Задний мост и дифференциал
Главная
» Информация
» Статьи
» ЗАПЧАСТИ
» Трансмиссия
» Мосты
» Задний мост и дифференциал
- 9941 просмотр
Посмотреть задний мост в каталоге «АВТОмаркет Интерком»
Задний мост — один из самых сложных механизмов автомобиля. Этот механизм распределяет вращающий момент на задние колёса, и к тому же в нём установлен механизм, который распределяет крутящий момент на то колесо, на которое нужно. Механизм этот называется — дифференциал. Он весьма связан с мостом.
Задний мост решает многие задачи. Картер выполняет функции специальной опоры для деталей подвески и держит вашу машину.

Полуоси заднего моста работают с разной частотой вращения, чтобы оставлять тот факт, что колесо на внешней стороне поворота меняется на значительное расстояние и поэтому будет работать с большей скоростью, чем колесо на внутренней окружности поворота. В заднем собранном мосте можно найти дифференциал.
Дифференциал — это деталь из зубчатых колес, который при надобности самостоятельно переносит крутящий момент от карданного вала к полуосям заднего моста.
Виды задних собранных мостов
Существуют 3 важных типа заднего моста в сборе, они зависят от разновидности поддержки полуоси и колеса:
• С полуразгруженными полуосями
• С полностью разгруженными полуосями
• С независимой подвеской.
В мосте с полуразгруженными полуосями применяются полуоси, которые, как правило, снабжены С-образными зажимами в картере моста. Эти С-образные зажимы закрепляются в канавку на шлицевом внутреннем конце полуоси. К тому же, С-образные зажимы входят в выемку в полуосевых шестеренках дифференциала, которые расположены в коробке дифференциала. Полуразгруженная полуось находится в водном прямом роликовом подшипнике, который можно обнаружить на наружной стороне полуоси.
Задний мост с полностью разгруженными полуосями создает грузоподъемность. Ступица держится на полуоси, делая упор на 2 по разному установленных конических роликовых подшипника. Вес задней части автомобиля держится на картере моста, и полуоси становятся свободными. Полуось просто заставляет крутиться колесо. Ступица находится на полуоси храповой гайкой, которая контрится в пазе на полуоси.
Самый последний тип заднего моста — это задний мост с независимой задней подвеской (IRS). Этот мост похож на другие виды, кроме того, что весь вес машины берет на себя отдельная система подвески, а не собранный мост. Никакие трубчатые полуоси не функционируют. Вместо них для объединения картера моста с ведущими колесами работают полуоси, похожие на карданные валы.
Шарниры равных угловых скоростей на двух концах полуосей способны функционировать под меняющимися углами и проводить изменение длины полуосей. Изменение длины полуоси исполняет работу подвески колеса и динамику движения. Короткий вал внутреннего шарнира равных угловых скоростей держится в полуосевой шестерне дифференциала специальным стопорным кольцом. Вал наружного шарнира устанавливается в ступицу и крепится через держатель ступицы колеса заднего моста.
Элементы заднего моста/ дифференциала
Простой задний мост в своем составе имеет:
• картер заднего моста
• ведущая шестерня главной передачи
• ведомая шестерня главной передачи
• коробка дифференциала
• полуосевые шестерни дифференциала
• сателлиты дифференциала
• подшипники коробки дифференциала
• подшипники ведущей шестерни
• регулировочные прокладки и уплотнения.
Запчасти на автомобили ваз можно купить в сети магазинов «АВТОмаркет Интерком». Любой товар можно заказать через интернет магазин на нашем сайте. Если возникли вопросы, то перейдите в раздел «Вопрос-ответ», и задайте его нашим специалистам.
