Роботизированная коробка передач
Основу роботизированной коробки передач составляет механическая коробка, но функции выключения сцепления и переключения передач автоматизированы. Работой коробки передач управляет электронный блок с заложенным алгоритмом управления.
Коробка-робот сочетает топливную экономичность и высокую надежность МКПП с комфортом автоматической коробки. Но при этом стоимость «робота» значительно ниже классической АКПП. Именно эти факторы поспособствовали тому, что большинство автопроизводителей в настоящее время оснащают свои транспортные средства роботизированными коробками. Они устанавливаются как на модели эконом, так и премиум класса.
Конструкция роботизированной коробки передач
В зависимости от компании-производителя конструкция роботизированных коробок может разниться. Однако следует выделить их общее устройство: механическая коробка передач с интегрированной системой управления сцеплением и передачами.
В автоматизированных КПП применяется сцепление фрикционного типа: это либо отдельный диск, либо пакет фрикционных дисков. Инновационным считается т.н. двойное сцепление, способное передавать крутящий момент без потери мощности.
Как указывалось выше, основу конструкции роботизированной коробки составляет МКПП. Производители, как правило, используют уже готовые технические решения. К примеру, на базе АКПП 7G-Tronic построена автоматизированная коробка передач Speedshift от Mercedes – в этом случае гидротрансформатор был заменен фрикционным многодисковым сцеплением. Базой для SMG от BMW служит 6-ступенчатая «механика», оснащенная электрогидравлическим приводом сцепления.
«Роботы» могут комплектоваться гидравлическим либо электрическим приводом сцепления и передач. В качестве исполнительных устройств в электрическом приводе используются сервомеханизмы (механическая передача и электродвигатель). Гидравлический привод приводится в действие посредством гидроцилиндров, которые находятся под управлением электромагнитных клапанов.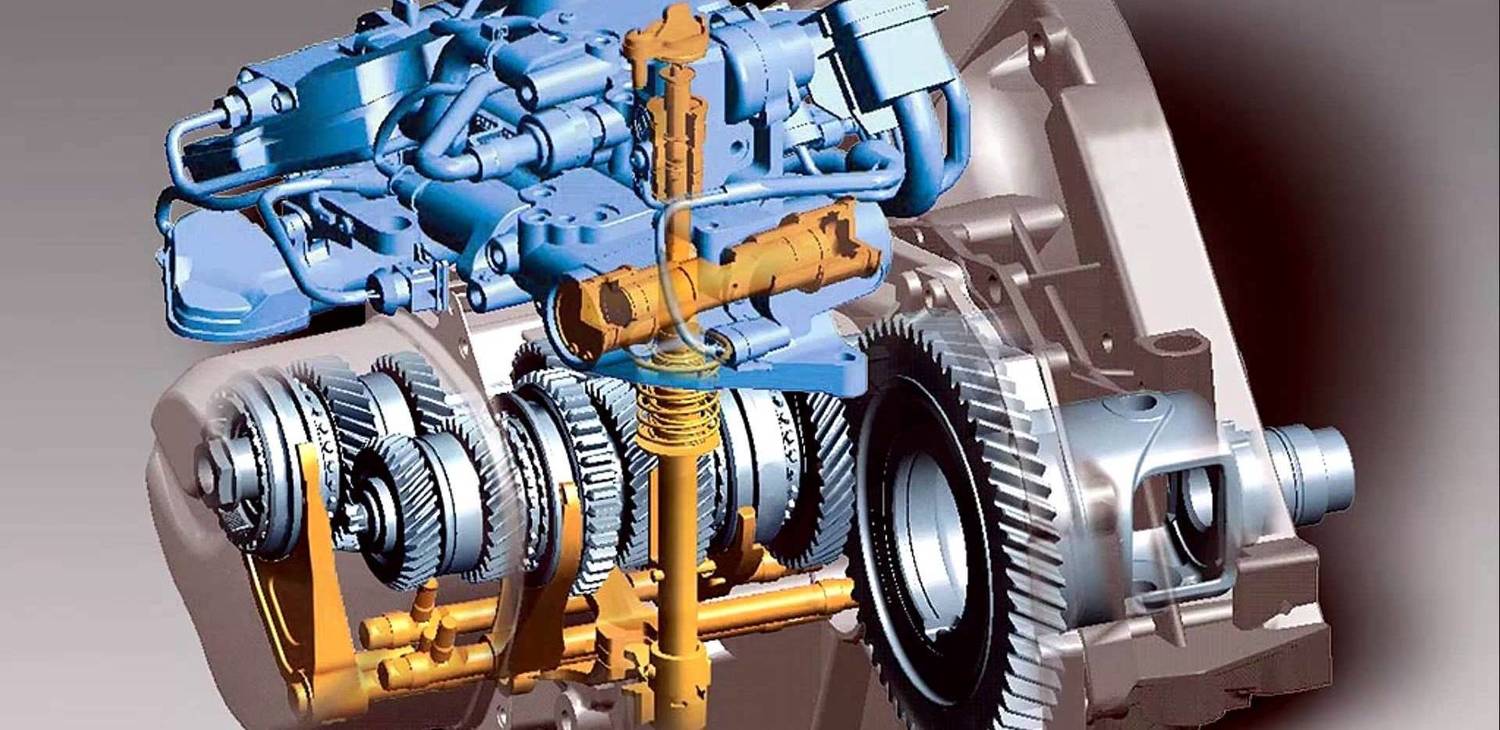
Электрический привод характеризуется меньшим энергопотреблением и невысокой скоростью работы – временной промежуток переключения передач варьируется в пределах 0,3–0,5 секунды. В гидравлическом приводе постоянно поддерживается давление в системе, поэтому он требует больших затрат энергии. Вместе с тем, он отличается более высокой скоростью работы. Некоторые коробки-роботы с гидроприводом, которыми комплектуются спортивные авто, отличаются поразительной скоростью переключения передач, например, у Lamboghini Aventador этот показатель составляет 0,05 cек., а у Ferrari 599GTO – 0,06 cек.
Эти качества определяют область применение агрегатов. Таким образом, «роботы» с электрическим приводом устанавливаются на бюджетные транспортные средства, а с гидравлическим – на автомобили сегмента премиум.
Электрическим приводом оснащаются следующие коробки передач:
- SensoDrive от компании Citroen;
- 2-Tronic от компании Peugeot;
- Easytronic от компании Opel;
- MultiMode от компании Toyota;
- Dualogic от компании Fiat;
- Allshift от компании Mitsubishi;
- Durashift EST от компании Ford.
Гидравлический привод устанавливается на следующие роботизированные коробки передач:
- SMG от компании BMW;
- R-Tronic от компании Audi;
- Quickshift от компании Renault;
- ISR от компании Lamborghini;
-
Selespeed от компании Alfa Romeo.
Электронная система осуществляет управление роботизированной коробкой передач. Она состоит из входных датчиков, исполнительных устройств и электронного блока управления. Задача входных датчиков заключается в отслеживании основных параметров коробки: положение селектора, положение вилок включения передач, частоту вращения на входе и выходе, температуру и давление трансмиссионного масла. Все параметры передаются в блок управления.
Учитывая входящие сигналы датчиков, электронный блок управления формирует команды для исполнительных устройств в соответствии с заложенной программой. Кроме того, электронный блок в процессе работы взаимодействует прочими электронными системами, среди которых система управления двигателем, система ABS (ESP). В коробках с гидравлическим приводом в систему управления также входит гидравлический блок управления (отвечает за управление гидроцилиндрами и давление в системе).
В зависимости от привода исполнительными механизмами выступают электромагнитные клапаны гидроцилиндров (гидравлический привод), электродвигатели (электрический привод).
Коробка передач с двойным сцеплением
Роботизированная коробка передач имеет достаточно весомый недостаток – относительно большой промежуток времени переключения передач. Данный недостаток влечет за собой провалы и рывки в процессе управлением машины, что в свою очередь приводит к снижению комфорта. Для решения данной проблемы была разработана коробка с двойным сцеплением, которая обеспечивает переключение без потери мощности.
При уже включенной передаче двойное сцепление позволяет выбрать следующую передачу и включить ее при первой потребности, при этом работа коробки передач не будет прервана. Отсюда исходит другое название – преселективная коробка передач (preselect – предварительный выбор).
Еще одним преимуществом «робота» с двойным сцеплением считается высокая скорость переключения. Причем, скорость зависит лишь от скорости переключения муфт (DCT M Drivelogic от BMW – 0,1 cек., DSG от Volkswagen – 0,2 cек.
