ΠΠ°ΠΊΠΎΠ΅ Π΄Π°Π²Π»Π΅Π½ΠΈΠ΅ Π² ΡΠΎΡΠΌΠΎΠ·Π½ΠΎΠΉ ΡΠΈΡΡΠ΅ΠΌΠ΅ Π°Π²ΡΠΎΠΌΠΎΠ±ΠΈΠ»Ρ?
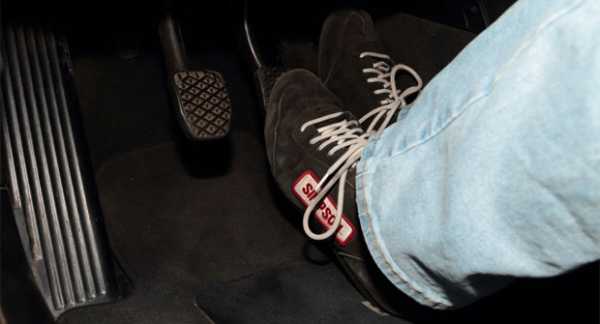
ΠΠ°ΠΊΠΎΠ΅ Π΄Π°Π²Π»Π΅Π½ΠΈΠ΅ Π² Π³ΠΈΠ΄ΡΠ°Π²Π»ΠΈΡΠ΅ΡΠΊΠΈΡ ΡΠΎΡΠΌΠΎΠ·Π°Ρ Π»Π΅Π³ΠΊΠΎΠ²ΡΡ Π°Π²ΡΠΎ?
ΠΠ·Π½Π°ΡΠ°Π»ΡΠ½ΠΎ Π΅ΡΡΡ ΡΠΌΡΡΠ» ΡΠ°Π·ΠΎΠ±ΡΠ°ΡΡΡΡ Π² ΡΠ°ΠΊΠΈΡ ΠΏΠΎΠ½ΡΡΠΈΡΡ , ΠΊΠ°ΠΊ Π΄Π°Π²Π»Π΅Π½ΠΈΠ΅ Π² Π³ΠΈΠ΄ΡΠ°Π²Π»ΠΈΡΠ΅ΡΠΊΠΎΠΉ ΡΠΈΡΡΠ΅ΠΌΠ΅ ΠΈ Π΄Π°Π²Π»Π΅Π½ΠΈΠ΅, ΠΎΠΊΠ°Π·ΡΠ²Π°Π΅ΠΌΠΎΠ΅ ΡΡΠΏΠΏΠΎΡΡΠ°ΠΌΠΈ ΠΈΠ»ΠΈ ΡΡΠΎΠΊΠ°ΠΌΠΈ ΡΠΈΠ»ΠΈΠ½Π΄ΡΠΎΠ² Π½Π΅ΠΏΠΎΡΡΠ΅Π΄ΡΡΠ²Π΅Π½Π½ΠΎ Π½Π° ΡΠΎΡΠΌΠΎΠ·Π½ΡΠ΅ ΠΊΠΎΠ»ΠΎΠ΄ΠΊΠΈ.
ΠΠ°Π²Π»Π΅Π½ΠΈΠ΅ Π² ΡΠ°ΠΌΠΎΠΉ Π³ΠΈΠ΄ΡΠ°Π²Π»ΠΈΡΠ΅ΡΠΊΠΎΠΉ ΡΠΈΡΡΠ΅ΠΌΠ΅ Π°Π²ΡΠΎ Π²ΠΎ Π²ΡΠ΅Ρ Π΅Ρ ΡΡΠ°ΡΡΠΊΠ°Ρ ΠΏΡΠΈΠΌΠ΅ΡΠ½ΠΎ ΠΎΠ΄ΠΈΠ½Π°ΠΊΠΎΠ²ΠΎΠ΅ ΠΈ ΡΠΎΡΡΠ°Π²Π»ΡΠ΅Ρ Π½Π° ΡΠ²ΠΎΡΠΌ ΠΏΠΈΠΊΠ΅ Ρ Π½Π°ΠΈΠ±ΠΎΠ»Π΅Π΅ ΡΠΎΠ²ΡΠ΅ΠΌΠ΅Π½Π½ΡΡ Π°Π²ΡΠΎ ΠΎΠΊΠΎΠ»ΠΎ 180 Π±Π°Ρ (Π΅ΡΠ»ΠΈ ΡΡΠΈΡΠ°ΡΡ Π² Π°ΡΠΌΠΎΡΡΠ΅ΡΠ°Ρ , ΡΠΎ ΡΡΠΎ ΠΏΡΠΈΠ±Π»ΠΈΠ·ΠΈΡΠ΅Π»ΡΠ½ΠΎ 177 Π°ΡΠΌ). Π ΡΠΏΠΎΡΡΠΈΠ²Π½ΡΡ ΠΈΠ»ΠΈ Π³ΡΠ°ΠΆΠ΄Π°Π½ΡΠΊΠΈΡ Π·Π°ΡΡΠΆΠ΅Π½Π½ΡΡ Π°Π²ΡΠΎ ΡΡΠΎ Π΄Π°Π²Π»Π΅Π½ΠΈΠ΅ ΠΌΠΎΠΆΠ΅Ρ Π΄ΠΎΡ ΠΎΠ΄ΠΈΡΡ Π΄ΠΎ 200 Π±Π°Ρ.
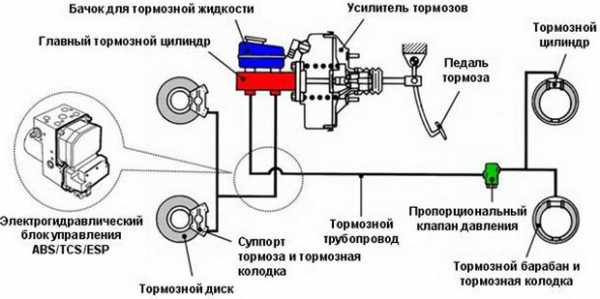
Π Π°Π·ΡΠΌΠ΅Π΅ΡΡΡ, ΡΡΠΎ ΡΠΎΠ»ΡΠΊΠΎ ΡΡΠΈΠ»ΠΈΠ΅ΠΌ ΠΌΡΡΠΊΡΠ»ΡΠ½ΠΎΠΉ ΡΠΈΠ»Ρ ΡΠ΅Π»ΠΎΠ²Π΅ΠΊΠ° Π½Π°ΠΏΡΡΠΌΡΡ ΡΠΎΠ·Π΄Π°ΡΡ ΠΏΠΎΠ΄ΠΎΠ±Π½ΠΎΠ΅ Π΄Π°Π²Π»Π΅Π½ΠΈΠ΅ Π½Π΅Π²ΠΎΠ·ΠΌΠΎΠΆΠ½ΠΎ. ΠΠΎΡΡΠΎΠΌΡ Π² ΡΠΎΡΠΌΠΎΠ·Π½ΠΎΠΉ ΡΠΈΡΡΠ΅ΠΌΠ΅ Π°Π²ΡΠΎ Π΅ΡΡΡ Π΄Π²Π° ΡΡΠΈΠ»ΠΈΠ²Π°ΡΡΠΈΡ ΡΠ°ΠΊΡΠΎΡΠ°.
- Π ΡΡΠ°Π³ ΠΏΠ΅Π΄Π°Π»ΠΈ. ΠΠ° ΡΡΠ΅Ρ ΡΡΡΠ°Π³Π°, ΠΊΠΎΡΠΎΡΡΠΉ ΠΎΠ±Π΅ΡΠΏΠ΅ΡΠΈΠ²Π°Π΅ΡΡΡ ΠΊΠΎΠ½ΡΡΡΡΠΊΡΠΈΠ΅ΠΉ ΠΏΠ΅Π΄Π°Π»ΡΠ½ΠΎΠ³ΠΎ ΡΠ·Π»Π°, ΠΈΠ·Π½Π°ΡΠ°Π»ΡΠ½ΠΎ ΠΏΡΠΈΠ»Π°Π³Π°Π΅ΠΌΠΎΠ΅ Π²ΠΎΠ΄ΠΈΡΠ΅Π»Π΅ΠΌ Π΄Π°Π²Π»Π΅Π½ΠΈΠ΅ Π½Π° ΠΏΠ΅Π΄Π°Π»Ρ ΡΠ²Π΅Π»ΠΈΡΠΈΠ²Π°Π΅ΡΡΡ Π² 4-8 ΡΠ°Π· Π² Π·Π°Π²ΠΈΡΠΈΠΌΠΎΡΡΠΈ ΠΎΡ ΠΌΠ°ΡΠΊΠΈ Π°Π²ΡΠΎ.
- ΠΠ°ΠΊΡΡΠΌΠ½ΡΠΉ ΡΡΠΈΠ»ΠΈΡΠ΅Π»Ρ. ΠΡΠΎΡ ΡΠ·Π΅Π» ΡΠ°ΠΊΠΆΠ΅ ΡΡΠΈΠ»ΠΈΠ²Π°Π΅Ρ Π΄Π°Π²Π»Π΅Π½ΠΈΠ΅ Π½Π° Π³Π»Π°Π²Π½ΡΠΉ ΡΠΎΡΠΌΠΎΠ·Π½ΠΎΠΉ ΡΠΈΠ»ΠΈΠ½Π΄Ρ ΠΏΡΠΈΠ±Π»ΠΈΠ·ΠΈΡΠ΅Π»ΡΠ½ΠΎ Π² 2 ΡΠ°Π·Π°. Π₯ΠΎΡΡ ΡΠ°Π·Π½ΡΠ΅ ΠΊΠΎΠ½ΡΡΡΡΠΊΡΠΈΠΈ ΡΡΠΎΠ³ΠΎ ΡΠ·Π»Π° ΠΏΡΠ΅Π΄ΡΡΠΌΠ°ΡΡΠΈΠ²Π°ΡΡ Π΄ΠΎΠ²ΠΎΠ»ΡΠ½ΠΎ Π±ΠΎΠ»ΡΡΡΡ ΡΠ°Π·Π±Π΅ΠΆΠΊΡ ΠΏΠΎ Π΄ΠΎΠΏΠΎΠ»Π½ΠΈΡΠ΅Π»ΡΠ½ΠΎΠΌΡ ΡΡΠΈΠ»ΠΈΡ Π² ΡΠΈΡΡΠ΅ΠΌΠ΅.
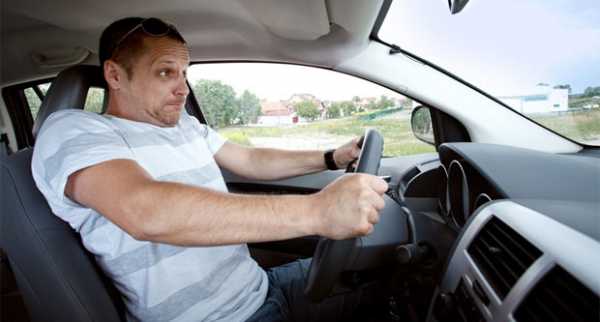
Π€Π°ΠΊΡΠΈΡΠ΅ΡΠΊΠΈ ΡΠ°Π±ΠΎΡΠ΅Π΅ Π΄Π°Π²Π»Π΅Π½ΠΈΠ΅ Π² ΡΠΎΡΠΌΠΎΠ·Π½ΠΎΠΉ ΡΠΈΡΡΠ΅ΠΌΠ΅ ΠΏΡΠΈ ΡΡΠ°ΡΠ½ΠΎΠΌ ΡΠ΅ΠΆΠΈΠΌΠ΅ ΡΠΊΡΠΏΠ»ΡΠ°ΡΠ°ΡΠΈΠΈ Π°Π²ΡΠΎ ΡΠ΅Π΄ΠΊΠΎ ΠΏΡΠ΅Π²ΡΡΠ°Π΅Ρ 100 Π°ΡΠΌΠΎΡΡΠ΅Ρ. Π ΡΠΎΠ»ΡΠΊΠΎ ΠΏΡΠΈ ΡΠΊΡΡΡΠ΅Π½Π½ΠΎΠΌ ΡΠΎΡΠΌΠΎΠΆΠ΅Π½ΠΈΠΈ Ρ ΠΎΡΠΎΡΠΎ ΡΠΈΠ·ΠΈΡΠ΅ΡΠΊΠΈ ΡΠ°Π·Π²ΠΈΡΡΠΉ ΡΠ΅Π»ΠΎΠ²Π΅ΠΊ ΡΠΏΠΎΡΠΎΠ±Π΅Π½ Π΄Π°Π²Π»Π΅Π½ΠΈΠ΅ΠΌ Π½ΠΎΠ³ΠΈ Π½Π° ΠΏΠ΅Π΄Π°Π»Ρ ΡΠΎΠ·Π΄Π°ΡΡ Π΄Π°Π²Π»Π΅Π½ΠΈΠ΅ Π² ΡΠΈΡΡΠ΅ΠΌΠ΅ Π²ΡΡΠ΅ 100 Π°ΡΠΌΠΎΡΡΠ΅Ρ, Π½ΠΎ ΠΏΡΠΎΠΈΡΡ ΠΎΠ΄ΠΈΡ ΡΡΠΎ ΡΠΎΠ»ΡΠΊΠΎ Π² ΠΈΡΠΊΠ»ΡΡΠΈΡΠ΅Π»ΡΠ½ΡΡ ΡΠ»ΡΡΠ°ΡΡ .
ΠΠ°Π²Π»Π΅Π½ΠΈΠ΅ ΠΏΠΎΡΡΠ½Ρ ΡΡΠΏΠΏΠΎΡΡΠ° ΠΈΠ»ΠΈ ΡΠ°Π±ΠΎΡΠΈΡ ΡΠΈΠ»ΠΈΠ½Π΄ΡΠΎΠ² Π½Π° ΠΊΠΎΠ»ΠΎΠ΄ΠΊΠΈ ΠΎΡΠ»ΠΈΡΠ°Π΅ΡΡΡ ΠΎΡ Π³ΠΈΠ΄ΡΠ°Π²Π»ΠΈΡΠ΅ΡΠΊΠΎΠ³ΠΎ Π΄Π°Π²Π»Π΅Π½ΠΈΡ Π² ΡΠΎΡΠΌΠΎΠ·Π½ΠΎΠΉ ΡΠΈΡΡΠ΅ΠΌΠ΅. ΠΠ΄Π΅ΡΡ ΡΠ°Π±ΠΎΡΠ°Π΅Ρ ΠΏΡΠΈΠ½ΡΠΈΠΏ, ΡΡ ΠΎΠ΄Π½ΡΠΉ Ρ ΠΏΡΠΈΠ½ΡΠΈΠΏΠΎΠΌ Π΄Π΅ΠΉΡΡΠ²ΠΈΡ ΡΡΡΠ½ΠΎΠ³ΠΎ Π³ΠΈΠ΄ΡΠ°Π²Π»ΠΈΡΠ΅ΡΠΊΠΎΠ³ΠΎ ΠΏΡΠ΅ΡΡΠ°, Π³Π΄Π΅ Π½Π°ΡΠΎΡΠ½ΡΠΉ ΡΠΈΠ»ΠΈΠ½Π΄Ρ ΠΌΠ°Π»Π΅Π½ΡΠΊΠΎΠ³ΠΎ ΡΠ΅ΡΠ΅Π½ΠΈΡ ΠΏΠ΅ΡΠ΅ΠΊΠ°ΡΠΈΠ²Π°Π΅Ρ ΠΆΠΈΠ΄ΠΊΠΎΡΡΡ Π² ΡΠΈΠ»ΠΈΠ½Π΄Ρ Π·Π½Π°ΡΠΈΡΠ΅Π»ΡΠ½ΠΎ Π±ΠΎΠ»ΡΡΠ΅Π³ΠΎ ΡΠ΅ΡΠ΅Π½ΠΈΡ. ΠΠΎΠ²ΡΡΠ΅Π½ΠΈΠ΅ ΡΡΠΈΠ»ΠΈΡ ΡΠ°ΡΡΡΠΈΡΡΠ²Π°Π΅ΡΡΡ ΠΊΠ°ΠΊ ΠΎΡΠ½ΠΎΡΠ΅Π½ΠΈΠ΅ Π΄ΠΈΠ°ΠΌΠ΅ΡΡΠΎΠ² ΡΠΈΠ»ΠΈΠ½Π΄ΡΠΎΠ². ΠΡΠ»ΠΈ ΠΎΠ±ΡΠ°ΡΠΈΡΡ Π²Π½ΠΈΠΌΠ°Π½ΠΈΠ΅ Π½Π° ΠΏΠΎΡΡΠ΅Π½Ρ ΡΠΎΡΠΌΠΎΠ·Π½ΠΎΠ³ΠΎ ΡΡΠΏΠΏΠΎΡΡΠ° Π»Π΅Π³ΠΊΠΎΠ²ΠΎΠ³ΠΎ Π°Π²ΡΠΎ, ΡΠΎ ΠΎΠ½ Π±ΡΠ΄Π΅Ρ Π² Π½Π΅ΡΠΊΠΎΠ»ΡΠΊΠΎ ΡΠ°Π· Π±ΠΎΠ»ΡΡΠ΅ ΠΏΠΎ Π΄ΠΈΠ°ΠΌΠ΅ΡΡΡ, ΡΠ΅ΠΌ ΠΏΠΎΡΡΠ΅Π½Ρ Π³Π»Π°Π²Π½ΠΎΠ³ΠΎ ΡΠΎΡΠΌΠΎΠ·Π½ΠΎΠ³ΠΎ ΡΠΈΠ»ΠΈΠ½Π΄ΡΠ°. ΠΠΎΡΡΠΎΠΌΡ ΠΈ Π΄Π°Π²Π»Π΅Π½ΠΈΠ΅ Π½Π° ΡΠ°ΠΌΠΈ ΠΊΠΎΠ»ΠΎΠ΄ΠΊΠΈ Π±ΡΠ΄Π΅Ρ ΡΠ²Π΅Π»ΠΈΡΠΈΠ²Π°ΡΡΡΡ Π·Π° ΡΡΡΡ ΡΠ°Π·Π½ΠΈΡΡ Π΄ΠΈΠ°ΠΌΠ΅ΡΡΠΎΠ² ΡΠΈΠ»ΠΈΠ½Π΄ΡΠΎΠ².
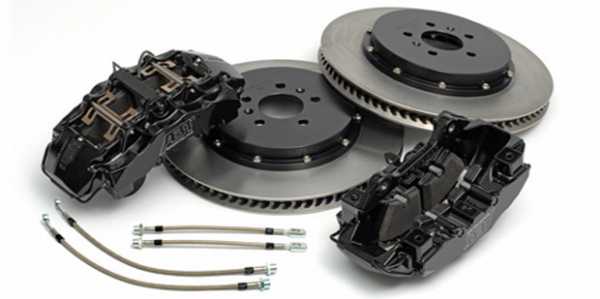
ΠΠ°Π²Π»Π΅Π½ΠΈΠ΅ ΠΏΠ½Π΅Π²ΠΌΠ°ΡΠΈΡΠ΅ΡΠΊΠΈΡ ΡΠΎΡΠΌΠΎΠ·ΠΎΠ²
ΠΡΠΈΠ½ΡΠΈΠΏ ΡΠ°Π±ΠΎΡΡ ΠΏΠ½Π΅Π²ΠΌΠ°ΡΠΈΡΠ΅ΡΠΊΠΎΠΉ ΡΠΈΡΡΠ΅ΠΌΡ Π½Π΅ΡΠΊΠΎΠ»ΡΠΊΠΎ ΠΎΡΠ»ΠΈΡΠ°Π΅ΡΡΡ ΠΎΡ Π³ΠΈΠ΄ΡΠ°Π²Π»ΠΈΡΠ΅ΡΠΊΠΎΠΉ. ΠΠΎ-ΠΏΠ΅ΡΠ²ΡΡ , Π΄Π°Π²ΡΡΠ΅Π΅ Π½Π° ΠΊΠΎΠ»ΠΎΠ΄ΠΊΠΈ ΡΡΠΈΠ»ΠΈΠ΅ ΡΠΎΠ·Π΄Π°ΡΡΡΡ Π½Π°ΠΏΠΎΡΠΎΠΌ Π²ΠΎΠ·Π΄ΡΡ Π°, Π° Π½Π΅ Π΄Π°Π²Π»Π΅Π½ΠΈΠ΅ΠΌ ΠΆΠΈΠ΄ΠΊΠΎΡΡΠΈ. ΠΠΎ-Π²ΡΠΎΡΡΡ , Π²ΠΎΠ΄ΠΈΡΠ΅Π»Ρ Π½Π΅ ΡΠΎΠ·Π΄Π°ΡΡ Π΄Π°Π²Π»Π΅Π½ΠΈΠ΅ ΠΌΡΡΠΊΡΠ»ΡΠ½ΠΎΠΉ ΡΠΈΠ»ΠΎΠΉ Π½ΠΎΠ³ΠΈ. ΠΠΎΠ·Π΄ΡΡ Π² ΡΠ΅ΡΠΈΠ²Π΅Ρ Π½Π°ΠΊΠ°ΡΠΈΠ²Π°Π΅ΡΡΡ ΠΊΠΎΠΌΠΏΡΠ΅ΡΡΠΎΡΠΎΠΌ, ΠΊΠΎΡΠΎΡΡΠΉ ΠΏΠΎΠ»ΡΡΠ°Π΅Ρ ΡΠ½Π΅ΡΠ³ΠΈΡ ΠΎΡ Π΄Π²ΠΈΠ³Π°ΡΠ΅Π»Ρ. Π Π²ΠΎΠ΄ΠΈΡΠ΅Π»Ρ Π½Π°ΠΆΠ°ΡΠΈΠ΅ΠΌ Π½Π° ΠΏΠ΅Π΄Π°Π»Ρ ΡΠΎΡΠΌΠΎΠ·Π° ΡΠΎΠ»ΡΠΊΠΎ ΠΎΡΠΊΡΡΠ²Π°Π΅Ρ ΠΊΡΠ°Π½, ΠΊΠΎΡΠΎΡΡΠΉ ΡΠ°ΡΠΏΡΠ΅Π΄Π΅Π»ΡΠ΅Ρ Π²ΠΎΠ·Π΄ΡΡΠ½ΡΠ΅ ΠΏΠΎΡΠΎΠΊΠΈ ΠΏΠΎ ΠΌΠ°Π³ΠΈΡΡΡΠ°Π»ΡΠΌ.
Π Π°ΡΠΏΡΠ΅Π΄Π΅Π»ΠΈΡΠ΅Π»ΡΠ½ΡΠΉ ΠΊΡΠ°Π½ Π² ΠΏΠ½Π΅Π²ΠΌΠ°ΡΠΈΡΠ΅ΡΠΊΠΎΠΉ ΡΠΈΡΡΠ΅ΠΌΠ΅ ΠΊΠΎΠ½ΡΡΠΎΠ»ΠΈΡΡΠ΅Ρ Π΄Π°Π²Π»Π΅Π½ΠΈΠ΅, ΠΊΠΎΡΠΎΡΠΎΠ΅ ΠΏΠΎΡΡΠ»Π°Π΅ΡΡΡ Π² ΡΠΎΡΠΌΠΎΠ·Π½ΡΠ΅ ΠΊΠ°ΠΌΠ΅ΡΡ. ΠΠ° ΡΡΡΡ ΡΡΠΎΠ³ΠΎ ΡΠ΅Π³ΡΠ»ΠΈΡΡΠ΅ΡΡΡ ΡΡΠΈΠ»ΠΈΠ΅ ΠΏΡΠΈΠΆΠ°ΡΠΈΡ ΠΊΠΎΠ»ΠΎΠ΄ΠΎΠΊ ΠΊ Π±Π°ΡΠ°Π±Π°Π½Π°ΠΌ.
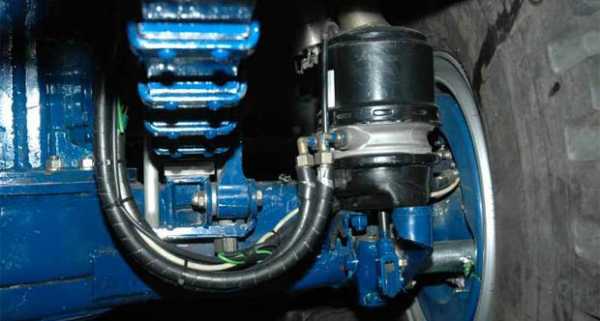
ΠΠ°ΠΊΡΠΈΠΌΠ°Π»ΡΠ½ΠΎΠ΅ Π΄Π°Π²Π»Π΅Π½ΠΈΠ΅ Π² ΠΌΠ°Π³ΠΈΡΡΡΠ°Π»ΡΡ ΠΏΠ½Π΅Π²ΠΌΠ°ΡΠΈΡΠ΅ΡΠΊΠΎΠΉ ΡΠΈΡΡΠ΅ΠΌΡ ΠΎΠ±ΡΡΠ½ΠΎ Π½Π΅ ΠΏΡΠ΅Π²ΡΡΠ°Π΅Ρ 10-12 Π°ΡΠΌΠΎΡΡΠ΅Ρ. ΠΡΠΎ ΡΠΎ Π΄Π°Π²Π»Π΅Π½ΠΈΠ΅, Π½Π° ΠΊΠΎΡΠΎΡΠΎΠ΅ ΡΠ°ΡΡΡΠΈΡΠ°Π½ ΡΠ΅ΡΠΈΠ²Π΅Ρ. ΠΠ΄Π½Π°ΠΊΠΎ ΡΠΈΠ»Π° ΠΏΡΠΈΠΆΠ°ΡΠΈΡ ΠΊΠΎΠ»ΠΎΠ΄ΠΎΠΊ ΠΊ Π±Π°ΡΠ°Π±Π°Π½Π°ΠΌ Π·Π½Π°ΡΠΈΡΠ΅Π»ΡΠ½ΠΎ Π²ΡΡΠ΅. Π£ΡΠΈΠ»Π΅Π½ΠΈΠ΅ ΠΏΡΠΎΠΈΡΡ ΠΎΠ΄ΠΈΡ Π² ΠΌΠ΅ΠΌΠ±ΡΠ°Π½Π½ΡΡ (ΡΠ΅ΠΆΠ΅ β ΠΏΠΎΡΡΠ½Π΅Π²ΡΡ ) ΠΏΠ½Π΅Π²ΠΌΠ°ΡΠΈΡΠ΅ΡΠΊΠΈΡ ΠΊΠ°ΠΌΠ΅ΡΠ°Ρ , ΠΊΠΎΡΠΎΡΡΠ΅ ΠΈ Π΄Π°Π²ΡΡ Π½Π° ΠΊΠΎΠ»ΠΎΠ΄ΠΊΠΈ.
ΠΠ½Π΅Π²ΠΌΠ°ΡΠΈΡΠ΅ΡΠΊΠ°Ρ ΡΠΎΡΠΌΠΎΠ·Π½Π°Ρ ΡΠΈΡΡΠ΅ΠΌΠ° Π½Π° Π»Π΅Π³ΠΊΠΎΠ²ΠΎΠΌ Π°Π²ΡΠΎΠΌΠΎΠ±ΠΈΠ»Π΅ Π²ΡΡΡΠ΅ΡΠ°Π΅ΡΡΡ ΡΠ΅Π΄ΠΊΠΎ. ΠΠ½Π΅Π²ΠΌΠ°ΡΠΈΠΊΠ° Π½Π°ΡΠΈΠ½Π°Π΅Ρ ΠΌΠ°ΡΡΠΎΠ²ΠΎ ΠΏΠΎΡΠ²Π»ΡΡΡΡΡ Π½Π° Π³ΡΡΠ·ΠΎΠΏΠ°ΡΡΠ°ΠΆΠΈΡΡΠΊΠΈΡ Π°Π²ΡΠΎ ΠΈΠ»ΠΈ Π½Π΅Π±ΠΎΠ»ΡΡΠΈΡ Π³ΡΡΠ·ΠΎΠ²ΠΈΠΊΠ°Ρ . ΠΠ½ΠΎΠ³Π΄Π° ΠΏΠ½Π΅Π²ΠΌΠ°ΡΠΈΡΠ΅ΡΠΊΠΈΠ΅ ΡΠΎΡΠΌΠΎΠ·Π° Π΄ΡΠ±Π»ΠΈΡΡΡΡ Π³ΠΈΠ΄ΡΠ°Π²Π»ΠΈΡΠ΅ΡΠΊΠΈΠ΅, ΡΠΎ Π΅ΡΡΡ ΡΠΈΡΡΠ΅ΠΌΠ° ΠΈΠΌΠ΅Π΅Ρ Π΄Π²Π° ΠΎΡΠ΄Π΅Π»ΡΠ½ΡΡ ΠΊΠΎΠ½ΡΡΡΠ°, ΡΡΠΎ ΡΡΠ»ΠΎΠΆΠ½ΡΠ΅Ρ ΠΊΠΎΠ½ΡΡΡΡΠΊΡΠΈΡ, Π½ΠΎ ΡΠ²Π΅Π»ΠΈΡΠΈΠ²Π°Π΅Ρ Π½Π°Π΄ΡΠΆΠ½ΠΎΡΡΡ ΡΠ°Π±ΠΎΡΡ ΡΠΎΡΠΌΠΎΠ·ΠΎΠ².
avtozhidkost.ru
Π’ΠΎΡΠΌΠΎΠ·Π° — ΠΏΡΠΎΠ±Π»Π΅ΠΌΡ ΠΈ Π½Π΅ΠΈΡΠΏΡΠ°Π²Π½ΠΎΡΡΠΈ
Π’ΠΎΡΠΌΠΎΠ·Π½Π°Ρ ΡΠΈΡΡΠ΅ΠΌΠ° ΡΠΎΠ²ΡΠ΅ΠΌΠ΅Π½Π½ΠΎΠ³ΠΎ Π»Π΅Π³ΠΊΠΎΠ²ΠΎΠ³ΠΎ Π°Π²ΡΠΎΠΌΠΎΠ±ΠΈΠ»Ρ ΠΏΡΠ΅Π΄ΡΡΠ°Π²Π»ΡΠ΅Ρ ΡΠΎΠ±ΠΎΠΉ Π·Π°ΠΌΠΊΠ½ΡΡΡΠΉ Π³ΠΈΠ΄ΡΠ°Π²Π»ΠΈΡΠ΅ΡΠΊΠΈΠΉ ΠΊΠΎΠ½ΡΡΡ. ΠΠΎΠ΄ΠΈΡΠ΅Π»Ρ, Π½Π°ΠΆΠ°Π² Π½Π° ΠΏΠ΅Π΄Π°Π»Ρ ΡΠΎΡΠΌΠΎΠ·Π°, ΡΠ²Π΅Π»ΠΈΡΠΈΠ²Π°Π΅Ρ Π΄Π°Π²Π»Π΅Π½ΠΈΠ΅ Π² ΡΠΈΡΡΠ΅ΠΌΠ΅ Π΄ΠΎ 100 Π°ΡΠΌΠΎΡΡΠ΅Ρ, ΡΡΠΎ ΡΠΎΠ±ΡΡΠ²Π΅Π½Π½ΠΎ ΠΈ Π²ΡΠ·ΡΠ²Π°Π΅Ρ Π΄Π²ΠΈΠΆΠ΅Π½ΠΈΠ΅ ΠΏΠΎΡΡΠ½Π΅ΠΉ Π² ΡΡΠΏΠΏΠΎΡΡΠ°Ρ . ΠΠΎΠ²ΡΠ΅ ΠΊΠΎΠΌΠΏΠΎΠ½Π΅Π½ΡΡ ΡΠΎΡΠΌΠΎΠ·Π½ΠΎΠΉ ΡΠΈΡΡΠ΅ΠΌΡ Π±Π΅Π· ΠΏΡΠΎΠ±Π»Π΅ΠΌ ΠΏΠ΅ΡΠ΅Π½ΠΎΡΡΡ ΡΡΠ΅Ρ ΠΊΡΠ°ΡΠ½ΠΎΠ΅ ΠΏΡΠ΅Π²ΡΡΠ΅Π½ΠΈΠ΅ ΡΠΊΠ°Π·Π°Π½Π½ΠΎΠ³ΠΎ Π΄Π°Π²Π»Π΅Π½ΠΈΡ, Π½ΠΎ Ρ ΡΠ΅ΡΠ΅Π½ΠΈΠ΅ΠΌ Π²ΡΠ΅ΠΌΠ΅Π½ΠΈ Π·Π°ΠΏΠ°Ρ ΠΏΡΠΎΡΠ½ΠΎΡΡΠΈ ΡΠ½ΠΈΠΆΠ°Π΅ΡΡΡ.
ΠΠΎΠ»ΡΠ½ΠΎΠΉ Π²ΠΎΠΏΡΠΎΡ
Π‘Π°ΠΌΠΎΠ΅ ΡΠ»Π°Π±ΠΎΠ΅ Π·Π²Π΅Π½ΠΎ Π² ΡΠΎΡΠΌΠΎΠ·Π½ΠΎΠΉ ΡΠΈΡΡΠ΅ΠΌΠ΅ β ΡΠ»Π°Π½Π³ΠΈ ΠΈ ΠΌΠ°Π³ΠΈΡΡΡΠ°Π»ΠΈ, ΠΊΠΎΡΠΎΡΡΠ΅ Π½Π΅ Π·Π°ΡΠΈΡΠ΅Π½Ρ ΠΎΡ Π²ΠΎΠ·Π΄Π΅ΠΉΡΡΠ²ΠΈΡ Π²Π½Π΅ΡΠ½Π΅ΠΉ ΡΡΠ΅Π΄Ρ. Π’Π°ΠΊ, Π½Π°ΠΏΡΠΈΠΌΠ΅Ρ, ΡΠ»Π°Π½Π³ΠΈ ΡΠ΅ΡΡΡΡ ΡΠ²ΠΎΠΈ ΡΠ²ΠΎΠΉΡΡΠ²Π° ΠΈ ΠΌΠΎΠ³ΡΡ ΠΏΠΎΡΡΠ΅ΡΠΊΠ°ΡΡΡΡ ΡΠΆΠ΅ ΡΠ΅ΡΠ΅Π· ΠΏΠ°ΡΡ Π»Π΅Ρ. Π’ΠΎΡΠΌΠΎΠ·Π½ΡΠ΅ ΡΡΡΠ±ΠΊΠΈ ΡΠ°ΡΠ΅ Π²ΡΠ΅Π³ΠΎ ΠΈΠ·Π³ΠΎΡΠΎΠ²Π»Π΅Π½Ρ ΠΈΠ· ΡΡΠ°Π»ΠΈ, ΠΊΠΎΡΠΎΡΠ°Ρ ΡΠΎ Π²ΡΠ΅ΠΌΠ΅Π½Π΅ΠΌ Π½Π°ΡΠΈΠ½Π°Π΅Ρ ΠΊΠΎΡΡΠΎΠ·ΠΈΡΠΎΠ²Π°ΡΡ. Π ΠΎΠ±ΠΎΠΈΡ ΡΠ»ΡΡΠ°ΡΡ ΠΈΠ·Π½ΠΎΡ Π»ΠΈΠ½ΠΈΠΉ Π½ΠΈΠΊΠ°ΠΊ Π½Π΅ Π΄Π°Π΅Ρ ΠΎ ΡΠ΅Π±Π΅ Π·Π½Π°ΡΡ, ΠΈ Π²ΠΎΠ΄ΠΈΡΠ΅Π»Ρ Π½Π°ΡΠΈΠ½Π°Π΅Ρ ΠΏΠΎΠ΄Π²Π΅ΡΠ³Π°ΡΡΡΡ ΠΎΠΏΠ°ΡΠ½ΠΎΠΌΡ ΡΠΈΡΠΊΡ.
Π ΠΎΠ½ ΠΎΠ³ΡΠΎΠΌΠ½ΡΠΉ! ΠΡΠΎΠ³ΡΠ΅ΡΡΠΈΡΡΡΡΠ°Ρ ΠΊΠΎΡΡΠΎΠ·ΠΈΡ Π·Π½Π°ΡΠΈΡΠ΅Π»ΡΠ½ΠΎ ΠΎΡΠ»Π°Π±Π»ΡΠ΅Ρ ΠΏΡΠΎΡΠ½ΠΎΡΡΡ ΠΌΠ΅ΡΡΠ° ΠΏΠΎΡΠ°ΠΆΠ΅Π½ΠΈΡ. ΠΠΎΠΊΠ° Π²ΠΎΠ΄ΠΈΡΠ΅Π»Ρ Π½Π΅ ΡΠΈΠ»ΡΠ½ΠΎ Π½Π°ΠΆΠΈΠΌΠ°Π΅Ρ Π½Π° ΠΏΠ΅Π΄Π°Π»Ρ ΡΠΎΡΠΌΠΎΠ·Π°, Π½ΠΈΡΠ΅Π³ΠΎ Π½Π΅ ΠΏΡΠΎΠΈΡΡ ΠΎΠ΄ΠΈΡ. ΠΠ΄Π½Π°ΠΊΠΎ ΠΏΠΎΠΏΡΡΠΊΠ° ΡΠ΅Π·ΠΊΠΎΠ³ΠΎ ΡΠΎΡΠΌΠΎΠΆΠ΅Π½ΠΈΡ ΠΌΠΎΠΆΠ΅Ρ Π·Π°ΠΊΠΎΠ½ΡΠΈΡΡΡΡ ΡΡΠ°Π³Π΅Π΄ΠΈΠ΅ΠΉ. Π ΠΌΠΎΠΌΠ΅Π½Ρ ΡΠ°Π·ΡΡΠ²Π° ΠΌΠ°Π³ΠΈΡΡΡΠ°Π»ΠΈ Π΄Π°Π²Π»Π΅Π½ΠΈΠ΅ Π² ΡΠΈΡΡΠ΅ΠΌΠ΅ ΡΠ΅Π·ΠΊΠΎ ΠΏΠ°Π΄Π°Π΅Ρ, ΡΡΠΎ ΡΡΡΠ΅ΡΡΠ²Π΅Π½Π½ΠΎ ΡΡ ΡΠ΄ΡΠ°Π΅Ρ ΡΡΡΠ΅ΠΊΡΠΈΠ²Π½ΠΎΡΡΡ ΡΠΎΡΠΌΠΎΠΆΠ΅Π½ΠΈΡ. ΠΠΎΠΏΠΎΠ»Π½ΠΈΡΠ΅Π»ΡΠ½ΠΎΠΉ ΠΏΡΠΎΠ±Π»Π΅ΠΌΠΎΠΉ ΡΠ²Π»ΡΠ΅ΡΡΡ ΡΠΎΡ ΡΠ°ΠΊΡ, ΡΡΠΎ Π·Π°ΡΠ°ΡΡΡΡ ΡΠΎΡΠΌΠΎΠ·Π½ΡΠ΅ Π»ΠΈΠ½ΠΈΠΈ ΠΏΡΠΎΠ»ΠΎΠΆΠ΅Π½Ρ ΡΠ°ΠΊ, ΡΡΠΎ ΡΡΡΠ΄Π½ΠΎ ΠΎΡΠ΅Π½ΠΈΡΡ ΠΈΡ ΡΠΎΡΡΠΎΡΠ½ΠΈΠ΅, Π΄Π°ΠΆΠ΅ ΠΏΡΠΈΠΏΠΎΠ΄Π½ΡΠ² Π°Π²ΡΠΎΠΌΠΎΠ±ΠΈΠ»Ρ Ρ ΠΏΠΎΠΌΠΎΡΡΡ Π΄ΠΎΠΌΠΊΡΠ°ΡΠ°.
ΠΠ½ΠΎΠ³ΠΈΠ΅ Π²ΠΎΠ΄ΠΈΡΠ΅Π»ΠΈ Π²ΠΎ Π²ΡΠ΅ΠΌΡ ΠΏΠΎΠ²ΡΠ΅Π΄Π½Π΅Π²Π½ΡΡ ΠΏΠΎΠ΅Π·Π΄ΠΎΠΊ Π½Π΅ Π΄Π°Π²ΡΡ Π½Π° ΠΏΠ΅Π΄Π°Π»Ρ ΡΠΎΡΠΌΠΎΠ·Π° Ρ Π±ΠΎΠ»ΡΡΠΎΠΉ ΡΠΈΠ»ΠΎΠΉ, ΠΏΠΎΡΡΠΎΠΌΡ Π½Π΅ΠΈΡΠΏΡΠ°Π²Π½ΠΎΡΡΡ ΠΌΠΎΠΆΠ½ΠΎ ΠΎΠ±Π½Π°ΡΡΠΆΠΈΡΡ Π»ΠΈΡΡ ΠΏΡΠΈ ΡΠ΅Ρ Π½ΠΈΡΠ΅ΡΠΊΠΎΠΌ ΠΎΠ±ΡΠ»Π΅Π΄ΠΎΠ²Π°Π½ΠΈΠΈ. ΠΠΈΠ°Π³Π½ΠΎΡΡΡ ΡΠ΅Π³ΡΠ»ΡΡΠ½ΠΎ Π²ΡΡΠ²Π»ΡΡΡ Π΄Π΅ΡΠ΅ΠΊΡΡ. ΠΠ½ΠΈ ΡΡΠ²Π΅ΡΠΆΠ΄Π°ΡΡ, ΡΡΠΎ ΠΏΠΎΡΡΠ΅ΡΠΊΠ°Π²ΡΠΈΠ΅ΡΡ ΡΠΎΡΠΌΠΎΠ·Π½ΡΠ΅ ΡΠ»Π°Π½Π³ΠΈ β ΡΠ΅Π°Π»ΡΠ½Π°Ρ ΠΏΡΠΎΠ±Π»Π΅ΠΌΠ°, ΠΊΠΎΡΠΎΡΠ°Ρ ΠΏΡΠΈΡΡΡΡΡΠ²ΡΠ΅Ρ Π² ΠΌΠ°ΡΡΠΎΠ²ΠΎΠΌ ΠΌΠ°ΡΡΡΠ°Π±Π΅. ΠΠΎΡΡΠΎΠΌΡ, ΡΡΠΈΡΡΠ²Π°Ρ ΠΎΠ³ΡΠΎΠΌΠ½ΡΠΉ ΡΠΈΡΠΊ, Π½Π΅ ΡΠ»Π΅Π΄ΡΠ΅Ρ Π½Π΅Π΄ΠΎΠΎΡΠ΅Π½ΠΈΠ²Π°ΡΡ ΠΊΠΎΠΌΠΌΠ΅Π½ΡΠ°ΡΠΈΠΈ ΡΠΏΠ΅ΡΠΈΠ°Π»ΠΈΡΡΠΎΠ², ΠΊΠ°ΡΠ°ΡΡΠΈΠ΅ΡΡ ΡΠΎΡΠΌΠΎΠ·Π½ΡΡ ΠΌΠ°Π³ΠΈΡΡΡΠ°Π»Π΅ΠΉ. ΠΡΠ»ΠΈ Π΅ΡΡΡ ΠΏΠΎΠ΄ΠΎΠ·ΡΠ΅Π½ΠΈΡ ΠΎΡΠ½ΠΎΡΠΈΡΠ΅Π»ΡΠ½ΠΎ ΠΈΡ ΡΠΎΡΡΠΎΡΠ½ΠΈΡ, ΡΠΎ ΡΠ»Π΅Π΄ΡΠ΅Ρ ΠΊΠ°ΠΊ ΠΌΠΎΠΆΠ½ΠΎ ΡΠΊΠΎΡΠ΅ΠΉ Π·Π°ΠΌΠ΅Π½ΠΈΡΡ ΡΠΎΠΌΠ½ΠΈΡΠ΅Π»ΡΠ½ΡΠ΅ ΡΠ»Π΅ΠΌΠ΅Π½ΡΡ.
Β
Β
Π§ΡΠΎ ΠΏΡΠΎΠΈΡΡ ΠΎΠ΄ΠΈΡ?
ΠΡΠΈΠ½ΡΠΈΠΏΠΈΠ°Π»ΡΠ½Π°Ρ ΡΡ Π΅ΠΌΠ° ΡΠΎΡΠΌΠΎΠ·Π½ΠΎΠΉ ΡΠΈΡΡΠ΅ΠΌΡ.
1 β Π³Π»Π°Π²Π½ΡΠΉ ΡΠΎΡΠΌΠΎΠ·Π½ΠΎΠΉ ΡΠΈΠ»ΠΈΠ½Π΄Ρ Ρ Π²Π°ΠΊΡΡΠΌΠ½ΡΠΌ ΡΡΠΈΠ»ΠΈΡΠ΅Π»Π΅ΠΌ.
2 β ΡΠ΅Π³ΡΠ»ΡΡΠΎΡ Π΄Π°Π²Π»Π΅Π½ΠΈΡ Π² Π·Π°Π΄Π½ΠΈΡ ΡΠΎΡΠΌΠΎΠ·Π½ΡΡ ΠΌΠ΅Ρ Π°Π½ΠΈΠ·ΠΌΠ°Ρ .
3,4 β ΡΠ°Π±ΠΎΡΠΈΠ΅ ΠΊΠΎΠ½ΡΡΡΡ.
ΠΠ° ΠΏΡΠΎΡΡΠΆΠ΅Π½ΠΈΠΈ ΠΌΠ½ΠΎΠ³ΠΈΡ Π»Π΅Ρ ΡΠΎΡΠΌΠΎΠ·Π½ΡΠ΅ ΡΠΈΡΡΠ΅ΠΌΡ Π°Π²ΡΠΎΠΌΠΎΠ±ΠΈΠ»Π΅ΠΉ ΠΎΠ±ΠΎΡΡΠ΄ΠΎΠ²Π°Π»ΠΈΡΡ Π΄Π²ΡΠΌΡ ΠΊΠΎΠ½ΡΡΡΠ°ΠΌΠΈ, ΠΊΠ°ΠΆΠ΄ΡΠΉ ΠΈΠ· ΠΊΠΎΡΠΎΡΡΡ ΠΎΡΠ²Π΅ΡΠ°Π΅Ρ Π·Π° Π΄Π²Π° ΠΊΠΎΠ»Π΅ΡΠ°. Π’Π°ΠΊΠ°Ρ ΡΡ Π΅ΠΌΠ° Π² ΡΠ»ΡΡΠ°Π΅ ΡΠ°Π·ΡΡΠ²Π° ΠΊΠ°Π½Π°Π»Π° ΠΏΠΎΠ·Π²ΠΎΠ»ΡΠ΅Ρ ΠΎΡΡΠ°Π½ΠΎΠ²ΠΈΡΡ Π°Π²ΡΠΎΠΌΠΎΠ±ΠΈΠ»Ρ Ρ ΠΏΠΎΠΌΠΎΡΡΡ ΠΎΡΡΠ°Π²ΡΠ΅Π³ΠΎΡΡ ΠΊΠΎΠ½ΡΡΡΠ°.
ΠΠ½ΠΎΠ³ΠΎΡΠΈΡΠ»Π΅Π½Π½ΡΠ΅ Π·Π°Π΅Π·Π΄Ρ, ΠΏΡΠΎΠ²Π΅Π΄Π΅Π½Π½ΡΠ΅ Ρ ΡΠ΅Π»ΡΡ Π·Π°ΠΌΠ΅ΡΠΈΡΡ ΡΡΡΠ΅ΠΊΡΠΈΠ²Π½ΠΎΡΡΡ ΡΠΎΡΠΌΠΎΠΆΠ΅Π½ΠΈΡ Ρ ΠΎΠ΄Π½ΠΈΠΌ ΠΈΡΠΏΡΠ°Π²Π½ΡΠΌ ΠΊΠΎΠ½ΡΡΡΠΎΠΌ, Π΄Π°Π»ΠΈ ΡΠΎΠΊΠΈΡΡΡΡΠΈΠΉ ΡΠ΅Π·ΡΠ»ΡΡΠ°Ρ. ΠΠΊΠ°Π·Π°Π»ΠΎΡΡ, ΡΡΠΎ ΡΡΠ΅Π΄Π½ΠΈΠΉ ΡΠΎΡΠΌΠΎΠ·Π½ΠΎΠΉ ΠΏΡΡΡ Π°Π²ΡΠΎΠΌΠΎΠ±ΠΈΠ»Ρ Β ΠΏΡΠΈ ΡΠΎΡΠΌΠΎΠΆΠ΅Π½ΠΈΠΈ ΡΠΎ 100 ΠΊΠΌ/Ρ ΡΠ²Π΅Π»ΠΈΡΠΈΠ²Π°Π΅ΡΡΡ Π² Π΄Π²Π° ΡΠ°Π·Π° β Ρ 40 Π΄ΠΎ 86 ΠΌΠ΅ΡΡΠΎΠ²!
ΠΠ«ΠΠΠ. ΠΠ΅ΠΈΡΠΏΡΠ°Π²Π½Π°Ρ ΡΠΎΡΠΌΠΎΠ·Π½Π°Ρ ΡΠΈΡΡΠ΅ΠΌΠ° Π·Π°ΡΠΈΡΠ°Π΅Ρ ΠΎΡ ΠΏΠΎΠ»Π½ΠΎΠΉ Β«ΠΏΠΎΡΠ΅ΡΠΈ ΡΠΎΡΠΌΠΎΠ·ΠΎΠ²Β», ΠΎΠ΄Π½Π°ΠΊΠΎ ΡΡΡΠ΅ΠΊΡΠΈΠ²Π½ΠΎΡΡΡ ΡΠΎΡΠΌΠΎΠΆΠ΅Π½ΠΈΡ Π·Π½Π°ΡΠΈΡΠ΅Π»ΡΠ½ΠΎ ΡΠ½ΠΈΠΆΠ°Π΅ΡΡΡ.
Β
Β
ΠΠ°ΠΊ Π·Π°ΡΠΈΡΠΈΡΡ ΡΠ΅Π±Ρ ΠΎΡ Π½Π΅ΠΎΠΆΠΈΠ΄Π°Π½Π½ΠΎΡΡΠΈ
Π Π°Π·ΡΡΠ²Ρ ΡΠΎΡΠΌΠΎΠ·Π½ΡΡ Π»ΠΈΠ½ΠΈΠΉ Π½Π΅ ΠΏΡΠ΅Π΄ΡΠ΅ΡΡΠ²ΡΡΡ Π½ΠΈΠΊΠ°ΠΊΠΈΠ΅ ΠΏΡΠΈΠ·Π½Π°ΠΊΠΈ, ΠΊΠΎΡΠΎΡΡΠ΅ ΠΌΠΎΠ³Π»ΠΈ Π±Ρ ΠΏΠΎΠ΄ΡΠΊΠ°Π·Π°ΡΡ ΠΎ ΠΏΡΠΎΠ±Π»Π΅ΠΌΠ΅. ΠΡΡΠ΅ΠΊΡΠΈΠ²Π½ΠΎΡΡΡ ΡΠΎΡΠΌΠΎΠ·ΠΎΠ² Π½Π΅ ΠΏΠ°Π΄Π°Π΅Ρ Π²ΠΏΠ»ΠΎΡΡ Π΄ΠΎ Β«ΡΡΠ°Π³Π΅Π΄ΠΈΠΈΒ». ΠΠΎΡΡΠΎΠΌΡ Π΅Π΄ΠΈΠ½ΡΡΠ²Π΅Π½Π½ΡΠΉ Π²ΡΡ ΠΎΠ΄ β ΡΠ΅Π³ΡΠ»ΡΡΠ½ΡΠΉ ΠΊΠΎΠ½ΡΡΠΎΠ»Ρ ΡΠΏΠ΅ΡΠΈΠ°Π»ΠΈΡΡΠ°ΠΌΠΈ, ΠΎΡΠΎΠ±Π΅Π½Π½ΠΎ Π²ΠΎ Π²ΡΠ΅ΠΌΡ Π’Π. ΠΠΈΠΊΠΎΠ³Π΄Π° Π½Π΅Π»ΡΠ·Ρ Π½Π΅Π΄ΠΎΠΎΡΠ΅Π½ΠΈΠ²Π°ΡΡ ΠΏΠΎΠ»ΡΡΠ΅Π½Π½ΡΡ ΠΎΡ ΠΌΠ΅Ρ Π°Π½ΠΈΠΊΠΎΠ² ΡΠ΅ΠΊΠΎΠΌΠ΅Π½Π΄Π°ΡΠΈΠΉ, ΠΊΠ°ΡΠ°ΡΡΠΈΡ ΡΡ ΡΠΎΡΠΌΠΎΠ·Π½ΠΎΠΉ ΡΠΈΡΡΠ΅ΠΌΡ.
Β
Β
Π¦Π΅Π½Π° Π±Π΅Π·ΠΎΠΏΠ°ΡΠ½ΠΎΡΡΠΈ
ΠΠ°ΡΡΠ°ΡΡ Π½Π° Π·Π°ΠΌΠ΅Π½Ρ ΡΠΎΡΠΌΠΎΠ·Π½ΡΡ Π»ΠΈΠ½ΠΈΠΉ ΠΎΡΠ»ΠΈΡΠ°ΡΡΡΡ Π² Π·Π°Π²ΠΈΡΠΈΠΌΠΎΡΡΠΈ ΠΎΡ ΡΠΈΠΏΠ° ΠΈ Π΄Π»ΠΈΠ½Ρ. Π Π±ΠΎΠ»ΡΡΠΈΠ½ΡΡΠ²Π΅ ΡΠ»ΡΡΠ°Π΅Π² Π½ΠΎΠ²ΡΠΉ ΡΠ»Π΅ΠΌΠ΅Π½Ρ Ρ ΡΠ°Π±ΠΎΡΠΎΠΉ ΠΏΠΎΡΡΠ΅Π±ΡΠ΅Ρ ΠΎΠΊΠΎΠ»ΠΎ 20-50 Π΄ΠΎΠ»Π»Π°ΡΠΎΠ². ΠΠ½ΠΎΠ³ΠΈΠ΅ ΡΠ΅ΡΠ²ΠΈΡΡ ΠΌΠ΅Π½ΡΡΡ ΠΆΠ΅ΡΡΠΊΠΈΠ΅ ΡΡΠ°Π»ΡΠ½ΡΠ΅ ΡΡΡΠ±ΠΊΠΈ Π½Π° Π±ΠΎΠ»Π΅Π΅ ΡΠ΄ΠΎΠ±Π½ΡΠ΅ Π² Π΄ΠΎΡΠ°Π±ΠΎΡΠΊΠ΅ ΠΌΠ΅Π΄Π½ΡΠ΅. Π‘Π»Π΅Π΄ΡΠ΅Ρ Π²Π·ΡΡΡ Π·Π° ΠΏΡΠ°Π²ΠΈΠ»ΠΎ ΠΏΠ΅ΡΠΈΠΎΠ΄ΠΈΡΠ΅ΡΠΊΠΈ ΠΏΡΠΎΠ²Π΅ΡΡΡΡ ΡΠΎΡΡΠΎΡΠ½ΠΈΠ΅ ΡΠΎΡΠΌΠΎΠ·Π½ΡΡ ΡΠ»Π°Π½Π³ΠΎΠ² ΠΈ ΡΡΡΠ±ΠΎΠΊ, Π΄Π°ΠΆΠ΅ Π΅ΡΠ»ΠΈ Π°Π²ΡΠΎΠΌΠΎΠ±ΠΈΠ»Ρ Π²ΡΠ΅Π³ΠΎ ΠΏΠ°ΡΠ° Π»Π΅Ρ.