+7 (351) 240-85-85 Многоканальный
+7 (351) 220-18-88 Интернет-магазин
ЗАДНИЙ МОСТ. ОСОБЕННОСТИ КОНСТРУКЦИИ
г. Москва, Авиамоторная 12
+7 495 125-20-00
Авто
Бренды
ВАЗ
Ремонт ВАЗ 2107
ТРАНСМИССИЯ
ЗАДНИЙ МОСТ. ОСОБЕННОСТИ КОНСТРУКЦИИ
Автор: Третий РимСредний
шагов 4
30 мин — 1 час
Комментарии: Избранное: 0
Шаг 1
К балке 10 (рис. 5.8) заднего моста прикреплен редуктор 28, в котором расположены главная передача и дифференциал. Ведущая 29 и ведомая 19 шестерни главной передачи подобраны в пару по пятну контакта и шуму, поэтому при повреждении одной из них заменяются обе. Между внутренними кольцами подшипников 23 ведущей шестерни расположена распорная втулка 22, которая, деформируясь при затягивании гайки ведущей шестерни, обеспечивает предварительный натяг в ее подшипниках. Между торцом ведущей шестерни и внутренним подшипником установлено регулировочное кольцо 21, определяющее правильное положение ведущей шестерни относительно ведомой.
Шаг 2
Рис. 5.8. Задний мост: 1 – полуось; 2 – болт крепления колеса; 3 – направляющий штифт; 4 – маслоотражатель; 5 – тормозной барабан; 6 – подшипник полуоси; 7 – запорное кольцо; 8 – фланец балки заднего моста; 9 – сальник полуоси; 10 – балка заднего моста; 11 – пластина крепления подшипника; 12 – щит заднего тормоза; 13 – направляющая полуоси; 14 – регулировочная гайка; 15 – подшипник коробки дифференциала; 16 – крышка подшипника; 17 – сапун; 18 – сателлит; 19 – ведомая шестерня; 20 – шестерня полуоси; 21 – регулировочное кольцо ведущей шестерни; 22 – распорная втулка; 23 – подшипники ведущей шестерни; 24 – сальник; 25 – грязеотражатель; 26 – фланец; 27 – маслоотражатель; 28 – картер редуктора заднего моста; 29 – ведущая шестерня; 30 – ось сателлитов; 31 – регулировочная шайба; 32 – коробка дифференциала
Шаг 3
Ведомая шестерня главной передачи прикреплена к фланцу коробки 32 дифференциала, которая вращается на двух подшипниках 15. Предварительный натяг в этих подшипниках, а также зазор между зубьями ведущей и ведомой шестерен регулируют гайками 14, завернутыми в разъемные постели подшипников. Полуосевые шестерни 20 установлены в цилиндрических гнездах коробки дифференциала и опираются на коробку через опорные шайбы 31. Подбором шайб по толщине устанавливают боковой зазор 0–0,1 мм между зубьями сателлитов и полуосевых шестерен. Полуось 1 внутренним концом входит в шлицевое отверстие полуосевой шестерни, а наружным опирается на шариковый подшипник 6, который закреплен на полуоси запорным кольцом 7. Подшипник полуоси уплотнен в гнезде балки с внутренней стороны самоподжимным сальником 9, а снаружи – резиновым кольцом, зажатым между щитом 12 тормоза и фланцем балки заднего моста. Подшипник закреплен в гнезде балки пластиной 11, которая совместно с маслоотражателем 4 и щитом прикреплена болтами к фланцу балки.
Шаг 4
Готово!
Axle Essentials — Часть 1 — Mark Williams Enterprises, Inc.
