Технические требования на дефектацию деталей
Работы по дефектации и сортировке деталей оказывают большое влияние на эффективность авторемонтного производства, а также на качество и надежность отремонтированных автомобилей. Поэтому дефектацию и сортировку деталей следует производить в строгом соответствии с техническими требованиями на дефектацию деталей. [c.66]Технические требования на дефектацию деталей [c.69]
Технические требования на дефектацию деталей составляются в виде карт (табл. П.4.1), которые по каждой детали в отдельности содержат следующие сведения общие сведения о детали, перечень возможных ее дефектов, способы выявления дефектов, допустимые без ремонта размеры детали и рекомендуемые способы устранения дефектов. [c.69]
Наибольшую сложность при разработке технических требований на дефектацию деталей представляет определение допустимых размеров деталей.
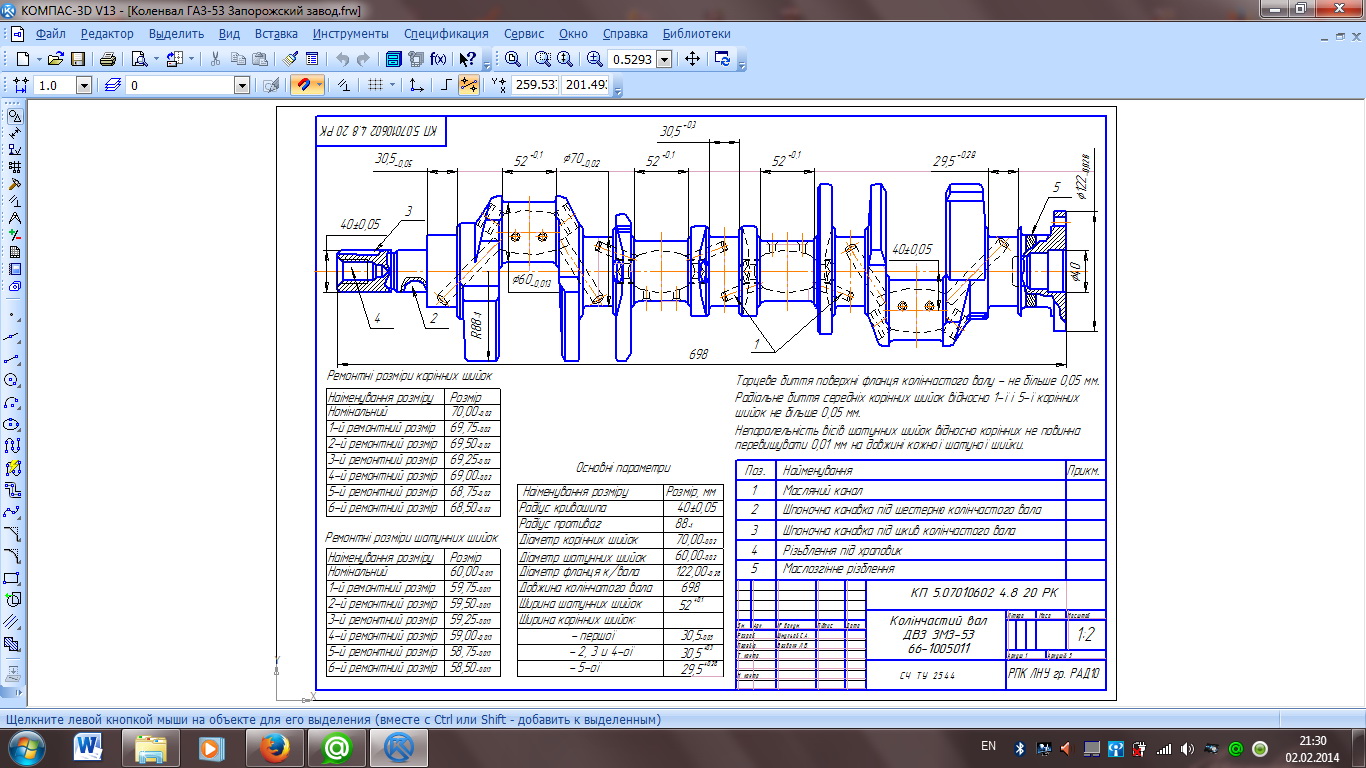
Промытые и очищенные соединения и детали поступают на рабочее место, расположенное непосредственно за последним этапом очистки деталей. Рабочее место должно быть обеспечено необходимым измерительным инструментом и техническими требованиями на дефектацию деталей и соединений по машине каждой марки. [c.156]
Определение абсолютных и относительных величин износа предельно изношенных (выбракованных) деталей по образцам или картам технических требований на дефектацию деталей. [c.345]
Дефектация кабин (кузовов) многостадийная и в значительной степени совмещается с операциями по ремонту. От правильного размещения постов дефектации зависит качество разборки деталей, а в последующем и ремонта. Окончательный контроль кабины (кузова) имеет своей целью выявление характера повреждений в корпусе и определение объема и трудоемкости ремонтных работ. При контроле необходимо руководствоваться техническими требованиями на дефектацию и сортировку деталей и техническими требованиями на ремонт кабины или кузова.
Способы и средства измерения деталей, указанные в технических требованиях на дефектацию, выбраны в зависимости от допуска на изготовление и конструктивных особенностей детали. При отсутствии технических требований способы и средства измерения назначает инженер, ответственный за организацию технического контроля. [c.157]
Для многих машин (электровозы, автомобили и др.) такие технические требования на дефектацию и ремонт деталей разработаны и применяются при ремонте машины.
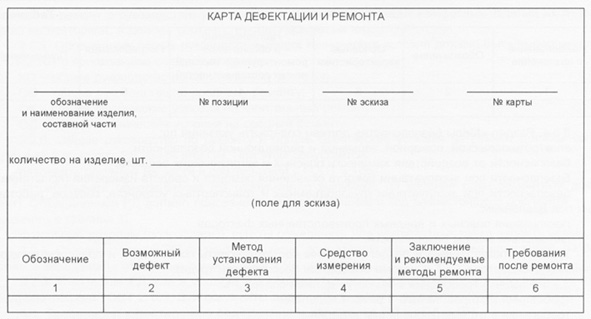
ОСТ 34-38-446-78 Технические условия на капитальный ремонт. Правила построения, изложения и оформления. Порядок согласования, утверждения и регистрации распространяется на технические условия (ТУ) на капитальный ремонт оборудования электростанций, подстанций, тепловых и электрических сетей и устанавливает технические требования к деталям, сборочным единицам и оборудованию в целом при дефектации, ремонте и контроле после ремонта. [c.13]
Дефектацию деталей проводят с целью определить их техническое состояние деформацию и износ поверхностей, целость материала, изменение свойств и характеристик рабочих поверхностей, сохранность формы. Дефектацию деталей осуществляют в соответствии с таблицами дефектации технических условий или требований на ремонт машин.
[c.68]
При разработке мероприятий по совершенствованию производственного процесса следует учитывать, что снижение качества ремонта автомобилей вызывается следующими основными причинами при разборке — повреждением деталей при выполнении моечно-очистных операций—оставленными загрязнениями на трущихся, подлежащих восстановлению и окраске поверхностях при дефектации — несоответствием показателей деталей, идущих на сборку, требованиям технических условий при комплектации — нарушением допусков на сборку сопряжений и несоответствием номенклатуры деталей при испытаниях — нарушением режимов, установленных техническими условиями при сборке — невыполнением требований технических условий на зазоры, натяги, положение деталей относительно друг друга при окраске — нарушением режимов нанесения покрытий и сушки.
Отступление от технических требований может привести к снижению качества и повышению стоимости ремонта автомобилей. Увеличение количества повторно используемых деталей позволяет снизить себестоимость ремонта, однако применение на сборке деталей с отклонениями от- технических требований ухудшает показатели качества отремонтированных автомобилей, Дефектацию деталей производят путем их внешнего осмотра, а также с помощью специального инструмента, приспособлений, приборов и оборудования.,
Общие сведения. Дефектацией называют процесс технического контроля соединений и деталей и сортировки их на группы в соответствии с техническими требованиями. [c.155]
В технических требованиях указаны марка и наименование машины или агрегата, чертеж, наименование и номер детали по каталогу по каждому соединению приведены нормальные, допускаемые и предельные зазоры или натяги, а по каждой детали показаны поверхности, подвергаемые износу перечислены возможные дефекты и указаны способы и средства их выявления приведены нормальные и ремонтные размеры, а также размеры, допускаемые в соединении с деталями, бывшими в эксплуатации, и новыми приведены условия на выбраковку деталей.
Прежде всего необходимо совершенствовать техническую документацию на контрольно-сортировочные работы. Действующие технические требования на дефектацию деталей автомобиля имеют определенные недостатки. В них, например, не всегда приводятся сведения о допустимых погрешностях во взаимном положении рабочих поверхностей деталей. Так, по такой ответственной базовой детали, как блок цилиндров, имеются лишь допустимые отклонения по соосности гнезд под владыши коренных подшипников. Сведения о допустимых погрешностях во взаимном положении других поверхностей блока отсутствуют.
Дефектация сварного корпуса кабины (кузова) — многостадийная и в значительной степени совмещается с операциями по ремонту. Окончательный контроль кабины (кузова) имеет своей целью выявление характера йовреждений в корпусе и определение объема и трудоемкости ремонтных работ. При контроле необходимо руководствоваться техническими условиями на дефектацию и сортировку деталей и техническими требованиями на ремонт каби- [c.240]
В соответствии с требованиями ГОСТ 2602—68 Ремонтные документы , входящего в ЕСКД, на все изделия серийного и массового производства должны разрабатываться документы, включающие руководства, технические условия и нормы расхода запасных частей на средние и капитальные ремонты. Руководства по ремонту включают технические требования (условия) на дефектацию и ремонт деталей, определяющие
Дефектация шатунов.
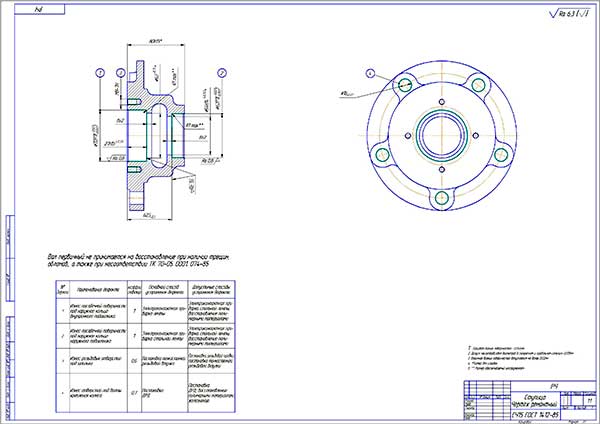
Лабораторная работа № 6
Дефектация шатунов.
Цель работы: Ознакомиться с дефектами шатунов и составить карту технических требований на дефектацию деталей.
Содержание работы:
Определить возможные дефекты шатунов. Выбрать способ установления дефекта.
Произвести основные замеры шатунов и сравнить их по рабочему чертежу. Дать заключение о дефекте.
Ход выполнения работы:
Повторить по конспекту тему дефектация деталей
Изучить способы установления дефектов и контрольно-измерительный инструмент.
Проделанную работу оформить в отчёт и составить карту технических требований на дефектацию деталей.
Теоретическая часть:
Шатуны относятся к классу некруглых
стержней. Их изготавливают в двигатели:
ЗИЛ-130 из стали 40, твёрдость НВ-217;248, ЗМЗ — из стали 45, твёрдость
НВ- 228;269, ЯМЗ- из стали 40Х, КАМАЗ — из стали 40ХН2А, твёрдостью НВ~225;245.
Шатуны и их крышки не должны разукомплектовываться. Шатунные болты должны затягиваться динамометрическим ключом. Момент затяжки у ЗИЛ-130 70-80 Н*М; КАМАЗ- до удлинения болтов на 0,25- 0,27 мм.
Основные дефекты шатунов:
Изгиб или скручивание: правят под прессом с помощью приспособления
Износ отверстий
в нижней головке шатуна: восстанавливают железнением,
или фрезерованием крышки
шатуна
Износ отверстий верхней головке шатуна: замена втулки
Уменьшение
расстояния между осями верхней и нижней головки: является
браковочным
признаком.
Обработка результатов и составление отчета.
1.Диаметр отверстия верхней головки шатуна под втулку: Номинальный, мм ~ 30,5 Допустимый, мм -31
2. Диаметр отверстия нижней головки:
Номинальный, мм — 72,4
Допустимый, мм — 72,9
3.Расстояние между осями верхней и нижней головок:
Номинальный, мм — 260
Допустимый, мм — 260,1
4. Допустимый
изгиб и скручивание шатуна, мм 5.Данные измерений шатуна, мм:
Диаметр отверстия верхей головки- 31,25.
нижней головки- 73,3.
Расстояние между осями верхней и нижней головок- 260,2
б.Заключение о дефектации шатуна:
а) по результатам внешнего осмотра:
Шатун изношен, видны следы задиров, следы деформации.
б) по результатам измерений:
Диаметр отверстия верхей головки шатуна превышает допустимый. Диаметр отверстия нижней головки шатуна превышает допустимый, но износилось больше верхнего.
Расстояние между осями верхней и нижней головок превышает допустимое.
Вывод:
Ознакомился с дефектами шатунов различных автомобилей, и составил карту технических требований на дефектацию деталей.
Технологический процесс восстановительного ремонта шатуна двигателя ЗМЗ-53
Изм.
Лист
№ докум.
Подпись
Дата
Лист
КП 190604.23. 00.00 ПЗ
ВВЕДЕНИЕ
Постоянная необеспеченность ремонтного производства запасными частями является серьёзным фактором снижения технической готовности автомобильного парка. Расширение же производства новых запасных частей связано с увеличением материальных и трудовых затрат. Вместе с тем около 75% деталей, выбраковываемых при первом капитальном ремонте автомобилей, являются ремонтопригодными, либо могут быть использованы вообще без восстановления.
Поэтому целесообразной альтернативой
является вторичное использование
изношенных деталей, восстанавливаемых
в процессе ремонта автомобилей
и его агрегатов. Из ремонтной
практики известно, что большинство
выбракованных по износу деталей
теряют не более 1-2% исходной массы. При
этом прочность деталей практически
сохраняется. Например, 95% деталей двс
выбрасывают при износах, не превышающих
0,3 мм, и большинство из них могут быть
вторично использованы после восстановления. С позиции материалоёмкости воспроизводства
машин экономическая целесообразность
ремонта обусловлена возможностью повторного
использования большинства деталей как
годных, так и предельно изношенных. Это
позволяет осуществлять ремонт в более
короткие сроки с меньшими затратами металла
и других материалов по сравнению с затратами
при изготовлении новых машин. Восстановление
деталей стало одним из важнейших показателей
хозяйственной деятельности крупных ремонтных,
специализированных предприятий. Создана
фактически новая отрасль производства
— восстановление изношенных деталей.
Вторичное потребление деталей значительно
больше, чем потребление новых запасных
частей. Так, например, восстановленными
блоками двигателей пользуются в 2,5 раза
больше, чем новыми, коленчатыми валами
в 1,9 раза, картерами коробок передач в
2,1 раза. Себестоимость восстановления
для большинства восстанавливаемых деталей
не превышает 75% стоимости новых, а расход
материалов в 15 — 20 раз ниже, чем на их изготовление.
Целенаправленная работа заводов — изготовителей
по повышению ресурса рам и кабин, доведению
его до срока службы автомобиля способствует
резкому сокращению сферы при
менения капитального ремонта (КР) полнокомплектных автомобилей. В последнее время он неуклонно снижается, а для грузовых автомобилей предусмотрен КР только агрегатов. Эта тенденция вызывает изменение функций авторемонтных заводов, которые становятся предприятиями по КР агрегатов. Организационно-техническая перестройка АТП в последние годы ускорилась в связи с изменением социально-экономических условий хозяйствования в нашей стране. Дальнейшее эффективное развитие АТП базируется на идеях и принципах, которые создаются в процессе изготовления новой техники заводами-изготовителями, выполняющими услуги по централизованному ТО и ремонту этой техники.
Целью курсового проектирования
является разработка технологического
процесса восстановления шатуна двигателя
ЗМЗ-53.
1. ОБЩАЯ ЧАСТЬ
- Характеристика детали
Шатун двигателя ЗМЗ-53 66-1004045-02 расположен в блоке цилиндров соединяет поршень с шатунной шейкой коленчатого вала и предназначен для передачи усилия от поршня (при рабочем ходе) на коленчатый вал и от коленчатого вала на поршень. Конструктивно шатун состоит из стального стержня, верхней неразъемной и нижней разъемной головок. Верхняя головка шатуна надета на поршневой палец и тем самым соединена с поршнем. Обе половинки нижней головки шатуна надеты на шатунную шейку коленчатого вала и соединены между собой стяжными болтами, гайки которых после затяжки шплинтуют. Чтобы уменьшить трение между деталями и, следовательно, их износ, в верхнюю головку шатуна вставляют бронзовую втулку, а в нижнюю — тонкостенные вкладыши, являющиеся подшипниками скольжения. Внутреннюю поверхность вкладышей заливают баббитом (сплавом олова и свинца).
Материал шатуна – сталь
45Г2, твёрдость материала шатуна
НВ 228¸269, ширина 100мм, высота 40мм, длина
255мм, вес 0,929кг.
В процессе работы двигателя шатуны испытывают значительные знакопеременные нагрузки. При движении поршня во время рабочего хода и такта сжатия шатун сжимается силами давления газов, воспринимаемыми поршнем. Силы инерции поршня стараются оторвать поршень от шатуна, а значит – растянуть шатун. При нормальных условиях работы износа шатуна не происходит. При отсутствии смазки или её низком качестве может произойти схватывание, а в следствии этого – проворачивание верхней втулки или вкладышей, что приводит к задирам нижней и верхней головки шатуна. Износ верхней головки шатуна может происходить из-за частой замены верхней втулки. Шероховатость поверхности отверстий головок шатунов Ra=0,63¸0,40 мкм.
1.2. Технические требования на дефектацию детали
Технические условия на контроль-сортировку
приводятся в карте технических
требований на дефектацию детали. В карте
дефектации указаны дефекты, размеры (номинальный,
допустимый без ремонта и допустимый для
ремонта), а также необходимые технические
воздействия. Схема шатуна с указанием
мест и значение размеров контроля и дефектовки
представлена на эскизе. При контроле
детали, поступившей в капитальный ремонт
проверяются следующие параметры указанные
в таблице 1.
Наименование детали (сборочной единицы). Шатун 66-1004045-02 | |||||
1 3 2 | Материал: Сталь 45Г2 | ||||
Твердость: НВ 228¸269 | |||||
Позиция на эскизе | Возможный дефект | Способ установления дефекта и средства контроля | Размер, мм | Заключение | |
По рабочему чертежу | Допустимый без ремонта | ||||
1 | Износ торцев нижней головки | Штангенциркуль Калибр скоба | 26,60 | 25,90 | Подлежит восстановлению хромированием |
2 | Износ отверстия под втулку верхней головки | Калибр пробка Штангенциркуль Нутромер | 24,3+0,045 | 25,007 | Подлежит восстановлению под ремонтный размер 26,27+0,023 |
3 | Задиры на поверхности отверстия нижней головки шатуна | Визуальный осомтр | 63,6+0,012 |
| Подлежит восстановлению железнением, хонингованием и шлифовкой |
Таблица 1 – Карта дефектации детали
- уменьшение расстояния между осями верхней и нижней головки, контролируется шаблоном 155,95 мм, бракуется при размере менее 155,95 мм;
- износ отверстия верхней головки шатуна под втулку.
