2.Карта дефектации
Карта технических требований на дефектацию блока цилиндров компрессора | ||||||
Деталь: | ||||||
Блок цилиндров | ||||||
Номер детали: | ||||||
№ 5320-3509028 | ||||||
Материал | Твердость | |||||
СЧ 18 | HB – 187-241 | |||||
Позиция на эскизе | Возможные дефекты | Способ установле-ния дефекта, измерительные инструменты | Размеры, мм | Заключение | ||
по рабочему чертежу | допустимый без ремонта | допустимый для ремонта | ||||
1 | Трещины, изломы, пробоины | Осмотр | – | – | – | Браковать |
2 | Задиры, риски на поверхности зеркала цилиндра | Осмотр, лупа | ○60+0,03 | Браковать при
наличии глубоких рисок и задиров. | ||
3 | Износ поверхности зеркала цилиндра | Индикаторный нутромер | ○60+0,03 | ○60,3 | – | Обработать в ремонтный размер |
1-ый ремонтный | ○60,4+0,03 | ○60,43 | ○60,23 | |||
2-ой ремонтный | ○60,8+0,03 | ○60,63 | ||||
4 | Коробление привалочных поверхностей под картер и головку цилиндра | Лекальная линейка | 92-0,24 | 91,7 | Обработать до выведения дефекта | |
5 | Износ поверхности под седло выпускного клапана | Осмотр | ○17+0,019 | 17,027 | Запрес- совать втулку | |
6 | Срыв резьбы | Осмотр | Поставить резьбовую вставку или ввертыш |
Обработка деталей под ремонтный
размер.
При этом способе восстановления одна из сопряженных деталей, обычно более дорогостоящая, обрабатывается под ремонтный размер, а вторая, сопряженная с ней, заменяется новой, так называемой ремонтной, или восстанавливается также до ремонтного размера. Обработкой под ремонтный размер восстанавливают геометрическую форму, требуемую шероховатость и точные параметры изношенных поверхностей деталей. Этот вид восстановления деталей эффективен лишь в случае, когда изменение размера не приводит к ликвидации термически обработанного поверхностного слоя детали.
Восстанавливаемые поверхности деталей
могут иметь несколько ремонтных размеров.
Их количество и конкретное значение
зависят от износа деталей за межремонтный
срок службы автомобиля, припуска на
обработку и запаса прочности детали.
Припуск на механическую обработку
зависит от вида обработки: при чистовом
точении и растачивании он составляет
0,05—0,10 мм, при шлифовании 0,03—0,05 мм на
радиус.
Обработкой деталей под ремонтный размер восстанавливают гильзы блока цилиндров, коренные и шатунные шейки коленчатого вала, опорные шейки распределительного вала и многие другие детали. К преимуществам восстановления деталей обработкой до ремонтного размера следует отнести простоту технологического процесса и высокую экономическую эффективность. К недостаткам этого способа относятся увеличение номенклатуры запасных частей, поставляемых промышленностью, и некоторое усложнение организации процессов комплектования деталей.
«Микрогеометрия» — это микропрофиль зеркала цилиндров. От того, какой получилась поверхность после ремонта, зависит трение и износ деталей, в первую очередь, поршневых колец. Для этого микропрофиль поверхности должен удовлетворять противоречивым требованиям — быть гладким, но одновременно и шероховатым, чтобы удерживать масло. Кроме того, необходимо, чтобы трущиеся детали имели минимальное время приработки.
Всем этим требованиям, как известно,
лучше всего соответствует поверхность,
имеющая впадины (риски) так называемой
основной шероховатости глубиной до
0,005-0,010 мм и сглаженные (плоские) вершины
— опорные поверхности. Такая поверхность
формируется в процессе плосковершинного
хонингования.
Оформление карты дефектации — Студопедия
Поделись
Оформление карты дефектации производится в соответствии с ГОСТ 3.1115 – 79. При применении МК в качестве КТПД:
– в графах «Наименование детали, сборочной единицы или материала» и «Обозначение, код» указывается наименование дефектной детали и ее обозначение, а данные по контролируемым дефектам, параметрам и средствам контроля следует записывать на отдельной строке со служебным символом «Д/Т». Блок со служебным символом вводится после строки со служебным символом «К/М». Блоки заполнения информации обозначение граф приведены в таблицах 2.1 и 2.2.
