ΠΠΎΠΊΠ°Π·Π°ΡΠ΅Π»ΠΈ Π½Π°Π΄Π΅ΠΆΠ½ΠΎΡΡΠΈ ΡΡΡΠΎΠΈΡΠ΅Π»ΡΠ½ΡΡ ΠΌΠ°ΡΠΈΠ½
ΠΠ°ΡΠ΅Π³ΠΎΡΠΈΡ:
Β Β Β Π‘ΡΡΠΎΠΈΡΠ΅Π»ΡΠ½Π°Ρ ΡΠ΅Ρ Π½ΠΈΠΊΠ° ΠΈ ΠΎΠ±ΠΎΡΡΠ΄ΠΎΠ²Π°Π½ΠΈΠ΅ 4
ΠΡΠ±Π»ΠΈΠΊΠ°ΡΠΈΡ:
Β Β Β ΠΠΎΠΊΠ°Π·Π°ΡΠ΅Π»ΠΈ Π½Π°Π΄Π΅ΠΆΠ½ΠΎΡΡΠΈ ΡΡΡΠΎΠΈΡΠ΅Π»ΡΠ½ΡΡ Β ΠΌΠ°ΡΠΈΠ½
Π§ΠΈΡΠ°ΡΡ Π΄Π°Π»Π΅Π΅:
ΠΠΎΠΊΠ°Π·Π°ΡΠ΅Π»ΠΈ Π½Π°Π΄Π΅ΠΆΠ½ΠΎΡΡΠΈ ΡΡΡΠΎΠΈΡΠ΅Π»ΡΠ½ΡΡ Β ΠΌΠ°ΡΠΈΠ½
ΠΠΎΠΊΠ°Π·Π°ΡΠ΅Π»Ρ Π½Π°Π΄Π΅ΠΆΠ½ΠΎΡΡΠΈ β ΡΡΠΎ ΠΊΠΎΠ»ΠΈΡΠ΅ΡΡΠ²Π΅Π½Π½Π°Ρ Ρ Π°ΡΠ°ΠΊΡΠ΅ΡΠΈΡΡΠΈΠΊΠ° ΠΎΠ΄Π½ΠΎΠ³ΠΎ ΠΈΠ»ΠΈ Π½Π΅ΡΠΊΠΎΠ»ΡΠΊΠΈΡ ΡΠ²ΠΎΠΉΡΡΠ², ΡΠΎΡΡΠ°Π²Π»ΡΡΡΠΈΡ Π½Π°Π΄Π΅ΠΆΠ½ΠΎΡΡΡ ΠΎΠ±ΡΠ΅ΠΊΡΠ°.
ΠΠ»Ρ ΡΡΡΠΎΠΈΡΠ΅Π»ΡΠ½ΡΡ ΠΌΠ°ΡΠΈΠ½ ΠΈ ΠΎΠ±ΠΎΡΡΠ΄ΠΎΠ²Π°Π½ΠΈΡ ΠΏΠΎΠΊΠ°Π·Π°ΡΠ΅Π»Ρ Π½Π°Π΄Π΅ΠΆΠ½ΠΎΡΡΠΈ Π±ΡΠ²Π°Π΅Ρ Π΅Π΄ΠΈΠ½ΠΈΡΠ½ΡΠΌ, Π½Π°ΠΏΡΠΈΠΌΠ΅Ρ, ΠΏΠΎΠΊΠ°Π·Π°ΡΠ΅Π»Ρ Π±Π΅Π·ΠΎΡΠΊΠ°Π·Π½ΠΎΡΡΠΈ, Π΄ΠΎΠ»Π³ΠΎΠ²Π΅ΡΠ½ΠΎΡΡΠΈ, ΡΠ΅ΠΌΠΎΠ½ΡΠΎΠΏΡΠΈΠ³ΠΎΠ΄Π½ΠΎΡΡΠΈ, ΠΈΠ»ΠΈ ΠΊΠΎΠΌΠΏΠ»Π΅ΠΊΡΠ½ΡΠΉ. Π ΡΠΈΡΠ»Ρ ΠΊΠΎΠΌΠΏΠ»Π΅ΠΊΡΠ½ΡΡ ΠΎΡΠ½ΠΎΡΠΈΡΡΡ ΠΊΠΎΡΡΡΠΈΡΠΈΠ΅Π½Ρ Π³ΠΎΡΠΎΠ²Π½ΠΎΡΡΠΈ, ΠΊΠΎΡΠΎΡΡΠΉ Ρ Π°ΡΠ°ΠΊΡΠ΅ΡΠΈΠ·ΡΠ΅Ρ Π²Π΅ΡΠΎΡΡΠ½ΠΎΡΡΡ ΡΠΎΠ³ΠΎ, ΡΡΠΎ ΠΈΠ·Π΄Π΅Π»ΠΈΠ΅ ΠΎΠΊΠ°ΠΆΠ΅ΡΡΡ ΡΠ°Π±ΠΎΡΠΎΡΠΏΠΎΡΠΎΠ±Π½ΡΠΌ Π² ΠΏΡΠΎΠΈΠ·Π²ΠΎΠ»ΡΠ½ΡΠΉ ΠΌΠΎΠΌΠ΅Π½Ρ Π²ΡΠ΅ΠΌΠ΅Π½ΠΈ, ΠΊΡΠΎΠΌΠ΅ ΠΏΠ»Π°Π½ΠΈΡΡΠ΅ΠΌΡΡ ΠΏΠ΅ΡΠΈΠΎΠ΄ΠΎΠ², Π² ΡΠ΅ΡΠ΅Π½ΠΈΠ΅ ΠΊΠΎΡΠΎΡΡΡ ΠΈΡΠΏΠΎΠ»ΡΠ·ΠΎΠ²Π°Π½ΠΈΠ΅ ΠΎΠ±ΡΠ΅ΠΊΡΠ° ΠΏΠΎ Π½Π°Π·Π½Π°ΡΠ΅Π½ΠΈΡ Π½Π΅ ΠΏΡΠ΅Π΄ΡΡΠΌΠ°ΡΡΠΈΠ²Π°Π΅ΡΡΡ.
ΠΠ΄ΠΈΠ½ΠΈΡΠ½ΡΠΉ ΠΏΠΎΠΊΠ°Π·Π°ΡΠ΅Π»Ρ ΠΊΠΎΠ»ΠΈΡΠ΅ΡΡΠ²Π΅Π½Π½ΠΎ Ρ
Π°ΡΠ°ΠΊΡΠ΅ΡΠΈΠ·ΡΠ΅Ρ ΡΠΎΠ»ΡΠΊΠΎ ΠΎΠ΄Π½ΠΎ ΡΠ²ΠΎΠΉΡΡΠ²ΠΎ, Π° ΠΊΠΎΠΌΠΏΠ»Π΅ΠΊΡΠ½ΡΠΉ β Π½Π΅ΡΠΊΠΎΠ»ΡΠΊΠΎ ΡΠ²ΠΎΠΉΡΡΠ², ΡΠΎΡΡΠ°Π²Π»ΡΡΡΠΈΡ
Π½Π°Π΄Π΅ΠΆΠ½ΠΎΡΡΡ ΠΎΠ±ΡΠ΅ΠΊΡΠ° (ΠΌΠ°ΡΠΈΠ½Ρ).
Π Π΅ΠΊΠ»Π°ΠΌΠ½ΡΠ΅ ΠΏΡΠ΅Π΄Π»ΠΎΠΆΠ΅Π½ΠΈΡ Π½Π° ΠΎΡΠ½ΠΎΠ²Π΅ Π²Π°ΡΠΈΡ ΠΈΠ½ΡΠ΅ΡΠ΅ΡΠΎΠ²:
ΠΡΠ½ΠΎΠ²Π½ΡΠΌ ΠΏΠΎΠΊΠ°Π·Π°ΡΠ΅Π»Π΅ΠΌ Π½Π°Π΄Π΅ΠΆΠ½ΠΎΡΡΠΈ ΡΡΡΠΎΠΈΡΠ΅Π»ΡΠ½ΡΡ ΠΌΠ°ΡΠΈΠ½ ΡΠ²Π»ΡΠ΅ΡΡΡ Π³Π°ΠΌΠΌΠ°-ΠΏΡΠΎΡΠ΅Π½ΡΠ½ΡΠΉ ΡΠ΅ΡΡΡΡ, ΠΊΠΎΡΠΎΡΡΠΉ ΠΎΠ±ΡΡΠ½ΠΎ ΡΠ΅Π³Π»Π°ΠΌΠ΅Π½ΡΠΈΡΡΠ΅ΡΡΡ Π»ΠΈΠ±ΠΎ Π³ΠΎΡΡΠ΄Π°ΡΡΡΠ²Π΅Π½Π½ΡΠΌ ΡΡΠ°Π½Π΄Π°ΡΡΠΎΠΌ, Π»ΠΈΠ±ΠΎ ΡΠ΅Ρ Π½ΠΈΡΠ΅ΡΠΊΠΈΠΌΠΈ ΡΡΠ»ΠΎΠ²ΠΈΡΠΌΠΈ Π½Π° Π΄Π°Π½Π½ΠΎΠ΅ ΠΈΠ·Π΄Π΅Π»ΠΈΠ΅. ΠΠ»Ρ ΠΌΠ½ΠΎΠ³ΠΈΡ ΠΌΠ°ΡΠΈΠ½ ΡΠ°ΡΠΏΡΠΎΡΡΡΠ°Π½Π΅Π½Π½ΡΠΌΠΈ Π΅Π΄ΠΈΠ½ΠΈΡΠ½ΡΠΌΠΈ ΠΏΠΎΠΊΠ°Π·Π°ΡΠ΅Π»ΡΠΌΠΈ Π½Π°Π΄Π΅ΠΆΠ½ΠΎΡΡΠΈ ΡΠ»ΡΠΆΠ°Ρ: Π’0 β Π½Π°ΡΠ°Π±ΠΎΡΠΊΠ° Π½Π° ΠΎΡΠΊΠ°Π·, Ρ Π°ΡΠ°ΠΊΡΠ΅ΡΠΈΠ·ΡΡΡΠ°Ρ Π±Π΅Π·ΠΎΡΠΊΠ°Π·Π½ΠΎΡΡΡ, ΠΈ Π’Π² β ΡΡΠ΅Π΄Π½Π΅Π΅ Π²ΡΠ΅ΠΌΡ Π²ΠΎΡΡΡΠ°Π½ΠΎΠ²Π»Π΅Π½ΠΈΡ, Ρ Π°ΡΠ°ΠΊΡΠ΅ΡΠΈΠ·ΡΡΡΠ΅Π΅ ΡΠ΅ΠΌΠΎΠ½ΡΠΎΠΏΡΠΈΠ³ΠΎΠ΄Π½ΠΎΡΡΡ.
ΠΠ½ΠΎΠ³Π΄Π° ΠΏΠΎΠ»ΡΠ·ΡΡΡΡΡ ΠΊΠΎΠΌΠΏΠ»Π΅ΠΊΡΠ½ΡΠΌ ΠΏΠΎΠΊΠ°Π·Π°ΡΠ΅Π»Π΅ΠΌ β ΠΊΠΎΡΡΡΠΈΡΠΈΠ΅Π½ΡΠΎΠΌ Π³ΠΎΡΠΎΠ²Π½ΠΎΡΡΠΈ.
ΠΠ· ΡΡΠΎΠΉ ΡΠΎΡΠΌΡΠ»Ρ Π²ΠΈΠ΄Π½ΠΎ, ΡΡΠΎ ΠΊΠΎΡΡΡΠΈΡΠΈΠ΅Π½Ρ Π³ΠΎΡΠΎΠ²Π½ΠΎΡΡΠΈ Ρ Π°ΡΠ°ΠΊΡΠ΅ΡΠΈΠ·ΡΠ΅Ρ ΠΎΠ΄Π½ΠΎΠ²ΡΠ΅ΠΌΠ΅Π½Π½ΠΎ Π΄Π²Π° ΡΠ°Π·Π»ΠΈΡΠ½Ρ ΡΠ²ΠΎΠΉΡΡΠ²Π° ΠΎΠ±ΡΠ΅ΠΊΡΠ° β Π΅Π³ΠΎ Π±Π΅Π·ΠΎΡΠΊΠ°Π·Π½ΠΎΡΡΡ ΠΈ ΡΠ΅ΠΌΠΎΠ½ΡΠΎΠΏΡΠΈΠ³ΠΎΠ΄Π½ΠΎΡΡΡ.
ΠΠ°Π΄Π΅ΠΆΠ½ΠΎΡΡΡ ΠΊΠ°ΠΊ ΠΊΠΎΠΌΠΏΠ»Π΅ΠΊΡΠ½ΠΎΠ΅ ΡΠ²ΠΎΠΉΡΡΠ²ΠΎ ΡΡΡΠ΅ΡΡΠ²Π΅Π½Π½ΠΎ ΠΎΡΠ»ΠΈΡΠ°Π΅ΡΡΡ ΠΎΡ Π΄ΡΡΠ³ΠΈΡ
ΡΠ²ΠΎΠΉΡΡΠ² ΠΈΠ·Π΄Π΅Π»ΠΈΡ. ΠΠ½Π°ΡΠΈΡΠ΅Π»ΡΠ½Π°Ρ ΡΠ°ΡΡΡ ΡΡΠΈΡ
ΡΠ²ΠΎΠΉΡΡΠ² Π½Π΅ Π²Π·Π°ΠΈΠΌΠΎΡΠ²ΡΠ·Π°Π½Π°.
Π‘ΠΎΠΎΡΠ½ΠΎΡΠ΅Π½ΠΈΠ΅ ΡΠ²ΠΎΠΉΡΡΠ² Π±Π΅Π·ΠΎΡΠΊΠ°Π·Π½ΠΎΡΡΠΈ, Π΄ΠΎΠ»Π³ΠΎΠ²Π΅ΡΠ½ΠΎΡΡΠΈ, ΡΠ΅ΠΌΠΎΠ½ΡΠΎΠΏΡΠΈΠ³ΠΎΠ΄Π½ΠΎΡΡΠΈ Π΄Π»Ρ Ρ Π°ΡΠ°ΠΊΡΠ΅ΡΠΈΡΡΠΈΠΊΠΈ Π½Π°Π΄Π΅ΠΆΠ½ΠΎΡΡΠΈ ΡΠ°Π·Π»ΠΈΡΠ½ΡΡ Π²ΠΈΠ΄ΠΎΠ² ΡΠ΅Ρ Π½ΠΈΠΊΠΈ Π½Π΅ΠΎΠ΄ΠΈΠ½Π°ΠΊΠΎΠ²ΠΎ. Π Π·Π°Π²ΠΈΡΠΈΠΌΠΎΡΡΠΈ ΠΎΡ Ρ Π°ΡΠ°ΠΊΡΠ΅ΡΠ° ΠΈ Π½Π°Π·Π½Π°ΡΠ΅Π½ΠΈΡ ΡΠ΅Ρ Π½ΠΈΠΊΠΈ Π½Π° ΠΏΠ΅ΡΠ²ΡΠΉ ΠΏΠ»Π°Π½ Π²ΡΠ΄Π²ΠΈΠ³Π°Π΅ΡΡΡ ΡΠΎ ΠΈΠ»ΠΈ ΠΈΠ½ΠΎΠ΅ ΡΠ²ΠΎΠΉΡΡΠ²ΠΎ. ΠΠ»Ρ ΠΎΠ΄Π½ΠΈΡ (ΡΡΠ°Π½ΡΠΏΠΎΡΡΠ½ΡΠ΅ ΡΡΠ΅Π΄ΡΡΠ²Π°) Π²Π°ΠΆΠ½Π΅ΠΉΡΠΈΠΌ ΠΌΠ΅ΡΠΈΠ»ΠΎΠΌ Π½Π°Π΄Π΅ΠΆΠ½ΠΎΡΡΠΈ ΡΠ²Π»ΡΠ΅ΡΡΡ Π±Π΅Π·ΠΎΡΠΊΠ°Π·Π½ΠΎΡΡΡ, Π΄Π»Ρ Π΄ΡΡΠ³ΠΈΡ (Π±ΠΎΠ»ΡΡΠΈΠ½ΡΡΠ²ΠΎ ΡΠ΅Ρ Π½ΠΎΠ»ΠΎΠ³ΠΈΡΠ΅ΡΠΊΠΎΠ³ΠΎ ΠΎΠ±ΠΎΡΡΠ΄ΠΎΠ²Π°Π½ΠΈΡ) β Π΄ΠΎΠ»Π³ΠΎΠ²Π΅ΡΠ½ΠΎΡΡΡ, Π΄Π»Ρ ΡΡΠ΅ΡΡΠΈΡ ΡΠ΅ΡΠ°ΡΡΠ΅ΠΉ ΡΠ²Π»ΡΠ΅ΡΡΡ ΡΠ΅ΠΌΠΎΠ½ΡΠΎΠΏΡΠΈΠ³ΠΎΠ΄Π½ΠΎΡΡΡ.
ΠΠ°Π΄Π΅ΠΆΠ½ΠΎΡΡΡ ΠΈΠΌΠ΅Π΅Ρ Π±ΠΎΠ»ΡΡΠΎΠ΅ ΡΠΊΠΎΠ½ΠΎΠΌΠΈΡΠ΅ΡΠΊΠΎΠ΅ Π·Π½Π°ΡΠ΅Π½ΠΈΠ΅. ΠΡΡ
ΠΎΠ΄ ΠΈΠ· ΡΡΡΠΎΡ Π½Π΅Π½Π°Π΄Π΅ΠΆΠ½ΠΎΠΉ ΡΠ΅Ρ
Π½ΠΈΠΊΠΈ ΠΈ ΡΡΡΡΠ°Π½Π΅Π½ΠΈΠ΅ Π½Π΅ΠΈΡΠΏΡΠ°Π²Π½ΠΎΡΡΠΈ ΡΠ½ΠΈΠΆΠ°ΡΡ ΡΠΎΠ½Π΄ ΡΠ°Π±ΠΎΡΠ΅Π³ΠΎ Π²ΡΠ΅ΠΌΠ΅Π½ΠΈ ΠΈ, ΡΠ»Π΅Π΄ΠΎΠ²Π°ΡΠ΅Π»ΡΠ½ΠΎ, Π΅Π΅ ΠΏΡΠΎΠΈΠ·Π²ΠΎΠ΄ΠΈΡΠ΅Π»ΡΠ½ΠΎΡΡΡ, ΠΏΠΎΠ²ΡΡΠ°ΡΡ ΡΠ΅Π±Π΅ΡΡΠΎΠΈΠΌΠΎΡΡΡ ΠΏΡΠΎΠ΄ΡΠΊΡΠΈΠΈ. ΠΡΠΎΠΌΠ΅ ΡΠΎΠ³ΠΎ, Π²ΡΡ
ΠΎΠ΄ ΠΈΠ· ΡΡΡΠΎΡ ΠΌΠΎΠΆΠ΅Ρ Π²ΡΠ·Π²Π°ΡΡ ΠΏΡΠΎΡΡΠΎΠΉ Π΄ΡΡΠ³ΠΎΠΉ, ΡΠ²ΡΠ·Π°Π½Π½ΠΎΠΉ Ρ Π½Π΅ΠΉ ΡΠ΅Ρ
Π½ΠΈΠΊΠΈ, Π° ΡΠ°ΠΊΠΆΠ΅ ΡΠ½ΠΈΠΆΠ΅Π½ΠΈΠ΅ ΠΎΠ±ΡΠ΅ΠΌΠ° ΠΏΡΠΎΠΈΠ·Π²ΠΎΠ΄ΡΡΠ²Π° ΠΈ Π΄Π°ΠΆΠ΅ ΠΏΠΎΡΡΡ ΠΏΡΠΎΠ΄ΡΠΊΡΠΈΠΈ.
ΠΠ°Π΄Π΅ΠΆΠ½ΠΎΡΡΡ ΠΌΠ°ΡΠΈΠ½Ρ Π·Π°ΠΊΠ»Π°Π΄ΡΠ²Π°Π΅ΡΡΡ ΠΏΡΠΈ Π΅Π΅ ΠΏΡΠΎΠ΅ΠΊΡΠΈΡΠΎΠ²Π°Π½ΠΈΠΈ ΠΈ ΠΎΠ±Π΅ΡΠΏΠ΅ΡΠΈΠ²Π°Π΅ΡΡΡ Π² ΠΏΡΠΎΡΠ΅ΡΡΠ΅ ΠΏΡΠΎΠΈΠ·Π²ΠΎΠ΄ΡΡΠ²Π°. ΠΠ΄Π½Π°ΠΊΠΎ ΠΏΡΠΈ Π½Π°ΡΡΠ½ΠΎ ΠΎΠ±ΠΎΡΠ½ΠΎΠ²Π°Π½Π½ΡΡ
ΠΌΠ΅ΡΠΎΠ΄Π°Ρ
ΡΠΊΡΠΏΠ»ΡΠ°ΡΠ°ΡΠΈΠΈ, Π²ΠΊΠ»ΡΡΠ°ΡΡΠΈΡ
ΡΠ΅Ρ
Π½ΠΈΡΠ΅ΡΠΊΠΎΠ΅ ΠΎΠ±ΡΠ»ΡΠΆΠΈΠ²Π°Π½ΠΈΠ΅, ΡΠ΅ΠΌΠΎΠ½Ρ ΠΈ ΡΠΎΠΎΡΠ²Π΅ΡΡΡΠ²ΡΡΡΠΈΠ΅ ΡΡΠ»ΠΎΠ²ΠΈΡ ΡΠ°Π±ΠΎΡΡ ΠΈ Ρ
ΡΠ°Π½Π΅Π½ΠΈΡ, ΡΠ΄Π°Π΅ΡΡΡ ΡΡΡΠ΅ΡΡΠ²Π΅Π½Π½ΠΎ ΡΠ²Π΅Π»ΠΈΡΠΈΡΡ Π²ΡΠ΅ΠΌΡ, Π² ΡΠ΅ΡΠ΅Π½ΠΈΠ΅ ΠΊΠΎΡΠΎΡΠΎΠ³ΠΎ ΡΠΎΡ
ΡΠ°Π½ΡΠ΅ΡΡΡ Π΄Π°Π½Π½ΡΠΉ ΡΡΠΎΠ²Π΅Π½Ρ Π½Π°Π΄Π΅ΠΆΠ½ΠΎΡΡΠΈ. ΠΠ°ΠΏΡΠΈΠΌΠ΅Ρ, Ρ Π½ΠΎΠ²ΠΎΠΉ ΠΌΠ°ΡΠΈΠ½Ρ Ρ Π³ΠΈΠ΄ΡΠ°Π²Π»ΠΈΡΠ΅ΡΠΊΠΈΠΌ ΠΏΡΠΈΠ²ΠΎΠ΄ΠΎΠΌ Π±ΡΠ»Π° Π²ΡΡΠΎΠΊΠ°Ρ Π²Π΅ΡΠΎΡΡΠ½ΠΎΡΡΡ Π±Π΅Π·ΠΎΡΠΊΠ°Π·Π½ΠΎΠΉ ΡΠ°Π±ΠΎΡΡ, Π½ΠΎ ΡΠ΅ΡΠ΅Π· ΠΎΠΏΡΠ΅Π΄Π΅Π»Π΅Π½Π½ΡΠΉ ΠΈΠ½ΡΠ΅ΡΠ²Π°Π» Π²ΡΠ΅ΠΌΠ΅Π½ΠΈ Π² ΡΠ΅Π·ΡΠ»ΡΡΠ°ΡΠ΅ ΠΈΠ·Π½ΠΎΡΠ° ΠΈ ΡΡΠ°ΡΠ΅Π½ΠΈΡ ΠΌΠ°ΡΠ΅ΡΠΈΠ°Π»Π° ΡΠΏΠ»ΠΎΡΠ½ΡΡΡΠΈΡ
ΡΠ»Π΅ΠΌΠ΅Π½ΡΠΎΠ² ΠΏΠΎΠ²ΡΡΠΈΠ»Π°ΡΡ Π²Π΅ΡΠΎΡΡΠ½ΠΎΡΡΡ ΠΏΠΎΡΠ΅ΡΠΈ Π³Π΅ΡΠΌΠ΅ΡΠΈΡΠ½ΠΎΡΡΠΈ, Ρ. Π΅. ΡΠΌΠ΅Π½ΡΡΠΈΠ»Π°ΡΡ Π½Π°Π΄Π΅ΠΆΠ½ΠΎΡΡΡ Π³ΠΈΠ΄ΡΠΎΠΏΡΠΈΠ²ΠΎΠ΄Π°, Π° ΡΠ»Π΅Π΄ΠΎΠ²Π°ΡΠ΅Π»ΡΠ½ΠΎ, ΠΈ ΠΌΠ°ΡΠΈΠ½Ρ. ΠΠ°ΠΌΠ΅Π½Π° ΡΠΏΠ»ΠΎΡΠ½ΡΡΡΠΈΡ
ΡΠ»Π΅ΠΌΠ΅Π½ΡΠΎΠ² ΠΏΠΎΠ·Π²ΠΎΠ»ΠΈΡ Π² ΡΠ»Π΅Π΄ΡΡΡΠ΅ΠΌ ΠΈΠ½ΡΠ΅ΡΠ²Π°Π»Π΅ Π²ΡΠ΅ΠΌΠ΅Π½ΠΈ ΡΠΎΡ
ΡΠ°Π½ΠΈΡΡ ΠΏΠ΅ΡΠ²ΠΎΠ½Π°ΡΠ°Π»ΡΠ½ΡΠΉ ΡΡΠΎΠ²Π΅Π½Ρ Π½Π°Π΄Π΅ΠΆΠ½ΠΎΡΡΠΈ, Ρ. Π΅. ΡΠ²ΠΎΠ΅Π²ΡΠ΅ΠΌΠ΅Π½Π½ΠΎ ΠΏΡΠΎΠ²Π΅Π΄Π΅Π½Π½ΠΎΠ΅ ΡΠ΅Ρ
Π½ΠΈΡΠ΅ΡΠΊΠΎΠ΅ ΠΎΠ±ΡΠ»ΡΠΆΠΈΠ²Π°Π½ΠΈΠ΅ ΠΏΠΎΠ·Π²ΠΎΠ»ΠΈΡ ΡΠ²Π΅Π»ΠΈΡΠΈΡΡ Π²ΡΠ΅ΠΌΡ ΡΠ°Π±ΠΎΡΡ ΡΠΈΡΡΠ΅ΠΌΡ Ρ Π·Π°Π΄Π°Π½Π½ΠΎΠΉ Π½Π°Π΄Π΅ΠΆΠ½ΠΎΡΡΡΡ. ΠΠΎΡΠ΅ΡΡ ΡΠ°Π±ΠΎΡΠΎΡΠΏΠΎΡΠΎΠ±Π½ΠΎΡΡΠΈ Π±ΠΎΠ»ΡΡΠΈΠ½ΡΡΠ²Π° Π΄Π΅ΡΠ°Π»Π΅ΠΉ ΠΌΠ°ΡΠΈΠ½Ρ ΡΠ²Π»ΡΠ΅ΡΡΡ ΡΡΠ½ΠΊΡΠΈΠ΅ΠΉ Π½Π°ΡΠ°Π±ΠΎΡΠΊΠΈ. ΠΠ·ΠΌΠ΅ΡΠΈΡΠ΅Π»Π΅ΠΌ Π½Π°ΡΠ°Π±ΠΎΡΠΊΠΈ Π΄Π»Ρ ΡΡΡΠΎΠΈΡΠ΅Π»ΡΠ½ΡΡ
ΠΌΠ°ΡΠΈΠ½ ΠΈ ΠΎΠ±ΠΎΡΡΠ΄ΠΎΠ²Π°Π½ΠΈΡ ΠΌΠΎΠΆΠ΅Ρ Π±ΡΡΡ Π°ΡΡΡΠΎΠ½ΠΎΠΌΠΈΡΠ΅ΡΠΊΠΎΠ΅ Π²ΡΠ΅ΠΌΡ (ΠΌΠ°Ρ.
ΠΠ°ΡΠ°Π±ΠΎΡΠΊΠ° ΡΡΠ΄Π° ΠΌΠ΅Ρ Π°Π½ΠΈΠ·ΠΌΠΎΠ² ΠΌΠΎΠΆΠ΅Ρ ΠΎΡΠ»ΠΈΡΠ°ΡΡΡΡ ΠΎΡ ΡΠ°Π±ΠΎΡΠ΅Π³ΠΎ Π²ΡΠ΅ΠΌΠ΅Π½ΠΈ ΠΌΠ°ΡΠΈΠ½Ρ. Π ΡΡΠΎΠΌ ΡΠ»ΡΡΠ°Π΅ ΠΏΡΠΈ ΡΠ°ΡΡΠ΅ΡΠ°Ρ ΠΈΡΠΏΠΎΠ»ΡΠ·ΡΡΡ ΠΊΠΎΡΡΡΠΈΡΠΈΠ΅Π½ΡΡ, ΡΡΠΈΡΡΠ²Π°ΡΡΠΈΠ΅ Π²ΡΠ΅ΠΌΠ΅Π½Π½ΡΡ Π·Π°Π³ΡΡΠ·ΠΊΡ ΠΌΠ΅Ρ Π°Π½ΠΈΠ·ΠΌΠΎΠ² ΠΎΡΠ½ΠΎΡΠΈΡΠ΅Π»ΡΠ½ΠΎ ΠΏΡΠΎΠ΄ΠΎΠ»ΠΆΠΈΡΠ΅Π»ΡΠ½ΠΎΡΡΠΈ ΡΠ°Π±ΠΎΡΡ ΠΌΠ°ΡΠΈΠ½Ρ (ΠΌΠΎΡΠΎ-Ρ).
ΠΠΏΡΠ΅Π΄Π΅Π»Π΅Π½ΠΈΠ΅ ΠΊΠΎΠ»ΠΈΡΠ΅ΡΡΠ²Π΅Π½Π½ΡΡ ΠΏΠΎΠΊΠ°Π·Π°ΡΠ΅Π»Π΅ΠΉ Π½Π°Π΄Π΅ΠΆΠ½ΠΎΡΡΠΈ ΠΏΡΠΎΠΈΠ·Π²ΠΎΠ΄ΡΡ Ρ ΠΏΠΎΠΌΠΎΡΡΡ ΡΡΠ΅Ρ ΠΌΠ΅ΡΠΎΠ΄ΠΎΠ²: ΡΠΊΡΠΏΠ΅ΡΠΈΠΌΠ΅Π½ΡΠ°Π»ΡΠ½ΠΎΠ³ΠΎ, ΠΎΡΡΡΠ΅ΡΡΠ²Π»ΡΠ΅ΠΌΠΎΠ³ΠΎ ΡΠ΅Ρ Π½ΠΈΡΠ΅ΡΠΊΠΈΠΌΠΈ ΠΈΠ·ΠΌΠ΅ΡΠΈΡΠ΅Π»ΡΠ½ΡΠΌΠΈ ΡΡΠ΅Π΄ΡΡΠ²Π°ΠΌΠΈ ΠΈΠ»ΠΈ Π½Π° ΠΎΡΠ½ΠΎΠ²Π΅ ΠΎΠ±Π½Π°ΡΡΠΆΠ΅Π½ΠΈΡ ΠΈ ΠΏΠΎΠ΄ΡΡΠ΅ΡΠ° ΠΊΠΎΠ»ΠΈΡΠ΅ΡΡΠ²Π° ΡΠΎΠ±ΡΡΠΈΠΉ; ΡΠ°ΡΡΠ΅ΡΠ½ΠΎΠ³ΠΎ, ΠΎΡΡΡΠ΅ΡΡΠ²Π»ΡΠ΅ΠΌΠΎΠ³ΠΎ ΠΏΡΠΈ ΠΏΠΎΠΌΠΎΡΠΈ Π²ΡΡΠΈΡΠ»Π΅Π½ΠΈΠΉ Ρ ΠΈΡΠΏΠΎΠ»ΡΠ·ΠΎΠ²Π°Π½ΠΈΠ΅ΠΌ Π·Π½Π°ΡΠ΅Π½ΠΈΠΉ ΠΏΠ°ΡΠ°ΠΌΠ΅ΡΡΠΎΠ², Π½Π°ΠΉΠ΄Π΅Π½Π½ΡΡ Π΄ΡΡΠ³ΠΈΠΌΠΈ ΠΌΠ΅ΡΠΎΠ΄Π°ΠΌΠΈ; ΠΊΠΎΠΌΠ±ΠΈΠ½ΠΈΡΠΎΠ²Π°Π½Π½ΠΎΠ³ΠΎ β ΡΠΊΡΠΏΠ΅ΡΠΈΠΌΠ΅Π½ΡΠ°Π»ΡΠ½ΠΎΠ³ΠΎ ΡΠΎΠ²ΠΌΠ΅ΡΡΠ½ΠΎ Ρ ΡΠ°ΡΡΠ΅ΡΠ½ΡΠΌ.
Π Π΅ΠΊΠ»Π°ΠΌΠ½ΡΠ΅ ΠΏΡΠ΅Π΄Π»ΠΎΠΆΠ΅Π½ΠΈΡ:
Π§ΠΈΡΠ°ΡΡ Π΄Π°Π»Π΅Π΅: Π’ΡΠ΅Π½ΠΈΠ΅ ΠΈ ΠΈΠ·Π½Π°ΡΠΈΠ²Π°Π½ΠΈΠ΅ ΠΏΠΎΠ²Π΅ΡΡ Π½ΠΎΡΡΠ΅ΠΉ Π΄Π΅ΡΠ°Π»Π΅ΠΉ ΡΡΡΠΎΠΈΡΠ΅Π»ΡΠ½ΡΡ ΠΌΠ°ΡΠΈΠ½
ΠΠ°ΡΠ΅Π³ΠΎΡΠΈΡ: — Π‘ΡΡΠΎΠΈΡΠ΅Π»ΡΠ½Π°Ρ ΡΠ΅Ρ Π½ΠΈΠΊΠ° ΠΈ ΠΎΠ±ΠΎΡΡΠ΄ΠΎΠ²Π°Π½ΠΈΠ΅ 4
ΠΠ»Π°Π²Π½Π°Ρ β Π‘ΠΏΡΠ°Π²ΠΎΡΠ½ΠΈΠΊ β Π‘ΡΠ°ΡΡΠΈ β Π€ΠΎΡΡΠΌ
Π‘Π²ΠΎΠΉΡΡΠ²Π° ΠΈ ΠΎΡΠ½ΠΎΠ²Π½ΡΠ΅ ΠΏΠΎΠΊΠ°Π·Π°ΡΠ΅Π»ΠΈ Π½Π°Π΄Π΅ΠΆΠ½ΠΎΡΡΠΈ Π°Π²ΡΠΎΠΌΠΎΠ±ΠΈΠ»Π΅ΠΉ
ΠΈΠ· «Π’Π΅Ρ Π½ΠΈΡΠ΅ΡΠΊΠ°Ρ ΡΠΊΡΠΏΠ»ΡΠ°ΡΠ°ΡΠΈΡ Π°Π²ΡΠΎΠΌΠΎΠ±ΠΈΠ»Π΅ΠΉ Π£ΡΠ΅Π±Π½ΠΈΠΊ Π΄Π»Ρ Π²ΡΠ·ΠΎΠ² »
Π Π°ΡΡΠΌΠΎΡΡΠ΅Π½Π½ΡΠ΅ Π²ΡΡΠ΅ ΠΌΠ°ΡΠ΅ΡΠΈΠ°Π»Ρ ΠΏΠΎΠΊΠ°Π·ΡΠ²Π°ΡΡ, ΡΡΠΎ Π½Π°Π΄Π΅ΠΆΠ½ΠΎΡΡΡ Π·Π°Π²ΠΈΡΠΈΡ Π½Π΅ ΡΠΎΠ»ΡΠΊΠΎ ΠΎΡ Π½Π°ΡΠ°Π±ΠΎΡΠΊΠΈ Π½Π° ΠΎΡΠΊΠ°Π·Ρ, Π½ΠΎ ΠΈ ΠΎΡ ΠΏΡΠΎΠ΄ΠΎΠ»ΠΆΠΈΡΠ΅Π»ΡΠ½ΠΎΡΡΠΈ ΠΈΡ ΡΡΡΡΠ°Π½Π΅Π½ΠΈΡ.
Π Π°ΡΡΠΌΠΎΡΡΠΈΠΌ ΠΊΠ°ΠΆΠ΄ΠΎΠ΅ ΠΈΠ· ΡΡΠΈΡ ΡΠ²ΠΎΠΉΡΡΠ². ΠΠ΅Π·ΠΎΡΠΊΠ°Π·Π½ΠΎΡΡΡ β ΡΡΠΎ ΡΠ²ΠΎΠΉΡΡΠ²ΠΎ Π°Π²ΡΠΎΠΌΠΎΠ±ΠΈΠ»Ρ Π½Π΅ΠΏΡΠ΅ΡΡΠ²Π½ΠΎ ΡΠΎΡ ΡΠ°Π½ΡΡΡ ΡΠ°Π±ΠΎΡΠΎΡΠΏΠΎΡΠΎΠ±Π½ΠΎΡΡΡ Π² ΡΠ΅ΡΠ΅Π½ΠΈΠ΅ ΠΎΠΏΡΠ΅Π΄Π΅Π»Π΅Π½Π½ΠΎΠ³ΠΎ Π²ΡΠ΅ΠΌΠ΅Π½ΠΈ ΠΈΠ»ΠΈ ΠΏΡΠΎΠ±Π΅Π³Π°. ΠΠ»Ρ ΠΎΡΠ΅Π½ΠΊΠΈ Π±Π΅Π·ΠΎΡΠΊΠ°Π·Π½ΠΎΡΡΠΈ ΠΏΡΠΈΠΌΠ΅Π½ΡΡΡ ΡΠ»Π΅Π΄ΡΡΡΠΈΠ΅ ΠΎΡΠ½ΠΎΠ²Π½ΡΠ΅ ΠΏΠΎΠΊΠ°Π·Π°ΡΠ΅Π»ΠΈ Π²Π΅ΡΠΎΡΡΠ½ΠΎΡΡΡ Π±Π΅Π·ΠΎΡΠΊΠ°Π·Π½ΠΎΠΉ ΡΠ°Π±ΠΎΡΡ ΡΡΠ΅Π΄Π½ΡΡ Π½Π°ΡΠ°Π±ΠΎΡΠΊΠ° Π΄ΠΎ ΠΎΡΠΊΠ°Π·Π° ΠΈ Π½Π° ΠΎΡΠΊΠ°Π· ΠΈΠ½ΡΠ΅Π½ΡΠΈΠ²Π½ΠΎΡΡΡ ΠΎΡΠΊΠ°Π·ΠΎΠ² Π΄Π»Ρ Π½Π΅Π²ΠΎΡΡΡΠ°Π½Π°Π²Π»ΠΈΠ²Π°Π΅ΠΌΡΡ ΠΈΠ·Π΄Π΅Π»ΠΈΠΉ ΠΏΠ°ΡΠ°ΠΌΠ΅ΡΡ ΠΏΠΎΡΠΎΠΊΠ° ΠΎΡΠΊΠ°Π·ΠΎΠ² Π΄Π»Ρ Π²ΠΎΡΡΡΠ°Π½Π°Π²Π»ΠΈΠ²Π°Π΅ΠΌΡΡ ΠΈΠ·Π΄Π΅Π»ΠΈΠΉ. [c.50]
ΠΡΠΈΠΌΠ΅Π½ΠΈΡΠ΅Π»ΡΠ½ΠΎ ΠΊ Π°Π²ΡΠΎΠΌΠΎΠ±ΠΈΠ»Ρ ΠΎΠ±ΡΡΠ½ΠΎ ΡΠ°ΡΡΠΌΠ°ΡΡΠΈΠ²Π°ΡΡ Π±Π΅Π·ΠΎΡΠΊΠ°Π·Π½ΠΎΡΡΡ Π² ΡΠ΅ΡΠ΅Π½ΠΈΠ΅ ΡΠΌΠ΅Π½Ρ (ΠΎΠ½Π° ΠΎΡΠΎΠ±Π΅Π½Π½ΠΎ Π²Π°ΠΆΠ½Π°), Π² ΡΠ΅ΡΠ΅Π½ΠΈΠ΅ Π·Π°Π΄Π°Π½Π½ΠΎΠ³ΠΎ ΠΏΡΠΎΠ±Π΅Π³Π° (Π½Π°ΠΏΡΠΈΠΌΠ΅Ρ, Π΄Π»Ρ ΠΌΠ΅ΠΆΠ΄ΡΠ½Π°ΡΠΎΠ΄Π½ΡΡ ΠΏΠ΅ΡΠ΅Π²ΠΎΠ·ΠΎΠΊ) ΠΈΠ»ΠΈ ΠΌΠ΅ΠΆΠ΄Ρ ΠΎΡΠ΅ΡΠ΅Π΄Π½ΡΠΌΠΈ Π²ΠΈΠ΄Π°ΠΌΠΈ Π’Π. Π ΠΏΠΎΡΠ»Π΅Π΄Π½Π΅ΠΌ ΡΠ»ΡΡΠ°Π΅ ΠΏΠΎΠΊΠ°Π·Π°ΡΠ΅Π»ΠΈ Π±Π΅Π·ΠΎΡΠΊΠ°Π·Π½ΠΎΡΡΠΈ Ρ Π°ΡΠ°ΠΊΡΠ΅ΡΠΈΠ·ΡΡΡ ΡΡΡΠ΅ΠΊΡΠΈΠ²Π½ΠΎΡΡΡ ΠΈ ΠΊΠ°ΡΠ΅ΡΡΠ²ΠΎ Π’Π. ΠΡΠ΅Π½ΠΊΠ° Π±Π΅Π·ΠΎΡΠΊΠ°Π·Π½ΠΎΡΡΠΈ ΠΏΠΎ ΠΈΠ½ΡΠ΅ΡΠ²Π°Π»Π°ΠΌ ΠΏΡΠΎΠ±Π΅Π³Π° Π² ΡΠ΅ΡΠ΅Π½ΠΈΠ΅ Π²ΡΠ΅Π³ΠΎ ΡΡΠΎΠΊΠ° ΡΠ°Π±ΠΎΡΡ Π°Π²ΡΠΎΠΌΠΎΠ±ΠΈΠ»Ρ Ρ Π°ΡΠ°ΠΊΡΠ΅ΡΠΈΠ·ΡΠ΅Ρ ΡΠ΅ΠΌΠΏ Π΅Π³ΠΎ ΡΡΠ°ΡΠ΅Π½ΠΈΡ.

ΠΠΎΠ»Π³ΠΎΠ²Π΅ΡΠ½ΠΎΡΡΡ β ΡΠ²ΠΎΠΉΡΡΠ²ΠΎ Π°Π²ΡΠΎΠΌΠΎΠ±ΠΈΠ»Ρ ΡΠΎΡ ΡΠ°Π½ΡΡΡ ΡΠ°Π±ΠΎΡΠΎΡΠΏΠΎΡΠΎΠ±Π½ΠΎΡΡΡ Π΄ΠΎ Π½Π°ΡΡΡΠΏΠ»Π΅Π½ΠΈΡ ΠΏΡΠ΅Π΄Π΅Π»ΡΠ½ΠΎΠ³ΠΎ ΡΠΎΡΡΠΎΡΠ½ΠΈΡ ΠΏΡΠΈ ΡΡΡΠ°Π½ΠΎΠ²Π»Π΅Π½Π½ΠΎΠΉ ΡΠΈΡΡΠ΅ΠΌΠ΅ ΠΏΡΠΎΠ²Π΅Π΄Π΅Π½ΠΈΡ ΡΠ°Π±ΠΎΡ Π’Π ΠΈ ΡΠ΅ΠΌΠΎΠ½ΡΠ°. [c.50]
ΠΠ»Ρ Π΄Π΅ΡΠ°Π»Π΅ΠΉ ΡΠΊΠ°Π·Π°Π½Π½ΡΠ΅ ΠΏΠΎΠΊΠ°Π·Π°ΡΠ΅Π»ΠΈ ΠΎΠΏΡΠ΅Π΄Π΅Π»ΡΡΡΡΡ ΠΏΡΠΈ ΠΏΡΠΎΠ²Π΅Π΄Π΅Π½ΠΈΠΈ ΠΈΡ ΡΠ΅ΠΌΠΎΠ½ΡΠ° ΠΈΠ»ΠΈ, ΡΡΠΎ ΡΠ΅ΠΆΠ΅, ΠΏΡΠΈ ΡΠΏΠΈΡΠ°Π½ΠΈΠΈ Π΄Π΅ΡΠ°Π»Π΅ΠΉ. ΠΠ»Ρ Π°Π³ΡΠ΅Π³Π°ΡΠΎΠ² ΠΎΠΏΡΠ΅Π΄Π΅Π»ΡΡΡΡΡ ΡΠ΅ΡΡΡΡΡ Π΄ΠΎ ΡΠ΅ΠΌΠΎΠ½ΡΠ° ΠΈ ΠΌΠ΅ΠΆΠ΄Ρ ΡΠ΅ΠΌΠΎΠ½ΡΠ°ΠΌΠΈ. ΠΠ»Ρ Π°Π²ΡΠΎΠΌΠΎΠ±ΠΈΠ»Π΅ΠΉ, ΠΊΡΠΎΠΌΠ΅ ΡΠ΅ΡΡΡΡΠΎΠ² Π΄ΠΎ ΡΠ΅ΠΌΠΎΠ½ΡΠ°, ΠΎΠΏΡΠ΅Π΄Π΅Π»ΡΡΡΡΡ ΠΈ Π½ΠΎΡΠΌΠΈΡΡΡΡΡΡ, ΠΊΠ°ΠΊ ΠΏΡΠ°Π²ΠΈΠ»ΠΎ, ΡΡΠΎΠΊΠΈ ΡΠ»ΡΠΆΠ±Ρ Π΄ΠΎ ΠΈΡ ΡΠΏΠΈΡΠ°Π½ΠΈΡ. [c.51]
Π Π΅ΠΌΠΎΠ½ΡΠΎΠΏΡΠΈΠ³ΠΎΠ΄Π½ΠΎΡΡΡ (ΡΠΊΡΠΏΠ»ΡΠ°ΡΠ°ΡΠΈΠΎΠ½Π½Π°Ρ ΡΠ΅Ρ Π½ΠΎΠ»ΠΎΠ³ΠΈΡΠ½ΠΎΡΡΡ) β ΡΠ²ΠΎΠΉΡΡΠ²ΠΎ Π°Π²ΡΠΎΠΌΠΎΠ±ΠΈΠ»Ρ, Π·Π°ΠΊΠ»ΡΡΠ°ΡΡΠ΅Π΅ΡΡ Π² Π΅Π³ΠΎ ΠΏΡΠΈΡΠΏΠΎΡΠΎΠ±Π»Π΅Π½Π½ΠΎΡΡΠΈ ΠΊ ΠΏΡΠ΅Π΄ΡΠΏΡΠ΅ΠΆΠ΄Π΅Π½ΠΈΡ ΠΈ ΠΎΠ±Π½Π°ΡΡΠΆΠ΅Π½ΠΈΡ ΠΏΡΠΈΡΠΈΠ½ Π²ΠΎΠ·Π½ΠΈΠΊΠ½ΠΎΠ²Π΅Π½ΠΈΡ ΠΎΡΠΊΠ°Π·ΠΎΠ², ΠΏΠΎΠ²ΡΠ΅ΠΆΠ΄Π΅Π½ΠΈΠΉ ΠΈ ΠΏΠΎΠ΄Π΄Π΅ΡΠΆΠ°Π½ΠΈΡ ΠΈ Π²ΠΎΡΡΡΠ°Π½ΠΎΠ²Π»Π΅Π½ΠΈΡ ΡΠ°Π±ΠΎΡΠΎΡΠΏΠΎΡΠΎΠ±Π½ΠΎΠ³ΠΎ ΡΠΎΡΡΠΎΡΠ½ΠΈΡ ΠΏΡΡΠ΅ΠΌ ΠΏΡΠΎΠ²Π΅Π΄Π΅Π½ΠΈΡ Π’Π ΠΈ ΡΠ΅ΠΌΠΎΠ½ΡΠ°. ΠΡΠ½ΠΎΠ²Π½ΡΠΌΠΈ ΠΏΠΎΠΊΠ°Π·Π°ΡΠ΅Π»ΡΠΌΠΈ ΡΠ΅ΠΌΠΎΠ½ΡΠΎΠΏΡΠΈΠ³ΠΎΠ΄Π½ΠΎΡΡΠΈ ΡΠ²Π»ΡΡΡΡΡ ΡΡΠ΅Π΄Π½ΠΈΠ΅ ΠΏΡΠΎΠ΄ΠΎΠ»ΠΆΠΈΡΠ΅Π»ΡΠ½ΠΎΡΡΡ ΠΈ ΡΡΡΠ΄ΠΎΠ΅ΠΌΠΊΠΎΡΡΡ Π²ΡΠΏΠΎΠ»Π½Π΅Π½ΠΈΡ ΠΎΠΏΠ΅ΡΠ°ΡΠΈΠΉ Π’Π ΠΈ ΡΠ΅ΠΌΠΎΠ½ΡΠ°, ΠΊΠΎΡΠΎΡΡΠ΅ ΠΏΡΠΈΠΌΠ΅Π½ΡΡΡΡΡ ΠΏΡΠΈ Π½ΠΎΡΠΌΠΈΡΠΎΠ²Π°Π½ΠΈΠΈ ΠΈ ΡΡΠ°Π²Π½Π΅Π½ΠΈΠΈ ΡΠ°Π·Π»ΠΈΡΠ½ΡΡ Π°Π²ΡΠΎΠΌΠΎΠ±ΠΈΠ»Π΅ΠΉ.
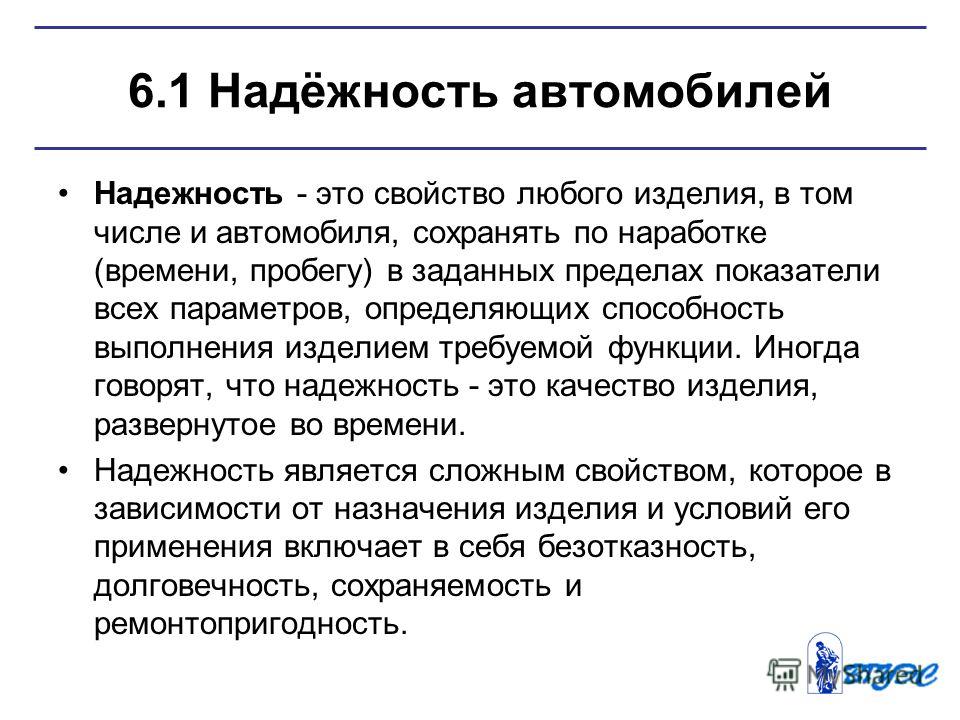
ΠΠΌΠ΅Ρ ΠΎΡΡΠ΅ΡΠ½ΡΠ΅ Π΄Π°Π½Π½ΡΠ΅ ΠΈΠ»ΠΈ Π²Π΅Π΄Ρ Π½Π°Π±Π»ΡΠ΄Π΅Π½ΠΈΡ Π·Π° ΠΈΠ·Π΄Π΅Π»ΠΈΡΠΌΠΈ (Π΄Π΅ΡΠ°Π»ΡΠΌΠΈ, Π°Π³ΡΠ΅Π³Π°ΡΠ°ΠΌΠΈ, Π°Π²ΡΠΎΠΌΠΎΠ±ΠΈΠ»ΡΠΌΠΈ), ΠΌΠΎΠΆΠ½ΠΎ Π΄Π°ΡΡ Π²Π΅ΡΠΎΡΡΠ½ΠΎΡΡΠ½ΡΡ Ρ Π°ΡΠ°ΠΊΡΠ΅ΡΠΈΡΡΠΈΠΊΡ ΡΠ²ΠΎΠΉΡΡΠ²Π°ΠΌ Π½Π°Π΄Π΅ΠΆΠ½ΠΎΡΡΠΈ, Π° ΡΠ°ΠΊΠΆΠ΅ ΠΎΡΠ΅Π½ΠΈΡΡ Π·Π°ΠΊΠΎΠ½ΠΎΠΌΠ΅ΡΠ½ΠΎΡΡΠΈ ΠΈΠ·ΠΌΠ΅Π½Π΅Π½ΠΈΡ ΡΠ΅Ρ Π½ΠΈΡΠ΅ΡΠΊΠΎΠ³ΠΎ ΡΠΎΡΡΠΎΡΠ½ΠΈΡ.

ΠΠ΅ΡΠ½ΡΡΡΡΡ ΠΊ ΠΎΡΠ½ΠΎΠ²Π½ΠΎΠΉ ΡΡΠ°ΡΡΠ΅
ΠΠ°Π΄Π΅ΠΆΠ½ΠΎΡΡΡ ΠΌΠ°ΡΠΈΠ½ — Π‘ΠΏΡΠ°Π²ΠΎΡΠ½ΠΈΠΊ Ρ ΠΈΠΌΠΈΠΊΠ° 21
ββββΠΠΎΠ²ΡΡΠ°ΡΡ Π½Π°Π΄Π΅ΠΆΠ½ΠΎΡΡΡ ΠΌΠ°ΡΠΈΠ½ ΠΈ Π°ΠΏΠΏΠ°ΡΠ°ΡΠΎΠ² Ρ ΠΈΠΌΠΈΡΠ΅ΡΠΊΠΎΠ³ΠΎ ΠΏΡΠΎΠΈΠ·Π²ΠΎΠ΄ΡΡΠ²Π°, ΡΠ°ΠΊ ΠΊΠ°ΠΊ Π°Π²Π°ΡΠΈΠΉΠ½Π°Ρ ΠΎΡΡΠ°Π½ΠΎΠ²ΠΊΠ° ΡΠΎΠ²ΡΠ΅ΠΌΠ΅Π½Π½ΠΎΠΉ Π²ΡΡΠΎΠΊΠΎΠΏΡΠΎΠΈΠ·Π²ΠΎΠ΄ΠΈΡΠ΅Π»ΡΠ½ΠΎΠΉ ΡΠ΅Ρ Π½ΠΎΠ»ΠΎΠ³ΠΈΡΠ΅ΡΠΊΠΎΠΉ ΡΠΈΡΡΠ΅ΠΌΡ ΠΈΠ½ΠΎΠ³Π΄Π° ΠΏΡΠΈΠ½ΠΎΡΠΈΡ ΡΠ±ΡΡΠΊΠΈ, ΠΏΡΠ΅Π²ΡΡΠ°ΡΡΠΈΠ΅ ΡΡΠΎΠΈΠΌΠΎΡΡΡ ΡΠ°ΠΌΠΎΠ³ΠΎ ΠΎΠ±ΠΎΡΡΠ΄ΠΎΠ²Π°Π½ΠΈΡ. Π§Π°ΡΡΡΠ΅ ΠΏΡΠΈΡΠΈΠ½ΠΈ Π²ΡΡ ΠΎΠ΄Π° ΠΈΠ· ΡΡΡΠΎΡ ΠΌΠ°ΡΠΈΠ½ ΠΈ Π°ΠΏΠΏΠ°ΡΠ°ΡΠΎΠ² Ρ ΠΈΠΌΠΈΡΠ΅ΡΠΊΠΎΠ³ΠΎ ΠΏΡΠΎΠΈΠ·Π²ΠΎΠ΄ΡΡΠ²Π° β ΠΊΠΎΡΡΠΎΠ·ΠΈΡ ΠΈ ΠΏΠΎΠ²ΡΠ΅ΠΆΠ΄Π΅Π½ΠΈΠ΅ Π½Π°ΠΈΠ±ΠΎΠ»Π΅Π΅ ΠΎΡΠ²Π΅ΡΡΡΠ²Π΅Π½Π½ΡΡ ΡΠ·Π»ΠΎΠ². β[c.5]ββββΠΠΎΠ»ΠΆΠ½Π° Π±ΡΡΡ Π΄ΠΎΠΊΠ°Π·Π°Π½Π° Π±Π΅Π·ΠΎΠΏΠ°ΡΠ½ΠΎΡΡΡ ΠΎΡΡΡΠ΅ΡΡΠ²Π»Π΅Π½ΠΈΡ ΠΏΡΠΎΡΠ΅ΡΡΠ° ΠΏΡΠΈ Π²ΡΡ ΠΎΠ΄Π΅ ΠΈΠ· ΡΡΡΠΎΡ ΡΠΏΡΠ°Π²Π»ΡΡΡΠ΅ΠΉ ΠΌΠ°ΡΠΈΠ½Ρ ΠΎΠ΄Π½Π°ΠΊΠΎ, Π½Π΅ΡΠΌΠΎΡΡΡ Π½Π° ΡΡΠΎ, ΠΊ Π½Π°Π΄Π΅ΠΆΠ½ΠΎΡΡΠΈ ΠΌΠ°ΡΠΈΠ½Ρ Π½ΡΠΆΠ½ΠΎ ΠΏΡΠ΅Π΄ΡΡΠ²Π»ΡΡΡ Π²ΡΡΠΎΠΊΠΈΠ΅ ΡΡΠ΅Π±ΠΎΠ²Π°Π½ΠΈΡ.β[c.163]
ββββΠΡΠΏ ΡΠ°Π·ΡΠ°Π±ΠΎΡΠΊΠ΅ ΠΎΠ±ΠΎΡΡΠ΄ΠΎΠ²Π°Π½ΠΈΡ Π΄Π»Ρ ΠΎΠ±Π΅ΡΠΏΠ΅ΡΠ΅Π½ΠΈΡ Π½Π°Π΄Π΅ΠΆΠ½ΠΎΡΡΠΈ ΠΌΠ°ΡΠΈΠ½Ρ Π½Π΅ΠΎΠ±Ρ
ΠΎΠ΄ΠΈΠΌΠΎ ΠΎΠ±Π΅ΡΠΏΠ΅ΡΠΈΡΡ Π½Π°Π΄Π΅ΠΆΠ½ΠΎΡΡΡ ΠΊΠ°ΠΆΠ΄ΠΎΠΉ Π΅Π΅ Π΄Π΅ΡΠ°Π»ΠΈ. ΠΠ»Ρ ΡΠ΅ΡΠΈΠΉΠ½ΠΎΠ³ΠΎ ΠΎΠ±ΠΎΡΡΠ΄ΠΎΠ²Π°Π½ΠΈΡ ΠΎΠ±ΡΠ·Π°ΡΠ΅Π»ΡΠ½Ρ ΠΎΡΡΠ°Π±ΠΎΡΠΊΠ°, ΡΠΎΠ·Π΄Π°Π½ΠΈΠ΅ ΠΈ ΠΈΡΠΏΡΡΠ°Π½ΠΈΠ΅ ΠΎΠΏΡΡΠ½ΡΡ
ΠΎΠ±ΡΠ°Π·ΡΠΎΠ². ΠΠΎΡΠΊΠΎΠ»ΡΠΊΡ Π½Π° Π½Π°Π΄Π΅ΠΆΠ½ΠΎΡΡΡ Π΄Π΅ΡΠ°Π»Π΅ΠΉ ΠΎΠΊΠ°Π·ΡΠ²Π°ΡΡ Π²Π»ΠΈΡΠ½ΠΈΠ΅ ΡΡΠ»ΠΎΠ²ΠΈΡ ΡΠΊΡΠΏΠ»ΡΠ°ΡΠ°ΡΠΈΠΈ, ΠΏΠΎΠ²ΡΡΠ΅Π½ΠΈΠ΅ Π½Π°Π΄Π΅ΠΆΠ½ΠΎΡΡΠΈ ΡΡΠ΅Π±ΡΠ΅Ρ ΠΏΠΎΠ»ΡΡΠ΅Π½ΠΈΡ ΠΈΠ½ΡΠΎΡΠΌΠ°ΡΠΈΠΈ ΠΎΡ ΠΏΡΠ΅Π΄ΠΏΡΠΈΡΡΠΈΠΉ, ΡΠΊΡΠΏΠ»ΡΠ°ΡΠΈΡΡΡΡΠΈΡ
ΠΎΠ±ΠΎΡΡΠ΄ΠΎΠ²Π°Π½ΠΈΠ΅, ΠΈ Π°Π½Π°Π»ΠΈΠ·Π° ΠΏΡΠΈΡΠΈΠ½ Π²ΡΡ
ΠΎΠ΄Π° ΠΈΠ· ΡΡΡΠΎΡ ΠΎΠ±ΠΎΡΡΠ΄ΠΎΠ²Π°Π½ΠΈΡ. ΠΡΠΎΠΌΠ΅ ΡΠΎΠ³ΠΎ, Π΄Π»Ρ ΠΎΠΏΡΠ΅Π΄Π΅Π»Π΅Π½ΠΈΡ Π½Π°Π΄Π΅ΠΆΠ½ΠΎΡΡΠΈ ΠΈΡΠΏΠΎΠ»ΡΠ·ΡΡΡΡΡ ΡΠΏΠ΅ΡΠΈΠ°Π»ΡΠ½ΡΠ΅ ΡΡΠΊΠΎΡΠ΅Π½Π½ΡΠ΅ ΠΈΡΠΏΡΡΠ°Π½ΠΈΡ Π½Π° ΡΡΠ΅Π½Π΄Π°Ρ
.β[c.51]
ββββΠ’ΡΠ΅Π±ΠΎΠ²Π°Π½ΠΈΠ΅ Π½Π°Π΄Π΅ΠΆΠ½ΠΎΡΡΠΈ ΠΎΠΊΠ°Π·ΡΠ²Π°Π΅Ρ Π²Π»ΠΈΡΠ½ΠΈΠ΅ Π½Π° ΠΊΠΎΠ½ΡΡΡΡΠΊΡΠΈΡ ΠΌΠ°ΡΠΈΠ½Ρ. ΠΡΠΈ ΡΠΌΠ΅Π½ΡΡΠ΅Π½ΠΈΠΈ ΡΠΈΡΠ»Π° ΠΊΠΎΠ½ΡΡΡΡΠΊΡΠΈΠ²Π½ΡΡ
ΡΠ»Π΅ΠΌΠ΅Π½ΡΠΎΠ² Π½Π°Π΄Π΅ΠΆΠ½ΠΎΡΡΡ ΠΌΠ°ΡΠΈΠ½Ρ ΡΠ²Π΅Π»ΠΈΡΠΈΠ²Π°Π΅ΡΡΡ. Π ΠΌΠ°ΡΠΈΠ½Π΅ ΡΠ»ΠΎΠΆΠ½ΠΎΠΉ ΠΊΠΎΠ½ΡΡΡΡΠΊΡΠΈΠΈ Π½Π΅ ΡΠ΄Π°Π΅ΡΡΡ Π΄ΠΎΠ±ΠΈΡΡΡΡ ΡΠ°Π²Π½ΠΎΠΏΡΠΎΡΠ½ΠΎΡΡΠΈ Π²ΡΠ΅Ρ
Π΄Π΅ΡΠ°Π»Π΅ΠΉ.β
ββββΠΠ° ΠΏΡΠ°ΠΊΡΠΈΠΊΠ΅ ΠΆΠ΅Π»Π°ΡΠ΅Π»ΡΠ½ΠΎ ΡΠ°Π±ΠΎΡΠ°ΡΡ Π² ΠΎΠ±Π»Π°ΡΡΠΈ Π²Π½Π΅Π·Π°ΠΏΠ½ΡΡ ΠΎΡΠΊΠ°Π·ΠΎΠ², Π½Π΅ Π΄ΠΎΠ²ΠΎΠ΄Ρ ΡΠΎΡΡΠΎΡΠ½ΠΈΠ΅ ΠΎΠ±ΠΎΡΡΠ΄ΠΎΠ²Π°Π½ΠΈΡ Π΄ΠΎ ΠΈΠ·Π½ΠΎΡΠ½ΡΡ ΠΎΡΠΊΠ°Π·ΠΎΠ². ΠΠ»Ρ ΡΡΠΎΠ³ΠΎ ΠΏΡΠΈΠΌΠ΅Π½ΡΡΡΡΡ ΠΏΡΠΎΡΠΈΠ»Π°ΠΊΡΠΈΡΠ΅ΡΠΊΠΈΠ΅ ΠΎΡΠΌΠΎΡΡΡ ΠΈ ΡΠ΅ΠΌΠΎΠ½ΡΡ. Π’Π°ΠΊΠΈΠΌ ΠΎΠ±ΡΠ°Π·ΠΎΠΌ, ΡΠΊΡΠΏΠΎΠ½Π΅Π½ΡΠΈΠ°Π»ΡΠ½ΡΠΉ Π·Π°ΠΊΠΎΠ½ ΠΏΡΠΈΠΎΠ±ΡΠ΅ΡΠ°Π΅Ρ Π²Π°ΠΆΠ½ΠΎΠ΅ Π·Π½Π°ΡΠ΅Π½ΠΈΠ΅ Π΄Π»Ρ ΡΠ΅ΠΎΡΠΈΠΈ Π½Π°Π΄Π΅ΠΆΠ½ΠΎΡΡΠΈ ΠΌΠ°ΡΠΈΠ½.β[c.59]
ββββΠ Π°ΡΡΠΌΠΎΡΡΠ΅Π½Π½ΡΠ΅ ΠΏΠΎΠ»ΠΎΠΆΠ΅Π½ΠΈΡ ΡΠ΅ΠΎΡΠΈΠΈ Π½Π°Π΄Π΅ΠΆΠ½ΠΎΡΡΠΈ ΠΌΠ°ΡΠΈΠ½ ΠΈ Π°ΠΏΠΏΠ°ΡΠ°ΡΠΎΠ² ΠΏΠΎΠΊΠ°Π·ΡΠ²Π°ΡΡ, ΡΡΠΎ ΡΠ΅ΠΌΠΎΠ½ΡΠ½Π°Ρ Ρ
Π°ΡΠ°ΠΊΡΠ΅ΡΠΈΡΡΠΈΠΊΠ° ΠΌΠ°ΡΠΈΠ½Ρ ΡΠ΅ΡΠ½ΠΎ ΡΠ²ΡΠ·Π°Π½Π° Ρ Π΅Π΅ Π½Π°Π΄Π΅ΠΆΠ½ΠΎΡΡΡΡ. Π Π½Π°ΡΡΠΎΡΡΠ΅Π΅ Π²ΡΠ΅ΠΌΡ ΠΌΠΎΠ΄Π΅ΡΠ½ΠΈΠ·Π°ΡΠΈΡ ΠΎΠ±ΠΎΡΡΠ΄ΠΎΠ²Π°Π½ΠΈΡ, ΠΏΠΎΠ²ΡΡΠ°ΡΡΠ°Ρ Π΅Π³ΠΎ Π½Π°Π΄Π΅ΠΆΠ½ΠΎΡΡΡ, ΠΎΡΡΡΠ΅ΡΡΠ²Π»ΡΠ΅ΡΡΡ Π² ΠΏΠ΅ΡΠΈΠΎΠ΄ ΠΎΡΡΠ°Π½ΠΎΠ²ΠΊΠΈ ΠΎΠ±ΠΎΡΡΠ΄ΠΎΠ²Π°Π½ΠΈΡ Π½Π° ΡΠ΅ΠΌΠΎΠ½Ρ. ΠΠΎΠ²ΡΡΠ΅Π½ΠΈΠ΅ Π½Π°Π΄Π΅ΠΆΠ½ΠΎΡΡΠΈ, Π° ΡΠ»Π΅Π΄ΠΎΠ²Π°ΡΠ΅Π»ΡΠ½ΠΎ, ΠΈ ΠΌΠ΅ΠΆΡΠ΅ΠΌΠΎΠ½ΡΠ½ΠΎΠ³ΠΎ ΠΏΡΠΎΠ±Π΅Π³Π° Π΄ΠΎΡΡΠΈΠ³Π°Π΅ΡΡΡ ΡΡΠΎΠ²Π΅ΡΡΠ΅Π½ΡΡΠ²ΠΎΠ²Π°Π½ΠΈΠ΅ΠΌ ΠΊΠΎΠ½ΡΡΡΡΠΊΡΠΈΠΈ ΠΎΡΠ΄Π΅Π»ΡΠ½ΡΡ
ΡΠ·Π»ΠΎΠ² Ρ ΠΈΡΠΏΠΎΠ»ΡΠ·ΠΎΠ²Π°Π½ΠΈΠ΅ΠΌ Π½ΠΎΠ²ΡΡ
ΠΊΠΎΡΡΠΎΠ·ΠΈΠΎΠ½Π½ΠΎΡΡΠΎΠΉΠΊΠΈΡ
ΠΌΠ°ΡΠ΅ΡΠΈΠ°Π»ΠΎΠ² ΠΈ ΡΠ°Π·Π»ΠΈΡΠ½ΡΡ
ΠΌΠ΅ΡΠΎΠ΄ΠΎΠ² ΡΠΏΡΠΎΡΠ½Π΅Π½ΠΈΡ ΠΏΠΎΠ²Π΅ΡΡ
Π½ΠΎΡΡΠΈ Π΄Π΅ΡΠ°Π»Π΅ΠΉ.β[c.63]
ββββΠΠ°Π΄Π΅ΠΆΠ½ΠΎΡΡΡ ΠΌΠ°ΡΠΈΠ½Ρ, ΡΠΎΡΡΠΎΡΡΠ΅ΠΉ ΠΈΠ· 40 Π΄Π΅ΡΠ°Π»Π΅ΠΉ, Π΄ΠΎΠ»ΠΆΠ½Π° Π±ΡΡΡ 0,9. ΠΠ°ΠΊΠΎΠΉ Π΄ΠΎΠ»ΠΆΠ½Π° Π±ΡΡΡ Π½Π°Π΄Π΅ΠΆΠ½ΠΎΡΡΡ Π΄Π΅ΡΠ°Π»ΠΈ Π½ΡΠ½ ΡΠ°Π²Π½ΠΎΠΉ ΠΈΠ½ΡΠ΅Π½ΡΠΈΠ²Π½ΠΎΡΡΠΈ ΠΎΡΠΊΠ°Π·ΠΎΠ² Π΄Π»Ρ Π²ΡΠ΅Ρ Π΄Π΅ΡΠ°Π»Π΅ΠΉ β[c.74]
ββββΠΠΎΠ½ΡΡΠΎΠ»Ρ ΡΠΈΡΡΠΎΡΡ Π½Π΅ΡΡΡΠ½ΡΡ ΠΌΠ°ΡΠ΅Π» Π΄Π°Π΅Ρ Π²ΠΎΠ·ΠΌΠΎΠΆΠ½ΠΎΡΡΡ ΠΎΡΠ΅Π½ΠΈΠ²Π°ΡΡ ΡΡΡΠ΅ΠΊΡΠΈΠ²Π½ΠΎΡΡΡ ΡΠΈΡΡΠ΅ΠΌ ΠΈΡ ΠΎΡΠΈΡΡΠΊΠΈ ΠΈ ΡΠ²ΠΎΠ΅Π²ΡΠ΅ΠΌΠ΅Π½Π½ΠΎ Π²ΡΡΠ²Π»ΡΡΡ Π½Π΅ΠΈΡΠΏΡΠ°Π²Π½ΠΎΡΡΠΈ ΠΏΡΠΈ ΡΠΊΡΠΏΠ»ΡΠ°ΡΠ°ΡΠΈΠΈ ΡΡΠΈΡ ΡΠΈΡΡΠ΅ΠΌ, ΡΡΠΎ ΠΏΠΎΠ·Π²ΠΎΠ»ΡΠ΅Ρ ΡΡΡΠ΅ΡΡΠ²Π΅Π½Π½ΠΎ ΡΠ½ΠΈΠΆΠ°ΡΡ Π·Π°Π³ΡΡΠ·Π½Π΅Π½Π½ΠΎΡΡΡ ΠΌΠ°ΡΠ΅Π» ΠΈ ΠΏΠΎΠ²ΡΡΠ°ΡΡ Π½Π°Π΄Π΅ΠΆΠ½ΠΎΡΡΡ ΠΌΠ°ΡΠΈΠ½, Π°Π³ΡΠ΅Π³Π°ΡΠΎΠ² ΠΈ ΡΠ·Π»ΠΎΠ², Π² ΠΊΠΎΡΠΎΡΡΡ ΡΡΠΈ ΠΌΠ°ΡΠ»Π° ΠΏΡΠΈΠΌΠ΅Π½ΡΡΡΡΡ.β[c.297]
ββββΠΠΎΠ»ΡΡΠΈΠ΅ Π·Π°Π΄Π°ΡΠΈ ΡΡΠΎΡΡ ΠΏΠ΅ΡΠ΅Π΄ Π³ΠΎΡΠ½ΠΎΠΉ Π½Π°ΡΠΊΠΎΠΉ ΠΏΠΎ ΡΠ°Π·ΡΠ°Π±ΠΎΡΠΊΠ΅ ΠΈ Π²Π½Π΅Π΄ΡΠ΅Π½ΠΈΡ Π½Π°ΠΈΠ±ΠΎΠ»Π΅Π΅ ΡΠΊΠΎΠ½ΠΎΠΌΠΈΡΠ½ΡΡ
ΡΠΏΠΎΡΠΎΠ±ΠΎΠ² Π΄ΠΎΠ±ΡΡΠΈ ΡΠ³Π»Ρ. ΠΠΎΡΠ½Π°Ρ Π½Π°ΡΠΊΠ° Π΄ΠΎΠ»ΠΆΠ½Π° ΠΎΠ±Π΅ΡΠΏΠ΅ΡΠΈΡΡ ΡΡΠΏΠ΅ΡΠ½ΠΎΠ΅ Π²Π½Π΅Π΄ΡΠ΅Π½ΠΈΠ΅ Π½Π° ΡΠ°Ρ
ΡΠ°Ρ
ΠΊΠΎΠΌΠΏΠ»Π΅ΠΊΡΠ½ΠΎΠΉ Π°Π²ΡΠΎΠΌΠ°ΡΠΈΠ·Π°ΡΠΈΠΈ ΠΈ Π²ΡΠ΅ΠΌΠΊΠΈ ΡΠ³Π»Ρ Π±Π΅Π· ΠΏΡΠΈΡΡΡΡΡΠ²ΠΈΡ Π»ΡΠ΄Π΅ΠΉ Π² ΠΎΡΠΈΡΡΠ½ΡΡ
Π·Π°Π±ΠΎΡΡ
, Π° ΡΠ°ΠΊΠΆΠ΅ ΡΠ°Π·ΡΠ°Π±ΠΎΡΠ°ΡΡ Π±Π΅Π·ΠΎΠΏΠ°ΡΠ½ΡΠ΅ ΡΠΏΠΎΡΠΎΠ±Ρ Π²ΡΠ΅ΠΌΠΊΠΈ ΡΠ³ΠΎΠ»ΡΠ½ΡΡ
ΠΏΠ»Π°ΡΡΠΎΠ² Π½Π° Π±ΠΎΠ»ΡΡΠΈΡ
Π³Π»ΡΠ±ΠΈΠ½Π°Ρ
Π² ΡΡΠ»ΠΎΠ²ΠΈΡΡ
ΠΏΠΎΠ²ΡΡΠ΅Π½Π½ΠΎΠ³ΠΎ Π³ΠΎΡΠ½ΠΎΠ³ΠΎ Π΄Π°Π²Π»Π΅Π½ΠΈΡ. ΠΠ΅ΠΎΠ±Ρ
ΠΎΠ΄ΠΈΠΌΠΎ Π·Π°Π²Π΅ΡΡΠΈΡΡ ΡΠΎΠ·Π΄Π°Π½ΠΈΠ΅ Π½Π°Π΄Π΅ΠΆΠ½ΡΡ
ΠΌΠ°ΡΠΈΠ½ Π΄Π»Ρ Π³ΠΈΠ΄ΡΠ°Π²Π»ΠΈΡΠ΅ΡΠΊΠΎΠ³ΠΎ ΡΠΏΠΎΡΠΎΠ±Π° Π΄ΠΎΠ±ΡΡΠΈ ΡΠ³Π»Ρ.β[c.205]
ββββΠΠ΅ΡΠΎΡΡΠ½ΠΎΡΡΡ Π²ΡΡ ΠΎΠ΄Π° Π΅Π΅ ΠΈΠ· ΡΡΡΠΎΡ Π² ΡΠ΅ΡΠ΅Π½ΠΈΠ΅ ΡΡΠΎΠ³ΠΎ ΠΏΠ΅ΡΠΈΠΎΠ΄Π° ΠΎΡΠ΅Π½Ρ ΠΌΠ°Π»Π°. ΠΠ±ΡΠ΅Π΅ ΠΎΠΏΡΠ΅Π΄Π΅Π»Π΅Π½ΠΈΠ΅ Π½Π°Π΄Π΅ΠΆΠ½ΠΎΡΡΠΈ Π½ΡΠΆΠ΄Π°Π΅ΡΡΡ Π² ΠΊΠΎΠ½ΠΊΡΠ΅ΡΠΈΠ·Π°ΡΠΈΠΈ ΠΏΡΠΈΠΌΠ΅Π½ΠΈΡΠ΅Π»ΡΠ½ΠΎ ΠΊ ΡΠ°Π·Π»ΠΈΡΠ½ΡΠΌ ΡΡΠ»ΠΎΠ²ΠΈΡΠΌ ΡΠ°Π±ΠΎΡΡ. Π ΠΎΠ΄Π½ΠΈΡ ΡΠ»ΡΡΠ°ΡΡ ΠΏΠΎΠ΄ Π½Π°Π΄Π΅ΠΆΠ½ΠΎΡΡΡΡ ΠΌΠ°ΡΠΈΠ½Ρ ΠΏΠΎΠ½ΠΈΠΌΠ°ΡΡ ΡΡΠ°Π±ΠΈΠ»ΡΠ½ΠΎΡΡΡ Π΅Π΅ ΠΏΠ°ΡΠ°ΠΌΠ΅ΡΡΠΎΠ² ΠΈ ΠΌΠΈΠ½ΠΈΠΌΠ°Π»ΡΠ½ΠΎΠ΅ ΡΡ ΡΠ΄ΡΠ΅Π½ΠΈΠ΅ ΡΠΊΡΠΏΠ»ΡΠ°ΡΠ°ΡΠΈΠΎΠ½Π½ΡΡ Ρ Π°ΡΠ°ΠΊΡΠ΅ΡΠΈΡΡΠΈΠΊ Π·Π° ΠΎΠΏΡΠ΅Π΄Π΅Π»Π΅Π½Π½ΡΠΉ ΠΏΠ΅ΡΠΈΠΎΠ΄ Π²ΡΠ΅ΠΌΠ΅Π½ΠΈ, Π² Π΄ΡΡΠ³ΠΈΡ β ΠΎΡΡΡΡΡΡΠ²ΠΈΠ΅ Π²Π½Π΅Π·Π°ΠΏΠ½ΡΡ Π²ΡΡ ΠΎΠ΄ΠΎΠ² ΠΈΠ· ΡΡΡΠΎΡ ΠΏΡΠΈ Π½ΠΎΡΠΌΠ°Π»ΡΠ½ΠΎΠΉ ΡΠ°Π±ΠΎΡΠ΅ Π·Π° ΠΎΠΏΡΠ΅Π΄Π΅Π»Π΅Π½Π½ΡΠΉ ΠΏΠ΅ΡΠΈΠΎΠ΄ Π²ΡΠ΅ΠΌΠ΅Π½ΠΈ, Π² Π΄ΡΡΠ³ΠΈΡ β ΠΎΡΡΡΡΡΡΠ²ΠΈΠ΅ Π²Π½Π΅Π·Π°ΠΏΠ½ΡΡ Π²ΡΡ ΠΎΠ΄ΠΎΠ² ΠΈΠ· ΡΡΡΠΎΡ ΠΏΡΠΈ Π½ΠΎΡΠΌΠ°Π»ΡΠ½ΠΎΠΉ ΡΠ°Π±ΠΎΡΠ΅ Π·Π° ΠΎΠΏΡΠ΅Π΄Π΅Π»Π΅Π½Π½ΡΠΉ ΠΏΠ΅ΡΠΈΠΎΠ΄ Π²ΡΠ΅ΠΌΠ΅Π½ΠΈ. ΠΠ΅ΠΎΠ±Ρ ΠΎΠ΄ΠΈΠΌΡ ΠΏΠΎΠΊΠ°Π·Π°ΡΠ΅Π»ΠΈ Π½Π°Π΄Π΅ΠΆΠ½ΠΎΡΡΠΈ ΠΌΠ°ΡΠΈΠ½Ρ, ΠΎΡΡΠ°ΠΆΠ°ΡΡΠΈΠ΅ ΡΠ°ΡΡΠΎΡΡ Π²Π½Π΅Π·Π°ΠΏΠ½ΡΡ Π²ΡΡ ΠΎΠ΄ΠΎΠ² Π΅Π΅ ΠΈΠ· ΡΡΡΠΎΡ ΠΈ ΡΡΠ΅ΠΏΠ΅Π½Ρ ΡΡ ΡΠ΄ΡΠ΅Π½ΠΈΡ Ρ Π°ΡΠ°ΠΊΡΠ΅ΡΠΈΡΡΠΈΠΊ ΡΠ°Π±ΠΎΡΡ ΠΌΠ°ΡΠΈΠ½Ρ Π²ΠΎ Π²ΡΠ΅ΠΌΠ΅Π½ΠΈ.