При размере более 25,007 мм производят растачивание до ремонтного размера 26,27+0,023 мм;
- дефектация или износ отверстия нижней головки шатуна. При размере более 63,512 мм ремонтируется.
- износ торцов нижней головки. Бракуется при размерах менее 25,90 мм.
1.3. Дефекты деталей и причины их возникновения
Износ отверстия в верхней головки шатуна устраняется расточкой до ремонтного размера втулки (26,27+0,023 мм) с использованием токарного станка типа 1М61.
Износ отверстия нижней головки шатуна устраняется железнением с последующим шлифованием и хонингованием до номинального размера.
Положительными особенностями этого способа является:
а). Высокая скорость осаждения металла на поверхность;
б). Возможность ремонта деталей с износом более 0,15 мм.
Процесс несения покрытия
включает в себя три группы операций:
подготовка деталей, нанесение покрытия,
обработка покрытия детали.
Подготовка включает механическую обработку: чистовое растачивание с целью исправления геометрических параметров изношенной поверхности. Далее идёт предварительное обезжиривание с промывкой в проточной воде и анодное травление. Анодное травление способствует повышению прочности сцепления покрытий с восстанавливаемой поверхностью.
Нанесение покрытия осуществляется безванным способом в холодном электролите на асимметричном токе. Обработка детали после железнения включает: промывку деталей в проточной воде, сушку и механическую обработку (шлифование и хонингование до требуемого размера).
1.4. План рациональной последовательности и содержание технологических операций
При составлении технологического маршрута необходимо учитывать следующие требования:
- одноимённые операции по всем дефектам маршрута должны быть объединены;
- каждая последующая операция должна обеспечить сохранность качества работы поверхностей детали, достигнутую при предыдущих операциях;
- в начале должны идти подготовительные операции, затем восстановительные, кузнечные, слесарно-механические, шлифовальные и доводочные.
План рациональной последовательности приведен в маршрутной карте
Маршрутная карта представлена в таблице 2.
Таблица 2 – маршрутная карта
Маршрутная карта | Группа | |||||
Наименование | код | материал | ||||
Шатун | 66-1004045-02 | Сталь 45Г2 | ||||
N | Наименование операции | Оборудование | Приспособление | Примечание | ||
1 | 2 | 3 | 4 | 5 | ||
1 | Мойка | Машина моечная ОМ-5360 | Моющий раствор Лабомид 201 | Все поверхности | ||
2 | Контрольные операции | Контрольно-измерительные приборы | Штангенциркуль, калибр
пробка, калибр скоба, нутромер индикаторный. | |||
3 | Расточная операция | Станок 1М61 | расточной резец 2140-0001 ГОСТ 18882-73 с углом в плане g=600 с пластинами из твёрдого сплава Т15К16 | Расточка отверстия в верхней головке шатуна под втулку ремонтного размера | ||
4 | Расточная операция | Станок 1М61 | расточной резец 2140-0001 ГОСТ 18882-73 с углом в плане g=600 с пластинами из твёрдого сплава Т15К16 | Чистовая расточка отверстия в нижней головке шатуна для исправления геометрии | ||
5 | Гальваническая операция | Абразивная обработка | Нанесения покрытия на поверхность отверстия в нижней головке шатуна | |||
6 | Шлифовальная операция | Токарный станок 3А228 | шлифовальный круг типа переключения передач диаметром 50 мм, высотой 30мм и зернистостью 40¸10, материал круга 4А20СМ28К5/ПСС4015 | Шлифовка восстановленного размера до номинального с учетом припуска на хонингование | ||
7 | Хонинговальная операция | Хонинговальный станок 3Б833 | Бруски АС4125/100-М1-100% | Хонингование до номинального размера | ||
8 | Контрольная операция | Контрольно-измерительные приборы |
1. 5. Выбор технологических
баз
Базовые поверхности следует выбирать с таким расчётом, чтобы при установке и замене деталь не смещалась с приданного местоположения и не деформировалась под воздействием сил резания и усилий закрепления. При выборе баз необходимо учитывать:
- по возможности выбирать те базы, которые использовались при изготовлении детали;
- базы должны иметь минимальный износ;
- базы должны быть жёстко связаны точными размерами с основными поверхностями детали, влияющими на работу в сборочной единице.
При расточке, шлифовке и хонинговании в качестве зажимного устройства используются призмы, т.е. шатун устанавливается в призмы с опорой на плоскость торцом кривошипной головки.
Рисунок 1 – схема базировния.
При обработке, для того,
чтобы лишить шатун подвижности
используют призмы и опору на плоскость
базовой поверхностью. При использовании
этой схемы обеспечивается достаточная
неподвижность детали и отсутствие
деформации при закреплении.
1.6. Выбор оборудования,
режущего и измерительного
При выборе оборудования для каждой технологической операции необходимо учитывать назначение обработки, габаритные размеры деталей, размер партии обрабатываемых деталей, расположение обрабатываемых поверхностей, требования к точности и качеству обрабатываемых поверхностей.
Для обработки деталей, восстанавливаемых гальванопокрытиями, чаще всего применяют абразивную обработку.
Для предварительного чистового растачивания используем токарный станок 1М61 с применением приспособления для центровки нижней головки шатуна. Для расточки используется расточной резец 2140-0001 ГОСТ 18882-73 с углом в плане g=60° с пластинами из твёрдого сплава Т15К16. Размеры контролируются индикаторным нутромером с ценой деления 10 мкм и пределами измерений 50¸75 мм.
После восстановления железнением
деталь подвергается абразивной обработке
до номинального размера. Для шлифования
используется токарный станок 3А228 с использованием
шлифовального круга вместо резца и приспособления
для центровки нижней головки шатуна.
При внутреннем шлифовании используют шлифовальный круг типа переключения передач диаметром 50 мм, высотой 30мм и зернистостью 40¸10, материал круга 4А20СМ28К5/ПСС4015. при контроле отверстия используется нутромер индикаторный, цена деления 10 мкм, пределы измерений 50¸100 мкм.
Дефектация деталей общего назначения » Привет Студент!
Дефектация деталей общего назначения
Цель работы:
Освоение методов дефектации деталей общего назначения
Краткие сведения о дефектации деталей
Дефектация деталей является ответственной операцией технологического процесса ремонта оборудования. Дефектация в конечном итоге оказывает существенное влияние на качество и стоимость ремонта. Она является операцией следующей обычно за разборкой и мойкой деталей.
Сборочные единицы, составные части и детали оборудования, поступающие на дефектацию должны быть чистыми и сухими.
Дефектация обычно проводится на специальном рабочем месте оборудованном необходимыми приборами, стендами, материальным инструментом.
Чтобы исключить субъективность оценок о допустимости и недопустимости дефектов, выявляемых внешним осмотром, технический отдел ремонтного предприятия или ОГМ должны отобрать для основной номенклатуры деталей и сборочных единиц образцы с допустимыми дефектами, утверждаемые начальником ОТК в качестве эталонов. Эталоны должны быть смазаны тонким слоем технического вазелина (только для эталонов из металлов), снабжены соответствующими бирками ОТК. Периодически, раз в шесть месяцев, ОТК должен контролировать состояние эталонов и при необходимости заменять их новыми. Прошедшие дефектацию детали обычно делятся на 3 группы:
— годные без ремонта, при работе в паре с деталью бывшей в эксплуатации;
— годные без ремонта при работе с новой сопряженной деталью;
— требующие ремонта;
— детали, не подлежащие ремонту и непригодные к дальнейшей эксплуатации.
Каждая группа деталей окрашивается несмываемой краской в свой цвет по принятой на предприятии схеме.
При узловом методе ремонта детали, обезличиваются за исключением некоторых деталей. Например, у двигателей и компрессоров не подлежат обезличиванию шатун и его крышка. Не подлежат обезличиванию сепараторы с роликами и кольца роликовых подшипников, конические шестерни. Отдельные сборочные единицы подлежат дефектации совместно с
деталями, соединяемыми между собой на неподвижной посадке. В этом случае разборке подлежат изделия, реставрация которых в сборе невозможна.
Основным документом, по которому осуществляется технологический процесс дефектации, является карта дефектации, где указываются возможные дефекты контролируемого изделия, способы их обнаружения и инструмент, допустимые без ремонта величины размеров и дается заключение о возможности использования детали при превышении допустимого износа. Карта дефектации составляется либо ОТМ предприятия, либо ведущим институтом отрасли.
Требования на дефектацию деталей и сборочных единиц общего назначения
Шестерни
- Состояние рабочих поверхностей зубьев контролируют осмотром, при этом не допускается:
— изломы, сколы и трещины на поверхности зуба;
— выкрашивание или сыпь на рабочей поверхности зуба;
— ступенчатая по длине выработка рабочей поверхности.
При наличии указанных дефектов шестерни следует браковать.
- Шестерни постоянно замкнутого зацепления при неравномернм износе зуба по толщине (конусности) более 0,05 мм на длине 10 мм следует браковать.
- Забоины и заусенцы на рабочих поверхностях шестерен не допускаются. Шестерни с такими дефектами следует ремонтировать.
- Шестерни, имеющие износ по толщине более допустимой нормы следует браковать или ремонтировать методом ремонтных размеров. Допустимый износ при капитальном ремонте определяется условиями работы машины и составляет до 10% (см. таблицу 5.1) от толщины зуба. Шестерни, подвергнутые закалке ТВЧ или ХТО, допускают износ на глубину не более 80% упрочненного слоя. Проверка величины износа осуществляется либо универсальным зубомером либо по шаблону.
Шкивы ременных передач
- Шкивы ременных передач подлежат выбраковке:
— при наличии трещин в ободе ступице, спицам. Трещины обнаруживают пробой на керосин или дефектоскопией, а также на звук простукиванием;
— при наличии скола ручьев длиной более 20-50 мм, в зависимости от типа ремня.
Цепи приводные роликовые
- Состояние цепей определяют осмотром и измерением величины их удлинения.
- Звенья, имеющие трещины, разрушение и деформацию деталей, нарушение посадки (проворачивание валиков и втулок в пластинах) бракуют.
- Цепи, имеющие более 50 % дефектных звеньев, бракуют.
- Износ определяют по удлинению 10 звеньев.
За результат измерения принимают полученное не менее чем на трех участках максимальное удлинение. При измерении транспортерных цепей необходимо чтобы в измеряемые участки входило не менее двух специальных звеньев, к которым крепятся несущие органы. При измерении цепь натягивают усилием 300-400 Н.
- Допустимую величину износа (удлинения) определяют по техническим условиям для данной цепи.
Например, у цепей с шагом 19,05 мм и 38 мм можно принять:
Шаг цепи 19,05 мм 38,0 мм
Длина 10 звеньев допустимая 194 мм 390 мм
Длина звеньев предельная 196 мм 395 мм
Звездочки
- Состояние звездочек контролируется осмотром, а величину износа зубьев, посадочных поверхностей, шпоночных пазов радиального и торцевого биений венцов измерением.
- Основными выбраковочными показателями звездочек является износ по толщине зуба, разрушение зуба, износ шпоночного паза.
Болты, шпильки, винты, пробки, гайки, резьба на деталях
- Поступающие на дефектацию детали с резьбой должны быть чистыми без окалины и коррозии.
- Состояние резьбы проверяют внешним осмотром и резьбовыми калибрами (пробкой резьбовой ГОСТ 17757-72 кольцом резьбовым ГОСТ 17764-72).
Вмятины, забоины, выкрашивания, вытянутость и срыв более двух ниток резьбы не допускается.
- Стержни болтов и шпилек не должны иметь изгиба и заметной выработки на головках болтов и гаек не допускается смятие граней и углов. Износ граней для размеров «под ключ» от 5,5 до 10 мм допускается не более 0,25 мм, от 12 до 17 мм не более 0,5 мм, от 13 до З0 мм не более 0,6 мм, от 32 до 50 мм не более 1 мм.
Отверстия для шплинтов в болтах и шпильках не должны быть забиты и заметно увеличены.
- При дефектации сборочных единиц исправные шпильки вывертывать из детали, не следует. Преходные посадки проверяются постукиванием; если при этом слышен дребезжащий звук следует вывернуть шпильку и восстановить посадку.
- Гайки, болты, шпильки, пробки и винты, имеющие дефекты, указанные в п. 1 и 2 следует (браковать, а резьбовые отверстия в корпусных деталях ремонтировать).
Шайбы, шайбы пружинные, пластины замковые и стопорные, шплинты
- Шайбы, шайбы стопорные, пластины, пластины замковые и стопорные при наличии трещин, надломов, глубоких задиров, смятий и деформации отверстий следует браковать.
- Шайбы пружинные при разводе концов менее полуторной толщины шайбы (нормальный развод равен двойной толщине) и заметном увеличении зазора в стыке следует браковать,
- Шплинты и шплинтовочная проволока повторному использованию не подлежат.
Цилиндрические штифты и их гнезда
При ослаблении посадки и выпадении из гнезда установочные штифты бракуются, а гнезда ремонтируются и комплектуются вновь изготовленными штифтами ремонтного размера.
Пружины сжатия и растяжения
- Пружины сжатия и растяжения дефектуют внешним осмотром и измерением. Внешним осмотром проверяют изгиб витков их поломку, наличие трещин. Измерению подвергается упругость пружины на специальном приборе ЛМН-10.
- Поломка витков, трещины не допускаются.
- При сжатии или растяжении нагрузкой оговоренной в технических условиях, на величину большую допускаемое прожиму следует браковать.
- Допускается неперпендикулярность опорных торцов пружин сжатая к ее оси не более 3 мм на длине 100 мм, и неравномерность шага витков пружины не более 20 %.
Трубопроводы, ниппеля, штуцера, угольники
- Внутренние и наружные поверхности трубопроводов систем смазки машин и систем питания двигателей должны быть чистыми. На их поверхностях не допускаются асфальто-смолистые отложения, окалины, ржавчина. На поверхностях трубопроводов горячей воды и пара не допускается отложение солей и накипи.
- Овальность в местах изгиба и вмятины на, стенках допускаются не более: при диаметре трубы от 6 до 10 мм — 2 мм, от 10 до 20 мм — 3 мм, от 20 до 40 мм — 4 мм, более 40 мм- 5 мм.
- Трубопроводы подлежат испытанию на герметичность номинальным давлением в сети сжатым воздухом в воде. Появление пузырьков воздуха не допускается.
- Ниппеля, должны свободно перемещаться по трубопроводу. Срыв резьбы на ниппеле более одной нитки и смятие граней не допускаются. На уплотняющих поверхностях трубопроводов (конуса, штуцера) не допускаются задиры, заусенцы, вмятины и деформация конуса. При наличии указанных дефектов трубопроводы подлежат ремонту.
- Стяжные хомутики подлежат выбраковке при наличии на стяжной ленте трещин надрывов и неравномерной вытянутости ленты по ширине. Уплотнительные металлические кольца штуцеров при капитальном ремонте подлежат 100 % выбраковке.
Уплотнения
- Все резиновые армированные манжеты, сальники, кольца, водочные уплотнения, картонные, поранитовые и резиновые прокладки подлежат при капитальном ремонте замене.
Примечание: На несоответственном оборудовании допускается повторное использование самоподжимных уплотнений, не имеющих рисок и заусенцев не рабочих кромках, соприкасающихся с валом, и обрывов и повреждений пружин. Там же допускается использовать повторно паронитовые прокладки, не имеющие перегибов и разрывов.
Клиновые ремни
- Состояние клиновых ремней проверяют осмотром.
- Не допускается на боковых (рабочих) поверхностях складок, трещин, выпуклостей, срывов резины, торчащих ниток и расслоения, трещин на поверхностях верхнего и нижнего оснований. При наличии указанных дефектов ремни подлежат выбраковке.
Порядок выполнения работы
- Подучить 3-5 деталей.
- Установить назначение детали.
- В соответствии с рекомендациями раздела 2 методических указаний определить, характер износа деталей.
- Заполнить карту дефектации.
- При дефектации зубчатых колес по чертежу или расчетом определить толщину колеса на высоте равной модулю.
Величину допустимого износа определить по таблице 2.
- Составить отчет по работе, который должен включать:
— цель работы;
— назначение и условия работы деталей;
— карту дефектации и ведомость дефектов;
— выводы по работе.
Материалы и инструмент
— приборы для контроля линейных размеров;
— резьбовые калибры-пробки;
— резьбовые калибры-кольца;
— зубомер;
— лупа 10х;
— прибор для контроля пружин.
Таблица 5.1 — Допустимый износ шестерен.
Режим работы |
Скорость, м/с |
Максимальный предельный износ в %к толщине зуба на высоте модуля при ремонтах |
||
малом |
среднем |
капитальном |
||
Передача мощности в 1-м направлении без ударной нагрузки |
до 2 2-5 свыше 5 |
20 15 10 |
15 10 7 |
10 8 5 |
Передача реверсивная при ударной нагрузке |
до 2 2-5 |
15 10 |
10 5 |
5 5 |
Таблица 5.2 — Форма карты дефектации.
Наименова-ние и обозначение контролируе-мой детали (сборочной единицы) и её эскиз |
Контролируемый дефект |
Размеры, мм |
Способы и средства контроля |
Заклю-чение |
||||
№ пози-ции на износе |
наиме-нова-ние |
по черте-жу |
допустимые сопряжения с деталями |
наиме-нова-ние |
обозначе-нияили погреш-ность из-мерения |
|||
бывшими в экспл. |
новы-ми |
|||||||
1 |
2 |
3 |
4 |
5 |
6 |
7 |
8 |
9 |
Примечания: 1. Для чугунных зубчатых колес приведенные с таблице данные уменьшить на 30 %.
- Для технологического оборудования хлебоприемных и хлебоперерабатывающих предприятий допустимый износ при текущем ремонте определяется как полусумма износа при среднем и малом ремонте.
Скачать: У вас нет доступа к скачиванию файлов с нашего сервера. КАК ТУТ СКАЧИВАТЬ
§ 15. Дефектовщик авиационной техники / КонсультантПлюс
6-й разряд
Характеристика работ. Дефектация технического состояния и определение вида ремонта летательных аппаратов среднего типа. Дефектация сложных и мощных газотурбинньх двигателей. Установление причин возникновения дефектов деталей, узлов, агрегатов, приборов, оборудования и систем вооружения летательных аппаратов среднего типа, выбор способов их восстановления. Проверка и настройка применяемых контрольно-измерительного инструмента, приборов и аппаратуры. Выбор способов дефектации деталей, агрегатов и систем вооружения летательных аппаратов среднего типа. Подбор взаимозаменяемых деталей по размерам, упругости, весу и частотам собственных колебаний с применением ЭВМ. Проведение контроля несъемных деталей неразрушающими методами контроля на изделии при проведении ремонта летательного аппарата. Проведение микрометрического обмера сложных и точных несъемных деталей. Заполнение карточек отказа и дефектов изделий летательных аппаратов среднего типа. Проверка формуляров двигателей. Выписка и оформление карт дефектации.
Должен знать: виды и методы ремонта авиационной техники; характерные и нехарактерные дефекты деталей летательных аппаратов среднего типа, в том числе из пластических масс и других неметаллических материалов, причины их возникновения и способы устранения; основы технологии механической обработки металлов; технологию сварочных, сборочно-клепальных и клеевых работ, правила наладки точных измерительных инструментов и приборов; оптимальные способы применения неразрушающих методов контроля деталей летательных аппаратов среднего типа; конструктивные отличия изделий летательных аппаратов среднего типа по сериям их изготовления; требования к сертифицированным изделиям летательных аппаратов среднего типа; основы механики, электротехники, электроники, радиотехники, баллистики, метрологии.