ΠΠ°ΠΊΠ»ΡΡΠ΅Π½ΠΈΠ΅
ΠΡΠΈΠ½ΠΈΠΌΠ°Ρ Π²ΠΎ Π²Π½ΠΈΠΌΠ°Π½ΠΈΠ΅ ΡΠΎ, ΠΊΠ°ΠΊ ΡΠ°ΡΡΠΎ ΠΎΠ±Π½Π°ΡΡΠΆΠΈΠ²Π°ΡΡΡΡ Π΄Π΅ΡΠ΅ΠΊΡΡ ΡΠΎΡΠΌΠΎΠ·Π½ΡΡ ΠΌΠ°Π³ΠΈΡΡΡΠ°Π»Π΅ΠΉ, ΠΏΡΠ΅Π΄ΡΡΠ°Π²ΡΡΠ΅ — ΡΠΊΠΎΠ»ΡΠΊΠΎ Π²ΠΎΠ΄ΠΈΡΠ΅Π»Π΅ΠΉ ΠΏΠ΅ΡΠ΅Π΄Π²ΠΈΠ³Π°Π΅ΡΡΡ Π½Π° ΡΠΌΠ΅ΡΡΠ΅Π»ΡΠ½ΠΎ ΠΎΠΏΠ°ΡΠ½ΡΡ Π°Π²ΡΠΎΠΌΠΎΠ±ΠΈΠ»ΡΡ . ΠΠΎΠ»ΠΈΡΠ΅ΡΡΠ²ΠΎ ΠΏΡΠΎΡΡΠΎ ΠΎΡΠ΅Π»ΠΎΠΌΠ»ΡΠ΅Ρ. Π Π³Π»Π°Π²Π½ΠΎΠ΅ β ΠΏΡΠΎΠ±Π»Π΅ΠΌΠ° ΠΊΠ°ΡΠ°Π΅ΡΡΡ Π½Π΅ ΡΠΎΠ»ΡΠΊΠΎ ΡΡΠ°ΡΡΡ ΠΌΠ°ΡΠΈΠ½. Β«ΠΡΠΊΠ°Π·Ρ ΡΠΎΡΠΌΠΎΠ·ΠΎΠ²Β» ΠΏΠΎΠ΄Π²Π΅ΡΠΆΠ΅Π½Ρ ΠΈ ΡΡΠ°Π²Π½ΠΈΡΠ΅Π»ΡΠ½ΠΎ ΠΌΠΎΠ»ΠΎΠ΄ΡΠ΅ Π°Π²ΡΠΎΠΌΠΎΠ±ΠΈΠ»ΠΈ, ΠΎΡΠΎΠ±Π΅Π½Π½ΠΎ ΡΠΊΡΠΏΠ»ΡΠ°ΡΠΈΡΡΠ΅ΠΌΡΠ΅ Π²ΠΎ Π²Π»Π°ΠΆΠ½ΠΎΠΌ ΠΊΠ»ΠΈΠΌΠ°ΡΠ΅ ΠΈΠ»ΠΈ Π½Π° Π·ΠΈΠΌΠ½ΠΈΡ Π΄ΠΎΡΠΎΠ³Π°Ρ , ΠΎΠ±ΠΈΠ»ΡΠ½ΠΎ ΠΏΠΎΠ»ΠΈΡΡΡ ΡΠ΅Π°Π³Π΅Π½ΡΠ°ΠΌΠΈ.Β
vvm-auto.ru
ΠΠ°ΠΊΠΎΠ΅ Π΄Π°Π²Π»Π΅Π½ΠΈΠ΅ Π² ΡΠΎΡΠΌΠΎΠ·Π½ΠΎΠΉ ΡΠΈΡΡΠ΅ΠΌΠ΅ Π°Π²ΡΠΎΠΌΠΎΠ±ΠΈΠ»Ρ?
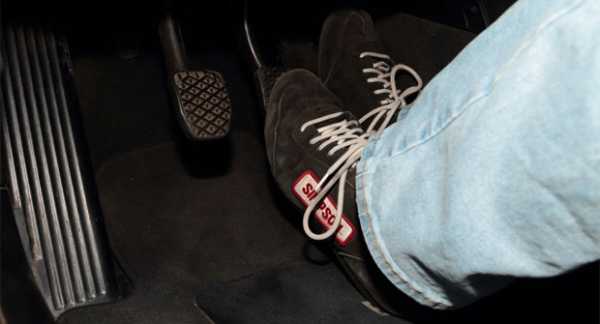
ΠΠΎΠΊΠ° ΡΠΎΡΠΌΠΎΠ·Π½Π°Ρ ΡΠΈΡΡΠ΅ΠΌΠ° ΠΈΡΠΏΡΠ°Π²Π½ΠΎ ΡΡΠ½ΠΊΡΠΈΠΎΠ½ΠΈΡΡΠ΅Ρ, ΡΠ΅Π΄ΠΊΠΈΠΉ Π²ΠΎΠ΄ΠΈΡΠ΅Π»Ρ Π·Π°Π΄ΡΠΌΡΠ²Π°Π΅ΡΡΡ, ΠΊΠ°ΠΊΠΈΠ΅ ΠΏΡΠΎΡΠ΅ΡΡΡ ΠΏΡΠΎΠΈΡΡ ΠΎΠ΄ΡΡ Π² Π½Π΅ΠΉ, ΠΈ ΠΊΠ°ΠΊΠΈΠΌΠΈ ΠΏΠ°ΡΠ°ΠΌΠ΅ΡΡΠ°ΠΌΠΈ ΠΎΠ±ΡΡΠ»ΠΎΠ²Π»Π΅Π½Π° Π΅Ρ ΡΠ°Π±ΠΎΡΠ°. ΠΠ°Π²Π°ΠΉΡΠ΅ ΡΠ°Π·Π±Π΅ΡΡΠΌΡΡ, ΠΊΠ°ΠΊΠΎΠ΅ Π΄Π°Π²Π»Π΅Π½ΠΈΠ΅ Π² ΡΠΎΡΠΌΠΎΠ·Π½ΠΎΠΉ ΡΠΈΡΡΠ΅ΠΌΠ΅ Π°Π²ΡΠΎΠΌΠΎΠ±ΠΈΠ»Ρ, ΠΈ Π½Π°ΡΠΊΠΎΠ»ΡΠΊΠΎ ΡΡΠ° Π²Π΅Π»ΠΈΡΠΈΠ½Π° ΡΠ°Π·Π»ΠΈΡΠ°Π΅ΡΡΡ Ρ Π³ΠΈΠ΄ΡΠ°Π²Π»ΠΈΡΠ΅ΡΠΊΠΎΠ³ΠΎ ΠΈ ΠΏΠ½Π΅Π²ΠΌΠ°ΡΠΈΡΠ΅ΡΠΊΠΎΠ³ΠΎ ΠΈΡΠΏΠΎΠ»Π½Π΅Π½ΠΈΡ.
ΠΠ°ΠΊΠΎΠ΅ Π΄Π°Π²Π»Π΅Π½ΠΈΠ΅ Π² Π³ΠΈΠ΄ΡΠ°Π²Π»ΠΈΡΠ΅ΡΠΊΠΈΡ ΡΠΎΡΠΌΠΎΠ·Π°Ρ Π»Π΅Π³ΠΊΠΎΠ²ΡΡ Π°Π²ΡΠΎ?
ΠΠ·Π½Π°ΡΠ°Π»ΡΠ½ΠΎ Π΅ΡΡΡ ΡΠΌΡΡΠ» ΡΠ°Π·ΠΎΠ±ΡΠ°ΡΡΡΡ Π² ΡΠ°ΠΊΠΈΡ ΠΏΠΎΠ½ΡΡΠΈΡΡ , ΠΊΠ°ΠΊ Π΄Π°Π²Π»Π΅Π½ΠΈΠ΅ Π² Π³ΠΈΠ΄ΡΠ°Π²Π»ΠΈΡΠ΅ΡΠΊΠΎΠΉ ΡΠΈΡΡΠ΅ΠΌΠ΅ ΠΈ Π΄Π°Π²Π»Π΅Π½ΠΈΠ΅, ΠΎΠΊΠ°Π·ΡΠ²Π°Π΅ΠΌΠΎΠ΅ ΡΡΠΏΠΏΠΎΡΡΠ°ΠΌΠΈ ΠΈΠ»ΠΈ ΡΡΠΎΠΊΠ°ΠΌΠΈ ΡΠΈΠ»ΠΈΠ½Π΄ΡΠΎΠ² Π½Π΅ΠΏΠΎΡΡΠ΅Π΄ΡΡΠ²Π΅Π½Π½ΠΎ Π½Π° ΡΠΎΡΠΌΠΎΠ·Π½ΡΠ΅ ΠΊΠΎΠ»ΠΎΠ΄ΠΊΠΈ.
ΠΠ°Π²Π»Π΅Π½ΠΈΠ΅ Π² ΡΠ°ΠΌΠΎΠΉ Π³ΠΈΠ΄ΡΠ°Π²Π»ΠΈΡΠ΅ΡΠΊΠΎΠΉ ΡΠΈΡΡΠ΅ΠΌΠ΅ Π°Π²ΡΠΎ Π²ΠΎ Π²ΡΠ΅Ρ Π΅Ρ ΡΡΠ°ΡΡΠΊΠ°Ρ ΠΏΡΠΈΠΌΠ΅ΡΠ½ΠΎ ΠΎΠ΄ΠΈΠ½Π°ΠΊΠΎΠ²ΠΎΠ΅ ΠΈ ΡΠΎΡΡΠ°Π²Π»ΡΠ΅Ρ Π½Π° ΡΠ²ΠΎΡΠΌ ΠΏΠΈΠΊΠ΅ Ρ Π½Π°ΠΈΠ±ΠΎΠ»Π΅Π΅ ΡΠΎΠ²ΡΠ΅ΠΌΠ΅Π½Π½ΡΡ Π°Π²ΡΠΎ ΠΎΠΊΠΎΠ»ΠΎ 180 Π±Π°Ρ (Π΅ΡΠ»ΠΈ ΡΡΠΈΡΠ°ΡΡ Π² Π°ΡΠΌΠΎΡΡΠ΅ΡΠ°Ρ , ΡΠΎ ΡΡΠΎ ΠΏΡΠΈΠ±Π»ΠΈΠ·ΠΈΡΠ΅Π»ΡΠ½ΠΎ 177 Π°ΡΠΌ). Π ΡΠΏΠΎΡΡΠΈΠ²Π½ΡΡ ΠΈΠ»ΠΈ Π³ΡΠ°ΠΆΠ΄Π°Π½ΡΠΊΠΈΡ Π·Π°ΡΡΠΆΠ΅Π½Π½ΡΡ Π°Π²ΡΠΎ ΡΡΠΎ Π΄Π°Π²Π»Π΅Π½ΠΈΠ΅ ΠΌΠΎΠΆΠ΅Ρ Π΄ΠΎΡ ΠΎΠ΄ΠΈΡΡ Π΄ΠΎ 200 Π±Π°Ρ.
Π Π°Π·ΡΠΌΠ΅Π΅ΡΡΡ, ΡΡΠΎ ΡΠΎΠ»ΡΠΊΠΎ ΡΡΠΈΠ»ΠΈΠ΅ΠΌ ΠΌΡΡΠΊΡΠ»ΡΠ½ΠΎΠΉ ΡΠΈΠ»Ρ ΡΠ΅Π»ΠΎΠ²Π΅ΠΊΠ° Π½Π°ΠΏΡΡΠΌΡΡ ΡΠΎΠ·Π΄Π°ΡΡ ΠΏΠΎΠ΄ΠΎΠ±Π½ΠΎΠ΅ Π΄Π°Π²Π»Π΅Π½ΠΈΠ΅ Π½Π΅Π²ΠΎΠ·ΠΌΠΎΠΆΠ½ΠΎ. ΠΠΎΡΡΠΎΠΌΡ Π² ΡΠΎΡΠΌΠΎΠ·Π½ΠΎΠΉ ΡΠΈΡΡΠ΅ΠΌΠ΅ Π°Π²ΡΠΎ Π΅ΡΡΡ Π΄Π²Π° ΡΡΠΈΠ»ΠΈΠ²Π°ΡΡΠΈΡ ΡΠ°ΠΊΡΠΎΡΠ°.
- Π ΡΡΠ°Π³ ΠΏΠ΅Π΄Π°Π»ΠΈ. ΠΠ° ΡΡΠ΅Ρ ΡΡΡΠ°Π³Π°, ΠΊΠΎΡΠΎΡΡΠΉ ΠΎΠ±Π΅ΡΠΏΠ΅ΡΠΈΠ²Π°Π΅ΡΡΡ ΠΊΠΎΠ½ΡΡΡΡΠΊΡΠΈΠ΅ΠΉ ΠΏΠ΅Π΄Π°Π»ΡΠ½ΠΎΠ³ΠΎ ΡΠ·Π»Π°, ΠΈΠ·Π½Π°ΡΠ°Π»ΡΠ½ΠΎ ΠΏΡΠΈΠ»Π°Π³Π°Π΅ΠΌΠΎΠ΅ Π²ΠΎΠ΄ΠΈΡΠ΅Π»Π΅ΠΌ Π΄Π°Π²Π»Π΅Π½ΠΈΠ΅ Π½Π° ΠΏΠ΅Π΄Π°Π»Ρ ΡΠ²Π΅Π»ΠΈΡΠΈΠ²Π°Π΅ΡΡΡ Π² 4-8 ΡΠ°Π· Π² Π·Π°Π²ΠΈΡΠΈΠΌΠΎΡΡΠΈ ΠΎΡ ΠΌΠ°ΡΠΊΠΈ Π°Π²ΡΠΎ.
- ΠΠ°ΠΊΡΡΠΌΠ½ΡΠΉ ΡΡΠΈΠ»ΠΈΡΠ΅Π»Ρ. ΠΡΠΎΡ ΡΠ·Π΅Π» ΡΠ°ΠΊΠΆΠ΅ ΡΡΠΈΠ»ΠΈΠ²Π°Π΅Ρ Π΄Π°Π²Π»Π΅Π½ΠΈΠ΅ Π½Π° Π³Π»Π°Π²Π½ΡΠΉ ΡΠΎΡΠΌΠΎΠ·Π½ΠΎΠΉ ΡΠΈΠ»ΠΈΠ½Π΄Ρ ΠΏΡΠΈΠ±Π»ΠΈΠ·ΠΈΡΠ΅Π»ΡΠ½ΠΎ Π² 2 ΡΠ°Π·Π°. Π₯ΠΎΡΡ ΡΠ°Π·Π½ΡΠ΅ ΠΊΠΎΠ½ΡΡΡΡΠΊΡΠΈΠΈ ΡΡΠΎΠ³ΠΎ ΡΠ·Π»Π° ΠΏΡΠ΅Π΄ΡΡΠΌΠ°ΡΡΠΈΠ²Π°ΡΡ Π΄ΠΎΠ²ΠΎΠ»ΡΠ½ΠΎ Π±ΠΎΠ»ΡΡΡΡ ΡΠ°Π·Π±Π΅ΠΆΠΊΡ ΠΏΠΎ Π΄ΠΎΠΏΠΎΠ»Π½ΠΈΡΠ΅Π»ΡΠ½ΠΎΠΌΡ ΡΡΠΈΠ»ΠΈΡ Π² ΡΠΈΡΡΠ΅ΠΌΠ΅.
Π€Π°ΠΊΡΠΈΡΠ΅ΡΠΊΠΈ ΡΠ°Π±ΠΎΡΠ΅Π΅ Π΄Π°Π²Π»Π΅Π½ΠΈΠ΅ Π² ΡΠΎΡΠΌΠΎΠ·Π½ΠΎΠΉ ΡΠΈΡΡΠ΅ΠΌΠ΅ ΠΏΡΠΈ ΡΡΠ°ΡΠ½ΠΎΠΌ ΡΠ΅ΠΆΠΈΠΌΠ΅ ΡΠΊΡΠΏΠ»ΡΠ°ΡΠ°ΡΠΈΠΈ Π°Π²ΡΠΎ ΡΠ΅Π΄ΠΊΠΎ ΠΏΡΠ΅Π²ΡΡΠ°Π΅Ρ 100 Π°ΡΠΌΠΎΡΡΠ΅Ρ. Π ΡΠΎΠ»ΡΠΊΠΎ ΠΏΡΠΈ ΡΠΊΡΡΡΠ΅Π½Π½ΠΎΠΌ ΡΠΎΡΠΌΠΎΠΆΠ΅Π½ΠΈΠΈ Ρ ΠΎΡΠΎΡΠΎ ΡΠΈΠ·ΠΈΡΠ΅ΡΠΊΠΈ ΡΠ°Π·Π²ΠΈΡΡΠΉ ΡΠ΅Π»ΠΎΠ²Π΅ΠΊ ΡΠΏΠΎΡΠΎΠ±Π΅Π½ Π΄Π°Π²Π»Π΅Π½ΠΈΠ΅ΠΌ Π½ΠΎΠ³ΠΈ Π½Π° ΠΏΠ΅Π΄Π°Π»Ρ ΡΠΎΠ·Π΄Π°ΡΡ Π΄Π°Π²Π»Π΅Π½ΠΈΠ΅ Π² ΡΠΈΡΡΠ΅ΠΌΠ΅ Π²ΡΡΠ΅ 100 Π°ΡΠΌΠΎΡΡΠ΅Ρ, Π½ΠΎ ΠΏΡΠΎΠΈΡΡ ΠΎΠ΄ΠΈΡ ΡΡΠΎ ΡΠΎΠ»ΡΠΊΠΎ Π² ΠΈΡΠΊΠ»ΡΡΠΈΡΠ΅Π»ΡΠ½ΡΡ ΡΠ»ΡΡΠ°ΡΡ .
ΠΠ°Π²Π»Π΅Π½ΠΈΠ΅ ΠΏΠΎΡΡΠ½Ρ ΡΡΠΏΠΏΠΎΡΡΠ° ΠΈΠ»ΠΈ ΡΠ°Π±ΠΎΡΠΈΡ ΡΠΈΠ»ΠΈΠ½Π΄ΡΠΎΠ² Π½Π° ΠΊΠΎΠ»ΠΎΠ΄ΠΊΠΈ ΠΎΡΠ»ΠΈΡΠ°Π΅ΡΡΡ ΠΎΡ Π³ΠΈΠ΄ΡΠ°Π²Π»ΠΈΡΠ΅ΡΠΊΠΎΠ³ΠΎ Π΄Π°Π²Π»Π΅Π½ΠΈΡ Π² ΡΠΎΡΠΌΠΎΠ·Π½ΠΎΠΉ ΡΠΈΡΡΠ΅ΠΌΠ΅. ΠΠ΄Π΅ΡΡ ΡΠ°Π±ΠΎΡΠ°Π΅Ρ ΠΏΡΠΈΠ½ΡΠΈΠΏ, ΡΡ ΠΎΠ΄Π½ΡΠΉ Ρ ΠΏΡΠΈΠ½ΡΠΈΠΏΠΎΠΌ Π΄Π΅ΠΉΡΡΠ²ΠΈΡ ΡΡΡΠ½ΠΎΠ³ΠΎ Π³ΠΈΠ΄ΡΠ°Π²Π»ΠΈΡΠ΅ΡΠΊΠΎΠ³ΠΎ ΠΏΡΠ΅ΡΡΠ°, Π³Π΄Π΅ Π½Π°ΡΠΎΡΠ½ΡΠΉ ΡΠΈΠ»ΠΈΠ½Π΄Ρ ΠΌΠ°Π»Π΅Π½ΡΠΊΠΎΠ³ΠΎ ΡΠ΅ΡΠ΅Π½ΠΈΡ ΠΏΠ΅ΡΠ΅ΠΊΠ°ΡΠΈΠ²Π°Π΅Ρ ΠΆΠΈΠ΄ΠΊΠΎΡΡΡ Π² ΡΠΈΠ»ΠΈΠ½Π΄Ρ Π·Π½Π°ΡΠΈΡΠ΅Π»ΡΠ½ΠΎ Π±ΠΎΠ»ΡΡΠ΅Π³ΠΎ ΡΠ΅ΡΠ΅Π½ΠΈΡ. ΠΠΎΠ²ΡΡΠ΅Π½ΠΈΠ΅ ΡΡΠΈΠ»ΠΈΡ ΡΠ°ΡΡΡΠΈΡΡΠ²Π°Π΅ΡΡΡ ΠΊΠ°ΠΊ ΠΎΡΠ½ΠΎΡΠ΅Π½ΠΈΠ΅ Π΄ΠΈΠ°ΠΌΠ΅ΡΡΠΎΠ² ΡΠΈΠ»ΠΈΠ½Π΄ΡΠΎΠ². ΠΡΠ»ΠΈ ΠΎΠ±ΡΠ°ΡΠΈΡΡ Π²Π½ΠΈΠΌΠ°Π½ΠΈΠ΅ Π½Π° ΠΏΠΎΡΡΠ΅Π½Ρ ΡΠΎΡΠΌΠΎΠ·Π½ΠΎΠ³ΠΎ ΡΡΠΏΠΏΠΎΡΡΠ° Π»Π΅Π³ΠΊΠΎΠ²ΠΎΠ³ΠΎ Π°Π²ΡΠΎ, ΡΠΎ ΠΎΠ½ Π±ΡΠ΄Π΅Ρ Π² Π½Π΅ΡΠΊΠΎΠ»ΡΠΊΠΎ ΡΠ°Π· Π±ΠΎΠ»ΡΡΠ΅ ΠΏΠΎ Π΄ΠΈΠ°ΠΌΠ΅ΡΡΡ, ΡΠ΅ΠΌ ΠΏΠΎΡΡΠ΅Π½Ρ Π³Π»Π°Π²Π½ΠΎΠ³ΠΎ ΡΠΎΡΠΌΠΎΠ·Π½ΠΎΠ³ΠΎ ΡΠΈΠ»ΠΈΠ½Π΄ΡΠ°. ΠΠΎΡΡΠΎΠΌΡ ΠΈ Π΄Π°Π²Π»Π΅Π½ΠΈΠ΅ Π½Π° ΡΠ°ΠΌΠΈ ΠΊΠΎΠ»ΠΎΠ΄ΠΊΠΈ Π±ΡΠ΄Π΅Ρ ΡΠ²Π΅Π»ΠΈΡΠΈΠ²Π°ΡΡΡΡ Π·Π° ΡΡΡΡ ΡΠ°Π·Π½ΠΈΡΡ Π΄ΠΈΠ°ΠΌΠ΅ΡΡΠΎΠ² ΡΠΈΠ»ΠΈΠ½Π΄ΡΠΎΠ².
ΠΠ°Π²Π»Π΅Π½ΠΈΠ΅ ΠΏΠ½Π΅Π²ΠΌΠ°ΡΠΈΡΠ΅ΡΠΊΠΈΡ ΡΠΎΡΠΌΠΎΠ·ΠΎΠ²
ΠΡΠΈΠ½ΡΠΈΠΏ ΡΠ°Π±ΠΎΡΡ ΠΏΠ½Π΅Π²ΠΌΠ°ΡΠΈΡΠ΅ΡΠΊΠΎΠΉ ΡΠΈΡΡΠ΅ΠΌΡ Π½Π΅ΡΠΊΠΎΠ»ΡΠΊΠΎ ΠΎΡΠ»ΠΈΡΠ°Π΅ΡΡΡ ΠΎΡ Π³ΠΈΠ΄ΡΠ°Π²Π»ΠΈΡΠ΅ΡΠΊΠΎΠΉ. ΠΠΎ-ΠΏΠ΅ΡΠ²ΡΡ , Π΄Π°Π²ΡΡΠ΅Π΅ Π½Π° ΠΊΠΎΠ»ΠΎΠ΄ΠΊΠΈ ΡΡΠΈΠ»ΠΈΠ΅ ΡΠΎΠ·Π΄Π°ΡΡΡΡ Π½Π°ΠΏΠΎΡΠΎΠΌ Π²ΠΎΠ·Π΄ΡΡ Π°, Π° Π½Π΅ Π΄Π°Π²Π»Π΅Π½ΠΈΠ΅ΠΌ ΠΆΠΈΠ΄ΠΊΠΎΡΡΠΈ. ΠΠΎ-Π²ΡΠΎΡΡΡ , Π²ΠΎΠ΄ΠΈΡΠ΅Π»Ρ Π½Π΅ ΡΠΎΠ·Π΄Π°ΡΡ Π΄Π°Π²Π»Π΅Π½ΠΈΠ΅ ΠΌΡΡΠΊΡΠ»ΡΠ½ΠΎΠΉ ΡΠΈΠ»ΠΎΠΉ Π½ΠΎΠ³ΠΈ. ΠΠΎΠ·Π΄ΡΡ Π² ΡΠ΅ΡΠΈΠ²Π΅Ρ Π½Π°ΠΊΠ°ΡΠΈΠ²Π°Π΅ΡΡΡ ΠΊΠΎΠΌΠΏΡΠ΅ΡΡΠΎΡΠΎΠΌ, ΠΊΠΎΡΠΎΡΡΠΉ ΠΏΠΎΠ»ΡΡΠ°Π΅Ρ ΡΠ½Π΅ΡΠ³ΠΈΡ ΠΎΡ Π΄Π²ΠΈΠ³Π°ΡΠ΅Π»Ρ. Π Π²ΠΎΠ΄ΠΈΡΠ΅Π»Ρ Π½Π°ΠΆΠ°ΡΠΈΠ΅ΠΌ Π½Π° ΠΏΠ΅Π΄Π°Π»Ρ ΡΠΎΡΠΌΠΎΠ·Π° ΡΠΎΠ»ΡΠΊΠΎ ΠΎΡΠΊΡΡΠ²Π°Π΅Ρ ΠΊΡΠ°Π½, ΠΊΠΎΡΠΎΡΡΠΉ ΡΠ°ΡΠΏΡΠ΅Π΄Π΅Π»ΡΠ΅Ρ Π²ΠΎΠ·Π΄ΡΡΠ½ΡΠ΅ ΠΏΠΎΡΠΎΠΊΠΈ ΠΏΠΎ ΠΌΠ°Π³ΠΈΡΡΡΠ°Π»ΡΠΌ.
Π Π°ΡΠΏΡΠ΅Π΄Π΅Π»ΠΈΡΠ΅Π»ΡΠ½ΡΠΉ ΠΊΡΠ°Π½ Π² ΠΏΠ½Π΅Π²ΠΌΠ°ΡΠΈΡΠ΅ΡΠΊΠΎΠΉ ΡΠΈΡΡΠ΅ΠΌΠ΅ ΠΊΠΎΠ½ΡΡΠΎΠ»ΠΈΡΡΠ΅Ρ Π΄Π°Π²Π»Π΅Π½ΠΈΠ΅, ΠΊΠΎΡΠΎΡΠΎΠ΅ ΠΏΠΎΡΡΠ»Π°Π΅ΡΡΡ Π² ΡΠΎΡΠΌΠΎΠ·Π½ΡΠ΅ ΠΊΠ°ΠΌΠ΅ΡΡ. ΠΠ° ΡΡΡΡ ΡΡΠΎΠ³ΠΎ ΡΠ΅Π³ΡΠ»ΠΈΡΡΠ΅ΡΡΡ ΡΡΠΈΠ»ΠΈΠ΅ ΠΏΡΠΈΠΆΠ°ΡΠΈΡ ΠΊΠΎΠ»ΠΎΠ΄ΠΎΠΊ ΠΊ Π±Π°ΡΠ°Π±Π°Π½Π°ΠΌ.
ΠΠ°ΠΊΡΠΈΠΌΠ°Π»ΡΠ½ΠΎΠ΅ Π΄Π°Π²Π»Π΅Π½ΠΈΠ΅ Π² ΠΌΠ°Π³ΠΈΡΡΡΠ°Π»ΡΡ ΠΏΠ½Π΅Π²ΠΌΠ°ΡΠΈΡΠ΅ΡΠΊΠΎΠΉ ΡΠΈΡΡΠ΅ΠΌΡ ΠΎΠ±ΡΡΠ½ΠΎ Π½Π΅ ΠΏΡΠ΅Π²ΡΡΠ°Π΅Ρ 10-12 Π°ΡΠΌΠΎΡΡΠ΅Ρ. ΠΡΠΎ ΡΠΎ Π΄Π°Π²Π»Π΅Π½ΠΈΠ΅, Π½Π° ΠΊΠΎΡΠΎΡΠΎΠ΅ ΡΠ°ΡΡΡΠΈΡΠ°Π½ ΡΠ΅ΡΠΈΠ²Π΅Ρ. ΠΠ΄Π½Π°ΠΊΠΎ ΡΠΈΠ»Π° ΠΏΡΠΈΠΆΠ°ΡΠΈΡ ΠΊΠΎΠ»ΠΎΠ΄ΠΎΠΊ ΠΊ Π±Π°ΡΠ°Π±Π°Π½Π°ΠΌ Π·Π½Π°ΡΠΈΡΠ΅Π»ΡΠ½ΠΎ Π²ΡΡΠ΅. Π£ΡΠΈΠ»Π΅Π½ΠΈΠ΅ ΠΏΡΠΎΠΈΡΡ ΠΎΠ΄ΠΈΡ Π² ΠΌΠ΅ΠΌΠ±ΡΠ°Π½Π½ΡΡ (ΡΠ΅ΠΆΠ΅ β ΠΏΠΎΡΡΠ½Π΅Π²ΡΡ ) ΠΏΠ½Π΅Π²ΠΌΠ°ΡΠΈΡΠ΅ΡΠΊΠΈΡ ΠΊΠ°ΠΌΠ΅ΡΠ°Ρ , ΠΊΠΎΡΠΎΡΡΠ΅ ΠΈ Π΄Π°Π²ΡΡ Π½Π° ΠΊΠΎΠ»ΠΎΠ΄ΠΊΠΈ.
ΠΠ½Π΅Π²ΠΌΠ°ΡΠΈΡΠ΅ΡΠΊΠ°Ρ ΡΠΎΡΠΌΠΎΠ·Π½Π°Ρ ΡΠΈΡΡΠ΅ΠΌΠ° Π½Π° Π»Π΅Π³ΠΊΠΎΠ²ΠΎΠΌ Π°Π²ΡΠΎΠΌΠΎΠ±ΠΈΠ»Π΅ Π²ΡΡΡΠ΅ΡΠ°Π΅ΡΡΡ ΡΠ΅Π΄ΠΊΠΎ. ΠΠ½Π΅Π²ΠΌΠ°ΡΠΈΠΊΠ° Π½Π°ΡΠΈΠ½Π°Π΅Ρ ΠΌΠ°ΡΡΠΎΠ²ΠΎ ΠΏΠΎΡΠ²Π»ΡΡΡΡΡ Π½Π° Π³ΡΡΠ·ΠΎΠΏΠ°ΡΡΠ°ΠΆΠΈΡΡΠΊΠΈΡ Π°Π²ΡΠΎ ΠΈΠ»ΠΈ Π½Π΅Π±ΠΎΠ»ΡΡΠΈΡ Π³ΡΡΠ·ΠΎΠ²ΠΈΠΊΠ°Ρ . ΠΠ½ΠΎΠ³Π΄Π° ΠΏΠ½Π΅Π²ΠΌΠ°ΡΠΈΡΠ΅ΡΠΊΠΈΠ΅ ΡΠΎΡΠΌΠΎΠ·Π° Π΄ΡΠ±Π»ΠΈΡΡΡΡ Π³ΠΈΠ΄ΡΠ°Π²Π»ΠΈΡΠ΅ΡΠΊΠΈΠ΅, ΡΠΎ Π΅ΡΡΡ ΡΠΈΡΡΠ΅ΠΌΠ° ΠΈΠΌΠ΅Π΅Ρ Π΄Π²Π° ΠΎΡΠ΄Π΅Π»ΡΠ½ΡΡ ΠΊΠΎΠ½ΡΡΡΠ°, ΡΡΠΎ ΡΡΠ»ΠΎΠΆΠ½ΡΠ΅Ρ ΠΊΠΎΠ½ΡΡΡΡΠΊΡΠΈΡ, Π½ΠΎ ΡΠ²Π΅Π»ΠΈΡΠΈΠ²Π°Π΅Ρ Π½Π°Π΄ΡΠΆΠ½ΠΎΡΡΡ ΡΠ°Π±ΠΎΡΡ ΡΠΎΡΠΌΠΎΠ·ΠΎΠ².
neauto.ru
β°ΠΡΠΈΠ½ΡΠΈΠΏ ΡΠ°Π±ΠΎΡΡ ΠΏΠ½Π΅Π²ΠΌΠ°ΡΠΈΡΠ΅ΡΠΊΠΎΠΉ ΡΠΎΡΠΌΠΎΠ·Π½ΠΎΠΉ ΡΠΈΡΡΠ΅ΠΌΡ Π°Π²ΡΠΎΠΌΠΎΠ±ΠΈΠ»Ρ
ΠΠ½Π΅Π²ΠΌΠ°ΡΠΈΡΠ΅ΡΠΊΠΈΠΉ ΡΠΎΡΠΌΠΎΠ·Π½ΠΎΠΉ ΠΏΡΠΈΠ²ΠΎΠ΄ — Π²ΠΈΠ΄ ΠΊΠΎΠ½ΡΡΡΡΠΊΡΠΈΠΈ ΡΠΎΡΠΌΠΎΠ·Π½ΠΎΠΉ ΡΠΈΡΡΠ΅ΠΌΡ, ΠΊΠΎΡΠΎΡΠ°Ρ ΠΈΡΠΏΠΎΠ»ΡΠ·ΡΠ΅Ρ Π² ΠΊΠ°ΡΠ΅ΡΡΠ²Π΅ ΡΠ½Π΅ΡΠ³ΠΎΠ½ΠΎΡΠΈΡΠ΅Π»Ρ ΡΠΆΠ°ΡΡΠΉ Π²ΠΎΠ·Π΄ΡΡ . ΠΠ½Π΅Π²ΠΌΠ°ΡΠΈΡΠ΅ΡΠΊΠΈΠ΅ ΡΠΎΡΠΌΠΎΠ·Π° ΠΈΡΠΏΠΎΠ»ΡΠ·ΡΡΡ Π² ΡΠ°Π·Π½ΡΡ Π²ΠΈΠ΄Π°Ρ ΡΡΠ°Π½ΡΠΏΠΎΡΡΠ°:
- ΠΏΠ°ΡΡΠ°ΠΆΠΈΡΡΠΊΠΈΠ΅ Π°Π²ΡΠΎΠ±ΡΡΡ;
- Π³ΡΡΠ·ΠΎΠ²ΡΠ΅ ΠΊΠΎΠΌΠΌΠ΅ΡΡΠ΅ΡΠΊΠΈΠ΅ Π°Π²ΡΠΎΠΌΠΎΠ±ΠΈΠ»ΠΈ;
- ΡΠΏΠ΅ΡΠΈΠ°Π»ΠΈΠ·ΠΈΡΠΎΠ²Π°Π½Π½Π°Ρ ΡΠ΅Ρ Π½ΠΈΠΊΠ° — Π³ΡΠ΅ΠΉΠ΄Π΅ΡΡ, Π±ΡΠ»ΡΠ΄ΠΎΠ·Π΅ΡΡ, ΠΏΠΎΠ³ΡΡΠ·ΡΠΈΠΊΠΈ, Π°Π²ΡΠΎΠΊΡΠ°Π½Ρ, Π΄ΡΡΠ³ΠΈΠ΅ ΠΊΡΡΠΏΠ½ΠΎ- ΠΈ ΠΌΠ°Π»ΠΎΠ³Π°Π±Π°ΡΠΈΡΠ½ΡΠ΅ ΡΠΏΠ΅ΡΡΡΠ΅Π΄ΡΡΠ²Π°;
- ΠΆΠ΅Π»Π΅Π·Π½ΠΎΠ΄ΠΎΡΠΎΠΆΠ½ΡΠΉ ΡΡΠ°Π½ΡΠΏΠΎΡΡ.
Π’ΡΠ³Π°Ρ DAF XF105 — ΠΏΡΠΈΠΌΠ΅Ρ Π³ΡΡΠ·ΠΎΠ²ΠΈΠΊΠ° Ρ ΠΏΠ½Π΅Π²ΠΌΠ°ΡΠΈΡΠ΅ΡΠΊΠΈΠΌΠΈ ΡΠΎΡΠΌΠΎΠ·Π°ΠΌΠΈ
ΠΠ°Ρ ΠΈΠ½ΡΠ΅ΡΠ΅ΡΡΠ΅Ρ ΠΈΠΌΠ΅Π½Π½ΠΎ Π°Π²ΡΠΎΠΌΠΎΠ±ΠΈΠ»ΡΠ½ΡΠΉ Π²Π°ΡΠΈΠ°Π½Ρ ΠΏΠ½Π΅Π²ΠΌΠ°ΡΠΈΡΠ΅ΡΠΊΠΎΠ³ΠΎ ΡΠΎΡΠΌΠΎΠ·Π½ΠΎΠ³ΠΎ ΠΏΡΠΈΠ²ΠΎΠ΄Π°. Π ΡΡΠ°ΡΡΠ΅ ΠΌΡ ΡΠ°ΡΡΠΊΠ°ΠΆΠ΅ΠΌ ΠΎ:
- Π²ΠΈΠ΄Π°Ρ ΠΏΠ½Π΅Π²ΠΌΠ°ΡΠΈΡΠ΅ΡΠΊΠΈΡ ΡΠΎΡΠΌΠΎΠ·Π½ΡΡ ΡΠΈΡΡΠ΅ΠΌ;
- ΠΊΠΎΠ½ΡΡΡΡΠΊΡΠΈΠΈ ΠΈ ΠΏΡΠΈΠ½ΡΠΈΠΏΠ΅ ΡΠ°Π±ΠΎΡΡ ΠΏΠ½Π΅Π²ΠΌΠΎΠΏΡΠΈΠ²ΠΎΠ΄Π°;
- ΠΎΡΠ½ΠΎΠ²Π½ΡΡ ΠΏΡΠ΅ΠΈΠΌΡΡΠ΅ΡΡΠ²Π°Ρ ΠΈ Π½Π΅Π΄ΠΎΡΡΠ°ΡΠΊΠ°Ρ ΠΏΠ½Π΅Π²ΠΌΠ°ΡΠΈΠΊΠΈ Π² ΡΡΠ°Π²Π½Π΅Π½ΠΈΠΈ Ρ Π³ΠΈΠ΄ΡΠ°Π²Π»ΠΈΡΠ΅ΡΠΊΠΈΠΌΠΈ ΡΠΎΡΠΌΠΎΠ·Π°ΠΌΠΈ;
- Π½Π΅ΠΈΡΠΏΡΠ°Π²Π½ΠΎΡΡΡΡ , ΠΊΠΎΡΠΎΡΡΠ΅ Π²ΠΎΠ·Π½ΠΈΠΊΠ°ΡΡ Π² ΡΠ°Π±ΠΎΡΠ΅ ΠΏΠ½Π΅Π²ΠΌΠΎΡΠΎΡΠΌΠΎΠ·ΠΎΠ², ΠΏΡΠΈΠ·Π½Π°ΠΊΠ°Ρ ΠΈ ΠΏΠΎΡΠ»Π΅Π΄ΡΡΠ²ΠΈΡΡ ΠΏΠΎΠ»ΠΎΠΌΠΎΠΊ, Π° ΡΠ°ΠΊΠΆΠ΅ Π΄Π°Π΄ΠΈΠΌ ΠΏΠΎΠ»Π΅Π·Π½ΡΠ΅ ΡΠΎΠ²Π΅ΡΡ ΠΊΠ°ΠΊ ΠΏΡΠΎΠ΄Π»ΠΈΡΡ ΡΡΠΎΠΊ ΡΠ»ΡΠΆΠ±Ρ ΡΠΎΡΠΌΠΎΠ·Π½ΠΎΠΉ ΡΠΈΡΡΠ΅ΠΌΡ.
ΠΠ»Π°ΡΡΠΈΡΠΈΠΊΠ°ΡΠΈΡ ΠΏΠ½Π΅Π²ΠΌΠ°ΡΠΈΡΠ΅ΡΠΊΠΈΡ ΡΠΎΡΠΌΠΎΠ·Π½ΡΡ ΡΠΈΡΡΠ΅ΠΌ
ΠΠ½Π΅Π²ΠΌΠ°ΡΠΈΡΠ΅ΡΠΊΠΈΠΉ ΡΠΎΡΠΌΠΎΠ·Π½ΠΎΠΉ ΠΏΡΠΈΠ²ΠΎΠ΄ ΠΈΡΠΏΠΎΠ»ΡΠ·ΡΡΡ ΠΎΡΠ΄Π΅Π»ΡΠ½ΠΎ ΠΈΠ»ΠΈ Π² ΠΊΠΎΠΌΠΏΠ»Π΅ΠΊΡΠ΅ Ρ Π΄ΡΡΠ³ΠΈΠΌΠΈ ΡΠΈΡΡΠ΅ΠΌΠ°ΠΌΠΈ (ΠΏΡΠΈΠΌΠ΅ΡΡ — ΠΊΠΎΠΌΠ±ΠΈΠ½ΠΈΡΠΎΠ²Π°Π½Π½ΡΠ΅ ΡΠΎΡΠΌΠΎΠ·Π½ΡΠ΅ ΡΠΈΡΡΠ΅ΠΌΡ ΡΠ»Π΅ΠΊΡΡΠΎΠΏΠ½Π΅Π²ΠΌΠ°ΡΠΈΡΠ΅ΡΠΊΠΎΠ³ΠΎ ΠΈΠ»ΠΈ ΠΏΠ½Π΅Π²ΠΌΠΎΠ³ΠΈΠ΄ΡΠ°Π²Π»ΠΈΡΠ΅ΡΠΊΠΎΠ³ΠΎ ΡΠΈΠΏΠ°).
ΠΠ½Π΅Π²ΠΌΠ°ΡΠΈΡΠ΅ΡΠΊΠΈΠ΅ ΡΠΎΡΠΌΠΎΠ·Π½ΡΠ΅ ΡΠΈΡΡΠ΅ΠΌΡ ΡΠ°ΠΊΠΆΠ΅ ΠΊΠ»Π°ΡΡΠΈΡΠΈΡΠΈΡΡΡΡ ΠΏΠΎ ΠΊΠΎΠ»ΠΈΡΠ΅ΡΡΠ²Ρ ΡΠ°Π±ΠΎΡΠΈΡ ΠΊΠΎΠ½ΡΡΡΠΎΠ²-ΠΌΠ°Π³ΠΈΡΡΡΠ°Π»Π΅ΠΉ. ΠΡΡΡΠ΅ΡΠ°ΡΡΡΡ 3 Π²ΠΈΠ΄Π° ΡΠΈΡΡΠ΅ΠΌ:
- ΠΎΠ΄Π½ΠΎΠΊΠΎΠ½ΡΡΡΠ½ΡΠ΅;
- Π΄Π²ΡΡ ΠΊΠΎΠ½ΡΡΡΠ½ΡΠ΅;
- ΠΌΠ½ΠΎΠ³ΠΎΠΊΠΎΠ½ΡΡΡΠ½ΡΠ΅.
ΠΠ΄Π½ΠΎΠΊΠΎΠ½ΡΡΡΠ½ΡΠ΅ ΡΠΈΡΡΠ΅ΠΌΡ. ΠΡΠΎΠ±Π΅Π½Π½ΠΎΡΡΡ — ΠΌΠ°Π³ΠΈΡΡΡΠ°Π»ΠΈ Π½Π° ΠΏΠ΅ΡΠ΅Π΄Π½ΠΈΠ΅ ΠΈ Π·Π°Π΄Π½ΠΈΠ΅ ΠΊΠΎΠ»Π΅ΡΠ° ΠΎΠ±ΡΠ΅Π΄ΠΈΠ½Π΅Π½Ρ Π² ΠΎΠ΄Π½Ρ Π²Π΅ΡΠΊΡ, Π° ΠΈΠ½ΡΠ΅Π½ΡΠΈΠ²Π½ΠΎΡΡΡ ΠΏΠΎΡΠΎΠΊΠ° ΡΠΆΠ°ΡΠΎΠ³ΠΎ Π²ΠΎΠ·Π΄ΡΡ Π° ΠΊΠΎΠ½ΡΡΠΎΠ»ΠΈΡΡΠ΅Ρ ΠΎΠ΄ΠΈΠ½ ΡΠΎΡΠΌΠΎΠ·Π½ΠΎΠΉ ΠΊΡΠ°Π½. ΠΠ΄Π½ΠΎΠΊΠΎΠ½ΡΡΡΠ½Π°Ρ ΠΌΠΎΠ΄Π΅Π»Ρ ΠΏΠ½Π΅Π²ΠΌΠ°ΡΠΈΡΠ΅ΡΠΊΠΎΠΉ ΡΠΎΡΠΌΠΎΠ·Π½ΠΎΠΉ ΡΠΈΡΡΠ΅ΠΌΡ — ΡΡΡΠ°ΡΠ΅Π²ΡΠΈΠΉ ΡΠΈΠΏ ΠΊΠΎΠ½ΡΡΡΡΠΊΡΠΈΠΈ, ΠΊΠΎΡΠΎΡΡΠΉ Π² Π±ΠΎΠ»ΡΡΠΈΠ½ΡΡΠ²Π΅ ΡΠ»ΡΡΠ°Π΅Π² Π²ΡΡΡΠ΅ΡΠ°Π΅ΡΡΡ ΡΠΎΠ»ΡΠΊΠΎ Π½Π° ΡΡΠ°ΡΡΡ ΠΌΠΎΠ΄Π΅Π»ΡΡ Π³ΡΡΠ·ΠΎΠ²ΡΡ Π°Π²ΡΠΎΠΌΠΎΠ±ΠΈΠ»Π΅ΠΉ ΠΈ Π°Π²ΡΠΎΠ±ΡΡΠΎΠ².
ΠΠ²ΡΡ ΠΊΠΎΠ½ΡΡΡΠ½ΡΠ΅ ΡΠΈΡΡΠ΅ΠΌΡ. ΠΡΠ»ΠΈΡΠΈΡ ΠΏΠΎΠ½ΡΡΠ½Ρ ΠΈΠ· Π½Π°Π·Π²Π°Π½ΠΈΡ — ΠΌΠ°Π³ΠΈΡΡΡΠ°Π»ΠΈ ΡΠΎΡΠΌΠΎΠ·Π½ΠΎΠΉ ΡΠΈΡΡΠ΅ΠΌΡ Π°Π²ΡΠΎΠΌΠΎΠ±ΠΈΠ»Ρ ΡΠ°Π·Π΄Π΅Π»Π΅Π½Ρ Π½Π° Π΄Π²Π΅ Π²Π΅ΡΠΊΠΈ. ΠΠ΄Π½Π° Π²Π΅ΡΠΊΠ° ΠΏΠ΅ΡΠ΅Π΄Π°Π΅Ρ ΡΠΆΠ°ΡΡΠΉ Π²ΠΎΠ·Π΄ΡΡ Π½Π° ΠΏΠ΅ΡΠ΅Π΄Π½ΠΈΠ΅ ΠΊΠΎΠ»Π΅ΡΠ°, Π²ΡΠΎΡΠ°Ρ — Π½Π° Π·Π°Π΄Π½ΠΈΠ΅. ΠΠΎΡΠΎΠΊ ΡΠ½Π΅ΡΠ³ΠΎΠ½ΠΎΡΠΈΡΠ΅Π»Ρ ΠΊΠΎΠ½ΡΡΠΎΠ»ΠΈΡΡΡΡ Π΄Π²Π° ΡΠΎΡΠΌΠΎΠ·Π½ΡΡ ΠΊΡΠ°Π½Π° — ΠΏΠΎ ΠΎΠ΄Π½ΠΎΠΌΡ Π½Π° ΠΊΠ°ΠΆΠ΄ΡΠΉ ΠΊΠΎΠ½ΡΡΡ ΠΌΠ°Π³ΠΈΡΡΡΠ°Π»Π΅ΠΉ. ΠΠ²ΡΡ ΠΊΠΎΠ½ΡΡΡΠ½Π°Ρ ΠΊΠΎΠ½ΡΡΡΡΠΊΡΠΈΡ Π½Π°Π΄Π΅ΠΆΠ½Π΅Π΅, ΡΠ΅ΠΌ ΠΎΠ΄Π½ΠΎΠΊΠΎΠ½ΡΡΡΠ½Π°Ρ. ΠΡΠ»ΠΈ Π²ΡΡΠ»Π° ΠΈΠ· ΡΡΡΠΎΡ Π²Π΅ΡΠΊΠ° Π·Π°Π΄Π½Π΅ΠΉ ΠΎΡΠΈ, ΠΏΠ΅ΡΠ΅Π΄Π½ΠΈΠ΅ ΡΠΎΡΠΌΠΎΠ·Π½ΡΠ΅ ΡΠ·Π»Ρ ΠΏΡΠΎΠ΄ΠΎΠ»ΠΆΠ°ΡΡ ΡΡΠ½ΠΊΡΠΈΠΎΠ½ΠΈΡΠΎΠ²Π°ΡΡ ΠΈ Π½Π°ΠΎΠ±ΠΎΡΠΎΡ.
ΠΠ½ΠΎΠ³ΠΎΠΊΠΎΠ½ΡΡΡΠ½ΡΠ΅ ΡΠΈΡΡΠ΅ΠΌΡ. ΠΡΠΎΠ±Π΅Π½Π½ΠΎΡΡΡ — ΡΠ»ΠΎΠΆΠ½Π°Ρ, Π½ΠΎ ΡΡΡΠ΅ΠΊΡΠΈΠ²Π½Π°Ρ ΠΈ Π½Π°Π΄Π΅ΠΆΠ½Π°Ρ ΠΊΠΎΠ½ΡΡΡΡΠΊΡΠΈΡ. ΠΠ½ΠΎΠ³ΠΎΠΊΠΎΠ½ΡΡΡΠ½ΡΠ΅ ΠΏΠ½Π΅Π²ΠΌΠ°ΡΠΈΡΠ΅ΡΠΊΠΈΠ΅ ΡΠΈΡΡΠ΅ΠΌΡ Π²ΡΡΡΠ΅ΡΠ°ΡΡΡΡ Π² ΠΊΡΡΠΏΠ½ΡΡ Π³ΡΡΠ·ΠΎΠ²ΡΡ Π°Π²ΡΠΎΠΌΠΎΠ±ΠΈΠ»ΡΡ ΠΈ ΡΠΎΡΡΠΎΡΡ ΠΈΠ· ΡΡΠ΅Ρ ΠΈ Π±ΠΎΠ»ΡΡΠ΅ ΠΊΠΎΠ½ΡΡΡΠΎΠ². ΠΠ½ΠΎΠ³ΠΎΠΊΠΎΠ½ΡΡΡΠ½Π°Ρ ΡΠΎΡΠΌΠΎΠ·Π½Π°Ρ ΠΏΠ½Π΅Π²ΠΌΠΎΡΠΈΡΡΠ΅ΠΌΠ° ΡΠ²Π΅Π»ΠΈΡΠΈΠ²Π°Π΅Ρ ΡΡΡΠΎΠΉΡΠΈΠ²ΠΎΡΡΡ, ΠΎΠ±Π»Π΅Π³ΡΠ°Π΅Ρ ΡΠΏΡΠ°Π²Π»Π΅Π½ΠΈΠ΅ ΠΈ ΠΎΡΡΠ°Π½ΠΎΠ²ΠΊΡ Π³ΡΡΠ·ΠΎΠ²ΠΈΠΊΠ°.
ΠΠΎΠ½ΡΡΡΡΠΊΡΠΈΡ ΠΏΠ½Π΅Π²ΠΌΠ°ΡΠΈΡΠ΅ΡΠΊΠΎΠΉ ΡΠΎΡΠΌΠΎΠ·Π½ΠΎΠΉ ΡΠΈΡΡΠ΅ΠΌΡ
ΠΠΎΠ½ΡΡΡΡΠΊΡΠΈΡ ΠΏΠ½Π΅Π²ΠΌΠ°ΡΠΈΡΠ΅ΡΠΊΠΎΠ³ΠΎ ΡΠΎΡΠΌΠΎΠ·Π½ΠΎΠ³ΠΎ ΠΏΡΠΈΠ²ΠΎΠ΄Π° ΠΏΡΠΈΠΌΠ΅ΡΠ½ΠΎ ΠΎΠ΄ΠΈΠ½Π°ΠΊΠΎΠ²Π°Ρ Π΄Π»Ρ Π²ΡΠ΅Ρ Π²ΠΈΠ΄ΠΎΠ² Π°Π²ΡΠΎΠΌΠΎΠ±ΠΈΠ»Π΅ΠΉ. ΠΡΠ»ΠΈΡΠ°ΡΡΡΡ ΠΌΠΎΠ³ΡΡ ΠΎΡΠ΄Π΅Π»ΡΠ½ΡΠ΅ ΡΠ·Π»Ρ ΠΈ ΡΠ»Π΅ΠΌΠ΅Π½ΡΡ.
ΠΠ±ΡΠΈΠΉ Π²ΠΈΠ΄ ΠΏΠ½Π΅Π²ΠΌΠ°ΡΠΈΡΠ΅ΡΠΊΠΎΠΉ ΡΠΎΡΠΌΠΎΠ·Π½ΠΎΠΉ ΡΠΈΡΡΠ΅ΠΌΡ: 1 — Π΄Π²ΡΡ ΡΠ΅ΠΊΡΠΈΠΎΠ½Π½ΡΠΉ ΡΠΎΡΠΌΠΎΠ·Π½ΠΎΠΉ ΠΊΡΠ°Π½, 2, 6 — ΡΠΎΡΠΌΠΎΠ·Π½ΡΠ΅ ΠΊΠ°ΠΌΠ΅ΡΡ (ΡΠΈΠ»ΠΎΠ²ΡΠ΅ ΡΠΈΠ»ΠΈΠ½Π΄ΡΡ), 3 — ΠΏΡΠ΅Π΄ΠΎΡ ΡΠ°Π½ΠΈΡΠ΅Π»ΡΠ½ΡΠΉ ΠΊΠ»Π°ΠΏΠ°Π½, 4 — ΡΠ΅Π³ΡΠ»ΡΡΠΎΡ Π΄Π°Π²Π»Π΅Π½ΠΈΡ, 5 — ΠΊΠΎΠΌΠΏΡΠ΅ΡΡΠΎΡ, 7 — ΠΊΡΠ°Π½ ΠΎΡΠ±ΠΎΡΠ° Π²ΠΎΠ·Π΄ΡΡ Π°, 8 ΠΈ 9 — ΡΠ°Π·ΠΎΠ±ΡΠΈΡΠ΅Π»ΡΠ½ΡΠΉ ΠΊΡΠ°Π½ Ρ ΡΠΎΠ΅Π΄ΠΈΠ½ΠΈΡΠ΅Π»ΡΠ½ΠΎΠΉ Π³ΠΎΠ»ΠΎΠ²ΠΊΠΎΠΉ, 10 — ΡΠ΅ΡΠΈΠ²Π΅ΡΡ (Π²ΠΎΠ·Π΄ΡΡΠ½ΡΠ΅ Π±Π°Π»Π»ΠΎΠ½Ρ), 11, 12 — ΡΠΎΡΠΌΠΎΠ·Π½ΡΠ΅ Π±Π°ΡΠ°Π±Π°Π½Ρ Π² ΡΠ±ΠΎΡΠ΅.
