Причины возникновения неисправностей в приборах
Неисправности в приборах возникают по самым различным причинам. Основными из них являются следующие:
Износ при длительной эксплуатации. В результате длительной эксплуатации изнашиваются керны, концы осей, камни, нарушается балансировка, изменяются свойства магнитов, ослабевает крепеж, окисляются (ржавеют) металлические части приборов.
Перегрузки. При перегрузках возникают механические и электрические неисправности. К таким неисправностям относятся нарушение изоляции, обрывы в цепях, короткие замыкания в катушках, рамках и добавочных сопротивлениях, обгорание зажимов, потемнение стекла и шкалы приборов, повреждение стрелки и смещение ее относительно оси, деформация подвижной части прибора.
Систематические вибрации вызывают чисто механические неисправности в приборах, связанные с появлением дополнительного трения в опорах.
Работа при пусковых режимах и частых включениях.
Вследствие
большой величины пусковых токов при
включении двигателей приборы работают
в особо тяжелых условиях.
Плохое уплотнение корпусов. Вследствие плохого уплотнения корпусов- внутрь приборов попадает пыль и ферромагнитные частицы. Пыль, попадая в углубление (кратер) камня, создает дополнительное трение, вызывает увеличение вариации, ускоряет износ керна и камня. Ферромагнитные частицы, попадая в зазоры постоянного магнита подвижной системы, в зазор магнита тормоза (у счетчиков) или в зазор магнита успокоителя, препятствует свободному перемещению подвижной системы прибора, образуют задевания (зацепления) ее деталей о детали неподвижной части.
Длительное
хранение приборов. При длительном хранении приборов часто
подвергаются коррозии оси (керны). В
результате этого у многих приборов
появляется затирание, т. е. несвободное
перемещение подвижной части. Кроме
того, имеют место и ряд других причин,
приводящих к возникновению неисправностей.
К ним относятся воздействие на приборы
высоких и низких температур, сырости,
агрессивных паров и газов, нарушение
правил и инструкций по эксплуатации
приборов, небрежное обращение с приборами
при эксплуатации и транспортировке и
др.
Общие неисправности электроизмерительных приборов
Среди всех возможных неисправностей, встречающихся в электроизмерительных приборах, можно указать на ряд неисправностей, характерных для всех приборов непосредственного отсчета.
Такими неисправностями являются: прибор не дает показаний; прибор дает заведомо неверные показания; вариация прибора превышает установленные нормы; погрешность прибора выше нормы; невозвращение указателя в нулевое положение превышает норму;
Кроме указанных выше неисправностей, в электроизмерительных приборах могут встречаться и другие неисправности или повреждения: трещины и вмятины на корпусе, разбито или отклеилось стекло, отсутствует часть крепежа; сломана или погнута стрелка, расшатаны зажимы и др.
Методика обнаружения неисправностей
Для
обнаружения неисправностей
электроизмерительные приборы подвергаются:
внешнему осмотру без вскрытия прибора;
внутреннему осмотру после вскрытия
прибора; проверке под током (напряжением).
Внешний осмотр прибора производится до снятия с прибора крышки или кожуха. При этом проверяют состояние корпуса, работу корректора, арретира, отсутствие повышенного трения в опорах, уравновешенность подвижной части, наличие свободного перемещения указателя, целость электрической цепи, величины сопротивлений постоянному току, отсутствие посторонних предметов, отсоединившихся деталей и т. п.
При проверке корпуса обращают внимание на отсутствие трещин, сколов, вмятин, плохого прилегания крышки (кожуха) к корпусу, стекла к крышке, на наличие необходимого крепежа, исправность зажимов и т. п.
Винт (головка) корректора при проверке должен свободно перемещаться в правую и левую стороны, при этом указатель прибора должен отклоняться в правую и левую стороны относительно нулевой отметки шкалы.
Исправный механический арретир в положении «Арр.» должен скреплять подвижную часть с неподвижной, снимая тем самым нагрузку с растяжек или подвесов прибора.
Наличие
дополнительного трения в опорах прибора
проверяется по несвободному (неплавному)
перемещению указателя при медленном и
многократном поворачивании винта
(головки) корректора. Наличие дополнительного
трения в опорах можно также определить
по величине смещения указателя. Для
этого указатель отклоняют корректором
на некоторый угол и затем замечают, на
какую величину сместится он относительно
установившегося положения при легком
постукивании карандашом (пальцем) по
крышке (стеклу) прибора. Если величина
смещения указателя больше допустимой,
то это указывает на наличие дефекта в
опорах: затупление керна, повреждение
камня или слишком сильное зажатие между
подпятниками подвижной системы.
Уравновешенность подвижной системы определяется по величине смещения указателя с нулевой отметки шкалы при наклоне прибора в. разные стороны на установленный для него угол. Если при этом величина перемещения указателя превышает установленную для прибора норму, подвижную часть прибора необходимо уравновесить (отбалансировать).
Свободное
перемещение указателя определяется
путем поворота прибора в горизонтальной:
плоскости вокруг оси подвижной части;
при этом наблюдают, насколько свободно
перемещается указатель прибора.
Исправность электрических цепей и величина их сопротивления определяются при помощи тестера (омметра).
Внутренний осмотр. После проведения внешнего осмотра и при наличии неисправностей прибора снимают его кожух (крышку) и производят внутренний осмотр с целью обнаружения неисправностей и установления характера повреждения (неисправности).
При внутреннем осмотре проверяется возможность свободного перемещения подвижной части по всей шкале, определяется место обрыва электрической цепи, состояние изоляции катушек, внутренних шунтов, моментных пружин, растяжек, отсутствие коррозии металлических деталей и т. п.
Возможность
свободного перемещения подвижной части,
вдоль всей шкалы определяется путем
дутья на стрелку прибора в направлении
ее движения. Доведя таким образом стрелку
до верхнего предела шкалы, прекращают
дутье и наблюдают за перемещением
стрелки. При наличии задеваний, стрелка
прибора будет возвращаться неплавно,
скачками, или остановится, не дойдя до
нулевой отметки.
Задевание может произойти между крылом или сектором успокоителя и стенками камеры или магнита успокоителя, между рамкой прибора и полюсными наконечниками, между стрелкой и неровностями, шероховатостями шкалы.
Определение места обрыва электрической цепи прибора производится при помощи тестера или пробника путем последовательной поэлементной проверки всей цепи, при этом наиболее вероятными точками обрыва цепи могут быть места соединения (спая) катушек, пружин, рамок, токоподводов и т. д. Поврежденный участок цепи (катушки, шунты, добавочные сопротивления) можно определить по изменению цвета изоляции и наличию характерного запаха.
