Тормозные механизмы автомобилей.
Тормозные механизмы
Тормозной механизм – устройство, непосредственно предназначенное для создания или изменения принудительного сопротивления движению автотранспортного средства.
В тормозных системах автомобилей в качестве тормозных механизмов наиболее часто используют фрикционные устройства, в которых искусственное сопротивление движению создается за счет сил трения между вращающимися деталями, связанными с колесом, и неподвижными деталями, связанными с ходовой частью, агрегатами трансмиссии или несущей системой автомобиля.
Исключение могут составлять вспомогательные тормозные системы, использующие для уменьшения скорости автомобиля естественные силы трения в трансмиссии и двигателе, а также противодавление в выпускной системе двигателя.
В качестве тормозной системы спортивных и гоночных автомобилей иногда применяются устройства, использующие внешние источники энергии, например, парашют. В массовом автомобилестроении такие тормозные системы не применяются.
- по форме вращающихся деталей различают барабанные, дисковые и шкивовые тормозные механизмы;
- по форме трущихся поверхностей — колодочные и ленточные;
- в зависимости от места установки различают колесные и трансмиссионные тормозные механизмы.
В рабочих, стояночных и запасных тормозных системах автомобилей в подавляющем большинстве применяются барабанные и дисковые тормозные механизмы, поскольку они наиболее полно отвечают предъявляемым требованиям – надежность и эффективность, хороший отвод тепла от деталей и узлов, обеспечение плавности торможения и высокий КПД. Используемые в конструкциях многих дорожных и сельскохозяйственных машин ленточные тормозные механизмы, использующие трение между тормозной лентой (или ремнем) и шкивом, на автомобилях применение не нашли.
В барабанных тормозных механизмах (
рис. 1) используются силы трения, возникающие между внутренней поверхностью цилиндрического барабана, вращающегося вместе с колесом или подвижным элементом трансмиссии, и тормозными колодками, шарнирно соединяемыми с неподвижными элементами ходовой части, несущей системы или трансмиссии.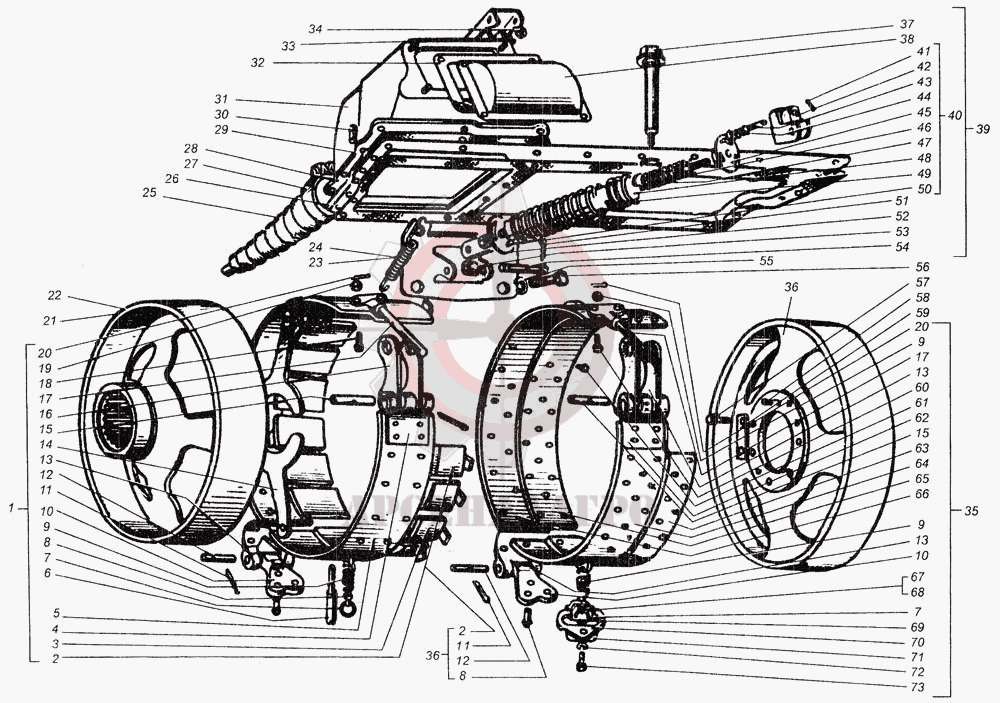
В дисковых тормозных механизмах (рис. 2) используются силы трения, возникающие между боковыми поверхностями металлического диска, вращающегося вместе с колесом, и колодками, корпус которых крепится к неподвижным элементам ходовой части. Тормозной привод в обоих механизмах воздействует на тормозные колодки, прижимая их к поверхностям барабана или диска, создавая силу трения требуемой эффективности.
***
Достоинства и недостатки тормозных механизмов
К достоинствам барабанных тормозных механизмов следует отнести более высокую эффективность при одинаковом усилии на исполнительные элементы (колодки) по сравнению с дисковым тормозным механизмом при прочих равных условиях. Это достигается возможностью использования большей площади трения между барабаном и колодками, а также создавать полученной силой трения крутящий момент с бóльшим плечом, равным внутреннему радиусу барабана.
Плечо силы трения, создаваемой дисковым механизмом, меньше наружного диаметра диска, поскольку суммарная сила трения приложена к его боковой поверхности на некотором расстоянии от обода, т. е. смещена к оси колеса. По этой причине, при одинаковой силе трения и габаритах тормозного механизма, барабанные тормоза создают больший тормозящий момент, чем дисковые.
Тормозные колодки барабанных механизмов имеют бóльшую площадь трения, чем колодки дисковых тормозов, поэтому они изнашиваются менее интенсивно. Детали барабанного тормозного механизма лучше защищены от неблагоприятного воздействия внешней среды, поэтом меньше подвержены механическим повреждениям, коррозии и абразивному износу.
Кроме этого, барабанные тормозные механизмы имеют более жесткую конструкцию тормозящего элемента (барабана), благодаря чему он менее подвержен деформации, чем диск. Однако пространственная форма барабана усложняет его балансировку.
Такие качества, как создаваемый эффективный тормозной момент и прочностные достоинства барабана являются основной причиной широкого применения барабанных тормозных механизмов в системах торможения грузовых автомбилей и автобусов. В современных легковых автомобилях их применение ограничено из-за сравнительно большой массы и габаритов.
К достоинствам дисковых тормозных механизмов можно отнести малые габариты и массу, эффективное охлаждение деталей механизма из-за большой площади охлаждения и возможности вентилирования, независимость действия тормозов от износа накладок и возможность работы с малыми зазорами, более равномерное распределение давлений и высокую стабильность работы.
У дисковых тормозов зависимость коэффициента эффективности от коэффициента трения имеет более благоприятный (линейный) характер, чем у барабанных.
Благодаря перечисленным достоинствам дисковые тормозные механизмы в последние годы практически вытеснили барабанные механизмы в конструкциях тормозных систем легковых автомобилей, и все чаще применяются на грузовых автомобилях.
Тем не менее, и тот и другой тип тормозных механизмов может использоваться в конструкции всех типов автомобилей, при этом барабанные тормозные механизмы чаще применяются в тормозных системах грузовых автомобилей, дисковые – в тормозных системах легковых автомобилей.
Встречаются и комбинации таких механизмов на одном автомобиле, например, тормозные механизмы задних колес легкового автомобиля могут быть барабанными, передних колес – дисковыми.
Барабанные тормозные механизмы, размещенные на элементах трансмиссии, нередко используются в стояночных тормозных системах грузовых автомобилей малой и средней грузоподъемности.
***
Элементы тормозных механизмов
Тормозные барабаны могут быть литые, штампованные и комбинированные. Их отливают из чугуна с примесью меди, молибдена, никеля и титана, а также из алюминиевых сплавов. Штампованные барабаны обычно выполняются из листовой стали, при этом имеют внутренний слой из легированного чугуна.
Тормозные диски изготовляют, как правило, из чугуна. Применяют также биметаллические диски, которые выполняют с фрикционным слоем из серого чугуна, размещаемого на алюминиевом или медном основании.
Колодки тормозных механизмов выполняют чаще всего литыми из чугуна или легких сплавов, а также штампованными или сварными.
Тормозные накладки могут быть прессованные или формованные или плетенные. Для накладок используют формованные и прессованные материалы на асбокаучуковой основе (коротковолокнистый асбест, наполнители и связующие материалы — чаще бакелито-формальдегидные смолы), а также металлокерамику.
***
Устройство тормозных механизмов различных марок отечественных автомобилей можно изучить, пройдя по приведенным ниже ссылкам (схемы откроются в отдельном окне браузера):
Тормозные механизмы автомобилей «ГАЗ» и «ЗИЛ»
Тормозные механизмы автомобилей «КамАЗ» и «МАЗ»
Дисковые тормозные механизмы автомобилей «Волга», «Москвич»
***
Назначение и общее устройство рулевого управления
Главная страница
Дистанционное образование
Специальности
Учебные дисциплины
Олимпиады и тесты
Конструкция тормозных механизмов
В настоящее время наибольшее распространение получили тормозные механизмы фрикционного типа. Принцип действия тормозного механизма фрикционного типа основан на силах трения, которые возникают между вращающимися и невращающимися деталями механизма. В зависимости от формы вращающиеся детали тормозного механизма делятся на дисковые и барабанные.
Эти тормозные механизмы, как правило, применяются на легковых автомобилях. На легковых автомобилях высокого класса дисковые тормозные механизмы ставятся на все колеса; на легковых автомобилях среднего и малого класса дисковые тормозные механизмы, как правило, ставят только на передние колеса, а на задние колеса ставят барабанные тормозные механизмы. В последнее время ряд зарубежных фирм начали применять дисковые тормозные механизмы на грузовых автомобилях.
Тормозной диск закрепляется на ступице переднего колеса. Скоба закрепляется на фланце поворотного кулака при помощи кронштейна. Она изготавливается из высокопрочного чугуна. В пазах скобы находятся тормозные легкосъемные колодки. В скобе размещены два алюминиевых тормозных цилиндра, которые находятся по разные стороны тормозного диска. Очень часто при раздельном или дублированном приводе тормозных механизмов в скобе размещают по два тормозных цилиндра с каждой стороны тормозного диска. Тормозные цилиндры соединяются между собой при помощи соединительной резиновой трубки. Внутри тормозного цилиндра находятся стальные поршни, которые уплотняются резиновыми кольцами. Благодаря этим кольцам стальные поршни возвращаются в свое исходное положение при растормаживании колес. Кроме этого при износе тормозных колодок резиновые кольца позволяют поршню перемещаться, сохраняя между колонкой и диском минимальный зазор (примерно 0,1 мм).