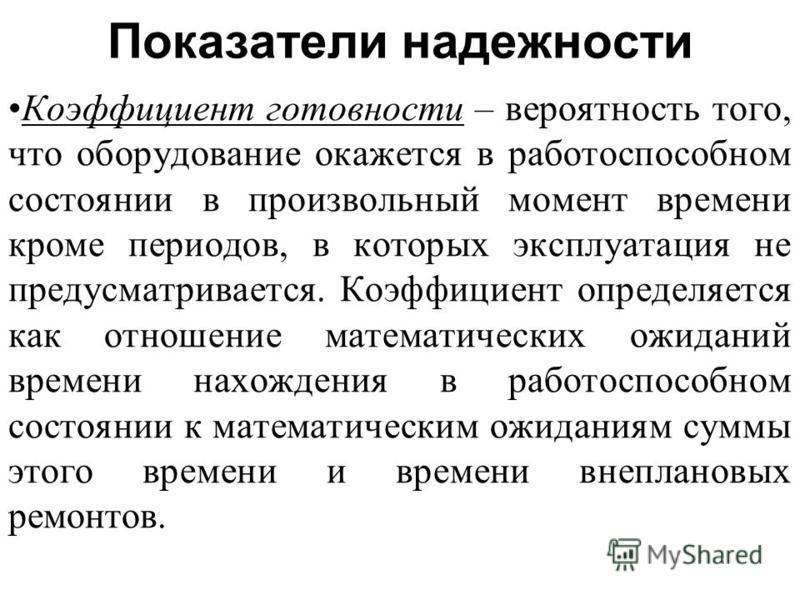
ββββΠΠ°ΡΡΠ΄Ρ Ρ Π½Π°Π΄Π΅ΠΆΠ½ΠΎΡΡΡΡ ΠΌΠ°ΡΠΈΠ½Ρ ΠΈΠ»ΠΈ Π°Π³ΡΠ΅Π³Π°ΡΠ° ΡΡΡΠ΅ΡΡΠ²ΡΠ΅Ρ ΠΏΠΎΠ½ΡΡΠΈΠ΅ Π½Π°Π΄Π΅ΠΆΠ½ΠΎΡΡΠΈ ΠΎΡΠ΄Π΅Π»ΡΠ½ΡΡ Π΄Π΅ΡΠ°Π»Π΅ΠΉ ΠΈ ΡΠ·Π»ΠΎΠ². ΠΠ°Π΄Π΅ΠΆΠ½ΠΎΡΡΡ Π΄Π΅ΡΠ°Π»Π΅ΠΉ ΠΎΠΏΡΠ΅Π΄Π΅Π»ΡΠ΅ΡΡΡ Π΄Π»ΠΈΡΠ΅Π»ΡΠ½ΠΎΡΡΡΡ ΠΌΠ΅ΠΆΡΠ΅ΠΌΠΎΠ½ΡΠ½ΠΎΠ³ΠΎ ΡΡΠΎΠΊΠ° ΠΈΡ ΡΠ»ΡΠΆΠ±Ρ ΡΠ΅ΠΌ Π²ΡΡΠ΅ Π³Π°ΡΠ°Π½ΡΠΈΠΉΠ½ΡΠΉ ΠΌΠ΅ΠΆΡΠ΅ΠΌΠΎΠ½ΡΠ½ΡΠΉ ΡΡΠΎΠΊ ΡΠ»ΡΠΆΠ±Ρ Π΄Π΅ΡΠ°Π»Π΅ΠΉ, ΡΠ΅ΠΌ Π²ΡΡΠ΅ ΠΈΡ Π½Π°Π΄Π΅ΠΆΠ½ΠΎΡΡΡ ΠΈ, ΠΊΠ°ΠΊ ΠΏΡΠ°Π²ΠΈΠ»ΠΎ, ΡΠ΅ΠΌ Π²ΡΡΠ΅ Π΄ΠΎΠ»Π³ΠΎΠ²Π΅ΡΠ½ΠΎΡΡΡ ΠΌΠ°ΡΠΈΠ½Ρ Π² ΡΠ΅Π»ΠΎΠΌ. ΠΠΎ Π½Π΅ ΡΠ»Π΅Π΄ΡΠ΅Ρ ΠΎΡΠΎΠΆΠ΄Π΅ΡΡΠ²Π»ΡΡΡ Π΄ΠΎΠ»Π³ΠΎΠ²Π΅ΡΠ½ΠΎΡΡΡ ΠΌΠ°ΡΠΈΠ½Ρ ΠΈ ΡΡΠΎΠΊ ΡΠ»ΡΠΆΠ±Ρ Π΅Π΅ ΠΎΡΠ΄Π΅Π»ΡΠ½ΡΡ Π΄Π΅ΡΠ°Π»Π΅ΠΉ ΠΈ ΡΠ·Π»ΠΎΠ².β[c.226]
ββββΠΠ°Π΄Π΅ΠΆΠ½ΠΎΡΡΡ ΠΌΠ°ΡΠΈΠ½Ρ Ρ Π°ΡΠ°ΠΊΡΠ΅ΡΠΈΠ·ΡΠ΅ΡΡΡ Π½Π΅ΠΏΡΠ΅ΡΡΠ²Π½ΠΎΡΡΡΡ ΠΈ Π΄Π»ΠΈΡΠ΅Π»ΡΠ½ΠΎΡΡΡΡ Π΅Π΅ ΡΠ°Π±ΠΎΡΡ Π±Π΅Π· ΡΠ΅ΠΌΠΎΠ½ΡΠ°. ΠΠ°Π΄Π΅ΠΆΠ½ΠΎΠΉ ΡΡΠΈΡΠ°Π΅ΡΡΡ ΠΊΠΎΠ½ΡΡΡΡΠΊΡΠΈΡ, ΠΎΠ±Π΅ΡΠΏΠ΅ΡΠΈΠ²Π°ΡΡΠ°Ρ Π±Π΅ΡΠΏΠ΅ΡΠ΅Π±ΠΎΠΉΠ½ΡΡ ΡΠ°Π±ΠΎΡΡ ΠΌΠ°ΡΠΈΠ½Ρ Π² ΡΠ΅ΡΠ΅Π½ΠΈΠ΅ ΠΎΠΏΡΠ΅Π΄Π΅Π»Π΅Π½Π½ΠΎΠ³ΠΎ, Π΄ΠΎΠ²ΠΎΠ»ΡΠ½ΠΎ Π΄Π»ΠΈΡΠ΅Π»ΡΠ½ΠΎΠ³ΠΎ ΡΡΠΎΠΊΠ° Π΅Π΅ ΡΠΊΡΠΏΠ»ΡΠ°ΡΠ°ΡΠΈΠΈ.β[c.517]
ββββΠΠΎΠ²ΡΡΠ΅Π½ΠΈΠ΅ Π½Π°Π΄Π΅ΠΆΠ½ΠΎΡΡΠΈ. ΠΠΎΠ²ΡΡΠ΅Π½ΠΈΠ΅ Π½Π°Π΄Π΅ΠΆΠ½ΠΎΡΡΠΈ ΠΌΠ°ΡΠΈΠ½ ΡΠ²Π»ΡΠ΅ΡΡΡ ΠΎΠ±ΡΠ΅ΠΉ ΡΠ΅Ρ
Π½ΠΈΡΠ΅ΡΠΊΠΎΠΉ Π·Π°Π΄Π°ΡΠ΅ΠΉ, ΠΊΠΎΡΠΎΡΠ°Ρ Π΄ΠΎΠ»ΠΆΠ½Π° ΡΠ΅ΡΠ°ΡΡΡΡ Π½Π° Π²ΡΠ΅Ρ
ΡΡΠ°ΠΏΠ°Ρ
ΠΏΡΠΎΠ΅ΠΊΡΠΈΡΠΎΠ²Π°Π½ΠΈΡ, ΠΈΠ·Π³ΠΎΡΠΎΠ²Π»Π΅Π½ΠΈΡ ΠΈ ΡΠΊΡΠΏΠ»ΡΠ°ΡΠ°ΡΠΈΠΈ. ΠΠΎΠ²ΡΡΠ΅Π½ΠΈΠ΅ Π½Π°Π΄Π΅ΠΆΠ½ΠΎΡΡΠΈ ΠΏΠΎΠ·Π²ΠΎΠ»ΡΠ΅Ρ ΡΠ²Π΅Π»ΠΈΡΠΈΡΡ ΠΏΠ΅ΡΠΈΠΎΠ΄ ΡΠ°Π±ΠΎΡΡ ΠΌΠ°ΡΠΈΠ½Ρ ΠΌΠ΅ΠΆΠ΄Ρ ΡΠ΅ΠΌΠΎΠ½ΡΠ°ΠΌΠΈ ΠΈ ΡΠΌΠ΅Π½ΡΡΠΈΡΡ ΡΠΈΡΠ»ΠΎ ΡΠ΅ΠΌΠΎΠ½ΡΠΎΠ² Π·Π° Π²ΡΠ΅ΠΌΡ ΡΠ»ΡΠΆΠ±Ρ ΠΌΠ°ΡΠΈΠ½Ρ. β[c.27]
ββββΠΠΎ Π½ΠΎΠΌΠΎΠ³ΡΠ°ΠΌΠΌΠ΅ ΠΎΡΠ½ΠΎΡΠ΅Π½ΠΈΡ Π΄Π°Π²Π»Π΅Π½ΠΈΠΉ Π² ΡΡΡΠΏΠ΅Π½ΡΡ ΡΠΌΠ΅Π½ΡΡΠ°ΡΡΡΡ ΠΎΡ ΠΏΠ΅ΡΠ²ΠΎΠΉ ΡΡΡΠΏΠ΅Π½ΠΈ ΠΊ ΠΏΠΎΡΠ»Π΅Π΄Π½Π΅ΠΉ. ΠΡΠΈ ΡΡΠΎΠΌ ΠΏΠΎΠ²ΡΡΠ°Π΅ΡΡΡ ΡΠΊΠΎΠ½ΠΎΠΌΠΈΡΠ½ΠΎΡΡΡ, Π΄ΠΎΡΡΠΈΠ³Π°ΡΡΡΡ ΡΠΊΡΠΏΠ»ΡΠ°ΡΠ°ΡΠΈΠΎΠ½Π½ΡΠ΅ ΠΏΡΠ΅ΠΈΠΌΡΡΠ΅ΡΡΠ²Π°. Π ΡΡΡΠΏΠ΅Π½ΡΡ Π²ΡΡΠΎΠΊΠΎΠ³ΠΎ Π΄Π°Π²Π»Π΅Π½ΠΈΡ ΠΎΡ Π»Π°ΠΆΠ΄Π΅Π½ΠΈΠ΅ ΡΠΈΠ»ΠΈΠ½Π΄ΡΠΎΠ² ΠΌΠ°Π»ΠΎ ΡΡΡΠ΅ΠΊΡΠΈΠ²Π½ΠΎ, Π²ΡΠ»Π΅Π΄ΡΡΠ²ΠΈΠ΅ ΡΠ΅Π³ΠΎ ΠΏΠΎΠΊΠ°Π·Π°ΡΠ΅Π»Ρ ΠΏΠΎΠ»ΠΈΡΡΠΎΠΏΡ ΡΠΆΠ°ΡΠΈΡ ΠΈ, ΡΠ»Π΅Π΄ΠΎΠ²Π°ΡΠ΅Π»ΡΠ½ΠΎ, ΡΠ΅ΠΌΠΏΠ΅ΡΠ°ΡΡΡΡ Π² ΡΠΈΠ»ΠΈΠ½Π΄ΡΠ°Ρ Π²ΡΡΠ΅, ΡΠ΅ΠΌ Π² ΡΡΡΠΏΠ΅Π½ΡΡ Π½ΠΈΠ·ΠΊΠΎΠ³ΠΎ Π΄Π°Π²Π»Π΅Π½ΠΈΡ. ΠΠΎΠ½ΠΈΠΆΠ΅Π½ΠΈΠ΅ ΠΎΡΠ½ΠΎ ΡΠ΅Π½ΠΈΡ Π΄Π°Π²Π»Π΅Π½ΠΈΠΉ Π² ΡΡΡΠΏΠ΅Π½ΡΡ Π²ΡΡΠΎΠΊΠΎΠ³ΠΎ Π΄Π°Π²Π»Π΅Π½ΠΈΡ Π²ΡΡΠ°Π²Π½ΠΈΠ²Π°Π΅Ρ ΡΠ΅ΠΌΠΏΠ΅ΡΠ°ΡΡΡΡ Π½Π°Π³Π½Π΅ΡΠ°Π½ΠΈΡ ΠΏΠΎ ΡΡΡΠΏΠ΅Π½ΡΠΌ, ΡΠ»ΡΡΡΠ°Π΅Ρ ΡΡΠ»ΠΎΠ²ΠΈΡ ΡΠΌΠ°Π·ΠΊΠΈ ΠΈ ΠΏΠΎΠ²ΡΡΠ°Π΅Ρ Π½Π°Π΄Π΅ΠΆΠ½ΠΎΡΡΡ ΠΌΠ°ΡΠΈΠ½Ρ.β[c.70]
ββββΠΠ°ΠΆΠ΄ΠΎΠΉ ΡΠΈΡΡΠ΅ΠΌΠ΅ Π² Π·Π°Π²ΠΈΡΠΈΠΌΠΎΡΡΠΈ ΠΎΡ Π΅Π΅ Π½Π°Π·Π½Π°ΡΠ΅Π½ΠΈΡ ΠΈ Π²Π°ΠΆΠ½ΠΎΡΡΠΈ Π²ΡΠΏΠΎΠ»Π½ΡΠ΅ΠΌΡΡ ΡΡΠ½ΠΊΡΠΈΠΉ ΡΡΡΠ°Π½Π°Π²Π»ΠΈΠ²Π°Π΅ΡΡΡ ΡΡΠ΅Π±ΡΠ΅ΠΌΡΠΉ ΠΊΠ»Π°ΡΡ ΡΠΈΡΡΠΎΡΡ ΠΆΠΈΠ΄ΠΊΠΎΡΡΠΈ. ΠΡΠΈ ΡΡΠΎΠΌ ΠΎΠ±ΡΠ·Π°ΡΠ΅Π»ΡΠ½ΠΎ ΡΡΠΈΡΡΠ²Π°ΡΡΡΡ ΡΡΠ΅Π±ΠΎΠ²Π°Π½ΠΈΡ ΠΏΠΎ Π½Π°Π΄Π΅ΠΆΠ½ΠΎΡΡΠΈ ΠΌΠ°ΡΠΈΠ½ ΠΈ ΠΌΠ΅Ρ Π°Π½ΠΈΠ·ΠΌΠΎΠ² ΠΈ ΡΡΡΠ°Π½Π°Π²Π»ΠΈΠ²Π°Π΅ΡΡΡ ΡΡΠΎΠΊ ΡΠ»ΡΠΆΠ±Ρ.β[c.17]
ββββΠΠ±ΡΠ°Π³ΠΈΠΌΠΎΠ² Π.Π., ΠΡΠ·Π΅Π΅Π² Π.Π ., Π€ΠΈΠ»ΠΈΠΌΠΎΠ½ΠΎΠ² Π.Π., ΠΠ°ΡΠ·ΠΈΡΠΎΠ² Π.Π. ΠΡΡΠ°ΡΠΎΡΠ½ΡΠ΅ ΡΠΎΠ»ΡΠΈΠ½Ρ ΡΡΠ΅Π½ΠΊΠΈ ΡΡΡΠ± ΠΊΠΎΠ½Π²Π΅ΠΊΡΠΈΠΎΠ½Π½ΡΡ
ΠΈ ΡΠ°Π΄ΠΈΠ°Π½ΡΠ½ΡΡ
ΡΠΊΡΠ°Π½ΠΎΠ² Π½Π°Π³ΡΠ΅Π²Π°ΡΠ΅Π»ΡΠ½ΡΡ
ΠΏΠ΅ΡΠ΅ΠΉ// ΠΠΎΠ²ΡΡΠ΅Π½ΠΈΠ΅ ΡΡΡΠ΅ΠΊΡΠΈΠ²Π½ΠΎΡΡΠΈ ΠΈ Π½Π°Π΄Π΅ΠΆΠ½ΠΎΡΡΠΈ ΠΌΠ°ΡΠΈΠ½ ΠΈ Π°ΠΏΠΏΠ°ΡΠ°ΡΠΎΠ² Π² ΠΎΡΠ½ΠΎΠ²Π½ΠΎΠΉ Ρ
ΠΈΠΌΠΈΠΈ. -Π‘ΡΠΌΡ, 1986.- Π‘.217-218.β[c.44]
ββββΠ Π 26-11-20-88. ΠΠ°Π΄Π΅ΠΆΠ½ΠΎΡΡΡ ΠΈΠ·Π΄Π΅Π»ΠΈΠΉ Ρ ΠΈΠΌΠΈΡΠ΅ΡΠΊΠΎΠ³ΠΎ ΠΈ Π½Π΅ΡΡΡΠ½ΠΎΠ³ΠΎ ΠΌΠ°ΡΠΈΠ½ΠΎΡΡΡΠΎΠ΅Π½ΠΈΡ. Π‘ΠΈΡΡΠ΅ΠΌΠ° ΠΊΠΎΠ½ΡΡΠΎΠ»Ρ ΠΈ ΠΎΡΠ΅Π½ΠΊΠΈ Π½Π°Π΄Π΅ΠΆΠ½ΠΎΡΡΠΈ ΠΌΠ°ΡΠΈΠ½ Π² ΡΠΊΡΠΏΠ»ΡΠ°ΡΠ°ΡΠΈΠΈ. ΠΠΎΠ½ΡΡΠΎΠ»Ρ Π½ΠΎΡΠΌΠΈΡΠΎΠ²Π°Π½Π½ΡΡ ΠΏΠΎΠΊΠ°Π·Π°ΡΠ΅Π»Π΅ΠΉ Π½Π°Π΄Π΅ΠΆΠ½ΠΎΡΡΠΈ ΠΈΠ·Π΄Π΅Π»ΠΈΠΉ Π΅Π΄ΠΈΠ½ΠΈΡΠ½ΠΎΠ³ΠΎ ΠΈ ΠΌΠ΅Π»ΠΊΠΎΡΠ΅ΡΠΈΠΉΠ½ΠΎΠ³ΠΎ ΠΏΡΠΎΠΈΠ·Π²ΠΎΠ΄ΡΡΠ²Π°. — Π. ΠΠΠΠ₯ΠΠΠΠΠ¨.β[c.291]
ββββΠ Π 26-11-21-88. ΠΠ΅ΡΠΎΠ΄ΠΈΡΠ΅ΡΠΊΠΈΠ΅ ΡΠΊΠ°Π·Π°Π½ΠΈΡ. ΠΠ°Π΄Π΅ΠΆΠ½ΠΎΡΡΡ ΠΈΠ·Π΄Π΅Π»ΠΈΠΉ Ρ ΠΈΠΌΠΈΡΠ΅ΡΠΊΠΎΠ³ΠΎ ΠΈ Π½Π΅ΡΡΡΠ½ΠΎΠ³ΠΎ ΠΌΠ°ΡΠΈΠ½ΠΎΡΡΡΠΎΠ΅Π½ΠΈΡ. Π‘ΠΈΡΡΠ΅ΠΌΠ° ΠΊΠΎΠ½ΡΡΠΎΠ»Ρ ΠΈ ΠΎΡΠ΅Π½ΠΊΠΈ Π½Π°Π΄Π΅ΠΆΠ½ΠΎΡΡΠΈ ΠΌΠ°ΡΠΈΠ½ Π² ΡΠΊΡΠΏΠ»ΡΠ°ΡΠ°ΡΠΈΠΈ. ΠΡΠ΅Π½ΠΊΠ° Π½Π°Π΄Π΅ΠΆΠ½ΠΎΡΡΠΈ ΠΈΠ·Π΄Π΅Π»ΠΈΠΉ ΠΏΠΎ ΡΠ΅Π·ΡΠ»ΡΡΠ°ΡΠ°ΠΌ ΡΠΊΡΠΏΠ»ΡΠ°ΡΠ°ΡΠΈΠΎΠ½Π½ΡΡ Π½Π°Π±Π»ΡΠ΄Π΅Π½ΠΈΠΉ (ΠΈΡΠΏΡΡΠ°Π½ΠΈΠΉ). — Π. ΠΠΠΠ₯ΠΠΠΠΠ¨, 1988.β[c.291]
ββββΠΡΠΎΠΌΠ΅ ΡΠ΅ΡΠΌΠΎΠ΄ΠΈΠ½Π°ΠΌΠΈΡΠ΅ΡΠΊΠΎΠΉ Π²Π΅ΡΠΎΡΡΠ½ΠΎΡΡΠΈ ΠΏΡΠΎΡΠ΅ΡΡΠ° Π½Π΅ΠΎΠ±Ρ ΠΎΠ΄ΠΈΠΌΠΎ ΡΠ°ΡΡΠΌΠ°ΡΡΠΈΠ²Π°ΡΡ ΠΊΠΈΠ½Π΅ΡΠΈΠΊΡ ΠΏΡΠΎΡΠ΅ΡΡΠ°, ΡΠ°ΠΊ ΠΊΠ°ΠΊ ΠΎΠ½Π° ΠΎΠΏΡΠ΅Π΄Π΅Π»ΡΠ΅Ρ Π΄ΠΎΠ»Π³ΠΎΠ²Π΅ΡΠ½ΠΎΡΡΡ ΠΈ Π½Π°Π΄Π΅ΠΆΠ½ΠΎΡΡΡ ΠΌΠ°ΡΠΈΠ½ ΠΈ ΠΊΠΎΠ½ΡΡΡΡΠΊΡΠΈΠΉ, ΡΠ°Π±ΠΎΡΠ°ΡΡΠΈΡ Π² ΠΊΠΎΡΡΠΎΠ·ΠΈΠΎΠ½Π½ΡΡ ΡΡΠ΅Π΄Π°Ρ .β[c.507]
ββββΠΠ°ΡΠΈΡΠ° ΠΌΠ΅ΡΠ°Π»Π»ΠΎΠ² ΠΎΡ ΠΊΠΎΡΡΠΎΠ·ΠΈΠΎΠ½Π½ΠΎΠ³ΠΎ ΡΠ°Π·ΡΡΡΠ΅Π½ΠΈΡ ΡΠΎΡΡΠΎΠΈΡ ΠΈΠ· ΡΠ΅Π»ΠΎΠ³ΠΎ ΠΊΠΎΠΌΠΏΠ»Π΅ΠΊΡΠ° ΠΌΠ΅ΡΠΎΠΏΡΠΈΡΡΠΈΠΉ ΠΏΠΎ ΡΠ²Π΅Π»ΠΈΡΠ΅Π½ΠΈΡ ΡΠ°Π±ΠΎΡΠΎΡΠΏΠΎΡΠΎΠ±Π½ΠΎΡΡΠΈ ΠΈ Π½Π°Π΄Π΅ΠΆΠ½ΠΎΡΡΠΈ ΠΌΠ°ΡΠΈΠ½ ΠΈ ΠΊΠΎΠ½ΡΡΡΡΠΊΡΠΈΠΉ Π² Π΄Π°Π½Π½ΠΎΠΉ ΡΡΠ΅Π΄Π΅. Π§Π°ΡΡΡ ΡΡΠΈΡ
ΠΌΠ΅Ρ Π·Π°ΠΊΠ»Π°Π΄ΡΠ²Π°Π΅ΡΡΡ Π΅ΡΠ΅ Π² ΠΏΡΠΎΡΠ΅ΡΡΠ΅ ΠΏΡΠΎΠ΅ΠΊΡΠΈΡΠΎΠ²Π°Π½ΠΈΡ, ΡΠ°ΡΡΡ β Π² ΠΏΡΠΎΡΠ΅ΡΡΠ΅ ΠΈΠ·Π³ΠΎΡΠΎΠ²Π»Π΅Π½ΠΈΡ ΠΌΠ°ΡΠΈΠ½ ΠΈΠ»ΠΈ ΠΊΠΎΠ½ΡΡΡΡΠΊΡΠΈΠΉ, Π° ΠΎΡΡΠ°Π»ΡΠ½ΡΠ΅ ΠΌΠ΅ΡΡ Π΄ΠΎΠ»ΠΆΠ½Ρ Π±ΡΡΡ ΠΏΡΠΈΠ½ΡΡΡ Π² ΠΏΡΠΎΡΠ΅ΡΡΠ΅ ΡΠΊΡΠΏΠ»ΡΠ°ΡΠ°ΡΠΈΠΈ.β[c.521]
ββββΠ’Π΅Ρ Π½ΠΈΠΊΠΎ-ΡΠΊΠΎΠ½ΠΎΠΌΠΈΡΠ΅ΡΠΊΠΈΠ΅ ΡΠ°ΡΡΠ΅ΡΡ ΠΏΠΎΠΊΠ°Π·ΡΠ²Π°ΡΡ, ΡΡΠΎ Π½Π°ΠΈΠΌΠ΅Π½ΡΡΠΈΠ΅ ΠΊΠ°ΠΏΠΈΡΠ°Π»ΡΠ½ΡΠ΅ ΠΈ ΡΠΊΡΠΏΠ»ΡΠ°ΡΠ°ΡΠΈΠΎΠ½Π½ΡΠ΅ Π·Π°ΡΡΠ°ΡΡ Π½Π° ΠΊΠΎΠΌΠΏΡΠΈΠΌΠΈΡΠΎΠ²Π°Π½ΠΈΠ΅ Π³Π°Π·Π° Π΄ΠΎΡΡΠΈΠ³Π°ΡΡΡΡ, ΠΊΠΎΠ³Π΄Π° ΠΏΡΠΎΠΈΠ·Π²ΠΎΠ΄ΠΈΡΠ΅Π»ΡΠ½ΠΎΡΡΡ ΠΊΠΎΠΌΠΏΡΠ΅ΡΡΠΎΡΠ° ΡΠ°Π²Π½Π° ΠΏΡΠΎΠΈΠ·Π²ΠΎΠ΄ΠΈΡΠ΅Π»ΡΠ½ΠΎΡΡΠΈ ΡΠ΅Ρ Π½ΠΎΠ»ΠΎΠ³ΠΈΡΠ΅ΡΠΊΠΎΠ³ΠΎ Π±Π»ΠΎΠΊΠ° (ΡΠ΅Ρ Π½ΠΎΠ»ΠΎΠ³ΠΈΡΠ΅ΡΠΊΠΎΠΉ Π»ΠΈΠ½ΠΈΠΈ). ΠΡΠΈ ΡΡΠΎΠΌ Π½Π°Π΄Π΅ΠΆΠ½ΠΎΡΡΡ ΠΌΠ°ΡΠΈΠ½Ρ Π΄ΠΎΠ»ΠΆΠ½Π° Π±ΡΡΡ ΡΠ°ΠΊΠΎΠΉ, ΡΡΠΎΠ±Ρ Π΅Π΅ ΠΌΠΎΠΆΠ½ΠΎ Π±ΡΠ»ΠΎ ΡΡΡΠ°Π½Π°Π²Π»ΠΈΠ²Π°ΡΡ Π±Π΅Π· ΡΠ΅Π·Π΅ΡΠ²Π°. ΠΠΎΡΡΠΎΠΌΡ Π²ΠΎΠ·Π½ΠΈΠΊΠ°Π΅Ρβ[c.375]
ββββΠ‘ΠΎΠ²ΡΠ΅ΠΌΠ΅Π½Π½ΡΠ΅ Ρ
ΠΈΠΌΠΈΠΊΠΎ-ΡΠ½Π΅ΡΠ³ΠΎΡΠ΅Ρ
Π½ΠΎΠ»ΠΎΠ³ΠΈΡΠ΅ΡΠΊΠΈΠ΅ ΡΠΈΡΡΠ΅ΠΌΡ (Π₯ΠΠ’Π‘) ΠΊΡΡΠΏΠ½ΠΎΡΠΎΠ½Π½Π°ΠΆΠ½ΡΡ
ΠΏΡΠΎΠΈΠ·Π²ΠΎΠ΄ΡΡΠ² Π°ΠΌΠΌΠΈΠ°ΠΊΠ° ΠΏΡΠ΅Π΄ΡΡΠ°Π²Π»ΡΡΡ ΡΠΎΠ±ΠΎΠΉ ΡΠΎΠ²ΠΎΠΊΡΠΏΠ½ΠΎΡΡΡ ΡΠ°Π·Π»ΠΈΡΠ½ΡΡ
Π₯Π’Π, ΡΠ½Π΅ΡΠ³ΠΎ- ΠΈ ΡΠ΅ΠΏΠ»ΠΎΡΠ΅Ρ
Π½ΠΈΡΠ΅ΡΠΊΠΈΡ
ΠΏΡΠΎΡΠ΅ΡΡΠΎΠ² [4, 13, 49, 93]. ΠΡΠ½ΠΎΠ²Π½ΡΠΌΠΈ ΠΏΡΠΈΡΠΈΠ½Π°ΠΌΠΈ ΠΌΠ½ΠΎΠ³ΠΈΡ
Π°Π²Π°ΡΠΈΠΉ ΠΈ Π½Π΅ΡΡΠ°ΡΡΠ½ΡΡ
ΡΠ»ΡΡΠ°Π΅Π², ΠΏΡΠΎΠΈΡΡΠ΅Π΄ΡΠΈΡ
Π² ΡΡΠΎΠΌ ΠΏΡΠΎΠΈΠ·Π²ΠΎΠ΄ΡΡΠ²Π΅, ΡΠ²Π»ΡΡΡΡΡ Π½Π°ΡΡΡΠ΅Π½ΠΈΡ ΡΠ΅Ρ
Π½ΠΎΠ»ΠΎΠ³ΠΈΡΠ΅ΡΠΊΠΎΠΉ Π΄ΠΈΡΡΠΈΠΏΠ»ΠΈΠ½Ρ, Π½Π΅Π΄ΠΎΡΡΠ°ΡΠΎΡΠ½ΠΎ Π²ΡΡΠΎΠΊΠ°Ρ Π½Π°Π΄Π΅ΠΆΠ½ΠΎΡΡΡ ΠΌΠ°ΡΠΈΠ½, Π°ΠΏΠΏΠ°ΡΠ°ΡΠΎΠ², Π°ΡΠΌΠ°ΡΡΡΡ, ΠΠΠ ΠΈ ΠΠ‘Π£, Π½Π΅ΡΠ΄ΠΎΠ²Π»Π΅ΡΠ²ΠΎΡΠΈΡΠ΅Π»ΡΠ½Π°Ρ ΠΎΡΠ³Π°Π½ΠΈΠ·Π°ΡΠΈΡ ΡΠ΅ΠΌΠΎΠ½ΡΠ½ΡΡ
ΡΠ°Π±ΠΎΡ ΠΈ ΡΠΊΡΠΏΠ»ΡΠ°ΡΠ°ΡΠΈΡ Π½Π΅ΠΈΡΠΏΡΠ°Π²Π½ΠΎΠ³ΠΎ ΠΎΠ±ΠΎΡΡΠ΄ΠΎΠ²Π°Π½ΠΈΡ, ΠΏΠ»ΠΎΡ
ΠΎΠ΅ ΡΠΎΠ±Π»ΡΠ΄Π΅Π½ΠΈΠ΅ ΡΡΠ΅Π±ΠΎΠ²Π°Π½ΠΈΠΉ ΡΠ΅Ρ
Π½ΠΈΠΊΠΈ Π±Π΅Π·ΠΎΠΏΠ°ΡΠ½ΠΎΡΡΠΈ. β[c.108]
ββββΠΠ΅Π±Π°Π»ΠΊ Π. Π., ΠΠ΅ΠΊΠΎΠ²ΠΈΡ Π., ΠΠΎΡΡΠ°Π½ΡΠ½ Π. Π. ΠΈ Π΄Ρ. β Π ΠΊΠ½. ΠΡΠ½ΠΎΠ²Π½ΡΠ΅ Π½Π°ΠΏΡΠ°Π²Π»Π΅Π½ΠΈΡ ΡΠΎΠ·Π΄Π°Π½ΠΈΡ ΠΈ ΠΏΠΎΠ²ΡΡΠ΅Π½ΠΈΡ ΡΠ΅Ρ Π½ΠΈΡΠ΅ΡΠΊΠΎΠ³ΠΎ ΡΡΠΎΠ²Π½Ρ, ΠΊΠ°ΡΠ΅ΡΡΠ²Π° ΠΈ Π½Π°Π΄Π΅ΠΆΠ½ΠΎΡΡΠΈ ΠΌΠ°ΡΠΈΠ½ ΠΈ Π°ΠΏΠΏΠ°ΡΠ°ΡΠΎΠ² Ρ ΠΈΠΌΠΈΡΠ΅ΡΠΊΠΎΠ³ΠΎ ΠΈ Π½Π΅ΡΡΠ΅ΠΏΠ΅ΡΠ΅ΡΠ°Π±Π°ΡΡΠ²Π°ΡΡΠ΅Π³ΠΎ ΠΌΠ°ΡΠΈΠ½ΠΎΡΡΡΠΎΠ΅Π½ΠΈΡ (ΠΠ±. ΡΠ΅ΡΠ΅ΡΠ°ΡΠΎΠ² Π΄ΠΎΠΊΠ»Π°Π΄ΠΎΠ²). Π., Π¦ΠΈΠ½ΡΠΈΡ ΠΈΠΌΠ½Π΅ΡΡΠ΅ΠΌΠ°Ρ, 1970, Ρ. 59β60.β[c.257]
ββββΠ£Π²Π΅Π»ΠΈΡΠ΅Π½ΠΈΠ΅ ΠΏΡΠΎΠΈΠ·Π²ΠΎΠ΄ΠΈΡΠ΅Π»ΡΠ½ΠΎΡΡΠΈ ΠΈ ΡΠΈΡΠΎΠΊΠΎΠ΅ Π²Π½Π΅Π΄ΡΠ΅Π½ΠΈΠ΅ Π°Π²ΡΠΎΠΌΠ°ΡΠΈΠ·Π°ΡΠΈΠΈ ΠΏΡΠ΅Π΄ΡΡΠ²Π»ΡΡΡ ΠΏΠΎΠ²ΡΡΠ΅Π½Π½ΡΠ΅ ΡΡΠ΅Π±ΠΎΠ²Π°Π½ΠΈΡ ΠΊ Π½Π°Π΄Π΅ΠΆΠ½ΠΎΡΡΠΈ ΠΌΠ°ΡΠΈΠ½ ΠΈ Π°ΠΏΠΏΠ°ΡΠ°ΡΠΎΠ². Π Π°ΡΡΠ΅ΡΠ½ΡΠΉ ΡΡΠΎΠΊ ΡΠ»ΡΠΆΠ±Ρ Π°ΠΏΠΏΠ°ΡΠ°ΡΠΎΠ² 10β12 Π»Π΅Ρ. ΠΡΠ»ΠΈ ΠΈ ΠΏΡΠΎΠΈΠ·Π²ΠΎΠ΄ΡΡΠ²Π΅ ΠΎΡΡΡΡΡΡΠ²ΡΠ΅Ρ Π·Π½Π°ΡΠΈΡΠ΅Π»ΡΠ½Π°Ρ ΠΊΠΎΡΡΠΎΠ·ΠΈΡ, ΡΠΎ Π°ΠΏΠΏΠ°ΡΠ°ΡΡ ΡΠ»ΡΠ» Π°Ρ Π΄ΠΎΠ»ΡΡΠ΅ ΡΠΊΠ°Π·Π°Π½Π½ΠΎΠ³ΠΎ ΡΡΠΎΠΊΠ°. ΠΠΎΠ»Π³ΠΎΠ²Π΅ΡΠ½ΠΎΡΡΡ ΠΈ Π½Π°Π΄Π΅ΠΆΠ½ΠΎΡΡΡ Π°ΠΏΠΏΠ°ΡΠ°ΡΡΡΡ ΠΏΠΎΠ²ΡΡΠ°ΡΡ ΠΏΡΡΠ΅ΠΌ ΠΈΡΠΏΠΎΠ»ΡΠ·ΠΎΠ²Π°Π½ΠΈΡ ΠΌΠ°ΡΠ΅ΡΠΈΠ°Π»ΠΎΠ², ΡΡΡΠΎΠΉΡΠΈΠ²ΡΡ ΠΊ ΠΊΠΎΡΡΠΎΠ·ΠΈΠΈ ΠΈ Π΄Π΅ΠΉΡΡΠ²ΠΈΡ Π²ΡΡΠΎΠΊΠΈΡ ΡΠ΅ΠΌΠΏΠ΅ΡΠ°ΡΡΡ, ΠΏΡΡΠ΅ΠΌ ΠΏΡΠΈΠΌΠ΅Π½Π΅Π½ΠΈΡ Π±Π΅Π·ΠΎΡΠΊΠ°Π·Π½ΠΎ ΡΠ°Π±ΠΎΡΠ°ΡΡΠΈΡ ΡΠ·Π»ΠΎΠ² ΠΈ ΠΌΠ΅Ρ Π°Π½ΠΈΠ·ΠΌΠΎΠ² ΠΈ ΠΊΠΎΠ½ΡΡΠΎΠ»Ρ Π·Π° ΡΠΎΡΡΠΎΡΠ½ΠΈΠ΅ΠΌ ΡΡΠ΅Π½ΠΎΠΊ Π°ΠΏΠΏΠ°ΡΠ°ΡΠ°, ΡΠ²Π°ΡΠ½ΡΡ ΡΠ²ΠΎΠ² ΠΈ Π°Π½ΡΠΈΠΊΠΎΡΡΠΎΠ·Π½ΠΎΠ½Π½Ρ)ΠΠΎΡΠΏΡΡ Π°ΠΏΠΏΠ°ΡΠ°ΡΠ° ΡΠ»ΡΠΆΠΈΡ ΠΎΠ±ΡΡΠ½ΠΎ Π·Π½Π°ΡΠΈΡΠ΅Π»ΡΠ½ΠΎ Π΄ΠΎΠ»ΡΡΠ΅, ΡΠ΅ΠΌ ΡΠ°Π·Π»ΠΈ ΠΏΡΡΠ΅ Π²Π½ΡΡΡΠ΅Π½Π½ΠΈΠ΅ ΡΡΡΡΠΎΠΉΡΡΠ²Π°, ΠΊΠΎΡΠΎΡΡΠ΅ ΠΏΠ΅ΡΠΈΠΎΠ΄ΠΈΡΠ΅ΡΠΊΠΈ ΠΌΠ΅Π½ΡΡΡ Π²ΠΎ Π²ΡΠ΅ΠΌΡ ΡΠ΅ΠΌΠΎΠ½ΡΠΎΠ².

ββββΠΠΎΠ»Π΅Π±Π°Π½ΠΈΡ ΠΈ Π²ΠΈΠ±ΡΠ°ΡΠΈΡ. ΠΠ½ΡΠ΅Π½ΡΠΈΡΠΈΠΊΠ°ΡΠΈΡ ΡΠ΅Ρ Π½ΠΎΠ»ΠΎΠ³ΠΈΡΠ΅ΡΠΊΠΈΡ ΠΏΡΠΎΡΠ΅ΡΡΠΎΠ², ΠΏΡΠΎΡΠ΅ΠΊΠ°ΡΡΠΈΡ Π² ΠΌΠ°ΡΠ½ΠΈΠ½Π°Ρ Ρ ΠΈΠΌΠΈΡΠ΅ΡΠΊΠΈΡ ΠΏΡΠΎΠΈΠ·Π²ΠΎΠ΄ΡΡΠ², Π½Π΅ΠΏΠΎΡΡΠ΅Π΄ΡΡΠ²Π΅Π½Π½ΠΎ ΡΠ²ΡΠ·Π°Π½Π° Ρ ΡΠΎΡΡΠΎΠΌ Π½Π°ΠΏΡΡΠΆΠ΅Π½Π½ΠΎΡΡΠΈ ΡΠ½Π΅ΡΠ³Π΅ΡΠΈΡΠ΅ΡΠΊΠΈΡ ΠΏΠΎΡΠΎΠΊΠΎΠ² ΠΎΡ Π΄Π²ΠΈΠ³Π°ΡΠ΅Π»Ρ ΠΊ ΡΠ°Π±ΠΎΡΠ΅ΠΉ ΠΌΠ°ΡΠΈΠ½Π΅, ΡΠ²Π΅Π»ΠΈΡΠ΅Π½ΠΈΠ΅ΠΌ ΡΠΊΠΎΡΠΎΡΡΠ΅ΠΉ Π΄Π²ΠΈΠΆΠ΅Π½ΠΈΡ ΠΈΡΠΏΠΎΠ»Π½ΠΈΡΠ΅Π»ΡΠ½ΡΡ ΠΎΡΠ³Π°Π½ΠΎΠ², ΠΏΠΎΠ²ΡΡΠ΅Π½ΠΈΠ΅ΠΌ ΡΡΠ΅Π±ΠΎΠ²Π°Π½ΠΈΠΉ ΠΊ Π½Π°Π΄Π΅ΠΆΠ½ΠΎΡΡΠΈ ΠΌΠ°ΡΠΈΠ½. ΠΠΎ ΡΡΠΈΠΌ ΠΏΡΠΈΡΠΈΠ½Π°ΠΌ ΠΎΡΠΎΠ±ΠΎΠ΅ Π²Π½ΠΈΠΌΠ°Π½ΠΈΠ΅ ΡΠ΄Π΅Π»ΡΡΡ ΠΈΠ·ΡΡΠ΅Π½ΠΈΡ ΠΌΠ΅Ρ Π°Π½ΠΈΡΠ΅ΡΠΊΠΈΡ ΠΊΠΎΠ»Π΅Π±Π°Π½ΠΈΠΉ, ΠΏΠΎΠ΄ ΠΊΠΎΡΠΎΡΡΠΌΠΈ ΠΏΠΎΠ½ΠΈΠΌΠ°ΡΡ ΠΌΠ½ΠΎΠ³ΠΎ-4 β[c.44]
ββββΠ Π΅ΠΌΠΎΠ½ΡΠΎΠΏΡΠΈΠ³ΠΎΠ΄Π½ΠΎΡΡΡ Π²Ρ
ΠΎΠ΄ΠΈΡ Π² ΠΏΠΎΠ½ΡΡΠΈΠ΅ Π½Π°Π΄Π΅ΠΆΠ½ΠΎΡΡΠΈ. ΠΠ΄Π½Π°ΠΊΠΎ Π²ΡΡΠΎΠΊΠ°Ρ Π½Π°Π΄Π΅ΠΆΠ½ΠΎΡΡΡ ΠΌΠ°ΡΠΈΠ½Ρ Π½Π΅ Π²ΡΠ΅Π³Π΄Π° ΠΎΠ·Π½Π°ΡΠ°Π΅Ρ Π²ΡΡΠΎΠΊΡΡ ΡΠ΅ΠΌΠΎΠ½ΡΠΎ-ΠΏΡΠΈΠ³ΠΎΠ΄ ΡΡΡΡ. ΠΠΎΡΡΠΎΠΌΡ ΠΏΡΠΈ ΡΠ°Π·ΡΠ°Π±ΠΎΡΠΊΠ΅ ΠΌΠ°ΡΠΈΠ½Ρ (Π°ΠΏΠΏΠ°ΡΠ°ΡΠ°) ΠΏΡΠΈΡ
ΠΎΠ΄ΠΈΡΡΡ ΠΎΠ±ΡΠ°ΡΠ°ΡΡ ΠΎΡΠΎΠ±ΠΎΠ΅ Π²Π½ΠΈΠΌΠ°Π½ΠΈΠ΅ Π½Π° ΠΎΠ±Π΅ΡΠΏΠ΅ΡΠ΅Π½ΠΈΠ΅ Π΄ΠΎΡΡΠ°ΡΠΎΡΠ½ΠΎΠ³ΠΎ ΡΡΠΎΠ²Π½Ρ ΡΠ΅ΠΌΠΎΠ½ΡΠΎΠΏΡΠΈΠ³ΠΎΠ΄Π½ΠΎΡΡΠΈ. Π Π΅ΠΌΠΎΠ½ΡΠΎΠΏΡΠΈΠ³ΠΎΠ΄Π½ΠΎΡΡΡ ΠΌΠΎΠΆΠ΅Ρ Π±ΡΡΡ ΠΏΡΠ΅Π΄ΡΡΠΌΠΎΡΡΠ΅Π½Π° ΠΏΡΠΈ ΠΏΡΠΎΠ΅ΠΊΡΠΈΡΠΎΠ²Π°Π½ΠΈΠΈ ΠΌΠ°ΡΠΈΠ½Ρ Π΄Π»Ρ ΡΡΡΠ΅ΡΡΠ²ΡΡΡΠ΅ΠΉ ΠΌΠ°ΡΠΈΠ½Ρ ΡΠΏΠΎΡΠΎΠ± ΠΏΠΎΠ²ΡΡΠ΅Π½ΠΈΡ ΡΠ΅ΠΌΠΎΠ½ΡΠΎΠΏΡΠΈΠ³ΠΎΠ΄Π½ΠΎΡΡΠΈ Π½Π°ΠΌΠ΅ΡΠ°Π΅ΡΡΡ Π² ΠΏΡΠΎΡΠ΅ΡΡΠ΅ Π΅Π΅ ΡΠΊΡΠΏΠ»ΡΠ°ΡΠ°ΡΠΈΠΈ ΠΈ ΠΎΡΡΡΠ΅ΡΡΠ²Π»ΡΠ΅ΡΡΡ ΠΊΠ°ΠΊ ΠΌΠΎΠ΄Π΅ΡΠ½ΠΈΠ·Π°ΡΠΈΡ, Π½Π°ΠΏΡΠ°Π²Π»Π΅Π½Π½Π°Ρ Π½Π° ΠΏΠΎΠ²ΡΡΠ΅Π½ΠΈΠ΅ ΡΠΊΡΠΏΠ»ΡΠ°ΡΠ°ΡΠΈΠΎΠ½Π½ΡΡ
Ρ
Π°ΡΠ°ΠΊΡΠ΅ΡΠΈΡΡΠΈΠΊ. β[c.67]
ββββΠΠ΅Π·ΠΎΠΏΠ°ΡΠ½ΠΎΡΡΡ Π₯ΠΠ’Π‘ ΠΏΡΠ°ΠΊΡΠΈΡΠ΅ΡΠΊΠΈ ΠΏΠΎΠ»Π½ΠΎΡΡΡΡ Π·Π°Π²ΠΈΡΠΈΡ ΠΎΡ ΠΏΠΎΠΊΠ°Π·Π°ΡΠ΅Π»Π΅ΠΉ Π½Π°Π΄Π΅ΠΆΠ½ΠΎΡΡΠΈ ΠΠ‘Π£ ΠΈ ΡΠΈΡΡΠ΅ΠΌ Π·Π°ΡΠΈΡΠ½ΡΡ Π±Π»ΠΎΠΊΠΈΡΠΎΠ²ΠΎΠΊ, Π½Π°Π΄Π΅ΠΆΠ½ΠΎΡΡΠΈ ΠΌΠ°ΡΠΈΠ½ ΠΈ ΠΎΠ±ΠΎΡΡΠ΄ΠΎΠ²Π°Π½ΠΈΡ, ΠΎΡ ΡΡΠΎΠ²Π½Ρ ΠΏΡΠΎΡΠ΅ΡΡΠΈΠΎΠ½Π°Π»ΡΠ½ΠΎΠΉ ΠΏΠΎΠ΄Π³ΠΎΡΠΎΠ²ΠΊΠΈ ΠΎΠ±ΡΠ»ΡΠΆΠΈΠ²Π°ΡΡΠ΅Π³ΠΎ ΠΏΠ΅ΡΡΠΎΠ½Π°Π»Π° ΠΈ ΠΏΡΠΎΠΈΠ·Π²ΠΎΠ΄ΡΡΠ²Π΅Π½Π½ΠΎΠΉ Π΄ΠΈΡΡΠΈΠΏΠ»ΠΈΠ½Ρ Π½Π° Π΄Π°Π½Π½ΠΎΠΌ ΠΏΡΠ΅Π΄ΠΏΡΠΈΡΡΠΈΠΈ. Π’ΡΠ΅Π±ΠΎΠ²Π°Π½ΠΈΠ΅ Π²ΡΡΠΎΠΊΠΎΠ³ΠΎ ΡΡΠΎΠ²Π½Ρβ[c.108]
ββββΠΠΎΠΌΠΏΡΠ΅ΡΡΠΎΡΡ ΠΌΠ°Π»ΠΎΠΉ ΠΏΡΠΎΠΈΠ·Π²ΠΎΠ΄ΠΈΡΠ΅Π»ΡΠ½ΠΎΡΡΠΈ Π΄ΠΎΠ»ΠΆΠ½Ρ Π±ΡΡΡ ΠΏΡΠΎΡΡΡΠΌΠΈ Π² ΠΌΠΎΠ½ΡΠ°ΠΆΠ΅ ΠΈ ΠΎΠ±ΡΠ»ΡΠΆΠΈΠ²Π°Π½ΠΈΠΈ, Π° ΠΏΡΠ΅Π΄Π½Π°Π·Π½Π°ΡΠ΅Π½Π½ΡΠ΅ Π΄Π»Ρ ΠΏΠ΅ΡΠ΅Π΄Π²ΠΈΠΆΠ½ΡΡ
ΡΡΡΠ°Π½ΠΎΠ²ΠΎΠΊ ΠΈ ΡΡΠ΄ΠΎΠ², ΠΊΡΠΎΠΌΠ΅ ΡΠΎΠ³ΠΎ, ΠΊΠΎΠΌΠΏΠ°ΠΊΡΠ½ΡΠΌΠΈ ΠΈ Π»Π΅Π³ΠΊΠΈΠΌΠΈ. ΠΠΎΠΌΠΏΡΠ΅ΡΡΠΎΡΡ Π±ΠΎΠ»ΡΡΠΎΠΉ ΠΏΡΠΎΠΈΠ·Π²ΠΎΠ΄ΠΈΡΠ΅Π»ΡΠ½ΠΎΡΡΠΈ Π΄ΠΎΠ»ΠΆΠ½Ρ Π±ΡΡΡ Π½Π°Π΄Π΅ΠΆΠ½ΡΠΌΠΈ ΠΈ ΡΠΊΠΎΠ½ΠΎΠΌΠΈΡΠ½ΡΠΌΠΈ. Π’ΡΠ΅Π±ΠΎΠ²Π°Π½ΠΈΡ ΠΏΡΠΎΡΡΠΎΡΡ ΠΎΠ±ΡΠ»ΡΠΆΠΈΠ²Π°Π½ΠΈΡ ΠΈ ΡΠ΅ΠΌΠΎΠ½ΡΠ° ΠΏΡΠ΅Π΄ΡΡΠ²Π»ΡΡΡΡΡ ΠΊΠΎ Π²ΡΠ΅ΠΌ ΠΌΠ°ΡΠΈΠ½Π°ΠΌ, Π½ΠΎ Π½Π΅Π»ΡΠ·Ρ Π½Π΅ ΡΡΠΈΡΡΠ²Π°ΡΡ, ΡΡΠΎ ΠΊΡΡΠΏΠ½ΡΠ΅ ΠΊΠΎΠΌΠΏΡΠ΅ΡΡΠΎΡΡ ΠΎΠ±ΡΠ»ΡΠΆΠΈΠ²Π°ΡΡΡΡ Π±ΠΎΠ»Π΅Π΅ ΠΊΠ²Π°Π»ΠΈΡΠΈΡΠΈΡΠΎΠ²Π°Π½Π½ΡΠΌ ΠΏΠ΅ΡΡΠΎΠ½Π°Π»ΠΎΠΌ, ΡΠ΅ΠΌ ΠΌΠ°Π»ΡΠ΅. ΠΠ°Π΄Π΅ΠΆΠ½ΠΎΡΡΡ Π² ΡΠ°Π±ΠΎΡΠ΅ β ΡΠΎΠΆΠ΅ ΠΎΠ±ΡΠ΅Π΅ ΡΡΠ΅Π±ΠΎΠ²Π°Π½ΠΈΠ΅, Π½ΠΎ ΠΎΠ½ΠΎ ΠΎΡΠΎΠ±ΠΎ ΡΡΡΠ΅ΡΡΠ²Π΅Π½Π½ΠΎ Π΄Π»Ρ ΠΊΡΡΠΏΠ½ΡΡ
ΠΊΠΎΠΌΠΈΡΠ΅ΡΡΠΎΡΠΎΠ², ΠΊΠΎΡΠΎΡΡΠ΅ ΡΠ°ΡΡΠΎ ΡΠ°Π±ΠΎΡΠ°ΡΡ Π±Π΅Π· ΠΎΡΡΠ°Π½ΠΎΠ²ΠΎΠΊ Π² ΡΠ΅ΡΠ΅Π½ΠΈΠ΅ Π΄Π²ΡΡ
-ΡΡΠ΅Ρ
ΠΌΠ΅ΡΡΡΠ΅Π², ΠΏΡΠΈΡΠΎΠΌ Π³ΠΎΠ΄ΠΎΠ²ΡΠ΅ ΠΏΡΠΎΡΡΠΎΠΈ ΠΈΠ·-Π·Π° ΡΠ΅ΠΌΠΎΠ½ΡΠΎΠ² Π½Π΅ Π΄ΠΎΠ»ΠΆΠ½Ρ Π±ΡΡΡ Π±ΠΎΠ»Π΅Π΅ 4% Π²ΡΠ΅ΠΌΠ΅Π½ΠΈ ΠΈΡ
ΡΠ°Π±ΠΎΡΡ. ΠΠ΅Π·Π°Π²Π°ΡΠΈΠΉΠ½ΠΎΡΡΡ ΡΠ²Π»ΡΠ΅ΡΡΡ ΠΏΠ΅ΡΠ²ΡΠΌ ΡΡΠ»ΠΎΠ²ΠΈΠ΅ΠΌ, ΡΠ°ΠΊ ΠΊΠ°ΠΊ Π·Π°ΡΡΠ°ΡΡ, Π½Π°ΠΏΡΠ°Π²Π»Π΅Π½Π½ΡΠ΅ Π½Π° ΠΏΠΎΠ²ΡΡΠ΅Π½ΠΈΠ΅ Π½Π°Π΄Π΅ΠΆΠ½ΠΎΡΡΠΈ ΠΌΠ°ΡΠΈΠ½Ρ, Π½Π΅Π·Π½Π°ΡΠΈΡΠ΅Π»ΡΠ½Ρ ΠΏΠΎ ΡΡΠ°Π²Π½Π΅Π½ΠΈΡ Ρ ΡΠ΅ΠΌΠΈ ΡΠ±ΡΡΠΊΠ°ΠΌΠΈ, ΠΊΠΎΡΠΎΡΡΠ΅ Π²ΡΠ·ΡΠ²Π°ΡΡΡΡ ΠΏΡΠΎΡΡΠΎΡΠΌΠΈ ΠΊΠΎΠΌΠΏΡΠ΅ΡΡΠΎΡΠ° Ρ ΠΎΡΡΠ°Π½ΠΎΠ²ΠΊΠΎΠΉ ΠΈΠ»ΠΈ ΡΠΎΠΊΡΠ°ΡΠ΅Π½ΠΈΠ΅ΠΌ ΠΈΠ·-Π·Π° ΡΡΠΎΠ³ΠΎ ΠΏΡΠΎΠΈΠ·Π²ΠΎΠ΄ΡΡΠ²Π°.β[c.126]
ββββΠΠ°ΠΉΠ½ΡΠ»Π»ΠΈΠ½ P. ., ΠΡΡΠ»Π°Π½ΠΎΠ²Π° Π€.Π., ΠΠ±Π΄Π΅Π΅Π² Π .Π. ΠΠΎΠ²ΡΡΠ΅Π½ΠΈΠ΅ ΠΏΡΠΎΡΠ½ΠΎΡΡΠΈ ΠΈ Π΄ΠΎΠ»Π³ΠΎΠ²Π΅ΡΠ½ΠΎΡΡΠΈ ΡΠ²Π°ΡΠ½ΡΡ ΡΠΎΠ΅Π΄ΠΈΠ½Π΅Π½ΠΈΠΉ Ρ ΠΈΠΌΠΈΡΠ΅ΡΠΊΠΈΡ Π°ΠΏΠΏΠ°ΡΠ°ΡΠΎΠ² ΠΏΡΠΈ Π½Π°Π»ΠΈΡΠΈΠΈ ΡΠΌΠ΅ΡΠ΅Π½ΠΈΡ ΠΊΡΠΎΠΌΠΎΠΊ //ΠΠΎΠ²ΡΡΠ΅Π½ΠΈΠ΅ ΡΡΡΠ΅ΠΊΡΠΈΠ²Π½ΠΎΡΡΠΈ ΠΈ Π½Π°Π΄Π΅ΠΆΠ½ΠΎΡΡΠΈ ΠΌΠ°ΡΠΈΠ½ ΠΈ Π°ΠΏΠΏΠ°ΡΠ°ΡΠΎΠ² Π² ΠΎΡΠ½ΠΎΠ²Π½ΠΎΠΉ Ρ ΠΈΠΌΠΈΠΈ Π’Π΅Π·ΠΈΡΡ Π΄ΠΎΠΊΠ». ΠΡΠ΅ΡΠΎΡΠ·Π½. ΠΊΠΎΠ½Ρ. /Π‘ΡΠΌΡ, 1986.- Π‘.69.β[c.408]
ΠΡΠΈΡΠ΅ΡΠΈΠΈ ΠΈ ΠΏΠΎΠΊΠ°Π·Π°ΡΠ΅Π»ΠΈ ΡΠΊΡΠΏΠ»ΡΠ°ΡΠ°ΡΠΈΠΎΠ½Π½ΠΎΠΉ Π½Π°Π΄Π΅ΠΆΠ½ΠΎΡΡΠΈ
ΠΠΊΡΠΏΠ»ΡΠ°ΡΠ°ΡΠΈΡ ΠΈ ΡΠ΅ΠΌΠΎΠ½Ρ ΠΌΠ°ΡΠΈΠ½ ΠΈ ΠΎΠ±ΠΎΡΡΠ΄ΠΎΠ²Π°Π½ΠΈΡ ΠΠΈΠ ΠΏΡΠΎΠΌΡΡΠ»ΠΎΠ².
ΠΠ΅ΠΊΡΠΈΡ 3.
ΠΡΠΈΡΠ΅ΡΠΈΠΈ ΠΈ ΠΏΠΎΠΊΠ°Π·Π°ΡΠ΅Π»ΠΈ ΡΠΊΡΠΏΠ»ΡΠ°ΡΠ°ΡΠΈΠΎΠ½Π½ΠΎΠΉ Π½Π°Π΄Π΅ΠΆΠ½ΠΎΡΡΠΈ.
ΠΠ΄Π½ΠΈΠΌ ΠΈΠ· Π²Π°ΠΆΠ½ΡΡ
ΡΠ²ΠΎΠΉΡΡΠ², Ρ
Π°ΡΠ°ΠΊΡΠ΅ΡΠΈΠ·ΡΡΡΠΈΡ
ΠΊΠ°ΡΠ΅ΡΡΠ²ΠΎ ΠΈ ΡΠ΅Ρ
Π½ΠΈΡΠ΅ΡΠΊΠΈΠΉ ΡΡΠΎΠ²Π΅Π½Ρ Π±ΡΡΠΎΠ²ΡΡ
ΠΌΠ°ΡΠΈΠ½ ΠΈ ΠΎΠ±ΠΎΡΡΠ΄ΠΎΠ²Π°Π½ΠΈΡ ΡΠ²Π»ΡΠ΅ΡΡΡ ΠΈΡ
Π½Π°Π΄Π΅ΠΆΠ½ΠΎΡΡΡ. Π‘ΠΎΠ³Π»Π°ΡΠ½ΠΎ ΠΏΡΠΈΠ½ΡΡΠΎΠΉ ΡΠ΅ΡΠΌΠΈΠ½ΠΎΠ»ΠΎΠ³ΠΈΠΈ (ΠΠΠ‘Π’ 24002-83), Π½Π°Π΄Π΅ΠΆΠ½ΠΎΡΡΡΡ Π½Π°Π·ΡΠ²Π°ΡΡ ΡΠ²ΠΎΠΉΡΡΠ²Π° ΡΠ΅Ρ
Π½ΠΈΡΠ΅ΡΠΊΠΎΠ³ΠΎ ΠΎΠ±ΡΠ΅ΠΊΡΠ° ΡΠΎΡ
ΡΠ°Π½ΡΡΡ Π²ΠΎ Π²ΡΠ΅ΠΌΠ΅Π½ΠΈ Π² ΡΡΡΠ°Π½ΠΎΠ²Π»Π΅Π½Π½ΡΡ
ΠΈΠ·Π΄Π΅Π»ΠΈΡΡ
Π·Π½Π°ΡΠ΅Π½ΠΈΡ Π²ΡΠ΅Ρ
ΠΏΠ°ΡΠ°ΠΌΠ΅ΡΡΠΎΠ², ΡΠΏΠΎΡΠΎΠ±Π½ΠΎΡΡΡ Π²ΡΠΏΠΎΠ»Π½ΡΡΡ ΡΡΠ΅Π±ΡΠ΅ΠΌΡΠ΅ ΡΡΠ½ΠΊΡΠΈΠΈ Π² Π·Π°Π΄Π°Π½Π½ΡΡ
ΡΠ΅ΠΆΠΈΠΌΠ°Ρ
ΠΈ ΡΡΠ»ΠΎΠ²ΠΈΡΡ
ΠΏΡΠΈΠΌΠ΅Π½Π΅Π½ΠΈΡ, ΡΠ΅Ρ
Π½ΠΈΡΠ΅ΡΠΊΠΎΠ³ΠΎ ΠΎΠ±ΡΠ»ΡΠΆΠΈΠ²Π°Π½ΠΈΡ, ΡΠ΅ΠΌΠΎΠ½ΡΠΎΠ², Ρ
ΡΠ°Π½Π΅Π½ΠΈΡ ΠΈ ΡΡΠ°Π½ΡΠΏΠΎΡΡΠΈΡΠΎΠ²Π°Π½ΠΈΡ.
ΠΠ° ΠΎΡΠ½ΠΎΠ²Π°Π½ΠΈΠΈ ΡΠ΅ΠΎΡΠΈΠΈ Π½Π°Π΄Π΅ΠΆΠ½ΠΎΡΡΠΈ ΡΡΡΠ°Π½Π°Π²Π»ΠΈΠ²Π°ΡΡΡΡ Π·Π°ΠΊΠΎΠ½ΠΎΠΌΠ΅ΡΠ½ΠΎΡΡΠΈ Π²ΠΎΠ·Π½ΠΈΠΊΠ½ΠΎΠ²Π΅Π½ΠΈΡ ΠΎΡΠΊΠ°Π·ΠΎΠ² ΠΈ Π²ΠΎΡΡΡΠ°Π½ΠΎΠ²Π»Π΅Π½ΠΈΡ ΡΠ°Π±ΠΎΡΠΎΡΠΏΠΎΡΠΎΠ±Π½ΠΎΡΡΠΈ, ΠΏΡΠΎΠ³Π½ΠΎΠ·ΠΈΡΡΡΡΡΡ Π²ΠΎΠ·ΠΌΠΎΠΆΠ½ΡΠ΅ ΠΎΡΠΊΠ°Π·Ρ, Π²ΡΡΠ²Π»ΡΡΡΡΡ ΡΠΏΠΎΡΠΎΠ±Ρ ΠΏΠΎΠ²ΡΡΠ΅Π½ΠΈΡ Π½Π°Π΄Π΅ΠΆΠ½ΠΎΡΡΠΈ ΠΏΡΠΈ ΠΊΠΎΠ½ΡΡΡΡΠΈΡΠΎΠ²Π°Π½ΠΈΠΈ, ΠΈΠ·Π³ΠΎΡΠΎΠ²Π»Π΅Π½ΠΈΠΈ ΠΈ ΡΠΊΡΠΏΠ»ΡΠ°ΡΠ°ΡΠΈΠΈ ΡΠ°Π·Π»ΠΈΡΠ½ΡΡ ΠΎΠ±ΡΠ΅ΠΊΡΠΎΠ², Π° ΡΠ°ΠΊ ΠΆΠ΅ ΡΠ°Π·ΡΠ°Π±Π°ΡΡΠ²Π°ΡΡΡΡ ΠΌΠ΅ΡΠΎΠ΄Ρ ΡΠ±ΠΎΡΠ°, ΡΡΠ΅ΡΠ° ΠΈ Π°Π½Π°Π»ΠΈΠ·Π° ΡΡΠ°ΡΠΈΡΡΠΈΡΠ΅ΡΠΊΠΈΡ Π΄Π°Π½Π½ΡΡ , Π½Π΅ΠΎΠ±Ρ ΠΎΠ΄ΠΈΠΌΡΡ Π΄Π»Ρ ΡΠ°ΡΡΠ΅ΡΠ° ΠΏΠΎΠΊΠ°Π·Π°ΡΠ΅Π»Π΅ΠΉ Π½Π°Π΄Π΅ΠΆΠ½ΠΎΡΡΠΈ. Π£ΡΠΎΠ²Π΅Π½Ρ Π½Π°Π΄Π΅ΠΆΠ½ΠΎΡΡΠΈ Π·Π°ΠΊΠ»Π°Π΄ΡΠ²Π°Π΅ΡΡΡ ΠΏΡΠΈ ΠΏΡΠΎΠ΅ΠΊΡΠΈΡΠΎΠ²Π°Π½ΠΈΠΈ, ΠΎΠ±Π΅ΡΠΏΠ΅ΡΠΈΠ²Π°Π΅ΡΡΡ Π² ΠΏΡΠΎΡΠ΅ΡΡΠ΅ ΠΈΠ·Π³ΠΎΡΠΎΠ²Π»Π΅Π½ΠΈΡ ΠΈ ΠΏΠΎΠ΄Π΄Π΅ΡΠΆΠΈΠ²Π°Π΅ΡΡΡ Π² ΡΠΊΡΠΏΠ»ΡΠ°ΡΠ°ΡΠΈΠΈ.
ΠΡΠ½ΠΎΠ²Π½ΠΎΠ΅ Π½Π°ΠΏΡΠ°Π²Π»Π΅Π½ΠΈΠ΅ ΠΈΡΡΠ»Π΅Π΄ΠΎΠ²Π°Π½ΠΈΠΉ Π½Π°Π΄Π΅ΠΆΠ½ΠΎΡΡΠΈ Π±ΡΡΠΎΠ²ΡΡ
ΠΌΠ°ΡΠΈΠ½ ΠΈ ΠΎΠ±ΠΎΡΡΠ΄ΠΎΠ²Π°Π½ΠΈΡ — ΠΈΠ·ΡΡΠ΅Π½ΠΈΠ΅ Π½Π°ΠΈΠ±ΠΎΠ»Π΅Π΅ Π²Π°ΠΆΠ½ΡΡ
Π΅Ρ Π°ΡΠΏΠ΅ΠΊΡΠΎΠ² Π½Π° ΠΎΡΠ½ΠΎΠ²Π΅ ΠΎΠ±ΡΠ΅ΠΉ ΡΠ΅ΠΎΡΠΈΠΈ Π½Π°Π΄Π΅ΠΆΠ½ΠΎΡΡΠΈ, ΠΏΡΠ°ΠΊΡΠΈΡΠ΅ΡΠΊΠΈΡ
Π΄ΠΎΡΡΠΈΠΆΠ΅Π½ΠΈΠΉ Π² ΡΠΌΠ΅ΠΆΠ½ΡΡ
ΠΎΠ±Π»Π°ΡΡΡΡ
ΡΠ΅ΠΎΡΠΈΠΈ ΠΈ Π½Π°ΠΊΠΎΠΏΠ»Π΅Π½Π½ΡΡ
ΡΡΠ°ΡΠΈΡΡΠΈΡΠ΅ΡΠΊΠΈΡ
Π΄Π°Π½Π½ΡΡ
. Π Π°ΡΡΠΈΡΠ΅Π½ΠΈΠ΅ ΡΠ°Π±ΠΎΡΡ Π² ΡΡΠΎΠΉ ΠΎΠ±Π»Π°ΡΡΠΈ ΠΈΠΌΠ΅Π΅Ρ ΠΏΠ΅ΡΠ²ΠΎΡΡΠ΅ΠΏΠ΅Π½Π½ΠΎΠ΅ Π·Π½Π°ΡΠ΅Π½ΠΈΠ΅ Π΄Π»Ρ Π΄Π°Π»ΡΠ½Π΅ΠΉΡΠ΅Π³ΠΎ ΡΠΎΡΡΠ° ΡΡΡΠ΅ΠΊΡΠΈΠ²Π½ΠΎΡΡΠΈ Π±ΡΡΠ΅Π½ΠΈΡ Π½Π΅ΡΡΡΠ½ΡΡ
ΠΈ Π³Π°Π·ΠΎΠ²ΡΡ
ΡΠΊΠ²Π°ΠΆΠΈΠ½ ΠΈ ΡΠΎΠΊΡΠ°ΡΠ΅Π½ΠΈΡ ΠΊΠ°ΠΏΠΈΡΠ°Π»ΡΠ½ΡΡ
Π·Π°ΡΡΠ°Ρ Π½Π° ΡΠΎΠ·Π΄Π°Π½ΠΈΠ΅ ΠΏΡΠΎΠΌΡΡΠ»ΠΎΠ²ΡΡ
ΡΠ΅ΠΌΠΎΠ½ΡΠ½ΡΡ
ΡΠ»ΡΠΆΠ± ΠΈ Π·Π°Π²ΠΎΠ΄ΠΎΠ², Π·Π°Π½ΡΡΡΡ
ΠΈΠ·Π³ΠΎΡΠΎΠ²Π»Π΅Π½ΠΈΠ΅ΠΌ ΡΠΌΠ΅Π½Π½ΠΎΠ³ΠΎ Π±ΡΡΠΎΠ²ΠΎΠ³ΠΎ ΠΎΠ±ΠΎΡΡΠ΄ΠΎΠ²Π°Π½ΠΈΡ, Π·Π°ΠΏΠ°ΡΠ½ΡΡ
ΡΠ°ΡΡΠ΅ΠΉ ΠΈ Π΄Π΅ΡΠ°Π»Π΅ΠΉ.
1.Β Β Β Β Β Π’Π΅ΡΠΌΠΈΠ½Ρ ΠΈ ΠΎΠΏΡΠ΅Π΄Π΅Π»Π΅Π½ΠΈΡ ΠΎΡΠ½ΠΎΠ²Π½ΡΡ ΠΏΠΎΠ½ΡΡΠΈΠΉ.
Π Π΅ΠΊΠΎΠΌΠ΅Π½Π΄ΡΠ΅ΠΌΡΠ΅ ΡΠ°ΠΉΠ»Ρ
Π’Π΅ΡΠΌΠΈΠ½Ρ ΠΈ ΠΎΠΏΡΠ΅Π΄Π΅Π»Π΅Π½ΠΈΡ ΠΎΡΠ½ΠΎΠ²Π½ΡΡ ΠΏΠΎΠ½ΡΡΠΈΠΉ Π½Π°Π΄Π΅ΠΆΠ½ΠΎΡΡΠΈ, ΠΏΡΠΈΠ½ΡΡΡΠ΅ Π² Π½Π°ΡΠΊΠ΅, ΡΠ΅Ρ Π½ΠΈΠΊΠ΅ ΠΈ ΠΏΡΠΎΠΈΠ·Π²ΠΎΠ΄ΡΡΠ²Π΅, ΡΡΡΠ°Π½ΠΎΠ²Π»Π΅Π½Ρ ΠΠΠ‘Π’ 27002-83 ΠΈ ΠΎΠ±ΡΠ·Π°ΡΠ΅Π»ΡΠ½Ρ Π΄Π»Ρ ΠΏΡΠΈΠΌΠ΅Π½Π΅Π½ΠΈΡ Π² Π΄ΠΎΠΊΡΠΌΠ΅Π½ΡΠ°ΡΠΈΠΈ Π²ΡΠ΅Ρ Π²ΠΈΠ΄ΠΎΠ². Π Π°ΡΡΠΌΠ°ΡΡΠΈΠ²Π°Π΅ΠΌΡΠ΅ ΡΠ΅ΡΠΌΠΈΠ½Ρ ΠΈ ΠΎΠΏΡΠ΅Π΄Π΅Π»Π΅Π½ΠΈΡ ΠΏΡΠΈΠΌΠ΅Π½ΠΈΠΌΡ ΠΊ ΠΠ£ Π² ΡΠ΅Π»ΠΎΠΌ, Π° ΡΠ°ΠΊΠΆΠ΅ ΠΈ ΠΎΡΠ΄Π΅Π»ΡΠ½ΡΠΌ Π°Π³ΡΠ΅Π³Π°ΡΠ°ΠΌ, Π΄Π΅ΡΠ°Π»ΡΠΌ ΠΈ ΠΎΠ±ΠΎΡΡΠ΄ΠΎΠ²Π°Π½ΠΈΡ. ΠΡΠΈ ΠΈΠ·ΡΡΠ΅Π½ΠΈΠΈ ΡΠ²ΠΎΠΉΡΡΠ² ΠΈ ΠΏΠΎΠΊΠ°Π·Π°ΡΠ΅Π»Π΅ΠΉ Π½Π°Π΄Π΅ΠΆΠ½ΠΎΡΡΠΈ ΠΏΠΎΠ»ΡΠ·ΡΡΡΡΡ ΠΏΠΎΠ½ΡΡΠΈΡΠΌΠΈ, Ρ Π°ΡΠ°ΠΊΡΠ΅ΡΠΈΠ·ΡΡΡΠΈΠΌΠΈ ΡΠ΅Ρ Π½ΠΈΡΠ΅ΡΠΊΠΎΠ΅ ΡΠΎΡΡΠΎΡΠ½ΠΈΠ΅ ΠΎΠ±ΡΠ΅ΠΊΡΠ° ΠΈ ΡΠΎΠ±ΡΡΠΈΠ΅. Π Π°Π·Π»ΠΈΡΠ°ΡΡ ΡΠ»Π΅Π΄ΡΡΡΠΈΠ΅ ΡΠΎΡΡΠΎΡΠ½ΠΈΡ: ΠΈΡΠΏΡΠ°Π²Π½ΠΎΠ΅, Π½Π΅ΠΈΡΠΏΡΠ°Π²Π½ΠΎΠ΅, ΡΠ°Π±ΠΎΡΠΎΡΠΏΠΎΡΠΎΠ±Π½ΠΎΠ΅, Π½Π΅ΡΠ°Π±ΠΎΡΠΎΡΠΏΠΎΡΠΎΠ±Π½ΠΎΠ΅ ΠΈ ΠΏΡΠ΅Π΄Π΅Π»ΡΠ½ΠΎΠ΅.
Π ΠΏΡΠ΅Π΄Π΅Π»ΡΠ½ΠΎΠΌ ΡΠΎΡΡΠΎΡΠ½ΠΈΠΈ ΠΎΠ±ΡΠ΅ΠΊΡ ΡΠΎΠΎΡΠ²Π΅ΡΡΡΠ²ΡΠ΅Ρ Π²ΡΠ΅ΠΌ ΡΡΠ΅Π±ΠΎΠ²Π°Π½ΠΈΡΠΌ Π½ΠΎΡΠΌΠ°ΡΠΈΠ²Π½ΠΎ-ΡΠ΅Ρ Π½ΠΈΡΠ΅ΡΠΊΠΎΠΉ ΠΈ ΠΊΠΎΠ½ΡΡΡΡΠΊΡΠΎΡΡΠΊΠΎΠΉ Π΄ΠΎΠΊΡΠΌΠ΅Π½ΡΠ°ΡΠΈΠΈ, Π² Π½Π΅ΠΈΡΠΏΡΠ°Π²Π½ΠΎΠΌ β Π½Π΅ ΡΠΎΠΎΡΠ²Π΅ΡΡΡΠ²ΡΠ΅Ρ Ρ ΠΎΡΡ Π±Ρ ΠΎΠ΄Π½ΠΎΠΌΡ ΠΈΠ· ΡΡΠΈΡ ΡΡΠ΅Π±ΠΎΠ²Π°Π½ΠΈΠΉ. Π Π°Π±ΠΎΡΠΎΡΠΏΠΎΡΠΎΠ±Π½ΠΎΡΡΡ β ΡΡΠΎ ΡΠΎΡΡΠΎΡΠ½ΠΈΠ΅ ΠΎΠ±ΡΠ΅ΠΊΡΠ°, ΠΏΡΠΈ ΠΊΠΎΡΠΎΡΠΎΠΌ Π·Π½Π°ΡΠ΅Π½ΠΈΡ Π²ΡΠ΅Ρ ΠΏΠ°ΡΠ°ΠΌΠ΅ΡΡΠΎΠ², Ρ Π°ΡΠ°ΠΊΡΠ΅ΡΠΈΠ·ΡΡΡΠΈΡ ΡΠΏΠΎΡΠΎΠ±Π½ΠΎΡΡΡ Π²ΡΠΏΠΎΠ»Π½ΡΡΡ Π·Π°Π΄Π°Π½Π½ΡΠ΅ ΡΡΠ½ΠΊΡΠΈΠΈ, ΡΠΎΠΎΡΠ²Π΅ΡΡΡΠ²ΡΡΡ ΡΡΠ΅Π±ΠΎΠ²Π°Π½ΠΈΡΠΌ Π½ΠΎΡΠΌΠ°ΡΠΈΠ²Π½ΠΎ-ΡΠ΅Ρ Π½ΠΈΡΠ΅ΡΠΊΠΎΠΉ ΠΈ ΠΊΠΎΠ½ΡΡΡΡΠΊΡΠΎΡΡΠΊΠΎΠΉ Π΄ΠΎΠΊΡΠΌΠ΅Π½ΡΠ°ΡΠΈΠΉ. Π Π°Π±ΠΎΡΠΎΡΠΏΠΎΡΠΎΠ±Π½ΠΎΡΡΡ ΠΎΠ±ΡΠ΅ΠΊΡΠ° Ρ Π°ΡΠ°ΠΊΡΠ΅ΡΠΈΠ·ΡΡΡ ΡΠΎΠ²ΠΎΠΊΡΠΏΠ½ΠΎΡΡΡΡ ΠΎΠΏΡΠ΅Π΄Π΅Π»Π΅Π½Π½ΡΡ ΠΏΡΠΈΠ·Π½Π°ΠΊΠΎΠ², Π½Π°Ρ ΠΎΠΆΠ΄Π΅Π½ΠΈΠ΅ΠΌ Π·Π½Π°ΡΠ΅Π½ΠΈΠΉ Π·Π°Π΄Π°Π½Π½ΡΡ ΠΏΠ°ΡΠ°ΠΌΠ΅ΡΡΠΎΠ² ΠΎΠ±ΡΠ΅ΠΊΡΠΎΠ² Π² ΠΏΡΠ΅Π΄Π΅Π»Π°Ρ Π΄ΠΎΠΏΡΡΠΊΠΎΠ², ΡΡΡΠ°Π½ΠΎΠ²Π»Π΅Π½Π½ΡΡ Π΄Π»Ρ ΡΡΠΈΡ ΠΏΠ°ΡΠ°ΠΌΠ΅ΡΡΠΎΠ². Π Π°Π±ΠΎΡΠΎΡΠΏΠΎΡΠΎΠ±Π½ΠΎΡΡΡ ΠΎΠ±ΡΠ΅ΠΊΡΠ° Ρ Π°ΡΠ°ΠΊΡΠ΅ΡΠΈΠ·ΡΡΡ ΡΡΠ΄ΠΎΠΌ ΠΊΠ°ΡΠ΅ΡΡΠ²Π΅Π½Π½ΡΡ ΠΏΡΠΈΠ·Π½Π°ΠΊΠΎΠ² Π½ΠΎΡΠΌΠ°Π»ΡΠ½ΠΎΠΉ ΡΠ°Π±ΠΎΡΡ. Π Π½Π΅ΡΠ°Π±ΠΎΡΠΎΡΠΏΠΎΡΠΎΠ±Π½ΠΎΠΌ ΡΠΎΡΡΠΎΡΠ½ΠΈΠΈ Π·Π½Π°ΡΠ΅Π½ΠΈΠ΅ Ρ ΠΎΡΡ Π±Ρ ΠΎΠ΄Π½ΠΎΠ³ΠΎ ΠΈΠ· ΠΏΠ°ΡΠ°ΠΌΠ΅ΡΡΠΎΠ² Π½Π΅ ΡΠΎΠΎΡΠ²Π΅ΡΡΡΠ²ΡΡΡ ΡΠΊΠ°Π·Π°Π½Π½ΡΠΌ ΡΡΠ΅Π±ΠΎΠ²Π°Π½ΠΈΡΠΌ. ΠΠΎΠ½ΡΡΠΈΠ΅ Β«ΠΈΡΠΏΡΠ°Π²Π½ΠΎΡΡΡΒ» ΡΠΈΡΠ΅ ΠΏΠΎΠ½ΡΡΠΈΡ Β«ΡΠ°Π±ΠΎΡΠΎΡΠΏΠΎΡΠΎΠ±Π½ΠΎΡΡΡΒ»: ΠΈΡΠΏΡΠ°Π²Π½ΡΠΉ ΠΎΠ±ΡΠ΅ΠΊΡ ΡΠ΄ΠΎΠ²Π»Π΅ΡΠ²ΠΎΡΡΠ΅Ρ Π²ΡΠ΅ΠΌ ΡΡΠ΅Π±ΠΎΠ²Π°Π½ΠΈΡΠΌ, Π° ΡΠ°Π±ΠΎΡΠΎΡΠΏΠΎΡΠΎΠ±Π½ΠΎΡΡΡ Π»ΠΈΡΡ ΡΠ΅ΠΌ, ΠΊΠΎΡΠΎΡΡΠ΅ ΠΎΠ±Π΅ΡΠΏΠ΅ΡΠΈΠ²Π°ΡΡ Π½ΠΎΡΠΌΠ°Π»ΡΠ½ΠΎΠ΅ ΡΡΠ½ΠΊΡΠΈΠΎΠ½ΠΈΡΠΎΠ²Π°Π½ΠΈΠ΅ ΠΎΠ±ΡΠ΅ΠΊΡΠ°. Π Π°Π±ΠΎΡΠΎΡΠΏΠΎΡΠΎΠ±Π½ΡΠΉ ΠΎΠ±ΡΠ΅ΠΊΡ ΠΌΠΎΠΆΠ΅Ρ Π±ΡΡΡ Π½Π΅ΠΈΡΠΏΡΠ°Π²Π½ΡΠΌ, Π½Π°ΠΏΡΠΈΠΌΠ΅Ρ Π½Π΅ ΡΠ΄ΠΎΠ²Π»Π΅ΡΠ²ΠΎΡΡΡΡ ΡΡΡΠ΅ΡΠΈΡΠ΅ΡΠΊΠΈΠΌ ΡΡΠ΅Π±ΠΎΠ²Π°Π½ΠΈΡΠΌ, Π΅ΡΠ»ΠΈ ΡΡ ΡΠ΄ΡΠ΅Π½ΠΈΠ΅ Π²Π½Π΅ΡΠ½Π΅Π³ΠΎ Π²ΠΈΠ΄Π° ΠΎΠ±ΡΠ΅ΠΊΡΠ° Π½Π΅ ΠΏΡΠ΅ΠΏΡΡΡΡΠ²ΡΠ΅Ρ Π΅Π³ΠΎ ΠΏΡΠΈΠΌΠ΅Π½Π΅Π½ΠΈΡ ΠΏΠΎ Π½Π°Π·Π½Π°ΡΠ΅Π½ΠΈΡ. ΠΡΠ΅Π΄Π΅Π»ΡΠ½ΡΠΌ Π½Π°Π·ΡΠ²Π°ΡΡ ΡΠ°ΠΊΠΎΠ΅ ΡΠΎΡΡΠΎΡΠ½ΠΈΠ΅ ΠΎΠ±ΡΠ΅ΠΊΡΠ°, ΠΏΡΠΈ ΠΊΠΎΡΠΎΡΠΎΠΌ Π΅Π³ΠΎ Π΄Π°Π»ΡΠ½Π΅ΠΉΡΠ΅Π΅ ΠΏΡΠΈΠΌΠ΅Π½Π΅Π½ΠΈΠ΅ ΠΏΠΎ Π½Π°Π·Π½Π°ΡΠ΅Π½ΠΈΡ Π½Π΅Π΄ΠΎΠΏΡΡΡΠΈΠΌΠΎ ΠΈΠ»ΠΈ Π½Π΅ΡΠ΅Π»Π΅ΡΠΎΠΎΠ±ΡΠ°Π·Π½ΠΎ. ΠΡΠ΅Π΄Π΅Π»ΡΠ½ΡΠ΅ ΡΠΎΡΡΠΎΡΠ½ΠΈΡ Π²ΠΎΠ·Π½ΠΈΠΊΠ°ΡΡ Π² ΡΠ»ΡΡΠ°Π΅ Π½Π΅ΡΡΡΡΠ°Π½ΠΈΠΌΠΎΠ³ΠΎ Π½Π°ΡΡΡΠ΅Π½ΠΈΡ ΡΡΠ΅Π±ΠΎΠ²Π°Π½ΠΈΠΉ Π±Π΅Π·ΠΎΠΏΠ°ΡΠ½ΠΎΡΡΠΈ (ΠΎΠ±ΠΎΡΠ²Π°Π½Ρ ΠΏΡΠΎΠ²ΠΎΠ»ΠΎΠΊΠΈ ΠΊΠ°Π½Π°ΡΠ°), Π½Π΅ΡΡΡΡΠ°Π½ΠΈΠΌΠΎΠ³ΠΎ ΠΏΡΠ΅Π²ΡΡΠ΅Π½ΠΈΡ Π·Π°Π΄Π°Π½Π½ΡΡ ΠΏΠ°ΡΠ°ΠΌΠ΅ΡΡΠΎΠ² (ΠΈΠ·Π½ΠΎΡ ΠΊΠ°Π½Π°Π²ΠΎΠΊ ΡΠΊΠΈΠ²ΠΎΠ²), Π½Π΅ΡΡΡΡΠ°Π½ΠΈΠΌΠΎΠ³ΠΎ ΡΠ½ΠΈΠΆΠ΅Π½ΠΈΡ ΡΡΡΠ΅ΠΊΡΠΈΠ²Π½ΠΎΡΡΠΈ ΡΠΊΡΠΏΠ»ΡΠ°ΡΠ°ΡΠΈΠΈ (ΠΈΠ·Π½ΠΎΡ ΡΠΈΠ»ΠΈΠ½Π΄ΡΠΎΠ²ΡΡ Π²ΡΡΠ»ΠΎΠΊ), ΠΏΡΠΈ Π½Π΅ΠΎΠ±Ρ ΠΎΠ΄ΠΈΠΌΠΎΡΡΠΈ ΠΏΡΠΎΠ²Π΅Π΄Π΅Π½ΠΈΡ ΡΠ΅ΠΊΡΡΠ΅Π³ΠΎ ΠΈΠ»ΠΈ ΠΊΠ°ΠΏΠΈΡΠ°Π»ΡΠ½ΠΎΠ³ΠΎ ΡΠ΅ΠΌΠΎΠ½ΡΠΎΠ².
ΠΡΡΡΠ΄Π° ΡΠ»Π΅Π΄ΡΠ΅Ρ, ΡΡΠΎ ΠΏΠ΅ΡΠ΅Ρ ΠΎΠ΄ ΠΎΠ±ΡΠ΅ΠΊΡΠ° Π² ΠΏΡΠ΅Π΄Π΅Π»ΡΠ½ΠΎΠ΅ ΡΠΎΡΡΠΎΡΠ½ΠΈΠ΅ Π²Π»Π΅ΡΠ΅Ρ Π·Π° ΡΠΎΠ±ΠΎΠΉ Π²ΡΠ΅ΠΌΠ΅Π½Π½ΠΎΠ΅ ΠΈΠ»ΠΈ ΠΎΠΊΠΎΠ½ΡΠ°ΡΠ΅Π»ΡΠ½ΠΎΠ΅ ΠΏΡΠ΅ΠΊΡΠ°ΡΠ΅Π½ΠΈΠ΅ ΠΏΡΠΈΠΌΠ΅Π½Π΅Π½ΠΈΠ΅ ΠΎΠ±ΡΠ΅ΠΊΡΠ° ΠΏΠΎ Π½Π°Π·Π½Π°ΡΠ΅Π½ΠΈΡ. Π ΠΏΠΎΠ½ΡΡΠΈΡ Β«ΡΠΎΠ±ΡΡΠΈΠ΅Β» ΠΎΡΠ½ΠΎΡΡΡΡΡ ΠΏΠΎΠ²ΡΠ΅ΠΆΠ΄Π΅Π½ΠΈΠ΅ ΠΈ ΠΎΡΠΊΠ°Π·, Π²ΡΠ»Π΅Π΄ΡΡΠ²ΠΈΠ΅ ΠΊΠΎΡΠΎΡΡΡ ΠΏΡΠΎΠΈΡΡ ΠΎΠ΄ΠΈΡ ΠΏΠ΅ΡΠ΅Ρ ΠΎΠ΄ ΠΎΠ±ΡΠ΅ΠΊΡΠ° ΠΈΠ· ΠΎΠ΄Π½ΠΎΠ³ΠΎ ΡΠΎΡΡΠΎΡΠ½ΠΈΡ Π² Π΄ΡΡΠ³ΠΎΠ΅. ΠΠΎΠ²ΡΠ΅ΠΆΠ΄Π΅Π½ΠΈΠ΅ΠΌ Π½Π°Π·ΡΠ²Π°ΡΡ ΡΠΎΠ±ΡΡΠΈΠ΅, Π·Π°ΠΊΠ»ΡΡΠ°ΡΡΠΈΠ΅ΡΡ Π² Π½Π°ΡΡΡΠ΅Π½ΠΈΠΈ ΠΈΡΠΏΡΠ°Π²Π½ΠΎΡΡΠΈ ΠΏΡΠΈ ΡΠΎΡ ΡΠ°Π½Π΅Π½ΠΈΠΈ ΡΠ°Π±ΠΎΡΠΎΡΠΏΠΎΡΠΎΠ±Π½ΠΎΠ³ΠΎ ΡΠΎΡΡΠΎΡΠ½ΠΈΡ. ΠΡΠΊΠ°Π· β ΡΠΎΠ±ΡΡΠΈΠ΅, Π·Π°ΠΊΠ»ΡΡΠ°ΡΡΠΈΠ΅ΡΡ Π² Π½Π°ΡΡΡΠ΅Π½ΠΈΠΈ ΡΠ°Π±ΠΎΡΠΎΡΠΏΠΎΡΠΎΠ±Π½ΠΎΠ³ΠΎ ΡΠΎΡΡΠΎΡΠ½ΠΈΡ. ΠΡΠΈΠ·Π½Π°ΠΊΠ°ΠΌΠΈ Π²ΠΎΠ·Π½ΠΈΠΊΠ½ΠΎΠ²Π΅Π½ΠΈΡ ΠΎΡΠΊΠ°Π·Π° ΡΠ²Π»ΡΡΡΡΡ Π½Π΅Π΄ΠΎΠΏΡΡΡΠΈΠΌΡΠ΅ ΠΈΠ·ΠΌΠ΅Π½Π΅Π½ΠΈΡ ΠΏΡΠΈΠ·Π½Π°ΠΊΠΎΠ² ΡΠ°Π±ΠΎΡΠΎΡΠΏΠΎΡΠΎΠ±Π½ΠΎΡΡΠΈ. ΠΠ°ΡΡΠ΄Ρ Ρ ΠΈΠ·Π½ΠΎΡΠΎΠΌ, ΠΊΠΎΡΡΠΎΠ·ΠΈΠ΅ΠΉ ΠΈ ΡΡΡΠ°Π»ΠΎΡΡΠ½ΡΠΌΠΈ ΡΠ°Π·ΡΡΡΠ΅Π½ΠΈΡΠΌΠΈ ΠΎΡΠΊΠ°Π·Ρ ΠΌΠΎΠ³ΡΡ Π±ΡΡΡ Π²ΡΠ·Π²Π°Π½Ρ Π³ΡΡΠ±ΡΠΌΠΈ Π½Π°ΡΡΡΠ΅Π½ΠΈΡΠΌΠΈ ΡΠ΅Ρ Π½ΠΎΠ»ΠΎΠ³ΠΈΠΈ ΠΈΠ·Π³ΠΎΡΠΎΠ²Π»Π΅Π½ΠΈΡ, ΠΏΡΠ°Π²ΠΈΠ» ΡΠΊΡΠΏΠ»ΡΠ°ΡΠ°ΡΠΈΠΈ ΠΈ ΡΠ΅Ρ Π½ΠΈΡΠ΅ΡΠΊΠΎΠ³ΠΎ ΠΎΠ±ΡΠ»ΡΠΆΠΈΠ²Π°Π½ΠΈΡ. ΠΡΠΈ ΡΠ΅ΡΠ΅Π½ΠΈΠΈ Π·Π°Π΄Π°Ρ Π½Π°Π΄Π΅ΠΆΠ½ΠΎΡΡΠΈ Π²Π°ΠΆΠ½ΠΎΠ΅ Π·Π½Π°ΡΠ΅Π½ΠΈΠ΅ ΠΈΠΌΠ΅ΡΡ Π°Π½Π°Π»ΠΈΠ· ΠΈ ΠΊΠ»Π°ΡΡΠΈΡΠΈΠΊΠ°ΡΠΈΡ ΠΎΡΠΊΠ°Π·ΠΎΠ². ΠΠΎ ΡΠ°ΡΡΠΈ ΠΎΡΠΊΠ°Π·ΠΎΠ², ΠΏΡΠΈΡΡΡΠ΅ΠΉ Π΄Π°Π½Π½ΠΎΠΌΡ ΠΎΠ±ΡΠ΅ΠΊΡΡ ΠΈ ΡΡΠ»ΠΎΠ²ΠΈΡΠΌ ΡΠΊΡΠΏΠ»ΡΠ°ΡΠ°ΡΠΈΠΈ, ΡΠ°Π·Π»ΠΈΡΠ°ΡΡ Π΅Π΄ΠΈΠ½ΠΈΡΠ½ΡΠ΅ΠΎΡΠΊΠ°Π·Ρ ΠΈ ΠΏΠΎΠ²ΡΠΎΡΡΡΡΠΈΠ΅ΡΡ ΠΎΡΠΊΠ°Π·Ρ.