Проверка прибора под током (напряжением) производится на специальных стендах (установках) постоянного и переменного тока с использованием образцовых мер и измерительных приборов,.
При
данной проверке определяют плавность
перемещения указателя вдоль всей, шкалы,
возвращение указателя, к нулевой отметке
шкалы, исправность электрических цепей,
величины погрешностей и вариации
показаний на основных (оцифрованных)
отметках и влияние наклона.
Плавность перемещения указателя вдоль всей шкалы проверяется путем плавного изменения тока (напряжения) от нуля до максимума « обратно при одновременном наблюдении за характером перемещения стрелки по всей шкале. Неплавное перемещение указателя свидетельствует о наличии затирания или задевания деталей подвижной части прибора о неподвижные. Затирание — неисправность, вызванная нарушением кернов, концов, осей, подпятников или малым зазором между осью и подпятником. Этот вид неисправности обычно определяется до включения прибора в схему.
Задевание в приборе не связано с нарушением кернов и подпятников. Оно обуславливается незначительным касанием подвижной части о неподвижную и выявляется в ‘большинстве случаев при включении прибора в схему.
Невозвращение
стрелки на нулевую отметку шкалы
определяется в процессе проверки
плавности ее перемещения при плавном
изменении тока (напряжения) от максимума
до нуля. Перед проверкой стрелка прибора
должна быть поставлена корректором на
нулевую отметку шкалы.
Если стрелка возвращается на нулевую отметку после легкого постукивания по прибору, то это указывает на наличие повышенного трения в опорах. Невозвращение стрелки на нуль может быть также и от уменьшения противодействующего момента, вызванного отжигом или деформацией спиральных пружин (растяжек), или вследствие незначительного задевания подвижной системы о какую-либо неподвижную часть прибора.
При включенном в схему приборе проверяются исправность электрических цепей, соответствие его классу точности по допускаемой погрешности и вариации показаний. При этом одновременно проверяется постоянство показаний прибора.
Непостоянство
показаний прибора может явиться
результатом плохого контакта, межвитковых
замыканий, плохого закрепления стрелки
или лепестка на оси прибора. Если стрелка
после установки на отметку смещается
с нее, в то время как стрелка образцового
прибора находится в покое, то это
указывает на слабый контакт в цепи
испытуемого прибора. Такой прибор
необходимо включить в схему омметра
или моста для измерения сопротивления
и слегка дотрагиваться изоляционной
палочкой, до отдельных проводников и
деталей прибора (исключая подвижную
часть). При непостоянном контакте стрелка
омметра или гальванометра моста будет
колебаться. Если слабый контакт не будет
обнаружен, необходимо после разборки
прибора проверить рамку. Часто плохой
контакт бывает в местах спая концов
обмотки рамки с пружинодержателем.
Основные неисправности и техническое обслуживание контрольно-измерительных приборов
Основными неисправностями спидометра являются неправильное показание скорости движения автомобиля из-за разрегулировки скоростного узла, колебание стрелки спидометра, заедание барабанчиков счетного узла. Перед устранением неисправности спидометра необходимо проверить исправность гибкого вала его привода: не ослабло ли крепление гаек, соединяющих гибкий вал со спидометром и с коробкой передачи, и не оборван ли трос. В случае обрыва троса перед установкой на автомобиль нового гибкого вала надо установить причины обрыва. Одной из причин обрыва троса может быть заедание в спидометре. Для Проверки этого нужно присоединить конец гибкого вала к спидометру и медленно проворачивать рукой свободный конец троса. При этом не должно ощущаться никаких заеданий и стрелка спидометра не должна отходить от нулевого деления. При резком проворачивании троса в рабочем направлении стрелка должна резко отклониться от нулевого деления, а затем свободно вернуться обратно.
Колебание стрелки спидометра возникает вследствие неправильного монтажа гибкого вала (плохое закрепление, изгибы с радиусом менее 150 мм), недостаточного количества смазки внутри оболочки гибкого вала и отсутствия продольного перемещения троса внутри оболочки при затянутой до отказа гайке крепления гибкого вала к спидометру. Отсутствие продольного перемещения троса вала объясняется попаданием грязи в отверстие валика спидометра.
Учитывая большое разнообразие конструкций и назначений контрольно-измерительных приборов, ниже в качестве примера приведены основные неисправности и способы проверки магнитоэлектрических термометров.
Опыт эксплуатации магнитоэлектрических термометров выявил следующие возможные их неисправности:
нарушение герметичности баллона датчика из-за чрезмерных усилий, прикладываемых к гайке датчика при его монтаже на двигателе. В этом случае вода, попадая внутрь датчика, выводит из строя терморезистор;
нарушение стабильности характеристик терморезистора. Чаще всего это нарушение происходит вследствие значительных и длительных перегревов терморезистора в процессе эксплуатации, например работа двигателя без охлаждающей жидкости;
смещение стрелки указателя на оси магнита из-за вибраций или ударов;
обрыв проводов внутри указателя.
При обнаружении неисправностей датчика или указателя рекомендуется заменить его исправным, а не подвергать ремонту, так как конструкция указателя и датчика выполнена неразборной и ремонт их в эксплуатации не предусмотрен.
Проверку исправности электромагнитных термометров рекомендуется производить в определенной последовательности.
Для проверки точности показания датчик и указатель должны быть сняты с автомобиля.
Проверка производится при температуре окружающей среды плюс 20°С. Указатель устанавливается в приспособлении в рабочем положении.
Датчик помещается в специальную герметичную ванну с водой, закрытую пробкой от автомобильного радиатора, которая дает возможность повышать температуру воды выше 100°С.
Термометры, предназначенные для замера температуры охлаждающей жидкости, можно проверять только в воде.
При нагреве в масле, при отсутствии интенсивного его перемещения увеличиваются погрешности измерения в результате изменений условий теплопередачи.
Термометры, предназначенные для замера температуры масла, проверяются в масляной ванне.
Схема включения комплекта указателя и датчика для проверки изображена на рис. 30, а.
Напряжение, подводимое к прибору, необходимо поддерживать равным 14 или 28 В (соответственно для приборов с номинальным напряжением 12 и 24 В).
Водяная или масляная ванна медленно подогревается, например, путем включения нагревательного элемента через лабораторный автотрансформатор.
Показания указателя сравниваются с показаниями контрольного ртутного термометра, установленного в ванне. Цена деления контрольного ртутного термометра в этом случае должна быть не более 0,5°С.