В дисковом тормозном механизме с плавающей скобой скоба может перемещаться в пазах кронштейна, который закрепляется на фланце поворотного кулака. В таких тормозных механизмах тормозной цилиндр располагается только с одной стороны, а в некоторых случаях ставят два или три цилиндра, которые также располагаются с одной стороны.
Кроме вышеперечисленных видов тормозных систем существуют дисковые тормозные механизмы с качающейся на маятниковом подвесе скобой. В такой конструкции тормозные цилиндры также располагаются с одной стороны, кроме этого в таких тормозных механизмах исключается возможность заедания скобы, что иногда наблюдается в конструкциях с плавающей скобой.
Барабанные тормозные механизмы могут быть с гидравлическим приводом и с пневматическим. Барабанный тормозной механизм с гидравлическим приводом состоит из двух колодок с фрикционными накладками, которые размещаются на опорном диске. Нижние концы тормозных колодок шарнирно закрепляются на опорах, а верхние концы опираются в поршни разжимного колесного рабочего цилиндра через стальные сухари. Стяжная пружина прижимает колодки к поршням цилиндра, благодаря этому обеспечивается зазор между колодками и тормозным барабаном в нерабочем состоянии тормозной системы. В тот момент, когда жидкость поступает из привода в колесный рабочий цилиндр, его поршни расходятся и раздвигают колодки до тех пор, пока те не начнут соприкасаться с тормозным барабаном, который вращается со ступицей колеса. Торможение колеса обеспечивает возникающая сила трения между тормозными колодками и барабаном. Когда давление жидкости на поршни рабочего цилиндра прекращается, стяжная пружина возвращает колодки в исходное положение, в результате этого торможение колеса прекращается.
Кроме этого на некоторых автомобилях применяется другая конструкция барабанного механизма торможения, в которой шарнирные опоры колодок располагаются на противоположных сторонах тормозного диска, привод каждой колодки осуществляется при помощи- отдельного тормозного цилиндра. В такой конструкции возникает больший тормозной момент, кроме этого тормозные колодки автомобиля изнашиваются более равномерно.
Барабанный тормозной механизм с пневматическим приводом отличается от конструкции барабанного тормозного механизма с гидравлическим приводом конструкцией разжимного устройства. Разжимное устройство барабанного тормозного механизма с пневматическим приводом выполнено по типу механического привода тормозного механизма. Для разведения колонок в таком механизме применяется разжимной кулак, который приводится в действие рычагом, посаженным на ось кулака. Рычаг отклоняется под действием усилия, возникающего в пневматической тормозной камере. Пневматическая камера работает от централизованной системы сжатого воздуха автомобиля. Возврат колонок в исходное положение при растормаживании колес автомобиля осуществляется под действием сжатой пружины. Нижние концы колонок закрепляются на эксцентриковых кольцах. Такие кольца дают возможность регулировать зазор между нижними частями тормозных колодок и барабаном. Верхние части тормозных колодок подводятся к тормозному барабану при регулировке зазора при помощи червячного механизма.
Тормозные барабаны для легковых и грузовых автомобилей малой или средней грузоподъемности, как правило, производят биметаллическими. Это может быть стальной диск с залитым внутрь чугунным ободом (например, на таких автомобилях, как ГАЗ-3102, ВАЗ-2105 или ГАЗ-53) или тормозной барабан из алюминиевого сплава с залитым внутрь чугунным кольцом (например, на автомобиле ВАЗ-2101). На грузовых автомобилях большой грузоподъемности (таких, как КамАЗ, ЗИЛ) применяют тормозные барабаны, которые чаще всего выполняются из серого чугуна.
Опорные диски, как правило, штампуют из листовой стали.
В дисковых тормозных механизмах рабочие цилиндры производят из алюминиевого сплава.
В барабанных тормозных механизмах с гидроприводом рабочие тормозные цилиндры производят из серого чугуна, поршни из цинкового или алюминиевого сплава. В барабанных тормозных механизмах с пневматическим приводом разжимной кулак делают из высокоуглеродистой стали с закалкой поверхности токами высокой частоты, его выполняют как одно целое с валом.
В настоящее время на многих автомобилях широкое распространение получили формованные фрикционные накладки, которые состоят из коротковолокнистого асбеста, наполнителей и связующих материалов. В роли связующих материалов применяют синтетические смолы, каучук и их комбинации. Но в последнее время все большее распространение начинают получать безасбестовые накладки, так как они являются более экологически чистыми. В некоторых случаях применяют пластмассовые фрикционные накладки, которые включают в себя эбонит и некоторые другие материалы. На отечественных автомобилях для дисковых и барабанных тормозных механизмов широко применяются накладки, выполненные их асбокаучуковой композиции.
Тормозные колодки чаще всего выштамповывают из листовой стали, но на некоторых грузовых автомобилях (например, ЗИЛ-431410) применяют тормозные колодки, выполненные из литого чугуна. На легковых автомобилях накладки чаще всего крепятся к тормозным колодкам при помощи клея, на грузовых автомобилях накладки прикрепляют к тормозным колодкам заклепками или болтами.
Изделия фрикционные тормозные. Общие технические требования – РТС-тендер
ГОСТ 32516-2013
МКС 21.140
Дата введения 2015-01-01
Цели, основные принципы и порядок проведения работ по межгосударственной стандартизации установлены ГОСТ 1. 0-92 «Межгосударственная система стандартизации. Основные положения» и ГОСТ 1.2-2009 «Межгосударственная система стандартизации. Стандарты межгосударственные, правила и рекомендации по межгосударственной стандартизации. Правила разработки, принятия, применения, обновления и отмены»
Сведения о стандарте
1 РАЗРАБОТАН Техническим комитетом по стандартизации ТК 160 «Продукция нефтехимического комплекса»
2 ВНЕСЕН Федеральным агентством по техническому регулированию и метрологии
3 ПРИНЯТ Межгосударственным советом по стандартизации, метрологии и сертификации (протокол от 14 ноября 2013 г. N 44-2013)
За принятие проголосовали:
Краткое наименование страны | Код страны | Сокращенное наименование национального органа по стандартизации |
Армения | AM | Минторгэкономразвития Республики Армения |
Беларусь | BY | Госстандарт Республики Беларусь |
Киргизия | KG | Кыргызстандарт |
Россия | RU | Росстандарт |
4 ВВЕДЕН ВПЕРВЫЕ
5 Приказом Федерального агентства по техническому регулированию и метрологии от 22 ноября 2013 г. N 1852-ст межгосударственный стандарт ГОСТ 32516-2013 введен в действие в качестве национального стандарта Российской Федерации с 1 января 2015 г.
Информация об изменениях к настоящему стандарту публикуется в ежегодно издаваемом информационном указателе «Национальные стандарты», а текст изменений и поправок — в ежемесячно издаваемом информационном указателе «Национальные стандарты». В случае пересмотра (замены) или отмены настоящего стандарта соответствующее уведомление будет опубликовано в ежемесячно издаваемом информационном указателе «Национальные стандарты». Соответствующая информация, уведомление и тексты размещаются также в информационной системе общего пользования — на официальном сайте Федерального агентства по техническому регулированию и метрологии в сети Интернет
Настоящий стандарт устанавливает требования назначения, маркировки, упаковки, транспортирования и хранения тормозных колодок, накладок, лент, фрикционных пластин, секторов, вкладышей (далее — изделий), применяемых в различных тормозных устройствах.
Вид климатического исполнения изделий — 0 (V) по ГОСТ 15150.
В настоящем стандарте использованы нормативные ссылки на следующие межгосударственные стандарты:
ГОСТ 4.79-87 Система показателей качества продукции. Изделия фрикционные для тормозных механизмов. Номенклатура показателей
ГОСТ 1198-93 Ленты асбестовые тормозные. Технические условия
ГОСТ 15150-69 Машины, приборы и другие технические изделия. Исполнения для различных климатических районов. Категории, условия эксплуатации, хранения и транспортирования в части воздействия климатических факторов внешней среды
ГОСТ 15853-70 Накладки тормозные. Размеры
ГОСТ 15960-96 Материалы асбестовые фрикционные эластичные и изделия из них. Технические условия
ГОСТ 27513-87 Изделия фрикционные. Маркировка, упаковка, транспортирование и хранение
Примечание — При пользовании настоящим стандартом целесообразно проверить действие ссылочных стандартов в информационной системе общего пользования — на официальном сайте Федерального агентства по техническому регулированию и метрологии в сети Интернет или по ежегодному информационному указателю «Национальные стандарты)», который опубликован по состоянию на 1 января текущего года, и по выпускам ежемесячного информационного указателя «Национальные стандарты» за текущий год. Если ссылочный стандарт заменен (изменен), то при пользовании настоящим стандартом следует руководствоваться заменяющим (измененным) стандартом. Если ссылочный стандарт отменен без замены, то положение, в котором дана ссылка на него, применяется в части, не затрагивающей эту ссылку.
В настоящем стандарте применены определения по техническому регламенту [1]*, а также следующие термины с соответствующими определениями:
________________
* Действует на территории стран-участников Таможенного союза.
3.1 изменение линейных размеров тормозной накладки при нагревании: Соотношение линейных размеров тормозной накладки до и после нагрева ее до заданной температуры.
3.2 предел прочности при срезе образцов тормозных накладок: Отношение силы, необходимой для разрушения образца при срезе, к его номинальной площади среза.
3.3 предел прочности соединения тормозной накладки с металлической колодкой: Отношение силы, необходимой для разрушения соединения тормозной накладки с металлической колодкой к номинальной площади соединения.
3.4 прочность схватывания тормозной накладки с металлическим контртелом в результате коррозии: Сила или момент силы, необходимый для разрушения соединения тормозной накладки с металлическим контртелом в результате коррозии.
3.5 сжимаемость: Уменьшение толщины накладки под действием заданной нагрузки.
3.6 стойкость к воздействию жидкостей: Способность изделий сохранять свойства в заданных пределах после воздействия жидкостей.
3.7 фрикционные свойства: Способность оказывать сопротивление относительному перемещению, возникающее между двумя телами в зонах соприкосновения поверхностей по касательной к ним при определенных параметрах режима трения (скорости скольжения, давления, температуры и др.).
Фрикционные свойства при торможении можно выражать тормозным путем (м), временем торможения (с), замедлением (м/с), моментом трения (Н·м) или коэффициентом трения в зависимости от установленных требований.
4.1 Изделия изготовляют в соответствии с требованиями настоящего стандарта и документов на конкретный ассортимент изделий по чертежам, согласованным изготовителем и потребителем, и технологической документации, утвержденной в установленном порядке.