Двойным сцеплением комплектуются многие роботизированные коробки передач:
- DSG от компании Volkswagen;
- Speedshift DCT от компании Mercedes;
- DCT M Drivelogic от компании BMW;
- PDK от компании Porsche;
- S-Tronic от компании Audi;
- Twin Clutch SST от компании Mitsubishi;
- Powershift от компаний Ford и Volvo;
-
TCT от компании Alfa Romeo.
Даже спортивный автомобиль Ferrari 458 Italia укомплектована коробкой с двойным сцеплением Doppelkupplungsgetriebe. Вышеуказанные коробки передач имеют гидравлический привод сцепления и передач. В настоящий момент лишь одна коробка использует электропривод устройств – EDC (Efficient Dual Clutch) от компании Renault. Стоит отметить, что время переключения передач составляет всего 0,29 сек.
Лидерами по массовому применению коробок передач с двумя сцеплениями по праву считаются компании Audi и Volkswagen, которые устанавливают на свои автомобили коробки S-tronic и DSG с 2003 года. S-tronic, в отличие от коробки DSG, устанавливается продольно на оси полноприводных и заднеприводных автомобилей.
DCT M Drivelogic – это автоматизированная коробка передач с функцией Drivelogic. Данная функция предусматривает 11 программ переключения передач, из которых 6 предполагают выполнение в ручном режиме, а остальные 5 – это автоматизированные программы переключения передач. С помощью этой функции можно адаптировать смену передач под стиль вождения конкретного человека.
Принцип работы роботизированной коробки передач
У данного типа коробки передач предусмотрено два режима работы: автоматический и полуавтоматический. В первом случае электронный блок управления задействует определенный алгоритм управления коробкой, учитывая при этом сигналы входных датчиков. Команды блока управления выполняют исполнительные механизмы.
Полуавтоматический режим переключения передач аналогичен функции Типтроник на АКПП. Благодаря данному режиму обеспечивается возможность последовательно переключать передачи посредством селектора и/или подрулевых лепестков. По этой причине роботизированную трансмиссию также называют секвентальной КПП (sequensum – последовательность).
Трансмиссия
Для IVECO STRALIS предлагаются три типа коробок передач:
- 9-и 16-скоростная МКПП
- Роботизированная коробка передач EUROTRONIC с управлением на рулевой колонке
- 6-ступенчатая АКПП
Все коробки передач отличаются высокой надежностью и низкими затратами на обслуживание. Передаточные отношения подверглись оптимизации для увеличения производительности и эффективности автомобиля.
Механические коробки передач
Быстрые и точные переключения передач.
На Stralis устанавливаются 9-скоростная и 16-скоростная механические коробки передач ZF.
16-скоростная механическая коробка передач оборудована сервоприводом переключения для более высокого комфорта и быстрой, точной смены передач.
Пневматический сервопривод снижает усилие водителя, требуемое для переключения передачи, на 50%, а ход рычага переключения был уменьшен на 40%.
Роботизированные коробки передач
Роботизированная коробка передач Eurotronic — это высокий комфорт и надежность.
Наряду с обычными механическими коробками передач для Stralis доступна технологичная роботизированная коробка передач EuroTronic с рычагом переключения на передней панели.
Она обладает рядом преимуществ, включая уменьшенную на 60 кг массу по сравнению с механической коробкой передач, более компактные размеры и меньшее число пневматических и электрических соединений.
За счет отсутствия синхронизаторов переключение передач происходит быстрее и безопаснее: система предотвращает включение неправильной передачи и защищает двигатель от превышения максимально допустимых оборотов.
Коробка передач EuroTronic может работать как в автоматическом, так и полуавтоматическом режиме. Автоматическая смена передач рассчитывается с учетом загрузки автомобиля, дорожной обстановки и стиля вождения водителя, в результате чего обеспечиваются оптимальные ускорение, расход топлива и комфорт.
Автоматические коробки передач
Идеальный выбор для работы в городе.
На Stralis устанавливается 6-ступенчатая автоматическая коробка передач Allison 3200. В данной трансмиссии используется гидротрансформатор, выполняющий роль сцепления, т.е. компоненты, подверженные износу, отсутствуют.
Благодаря своим техническим особенностям она крайне надежна и отлично подходит для эксплуатации с частыми разгонами и остановками – например, для перевозки грузов по городу, доставки товаров и уборки мусора.
Передние и задние оси
Безопасность и абсолютная надежность.Для всех моделей Stralis предлагаются различные типы осей в зависимости от требований эксплуатации.
Все они различаются по:
- типу конструкции
- максимально допустимой нагрузке
- передаточному отношению главной передачи (только для задних осей)
Задние оси имеют конструкцию с одной главной передачей, при этом максимально допустимая нагрузка может составлять до 13 000 кг.
В качестве опции можно заказать заднюю ось с двойной главной передачей (центральной главной передачей и главной передачей в колесных редукторах).
Многочисленные передаточные числа главной передачи (от 2,64 до 5,29) обеспечивают оптимальную динамику при выполнении любых задач и высокую экономичность двигателя на любых маршрутах.
Чтобы модельная линейка была максимально полной, компания IVECO предлагает целый ряд автомобилей с фиксированными или поднимаемыми, неведущими или управляемыми третьими осями, с одинарной или двойной ошиновкой.
Рама и подвеска
Решения для непревзойденной прочности.
Одной из самых сильных сторон всех автомобилей Iveco всегда была надежная и прочная рама.
Рама состоит из балок C-образного сечения с двойным сужением, изготовленных из высокопрочной стали, и доступна в исполнении с толщиной 6,7 мм и 7,7 мм в зависимости от колесной базы и модели/версии.
На Stralis могут быть установлены различные подвески:
- параболическая
- задняя пневматическая
- полностью пневматическая.
Роботизированная коробка передач
Можно сказать, что роботизированная коробка передач занимает промежуточное положение между механической и автоматической трансмиссиями. Идея создания «робота» заключалась в том, чтобы в одной коробке передач сочетались бы комфорт, надежность и экономичность с точки зрения топлива. При этом роботизированная коробка должна была стоить намного дешевле классического «автомата». Как показывает практика, обе цели в итоге были достигнуты.
По сути, роботизированная коробка передач является «эволюцией» обычной механической трансмиссии. Устройство и принцип работы «механики» довольно простой. Главными составляющими элементами являются первичный (ведущий) и вторичный (ведомый) валы. На ведущий вал передается крутящий момент от двигателя. Ведомый вал преобразовывает крутящий момент и передает его на передние или задние колеса в зависимости от типа привода автомобиля.
На каждом из валов присутствуют шестерни. На ведущем валу они жестко закреплены, а на ведомом свободно вращаются. Именно поэтому, когда коробка передач находится в нейтральном положении, ведущие колеса не получают крутящий момент.
На автомобиле с обычной механической коробкой передач, водитель сначала выжимает сцепление, тем самым отсоединяя первичный вал от мотора. После этого, с помощью рычага коробки на вторичном валу начинают двигаться и перемещаться синхронизаторы, которые не позволяют муфте заблокировать шестерню, пока их скорости вращения не станут одинаковыми. Когда это условие выполнено, синхронизатор жестко блокирует шестерню выбранной передачи на вторичном валу. Чтобы крутящий момент сначала попал на ведомый вал, а от него на главную передачу и ведущие колеса, необходимо включить сцепление.
Но если механической трансмиссией управляет водитель, т.е. он включает и выключает сцепление, выбирает необходимую передачу, то в роботизированной коробке все эти функции выполняет электроника, которая состоит из входных датчиков, электронного блока управления и исполнительные механизмы.
Основная функция входных датчиков заключается в постоянном контроле основных параметров коробки передач. Полученная датчиками информация далее передается в электронный блок управления, который взаимодействует с различными системами автомобиля, такими как ABS, ESP, отслеживает обороты двигателя, скорость движения. Кроме этого, в блок заложена программа управления исполнительными механизмами. На основе полученных данных, электронный блок дает команды исполнительным механизмам, которыми являются сервоприводы – актуаторы.
Как только от электронного блока поступает команда на включение передачи, один сервопривод выжимает сцепление, второй передвигает муфту и включает выбранную передачу. Сразу после включения передачи первый сервопривод плавно отпускает сцепление. Таким образом, водителю не нужно выжимать педаль сцепления, да ее собственно и нет, так как все делает электроника.
Большинство «роботов» имеют два режима работы. В автоматическом режиме все команды, касающиеся работы сцепления и включения необходимой в данный момент передачи, поступают от электронного блока управления. В ручном режиме, водитель самостоятельно переключает передачи.