На каждой контрольной отметке шкалы перед отсчетом показаний должна производиться выдержка не менее 2 мин.
Комплект указателя и датчика можно считать исправным, если погрешность не превышает данных, приведенных в табл. 5.
В случае увеличенной погрешности комплекта необходимо проверить указатель и датчик отдельно.
5. Допустимые погрешности указателя и датчика термометра
Проверяемые точки шкалы |
Допускаемая погрешность, °С |
40 |
±8 |
80 |
±5 |
100 |
±5 |
110 |
±6 |
120 |
±6 |
Проверка указателя осуществляется при помощи контрольного реостата или магазина сопротивлений, включенного в цепь указателя вместо датчика (рис. 30, б) при температуре окружающей среды плюс 20 ±5°С и питающем напряжении 14 или 28 В.
Перед проверкой показаний указателя последний выдерживают во включенном положении на предельной отметке 110 или 120°С в течение 2 мин.
При положении стрелки на контрольной отметке шкалы фиксируется значение сопротивления контрольного реостата.
Показания указателя считают удовлетворительными, если контрольные положения стрелки соответствуют величине сопротивления контрольного реостата (табл. 6).
6. Сопротивления контрольного реостата для различных точек шкалы
Проверяемые точки шкалы |
Сопротивление, Ом |
40 |
320—440 |
80 |
128—142 |
100 |
82—91 |
110 |
66—74 |
120 |
55-62 |
Погрешность указателя в градусах определяется как разность между показаниями приемника и контрольного ртутного термометра.
Указатель можно считать исправным, если его погрешности не выходят за пределы, указанные в табл. 5.
Проверка датчика проводится с эталонным указателем (рис. 30, в), сопротивление катушки которого между клеммами Б и Д равно 10±1 Ом. При проверке используют контрольный ртутный термометр с ценой делений 0,ГС.
Проверка датчика заключается в определении величины его сопротивления при контрольных температурах и работе его в комплекте с эталонным указателем. Такая проверка может быть выполнена при помощи амперметра и вольтметра. Применяемый при этом испытании вольтметр должен иметь класс точности не ниже 0,5.
Величина сопротивления датчика не должна выходить из пределов, указанных в табл. 7.
7. Сопротивление датчика ТМ 100 при различных температурах.
Контрольные температуры, ºC | Сопротивление, Ом |
40 | 318-418 |
60 | 194-234 |
80 | 124-144 |
100 | 80-92 |
120 | 54-62 |
Поделитесь этой страницей с друзьями!
Анализ отказа оборудования [Анализ основных причин отказа]
16 сентября 2020 г.
Почему оборудование продолжает выходить из строя
Наверное, все согласятся с тем, что неспособность найти и устранить причины отказов оборудования приводит к дополнительным отказам и проблемам с надежностью. Итак, если люди согласны, почему мы продолжаем сталкиваться с неудачами в поиске и устранении основных причин сбоев оборудования? Ответ … плохой анализ отказов оборудования/анализ основных причин отказов.
Эту проблему я исследовал в конце 1990-е. Я обсуждал проблему с некоторыми очень умными людьми. Одним из них был Хайнц Блох, известный специалист по надежности оборудования.
Результатом нашего обсуждения стало то, что многие специалисты по техническому обслуживанию, менеджеры по техническому обслуживанию и инженеры по надежности оборудования не использовали систематический подход к устранению неполадок и анализу основных причин.
Что они сделали?
- Замена деталей или целых узлов (методом проб и ошибок)
- Угадайте ответы, используя свой опыт
- Угадывать ответы на основе советов других (возможно, поставщиков)
- Использование нестандартных методов, таких как 5-Whys
Это приводит к неправильному устранению неполадок и неспособности найти основные причины сбоев.
Без обнаружения причин и коренных причин сбоя предпринимаемые действия обычно возвращают оборудование в исходное состояние, при этом причины сбоя остаются на месте. Таким образом, обязательно произойдет еще один повторный сбой.
Иногда это случалось так много раз, что люди начинают думать, что оборудование просто ненадежно. Ведь так было всегда. Люди считают, что нет никакого способа повысить надежность.
Создание системы анализа отказов оборудования/анализа основных причин отказов
Мы с Хайнцем не согласились с ответом, что повышение надежности было «слишком сложно». Хайнц знал эффективные методы устранения неполадок оборудования. И я знал передовые методы анализа первопричин. Мы решили объединить их в систематический процесс для устранения неполадок и поиска основных причин проблем с надежностью оборудования. Компания System Improvement лицензировала методы устранения неполадок Хайнца Блоха для создания системы.
Это был 1997 год. Нам потребовалось несколько лет на разработку методики, разработку курсов, разработку программного обеспечения и тестирование, прежде чем мы получили проверенную систему. Он объединил лучшие методы устранения неполадок Heinz с усовершенствованной системой анализа основных причин TapRooT®, чтобы создать новый способ поиска и устранения основных причин проблем с оборудованием.
Использование этой системы в полевых условиях доказало, что эффективное устранение неполадок и анализ первопричин могут повысить производительность предприятия/процесса за счет повышения надежности оборудования. Но, как сказал адмирал Риковер:
Хорошие идеи не принимаются автоматически. Их нужно претворять в жизнь с мужественным нетерпением. После того, как они будут реализованы, их можно легко отменить или подорвать из-за апатии или отсутствия последующих действий, поэтому требуются постоянные усилия.
Возможно, поэтому даже спустя 20 лет многие до сих пор не знают об этих передовых инструментах или забыли применить полученные знания.
Процесс анализа отказов оборудования/анализ основных причин отказов
Процесс анализа отказа оборудования/анализа первопричин отказа состоит из шести основных шагов. Это:
Шаг 1. Что произошло
Шаг 2. Устранение неполадок
Шаг 3. Причинные факторы
Шаг 4. Основные причины
Шаг 5. Комбинированные корректирующие действия
в блок-схему анализа отказов оборудования…
Весь процесс описан в Использование инструментов устранения неполадок Equifactor® и анализа основных причин TapRooT® для повышения надежности оборудования .
Давайте рассмотрим каждый шаг и причину каждого шага, чтобы понять, зачем нужны все эти шаги.
Шаг 1. Что произошло
Люди часто совершают ошибку, пытаясь исправить проблемы (корректирующие действия) или найти первопричины ДО того, как они поймут, что произошло. Почему они это сделали? Потому что они думали, что уже знают ответ. Они «видели это раньше». Таким образом, они думали, что им не нужно спрашивать о том, что произошло.