ΠΠΎΠΌΠΏΡΠ΅ΡΡΠΎΡ. ΠΠ°Π³Π½Π΅ΡΠ°Π΅Ρ Π²ΠΎΠ·Π΄ΡΡ Π² ΡΠ΅ΡΠΈΠ²Π΅ΡΠ°Ρ (Π±Π°Π»Π»ΠΎΠ½Π°Ρ ). ΠΠΎΠΌΠΏΡΠ΅ΡΡΠΎΡ ΡΡΡΠ°Π½Π°Π²Π»ΠΈΠ²Π°ΡΡ Π² ΠΏΠ΅ΡΠ΅Π΄Π½ΡΡ ΡΠ°ΡΡΡ Π°Π²ΡΠΎΠΌΠΎΠ±ΠΈΠ»Ρ Π²ΠΎΠ·Π»Π΅ Π±Π»ΠΎΠΊΠ° Π΄Π²ΠΈΠ³Π°ΡΠ΅Π»Ρ. ΠΠ³ΡΠ΅Π³Π°Ρ ΡΠ°Π±ΠΎΡΠ°Π΅Ρ ΠΎΡ ΠΊΠ»ΠΈΠ½ΠΎΠ²ΠΈΠ΄Π½ΠΎΠ³ΠΎ ΡΠ΅ΠΌΠ½Ρ, ΠΊΠΎΡΠΎΡΡΠΉ ΡΠΎΠ΅Π΄ΠΈΠ½ΡΠ΅Ρ ΡΠΊΠΈΠ² ΠΊΠΎΠΌΠΏΡΠ΅ΡΡΠΎΡΠ° ΠΈ ΡΠΊΠΈΠ² ΡΠ°Π΄ΠΈΠ°ΡΠΎΡΠ½ΠΎΠ³ΠΎ Π²Π΅Π½ΡΠΈΠ»ΡΡΠΎΡΠ°.
Π Π΅ΡΠΈΠ²Π΅ΡΡ ΠΈΠ»ΠΈ Π±Π°Π»Π»ΠΎΠ½Ρ. Π ΡΠ΅ΡΠΈΠ²Π΅ΡΠ°Ρ Ρ ΡΠ°Π½ΠΈΡΡΡ Π·Π°ΠΏΠ°Ρ ΡΠΆΠ°ΡΠΎΠ³ΠΎ Π²ΠΎΠ·Π΄ΡΡ Π°. ΠΠ½Π΅Π²ΠΌΠ°ΡΠΈΡΠ΅ΡΠΊΠΈΠ΅ ΡΠΎΡΠΌΠΎΠ·Π° ΠΎΠ±ΠΎΡΡΠ΄ΠΎΠ²Π°Π½Ρ Π΄Π²ΡΠΌΡ ΡΠ΅ΡΠΈΠ²Π΅ΡΠ°ΠΌΠΈ. ΠΠ΅ΡΠ²ΡΠΉ Π±Π°Π»Π»ΠΎΠ½, ΠΊΠΎΡΠΎΡΡΠΉ Π² Π½Π°ΡΠΎΠ΄Π΅ Π½Π°Π·ΡΠ²Π°ΡΡ βΠΌΠΎΠΊΡΡΠΌβ, ΠΎΠ±ΠΎΡΡΠ΄ΠΎΠ²Π°Π½ ΠΏΡΠ΅Π΄ΠΎΡ ΡΠ°Π½ΠΈΡΠ΅Π»ΡΠ½ΡΠΌ ΠΊΠ»Π°ΠΏΠ°Π½ΠΎΠΌ ΠΈ ΠΊΡΠ°Π½ΠΎΠΌ Π΄Π»Ρ ΡΠ»ΠΈΠ²Π° ΠΊΠΎΠ½Π΄Π΅Π½ΡΠ°ΡΠ°. ΠΠ° Π²ΡΠΎΡΠΎΠΌ ΡΠ΅ΡΠΈΠ²Π΅ΡΠ΅ Π΅ΡΡΡ ΡΠΎΠ»ΡΠΊΠΎ ΠΊΡΠ°Π½ Π΄Π»Ρ ΡΠ»ΠΈΠ²Π° ΠΊΠΎΠ½Π΄Π΅Π½ΡΠ°ΡΠ°. ΠΡΠ΅Π΄ΠΎΡ ΡΠ°Π½ΠΈΡΠ΅Π»ΡΠ½ΡΠΉ ΠΊΠ»Π°ΠΏΠ°Π½, ΠΊΠΎΡΠΎΡΡΠΉ ΠΊΠΎΠ½ΡΡΠΎΠ»ΠΈΡΡΠ΅Ρ Π΄Π°Π²Π»Π΅Π½ΠΈΠ΅ Π²ΠΎ Π²ΡΠΎΡΠΎΠΌ Π±Π°Π»Π»ΠΎΠ½Π΅, ΡΡΡΠ°Π½ΠΎΠ²Π»Π΅Π½ Π΄Π°Π»ΡΡΠ΅ ΠΏΠΎ ΠΌΠ°Π³ΠΈΡΡΡΠ°Π»ΠΈ Π² ΡΠΎΡΠΌΠΎΠ·Π½ΠΎΠΌ ΠΊΡΠ°Π½Π΅.
ΠΡΠ΅Π΄ΠΎΡ ΡΠ°Π½ΠΈΡΠ΅Π»ΡΠ½ΡΠΉ ΠΊΠ»Π°ΠΏΠ°Π½. ΠΠ°ΡΠΈΡΠ°Π΅Ρ ΡΠΈΡΡΠ΅ΠΌΡ ΠΎΡ ΠΏΠ΅ΡΠ΅Π³ΡΡΠ·ΠΊΠΈ ΠΈ ΡΠ±ΡΠ°ΡΡΠ²Π°Π΅Ρ ΠΈΠ·Π±ΡΡΠΎΡΠ½ΠΎΠ΅ Π΄Π°Π²Π»Π΅Π½ΠΈΠ΅. ΠΠΎΠ»ΠΈΡΠ΅ΡΡΠ²ΠΎ Π·Π°ΡΠΈΡΠ½ΡΡ ΠΊΠ»Π°ΠΏΠ°Π½ΠΎΠ² Π·Π°Π²ΠΈΡΠΈΡ ΠΎΡ ΡΠΈΠΏΠ° ΠΊΠΎΠ½ΡΡΡΡΠΊΡΠΈΠΈ ΠΈ ΠΊΠΎΠ»ΠΈΡΠ΅ΡΡΠ²ΠΎ ΠΊΠΎΠ½ΡΡΡΠΎΠ² ΠΌΠ°Π³ΠΈΡΡΡΠ°Π»Π΅ΠΉ.
Π Π΅Π³ΡΠ»ΡΡΠΎΡ Π΄Π°Π²Π»Π΅Π½ΠΈΡ. ΠΠΎΠ½ΡΡΠΎΠ»ΠΈΡΡΠ΅Ρ ΠΈ ΠΏΠΎΠ΄Π΄Π΅ΡΠΆΠΈΠ²Π°Π΅Ρ ΠΎΠΏΡΠΈΠΌΠ°Π»ΡΠ½ΠΎΠ΅ Π΄Π°Π²Π»Π΅Π½ΠΈΠ΅ Π² ΡΠΈΡΡΠ΅ΠΌΠ΅, Π° ΠΏΡΠΈ Π½Π΅ΠΎΠ±Ρ ΠΎΠ΄ΠΈΠΌΠΎΡΡΠΈ Π²ΠΏΡΡΠΊΠ°Π΅Ρ ΠΈΠ»ΠΈ Π²ΡΠΏΡΡΠΊΠ°Π΅Ρ Π²ΠΎΠ·Π΄ΡΡ Π² ΡΡΡΡΠΎΠΉΡΡΠ²ΠΎ ΡΠ°Π·Π³ΡΡΠ·ΠΊΠΈ ΠΊΠΎΠΌΠΏΡΠ΅ΡΡΠΎΡΠ°.
Π’ΠΎΡΠΌΠΎΠ·Π½ΠΎΠΉ ΠΊΡΠ°Π½. ΠΠΎΠΌΠ±ΠΈΠ½ΠΈΡΠΎΠ²Π°Π½Π½ΡΠΉ ΠΏΠΎΡΡΠ½Π΅Π²ΠΎΠΉ ΡΠ·Π΅Π», ΠΊΠΎΡΠΎΡΡΠΉ ΡΠ°ΡΠΏΡΠ΅Π΄Π΅Π»ΡΠ΅Ρ ΠΏΠΎΡΠΎΠΊΠΈ ΡΠΆΠ°ΡΠΎΠ³ΠΎ Π²ΠΎΠ·Π΄ΡΡ Π° ΠΏΠΎ ΡΠΈΡΡΠ΅ΠΌΠ΅, ΠΏΠΎΡΠ»Π΅Π΄ΠΎΠ²Π°ΡΠ΅Π»ΡΠ½ΠΎ Π·Π°ΠΏΠΎΠ»Π½ΡΠ΅Ρ ΡΠ½Π΅ΡΠ³ΠΎΠ½ΠΎΡΠΈΡΠ΅Π»Π΅ΠΌ Π²ΡΠ΅ ΠΊΠΎΠ½ΡΡΡΡ ΠΏΠ½Π΅Π²ΠΌΠΎΡΠΈΡΡΠ΅ΠΌΡ ΠΈ ΡΠΎΡΠΌΠΎΠ·Π½ΡΠ΅ ΠΊΠ°ΠΌΠ΅ΡΡ. Π’ΠΎΡΠΌΠΎΠ·Π½ΠΎΠΉ ΠΊΡΠ°Π½ — ΡΠ²ΡΠ·ΡΡΡΠΈΠΉ ΡΠ·Π΅Π» ΠΌΠ΅ΠΆΠ΄Ρ ΡΠ΅ΡΠΈΠ²Π΅ΡΠ°ΠΌΠΈ ΠΈ ΡΠΎΡΠΌΠΎΠ·Π½ΡΠΌΠΈ ΡΠΈΠ»ΠΈΠ½Π΄ΡΠ°ΠΌΠΈ ΠΊΠΎΠ»Π΅Ρ. ΠΠΎΠ»ΠΈΡΠ΅ΡΡΠ²ΠΎ ΡΠΎΡΠΌΠΎΠ·Π½ΡΡ ΠΊΡΠ°Π½ΠΎΠ² Π² ΠΏΠ½Π΅Π²ΠΌΠ°ΡΠΈΡΠ΅ΡΠΊΠΎΠΉ ΡΠΈΡΡΠ΅ΠΌΠ΅ Π·Π°Π²ΠΈΡΠΈΡ ΠΎΡ ΠΊΠΎΠ»ΠΈΡΠ΅ΡΡΠ²ΠΎ ΠΊΠΎΠ½ΡΡΡΠΎΠ².
ΠΡΡΡΠΈΡΠ΅Π»Ρ Π²ΠΎΠ·Π΄ΡΡ Π°. ΠΡΠ΄Π΅Π»ΡΠ΅Ρ ΠΏΠ°ΡΡ Π²ΠΎΠ΄Ρ ΠΈ Π΄ΡΡΠ³ΠΈΠ΅ ΠΏΡΠΈΠΌΠ΅ΡΠΈ (Π½Π°ΠΏΡΠΈΠΌΠ΅Ρ, ΠΏΠ°ΡΡ ΠΌΠ°ΡΠ»Π°) ΠΈΠ· Π²ΡΠ°ΡΡΠ²Π°Π΅ΠΌΠΎΠ³ΠΎ Π²ΠΎΠ·Π΄ΡΡ Π°. Π ΡΠΎΠ²ΡΠ΅ΠΌΠ΅Π½Π½ΡΡ ΠΌΠΎΠ΄Π΅Π»ΡΡ Π°Π²ΡΠΎΠΌΠΎΠ±ΠΈΠ»Π΅ΠΉ ΠΎΡΡΡΠΈΡΠ΅Π»Ρ ΡΠΎΠ²ΠΌΠ΅ΡΠ΅Π½ Ρ ΡΠ΅Π³ΡΠ»ΡΡΠΎΡΠΎΠΌ Π΄Π°Π²Π»Π΅Π½ΠΈΡ, ΠΏΠΎΡΡΠΎΠΌΡ ΠΏΠΎΡΠ»Π΅Π΄Π½ΠΈΠΉ ΠΊΠ°ΠΊ ΠΎΡΠ΄Π΅Π»ΡΠ½ΡΠΉ ΡΠ·Π΅Π» ΠΎΡΡΡΡΡΡΠ²ΡΠ΅Ρ.
Π’ΠΎΡΠΌΠΎΠ·Π½ΡΠ΅ ΡΠ·Π»Ρ Ρ ΡΠΈΠ»ΠΎΠ²ΡΠΌΠΈ ΡΠΈΠ»ΠΈΠ½Π΄ΡΠ°ΠΌΠΈ (ΡΠΎΡΠΌΠΎΠ·Π½ΡΠΌΠΈ ΠΊΠ°ΠΌΠ΅ΡΠ°ΠΌΠΈ). Π£ΡΡΠ°Π½ΠΎΠ²Π»Π΅Π½Ρ Π½Π° ΠΊΠΎΠ»Π΅ΡΠ°Ρ Π°Π²ΡΠΎΠΌΠΎΠ±ΠΈΠ»Ρ, ΠΎΡΠ²Π΅ΡΠ°ΡΡ Π·Π° ΠΎΡΡΠ°Π½ΠΎΠ²ΠΊΡ ΡΡΠ°Π½ΡΠΏΠΎΡΡΠ½ΠΎΠ³ΠΎ ΡΡΠ΅Π΄ΡΡΠ²Π°. ΠΠ°ΠΆΠ΄ΡΠΉ ΡΠ·Π΅Π» ΠΎΠ±ΠΎΡΡΠ΄ΠΎΠ²Π°Π½ ΡΠΎΡΠΌΠΎΠ·Π½ΡΠΌ ΡΠΈΠ»ΠΈΠ½Π΄ΡΠΎΠΌ, Π² ΠΊΠΎΡΠΎΡΡΠΉ ΠΏΠΎ ΡΡΡΠ±ΠΎΠΏΡΠΎΠ²ΠΎΠ΄Ρ ΠΏΠΎΠ΄ Π΄Π°Π²Π»Π΅Π½ΠΈΠ΅ΠΌ ΠΏΠΎΡΡΡΠΏΠ°Π΅Ρ Π²ΠΎΠ·Π΄ΡΡ ΠΈ ΠΊΠΎΡΠΎΡΡΠΉ ΠΏΡΠΈΠΆΠΈΠΌΠ°Π΅Ρ ΡΠΎΡΠΌΠΎΠ·Π½ΡΠ΅ ΠΊΠΎΠ»ΠΎΠ΄ΠΊΠΈ ΠΊ Π±Π°ΡΠ°Π±Π°Π½Ρ.
Π Π°Π·ΠΎΠ±ΡΠΈΡΠ΅Π»ΡΠ½ΡΠΉ ΠΊΡΠ°Π½. ΠΠ»Π΅ΠΌΠ΅Π½Ρ Π²ΡΡΡΠ΅ΡΠ°Π΅ΡΡΡ ΡΠΎΠ»ΡΠΊΠΎ Π² ΡΡΠ³Π°ΡΠ°Ρ Ρ ΠΏΡΠΈΡΠ΅ΠΏΠ°ΠΌΠΈ. Π§Π΅ΡΠ΅Π· ΠΊΡΠ°Π½ ΠΏΠ½Π΅Π²ΠΌΠ°ΡΠΈΡΠ΅ΡΠΊΡΡ ΡΠΎΡΠΌΠΎΠ·Π½ΡΡ ΡΠΈΡΡΠ΅ΠΌΡ ΡΡΠ³Π°ΡΠ° ΡΠΎΠ΅Π΄ΠΈΠ½ΡΡΡ Ρ ΡΠΎΡΠΌΠΎΠ·Π½ΠΎΠΉ ΠΌΠ°Π³ΠΈΡΡΡΠ°Π»ΡΡ ΠΏΡΠΈΡΠ΅ΠΏΠ°. ΠΡΠ°Π½ ΠΎΠ±ΡΠ΅Π΄ΠΈΠ½ΡΠ΅Ρ Π΄Π²Π΅ ΡΠΈΡΡΠ΅ΠΌΡ, ΡΠ²Π΅Π»ΠΈΡΠΈΠ²Π°Π΅Ρ ΡΡΡΠΎΠΉΡΠΈΠ²ΠΎΡΡΡ ΠΈ ΡΠΏΡΠ°Π²Π»ΡΠ΅ΠΌΠΎΡΡΡ Π°Π²ΡΠΎΠΌΠΎΠ±ΠΈΠ»Ρ, ΡΠΌΠ΅Π½ΡΡΠ°Π΅Ρ ΡΠΈΡΠΊ Π·Π°Π½ΠΎΡΠ° ΠΏΡΠΈΡΠ΅ΠΏΠ° ΠΏΡΠΈ ΡΠΎΡΠΌΠΎΠΆΠ΅Π½ΠΈΠΈ.
ΠΠ½Π΅Π²ΠΌΠΎΡΡΠΈΠ»ΠΈΡΠ΅Π»ΠΈ. ΠΠ³ΡΠ΅Π³Π°ΡΡ ΡΠ²Π΅Π»ΠΈΡΠΈΠ²Π°ΡΡ ΠΏΠΎΠΊΠ°Π·Π°ΡΠ΅Π»ΠΈ Π΄Π°Π²Π»Π΅Π½ΠΈΡ Π΄ΠΎ Π½Π΅ΠΎΠ±Ρ ΠΎΠ΄ΠΈΠΌΠΎΠ³ΠΎ ΡΡΠΎΠ²Π½Ρ ΠΈ ΡΠΌΠ΅Π½ΡΡΠ°ΡΡ Π½Π°Π³ΡΡΠ·ΠΊΡ Π½Π° ΠΊΠΎΠΌΠΏΡΠ΅ΡΡΠΎΡ. ΠΠΎΠ»ΠΈΡΠ΅ΡΡΠ²ΠΎ ΡΡΠΈΠ»ΠΈΡΠ΅Π»Π΅ΠΉ ΠΎΡΠ»ΠΈΡΠ°Π΅ΡΡΡ Π² ΡΠ°Π·Π»ΠΈΡΠ½ΡΡ ΠΌΠΎΠ΄Π΅Π»ΡΡ Π°Π²ΡΠΎΠΌΠΎΠ±ΠΈΠ»Π΅ΠΉ.
Π’ΡΡΠ±ΠΎΠΏΡΠΎΠ²ΠΎΠ΄. Π‘ΠΈΡΡΠ΅ΠΌΠ° ΡΡΡΠ± ΠΈ ΡΠ»Π°Π½Π³ΠΎΠ² ΡΠΎΠ΅Π΄ΠΈΠ½ΡΠ΅Ρ Π²ΡΠ΅ ΡΠ·Π»Ρ ΠΈ ΡΠ»Π΅ΠΌΠ΅Π½ΡΡ. ΠΠΎΠ»ΠΈΡΠ΅ΡΡΠ²ΠΎ ΠΎΡΠ²Π΅ΡΠ²Π»Π΅Π½ΠΈΠΉ ΡΡΡΠ±ΠΎΠΏΡΠΎΠ²ΠΎΠ΄Π° Π·Π°Π²ΠΈΡΠΈΡ ΠΎΡ ΠΊΠΎΠ»ΠΈΡΠ΅ΡΡΠ²Π° ΠΊΠΎΠ½ΡΡΡΠΎΠ² ΠΏΠ½Π΅Π²ΠΌΠ°ΡΠΈΡΠ΅ΡΠΊΠΎΠΉ ΡΠΎΡΠΌΠΎΠ·Π½ΠΎΠΉ ΡΠΈΡΡΠ΅ΠΌΡ.
ΠΠ΅Π΄Π°Π»Ρ ΡΠΎΡΠΌΠΎΠ·Π°. ΠΠ»Π΅ΠΌΠ΅Π½Ρ ΠΏΠ΅ΡΠ΅Π΄Π°Π΅Ρ ΡΡΠΈΠ»ΠΈΠ΅ Π½Π° ΠΏΠΎΡΡΠ½ΠΈ ΡΠΎΡΠΌΠΎΠ·Π½ΠΎΠ³ΠΎ ΠΊΡΠ°Π½Π° ΠΈ ΠΎΡΠΊΡΡΠ²Π°Π΅Ρ ΠΊΠ°Π½Π°Π»Ρ Π΄Π»Ρ ΡΠΆΠ°ΡΠΎΠ³ΠΎ Π²ΠΎΠ·Π΄ΡΡ Π° ΠΎΡ ΡΠ΅ΡΠΈΠ²Π΅ΡΠΎΠ² Π½Π° ΡΠΎΡΠΌΠΎΠ·Π½ΡΠ΅ ΠΊΠ°ΠΌΠ΅ΡΡ ΠΊΠΎΠ»Π΅Ρ.
Π ΡΡΠ°Π³ ΡΡΡΠ½ΠΎΠ³ΠΎ ΡΠΎΡΠΌΠΎΠ·Π°.
ΠΠ·ΠΌΠ΅ΡΠΈΡΠ΅Π»ΡΠ½ΡΠ΅ ΠΏΡΠΈΠ±ΠΎΡΡ ΠΈ Π΄Π°ΡΡΠΈΠΊΠΈ. ΠΠΎΠ½ΡΡΠΎΠ»ΠΈΡΡΡΡΠΈΠ΅ ΡΠ»Π΅ΠΌΠ΅Π½ΡΡ, ΠΏΠΎ ΠΊΠΎΡΠΎΡΡΠΌ Π²ΠΎΠ΄ΠΈΡΠ΅Π»Ρ ΡΠ»Π΅Π΄ΠΈΡ Π·Π° ΡΠΎΡΡΠΎΡΠ½ΠΈΠ΅ΠΌ ΠΈ ΡΠ°Π±ΠΎΡΠΎΡΠΏΠΎΡΠΎΠ±Π½ΠΎΡΡΡΡ ΡΠΎΡΠΌΠΎΠ·Π½ΠΎΠΉ ΡΠΈΡΡΠ΅ΠΌΡ. Π Π½ΠΈΠΌ ΠΎΡΠ½ΠΎΡΡΡΡΡ Π΄Π°ΡΡΠΈΠΊΠΈ, ΠΊΠΎΡΠΎΡΡΠ΅ Π½Π°Ρ ΠΎΠ΄ΡΡΡΡ Π² ΡΠ΅ΡΠΈΠ²Π΅ΡΠ°Ρ ΠΈ ΡΠΎΡΠΌΠΎΠ·Π½ΡΡ ΠΊΠ°ΠΌΠ΅ΡΠ°Ρ , ΠΈ Π΄Π²ΡΡ ΡΡΡΠ΅Π»ΠΎΡΠ½ΡΠΉ ΠΌΠ°Π½ΠΎΠΌΠ΅ΡΡ. ΠΠ΄Π½Π° ΡΡΡΠ΅Π»ΠΊΠ° ΠΌΠ°Π½ΠΎΠΌΠ΅ΡΡΠ° ΠΏΠΎΠΊΠ°Π·ΡΠ²Π°Π΅Ρ Π΄Π°Π²Π»Π΅Π½ΠΈΠ΅ Π² Π±Π°Π»Π»ΠΎΠ½Π°Ρ , Π° Π²ΡΠΎΡΠ°Ρ — Π² ΡΠΎΡΠΌΠΎΠ·Π½ΡΡ ΠΊΠ°ΠΌΠ΅ΡΠ°Ρ . Π ΡΡΠ°ΡΡΡ ΠΌΠΎΠ΄Π΅Π»ΡΡ Π°Π²ΡΠΎΠΌΠΎΠ±ΠΈΠ»Π΅ΠΉ ΠΌΠ°Π½ΠΎΠΌΠ΅ΡΡΠΎΠ² Π±ΡΠ»ΠΎ Π΄Π²Π° ΠΈ ΠΊΠ°ΠΆΠ΄ΡΠΉ ΠΎΡΠ²Π΅ΡΠ°Π» Π·Π° ΡΠ²ΠΎΠΉ ΡΠ·Π΅Π».
ΠΡΠΈΠ½ΡΠΈΠΏ ΡΠ°Π±ΠΎΡΡ ΠΈ ΡΡΠ½ΠΊΡΠΈΠΎΠ½Π°Π» ΠΏΠ½Π΅Π²ΠΌΠ°ΡΠΈΡΠ΅ΡΠΊΠΎΠ³ΠΎ ΡΠΎΡΠΌΠΎΠ·Π½ΠΎΠ³ΠΎ ΠΏΡΠΈΠ²ΠΎΠ΄Π°
ΠΠ»Π°Π²Π½Π°Ρ ΠΈ Π΅Π΄ΠΈΠ½ΡΡΠ²Π΅Π½Π½Π°Ρ ΡΡΠ½ΠΊΡΠΈΡ Π»ΡΠ±ΠΎΠΉ ΡΠΎΡΠΌΠΎΠ·Π½ΠΎΠΉ ΡΠΈΡΡΠ΅ΠΌΡ — Π²ΠΎΠ²ΡΠ΅ΠΌΡ ΠΎΡΡΠ°Π½ΠΎΠ²ΠΈΡΡ Π°Π²ΡΠΎΠΌΠΎΠ±ΠΈΠ»Ρ Π½Π΅ Π·Π°Π²ΠΈΡΠΈΠΌΠΎ ΠΎΡ ΡΡΠ»ΠΎΠ²ΠΈΠΉ ΠΈ Π²Π½Π΅ΡΠ½ΠΈΡ ΡΠ°ΠΊΡΠΎΡΠΎΠ². ΠΠ΅Π²Π°ΠΆΠ½ΠΎ, Π½ΡΠΆΠ½ΠΎ ΠΏΠ»Π°Π²Π½ΠΎ ΠΎΡΡΠ°Π½ΠΎΠ²ΠΈΡΡ Π°Π²ΡΠΎ ΠΏΠ΅ΡΠ΅Π΄ ΠΏΠ΅ΡΠ΅ΠΊΡΠ΅ΡΡΠΊΠΎΠΌ ΠΈΠ»ΠΈ ΡΠ΅Π·ΠΊΠΎ Π·Π°ΡΠΎΡΠΌΠΎΠ·ΠΈΡΡ ΠΈΠ·-Π·Π° Π½Π΅ΠΎΠΆΠΈΠ΄Π°Π½Π½ΠΎ Π²ΠΎΠ·Π½ΠΈΠΊΡΠ΅ΠΉ ΠΏΡΠ΅Π³ΡΠ°Π΄Ρ — Π°Π²ΡΠΎΠΌΠΎΠ±ΠΈΠ»Ρ Π΄ΠΎΠ»ΠΆΠ΅Π½ ΠΎΡΡΠ°Π½ΠΎΠ²ΠΈΡΡΡ Π±Π΅Π· ΡΡΠ΅ΡΠ±Π° Π΄Π»Ρ Π²ΠΎΠ΄ΠΈΡΠ΅Π»Ρ, ΡΡΠ°Π½ΡΠΏΠΎΡΡΠ½ΠΎΠ³ΠΎ ΡΡΠ΅Π΄ΡΡΠ²Π°, Π΄ΡΡΠ³ΠΈΡ ΡΡΠ°ΡΡΠ½ΠΈΠΊΠΎΠ² Π΄ΠΎΡΠΎΠΆΠ½ΠΎΠ³ΠΎ Π΄Π²ΠΈΠΆΠ΅Π½ΠΈΡ.
Π Π°ΡΡΠΌΠΎΡΡΠΈΠΌ ΠΎΡΠ½ΠΎΠ²Π½ΡΠ΅ ΡΡΠ°ΠΏΡ ΠΈ ΠΏΡΠΎΡΠ΅ΡΡΡ, ΠΊΠΎΡΠΎΡΡΠ΅ ΠΏΡΠΎΠΈΡΡ ΠΎΠ΄ΡΡ Π² ΠΏΠ½Π΅Π²ΠΌΠ°ΡΠΈΡΠ΅ΡΠΊΠΎΠΉ ΡΠΎΡΠΌΠΎΠ·Π½ΠΎΠΉ ΡΠΈΡΡΠ΅ΠΌΠ΅.
ΠΠ½Π΅Π²ΠΌΠΎΠΊΠΎΠΌΠΏΡΠ΅ΡΡΠΎΡ Π΄Π»Ρ Π°Π²ΡΠΎΠΌΠΎΠ±ΠΈΠ»Π΅ΠΉ ΠΠΠ Ρ Π΄Π²ΠΈΠ³Π°ΡΠ΅Π»Π΅ΠΌ OM 906 LA
ΠΠΎΠΌΠΏΡΠ΅ΡΡΠΎΡ ΡΠΎΡΠΌΠΎΠ·Π½ΠΎΠΉ ΡΠΈΡΡΠ΅ΠΌΡ — ΠΏΡΠΈΠ²ΠΎΠ΄Π½ΠΎΠΉ Π°Π³ΡΠ΅Π³Π°Ρ, ΠΊΠΎΡΠΎΡΡΠΉ ΡΠ°Π±ΠΎΡΠ°Π΅Ρ ΡΠΎΠ»ΡΠΊΠΎ ΠΊΠΎΠ³Π΄Π° Π·Π°ΠΏΡΡΠ΅Π½ Π΄Π²ΠΈΠ³Π°ΡΠ΅Π»Ρ. Π§Π΅ΡΠ΅Π· Π²ΠΎΠ·Π΄ΡΡΠ½ΡΠΉ ΡΠΈΠ»ΡΡΡ Π² ΠΊΠΎΠΌΠΏΡΠ΅ΡΡΠΎΡ ΠΏΠΎΡΡΡΠΏΠ°Π΅Ρ Π²ΠΎΠ·Π΄ΡΡ , ΠΊΠΎΡΠΎΡΡΠΉ Π°Π³ΡΠ΅Π³Π°Ρ ΡΠ΅ΡΠ΅Π· ΡΠ΅Π³ΡΠ»ΡΡΠΎΡ Π΄Π°Π²Π»Π΅Π½ΠΈΡ Π·Π°ΠΊΠ°ΡΠΈΠ²Π°Π΅Ρ Π² ΡΠ΅ΡΠΈΠ²Π΅ΡΡ.
Π Π΅Π³ΡΠ»ΡΡΠΎΡ Π΄Π°Π²Π»Π΅Π½ΠΈΡ, ΠΊΠΎΡΠΎΡΡΠΉ ΡΠ°ΡΠΏΠΎΠ»ΠΎΠΆΠ΅Π½ Π»ΠΈΠ±ΠΎ ΠΊΠ°ΠΊ ΠΎΡΠ΄Π΅Π»ΡΠ½ΡΠΉ ΡΠ·Π΅Π», Π»ΠΈΠ±ΠΎ Π²ΡΡΡΠΎΠ΅Π½ Π² ΠΎΡΡΡΠΈΡΠ΅Π»Ρ, ΠΊΠΎΠ½ΡΡΠΎΠ»ΠΈΡΡΠ΅Ρ ΠΈ ΠΎΠΏΡΠΈΠΌΠΈΠ·ΠΈΡΡΠ΅Ρ Π΄Π°Π²Π»Π΅Π½ΠΈΠ΅ Π²ΠΎΠ·Π΄ΡΡ Π°, Π° ΠΊΠΎΠ³Π΄Π° ΡΠ΅ΡΠΈΠ²Π΅ΡΡ Π·Π°ΠΏΠΎΠ»Π½Π΅Π½Ρ ΠΏΠΎΠ»Π½ΠΎΡΡΡΡ, ΠΎΠ±Π΅ΡΠΏΠ΅ΡΠΈΠ²Π°Π΅Ρ Ρ ΠΎΠ»ΠΎΡΡΠΎΠΉ Ρ ΠΎΠ΄ ΠΊΠΎΠΌΠΏΡΠ΅ΡΡΠΎΡΠ°. ΠΡΠ»ΠΈ ΡΠ΅Π³ΡΠ»ΡΡΠΎΡ Π΄Π°Π²Π»Π΅Π½ΠΈΡ Π½Π΅ ΡΠ°Π±ΠΎΡΠ°Π΅Ρ, Π΅Π³ΠΎ ΠΏΠΎΠ΄ΠΌΠ΅Π½ΡΠ΅Ρ ΠΏΡΠ΅Π΄ΠΎΡ ΡΠ°Π½ΠΈΡΠ΅Π»ΡΠ½ΡΠΉ ΠΊΠ»Π°ΠΏΠ°Π½.
Π Π΅ΡΠΈΠ²Π΅ΡΡ ΡΠΈΡΡΠ΅ΠΌΡ ΡΠΎΠ΅Π΄ΠΈΠ½Π΅Π½Ρ ΠΏΠΎΡΠ»Π΅Π΄ΠΎΠ²Π°ΡΠ΅Π»ΡΠ½ΠΎ. Π Π½ΠΈΠΆΠ½Π΅ΠΉ ΡΠ°ΡΡΠΈ ΠΏΠ΅ΡΠ²ΠΎΠ³ΠΎ Π±Π°Π»Π»ΠΎΠ½Π° Π½Π°Ρ ΠΎΠ΄ΠΈΡΡΡ ΡΠΏΡΡΠΊΠ½ΠΎΠΉ ΠΊΡΠ°Π½, ΡΠ΅ΡΠ΅Π· ΠΊΠΎΡΠΎΡΡΠΉ ΠΈΠ· ΡΠ½Π΅ΡΠ³ΠΎΠ½ΠΎΡΠΈΡΠ΅Π»Ρ Π²ΡΠ²ΠΎΠ΄ΠΈΡΡΡ ΠΊΠΎΠ½Π΄Π΅Π½ΡΠ°Ρ ΠΈ ΠΏΠ°ΡΡ ΠΌΠ°ΡΠ»Π°. ΠΡΠΎΡΠΎΠΉ Π±Π°Π»Π»ΠΎΠ½ ΡΠΎΠ΅Π΄ΠΈΠ½Π΅Π½ Ρ ΠΊΡΠ°Π½ΠΎΠΌ, ΠΊΠΎΡΠΎΡΡΠΉ ΠΎΠ±ΠΎΡΡΠ΄ΠΎΠ²Π°Π½ ΡΠ΅Π³ΡΠ»ΡΡΠΎΡΠΎΠΌ Π΄Π°Π²Π»Π΅Π½ΠΈΡ ΠΈ ΠΏΡΠ΅Π΄ΠΎΡ ΡΠ°Π½ΠΈΡΠ΅Π»ΡΠ½ΡΠΌ ΠΊΠ»Π°ΠΏΠ°Π½ΠΎΠΌ. ΠΠΎΡΠ»Π΅Π΄Π½ΠΈΠ΅ ΡΠ±ΡΠ°ΡΡΠ²Π°ΡΡ Π»ΠΈΡΠ½ΠΈΠΉ Π²ΠΎΠ·Π΄ΡΡ ΠΈ Π½ΠΎΡΠΌΠ°Π»ΠΈΠ·ΡΡΡ Π΄Π°Π²Π»Π΅Π½ΠΈΠ΅ Π² ΡΠΈΡΡΠ΅ΠΌΠ΅, Π΅ΡΠ»ΠΈ ΠΎΠ½ΠΎ ΠΏΡΠ΅Π²ΡΡΠ°Π΅Ρ Π΄ΠΎΠΏΡΡΡΠΈΠΌΠΎΠ΅.
Π’ΠΎΡΠΌΠΎΠ·Π½ΠΎΠΉ ΠΊΡΠ°Π½ ΠΊΠΎΠ½ΡΡΠΎΠ»ΠΈΡΡΠ΅Ρ ΠΈ ΠΏΠ΅ΡΠ΅Π½Π°ΠΏΡΠ°Π²Π»ΡΠ΅Ρ ΠΏΠΎΡΠΎΠΊ ΡΠΆΠ°ΡΠΎΠ³ΠΎ Π²ΠΎΠ·Π΄ΡΡ Π° Π² ΠΊΠ°ΠΌΠ΅ΡΡ ΡΠΈΠ»ΠΎΠ²ΡΡ ΡΠΈΠ»ΠΈΠ½Π΄ΡΠΎΠ², ΠΊΠΎΡΠΎΡΡΠ΅ Π½Π°Ρ ΠΎΠ΄ΡΡΡΡ Π² ΡΠΎΡΠΌΠΎΠ·Π½ΡΡ ΡΠ·Π»Π°Ρ ΠΊΠΎΠ»Π΅Ρ. Π ΠΎΠ΄Π½ΠΎΠΊΠΎΠ½ΡΡΡΠ½ΠΎΠΉ ΡΠΈΡΡΠ΅ΠΌΠ΅ Π·Π° ΠΏΠ΅ΡΠ΅Π΄Π½ΠΈΠ΅ ΠΊΠΎΠ»Π΅ΡΠ° Π°Π²ΡΠΎΠΌΠΎΠ±ΠΈΠ»Ρ ΠΎΡΠ²Π΅ΡΠ°Π΅Ρ Π½ΠΈΠΆΠ½ΠΈΠΉ ΡΠΈΠ»ΠΈΠ½Π΄Ρ ΠΊΡΠ°Π½Π°, Π° Π·Π° Π·Π°Π΄Π½ΠΈΠ΅ ΠΊΠΎΠ»Π΅ΡΠ° ΡΡΠ³Π°ΡΠ° ΠΈ ΠΊΠΎΠ»Π΅ΡΠ° ΠΏΡΠΈΡΠ΅ΠΏΠ° (Π΅ΡΠ»ΠΈ Π΅ΡΡΡ) — Π²Π΅ΡΡ Π½ΠΈΠΉ ΡΠΈΠ»ΠΈΠ½Π΄Ρ. ΠΠ½Π΅Π²ΠΌΠ°ΡΠΈΡΠ΅ΡΠΊΠΈΠ΅ ΡΠΎΡΠΌΠΎΠ·Π° ΠΏΡΠΈΡΠ΅ΠΏΠ° ΠΏΡΠΈΡΠΎΠ΅Π΄ΠΈΠ½ΡΡΡ ΠΊ Π°Π²ΡΠΎΠΌΠΎΠ±ΠΈΠ»Ρ ΡΠ΅ΡΠ΅Π· ΡΠ°Π·ΠΎΠ±ΡΠΈΡΠ΅Π»ΡΠ½ΡΠΉ ΠΊΡΠ°Π½ ΠΈ ΡΠΎΠ΅Π΄ΠΈΠ½ΠΈΡΠ΅Π»ΡΠ½ΡΡ Π³ΠΎΠ»ΠΎΠ²ΠΊΡ.
ΠΠΎΠ³Π΄Π° Π²ΠΎΠ΄ΠΈΡΠ΅Π»Ρ Π½Π°ΠΆΠΈΠΌΠ°Π΅Ρ ΠΏΠ΅Π΄Π°Π»Ρ ΡΠΎΡΠΌΠΎΠ·Π°, ΡΠΎΡΠΌΠΎΠ·Π½ΠΎΠΉ ΠΊΡΠ°Π½ ΠΎΡΠΊΡΡΠ²Π°Π΅Ρ Π΄ΠΎΡΡΡΠΏ Π΄Π»Ρ ΡΠΆΠ°ΡΠΎΠ³ΠΎ Π²ΠΎΠ·Π΄ΡΡ Π°, ΠΊΠΎΡΠΎΡΡΠΉ ΠΈΠ· ΡΠ΅ΡΠΈΠ²Π΅ΡΠΎΠ² ΠΏΠΎΡΡΡΠΏΠ°Π΅Ρ Π² ΡΠΎΡΠΌΠΎΠ·Π½ΡΠ΅ ΠΊΠ°ΠΌΠ΅ΡΡ ΠΊΠΎΠ»Π΅Ρ. Π ΡΠΈΠ»ΠΈΠ½Π΄ΡΠ°Ρ ΡΠ²Π΅Π»ΠΈΡΠΈΠ²Π°Π΅ΡΡΡ Π΄Π°Π²Π»Π΅Π½ΠΈΠ΅, ΡΠ°Π·ΠΆΠΈΠΌΠ½ΡΠ΅ ΠΊΡΠ»Π°ΠΊΠΈ ΠΏΡΠΈΠΆΠΈΠΌΠ°ΡΡ ΠΊΠΎΠ»ΠΎΠ΄ΠΊΠΈ ΠΊ ΡΠΎΡΠΌΠΎΠ·Π½ΡΠΌ Π±Π°ΡΠ°Π±Π°Π½Π°ΠΌ ΠΊΠΎΠ»Π΅Ρ ΠΈ ΠΎΡΡΠ°Π½Π°Π²Π»ΠΈΠ²Π°ΡΡ Π°Π²ΡΠΎΠΌΠΎΠ±ΠΈΠ»Ρ. ΠΠΎΠ³Π΄Π° Π²ΠΎΠ΄ΠΈΡΠ΅Π»Ρ ΠΎΡΠΏΡΡΠΊΠ°Π΅Ρ ΠΏΠ΅Π΄Π°Π»Ρ, ΠΊΠ»Π°ΠΏΠ°Π½Ρ ΡΠΎΡΠΌΠΎΠ·Π½ΡΡ ΠΊΠ°ΠΌΠ΅Ρ ΠΊΠΎΠ»Π΅Ρ Π²ΡΠ²ΠΎΠ΄Ρ Π²ΠΎΠ·Π΄ΡΡ ΠΈ ΠΊΠΎΠ»ΠΎΠ΄ΠΊΠΈ Π²ΠΎΠ·Π²ΡΠ°ΡΠ°ΡΡΡΡ Π² ΠΈΡΡ ΠΎΠ΄Π½ΠΎΠ΅ ΠΏΠΎΠ»ΠΎΠΆΠ΅Π½ΠΈΠ΅.
ΠΠ½Π΅Π²ΠΌΠ°ΡΠΈΡΠ΅ΡΠΊΠΈΠΉ Π±Π°ΡΠ°Π±Π°Π½Π½ΡΠΉ ΡΠΎΡΠΌΠΎΠ·Π½ΠΎΠΉ ΡΠ·Π΅Π» Π² ΡΠ±ΠΎΡΠ΅ Π½Π° Π°Π²ΡΠΎΠΌΠΎΠ±ΠΈΠ»Π΅
ΠΠΎΠ΄ΠΈΡΠ΅Π»Ρ ΠΌΠΎΠΆΠ΅Ρ ΡΠ»Π΅Π΄ΠΈΡΡ Π·Π° ΡΠΎΡΡΠΎΡΠ½ΠΈΠ΅ΠΌ ΠΏΠ½Π΅Π²ΠΌΠ°ΡΠΈΡΠ΅ΡΠΊΠΎΠΉ ΡΠΎΡΠΌΠΎΠ·Π½ΠΎΠΉ ΡΠΈΡΡΠ΅ΠΌΡ ΠΏΠΎ ΠΌΠ°Π½ΠΎΠΌΠ΅ΡΡΡ, ΠΊΠΎΡΠΎΡΡΠΉ ΠΏΠΎΠΊΠ°Π·ΡΠ²Π°ΡΡ Π΄Π°Π²Π»Π΅Π½ΠΈΠ΅ ΡΠΆΠ°ΡΠΎΠ³ΠΎ Π²ΠΎΠ·Π΄ΡΡ Π° Π² ΡΠ΅ΡΠΈΠ²Π΅ΡΠ°Ρ ΠΈ ΡΠΎΡΠΌΠΎΠ·Π½ΡΡ ΠΊΠ°ΠΌΠ΅ΡΠ°Ρ . ΠΠ°Π½ΠΎΠΌΠ΅ΡΡ ΡΠΎΠ΅Π΄ΠΈΠ½Π΅Π½ Ρ Π΄Π°ΡΡΠΈΠΊΠ°ΠΌΠΈ Π΄Π°Π²Π»Π΅Π½ΠΈΡ, ΠΊΠΎΡΠΎΡΡΠ΅ ΠΏΠ΅ΡΠ΅Π΄Π°ΡΡ Π΄Π°Π½Π½ΡΠ΅ Π½Π° ΠΏΡΠΈΠ±ΠΎΡΠ½ΡΡ ΠΏΠ°Π½Π΅Π»Ρ Π² ΠΊΠ°Π±ΠΈΠ½Ρ Π²ΠΎΠ΄ΠΈΡΠ΅Π»Ρ.
ΠΡΠ΅ΠΈΠΌΡΡΠ΅ΡΡΠ²Π° ΠΈ Π½Π΅Π΄ΠΎΡΡΠ°ΡΠΊΠΈ ΠΏΠ½Π΅Π²ΠΌΠ°ΡΠΈΠΊΠΈ
ΠΠ½Π΅Π²ΠΌΠ°ΡΠΈΡΠ΅ΡΠΊΠ°Ρ ΠΈ Π³ΠΈΠ΄ΡΠ°Π²Π»ΠΈΡΠ΅ΡΠΊΠΈΠ΅ ΡΠΎΡΠΌΠΎΠ·Π½ΡΠ΅ ΡΠΈΡΡΠ΅ΠΌΡ — ΡΡΠΎ Π΄Π²Π° Π°Π½Π°Π»ΠΎΠ³ΠΎΠ²ΡΡ ΡΠΎΡΠΌΠΎΠ·Π½ΡΡ ΠΏΡΠΈΠ²ΠΎΠ΄Π°, ΠΊΠ°ΠΆΠ΄ΡΠΉ ΠΈΠ· ΠΊΠΎΡΠΎΡΡΡ ΠΎΠ±Π»Π°Π΄Π°Π΅Ρ ΡΠ²ΠΎΠΈΠΌΠΈ ΠΏΡΠ΅ΠΈΠΌΡΡΠ΅ΡΡΠ²Π°ΠΌΠΈ ΠΈ Π½Π΅Π΄ΠΎΡΡΠ°ΡΠΊΠ°ΠΌΠΈ. ΠΠ΅ΡΠ²ΡΠΉ ΡΠΈΠΏ ΠΏΡΠΈΠ²ΠΎΠ΄Π° ΠΈΡΠΏΠΎΠ»ΡΠ·ΡΡΡ Π² ΠΎΡΠ½ΠΎΠ²Π½ΠΎΠΌ Π² ΡΡΠΆΠ΅Π»ΡΡ Π°Π²ΡΠΎΠΌΠΎΠ±ΠΈΠ»ΡΡ , Π° Π²ΡΠΎΡΠΎΠΉ ΡΠ°ΡΠ΅ Π²ΡΡΡΠ΅ΡΠ°Π΅ΡΡΡ Π½Π° ΡΡΠ°Π½ΡΠΏΠΎΡΡΠ½ΡΡ ΡΡΠ΅Π΄ΡΡΠ²Π°Ρ ΠΏΠΎΠ²ΡΠ΅Π΄Π½Π΅Π²Π½ΠΎΠ³ΠΎ ΠΈΡΠΏΠΎΠ»ΡΠ·ΠΎΠ²Π°Π½ΠΈΡ.
Π§Π΅ΠΌ ΠΏΠ½Π΅Π²ΠΌΠ°ΡΠΈΡΠ΅ΡΠΊΠΈΠ΅ ΡΠΎΡΠΌΠΎΠ·Π° Π»ΡΡΡΠ΅ Π³ΠΈΠ΄ΡΠ°Π²Π»ΠΈΡΠ΅ΡΠΊΠΈΡ :
- ΠΊΠΎΠ³Π΄Π° Π²ΠΎΠ΄ΠΈΡΠ΅Π»Ρ ΠΎΡΠΏΡΡΠΊΠ°Π΅Ρ ΠΏΠ΅Π΄Π°Π»Ρ ΡΠΎΡΠΌΠΎΠ·Π°, ΡΠΆΠ°ΡΡΠΉ Π²ΠΎΠ·Π΄ΡΡ Π½Π΅ Π²ΠΎΠ·Π²ΡΠ°ΡΠ°Π΅ΡΡΡ ΠΎΠ±ΡΠ°ΡΠ½ΠΎ Π² ΡΠΈΡΡΠ΅ΠΌΡ, Π° Π²ΡΡ ΠΎΠ΄ΠΈΡ ΡΠ΅ΡΠ΅Π· ΠΊΠ»Π°ΠΏΠ°Π½Ρ ΡΠ±ΡΠΎΡΠ° Π² Π°ΡΠΌΠΎΡΡΠ΅ΡΡ;
- ΠΏΠ½Π΅Π²ΠΌΠ°ΡΠΈΡΠ΅ΡΠΊΠ°Ρ ΡΠΈΡΡΠ΅ΠΌΠ° ΡΠΊΠΎΠ½ΠΎΠΌΠΈΡΠ½Π΅Π΅, ΡΠ°ΠΊ ΠΊΠ°ΠΊ ΠΈΡΠΏΠΎΠ»ΡΠ·ΡΠ΅Ρ ΡΠΆΠ°ΡΡΠΉ Π²ΠΎΠ·Π΄ΡΡ , ΠΊΠΎΡΠΎΡΡΠΉ ΠΊΠΎΠΌΠΏΡΠ΅ΡΡΠΎΡ Π·Π°Π±ΠΈΡΠ°Π΅Ρ ΠΈΠ· Π°ΡΠΌΠΎΡΡΠ΅ΡΡ;
- Π²ΠΎΠ·Π΄ΡΡ ΠΌΠ΅Π½ΡΡΠ΅ ΠΈΠ·Π½Π°ΡΠΈΠ²Π°Π΅Ρ ΡΠΈΡΡΠ΅ΠΌΡ, ΡΠ΅ΠΌ ΠΆΠΈΠ΄ΠΊΠΎΡΡΠ½ΡΠΉ Π½Π°ΠΏΠΎΠ»Π½ΠΈΡΠ΅Π»Ρ;
- ΡΠΆΠ°ΡΡΠΉ Π²ΠΎΠ·Π΄ΡΡ — Π½Π΅ΠΉΡΡΠ°Π»ΡΠ½Π°Ρ ΡΡΠ΅Π΄Π°, ΠΏΠΎΡΡΠΎΠΌΡ Π²Π΅ΡΠΎΡΡΠ½ΠΎΡΡΡ ΡΠΎΠ³ΠΎ, ΡΡΠΎ ΡΠ½Π΅ΡΠ³ΠΎΠ½ΠΎΡΠΈΡΠ΅Π»Ρ ΠΏΠΎΡΠ΅ΡΡΠ΅Ρ ΡΠ²ΠΎΠΉΡΡΠ²Π°, Π³ΠΎΡΠ°Π·Π΄ΠΎ ΠΌΠ΅Π½ΡΡΠ΅. ΠΠΈΠ΄ΡΠ°Π²Π»ΠΈΡΠ΅ΡΠΊΠΈΠ΅ ΡΠΌΠ΅ΡΠΈ Π΄Π»Ρ ΡΠΎΡΠΌΠΎΠ·Π½ΡΡ ΡΠΈΡΡΠ΅ΠΌ ΡΠΈΠ»ΡΠ½ΠΎ ΠΎΡΠ»ΠΈΡΠ°ΡΡΡΡ Π΄ΡΡΠ³ ΠΎΡ Π΄ΡΡΠ³Π° ΠΏΠΎ ΡΠΎΡΡΠ°Π²Ρ, ΡΠΌΠ΅ΡΠΈΠ²Π°ΡΡ ΠΈΡ Π½Π΅Π»ΡΠ·Ρ, Π° Π²ΡΠ²Π΅ΡΡΠΈ ΠΈΠ· ΡΡΡΠΎΡ ΡΠΈΡΡΠ΅ΠΌΡ ΠΌΠΎΠΆΠ΅Ρ Π»ΡΠ±Π°Ρ ΠΏΠΎΡΡΠΎΡΠΎΠ½Π½ΡΡ ΠΏΡΠΈΠΌΠ΅ΡΡ;
- ΠΏΠ½Π΅Π²ΠΌΠ°ΡΠΈΡΠ΅ΡΠΊΠ°Ρ ΡΠΎΡΠΌΠΎΠ·Π½Π°Ρ ΡΠΈΡΡΠ΅ΠΌΠ° Π»Π΅Π³ΡΠ΅ ΠΏΠ΅ΡΠ΅Π½ΠΎΡΠΈΡ ΡΠ΅ΠΌΠΏΠ΅ΡΠ°ΡΡΡΠ½ΡΠ΅ ΠΏΠ΅ΡΠ΅ΠΏΠ°Π΄Ρ ΠΊΠ°ΠΊ ΠΎΠΊΡΡΠΆΠ°ΡΡΠ΅ΠΉ ΡΡΠ΅Π΄Ρ, ΡΠ°ΠΊ ΠΈ Π²Π½ΡΡΡΠΈ ΡΠΈΡΡΠ΅ΠΌΡ. ΠΠΈΠ΄ΡΠ°Π²Π»ΠΈΡΠ΅ΡΠΊΠΈΠΉ ΡΠ½Π΅ΡΠ³ΠΎΠ½ΠΎΡΠΈΡΠ΅Π»Ρ ΠΌΠΎΠΆΠ΅Ρ Π·Π°ΠΊΠΈΠΏΠ΅ΡΡ ΠΈΠ»ΠΈ Π·Π°ΠΌΠ΅ΡΠ·Π½ΡΡΡ ΠΎΡ ΡΠ΅Π·ΠΊΠΎΠ³ΠΎ ΡΠΊΠ°ΡΠΊΠ° ΡΠ΅ΠΌΠΏΠ΅ΡΠ°ΡΡΡΡ, Π² ΡΠ΅Π·ΡΠ»ΡΡΠ°ΡΠ΅ ΡΠΎΡΠΌΠΎΠ·Π° Π»ΠΎΠΌΠ°ΡΡΡΡ;
- ΠΏΠ½Π΅Π²ΠΌΠ°ΡΠΈΠΊΠ° ΠΌΠ΅Π½ΡΡΠ΅ Π±ΠΎΠΈΡΡΡ ΠΌΠ΅Π»ΠΊΠΈΡ ΡΡΠ΅ΡΠ΅ΠΊ, ΡΠ°ΠΊ ΠΊΠ°ΠΊ ΠΊΠΎΠΌΠΏΡΠ΅ΡΡΠΎΡ ΡΠ°Π±ΠΎΡΠ°Π΅Ρ Π²ΡΠ΅ Π²ΡΠ΅ΠΌΡ ΠΈ Π² ΡΠ»ΡΡΠ°Π΅ ΡΡΠ΅ΡΠΊΠΈ ΡΠ°Π±ΠΎΡΠ΅Π³ΠΎ Π³Π°Π·Π° Π±ΡΡΡΡΠΎ Π²ΠΎΡΠΏΠΎΠ»Π½ΠΈΡ Π½Π΅Π΄ΠΎΡΡΠ°ΡΡ.