Π―Π²Π»Π΅Π½ΠΈΡ, ΠΏΡΠΎΡΠ΅ΡΡΡ, ΡΠΎΠ±ΡΡΠΈΡ ΠΈ ΡΠΎΡΡΠΎΡΠ½ΠΈΡ, ΠΎΠ±ΡΡΠ»ΠΎΠ²Π»Π΅Π½Π½ΡΠ΅ Π²ΠΎΠ·Π½ΠΈΠΊΠ½ΠΎΠ²Π΅Π½ΠΈΠ΅ΠΌ ΠΎΡΠΊΠ°Π·Π°, Π½Π°Π·ΡΠ²Π°ΡΡΡΡ ΠΏΠΎΡΠ»Π΅Π΄ΡΡΠ²ΠΈΡΠΌΠΈ ΠΎΡΠΊΠ°Π·ΠΎΠ². ΠΡΠΊΠ°Π·Ρ Π±ΡΡΠΎΠ²ΡΡ ΠΌΠ°ΡΠΈΠ½ ΠΈ ΠΎΠ±ΠΎΡΡΠ΄ΠΎΠ²Π°Π½ΠΈΡ ΡΡΠ»ΠΎΠ²Π½ΠΎ ΠΌΠΎΠΆΠ½ΠΎ ΡΠ°Π·Π΄Π΅Π»ΠΈΡΡ Π½Π° ΡΡΠΈ Π²ΠΈΠ΄Π°. Π ΠΏΠ΅ΡΠ²ΠΎΠΌΡ ΠΎΡΠ½ΠΎΡΡΡΡΡ ΠΎΡΠΊΠ°Π·Ρ, Π²ΡΠ·ΡΠ²Π°ΡΡΠΈΠ΅ ΡΠΎΠ»ΡΠΊΠΎ ΠΌΠ°ΡΠ΅ΡΠΈΠ°Π»ΡΠ½ΡΠ΅ Π·Π°ΡΡΠ°ΡΡ, ΡΠ²ΡΠ·Π°Π½Π½ΡΠ΅ ΡΠΎ ΡΠΌΠ΅Π½ΠΎΠΉ ΠΈ ΡΠ΅ΠΌΠΎΠ½ΡΠΎΠΌ ΠΎΡΠΊΠ°Π·Π°Π²ΡΠ΅Π³ΠΎ ΠΎΠ±ΠΎΡΡΠ΄ΠΎΠ²Π°Π½ΠΈΡ.
ΠΡΠΎΡΠΎΠΉ Π²ΠΈΠ΄ ΠΎΡΠΊΠ°Π·ΠΎΠ² Ρ Π°ΡΠ°ΠΊΡΠ΅ΡΠΈΠ·ΡΠ΅ΡΡΡ ΡΠΊΠΎΠ½ΠΎΠΌΠΈΡΠ΅ΡΠΊΠΈΠΌΠΈ ΠΏΠΎΡΠ΅ΡΡΠΌΠΈ Π²ΡΠ»Π΅Π΄ΡΡΠ²ΠΈΠ΅ Π²ΡΠ½ΡΠΆΠ΄Π΅Π½Π½ΡΡ ΠΏΡΠΎΡΡΠΎΠ΅Π².
Π ΡΡΠ΅ΡΡΠ΅ΠΌΡ Π²ΠΈΠ΄Ρ ΠΎΡΠ½ΠΎΡΡΡΡΡ ΠΎΡΠΊΠ°Π·Ρ, Π²ΡΠ·ΡΠ²Π°ΡΡΠΈΠ΅ Π±ΠΎΠ»ΡΡΠΈΠ΅ ΡΠΊΠΎΠ½ΠΎΠΌΠΈΡΠ΅ΡΠΊΠΈΠ΅ ΠΏΠΎΡΠ΅ΡΠΈ, Π²ΠΎΠ·ΠΌΠΎΠΆΠ½ΡΠ΅ Π°Π²Π°ΡΠΈΠΈ, ΡΠ³ΡΠΎΠΆΠ°ΡΡΠΈΠ΅ Π±Π΅Π·ΠΎΠΏΠ°ΡΠ½ΠΎΡΡΠΈ ΠΏΠ΅ΡΡΠΎΠ½Π°Π»Π°.
ΠΠΎ Π²ΠΎΠ·ΠΌΠΎΠΆΠ½ΠΎΡΡΠΈ ΡΡΡΡΠ°Π½Π΅Π½ΠΈΡ ΠΎΡΠΊΠ°Π·ΠΎΠ² ΠΌΠ°ΡΠΈΠ½Ρ ΠΈ ΠΎΠ±ΠΎΡΡΠ΄ΠΎΠ²Π°Π½ΠΈΠ΅ ΠΏΠΎΠ΄ΡΠ°Π·Π΄Π΅Π»ΡΡΡΡΡ Π½Π° Π²ΠΎΡΡΡΠ°Π½Π°Π²Π»ΠΈΠ²Π°Π΅ΠΌΡΠ΅ ΠΈ Π½Π΅Π²ΠΎΡΡΡΠ°Π½Π°Π²Π»ΠΈΠ²Π°Π΅ΠΌΡΠ΅. ΠΠΎΡΡΡΠ°Π½Π°Π²Π»ΠΈΠ²Π°Π΅ΠΌΡΠ΅ β ΠΎΠ±ΡΠ΅ΠΊΡΡ, Π΄Π»Ρ ΠΊΠΎΡΠΎΡΡΡ Π²ΠΎΡΡΡΠ°Π½ΠΎΠ²Π»Π΅Π½ΠΈΠ΅ ΡΠ°Π±ΠΎΡΠΎΡΠΏΠΎΡΠΎΠ±Π½ΠΎΠ³ΠΎ ΡΠΎΡΡΠΎΡΠ½ΠΈΡ ΠΏΡΠ΅Π΄ΡΡΠΌΠΎΡΡΠ΅Π½ΠΎ Π² Π½ΠΎΡΠΌΠ°ΡΠΈΠ²Π½ΠΎ-ΡΠ΅Ρ Π½ΠΈΡΠ΅ΡΠΊΠΎΠΉ ΠΈ ΠΊΠΎΠ½ΡΡΡΡΠΊΡΠΈΠ²Π½ΠΎΠΉ Π΄ΠΎΠΊΡΠΌΠ΅Π½ΡΠ°ΡΠΈΠΈ. Π Π½Π΅Π²ΠΎΡΡΡΠ°Π½Π°Π²Π»ΠΈΠ²Π°Π΅ΠΌΡΠΌ ΠΎΡΠ½ΠΎΡΡΡΡΡ: ΡΠ°Π»Π΅Π²ΡΠΉ ΠΊΠ°Π½Π°Ρ, ΡΠΎΡΠΌΠΎΠ·Π½ΡΠ΅ Π½Π°ΠΊΠ»Π°Π΄ΠΊΠΈ, ΠΊΠ»Π°ΠΏΠ°Π½Ρ Π±ΡΡΠΎΠ²ΠΎΠ³ΠΎ Π½Π°ΡΠΎΡΠ°, Π΄ΠΎΠ»ΠΎΡΠ°, ΠΏΡΡΠΆΠΈΠ½Ρ, ΠΏΠΎΠ΄ΡΠΈΠΏΠ½ΠΈΠΊΠΈ ΠΈ Ρ.Π΄. ΠΈΡ Π²ΠΎΡΡΡΠ°Π½ΠΎΠ²Π»Π΅Π½ΠΈΠ΅ Π½Π΅ ΠΏΡΠ΅Π΄ΡΡΠΌΠΎΡΡΠ΅Π½ΠΎ ΡΠ΅Ρ Π½ΠΈΡΠ΅ΡΠΊΠΎΠΉ Π΄ΠΎΠΊΡΠΌΠ΅Π½ΡΠ°ΡΠΈΠ΅ΠΉ.
ΠΠ°ΡΡΠ΄Ρ Ρ ΡΡΠΈΠΌ ΡΠ°Π·Π»ΠΈΡΠ°ΡΡ ΡΠ΅ΠΌΠΎΠ½ΡΠΈΡΡΠ΅ΠΌΡΠ΅ ΠΈ Π½Π΅ΡΠ΅ΠΌΠΎΠ½ΡΠΈΡΡΠ΅ΠΌΡΠ΅ ΠΎΠ±ΡΠ΅ΠΊΡΡ. Π ΡΠ΅ΠΌΠΎΠ½ΡΠΈΡΡΠ΅ΠΌΡΠΌ ΠΎΡΠ½ΠΎΡΡΡΡΡ ΠΎΠ±ΡΠ΅ΠΊΡΡ, Π΄Π»Ρ ΠΊΠΎΡΠΎΡΡΡ ΠΏΡΠΎΠ²Π΅Π΄Π΅Π½ΠΈΠ΅ ΡΠ΅ΠΌΠΎΠ½ΡΠΎΠ² ΠΏΡΠ΅Π΄ΡΡΠΌΠΎΡΡΠ΅Π½ΠΎ Π² ΡΠ΅Ρ Π½ΠΈΡΠ΅ΡΠΊΠΎΠΉ Π΄ΠΎΠΊΡΠΌΠ΅Π½ΡΠ°ΡΠΈΠΈ.
ΠΠ°Π΄Π΅ΠΆΠ½ΠΎΡΡΡ ΠΎΠ±ΡΠ΅ΠΊΡΠ° ΠΎΠΏΡΠ΅Π΄Π΅Π»ΡΠ΅ΡΡΡ Π΅Π³ΠΎ Π±Π΅Π·ΠΎΡΠΊΠ°Π·Π½ΠΎΡΡΡΡ, Π΄ΠΎΠ»Π³ΠΎΠ²Π΅ΡΠ½ΠΎΡΡΡΡ, ΡΠ΅ΠΌΠΎΠ½ΡΠΎΠΏΡΠΈΠ³ΠΎΠ΄Π½ΠΎΡΡΡΡ ΠΈ ΡΠΎΡ ΡΠ°Π½ΡΠ΅ΠΌΠΎΡΡΡΡ.
ΠΠ΅Π·ΠΎΡΠΊΠ°Π·Π½ΠΎΡΡΡ β ΡΡΠΎ ΡΠ²ΠΎΠΉΡΡΠ²ΠΎ ΠΎΠ±ΡΠ΅ΠΊΡΠ° Π½Π΅ΠΏΡΠ΅ΡΡΠ²Π½ΠΎ ΡΠΎΡ ΡΠ°Π½ΡΡΡ ΡΠ°Π±ΠΎΡΠΎΡΠΏΠΎΡΠΎΠ±Π½ΠΎΡΡΡ Π² ΡΠ΅ΡΠ΅Π½ΠΈΠΈ Π½Π΅ΠΊΠΎΡΠΎΡΠΎΠ³ΠΎ Π²ΡΠ΅ΠΌΠ΅Π½ΠΈ ΠΈΠ»ΠΈ Π½Π΅ΠΊΠΎΡΠΎΡΠΎΠΉ Π½Π°ΡΠ°Π±ΠΎΡΠΊΠΈ. ΠΠ΅Π·ΠΎΡΠΊΠ°Π·Π½ΠΎΡΡΡ ΠΌΠΎΠΆΠ΅Ρ ΡΠ°ΡΡΠΌΠ°ΡΡΠΈΠ²Π°ΡΡΡΡ Π½Π΅ ΡΠΎΠ»ΡΠΊΠΎ Π² ΡΠ΅ΠΆΠΈΠΌΠ΅ ΡΠ°Π±ΠΎΡΡ ΠΎΠ±ΡΠ΅ΠΊΡΠ°, Π½ΠΎ ΠΈ ΠΏΡΠΈ Ρ ΡΠ°Π½Π΅Π½ΠΈΠΈ ΠΈ ΡΡΠ°Π½ΡΠΏΠΎΡΡΠΈΡΠΎΠ²ΠΊΠ΅ Π΅Π³ΠΎ.
ΠΠΎΠ»Π³ΠΎΠ²Π΅ΡΠ½ΠΎΡΡΡ β ΡΡΠΎ ΡΠ²ΠΎΠΉΡΡΠ²ΠΎ ΠΎΠ±ΡΠ΅ΠΊΡΠ° ΡΠΎΡ ΡΠ°Π½ΡΡΡ ΡΠ°Π±ΠΎΡΠΎΡΠΏΠΎΡΠΎΠ±Π½ΠΎΡΡΡ Π΄ΠΎ Π½Π°ΡΡΡΠΏΠ»Π΅Π½ΠΈΡ ΠΏΡΠ΅Π΄Π΅Π»ΡΠ½ΠΎΠ³ΠΎ ΡΠΎΡΡΠΎΡΠ½ΠΈΡ (Π½Π΅ΡΡΡΡΠ°Π½ΠΈΠΌΠΎΠ³ΠΎ ΠΎΡΠΊΠ°Π·Π°) ΠΏΡΠΈ ΡΡΡΠ°Π½ΠΎΠ²Π»Π΅Π½Π½ΠΎΠΉ ΡΠΈΡΡΠ΅ΠΌΠ΅ ΡΠ΅Ρ Π½ΠΈΡΠ΅ΡΠΊΠΎΠ³ΠΎ ΠΎΠ±ΡΠ»ΡΠΆΠΈΠ²Π°Π½ΠΈΡ ΠΈ ΡΠ΅ΠΌΠΎΠ½ΡΠ°. ΠΡΠΎ ΡΠΎΡΡΠΎΡΠ½ΠΈΠ΅ ΠΌΠΎΠΆΠ΅Ρ Π½Π°ΡΡΡΠΏΠ°ΡΡ Π²ΡΠ»Π΅Π΄ΡΡΠ²ΠΈΠ΅ ΠΈΠ·Π½ΠΎΡΠ°, ΠΏΠΎΠ»ΠΎΠΌΠΊΠΈ, ΠΊΠΎΡΡΠΎΠ·ΠΈΠΈ ΠΈ Ρ.Π΄. Π½Π°ΡΠ°Π±ΠΎΡΠΊΠ° ΠΎΠ±ΡΠ΅ΠΊΡΠ° ΠΎΡ Π½Π°ΡΠ°Π»Π° Π΅Π³ΠΎ ΡΠΊΡΠΏΠ»ΡΠ°ΡΠ°ΡΠΈΠΈ Π΄ΠΎ Π½Π°ΡΡΡΠΏΠ»Π΅Π½ΠΈΡ ΠΏΡΠ΅Π΄Π΅Π»ΡΠ½ΠΎΠ³ΠΎ ΡΠΎΡΡΠΎΡΠ½ΠΈΡ Π½Π°Π·ΡΠ²Π°Π΅ΡΡΡ ΡΠ΅Ρ Π½ΠΈΡΠ΅ΡΠΊΠΈΠΌ ΡΠ΅ΡΡΡΡΠΎΠΌ. ΠΠ°Π»Π΅Π½Π΄Π°ΡΠ½Π°Ρ ΠΏΡΠΎΠ΄ΠΎΠ»ΠΆΠΈΡΠ΅Π»ΡΠ½ΠΎΡΡΡ ΠΎΡ Π½Π°ΡΠ°Π»Π° ΡΠΊΡΠΏΠ»ΡΠ°ΡΠ°ΡΠΈΠΈ ΠΎΠ±ΡΠ΅ΠΊΡΠ° Π΄ΠΎ ΠΏΠ΅ΡΠ΅Ρ ΠΎΠ΄Π° Π² ΠΏΡΠ΅Π΄Π΅Π»ΡΠ½ΠΎΠ΅ ΡΠΎΡΡΠΎΡΠ½ΠΈΠ΅ Π½Π°Π·ΡΠ²Π°Π΅ΡΡΡ ΡΡΠΎΠΊΠΎΠΌ ΡΠ»ΡΠΆΠ±Ρ.
Π Π΅ΠΌΠΎΠ½ΡΠΎΠΏΡΠΈΠ³ΠΎΠ΄Π½ΠΎΡΡΡΡ Π½Π°Π·ΡΠ²Π°ΡΡ ΡΠ²ΠΎΠΉΡΡΠ²ΠΎ ΠΎΠ±ΡΠ΅ΠΊΡΠ°, Π·Π°ΠΊΠ»ΡΡΠ°ΡΡΠ΅Π΅ΡΡ Π² ΠΏΡΠΈΡΠΏΠΎΡΠΎΠ±Π»Π΅Π½Π½ΠΎΡΡΠΈ ΠΊ ΠΏΡΠ΅Π΄ΡΠΏΡΠ΅ΠΆΠ΄Π΅Π½ΠΈΡ ΠΈ ΠΎΠ±Π½Π°ΡΡΠΆΠ΅Π½ΠΈΡ ΠΏΡΠΈΡΠΈΠ½ Π²ΠΎΠ·Π½ΠΈΠΊΠ½ΠΎΠ²Π΅Π½ΠΈΡ ΠΎΡΠΊΠ°Π·ΠΎΠ², ΠΏΠΎΠ²ΡΠ΅ΠΆΠ΄Π΅Π½ΠΈΠΉ ΠΈ ΠΏΠΎΠ΄Π΄Π΅ΡΠΆΠ°Π½ΠΈΡ ΠΈ Π²ΠΎΡΡΡΠ°Π½ΠΎΠ²Π»Π΅Π½ΠΈΡ ΡΠ°Π±ΠΎΡΠΎΡΠΏΠΎΡΠΎΠ±Π½ΠΎΠ³ΠΎ ΡΠΎΡΡΠΎΡΠ½ΠΈΡ ΠΏΡΡΠ΅ΠΌ ΡΠ΅Ρ Π½ΠΈΡΠ΅ΡΠΊΠΎΠ³ΠΎ ΠΎΠ±ΡΠ»ΡΠΆΠΈΠ²Π°Π½ΠΈΡ ΠΈ ΡΠ΅ΠΌΠΎΠ½ΡΠΎΠ². ΠΠ»Ρ Π±ΡΡΠΎΠ²ΠΎΠ³ΠΎ ΠΈ ΠΏΡΠΎΠΌΡΡΠ»ΠΎΠ²ΠΎΠ³ΠΎ ΠΎΠ±ΠΎΡΡΠ΄ΠΎΠ²Π°Π½ΠΈΡ ΠΈΠΌΠ΅Π΅ΡΡΡ Π² Π²ΠΈΠ΄Ρ ΠΈΡ ΠΏΡΠΈΡΠΏΠΎΡΠΎΠ±Π»Π΅Π½Π½ΠΎΡΡΡ ΠΊ ΡΠ΅ΠΌΠΎΠ½ΡΠ°ΠΌ Π² ΠΏΠΎΠ»Π΅Π²ΡΡ ΡΡΠ»ΠΎΠ²ΠΈΡΡ . ΠΠΎΠ»ΠΈΡΠ΅ΡΡΠ²Π΅Π½Π½ΠΎ ΡΠ΅ΠΌΠΎΠ½ΡΠΎΠΏΡΠΈΠ³ΠΎΠ΄Π½ΠΎΡΡΡ ΠΎΠΏΡΠ΅Π΄Π΅Π»ΡΠ΅ΡΡΡ Π·Π°ΡΡΠ°ΡΠ°ΠΌΠΈ ΡΡΡΠ΄Π° ΠΈ ΡΡΠ΅Π΄ΡΡΠ². Π Π΅ΠΌΠΎΠ½ΡΠΎΠΏΡΠΈΠ³ΠΎΠ΄Π½ΠΎΡΡΡ ΠΎΠΏΡΠ΅Π΄Π΅Π»ΡΠ΅ΡΡΡ Π΄ΠΎΡΡΡΠΏΠ½ΠΎΡΡΡΡ, ΠΊΠΎΠ½ΡΡΠΎΠ»ΠΈΡΡΠ΅ΠΌΠΎΡΡΡΡ, Π»Π΅Π³ΠΊΠΎΡΡΠ΅ΠΌΠ½ΠΎΡΡΡΡ, Π²Π·Π°ΠΈΠΌΠΎΠ·Π°ΠΌΠ΅Π½ΡΠ΅ΠΌΠΎΡΡΡΡ, ΡΡΠ΅ΠΏΠ΅Π½ΡΡ ΡΠ½ΠΈΡΠΈΠΊΠ°ΡΠΈΠΈ ΠΈ Ρ.Π΄.
Π‘ΠΎΡ ΡΠ°Π½ΡΠ΅ΠΌΠΎΡΡΡ β ΡΠ²ΠΎΠΉΡΡΠ²ΠΎ ΠΎΠ±ΡΠ΅ΠΊΡΠ° ΡΠΎΡ ΡΠ°Π½ΡΡΡ Π·Π½Π°ΡΠ΅Π½ΠΈΡ ΠΏΠΎΠΊΠ°Π·Π°ΡΠ΅Π»Π΅ΠΉ Π±Π΅Π·ΠΎΡΠΊΠ°Π·Π½ΠΎΡΡΠΈ, Π΄ΠΎΠ»Π³ΠΎΠ²Π΅ΡΠ½ΠΎΡΡΠΈ ΠΈ ΡΠ΅ΠΌΠΎΠ½ΡΠΎΠΏΡΠΈΠ³ΠΎΠ΄Π½ΠΎΡΡΠΈ Π² ΡΠ΅ΡΠ΅Π½ΠΈΠΈ ΠΈΠ»ΠΈ ΠΏΠΎΡΠ»Π΅ Ρ ΡΠ°Π½Π΅Π½ΠΈΡ ΠΈ ΡΡΠ°Π½ΡΠΏΠΎΡΡΠΈΡΠΎΠ²ΠΊΠΈ. Π‘ΠΎΡ ΡΠ°Π½ΡΠ΅ΠΌΠΎΡΡΡ ΠΈΠΌΠ΅Π΅Ρ Π΄Π²Π΅ ΡΠΎΡΡΠ°Π²Π»ΡΡΡΠΈΡ : ΠΎΠ΄Π½Π° Π²ΠΎ Π²ΡΠ΅ΠΌΡ Ρ ΡΠ°Π½Π΅Π½ΠΈΡ, Π΄ΡΡΠ³Π°Ρ β Π²ΠΎ Π²ΡΠ΅ΠΌΡ ΠΏΡΠΈΠΌΠ΅Π½Π΅Π½ΠΈΡ ΠΏΠΎΡΠ»Π΅ Ρ ΡΠ°Π½Π΅Π½ΠΈΡ.
Π‘ΡΠΎΠΊ ΡΠΎΡ ΡΠ°Π½ΡΠ΅ΠΌΠΎΡΡΠΈ β ΡΠ°ΠΊΠ°Ρ ΠΏΡΠΎΠ΄ΠΎΠ»ΠΆΠΈΡΠ΅Π»ΡΠ½ΠΎΡΡΡ ΠΏΡΠ΅Π±ΡΠ²Π°Π½ΠΈΡ ΠΎΠ±ΡΠ΅ΠΊΡΠ° Π² ΡΠ΅ΠΆΠΈΠΌΠ°Ρ Ρ ΡΠ°Π½Π΅Π½ΠΈΡΒ ΠΈ ΡΡΠ°Π½ΡΠΏΠΎΡΡΠΈΡΠΎΠ²Π°Π½ΠΈΡ ΠΏΡΠΈ ΠΊΠΎΡΠΎΡΡΡ ΠΏΡΠΈ ΠΊΠΎΡΠΎΡΠΎΠΉ ΠΈΠ·ΠΌΠ΅Π½Π΅Π½ΠΈΡ ΠΏΠΎΠΊΠ°Π·Π°ΡΠ΅Π»Π΅ΠΉ Π±Π΅Π·ΠΎΡΠΊΠ°Π·Π½ΠΎΡΡΠΈ, Π΄ΠΎΠ»Π³ΠΎΠ²Π΅ΡΠ½ΠΎΡΡΠΈ ΠΈ ΡΠ΅ΠΌΠΎΠ½ΡΠΎΠΏΡΠΈΠ³ΠΎΠ΄Π½ΠΎΡΡΠΈ Π½Π°Ρ ΠΎΠ΄ΡΡΡΡ Π² Π΄ΠΎΠΏΡΡΡΠΈΠΌΡΡ ΠΏΡΠ΅Π΄Π΅Π»Π°Ρ . Π‘ΠΎΡ ΡΠ°Π½ΡΠ΅ΠΌΠΎΡΡΡ Ρ Π°ΡΠ°ΠΊΡΠ΅ΡΠΈΠ·ΡΠ΅Ρ ΡΠΎΠΏΡΠΎΡΠΈΠ²Π»ΡΠ΅ΠΌΠΎΡΡΡ ΠΎΠ±ΡΠ΅ΠΊΡΠ° Π²ΠΎΠ·Π΄Π΅ΠΉΡΡΠ²ΠΈΡ Π²Π»Π°ΠΆΠ½ΠΎΡΡΠΈ, Π°ΡΠΌΠΎΡΡΠ΅ΡΠ½ΠΎΠ³ΠΎ Π΄Π°Π²Π»Π΅Π½ΠΈΡ ΠΈ ΡΠ΅ΠΌΠΏΠ΅ΡΠ°ΡΡΡΡ, Π·Π°Π³ΡΡΠ·Π½Π΅Π½Π½ΠΎΡΡΠΈ ΡΠ°Π±ΠΎΡΠ΅Π³ΠΎ ΠΌΠ΅ΡΡΠ°. ΠΡΡΠΎΠΊΠΈΠ΅ ΠΏΠΎΠΊΠ°Π·Π°ΡΠ΅Π»ΠΈ ΡΠΎΡ ΡΠ°Π½ΡΠ΅ΠΌΠΎΡΡΠΈ Π΄ΠΎΡΡΠΈΠ³Π°ΡΡΡΡ ΠΏΡΡΠ΅ΠΌ Π³Π΅ΡΠΌΠ΅ΡΠΈΠ·Π°ΡΠΈΠΈ, ΠΏΠΎΠΊΡΠ°ΡΠΊΠ°, ΠΏΡΠΈΠΌΠ΅Π½Π΅Π½ΠΈΡ Π·Π°Π³Π»ΡΡΠ΅ΠΊ, ΠΎΠΏΠΎΡ ΠΈ Ρ.Π΄.
ΠΠ°ΠΆΠ½ΠΎΠ΅ ΠΏΠΎΠ½ΡΡΠΈΠ΅, ΠΎΡΠ½ΠΎΡΡΡΠ΅Π΅ΡΡ ΠΊ Π½Π°Π΄Π΅ΠΆΠ½ΠΎΡΡΠΈ — ΡΠ΅Π·Π΅ΡΠ²ΠΈΡΠΎΠ²Π°Π½ΠΈΠ΅. ΠΠΎΠ΄ Π½ΠΈΠΌ ΠΏΠΎΠ½ΠΈΠΌΠ°Π΅ΡΡΡ ΡΡΠ΅Π΄ΡΡΠ²ΠΎ ΠΏΠΎΠ²ΡΡΠ΅Π½ΠΈΡ ΡΡΠΎΠ²Π½Ρ Π½Π°Π΄Π΅ΠΆΠ½ΠΎΡΡΠΈ Π²Π²Π΅Π΄Π΅Π½ΠΈΠ΅ΠΌ Π΄ΠΎΠΏΠΎΠ»Π½ΠΈΡΠ΅Π»ΡΠ½ΡΡ ΡΡΠ΅Π΄ΡΡΠ² ΠΈ Π²ΠΎΠ·ΠΌΠΎΠΆΠ½ΠΎΡΡΠ΅ΠΉ. Π¦Π΅Π»Ρ ΡΠ΅Π·Π΅ΡΠ²ΠΈΡΠΎΠ²Π°Π½ΠΈΡ β ΠΎΠ±Π΅ΡΠΏΠ΅ΡΠΈΠ²Π°ΡΡ ΠΎΡΠΊΠ°Π·ΠΎΡΡΡΠΎΠΉΡΠΈΠ²ΠΎΡΡΡ ΠΎΠ±ΡΠ΅ΠΊΡΠ° Π² ΡΠ΅Π»ΠΎΠΌ. Π ΠΠ£ ΠΈΡΠΏΠΎΠ»ΡΠ·ΡΡΡΡΡ ΡΠ»Π΅Π΄ΡΡΡΠΈΠ΅ Π²ΠΈΠ΄Ρ ΡΠ΅Π·Π΅ΡΠ²ΠΈΡΠΎΠ²Π°Π½ΠΈΡ: ΠΎΠ±ΡΠ΅Π΅ β ΠΊΠΎΠ³Π΄Π° ΠΎΠ±ΡΠ΅ΠΊΡ ΡΠ΅Π·Π΅ΡΠ²ΠΈΡΡΠ΅ΡΡΡ Π² ΡΠ΅Π»ΠΎΠΌ β ΠΊΠΎΠΌΠΏΡΠ΅ΡΡΠΎΡΡ. Π Π°Π·Π΄Π΅Π»ΡΠ½ΠΎΠ΅ β ΠΊΠΎΠ³Π΄Π° ΡΠ΅Π·Π΅ΡΠ²ΠΈΡΡΡΡΡΡ ΠΎΡΠ΄Π΅Π»ΡΠ½ΡΠ΅ ΠΎΠ±ΡΠ΅ΠΊΡΡ ΠΎΠ±ΠΎΡΡΠ΄ΠΎΠ²Π°Π½ΠΈΡ β ΠΏΡΠΎΡΠΈΠ²ΠΎΠ²ΡΠ±ΡΠΎΡΠΎΠ²ΠΎΠ΅; Π·Π°ΠΌΠ΅ΡΠ΅Π½ΠΈΠ΅ βΠΏΡΠΈ ΠΊΠΎΡΠΎΡΠΎΠΌ ΡΡΠ½ΠΊΡΠΈΠΈ ΠΎΠ±ΡΠ΅ΠΊΡΠ° Π²ΡΠΏΠΎΠ»Π½ΡΡΡΡΡ Π΄ΡΡΠ³ΠΈΠΌ β Π°Π²ΡΠΎΠΌΠ°ΡΠΈΡΠ΅ΡΠΊΠ°Ρ ΠΏΠΎΠ΄Π°ΡΠ° Π΄ΠΎΠ»ΠΎΡΠ°. ΠΡΠ½ΠΎΡΠ΅Π½ΠΈΠ΅ ΡΠΈΡΠ»Π° ΡΠ΅Π·Π΅ΡΠ²Π½ΡΡ ΠΈΠ·Π΄Π΅Π»ΠΈΠΉ ΠΊ ΡΠΈΡΠ»Ρ ΡΠ΅Π·Π΅ΡΠ²ΠΈΡΡΠ΅ΠΌΡΡ Π½Π°Π·ΡΠ²Π°Π΅ΡΡΡ ΠΊΡΠ°ΡΠ½ΠΎΡΡΡΡ ΡΠ΅Π·Π΅ΡΠ²ΠΈΡΠΎΠ²Π°Π½ΠΈΡ. Π Π΅Π·Π΅ΡΠ²ΠΈΡΠΎΠ²Π°Π½ΠΈΠ΅ Ρ ΠΊΡΠ°ΡΠ½ΠΎΡΡΡΡ ΡΠ°Π²Π½ΠΎΠΉ Π΅Π΄ΠΈΠ½ΠΈΡΠ΅ Π½Π°Π·ΡΠ²Π°Π΅ΡΡΡ Π΄ΡΠ±Π»ΠΈΡΠΎΠ²Π°Π½ΠΈΠ΅ΠΌ.
Π Π°Π·Π»ΠΈΡΠ°ΡΡ Π΅Π΄ΠΈΠ½ΠΈΡΠ½ΡΠ΅ ΠΈ ΠΊΠΎΠΌΠΏΠ»Π΅ΠΊΡΠ½ΡΠ΅ ΠΏΠΎΠΊΠ°Π·Π°ΡΠ΅Π»ΠΈ Π½Π°Π΄Π΅ΠΆΠ½ΠΎΡΡΠΈ. ΠΠ΄ΠΈΠ½ΠΈΡΠ½ΡΠΉ ΠΏΠΎΠΊΠ°Π·Π°ΡΠ΅Π»Ρ ΠΊΠΎΠ»ΠΈΡΠ΅ΡΡΠ²Π΅Π½Π½ΠΎ Ρ Π°ΡΠ°ΠΊΡΠ΅ΡΠΈΠ·ΡΠ΅Ρ ΠΎΠ΄Π½ΠΎ ΠΈΠ· ΡΠ²ΠΎΠΉΡΡΠ², ΡΠΎΡΡΠ°Π²Π»ΡΡΡΠΈΡ Π½Π°Π΄Π΅ΠΆΠ½ΠΎΡΡΡ ΠΎΠ±ΡΠ΅ΠΊΡΠ°. ΠΠΎΠΌΠΏΠ»Π΅ΠΊΡΠ½ΡΠΉ Π½Π΅ ΠΌΠ΅Π½Π΅Π΅ Π΄Π²ΡΡ . ΠΠ°ΠΏΡΠΈΠΌΠ΅Ρ Π±Π΅Π·ΠΎΡΠΊΠ°Π·Π½ΠΎΡΡΡ ΠΈ ΡΠ΅ΠΌΠΎΠ½ΡΠΎΠΏΡΠΈΠ³ΠΎΠ΄Π½ΠΎΡΡΡ.
ΠΡΠ½ΠΎΠ²Π½ΡΠΌ ΠΏΠΎΠΊΠ°Π·Π°ΡΠ΅Π»Π΅ΠΌ Π±Π΅Π·ΠΎΡΠΊΠ°Π·Π½ΠΎΡΡΠΈ ΡΠ²Π»ΡΠ΅ΡΡΡ Π²Π΅ΡΠΎΡΡΠ½ΠΎΡΡΡ Π±Π΅Π·ΠΎΡΠΊΠ°Π·Π½ΠΎΠΉ ΡΠ°Π±ΠΎΡΡ Π (t0), ΠΎΠΏΡΠ΅Π΄Π΅Π»ΡΡΡΠ°Ρ Π²Π΅ΡΠΎΡΡΠ½ΠΎΡΡΡ ΡΠΎΠ³ΠΎ, ΡΡΠΎ Π² Π·Π°Π΄Π°Π½Π½ΠΎΠΌ ΠΈΠ½ΡΠ΅ΡΠ²Π°Π»Π΅ Π²ΡΠ΅ΠΌΠ΅Π½ΠΈ t0=Π’ Π½Π΅ Π²ΠΎΠ·Π½ΠΈΠΊΠ½Π΅Ρ ΠΎΡΠΊΠ°Π· ΠΎΠ±ΡΠ΅ΠΊΡΠ°. ΠΠ½Π°ΡΠ΅Π½ΠΈΠ΅ Π (t0) ΠΊΠ°ΠΊ Π²ΡΡΠΊΠΎΠΉ Π²Π΅ΡΠΎΡΡΠ½ΠΎΡΡΠΈ Π½Π°Ρ ΠΎΠ΄ΠΈΡΡΡ Π² ΠΏΡΠ΅Π΄Π΅Π»Π°Ρ 0β€ Π (t0)β€1.
ΠΠ°ΠΏΡΠΈΠΌΠ΅Ρ, Π΅ΡΠ»ΠΈ Π²Π΅ΡΠΎΡΡΠ½ΠΎΡΡΡ Π±Π΅Π·ΠΎΡΠΊΠ°Π·Π½ΠΎΠΉ ΡΠ°Π±ΠΎΡΡ ΠΌΠ°ΡΠΈΠ½Ρ Π·Π° Π²ΡΠ΅ΠΌΡ Π’=1000 Ρ ΡΠ°Π²Π½Π° 0,95, ΡΠΎ ΡΡΠΎ ΠΎΠ·Π½Π°ΡΠ°Π΅Ρ, ΡΡΠΎ ΠΈΠ· ΠΎΠ±ΡΠ΅Π³ΠΎ ΡΠΈΡΠ»Π° ΠΎΠ΄Π½ΠΎΡΠΈΠΏΠ½ΡΡ ΠΊΠΎΠ½ΡΡΡΡΠΊΡΠΈΠΉ Π² ΡΡΠ΅Π΄Π½Π΅ΠΌ ΠΎΠΊΠΎΠ»ΠΎ 5% Π±ΡΠ΄ΡΡ ΠΈΠΌΠ΅ΡΡ ΠΎΡΠΊΠ°Π·Ρ ΡΠ°Π½ΡΡΠ΅ ΡΠ΅ΠΌ ΡΠ΅ΡΠ΅Π· 1000 Ρ ΡΠ°Π±ΠΎΡΡ. Π’Π°ΠΊ ΠΊΠ°ΠΊ Π±Π΅Π·ΠΎΡΠΊΠ°Π·Π½Π°Ρ ΡΠ°Π±ΠΎΡΠ° ΠΈ ΠΎΡΠΊΠ°Π· Π²Π·Π°ΠΈΠΌΠΎΠΏΡΠΎΡΠΈΠ²ΠΎΠΏΠΎΠ»ΠΎΠΆΠ½ΡΠ΅ ΡΠΎΠ±ΡΡΠΈΡ, ΡΠΎ ΡΡΠΌΠΌΠ° ΠΈΡ Π²Π΅ΡΠΎΡΡΠ½ΠΎΡΡΠ΅ΠΉ ΡΠ°Π²Π½Π° 1.
Π (t0)+Q(t0)=1,Β Β Β Β Β Β Β Β Β Β Β Β Β Β Β Β Β Β Β Β Β Β 0β€tβ€1.
Π ΠΏΠΎΠΊΠ°Π·Π°ΡΠ΅Π»ΡΠΌ Π±Π΅Π·ΠΎΡΠΊΠ°Π·Π½ΠΎΡΡΠΈ ΠΎΡΠ½ΠΎΡΡΡΡΡ ΡΡΠ΅Π΄Π½ΡΡ Π½Π°ΡΠ°Π±ΠΎΡΠΊΠ° Π΄ΠΎ ΠΎΡΠΊΠ°Π·Π°, Π³Π°ΠΌΠΌΠ°-ΠΏΡΠΎΡΠ΅Π½ΡΠ½Π°Ρ Π½Π°ΡΠ°Π±ΠΎΡΠΊΠ° Π΄ΠΎ ΠΎΡΠΊΠ°Π·Π°, ΡΡΠ΅Π΄Π½ΡΡ Π½Π°ΡΠ°Π±ΠΎΡΠΊΠ° Π½Π° ΠΎΡΠΊΠ°Π·, ΠΈΠ½ΡΠ΅Π½ΡΠΈΠ²Π½ΠΎΡΡΡ ΠΎΡΠΊΠ°Π·ΠΎΠ² ΠΈ ΠΏΠ°ΡΠ°ΠΌΠ΅ΡΡ ΠΏΠΎΡΠΎΠΊΠ° ΠΎΡΠΊΠ°Π·ΠΎΠ². Π ΡΠ»ΡΡΠ°ΡΡ Π»Π΅Π³ΠΊΠΎ ΡΡΡΡΠ°Π½ΠΈΠΌΡΡ ΠΎΡΠΊΠ°Π·ΠΎΠ² ΠΏΠΎΠΊΠ°Π·Π°ΡΠ΅Π»Π΅ΠΌ Π±Π΅Π·ΠΎΡΠΊΠ°Π·Π½ΠΎΡΡΠΈ ΡΠ²Π»ΡΠ΅ΡΡΡ ΡΡΠ΅Π΄Π½ΡΡ Π½Π°ΡΠ°Π±ΠΎΡΠΊΠ° Π½Π° ΠΎΡΠΊΠ°Π·, ΠΎΠΏΡΠ΅Π΄Π΅Π»ΡΠ΅ΠΌΠ°Ρ ΠΎΡΠ½ΠΎΡΠ΅Π½ΠΈΠ΅ΠΌ Π½Π°ΡΠ°Π±ΠΎΡΠΊΠΈ Π²ΠΎΡΡΡΠ°Π½Π°Π²Π»ΠΈΠ²Π°Π΅ΠΌΠΎΠ³ΠΎ ΠΎΠ±ΡΠ΅ΠΊΡΠ° ΠΊ ΠΎΠΆΠΈΠ΄Π°Π΅ΠΌΠΎΠΌΡ ΡΠΈΡΠ»Ρ Π΅Π³ΠΎ ΠΎΡΠΊΠ°Π·ΠΎΠ² Π² ΡΠ΅ΡΠ΅Π½ΠΈΠΈ ΡΡΠΎΠΉ Π½Π°ΡΠ°Π±ΠΎΡΠΊΠΈ.Β Π‘ΡΠ΅Π΄Π½ΡΡ Π½Π°ΡΠ°Π±ΠΎΡΠΊΠ° Π½Π° ΠΎΡΠΊΠ°Π· ΠΎΠ·Π½Π°ΡΠ°Π΅Ρ Π½Π°ΡΠ°Π±ΠΎΡΠΊΡ Π²ΠΎΡΡΡΠ°Π½Π°Π²Π»ΠΈΠ²Π°Π΅ΠΌΠΎΠ³ΠΎ ΠΎΠ±ΡΠ΅ΠΊΡΠ° Π² ΡΡΠ΅Π΄Π½Π΅ΠΌ Π½Π° ΠΎΠ΄ΠΈΠ½ ΠΎΡΠΊΠ°Π· Π² ΡΠ°ΡΡΠΌΠ°ΡΡΠΈΠ²Π°Π΅ΠΌΠΎΠΌ ΠΈΠ½ΡΠ΅ΡΠ²Π°Π»Π΅ ΡΡΠΌΠΌΠ°ΡΠ½ΠΎΠΉ Π½Π°ΡΠ°Π±ΠΎΡΠΊΠΈ ΠΈΠ»ΠΈ ΠΎΠΏΡΠ΅Π΄Π΅Π»Π΅Π½Π½ΠΎΠΉ ΠΏΡΠΎΠ΄ΠΎΠ»ΠΆΠΈΡΠ΅Π»ΡΠ½ΠΎΡΡΠΈ ΡΠΊΡΠΏΠ»ΡΠ°ΡΠ°ΡΠΈΠΈ.
ΠΠ°ΡΠ°ΠΌΠ΅ΡΡ ΠΏΠΎΡΠΎΠΊΠ° ΠΎΡΠΊΠ°Π·ΠΎΠ² ΠΎΠΏΡΠ΅Π΄Π΅Π»ΡΠ΅ΡΡΡ ΠΎΡΠ½ΠΎΡΠ΅Π½ΠΈΠ΅ΠΌ ΡΡΠ΅Π΄Π½Π΅Π³ΠΎ ΡΠΈΡΠ»Π° ΠΎΡΠΊΠ°Π·ΠΎΠ² Π²ΠΎΡΡΡΠ°Π½Π°Π²Π»ΠΈΠ²Π°Π΅ΠΌΠΎΠ³ΠΎ ΠΎΠ±ΡΠ΅ΠΊΡΠ° Π·Π° ΠΏΡΠΎΠΈΠ·Π²ΠΎΠ»ΡΠ½ΠΎ ΠΌΠ°Π»ΡΡ Π΅Π³ΠΎ Π½Π°ΡΠ°Π±ΠΎΡΠΊΡ ΠΊ Π·Π½Π°ΡΠ΅Π½ΠΈΡ ΡΡΠΎΠΉ Π½Π°ΡΠ°Π±ΠΎΡΠΊΠΈ.
Π’Π΅ΡΠΌΠΈΠ½ ΠΈΠ½ΡΠ΅Π½ΡΠΈΠ²Π½ΠΎΡΡΡ ΠΎΡΠΊΠ°Π·ΠΎΠ² ΠΎΠ·Π½Π°ΡΠ°Π΅Ρ ΡΡΠ»ΠΎΠ²Π½ΡΡ ΠΏΠ»ΠΎΡΠ½ΠΎΡΡΡ Π²Π΅ΡΠΎΡΡΠ½ΠΎΡΡΠΈ Π²ΠΎΠ·Π½ΠΈΠΊΠ½ΠΎΠ²Π΅Π½ΠΈΡ ΠΎΡΠΊΠ°Π·Π° Π½Π΅Π²ΠΎΡΡΡΠ°Π½Π°Π²Π»ΠΈΠ²Π°Π΅ΠΌΠΎΠ³ΠΎ ΠΎΠ±ΡΠ΅ΠΊΡΠ°, ΠΎΠΏΡΠ΅Π΄Π΅Π»ΡΠ΅ΠΌΡΡ Π΄Π»Ρ ΡΠ°ΡΡΠΌΠ°ΡΡΠΈΠ²Π°Π΅ΠΌΠΎΠ³ΠΎ ΠΌΠΎΠΌΠ΅Π½ΡΠ° Π²ΡΠ΅ΠΌΠ΅Π½ΠΈ ΠΏΡΠΈ ΡΡΠ»ΠΎΠ²ΠΈΠΈ, ΡΡΠΎ Π΄ΠΎ ΡΡΠΎΠ³ΠΎ ΠΌΠΎΠΌΠ΅Π½ΡΠ° ΠΎΡΠΊΠ°Π· Π½Π΅ Π²ΠΎΠ·Π½ΠΈΠΊ. ΠΠ»Ρ ΡΠ°Π»Π΅Π²ΡΡ ΠΊΠ°Π½Π°ΡΠΎΠ², ΠΏΠΎΠ΄ΡΠΈΠΏΠ½ΠΈΠΊΠΎΠ² ΠΈ Π΄ΡΡΠ³ΠΈΡ Π½Π΅Π²ΠΎΡΡΡΠ°Π½Π°Π²Π»ΠΈΠ²Π°Π΅ΠΌΡΡ ΠΎΠ±ΡΠ΅ΠΊΡΠΎΠ² ΠΏΠΎΠΊΠ°Π·Π°ΡΠ΅Π»Π΅ΠΌ Π±Π΅Π·ΠΎΡΠΊΠ°Π·Π½ΠΎΡΡΠΈ ΡΠ²Π»ΡΠ΅ΡΡΡ ΡΡΠ΅Π΄Π½ΡΡ Π½Π°ΡΠ°Π±ΠΎΡΠΊΠ° Π΄ΠΎ ΠΎΡΠΊΠ°Π·Π°.
Π ΠΊΠ°ΡΠ΅ΡΡΠ²Π΅ ΠΏΠΎΠΊΠ°Π·Π°ΡΠ΅Π»Π΅ΠΉ Π΄ΠΎΠ»Π³ΠΎΠ²Π΅ΡΠ½ΠΎΡΡΠΈ ΠΈΡΠΏΠΎΠ»ΡΠ·ΡΠ΅ΡΡΡ ΡΡΠ΅Π΄Π½ΠΈΠΉ ΡΠ΅ΡΡΡΡ, Π³Π°ΠΌΠΌΠ°-ΠΏΡΠΎΡΠ΅Π½ΡΠ½ΡΠΉ ΡΠ΅ΡΡΡΡ. Π‘ΡΠ΅Π΄Π½ΠΈΠΌ ΡΠ΅ΡΡΡΡΠΎΠΌ Π½Π°Π·ΡΠ²Π°ΡΡ ΠΌΠ°ΡΠ΅ΠΌΠ°ΡΠΈΡΠ΅ΡΠΊΠΎΠ΅ ΠΎΠΆΠΈΠ΄Π°Π½ΠΈΠ΅ ΡΠ΅ΡΡΡΡΠ°.
ΠΠ°ΠΌΠΌΠ°-ΠΏΡΠΎΡΠ΅Π½ΡΠ½ΡΠΉ ΡΠ΅ΡΡΡΡ β Π½Π°ΡΠ°Π±ΠΎΡΠΊΠ°, Π² ΡΠ΅ΡΠ΅Π½ΠΈΠΈ ΠΊΠΎΡΠΎΡΠΎΠΉ ΠΎΠ±ΡΠ΅ΠΊΡ Π½Π΅ Π΄ΠΎΡΡΠΈΠ³Π°Π΅Ρ ΠΏΡΠ΅Π΄Π΅Π»ΡΠ½ΠΎΠ³ΠΎ ΡΠΎΡΡΠΎΡΠ½ΠΈΡ Ρ Π·Π°Π΄Π°Π½Π½ΠΎΠΉ Π²Π΅ΡΠΎΡΡΠ½ΠΎΡΡΡΡ Ξ³- Π³Π°ΠΌΠΌΠ° Π²ΡΡΠ°ΠΆΠ΅Π½Π½ΠΎΠΉ Π² ΠΏΡΠΎΡΠ΅Π½ΡΠ°Ρ .
ΠΠ»Ρ Π½Π΅Π²ΠΎΡΡΡΠ°Π½Π°Π²Π»ΠΈΠ²Π°Π΅ΠΌΡΡ ΠΎΠ±ΡΠ΅ΠΊΡΠΎΠ² ΠΎΡΠ²Π΅ΡΡΡΠ²Π΅Π½Π½ΠΎΠ³ΠΎ Π½Π°Π·Π½Π°ΡΠ΅Π½ΠΈΡ ΠΏΠΎΠΊΠ°Π·Π°ΡΠ΅Π»ΠΈ Π΄ΠΎΠ»Π³ΠΎΠ²Π΅ΡΠ½ΠΎΡΡΠΈ ΡΠ²Π»ΡΠ΅ΡΡΡ Π½Π°Π·Π½Π°ΡΠ΅Π½Π½ΡΠΉ ΡΠ΅ΡΡΡΡ (ΡΡΠΎΠΊ ΡΠ»ΡΠΆΠ±Ρ). ΠΠΎΠΊΠ°Π·Π°ΡΠ΅Π»Π΅ΠΌ ΡΠ΅ΠΌΠΎΠ½ΡΠΎΡΠΏΠΎΡΠΎΠ±Π½ΠΎΡΡΠΈ ΡΠ²Π»ΡΠ΅ΡΡΡ ΡΡΠ΅Π΄Π½Π΅Π΅ Π²ΡΠ΅ΠΌΡ Π²ΠΎΡΡΡΠ°Π½ΠΎΠ²Π»Π΅Π½ΠΈΡ.Β ΠΡΠ΅ΠΌΡ Π²ΠΎΡΡΡΠ°Π½ΠΎΠ²Π»Π΅Π½ΠΈΡ ΡΠ»Π°Π³Π°Π΅ΡΡΡ ΠΈΠ· Π²ΡΠ΅ΠΌΠ΅Π½ΠΈ ΠΎΠ±Π½Π°ΡΡΠΆΠ΅Π½ΠΈΡ, ΠΏΠΎΠΈΡΠΊΠ° ΠΏΡΠΈΡΠΈΠ½Ρ ΠΎΡΠΊΠ°Π·Π° ΠΈ ΡΡΡΡΠ°Π½Π΅Π½ΠΈΡ ΠΏΠΎΡΠ»Π΅Π΄ΡΡΠ²ΠΈΠΉ ΠΎΡΠΊΠ°Π·Π°. ΠΠ»Ρ ΠΎΡΠ΅Π½ΠΊΠΈ ΡΠΎΡ ΡΠ°Π½ΡΠ΅ΠΌΠΎΡΡΠΈ ΠΈΠ·Π΄Π΅Π»ΠΈΠΉ ΠΏΠΎΠ»ΡΠ·ΡΡΡΡΡ ΠΏΠΎΠΊΠ°Π·Π°ΡΠ΅Π»Π΅ΠΌ ΡΡΠ΅Π΄Π½ΠΈΠΉ ΡΡΠΎΠΊ ΡΠΎΡ ΡΠ°Π½ΡΠ΅ΠΌΠΎΡΡΠΈ β ΠΎΠ·Π½Π°ΡΠ°Π΅Ρ ΠΎΠΆΠΈΠ΄Π°Π΅ΠΌΡΠΉ ΡΡΠΎΠΊ ΡΠΎΡ ΡΠ°Π½Π½ΠΎΡΡΠΈ, Π²ΠΊΠ»ΡΡΠ°ΡΡΠ΅ΠΉ ΠΏΡΠΎΠ΄ΠΎΠ»ΠΆΠΈΡΠ΅Π»ΡΠ½ΠΎΡΡΡ Ρ ΡΠ°Π½Π΅Π½ΠΈΡ, ΡΡΠ°Π½ΡΠΏΠΎΡΡΠΈΡΠΎΠ²ΠΊΠΈ ΠΎΠ±ΡΠ΅ΠΊΡΠ° Π² Π·Π°Π΄Π°Π½Π½ΡΡ ΡΡΠ»ΠΎΠ²ΠΈΡΡ , Π² ΡΠ΅ΡΠ΅Π½ΠΈΠΈ ΠΈ ΠΏΠΎΡΠ»Π΅ ΠΊΠΎΡΠΎΡΠΎΠΉ ΡΠΎΡ ΡΠ°Π½ΡΠ΅ΡΡΡ Π·Π½Π°ΡΠ΅Π½ΠΈΠ΅ Π·Π°Π΄Π°Π½Π½ΡΡ ΠΏΠΎΠΊΠ°Π·Π°ΡΠ΅Π»Π΅ΠΉ Π² ΡΡΡΠ°Π½ΠΎΠ²Π»Π΅Π½Π½ΡΡ ΠΏΡΠ΅Π΄Π΅Π»Π°Ρ .
Π ΠΊΠΎΠΌΠΏΠ»Π΅ΠΊΡΠ½ΡΠΌ ΠΏΠΎΠΊΠ°Π·Π°ΡΠ΅Π»ΡΠΌ Π½Π°Π΄Π΅ΠΆΠ½ΠΎΡΡΠΈ ΠΎΡΠ½ΠΎΡΠΈΡΡΡ ΠΊΠΎΡΡΡΠΈΡΠΈΠ΅Π½Ρ Π³ΠΎΡΠΎΠ²Π½ΠΎΡΡΠΈ
Π³Π΄Π΅ Π’0— Π½Π°ΡΠ°Π±ΠΎΡΠΊΠ° Π½Π° ΠΎΡΠΊΠ°Π·;
Β Β Β Β Β Π’Π— ΡΡΠ΅Π΄Π½Π΅Π΅ Π²ΡΠ΅ΠΌΡ Π²ΠΎΡΡΡΠ°Π½ΠΎΠ²Π»Π΅Π½ΠΈΡ.
ΠΠΎΡΡΡΠΈΡΠΈΠ΅Π½Ρ Π³ΠΎΡΠΎΠ²Π½ΠΎΡΡΠΈ Ρ Π°ΡΠ°ΠΊΡΠ΅ΡΠΈΠ·ΡΠ΅Ρ Π΄Π²Π° ΡΠ²ΠΎΠΉΡΡΠ²Π°: Π±Π΅Π·ΠΎΡΠΊΠ°Π·Π½ΠΎΡΡΡ ΠΈ ΡΠ΅ΠΌΠΎΠ½ΡΠΈΡΡΠ΅ΠΌΠΎΡΡΡ. ΠΡΠ΅ΠΌΡ Π½Π° Π²ΠΎΡΡΡΠ°Π½ΠΎΠ²Π»Π΅Π½ΠΈΡ ΡΠ°Π±ΠΎΡΠΎΡΠΏΠΎΡΠΎΠ±Π½ΠΎΡΡΠΈ Π² ΡΡΠ»ΠΎΠ²ΠΈΡΡ ΡΠΊΡΠΏΠ»ΡΠ°ΡΠ°ΡΠΈΠΈ ΠΏΡΠΈΠ½ΡΡΠΎ ΡΡΠΈΡΠ°ΡΡ ΠΏΡΠΎΡΡΠΎΠ΅ΠΌ.
ΠΠ»Ρ ΠΎΡΠ΅Π½ΠΊΠΈ Π½Π°Π΄Π΅ΠΆΠ½ΠΎΡΡΠΈ Π±ΡΡΠΎΠ²ΡΡ ΠΌΠ°ΡΠΈΠ½ ΠΌΠΎΠΆΠ΅Ρ ΡΠ»ΡΠΆΠΈΡΡ ΠΊΠΎΡΡΡΠΈΡΠΈΠ΅Π½Ρ ΡΠ΅Ρ Π½ΠΈΡΠ΅ΡΠΊΠΎΠ³ΠΎ ΠΈΡΠΏΠΎΠ»ΡΠ·ΠΎΠ²Π°Π½ΠΈΡ, Π²ΡΡΠ°ΠΆΠ°ΡΡΠΈΠΉ ΠΎΡΠ½ΠΎΡΠ΅Π½ΠΈΠ΅ Π²ΡΠ΅ΠΌΠ΅Π½ΠΈ ΠΏΡΠ΅Π±ΡΠ²Π°Π½ΠΈΡ ΠΎΠ±ΡΠ΅ΠΊΡΠ° Π² ΡΠ°Π±ΠΎΡΠΎΡΠΏΠΎΡΠΎΠ±Π½ΠΎΠΌ ΡΠΎΡΡΠΎΡΠ½ΠΈΠΈ ΠΊ ΡΡΠΌΠΌΠ΅ Π²ΡΠ΅ΠΌΠ΅Π½ΠΈ Π² ΡΠ°Π±ΠΎΡΠΎΡΠΏΠΎΡΠΎΠ±Π½ΠΎΠΌ ΡΠΎΡΡΠΎΡΠ½ΠΈΠΈ ΠΈ Π²ΡΠ΅ΠΌΠ΅Π½ΠΈ ΠΎΠ±ΡΠ»ΡΠΆΠΈΠ²Π°Π½ΠΈΡ ΠΈ ΡΠ΅ΠΌΠΎΠ½ΡΠΎΠ².
.
ΠΠΊΠΎΠ½ΠΎΠΌΠΈΡΠ΅ΡΠΊΠΈΠΌ ΠΏΠΎΠΊΠ°Π·Π°ΡΠ΅Π»Π΅ΠΌ Π½Π°Π΄Π΅ΠΆΠ½ΠΎΡΡΠΈ Π±ΡΡΠΎΠ²ΡΡ ΠΌΠ°ΡΠΈΠ½ ΠΈ ΠΎΠ±ΠΎΡΡΠ΄ΠΎΠ²Π°Π½ΠΈΡ ΠΌΠΎΠΆΠ΅Ρ ΡΠ»ΡΠΆΠΈΡΡ ΡΡΠΌΠΌΠ° Π·Π°ΡΡΠ°Ρ Π½Π° ΠΏΡΠΎΠ²Π΅Π΄Π΅Π½ΠΈΡ ΡΠ΅Ρ Π½ΠΈΡΠ΅ΡΠΊΠΎΠ³ΠΎ ΠΎΠ±ΡΠ»ΡΠΆΠΈΠ²Π°Π½ΠΈΡ Π·Π° Π²ΡΠ΅ΠΌΡ Π±ΡΡΠ΅Π½ΠΈΡ ΡΠΊΠ²Π°ΠΆΠΈΠ½.
2.Β Β Β Β Β Β Β ΠΡΠ±ΠΎΡ Π½ΠΎΠΌΠ΅Π½ΠΊΠ»Π°ΡΡΡΡ ΠΏΠΎΠΊΠ°Π·Π°ΡΠ΅Π»Π΅ΠΉ Π½Π°Π΄Π΅ΠΆΠ½ΠΎΡΡΠΈ Π±ΡΡΠΎΠ²ΡΡ ΠΌΠ°ΡΠΈΠ½ ΠΈ ΠΎΠ±ΠΎΡΡΠ΄ΠΎΠ²Π°Π½ΠΈΡ.
ΠΠΎΠΌΠ΅Π½ΠΊΠ»Π°ΡΡΡΠ° ΠΏΠΎΠΊΠ°Π·Π°ΡΠ΅Π»Π΅ΠΉ Π½Π°Π΄Π΅ΠΆΠ½ΠΎΡΡΠΈ Π²ΡΠ±ΠΈΡΠ°Π΅ΡΡΡ Π² Π·Π°Π²ΠΈΡΠΈΠΌΠΎΡΡΠΈ ΠΎΡ ΡΠ΅Ρ Π½ΠΈΡΠ΅ΡΠΊΠΈΡ , ΡΠΊΡΠΏΠ»ΡΠ°ΡΠ°ΡΠΈΠΎΠ½Π½ΡΡ ΠΈ ΡΠΊΠΎΠ½ΠΎΠΌΠΈΡΠ΅ΡΠΊΠΈΡ ΠΏΠ°ΡΠ°ΠΌΠ΅ΡΡΠΎΠ² ΠΈ ΠΎΡΠΎΠ±Π΅Π½Π½ΠΎΡΡΠ΅ΠΉ ΡΠ°ΡΡΠΌΠ°ΡΡΠΈΠ²Π°Π΅ΠΌΡΡ ΠΌΠ°ΡΠΈΠ½ ΠΈ ΠΎΠ±ΠΎΡΡΠ΄ΠΎΠ²Π°Π½ΠΈΡ. Π§ΠΈΡΠ»ΠΎ Π²ΡΠ±ΡΠ°Π½Π½ΡΡ ΠΏΠ°ΡΠ°ΠΌΠ΅ΡΡΠΎΠ² Π½Π°Π΄Π΅ΠΆΠ½ΠΎΡΡΠΈ Π΄ΠΎΠ»ΠΆΠ½ΠΎ Π±ΡΡΡ ΠΌΠΈΠ½ΠΈΠΌΠ°Π»ΡΠ½ΡΠΌ, Π½ΠΎ Π΄ΠΎΡΡΠ°ΡΠΎΡΠ½ΡΠΌ Π΄Π»Ρ ΠΎΡΠ΅Π½ΠΊΠΈ. Π Π·Π°Π²ΠΈΡΠΈΠΌΠΎΡΡΠΈ ΠΎΡ ΠΏΠΎΡΠ»Π΅Π΄ΡΡΠ²ΠΈΠΉ ΠΎΡΠΊΠ°Π·Π°, ΡΠ΅ΠΌΠΎΠ½ΡΠΎΠΏΡΠΈΠ³ΠΎΠ΄Π½ΠΎΡΡΠΈ ΠΈ ΠΏΡΠΈΠ·Π½Π°ΠΊΠΎΠ² ΠΎΠΏΡΠ΅Π΄Π΅Π»ΡΡΡΠΈΡ Π½Π΅ΠΎΠ±Ρ ΠΎΠ΄ΠΈΠΌΠΎΡΡΡ ΠΏΡΠ΅ΠΊΡΠ°ΡΠ΅Π½ΠΈΡ ΡΠΊΡΠΏΠ»ΡΠ°ΡΠ°ΡΠΈΠΈ, Π±ΡΡΠΎΠ²ΡΠ΅ ΠΌΠ°ΡΠΈΠ½Ρ ΠΈ ΠΎΠ±ΠΎΡΡΠ΄ΠΎΠ²Π°Π½ΠΈΠ΅ ΠΏΠΎΠ΄ΡΠ°Π·Π΄Π΅Π»ΡΡΡΡΡ Π½Π° ΠΎΡΠ΄Π΅Π»ΡΠ½ΡΠ΅ Π³ΡΡΠΏΠΏΡ.
I Π³ΡΡΠΏΠΏΠ° ΠΎΠ±ΡΠ΅Π΄ΠΈΠ½ΡΠ΅Ρ ΡΠ΅ΠΌΠΎΠ½ΡΠΈΡΡΠ΅ΠΌΡΠ΅ ΠΈ ΡΠΊΡΠΏΠ»ΡΠ°ΡΠΈΡΡΡΡΠΈΠ΅ΡΡ Π΄ΠΎ ΠΎΠΏΡΠ΅Π΄Π΅Π»Π΅Π½Π½ΠΎΠ³ΠΎ ΡΠΎΡΡΠΎΡΠ½ΠΈΡ ΠΌΠ°ΡΠΈΠ½Ρ ΠΈ ΠΎΠ±ΠΎΡΡΠ΄ΠΎΠ²Π°Π½ΠΈΠ΅, ΠΏΠΎΡΠ»Π΅Π΄ΡΡΠ²ΠΈΠ΅ΠΌ ΠΎΡΠΊΠ°Π·ΠΎΠ² ΠΊΠΎΡΠΎΡΡΡ , ΡΠ²Π»ΡΡΡΡΡ ΠΏΠΎΡΠ΅ΡΠΈ ΠΎΡ Π²ΡΠ½ΡΠΆΠ΄Π΅Π½Π½ΡΡ ΠΏΡΠΎΡΡΠΎΠ΅Π². ΠΡΠΎ ΠΠ£ Π² ΡΠ΅Π»ΠΎΠΌ, ΠΠ¦Π‘, Π±ΡΡΠΎΠ²ΡΠ΅ Π½Π°ΡΠΎΡΡ, Π»Π΅Π±Π΅Π΄ΠΊΠΈ. ΠΠΊΠΎΠ½ΠΎΠΌΠΈΡΠ΅ΡΠΊΠΈΠΉ ΡΡΡΠ΅ΠΊΡ ΠΎΡ ΡΠΊΡΠΏΠ»ΡΠ°ΡΠ°ΡΠΈΠΈ ΡΡΠΈΡ ΠΌΠ°ΡΠΈΠ½ Π·Π°Π²ΠΈΡΠΈΡ ΠΎΡ Π΄Π»ΠΈΡΠ΅Π»ΡΠ½ΠΎΡΡΠΈ ΠΈΡ Π±Π΅Π·ΠΎΡΠΊΠ°Π·Π½ΠΎΠΉ ΡΠ°Π±ΠΎΡΡ ΠΈ Π²ΡΠ΅ΠΌΠ΅Π½ΠΈ ΠΏΡΠΎΡΡΠΎΠ΅Π² Π·Π° ΠΎΡΠ½ΠΎΠ²Π½ΡΠ΅ ΠΏΠΎΠΊΠ°Π·Π°ΡΠ΅Π»ΠΈ Π½Π°Π΄Π΅ΠΆΠ½ΠΎΡΡΠΈ ΡΡΠΎΠΉ Π³ΡΡΠΏΠΏΡ ΠΌΠ°ΡΠΈΠ½ ΠΏΡΠΈΠ½ΠΈΠΌΠ°ΡΡΡΡ:
1)Β Β Β Β Β Β Β ΠΠΎΡΡΡΠΈΡΠΈΠ΅Π½Ρ Π³ΠΎΡΠΎΠ²Π½ΠΎΡΡΠΈ ΠΈΠ»ΠΈ ΠΊΠΎΡΡΡΠΈΡΠΈΠ΅Π½Ρ ΡΠ΅Ρ Π½ΠΈΡΠ΅ΡΠΊΠΎΠ³ΠΎ ΠΈΡΠΏΠΎΠ»ΡΠ·ΠΎΠ²Π°Π½ΠΈΡ.
2)Β Β Β Β Β Β Β ΠΠ°ΡΠ°Π±ΠΎΡΠΊΠ° Π½Π° ΠΎΡΠΊΠ°Π·.
3)Β Β Β Β Β Β Β Π‘ΡΠ΅Π΄Π½ΠΈΠΉ ΡΠ΅ΡΡΡΡ Π΄ΠΎ ΠΊΠ°ΠΏΡΠ΅ΠΌΠΎΠ½ΡΠ° ΠΈΠ»ΠΈ ΠΏΠΎΠ»Π½ΡΠΉ ΡΡΠ΅Π΄Π½ΠΈΠΉ ΡΠ΅ΡΡΡΡ.
II Π³ΡΡΠΏΠΏΠ° β Π²ΡΡΠΊΠ°, ΡΠ°Π»Π΅Π²ΡΠΉ ΠΊΠ°Π½Π°Ρ β ΠΈΡΠΏΡΡΡΠ²Π°ΡΡΠΈΠ΅ ΡΠΈΠΊΠ»ΠΈΡΠ΅ΡΠΊΠΈΠ΅ Π½Π°Π³ΡΡΠ·ΠΊΠΈ. ΠΠΎΡΠΌΠΈΡΡΠ΅ΠΌΡΠΌ ΠΏΠΎΠΊΠ°Π·Π°ΡΠ΅Π»Π΅ΠΌ Π½Π°Π΄Π΅ΠΆΠ½ΠΎΡΡΠΈ Π² ΡΠ²ΡΠ·ΠΈ Ρ ΡΡΠΈΠΌ ΡΠ²Π»ΡΡΡΡΡ:
1)Β Β Β Β Β Β Β ΠΠ΅ΡΠΎΡΡΠ½ΠΎΡΡΡ Π±Π΅Π·ΠΎΡΠΊΠ°Π·Π½ΠΎΠΉ ΡΠ°Π±ΠΎΡΡ Π·Π° Π²ΡΠ΅ΠΌΡ t.
2)Β Β Β Β Β Β Β Π‘ΡΠ΅Π΄Π½ΠΈΠΉ ΡΠ΅ΡΡΡΡ ΠΈ ΡΡΠ΅Π΄Π½ΠΈΠΉ ΡΡΠΎΠΊ ΡΠ»ΡΠΆΠ±Ρ.
III Π³ΡΡΠΏΠΏΠ° β ΡΠ΅ΠΌΠΎΠ½ΡΠΈΡΡΠ΅ΠΌΠΎΠ΅ ΠΎΠ±ΠΎΡΡΠ΄ΠΎΠ²Π°Π½ΠΈΠ΅ ΠΏΠ΅ΡΠ²ΡΠΉ ΠΎΡΠΊΠ°Π· ΠΊΠΎΡΠΎΡΠΎΠ³ΠΎ ΡΠΎΠ²ΠΏΠ°Π΄Π°Π΅Ρ Ρ Π½Π°ΡΡΡΠΏΠ»Π΅Π½ΠΈΠ΅ΠΌ Π΅Π³ΠΎ ΠΏΡΠ΅Π΄Π΅Π»ΡΠ½ΠΎΠ³ΠΎ ΡΠΎΡΡΠΎΡΠ½ΠΈΡ ΠΈ ΠΎΡΠ΄Π΅Π»ΡΠ½ΡΠ΅ ΡΠ»Π΅ΠΌΠ΅Π½ΡΡ ΠΎΠ±ΠΎΡΡΠ΄ΠΎΠ²Π°Π½ΠΈΡ, ΠΊΠΎΡΠΎΡΡΠ΅ ΡΠΊΡΠΏΠ»ΡΠ°ΡΠΈΡΡΡΡΡΡ Π΄ΠΎ ΠΏΠ΅ΡΠ²ΠΎΠ³ΠΎ ΠΎΡΠΊΠ°Π·Π° Π½Π΅ ΠΏΠΎΠ΄Π»Π΅ΠΆΠ°Ρ ΡΠ΅ΠΌΠΎΠ½ΡΡ. Π ΡΡΠΎΠΌΡ ΠΎΠ±ΠΎΡΡΠ΄ΠΎΠ²Π°Π½ΠΈΡ ΠΎΡΠ½ΠΎΡΠΈΡΡΡ ΡΠΎΡΠΎΡ.Ρ Π° ΠΊ ΡΠ»Π΅ΠΌΠ΅Π½ΡΠ°ΠΌ β ΡΠΏΠ»ΠΎΡΠ½Π΅Π½ΠΈΡ, ΠΏΠΎΡΡΠ½ΠΈ, ΠΊΠ»Π°ΠΏΠ°Π½Ρ. Π ΠΊΠ°ΡΠ΅ΡΡΠ²Π΅ ΠΏΠΎΠΊΠ°Π·Π°ΡΠ΅Π»Π΅ΠΉ Π½Π°Π΄Π΅ΠΆΠ½ΠΎΡΡΠΈ ΠΏΡΠΈΠ½ΠΈΠΌΠ°ΡΡΡΡ:
1)Β Β Β Β Β Β Β Π‘ΡΠ΅Π΄Π½ΠΈΠΉ ΡΠ΅ΡΡΡΡ Π΄ΠΎ ΠΊΠ°ΠΏΡΠ΅ΠΌΠΎΠ½ΡΠ°.
2)Β Β Β Β Β Β Β Π‘ΡΠ΅Π΄Π½ΠΈΠΉ ΡΠ΅ΡΡΡΡ.
IV Π³ΡΡΠΏΠΏΠ° β Π½Π°ΠΈΠ±ΠΎΠ»Π΅Π΅ ΠΌΠ½ΠΎΠ³ΠΎΡΠΈΡΠ»Π΅Π½Π½Π°Ρ, ΡΠΊΡΠΏΠ»ΡΠ°ΡΠΈΡΡΠ΅ΠΌΠ°Ρ Π΄ΠΎ ΠΏΡΠ΅Π΄Π΅Π»ΡΠ½ΠΎΠ³ΠΎ ΡΠΎΡΡΠΎΡΠ½ΠΈΡ. Π‘ΡΠ΄Π° ΠΎΡΠ½ΠΎΡΡΡΡΡ ΡΠ·Π»Ρ ΡΠ°Π»Π΅Π²ΠΎΠ³ΠΎ ΠΌΠ΅Ρ Π°Π½ΠΈΠ·ΠΌΠ°, ΡΠ΅ΠΏΠ½ΡΠ΅ ΠΏΠ΅ΡΠ΅Π΄Π°ΡΠΈ, Π²Π΅ΡΡΠ»ΡΠ³ΠΈ, Π·Π°ΠΏΠΎΡΠ½ΡΠ΅ ΡΡΡΡΠΎΠΉΡΡΠ²Π°.
ΠΠΎΠΊΠ°Π·Π°ΡΠ΅Π»ΡΠΌΠΈ Π½Π°Π΄Π΅ΠΆΠ½ΠΎΡΡΠΈ ΡΠ²Π»ΡΡΡΡΡ:
1)Β Β Β Β Β Β Β ΠΠΎΡΡΡΠΈΡΠΈΠ΅Π½Ρ Π³ΠΎΡΠΎΠ²Π½ΠΎΡΡΠΈ ΠΈΠ»ΠΈ ΠΊΠΎΡΡΡΠΈΡΠΈΠ΅Π½Ρ ΡΠ΅Ρ Π½ΠΈΡΠ΅ΡΠΊΠΎΠ³ΠΎ ΠΈΡΠΏΠΎΠ»ΡΠ·ΠΎΠ²Π°Π½ΠΈΡ.
2)Β Β Β Β Β Β Β Π‘ΡΠ΅Π΄Π½ΠΈΠΉ ΡΠ΅ΡΡΡΡ Π΄ΠΎ ΠΊΠ°ΠΏΠΈΡΠ°Π»ΡΠ½ΠΎΠ³ΠΎ ΡΠ΅ΠΌΠΎΠ½ΡΠ° Π»ΠΈΠ±ΠΎ ΠΏΠΎΠ»Π½ΡΠΉ ΡΡΠ΅Π΄Π½ΠΈΠΉ ΡΠ΅ΡΡΡΡ.
V Π³ΡΡΠΏΠΏΠ° β ΡΠ΅ΠΌΠΎΠ½ΡΠΈΡΡΠ΅ΠΌΠΎΠ΅ ΠΎΠ±ΠΎΡΡΠ΄ΠΎΠ²Π°Π½ΠΈΠ΅, ΡΠΊΡΠΏΠ»ΡΠ°ΡΠΈΡΡΠ΅ΠΌΠΎΠ΅ Π΄ΠΎ ΠΏΡΠ΅Π΄Π΅Π»ΡΠ½ΠΎΠ³ΠΎ ΡΠΎΡΡΠΎΡΠ½ΠΈΡ, ΠΏΠΎΡΠ»Π΅ ΠΊΠΎΡΠΎΡΠΎΠ³ΠΎ Π½Π΅ΠΎΠ±Ρ ΠΎΠ΄ΠΈΠΌ ΠΊΠ°ΠΏΠΈΡΠ°Π»ΡΠ½ΡΠΉ ΡΠ΅ΠΌΠΎΠ½Ρ. ΠΡΠΊΠ°Π·Ρ ΡΡΠΎΠΉ Π³ΡΡΠΏΠΏΡ Π½Π΅ Π²ΡΠ·ΡΠ²Π°ΡΡ ΠΏΡΠΎΡΡΠΎΠ΅Π² ΠΠ£. ΡΡΠ΄Π° ΠΎΡΠ½ΠΎΡΡΡΡΡ: ΠΊΠΎΠΌΠΏΡΠ΅ΡΡΠΎΡΠ½ΡΠ΅ Π±Π»ΠΎΠΊΠΈ, ΡΡΡΠ°Π½ΠΎΠ²ΠΊΠΈ ΠΎΡΠΈΡΡΠΊΠΈ ΡΠ°ΡΡΠ²ΠΎΡΠ°. ΠΡΠ½ΠΎΠ²Π½ΡΠΌΠΈ ΠΏΠΎΠΊΠ°Π·Π°ΡΠ΅Π»ΡΠΌΠΈ Π½Π°Π΄Π΅ΠΆΠ½ΠΎΡΡΠΈ ΡΠ²Π»ΡΡΡΡΡ:
1)Β Β Β Β Β Β Β ΠΠ°ΡΠ°Π±ΠΎΡΠΊΠ° Π½Π° ΠΎΡΠΊΠ°Π·.
2)Β Β Β Β Β Β Β Π‘ΡΠ΅Π΄Π½ΠΈΠΉ ΡΠ΅ΡΡΡΡ Π΄ΠΎ ΠΊΠ°ΠΏΠΈΡΠ°Π»ΡΠ½ΠΎΠ³ΠΎ ΡΠ΅ΠΌΠΎΠ½ΡΠ°.
VI Π³ΡΡΠΏΠΏΠ° β ΡΡΡΡΠΎΠΉΡΡΠ²Π°, ΠΈΡΠΏΠΎΠ»ΡΠ·ΡΠ΅ΠΌΡΠ΅ Π΄Π»Ρ ΠΎΠ±Π΅ΡΠΏΠ΅ΡΠ΅Π½ΠΈΡ Π±Π΅Π·ΠΎΠΏΠ°ΡΠ½ΠΎΡΡΠΈ ΠΈ ΡΡΡΡΠ°Π½Π΅Π½ΠΈΡ Π°Π²Π°ΡΠΈΠΉ. ΠΠ»Ρ ΡΡΠΎΠΉ Π³ΡΡΠΏΠΏΡ Ρ Π°ΡΠ°ΠΊΡΠ΅ΡΠ½Ρ ΡΠ΅ΠΆΠΈΠΌΡ ΠΎΠΆΠΈΠ΄Π°Π½ΠΈΡ ΡΠ°Π±ΠΎΡΡ Ρ Π°ΡΠ°ΠΊΡΠ΅ΡΠ½Ρ ΡΠ΅ΠΆΠΈΠΌΡ ΠΎΠΆΠΈΠ΄Π°Π½ΠΈΡ ΡΠ°Π±ΠΎΡΡ (ΠΏΡΠΎΡΠΈΠ²ΠΎΠ²ΡΠ±ΡΠΎΡΠΎΠ²ΠΎΠ΅ ΠΎΠ±ΠΎΡΡΠ΄ΠΎΠ²Π°Π½ΠΈΠ΅, ΠΎΠ³ΡΠ°Π½ΠΈΡΠΈΡΠ΅Π»Ρ ΠΏΠΎΠ΄ΡΠ΅ΠΌΠ° ΡΠ°Π»ΡΠ±Π»ΠΎΠΊΠ°) ΠΏΠΎΠΊΠ°Π·Π°Π½ΠΈΡΠΌΠΈ Π½Π°Π΄Π΅ΠΆΠ½ΠΎΡΡΠΈ ΡΠ²Π»ΡΡΡΡΡ:
1)Β Β Β Β Β Β Β ΠΠΎΡΡΡΠΈΡΠΈΠ΅Π½Ρ ΠΎΠΏΠ΅ΡΠ°ΡΠΈΠ²Π½ΠΎΠΉ Π³ΠΎΡΠΎΠ²Π½ΠΎΡΡΠΈ.
2)Β Β Β Β Β Β Β ΠΠ°Π·Π½Π°ΡΠ΅Π½Π½ΡΠΉ ΡΠ΅ΡΡΡΡ.
ΠΠ΅ΡΡ ΠΏΠ΅ΡΠΈΠΎΠ΄ ΡΠΊΡΠΏΠ»ΡΠ°ΡΠ°ΡΠΈΠΈ ΠΎΠ±ΠΎΡΡΠ΄ΠΎΠ²Π°Π½ΠΈΡ ΡΠΎΡΡΠΎΠΈΡ ΠΈΠ· ΡΡΠ΅Ρ :
«15.3 ΠΠ½Π³Π»ΠΈΠΉΡΠΊΠΈΠΉ ΡΠΎΠΌΠ°Π½ XVIII Π²Π΅ΠΊΠ°» — ΡΡΡ ΡΠΎΠΆΠ΅ ΠΌΠ½ΠΎΠ³ΠΎ ΠΏΠΎΠ»Π΅Π·Π½ΠΎΠ³ΠΎ Π΄Π»Ρ ΠΠ°Ρ.
I.Β Β Β Β Β Β Β Β Β ΠΠ΅ΡΠΈΠΎΠ΄ ΠΏΠΎΠ²ΡΡΠ΅Π½Π½ΠΎΠ³ΠΎ Π·Π½Π°ΡΠ΅Π½ΠΈΡ ΠΏΠΎΡΠΎΠΊΠ° ΠΎΡΠΊΠ°Π·ΠΎΠ² (Π²ΡΠ»Π΅Π΄ΡΡΠ²ΠΈΠ΅ ΡΠΊΡΡΡΡΡ Π΄Π΅ΡΠ΅ΠΊΡΠΎΠ² ΠΊΠΎΠ½ΡΡΡΡΠΊΡΠΎΡΡΠΊΠΎΠ³ΠΎ ΠΈ ΠΏΡΠΎΠΈΠ·Π²ΠΎΠ΄ΡΡΠ²Π΅Π½Π½ΠΎΠ³ΠΎ Ρ Π°ΡΠ°ΠΊΡΠ΅ΡΠ°).
II.Β Β Β Β Β Β Β Β Β ΠΠ΅ΡΠΈΠΎΠ΄ Π½ΠΎΡΠΌΠ°Π»ΡΠ½ΠΎΠΉ ΡΠΊΡΠΏΠ»ΡΠ°ΡΠ°ΡΠΈΠΈ, Π½Π°ΠΊΠΎΠΏΠ»Π΅Π½ΠΈΠ΅ ΠΏΠΎΠ²ΡΠ΅ΠΆΠ΄Π΅Π½ΠΈΠΉ ΠΈ ΡΠ΅Π΄ΠΊΠΈΠ΅ ΠΎΡΠΊΠ°Π·Ρ.
III.Β Β Β Β Β Β Β Β Β ΠΠ΅ΡΠΈΠΎΠ΄ ΠΈΠ½ΡΠ΅Π½ΡΠΈΠ²Π½ΠΎΠ³ΠΎ ΡΠΎΡΡΠ° ΠΎΡΠΊΠ°Π·ΠΎΠ².
Π Π±ΠΎΠ»ΡΡΠΈΠ½ΡΡΠ²Π΅ ΡΠ»ΡΡΠ°Π΅Π² Π½Π°ΡΠ°Π±ΠΎΡΠΊΠ° ΠΎΠ±ΠΎΡΡΠ΄ΠΎΠ²Π°Π½ΠΈΡ ΠΈΠ·ΠΌΠ΅ΡΡΠ΅ΡΡΡ ΠΌΠ°ΡΠΈΠ½Π½ΡΠΌ Π²ΡΠ΅ΠΌΠ΅Π½Π΅ΠΌ Π² ΡΠ°ΡΠ°Ρ . Π€Π°ΠΊΡΠΎΡΡ Π²Π»ΠΈΡΡΡΠΈΠ΅ Π½Π° Π½Π°Π΄Π΅ΠΆΠ½ΠΎΡΡΡ Π±ΡΡΠΈΠ»ΡΠ½ΡΡ ΠΌΠ°ΡΠΈΠ½ ΠΈ ΠΎΠ±ΠΎΡΡΠ΄ΠΎΠ²Π°Π½ΠΈΡ Π½ΠΎΡΡ ΡΠ»ΡΡΠ°ΠΉΠ½ΡΠΉ Ρ Π°ΡΠ°ΠΊΡΠ΅Ρ. Π ΡΡΠΎΠΉ ΡΠ²ΡΠ·ΠΈ ΠΎΡΠ½ΠΎΠ²Π½ΠΎΠΉ ΠΌΠ΅ΡΠΎΠ΄ ΠΈΠ·ΡΡΠ΅Π½ΠΈΡ Π½Π°Π΄Π΅ΠΆΠ½ΠΎΡΡΠΈ β ΡΡΠ°ΡΠΈΡΡΠΈΡΠ΅ΡΠΊΠΈΠΉ, Π° Π΄Π»Ρ ΡΠ΅ΡΠ΅Π½ΠΈΡ ΡΠ΅ΠΎΡΠ΅ΡΠΈΡΠ΅ΡΠΊΠΈΡ Π·Π°Π΄Π°Ρ ΠΈΡΠΏΠΎΠ»ΡΠ·ΡΠ΅ΡΡΡ ΡΠ΅ΠΎΡΠΈΡ Π²Π΅ΡΠΎΡΡΠ½ΠΎΡΡΠ΅ΠΉ.
ΠΠΈΡΠ΅ΡΠ°ΡΡΡΠ°:
1. ΠΠ°Π³ΡΠ°ΠΌΠΎΠ² Π .Π. Β«ΠΡΡΠΎΠ²ΡΠ΅ ΠΌΠ°ΡΠΈΠ½Ρ ΠΈ ΠΊΠΎΠΌΠΏΠ»Π΅ΠΊΡΡΒ», ΠΈΠ·Π΄. ΠΠ΅Π΄ΡΠ° 1988.