К сожалению, обычно они ошибались. Почему? Потому что причин много, а они знали лишь некоторые.
Итак, одна из первых вещей, которые я узнал об анализе основных причин, это:
Вам нужно понять, что произошло, ПРЕЖДЕ чем вы сможете понять, почему это произошло.
Таким образом, во всех наших процессах анализа первопричин мы начинаем с разработки SnapCharT®, визуальной блок-схемы того, что произошло. Разработка SnapCharT® помогает человеку, исследующему проблему, понять, что произошло, прежде чем он начнет анализ основной причины.
Ниже приведен пример SnapCharT®, связанного с отказом оборудования…
Я не знаю, сколько раз меня просили помочь с застопорившимся расследованием (они просто не могут найти основные причины), и я начал рисовать SnapCharT®, который помог им задать вопросы, которые они раньше упустили из виду и нашли новые и важные доказательства, которые привели к выявлению важных коренных причин, которые действительно требовали устранения.
Шаг 2: Устранение неполадок
Здесь пригодился опыт Хайнца Блоха. Он разработал систематизированную систему устранения неполадок (набор таблиц), которая обеспечила последовательный способ понять, что вызвало отказ части оборудования. Ниже приведена блок-схема того, как применять таблицы…
В примере с насосом SnapCharT® симптомом была недостаточная производительность. Для этого симптома Heinz разработал следующую таблицу возможных причин…
Таким образом, вы можете разработать процедуру устранения неполадок, чтобы выбрать или устранить каждую из этих потенциальных причин и обнаружить причину проблемы.
В примере было обнаружено, что рабочее колесо установлено задом наперед. Но прежде чем это было обнаружено, были проверены и устранены другие причины, прежде чем они решили разобрать насос для проверки.
После завершения устранения неполадок полученная информация добавляется в SnapCharT®…
Обладая этими знаниями, вы готовы решить, есть ли что-то еще, что можно узнать, выполнив анализ основных причин, ИЛИ мы должны просто остановиться здесь и выполнить ремонт.
Другими словами, нужно ли нам просто установить рабочее колесо в правильном направлении и восстановить насос, ИЛИ есть ли что-то, что нам нужно узнать о том, почему рабочее колесо насоса было установлено задом наперед и как мы можем предотвратить это в будущем.
Если вы решите узнать больше, вы готовы определить причинные факторы.
Шаг 3: Причинные факторы
Мы знаем, что это за инцидент, но какие проблемы привели к нему. Это причинные факторы. Мы определяем Причинные факторы следующим образом:
Причинный фактор:
Ошибка, ошибка или сбой, которые непосредственно приводят к
(или вызывают) Инцидент (круг на SnapCharT®) или
не могут смягчить последствия первоначальной ошибки.
Для получения дополнительной информации об определении причинных факторов см. пост о наших новых таблицах причинных факторов. Существует четыре типа рабочих таблиц Causal Facor для каждого из этих типов проблем:
- Инциденты, связанные с отказом оборудования.
- Инциденты, связанные с безопасностью.
- Инциденты, связанные с качеством.
- Инциденты, связанные с безопасностью пациентов.
После того, как вы определите Причинные факторы, каждый Причинный фактор будет проанализирован, чтобы найти основные причины Причинного фактора.
Шаг 4: Основные причины
Как использовать диаграмму TapRooT® Root Cause Tree® для поиска основных причин каждого из причинных факторов, описано в предыдущих статьях. Чтобы получить информационный документ, в котором объясняется, как работает Root Cause Tree®, используйте форму ниже.
Шаг 5. Действия по устранению неполадок
Как только вы узнаете основные причины, следующим шагом будет их устранение. Для этого вы используете Помощник по корректирующим действиям® (книга) или Модуль (программное обеспечение). Руководство содержит предложения по разработке эффективных корректирующих действий для каждой основной причины в дереве основных причин®. Опять же, использование Руководства для разработки корректирующих действий описано в официальном документе выше.
Этап 6: Ремонт и усовершенствование
Последним этапом является починка оборудования и выполнение корректирующих действий.
Benna & Ken Покажите пример использования программного обеспечения TapRooT®
Что делает этот процесс анализа отказа оборудования уникальным?
Уникальной эту версию Анализа отказов оборудования/Анализа основных причин отказа делают четыре вещи:
- SnapCharT® для организации и отображения того, что произошло.
- Знания Хайнца Блоха включены в Таблицы устранения неполадок Equifactor®.
- Диаграмма TapRooT® Root Cause Tree® для поиска основных причин проблем, связанных с работоспособностью человека и оборудованием.
- Руководство/модуль Corrective Action Helper® для разработки эффективных корректирующих действий.
Без этих инструментов люди зависят только от своих знаний. У большинства людей нет:
- подробных знаний по поиску и устранению неисправностей оборудования
- подробные знания о человеческом факторе
- нестандартных идей по устранению проблем
Плюс, Equifactor® и TapRooT® делают процесс систематическим и воспроизводимым. Это процесс, которому вы можете научить механиков и инженеров и получить стабильные, надежные результаты, которые работают на повышение надежности оборудования.
Наконец, этот процесс помогает людям понять, что многие проблемы, которые считаются проблемами оборудования, на самом деле являются проблемами производительности человека. И когда они применяют инструменты TapRooT®, они могут найти и устранить основные причины этих проблем с производительностью человека, которые они ранее не распознавали.
Как вы можете изучить этот процесс анализа отказа оборудования/анализа основных причин отказа?
Во-первых, вы можете прочитать книгу Использование инструментов Equifactor® для устранения неполадок и анализа основных причин TapRooT® для повышения надежности оборудования . Но лучше посетить двухдневный тренинг по устранению неполадок оборудования Equifactor® и анализу основных причин TapRooT®. Вот план курса:
План курса
ДЕНЬ ПЕРВЫЙ
- Введение
- Понимание того, что произошло — SnapCharT ® Основы
- SnapChart ® Упражнение
- Сбор информации
- Режимы отказа и агенты отказа
- Таблицы поиска и устранения неисправностей Equifactor®
- Человеческие ошибки
- Устранение неполадок процесса
- Пример: поиск и устранение неисправностей насоса забортной воды
ДЕНЬ ВТОРОЙ
- Введение в программное обеспечение TapRooT®/Equifactor®
- Выявление причинных факторов
- Введение в дерево основных причин®
- Упражнение: Анализ дерева первопричин®
- Упражнение: команды находят первопричины с помощью дерева первопричин®
- Анализ изменений
- Упражнение по анализу изменений
- Заключительное упражнение: решение серьезной проблемы с оборудованием
Материалы курса включают книгу Использование инструментов устранения неполадок Equifactor® и анализа основных причин TapRooT® для повышения надежности оборудования , дерево основных причин TapRooT®, Root Cause Tree® Dictionary и Correction Action Helper® Guide стоимостью 129 долларов США. Книга включает в себя полный набор таблиц устранения неполадок Хайнца Блоха.