ΠΠ΄Π½Π°ΠΊΠΎ ΠΈ Ρ Π³ΠΈΠ΄ΡΠ°Π²Π»ΠΈΠΊΠΈ Π΅ΡΡΡ ΡΠ²ΠΎΠΈ ΠΏΡΠ΅ΠΈΠΌΡΡΠ΅ΡΡΠ²Π°:
- Π³ΠΈΠ΄ΡΠΎΡΠΎΡΠΌΠΎΠ· ΡΡΠ°Π±Π°ΡΡΠ²Π°Π΅Ρ Π±ΡΡΡΡΠ΅Π΅ Π·Π° ΡΡΠ΅Ρ ΡΠΎΠ³ΠΎ, ΡΡΠΎ ΡΠ½Π΅ΡΠ³ΠΎΠ½ΠΎΡΠΈΡΠ΅Π»Ρ ΠΎΠ±Π»Π°Π΄Π°Π΅Ρ Π²ΡΡΠΎΠΊΠΎΠΉ ΠΏΠ»ΠΎΡΠ½ΠΎΡΡΡΡ ΠΈ Π½Π΅ ΡΠΆΠΈΠΌΠ°Π΅ΡΡΡ, ΠΊΠ°ΠΊ Π²ΠΎΠ·Π΄ΡΡ ;
- Ρ Π³ΠΈΠ΄ΡΠ°Π²Π»ΠΈΡΠ΅ΡΠΊΠΎΠ³ΠΎ ΠΏΡΠΈΠ²ΠΎΠ΄Π° ΠΊΠΎΠ½ΡΡΡΡΠΊΡΠΈΡ Π·Π½Π°ΡΠΈΡΠ΅Π»ΡΠ½ΠΎ ΠΏΡΠΎΡΠ΅, ΡΠ΅ΠΌ Ρ ΠΏΠ½Π΅Π²ΠΌΠ°ΡΠΈΡΠ΅ΡΠΊΠΎΠΉ ΡΠΎΡΠΌΠΎΠ·Π½ΠΎΠΉ ΡΠΈΡΡΠ΅ΠΌΡ
- Π³ΠΈΠ΄ΡΠ°Π²Π»ΠΈΡΠ΅ΡΠΊΠΈΠΉ ΠΏΡΠΈΠ²ΠΎΠ΄ ΡΡΠ½ΠΊΡΠΈΠΎΠ½ΠΈΡΡΠ΅Ρ ΠΊΠ°ΠΊ ΠΎΡΠ΄Π΅Π»ΡΠ½Π°Ρ ΡΠΈΡΡΠ΅ΠΌΠ° Π² ΠΎΡΠ»ΠΈΡΠΈΠ΅ ΠΎΡ ΠΏΠ½Π΅Π²ΠΌΠ°ΡΠΈΡΠ΅ΡΠΊΠΎΠ³ΠΎ, Π² ΠΊΠΎΡΠΎΡΠΎΠΌ ΡΠ°Π±ΠΎΡΠ° ΠΊΠΎΠΌΠΏΡΠ΅ΡΡΠΎΡΠ° Π·Π°Π²ΠΈΡΠΈΡ ΠΎΡ ΡΠ°Π±ΠΎΡΡ Π΄Π²ΠΈΠ³Π°ΡΠ΅Π»Ρ;
- Π½Π΅ΡΠΌΠΎΡΡΡ Π½Π° ΡΠΎ, ΡΡΠΎ ΠΏΠ½Π΅Π²ΠΌΠ°ΡΠΈΡΠ΅ΡΠΊΠΈΠ΅ ΡΠΎΡΠΌΠΎΠ·Π° ΡΡΠ°Π±Π°ΡΡΠ²Π°ΡΡ Π±ΡΡΡΡΠ΅Π΅, ΠΠΠ Π³ΠΈΠ΄ΡΠ°Π²Π»ΠΈΡΠ΅ΡΠΊΠΈΡ ΡΠΎΡΠΌΠΎΠ·ΠΎΠ² Π²ΡΡΠ΅ Π·Π° ΡΡΠ΅Ρ ΠΌΠ΅Π½ΡΡΠ΅ΠΉ ΠΏΠΎΡΠ΅ΡΠΈ ΡΠ½Π΅ΡΠ³ΠΈΠΈ ΠΏΡΠΈ ΠΏΠ΅ΡΠ΅ΠΌΠ΅ΡΠ΅Π½ΠΈΠΈ ΡΠ½Π΅ΡΠ³ΠΎΠ½ΠΎΡΠΈΡΠ΅Π»Ρ ΠΏΠΎ ΡΡΡΠ±ΠΎΠΏΡΠΎΠ²ΠΎΠ΄Ρ.
ΠΡ ΠΈ ΡΠ°ΠΌΠΎΠ΅ Π³Π»Π°Π²Π½ΠΎΠ΅ ΠΎΡΠ»ΠΈΡΠΈΠ΅ ΠΌΠ΅ΠΆΠ΄Ρ Π³ΠΈΠ΄ΡΠ°Π²Π»ΠΈΠΊΠΎΠΉ ΠΈ ΠΏΠ½Π΅Π²ΠΌΠ°ΡΠΈΠΊΠΎΠΉ — ΡΠ΅Π½Π° Π½Π° Π·Π°ΠΏΡΠ°ΡΡΠΈ ΠΈ Π°Π³ΡΠ΅Π³Π°ΡΡ. Π₯ΠΎΡΡ ΡΡΠΆΠ΅Π»ΠΎ ΡΡΠ°Π²Π½ΠΈΠ²Π°ΡΡ, Π½Π°ΠΏΡΠΈΠΌΠ΅Ρ, ΡΡΠΎΠΈΠΌΠΎΡΡΡ ΡΠΎΡΠΌΠΎΠ·Π½ΠΎΠ³ΠΎ ΡΡΠΏΠΏΠΎΡΡΠ° Π»Π΅Π³ΠΊΠΎΠ²ΠΎΠ³ΠΎ Π°Π²ΡΠΎΠΌΠΎΠ±ΠΈΠ»Ρ ΠΈ Π±Π°ΡΠ°Π±Π°Π½Π½ΡΠΉ ΡΠΎΡΠΌΠΎΠ· ΡΡΠΆΠ΅Π»ΠΎΠ³ΠΎ ΡΡΠ³Π°ΡΠ°, ΠΊΠ°ΠΊ ΠΌΠΈΠ½ΠΈΠΌΡΠΌ ΠΈΠ·-Π·Π° Π±ΠΎΠ»ΡΡΠΎΠΉ ΡΠ°Π·Π½ΠΈΡΡ Π² Π³Π°Π±Π°ΡΠΈΡΠ°Ρ ΠΈ ΠΊΠΎΠ½ΡΡΡΡΠΊΡΠΈΠΈ.
ΠΠΌΠ΅Π½Π½ΠΎ Π±Π»Π°Π³ΠΎΠ΄Π°ΡΡ ΠΎΡΠ»ΠΈΡΠΈΡΠΌ ΠΌΠ΅ΠΆΠ΄Ρ Π΄Π²ΡΠΌΡ Π²ΠΈΠ΄Π°ΠΌΠΈ ΡΠΎΡΠΌΠΎΠ·Π½ΡΡ ΠΏΡΠΈΠ²ΠΎΠ΄ΠΎΠ² ΠΊΠ°ΠΆΠ΄ΡΠΉ ΠΈΠ· ΡΠΈΠΏΠΎΠ² Π·Π°Π½ΠΈΠΌΠ°Π΅Ρ ΡΠ²ΠΎΡ Π½ΠΈΡΡ ΠΈ ΠΏΡΠ°ΠΊΡΠΈΡΠ΅ΡΠΊΠΈ Π½Π΅ ΠΊΠΎΠ½ΠΊΡΡΠΈΡΡΠ΅Ρ Ρ Π°Π½Π°Π»ΠΎΠ³ΠΎΠΌ.
ΠΠ΅ΠΈΡΠΏΡΠ°Π²Π½ΠΎΡΡΠΈ ΠΏΠ½Π΅Π²ΠΌΠ°ΡΠΈΡΠ΅ΡΠΊΠΎΠΉ ΡΠΎΡΠΌΠΎΠ·Π½ΠΎΠΉ ΡΠΈΡΡΠ΅ΠΌΡ. ΠΡΠΈΡΠΈΠ½Ρ ΠΈ ΠΏΡΠΈΠ·Π½Π°ΠΊΠΈ ΠΏΠΎΠ»ΠΎΠΌΠΎΠΊ. ΠΠ°ΠΊ ΠΏΡΠΎΠ΄Π»ΠΈΡΡ ΡΡΠΎΠΊ ΡΠ»ΡΠΆΠ±Ρ ΡΠΎΡΠΌΠΎΠ·ΠΎΠ²
ΠΡΠ½ΠΎΠ²Π½ΡΠ΅ Π½Π΅ΠΈΡΠΏΡΠ°Π²Π½ΠΎΡΡΠΈ ΠΏΠ½Π΅Π²ΠΌΠ°ΡΠΈΡΠ΅ΡΠΊΠΎΠΉ ΡΠΎΡΠΌΠΎΠ·Π½ΠΎΠΉ ΡΠΈΡΡΠ΅ΠΌΠ΅:
- ΡΠΎΡΠΌΠΎΠ·Π° Π°Π²ΡΠΎΠΌΠΎΠ±ΠΈΠ»Ρ Π½Π΅ ΡΠ΅Π°Π³ΠΈΡΡΡΡ Π½Π° Π½Π°ΠΆΠΈΠΌ ΠΏΠ΅Π΄Π°Π»ΠΈ ΠΈΠ»ΠΈ ΡΠ΅Π°Π³ΠΈΡΡΡΡ Ρ Π±ΠΎΠ»ΡΡΠΈΠΌ ΠΎΠΏΠΎΠ·Π΄Π°Π½ΠΈΠ΅ΠΌ. ΠΡΠΈΡΠΈΠ½Ρ — ΡΠΆΠ°ΡΡΠΉ Π²ΠΎΠ·Π΄ΡΡ Π²ΡΡ ΠΎΠ΄ΠΈΡ ΡΠ΅ΡΠ΅Π· ΡΡΠ΅ΡΠΈΠ½Ρ Π² ΡΡΡΠ±ΠΎΠΏΡΠΎΠ²ΠΎΠ΄Π΅ ΠΈΠ»ΠΈ ΡΠ΅ΡΠΈΠ²Π΅ΡΠ΅, Π²ΡΡΠ΅Π» ΠΈΠ· ΡΡΡΠΎΡ ΠΊΠΎΠΌΠΏΡΠ΅ΡΡΠΎΡ. ΠΠ΅ΠΈΡΠΏΡΠ°Π²Π½ΠΎΡΡΠΈ Π²ΠΎΠ·Π½ΠΈΠΊΠ°ΡΡ Π² ΡΠ΅Π·ΡΠ»ΡΡΠ°ΡΠ΅ ΡΠ΅Π·ΠΊΠΎΠ³ΠΎ ΡΠ΄Π°ΡΠ°, ΠΊΠΎΡΠΎΡΡΠΉ ΠΏΠΎΠ²ΡΠ΅Π΄ΠΈΠ» ΠΏΠ½Π΅Π²ΠΌΠΎΡΠΈΡΡΠ΅ΠΌΡ, ΠΏΠΎΡΡΠ΅ΠΏΠ΅Π½Π½ΠΎΠ³ΠΎ ΠΈΠ·Π½ΠΎΡΠ° ΠΏΡΠΈΠ²ΠΎΠ΄Π°, ΡΠ°Π·ΡΡΠ²Π° ΠΏΡΠΈΠ²ΠΎΠ΄Π½ΠΎΠ³ΠΎ ΡΠ΅ΠΌΠ½Ρ, ΠΊΠΎΡΠΎΡΡΠΉ Π·Π°ΠΏΡΡΠΊΠ°Π΅Ρ ΠΊΠΎΠΌΠΏΡΠ΅ΡΡΠΎΡ. ΠΡΡ ΠΎΠ΄ — ΠΎΠ±ΡΠ°ΡΠΈΡΡΡΡ Π½Π° Π΄ΠΈΠ°Π³Π½ΠΎΡΡΠΈΠΊΡΒ Π½Π° ΡΡΠ°Π½ΡΠΈΠΈ ΡΠ΅Ρ ΠΎΠ±ΡΠ»ΡΠΆΠΈΠ²Π°Π½ΠΈΡ;
- ΡΠ²Π΅Π»ΠΈΡΠΈΠ»ΡΡ ΡΠΎΡΠΌΠΎΠ·Π½ΠΎΠΉ ΠΏΡΡΡ Π°Π²ΡΠΎΠΌΠΎΠ±ΠΈΠ»Ρ. ΠΡΠΈΡΠΈΠ½Ρ ΡΠ°ΠΊΠΆΠ΅ ΠΌΠΎΠ³ΡΡ Π±ΡΡΡ ΡΠ°Π·Π½ΡΠ΅. ΠΠ°ΠΏΡΠΈΠΌΠ΅Ρ, ΡΠ°Π·Π±ΠΎΠ»ΡΠ°Π»Π°ΡΡ ΠΏΠ΅Π΄Π°Π»Ρ ΡΠΎΡΠΌΠΎΠ·Π°, ΠΈΠ·Π½ΠΎΡΠΈΠ»ΠΈΡΡ ΡΠΎΡΠΌΠΎΠ·Π½ΡΠ΅ ΠΊΠΎΠ»ΠΎΠ΄ΠΊΠΈ ΠΈΠ»ΠΈ Π±Π°ΡΠ°Π±Π°Π½Ρ, ΠΏΠΎΠ²ΡΠ΅ΠΆΠ΄Π΅Π½ ΠΎΠ΄ΠΈΠ½ ΠΈΠ· ΠΊΠΎΠ½ΡΡΡΠΎΠ² ΠΌΠ°Π³ΠΈΡΡΡΠ°Π»ΠΈ. ΠΠ΅ΠΈΡΠΏΡΠ°Π²Π½ΠΎΡΡΠΈ Π²ΠΎΠ·Π½ΠΈΠΊΠ°ΡΡ Π² ΡΠ΅Π·ΡΠ»ΡΡΠ°ΡΠ΅ Π΅ΡΡΠ΅ΡΡΠ²Π΅Π½Π½ΠΎΠ³ΠΎ ΠΈΠ·Π½ΠΎΡΠ°, ΡΠ΅Π·ΠΊΠΎΠ³ΠΎ ΠΏΠ΅ΡΠ΅ΠΏΠ°Π΄Π° Π΄Π°Π²Π»Π΅Π½ΠΈΡ ΠΈΠ»ΠΈ Π½Π΅ΠΏΡΠ°Π²ΠΈΠ»ΡΠ½ΠΎΠΉ ΡΠ°Π±ΠΎΡΡ ΠΏΠ΅ΡΠ΅ΠΏΡΡΠΊΠ½ΡΡ ΠΊΠ»Π°ΠΏΠ°Π½ΠΎΠ² ΠΈ ΡΠΎΡΠΌΠΎΠ·Π½ΡΡ ΠΊΡΠ°Π½ΠΎΠ². Π Π΅ΡΠ΅Π½ΠΈΠ΅ — ΠΏΠΎΡΠ΅ΡΠΈΡΠ΅ Π°Π²ΡΠΎΡΠ΅ΡΠ²ΠΈΡ ΠΈ ΠΏΡΠΎΠΉΠ΄ΠΈΡΠ΅ Π΄ΠΈΠ°Π³Π½ΠΎΡΡΠΈΠΊΡ ΠΏΠ½Π΅Π²ΠΌΠΎΡΠΎΡΠΌΠΎΠ·ΠΎΠ²;
- Π·Π°Π½ΠΎΡ ΠΏΡΠΈΡΠ΅ΠΏΠ° Π²ΠΎ Π²ΡΠ΅ΠΌΡ ΡΠΎΡΠΌΠΎΠΆΠ΅Π½ΠΈΡ. ΠΡΠΎΠ±Π»Π΅ΠΌΠ° Π³ΠΎΠ²ΠΎΡΠΈΡ ΠΎ Π½Π΅ΠΈΡΠΏΡΠ°Π²Π½ΠΎΡΡΠΈ ΡΠ°Π·ΠΎΠ±ΡΠΈΡΠ΅Π»ΡΠ½ΠΎΠ³ΠΎ ΠΊΠ»Π°ΠΏΠ°Π½Π°, ΠΊΠΎΡΠΎΡΡΠΉ ΡΠΎΠ΅Π΄ΠΈΠ½ΡΠ΅Ρ ΠΏΠ½Π΅Π²ΠΌΠΎΡΠΈΡΡΠ΅ΠΌΡ ΡΡΠ³Π°ΡΠ° ΠΈ ΡΠΎΡΠΌΠΎΠ·Π½ΡΠ΅ ΠΊΠ°ΠΌΠ΅ΡΡ ΠΏΡΠΈΡΠ΅ΠΏΠ°. Π ΡΠ΅Π·ΡΠ»ΡΡΠ°ΡΠ΅, ΠΊΠΎΠ³Π΄Π° Π²ΠΎΠ΄ΠΈΡΠ΅Π»Ρ ΡΠΎΡΠΌΠΎΠ·ΠΈΡ, Π²ΠΎΠ·Π΄ΡΡ ΠΏΠΎΡΡΡΠΏΠ°Π΅Ρ ΡΠΎΠ»ΡΠΊΠΎ Π² ΡΠΎΡΠΌΠΎΠ·Π½ΡΠ΅ ΠΊΠ°ΠΌΠ΅ΡΡ, Π° ΠΏΡΠΈΡΠ΅ΠΏ ΠΏΡΠΎΠ΄ΠΎΠ»ΠΆΠ°Π΅Ρ Π΄Π²ΠΈΠΆΠ΅Π½ΠΈΠ΅. ΠΡΡ ΠΎΠ΄ΠΈΡ, ΡΡΠΎ ΠΏΡΠΈΡΠ΅ΠΏ ΠΈ ΡΡΠ³Π°Ρ Π½Π°ΡΠΈΠ½Π°ΡΡ Π΄Π²ΠΈΠ³Π°ΡΡΡΡ Π½Π°Π²ΡΡΡΠ΅ΡΡ Π΄ΡΡΠ³ Π΄ΡΡΠ³Ρ, Π² ΡΠ΅Π·ΡΠ»ΡΡΠ°ΡΠ΅ ΡΠ΅Π³ΠΎ ΠΏΡΠΈΡΠ΅ΠΏ ΠΊΠ°ΠΊ Π±ΠΎΠ»Π΅Π΅ Π΄Π»ΠΈΠ½Π½ΡΠΉ ΠΈ ΠΌΠ΅Π½Π΅Π΅ ΡΡΡΠΎΠΉΡΠΈΠ²ΡΠΉ ΠΎΠ±ΡΠ΅ΠΊΡ Π²Π΅Π΄Π΅Ρ Π² ΡΡΠΎΡΠΎΠ½Ρ. Π§ΡΠΎΠ±Ρ ΡΡΡΡΠ°Π½ΠΈΡΡ ΠΏΠΎΠ»ΠΎΠΌΠΊΡ, Π΄ΠΎΡΡΠ°ΡΠΎΡΠ½ΠΎ Π·Π°ΠΌΠ΅Π½ΠΈΡΡ ΡΠ°Π·ΠΎΠ±ΡΠΈΡΠ΅Π»ΡΠ½ΡΠΉ ΠΊΡΠ°Π½;
- Π°Π²ΡΠΎΠΌΠΎΠ±ΠΈΠ»Ρ Π²Π΅Π΄Π΅Ρ Π² ΡΡΠΎΡΠΎΠ½Ρ ΠΏΡΠΈ ΡΠΎΡΠΌΠΎΠΆΠ΅Π½ΠΈΠΈ. ΠΡΠΈΡΠΈΠ½Π° — ΡΠΎΡΠΌΠΎΠ·Π° ΡΠ°Π±ΠΎΡΠ°ΡΡ Π½Π΅ΡΠΈΠ½Ρ ΡΠΎΠ½Π½ΠΎ, ΠΊΠΎΠ»Π΅ΡΠ° ΡΠΎΡΠΌΠΎΠ·ΡΡ Π² ΡΠ°Π·Π½ΠΎΠ΅ Π²ΡΠ΅ΠΌΡ, ΠΈ Π°Π²ΡΠΎΠΌΠΎΠ±ΠΈΠ»Ρ ΠΌΠΎΠΆΠ΅Ρ Π·Π°Π½Π΅ΡΡΠΈ. ΠΡΠΎΠ±Π»Π΅ΠΌΠ° Π²ΠΎΠ·Π½ΠΈΠΊΠ°Π΅Ρ, ΠΊΠΎΠ³Π΄Π° Π½Π΅ΡΠ°Π²Π½ΠΎΠΌΠ΅ΡΠ½ΠΎ ΠΈΠ·Π½Π°ΡΠΈΠ²Π°ΡΡΡΡ ΡΠΎΡΠΌΠΎΠ·Π½ΡΠ΅ ΠΊΠΎΠ»ΠΎΠ΄ΠΊΠΈ ΠΈ Π±Π°ΡΠ°Π±Π°Π½Ρ ΠΈΠ»ΠΈ ΠΎΠ΄Π½Π° ΠΈΠ· ΡΠΎΡΠΌΠΎΠ·Π½ΡΡ ΠΊΠ°ΠΌΠ΅Ρ ΠΏΡΠΎΠΏΡΡΠΊΠ°Π΅Ρ Π²ΠΎΠ·Π΄ΡΡ .
Π‘Π²ΠΎΠ΅Π²ΡΠ΅ΠΌΠ΅Π½Π½ΡΠΉ ΡΠ΅ΠΌΠΎΠ½Ρ — Π·Π°Π»ΠΎΠ³ Π±Π΅Π·ΠΎΠΏΠ°ΡΠ½ΠΎΡΡΠΈ ΠΈ ΠΊΠΎΠΌΡΠΎΡΡΠ°
Π§ΡΠΎΠ±Ρ Π½Π΅ Π΄ΠΎΠΏΡΡΡΠΈΡΡ Π½Π΅ΠΈΡΠΏΡΠ°Π²Π½ΠΎΡΡΠΈ, Π΄ΠΎΡΡΠ°ΡΠΎΡΠ½ΠΎ ΡΠ΅Π³ΡΠ»ΡΡΠ½ΠΎ ΠΏΡΠΎΠ²Π΅ΡΡΡΡ ΡΠΎΡΡΠΎΡΠ½ΠΈΠ΅ ΡΠΎΡΠΌΠΎΠ·Π½ΠΎΠΉ ΡΠΈΡΡΠ΅ΠΌΡ Π°Π²ΡΠΎΠΌΠΎΠ±ΠΈΠ»Ρ, ΡΠ»Π΅Π΄ΠΈΡΡ Π·Π° ΠΏΠΎΠΊΠ°Π·Π°ΡΠ΅Π»ΠΈ ΠΌΠ°Π½ΠΎΠΌΠ΅ΡΡΠΎΠ² ΠΈ Π΄Π°ΡΡΠΈΠΊΠΎΠ², Π²ΠΎΠ²ΡΠ΅ΠΌΡ ΠΏΡΠΎΡ ΠΎΠ΄ΠΈΡΡ Π’Π, ΠΈΡΠΏΠΎΠ»ΡΠ·ΠΎΠ²Π°ΡΡ ΠΊΠ°ΡΠ΅ΡΡΠ²Π΅Π½Π½ΡΠ΅ ΠΈ ΠΏΠΎΠ΄Ρ ΠΎΠ΄ΡΡΠΈΠ΅ ΠΏΠΎ Π΄ΠΎΠΏΡΡΠΊΠ°ΠΌ Π·Π°ΠΏΡΠ°ΡΡΠΈ, ΠΊΠΎΠΌΠΏΠ»Π΅ΠΊΡΡΡΡΠΈΠ΅ ΠΈ ΡΠΌΠ΅Π½Π½ΡΠ΅ ΡΠ·Π»Ρ. ΠΠΌΠ΅Π½Π½ΠΎ ΠΎΡ ΠΎΡΠ½ΠΎΡΠ΅Π½ΠΈΡ Π²ΠΎΠ΄ΠΈΡΠ΅Π»Ρ ΠΊ Π°Π²ΡΠΎΠΌΠΎΠ±ΠΈΠ»Ρ Π·Π°Π²ΠΈΡΠΈΡ ΡΡΠΎΠΊ ΡΠ»ΡΠΆΠ±Ρ ΡΡΠ°Π½ΡΠΏΠΎΡΡΠ½ΠΎΠ³ΠΎ ΡΡΠ΅Π΄ΡΡΠ²Π°. ΠΡΠΎ ΠΏΡΠ°Π²ΠΈΠ»ΠΎ, ΠΊΠΎΡΠΎΡΡΠ΅ Π΄ΠΎΠ»ΠΆΠ΅Π½ Π·Π½Π°ΡΡ ΠΈ ΡΠΎΠ±Π»ΡΠ΄Π°ΡΡ ΠΊΠ°ΠΆΠ΄ΡΠΉ Π²ΠΎΠ΄ΠΈΡΠ΅Π»Ρ Π½Π΅Π·Π°Π²ΠΈΡΠΈΠΌΠΎ ΠΎΡ ΡΠΎΠ³ΠΎ, Π½Π° ΡΠ΅ΠΌ Π΅Π·Π΄ΠΈΡ ΡΠ΅Π»ΠΎΠ²Π΅ΠΊ — Π½Π° Π»Π΅Π³ΠΊΠΎΠ²ΡΡΠΊΠ΅ ΠΈΠ»ΠΈ ΡΡΠ³Π°ΡΠ΅ Ρ ΠΏΡΠΈΡΠ΅ΠΏΠΎΠΌ.
steering.com.ua
ΠΠ°ΠΊΠΎΠ΅ Π΄Π°Π²Π»Π΅Π½ΠΈΠ΅ Π² ΡΠΎΡΠΌΠΎΠ·Π½ΠΎΠΉ ΡΠΈΡΡΠ΅ΠΌΠ΅ Π°Π²ΡΠΎΠΌΠΎΠ±ΠΈΠ»Ρ
Π’ΠΎΡΠΌΠΎΠ·Π½Π°Ρ ΡΠΈΡΡΠ΅ΠΌΠ° Π°Π²ΡΠΎΠΌΠΎΠ±ΠΈΠ»Ρ: ΡΡΡΡΠΎΠΉΡΡΠ²ΠΎ, Π½Π°Π·Π½Π°ΡΠ΅Π½ΠΈΠ΅ ΠΈ ΠΏΡΠΈΠ½ΡΠΈΠΏ Π΄Π΅ΠΉΡΡΠ²ΠΈΡ ΡΠΎΡΠΌΠΎΠ·ΠΎΠ²
ΠΠ΄Π½ΠΎΠΉ ΠΈΠ· ΡΠ°ΠΌΡΡ Π²Π°ΠΆΠ½ΡΡ ΡΠΈΡΡΠ΅ΠΌ Π² Π°Π²ΡΠΎΠΌΠΎΠ±ΠΈΠ»Π΅, ΡΠ²Π»ΡΠ΅ΡΡΡ ΡΠΈΡΡΠ΅ΠΌΠ° ΡΠΎΡΠΌΠΎΠΆΠ΅Π½ΠΈΡ. ΠΡΠΈ Π΅Π΅ Π½Π΅ΠΈΡΠΏΡΠ°Π²Π½ΠΎΡΡΠΈ Π°Π²ΡΠΎΠΌΠΎΠ±ΠΈΠ»Ρ ΡΡΠ°Π½ΠΎΠ²ΠΈΡΡΡ ΡΠΌΠ΅ΡΡΠ΅Π»ΡΠ½ΠΎ ΠΎΠΏΠ°ΡΠ½ΡΠΌ ΠΊΠ°ΠΊ Π΄Π»Ρ Π²ΠΎΠ΄ΠΈΡΠ΅Π»Ρ, Π΅Π΄ΡΡΠΈΡ Ρ Π½ΠΈΠΌ ΠΏΠ°ΡΡΠ°ΠΆΠΈΡΠΎΠ², ΡΠ°ΠΊ ΠΈ Π΄Π»Ρ Π²ΡΠ΅Ρ ΠΎΡΡΠ°Π»ΡΠ½ΡΡ ΡΡΠ°ΡΡΠ½ΠΈΠΊΠΎΠ² Π΄ΠΎΡΠΎΠΆΠ½ΠΎΠ³ΠΎ Π΄Π²ΠΈΠΆΠ΅Π½ΠΈΡ, Π²ΠΊΠ»ΡΡΠ°Ρ Π²Π΅Π·Π΄Π΅ΡΡΡΠΈΡ ΠΏΠ΅ΡΠ΅Ρ ΠΎΠ΄ΠΎΠ². ΠΠΎΡΡΠΎΠΌΡ ΠΈΡΠΏΡΠ°Π²Π½ΠΎΡΡΡ ΡΠΎΡΠΌΠΎΠ·Π½ΠΎΠΉ ΡΠΈΡΡΠ΅ΠΌΡ Π°Π²ΡΠΎΠΌΠΎΠ±ΠΈΠ»Ρ — Π·Π°Π»ΠΎΠ³ ΡΠΎΡ ΡΠ°Π½Π½ΠΎΡΡΠΈ Π½Π΅ ΡΠΎΠ»ΡΠΊΠΎ Π·Π΄ΠΎΡΠΎΠ²ΡΡ, Π½ΠΎ ΠΈ ΠΆΠΈΠ·Π½ΠΈ.
Π’ΠΎΡΠΌΠΎΠ·Π½Π°Ρ ΡΠΈΡΡΠ΅ΠΌΠ° Π°Π²ΡΠΎΠΌΠΎΠ±ΠΈΠ»Ρ ΠΏΡΠ΅Π΄Π½Π°Π·Π½Π°ΡΠ΅Π½Π° Π΄Π»Ρ Π·Π°ΠΌΠ΅Π΄Π»Π΅Π½ΠΈΡ ΠΈΠ»ΠΈ ΠΎΡΡΡΠ΅ΡΡΠ²Π»Π΅Π½ΠΈΡ ΠΏΠΎΠ»Π½ΠΎΠΉ ΠΎΡΡΠ°Π½ΠΎΠ²ΠΊΠΈ ΡΡΠ°Π½ΡΠΏΠΎΡΡΠ½ΠΎΠ³ΠΎ ΡΡΠ΅Π΄ΡΡΠ²Π°. Π ΡΠΎΡΠΌΠΎΠ·Π½ΡΡ ΡΠΈΡΡΠ΅ΠΌΡ Π²Ρ ΠΎΠ΄ΠΈΡ ΡΡΠ΄ ΡΠΎΡΡΠ°Π²Π½ΡΡ ΡΠ°ΡΡΠ΅ΠΉ β ΡΡΠΎ ΡΠΎΡΠΌΠΎΠ·Π½ΡΠ΅ ΠΊΠΎΠ»ΠΎΠ΄ΠΊΠΈ, ΡΠ»Π°Π½Π³ΠΈ, ΡΠΎΡΠΌΠΎΠ·Π½ΡΠ΅ ΡΠΈΠ»ΠΈΠ½Π΄ΡΡ, Π²Π°ΠΊΡΡΠΌΠ½ΡΠΉ ΡΡΠΈΠ»ΠΈΡΠ΅Π»Ρ, Π±Π°ΡΠ°Π±Π°Π½Ρ ΠΈΠ»ΠΈ Π΄ΠΈΡΠΊΠΈ.
ΠΡΠ΅ ΡΠΎΠ²ΡΠ΅ΠΌΠ΅Π½Π½ΡΠ΅ Π°Π²ΡΠΎΠΌΠΎΠ±ΠΈΠ»ΠΈ ΠΎΠ±ΠΎΡΡΠ΄ΡΡΡΡΡ ΡΡΠΈΠΊΡΠΈΠΎΠ½Π½ΡΠΌΠΈ ΡΠΎΡΠΌΠΎΠ·Π°ΠΌΠΈ. Π ΠΎΡΠ½ΠΎΠ²Π΅ ΡΠ°Π±ΠΎΡΠΎΡΠΏΠΎΡΠΎΠ±Π½ΠΎΡΡΠΈ ΡΡΠΈΠΊΡΠΈΠΎΠ½Π½ΡΡ ΡΠΎΡΠΌΠΎΠ·ΠΎΠ² ΠΈΡΠΏΠΎΠ»ΡΠ·ΡΠ΅ΡΡΡ ΡΠΈΠ»Π° ΡΡΠ΅Π½ΠΈΡ Π½Π΅ΠΏΠΎΠ΄Π²ΠΈΠΆΠ½ΡΡ Π΄Π΅ΡΠ°Π»Π΅ΠΉ ΠΌΠ΅Ρ Π°Π½ΠΈΠ·ΠΌΠ° ΠΎ ΠΏΠΎΠ΄Π²ΠΈΠΆΠ½ΡΠ΅.
Π’ΠΎΡΠΌΠΎΠ·Π½Π°Ρ ΡΠΈΡΡΠ΅ΠΌΠ° ΡΠ°Π·Π΄Π΅Π»ΡΠ΅ΡΡΡ Π½Π° Π΄Π²Π° Π²ΠΈΠ΄Π°: ΡΠ°Π±ΠΎΡΠ°Ρ, ΠΊΠΎΡΠΎΡΠ°Ρ ΠΏΡΠ΅Π΄Π½Π°Π·Π½Π°ΡΠ΅Π½Π° Π΄Π»Ρ ΡΠ½ΠΈΠΆΠ΅Π½ΠΈΡ ΡΠΊΠΎΡΠΎΡΡΠΈ ΠΈ ΠΎΡΡΠ°Π½ΠΎΠ²ΠΊΠΈ Π°Π²ΡΠΎΠΌΠΎΠ±ΠΈΠ»Ρ ΠΈ ΡΡΠΎΡΠ½ΠΎΡΠ½Π°Ρ, ΠΊΠΎΡΠΎΡΠ°Ρ ΠΈΡΠΏΠΎΠ»ΡΠ·ΡΠ΅ΡΡΡ Π΄Π»Ρ ΡΠΎΠ³ΠΎ, ΡΡΠΎΠ±Ρ ΡΠ΄Π΅ΡΠΆΠ°ΡΡ Π°Π²ΡΠΎΠΌΠΎΠ±ΠΈΠ»Ρ Π½Π° Π½Π΅ΡΠΎΠ²Π½ΠΎΠΉ ΠΏΠΎΠ²Π΅ΡΡ Π½ΠΎΡΡΠΈ (ΡΡΡΠ½ΠΈΠΊ, Π½ΠΎ Π² ΡΠΎΠ²ΡΠ΅ΠΌΠ΅Π½Π½ΡΡ Π°Π²ΡΠΎΠΌΠΎΠ±ΠΈΠ»ΡΡ Π±ΡΠ²Π°Π΅Ρ ΠΈ Π°Π²ΡΠΎΠΌΠ°ΡΠΈΡΠ΅ΡΠΊΠΈΠΉ ΡΡΠΎΡΠ½ΠΎΡΠ½ΡΠΉ ΡΠΎΡΠΌΠΎΠ·). Π‘ΠΎΠ³Π»Π°ΡΠ½ΠΎ ΡΡΠ΅Π±ΠΎΠ²Π°Π½ΠΈΠΉ, ΠΊΠΎΡΠΎΡΡΠ΅ ΠΏΡΠ΅Π΄ΡΡΠ²Π»ΡΡΡΡΡ ΡΡΡΠ°Π½Π°ΠΌΠΈ, Π²Ρ ΠΎΠ΄ΡΡΠΈΠΌΠΈ Π² ΠΠΠ‘, ΡΠ°Π±ΠΎΡΠ΅ΠΉ ΠΈ ΡΡΠΎΡΠ½ΠΎΡΠ½ΠΎΠΉ ΡΠΎΡΠΌΠΎΠ·Π½ΠΎΠΉ ΡΠΈΡΡΠ΅ΠΌΠ°ΠΌΠΈ Π΄ΠΎΠ»ΠΆΠ΅Π½ Π±ΡΡΡ ΠΎΠ±ΠΎΡΡΠ΄ΠΎΠ²Π°Π½ ΠΊΠ°ΠΆΠ΄ΡΠΉ ΠΏΡΠΎΠΈΠ·Π²ΠΎΠ΄ΠΈΠΌΡΠΉ Π°Π²ΡΠΎΠΌΠΎΠ±ΠΈΠ»Ρ.
ΠΠ±Π΅ΡΠΏΠ΅ΡΠΈΡΡ Π±Π΅Π·ΠΎΠΏΠ°ΡΠ½ΡΡ ΡΠΊΡΠΏΠ»ΡΠ°ΡΠ°ΡΠΈΡ ΡΡΠ°Π½ΡΠΏΠΎΡΡΠ½ΡΡ ΡΡΠ΅Π΄ΡΡΠ² Π±Π΅Π· Π²ΡΡΠΎΠΊΠΎ-ΡΡΡΠ΅ΠΊΡΠΈΠ²Π½ΠΎΠΉ ΠΈ ΠΊΡΠ°ΠΉΠ½Π΅ Π½Π°Π΄Π΅ΠΆΠ½ΠΎΠΉ ΡΠΎΡΠΌΠΎΠ·Π½ΠΎΠΉ ΡΠΈΡΡΠ΅ΠΌΡ Π½Π΅ ΠΏΡΠ΅Π΄ΡΡΠ°Π²Π»ΡΠ΅ΡΡΡ Π²ΠΎΠ·ΠΌΠΎΠΆΠ½ΡΠΌ. ΠΠ΅ΡΠ΅Π΄ ΠΈΠ½ΠΆΠ΅Π½Π΅ΡΠ°ΠΌΠΈ, ΡΠ°Π±ΠΎΡΠ°ΡΡΠΈΠΌΠΈ Π² Π°Π²ΡΠΎΠΌΠΎΠ±ΠΈΠ»Π΅ΡΡΡΠΎΠ΅Π½ΠΈΠΈ, ΠΏΠΎΡΡΠΎΡΠ½Π½ΠΎ ΡΡΠΎΠΈΡ Π·Π°Π΄Π°ΡΠ° ΡΠΎΠ²Π΅ΡΡΠ΅Π½ΡΡΠ²ΠΎΠ²Π°Π½ΠΈΡ ΡΠΎΡΠΌΠΎΠ·Π½ΡΡ ΡΠΈΡΡΠ΅ΠΌ. ΠΠ½ΠΎΠ³ΠΈΠ΅ ΠΈΠ· ΡΡΠΈΡ ΡΡΠΎΠ²Π΅ΡΡΠ΅Π½ΡΡΠ²ΠΎΠ²Π°Π½ΠΈΠΉ, ΠΊ ΡΠΎΠΆΠ°Π»Π΅Π½ΠΈΡ, ΠΏΡΠ΅Π΄Π»Π°Π³Π°ΡΡΡΡ ΡΠΎΠ»ΡΠΊΠΎ Π² Π΄ΠΎΠΏΠΎΠ»Π½ΠΈΡΠ΅Π»ΡΠ½ΡΡ ΠΎΠΏΡΠΈΡΡ ΠΊ Π°Π²ΡΠΎΠΌΠΎΠ±ΠΈΠ»Ρ ΠΈΠ»ΠΈ ΡΠΎΠ»ΡΠΊΠΎ Π² Π΄ΠΎΡΠΎΠ³ΠΈΡ ΠΊΠΎΠΌΠΏΠ»Π΅ΠΊΡΠ°ΡΠΈΡΡ , Π·Π° ΠΊΠΎΡΠΎΡΡΠ΅ ΠΏΡΠΈΡ ΠΎΠ΄ΠΈΡΡΡ ΠΏΠ»Π°ΡΠΈΡΡ Π±ΠΎΠ»ΡΡΠ΅. ΠΠΎ ΡΡΠΎΠΈΡ Π»ΠΈ ΡΠΊΠΎΠ½ΠΎΠΌΠΈΡΡ Π½Π° ΡΠΎΠ±ΡΡΠ²Π΅Π½Π½ΠΎΠΉ Π±Π΅Π·ΠΎΠΏΠ°ΡΠ½ΠΎΡΡΠΈ? ΠΡΠΎ ΡΠ΅ΡΠ°Π΅Ρ ΠΊΠ°ΠΆΠ΄ΡΠΉ Π°Π²ΡΠΎΠ»ΡΠ±ΠΈΡΠ΅Π»Ρ ΡΠ°ΠΌΠΎΡΡΠΎΡΡΠ΅Π»ΡΠ½ΠΎ.
ΠΡΠΈΠ½ΡΠΈΠΏ Π΄Π΅ΠΉΡΡΠ²ΠΈΡ ΡΠΎΡΠΌΠΎΠ·Π½ΠΎΠΉ ΡΠΈΡΡΠ΅ΠΌΡ
Π‘Ρ
Π΅ΠΌΠ° ΠΏΠΎΠ΄Π³ΠΎΡΠΎΠ²Π»Π΅Π½Π° ΠΏΠΎ ΠΌΠ°ΡΠ΅ΡΠΈΠ°Π»Π°ΠΌ automn.ru ΠΈ systemsauto.ru
- ΡΡΡΠ±ΠΎΠΏΡΠΎΠ²ΠΎΠ΄ ΠΊΠΎΠ½ΡΡΡΠ° Β«Π»Π΅Π²ΡΠΉ ΠΏΠ΅ΡΠ΅Π΄Π½ΠΈΠΉ-ΠΏΡΠ°Π²ΡΠΉ Π·Π°Π΄Π½ΠΈΠΉ ΡΠΎΡΠΌΠΎΠ·Π½ΡΠ΅ ΠΌΠ΅Ρ Π°Π½ΠΈΠ·ΠΌΡΒ»
- ΡΠΈΠ³Π½Π°Π»ΡΠ½ΠΎΠ΅ ΡΡΡΡΠΎΠΉΡΡΠ²ΠΎ
- ΡΡΡΠ±ΠΎΠΏΡΠΎΠ²ΠΎΠ΄ ΠΊΠΎΠ½ΡΡΡΠ° Β«ΠΏΡΠ°Π²ΡΠΉ ΠΏΠ΅ΡΠ΅Π΄Π½ΠΈΠΉ — Π»Π΅Π²ΡΠΉ Π·Π°Π΄Π½ΠΈΠΉ ΡΠΎΡΠΌΠΎΠ·Π½ΡΠ΅ ΠΌΠ΅Ρ Π°Π½ΠΈΠ·ΠΌΡΒ»
- Π±Π°ΡΠΎΠΊ Π³Π»Π°Π²Π½ΠΎΠ³ΠΎ ΡΠΎΡΠΌΠΎΠ·Π½ΠΎΠ³ΠΎ ΡΠΈΠ»ΠΈΠ½Π΄ΡΠ°
- Π³Π»Π°Π²Π½ΡΠΉ ΡΠΎΡΠΌΠΎΠ·Π½ΠΎΠΉ ΡΠΈΠ»ΠΈΠ½Π΄Ρ
- Π²Π°ΠΊΡΡΠΌΠ½ΡΠΉ ΡΡΠΈΠ»ΠΈΡΠ΅Π»Ρ ΡΠΎΡΠΌΠΎΠ·ΠΎΠ²
- ΠΏΠ΅Π΄Π°Π»Ρ ΡΠΎΡΠΌΠΎΠ·Π°
- ΡΠ΅Π³ΡΠ»ΡΡΠΎΡ Π΄Π°Π²Π»Π΅Π½ΠΈΡ
- ΡΡΠΎΡ ΡΡΠΎΡΠ½ΠΎΡΠ½ΠΎΠ³ΠΎ ΡΠΎΡΠΌΠΎΠ·Π°
- ΡΠΎΡΠΌΠΎΠ·Π½ΠΎΠΉ ΠΌΠ΅Ρ Π°Π½ΠΈΠ·ΠΌ Π·Π°Π΄Π½Π΅Π³ΠΎ ΠΊΠΎΠ»Π΅ΡΠ°
- ΡΠ΅Π³ΡΠ»ΠΈΡΠΎΠ²ΠΎΡΠ½ΡΠΉ Π½Π°ΠΊΠΎΠ½Π΅ΡΠ½ΠΈΠΊ ΡΡΠΎΡΠ½ΠΎΡΠ½ΠΎΠ³ΠΎ ΡΠΎΡΠΌΠΎΠ·Π°
- ΡΡΡΠ°Π³ ΠΏΡΠΈΠ²ΠΎΠ΄Π° ΡΡΠΎΡΠ½ΠΎΡΠ½ΠΎΠ³ΠΎ ΡΠΎΡΠΌΠΎΠ·Π°
- ΡΠΎΡΠΌΠΎΠ·Π½ΠΎΠΉ ΠΌΠ΅Ρ Π°Π½ΠΈΠ·ΠΌ ΠΏΠ΅ΡΠ΅Π΄Π½Π΅Π³ΠΎ ΠΊΠΎΠ»Π΅ΡΠ°
ΠΡΠΈ Π½Π°ΠΆΠ°ΡΠΈΠΈ Π½Π° ΠΏΠ΅Π΄Π°Π»Ρ ΡΠΎΡΠΌΠΎΠ·Π° Π² ΡΠΎΡΠΌΠΎΠ·Π½ΠΎΠΉ ΡΠΈΡΡΠ΅ΠΌΠ΅ ΡΠΎΠ·Π΄Π°Π΅ΡΡΡ Π΄Π°Π²Π»Π΅Π½ΠΈΠ΅, ΠΊΠΎΡΠΎΡΠΎΠ΅ ΡΡΠΈΠ»ΠΈΠ²Π°Π΅ΡΡΡ Π²Π°ΠΊΡΡΠΌΠ½ΡΠΌ ΡΡΠΈΠ»ΠΈΡΠ΅Π»Π΅ΠΌ ΠΈ ΠΏΠ΅ΡΠ΅Π΄Π°Π΅ΡΡΡ ΡΠ΅ΡΠ΅Π· ΡΠΎΡΠΌΠΎΠ·Π½ΡΠ΅ ΡΠ»Π°Π½Π³ΠΈ Π½Π° Π½Π΅ΠΏΠΎΠ΄Π²ΠΈΠΆΠ½ΡΠ΅ ΡΠ°ΡΡΠΈ ΡΠΎΡΠΌΠΎΠ·Π½ΠΎΠ³ΠΎ ΠΌΠ΅Ρ Π°Π½ΠΈΠ·ΠΌΠ° — ΠΊΠΎΠ»ΠΎΠ΄ΠΊΠΈ.
Π’Π΅ΠΌ ΡΠ°ΠΌΡΠΌ ΡΠΎΡΠΌΠΎΠ·Π½ΡΠ΅ ΠΊΠΎΠ»ΠΎΠ΄ΠΊΠΈ ΠΏΡΠΈΠ²ΠΎΠ΄ΡΡΡΡ Π² Π΄Π²ΠΈΠΆΠ΅Π½ΠΈΠ΅ ΠΈ Π»ΠΈΠ±ΠΎ Π·Π°ΠΆΠΈΠΌΠ°ΡΡ ΡΠΎΡΠΌΠΎΠ·Π½ΠΎΠΉ Π΄ΠΈΡΠΊ (Π² Π΄ΠΈΡΠΊΠΎΠ²ΡΡ ΡΠΎΡΠΌΠΎΠ·Π°Ρ ), Π»ΠΈΠ±ΠΎ ΡΠΏΠΈΡΠ°ΡΡΡΡ Π² ΡΡΠ΅Π½ΠΊΠΈ Π±Π°ΡΠ°Π±Π°Π½Π° (Π² ΡΠΎΡΠΌΠΎΠ·Π°Ρ Π±Π°ΡΠ°Π±Π°Π½Π½ΠΎΠ³ΠΎ ΡΠΈΠΏΠ°), ΡΡΠΎ ΠΎΠ±Π΅ΡΠΏΠ΅ΡΠΈΠ²Π°Π΅Ρ ΡΠΎΡΠΌΠΎΠΆΠ΅Π½ΠΈΠ΅.
ΠΠΈΡΠΊΠΎΠ²ΡΠ΅ ΡΠΎΡΠΌΠΎΠ·Π° Ρ ΠΎΡΡ ΠΈ Π±ΠΎΠ»Π΅Π΅ Π΄ΠΎΡΠΎΠ³ΠΈΠ΅, Π½ΠΎ Π±ΠΎΠ»Π΅Π΅ Π½Π°Π΄Π΅ΠΆΠ½ΡΠ΅, ΠΏΠΎΡΡΠΎΠΌΡ Π±Π°ΡΠ°Π±Π°Π½Π½ΡΠ΅ ΡΠΎΡΠΌΠΎΠ·Π° ΠΈΡΠΏΠΎΠ»ΡΠ·ΡΡΡΡΡ Π»ΠΈΡΡ Π½Π° Π·Π°Π΄Π½ΠΈΡ ΠΊΠΎΠ»Π΅ΡΠ°Ρ Π±ΡΠ΄ΠΆΠ΅ΡΠ½ΡΡ Π°Π²ΡΠΎΠΌΠΎΠ±ΠΈΠ»Π΅ΠΉ.
Π‘Ρ Π΅ΠΌΠ° Π΄ΠΈΡΠΊΠΎΠ²ΡΡ ΡΠΎΡΠΌΠΎΠ·ΠΎΠ²
ΠΠΈΡΠΊΠΎΠ²ΡΠΉ ΡΠΎΡΠΌΠΎΠ·Π½ΠΎΠΉ ΠΌΠ΅Ρ Π°Π½ΠΈΠ·ΠΌ ΡΠΎΡΡΠΎΠΈΡ ΠΈΠ· ΡΠΎΡΠΌΠΎΠ·Π½ΠΎΠ³ΠΎ Π΄ΠΈΡΠΊΠ°, ΠΊΠΎΡΠΎΡΡΠΉ Π·Π°ΠΊΡΠ΅ΠΏΠ»Π΅Π½ Π½Π° ΠΊΠΎΠ»Π΅ΡΠ΅ ΠΈ Π²ΡΠ°ΡΠ°Π΅ΡΡΡ Π²ΠΌΠ΅ΡΡΠ΅ Ρ Π½ΠΈΠΌ, Π΄Π²ΡΡ Π½Π΅ΠΏΠΎΠ΄Π²ΠΈΠΆΠ½ΡΡ ΠΊΠΎΠ»ΠΎΠ΄ΠΎΠΊ, ΠΊΠΎΡΠΎΡΡΠ΅ ΡΡΡΠ°Π½ΠΎΠ²Π»Π΅Π½Ρ Π²Π½ΡΡΡΠΈ ΡΡΠΏΠΏΠΎΡΡΠ° ΠΏΠΎ ΠΎΠ±Π΅ ΡΡΠΎΡΠΎΠ½Ρ ΠΎΡ ΡΠΎΡΠΌΠΎΠ·Π½ΠΎΠ³ΠΎ Π΄ΠΈΡΠΊΠ°.
Π‘ΡΠΏΠΏΠΎΡΡ ΠΊΡΠ΅ΠΏΠΈΡΡΡ Π½Π° ΠΊΡΠΎΠ½ΡΡΠ΅ΠΉΠ½Π΅. ΠΠ° ΡΡΠΏΠΏΠΎΡΡΠ΅, Π² Π΅Π³ΠΎ ΠΏΠ°Π·Π°Ρ ΡΠ°ΠΊΠΆΠ΅ ΠΊΡΠ΅ΠΏΡΡΡΡ ΡΠ°Π±ΠΎΡΠΈΠ΅ ΡΠΈΠ»ΠΈΠ½Π΄ΡΡ, ΠΊΠΎΡΠΎΡΡΠ΅ Π²ΠΎ Π²ΡΠ΅ΠΌΡ ΡΠΎΡΠΌΠΎΠΆΠ΅Π½ΠΈΡ ΠΏΡΠΈΠΆΠΈΠΌΠ°ΡΡ ΡΠΎΡΠΌΠΎΠ·Π½ΡΠ΅ ΠΊΠΎΠ»ΠΎΠ΄ΠΊΠΈ ΠΊ Π΄ΠΈΡΠΊΡ.
Π’ΠΎΡΠΌΠΎΠ·Π½ΡΠ΅ ΠΊΠΎΠ»ΠΎΠ΄ΠΊΠΈ ΠΏΠΎΡΠ»Π΅ ΠΎΡΠΏΡΡΠΊΠ°Π½ΠΈΡ ΠΏΠ΅Π΄Π°Π»ΠΈ ΡΠΎΡΠΌΠΎΠ·Π° Π²ΠΎΠ·Π²ΡΠ°ΡΠ°ΡΡΡΡ Π² ΠΈΡΡ ΠΎΠ΄Π½ΠΎΠ΅ ΠΏΠΎΠ»ΠΎΠΆΠ΅Π½ΠΈΠ΅ ΠΏΡΡΠΆΠΈΠ½Π½ΡΠΌΠΈ ΡΠ»Π΅ΠΌΠ΅Π½ΡΠ°ΠΌΠΈ.
Π’ΠΎΡΠΌΠΎΠ·Π½ΠΎΠΉ Π΄ΠΈΡΠΊ Π² ΠΏΡΠΎΡΠ΅ΡΡΠ΅ ΡΠΎΡΠΌΠΎΠΆΠ΅Π½ΠΈΡ, ΠΏΠΎΠ΄ Π²ΠΎΠ·Π΄Π΅ΠΉΡΡΠ²ΠΈΠ΅ΠΌ ΡΠΈΠ» ΡΡΠ΅Π½ΠΈΡ ΡΠΈΠ»ΡΠ½ΠΎ Π½Π°Π³ΡΠ΅Π²Π°Π΅ΡΡΡ. ΠΡ Π»Π°ΠΆΠ΄Π΅Π½ΠΈΠ΅ ΡΠΎΡΠΌΠΎΠ·Π½ΡΡ Π΄ΠΈΡΠΊΠΎΠ² ΠΏΡΠΎΠΈΡΡ ΠΎΠ΄ΠΈΡ Π·Π° ΡΡΠ΅Ρ ΠΊΠΎΠ½Π²Π΅ΠΊΡΠΈΠ²Π½ΠΎΠ³ΠΎ ΠΎΠΌΠΎΠ²Π΅Π½ΠΈΡ ΠΏΠΎΡΠΎΠΊΠΎΠΌ Π²ΠΎΠ·Π΄ΡΡ Π°. ΠΠ»Ρ ΡΠ»ΡΡΡΠ΅Π½ΠΈΡ ΠΎΡΠ²ΠΎΠ΄Π° Π½Π°ΠΊΠ°ΠΏΠ»ΠΈΠ²Π°Π΅ΠΌΠΎΠ³ΠΎ Π΄ΠΈΡΠΊΠΎΠΌ ΡΠ΅ΠΏΠ»Π° Π² Π½Π΅ΠΌ Π΄Π΅Π»Π°ΡΡΡΡ ΡΠΏΠ΅ΡΠΈΠ°Π»ΡΠ½ΡΠ΅ ΠΎΡΠ²Π΅ΡΡΡΠΈΡ ΠΈ Π² ΡΡΠΎΠΌ ΡΠ»ΡΡΠ°Π΅ Π΄ΠΈΡΠΊ ΡΠ²Π»ΡΠ΅ΡΡΡ Π²Π΅Π½ΡΠΈΠ»ΠΈΡΡΠ΅ΠΌΡΠΌ. ΠΠ»Ρ Π΅ΡΠ΅ Π±ΠΎΠ»ΡΡΠ΅Π³ΠΎ ΠΏΠΎΠ²ΡΡΠ΅Π½ΠΈΡ ΡΡΡΠ΅ΠΊΡΠΈΠ²Π½ΠΎΡΡΠΈ ΠΏΡΠΎΡΠ΅ΡΡΠ° ΡΠΎΡΠΌΠΎΠΆΠ΅Π½ΠΈΡ ΠΈ Π½ΠΈΠ²Π΅Π»ΠΈΡΠΎΠ²Π°Π½ΠΈΡ ΠΏΠΎΡΠ»Π΅Π΄ΡΡΠ²ΠΈΠΉ ΠΏΠ΅ΡΠ΅Π³ΡΠ΅Π²Π° Π΄ΠΈΡΠΊΠ° Π½Π° ΡΠΏΠΎΡΡΠΈΠ²Π½ΡΡ ΠΈ ΡΠΊΠΎΡΠΎΡΡΠ½ΡΡ Π°Π²ΡΠΎΠΌΠΎΠ±ΠΈΠ»ΡΡ ΡΡΡΠ°Π½Π°Π²Π»ΠΈΠ²Π°ΡΡ ΡΠΎΡΠΌΠΎΠ·Π½ΡΠ΅ Π΄ΠΈΡΠΊΠΈ, ΠΈΠ·Π³ΠΎΡΠΎΠ²Π»Π΅Π½Π½ΡΠ΅ Ρ ΠΏΡΠΈΠΌΠ΅Π½Π΅Π½ΠΈΠ΅ΠΌ ΡΠΏΠ΅ΡΠΈΠ°Π»ΡΠ½ΡΡ ΠΊΠ΅ΡΠ°ΠΌΠΈΡΠ΅ΡΠΊΠΈΡ ΠΌΠ°ΡΠ΅ΡΠΈΠ°Π»ΠΎΠ².