ΠΠ°Π΄Π΅ΠΆΠ½ΠΎΡΡΡ Π°Π²ΡΠΎΠΌΠΎΠ±ΠΈΠ»Ρ ΡΡΠΎ
ΠΠ°Π΄Π΅ΠΆΠ½ΠΎΡΡΡ Π°Π²ΡΠΎΠΌΠΎΠ±ΠΈΠ»Ρ ΠΈ Π΅Π΅ ΠΎΡΠ½ΠΎΠ²Π½ΡΠ΅ Ρ Π°ΡΠ°ΠΊΡΠ΅ΡΠΈΡΡΠΈΠΊΠΈ
ΠΠ°Π΄Π΅ΠΆΠ½ΠΎΡΡΡ Π°Π²ΡΠΎΠΌΠΎΠ±ΠΈΠ»Ρ β ΡΡΠΎ ΡΠ²ΠΎΠΉΡΡΠ²ΠΎ Π°Π²ΡΠΎΠΌΠΎΠ±ΠΈΠ»Ρ Π²ΡΠΏΠΎΠ»Π½ΡΡΡ Π·Π°Π΄Π°Π½Π½ΡΠ΅ ΡΡΠ½ΠΊΡΠΈΠΈ, ΡΠΎΡ ΡΠ°Π½ΡΡ Π·Π½Π°ΡΠ΅Π½ΠΈΡ ΡΡΡΠ°Π½ΠΎΠ²Π»Π΅Π½Π½ΡΡ ΡΠΊΡΠΏΠ»ΡΒΠ°ΡΠ°ΡΠΈΠΎΠ½Π½ΡΡ ΠΏΠΎΠΊΠ°Π·Π°ΡΠ΅Π»Π΅ΠΉ Π² ΠΏΡΠ΅Π΄Π΅Π»Π°Ρ , ΡΠΎΠΎΡΠ²Π΅ΡΡΡΠ²ΡΡΡΠΈΡ Π·Π°Π΄Π°Π½Π½ΡΠΌ ΡΠ΅ΠΆΠΈΠΌΠ°ΠΌ ΠΈ ΡΡΠ»ΠΎΠ²ΠΈΡΠΌ ΠΈΡΠΏΠΎΠ»ΡΠ·ΠΎΠ²Π°Π½ΠΈΡ, ΡΠ΅Ρ Π½ΠΈΡΠ΅ΡΠΊΠΎΠ³ΠΎ ΠΎΠ±ΡΠ»ΡΠΆΠΈΠ²Π°Π½ΠΈΡ, ΡΠ΅ΠΌΠΎΠ½ΡΠ°, Ρ ΡΠ°Π½Π΅Π½ΠΈΡ ΠΈ ΡΡΠ°Π½ΡΠΏΠΎΡΡΠΈΡΠΎΠ²Π°Π½ΠΈΡ.
ΠΠ°Π΄Π΅ΠΆΠ½ΠΎΡΡΡ ΡΠ²Π»ΡΠ΅ΡΡΡ ΠΊΠΎΠΌΠΏΠ»Π΅ΠΊΡΠ½ΡΠΌ ΡΠ²ΠΎΠΉΡΡΠ²ΠΎΠΌ, ΠΊΠΎΡΠΎΡΠΎΠ΅ Π² Π·Π°Π²ΠΈΡΠΈΠΌΠΎΡΡΠΈ ΠΎΡ Π½Π°Π·Π½Π°ΡΠ΅Π½ΠΈΡ Π°Π²ΡΠΎΠΌΠΎΠ±ΠΈΠ»Ρ ΠΈ ΡΡΠ»ΠΎΠ²ΠΈΠΉ Π΅Π³ΠΎ ΡΠΊΡΠΏΠ»ΡΠ°ΡΠ°ΡΠΈΠΈ ΠΌΠΎΠΆΠ΅Ρ Π²ΠΊΠ»ΡΡΠ°ΡΡ Π±Π΅Π·ΠΎΡΠΊΠ°Π·Π½ΠΎΡΡΡ, Π΄ΠΎΠ»Π³ΠΎΠ²Π΅ΡΠ½ΠΎΡΡΡ, ΡΠ΅ΠΌΠΎΠ½ΡΠΎΠΏΡΠΈΠ³ΠΎΠ΄Π½ΠΎΡΡΡ ΠΈ ΡΠΎΡ ΡΠ°Π½ΡΠ΅ΠΌΠΎΡΡΡ Π² ΠΎΡΠ΄Π΅Π»ΡΠ½ΠΎΡΡΠΈ ΠΈΠ»ΠΈ ΠΎΠΏΡΠ΅Π΄Π΅Π»Π΅Π½Π½ΠΎΠ΅ ΡΠΎΡΠ΅ΡΠ°Π½ΠΈΠ΅ ΡΡΠΈΡ ΡΠ²ΠΎΠΉΡΡΠ² ΠΊΠ°ΠΊ Π΄Π»Ρ Π°Π²ΡΠΎΠΌΠΎΠ±ΠΈΠ»Ρ, ΡΠ°ΠΊ ΠΈ Π΄Π»Ρ Π΅Π³ΠΎ Π°Π³ΡΠ΅Π³Π°ΡΠΎΠ² (ΡΠΈΡΡΠ΅ΠΌ, ΡΠ·Π»ΠΎΠ² ΠΈ Π΄Π΅ΡΠ°Π»Π΅ΠΉ), Π½Π°ΠΏΡΠ°Π²Π»Π΅Π½Π½ΡΠΌ Π½Π° Π²ΡΠΏΠΎΠ»Π½Π΅Π½ΠΈΠ΅ Π°Π²ΡΠΎΠΌΠΎΠ±ΠΈΠ»Π΅ΠΌ ΡΠ°Π±ΠΎΡΠΈΡ ΡΡΠ½ΠΊΡΠΈΠΉ Ρ ΡΡΡΠ°Π½ΠΎΠ²Π»Π΅Π½Π½ΡΠΌΠΈ ΠΏΠΎΠΊΠ°Π·Π°ΡΠ΅Π»ΡΠΌΠΈ Π² ΡΠ΅ΡΠ΅Π½ΠΈΠ΅ ΡΠ΅ΡΡΡΡΠ° Π΄ΠΎ ΠΊΠ°ΠΏΠΈΡΠ°Π»ΡΠ½ΠΎΠ³ΠΎ ΡΠ΅ΠΌΠΎΠ½ΡΠ°.
ΠΠ°Π΄Π΅ΠΆΠ½ΠΎΡΡΡ Π°Π²ΡΠΎΠΌΠΎΠ±ΠΈΠ»Ρ Π½Π΅ ΠΎΡΡΠ°Π΅ΡΡΡ ΠΏΠΎΡΡΠΎΡΠ½Π½ΠΎΠΉ Π² ΡΠ΅ΡΠ΅Π½ΠΈΠ΅ Π²ΡΠ΅Π³ΠΎ ΡΡΠΎΠΊΠ° Π΅Π³ΠΎ ΡΠ»ΡΠΆΠ±Ρ. ΠΠΎ ΠΌΠ΅ΡΠ΅ ΠΈΠ·Π½Π°ΡΠΈΠ²Π°Π½ΠΈΡ Π΄Π΅ΡΠ°Π»Π΅ΠΉ, ΠΌΠ΅Ρ Π°Π½ΠΈΠ·ΠΌΠΎΠ² ΠΈ Π°Π³ΡΠ΅Π³Π°ΡΠΎΠ² Π½Π°Π΄Π΅ΠΆΠ½ΠΎΡΡΡ ΡΠΌΠ΅Π½ΡΡΠ°Π΅ΡΡΡ, ΡΠ°ΠΊ ΠΊΠ°ΠΊ Π²Π΅ΡΠΎΡΡΠ½ΠΎΡΡΡ Π²ΡΡ ΠΎΠ΄Π° ΠΈΠ· ΡΡΡΠΎΡ Π΄Π΅ΡΠ°Π»Π΅ΠΉ ΡΠ²Π΅Π»ΠΈΡΠΈΠ²Π°Π΅ΡΡΡ. ΠΠΎΠ²ΡΠ΅ Π°Π²ΡΠΎΠΌΠΎΠ±ΠΈΠ»ΠΈ Π²ΡΠ΅Π³Π΄Π° Π±ΠΎΠ»Π΅Π΅ Π½Π°Π΄Π΅ΠΆΠ½Ρ ΠΏΠΎ ΡΡΠ°Π²Π½Π΅Π½ΠΈΡ Ρ Π°Π²ΡΠΎΠΌΠΎΠ±ΠΈΠ»ΡΠΌΠΈ, ΠΈΠΌΠ΅ΡΡΠΈΠΌΠΈ Π±ΠΎΠ»ΡΡΠΎΠΉ ΠΏΡΠΎΠ±Π΅Π³ ΠΈΠ»ΠΈ ΠΏΡΠΎΡΠ΅Π΄ΡΠΈΠΌΠΈ ΠΊΠ°ΠΏΠΈΡΠ°Π»ΡΠ½ΡΠΉ ΡΠ΅ΠΌΠΎΠ½Ρ. Π‘Π»Π΅Π΄ΠΎΠ²Π°ΡΠ΅Π»ΡΠ½ΠΎ, Π·Π°Π΄Π°Π½Π½Π°Ρ ΡΡΠ΅ΠΏΠ΅Π½Ρ Π½Π°Π΄Π΅ΠΆΠ½ΠΎΡΡΠΈ Π°Π²ΡΠΎΠΌΠΎΠ±ΠΈΠ»Ρ ΡΠ°ΡΡΠΌΠ°ΡΡΠΈΠ²Π°Π΅ΡΡΡ Π² ΡΠ²ΡΠ·ΠΈ Ρ ΠΎΠΏΡΠ΅Π΄Π΅ΒΠ»Π΅Π½Π½ΡΠΌ ΠΏΡΠΎΠ±Π΅Π³ΠΎΠΌ. ΠΠ°Π΄Π΅ΠΆΠ½ΠΎΡΡΡ Π·Π°Π²ΠΈΡΠΈΡ ΡΠ°ΠΊΠΆΠ΅ ΠΈ ΠΎΡ ΡΠΎΠ³ΠΎ, Π² ΠΊΠ°ΠΊΠΈΡ ΡΡΠ»ΠΎΠ²ΠΈΡΡ ΡΠ°Π±ΠΎΡΠ°Π΅Ρ Π°Π²ΡΠΎΠΌΠΎΠ±ΠΈΠ»Ρ.
ΠΡΠΈ ΡΠ°Π±ΠΎΡΠ΅, Π½Π°ΠΏΡΠΈΠΌΠ΅Ρ, Π½Π° Π΄ΠΎΡΠΎΠ³Π°Ρ Ρ ΡΠ²Π΅ΡΠ΄ΡΠΌ ΡΡΠΎΠ²Π΅ΡΡΠ΅Π½ΡΡΠ²ΠΎΠ²Π°Π½ΒΠ½ΡΠΌ ΠΏΠΎΠΊΡΡΡΠΈΠ΅ΠΌ Π½Π°Π΄Π΅ΠΆΠ½ΠΎΡΡΡ Π°Π²ΡΠΎΠΌΠΎΠ±ΠΈΠ»Ρ Π±ΠΎΠ»ΡΡΠ΅, ΡΠ΅ΠΌ ΠΏΡΠΈ ΡΠ°Π±ΠΎΡΠ΅ ΠΏΠΎ Π±Π΅Π·Π΄ΠΎΡΠΎΠΆΡΡ. ΠΠ°Π΄Π΅ΠΆΠ½ΠΎΡΡΡ Π»Π΅ΡΠΎΠΌ Π²ΡΠ΅Π³Π΄Π° Π²ΡΡΠ΅, ΡΠ΅ΠΌ Π·ΠΈΠΌΠΎΠΉ, ΠΏΡΠΈ ΠΏΡΠΎΡΠΈΡ ΡΠ°Π²Π½ΡΡ ΡΡΠ»ΠΎΠ²ΠΈΡΡ . ΠΠΎΡΡΠΎΠΌΡ, ΠΏΠΎΠ½ΡΡΠΈΠ΅ Β«Π½Π°Π΄Π΅ΠΆΠ½ΠΎΡΡΡ Π°Π²ΡΠΎΠΌΠΎΠ±ΠΈΠ»ΡΒ» ΡΠ΅ΡΠ½ΠΎ ΡΠ²ΡΠ·ΡΠ²Π°Π΅ΡΡΡ Ρ ΡΡΠ»ΠΎΠ²ΠΈΡΠΌΠΈ Π΅Π³ΠΎ ΡΠΊΡΠΏΠ»ΡΠ°ΡΠ°ΡΠΈΠΈ. ΠΠ°Π΄Π΅ΠΆΠ½ΠΎΡΡΡ Π°Π³ΡΠ΅Π³Π°ΡΠΎΠ² ΠΈ ΡΠ·Π»ΠΎΠ² ΠΎΠΏΡΠ΅Π΄Π΅Π»ΡΠ΅ΡΡΡ Π³Π»Π°Π²Π½ΡΠΌ ΠΎΠ±ΡΠ°Π·ΠΎΠΌ Π΄ΠΎΠ»Π³ΠΎΠ²Π΅ΡΠ½ΠΎΡΡΡΡ Π΄Π΅ΡΠ°Π»Π΅ΠΉ. ΠΠΎΡΡΠΎΠΌΡ ΠΏΡΠ΅ΠΆΠ΄Π΅ Π²ΡΠ΅Π³ΠΎ Π½Π΅ΠΎΠ±Ρ ΠΎΠ΄ΠΈΠΌΠΎ ΡΠΈΡΠΎΠΊΠΎΠ΅ ΡΠΊΡΠΏΠ΅ΡΠΈΠΌΠ΅Π½ΡΠ°Π»ΡΠ½ΠΎΠ΅ ΠΈΡΡΠ»Π΅Π΄ΠΎΠ²Π°Π½ΠΈΠ΅, Π²ΡΡΠ²Π»ΡΡΡΠ΅Π΅ Π΄Π΅ΡΠ°Π»ΠΈ, ΠΊΡΠΈΡΠΈΡΠ΅ΡΠΊΠΈΠ΅ ΠΏΠΎ Π½Π°Π΄Π΅ΠΆΠ½ΠΎΡΡΠΈ.
Π‘ΠΎΠ²ΡΠ΅ΠΌΠ΅Π½Π½Π°Ρ Π½Π°ΡΠΊΠ° ΠΈ ΡΠ΅Ρ Π½ΠΈΠΊΠ° Π² ΠΎΠ±Π»Π°ΡΡΠΈ Π°Π²ΡΠΎΠΌΠΎΠ±ΠΈΠ»Π΅ΡΡΡΠΎΠ΅Π½ΠΈΡ ΠΏΠΎΠ·Π²ΠΎΠ»ΡΡΡ ΠΎΠ±Π΅ΡΠΏΠ΅ΡΠΈΠ²Π°ΡΡ ΡΠ΅ΡΡΡΡ ΠΎΡΠ½ΠΎΠ²Π½ΡΡ Π°Π³ΡΠ΅Π³Π°ΡΠΎΠ², Π² ΡΠΎΠΌ ΡΠΈΡΠ»Π΅ Π΄Π²ΠΈΠ³Π°ΡΠ΅Π»Ρ Π΄ΠΎ ΠΊΠ°ΠΏΠΈΡΠ°Π»ΡΠ½ΠΎΠ³ΠΎ ΡΠ΅ΠΌΠΎΠ½ΡΠ° ΠΈ Π±ΠΎΠ»Π΅Π΅, Π½Π°ΠΌΠ½ΠΎΠ³ΠΎ ΡΠ²Π΅Π»ΠΈΡΠΈΠ²Π°ΡΡ Π½Π°ΡΠ°Π±ΠΎΡΠΊΡ Π½Π° ΠΎΡΠΊΠ°Π· Π΄ΡΡΠ³ΠΈΡ Π°Π³ΡΠ΅Π³Π°ΡΠΎΠ² ΠΈ ΠΌΠ΅Ρ Π°Π½ΠΈΠ·ΠΌΠΎΠ². ΠΠΎΠ²ΡΡΠ΅Π½ΠΈΠ΅ Π½Π°Π΄Π΅ΠΆΠ½ΠΎΡΡΠΈ Π°Π²ΡΠΎΠΌΠΎΠ±ΠΈΠ»Π΅ΠΉ, ΠΎΠ±Π΅ΡΠΏΠ΅ΡΠ΅Π½ΠΈΠ΅ ΡΠ΄ΠΎΠ±Π½ΠΎΠ³ΠΎ Π΄ΠΎΡΡΡΠΏΠ° ΠΊ ΠΎΠ±ΡΠ»ΡΠΆΠΈΒΠ²Π°Π΅ΠΌΡΠΌ Π°Π³ΡΠ΅Π³Π°ΡΠ°ΠΌ ΠΈ ΡΠ·Π»Π°ΠΌ, ΠΈΡ ΡΠΎΠ²Π΅ΡΡΠ΅Π½ΡΡΠ²ΠΎΠ²Π°Π½ΠΈΠ΅ Π΄Π»Ρ ΠΎΠ±Π»Π΅Π³ΡΠ΅Π½ΠΈΡ ΠΎΠ±ΡΠ»ΡΠΆΠΈΠ²Π°Π½ΠΈΡ ΠΈ ΡΠ΅ΠΌΠΎΠ½ΡΠ°, ΡΠΌΠ΅Π½ΡΡΠ΅Π½ΠΈΠ΅ ΠΊΠΎΠ»ΠΈΡΠ΅ΡΡΠ²Π° ΡΠΎΡΠ΅ΠΊ ΡΠΌΠ°Π·ΠΊΠΈ, ΡΠ²Π΅Π»ΠΈΡΠ΅Π½ΠΈΠ΅ ΠΏΠ΅ΡΠΈΠΎΠ΄ΠΈΡΠ½ΠΎΡΡΠΈ ΡΠ΅Ρ Π½ΠΈΡΠ΅ΡΠΊΠΎΠ³ΠΎ ΠΎΠ±ΡΠ»ΡΠΆΠΈΠ²Π°Π½ΠΈΡ ΠΏΠΎΠ·Π²ΠΎΠ»ΡΡΡ ΡΠΎΠΊΡΠ°ΡΠΈΡΡ ΠΏΡΠΎΡΡΠΎΠΈ Π°Π²ΡΠΎΠΌΠΎΠ±ΠΈΠ»Π΅ΠΉ Π² ΡΠ΅Ρ Π½ΠΈΡΠ΅ΡΠΊΠΎΠΌ ΠΎΠ±ΡΠ»ΡΠΆΠΈΠ²Π°Π½ΠΈΠΈ ΠΈ ΡΠ΅ΠΌΠΎΠ½ΡΠ΅ ΠΈ ΡΠ΅ΠΌ ΡΠ°ΠΌΡΠΌ ΠΏΠΎΠ²ΡΡΠΈΡΡ ΠΈΡ ΠΏΡΠΎΠΈΠ·Π²ΠΎΠ΄ΠΈΡΠ΅Π»ΡΠ½ΠΎΡΡΡ.
ΠΠ²ΡΠΎΠΌΠΎΠ±ΠΈΠ»Ρ, ΠΊΠ°ΠΊ ΠΏΡΠ°Π²ΠΈΠ»ΠΎ, ΡΠ°ΡΡΡΠΈΡΡΠ²Π°Π΅ΡΡΡ Π½Π° Π΄Π»ΠΈΡΠ΅Π»ΡΠ½ΡΡ ΡΠ°Π±ΠΎΡΡ. Π Π°Π·Π½ΠΎΡΡΠΎΠΉΠΊΠΎΡΡΡ ΡΠΎΠΏΡΡΠΆΠ΅Π½ΠΈΠΉ Π°Π³ΡΠ΅Π³Π°ΡΠΎΠ² Π°Π²ΡΠΎΠΌΠΎΠ±ΠΈΠ»Ρ ΡΡΠ΅Π±ΡΠ΅Ρ ΠΏΠ΅ΡΠΈΠΎΠ΄ΠΈΒΡΠ΅ΡΠΊΠΈΡ ΠΎΡΡΠ°Π½ΠΎΠ²ΠΎΠΊ Π΄Π»Ρ Π΅Π³ΠΎ ΠΎΠ±ΡΠ»ΡΠΆΠΈΠ²Π°Π½ΠΈΡ ΠΈ Π·Π°ΠΌΠ΅Π½Ρ Π½Π°ΠΈΠΌΠ΅Π½Π΅Π΅ ΡΡΠΎΠΉΠΊΠΈΡ Π΄Π΅ΡΠ°Π»Π΅ΠΉ. ΠΠΎΡΡΠΎΠΌΡ Π½Π΅ΠΎΠ±Ρ ΠΎΠ΄ΠΈΠΌΠΎ ΡΡΡΠ΅ΠΌΠΈΡΡΡΡ ΠΊ ΡΠΎΠΌΡ, ΡΡΠΎΠ±Ρ ΡΡΠΈ ΠΎΡΡΠ°Π½ΠΎΠ²ΠΊΠΈ Π±ΡΠ»ΠΈ ΡΠ΅ΠΆΠ΅ ΠΈ ΡΡΠ΅Π±ΠΎΠ²Π°Π»ΠΈ ΠΌΠΈΠ½ΠΈΠΌΠ°Π»ΡΠ½ΡΡ ΡΡΡΠ΄ΠΎΠ²ΡΡ ΠΈ ΠΌΠ°ΡΠ΅ΡΠΈΒΠ°Π»ΡΠ½ΡΡ Π·Π°ΡΡΠ°Ρ. Π‘Π»Π΅Π΄ΠΎΠ²Π°ΡΠ΅Π»ΡΠ½ΠΎ, Π½Π°Π΄Π΅ΠΆΠ½ΠΎΡΡΡ Π΄ΠΎΠ»ΠΆΠ½Π° ΡΠΎΠ΄Π΅ΡΠΆΠ°ΡΡ Π½Π΅ ΡΠΎΠ»ΡΠΊΠΎ Π²Π΅ΡΠΎΡΡΠ½ΠΎΡΡΡ Π±Π΅Π·ΠΎΡΠΊΠ°Π·Π½ΠΎΠΉ ΡΠ°Π±ΠΎΡΡ Π² ΡΠ΅ΡΠ΅Π½ΠΈΠ΅ Π·Π°Π΄Π°Π½Π½ΠΎΠ³ΠΎ Π²ΡΠ΅ΠΌΠ΅Π½ΠΈ, Π½ΠΎ ΠΈ ΠΏΠΎΠΊΠ°Π·Π°ΡΠ΅Π»ΠΈ, Ρ Π°ΡΠ°ΠΊΡΠ΅ΡΠΈΠ·ΡΡΡΠΈΠ΅ Π²ΡΠΏΠΎΠ»Π½Π΅Π½ΠΈΠ΅ ΡΠ°Π±ΠΎΡ ΠΏΠΎ ΡΠ΅Ρ Π½ΠΈΡΠ΅ΒΡΠΊΠΎΠΌΡ ΠΎΠ±ΡΠ»ΡΠΆΠΈΠ²Π°Π½ΠΈΡ ΠΈ ΡΠ΅ΠΌΠΎΠ½ΡΡ Π² ΠΊΡΠ°ΡΡΠ°ΠΉΡΠΈΠ΅ ΡΡΠΎΠΊΠΈ Ρ ΠΌΠΈΠ½ΠΈΠΌΠ°Π»ΡΠ½ΡΠΌΠΈ ΡΡΡΠ΄ΠΎΠ²ΡΠΌΠΈ ΠΈ ΠΌΠ°ΡΠ΅ΡΠΈΠ°Π»ΡΠ½ΡΠΌΠΈ Π·Π°ΡΡΠ°ΡΠ°ΠΌΠΈ.
Π£ΠΌΠ΅Π½ΡΡΠΈΡΡ ΠΎΠ±ΡΠ΅ΠΌ ΡΠ°Π±ΠΎΡ ΠΏΠΎ ΡΠ΅Ρ Π½ΠΈΡΠ΅ΡΠΊΠΎΠΌΡ ΠΎΠ±ΡΠ»ΡΠΆΠΈΠ²Π°Π½ΠΈΡ ΠΈ ΡΠ΅ΠΌΠΎΠ½ΡΡ ΠΈ ΠΈΡ ΡΡΡΠ΄ΠΎΠ΅ΠΌΠΊΠΎΡΡΡ ΠΌΠΎΠΆΠ½ΠΎ Π»ΠΈΠ±ΠΎ Π·Π° ΡΡΠ΅Ρ ΡΠ²Π΅Π»ΠΈΡΠ΅Π½ΠΈΡ Π΄ΠΎΠ»Π³ΠΎΒΠ²Π΅ΡΠ½ΠΎΡΡΠΈ Π΄Π΅ΡΠ°Π»Π΅ΠΉ, Π»ΠΈΠ±ΠΎ Π·Π° ΡΡΠ΅Ρ ΠΏΡΠΈΡΠΏΠΎΡΠΎΠ±Π»Π΅Π½ΠΈΡ ΠΊΠΎΠ½ΡΡΡΡΠΊΡΠΈΠΈ Π°Π²ΡΠΎΠΌΠΎΠ±ΠΈΠ»Ρ ΠΈ Π΅Π³ΠΎ Π°Π³ΡΠ΅Π³Π°ΡΠΎΠ² ΠΊ Π±ΡΡΡΡΠΎΠΉ Π·Π°ΠΌΠ΅Π½Π΅ ΠΈΠ·Π½ΠΎΡΠΈΠ²ΡΠΈΡ ΡΡ ΡΠΎΠΏΡΡΒΠΆΠ΅Π½ΠΈΠΉ ΠΈ ΡΠ·Π»ΠΎΠ², Ρ. Π΅. Π·Π° ΡΡΠ΅Ρ ΡΠ»ΡΡΡΠ΅Π½ΠΈΡ ΡΠ΅ΠΌΠΎΠ½ΡΠΎΠΏΡΠΈΠ³ΠΎΠ΄Π½ΠΎΡΡΠΈ, Π»ΠΈΠ±ΠΎ Π·Π° ΡΡΠ΅Ρ ΠΎΠ΄Π½ΠΎΠ²ΡΠ΅ΠΌΠ΅Π½Π½ΠΎΠ³ΠΎ ΡΠ»ΡΡΡΠ΅Π½ΠΈΡ ΠΏΠΎΠΊΠ°Π·Π°ΡΠ΅Π»Π΅ΠΉ Π΄ΠΎΠ»Π³ΠΎΠ²Π΅ΡΠ½ΠΎΡΡΠΈ ΠΈ ΡΠ΅ΠΌΠΎΠ½ΡΠΎΠΏΡΠΈΠ³ΠΎΠ΄Π½ΠΎΡΡΠΈ.
ΠΠΎΠ»Π³ΠΎΠ²Π΅ΡΠ½ΠΎΡΡΡ Π΄Π΅ΡΠ°Π»Π΅ΠΉ, ΡΠ·Π»ΠΎΠ² ΠΈ Π°Π³ΡΠ΅Π³Π°ΡΠΎΠ² ΠΈ ΡΠ΅ΠΌΠΎΠ½ΡΠΎΠΏΡΠΈΠ³ΠΎΠ΄Π½ΠΎΡΡΡ ΠΊΠΎΠ½ΡΡΡΡΠΊΡΠΈΠΈ Π°Π²ΡΠΎΠΌΠΎΠ±ΠΈΠ»Ρ β ΡΡΠΎ Π΄Π²Π° ΠΌΠΎΡΠ½ΡΡ ΡΡΡΠ°Π³Π°, Ρ ΠΏΠΎΠΌΠΎΡΡΡ ΠΊΠΎΡΠΎΡΡΡ ΠΌΠΎΠΆΠ½ΠΎ ΠΏΠΎΠ²ΡΡΠΈΡΡ Π΅Π³ΠΎ Π½Π°Π΄Π΅ΠΆΠ½ΠΎΡΡΡ Π½Π° ΡΡΠ°Π΄ΠΈΠΈ ΠΏΡΠΎΠ΅ΠΊΡΠΈΡΠΎΠ²Π°Π½ΠΈΡ ΠΈ Π² ΠΏΡΠΎΡΠ΅ΡΡΠ΅ ΠΌΠΎΠ΄Π΅ΡΠ½ΠΈΠ·Π°ΡΠΈΠΈ.
ΠΡΠΎΠ±Π»Π΅ΠΌΠ° Π½Π°Π΄Π΅ΠΆΠ½ΠΎΡΡΠΈ ΠΎΠ±Π΅ΡΠΏΠ΅ΡΠΈΠ²Π°Π΅ΡΡΡ Π½Π° ΡΠ΅ΡΡΡΠ΅Ρ ΠΎΡΠ½ΠΎΠ²Π½ΡΡ ΡΡΠ°ΠΏΠ°Ρ :
- ΠΎΠΏΡΠ΅Π΄Π΅Π»Π΅Π½ΠΈΠ΅ ΠΈΡΡ ΠΎΠ΄Π½ΡΡ ΡΡΠ΅Π±ΠΎΠ²Π°Π½ΠΈΠΉ ΠΊ ΠΊΠ°ΡΠ΅ΡΡΠ²Ρ Π½ΠΎΠ²ΠΎΠΉ ΠΌΠΎΠ΄Π΅Π»ΠΈ Ρ ΡΡΠ΅ΡΠΎΠΌ ΡΡΠΎΠ²Π½Ρ ΡΠΎΠ²ΡΠ΅ΠΌΠ΅Π½Π½ΠΎΠΉ ΡΠ΅Ρ Π½ΠΈΠΊΠΈ, ΠΈΠΌΠ΅ΡΡΠΈΡ ΡΡ Π°Π½Π°Π»ΠΎΠ³ΠΎΠ², ΠΊΠΎΠ½ΡΡΠ½ΠΊΡΡΡΡ ΡΡΠ½ΠΊΠ° ΠΈ ΠΈΠ½ΡΠ΅ΡΠ΅ΡΠΎΠ² ΠΏΠΎΡΡΠ΅Π±ΠΈΡΠ΅Π»Π΅ΠΉ
- ΠΏΡΠΎΠ΅ΠΊΡΠΈΡΠΎΠ²Π°Π½ΠΈΠ΅, Ρ. Π΅. ΡΠ°Π·ΡΠ°Π±ΠΎΡΠΊΠ° ΠΊΠΎΠ½ΡΡΡΡΠΊΡΠΎΡΡΠΊΠΎΠΉ Π΄ΠΎΠΊΡΠΌΠ΅Π½ΡΠ°ΡΠΈΠΈ, Π²ΡΠΏΠΎΠ»Π½Π΅Π½ΠΈΠ΅ ΠΊΠΎΠΌΠΏΠ»Π΅ΠΊΡΒΠ½ΡΡ ΡΡΠ΅Π½Π΄ΠΎΠ²ΡΡ ΠΈ Π΄ΠΎΡΠΎΠΆΠ½ΡΡ ΠΈΡΠΏΡΡΠ°Π½ΠΈΠΉ
- ΠΏΡΠΎΠΈΠ·Π²ΠΎΠ΄ΡΡΠ²ΠΎ
- ΡΠ°Π±ΠΎΡΠ° Ρ ΠΏΠΎΡΡΠ΅Π±ΠΈΡΠ΅Π»ΡΠΌΠΈ (ΡΠ±ΠΎΡ ΠΈΠ½ΡΠΎΡΠΌΠ°ΡΠΈΠΈ ΠΎ Π²ΡΠ΅Ρ ΠΎΡΠΊΠ°Π·Π°Ρ ΠΈ Π½Π΅ΠΈΡΠΏΡΠ°Π²Π½ΠΎΡΡΡΡ , Π²ΠΎΠ·Π½ΠΈΠΊΠ°ΡΡΠΈΡ Π² ΠΏΡΠΎΡΠ΅ΡΡΠ΅ ΡΠΊΡΠΏΠ»ΡΠ°ΡΠ°ΡΠΈΠΈ, ΡΠΏΡΠΎΡΠ΅Π½ΠΈΠ΅ ΠΈ ΡΠ½ΠΈΠΆΠ΅Π½ΠΈΠ΅ ΡΡΡΠ΄ΠΎΠ΅ΠΌΠΊΠΎΡΡΠΈ ΡΠ΅Ρ Π½ΠΈΡΠ΅ΡΠΊΠΎΠ³ΠΎ ΠΎΠ±ΡΠ»ΡΠΆΠΈΠ²Π°Π½ΠΈΡ ΠΈ ΡΠ΅ΠΌΠΎΠ½ΡΠ½ΡΡ ΡΠ°Π±ΠΎΡ, ΠΎΠ±Π΅ΡΠΏΠ΅ΡΠ΅Π½ΠΈΠ΅ Π·Π°ΠΏΠ°ΡΠ½ΡΠΌΠΈ ΡΠ°ΡΡΡΠΌΠΈ)
ΠΡΠΈ ΠΊΠΎΠ½ΡΡΡΡΠΈΡΠΎΠ²Π°Π½ΠΈΠΈ Π°Π²ΡΠΎΠΌΠΎΠ±ΠΈΠ»Π΅ΠΉ Π΄ΠΎΠ»ΠΆΠ½ΠΎ ΡΠΎΠ±Π»ΡΠ΄Π°ΡΡΡΡ ΠΏΡΠ°Π²ΠΈΠ»ΠΎ, ΡΠ΅ΠΌ ΠΌΠ΅Π½ΡΡΠ΅ ΠΎΠΆΠΈΠ΄Π°Π΅ΠΌΠ°Ρ Π΄ΠΎΠ»Π³ΠΎΠ²Π΅ΡΠ½ΠΎΡΡΡ ΡΠΎΠΉ ΠΈΠ»ΠΈ ΠΈΠ½ΠΎΠΉ Π΄Π΅ΡΠ°Π»ΠΈ ΡΠΎΠΏΡΡΠΆΠ΅Π½ΠΈΡ, ΡΠ΅ΠΌ Π±ΠΎΠ»ΡΡΠ΅ΠΉ ΡΠ΅ΠΌΠΎΠ½ΡΠΎΠΏΡΠΈΠ³ΠΎΠ΄Π½ΠΎΡΡΡΡ Π΄ΠΎΠ»ΠΆΠ½Π° ΠΎΠ±Π»Π°Π΄Π°ΡΡ ΠΊΠΎΠ½ΡΡΡΡΠΊΡΠΈΡ Π°Π²ΡΠΎΠΌΠΎΠ±ΠΈΠ»Ρ. ΠΠΎΡΡΠΎΠΌΡ Π½Π°Π΄Π΅ΠΆΠ½ΠΎΡΡΡ Π°Π²ΡΠΎΠΌΠΎΠ±ΠΈΠ»Ρ β ΠΊΠ°ΡΠ΅ΒΠ³ΠΎΡΠΈΡ Π½Π΅ ΡΠΎΠ»ΡΠΊΠΎ ΡΠ΅Ρ Π½ΠΈΡΠ΅ΡΠΊΠ°Ρ, Π½ΠΎ ΠΈ ΡΠΊΠΎΠ½ΠΎΠΌΠΈΡΠ΅ΡΠΊΠ°Ρ. ΠΠ½Π° Π΄ΠΎΠ»ΠΆΠ½Π° ΠΎΡΡΠ°ΠΆΠ°ΡΡ Π·Π°ΡΡΠ°ΡΡ ΠΎΠ±ΡΠ΅ΡΡΠ²Π΅Π½Π½ΠΎ Π½Π΅ΠΎΠ±Ρ ΠΎΠ΄ΠΈΠΌΠΎΠ³ΠΎ ΡΡΡΠ΄Π° Π½Π° ΡΠΎΠ·Π΄Π°Π½ΠΈΠ΅ Π°Π²ΡΠΎΠΌΠΎΠ±ΠΈΠ»Ρ ΠΈ ΠΏΠΎΠ΄Π΄Π΅ΡΠΆΠ°Π½ΠΈΠ΅ Π΅Π³ΠΎ Π² ΡΠ°Π±ΠΎΡΠΎΡΠΏΠΎΡΠΎΠ±Π½ΠΎΠΌ ΡΠΎΡΡΠΎΡΠ½ΠΈΠΈ Π² ΠΏΡΠΎΡΠ΅ΡΡΠ΅ ΡΠΊΡΠΏΠ»ΡΠ°ΡΠ°ΡΠΈΠΈ. ΠΠ°Π΄Π΅ΠΆΠ½ΠΎΡΡΡ Π·Π°Π²ΠΈΡΠΈΡ ΠΏΡΠ΅ΠΆΠ΄Π΅ Π²ΡΠ΅Π³ΠΎ ΠΎΡ ΡΡΠΎΠ²Π½Ρ ΡΠ΅Ρ Π½ΠΈΡΠ΅ΡΠΊΠΎΠ³ΠΎ ΠΎΡΠ½Π°ΡΠ΅Π½ΠΈΡ Π·Π°Π²ΠΎΠ΄Π°-ΠΈΠ·Π³ΠΎΡΠΎΠ²ΠΈΡΠ΅Π»Ρ, Π·Π°Π²ΠΎΠ΄ΠΎΠ² β ΠΏocΠΏΠΎΡΡΠ°Π²ΡΠΈΠΊΠΎΠ² ΡΡΡΡΡ, ΠΊΠ°ΡΠ΅ΡΡΠ²Π° ΠΌΠ°ΡΠ΅ΡΠΈΠ°Π»ΠΎΠ², ΠΏΠΎΠ»ΡΡΠ°Π±ΡΠΈΠΊΠ°ΡΠΎΠ² ΠΈ Π³ΠΎΡΠΎΠ²ΡΡ Π΄Π΅ΡΠ°Π»Π΅ΠΉ. Π Π΅ΡΠ΅Π½ΠΈΠ΅ ΡΠ»ΠΎΠΆΠ½ΡΡ ΠΏΡΠΎΠ±Π»Π΅ΠΌ Π½Π°Π΄Π΅ΠΆΠ½ΠΎΡΡΠΈ ΡΠΎΠ²ΡΠ΅ΠΌΠ΅Π½Π½ΡΡ Π°Π²ΡΠΎΠΌΠΎΠ±ΠΈΠ»Π΅ΠΉ Π½Π΅Π²ΠΎΠ·ΠΌΠΎΠΆΠ½ΠΎ Π±Π΅Π· Π³Π»ΡΠ±ΠΎΠΊΠΎΠ³ΠΎ ΡΠ΅ΠΎΡΠ΅ΡΠΈΡΠ΅ΡΠΊΠΎΠ³ΠΎ ΠΈΠ·ΡΡΠ΅Π½ΠΈΡ ΡΠΈΠ·ΠΈΠΊΠΎ-Ρ ΠΈΠΌΠΈΡΠ΅ΡΠΊΠΈΡ ΠΏΡΠΎΡΠ΅ΡΡΠΎΠ², Π²ΡΠ·ΡΠ²Π°ΡΡΠΈΡ ΠΈΠ·Π½ΠΎΡ ΠΈ ΠΏΠΎΠ»ΠΎΠΌΠΊΡ Π΄Π΅ΡΠ°Π»Π΅ΠΉ, ΠΈ ΡΠ°Π·ΡΠ°Π±ΠΎΡΠΊΠΈ Π½Π° ΡΡΠΎΠΉ Π±Π°Π·Π΅ ΡΠΎΠΎΡΠ²Π΅ΡΡΡΠ²ΡΡΡΠΈΡ ΠΏΡΠ°ΠΊΡΠΈΡΠ΅ΡΠΊΠΈΡ ΡΠ΅ΠΊΠΎΠΌΠ΅Π½Π΄Π°ΡΠΈΠΈ ΠΏΠΎ ΠΊΠΎΠ½ΡΡΡΡΠΈΡΠΎΠ²Π°Π½ΠΈΡ, ΠΏΡΠΎΠΈΠ·Π²ΠΎΠ΄ΡΡΠ²Ρ ΠΈ ΡΠΊΡΠΏΠ»ΡΠ°ΡΠ°ΡΠΈΠΈ Π°Π²ΡΠΎΠΌΠΎΠ±ΠΈΠ»Π΅ΠΉ.
ΠΡΠΈΠ½ΡΡΡΠ΅ Π½Π° ΡΠ΅ΡΠΈΠΉΠ½ΠΎΠ΅ ΠΏΡΠΎΠΈΠ·Π²ΠΎΠ΄ΡΡΠ²ΠΎ Π°Π²ΡΠΎΠΌΠΎΠ±ΠΈΠ»ΠΈ Π² ΡΠ΅ΡΠ΅Π½ΠΈΠ΅ Π²ΡΠ΅Π³ΠΎ Π²ΡΠ΅ΠΌΠ΅Π½ΠΈ Π½Π°Ρ ΠΎΠΆΠ΄Π΅Π½ΠΈΡ ΠΈΡ Π½Π° ΠΏΡΠΎΠΈΠ·Π²ΠΎΠ΄ΡΡΠ²Π΅ ΠΏΠΎΠ΄Π²Π΅ΡΠ³Π°ΡΡΡΡ Π·Π°Π²ΠΎΠ΄Π°ΠΌΠΈ-ΠΈΠ·Π³ΠΎΡΠΎΠ²ΠΈΡΠ΅Π»ΡΠΌΠΈ ΠΊΠΎΠ½ΡΡΡΡΠΊΡΠΈΠ²Π½ΠΎΠΌΡ ΡΠ»ΡΡΡΠ΅Π½ΠΈΡ Ρ ΡΠ΅Π»ΡΡ ΠΏΠΎΠ²ΡΡΠ΅Π½ΠΈΡ ΠΊΠ°ΡΠ΅ΡΡΠ²Π° ΠΈ ΡΠΊΡΠΏΠ»ΡΠ°ΡΠ°ΡΠΈΠΎΠ½Π½ΡΡ ΠΏΠΎΠΊΠ°Π·Π°ΡΠ΅Π»Π΅ΠΉ. ΠΠ°ΡΠ΅ΡΡΠ²ΠΎ ΠΈΠ·Π³ΠΎΡΠΎΠ²Π»Π΅Π½ΠΈΡ Π°Π²ΡΠΎΠΌΠΎΠ±ΠΈΠ»Ρ ΠΎΠΏΡΠ΅Π΄Π΅Π»ΡΠ΅ΡΡΡ ΡΠ΅Ρ Π½ΠΈΡΠ΅ΡΠΊΠΈΠΌ ΠΈ ΡΠ΅Ρ Π½ΠΎΠ»ΠΎΠ³ΠΈΡΠ΅ΡΠΊΠΈΠΌ ΡΡΠΎΠ²Π½ΡΠΌΠΈ ΠΏΡΠΎΠΈΠ·Π²ΠΎΠ΄ΡΡΠ²Π°, ΠΊΠ²Π°Π»ΠΈΡΠΈΠΊΠ°ΡΠΈΠ΅ΠΉ ΠΏΠ΅ΡΡΠΎΠ½Π°Π»Π°, ΠΏΡΠΈΠΌΠ΅Π½ΡΠ΅ΠΌΡΠΌΠΈ ΠΌΠ°ΡΠ΅ΡΠΈΠ°Π»Π°ΠΌΠΈ ΠΈ ΡΡΠΎΠ²Π½Π΅ΠΌ ΠΎΡΠ³Π°Π½ΠΈΠ·Π°ΡΠΈΠΎΠ½Π½ΠΎ-ΡΠΏΡΠ°Π²Π»Π΅Π½ΡΠ΅ΡΠΊΠΎΠ³ΠΎ ΡΠ΅Π³ΡΠ»ΠΈΡΠΎΠ²Π°Π½ΠΈΡ ΠΏΡΠΎΠΈΠ·Π²ΠΎΠ΄ΡΡΠ²Π°. Π ΡΡΠ»ΠΎΠ²ΠΈΡΡ ΡΠ΅ΡΠΈΠΉΠ½ΠΎΠ³ΠΎ ΠΈ ΠΌΠ°ΡΡΠΎΠ²ΠΎΠ³ΠΎ ΠΏΡΠΎΠΈΠ·Π²ΠΎΠ΄ΡΡΠ²Π° ΠΈΠ·ΒΠ³ΠΎΡΠΎΠ²ΠΈΡΡ Π±Π΅Π·Π΄Π΅ΡΠ΅ΠΊΡΠ½ΡΠ΅ Π°Π²ΡΠΎΠΌΠΎΠ±ΠΈΠ»ΠΈ ΠΏΡΠ°ΠΊΡΠΈΡΠ΅ΡΠΊΠΈ Π½Π΅Π²ΠΎΠ·ΠΌΠΎΠΆΠ½ΠΎ, ΠΏΠΎΡΠΎΠΌΡ ΡΡΠΎ Π²ΡΠ΅Π³Π΄Π° ΠΈΠΌΠ΅ΡΡΡΡ ΡΠ»ΡΡΠ°ΠΉΠ½ΡΠ΅ ΡΠ°ΠΊΡΠΎΡΡ, ΠΊΠΎΡΠΎΡΡΠ΅ ΡΠ²Π»ΡΡΡΡΡ ΠΏΡΠΈΡΠΈΠ½ΠΎΠΉ ΠΏΠΎΡΠ²Π»Π΅Π½ΠΈΡ Π΄Π΅ΡΠ΅ΠΊΡΠΎΠ². Π’Π°ΠΊΠΈΠΌΠΈ ΡΠ°ΠΊΡΠΎΡΠ°ΠΌΠΈ ΠΌΠΎΠ³ΡΡ Π±ΡΡΡ ΠΏΠΎΠ³ΡΠ΅ΡΠ½ΠΎΡΡΠΈ ΡΠ΅Ρ Π½ΠΎΠ»ΠΎΠ³ΠΈΡΠ΅ΡΠΊΠΎΠ³ΠΎ ΠΎΠ±ΠΎΡΡΠ΄ΠΎΠ²Π°Π½ΠΈΡ, ΠΈΠ½ΡΡΡΡΠΌΠ΅Π½ΡΠ°, ΠΏΡΠΈΡΠΏΠΎΡΠΎΠ±Π»Π΅Π½ΠΈΠΉ, ΡΠ΅ΠΆΠΈΠΌΠΎΠ² ΠΎΠ±ΡΠ°Π±ΠΎΡΠΊΠΈ, ΠΌΠ°ΡΠ΅ΡΠΈΠ°Π»ΠΎΠ² (Π½Π°ΠΏΡΠΈΠΌΠ΅Ρ, Π½Π΅ΠΎΠ΄Π½ΠΎΡΠΎΠ΄Π½ΠΎΡΡΡ ΡΡΡΡΠΊΡΡΒΡΡ), Π½Π°ΡΡΡΠΎΠΉΠΊΠΈ ΠΈΠ·ΠΌΠ΅ΡΠΈΡΠ΅Π»ΡΠ½ΡΡ ΡΡΠ΅Π΄ΡΡΠ². Π’Π°ΠΊΠΈΠΌ ΠΎΠ±ΡΠ°Π·ΠΎΠΌ, Π΄Π΅ΡΠ΅ΠΊΡΡ ΠΈ Π½Π΅ΠΈΡΠΏΡΠ°Π²Π½ΠΎΡΡΠΈ Π½ΠΎΠ²ΡΡ Π°Π²ΡΠΎΠΌΠΎΠ±ΠΈΠ»Π΅ΠΉ β ΠΎΠ±ΡΠ΅ΠΊΡΠΈΠ²Π½Π°Ρ Π·Π°ΠΊΠΎΠ½ΠΎΠΌΠ΅ΡΠ½ΠΎΡΡΡ ΠΈΡ ΠΏΡΠΎΠΈΠ·Π²ΠΎΠ΄ΡΡΠ²Π°. ΠΡΠΎΠ²Π΅Π΄Π΅Π½ΠΈΠ΅ ΠΆΠ΅ ΡΠΏΠ»ΠΎΡΠ½ΠΎΠ³ΠΎ ΠΊΠΎΠ½ΡΡΠΎΠ»Ρ ΠΊΠ°ΡΠ΅ΡΡΠ²Π° Π°Π²ΡΠΎΠΌΠΎΠ±ΠΈΠ»Π΅ΠΉ, ΡΡ ΠΎΠ΄ΡΡΠΈΡ Ρ ΠΊΠΎΠ½Π²Π΅ΠΉΠ΅ΡΠ° Π·Π°Π²ΠΎΠ΄ΠΎΠ², ΠΏΡΠ°ΠΊΡΠΈΡΠ΅ΡΠΊΠΈ Π½Π΅Π²ΠΎΠ·ΠΌΠΎΠΆΠ½ΠΎ ΠΈ ΡΠΊΠΎΠ½ΠΎΠΌΠΈΡΠ΅ΡΠΊΠΈ Π½Π΅ΡΠ΅Π»Π΅ΡΠΎΠΎΠ±ΡΠ°Π·Π½ΠΎ. ΠΠΎΡΡΠΎΠΌΡ Π΄Π»Ρ ΠΎΠΏΡΠ΅Π΄Π΅Π»Π΅Π½ΠΈΡ ΠΏΠΎΠΊΠ°Π·Π°ΡΠ΅Π»Π΅ΠΉ Π½Π°Π΄Π΅ΠΆΠ½ΠΎΡΡΠΈ Π½Π΅ΠΎΠ±Ρ ΠΎΠ΄ΠΈΠΌΠΎ ΠΎΡΡΡΠ΅ΡΡΠ²Π»ΡΡΡ ΡΠΈΡΡΠ΅ΠΌΠ°ΡΠΈΡΠ΅ΡΠΊΠΎΠ΅ Π½Π°Π±Π»ΡΠ΄Π΅Π½ΠΈΠ΅ Π·Π° ΡΠ°Π±ΠΎΡΠΎΠΉ Π°Π²ΡΠΎΠΌΠΎΠ±ΠΈΠ»Π΅ΠΉ Π² ΡΠ°Π·Π»ΠΈΡΠ½ΡΡ ΡΡΠ»ΠΎΠ²ΠΈΡΡ ΡΠΊΡΠΏΠ»ΡΠ°ΒΡΠ°ΡΠΈΠΈ Π² ΡΠ΅ΡΠ΅Π½ΠΈΠ΅ Π²ΡΠ΅Π³ΠΎ Π³Π°ΡΠ°Π½ΡΠΈΠΉΠ½ΠΎΠ³ΠΎ ΠΈ ΠΌΠ΅ΠΆΡΠ΅ΠΌΠΎΠ½ΡΠ½ΠΎΠ³ΠΎ ΠΏΡΠΎΠ±Π΅Π³ΠΎΠ². Π ΡΡΠΈΡ ΡΠ΅Π»ΡΡ , Π° ΡΠ°ΠΊΠΆΠ΅ Π΄Π»Ρ ΠΎΡΡΠ°Π±ΠΎΡΠΊΠΈ ΠΎΠ±ΠΎΡΠ½ΠΎΠ²Π°Π½Π½ΡΡ Π½ΠΎΡΠΌΠ°ΡΠΈΠ²ΠΎΠ² ΠΏΠΎ ΡΠ΅Ρ Π½ΠΈΡΠ΅ΡΠΊΠΎΠΌΡ ΠΎΠ±ΡΠ»ΡΠΆΠΈΠ²Π°Π½ΠΈΡ ΠΈ ΡΠ΅ΠΌΠΎΠ½ΡΡ Π°Π²ΡΠΎΠΌΠΎΠ±ΠΈΠ»Π΅ΠΉ, Π½Π°ΠΈΠ±ΠΎΠ»Π΅Π΅ ΠΏΠΎΒΠ»Π½ΠΎΠΎΡΠ²Π΅ΡΠ°ΡΡΠΈΡ ΡΡΠ»ΠΎΠ²ΠΈΡΠΌ ΡΠΊΡΠΏΠ»ΡΠ°ΡΠ°ΡΠΈΠΈ Π² ΡΠ°Π·Π»ΠΈΡΠ½ΡΡ Π³Π΅ΠΎΠ³ΡΠ°ΡΠΈΡΠ΅ΒΡΠΊΠΈΡ ΠΈ ΠΊΠ»ΠΈΠΌΠ°ΡΠΈΡΠ΅ΡΠΊΠΈΡ Π·ΠΎΠ½Π°Ρ ΡΡΡΠ°Π½Ρ, ΠΎΡΠ³Π°Π½ΠΈΠ·ΡΠ΅ΡΡΡ ΠΎΠΏΡΡΠ½Π°Ρ ΡΠΊΡΠΏΠ»ΡΠ°ΡΠ°ΡΠΈΡ Π°Π²ΡΠΎΠΌΠΎΠ±ΠΈΠ»Π΅ΠΉ.
Π’Π΅ΡΠΌΠΈΠ½Ρ Π½Π°Π΄Π΅ΠΆΠ½ΠΎΡΡΠΈ
ΠΠ»Ρ ΡΠΎΠ³ΠΎ ΡΡΠΎΠ±Ρ Π΄Π°ΡΡ ΠΎΡΠ΅Π½ΠΊΡ Π½Π°Π΄Π΅ΠΆΠ½ΠΎΡΡΠΈ Π°Π²ΡΠΎΠΌΠΎΠ±ΠΈΠ»Ρ, Π½Π΅ΠΎΠ±Ρ ΠΎΠ΄ΠΈΠΌΠΎ ΠΏΡΠ°Π²ΠΈΠ»ΡΠ½ΠΎ ΠΊΠ»Π°ΡΡΠΈΡΠΈΡΠΈΡΠΎΠ²Π°ΡΡ ΡΠ΅ΡΠΌΠΈΠ½Ρ Π½Π°Π΄Π΅ΠΆΠ½ΠΎΡΡΠΈ.
ΠΡΠΏΡΠ°Π²Π½ΠΎΡΡΡ β ΡΡΠΎ ΡΠΎΡΡΠΎΡΠ½ΠΈΠ΅ Π°Π²ΡΠΎΠΌΠΎΠ±ΠΈΠ»Ρ, ΠΏΡΠΈ ΠΊΠΎΡΠΎΡΠΎΠΌ ΠΎΠ½ ΡΠΎΠΎΡΠ²Π΅ΡΡΡΠ²ΡΠ΅Ρ Π²ΡΠ΅ΠΌ ΡΠ΅Ρ ΒΠ½ΠΈΡΠ΅ΡΠΊΠΈΠΌ ΡΡΠ΅Π±ΠΎΠ²Π°Π½ΠΈΡΠΌ, ΡΡΡΠ°Π½ΠΎΠ²Π»Π΅Π½Π½ΡΠΌ Π½ΠΎΡΠΌΠ°ΡΠΈΠ²Π½ΠΎ-ΡΠ΅Ρ Π½ΠΈΡΠ΅ΡΠΊΠΎΠΉ Π΄ΠΎΒΠΊΡΠΌΠ΅Π½ΡΠ°ΡΠΈΠ΅ΠΉ ΠΊΠ°ΠΊ Π² ΠΎΡΠ½ΠΎΡΠ΅Π½ΠΈΠΈ ΠΎΡΠ½ΠΎΠ²Π½ΡΡ ΠΏΠ°ΡΠ°ΠΌΠ΅ΡΡΠΎΠ², Ρ Π°ΡΠ°ΠΊΡΠ΅ΡΠΈΒΠ·ΡΡΡΠΈΡ Π½ΠΎΡΠΌΠ°Π»ΡΠ½ΠΎΠ΅ Π²ΡΠΏΠΎΠ»Π½Π΅Π½ΠΈΠ΅ Π·Π°Π΄Π°Π½Π½ΡΡ ΡΡΠ½ΠΊΡΠΈΠΉ, ΡΠ°ΠΊ ΠΈΠ² ΠΎΡΠ½ΠΎΡΠ΅Π½ΠΈΠΈ Π²ΡΠΎΡΠΎΡΡΠ΅ΠΏΠ΅Π½Π½ΡΡ ΠΏΠ°ΡΠ°ΠΌΠ΅ΡΡΠΎΠ², Ρ Π°ΡΠ°ΠΊΡΠ΅ΡΠΈΠ·ΡΡΡΠΈΡ Π²Π½Π΅ΡΠ½ΠΈΠΉ Π²ΠΈΠ΄, ΡΠ΄ΠΎΠ±ΡΡΠ²ΠΎ ΡΠΊΡΠΏΠ»ΡΠ°ΡΠ°ΡΠΈΠΈ ΠΈ Ρ. Π΄.
ΠΠ΅ΠΈΡΠΏΡΠ°Π²Π½ΠΎΡΡΡ β ΡΡΠΎ ΡΠΎΡΡΠΎΡΠ½ΠΈΠ΅ Π°Π²ΡΠΎΠΌΠΎΠ±ΠΈΠ»Ρ, ΠΏΡΠΈ ΠΊΠΎΡΠΎΡΠΎΠΌ ΠΎΠ½ Π² Π΄Π°Π½Π½ΡΠΉ ΠΌΠΎΠΌΠ΅Π½Ρ Π²ΡΠ΅ΠΌΠ΅Π½ΠΈ Π½Π΅ ΡΠ΄ΠΎΠ²Π»Π΅ΡΠ²ΠΎΡΡΠ΅Ρ Ρ ΠΎΡΡ Π±Ρ ΠΎΠ΄Π½ΠΎΠΌΡ ΠΈΠ· ΡΡΠ΅ΒΠ±ΠΎΠ²Π°Π½ΠΈΠΉ, ΡΡΡΠ°Π½ΠΎΠ²Π»Π΅Π½Π½ΡΡ Π½ΠΎΡΠΌΠ°ΡΠΈΠ²Π½ΠΎ-ΡΠ΅Ρ Π½ΠΈΡΠ΅ΡΠΊΠΎΠΉ Π΄ΠΎΠΊΡΠΌΠ΅Π½ΡΠ°ΡΠΈΠ΅ΠΉ.
Π Π°Π±ΠΎΡΠΎΡΠΏΠΎΡΠΎΠ±Π½ΠΎΡΡΡ β ΡΡΠΎ ΡΠΎΡΡΠΎΡΠ½ΠΈΠ΅ Π°Π²ΡΠΎΠΌΠΎΠ±ΠΈΠ»Ρ, ΠΏΡΠΈ ΠΊΠΎΡΠΎΡΠΎΠΌ ΠΎΠ½ ΡΠΏΠΎΡΠΎΠ±Π΅Π½ Π²ΡΠΏΠΎΠ»Π½ΡΡΡ Π·Π°Π΄Π°Π½Π½ΡΠ΅ ΡΡΠ½ΠΊΡΠΈΠΈ, ΡΠΎΡ ΡΠ°Π½ΡΡ Π·Π½Π°ΡΠ΅Π½ΠΈΡ Π·Π°Π΄Π°Π½Π½ΡΡ ΠΏΠ°ΡΠ°ΠΌΠ΅ΡΡΠΎΠ² Π² ΠΏΡΠ΅Π΄Π΅Π»Π°Ρ , ΡΡΡΠ°Π½ΠΎΠ²Π»Π΅Π½Π½ΡΡ Π½ΠΎΡΠΌΠ°ΡΠΈΠ²Π½ΠΎ-ΡΠ΅Ρ Π½ΠΈΡΠ΅ΡΠΊΠΎΠΉ Π΄ΠΎΠΊΡΠΌΠ΅Π½ΡΠ°ΡΠΈΠ΅ΠΉ.
ΠΠ½Π°ΡΠΈΡ, ΠΌΠ΅ΠΆΠ΄Ρ ΡΠ°Π±ΠΎΡΠΎΡΠΏΠΎΡΠΎΠ±Π½ΠΎΡΡΡΡ ΠΈ ΠΈΡΠΏΡΠ°Π²Π½ΠΎΡΡΡΡ ΡΡΡΠ΅ΡΡΠ²ΡΠ΅Ρ ΠΎΡΠ΅Π½Ρ Π²Π°ΠΆΠ½ΠΎΠ΅ ΡΠ°Π·Π»ΠΈΡΠΈΠ΅: ΠΈΡΠΏΡΠ°Π²Π½ΠΎΡΡΡ ΠΏΡΠ΅Π΄ΠΏΠΎΠ»Π°Π³Π°Π΅Ρ, ΡΡΠΎ Π²ΡΠΏΠΎΠ»Π½ΡΡΡΡΡ Π²ΡΠ΅ ΡΡΠ΅Π±ΠΎΠ²Π°Π½ΠΈΡ, ΠΎΡΠ½ΠΎΡΡΡΠΈΠ΅ΡΡ ΠΊΠ°ΠΊ ΠΊ ΠΎΡΠ½ΠΎΠ²Π½ΡΠΌ, ΡΠ°ΠΊ ΠΈ ΠΊ Π²ΡΠΎΡΠΎΡΡΠ΅ΠΏΠ΅Π½Π½ΡΠΌ ΠΏΠ°ΡΠ°ΠΌΠ΅ΡΡΠ°ΠΌ, ΡΡΡΠ°Π½ΠΎΠ²Π»Π΅Π½Π½ΡΠΌ Π½ΠΎΡΠΌΠ°ΡΠΈΠ²Π½ΠΎ-ΡΠ΅Ρ Π½ΠΈΡΠ΅ΡΠΊΠΎΠΉ Π΄ΠΎΠΊΡΠΌΠ΅Π½ΡΠ°ΡΠΈΠ΅ΠΉ. Π Π°Π±ΠΎΡΠΎΡΠΏΠΎΡΠΎΠ±Π½ΠΎΡΡΡ Ρ Π°ΡΠ°ΠΊΡΠ΅ΡΠΈΠ·ΡΠ΅Ρ ΡΠΎΠ»ΡΠΊΠΎ ΡΡΠ΅Π±ΠΎΠ²Π°Π½ΠΈΡ, ΠΎΡΠ½ΠΎΡΡΡΠΈΠ΅ΡΡ ΠΊ ΠΎΡΠ½ΠΎΠ²Π½ΡΠΌ ΠΏΠ°ΡΠ°ΠΌΠ΅ΡΡΠ°ΠΌ. Π’ΡΠ΅Π±ΠΎΠ²Π°Π½ΠΈΡ, ΠΎΡΠ½ΠΎΡΡΡΠΈΠ΅ΡΡ ΠΊ Π²ΡΠΎΡΠΎΡΡΠ΅ΠΏΠ΅Π½Π½ΡΠΌ ΠΏΠ°ΡΠ°ΠΌΠ΅ΡΡΠ°ΠΌ, ΠΌΠΎΠ³ΡΡ Π½Π΅ Π²ΡΠΏΠΎΠ»Π½ΡΡΡΡΡ. Π’Π°ΠΊ, Π½Π°ΠΏΡΠΈΠΌΠ΅Ρ, Π°Π²ΡΠΎΠΌΠΎΠ±ΠΈΠ»Ρ ΠΎΡΡΠ°Π΅ΡΡΡ ΡΠ°Π±ΠΎΡΠΎΡΠΏΠΎΡΠΎΠ±Π½ΡΠΌ, ΠΊΠΎΠ³Π΄Π° Ρ Π½Π΅Π³ΠΎ ΠΏΠΎΠ²ΡΠ΅ΠΆΠ΄Π΅Π½Ρ Π»Π°ΠΊΠΎΠΊΡΠ°ΡΠΎΡΠ½ΡΠ΅ ΠΈΠ»ΠΈ Π°Π½ΡΠΈΠΊΠΎΡΡΠΎΠ·ΠΈΠΎΠ½Π½ΡΠ΅ ΠΏΠΎΠΊΡΡΡΠΈΡ, ΡΠ³ΠΎΡΠ΅Π»Π° Π»Π°ΠΌΠΏΠΎΡΠΊΠ° ΠΎΡΠ²Π΅ΡΠ΅Π½ΠΈΡ ΡΠΈΡΠΊΠ° ΠΏΡΠΈΠ±ΠΎΡΠΎΠ² ΠΈ Ρ.Π΄.
ΠΡΠΊΠ°Π· ΠΈ Π΅Π³ΠΎ Π²ΠΈΠ΄Ρ
ΠΡΡΠ°Π½ΠΎΠ²ΠΊΠ° Π°Π²ΡΠΎΠΌΠΎΠ±ΠΈΠ»Ρ ΠΈΠ·-Π·Π° Π²ΠΎΠ·Π½ΠΈΠΊΡΠΈΡ ΡΠ΅Ρ Π½ΠΈΡΠ΅ΡΠΊΠΈΡ Π½Π΅ΠΈΡΠΏΡΠ°Π²ΒΠ½ΠΎΡΡΠ΅ΠΉ ΠΈΠ»ΠΈ ΡΠ°Π±ΠΎΡΠ° Ρ Π½Π΅Π΄ΠΎΠΏΡΡΡΠΈΠΌΡΠΌΠΈ ΠΎΡΠΊΠ»ΠΎΠ½Π΅Π½ΠΈΡΠΌΠΈ ΠΎΡ Π·Π°Π΄Π°Π½Π½ΡΡ ΡΠ°Π±ΠΎΡΠΈΡ Ρ Π°ΡΠ°ΠΊΡΠ΅ΡΠΈΡΡΠΈΠΊ Π½Π°Π·ΡΠ²Π°Π΅ΡΡΡ ΠΎΡΠΊΠ°Π·ΠΎΠΌ.
ΠΡΠΊΠ°Π· Π°Π²ΡΠΎΠΌΠΎΠ±ΠΈΠ»Ρ ΠΌΠΎΠΆΠ½ΠΎ ΡΠ°ΠΊΠΆΠ΅ ΠΎΠΏΡΠ΅Π΄Π΅Π»ΠΈΡΡ ΠΊΠ°ΠΊ ΠΏΠΎΠ»Π½ΡΡ ΠΈΠ»ΠΈ ΡΠ°ΡΡΠΈΡΠ½ΡΡ ΡΡΡΠ°ΡΡ ΠΈΠΌ ΡΠ°Π±ΠΎΡΠΎΡΠΏΠΎΡΠΎΠ±Π½ΠΎΡΡΠΈ.
ΠΠΎΠ»Π½ΡΠΉ ΠΎΡΠΊΠ°Π· β ΡΡΠΎ ΠΎΡΠΊΠ°Π·, Π»ΠΈΡΠ°ΡΡΠΈΠΉ Π°Π²ΡΠΎΠΌΠΎΠ±ΠΈΠ»Ρ ΠΏΠΎΠ΄Π²ΠΈΠΆΠ½ΠΎΡΡΠΈ.
Π§Π°ΡΡΠΈΡΠ½ΡΠΉ ΠΎΡΠΊΠ°Π· β ΡΡΠΎ ΡΠ½ΠΈΠΆΠ΅Π½ΠΈΠ΅Β ΡΠΊΡΠΏΠ»ΡΠ°ΡΠ°ΡΠΈΠΎΠ½Π½ΡΡ Β ΠΊΠ°ΡΠ΅ΡΡΠ²Π° Π°Π²ΡΠΎΠΌΠΎΠ±ΠΈΠ»Ρ.
ΠΠ΅ΠΈΡΠΏΡΠ°Π²Π½ΠΎΡΡΠΈ, ΡΡΡΡΠ°Π½ΡΠ΅ΠΌΡΠ΅ Π²ΠΎΠ΄ΠΈΡΠ΅Π»Π΅ΠΌ Π² ΠΏΡΡΠΈ Ρ ΠΏΠΎΠΌΠΎΡΡΡ ΠΈΠ½ΒΠ΄ΠΈΠ²ΠΈΠ΄ΡΠ°Π»ΡΠ½ΠΎΠ³ΠΎ ΠΊΠΎΠΌΠΏΠ»Π΅ΠΊΡΠ° ΠΠΠ ΠΈ Π·Π° Π²ΡΠ΅ΠΌΡ ΠΏΡΠΎΠ²Π΅Π΄Π΅Π½ΠΈΡ Π΅ΠΆΠ΅Π΄Π½Π΅Π²Π½ΠΎΠ³ΠΎ ΡΠ΅Ρ Π½ΠΈΡΠ΅ΡΠΊΠΎΠ³ΠΎ ΠΎΠ±ΡΠ»ΡΠΆΠΈΠ²Π°Π½ΠΈΡ, ΠΈ Π½Π΅ΠΈΡΠΏΡΠ°Π²Π½ΠΎΡΡΠΈ, Π½Π΅ Π²Π»ΠΈΡΡΡΠΈΠ΅ Π½Π° ΡΠ°ΒΠ±ΠΎΡΠΎΡΠΏΠΎΡΠΎΠ±Π½ΠΎΡΡΡ Π°Π²ΡΠΎΠΌΠΎΠ±ΠΈΠ»Ρ, Π² ΠΎΡΠΊΠ°Π·Ρ Π½Π΅ Π²ΠΊΠ»ΡΡΠ°ΡΡΡΡ.
Π Π·Π°Π²ΠΈΡΠΈΠΌΠΎΡΡΠΈ ΠΎΡ ΠΏΡΠΈΡΠΈΠ½Ρ ΠΏΠΎΡΠ²Π»Π΅Π½ΠΈΡ ΠΎΡΠΊΠ°Π·Ρ ΠΏΠΎΠ΄ΡΠ°Π·Π΄Π΅Π»ΡΡΡΡΡ Π½Π° Π·Π°Π²ΠΎΠ΄ΡΠΊΠΈΠ΅ ΠΈ ΡΠΊΡΠΏΠ»ΡΠ°ΡΠ°ΡΠΈΠΎΠ½Π½ΡΠ΅.
ΠΠ°Π²ΠΎΠ΄ΡΠΊΠΈΠ΅Β ΠΎΡΠΊΠ°Π·Ρ β ΡΡΠΎ ΠΎΡΠΊΠ°Π·Ρ, ΠΏΠΎΡΠ²ΠΈΠ²ΡΠΈΠ΅ΡΡ ΠΏΠΎ Π²ΠΈΠ½Π΅ Π·Π°Π²ΠΎΠ΄Π° β ΠΈΠ·Π³ΠΎΡΠΎΠ²ΠΈΡΠ΅Π»Ρ Π°Π²ΡΠΎΠΌΠΎΠ±ΠΈΠ»Ρ. ΠΠ½ΠΈ ΠΏΠΎΠ΄ΡΠ°Π·Π΄Π΅Π»ΡΡΡΡΡ Π½Π° ΠΊΠΎΠ½ΡΡΡΡΠΊΡΠΈΠ²Π½ΡΠ΅ ΠΈ ΠΏΡΠΎΠΈΠ·Π²ΠΎΠ΄ΡΡΠ²Π΅Π½Π½ΡΠ΅.
ΠΠΊΡΠΏΠ»ΡΠ°ΡΠ°ΡΠΈΠΎΠ½Π½ΡΠ΅ ΠΎΡΠΊΠ°Π·Ρ β ΡΡΠΎ ΠΎΡΠΊΠ°Π·Ρ, ΠΎΠ±ΡΡΠ»ΠΎΠ²Π»Π΅Π½Π½ΡΠ΅ Π½Π°ΡΡΡΠ΅Π½ΠΈΠ΅ΠΌ ΠΏΡΠ°Π²ΠΈΠ» ΡΠΊΡΠΏΠ»ΡΠ°ΡΠ°ΡΠΈΠΈ ΠΈ Π²Π½Π΅ΡΠ½ΠΈΠΌΠΈ Π²ΠΎΠ·Π΄Π΅ΠΉΡΡΠ²ΠΈΡΠΌΠΈ, Π½Π΅ ΡΠ²ΠΎΠΉΡΡΒΠ²Π΅Π½Π½ΡΠΌΠΈ Π½ΠΎΡΠΌΠ°Π»ΡΠ½ΠΎΠΉ ΡΠΊΡΠΏΠ»ΡΠ°ΡΠ°ΡΠΈΠΈ. ΠΠΊΡΠΏΠ»ΡΠ°ΡΠ°ΡΠΈΠΎΠ½Π½ΡΠ΅ ΠΎΡΠΊΠ°Π·Ρ ΠΈ Π½Π΅ΠΈΡΠΏΡΠ°Π²Π½ΠΎΡΡΠΈ ΠΏΡΠΈ ΠΎΡΠ΅Π½ΠΊΠ΅ Π½Π°Π΄Π΅ΠΆΠ½ΠΎΡΡΠΈ Π°Π²ΡΠΎΠΌΠΎΠ±ΠΈΠ»Ρ Π½Π΅ ΡΡΠΈΡΡΠ²Π°ΡΡΡΡ.
ΠΡΠΊΠ°Π·Ρ ΠΈ Π½Π΅ΠΈΡΠΏΡΠ°Π²Π½ΠΎΡΡΠΈ, ΡΡΠΈΡΡΠ²Π°Π΅ΠΌΡΠ΅ ΠΏΡΠΈ ΠΎΡΠ΅Π½ΠΊΠ΅ Π½Π°Π΄Π΅ΠΆΠ½ΠΎΡΡΠΈ Π°Π²ΡΠΎΠΌΠΎΠ±ΠΈΠ»Ρ, ΠΌΠΎΠ³ΡΡ Π·Π½Π°ΡΠΈΡΠ΅Π»ΡΠ½ΠΎ ΠΎΡΠ»ΠΈΡΠ°ΡΡΡΡ ΠΏΠΎ ΡΡΠ΅ΠΏΠ΅Π½ΠΈ Π²Π»ΠΈΡΠ½ΠΈΡ Π½Π° Π΅Π³ΠΎ ΡΠ°Π±ΠΎΡΠΎΡΠΏΠΎΡΠΎΠ±Π½ΠΎΡΡΡ ΠΈ ΡΠ»ΠΎΠΆΠ½ΠΎΡΡΠΈ ΠΈΡ ΡΡΡΡΠ°Π½Π΅Π½ΠΈΡ. ΠΠΎΡΡΠΎΠΌΡ Π½Π΅ΠΎΠ±Ρ ΠΎΠ΄ΠΈΠΌΠΎ ΠΈΡ ΠΊΠ»Π°ΡΡΠΈΡΠΈΡΠΈΡΠΎΠ²Π°ΡΡ ΠΈ ΠΏΠΎ ΡΡΠΈΠΌ ΠΏΡΠΈΠ·Π½Π°ΠΊΠ°ΠΌ.
ΠΠΎ ΠΏΡΠΈΠ·Π½Π°ΠΊΡ Β«ΡΡΠ΅ΠΏΠ΅Π½Ρ Π²Π»ΠΈΡΠ½ΠΈΡ Π½Π° ΡΠ°Π±ΠΎΡΠΎΡΠΏΠΎΡΠΎΠ±Π½ΠΎΡΡΡΒ» ΠΎΡΠΊΠ°Π·Ρ ΠΈ Π½Π΅ΠΈΡΠΏΡΠ°Π²Π½ΠΎΡΡΠΈ ΡΠ°ΡΠΏΡΠ΅Π΄Π΅Π»ΡΡΡΡΡ Π½Π° ΡΡΠΈ Π³ΡΡΠΏΠΏΡ:
- Π»ΠΈΡΠ°ΡΡΠΈΠ΅Β Π°Π²ΡΠΎΠΌΠΎΠ±ΠΈΠ»ΡΒ ΠΏΠΎΠ΄Π²ΠΈΠΆΠ½ΠΎΡΡΠΈ
- ΡΠ½ΠΈΠΆΠ°ΡΡΠΈΠ΅ ΡΠΊΡΠΏΠ»ΡΠ°ΡΠ°ΡΠΈΠΎΠ½Π½ΡΠ΅ ΠΊΠ°ΡΠ΅ΡΡΠ²Π°
- Π½Π΅ Π²Π»ΠΈΡΡΡΠΈΠ΅ Π½Π° ΡΠ°Π±ΠΎΡΠΎΡΠΏΠΎΡΠΎΠ±Π½ΠΎΡΡΡ Π°Π²ΡΠΎΠΌΠΎΠ±ΠΈΠ»Ρ
Π Π³ΡΡΠΏΠΏΠ΅ Π»ΠΈΡΠ°ΡΡΠΈΡ Π°Π²ΡΠΎΠΌΠΎΠ±ΠΈΠ»Ρ ΠΏΠΎΠ΄Π²ΠΈΠΆΠ½ΠΎΡΡΠΈ ΠΎΡΠ½ΠΎΡΡΡΡΡ ΠΎΡΠΊΠ°Π·Ρ, Π±Π΅Π· ΡΡΡΡΠ°Π½Π΅Π½ΠΈΡ ΠΊΠΎΡΠΎΡΡΡ Π΄Π°Π»ΡΠ½Π΅ΠΉΡΠ΅Π΅ Π΅Π³ΠΎ ΠΈΡΠΏΠΎΠ»ΡΠ·ΠΎΠ²Π°Π½ΠΈΠ΅ Π½Π΅Π²ΠΎΠ·ΠΌΠΎΠΆΠ½ΠΎ (ΠΎΡΡΡΡΡΡΠ²ΠΈΠ΅ ΠΏΠΎΠ΄Π°ΡΠΈ ΡΠΎΠΏΠ»ΠΈΠ²Π°, ΠΏΠΎΠ»ΠΎΠΌΠΊΠ° Π±ΡΠΊΡΠΈΡΠ½ΠΎΠ³ΠΎ ΠΊΡΡΠΊΠ° ΡΡΠ³Π°ΡΠ° ΠΈ Π΄Ρ.) ΠΈΠ»ΠΈ Π½Π΅Π΄ΠΎΠΏΡΡΡΠΈΠΌΠΎ (ΠΎΡΡΡΡΡΡΠ²ΠΈΠ΅ Π΄Π°Π²Π»Π΅Π½ΠΈΡ Π² ΡΠΈΡΡΠ΅ΠΌΠ΅ ΡΠΌΠ°Π·ΠΊΠΈ Π΄Π²ΠΈΠ³Π°ΡΠ΅Π»Ρ, ΠΎΡΠΊΠ°Π· ΡΠΎΡΠΌΠΎΠ·ΠΎΠ² ΠΈ Ρ. ΠΏ.).
ΠΠ΅ΠΈΡΠΏΡΠ°Π²Π½ΠΎΡΡΠΈ ΡΡΠΎΠΉ Π³ΡΡΠΏΠΏΡ ΡΠ²Π»ΡΡΡΡΡ ΠΏΠΎΠ»Π½ΡΠΌΠΈ ΠΎΡΠΊΠ°Π·Π°ΠΌΠΈ Π°Π²ΡΠΎΠΌΠΎΠ±ΠΈΠ»Ρ. ΠΡ ΠΏΠΎΡΠ²Π»Π΅Π½ΠΈΠ΅ Π²ΡΠ·ΡΠ²Π°Π΅Ρ Π½Π΅ΠΎΠ±Ρ ΠΎΠ΄ΠΈΠΌΠΎΡΡΡ Π²ΠΎΡΡΡΠ°Π½Π°Π²Π»ΠΈΠ²Π°ΡΡ Π°Π²ΡΠΎΠΌΠΎΠ±ΠΈΠ»Ρ Π½Π° ΠΌΠ΅ΡΡΠ΅ Π²ΡΡ ΠΎΠ΄Π° ΠΈΠ· ΡΡΡΠΎΡ ΠΈΠ»ΠΈ Π±ΡΠΊΡΠΈΡΠΎΠ²Π°ΡΡ Π² Π°Π²ΡΠΎΡΡΠ°Π½ΡΒΠΏΠΎΡΡΠ½ΠΎΠ΅ ΠΏΡΠ΅Π΄ΠΏΡΠΈΡΡΠΈΠ΅.
Π Π³ΡΡΠΏΠΏΠ΅ ΠΎΡΠΊΠ°Π·ΠΎΠ², ΡΠ½ΠΈΠΆΠ°ΡΡΠΈΡ ΡΠΊΡΠΏΠ»ΡΠ°ΡΠ°ΡΠΈΠΎΠ½Π½ΡΠ΅ ΠΊΠ°ΡΠ΅ΡΡΠ²Π°, ΠΎΡΠ½ΠΎΡΡΡΡΡ ΠΎΡΠΊΠ°Π·Ρ ΠΈ Π½Π΅ΠΈΡΠΏΡΠ°Π²Π½ΠΎΡΡΠΈ, ΡΡ ΡΠ΄ΡΠ°ΡΡΠΈΠ΅ ΡΠ°ΠΊΠΈΠ΅ ΠΏΠΎΠΊΠ°Π·Π°ΡΠ΅Π»ΠΈ, ΠΊΠ°ΠΊ Π²ΡΠ΅ΠΌΡ ΠΏΠΎΠ΄Π³ΠΎΡΠΎΠ²ΠΊΠΈ ΠΊ Π΄Π²ΠΈΠΆΠ΅Π½ΠΈΡ, ΡΡΠ΅Π΄Π½ΡΡ ΡΠΊΠΎΡΠΎΡΡΡ Π΄Π²ΠΈΠΆΠ΅Π½ΠΈΡ, Π³ΡΡΠ·ΠΎΠΏΠΎΠ΄ΡΠ΅ΠΌΠ½ΠΎΡΡΡ, ΠΏΡΠΎΡ ΠΎΠ΄ΠΈΠΌΠΎΡΡΡ, ΡΠ°ΡΡ ΠΎΠ΄ ΠΠ‘Π ΠΈ Ρ. Π΄., Π½ΠΎ Π΄ΠΎΠΏΡΡΠΊΠ°ΡΡΠΈΠ΅ ΠΈΡΠΏΠΎΠ»ΡΠ·ΠΎΠ²Π°Π½ΠΈΠ΅ Π°Π²ΡΠΎΠΌΠΎΠ±ΠΈΠ»Ρ ΠΏΠΎ Π½Π°Π·Π½Π°ΡΠ΅Π½ΠΈΡ Π² ΡΠ΅ΡΠ΅Π½ΠΈΠ΅ Π½Π΅ΠΊΠΎΡΠΎΡΠΎΠ³ΠΎ Π²ΡΠ΅ΠΌΠ΅Π½ΠΈ.
Π Π³ΡΡΠΏΠΏΠ΅ Π½Π΅ΠΈΡΠΏΡΠ°Π²Π½ΠΎΡΡΠ΅ΠΉ, Π½Π΅ Π²Π»ΠΈΡΡΡΠΈΡ Π½Π° ΡΠ°Π±ΠΎΡΠΎΡΠΏΠΎΡΠΎΠ±Π½ΠΎΡΡΡ, ΠΎΡΠ½ΠΎΡΡΡΡΡ Π½Π΅ΠΈΡΠΏΡΠ°Π²Π½ΠΎΡΡΠΈ, Π½Π΅ ΡΡ ΡΠ΄ΡΠ°ΡΡΠΈΠ΅ ΠΎΡΠ½ΠΎΠ²Π½ΡΠ΅ Ρ Π°ΡΠ°ΠΊΡΠ΅ΡΠΈΡΡΠΈΠΊΠΈ Π°Π²ΡΠΎΠΌΠΎΠ±ΠΈΠ»Ρ, Π½Π΅ ΡΠΎΠ·Π΄Π°ΡΡΠΈΠ΅ Π½Π΅ΡΠ΄ΠΎΠ±ΡΡΠ²Π° ΠΏΡΠΈ Π΅Π³ΠΎ ΡΠΊΡΠΏΠ»ΡΠ°ΡΠ°ΡΠΈΠΈ ΠΈ ΡΡΒΡΡΠ°Π½Π΅Π½ΠΈΠ΅ ΠΊΠΎΡΠΎΡΡΡ ΠΌΠΎΠΆΠ΅Ρ Π±ΡΡΡ ΠΎΡΠ»ΠΎΠΆΠ΅Π½ΠΎ Π΄ΠΎ ΠΎΡΠ΅ΡΠ΅Π΄Π½ΠΎΠ³ΠΎ Π½ΠΎΠΌΠ΅ΡΠ½ΠΎΠ³ΠΎ ΡΠ΅Ρ Π½ΠΈΡΠ΅ΡΠΊΠΎΠ³ΠΎ ΠΎΠ±ΡΠ»ΡΠΆΠΈΠ²Π°Π½ΠΈΡ (Π½Π΅Π·Π½Π°ΡΠΈΡΠ΅Π»ΡΠ½ΡΠ΅ ΠΏΠΎΠ΄ΡΠ΅ΠΊΠ°Π½ΠΈΡ ΡΠΌΠ°Π·ΠΎΡΠ½ΠΎΠ³ΠΎ ΠΌΠ°ΡΠ΅ΡΠΈΠ°Π»Π° ΡΠ΅ΡΠ΅Π· ΡΠΏΠ»ΠΎΡΠ½Π΅Π½ΠΈΡ, ΡΡΠ΅ΡΠΈΠ½Ρ ΡΠ»Π΅ΠΌΠ΅Π½ΡΠΎΠ² ΠΎΠ±Π»ΠΈΡΠΎΠ²ΠΊΠΈ, ΠΎΡΒΡΠ»ΠΎΠ΅Π½ΠΈΠ΅ Π»Π°ΠΊΠΎΠΊΡΠ°ΡΠΎΡΠ½ΡΡ ΠΏΠΎΠΊΡΡΡΠΈΠΉ ΠΈ Ρ. ΠΏ.).
ΠΡΠΊΠ°Π·Ρ ΠΊΠ°ΠΊ ΡΠ»ΡΡΠ°ΠΉΠ½ΡΠ΅ ΡΠΎΠ±ΡΡΠΈΡ ΠΌΠΎΠ³ΡΡ Π±ΡΡΡ Π½Π΅Π·Π°Π²ΠΈΡΠΈΠΌΡΠΌΠΈ ΠΈ Π·Π°Π²ΠΈΡΠΈΠΌΡΠΌΠΈ. ΠΠ΅Π·Π°Π²ΠΈΡΠΈΠΌΡΠΉ ΠΎΡΠΊΠ°Π· β ΡΡΠΎ ΠΎΡΠΊΠ°Π·, ΠΊΠΎΡΠΎΡΡΠΉ Π½Π΅ ΠΏΡΠΈΠ²ΠΎΠ΄ΠΈΡ ΠΊ ΠΎΡΠΊΠ°Π·Ρ Π΄ΡΡΠ³ΠΈΡ ΡΠ»Π΅ΠΌΠ΅Π½ΡΠΎΠ² Π°Π²ΡΠΎΠΌΠΎΠ±ΠΈΠ»Ρ. ΠΡΠΊΠ°Π·, ΠΏΡΠΎΡΠ²ΠΈΠ²ΡΠΈΠΉΡΡ Π² ΡΠ΅Π·ΡΠ»ΡΡΠ°ΡΠ΅ ΠΎΡΠΊΠ°Π·Π° Π΄ΡΡΠ³ΠΈΡ ΡΠ»Π΅ΠΌΠ΅Π½ΡΠΎΠ², Π½Π°Π·ΡΠ²Π°Π΅ΡΡΡ Π·Π°Π²ΠΈΡΠΈΠΌΡΠΌ. ΠΡΠΊΠ°Π· ΠΌΠΎΠΆΠ΅Ρ Π±ΡΡΡ Π²Π½Π΅Π·Π°ΠΏΠ½ΡΠΌ, Π΅ΡΠ»ΠΈ ΠΏΠΎΠ²ΡΠ΅ΠΆΠ΄Π΅Π½ΠΈΡ Π°Π³ΡΠ΅Π³Π°ΡΠΎΠ² Π°Π²ΡΠΎΠΌΠΎΠ±ΠΈΠ»Ρ Π½Π°ΡΡΡΠΏΠ°ΡΡ ΠΌΠ³Π½ΠΎΠ²Π΅Π½Π½ΠΎ, ΠΈ ΠΏΠΎΡΡΠ΅ΠΏΠ΅Π½Π½ΡΠΌ, Π² ΡΠ΅Π·ΡΠ»ΡΡΠ°ΡΠ΅ Π΄Π»ΠΈΡΠ΅Π»ΡΠ½ΠΎΠ³ΠΎ, ΠΏΠΎΡΡΠ΅ΠΏΠ΅Π½Π½ΠΎΠ³ΠΎ ΠΈΠ·ΠΌΠ΅Π½Π΅Π½ΠΈΡ ΠΏΠ°ΡΠ°ΠΌΠ΅ΡΡΠΎΠ² ΡΠ»Π΅ΠΌΠ΅Π½ΡΠΎΠ² (ΡΡΡΠ°Π»ΠΎΡΡΡ ΠΌΠ΅ΡΠ°Π»Π»Π°, ΠΈΠ·Π½Π°ΡΠΈΠ²Π°Π½ΠΈΠ΅ ΠΏΠΎΠ²Π΅ΡΡ Π½ΠΎΡΡΠΈ ΠΈ ΠΏΡ.).