По завершении курса участники получат сертификат об окончании и 90-дневную подписку на программное обеспечение TapRooT® VI, наше динамическое облачное программное обеспечение, которое компьютеризирует методы Equifactor® и TapRooT®.
Вот ссылка на даты и места проведения ближайших общедоступных курсов:
ПРЕДСТОЯЩИЕ КУРСЫ ПО ВСЕМУ МИРУ
Или вы можете спонсировать курс на своем предприятии для своих экспертов по поиску и устранению неисправностей и анализу отказов оборудования. Позвоните нам по телефону 865-539-2139 для получения дополнительной информации. Или НАЖМИТЕ ЗДЕСЬ, чтобы связаться с нами.
Но не ждите. Ненадежное оборудование дорого обходится в производственных процессах. Каждый день просрочки — это потраченные впустую тысячи долларов.
Категории
Надежность оборудования / Equifactor®Другие статьи, которые могут вас заинтересовать.
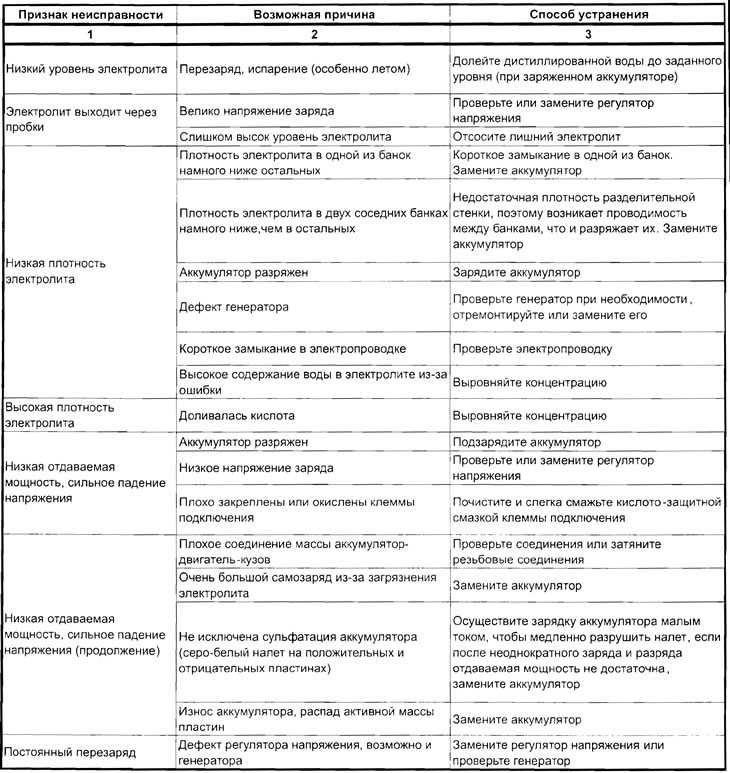
Методы анализа сбоев для PDE: поиск источников ошибок
Хотя в настоящее время это может вызывать разочарование, устранение сбоев и обеспечение запуска без дефектов — одна из самых приятных частей разработки продукта. Понимание того, как обнаруживать сбои, где их искать, а также общие методы анализа сбоев могут упорядочить ваши рабочие процессы и уменьшить количество ошибок в вашей программе, повышая шансы вашего продукта на запуск вовремя и в рамках бюджета.
Поскольку очень трудно понять, с чего начать, команда инженеров-проектировщиков компании Instrumental написала эту серию из трех частей, чтобы помочь вам. В Части 1 ниже мы обсудим инструменты, которые вы можете использовать для выявления общих источников проблем, и способы, которые вы можете уменьшить в первую очередь. Часть 2 будет посвящена общим процессам и методам анализа отказов, а часть 3 познакомит вас с некоторыми ключевыми вопросами, которые следует задать во время анализа отказов.
Никто не хочет иметь дело с неудачами, но лучше быть готовым, когда они случаются. Мы по-прежнему выступаем за профилактику как за лучший способ уменьшить количество проблем, поэтому она помогает быть организованным и бдительным с самого начала при записи как можно большего количества информации о конструкции. Задокументируйте, как ваш продукт движется по цепочке поставок и сборочной линии, а также как были вызваны и идентифицированы сбои. Чем больше у вас хороших источников информации, тем лучше ваша команда будет подготовлена к преодолению сбоев, которые неизбежно произойдут.
- Создайте документацию и критерии тестирования для выявления проблем в ваших разработках, особенно тех, которые возникают на критических узлах
- Критические узлы в вашей разработке возникают на любом этапе процесса, который изменяет форму или функцию продукта может привести к повреждению устройства.
- Многие глупые ошибки можно смягчить с помощью улучшенных процессов и контрольных списков.
- Обязательно усовершенствуйте свои процессы разработки на основе прошлого опыта.
- О любых других возникающих проблемах см. в следующих статьях по этой теме.
Все знают, что такое сбои, или знают? Есть очевидные проблемы, когда что-то не подходит или ломается в тесте, но на самом деле сбои происходят во многих местах на протяжении всего процесса разработки. Поскольку предстоит сделать так много и принять участие так много сторон, каждый шаг на этом пути является потенциальным источником ошибок, которые могут вызвать непредвиденные проблемы на линии прототипа или при использовании потребителями.
Поскольку вы не можете выполнить какой-либо анализ проблем, которые остались незамеченными, Анализ отказов начинается с понимания того, откуда возникают эти проблемы. Это означает знание того, что такое сбои и как их обнаружить. Затем вы можете триангулировать, где в цикле разработки возникают различные типы проблем, и внедрить процессы для смягчения наиболее вопиющих ошибок. Если вы не потратите время на соблюдение этих процессов, что-то может быть упущено на ранних стадиях проектирования, распространено в процессе разработки и в итоге окажется в готовом изделии 9.0287 .
Лучший способ найти отказы — внедрить процессы проверки и тестирования на критических этапах разработки вашего продукта. Критические соединения возникают каждый раз, когда выполняется процесс, который изменяет форму или функцию продукта или подвергает продукт экстремальным условиям. Примеры включают передачу ответственности между компаниями, например выпуск инструмента или отправку деталей от поставщика производителю по контракту. Они также происходят в меньшем масштабе на заводе, когда детали добавляются к сборкам, а сборки перемещаются с одной станции на линии на другую.