Π’ΠΎΡΠΌΠΎΠ·Π½ΠΎΠΉ ΠΏΡΠΈΠ²ΠΎΠ΄ ΡΠ»ΡΠΆΠΈΡ Π΄Π»Ρ ΠΎΠ±Π΅ΡΠΏΠ΅ΡΠ΅Π½ΠΈΡ ΡΠΏΡΠ°Π²Π»Π΅Π½ΠΈΡ Π²ΡΠ΅ΠΌΠΈ ΡΠΎΡΡΠ°Π²Π»ΡΡΡΠΈΠΌΠΈ ΡΠΎΡΠΌΠΎΠ·Π½ΠΎΠ³ΠΎ ΠΌΠ΅Ρ Π°Π½ΠΈΠ·ΠΌΠ°. Π ΡΠΎΠ²ΡΠ΅ΠΌΠ΅Π½Π½ΡΡ ΡΠΎΡΠΌΠΎΠ·Π½ΡΡ ΡΠΈΡΡΠ΅ΠΌΠ°Ρ ΠΏΡΠΈΠΌΠ΅Π½ΡΡΡΡΡ ΡΠ°ΠΊΠΈΠ΅ ΡΠΈΠΏΡ ΡΠΎΡΠΌΠΎΠ·Π½ΡΡ ΠΏΡΠΈΠ²ΠΎΠ΄ΠΎΠ²: ΠΌΠ΅Ρ Π°Π½ΠΈΡΠ΅ΡΠΊΠΈΠΉ, ΠΏΠ½Π΅Π²ΠΌΠ°ΡΠΈΡΠ΅ΡΠΊΠΈΠΉ, Π³ΠΈΠ΄ΡΠ°Π²Π»ΠΈΡΠ΅ΡΠΊΠΈΠΉ, ΡΠ»Π΅ΠΊΡΡΠΈΡΠ΅ΡΠΊΠΈΠΉ ΠΈ ΠΊΠΎΠΌΠ±ΠΈΠ½ΠΈΡΠΎΠ²Π°Π½Π½ΡΠΉ.
ΠΠ΅Ρ Π°Π½ΠΈΡΠ΅ΡΠΊΠΈΠΉ ΠΏΡΠΈΠ²ΠΎΠ΄ ΠΏΡΠΈΠΌΠ΅Π½ΡΠ΅ΡΡΡ Π² ΡΡΠΎΡΠ½ΠΎΡΠ½ΠΎΠΉ ΡΠΎΡΠΌΠΎΠ·Π½ΠΎΠΉ ΡΠΈΡΡΠ΅ΠΌΠ΅ (ΡΡΡΠ½ΠΈΠΊ). ΠΠ΅Ρ Π°Π½ΠΈΡΠ΅ΡΠΊΠΈΠΉ ΠΏΡΠΈΠ²ΠΎΠ΄ — ΡΡΠΎ ΡΠΈΡΡΠ΅ΠΌΠ° ΡΡΠ³, ΡΡΠΎΡΠΎΠ² ΠΈ ΡΡΡΠ°Π³ΠΎΠ², ΠΊΠΎΡΠΎΡΡΠ΅ ΡΠ»ΡΠΆΠ°Ρ Π΄Π»Ρ ΡΠΎΠ΅Π΄ΠΈΠ½Π΅Π½ΠΈΡ ΡΡΡΠ°Π³Π° ΡΡΠΎΡΠ½ΠΎΡΠ½ΠΎΠ³ΠΎ ΡΠΎΡΠΌΠΎΠ·Π° Ρ ΡΠΎΡΠΌΠΎΠ·Π½ΡΠΌ ΠΌΠ΅Ρ Π°Π½ΠΈΠ·ΠΌΠΎΠΌ Π·Π°Π΄Π½ΠΈΡ ΠΊΠΎΠ»Π΅Ρ Π°Π²ΡΠΎΠΌΠΎΠ±ΠΈΠ»Ρ.
Π‘ΡΡΠ΅ΡΡΠ²ΡΠ΅Ρ ΡΠ°ΠΊΠΆΠ΅ ΡΠΈΡΡΠ΅ΠΌΠ° ΠΌΠ΅Ρ Π°Π½ΠΈΡΠ΅ΡΠΊΠΎΠ³ΠΎ ΠΏΡΠΈΠ²ΠΎΠ΄Π° ΡΡΠΎΡΠ½ΠΎΡΠ½ΠΎΠ³ΠΎ ΡΠΎΡΠΌΠΎΠ·Π°, ΠΏΡΠΈΠ²ΠΎΠ΄ΠΈΠΌΠ°Ρ Π² Π΄Π΅ΠΉΡΡΠ²ΠΈΠ΅ Ρ ΠΏΠΎΠΌΠΎΡΡΡ Π½ΠΎΠΆΠ½ΠΎΠΉ ΠΏΠ΅Π΄Π°Π»ΠΈ.
ΠΠΈΠ΄ΡΠ°Π²Π»ΠΈΡΠ΅ΡΠΊΠΈΠΉ ΠΏΡΠΈΠ²ΠΎΠ΄ ΡΠ²Π»ΡΠ΅ΡΡΡ Π½Π°ΠΈΠ±ΠΎΠ»Π΅Π΅ ΡΠ°ΡΠΏΡΠΎΡΡΡΠ°Π½Π΅Π½Π½ΡΠΌ ΡΠΈΠΏΠΎΠΌ ΠΏΡΠΈΠ²ΠΎΠ΄Π° Π² ΡΠ°Π±ΠΎΡΠ΅ΠΉ ΡΠΈΡΡΠ΅ΠΌΠ΅ ΡΠΎΡΠΌΠΎΠ·ΠΎΠ². ΠΠΎΠ½ΡΡΡΡΠΊΡΠΈΡ Π³ΠΈΠ΄ΡΠ°Π²Π»ΠΈΡΠ΅ΡΠΊΠΎΠ³ΠΎ ΠΏΡΠΈΠ²ΠΎΠ΄Π° Π²ΠΊΠ»ΡΡΠ°Π΅Ρ: ΠΏΠ΅Π΄Π°Π»Ρ ΡΠΎΡΠΌΠΎΠ·Π°, Π³Π»Π°Π²Π½ΡΠΉ ΡΠΎΡΠΌΠΎΠ·Π½ΠΎΠΉ ΡΠΈΠ»ΠΈΠ½Π΄Ρ, Π²Π°ΠΊΡΡΠΌΠ½ΡΠΉ ΡΡΠΈΠ»ΠΈΡΠ΅Π»Ρ ΡΠΎΡΠΌΠΎΠ·ΠΎΠ², ΡΠ°Π±ΠΎΡΠΈΠ΅ ΡΠΈΠ»ΠΈΠ½Π΄ΡΡ, ΡΠ»Π°Π½Π³ΠΈ ΠΈ ΡΡΡΠ±ΠΎΠΏΡΠΎΠ²ΠΎΠ΄Ρ.
ΠΡΠΈΠ½ΡΠΈΠΏ ΡΠ°Π±ΠΎΡΡ Π³ΠΈΠ΄ΡΠ°Π²Π»ΠΈΡΠ΅ΡΠΊΠΎΠ³ΠΎ ΠΏΡΠΈΠ²ΠΎΠ΄Π° ΡΠΎΡΠΌΠΎΠ·ΠΎΠ² ΠΎΠΏΠΈΡΠ°Π½ ΡΡΡΡ Π²ΡΡΠ΅.
ΠΠ»Ρ ΠΎΠ±Π΅ΡΠΏΠ΅ΡΠ΅Π½ΠΈΡ Π½Π°Π΄Π΅ΠΆΠ½ΠΎΡΡΠΈ ΡΠΎΡΠΌΠΎΠ·Π½ΠΎΠΉ ΡΠΈΡΡΠ΅ΠΌΡ ΡΠ°Π±ΠΎΡΠ° Π³ΠΈΠ΄ΡΠ°Π²Π»ΠΈΡΠ΅ΡΠΊΠΎΠ³ΠΎ ΠΏΡΠΈΠ²ΠΎΠ΄Π° ΠΎΡΠ³Π°Π½ΠΈΠ·ΡΠ΅ΡΡΡ ΠΏΠΎ Π΄Π²ΡΠΌ (ΠΊΠ°ΠΊ ΠΏΡΠ°Π²ΠΈΠ»ΠΎ) Π½Π΅Π·Π°Π²ΠΈΡΠΈΠΌΡΠΌ ΠΊΠΎΠ½ΡΡΡΠ°ΠΌ. ΠΡΠΈ ΠΏΠΎΠ»ΠΎΠΌΠΊΠ΅ ΠΎΠ΄Π½ΠΎΠ³ΠΎ ΠΊΠΎΠ½ΡΡΡΠ°, Π΅Π³ΠΎ ΡΡΠ½ΠΊΡΠΈΠΈ Π±Π΅ΡΠ΅Ρ Π½Π° ΡΠ΅Π±Ρ Π΄ΡΡΠ³ΠΎΠΉ ΠΊΠΎΠ½ΡΡΡ. Π Π°Π±ΠΎΡΠΈΠ΅ ΠΊΠΎΠ½ΡΡΡΡ ΠΌΠΎΠ³ΡΡ Π΄ΡΠ±Π»ΠΈΡΠΎΠ²Π°ΡΡ ΡΡΠ½ΠΊΡΠΈΠΈ Π΄ΡΡΠ³-Π΄ΡΡΠ³Π° Π»ΠΈΠ±ΠΎ Π²ΡΠΏΠΎΠ»Π½ΡΡΡ ΡΠ°ΡΡΡ ΠΊΠ°ΠΊΡΡ-ΡΠΎ ΡΠ°ΡΡΡ ΡΡΠ½ΠΊΡΠΈΠΉ Π²ΡΠΎΡΠΎΠ³ΠΎ ΠΊΠΎΠ½ΡΡΡΠ°. ΠΠΎΠ·ΠΌΠΎΠΆΠ½ΠΎ ΡΠ°ΠΊΠΆΠ΅ ΠΈ Π²ΡΠΏΠΎΠ»Π½Π΅Π½ΠΈΠ΅ ΠΊΠ°ΠΆΠ΄ΡΠΌ ΠΊΠΎΠ½ΡΡΡΠΎΠΌ ΡΡΡΠΎΠ³ΠΎ ΡΠ²ΠΎΠΈΡ ΡΡΠ½ΠΊΡΠΈΠΉ. ΠΠ°ΠΈΠ±ΠΎΠ»Π΅Π΅ ΡΠ°ΡΠΏΡΠΎΡΡΡΠ°Π½Π΅Π½Π½ΠΎΠΉ ΡΠ²Π»ΡΠ΅ΡΡΡ Π΄ΠΈΠ°Π³ΠΎΠ½Π°Π»ΡΠ½Π°Ρ ΡΡ Π΅ΠΌΠ° ΡΠ°Π±ΠΎΡΡ ΠΊΠΎΠ½ΡΡΡΠΎΠ².
ΠΠ½Π΅Π²ΠΌΠ°ΡΠΈΡΠ΅ΡΠΊΠΈΠΉ ΠΏΡΠΈΠ²ΠΎΠ΄ ΠΈΡΠΏΠΎΠ»ΡΠ·ΡΠ΅ΡΡΡ ΠΏΡΠ΅ΠΈΠΌΡΡΠ΅ΡΡΠ²Π΅Π½Π½ΠΎ Π² ΡΠΎΡΠΌΠΎΠ·Π½ΠΎΠΉ ΡΠΈΡΡΠ΅ΠΌΠ΅ Π³ΡΡΠ·ΠΎΠ²ΡΡ Π°Π²ΡΠΎΠΌΠΎΠ±ΠΈΠ»Π΅ΠΉ.
ΠΠΎΠΌΠ±ΠΈΠ½ΠΈΡΠΎΠ²Π°Π½Π½ΡΠΉ ΡΠΎΡΠΌΠΎΠ·Π½ΠΎΠΉ ΠΏΡΠΈΠ²ΠΎΠ΄, ΠΊΠ°ΠΊ ΡΠ»Π΅Π΄ΡΠ΅Ρ ΠΈΠ· Π½Π°Π·Π²Π°Π½ΠΈΡ, ΠΏΡΠ΅Π΄ΡΡΠ°Π²Π»ΡΠ΅Ρ ΡΠΎΠ±ΠΎΠΉ ΡΠΎΡΠ΅ΡΠ°Π½ΠΈΠ΅ (ΠΊΠΎΠΌΠ±ΠΈΠ½Π°ΡΠΈΡ) Π΄Π²ΡΡ Π²ΠΈΠ΄ΠΎΠ² ΠΏΡΠΈΠ²ΠΎΠ΄Π° (ΡΠ»Π΅ΠΊΡΡΠΎΠΏΠ½Π΅Π²ΠΌΠ°ΡΠΈΡΠ΅ΡΠΊΠΈΠΉ, Π½Π°ΠΏΡΠΈΠΌΠ΅Ρ).
ΠΠ°Π»Π΅Π΅ ΡΠΊΠ°ΠΆΠ΅ΠΌ ΠΏΠ°ΡΡ ΡΠ»ΠΎΠ² ΠΎ Π΄ΠΎΠΏΠΎΠ»Π½ΠΈΡΠ΅Π»ΡΠ½ΡΡ ΡΠΈΡΡΠ΅ΠΌΠ°Ρ , ΠΊΠΎΡΠΎΡΡΠ΅ Π΄Π΅Π»Π°ΡΡ Π°Π²ΡΠΎΠΌΠΎΠ±ΠΈΠ»Ρ Π±ΠΎΠ»Π΅Π΅ Π±Π΅Π·ΠΎΠΏΠ°ΡΠ½ΡΠΌ…
ΠΠ½ΡΠΈ-Π±Π»ΠΎΠΊΠΈΡΠΎΠ²ΠΎΡΠ½Π°Ρ ΡΠΈΡΡΠ΅ΠΌΠ° ABS, ΠΏΡΠ΅Π΄Π½Π°Π·Π½Π°ΡΠ°Π΅ΡΡΡ Π΄Π»Ρ ΠΏΡΠ΅Π΄ΠΎΡΠ²ΡΠ°ΡΠ΅Π½ΠΈΡ Π±Π»ΠΎΠΊΠΈΡΠΎΠ²Π°Π½ΠΈΡ ΠΊΠΎΠ»Π΅Ρ Π°Π²ΡΠΎΠΌΠΎΠ±ΠΈΠ»Ρ Π²ΠΎ Π²ΡΠ΅ΠΌΡ ΠΎΡΠ΅Π½Ρ ΡΠΈΠ»ΡΠ½ΠΎΠ³ΠΎ Π½Π°ΠΆΠ°ΡΠΈΡ Π½Π° ΠΏΠ΅Π΄Π°Π»Ρ ΡΠΎΡΠΌΠΎΠ·Π°, ΡΡΠΎ ΠΏΠΎΠ·Π²ΠΎΠ»ΡΠ΅Ρ ΠΈΠ·Π±Π΅ΠΆΠ°ΡΡ Π΄Π²ΠΈΠΆΠ΅Π½ΠΈΡ ΡΠ·ΠΎΠΌ, ΠΈ ΡΠΎΡ ΡΠ°Π½ΠΈΡΡ ΠΊΠΎΠ½ΡΡΠΎΠ»Ρ Π½Π°Π΄ Π°Π²ΡΠΎΠΌΠΎΠ±ΠΈΠ»Π΅ΠΌ. Π ΡΠΎΡΡΠ°Π² ΡΠΈΡΡΠ΅ΠΌΡ ABS (Antilock Brake System) Π²Ρ ΠΎΠ΄ΡΡ ΡΡΠΈ ΡΠ»Π΅ΠΌΠ΅Π½ΡΠ° β ΡΡΠΎ Π΄Π°ΡΡΠΈΠΊ ΠΈΠ·ΠΌΠ΅ΡΠ΅Π½ΠΈΡ ΡΠΊΠΎΡΠΎΡΡΠΈ, ΠΊΠΎΡΠΎΡΡΠΉ ΡΡΡΠ°Π½Π°Π²Π»ΠΈΠ²Π°Π΅ΡΡΡ Π½Π° ΠΊΠ°ΠΆΠ΄ΠΎΠΌ ΠΊΠΎΠ»Π΅ΡΠ΅, ΠΌΠΎΠ΄ΡΠ»ΡΡΠΎΡ Π΄Π°Π²Π»Π΅Π½ΠΈΡ ΡΠΎΡΠΌΠΎΠ·Π½ΠΎΠΉ ΠΆΠΈΠ΄ΠΊΠΎΡΡΠΈ ΠΈ Π±Π»ΠΎΠΊ ΡΠΏΡΠ°Π²Π»Π΅Π½ΠΈΡ ΡΠΈΡΡΠ΅ΠΌΠΎΠΉ ABS.
Π‘ΠΈΡΡΠ΅ΠΌΠ° TCS ΡΠΎΠ·Π΄Π°Π½Π° Π½Π° ΠΎΡΠ½ΠΎΠ²Π΅ ΡΠΈΡΡΠ΅ΠΌΡ ABS ΠΈ ΠΏΡΠ΅Π΄Π½Π°Π·Π½Π°ΡΠ΅Π½Π° Π΄Π»Ρ ΠΏΡΠ΅Π΄ΠΎΡΠ²ΡΠ°ΡΠ΅Π½ΠΈΡ ΠΏΡΠΎΠ±ΡΠΊΡΠΎΠ²ΡΠ²Π°Π½ΠΈΡ ΠΊΠΎΠ»Π΅Ρ Π²ΠΎ Π²ΡΠ΅ΠΌΡ ΡΠ»ΠΈΡΠΊΠΎΠΌ ΡΠ΅Π·ΠΊΠΎΠ³ΠΎ ΡΡΠ°ΡΡΠ° ΠΈΠ»ΠΈ Π½Π° ΡΠΊΠΎΠ»ΡΠ·ΠΊΠΎΠΉ Π΄ΠΎΡΠΎΠ³Π΅. Π‘ΠΈΡΡΠ΅ΠΌΠ° (Traction Control System) ΡΡΡΠ΅ΡΡΠ²ΡΠ΅Ρ ΠΈ ΠΏΠΎΠ΄ Π½Π°Π·Π²Π°Π½ΠΈΡΠΌΠΈ: ASR, ASC, ETS. ΠΠ½Π° ΠΎΡΠ»ΠΈΡΠ°Π΅ΡΡΡ ΠΎΡ ΡΠΈΡΡΠ΅ΠΌΡ ABS ΡΠΎΠ»ΡΠΊΠΎ Π½Π°Π»ΠΈΡΠΈΠ΅ΠΌ ΠΌΠΎΠ΄ΠΈΡΠΈΡΠΈΡΠΎΠ²Π°Π½Π½ΠΎΠ³ΠΎ Π±Π»ΠΎΠΊΠ° ΡΠΏΡΠ°Π²Π»Π΅Π½ΠΈΡ.
ESP. ΠΡΠ΅ ΠΎΠ΄Π½ΠΎΠΉ ΠΏΠΎΠ»Π΅Π·Π½ΠΎΠΉ ΡΠΈΡΡΠ΅ΠΌΠΎΠΉ, ΠΊΠΎΡΠΎΡΠ°Ρ ΠΌΠΎΠΆΠ΅Ρ ΡΡΡΠ°Π½Π°Π²Π»ΠΈΠ²Π°ΡΡΡΡ Π½Π° Π°Π²ΡΠΎΠΌΠΎΠ±ΠΈΠ»Π΅, ΡΠ²Π»ΡΠ΅ΡΡΡ ΡΠΈΡΡΠ΅ΠΌΠ° ΡΠ»Π΅ΠΊΡΡΠΎΠ½Π½ΠΎΠΉ ΡΡΠ°Π±ΠΈΠ»ΠΈΠ·Π°ΡΠΈΠΈ ΠΊΠΎΠ»Π΅Ρ ESP. ΠΡΠ° ΡΠΈΡΡΠ΅ΠΌΠ° ΡΠ°Π±ΠΎΡΠ°Π΅Ρ Π² ΠΏΠΎΠ²ΠΎΡΠΎΡΠ΅, ΠΏΡΠΈΡΠ΅ΠΌ Π΅Π³ΠΎ ΡΠ³ΠΎΠ» ΠΈ ΡΠΊΠΎΡΠΎΡΡΡ Π½Π΅ ΠΈΠΌΠ΅ΡΡ Π·Π½Π°ΡΠ΅Π½ΠΈΡ, ΠΏΡΠΈ Π²ΠΎΠ·Π½ΠΈΠΊΠ½ΠΎΠ²Π΅Π½ΠΈΠΈ Π·Π°Π½ΠΎΡΠ° Π·Π°Π΄Π½Π΅ΠΉ ΠΎΡΠΈ Π°Π²ΡΠΎΠΌΠΎΠ±ΠΈΠ»Ρ, ESP (Electronic Stability Program) ΠΎΠ±Π΅ΡΠΏΠ΅ΡΠΈΠ²Π°Π΅Ρ ΠΏΠΎΠ΄ΡΠΎΡΠΌΠ°ΠΆΠΈΠ²Π°Π½ΠΈΠ΅ ΠΏΠ΅ΡΠ΅Π΄Π½Π΅Π³ΠΎ Π½Π°ΡΡΠΆΠ½ΠΎΠ³ΠΎ ΠΊΠΎΠ»Π΅ΡΠ°. Π ΡΠ°ΠΊΠΎΠΉ ΡΠΈΡΡΠ°ΡΠΈΠΈ ΠΎΠ±ΡΠ°Π·ΡΠ΅ΡΡΡ ΡΡΠ°Π±ΠΈΠ»ΠΈΠ·ΠΈΡΡΡΡΠΈΠΉ ΠΌΠΎΠΌΠ΅Π½Ρ, Π²ΠΎΠ·Π½ΠΈΠΊΠ°ΡΡΠΈΠΉ ΠΌΠ΅ΠΆΠ΄Ρ ΠΊΠΎΠ»Π΅ΡΠ°ΠΌΠΈ Π°Π²ΡΠΎΠΌΠΎΠ±ΠΈΠ»Ρ, ΠΊΠΎΡΠΎΡΡΠΉ Π²ΠΎΠ·Π²ΡΠ°ΡΠ°Π΅Ρ Π΄Π²ΠΈΠΆΡΡΠΈΠΉΡΡ Π°Π²ΡΠΎΠΌΠΎΠ±ΠΈΠ»Ρ Π½Π° Π±Π΅Π·ΠΎΠΏΠ°ΡΠ½ΡΡ ΡΡΠ°Π΅ΠΊΡΠΎΡΠΈΡ.
ΠΠΈΠ΄Π΅ΠΎ: ΠΏΡΠΈΠ½ΡΠΈΠΏ ΡΠ°Π±ΠΎΡΡ ΡΠΎΡΠΌΠΎΠ·Π½ΠΎΠΉ ΡΠΈΡΡΠ΅ΠΌΡ
Π§ΠΈΡΠ°ΠΉΡΠ΅ ΡΠ°ΠΊΠΆΠ΅, ΠΊΠ°ΠΊΠΈΠ΅ Π½Π΅ΠΈΡΠΏΡΠ°Π²Π½ΠΎΡΡΠΈ ΡΠΎΡΠΌΠΎΠ·Π½ΠΎΠΉ ΡΠΈΡΡΠ΅ΠΌΡ Π½Π°ΠΈΠ±ΠΎΠ»Π΅Π΅ ΡΠ°ΡΡΠΎ Π²ΡΡΡΠ΅ΡΠ°ΡΡΡΡ…
ΠΡΡΠ³ΠΈΠ΅ ΠΌΠ°ΡΠ΅ΡΠΈΠ°Π»Ρ ΠΏΠΎ ΡΠ΅ΠΌΠ΅:
www.auto-infosite.ru
Π’ΠΎΡΠΌΠΎΠ·Π½Π°Ρ ΡΠΈΡΡΠ΅ΠΌΠ° Π°Π²ΡΠΎΠΌΠΎΠ±ΠΈΠ»Ρ
_____________________________________________________________________________________________________________________ |
Π Π·Π½Π°Π΅ΡΠ΅, Π² ΡΠ°ΠΌΠΎΠ»Π΅ΡΠ΅ ΡΠΎΠΆΠ΅ Π΅ΡΡΡ ΡΠΎΡΠΌΠΎΠ·Π°! ΠΡΠ°Π²Π΄Π°, ΡΠ°Π±ΠΎΡΠ°ΡΡ ΠΎΠ½ΠΈ Π½Π΅ Π² Π²ΠΎΠ·Π΄ΡΡ Π΅, Π° Π½Π° Π²Π·Π»Π΅ΡΠ½ΠΎΠΉ ΠΏΠΎΠ»ΠΎΡΠ΅, Π²ΠΎ Π²ΡΠ΅ΠΌΡ ΠΎΡΡΠ°Π½ΠΎΠ²ΠΊΠΈ ΡΠ°ΠΌΠΎΠ»Π΅ΡΠ° ΠΏΠΎΡΠ»Π΅ ΠΏΠΎΡΠ°Π΄ΠΊΠΈ. ΠΡ Π° Π² Π°Π²ΡΠΎΠΌΠΎΠ±ΠΈΠ»Π΅ β Β«ΡΠ°ΠΌ ΠΠΎΠ³ Π²Π΅Π»Π΅Π»Β», ΠΏΡΠΈΠΌΠ΅Π½ΠΈΡΡ ΡΠΎΡΠΌΠΎΠ·Π½ΡΡ ΡΠΈΡΡΠ΅ΠΌΡ.
ΠΡΠ°ΠΊ, ΡΠΎΡΠΌΠΎΠ·Π½Π°Ρ ΡΠΈΡΡΠ΅ΠΌΠ° ΠΏΡΠ΅Π΄Π½Π°Π·Π½Π°ΡΠ΅Π½Π° Π΄Π»Ρ ΠΈΠ·ΠΌΠ΅Π½Π΅Π½ΠΈΡ ΡΠΊΠΎΡΠΎΡΡΠΈ Π΄Π²ΠΈΠΆΠ΅Π½ΠΈΡ Π°Π²ΡΠΎΠΌΠΎΠ±ΠΈΠ»Ρ, ΠΏΠΎ ΠΊΠΎΠΌΠ°Π½Π΄Π΅ Π²ΠΎΠ΄ΠΈΡΠ΅Π»Ρ, ΠΈΠ»ΠΈ ΡΠ»Π΅ΠΊΡΡΠΎΠ½Π½ΠΎΠΉ ΡΠΈΡΡΠ΅ΠΌΡ ΡΠΏΡΠ°Π²Π»Π΅Π½ΠΈΡ. ΠΡΠΎΡΠΎΠ΅ Π½Π°Π·Π½Π°ΡΠ΅Π½ΠΈΠ΅ ΡΠΎΡΠΌΠΎΠ·Π½ΠΎΠΉ ΡΠΈΡΡΠ΅ΠΌΡ —Β ΡΠ΄Π΅ΡΠΆΠ°Π½ΠΈΠ΅ Π°Π²ΡΠΎΠΌΠΎΠ±ΠΈΠ»Ρ Π² Π½Π΅ΠΏΠΎΠ΄Π²ΠΈΠΆΠ½ΠΎΠΌ ΡΠΎΡΡΠΎΡΠ½ΠΈΠΈ ΠΎΡΠ½ΠΎΡΠΈΡΠ΅Π»ΡΠ½ΠΎ Π΄ΠΎΡΠΎΠΆΠ½ΠΎΠ³ΠΎ ΠΏΠΎΠΊΡΡΡΠΈΡ, Π½Π° Π²ΡΠ΅ΠΌΡ ΡΡΠΎΡΠ½ΠΊΠΈ. Π Π°Π·Π»ΠΈΡΠ°ΡΡ ΡΡΠΈ Π²ΠΈΠ΄Π° ΡΠΎΡΠΌΠΎΠ·Π½ΡΡ ΡΠΈΡΡΠ΅ΠΌ:
- ΡΠ°Π±ΠΎΡΠ°Ρ
- ΡΡΠΎΡΠ½ΠΎΡΠ½Π°Ρ, Π² Π½Π°ΡΠΎΠ΄Π΅ ΠΈΠΌΠ΅Π½ΡΠ΅ΠΌΠ°Ρ ΡΡΡΠ½ΠΈΠΊ.
- Π·Π°ΠΏΠ°ΡΠ½Π°Ρ, ΠΈΠ»ΠΈ ΡΠΈΡΡΠ΅ΠΌΠ° ΡΠΊΡΡΡΠ΅Π½Π½ΠΎΠ³ΠΎ ΡΠΎΡΠΌΠΎΠΆΠ΅Π½ΠΈΡ.
Π Π°Π±ΠΎΡΠ°Ρ ΡΠΈΡΡΠ΅ΠΌΠ°, ΡΡΠΎ ΠΎΡΠ½ΠΎΠ²Π½ΠΎΠΉ ΡΠ·Π΅Π» ΡΠΏΡΠ°Π²Π»Π΅Π½ΠΈΡ ΠΈ Π±Π΅Π·ΠΎΠΏΠ°ΡΠ½ΠΎΡΡΠΈ Π² Π°Π²ΡΠΎΠΌΠΎΠ±ΠΈΠ»Π΅, ΠΎΡ Π½Π°Π΄Π΅ΠΆΠ½ΠΎΡΡΠΈ ΠΊΠΎΡΠΎΡΠΎΠ³ΠΎ, Π·Π°Π²ΠΈΡΡΡ ΠΆΠΈΠ·Π½ΠΈ ΠΏΠ°ΡΡΠ°ΠΆΠΈΡΠΎΠ².
Π ΡΡΠ½ΠΈΠΊ, ΠΈΠ»ΠΈ ΡΡΠΎΡΠ½ΠΎΡΠ½ΡΠΉ ΡΠΎΡΠΌΠΎΠ· ΠΏΡΠΈΠ²ΠΎΠ΄ΠΈΡΡΡ Π² Π΄Π΅ΠΉΡΡΠ²ΠΈΠ΅, ΠΏΡΠΈ Π΄Π»ΠΈΡΠ΅Π»ΡΠ½ΠΎΠΉ ΡΡΠΎΡΠ½ΠΊΠ΅ Π°Π²ΡΠΎΠΌΠΎΠ±ΠΈΠ»Ρ, Π΄Π»Ρ ΠΈΡΠΊΠ»ΡΡΠ΅Π½ΠΈΡ ΡΠ°ΠΌΠΎΠΏΡΠΎΠΈΠ·Π²ΠΎΠ»ΡΠ½ΠΎΠ³ΠΎ Π΄Π²ΠΈΠΆΠ΅Π½ΠΈΡ, ΠΎΡΠΎΠ±Π΅Π½Π½ΠΎ Π½Π° ΡΡΠ°ΡΡΠΊΠ°Ρ Π΄ΠΎΡΠΎΠ³ΠΈ ΠΈΠΌΠ΅ΡΡΠΈΡ ΡΠΊΠ»ΠΎΠ½. ΠΠΎΠΆΠ΅Ρ ΠΈΡΠΏΠΎΠ»ΡΠ·ΠΎΠ²Π°ΡΡΡΡ ΠΈ ΠΊΠ°ΠΊ ΡΠΈΡΡΠ΅ΠΌΠ° ΡΠΊΡΡΡΠ΅Π½Π½ΠΎΠ³ΠΎ ΡΠΎΡΠΌΠΎΠΆΠ΅Π½ΠΈΡ. Π Ρ Π»ΡΠ±ΠΈΡΠ΅Π»Π΅ΠΉ Π΄ΡΠ°ΠΉΠ²Π°, ΡΡΡΡΠΎΠΉΡΡΠ²ΠΎΠΌ Π±Π»ΠΎΠΊΠΈΡΠΎΠ²ΠΊΠΈ Π·Π°Π΄Π½ΠΈΡ ΠΊΠΎΠ»Π΅Ρ (Π΄Π»Ρ ΠΏΠ΅ΡΠ΅Π΄Π½Π΅Π³ΠΎ ΠΏΡΠΈΠ²ΠΎΠ΄Π°) Π΄Π»Ρ Π²ΡΠΏΠΎΠ»Π½Π΅Π½ΠΈΡ ΡΠ΅Π·ΠΊΠΎΠ³ΠΎ ΡΠ°Π·Π²ΠΎΡΠΎΡΠ°, ΡΠ°ΠΊ Π½Π°Π·ΡΠ²Π°Π΅ΠΌΡΠΉ Β«ΠΏΠΎΠ»ΠΈΡΠ΅ΠΉΡΠΊΠΈΠΉ ΡΠ°Π·Π²ΠΎΡΠΎΡΒ».
ΠΠ°ΠΏΠ°ΡΠ½Π°Ρ ΡΠΈΡΡΠ΅ΠΌΠ° ΡΠΎΡΠΌΠΎΠΆΠ΅Π½ΠΈΡ ΡΡΠ°Π»Π° ΠΏΡΠΈΠΌΠ΅Π½ΡΡΡΡΡ ΡΡΠ°Π²Π½ΠΈΡΠ΅Π»ΡΠ½ΠΎ Π½Π΅Π΄Π°Π²Π½ΠΎ ΠΈ ΡΠ»ΡΠΆΠΈΡ Π΄Π»Ρ ΡΠΊΡΡΡΠ΅Π½Π½ΠΎΠ³ΠΎ ΡΠΎΡΠΌΠΎΠΆΠ΅Π½ΠΈΡ Π²ΠΎ Π²ΡΠ΅ΠΌΡ ΠΎΡΠΊΠ°Π·Π° ΡΠ°Π±ΠΎΡΠ΅ΠΉ ΡΠΈΡΡΠ΅ΠΌΡ. Π£ΡΡΠ°Π½Π°Π²Π»ΠΈΠ²Π°Π΅ΡΡΡ, ΠΊΠ°ΠΊ ΠΏΡΠ°Π²ΠΈΠ»ΠΎ, Π½Π° Π°Π²ΡΠΎΠΌΠΎΠ±ΠΈΠ»ΡΡ Ρ ΡΠ»Π΅ΠΊΡΡΠΈΡΠ΅ΡΠΊΠΈΠΌ ΡΡΡΠ½ΠΈΠΊΠΎΠΌ. Π’Π°ΠΊ ΠΊΠ°ΠΊ ΡΡΡΠ½ΠΈΠΊ Π²ΠΎ Π²ΡΠ΅ΠΌΡ Π΄Π²ΠΈΠΆΠ΅Π½ΠΈΡ Π½Π΅ ΡΠΌΠΎΠΆΠ΅Ρ Π²ΠΊΠ»ΡΡΠΈΡΡΡΡ, ΡΠΎ ΠΏΡΠΎΡΡΡΠΌ Π΄Π²ΠΈΠΆΠ΅Π½ΠΈΠ΅ΠΌ ΡΡΡΠ°Π³Π° ΡΠΊΡΡΡΠ΅Π½Π½ΠΎΠ³ΠΎ ΡΠΎΡΠΌΠΎΠΆΠ΅Π½ΠΈΡ Π±Π»ΠΎΠΊΠΈΡΡΡΡΡΡ ΠΊΠΎΠ»Π΅ΡΠ° ΠΈ Π°Π²ΡΠΎΠΌΠΎΠ±ΠΈΠ»Ρ ΠΎΡΡΠ°Π½ΠΎΠ²ΠΈΡΡΡ. ΠΠ°ΠΏΠ°ΡΠ½Π°Ρ ΡΠΈΡΡΠ΅ΠΌΠ° ΠΌΠΎΠΆΠ΅Ρ Π±ΡΡΡ ΡΠ΅Π°Π»ΠΈΠ·ΠΎΠ²Π°Π½Π° ΠΊΠ°ΠΊ ΠΎΡΠ΄Π΅Π»ΡΠ½ΡΠΉ ΡΠ·Π΅Π», ΠΈΠ»ΠΈ ΠΊΠ°ΠΊ ΡΠ°ΡΡΡ ΡΠ°Π±ΠΎΡΠ΅ΠΉ ΡΠΈΡΡΠ΅ΠΌΡ.
Π’ΠΎΡΠΌΠΎΠ·Π½Π°Ρ ΡΠΈΡΡΠ΅ΠΌΠ° Π°Π²ΡΠΎΠΌΠΎΠ±ΠΈΠ»Ρ ΠΎΡΠ½ΠΎΠ²Π°Π½Π° Π½Π° ΡΠΈΠ·ΠΈΡΠ΅ΡΠΊΠΎΠΌ ΡΠ²Π»Π΅Π½ΠΈΠΈ — ΡΡΠ΅Π½ΠΈΠΈ. ΠΠΌΠ΅Π½Π½ΠΎ ΠΈΠ·-Π·Π° ΡΡΠ΅Π½ΠΈΡ ΠΌΠ΅ΠΆΠ΄Ρ Π½Π΅ΠΏΠΎΠ΄Π²ΠΈΠΆΠ½ΠΎΠΉ Π΄Π΅ΡΠ°Π»ΡΡ ΠΈ Π²ΡΠ°ΡΠ°ΡΡΠ΅ΠΉΡΡ, Π΄ΠΎΡΡΠΈΠ³Π°Π΅ΡΡΡ ΡΡΡΠ΅ΠΊΡ ΡΠΎΡΠΌΠΎΠΆΠ΅Π½ΠΈΡ, Π° Π²ΠΎΡ ΠΊΠ°ΠΊ ΡΡΠΎ ΠΏΡΠΎΠΈΡΡ ΠΎΠ΄ΠΈΡ, ΠΏΠΎΠ³ΠΎΠ²ΠΎΡΠΈΠΌ Π½ΠΈΠΆΠ΅.
ΠΠΎ Π²ΡΠ΅ΠΌΡ ΡΠΎΡΠΌΠΎΠΆΠ΅Π½ΠΈΡ, ΡΡΠ΅Π½ΠΈΠ΅ Π²ΠΎΠ·Π½ΠΈΠΊΠ°Π΅Ρ ΠΌΠ΅ΠΆΠ΄Ρ ΡΡΠΈΠΊΡΠΈΠΎΠ½Π½ΡΠΌΠΈ Π½Π°ΠΊΠ»Π°Π΄ΠΊΠ°ΠΌΠΈ ΡΠΎΡΠΌΠΎΠ·Π½ΡΡ ΠΊΠΎΠ»ΠΎΠ΄ΠΎΠΊ ΠΈΠ· ΠΌΡΠ³ΠΊΠΎΠ³ΠΎ ΠΌΠ°ΡΠ΅ΡΠΈΠ°Π»Π° ΠΈ Π²ΡΠ°ΡΠ°ΡΡΠΈΠΌΡΡ ΡΠΎΡΠΌΠΎΠ·Π½ΡΠΌ Π΄ΠΈΡΠΊΠΎΠΌ ΠΈΠ»ΠΈ ΡΠΎΡΠΌΠΎΠ·Π½ΡΠΌ Π±Π°ΡΠ°Π±Π°Π½ΠΎΠΌ. ΠΠ·-Π·Π° ΡΡΠΎΠΉ ΠΎΡΠΎΠ±Π΅Π½Π½ΠΎΡΡΠΈ ΡΠΎΡΠΌΠΎΠ·Π° ΠΏΠΎΠ΄ΡΠ°Π·Π΄Π΅Π»ΡΡΡΡΡ Π½Π° Π΄ΠΈΡΠΊΠΎΠ²ΡΠ΅ ΠΈ Π±Π°ΡΠ°Π±Π°Π½Π½ΡΠ΅. ΠΠΎ Π² ΡΠΎΠ²ΡΠ΅ΠΌΠ΅Π½Π½ΠΎΠΌ Π°Π²ΡΠΎΠΌΠΎΠ±ΠΈΠ»Π΅, ΠΊΠ°ΠΊ ΠΏΡΠ°Π²ΠΈΠ»ΠΎ, ΠΏΡΠΈΠΌΠ΅Π½ΡΠ΅ΡΡΡ ΠΈΡ ΡΠΈΠΌΠ±ΠΈΠΎΠ· β ΠΏΠ΅ΡΠ΅Π΄Π½ΠΈΠ΅ ΡΠΎΡΠΌΠΎΠ·Π° Π΄ΠΈΡΠΊΠΎΠ²ΡΠ΅, Π·Π°Π΄Π½ΠΈΠ΅ Π±Π°ΡΠ°Π±Π°Π½Π½ΡΠ΅, Π½ΠΎ Π²ΠΎΠ·ΠΌΠΎΠΆΠ½Ρ Π²Π°ΡΠΈΠ°Π½ΡΡ, Π²ΡΠ΅ Π·Π°Π²ΠΈΡΠΈΡ ΠΎΡ ΠΊΠΎΠ½ΡΡΡΡΠΊΡΠΎΡΠΎΠ².
ΠΠΎ ΡΠΏΠΎΡΠΎΠ±Ρ ΠΏΡΠΈΠ²ΠΎΠ΄Π° Π² Π΄Π΅ΠΉΡΡΠ²ΠΈΠ΅, ΡΠΎΡΠΌΠΎΠ·Π½ΡΠ΅ ΡΠΈΡΡΠ΅ΠΌΡ ΠΏΠΎΠ΄ΡΠ°Π·Π΄Π΅Π»ΡΡΡΡΡ Π½Π°:
- ΠΠΈΠ΄ΡΠ°Π²Π»ΠΈΡΠ΅ΡΠΊΠΈΠ΅
- ΠΠ½Π΅Π²ΠΌΠ°ΡΠΈΡΠ΅ΡΠΊΠΈΠ΅
- ΠΠ΅Ρ Π°Π½ΠΈΡΠ΅ΡΠΊΠΈΠ΅
- ΠΠ»Π΅ΠΊΡΡΠΎΠΌΠ΅Ρ Π°Π½ΠΈΡΠ΅ΡΠΊΠΈΠ΅
- ΠΠ»Π΅ΠΊΡΡΠΎΠΏΠ½Π΅Π²ΠΌΠ°ΡΠΈΡΠ΅ΡΠΊΠΈΠ΅
Π Π°ΡΡΠΌΠΎΡΡΠΈΠΌ ΡΠ°Π±ΠΎΡΡ Π³ΠΈΠ΄ΡΠ°Π²Π»ΠΈΡΠ΅ΡΠΊΠΎΠΉ ΡΠ°Π±ΠΎΡΠ΅ΠΉ ΡΠΎΡΠΌΠΎΠ·Π½ΠΎΠΉ ΡΠΈΡΡΠ΅ΠΌΡ, ΠΊΠΎΡΠΎΡΠ°Ρ ΡΠΎΡΡΠΎΠΈΡ ΠΈΠ·:
- ΠΠ΅Π΄Π°Π»ΠΈ ΠΏΡΠΈΠ²ΠΎΠ΄Π° ΡΠΎΡΠΌΠΎΠ·Π½ΠΎΠΉ ΡΠΈΡΡΠ΅ΠΌΡ
- ΠΠ»Π°Π²Π½ΠΎΠ³ΠΎ Π³ΠΈΠ΄ΡΠ°Π²Π»ΠΈΡΠ΅ΡΠΊΠΎΠ³ΠΎ ΡΠΈΠ»ΠΈΠ½Π΄ΡΠ°
- Π Π°Π±ΠΎΡΠΈΡ ΡΠΈΠ»ΠΈΠ½Π΄ΡΠΎΠ² (Π΄Π»Ρ ΠΊΠ°ΠΆΠ΄ΠΎΠ³ΠΎ ΠΊΠΎΠ»Π΅ΡΠ°)
- Π’ΡΡΠ±ΠΎΠΊ, ΡΠ»Π°Π½Π³ΠΎΠ² Π²ΡΡΠΎΠΊΠΎΠ³ΠΎ Π΄Π°Π²Π»Π΅Π½ΠΈΡ
- Π’ΠΎΡΠΌΠΎΠ·Π½ΡΡ ΠΊΠΎΠ»ΠΎΠ΄ΠΎΠΊ
- ΠΠ°ΡΠΊΠ°
- Π’ΠΎΡΠΌΠΎΠ·Π½ΠΎΠΉ ΠΆΠΈΠ΄ΠΊΠΎΡΡΠΈ
ΠΡΠΈ Π½Π°ΠΆΠ°ΡΠΈΠΈ Π½Π° ΠΏΠ΅Π΄Π°Π»Ρ ΡΠΎΡΠΌΠΎΠ·Π° ΠΏΡΠΈΠ²ΠΎΠ΄ΠΈΡΡΡ Π² Π΄Π΅ΠΉΡΡΠ²ΠΈΠ΅ ΡΡΠΎΠΊ Π³Π»Π°Π²Π½ΠΎΠ³ΠΎ ΡΠΈΠ»ΠΈΠ½Π΄ΡΠ°. Π¨ΡΠΎΠΊ ΡΠΎΠ»ΠΊΠ°Π΅Ρ ΠΏΠΎΡΡΠ΅Π½Π΅ΠΊ, ΠΊΠΎΡΠΎΡΡΠΉ Π½Π°Π³Π½Π΅ΡΠ°Π΅Ρ Π΄Π°Π²Π»Π΅Π½ΠΈΠ΅ ΡΠ°Π±ΠΎΡΠ΅ΠΉ ΠΆΠΈΠ΄ΠΊΠΎΡΡΠΈ Π² ΡΡΡΠ±ΠΊΠ°Ρ ΡΠΈΡΡΠ΅ΠΌΡ, Π΄Π°Π»Π΅Π΅ Π² ΡΠ°Π±ΠΎΡΠ΅ΠΌ ΡΠΈΠ»ΠΈΠ½Π΄ΡΠ΅. ΠΠΎΡΡΠ½ΠΈ ΡΠ°Π±ΠΎΡΠΈΡ ΡΠΈΠ»ΠΈΠ½Π΄ΡΠΎΠ² Π½Π°ΠΆΠΈΠΌΠ°ΡΡ Π½Π° ΡΠΎΡΠΌΠΎΠ·Π½ΡΠ΅ ΠΊΠΎΠ»ΠΎΠ΄ΠΊΠΈ (Π²Π°ΡΠΈΠ°Π½Ρ Π΄ΠΈΡΠΊΠΎΠ²ΡΡ ΡΠΎΡΠΌΠΎΠ·ΠΎΠ²). Π Π±Π°ΡΠ°Π±Π°Π½Π½ΡΡ ΡΠΎΡΠΌΠΎΠ·Π°Ρ Π² ΡΠ°Π±ΠΎΡΠ΅ΠΌ ΡΠΈΠ»ΠΈΠ½Π΄ΡΠ΅ Π½Π°Ρ ΠΎΠ΄ΡΡΡΡ Π΄Π²Π° ΠΏΠΎΡΡΠ΅Π½ΡΠΊΠ°, ΠΊΠΎΡΠΎΡΡΠ΅ Π·Π°ΡΡΠ°Π²Π»ΡΡΡ ΠΊΠΎΠ»ΠΎΠ΄ΠΊΠΈ ΡΠ°Π·ΠΎΠΉΡΠΈΡΡ ΠΏΠΎ ΡΡΠΎΡΠΎΠ½Π°ΠΌ ΠΈ ΠΏΡΠΈΠΆΠ°ΡΡΡΡ ΠΊ Π²Π½ΡΡΡΠ΅Π½Π½Π΅ΠΉ ΡΡΠ΅Π½ΠΊΠ΅ Π±Π°ΡΠ°Π±Π°Π½Π°.
ΠΠ°Π΄ΠΎ ΠΎΡΠΌΠ΅ΡΠΈΡΡ, ΡΡΠΎ Π΄Π°Π²Π»Π΅Π½ΠΈΠ΅ Π² ΡΠΈΡΡΠ΅ΠΌΠ΅ ΡΠΎΡΠΌΠΎΠ·ΠΎΠΌ Π΄ΠΎΡΡΠΈΠ³Π°Π΅Ρ 20 Π°ΡΠΌΠΎΡΡΠ΅Ρ, ΠΏΠΎΡΡΠΎΠΌΡ Π΄Π»Ρ ΡΠΌΠ΅Π½ΡΡΠ΅Π½ΠΈΡ ΡΡΠΈΠ»ΠΈΡ Π²ΠΎΠ΄ΠΈΡΠ΅Π»Ρ ΠΏΡΠΈ Π½Π°ΠΆΠ°ΡΠΈΠΈ Π½Π° ΠΏΠ΅Π΄Π°Π»Ρ ΡΠΎΡΠΌΠΎΠ·Π°, Π² ΡΠΈΡΡΠ΅ΠΌΡ Π²Π²ΠΎΠ΄ΠΈΡΡΡ Π²Π°ΠΊΡΡΠΌΠ½ΡΠΉ ΡΡΠΈΠ»ΠΈΡΠ΅Π»Ρ ΡΠΎΡΠΌΠΎΠ·ΠΎΠ², ΡΠ°Π±ΠΎΡΡ ΠΊΠΎΡΠΎΡΠΎΠ³ΠΎ ΡΠ°ΡΡΠΌΠΎΡΡΠΈΠΌ ΠΎΡΠ΄Π΅Π»ΡΠ½ΠΎ.
ΠΠ»Ρ ΡΠ»ΡΡΡΠ΅Π½ΠΈΡ Ρ Π°ΡΠ°ΠΊΡΠ΅ΡΠΈΡΡΠΈΠΊ ΡΠΎΡΠΌΠΎΠ·Π½ΠΎΠΉ ΡΠΈΡΡΠ΅ΠΌΡ, Π° ΡΠ°ΠΊ ΠΆΠ΅ Π΅Π΅ Π½Π°Π΄Π΅ΠΆΠ½ΠΎΡΡΠΈ ΠΏΡΠΈΠΌΠ΅Π½ΡΡΡΡΡ Π΅ΡΠ΅ Π½Π΅ΡΠΊΠΎΠ»ΡΠΊΠΎ ΡΡΠΎΠ²Π΅ΡΡΠ΅Π½ΡΡΠ²ΠΎΠ²Π°Π½ΠΈΠΉ. ΠΡΠΎ:
- ABS (Π°Π½ΡΠΈΠ±Π»ΠΎΠΊΠΈΡΠΎΠ²ΠΎΡΠ½Π°Ρ ΡΠΈΡΡΠ΅ΠΌΠ°)
- ASR (Π°Π½ΡΠΈΠΏΡΠΎΠ±ΡΠΊΡΠΎΠ²ΠΎΡΠ½Π°Ρ ΡΠΈΡΡΠ΅ΠΌΠ°)
- ESP (ΡΠΈΡΡΠ΅ΠΌΠ° ΠΊΡΡΡΠΎΠ²ΠΎΠΉ ΡΡΡΠΎΠΉΡΠΈΠ²ΠΎΡΡΠΈ)
- BAS (ΡΡΠΈΠ»ΠΈΡΠ΅Π»Ρ ΡΠΊΡΡΡΠ΅Π½Π½ΠΎΠ³ΠΎ ΡΠΎΡΠΌΠΎΠΆΠ΅Π½ΠΈΡ)
- EBD (ΡΠΈΡΡΠ΅ΠΌΠ° ΡΠ°ΡΠΏΡΠ΅Π΄Π΅Π»Π΅Π½ΠΈΡ ΡΠΎΡΠΌΠΎΠ·Π°)
- EDS (Π±Π»ΠΎΠΊΠΈΡΠΎΠ²ΠΊΠ° Π΄ΠΈΡΡΠ΅ΡΠ΅Π½ΡΠΈΠ°Π»Π°)
ΠΠ΅Ρ Π°Π½ΠΈΡΠ΅ΡΠΊΠ°Ρ ΡΠΎΡΠΌΠΎΠ·Π½Π°Ρ ΡΠΈΡΡΠ΅ΠΌΠ° ΠΏΡΠΈΠΌΠ΅Π½ΡΠ΅ΡΡΡ Π² ΡΠ°Π±ΠΎΡΠ΅ ΡΡΠΎΡΠ½ΠΎΡΠ½ΠΎΠ³ΠΎ ΡΠΎΡΠΌΠΎΠ·Π° ΠΈ ΡΠΊΡΡΡΠ΅Π½Π½ΠΎΠ³ΠΎ ΡΠΎΡΠΌΠΎΠΆΠ΅Π½ΠΈΡ. ΠΠ±ΡΡΠ½ΠΎ ΡΡΡΠ½ΠΈΠΊ ΡΠΎΠ²ΠΌΠ΅ΡΠ°Π΅ΡΡΡ Ρ Π³ΠΈΠ΄ΡΠ°Π²Π»ΠΈΡΠ΅ΡΠΊΠΎΠΉ ΡΠΈΡΡΠ΅ΠΌΠΎΠΉ, Π½ΠΎ Π΅ΡΠ»ΠΈ Π½Π° Π·Π°Π΄Π½ΠΈΡ ΠΊΠΎΠ»Π΅ΡΠ°Ρ ΠΏΡΠΈΠΌΠ΅Π½ΡΡΡΡΡ Π΄ΠΈΡΠΊΠΎΠ²ΡΠ΅ ΡΠΎΡΠΌΠΎΠ·Π°, ΡΠΎ ΡΡΠΎΡΠ½ΠΎΡΠ½ΡΠΉ ΡΠΎΡΠΌΠΎΠ· ΡΠ΅Π°Π»ΠΈΠ·ΠΎΠ²Π°Π½ ΠΎΡΠ΄Π΅Π»ΡΠ½ΠΎ. Π Π½Π΅ΠΊΠΎΡΠΎΡΡΡ Π°Π²ΡΠΎΠΌΠΎΠ±ΠΈΠ»ΡΡ ΡΡΠΎΡΠ½ΠΎΡΠ½ΡΠΉ ΡΠΎΡΠΌΠΎΠ· Π±Π»ΠΎΠΊΠΈΡΡΠ΅Ρ Π½Π΅ ΠΊΠΎΠ»Π΅ΡΠ°, Π° Π±Π°ΡΠ°Π±Π°Π½ ΡΠΎΡΠΌΠΎΠ·Π½ΠΎΠΉ, ΠΊΠΎΡΠΎΡΡΠΉ Π½Π°Ρ ΠΎΠ΄ΠΈΡΡΡ Π½Π° ΠΏΡΠΈΠ²ΠΎΠ΄Π΅ ΡΡΠ°Π½ΡΠΌΠΈΡΡΠΈΠΈ.
ΠΡΠΈΠ½ΡΠΈΠΏ ΡΠ°Π±ΠΎΡΡ ΠΎΡΠ΅Π½Ρ ΠΏΡΠΎΡΡ, ΠΏΡΠΈΠ²ΠΎΠ΄Ρ Π² Π΄Π΅ΠΉΡΡΠ²ΠΈΠ΅ ΡΡΡΠ°Π³ ΡΡΡΠ½ΠΈΠΊΠ°, Π½Π°ΡΡΠ³ΠΈΠ²Π°Π΅ΡΡΡ ΡΡΠΎΡ, ΠΊΠΎΡΠΎΡΡΠΉ ΡΠΎΠ΅Π΄ΠΈΠ½Π΅Π½ Ρ ΡΠΎΡΠΌΠΎΠ·Π½ΡΠΌΠΈ ΠΊΠΎΠ»ΠΎΠ΄ΠΊΠ°ΠΌΠΈ. ΠΠΎΠ»ΠΎΠ΄ΠΊΠΈ ΡΠ°ΡΡ ΠΎΠ΄ΡΡΡΡ ΠΈ Π±Π»ΠΎΠΊΠΈΡΡΡΡ Π±Π°ΡΠ°Π±Π°Π½ ΠΈΠ»ΠΈ Π΄ΠΈΡΠΊ ΠΈΠ·Π½ΡΡΡΠΈ.