Недостаток роботизированной коробки передачПри смене передач в автоматическом режиме «робот» надолго прерывает идущую к колесам мощность от двигателя. Причем такие разрывы достаточно продолжительны во времени, чтобы водитель успел их заметить и ощутить.
Чтобы полностью исключить такие провалы или хотя бы существенно сократить время, затрачиваемое на переключение передач, в начале 1980-х годов была разработана роботизированная коробка передач с двойным сцеплением — DCT (dual clutch transmission). Самым известным представителем подобной трансмиссии является коробка DSG, которая применяется на автомобилях Volkswagen, Audi и др.
Лада АМТ — роботизированная коробка ВАЗ 2182
Идею создания собственного автомата очень много лет вынашивали конструкторы АвтоВАЗа, но квалификации не хватало. Поэтому снова решили обратиться к зарубежным специалистам.
Сперва переговоры довольно долго велись с известной итальянской компанией Magneti Marelli, но полученное позже предложение немецкого концерна ZF оказалось гораздо более выгодным. В результате руководство АвтоВАЗа решило оснастить самую современную на данный момент отечественную механику ВАЗ 2180 электромеханическими актуаторами от немецкой компании.
Исполнительный механизм состоит из следующих узлов:
А — актуатор включения сцепления; Б — актуатор переключения передач; В — вилка включения сцепления; Г — датчик скорости на первичном валу; Д — ручка управления в салоне.
Исполнительный механизм переключения передач:
1 — шток выбора передач; 2 — привод включения передач; 3 — привод выбора передач; 4 — электромоторы.
Исполнительный механизм включения сцепления:
1 — приводная шестерня; 2 — шток вилки сцепления; 3 — компенсатор износа; 4 — компенсационная пружина; 5 — электромоторы.
В итоге получился типичный робот с электрическим приводом единственного диска сцепления. Такие модели были популярны у европейских либо японских производителей лет десять назад. На данный момент почти все ведущие автомобильные концерны мира от них давно отказались в пользу еще более современной трансмиссии: преселективных роботов с двумя сцеплениями.
5em;text-align:center;font:6em/1.5 sans-serif;color:white;text-shadow:0 0 0.5em black}</style> <a href=https://www.youtube.com/embed/oZ2oWpycR0U?autoplay=1> <img src=https://img.youtube.com/vi/oZ2oWpycR0U/hqdefault.jpg alt=’Ладная механика: Лайфхаки АМТ!’><span>►</span></a>» allow=»accelerometer; autoplay; encrypted-media; gyroscope; picture-in-picture» allowfullscreen=»» title=»Ладная механика: Лайфхаки АМТ!»/>
Аналогичные трансмиссии других производителей:
Роботизированная коробка передач DSG, или новое это хорошо забытое старое.
Роботизированная коробка передач DSG (Direct Shift Gearbox). Это коробка передач прямого переключения. В настоящее время она является самой совершенной автоматизированной коробкой, устанавливаемой на массовые модели легковых автомобилей – так, или примерно так начинаются все описания данного агрегата во многих, если не сказать во всех, рекламных источниках. Давайте разберемся, что это такое и так ли это на самом деле.
Эту коробку изобрел пионер автомобилестроения Адольф Кегресс (Adolphe Kegresse) (1879-1943), больше известный изобретением полугусеничных машин, оснащенных резиновыми гусеницами, которые помогают ездить по различным формам рельефа. Кстати, интересный факт, Адольф Кегресс с 1904 года работал в России, организовывая там автомобильную почту. С 1906 года А. Кегресс стал техническим директором гаража царя Николая II, а после – личным шофером императора.
Так вот, в 1939 году Кегресс впервые сформулировал идею КПП с двойным сцеплением, которую он надеялся воплотить в легендарном Citroen Traction. К сожалению, неблагоприятные условия бизнеса, а затем вторая мировая война, не позволили претворить идею в жизнь.
К идее создания КПП с двойным сцеплением вернулись только в 80-х годах прошлого века разработчики спортивных болидов. Они смогли автоматически переключать механические КПП. В автомобиле педалью сцепления и кулисой переключения передач управляет электроника, все действия совершаются электромагнитными или гидравлическими механизмами.
Давайте разберемся, как это работает. Для того, чтобы понять, как это работает, необходимо вспомнить, как работает механика.
Итак, как работает механическая КПП? Прежде чем переключить передачу с помощью кулисы переключения передач, необходимо выжать педаль сцепление, которая отсоединяет двигатель от коробки передач и прекращает подачу силового потока к коробке. Когда водитель выбирает нужную передачу с помощью кулисы, зубчатая муфта перемещается от одной шестерни к другой, синхронизаторы выравнивают скорость вращения муфты, после чего передача безударно включается. После того, как шестерня пришла в движение, необходимо отпустить педаль сцепления, после чего происходит повторное соединение двигателя с трансмиссией и посылает крутящий момент на колеса. Таким образом, в обычной механической коробке передач, поток мощности от двигателя к колесам при переключении скоростей прерывается. Это вызывает толчок переключения передачи или прерывание крутящего момента. В случаях неправильного, или несвоевременного включения передачи, автомобиль может заметно подергиваться, или как говорят в народе – «козлить».
Коробка DSG работает по-другом, она объединяет в одном корпусе две механические коробки передач, одну для четных скоростей, а другую для нечетных, и каждая из которых оснащена своим сцеплением, Но зачем это нужно? Оказывается, для того, чтобы включать две передачи одновременно!
Пока автомобиль разгоняется на четной скорости, шестерни следующей, нечетной, уже находятся в зацеплении. Когда обороты двигателя достигают точки включения следующей передачи, сцепление четной передачи размыкается, а нечетной одновременно замыкается, при этом передача тяги между коробками происходит без разрыва потока мощности, а смена скорости получается быстрой и почти незаметной. И все это при минимальных потерях энергии – будучи производной от обычной “механики” коробка наследует и высокую эффективность передачи мощности. Управляется все это автоматикой, поэтому в системе отсутствует педаль сцепления, как таковая, и ручка управления КПП такая, как у автоматической коробки.
“Вот она, идеальная трансмиссия”- воскликнет восторженный читатель, но… Как говорил известный персонаж товарищ Саахов из Кавказской пленницы – “э нет… тарапица не надо”. Коробка DSG, как уже было сказано выше, управляется электроникой, и при наборе скорости компьютер почти мгновенно переключает передачи, экономя топливо, сохраняя динамику и сглаживая рывки, потому что сразу после включения, например, четвертой передачи он готов включить пятую. А если Вы в процессе разгона решили притормозить, а такое в пробках и на трассе бывает часто? А система управления об этом не знала и готовилась включить передачу выше? Ей нужно гораздо больше времени для отключения более высокой передачи и подготовки к включении более низкой передачи. На это уходит уже не 100 мс, а до полусекунды. Вы скажете, “Ну и что этого и не заметишь”, и будете правы, при торможении этого практически не заметно, но автоматам такое угадывание не свойственно. Это минус.
Не всегда удается обеспечить и низкие потери энергии. Проблема в том, что сухие сцепления (такие же, как и у ручных коробок) в DSG трансмиссиях могут перегреваться, поэтому в моделях, рассчитанных на мощные моторы, вместо них применяются пакеты фрикционов, работающие в масле. Они лучше держат нагрузки, но из-за большего проскальзывания и гидродинамических потерь эффективность передачи мощности снижается до 96%, в то время как ручные коробки и их роботизированные версии достигают величины в 98-99%. Впрочем, это, конечно, лучше обычного “автомата” с его 91-94%. Разработчики заявляют, что коробка DSG экономит до 10% топлива. Ой, как я сомневаюсь. Несколько процентов – да, и это безусловно радует.
Неоспоримым минусом является стоимость коробки и огромные проблемы с ремонтопригодностью. В связи с чем, возникает необходимость правильного обслуживания КПП и своевременной замены масла. Так как это, как не крути, рекламная статья, не примену возможностью обратить Ваше внимание, что компания North Sea Lubricants для таких коробок производит специальное масло ATF POWER DSG.
Так почему же коробки передач DSG стали так популярны? Ведь по каждому из параметров обязательно находится какой-то более подходящий тип трансмиссии. А секрет заключается в том, что, не являясь лидером в отдельных номинациях, эти коробки, тем не менее, совместили в себе удачный набор характеристик: достаточно эффективные, относительно недорогие, вполне комфортные и довольно быстрые. Золотая середина.
Катайтесь на машинах с коробками DSG и получайте от этого удовольствие.