Поиск ошибок в механических чертежах Начиная с проектирования, если что-то не является идеальным воссозданием ваших файлов САПР, вы должны иметь возможность определить, какой уровень расхождений является приемлемым, и установить пределы соответствия/несоответствия. Допуски на размеры на чертежах должны соответствовать ограничениям в вашей конструкции, основанным на вашем анализе допусков, но они также должны соответствовать технологическим возможностям ваших поставщиков. Слишком свободные размеры могут вызвать проблемы с посадкой и отделкой, но слишком узкие могут привести к выпадению большого количества урожая.
Элементы, важные для функционирования, должны быть измерены на статистически значимом наборе образцов, чтобы убедиться, что детали попадают в допустимый диапазон. Эти важные параметры должны быть измерены вашим поставщиком при исходящей проверке качества (OQC), а ваш контрактный производитель — при входной проверке качества (IQC). В идеале измерения должны выполняться с использованием одной и той же установки, оборудования и методики, чтобы они хорошо коррелировали. Но не думайте, что каждая деталь будет измерена полностью, потому что проверка всех критических размеров каждой детали займет довольно много времени.
Поиск сбоев в процессах и тестах сборочной линии В процессе FATP ваши операторы будут обучены следовать Стандартной рабочей процедуре (СОП). Чем больше времени ваша команда потратит на проверку каждой детали процедуры перед сборкой, тем лучше вы сможете выявить потенциальные ошибки и определить, что делать с любыми неудачными сборками. Все, начиная от порядка свинчивания компонентов и заканчивая положением избыточного провисания кабеля, должно быть определено, чтобы вы могли быть уверены, что каждое устройство будет собрано последовательно.
Аналогично допускам на размеры, функциональные испытания входных и выходных компонентов также требуют ограничений. Эти ограничения должны быть установлены между минимальным уровнем приемлемой функциональности и максимальной теоретической производительностью. Если вы не уверены, какими должны быть эти пределы, вы можете установить их на каждой испытательной станции, используя тесты на повторяемость и воспроизводимость (GR&R) до начала основной сборки. В идеале вы получите узкую полосу изменения производительности для ключевых компонентов, которая также укладывается в теоретические пределы. По мере прохождения сборки следите за устройствами, которые выходят за пределы начальных диапазонов, и при необходимости вносите коррективы.
Несмотря на всю хаотичность процесса сборки прототипа, обязательно проводите визуальные проверки на протяжении всего процесса, особенно при любых процессах сборки вслепую. Это невероятно полезно до и после этапов слепой сборки, особенно при работе с хрупкими косметическими компонентами со специальной отделкой, такой как краска или анодирование. Небольшие незадокументированные процессы на линии, такие как перемещение продукта между станциями или то, как конкретная испытательная станция зажимает продукт, могут повредить незащищенные компоненты.
При визуальном осмотре убедитесь, что условия освещения хорошие для просмотра и осмотра под разными углами. Ранние проверки сборки могут также включать тест на встряхивание на предмет необычного дребезжания из-за дополнительных деталей или ослабленных винтов.
Остановка линии Во время сборки прототипа важно остановить линию, если возникла проблема, чтобы последующие устройства не собирались с этой конкретной проблемой. Целью этапов сборки является обнаружение проблем и их устранение до запуска в массовое производство, и чем раньше, тем лучше. Так что используйте этот ключевой рычаг для выявления сбоев и позвольте вашей команде сделать паузу, проанализировать ситуацию и составить план, как ее исправить.
Используя описанные выше методы обнаружения, вы можете заранее выявить источники ошибок. Еще лучше было бы предотвратить их появление.
В Instrumental нам нравится разбивать источники отказов на 5 категорий. Каждая из этих категорий представляет собой важную фазу развития. Поскольку на разных этапах разработки возникают разные виды ошибок, вы можете включить описанные выше методы обнаружения в процессы разработки, чтобы предотвратить слишком далекое распространение проблем.
1. Анализ ошибок проектирования и архитектуры Ошибки проектирования и архитектуры возникают, когда что-то было упущено при создании фундаментальной архитектуры продукта и ее преобразовании в 3D-модели CAD. Лучше всего найти и устранить сбои до того, как проект будет заблокирован, потому что у вас есть наибольшая гибкость для внесения изменений. Однако это сложно, потому что у вас еще нет четкого представления о том, как продукт будет работать в реальной жизни. У вас также может быть плотный график и множество заинтересованных сторон, которые необходимо удовлетворить. Просто помните, что как только вы вкладываете большие средства в сборку или инструменты, влияние каждой ошибки возрастает, и исправить ее становится все труднее.
Иногда сбои в проектировании являются глупыми ошибками, такими как пропущенное вмешательство или неуместная функция, которая не учитывала способ сборки продукта. В других случаях вы можете раздвинуть границы возможностей процесса для достижения целей промышленного дизайна только для того, чтобы позже обнаружить, что это не сработает. Чем сложнее дизайн, тем больше вероятность того, что небольшие проблемы перерастут в большие проблемы.
Одним из особенно болезненных опытов, с которым столкнулся один из наших инженеров, был проект очень простой гибкой печатной платы (FPC или flex). Проще говоря, FPC был просто плоским проводом с разъемами на обоих концах и несколькими дорожками посередине, что облегчало разработку конструкции. Но команда инженеров упустила из виду, что один из сигнальных переходов был открыт для заземленного механического элемента жесткости на задней панели. Это означало, что сам сигнал, для передачи которого был разработан гибкий кабель, был привязан непосредственно к земле, а это означало, что весь гибкий кабель был бесполезен.
Чтобы решить эту проблему, команде пришлось повторно раскрутить дизайн и сделать новые изгибы, что заняло 3 недели, и все потому, что они не потратили 30 минут на тщательную проверку дизайна. Для таких сложных вещей команда инженеров разработала контрольный список (по сути, список всех вещей, которые раньше пошли не так), чтобы проверять каждый новый проект. Обновление этого списка с каждым новым выпуском избавит вас от повторения одних и тех же ошибок снова и снова.
Чтобы справиться с этими проблемами на этапе проектирования, не забудьте запланировать соответствующее количество времени для проверки проекта. Это время должно соответствовать сложности дизайна и рискам, которые команда берет на себя при работе с каждой программой. В обзорах проекта команда должна описать основную архитектуру, основные компоненты, критические стеки и анализ допусков, а также потенциальные риски, связанные с проектом, и то, как они были или будут устранены.