Требуется среднее профессиональное образование.
Примеры работ
1. Агрегаты и узлы управления летательного аппарата — дефектация.
2. Агрегаты топливной автоматики типа ЦИА, ИМТ, ТППО — дефектация с применением измерительных и оптических приборов повышенной точности.
3. Агрегаты топливной системы типа РСФ, насосы топливные — дефектация.
4. Аппаратура радиолокационная — проверка и дефектация.
5. Блоки электронные, электрические, механические пилотажных приборов — комплексная дефектация.
6. Бортовые вычислители — дефектация.
7. Винты воздушные, соосные — дефектация.
8. Гермовыводы управления и штурвальной колонки летательных аппаратов среднего типа — дефектация.
9. Замки шасси и грузолюков — дефектация.
10. Зеркала антенн и облучателей радиолокационной аппаратуры — проверка согласно техническим условиям.
11. Камеры сгорания — осмотр с прибором ПДК.
12. Корпусы форсажных диффузоров, жаровые трубы — дефектация.
13. Пары золотниковые, плунжеры топливных насосов — дефектация.
14. Подшипники опор турбокомпрессоров ГТД — подсчет радиальных и осевых зазоров, посадок.
15. Разъемы штепсельные — дефектация.
16. Редукторы вертолетов — дефектация.
17. Регуляторы оборотов, датчики давления масла, топлива, сигнализации — дефектация.
18. Узлы двигателей — динамическая балансировка при дефектации.
19. Устройства силовые вспомогательные, неразъемные детали ВСУ и двигателя — дефектация.
20. Центропланы, гермокабины, фюзеляжи, мотогондолы, силовые элементы конструкций планера — дефектация.
21. Электроаппаратура радиоцепей — дефектация.
Открыть полный текст документа
автореферат диссертации по процессам и машинам агроинженерных систем, 05.20.03, диссертация на тему:Совершенствование методики обоснования требований технических условий на дефектацию деталей при их ремонте
Автореферат диссертации по теме «Совершенствование методики обоснования требований технических условий на дефектацию деталей при их ремонте»
На правах рукописи
Гузёма Анатолий Борисович
Совершенствование методики обоснования требований технических условий на дефектацию деталей при их ремонте (на примере коробок передач)
Специальность 05 20 03 — Технологии и средства технического обслуживания
в сельском хозяйстве
Автореферат диссертации на соискание ученой степени кандидата технических наук
Москва 2008
003167738
Работа выполнена в Московском автомобильно-дорожном институте (государственном техническом университете)
Научный руководитель — кандидат технических наук, профессор Штоль Ю Л Официальные оппоненты — доктор технических наук, профессор Михлин В М
Ведущая организация — ФГОУ ВПО «Российский государственный аграрный заочный университет»
Защита состоится 15 мая 2008 г в 10 00 часов на заседании диссертационного совета Д 006 034 01 Государственного научного учреждения «Всероссийский научно-исследовательский технологический институт ремонта и эксплуатации машинно-тракторного парка» (ГНУ ГОСНИТИ) по адресу 109428, г Москва, 1-й Институтский пр, д 1
С диссертацией можно ознакомиться в библиотеке ГНУ ГОСНИТИ
Автореферат разослан и опубликован на сайте http //www gosniti ru 14 апреля 2008 г
— доктор технических наук, профессор Кутарев JIБ
Учёный секретарь диссертационного совета
Соловьев Р Ю
Общая характеристика работы Актуальность работы
В последнее время мобильная техника в нашей стране интенсивно обновляется новыми машинами как российского, так и зарубежного производства Со временем возникает потребность в ремонте этих машин Одним из этапов технологического процесса ремонта является дефектация, которая позволяет оценить техническое состояние деталей и агрегатов в целом Для проведения этого этапа необходимы требования технических условий (ТУ) на дефектацию Но на многие модели современных машин отсутствует выше упомянутая техническая документация, прежде всего это касается машин зарубежного производства Такая ситуация ведёт к увеличению стоимости ремонта, поскольку многие детали с незначительными износами бракуются и заменяются новыми Методика, которая существует на сегодняшний день для обоснования требований ТУ на дефектацию, базируется на сборе большого объёма статистики об гоносах рабочих поверхностей деталей в зависимости от наработки, а это занимает очень длительный период времени Под обоснованием требований ТУ на дефектацию в данной работе имеется в виду расчёт допустимых без ремонта размеров рабочих поверхностей деталей Теорией расчета допустимых без ремонта размеров занимались следующие авторы Ефремов В В , Долгополов Б П, Дехтеринский Л В, Челпан Л К, Михлин В.М и другие
Целью диссертационной работы является совершенствование методики обоснования требований ТУ на дефектацию деталей при капитальном ремонте в условиях ограниченных исходных данных
Для достижения поставленной цели в работе решались следующие задачи (на примере коробок передач грузовых автомобилей) — анализ состава и технического состояния современного автомобильного парка РФ и обеспеченности авторемонтных предприятий необходимой документацией,
— оценка существующей методики обоснования требований ТУ на дефектацию деталей с точки зрения её универсальности, простоты и достоверности,
— совершенствование методики обоснования требований ТУ на дефектацию деталей при капитальном ремонте,
— экспериментальная проверка усовершенствованной методики,
— реализация усовершенствованной методики на примере выбранного агрегата машины зарубежного производства,
— оценка эффективности усовершенствованной методики
Объектом исследования являются действующие технические условия на дефектацию деталей ряда базовых машин, а также техническое состояние деталей агрегатов (на примере коробок передач) Под базовыми машинами имеются в виду ранее выпущенные и эксплуатируемые машины, на которые есть техническая документация
Научная новизна работы состоит
— в использовании для расчёта допустимых без ремонта размеров рабочих поверхностей деталей коэффициента относительного допуска, представляющего собой отношение ремонтного допуска к производственному,
— в разработке компьютерной программы для расчёта допустимых без ремонта размеров рабочих поверхностей деталей на примере коробок передач
Практическая значимость работы состоит
— в обеспечении заводов-изготовителей и научно-исследовательских институтов усовершенствованной методикой обоснования требований ТУ на дефектацию деталей для новых машин в условиях ограниченной исходной информации Усовершенствованной методикой могут также воспользоваться ремонтные предприятия для расчёта или уточнения допустимых без ремонта размеров поверхностей деталей и параметров соединений,
— в создании компьютерной программы для расчёта допустимых без ремонта размеров рабочих поверхностей деталей коробок передач,
— в разработке и внедрении к использованию карт дефектации ряда
деталей коробки передач ZF16S151 грузового автомобиля MAN
Реализация работы. С использованием усовершенствованной методики были рассчитаны допустимые без ремонта размеры поверхностей ряда деталей коробки передач ZF16S151 грузового автомобиля MAN Также были составлены карты дефектации 19 наиболее нагруженных основных деталей этой коробки передач По разработанным картам дефектации на одном из московских ремонтных предприятий с февраля 2007 года осуществляется дефектация деталей коробок передач ZF16S151 Усовершенствованная методика практически используется на ремонтном предприятии СУПНР (Специализированное управление пуско-наладочных работ) в городе Магнитогорске
На защиту выносится
— усовершенствованная методика обоснования требований ТУ на дефектацию деталей при капитальном ремонте автомобилей,
— результаты расчётов для обоснования требований ТУ на дефектацию деталей при капитальном ремонте машин зарубежного производства,
— комплект ремонтных документов на дефектацию деталей при капитальном ремонте машин
Достоверность и обоснованность научных положений работы подтверждаются использованием современных контрольно-измерительных приборов, оборудования и инструмента, применения математической обработки опытных данных с использованием ПЭВМ, хорошей сходимостью результатов расчётов по существующей и предлагаемой методике
Апробация работы. Диссертационная работа заслушивалась и обсуждалась на заседании научно-технического семинара кафедры «Производство и ремонт автомобилей и дорожных машин» МАДИ (ГТУ), а также на заседании диссертационного совета при ПТУ ГОСНИТИ. Результаты диссертационной работы докладывались на 64-ой (2006 г), 65-ой (2007 г) и 66-ой (2008 г) научно-исследовательских конференциях МАДИ (ГТУ), а также на международной научно-технической конференции (2007 г) ГНУ
госнити
Публикации. По материалам диссертационной работы опубликовано 6 научных статей, в том числе две статьи в изданиях, рекомендуемых ВАК
Структура и объём работы. Диссертация состоит из введения, четырёх глав, основных выводов, списка литературы (75 наименований) и четырёх приложений Диссертация изложена на 143 страницах машинописного текста, содержит 25 таблиц и 48 рисунков
Содержание работы Первая глава посвящена постановке актуальности проблемы, связанной с отсутствием требований ТУ на дефекгацию деталей современных машин Первая причина заключается в том, что сейчас распалась система и структура организаций по разработке ремонтно-технической документации, а эта техническая документация является обязательной при ремонте Вторая причина заключается в том, что зарубежные фирмы, которые поставляют свои машины в Россию, не обеспечивают потребителей и дилеров всей необходимой ремонтно-технической документацией и, в частности, техническими условиями на дефекгацию Из-за отсутствия требований ТУ на дефекгацию деталей для зарубежных машин при ремонте рабочие часто вынуждены браковать детали с незначительными износами, в результате происходит недоиспользование заложенного ресурса деталей И третья причина заключается в том, что существующая методика обоснования требований ТУ на дефекгацию является слишком трудоёмкой при своей реализации
Указанные причины послужили поводом для усовершенствования методики обоснования требований ТУ на дефекгацию деталей, чтобы она обеспечивала быстроту выполнения работы при ограниченных исходных данных (отсутствие рабочих чертежей деталей, статистики об износах рабочих поверхностей деталей, нормативных пробегов агрегатов до капитального ремонта и т д)
Во второй главе производилась разработка по совершенствованию методики обоснования требований ТУ на дефектацию деталей при капитальном ремонте Самым сложным при составлении карт дефектации деталей является расчет допустимых без ремонта размеров Поэтому можно считать, что методика обоснования требований ТУ на дефектацию заключается в основном в расчёте допустимых без ремонта размеров Допустимым без ремонта размером, как известно, называется такой размер, при котором деталь считается годной для дальнейшей эксплуатации на заданную величину наработки после капитального ремонта
Согласно предлагаемой в этой работе методике рассчитать допустимый без ремонта размер поверхности детали можно с использованием так называемого коэффициента относительного допуска Ка Данный коэффициент представляет собой отношение ремонтного допуска поверхности детали к производственному
5Р
°п
По картам дефекгации деталей базовых машин можно рассчитать значения этих коэффициентов Производственный допуск поверхности детали рассчитывается как разность верхнего и нижнего отклонения номинального размера или как разность наибольшего и наименьшего предельных размеров Ремонтный допуск — это допустимая величина износа рабочей поверхности детали за определённую наработку Для вала ремонтный допуск рассчитывается как разность наибольшего предельного размера и допустимого без ремонта А для отверстия ремонтный допуск рассчитывается как разность допустимого без ремонта размера и наименьшего предельного размера Допустимые без ремонта размеры и наибольшие и наименьшие предельные размеры берутся из карт дефектации деталей базовых машин
Ремонтный допуск рабочей поверхности детали
— для вала 8р =
^наиб пред диаметр » ^доп без ремонта > ММ
— для отверстия 5Р = ‘ Ццоп бо ремонта » Окаим пред диаметр > ММ
На рис 1 показан ремонтный и производственный допуск для рабочих поверхностей деталей
1доп без ремонта
1 паям пред диаметр
[ наиб пред диаметр
бп/2
§р/2
В доп без ремонта
Р наиб, пред диаметр
Б
наим пред диаметр
5пЛ
Л2/2
Вал Отверстие
Рис 1 Ремонтные и производственные допуски рабочих поверхностей
деталей
Ниже представлены формулы для расчёта допустимых без ремонта размеров рабочих поверхностей деталей
-для вала ¿доп без ремонта ^наиб пред. диаметр » П 9 (1)
— ДЛЯ отверстия ВД0„.6И ремонта = Внанм пред диаметр + К5 ‘5П , (2)
где ¿д0пбез ремонта, Цюпби ремонта — допустимые без ремонта диаметры поверхностей деталей НОВОЙ машины, <1„аиб пред диамеп» Онаим пред диаметр -наибольший и наименьший предельные диаметры поверхности детали новой машины, К5- коэффициент относительного допуска, рассчитанный по рабочей поверхности детали базовой машины, бп — производственный допуск поверхности детали новой машины
Поскольку в технические условия на дефектацию деталей иногда вносится допустимая величина зазора в соединении, то был взят ещё один коэффициент для расчёта зазоров Данный коэффициент в этой работе был назван коэффициентом посадки Он представляет собой отношение допустимого без ремонта зазора пары деталей к максимальному зазору
Кд
_ «доп. без ремонт
1тах
где Адоп. без ремонта — допустимый без ремонта зазор пары деталей базовой машины, Дщах — максимальный зазор, рассчитанный для требуемого сопряжения
Ддоп. — максимальный зазор в соединении деталей новой машины
Чтобы рассчитать допустимые без ремонта размеры и зазоры в соединениях деталей новой машины, необходимо составить таблицы информационного поля значений коэффициентов относительного допуска и коэффициентов посадки Ниже представлен фрагмент такой таблицы на примере деталей коробки передач грузового автомобиля ЗИЛ-433102
Таблица 1
Информационное поле значений коэффициентов
Модель машины ЗШЕ-433102
№ Деталь и се рабочие поверхности Размеры, мм Коэффициенты Материал Твердость Шероховатость
1 Ведущий вал коробки передач Номинальный Допустимый без ремонта Кв Кл Сталь 25ХГМ же 60 65 Кл
1 1 Шлицевые зубья по толщине -0 025 > -0,075 5,76 2,1 1,92 Тоже То же 1,25
12 Шейха под передний шариковый подшипник -002 » -0 04 24,93 2,5 Тоже Тоже Тоже
и Отверстие под роликовый подшипник +0,027 43 98 44,06 2,962 — Тоже Тоже Тоже
14 Шейка под задний шариковый подшипник +0 023 60 +0,003 59,98 2,15 — Тоже Тоже Тоже
15 Зубья постоянного зацепления по толщине -0 10 6,95 6,5 — Тоже Тоже 1,25
2 Картер коробки передач — — — — СЧ18-36 1Ш 170 229 Ла
21 Отверстие под подшипник ведущего вала по*1’023 ш-0012 110,05 1,771 — Тоже Тоже 0,63
22 Отверстие под передний подшипник промежуточного вала 7? 72 -0 01 72,04 1,666 — Тоже Тоже Тоже
23 Отверстие под задний подшипник промежуточного вала ™ -0 012 90,05 1,771 — Тоже Тоже Тоже
24 Отверстие под подшипник ведомого вала „„+0 023 НО.0,012 110,05 1,771 — Тоже Тоже Тоже
25 Отверстие под передний конеп оси блока тпестелен заднего хода +0020 30 -0 013 30,04 1,606 1,6666 Тоже Тоже Тоже
26 Отверстие под задний конец оси блока шестерен заднего хода 32+0 039 32,06 1,538 7,5 Тоже Тоже Тоже
Чтобы рассчитать с использованием усовершенствованной методики допустимые без ремонта размеры поверхностей деталей новой машины, нужны следующие исходные данные:
1 Таблицы информационного поля значений коэффициентов,
2 Номинальные размеры и производственные допуски поверхностей деталей новой машины,
3. Марки материалов деталей новой машины,
4 Твёрдости рабочих поверхностей деталей новой машины,
5 Величины шероховатости
Таблицы информационного поля значений коэффициентов составляются на основе карт дефектации деталей базовых машин А остальные исходные данные берутся из рабочих чертежей деталей
Алгоритм расчёта допустимых без ремонта размеров и зазоров по усовершенствованной методике:
1 Выбор машины, для которой необходимо обосновать требования ТУ на дефектацию деталей при капитальном ремонте,
2 Отнесение выбранной модели машины к тому или иному классу (легковые автомобили, грузовые, автобусы, трактора и т д),
3 Подбор карт дефектации деталей при капитальном ремонте по базовым машинам Для получения достоверных результатов в классе должно быть не менее 5 машин (малая статистическая выборка начинается от пяти),
4 Составление таблиц информационного поля значений коэффициентов,
5. Расчёт допустимых без ремонта размеров рабочих поверхностей деталей и зазоров в соединениях с использованием коэффициентов относительного допуска и коэффициентов посадки с соблюдением ряда определённых условий Такими условиями являются:
1 Идентичность материалов деталей Материал новой детали, для которой рассчитываются допустимые без ремонта размеры, должен быть точно таким же или близким по твёрдости и шероховатости рабочих
поверхностей, как и у аналогичных деталей базовых машин, по которым определялись коэффициенты относительного допуска В зависимости от материалов деталей новой машины и базовой выбираются различные значения коэффициентов для дальнейшего расчёта допустимых без ремонта размеров.
2 Одинаковые природно-климатические условия эксплуатации Согласно усовершенствованной методике машина, для которой разрабатываются требования ТУ на дефектацию деталей, должна эксплуатироваться в тех же природно-климатических условиях, как и те базовые машины, по картам дефектации деталей которых рассчитывались коэффициенты относительного допуска и коэффициенты посадки То есть если нужно обосновать требования ТУ на дефектацию деталей для машины, эксплуатация которой предполагается, к примеру, на территории Германии, то нужно рассчитать коэффициенты относительного допуска и посадки по рабочим поверхностям деталей базовых машин, которые эксплуатировались в Германии
3 Соответствие классов машин Если производится обоснование требования ТУ на дефектацию деталей для новой машины, то нужно использовать коэффициенты относительного допуска рабочих поверхностей деталей ранее выпущенных машин того же класса, так как это упрощает расчёты и повышает точность в том же классе То есть если нужно обосновать требования ТУ на дефектацию деталей, к примеру, для нового трактора, то соответственно нужно определить коэффициенты относительного допуска поверхностей деталей ряда тракторов различных моделей, на которые имеются требования ТУ на дефектацию
Для расчёта с использованием усовершенствованной методики допустимых без ремонта размеров поверхностей деталей коробок передач была написана специальная компьютерная программа Чтобы рассчитать допустимый без ремонта размер поверхности детали, нужно в программу ввести номинальный размер поверхности новой детали с производственным
допуском и марку материала детали
Усовершенствованная методика может также использоваться и для обоснования требований ТУ на дефектацию деталей при текущем ремонте Для этого необходимо определить коэффициенты относительного допуска и посадки на основе карт дефектации деталей при текущем ремонте
Третья глава посвящена экспериментальной проверке усовершенствованной методики Чтобы проверить достоверность методики, для поверхностей ряда деталей были рассчитаны допустимые без ремонта размеры по усовершенствованной и ныне существующей методике И в заключении полученные результаты сравнивались между собой Расчёт допустимых без ремонта размеров производился для рабочих поверхностей трёх деталей коробки передач ЯМЭ-238 — это первичный вал и шестерни второй и пятой передач вторичного вала Чтобы рассчитать допустимые без ремонта размеры по существующей методике, необходим сбор статистических данных об износах рабочих поверхностей деталей в зависимости от наработки На предприятии ЗАО «АиР» в процессе дефектации деталей коробок передач ЯМЭ-238 производились измерения рабочих поверхностей исследуемых деталей, фиксировались пробеги коробок передач, поступающих в ремонт, и отмечались характерные дефекты рабочих поверхностей Объём выборки исследуемых деталей составлял 100 единиц На основе этих данных были построены гистограммы оценочных контролируемых параметров, подобраны теоретические законы распределения, построены характеристики изнашивания рабочих поверхностей и рассчитаны предельные размеры рабочих поверхностей исследуемых деталей На рис 2 представлена в качестве примера построенная характеристика изнашивания зуба по толщине шестерни второй передачи вторичного вала Зуб по толщине измерялся штангензубомером на определённой высоте, которая указана в карте дефектации шестерни
-1-1-1-1-1-1-1 » |-1-1 ^ |«*|>-1-
0 25 50 75 100 125 150 175 200 225 250 275 300 325 350 375
Б доп. Шейка 24,94 24,93 0,04
й 1 Шлицы по толщине 5,78 5,80 0,52
2 ! я е в в м 1 2 Зубья по толщине 6,26 6,28 0,32
||§ В И 1 3 в Отверстие под подшипник 78,05 78,07 0,025
Шестерня пятой передачи вторичного вала Зубья по толщине 8,23 8,21 0,24
3 Отверстие под подшипник 68,05 68,07 0,029
Расхождение рассчитанных размеров по существующей и усовершенствованной методике составляет от одной до двух сотых миллиметра, что соответствует точности изготовления этих деталей Таким образом, усовершенствованная в этой работе методика является достоверной
Для опытной проверки методики были собраны коробки передач ЯМЗ-238 (30 пггук) С использованием усовершенствованной методики были рассчитаны допустимые без ремонта размеры, и по этим размерам были отдефектованы детали коробок передач, поступивших в капитальный ремонт После сборки эти агрегаты установили на грузовые автомобили МАЗ Эксплуатируемые коробки передач имеют наработку около 40 тыс км и находятся в исправном техническом состоянии Средний остаточный ресурс 30 эксплуатируемых коробок передач ЯМЭ-238, имеющих уже наработку
около 40 тыс. \ ……. 2 з \ iffiu 6 \ Ёк
Деталь: Первичный вал
№ Детали 81.32205-0267
Материал: Сталь типа 18ХГ Твёрдость: 60…62 HRC
II Наименование дефектов Способ установления дефекта и измерительные инструменты Размеры, мм Заключение
t * Is о Наименьший предельный и наибольший предельный Допустимый без ремонта
1 Сколы зубьев Осмотр — — Браковать
2 Износ шейки под шестерню постоянного зацепления Микрометр 75-100 мм 99,97-99,98 99,94 Ремонтировать, Хромирование. Железнение.