Блок информации по дефектации приведен в таблице 2.1
Блок информации по дефектации Таблица 2.1
Код, | ПЗП | ПЗПР | ДЗП | СТО | ||||
РД | наименование | |||||||
дефекта | ||||||||
Графы блока следует заполнять в соответствии с таблицей 2. 2
Таблица 2.2 – Обозначение граф карты дефектации
Номер графы | Условное обозначение графы ПРИ | Содержание графы | |
ручном способе заполнения | автоматизированном способе заполнения | ||
Код, наименование дефекта | КД | Код, наименование дефекта. Код допускается не указывать | |
ПЗП | ПЗП | предельное значение контролируемого параметра по конструкторскому или нормативно техническому документу | |
ПЗПР | ПЗПР | предельное значение контролируемого параметра по ремонтному конструкторскому или нормативно техническому документу | |
ДЗП | ДЗП | действительное значение контролируемого параметра | |
СТО | СТО | Обозначение (код), наименование применяемых средств контроля | |
— | — | резервная графа.![]() |
Примеры оформления карты дефектации приведены на рисунках 2.1 и 2.2.
Порядок выполнения
1. Описать назначение карты дефектации.
2. Привести таблицу с примером заполнения блоков информации.
3. Заполнить карту дефектации на примере валика гидравлического гасителя колебаний (Допускается оформление маршрутной карты на любую другую тему, связанную с ремонтной тематикой, железнодорожного транспорта, выданную преподавателем).
Примечание: Карту дефектации выполнять на основе маршрутной карты.
При описании процесса необходимо учитывать требования нормативно – технической документации, предъявляемые к конкретному технологическому процессу.
Содержание отчета
1. Поясните сущность и предназначение процесса дефектации.
2. Поясните предназначение технологических карт дефектации.
3. Сведения, вносимые в графы и строки маршрутной карты
4. Выводы.
Контрольные вопросы
1. Какая информация вносится в графу с обозначением «ПЗП»?
2. Какая информация вносится в графу с обозначением «ПЗПР»?
3. В какой последовательности вносится информация о применяемой технологической оснастке?
4. Каким образом обозначается информация о применяемых средствах технологического оснащения?
5. В каких графах указывается наименование дефектной детали и ее обозначение?
6. Какие данные следует записывать на отдельной строке со служебным символом «Д/Т»?
7. В какой строке следует записывать данные по контролируемым дефектам, параметрам и средствам контроля?
Рисунок 2.1 Пример заполнения карты дефектации при применении МК в качестве КТПД.
Рисунок 2.2 Пример заполнения карты дефектации совместно с картой эскизов при применении МК.
Местоположение неисправности — атрибутивный контроль — Карта дефектов [2/2]
Атрибутивный контроль аспектных дефектов в подходе SPC осуществляется с использованием классических диаграмм отслеживания атрибутов NP (количество несоответствующих деталей), C (количество несоответствий ), P (доля несоответствующих деталей) или U (доля несоответствий на единицу).
Если C-карта используется для деталей с высокой добавленной стоимостью при 100% контроле, будет отслеживаться изменение количества дефектов на деталь. В некоторых случаях этого наблюдения достаточно. С другой стороны, можно представить себе и другие случаи, для которых информации о количестве дефектов недостаточно.
Чтобы преодолеть этот недостаток, для атрибутивных элементов управления можно ввести понятие местоположения дефекта (или карты дефекта). Вместо того, чтобы документировать только наличие дефекта, также документируется местонахождение дефекта на детали.
На этом изображении арендодатель отмечает два дефекта: первый дефект на капоте, второй дефект на левом переднем крыле. На изображении компания по аренде автомобилей сообщает о дефектах, возникших, когда клиент возвращает арендованный автомобиль. В этом примере компания по аренде автомобилей находит два дефекта: первый дефект на капоте, второй дефект на левом переднем крыле.