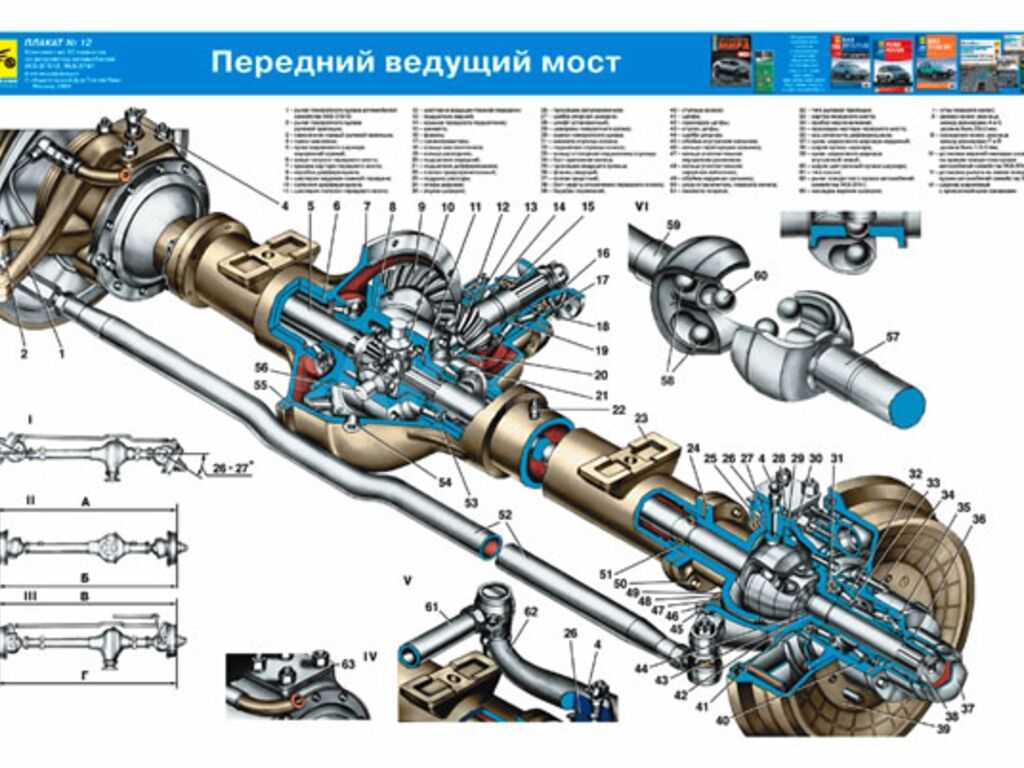
by Wayne Scraba Подумаешь? Как только вы увидите гоночный автомобиль, который только что наклонил колесо (чаще всего с прикрепленным куском оси), вы гораздо лучше поймете, почему оси имеют решающее значение. Это также причина, по которой большинство органов, санкционирующих гонки, имеют правила, в которых изложено, что вы можете и что не можете иметь, когда дело доходит до осей (показательный пример: какое-то устройство принудительной фиксации оси, которое означает отсутствие зажимов). |
Так выглядит набор качественных осей после ковки, механической обработки и термообработки. |
Но начнем с самого начала. Автомобильные оси оригинального оборудования обычно изготавливаются из стали 1055 или 1541. Как правило, они находятся на границе между средне- и высокоуглеродистой сталью с относительно большим содержанием марганца. 1055 имеет содержание углерода от 0,50% до 0,60%, а 1541 — от 0,36 до 0,44%.
|
Когда речь идет о осях, обычно используются два различных типа термической обработки. |
При индукционной закалке полуось проходит через электромагнитную катушку. В металле возникают вихревые токи, которые, в свою очередь, нагревают вал. Затем вал закаливают. Этот процесс закалки оставляет вал с поверхностной твердостью 55-58 по Роквеллу, проникая на глубину примерно 0,150-0,300 дюйма. Сердцевина оси остается относительно мягкой, но поверхность очень твердая – почти ломкая. Пока все хорошо, но этот тип оси с мягким фланцем лучше подходит для людей, бьющих по бордюрам, чем для того, чтобы выдерживать ударные нагрузки чего-то вроде гоночного автомобиля.
|
На этой фотографии Марка Уильямса показан процесс закалки, который они используют для осей Hi-Torque. |
Но бордюры и выбоины не являются самой большой проблемой для гоночного автомобиля (или даже для уличной машины). Факторы для этих приложений включают определение того, какая нагрузка будет приходиться на оси при запуске, общий вес различных частей трансмиссии (подробнее об этом позже) и, конечно же, размер вашего бюджета. Рассчитать величину крутящего момента, прикладываемого к оси, очень просто: возьмите выходной крутящий момент двигателя и умножьте его на передаточное число первой и задней передачи трансмиссии. Если это автомат, в смесь также следует добавить коэффициент умножения от гидротрансформатора. В целом, на самом деле нет ничего необычного в том, чтобы увидеть цифры более 10 000 футо-фунтов. крутящего момента, передаваемого на оси. Это куча. Для такого рода нагрузок важно нечто большее, чем просто прочность материала на растяжение. Перемотать пару абзацев назад. Помните, что индукционная закалка применялась на OEM-осях? Хотя это может быть здорово для борьбы с ударами о бордюры и выбоины, для гоночных автомобилей и сверхмощных деталей требуется что-то еще. Мы обратились в компанию Mark Williams Enterprises за информацией о характеристиках осей и особенно о пластичности: Для достижения пластичности, необходимой для гоночных целей, Mark Williams Enterprises применяет процесс аустенизации исключительно для своих осей Hi-Torque из никель-хромомолибденового сплава. Этот процесс термообработки включает погружение оси в расплавленный раствор при температуре более 1500 градусов (F), а затем закалку компонентов в расплавленном соляном растворе. Другими важными преимуществами Austempering являются повышенная ударная и усталостная прочность осей, стойкость к водородному охрупчиванию, более равномерная твердость и повышенная износостойкость. В конце концов, выбор материалов в сочетании с процессом Austempering обеспечивает ось с предельным пределом прочности на растяжение 225 000–253 000 фунтов на квадратный дюйм наряду с исключительной пластичностью (способностью изменять форму без разрушения). Твердость поверхности вала составляет приблизительно 50 по шкале Роквелла, что оказывается гораздо менее хрупким, чем ось из углеродистой стали, подвергнутой индукционной закалке.