4.2 Основные показатели назначения изделий приведены в таблице 1.
Таблица 1
Наименование показателя | Метод испытаний | Область распространения |
1 Фрикционные свойства | — | Тормозные фрикционные изделия |
2 Продел прочности соединения тормозной накладки с металлической колодкой | По стандарту [2] | Тормозные накладки дисковых тормозов автомобилей, тормозные накладки барабанных тормозов автомобилей (в случае их приклейки) |
3 Прочность схватывания тормозной накладки с металлическим контртелом в результате коррозии | По стандарту [3] | Тормозные накладки барабанных и дисковых тормозов легковых автомобилей |
4 Предел прочности при срезе образцов тормозных накладок | По стандарту [4] | То же |
5 Стойкость к воздействию жидкостей | По стандарту [5] | « |
6 Сжимаемость | По стандарту [6] | Тормозные накладки с колодками в сборе дисковых тормозов автомобилей |
7 Изменение линейных размеров накладки при нагреве | По стандарту [7] | То же |
Примечания 1 Для колодок с накладками в сборе дисковых и барабанных тормозов, фрикционных накладок для барабанных и дисковых тормозов транспортных средств категорий L, M, N и O обязательность показателей определяется требованиями технического регламента [1]. 2 Фрикционные свойства колодок с накладками в сборе для дисковых и барабанных тормозов, фрикционных накладок для барабанных и дисковых тормозов транспортных средств категорий L, M, N и O определяют по стандарту [8]. альтернативно для транспортных средства категорий M, M, N, O — по правилам [9], для транспортных средств категорий M — по стандарту [10], для транспортных средств категории L — по правилам [11], для транспортных средств категории N — по правилам [9] или [10]. 3 Для колодок с накладками в сборе для дисковых и барабанных тормозов и фрикционных накладок для барабанных и дисковых тормозов, поставляемых для послепродажного обслуживания транспортных средств категорий L, M, N и O, требования правил [9] (5.1.1.3), [10] (5.1.1.3), [11] (5.1.1.3), [8] (5.1 (d) факультативны. 4 Испытания изделий по определению фрикционных свойств (показатель 1), кроме колодок с накладками в сборе для дисковых и барабанных тормозов, фрикционных накладок для барабанных и дисковых тормозов транспортных средств категорий L, M, N и O, проводят по методам, согласованным с потребителем. |
4.2.1 Значения показателей, установленные в документах на тормозное изделие, должны соответствовать требованиям международных, национальных или отраслевых стандартов.
Если в международных, национальных или отраслевых стандартах требования отсутствуют, значения показателей устанавливают по согласованию между потребителем и изготовителем.
4.2.2 Периодичность контроля показателей устанавливают в документах на тормозные изделия.
4.2.3 Для контроля продукции при ее выпуске в документах по согласованию изготовителя и потребителя могут быть установлены дополнительные показатели качества в соответствии с ГОСТ 4.79, характеризующие физико-механические свойства тормозных изделий.
5.1 Изделия маркируют, упаковывают, транспортируют и хранят по ГОСТ 27513.
Дополнительные требования к маркировке, упаковке, транспортированию и хранению указывают в документе на тормозные изделия.
5.2 Маркировка накладок в сборе для дисковых и барабанных тормозов, фрикционных накладок для барабанных и дисковых тормозов транспортных средств категорий L, M, N и O единым знаком обращения продукции на рынке
5.2.1 Графическое изображение единого знака обращения продукции на рынке устанавливается Решением Комиссии Таможенного союза.
Единым знаком обращения продукции на рынке маркируют изделия, на которые оформлены сертификаты соответствия или декларации о соответствии требованиям технического регламента [1]. Маркирование осуществляют любым удобным способом, обеспечивающим четкость изображения и исключающим истирание.
При маркировании изделий единый знак обращения продукции на рынке государств-членов Таможенного союза должен быть нанесен непосредственно на единицу продукции (если это технически возможно) и/или ярлык (при наличии), а также упаковку и сопроводительную техническую документацию. Единый знак обращения продукции на рынке государств-членов Таможенного союза должен быть нанесен, по возможности, рядом с товарным знаком изготовителя. Маркировка компонентов знаками официального утверждения «Е» или «е» по техническому регламенту [1] приравнивается к маркировке единым знаком обращения продукции на рынке государств-членов Таможенного союза. При наличии на изделии маркировки знаками официального утверждения «E» или «e» маркировка единым знаком обращения на рынке государств-членов Таможенного союза не требуется.
5.3 Гарантийный срок хранения и эксплуатации изделий устанавливают в документе на тормозные изделия, согласованном с потребителем.
6.1 Конструктивные требования к равнотолщинным тормозным накладкам барабанных тормозов приведены в следующих стандартах:
ГОСТ 15853 -для дорожных и сельскохозяйственных транспортных машин;
ГОСТ 1198 — для тканых тормозных лент:
ГОСТ 15960 — для вальцованных лент и накладок.
6.2 Конструктивные требования к разнотолщинным тормозным накладкам барабанного тормоза, колодкам, накладкам дискового тормоза, фрикционным вкладышам и секторам, не приведенные в 6. 1, должны быть указаны в соответствующих чертежах и документах, согласованных между изготовителем и потребителем.
[1] | Технический регламент Таможенного союза | Технический регламент Таможенного союза 018/2011 «О безопасности колесных транспортных средств», утвержден решением Комиссии Таможенного союза от 09.12.2011 г. N 877* | |
[2] | ИСО 6312:2010 (ISO 6312:2010) | Транспорт дорожный. Тормозные накладки. Метод испытания на сдвиг накладки с колодкой в сборе для дисковых и барабанных тормозов (Road vehicles — Brake linings — Shear test procedure for disc brake pad and drum brake shoe assemblies) | |
[3] | ИСО 6315:1980 (ISO 6315:1980) | Транспорт дорожный. (Road vehicles — Brake linings — Seizure to ferrous mating surface due to corrosion; Test procedure) | |
[4] | ИСО 6311:1980 (ISO 6311:1980) | Транспорт дорожный. Фрикционные тормозные накладки. Сопротивление внутреннему срезу. Метод испытания (Road vehicles — Brake linings: Internal shear strength of lining material — Test procedure) | |
[5] | ИСО 6314:1980 (ISO 6314:1980) | Транспорт дорожный. Накладки тормозные. Водостойкость, стойкость к солевому раствору, маслу и тормозной жидкости. Метод испытания (Road vehicles — Brake linings — Resistance to water, saline solution, oil and brake fluid — Test procedure) | |
[6] | ИСО 6314:1980 (ISO 6314:1980) | Транспорт дорожный. (Road vehicles — Brake linings — Compressive strain test methods) | |
[7] | ИСО 6310:2009 (ISO 6310:2009) | Транспорт дорожный. Фрикционные тормозные накладки. Влияние тепла на размеры и форму накладок дискового тормоза. Метод испытания (Road vehicles — Brake linings — Effects of heat on dimensions and form of disc brake pads — Test procedure) | |
[8] | Правила ЕЭК ООН N 90 (Regulation EEC UN N 90) | Единообразные предписания, касающиеся официального утверждения сменных тормозных накладок в сборе и накладок барабанных тормозов для механических транспортных средств и их прицепов (Uniform provisions concerning the approval of replacement brake lining assemblies and drum-brake linings for power-driven vehicles and their trailers) | |
[9] | Правила ЕЭК ООН N 13 (Regulation EEC UN N 13) | Единообразные предписания, касающиеся официального утверждения транспортных средств категорий M, N и O в отношении торможения (Uniform provisions concerning the vehicles of categories M, N and O with regard to braking) | |
[10] | Правила ЕЭК ООН 13 Н (Regulation EEC UN N 13 N) | Единообразные предписания, касающиеся официального утверждения легковых автомобилей в отношении торможения (Uniform provisions concerning the approval of passenger cars with regard to braking) | |
[11] | Правила ЕЭК ООН N 78 (Regulation EEC UN N 78) | Единообразные предписания, касающиеся официального утверждения транспортных средств категории L в отношении торможения (Uniform provisions concerning the type approval of vehicles of category L with regard to braking) |
Фрикционные диски тормоза лебедки – Эксплуатация, уход и замена
Дата публикации: 22. 07.2020 02:53
Фрикционные (тормозные) диски КМУ: особенности эксплуатации, обслуживания и замены
Фрикционные диски — это небольшие, но очень важные детали, которые позволяют тормозить грузоподъемный механизм и фиксировать тяжести, закрепленные на грузовой подвеске. От состояния и исправности этих компонентов зависит эффективность и безопасность используемой техники.
Владельцы крановых манипуляторов часто сталкиваются с проблемой неисправности тормозов подъемного механизма. Если владелец не уделяет достаточно внимания техническому обслуживанию устройства, не меняет вовремя смазку или использует некачественное масло, фрикцион тормоза грузовой лебедки быстро изнашивается.
Главный признак износа тормозной системы: лебедка кран-манипулятора перестала фиксировать переносимые тяжести, вследствие чего груз падает. Это происходит потому, что при избыточном истирании диски не способны дать необходимый тормозной эффект. Единственное решение проблемы — заменить фрикционы лебедки.
Особенности использования фрикционных дисков и причины износа
Тормоз лебедки крана представляет собой важнейшую деталь, без которой не способен исправно работать и выполнять возложенные задачи грузоподъемный механизм. Эти устройства выдерживают огромные нагрузки, и поэтому требуют специального обслуживания. В него входит:
- регулярный осмотр;
- использование качественного масла;
- периодическая полная замена смазки;
- правильная регулировка тормозных фрикционов.
Если в редукторе лебедки, в котором находятся тормозные элементы, нет масла, или есть, но плохого качества, механизм изнашивается быстрее. В него попадает грязь, влага, воздух, которые периодически нужно удалять путем замены смазки. Также на долговечность устройства влияет правильность регулировки фрикционов. При соблюдении всех правил эксплуатации, фрикционный диск лебедки прослужит не менее 3 лет.
Замена фрикционов и наладка тормоза
Согласно инструкции по эксплуатации большинства кранов-манипуляторов, тормозной фрикционный диск должен меняться каждые 3 года использования, независимо от его визуального состояния.
Это довольно дорогие детали, поэтому отечественные умельцы пытаются сделать тормоза своими руками. Такая затея ничем хорошим не закончится, ведь тормоз подъемника — ответственный узел механизма и невнимание к его состоянию может привести к серьезной аварии. Не стоит рисковать своим здоровьем и здоровьем работников. Применяйте только качественные комплектующие для починки КМУ.