Используя анализ допусков и опыт работы с инструментами и производственными процессами, вы можете установить начальные пределы на чертежах с размерами. Но вам все равно нужно будет пройти проверку «Проектирование для производства» (DFM) вместе с вашими поставщиками, чтобы убедиться, что их инструментальные возможности соответствуют вашим проектным допускам. Если они не могут, вам, возможно, придется либо переработать свои анализы и обновить CAD, чтобы отразить то, что возможно, либо работать с вашими технологическими группами и поставщиками, чтобы искать любые новые способы гарантировать более жесткие допуски. Важно использовать свой опыт и суждения при оценке риска любого варианта, который может включать время и затраты, связанные с дополнительными исследованиями и переоснащением.
Межфункциональные группы должны проверить и утвердить, как важные компоненты, такие как антенны, дисплеи и динамики, подключаются к основной плате и остаются в корпусах. Используйте эти обзоры, чтобы найти нарушителей условий сделки для каждой команды. Это может помочь ограничить ваш выбор, если вам нужно будет внести изменения в дизайн в будущем. Например, если рассматривается металлическое ребро для придания жесткости конструкции, обязательно обсудите это с командой антенн, если это может изменить ожидаемые характеристики.
Операционные группы, ответственные за проектирование процессов и приспособлений для сборки (DFA), также должны понимать замысел конструкции и рекомендуемый метод сборки. Это позволяет им проектировать линию с учетом того, как устройство подходит друг к другу, и создавать приспособления и методы испытаний, чтобы свести к минимуму косметические повреждения. Быстрые и простые прототипы, напечатанные на 3D-принтере или обработанные на станке с ЧПУ, могут помочь команде визуализировать, как детали подходят друг к другу, и внести элемент масштаба в обсуждение размеров элементов. Они также являются отличной проверкой работоспособности для определения размеров гнезд тестовых приспособлений.
Будьте осторожны с последними изменениями в критических функциях и призывайте команду провести еще одну проверку проекта, если необходимо внести какие-либо существенные изменения. Ошибки часто возникают, когда ваши команды спешат уложиться в срок. Изменения объема или дизайна в последнюю минуту часто остаются незамеченными, поскольку ваши инженеры пытаются внести изменения непосредственно перед выпуском инструмента. Даже если вы отпустите свои детали для оснастки на 1-2 недели позже, чем вам хотелось бы, вы неизбежно сэкономите гораздо больше времени и денег, обнаружив проблемы до того, как они будут встроены в оснастку. Кроме того, если вы обнаружите какие-либо проблемы по пути, запишите их, чтобы вы могли собрать их в контрольный список для будущего использования. Узнайте, как инженеры P2i утроили свою эффективность FA с помощью Instrumental.
2. Компонент и поставщик Анализ отказов Для любой нестандартной детали у ваших поставщиков есть собственный процесс разработки для проектирования инструментов, резки стали и, в конечном итоге, создания стабильных качественных компонентов. Некоторые производственные процессы хорошо отлажены и легко моделируются, но если вы выходите за рамки своего дизайна или сроков, будьте готовы к некоторым задержкам, пока их команда набирает параметры обработки.
Будьте осторожны при использовании первых деталей для чего-либо, кроме проверки приспособления, поскольку они могут иметь широкий спектр проблем с качеством. Все, от отсутствующих элементов до значительно деформированных или недостаточно заполненных частей, довольно часто встречается при наборе параметров. Также могла быть проблема с конструкцией инструмента, например, с неподходящими линиями охлаждения или неправильным расположением литника. Вторичные процессы, такие как ЧПУ, многослойное формование, обрезка, косметическая обработка и подсборка, только добавляют к возможным источникам ошибок. Кроме того, если у вас есть обширная база поставщиков, любые чувствительные компоненты могут быть повреждены при транспортировке или из-за плохой упаковки.
Пример изображения из Moldex3D
Чтобы решить эти проблемы, вам потребуется, чтобы ваша группа по инструментам рассмотрела конструкции деталей и инструментов на этапе DFM и удостоверилась, что ваши поставщики документируют свои технологические параметры. Фотографии процесса и компонентов, проходящих измерения FAI, и документирование их критериев «годен/не годен» могут помочь определить недостающие функции и детали низкого качества до того, как они будут отправлены CM. Кроме того, не забудьте получить отчеты о выходе и инспекции, чтобы ссылаться на них в случае несоответствия.
В начале программы у вас может не быть другого выбора, кроме как использовать эти разрабатываемые части. Но когда вы отказываетесь от их использования, имейте в виду потенциальные последующие последствия, которые могут быть вызваны качеством детали, такие как плохая посадка, косметические проблемы или низкая надежность.
Даже когда компоненты поступают на завод вовремя, они проходят несколько этапов, прежде чем их можно будет собрать на линии. Детали обычно хранятся на складе вашего CM. Образцы этих деталей отправляются в IQC для измерения, и в процессе они могут перемещаться между этажами здания несколько раз в ожидании сборки. Неисправности, обнаруженные в IQC, могут привести к отклонению партии и дополнительным затратам времени на выяснение того, действительно ли деталь выходит из строя и кто виноват. Некоторые клиенты Instrumental полностью избежали этой потери времени, интегрировав испытательные станции со своими вышестоящими поставщиками, что позволило инженерам иметь единую справочную базу данных, показывающую им четкое представление обо всех деталях по мере их движения по цепочке поставок.
EXAMPLE:
Kindle Voyage Cosmetic Mid-Frame
- 10 different process steps:
- Factory 1
- Die-cast
- Rough Trim
- Fine Trim
- CNC 1
- CNC 2
- Passivation
- Фабрика 2
- Форма-вкладыш из стеклонаполненного нейлона
- Формовочная накладка из ТПУ
- Лазерное травление
- Клеевой узел
После того, как все ваши материалы поставлены на конвейер, в процессе сборки часто возникают проблемы. Мы рекомендуем иметь несколько дополнительных наборов компонентов, которые ваши инженеры-технологи и проектировщики могут использовать для физического соблюдения SOP и испытательных станций для проверки процессов сборки и установки пределов соответствия/несоответствия.