Π₯Π°ΡΠ°ΠΊΡΠ΅ΡΠΈΡΡΠΈΠΊΠΈ Π½Π°Π΄Π΅ΠΆΠ½ΠΎΡΡΠΈ
Π§ΡΠΎΠ±Ρ ΠΎΡΠ΅Π½ΠΈΡΡ ΠΊΠ°ΡΠ΅ΡΡΠ²ΠΎ ΠΏΡΠΎΠ΄ΡΠΊΡΠΈΠΈ, Π²ΡΠΏΡΡΠΊΠ°Π΅ΠΌΠΎΠΉ Π°Π²ΡΠΎΠΌΠΎΠ±ΠΈΠ»ΡΠ½ΠΎΠΉ ΠΏΡΠΎΠΌΡΡΠ»Π΅Π½Π½ΠΎΡΡΡΡ, ΠΏΡΠΈΠΌΠ΅Π½ΠΈΡΠ΅Π»ΡΠ½ΠΎ ΠΊ ΠΊΠΎΠ½ΠΊΡΠ΅ΡΠ½ΡΠΌ ΡΡΠ»ΠΎΠ²ΠΈΡΠΌ ΡΠΊΡΠΏΠ»ΡΒΠ°ΡΠ°ΡΠΈΠΈ, Π½Π΅ΠΎΠ±Ρ ΠΎΠ΄ΠΈΠΌΠΎ ΠΈΠ·ΡΡΠ°ΡΡ Π½Π°Π΄Π΅ΠΆΠ½ΠΎΡΡΡ Π°Π²ΡΠΎΠΌΠΎΠ±ΠΈΠ»Π΅ΠΉ ΠΏΠΎΡΠ»Π΅ ΠΈΡ ΠΎΠ±ΠΊΠ°ΡΠΊΠΈ.
Π‘ΡΠ°Π²Π½Π΅Π½ΠΈΠ΅ Π½Π°Π΄Π΅ΠΆΠ½ΠΎΡΡΠΈ Π½ΠΎΠ²ΡΡ ΠΈ ΠΊΠ°ΠΏΠΈΡΠ°Π»ΡΠ½ΠΎ ΠΎΡΡΠ΅ΠΌΠΎΠ½ΡΠΈΡΠΎΠ²Π°Π½Π½ΡΡ Π°Π²ΡΠΎΠΌΠΎΠ±ΠΈΠ»Π΅ΠΉ, ΡΠ°Π±ΠΎΡΠ°ΡΡΠΈΡ Π² ΠΎΠ΄ΠΈΠ½Π°ΠΊΠΎΠ²ΡΡ ΡΡΠ»ΠΎΠ²ΠΈΡΡ , ΠΌΠΎΠΆΠ΅Ρ Π΄Π°ΡΡ ΠΎΠ±ΡΠ΅ΠΊΡΠΈΠ²Π½ΡΡ ΠΎΡΠ΅Π½ΠΊΡ ΠΊΠ°ΡΠ΅ΡΡΠ²Π° ΡΠ΅ΠΌΠΎΠ½ΡΠ°.
ΠΠΎΠ»ΠΈΡΠ΅ΡΡΠ²Π΅Π½Π½ΡΠ΅ Ρ Π°ΡΠ°ΠΊΡΠ΅ΡΠΈΡΡΠΈΠΊΠΈ Π½Π°Π΄Π΅ΠΆΠ½ΠΎΡΡΠΈ ΠΎΠ΄Π½ΠΎΠΌΠ°ΡΠΎΡΠ½ΡΡ Π°Π²ΒΡΠΎΠΌΠΎΠ±ΠΈΠ»Π΅ΠΉ, ΠΏΠΎΠ»ΡΡΠ΅Π½Π½ΡΠ΅ ΡΠ°Π·Π»ΠΈΡΠ½ΡΠΌΠΈ Π°Π²ΡΠΎΡΡΠ°Π½ΡΠΏΠΎΡΡΠ½ΡΠΌΠΈ ΠΏΡΠ΅Π΄ΠΏΡΠΈΡΒΡΠΈΡΠΌΠΈ, Π½ΠΎ ΡΠ°Π±ΠΎΡΠ°ΡΡΠΈΡ Π² ΠΎΠ΄ΠΈΠ½Π°ΠΊΠΎΠ²ΡΡ ΡΡΠ»ΠΎΠ²ΠΈΡΡ , ΡΠ²Π»ΡΡΡΡΡ Π΄ΠΎΡΡΠ°ΡΠΎΡΠ½ΠΎ ΡΠΎΡΠ½ΡΠΌΠΈ Ρ Π°ΡΠ°ΠΊΡΠ΅ΡΠΈΡΡΠΈΠΊΠ°ΠΌΠΈ ΡΡΠΎΠ²Π½Ρ ΡΠ΅Ρ Π½ΠΈΡΠ΅ΡΠΊΠΎΠΉ ΡΠΊΡΠΏΠ»ΡΠ°ΡΠ°ΡΠΈΠΈ Π°Π²ΡΠΎΠΌΠΎΠ±ΠΈΠ»Π΅ΠΉ Π² ΠΊΠΎΠ½ΠΊΡΠ΅ΡΠ½ΠΎΠΌ Π°Π²ΡΠΎΡΡΠ°Π½ΡΠΏΠΎΡΡΠ½ΠΎΠΌ ΠΏΡΠ΅Π΄ΠΏΡΠΈΡΡΠΈΠΈ.
ΠΠ½Π°Π»ΠΈΠ· Ρ Π°ΡΠ°ΠΊΡΠ΅ΡΠΈΡΡΠΈΠΊ Π½Π°Π΄Π΅ΠΆΠ½ΠΎΡΡΠΈ Π°Π²ΡΠΎΠΌΠΎΠ±ΠΈΠ»Π΅ΠΉ ΠΏΠΎΠ·Π²ΠΎΠ»ΡΠ΅Ρ Π²ΡΡΒΠ²ΠΈΡΡ ΡΠ·ΠΊΠΈΠ΅ ΠΌΠ΅ΡΡΠ° Π² ΠΎΡΠ³Π°Π½ΠΈΠ·Π°ΡΠΈΠΈ ΠΈ ΡΠ΅Ρ Π½ΠΎΠ»ΠΎΠ³ΠΈΠΈ ΡΠ΅Ρ Π½ΠΈΡΠ΅ΡΠΊΠΎΠ³ΠΎ ΠΎΠ±ΡΠ»ΡΒΠΆΠΈΠ²Π°Π½ΠΈΡ ΠΈ ΡΠ΅ΠΌΠΎΠ½ΡΠ°. ΠΡΠΈ Π΄Π°Π½Π½ΡΠ΅ ΠΌΠΎΠ³ΡΡ Π±ΡΡΡ ΠΈΡΠΏΠΎΠ»ΡΠ·ΠΎΠ²Π°Π½Ρ Π΄Π»Ρ ΠΎΠ±ΠΎΡΠ½ΠΎΠ²Π°Π½Π½ΡΡ Π·Π°ΡΠ²ΠΎΠΊ Π½Π° Π·Π°ΠΏΠ°ΡΠ½ΡΠ΅ ΡΠ°ΡΡΠΈ ΠΈ ΠΌΠ°ΡΠ΅ΡΠΈΠ°Π»Ρ.
ΠΠ»Ρ Ρ Π°ΡΠ°ΠΊΡΠ΅ΡΠΈΡΡΠΈΠΊΠΈ Π½Π°Π΄Π΅ΠΆΠ½ΠΎΡΡΠΈ Π°Π²ΡΠΎΠΌΠΎΠ±ΠΈΠ»Ρ Π² Π·Π°Π²ΠΈΡΠΈΠΌΠΎΡΡΠΈ ΠΎΡ ΠΊΠΎΠ½ΡΡΡΡΠΊΡΠΈΠ²Π½ΠΎ-ΡΠ΅Ρ Π½ΠΎΠ»ΠΎΠ³ΠΈΡΠ΅ΡΠΊΠΈΡ ΠΈ ΡΠΊΡΠΏΠ»ΡΠ°ΡΠ°ΡΠΈΠΎΠ½Π½ΡΡ ΡΠ°ΠΊΡΠΎΡΠΎΠ² ΠΏΡΠΈΠ½ΠΈΠΌΠ°ΡΡ ΡΠΈΡΡΠ΅ΠΌΡ ΠΊΡΠΈΡΠ΅ΡΠΈΠ΅Π², ΠΏΠΎΠ·Π²ΠΎΠ»ΡΡΡΠΈΡ ΠΎΡΠ΅Π½ΠΈΠ²Π°ΡΡ Π½Π°Π΄Π΅ΠΆΠ½ΠΎΡΡΡ Π²ΡΠ΅Π³ΠΎ Π°Π²ΡΠΎΠΌΠΎΠ±ΠΈΠ»Ρ ΠΈΠ»ΠΈ ΠΎΡΠ΄Π΅Π»ΡΠ½ΡΡ Π΅Π³ΠΎ ΡΠ»Π΅ΠΌΠ΅Π½ΡΠΎΠ² Π² ΡΠΈΡΠ»ΠΎΠ²ΡΡ ΠΏΠΎΠΊΠ°ΒΠ·Π°ΡΠ΅Π»ΡΡ . Π’ΠΎΠ»ΡΠΊΠΎ Π² ΡΡΠΎΠΌ ΡΠ»ΡΡΠ°Π΅ ΠΌΠΎΠΆΠ½ΠΎ ΡΡΠ°Π²Π½ΠΈΠ²Π°ΡΡ Π½Π°Π΄Π΅ΠΆΠ½ΠΎΡΡΡ ΡΠ°Π·Π»ΠΈΡΠ½ΡΡ ΠΌΠ°ΡΠΎΠΊ ΠΈ ΠΌΠΎΠ΄Π΅Π»Π΅ΠΉ Π°Π²ΡΠΎΠΌΠΎΠ±ΠΈΠ»Π΅ΠΉ ΠΈ Π²Π΅ΡΡΠΈ ΡΠ°Π±ΠΎΡΡ ΠΏΠΎ ΠΏΠΎΠ²ΡΡΠ΅Π½ΠΈΡ ΠΈΡ Π½Π°Π΄Π΅ΠΆΠ½ΠΎΡΡΠΈ.
ΠΠ»Ρ ΠΎΠ±Π΅ΡΠΏΠ΅ΡΠ΅Π½ΠΈΡ Π½Π°Π΄Π΅ΠΆΠ½ΠΎΡΡΠΈ Π°Π²ΡΠΎΠΌΠΎΠ±ΠΈΠ»Π΅ΠΉ Π½Π΅ΠΎΠ±Ρ ΠΎΠ΄ΠΈΠΌΠΎ, ΡΡΠΎΠ±Ρ ΠΏΠΎΠΊΠ°Π·Π°ΡΠ΅Π»ΠΈ Π½Π°Π΄Π΅ΠΆΠ½ΠΎΡΡΠΈ Π·Π°Π΄Π°Π²Π°Π»ΠΈΡΡ Π² ΡΠ΅Ρ Π½ΠΈΡΠ΅ΡΠΊΠΎΠΌ Π·Π°Π΄Π°Π½ΠΈΠΈ Π½Π° ΠΏΡΠΎΒΠ΅ΠΊΡΠΈΡΠΎΠ²Π°Π½ΠΈΠ΅ ΠΈ ΠΊΠΎΠ½ΡΡΠΎΠ»ΠΈΡΠΎΠ²Π°Π»ΠΈΡΡ ΠΏΡΠΈ ΡΠ°Π·ΡΠ°Π±ΠΎΡΠΊΠ΅ ΠΊΠΎΠ½ΡΡΡΡΠΊΡΠΈΠΈ, ΠΈΠ·ΒΠ³ΠΎΡΠΎΠ²Π»Π΅Π½ΠΈΠΈ ΠΈ ΡΠΊΡΠΏΠ»ΡΠ°ΡΠ°ΡΠΈΠΈ. Π‘Π»Π΅Π΄ΠΎΠ²Π°ΡΠ΅Π»ΡΠ½ΠΎ, Π΄Π»Ρ ΠΊΠ°ΠΆΠ΄ΠΎΠ³ΠΎ ΡΠΈΠΏΠ° Π°Π²ΡΠΎΠΌΠΎΠ±ΠΈΠ»Π΅ΠΉ Π² Π·Π°Π²ΠΈΡΠΈΠΌΠΎΡΡΠΈ ΠΎΡ ΡΡΠ»ΠΎΠ²ΠΈΠΉ ΠΈΡ ΡΠΊΡΠΏΠ»ΡΠ°ΡΠ°ΡΠΈΠΈ Π΄ΠΎΠ»ΠΆΠ½Ρ ΡΡΡΠ°ΒΠ½Π°Π²Π»ΠΈΠ²Π°ΡΡΡΡ Π½Π΅ΠΊΠΎΡΠΎΡΠ°Ρ ΡΠΎΠ²ΠΎΠΊΡΠΏΠ½ΠΎΡΡΡ ΠΏΠΎΠΊΠ°Π·Π°ΡΠ΅Π»Π΅ΠΉ Π½Π°Π΄Π΅ΠΆΠ½ΠΎΡΡΠΈ, Π·Π½Π°ΡΠ΅Π½ΠΈΡ ΠΈ ΠΌΠ΅ΡΠΎΠ΄Ρ ΠΈΡ ΠΊΠΎΠ»ΠΈΡΠ΅ΡΡΠ²Π΅Π½Π½ΠΎΠΉ ΠΎΡΠ΅Π½ΠΊΠΈ.
ΠΠ°Π΄Π΅ΠΆΠ½ΠΎΡΡΡ Π°Π²ΡΠΎΠΌΠΎΠ±ΠΈΠ»Ρ Ρ Π°ΡΠ°ΠΊΡΠ΅ΡΠΈΠ·ΡΠ΅ΡΡΡ ΡΠ΅ΡΡΡΡΠΌΡ ΡΠ²ΠΎΠΉΡΡΠ²Π°ΠΌΠΈ:
- Π±Π΅Π·ΠΎΡΠΊΠ°Π·Π½ΠΎΡΡΡΡ
- ΡΠ΅ΠΌΠΎΠ½ΡΠΎΠΏΡΠΈΠ³ΠΎΠ΄Π½ΠΎΡΡΡΡ
- Π΄ΠΎΠ»Π³ΠΎΠ²Π΅ΡΠ½ΠΎΡΡΡΡ
- ΡΠΎΡ ΡΠ°Π½ΡΠ΅ΠΌΠΎΡΡΡΡ
ΠΠ΅Π·ΠΎΡΠΊΠ°Π·Π½ΠΎΡΡΡ β ΡΠ²ΠΎΠΉΡΡΠ²ΠΎ Π°Π²ΡΠΎΠΌΠΎΠ±ΠΈΠ»Ρ Π½Π΅ΠΏΡΠ΅ΡΡΠ²Π½ΠΎ ΡΠΎΡ ΡΠ°Π½ΡΡΡ ΡΠ°Π±ΠΎΡΠΎΡΠΏΠΎΡΠΎΠ±Π½ΠΎΠ΅ ΡΠΎΡΡΠΎΡΠ½ΠΈΠ΅ Π² ΡΠ΅ΡΠ΅Π½ΠΈΠ΅ Π½Π΅ΠΊΠΎΡΠΎΡΠΎΠ³ΠΎ Π²ΡΠ΅ΠΌΠ΅Π½ΠΈ ΠΈΠ»ΠΈ Π½Π΅ΠΊΠΎΡΠΎΡΠΎΠΉ Π½Π°ΡΠ°Π±ΠΎΡΠΊΠΈ.
ΠΠΎΠ»ΠΈΡΠ΅ΡΡΠ²Π΅Π½Π½ΠΎ ΠΎΠ½ΠΎ ΠΎΡΠ΅Π½ΠΈΠ²Π°Π΅ΡΡΡ Π²Π΅ΡΠΎΡΡΠ½ΠΎΡΡΡΡ Π±Π΅Π·ΠΎΡΠΊΠ°Π·Π½ΠΎΠΉ ΡΠ°Π±ΠΎΡΡ, ΡΡΠ΅Π΄Π½Π΅ΠΉ Π½Π°ΡΠ°Π±ΠΎΡΠΊΠΎΠΉ Π΄ΠΎ ΠΎΡΠΊΠ°Π·Π°, ΠΈΠ½ΡΠ΅Π½ΡΠΈΠ²Π½ΠΎΡΡΡΡ ΠΎΡΠΊΠ°Π·ΠΎΠ², ΡΡΠ΅Π΄Π½Π΅ΠΉ Π½Π°ΡΠ°Π±ΠΎΡΠΊΠΎΠΉ Π½Π° ΠΎΡΠΊΠ°Π· ΠΈ ΠΏΠ°ΡΠ°ΠΌΠ΅ΡΡΠΎΠΌ ΠΏΠΎΡΠΎΠΊΠ° ΠΎΡΠΊΠ°Π·ΠΎΠ².
Π Π΅ΠΌΠΎΠ½ΡΠΎΠΏΡΠΈΠ³ΠΎΠ΄Π½ΠΎΡΡΡ β ΡΠ²ΠΎΠΉΡΡΠ²ΠΎ Π°Π²ΡΠΎΠΌΠΎΠ±ΠΈΠ»Ρ, Π·Π°ΠΊΠ»ΡΡΠ°ΡΡΠ΅Π΅ΡΡ Π² ΠΏΡΠΈΡΠΏΠΎΡΠΎΠ±Π»Π΅Π½Π½ΠΎΡΡΠΈ ΠΊ ΠΏΡΠ΅Π΄ΡΠΏΡΠ΅ΠΆΠ΄Π΅Π½ΠΈΡ ΠΈ ΠΎΠ±Π½Π°ΡΡΠΆΠ΅Π½ΠΈΡ ΠΏΡΠΈΡΠΈΠ½ Π²ΠΎΠ·Π½ΠΈΠΊΠ½ΠΎΠ²Π΅Π½ΠΈΡ ΠΎΡΠΊΠ°Π·ΠΎΠ², ΠΏΠΎΠ²ΡΠ΅ΠΆΠ΄Π΅Π½ΠΈΠΉ ΠΈ ΠΏΠΎΠ΄Π΄Π΅ΡΠΆΠ°Π½ΠΈΡ ΠΈ Π²ΠΎΡΡΡΠ°Π½ΠΎΠ²ΒΠ»Π΅Π½ΠΈΡ ΡΠ°Π±ΠΎΡΠΎΡΠΏΠΎΡΠΎΠ±Π½ΠΎΠ³ΠΎ ΡΠΎΡΡΠΎΡΠ½ΠΈΡ ΠΏΡΡΠ΅ΠΌ ΠΏΡΠΎΠ²Π΅Π΄Π΅Π½ΠΈΡ ΡΠ΅Ρ Π½ΠΈΡΠ΅ΡΠΊΠΎΠ³ΠΎ ΠΎΠ±ΡΠ»ΡΠΆΠΈΠ²Π°Π½ΠΈΡ ΠΈ ΡΠ΅ΠΌΠΎΠ½ΡΠΎΠ².
ΠΠΎΠ»ΠΈΡΠ΅ΡΡΠ²Π΅Π½Π½ΠΎ ΠΎΠ½ΠΎ ΠΎΡΠ΅Π½ΠΈΠ²Π°Π΅ΡΡΡ ΡΡΠ΅Π΄Π½ΠΈΠΌ Π²ΡΠ΅ΠΌΠ΅Π½Π΅ΠΌ Π²ΠΎΡΡΡΠ°Π½ΠΎΠ²Π»Π΅ΒΠ½ΠΈΡ, ΡΡΠ΅Π΄Π½Π΅ΠΉ ΡΠ΄Π΅Π»ΡΠ½ΠΎΠΉ ΡΡΡΠ΄ΠΎΠ΅ΠΌΠΊΠΎΡΡΡΡ ΡΠ΅Ρ Π½ΠΈΡΠ΅ΡΠΊΠΎΠ³ΠΎ ΠΎΠ±ΡΠ»ΡΠΆΠΈΠ²Π°Π½ΠΈΡ ΠΈ ΡΠ΅ΠΊΡΡΠ΅Π³ΠΎ ΡΠ΅ΠΌΠΎΠ½ΡΠ°, Π²Π΅ΡΠΎΡΡΠ½ΠΎΡΡΡΡ Π²ΠΎΡΡΡΠ°Π½ΠΎΠ²Π»Π΅Π½ΠΈΡ ΡΠ°Π±ΠΎΡΠΎΡΠΏΠΎΡΠΎΠ±Π½ΠΎΡΡΠΈ Π² Π·Π°Π΄Π°Π½Π½ΠΎΠ΅ ΠΊΠΎΡΡΡΠΈΡΠΈΠ΅Π½ΡΠΎΠΌ Π³ΠΎΡΠΎΠ²Π½ΠΎΡΡΠΈ, ΠΊΠΎΡΡΡΠΈΡΠΈΠ΅Π½ΡΠΎΠΌ ΡΠ΅Ρ Π½ΠΈΡΠ΅ΡΠΊΠΎΠ³ΠΎ ΠΈΡΠΏΠΎΠ»ΡΠ·ΠΎΠ²Π°Π½ΠΈΡ Π²ΡΠ΅ΠΌΡ ΠΈ ΠΊΠΎΡΡΡΠΈΡΠΈΠ΅Π½ΡΠΎΠΌ ΡΠ»ΠΎΠΆΠ½ΠΎΡΡΠΈ ΠΎΡΠΊΠ°Π·ΠΎΠ².
ΠΡΠΈ ΡΡΠ°Π²Π½ΠΈΡΠ΅Π»ΡΠ½ΠΎΠΉ ΠΎΡΠ΅Π½ΠΊΠ΅ ΡΠ°Π·Π»ΠΈΡΠ½ΡΡ ΡΠΈΠΏΠΎΠ² Π°Π²ΡΠΎΠΌΠΎΠ±ΠΈΠ»Π΅ΠΉ Π½Π΅ΠΎΠ±Ρ ΠΎΠ΄ΠΈΠΌΠΎ ΠΈΠΌΠ΅ΡΡ Π² Π²ΠΈΠ΄Ρ, ΡΡΠΎ Π²ΡΠ΅ΠΌΡ ΠΈΡ ΠΏΡΠΎΡΡΠΎΡ Π² ΡΠ²ΡΠ·ΠΈ Ρ ΠΏΡΠΎΠ²Π΅Π΄Π΅Π½ΠΈΠ΅ΠΌ ΡΠ΅Ρ Π½ΠΈΡΠ΅ΡΠΊΠΎΠ³ΠΎ ΠΎΠ±ΡΠ»ΡΠΆΠΈΠ²Π°Π½ΠΈΡ ΠΈΠ»ΠΈ ΡΠ΅ΠΌΠΎΠ½ΡΠ° Π·Π°Π²ΠΈΡΠΈΡ ΠΎΡ ΡΡΠΎΠ²Π½Ρ ΠΎΡΠ³Π°ΒΠ½ΠΈΠ·Π°ΡΠΈΠΈ ΡΡΠΈΡ ΡΠ°Π±ΠΎΡ, ΠΈΡ ΡΠ΅Ρ Π½ΠΈΡΠ΅ΡΠΊΠΎΠ³ΠΎ ΠΎΡΠ½Π°ΡΠ΅Π½ΠΈΡ, ΠΊΠ²Π°Π»ΠΈΡΠΈΠΊΠ°ΡΠΈΠΈ ΠΏΠ΅ΡΡΠΎΠ½Π°Π»Π° ΠΈ ΡΡΠ΄Π° Π΄ΡΡΠ³ΠΈΡ ΡΠ°ΠΊΡΠΎΡΠΎΠ² ΡΠΊΡΠΏΠ»ΡΠ°ΡΠ°ΡΠΈΠΎΠ½Π½ΠΎΠ³ΠΎ Ρ Π°ΡΠ°ΠΊΡΠ΅ΡΠ°.
ΠΠΎΠ»Π³ΠΎΠ²Π΅ΡΠ½ΠΎΡΡΡ β ΡΠ²ΠΎΠΉΡΡΠ²ΠΎ Π°Π²ΡΠΎΠΌΠΎΠ±ΠΈΠ»Ρ ΡΠΎΡ ΡΠ°Π½ΡΡΡ ΡΠ°Π±ΠΎΡΠΎΡΠΏΠΎΡΠΎΠ±ΒΠ½ΠΎΠ΅ ΡΠΎΡΡΠΎΡΠ½ΠΈΠ΅ Π΄ΠΎ Π½Π°ΡΡΡΠΏΠ»Π΅Π½ΠΈΡ ΠΏΡΠ΅Π΄Π΅Π»ΡΠ½ΠΎΠ³ΠΎ ΡΠΎΡΡΠΎΡΠ½ΠΈΡ ΠΏΡΠΈ ΡΡΡΠ°Π½ΠΎΠ²ΒΠ»Π΅Π½Π½ΠΎΠΉ ΡΠΈΡΡΠ΅ΠΌΠ΅ ΡΠ΅Ρ Π½ΠΈΡΠ΅ΡΠΊΠΎΠ³ΠΎ ΠΎΠ±ΡΠ»ΡΠΆΠΈΠ²Π°Π½ΠΈΡ ΠΈ ΡΠ΅ΠΌΠΎΠ½ΡΠ°.
ΠΠ΅Π·ΠΎΡΠΊΠ°Π·Π½ΠΎΡΡΡ ΠΈ Π΄ΠΎΠ»Π³ΠΎΠ²Π΅ΡΠ½ΠΎΡΡΡ β ΡΠ²ΠΎΠΉΡΡΠ²Π° Π°Π²ΡΠΎΠΌΠΎΠ±ΠΈΠ»Ρ ΡΠΎΡ ΡΠ°Π½ΡΡΡ ΡΠ°Π±ΠΎΡΠΎΡΠΏΠΎΡΠΎΠ±Π½ΠΎΠ΅ ΡΠΎΡΡΠΎΡΠ½ΠΈΠ΅. ΠΠΎ Π±Π΅Π·ΠΎΡΠΊΠ°Π·Π½ΠΎΡΡΡ β ΡΠ²ΠΎΠΉΡΡΠ²ΠΎ Π°Π²ΡΠΎΠΌΠΎΠ±ΠΈΠ»Ρ Π½Π΅ΠΏΡΠ΅ΡΡΠ²Π½ΠΎ ΡΠΎΡ ΡΠ°Π½ΡΡΡ ΡΠ°Π±ΠΎΡΠΎΡΠΏΠΎΡΠΎΠ±Π½ΠΎΠ΅ ΡΠΎΡΡΠΎΡΠ½ΠΈΠ΅, Π° Π΄ΠΎΠ»Π³ΠΎΠ²Π΅ΡΒΠ½ΠΎΡΡΡ β ΡΠ²ΠΎΠΉΡΡΠ²ΠΎ Π°Π²ΡΠΎΠΌΠΎΠ±ΠΈΠ»Ρ Π΄Π»ΠΈΡΠ΅Π»ΡΠ½ΠΎ ΡΠΎΡ ΡΠ°Π½ΡΡΡ ΡΠ°Π±ΠΎΡΠΎΡΠΏΠΎΡΠΎΠ±Π½ΠΎΠ΅ ΡΠΎΡΡΠΎΡΠ½ΠΈΠ΅ Ρ Π½Π΅ΠΎΠ±Ρ ΠΎΠ΄ΠΈΠΌΡΠΌΠΈ ΠΏΠ΅ΡΠ΅ΡΡΠ²Π°ΠΌΠΈ Π΄Π»Ρ ΡΠ΅Ρ Π½ΠΈΡΠ΅ΡΠΊΠΎΠ³ΠΎ ΠΎΠ±ΡΠ»ΡΠΆΠΈΒΠ²Π°Π½ΠΈΡ ΠΈ ΡΠ΅ΠΌΠΎΠ½ΡΠ°.
ΠΠΏΡΠ΅Π΄Π΅Π»Π΅Π½ΠΈΠ΅ Π΄ΠΎΠ»Π³ΠΎΠ²Π΅ΡΠ½ΠΎΡΡΠΈ Π°Π²ΡΠΎΠΌΠΎΠ±ΠΈΠ»Π΅ΠΉ, Π°Π³ΡΠ΅Π³Π°ΡΠΎΠ², Π΄Π΅ΡΠ°Π»Π΅ΠΉ Π΄ΠΎΠ»ΠΆΠ½ΠΎ ΠΎΡΡΡΠ΅ΡΡΠ²Π»ΡΡΡΡΡ Π½Π° ΡΡΠ°Π΄ΠΈΠΈ ΠΏΡΠΎΠ΅ΠΊΡΠΈΡΠΎΠ²Π°Π½ΠΈΡ ΠΎΠ΄Π½ΠΎΠ²ΡΠ΅ΠΌΠ΅Π½Π½ΠΎ Ρ ΠΎΠΏΒΡΠ΅Π΄Π΅Π»Π΅Π½ΠΈΠ΅ΠΌ ΡΠΊΡΠΏΠ»ΡΠ°ΡΠ°ΡΠΈΠΎΠ½Π½ΡΡ Π·Π°ΡΡΠ°Ρ Π½Π° ΠΈΡ ΡΠ΅Ρ Π½ΠΈΡΠ΅ΡΠΊΠΎΠ΅ ΡΠΎΠ΄Π΅ΡΠΆΠ°Π½ΠΈΠ΅.
ΠΠΎΠ»ΠΈΡΠ΅ΡΡΠ²Π΅Π½Π½ΠΎ Π΄ΠΎΠ»Π³ΠΎΠ²Π΅ΡΠ½ΠΎΡΡΡ ΠΎΡΠ΅Π½ΠΈΠ²Π°Π΅ΡΡΡ ΡΡΠ΅Π΄Π½ΠΈΠΌ ΡΠ΅ΡΡΡΡΠΎΠΌ Π°Π²ΡΠΎΠΌΠΎΠ±ΠΈΠ»Ρ Π΄ΠΎ ΠΊΠ°ΠΏΠΈΡΠ°Π»ΡΠ½ΠΎΠ³ΠΎ ΡΠ΅ΠΌΠΎΠ½ΡΠ°, ΡΡΠ΅Π΄Π½Π΅ΠΉ Π½Π°ΡΠ°Π±ΠΎΡΠΊΠΎΠΉ Π½Π° ΠΎΡΠΊΠ°Π· Π°Π²ΡΠΎΠΌΠΎΠ±ΠΈΠ»Ρ Π·Π° ΠΏΡΠΎΠ±Π΅Π³ Π΄ΠΎ ΠΊΠ°ΠΏΠΈΡΠ°Π»ΡΠ½ΠΎΠ³ΠΎ ΡΠ΅ΠΌΠΎΠ½ΡΠ°, ΡΡΠ΅Π΄Π½Π΅ΠΉ Π½Π°ΡΠ°Π±ΠΎΡΠΊΠΎΠΉ Π΄ΠΎ ΠΊΠ°ΠΏΠΈΡΠ°Π»ΡΠ½ΠΎΠ³ΠΎ ΡΠ΅ΠΌΠΎΠ½ΡΠ° ΠΎΡΠ½ΠΎΠ²Π½ΠΎΠ³ΠΎ Π°Π³ΡΠ΅Π³Π°ΡΠ°, Π³Π°ΠΌΠΌΠ°-ΠΏΡΠΎΡΠ΅Π½ΡΠ½ΡΠΌ ΡΠ΅ΡΡΡΡΠΎΠΌ.
ΠΠ°ΠΆΠ΄Π°Ρ Π½ΠΎΠ²Π°Ρ ΠΌΠΎΠ΄Π΅Π»Ρ Π°Π²ΡΠΎΠΌΠΎΠ±ΠΈΠ»Ρ Π΄ΠΎΠ»ΠΆΠ½Π° Π±ΡΡΡ Π±ΠΎΠ»Π΅Π΅ ΡΠΎΠ²Π΅ΡΡΠ΅Π½Π½ΠΎΠΉ ΠΏΠΎ ΡΡΠ°Π²Π½Π΅Π½ΠΈΡ Ρ ΠΏΡΠ΅Π΄ΡΠ΄ΡΡΠ΅ΠΉ ΠΈ ΡΠΎΠΎΡΠ²Π΅ΡΡΡΠ²ΠΎΠ²Π°ΡΡ Π»ΡΡΡΠΈΠΌ ΠΌΠΈΡΠΎΠ²ΡΠΌ ΠΎΠ±ΡΠ°Π·ΡΠ°ΠΌ. Π‘ΠΎΠ²Π΅ΡΡΠ΅Π½ΡΡΠ²ΠΎ Π² Π΄Π°Π½Π½ΠΎΠΌ ΡΠ»ΡΡΠ°Π΅ ΠΎΠΏΡΠ΅Π΄Π΅Π»ΡΠ΅ΡΡΡ ΡΠ½ΠΈΠΆΠ΅Π½ΠΈΠ΅ΠΌ ΡΡΠΌΠΌΠ°ΡΠ½ΡΡ ΡΠ΄Π΅Π»ΡΠ½ΡΡ Π·Π°ΡΡΠ°Ρ Π½Π° ΠΈΠ·Π³ΠΎΡΠΎΠ²Π»Π΅Π½ΠΈΠ΅ ΠΈ ΡΠ΅Ρ Π½ΠΈΡΠ΅ΡΠΊΠΎΠ΅ ΡΠΎΠ΄Π΅ΡΒΠΆΠ°Π½ΠΈΠ΅, Π° ΡΠ°ΠΊΠΆΠ΅ ΡΡΡΡΠΊΡΡΡΠΎΠΉ ΡΡΠΈΡ Π·Π°ΡΡΠ°Ρ, Ρ. Π΅. Π²ΠΎΠ·ΠΌΠΎΠΆΠ½ΡΠΌ ΡΠ½ΠΈΠΆΠ΅Π½ΠΈΠ΅ΠΌ Π΄ΠΎΠ»ΠΈ Π·Π°ΡΡΠ°Ρ Π² ΡΠΊΡΠΏΠ»ΡΠ°ΡΠ°ΡΠΈΠΈ. ΠΠ΄Π½ΠΎΠ²ΡΠ΅ΠΌΠ΅Π½Π½ΠΎ ΠΎΠΏΡΠ΅Π΄Π΅Π»ΡΡΡΡΡ ΠΏΠΎΠΊΠ°Π·Π°ΡΠ΅Π»ΠΈ Π΄ΠΎΠ»Π³ΠΎΠ²Π΅ΡΠ½ΠΎΡΡΠΈ, ΠΊΠΎΡΠΎΡΡΠ΅ ΠΈΠΌΠ΅ΡΡ, ΠΊΠ°ΠΊ ΠΏΡΠ°Π²ΠΈΠ»ΠΎ, ΡΠ΅Π½Π΄Π΅Π½ΡΠΈΡ ΠΊ ΡΠ²Π΅Π»ΠΈΡΠ΅Π½ΠΈΡ.
ΠΠΎΠ»Π³ΠΎΠ²Π΅ΡΠ½ΠΎΡΡΡ Π°Π²ΡΠΎΠΌΠΎΠ±ΠΈΠ»Π΅ΠΉ ΠΏΠΎΠ²ΡΡΠ°Π΅ΡΡΡ Π² ΡΠ΅Π·ΡΠ»ΡΡΠ°ΡΠ΅ ΡΠΎΠ²Π΅ΡΡΠ΅Π½ΒΡΡΠ²ΠΎΠ²Π°Π½ΠΈΡ ΠΈΡ ΠΊΠΎΠ½ΡΡΡΡΠΊΡΠΈΠΈ, ΡΠ΅Ρ Π½ΠΎΠ»ΠΎΠ³ΠΈΠΈ ΠΈΠ·Π³ΠΎΡΠΎΠ²Π»Π΅Π½ΠΈΡ ΠΈ ΡΠ»ΡΡΡΠ΅Π½ΠΈΡ ΠΎΡΠ³Π°Π½ΠΈΠ·Π°ΡΠΈΠΈ ΡΠ΅Ρ Π½ΠΈΡΠ΅ΡΠΊΠΎΠΉ ΡΠΊΡΠΏΠ»ΡΠ°ΡΠ°ΡΠΈΠΈ.
Π‘ΠΎΡ ΡΠ°Π½ΡΠ΅ΠΌΠΎΡΡΡ β ΡΠ²ΠΎΠΉΡΡΠ²ΠΎ Π°Π²ΡΠΎΠΌΠΎΠ±ΠΈΠ»Ρ ΡΠΎΡ ΡΠ°Π½ΡΡΡ Π·Π½Π°ΡΠ΅Π½ΠΈΡ ΠΏΠΎΠΊΠ°Π·Π°ΡΠ΅Π»Π΅ΠΉ Π±Π΅Π·ΠΎΡΠΊΠ°Π·Π½ΠΎΡΡΠΈ, Π΄ΠΎΠ»Π³ΠΎΠ²Π΅ΡΠ½ΠΎΡΡΠΈ ΠΈ ΡΠ΅ΠΌΠΎΠ½ΡΠΎΠΏΡΠΈΠ³ΠΎΠ΄Π½ΠΎΡΡΠΈ Π² ΡΠ΅ΡΠ΅Π½ΠΈΠ΅ ΠΈ ΠΏΠΎΡΠ»Π΅ Ρ ΡΠ°Π½Π΅Π½ΠΈΡ ΠΈ ΡΡΠ°Π½ΡΠΏΠΎΡΡΠΈΡΠΎΠ²Π°Π½ΠΈΡ.
ΠΡΠ½ΠΎΠ²Π½ΡΠΌ ΠΏΠΎΠΊΠ°Π·Π°ΡΠ΅Π»Π΅ΠΌ ΡΠΎΡ ΡΠ°Π½ΡΠ΅ΠΌΠΎΡΡΠΈ Π°Π²ΡΠΎΠΌΠΎΠ±ΠΈΠ»Π΅ΠΉ Π΄ΠΎΠ»ΠΆΠ½Π° Π±ΡΡΡ Π²Π΅ΡΠΎΡΡΠ½ΠΎΡΡΡ ΡΠΎΡ ΡΠ°Π½Π΅Π½ΠΈΡ Π±Π΅Π·ΠΎΡΠΊΠ°Π·Π½ΠΎΡΡΠΈ. ΠΡΠΎΡ ΠΏΠΎΠΊΠ°Π·Π°ΡΠ΅Π»Ρ Ρ Π°ΡΠ°ΠΊΡΠ΅ΡΠΈΠ·ΡΠ΅Ρ Π³ΠΎΡΠΎΠ²Π½ΠΎΡΡΡ Π°Π²ΡΠΎΠΌΠΎΠ±ΠΈΠ»Π΅ΠΉ ΠΊ Π½Π΅ΠΌΠ΅Π΄Π»Π΅Π½Π½ΠΎΠΌΡ Π²ΡΠΏΠΎΠ»Π½Π΅Π½ΠΈΡ ΡΡΠ°Π½ΡΒΠΏΠΎΡΡΠ½ΠΎΠΉ ΡΠ°Π±ΠΎΡΡ ΠΏΠΎΡΠ»Π΅ ΠΎΠΏΡΠ΅Π΄Π΅Π»Π΅Π½Π½ΠΎΠ³ΠΎ ΡΡΠΎΠΊΠ° Ρ ΡΠ°Π½Π΅Π½ΠΈΡ.
ΠΠΎΠΊΠ°Π·Π°ΡΠ΅Π»Π΅ΠΌ ΡΠΎΡ ΡΠ°Π½ΡΠ΅ΠΌΠΎΡΡΠΈ ΡΠ²Π»ΡΠ΅ΡΡΡ ΡΠ°ΠΊΠΆΠ΅ ΡΡΠ΅Π΄Π½ΠΈΠΉ ΡΡΠΎΠΊ ΡΠΎΡ ΡΠ°ΒΠ½ΡΠ΅ΠΌΠΎΡΡΠΈ Π°Π²ΡΠΎΠΌΠΎΠ±ΠΈΠ»Π΅ΠΉ ΠΏΡΠΈ Π΄Π»ΠΈΡΠ΅Π»ΡΠ½ΠΎΠΌ Ρ ΡΠ°Π½Π΅Π½ΠΈΠΈ.
ΠΠ΅ΡΠ΅ΡΠΈΡΠ»Π΅Π½Π½ΡΠ΅ ΡΠ²ΠΎΠΉΡΡΠ²Π° ΠΎΡΡΠ°ΠΆΠ°ΡΡ ΠΏΠΎΡΠ΅Π½ΡΠΈΠ°Π»ΡΠ½ΡΠ΅ Π²ΠΎΠ·ΠΌΠΎΠΆΠ½ΠΎΡΡΠΈ ΠΊΠΎΠ½ΡΡΡΡΠΊΡΠΈΠΈ Π°Π²ΡΠΎΠΌΠΎΠ±ΠΈΠ»Ρ. ΠΠ½ΠΈ ΡΠΎΡΠΌΠΈΡΡΡΡΡΡ ΠΏΡΠΈ ΠΏΡΠΎΠ΅ΠΊΡΠΈΡΠΎΠ²Π°Π½ΠΈΠΈ ΠΈ ΠΏΡΠΎΠΈΠ·Π²ΠΎΠ΄ΡΡΠ²Π΅, ΡΠ²Π»ΡΡΡΡΡ Π²Π½ΡΡΡΠ΅Π½Π½ΠΈΠΌΠΈ ΠΏΡΠΈΡΠΈΠ½Π°ΠΌΠΈ, ΠΎΡ ΠΊΠΎΡΠΎΡΡΡ Π·Π°Π²ΠΈΡΠΈΡ ΡΡΠ΅ΠΏΠ΅Π½Ρ Π½Π°Π΄Π΅ΠΆΠ½ΠΎΡΡΠΈ Π°Π²ΡΠΎΠΌΠΎΠ±ΠΈΠ»Ρ.
ΠΠ°Π΄Π΅ΠΆΠ½ΠΎΡΡΡΒ Π°Π²ΡΠΎΠΌΠΎΠ±ΠΈΠ»Ρ
ΠΠ°ΡΠ΅Π³ΠΎΡΠΈΡ:
Β Β Β Π’Π΅Ρ Π½ΠΈΡΠ΅ΡΠΊΠ°Ρ ΡΠΊΡΠΏΠ»ΡΠ°ΡΠ°ΡΠΈΡ Π°Π²ΡΠΎΠΌΠΎΠ±ΠΈΠ»Π΅ΠΉ
ΠΠ°Π΄Π΅ΠΆΠ½ΠΎΡΡΡΒ Π°Π²ΡΠΎΠΌΠΎΠ±ΠΈΠ»Ρ
ΠΡΠ½ΠΎΠ²Π½ΡΠ΅ ΠΏΠΎΠ½ΡΡΠΈΡ ΠΈ ΠΎΠΏΡΠ΅Π΄Π΅Π»Π΅Π½ΠΈΡ. ΠΠ°ΡΠ΅ΡΡΠ²ΠΎΠΌ Π»ΡΠ±ΠΎΠΉ ΠΌΠ°ΡΠΈΠ½Ρ, Π² ΡΠΎΠΌ ΡΠΈΡΠ»Π΅ ΠΈ Π°Π²ΡΠΎΠΌΠΎΠ±ΠΈΠ»Ρ, Π½Π°Π·ΡΠ²Π°ΡΡ ΡΠΎΠ²ΠΎΠΊΡΠΏΠ½ΠΎΡΡΡ ΡΠ²ΠΎΠΉΡΡΠ², ΠΎΠΏΡΠ΅Π΄Π΅Π»ΡΡΡΠΈΡ ΡΡΠ΅ΠΏΠ΅Π½Ρ ΠΏΡΠΈΠ³ΠΎΠ΄Π½ΠΎΡΡΠΈ Π΅Π΅ Π΄Π»Ρ ΠΈΡΠΏΠΎΠ»ΡΠ·ΠΎΠ²Π°Π½ΠΈΡ ΠΏΠΎ Π½Π°Π·Π½Π°ΡΠ΅Π½ΠΈΡ. ΠΠ°ΡΠ΅ΡΡΠ²ΠΎ Π°Π²ΡΠΎΠΌΠΎΠ±ΠΈΠ»Ρ ΠΎΠ±ΡΡΠ»ΠΎΠ²Π»ΠΈΠ²Π°Π΅ΡΡΡ ΡΠ°ΠΊΠΈΠΌΠΈ ΡΠ²ΠΎΠΉΡΡΠ²Π°ΠΌΠΈ, ΠΊΠ°ΠΊ Π΄ΠΈΠ½Π°ΠΌΠΈΡΠ½ΠΎΡΡΡ, ΡΠΎΠΏΠ»ΠΈΠ²Π½Π°Ρ ΡΠΊΠΎΠ½ΠΎΠΌΠΈΡΠ½ΠΎΡΡΡ, ΡΠΏΡΠ°Π²Π»ΡΠ΅ΠΌΠΎΡΡΡ, ΠΏΡΠΎΡ ΠΎΠ΄ΠΈΠΌΠΎΡΡΡ, ΠΏΡΠΈΡΠΏΠΎΡΠΎΠ±Π»Π΅Π½Π½ΠΎΡΡΡ ΠΊ ΡΠ΅Ρ Π½ΠΈΡΠ΅ΡΠΊΠΎΠΌΡ ΠΎΠ±ΡΠ»ΡΠΆΠΈΠ²Π°Π½ΠΈΡ ΠΈ ΡΠ΅ΠΌΠΎΠ½ΡΡ.
Π Π·Π°Π²ΠΈΡΠΈΠΌΠΎΡΡΠΈ ΠΎΡ ΡΠΈΠΏΠ° ΠΈ Π½Π°Π·Π½Π°ΡΠ΅Π½ΠΈΡ Π°Π²ΡΠΎΠΌΠΎΠ±ΠΈΠ»Ρ, ΠΊΠΎΠ½ΠΊΡΠ΅ΡΠ½ΡΡ ΡΡΠ»ΠΎΠ²ΠΈΠΉ ΡΠΊΡΠΏΠ»ΡΠ°ΡΠ°ΡΠΈΠΈ ΡΡΠ΅Π±ΠΎΠ²Π°Π½ΠΈΡ ΠΊ Π΅Π³ΠΎ ΡΠ²ΠΎΠΉΡΡΠ²Π°ΠΌ Π½Π΅ ΠΎΠ΄ΠΈΠ½Π°ΠΊΠΎΠ²Ρ ΠΈ ΠΌΠΎΠ³ΡΡ ΠΈΠ·ΠΌΠ΅Π½ΡΡΡΡΡ Π² ΡΠΈΡΠΎΠΊΠΈΡ ΠΏΡΠ΅Π΄Π΅Π»Π°Ρ . ΠΠΎΠ·ΠΌΠΎΠΆΠ½ΠΎΡΡΡ ΡΠ΅Π°Π»ΠΈΠ·Π°ΡΠΈΠΈ ΡΠ²ΠΎΠΉΡΡΠ², Π·Π°Π»ΠΎΠΆΠ΅Π½Π½ΡΡ Π² ΠΊΠΎΠ½ΡΡΡΡΠΊΡΠΈΡ Π»ΡΠ±ΠΎΠ³ΠΎ Π°Π²ΡΠΎΠΌΠΎΠ±ΠΈΠ»Ρ, Π² Π±ΠΎΠ»ΡΡΠΎΠΉ ΡΡΠ΅ΠΏΠ΅Π½ΠΈ ΠΎΠΏΡΠ΅Π΄Π΅Π»ΡΠ΅ΡΡΡ Π΅Π³ΠΎ Π½Π°Π΄Π΅ΠΆΠ½ΠΎΡΡΡΡ. ΠΠ°Π΄Π΅ΠΆΠ½ΠΎΡΡΡ ΡΠ²Π»ΡΠ΅ΡΡΡ ΠΎΠ΄Π½ΠΈΠΌ ΠΈΠ· Π²Π°ΠΆΠ½Π΅ΠΉΡΠΈΡ ΡΠ²ΠΎΠΉΡΡΠ² Π°Π²ΡΠΎΠΌΠΎΠ±ΠΈΠ»Ρ, ΠΎΡ ΠΊΠΎΡΠΎΡΠΎΠΉ Π·Π°Π²ΠΈΡΠΈΡ ΡΡΡΠ΅ΠΊΡΠΈΠ²Π½ΠΎΡΡΡ ΠΈΡΠΏΠΎΠ»ΡΠ·ΠΎΠ²Π°Π½ΠΈΡ Π°Π²ΡΠΎΠΌΠΎΠ±ΠΈΠ»Ρ ΠΏΠΎ Π½Π°Π·Π½Π°ΡΠ΅Π½ΠΈΡ.
ΠΠ°Π΄Π΅ΠΆΠ½ΠΎΡΡΡ Π°Π²ΡΠΎΠΌΠΎΠ±ΠΈΠ»Ρ β ΡΠ²ΠΎΠΉΡΡΠ²ΠΎ Π²ΡΠΏΠΎΠ»Π½ΡΡΡ Π·Π°Π΄Π°Π½Π½ΡΠ΅ ΡΡΠ½ΠΊΡΠΈΠΈ, ΡΠΎΡ ΡΠ°Π½ΡΡ ΡΠ²ΠΎΠΈ ΡΠΊΡΠΏΠ»ΡΠ°ΡΠ°ΡΠΈΠΎΠ½Π½ΡΠ΅ ΠΏΠΎΠΊΠ°Π·Π°ΡΠ΅Π»ΠΈ Π² Π·Π°Π΄Π°Π½Π½ΡΡ ΠΏΡΠ΅Π΄Π΅Π»Π°Ρ Π² ΡΠ΅ΡΠ΅Π½ΠΈΠ΅ ΡΡΠ΅Π±ΡΠ΅ΠΌΠΎΠ³ΠΎ Π²ΡΠ΅ΠΌΠ΅Π½ΠΈ ΠΈΠ»ΠΈ ΡΡΠ΅Π±ΡΠ΅ΠΌΠΎΠΉ Π½Π°ΡΠ°Π±ΠΎΡΠΊΠΈ. ΠΠ°ΡΠ°Π±ΠΎΡΠΊΠ° Π°Π²ΡΠΎΠΌΠΎΠ±ΠΈΠ»Ρ (ΠΎΠ±ΡΠ΅ΠΌ ΡΠ°Π±ΠΎΡΡ) ΠΎΠ±ΡΡΠ½ΠΎ ΠΈΠ·ΠΌΠ΅ΡΡΠ΅ΡΡΡ Π² ΠΊΠΈΠ»ΠΎΠΌΠ΅ΡΡΠ°Ρ ΠΏΡΠΎΠ±Π΅Π³Π° ΠΈΠ»ΠΈ ΡΠΎΠ½Π½ΠΎ-ΠΊΠΈΠ»ΠΎΠΌΠ΅ΡΡΠ°Ρ . Π ΠΎΡΠ΄Π΅Π»ΡΠ½ΡΡ ΡΠ»ΡΡΠ°ΡΡ Π½Π°ΡΠ°Π±ΠΎΡΠΊΠ° Π°Π²ΡΠΎΠΌΠΎΠ±ΠΈΠ»Ρ ΠΌΠΎΠΆΠ΅Ρ ΠΈΠ·ΠΌΠ΅ΡΡΡΡΡΡ Π² ΡΠ°ΡΠ°Ρ . Π Π΄Π°Π»ΡΠ½Π΅ΠΉΡΠ΅ΠΌ ΠΏΠΎΠ΄ ΡΠ΅ΡΠΌΠΈΠ½ΠΎΠΌ Π½Π°ΡΠ°Π±ΠΎΡΠΊΠ° ΠΌΡ Π±ΡΠ΄Π΅ΠΌ ΠΏΠΎΠ½ΠΈΠΌΠ°ΡΡ ΠΏΡΠΎΠ±Π΅Π³ Π°Π²ΡΠΎΠΌΠΎΠ±ΠΈΠ»Ρ Π² ΠΊΠΈΠ»ΠΎΠΌΠ΅ΡΡΠ°Ρ . Π‘Π»Π΅Π΄ΠΎΠ²Π°ΡΠ΅Π»ΡΠ½ΠΎ, Π½Π°Π΄Π΅ΠΆΠ½ΠΎΡΡΡ β ΡΡΠΎ ΠΌΠ΅ΡΠ° ΡΠΏΠΎΡΠΎΠ±Π½ΠΎΡΡΠΈ Π°Π²ΡΠΎΠΌΠΎΠ±ΠΈΠ»Ρ ΡΠ°Π±ΠΎΡΠ°ΡΡ Π±Π΅Π· ΠΏΠΎΠ»ΠΎΠΌΠΎΠΊ ΠΈ ΠΏΡΠ΅ΠΆΠ΄Π΅Π²ΡΠ΅ΠΌΠ΅Π½Π½ΠΎΠ³ΠΎ ΠΈΠ·Π½ΠΎΡΠ° Π΄Π΅ΡΠ°Π»Π΅ΠΉ, Π½Π°ΡΡΡΠ΅Π½ΠΈΡ ΡΠ΅Π³ΡΠ»ΠΈΡΠΎΠ²ΠΎΠΊ ΠΌΠ΅Ρ Π°Π½ΠΈΠ·ΠΌΠΎΠ² ΠΈ ΡΠΈΡΡΠ΅ΠΌΡ. Π΅. ΡΠ°Π±ΠΎΡΠ°ΡΡ Π±Π΅Π· ΠΎΡΡΠ°Π½ΠΎΠ²ΠΎΠΊ ΠΏΠΎ ΡΠ΅Ρ Π½ΠΈΡΠ΅ΡΠΊΠΈΠΌ Π½Π΅ΠΈΡΠΏΡΠ°Π²Π½ΠΎΡΡΡΠΌ.
ΠΠ°Π΄Π΅ΠΆΠ½ΠΎΡΡΡ Π°Π²ΡΠΎΠΌΠΎΠ±ΠΈΠ»Ρ Π² ΡΠΈΡΠΎΠΊΠΎΠΌ ΡΠΌΡΡΠ»Π΅ ΠΎΠ±ΡΡΠ»ΠΎΠ²Π»ΠΈΠ²Π°Π΅ΡΡΡ Π΅Π³ΠΎ Π±Π΅Π·ΠΎΡΠΊΠ°Π·Π½ΠΎΡΡΡΡ, ΡΠ΅ΠΌΠΎΠ½ΡΠΎΠΏΡΠΈΠ³ΠΎΠ΄Π½ΠΎΡΡΡΡ, ΡΠΎΡ ΡΠ°Π½ΡΠ΅ΠΌΠΎΡΡΡΡ, Π° ΡΠ°ΠΊΠΆΠ΅ Π΄ΠΎΠ»Π³ΠΎΠ²Π΅ΡΠ½ΠΎΡΡΡΡ Π΅Π³ΠΎ Π°Π³ΡΠ΅Π³Π°ΡΠΎΠ², ΡΠ·Π»ΠΎΠ² ΠΈ Π΄Π΅ΡΠ°Π»Π΅ΠΉ.
ΠΠ΅Π·ΠΎΡΠΊΠ°Π·Π½ΠΎΡΡΡ Π°Π²ΡΠΎΠΌΠΎΠ±ΠΈΠ»Ρ β ΡΠ²ΠΎΠΉΡΡΠ²ΠΎ ΡΠΎΡ ΡΠ°Π½ΡΡΡ ΡΠ°Π±ΠΎΡΠΎΡΠΏΠΎΡΠΎΠ±Π½ΠΎΡΡΡ Π² ΡΠ΅ΡΠ΅Π½ΠΈΠ΅ Π½Π΅ΠΊΠΎΡΠΎΡΠΎΠ³ΠΎ ΠΏΡΠΎΠ±Π΅Π³Π° Π±Π΅Π· Π²ΡΠ½ΡΠΆΠ΄Π΅Π½Π½ΡΡ ΠΏΠ΅ΡΠ΅ΡΡΠ²ΠΎΠ². ΠΠΎΠΊΠ°Π·Π°ΡΠ΅Π»ΡΠΌΠΈ Π±Π΅Π·ΠΎΡΠΊΠ°Π·Π½ΠΎΡΡΠΈ Π°Π²ΡΠΎΠΌΠΎΠ±ΠΈΠ»Ρ ΠΌΠΎΠ³ΡΡ ΡΠ»ΡΠΆΠΈΡΡ, Π½Π°ΠΏΡΠΈΠΌΠ΅Ρ, Π²Π΅ΡΠΎΡΡΠ½ΠΎΡΡΡ Π±Π΅Π·ΠΎΡΠΊΠ°Π·Π½ΠΎΠΉ ΡΠ°Π±ΠΎΡΡ, Π½Π°ΡΠ°Π±ΠΎΡΠΊΠΈ Π½Π° ΠΎΡΠΊΠ°Π·, ΠΏΠ°ΡΠ°ΠΌΠ΅ΡΡ ΠΏΠΎΡΠΎΠΊΠ° ΠΎΡΠΊΠ°Π·ΠΎΠ², ΠΊΠΎΡΡΡΠΈΡΠΈΠ΅Π½Ρ Π³ΠΎΡΠΎΠ²Π½ΠΎΡΡΠΈ.
ΠΠ²ΡΠΎΠΌΠΎΠ±ΠΈΠ»Ρ ΡΠ²Π»ΡΠ΅ΡΡΡ Π²ΠΎΡΡΡΠ°Π½Π°Π²Π»ΠΈΠ²Π°Π΅ΠΌΠΎΠΉ ΡΠΈΡΡΠ΅ΠΌΠΎΠΉ, ΠΌΠΎΠΆΠ΅Ρ ΠΌΠ½ΠΎΠ³ΠΎΠΊΡΠ°ΡΠ½ΠΎ ΠΏΠΎΠ΄Π²Π΅ΡΠ³Π°ΡΡΡΡ ΡΠ°Π·Π»ΠΈΡΠ½ΡΠΌ Π²ΠΈΠ΄Π°ΠΌ ΡΠ΅Ρ Π½ΠΈΡΠ΅ΡΠΊΠΎΠ³ΠΎ ΠΎΠ±ΡΠ»ΡΠΆΠΈΠ²Π°Π½ΠΈΡ ΠΈ ΡΠ΅ΠΌΠΎΠ½ΡΠ°ΠΌ, Ρ. Π΅. ΠΎΠ½ ΡΠ΅ΠΌΠΎΠ½ΡΠΎΠΏΡΠΈΠ³ΠΎΠ΄Π½ΡΠΉ.
Π Π΅ΠΌΠΎΠ½ΡΠΎΠΏΡΠΈΠ³ΠΎΠ΄Π½ΠΎΡΡΡ β ΡΠ²ΠΎΠΉΡΡΠ²ΠΎ, Π·Π°ΠΊΠ»ΡΡΠ°ΡΡΠ΅Π΅ΡΡ Π² Π΅Π³ΠΎ ΠΏΡΠΈΡΠΏΠΎΡΠΎΠ±Π»Π΅Π½Π½ΠΎΡΡΠΈ ΠΊ ΠΏΡΠ΅Π΄ΡΠΏΡΠ΅ΠΆΠ΄Π΅Π½ΠΈΡ, ΠΎΠ±Π½Π°ΡΡΠΆΠ΅Π½ΠΈΡ ΠΈ ΡΡΡΡΠ°Π½Π΅Π½ΠΈΡ ΠΎΡΠΊΠ°Π·ΠΎΠ² ΠΈ Π½Π΅ΠΈΡΠΏΡΠ°Π²Π½ΠΎΡΡΠ΅ΠΉ ΠΏΡΡΠ΅ΠΌ ΠΏΡΠΎΠ²Π΅Π΄Π΅Π½ΠΈΡ ΡΠ΅Ρ Π½ΠΈΡΠ΅ΡΠΊΠΈΡ ΠΎΠ±ΡΠ»ΡΠΆΠΈΠ²Π°Π½ΠΈΠΉ ΠΈ ΡΠ΅ΠΌΠΎΠ½ΡΠΎΠ². Π Π·Π°Π²ΠΈΡΠΈΠΌΠΎΡΡΠΈ ΠΎΡ ΡΡΠΎΠ²Π½Ρ ΡΠ΅ΠΌΠΎΠ½ΡΠΎΠΏΡΠΈΠ³ΠΎΠ΄Π½ΠΎΡΡΠΈ Π°Π²ΡΠΎΠΌΠΎΠ±ΠΈΠ»Ρ ΠΈΠ·ΠΌΠ΅Π½ΡΠ΅ΡΡΡ ΠΏΡΠΎΠ΄ΠΎΠ»ΠΆΠΈΡΠ΅Π»ΡΠ½ΠΎΡΡΡ ΠΏΡΠΎΡΡΠΎΡ ΠΏΡΠΈ ΡΠ΅Ρ Π½ΠΈΡΠ΅ΡΠΊΠΎΠΌ ΠΎΠ±ΡΠ»ΡΠΆΠΈΠ²Π°Π½ΠΈΠΈ ΠΈ ΡΠ΅ΠΌΠΎΠ½ΡΠ΅, Π° ΡΠ°ΠΊΠΆΠ΅ ΡΡΡΠ΄ΠΎΠ΅ΠΌΠΊΠΎΡΡΡ ΡΡΠΈΡ ΡΠ°Π±ΠΎΡ. ΠΠΎΠΊΠ°Π·Π°ΡΠ΅Π»ΡΠΌΠΈ ΡΠ΅ΠΌΠΎΠ½ΡΠΎΠΏΡΠΈΠ³ΠΎΠ΄Π½ΠΎΡΡΠΈ Π°Π²ΡΠΎΠΌΠΎΠ±ΠΈΠ»Ρ ΠΌΠΎΠ³ΡΡ ΡΠ»ΡΠΆΠΈΡΡ, Π½Π°ΠΏΡΠΈΠΌΠ΅Ρ, Π²Π΅ΡΠΎΡΡΠ½ΠΎΡΡΡ Π²ΡΠΏΠΎΠ»Π½Π΅Π½ΠΈΡ ΡΠ΅ΠΌΠΎΠ½ΡΠ° Π² Π·Π°Π΄Π°Π½Π½ΠΎΠ΅ Π²ΡΠ΅ΠΌΡ, ΡΠ΄Π΅Π»ΡΠ½Π°Ρ ΡΡΡΠ΄ΠΎΠ΅ΠΌΠΊΠΎΡΡΡ ΠΈ ΡΡΠ΅Π΄Π½ΡΡ ΡΡΠΎΠΈΠΌΠΎΡΡΡ ΡΠ΅Ρ Π½ΠΈΡΠ΅ΡΠΊΠΎΠ³ΠΎ ΠΎΠ±ΡΠ»ΡΠΆΠΈΠ²Π°Π½ΠΈΡ.
Π‘ΠΎΡ ΡΠ°Π½ΡΠ΅ΠΌΠΎΡΡΡ β ΡΠ²ΠΎΠΉΡΡΠ²ΠΎ Π°Π²ΡΠΎΠΌΠΎΠ±ΠΈΠ»Ρ ΡΠΎΡ ΡΠ°Π½ΡΡΡ ΠΎΠ±ΡΡΠ»ΠΎΠ²Π»Π΅Π½Π½ΡΠ΅ ΡΠΊΡΠΏΠ»ΡΠ°ΡΠ°ΡΠΈΠΎΠ½Π½ΡΠ΅ ΠΏΠΎΠΊΠ°Π·Π°ΡΠ΅Π»ΠΈ Π² ΡΠ΅ΡΠ΅Π½ΠΈΠ΅ ΠΈ ΠΏΠΎΡΠ»Π΅ ΡΡΠΎΠΊΠ° Ρ ΡΠ°Π½Π΅Π½ΠΈΡ ΠΈ ΡΡΠ°Π½ΡΠΏΠΎΡΡΠΈΡΠΎΠ²Π°Π½ΠΈΡ, ΡΡΡΠ°Π½ΠΎΠ²Π»Π΅Π½Π½ΠΎΠ³ΠΎ Π² ΡΠ΅Ρ Π½ΠΈΡΠ΅ΡΠΊΠΎΠΉ Π΄ΠΎΠΊΡΠΌΠ΅Π½ΡΠ°ΡΠΈΠΈ. Π‘ΠΎΡ ΡΠ°Π½ΡΠ΅ΠΌΠΎΡΡΡΡ ΠΎΠΏΡΠ΅Π΄Π΅Π»ΡΡΡΡΡ ΡΠ΅Π»Π΅ΡΠΎΠΎΠ±ΡΠ°Π·Π½ΡΠ΅ ΡΡΠΎΠΊΠΈ Ρ ΡΠ°Π½Π΅Π½ΠΈΡ ΠΈ ΠΊΠΎΠ½ΡΠ΅ΡΠ²Π°ΡΠΈΠΈ Π°Π²ΡΠΎΠΌΠΎΠ±ΠΈΠ»Π΅ΠΉ, Π° ΡΠ°ΠΊΠΆΠ΅ Π΄ΠΎΠΏΡΡΡΠΈΠΌΡΠ΅ ΡΠ°ΡΡΡΠΎΡΠ½ΠΈΡ (Π²ΡΠ΅ΠΌΡ) ΡΡΠ°Π½ΡΠΏΠΎΡΡΠΈΡΠΎΠ²Π°Π½ΠΈΡ, ΠΏΠΎΡΠ»Π΅ ΠΊΠΎΡΠΎΡΡΡ Π°Π²ΡΠΎΠΌΠΎΠ±ΠΈΠ»Ρ ΠΎΡΡΠ°Π΅ΡΡΡ ΠΏΡΠΈΠ³ΠΎΠ΄Π½ΡΠΌ ΠΊ Π΄Π°Π»ΡΠ½Π΅ΠΉΡΠ΅ΠΉ ΡΠΊΡΠΏΠ»ΡΠ°ΡΠ°ΡΠΈΠΈ Π±Π΅Π· ΡΠ΅ΠΌΠΎΠ½ΡΠ°. ΠΠΎΠΊΠ°Π·Π°ΡΠ΅Π»Π΅ΠΌ ΡΠΎΡ ΡΠ°Π½ΡΠ΅ΠΌΠΎΡΡΠΈ ΠΌΠΎΠΆΠ΅Ρ ΡΠ»ΡΠΆΠΈΡΡ, Π½Π°ΠΏΡΠΈΠΌΠ΅Ρ, ΡΡΠ΅Π΄Π½ΠΈΠΉ ΡΡΠΎΠΊ ΡΠΎΡ ΡΠ°Π½Π½ΠΎΡΡΠΈ.
Π‘ΠΎΡ ΡΠ°Π½ΡΠ΅ΠΌΠΎΡΡΡ Π°Π²ΡΠΎΠΌΠΎΠ±ΠΈΠ»Ρ Π·Π°Π²ΠΈΡΠΈΡ ΠΎΡ ΠΊΠ°ΡΠ΅ΡΡΠ²Π° Π΅Π³ΠΎ ΠΈΠ·Π³ΠΎΡΠΎΠ²Π»Π΅Π½ΠΈΡ, ΠΈΠ½ΡΠ΅Π½ΡΠΈΠ²Π½ΠΎΡΡΠΈ ΠΏΡΠΎΡΠ΅ΠΊΠ°Π½ΠΈΡ Π² Π΅Π³ΠΎ ΡΠ»Π΅ΠΌΠ΅Π½ΡΠ°Ρ Π½Π΅ΠΎΠ±ΡΠ°ΡΠΈΠΌΡΡ ΠΏΡΠΎΡΠ΅ΡΡΠΎΠ² (ΡΡΠ°ΡΠ΅Π½ΠΈΡ, ΠΊΠΎΡΡΠΎΠ·ΠΈΠΈ), Π²Π½Π΅ΡΠ½ΠΈΡ ΡΠ°ΠΊΡΠΎΡΠΎΠ² (ΡΠ΅ΠΌΠΏΠ΅ΡΠ°ΡΡΡΡ ΠΈ Π²Π»Π°ΠΆΠ½ΠΎΡΡΠΈ Π²ΠΎΠ·Π΄ΡΡ Π°, Π°Π³ΡΠ΅ΡΡΠΈΠ²Π½ΠΎΡΡΠΈ ΡΡΠ΅Π΄Ρ, ΡΠΎΠ»Π½Π΅ΡΠ½ΠΎΠΉ ΡΠ°Π΄ΠΈΠ°ΡΠΈΠΈ). ΠΠ° ΡΡΠΎΠΊ ΡΠΎΡ ΡΠ°Π½ΡΠ΅ΠΌΠΎΡΡΠΈ Π±ΠΎΠ»ΡΡΠΎΠ΅ Π²Π»ΠΈΡΠ½ΠΈΠ΅ ΠΎΠΊΠ°Π·ΡΠ²Π°Π΅Ρ ΠΊΠ°ΡΠ΅ΡΡΠ²ΠΎ ΠΊΠΎΠ½ΡΠ΅ΡΠ²Π°ΡΠΈΠΈ ΠΈ ΠΎΠ±ΡΠ»ΡΠΆΠΈΠ²Π°Π½ΠΈΡ Π°Π²ΡΠΎΠΌΠΎΠ±ΠΈΠ»Ρ Π² ΠΏΡΠΎΡΠ΅ΡΡΠ΅ Ρ ΡΠ°Π½Π΅Π½ΠΈΡ, Π° ΡΠ°ΠΊΠΆΠ΅ ΡΠ²ΠΎΠΉΡΡΠ²ΠΎ ΠΏΡΠΈΠΌΠ΅Π½ΡΠ΅ΠΌΡΡ ΡΠΊΡΠΏΠ»ΡΠ°ΡΠ°ΡΠΈΠΎΠ½Π½ΡΡ ΠΌΠ°ΡΠ΅ΡΠΈΠ°Π»ΠΎΠ².
ΠΠΎΠ»Π³ΠΎΠ²Π΅ΡΠ½ΠΎΡΡΡ Π°Π²ΡΠΎΠΌΠΎΠ±ΠΈΠ»Ρ β ΡΠ²ΠΎΠΉΡΡΠ²ΠΎ ΡΠΎΡ ΡΠ°Π½ΡΡΡ ΡΠ°Π±ΠΎΡΠΎΡΠΏΠΎΡΠΎΠ±Π½ΠΎΡΡΡ Π΄ΠΎ ΠΏΡΠ΅Π΄Π΅Π»ΡΠ½ΠΎΠ³ΠΎ ΡΠΎΡΡΠΎΡΠ½ΠΈΡ Ρ Π½Π΅ΠΎΠ±Ρ ΠΎΠ΄ΠΈΠΌΡΠΌΠΈ ΠΏΠ΅ΡΠ΅ΡΡΠ²Π°ΠΌΠΈ Π΄Π»Ρ ΡΠ΅Ρ Π½ΠΈΡΠ΅ΡΠΊΠΈΡ ΠΎΠ±ΡΠ»ΡΠΆΠΈΠ²Π°Π½ΠΈΠΉ ΠΈ ΡΠ΅ΠΌΠΎΠ½ΡΠΎΠ². ΠΡΠ΅Π΄Π΅Π»ΡΠ½ΠΎΠ΅ ΡΠΎΡΡΠΎΡΠ½ΠΈΠ΅ Π°Π²ΡΠΎΠΌΠΎΠ±ΠΈΠ»Ρ ΠΌΠΎΠΆΠ΅Ρ ΠΎΠΏΡΠ΅Π΄Π΅Π»ΡΡΡΡΡ ΠΏΠΎ ΠΈΠ·Π½ΠΎΡΡ Π΅Π³ΠΎ Π±Π°Π·ΠΎΠ²ΡΡ ΠΈ ΠΎΡΠ½ΠΎΠ²Π½ΡΡ Π΄Π΅ΡΠ°Π»Π΅ΠΉ, ΠΏΠΎ ΡΡΠ»ΠΎΠ²ΠΈΡΠΌ Π±Π΅Π·ΠΎΠΏΠ°ΡΠ½ΠΎΡΡΠΈ Π΄Π²ΠΈΠΆΠ΅Π½ΠΈΡ, ΠΏΠΎ ΠΈΠ·ΠΌΠ΅Π½Π΅Π½ΠΈΡ ΡΠΊΡΠΏΠ»ΡΠ°ΡΠ°ΡΠΈΠΎΠ½Π½ΡΡ ΡΠ²ΠΎΠΉΡΡΠ² ΠΈ ΠΎΠ³ΠΎΠ²Π°ΡΠΈΠ²Π°Π΅ΡΡΡ Π² ΡΠ΅Ρ Π½ΠΈΡΠ΅ΡΠΊΠΎΠΉ Π΄ΠΎΠΊΡΠΌΠ΅Π½ΡΠ°ΡΠΈΠΈ. ΠΠ°ΠΈΠ±ΠΎΠ»Π΅Π΅ ΡΠ°ΡΡΠΎ ΠΏΡΠ΅Π΄Π΅Π»ΡΠ½ΠΎΠ΅ ΡΠΎΡΡΠΎΡΠ½ΠΈΠ΅ Π°Π²ΡΠΎΠΌΠΎΠ±ΠΈΠ»Ρ ΠΎΠΏΡΠ΅Π΄Π΅Π»ΡΡΡ ΠΏΠΎ ΡΠΊΠΎΠ½ΠΎΠΌΠΈΡΠ΅ΡΠΊΠΈΠΌ ΠΏΠΎΠΊΠ°Π·Π°ΡΠ΅Π»ΡΠΌ.
ΠΠΎΠΊΠ°Π·Π°ΡΠ΅Π»ΡΠΌΠΈ Π΄ΠΎΠ»Π³ΠΎΠ²Π΅ΡΠ½ΠΎΡΡΠΈ Π°Π²ΡΠΎΠΌΠΎΠ±ΠΈΠ»Ρ ΠΌΠΎΠ³ΡΡ ΡΠ»ΡΠΆΠΈΡΡ, Π½Π°ΠΏΡΠΈΠΌΠ΅Ρ, ΡΠ΅ΡΡΡΡ (ΠΏΡΠΎΠ±Π΅Π³ Π°Π²ΡΠΎΠΌΠΎΠ±ΠΈΠ»Ρ ΠΈΠ»ΠΈ Π΅Π³ΠΎ Π°Π³ΡΠ΅Π³Π°ΡΠ° Π΄ΠΎ ΠΏΡΠ΅Π΄Π΅Π»ΡΠ½ΠΎΠ³ΠΎ ΡΠΎΡΡΠΎΡΠ½ΠΈΡ, ΠΎΠ³ΠΎΠ²ΠΎΡΠ΅Π½Π½ΠΎΠ³ΠΎ Π² ΡΠ΅Ρ Π½ΠΈΡΠ΅ΡΠΊΠΎΠΉ Π΄ΠΎΠΊΡΠΌΠ΅Π½ΡΠ°ΡΠΈΠΈ) ΠΈΠ»ΠΈ ΡΡΠΎΠΊ ΡΠ»ΡΠΆΠ±Ρ (ΠΊΠ°Π»Π΅Π½Π΄Π°ΡΠ½Π°Ρ ΠΏΡΠΎΠ΄ΠΎΠ»ΠΆΠΈΡΠ΅Π»ΡΠ½ΠΎΡΡΡ ΡΠΊΡΠΏΠ»ΡΠ°ΡΠ°ΡΠΈΠΈ Π°Π²ΡΠΎΠΌΠΎΠ±ΠΈΠ»Ρ Π΄ΠΎ ΠΏΡΠ΅Π΄Π΅Π»ΡΠ½ΠΎΠ³ΠΎ ΡΠΎΡΡΠΎΡΠ½ΠΈΡ, ΠΎΠ³ΠΎΠ²ΠΎΡΠ΅Π½Π½ΠΎΠ³ΠΎ Π² ΡΠ΅Ρ Π½ΠΈΡΠ΅ΡΠΊΠΎΠΉ Π΄ΠΎΠΊΡΠΌΠ΅Π½ΡΠ°ΡΠΈΠΈ). Π ΠΏΡΠ°ΠΊΡΠΈΠΊΠ΅ ΡΠΊΡΠΏΠ»ΡΠ°ΡΠ°ΡΠΈΠΈ Π°Π²ΡΠΎΠΌΠΎΠ±ΠΈΠ»Π΅ΠΉ ΠΎΡΠ½ΠΎΠ²Π½ΡΠΌ ΠΏΠΎΠΊΠ°Π·Π°ΡΠ΅Π»Π΅ΠΌ Π΄ΠΎΠ»Π³ΠΎΠ²Π΅ΡΠ½ΠΎΡΡΠΈ Π°Π²ΡΠΎΠΌΠΎΠ±ΠΈΠ»Ρ (Π°Π³ΡΠ΅Π³Π°ΡΠ°) ΠΏΡΠΈΠ½ΠΈΠΌΠ°ΡΡ ΡΡΠ΅Π΄Π½ΠΈΠΉ ΠΏΡΠΎΠ±Π΅Π³ Π΄ΠΎ ΠΏΠ΅ΡΠ²ΠΎΠ³ΠΎ ΠΊΠ°ΠΏΠΈΡΠ°Π»ΡΠ½ΠΎΠ³ΠΎ ΡΠ΅ΠΌΠΎΠ½ΡΠ°. Π ΡΡΠΎΠΌ ΡΠ»ΡΡΠ°Π΅ ΠΎΡΠ΅Π½Ρ Π²Π°ΠΆΠ½ΠΎ ΡΠΎΡΠ½ΠΎ ΠΎΠ³ΠΎΠ²ΠΎΡΠΈΡΡ ΠΏΠΎΠ½ΡΡΠΈΠ΅ Β«ΠΊΠ°ΠΏΠΈΡΠ°Π»ΡΠ½ΡΠΉ ΡΠ΅ΠΌΠΎΠ½ΡΒ» ΠΏΡΠΈΠΌΠ΅Π½ΠΈΡΠ΅Π»ΡΠ½ΠΎ ΠΊ Π°Π²ΡΠΎΠΌΠΎΠ±ΠΈΠ»Ρ ΠΈΠ»ΠΈ Π°Π³ΡΠ΅Π³Π°ΡΡ (ΡΠ·Π»Ρ).
Π Π°Π±ΠΎΡΠΎΡΠΏΠΎΡΠΎΠ±Π½ΠΎΡΡΡ Π°Π²ΡΠΎΠΌΠΎΠ±ΠΈΠ»Ρ β ΡΠΎΡΡΠΎΡΠ½ΠΈΠ΅, ΠΏΡΠΈ ΠΊΠΎΡΠΎΡΠΎΠΌ ΠΎΠ½ ΠΌΠΎΠΆΠ΅Ρ Π²ΡΠΏΠΎΠ»Π½ΡΡΡ Π·Π°Π΄Π°Π½Π½ΡΠ΅ ΡΡΠ½ΠΊΡΠΈΠΈ Ρ ΠΏΠ°ΡΠ°ΠΌΠ΅ΡΡΠ°ΠΌΠΈ, ΡΡΡΠ°Π½ΠΎΠ²Π»Π΅Π½Π½ΡΠΌΠΈ ΡΡΠ΅Π±ΠΎΠ²Π°Π½ΠΈΡΠΌΠΈ ΡΠ΅Ρ Π½ΠΈΡΠ΅ΡΠΊΠΎΠΉ Π΄ΠΎΠΊΡΠΌΠ΅Π½ΡΠ°ΡΠΈΠΈ.
ΠΠ°Π΄Π΅ΠΆΠ½ΠΎΡΡΡ Π°Π²ΡΠΎΠΌΠΎΠ±ΠΈΠ»Ρ Π·Π°ΠΊΠ»Π°Π΄ΡΠ²Π°Π΅ΡΡΡ ΠΏΡΠΈ Π΅Π³ΠΎ ΠΏΡΠΎΠ΅ΠΊΡΠΈΡΠΎΠ²Π°Π½ΠΈΠΈ ΠΈ Π΄ΠΎΠ²ΠΎΠ΄ΠΊΠ΅ ΠΎΠΏΡΡΠ½ΠΎΠ³ΠΎ ΠΎΠ±ΡΠ°Π·ΡΠ°, ΠΎΠ±Π΅ΡΠΏΠ΅ΡΠΈΠ²Π°Π΅ΡΡΡ Π² ΠΏΡΠΎΡΠ΅ΡΡΠ΅ ΠΏΡΠΎΠΈΠ·Π²ΠΎΠ΄ΡΡΠ²Π° ΠΈ ΠΊΠ°ΠΊ ΠΎΠ΄Π½ΠΎ ΠΈΠ· Π²Π°ΠΆΠ½Π΅ΠΉΡΠΈΡ ΡΠΊΡΠΏΠ»ΡΠ°ΡΠ°ΡΠΈΠΎΠ½Π½ΡΡ ΡΠ²ΠΎΠΉΡΡΠ² ΠΏΡΠΎΡΠ²Π»ΡΠ΅ΡΡΡ ΠΈ ΠΏΠΎΠ΄Π΄Π΅ΡΠΆΠΈΠ²Π°Π΅ΡΡΡ Π² ΠΏΡΠΎΡΠ΅ΡΡΠ΅ ΡΠΊΡΠΏΠ»ΡΠ°ΡΠ°ΡΠΈΠΈ. ΠΡΡ ΠΎΠ΄Ρ ΠΈΠ· ΡΡΠΎΠ³ΠΎ, ΡΠ»Π΅Π΄ΡΠ΅Ρ ΡΠ°ΡΡΠΌΠ°ΡΡΠΈΠ²Π°ΡΡ ΠΊΠΎΠ½ΡΡΡΡΠΊΡΠΈΠ²Π½ΡΡ, ΠΏΡΠΎΠΈΠ·Π²ΠΎΠ΄ΡΡΠ²Π΅Π½Π½ΡΡ ΠΈ ΡΠΊΡΠΏΠ»ΡΠ°ΡΠ°ΡΠΈΠΎΠ½Π½ΡΡ Π½Π°Π΄Π΅ΠΆΠ½ΠΎΡΡΡ Π°Π²ΡΠΎΠΌΠΎΠ±ΠΈΠ»Ρ. ΠΠΎ ΠΌΠ΅ΡΠ΅ ΡΠ°Π·Π²ΠΈΡΠΈΡ ΠΈ ΡΠΎΠ²Π΅ΡΡΠ΅Π½ΡΡΠ²ΠΎΠ²Π°Π½ΠΈΡ ΠΌΠ΅ΡΠΎΠ΄ΠΎΠ² ΡΠ°ΡΡΠ΅ΡΠΎΠ², ΠΊΠΎΠ½ΡΡΡΡΠΈΡΠΎΠ²Π°Π½ΠΈΡ ΠΈ ΡΠ΅Ρ Π½ΠΎΠ»ΠΎΠ³ΠΈΠΈ ΠΏΡΠΎΠΈΠ·Π²ΠΎΠ΄ΡΡΠ²Π° Π°Π²ΡΠΎΠΌΠΎΠ±ΠΈΠ»Π΅ΠΉ, Π²Π½Π΅Π΄ΡΠ΅Π½ΠΈΡ Π½Π°ΡΡΠ½ΠΎ ΠΎΠ±ΠΎΡΠ½ΠΎΠ²Π°Π½Π½ΡΡ ΠΌΠ΅ΡΠΎΠ΄ΠΎΠ² ΡΠ΅Ρ Π½ΠΈΡΠ΅ΡΠΊΠΎΠΉ ΡΠΊΡΠΏΠ»ΡΠ°ΡΠ°ΡΠΈΠΈ, ΡΠΊΡΠΏΠ»ΡΠ°ΡΠ°ΡΠΈΠΎΠ½Π½Π°Ρ Π½Π°Π΄Π΅ΠΆΠ½ΠΎΡΡΡ Π°Π²ΡΠΎΠΌΠΎΠ±ΠΈΠ»Ρ ΠΏΠΎ ΡΠ²ΠΎΠ΅ΠΌΡ ΡΡΠΎΠ²Π½Ρ Π±ΡΠ΄Π΅Ρ ΠΏΡΠΈΠ±Π»ΠΈΠΆΠ°ΡΡΡΡ ΠΊ ΠΊΠΎΠ½ΡΡΡΡΠΊΡΠΈΠ²Π½ΠΎΠΉ Π½Π°Π΄Π΅ΠΆΠ½ΠΎΡΡΠΈ.
ΠΠ°Π΄Π΅ΠΆΠ½ΠΎΡΡΡ Π°Π²ΡΠΎΠΌΠΎΠ±ΠΈΠ»Ρ Π½Π΅ ΠΎΡΡΠ°Π΅ΡΡΡ ΠΏΠΎΡΡΠΎΡΠ½Π½ΠΎΠΉ Π² ΡΠ΅ΡΠ΅Π½ΠΈΠ΅ Π²ΡΠ΅Π³ΠΎ ΡΡΠΎΠΊΠ° ΡΠ»ΡΠΆΠ±Ρ. ΠΠΎ ΠΌΠ΅ΡΠ΅ ΠΈΠ·Π½Π°ΡΠΈΠ²Π°Π½ΠΈΡ Π΄Π΅ΡΠ°Π»Π΅ΠΉ, Π½Π°ΠΊΠΎΠΏΠ»Π΅Π½ΠΈΡ Π² Π½ΠΈΡ Π½Π΅ΠΎΠ±ΡΠ°ΡΠΈΠΌΡΡ ΠΏΡΠΎΡΠ΅ΡΡΠΎΠ² (ΡΡΡΠ°Π»ΠΎΡΡΠ½ΡΡ ΡΠ²Π»Π΅Π½ΠΈΠΉ, ΠΈΠ·Π½ΠΎΡΠ°, ΠΊΠΎΡΡΠΎΠ·ΠΈΠΈ) ΡΠ²Π΅Π»ΠΈΡΠΈΠ²Π°Π΅ΡΡΡ Π²Π΅ΡΠΎΡΡΠ½ΠΎΡΡΡ ΠΏΠΎΡΠ²Π»Π΅Π½ΠΈΡ Π½Π΅ΠΈΡΠΏΡΠ°Π²Π½ΠΎΡΡΠ΅ΠΉ ΠΈ ΠΎΡΠΊΠ°Π·ΠΎΠ². ΠΠΎΠ²ΡΠ΅ Π°Π²ΡΠΎΠΌΠΎΠ±ΠΈΠ»ΠΈ Π²ΡΠ΅Π³Π΄Π° ΠΈΠΌΠ΅ΡΡ Π±ΠΎΠ»Π΅Π΅ Π²ΡΡΠΎΠΊΡΡ Π½Π°Π΄Π΅ΠΆΠ½ΠΎΡΡΡ ΠΏΠΎ ΡΡΠ°Π²Π½Π΅Π½ΠΈΡ Ρ Π°Π²ΡΠΎΠΌΠΎΠ±ΠΈΠ»ΡΠΌΠΈ, ΠΈΠΌΠ΅ΡΡΠΈΠΌΠΈ Π±ΠΎΠ»ΡΡΠΎΠΉ ΠΏΡΠΎΠ±Π΅Π³ ΠΈΠ»ΠΈ ΠΏΡΠΎΡΠ΅Π΄ΡΠΈΠΌΠΈ ΠΊΠ°ΠΏΠΈΡΠ°Π»ΡΠ½ΡΠΉ ΡΠ΅ΠΌΠΎΠ½Ρ.
ΠΡΠ½ΠΎΠ²Π½Π°Ρ Π·Π°Π΄Π°ΡΠ° ΡΠ°ΡΠΈΠΎΠ½Π°Π»ΡΠ½ΠΎΠΉ ΡΠ΅Ρ Π½ΠΈΡΠ΅ΡΠΊΠΎΠΉ ΡΠΊΡΠΏΠ»ΡΠ°ΡΠ°ΡΠΈΠΈ Π°Π²ΡΠΎΠΌΠΎΠ±ΠΈΠ»Ρ Π·Π°ΠΊΠ»ΡΡΠ°Π΅ΡΡΡ ΠΏΡΠ΅ΠΆΠ΄Π΅ Π²ΡΠ΅Π³ΠΎ Π² ΡΠΎΠΌ, ΡΡΠΎΠ±Ρ ΠΊΠ°ΠΊ ΠΌΠΎΠΆΠ½ΠΎ Π΄ΠΎΠ»ΡΡΠ΅ ΡΠΎΡ ΡΠ°Π½ΠΈΡΡ Π·Π°Π»ΠΎΠΆΠ΅Π½Π½ΡΡ Π² Π½Π΅ΠΌ Π½Π°Π΄Π΅ΠΆΠ½ΠΎΡΡΡ.