ΠΠ½Π΅Π²ΠΌΠ°ΡΠΈΡΠ΅ΡΠΊΠΈΠ΅ ΡΠΎΡΠΌΠΎΠ·Π° ΡΡ ΠΎΠΆΠΈ Ρ Π³ΠΈΠ΄ΡΠ°Π²Π»ΠΈΡΠ΅ΡΠΊΠΈΠΌΠΈ, Π½ΠΎ Π²ΠΌΠ΅ΡΡΠΎ ΡΠΎΡΠΌΠΎΠ·Π½ΠΎΠΉ ΠΆΠΈΠ΄ΠΊΠΎΡΡΠΈ Π² ΡΠΈΡΡΠ΅ΠΌΠ΅ ΡΠΆΠ°ΡΡΠΉ Π²ΠΎΠ·Π΄ΡΡ . ΠΠ»Ρ ΡΡΠΎΠ³ΠΎ Π² ΡΠΈΡΡΠ΅ΠΌΡ Π²Π²Π΅Π΄Π΅Π½Ρ ΡΠ΅ΡΠΈΠ²Π΅ΡΡ Π΄Π»Ρ Π΅Π³ΠΎ Π½Π°ΠΊΠΎΠΏΠ»Π΅Π½ΠΈΡ.
Π ΡΠ»Π΅ΠΊΡΡΠΎΠΌΠ΅Ρ Π°Π½ΠΈΡΠ΅ΡΠΊΠΈΡ ΡΠΎΡΠΌΠΎΠ·Π°Ρ ΡΡΠΎΡ ΠΏΡΠΈΠ²ΠΎΠ΄ΠΈΡ Π² Π΄Π΅ΠΉΡΡΠ²ΠΈΠ΅ ΡΠ»Π΅ΠΊΡΡΠΎΠ΄Π²ΠΈΠ³Π°ΡΠ΅Π»Ρ.
Π ΠΠΠΠΠΠΠΠ£ΠΠ Π’ΠΠΠΠ ΠΠ ΠΠ§ΠΠ’ΠΠ’Π¬: _____________________________________________________________________________________________________________________ |
autoustroistvo.ru
ΠΠΈΠ°Π³Π½ΠΎΡΡΠΈΠΊΠ° ΠΏΠ½Π΅Π²ΠΌΠΎΠΏΡΠΈΠ²ΠΎΠ΄Π° ΡΠΎΡΠΌΠΎΠ·Π½ΡΡ ΡΠΈΡΡΠ΅ΠΌ ΠΠ°ΠΌΠΠ
Π‘ΡΡΠ°Π½ΠΈΡΠ° 1 ΠΈΠ· 2
ΠΠ»Ρ ΠΏΡΠΎΠ²Π΅Π΄Π΅Π½ΠΈΡ Π΄ΠΈΠ°Π³Π½ΠΎΡΡΠΈΡΠΎΠ²Π°Π½ΠΈΡ ΠΏΠ½Π΅Π²ΠΌΠΎΠΏΡΠΈΠ²ΠΎΠ΄Π° ΡΠΎΡΠΌΠΎΠ·Π½ΡΡ ΡΠΈΡΡΠ΅ΠΌ Π½Π΅ΠΎΠ±Ρ ΠΎΠ΄ΠΈΠΌΠΎ ΠΈΠΌΠ΅ΡΡ Ρ ΠΎΡΡ Π±Ρ ΠΎΠ΄ΠΈΠ½ ΠΊΠΎΠ½ΡΡΠΎΠ»ΡΠ½ΡΠΉ ΠΌΠ°Π½ΠΎΠΌΠ΅ΡΡ ΠΈ ΠΈΡΠΏΠΎΠ»ΡΠ·ΠΎΠ²Π°ΡΡ ΠΊΠ»Π°ΠΏΠ°Π½Ρ ΠΊΠΎΠ½ΡΡΠΎΠ»ΡΠ½ΠΎΠ³ΠΎ Π²ΡΠ²ΠΎΠ΄Π°, ΠΈΠΌΠ΅ΡΡΠΈΠ΅ΡΡ Π½Π° Π°Π²ΡΠΎΠΌΠΎΠ±ΠΈΠ»Π΅. ΠΠ΄Π½Π°ΠΊΠΎ ΡΠ°Π±ΠΎΡΠ° Ρ ΠΎΠ΄Π½ΠΈΠΌ ΠΌΠ°Π½ΠΎΠΌΠ΅ΡΡΠΎΠΌ ΡΠ²Π»ΡΠ΅ΡΡΡ Π²Π΅ΡΡΠΌΠ° ΡΡΡΠ΄ΠΎΠ΅ΠΌΠΊΠΎΠΉ, Π° ΠΈΡΠΏΠΎΠ»ΡΠ·ΠΎΠ²Π°Π½ΠΈΠ΅ ΡΠΎΠ»ΡΠΊΠΎ ΡΡΠ°ΡΠ½ΡΡ ΠΊΠ»Π°ΠΏΠ°Π½ΠΎΠ² ΠΊΠΎΠ½ΡΡΠΎΠ»ΡΠ½ΠΎΠ³ΠΎ Π²ΡΠ²ΠΎΠ΄Π° Π·Π½Π°ΡΠΈΡΠ΅Π»ΡΠ½ΠΎ Π·Π°ΡΡΡΠ΄Π½ΡΠ΅Ρ ΠΏΠΎΠΈΡΠΊ Π½Π΅ΠΈΡΠΏΡΠ°Π²Π½ΠΎΡΡΠ΅ΠΉ ΡΠ΅Π»ΠΎΠ³ΠΎ ΡΡΠ΄Π° ΠΏΡΠΈΠ±ΠΎΡΠΎΠ².
ΠΠΎΡΡΠΎΠΌΡ ΠΏΡΠΈ ΡΠ³Π»ΡΠ±Π»Π΅Π½Π½ΠΎΠΉ ΠΏΡΠΎΠ²Π΅ΡΠΊΠ΅ ΡΠ°Π±ΠΎΡΠΎΡΠΏΠΎΡΠΎΠ±Π½ΠΎΡΡΠΈ ΠΏΠ½Π΅Π²ΠΌΠΎΠΏΡΠΈΠ²ΠΎΠ΄Π° ΡΠ»Π΅Π΄ΡΠ΅Ρ ΠΏΠΎΠ»ΡΠ·ΠΎΠ²Π°ΡΡΡΡ ΠΊΠΎΠΌΠΏΠ»Π΅ΠΊΡΠΎΠΌ ΠΊΠΎΠ½ΡΡΠΎΠ»ΡΠ½ΡΡ ΠΌΠ°Π½ΠΎΠΌΠ΅ΡΡΠΎΠ², Π° ΡΠ°ΠΊΠΆΠ΅ Π½Π°Π±ΠΎΡΠΎΠΌ ΡΡΡΡΠ΅ΡΠΎΠ², ΠΏΠ΅ΡΠ΅Ρ ΠΎΠ΄Π½ΠΈΠΊΠΎΠ² ΠΈ ΡΠΎΠ΅Π΄ΠΈΠ½ΠΈΡΠ΅Π»ΡΠ½ΡΡ Π³ΠΎΠ»ΠΎΠ²ΠΎΠΊ, ΠΏΠΎΠ·Π²ΠΎΠ»ΡΡΡΠΈΡ ΠΈΠ·ΠΌΠ΅ΡΠΈΡΡ Π΄Π°Π²Π»Π΅Π½ΠΈΠ΅ Π² Π»ΡΠ±ΠΎΠΉ ΠΌΠ°Π³ΠΈΡΡΡΠ°Π»ΠΈ.
Π Π½Π°ΡΠ°Π»Π΅ ΠΏΡΠΎΠ²Π΅ΡΡΠ΅ΡΡΡ ΠΈΡΠΏΡΠ°Π²Π½ΠΎΡΡΡ Π»Π°ΠΌΠΏ ΠΈ Π·ΡΠΌΠΌΠ΅ΡΠ°. ΠΡΠΈ Π½Π°ΠΆΠ°ΡΠΈΠΈ Π½Π° ΠΊΠ½ΠΎΠΏΠΊΡ Π² Π±Π»ΠΎΠΊΠ΅ ΠΊΠΎΠ½ΡΡΠΎΠ»ΡΠ½ΡΠ΅ Π»Π°ΠΌΠΏΡ Π΄ΠΎΠ»ΠΆΠ½Ρ Π·Π°Π³ΠΎΡΠ°ΡΡΡΡ. ΠΠ°ΠΌΠΏΡ Π³ΠΎΡΡΡ, Π΅ΡΠ»ΠΈ Π΄Π°Π²Π»Π΅Π½ΠΈΠ΅ Π² ΡΠΎΠΎΡΠ²Π΅ΡΡΡΠ²ΡΡΡΠΈΡ Π±Π°Π»Π»ΠΎΠ½Π°Ρ Π½ΠΈΠΆΠ΅ 4,8…5,2 ΠΊΠ³Ρ/ΡΠΌ2. ΠΡΠΌΠΌΠ΅Ρ ΡΠ°Π±ΠΎΡΠ°Π΅Ρ, Π΅ΡΠ»ΠΈ Π³ΠΎΡΠΈΡ Ρ ΠΎΡΡ Π±Ρ ΠΎΠ΄Π½Π° Π»Π°ΠΌΠΏΠ°.
ΠΠ°Π»Π΅Π΅, Π·Π°ΠΏΡΡΡΠΈΠ² Π΄Π²ΠΈΠ³Π°ΡΠ΅Π»Ρ, Π·Π°ΠΏΠΎΠ»Π½ΡΠΉΡΠ΅ ΠΏΠ½Π΅Π²ΠΌΠΎΠΏΡΠΈΠ²ΠΎΠ΄ ΡΠΆΠ°ΡΡΠΌ Π²ΠΎΠ·Π΄ΡΡ ΠΎΠΌ. ΠΡΠΈ ΡΠ°ΡΡΠΎΡΠ΅ Π²ΡΠ°ΡΠ΅Π½ΠΈΡ ΠΊΠΎΠ»Π΅Π½ΡΠ°ΡΠΎΠ³ΠΎ Π²Π°Π»Π° Π΄Π²ΠΈΠ³Π°ΡΠ΅Π»Ρ 2200 ΠΎΠ±/ΠΌΠΈΠ½ ΠΈΡΠΏΡΠ°Π²Π½ΡΠΉ ΠΊΠΎΠΌΠΏΡΠ΅ΡΡΠΎΡ Π·Π°ΠΊΠ°ΡΠΈΠ²Π°Π΅Ρ ΡΠΎΡΠΌΠΎΠ·Π½ΡΡ ΡΠΈΡΡΠ΅ΠΌΡ (Π»Π°ΠΌΠΏΠΎΡΠΊΠΈ Π³Π°ΡΠ½ΡΡ) Π·Π° 8 ΠΌΠΈΠ½. ΠΡΠ»ΠΈ Π²ΡΠ΅ΠΌΡ Π·Π°ΠΏΠΎΠ»Π½Π΅Π½ΠΈΡ Π±ΠΎΠ»ΡΡΠ΅, ΡΠΎ Π²ΠΎΠ·ΠΌΠΎΠΆΠ½Π° Π½Π΅Π³Π΅ΡΠΌΠ΅ΡΠΈΡΠ½ΠΎΡΡΡ ΠΏΠ½Π΅Π²ΠΌΠΎΠΏΡΠΈΠ²ΠΎΠ΄Π°, Π·Π°Π³ΡΡΠ·Π½Π΅Π½ ΠΈΠ»ΠΈ Π·Π°ΠΌΠ΅ΡΠ· ΡΠΈΠ»ΡΡΡ Π² ΡΠ΅Π³ΡΠ»ΡΡΠΎΡΠ΅ ΠΈΠ»ΠΈ Π² ΠΊΠΎΠΌΠΏΡΠ΅ΡΡΠΎΡΠ΅ Π½Π΅ΠΈΡΠΏΡΠ°Π²Π½Ρ ΠΊΠ»Π°ΠΏΠ°Π½Ρ. ΠΡΠ»ΠΈ ΠΈΠ·Π½ΠΎΡΠ΅Π½Π° ΡΠΈΠ»ΠΈΠ½Π΄ΡΠΎΠΏΠΎΡΡΠ½Π΅Π²Π°Ρ Π³ΡΡΠΏΠΏΠ°, ΡΠΎ, ΠΈΠΌΠ΅Ρ ΠΌΠ°Π»ΡΡ ΠΏΡΠΎΠΈΠ·Π²ΠΎΠ΄ΠΈΡΠ΅Π»ΡΠ½ΠΎΡΡΡ, ΠΊΠΎΠΌΠΏΡΠ΅ΡΡΠΎΡ Π²ΠΌΠ΅ΡΡΠ΅ Ρ Π²ΠΎΠ·Π΄ΡΡ ΠΎΠΌ Π±ΡΠ΄Π΅Ρ ΠΏΠΎΠ΄Π°Π²Π°ΡΡ Π² ΠΏΠ½Π΅Π²ΠΌΠΎΠΏΡΠΈΠ²ΠΎΠ΄ ΠΌΠ°ΡΠ»ΠΎ, ΠΊΠΎΡΠΎΡΠΎΠ΅ ΡΠΊΠ°ΠΏΠ»ΠΈΠ²Π°Π΅ΡΡΡ Π²ΠΌΠ΅ΡΡΠ΅ Ρ ΠΊΠΎΠ½Π΄Π΅Π½ΡΠ°ΡΠΎΠΌ Π² Π±Π°Π»Π»ΠΎΠ½Π°Ρ ΠΈ Π²ΡΠ±ΡΠ°ΡΡΠ²Π°Π΅ΡΡΡ ΠΈΠ· ΡΠ΅Π³ΡΠ»ΡΡΠΎΡΠ° Π΄Π°Π²Π»Π΅Π½ΠΈΡ.
ΠΡΠΈ Π΄ΠΎΡΡΠΈΠΆΠ΅Π½ΠΈΠΈ Π΄Π°Π²Π»Π΅Π½ΠΈΡ Π² ΡΠΈΡΡΠ΅ΠΌΠ΅ 7,0 … 7,5 ΠΊΠ³Ρ/ΡΠΌ2 ΡΠ΅Π³ΡΠ»ΡΡΠΎΡ Π΄Π°Π²Π»Π΅Π½ΠΈΡ ΡΡΠ°Π±Π°ΡΡΠ²Π°Π΅Ρ, ΠΈ Π²ΠΎΠ·Π΄ΡΡ ΠΎΡ ΠΊΠΎΠΌΠΏΡΠ΅ΡΡΠΎΡΠ° Π½Π΅ΠΏΡΠ΅ΡΡΠ²Π½ΠΎ Π²ΡΡ ΠΎΠ΄ΠΈΡ ΡΠ΅ΡΠ΅Π· Π°ΡΠΌΠΎΡΡΠ΅ΡΠ½ΡΠΉ Π²ΡΠ²ΠΎΠ΄. ΠΠ΅ΡΠΊΠΎΠ»ΡΠΊΠΎ ΡΠ°Π· Π½Π°ΠΆΠΌΠΈΡΠ΅ ΠΈ ΠΎΡΠΏΡΡΡΠΈΡΠ΅ ΠΏΠ΅Π΄Π°Π»Ρ ΡΠΎΡΠΌΠΎΠ·Π°. ΠΠ°Π²Π»Π΅Π½ΠΈΠ΅ Π² ΠΏΠ½Π΅Π²ΠΌΠΎΠΏΡΠΈΠ²ΠΎΠ΄Π΅ ΡΠΌΠ΅Π½ΡΡΠΈΡΡΡ Π΄ΠΎ 6.2 … 6,5 ΠΊΠ³Ρ/ΡΠΌ2. Π ΡΠ΅Π³ΡΠ»ΡΡΠΎΡΠ΅ Π΄Π°Π²Π»Π΅Π½ΠΈΡ Π·Π°ΠΊΡΠΎΠ΅ΡΡΡ ΡΠ°Π·Π³ΡΡΠ·ΠΎΡΠ½ΡΠΉ ΠΊΠ»Π°ΠΏΠ°Π½, ΠΈ ΠΊΠΎΠΌΠΏΡΠ΅ΡΡΠΎΡ Π²Π½ΠΎΠ²Ρ ΡΠ²Π΅Π»ΠΈΡΠΈΡ Π΄Π°Π²Π»Π΅Π½ΠΈΠ΅ Π² ΠΏΠ½Π΅Π²ΠΌΠΎΠΏΡΠΈΠ²ΠΎΠ΄Π΅ Π΄ΠΎ 7,0 … 7,5 Π³Ρ/ΡΠΌ2. ΠΠ°Π²Π»Π΅Π½ΠΈΠ΅ ΠΎΡΠΊΡΡΡΠΈΡ ΠΈ Π·Π°ΠΊΡΡΡΠΈΡ ΠΊΠ»Π°ΠΏΠ°Π½Π° Π² ΡΠ΅Π³ΡΠ»ΡΡΠΎΡΠ΅ Π΄Π°Π²Π»Π΅Π½ΠΈΡ ΠΊΠΎΠ½ΡΡΠΎΠ»ΠΈΡΡΠ΅ΡΡΡ ΠΏΠΎ Π΄Π²ΡΡ ΡΡΡΠ΅Π»ΠΎΡΠ½ΠΎΠΌΡ ΠΌΠ°Π½ΠΎΠΌΠ΅ΡΡΡ Π² ΠΊΠ°Π±ΠΈΠ½Π΅ ΠΈΠ»ΠΈ ΠΏΠΎ ΠΌΠ°Π½ΠΎΠΌΠ΅ΡΡΡ, ΠΏΠΎΠ΄ΡΠΎΠ΅Π΄ΠΈΠ½Π΅Π½Π½ΠΎΠΌΡ ΠΊ ΠΊΠ»Π°ΠΏΠ°Π½Ρ ΠΊΠΎΠ½ΡΡΠΎΠ»ΡΠ½ΠΎΠ³ΠΎ Π²ΡΠ²ΠΎΠ΄Π° Π½Π° ΠΊΠΎΠ½Π΄Π΅Π½ΡΠ°ΡΠΈΠΎΠ½Π½ΠΎΠΌ Π±Π°Π»Π»ΠΎΠ½Π΅. Π Π΅Π³ΡΠ»ΠΈΡΠΎΠ²Π°ΡΡ Π΄Π°Π²Π»Π΅Π½ΠΈΠ΅ Π²ΠΎΠ·Π΄ΡΡ Π° Π² ΠΏΠ½Π΅Π²ΠΌΠΎΠΏΡΠΈΠ²ΠΎΠ΄Π΅ Π½ΡΠΆΠ½ΠΎ Π²ΠΈΠ½ΡΠΎΠΌ ΡΠ²Π΅ΡΡ Ρ ΡΠ΅Π³ΡΠ»ΡΡΠΎΡΠ° Π΄Π°Π²Π»Π΅Π½ΠΈΡ. ΠΡΠΊΠ»ΠΎΠ½Π΅Π½ΠΈΡ Π² ΡΠ°Π±ΠΎΡΠ΅ ΡΠ΅Π³ΡΠ»ΡΡΠΎΡΠ° Π΄Π°Π²Π»Π΅Π½ΠΈΡ: ΡΠ΅Π·ΠΊΠΈΠΉ ΡΠ±ΡΠΎΡ Π²ΠΎΠ·Π΄ΡΡ Π° Π² ΠΏΡΠΎΡΠ΅ΡΡΠ΅ Π·Π°ΠΏΠΎΠ»Π½Π΅Π½ΠΈΡ ΡΠΈΡΡΠ΅ΠΌΡ, ΠΎΡΠΊΡΡΡΠΈΠ΅ ΠΊΠ»Π°ΠΏΠ°Π½Π° ΠΏΡΠΈ Π½ΠΈΠ·ΠΊΠΎΠΌ ΠΈΠ»ΠΈ Π²ΡΡΠΎΠΊΠΎΠΌ Π΄Π°Π²Π»Π΅Π½ΠΈΠΈ ΠΈ Π½Π΅Π²ΠΎΠ·ΠΌΠΎΠΆΠ½ΠΎΡΡΡ Π΅Π³ΠΎ ΡΠ΅Π³ΡΠ»ΠΈΡΠΎΠ²ΠΊΠΈ β ΡΠΊΠ°Π·ΡΠ²Π°ΡΡ Π½Π° Π½Π΅ΠΈΡΠΏΡΠ°Π²Π½ΠΎΡΡΡ ΠΏΡΠΈΠ±ΠΎΡΠ° ΠΈ Π½Π΅ΠΎΠ±Ρ ΠΎΠ΄ΠΈΠΌΠΎΡΡΡ Π΅Π³ΠΎ ΡΠ΅ΠΌΠΎΠ½ΡΠ°.
ΠΡΠΎΠ²Π΅ΡΡΡΠ΅ ΠΏΠ½Π΅Π²ΠΌΠ°ΡΠΈΡΠ΅ΡΠΊΠΈΠΉ ΡΠΎΡΠΌΠΎΠ·Π½ΠΎΠΉ ΠΏΡΠΈΠ²ΠΎΠ΄ Π½Π° Π³Π΅ΡΠΌΠ΅ΡΠΈΡΠ½ΠΎΡΡΡ
ΠΡΠΈ Π½Π΅ΡΠ°Π±ΠΎΡΠ°ΡΡΠ΅ΠΌ ΠΊΠΎΠΌΠΏΡΠ΅ΡΡΠΎΡΠ΅ ΠΈ Π²ΡΠΊΠ»ΡΡΠ΅Π½Π½ΡΡ ΠΏΠΎΡΡΠ΅Π±ΠΈΡΠ΅Π»ΡΡ (ΡΠΎΡΠΌΠΎΠ·Π½Π°Ρ ΠΏΠ΅Π΄Π°Π»Ρ ΠΎΡΠΏΡΡΠ΅Π½Π°, ΡΡΠΎΡΠ½ΠΎΡΠ½ΡΠΉ ΡΠΎΡΠΌΠΎΠ· Π²ΠΊΠ»ΡΡΠ΅Π½) ΠΏΠ°Π΄Π΅Π½ΠΈΠ΅ Π΄Π°Π²Π»Π΅Π½ΠΈΡ Π·Π° 30 ΠΌΠΈΠ½ΡΡ ΠΏΡΠΎΠ²Π΅ΡΠΊΠΈ Π΄ΠΎΠ»ΠΆΠ½ΠΎ Π±ΡΡΡ ΠΌΠ΅Π½Π΅Π΅ 0,5 ΠΊΠ³Ρ/ΡΠΌ2. ΠΡΠΈ Π²ΠΊΠ»ΡΡΠ΅Π½Π½ΡΡ ΠΏΠΎΡΡΠ΅Π±ΠΈΡΠ΅Π»ΡΡ (ΡΠΎΡΠΌΠΎΠ·Π½Π°Ρ ΠΏΠ΅Π΄Π°Π»Ρ Π½Π°ΠΆΠ°ΡΠ°, ΡΡΠΎΡΠ½ΠΎΡΠ½ΡΠΉ ΡΠΎΡΠΌΠΎΠ· Π²ΡΠΊΠ»ΡΡΠ΅Π½) ΠΏΠ°Π΄Π΅Π½ΠΈΠ΅ Π΄Π°Π²Π»Π΅Π½ΠΈΡ Π·Π° 15 ΠΌΠΈΠ½ΡΡ ΠΏΡΠΎΠ²Π΅ΡΠΊΠΈ Π΄ΠΎΠ»ΠΆΠ½ΠΎ Π±ΡΡΡ ΡΠ°ΠΊΠΆΠ΅ ΠΌΠ΅Π½Π΅Π΅ 0,5 ΠΊΠ³Ρ/ΡΠΌ2.
ΠΠ»Ρ ΠΏΡΠΎΠ²Π΅ΡΠΊΠΈ ΡΠ°Π±ΠΎΡΡ Π·Π°ΡΠΈΡΠ½ΡΡ ΠΊΠ»Π°ΠΏΠ°Π½ΠΎΠ² ΠΏΠΎΠ΄ΠΊΠ»ΡΡΠΈΡΠ΅ ΠΊ ΠΊΠ»Π°ΠΏΠ°Π½Ρ ΠΊΠΎΠ½ΡΡΠΎΠ»ΡΠ½ΠΎΠ³ΠΎ Π²ΡΠ²ΠΎΠ΄Π° Π½Π° Π±Π°Π»Π»ΠΎΠ½Π΅ ΡΡΠΎΡΠ½ΠΎΡΠ½ΠΎΠ³ΠΎ ΡΠΎΡΠΌΠΎΠ·Π° ΠΌΠ°Π½ΠΎΠΌΠ΅ΡΡ. Π‘ΡΡΠ°Π²ΠΈΡΠ΅ Π²ΠΎΠ·Π΄ΡΡ ΠΈΠ· Π±Π°Π»Π»ΠΎΠ½Π° ΠΏΠ΅ΡΠ΅Π΄Π½Π΅Π³ΠΎ ΠΌΠΎΡΡΠ°, ΠΈΡΠΏΠΎΠ»ΡΠ·ΡΡ ΠΊΠ»Π°ΠΏΠ°Π½ Π΄Π»Ρ ΡΠ»ΠΈΠ²Π° ΠΊΠΎΠ½Π΄Π΅Π½ΡΠ°ΡΠ°. ΠΠ°Π΄Π΅Π½ΠΈΠ΅ Π΄Π°Π²Π»Π΅Π½ΠΈΡ ΠΏΡΠΈ ΡΡΠΎΠΌ Π΄ΠΎΠ»ΠΆΠ½Π° ΠΏΠΎΠΊΠ°Π·ΡΠ²Π°ΡΡ ΡΠΎΠ»ΡΠΊΠΎ Π²Π΅ΡΡ Π½ΡΡ ΡΡΡΠ΅Π»ΠΊΠ° ΡΡΠ°ΡΠ½ΠΎΠ³ΠΎ ΠΌΠ°Π½ΠΎΠΌΠ΅ΡΡΠ°. ΠΠ°Π²Π»Π΅Π½ΠΈΠ΅ Π² Π±Π°Π»Π»ΠΎΠ½Π°Ρ Π·Π°Π΄Π½Π΅ΠΉ ΡΠ΅Π»Π΅ΠΆΠΊΠΈ ΠΈ ΡΡΠΎΡΠ½ΠΎΡΠ½ΠΎΠ³ΠΎ ΡΠΎΡΠΌΠΎΠ·Π° ΠΈΠ·ΠΌΠ΅Π½ΠΈΡΡΡΡ Π½Π΅ Π΄ΠΎΠ»ΠΆΠ½ΠΎ. ΠΡΠ»ΠΈ Π΄Π°Π²Π»Π΅Π½ΠΈΠ΅ ΡΠΌΠ΅Π½ΡΡΠ°Π΅ΡΡΡ Π² Π±Π°Π»Π»ΠΎΠ½Π°Ρ Π·Π°Π΄Π½Π΅ΠΉ ΡΠ΅Π»Π΅ΠΆΠΊΠΈ, ΡΠΎ Π½Π΅ΠΈΡΠΏΡΠ°Π²Π΅Π½ ΡΡΠΎΠΉΠ½ΠΎΠΉ Π·Π°ΡΠΈΡΠ½ΡΠΉ ΠΊΠ»Π°ΠΏΠ°Π½, Π° ΠΏΠ°Π΄Π΅Π½ΠΈΠ΅ Π΄Π°Π²Π»Π΅Π½ΠΈΡ Π² Π±Π°Π»Π»ΠΎΠ½Π°Ρ ΡΡΠΎΡΠ½ΠΎΡΠ½ΠΎΠ³ΠΎ ΡΠΎΡΠΌΠΎΠ·Π° ΡΠΊΠ°Π·ΡΠ²Π°Π΅Ρ Π½Π° Π½Π΅ΠΈΡΠΏΡΠ°Π²Π½ΠΎΡΡΡ Π΄Π²ΠΎΠΉΠ½ΠΎΠ³ΠΎ ΠΈΠ»ΠΈ ΠΎΠ΄ΠΈΠ½Π°ΡΠ½ΠΎΠ³ΠΎ Π·Π°ΡΠΈΡΠ½ΠΎΠ³ΠΎ ΠΊΠ»Π°ΠΏΠ°Π½Π° (Π² Π·Π°Π²ΠΈΡΠΈΠΌΠΎΡΡΠΈ ΠΎΡ ΠΊΠΎΠΌΠΏΠΎΠ½ΠΎΠ²ΠΊΠΈ ΠΏΠ½Π΅Π²ΠΌΠΎΠΏΡΠΈΠ²ΠΎΠ΄Π°), ΠΏΠΈΡΠ°ΡΡΠ΅Π³ΠΎ ΡΡΠΎΡ ΠΊΠΎΠ½ΡΡΡ.
ΠΠ»Ρ ΡΠΎΠ³ΠΎ ΡΡΠΎΠ±Ρ ΠΏΡΠΎΠ²Π΅ΡΠΈΡΡ ΠΈΡΠΏΡΠ°Π²Π½ΠΎΡΡΡ ΠΏΠ½Π΅Π²ΠΌΠ°ΡΠΈΡΠ΅ΡΠΊΠΎΠ³ΠΎ ΠΏΡΠΈΠ²ΠΎΠ΄Π° ΡΠ°Π±ΠΎΡΠ΅Π³ΠΎ ΡΠΎΡΠΌΠΎΠ·Π°, Π½ΡΠΆΠ½ΠΎ ΠΏΡΠΈΡΠΎΠ΅Π΄ΠΈΠ½ΠΈΡΡ ΠΌΠ°Π½ΠΎΠΌΠ΅ΡΡΡ ΠΊ ΠΊΠ»Π°ΠΏΠ°Π½Π°ΠΌ ΠΊΠΎΠ½ΡΡΠΎΠ»ΡΠ½ΠΎΠ³ΠΎ Π²ΡΠ²ΠΎΠ΄Π° Π½Π° ΠΎΠ³ΡΠ°Π½ΠΈΡΠΈΡΠ΅Π»Π΅ Π΄Π°Π²Π»Π΅Π½ΠΈΡ ΠΈ ΡΠ·Π°Π΄ΠΈ Π½Π° ΡΠ°ΠΌΠ΅ Π½Π°Π΄ Π·Π°Π΄Π½ΠΈΠΌ ΠΌΠΎΡΡΠΎΠΌ. ΠΠΎΠΊΠ°Π·Π°Π½ΠΈΡ ΡΡΠΈΡ ΠΌΠ°Π½ΠΎΠΌΠ΅ΡΡΠΎΠ² ΡΠΎΠΎΡΠ²Π΅ΡΡΡΠ²ΡΡΡ Π΄Π°Π²Π»Π΅Π½ΠΈΡ Π² ΠΏΠ΅ΡΠ΅Π΄Π½ΠΈΡ ΡΠΎΡΠΌΠΎΠ·Π½ΡΡ ΠΊΠ°ΠΌΠ΅ΡΠ°Ρ ΠΈ ΡΠΎΡΠΌΠΎΠ·Π½ΡΡ ΠΊΠ°ΠΌΠ΅ΡΠ°Ρ Π·Π°Π΄Π½Π΅ΠΉ ΡΠ΅Π»Π΅ΠΆΠΊΠΈ. ΠΡΠΈ Π½Π°ΠΆΠ°ΡΠΈΠΈ Π½Π° ΠΏΠ΅Π΄Π°Π»Ρ ΡΠΎΡΠΌΠΎΠ·Π° Π΄ΠΎ ΡΠΏΠΎΡΠ° Π΄Π°Π²Π»Π΅Π½ΠΈΠ΅ ΠΏΠΎ Π΄Π²ΡΡ ΡΡΡΠ΅Π»ΠΎΡΠ½ΠΎΠΌΡ ΠΌΠ°Π½ΠΎΠΌΠ΅ΡΡΡ Π΄ΠΎΠ»ΠΆΠ½ΠΎ ΡΠ½ΠΈΠ·ΠΈΡΡΡΡ Π½Π΅ Π±ΠΎΠ»Π΅Π΅ ΡΠ΅ΠΌ Π½Π° 0,5 ΠΊΠ³Ρ/ΡΠΌ2 (Π²ΠΎΠ·Π΄ΡΡ ΠΈΠ· Π±Π°Π»Π»ΠΎΠ½ΠΎΠ² ΠΏΠΎΡΡΡΠΏΠΈΠ» Π² ΡΠΎΡΠΌΠΎΠ·Π½ΡΠ΅ ΠΊΠ°ΠΌΠ΅ΡΡ, ΠΈ Π΄Π°Π²Π»Π΅Π½ΠΈΠ΅ ΡΠΏΠ°Π»ΠΎ), Π΄Π°Π²Π»Π΅Π½ΠΈΠ΅ Π² ΠΏΠ΅ΡΠ΅Π΄Π½ΠΈΡ ΡΠΎΡΠΌΠΎΠ·Π½ΡΡ ΠΊΠ°ΠΌΠ΅ΡΠ°Ρ Π΄ΠΎΠ»ΠΆΠ½ΠΎ Π²ΠΎΠ·ΡΠ°ΡΡΠΈ Π΄ΠΎ 7,0 ΠΊΠ³Ρ/ΡΠΌ2 ΠΈ ΡΡΠ°ΡΡ ΡΠ°Π²Π½ΡΠΌ ΠΏΠΎΠΊΠ°Π·Π°Π½ΠΈΡΠΌ Π²Π΅ΡΡ Π½Π΅ΠΉ ΡΠΊΠ°Π»Ρ ΠΌΠ°Π½ΠΎΠΌΠ΅ΡΡΠ° Π² ΠΊΠ°Π±ΠΈΠ½Π΅. ΠΠ°Π²Π»Π΅Π½ΠΈΠ΅ Π² Π·Π°Π΄Π½ΠΈΡ ΡΠΎΡΠΌΠΎΠ·Π½ΡΡ ΠΊΠ°ΠΌΠ΅ΡΠ°Ρ ΡΠ°ΠΊΠΆΠ΅ Π²ΠΎΠ·ΡΠ°ΡΡΠ°Π΅Ρ Π΄ΠΎ 2,5 … 3,0 ΠΊΠ³Ρ/ΡΠΌ2 Π΄Π»Ρ ΠΏΠΎΡΠΎΠΆΠ½Π΅Π³ΠΎ Π°Π²ΡΠΎΠΌΠΎΠ±ΠΈΠ»Ρ. ΠΡΠ»ΠΈ ΠΏΠΎΠ΄Π½ΡΡΡ Π²Π²Π΅ΡΡ Π²Π΅ΡΡΠΈΠΊΠ°Π»ΡΠ½ΡΡ ΡΡΠ³Ρ ΠΏΡΠΈΠ²ΠΎΠ΄Π° ΡΠ΅Π³ΡΠ»ΡΡΠΎΡΠ° ΡΠΎΡΠΌΠΎΠ·Π½ΡΡ ΡΠΈΠ» Π½Π° Π²Π΅Π»ΠΈΡΠΈΠ½Ρ ΡΡΠ°ΡΠΈΡΠ΅ΡΠΊΠΎΠ³ΠΎ ΠΏΡΠΎΠ³ΠΈΠ±Π° ΠΏΠΎΠ΄Π²Π΅ΡΠΊΠΈ, ΡΠΎ Π΄Π°Π²Π»Π΅Π½ΠΈΠ΅ Π² Π·Π°Π΄Π½ΠΈΡ ΡΠΎΡΠΌΠΎΠ·Π½ΡΡ ΠΊΠ°ΠΌΠ΅ΡΠ°Ρ Π΄ΠΎΠ»ΠΆΠ½ΠΎ Π²ΠΎΠ·ΡΠ°ΡΡΠΈ Π΄ΠΎ 7,0 ΠΊΠ³Ρ/ΡΠΌ2 (ΠΏΠΎΠΊΠ°Π·Π°Π½ΠΈΠ΅ Π½ΠΈΠΆΠ½Π΅ΠΉ ΡΠΊΠ°Π»Ρ ΠΌΠ°Π½ΠΎΠΌΠ΅ΡΡΠ°).
Π‘ΡΠ°ΡΠΈΡΠ΅ΡΠΊΠΈΠΉ ΠΏΡΠΎΠ³ΠΈΠ± ΠΏΠΎΠ΄Π²Π΅ΡΠΊΠΈ ΠΏΡΠΈ Π·Π°Π³ΡΡΠ·ΠΊΠ΅ Π·Π°Π²ΠΈΡΠΈΡ ΠΎΡ ΠΆΠ΅ΡΡΠΊΠΎΡΡΠΈ ΡΠ΅ΡΡΠΎΡ, ΡΠ°ΠΊ, Π΄Π»Ρ Π±Π°Π·ΠΎΠ²ΡΡ ΠΌΠΎΠ΄Π΅Π»Π΅ΠΉ ΠΎΠ½ ΡΠΎΡΡΠ°Π²Π»ΡΠ΅Ρ ΡΠΎΠΎΡΠ²Π΅ΡΡΡΠ²Π΅Π½Π½ΠΎ: ΠΠ°ΠΌΠΠ-5320 β 40 ΠΌΠΌ, ΠΠ°ΠΌΠΠ-5410 β 42 ΠΌΠΌ, ΠΠ°ΠΌΠΠ-5511 β 34 ΠΌΠΌ.
ΠΡΠΈΠ²ΠΎΠ΄ ΡΠ΅Π³ΡΠ»ΡΡΠΎΡΠ° ΡΠΎΡΠΌΠΎΠ·Π½ΡΡ ΡΠΈΠ» ΡΠ΅Π³ΡΠ»ΠΈΡΡΠ΅ΡΡΡ ΠΈΠ·ΠΌΠ΅Π½Π΅Π½ΠΈΠ΅ΠΌ Π΄Π»ΠΈΠ½Ρ Π²Π΅ΡΡΠΈΠΊΠ°Π»ΡΠ½ΠΎΠΉ ΡΡΠ³ΠΈ ΠΈ ΠΈΠ·ΠΌΠ΅Π½Π΅Π½ΠΈΠ΅ΠΌ Π΄Π»ΠΈΠ½Ρ ΡΡΡΠ°Π³Π° ΡΠ΅Π³ΡΠ»ΡΡΠΎΡΠ°. ΠΠ»ΠΈΠ½Ρ ΡΡΠ³ΠΈ ΡΡΡΠ°Π½Π°Π²Π»ΠΈΠ²Π°ΡΡ ΡΠ°ΠΊΠΈΠΌ ΠΎΠ±ΡΠ°Π·ΠΎΠΌ, ΡΡΠΎΠ±Ρ Π½Π° ΠΏΠΎΡΠΎΠΆΠ½Π΅ΠΌ Π°Π²ΡΠΎΠΌΠΎΠ±ΠΈΠ»Π΅ ΠΏΡΠΈ ΠΏΠΎΠ»Π½ΠΎΡΡΡΡ Π½Π°ΠΆΠ°ΡΠΎΠΉ ΠΏΠ΅Π΄Π°Π»ΠΈ ΡΠΎΡΠΌΠΎΠ·Π° Π΄Π°Π²Π»Π΅Π½ΠΈΠ΅ Π² Π·Π°Π΄Π½ΠΈΡ ΡΠΎΡΠΌΠΎΠ·Π½ΡΡ ΠΊΠ°ΠΌΠ΅ΡΠ°Ρ Π±ΡΠ»ΠΎ Π½Π΅ Π½ΠΈΠΆΠ΅ 2,5 ΠΊΠ³Ρ/ΡΠΌ2. Π΄Π»ΠΈΠ½Π° Π ΡΡΠ°Π³Π° ΡΠ΅Π³ΡΠ»ΡΡΠΎΡΠ° ΡΡΡΠ°Π½Π°Π²Π»ΠΈΠ²Π°Π΅ΡΡΡ ΠΏΠΎΡΡΠΎΡΠ½Π½ΠΎΠΉ Π΄Π»Ρ Π΄Π°Π½Π½ΠΎΠΉ ΠΌΠΎΠ΄Π΅Π»ΠΈ:
ΠΠ°ΠΌΠΠ-5320β105 ΠΌΠΌ, ΠΠ°ΠΌΠΠ-5410β105 ΠΌΠΌ, ΠΠ°ΠΌΠΠ-5511β95 ΠΌΠΌ. ΠΠΎΡΠ»Π΅ ΠΎΡΠΏΡΡΠΊΠ°Π½ΠΈΡ ΠΏΠ΅Π΄Π°Π»ΠΈ ΡΠΎΡΠΌΠΎΠ·Π° Π²ΠΎΠ·Π΄ΡΡ ΠΈΠ· ΡΠΎΡΠΌΠΎΠ·Π½ΡΡ ΠΊΠ°ΠΌΠ΅Ρ Π΄ΠΎΠ»ΠΆΠ΅Π½ Π²ΡΡ ΠΎΠ΄ΠΈΡΡ Π±Π΅Π· Π·Π°Π΄Π΅ΡΠΆΠΊΠΈ ΠΈ ΠΏΠΎΠ»Π½ΠΎΡΡΡΡ.
ΠΡΠ»ΠΈ Π½Π΅ ΠΎΠ±Π΅ΡΠΏΠ΅ΡΠΈΠ²Π°Π΅ΡΡΡ Π½ΠΎΠΌΠΈΠ½Π°Π»ΡΠ½ΠΎΠ΅ Π΄Π°Π²Π»Π΅Π½ΠΈΠ΅ (7,0 ΠΊΠ³Ρ/ΡΠΌ2) Π² ΠΏΠ΅ΡΠ΅Π΄Π½ΠΈΡ ΠΈ Π·Π°Π΄Π½ΠΈΡ ΡΠΎΡΠΌΠΎΠ·Π½ΡΡ ΠΊΠ°ΠΌΠ΅ΡΠ°Ρ ΠΏΡΠΈ ΠΏΠΎΠ»Π½ΠΎΠΌ Π½Π°ΠΆΠ°ΡΠΈΠΈ Π½Π° ΠΏΠ΅Π΄Π°Π»Ρ, ΡΠΎ Π½Π΅ΠΎΠ±Ρ ΠΎΠ΄ΠΈΠΌΠΎ, ΠΏΡΠ΅ΠΆΠ΄Π΅ Π²ΡΠ΅Π³ΠΎ, ΠΏΡΠΎΠ²Π΅ΡΠΈΡΡ ΠΏΡΠ°Π²ΠΈΠ»ΡΠ½ΠΎΡΡΡ ΡΠ΅Π³ΡΠ»ΠΈΡΠΎΠ²ΠΊΠΈ ΠΌΠ΅Ρ Π°Π½ΠΈΡΠ΅ΡΠΊΠΎΠ³ΠΎ ΠΏΡΠΈΠ²ΠΎΠ΄Π° ΡΠΎΡΠΌΠΎΠ·Π½ΠΎΠ³ΠΎ ΠΊΡΠ°Π½Π° (ΡΠΈΡ. 1).
ΠΡΠΈΠ²ΠΎΠ΄ ΠΈΠΌΠ΅Π΅Ρ Π΄Π²Π΅ ΡΠ΅Π³ΡΠ»ΠΈΡΠΎΠ²ΠΎΡΠ½ΡΠ΅ Π²ΠΈΠ»ΠΊΠΈ: Π½Π° ΡΡΠ³Π΅ ΠΏΠ΅Π΄Π°Π»ΠΈ ΠΈ Π½Π° ΠΏΡΠΎΠΌΠ΅ΠΆΡΡΠΎΡΠ½ΠΎΠΉ ΡΡΠ³Π΅ Π΄ΠΎΡΡΡΠΏ ΠΊ ΠΏΠ΅ΡΠ²ΠΎΠΉ ΡΠ΅Π³ΡΠ»ΠΈΡΠΎΠ²ΠΎΡΠ½ΠΎΠΉ Π²ΠΈΠ»ΠΊΠ΅ ΠΎΠ±Π΅ΡΠΏΠ΅ΡΠΈΠ²Π°Π΅ΡΡΡ ΠΏΡΠΈ ΠΏΠΎΠ΄Π½ΡΡΠΎΠΉ ΠΎΠ±Π»ΠΈΡΠΎΠ²ΠΊΠ΅ ΠΏΠ΅ΡΠ΅Π΄ΠΊΠ°. Π£ΠΊΠΎΡΠ°ΡΠΈΠ²Π°Ρ ΡΡΠ³Ρ ΠΏΠ΅Π΄Π°Π»ΠΈ, ΠΌΡ ΠΏΠΎΠ΄Π½ΠΈΠΌΠ°Π΅ΠΌ ΠΏΠ΅Π΄Π°Π»Ρ Π² ΠΊΠ°Π±ΠΈΠ½Π΅, ΠΏΠΎΠ»Π½ΡΠΉ Ρ ΠΎΠ΄ ΠΏΠ΅Π΄Π°Π»ΠΈ ΡΠ²Π΅Π»ΠΈΡΠΈΠ²Π°Π΅ΡΡΡ, ΠΎΠ½ Π΄ΠΎΠ»ΠΆΠ΅Π½ Π±ΡΡΡ ΡΠ°Π²Π΅Π½ 100 … 140 ΠΌΠΌ. ΠΡΠΈ ΠΏΠΎΠ»Π½ΠΎΠΌ Π½Π°ΠΆΠ°ΡΠΈΠΈ Π½Π° ΠΏΠ΅Π΄Π°Π»Ρ Ρ ΠΎΠ΄ ΡΡΡΠ°Π³Π° Π΄Π²ΡΡ ΡΠ΅ΠΊΡΠΈΠΎΠ½Π½ΠΎΠ³ΠΎ ΡΠΎΡΠΌΠΎΠ·Π½ΠΎΠ³ΠΎ ΠΊΡΠ°Π½Π° ΡΠΎΡΡΠ°Π²Π»ΡΠ΅Ρ 31 ΠΌΠΌ.
Π ΡΠΊΡΠΏΠ»ΡΠ°ΡΠ°ΡΠΈΠΈ Π²ΡΡΡΠ΅ΡΠ°ΡΡΡΡ Π°Π²ΡΠΎΠΌΠΎΠ±ΠΈΠ»ΠΈ, Ρ ΠΊΠΎΡΠΎΡΡΡ Π²Π΅Π»ΠΈΠΊΠΎ Π²ΡΠ΅ΠΌΡ ΡΠ°ΡΡΠΎΡΠΌΠ°ΠΆΠΈΠ²Π°Π½ΠΈΡ, Π·Π°ΡΠ°ΡΡΡΡ ΡΡΠΎ ΡΠ²ΡΠ·Π°Π½ΠΎ Ρ ΠΎΡΡΡΡΡΡΠ²ΠΈΠ΅ΠΌ ΡΠ²ΠΎΠ±ΠΎΠ΄Π½ΠΎΠ³ΠΎ Ρ ΠΎΠ΄Π° ΠΏΠ΅Π΄Π°Π»ΠΈ ΡΠΎΡΠΌΠΎΠ·Π°, ΠΊΠΎΡΠΎΡΡΠΉ ΡΠ΅Π³ΡΠ»ΠΈΡΡΠ΅ΡΡΡ Π²ΠΈΠ»ΠΊΠΎΠΉ Π½Π° ΠΏΡΠΎΠΌΠ΅ΠΆΡΡΠΎΡΠ½ΠΎΠΉ ΡΡΠ³Π΅ ΠΈ Π΄ΠΎΠ»ΠΆΠ΅Π½ ΡΠΎΡΡΠ°Π²Π»ΡΡΡ 20…40 ΠΌΠΌ.
ΠΡΠ»ΠΈ Π½Π΅ ΠΎΠ±Π΅ΡΠΏΠ΅ΡΠΈΠ²Π°Π΅ΡΡΡ ΠΌΠ°ΠΊΡΠΈΠΌΠ°Π»ΡΠ½ΠΎΠ΅ Π΄Π°Π²Π»Π΅Π½ΠΈΠ΅ Π² ΠΎΠ΄Π½ΠΎΠΌ ΠΈΠ· ΠΊΠΎΠ½ΡΡΡΠΎΠ² ΡΠ°Π±ΠΎΡΠ΅Π³ΠΎ ΡΠΎΡΠΌΠΎΠ·Π°, Π° Π΄Π°Π²Π»Π΅Π½ΠΈΠ΅ Π² Π΄ΡΡΠ³ΠΎΠΌ Π½ΠΎΡΠΌΠ°Π»ΡΠ½ΠΎΠ΅, ΡΠΎ Π½Π΅ΠΎΠ±Ρ ΠΎΠ΄ΠΈΠΌΠΎ ΠΏΡΠΈΡΠΎΠ΅Π΄ΠΈΠ½ΠΈΡΡ ΠΌΠ°Π½ΠΎΠΌΠ΅ΡΡ ΠΊ Π²ΡΡ ΠΎΠ΄Ρ ΡΠΎΠΎΡΠ²Π΅ΡΡΡΠ²ΡΡΡΠ΅ΠΉ ΡΠ΅ΠΊΡΠΈΠΈ ΡΠΎΡΠΌΠΎΠ·Π½ΠΎΠ³ΠΎ ΠΊΡΠ°Π½Π°: ΠΊ Π²Π΅ΡΡ Π½Π΅ΠΉ β ΠΏΡΠΈ ΠΏΠ»ΠΎΡ ΠΎΠΉ ΡΠ°Π±ΠΎΡΠ΅ ΠΊΠΎΠ½ΡΡΡΠ° Π·Π°Π΄Π½Π΅ΠΉ ΡΠ΅Π»Π΅ΠΆΠΊΠΈ, ΠΊ Π½ΠΈΠΆΠ½Π΅ΠΉ β ΠΏΡΠΈ ΠΏΠ»ΠΎΡ ΠΎΠΉ ΡΠ°Π±ΠΎΡΠ΅ ΠΊΠΎΠ½ΡΡΡΠ° ΠΏΠ΅ΡΠ΅Π΄Π½Π΅Π³ΠΎ ΠΌΠΎΡΡΠ°. ΠΠ°Π½ΠΎΠΌΠ΅ΡΡΡ Π½ΡΠΆΠ½ΠΎ ΠΏΡΠΈΡΠΎΠ΅Π΄ΠΈΠ½ΡΡΡ ΠΊ Π±ΠΎΠΊΠΎΠ²ΡΠΌ (ΠΏΠΎ Ρ ΠΎΠ΄Ρ Π°Π²ΡΠΎΠΌΠΎΠ±ΠΈΠ»Ρ) Π²ΡΠ²ΠΎΠ΄Π°ΠΌ Π²ΠΌΠ΅ΡΡΠΎ Π΄Π°ΡΡΠΈΠΊΠΎΠ² Β«ΡΡΠΎΠΏΒ» — ΡΠΈΠ³Π½Π°Π»ΠΎΠ² Π½Π° ΡΠ°ΠΌΠΎΡΠ²Π°Π»Π°Ρ ΠΈΠ»ΠΈ ΡΡΡΠ±ΠΎΠΏΡΠΎΠ²ΠΎΠ΄ΠΎΠ², ΠΈΠ΄ΡΡΠΈΡ ΠΊ Π΄Π²ΡΡ ΠΏΡΠΎΠ²ΠΎΠ΄Π½ΠΎΠΌΡ ΠΊΠ»Π°ΠΏΠ°Π½Ρ Π½Π° Π°Π²ΡΠΎΠΌΠΎΠ±ΠΈΠ»ΡΡ -ΡΡΠ³Π°ΡΠ°Ρ . ΠΡΠΈ Π½Π°ΠΆΠ°ΡΠΈΠΈ Π½Π° ΠΏΠ΅Π΄Π°Π»Ρ Π½Π΅ΠΎΠ±Ρ ΠΎΠ΄ΠΈΠΌΠΎ ΡΡΠ°Π²Π½ΠΈΡΡ Π΄Π°Π²Π»Π΅Π½ΠΈΠ΅ Π½Π° Π²ΡΡ ΠΎΠ΄Π΅ ΡΠΎΡΠΌΠΎΠ·Π½ΠΎΠ³ΠΎ ΠΊΡΠ°Π½Π° ΠΈ Π² ΡΠΎΡΠΌΠΎΠ·Π½ΡΡ ΠΊΠ°ΠΌΠ΅ΡΠ°Ρ . ΠΡΠΈ ΠΏΠΎΠ»Π½ΠΎΠΌ Π½Π°ΠΆΠ°ΡΠΈΠΈ Π½Π° ΠΏΠ΅Π΄Π°Π»Ρ Π²Π΅Π»ΠΈΡΠΈΠ½Ρ Π΄Π°Π²Π»Π΅Π½ΠΈΡ Π½Π° Π²ΡΡ ΠΎΠ΄Π΅ ΡΠΎΡΠΌΠΎΠ·Π½ΠΎΠ³ΠΎ ΠΊΡΠ°Π½Π° ΠΈ ΠΎΠ³ΡΠ°Π½ΠΈΡΠΈΡΠ΅Π»Ρ Π΄Π°Π²Π»Π΅Π½ΠΈΡ Π΄ΠΎΠ»ΠΆΠ½Ρ ΡΡΠ°Π²Π½ΡΡΡΡΡ. ΠΠ°Π²Π»Π΅Π½ΠΈΠ΅ Π² Π·Π°Π΄Π½ΠΈΡ ΡΠΎΡΠΌΠΎΠ·Π½ΡΡ ΠΊΠ°ΠΌΠ΅ΡΠ°Ρ Π·Π°Π²ΠΈΡΠΈΡ ΠΎΡ ΠΏΠΎΠ»ΠΎΠΆΠ΅Π½ΠΈΡ ΡΡΡΠ°Π³Π° ΡΠ΅Π³ΡΠ»ΡΡΠΎΡΠ° ΡΠΎΡΠΌΠΎΠ·Π½ΡΡ ΡΠΈΠ»: Π² Π½ΠΈΠΆΠ½Π΅ΠΌ ΠΏΠΎΠ»ΠΎΠΆΠ΅Π½ΠΈΠΈ Β«ΠΏΠΎΡΠΎΠΆΠ½ΠΈΠΉΒ» β 2,5 ΠΊΠ³Ρ/ΡΠΌ2, Π² Π²Π΅ΡΡ Π½Π΅ΠΌ ΠΏΠΎΠ»ΠΎΠΆΠ΅Π½ΠΈΠΈ Β«Π³ΡΡΠΆΠ΅Π½ΡΠΉΒ» β 7,0 ΠΊΠ³Ρ/ΡΠΌ2. Π‘ΡΠ°Π²Π½ΠΈΠ²Π°Ρ ΠΏΠΎΠΊΠ°Π·Π°Π½ΠΈΡ ΠΌΠ°Π½ΠΎΠΌΠ΅ΡΡΠΎΠ² ΠΈ Π·Π½Π°Ρ Ρ Π°ΡΠ°ΠΊΡΠ΅ΡΠΈΡΡΠΈΠΊΠΈ ΠΏΡΠΈΠ±ΠΎΡΠΎΠ², ΠΌΠΎΠΆΠ½ΠΎ Π»Π΅Π³ΠΊΠΎ ΠΎΠ±Π½Π°ΡΡΠΆΠΈΡΡ, ΠΊΠ°ΠΊΠΎΠΉ ΠΈΠ· Π½ΠΈΡ Π½Π΅ΠΈΡΠΏΡΠ°Π²Π΅Π½. ΠΡΠΈ ΡΠΎΡΠΌΠΎΠΆΠ΅Π½ΠΈΠΈ ΡΠ°Π±ΠΎΡΠΈΠΌ ΡΠΎΡΠΌΠΎΠ·ΠΎΠΌ Π½ΡΠΆΠ½ΠΎ ΠΏΡΠΎΠ²Π΅ΡΠΈΡΡ Ρ ΠΎΠ΄ ΡΡΠΎΠΊΠΎΠ² ΡΠΎΡΠΌΠΎΠ·Π½ΡΡ ΠΊΠ°ΠΌΠ΅Ρ. ΠΠ»Ρ Π°Π²ΡΠΎΠΌΠΎΠ±ΠΈΠ»Π΅ΠΉ ΠΠ°ΠΌΠΠ-5320, 5410, 55102 ΠΎΠ½ ΡΠ°Π²Π΅Π½ 20 … 30 ΠΌΠΌ, ΠΠ°ΠΌΠΠ-5511, ΠΠ°ΠΌΠΠ-53212, 54112 β 25 … 35 ΠΌΠΌ. Π΄ΠΎΠΏΡΡΠΊΠ°Π΅ΡΡΡ ΡΠ°Π·Π½ΠΈΡΠ° Π² Ρ ΠΎΠ΄Π΅ ΡΡΠΎΠΊΠΎΠ² ΡΠΎΡΠΌΠΎΠ·Π½ΡΡ ΠΊΠ°ΠΌΠ΅Ρ Π½Π° ΠΎΠ΄Π½ΠΎΠΌ ΠΌΠΎΡΡΡ β 2…3 ΠΌΠΌ.
autoruk.ru
Β
«ΠΠΈΡΠ΅Ρ — ΠΠ’»
ΠΠΠ 780703320484
ΠΠΠ ΠΠΠ 313784720500453
piter-at.ru
ΠΠΈΠ°Π³Π½ΠΎΡΡΠΈΠΊΠ° ΠΏΠ½Π΅Π²ΠΌΠΎΠΏΡΠΈΠ²ΠΎΠ΄Π° ΡΠΎΡΠΌΠΎΠ·Π½ΡΡ ΡΠΈΡΡΠ΅ΠΌ ΠΠ°ΠΌΠΠ
Π‘ΡΡΠ°Π½ΠΈΡΠ° 1 ΠΈΠ· 2
ΠΠ»Ρ ΠΏΡΠΎΠ²Π΅Π΄Π΅Π½ΠΈΡ Π΄ΠΈΠ°Π³Π½ΠΎΡΡΠΈΡΠΎΠ²Π°Π½ΠΈΡ ΠΏΠ½Π΅Π²ΠΌΠΎΠΏΡΠΈΠ²ΠΎΠ΄Π° ΡΠΎΡΠΌΠΎΠ·Π½ΡΡ ΡΠΈΡΡΠ΅ΠΌ Π½Π΅ΠΎΠ±Ρ ΠΎΠ΄ΠΈΠΌΠΎ ΠΈΠΌΠ΅ΡΡ Ρ ΠΎΡΡ Π±Ρ ΠΎΠ΄ΠΈΠ½ ΠΊΠΎΠ½ΡΡΠΎΠ»ΡΠ½ΡΠΉ ΠΌΠ°Π½ΠΎΠΌΠ΅ΡΡ ΠΈ ΠΈΡΠΏΠΎΠ»ΡΠ·ΠΎΠ²Π°ΡΡ ΠΊΠ»Π°ΠΏΠ°Π½Ρ ΠΊΠΎΠ½ΡΡΠΎΠ»ΡΠ½ΠΎΠ³ΠΎ Π²ΡΠ²ΠΎΠ΄Π°, ΠΈΠΌΠ΅ΡΡΠΈΠ΅ΡΡ Π½Π° Π°Π²ΡΠΎΠΌΠΎΠ±ΠΈΠ»Π΅. ΠΠ΄Π½Π°ΠΊΠΎ ΡΠ°Π±ΠΎΡΠ° Ρ ΠΎΠ΄Π½ΠΈΠΌ ΠΌΠ°Π½ΠΎΠΌΠ΅ΡΡΠΎΠΌ ΡΠ²Π»ΡΠ΅ΡΡΡ Π²Π΅ΡΡΠΌΠ° ΡΡΡΠ΄ΠΎΠ΅ΠΌΠΊΠΎΠΉ, Π° ΠΈΡΠΏΠΎΠ»ΡΠ·ΠΎΠ²Π°Π½ΠΈΠ΅ ΡΠΎΠ»ΡΠΊΠΎ ΡΡΠ°ΡΠ½ΡΡ ΠΊΠ»Π°ΠΏΠ°Π½ΠΎΠ² ΠΊΠΎΠ½ΡΡΠΎΠ»ΡΠ½ΠΎΠ³ΠΎ Π²ΡΠ²ΠΎΠ΄Π° Π·Π½Π°ΡΠΈΡΠ΅Π»ΡΠ½ΠΎ Π·Π°ΡΡΡΠ΄Π½ΡΠ΅Ρ ΠΏΠΎΠΈΡΠΊ Π½Π΅ΠΈΡΠΏΡΠ°Π²Π½ΠΎΡΡΠ΅ΠΉ ΡΠ΅Π»ΠΎΠ³ΠΎ ΡΡΠ΄Π° ΠΏΡΠΈΠ±ΠΎΡΠΎΠ².