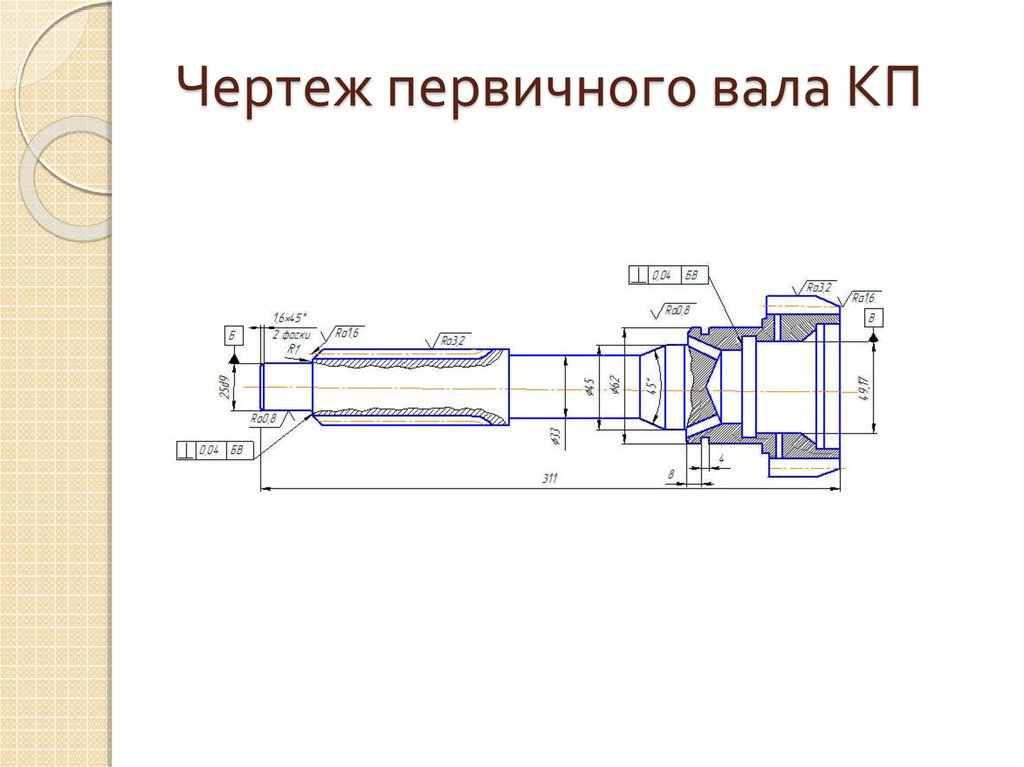
В промышленной сфере можно представить себе множество приложений, которым необходимо знать, где находится дефект, чтобы иметь возможность решить, отбраковывать деталь или нет.
В аэронавтике мы можем принять трещину, расположенную в области низкой физической нагрузки. С другой стороны, та же трещина приведет к слому детали, если она находится в зоне, подверженной высоким физическим нагрузкам.
Для производителя часов допустима царапина, если она находится в невидимой области конечной детали. Однако, если царапина находится в середине безеля, что хорошо видно покупателю, тот же дефект приведет к тому, что деталь будет утилизирована.
Примеры, приведенные выше, показывают случаи, когда местонахождение дефекта играет определяющую роль в принятии решения об отказе от брака. Можно также представить случаи, когда для принятия решения важна дополнительная информация о дефекте (длина дефекта, площадь дефекта).
Как и в случае с его местоположением, можно попросить указать каждый дефект с определенным объемом дополнительной информации.
В зависимости от размера царапины или удара по капоту решение арендодателя не будет одинаковым: он может принять возврат как есть или запросить ремонт и прибегнуть к страховке.
Таким образом, он должен охарактеризовать эти дефекты либо путем их классификации (маленькие, средние, большие), либо путем их измерения (царапина длиной 15 мм).
В некоторых местах допустимой считается трещина, если ее длина не превышает четырех миллиметров. Если она длиннее, деталь следует выбросить. Для производителя стекла радужность может считаться не вызывающей беспокойства, если ее поверхность не превышает 5 мм².
Все эти примеры иллюстрируют возможность использования карты дефектов для принятия правильных решений, когда дело доходит до принятия решения об утилизации детали. Если вы ограничите использование карты дефектов этой поддержкой принятия решений, к сожалению, вы не увидите уменьшения количества дефектов.
Как мы можем воспользоваться этой дополнительной информацией (местоположение, характеристика), чтобы уменьшить количество дефектов?
Представим, что наша компания по аренде автомобилей сейчас «накладывает» дефекты, обнаруженные на все автомобили, взятые в аренду за определенный период. В результате получается карта дефектов, показывающая, в каких областях автомобиля обнаружено наибольшее количество дефектов.
Глядя на приведенную выше карту, он может предпринять корректирующие действия, чтобы ограничить количество столкновений в определенных областях и попросить установить реверсивные радары, чтобы ограничить проблемы с задней частью транспортных средств!
Перенося этот пример в промышленную область, мы видим, что с помощью карты дефектов мы можем легко определить области, в которых часто возникают дефекты, и найти причину их накопления. При устранении выявленной причины автоматически достигается уменьшение дефектов.