Стандартные рабочие процедуры могут вызывать беспокойство, если этапы плохо определены или неясны. Хотя документы часто пишутся как на английском, так и на родном языке, операторы могут быть не в состоянии читать и полагаться на обучение линейных руководителей. Убедитесь, что у вас есть последовательные линейные лидеры во время сборки и, если возможно, от сборки к сборке, и убедитесь, что они понимают, что они должны делать. Также должно быть ясно, что возможные проблемы могут возникнуть, если они сделают что-то неправильно. Использование изображений с графическими наложениями может помочь более четко передать цель процесса, а выделение примеров сбоев может помочь научить их выявлять проблемы до того, как они станут шаблоном. Неисправные компоненты или сборки также являются полезными иллюстрациями для сравнения. В некоторых случаях операторы, которые не полностью понимают SOP, могут предпочесть выполнить операцию более простым или небрежным способом, который создает несоответствия в ваших прототипах, поэтому важно, чтобы кто-то на месте наблюдал за процессом. Во время COVID-19, вы можете использовать фотографии и видео, чтобы задокументировать процесс на потом.
Если вы хотите проверить 100 % ваших деталей для определенной сборки, вы можете использовать датчики годности/негодности, чтобы определить, будет ли данная деталь приемлемой. Это будет быстрее, чем 100%-ое измерение, потому что эти датчики должны легко позволять хорошим деталям продолжать процесс, немедленно идентифицируя и отбраковывая плохие детали. Однако простые датчики не являются наиболее полезными для сбора и хранения данных о каждом компоненте отслеживаемым образом. Такие инструменты, как платформа оптимизации Instrumental и данные изображений, могут помочь преодолеть этот разрыв, делая фотографии каждого сериализованного компонента и устройства для дальнейшего использования.
На функциональных тестовых станциях производительность может быть непостоянной из-за неправильной конструкции платы или из-за проблем с подключением самой тестовой станции к тестируемому устройству. Кроме того, прошивка для поднятия вашей платы может быть еще не доработана. Плохой драйвер может привести к сбою теста и привести вашу команду к поиску оборудования, когда решением может быть исправление программного обеспечения. Убедитесь, что соответствующие группы программного и аппаратного обеспечения совместно рассматривают проблемы в процессе FA. Если приспособление или испытательная станция были откалиброваны и проверены перед сборкой, вы должны быть гораздо более уверены в выявлении неэффективных устройств. Если многие устройства выходят из строя, вы можете расширить свои ограничения
Если ваша команда не может быть на месте, убедитесь, что команда CM на месте записывает каждый шаг процесса сборки и тестирует с помощью видео и фотографий. Иногда шаги, предпринятые за пределами сборочных станций, могут вызвать проблемы, поэтому попросите проследить весь блок от начала до конца. Для еще лучшего наблюдения за удаленной сборкой испытательные станции Instrumental могут быть встроены в ключевые точки, чтобы не только делать снимки каждой станции, но и заранее выявлять расхождения в разных сборках уже после нескольких наборов данных.
Пример фотографии из Memeburn.
После завершения прототипа вы, вероятно, обнаружите сбои во время тестирования надежности. Эти тесты предназначены для того, чтобы довести ваш продукт до предела и воспроизвести фактическое использование вашими будущими клиентами.
Если вы строите что-то в первый раз, может быть полезно создать симуляцию определенных механических испытаний, таких как испытание на падение. После того, как вы завершите тест на надежность, сравните фактическую работу ваших устройств с их смоделированной производительностью.
Иногда вам может повезти, если вы не обнаружите никаких сбоев, но в этом случае вам следует учитывать возможность ложноотрицательного результата. Кроме того, будьте осторожны с созданием продуктов, которые просто проходят определенные контролируемые испытания, потому что реальный мир может быть более сложным. Большинство дизайнеров вряд ли когда-либо будут подвергать сомнению результаты прохождения, но изо всех сил борются за то, чтобы придумать правдоподобные внешние объяснения того, почему они могли провалиться, включая обвинение в тесте, плохих материалах или сборке. Чтобы бороться с этим предубеждением, тестируйте свои ранние прототипы до отказа. Все продукты не работают, вы просто хотите знать, при каких условиях они могут выйти из строя.
При тестировании надежности очень важно получить как можно больше подробностей о неисправных продуктах, включая изображения критических сборок, результаты функциональных тестов и каскадную последовательность тестов надежности, через которые прошло рассматриваемое устройство. Платформа компании Instrumental для оптимизации производства обеспечивает легкий доступ к сериализованным данным об изображениях продуктов и любой информации о тестовых станциях, которую вы хотите интегрировать. Вы можете использовать эту платформу для обратного поиска отказоустойчивых устройств, чтобы быстро агрегировать огромное количество имеющихся у вас данных и быстро начать процесс анализа отказов.
5. Необъяснимые сбои Последняя категория сбоев — настоящая головная боль. Это те, где ваши методы обнаружения потерпели неудачу, и нет очевидного места для начала. Вы не всегда можете предсказать, как и почему они возникают, или они могут проявиться только в конце тестирования надежности, что может задержать вашу программу. Анализ отказов с неполными данными об изделии может привести к экспоненциальной задержке, если отказ сам по себе является неожиданным.
Это наиболее сбивающие с толку, потому что это означает, что продукт прошел через все определенные контрольно-пропускные пункты на своем пути и все же сумел уйти. Возможно, один из многих шагов в вашем развитии плохо контролируется или не понимается, или может случиться так, что что-то, на что вы не обращали внимания, внезапно становится вашей главной проблемой.
Некоторые из наиболее сложных проблем представляют собой сочетание многих незначительных факторов, которые проявляются только при определенных обстоятельствах. Проблемы возникают постоянно, поскольку потребители используют продукты по-новому в разных средах по всему миру.
При возникновении проблем такого типа лучше всего вернуться к основным принципам и задокументировать все, что вам известно о проблеме, и просмотреть все шаги на этом пути, чтобы найти возможные источники отклонений.
Размышляя над своими прошлыми программами, подумайте, сможете ли вы найти закономерность возникновения наиболее сложных проблем. Если вы заметили какие-либо распространенные источники ошибок, скорректируйте процессы разработки продукта, чтобы в следующий раз лучше выявлять проблемы, прежде чем они превратятся в снежный ком. Из журнала проблем в каждой сборке вы можете создать обобщенные контрольные списки для использования в следующей программе. Записывая, кто нашел и решил проблему, вы можете создать отличный набор ресурсов для будущих дизайнеров, к которым можно обратиться, если они столкнутся с похожими проблемами.
Если вам удалось создать отличные процессы для предотвращения проблем, но все еще есть некоторые сложные необъяснимые сбои, которые нужно решить, обратите внимание на следующие выпуски, в которых мы рассмотрим некоторые отличные методы и инструменты для использования в FA и углубимся в некоторые ключевые вопросы. вы можете использовать для допроса любой вопрос.