевидно, какие типы данных вам нужны для того типа расследования, которое вы проводите.
Иногда для решения определенных типов проблем требуются дополнительные инструменты сбора данных TapRooT®. Equifactor® — один из таких инструментов. Он разработан, чтобы помочь специалистам по техобслуживанию и надёжности вашего оборудования выяснить основные причины отказов механического или электрического оборудования.
Зачем нужен поиск и устранение неисправностей оборудования Equifactor®?В ходе расследования вы можете обнаружить, что одна из ваших проблем связана с неисправностью оборудования.Например, вы можете обнаружить, что компрессор вибрирует выше ожидаемого. Вы можете поместить этот факт в свой SnapCharT®, но что теперь? Что вы делаете с этой информацией? Чтобы преодолеть этот момент в SnapCharT®, вам действительно нужен ответ от вашей группы устранения неполадок: «Почему компрессор вибрирует?» К сожалению, если бы вы знали это, вам не нужно было бы задавать вопрос в первую очередь о вашем SnapCharT®! Вам необходимо знать физическую причину вибрации, чтобы перейти к более подробному анализу SnapCharT® с причинными факторами.
Equifactor® Обнаружение и устранение неисправностей оборудования в деталяхЗдесь на помощь приходит Equifactor®. Чтобы помочь специалистам по вашему оборудованию выяснить физическую причину вибрации, они, вероятно, будут полагаться на свой опыт и местные руководства для получения советов по поиску и устранению неисправностей. Они рассмотрят возможные причины, с которыми они знакомы, и, надеюсь, найдут проблему. Однако мы не можем полагаться на надежду. Что происходит, когда они проверяют элементы, с которыми они знакомы, а проблема не обнаруживается? Тогда они могут обратиться за помощью к таблицам поиска и устранения неисправностей оборудования Equifactor®.В таблицах приведен исчерпывающий список возможных причин вибрации компрессора. Ваши специалисты могут просмотреть эти таблицы, чтобы определить все возможные причины, относящиеся к вашему компрессору, а затем использовать этот список возможных причин для разработки подробного плана устранения неполадок для выявления проблемы. Эти таблицы служат отличным руководством для вашей группы технического обслуживания при поиске и устранении неисправностей. Эти предметы довольно часто являются вещами, которых они никогда раньше не видели, а потому и не думали искать.
Устранение неполадок оборудования Equifactor® — инструмент анализа первопричин TapRooT®Как только ваша команда обнаружит физическую причину вибрации компрессора (например, возможно, использовались неправильные соединительные болты, что нарушило баланс машины), мы еще не закончили. Многие компании останавливались на этом и заявляли, что «основная причина заключалась в том, что механики установили неправильные стяжные болты». Оглядываясь назад, это кажется глупой первопричиной. К сожалению, это тоже обычное дело!
Equifactor® НЕ является отдельным независимым инструментом.Он разработан для использования в качестве инструмента сбора данных для расследования TapRooT®. Таким образом, обнаруженная проблема (неправильные соединительные болты) теперь добавлена в исходный SnapCharT®, и теперь мы можем продолжить наше обычное расследование TapRooT®. Я почти уверен, что болты не установились волшебным образом; был вовлечен человек. Теперь мы можем обнаружить проблемы с производительностью человека, которые заставляют механиков использовать неправильные болты. Мы продолжаем добавлять информацию в наш SnapCharT®, пока не сможем проанализировать все причинные факторы (одним из которых, вероятно, будет «Механики собрали муфту с использованием неправильных болтов») через дерево первопричин®.Теперь мы можем применить эффективные корректирующие действия к проблеме. Вместо того, чтобы обвинять механика («Консультировал механика о важности использования разрешенных запасных частей во время сборки муфты»), теперь мы можем нацелить наши корректирующие действия на причину, механик использовал неправильные болты (правильные болты недоступны, общие использование «ящиков для запчастей» для ремонта оборудования, неправильный номер детали в заказе на ремонт и т. д.).
Equifactor® — отличный инструмент, который поможет вашим специалистам по техобслуживанию и надёжности найти физическую причину неисправности оборудования.Это инструмент, который поможет вам в проведении расследования TapRooT®, когда проблема оборудования является частью этого расследования. Научитесь использовать эти таблицы, чтобы сэкономить время и силы при устранении неполадок с оборудованием.
Кому следует пройти обучение по поиску и устранению неисправностей оборудования Equifactor®?Очевидно, чтобы хорошо владеть инструментом, вы должны быть обучены его использованию. Обучение Equifactor® было настроено так, чтобы быть чрезвычайно гибким для удовлетворения различных потребностей в обучении.
Этот курс представляет собой двухдневный курс TapRooT® / Equifactor®:
- В первый день мы научим методам устранения неполадок Equifactor®. В этот день может принять участие любой из специалистов по надежности и обслуживанию вашего оборудования. Они узнают, как использовать SnapCharT® для сбора информации об устранении неполадок и таблицы устранения неполадок Equifactor® для анализа отказов оборудования.
- День 2 будет обучать остальным техникам TapRooT®. Те, кто хотел бы изучить полную систему TapRooT®, но на примерах оборудования, останутся на оба дня и пройдут полный курс.
Сообщите нам, если вы хотите увидеть демонстрацию системы. Мы будем рады показать вам, как TapRooT® и Equifactor® вместе могут стать мощной частью программ обслуживания и повышения надежности вашего оборудования.
Узнать больше
Свяжитесь с нами
Категории
Надежность оборудования / Equifactor®Next ПредыдущийУстранение неполадок Распространенные проблемы AV-оборудования
Традиционный цикл решения проблем
Ваше мероприятие планировалось уже несколько месяцев.Сотни людей приезжают за несколько дней, и все готово к работе. Вам даже помогли выбрать подходящее аудио-видео оборудование, и вы уверены, что все пойдет гладко.