Π€ΡΠ½Π΄Π°ΠΌΠ΅Π½ΡΠ°Π»ΡΠ½ΡΠΌ ΠΏΠΎΠ½ΡΡΠΈΠ΅ΠΌ Π² ΡΠ΅ΠΎΡΠΈΠΈ Π½Π°Π΄Π΅ΠΆΠ½ΠΎΡΡΠΈ ΡΠ²Π»ΡΠ΅ΡΡΡ ΠΏΠΎΠ½ΡΡΠΈΠ΅ ΠΎΡΠΊΠ°Π·Π°.
ΠΡΠΊΠ°Π· Π°Π²ΡΠΎΠΌΠΎΠ±ΠΈΠ»Ρ βΡΡΠΎ ΡΠΎΠ±ΡΡΠΈΠ΅, Π·Π°ΠΊΠ»ΡΡΠ°ΡΡΠ΅Π΅ΡΡ Π² Π½Π°ΡΡΡΠ΅Π½ΠΈΠΈ ΡΠ°Π±ΠΎΡΠΎΡΠΏΠΎΡΠΎΠ±Π½ΠΎΡΡΠΈ. ΠΡΠΊΠ°Π· ΠΌΠΎΠΆΠ΅Ρ ΠΏΡΠΎΠΈΠ·ΠΎΠΉΡΠΈ Π²ΡΠ»Π΅Π΄ΡΡΠ²ΠΈΠ΅ ΡΠ°Π·ΡΡΡΠ΅Π½ΠΈΡ, Π΄Π΅ΡΠΎΡΠΌΠ°ΡΠΈΠΈ ΠΈΠ»ΠΈ ΠΈΠ·Π½ΠΎΡΠ° Π΄Π΅ΡΠ°Π»Π΅ΠΉ, Π½Π°ΡΡΡΠ΅Π½ΠΈΡ ΡΠ΅Π³ΡΠ»ΠΈΡΠΎΠ²ΠΎΠΊ ΠΌΠ΅Ρ Π°Π½ΠΈΠ·ΠΌΠΎΠ² ΠΈΠ»ΠΈ ΡΠΈΡΡΠ΅ΠΌ, ΠΏΡΠ΅ΠΊΡΠ°ΡΠ΅Π½ΠΈΡ ΠΏΠΎΠ΄Π°ΡΠΈ ΡΠΎΠΏΠ»ΠΈΠ²Π°, ΡΠΌΠ°Π·ΠΊΠΈ ΠΈΠ»ΠΈ ΡΠ°ΠΊΠΎΠ³ΠΎ ΠΈΠ·ΠΌΠ΅Π½Π΅Π½ΠΈΡ ΡΠ°Π±ΠΎΡΠΈΡ Ρ Π°ΡΠ°ΠΊΡΠ΅ΡΠΈΡΡΠΈΠΊ Π°Π²ΡΠΎΠΌΠΎΠ±ΠΈΠ»Ρ (ΠΏΠΎΡΠ΅ΡΡ ΠΌΠΎΡΠ½ΠΎΡΡΠΈ, ΠΏΠ΅ΡΠ΅ΡΠ°ΡΡ ΠΎΠ΄ ΡΠΌΠ°Π·ΠΊΠΈ, Π±ΠΎΠ»ΡΡΠΎΠΉ ΡΠΎΡΠΌΠΎΠ·Π½ΠΎΠΉ ΠΏΡΡΡ ΠΈ Π΄Ρ.) ΠΈΠ»ΠΈ Π΅Π³ΠΎ ΡΠ»Π΅ΠΌΠ΅Π½ΡΠΎΠ², ΠΊΠΎΠ³Π΄Π° ΠΎΠ½ΠΈ Π²ΡΡ ΠΎΠ΄ΡΡ Π·Π° ΠΏΡΠ΅Π΄Π΅Π»Ρ Π΄ΠΎΠΏΡΡΡΠΈΠΌΡΡ Π½ΠΎΡΠΌ, ΠΎΠ³ΠΎΠ²ΠΎΡΠ΅Π½Π½ΡΡ ΡΠ΅Ρ Π½ΠΈΡΠ΅ΡΠΊΠΈΠΌΠΈ ΡΡΠ»ΠΎΠ²ΠΈΡΠΌΠΈ.
ΠΠ΅ΠΎΠ±Ρ ΠΎΠ΄ΠΈΠΌΠΎ ΡΠ°Π·Π»ΠΈΡΠ°ΡΡ ΡΠ°ΠΊΠΆΠ΅ ΠΏΠΎΠ½ΡΡΠΈΠ΅ Π½Π΅ΠΈΡΠΏΡΠ°Π²Π½ΠΎΡΡΡ Π°Π²ΡΠΎΠΌΠΎΠ±ΠΈΠ»Ρ (ΠΈΠ»ΠΈ Π΅Π³ΠΎ ΡΠ»Π΅ΠΌΠ΅Π½ΡΠ°) β ΡΠΎΡΡΠΎΡΠ½ΠΈΠ΅, ΠΏΡΠΈ ΠΊΠΎΡΠΎΡΠΎΠΌ ΠΎΠ½ Π½Π΅ ΡΠΎΠΎΡΠ²Π΅ΡΡΡΠ²ΡΠ΅Ρ Ρ ΠΎΡΡ Π±Ρ ΠΎΠ΄Π½ΠΎΠΌΡ ΠΈΠ· ΡΡΠ΅Π±ΠΎΠ²Π°Π½ΠΈΠΉ ΡΠ΅Ρ Π½ΠΈΡΠ΅ΡΠΊΠΎΠΉ Π΄ΠΎΠΊΡΠΌΠ΅Π½ΡΠ°ΡΠΈΠΈ. Π Π°Π·Π»ΠΈΡΠ°ΡΡ Π½Π΅ΠΈΡΠΏΡΠ°Π²Π½ΠΎΡΡΠΈ, Π½Π΅ ΠΏΡΠΈΠ²ΠΎΠ΄ΡΡΠΈΠ΅ ΠΊ ΠΎΡΠΊΠ°Π·Π°ΠΌ (ΡΠ°Π·ΡΡΡΠ΅Π½ΠΈΠ΅ ΠΎΠΊΡΠ°ΡΠΊΠΈ ΠΊΡΠ·ΠΎΠ²Π° Π°Π²ΡΠΎΠΌΠΎΠ±ΠΈΠ»Ρ, Π²ΠΌΡΡΠΈΠ½Ρ Π² ΠΊΠ°Π±ΠΈΠ½Π΅ ΠΈ Π΄ΡΡΠ³ΠΈΠ΅), ΠΈ Π½Π΅ΠΈΡΠΏΡΠ°Π²Π½ΠΎΡΡΠΈ (ΠΈ ΠΈΡ ΡΠΎΡΠ΅ΡΠ°Π½ΠΈΡ), Π²ΡΠ·ΡΠ²Π°ΡΡΠΈΠ΅ ΠΎΡΠΊΠ°Π·Ρ.
ΠΠ»Ρ ΡΠΎΠ³ΠΎ ΡΡΠΎΠ±Ρ ΡΠΎΡΠ½ΠΎ ΠΎΠΏΡΠ΅Π΄Π΅Π»ΠΈΡΡ ΠΏΠΎΠ½ΡΡΠΈΠ΅ ΠΎΡΠΊΠ°Π· ΠΈ Π·Π°ΡΠΈΠΊΡΠΈΡΠΎΠ²Π°ΡΡ Π²ΡΠ΅ ΡΠ»ΡΡΠ°ΠΈ ΠΎΡΠΊΠ°Π·ΠΎΠ², Π½Π΅ΠΎΠ±Ρ ΠΎΠ΄ΠΈΠΌΠΎ ΡΠΎΡΠ½ΠΎ ΡΡΠΎΡΠΌΡΠ»ΠΈΡΠΎΠ²Π°ΡΡ ΠΏΠΎΠ½ΡΡΠΈΠ΅ Π½ΠΎΡΠΌΠ°Π»ΡΠ½ΠΎΠ³ΠΎ ΡΡΠ½ΠΊΡΠΈΠΎΠ½ΠΈΡΠΎΠ²Π°Π½ΠΈΡ Π°Π²ΡΠΎΠΌΠΎΠ±ΠΈΠ»Ρ (ΠΎΠ±ΡΡΠ»ΠΎΠ²ΠΈΡΡ ΠΏΡΠ΅Π΄Π΅Π»Ρ Π΄ΠΎΠΏΡΡΡΠΈΠΌΠΎΠ³ΠΎ ΠΈΠ·ΠΌΠ΅Π½Π΅Π½ΠΈΡ ΡΠ°Π±ΠΎΡΠΈΡ Ρ Π°ΡΠ°ΠΊΡΠ΅ΡΠΈΡΡΠΈΠΊ Π°Π²ΡΠΎΠΌΠΎΠ±ΠΈΠ»Ρ Π² ΡΠ΅Π»ΠΎΠΌ ΠΈ Π΅Π³ΠΎ ΠΎΡΠ΄Π΅Π»ΡΠ½ΡΡ ΡΠ»Π΅ΠΌΠ΅Π½ΡΠΎΠ² Ρ ΡΡΠ΅ΡΠΎΠΌ ΡΡΠ΅Π±ΠΎΠ²Π°Π½ΠΈΠΉ ΡΠΊΡΠΏΠ»ΡΠ°ΡΠ°ΡΠΈΠΈ).
Π Π·Π°Π²ΠΈΡΠΈΠΌΠΎΡΡΠΈ ΠΎΡ ΠΏΠΎΡΡΠ°Π²Π»Π΅Π½Π½ΠΎΠΉ ΠΈΡΡΠ»Π΅Π΄ΠΎΠ²Π°ΡΠ΅Π»Π΅ΠΌ Π·Π°Π΄Π°ΡΠΈ ΠΎΡΠΊΠ°Π·Ρ Π°Π²ΡΠΎΠΌΠΎΠ±ΠΈΠ»Ρ ΠΌΠΎΠΆΠ½ΠΎ ΠΊΠ»Π°ΡΡΠΈΡΠΈΡΠΈΡΠΎΠ²Π°ΡΡ ΠΏΠΎ ΡΠ°Π·Π»ΠΈΡΠ½ΡΠΌ ΠΏΡΠΈΠ·Π½Π°ΠΊΠ°ΠΌ. ΠΠ»Ρ Π°Π½Π°Π»ΠΈΠ·Π° ΡΠΈΠ·ΠΈΡΠ΅ΡΠΊΠΎΠΉ ΠΏΡΠΈΡΠΎΠ΄Ρ ΠΎΡΠΊΠ°Π·ΠΎΠ², ΠΈΡ Π²Π·Π°ΠΈΠΌΠΎΡΠ²ΡΠ·ΠΈ Π΄Π»Ρ ΡΠ°Π·ΡΠ°Π±ΠΎΡΠΊΠΈ ΠΌΠ΅Ρ ΠΏΠΎ ΠΈΡ ΠΏΡΠΎΠ³Π½ΠΎΠ·ΠΈΡΠΎΠ²Π°Π½ΠΈΡ ΠΎΡΠΊΠ°Π·Ρ ΡΠ΅Π»Π΅ΡΠΎΠΎΠ±ΡΠ°Π·Π½ΠΎ ΠΊΠ»Π°ΡΡΠΈΡΠΈΡΠΈΡΠΎΠ²Π°ΡΡ ΠΏΠΎ ΡΠ»Π΅Π΄ΡΡΡΠΈΠΌ ΠΏΡΠΈΠ·Π½Π°ΠΊΠ°ΠΌ: ΠΏΠΎ ΠΈΡ Π²Π·Π°ΠΈΠΌΠΎΡΠ²ΡΠ·ΠΈ β Π½Π° Π·Π°Π²ΠΈΡΠΈΠΌΡΠ΅, Ρ. Π΅. Π²ΠΎΠ·Π½ΠΈΠΊΡΠΈΠ΅ Π² ΡΠ΅Π·ΡΠ»ΡΡΠ°ΡΠ΅ ΠΎΡΠΊΠ°Π·Π° Π΄ΡΡΠ³ΠΈΡ ΡΠ»Π΅ΠΌΠ΅Π½ΡΠΎΠ², ΠΈ Π½Π΅Π·Π°Π²ΠΈΡΠΈΠΌΡΠ΅. ΠΡΠΈ Π°Π½Π°Π»ΠΈΠ·Π΅ ΡΠΊΡΠΏΠ»ΡΠ°ΡΠ°ΡΠΈΠΎΠ½Π½ΠΎΠΉ Π½Π°Π΄Π΅ΠΆΠ½ΠΎΡΡΠΈ Π°Π²ΡΠΎΠΌΠΎΠ±ΠΈΠ»Ρ Π³Π»Π°Π²Π½ΠΎΠ΅ Π²Π½ΠΈΠΌΠ°Π½ΠΈΠ΅ ΡΠ»Π΅Π΄ΡΠ΅Ρ ΡΠ΄Π΅Π»ΡΡΡ ΠΏΠ΅ΡΠ²ΠΎΠΏΡΠΈΡΠΈΠ½Π°ΠΌ, ΠΎΠ±ΡΡΠ»ΠΎΠ²Π»ΠΈΠ²Π°ΡΡΠΈΠΌ Π²ΠΎΠ·Π½ΠΈΠΊΠ½ΠΎΠ²Π΅Π½ΠΈΠ΅ Π·Π°Π²ΠΈΡΠΈΠΌΡΡ ΠΎΡΠΊΠ°Π·ΠΎΠ². ΠΠΎΡΠΎΠΊ Π·Π°Π²ΠΈΡΠΈΠΌΡΡ ΠΎΡΠΊΠ°Π·ΠΎΠ² Π² ΠΏΡΠΎΡΠ΅ΡΡΠ΅ ΡΠΊΡΠΏΠ»ΡΠ°ΡΠ°ΡΠΈΠΈ ΡΠ²ΠΈΠ΄Π΅ΡΠ΅Π»ΡΡΡΠ²ΡΠ΅Ρ ΠΎ Π½Π΅ΡΠΎΠ²Π΅ΡΡΠ΅Π½ΡΡΠ²Π΅ Π²ΡΠ±ΡΠ°Π½Π½ΠΎΠΉ ΡΡΡΡΠΊΡΡΡΠ½ΠΎΠΉ ΡΡ Π΅ΠΌΡ ΡΠ»ΠΎΠΆΠ½ΡΡ ΡΠ»Π΅ΠΌΠ΅Π½ΡΠΎΠ² Π°Π²ΡΠΎΠΌΠΎΠ±ΠΈΠ»Ρ.
ΠΠΎ ΠΏΠΎΡΠ»Π΅Π΄ΡΡΠ²ΠΈΡΠΌ ΠΎΡΠΊΠ°Π·Ρ Π΄Π΅Π»ΡΡΡΡ Π½Π° ΠΎΠΏΠ°ΡΠ½ΡΠ΅ ΠΈ Π±Π΅Π·ΠΎΠΏΠ°ΡΠ½ΡΠ΅. ΠΠΏΠ°ΡΠ½ΡΠ΅ ΠΎΡΠΊΠ°Π·Ρ β ΡΡΠΎ ΡΠ°ΠΊΠΈΠ΅, Π²ΠΎΠ·Π½ΠΈΠΊΠ½ΠΎΠ²Π΅Π½ΠΈΠ΅ ΠΊΠΎΡΠΎΡΡΡ ΠΏΡΠ΅Π΄ΡΡΠ°Π²Π»ΡΠ΅Ρ ΠΎΠΏΠ°ΡΠ½ΠΎΡΡΡ Π΄Π»Ρ ΠΆΠΈΠ·Π½ΠΈ ΠΈΠ»ΠΈ Π·Π΄ΠΎΡΠΎΠ²ΡΡ Π»ΡΠ΄Π΅ΠΉ, ΠΎΠ±ΡΠ»ΡΠΆΠΈΠ²Π°ΡΡΠΈΡ ΠΈΠ»ΠΈ ΠΏΠΎΠ»ΡΠ·ΡΡΡΠΈΡ ΡΡ Π°Π²ΡΠΎΠΌΠΎΠ±ΠΈΠ»Π΅ΠΌ. ΠΠΏΠ°ΡΠ½ΡΠ΅ ΠΎΡΠΊΠ°Π·Ρ ΠΌΠΎΠ³ΡΡ Π²ΠΎΠ·Π½ΠΈΠΊΠ°ΡΡ Π² ΠΌΠ΅Ρ Π°Π½ΠΈΠ·ΠΌΠ°Ρ ΡΠΏΡΠ°Π²Π»Π΅Π½ΠΈΡ Π°Π²ΡΠΎΠΌΠΎΠ±ΠΈΠ»Ρ (ΡΡΠ»Π΅Π²ΠΎΠΌ ΡΠΏΡΠ°Π²Π»Π΅Π½ΠΈΠΈ, ΡΠΎΡΠΌΠΎΠ·Π°Ρ ).
ΠΠΎ Ρ Π°ΡΠ°ΠΊΡΠ΅ΡΡ ΠΈΠ·ΠΌΠ΅Π½Π΅Π½ΠΈΡ ΡΠΎΡΡΠΎΡΠ½ΠΈΡ Π°Π²ΡΠΎΠΌΠΎΠ±ΠΈΠ»Ρ (Π°Π³ΡΠ΅Π³Π°ΡΠ°, ΠΌΠ΅Ρ Π°Π½ΠΈΠ·ΠΌΠ°) ΠΎΡΠΊΠ°Π·Ρ ΠΌΠΎΠ³ΡΡ Π±ΡΡΡ Π²Π½Π΅Π·Π°ΠΏΠ½ΡΠ΅ ΠΈΠ»ΠΈ ΠΏΠΎΡΡΠ΅ΠΏΠ΅Π½Π½ΡΠ΅. Π’Π°ΠΊΠΎΠ΅ Π΄Π΅Π»Π΅Π½ΠΈΠ΅ ΠΎΡΠΊΠ°Π·ΠΎΠ² ΡΠ²Π»ΡΠ΅ΡΡΡ ΡΡΠ»ΠΎΠ²Π½ΡΠΌ. ΠΠ½Π΅Π·Π°ΠΏΠ½ΡΠ΅ ΠΎΡΠΊΠ°Π·Ρ Π² Π±ΠΎΠ»ΡΡΠΈΠ½ΡΡΠ²Π΅ ΡΠ»ΡΡΠ°Π΅Π² ΡΠ²Π»ΡΡΡΡΡ ΡΠ»Π΅Π΄ΡΡΠ²ΠΈΠ΅ΠΌ ΠΏΠΎΡΡΠ΅ΠΏΠ΅Π½Π½ΠΎΠ³ΠΎ ΠΊΠ°ΡΠ΅ΡΡΠ²Π΅Π½Π½ΠΎΠ³ΠΎ ΠΈΠ·ΠΌΠ΅Π½Π΅Π½ΠΈΡ ΡΠΈΠ·ΠΈΠΊΠΎ-ΠΌΠ΅Ρ Π°Π½ΠΈΡΠ΅ΡΠΊΠΈΡ ΡΠ²ΠΎΠΉΡΡΠ² ΠΌΠ°ΡΠ΅ΡΠΈΠ°Π»ΠΎΠ², Π½ΠΎ ΡΠΊΡΡΡΠΎΠ³ΠΎ ΠΎΡ Π½Π°Π±Π»ΡΠ΄Π°ΡΠ΅Π»Ρ Π΄ΠΎ ΠΌΠΎΠΌΠ΅Π½ΡΠ° Π²Π½Π΅ΡΠ½Π΅Π³ΠΎ ΠΈΡ ΠΏΡΠΎΡΠ²Π»Π΅Π½ΠΈΡ.
ΠΠ»Ρ ΡΠ°Π·ΡΠ°Π±ΠΎΡΠΊΠΈ ΠΌΠ΅ΡΠΎΠΏΡΠΈΡΡΠΈΠΉ ΠΏΠΎ ΠΏΠΎΠ²ΡΡΠ΅Π½ΠΈΡ Π½Π°Π΄Π΅ΠΆΠ½ΠΎΡΡΠΈ Π°Π²ΡΠΎΠΌΠΎΠ±ΠΈΠ»Π΅ΠΉ Π²Π°ΠΆΠ½ΠΎΠ΅ Π·Π½Π°ΡΠ΅Π½ΠΈΠ΅ ΠΈΠΌΠ΅Π΅Ρ ΠΊΠ»Π°ΡΡΠΈΡΠΈΠΊΠ°ΡΠΈΡ ΠΎΡΠΊΠ°Π·ΠΎΠ² ΠΏΠΎ ΠΏΡΠΈΡΠΈΠ½Π°ΠΌ ΠΈΡ Π²ΠΎΠ·Π½ΠΈΠΊΠ½ΠΎΠ²Π΅Π½ΠΈΡ. ΠΠΎ ΡΡΠΎΠΉ ΠΊΠ»Π°ΡΡΠΈΡΠΈΠΊΠ°ΡΠΈΠΈ ΠΎΡΠΊΠ°Π·Ρ Π΄Π΅Π»ΡΡΡΡ Π½Π° ΠΊΠΎΠ½ΡΡΡΡΠΊΡΠΈΠΎΠ½Π½ΡΠ΅, ΡΠ΅Ρ Π½ΠΎΠ»ΠΎΠ³ΠΈΡΠ΅ΡΠΊΠΈΠ΅, ΡΠΊΡΠΏΠ»ΡΠ°ΡΠ°ΡΠΈΠΎΠ½Π½ΡΠ΅ ΠΈ ΠΈΠ·Π½ΠΎΡΠ½ΡΠ΅, ΠΎΠ±ΡΡΠ»ΠΎΠ²Π»Π΅Π½Π½ΡΠ΅ ΡΡΠ°ΡΠ΅Π½ΠΈΠ΅ΠΌ ΡΠ»Π΅ΠΌΠ΅Π½ΡΠΎΠ².
ΠΠΎΠ½ΡΡΡΡΠΊΡΠΈΠΎΠ½Π½ΡΠ΅ ΠΎΡΠΊΠ°Π·Ρ ΠΎΠ±ΡΡΠ»ΠΎΠ²Π»ΠΈΠ²Π°ΡΡΡΡ Π½Π΅ΡΠΎΠ²Π΅ΡΡΠ΅Π½Π½ΡΠΌΠΈ ΠΌΠ΅ΡΠΎΠ΄Π°ΠΌΠΈ ΠΊΠΎΠ½ΡΡΡΡΠΈΡΠΎΠ²Π°Π½ΠΈΡ Π°Π²ΡΠΎΠΌΠΎΠ±ΠΈΠ»Ρ ΠΈΠ»ΠΈ Π΅Π³ΠΎ ΡΠ»Π΅ΠΌΠ΅Π½ΡΠΎΠ², ΠΎΡΠΈΠ±ΠΊΠ°ΠΌΠΈ ΠΈ ΠΏΡΠΎΡΡΠ΅ΡΠ°ΠΌΠΈ, Π΄ΠΎΠΏΡΡΠ΅Π½Π½ΡΠΌΠΈ ΠΊΠΎΠ½ΡΡΡΡΠΊΡΠΎΡΠΎΠΌ. ΠΡΠΈ ΠΎΡΠΊΠ°Π·Ρ ΠΌΠΎΠ³ΡΡ ΠΏΠΎΡΠ²Π»ΡΡΡΡΡ, ΠΊΠΎΠ³Π΄Π° Π½Π΅ ΡΡΠΈΡΡΠ²Π°ΡΡΡΡ Β«ΠΏΠΈΠΊΠΎΠ²ΡΠ΅Β» (ΡΠ»ΡΡΠ°ΠΉΠ½ΡΠ΅) Π½Π°Π³ΡΡΠ·ΠΊΠΈ, Π²Π΅Π»ΠΈΡΠΈΠ½Π° ΠΊΠΎΡΠΎΡΡΡ Π·Π½Π°ΡΠΈΡΠ΅Π»ΡΠ½ΠΎ ΠΏΡΠ΅Π²ΡΡΠ°Π΅Ρ ΡΠΊΡΠΏΠ»ΡΠ°ΡΠ°ΡΠΈΠΎΠ½Π½ΡΠ΅ Π½Π°Π³ΡΡΠ·ΠΊΠΈ, Π½Π° ΠΊΠΎΡΠΎΡΡΠ΅ ΡΠ°ΡΡΡΠΈΡΠ°Π½ Π°Π²ΡΠΎΠΌΠΎΠ±ΠΈΠ»Ρ. ΠΡΠΎΡΠ²Π»ΡΡΡΡΡ ΠΊΠΎΠ½ΡΡΡΡΠΊΡΠΈΠΎΠ½Π½ΡΠ΅ ΠΎΡΠΊΠ°Π·Ρ ΠΏΡΠ΅ΠΈΠΌΡΡΠ΅ΡΡΠ²Π΅Π½Π½ΠΎ Π² ΠΏΠ΅ΡΠ²ΡΠ΅ ΠΏΠ΅ΡΠΈΠΎΠ΄Ρ ΡΠΊΡΠΏΠ»ΡΠ°ΡΠ°ΡΠΈΠΈ Π°Π²ΡΠΎΠΌΠΎΠ±ΠΈΠ»Ρ, ΠΎΠ΄Π½Π°ΠΊΠΎ ΠΎΠ½ΠΈ ΠΌΠΎΠ³ΡΡ Π²ΠΎΠ·Π½ΠΈΠΊΠ½ΡΡΡ ΠΈ Π½Π° Π±ΠΎΠ»Π΅Π΅ ΠΏΠΎΠ·Π΄Π½Π΅ΠΉ ΡΡΠ°Π΄ΠΈΠΈ ΡΠΊΡΠΏΠ»ΡΠ°ΡΠ°ΡΠΈΠΈ. Π₯Π°ΡΠ°ΠΊΡΠ΅ΡΠ½ΠΎΠΉ ΠΎΡΠΎΠ±Π΅Π½Π½ΠΎΡΡΡΡ ΡΡΠΈΡ ΠΎΡΠΊΠ°Π·ΠΎΠ² ΡΠ²Π»ΡΠ΅ΡΡΡ ΡΠΎ, ΡΡΠΎ ΠΎΠ½ΠΈ ΠΏΡΠΈΡΡΡΠΈ ΠΏΠΎ ΠΌΠ΅ΡΡΡ ΠΈ Π²ΡΠ΅ΠΌΠ΅Π½ΠΈ Π²ΡΠ΅ΠΌ ΡΠΊΠ·Π΅ΠΌΠΏΠ»ΡΡΠ°ΠΌ Π΄Π°Π½Π½ΠΎΠΉ ΡΠΈΡΡΠ΅ΠΌΡ (ΡΠ»Π΅ΠΌΠ΅Π½ΡΠ°).
Π’Π΅Ρ Π½ΠΎΠ»ΠΎΠ³ΠΈΡΠ΅ΡΠΊΠΈΠ΅ ΠΎΡΠΊΠ°Π·Ρ ΠΈΠΌΠ΅ΡΡ Π² ΡΠ²ΠΎΠ΅ΠΉ ΠΎΡΠ½ΠΎΠ²Π΅ Π½Π΅ΠΏΡΠ°Π²ΠΈΠ»ΡΠ½ΠΎ Π½Π°Π·Π½Π°ΡΠ΅Π½Π½ΡΠ΅ ΡΠ΅Ρ Π½ΠΎΠ»ΠΎΠ³ΠΈΡΠ΅ΡΠΊΠΈΠ΅ ΠΏΡΠΎΡΠ΅ΡΡΡ ΠΈΠ·Π³ΠΎΡΠΎΠ²Π»Π΅Π½ΠΈΡ Π΄Π΅ΡΠ°Π»Π΅ΠΉ ΠΈΠ»ΠΈ ΡΠ²Π»ΡΡΡΡΡ ΡΠ»Π΅Π΄ΡΡΠ²ΠΈΠ΅ΠΌ Π½Π°ΡΡΡΠ΅Π½ΠΈΡ ΠΏΡΠΈΠ½ΡΡΠΎΠΉ ΡΠ΅Ρ Π½ΠΎΠ»ΠΎΠ³ΠΈΠΈ ΡΠ±ΠΎΡΠΊΠΈ, ΡΠ΅Π³ΡΠ»ΠΈΡΠΎΠ²ΠΊΠΈ, ΠΏΡΠΈΡΠ°Π±ΠΎΡΠΊΠΈ ΠΈΠ»ΠΈ ΠΈΡΠΏΡΡΠ°Π½ΠΈΡ Π°Π²ΡΠΎΠΌΠΎΠ±ΠΈΠ»Ρ (Π°Π³ΡΠ΅Π³Π°ΡΠΎΠ²) Π½Π΅ΠΏΡΠ°Π²ΠΈΠ»ΡΠ½ΠΎ Π²ΡΠ±ΡΠ°Π½Π½ΡΠ΅ ΠΌΠ°ΡΠ΅ΡΠΈΠ°Π»Ρ, Π½Π΅ΡΡΠ°Π±ΠΈΠ»ΡΠ½ΠΎΡΡΡ ΠΈΡ ΡΠ²ΠΎΠΉΡΡΠ². ΠΠ½ΠΈ ΠΏΡΠΎΡΠ²Π»ΡΡΡΡΡ Π½Π° ΡΠ°ΠΌΠΎΠΉ ΡΠ°Π½Π½Π΅ΠΉ ΡΡΠ°Π΄ΠΈΠΈ ΡΠΊΡΠΏΠ»ΡΠ°ΡΠ°ΡΠΈΠΈ Π°Π²ΡΠΎΠΌΠΎΠ±ΠΈΠ»Ρ.
ΠΠΊΡΠΏΠ»ΡΠ°ΡΠ°ΡΠΈΠΎΠ½Π½ΡΠ΅ ΠΎΡΠΊΠ°Π·Ρ Π²ΠΎΠ·Π½ΠΈΠΊΠ°ΡΡ Π² ΡΠ»ΡΡΠ°Π΅ Π½Π°ΡΡΡΠ΅Π½ΠΈΡ ΡΡΡΠ°Π½ΠΎΠ²Π»Π΅Π½Π½ΡΡ ΠΏΡΠ°Π²ΠΈΠ» ΡΠ΅Ρ Π½ΠΈΡΠ΅ΡΠΊΠΎΠΉ ΡΠΊΡΠΏΠ»ΡΠ°ΡΠ°ΡΠΈΠΈ Π°Π²ΡΠΎΠΌΠΎΠ±ΠΈΠ»Ρ, Π° ΡΠ°ΠΊΠΆΠ΅ ΠΏΡΠΈ Π½Π΅ΡΠΎΠΎΡΠ²Π΅ΡΡΡΠ²ΠΈΠΈ ΠΊΠΎΠ½ΡΡΡΡΠΊΡΠΈΠΈ Π°Π²ΡΠΎΠΌΠΎΠ±ΠΈΠ»Ρ ΡΡΠ»ΠΎΠ²ΠΈΡΠΌ Π²Π½Π΅ΡΠ½Π΅ΠΉ ΡΡΠ΅Π΄Ρ ΠΈ Π·Π°Π΄Π°Π½Π½ΡΠΌ ΡΠ΅ΠΆΠΈΠΌΠ°ΠΌ ΡΠ°Π±ΠΎΡΡ.
ΠΠ·Π½ΠΎΡΠ½ΡΠ΅ ΠΎΡΠΊΠ°Π·Ρ ΠΎΠ±ΡΡΠ»ΠΎΠ²Π»Π΅Π½Ρ ΡΡΠ°ΡΠ΅Π½ΠΈΠ΅ΠΌ ΡΠΈΡΡΠ΅ΠΌΡ ΠΈ Π²ΠΎΠ·Π½ΠΈΠΊΠ°ΡΡ Π² ΡΠ΅Π·ΡΠ»ΡΡΠ°ΡΠ΅ ΠΏΠΎΡΡΠ΅ΠΏΠ΅Π½Π½ΠΎΠ³ΠΎ Π½Π°ΠΊΠ°ΠΏΠ»ΠΈΠ²Π°Π½ΠΈΡ Π² ΡΠ»Π΅ΠΌΠ΅Π½ΡΠ°Ρ Π½Π΅ΠΎΠ±ΡΠ°ΡΠΈΠΌΡΡ ΠΈΠ·ΠΌΠ΅Π½Π΅Π½ΠΈΠΉ (ΡΠ΅ΠΊΡΠΈΡΡΠ°Π»Π»ΠΈΠ·Π°ΡΠΈΡ ΠΌΠ΅ΡΠ°Π»Π»Π°, ΠΊΠΎΡΡΠΎΠ·ΠΈΡ, ΡΡΡΠ°Π»ΠΎΡΡΠ½ΡΠ΅ ΡΠ²Π»Π΅Π½ΠΈΡ, ΠΈΠ·ΠΌΠ΅Π½Π΅Π½ΠΈΡ ΡΠΎΡΠΌΡ Π΄Π΅ΡΠ°Π»Π΅ΠΉ ΠΈ Ρ. Π΄.). ΠΠ·Π½ΠΎΡΠ½ΡΠ΅ ΠΎΡΠΊΠ°Π·Ρ Π²ΠΎΠ·Π½ΠΈΠΊΠ°ΡΡ Π²ΡΠ»Π΅Π΄ΡΡΠ²ΠΈΠ΅ ΡΠΎΠ²ΠΌΠ΅ΡΡΠ½ΠΎΠ³ΠΎ Π΄Π΅ΠΉΡΡΠ²ΠΈΡ Π½Π΅ΡΠΊΠΎΠ»ΡΠΊΠΈΡ ΠΏΡΠΈΡΠΈΠ½, ΠΏΠΎΡΡΠΎΠΌΡ Π²Π°ΠΆΠ½ΠΎ ΡΡΡΠ°Π½ΠΎΠ²ΠΈΡΡ Π³Π»Π°Π²Π½ΡΡ ΠΏΡΠΈΡΠΈΠ½Ρ Π²ΠΎΠ·Π½ΠΈΠΊΠ½ΠΎΠ²Π΅Π½ΠΈΡ ΠΎΡΠΊΠ°Π·Π° ΠΈ ΡΡΡΡΠ°Π½ΠΈΡΡ Π΅Π΅.
ΠΡΠ»ΠΈ ΠΏΡΠΈ ΠΈΡΠΏΡΡΠ°Π½ΠΈΠΈ Π½ΠΎΠ²ΠΎΠΉ ΠΌΠ°ΡΠΈΠ½Ρ ΠΏΡΠΎΠΈΠ·ΠΎΡΠ΅Π» ΠΎΡΠΊΠ°Π·, ΡΠ»Π΅Π΄ΠΎΠ²Π°ΡΠ΅Π»ΡΠ½ΠΎ, Π½Π° ΡΡΠ°Π΄ΠΈΠΈ ΠΏΡΠΎΠ΅ΠΊΡΠΈΡΠΎΠ²Π°Π½ΠΈΡ ΡΡΠΎΠ²Π΅Π½Ρ ΠΏΡΠΎΡΠ½ΠΎΡΡΠΈ Π½Π΅ Π±ΡΠ» ΡΠΊΠΎΠΎΡΠ΄ΠΈΠ½ΠΈΡΠΎΠ²Π°Π½ Ρ ΡΡΠΎΠ²Π½Π΅ΠΌ Π½Π°Π³ΡΡΠ·ΠΊΠΈ. ΠΠΎΡΡΠΎΠΌΡ Π½ΡΠΆΠ½ΠΎ Ρ ΠΎΡΠΎΡΠΎ Π·Π½Π°ΡΡ Π²Π½Π΅ΡΠ½ΠΈΠ΅ ΡΡΠ»ΠΎΠ²ΠΈΡ ΡΠ°Π±ΠΎΡΡ ΠΌΠ°ΡΠΈΠ½Ρ, Π½Π°Π³ΡΡΠ·ΠΊΠΈ, Π²ΠΎΡΠΏΡΠΈΠ½ΠΈΠΌΠ°Π΅ΠΌΡΠ΅ ΠΌΠ°ΡΠΈΠ½ΠΎΠΉ, Π°ΠΌΠΏΠ»ΠΈΡΡΠ΄Ρ ΠΈΡ ΡΠ°ΡΡΠ΅ΠΈΠ²Π°Π½ΠΈΡ ΠΈ ΠΏΡ. ΠΡΠΈ ΡΠ°ΠΊΠΎΠΌ ΠΏΠΎΠ΄Ρ ΠΎΠ΄Π΅ ΠΊ ΠΏΠΎΠ½ΠΈΠΌΠ°Π½ΠΈΡ ΠΎΡΠΊΠ°Π·ΠΎΠ² Π½Π°Π΄Π΅ΠΆΠ½ΠΎΡΡΡ ΠΌΠΎΠΆΠ½ΠΎ ΠΎΠΏΡΠ΅Π΄Π΅Π»ΠΈΡΡ ΠΊΠ°ΠΊ ΡΠ²ΠΎΠΉΡΡΠ²ΠΎ ΠΌΠ°ΡΠΈΠ½Ρ (ΡΠ»Π΅ΠΌΠ΅Π½ΡΠ°) Π½Π΅ΠΏΡΠ΅ΡΡΠ²Π½ΠΎ ΡΠΎΡ ΡΠ°Π½ΡΡΡ ΡΠ°Π±ΠΎΡΠΎΡΠΏΠΎΡΠΎΠ±Π½ΠΎΡΡΡ Π² ΠΎΠΏΡΠ΅Π΄Π΅Π»Π΅Π½Π½ΡΡ ΡΡΠ»ΠΎΠ²ΠΈΡΡ ΡΠΊΡΠΏΠ»ΡΠ°ΡΠ°ΡΠΈΠΈ Π² ΡΠ΅ΡΠ΅Π½ΠΈΠ΅ Π·Π°Π΄Π°Π½Π½ΠΎΠ³ΠΎ ΠΏΠ΅ΡΠΈΠΎΠ΄Π° Π²ΡΠ΅ΠΌΠ΅Π½ΠΈ.
ΠΠ°Π΄Π΅ΠΆΠ½ΠΎΡΡΡ Π°Π²ΡΠΎΠΌΠΎΠ±ΠΈΠ»Ρ ΠΎΡΠ΅Π½ΠΈΠ²Π°Π΅ΡΡΡ Π²Π΅ΡΠΎΡΡΠ½ΠΎΡΡΠ½ΡΠΌΠΈ, ΡΠΈΡΠ»Π΅Π½Π½ΡΠΌΠΈ Ρ Π°ΡΠ°ΠΊΡΠ΅ΡΠΈΡΡΠΈΠΊΠ°ΠΌΠΈ, ΠΊΠΎΡΠΎΡΡΠ΅ ΠΌΠΎΠ³ΡΡ Π±ΡΡΡ ΠΏΠΎΠ»ΡΡΠ΅Π½Ρ Π½Π° ΠΎΡΠ½ΠΎΠ²Π°Π½ΠΈΠΈ ΠΌΠ°ΡΠ΅ΠΌΠ°ΡΠΈΡΠ΅ΡΠΊΠΎΠΉ ΠΎΠ±ΡΠ°Π±ΠΎΡΠΊΠΈ Π΄ΠΎΡΡΠ°ΡΠΎΡΠ½ΠΎΠΉ ΡΡΠ°ΡΠΈΡΡΠΈΡΠ΅ΡΠΊΠΎΠΉ ΠΈΠ½ΡΠΎΡΠΌΠ°ΡΠΈΠΈ.
Π’Π΅ΠΎΡΠΈΡ Π½Π°Π΄Π΅ΠΆΠ½ΠΎΡΡΠΈ Π°Π²ΡΠΎΠΌΠΎΠ±ΠΈΠ»Ρ ΡΠ²Π»ΡΠ΅ΡΡΡ ΡΠ°Π·Π΄Π΅Π»ΠΎΠΌ ΠΎΠ±ΡΠ΅ΠΉ ΡΠ΅ΠΎΡΠΈΠΈ Π½Π°Π΄Π΅ΠΆΠ½ΠΎΡΡΠΈ ΠΌΠ°ΡΠΈΠ½ ΠΈ ΡΠ°Π·Π²ΠΈΠ²Π°Π΅ΡΡΡ Π½Π° Π±Π°Π·Π΅ ΡΠ΅ΠΎΡΠΈΠΈ Π²Π΅ΡΠΎΡΡΠ½ΠΎΡΡΠ΅ΠΉ ΠΈ ΠΌΠ°ΡΠ΅ΠΌΠ°ΡΠΈΡΠ΅ΡΠΊΠΎΠΉ ΡΡΠ°ΡΠΈΡΡΠΈΠΊΠΈ, Π ΡΡΠ΄Π΅ ΡΠ°Π·Π΄Π΅Π»ΠΎΠ² ΡΠ΅ΠΎΡΠΈΠΈ Π½Π°Π΄Π΅ΠΆΠ½ΠΎΡΡΠΈ ΡΠΈΡΠΎΠΊΠΎΠ΅ ΠΏΡΠΈΠΌΠ΅Π½Π΅Π½ΠΈΠ΅ ΠΏΠΎΠ»ΡΡΠ°ΡΡ ΠΌΠ΅ΡΠΎΠ΄Ρ ΡΠ΅ΠΎΡΠΈΠΈ ΠΈΠ½ΡΠΎΡΠΌΠ°ΡΠΈΠΈ, ΡΠ΅ΠΎΡΠΈΠΈ ΠΌΠ°ΡΡΠΎΠ²ΠΎΠ³ΠΎ ΠΎΠ±ΡΠ»ΡΠΆΠΈΠ²Π°Π½ΠΈΡ, Π»ΠΈΠ½Π΅ΠΉΠ½ΠΎΠ³ΠΎ ΠΈ Π½Π΅Π»ΠΈΠ½Π΅ΠΉΠ½ΠΎΠ³ΠΎ ΠΏΡΠΎΠ³ΡΠ°ΠΌΠΌΠΈΡΠΎΠ²Π°Π½ΠΈΡ ΠΈ Π΄Ρ.
Β«ΠΡΠΈ ΡΠ΅ΡΠ΅Π½ΠΈΠΈ Π·Π°Π΄Π°Ρ ΡΠ΅ΠΎΡΠΈΡ Π½Π°Π΄Π΅ΠΆΠ½ΠΎΡΡΠΈ ΠΈΡΠΏΠΎΠ»ΡΠ·ΡΠ΅Ρ ΡΠ΅Π·ΡΠ»ΡΡΠ°ΡΡ ΠΈΡΡΠ»Π΅Π΄ΠΎΠ²Π°Π½ΠΈΠΉ ΡΠΈΠ·ΠΈΡΠ΅ΡΠΊΠΈΡ ΠΈ Ρ ΠΈΠΌΠΈΡΠ΅ΡΠΊΠΈΡ ΠΏΡΠΎΡΠ΅ΡΡΠΎΠ², Π»Π΅ΠΆΠ°ΡΠΈΡ Π² ΠΎΡΠ½ΠΎΠ²Π΅ ΡΠ²Π»Π΅Π½ΠΈΠΉ, ΡΠ²ΡΠ·Π°Π½Π½ΡΡ Ρ ΠΏΠΎΡΠ΅ΡΠ΅ΠΉ ΠΊΠ°ΡΠ΅ΡΡΠ²Π°Β».
ΠΠ΅ΠΏΡΠ΅ΡΡΠ²Π½ΠΎΠ΅ ΡΠΎΠ²Π΅ΡΡΠ΅Π½ΡΡΠ²ΠΎΠ²Π°Π½ΠΈΠ΅ ΡΠ΅Ρ Π½ΠΈΠΊΠΈ, ΡΡΠ»ΠΎΠΆΠ½Π΅Π½ΠΈΠ΅ ΡΡΠ½ΠΊΡΠΈΠΉ, Π²ΡΠΏΠΎΠ»Π½ΡΠ΅ΠΌΡΡ ΠΌΠ°ΡΠΈΠ½Π°ΠΌΠΈ ΠΈ ΡΠ΅Ρ Π½ΠΈΡΠ΅ΡΠΊΠΈΠΌΠΈ ΡΠΈΡΡΠ΅ΠΌΠ°ΠΌΠΈ, Π²Π΅Π΄Π΅Ρ ΠΊ ΡΡΠ»ΠΎΠΆΠ½Π΅Π½ΠΈΡ ΠΈ ΡΠ°ΠΌΠΈΡ ΠΌΠ°ΡΠΈΠ½. Π§Π΅ΠΌ ΡΠ»ΠΎΠΆΠ½Π΅Π΅ ΠΌΠ°ΡΠΈΠ½Π°, ΡΠ΅ΠΌ, ΠΏΡΠΈ ΠΏΡΠΎΡΠΈΡ ΡΠ°Π²Π½ΡΡ ΡΡΠ»ΠΎΠ²ΠΈΡΡ , ΠΎΠ½Π° ΠΌΠ΅Π½Π΅Π΅ Π½Π°Π΄Π΅ΠΆΠ½Π°. ΠΠ»Ρ ΡΠ½ΡΡΠΈΡ ΡΡΠΎΠ³ΠΎ ΠΏΡΠΎΡΠΈΠ²ΠΎΡΠ΅ΡΠΈΡ Π² ΡΠ΅ΠΎΡΠΈΠΈ Π½Π°Π΄Π΅ΠΆΠ½ΠΎΡΡΠΈ ΡΠ°Π·ΡΠ°Π±Π°ΡΡΠ²Π°ΡΡΡΡ ΠΌΠ΅ΡΠΎΠ΄Ρ ΡΠΎΠ·Π΄Π°Π½ΠΈΡ Π½Π°Π΄Π΅ΠΆΠ½ΡΡ ΠΌΠ°ΡΠΈΠ½ ΠΈ ΡΠΈΡΡΠ΅ΠΌ ΠΏΡΡΠ΅ΠΌ ΡΠ°Π·Π΅ΡΠ²ΠΈΡΠΎΠ²Π°Π½ΠΈΡ, Π²ΡΠ±ΠΎΡΠ° ΠΎΠΏΡΠΈΠΌΠ°Π»ΡΠ½ΠΎΠΉ ΡΡΡΡΠΊΡΡΡΠ½ΠΎΠΉ ΠΈ ΡΡΠ½ΠΊΡΠΈΠΎΠ½Π°Π»ΡΠ½ΠΎΠΉ ΡΡ Π΅ΠΌ, ΡΠ°ΡΠΈΠΎΠ½Π°Π»ΡΠ½ΡΡ ΠΌΠ΅ΡΠΎΠ΄ΠΎΠ² ΠΈ ΠΏΡΠΈΠ΅ΠΌΠΎΠ² ΡΠ΅Ρ Π½ΠΈΡΠ΅ΡΠΊΠΎΠΉ ΡΠΊΡΠΏΠ»ΡΠ°ΡΠ°ΡΠΈΠΈ ΠΈ ΡΠ΅ΠΌΠΎΠ½ΡΠ°.
ΠΡΠΈΠΌΠ΅Π½ΠΈΡΠ΅Π»ΡΠ½ΠΎ ΠΊ Π°Π²ΡΠΎΠΌΠΎΠ±ΠΈΠ»Ρ Π·Π°Π΄Π°ΡΠΈ ΡΠ΅ΠΎΡΠΈΠΈ Π½Π°Π΄Π΅ΠΆΠ½ΠΎΡΡΠΈ ΡΠΎΡΡΠΎΡΡ Π² ΡΠΎΠΌ, ΡΡΠΎΠ±Ρ ΡΡΡΠ°Π½Π°Π²Π»ΠΈΠ²Π°ΡΡ ΠΈ ΠΈΠ·ΡΡΠ°ΡΡ ΠΊΠΎΠ»ΠΈΡΠ΅ΡΡΠ²Π΅Π½Π½ΡΠ΅ Ρ Π°ΡΠ°ΠΊΡΠ΅ΡΠΈΡΡΠΈΠΊΠΈ Π½Π°Π΄Π΅ΠΆΠ½ΠΎΡΡΠΈ, Π·Π°ΠΊΠΎΠ½ΠΎΠΌΠ΅ΡΠ½ΠΎΡΡΠΈ Π²ΠΎΠ·Π½ΠΈΠΊΠ½ΠΎΠ²Π΅Π½ΠΈΡ ΠΎΡΠΊΠ°Π·ΠΎΠ², ΠΌΠ΅ΡΠΎΠ΄Ρ Π°Π½Π°Π»ΠΈΠ·Π° ΠΈ ΠΏΡΠΎΠ³Π½ΠΎΠ·ΠΈΡΠΎΠ²Π°Π½ΠΈΡ ΠΎΡΠΊΠ°Π·ΠΎΠ², ΠΌΠ΅ΡΠΎΠ΄ΠΈΠΊΡ ΠΈΡΠΏΡΡΠ°Π½ΠΈΡ ΠΈ ΠΌΠ°ΡΠ΅ΠΌΠ°ΡΠΈΡΠ΅ΡΠΊΠΎΠΉ ΠΎΠ±ΡΠ°Π±ΠΎΡΠΊΠΈ ΡΡΠ°ΡΠΈΡΡΠΈΡΠ΅ΡΠΊΠΈΡ ΠΏΠΎΠΊΠ°Π·Π°ΡΠ΅Π»Π΅Π½.
ΠΠ»Ρ ΡΠΏΠ΅ΡΠΈΠ°Π»ΠΈΡΡΠΎΠ², Π·Π°Π½ΠΈΠΌΠ°ΡΡΠΈΡ ΡΡ ΡΠ΅Ρ Π½ΠΈΡΠ΅ΡΠΊΠΎΠΉ ΡΠΊΡΠΏΠ»ΡΠ°ΡΠ°ΡΠΈΠ΅ΠΉ Π°Π²ΡΠΎΠΌΠΎΠ±ΠΈΠ»Ρ, ΡΠ΅ΠΎΡΠΈΡ Π½Π°Π΄Π΅ΠΆΠ½ΠΎΡΡΠΈ Π΄Π°Π΅Ρ ΠΌΠ΅ΡΠΎΠ΄Ρ, ΠΏΠΎΠ·Π²ΠΎΠ»ΡΡΡΠΈΠ΅ ΠΎΠΏΡΠ΅Π΄Π΅Π»ΡΡΡ Π²Π΅ΡΠΎΡΡΠ½ΠΎΡΡΡ Π±Π΅Π·ΠΎΡΠΊΠ°Π·Π½ΠΎΠΉ ΡΠ°Π±ΠΎΡΡ Π°Π²ΡΠΎΠΌΠΎΠ±ΠΈΠ»Ρ Π² Π·Π°Π΄Π°Π½Π½ΠΎΠΌ ΠΈΠ½ΡΠ΅ΡΠ²Π°Π»Π΅ ΠΏΡΠΎΠ±Π΅Π³Π°, Π½Π°ΡΡΠ½ΠΎ ΠΎΠ±ΠΎΡΠ½ΠΎΠ²ΡΠ²Π°ΡΡ ΠΎΠΏΡΠΈΠΌΠ°Π»ΡΠ½ΡΠ΅ ΡΠ΅ΠΆΠΈΠΌΡ ΡΠ΅Ρ Π½ΠΈΡΠ΅ΡΠΊΠΎΠ³ΠΎ ΠΎΠ±ΡΠ»ΡΠΆΠΈΠ²Π°Π½ΠΈΡ, ΡΠ°ΡΡΡΠΈΡΡΠ²Π°ΡΡ ΠΎΠΏΡΠΈΠΌΠ°Π»ΡΠ½ΡΡ ΠΏΠΎΡΡΠ΅Π±Π½ΠΎΡΡΡ Π² Π·Π°ΠΏΠ°ΡΠ½ΡΡ ΡΠ°ΡΡΡΡ ΠΈ ΡΠ΅ΠΌΠΎΠ½ΡΠ½ΠΎ-ΡΠ΅Ρ Π½ΠΈΡΠ΅ΡΠΊΠΈΡ ΡΡΠ΅Π΄ΡΡΠ²Π°Ρ Π΄Π»Ρ ΠΏΠΎΠ΄Π΄Π΅ΡΠΆΠ°Π½ΠΈΡ Π½Π°Π΄Π΅ΠΆΠ½ΠΎΡΡΠΈ Π°Π²ΡΠΎΠΌΠΎΠ±ΠΈΠ»Π΅ΠΉ Π½Π° Π·Π°Π΄Π°Π½Π½ΠΎΠΌ ΡΡΠΎΠ²Π½Π΅, Π½ΠΎΡΠΌΠΈΡΠΎΠ²Π°ΡΡ ΠΈ ΡΠΏΡΠ°Π²Π»ΡΡΡ ΠΌΠ΅ΠΆΡΠ΅ΠΌΠΎΠ½ΡΠ½ΡΠΌΠΈ ΠΏΡΠΎΠ±Π΅Π³Π°ΠΌΠΈ.
ΠΡΠ½ΠΎΠ²Π½ΡΠ΅ ΠΏΠΎΠΊΠ°Π·Π°ΡΠ΅Π»ΠΈ, Ρ Π°ΡΠ°ΠΊΡΠ΅ΡΠΈΠ·ΡΡΡΠΈΠ΅ Π½Π°Π΄Π΅ΠΆΠ½ΠΎΡΡΡ Π°Π²ΡΠΎΠΌΠΎΠ±ΠΈΠ»Ρ. ΠΠ°Π΄Π΅ΠΆΠ½ΠΎΡΡΡ Π°Π²ΡΠΎΠΌΠΎΠ±ΠΈΠ»Ρ Π·Π°Π²ΠΈΡΠΈΡ ΠΎΡ Π±ΠΎΠ»ΡΡΠΎΠ³ΠΎ ΠΊΠΎΠ»ΠΈΡΠ΅ΡΡΠ²Π° ΠΊΠΎΠ½ΡΡΡΡΠΊΡΠΈΠ²Π½ΠΎ-ΡΠ΅Ρ Π½ΠΎΠ»ΠΎΠ³ΠΈΡΠ΅ΡΠΊΠΈΡ ΠΈ ΡΠΊΡΠΏΠ»ΡΠ°ΡΠ°ΡΠΈΠΎΠ½Π½ΡΡ ΡΠ°ΠΊΡΠΎΡΠΎΠ² ΠΈ ΠΏΠΎΡΡΠΎΠΌΡ Π½Π΅ ΠΌΠΎΠΆΠ΅Ρ Π±ΡΡΡ ΠΎΡΠ΅Π½Π΅Π½Π° ΠΎΠ΄Π½ΠΎΠ·Π½Π°ΡΠ½ΠΎ. ΠΠ»Ρ ΠΎΡΠ΅Π½ΠΊΠΈ Π½Π°Π΄Π΅ΠΆΠ½ΠΎΡΡΠΈ Π°Π²ΡΠΎΠΌΠΎΠ±ΠΈΠ»Ρ ΠΏΡΠΈΠΌΠ΅Π½ΡΡΡ ΡΠΈΡΡΠ΅ΠΌΡ ΠΏΠΎΠΊΠ°Π·Π°ΡΠ΅Π»Π΅ΠΉ (ΠΊΡΠΈΡΠ΅ΡΠΈΠ΅Π²), ΠΏΠΎΠ·Π²ΠΎΠ»ΡΡΡΠΈΡ ΠΎΡΠ΅Π½ΠΈΠ²Π°ΡΡ Π½Π°Π΄Π΅ΠΆΠ½ΠΎΡΡΡ Π²ΡΠ΅Π³ΠΎ Π°Π²ΡΠΎΠΌΠΎΠ±ΠΈΠ»Ρ ΠΈΠ»ΠΈ Π΅Π³ΠΎ ΡΠ»Π΅ΠΌΠ΅Π½ΡΠΎΠ² Π² ΡΠΈΡΠ»Π΅Π½Π½ΡΡ Π·Π½Π°ΡΠ΅Π½ΠΈΡΡ . ΠΡΠΈΡΠ΅ΡΠΈΠΈ Π½Π°Π΄Π΅ΠΆΠ½ΠΎΡΡΠΈ ΠΌΠΎΠ³ΡΡ ΠΎΡΠ΅Π½ΠΈΠ²Π°ΡΡΡΡ ΡΠ΅ΠΎΡΠ΅ΡΠΈΡΠ΅ΡΠΊΠΈΠΌΠΈ (ΡΠΎΡΠ½ΡΠΌΠΈ) ΠΈ ΡΡΠ°ΡΠΈΡΡΠΈΡΠ΅ΡΠΊΠΈΠΌΠΈ (ΠΏΡΠΈΠ±Π»ΠΈΠΆΠ΅Π½Π½ΡΠΌΠΈ) ΡΡΠ°Π²Π½Π΅Π½ΠΈΡΠΌΠΈ.
ΠΠ΅ΠΈΠ·Π±Π΅ΠΆΠ½ΡΠ΅ ΠΊΠΎΠ»Π΅Π±Π°Π½ΠΈΡ ΠΊΠ°ΡΠ΅ΡΡΠ²Π° ΠΌΠ°ΡΠ΅ΡΠΈΠ°Π»ΠΎΠ², ΠΏΡΠΎΠΈΠ·Π²ΠΎΠ΄ΡΡΠ²Π΅Π½Π½ΡΡ ΡΠ°ΠΊΡΠΎΡΠΎΠ² ΠΈ ΡΡΠ»ΠΎΠ²ΠΈΠΉ ΡΠΊΡΠΏΠ»ΡΠ°ΡΠ°ΡΠΈΠΈ ΠΏΡΠΈΠ²ΠΎΠ΄ΡΡ ΠΊ ΡΠ°Π·Π±ΡΠΎΡΡ ΡΠ²ΠΎΠΉΡΡΠ², Ρ Π°ΡΠ°ΠΊΡΠ΅ΡΠΈΠ·ΡΡΡΠΈΡ Π½Π°Π΄Π΅ΠΆΠ½ΠΎΡΡΡ Π°Π²ΡΠΎΠΌΠΎΠ±ΠΈΠ»Ρ. ΠΡΠ»Π΅Π΄ΡΡΠ²ΠΈΠ΅ ΡΡΠΎΠ³ΠΎ ΠΊΡΠΈΡΠ΅ΡΠΈΠΈ Π½Π°Π΄Π΅ΠΆΠ½ΠΎΡΡΠΈ ΡΠ°ΡΡΠΌΠ°ΡΡΠΈΠ²Π°ΡΡ ΠΊΠ°ΠΊ Π²Π΅ΡΠΎΡΡΠ½ΠΎΡΡΠ½ΡΠ΅ ΡΡΠ°ΡΠΈΡΡΠΈΡΠ΅ΡΠΊΠΈΠ΅ Π²Π΅Π»ΠΈΡΠΈΠ½Ρ, ΠΎΡΠ½ΠΎΠ²Π°Π½Π½ΡΠ΅ Π½Π° Π΄ΠΎΡΡΠ°ΡΠΎΡΠ½ΠΎΠΉ ΠΈΠ½ΡΠΎΡΠΌΠ°ΡΠΈΠΈ. ΠΠ°Π΄Π΅ΠΆΠ½ΠΎΡΡΡ Π°Π²ΡΠΎΠΌΠΎΠ±ΠΈΠ»Ρ Π².Π·Π½Π°ΡΠΈΡΠ΅Π»ΡΠ½ΠΎΠΉ ΡΡΠ΅ΠΏΠ΅Π½ΠΈ Π·Π°Π²ΠΈΡΠΈΡ ΠΎΡ ΠΊΠΎΠΌΠΏΠ»Π΅ΠΊΡΠ° ΡΡΠ»ΠΎΠ²ΠΈΠΉ ΡΠΊΡΠΏΠ»ΡΠ°ΡΠ°ΡΠΈΠΈ, ΠΏΠΎΡΡΠΎΠΌΡ ΡΠΈΡΠ»Π΅Π½Π½ΡΠ΅ Π·Π½Π°ΡΠ΅Π½ΠΈΡ ΠΊΡΠΈΡΠ΅ΡΠΈΠ΅Π² Π½Π°Π΄Π΅ΠΆΠ½ΠΎΡΡΠΈ ΠΈΠΌΠ΅ΡΡ ΡΠΌΡΡΠ» Π»ΠΈΡΡ Π² ΡΠΎΠΌ ΡΠ»ΡΡΠ°Π΅, ΠΊΠΎΠ³Π΄Π° ΠΎΠ½ΠΈ ΠΎΠΏΡΠ΅Π΄Π΅Π»Π΅Π½Ρ Π΄Π»Ρ ΠΊΠΎΠ½ΠΊΡΠ΅ΡΠ½ΡΡ (ΠΎΠ³ΠΎΠ²ΠΎΡΠ΅Π½Π½ΡΡ ) ΡΡΠ»ΠΎΠ²ΠΈΠΉ ΡΠΊΡΠΏΠ»ΡΠ°ΡΠ°ΡΠΈΠΈ.
ΠΡΠΈ ΡΠ°ΡΡΠΌΠΎΡΡΠ΅Π½ΠΈΠΈ Π²ΠΎΠΏΡΠΎΡΠΎΠ² Π½Π°Π΄Π΅ΠΆΠ½ΠΎΡΡΠΈ Π°Π²ΡΠΎΠΌΠΎΠ±ΠΈΠ»Ρ Π±ΡΠ΄Π΅ΠΌ ΠΏΠΎΠ»ΡΠ·ΠΎΠ²Π°ΡΡΡΡ ΡΠ΅ΡΠΌΠΈΠ½Π°ΠΌΠΈ Β«ΡΠ»Π΅ΠΌΠ΅Π½ΡΒ» ΠΈ Β«ΡΠΈΡΡΠ΅ΠΌΠ°Β». ΠΠΎΠ΄ ΡΠ»ΠΎΠ²ΠΎΠΌ Β«ΡΠ»Π΅ΠΌΠ΅Π½ΡΒ» Π±ΡΠ΄Π΅ΠΌ ΠΏΠΎΠ½ΠΈΠΌΠ°ΡΡ Π½Π΅ ΡΠΎΠ»ΡΠΊΠΎ Π½Π΅ΡΠ°Π·Π»ΠΎΠΆΠΈΠΌΡΡ ΡΠ°ΡΡΡ ΡΠΈΡΡΠ΅ΠΌΡ (Π΄Π΅ΡΠ°Π»Ρ), Π½ΠΎ ΠΈ Π»ΡΠ±ΠΎΠ΅ ΡΡΡΡΠΎΠΉΡΡΠ²ΠΎ (ΡΠ·Π΅Π», Π°Π³ΡΠ΅Π³Π°Ρ), Π½Π°Π΄Π΅ΠΆΠ½ΠΎΡΡΡ ΠΊΠΎΡΠΎΡΠΎΠ³ΠΎ ΠΈΡΡΠ»Π΅Π΄ΡΠ΅ΡΡΡ Π½Π΅Π·Π°Π²ΠΈΡΠΈΠΌΠΎ ΠΎΡ Π½Π°Π΄Π΅ΠΆΠ½ΠΎΡΡΠΈ ΡΠΎΡΡΠ°Π²Π»ΡΡΡΠΈΡ Π΅Π³ΠΎ ΡΠ°ΡΡΠ΅ΠΉ. ΠΠ²ΡΠΎΠΌΠΎΠ±ΠΈΠ»Ρ ΠΌΠΎΠΆΠ½ΠΎ ΡΠ°ΡΡΠΌΠ°ΡΡΠΈΠ²Π°ΡΡ ΠΊΠ°ΠΊ ΡΠΈΡΡΠ΅ΠΌΡ, ΡΠΎΡΡΠΎΡΡΡΡ ΠΈΠ· ΠΎΡΠ΄Π΅Π»ΡΠ½ΡΡ ΡΠ»Π΅ΠΌΠ΅Π½ΡΠΎΠ² (Π΄Π΅ΡΠ°Π»Ρ, ΡΠ·Π΅Π», Π°Π³ΡΠ΅Π³Π°Ρ). Π ΡΠΎ ΠΆΠ΅ Π²ΡΠ΅ΠΌΡ Π°Π³ΡΠ΅Π³Π°Ρ ΠΌΠΎΠΆΠ½ΠΎ ΡΠ°ΡΡΠΌΠ°ΡΡΠΈΠ²Π°ΡΡ ΠΊΠ°ΠΊ ΡΠΈΡΡΠ΅ΠΌΡ, ΡΠΎΡΡΠΎΡΡΡΡ ΠΈΠ· ΡΠ·Π»ΠΎΠ² ΠΈ Π΄Π΅ΡΠ°Π»Π΅ΠΉ.
ΠΡΠ΅ ΡΠ»Π΅ΠΌΠ΅Π½ΡΡ Π°Π²ΡΠΎΠΌΠΎΠ±ΠΈΠ»Ρ ΡΠ°Π·Π΄Π΅Π»ΡΡΡ Π½Π° Π΄Π²Π° ΠΊΠ»Π°ΡΡΠ°: β ΡΠ΅ΠΌΠΎΠ½ΡΠΈΡΡΠ΅ΠΌΡΠ΅ (Π²ΠΎΡΡΡΠ°Π½Π°Π²Π»ΠΈΠ²Π°Π΅ΠΌΡΠ΅), ΡΠ°Π±ΠΎΡΠΎΡΠΏΠΎΡΠΎΠ±Π½ΠΎΡΡΡ ΠΊΠΎΡΠΎΡΡΡ Π²ΠΎΡΡΡΠ°Π½Π°Π²Π»ΠΈΠ²Π°Π΅ΡΡΡ ΠΏΠΎΡΠ»Π΅ Π²ΠΎΠ·Π½ΠΈΠΊΠ½ΠΎΠ²Π΅Π½ΠΈΡ ΠΎΡΠΊΠ°Π·ΠΎΠ²;
β ΠΏΠ΅ΡΠ΅ΠΌΠΎΠ½ΡΠΈΡΡΠ΅ΠΌΡΠ΅ (Π½Π΅Π²ΠΎΡΡΡΠ°Π½Π°Π²Π»ΠΈΠ²Π°Π΅ΠΌΡΠ΅), ΡΠ°Π±ΠΎΡΠΎΡΠΏΠΎΡΠΎΠ±Π½ΠΎΡΡΡ ΠΊΠΎΡΠΎΡΡΡ ΠΏΠΎΡΠ»Π΅ Π²ΠΎΠ·Π½ΠΈΠΊΠ½ΠΎΠ²Π΅Π½ΠΈΡ ΠΎΡΠΊΠ°Π·Π° Π½Π΅ ΠΌΠΎΠΆΠ΅Ρ Π±ΡΡΡ Π²ΠΎΡΡΡΠ°Π½ΠΎΠ²Π»Π΅Π½Π°.
Π’ΠΈΠΏΠΈΡΠ½ΡΠΌΠΈ Π½Π΅ΡΠ΅ΠΌΠΎΠ½ΡΠΈΡΡΠ΅ΠΌΡΠΌΠΈ Π΄Π΅ΡΠ°Π»ΡΠΌΠΈ Π°Π²ΡΠΎΠΌΠΎΠ±ΠΈΠ»Ρ ΡΠ²Π»ΡΡΡΡΡ ΠΏΠΎΡΡΠ½Π΅Π²ΡΠ΅ ΠΊΠΎΠ»ΡΡΠ°, ΡΠΎΠ½ΠΊΠΎΡΡΠ΅Π½Π½ΡΠ΅ Π²ΠΊΠ»Π°Π΄ΡΡΠΈ ΠΊΠΎΠ»Π΅Π½ΡΠ°ΡΠΎΠ³ΠΎ Π²Π°Π»Π°, ΠΏΡΡΠΆΠΈΠ½Ρ ΠΊΠ»Π°ΠΏΠ°Π½ΠΎΠ², Π΄Π΅ΡΠ°Π»ΠΈ ΠΏΠΎΠ΄Π²Π΅ΡΠΊΠΈ, ΡΡΠΈΠΊΡΠΈΠΎΠ½Π½ΡΠ΅ Π½Π°ΠΊΠ»Π°Π΄ΠΊΠΈ ΡΠΎΡΠΌΠΎΠ·ΠΎΠ² ΠΈ ΡΡΠ΅ΠΏΠ»Π΅Π½ΠΈΡ, ΠΏΠΎΠ΄ΡΠΈΠΏΠ½ΠΈΠΊΠΈ ΠΊΠ°ΡΠ΅Π½ΠΈΡ, ΠΏΡΠ΅ΡΠΈΠ·ΠΈΠΎΠ½Π½ΡΠ΅ Π΄Π΅ΡΠ°Π»ΠΈ ΡΠΎΠΏΠ»ΠΈΠ²Π½ΠΎΠΉ Π°ΠΏΠΏΠ°ΡΠ°ΡΡΡΡ Π΄ΠΈΠ·Π΅Π»Π΅ΠΉ, Π·Π°ΠΏΠ°Π»ΡΠ½ΡΠ΅ ΡΠ²Π΅ΡΠΈ, ΠΌΠ΅Π΄Π½ΠΎ-Π°ΡΠ±Π΅ΡΡΠΎΠ²ΡΠ΅ ΠΈ ΡΠ΅Π·ΠΈΠ½ΠΎΠ²ΡΠ΅ ΠΏΡΠΎΠΊΠ»Π°Π΄ΠΊΠΈ ΠΈ Π΄Ρ
Π’ΠΈΠΏΠΈΡΠ½ΡΠΌΠΈ ΡΠ΅ΠΌΠΎΠ½ΡΠΈΡΡΠ΅ΠΌΡΠΌΠΈ Π΄Π΅ΡΠ°Π»ΡΠΌΠΈ Π°Π²ΡΠΎΠΌΠΎΠ±ΠΈΠ»Ρ ΠΌΠΎΠΆΠ½ΠΎ Π½Π°Π·Π²Π°ΡΡ Π±Π»ΠΎΠΊ ΠΈ Π³ΠΈΠ»ΡΠ·Ρ ΡΠΈΠ»ΠΈΠ½Π΄ΡΠΎΠ², ΠΊΠΎΠ»Π΅Π½ΡΠ°ΡΡΠΉ Π²Π°Π», Π½Π°ΠΏΡΠ°Π²Π»ΡΡΡΠΈΠ΅ Π²ΡΡΠ»ΠΊΠΈ ΠΊΠ»Π°ΠΏΠ°Π½ΠΎΠ², ΠΊΠ»Π°ΠΏΠ°Π½Ρ, ΡΠΎΡΠΌΠΎΠ·Π½ΡΠ΅ Π±Π°ΡΠ°Π±Π°Π½Ρ, Π±Π°Π»ΠΊΡ ΠΏΠ΅ΡΠ΅Π΄Π½Π΅ΠΉ ΠΎΡΠΈ, ΡΠ°ΠΌΡ ΠΈ Π΄Ρ.
Π Π·Π°Π²ΠΈΡΠΈΠΌΠΎΡΡΠΈ ΠΎΡ ΠΊΠ»Π°ΡΡΠ° ΡΠ»Π΅ΠΌΠ΅Π½ΡΠ° ΠΊ Π½Π΅ΠΌΡ ΠΌΠΎΠ³ΡΡ ΠΏΡΠΈΠΌΠ΅Π½ΡΡΡΡΡ ΡΠ΅ ΠΈΠ»ΠΈ ΠΈΠ½ΡΠ΅ ΠΊΡΠΈΡΠ΅ΡΠΈΠΈ Π½Π°Π΄Π΅ΠΆΠ½ΠΎΡΡΠΈ. ΠΠ³Π½ΠΎΡΠΈΡΠΎΠ²Π°Π½ΠΈΠ΅ ΡΡΠΎΠ³ΠΎ ΠΏΠΎΠ»ΠΎΠΆΠ΅Π½ΠΈΡ ΠΌΠΎΠΆΠ΅Ρ ΠΏΡΠΈΠ²Π΅ΡΡΠΈ ΠΊ ΡΠ΅ΡΡΠ΅Π·Π½ΡΠΌ ΠΎΡΠΈΠ±ΠΊΠ°ΠΌ Π² ΠΎΡΠ΅Π½ΠΊΠ΅ Π½Π°Π΄Π΅ΠΆΠ½ΠΎΡΡΠΈ.
ΠΠ°ΡΠ°Π±ΠΎΡΠΊΠ° Π°Π²ΡΠΎΠΌΠΎΠ±ΠΈΠ»Ρ Π΄ΠΎ ΠΎΡΠΊΠ°Π·Π° (Π² ΡΠ°ΡΠ°Ρ ΠΈΠ»ΠΈ ΠΊΠΈΠ»ΠΎΠΌΠ΅ΡΡΠ°Ρ ΠΏΡΠΎΠ±Π΅Π³Π°) ΡΠ²Π»ΡΠ΅ΡΡΡ ΡΠ»ΡΡΠ°ΠΉΠ½ΠΎΠΉ Π½Π΅ΠΏΡΠ΅ΡΡΠ²Π½ΠΎΠΉ Π²Π΅Π»ΠΈΡΠΈΠ½ΠΎΠΉ. Π ΡΠΎ ΠΆΠ΅ Π²ΡΠ΅ΠΌΡ ΠΊΠΎΠ»ΠΈΡΠ΅ΡΡΠ²ΠΎ ΠΎΡΠΊΠ°Π·ΠΎΠ² Π°Π²ΡΠΎΠΌΠΎΠ±ΠΈΠ»Ρ Π·Π° ΡΠΈΠΊΡΠΈΡΠΎΠ²Π°Π½Π½ΡΠΉ Π΄Π΅ΠΉΡΡΠ²ΠΈΡΠ΅Π»ΡΠ½ΡΠΉ ΠΏΡΠΎΠ±Π΅Π³ ΡΠ²Π»ΡΠ΅ΡΡΡ ΡΠ»ΡΡΠ°ΠΉΠ½ΠΎΠΉ Π΄ΠΈΡΠΊΡΠ΅ΡΠ½ΠΎΠΉ (ΠΏΡΠ΅ΡΡΠ²Π½ΠΎΠΉ) Π²Π΅Π»ΠΈΡΠΈΠ½ΠΎΠΉ.
ΠΡΡΠ΅ΡΠΏΡΠ²Π°ΡΡΠ΅ΠΉ Ρ Π°ΡΠ°ΠΊΡΠ΅ΡΠΈΡΡΠΈΠΊΠΎΠΉ ΡΠ»ΡΡΠ°ΠΉΠ½ΠΎΠΉ Π²Π΅Π»ΠΈΡΠΈΠ½Ρ ΡΠ²Π»ΡΠ΅ΡΡΡ Π·Π°ΠΊΠΎΠ½ ΡΠ°ΡΠΏΡΠ΅Π΄Π΅Π»Π΅Π½ΠΈΡ, ΡΡΡΠ°Π½Π°Π²Π»ΠΈΠ²Π°ΡΡΠΈΠΉ ΡΠ²ΡΠ·Ρ ΠΌΠ΅ΠΆΠ΄Ρ Π²ΠΎΠ·ΠΌΠΎΠΆΠ½ΡΠΌΠΈ Π΅Π΅ Π·Π½Π°ΡΠ΅Π½ΠΈΡΠΌΠΈ ΠΈ ΡΠΎΠΎΡΠ²Π΅ΡΡΡΠ²ΡΡΡΠΈΠΌΠΈ ΠΈΠΌ Π²Π΅ΡΠΎΡΡΠ½ΠΎΡΡΡΠΌΠΈ.
ΠΠ»Ρ Π΄ΠΈΡΠΊΡΠ΅ΡΠ½ΠΎΠΉ ΡΠ»ΡΡΠ°ΠΉΠ½ΠΎΠΉ Π²Π΅Π»ΠΈΡΠΈΠ½Ρ Π·Π°ΠΊΠΎΠ½ ΡΠ°ΡΠΏΡΠ΅Π΄Π΅Π»Π΅Π½ΠΈΡ Π·Π°Π΄Π°Π΅ΡΡΡ Π². Π²ΠΈΠ΄Π΅ ΡΡΠ΄Π° ΡΠ°ΡΠΏΡΠ΅Π΄Π΅Π»Π΅Π½ΠΈΡ. Π£Π½ΠΈΠ²Π΅ΡΡΠ°Π»ΡΠ½ΠΎΠΉ Ρ Π°ΡΠ°ΠΊΡΠ΅ΡΠΈΡΡΠΈΠΊΠΎΠΉ ΠΊΠ°ΠΊ Π΄ΠΈΡΠΊΡΠ΅ΡΠ½ΡΡ , ΡΠ°ΠΊ ΠΈ Π½Π΅ΠΏΡΠ΅ΡΡΠ²Π½ΡΡ ΡΠ»ΡΡΠ°ΠΉΠ½ΡΡ Π²Π΅Π»ΠΈΡΠΈΠ½ ΡΠ²Π»ΡΠ΅ΡΡΡ ΡΡΠ½ΠΊΡΠΈΡ ΡΠ°ΡΠΏΡΠ΅Π΄Π΅Π»Π΅Π½ΠΈΡ.
Π ΠΈΡ. 1. ΠΡΠ°ΡΠΈΠΊ ΠΊΠΎΡΡΡΠΈΡΠΈΠ΅Π½ΡΠΎΠ² ΠΎΡΠΊΠ°Π·ΠΎΠ² Π°Π²ΡΠΎΠΌΠΎΠ±ΠΈΠ»Π΅ΠΉ ΠΠΠ-21 Β«ΠΠΎΠ»Π³Π°Β» Π² ΠΈΠ½ΡΠ΅ΡΠ²Π°Π»Π΅ ΠΏΡΠΎΠ±Π΅Π³Π° 0β60 ΡΡΡ. ΠΊΠΌ: 1 β Π΄Π²ΠΈΠ³Π°ΡΠ΅Π»Ρ; 2 β ΡΡΠ΅ΠΏΠ»Π΅Π½ΠΈΠ΅; 3 β ΠΊΠΎΡΠΎΠ±ΠΊΠ° ΠΏΠ΅ΡΠ΅Π΄Π°Ρ; 4 β ΠΊΠ°ΡΠ΄Π°Π½Π½Π°Ρ ΠΏΠ΅ΡΠ΅Π΄Π°ΡΠ°; 5 β ΡΠΎΡΠΌΠΎΠ·Π°; 6 β ΡΡΠ»Π΅Π²ΠΎΠ΅ ΡΠΏΡΠ°Π²Π»Π΅Π½ΠΈΠ΅; 7 β ΡΠ»Π΅ΠΊΡΡΠΎΠΎΠ±ΠΎΡΡΠ΄ΠΎΠ²Π°Π½ΠΈΠ΅; 8 β ΠΏΠΎΠ΄Π²Π΅ΡΠΊΠ°; 9 β ΠΊΠΎΠ»Π΅ΡΠ° ΠΈ ΡΠΈΠ½Ρ; 10 β ΠΊΡΠ·ΠΎΠ²; 11 β ΠΏΡΠΎΡΠΈΠ΅ ΡΠ·Π»Ρ ΠΈ Π°Π³ΡΠ΅Π³Π°ΡΡ; Π° β Π½ΠΎΠ²ΡΠ΅ Π°Π²ΡΠΎΠΌΠΎΠ±ΠΈΠ»ΠΈ; Π± β Π°Π²ΡΠΎΠΌΠΎΠ±ΠΈΠ»ΠΈ ΠΏΠΎΡΠ»Π΅ ΠΊΠ°ΠΏΠΈΡΠ°Π»ΡΠ½ΠΎΠ³ΠΎ ΡΠ΅ΠΌΠΎΠ½ΡΠ° (II ΠΊΠ°ΡΠ΅Π³ΠΎΡΠΈΡ ΡΡΠ»ΠΎΠ²ΠΈΠΉ ΡΠΊΡΠΏΠ»ΡΠ°ΡΠ°ΡΠΈΠΈ)
ΠΠΏΡΠ΅Π΄Π΅Π»Π΅Π½ΠΈΠ΅ ΡΡΠ΅Π΄Π½Π΅Π³ΠΎ ΡΠ΅ΡΡΡΡΠ° ΡΠ΅ΠΌΠΎΠ½ΡΠΈΡΡΠ΅ΠΌΠΎΠ³ΠΎ ΡΠ»Π΅ΠΌΠ΅Π½ΡΠ° Π°Π²ΡΠΎΠΌΠΎΠ±ΠΈΠ»Ρ ΠΈ ΡΡΠ΅Π΄Π½Π΅ΠΉ Π½Π°ΡΠ°Π±ΠΎΡΠΊΠΈ Π΄ΠΎ ΠΏΠ΅ΡΠ²ΠΎΠ³ΠΎ ΠΎΡΠΊΠ°Π·Π° ΠΏΡΠΎΠΈΠ·Π²ΠΎΠ΄ΠΈΡΡΡ ΠΏΠΎ ΡΠ°ΠΊΠΈΠΌ ΠΆΠ΅ ΡΡΠ°Π²Π½Π΅Π½ΠΈΡΠΌ, ΠΊΠ°ΠΊ ΠΈ Π΄Π»Ρ Π½Π΅ΡΠ΅ΠΌΠΎΠ½ΡΠΈΡΡΠ΅ΠΌΡΡ ΡΠ»Π΅ΠΌΠ΅Π½ΡΠΎΠ².
ΠΡΠΎΠΌΠ΅ ΠΏΠ΅ΡΠ΅ΡΠΈΡΠ»Π΅Π½Π½ΡΡ ΠΏΠΎΠΊΠ°Π·Π°ΡΠ΅Π»Π΅ΠΉ Π½Π°Π΄Π΅ΠΆΠ½ΠΎΡΡΠΈ, ΠΌΠΎΠ³ΡΡ ΠΏΡΠΈΠΌΠ΅Π½ΡΡΡΡΡ ΠΈ Π΄ΡΡΠ³ΠΈΠ΅ β Π² Π·Π°Π²ΠΈΡΠΈΠΌΠΎΡΡΠΈ ΠΎΡ ΠΏΠΎΡΡΠ°Π²Π»Π΅Π½Π½ΠΎΠΉ Π·Π°Π΄Π°ΡΠΈ, ΠΎΡ ΡΡΡΡΠΎΠΉΡΡΠ²Π° ΠΈ Π½Π°Π·Π½Π°ΡΠ΅Π½ΠΈΡ ΡΠ»Π΅ΠΌΠ΅Π½ΡΠ°.
ΠΠ»Ρ ΠΎΡΠ΅Π½ΠΊΠΈ ΡΠ΅ΠΌΠΎΠ½ΡΠΎΠΏΡΠΈΠ³ΠΎΠ΄Π½ΠΎΡΡΠΈ Π°Π²ΡΠΎΠΌΠΎΠ±ΠΈΠ»Ρ ΠΏΡΠΈΠ½ΠΈΠΌΠ°ΡΡ ΡΠ°ΠΊΠΈΠ΅ ΠΏΠΎΠΊΠ°Π·Π°ΡΠ΅Π»ΠΈ, ΠΊΠ°ΠΊ ΡΠ΄Π΅Π»ΡΠ½ΡΠ΅ ΡΡΡΠ΄ΠΎΠ²ΡΠ΅ Π·Π°ΡΡΠ°ΡΡ, ΡΠ²ΡΠ·Π°Π½Π½ΡΠ΅ Ρ ΡΡΡΡΠ°Π½Π΅Π½ΠΈΠ΅ΠΌ ΠΎΡΠΊΠ°Π·ΠΎΠ² (Ρ. Π΅. Π·Π°ΡΡΠ°ΡΡ, ΠΎΡΠ½Π΅ΡΠ΅Π½Π½ΡΠ΅ ΠΊ ΠΊΠΈΠ»ΠΎΠΌΠ΅ΡΡΠ°ΠΌ ΠΏΡΠΎΠ±Π΅Π³Π° Π°Π²ΡΠΎΠΌΠΎΠ±ΠΈΠ»Ρ), ΡΠ΄Π΅Π»ΡΠ½ΡΠ΅ ΡΡΠΎΠΈΠΌΠΎΡΡΠ½ΡΠ΅ Π·Π°ΡΡΠ°ΡΡ (ΡΠ°ΡΡ ΠΎΠ΄ Π·Π°ΠΏΠ°ΡΠ½ΡΡ ΡΠ°ΡΡΠ΅ΠΉ ΠΈ ΠΌΠ°ΡΠ΅ΡΠΈΠ°Π»ΠΎΠ² Π½Π° ΠΊΠΈΠ»ΠΎΠΌΠ΅ΡΡ ΠΏΡΠΎΠ±Π΅Π³Π°) ΠΈ Π΄Ρ.
Π Π΅ΠΊΠ»Π°ΠΌΠ°:
Π§ΠΈΡΠ°ΡΡ Π΄Π°Π»Π΅Π΅: ΠΠΎΠ»Π³ΠΎΠ²Π΅ΡΠ½ΠΎΡΡΡ Π°Π²ΡΠΎΠΌΠΎΠ±ΠΈΠ»ΡΠΠ°ΡΠ΅Π³ΠΎΡΠΈΡ: — Π’Π΅Ρ Π½ΠΈΡΠ΅ΡΠΊΠ°Ρ ΡΠΊΡΠΏΠ»ΡΠ°ΡΠ°ΡΠΈΡ Π°Π²ΡΠΎΠΌΠΎΠ±ΠΈΠ»Π΅ΠΉ
ΠΠ»Π°Π²Π½Π°Ρ β Π‘ΠΏΡΠ°Π²ΠΎΡΠ½ΠΈΠΊ β Π‘ΡΠ°ΡΡΠΈ β Π€ΠΎΡΡΠΌ
ΠΠ°ΡΠ΅ΡΡΠ²ΠΎ ΠΈ Π½Π°Π΄Π΅ΠΆΠ½ΠΎΡΡΡ ΠΌΠ°ΡΠΈΠ½
ΠΠ°ΡΠ΅ΡΡΠ²ΠΎ Π²ΡΠΏΡΡΠΊΠ°Π΅ΠΌΠΎΠΉ ΠΏΡΠΎΠ΄ΡΠΊΡΠΈΠΈ ΡΠ²Π»ΡΠ΅ΡΡΡ ΠΎΠ΄Π½ΠΈΠΌ ΠΈΠ· Π²Π°ΠΆΠ½Π΅ΠΉΡΠΈΡ ΠΏΠΎΠΊΠ°Π·Π°ΡΠ΅Π»Π΅ΠΉ Π΄Π΅ΡΡΠ΅Π»ΡΠ½ΠΎΡΡΠΈ ΠΏΡΠ΅Π΄ΠΏΡΠΈΡΡΠΈΡ.