ΠΠΎΡΡΠΎΠΌΡ ΠΏΡΠΈ ΡΠ³Π»ΡΠ±Π»Π΅Π½Π½ΠΎΠΉ ΠΏΡΠΎΠ²Π΅ΡΠΊΠ΅ ΡΠ°Π±ΠΎΡΠΎΡΠΏΠΎΡΠΎΠ±Π½ΠΎΡΡΠΈ ΠΏΠ½Π΅Π²ΠΌΠΎΠΏΡΠΈΠ²ΠΎΠ΄Π° ΡΠ»Π΅Π΄ΡΠ΅Ρ ΠΏΠΎΠ»ΡΠ·ΠΎΠ²Π°ΡΡΡΡ ΠΊΠΎΠΌΠΏΠ»Π΅ΠΊΡΠΎΠΌ ΠΊΠΎΠ½ΡΡΠΎΠ»ΡΠ½ΡΡ ΠΌΠ°Π½ΠΎΠΌΠ΅ΡΡΠΎΠ², Π° ΡΠ°ΠΊΠΆΠ΅ Π½Π°Π±ΠΎΡΠΎΠΌ ΡΡΡΡΠ΅ΡΠΎΠ², ΠΏΠ΅ΡΠ΅Ρ ΠΎΠ΄Π½ΠΈΠΊΠΎΠ² ΠΈ ΡΠΎΠ΅Π΄ΠΈΠ½ΠΈΡΠ΅Π»ΡΠ½ΡΡ Π³ΠΎΠ»ΠΎΠ²ΠΎΠΊ, ΠΏΠΎΠ·Π²ΠΎΠ»ΡΡΡΠΈΡ ΠΈΠ·ΠΌΠ΅ΡΠΈΡΡ Π΄Π°Π²Π»Π΅Π½ΠΈΠ΅ Π² Π»ΡΠ±ΠΎΠΉ ΠΌΠ°Π³ΠΈΡΡΡΠ°Π»ΠΈ.
Π Π½Π°ΡΠ°Π»Π΅ ΠΏΡΠΎΠ²Π΅ΡΡΠ΅ΡΡΡ ΠΈΡΠΏΡΠ°Π²Π½ΠΎΡΡΡ Π»Π°ΠΌΠΏ ΠΈ Π·ΡΠΌΠΌΠ΅ΡΠ°. ΠΡΠΈ Π½Π°ΠΆΠ°ΡΠΈΠΈ Π½Π° ΠΊΠ½ΠΎΠΏΠΊΡ Π² Π±Π»ΠΎΠΊΠ΅ ΠΊΠΎΠ½ΡΡΠΎΠ»ΡΠ½ΡΠ΅ Π»Π°ΠΌΠΏΡ Π΄ΠΎΠ»ΠΆΠ½Ρ Π·Π°Π³ΠΎΡΠ°ΡΡΡΡ.
ΠΠ°ΠΌΠΏΡ Π³ΠΎΡΡΡ, Π΅ΡΠ»ΠΈ Π΄Π°Π²Π»Π΅Π½ΠΈΠ΅ Π² ΡΠΎΠΎΡΠ²Π΅ΡΡΡΠ²ΡΡΡΠΈΡ Π±Π°Π»Π»ΠΎΠ½Π°Ρ Π½ΠΈΠΆΠ΅ 4,8…5,2 ΠΊΠ³Ρ/ΡΠΌ2. ΠΡΠΌΠΌΠ΅Ρ ΡΠ°Π±ΠΎΡΠ°Π΅Ρ, Π΅ΡΠ»ΠΈ Π³ΠΎΡΠΈΡ Ρ ΠΎΡΡ Π±Ρ ΠΎΠ΄Π½Π° Π»Π°ΠΌΠΏΠ°.
ΠΠ°Π»Π΅Π΅, Π·Π°ΠΏΡΡΡΠΈΠ² Π΄Π²ΠΈΠ³Π°ΡΠ΅Π»Ρ, Π·Π°ΠΏΠΎΠ»Π½ΡΠΉΡΠ΅ ΠΏΠ½Π΅Π²ΠΌΠΎΠΏΡΠΈΠ²ΠΎΠ΄ ΡΠΆΠ°ΡΡΠΌ Π²ΠΎΠ·Π΄ΡΡ ΠΎΠΌ.
ΠΡΠΈ ΡΠ°ΡΡΠΎΡΠ΅ Π²ΡΠ°ΡΠ΅Π½ΠΈΡ ΠΊΠΎΠ»Π΅Π½ΡΠ°ΡΠΎΠ³ΠΎ Π²Π°Π»Π° Π΄Π²ΠΈΠ³Π°ΡΠ΅Π»Ρ 2200 ΠΎΠ±/ΠΌΠΈΠ½ ΠΈΡΠΏΡΠ°Π²Π½ΡΠΉ ΠΊΠΎΠΌΠΏΡΠ΅ΡΡΠΎΡ Π·Π°ΠΊΠ°ΡΠΈΠ²Π°Π΅Ρ ΡΠΎΡΠΌΠΎΠ·Π½ΡΡ ΡΠΈΡΡΠ΅ΠΌΡ (Π»Π°ΠΌΠΏΠΎΡΠΊΠΈ Π³Π°ΡΠ½ΡΡ) Π·Π° 8 ΠΌΠΈΠ½.
ΠΡΠ»ΠΈ Π²ΡΠ΅ΠΌΡ Π·Π°ΠΏΠΎΠ»Π½Π΅Π½ΠΈΡ Π±ΠΎΠ»ΡΡΠ΅, ΡΠΎ Π²ΠΎΠ·ΠΌΠΎΠΆΠ½Π° Π½Π΅Π³Π΅ΡΠΌΠ΅ΡΠΈΡΠ½ΠΎΡΡΡ ΠΏΠ½Π΅Π²ΠΌΠΎΠΏΡΠΈΠ²ΠΎΠ΄Π°, Π·Π°Π³ΡΡΠ·Π½Π΅Π½ ΠΈΠ»ΠΈ Π·Π°ΠΌΠ΅ΡΠ· ΡΠΈΠ»ΡΡΡ Π² ΡΠ΅Π³ΡΠ»ΡΡΠΎΡΠ΅ ΠΈΠ»ΠΈ Π² ΠΊΠΎΠΌΠΏΡΠ΅ΡΡΠΎΡΠ΅ Π½Π΅ΠΈΡΠΏΡΠ°Π²Π½Ρ ΠΊΠ»Π°ΠΏΠ°Π½Ρ.
ΠΡΠ»ΠΈ ΠΈΠ·Π½ΠΎΡΠ΅Π½Π° ΡΠΈΠ»ΠΈΠ½Π΄ΡΠΎΠΏΠΎΡΡΠ½Π΅Π²Π°Ρ Π³ΡΡΠΏΠΏΠ°, ΡΠΎ, ΠΈΠΌΠ΅Ρ ΠΌΠ°Π»ΡΡ ΠΏΡΠΎΠΈΠ·Π²ΠΎΠ΄ΠΈΡΠ΅Π»ΡΠ½ΠΎΡΡΡ, ΠΊΠΎΠΌΠΏΡΠ΅ΡΡΠΎΡ Π²ΠΌΠ΅ΡΡΠ΅ Ρ Π²ΠΎΠ·Π΄ΡΡ ΠΎΠΌ Π±ΡΠ΄Π΅Ρ ΠΏΠΎΠ΄Π°Π²Π°ΡΡ Π² ΠΏΠ½Π΅Π²ΠΌΠΎΠΏΡΠΈΠ²ΠΎΠ΄ ΠΌΠ°ΡΠ»ΠΎ, ΠΊΠΎΡΠΎΡΠΎΠ΅ ΡΠΊΠ°ΠΏΠ»ΠΈΠ²Π°Π΅ΡΡΡ Π²ΠΌΠ΅ΡΡΠ΅ Ρ ΠΊΠΎΠ½Π΄Π΅Π½ΡΠ°ΡΠΎΠΌ Π² Π±Π°Π»Π»ΠΎΠ½Π°Ρ ΠΈ Π²ΡΠ±ΡΠ°ΡΡΠ²Π°Π΅ΡΡΡ ΠΈΠ· ΡΠ΅Π³ΡΠ»ΡΡΠΎΡΠ° Π΄Π°Π²Π»Π΅Π½ΠΈΡ.
ΠΡΠΈ Π΄ΠΎΡΡΠΈΠΆΠ΅Π½ΠΈΠΈ Π΄Π°Π²Π»Π΅Π½ΠΈΡ Π² ΡΠΈΡΡΠ΅ΠΌΠ΅ 7,0 … 7,5 ΠΊΠ³Ρ/ΡΠΌ2 ΡΠ΅Π³ΡΠ»ΡΡΠΎΡ Π΄Π°Π²Π»Π΅Π½ΠΈΡ ΡΡΠ°Π±Π°ΡΡΠ²Π°Π΅Ρ, ΠΈ Π²ΠΎΠ·Π΄ΡΡ ΠΎΡ ΠΊΠΎΠΌΠΏΡΠ΅ΡΡΠΎΡΠ° Π½Π΅ΠΏΡΠ΅ΡΡΠ²Π½ΠΎ Π²ΡΡ ΠΎΠ΄ΠΈΡ ΡΠ΅ΡΠ΅Π· Π°ΡΠΌΠΎΡΡΠ΅ΡΠ½ΡΠΉ Π²ΡΠ²ΠΎΠ΄. ΠΠ΅ΡΠΊΠΎΠ»ΡΠΊΠΎ ΡΠ°Π· Π½Π°ΠΆΠΌΠΈΡΠ΅ ΠΈ ΠΎΡΠΏΡΡΡΠΈΡΠ΅ ΠΏΠ΅Π΄Π°Π»Ρ ΡΠΎΡΠΌΠΎΠ·Π°.
ΠΠ°Π²Π»Π΅Π½ΠΈΠ΅ Π² ΠΏΠ½Π΅Π²ΠΌΠΎΠΏΡΠΈΠ²ΠΎΠ΄Π΅ ΡΠΌΠ΅Π½ΡΡΠΈΡΡΡ Π΄ΠΎ 6.2 … 6,5 ΠΊΠ³Ρ/ΡΠΌ2. Π ΡΠ΅Π³ΡΠ»ΡΡΠΎΡΠ΅ Π΄Π°Π²Π»Π΅Π½ΠΈΡ Π·Π°ΠΊΡΠΎΠ΅ΡΡΡ ΡΠ°Π·Π³ΡΡΠ·ΠΎΡΠ½ΡΠΉ ΠΊΠ»Π°ΠΏΠ°Π½, ΠΈ ΠΊΠΎΠΌΠΏΡΠ΅ΡΡΠΎΡ Π²Π½ΠΎΠ²Ρ ΡΠ²Π΅Π»ΠΈΡΠΈΡ Π΄Π°Π²Π»Π΅Π½ΠΈΠ΅ Π² ΠΏΠ½Π΅Π²ΠΌΠΎΠΏΡΠΈΠ²ΠΎΠ΄Π΅ Π΄ΠΎ 7,0 … 7,5 Π³Ρ/ΡΠΌ2.
ΠΠ°Π²Π»Π΅Π½ΠΈΠ΅ ΠΎΡΠΊΡΡΡΠΈΡ ΠΈ Π·Π°ΠΊΡΡΡΠΈΡ ΠΊΠ»Π°ΠΏΠ°Π½Π° Π² ΡΠ΅Π³ΡΠ»ΡΡΠΎΡΠ΅ Π΄Π°Π²Π»Π΅Π½ΠΈΡ ΠΊΠΎΠ½ΡΡΠΎΠ»ΠΈΡΡΠ΅ΡΡΡ ΠΏΠΎ Π΄Π²ΡΡ ΡΡΡΠ΅Π»ΠΎΡΠ½ΠΎΠΌΡ ΠΌΠ°Π½ΠΎΠΌΠ΅ΡΡΡ Π² ΠΊΠ°Π±ΠΈΠ½Π΅ ΠΈΠ»ΠΈ ΠΏΠΎ ΠΌΠ°Π½ΠΎΠΌΠ΅ΡΡΡ, ΠΏΠΎΠ΄ΡΠΎΠ΅Π΄ΠΈΠ½Π΅Π½Π½ΠΎΠΌΡ ΠΊ ΠΊΠ»Π°ΠΏΠ°Π½Ρ ΠΊΠΎΠ½ΡΡΠΎΠ»ΡΠ½ΠΎΠ³ΠΎ Π²ΡΠ²ΠΎΠ΄Π° Π½Π° ΠΊΠΎΠ½Π΄Π΅Π½ΡΠ°ΡΠΈΠΎΠ½Π½ΠΎΠΌ Π±Π°Π»Π»ΠΎΠ½Π΅.
Π Π΅Π³ΡΠ»ΠΈΡΠΎΠ²Π°ΡΡ Π΄Π°Π²Π»Π΅Π½ΠΈΠ΅ Π²ΠΎΠ·Π΄ΡΡ Π° Π² ΠΏΠ½Π΅Π²ΠΌΠΎΠΏΡΠΈΠ²ΠΎΠ΄Π΅ Π½ΡΠΆΠ½ΠΎ Π²ΠΈΠ½ΡΠΎΠΌ ΡΠ²Π΅ΡΡ Ρ ΡΠ΅Π³ΡΠ»ΡΡΠΎΡΠ° Π΄Π°Π²Π»Π΅Π½ΠΈΡ.
ΠΡΠΊΠ»ΠΎΠ½Π΅Π½ΠΈΡ Π² ΡΠ°Π±ΠΎΡΠ΅ ΡΠ΅Π³ΡΠ»ΡΡΠΎΡΠ° Π΄Π°Π²Π»Π΅Π½ΠΈΡ: ΡΠ΅Π·ΠΊΠΈΠΉ ΡΠ±ΡΠΎΡ Π²ΠΎΠ·Π΄ΡΡ Π° Π² ΠΏΡΠΎΡΠ΅ΡΡΠ΅ Π·Π°ΠΏΠΎΠ»Π½Π΅Π½ΠΈΡ ΡΠΈΡΡΠ΅ΠΌΡ, ΠΎΡΠΊΡΡΡΠΈΠ΅ ΠΊΠ»Π°ΠΏΠ°Π½Π° ΠΏΡΠΈ Π½ΠΈΠ·ΠΊΠΎΠΌ ΠΈΠ»ΠΈ Π²ΡΡΠΎΠΊΠΎΠΌ Π΄Π°Π²Π»Π΅Π½ΠΈΠΈ ΠΈ Π½Π΅Π²ΠΎΠ·ΠΌΠΎΠΆΠ½ΠΎΡΡΡ Π΅Π³ΠΎ ΡΠ΅Π³ΡΠ»ΠΈΡΠΎΠ²ΠΊΠΈ β ΡΠΊΠ°Π·ΡΠ²Π°ΡΡ Π½Π° Π½Π΅ΠΈΡΠΏΡΠ°Π²Π½ΠΎΡΡΡ ΠΏΡΠΈΠ±ΠΎΡΠ° ΠΈ Π½Π΅ΠΎΠ±Ρ ΠΎΠ΄ΠΈΠΌΠΎΡΡΡ Π΅Π³ΠΎ ΡΠ΅ΠΌΠΎΠ½ΡΠ°.
ΠΡΠΎΠ²Π΅ΡΡΡΠ΅ ΠΏΠ½Π΅Π²ΠΌΠ°ΡΠΈΡΠ΅ΡΠΊΠΈΠΉ ΡΠΎΡΠΌΠΎΠ·Π½ΠΎΠΉ ΠΏΡΠΈΠ²ΠΎΠ΄ Π½Π° Π³Π΅ΡΠΌΠ΅ΡΠΈΡΠ½ΠΎΡΡΡ
ΠΡΠΈ Π½Π΅ΡΠ°Π±ΠΎΡΠ°ΡΡΠ΅ΠΌ ΠΊΠΎΠΌΠΏΡΠ΅ΡΡΠΎΡΠ΅ ΠΈ Π²ΡΠΊΠ»ΡΡΠ΅Π½Π½ΡΡ ΠΏΠΎΡΡΠ΅Π±ΠΈΡΠ΅Π»ΡΡ (ΡΠΎΡΠΌΠΎΠ·Π½Π°Ρ ΠΏΠ΅Π΄Π°Π»Ρ ΠΎΡΠΏΡΡΠ΅Π½Π°, ΡΡΠΎΡΠ½ΠΎΡΠ½ΡΠΉ ΡΠΎΡΠΌΠΎΠ· Π²ΠΊΠ»ΡΡΠ΅Π½) ΠΏΠ°Π΄Π΅Π½ΠΈΠ΅ Π΄Π°Π²Π»Π΅Π½ΠΈΡ Π·Π° 30 ΠΌΠΈΠ½ΡΡ ΠΏΡΠΎΠ²Π΅ΡΠΊΠΈ Π΄ΠΎΠ»ΠΆΠ½ΠΎ Π±ΡΡΡ ΠΌΠ΅Π½Π΅Π΅ 0,5 ΠΊΠ³Ρ/ΡΠΌ2.
ΠΡΠΈ Π²ΠΊΠ»ΡΡΠ΅Π½Π½ΡΡ ΠΏΠΎΡΡΠ΅Π±ΠΈΡΠ΅Π»ΡΡ (ΡΠΎΡΠΌΠΎΠ·Π½Π°Ρ ΠΏΠ΅Π΄Π°Π»Ρ Π½Π°ΠΆΠ°ΡΠ°, ΡΡΠΎΡΠ½ΠΎΡΠ½ΡΠΉ ΡΠΎΡΠΌΠΎΠ· Π²ΡΠΊΠ»ΡΡΠ΅Π½) ΠΏΠ°Π΄Π΅Π½ΠΈΠ΅ Π΄Π°Π²Π»Π΅Π½ΠΈΡ Π·Π° 15 ΠΌΠΈΠ½ΡΡ ΠΏΡΠΎΠ²Π΅ΡΠΊΠΈ Π΄ΠΎΠ»ΠΆΠ½ΠΎ Π±ΡΡΡ ΡΠ°ΠΊΠΆΠ΅ ΠΌΠ΅Π½Π΅Π΅ 0,5 ΠΊΠ³Ρ/ΡΠΌ2.
ΠΠ»Ρ ΠΏΡΠΎΠ²Π΅ΡΠΊΠΈ ΡΠ°Π±ΠΎΡΡ Π·Π°ΡΠΈΡΠ½ΡΡ ΠΊΠ»Π°ΠΏΠ°Π½ΠΎΠ² ΠΏΠΎΠ΄ΠΊΠ»ΡΡΠΈΡΠ΅ ΠΊ ΠΊΠ»Π°ΠΏΠ°Π½Ρ ΠΊΠΎΠ½ΡΡΠΎΠ»ΡΠ½ΠΎΠ³ΠΎ Π²ΡΠ²ΠΎΠ΄Π° Π½Π° Π±Π°Π»Π»ΠΎΠ½Π΅ ΡΡΠΎΡΠ½ΠΎΡΠ½ΠΎΠ³ΠΎ ΡΠΎΡΠΌΠΎΠ·Π° ΠΌΠ°Π½ΠΎΠΌΠ΅ΡΡ.
Π‘ΡΡΠ°Π²ΠΈΡΠ΅ Π²ΠΎΠ·Π΄ΡΡ ΠΈΠ· Π±Π°Π»Π»ΠΎΠ½Π° ΠΏΠ΅ΡΠ΅Π΄Π½Π΅Π³ΠΎ ΠΌΠΎΡΡΠ°, ΠΈΡΠΏΠΎΠ»ΡΠ·ΡΡ ΠΊΠ»Π°ΠΏΠ°Π½ Π΄Π»Ρ ΡΠ»ΠΈΠ²Π° ΠΊΠΎΠ½Π΄Π΅Π½ΡΠ°ΡΠ°.
ΠΠ°Π΄Π΅Π½ΠΈΠ΅ Π΄Π°Π²Π»Π΅Π½ΠΈΡ ΠΏΡΠΈ ΡΡΠΎΠΌ Π΄ΠΎΠ»ΠΆΠ½Π° ΠΏΠΎΠΊΠ°Π·ΡΠ²Π°ΡΡ ΡΠΎΠ»ΡΠΊΠΎ Π²Π΅ΡΡ Π½ΡΡ ΡΡΡΠ΅Π»ΠΊΠ° ΡΡΠ°ΡΠ½ΠΎΠ³ΠΎ ΠΌΠ°Π½ΠΎΠΌΠ΅ΡΡΠ°.
ΠΠ°Π²Π»Π΅Π½ΠΈΠ΅ Π² Π±Π°Π»Π»ΠΎΠ½Π°Ρ Π·Π°Π΄Π½Π΅ΠΉ ΡΠ΅Π»Π΅ΠΆΠΊΠΈ ΠΈ ΡΡΠΎΡΠ½ΠΎΡΠ½ΠΎΠ³ΠΎ ΡΠΎΡΠΌΠΎΠ·Π° ΠΈΠ·ΠΌΠ΅Π½ΠΈΡΡΡΡ Π½Π΅ Π΄ΠΎΠ»ΠΆΠ½ΠΎ.
ΠΡΠ»ΠΈ Π΄Π°Π²Π»Π΅Π½ΠΈΠ΅ ΡΠΌΠ΅Π½ΡΡΠ°Π΅ΡΡΡ Π² Π±Π°Π»Π»ΠΎΠ½Π°Ρ Π·Π°Π΄Π½Π΅ΠΉ ΡΠ΅Π»Π΅ΠΆΠΊΠΈ, ΡΠΎ Π½Π΅ΠΈΡΠΏΡΠ°Π²Π΅Π½ ΡΡΠΎΠΉΠ½ΠΎΠΉ Π·Π°ΡΠΈΡΠ½ΡΠΉ ΠΊΠ»Π°ΠΏΠ°Π½, Π° ΠΏΠ°Π΄Π΅Π½ΠΈΠ΅ Π΄Π°Π²Π»Π΅Π½ΠΈΡ Π² Π±Π°Π»Π»ΠΎΠ½Π°Ρ ΡΡΠΎΡΠ½ΠΎΡΠ½ΠΎΠ³ΠΎ ΡΠΎΡΠΌΠΎΠ·Π° ΡΠΊΠ°Π·ΡΠ²Π°Π΅Ρ Π½Π° Π½Π΅ΠΈΡΠΏΡΠ°Π²Π½ΠΎΡΡΡ Π΄Π²ΠΎΠΉΠ½ΠΎΠ³ΠΎ ΠΈΠ»ΠΈ ΠΎΠ΄ΠΈΠ½Π°ΡΠ½ΠΎΠ³ΠΎ Π·Π°ΡΠΈΡΠ½ΠΎΠ³ΠΎ ΠΊΠ»Π°ΠΏΠ°Π½Π° (Π² Π·Π°Π²ΠΈΡΠΈΠΌΠΎΡΡΠΈ ΠΎΡ ΠΊΠΎΠΌΠΏΠΎΠ½ΠΎΠ²ΠΊΠΈ ΠΏΠ½Π΅Π²ΠΌΠΎΠΏΡΠΈΠ²ΠΎΠ΄Π°), ΠΏΠΈΡΠ°ΡΡΠ΅Π³ΠΎ ΡΡΠΎΡ ΠΊΠΎΠ½ΡΡΡ.
ΠΠ»Ρ ΡΠΎΠ³ΠΎ ΡΡΠΎΠ±Ρ ΠΏΡΠΎΠ²Π΅ΡΠΈΡΡ ΠΈΡΠΏΡΠ°Π²Π½ΠΎΡΡΡ ΠΏΠ½Π΅Π²ΠΌΠ°ΡΠΈΡΠ΅ΡΠΊΠΎΠ³ΠΎ ΠΏΡΠΈΠ²ΠΎΠ΄Π° ΡΠ°Π±ΠΎΡΠ΅Π³ΠΎ ΡΠΎΡΠΌΠΎΠ·Π°, Π½ΡΠΆΠ½ΠΎ ΠΏΡΠΈΡΠΎΠ΅Π΄ΠΈΠ½ΠΈΡΡ ΠΌΠ°Π½ΠΎΠΌΠ΅ΡΡΡ ΠΊ ΠΊΠ»Π°ΠΏΠ°Π½Π°ΠΌ ΠΊΠΎΠ½ΡΡΠΎΠ»ΡΠ½ΠΎΠ³ΠΎ Π²ΡΠ²ΠΎΠ΄Π° Π½Π° ΠΎΠ³ΡΠ°Π½ΠΈΡΠΈΡΠ΅Π»Π΅ Π΄Π°Π²Π»Π΅Π½ΠΈΡ ΠΈ ΡΠ·Π°Π΄ΠΈ Π½Π° ΡΠ°ΠΌΠ΅ Π½Π°Π΄ Π·Π°Π΄Π½ΠΈΠΌ ΠΌΠΎΡΡΠΎΠΌ.
ΠΠΎΠΊΠ°Π·Π°Π½ΠΈΡ ΡΡΠΈΡ ΠΌΠ°Π½ΠΎΠΌΠ΅ΡΡΠΎΠ² ΡΠΎΠΎΡΠ²Π΅ΡΡΡΠ²ΡΡΡ Π΄Π°Π²Π»Π΅Π½ΠΈΡ Π² ΠΏΠ΅ΡΠ΅Π΄Π½ΠΈΡ ΡΠΎΡΠΌΠΎΠ·Π½ΡΡ ΠΊΠ°ΠΌΠ΅ΡΠ°Ρ ΠΈ ΡΠΎΡΠΌΠΎΠ·Π½ΡΡ ΠΊΠ°ΠΌΠ΅ΡΠ°Ρ Π·Π°Π΄Π½Π΅ΠΉ ΡΠ΅Π»Π΅ΠΆΠΊΠΈ.
ΠΡΠΈ Π½Π°ΠΆΠ°ΡΠΈΠΈ Π½Π° ΠΏΠ΅Π΄Π°Π»Ρ ΡΠΎΡΠΌΠΎΠ·Π° Π΄ΠΎ ΡΠΏΠΎΡΠ° Π΄Π°Π²Π»Π΅Π½ΠΈΠ΅ ΠΏΠΎ Π΄Π²ΡΡ ΡΡΡΠ΅Π»ΠΎΡΠ½ΠΎΠΌΡ ΠΌΠ°Π½ΠΎΠΌΠ΅ΡΡΡ Π΄ΠΎΠ»ΠΆΠ½ΠΎ ΡΠ½ΠΈΠ·ΠΈΡΡΡΡ Π½Π΅ Π±ΠΎΠ»Π΅Π΅ ΡΠ΅ΠΌ Π½Π° 0,5 ΠΊΠ³Ρ/ΡΠΌ2 (Π²ΠΎΠ·Π΄ΡΡ ΠΈΠ· Π±Π°Π»Π»ΠΎΠ½ΠΎΠ² ΠΏΠΎΡΡΡΠΏΠΈΠ» Π² ΡΠΎΡΠΌΠΎΠ·Π½ΡΠ΅ ΠΊΠ°ΠΌΠ΅ΡΡ, ΠΈ Π΄Π°Π²Π»Π΅Π½ΠΈΠ΅ ΡΠΏΠ°Π»ΠΎ), Π΄Π°Π²Π»Π΅Π½ΠΈΠ΅ Π² ΠΏΠ΅ΡΠ΅Π΄Π½ΠΈΡ ΡΠΎΡΠΌΠΎΠ·Π½ΡΡ ΠΊΠ°ΠΌΠ΅ΡΠ°Ρ Π΄ΠΎΠ»ΠΆΠ½ΠΎ Π²ΠΎΠ·ΡΠ°ΡΡΠΈ Π΄ΠΎ 7,0 ΠΊΠ³Ρ/ΡΠΌ2 ΠΈ ΡΡΠ°ΡΡ ΡΠ°Π²Π½ΡΠΌ ΠΏΠΎΠΊΠ°Π·Π°Π½ΠΈΡΠΌ Π²Π΅ΡΡ Π½Π΅ΠΉ ΡΠΊΠ°Π»Ρ ΠΌΠ°Π½ΠΎΠΌΠ΅ΡΡΠ° Π² ΠΊΠ°Π±ΠΈΠ½Π΅.
ΠΠ°Π²Π»Π΅Π½ΠΈΠ΅ Π² Π·Π°Π΄Π½ΠΈΡ ΡΠΎΡΠΌΠΎΠ·Π½ΡΡ ΠΊΠ°ΠΌΠ΅ΡΠ°Ρ ΡΠ°ΠΊΠΆΠ΅ Π²ΠΎΠ·ΡΠ°ΡΡΠ°Π΅Ρ Π΄ΠΎ 2,5 … 3,0 ΠΊΠ³Ρ/ΡΠΌ2 Π΄Π»Ρ ΠΏΠΎΡΠΎΠΆΠ½Π΅Π³ΠΎ Π°Π²ΡΠΎΠΌΠΎΠ±ΠΈΠ»Ρ.
ΠΡΠ»ΠΈ ΠΏΠΎΠ΄Π½ΡΡΡ Π²Π²Π΅ΡΡ Π²Π΅ΡΡΠΈΠΊΠ°Π»ΡΠ½ΡΡ ΡΡΠ³Ρ ΠΏΡΠΈΠ²ΠΎΠ΄Π° ΡΠ΅Π³ΡΠ»ΡΡΠΎΡΠ° ΡΠΎΡΠΌΠΎΠ·Π½ΡΡ ΡΠΈΠ» Π½Π° Π²Π΅Π»ΠΈΡΠΈΠ½Ρ ΡΡΠ°ΡΠΈΡΠ΅ΡΠΊΠΎΠ³ΠΎ ΠΏΡΠΎΠ³ΠΈΠ±Π° ΠΏΠΎΠ΄Π²Π΅ΡΠΊΠΈ, ΡΠΎ Π΄Π°Π²Π»Π΅Π½ΠΈΠ΅ Π² Π·Π°Π΄Π½ΠΈΡ ΡΠΎΡΠΌΠΎΠ·Π½ΡΡ ΠΊΠ°ΠΌΠ΅ΡΠ°Ρ Π΄ΠΎΠ»ΠΆΠ½ΠΎ Π²ΠΎΠ·ΡΠ°ΡΡΠΈ Π΄ΠΎ 7,0 ΠΊΠ³Ρ/ΡΠΌ2 (ΠΏΠΎΠΊΠ°Π·Π°Π½ΠΈΠ΅ Π½ΠΈΠΆΠ½Π΅ΠΉ ΡΠΊΠ°Π»Ρ ΠΌΠ°Π½ΠΎΠΌΠ΅ΡΡΠ°).
Π‘ΡΠ°ΡΠΈΡΠ΅ΡΠΊΠΈΠΉ ΠΏΡΠΎΠ³ΠΈΠ± ΠΏΠΎΠ΄Π²Π΅ΡΠΊΠΈ ΠΏΡΠΈ Π·Π°Π³ΡΡΠ·ΠΊΠ΅ Π·Π°Π²ΠΈΡΠΈΡ ΠΎΡ ΠΆΠ΅ΡΡΠΊΠΎΡΡΠΈ ΡΠ΅ΡΡΠΎΡ, ΡΠ°ΠΊ, Π΄Π»Ρ Π±Π°Π·ΠΎΠ²ΡΡ ΠΌΠΎΠ΄Π΅Π»Π΅ΠΉ ΠΎΠ½ ΡΠΎΡΡΠ°Π²Π»ΡΠ΅Ρ ΡΠΎΠΎΡΠ²Π΅ΡΡΡΠ²Π΅Π½Π½ΠΎ: ΠΠ°ΠΌΠΠ-5320 β 40 ΠΌΠΌ, ΠΠ°ΠΌΠΠ-5410 β 42 ΠΌΠΌ, ΠΠ°ΠΌΠΠ-5511 β 34 ΠΌΠΌ.
ΠΡΠΈΠ²ΠΎΠ΄ ΡΠ΅Π³ΡΠ»ΡΡΠΎΡΠ° ΡΠΎΡΠΌΠΎΠ·Π½ΡΡ ΡΠΈΠ» ΡΠ΅Π³ΡΠ»ΠΈΡΡΠ΅ΡΡΡ ΠΈΠ·ΠΌΠ΅Π½Π΅Π½ΠΈΠ΅ΠΌ Π΄Π»ΠΈΠ½Ρ Π²Π΅ΡΡΠΈΠΊΠ°Π»ΡΠ½ΠΎΠΉ ΡΡΠ³ΠΈ ΠΈ ΠΈΠ·ΠΌΠ΅Π½Π΅Π½ΠΈΠ΅ΠΌ Π΄Π»ΠΈΠ½Ρ ΡΡΡΠ°Π³Π° ΡΠ΅Π³ΡΠ»ΡΡΠΎΡΠ°. ΠΠ»ΠΈΠ½Ρ ΡΡΠ³ΠΈ ΡΡΡΠ°Π½Π°Π²Π»ΠΈΠ²Π°ΡΡ ΡΠ°ΠΊΠΈΠΌ ΠΎΠ±ΡΠ°Π·ΠΎΠΌ, ΡΡΠΎΠ±Ρ Π½Π° ΠΏΠΎΡΠΎΠΆΠ½Π΅ΠΌ Π°Π²ΡΠΎΠΌΠΎΠ±ΠΈΠ»Π΅ ΠΏΡΠΈ ΠΏΠΎΠ»Π½ΠΎΡΡΡΡ Π½Π°ΠΆΠ°ΡΠΎΠΉ ΠΏΠ΅Π΄Π°Π»ΠΈ ΡΠΎΡΠΌΠΎΠ·Π° Π΄Π°Π²Π»Π΅Π½ΠΈΠ΅ Π² Π·Π°Π΄Π½ΠΈΡ ΡΠΎΡΠΌΠΎΠ·Π½ΡΡ ΠΊΠ°ΠΌΠ΅ΡΠ°Ρ Π±ΡΠ»ΠΎ Π½Π΅ Π½ΠΈΠΆΠ΅ 2,5 ΠΊΠ³Ρ/ΡΠΌ2. Π΄Π»ΠΈΠ½Π° Π ΡΡΠ°Π³Π° ΡΠ΅Π³ΡΠ»ΡΡΠΎΡΠ° ΡΡΡΠ°Π½Π°Π²Π»ΠΈΠ²Π°Π΅ΡΡΡ ΠΏΠΎΡΡΠΎΡΠ½Π½ΠΎΠΉ Π΄Π»Ρ Π΄Π°Π½Π½ΠΎΠΉ ΠΌΠΎΠ΄Π΅Π»ΠΈ:
ΠΠ°ΠΌΠΠ-5320β105 ΠΌΠΌ, ΠΠ°ΠΌΠΠ-5410β105 ΠΌΠΌ, ΠΠ°ΠΌΠΠ-5511β95 ΠΌΠΌ. ΠΠΎΡΠ»Π΅ ΠΎΡΠΏΡΡΠΊΠ°Π½ΠΈΡ ΠΏΠ΅Π΄Π°Π»ΠΈ ΡΠΎΡΠΌΠΎΠ·Π° Π²ΠΎΠ·Π΄ΡΡ ΠΈΠ· ΡΠΎΡΠΌΠΎΠ·Π½ΡΡ ΠΊΠ°ΠΌΠ΅Ρ Π΄ΠΎΠ»ΠΆΠ΅Π½ Π²ΡΡ ΠΎΠ΄ΠΈΡΡ Π±Π΅Π· Π·Π°Π΄Π΅ΡΠΆΠΊΠΈ ΠΈ ΠΏΠΎΠ»Π½ΠΎΡΡΡΡ.
ΠΡΠ»ΠΈ Π½Π΅ ΠΎΠ±Π΅ΡΠΏΠ΅ΡΠΈΠ²Π°Π΅ΡΡΡ Π½ΠΎΠΌΠΈΠ½Π°Π»ΡΠ½ΠΎΠ΅ Π΄Π°Π²Π»Π΅Π½ΠΈΠ΅ (7,0 ΠΊΠ³Ρ/ΡΠΌ2) Π² ΠΏΠ΅ΡΠ΅Π΄Π½ΠΈΡ ΠΈ Π·Π°Π΄Π½ΠΈΡ ΡΠΎΡΠΌΠΎΠ·Π½ΡΡ ΠΊΠ°ΠΌΠ΅ΡΠ°Ρ ΠΏΡΠΈ ΠΏΠΎΠ»Π½ΠΎΠΌ Π½Π°ΠΆΠ°ΡΠΈΠΈ Π½Π° ΠΏΠ΅Π΄Π°Π»Ρ, ΡΠΎ Π½Π΅ΠΎΠ±Ρ ΠΎΠ΄ΠΈΠΌΠΎ, ΠΏΡΠ΅ΠΆΠ΄Π΅ Π²ΡΠ΅Π³ΠΎ, ΠΏΡΠΎΠ²Π΅ΡΠΈΡΡ ΠΏΡΠ°Π²ΠΈΠ»ΡΠ½ΠΎΡΡΡ ΡΠ΅Π³ΡΠ»ΠΈΡΠΎΠ²ΠΊΠΈ ΠΌΠ΅Ρ Π°Π½ΠΈΡΠ΅ΡΠΊΠΎΠ³ΠΎ ΠΏΡΠΈΠ²ΠΎΠ΄Π° ΡΠΎΡΠΌΠΎΠ·Π½ΠΎΠ³ΠΎ ΠΊΡΠ°Π½Π° (ΡΠΈΡ. 1).
ΠΡΠΈΠ²ΠΎΠ΄ ΠΈΠΌΠ΅Π΅Ρ Π΄Π²Π΅ ΡΠ΅Π³ΡΠ»ΠΈΡΠΎΠ²ΠΎΡΠ½ΡΠ΅ Π²ΠΈΠ»ΠΊΠΈ: Π½Π° ΡΡΠ³Π΅ ΠΏΠ΅Π΄Π°Π»ΠΈ ΠΈ Π½Π° ΠΏΡΠΎΠΌΠ΅ΠΆΡΡΠΎΡΠ½ΠΎΠΉ ΡΡΠ³Π΅ Π΄ΠΎΡΡΡΠΏ ΠΊ ΠΏΠ΅ΡΠ²ΠΎΠΉ ΡΠ΅Π³ΡΠ»ΠΈΡΠΎΠ²ΠΎΡΠ½ΠΎΠΉ Π²ΠΈΠ»ΠΊΠ΅ ΠΎΠ±Π΅ΡΠΏΠ΅ΡΠΈΠ²Π°Π΅ΡΡΡ ΠΏΡΠΈ ΠΏΠΎΠ΄Π½ΡΡΠΎΠΉ ΠΎΠ±Π»ΠΈΡΠΎΠ²ΠΊΠ΅ ΠΏΠ΅ΡΠ΅Π΄ΠΊΠ°. Π£ΠΊΠΎΡΠ°ΡΠΈΠ²Π°Ρ ΡΡΠ³Ρ ΠΏΠ΅Π΄Π°Π»ΠΈ, ΠΌΡ ΠΏΠΎΠ΄Π½ΠΈΠΌΠ°Π΅ΠΌ ΠΏΠ΅Π΄Π°Π»Ρ Π² ΠΊΠ°Π±ΠΈΠ½Π΅, ΠΏΠΎΠ»Π½ΡΠΉ Ρ ΠΎΠ΄ ΠΏΠ΅Π΄Π°Π»ΠΈ ΡΠ²Π΅Π»ΠΈΡΠΈΠ²Π°Π΅ΡΡΡ, ΠΎΠ½ Π΄ΠΎΠ»ΠΆΠ΅Π½ Π±ΡΡΡ ΡΠ°Π²Π΅Π½ 100 … 140 ΠΌΠΌ. ΠΡΠΈ ΠΏΠΎΠ»Π½ΠΎΠΌ Π½Π°ΠΆΠ°ΡΠΈΠΈ Π½Π° ΠΏΠ΅Π΄Π°Π»Ρ Ρ ΠΎΠ΄ ΡΡΡΠ°Π³Π° Π΄Π²ΡΡ ΡΠ΅ΠΊΡΠΈΠΎΠ½Π½ΠΎΠ³ΠΎ ΡΠΎΡΠΌΠΎΠ·Π½ΠΎΠ³ΠΎ ΠΊΡΠ°Π½Π° ΡΠΎΡΡΠ°Π²Π»ΡΠ΅Ρ 31 ΠΌΠΌ.
Π ΡΠΊΡΠΏΠ»ΡΠ°ΡΠ°ΡΠΈΠΈ Π²ΡΡΡΠ΅ΡΠ°ΡΡΡΡ Π°Π²ΡΠΎΠΌΠΎΠ±ΠΈΠ»ΠΈ, Ρ ΠΊΠΎΡΠΎΡΡΡ Π²Π΅Π»ΠΈΠΊΠΎ Π²ΡΠ΅ΠΌΡ ΡΠ°ΡΡΠΎΡΠΌΠ°ΠΆΠΈΠ²Π°Π½ΠΈΡ, Π·Π°ΡΠ°ΡΡΡΡ ΡΡΠΎ ΡΠ²ΡΠ·Π°Π½ΠΎ Ρ ΠΎΡΡΡΡΡΡΠ²ΠΈΠ΅ΠΌ ΡΠ²ΠΎΠ±ΠΎΠ΄Π½ΠΎΠ³ΠΎ Ρ ΠΎΠ΄Π° ΠΏΠ΅Π΄Π°Π»ΠΈ ΡΠΎΡΠΌΠΎΠ·Π°, ΠΊΠΎΡΠΎΡΡΠΉ ΡΠ΅Π³ΡΠ»ΠΈΡΡΠ΅ΡΡΡ Π²ΠΈΠ»ΠΊΠΎΠΉ Π½Π° ΠΏΡΠΎΠΌΠ΅ΠΆΡΡΠΎΡΠ½ΠΎΠΉ ΡΡΠ³Π΅ ΠΈ Π΄ΠΎΠ»ΠΆΠ΅Π½ ΡΠΎΡΡΠ°Π²Π»ΡΡΡ 20…40 ΠΌΠΌ.
ΠΡΠ»ΠΈ Π½Π΅ ΠΎΠ±Π΅ΡΠΏΠ΅ΡΠΈΠ²Π°Π΅ΡΡΡ ΠΌΠ°ΠΊΡΠΈΠΌΠ°Π»ΡΠ½ΠΎΠ΅ Π΄Π°Π²Π»Π΅Π½ΠΈΠ΅ Π² ΠΎΠ΄Π½ΠΎΠΌ ΠΈΠ· ΠΊΠΎΠ½ΡΡΡΠΎΠ² ΡΠ°Π±ΠΎΡΠ΅Π³ΠΎ ΡΠΎΡΠΌΠΎΠ·Π°, Π° Π΄Π°Π²Π»Π΅Π½ΠΈΠ΅ Π² Π΄ΡΡΠ³ΠΎΠΌ Π½ΠΎΡΠΌΠ°Π»ΡΠ½ΠΎΠ΅, ΡΠΎ Π½Π΅ΠΎΠ±Ρ ΠΎΠ΄ΠΈΠΌΠΎ ΠΏΡΠΈΡΠΎΠ΅Π΄ΠΈΠ½ΠΈΡΡ ΠΌΠ°Π½ΠΎΠΌΠ΅ΡΡ ΠΊ Π²ΡΡ ΠΎΠ΄Ρ ΡΠΎΠΎΡΠ²Π΅ΡΡΡΠ²ΡΡΡΠ΅ΠΉ ΡΠ΅ΠΊΡΠΈΠΈ ΡΠΎΡΠΌΠΎΠ·Π½ΠΎΠ³ΠΎ ΠΊΡΠ°Π½Π°: ΠΊ Π²Π΅ΡΡ Π½Π΅ΠΉ β ΠΏΡΠΈ ΠΏΠ»ΠΎΡ ΠΎΠΉ ΡΠ°Π±ΠΎΡΠ΅ ΠΊΠΎΠ½ΡΡΡΠ° Π·Π°Π΄Π½Π΅ΠΉ ΡΠ΅Π»Π΅ΠΆΠΊΠΈ, ΠΊ Π½ΠΈΠΆΠ½Π΅ΠΉ β ΠΏΡΠΈ ΠΏΠ»ΠΎΡ ΠΎΠΉ ΡΠ°Π±ΠΎΡΠ΅ ΠΊΠΎΠ½ΡΡΡΠ° ΠΏΠ΅ΡΠ΅Π΄Π½Π΅Π³ΠΎ ΠΌΠΎΡΡΠ°.
ΠΠ°Π½ΠΎΠΌΠ΅ΡΡΡ Π½ΡΠΆΠ½ΠΎ ΠΏΡΠΈΡΠΎΠ΅Π΄ΠΈΠ½ΡΡΡ ΠΊ Π±ΠΎΠΊΠΎΠ²ΡΠΌ (ΠΏΠΎ Ρ ΠΎΠ΄Ρ Π°Π²ΡΠΎΠΌΠΎΠ±ΠΈΠ»Ρ) Π²ΡΠ²ΠΎΠ΄Π°ΠΌ Π²ΠΌΠ΅ΡΡΠΎ Π΄Π°ΡΡΠΈΠΊΠΎΠ² Β«ΡΡΠΎΠΏΒ» — ΡΠΈΠ³Π½Π°Π»ΠΎΠ² Π½Π° ΡΠ°ΠΌΠΎΡΠ²Π°Π»Π°Ρ ΠΈΠ»ΠΈ ΡΡΡΠ±ΠΎΠΏΡΠΎΠ²ΠΎΠ΄ΠΎΠ², ΠΈΠ΄ΡΡΠΈΡ ΠΊ Π΄Π²ΡΡ ΠΏΡΠΎΠ²ΠΎΠ΄Π½ΠΎΠΌΡ ΠΊΠ»Π°ΠΏΠ°Π½Ρ Π½Π° Π°Π²ΡΠΎΠΌΠΎΠ±ΠΈΠ»ΡΡ -ΡΡΠ³Π°ΡΠ°Ρ .
ΠΡΠΈ Π½Π°ΠΆΠ°ΡΠΈΠΈ Π½Π° ΠΏΠ΅Π΄Π°Π»Ρ Π½Π΅ΠΎΠ±Ρ ΠΎΠ΄ΠΈΠΌΠΎ ΡΡΠ°Π²Π½ΠΈΡΡ Π΄Π°Π²Π»Π΅Π½ΠΈΠ΅ Π½Π° Π²ΡΡ ΠΎΠ΄Π΅ ΡΠΎΡΠΌΠΎΠ·Π½ΠΎΠ³ΠΎ ΠΊΡΠ°Π½Π° ΠΈ Π² ΡΠΎΡΠΌΠΎΠ·Π½ΡΡ ΠΊΠ°ΠΌΠ΅ΡΠ°Ρ . ΠΡΠΈ ΠΏΠΎΠ»Π½ΠΎΠΌ Π½Π°ΠΆΠ°ΡΠΈΠΈ Π½Π° ΠΏΠ΅Π΄Π°Π»Ρ Π²Π΅Π»ΠΈΡΠΈΠ½Ρ Π΄Π°Π²Π»Π΅Π½ΠΈΡ Π½Π° Π²ΡΡ ΠΎΠ΄Π΅ ΡΠΎΡΠΌΠΎΠ·Π½ΠΎΠ³ΠΎ ΠΊΡΠ°Π½Π° ΠΈ ΠΎΠ³ΡΠ°Π½ΠΈΡΠΈΡΠ΅Π»Ρ Π΄Π°Π²Π»Π΅Π½ΠΈΡ Π΄ΠΎΠ»ΠΆΠ½Ρ ΡΡΠ°Π²Π½ΡΡΡΡΡ.
ΠΠ°Π²Π»Π΅Π½ΠΈΠ΅ Π² Π·Π°Π΄Π½ΠΈΡ ΡΠΎΡΠΌΠΎΠ·Π½ΡΡ ΠΊΠ°ΠΌΠ΅ΡΠ°Ρ Π·Π°Π²ΠΈΡΠΈΡ ΠΎΡ ΠΏΠΎΠ»ΠΎΠΆΠ΅Π½ΠΈΡ ΡΡΡΠ°Π³Π° ΡΠ΅Π³ΡΠ»ΡΡΠΎΡΠ° ΡΠΎΡΠΌΠΎΠ·Π½ΡΡ ΡΠΈΠ»: Π² Π½ΠΈΠΆΠ½Π΅ΠΌ ΠΏΠΎΠ»ΠΎΠΆΠ΅Π½ΠΈΠΈ Β«ΠΏΠΎΡΠΎΠΆΠ½ΠΈΠΉΒ» β 2,5 ΠΊΠ³Ρ/ΡΠΌ2, Π² Π²Π΅ΡΡ Π½Π΅ΠΌ ΠΏΠΎΠ»ΠΎΠΆΠ΅Π½ΠΈΠΈ Β«Π³ΡΡΠΆΠ΅Π½ΡΠΉΒ» β 7,0 ΠΊΠ³Ρ/ΡΠΌ2.
Π‘ΡΠ°Π²Π½ΠΈΠ²Π°Ρ ΠΏΠΎΠΊΠ°Π·Π°Π½ΠΈΡ ΠΌΠ°Π½ΠΎΠΌΠ΅ΡΡΠΎΠ² ΠΈ Π·Π½Π°Ρ Ρ Π°ΡΠ°ΠΊΡΠ΅ΡΠΈΡΡΠΈΠΊΠΈ ΠΏΡΠΈΠ±ΠΎΡΠΎΠ², ΠΌΠΎΠΆΠ½ΠΎ Π»Π΅Π³ΠΊΠΎ ΠΎΠ±Π½Π°ΡΡΠΆΠΈΡΡ, ΠΊΠ°ΠΊΠΎΠΉ ΠΈΠ· Π½ΠΈΡ Π½Π΅ΠΈΡΠΏΡΠ°Π²Π΅Π½.