Затем наступает важный день, и ничто не хочет работать. Не работают проекторы, не работают мониторы, в некоторых местах нет звука. Что теперь? Наем стороннего поставщика AV-услуг может облегчить большую часть беспокойства, связанного с использованием AV-оборудования, поскольку у них есть многолетний опыт настройки и эксплуатации оборудования, а также устранения любых возникающих проблем.Но если вы не можете нанять для своего мероприятия по какой-либо причине или не можете вовремя найти поставщика, следуйте этим советам по устранению распространенных проблем с AV-оборудованием, чтобы вы могли вернуться к его проведению!
Устранение распространенных проблем AV
- Звук не работает. Устранение неполадок со звуком можно найти в нескольких простых местах.
- Сначала запустите тест, чтобы убедиться, что звук действительно не работает.Вы можете сделать это, перезапустив систему и прислушиваясь к звукам запуска. Если ничего не слышно, переходите к следующим шагам.
- Дважды щелкните значок «Громкость» на панели задач, чтобы убедиться, что на вашем компьютере не выключена или отключена громкость.
- Вы также можете нажать «Настройки» -> «Панель управления» -> «Звуки и аудиоустройства», чтобы узнать, отключен ли звук.
- Убедитесь, что в той же области не выбран параметр «Наушники».
- Если вы по-прежнему не получаете звук, проверьте регуляторы громкости на другом подключенном оборудовании, чтобы убедиться, что звук не отключен или не выключен.
2) Визуальные дисплеи не подключаются. Иногда на экране отображается сообщение об отсутствии синхронизации или сигнала. В таких случаях следуйте этим советам по устранению неполадок.
- Убедитесь, что все ваши кабели надежно подключены. Ослабленный кабель или неправильно подключенный кабель могут вызвать проблемы с AV.
- Убедитесь, что вы подключены к правильному устройству. Если вы подключаетесь к ноутбуку, но основные кабели подключены к настольному компьютеру, вам необходимо переключить соединения.
- Убедитесь, что сетевое соединение активно. Иногда системы работают только тогда, когда они подключены к сети, поэтому убедитесь, что все оборудование подключено к одной и той же сети, чтобы обеспечить совместимость.
3) Визуальные дисплеи не показывают изображения. Если ваш компьютер подключен к дисплею, но изображение по-прежнему не отображается, выполните следующие действия:
- В некоторых системах есть главный элемент управления, который может переключать выбранное оборудование для проецирования или отображения.Убедитесь, что переключатель установлен на то оборудование, которое вы хотите отображать.
- Убедитесь, что переключатель на вашем оборудовании настроен на отображение внешнего источника. Даже если переключатель на оборудовании переключается на отображение с вашего компьютера, вам необходимо убедиться, что ваш компьютер настроен на отображение внешнего источника.
- Большинство новых ноутбуков с Windows и Mac автоматически определяют, что к устройству подключен внешний источник. Однако, если изображение не появляется, возможно, необходимо изменить некоторые настройки компьютера.Проверьте свою панель управления, чтобы убедиться, что установлены соответствующие параметры отображения.
4) Проблемы с проектором. Проекторы могут добавить к этому сложный уровень поиска и устранения неисправностей AV. Если у вас возникли проблемы с проектором, вам могут помочь следующие советы:
- Если ваш монитор включен, но экран черный, возможно, компьютер спит и его нужно «разбудить» встряхиванием мыши на коврике для мыши. Кажется простым решением, но его часто упускают из виду.
- При использовании портативного компьютера с проектором проектор следует сначала включить, а затем включить портативный компьютер.Если вы этого не сделали, просто выключите все и начните снова в правильном порядке.
- В некоторых случаях ноутбукам Mac требуется адаптер VGA для подключения к кабелям VGA, используемым для подключения к проекторам. Эти адаптеры поставляются вместе с Mac при покупке, так что они должны быть у вас под рукой. Всегда полезно иметь под рукой дополнительные адаптеры VGA на всякий случай.
Наем сторонней службы AV для оказания помощи
Следование этим советам и приемам гарантирует, что ваше мероприятие быстро и легко вернется в нужное русло.Не позволяйте AV-проблемам подкрадываться к вам, найдите стороннего поставщика AV-услуг, которому вы можете доверять, чтобы сделать работу правильно с первого раза! Один из лучших вариантов, доступных вам, — это системы для проведения мероприятий ATX в Остине, штат Техас. Наша репутация производителя безупречного исполнения с непревзойденным профессионализмом хорошо известна во всем штате Техас, включая Даллас, Сан-Антонио и Хьюстон. Позвоните нам. Мы будем рады вам помочь.
Требования к оборудованию и помощь — ProctorU
Связаться со службой поддержки- ProctorU
- Тестируемый
- Требования к оборудованию и помощь
- Требования к оборудованию
- Подключение к Интернету / пропускная способность
- Устранение неполадок камеры
- Устранение неполадок микрофона
- Какие браузеры поддерживаются?
- Несколько мониторов / дисплеев
- Настройки Windows
- Настройки MAC-адреса
- Участники тестирования из Великобритании — Настройка TalkTalk / HomeSafe
- Какие операционные системы / устройства поддерживаются?
- Динамики
- ИСПЫТАНИЯ
- Регистрация Вход Ресурсный центр для тестируемых Автоматическая проверка оборудования
- О PROCTORU
- Карьера Исполнительная биография Политика конфиденциальности Условия использования Заявление о доступности
- НАШИ ОФИСЫ
- Плезантон, Калифорния Бирмингем, штат Алабама Фолсом Калифорния