Карта дефектов, расположение дефектов
Путем наложения производственной партии (например, 20 штук в неделю) мы понимаем, что у нас есть зона, в которой сосредоточено большое количество дефектов (от R2-S2 до R3-S5): мы бы не понял этого, изучив куски 1 на 1!
В заключение, мы можем усилить статистический аспект карт атрибутов:
- мы добавляем информацию о дефектах (что позволяет нам получать информацию анализа быстрее, с меньшим количеством деталей)
- , «накладывая» карту дефектов на части, мы воссоздаем образец эффекта и можем обеспечить мониторинг и развитие с течением времени.
Фредерик Хенрионне
Менеджер по обеспечению качества, Infodream
Андреас Фёлькер
Менеджер по продукту, Infodream
Узнайте больше о Qual@xy SPC
Узнайте больше о карте дефектов
Автоматический анализ дефектов (ADR) 300-мм пластин без покрытия с помощью автоматизированного АСМ контроль дефектов на пластинах. Для того чтобы охарактеризовать дефекты, необходимы инструменты как для проверки, так и для проверки. Инструменты контроля, такие как системы контроля сканирования поверхности (SSIS), используются в первую очередь для обнаружения и картирования участков дефектов, а инструменты обзора, такие как сканирующая электронная микроскопия (СЭМ), используются для получения морфологической информации.
Крупные дефекты, видимые с помощью оптической микроскопии, могут быть легко обнаружены с помощью контрольного прибора и отображены с помощью контрольного прибора. Однако по мере того, как требования к обработке становятся более строгими, интересующий размер дефекта становится меньше, ниже дифракционного предела оптической микроскопии. Чтобы найти и идентифицировать небольшие дефекты, инструмент просмотра должен выполнить большое обзорное сканирование, чтобы найти точное местоположение дефектов.
Рис. 1. Цель проверки дефектов состоит в том, чтобы определить местонахождение дефекта, идентифицированного с помощью инструмента проверки, и отобразить дефект с помощью инструмента проверки
Обзор дефектов Сканирующий электронный микроскоп (СЭМ) использовался для визуализации дефектов голой пластины после картирования дефектных участков с помощью инструментов для дефектоскопии лазерного рассеяния, таких как Surfscan от KLA-Tencor. Тем не менее, визуализация с помощью SEM для просмотра дефектов ограничена 2D и не может предоставить 3D информацию, которая в последние дни стала более важной для контроля производства голых пластин. Кроме того, более мелкие дефекты, менее 50 нм, все чаще не обнаруживаются с помощью СЭМ для проверки дефектов.
Зачем нужен автоматический анализ дефектов АСМ?
Атомно-силовая микроскопия (АСМ) в последние дни приобретает все большее значение в качестве инструмента для обзора, поскольку она позволяет напрямую измерять размеры дефекта (высоту и ширину, следовательно, форму) и физические свойства интересующих дефектов. Однако для инженеров и исследователей, работающих с голыми пластинами, процесс выявления наноразмерных дефектов с помощью обычного ручного АСМ требует много времени, что снижает производительность, не говоря уже о пропускной способности. Таким образом, важно иметь автоматизированное решение как для анализа отказов, так и для инженеров-технологов, которым необходимо найти причину дефектов на голых пластинах и свести их к минимуму.
Рисунок 2. Типичная процедура проверки дефектов с помощью ручной АСМ имеет очень низкую производительность, в лучшем случае 10 дефектов в день. Кроме того, стоимость подсказки может быть высокой, если используется деструктивный режим сканирования, такой как постукивание.
Чтобы удовлетворить эту потребность, компания Park Systems разработала АСМ для автоматического просмотра дефектов (ADR), который ускоряет и улучшает способ визуализации и анализа дефектов. С помощью этого решения пользователи теперь могут получать дополнительные сведения и информацию о высоте/глубине дефектов, которые невозможно или слишком дорого получить с помощью ADR на основе SEM.
Как перенести карту дефектов из инструмента контроля в АСМ для просмотра
Общая концепция просмотра дефектов проста, но сложна, когда она выполняется в нанометровом масштабе. Просто, потому что все, что для этого потребуется, — это правильный перенос карты дефектов из инструмента проверки и повторное определение местоположения тех же самых дефектов в инструменте обзора. Координаты из инструмента проверки передаются в инструмент просмотра, который используется для увеличения и отображения деталей дефекта, раскрывая его характеристики. Сложная часть вступает в игру, когда вы пытаетесь точно подойти достаточно близко к месту дефекта, чтобы отобразить его, и сделать все это в автоматическом режиме. Когда два этапа инструмента проверки и инструмента обзора связаны между собой, необходимо учитывать различные ошибки. Успешный результат процесса автоматической проверки дефектов зависит от точности двухэтапного сопоставления.