Итак, если не держит груз лебедка КМУ и причина в изношенности фрикционов, нужно выполнить 3 шага: заменить тормозной диск, отрегулировать тормоз, поменять масло в редукторе. Рассмотрим их более детально.
Замена фрикционного диска
Это процедуру лучше не выполнять самостоятельно, а доверить специалистам. Только мастер с достаточной квалификацией сможет качественно и надежно поменять диски.
Регулировка тормоза
Для регулировки тормоза нужно вручную затянуть корончатую гайку. После ее необходимо ослабить на 1/6 оборота и закрепить шплинтом. Все это можно сделать самостоятельно. Ключ не рекомендуется использовать.
Замена масла
В процессе работы КМУ лебедка естественно изнашивается. В редуктор грузовой лебедки проникает воздух, загрязнения, вода. Чтобы предотвратить быстрый износ грузовой лебедки, следует периодически удалять все эти сторонние продукты путем замены смазочного материала.
Первый раз масло меняется через 6 месяцев после начала эксплуатации крановой установки, далее — один раз в год.
Систематичное и своевременное обслуживание систем кран-манипулятора повышает их производительность и продлевает срок эксплуатации.
Произвести диагностику и приобрести оригинальные тормозные диски для лебедок КМУ Soosan, Kanglim, Dong Yang, Hiab, Unic и Tadano вы сможете в нашей компании.
На товар нашего интернет-магазина мы предоставляем гарантии и четко соблюдаем сроки поставок.
Современные системы торможения на основе фрикционных материалов
Современная система тормозного управления транспортных средств состоит из запасной (дублирующей), основной и стояночной тормозных систем. Запасная и основная тормозные системы предназначены для замедления автомобиля во время движения, при этом активация дублирующей системы происходит в случае выхода из строя основной. Стояночная система (ручной тормоз) используется для удержания авто во время стоянки. Наиболее эффективными и безопасными являются тормозные системы, изготовленные из фрикционных композитных материалов.
Для придания системам торможения максимальной степени эффективности и эксплуатационной надежности, многие производители активно занимаются исследованием новых видов фрикционных материалов, которые обладают более высокими техническими характеристиками. Сегодня, основой практически всех систем тормозного управления являются такие фрикционные материалы, как:
- асбополимеры и чугун, ретинакс;
- ряд композиционных изделий с полимерной матрицей;
- порошковые фрикционные материалы из различных металлов;
- металлокерамика, трибонит;
- материалы с керамической и углеродной матрицей.
Использование в производстве тормозных механизмов усовершенствованных фрикционных материалов, позволяют создать более надежную тормозную систему, обладающую минимальным нагревом между фрикционными деталями системы во время торможения. Это увеличивает износоустойчивость механизмов, повышает коэффициент трения и допустимую температурную норму поверхностного трения деталей.
Усовершенствование узлов тормозных систем
С повышением мощности современных транспортных средств, возрастает и средняя скорость движения автомобиля, что напрямую связано с ростом количества циклов торможения. Для повышения безопасности движения и жизни человека, к системам торможения предъявляются оптимально жесткие требования. Компания «Ретинакс», уже сегодня готова представить новейшие разработки в области фрикционных материалов, которые позволяют в два раза повысить эксплуатационный срок систем тормозного управления, рабочую надежность и безопасность.
В разработках используются такие материалы, как: трибонит, ретинакс, пресскомпозицию, в которые входят вкрапления стружки латуни, асбест, барит, различные нефтепродукты и вода. Использование во фрикционных композитных составах некоторых материалов, было предложено компанией впервые, например, борная кислота и полиметиленэфир фенолы. Это позволило достичь максимальной стабильности эксплуатационных характеристик и значительно повысить рабочий срок систем торможения.
Главной целью является создание фрикционных материалов (вкладышей, дисков, пластин) нового поколения, которые будут активно использоваться в производстве современных систем торможения. Разрабатывая фрикционные материалы, повышающие эксплуатационный срок и безопасность функционирования тормозных систем, компания «Ретинакс» использует только инновационные технологии.
Взгляд в будущее
По утверждениям профильных экспертов в ближайшем будущем, тормозные системы на основе фрикционных композитных материалов, будут использоваться повсеместно. Уже сейчас перспективными направлениями для внедрения таких систем торможения рассматриваются высоконагруженные системы лифтов, тракторов, промышленных установок, тяжелых танков, элеваторов, авиакосмической и авиационной техники. Фрикционные материалы — это главная составляющая высококачественных, безопасных и надежных систем торможения.
Тормоз фрикционный дисковый — Энциклопедия по машиностроению XXL
Тормоза фрикционные дисковые 9 — 808 —Тормоза фрикционные конические 9—808 — Тормоза центробежные 9 — 809 [c.205]Привод ножниц осуществляется от индивидуального электродвигателя через клиноременную и зубчатую одно- или двухступенчатую передачи. Муфта и тормоз — фрикционные дисковые с электропневматическим управлением. [c.68]
Б р е н е в Г. Е. Выбор основных размеров фрикционных дисковых муфт и тормозов кузнечно-прессовых машин — Кузнечно-штамповочное производство , 1959, № 11. [c.667]
Тормоз Т (фиг. 115, б и 116. —фрикционный, дисковый, пневматический, расположен на приводном валу, рядом с муфтой, с которой он составляет связанную конструкцию.

Фиг. 23, Схема конического Фиг, 24. Схема дискового фрикционного тормоза. фрикционного тормоза. |
При включении пневмоклапана 8 или 9 сжатый воздух соответственно поступает в пневмокамеру 17 или 18 фрикционных дисковых муфт, включающих стреловую лебедку одна камера — на подъем стрелы, другая — на опускание стрелы. Одновременно включается пневмоклапан 7 и сжатый воздух поступает в пневмокамеру 16 тормоза стреловой лебедки и размыкает его.
[c.95]
При включении пневмоклапанов 11 и 12 сжатый воздух соответственно поступает в пневмокамеру 20 или 21 фрикционных дисковых муфт, включающих поворотный механизм одна камера — на поворот вправо, другая — на поворот влево. Одновременно включается пневмоклапан 10 и сжатый воздух поступает в пневмокамеру 19 тормоза механизма поворота и размыкает его. [c.95]
Пуск и остановка шпинделя станка производятся либо рукояткой 36, непосредственно связанной с коробкой скоростей, либо рукояткой 27, расположенной на фартуке и связанной с валиком переключения (при помощи обеих рукояток управляют фрикционной дисковой муфтой 5). Кроме того, при пуске и остановке шпинделя используется ленточный тормоз, перемещающийся в коробке скоростей. Этот тормоз на рисунке не виден. [c.80]
При включении пневмоклапанов 5 или 6 сжатый воздух соответственно поступает в пневмокамеры 14 или 15, которые управляют фрикционными дисковыми муфтами, включающими грузовую лебедку одна камера — на подъем груза, другая — на опускание груза. Одновременно включается пневмоклапан 4 и сжатый воздух поступает в пневмокамеру 13 тормоза грузовой лебедки и размыкает его.
[c.140]
Шарнирно-рычажная система, состоящая из тяг 2—4, рычагов 16, валиков 11 и 14, рычагов 15 и тяг 10, 12, 13, связывает рычаги 1 и 5 управления лебедками и механизмом поворота с соответствующими рычагами 17 блоков 7—9 кулачков. Блок 18 пневмоклапанов состоит из девяти пневмоклапанов, управляемых тремя блоками 7—9 кулачков. Каждый блок управляет тремя пневмоклапанами пневмоклапаном управления тормозом соответствующего механизма (грузовой или стреловой лебедки или механизма поворота) и двумя пневмоклапанами (попеременно) управления фрикционными дисковыми муфтами реверсивно-распределительного механизма. [c.142]
Муфта и тормоз прессов — дисковые фрикционные с электропневматическим управлением, аналогичные применяемым в закрытых прессах простого действия.
[c.56]
При включении дифференциальных золотников 6 или 7 сжатый воздух соответственно поступает в пневмокамеры фрикционных дисковых муфт, включающие стреловую лебедку камера 20 — подъем стрелы, камера 18 — опускание стрелы. В пневмокамеру 20 сжатый воздух поступает через конечный выключатель И ограничителя подъема стрелы. Через двойной клапан 17 сжатый воздух одновременно поступает в пневмокамеру 19 тормоза стреловой лебедки и размыкает его. [c.125]
При включении дифференциальных золотников 8 или 10 сжатый воздух соответственно поступает в пневмокамеры 16 (через конечный выключатель 12 ограничителя подъема крюка) или 14, которые управляют фрикционными дисковыми муфтами, включающими грузовую лебедку камера 16 — подъем груза, камера 14 — опускание груза. Одновременно сжатый воздух через двойной клапан 13 поступает в пневмокамеру 15 тормоза грузовой лебедки и размыкает его.
[c.125]
Каждый блок управляет тремя золотниками золотником управления тормозом соответствующего механизма (грузовой или стреловой лебедки или механизма поворота) и двумя золотниками (попеременно) управления фрикционными дисковыми муфтами распределительного механизма. [c.128]
При включении электропневматических вентилей 6 или 7 сжатый воздух соответственно поступает в пневмокамеры фрикционных дисковых муфт, включающие поворотный механизм камера 27 — поворот вправо, а камера 24 —поворот влево. Поступая в пневмокамеры 24 или 27, сжатый воздух одновременно через двойной клапан 26 поступает и в пневмокамеру 25 тормоза механизма поворота, размыкая его. [c.131]
Электромагнитный фрикционный дисковый тормоз имеет вал, на котором закреплена шестерня, сцепляющаяся с шестерней 15 отслеживающего диска. Внутри корпуса тормоза посредством шпонки с валом соединен фрикционный диск, который зажимается спиральной пружиной между стаканом и тарелкой. Усилие пружины регулируется винтом, что дает возможность регулировать тормозной момент. Растормаживание осуществляется электромагнитной катушкой, которая, притягивая к себе якорь магнита, сжимает пружину и тем самым освобождает фрикционный диск. Катушка электромагнита питается постоянным током напряжением 110 В, снимаемым с выпрямляющего устройства, собранного на полупроводниковых диодах и смонтированного в корпусе.
[c.271]
Движение от электродвигателя / передается клиноременной передачей 2 через шестерни 3, 4 и дисковую муфту 5 кривошипному валу 6, шатуну 7 и ползуну 8. Кривошипный вал 6 приходит в движение только тогда, когда включена фрикционная дисковая муфта 5 с пневматическим нажимом. Тормоз 9 служит для остановки вращения кривошипного вала после выключения муфты.