|
Это второй тип процесса закалки, используемый для осей. Это называется индукционной закалкой. |
ОК. Если все это необходимо для создания хороших осей, то почему вы так дешево рекламируете легкосплавные оси? Реальность такова, что эти компоненты на самом деле производятся OEM-компанией по ковке осей. Основным направлением деятельности этой компании является производство осей для тяжелых грузовиков и строительной отрасли. И да, используемый материал — углеродистая сталь, обычная для осей оригинального оборудования. В этом случае производитель изготавливает заготовку оси. Компания, продающая эти недорогие оси из сплава, обрезает ось по длине, а затем нарезает ее шлицами. Эти оси изготовлены из того же материала, что и стандартные оси, и проходят такую же термообработку. Единственная реальная разница в том, что они доступны в более коротких длинах и с другими шлицами. Теперь вы знаете, почему они дешевые. И вы получаете то, за что платите. На следующей неделе мы поговорим о сплайнах. |
Полную и оригинальную статью можно найти здесь, на RacingJunk. ![]() Хотите прочитать всю серию? Статьи 1-4 можно найти здесь. |
Осевой вал внедорожника Факты
Никому не нравится получать вал в общеизвестном смысле. Но выбор правильного вала для вашей оси может уберечь вас от застревания в дерьме без крутящего момента на шинах. В этой статье подробно рассказывается о материалах и производстве оригинальных и неоригинальных полуосей. Мы ограничиваем его задними валами; передние валы могут быть освещены в следующем выпуске.
Материалы
Общая прочность полуоси определяется тем, что Randy’s Ring & Pinion называет DMD: диаметр, материалы, конструкция. Начнем с материалов.
Большинство читателей знают, что сталь — это общее название различных сплавов или смесей железа. Железо (Fe) является основным металлом стали, с углеродом (C) и такими другими элементами, как марганец (Mn), фосфор (P), сера (S), кремний (Si), никель (Ni), хром (Cr), молибден. (Mo) и ванадий (V) иногда добавляют для улучшения твердости, обрабатываемости и термообработки.
Оси обычно изготавливаются из среднеуглеродистой стали. Углерод увеличивает прочность, но делает сталь менее пластичной и гибкой. Валы из сплава вторичного рынка часто имеют более высокое содержание углерода, чем валы оригинального оборудования, а также содержат другие металлы, такие как хром, молибден и никель. Эти металлы повышают прочность и улучшают поверхностное упрочнение.
Ниже представлен обзор марок материалов AISI (Американский институт чугуна и стали), наиболее часто используемых для автомобильных полуосей. (Общество автомобильных инженеров склонно использовать обозначения AISI; обозначения MIL-Spec, ASTM, ASM и международные обозначения могут различаться.) Сырье иногда включает сокращения, относящиеся к производственному процессу: H — горячекатаный, CD — холоднокатаный. вытягивается, A отжигается, а Q закаливается, например.
Первые две цифры относятся к сплаву, а последние две — к среднему содержанию углерода. Цифры 1xxx в первую очередь относятся к углеродной группе, 4xxx включает множество членов группы никель-хром-молибден (хромомолибден), а трехзначные обозначения считаются авиационными сталями.