В случае узорчатой пластины метки совмещения используются в качестве опорных точек для сопоставления двух этапов между инструментом контроля и АСМ, и можно точно оценить погрешность положения обоих инструментов. Первоначальный успех Park Systems в решении автоматизированной проверки дефектов (ADR) AFM был реализован в индустрии жестких дисков с использованием контрольных меток, нанесенных инструментом оптического контроля, таким как серия Candela компании KLA Tencor. Используя эти метки, можно было точно и надежно передавать карты дефектов жесткого диска или подложки, а автоматический обзорный АСМ серии Park HDM мог подойти достаточно близко к дефекту, чтобы провести обзорное сканирование, а затем выполнить контрольное сканирование. сканирование с увеличением, чтобы предоставить детали, необходимые пользователю. В целом это решение оказалось эффективным, повысив производительность лабораторий FA индустрии HDD до 1000%.
Автоматизированный и точный перенос карты дефектов БЕЗ контрольных меток
Успех в производстве жестких дисков привел к тому, что аналогичные запросы поступили и от полупроводниковой промышленности. Поскольку требования к уровню чистоты для полупроводниковой промышленности намного строже, чем для жестких дисков, создание маркеров на голых пластинах было невозможно, поэтому необходим процесс ADR БЕЗ какой-либо контрольной маркировки на голых пластинах.
Без установочных меток положение дефектов оценивается приблизительно [1, 2]. Следовательно, требуется дополнительный процесс выравнивания для уменьшения позиционной ошибки [3] во время передачи карты дефектов. Для решения этой проблемы был разработан новый метод, в котором в качестве контрольных точек используются край пластины, надрез и крупные дефекты, видимые с помощью оптической микроскопии. Усовершенствованный метод переназначения в сочетании с улучшенным зрением не требует использования эталонного маркера на голой пластине. Также не требуется какой-либо отдельный шаг для калибровки этапа целевой системы контроля.
Рис. 3. Край пластины и фактические дефекты используются для ориентации пластины и преобразования координат между инструментом контроля и АСМ Park.
Вероятность успеха 300-мм ADR без покрытия пластины зависит от двух факторов: точности картирования сцены и размера исходного скана. Чем точнее картирование стадий, тем меньший размер сканируемого изображения можно использовать и, следовательно, тем выше успех обнаружения дефектов. Новая методика картирования стадий значительно повысила точность за счет применения усовершенствованного алгоритма переназначения и улучшенной техники визуализации.
Среднеквадратичная погрешность позиционирования обзорных сканов составляет менее 5 мкм независимо от положения загрузки пластины. Это означает, что все дефекты расположены в пределах ± 5 мкм с использованием карты дефектов, предоставленной инструментом проверки дефектов
Рис. среднеквадратичное значение Позиционная ошибка остается практически неизменной независимо от положения загрузки пластины.
Результаты ADR 300-мм пластины без покрытия от Park NX-Wafer
Используя усовершенствованную технику преобразования координат, карта дефектов, полученная с помощью лазерного инструмента для проверки дефектов, такого как Surfscan от KLA-Tencor, может быть точно передана в 300-мм АСМ-систему, что позволяет полностью автоматизировать высокопроизводительную визуализацию дефектов.
С новой 300-миллиметровой пластиной ADR типичный автоматический цикл измерения будет проходить следующим образом.
— Неизолированная пластина обрабатывается с помощью лазерного дефектоскопа (например, Surfscan).
— Координаты карты дефектов автоматически устраняются, и активируется связь между двумя этапами между инструментом проверки и Park NX-Wafer. образец голой вафли.
В следующем наборе данных показаны результаты ADR 300-мм пластины без покрытия с пластиной Park NX-Wafer. Типичный показатель успеха превышает 95% независимо от ориентации пластины. Увеличенные сканы показывают подробную морфологию дефектов, четко различая различные типы, такие как ямки, бугры и царапины.
Рис. 5. 300-мм АСМ ADR без покрытия пластины правильно определяет местонахождение всех участков дефектов, выявленных с помощью инструмента для проверки, и автоматически увеличивает масштаб для детального изображения.
Рисунок 5 (a)
Рисунок 5 (b)
Рисунок 5 (c)
Примечательно, что рассмотрение дефекта листья Destradiation Marks, Square-Shaped.