Муфта включения — пневматическая, фрикционная, дисковая, с вкладышами из ретинакса. Тормоз — фрикционный, ленточный, сблокирован с муфтой. [c.90]
Муфта включения — фрикционная, дисковая, с пневматическим включением. Взаимодействие муфты с дисковым тормозом обеспечивается электро- [c.208]
Муфта н тормоз пневматические фрикционные дисковые. [c.3]
На левом конце эксцентрикового вала смонтирован тормоз фрикционный пневматический дисковый. Муфта фрикционная пневматическая дисковая кренится к зубчатому колесу, расположенному на эксцентриковом валу. [c.47]
Современные модели чеканочных прессов всех размеров оборудуют пневматическими фрикционными дисковыми муфтами, установленными на приемном валу в одном блоке с дисковыми тормозами или раздельно, причем тормоз тогда выполняют ленточным. Конструкция чеканочных прессов общего назначения предусматривает возможность установки автоматических или полуавтоматических подач.
[c.52]
Привод ножниц — от индивидуального электродвигателя через клиноременную и зубчатую одно- или двухступенчатую передачи. У малых ножниц муфта включения жесткая шпоночная и ленточный тормоз, у больших — фрикционная дисковая муфта в блоке с тормозом. [c.67]
Тормоз преобразует в теплоту всю кинетическую энергию останавливаемой машины. Поэтому нагревание и теплоотвод для него имеют большее значение, чем для фрикционных муфт. Дисковые тормоза, устройство которых не отличается от устройства дисковых фрикционных муфт, применяют сравнительно редко. Более широко распространены барабанные колодочные тормоза с наружным (рельсовый транспорт) и внутренним (автомобили) расположением тормозных колодок, которые имеют хорошо развитую поверхность охлаждения. [c.393]
При работе дискового тормоза со смазкой снижается значение коэффициента трения фрикционного материала по металлу, но это уменьшение компенсируется тем, что тормоз может работать со значительно большими давлениями и его конструкция может получиться более компактной. Однако при работе со смазкой конструкция тормоза несколько усложняется из-за необходимости обеспечения смазкой трущихся поверхностей. Кроме того, при изменении температурных условий изменяется вязкость масла, что может привести к изменению коэффициента трения, а при низких температурах даже к застыванию смазки и к замерзанию всей тормозной системы. В этих случаях требуется или применять специальные масла, или предварительно прогревать тормозное устройство. Замыкание тормоза, работающего в масляной ванне, происходит более плавно, чем при работе без смазки, так как смазка, выдавливающаяся с поверхности трения, смягчает толчки, возможные в процессе замыкания.
[c.225]
Тормоз фрикционный дисковый пружинный с пневматическим растормаживанием — Принцип работы 50 ТУ38-4044—73 150 [c.217]
Муфта и тормоз — фрикционные дисковые с электронневматическим управлением. [c.117]
В последних конструкциях прессов передача от электродвигателя выполняется клино-рсмённой муфта включения применяется фрикционная дисковая, сблокированная с дисковым тормозом. В крупных прессах управление электропнеаматическое.
[c.547]
Передние бабки средних токарных и то-карно ьинторезных станков имеют (обычно на первом валике) фрикционные муфты и тормоз (ленточный, дисковый или конусный). [c.255]
К блоку 3 подсоединены пневмоклапаны непрямого действия 4—12, подающие воздух в соответствующие пневмокамеры 13—21. При включении пневмоклапана 5 или 6 сжатый воздух соответственно поступает в пневмокамеру 14 или 15, которые управляют фрикционными дисковыми муфтами, включающими грузовую лебедку одна камера подъема груза, другая — на опускание груза. Одновременно включается пиевмоклапан 4 и сжатый воздух поступает в пневмокамеру 13 тормоза грузовой лебедки и размыкает его. [c.95]
Тормоз прессов моделей К3534А, К3536, К3537 и др. фрикционный дисковый пружинный с пневматическим растормаживанием (рис. 19). Тормоз, как и муфта, — мембранного типа. Неподвижный фланец 3 жестко соединен с корпусом 5, прикрепленным к станине пресса. Пружины 6, упираясь в неподвижный фланец 3, прижимают через нажимной диск 7 фрикционный диск 9. Последний вращается вместе с валом 8, получающим вращение от муфты пресса. Вследствие зажатия фрикционного диска между неподвижными элементами корпуса 5 и нажимного диска 7 вал затормаживается. Таким образом, при отсутствии в системе сжатого воздуха вал 8 всегда заторможен. При подаче воздуха в полость фланца 3 мембрана 1 перемещает поршень 2, который через тяги 10 отводит влево нажимной диск 7, сжимая пружины 6. Фрикционный диск 9 освобождается и при включении муфты может вращаться вместе с валом 8. Растормаживание продолжается до тех пор, пока в полость фланца 3 поступает сжатый воздух.
[c.50]
Разматывающее устройство УР1-50 (рис. 56, а) предназначено для плавного разматывания рулонов металлической ленты и создания компенсационной петли (с небольшим колебанием ее величины). При включении электродвигателя 5 вращение через редуктор 6, ременную передачу 7 и дисковую фрикционную муфту 8 передается на диск 1 рулонодержателя. Лента сматывается и механизмом подачи 2 пресса-автомата подается в штамп. Так как скорость сматывания всегда больше скорости подачи ленты в пресс, то штанга 3, следующая за петлей ленты, опускается, поворачивая рычаг 12 и ротор 14. Открывается отверстие в корпусе 15 распределительного устройства 13, и воздух поступает в пневмоцилиндр 11. Каналы для воздуха в распределительном устройстве выполнены таким образом, что в зависимости от угла поворота ротора происходит переключение подачи воздуха в полости пневмоцилиндра. Пневмоцилиндр клином 10 воздействует через рычаги 9 на колодки 4, которые давят на тормозные накладки, и тормозит диск рулонодержателя. Фрикционная дисковая муфта работает с проскальзыванием. Скорость вращения диска рулонодержателя падает, и петля ленты начинает уменьшаться, в ре-
[c.108]
На рис. 160 приведена кинематическая схема кривошипного пресса. Через клиноременную передачу 4 движение от электромотора 5 передается на маховик 3, находящийся на передаточном валу 6. Зубчатая передача 7 передает движение на кривошипношатунный механизм, состоящий из кривошипного вала 9, шатунаползуна 1. Пресс имеет фрикционную дисковую муфту включения 8, с помощью которой осуществляется пуск пресса на рабочий ход. Для остановки вращения кривошипного вала 9 после выключения муфты служит тормоз 2, который останавливает пол- [c.265]
Муфта включения — дисковая, фрикционная, с ретинаксовыми вкладышами, сблокирована с фрикционным дисковым тормозом. [c.165]
В столе пресса расположены три пиевматичеокие подушки, используемые как нижний выталкиватель и для прижима заготовок при неглубокой вытяжке. Муфта и тормоз пневматические фрикционные дисковые. [c.49]
Такие тормоза, подобно дисковым фрикционным муфтам сцепления, могут работать со смазкой и без смазки трущихся поверхностей. Это обстоятельство следует иметь в виду нри выборе значений коэффициента трения скольжения /, для гювышения значений которого на диски / и 7 приклепывают или приклеивают накладки из указанных фрикционных материалов. Рекомендуемое соотношение между наружным и внутренним радиусами поверхности трения дисков имеет вид R (1.25ч-2,5) R , причем разность / / не должна превышать 60 мм. [c.58]
Дисковые тормоза, В качесгве тормоза может быть использована фрикционная дисковая муфта любой к нструкции, если ее наружный корпус (чашку) яли флансц в однодисковой муф е скрепить с нeпo. u ижндисковые муфты, изображенные выше, на стр, 445 — 449, поясняют одноипеменно л конструкции дисковых тормозов. [c.470]
От электродвигателя 1 мощностью 40 кВт с помощью клиноременной передачи 2 крутящий момент передается на маховик 5, который при включении фрикционной пневматической муфты 4 связывается с главным валом. На валу предусмотрен фрикционный дисковый тормоз с пневматическим управлением. Посредством зубчатой пе )едачи с колесами 5 и б вращение передается на промежуточный вал с цилиндрическим колесом 7, которое с помошью колеса 8 приводит колеса 9 к 10 зубчатого зацепления, а также рабочие валки 11 первой клети. Валки рабочей клети вращаются навстречу друг другу с частотой 85 мин». [c.75]
Дисковые тормоза. В дисковых тормозах необходимый момент трения создается прижатием неподвижных дисков ] к дискам 2, вращающимся вместе с тормозным валом (рис. 99). Источником замыкающей силы могут быть сила пружины, вес груза или усилие человека, прилагаемое посредством рычажной, гидравлической или пневма ической. системы. Дисковые тормоза могут применяться во всех механизмах подъемно-транспортных машин. Они имеют ряд достоинств, к которьлм следует отнести возможность получения больших тормозных моментов при относительно малых габаритах за счет увеличения числа дисков возможность обеспечения защиты тормозов от влияния окружающей среды, вплоть до создания полной герметизации уравновешенность тормоза из-за отсутствия радиально действующих на вал сил — осевые силы могут быть замкнуты внутри тормозного устройства и не восприниматься валом и подшипниками машины более равномерный износ фрикционного материала. Широкое распространение осевые тормоза получили там, где необходимы особо компактные конструкции. [c.170]
Тормозные накладки. Виды, способы производства и материал фрикционных накладок.
Накладка фрикционная тормозная – это часть тормозной колодки автомобиля, благодаря которой создается тормозной момент. В основе работы устройства – сила трения. В момент торможения изделие взаимодействует с металлическим барабаном, поглощая кинетическую энергию автомобиля.
Снижение скорости и остановка транспорта происходит благодаря силе трения. Плотно прикрепленная к металлической части тормозной колодки накладка способствует торможению. Кинетическая энергия движения транспортного средства преобразуется в тепловую, которую колодка и тормозной диск рассеивают в окружающей среде.
Устанавливаются в дисковых, конических, барабанных тормозах:легковых машин;
грузовиков;
сельскохозяйственной и промышленной техники.
ОАО «Тамбов АТИ» специализируется на производстве накладок тормозных для грузовых автомобилей отечественного и иностранного производства, а также для высоконагруженных транспортных средств (ракетовозов, автомобильных кранов и т.п.)
Качественные накладки на тормозные колодки обеспечивают эффективное торможение даже при высокой частоте и сложных условиях.
Разновидности тормозных накладок
По назначению накладки бывают для тормозных механизмов:барабанных;
дисковых.
Накладки для барабанных тормозных механизмов выполнены в виде дугообразной пластины, наружный радиус которой равен внутреннему радиусу барабана. Устанавливаются в каждом колесном тормозном механизме по две штуки.