3 Износ шейки под подшипник в картере сцепления Микрометр 75-100 лш 85,05-85,06 85,02 То же
4 Износ шлицов по толщине Штантегоубомер 7,75-7,76 7,70 Браковать при размере менее 7,70 мм
5 Износ шейки под подшипник маховика Микрометр 0-25 мм 24,97-24,98 24,94 Ремонтировать. Хромирование. Железнение.
6 Износ отверстая под подшипник вторичного вала Нутромер 50-100 мм 82,04-82,05 82,08 Браковать при размере более 82,08 мм
Рис. 3. Карта дефектации первичного вала коробки передач ZF16S151.
На одном из московских ремонтных предприятий с февраля 2007 года по разработанным картам дефектации осуществляется техническая оценка деталей коробок передач 2П68151
Усовершенствованная методика практически используется на ремонтном предприятии СУПНР (Специализированное управление пуско-наладочных работ) в городе Магнитогорске Данное предприятие производит капитальный ремонт дорожно-строительной техники зарубежного производства
Усовершенствованная методика используется в учебном процессе кафедры ПРАДМ института МАДИ (ГТУ)
Целесообразность использования усовершенствованной методики подтверждается экономическим расчётом на примере коробки передач 7$ 168151 Для научно-исследовательского института стоимость расчёта допустимых без ремонта размеров рабочих поверхностей всех деталей коробки передач по существующей методике составляет 417 тыс руб, а по усовершенствованной методике стоимость расчёта составляет 105 тыс руб, что в 4 раза дешевле Снижение стоимости достигается за счёт значительного уменьшения трудоёмкости работы (при расчёте допустимых без ремонта размеров с использованием усовершенствованной методики не требуется длительный сбор статистических данных об износах рабочих поверхностей деталей в зависимости от наработки) Экономия от использования усовершенствованной методики взамен существующей только на одной коробке передач составляет 312 тыс руб
ОБЩИЕ ВЫВОДЫ 1 Произведено совершенствование методики расчёта допустимых без ремонта размеров и зазоров при текущем и капитальном ремонте новых машин с учётом коэффициента относительного допуска и коэффициента посадки
2 Разработана компьютерная программа по расчёту допустимых без ремонта размеров рабочих поверхностей основных деталей на примере коробок передач, которая позволяет сокращать время по расчёту на 20 — 30%
3 Произведена экспериментальная проверка предложенной методики по сравнению с существующей Полученные допустимые без ремонта размеры различаются между собой не более чем на один процент Расхождение рассчитанных размеров по существующей и предлагаемой методике составляет от одной до двух сотых миллиметра, что соответствует точности изготовления этих деталей
4 По предложенной методике были рассчитаны допустимые без ремонта размеры поверхностей ряда деталей зарубежной коробки передач ZF16S151, также составлены карты дефектации 19 наиболее нагруженных, основных деталей этой коробки передач, которые сейчас используются на ремонтном предприятии
5 Полученные результаты работы используются в ремонтном производстве По разработанным картам дефектации деталей на одном из московских ремонтных предприятий осуществляется техническая оценка деталей коробок передач ZF16S151 грузовых автомобилей MAN Усовершенствованная методика практически используется на ремонтном предприятии СУПНР (Специализированное управление пуско-наладочных работ) в городе Магнитогорске Данное предприятие производит ремонт дорожно-строительной техники зарубежного производства
6 Экономическая эффективность усовершенствованной методики подтверждается в условиях реального производства Стоимость расчёта допустимых без ремонта размеров рабочих поверхностей деталей коробки передач ZF16S151 по предлагаемой методике в 4 раза меньше, чем по существующей
Основные положения диссертации изложены в научных журналах, рекомендуемых ВАК:
1. Гузёма А Б Оценка технического состояния коробок передач ЯМЗ-236, 238 — М Грузовое и пассажирское автохозяйство, 2006, №9, с 59-63
2 Гузёма А Б Новый подход к обоснованию требований технических условий на дефектацию -М Автотранспортное предприятие, 2007, №5, с 3640
Публикации в других изданиях:
1 Долгополов БП, Гузёма А Б Ремонт автомобилей с учётом требований технических условий — М Грузовик, 2006, №7, с 26-28.
2 Гузёма А Б Предельное состояние шестерен в коробке передач ЯМЗ -М Техника и технология, 2006, №4, с 16-21
3 Гузёма А Б, Штоль Ю Л Как рассчитать размеры, по которым дефектуют детали при капитальном ремонте — М Автомобиль и сервис, 2008, №1, с 42-43
4 Гузёма А Б, Штоль Ю Л Расчет — это просто — М Новости авторемонта, 2008, №3, с 70-74
Отпечатано в ООО «Компания Спутник+» ПД № 1-00007 от 25.09.2000 г. Подписано в печать 31.03.08 Тираж 100 экз. Уел пл. 1,13 Печать авторефератов (495) 730-47-74,778-45-60
Дефектация и сортировка деталей (Реферат)
Дефектация и сортировка деталей
1. Детали автомобиля после мойки и очистки от загрязнений в соответствии с технологическим процессом подвергаются дефектации, т. е. контролю с целью обнаружения дефектов. Под дефектами детали понимают всякие отклонения ее параметров от величин, установленных техническими условиями или рабочим чертежом.
Основными задачами дефектации и сортировки деталей являются: контроль деталей для определения их технического состояния; сортировка деталей на три группы: годные для дальнейшего использования, подлежащие восстановлению и негодные; накопление информации о результатах дефектации и сортировки с целью использования ее при совершенствовании технологических процессов и для определения коэффициентов годности, сменности и восстановления деталей; сортировка деталей по маршрутам восстановления.
Работы по дефектации и сортировке деталей оказывают большое влияние на эффективность авторемонтного производства, а также на качество и надежность отремонтированных автомобилей. Поэтому дефектацию и сортировку деталей следует производить в строгом соответствии с техническими условиями.
Отступление от технических условий может привести к снижению качества и повышению стоимости ремонта автомобилей. Увеличение количества повторно используемых деталей позволяет снизить себестоимость ремонта, однако применение на сборке деталей с отклонениями от технических условий ухудшает показатели качества отремонтированных автомобилей.
Дефектацию деталей производят путем их внешнего осмотра, а также с помощью специального инструмента, приспособлений, приборов и оборудования.
Результаты дефектации и сортировки фиксируют путем маркировки деталей краской. При этом зеленой краской отмечают годные для дальнейшего использования детали, красной — негодные, желтой — требующие восстановления. Количественные показатели дефектации и сортировки деталей фиксируют также в дефектовочных ведомостях или при помощи специальных суммирующих счетных устройств. Эти данные после статистической обработки позволяют определять или корректировать коэффициенты годности, сменности и восстановления деталей.
Годные детали после дефектации направляются на комплектовочный участок предприятия и далее на сборку агрегатов и автомобилей, а негодные — на склад утиля. Детали, требующие восстановления, после определения маршрута ремонта поступают на склад деталей, ожидающих ремонта, и далее на соответствующие участки восстановления.
1. Методы контроля
В целях экономии времени при дефектации деталей придерживаются следующего порядка. Сначала производят внешний осмотр деталей с целью обнаружения повреждений, видимых невооруженным глазом: крупных трещин, пробоин, изломов, задиров, рисок, коррозии и т. п. Затем детали проверяют на специальных приспособлениях для обнаружения дефектов, связанных с нарушением взаимного расположения рабочих поверхностей и физико-механических свойств материала деталей. После этого детали контролируют на отсутствие скрытых дефектов (невидимых трещин и внутренних пороков). В заключение производят контроль размеров и геометрической формы рабочих поверхностей деталей.
Контроль взаимного расположения рабочих поверхностей. Методы контроля погрешностей взаимного расположения рабочих поверхностей рассмотрим на примере деталей класса валов и корпусных деталей. В деталях класса валов наиболее часто контролируют несоосность шеек и неперпендикулярность фланцев к оси валов.
Контроль несоосности шеек валов производят путем замера их радиального биения с помощью индикатора. Контролируемый вал при этом устанавливают в центрах. Величина радиального биения шеек определяется как разность наибольшего и наименьшего показаний индикатора за один оборот вала.
Контроль неперпендикулярности фланца к оси вала производят также при установке вала в центрах. При помощи индикатора замеряют торцевое биение фланца на определенном радиусе R.
В корпусных деталях контролируют следующие погрешности взаимного расположения поверхностей: несоосность отверстий, непараллельность оси отверстий относительно плоскости, непараллельность осей отверстий и нарушение межцентрового расстояния, неперпендикулярность осей отверстий, неперпендикулярность оси отверстия к плоскости.
Контроль несоосности отверстий в корпусных деталях производят с помощью оптических, пневматических и индикаторных приспособлений. Наибольшее применение в авторемонтном производстве нашли индикаторные приспособления. Приспособление состоит из контрольной оправки, втулок и индикатора часового типа. При проверке несоосности вращают втулку с индикатором и замеряют величину радиального биения. Радиальное биение покажет удвоенную величину несоосности (смещения осей). Несоосность отверстий контролируют в блоках цилиндров двигателей, картерах коробок передач, картерах редукторов и других деталях.
Контроль межцентрового расстояния и непараллельности осей отверстий производят путем измерения расстояний а1 и а2 между внутренними образующими контрольных оправок при помощи штихмаса или индикаторного нутромера
Межцентровое расстояние определяют расчетом по формуле
А = а1 и а2 + d1 + d2
2 2
где d1 и d2 — диаметры контрольных оправок.
Непараллельность осей отверстий определяют как разность замеров а1—а2 на длине L.
Контроль неперпендикулярности осей отверстий производят при помощи оправки с индикатором или калибром путем измерения зазоров ∆1 и ∆2 на длине L. Величина неперпендикулярности осей в первом случае определяется как разность показаний индикатора в двух противоположных положениях, а во втором — как разность зазоров.
Контроль неперпендикулярности оси отверстий к плоскости можно выполнить при помощи индикаторного приспособления или специального калибра. В первом случае неперпендикулярность оси отверстия к торцевой плоскости на диаметре Д определяют как разность показаний индикатора при вращении его относительно оси отверстия, во втором случае — измерением зазоров в двух диаметрально противоположных точках по периферии контрольного диска. Величина неперпендикулярности в этом случае будет равна разности зазоров ∆1—∆2 на диаметре Д.
Контроль нарушения физико-механических свойств материала деталей. Нарушение физико-механических свойств материала деталей может проявляться в виде изменения твердости детали или ее жесткости. Изменение жесткости может иметь место в таких деталях, как рессоры и пружины.
Нарушение твердости контролируют с помощью универсальных приборов для измерения твердости.
дефектация сортировка деталь
2. Контроль скрытых дефектов
При контроле деталей очень важно проверять их на наличие скрытых дефектов (поверхностных и внутренних трещин). Этот контроль особенно необходим для деталей, от которых зависит безопасность движения автомобиля.
Существует большое количество различных методов обнаружения скрытых дефектов на деталях. В авторемонтном производстве нашли применение следующие методы: опрессовки, красок, люминесцентный, намагничивания, ультразвуковой.
Метод опрессовки применяют для обнаружения скрытых дефектов в полых деталях. Опрессовку деталей производят водой (гидравлический метод) и сжатым воздухом (пневматический метод).
Метод гидравлического испытания применяют для выявления трещин в корпусных деталях (блок и головка цилиндров). Испытание производится на специальных стендах, которые обеспечивают герметизацию всех отверстий в контролируемых деталях. При испытании полость детали заполняют горячей водой под давлением 0,3.. .0,4 МПа. О наличии трещин судят по подтеканию воды.
Метод пневматического испытания применяют при контроле на герметичность таких деталей, как радиаторы, баки, трубопроводы и др. Полость детали в этом случае заполняют сжатым воздухом под давлением, соответствующим техническим условиям на испытание, и затем погружают в ванну с водой. Выходящие из трещины пузырьки воздуха укажут место нахождения дефектов.
Все, что вам нужно знать о визуальном осмотре с AI
Как машинное зрение и глубокое обучение меняют сферу автоматизированного контроля на производстве.
Искусственный интеллект меняет правила игры, предлагая бесчисленное множество приложений почти во всех сферах. Теперь он пробивается в области производства и производства, позволяя использовать возможности глубокого обучения и тем самым обеспечивая автоматизацию, которая работает быстрее, дешевле и лучше.Эта статья призвана дать краткое представление об автоматической визуальной оценке и о том, как подход глубокого обучения может значительно сэкономить время и усилия.
Что такое визуальный осмотр?
Выявление дефектов с использованием технологии автоматизированного визуального контроляОн включает в себя анализ продукции на производственной линии с целью контроля качества. Визуальный осмотр также может использоваться для внутренней и внешней оценки различного оборудования на производственном объекте, такого как резервуары для хранения, сосуды под давлением, трубопроводы и другое оборудование.
Классификация компонентов печатной платы (Источник: Radiant Vision Systems)Это процесс, который происходит через определенные промежутки времени, например, изо дня в день. Неоднократно было показано, что визуальный осмотр приводит к обнаружению большинства скрытых дефектов в процессе производства.
Когда и где нужен визуальный осмотр?
В то время как визуальный осмотр используется на производстве для оценки качества или дефектов, в непроизводственной среде его можно использовать для определения наличия признаков, указывающих на «цель», и предотвращения потенциальных негативных воздействий.
Некоторые сценарии, при которых необходим визуальный осмотр. Отрасли, использующие визуальный осмотр. (источник: NECAM)Среди многих отраслей, где требуется визуальный осмотр, есть несколько, где визуальный осмотр считается очень серьезным и высокоприоритетным мероприятием из-за потенциально высокой стоимости любых ошибок, которые могут возникнуть в результате осмотра, например в виде травм, смертельного исхода, потери дорогостоящего оборудования, бракованного оборудования, переделки или потери клиентов. Области, в которых визуальный осмотр является приоритетным, включают ядерное оружие, ядерную энергетику, досмотр багажа в аэропортах, техническое обслуживание самолетов, пищевую промышленность, медицину и фармацевтику.
Разбивка отраслей с использованием визуального контроляПочему бы просто не придерживаться ручного контроля?
Хотя старый может быть золотом, можно утверждать, что есть несколько ограничений на использование старомодного способа проверки.
Ручная проверка требует присутствия лица, инспектора, который проводит оценку рассматриваемого объекта и выносит по нему заключение в соответствии с некоторой подготовкой или предыдущими знаниями. Никакого оборудования не требуется, кроме невооруженного глаза обученного инспектора.
Согласно исследованиям, ошибки визуального контроля обычно составляют от 20% до 30% (Drury & Fox, 1975). Некоторые недостатки можно отнести на счет ошибки человека, а другие — из-за нехватки места. Некоторые ошибки можно уменьшить с помощью обучения и практики, но нельзя полностью устранить.
Инспекционный процесс. (Источник: Роль визуального контроля в 21 веке (See & Drury, 2017) Факторы, влияющие на эффективность проверкиОшибки при визуальном контроле при производстве принимают одну из двух форм — отсутствие существующего дефекта или неправильное определение несуществующего дефекта (ложь положительный).Пропуски, как правило, происходят гораздо чаще, чем ложные срабатывания (см. 2012 г.). Промахи могут привести к снижению качества, а ложные срабатывания могут привести к ненужным производственным затратам и общим потерям.
Ограничения ручного осмотраКроме того, ручной осмотр страдает и другими ограничениями, такими как эти
- Остается факт, что человеческий глаз, хотя и более технологически продвинутый, чем любая механическая камера, также может быть легко обманут. Рассмотрим некоторые из этих недостатков, связанных с визуальным осмотром:
Одно человеческое зрение ненадежно. — Оптические иллюзии, подобные тем, что слева, могут продемонстрировать, насколько ненадежным может быть человеческий глаз. Это не обязательно означает, что ручная проверка совершенно бесполезна, но было бы неразумно полностью полагаться на нее.
Кажется, что параллельные линии имеют наклон.Неточность зрения — Человеческий глаз неспособен производить точные измерения, особенно в очень маленьком масштабе. Даже сравнивая два похожих объекта, глаз может не заметить, что один немного меньше или больше другого.Эта концепция также применима к таким характеристикам, как шероховатость поверхности, размер и любой другой фактор, который необходимо измерить.
Стоимость рабочей силы — Ручной осмотр остается дорогостоящим мероприятием из-за назначения (нескольких) обученных специалистов. С точки зрения затрат операторы, выполняющие ручную инспекцию, могут получать годовую зарплату от 50 000 до 60 000 долларов.
Источник: GlassdoorАльтернатива новой эпохи
Автоматизированный визуальный осмотр может преодолеть эти проблемы, сделав всю процедуру визуального осмотра независимой от какого-либо участия человека.Использование автоматизированных систем обычно превосходит стандарт ручной проверки.
Источник: Digital TwinsИспользование глубокого обучения и машинного зрения не только возможно, но и вполне достижимо для создания интеллектуальных систем, которые проводят тщательную проверку качества до мельчайших деталей. Нам не нужны ходячие говорящие роботы-андроиды, чтобы автоматизировать производство, например инспекцию. Минимальное физическое оборудование необходимо для автоматизации процесса визуального контроля. Вместо этого процесс становится умнее за счет использования глубокого обучения.Этот подход обычно включает в себя такие шаги, как получение изображения, предварительная обработка, извлечение признаков, классификация и т. Д. Это также относится к распознаванию изображений широкой группы.