Роботизированная коробка передач — что это такое, устройство и принцип работы коробки робот
Современные автомобили все чаще оснащаются коробками передач роботизированного типа. В обиходе такие коробки еще называют «роботами». Само наименование «роботизированная КПП» указывает на то, что действиями водителя с учетом условий движения автомобиля, формируется «входная информация» для электронного блока коробки (робота), который, посредством заложенных алгоритмов, руководит работой всего узла. Главным преимуществом роботизированных коробок передач является то, что эти агрегаты эффективно сочетают комфорт и удобство в эксплуатации привычной автоматической коробки с надежностью и топливной экономичностью обыкновенной «механики». Кроме того, как правило, коробка-робот существенно дешевле традиционной автоматической коробки. Сегодня «роботы» устанавливаются как на дорогие модели премиум-класса, так и на автомобили массового и даже бюджетного сегмента.
Роботизированная коробка передач способна работать в автоматическом, а также полуавтоматическом режимах. Для водителя работа роботизированной КПП будет практически неотличима от работы обычной коробки-автомата. При достижении определенной скорости движения электронный блок, на основании поступающих сигналов от входных датчиков, обеспечивает нужный алгоритм работы коробки при помощи исполнительных механизмов. Помимо этого, любая роботизированная коробка передач обладает функцией ручного переключения передач, называемой типтроник. Правда, в отличие от обычной «механики», при ручном переключении рычаг «робота» не нужно устанавливать в конкретное положение, определенное для той или иной передачи. Переключение в ручном режиме производится последовательно с низшей на высшую передачу и наоборот простым покачиванием селектора вперед или назад. Иногда роботизированную КПП, благодаря особенности последовательного переключения передач в ручном режиме, называют еще секвентальной (sequensum – последовательность). Для некоторых разновидностей роботизированных коробок дополнительно предусмотрены подрулевые лепестки, при помощи которых можно переключать передачи, не отрывая рук от рулевого колеса.
Устройство роботизированной коробки передач
Роботизированные коробки разных производителей могут несколько разниться по конструкции, но общий принцип функционирования таких агрегатов единый – любая роботизированная КПП представляет собой механическую коробку передач, которая наделена системой, управляющей передачами и сцеплением.
В коробках-«роботах» применяется фрикционный механизм сцепления. Для этого может использоваться отдельный диск, либо набор фрикционных дисков. Многие современные роботизированные коробки передач оборудуются системой двойного сцепления, при помощи которой обеспечивается передача крутящего момента с постоянным потоком мощности. Учитывая что основой любой роботизированной коробки передач является агрегат механического типа, производители используют, как правило, уже готовые решения. Так, к примеру, известный агрегат Speedshift, выпускаемый на мощностях Mercedes-Benz, построен на основе коробки 7G-Tronic, у которой гидротрансформатор заменен на многодисковое сцепление фрикционного типа. А для создания баварской роботизированной коробки SMG использован шестиступенчатый механический агрегат, доработанный сцеплением с электрогидравлическим приводом.
Примечательно, что «роботы» могут располагать, как гидравлическим, так и электрическим приводом передач и сцепления. Исполнительными узлами электрического привода коробки выступают сервомеханизмы (механическая передача с электромотором). Работа гидравлического привода коробки-робота осуществляется при помощи гидроцилиндров, управляемых электромагнитными клапанами. Подобная разновидность привода нередко именуется электрогидравлическим приводом. В некоторых роботизированных коробках передач, оснащаемых приводом электрического типа, например, Durashift, устанавливаемых на ряд моделей Ford, применяется гидромеханический блок, комплектуемый электродвигателем, который перемещает главный цилиндр привода сцепления.
Коробки-роботы с электроприводом устанавливают обычно на недорогие модели массовых брендов. Ведь электропривод, хотя и отличается невысоким энергопотреблением, не может обеспечить высокую скорость работы – переключение передачи составляет от 0.3 до 0.5 секунды. Система гидропривода в коробке требует наличие постоянного давления, достигаемое более высоким энергопотреблением. Роботы с гидравлическим приводом намного более быстродейственны – нередко роботизированные коробки с гидроприводом устанавливают даже на спортивные автомобили.
Управление «роботом» обеспечивается электронной системой, ответственной за включение и работу блока управления, входных датчиков и исполнительных механизмов. Такие основные параметры, как частота вращения, положение селектора или состояние вилок включения передачи, а также температура и давление масла (для системы с гидравлическим приводом) считываются датчиками и передаются к блоку управления. Затем электронный блок, на основании заложенной программы, вызывает необходимые воздействия на механизмы-исполнители. Стоит отметить, что в роботизированной КПП с гидроприводом система управления дополнена блоком, обеспечивающим функционирование гидроцилиндрами и обеспечивающим необходимый уровень давления.
В зависимости от типа привода, роль исполнительных механизмов роботизированной КПП выполняют электромоторы или электромагнитные клапаны, которыми оснащаются гидроцилиндры.
Коробка-робот с двойным сцеплением
Широкое распространение за последние пару лет получили роботизированные коробки передач с системой двойного сцепления. Дело в том, что главным недостатком стандартной коробки-робота считается довольно длительное время, требуемое агрегату на переключение передачи. Зачастую это вызывает провалы в динамике и рывки при активном стиле вождения, что негативно сказывается на уровне комфорта всей поездки в целом. Такая негативная особенность отпугивает немалое количество потенциальных автолюбителей от перспективы приобретения автомобиля, оборудованного роботизированной коробкой передач. Решением проблемы стало использование системы двойного сцепления, которая исключает разрыв потока мощности в момент переключения передачи. Двойное сцепление дает возможность выбрать требуемую передачу еще при включенной предыдущей передаче, и, в случае необходимости, включить следующую передачу не допуская перерыва в работе КПП. Благодаря такой конструктивной характеристике коробки передач с двойным сцеплением получили название преселективных коробок передач.
Еще одно важное достоинство коробок с двойным сцеплением – быстродействие при переключении передач. Здесь скорость перехода с одной передачи на другую зависит исключительно от скорости работы муфт. Так, «роботы» DSG от Volkswagen тратят на переключение не более 0.2 сек., а агрегаты DCT M Drivelogic, производимые компанией BMW, – всего 0.1 cек. Кроме того, «робот», оборудованный двумя сцеплениями, представляет собой весьма компактный агрегат, что особенно актуально для небольших городских малолитражек.
Отличия «робота» от «автомата»
Неискушенный автомобилист может не найти отличий между автомобилями, оборудованными автоматической и роботизированной коробками передач. Ведь в салонах таких машин отсутствуют педали сцепления, а селекторы переключения передач выглядят практически одинаково. Но на самом деле, с технической точки зрения, эти агрегаты значительно различаются между собой. Более того, конструктивно робот даже больше схож с механической коробкой. В отличие от «робота» или стандартной МКПП, основными узлами автоматической коробки являются редуктор и гидротрансоформатор, обеспечивающий плавное переключение передач. Именно гидротрансформатор выполняет функцию сцепления обычной МКПП, которым оснащается и РКПП. Таким образом, «робот» является механической коробкой передач, у которой за своевременность переключения передач отвечает электронный блок. А сами переключения производятся автоматически, посредством гидравлики и электронного управления.
Преимущества и недостатки роботизированных коробок передач
Оценивая плюсы и минусы роботизированных коробок передач, стоит отметить, что «робот» удобнее МКПП, ведь здесь не приходится постоянно орудовать рычагом переключения, а отсутствие необходимости выжимать педаль сцепления значительно уменьшает утомляемость водителя. Относительно АКПП, роботизированные коробки обеспечивают большую топливную экономичность и, как правило, имеют меньшую массу. Расход топлива у автомобиля с РКПП приближен к топливному расходу машины с «механикой». Стоимость роботизированной коробки передач также ниже по сравнению с коробкой-автоматом.
Что касается недостатков, то основные из них были названы выше – это ощутимые рывки и дергания при переключении передач, свойственные бюджетным автомобилям, оборудованным «роботами». Мало кого порадуют и длительные паузы при переходе с одной передачи на другую. Кроме того, начиная движение в горку, машина с РКПП, как и автомобиль с механической коробкой, может немного откатиться назад.
Впрочем, для объективности картины, стоит отметить, что все перечисленные недостатки устранены на агрегатах с двумя сцеплениями. Роботизированные коробки передач такого типа можно было бы считать оптимальными агрегатами, если бы не их высокая цена.
Роботизированная коробка Тойота: принцип работы коробки Toyota
За основу трансмиссии Freetronic была взята традиционная «механика» оснащенная электроприводами. Другое известное название «робота» Freetronic — ММТ (Multimode). Роботизированная трансмиссия может работать как в режиме «автомат», так и в ручном режиме.