1340: Этот сорт с высоким содержанием марганца много лет назад использовался в качестве оригинального материала. Многие ранние полуоси Dana/Spicer использовали 1340. Современные высокопроизводительные устройства требуют более прочного материала.
1040: Оригинальные полуоси обычно изготавливаются из сплава 1040 с индукционной закалкой, потому что он обеспечивает компромисс между прочностью и пластичностью. 1040 также легче обрабатывать, чем более твердые сплавы.
1050: Благодаря более высокому содержанию углерода, 1050 примерно на 38 процентов прочнее, чем 1040. Он используется в некоторых областях применения оригинального оборудования, а также для некоторых валов, заменяющих оригинальные запчасти.
1541: Этот высоколегированный сплав популярен среди производителей запчастей.
1541H: Еще лучший материал для вторичного рынка, этот сорт содержит кремний, добавленный в 1541 для повышения прочности и способности к термообработке. 1541H может быть на 50 процентов прочнее, чем OE 1040, и примерно на 12 процентов толще, чем 1050.
4140: 41xx обозначает группу хрома. Хром предлагает три преимущества: повышенную твердость, лучшую эластичность при закалке и большую коррозионную стойкость. Молибден и никель дополнительно повышают твердость. Эта сталь также широко используется для U-образных соединений, шпинделей и распределительных валов.
4340: Также в семействе хромомолибденовых сплавов 4340 примерно в два раза прочнее OE 1040. Он также достаточно пластичен, чтобы поглощать удары при резком ускорении, разгружая дифференциал. 4340 популярен для изготовления передних валов послепродажного обслуживания, потому что он прочный и более доступный, чем некоторые из более экзотических сплавов.
300M: Также известный как 4340M, он похож на 4340, только с добавлением ванадия, дополнительного кремния и немного большего количества углерода и марганца. Он в основном используется в авиастроении, где требуется высокая прочность и пластичность для таких компонентов, как шасси. 300M также обычно имеет сквозную закалку и примерно на 150 процентов прочнее, чем OE 1040. Он дорог, труднее в обработке, чем другие материалы для валов, и производится в гораздо меньших количествах, чем другие марки стали.
Hy-Tuf: (ASM-6418, SAE 4625M4, MIL S-71083, он же Maxi-Drive) — хромомолибден, хорошо известный в кругах дрэг-рейсинга. Strange Engineering и другие компании продают валы Hy-Tuf с твердостью по шкале Роквелла (HRC) 46-48. (Hy-Tuf обычно проходит сквозную закалку.) В рецепте много кремния и марганца. Hy-Tuf более доступен и доступен, чем 300M.
8620: Также в никель-хромово-молибденовой группе этот низколегированный (с низким содержанием углерода) сорт не подходит для ведущих мостов — прочность на растяжение составляет примерно половину от материала 1040, обычно используемого для оригинальных валов. 8620 обычно используется для компонентов, которым требуется твердая поверхность для защиты от износа и пластичный сердечник, таких как зубчатые колеса и шестерни.
Каждая марка стали имеет допустимый диапазон содержания углерода и других элементов. (Показатели прочности в прилагаемой таблице являются приблизительными; фактическая прочность вала определяется конкретным рецептом, используемым сталелитейным заводом, процессом закалки и размером.) Стоимость готового продукта часто отражает качество материалов. Необработанная сталь, которая постоянно находится в верхней части спецификации, как правило, стоит больше, чем поставки, которые варьируются от партии к партии или находятся в нижней части допустимого диапазона. Более твердые сплавы сложнее обрабатывать, что также увеличивает стоимость.
Производство
Здесь представлен обзор производства задней полуоси.
Шлицы:
• Зубчатые: В ходе этого процесса на валу вырезаются эвольвентные (изогнутые) шлицы. Шлицы боковой шестерни дифференциала эвольвентные, поэтому крутящий момент распределяется более равномерно, когда шлицы совпадают. Некоторые предприятия меньшего объема вырезают сплайны прямо. Это концентрирует нагрузку только на части зуба вместо более равномерного распределения нагрузки. Прямая резка также может проникать ниже цементируемого участка вала.