Что такое глубокое обучение и как оно влияет?
Технология глубокого обучения использует нейронные сети, содержащие тысячи слоев, которые способны имитировать человеческий уровень интеллекта, чтобы различать аномалии, части и символы, допуская естественные вариации в сложных образцах. Таким образом, глубокое обучение объединяет адаптируемость визуального контроля человека со скоростью и надежностью компьютеризированной системы.
Глубокое обучение учит машины делать то, что естественно для людей: учиться на собственном примере. Новое дешевое оборудование сделало практичным развертывание многослойных «глубоких» нейронных сетей, имитирующих нейронные сети в человеческом мозгу. Это дает производственным технологиям удивительные новые возможности распознавать изображения, различать тенденции и делать разумные прогнозы и решения. Начиная с базовой логики, разработанной во время начального обучения, глубокие нейронные сети могут постоянно улучшать свою производительность, поскольку им предоставляются новые изображения, речь и текст.
Послойная разбивка процедуры глубокого обучения (Источник)Так что же тогда такое машинное зрение?
Машинное зрение — это технология и методы, используемые для автоматического контроля на основе изображений. Это система, которая использует технологию визуальных вычислений для механического «наблюдения» за действиями, которые происходят одно за другим на производственной линии. Компоненты автоматической системы контроля обычно включают в себя освещение, камеру или другое устройство для получения изображения, процессор, программное обеспечение и устройства вывода.
Машинное зрение превосходит человеческое зрение в количественном и качественном измерении структурированной сцены благодаря своей скорости, точности и воспроизводимости. Система машинного зрения может легко оценить детали объекта, слишком мелкие, чтобы их мог увидеть человеческий глаз, и исследовать их с большей надежностью и меньшими ошибками. На производственной линии системы машинного зрения могут надежно и многократно проверять сотни или тысячи деталей в минуту, что намного превышает возможности проверки людьми.
Оптическое распознавание символов (слева) и обнаружение дефектов (справа) — общие аспекты машинного зрения в AVI. Традиционная автоматизированная система, в то время как минимизация затрат и повышение эффективности не обладают гибкостью или допуском к вариациям, которые делают люди. Инспекторы, работающие вручную, могут различать незначительные, косметические и функциональные недостатки и могут интерпретировать изменения внешнего вида деталей, которые могут повлиять на воспринимаемое качество. Хотя скорость обработки информации ограничена, люди обладают уникальной способностью концептуализировать и обобщать.Люди преуспевают в обучении на примере и могут различать, что действительно важно, когда дело доходит до небольших аномалий между частями. Возникает вопрос о том, как машинное зрение может во многих случаях сделать лучший выбор для качественной интерпретации сложной неструктурированной сцены, особенно с небольшими дефектами и непредсказуемыми изъянами.
Почему машинное зрение и глубокое обучение идут рука об руку в этом сценарии
Хотя системы машинного зрения допускают некоторые отклонения во внешнем виде детали из-за масштабирования, поворота и искажения позы, сложные текстуры поверхности и проблемы с качеством изображения вызывают серьезную проверку проблемы.Сами по себе системы машинного зрения не способны оценить огромную возможность вариаций и отклонений между очень похожими визуально изображениями.
Источник: CognexСистемы на основе глубокого обучения хорошо подходят для более сложных по своей природе визуальных проверок: шаблоны, которые различаются тонкими, но приемлемыми способами. Глубокое обучение помогает устранять сложные поверхностные и косметические дефекты, такие как царапины и вмятины на точеных, отшлифованных или блестящих деталях. Анализ изображений на основе глубокого обучения отличается от традиционного машинного зрения способностью концептуализировать и обобщать внешний вид детали.
Сложные ситуации, которые можно эффективно решить с помощью глубокого обучения (Источник: Cognex)И это еще не все
Вот еще несколько причин выбрать автоматизированный визуальный контроль, когда дело доходит до производства:
Лучшее восприятие
Машинное зрение имеет очень высокое оптическое разрешение, которое зависит от технологии и оборудования, используемого для получения изображений.
По сравнению с человеческим зрением, машинное зрение имеет «более широкий» спектр визуального восприятия с возможностью проводить наблюдения в ультрафиолетовой, рентгеновской и инфракрасной областях спектра.
Быстрее — Наблюдения и выводы делаются очень быстро, со скоростью компьютера, измеряемой в FLOP, а также они приводят к точным вычислениям.
Система обладает всеми возможностями, связанными с более высокими скоростями обработки, а также потенциально неограниченным объемом памяти.
Надежность — Система беспристрастна и программируется по мере необходимости, без вопросов следуя инструкциям.
Accurate — Автоматизированная система способна измерять абсолютные размеры стандартизированным способом.
Независимо от окружающей среды — Такая система может быть развернута в опасных и опасных условиях или средах, где участие человека может оказаться рискованным.
Как начать работу с автоматизированной визуальной проверкой
С точки зрения требований, AVI не требует большого количества физического оборудования. Оборудование, необходимое для запуска автоматизации визуального контроля, можно разделить на аппаратных ресурсов и программных ресурсов.
Аппаратное обеспечение
Эти ресурсы включают основное оборудование, такое как камера, фотометр, колориметр и дополнительное вторичное оборудование, необходимое для сортировки или сортировки, которое будет зависеть от отрасли и процессов автоматизации.
Мы, по сути, фотографируем и анализируем изображение, камера — это все, что вам нужно!
В зависимости от отрасли, в которой оно используется, физическое оборудование можно фактически разделить на три подсистемы
- Система подачи — равномерно распределяет предметы и перемещает их с постоянной скоростью, чтобы оптическая система могла захватывать кадры отдельных предметов.
- Оптическая система — Состоит из специально настроенного источника освещения и датчика (обычно цифровой камеры).Оптическая система фиксирует изображения проверенных предметов, чтобы программное обеспечение могло их обрабатывать и анализировать.
- Система разделения — Удаляет дефектные элементы и / или сорта и разделяет продукты на несколько категорий в соответствии с их качеством.
Программное обеспечение
Основным требованием к AVI является уровень программного обеспечения, в основе которого лежит технология компьютерного зрения, которая помогает проверять продукты или любой интересующий объект на предмет дефектов и отсутствия / наличия определенных частей.
Программная часть автоматизированной системы визуального контроля требует сложных алгоритмов анализа изображений и сложного программирования. Эти алгоритмы обрабатывают изображения, чтобы настроить их качество, найти интересные точки и области и, наконец, принять решение на основе особенностей, обнаруженных в этих регионах.
Технологии глубокого обучения позволили автоматизировать системы визуального контроля, которые превосходят человеческие или традиционные процессы машинного зрения.
Модели глубокого обучения оказались незаменимой частью программного обеспечения благодаря огромному успеху, который они продемонстрировали в решении задач контроля.Их можно обучить на тысячах изображений, скажем, болтов, алгоритм глубокого обучения постепенно учится обнаруживать любые значимые отклонения от «стандартного» внешнего вида болта. В зависимости от вашего варианта использования ваша проблема проверки может быть решена с помощью одной или комбинации различных задач, таких как обнаружение объектов, семантическая сегментация и классификация изображений. Он также может включать модели OCR для чтения серийных номеров или штрих-кодов.
Чтобы поддерживать высокую скорость обработки изображений, обученная модель глубокого обучения обычно должна быть развернута на компьютерах с высокими ресурсами.Например, для получения результатов в реальном времени необходим графический процессор.
Несколько факторов играют роль в результирующей точности и производительности модели проверки — условия освещения, количество продуктов для проверки, типы дефектов, которые необходимо искать, размер дефектов / объектов, разрешение изображения, чтобы назвать немного. Таким образом, для автоматизированной системы визуального контроля требуется команда опытных инженеров-исследователей, способных создавать такие сложные системы.
Каждая производственная единица имеет разные и часто уникальные данные (изображения) — это может быть из-за другого типа камеры, внутреннего освещения или самого продукта.Поэтому программная часть AVI — это всегда индивидуальное решение, адаптированное к конкретным потребностям проверки.
Nanonets помогает создавать и развертывать модели глубокого обучения, необходимые для разработки программного обеспечения для автоматизации визуального контроля.
Эксперименты с новой неизведанной областью для улучшения бизнеса требуют эффективной команды с многолетним опытом и проверенной репутацией в области построения. решения для глубокого обучения для бизнеса.
При обучении моделей глубокого обучения необходимо учитывать множество других факторов, например, как вы собираетесь предварительно обработать данные, определить модель и получить компьютер, достаточно мощный для запуска модели.
Nanonets предоставляет простые в использовании API-интерфейсы для обучения и развертывания моделей глубокого обучения, адаптированных к конкретным потребностям бизнеса. Он берет на себя всю тяжелую работу, необходимую для создания готовой к производству высокоточной модели — увеличение данных, трансферное обучение и, да, оптимизацию гиперпараметров!
Найдя лучшую модель, Nanonets предоставляет ее в своем облаке, чтобы вы могли протестировать модель с помощью своего веб-интерфейса или интегрировать ее в свою программу с помощью двух строк кода.Nanonets также предоставляет образы Docker, содержащие обученную модель, которая позволяет вам развертывать модели на ваших собственных машинах — это означает, что ваши данные / изображения никогда не должны покидать ваше помещение / локальную сеть.
Вот некоторые типичные варианты использования наносет:
• Продукты для контроля качества перед тем, как они покинут производственную линию
• Оценка качества урожая
• Проверка страховых требований
• Осмотр деталей на предмет дефектов на производственной линии
• Выявление и выявить дефекты инженерной инфраструктуры
Хотите автоматизировать визуальный осмотр? лень писать код, не хочешь тратиться на графические процессоры? Отправляйтесь в Nanonets и начните строить свою модель бесплатно!
Что мы можем извлечь из всего этого?
Искусственный интеллект уже произвел революцию в нашей повседневной жизни здесь и сейчас.От поиска в Google по изображению до сложных промышленных систем, обеспечивающих качество продукции — машинное зрение облегчает нашу жизнь при выполнении самых простых и сложных задач. И возможно, что очень скоро задачи визуального контроля качества будут в основном машинными, что позволит людям сосредоточиться на более сложных задачах.
По мере того как технологии становятся все более распространенным явлением, стоимость систем искусственного интеллекта постоянно снижается, в то время как эффективность растет без остановки для дыхания. Текущая тенденция в автоматизации в промышленном секторе породила тему, известную как Индустрия 4.0, который включает киберфизические системы, Интернет вещей, облачные вычисления и когнитивные вычисления. Индустрию 4.0 обычно называют четвертой промышленной революцией.
Автоматизация будет играть решающую роль в так называемой «Индустрии 4.0». (Источник: ООН)Индустрия 4.0 способствует тому, что называют «умной фабрикой». В рамках умных фабрик с модульной структурой киберфизические системы отслеживают физические процессы, создают виртуальную копию физического мира и принимают децентрализованные решения.Через Интернет вещей киберфизические системы обмениваются данными и взаимодействуют друг с другом и с людьми в режиме реального времени как внутри организации, так и в рамках услуг организации, предлагаемых и используемых участниками цепочки создания стоимости.
Нет сомнений в том, что машинное зрение и глубокое обучение станут неотъемлемой частью этой промышленной революции, которая выведет мировых производителей на новый уровень эффективности и производительности.
Создайте свои собственные модели визуального осмотра сегодня!
Учить больше
Возможно, вас заинтересуют наши последние сообщения на:
(PDF) Система реального времени для автоматического обнаружения дефектов поверхности холодной полосы
FME Transactions VOL.47, No 4, 2019 ▪ 773
наука Российской Федерации, постановление Правительства
№ 2.7905.2017 и № 8.9694.2017.
В данном исследовании использовались ресурсы суперкомпьютера
Южно-Уральского государственного университета [32].
СПИСОК ЛИТЕРАТУРЫ
[1] Baindorf, I., Anstots, T., Eberle, A., Ernenpuch, L.
Holzhauser J .: Оптимизация процесса и качества
коррозионностойкой системы 9000 черных систем на базе 4 Встретились., Vol. 3, pp.
45–56, 2005.
[2] Лимон, С .: Автоматический осмотр поверхности
полосы для обеспечения второго контроля
качества в линии, Черные мет., Vol. 4, pp. 49–54,
2003.
[3] Stolzenberg, M., Gruber, K., Henkenmayer, H. и
Joncourt, K .: Система осмотра поверхности листовой
сталь: Результаты исследований, Черные мет., Т.
12, стр. 40–48, 2002.
[4] Ветошкин Н., Валкевич Н., Костенецкий П .:
Разработка пользовательского интерфейса для системы
автоматического контроля качества поверхности
листовой стали с покрытием, 2018- 400.
[5] Калеб П. и Штойер М .: Классификация поверхностных дефектов
горячекатаной стали с использованием методов адаптивного обучения
, в: KES’2000. Четвертая международная конференция
по интеллектуальным технологиям, основанным на знаниях
Технические системы и смежные технологии.
Proceedings, (Cat. No. 00TH8516), 2000, Vol. 1,
с. 103–108.
[6] Guifang Wu, Hoonsung Kwak, Seyoung Jang, Ke
Xu и Jinwu Xu: Проектирование онлайн-системы контроля поверхности
горячекатаных полос, в: 2008
Международная конференция IEEE по автоматизации и
Логистика , 2008, стр. 2291–2295.
[7] Masci, J., Meier, U., Ciresan, D., Schmidhuber, J.
и Fricout, G .: Классификация стальных дефектов с использованием сверточных нейронных сетей
Max-Pooling, in:
The 2012 Международная совместная конференция по нейронным сетям
(IJCNN), 2012, стр.1–6.
[8] Попат М. и Бараи С. В. Обнаружение дефектов и классификация
с использованием классификатора машинного обучения.
[9] Неоги, Н., Моханта, Д. К. и Датта, П. К .:
Обзор систем визуального контроля стальных поверхностей
, EURASIP — J. Image Video Process., Vol.
2014, вып. 1, стр. 50, декабрь 2014.
[10] Навицкас В., Кузнецова С.В. Грузаускас: Cyber-
Выражение физических систем в Индустрии 4.0 Conte-
xt — Финансово-кредитная деятельность: проблемы теории и практики. т.5, вып. 23, стр. 188–197, 2017.
[11] Санфеличе Р.Г.: Анализ и проектирование Cyber-
Физические системы: гибридные системы управления
Подход— Киберфизические системы: от теории
к практике, с. 3–31, 2015.
[12] Ранков В., Локк Р.Дж., Иденс Р.Дж., Барбер, PR
и Войнович Б.: Алгоритм сшивания изображений
и смешивания — SPIE Newsroom, Vol. 5701, No.
March, pp. 190–199, 2005.
[13] Gupta S.и Мазумдар, С.Г .: Sobel Edge
Алгоритм обнаружения — Int. J. Comput. Sci. Manag.
Res., Vol. 2, No. 2, pp. 1578–1583, 2013.
[14] Сентилкумаран Н., Вайтеги С.: Image Segmen-
tation by using Thresholding Techniques for Me-
dical Images — Comput. Sci. Англ. Int. J., Vol. 6,
No. 1, pp. 1–13, 2016.
[15] Chudasama, D .: Image Segmentation using Morp-
hological Operations — Int. J. Comput. Прил., Vol.
117, № 18, стр. 16–19, 2015.
[16] Йованович, Р. Э., Сретенович, А.А.: Ансамбль
радиальных базисных нейронных сетейс кластерами K-средних —
для прогноз потребления тепловой энергии —
FME Trans., Vol. 45, pp. 51–57, 2017.
[17] Парк, К., Вон, С .: Автоматизированная проверка поверхности полотна
для катанки горячего электрода с использованием недецимации
вейвлет-преобразования и машины опорных векторов, in:
2009 35-я ежегодная конференция IEEE Industrial
Electronics, 2009, стр.2411–2415.
[18] Хунбинь Цзя, Мерфи, Ю.Л., Цзинаджун Ши, Цзы-
Шу Чанг: интеллектуальная система технического зрения в реальном времени
для обнаружения поверхностных дефектов, в: Труды
17-й Международной конференции по распознаванию образов.
nition, 2004. ICPR 2004, 2004, p. 239–242 Т. 3.
[19] Ghorai, S., Mukherjee, A., Gangadaran, M. и
Dutta, P.K .: Автоматическое обнаружение дефектов горячекатаного плоского стального проката
, IEEE Trans.- Instrum.
Измер., Об. 62, No. 3, pp. 612–621, март 2013 г.
[20] Цзе Чжао, Юнминь Ян и Гэ Ли: Холодная
проверка дефектов поверхности прокатной полосы в режиме онлайн
Система, основанная на машинном зрении, in: 2010 Вторая
Азиатско-Тихоокеанская конференция по схемам, Коммуникация
катионов и систем, 2010, стр. 402–405.
[21] Бацуури, С., Ан, Дж. И Ко, Дж .: Обнаружение и классификация дефектов стальной поверхности
с использованием SIFT и стратегии голосования
, — Int.J. Softw. Англ. Его приложение, Vol.
6, 2012.
[22] Беттин, Ф., Амедда, Х. и Манаа, Р .: Подход нейронной сети
для прогнозирования кинематических ошибок
Решения для трохоидальной обработки на станке Matsuura
MX-330 пятиосевой станок, — FME Trans., Vol. 46,
pp. 453–462, 2018.
[23] Yazdchi, MR, Mahyari, AG and Nazeri, A .:
Обнаружение и классификация поверхностных дефектов стали
для холодной прокатки с использованием морфологии иНейронная сеть, в: 2008 International Conference
on Computational Intelligence for Modeling
Control & Automation, 2008, pp.1071–1076.
[24] Сонг, К. и Юньхуи, Ю.: Поверхностный дефект NEU
, база данных. [Онлайн]. Доступно: http: //faculty.neu.
edu.cn/yunhyan/NEU_surface_defect_database.htm
л. [Доступ: 01 февраля 2018 г.].
[25] LeCun, Y., Bengio, Y. и Hinton, G .: Deep
Learning, — Nature, Vol. 521, No. 7553, pp. 436–
444, May 2015.
[26] Крижевский, А., Суцкевер, И. и Хинтон, GE:
Классификация ImageNet с глубокими сверточными нейронными сетями
, — Commun. .ACM, Vol. 60, No. 6,
pp. 84–90, May 2017.
Defect Detection Accelerated Application
Defect Detection Accelerated ApplicationВы используете устаревший браузер. Xilinx больше не поддерживает Internet Explorer.
Приложение ускоренного обнаружения дефектов — это приложение машинного зрения, которое автоматизирует обнаружение дефектов (например,g., фрукты, печатные платы) и сортировку в высокоскоростных производственных конвейерах с использованием функций библиотеки Vitis Vision.
Характеристики:
- Конвейер обнаружения дефектов с малой задержкой
- Обнаружение дефектов и сортировка фруктов
- Выход HDMI или DisplayPort
- Программируемые пользователем функции библиотеки Vitis Vision
- Полное приложение с аппаратным обеспечением
Дополнительные инструменты и ресурсы
Часто задаваемые вопросы
Вам нужен опыт проектирования FPGA для этого приложения?
Нет, приложение не требует опыта проектирования FPGA.
Какие варианты лицензирования доступны?
Это приложение бесплатно от Xilinx.
Проверялось ли приложение для других датчиков?
Нет, приложение оптимизировано и протестировано для OnSemi AR0144.Чтобы адаптировать приложение для другого датчика, вам необходимо обновить дизайн и оптимизировать приложение для нового датчика.