Переключение передач в трансмиссии происходит при помощи трех электродвигателей. Один из них отвечает за выключение (выжим) сцепления, а два других за смену передач. Работой приводов управляет электронный блок управления (ТСМ), путем обработки сигналов с бесконтактных датчиков.
Трансмиссией Freetronic комплектовались автомобили марки Toyota с 2005 по 2009 гг. Это такие модели как: Corolla, Auris, Yaris, Aygo,Echo, Prius и другие. На моделях Yaris и Echo концерн Тойота впервые стал устанавливать автоматическое сцепление TFT.
Общее устройство
1 — индикатор в автомобиле, 2 — концевой выключатель рычага КПП, 3 — привод, 4 — датчик 1-2, 5 — датчик заднего хода, 6 — датчик нейтрали, 7 — датчик частоты вращения (КПП), 8 — датчик положения сцепления, 9 — электронный блок управления MMT — Фритроник.
Выключение и включение сцепления TFT в трансмиссии Freetronic происходит путем управления величиной давления жидкости, которая подводится к главному цилиндру сцепления. Коробка переключения передач оснащена датчиками, одни из которых следят за реальным положением селектора передач, а другие измеряют частоту вращения первичного вала КПП. Рычаг переключения оснащен концевыми выключателями упреждающими блок управления о намерениях водителя задействовать рычаг коробки переключения передач. При наличии неисправностей на панели приборов начинает мигать индикатор. Индикатор также сигнализирует водителю при его попытке неверного переключения.
Принцип работы роботизированной коробки Toyota
- До запуска двигателя сцепления всегда включено
- Пуск. После поворота ключа в положение зажигание (положение КПП – нейтраль) блок ММТ выполняет «выжим» сцепления и можно запускать двигатель
-
Начало движения. При включении первой передачи или передачи заднего хода и нажатии педали газа, блок ММТ мгновенно получает информацию об этом путем сигнала от датчиков и выдает команду золотниковому клапану на понижение давления, что ведет к включению сцепления и автомобиль трогается. Для плавного включения сцепления клапан золотника открывается постепенно, и полное его включение происходит после выравнивания частоты вращения коленвала и первичного вала КПП. Блок в этот момент дает команду на полное открытие канала главного цилиндра сцепления на слив.
- Смена передач. При отпускании педали газа и изменении положения рычага КПП, соответствующие датчики сообщают об этом в блок ММТ. Блок дает команду на «выжим» сцепления. Дальнейшее включение сцепления происходит после получения сигналов от датчиков нейтрали и «концевиков» рычага.
- Остановка. В момент торможения автомобиля входной вал КПП начинает вращаться с меньшим числом оборотов (ниже заданной нормы) и блок управления TFT выполняет «выжим» сцепления.
- Зуммер. Включается при возникновении внештатных ситуаций: ошибка при переключении вниз, попытка начала движения с передачи выше 3-й, чрезмерная нагрузка на сцепление, попытка запуска при включенной передаче, открыта дверь водителя при запущенном двигателе и положении рычага селектора соответствующее движению вперед или назад ( не нейтраль).
Box Robotics ускоряет AGV с помощью лидарных датчиков Ouster.

Том Панцарелла и Джон Сплетцер хорошо разбираются в складских помещениях. Как профессиональные робототехники и давние участники открытого исходного кода Robot Operating System (ROS), они помогли индустрии роботизированной автоматизации расти и развиваться до того уровня, на котором она находится сегодня. Теперь они думают, что готов к прорыву роста.
Том (слева) и Джон (справа) работают над своим программным обеспечением AGV на складе
После выхода из своего предыдущего стартапа Love Park Robotics в начале 2018 года Panzarella и Spletzer переключили свое внимание с чисто трехмерных задач компьютерного зрения и восприятия на алгоритмы, которые влияют на ходовые качества и автономность промышленных мобильных роботов.Они создают и коммерциализируют программный стек HD Mapping, а также поставляют на склад 3D-лидары дальнего действия через свою новую компанию Box Robotics.
youtube.com/embed/zCaH7fpxdF0″ frameborder=»0″ allowfullscreen=»allowfullscreen» data-service=»youtube»/>
Box Robotics, использующая Ouster OS1 с алогритом SLAM для отображения склада
Склады и производственные цеха — привлекательные места для роботизированной автоматизации, особенно при перемещении инвентаря с места на место. Склады предлагают структурированную среду с повторяющимися задачами, что делает их хорошо подходящими для роботизированной автоматизации.
Компании используют парк автоматизированных транспортных средств (AGV) для перемещения товаров по складу без участия человека-оператора. Эти развертывания приносят положительную отдачу от инвестиций в ответ на значительную нехватку рабочей силы и высокую текучесть кадров. Интерес отрасли к грузовым автомобилям с легким двигателем и беспилотным вилочным погрузчикам быстро растет.
Ранняя технология AGV опирается на примитивную систему наведения, состоящую из однолинейных планарных лазерных сканеров, которые часто также полагаются на тщательно размещенные отражающие маркеры, позволяющие транспортному средству определять свое местоположение и перемещаться по простой схеме. Эти системы ограничены в объеме возможностей, которые может выполнять робот, блокировать транспортное средство на заранее определенном «пути следования» и двигаться медленно. Людям часто приходится вмешиваться, чтобы спасти AGV из-за блокировок на направляющей, сбоев локализации из-за оборота запасов или столкновений с объектами, невидимыми для их примитивной системы безопасности. Даже когда они хорошо работают, они все равно двигаются медленно.
3D-лидар способен улавливать препятствия на складе, которые пропускаются традиционными 2D-лидарными датчиками.
Но с годами AGV стали умнее и быстрее.Используя комбинацию лидарных датчиков и камер с низким разрешением, AGV теперь могут выполнять относительно сложные задачи с приемлемой скоростью, обычно от 1,5 до 2,0 метров в секунду, в менее четко определенной среде.
Но Box Robotics не удовлетворены просто приемлемыми скоростями. Вилочные погрузчики с ручным приводом движутся со скоростью, вдвое превышающей скорость современных AGV, и с гораздо большей маневренностью. Зная, что чем быстрее робот может безопасно путешествовать, тем эффективнее и рентабельнее он будет, Том и его команда черпали вдохновение из индустрии беспилотных автомобилей и решили создать совершенно новый стек автономности HD Mapping.
Алгоритм сегментации Box Robotics при обнаружении людей на складе
Решение Box Robotics, Warehouse HD, , состоящее из проприетарного программного обеспечения, готового оборудования и поддерживаемое набором профессиональных услуг, может быть модернизировано на платформах AGV и легко интегрируется с существующими системами управления приводом транспортных средств.
Датчик 3D LiDAR с высоким разрешением — ключевой компонент Warehouse HD. «Мы опробовали и протестировали каждый датчик, который вы могли купить за последние 15 с лишним лет, начиная с очень простых однолинейных сканеров, стереокамер, 3D LiDAR низкого разрешения, а теперь и 3D LiDAR высокого разрешения от Ouster. LiDAR с высоким разрешением и большим радиусом действия абсолютно необходим для безопасного увеличения скорости AGV », — говорит генеральный директор Box Robotics Том Панцарелла.
Для коммерческого развертывания AGV скорость является критическим фактором затрат
Сегодня большинство промышленных AGV движутся с максимальной скоростью 1,5–2,0 метра в секунду. Но можно получить огромную экономию средств — до 35% — за счет увеличения скорости до 3,0 метров в секунду. Box Robotics работает напрямую с производителями AGV и поставщиками решений для этого, и датчики Ouster являются ключевым инструментом для Тома, Джона и остальной команды Box.
Можно сказать, что им нужна… жажда скорости.
«Датчики Ouster действительно потрясли рынок своей великолепной производительностью и агрессивной ценой, которую мы можем оправдать с точки зрения преимуществ, которые дает нам более высокое разрешение. Мы пишем алгоритмы, которые локализуют, классифицируют интересующие объекты и планируют траектории движения транспортных средств через участки, загроможденные препятствиями, включая людей и другие объекты, которые современные сканеры безопасности просто не видят. Мы делаем это на более высоких скоростях, чем когда-либо прежде. Для этого абсолютно необходимо разрешение, которое дает нам Оустер », — добавляет Джон Сплетцер, технический директор.
Ouster очень рад стать предпочтительным 3D-лидаром для команды робототехники Box и надеется увидеть их прогресс в ближайшие годы.
КомпанияBox Robotics была основана в 2019 году и была приобретена Seegrid в октябре 2020 года. Подробнее: https://seegrid.com/box-robotics/
Box Robotics использует OS1-16 и OS1-32 (конфигурация луча ниже горизонта).Узнайте больше о датчиках здесь.