ΠΠ°ΡΠ΅ΡΡΠ²ΠΎ ΠΏΡΠΎΠ΄ΡΠΊΡΠΈΠΈ β ΡΡΠΎ ΡΠΎΠ²ΠΎΠΊΡΠΏΠ½ΠΎΡΡΡ ΡΠ²ΠΎΠΉΡΡΠ², ΠΎΠ±ΡΡΠ»ΠΎΠ²Π»ΠΈΠ²Π°ΡΡΠΈΡ Π΅Π΅ ΠΏΡΠΈΠ³ΠΎΠ΄Π½ΠΎΡΡΡ ΡΠ΄ΠΎΠ²Π»Π΅ΡΠ²ΠΎΡΡΡΡ ΠΎΠΏΡΠ΅Π΄Π΅Π»Π΅Π½Π½ΡΠ΅ ΠΏΠΎΡΡΠ΅Π±Π½ΠΎΡΡΠΈ Π² ΡΠΎΠΎΡΠ²Π΅ΡΡΡΠ²ΠΈΠΈ Ρ Π½Π°Π·Π½Π°ΡΠ΅Π½ΠΈΠ΅ΠΌ; ΡΠ²ΠΎΠΉΡΡΠ²ΠΎ ΠΏΡΠΎΠ΄ΡΠΊΡΠΈΠΈ β ΠΎΠ±ΡΠ΅ΠΊΡΠΈΠ²Π½Π°Ρ ΠΎΡΠΎΠ±Π΅Π½Π½ΠΎΡΡΡ ΠΏΡΠΎΠ΄ΡΠΊΡΠΈΠΈ, ΠΏΡΠΎΡΠ²Π»ΡΡΡΠ°ΡΡΡ ΠΏΡΠΈ Π΅Π΅ ΡΠΎΠ·Π΄Π°Π½ΠΈΠΈ ΠΈ ΠΈΡΠΏΠΎΠ»ΡΠ·ΠΎΠ²Π°Π½ΠΈΠΈ. ΠΠ· ΡΡΠΎΠΉ ΡΠΎΡΠΌΡΠ»ΠΈΡΠΎΠ²ΠΊΠΈ ΡΠ»Π΅Π΄ΡΠ΅Ρ, ΡΡΠΎ Π½Π΅ Π²ΡΠ΅ ΡΠ²ΠΎΠΉΡΡΠ²Π° ΠΈΠ·Π΄Π΅Π»ΠΈΡ ΠΈΠΌΠ΅ΡΡ ΠΎΠ΄ΠΈΠ½Π°ΠΊΠΎΠ²ΡΡ Π·Π½Π°ΡΠΈΠΌΠΎΡΡΡ ΠΈ Π²Ρ ΠΎΠ΄ΡΡ Π² ΠΏΠΎΠ½ΡΡΠΈΠ΅ Β«ΠΊΠ°ΡΠ΅ΡΡΠ²ΠΎΒ». ΠΠ°ΠΏΡΠΈΠΌΠ΅Ρ, ΠΊΠ°ΡΠ΅ΡΡΠ²ΠΎ ΡΡΠ°ΠΊΡΠΎΡΠ° Π±ΡΠ΄Π΅Ρ ΠΎΠΏΡΠ΅Π΄Π΅Π»ΡΡΡΡΡ ΡΡΠ³ΠΎΠ²ΡΠΌ ΡΡΠΈΠ»ΠΈΠ΅ΠΌ, ΡΠ΄Π΅Π»ΡΠ½ΡΠΌ ΡΠ°ΡΡ ΠΎΠ΄ΠΎΠΌ ΡΠΎΠΏΠ»ΠΈΠ²Π°, Π½Π°ΡΠ°Π±ΠΎΡΠΊΠΎΠΉ Π΄ΠΎ ΠΊΠ°ΠΏΠΈΡΠ°Π»ΡΠ½ΠΎΠ³ΠΎ ΡΠ΅ΠΌΠΎΠ½ΡΠ° ΠΈ Π΄Ρ.
ΠΠΎΠΊΠ°Π·Π°ΡΠ΅Π»ΠΈ ΠΊΠ°ΡΠ΅ΡΡΠ²Π° ΠΏΡΠΎΠ΄ΡΠΊΡΠΈΠΈ β ΠΊΠΎΠ»ΠΈΡΠ΅ΡΡΠ²Π΅Π½Π½Π°Ρ Ρ Π°ΡΠ°ΠΊΡΠ΅ΡΠΈΡΡΠΈΠΊΠ° ΡΠ²ΠΎΠΉΡΡΠ² ΠΏΡΠΎΠ΄ΡΠΊΡΠΈΠΈ, ΡΠ°ΡΡΠΌΠ°ΡΡΠΈΠ²Π°Π΅ΠΌΠ°Ρ ΠΏΡΠΈΠΌΠ΅Π½ΠΈΡΠ΅Π»ΡΠ½ΠΎ ΠΊ ΠΎΠΏΡΠ΅Π΄Π΅Π»Π΅Π½Π½ΡΠΌ ΡΡΠ»ΠΎΠ²ΠΈΡΠΌ Π΅Π΅ ΡΠΎΠ·Π΄Π°Π½ΠΈΡ ΠΈΠ»ΠΈ ΡΠΊΡΠΏΠ»ΡΠ°ΡΠ°ΡΠΈΠΈ. ΠΡΡΠ³ΠΈΠΌΠΈ ΡΠ»ΠΎΠ²Π°ΠΌΠΈ, ΠΏΠΎΠΊΠ°Π·Π°ΡΠ΅Π»ΡΠΌΠΈ ΠΊΠ°ΡΠ΅ΡΡΠ²Π° ΠΏΡΠΎΠ΄ΡΠΊΡΠΈΠΈ ΡΠ²Π»ΡΡΡΡΡ ΠΏΠ°ΡΠ°ΠΌΠ΅ΡΡΡ, ΠΊΠΎΡΠΎΡΡΠ΅ Ρ Π°ΡΠ°ΠΊΡΠ΅ΡΠΈΠ·ΡΡΡ ΠΊΠ°ΡΠ΅ΡΡΠ²ΠΎ.
ΠΠ°ΡΠ΅ΡΡΠ²ΠΎ Π°Π²ΡΠΎΠΌΠΎΠ±ΠΈΠ»Ρ β ΡΡΠΎ ΡΠΎΠ²ΠΎΠΊΡΠΏΠ½ΠΎΡΡΡ ΡΠ²ΠΎΠΉΡΡΠ², ΠΎΠΏΡΠ΅Π΄Π΅Π»ΡΡΡΠΈΡ Π΅Π³ΠΎ ΡΠΏΠΎΡΠΎΠ±Π½ΠΎΡΡΡ Π²ΡΠΏΠΎΠ»Π½ΡΡΡ ΡΠ²ΠΎΠΈ ΡΡΠ½ΠΊΡΠΈΠΈ Π² ΡΠΎΠΎΡΠ²Π΅ΡΡΡΠ²ΠΈΠΈ Ρ ΡΡΠ΅Π±ΠΎΠ²Π°Π½ΠΈΡΠΌΠΈ. ΠΡΠ΅ ΠΏΠΎΠΊΠ°Π·Π°ΡΠ΅Π»ΠΈ ΠΊΠ°ΡΠ΅ΡΡΠ²Π° Π°Π²ΡΠΎΠΌΠΎΠ±ΠΈΠ»Ρ Π΄Π΅Π»ΡΡΡΡ Π½Π° Π½Π΅ΡΠΊΠΎΠ»ΡΠΊΠΎ Π³ΡΡΠΏΠΏ:
- ΠΠΎΠΊΠ°Π·Π°ΡΠ΅Π»ΠΈ Π½Π°Π·Π½Π°ΡΠ΅Π½ΠΈΡ Ρ Π°ΡΠ°ΠΊΡΠ΅ΡΠΈΠ·ΡΡΡ ΠΏΡΠΈΡΠΏΠΎΡΠΎΠ±Π»Π΅Π½Π½ΠΎΡΡΡ Π°Π²ΡΠΎΠΌΠΎΠ±ΠΈΠ»Ρ ΠΊ ΠΈΡΠΏΠΎΠ»ΡΠ·ΠΎΠ²Π°Π½ΠΈΡ ΠΏΠΎ Π½Π°Π·Π½Π°ΡΠ΅Π½ΠΈΡ, Π΅Π³ΠΎ ΡΠ΅Ρ Π½ΠΈΡΠ΅ΡΠΊΠΈΠ΅ ΠΈ ΡΠΊΡΠΏΠ»ΡΠ°ΡΠ°ΡΠΈΠΎΠ½Π½ΡΠ΅ Π²ΠΎΠ·ΠΌΠΎΠΆΠ½ΠΎΡΡΠΈ (ΠΌΠΎΡΠ½ΠΎΡΡΡ, ΠΏΡΠΎΠΈΠ·Π²ΠΎΠ΄ΠΈΡΠ΅Π»ΡΠ½ΠΎΡΡΡ, ΡΠΊΠΎΡΠΎΡΡΡ ΠΈ Π΄Ρ.).
- ΠΠΎΠΊΠ°Π·Π°ΡΠ΅Π»ΠΈ ΡΠ΅Ρ Π½ΠΎΠ»ΠΎΠ³ΠΈΡΠ½ΠΎΡΡΠΈ Ρ Π°ΡΠ°ΠΊΡΠ΅ΡΠΈΠ·ΡΡΡ ΡΡΡΠ΅ΠΊΡΠΈΠ²Π½ΠΎΡΡΡ ΠΊΠΎΠ½ΡΡΡΡΠΊΡΠΈΠΈ ΠΈ ΡΠ΅Ρ Π½ΠΎΠ»ΠΎΠ³ΠΈΡ Π΅Π΅ ΠΏΡΠΎΠΈΠ·Π²ΠΎΠ΄ΡΡΠ²Π°.
- ΠΡΠ³ΠΎΠ½ΠΎΠΌΠΈΡΠ΅ΡΠΊΠΈΠ΅ ΠΏΠΎΠΊΠ°Π·Π°ΡΠ΅Π»ΠΈ ΡΡΠΈΡΡΠ²Π°ΡΡ Π΅Π³ΠΎ ΠΏΡΠΈΡΠΏΠΎΡΠΎΠ±Π»Π΅Π½Π½ΠΎΡΡΡ ΠΊ Π°Π½ΡΡΠΎΠΏΠΎΠΌΠ΅ΡΡΠΈΡΠ΅ΡΠΊΠΈΠΌ, ΡΠΈΠ·ΠΈΠΎΠ»ΠΎΠ³ΠΈΡΠ΅ΡΠΊΠΈΠΌ, ΠΏΡΠΈΡ ΠΎΠ»ΠΎΠ³ΠΈΡΠ΅ΡΠΊΠΈΠΌ, Π±ΠΈΠΎΠΌΠ΅Ρ Π°Π½ΠΈΡΠ΅ΡΠΊΠΈΠΌ ΠΈ Π΄ΡΡΠ³ΠΈΠΌ ΡΠ²ΠΎΠΉΡΡΠ²Π°ΠΌ ΡΠ΅Π»ΠΎΠ²Π΅ΠΊΠ°, ΠΏΡΠΎΡΠ²Π»ΡΡΡΠΈΠΌΡΡ Π² ΠΏΡΠΎΠΈΠ·Π²ΠΎΠ΄ΡΡΠ²Π΅Π½Π½ΡΡ ΠΏΡΠΎΡΠ΅ΡΡΠ°Ρ (ΡΡΠΌ, Π²ΠΈΠ±ΡΠ°ΡΠΈΡ, ΡΡΠΈΠ»ΠΈΠ² Π½Π° ΡΡΡΠ°Π³Π°Ρ ΠΈ Π΄Ρ.).
- ΠΠΎΠΊΠ°Π·Π°ΡΠ΅Π»ΠΈ ΡΠ½ΠΈΡΠΈΠΊΠ°ΡΠΈΠΈ ΠΈ ΡΡΠ°Π½Π΄Π°ΡΡΠΈΠ·Π°ΡΠΈΠΈ Ρ Π°ΡΠ°ΠΊΡΠ΅ΡΠΈΠ·ΡΡΡ ΡΡΠ΅ΠΏΠ΅Π½Ρ ΠΈΡΠΏΠΎΠ»ΡΠ·ΠΎΠ²Π°Π½ΠΈΡ ΠΎΠ΄ΠΈΠ½Π°ΠΊΠΎΠ²ΡΡ ΠΏΠΎ ΡΠ²ΠΎΠ΅ΠΌΡ ΡΡΠ½ΠΊΡΠΈΠΎΠ½Π°Π»ΡΠ½ΠΎΠΌΡ Π½Π°Π·Π½Π°ΡΠ΅Π½ΠΈΡ Π΄Π΅ΡΠ°Π»Π΅ΠΉ ΡΠ±ΠΎΡΠΎΡΠ½ΡΡ Π΅Π΄ΠΈΠ½ΠΈΡ, ΠΏΡΠΈΠΌΠ΅Π½ΡΠ΅ΠΌΡΡ Π½Π° ΡΠ°Π·Π»ΠΈΡΠ½ΡΡ Π°Π²ΡΠΎΠΌΠΎΠ±ΠΈΠ»ΡΡ , ΠΈ ΡΡΠ°Π½Π΄Π°ΡΡΠ½ΡΡ Π΄Π΅ΡΠ°Π»Π΅ΠΉ ΠΈ ΡΠ·Π»ΠΎΠ².
- ΠΠΊΠΎΠ½ΠΎΠΌΠΈΡΠ΅ΡΠΊΠΈΠ΅ ΠΏΠΎΠΊΠ°Π·Π°ΡΠ΅Π»ΠΈ ΠΎΡΡΠ°ΠΆΠ°ΡΡ Π·Π°ΡΡΠ°ΡΡ Π½Π° ΡΠ°Π·ΡΠ°Π±ΠΎΡΠΊΡ, ΠΈΠ·Π³ΠΎΡΠΎΠ²Π»Π΅Π½ΠΈΠ΅ ΠΈ ΠΈΡΠΏΠΎΠ»ΡΠ·ΠΎΠ²Π°Π½ΠΈΠ΅ Π°Π²ΡΠΎΠΌΠΎΠ±ΠΈΠ»Ρ, ΡΡΡΠ΄ΠΎΠ΅ΠΌΠΊΠΎΡΡΡ ΠΈ ΡΡΠΎΠΈΠΌΠΎΡΡΡ ΡΠ΅Ρ Π½ΠΈΡΠ΅ΡΠΊΠΎΠ³ΠΎ ΠΎΠ±ΡΠ»ΡΠΆΠΈΠ²Π°Π½ΠΈΡ ΠΈ ΡΠ΅ΠΌΠΎΠ½ΡΠ°.
- ΠΠΊΠΎΠ»ΠΎΠ³ΠΈΡΠ΅ΡΠΊΠΈΠ΅ ΠΏΠΎΠΊΠ°Π·Π°ΡΠ΅Π»ΠΈ Ρ Π°ΡΠ°ΠΊΡΠ΅ΡΠΈΠ·ΡΡΡ ΡΠΈΡΡΠ΅ΠΌΡ ΡΠ΅Π»ΠΎΠ²Π΅ΠΊβΠΌΠ°ΡΠΈΠ½Π°βΡΡΠ΅Π΄Π° Ρ ΡΠΎΡΠΊΠΈ Π·ΡΠ΅Π½ΠΈΡ ΡΡΠΎΠ²Π½Ρ Π²ΡΠ΅Π΄Π½ΡΡ Π²ΠΎΠ·Π΄Π΅ΠΉΡΡΠ²ΠΈΠΉ Π½Π° ΠΏΡΠΈΡΠΎΠ΄Ρ, Π²ΠΎΠ·Π½ΠΈΠΊΠ°ΡΡΠΈΡ Π² ΠΏΡΠΎΡΠ΅ΡΡΠ΅ ΡΠΊΡΠΏΠ»ΡΠ°ΡΠ°ΡΠΈΠΈ ΠΌΠ°ΡΠΈΠ½Ρ.
- ΠΡΡΠ΅ΡΠΈΡΠ΅ΡΠΊΠΈΠ΅ ΠΏΠΎΠΊΠ°Π·Π°ΡΠ΅Π»ΠΈ ΠΎΡΡΠ°ΠΆΠ°ΡΡ ΡΠ°ΠΊΠΈΠ΅ ΡΠ²ΠΎΠΉΡΡΠ²Π° Π°Π²ΡΠΎΠΌΠΎΠ±ΠΈΠ»Ρ, ΠΊΠ°ΠΊ ΡΠΎΡΠΌΠ°, Π²Π½Π΅ΡΠ½ΠΈΠΉ Π²ΠΈΠ΄. ΠΠ½ΠΈ ΠΎΠΏΡΠ΅Π΄Π΅Π»ΡΡΡΡΡ ΡΡΠΎΠ²Π½Π΅ΠΌ Ρ ΡΠ΄ΠΎΠΆΠ΅ΡΡΠ²Π΅Π½Π½ΠΎΠ³ΠΎ ΠΊΠΎΠ½ΡΡΡΡΠΈΡΠΎΠ²Π°Π½ΠΈΡ.
- ΠΠ°ΡΠ΅Π½ΡΠ½ΠΎ-ΠΏΡΠ°Π²ΠΎΠ²ΡΠ΅ ΠΏΠΎΠΊΠ°Π·Π°ΡΠ΅Π»ΠΈ Ρ Π°ΡΠ°ΠΊΡΠ΅ΡΠΈΠ·ΡΡΡ Π²Π΅ΡΠΎΠΌΠΎΡΡΡ Π½ΠΎΠ²ΡΡ ΠΈΠ·ΠΎΠ±ΡΠ΅ΡΠ΅Π½ΠΈΠΉ, ΡΠ΅Π°Π»ΠΈΠ·ΠΎΠ²Π°Π½Π½ΡΡ Π² Π°Π²ΡΠΎΠΌΠΎΠ±ΠΈΠ»Π΅.
ΠΠ°Π΄Π΅ΠΆΠ½ΠΎΡΡΡ Π°Π²ΡΠΎΠΌΠΎΠ±ΠΈΠ»Ρ β ΠΎΠ΄ΠΈΠ½ ΠΈΠ· Π²Π°ΠΆΠ½Π΅ΠΉΡΠΈΡ ΠΏΠΎΠΊΠ°Π·Π°ΡΠ΅Π»Π΅ΠΉ ΠΊΠ°ΡΠ΅ΡΡΠ²Π°. ΠΠ°Π΄Π΅ΠΆΠ½ΠΎΡΡΡ β ΡΡΠΎ ΡΠ²ΠΎΠΉΡΡΠ²ΠΎ ΠΈΠ·Π΄Π΅Π»ΠΈΡ, ΠΎΠ±Π΅ΡΠΏΠ΅ΡΠΈΠ²Π°ΡΡΠ΅Π΅ Π²ΡΠΏΠΎΠ»Π½Π΅Π½ΠΈΠ΅ Π·Π°Π΄Π°Π½Π½ΡΡ ΡΡΠ½ΠΊΡΠΈΠΉ ΠΏΡΠΈ ΡΠΎΡ ΡΠ°Π½Π΅Π½ΠΈΠΈ ΡΠΊΡΠΏΠ»ΡΠ°ΡΠ°ΡΠΈΠΎΠ½Π½ΡΡ ΠΏΠΎΠΊΠ°Π·Π°ΡΠ΅Π»Π΅ΠΉ Π² ΡΠ΅ΡΠ΅Π½ΠΈΠ΅ ΡΡΠ΅Π±ΡΠ΅ΠΌΠΎΠ³ΠΎ ΠΏΡΠΎΠΌΠ΅ΠΆΡΡΠΊΠ° Π²ΡΠ΅ΠΌΠ΅Π½ΠΈ ΠΈΠ»ΠΈ ΡΡΠ΅Π±ΡΠ΅ΠΌΠΎΠΉ Π½Π°ΡΠ°Π±ΠΎΡΠΊΠΈ.
ΠΠ°ΡΠ°Π±ΠΎΡΠΊΠ° β ΠΏΡΠΎΠ΄ΠΎΠ»ΠΆΠΈΡΠ΅Π»ΡΠ½ΠΎΡΡΡ ΡΡΠ½ΠΊΡΠΈΠΎΠ½ΠΈΡΠΎΠ²Π°Π½ΠΈΡ ΠΈΠ»ΠΈ ΠΎΠ±ΡΠ΅ΠΌ ΡΠ°Π±ΠΎΡΡ, Π²ΡΠΏΠΎΠ»Π½Π΅Π½Π½ΡΠΉ Π°Π²ΡΠΎΠΌΠΎΠ±ΠΈΠ»Π΅ΠΌ, ΠΊΠΎΡΠΎΡΡΠ΅ ΠΈΠ·ΠΌΠ΅ΡΡΡΡ Π² ΡΠ°ΡΠ°Ρ , ΠΌΠΎΡΠΎΡΠ°ΡΠ°Ρ , Π³Π΅ΠΊΡΠ°ΡΠ°Ρ , ΡΡΠ»ΠΎΠ²Π½ΡΡ ΡΡΠ°Π»ΠΎΠ½Π½ΡΡ Π³Π΅ΠΊΡΠ°ΡΠ°Ρ . ΠΡΠΈ ΡΠΊΡΠΏΠ»ΡΠ°ΡΠ°ΡΠΈΠΈ Π°Π²ΡΠΎΠΌΠΎΠ±ΠΈΠ»Π΅ΠΉ ΡΠ°Π·Π»ΠΈΡΠ°ΡΡ Π½Π°ΡΠ°Π±ΠΎΡΠΊΡ: ΡΠΌΠ΅Π½Π½ΡΡ, ΡΡΡΠΎΡΠ½ΡΡ, ΠΌΠ΅ΡΡΡΠ½ΡΡ ΠΈΠ»ΠΈ Π³ΠΎΠ΄ΠΎΠ²ΡΡ, Π΄ΠΎ ΠΏΠ΅ΡΠ²ΠΎΠ³ΠΎ ΠΎΡΠΊΠ°Π·Π°, ΠΌΠ΅ΠΆΠ΄Ρ ΠΎΡΠΊΠ°Π·Π°ΠΌΠΈ ΠΈ Ρ. ΠΏ.
ΠΡΠΊΠ°Π· β Π½Π°ΡΡΡΠ΅Π½ΠΈΠ΅ ΡΠ°Π±ΠΎΡΠΎΡΠΏΠΎΡΠΎΠ±Π½ΠΎΡΡΠΈ Π°Π²ΡΠΎΠΌΠΎΠ±ΠΈΠ»Ρ (Π΄Π΅ΡΠ°Π»ΠΈ, ΡΠ·Π»Π° ΠΈ Ρ. ΠΏ.). ΠΠΎΠ²ΡΠ΅ΠΆΠ΄Π΅Π½ΠΈΠ΅ Π·Π°ΠΊΠ»ΡΡΠ°Π΅ΡΡΡ Π² Π½Π°ΡΡΡΠ΅Π½ΠΈΠΈ ΠΈΡΠΏΡΠ°Π²Π½ΠΎΡΡΠΈ. Π ΡΠΎΠΎΡΠ²Π΅ΡΡΡΠ²ΠΈΠΈ Ρ ΡΠ΅ΠΎΡΠΈΠ΅ΠΉ Π½Π°Π΄Π΅ΠΆΠ½ΠΎΡΡΠΈ Π°Π²ΡΠΎΠΌΠΎΠ±ΠΈΠ»Ρ ΠΌΠΎΠΆΠ΅Ρ Π½Π°Ρ ΠΎΠ΄ΠΈΡΡΡΡ Π² ΡΠΎΡΡΠΎΡΠ½ΠΈΠΈ ΡΠ°Π±ΠΎΡΠΎΡΠΏΠΎΡΠΎΠ±Π½ΠΎΡΡΠΈ ΠΈΠ»ΠΈ Π½Π΅ΡΠ°Π±ΠΎΡΠΎΡΠΏΠΎΡΠΎΠ±Π½ΠΎΡΡΠΈ, ΠΈΡΠΏΡΠ°Π²Π½ΠΎΡΡΠΈ ΠΈΠ»ΠΈ Π½Π΅ΠΈΡΠΏΡΠ°Π²Π½ΠΎΡΡΠΈ.
Π Π°Π±ΠΎΡΠΎΡΠΏΠΎΡΠΎΠ±Π½ΠΎΡΡΡ β ΡΠΎΡΡΠΎΡΠ½ΠΈΠ΅ Π°Π²ΡΠΎΠΌΠΎΠ±ΠΈΠ»Ρ ΠΈΠ»ΠΈ ΡΠ±ΠΎΡΠΎΡΠ½ΡΡ Π΅Π΄ΠΈΠ½ΠΈΡ, ΠΏΡΠΈ ΠΊΠΎΡΠΎΡΠΎΠΌ Π·Π½Π°ΡΠ΅Π½ΠΈΡ Π²ΡΠ΅Ρ ΠΏΠ°ΡΠ°ΠΌΠ΅ΡΡΠΎΠ², Ρ Π°ΡΠ°ΠΊΡΠ΅ΡΠΈΠ·ΡΡΡΠΈΡ ΡΠΏΠΎΡΠΎΠ±Π½ΠΎΡΡΡ Π²ΡΠΏΠΎΠ»Π½ΡΡΡ Π·Π°Π΄Π°Π½Π½ΡΠ΅ ΡΡΠ½ΠΊΡΠΈΠΈ, ΡΠΎΠΎΡΠ²Π΅ΡΡΡΠ²ΡΡΡ Π½ΠΎΡΠΌΠ°ΡΠΈΠ²Π½ΠΎ-ΡΠ΅Ρ Π½ΠΈΡΠ΅ΡΠΊΠΎΠΉ (ΡΡΠ°Π½Π΄Π°ΡΡΡ, ΡΠ΅Ρ Π½ΠΈΡΠ΅ΡΠΊΠΈΠ΅ ΡΡΠ»ΠΎΠ²ΠΈΡ ΠΈ Ρ. Π΄.) ΠΈ (ΠΈΠ»ΠΈ) ΠΊΠΎΠ½ΡΡΡΡΠΊΡΠΎΡΡΠΊΠΎΠΉ Π΄ΠΎΠΊΡΠΌΠ΅Π½ΡΠ°ΡΠΈΠΈ (ΠΌΠΎΡΠ½ΠΎΡΡΡ Π΄Π²ΠΈΠ³Π°ΡΠ΅Π»Ρ, ΡΠΈΠ»Π° ΡΡΠ³ΠΈ Π½Π° ΠΊΡΡΠΊΠ΅, ΡΠ°ΡΡ ΠΎΠ΄ ΡΠΎΠΏΠ»ΠΈΠ²Π° ΠΈ Ρ. Π΄.).
ΠΠ΅ΡΠ°Π±ΠΎΡΠΎΡΠΏΠΎΡΠΎΠ±Π½ΠΎΡΡΡ β ΡΠΎΡΡΠΎΡΠ½ΠΈΠ΅ Π°Π²ΡΠΎΠΌΠΎΠ±ΠΈΠ»Ρ, ΠΏΡΠΈ ΠΊΠΎΡΠΎΡΠΎΠΌ Π·Π½Π°ΡΠ΅Π½ΠΈΠ΅ Ρ ΠΎΡΡ Π±Ρ ΠΎΠ΄Π½ΠΎΠ³ΠΎ Π·Π°Π΄Π°Π½Π½ΠΎΠ³ΠΎ ΠΏΠ°ΡΠ°ΠΌΠ΅ΡΡΠ°, Ρ Π°ΡΠ°ΠΊΡΠ΅ΡΠΈΠ·ΡΡΡΠ΅Π³ΠΎ ΡΠΏΠΎΡΠΎΠ±Π½ΠΎΡΡΡ Π²ΡΠΏΠΎΠ»Π½ΡΡΡ Π·Π°Π΄Π°Π½Π½ΡΠ΅ ΡΡΠ½ΠΊΡΠΈΠΈ, Π½Π΅ ΡΠΎΠΎΡΠ²Π΅ΡΡΡΠ²ΡΠ΅Ρ ΡΡΠ΅Π±ΠΎΠ²Π°Π½ΠΈΡΠΌ Π½ΠΎΡΠΌΠ°ΡΠΈΠ²Π½ΠΎ-ΡΠ΅Ρ Π½ΠΈΡΠ΅ΡΠΊΠΎΠΉ ΠΈ (ΠΈΠ»ΠΈ) ΠΊΠΎΠ½ΡΡΡΡΠΊΡΠΎΡΡΠΊΠΎΠΉ Π΄ΠΎΠΊΡΠΌΠ΅Π½ΡΠ°ΡΠΈΠΈ.
ΠΡΠΏΡΠ°Π²Π½ΠΎΡΡΡ β ΡΠΎΡΡΠΎΡΠ½ΠΈΠ΅ Π°Π²ΡΠΎΠΌΠΎΠ±ΠΈΠ»Ρ, ΠΏΡΠΈ ΠΊΠΎΡΠΎΡΠΎΠΌ ΠΎΠ½ ΡΠΎΠΎΡΠ²Π΅ΡΡΡΠ²ΡΠ΅Ρ Π²ΡΠ΅ΠΌ ΡΡΠ΅Π±ΠΎΠ²Π°Π½ΠΈΡΠΌ, ΡΡΡΠ°Π½ΠΎΠ²Π»Π΅Π½Π½ΡΠΌ Π½ΠΎΡΠΌΠ°ΡΠΈΠ²Π½ΠΎ-ΡΠ΅Ρ Π½ΠΈΡΠ΅ΡΠΊΠΎΠΉ ΠΈ (ΠΈΠ»ΠΈ) ΠΊΠΎΠ½ΡΡΡΡΠΊΡΠΎΡΡΠΊΠΎΠΉ Π΄ΠΎΠΊΡΠΌΠ΅Π½ΡΠ°ΡΠΈΠ΅ΠΉ.
ΠΠ΅ΠΈΡΠΏΡΠ°Π²Π½ΠΎΡΡΡ β ΡΠΎΡΡΠΎΡΠ½ΠΈΠ΅ Π°Π²ΡΠΎΠΌΠΎΠ±ΠΈΠ»Ρ, ΠΏΡΠΈ ΠΊΠΎΡΠΎΡΠΎΠΌ ΠΎΠ½ Π½Π΅ ΡΠΎΠΎΡΠ²Π΅ΡΡΡΠ²ΡΠ΅Ρ Ρ ΠΎΡΡ Π±Ρ ΠΎΠ΄Π½ΠΎΠΌΡ ΠΈΠ· ΡΡΠΈΡ ΡΡΠ΅Π±ΠΎΠ²Π°Π½ΠΈΠΉ.
ΠΠΎΠ½ΡΡΠΈΠ΅ Β«ΠΈΡΠΏΡΠ°Π²Π½ΠΎΡΡΡΒ» ΡΠΈΡΠ΅, ΡΠ΅ΠΌ Β«ΡΠ°Π±ΠΎΡΠΎΡΠΏΠΎΡΠΎΠ±Π½ΠΎΡΡΡΒ». Π Π°Π±ΠΎΡΠΎΡΠΏΠΎΡΠΎΠ±Π½ΡΠΉ Π°Π²ΡΠΎΠΌΠΎΠ±ΠΈΠ»Ρ Π² ΠΎΡΠ»ΠΈΡΠΈΠ΅ ΠΎΡ ΠΈΡΠΏΡΠ°Π²Π½ΠΎΠ³ΠΎ ΡΠ΄ΠΎΠ²Π»Π΅ΡΠ²ΠΎΡΡΠ΅Ρ Π»ΠΈΡΡ ΡΠ΅ΠΌ ΡΡΠ΅Π±ΠΎΠ²Π°Π½ΠΈΡΠΌ Π½ΠΎΡΠΌΠ°ΡΠΈΠ²Π½ΠΎ-ΡΠ΅Ρ Π½ΠΈΡΠ΅ΡΠΊΠΎΠΉ Π΄ΠΎΠΊΡΠΌΠ΅Π½ΡΠ°ΡΠΈΠΈ, ΠΊΠΎΡΠΎΡΡΠ΅ ΠΎΠ±Π΅ΡΠΏΠ΅ΡΠΈΠ²Π°ΡΡ Π΅Π³ΠΎ Π½ΠΎΡΠΌΠ°Π»ΡΠ½ΠΎΠ΅ ΡΡΠ½ΠΊΡΠΈΠΎΠ½ΠΈΡΠΎΠ²Π°Π½ΠΈΠ΅ ΠΏΡΠΈ Π²ΡΠΏΠΎΠ»Π½Π΅Π½ΠΈΠΈ Π·Π°Π΄Π°Π½Π½ΡΡ ΡΡΠ½ΠΊΡΠΈΠΉ. ΠΠ΄Π½Π°ΠΊΠΎ Π°Π²ΡΠΎΠΌΠΎΠ±ΠΈΠ»Ρ ΠΌΠΎΠΆΠ΅Ρ Π½Π΅ ΡΠ΄ΠΎΠ²Π»Π΅ΡΠ²ΠΎΡΡΡΡ, Π½Π°ΠΏΡΠΈΠΌΠ΅Ρ, ΡΡΠ΅Π±ΠΎΠ²Π°Π½ΠΈΡΠΌ, ΠΎΡΠ½ΠΎΡΡΡΠΈΠΌΡΡ ΠΊ Π²Π½Π΅ΡΠ½Π΅ΠΌΡ Π²ΠΈΠ΄Ρ (Π΄Π΅ΡΠ΅ΠΊΡΡ ΠΊΠ°Π±ΠΈΠ½Ρ, ΠΎΠ±Π»ΠΈΡΠΎΠ²ΠΊΠΈ ΠΈ Π΄Ρ.). Π‘Π»Π΅Π΄ΠΎΠ²Π°ΡΠ΅Π»ΡΠ½ΠΎ, ΡΠ°Π±ΠΎΡΠΎΡΠΏΠΎΡΠΎΠ±Π½ΡΠΉ Π°Π²ΡΠΎΠΌΠΎΠ±ΠΈΠ»Ρ ΠΌΠΎΠΆΠ΅Ρ Π±ΡΡΡ Π½Π΅ΠΈΡΠΏΡΠ°Π²Π½ΡΠΌ, ΠΎΠ΄Π½Π°ΠΊΠΎ Π΅Π³ΠΎ ΠΏΠΎΠ²ΡΠ΅ΠΆΠ΄Π΅Π½ΠΈΡ Π½Π΅ ΠΏΡΠ΅ΠΏΡΡΡΡΠ²ΡΡΡ Π½ΠΎΡΠΌΠ°Π»ΡΠ½ΠΎΠΌΡ ΡΡΠ½ΠΊΡΠΈΠΎΠ½ΠΈΡΠΎΠ²Π°Π½ΠΈΡ.
ΠΠ°Π΄Π΅ΠΆΠ½ΠΎΡΡΡ Π°Π²ΡΠΎΠΌΠΎΠ±ΠΈΠ»Ρ β ΠΊΠΎΠΌΠΏΠ»Π΅ΠΊΡΠ½ΠΎΠ΅ ΡΠ²ΠΎΠΉΡΡΠ²ΠΎ, ΠΊΠΎΡΠΎΡΠΎΠ΅ Ρ Π°ΡΠ°ΠΊΡΠ΅ΡΠΈΠ·ΡΠ΅ΡΡΡ Π±Π΅Π·ΠΎΡΠΊΠ°Π·Π½ΠΎΡΡΡΡ, ΡΠ΅ΠΌΠΎΠ½ΡΠΎΠΏΡΠΈΠ³ΠΎΠ΄Π½ΠΎΡΡΡΡ, Π΄ΠΎΠ»Π³ΠΎΠ²Π΅ΡΠ½ΠΎΡΡΡΡ ΠΈ ΡΠΎΡ ΡΠ°Π½ΡΠ΅ΠΌΠΎΡΡΡΡ. ΠΠ°ΠΆΠ΄ΠΎΠ΅ ΠΈΠ· ΡΠΊΠ°Π·Π°Π½Π½ΡΡ ΡΠ²ΠΎΠΉΡΡΠ² Π½Π°Π΄Π΅ΠΆΠ½ΠΎΡΡΠΈ ΠΎΡΠ΅Π½ΠΈΠ²Π°Π΅ΡΡΡ ΡΡΠ΄ΠΎΠΌ ΡΠ΅Ρ Π½ΠΈΡΠ΅ΡΠΊΠΈΡ ΠΈ ΡΠΊΠΎΠ½ΠΎΠΌΠΈΡΠ΅ΡΠΊΠΈΡ ΠΏΠΎΠΊΠ°Π·Π°ΡΠ΅Π»Π΅ΠΉ, ΡΠΈΠ·ΠΈΡΠ΅ΡΠΊΠ°Ρ ΡΡΡΠ½ΠΎΡΡΡ ΠΈ ΠΊΠΎΠ»ΠΈΡΠ΅ΡΡΠ²ΠΎ ΠΊΠΎΡΠΎΡΡΡ Π·Π°Π²ΠΈΡΠΈΡ ΠΎΡ ΠΊΠΎΠ½ΡΡΡΡΠΊΡΠΈΠΈ Π°Π²ΡΠΎΠΌΠΎΠ±ΠΈΠ»Ρ, ΡΠ΅Ρ Π½ΠΎΠ»ΠΎΠ³ΠΈΠΈ ΠΈΠ·Π³ΠΎΡΠΎΠ²Π»Π΅Π½ΠΈΡ ΠΈ ΡΡΠ»ΠΎΠ²ΠΈΠΉ ΡΠΊΡΠΏΠ»ΡΠ°ΡΠ°ΡΠΈΠΈ, ΠΊΠ°ΡΠ΅ΡΡΠ²Π° ΡΠ΅Ρ Π½ΠΈΡΠ΅ΡΠΊΠΎΠ³ΠΎ ΠΎΠ±ΡΠ»ΡΠΆΠΈΠ²Π°Π½ΠΈΡ ΠΈ ΡΠ΅ΠΌΠΎΠ½ΡΠ°.
ΠΠ΅Π·ΠΎΡΠΊΠ°Π·Π½ΠΎΡΡΡ β ΡΠ²ΠΎΠΉΡΡΠ²ΠΎ Π°Π²ΡΠΎΠΌΠΎΠ±ΠΈΠ»Ρ ΡΠΎΡ ΡΠ°Π½ΡΡΡ ΡΠ°Π±ΠΎΡΠΎΡΠΏΠΎΡΠΎΠ±Π½ΠΎΡΡΡ ΠΏΡΠΈ ΡΠΊΡΠΏΠ»ΡΠ°ΡΠ°ΡΠΈΠΈ Π² ΡΠ΅ΡΠ΅Π½ΠΈΠ΅ ΠΎΠΏΡΠ΅Π΄Π΅Π»Π΅Π½Π½ΠΎΠ³ΠΎ Π²ΡΠ΅ΠΌΠ΅Π½ΠΈ ΠΈΠ»ΠΈ Π½Π°ΡΠ°Π±ΠΎΡΠΊΠΈ Π±Π΅Π· Π²ΡΠ½ΡΠΆΠ΄Π΅Π½Π½ΡΡ ΠΏΠ΅ΡΠ΅ΡΡΠ²ΠΎΠ². ΠΠΎΠΊΠ°Π·Π°ΡΠ΅Π»ΠΈ Π±Π΅Π·ΠΎΡΠΊΠ°Π·Π½ΠΎΡΡΠΈ ΠΎΠΏΡΠ΅Π΄Π΅Π»ΡΡΡΡΡ ΠΎΠΏΡΡΠ½ΡΠΌ ΠΏΡΡΠ΅ΠΌ.
Π Π΅ΠΌΠΎΠ½ΡΠΎΠΏΡΠΈΠ³ΠΎΠ΄Π½ΠΎΡΡΡ β ΡΠ²ΠΎΠΉΡΡΠ²ΠΎ Π°Π²ΡΠΎΠΌΠΎΠ±ΠΈΠ»Ρ, Π·Π°ΠΊΠ»ΡΡΠ°ΡΡΠ΅Π΅ΡΡ Π² ΠΏΡΠΈΡΠΏΠΎΡΠΎΠ±Π»Π΅Π½Π½ΠΎΡΡΠΈ Π΅Π³ΠΎ ΠΊΠΎΠ½ΡΡΡΡΠΊΡΠΈΠΈ ΠΊ ΠΏΡΠ΅Π΄ΡΠΏΡΠ΅ΠΆΠ΄Π΅Π½ΠΈΡ, ΠΎΠ±Π½Π°ΡΡΠΆΠ΅Π½ΠΈΡ ΠΈ ΡΡΡΡΠ°Π½Π΅Π½ΠΈΡ ΠΎΡΠΊΠ°Π·ΠΎΠ² ΠΈ Π½Π΅ΠΈΡΠΏΡΠ°Π²Π½ΠΎΡΡΠ΅ΠΉ ΠΏΡΡΠ΅ΠΌ ΠΏΡΠΎΠ²Π΅Π΄Π΅Π½ΠΈΡ ΡΠ΅Ρ Π½ΠΈΡΠ΅ΡΠΊΠΎΠ³ΠΎ ΠΎΠ±ΡΠ»ΡΠΆΠΈΠ²Π°Π½ΠΈΡ ΠΈ ΡΠ΅ΠΌΠΎΠ½ΡΠΎΠ² Π΄Π»Ρ ΠΏΠΎΠ΄Π΄Π΅ΡΠΆΠ°Π½ΠΈΡ ΠΈ Π²ΠΎΡΡΡΠ°Π½ΠΎΠ²Π»Π΅Π½ΠΈΡ ΡΠ°Π±ΠΎΡΠΎΡΠΏΠΎΡΠΎΠ±Π½ΠΎΡΡΠΈ. ΠΡΡΠ³ΠΈΠΌΠΈ ΡΠ»ΠΎΠ²Π°ΠΌΠΈ, ΡΠ΅ΠΌΠΎΠ½ΡΠΎΠΏΡΠΈΠ³ΠΎΠ΄Π½ΠΎΡΡΡ β ΡΠΊΡΠΏΠ»ΡΠ°ΡΠ°ΡΠΈΠΎΠ½Π½ΠΎ-ΡΠ΅Ρ Π½ΠΈΡΠ΅ΡΠΊΠΎΠ΅ ΡΠ²ΠΎΠΉΡΡΠ²ΠΎ Π°Π²ΡΠΎΠΌΠΎΠ±ΠΈΠ»Ρ, Ρ Π°ΡΠ°ΠΊΡΠ΅ΡΠΈΠ·ΡΡΡΠ΅Π΅ ΠΏΡΠΈΡΠΏΠΎΡΠΎΠ±Π»Π΅Π½Π½ΠΎΡΡΡ Π΅Π³ΠΎ ΠΊΠΎΠ½ΡΡΡΡΠΊΡΠΈΠΈ ΠΊ ΡΠ΅ΠΌΠΎΠ½ΡΠ½ΠΎ-ΠΎΠ±ΡΠ»ΡΠΆΠΈΠ²Π°ΡΡΠΈΠΌ ΡΠ°Π±ΠΎΡΠ°ΠΌ (ΠΏΡΠΎΠ²Π΅ΡΠΊΠ° ΡΠ΅Ρ Π½ΠΈΡΠ΅ΡΠΊΠΎΠ³ΠΎ ΡΠΎΡΡΠΎΡΠ½ΠΈΡ, ΡΠ΅Π³ΡΠ»ΠΈΡΠΎΠ²ΠΊΠ° ΡΠΎΠΏΡΡΠΆΠ΅Π½ΠΈΠΉ, ΡΡΡΡΠ°Π½Π΅Π½ΠΈΠ΅ ΠΎΡΠΊΠ°Π·ΠΎΠ², Π·Π°ΠΌΠ΅Π½Π° Π΄Π΅ΡΠ°Π»Π΅ΠΉ ΠΈ Ρ. Π΄.).
ΠΠΎΠ»Π³ΠΎΠ²Π΅ΡΠ½ΠΎΡΡΡ β ΡΠ²ΠΎΠΉΡΡΠ²ΠΎ Π°Π²ΡΠΎΠΌΠΎΠ±ΠΈΠ»Ρ ΡΠΎΡ ΡΠ°Π½ΡΡΡ ΡΠ°Π±ΠΎΡΠΎΡΠΏΠΎΡΠΎΠ±Π½ΠΎΡΡΡ Ρ Π½Π΅ΠΎΠ±Ρ ΠΎΠ΄ΠΈΠΌΡΠΌΠΈ ΠΏΠ΅ΡΠ΅ΡΡΠ²Π°ΠΌΠΈ Π΄Π»Ρ ΡΠ΅Ρ Π½ΠΈΡΠ΅ΡΠΊΠΎΠ³ΠΎ ΠΎΠ±ΡΠ»ΡΠΆΠΈΠ²Π°Π½ΠΈΡ ΠΈ ΡΠ΅ΠΌΠΎΠ½ΡΠ° Π΄ΠΎ ΠΏΡΠ΅Π΄Π΅Π»ΡΠ½ΠΎΠ³ΠΎ ΡΠΎΡΡΠΎΡΠ½ΠΈΡ, ΡΠΊΠ°Π·Π°Π½Π½ΠΎΠ³ΠΎ Π² Π½ΠΎΡΠΌΠ°ΡΠΈΠ²Π½ΠΎ-ΡΠ΅Ρ Π½ΠΈΡΠ΅ΡΠΊΠΎΠΉ Π΄ΠΎΠΊΡΠΌΠ΅Π½ΡΠ°ΡΠΈΠΈ.
ΠΡΠ΅Π΄Π΅Π»ΡΠ½ΠΎΠ΅ ΡΠΎΡΡΠΎΡΠ½ΠΈΠ΅ β ΡΠΎΡΡΠΎΡΠ½ΠΈΠ΅ Π°Π²ΡΠΎΠΌΠΎΠ±ΠΈΠ»Ρ, ΠΏΡΠΈ ΠΊΠΎΡΠΎΡΠΎΠΌ Π΅Π³ΠΎ Π΄Π°Π»ΡΠ½Π΅ΠΉΡΠ΅Π΅ ΠΏΡΠΈΠΌΠ΅Π½Π΅Π½ΠΈΠ΅ ΠΏΠΎ Π½Π°Π·Π½Π°ΡΠ΅Π½ΠΈΡ Π½Π΅Π΄ΠΎΠΏΡΡΡΠΈΠΌΠΎ ΠΈΠ»ΠΈ Π½Π΅ΡΠ΅Π»Π΅ΡΠΎΠΎΠ±ΡΠ°Π·Π½ΠΎ, Π»ΠΈΠ±ΠΎ Π²ΠΎΡΡΡΠ°Π½ΠΎΠ²Π»Π΅Π½ΠΈΠ΅ Π΅Π³ΠΎ ΡΠ°Π±ΠΎΡΠΎΡΠΏΠΎΡΠΎΠ±Π½ΠΎΠ³ΠΎ ΠΈΠ»ΠΈ ΠΈΡΠΏΡΠ°Π²Π½ΠΎΠ³ΠΎ ΡΠΎΡΡΠΎΡΠ½ΠΈΡ Π½Π΅Π²ΠΎΠ·ΠΌΠΎΠΆΠ½ΠΎ ΠΈΠ»ΠΈ Π½Π΅ΡΠ΅Π»Π΅ΡΠΎΠΎΠ±ΡΠ°Π·Π½ΠΎ.
Π‘ΠΎΡ ΡΠ°Π½ΡΠ΅ΠΌΠΎΡΡΡ β ΡΠ²ΠΎΠΉΡΡΠ²ΠΎ Π°Π²ΡΠΎΠΌΠΎΠ±ΠΈΠ»Ρ ΡΠΎΡ ΡΠ°Π½ΡΡΡ Π·Π½Π°ΡΠ΅Π½ΠΈΡ ΠΏΠΎΠΊΠ°Π·Π°ΡΠ΅Π»Π΅ΠΉ Π±Π΅Π·ΠΎΡΠΊΠ°Π·Π½ΠΎΡΡΠΈ, ΡΠ΅ΠΌΠΎΠ½ΡΠΎΠΏΡΠΈΠ³ΠΎΠ΄Π½ΠΎΡΡΠΈ ΠΈ Π΄ΠΎΠ»Π³ΠΎΠ²Π΅ΡΠ½ΠΎΡΡΠΈ Π² ΡΠ΅ΡΠ΅Π½ΠΈΠ΅ ΠΈ ΠΏΠΎΡΠ»Π΅ Ρ ΡΠ°Π½Π΅Π½ΠΈΡ ΠΈ (ΠΈΠ»ΠΈ) ΡΡΠ°Π½ΡΠΏΠΎΡΡΠΈΡΠΎΠ²Π°Π½ΠΈΡ.
ΠΠ»Ρ ΠΎΡΠ΅Π½ΠΊΠΈ Π½Π°Π΄Π΅ΠΆΠ½ΠΎΡΡΠΈ Π°Π²ΡΠΎΠΌΠΎΠ±ΠΈΠ»Ρ ΠΈΠ»ΠΈ ΡΠ±ΠΎΡΠΎΡΠ½ΠΎΠΉ Π΅Π΄ΠΈΠ½ΠΈΡΡ ΠΈΡΠΏΠΎΠ»ΡΠ·ΡΡΡΡΡ Π΅Π΄ΠΈΠ½ΠΈΡΠ½ΡΠ΅ ΠΈ ΠΊΠΎΠΌΠΏΠ»Π΅ΠΊΡΠ½ΡΠ΅ ΠΏΠΎΠΊΠ°Π·Π°ΡΠ΅Π»ΠΈ Π½Π°Π΄Π΅ΠΆΠ½ΠΎΡΡΠΈ.
1. ΠΠ°Π΄Π΅ΠΆΠ½ΠΎΡΡΡ ΠΌΠ°ΡΠΈΠ½, ΠΎΡΠ½ΠΎΠ²Π½ΡΠ΅ ΠΏΠΎΠ½ΡΡΠΈΡ Π½Π°Π΄Π΅ΠΆΠ½ΠΎΡΡΠΈ
ΠΠ°Π΄Π΅ΠΆΠ½ΠΎΡΡΡ — ΡΠ²ΠΎΠΉΡΡΠ²ΠΎ ΠΎΠ±ΡΠ΅ΠΊΡΠ° ΡΠΎΡ ΡΠ°Π½ΡΡΡ Π²ΠΎ Π²ΡΠ΅ΠΌΠ΅Π½ΠΈ Π² ΡΡΡΠ°Π½ΠΎΠ²Π»Π΅Π½Π½ΡΡ ΠΏΡΠ΅Π΄Π΅Π»Π°Ρ Π·Π½Π°ΡΠ΅Π½ΠΈΡ Π²ΡΠ΅Ρ ΠΏΠ°ΡΠ°ΠΌΠ΅ΡΡΠΎΠ², Ρ Π°ΡΠ°ΠΊΡΠ΅ΡΠΈΠ·ΡΡΡΠΈΡ ΡΠΏΠΎΡΠΎΠ±Π½ΠΎΡΡΡ Π²ΡΠΏΠΎΠ»Π½ΡΡΡ ΡΡΠ΅Π±ΡΠ΅ΠΌΡΠ΅ ΡΡΠ½ΠΊΡΠΈΠΈ Π² Π·Π°Π΄Π°Π½Π½ΡΡ ΡΠ΅ΠΆΠΈΠΌΠ°Ρ ΠΈ ΡΡΠ»ΠΎΠ²ΠΈΡΡ ΠΏΡΠΈΠΌΠ΅Π½Π΅Π½ΠΈΡ, ΡΠ΅Ρ Π½ΠΈΡΠ΅ΡΠΊΠΎΠ³ΠΎ ΠΎΠ±ΡΠ»ΡΠΆΠΈΠ²Π°Π½ΠΈΡ, Ρ ΡΠ°Π½Π΅Π½ΠΈΡ ΠΈ ΡΡΠ°Π½ΡΠΏΠΎΡΡΠΈΡΠΎΠ²Π°Π½ΠΈΡ.
ΠΠ°Π΄Π΅ΠΆΠ½ΠΎΡΡΡ ΡΠ²Π»ΡΠ΅ΡΡΡ ΠΊΠΎΠΌΠΏΠ»Π΅ΠΊΡΠ½ΡΠΌ ΡΠ²ΠΎΠΉΡΡΠ²ΠΎΠΌ, ΠΊΠΎΡΠΎΡΠΎΠ΅ Π² Π·Π°Π²ΠΈΡΠΈΠΌΠΎΡΡΠΈ ΠΎΡ Π½Π°Π·Π½Π°ΡΠ΅Π½ΠΈΡ ΠΎΠ±ΡΠ΅ΠΊΡΠ° ΠΈ ΡΡΠ»ΠΎΠ²ΠΈΠΉ Π΅Π³ΠΎ ΠΏΡΠΈΠΌΠ΅Π½Π΅Π½ΠΈΡ ΠΌΠΎΠΆΠ΅Ρ Π²ΠΊΠ»ΡΡΠ°ΡΡ Π±Π΅Π·ΠΎΡΠΊΠ°Π·Π½ΠΎΡΡΡ, Π΄ΠΎΠ»Π³ΠΎΠ²Π΅ΡΠ½ΠΎΡΡΡ, ΡΠ΅ΠΌΠΎΠ½ΡΠΎΠΏΡΠΈΠ³ΠΎΠ΄Π½ΠΎΡΡΡ ΠΈ ΡΠΎΡ ΡΠ°Π½ΡΠ΅ΠΌΠΎΡΡΡ ΠΈΠ»ΠΈ ΠΎΠΏΡΠ΅Π΄Π΅Π»Π΅Π½Π½ΡΠ΅ ΡΠΎΡΠ΅ΡΠ°Π½ΠΈΡ ΡΡΠΈΡ ΡΠ²ΠΎΠΉΡΡΠ².
ΠΠ΅Π·ΠΎΡΠΊΠ°Π·Π½ΠΎΡΡΡ — ΡΠ²ΠΎΠΉΡΡΠ²ΠΎ ΠΎΠ±ΡΠ΅ΠΊΡΠ° Π½Π΅ΠΏΡΠ΅ΡΡΠ²Π½ΠΎ ΡΠΎΡ ΡΠ°Π½ΡΡΡ ΡΠ°Π±ΠΎΡΠΎΡΠΏΠΎΡΠΎΠ±Π½ΠΎΠ΅ ΡΠΎΡΡΠΎΡΠ½ΠΈΠ΅ Π² ΡΠ΅ΡΠ΅Π½ΠΈΠ΅ Π½Π΅ΠΊΠΎΡΠΎΡΠΎΠ³ΠΎ Π²ΡΠ΅ΠΌΠ΅Π½ΠΈ ΠΈΠ»ΠΈ Π½Π°ΡΠ°Π±ΠΎΡΠΊΠΈ
ΠΠΎΠ»Π³ΠΎΠ²Π΅ΡΠ½ΠΎΡΡΡ — ΡΠ²ΠΎΠΉΡΡΠ²ΠΎ ΠΎΠ±ΡΠ΅ΠΊΡΠ° ΡΠΎΡ ΡΠ°Π½ΡΡΡ ΡΠ°Π±ΠΎΡΠΎΡΠΏΠΎΡΠΎΠ±Π½ΠΎΠ΅ ΡΠΎΡΡΠΎΡΠ½ΠΈΠ΅ Π΄ΠΎ Π½Π°ΡΡΡΠΏΠ»Π΅Π½ΠΈΡ ΠΏΡΠ΅Π΄Π΅Π»ΡΠ½ΠΎΠ³ΠΎ ΡΠΎΡΡΠΎΡΠ½ΠΈΡ ΠΏΡΠΈ ΡΡΡΠ°Π½ΠΎΠ²Π»Π΅Π½Π½ΠΎΠΉ ΡΠΈΡΡΠ΅ΠΌΠ΅ ΡΠ΅Ρ Π½ΠΈΡΠ΅ΡΠΊΠΎΠ³ΠΎ ΠΎΠ±ΡΠ»ΡΠΆΠΈΠ²Π°Π½ΠΈΡ ΠΈ ΡΠ΅ΠΌΠΎΠ½ΡΠ°
Π Π΅ΠΌΠΎΠ½ΡΠΎΠΏΡΠΈΠ³ΠΎΠ΄Π½ΠΎΡΡΡ — ΡΠ²ΠΎΠΉΡΡΠ²ΠΎ ΠΎΠ±ΡΠ΅ΠΊΡΠ°, Π·Π°ΠΊΠ»ΡΡΠ°ΡΡΠ΅Π΅ΡΡ Π² ΠΏΡΠΈΡΠΏΠΎΡΠΎΠ±Π»Π΅Π½Π½ΠΎΡΡΠΈ ΠΊ ΠΏΠΎΠ΄Π΄Π΅ΡΠΆΠ°Π½ΠΈΡ ΠΈ Π²ΠΎΡΡΡΠ°Π½ΠΎΠ²Π»Π΅Π½ΠΈΡ ΡΠ°Π±ΠΎΡΠΎΡΠΏΠΎΡΠΎΠ±Π½ΠΎΠ³ΠΎ ΡΠΎΡΡΠΎΡΠ½ΠΈΡ ΠΏΡΡΠ΅ΠΌ ΡΠ΅Ρ Π½ΠΈΡΠ΅ΡΠΊΠΎΠ³ΠΎ ΠΎΠ±ΡΠ»ΡΠΆΠΈΠ²Π°Π½ΠΈΡ ΠΈ ΡΠ΅ΠΌΠΎΠ½ΡΠ°
Π‘ΠΎΡ ΡΠ°Π½ΡΠ΅ΠΌΠΎΡΡΡ — ΡΠ²ΠΎΠΉΡΡΠ²ΠΎ ΠΎΠ±ΡΠ΅ΠΊΡΠ° ΡΠΎΡ ΡΠ°Π½ΡΡΡ Π² Π·Π°Π΄Π°Π½Π½ΡΡ ΠΏΡΠ΅Π΄Π΅Π»Π°Ρ Π·Π½Π°ΡΠ΅Π½ΠΈΡ ΠΏΠ°ΡΠ°ΠΌΠ΅ΡΡΠΎΠ², Ρ Π°ΡΠ°ΠΊΡΠ΅ΡΠΈΠ·ΡΡΡΠΈΡ ΡΠΏΠΎΡΠΎΠ±Π½ΠΎΡΡΠΈ ΠΎΠ±ΡΠ΅ΠΊΡΠ° Π²ΡΠΏΠΎΠ»Π½ΡΡΡ ΡΡΠ΅Π±ΡΠ΅ΠΌΡΠ΅ ΡΡΠ½ΠΊΡΠΈΠΈ, Π² ΡΠ΅ΡΠ΅Π½ΠΈΠ΅ ΠΈ ΠΏΠΎΡΠ»Π΅ Ρ ΡΠ°Π½Π΅Π½ΠΈΡ ΠΈ (ΠΈΠ»ΠΈ) ΡΡΠ°Π½ΡΠΏΠΎΡΡΠΈΡΠΎΠ²Π°Π½ΠΈΡ.
ΠΠ°Π΄Π΅ΠΆΠ½ΠΎΡΡΡ ΠΏΠΎΠ΄ΡΠ°Π·Π΄Π΅Π»ΡΠ΅ΡΡΡ Π½Π°:
ΠΠ΄ΠΈΠ½ΠΈΡΠ½ΡΠ΅ — Ρ Π°ΡΠ°ΠΊΡΠ΅ΡΠΈΠ·ΡΡΡ ΠΎΠ΄Π½ΠΎ ΠΈΠ· ΡΠ²ΠΎΠΉΡΡΠ² Π½Π°Π΄Π΅ΠΆΠ½ΠΎΡΡΠΈ (Π±Π΅Π·ΠΎΡΠΊΠ°Π·Π½ΠΎΡΡΡ, Π΄ΠΎΠ»Π³ΠΎΠ²Π΅ΡΠ½ΠΎΡΡΡ ΠΈ ΡΠ΄.).
ΠΠΎΠΌΠΏΠ»Π΅ΠΊΡΠ½ΡΠ΅ — Ρ Π°ΡΠ°ΠΊΡΠ΅ΡΠΈΠ·ΡΡΡ ΠΎΠ΄Π½ΠΎΠ²ΡΠ΅ΠΌΠ΅Π½Π½ΠΎ Π½Π΅ΡΠΊΠΎΠ»ΡΠΊΠΎ ΡΠ²ΠΎΠΉΡΡΠ², Ρ.Π΅. 2 ΠΈ Π±ΠΎΠ»Π΅Π΅ ΡΠΎΡΡΠ°Π²Π»ΡΡΡΠΈΡ Π½Π°Π΄Π΅ΠΆΠ½ΠΎΡΡΠΈ ΠΈΠ·Π΄Π΅Π»ΠΈΡ.
Π Π°ΡΡΠ΅ΡΠ½ΡΠ΅ — ΡΠ΅ ΠΊΠΎΡΠΎΡΡΠ΅ ΠΎΠΏΡΠ΅Π΄Π΅Π»ΡΡΡΡΡ ΡΠ°ΡΡΠ΅ΡΠ½ΡΠΌ ΠΏΡΡΠ΅ΠΌ.
ΠΠΊΡΠΏΠ΅ΡΠΈΠΌΠ΅Π½ΡΠ°Π»ΡΠ½ΡΠ΅ — ΡΠ΅ ΠΊΠΎΡΠΎΡΡΠ΅ ΠΎΠΏΡΠ΅Π΄Π΅Π»ΡΡΡΡΡ Π² ΠΏΡΠΎΡΠ΅ΡΡΠ΅ ΠΈΡΡΠ»Π΅Π΄ΠΎΠ²Π°Π½ΠΈΠΉ (ΡΠΊΡΠΏΠ΅ΡΠΈΠΌΠ΅Π½ΡΠ°Π»ΡΠ½ΠΎ).
ΠΡΡΠΏΠΏΠΎΠ²ΡΠ΅ — ΡΠ΅ ΠΊΠΎΡΠΎΡΡΠ΅ ΡΠ»ΡΠΆΠ°Ρ Π΄Π»Ρ ΠΎΡΠ΅Π½ΠΊΠΈ Π½Π°Π΄Π΅ΠΆΠ½ΠΎΡΡΠΈ ΡΠΎΠ²ΠΎΠΊΡΠΏΠ½ΠΎΡΡΠΈ ΠΈΠ·Π΄Π΅Π»ΠΈΡ Π΄Π°Π½Π½ΠΎΠ³ΠΎ ΡΠΈΠΏΠ°.
ΠΠ½Π΄ΠΈΠ²ΠΈΠ΄ΡΠ°Π»ΡΠ½ΡΠ΅ — ΠΏΡΠ΅Π΄Π½Π°Π·Π½Π°ΡΠ΅Π½Ρ Π΄Π»Ρ ΠΎΡΠ΅Π½ΠΊΠΈ Π½Π°Π΄Π΅ΠΆΠ½ΠΎΡΡΠΈ ΠΈΠ·Π΄Π΅Π»ΠΈΠΉ Π΄Π°Π½Π½ΠΎΠ³ΠΎ ΡΠΈΠΏΠ°.
2. Π‘ΡΡΠ½ΠΎΡΡΡ ΠΈ ΠΎΠ±Π»Π°ΡΡΡ ΠΏΡΠΈΠΌΠ΅Π½Π΅Π½ΠΈΡ ΡΡΡΠ΅ΡΡΠ²ΡΡΡΠΈΡ ΠΌΠ΅ΡΠΎΠ΄ΠΎΠ² ΠΎΠ±Π½Π°ΡΡΠΆΠ΅Π½ΠΈΡ ΡΠΊΡΡΡΡΡ Π΄Π΅ΡΠ΅ΠΊΡΠΎΠ².
ΠΠΎΠ»ΡΡΡΡ ΡΠ»ΠΎΠΆΠ½ΠΎΡΡΡ ΠΏΡΠΈ Π΄Π΅ΡΠ΅ΠΊΡΠ°ΡΠΈΠΈ Π΄Π΅ΡΠ°Π»Π΅ΠΉ ΠΈΠΌΠ΅Π΅Ρ ΠΎΠΏΡΠ΅Π΄Π΅Π»Π΅Π½ΠΈΠ΅ ΡΠΊΡΡΡΡΡ Π΄Π΅ΡΠ΅ΠΊΡΠΎΠ². Π‘ΡΡΠ΅ΡΡΠ²ΡΡΡ ΡΠ»Π΅Π΄ΡΡΡΠΈΠ΅ ΠΌΠ΅ΡΠΎΠ΄Ρ ΠΎΠ±Π½Π°ΡΡΠΆΠ΅Π½ΠΈΡ Π΄Π΅ΡΠ΅ΠΊΡΠΎΠ²:
ΠΠ½Π΅Π²ΠΌΠ°ΡΠΈΡΠ΅ΡΠΊΠΈΠΉ — Π² ΠΊΠΎΠ½ΡΡΠΎΠ»ΠΈΡΡΠ΅ΠΌΠΎΠ΅ ΠΈΠ·Π΄Π΅Π»ΠΈΠ΅ ΠΏΠΎΠ΄Π°Π΅ΡΡΡ Π²ΠΎΠ·Π΄ΡΡ ΠΏΠΎΠ΄ Π΄Π°Π²Π»Π΅Π½ΠΈΠ΅ΠΌ 0,1-0,2 ΠΠΠ°, ΠΈ ΠΏΠΎΠ³ΡΡΠΆΠ°ΡΡ Π΅Π³ΠΎ Π² Π²ΠΎΠ΄Ρ, ΠΈΠ»ΠΈ ΡΠΌΠ°Π·ΡΠ²Π°ΡΡ ΠΌΡΠ»ΡΠ½ΡΠΌ ΡΠ°ΡΡΠ²ΠΎΡΠΎΠΌ. ΠΠ°Π»ΠΈΡΠΈΠ΅ ΠΏΡΠ·ΡΡΡΠΊΠΎΠ² ΡΠ²ΠΈΠ΄Π΅ΡΠ΅Π»ΡΡΡΠ²ΡΠ΅Ρ ΠΎ Π½Π°Π»ΠΈΡΠΈΠΈ ΡΡΠ΅ΡΠΈΠ½ (ΡΡΡΠ±ΠΎΠΏΡΠΎΠ²ΠΎΠ΄Ρ, Π±Π°ΠΊΠΈ, ΡΠ°Π΄ΠΈΠ°ΡΠΎΡΡ, ΡΠΈΠ½Ρ, Π΅ΠΌΠΊΠΎΡΡΠΈ).
ΠΠΈΠ΄ΡΠ°Π²Π»ΠΈΡΠ΅ΡΠΊΠΈΠΉ — Π² ΠΏΠΎΠ»ΠΎΡΡΠΈ ΠΏΠΎΠ΄Π°Π΅ΡΡΡ Π²ΠΎΠ΄Π° ΠΏΠΎΠ΄ Π΄Π°Π²Π»Π΅Π½ΠΈΠ΅ΠΌ 0,5-0,6 ΠΠΠ° ΠΈ Π²ΡΠ΄Π΅ΡΠΆΠΈΠ²Π°ΡΡ Π΄ΠΎ 10 ΠΌΠΈΠ½. Π‘Π½ΠΈΠΆΠ΅Π½ΠΈΠ΅ Π΄Π°Π²Π»Π΅Π½ΠΈΡ ΡΠ²ΠΈΠ΄Π΅ΡΠ΅Π»ΡΡΡΠ²ΡΠ΅Ρ ΠΎ ΡΡΠ΅ΡΠΈΠ½Π°Ρ . Π Π΅ΡΠ»ΠΈ Π΄ΠΎΠ±Π°Π²ΠΈΡΡ 10 Π³. ΠΏΠΎΠ²Π°ΡΠ΅Π½Π½ΠΎΠΉ ΡΠΎΠ»ΠΈ, ΡΠΎ ΡΠ΅ΡΠ΅Π· 30-60 ΠΌΠΈΠ½. ΠΏΡΠΈ Π½Π°Π»ΠΈΡΠΈΠΈ Π·Π°ΡΠΎΠΆΠ΄Π°ΡΡΠΈΡ ΡΡ ΡΡΠ΅ΡΠΈΠ½ Π½Π° ΠΈΡ ΠΌΠ΅ΡΡΠ΅ ΠΏΠΎΡΠ²ΡΡΡΡ ΡΠ»Π΅Π΄Ρ ΡΠΆΠ°Π²ΡΠΈΠ½Ρ (Π±Π»ΠΎΠΊΠΈ, Π³ΠΎΠ»ΠΎΠ²ΠΊΠΈ Π±Π»ΠΎΠΊΠΎΠ², ΡΡΡΠ±ΠΎΠΏΡΠΎΠ²ΠΎΠ΄Ρ ΠΈ Ρ.Π΄.).
ΠΠ°Π³Π½ΠΈΡΠ½ΡΠΉ — ΠΎΡΠ½ΠΎΠ²ΡΠ²Π°Π΅ΡΡΡ Π½Π° ΠΎΠ±ΡΠ°Π·ΠΎΠ²Π°Π½ΠΈΠΈ ΠΌΠ°Π³Π½ΠΈΡΠ½ΠΎΠ³ΠΎ ΠΏΠΎΠ»Ρ ΡΠ°ΡΡΠ΅ΠΈΠ²Π°Π½ΠΈΡ ΠΏΡΠΈ Π½Π°Π»ΠΈΡΠΈΠΈ Π΄Π΅ΡΠ΅ΠΊΡΠΎΠ² Π½Π° ΠΏΠΎΠ²Π΅ΡΡ Π½ΠΎΡΡΠΈ ΠΈ ΠΏΠΎΠ΄ ΠΏΠΎΠ²Π΅ΡΡ Π½ΠΎΡΡΡΡ Π΄Π΅ΡΠ°Π»ΠΈ. ΠΠ»Ρ ΠΎΠ±Π½Π°ΡΡΠΆΠ΅Π½ΠΈΡ Π΄Π΅ΡΠ΅ΠΊΡΠΎΠ² ΠΏΡΠΎΠΌ. Π²ΡΠΏΡΡΠΊΠ°ΡΡΡΡ Π΄Π΅ΡΠ΅ΠΊΡΠΎΡΠΊΠΎΠΏΡ ΠΠ-70, Π£ΠΠ-900. ΠΠ°ΠΌΠ°Π³Π½ΠΈΡΠΈΠ²Π°Π½ΠΈΠ΅ ΠΌΠΎΠΆΠ΅Ρ ΠΎΡΡΡΠ΅ΡΡΠ²Π»ΡΡΡΡΡ Π² ΠΏΡΠΈΠ»ΠΎΠΆΠ΅Π½Π½ΠΎΠΌ ΠΈ ΠΎΡΡΠ°ΡΠΎΡΠ½ΠΎΠΌ ΠΏΠΎΠ»Π΅. ΠΠ΅Π»ΠΈΡΠΈΠ½Π° ΡΠΎΠΊΠ° Π½Π°ΠΌΠ°Π³Π½ΠΈΡΠΈΠ²Π°Π½ΠΈΡ Π² ΠΏΡΠΈΠ»ΠΎΠΆΠ΅Π½Π½ΠΎΠΌ ΠΏΠΎΠ»Π΅. ΠΠ΅Π»ΠΈΡΠΈΠ½Π° ΡΠΎΠΊΠ°
ΠΌΠΌ — ΠΏΡΠΈΠ»ΠΎΠΆΠ΅Π½Π½ΠΎΠ΅ ΠΏΠΎΠ»Π΅.
ΠΌΠΌ — ΠΎΡΡΠ°ΡΠΎΡΠ½ΠΎΠ΅ ΠΏΠΎΠ»Π΅.
D — Π»ΠΈΠ½Π΅ΠΉΠ½ΡΠΉ ΡΠ°Π·ΠΌΠ΅Ρ ΠΊΠΎΠ½ΡΡΠΎΠ»ΠΈΡΡΠ΅ΠΌΠΎΠ³ΠΎ ΡΠ΅ΡΠ΅Π½ΠΈΡ Π΄Π΅ΡΠ°Π»ΠΈ.
ΠΠ»Ρ Π²ΡΡΠ²Π»Π΅Π½ΠΈΡ ΠΌΠ°Π³Π½ΠΈΡΠ½ΠΎΠ³ΠΎ ΠΏΠΎΠ»Ρ ΠΈΡΠΏΠΎΠ»ΡΠ·ΡΡΡ ΡΠ΅ΡΠΎΠΌΠ°Π³Π½ΠΈΡΠ½ΡΠΉ ΠΏΠ°ΡΠ°ΡΠΎΠΊ. ΠΠΎΠ»Π΅Π΅ ΡΡΡΠ΅ΠΊΡΠΈΠ²Π½ΠΎΠΉ ΡΠ²Π»ΡΠ΅ΡΡΡ Π΄Π΅ΡΠ΅ΠΊΡΠ°ΡΠΈΡ Π² ΠΏΡΠΈΠ»ΠΎΠΆΠ΅Π½Π½ΠΎΠΌ ΠΏΠΎΠ»Π΅. ΠΠΎΡΠ»Π΅ ΠΊΠΎΠ½ΡΡΠΎΠ»Ρ Π΄Π΅ΡΠ°Π»ΠΈ ΡΠ°Π·ΠΌΠ°Π³Π½ΠΈΡΠΈΠ²Π°ΡΡ, ΠΏΠΎΠΌΠ΅ΡΠ°Ρ ΠΈΡ Π² ΡΠΎΠ»Π΅Π½ΠΎΠΈΠ΄.
Π£Π»ΡΡΡΠ°Π·Π²ΡΠΊΠΎΠ²ΠΎΠΉ — ΠΎΠ½ ΠΎΡΠ½ΠΎΠ²Π°Π½ Π½Π° ΡΠΏΠΎΡΠΎΠ±Π½ΠΎΡΡΠΈ ΠΌΠ°ΡΠ΅ΡΠΈΠ°Π»ΠΎΠ², ΠΏΠ΅ΡΠ΅Π΄Π°Π²Π°ΡΡ Ρ Π²ΡΡΠΎΠΊΠΎΠΉ ΡΠΊΠΎΡΠΎΡΡΡΡ ΡΠ»ΡΡΡΠ°Π·Π²ΡΠΊΠΎΠ²ΡΠ΅ ΠΊΠΎΠ»Π΅Π±Π°Π½ΠΈΡ Π½Π° Π±ΠΎΠ»ΡΡΠΈΠ΅ ΡΠ°ΡΡΡΠΎΡΠ½ΠΈΡ Π² Π²ΠΈΠ΄Π΅ Π½Π°ΠΏΡΠ°Π²Π»Π΅Π½Π½ΡΡ ΠΏΡΡΠΊΠΎΠ². ΠΠ»Ρ ΡΠ΅Π°Π»ΠΈΠ·Π°ΡΠΈΠΈ ΡΠ°ΠΊΠΎΠ³ΠΎ ΠΊΠΎΠ½ΡΡΠΎΠ»Ρ ΠΏΡΠΎΠΌΡΡΠ»Π΅Π½Π½ΠΎΡΡΡΡ Π²ΡΠΏΡΡΠΊΠ°Π΅ΡΡΡ Π£Π Π΄Π΅ΡΠ΅ΠΊΡΠΎΡΠΊΠΎΠΏΡ ΠΠ£Π-6, ΠΠ£Π-5Π, Π£ΠΠ-10Π ΠΈ Π΄.Ρ.
ΠΠ°ΠΏΠΈΠ»Π»ΡΡΠ½ΡΠΉ — ΠΎΠ½ ΠΏΠΎΠ΄ΡΠ°Π·Π΄Π΅Π»ΡΠ΅ΡΡΡ Π½Π° 2 ΠΌΠ΅ΡΠΎΠ΄Π°: Π»ΡΠΌΠΈΠ½Π΅ΡΡΠ΅Π½ΡΠ½ΡΠΉ ΠΈ ΡΠ²Π΅ΡΠΎΠ²ΠΎΠΉ.
ΠΡΠΌΠΈΠ½Π΅ΡΡΠ΅Π½ΡΠ½ΡΠΉ — ΠΎΡΠ½ΠΎΠ²Π°Π½ Π½Π° ΡΠΏΠΎΡΠΎΠ±Π½ΠΎΡΡΠΈ Π²-Π² ΠΏΠΎΠ³Π»ΠΎΡΠ°ΡΡ Π»ΡΡΠΈΡΡΡΡ ΡΠ½Π΅ΡΠ³ΠΈΡ. ΠΠ°ΠΈΠ±ΠΎΠ»Π΅Π΅ ΡΠ°ΡΠΏΡΠΎΡΡΡΠ°Π½Π΅Π½: ΡΡΠ°Π½ΡΡΠΎΡΠΌΠ°ΡΠΎΡΠ½ΠΎΠ΅ ΠΌΠ°ΡΠ»ΠΎ (1), ΠΊΠ΅ΡΠΎΡΠΈΠ½ (2), Π±Π΅Π½Π·ΠΈΠ½ Π-66 (1) + 2 Π³ΡΠ°ΠΌΠΌΠ° Π½Π° Π»ΠΈΡΡ Π·ΠΎΠ»ΠΎΡΠΈΡΡΠΎΠ³ΠΎ Π΄Π΅ΡΡΠ΅ΠΊΡΠΎΠ»Ρ. ΠΡΠΈ Π²ΠΎΠ·Π΄Π΅ΠΉΡΡΠ²ΠΈΠΈ Π£Π€ Π»ΡΡΠ΅ΠΉ Π½Π° ΡΡΡ ΡΠΌΠ΅ΡΡ ΠΌΠ΅ΡΡΠ° ΡΡΠ΅ΡΠΈΠ½ ΡΠ²Π΅ΡΡΡΡΡ Π½Π°ΠΈΠ±ΠΎΠ»Π΅Π΅ ΠΈΠ½ΡΠ΅Π½ΡΠΈΠ²Π½ΠΎ Ρ.ΠΊ Π±ΠΎΠ»ΡΡΠ΅ ΡΠ°ΡΡΠ²ΠΎΡΠ°.
Π¦Π²Π΅ΡΠΎΠ²ΠΎΠΉ — Π½Π° ΠΎΠ±Π΅Π·ΠΆΠΈΡΠ΅Π½Π½ΡΡ ΠΏΠΎΠ²Π΅ΡΡ Π½ΠΎΡΡΡ Π½Π°Π½ΠΎΡΡΡ ΡΠ°ΡΡΠ²ΠΎΡ ΡΠΎΡΡΠΎΡΡΠΈΠΉ ΠΈΠ· 65% ΠΊΠ΅ΡΠΎΡΠΈΠ½Π°, 30% ΡΡΠ°Π½ΡΡΠΎΡΠΌΠ°ΡΠΎΡΠ½ΠΎΠ³ΠΎ ΠΌΠ°ΡΠ»Π°, 5% ΡΠΊΠΈΠΏΠΈΠ΄Π°ΡΠ° + 5Π³Ρ/Π»ΠΈΡΡ ΠΊΡΠ°ΡΠΈΡΠ΅Π»Ρ (ΡΡΠ΄Π°Π½). Π Π°ΡΡΠ²ΠΎΡ ΠΎΠ±Π»Π°Π΄Π°Π΅Ρ Ρ ΠΎΡΠΎΡΠ΅ΠΉ ΡΠΌΠ°ΡΠΈΠ²Π°ΡΡΠ΅ΠΉ ΡΠΏΠΎΡΠΎΠ±Π½ΠΎΡΡΡΡ ΠΈ ΠΏΠΎΠΏΠ°Π΄Π°Π΅Ρ Π²ΠΎ Π²ΡΠ΅ ΡΡΠ΅ΡΠΈΠ½Ρ, ΡΠ΅ΡΠ΅Π· 10 ΠΌΠΈΠ½ Π΅Π³ΠΎ ΡΠΌΡΠ²Π°ΡΡ ΠΈ Π½Π°Π½ΠΎΡΡΡ ΡΠ»ΠΎΠΉ Π±Π΅Π»ΠΎΠΉ Π³Π»ΠΈΠ½Ρ ΠΈΠ»ΠΈ ΠΌΠ΅Π»Π° ΠΏΠΎΡΠ»Π΅ Π²ΡΡΡΡ Π°Π½ΠΈΡ ΠΊΡΠ°ΡΠΊΠΈ Π½Π° ΠΏΠΎΠ²Π΅ΡΡ Π½ΠΎΡΡΠΈ Π΄Π°ΡΡ ΠΎΡΠ΅ΡΡΠ°Π½ΠΈΡ ΡΡΠ΅ΡΠΈΠ½.
Π Π΅Π½ΡΠ³Π΅Π½ΠΎΠ³ΡΠ°ΡΠΈΡΠ΅ΡΠΊΠΈΠΉ — ΠΎΠ½ ΠΈΡΠΏΠΎΠ»ΡΠ·ΡΠ΅ΡΡΡ Π΄Π»Ρ Π²ΡΡΠ²Π»Π΅Π½ΠΈΡ Π΄Π΅ΡΠ΅ΠΊΡΠΎΠ² Π² ΠΎΡΠ²Π΅ΡΡΡΠ²Π΅Π½Π½ΡΡ Π΄Π΅ΡΠ°Π»ΡΡ ΠΏΡΠΈ ΠΈΡ ΠΈΠ·Π³ΠΎΡΠΎΠ²Π»Π΅Π½ΠΈΠΈ ΠΈ ΡΠΊΡΠΏΠ»ΡΠ°ΡΠ°ΡΠΈΠΈ.
ο»ΏΠ Π°Π±ΠΎΡΠΎΡΠΏΠΎΡΠΎΠ±Π½ΠΎΡΡΡ ΠΈ Π½Π°Π΄Π΅ΠΆΠ½ΠΎΡΡΡ ΠΈΠ·Π΄Π΅Π»ΠΈΠΉ.
Π Π°Π±ΠΎΡΠΎΡΠΏΠΎΡΠΎΠ±Π½ΠΎΡΡΡ ΠΈ Π½Π°Π΄Π΅ΠΆΠ½ΠΎΡΡΡ Π΄Π΅ΡΠ°Π»Π΅ΠΉ, ΠΌΠ΅Ρ Π°Π½ΠΈΠ·ΠΌΠΎΠ² ΠΈ ΠΌΠ°ΡΠΈΠ½
ο»ΏΠΠΎΠ½ΡΡΠΈΠ΅ Π½Π°Π΄Π΅ΠΆΠ½ΠΎΡΡΠΈ ΠΌΠ°ΡΠΈΠ½Ρ
Π Π°Π±ΠΎΡΠΎΡΠΏΠΎΡΠΎΠ±Π½ΠΎΡΡΡ — ΡΠΎΡΡΠΎΡΠ½ΠΈΠ΅ ΠΈΠ·Π΄Π΅Π»ΠΈΡ, ΠΏΡΠΈ ΠΊΠΎΡΠΎΡΠΎΠΌ Π² Π΄Π°Π½Π½ΡΠΉ ΠΌΠΎΠΌΠ΅Π½Ρ Π²ΡΠ΅ΠΌΠ΅Π½ΠΈ Π΅Π³ΠΎ ΠΎΡΠ½ΠΎΠ²Π½ΡΠ΅ ΠΏΠ°ΡΠ°ΠΌΠ΅ΡΡΡ Π½Π°Ρ ΠΎΠ΄ΡΡΡΡ Π² ΠΏΡΠ΅Π΄Π΅Π»Π°Ρ , ΡΡΡΠ°Π½ΠΎΠ²Π»Π΅Π½Π½ΡΡ ΡΡΠ΅Π±ΠΎΠ²Π°Π½ΠΈΡΠΌΠΈ Π½ΠΎΡΠΌΠ°ΡΠΈΠ²Π½ΠΎ-ΡΠ΅Ρ Π½ΠΈΡΠ΅ΡΠΊΠΎΠΉ Π΄ΠΎΠΊΡΠΌΠ΅Π½ΡΠ°ΡΠΈΠΈ ΠΈ Π½Π΅ΠΎΠ±Ρ ΠΎΠ΄ΠΈΠΌΡΡ Π΄Π»Ρ Π²ΡΠΏΠΎΠ»Π½Π΅Π½ΠΈΡ Π΅Π³ΠΎ ΡΡΠ½ΠΊΡΠΈΠΎΠ½Π°Π»ΡΠ½ΠΎΠΉ Π·Π°Π΄Π°ΡΠΈ. ΠΠΎΠΏΡΠΎΡΡΡ Π³ΠΎΠ²ΠΎΡΡ, ΡΠ°Π±ΠΎΡΠΎΡΠΏΠΎΡΠΎΠ±Π½ΠΎΡΡΡ ΠΈΠ·Π΄Π΅Π»ΠΈΡ β ΡΡΠΎ Π΅Π³ΠΎ ΡΠΏΠΎΡΠΎΠ±Π½ΠΎΡΡΡ Π½ΠΎΡΠΌΠ°Π»ΡΠ½ΠΎ Π²ΡΠΏΠΎΠ»Π½ΡΡΡ Π·Π°Π΄Π°Π½Π½ΡΠ΅ ΡΡΠ½ΠΊΡΠΈΠΈ.
Π Π°Π±ΠΎΡΠΎΡΠΏΠΎΡΠΎΠ±Π½ΠΎΡΡΡ ΠΊΠΎΠ»ΠΈΡΠ΅ΡΡΠ²Π΅Π½Π½ΠΎ ΠΎΡΠ΅Π½ΠΈΠ²Π°Π΅ΡΡΡ ΡΠ»Π΅Π΄ΡΡΡΠΈΠΌΠΈ ΠΏΠΎΠΊΠ°Π·Π°ΡΠ΅Π»ΡΠΌΠΈ:
- ΠΡΠΎΡΠ½ΠΎΡΡΡ — ΡΠΏΠΎΡΠΎΠ±Π½ΠΎΡΡΡ Π΄Π΅ΡΠ°Π»ΠΈ Π²ΡΠ΄Π΅ΡΠΆΠΈΠ²Π°ΡΡ Π·Π°Π΄Π°Π½Π½ΡΠ΅ Π½Π°Π³ΡΡΠ·ΠΊΠΈ Π² ΡΠ΅ΡΠ΅Π½ΠΈΠ΅ Π·Π°Π΄Π°Π½Π½ΠΎΠ³ΠΎ ΡΡΠΎΠΊΠ° Π±Π΅Π· Π½Π°ΡΡΡΠ΅Π½ΠΈΡ ΡΠ°Π±ΠΎΡΠΎΡΠΏΠΎΡΠΎΠ±Π½ΠΎΡΡΠΈ.
- ΠΠ΅ΡΡΠΊΠΎΡΡΡ — ΡΠΏΠΎΡΠΎΠ±Π½ΠΎΡΡΡ Π΄Π΅ΡΠ°Π»ΠΈ Π²ΡΠ΄Π΅ΡΠΆΠΈΠ²Π°ΡΡ Π·Π°Π΄Π°Π½Π½ΡΠ΅ Π½Π°Π³ΡΡΠ·ΠΊΠΈ Π±Π΅Π· ΠΈΠ·ΠΌΠ΅Π½Π΅Π½ΠΈΡ ΡΠΎΡΠΌΡ ΠΈ ΡΠ°Π·ΠΌΠ΅ΡΠΎΠ².
- ΠΠ·Π½ΠΎΡΠΎΡΡΠΎΠΉΠΊΠΎΡΡΡ — ΡΠΏΠΎΡΠΎΠ±Π½ΠΎΡΡΡ Π΄Π΅ΡΠ°Π»ΠΈ ΡΠΎΠΏΡΠΎΡΠΈΠ²Π»ΡΡΡΡΡ ΠΈΠ·Π½Π°ΡΠΈΠ²Π°Π½ΠΈΡ.
- Π‘ΡΠΎΠΉΠΊΠΎΡΡΡ ΠΊ ΡΠΏΠ΅ΡΠΈΠ°Π»ΡΠ½ΡΠΌ Π²ΠΎΠ·Π΄Π΅ΠΉΡΡΠ²ΠΈΡΠΌ — ΡΠΏΠΎΡΠΎΠ±Π½ΠΎΡΡΡ Π΄Π΅ΡΠ°Π»ΠΈ ΡΠΎΡ ΡΠ°Π½ΡΡΡ ΡΠ°Π±ΠΎΡΠΎΡΠΏΠΎΡΠΎΠ±Π½ΠΎΠ΅ ΡΠΎΡΡΠΎΡΠ½ΠΈΠ΅ ΠΏΡΠΈ ΠΏΡΠΎΡΠ²Π»Π΅Π½ΠΈΠΈ ΡΠΏΠ΅ΡΠΈΠ°Π»ΡΠ½ΡΡ Π²ΠΎΠ·Π΄Π΅ΠΉΡΡΠ²ΠΈΠΉ (ΡΠ΅ΠΏΠ»ΠΎΡΡΠΎΠΉΠΊΠΎΡΡΡ, Π²ΠΈΠ±ΡΠΎΡΡΠΎΠΉΠΊΠΎΡΡΡ, ΡΠ°Π΄ΠΈΠ°ΡΠΈΠΎΠ½Π½Π°Ρ ΡΡΠΎΠΉΠΊΠΎΡΡΡ, ΠΊΠΎΡΡΠΎΠ·ΠΈΠΎΠ½Π½Π°Ρ ΡΡΠΎΠΉΠΊΠΎΡΡΡ ΠΈ Ρ.ΠΏ.).