ΠΡΠΈ ΡΠΎΡΠΌΠΎΠΆΠ΅Π½ΠΈΠΈ ΡΠ°Π±ΠΎΡΠΈΠΌ ΡΠΎΡΠΌΠΎΠ·ΠΎΠΌ Π½ΡΠΆΠ½ΠΎ ΠΏΡΠΎΠ²Π΅ΡΠΈΡΡ Ρ ΠΎΠ΄ ΡΡΠΎΠΊΠΎΠ² ΡΠΎΡΠΌΠΎΠ·Π½ΡΡ ΠΊΠ°ΠΌΠ΅Ρ.
ΠΠ»Ρ Π°Π²ΡΠΎΠΌΠΎΠ±ΠΈΠ»Π΅ΠΉ ΠΠ°ΠΌΠΠ-5320, 5410, 55102 ΠΎΠ½ ΡΠ°Π²Π΅Π½ 20 … 30 ΠΌΠΌ, ΠΠ°ΠΌΠΠ-5511, ΠΠ°ΠΌΠΠ-53212, 54112 β 25 … 35 ΠΌΠΌ. Π΄ΠΎΠΏΡΡΠΊΠ°Π΅ΡΡΡ ΡΠ°Π·Π½ΠΈΡΠ° Π² Ρ ΠΎΠ΄Π΅ ΡΡΠΎΠΊΠΎΠ² ΡΠΎΡΠΌΠΎΠ·Π½ΡΡ ΠΊΠ°ΠΌΠ΅Ρ Π½Π° ΠΎΠ΄Π½ΠΎΠΌ ΠΌΠΎΡΡΡ β 2…3 ΠΌΠΌ.
autoruk.ru
ΠΡΠΎΠ²Π΅ΡΠΊΠ° Π³Π΅ΡΠΌΠ΅ΡΠΈΡΠ½ΠΎΡΡΠΈ ΡΠΎΡΠΌΠΎΠ·Π½ΡΡ ΡΠΈΡΡΠ΅ΠΌ | ΠΠΈΠ°Π³Π½ΠΎΡΡΠΈΡΠΎΠ²Π°Π½ΠΈΠ΅ Π°Π²ΡΠΎΠΌΠΎΠ±ΠΈΠ»Ρ
ΠΠ»Ρ ΡΡΠ°Π½ΡΠΏΠΎΡΡΠ½ΡΡ ΡΡΠ΅Π΄ΡΡΠ² Ρ Π³ΠΈΠ΄ΡΠΎΠΏΡΠΈΠ²ΠΎΠ΄ΠΎΠΌ
ΠΠ»Ρ ΡΡΠ°Π½ΡΠΏΠΎΡΡΠ½ΡΡ ΡΡΠ΅Π΄ΡΡΠ² Ρ Π³ΠΈΠ΄ΡΠΎΠΏΡΠΈΠ²ΠΎΠ΄ΠΎΠΌ Π΄Π°Π½Π½Π°Ρ ΠΏΡΠΎΠ²Π΅ΡΠΊΠ° Π·Π°ΠΊΠ»ΡΡΠ°Π΅ΡΡΡ Π² ΠΎΡΠΌΠΎΡΡΠ΅ Π²ΡΠ΅Ρ ΠΎΡΠ½ΠΎΠ²Π½ΡΡ ΡΠ»Π΅ΠΌΠ΅Π½ΡΠΎΠ² Π³ΠΈΠ΄ΡΠΎΠΏΡΠΈΠ²ΠΎΠ΄Π° Π½Π° ΠΎΡΡΡΡΡΡΠ²ΠΈΠ΅ ΡΡΠ΅ΡΠ΅ΠΊ ΡΠΎΡΠΌΠΎΠ·Π½ΠΎΠΉ ΠΆΠΈΠ΄ΠΊΠΎΡΡΠΈ. ΠΡΠΈ ΡΡΠΎΠΌ ΠΎΡΠΎΠ±ΠΎΠ΅ Π²Π½ΠΈΠΌΠ°Π½ΠΈΠ΅ Π½Π΅ΠΎΠ±Ρ ΠΎΠ΄ΠΈΠΌΠΎ ΡΠ΄Π΅Π»ΡΡΡ ΡΠ»Π΅Π΄ΡΡΡΠΈΠΌ ΡΠ»Π΅ΠΌΠ΅Π½ΡΠ°ΠΌ:
- Π³Π»Π°Π²Π½ΠΎΠΌΡ ΡΠΎΡΠΌΠΎΠ·Π½ΠΎΠΌΡ ΡΠΈΠ»ΠΈΠ½Π΄ΡΡ Π² ΠΌΠ΅ΡΡΠ΅ ΠΏΠΎΠ΄ΡΠΎΠ΅Π΄ΠΈΠ½Π΅Π½ΠΈΡ ΠΊ Π½Π΅ΠΌΡ Π±Π°ΡΠΊΠ° Π΄Π»Ρ ΡΠΎΡΠΌΠΎΠ·Π½ΠΎΠΉ ΠΆΠΈΠ΄ΠΊΠΎΡΡΠΈ
- ΠΊΠΎΠ»ΠΈΡΠ΅ΡΡΠ²Ρ ΠΆΠΈΠ΄ΠΊΠΎΡΡΠΈ Π² ΡΠ°ΠΌΠΎΠΌ Π±Π°ΡΠΊΠ΅
- ΡΡΡΡΠ΅ΡΠ°ΠΌ ΡΠΎΠ΅Π΄ΠΈΠ½Π΅Π½ΠΈΡ ΡΡΡΠ±ΠΎΠΏΡΠΎΠ²ΠΎΠ΄ΠΎΠ² ΡΠΎΡΠΌΠΎΠ·Π½ΠΎΠΉ ΡΠΈΡΡΠ΅ΠΌΡ
- ΡΡΡΡΠ΅ΡΠ°ΠΌ Π΄Π»Ρ ΡΠ΄Π°Π»Π΅Π½ΠΈΡ Π²ΠΎΠ·Π΄ΡΡ Π° ΠΈΠ· ΡΠΈΡΡΠ΅ΠΌΡ
- ΡΠ΅Π·ΠΈΠ½ΠΎΠ²ΡΠΌ ΡΠ»Π°Π½Π³Π°ΠΌ, ΠΎΡΠΎΠ±Π΅Π½Π½ΠΎ Π² ΠΌΠ΅ΡΡΠ°Ρ ΠΈΡ ΠΎΠ±ΠΆΠ°ΡΠΈΡ
- ΡΠ°Π±ΠΎΡΠΈΠΌ ΡΠΈΠ»ΠΈΠ½Π΄ΡΠ°ΠΌ ΠΈ ΠΏΡΠΎΡΡΡΠ°Π½ΡΡΠ²Ρ Π²ΠΎΠΊΡΡΠ³ Π½ΠΈΡ
ΠΠΎΠ΄ΡΠ΅ΠΊΠ°Π½ΠΈΠ΅ ΡΠΎΡΠΌΠΎΠ·Π½ΠΎΠΉ ΠΆΠΈΠ΄ΠΊΠΎΡΡΠΈ Π² ΡΠ»Π΅ΠΌΠ΅Π½ΡΠ°Ρ ΠΏΡΠΈΠ²ΠΎΠ΄Π° Π½Π΅ Π΄ΠΎΠΏΡΡΠΊΠ°Π΅ΡΡΡ. ΠΡΠΈ ΡΡΠΎΠΌ ΠΏΠΎΠ΄ ΠΏΠΎΠ΄ΡΠ΅ΠΊΠ°Π½ΠΈΠ΅ΠΌ ΡΠ»Π΅Π΄ΡΠ΅Ρ ΠΏΠΎΠ½ΠΈΠΌΠ°ΡΡ ΠΏΠΎΡΠ²Π»Π΅Π½ΠΈΠ΅ ΠΆΠΈΠ΄ΠΊΠΎΡΡΠΈ Π½Π° ΠΏΠΎΠ²Π΅ΡΡ Π½ΠΎΡΡΠΈ Π΄Π΅ΡΠ°Π»Π΅ΠΉ Π³Π΅ΡΠΌΠ΅ΡΠΈΡΠ½ΡΡ ΡΠΈΡΡΠ΅ΠΌ ΠΏΡΠΈΠ²ΠΎΠ΄Π° ΠΈΠ»ΠΈ ΠΏΠΈΡΠ°Π½ΠΈΡ, Π²ΠΎΡΠΏΡΠΈΠ½ΠΈΠΌΠ°Π΅ΠΌΠΎΠ΅ Π½Π° ΠΎΡΡΠΏΡ. ΠΠ΅ Π΄ΠΎΠΏΡΡΠΊΠ°ΡΡΡΡ ΡΠ°ΠΊΠΆΠ΅ ΠΏΠ΅ΡΠ΅Π³ΠΈΠ±Ρ ΡΡΡΠ±ΠΎΠΏΡΠΎΠ²ΠΎΠ΄ΠΎΠ² ΡΠΎΡΠΌΠΎΠ·Π½ΠΎΠ³ΠΎ ΠΏΡΠΈΠ²ΠΎΠ΄Π°, ΠΈΡ ΠΏΠ΅ΡΠ΅ΡΠΈΡΠ°Π½ΠΈΠ΅, ΠΊΠΎΡΡΠΎΠ·ΠΈΡ, Π³ΡΠΎΠ·ΡΡΠ°Ρ ΠΏΠΎΡΠ΅ΡΠ΅ΠΉ Π³Π΅ΡΠΌΠ΅ΡΠΈΡΠ½ΠΎΡΡΠΈ ΠΈΠ»ΠΈ ΡΠ°Π·ΡΡΡΠ΅Π½ΠΈΠ΅ΠΌ.
Π£ΡΠΎΠ²Π΅Π½Ρ ΠΆΠΈΠ΄ΠΊΠΎΡΡΠΈ Π² Π±Π°ΡΠΊΠ΅ Π΄ΠΎΠ»ΠΆΠ΅Π½ Π½Π°Ρ ΠΎΠ΄ΠΈΡΡΡΡ ΠΌΠ΅ΠΆΠ΄Ρ ΠΌΠ΅ΡΠΊΠ°ΠΌΠΈ, ΡΠΎΠΎΡΠ²Π΅ΡΡΡΠ²ΡΡΡΠΈΠΌΠΈ ΠΌΠ°ΠΊΡΠΈΠΌΠ°Π»ΡΠ½ΠΎΠΌΡ ΠΈ ΠΌΠΈΠ½ΠΈΠΌΠ°Π»ΡΠ½ΠΎΠΌΡ ΠΏΠΎΠ»ΠΎΠΆΠ΅Π½ΠΈΡ. Π’ΡΠ΅ΡΠΈΠ½Ρ ΠΈ ΠΏΠΎΠ²ΡΠ΅ΠΆΠ΄Π΅Π½ΠΈΡ ΡΠΎΡΠΌΠΎΠ·Π½ΡΡ ΡΠ»Π°Π½Π³ΠΎΠ², Π΄ΠΎΡ ΠΎΠ΄ΡΡΠΈΠ΅ Π΄ΠΎ ΡΠ»ΠΎΡ Π°ΡΠΌΠΈΡΠΎΠ²Π°Π½ΠΈΡ, Π° ΡΠ°ΠΊΠΆΠ΅ ΠΈΡ Π²Π·Π΄ΡΡΠΈΠ΅ ΠΏΡΠΈ ΠΏΠΎΠ²ΡΡΠ΅Π½ΠΈΠΈ Π΄Π°Π²Π»Π΅Π½ΠΈΡ Π² ΡΠΎΡΠΌΠΎΠ·Π½ΠΎΠΌ ΠΏΡΠΈΠ²ΠΎΠ΄Π΅ Π½Π΅ Π΄ΠΎΠΏΡΡΠΊΠ°ΡΡΡΡ.
ΠΠ»Ρ ΡΡΠ°Π½ΡΠΏΠΎΡΡΠ½ΡΡ ΡΡΠ΅Π΄ΡΡΠ² Ρ ΠΏΠ½Π΅Π²ΠΌΠΎΠΏΡΠΈΠ²ΠΎΠ΄ΠΎΠΌ
ΠΠ»Ρ ΡΡΠ°Π½ΡΠΏΠΎΡΡΠ½ΡΡ ΡΡΠ΅Π΄ΡΡΠ² Ρ ΠΏΠ½Π΅Π²ΠΌΠΎΠΏΡΠΈΠ²ΠΎΠ΄ΠΎΠΌ ΠΏΡΠΎΠ²Π΅ΡΠΊΠ° Π·Π°ΠΊΠ»ΡΡΠ°Π΅ΡΡΡ Π² ΠΎΡΠΌΠΎΡΡΠ΅ ΠΈ ΠΏΡΠΎΡΠ»ΡΡΠΈΠ²Π°Π½ΠΈΠΈ ΠΎΡΠ½ΠΎΠ²Π½ΡΡ ΡΠ»Π΅ΠΌΠ΅Π½ΡΠΎΠ² ΠΏΠ½Π΅Π²ΠΌΠΎΠΏΡΠΈΠ²ΠΎΠ΄Π° Π½Π° ΠΎΡΡΡΡΡΡΠ²ΠΈΠ΅ ΡΡΠ΅ΡΠ΅ΠΊ ΡΠΆΠ°ΡΠΎΠ³ΠΎ Π²ΠΎΠ·Π΄ΡΡ Π°. ΠΡΠΎΠ²Π΅ΡΠΊΠ° Π΄ΠΎΠ»ΠΆΠ½Π° ΠΏΡΠΎΠ²ΠΎΠ΄ΠΈΡΡΡΡ ΠΏΡΠΈ ΡΠ²ΠΎΠ±ΠΎΠ΄Π½ΠΎΠΌ ΠΏΠΎΠ»ΠΎΠΆΠ΅Π½ΠΈΠΈ ΠΏΠ΅Π΄Π°Π»ΠΈ ΡΠΏΡΠ°Π²Π»Π΅Π½ΠΈΡ ΡΠ°Π±ΠΎΡΠ΅ΠΉ ΡΠΎΡΠΌΠΎΠ·Π½ΠΎΠΉ ΡΠΈΡΡΠ΅ΠΌΠΎΠΉ ΠΈ Π΄Π΅Π°ΠΊΡΠΈΠ²ΠΈΡΠΎΠ²Π°Π½Π½ΠΎΠΌ ΡΡΠΎΡΠ½ΠΎΡΠ½ΠΎΠΌ ΡΠΎΡΠΌΠΎΠ·Π΅. ΠΠΎΠ΄ ΠΊΠΎΠ»Π΅ΡΠ° ΡΡΠ°Π½ΡΠΏΠΎΡΡΠ½ΠΎΠ³ΠΎ ΡΡΠ΅Π΄ΡΡΠ²Π° Ρ ΠΎΠ±Π΅ΠΈΡ ΡΡΠΎΡΠΎΠ½ Π½Π΅ΠΎΠ±Ρ ΠΎΠ΄ΠΈΠΌΠΎ ΠΏΠΎΠ΄Π»ΠΎΠΆΠΈΡΡ ΠΏΡΠΎΡΠΈΠ²ΠΎΠΎΡΠΊΠ°ΡΠ½ΡΠ΅ ΡΠΏΠΎΡΡ. ΠΡΠΈ Π΄Π°Π½Π½ΠΎΠΉ ΠΏΡΠΎΠ²Π΅ΡΠΊΠ΅ ΠΎΡΠΎΠ±ΠΎΠ΅ Π²Π½ΠΈΠΌΠ°Π½ΠΈΠ΅ ΡΠ΄Π΅Π»ΡΠ΅ΡΡΡ ΡΠ»Π΅Π΄ΡΡΡΠΈΠΌ ΡΠ»Π΅ΠΌΠ΅Π½ΡΠ°ΠΌ:
- ΠΎΡΡΡΠΈΡΠ΅Π»Ρ
- ΠΊΠ»Π°ΠΏΠ°Π½Π°ΠΌ ΠΈ ΠΊΡΠ°Π½Π°ΠΌ ΡΠΎΡΠΌΠΎΠ·Π½ΠΎΠΉ ΡΠΈΡΡΠ΅ΠΌΡ
- ΡΠΎΡΠΌΠΎΠ·Π½ΡΠΌ ΠΊΠ°ΠΌΠ΅ΡΠ°ΠΌ ΠΈ ΡΠ½Π΅ΡΠ³ΠΎΠ°ΠΊΠΊΡΠΌΡΠ»ΡΡΠΎΡΠ°ΠΌ
- ΠΌΠΎΠ΄ΡΠ»ΡΡΠΎΡΠ°ΠΌ ΠΠΠ‘
- ΡΠ΅Π·ΠΈΠ½ΠΎΠ²ΡΠΌ ΡΠ»Π°Π½Π³Π°ΠΌ ΠΏΠΎ Π²ΡΠ΅ΠΉ Π΄Π»ΠΈΠ½Π΅
ΠΡΠΎΠΌΠ΅ ΡΠΎΠ³ΠΎ, Π½Π°Π΄ΠΎ ΠΏΡΠΎΠ²Π΅ΡΠΈΡΡ Π½Π° ΡΡΠ΅ΡΠΊΠΈ ΠΏΡΠΎΡΠΈΠ΅ ΡΠ»Π΅ΠΌΠ΅Π½ΡΡ ΠΊΠΎΠ½ΡΡΡΡΠΊΡΠΈΠΈ ΡΡΠ°Π½ΡΠΏΠΎΡΡΠ½ΠΎΠ³ΠΎ ΡΡΠ΅Π΄ΡΡΠ²Π°, ΠΈΠΌΠ΅ΡΡΠΈΠ΅ ΠΏΠ½Π΅Π²ΠΌΠ°ΡΠΈΡΠ΅ΡΠΊΠΈΠΉ ΠΏΡΠΈΠ²ΠΎΠ΄: ΠΏΠ½Π΅Π²ΠΌΠΎΡΠ΅ΡΡΠΎΡΡ ΠΈ ΠΊΡΠ°Π½Ρ ΠΏΠΎΠ΄Π²Π΅ΡΠΊΠΈ ΠΊΠ°Π±ΠΈΠ½Ρ, ΡΠΈΠ΄Π΅Π½ΡΡ ΠΈ ΡΠ°ΡΡΠΈ. Π‘Π»Π΅Π΄ΡΠ΅Ρ ΠΎΡΠΌΠ΅ΡΠΈΡΡ, ΡΡΠΎ ΡΠΏΡΠ°Π²Π»ΡΡΡΠΈΠ΅ ΡΠ»Π΅ΠΌΠ΅Π½ΡΡ ΠΏΠ½Π΅Π²ΠΌΠΎΠΏΠΎΠ΄Π²Π΅ΡΠΎΠΊ ΠΌΠΎΠ³ΡΡ ΡΠ΅Π³ΡΠ»ΠΈΡΠΎΠ²Π°ΡΡ ΡΠ²ΠΎΠ΅ ΠΏΠΎΠ»ΠΎΠΆΠ΅Π½ΠΈΠ΅ ΠΏΡΡΠ΅ΠΌ ΡΠ°ΡΡΠΈΡΠ½ΠΎΠ³ΠΎ ΡΠ±ΡΠΎΡΠ° Π²ΠΎΠ·Π΄ΡΡ Π° ΠΈΠ· ΠΊΡΠ°Π½ΠΎΠ² ΡΠ΅Π³ΡΠ»ΠΈΡΠΎΠ²ΠΊΠΈ ΡΡΠΎΠ²Π½Ρ, ΠΏΠΎΡΡΠΎΠΌΡ Π² Π½Π°ΡΠ°Π»ΡΠ½ΡΠΉ ΠΌΠΎΠΌΠ΅Π½Ρ ΠΏΠΎΡΠ»Π΅ ΠΎΡΡΠ°Π½ΠΎΠ²ΠΊΠΈ ΡΡΠ°Π½ΡΠΏΠΎΡΡΠ½ΠΎΠ³ΠΎ ΡΡΠ΅Π΄ΡΡΠ²Π° (ΠΏΡΠΈΠΌΠ΅ΡΠ½ΠΎ Π² ΡΠ΅ΡΠ΅Π½ΠΈΠ΅ 0,5.1,0 ΠΌΠΈΠ½) ΠΌΠΎΠΆΠ΅Ρ ΠΏΡΠΎΡΠ»ΡΡΠΈΠ²Π°ΡΡΡΡ ΡΡΠ΅ΡΠΊΠ° ΡΠΆΠ°ΡΠΎΠ³ΠΎ Π²ΠΎΠ·Π΄ΡΡ Π° ΠΈΠ· ΡΠ°ΠΊΠΈΡ ΡΠ»Π΅ΠΌΠ΅Π½ΡΠΎΠ², ΠΊΠΎΡΠΎΡΠ°Ρ Π·Π°ΡΠ΅ΠΌ ΠΏΡΠ΅ΠΊΡΠ°ΡΠ°Π΅ΡΡΡ.
Π ΠΈΡ. ΠΡΠ½ΠΎΠ²Π½ΡΠ΅ ΠΌΠ΅ΡΡΠ° ΠΊΠΎΠ½ΡΡΠΎΠ»Ρ ΡΠΎΡΠΌΠΎΠ·Π½ΡΡ ΡΠΈΡΡΠ΅ΠΌ Ρ Π³ΠΈΠ΄ΡΠΎΠΏΡΠΈΠ²ΠΎΠ΄ΠΎΠΌ: 1 β Π΄ΠΈΡΠΊΠΎΠ²ΡΠΉ ΡΠΎΡΠΌΠΎΠ·Π½ΠΎΠΉ ΠΌΠ΅Ρ Π°Π½ΠΈΠ·ΠΌ; 2 β ΠΊΠ»Π°ΠΏΠ°Π½Ρ Π³ΠΈΠ΄ΡΠΎΠΏΡΠΈΠ²ΠΎΠ΄Π°; 3 β Π³Π»Π°Π²Π½ΡΠΉ ΡΠΎΡΠΌΠΎΠ·Π½ΠΎΠΉ ΡΠΈΠ»ΠΈΠ½Π΄Ρ; 4 β ΡΠ΅Π·ΠΈΠ½ΠΎΠ²ΡΠ΅ ΡΠ»Π°Π½Π³ΠΈ; 5 β ΡΡΠΎΡ ΠΏΡΠΈΠ²ΠΎΠ΄Π° ΡΡΠΎΡΠ½ΠΎΡΠ½ΠΎΠ³ΠΎ ΡΠΎΡΠΌΠΎΠ·Π°; 6 β Π±Π°ΡΠ°Π±Π°Π½Π½ΡΠΉ ΡΠΎΡΠΌΠΎΠ·Π½ΠΎΠΉ ΠΌΠ΅Ρ Π°Π½ΠΈΠ·ΠΌ
Π£ΠΊΠ°Π·Π°Π½Π½ΡΡ ΠΏΡΠΎΠ²Π΅ΡΠΊΡ Π½Π΅ΠΎΠ±Ρ ΠΎΠ΄ΠΈΠΌΠΎ ΠΏΠΎΠ²ΡΠΎΡΠΈΡΡ ΠΏΡΠΈ ΠΏΡΠΈΠ²Π΅Π΄Π΅Π½Π½ΠΎΠΉ Π² Π΄Π΅ΠΉΡΡΠ²ΠΈΠ΅ ΠΏΠ΅Π΄Π°Π»ΠΈ ΡΠΏΡΠ°Π²Π»Π΅Π½ΠΈΡ ΡΠ°Π±ΠΎΡΠ΅ΠΉ ΡΠΎΡΠΌΠΎΠ·Π½ΠΎΠΉ ΡΠΈΡΡΠ΅ΠΌΠΎΠΉ.
ΠΡΠΈ ΠΎΠ±Π½Π°ΡΡΠΆΠ΅Π½ΠΈΠΈ ΡΡΠ΅ΡΠΊΠΈ ΡΠΆΠ°ΡΠΎΠ³ΠΎ Π²ΠΎΠ·Π΄ΡΡ Π° Π΅Π΅ ΠΈΠ½ΡΠ΅Π½ΡΠΈΠ²Π½ΠΎΡΡΡ ΠΏΡΠΎΠ²Π΅ΡΡΡΡ Π² ΡΠΊΠ°Π·Π°Π½Π½ΠΎΠΌ Π½ΠΈΠΆΠ΅ ΠΏΠΎΡΡΠ΄ΠΊΠ΅:
- Π‘ ΠΏΠΎΠΌΠΎΡΡΡ ΡΠ΅Π³ΡΠ»ΡΡΠΎΡΠ° Π΄Π°Π²Π»Π΅Π½ΠΈΡ ΡΡΡΠ°Π½ΠΎΠ²ΠΈΡΡ Π΄Π°Π²Π»Π΅Π½ΠΈΠ΅ Π² ΠΏΠΈΡΠ°ΡΡΠ΅ΠΌ ΠΊΠΎΠ½ΡΡΡΠ΅ ΠΏΠ½Π΅Π²ΠΌΠΎΡΠΈΡΡΠ΅ΠΌΡ Π½Π° ΡΡΠΎΠ²Π½Π΅ Π½ΠΈΠΆΠ½Π΅Π³ΠΎ ΠΏΡΠ΅Π΄Π΅Π»Π° ΡΠ΅Π³ΡΠ»ΠΈΡΠΎΠ²Π°Π½ΠΈΡ. ΠΠ°Π½Π½ΡΠΉ ΠΏΡΠ΅Π΄Π΅Π» ΡΠΎΠΎΡΠ²Π΅ΡΡΡΠ²ΡΠ΅Ρ Π΄Π°Π²Π»Π΅Π½ΠΈΡ Π² ΡΠΊΠ°Π·Π°Π½Π½ΠΎΠΌ ΠΊΠΎΠ½ΡΡΡΠ΅, ΠΏΡΠΈ ΠΊΠΎΡΠΎΡΠΎΠΌ Π²ΡΡΡΠΏΠ°Π΅Ρ Π² ΡΠ°Π±ΠΎΡΡ ΠΊΠΎΠΌΠΏΡΠ΅ΡΡΠΎΡ. Π§ΡΠΎΠ±Ρ ΠΎΠΏΡΠ΅Π΄Π΅Π»ΠΈΡΡ ΡΡΠΎ Π΄Π°Π²Π»Π΅Π½ΠΈΠ΅, Π½Π΅ΠΎΠ±Ρ ΠΎΠ΄ΠΈΠΌΠΎ Π·Π°Π²Π΅ΡΡΠΈ Π΄Π²ΠΈΠ³Π°ΡΠ΅Π»Ρ ΠΈ Π΄ΠΎΠ²Π΅ΡΡΠΈ Π΄Π°Π²Π»Π΅Π½ΠΈΠ΅ Π² ΠΏΠ½Π΅Π²ΠΌΠΎΡΠΈΡΡΠ΅ΠΌΠ΅ Π΄ΠΎ ΡΡΠΎΠ²Π½Ρ, ΠΏΡΠΈ ΠΊΠΎΡΠΎΡΠΎΠΌ ΡΡΠ°Π±Π°ΡΡΠ²Π°Π΅Ρ ΡΠ°Π·Π³ΡΡΠ·ΠΎΡΠ½ΠΎΠ΅ ΡΡΡΡΠΎΠΉΡΡΠ²ΠΎ ΠΎΡΡΡΠΈΡΠ΅Π»Ρ Π²ΠΎΠ·Π΄ΡΡ Π° ΠΈΠ»ΠΈ ΡΠ΅Π³ΡΠ»ΡΡΠΎΡ Π΄Π°Π²Π»Π΅Π½ΠΈΡ ΠΈ ΠΏΡΠΎΠΈΡΡ ΠΎΠ΄ΠΈΡ ΠΎΡΠΊΠ»ΡΡΠ΅Π½ΠΈΠ΅ ΠΏΠΎΠ΄Π°ΡΠΈ ΠΊΠΎΠΌΠΏΡΠ΅ΡΡΠΎΡΠ°. ΠΠΎΡΠ»Π΅ ΡΡΠΎΠ³ΠΎ, Π½Π΅ ΠΎΡΡΠ°Π½Π°Π²Π»ΠΈΠ²Π°Ρ Π΄Π²ΠΈΠ³Π°ΡΠ΅Π»Ρ, ΠΊΡΠ°ΡΠΊΠΎΠ²ΡΠ΅ΠΌΠ΅Π½Π½ΡΠΌΠΈ ΠΈΠ½ΡΠ΅Π½ΡΠΈΠ²Π½ΡΠΌΠΈ Π½Π°ΠΆΠ°ΡΠΈΡΠΌΠΈ Π½Π° ΠΏΠ΅Π΄Π°Π»Ρ ΡΠΎΡΠΌΠΎΠ·Π° ΡΠ½ΠΈΠ·ΠΈΡΡ Π΄Π°Π²Π»Π΅Π½ΠΈΠ΅ Π² ΠΏΠ½Π΅Π²ΠΌΠΎΡΠΈΡΡΠ΅ΠΌΠ΅ Π΄ΠΎ ΡΡΠΎΠ²Π½Ρ, ΠΏΡΠΈ ΠΊΠΎΡΠΎΡΠΎΠΌ ΠΊΠΎΠΌΠΏΡΠ΅ΡΡΠΎΡ ΡΠ½ΠΎΠ²Π° Π½Π°ΡΠ½Π΅Ρ ΠΏΠΎΠ΄Π°Π²Π°ΡΡ Π²ΠΎΠ·Π΄ΡΡ Π² ΡΠΈΡΡΠ΅ΠΌΡ. ΠΠ΅ΠΌΠ΅Π΄Π»Π΅Π½Π½ΠΎ Π·Π°Π³Π»ΡΡΠΈΡΡ Π΄Π²ΠΈΠ³Π°ΡΠ΅Π»Ρ ΠΈ ΡΡΠΈΡΠ°ΡΡ ΡΡΡΠ°Π½ΠΎΠ²ΠΈΠ²ΡΠ΅Π΅ΡΡ Π² ΠΏΠΈΡΠ°ΡΡΠ΅ΠΌ ΠΊΠΎΠ½ΡΡΡΠ΅ Π΄Π°Π²Π»Π΅Π½ΠΈΠ΅ Π½ΠΈΠΆΠ½ΠΈΠΌ ΠΏΡΠ΅Π΄Π΅Π»ΠΎΠΌ ΡΠ΅Π³ΡΠ»ΠΈΡΠΎΠ²Π°Π½ΠΈΡ ΡΠ΅Π³ΡΠ»ΡΡΠΎΡΠ° Π΄Π°Π²Π»Π΅Π½ΠΈΡ. ΠΡΠ»ΠΈ ΠΏΡΠΈ ΡΡΠΎΠΌ Π²ΠΎΠ·Π½ΠΈΠΊΠ°ΡΡ ΡΡΡΠ΄Π½ΠΎΡΡΠΈ Ρ ΠΎΠΏΡΠ΅Π΄Π΅Π»Π΅Π½ΠΈΠ΅ΠΌ Β«Π½Π° ΡΠ»ΡΡ Β» ΠΌΠΎΠΌΠ΅Π½ΡΠ° Π²ΡΡΡΠΏΠ»Π΅Π½ΠΈΡ ΠΊΠΎΠΌΠΏΡΠ΅ΡΡΠΎΡΠ° Π² ΡΠ°Π±ΠΎΡΡ, ΠΌΠΎΠΆΠ½ΠΎ ΡΡΠ»ΠΎΠ²Π½ΠΎ ΡΡΠΈΡΠ°ΡΡ Π½ΠΈΠΆΠ½ΠΈΠΌ ΠΏΡΠ΅Π΄Π΅Π»ΠΎΠΌ ΡΠ΅Π³ΡΠ»ΠΈΡΠΎΠ²Π°Π½ΠΈΡ Π΄Π°Π²Π»Π΅Π½ΠΈΠ΅, Π½Π° 0,12.0,15 ΠΠΠ° ΠΌΠ΅Π½ΡΡΠ΅Π΅, ΡΠ΅ΠΌ Π΄Π°Π²Π»Π΅Π½ΠΈΠ΅ ΡΡΠ°Π±Π°ΡΡΠ²Π°Π½ΠΈΡ ΡΠ°Π·Π³ΡΡΠ·ΠΎΡΠ½ΡΡ ΡΡΡΡΠΎΠΉΡΡΠ² ΠΈ ΠΎΡΠΊΠ»ΡΡΠ΅Π½ΠΈΡ ΠΊΠΎΠΌΠΏΡΠ΅ΡΡΠΎΡΠ°.
- ΠΠ°ΡΠΈΠΊΡΠΈΡΠΎΠ²Π°ΡΡ Π½Π°ΡΠ°Π»ΡΠ½ΠΎΠ΅ Π·Π½Π°ΡΠ΅Π½ΠΈΠ΅ Π΄Π°Π²Π»Π΅Π½ΠΈΡ Π² ΠΏΠ½Π΅Π²ΠΌΠΎΡΠΈΡΡΠ΅ΠΌΠ΅ ΠΈ Π½Π°ΡΠ°ΡΡ ΠΎΡΡΡΠ΅Ρ Π²ΡΠ΅ΠΌΠ΅Π½ΠΈ ΠΏΠΎ ΡΠ΅ΠΊΡΠ½Π΄ΠΎΠΌΠ΅ΡΡ.
- Π ΡΠ΅ΡΠ΅Π½ΠΈΠ΅ ΡΠ΅Π³Π»Π°ΠΌΠ΅Π½ΡΠΈΡΠΎΠ²Π°Π½Π½ΠΎΠ³ΠΎ Π²ΡΠ΅ΠΌΠ΅Π½ΠΈ Π½Π΅ ΠΏΡΠΈΠ²ΠΎΠ΄ΠΈΡΡ Π² Π΄Π΅ΠΉΡΡΠ²ΠΈΠ΅ ΠΊΠ°ΠΊΠΈΠ΅-Π»ΠΈΠ±ΠΎ ΠΎΡΠ³Π°Π½Ρ ΡΠΏΡΠ°Π²Π»Π΅Π½ΠΈΡ ΠΏΠ½Π΅Π²ΠΌΠΎΠΏΡΠΈΠ²ΠΎΠ΄ΠΎΠΌ. ΠΠ»Ρ Π°Π²ΡΠΎΠΌΠΎΠ±ΠΈΠ»Π΅ΠΉ, ΠΎΡΠ½Π°ΡΠ΅Π½Π½ΡΡ ΠΏΠ½Π΅Π²ΠΌΠΎΠΏΠΎΠ΄Π²Π΅ΡΠΊΠΎΠΉ ΡΠ°ΡΡΠΈ ΠΈΠ»ΠΈ ΠΊΠ°Π±ΠΈΠ½Ρ, Π½Π΅ Π΄ΠΎΠΏΡΡΠΊΠ°ΡΡ ΠΊΠΎΠ»Π΅Π±Π°Π½ΠΈΠΉ ΡΠ°ΠΌΡ ΠΈΠ»ΠΈ ΠΊΠ°Π±ΠΈΠ½Ρ. ΠΠΎ ΠΈΡΡΠ΅ΡΠ΅Π½ΠΈΠΈ ΡΠ΅Π³Π»Π°ΠΌΠ΅Π½ΡΠΈΡΠΎΠ²Π°Π½Π½ΠΎΠ³ΠΎ Π²ΡΠ΅ΠΌΠ΅Π½ΠΈ ΠΎΠΏΡΠ΅Π΄Π΅Π»ΠΈΡΡ ΠΊΠΎΠ½Π΅ΡΠ½ΠΎΠ΅ Π·Π½Π°ΡΠ΅Π½ΠΈΠ΅ Π΄Π°Π²Π»Π΅Π½ΠΈΡ Π² ΠΏΠ½Π΅Π²ΠΌΠΎΡΠΈΡΡΠ΅ΠΌΠ΅.
- ΠΠΎΠ²ΡΠΎΡΠ½ΠΎ Π·Π°ΠΏΡΡΡΠΈΡΡ Π΄Π²ΠΈΠ³Π°ΡΠ΅Π»Ρ ΡΡΠ°Π½ΡΠΏΠΎΡΡΠ½ΠΎΠ³ΠΎ ΡΡΠ΅Π΄ΡΡΠ²Π° ΠΈ Π΄ΠΎΠ²Π΅ΡΡΠΈ Π΄Π°Π²Π»Π΅Π½ΠΈΠ΅ Π² ΠΏΠ½Π΅Π²ΠΌΠΎΡΠΈΡΡΠ΅ΠΌΠ΅ Π΄ΠΎ ΡΡΠΎΠ²Π½Ρ Π½ΠΈΠΆΠ½Π΅Π³ΠΎ ΠΏΡΠ΅Π΄Π΅Π»Π° ΡΠ΅Π³ΡΠ»ΠΈΡΠΎΠ²Π°Π½ΠΈΡ ΡΠΎΠ³Π»Π°ΡΠ½ΠΎ ΠΏ. 1.
- ΠΠΎΠ»Π½ΠΎΡΡΡΡ Π²ΡΠΆΠ°ΡΡ ΠΏΠ΅Π΄Π°Π»Ρ ΡΠΎΡΠΌΠΎΠ·Π°, ΠΏΠΎΡΠ»Π΅ ΡΠ΅Π³ΠΎ Π·Π°ΡΠΈΠΊΡΠΈΡΠΎΠ²Π°ΡΡ Π½Π°ΡΠ°Π»ΡΠ½ΠΎΠ΅ Π΄Π°Π²Π»Π΅Π½ΠΈΠ΅ Π² ΠΏΠ½Π΅Π²ΠΌΠΎΡΠΈΡΡΠ΅ΠΌΠ΅ ΠΈ Π½Π°ΡΠ°ΡΡ ΠΎΡΡΡΠ΅Ρ Π²ΡΠ΅ΠΌΠ΅Π½ΠΈ ΠΏΠΎ ΡΠ΅ΠΊΡΠ½Π΄ΠΎΠΌΠ΅ΡΡ.
- ΠΠΎ ΠΈΡΡΠ΅ΡΠ΅Π½ΠΈΠΈ ΡΠ΅Π³Π»Π°ΠΌΠ΅Π½ΡΠΈΡΠΎΠ²Π°Π½Π½ΠΎΠ³ΠΎ Π²ΡΠ΅ΠΌΠ΅Π½ΠΈ ΠΎΠΏΡΠ΅Π΄Π΅Π»ΠΈΡΡ ΠΊΠΎΠ½Π΅ΡΠ½ΠΎΠ΅ Π·Π½Π°ΡΠ΅Π½ΠΈΠ΅ Π΄Π°Π²Π»Π΅Π½ΠΈΡ Π² ΠΏΠ½Π΅Π²ΠΌΠΎΡΠΈΡΡΠ΅ΠΌΠ΅.
ΠΡΠΈ ΠΊΠΎΠ½ΡΡΠΎΠ»Π΅ ΡΠ΅Ρ Π½ΠΈΡΠ΅ΡΠΊΠΎΠ³ΠΎ ΡΠΎΡΡΠΎΡΠ½ΠΈΡ Π°Π²ΡΠΎΠΏΠΎΠ΅Π·Π΄Π° Π³Π΅ΡΠΌΠ΅ΡΠΈΡΠ½ΠΎΡΡΡ ΠΏΠ½Π΅Π²ΠΌΠΎΠΏΡΠΈΠ²ΠΎΠ΄Π° ΡΡΠ³Π°ΡΠ° ΠΈ ΠΏΡΠΈΡΠ΅ΠΏΠ° ΠΏΡΠΎΠ²Π΅ΡΡΠ΅ΡΡΡ ΡΠ°Π·Π΄Π΅Π»ΡΠ½ΠΎ ΠΏΡΠΈ ΠΎΡΡΠΎΠ΅Π΄ΠΈΠ½Π΅Π½Π½ΡΡ ΠΏΠ½Π΅Π²ΠΌΠ°ΡΠΈΡΠ΅ΡΠΊΠΈΡ ΡΡΡΠ±ΠΎΠΏΡΠΎΠ²ΠΎΠ΄Π°Ρ ΠΏΡΠΈΡΠ΅ΠΏΠ°. ΠΡΠΈ ΡΡΠΎΠΌ Π΄Π»Ρ ΠΏΡΠΎΠ²Π΅ΡΠΊΠΈ Π² ΡΠΎΡΡΠΎΡΠ½ΠΈΠΈ ΠΏΠΎΠ»Π½ΠΎΠ³ΠΎ ΠΏΡΠΈΠ²Π΅Π΄Π΅Π½ΠΈΡ Π² Π΄Π΅ΠΉΡΡΠ²ΠΈΠ΅ ΠΎΡΠ³Π°Π½ΠΎΠ² ΡΠΏΡΠ°Π²Π»Π΅Π½ΠΈΡ Π½Π° ΡΠΏΡΠ°Π²Π»ΡΡΡΡΡ ΠΌΠ°Π³ΠΈΡΡΡΠ°Π»Ρ ΠΏΡΠΈΡΠ΅ΠΏΠ° ΠΏΠΎΠ΄Π°Π΅ΡΡΡ ΡΠΆΠ°ΡΡΠΉ Π²ΠΎΠ·Π΄ΡΡ ΠΏΠΎΠ΄ Π΄Π°Π²Π»Π΅Π½ΠΈΠ΅ΠΌ 0,65 ΠΠΠ° ΠΎΡ Π²Π½Π΅ΡΠ½Π΅Π³ΠΎ ΠΈΡΡΠΎΡΠ½ΠΈΠΊΠ°, ΠΊΠΎΡΠΎΡΡΠΉ ΠΏΠΎΡΠ»Π΅ ΠΏΠΎΠ»Π½ΠΎΠ³ΠΎ ΡΡΠ°Π±Π°ΡΡΠ²Π°Π½ΠΈΡ ΡΠΎΡΠΌΠΎΠ·Π½ΡΡ ΠΊΠ°ΠΌΠ΅Ρ ΠΎΡΠΊΠ»ΡΡΠ°Π΅ΡΡΡ. ΠΡΠΈ ΡΡΠΎΠΌ Π΄Π°Π²Π»Π΅Π½ΠΈΠ΅ Π² ΠΏΠΈΡΠ°ΡΡΠ΅ΠΉ ΠΌΠ°Π³ΠΈΡΡΡΠ°Π»ΠΈ ΠΏΡΠΈΡΠ΅ΠΏΠ° Π΄ΠΎΠ»ΠΆΠ½ΠΎ ΡΠΎΠΎΡΠ²Π΅ΡΡΡΠ²ΠΎΠ²Π°ΡΡ Π½ΠΎΠΌΠΈΠ½Π°Π»ΡΠ½ΠΎΠΌΡ.
ΠΠ°ΡΡΡΠ΅Π½ΠΈΠ΅ Π³Π΅ΡΠΌΠ΅ΡΠΈΡΠ½ΠΎΡΡΠΈ ΠΏΠ½Π΅Π²ΠΌΠ°ΡΠΈΡΠ΅ΡΠΊΠΎΠ³ΠΎ ΡΠΎΡΠΌΠΎΠ·Π½ΠΎΠ³ΠΎ ΠΏΡΠΈΠ²ΠΎΠ΄Π° Π½Π΅ Π΄ΠΎΠ»ΠΆΠ½ΠΎ Π²ΡΠ·ΡΠ²Π°ΡΡ ΠΏΡΠΈ Π½Π΅ΡΠ°Π±ΠΎΡΠ°ΡΡΠ΅ΠΌ Π΄Π²ΠΈΠ³Π°ΡΠ΅Π»Π΅ ΡΠ½ΠΈΠΆΠ΅Π½ΠΈΡ Π΄Π°Π²Π»Π΅Π½ΠΈΡ Π²ΠΎΠ·Π΄ΡΡ Π° Π±ΠΎΠ»Π΅Π΅ ΡΠ΅ΠΌ Π½Π° 0,05 ΠΠΠ° ΠΏΠΎ ΡΡΠ°Π²Π½Π΅Π½ΠΈΡ Ρ Π½Π°ΡΠ°Π»ΡΠ½ΡΠΌ Π΄Π°Π²Π»Π΅Π½ΠΈΠ΅ΠΌ, ΡΡΡΠ°Π½ΠΎΠ²Π»Π΅Π½Π½ΡΠΌ ΡΠΎΠ³Π»Π°ΡΠ½ΠΎ ΠΏ. 1, Π² ΡΠ΅ΡΠ΅Π½ΠΈΠ΅ 30 ΠΌΠΈΠ½ ΠΏΡΠΈ ΡΠ²ΠΎΠ±ΠΎΠ΄Π½ΠΎΠΌ ΠΏΠΎΠ»ΠΎΠΆΠ΅Π½ΠΈΠΈ ΠΎΡΠ³Π°Π½ΠΎΠ² ΡΠΏΡΠ°Π²Π»Π΅Π½ΠΈΡ ΡΠΎΡΠΌΠΎΠ·Π½ΠΎΠΉ ΡΠΈΡΡΠ΅ΠΌΠΎΠΉ ΠΈ 15 ΠΌΠΈΠ½ ΠΏΠΎΡΠ»Π΅ ΠΏΠΎΠ»Π½ΠΎΠ³ΠΎ ΠΏΡΠΈΠ²Π΅Π΄Π΅Π½ΠΈΡ Π² Π΄Π΅ΠΉΡΡΠ²ΠΈΠ΅ ΠΎΡΠ³Π°Π½ΠΎΠ² ΡΠΏΡΠ°Π²Π»Π΅Π½ΠΈΡ ΡΠΎΡΠΌΠΎΠ·Π½ΠΎΠΉ ΡΠΈΡΡΠ΅ΠΌΠΎΠΉ.
ΠΡΠΈ ΠΏΡΠΎΠ²Π΅ΡΠΊΠ΅ Π³Π΅ΡΠΌΠ΅ΡΠΈΡΠ½ΠΎΡΡΠΈ ΠΏΠ½Π΅Π²ΠΌΠ°ΡΠΈΡΠ΅ΡΠΊΠΎΠ³ΠΎ ΠΈ ΠΏΠ½Π΅Π²ΠΌΠΎΠ³ΠΈΠ΄ΡΠ°Π²Π»ΠΈΡΠ΅ΡΠΊΠΎΠ³ΠΎ ΡΠΎΡΠΌΠΎΠ·Π½ΡΡ ΠΏΡΠΈΠ²ΠΎΠ΄ΠΎΠ² Π΄ΠΎΠΏΡΡΠΊΠ°Π΅ΡΡΡ ΠΊΠΎΡΡΠ΅ΠΊΡΠΈΡΠΎΠ²ΠΊΠ° ΡΡΡΠ°Π½ΠΎΠ²Π»Π΅Π½Π½ΠΎΠ³ΠΎ Π½ΠΎΡΠΌΠ°ΡΠΈΠ²Π½ΠΎΠ³ΠΎ ΠΏΠ΅ΡΠΈΠΎΠ΄Π° ΠΎΠΏΡΠ΅Π΄Π΅Π»Π΅Π½ΠΈΡ ΠΏΠ°Π΄Π΅Π½ΠΈΡ Π΄Π°Π²Π»Π΅Π½ΠΈΡ Π²ΠΎΠ·Π΄ΡΡ Π° Π² ΡΠΎΡΠΌΠΎΠ·Π½ΠΎΠΌ ΠΏΡΠΈΠ²ΠΎΠ΄Π΅ ΠΈ ΠΏΡΠ΅Π΄Π΅Π»ΡΠ½ΠΎ Π΄ΠΎΠΏΡΡΡΠΈΠΌΠΎΠ³ΠΎ ΠΏΠ°Π΄Π΅Π½ΠΈΡ Π΄Π°Π²Π»Π΅Π½ΠΈΡ Π²ΠΎΠ·Π΄ΡΡ Π° Π² ΠΏΡΠΈΠ²ΠΎΠ΄Π΅.
ΠΠΎΡΠΌΠ°ΡΠΈΠ²Ρ ΠΏΡΠ΅Π΄Π΅Π»ΡΠ½ΠΎ Π΄ΠΎΠΏΡΡΡΠΈΠΌΠΎΠ³ΠΎ ΠΏΠ°Π΄Π΅Π½ΠΈΡ Π΄Π°Π²Π»Π΅Π½ΠΈΡ Π²ΠΎΠ·Π΄ΡΡ Π° Π² ΠΏΠ½Π΅Π²ΠΌΠ°ΡΠΈΡΠ΅ΡΠΊΠΎΠΌ ΠΈ ΠΏΠ½Π΅Π²ΠΌΠΎΠ³ΠΈΠ΄ΡΠ°Π²Π»ΠΈΡΠ΅ΡΠΊΠΎΠΌ ΡΠΎΡΠΌΠΎΠ·Π½ΡΡ ΠΏΡΠΈΠ²ΠΎΠ΄Π°Ρ ΡΡΠ°Π½ΡΠΏΠΎΡΡΠ½ΠΎΠ³ΠΎ ΡΡΠ΅Π΄ΡΡΠ²Π° ΠΏΡΠΈ ΠΈΠ·ΠΌΠ΅ΡΠ΅Π½ΠΈΠΈ Π΄Π°Π²Π»Π΅Π½ΠΈΡ Ρ ΠΏΠΎΠ³ΡΠ΅ΡΠ½ΠΎΡΡΡΡ, ΠΌΠ΅Π½ΡΡΠ΅ΠΉ Β±5,0 %, Π΄ΠΎΠΏΡΡΠΊΠ°Π΅ΡΡΡ ΠΊΠΎΡΡΠ΅ΠΊΡΠΈΡΠΎΠ²Π°ΡΡ ΠΏΠΎ ΡΠ»Π΅Π΄ΡΡΡΠΈΠΌ ΡΠΎΡΠΌΡΠ»Π°ΠΌ:
Π³Π΄Π΅ Π β ΠΏΡΠ΅Π΄Π΅Π»ΡΠ½ΠΎ Π΄ΠΎΠΏΡΡΡΠΈΠΌΠ°Ρ Π²Π΅Π»ΠΈΡΠΈΠ½Π° ΠΏΠ°Π΄Π΅Π½ΠΈΡ Π΄Π°Π²Π»Π΅Π½ΠΈΡ Π²ΠΎΠ·Π΄ΡΡ Π° Π² ΠΏΡΠΈΠ²ΠΎΠ΄Π΅ ΠΎΡ Π·Π½Π°ΡΠ΅Π½ΠΈΡ Π½ΠΈΠΆΠ½Π΅Π³ΠΎ ΠΏΡΠ΅Π΄Π΅Π»Π° ΡΠ΅Π³ΡΠ»ΠΈΡΠΎΠ²Π°Π½ΠΈΡ ΡΠ΅Π³ΡΠ»ΡΡΠΎΡΠΎΠΌ Π΄Π°Π²Π»Π΅Π½ΠΈΡ ΠΏΡΠΈ Π½Π΅ΡΠ°Π±ΠΎΡΠ°ΡΡΠ΅ΠΌ Π΄Π²ΠΈΠ³Π°ΡΠ΅Π»Π΅ ΠΈ ΠΎΠ±Π΅ΡΠΏΠ΅ΡΠΈΠ²Π°Π΅ΠΌΠΎΠΉ ΠΏΡΠΈΠ±ΠΎΡΠΎΠΌ ΠΌΠ°ΠΊΡΠΈΠΌΠ°Π»ΡΠ½ΠΎΠΉ ΠΏΠΎΠ³ΡΠ΅ΡΠ½ΠΎΡΡΠΈ ΠΈΠ·ΠΌΠ΅ΡΠ΅Π½ΠΈΡ Π΄Π°Π²Π»Π΅Π½ΠΈΡ Π½Π΅ Π±ΠΎΠ»Π΅Π΅ m %; ΠΠ½ β Π½ΠΎΡΠΌΠ°ΡΠΈΠ²Π½Π°Ρ ΠΏΡΠ΅Π΄Π΅Π»ΡΠ½ΠΎ Π΄ΠΎΠΏΡΡΡΠΈΠΌΠ°Ρ Π²Π΅Π»ΠΈΡΠΈΠ½Π° ΠΏΠ°Π΄Π΅Π½ΠΈΡ Π΄Π°Π²Π»Π΅Π½ΠΈΡ Π²ΠΎΠ·Π΄ΡΡ Π° Π² ΠΏΡΠΈΠ²ΠΎΠ΄Π΅ ΠΎΡ Π·Π½Π°ΡΠ΅Π½ΠΈΡ Π½ΠΈΠΆΠ½Π΅Π³ΠΎ ΠΏΡΠ΅Π΄Π΅Π»Π° ΡΠ΅Π³ΡΠ»ΠΈΡΠΎΠ²Π°Π½ΠΈΡ ΡΠ΅Π³ΡΠ»ΡΡΠΎΡΠΎΠΌ Π΄Π°Π²Π»Π΅Π½ΠΈΡ ΠΏΡΠΈ Π½Π΅ΡΠ°Π±ΠΎΡΠ°ΡΡΠ΅ΠΌ Π΄Π²ΠΈΠ³Π°ΡΠ΅Π»Π΅ ΠΈ Π½ΠΎΡΠΌΠ°ΡΠΈΠ²Π½ΠΎΠΉ Π²Π΅Π»ΠΈΡΠΈΠ½Π΅ ΠΌΠ°ΠΊΡΠΈΠΌΠ°Π»ΡΠ½ΠΎΠΉ ΠΏΠΎΠ³ΡΠ΅ΡΠ½ΠΎΡΡΠΈ ΠΈΠ·ΠΌΠ΅ΡΠ΅Π½ΠΈΡ Π΄Π°Π²Π»Π΅Π½ΠΈΡ mΠ½ = 5 %; Π’ β ΠΌΠΈΠ½ΠΈΠΌΠ°Π»ΡΠ½ΠΎ Π΄ΠΎΠΏΡΡΡΠΈΠΌΡΠΉ ΠΏΠ΅ΡΠΈΠΎΠ΄ Π²ΡΠ΅ΠΌΠ΅Π½ΠΈ ΠΎΠΏΡΠ΅Π΄Π΅Π»Π΅Π½ΠΈΡ Π²Π΅Π»ΠΈΡΠΈΠ½Ρ ΠΏΠ°Π΄Π΅Π½ΠΈΡ Π΄Π°Π²Π»Π΅Π½ΠΈΡ Π²ΠΎΠ·Π΄ΡΡ Π° Π² ΡΠΎΡΠΌΠΎΠ·Π½ΠΎΠΌ ΠΏΡΠΈΠ²ΠΎΠ΄Π΅ ΠΏΡΠΈ ΠΎΠ±Π΅ΡΠΏΠ΅ΡΠΈΠ²Π°Π΅ΠΌΠΎΠΉ ΠΏΡΠΈΠ±ΠΎΡΠΎΠΌ ΡΠΎΡΠ½ΠΎΡΡΠΈ ΠΈΠ·ΠΌΠ΅ΡΠ΅Π½ΠΈΡ Π΄Π°Π²Π»Π΅Π½ΠΈΡ Π½Π΅ Π±ΠΎΠ»Π΅Π΅ m %, Ρ; Π’Π½ β Π½ΠΎΡΠΌΠ°ΡΠΈΠ²Π½Π°Ρ Π²Π΅Π»ΠΈΡΠΈΠ½Π° ΠΏΠ΅ΡΠΈΠΎΠ΄Π° Π²ΡΠ΅ΠΌΠ΅Π½ΠΈ ΠΎΠΏΡΠ΅Π΄Π΅Π»Π΅Π½ΠΈΡ ΠΏΠ°Π΄Π΅Π½ΠΈΡ Π΄Π°Π²Π»Π΅Π½ΠΈΡ Π²ΠΎΠ·Π΄ΡΡ Π° Π² ΡΠΎΡΠΌΠΎΠ·Π½ΠΎΠΌ ΠΏΡΠΈΠ²ΠΎΠ΄Π΅, Ρ.
ustroistvo-avtomobilya.ru