Boston Dynamics представляет Stretch: нового робота, предназначенного для перемещения ящиков на складах
Boston Dynamics наиболее известна своей роботизированной собакой Spot, машиной, предназначенной для работы в различных средах, от морских нефтяных вышек до глубоких подземных шахт. Но в последние годы компания все больше внимания уделяет логистике, и сегодня она представляет нового робота, предназначенного только для одного применения: перемещение ящиков на складах.
Робот называется Stretch и выглядит довольно скучно для творения Boston Dynamics.Он не создан по образцу людей или животных, а нацелен на то, чтобы быть максимально практичным. Он имеет квадратную мобильную базу, содержащую набор колес, «мачту восприятия» с камерами и другими датчиками, а также огромную роботизированную руку с семью степенями свободы и набор присосок на конце, который может захватывать и перемещать ящики до 23 килограммы (50 фунтов) в весе.
Что связывает Stretch с другими машинами Boston Dynamics, так это мобильность. Обычно, когда оборудование для автоматизации устанавливается на складах, система крепится болтами в одном месте с моделированием рабочего процесса вокруг этого.Stretch, для сравнения, предназначен для того, чтобы скользить в любое существующее рабочее место, где он может быть полезен при загрузке или разгрузке товаров.
«Все зависит от того, в чем проблема сегодняшнего дня».
«Вот что замечательно в этой системе: она может обеспечить автоматизацию сред, в которых нет инфраструктуры автоматизации», — сказал The Verge вице-президент Boston Dynamics по развитию бизнеса Майкл Перри. «Вы можете воспользоваться этой возможностью, и вы можете переместить ее в кузов грузовика, вы можете переместить ее в проходы, вы можете переместить ее рядом с вашими конвейерами.Все зависит от того, в чем проблема сегодняшнего дня ».
Это позволит Boston Dynamics ориентироваться на клиентов, которые в противном случае избегали бы автоматизации, поскольку ее интеграция слишком дорога или требует много времени, — говорит Перри. Около 80 процентов складов в мире не имеют оборудования для автоматизации, что дает компании значительный доступный рынок.Но у Stretch пока нет ценника, и вполне возможно, что для предприятий с низкой рентабельностью робот не стоит хлопот, независимо от того, насколько он мобильный.
Boston Dynamics проявляет интерес к логистике с 2019 года, когда она приобрела Kinema Systems, компанию, которая производит программное обеспечение машинного зрения для роботов на складах. Затем он разработал колесного робота под названием Ручка, который мог перемещать ящики с помощью роботизированной руки, балансируя себя с помощью огромного качающегося противовеса, такого как хвост.
Перри говорит, что Handle имеет «подходящую площадь и зону действия» для складов, но не может работать достаточно быстро. Рука робота прикреплена непосредственно к его основному корпусу, что означает, что вся машина должна перемещаться с каждым грузом. Для сравнения, рука Stretch свободно поворачивается благодаря некоторым умным (и запатентованным) противовесам, спрятанным внутри его квадратного основания.
«Это действительно секретный соус», — говорит Перри. «Эта основа способна выдерживать инерционную силу руки, а также коробку, раскачивающуюся под большим весом, без необходимости полагаться на стальную пластину весом в несколько тысяч килограммов, прикрученную к полу.”
Вакуумные захваты Stretch означают, что они могут работать только с коробками с плоскими поверхностями, что ограничивает их полезность на определенных складах.
Stretch можно проследить до двуногого робота Atlas от Boston Dynamics, который так плавно балансирует свой вес, что может бегать, прыгать, сальто и т. Д. «Атлас, поднимающий коробку, — это не просто вытягивание рук и их перемещение, а координация бедер, ног и туловища», — говорит Перри.«Многое из того же дизайнерского мышления вошло в Stretch».
В результате Boston Dynamics утверждает, что Stretch может перемещать до 800 ящиков в час, что сопоставимо с производительностью человека-сотрудника. Аккумуляторы большой емкости означают, что Stretch может работать в течение восьми часов подряд, прежде чем потребуется подзарядка.
Однако к такой пропускной способности следует относиться скептически. Заставить роботов работать на складах невероятно сложно из-за большого разнообразия этих пространств.Рабочие процессы могут меняться каждый день по мере того, как приходят и уходят разные товары, и часто ценится гибкость. Неспособность машин справиться с этими проблемами до сих пор привела к динамике автоматизации по принципу «все или ничего». Вы либо переделываете весь склад, чтобы он был достаточно регулярным, чтобы его могли понять машины, либо вы остаетесь с людьми, хозяевами неизвестного.
Boston Dynamics заявляет, что Stretch сможет преодолеть этот разрыв. Компания заявляет, что роботом может управлять любой человек, прошедший всего несколько часов обучения, и что его мобильная база означает, что он может размещаться в пространствах, предназначенных для людей.Это будет работать? Мы узнаем об этом только тогда, когда Stretch возьмется за дело. Boston Dynamics заявляет, что в настоящее время ищет клиентов для пилотного тестирования Stretch и планирует коммерческое внедрение в 2022 году.
Автоматическая машина для резки коробок | CASi-IBOD | CASI
CASi-IBOD (интеллектуальное устройство открывания ящиков) является краеугольным камнем решений CASI по автоматизации. CASi-IBOD — это встроенный проходной открыватель ящиков и открыватель ящиков с автоматической обрезкой ящиков для безопасного извлечения инвентаря. Интеграция автоматической резки коробок позволяет быстрее извлекать продукт за счет безопасного разрезания и извлечения предметов, устраняя необходимость использования резака человеком.
Благодаря встроенному интеллектуальному устройству, измеряющему размер каждого поступающего ящика, в каждой ящике делаются точные надрезы. Коробки можно кормить в любом порядке любого размера. CASi-IBOD повысит производительность, исключит травмы и сведет к минимуму повреждение продуктов, связанных с ручной резкой коробок.
Как это работает
CASi-IBOD — это полностью автоматическая, самоподдерживающаяся и самоустанавливающаяся система. В системе используются фотооптические измерения и измерения линейного смещения для измерения каждой коробки. После того, как коробка определена по размеру, она автоматически захватывается и размещается для резки.
Программируемое устройство перемещения преобразует предписанный шаблон вырезки для каждого размера коробки. Упоры для лезвий и коробчатый упор используются вместе, чтобы дать режущему роботу квадратную и неподвижную цель. Затем робот IBOD использует интеллектуальное программное обеспечение для автоматизации, чтобы разрезать коробки в соответствии с точными спецификациями, определенными заказчиком.
Прочная конструкция
IBOD имеет прочную сварную стальную конструкцию. Компоненты изготовлены из четырехдюймовой сварной стальной трубы с толстыми стальными панелями и ограждением.Передняя боковая панель и дверца доступа сделаны из акрила толщиной 0,70 дюйма для обеспечения жесткости и безопасности.
ХарактеристикиДва варианта
- IBOD Single может разрезать верхние ящики со скоростью до 500 коробок в час
- IBOD Duo способен открывать до 900 коробок в час.
Три основных конфигурации резки
- Верх коробки
- Переднее окно подборщика
- Разрезы для уплотнения ленты
- По запросу может быть разработан индивидуальный разрез
Другие особенности
- Интегрированная система измерения размеров
- Простота использования сенсорный экран Человек Интерфейс (HMI)
- Интегрированная диагностика
- Выбор динамической схемы реза
- Динамически программируемая глубина резания
- Автоматический контроль износа полотна
GoBox — подписка на робота — Dexter Industries
Вдохновляет всех учащихся.