• Катаный: Станок с дорогими штампами формирует эвольвентные шлицы под высоким давлением. Материал не удаляется.
Диаметр основного шлица: Максимальное расстояние между шлицами (определяется штангенциркулем).
Малый диаметр шлица: Диаметр основания шлица, который может быть или не быть минимальным диаметром вала.
Диаметр шага: Диаметр в средних точках шлицов.
Минимальный диаметр: Самая тонкая часть вала, которая иногда имеет меньший диаметр шлица, но также может быть суженной областью в другом месте вала.
Диаметральный шаг: Математический расчет, разработанный для того, чтобы осевые линии шлицев оставались постоянными при любом диаметре. Текущий стандарт — 24 шага. Это означает, что средние точки шлицев на валу с 24 шлицами имеют диаметр 1 дюйм, средние точки вала с 35 шлицами имеют диаметр 1 1/2 дюйма и так далее.
Угол давления: Угол зуба шлица. Он различается у разных производителей и не является взаимозаменяемым: например, 30-градусные внутренние шлицы Dana несовместимы с 45-градусными дифференциалами Ford или Toyota, даже если количество шлицов одинаково. Шлицы с большим углом производят немного более прочные валы, потому что меньший диаметр шлица больше.
Как правило, большее количество шлицов означает вал большего диаметра и более прочный (исключением является 30-шлицевой вал с 14 болтами). Точно так же, как крепежные детали с мелкой резьбой распределяют нагрузку по большей поверхности по сравнению с резьбой с крупной резьбой, меньшие зубья/большее количество шлицов прочнее, чем «крупные» шлицы, которые врезаны глубже в вал (сводя к минимуму меньший диаметр). По данным Dynatrac, валы послепродажного обслуживания для полноприводных автомобилей с большими шинами начинаются с 35-шлицевого сечения.
Закалка/финишная обработка
Закалка повышает прочность вала за счет изменения кристаллической структуры металла. Тепло создает атомы углерода, которые улавливаются благодаря быстрой закалке маслом или водой. Шкала Роквелла, выраженная в HRC, является наиболее распространенной системой измерения твердости полуосей.
Сквозное закаливание: Весь кусок металла теоретически закаляется равномерно от кожуха до сердцевины.
Индукционная закалка: Метод, наиболее часто используемый для полуосей. Электромагнитное поле, сила тока которого может варьироваться в зависимости от диаметра материала и желаемой глубины закаленного слоя, нагревает металл. Вскоре после этого вал охлаждается.
Азотирование: В этом процессе используется раствор с высоким содержанием азота, такой как аммиак, для упрочнения поверхности при нагревании металла в корпусе.
Другие виды обработки металлов и отделочные процессы еще больше повышают долговечность вала. Некоторые из возможностей заключаются в следующем.
Полировка: Микрополировка повышает прочность за счет сведения к минимуму неровностей поверхности и концентраторов напряжения. Хроммолибденовая сталь 4340 имеет довольно плотное зерно и не так хорошо полируется, как стали углеродистой группы. Участки подшипника/уплотнения обычно шлифуют или полируют, чтобы свести к минимуму задиры или обеспечить максимальную герметизацию этих контактных площадей.
Криогенная заморозка: Газообразный азот используется для охлаждения детали примерно до 300 градусов по Фаренгейту ниже нуля. Это сжимает зерна металла и улучшает сопротивление усталости в большей степени, чем общую прочность. Это одна из самых дорогих процедур.
Черный оксид: Это покрытие в первую очередь предназначено для защиты от коррозии.
Пистолетное сверление: Этот процесс высверливает сердцевину вала. При правильном выполнении он позволяет снизить вес с минимальной потерей прочности. Пистолетное бурение и криогенная заморозка не пользуются большим спросом на рынке полноприводных автомобилей для отдыха. Эти варианты изучаются в основном гонщиками, ищущими все доступные преимущества.
Отжиг: Этот процесс фактически размягчает металл посредством нагрева и медленного охлаждения.
Дробеструйная обработка: Дробеструйная очистка для снятия поверхностного напряжения предназначена для аэрокосмической промышленности некоторых деталей. Foote Axle & Forge считает, что надлежащее производство, включая точную индукционную закалку, исключает необходимость дробеструйной обработки, которую трудно точно регулировать.