Ускорьте ваше пограничное решение с поддержкой AI с помощью Adaptive Computing
Знакомство с адаптивной системой на модулях
Узнайте все об адаптивных SOM, включая примеры того, почему и как они могут быть развернуты в пограничных приложениях следующего поколения, и как поставщики интеллектуального машинного зрения извлекают выгоду из производительности, гибкости и быстрой разработки, которые могут быть достигнуты только с помощью адаптивного SOM.
Дефекты продукта и производительность
Многие люди по эту сторону океана с зевотой встретили шумиху по поводу чудесных достижений Японии в производстве за последнее десятилетие. «Так что же тут нового?» они говорят. «Деминг сказал это много лет назад». У. Эдвардс Деминг — если не настоящий отец, то крестный отец продуктивности растений.Он в основном отвечал за внедрение на заводах процедур статистического контроля, которые так ловко переняли японцы. В этой статье описывается подход Деминга к производительности и качеству: поскольку только руководство имеет право изменять производственную систему для их устранения, дефекты продукции являются ответственностью руководства.
Чтобы изменить систему, руководство сначала должно отличить ненормальное от нормального отклонения. Также необходимо оперативно указать, что должна производить система.Имея эти средства контроля, организация может прогнозировать производительность, затраты и уровни качества, а менеджеры могут эффективно общаться с клиентами и людьми в цехе. И это наиболее важно, поскольку, когда руководство видит причину проблем в системе, а не в рабочих, исчезают многие из подрывающих моральный дух результатов плохих решений, целей, в которые никто не верит, и мотивирующих лозунгов, косвенно обвиняющих рабочих.
Джон Генри, президент Global Manufacturing Company, откинулся на спинку стула, вздохнул и уставился в потолок.На столе перед ним лежал отчет двух статистиков о проблемах производительности и качества на фабрике Global’s Nightingale.
Генри и его вице-президенты знали, что дела идут плохо. Клиенты жаловались, цены были слишком высокими, дебиторская задолженность росла, звонки на ремонт росли, затраты росли, моральный дух рабочих падал, а профсоюз грозил забастовкой из-за непрекращающихся требований руководства к повышению производительности. Кроме того, большинство машин было не для работы.Но они не договорились, с сожалением подумал Генри, о том, что найдут статистики. Он взял отчет, вздохнул в другой раз и снова посмотрел на него.
«Ваша фабрика в Nightingale, — говорится в отчете, — работает изо дня в день, отправляя товары, 15% из которых (в среднем) имеют один или несколько серьезных дефектов … Эта доля серьезных дефектов в вашем продукте вполне может объяснить некоторые из ваших проблем с продажами и прибылью. Количество переделок, которые операторы должны выполнять на производственной линии, также снижает вашу прибыль.
«Так начинаются ваши проблемы. Оператор на линии превращает элемент. Она смотрит на это. Если она обнаружит серьезный дефект, она может исправить его сама, потому что знает, что в противном случае он может вернуться к ней позже, чтобы исправить. Но, думает она, инспектор, возможно, не заметит этот дефект. Если она это сделает, она может переделать его или отправить обратно оператору. Но даже если инспектор увидит это, супервайзер может перехватить предмет на обратном пути к оператору и отправить его на производство, чтобы избежать короткого замыкания на более позднем этапе производства.
«Почему бы с точки зрения оператора не рискнуть и с мелкими, и с серьезными дефектами? Отправьте их по очереди; скорее всего, они не вернутся. С точки зрения инспектора, руководитель может вмешаться, поэтому исправление дефектов может быть пустой тратой времени. С точки зрения руководителя, она может рискнуть дефектом. Она не может проиграть и может выиграть, если будет поддерживать рекорд производительности.
«Другими словами, мистер Генри, работа вашего оператора — устранять дефекты. Ей платят за них.Это система, и оператор не несет за нее ответственности. Управление есть ».
Суть записки статистиков бедному Джону Генри заключается в том, что дефектов не бесплатны: кто-то делает дефекты и получает деньги за их изготовление. Если значительная часть рабочей силы исправляет дефекты, то компания платит как за исправление дефектов, так и за их устранение. Если фабрика Nightingale производит 15% бракованной продукции, то 15% от общей стоимости тратится на изготовление дефектных единиц.Очевидно, что низкое качество означает высокую стоимость.
Все проблемы Генри и его вице-президентов возникли из-за неправильного управления качеством. Другими словами, и это может быть вторым моментом для статистиков, менеджмент обеспечивает получение высококачественного продукта за счет совершенствования процесса. Если менеджеры смогут улучшить производственный процесс, они смогут перенаправить ресурсы с производства дефектных продуктов на производство дополнительных хороших продуктов.
Предположим, что руководство компании Nightingale способно улучшить процесс, внеся некоторые изменения без дополнительных затрат, так что только 9% выходных данных являются дефектными.Чего удалось достичь менеджменту?
1. Производительность повысилась. Теперь фабрика производит на 6% больше единиц по той же цене. (Если завод исправляет дефекты, то операторы могут использовать время, которое они потратили бы на переработку 6% дефектов, чтобы сделать более качественный продукт. Это дает дополнительное — бесплатное — повышение производительности.)
2. Совокупное качество улучшилось. Теперь неисправно только 9% продукции вместо 15%.
3. Емкость увеличилась. Завод производит на 6% больше хороших единиц с той же системой — рабочая сила, машины, материалы и так далее.
4. Стоимость единицы ниже. Фабрика производит больше единиц по той же цене.
5. Цену можно снизить.
Видно, что контроль процесса (то есть надлежащее управление качеством) может облегчить проблемы Джона Генри. С повышением качества клиенты перестанут жаловаться, и возврат упадет, продавцы смогут эффективно конкурировать за счет более качественного продукта и более низкой цены, количество обращений за обслуживанием и ремонтом снизится, дебиторская задолженность снизится (поскольку, скорее всего, довольные клиенты будут платить по счетам), расходы снизятся, производительность повысится, профсоюз перестанет угрожать забастовкой, а у руководства появится капитал для надлежащего обслуживания оборудования.
Улучшение процесса — ключ к повышению производительности и качества, а также к снижению затрат на единицу продукции. Менеджеры могут достичь этих целей, понимая источники вариаций в процессе и используя соответствующие операционные определения.
Источники вариаций
Давайте посмотрим на производственный процесс, при котором производятся стальные стержни. Хотя средний диаметр стержней составляет 2,00 дюйма, мы не можем ожидать, что диаметр каждого стержня будет точно таким. Мы ожидаем некоторых вариаций в зависимости от того, как округлить результат измерения.
Изменения в процессе естественны. Фактически, мы все должны этого ожидать и не удивляться, когда это произойдет. Но процессы подвержены двум источникам вариаций: нормальным и ненормальным. Ненормальные отклонения возникают по особой или конкретной причине и могут присутствовать или не присутствовать в процессе. В нашем примере предположим, что мы производим стержень диаметром 1,96 дюйма. Несоответствие 0,04 дюйма является ненормальным изменением процесса? Или это нормальный вариант, которого мы должны ожидать? Если это ненормальное изменение, мы хотели бы вмешаться и, скажем, отрегулировать машину.Если это не так, нам не следует вмешиваться. Фактически, регулируя машину без причины, мы рискуем вывести процесс из строя.
По оценкам некоторых исследователей, аномальные отклонения вызывают 15% проблем в процессе, а нормальные отклонения вызывают оставшиеся 85%. 1 Нормальные вариации присущи всем элементам процесса — целой группе рабочих, целому отделу и даже целой компании — и создают большую часть высоких затрат на производство и обслуживание и проблемы с низкой производительностью.Путаница между общими и частными причинами вариаций приводит к разочарованию на всех уровнях, большему разнообразию и более высоким затратам. Не имея возможности различить два источника отклонений, руководство может отреагировать, обвиняя рабочих.
Рабочий бессилен устранить обычную причину изменения. У рабочих нет полномочий уточнять определения и тесты, определяющие приемлемое качество. Они мало что могут сделать с вышедшими из строя машинами или испытательным оборудованием. Они могут сообщать о таких событиях, но руководство должно следить за ними и вносить необходимые изменения.Рабочие также не могут изменять спецификации и политику закупки входящих материалов, и они не несут ответственности за дизайн продукта. Все они являются частью системы, и только менеджеры могут изменять систему.
Трудно переоценить, насколько высок моральный дух на большинстве заводов, если бы руководство возлагало на рабочих ответственность только за то, что они могли контролировать, а не за недостатки системы.
Что это за вариация?
Поскольку работники не могут нести ответственность за систему, менеджеры должны уметь различать ненормальные и нормальные отклонения, чтобы они знали, когда и как изменить процесс.Единственный безопасный способ различить два источника вариаций в процессе — использовать статистические сигналы, генерируемые контрольными диаграммами.
Контрольные карты
Контрольная диаграмма системы имеет центральную линию, которая представляет собой среднее значение процесса, и два контрольных предела, верхний и нижний. Предположим, вы хотите изучить операцию перфорирования клавиш в отделе обработки данных. Во-первых, согласно статистической теории, вы определяете размер выборки, скажем, 200 карточек в день. 2 Затем вы берете случайные выборки из 200 карточек из ежедневных выходных документов и проверяете их на наличие ошибок.На рисунке I показано, как построить контрольную диаграмму для операции нажатия клавиш.
Приложение I Формулировка контрольной диаграммы для работы с клавиатурой Примечание. Обе точки (день 8 и день 22), расположенные над UCL, посылают статистический сигнал руководству для поиска возможных источников аномальных колебаний в день 8 и день 22.
Приложение Ia показывает процент дефектных перфокарт. Приложение Ib представляет собой график зависимости «процента дефектных изделий» (столбец 4 в Ia) от «дня» (столбец 1 в Ia). Приложение Ic показывает вычисления, которые потребуются вам для построения центральной линии (в этом примере средний процент дефектов для процесса), а также верхнего и нижнего контрольных пределов.
Вы создаете контрольную диаграмму (идентификатор приложения) , соединив точки, нанесенные на график в Ib, и проведя через эти точки центральную линию, а также верхний и нижний контрольные пределы. Наконец, вы анализируете контрольную диаграмму. Если значение выборки попадает в верхний и нижний контрольные пределы и если тренд или какой-либо другой систематический образец отсутствует, вариация, вероятно, нормальная.Если, однако, значение выборки выходит за контрольные пределы, вероятно, отклонение ненормально.
Диаграмма, показанная на Приложении I, является лишь одним из многих видов контрольных диаграмм, каждая из которых имеет особое назначение. (Примеры других графиков вы можете найти в источниках, перечисленных в конце статьи.)
Если отклонение ненормальное
Сравнивая Ib и Id, читатель увидит, насколько сложно невооруженным глазом различить две причины вариации.Приложение Ib не позволяет менеджерам различать два источника отклонений, в то время как Exhibit Id ясно показывает, что в дни 8 и 22 произошло что-то ненормальное, не связанное с системой, что привело к перфорации дефектных карт.
Когда менеджер определяет, что причина отклонения является ненормальной, он должен искать и устранять причины, связанные с конкретным рабочим или группой рабочих, машиной, новой партией сырья и т. Д. Как только руководство устраняет все приписываемые причины отклонений, остается стабильный процесс, находящийся под статистическим контролем.
Давайте еще раз рассмотрим операцию перфорирования клавиш, показанную на Приложении I. Посмотрите на контрольную диаграмму процент карточек с ошибками (Id).
Принято основывать контрольные пределы на кратной стандартной ошибке. Обычно это кратное 3, и пределы называются пределами 3-сигма. Это означает, что есть приблизительно 3 шанса из 1000, что расположение точки вне пределов обусловлено естественным случайным изменением системы. Если мы посмотрим на графики в Приложениях I и II, мы увидим, что две точки находятся за пределами верхнего контрольного предела, что указывает на то, что процесс не находится в статистическом контроле.
Exhibit II Control Charts для клавишных перфораторов
Каким должен быть следующий шаг менеджменту? Чтобы взять процесс под контроль, руководство должно исследовать моменты, которые вышли из-под контроля, чтобы удалить из процесса назначаемые причины отклонений. Предположим, что руководство обнаружило, что на 8-й день к персоналу был добавлен новый оператор клавишного ввода, и что один день, который потребовался работнику, чтобы привыкнуть к новой среде, вероятно, вызвал необычно большое количество ошибок набора клавиш.Чтобы гарантировать, что эта назначаемая причина не повторится, компания ввела однодневную программу обучения.
Расследование дня 22 показало, что накануне вечером в отделе закончились карточки от обычного продавца, и он не ожидал новой поставки до утра 23 дня. Следовательно, отдел закупил однодневный запас карточек у нового поставщика. . Руководство обнаружило, что эти карты были низкого качества, что приводило к большому количеству ошибок при перфорации клавиш. Чтобы исправить это назначаемое отклонение, руководство ввело пересмотренную политику инвентаризации и оперативно определило приемлемое качество перфокарт.
После исключения дней, для которых были обнаружены приписываемые причины отклонений, менеджеры пересчитали статистику контрольной диаграммы:
Приложение IIb показывает исправленную контрольную диаграмму (IIa показывает исходную диаграмму). Теперь процесс стабилен, находится под статистическим контролем.
Стабильный процесс, который демонстрирует только вариации из-за внутренних ограничений системы, позволяет менеджеру определить его возможности, то есть то, что является нормальным. Вот некоторые из преимуществ достижения стабильного процесса:
1.Руководство знает возможности процесса и может спрогнозировать его производительность, затраты и уровни качества.
2. При существующей системе производительность максимальна, а затраты минимальны.
3. Руководство может измерять влияние изменений в системе с большей скоростью и надежностью.
4. Если руководство хочет изменить пределы спецификации, у него есть данные для резервного копирования своего аргумента.
Возможности процесса становятся данностью. Стабильный процесс, который приводит к недопустимому количеству дефектов, будет продолжать работать до тех пор, пока система, как она определена в настоящее время, остается прежней.И только руководство несет ответственность за изменение системы.
Нормальное изменение
Как только процесс достигает стабильности, что является не естественным состоянием, а достижением, руководство готово воздействовать на систему для повышения производительности и качества. Менеджеры могут улучшить систему:
1. Смещение среднего значения процесса. Например, руководство может захотеть уменьшить процент дефектов или увеличить средний результат.
2. Изменение степени вариации.Учитывая экономические требования рынка, руководство может захотеть уменьшить количество вариаций, чтобы получить более стабильно однородный продукт, или увеличить его, чтобы получить менее однородный продукт.
Определенные входные данные и процедуры, такие как труд, обучение, надзор, сырье, машины и рабочие определения, определяют систему. Чтобы улучшить систему, руководство должно изменить эти факторы. Мы снова подчеркиваем, что только руководство несет ответственность и имеет право вносить эти изменения.Сами по себе рабочие не могут повлиять на систему.
Как руководство может изменить процесс ввода клавиш для повышения производительности и качества? Внедряя процедуры обучения, которые снижают средний процент дефектных карточек и количество общих отклонений (что приводит к более узким контрольным пределам), руководство может помочь сотрудникам последовательно выпускать больше безошибочных карточек.
Приложение IIc показывает новую контрольную диаграмму после того, как руководство ввело обучение и процедурные изменения.Средний процент перфокарт с ошибками снизился с 0,017 до 0,008, а также уменьшились вариации процесса.
Важно подчеркнуть, что обсуждаемые нами концепции охватывают не только контрольные диаграммы. Компании могут использовать контрольные карты без какого-либо понимания подхода, который нас интересует, а именно ответственности руководства за улучшение системы, отсутствия привычной зависимости от окончательной проверки, исключения лозунгов, устранения произвольных стандартов работы и так далее.
Круг замкнулся. Мы знаем, что улучшение процесса увеличивает производительность и качество. Различая аномальные и нормальные отклонения и устраняя аномальные отклонения, менеджеры могут получить статистический контроль. Но одного этого недостаточно для повышения производительности и качества.
Если бы руководство полностью понимало источники отклонений, а также осознавало свою ответственность за улучшение процесса, но не понимало операционных определений, его усилия все равно были бы напрасными.
Что производится?
Если руководство не может точно определить свои продукты, как оно может их продать, описать, чего оно хочет, людям в цеху или улучшить производственный процесс? Не может. Без операционного определения люди не могут вести бизнес. Вот пример путаницы, которую может вызвать отсутствие точного представления о том, что производится:
«Этикетка на одеяле гласит« 50% шерсть ». Что это означает? Полушерсть в среднем поверх этого одеяла или полушерсть за месяц производства? Что такое полушерсть? Половина по весу? Если да, то при какой влажности? Каким методом химического анализа? Сколько анализов? Нижняя половина одеяла шерстяная, а верхняя — что-то другое? Это 50% шерсть? Означает ли 50 процентов шерсти, что в любом случайном сечении должно быть немного шерсти размером в полдоллара? Если да, то сколько разрезов следует проверить? Как вы их выбираете? Какому критерию должно удовлетворять среднее значение? И насколько допустимы отклонения между разрезами? Очевидно, что значение 50% шерсти можно определить только в статистических терминах.” 3
Каково точное или истинное определение термина? Например, что такое «точно круглый»? Не существует единого определения, которое помогло бы нам определить, действительно ли что-то круглое. Словарь тоже не поможет. Вебстер говорит, что фигура является круглой, если у нее «каждая часть поверхности или окружности равноудалена от центра». Это определение очень полезно для формальной логики, но если мы попытаемся использовать его, чтобы определить, круглый ли наш диск, мы столкнемся с непреодолимой трудностью. Словарь дает понятие, а не определение для использования в промышленности.
Как тогда мы можем определить термин, понятный на уровне магазина? Операционные определения бывают двух типов: одно для атрибутов, например, успех или неудача, и другое для переменных, например, объема продаж. Рабочее определение атрибута состоит из:
1. Критерий, применяемый к объекту или группе.
2. Процедура выбора исследуемого объекта.
3. Операция, например измерение или наблюдение за объектом.
4.Запись результата.
5. Тест объекта на соответствие критерию.
6. Решение «да» или «нет» относительно того, соответствует ли объект критерию.
Чтобы получить операционное определение переменной, менеджеры предпримут те же первые четыре шага, которые они предприняли для получения определения атрибута. (Шаги 5 и 6 для атрибутов не применяются к переменным.)
Теперь возникает вопрос: какое значение имеют операционные определения для производительности компании? Мы знаем, насколько важно, чтобы производители и пользователи понимали друг друга.Без рабочих определений спецификация бессмысленна. Конфликты и путаница между компаниями и между отделами компании возникают из-за того, что менеджеры не могут заранее в значимых терминах указать спецификации элемента или его характеристики. Подумайте о проблемах производительности и качества, которые могут возникнуть, когда инспектор, ответственный за обнаружение дефектов, со временем не согласуется в своих суждениях или когда инспекторы несовместимы друг с другом. Рабочие не знают, что приемлемо, а что нет.Им нужно оперативное определение бракованного продукта.
Допустим, мы производим круглые диски. Диски круглые? Почему нас это волнует? Если диск слишком далек от круглой формы, это приведет к заклиниванию машины клиента, повреждению оборудования и простоям. Если мы хотим оставаться в бизнесе, о нас лучше заботиться.
Запишем рабочее определение раунда для диска. Поскольку мы измеряем атрибут (округление или не округление), мы будем работать над первым типом операционного определения.
Шаг 1: Сначала мы хотим вывести критерий для объекта.
а. «Используйте штангенциркуль в достаточно хорошем состоянии». (Вы сразу чувствуете необходимость подвергать сомнению каждое слово.)
«Что такое« достаточно хороший порядок »?» (Мы решаем вопрос, позволяя вам пользоваться штангенциркулем.)
«Но как мне их использовать?»
«Мы будем довольны, если вы будете использовать их как обычно».