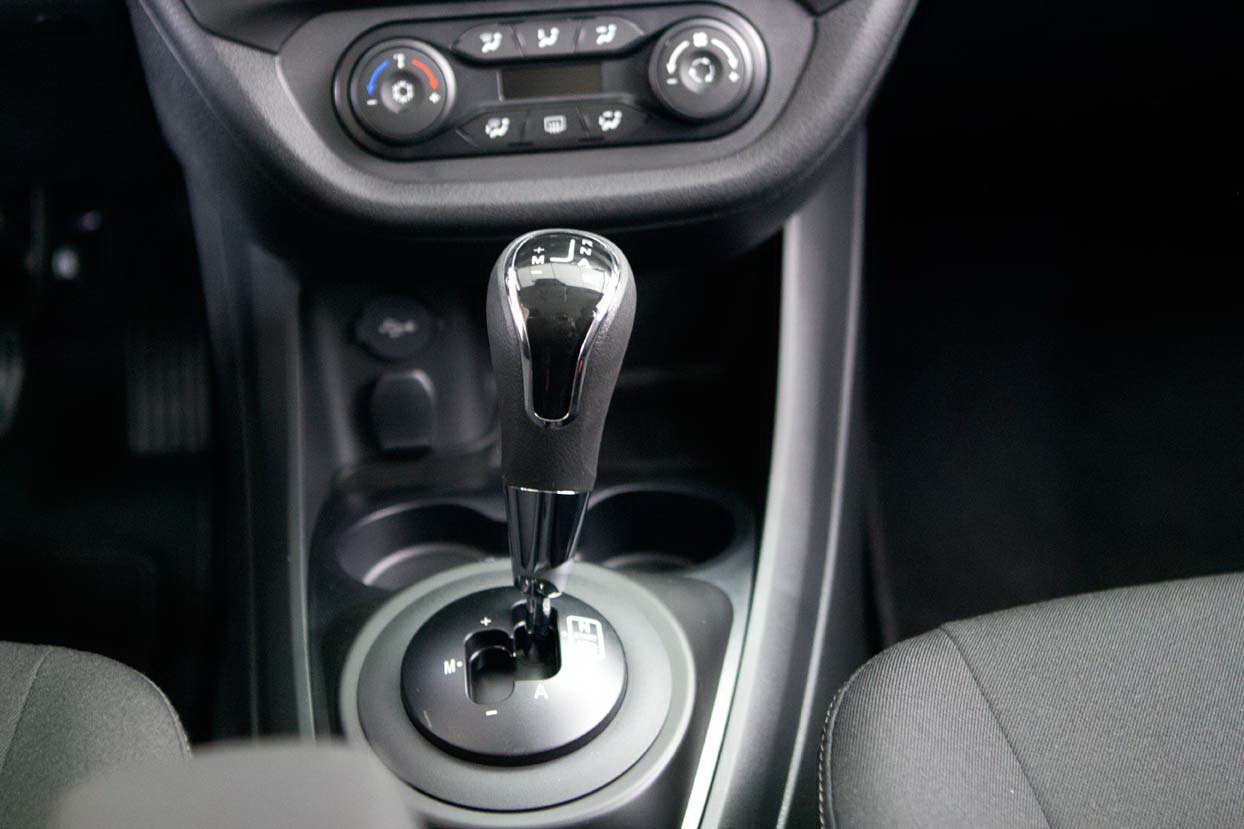
Мы считаем, что чем больше кто-то знает о том, как работают технологии, тем эффективнее и успешнее он будет в любой выбранной ими карьере. Однако способ преподавания технологий, таких как инженерия и информатика, ориентирован на людей с особым стилем обучения и часто может быть скучным и разочаровывающим для многих из нас, потому что он требует огромных базовых знаний.
Чтобы решить эту проблему, мы создаем простой в использовании набор для роботов, который позволит любому человеку с любым опытом узнать о программировании и технологиях.
Что такое GoPiGo? GoPiGo — это основа GoBox. GoPiGo — это автомобиль-робот, который мы спроектировали и построили. Благодаря потрясающим отзывам, которые мы получили от тысяч пользователей и нашего процветающего творческого сообщества, мы узнали, как упростить сборку, сделать его более долговечным и сделать его более интересным в использовании! Все эти улучшения были внесены в GoPiGo3.
Электроника и программирование
GoPiGo построен на основе действительно изящного одноплатного компьютера Raspberry Pi за 40 долларов.Он был разработан британским фондом несколько лет назад и покорил мир образования, благодаря чему молодым людям стало проще, чем когда-либо, получить электронику и научиться программировать. Ее легко использовать, и мы считаем, что это лучшая платформа для новичков, поскольку не требует каких-либо предварительных знаний.
Узнайте больше о Raspberry Pi и некоммерческом фонде, который его поддерживает, здесь.
GoBox и автомобиль-робот GoPiGo Raspberry Pi являются частью сообщества разработчиков оборудования с открытым исходным кодом.
Языки программирования
GoBox отлично подходит для новичков, потому что все миссии находятся в Bloxter, нашем блочном языке, похожем на Scratch. Вы также можете запрограммировать робота GoPiGo на многих других языках, включая Python, Scratch, Node.js и Go. Наше замечательное сообщество даже разработало Windows10 для GoPiGo! Не знаете, что это за языки? Не волнуйтесь, GoBox поможет вам изучить основы!
Когда мы рассмотрели, как сделать GoBox доступным и интересным для всех уровней навыков, мы решили использовать Bloxter, наш новый блочный язык, похожий на Scratch.
Bloxter — это простой язык перетаскивания, который мы разработали для обучения новых программистов программированию. Вместо типичных строк кода вы будете использовать простые формы и графику для программирования своего робота.
Почему ежемесячная подписка?
Это дар, который дарить не перестает. Ваш ежемесячный GoBox поставляется со всем необходимым для выполнения новой миссии, изучение которой продолжается месяц за месяцем.В большинстве миссий также есть датчик, который вы можете прикрепить к GoPiGo и использовать для выполнения миссии! Каждая миссия основывается на следующей, поэтому вы осваиваете новые навыки и продолжаете заниматься в течение определенного периода времени — что, по нашему мнению, является ключом к успеху!
Что такое миссия?
Что может быть интереснее миссии? Наша команда иллюстраторов, учителей, инженеров и дизайнеров создает красивые и простые для понимания материалы, которые проведут вас через историю, которая поможет вам достичь чего-то интересного с вашим GoPiGo и каждым новым датчиком.
Миссия 3, например, не только обучает концепциям биомимикрии, но и делает это таким образом, что объясняет такие концепции программирования, как , если и , иначе операторы , то, как роботы считывают данные датчиков, такие понятия, как пороги , и математические понятия, такие как средние значения . и как они применяются в кодировании.
Каждая миссия будет сопровождаться полезными видеороликами, которые помогут вам начать работу и проведут вас через определенные части миссии.
Учимся в игреИнженерные концепции
В каждой миссии заложены фундаментальные инженерные принципы. GoBox учит новым способам думать о том, как подходить к проблемам и решать их.
Каждая миссия представляет проблему и предоставляет инструменты для решения проблемы по-своему. Наши миссии поощряют подход теории дизайна: сформулировать проблему, спроектировать, построить, написать код, протестировать и повторить.
Это позволяет студентам находить свои собственные ответы и побуждает их придумывать свои собственные миссии!
Концепции программирования: делаем их осязаемыми.
С GoBox вы не просто играете с роботом, вы фактически изучаете концепции программирования, даже не чувствуя себя на уроке информатики. Робот делает весь процесс программирования и программирования осязаемым и реальным.
Некоторые концепции, которым обучают в 12 миссиях GoBox, включают: структуру программы, операторы if then, навсегда до управляющих структур, переменные, циклы, вложенные циклы, ожидания, последовательность, конечный автомат, входы и выходы, широковещание, условные операторы, итерация, переменные, случайные числа, обработка событий, параллельное выполнение и логическая логика.
Не знаете, что означают все эти термины? Нет проблем — это именно то, чему GoBox призван научить.
Не просто игрушка…
Поскольку GoPiGo также можно программировать на Python, Go, Node. js и растущем списке других языков, поддерживаемых нашим сообществом, когда вы или ваш ребенок перерастете Bloxter, вас ждет целый мир мощных языков программирования! Кроме того, поскольку GoPiGo имеет открытый исходный код, наше активное сообщество постоянно добавляет новые примеры, языки и функции.
- GoPiGo3 — новая улучшенная версия GoPiGo! Вы получите совершенно новую версию робота GoPiGo для Raspberry Pi. Робот прост в сборке и превращает ваш Raspberry Pi в роботизированную машину! (работает со всеми версиями Raspberry Pi)
- Миссии — Все миссии доступны через нашу онлайн-платформу Dexter Studio.
- Дополнительные припасы — Каждая миссия будет сопровождаться дополнительными припасами, которые помогут вам добавить больше функций к вашему GoPiGo для выполнения миссий.
- GoPiGo Line Follower — Датчик GoPiGo Line Follower помогает запрограммировать GoPiGo на поиск линий, написанных на поверхности, и следование им.
- Датчик освещенности и цвета — Датчик освещенности определяет различные уровни света вокруг GoPiGo и позволяет вам запрограммировать робота, чтобы он реагировал на эти показания любым способом, который вы выберете! Он также может определять разные цвета.
- Датчик звука — Датчик звука считывает уровень шума вокруг GoPiGo и позволяет использовать эти данные, чтобы заставить GoPiGo реагировать на изменения шума.
- Датчик расстояния — Датчик расстояния показывает, как далеко GoPiGo находится от твердого объекта. Его можно использовать для измерения расстояния до стены, человека или другого объекта.