Накладки в виде плоских серпообразных пластины используют для дисковых тормозов.
По месту монтажа:
установка в колесных тормозных механизмах;
установка в механизме стояночного тормоза.
Материалы изготовления накладок
Изготавливают накладки тормозных колодок из смеси полимеров, асбестов и других веществ. Раствор включает в себя множества различных компонентов. В качестве основы выступает либо асбест, либо полимер.Поэтому все эти накладки делятся на две большие категории: асбестовые и безасбестовые.
Асбестовые
В основе изделия – асбестовые волокна, в частности хризотил-асбест. Он используется в качестве каркаса, скрепляя и удерживая остальные составляющие. Изделия получаются мягкими, но отличаются высоким коэффициентом трения. Значительно снижают износ тормозного механизма.
Безасбестовые
В качестве основного компонента используются полимеры или минеральные волокна. Более жесткие и шумные, по сравнению с асбестовыми. Но являются менее вредными для окружающей среды.
В качестве дополнительных компонентов каждый производитель использует разные материалы: металлическую стружку, каучук, керамику, медь, полимеры.
Состав смеси постоянно дорабатывается, меняется процентное соотношение компонентов. Производители держат в секреты собственные рецепты и разработки.
Наше предприятие производит фрикционные накладки тормозных колодок как из асбестовых, так и безасбестовых материалов.
Способы производства тормозных накладок
Для производства тормозных фрикционных накладок готовят смесь из основного компонента и дополнительных веществ. Затем помешают в форму и под пресс либо при стандартных температурах, либо при высоких.При стандартных температурах
Смешанные компоненты укладывается в подготовленные формы, попадают по пресс без какого-либо воздействия температур. Некоторые компании подвергают накладки воздействию высоких температур уже после формовки. Такие изделия стоят дешевле, но не отличаются долговечностью.
При высоких температурах
Раствор укладывают в форму и прессуют под воздействием высокой температуры. Изготовленные таким способом фрикционные тормозные накладки отличаются долгим сроком службы. Независимо от типа прессования, конечный этап изготовления – шлифование.
Производители фрикционных накладок учитывают конструктивные и технические особенности транспортных средств, поэтому для каждого автомобиля создаются отдельные модели накладок.
Для определения степени износа тормозных накладок и необходимости их замены используют один из трех индикаторов: специальную метку, углубление или ступеньку. Некоторые производители рекомендуют менять накладки каждые 15 000 км пробега.
Ассортимент фрикционных накладок тормозных колодок производства ОАО «Тамбов АТИ» можно посмотреть в Каталоге.
Также у нас вы можете заказать изготовление тормозных накладок по чертежу.
Торможение — образование в области энергетики
Тепловая энергия, генерируемая во время фрикционного торможения, может быть замечена в этой установке фрикционного тормоза / ротора во время нагрузочных испытаний. [1]Торможение — это процесс управления скоростью объекта путем ограничения его движения. Движущийся объект обладает кинетической энергией и чтобы остановить объект, эту кинетическую энергию необходимо удалить. Удаление кинетической энергии может быть достигнуто путем рассеивания энергии в атмосфере посредством трения или преобразования ее в другую форму энергии.Самый распространенный тип торможения — это механический тормоз, который препятствует движению через фрикционные тормозные колодки. Механический тормоз применяет силу трения для преобразования кинетической энергии транспортного средства в тепловую энергию, которая затем рассеивается в атмосфере. [2] Тормозные системы, в которых не используется трение, называются системами рекуперативного торможения (RBS). В RBS кинетическая энергия преобразуется в другие формы полезной энергии, которая может быть сохранена для дальнейшего использования, повышая эффективность использования топлива.2)} {2} [/ math] где,
• [math] m [/ math] — масса объекта в килограммах (кг).
• [math] v [/ math] — скорость объекта в метрах в секунду (м / с).
• [math] E_ {kinetic} [/ math] — кинетическая энергия в джоулях (Дж).
Из этого уравнения и при условии, что масса объекта постоянна, ясно, что для того, чтобы убрать кинетическую энергию из системы, скорость должна быть сведена к нулю.
Торможение трением
Торможение трением — это наиболее часто используемый метод торможения в современных транспортных средствах.Он включает в себя преобразование кинетической энергии в тепловую путем приложения трения к движущимся частям системы. Сила трения сопротивляется движению и, в свою очередь, выделяет тепло, в конечном итоге доводя скорость до нуля. Энергия, взятая из системы, определяется следующим уравнением:
[math] E_ {Thermal} = F_f \ times d [/ math] где,
• [math] F_f [/ math] — сила трения в ньютонах (Н).
• [math] d [/ math] — тормозной путь в метрах (м).
• [math] E_ {Thermal} [/ math] — тепловая энергия, производимая тормозами, в Джоулях.2)} {2d} [/ математика]
Из этого уравнения видно, что увеличение скорости или массы объекта означает, что приложенная сила трения должна быть увеличена, чтобы остановить объект на том же расстоянии.
Торможение в автотранспортных средствах
Механическое торможение
Самый распространенный метод торможения в автотранспортных средствах — механическое или фрикционное торможение. В этом методе некоторые или все колеса транспортных средств оснащены тормозными колодками, которые создают силу трения, которая препятствует движению колес.Торможение трением приводит к преобразованию кинетической энергии, полученной от расхода топлива, в тепловую энергию. Эта тепловая энергия затем рассеивается в атмосферу в виде отработанного тепла.
Могут потребоваться большие силы трения, чтобы препятствовать движению транспортного средства, особенно в больших машинах и грузовиках, которые имеют большую массу и, следовательно, высокую кинетическую энергию. Тормозные колодки, отвечающие за приложение силы трения, изнашиваются в течение всего срока службы из-за этой силы трения.Износ тормозных колодок снижает эффективность тормозов в течение срока их службы и требует регулярной замены.
Рекуперативное торможение
- основная статья
Система рекуперативного торможения включает удаление кинетической энергии движущегося объекта путем преобразования ее в другую форму полезной энергии, такую как электрическая, пневматическая или накопленная кинетическая энергия. Использование рекуперативного торможения может повысить общую эффективность транспортного средства за счет сохранения некоторой его кинетической энергии, которая затем может быть использована для восстановления скорости транспортного средства.
Для дальнейшего чтения
Для получения дополнительной информации см. Соответствующие страницы ниже:
Список литературы
Фрикционные материалы | Тормоза для автомобилей | Продукт | Продукты и технологии
Дисковые тормоза и барабанные тормоза оснащены фрикционным материалом, называемым тормозными колодками и тормозными накладками соответственно.
Дисковые тормоза и барабанные тормоза оснащены фрикционным материалом, называемым тормозными колодками и тормозными накладками соответственно.
Фрикционные материалы играют важную роль в тормозной системе, поскольку тормоза используют трение для торможения (замедления и остановки).
Тормозные колодки и тормозные накладки изготавливаются из смеси не менее 10-20 видов сырья. Смешивание материалов, подходящих для требуемых условий и характеристик, — очень сложная задача, требующая специальных знаний, включая передовой опыт Akebono.
Качество фрикционных материалов также меняется в зависимости от производственного процесса.Благодаря развитию и совершенствованию технологий производства на протяжении многих лет, Akebono предлагает высокоэффективные и высококачественные фрикционные материалы, отвечающие потребностям наших клиентов.
Смесь сырья для наших фрикционных материалов (тормозные колодки, тормозные накладки)
Колодки дисковых тормозов и накладки барабанных тормозов изготавливаются из смеси от 10 до 20 видов сырья. В зависимости от их конкретных ролей сырье делится на три категории; «связующий материал», «элемент жесткости» и «материал для регулирования трения.”
Связующий материал упрочняет сырье и придает им прочность. В настоящее время используется в основном фенольная смола.
Элемент жесткости придает фрикционным материалам дополнительную прочность. Используются различные виды органических и неорганических волокон, такие как арамидные волокна и металлические волокна.
Материал для регулировки трения в основном регулирует эффективность фрикционных материалов. Он используется для повышения эффективности или стабилизации характеристик фрикционных материалов.При необходимости смешивают различное сырье, такое как смазочные материалы, органические наполнители, неорганические наполнители, абразивный материал и металлический порошок.
Фрикционное сырье
Виды фрикционных материалов
- * 1 Спеченный сплав: Явление, при котором частицы порошкового материала соединяются вместе и превращаются в твердое вещество в результате сжатия и изготовления порошкового материала и его нагревания до температуры ниже точки плавления.Материал, который получают не путем плавления металла, а путем спекания металлических порошков, называется спеченным сплавом.
- * 2 C / C композит: Углеродный композит, армированный углеродным волокном. Углеродный композитный материал усилен углеродным волокном. Он чрезвычайно термостойкий и легкий. Этот материал часто используется для изготовления тормозных дисков и тормозных колодок самолетов и гоночных автомобилей.
Требования к характеристикам фрикционных материалов (тормозные колодки, тормозные накладки)
Кроме того, фрикционные материалы необходимы для обеспечения стабильной эффективности (минимальные колебания эффективности) в различных условиях, таких как скорость автомобиля, полная масса или изменение температуры в результате использования тормозов, а также при различных воздействиях окружающей среды, включая влажность, воду и грязь. .Прочность, позволяющая противостоять тепловым возмущениям, и механическая прочность также являются важными критериями проектирования.
Прочность — еще одно важное свойство фрикционных материалов, поскольку они изнашиваются в процессе эксплуатации. Кроме того, при торможении необходимо свести к минимуму визг, шум и вибрацию. Кроме того, фрикционные материалы не должны вызывать повреждения материала, с которым они контактируют, например, роторов дисков. Фрикционные материалы также должны иметь низкую теплопроводность, чтобы предотвратить повышение температуры самих тормозов или тормозного масла.
Основные эксплуатационные требования к фрикционным материалам:
- — Оптимальная эффективность, т.е. соответствующий коэффициент трения (μ)
- — Стабильная эффективность при различных условиях использования и / или окружающей среды
- — Устойчивость к тепловым воздействиям и механическая прочность
- — Высокая прочность
- — Минимальный визг, шум и вибрации тормозов
- — Низкое повреждение контактного материала, такого как дисковый ротор
- — Низкая теплопроводность
Фрикционные материалы Akebono (тормозные колодки, тормозные накладки)
Akebono разрабатывает и производит широкий ассортимент тормозных колодок и тормозных накладок, в том числе для автомобилей, сверхскоростных поездов Синкансэн и высокопроизводительных автомобилей для автоспорта.В зависимости от того, где используются тормоза, используются различные типы материалов. Когда требуется высокая интенсивность торможения в условиях высокой температуры и высоких нагрузок, например, при скоростном движении сверхскоростных поездов Синкансэн, используются металлические фрикционные материалы. Для автомобилей, используемых в Европе, где относительно распространено торможение на высоких скоростях, используются фрикционные материалы с низким содержанием стали.