На приведенных здесь фотографиях и подписях показано, как компания Foote Axle & Forge изготавливает валы из необработанных круглых прутков. Многие хорошо известные «производители» осей на самом деле являются финишерами, покупая заготовки у таких компаний, как Foote, а затем обрабатывая их по мере необходимости до нужной длины, спецификации шлицев и рисунка колесных болтов. Финишеры иногда предлагают дополнительные услуги, такие как сверление пистолетом и криозаморозка.
Дизайн
В дополнение к марке металла и толщине профиль оси помогает определить ее общую прочность. Вот обзор популярных стилей заднего конца.
Конический двухкомпонентный: Этот тип имеет отдельный вал и фланец. В полупоплавках используется шпонка в шпоночном пазу для сопряжения валов и фланцев. Гайки крепят внешние концы валов к фланцам в этом стиле.
Полуплавающий: В этом типе обычно используется цельная фланцевая ось для соединения дифференциала и колеса. Полуплавающие полуоси выполняют двойную функцию: они передают крутящий момент и поддерживают вес автомобиля. В некоторых полуплавающих мостах внутри дифференциала используются С-образные зажимы для удержания валов на автомобиле, а не запрессованные подшипник и фланец. Поскольку фланцы валов крепятся болтами к колесам, а не к буксе, поломка вала может привести к тому, что шина/колесо отойдет от буксы. Комплекты фиксаторов C-образных зажимов для популярных осей, таких как Dana 35C, Ford 8.8 и Chevy с 12 болтами, включают в себя концы полуосей, запрессованные подшипники и стопорные пластины подшипников для надежного удержания полуосей в осях. Самодельные комплекты маслоотделителя, которые имеют концы корпуса с болтовым креплением, как правило, допускают большую боковую нагрузку на подшипники и валы, чем концы с приваркой. Однако приварные концы требуют для установки выравнивающей планки, чтобы гарантировать правильность осевой линии трубы корпуса.
Полностью плавающий: Этот тип задней части предпочтителен для транспортных средств, которые перевозят более тяжелые грузы, обычно 3/4 тонны и выше. Как и передние, полностью плавающие задние полуоси соединяются со ступицами, которые вращают колеса. Ступица поддерживает вес автомобиля. В случае поломки полностью плавающего вала ступица и колесо обычно остаются прикрепленными болтами к картеру оси. Полностью плавающие валы могут иметь шлицевые внешние концы, которые крепятся к ступицам, или приводные фланцы, которые болтами крепятся к ступицам колес.
Прочность
На прилагаемой диаграмме (справа) показан предел текучести в миниатюре (точка до того, как металл окончательно деформируется) для полуосей различных диаметров. Эта информация может быть использована для расчета крутящего момента полуоси по приведенным выше формулам. Радиус и диаметр указаны в дюймах; чтобы преобразовать крутящий момент в фунт-футы, разделите фунт-дюймы на 12.
Итак, какой крутящий момент требуется для полуосей вашего автомобиля 4×4? Максимальный выходной крутящий момент трансмиссии можно рассчитать, умножив крутящий момент коленчатого вала двигателя на передаточное число, а затем используя поправочный коэффициент 0,85 для компенсации наклона трансмиссии. Вот расчет для стандартного JK Rubicon 12 года с пятиступенчатой автоматической коробкой передач.
250 фунт-фут двигатель x 3,59 Первые
x 4,0 Т-сэза x 4,10 Ось = 14 719
14 719 x 0,85 Паразитовая потеря = 12 511
12111 = 3128 LB-FT на шал. квазиравные по длине; они теоретически делят нагрузку пополам при нормальных тяговых ситуациях и при задействовании фиксатора или катушки.
Выбор вала
Какой вал подходит именно вам? Мы надеемся, что приведенные здесь факты и цифры помогут сузить выбор. Интернет-форумы — еще один возможный ресурс, если вы можете найти знающих авторов, которые используют предложенную вами установку и атакуют схожую местность. Соответствующие посты часто рекомендуют определенных производителей. Используя технические линии этих производителей, можно сосредоточиться на том, что лучше сейчас и, возможно, в будущем, исходя из текущих и предполагаемых настроек автомобиля, бюджета и так далее.