- Зуммер — Зуммер добавляет к GoPiGo звук и оповещения. Сделайте звук с помощью GoPiGo, чтобы отправить оповещение или напугать своих кошек!
- LED — Светодиод добавляет подсветку вашему GoPiGo. Этот светодиод можно прикрепить к GoPiGo, чтобы добавить немного персонализации, помочь отладить программы и осветить комнату.
- Датчик движения — Датчик движения обнаруживает движущиеся объекты вокруг GoPiGo.
- Кнопка — Добавьте кнопку на свой GoPiGo. Вы можете подключить датчик кнопки к GoPiGo, чтобы приказать роботу двигаться разными способами и делать разные вещи.
- Инфракрасный датчик и пульт дистанционного управления — Отправляйте команды на GoPiGo с пульта дистанционного управления!
Роботизированная укладка ящиков на поддоны
Роботизированная укладка ящиков на поддоны
Дата коробки
Картонные коробки изготовлены из перерабатываемых материалов, используемых для упаковки товаров и расходных материалов.Это может относиться к различным плотным материалам, похожим на бумагу, включая картон. До изобретения ящиков преимущественно использовались деревянные ящики. Стоимость этих ящиков и сложность их изготовления привели к использованию посылок.
Производство коробок было впервые осуществлено сэром Малькольмом Торнхиллом в 1817 году. В начале 1900-х годов компания Kellogg Brothers сделала использование картона популярным во всем мире.
Производство коробки
Гофрированный картон проходит через машины, чтобы превратить его в картонные коробки после производственного процесса.В соответствии с сегодняшними технологиями сложенный картон готовится путем прохождения через блоки печати, резки и упаковки в машинном парке.
Использование коробки
Karon используется в таких областях, как коробки, косметика, ювелирные изделия, текстиль, готовая одежда, продукты питания, электронная коммерция, розничная торговля, бытовая техника, промышленность, подарки, логистика, сухие продукты для тортов, мороженое в порошковые стиральные порошки, игрушки. , текстиль, кожгалантерея.
Роботизированная укладка ящиков на поддоны
Воспользуйтесь многими преимуществами роботизированного укладывания на поддоны, включая гибкость и надежность. Он признает, что роботизированные системы укладывания на поддоны имеют значительное снижение стоимости владения по сравнению с обычными укладчиками на поддоны. Нет необходимости в ежегодной регулировке или замене цепи и пневмоцилиндра, что снижает затраты на текущее обслуживание. Сегодняшние роботы доказали рекордное время наработки на отказ (среднее время наработки на отказ) более 60 000 часов.
Роботизированный укладчик ящиков на поддоны предлагает комплексные решения для укладки на поддоны, которые включают конвейеры, межслойную подачу, подачу многослойных листов, устройства подачи поддонов.
Роботизированная укладка ящиков на поддоны позволяет быстро и легко регулировать штабель поддонов, загружать сохраненные конфигурации поддонов или создавать новые конструкции поддонов, адаптированные для легкого управления оператором и расширенного программирования поддонов.Он сочетает в себе мощное программирование с оперативным обменом данными и обменом данными между несколькими сайтами. Конфигурации поддонов, спроектированные на одной линии или в одном месте, могут быть переданы и использованы для всех заводских роботизированных ящичных поддонов.
Этот революционный дизайн улучшает предыдущие разработки, делая дизайн действительно прочным. Роботизированная укладка ящиков на поддоны гарантирует, что ящики можно укладывать на поддоны без каких-либо повреждений и с большим количеством пневматического оборудования с более прочной механической конструкцией и улучшенной динамической структурой, чтобы они работали долгие годы.
Прослеживаемость обеспечивается путем наклеивания желаемого штрих-кода и этикетки на каждую производимую коробку, обеспечивая полную автоматическую работу линии с открытием и обвязкой коробок, а за счет интеграции с системой ERP экономится время обращения бумаги и записи.
Преимущества роботизированной укладки ящиков на поддоны
Укладка ящиков и посылок на поддоны выполняется точнее и быстрее.
Снижены затраты на рабочую силу.
Предотвращены повреждения, вызванные человеческим фактором.
Благодаря специально разработанным роботизированным руками, роботизированная укладка ящиков на поддоны происходит без повреждения продуктов.
Объем вашей продукции увеличивается с появлением серийной производственной линии.
У вас будет измеримая производственная линия, ваше общение с клиентами станет более эффективным и надежным.
Предотвращаются несчастные случаи с рабочими, которые происходят во время укладки тяжелых посылок и ящиков на поддоны.
Ваше производство никогда не останавливается, оно продолжается 24 часа в сутки, 7 дней в неделю.
Heads Up Display — Библиотека Boom Box
ПОДРОБНЕЕ
- 621 звуковой эффект
- 150 стерео.wav файлы
- 1,28 ГБ
- 24 бит / 96 кГц
- встроенные метаданные
ОПИСАНИЕ
Библиотека звуковых эффектов Heads Up Display — первая часть коллекции Robotic Creations. Каждая библиотека из коллекции Robotic Creations Collection содержит звуковые эффекты, разработанные для соответствия пяти различным роботам-личностям с их собственными уникальными звуковыми характеристиками: Мимо, приятель-робот; Q5, винтажный робот; NGage, экзокостюм; Грегори, андроид; и брандмауэр, механический костюм.
Наша библиотека выглядит так, как будто она содержит всего 150 файлов, но каждый файл включает множество звуковых эффектов для удобства использования при редактировании. Чтобы помочь вам работать быстрее и эффективнее, вы найдете:
- Все более короткие звуковые файлы включают несколько итераций, предоставляя вам множество опций в рамках одного звукового семейства. Больше не нужно искать новый файл или манипулировать одним отличным звуком, когда вам нужно ввести тонкие вариации.
- Все более длинные звуки плавно повторяются.Не нужно тратить драгоценное время на поиск нужного места для создания петли.
Эта библиотека содержит внутренние технические звуки, которые вы можете услышать на каждом отдельном дисплее робота, например:
- 150+ звуковых сигналов интерфейса
- 80+ звуковых сигналов успеха
- 70+ аварийных сигналов
- 50+ считываний данных
- 45+ обратных отсчетов
- 15+ сигналов тревоги
- 100+ бонусов
- 95+ отключений питания
ТЕХНИЧЕСКИЙ ЛИСТ
ПЯТЬ ЛИЧНОСТЕЙ РОБОТОВ, БЕСКОНЕЧНЫЕ ВОЗМОЖНОСТИ
Каждая библиотека из коллекции Robotic Creations Collection содержит звуковые эффекты, разработанные для соответствия пяти различным роботам-личностям с их собственными уникальными звуковыми характеристиками.
СКАЧАТЬ ЦИФРОВУЮ
Вы получите ссылку для скачивания в течение 24 часов после покупки.
БЕЗ ВОЗВРАТА / ОБМЕНА
Мы не предлагаем возврат или обмен, так как это цифровой продукт.
Робот-страус Boston Dynamics может «справиться» с задачами укладки ящиков
Робот Boston Dynamics подбирает и складывает коробки.(Boston Dynamics через YouTube) Последнее роботизированное созданиеBoston Dynamics может быть симпатичнее, чем его жуткие собаки-роботы, но его потенциальное применение может, тем не менее, насторожить складских рабочих.
Робот Handle, показанный в видео на YouTube, опубликованном в четверг, представляет собой длинношеего робота, который очень похож на двухколесного механического страуса. «Голова» робота состоит из присосок, которые могут поднимать коробки с поддона, а затем отпускать их, образуя аккуратную стопку.
Вот как Boston Dynamics описывает Handle в описании видео:
«Handle — это мобильный робот-манипулятор, разработанный для логистики.Handle самостоятельно выполняет сборку поддонов со смешанными SKU и депалетизацию после инициализации и локализации на поддонах. Бортовая система технического зрения на ручке отслеживает отмеченные поддоны для навигации и находит отдельные коробки для захвата и размещения.
«Когда Handle помещает коробки на поддон, она использует контроль силы, чтобы прижать каждую коробку к своим соседям. Ящики, использованные в видео, весят около 5 кг (11 фунтов), но робот предназначен для работы с ящиками до 15 кг (33 фунта).Эта версия Handle работает с поддонами глубиной 1,2 м и высотой 1,7 м (48 дюймов в глубину и 68 дюймов в высоту) ».
Склады служили демонстрационными площадками для многих других существ Boston Dynamics, включая воплощения четвероногого собачьего SpotMini (которые выглядят как робо-доберманы в страшном эпизоде сериала Netflix «Черное зеркало») и его гуманоида.