Для легковых автомобилей обычно используются «не стальные» тормозные колодки, поскольку они сбалансированы между эффективностью, интенсивностью и сопротивлением визгу тормозов.«Нестальные» тормозные колодки — это основная продукция Akebono.
Akebono продолжает разрабатывать высокопроизводительные тормоза с целью совершенствования новейших тормозных технологий. Высокопроизводительные тормоза Akebono поставляются различным автоспортивным командам. Опыт, накопленный в автоспорте, который позволяет максимально эффективно использовать тормоза, применяется при разработке тормозных колодок и тормозных накладок для легковых автомобилей.
Тормозные колодки для 24-часовой гонки на выносливость в Нюрбургринге
10-поршневые тормозные колодки для высокопроизводительных серийных автомобилей
6-поршневые тормозные колодки для высокопроизводительных серийных автомобилей
Разработка фрикционных материалов (колодки тормозные, накладки тормозные)
При разработке фрикционных материалов необходимо принимать во внимание рабочие характеристики, а также качество, обеспечивающее длительный срок службы.Это достигается за счет подбора правильного сочетания сырья, а также за счет оптимизации условий производства. Есть много шагов, которые необходимо предпринять, прежде чем продукт будет доставлен нашим клиентам. Для завершения этого процесса может потребоваться несколько месяцев или даже несколько лет. Оценены физико-химические свойства фрикционных материалов. Испытательный прибор, называемый динамометром, на котором может быть установлен настоящий тормоз, используется для оценки фрикционных свойств. Реальные автомобили используются для оценки совместимости автомобиля и тормоза.Мы также разрабатываем сырье, минимизирующее воздействие на окружающую среду.
В Akebono мы постоянно стремимся стать экспертами в области фрикционных материалов. У нас есть собственные испытательные центры, с помощью которых мы можем оценивать основные свойства от начальных этапов разработки до финальной стадии оценки с использованием реального автомобиля.
Процесс изготовления фрикционных материалов (тормозные колодки, тормозные накладки)
Фрикционные материалы перед изготовлением производятся в процессе производства, контроля и испытаний.
При разработке фрикционных материалов, где должны выполняться различные требования к характеристикам, эффективное смешивание различных сырьевых материалов является одним из важнейших технологических навыков. То, как производятся материалы, также влияет на качество, поэтому технология производства также важна. Компания Akebono способна обеспечить стабильную производительность и качество своих колодок для дисковых тормозов благодаря своим разработкам и технологиям производства, совершенствовавшимся на протяжении многих лет.
Процессы контроля и испытаний фрикционных материалов (тормозные колодки, тормозные накладки)
Для проверки и испытаний фрикционных материалов используются различные методы проверки их качества. Процессы включают оценку физических свойств, таких как твердость и интенсивность фрикционных материалов, а также химический анализ органических материалов. Для проверки эффективности, износа и визга тормозов используется динамометр, на котором можно установить и протестировать настоящий тормоз.
Для тестирования наших фрикционных материалов с точки зрения клиента мы используем «Ай-Ринг», который является крупнейшим в своем роде испытательным полигоном среди производителей автомобильных запчастей.
На полигоне «Ай-Ринг» можно проводить различные испытания тормозов, от оценки на испытательном стенде до оценки на реальном автомобиле.
Решение вопросов, связанных с ингредиентами наших фрикционных материаловЗа долгую историю разработки и производства фрикционных материалов компания Akebono неизменно придерживалась темы «Безопасность и спокойствие».»
Примерно до 2000 года асбест широко использовался в качестве сырья для фрикционных материалов из-за его благоприятных свойств для тормозов, таких как превосходная термическая стабильность. В 1970-х годах из-за границы стали поступать сообщения о вреде асбеста для здоровья. Сразу после этого Akebono стала одной из первых компаний в Японии, которая приступила к разработке безасбестовых продуктов. Мы лидировали в отрасли по внедрению безасбестовых продуктов, и в 1992 году все OEM (для автомобильных заводов) продукты для легковых автомобилей были переведены на безасбестовые.За этим последовал полный переход на неасбестовые OEM-продукты для коммерческих автомобилей в 1994 году. Начиная с 2000 года, производство асбестовых продуктов, включая запасные части, было прекращено.
Столкнувшись с экологическими нормами в отношении меди, которая использовалась для изготовления фрикционных материалов из-за ее термической стабильности, мы приступили к разработке и производству фрикционных материалов без меди * . С 2007 года мы поставляем запасные части без содержания меди, а с 2014 года — фрикционные материалы OEM.Технологии следующего поколения также находятся в стадии разработки. Akebono разрабатывает тормозные колодки, изготовленные из природных ресурсов (биомассы), а также тормозные колодки, которые не образуют тормозную пыль.
- * Фрикционный материал без меди: Материалы с содержанием меди ниже указанного значения.
Что такое фрикционный тормоз? (с иллюстрациями)
Термин «фрикционный тормоз» применяется ко всему, в тормозной системе используется трение.Трение, трение двух предметов друг о друга, снижает подвижность и является одним из факторов, влияющих на работу тормозов. В автомобилях используется какая-то форма фрикционного тормоза в сочетании с другими методами, чтобы помочь им остановиться, когда водитель нажимает на педаль тормоза. Часть тормоза прижимается к колесам, и трение двух поверхностей, трущихся друг о друга, в конечном итоге заставляет колеса замедляться и перестать вращаться. Фрикционный тормоз делится на две категории: барабанный или дисковый.
В автомобиле с дисковыми тормозами сила прилагается к внешней стороне диска, расположенного в середине колеса.Эта сила замедляет колесо, пока оно не остановится. Более сильное нажатие на педаль тормоза создает большее трение и давление на колесо, тем самым останавливая его быстрее. Сегодняшние автомобили оснащены системой силового торможения, которая использует как гидравлическую систему, известную как силовое торможение, так и трение для остановки автомобиля. У старых автомобилей не было силового торможения, их труднее было остановить, и у них было более медленное время реакции.
Когда водитель нажимает на педаль тормоза автомобиля, гидравлическое давление передается на набор поршней, которые под действием силы выталкиваются наружу.Гидравлическое давление означает просто использование жидкости под давлением для перемещения частей автомобиля. Гидравлическое давление на поршни прижимает их к комплекту тормозных колодок, а тормозные колодки, в свою очередь, прижимаются к ротору, чтобы остановить его движение. Дисковые тормоза распространены на передних колесах автомобилей, и многие автомобили используют дисковые тормоза для всех четырех колес.
Барабанные тормоза — это второй тип фрикционных тормозов, в которых используется несколько иной подход к остановке автомобиля.Гидравлическое давление вызывается педалью тормоза и воздействует на цилиндр, расположенный в колесах. Выступы из цилиндра выталкиваются наружу и давят на комплект тормозных колодок. Тормозные колодки прижимаются к металлическому барабану внутри колеса, который замедляет его движение. В то время как дисковые тормоза прикладывают силу к внешней стороне ротора, барабанные тормоза прикладывают силу к внутренней части барабана.
Эти системы сочетают в себе использование фрикционного торможения с гидравликой и даже могут включать в себя другие системы.Цель при разработке эффективной тормозной системы — создать такую, которая быстро реагирует, не блокируется и выделяет наименьшее количество тепла при использовании. Тепло, выделяющееся при трении, должно постепенно отводиться от автомобиля. Слишком много тепла может вызвать проблемы и осложнения, когда система больше не может справляться с избыточной температурой.
В то время как современные автомобили могут использовать оба типа фрикционных тормозных систем, дисковые тормоза считаются лучшими с точки зрения того, как они справляются с нагревом.Тепло отводится легче, что предотвращает перегрев. Перегрев может привести к тому, что тормоза не сработают так быстро, как должны. В более новых автомобилях используются либо все дисковые тормозные системы, либо дисковые тормоза на передних колесах и барабанные тормоза на задних.
Абразивное трение и прилипшее трение Часть 2 — Роторы PureForge®
При нажатии на педаль тормоза возникает трение двух типов: абразивное трение и трение прилипания.Во второй части мы рассмотрим, что такое адгезионное трение и лучше или хуже, чем абразивное трение.
Прилипающее трение — это механизм трения, при котором тонкий слой материала тормозной колодки сцепляется с поверхностью ротора. Этот переносящий слой материала тормозных колодок, однажды равномерно нанесенный на ротор, входит в контакт с поверхностью тормозных колодок во время процесса торможения.
Когда материал тормозной колодки в достаточной степени переносится на поверхность ротора, он создает то, что мы называем липкими тормозами.Перенесенный материал действует как своего рода клей, который буквально прилипает к тормозной колодке, когда она прижимается к ротору. Это создает барьер между колодками и роторами, чтобы ротор не измельчался до порошка тормозными колодками. На самом деле это преимущество означает, что ваши тормоза прослужат значительно дольше. Поскольку ротор не шлифуется, роторы почти не изнашиваются, а это означает, что они прослужат очень долго без повреждений. Тормозной пыли нет.Опять же, потому что нет износа, нет тормозной пыли. Подушечки прослужат в 10-20 раз дольше. Прилегающее трение не так разрушительно, поэтому тормозные колодки изнашиваются не так быстро. Увеличенный тормозной путь. Поскольку здесь действуют две силы, сцепляющее трение и давление, тормоза останавливают автомобиль на 20 процентов быстрее. Это действительно важный момент. Нам всем нужны тормоза, которые прослужат долгое время, но, в конце концов, нам нужны тормоза, которые спасут нам жизнь.Уверенность в том, что ваш автомобиль может каждый раз останавливаться на копейке, стоит инвестировать. разница. Когда вы впервые нажимаете на тормоз, материал от колодок к роторам еще не передается, поэтому, когда вы впервые поедете на них, они не почувствуют никакой разницы. Чтобы действительно нарастить пленку на роторах, потребуется 50-100 миль торможения.Как только пленка будет полностью наложена, вы заметите огромную разницу в ваших тормозах. Так что дайте ему время, и вы заметите разницу. Вы даже сможете увидеть пленку на роторах, она будет выглядеть как ровная черная полоса вокруг ротора. Это может выглядеть не очень хорошо, но это именно то, что должно было случиться, это секрет тормозов, обладающих такой большой тормозной способностью. Как только вы увидите полосу на роторах, вы поймете, что тормоза установлены правильно.