«При какой температуре?»
«Температура в этой комнате.”
г. «Возьмите 6 мерок диаметром примерно 30 градусов друг от друга. Запишите результаты ».
«Но что такое« примерно 30 градусов друг от друга »? Разве вы не имеете в виду ровно 30 градусов? »
«Нет, в физическом мире не бывает ровно 30 градусов. Так что попробуйте на 30 градусов; мы будем довольны ».
г. Если диапазон между 6 диаметрами не превышает 0,007 сантиметра, мы объявляем диск круглым. Мы определились с критерием.
Шаг 2: Давайте выберем конкретный диск.(На этом этапе мы могли бы указать некоторую схему выборки.)
Шаги 3 и 4: Выполните измерения и запишите результаты в сантиметрах — 3,365, 3,363, 3,368, 3,366, 3,366 и 3,369.
Шаг 5: Диапазон составляет от 3,369 до 3,363, или 0,006 разницы. Мы проверяем соответствие, сравнивая диапазон 0,006 с диапазоном критерия меньше или равным 0,007 (из шага 1).
Шаг 6: Поскольку диск прошел предписанный тест на округлость, мы объявляем его круглым.
Если в компании есть работники, которые понимают, что означает раунд, и заказчик, который соглашается, проблемы, которые могли возникнуть у компании, чтобы удовлетворить клиента, исчезнут.
Давайте посмотрим на другой пример, где операционные определения улучшают понимание внутри компании. В этом примере мы измеряем переменную (продажи), поэтому мы используем второй тип операционного определения.
Продавцу говорят, что о ее работе будут судить по проценту изменения продаж в этом году по сравнению с продажами в прошлом году.Что это значит? Среднее процентное изменение каждый месяц? Каждую неделю? Каждый день? Для каждого продукта? Процентное изменение продаж с 31 декабря 1980 г. по 31 декабря 1981 г.?
Как мы измеряем продажи: валовую, чистую, валовую прибыль, чистую прибыль и т. Д.? Процентное изменение выражено в постоянных или завышенных долларах? Если это в постоянных долларах, каков базовый год? Если оно в завышенных долларах, то по ценам прошлого года или этого года? В каких экономических условиях?
Расплывчатое определение процентного изменения может привести только к путанице, разочарованию и недоброжелательности между менеджментом и продавцами — вряд ли способ повысить производительность.Как руководство должно оперативно определять процентное изменение продаж?
Шаг 1: Процентное изменение продаж — это разница между продажами 1981 г. (с 1 января 1981 г. по 31 декабря 1981 г.) и продажами 1980 г. (с 1 января 1980 г. по 31 декабря 1980 г.), деленная на объем продаж 1980 г .:
S80 измеряется в постоянных долларах с 1979 г. в качестве базового года с использованием цен на 15 июня 1979 г. и 15 июня 1980 г. для получения постоянных долларовых цен и общего объема продаж единицы продукции за вычетом прибыли (по любой причине) по состоянию на 31 декабря. 1980 для каждого продукта.
S81 измеряется в постоянных долларах с 1979 г. в качестве базового года с использованием цен на 15 июня 1979 г. и 15 июня 1981 г. для получения постоянных долларовых цен и общего объема продаж единицы продукции за вычетом прибыли (по любой причине) по состоянию на 31 декабря 1981 г. для каждого продукта. (Pi79 остается неизменным для всех продуктов.)
Эта процедура для расчета процентного изменения продаж в период с 1980 по 1981 год будет действовать независимо от экономических условий. Кроме того, руководство может пересмотреть определение процентного изменения продаж после оценки продаж 1985 года, но не раньше, если торговый персонал и руководство продаж не согласятся.
Шаг 2: Продавец и ее записи о продажах являются объектом исследования.
Шаги 3 и 4: Менеджер по продажам будет использовать все счета-фактуры за 1980 и 1981 годы и квитанции о продажах, чтобы вычислить чистое количество единиц, проданных для каждого продукта в 1980 и 1981 годах. Менеджер по продажам будет записывать вычисления и результаты.
Предыдущее определение продаж может не подходить другому менеджеру или продавцу; однако, если менеджер по продажам принимает его, а продавцы понимают его, это операционное определение.
Операционные определения нетривиальны. Если руководство не определит многие критические переменные и атрибуты так, чтобы их согласовали и работники, и клиенты, последуют серьезные проблемы. Контрольная диаграмма становится бесполезным управленческим инструментом из-за совершенно нового источника вариаций: вариаций измерения. Оперативное определение характеристик, отображаемых на карте, является обязанностью руководства. Если инспекторы не соглашаются друг с другом или с самими собой изо дня в день, разовьется хаос.Рабочие не знают, чего от них ждут. Их вывод подходит для Инспектора 1, но не для Инспектора 2; работа сотрудника могла быть сдана инспектором 1 вчера, но не сегодня.
Должность высшего руководства
Ряд людей недавно написали руководящие принципы, которые говорят руководству, что ему следует делать для повышения производительности:
Создайте организацию с постоянной целью и долгосрочными обязательствами высшего руководства.
Разрушайте барьеры между отделами.
Создайте среду, в которой люди не боятся сообщать о проблемах.
Обезвредить встроенные уровни дефектов, ошибок, некачественных материалов и т. Д.
Не вините рабочих в проблемах производительности и качества.
Читатель, несомненно, знаком с ними. Однако из изложенного здесь подхода вытекают дополнительные руководящие принципы, которые могут быть не столь очевидными.
1. Не ждите, что проверка решит проблему качества. К моменту проведения проверки товар уже годен или неисправен. Вы не можете проверить качество продукта.
Массовая проверка не позволяет четко отделить хорошие предметы от плохих. Лучшим способом является наблюдение за небольшими образцами продукта для контрольных диаграмм для достижения или поддержания статистического контроля. Таким образом менеджеры могут избавиться от необходимости инспектировать и использовать таланты инспекторов для других целей. Продавцы и покупатели также могли сравнить свои инструменты и тесты; продавцы и покупатели могли начать говорить на одном языке.Осмотр под давлением часто оказывается фарсом: идет он или уходит, все проходит. А поскольку разделение ответственности означает, что никто не несет ответственности, 200% проверка менее надежна, чем 100% проверка.
2. В соответствии с политикой, прекратите предоставлять бизнес лицу, предложившему самую низкую цену. Без оценки качества покупаемого товара цена не имеет значения.
Чтобы судить о качестве, менеджерам по закупкам требуется образование и опыт в оценке статистических свидетельств качества.Если покупатели станут экспертами в оценке качества, большинство из них резко сократит количество поставщиков, с которыми они имеют дело. Поставщик, который не знает ни своих затрат, ни того, сможет ли он повторить сегодняшнее распределение качества завтра, не является хорошим деловым партнером.
3. Избавьтесь от целей, числовых целей, лозунгов («ноль дефектов»), изображений и плакатов, которые руководители так часто наклеивают на предприятиях, призывая людей повышать производительность. К сожалению, такие программы «повышения производительности» оставляют дефекты там, где они есть.Они не выявляют и не исправляют неисправности системы, а также не предоставляют менеджерам статистических сигналов, которые необходимы для принятия корректирующих действий. Они не отвечают на важный вопрос: «Как мы можем повысить производительность?»
4. Устранение квот на работу. Рабочие квоты не учитывают обычные изменения в системе. Они не включают способ обнаружения необходимости в корректирующих действиях или способ возложить ответственность на руководство или на представителя руководства на линии. Например, менеджер банка может определить количество клиентов, которые, по его мнению, кассир должен обработать за час, количество вычислений процентов и штрафов, которые кто-то должен вычислить за час, и аналогичный показатель для всех остальных действий.Однако стандарты ничего не говорят о качестве работы и не дают руководителю возможности понять различия в процессе. Стандарты не указывают, какие действия следует предпринять менеджерам или как улучшить процесс.
5. Разработайте учебные программы по статистике, чтобы менеджеры и руководители могли понять, как управлять качеством. Надзор является частью системы и, разумеется, является обязанностью руководства. Статистические методы являются жизненно важными помощниками для мастеров и руководителей производства в выявлении причин потерь, низкой производительности и низкого качества.Менеджеры также могут использовать их, чтобы определить, когда сотрудники полностью обучены и когда поможет дальнейшее обучение.
• • •
Настоящее руководство указывает, что высшее руководство должно делать для повышения производительности и качества. Хотя следование каждому из руководящих принципов не принесет ощутимых результатов, в то же время компания, начавшая сегодня с полной отдачей, вскоре добьется впечатляющих результатов.
Ближайшая секунда для быстрых результатов — это избавление от страха, помощь людям в безопасности и преодоление страха сообщать о проблемах с оборудованием или с поступающими материалами.Менеджеры могут достичь этой цели за два-три года и получить серьезные экономические результаты.
1. См., Например, Джозеф М. Джуран, Справочник по контролю качества , 3-е изд. (Нью-Йорк: McGraw-Hill, 1974).
2. Обсуждение того, как вычислить размер выборки, можно найти в многочисленных текстах, некоторые из которых мы перечислили в конце статьи.
3. У. Эдвардс Деминг, Качество, производительность и экономическое положение (Кембридж: Центр перспективных разработок Массачусетского технологического института, 1982 г.).
Версия этой статьи появилась в выпуске Harvard Business Review за сентябрь 1983 г.% PDF-1.5 % 1 0 объект > / Метаданные 2 0 R / Контуры 3 0 R / PageLayout / OneColumn / Страницы 4 0 R / StructTreeRoot 5 0 R / Тип / Каталог >> эндобдж 6 0 obj > эндобдж 2 0 obj > транслировать 2019-03-04T23: 24: 13 + 02: 002019-03-04T23: 24: 04 + 02: 002019-03-04T23: 24: 13 + 02: 00Acrobat PDFMaker 11 для Worduuid: 5474a108-b0c5-4021-90e6- 86f7febe64eduuid: 7382d56a-5a06-486d-941c-b18bac8e411f
Исследование алгоритма обнаружения дефектов изолятора ЛЭП на базе CenterNet
Реферат
От надежности изолятора напрямую зависит стабильная работа электроэнергетической системы. Обнаружение дефектных изоляторов всегда было важной проблемой в интеллектуальных энергосистемах. Однако традиционный метод обнаружения линии передачи имеет низкую точность и низкую производительность в реальном времени. Мы представляем метод обнаружения дефектов изолятора на основе CenterNet.Чтобы повысить эффективность обнаружения, мы упростили магистральную сеть. Кроме того, используется механизм внимания для подавления бесполезной информации и повышения точности обнаружения сети. При предварительной обработке изображений размытие некоторых обнаруженных изображений приводит к тому, что образцы отбрасываются, поэтому мы используем алгоритм восстановления сверхвысокого разрешения для восстановления размытых изображений для улучшения набора данных. Результаты показывают, что AP предлагаемого метода достигает 96,16%, а скорость рассуждения достигает 30 кадров в секунду в условиях тестирования NVIDIA GTX 1080.По сравнению с Faster R-CNN, YOLOV3, RetinaNet и FSAF точность обнаружения предлагаемого метода значительно улучшена, что полностью доказывает эффективность предложенного метода.
Образец цитирования: Wu C, Ma X, Kong X, Zhu H (2021) Исследование алгоритма обнаружения дефектов изолятора линии передачи на основе CenterNet. PLoS ONE 16 (7): e0255135. https://doi.org/10.1371/journal.pone.0255135
Редактор: Чи-Хуа Чен, Университет Фучжоу, КИТАЙ
Поступила: 17 июня 2021 г .; Принят в печать: 9 июля 2021 г .; Опубликован: 29 июля 2021 г.
Авторские права: © 2021 Wu et al.Это статья в открытом доступе, распространяемая в соответствии с условиями лицензии Creative Commons Attribution License, которая разрешает неограниченное использование, распространение и воспроизведение на любом носителе при условии указания автора и источника.
Доступность данных: Изображения и данные этого исследования доступны на Figshare по адресу: https://figshare.com/articles/dataset/66KVimage_zip/14992944 (https://doi.org/10.6084/m9.figshare.14992944) .v1).
Финансирование: Автор (ы) не получил специального финансирования для этой работы.
Конкурирующие интересы: Авторы заявили об отсутствии конкурирующих интересов.
1 Введение
В современном обществе спрос на электроэнергию растет день ото дня, что представляет собой огромную проблему для проверки и обслуживания электросети. Ежедневный осмотр — необходимое средство для решения этой задачи и обеспечения безопасной и стабильной работы электросети [1]. Самоуничтожение изолятора, являющегося незаменимым устройством в энергосистеме, серьезно угрожает безопасной эксплуатации энергосистемы.Поэтому особенно важно регулярно проводить обнаружение состояния и диагностику неисправностей. С развитием интеллектуальных сетей все больше и больше внимания уделяется проверке БПЛА. Есть также больше приложений в работе по контролю мощности.
В последние годы традиционные алгоритмы обнаружения дефектов изолятора в основном основывались на локальных особенностях изображений. Martinez et al. В [2] предложен метод обнаружения и классификации опор ЛЭП на основе функции HOG и нейронной сети MLP.Wang et al. [3] предложили объединить информацию о форме, цвете и текстуре изоляторов для обнаружения, что эффективно снижает влияние текстуры фона и освещения. Однако описанный выше метод неэффективен при обнаружении закрытых объектов. Поскольку трудно выделить полные особенности обнаруженного изображения для идентификации изолятора, трудно достичь ожидаемой точности. С 2012 года глубокое обучение [4] привлекло широкое внимание. Существовали две ветви модели обнаружения объектов: двухэтапная и одноэтапная модель обнаружения.Двухэтапный процесс делит весь процесс на две части с высокой точностью обнаружения, но для достижения эффекта обнаружения в реальном времени требуется слишком много времени. В настоящее время разработано много улучшенных двухэтапных алгоритмов, например, R-CNN [5], Fast R-CNN [6], Faster R-CNN [7], R-FCN [8] и др. По сравнению с двухступенчатый, одноступенчатый может обеспечить сквозное обнаружение и имеет более высокую скорость обнаружения, но его точность снижается, в основном включая: YOLO [9], SSD [10], YOLOv2 [11], YOLOv3 [ 12], CenterNet [13] и др.
Будь то двухэтапная модель обнаружения или одноэтапная модель обнаружения, информационная помощь априорного блока обычно необходима для регресса к истине. Однако размер и форма дефектов меняются в зависимости от окружающей среды. В этих условиях сложно спроектировать подходящие анкерные рамы, а использование анкерных ящиков требует больших вычислительных затрат. Поскольку Ло и Дэн предложили модель Корнернета без якорных ящиков [14], некоторые соответствующие модели без якорных каркасов привлекли широкое внимание ученых [13, 15–18].Большинство этих детекторов принимают ключевые точки, такие как углы или центры, как положительные образцы для регрессии к объектам.
Таким образом, на основе вышеупомянутого исследования мы предлагаем алгоритм обнаружения дефектного изолятора, основанный на WDSR и CenterNet, который использует ResNet50 в качестве магистральной сети. Алгоритм WDSR используется для восстановления сверхвысокого разрешения. Затем сеть выявляет дефектные изоляторы. Кроме того, глубоко анализируются создание набора данных, выбор показателей оценки, выбор параметров сети и так далее.Экспериментальные результаты показывают, что по сравнению с YOLOv3 [12], RetinaNet [19], FSAF [18] и Faster R-CNN [7], предлагаемый метод имеет улучшение AP более чем на 6,45% и улучшение показателя F1 более чем на 3,56%. Доказано, что этот метод имеет лучший эффект распознавания на изображении обнаружения БПЛА.
Ниже приводится расположение других частей документа: второй раздел знакомит с принципом обнаружения дефектов изолятора линии передачи и конструкцией каждой части каркаса.В третьем разделе обсуждаются набор данных, экспериментальная среда, дизайн результатов, метрики оценки, план эксперимента и анализ результатов. Наконец, четвертый раздел подводит итоги работы.
2 Метод
В этом разделе представлена структура обнаружения дефектов для изоляторов линий передачи. Как показано в Рис. 1 . Процесс обнаружения дефектного изолятора включает в себя предварительную обработку изображения и обнаружение дефектного изолятора.
Конкретный процесс обнаружения выглядит следующим образом:
- Разделите исходный набор инспекционных изображений БПЛА на две категории: набор квалифицированных изображений и набор нечетких изображений с низким разрешением.В этой статье для классификации изображений используется алгоритм дисперсии Лапласа.
- Реконструкция сверхвысокого разрешения через WDSR. Обработанное изображение объединяется с исходным изображением для получения подходящего набора контрольных изображений посредством улучшения данных.
- Отрегулируйте разрешение нового изображения изолятора, равное 512 × 512, и напрямую введите его в сеть ResNet50 для создания тепловой карты. Пик на тепловой карте — это центр объекта.
- Генерация от точки до ограничивающей рамки проходит через три части: прогнозирование центральной точки, прогнозирование смещения центральной точки и прогнозирование ограничивающей рамки.
- Результаты тестирования сетевого выхода.
2.1 Магистраль
Для ускорения процесса оптимизации и уменьшения исчезновения градиента в [20] предлагается остаточная сеть. Позже многие другие эксперименты также доказали, что остаточная сеть очень эффективна. В этом эксперименте используется базовая магистральная сеть ResNet50. Однако, ограниченное объемом данных в этом эксперименте, использование сложной сверточной нейронной сети может привести к чрезмерной подгонке.Следовательно, мы улучшаем исходную сеть CenterNet, используя ResNet50 в качестве магистрали.
Принимая во внимание характеристики набора данных изолятора, такие как большая область наблюдения, большой объем информации, большая разница в размерах объектов, небольшое количество независимых крупных объектов и множество сконцентрированных мелких объектов, вводится механизм внимания. Механизм внимания может хорошо изучить особенности изображений изолятора, подавить не-объектные особенности, выделить информацию об экземпляре, подавить фоновую информацию и повысить точность обнаружения.В этой статье выбран CBAM [21], чтобы помочь модели лучше выбирать промежуточные характеристики. Модуль CBAM является универсальным и легким модулем, поэтому его можно вставить в модуль свертки всей сети для обеспечения сквозного синхронного обучения. Мы в основном вставляем модуль внимания 7 × 7 в модуль свертки до того, как изображение будет введено в магистральную сеть ResNet50. Этот модуль может повысить точность обнаружения мелких объектов в наборе данных, поскольку он помогает сети извлекать больше ключевой информации из изображения.Модуль CBAM показан на рис. 2 .
Согласно [22], в первом сверточном слое шаг понижающей дискретизации может ухудшить характеристики модели, особенно для небольших объектов. В ответ на эту ситуацию мы заменяем сверточный слой 7 × 7 (шаг 2) исходной сети тремя сложенными друг на друга сверточными слоями 3 × 3 (шаг 1). Среди них канал каждого сверточного слоя 3 × 3 установлен равным 64, что предназначено для экономии вычислительных затрат. При этом легко удаляем объединяющий слой.Сравнение структуры исходной модели и улучшенной модели показано на рис. , рис. 3 .
2.2 Центры обнаружения
Процесс от ограничивающей рамки до точки показан на рис. , рис. 4 . Помеченное изображение помещается в сеть извлечения признаков для получения выходной карты признаков. Затем ветвь Y прогнозирования ключевой точки, ветвь O отклонения центральной точки и ветвь S размера объекта совместно используют одну и ту же сеть извлечения признаков для обучения соответственно.