Прикрепленные фрикционные тормоза стоят каждой копейки.Они останавливаются быстрее, служат дольше и безвредны для окружающей среды. Это действительно и ежу понятно. Можете ли вы представить себе, что вам больше никогда не придется менять тормоза или роторы? Тогда попробуйте роторы PureForge®, вы не пожалеете об этом.
Что такое обычные фрикционные тормоза и рекуперативная тормозная система
И все же за десятилетия революционных достижений в области эффективности, производительности и безопасности, казалось, упустили из виду одну вещь. Возможность собрать потерянную энергию.В 1967 году AMC Amitron был представлен в U.S. Хотя он выглядел как версия Ford Pinto для картинга, он намного опередил свое время, и представленная им революционная тормозная система заняла еще полвека, чтобы стать обычным явлением в автомобильной промышленности. Обычные фрикционные тормоза
Неотъемлемой частью традиционной тормозной системы является гидросистема, приводящая ее в действие. Он состоит из главного или главного цилиндра, заполненного жидкостью, который соединен со вторичным, подчиненным цилиндром.
Главный цилиндр включает в себя поршень, который нажимает при нажатии на педаль тормоза, выталкивая жидкость через контур в подчиненные цилиндры, установленные на каждом колесе, которые, в свою очередь, толкают поршни, чтобы эффективно задействовать тормоза.
Эта система развивалась на протяжении многих лет с такими инновациями, как дисковые тормоза, плавающие и многопоршневые суппорты или механические тормоза, которые делают торможение более эффективным и комфортным для водителя, особенно с увеличенной выходной мощностью в современных двигателях.В автомобилях нашей эпохи жидкость из резервуара подается из главных цилиндров в тандемном желобе по двойным гидравлическим контурам и непосредственно к поршням суппорта, чтобы замедлить или остановить тормозной диск, прикрепленный к ступице колеса.
Большинство современных автомобилей также оснащены тормозами с усилителем.В этих случаях между главным цилиндром и педалью тормоза размещается сервомеханизм, в большинстве случаев вакуумный насос, который эффективно увеличивает тормозную мощность при торможении. Рекуперативное торможение
Идея этой системы не нова, как мы указывали в начале этой статьи. Он основан на простом принципе. Используйте как можно больше потерянной энергии и преобразуйте ее в электрическую энергию, которая может храниться в батарее большой емкости.
По сути, эта система создает энергию при торможении, приводя электродвигатель в обратном направлении, когда водитель нажимает на педаль тормоза.Это достигается за счет использования собственного импульса транспортного средства, а полученная энергия доставляется и сохраняется в аккумуляторном блоке автомобиля.
В гибридных автомобилях эта система работает вместе с обычным контуром фрикционного тормоза, который включается, когда электродвигатель не производит достаточного тормозного усилия.
Гидравлической системе помогает двигатель, который работает в обратном направлении и вырабатывает электричество, которое подается в аккумулятор, когда водитель нажимает ногу на педаль. Последовательность торможения не только замедляет автомобиль, но и превращает электродвигатель в генератор., создавая таким образом энергию.Рекуперативные тормоза лучше всего работают при остановках и остановках, когда они могут улавливать почти половину энергии, потерянной из-за трения. В результате аккумулятор заряжается и может использоваться в течение длительного периода времени, и в результате значительно снижается расход топлива.
Можно сделать вывод, что система рекуперативного торможения намного сложнее и, учитывая ее способность производить электроэнергию, является развитием традиционной системы. По мере того, как технологии и материалы становятся более доступными, они в конечном итоге заменят их на всех наших повседневных автомобилях.
Производитель фрикционной муфты, фрикционного тормоза
Как работают фрикционные муфты и фрикционные тормоза
Фрикционные муфты и фрикционные тормоза используют фрикционные диски для передачи энергии от одного вращающегося элемента ко второму вращающемуся элементу. Трение между дисками двух корпусов позволяет фрикционной муфте или фрикционному тормозу передавать крутящий момент. Фрикционные диски представляют собой плоские гладкие поверхности, которые попеременно прикреплены к вращающимся и невращающимся элементам.Последовательность и тип фрикционной поверхности, а также нагрузка, оказываемая на фрикционную муфту или фрикционный тормоз, будут определять размер и количество фрикционных поверхностей, которые используются для передачи крутящего момента.
При превышении крутящего момента поверхности фрикционного диска фрикционная муфта проскальзывает. Эти фрикционные муфты и фрикционные тормоза также будут проскальзывать во время зацепления и расцепления, в то время как фрикционные диски постепенно сжимаются вместе независимо от используемого метода приведения в действие.Это обеспечивает плавную передачу крутящего момента от одного устройства к другому, позволяя плавные пуски (для фрикционных муфт) и контролируемые остановки (для фрикционных тормозов).
Материалы фрикционной муфты и фрикционного тормоза
Фрикционные диски, используемые в фрикционах и фрикционных тормозах, могут быть изготовлены из различных материалов. Металлы с покрытием и без покрытия, различные сплавы, композитные фрикционные материалы на связке и их комбинации могут быть подходящими в зависимости от области применения.Carlyle Johnson предлагает широкий выбор типов поверхностей для фрикционных муфт и фрикционных тормозов, а также множество поверхностей с различными размерами и типами фрикционных муфт. Подробное описание методов включения наших фрикционных муфт и фрикционных тормозов доступно на нашей странице сравнения срабатываний.
Однодисковые и многодисковые конструкции
Фрикционные муфты и узлы фрикционного тормоза
Тип | Крутящая нагрузка | Стоимость | Скорость наконечника * |
Однодисковый | Низкая производительность | Нижний | 775 фут / сек |
Многодисковый | Высокая емкость | Высшее | 200 фут / сек |
* При 5000 об / мин
Типы фрикционных муфт и тормозов
Carlyle Johnson предлагает как однодисковые, так и многодисковые фрикционные муфты и фрикционные тормоза.Во многих приложениях, где требуется низкая стоимость и только небольшой крутящий момент, достаточно одной поверхности трения. Многодисковые фрикционные муфты и фрикционные тормоза позволяют справляться с нагрузками с высоким крутящим моментом в компактном устройстве.
Многодисковое сцепление с семью наборами дисков обеспечивает четырнадцать поверхностей трения. Общая площадь этих четырнадцати поверхностей потребует очень большой однодисковой муфты или тормоза, чтобы обеспечить равный крутящий момент.Причина кроется в элементарной тригонометрии. Устройство с четырнадцатью поверхностями диаметром 9,50 дюйма имеет такую же площадь, как устройство с одной поверхностью в 35,5 дюйма! В большинстве приложений с высоким крутящим моментом не существует места для размещения однодискового устройства такого большого размера.
Фрикционная муфта и максимальная скорость тормоза
Точно так же при высоких скоростях вращения кончик большого однодискового устройства может стать угрозой безопасности. 35,5-дюймовое устройство, вращающееся со скоростью 5000 об / мин, имеет скорость на внешнем крае почти 775 футов в секунду.Насколько это быстро? Что ж, это достаточно быстро, чтобы его можно было измерить как «число Маха» — в данном случае 0,69 Маха. Для сравнения: 9,5-дюймовое многодисковое устройство, вращающееся с той же скоростью, имеет скорость около 200 футов в секунду.
Размер фрикционной муфты и тормоза
Большая однодисковая конструкция требует инженерных соображений и усложняет конструкцию подшипников, инерционные нагрузки, размер компонентов, экранирование и т. Д. Эти факторы могут сделать многодисковые фрикционные муфты и фрикционные тормоза предпочтительным решением для передачи мощности при высоких крутящих моментах.Однодисковые фрикционные муфты и тормоза, как правило, больше, но дешевле, чем многодисковые фрикционные муфты и тормоза, потому что они содержат меньше деталей и их проще спроектировать, изготовить и собрать.
Стоимость фрикционной муфты и тормоза
Многодисковые фрикционные муфты и фрикционные тормоза обычно намного компактнее, хотя и имеют меньшую стоимость из-за их повышенной сложности.
НЕКОТОРЫЕ ФАКТОРЫ, ВЛИЯЮЩИЕ НА ТРЕНИЕ ТОРМОЗОВ
Изменение тормозных сил на тормозах автомобильных транспортных средств при заданном положении педали или заданном давлении на педаль часто происходит из-за обычного износа тормозных накладок или других деталей и может быть легко предотвращено периодическим осмотром и регулировкой.Иногда, однако, внезапное и серьезное снижение тормозной способности происходит, когда тормоза использовались в течение сравнительно длительных периодов времени с короткими интервалами охлаждения, или когда тормоза были намочены или масло достигло накладок. Лабораторные испытания тормозных материалов показали, что заметное повышение температуры обычно приводит к снижению коэффициента трения асбестовых текстильных материалов тормозных накладок и что масло и вода имеют аналогичный эффект временного характера.В настоящем документе лабораторные испытания сопровождаются серией экспериментов, предпринятых с целью получения данных об условиях работы тормозов легкового автомобиля в реальной эксплуатации, при этом особое внимание уделяется природе и величине причин, которые приводят к вариациям тормозной способности. Было проведено три серии испытаний: ( a ) с сухими тормозными накладками, ( b ) после того, как накладки были пропитаны водой и ( c ) после того, как накладки были высушены и обработаны обильным зелья из масла.
Дается подробное описание испытательного устройства, двумя особенностями которого были установка термопары, состоящая из восьми пар медь-константан, по одной в каждой тормозной колодке, и децелерометр для измерения замедления, полученного в футах в секунду. в секунду, пока машина была остановлена. Результаты испытаний поясняются и графически изображаются в виде ряда кривых.
Сделанные выводы заключаются в том, что ( a ) с накладками, которые считаются типичными для обычно используемых в автомобильных транспортных средствах, кажущийся коэффициент трения падает с повышением температуры; ( b ) падение кажущегося коэффициента трения с повышением температуры может быть в значительной степени, если не полностью, из-за влияния повышения температуры на насыщающий агент; ( c ) уменьшение кажущегося коэффициента трения с повышением температуры кажется меньше для твердых, плотных покрытий, чем для других; ( d ) не было очевидных различий в характеристиках при изменении температуры между ткаными пропитанными асфальтом футеровками и прорезиненными, или вулканизированными, сложенными и прошитыми футеровками; ( и ) тенденция к быстрому увеличению кажущегося коэффициента трения кажется большей для прорезиненных или вулканизированных футеровок после пропитки водой, чем для твердых тканых, пропитанных асфальтом футеровок; ни увеличения, ни уменьшения коэффициента трения при пропитке водой не наблюдалось; и ( f ) коэффициент трения всех накладок имеет тенденцию к уменьшению после того, как они пропитаны маслом, и их тенденция к восстановлению после такого состояния не является быстрой.