Мы используем центральную тепловую карту для классификации и определения местоположения дефектных изоляторов, но, чтобы избежать влияния на оценку прогноза переднего плана, фоновый канал не используется. Разрешение изображения уменьшается в 4 раза с помощью ResNet50, а затем карта функций подвергается повышенной дискретизации и восстанавливается до исходного размера. Короче говоря, разрешение входного изображения равно разрешению центральной тепловой карты. Предполагая, что размер входного изображения составляет Ш × В × 3, размер соответствующей тепловой карты составляет C × Ш × В, где канал C представляет категорию C.Поскольку мы обнаруживаем только самовзрыв изолятора, для C установлено значение 1. Для дефектной гирлянды изолятора положительным является только центр его ограничивающего прямоугольника со значением 1. Все остальные положения отрицательны со значением 0. Однако, это может вызвать серьезный дисбаланс между положительными и отрицательными образцами, что может снизить способность модели к обобщению. Поэтому мы используем функции Гаусса [13, 14] для обработки точек вокруг центра и уменьшения их вклада в потери. Функция задается: (1) где и — координата центральной точки, σ — дисперсия.Величина σ зависит от радиуса r области вокруг центра. Параметр r определяется методом, описанным в [14], то есть значение IoU блока предсказания и наземной истины достигает не менее 0,3, поэтому устанавливается σ = 1 / 3r.
Центральный значок тепловой карты показан на Рис. 5 .
Здесь потеря обучения относится к [14] и выводится из Focal Loss [19], которая определяется как: (2) где N — количество дефектных частей изолятора. p cij — это прогнозируемая оценка класса C в точке (i, j) и соответствующая метка.α и β — гиперпараметры. А β используется для контроля веса точек вокруг положительного образца. Установите α = 2 и β = 4.
2.3 Регрессия ограничивающих прямоугольников
Возвращаемся к ограничивающей рамке через центральную точку (положительную точку). Предположим, что дефект i имеет метку ( x i min , y i min , x i max , y i max ). Таким образом, ограничивающая рамка может быть выражена как box i = ( x i max — x i min , y i max — y и мин. ).Тогда мы используем потерю на обучение — это потеря L1 [6]: (3) (4) где — прогнозируемое значение ограничивающей рамки.
2.4 Подробности реализации
Разрешение изображения в наборе данных необходимо отрегулировать до 512 × 512. Чтобы улучшить дисбаланс сэмплов, мы добавляем больше отрицательных сэмплов к некоторым изображениям. Кроме того, в части улучшения данных используются случайное отсечение, переворачивание и сглаживание цветов, что может облегчить проблему переобучения. Мы также используем оптимизатор Adam [23].Сумма убытков двух ветвей и есть общий убыток. (5) где α = 1,0 — вес L cls , а β = 0,1 — вес L reg . Поскольку структура модели относительно проста, обучать модель может только один графический процессор. Мы можем использовать пакет размером 16 и обучить всю сеть за 50 эпох с начальной скоростью обучения 1,5 × 10–4. Среди них скорость обучения снижается до 2,5 × 10–5 после 30 эпох.
3. Эксперимент
3.1 Набор данных и сравниваемые методы
При подготовке набора обучающих данных для WDSE мы следуем методам обучения, описанным в [24] и [25]. В то же время чистое изображение обрабатывается методом размытия движения, где радиус размытия установлен равным 7. Наконец, размытое изображение и соответствующее четкое изображение объединяются в обучающую пару в качестве обучающего набора. Изображение изолятора после размытия движения показано на рис. 6, .
Набор данных части обнаружения изолятора в этом эксперименте состоит из двух частей: 1507 сетевых изображений и 931 аэрофотоснимка БПЛА.Все изображения БПЛА, использованные в этом эксперименте, взяты из инспекции энергетической компании в провинции Гуандун. Обучающий набор и тестовый набор состоят из 1958 и 480 изображений соответственно. Частичное изображение набора данных показано на рис. 7, .
Для удобства управления образцами и индексации образцы названы XXX_ x. Формат jpg. Схема маркировки LabelImg показана на Рис. 8 .
В этой статье экспериментальные настройки, используемые для сравнения, следующие: YOLOv3 [12], RetinaNet [19] и FSAF [18] выбраны как одноступенчатое обнаружение.Двухэтапное обнаружение использует Faster R-CNN [7].
Эффект обнаружения YOLOv3 на небольших объектах лучше, потому что он использует информацию пирамиды функций для обнаружения. Чтобы обеспечить производительность сети, в этом эксперименте в качестве основы выбирается предварительно обученный darknet-53.
RetinaNet повышает точность двухэтапного обнаружения, поскольку использует потерю фокуса для уменьшения веса большого количества простых отрицательных выборок при обучении. Этот метод требует, чтобы входное изображение было 640 × 640, и в этом эксперименте в качестве основы используется ResNet50.
FSAF имеет два ответвления: ответвление с основанием и ответвление без якоря. Каждый объект динамически выбирает лучший векторный слой. После того, как выбор сделан, метод привязки используется для последующей классификации и позиционного регресса. Основной магистралью, выбранной в этом эксперименте, также является ResNet50.
Детектор Faster R-CNN очень популярен благодаря своей высокой точности обнаружения. Метод Faster R-CNN для получения блоков кандидатов — это RPN (сеть предложений регионов), а затем детектор классифицирует эти области.Обе части используют ResNet50 в качестве магистрали.
Вышеупомянутые сравнительные эксперименты с использованием ResNet50 в качестве основы, все магистрали предварительно обучены на наборе данных MS COCO. За 200 эпох обучения мы используем оптимизатор Adam [23] для всех методов. Установите начальную скорость обучения 10–4 в первые 90 эпох, снизьте до 10–5 в 90 эпох и 10–6 в 150 эпох. Чтобы обеспечить сопоставимость результатов, на нашем наборе данных выполняются как обучение, так и тестирование.
3.2 Метрики оценки и результаты обнаружения
Прецизионность, отзыв и PRC (кривая точного отзыва) [26] используются для измерения эффективности вышеупомянутых методов.Методы расчета отзыва и точности следующие: (6) (7) где TP, FP и FN представляют собой истинно положительный, ложноположительный и ложно отрицательный соответственно.
AP (средняя точность), оценка F1 и FPS (кадров в секунду) также используются в качестве показателей оценки. Оценка F1 представляет собой золотое сечение точности и запоминания, то есть взвешенное среднее гармоническое значение точности и запоминания. FPS обнаруживается с помощью камеры для имитации видеопотока, получаемого БПЛА в среде одной видеокарты NVIDIA GTX1080 в рабочей станции глубокого обучения micro-star в этой статье.Среднее время обнаружения 100 изображений рассчитывается для получения индекса скорости вывода этой модели. Методика расчета следующая: (8) (9)
PRC всех сетей показаны на Рис. 9 . Наши результаты по данным о дефектах показаны в Таблице 1. Качественные сравнения с другими методами показаны на Рис. 10 .
Из рисунка можно сделать четкий вывод, что наши методы хорошо работают с точки зрения точности и запоминаемости. В частности, уровень точности лишь немного выше, чем у других сетей, но скорость отзыва намного выше, чем у других показателей отзыва.Хотя Faster R-CNN — двухступенчатая модель, ее отзывчивость на удивление хороша. Это связано с тем, что RPN создает подходящую анкерную коробку для возможных изоляторов. YOLOv3 по точности уступает только предложенному нами методу, но цена заключается в том, что его отзывчивость является самой низкой среди вышеперечисленных методов. Из визуального вывода YOLOv3 можно увидеть, что причина, приводящая к самой низкой скорости отзыва, заключается в том, что некоторые изоляторы выбираются через ограничивающий прямоугольник, но размер и положение ограничивающего прямоугольника недостаточно точны.RetinaNet — полная противоположность YOLOv3. У него более высокая степень отзыва, но более низкая точность. Всестороннее сравнение, производительность FSAF самая стабильная.
Таблица 1 показывает, что улучшенный метод с CBMA дает наилучшие оценки AP и F1. За счет улучшения ResNet50 значение AP сети достигает 95,48%, а оценка F1 достигает 92,72%. Кроме того, FPS также является быстрым, занимая второе место среди вышеупомянутых методов, и может быть обнаружен в режиме реального времени. Кроме того, после добавления механизма внимания баллы AP и F1 достигают 96,16% и 95% соответственно, что является наивысшим баллом среди вышеперечисленных методов, что доказывает эффективность этого метода.Среди всех сравниваемых сетей AP FSAF наиболее близок к нашему эффекту. Для сравнения, FASF хорошо работает при обнаружении небольших дефектных изоляторов, а три других метода хорошо работают при обнаружении крупных дефектных изоляторов, но плохо обнаруживают небольшие дефектные изоляторы и изоляторы неполной формы.
Из рисунка 10 видно, что по сравнению с другими методами наши методы более устойчивы к обнаружению дефектных изоляторов. Это отражается в эффекте обнаружения похожих объектов, расположенных рядом объектов и многомасштабных объектов.
4. Заключение
На основе ResNet50 мы улучшаем исходную CenterNet, упрощаем всю магистральную сеть и реализуем обнаружение выпадения изолятора. Эксперимент показывает, что результат обнаружения падения листа изолятора достигает AP (96.16). Подтверждено, что улучшенный CenterNet имеет превосходный эффект, его также можно обнаруживать в режиме реального времени и имеет особое практическое значение для улучшения технологии обнаружения мощности.
Линия инспекции БПЛА является общим направлением инспекции электроэнергии.Нашим следующим шагом в этой области является создание единой базы данных изоляторов и точное различение типов повреждений, включая удар молнии, обледенение, самовзрыв и т. Д. Таким образом, может быть реализовано не только обнаружение неисправностей изоляторов, но и их дефекты можно классифицировать.
Благодарности
Авторы хотели бы поблагодарить анонимных рецензентов за их критические и конструктивные комментарии, их вдумчивые предложения помогли существенно улучшить эту статью.
Ссылки
- 1. Нгуен В. Н., Йенсен Р., Роверсо Д. Автоматическая автономная проверка линии электропередачи на основе технического зрения: обзор текущего состояния и потенциальной роли глубокого обучения. Международный журнал электроэнергетических и энергетических систем. 2018; 99: 107–120. https://doi.org/10.1016/j.ijepes.2017.12.016
- 2. Мартинес К., Сампедро С., Чаухан А., Кампой П. На пути к автономному обнаружению и отслеживанию электрических вышек для проверки воздушных линий электропередачи.Международная конференция по беспилотным авиационным системам. 2014; 284–295. http://dx.doi.org/10.1109/ICUAS.2014.6842267
- 3. Xing W, Bai P, Zhang S, Bao P. Обнаружение пешеходов в зависимости от сцены на основе передачи обучения и обнаружения значимости для видеонаблюдения. Автоматическое управление и компьютерные науки. 2017; 51 (3): 180–192. http://dx.doi.org/10.3103/S0146411617030099
- 4. Хао Х, Чжан Г, Ма С. Глубокое обучение. Международный журнал семантических вычислений.2016; 10 (03): 417–439. https://doi.org/10.1142/S1793351X16500045
- 5. Гиршик Р., Донахью Дж., Даррелл Т., Малик Дж. Богатые иерархии функций для точного обнаружения объектов и семантической сегментации. 27-я конференция IEEE по компьютерному зрению и распознаванию образов (CVPR). 2014; 580–587. http://dx.doi.org/10.1109/CVPR.2014.81
- 6. Гиршик Р. Быстрый R-CNN. Международная конференция IEEE по компьютерному зрению. 2015; 1440–1448. http://dx.doi.org/10.1109/ICCV.2015.169
- 7. Рен С., Хе К., Гиршик Р., Сан Дж. Быстрее R-CNN: на пути к обнаружению объектов в реальном времени с помощью региональных сетей. IEEE Transactions по анализу шаблонов и машинному анализу. 2017; 39 (6): 1137–1149. pmid: 27295650
- 8. Дай Дж, Ли Й, Хе К., Сан Дж. R-FCN: Обнаружение объектов с помощью полностью сверточных сетей на основе регионов. Достижения в системах обработки нейронной информации. 2016; 29: 379–387.
- 9. Редом Дж., Диввала С., Гиршик Р., Фархади А.Вы смотрите только один раз: Единое обнаружение объектов в реальном времени. IEEE. 2016; 779–788. https://doi.org/10.1109/CVPR.2016.91
- 10. Лю В., Ангелов Д., Эрхан Д., Сегеди С., Рид С., Фу С. Ю. SSD: одноразовый мульти-бокс-детектор. Европейская конференция по компьютерному зрению Springer. 2016; 9905: 21–37. https://doi.org/10.1007/978-3-319-46448-0_2
- 11. Редмон Дж., Фархади А. YOLO9000: лучше, быстрее, сильнее. IEEE. 2017; 6517–6525. http://dx.doi.org/10.1109/CVPR.2017.690
- 12.Редмон Дж., Фархади А. YOLOv3: Постепенное улучшение. Препринт arXiv arXiv: 1804.02767, 2018.
- 13. Чжоу X, Ван Д., Кхенбюль П. Объекты как точки. Препринт arXiv arXiv: 1904.07850, 2019.
- 14. Закон Х., Дэн Дж. Корнернет: Обнаружение объектов как парных ключевых точек. Международный журнал компьютерного зрения. 2020; 128 (3): 642–656. https://doi.org/10.1007/978-3-030-01264-9_45
- 15. Тиан З., Шен К., Чен Х, Хе Т. FCOS: Полностью сверточное одноэтапное обнаружение объектов.Международная конференция IEEE / CVF по компьютерному зрению (ICCV), 2019 г. 2019: 9626–9635. http://dx.doi.org/10.1109/ICCV.2019.00972
- 16. Яо Дж, Ян Х, Доу Р. Анизотропно-устойчивый алгоритм локализации с контролем ошибок в беспроводной сенсорной сети. Автоматическое управление и компьютерные науки. 2017; 51 (6): 442–452. https://doi.org/10.3103/S0146411617060104
- 17. Kong T, Sun F, Liu H, Jiang Y, Shi J. Foveabox: За пределами детектора объектов на основе якоря. IEEE Transactions по обработке изображений.2020; 29: 7389–7398. Https://doi.org/10.1109/TIP.2020.3002345
- 18. Чжу Ч., Хе Й., Саввидес М. Функциональный избирательный модуль без привязки для однократного обнаружения объектов. Конференция IEEE / CVF по компьютерному зрению и распознаванию образов (CVPR) 2019 г. 2019; 840–849. http://dx.doi.org/10.1109/CVPR.2019.00093
- 19. Лин Т. И, Гойал П., Гиршик Р., Хе К., Доллар П. Потеря фокусировки при обнаружении плотных объектов. IEEE Transactions по анализу шаблонов и машинному анализу.2017; 99: 2999–3007. http://dx.doi.org/10.1109/TPAMI.2018.2858826
- 20. He K, Zhang X, Ren S, Sun J. Глубокое остаточное обучение для распознавания изображений. IEEE. 2016; 770–778. https://doi.org/10.1109/CVPR.2016.90
- 21. Woo S, Park J, Lee J Y, Kweon I.S. CBAM: модуль внимания сверточного блока. Европейская конференция по компьютерному зрению. 2018; 11211: 3–19. https://doi.org/10.1007/978-3-030-01234-2_1
- 22. Чжу Р., Чжан С., Ван Х, Вэнь Л., Мэй Т.ScratchDet: обучение детекторов объектов с нуля. Конференция IEEE / CVF по компьютерному зрению и распознаванию образов (CVPR). 2019; 2268–2277. http://dx.doi.org/10.1109/CVPR.2019.00237
- 23. Кингма Д., Ба Дж. Адам: метод стохастической оптимизации. Информатика. 2014.
- 24. Донг Ц., Лой Ц., Хе К., Тан X. Сверхразрешение изображения с использованием глубоких сверточных сетей. IEEE Trans Pattern Anal Mach Intell. 2016; 38 (2): 295–307. pmid: 26761735
- 25.Чао Д., Чен С. Л., Тан X. Ускорение сверточной нейронной сети сверхвысокого разрешения. Springer. 2016; 9906: 391–407. https://doi.org/10.1007/978-3-319-46475-6_25
- 26. Саджади М. С. М., Бахем О., Лючич М. Оценка генеративных моделей с помощью точности и отзыва, 32-я конференция по системам обработки нейронной информации (NIPS), Монреаль, 2018 г .; 31–41.
, интеллектуальный периферийный компьютер, одноплатный компьютер
Огромный рост популярности интеллектуальных устройств означает, что спрос на стеклянные панели дисплея, используемые для экранов, резко возрос.Контроль качества этих компонентов является ключевой частью производственного процесса. Хотя такие проверки иногда по-прежнему выполняются вручную, это требует времени и затрат. Более того, проверки, проводимые людьми-операторами, могут сами по себе привести к отказу, будь то отвлечение внимания, усталость или любое количество других факторов. Вот почему многие процессы обеспечения качества автоматизируются, и оборудование ASUS IoT находится в авангарде этой неудержимой производственной тенденции.
Проблема: интеграция автоматизированного контроля в существующие производственные линии
Выявление дефектов в стеклянных дисплеях является важной частью процесса контроля качества при производстве мобильных телефонов, планшетов и аналогичных современных интеллектуальных устройств.В большинстве случаев это высокопроизводительные процессы, поэтому осмотр человеческими глазами зачастую непрактичен: скорость современных производственных линий просто становится слишком высокой, чтобы люди могли выполнять задачу в соответствии с приемлемыми стандартами. По этой причине многие производители установили автоматизированные системы контроля, которые вместо этого используют машины.
Нашему клиенту, ведущему системному интегратору промышленного оборудования (SI), была нужна система, которая могла бы интегрироваться с существующими производственными линиями — и даже существующим оборудованием для обнаружения дефектов — чтобы специально сосредоточиться на обнаружении дефектов при производстве стеклянных экранов. .Требуемая система должна была продемонстрировать неизменную надежность, превосходную совместимость и исключительную простоту использования. Он также должен был быть простым в обслуживании.
Решение: высокоскоростное и точное обнаружение дефектов на базе ASUS IoT
В сотрудничестве с SI команда ASUS IoT объединила промышленную материнскую плату ASUS IoT Q170A-IM-A с ASUS IoT EBE Базовый сервер размером 4U, монтируемый в стойку, для поддержки специальной машины для проверки стекла при производстве смартфонов.Сочетание этих двух универсальных продуктов с широкими возможностями подключения, предлагаемыми Q170A-IM-A, позволило SI создать промышленную инспекционную машину с возможностью значительного расширения.
В процессе визуального осмотра эта специализированная машина может работать автономно и надежно в течение длительного периода времени. В промышленных цифровых камерах используется высокая частота кадров для обнаружения дефектов поверхности, что позволяет быстро и точно отделить экраны с дефектными стеклами.
Команда ASUS IoT помогла создать решение на основе сценариев.Благодаря четырем слотам PCI Express® и трем традиционным слотам PCI он достаточно гибкий, чтобы в нем можно было разместить все виды специализированных карт расширения — от графических процессоров и карт видеозахвата до устройств захвата кадров. Это создает компактную систему, которая может расти или адаптироваться к потребностям бизнеса.
Результат: новая эра цифровых визуальных проверок
Производство стеклянных экранов для мобильных устройств — это высокоскоростной процесс, который также требует исключительной точности. В настоящее время невозможно полностью устранить дефекты в процессе, поэтому визуальный контроль качества является жизненно важной частью производственной среды.
С помощью команды ASUS IoT и оборудования ASUS IoT, созданная нашим заказчиком автономная контрольная машина — SI — минимизирует человеческий фактор и максимизирует эффективность. Методы глубокого обучения на основе искусственного интеллекта используются для классификации различных классов дефектов с конечной целью уменьшения количества ложных срабатываний.