ΠΠ΅ΡΠ°Π±ΠΎΡΠΎΡΠΏΠΎΡΠΎΠ±Π½ΠΎΠ΅ ΡΠΎΡΡΠΎΡΠ½ΠΈΠ΅ Π½Π°ΡΡΡΠΏΠ°Π΅Ρ Π²ΡΠ»Π΅Π΄ΡΡΠ²ΠΈΠ΅ ΠΎΡΠΊΠ°Π·Π°.
ΠΡΠΊΠ°Π· — ΡΠΎΠ±ΡΡΠΈΠ΅, Π½Π°ΡΡΡΠ°ΡΡΠ΅Π΅ ΡΠ°Π±ΠΎΡΠΎΡΠΏΠΎΡΠΎΠ±Π½ΠΎΡΡΡ.
ΠΡΠΊΠ°Π·Ρ Π΄Π΅Π»ΡΡΡΡ Π½Π° ΠΏΠΎΡΡΠ΅ΠΏΠ΅Π½Π½ΡΠ΅ ΠΈ Π²Π½Π΅Π·Π°ΠΏΠ½ΡΠ΅; ΠΏΠΎΠ»Π½ΡΠ΅ ΠΈ ΡΠ°ΡΡΠΈΡΠ½ΡΠ΅; ΡΡΡΡΠ°Π½ΠΈΠΌΡΠ΅ ΠΈ Π½Π΅ΡΡΡΡΠ°Π½ΠΈΠΌΡΠ΅.
ΠΠ°Π΄Π΅ΠΆΠ½ΠΎΡΡΡ β ΡΠ²ΠΎΠΉΡΡΠ²ΠΎ ΠΈΠ·Π΄Π΅Π»ΠΈΡ ΡΠΎΡ
ΡΠ°Π½ΡΡΡ Π²ΠΎ Π²ΡΠ΅ΠΌΠ΅Π½ΠΈ ΡΠΏΠΎΡΠΎΠ±Π½ΠΎΡΡΡ ΠΊ Π²ΡΠΏΠΎΠ»Π½Π΅Π½ΠΈΡ ΡΡΠ΅Π±ΡΠ΅ΠΌΡΡ
ΡΡΠ½ΠΊΡΠΈΠΉ Π² Π·Π°Π΄Π°Π½Π½ΡΡ
ΡΠ΅ΠΆΠΈΠΌΠ°Ρ
ΠΈ ΡΡΠ»ΠΎΠ²ΠΈΡΡ
ΠΏΡΠΈΠΌΠ΅Π½Π΅Π½ΠΈΡ, ΡΠ΅Ρ
Π½ΠΈΡΠ΅ΡΠΊΠΎΠ³ΠΎ ΠΎΠ±ΡΠ»ΡΠΆΠΈΠ²Π°Π½ΠΈΡ, Ρ
ΡΠ°Π½Π΅Π½ΠΈΡ ΠΈ ΡΡΠ°Π½ΡΠΏΠΎΡΡΠΈΡΠΎΠ²Π°Π½ΠΈΡ.
ΠΠ°Π΄Π΅ΠΆΠ½ΠΎΡΡΡ Ρ
Π°ΡΠ°ΠΊΡΠ΅ΡΠΈΠ·ΡΡΡ ΡΠΎΡΡΠΎΡΠ½ΠΈΡΠΌΠΈ ΠΈ ΡΠΎΠ±ΡΡΠΈΡΠΌΠΈ.
Π‘Π²ΠΎΠΉΡΡΠ²ΠΎ Π½Π°Π΄Π΅ΠΆΠ½ΠΎΡΡΠΈ ΠΊΠΎΠ»ΠΈΡΠ΅ΡΡΠ²Π΅Π½Π½ΠΎ ΠΎΡΠ΅Π½ΠΈΠ²Π°Π΅ΡΡΡ ΡΠ»Π΅Π΄ΡΡΡΠΈΠΌΠΈ ΠΏΠΎΠΊΠ°Π·Π°ΡΠ΅Π»ΡΠΌΠΈ: Π½Π°ΡΠ°Π±ΠΎΡΠΊΠΎΠΉ Π½Π° ΠΎΡΠΊΠ°Π· (ΡΡΠ΅Π΄Π½Π΅Π΅ Π²ΡΠ΅ΠΌΡ ΡΠ°Π±ΠΎΡΡ ΠΈΠ·Π΄Π΅Π»ΠΈΡ ΠΌΠ΅ΠΆΠ΄Ρ Π΄Π²ΡΠΌΡ, ΡΠΎΡΠ΅Π΄Π½ΠΈΠΌΠΈ ΠΏΠΎ Π²ΡΠ΅ΠΌΠ΅Π½ΠΈ ΠΎΡΠΊΠ°Π·Π°ΠΌΠΈ), ΠΊΠΎΡΡΡΠΈΡΠΈΠ΅Π½ΡΠΎΠΌ Π³ΠΎΡΠΎΠ²Π½ΠΎΡΡΠΈ ΠΈΠ»ΠΈ ΠΊΠΎΡΡΡΠΈΡΠΈΠ΅Π½ΡΠΎΠΌ ΡΠ΅Ρ Π½ΠΈΡΠ΅ΡΠΊΠΎΠ³ΠΎ ΠΈΡΠΏΠΎΠ»ΡΠ·ΠΎΠ²Π°Π½ΠΈΡ (ΠΎΡΠ½ΠΎΡΠ΅Π½ΠΈΠ΅ Π²ΡΠ΅ΠΌΠ΅Π½ΠΈ ΡΠ°Π±ΠΎΡΡ ΠΈΠ·Π΄Π΅Π»ΠΈΡ ΠΊ ΡΡΠΌΠΌΠ΅ Π²ΡΠ΅ΠΌΠ΅Π½ ΡΠ°Π±ΠΎΡΡ, ΠΎΠ±ΡΠ»ΡΠΆΠΈΠ²Π°Π½ΠΈΡ ΠΈ ΡΠ΅ΠΌΠΎΠ½ΡΠ° Π² ΡΠ΅ΡΠ΅Π½ΠΈΠ΅ Π·Π°Π΄Π°Π½Π½ΠΎΠ³ΠΎ ΡΡΠΎΠΊΠ° ΡΠΊΡΠΏΠ»ΡΠ°ΡΠ°ΡΠΈΠΈ), Π²Π΅ΡΠΎΡΡΠ½ΠΎΡΡΡΡ Π±Π΅Π·ΠΎΡΠΊΠ°Π·Π½ΠΎΠΉ ΡΠ°Π±ΠΎΡΡ ΠΈ Π½Π΅ΠΊΠΎΡΠΎΡΡΠΌΠΈ Π΄ΡΡΠ³ΠΈΠΌΠΈ.
ΠΠΎΠΊΠ°Π·Π°ΡΠ΅Π»ΠΈ ΠΊΠ°ΡΠ΅ΡΡΠ²Π° ΠΈΠ·Π΄Π΅Π»ΠΈΡ ΠΏΠΎ Π½Π°Π΄Π΅ΠΆΠ½ΠΎΡΡΠΈ: Π±Π΅Π·ΠΎΡΠΊΠ°Π·Π½ΠΎΡΡΡ, Π΄ΠΎΠ»Π³ΠΎΠ²Π΅ΡΠ½ΠΎΡΡΡ ΠΈ ΡΠ΅ΠΌΠΎΠ½ΡΠΎΠΏΡΠΈΠ³ΠΎΠ΄Π½ΠΎΡΡΡ.
ΠΠ΅Π·ΠΎΡΠΊΠ°Π·Π½ΠΎΡΡΡ β ΡΠ²ΠΎΠΉΡΡΠ²ΠΎ ΠΈΠ·Π΄Π΅Π»ΠΈΡ Π½Π΅ΠΏΡΠ΅ΡΡΠ²Π½ΠΎ ΡΠΎΡ ΡΠ°Π½ΡΡΡ ΡΠ°Π±ΠΎΡΠΎΡΠΏΠΎΡΠΎΠ±Π½ΠΎΡΡΡ Π² ΡΠ΅ΡΠ΅Π½ΠΈΠ΅ Π·Π°Π΄Π°Π½Π½ΠΎΠ³ΠΎ Π²ΡΠ΅ΠΌΠ΅Π½ΠΈ.
ΠΠΎΠ»Π³ΠΎΠ²Π΅ΡΠ½ΠΎΡΡΡ β ΡΠ²ΠΎΠΉΡΡΠ²ΠΎ ΠΈΠ·Π΄Π΅Π»ΠΈΡ Π΄Π»ΠΈΡΠ΅Π»ΡΠ½ΠΎ ΡΠΎΡ ΡΠ°Π½ΡΡΡ ΡΠ°Π±ΠΎΡΠΎΡΠΏΠΎΡΠΎΠ±Π½ΠΎΡΡΡ Π΄ΠΎ Π½Π°ΡΡΡΠΏΠ»Π΅Π½ΠΈΡ ΠΏΡΠ΅Π΄Π΅Π»ΡΠ½ΠΎΠ³ΠΎ ΡΠΎΡΡΠΎΡΠ½ΠΈΡ ΠΏΡΠΈ ΡΠΎΠ±Π»ΡΠ΄Π΅Π½ΠΈΠΈ Π½ΠΎΡΠΌ ΡΠΊΡΠΏΠ»ΡΠ°ΡΠ°ΡΠΈΠΈ. ΠΠΎΠ΄ ΠΏΡΠ΅Π΄Π΅Π»ΡΠ½ΡΠΌ ΠΏΠΎΠ½ΠΈΠΌΠ°ΡΡ ΡΠ°ΠΊΠΎΠ΅ ΡΠΎΡΡΠΎΡΠ½ΠΈΠ΅ ΠΈΠ·Π΄Π΅Π»ΠΈΡ, ΠΏΡΠΈ ΠΊΠΎΡΠΎΡΠΎΠΌ Π΅Π³ΠΎ Π΄Π°Π»ΡΠ½Π΅ΠΉΡΠ°Ρ ΡΠΊΡΠΏΠ»ΡΠ°ΡΠ°ΡΠΈΡ Π½Π΅Π΄ΠΎΠΏΡΡΡΠΈΠΌΠ° ΠΈΠ»ΠΈ Π½Π΅ΡΠ΅Π»Π΅ΡΠΎΠΎΠ±ΡΠ°Π·Π½Π°.
Π Π΅ΠΌΠΎΠ½ΡΠΎΠΏΡΠΈΠ³ΠΎΠ΄Π½ΠΎΡΡΡ β ΡΠ²ΠΎΠΉΡΡΠ²ΠΎ ΠΈΠ·Π΄Π΅Π»ΠΈΡ, Π·Π°ΠΊΠ»ΡΡΠ°ΡΡΠ΅Π΅ΡΡ Π² ΠΏΡΠΈΡΠΏΠΎΡΠΎΠ±Π»Π΅Π½Π½ΠΎΡΡΠΈ ΠΊ ΠΏΠΎΠ΄Π΄Π΅ΡΠΆΠ°Π½ΠΈΡ ΠΈ Π²ΠΎΡΡΡΠ°Π½ΠΎΠ²Π»Π΅Π½ΠΈΡ ΡΠ°Π±ΠΎΡΠΎΡΠΏΠΎΡΠΎΠ±Π½ΠΎΡΡΠΈ ΠΏΡΡΠ΅ΠΌ ΡΠ΅Ρ Π½ΠΈΡΠ΅ΡΠΊΠΎΠ³ΠΎ ΠΎΠ±ΡΠ»ΡΠΆΠΈΠ²Π°Π½ΠΈΡ ΠΈ ΡΠ΅ΠΌΠΎΠ½ΡΠ°.
ΠΠΎΠ½ΡΡΠΈΡ Π½Π°Π΄Π΅ΠΆΠ½ΠΎΡΡΠΈ Π²ΠΎ Π²ΡΠ΅ΠΌΠ΅Π½ΠΈ: Π½Π°ΡΠ°Π±ΠΎΡΠΊΠ°, ΡΠ΅ΡΡΡΡ ΠΈ ΡΡΠΎΠΊ ΡΠ»ΡΠΆΠ±Ρ.
ΠΠ°ΡΠ°Π±ΠΎΡΠΊΠ° β ΠΏΡΠΎΠ΄ΠΎΠ»ΠΆΠΈΡΠ΅Π»ΡΠ½ΠΎΡΡΡ ΠΈΠ»ΠΈ ΠΎΠ±ΡΠ΅ΠΌ ΡΠ°Π±ΠΎΡΡ ΠΈΠ·Π΄Π΅Π»ΠΈΡ (Π² ΡΠ°ΡΠ°Ρ , ΠΊΠΈΠ»ΠΎΠΌΠ΅ΡΡΠ°Ρ ΠΏΡΠΎΠ±Π΅Π³Π°, ΡΠΈΡΠ»Π°Ρ ΡΠΈΠΊΠ»ΠΎΠ² Π½Π°Π³ΡΡΠΆΠ΅Π½ΠΈΡ).
Π Π΅ΡΡΡΡ β ΡΡΠΌΠΌΠ°ΡΠ½Π°Ρ Π½Π°ΡΠ°Π±ΠΎΡΠΊΠ° ΠΈΠ·Π΄Π΅Π»ΠΈΡ ΠΎΡ Π½Π°ΡΠ°Π»Π° ΡΠΊΡΠΏΠ»ΡΠ°ΡΠ°ΡΠΈΠΈ Π΄ΠΎ ΠΏΠ΅ΡΠ΅Ρ ΠΎΠ΄Π° Π² ΠΏΡΠ΅Π΄Π΅Π»ΡΠ½ΠΎΠ΅ ΡΠΎΡΡΠΎΡΠ½ΠΈΠ΅ (Π² ΡΠ°ΡΠ°Ρ , ΠΊΠΈΠ»ΠΎΠΌΠ΅ΡΡΠ°Ρ ΠΏΡΠΎΠ±Π΅Π³Π° ΠΈ Π΄Ρ.).
Π‘ΡΠΎΠΊ ΡΠ»ΡΠΆΠ±Ρ β ΠΊΠ°Π»Π΅Π½Π΄Π°ΡΠ½Π°Ρ ΠΏΡΠΎΠ΄ΠΎΠ»ΠΆΠΈΡΠ΅Π»ΡΠ½ΠΎΡΡΡ ΡΠΊΡΠΏΠ»ΡΠ°ΡΠ°ΡΠΈΠΈ ΠΈΠ·Π΄Π΅Π»ΠΈΡ ΠΎΡ Π½Π°ΡΠ°Π»Π° Π΄ΠΎ ΠΏΠ΅ΡΠ΅Ρ ΠΎΠ΄Π° Π² ΠΏΡΠ΅Π΄Π΅Π»ΡΠ½ΠΎΠ΅ ΡΠΎΡΡΠΎΡΠ½ΠΈΠ΅. ΠΡΡΠ°ΠΆΠ°ΡΡ ΠΎΠ±ΡΡΠ½ΠΎ Π² Π³ΠΎΠ΄Π°Ρ . Π‘ΡΠΎΠΊ ΡΠ»ΡΠΆΠ±Ρ Π²ΠΊΠ»ΡΡΠ°Π΅Ρ Π½Π°ΡΠ°Π±ΠΎΡΠΊΡ ΠΈΠ·Π΄Π΅Π»ΠΈΡ ΠΈ Π²ΡΠ΅ΠΌΡ ΠΏΡΠΎΡΡΠΎΠ΅Π².
ΠΡΠ½ΠΎΠ²Π½ΡΠΌΠΈ ΠΏΠΎΠΊΠ°Π·Π°ΡΠ΅Π»ΡΠΌΠΈ Π½Π°Π΄Π΅ΠΆΠ½ΠΎΡΡΠΈ ΡΠ²Π»ΡΡΡΡΡ:
- ΠΏΠΎ Π±Π΅Π·ΠΎΡΠΊΠ°Π·Π½ΠΎΡΡΠΈ β Π²Π΅ΡΠΎΡΡΠ½ΠΎΡΡΡ Π±Π΅Π·ΠΎΡΠΊΠ°Π·Π½ΠΎΠΉ ΡΠ°Π±ΠΎΡΡ ΠΈ ΠΈΠ½ΡΠ΅Π½ΡΠΈΠ²Π½ΠΎΡΡΡ ΠΎΡΠΊΠ°Π·ΠΎΠ²;
- ΠΏΠΎ Π΄ΠΎΠ»Π³ΠΎΠ²Π΅ΡΠ½ΠΎΡΡΠΈ β ΡΡΠ΅Π΄Π½ΠΈΠΉ ΠΈ Π³Π°ΠΌΠΌΠ°βΠΏΡΠΎΡΠ΅Π½ΡΠ½ΡΠΉ ΡΠ΅ΡΡΡΡ;
- ΠΏΠΎ ΡΠ΅ΠΌΠΎΠ½ΡΠΎΠΏΡΠΈΠ³ΠΎΠ΄Π½ΠΎΡΡΠΈ β Π²Π΅ΡΠΎΡΡΠ½ΠΎΡΡΡ Π²ΠΎΡΡΡΠ°Π½ΠΎΠ²Π»Π΅Π½ΠΈΡ.
***
ο»ΏΠΠ°Π΄Π΅ΠΆΠ½ΠΎΡΡΡ ΠΌΠ°ΡΠΈΠ½ ΠΈ ΡΠ΅ΠΎΡΠΈΡ Π²Π΅ΡΠΎΡΡΠ½ΠΎΡΡΠΈ
ΠΠΎΠ΄ Π²Π΅ΡΠΎΡΡΠ½ΠΎΡΡΡΡ P(t) Π±Π΅Π·ΠΎΡΠΊΠ°Π·Π½ΠΎΠΉ ΡΠ°Π±ΠΎΡΡ ΠΏΠΎΠ½ΠΈΠΌΠ°ΡΡ Π²Π΅ΡΠΎΡΡΠ½ΠΎΡΡΡ ΡΠΎΠ³ΠΎ, ΡΡΠΎ Π² Π·Π°Π΄Π°Π½Π½ΠΎΠΌ ΠΈΠ½ΡΠ΅ΡΠ²Π°Π»Π΅ Π²ΡΠ΅ΠΌΠ΅Π½ΠΈ ΠΈΠ»ΠΈ Π² ΠΏΡΠ΅Π΄Π΅Π»Π°Ρ
Π·Π°Π΄Π°Π½Π½ΠΎΠΉ Π½Π°ΡΠ°Π±ΠΎΡΠΊΠΈ Π½Π΅ Π²ΠΎΠ·Π½ΠΈΠΊΠ°Π΅Ρ ΠΎΡΠΊΠ°Π· ΠΈΠ·Π΄Π΅Π»ΠΈΡ.
ΠΡΠ»ΠΈ Π·Π° Π²ΡΠ΅ΠΌΡ t Π½Π°ΡΠ°Π±ΠΎΡΠΊΠΈ ΠΈΠ· ΡΠΈΡΠ»Π° N ΠΎΠ΄ΠΈΠ½Π°ΠΊΠΎΠ²ΡΡ
ΠΈΠ·Π΄Π΅Π»ΠΈΠΉ Π±ΡΠ»ΠΈ ΠΈΠ·ΡΡΡΡ ΠΈΠ·-Π·Π° ΠΎΡΠΊΠ°Π·ΠΎΠ² n ΠΈΠ·Π΄Π΅Π»ΠΈΠΉ, ΡΠΎ Π²Π΅ΡΠΎΡΡΠ½ΠΎΡΡΡ Π±Π΅Π·ΠΎΡΠΊΠ°Π·Π½ΠΎΠΉ ΡΠ°Π±ΠΎΡΡ ΠΈΠ·Π΄Π΅Π»ΠΈΡ:
P(t) = (N β n)/N = 1 β n/N.
ΠΠ΅ΡΠΎΡΡΠ½ΠΎΡΡΡ Π±Π΅Π·ΠΎΡΠΊΠ°Π·Π½ΠΎΠΉ ΡΠ°Π±ΠΎΡΡ ΡΠ»ΠΎΠΆΠ½ΠΎΠ³ΠΎ ΠΈΠ·Π΄Π΅Π»ΠΈΡ ΡΠ°Π²Π½Π° ΠΏΡΠΎΠΈΠ·Π²Π΅Π΄Π΅Π½ΠΈΡ Π²Π΅ΡΠΎΡΡΠ½ΠΎΡΡΠ΅ΠΉ Π±Π΅Π·ΠΎΡΠΊΠ°Π·Π½ΠΎΠΉ ΡΠ°Π±ΠΎΡΡ ΠΎΡΠ΄Π΅Π»ΡΠ½ΡΡ Π΅Π³ΠΎ ΡΠ»Π΅ΠΌΠ΅Π½ΡΠΎΠ²:
P(t) = P1(t)ΓP2(t)ΓP3(t)Γ…ΓPn(t).
ΠΡΡΡΠ΄Π° ΡΠ»Π΅Π΄ΡΠ΅Ρ, ΡΡΠΎ ΡΠ΅ΠΌ Π±ΠΎΠ»ΡΡΠ΅ ΡΠ»Π΅ΠΌΠ΅Π½ΡΠΎΠ² Π² ΠΈΠ·Π΄Π΅Π»ΠΈΠΈ, ΡΠ΅ΠΌ Π½ΠΈΠΆΠ΅ Π΅Π³ΠΎ Π½Π°Π΄Π΅ΠΆΠ½ΠΎΡΡΡ.
ΠΠΊΡΠΏΠ»ΡΠ°ΡΠ°ΡΠΈΡ ΠΈΠ·Π΄Π΅Π»ΠΈΡ Ρ Π½ΠΈΠ·ΠΊΠΈΠΌ ΠΏΠΎΠΊΠ°Π·Π°ΡΠ΅Π»Π΅ΠΌ P(t) ΠΌΠΎΠΆΠ΅Ρ ΠΎΠΊΠ°Π·Π°ΡΡΡΡ Π½Π΅ΡΠ΅Π»Π΅ΡΠΎΠΎΠ±ΡΠ°Π·Π½ΠΎΠΉ.
ΠΠ½ΡΠ΅Π½ΡΠΈΠ²Π½ΠΎΡΡΡ ΠΎΡΠΊΠ°Π·ΠΎΠ² (t).
Π ΡΠ°Π·Π½ΡΠ΅ ΠΏΠ΅ΡΠΈΠΎΠ΄Ρ ΡΠΊΡΠΏΠ»ΡΠ°ΡΠ°ΡΠΈΠΈ ΠΈΠ»ΠΈ ΠΈΡΠΏΡΡΠ°Π½ΠΈΠΉ ΠΈΠ·Π΄Π΅Π»ΠΈΠΉ ΡΠΈΡΠ»ΠΎ ΠΎΡΠΊΠ°Π·ΠΎΠ² Π² Π΅Π΄ΠΈΠ½ΠΈΡΡ Π²ΡΠ΅ΠΌΠ΅Π½ΠΈ ΡΠ°Π·Π»ΠΈΡΠ½ΠΎ.
ΠΠ½ΡΠ΅Π½ΡΠΈΠ²Π½ΠΎΡΡΡΡ ΠΎΡΠΊΠ°Π·ΠΎΠ² Π½Π°Π·ΡΠ²Π°ΡΡ ΠΎΡΠ½ΠΎΡΠ΅Π½ΠΈΠ΅ ΡΠΈΡΠ»Π° ΠΏ ΠΎΡΠΊΠ°Π·Π°Π²ΡΠΈΡ
Π² Π΅Π΄ΠΈΠ½ΠΈΡΡ Π²ΡΠ΅ΠΌΠ΅Π½ΠΈ t ΠΈΠ·Π΄Π΅Π»ΠΈΠΉ ΠΊ ΡΠΈΡΠ»Ρ ΠΈΠ·Π΄Π΅Π»ΠΈΠΉ (N β n), ΠΈΡΠΏΡΠ°Π²Π½ΠΎ ΡΠ°Π±ΠΎΡΠ°ΡΡΠΈΡ
Π² Π΄Π°Π½Π½ΡΠΉ ΠΎΡΡΠ΅Π·ΠΎΠΊ Π²ΡΠ΅ΠΌΠ΅Π½ΠΈ, ΠΏΡΠΈ ΡΡΠ»ΠΎΠ²ΠΈΠΈ, ΡΡΠΎ ΠΎΡΠΊΠ°Π·Π°Π²ΡΠΈΠ΅ ΠΈΠ·Π΄Π΅Π»ΠΈΡ Π½Π΅ Π²ΠΎΡΡΡΠ°Π½Π°Π²Π»ΠΈΠ²Π°ΡΡ ΠΈ Π½Π΅ Π·Π°ΠΌΠ΅Π½ΡΡΡ Π½ΠΎΠ²ΡΠΌΠΈ:
Ξ»(t) = n/[(N β n)Γt].
ΠΠ΅ΡΠΎΡΡΠ½ΠΎΡΡΡ Π±Π΅Π·ΠΎΡΠΊΠ°Π·Π½ΠΎΠΉ ΡΠ°Π±ΠΎΡΡ ΠΌΠΎΠΆΠ½ΠΎ ΠΎΡΠ΅Π½ΠΈΡΡ ΠΏΠΎ ΠΈΠ½ΡΠ΅Π½ΡΠΈΠ²Π½ΠΎΡΡΠΈ ΠΎΡΠΊΠ°Π·ΠΎΠ²:
P(t) = 1 β Ξ»(t)Γt.
ΠΠ»Ρ Π΄Π΅ΡΠ°Π»Π΅ΠΉ ΠΌΠ°ΡΠΈΠ½ Π² ΠΊΠ°ΡΠ΅ΡΡΠ²Π΅ ΠΏΠΎΠΊΠ°Π·Π°ΡΠ΅Π»Ρ Π΄ΠΎΠ»Π³ΠΎΠ²Π΅ΡΠ½ΠΎΡΡΠΈ ΠΈΡΠΏΠΎΠ»ΡΠ·ΡΡΡ ΡΡΠ΅Π΄Π½ΠΈΠΉ ΡΠ΅ΡΡΡΡ (ΠΌΠ°ΡΠ΅ΠΌΠ°ΡΠΈΡΠ΅ΡΠΊΠΎΠ΅ ΠΎΠΆΠΈΠ΄Π°Π½ΠΈΠ΅ ΡΠ΅ΡΡΡΡΠ° Π² ΡΠ°ΡΠ°Ρ
ΡΠ°Π±ΠΎΡΡ, ΠΊΠΈΠ»ΠΎΠΌΠ΅ΡΡΠ°Ρ
ΠΏΡΠΎΠ±Π΅Π³Π°, ΠΌΠΈΠ»Π»ΠΈΠΎΠ½Π°Ρ
ΠΎΠ±ΠΎΡΠΎΡΠΎΠ²) ΠΈΠ»ΠΈ Π³Π°ΠΌΠΌΠ°βΠΏΡΠΎΡΠ΅Π½ΡΠ½ΡΠΉ ΡΠ΅ΡΡΡΡ (ΡΡΠΌΠΌΠ°ΡΠ½Π°Ρ Π½Π°ΡΠ°Π±ΠΎΡΠΊΠ°, Π² ΡΠ΅ΡΠ΅Π½ΠΈΠ΅ ΠΊΠΎΡΠΎΡΠΎΠΉ ΠΈΠ·Π΄Π΅Π»ΠΈΠ΅ Π½Π΅ Π΄ΠΎΡΡΠΈΠ³Π°Π΅Ρ ΠΏΡΠ΅Π΄Π΅Π»ΡΠ½ΠΎΠ³ΠΎ ΡΠΎΡΡΠΎΡΠ½ΠΈΡ Ρ Π²Π΅ΡΠΎΡΡΠ½ΠΎΡΡΡΡ, Π²ΡΡΠ°ΠΆΠ΅Π½Π½ΠΎΠΉ Π² ΠΏΡΠΎΡΠ΅Π½ΡΠ°Ρ
).
ΠΠ»Ρ ΠΈΠ·Π΄Π΅Π»ΠΈΠΉ ΡΠ΅ΡΠΈΠΉΠ½ΠΎΠ³ΠΎ ΠΈ ΠΌΠ°ΡΡΠΎΠ²ΠΎΠ³ΠΎ ΠΏΡΠΎΠΈΠ·Π²ΠΎΠ΄ΡΡΠ²Π° Π½Π°ΠΈΠ±ΠΎΠ»Π΅Π΅ ΡΠ°ΡΡΠΎ ΠΈΡΠΏΠΎΠ»ΡΠ·ΡΡΡ Π³Π°ΠΌΠΌΠ°βΠΏΡΠΎΡΠ΅Π½ΡΠ½ΡΠΉ ΡΠ΅ΡΡΡΡ: Π΄Π»Ρ ΠΏΠΎΠ΄ΡΠΈΠΏΠ½ΠΈΠΊΠΎΠ² ΠΊΠ°ΡΠ΅Π½ΠΈΡ, Π½Π°ΠΏΡΠΈΠΌΠ΅Ρ, 90 %-Π½ΡΠΉ ΡΠ΅ΡΡΡΡ.
ΠΠΎΠ΄ Π²Π΅ΡΠΎΡΡΠ½ΠΎΡΡΡΡ Π²ΠΎΡΡΡΠ°Π½ΠΎΠ²Π»Π΅Π½ΠΈΡ ΠΏΠΎΠ½ΠΈΠΌΠ°ΡΡ Π²Π΅ΡΠΎΡΡΠ½ΠΎΡΡΡ ΡΠΎΠ³ΠΎ, ΡΡΠΎ Π²ΡΠ΅ΠΌΡ Π²ΠΎΡΡΡΠ°Π½ΠΎΠ²Π»Π΅Π½ΠΈΡ ΡΠ°Π±ΠΎΡΠΎΡΠΏΠΎΡΠΎΠ±Π½ΠΎΠ³ΠΎ ΡΠΎΡΡΠΎΡΠ½ΠΈΡ ΠΈΠ·Π΄Π΅Π»ΠΈΡ Π½Π΅ ΠΏΡΠ΅Π²ΡΡΠΈΡ Π·Π°Π΄Π°Π½Π½ΠΎΠ΅ Π·Π½Π°ΡΠ΅Π½ΠΈΠ΅.
ΠΡΠ½ΠΎΠ²Ρ Π½Π°Π΄Π΅ΠΆΠ½ΠΎΡΡΠΈ Π·Π°ΠΊΠ»Π°Π΄ΡΠ²Π°Π΅Ρ ΠΊΠΎΠ½ΡΡΡΡΠΊΡΠΎΡ ΠΏΡΠΈ ΠΏΡΠΎΠ΅ΠΊΡΠΈΡΠΎΠ²Π°Π½ΠΈΠΈ ΠΈΠ·Π΄Π΅Π»ΠΈΡ (ΡΠΎΡΠ½ΠΎΡΡΡΡ ΡΠΎΡΡΠ°Π²Π»Π΅Π½ΠΈΡ ΡΠ°ΡΡΠ΅ΡΠ½ΠΎΠΉ ΡΡ
Π΅ΠΌΡ). ΠΠΏΡΠ΅Π΄Π΅Π»Π΅Π½ΠΈΠ΅ ΠΏΠΎΠΊΠ°Π·Π°ΡΠ΅Π»Π΅ΠΉ Π½Π°Π΄Π΅ΠΆΠ½ΠΎΡΡΠΈ Π²ΡΠΏΠΎΠ»Π½ΡΡΡ ΠΌΠ΅ΡΠΎΠ΄Π°ΠΌΠΈ ΡΠ΅ΠΎΡΠΈΠΈ Π²Π΅ΡΠΎΡΡΠ½ΠΎΡΡΠ΅ΠΉ, ΠΈΡ
ΠΈΡΠΏΠΎΠ»ΡΠ·ΡΡΡ ΠΏΡΠΈ Π²ΡΠ±ΠΎΡΠ΅ ΠΎΠΏΡΠΈΠΌΠ°Π»ΡΠ½ΡΡ
Π²Π°ΡΠΈΠ°Π½ΡΠΎΠ² ΠΊΠΎΠ½ΡΡΡΡΠΊΡΠΈΠΈ.
ΠΠ°Π΄Π΅ΠΆΠ½ΠΎΡΡΡ Π·Π°Π²ΠΈΡΠΈΡ ΡΠ°ΠΊΠΆΠ΅ ΠΎΡ ΠΊΠ°ΡΠ΅ΡΡΠ²Π° ΠΈΠ·Π³ΠΎΡΠΎΠ²Π»Π΅Π½ΠΈΡ (Π½Π΅ΡΠΎΡΠ½ΠΎΡΡΠΈ Π²Π»ΠΈΡΡΡ Π½Π° ΡΠ°ΡΠΏΡΠ΅Π΄Π΅Π»Π΅Π½ΠΈΠ΅ Π½Π°Π³ΡΡΠ·ΠΎΠΊ Π² Π·ΠΎΠ½Π΅ ΡΠΈΠ»ΠΎΠ²ΠΎΠ³ΠΎ Π²Π·Π°ΠΈΠΌΠΎΠ΄Π΅ΠΉΡΡΠ²ΠΈΡ) ΠΈ ΠΎΡ ΡΠΎΠ±Π»ΡΠ΄Π΅Π½ΠΈΡ Π½ΠΎΡΠΌ ΡΠΊΡΠΏΠ»ΡΠ°ΡΠ°ΡΠΈΠΈ.
***
ΠΡΠΈΡΠ΅ΡΠΈΠΈ ΡΠ°Π±ΠΎΡΠΎΡΠΏΠΎΡΠΎΠ±Π½ΠΎΡΡΠΈ Π΄Π΅ΡΠ°Π»Π΅ΠΉ ΠΌΠ°ΡΠΈΠ½
ο»ΏΠΠ»Π°Π²Π½Π°Ρ ΡΡΡΠ°Π½ΠΈΡΠ°
ΠΠΈΡΡΠ°Π½ΡΠΈΠΎΠ½Π½ΠΎΠ΅ ΠΎΠ±ΡΠ°Π·ΠΎΠ²Π°Π½ΠΈΠ΅
Π‘ΠΏΠ΅ΡΠΈΠ°Π»ΡΠ½ΠΎΡΡΠΈ
Π£ΡΠ΅Π±Π½ΡΠ΅ Π΄ΠΈΡΡΠΈΠΏΠ»ΠΈΠ½Ρ
ΠΠ»ΠΈΠΌΠΏΠΈΠ°Π΄Ρ ΠΈ ΡΠ΅ΡΡΡ
«ΠΠ°Π΄Π΅ΠΆΠ½ΠΎΡΡΡ ΠΌΠ°ΡΠΈΠ½ ΠΈ ΡΠΏΡΠ°Π²Π»Π΅Π½ΠΈΠ΅ ΠΊΠ°ΡΠ΅ΡΡΠ²ΠΎΠΌ»
ΠΠΠΠΠΠΠΠ‘Π’Π¬ ΠΠΠ¨ΠΠ Π Π£ΠΠ ΠΠΠΠΠΠΠ ΠΠΠ§ΠΠ‘Π’ΠΠΠ
Π£Π§ΠΠΠΠΠ ΠΠΠ‘ΠΠΠΠ
ΠΏΠΎ ΠΏΡΠΎΠ²Π΅Π΄Π΅Π½ΠΈΡ ΠΏΡΠ°ΠΊΡΠΈΡΠ΅ΡΠΊΠΈΡ Π·Π°Π½ΡΡΠΈΠΉ
ΠΏΠΎ ΡΠ΅ΠΌΠ΅ 2.2 ΠΠΠ.02.02.ΠΠΈΠ°Π³Π½ΠΎΡΡΠΈΡΠ΅ΡΠΊΠΎΠ΅ ΠΈ ΡΠ΅Ρ Π½ΠΎΠ»ΠΎΠ³ΠΈΡΠ΅ΡΠΊΠΎΠ΅ ΠΎΠ±ΠΎΡΡΠ΄ΠΎΠ²Π°Π½ΠΈΠ΅ ΠΏΠΎ ΡΠ΅Ρ Π½ΠΈΡΠ΅ΡΠΊΠΎΠΌΡ ΠΎΠ±ΡΠ»ΡΠΆΠΈΠ²Π°Π½ΠΈΡ, ΡΠ΅ΠΌΠΎΠ½ΡΡ ΠΏΠΎΠ΄ΡΠ΅ΠΌΠ½ΠΎ-ΡΡΠ°Π½ΡΠΏΠΎΡΡΠ½ΡΡ , ΡΡΡΠΎΠΈΡΠ΅Π»ΡΠ½ΡΡ , Π΄ΠΎΡΠΎΠΆΠ½ΡΡ ΠΌΠ°ΡΠΈΠ½ ΠΈ ΠΎΠ±ΠΎΡΡΠ΄ΠΎΠ²Π°Π½ΠΈΡ ΠΠ.02. Π’Π΅Ρ Π½ΠΈΡΠ΅ΡΠΊΠΎΠ΅ ΠΎΠ±ΡΠ»ΡΠΆΠΈΠ²Π°Π½ΠΈΠ΅ ΠΈ ΡΠ΅ΠΌΠΎΠ½Ρ ΠΏΠΎΠ΄ΡΠ΅ΠΌΠ½ΠΎ-ΡΡΠ°Π½ΡΠΏΠΎΡΡΠ½ΡΡ , ΡΡΡΠΎΠΈΡΠ΅Π»ΡΠ½ΡΡ , Π΄ΠΎΡΠΎΠΆΠ½ΡΡ ΠΌΠ°ΡΠΈΠ½ ΠΈ ΠΎΠ±ΠΎΡΡΠ΄ΠΎΠ²Π°Π½ΠΈΡ Π² ΡΡΠ°ΡΠΈΠΎΠ½Π°ΡΠ½ΡΡ ΠΌΠ°ΡΡΠ΅ΡΡΠΊΠΈΡ ΠΈ Π½Π° ΠΌΠ΅ΡΡΠ΅ Π²ΡΠΏΠΎΠ»Π½Π΅Π½ΠΈΡ ΡΠ°Π±ΠΎΡ
Π΄Π»Ρ ΡΠΏΠ΅ΡΠΈΠ°Π»ΡΠ½ΠΎΡΡΠΈ
23.02.04 Π’Π΅Ρ Π½ΠΈΡΠ΅ΡΠΊΠ°Ρ ΡΠΊΡΠΏΠ»ΡΠ°ΡΠ°ΡΠΈΡ ΠΏΠΎΠ΄ΡΠ΅ΠΌΠ½ΠΎ-ΡΡΠ°Π½ΡΠΏΠΎΡΡΠ½ΡΡ , ΡΡΡΠΎΠΈΡΠ΅Π»ΡΠ½ΡΡ , Π΄ΠΎΡΠΎΠΆΠ½ΡΡ ΠΌΠ°ΡΠΈΠ½ ΠΈ ΠΎΠ±ΠΎΡΡΠ΄ΠΎΠ²Π°Π½ΠΈΡ
(ΠΏΠΎ ΠΎΡΡΠ°ΡΠ»ΡΠΌ) (Π½Π° ΠΆΠ΅Π»Π΅Π·Π½ΠΎΠ΄ΠΎΡΠΎΠΆΠ½ΡΠΉ ΡΡΠ°Π½ΡΠΏΠΎΡΡΠ΅)
Π±Π°Π·ΠΎΠ²ΡΠΉ ΡΡΠΎΠ²Π΅Π½Ρ
ΡΡΠ΅Π΄Π½Π΅Π³ΠΎ ΠΏΡΠΎΡΠ΅ΡΡΠΈΠΎΠ½Π°Π»ΡΠ½ΠΎΠ³ΠΎ ΠΎΠ±ΡΠ°Π·ΠΎΠ²Π°Π½ΠΈΡ
ΠΠ²ΡΠΎΡ:
ΠΡΠ΅ΠΏΠΎΠ΄Π°Π²Π°ΡΠ΅Π»Ρ
ΠΠ°Π»ΡΠΆΡΠΊΠΎΠ³ΠΎ ΠΏΠΎΠ΄ΡΠ°Π·Π΄Π΅Π»Π΅Π½ΠΈΡ
ΠΠΎΡΠΊΠΎΠ²ΡΠΊΠΎΠ³ΠΎ ΡΡΠ΅Π±Π½ΠΎΠ³ΠΎ ΡΠ΅Π½ΡΡΠ° ΠΏΡΠΎΡΠ΅ΡΡΠΈΠΎΠ½Π°Π»ΡΠ½ΡΡ ΠΊΠ²Π°Π»ΠΈΡΠΈΠΊΠ°ΡΠΈΠΉ β
ΡΡΡΡΠΊΡΡΡΠ½ΠΎΠ³ΠΎ ΠΏΠΎΠ΄ΡΠ°Π·Π΄Π΅Π»Π΅Π½ΠΈΡ ΠΠΎΡΠΊΠΎΠ²ΡΠΊΠΎΠΉ ΠΆΠ΅Π»Π΅Π·Π½ΠΎΠΉ Π΄ΠΎΡΠΎΠ³ΠΈ β
ΡΠΈΠ»ΠΈΠ°Π»Π° ΠΠΠ Β«Π ΠΠΒ»
ΠΠΊΡΠ»ΠΎΠ²Π° Π.Π.
2019
ΠΠ½Π½ΠΎΡΠ°ΡΠΈΡ
Π£ΡΠ΅Π±Π½ΠΎΠ΅ ΠΏΠΎΡΠΎΠ±ΠΈΠ΅ ΡΠ°Π·ΡΠ°Π±ΠΎΡΠ°Π½ΠΎ Π² ΡΠΎΠΎΡΠ²Π΅ΡΡΡΠ²ΠΈΠΈ Ρ ΠΏΡΠΈΠΌΠ΅ΡΠ½ΠΎΠΉ ΠΏΡΠΎΠ³ΡΠ°ΠΌΠΌΠΎΠΉ ΠΏΡΠΎΡΠ΅ΡΡΠΈΠΎΠ½Π°Π»ΡΠ½ΠΎΠ³ΠΎ ΠΌΠΎΠ΄ΡΠ»Ρ ΠΠ.02 Π’Π΅Ρ Π½ΠΈΡΠ΅ΡΠΊΠΎΠ΅ ΠΎΠ±ΡΠ»ΡΠΆΠΈΠ²Π°Π½ΠΈΠ΅ ΠΈ ΡΠ΅ΠΌΠΎΠ½Ρ ΠΏΠΎΠ΄ΡΠ΅ΠΌΠ½ΠΎ β ΡΡΠ°Π½ΡΠΏΠΎΡΡΠ½ΡΡ , ΡΡΡΠΎΠΈΡΠ΅Π»ΡΠ½ΡΡ , Π΄ΠΎΡΠΎΠΆΠ½ΡΡ ΠΌΠ°ΡΠΈΠ½ ΠΈ ΠΎΠ±ΠΎΡΡΠ΄ΠΎΠ²Π°Π½ΠΈΡ Π² ΡΡΠ°ΡΠΈΠΎΠ½Π°ΡΠ½ΡΡ ΠΌΠ°ΡΡΠ΅ΡΡΠΊΠΈΡ ΠΈ Π½Π° ΠΌΠ΅ΡΡΠ΅ Π²ΡΠΏΠΎΠ»Π½Π΅Π½ΠΈΡ ΡΠ°Π±ΠΎΡ ΠΠΠ 02.02 ΠΠΈΠ°Π³Π½ΠΎΡΡΠΈΡΠ΅ΡΠΊΠΎΠ΅ ΠΈ ΡΠ΅Ρ Π½ΠΎΠ»ΠΎΠ³ΠΈΡΠ΅ΡΠΊΠΎΠ΅ ΠΎΠ±ΠΎΡΡΠ΄ΠΎΠ²Π°Π½ΠΈΠ΅ ΠΏΠΎ ΡΠ΅Ρ Π½ΠΈΡΠ΅ΡΠΊΠΎΠΌΡ ΠΎΠ±ΡΠ»ΡΠΆΠΈΠ²Π°Π½ΠΈΡ, ΡΠ΅ΠΌΠΎΠ½ΡΡ ΠΏΠΎΠ΄ΡΠ΅ΠΌΠ½ΠΎ-ΡΡΠ°Π½ΡΠΏΠΎΡΡΠ½ΡΡ , ΡΡΡΠΎΠΈΡΠ΅Π»ΡΠ½ΡΡ , Π΄ΠΎΡΠΎΠΆΠ½ΡΡ ΠΌΠ°ΡΠΈΠ½ ΠΈ ΠΎΠ±ΠΎΡΡΠ΄ΠΎΠ²Π°Π½ΠΈΡ ΡΠ΅ΠΌΠ° 2.2. ΠΠ°Π΄Π΅ΠΆΠ½ΠΎΡΡΡ ΠΌΠ°ΡΠΈΠ½ ΠΈ ΡΠΏΡΠ°Π²Π»Π΅Π½ΠΈΠ΅ ΠΊΠ°ΡΠ΅ΡΡΠ²ΠΎΠΌ ΠΏΠΎ ΡΠΏΠ΅ΡΠΈΠ°Π»ΡΠ½ΠΎΡΡΠΈ 23.02.04 Β«Π’Π΅Ρ Π½ΠΈΡΠ΅ΡΠΊΠ°Ρ ΡΠΊΡΠΏΠ»ΡΠ°ΡΠ°ΡΠΈΡ ΠΏΠΎΠ΄ΡΠ΅ΠΌΠ½ΠΎ-ΡΡΠ°Π½ΡΠΏΠΎΡΡΠ½ΡΡ , ΡΡΡΠΎΠΈΡΠ΅Π»ΡΠ½ΡΡ , Π΄ΠΎΡΠΎΠΆΠ½ΡΡ ΠΌΠ°ΡΠΈΠ½ ΠΈ ΠΎΠ±ΠΎΡΡΠ΄ΠΎΠ²Π°Π½ΠΈΡΒ» (ΠΏΠΎ ΠΎΡΡΠ°ΡΠ»ΡΠΌ) (Π½Π° ΠΆΠ΅Π»Π΅Π·Π½ΠΎΠ΄ΠΎΡΠΎΠΆΠ½ΠΎΠΌ ΡΡΠ°Π½ΡΠΏΠΎΡΡΠ΅).
Π Π°ΡΡΠΌΠ°ΡΡΠΈΠ²Π°ΡΡΡΡ ΠΎΡΠ½ΠΎΠ²Π½ΡΠ΅ ΠΏΠΎΠ½ΡΡΠΈΡ ΠΈ ΠΎΠΏΡΠ΅Π΄Π΅Π»Π΅Π½ΠΈΡ ΡΠ΅ΠΎΡΠΈΠΈ Π½Π°Π΄Π΅ΠΆΠ½ΠΎΡΡΠΈ, ΡΠΈΠ·ΠΈΡΠ΅ΡΠΊΠ°Ρ ΡΡΡΠ½ΠΎΡΡΡ ΠΈ Π·Π°ΠΊΠΎΠ½ΠΎΠΌΠ΅ΡΠ½ΠΎΡΡΠΈ ΠΈΠ·ΠΌΠ΅Π½Π΅Π½ΠΈΡ ΡΠ΅Ρ Π½ΠΈΡΠ΅ΡΠΊΠΎΠ³ΠΎ ΡΠΎΡΡΠΎΡΠ½ΠΈΡ ΠΌΠ°ΡΠΈΠ½; ΡΠ°ΠΊΡΠΎΡΡ, ΠΎΠΏΡΠ΅Π΄Π΅Π»ΡΡΡΠΈΠ΅ ΠΈΠ½ΡΠ΅Π½ΡΠΈΠ²Π½ΠΎΡΡΡ ΠΈΠ·Π½Π°ΡΠΈΠ²Π°Π½ΠΈΡ; ΠΎΡΠ½ΠΎΠ²Π½ΡΠ΅ ΠΌΠ΅ΡΠΎΠ΄Ρ ΠΏΠΎΠ»ΡΡΠ΅Π½ΠΈΡ ΠΈ Π°Π½Π°Π»ΠΈΠ·Π° ΠΈΠ½ΡΠΎΡΠΌΠ°ΡΠΈΠΈ ΠΎΠ± ΠΎΡΠΊΠ°Π·Π°Ρ ΠΈ Π½Π΅ΠΈΡΠΏΡΠ°Π²Π½ΠΎΡΡΡΡ ; ΠΎΠ±Π΅ΡΠΏΠ΅ΡΠ΅Π½ΠΈΡ Π½Π°Π΄Π΅ΠΆΠ½ΠΎΡΡΠΈ ΠΌΠ°ΡΠΈΠ½ Π½Π° ΡΡΠ°ΠΏΠ°Ρ ΠΏΡΠΎΠ΅ΠΊΡΠΈΡΠΎΠ²Π°Π½ΠΈΡ, ΠΏΡΠΎΠΈΠ·Π²ΠΎΠ΄ΡΡΠ²Π° ΠΈ ΡΠΊΡΠΏΠ»ΡΠ°ΡΠ°ΡΠΈΠΈ. Π Π°ΡΡΠΌΠ°ΡΡΠΈΠ²Π°ΡΡΡΡ Π²ΠΎΠΏΡΠΎΡΡ ΡΠ°ΡΠΈΠΎΠ½Π°Π»ΡΠ½ΠΎΠΉ ΠΎΡΠ³Π°Π½ΠΈΠ·Π°ΡΠΈΠΈ ΡΠ΅Ρ Π½ΠΈΡΠ΅ΡΠΊΠΎΠΉ ΡΠΊΡΠΏΠ»ΡΠ°ΡΠ°ΡΠΈΠΈ ΠΌΠ°ΡΠΈΠ½, ΠΎΠ±ΠΎΡΠ½ΠΎΠ²Π°Π½ΠΈΡ ΠΏΠ΅ΡΠΈΠΎΠ΄ΠΈΡΠ½ΠΎΡΡΠ΅ΠΉ ΠΈ ΡΡΡΠ΄ΠΎΠ΅ΠΌΠΊΠΎΡΡΠ΅ΠΉ ΡΠ΅Ρ Π½ΠΈΡΠ΅ΡΠΊΠΈΡ Π²ΠΎΠ·Π΄Π΅ΠΉΡΡΠ²ΠΈΠΉ ΠΏΡΠΈ ΠΏΡΠΎΠ²Π΅Π΄Π΅Π½ΠΈΠΈ Π’Π ΠΈ ΡΠ΅ΠΌΠΎΠ½ΡΠΎΠ², ΡΠ½ΠΈΠΆΠ΅Π½ΠΈΡ ΡΡΡΠ΄ΠΎΠ²ΡΡ ΠΈ ΠΌΠ°ΡΠ΅ΡΠΈΠ°Π»ΡΠ½ΡΡ Π·Π°ΡΡΠ°Ρ Π½Π° ΠΏΠΎΠ΄Π΄Π΅ΡΠΆΠ°Π½ΠΈΠ΅ ΠΌΠ°ΡΠΈΠ½ Π² ΡΠ°Π±ΠΎΡΠΎΡΠΏΠΎΡΠΎΠ±Π½ΠΎΠΌ ΡΠΎΡΡΠΎΡΠ½ΠΈΠΈ.
ΠΠΎΡΠΎΠ±ΠΈΠ΅ ΠΈΠΌΠ΅Π΅Ρ ΡΠ΅Π»Ρ Π½Π°ΡΡΠΈΡΡΡΡ ΠΎΠΏΡΠ΅Π΄Π΅Π»ΡΡΡ ΡΠ°ΡΡΠ΅ΡΠ½ΡΠ΅ ΠΏΠΎΠΊΠ°Π·Π°ΡΠ΅Π»ΠΈ Π½Π°Π΄Π΅ΠΆΠ½ΠΎΡΡΠΈ; ΠΎΡΠ½ΠΎΠ²Π½ΡΠ΅ ΠΌΠ΅ΡΠΎΠ΄Ρ ΠΎΡΠ΅Π½ΠΊΠΈ ΠΊΠ°ΡΠ΅ΡΡΠ²Π° ΠΈ Π½Π°Π΄Π΅ΠΆΠ½ΠΎΡΡΠΈ ΠΎΠ±ΡΠ΅ΠΊΡΠΎΠ² ΠΈ ΡΠΏΠ΅ΡΠΈΠ°Π»ΡΠ½ΡΡ ΡΠ΅ΡΠΌΠΈΠ½ΠΎΠ»ΠΎΠ³ΠΈΡ, ΡΠΏΠΎΡΠΎΠ±Ρ ΠΎΠ±Π΅ΡΠΏΠ΅ΡΠ΅Π½ΠΈΡ ΠΈ ΠΏΠΎΠ΄Π΄Π΅ΡΠΆΠ°Π½ΠΈΡ Π½Π°Π΄Π΅ΠΆΠ½ΠΎΡΡΠΈ ΠΏΠΎΠ΄ΡΠ΅ΠΌΠ½ΠΎ-ΡΡΠ°Π½ΡΠΏΠΎΡΡΠ½ΡΡ , ΡΡΡΠΎΠΈΡΠ΅Π»ΡΠ½ΡΡ ΠΈ Π΄ΠΎΡΠΎΠΆΠ½ΡΡ ΠΌΠ°ΡΠΈΠ½ Π² ΡΠΊΡΠΏΠ»ΡΠ°ΡΠ°ΡΠΈΠΈ; ΠΎΡΠ½ΠΎΠ²Π½ΡΠ΅ ΠΏΡΠΈΠ½ΡΠΈΠΏΡ Π²Π΅ΡΠΎΡΡΠ½ΠΎΡΡΠ½ΠΎΠ³ΠΎ ΠΏΡΠΎΠ³Π½ΠΎΠ·ΠΈΡΠΎΠ²Π°Π½ΠΈΡ ΡΠ΅ΡΡΡΡΠ° ΠΎΠ±ΡΠ΅ΠΊΡΠΎΠ²; ΠΎΠ±ΡΠ°Π±Π°ΡΡΠ²Π°ΡΡ ΡΡΠ°ΡΠΈΡΡΠΈΡΠ΅ΡΠΊΡΡ ΠΈΠ½ΡΠΎΡΠΌΠ°ΡΠΈΡ ΠΎ Π±Π΅Π·ΠΎΡΠΊΠ°Π·Π½ΠΎΡΡΠΈ, ΡΠ΅ΠΌΠΎΠ½ΡΠΎΠΏΡΠΈΠ³ΠΎΠ΄Π½ΠΎΡΡΠΈ ΠΈ Π΄ΠΎΠ»Π³ΠΎΠ²Π΅ΡΠ½ΠΎΡΡΠΈ ΠΎΠ±ΡΠ΅ΠΊΡΠ°; ΡΠΎΡΡΠ°Π²Π»ΡΡΡ Π΄ΠΎΠ½Π΅ΡΠ΅Π½ΠΈΠ΅ ΠΎΠ± ΠΎΡΠΊΠ°Π·Π΅, ΡΠΈΡΡΠ΅ΠΌΠ°ΡΠΈΠ·ΠΈΡΠΎΠ²Π°ΡΡ ΡΡΠ°ΡΠΈΡΡΠΈΡΠ΅ΡΠΊΡΡ ΠΈΠ½ΡΠΎΡΠΌΠ°ΡΠΈΡ; ΠΎΠ±ΡΠ°Π±Π°ΡΡΠ²Π°ΡΡ ΡΠ΅Π·ΡΠ»ΡΡΠ°ΡΡ ΡΠΊΡΠΏΠ΅ΡΠΈΠΌΠ΅Π½ΡΠ°.
ΠΡΠ΅Π΄Π½Π°Π·Π½Π°ΡΠ΅Π½ΠΎ Π΄Π»Ρ ΡΡΡΠ΄Π΅Π½ΡΠΎΠ² ΡΠ΅Ρ Π½ΠΈΠΊΡΠΌΠΎΠ² ΠΈ ΠΊΠΎΠ»Π»Π΅Π΄ΠΆΠ΅ΠΉ ΡΠΏΠ΅ΡΠΈΠ°Π»ΡΠ½ΠΎΡΡΠ΅ΠΉ 23.02.04 Β«Π’Π΅Ρ Π½ΠΈΡΠ΅ΡΠΊΠ°Ρ ΡΠΊΡΠΏΠ»ΡΠ°ΡΠ°ΡΠΈΡ ΠΏΠΎΠ΄ΡΠ΅ΠΌΠ½ΠΎ-ΡΡΠ°Π½ΡΠΏΠΎΡΡΠ½ΡΡ , ΡΡΡΠΎΠΈΡΠ΅Π»ΡΠ½ΡΡ , Π΄ΠΎΡΠΎΠΆΠ½ΡΡ ΠΌΠ°ΡΠΈΠ½ ΠΈ ΠΎΠ±ΠΎΡΡΠ΄ΠΎΠ²Π°Π½ΠΈΡΒ» (ΠΏΠΎ ΠΎΡΡΠ°ΡΠ»ΡΠΌ) (Π½Π° ΠΆΠ΅Π»Π΅Π·Π½ΠΎΠ΄ΠΎΡΠΎΠΆΠ½ΠΎΠΌ ΡΡΠ°Π½ΡΠΏΠΎΡΡΠ΅), ΡΠ»ΡΡΠ°ΡΠ΅Π»Π΅ΠΉ Π΄ΠΎΡΠΎΠΆΠ½ΠΎ β ΡΠ΅Ρ Π½ΠΈΡΠ΅ΡΠΊΠΈΡ ΡΠΊΠΎΠ» (Π½Π΅ΠΊΠΎΡΠΎΡΡΠ΅ ΡΠ°Π·Π΄Π΅Π»Ρ), Π° ΡΠ°ΠΊΠΆΠ΅ Π΄Π»Ρ ΠΈΠ½ΠΆΠ΅Π½Π΅ΡΠ½ΠΎ- ΡΠ΅Ρ Π½ΠΈΡΠ΅ΡΠΊΠΈΡ ΡΠ°Π±ΠΎΡΠ½ΠΈΠΊΠΎΠ² ΠΏΡΠ΅Π΄ΠΏΡΠΈΡΡΠΈΠΉ ΠΆΠ΅Π»Π΅Π·Π½ΠΎΠ΄ΠΎΡΠΎΠΆΠ½ΠΎΠ³ΠΎ ΡΡΠ°Π½ΡΠΏΠΎΡΡΠ°.
Π‘ΠΠΠΠ ΠΠΠΠΠ
Π Π°Π·Π΄Π΅Π» 1. ΠΡΠ½ΠΎΠ²Π½ΡΠ΅ ΠΏΠΎΠ½ΡΡΠΈΡ ΠΈ ΠΎΠΏΡΠ΅Π΄Π΅Π»Π΅Π½ΠΈΡ Π½Π°Π΄Π΅ΠΆΠ½ΠΎΡΡΠΈ ΠΌΠ°ΡΠΈΠ½
ΠΠ±ΡΠΈΠ΅ ΠΏΠΎΠ½ΡΡΠΈΡ Π½Π°ΡΠΊΠΈ ΠΎ Π½Π°Π΄Π΅ΠΆΠ½ΠΎΡΡΠΈ
Π’Π΅ΡΠΌΠΈΠ½Ρ ΠΈ ΠΎΠΏΡΠ΅Π΄Π΅Π»Π΅Π½ΠΈΡ
ΠΠ»Π΅ΠΌΠ΅Π½ΡΡ ΡΠ΅ΠΎΡΠΈΠΈ Π²Π΅ΡΠΎΡΡΠ½ΠΎΡΡΠ΅ΠΉ, ΠΈΡΠΏΠΎΠ»ΡΠ·ΡΠ΅ΠΌΡΠ΅ Π² ΡΠ΅ΠΎΡΠΈΠΈ Π½Π°Π΄Π΅ΠΆΠ½ΠΎΡΡΠΈ
ΠΠΎΠ½ΡΡΠΈΠ΅ ΠΎ ΡΠ΅ΠΎΡΠΈΠΈ Π½Π°Π΄Π΅ΠΆΠ½ΠΎΡΡΠΈ.
ΠΠ°ΠΊΠΎΠ½Ρ ΡΠ°ΡΠΏΡΠ΅Π΄Π΅Π»Π΅Π½ΠΈΡ Π½Π°ΡΠ°Π±ΠΎΡΠΎΠΊ ΠΌΠ°ΡΠΈΠ½, ΠΈΡ Π°Π³ΡΠ΅Π³Π°ΡΠΎΠ², Π΄Π΅ΡΠ°Π»Π΅ΠΉ ΠΈ ΡΠΈΡΡΠ΅ΠΌ.
ΠΠΎΠ»ΠΈΡΠ΅ΡΡΠ²Π΅Π½Π½ΡΠ΅ ΠΏΠΎΠΊΠ°Π·Π°ΡΠ΅Π»ΠΈ Π½Π°Π΄Π΅ΠΆΠ½ΠΎΡΡΠΈ
ΠΠΎΠΊΠ°Π·Π°ΡΠ΅Π»ΠΈ Π±Π΅Π·ΠΎΡΠΊΠ°Π·Π½ΠΎΡΡΠΈ
ΠΠΎΠΊΠ°Π·Π°ΡΠ΅Π»ΠΈ Π΄ΠΎΠ»Π³ΠΎΠ²Π΅ΡΠ½ΠΎΡΡΠΈ
ΠΠΎΠΊΠ°Π·Π°ΡΠ΅Π»ΠΈ ΡΠ΅ΠΌΠΎΠ½ΡΠΎΠΏΡΠΈΠ³ΠΎΠ΄Π½ΠΎΡΡΠΈ
ΠΠΎΠΊΠ°Π·Π°ΡΠ΅Π»ΠΈ ΡΠΎΡ ΡΠ°Π½ΡΠ΅ΠΌΠΎΡΡΠΈ
ΠΠΎΠΌΠΏΠ»Π΅ΠΊΡΠ½ΡΠ΅ ΠΏΠΎΠΊΠ°Π·Π°ΡΠ΅Π»ΠΈ Π½Π°Π΄Π΅ΠΆΠ½ΠΎΡΡΠΈ
Π Π°Π·Π΄Π΅Π» 2. ΠΡΠΈΡΠΈΠ½Ρ ΠΏΠΎΡΠ΅ΡΠΈ ΠΌΠ°ΡΠΈΠ½ΠΎΠΉ ΡΠ°Π±ΠΎΡΠΎΡΠΏΠΎΡΠΎΠ±Π½ΠΎΡΡΠΈ
2.1. ΠΡΡΠΎΡΠ½ΠΈΠΊΠΈ ΠΈ ΠΏΡΠΈΡΠΈΠ½Ρ ΠΈΠ·ΠΌΠ΅Π½Π΅Π½ΠΈΡ Π½Π°ΡΠ°Π»ΡΠ½ΡΡ ΠΏΠ°ΡΠ°ΠΌΠ΅ΡΡΠΎΠ² ΠΌΠ°ΡΠΈΠ½Ρ
2.2. ΠΡΠΎΡΠ΅ΡΡΡ, ΡΠ½ΠΈΠΆΠ°ΡΡΠΈΠ΅ ΡΠ°Π±ΠΎΡΠΎΡΠΏΠΎΡΠΎΠ±Π½ΠΎΡΡΡ ΠΈΠ·Π΄Π΅Π»ΠΈΡ
2.3. ΠΠ»Π°ΡΡΠΈΡΠΈΠΊΠ°ΡΠΈΡ ΠΏΡΠΎΡΠ΅ΡΡΠΎΠ², Π΄Π΅ΠΉΡΡΠ²ΡΡΡΠΈΡ Π½Π° ΠΌΠ°ΡΠΈΠ½Ρ ΠΏΠΎ ΡΠΊΠΎΡΠΎΡΡΠΈ ΠΈΡ ΠΏΡΠΎΡΠ΅ΠΊΠ°Π½ΠΈΡ
2.4. ΠΠΈΠ΄Ρ ΠΏΠΎΠ²ΡΠ΅ΠΆΠ΄Π΅Π½ΠΈΠΉ Π΄Π΅ΡΠ°Π»Π΅ΠΉ ΠΈ ΡΠΎΠΏΡΡΠΆΠ΅Π½ΠΈΠΉ
2.5. ΠΠ°ΡΠ°ΠΌΠ΅ΡΡΠΈΡΠ΅ΡΠΊΠ°Ρ Π½Π°Π΄Π΅ΠΆΠ½ΠΎΡΡΡ ΠΌΠ°ΡΠΈΠ½
2.6. ΠΡΠΊΠ°Π·Ρ ΠΌΠ°ΡΠΈΠ½ ΠΈ ΡΠ»Π΅ΠΌΠ΅Π½ΡΠΎΠ²
2.7. ΠΡΠ΅Π½ΠΊΠ° ΠΏΡΠ΅Π΄Π΅Π»ΡΠ½ΠΎΠ³ΠΎ ΡΠΎΡΡΠΎΡΠ½ΠΈΡ ΠΈΠ·Π΄Π΅Π»ΠΈΡ
2.7.1. ΠΡΠ΅Π΄Π΅Π»ΡΠ½ΡΠ΅ Π²Π΅Π»ΠΈΡΠΈΠ½Ρ ΠΈΠ·Π½ΠΎΡΠ° Π΄Π΅ΡΠ°Π»Π΅ΠΉ
2.7.2. ΠΡΠΈΡΠ΅ΡΠΈΠΈ ΠΎΡΠ΅Π½ΠΊΠΈ ΠΏΡΠ΅Π΄Π΅Π»ΡΠ½ΠΎΠ³ΠΎ ΡΠΎΡΡΠΎΡΠ½ΠΈΡ ΠΈΠ·Π΄Π΅Π»ΠΈΡ
Π Π°Π·Π΄Π΅Π» 3 ΠΠ°Π΄Π΅ΠΆΠ½ΠΎΡΡΡ ΡΠ»ΠΎΠΆΠ½ΡΡ ΡΠΈΡΡΠ΅ΠΌ
3.1. ΠΠ±ΡΠΈΠ΅ ΠΏΡΠ΅Π΄ΡΡΠ°Π²Π»Π΅Π½ΠΈΡ ΠΎ ΡΠ»ΠΎΠΆΠ½ΡΡ ΡΠΈΡΡΠ΅ΠΌΠ°Ρ
3.2. Π‘Π»ΠΎΠΆΠ½ΡΠ΅ ΡΠΈΡΡΠ΅ΠΌΡ Ρ ΠΏΠΎΡΠ»Π΅Π΄ΠΎΠ²Π°ΡΠ΅Π»ΡΠ½ΡΠΌ ΡΠΎΠ΅Π΄ΠΈΠ½Π΅Π½ΠΈΠ΅ΠΌ ΡΠ»Π΅ΠΌΠ΅Π½ΡΠΎΠ²
3.3. Π‘Π»ΠΎΠΆΠ½ΡΠ΅ ΡΠΈΡΡΠ΅ΠΌΡ Ρ ΠΏΠ°ΡΠ°Π»Π»Π΅Π»ΡΠ½ΡΠΌ ΡΠΎΠ΅Π΄ΠΈΠ½Π΅Π½ΠΈΠ΅ΠΌ ΡΠ»Π΅ΠΌΠ΅Π½ΡΠΎΠ²
3.4. Π‘Π»ΠΎΠΆΠ½ΡΠ΅ ΡΠΈΡΡΠ΅ΠΌΡ Ρ ΠΊΠΎΠΌΠ±ΠΈΠ½ΠΈΡΠΎΠ²Π°Π½Π½ΡΠΌ ΡΠΎΠ΅Π΄ΠΈΠ½Π΅Π½ΠΈΠ΅ΠΌ ΡΠ»Π΅ΠΌΠ΅Π½ΡΠΎΠ²
3.5. Π‘ΠΈΡΡΠ΅ΠΌΡ Ρ ΡΠ΅Π·Π΅ΡΠ²ΠΈΡΠΎΠ²Π°Π½ΠΈΠ΅ΠΌ ΡΠ»Π΅ΠΌΠ΅Π½ΡΠΎΠ²
3.6. ΠΡΠ΅Π½ΠΊΠ° ΠΏΠ°ΡΠ°ΠΌΠ΅ΡΡΠΈΡΠ΅ΡΠΊΠΎΠΉ Π±Π΅Π·ΠΎΡΠΊΠ°Π·Π½ΠΎΡΡΠΈ ΠΈ Π΄ΠΎΠ»Π³ΠΎΠ²Π΅ΡΠ½ΠΎΡΡΠΈ ΠΈΠ·Π΄Π΅Π»ΠΈΠΉ
3.7. ΠΠ΅Π·ΠΎΡΠΊΠ°Π·Π½ΠΎΡΡΡ ΡΠ»ΠΎΠΆΠ½ΠΎΠΉ ΡΠΈΡΡΠ΅ΠΌΡ ΠΏΡΠΈ ΡΡΡΠ°Π½ΠΎΠ²ΠΈΠ²ΡΠ΅ΠΌΡΡ ΠΏΠΎΡΠΎΠΊΠ΅ ΠΎΡΠΊΠ°Π·ΠΎΠ²
Π Π°Π·Π΄Π΅Π» 4. ΠΠ·Π½ΠΎΡ ΠΌΠ°ΡΠΈΠ½
4.1. ΠΠΈΠ΄Ρ ΡΡΠ΅Π½ΠΈΡ
4.2. ΠΡΠΈΡΠΎΠ΄Π° ΠΈ ΠΊΠ»Π°ΡΡΠΈΡΠΈΠΊΠ°ΡΠΈΡ ΠΏΡΠΎΡΠ΅ΡΡΠΎΠ² ΠΈΠ·Π½Π°ΡΠΈΠ²Π°Π½ΠΈΡ
4.3. Π‘ΠΌΠ°Π·ΠΊΠ° ΠΌΠ°ΡΠΈΠ½
4.4. ΠΠΎΠΊΠ°Π·Π°ΡΠ΅Π»ΠΈ ΠΈΠ·Π½ΠΎΡΠΎΡΡΠΎΠΉΠΊΠΎΡΡΠΈ
4.5. ΠΡΠ΅Π½ΠΊΠ° ΠΈ ΠΏΡΠΎΠ³Π½ΠΎΠ·ΠΈΡΠΎΠ²Π°Π½ΠΈΠ΅ ΡΠ΅ΡΡΡΡΠ° ΡΠΎΠ΅Π΄ΠΈΠ½Π΅Π½ΠΈΠΉ
4.6. ΠΠΎΡΠ°Π»ΡΠ½ΠΎΠ΅ ΡΡΠ°ΡΠ΅Π½ΠΈΠ΅ ΠΌΠ°ΡΠΈΠ½
Π Π°Π·Π΄Π΅Π» 5. ΠΠ±Π΅ΡΠΏΠ΅ΡΠ΅Π½ΠΈΠ΅ Π½Π°Π΄Π΅ΠΆΠ½ΠΎΡΡΠΈ ΠΌΠ°ΡΠΈΠ½ Π½Π° ΡΡΠ°ΠΏΠ°Ρ ΠΏΡΠΎΠ΅ΠΊΡΠΈΡΠΎΠ²Π°Π½ΠΈΡ ΠΈ ΠΈΠ·Π³ΠΎΡΠΎΠ²Π»Π΅Π½ΠΈΡ
5.1. ΠΠΎΠ½ΡΡΡΡΠΊΡΠΈΠ²Π½ΡΠ΅ ΠΌΠ΅ΡΠΎΠ΄Ρ ΠΎΠ±Π΅ΡΠΏΠ΅ΡΠ΅Π½ΠΈΡ Π½Π°Π΄Π΅ΠΆΠ½ΠΎΡΡΠΈ ΠΌΠ°ΡΠΈΠ½
5.1.1 ΠΠΏΡΠΈΠΌΠΈΠ·Π°ΡΠΈΡ ΠΊΠΎΠΌΠΏΠΎΠ½ΠΎΠ²ΠΎΡΠ½ΠΎΠ³ΠΎ ΡΠ΅ΡΠ΅Π½ΠΈΡ ΠΌΠ°ΡΠΈΠ½Ρ
5.1.2. Π Π°ΡΠΈΠΎΠ½Π°Π»ΡΠ½ΡΠΉ Π²ΡΠ±ΠΎΡ ΠΌΠ°ΡΠ΅ΡΠΈΠ°Π»ΠΎΠ² Π΄Π΅ΡΠ°Π»Π΅ΠΉ
5.1.3. ΠΠΏΡΠΈΠΌΠΈΠ·Π°ΡΠΈΡ Π³Π΅ΠΎΠΌΠ΅ΡΡΠΈΡΠ΅ΡΠΊΠΎΠΉ ΡΠΎΡΠΌΡ Π΄Π΅ΡΠ°Π»Π΅ΠΉ ΡΠ·Π»ΠΎΠ² ΡΡΠ΅Π½ΠΈΡ
5.1.4. ΠΠ±Π΅ΡΠΏΠ΅ΡΠ΅Π½ΠΈΠ΅ Π½ΠΎΡΠΌΠ°Π»ΡΠ½ΡΡ ΡΡΠ»ΠΎΠ²ΠΈΠΉ ΡΠ°Π±ΠΎΡΡ
5.1.5. ΠΠΎΠ²ΡΡΠ΅Π½ΠΈΠ΅ ΡΡΠΎΠ²Π½Ρ ΡΠ΅ΠΌΠΎΠ½ΡΠΎΠΏΡΠΈΠ³ΠΎΠ΄Π½ΠΎΡΡΠΈ
5.1.6. Π Π΅Π·Π΅ΡΠ²ΠΈΡΠΎΠ²Π°Π½ΠΈΠ΅ ΡΠ»Π΅ΠΌΠ΅Π½ΡΠΎΠ² ΠΈ ΡΠΈΡΡΠ΅ΠΌ
5.2. ΠΠ±Π΅ΡΠΏΠ΅ΡΠ΅Π½ΠΈΠ΅ Π½Π°Π΄Π΅ΠΆΠ½ΠΎΡΡΠΈ ΠΌΠ°ΡΠΈΠ½ ΠΏΡΠΈ ΠΈΡ ΠΏΡΠΎΠΈΠ·Π²ΠΎΠ΄ΡΡΠ²Π΅
Π Π°Π·Π΄Π΅Π» 6. ΠΡΠ½ΠΎΠ²Π½ΡΠ΅ ΡΠΏΠΎΡΠΎΠ±Ρ ΠΏΠΎΠ»ΡΡΠ΅Π½ΠΈΡ ΠΈΠ½ΡΠΎΡΠΌΠ°ΡΠΈΠΈ ΠΎ Π½Π°Π΄Π΅ΠΆΠ½ΠΎΡΡΠΈ
6.1. ΠΠ»Π°Π½Ρ ΠΈΡΠΏΡΡΠ°Π½ΠΈΠΉ Π½Π° Π½Π°Π΄Π΅ΠΆΠ½ΠΎΡΡΡ
Π Π°Π·Π΄Π΅Π» 7. ΠΠΏΡΠ΅Π΄Π΅Π»Π΅Π½ΠΈΠ΅ ΠΏΠ°ΡΠ°ΠΌΠ΅ΡΡΠΎΠ² ΠΊΠΎΠ½ΡΡΠΎΠ»ΡΠ½ΡΡ ΠΈΡΠΏΡΡΠ°Π½ΠΈΠΉ ΠΎΠ³ΡΠ°Π½ΠΈΡΠ΅Π½Π½ΠΎΠΉ ΠΏΡΠΎΠ΄ΠΎΠ»ΠΆΠΈΡΠ΅Π»ΡΠ½ΠΎΡΡΠΈ ΡΠ°Π±ΠΎΡΡ
Π Π°Π·Π΄Π΅Π» 8. Π Π΅Π°Π»ΠΈΠ·Π°ΡΠΈΡ ΠΈ Π²ΠΎΡΡΡΠ°Π½ΠΎΠ²Π»Π΅Π½ΠΈΠ΅ Π½Π°Π΄Π΅ΠΆΠ½ΠΎΡΡΠΈ ΠΏΡΠΈ ΡΠΊΡΠΏΠ»ΡΠ°ΡΠ°ΡΠΈΠΈ ΠΌΠ°ΡΠΈΠ½
8.1 Π€Π°ΠΊΡΠΎΡΡ, Π²Π»ΠΈΡΡΡΠΈΠ΅ Π½Π° Π½Π°Π΄Π΅ΠΆΠ½ΠΎΡΡΡ ΠΌΠ°ΡΠΈΠ½ Π² ΠΏΠ΅ΡΠΈΠΎΠ΄ ΡΠΊΡΠΏΠ»ΡΠ°ΡΠ°ΡΠΈΠΈ
8.2 Π’Π΅Ρ Π½ΠΈΡΠ΅ΡΠΊΠΎΠ΅ ΠΎΠ±ΡΠ»ΡΠΆΠΈΠ²Π°Π½ΠΈΠ΅ ΠΈ ΡΠ΅ΠΌΠΎΠ½Ρ ΠΌΠ°ΡΠΈΠ½
8.2.1 Π‘ΡΡΠ½ΠΎΡΡΡ ΠΈ Π·Π½Π°ΡΠ΅Π½ΠΈΠ΅ ΡΠΈΡΡΠ΅ΠΌΡ ΠΏΠ»Π°Π½ΠΎΠ²ΠΎ β ΠΏΡΠ΅Π΄ΡΠΏΡΠ΅Π΄ΠΈΡΠ΅Π»ΡΠ½ΠΎΠ³ΠΎ ΡΠ΅Ρ Π½ΠΈΡΠ΅ΡΠΊΠΎΠ³ΠΎ ΠΎΠ±ΡΠ»ΡΠΆΠΈΠ²Π°Π½ΠΈΡ ΠΈ ΡΠ΅ΠΌΠΎΠ½ΡΠ° ΠΏΡΡΠ΅Π²ΡΡ ΠΌΠ°ΡΠΈΠ½ ΠΈ ΠΌΠ΅Ρ Π°Π½ΠΈΠ·ΠΌΠΎΠ²
8.2.2 ΠΡΠ½ΠΎΠ²Π½ΡΠ΅ ΡΠ΅ΡΠΌΠΈΠ½Ρ ΠΈ ΠΎΠΏΡΠ΅Π΄Π΅Π»Π΅Π½ΠΈΡ
8.2.3 ΠΡΠ½ΠΎΠ²Π½ΡΠ΅ ΡΠ°Π±ΠΎΡΡ ΠΏΠΎ ΡΠ΅Ρ Π½ΠΈΡΠ΅ΡΠΊΠΎΠΌΡ ΠΎΠ±ΡΠ»ΡΠΆΠΈΠ²Π°Π½ΠΈΡ ΠΈ ΡΠ΅ΠΌΠΎΠ½ΡΡ ΠΏΡΡΠ΅Π²ΡΡ ΠΌΠ°ΡΠΈΠ½ ΠΈ ΠΌΠ΅Ρ Π°Π½ΠΈΠ·ΠΌΠΎΠ²
8.3. ΠΠΈΠ°Π³Π½ΠΎΡΡΠΈΠΊΠ° ΡΠ΅Ρ Π½ΠΈΡΠ΅ΡΠΊΠΎΠ³ΠΎ ΡΠΎΡΡΠΎΡΠ½ΠΈΡ ΠΌΠ°ΡΠΈΠ½
8.3.1.ΠΡΠ½ΠΎΠ²Π½ΡΠ΅ ΠΏΠΎΠ½ΡΡΠΈΡ ΠΈ ΠΎΠΏΡΠ΅Π΄Π΅Π»Π΅Π½ΠΈΡ ΡΠ΅Ρ Π½ΠΈΡΠ΅ΡΠΊΠΎΠΉ Π΄ΠΈΠ°Π³Π½ΠΎΡΡΠΈΠΊΠΈ
8.3.2. ΠΠΈΠ°Π³Π½ΠΎΡΡΠΈΡΠ΅ΡΠΊΠΈΠ΅ Π½ΠΎΡΠΌΠ°ΡΠΈΠ²Ρ
8.4. ΠΠ°ΡΠΈΠ½Π° ΠΊΠ°ΠΊ ΠΎΠ±ΡΠ΅ΠΊΡ Π΄ΠΈΠ°Π³Π½ΠΎΡΡΠΈΡΠΎΠ²Π°Π½ΠΈΡ
8.4.1. ΠΠ°ΡΠΈΠ½Π° ΠΊΠ°ΠΊ ΡΠΈΡΡΠ΅ΠΌΠ° ΡΠ»Π΅ΠΌΠ΅Π½ΡΠΎΠ²
8.4.2. Π Π°ΡΠΏΡΠ΅Π΄Π΅Π»Π΅Π½ΠΈΠ΅ ΠΎΡΡΠ°ΡΠΎΡΠ½ΠΎΠ³ΠΎ ΡΠ΅ΡΡΡΡΠ°
8.4.3. ΠΠ·ΠΌΠ΅Π½Π΅Π½ΠΈΠ΅ ΡΡΡΡΠΊΡΡΡΠ½ΡΡ ΠΏΠ°ΡΠ°ΠΌΠ΅ΡΡΠΎΠ² ΠΌΠ°ΡΠΈΠ½Ρ
8.4.4. Π‘ΡΡΡΠΊΡΡΡΠ½ΠΎ β ΡΠ»Π΅Π΄ΡΡΠ²Π΅Π½Π½Π°Ρ ΠΌΠΎΠ΄Π΅Π»Ρ ΠΎΠ±ΡΠ΅ΠΊΡΠ° Π΄ΠΈΠ°Π³Π½ΠΎΡΡΠΈΡΠΎΠ²Π°Π½ΠΈΡ
8.4.5. Π€ΡΠ½ΠΊΡΠΈΠΎΠ½Π°Π»ΡΠ½Π°Ρ ΠΌΠΎΠ΄Π΅Π»Ρ ΠΎΠ±ΡΠ΅ΠΊΡΠ° Π΄ΠΈΠ°Π³Π½ΠΎΡΡΠΈΡΠΎΠ²Π°Π½ΠΈΡ
8.4.6. ΠΠΎΠ½ΡΡΠΎΠ»Π΅ΠΏΡΠΈΠ³ΠΎΠ΄Π½ΠΎΡΡΡ ΠΌΠ°ΡΠΈΠ½Ρ
8.5 ΠΠ΅ΡΠΎΠ΄Ρ Π΄ΠΈΠ°Π³Π½ΠΎΡΡΠΈΡΠΎΠ²Π°Π½ΠΈΡ ΠΌΠ°ΡΠΈΠ½
8.5.1 ΠΠ΅ΡΠΎΠ΄Ρ Π±Π΅Π·ΡΠ°Π·Π±ΠΎΡΠ½ΠΎΠΉ Π΄ΠΈΠ°Π³Π½ΠΎΡΡΠΈΠΊΠΈ ΠΌΠ°ΡΠΈΠ½
8.6. Π‘ΡΠ΅Π΄ΡΡΠ²Π° ΡΠ΅Ρ Π½ΠΈΡΠ΅ΡΠΊΠΎΠ³ΠΎ Π΄ΠΈΠ°Π³Π½ΠΎΡΡΠΈΡΠΎΠ²Π°Π½ΠΈΡ ΠΈ ΠΈΡ ΠΊΠ»Π°ΡΡΠΈΡΠΈΠΊΠ°ΡΠΈΡ
8.7. ΠΠ°ΠΏΡΠ°Π²Π»Π΅Π½ΠΈΡ ΠΏΠΎΠ΄Π΄Π΅ΡΠΆΠ°Π½ΠΈΡ ΠΈ Π²ΠΎΡΡΡΠ°Π½ΠΎΠ²Π»Π΅Π½ΠΈΡ ΡΡΠΎΠ²Π½Ρ Π½Π°Π΄Π΅ΠΆΠ½ΠΎΡΡΠΈ ΠΌΠ°ΡΠΈΠ½.
8.7.1. ΠΠΎΠ²ΡΡΠ΅Π½ΠΈΠ΅ ΡΠΎΠΏΡΠΎΡΠΈΠ²Π»ΡΠ΅ΠΌΠΎΡΡΠΈ ΠΌΠ°ΡΠΈΠ½ Π²Π½Π΅ΡΠ½ΠΈΠΌ Π²ΠΎΠ·Π΄Π΅ΠΉΡΡΠ²ΠΈΡΠΌ
8.7.2 ΠΠ·ΠΎΠ»ΡΡΠΈΡ ΠΌΠ°ΡΠΈΠ½ ΠΎΡ Π²ΡΠ΅Π΄Π½ΡΡ Π²ΠΎΠ·Π΄Π΅ΠΉΡΡΠ²ΠΈΠΉ
8.7.3. Π‘ΠΎΠ·Π΄Π°Π½ΠΈΠ΅ ΠΎΠΏΡΠΈΠΌΠ°Π»ΡΠ½ΠΎΠΉ ΠΊΠΎΠ½ΡΡΡΡΠΊΡΠΈΠΈ ΠΌΠ°ΡΠΈΠ½Ρ
8.7.4. ΠΡΠΈΠΌΠ΅Π½Π΅Π½ΠΈΠ΅ Π°Π²ΡΠΎΠΌΠ°ΡΠΈΠ·Π°ΡΠΈΠΈ Π΄Π»Ρ ΠΏΠΎΠ²ΡΡΠ΅Π½ΠΈΡ Π½Π°Π΄Π΅ΠΆΠ½ΠΎΡΡΠΈ ΠΌΠ°ΡΠΈΠ½
8.7.5 Π‘ΠΎΠ·Π΄Π°Π½ΠΈΠ΅ ΠΌΠ°ΡΠΈΠ½ Ρ ΡΠ΅Π³Π»Π°ΠΌΠ΅Π½ΡΠΈΡΠΎΠ²Π°Π½Π½ΡΠΌΠΈ ΠΏΠΎΠΊΠ°Π·Π°ΡΠ΅Π»ΡΠΌΠΈ Π½Π°Π΄Π΅ΠΆΠ½ΠΎΡΡΠΈ
Π’Π΅ΡΠΌΠΈΠ½Ρ ΠΈ ΠΎΠΏΡΠ΅Π΄Π΅Π»Π΅Π½ΠΈΡ (ΠΏΠΎΠ΄Π±ΠΎΡ ΠΏΠΎ ΡΠ°Π·Π΄Π΅Π»Π°ΠΌ)
ΠΡΠΈΠ»ΠΎΠΆΠ΅Π½ΠΈΠ΅ 1
ΠΡΠΈΠ»ΠΎΠΆΠ΅Π½ΠΈΠ΅ 2
ΠΡΠΈΠ»ΠΎΠΆΠ΅Π½ΠΈΠ΅ 3
ΠΡΠΈΠ»ΠΎΠΆΠ΅Π½ΠΈΠ΅ 4
ΠΡΠΈΠ»ΠΎΠΆΠ΅Π½ΠΈΠ΅ 5
ΠΡΠΈΠ»ΠΎΠΆΠ΅Π½ΠΈΠ΅ 6
ΠΡΠΈΠ»ΠΎΠΆΠ΅Π½ΠΈΠ΅ 7
ΠΡΠΈΠ»ΠΎΠΆΠ΅Π½ΠΈΠ΅ 8
Π Π΅ΠΊΠΎΠΌΠ΅Π½Π΄ΡΠ΅ΠΌΠ°Ρ Π»ΠΈΡΠ΅ΡΠ°ΡΡΡΠ°
ΠΠ²Π΅Π΄Π΅Π½ΠΈΠ΅
Π ΡΠ²ΡΠ·ΠΈ Ρ ΡΠ°Π·Π²ΠΈΡΠΈΠ΅ΠΌ ΡΠ΅Ρ Π½ΠΈΡΠ΅ΡΠΊΠΎΠ³ΠΎ ΠΏΡΠΎΠ³ΡΠ΅ΡΡΠ° Π²ΡΠ΅ Π±ΠΎΠ»Π΅Π΅ Π°ΠΊΡΡΠ°Π»ΡΠ½ΡΠΌΠΈ ΡΡΠ°Π½ΠΎΠ²ΡΡΡΡ Π²ΠΎΠΏΡΠΎΡΡ ΠΏΠΎΠ²ΡΡΠ΅Π½ΠΈΡ Π½Π°Π΄Π΅ΠΆΠ½ΠΎΡΡΠΈ ΡΠ°Π·Π½ΠΎΠΎΠ±ΡΠ°Π·Π½ΡΡ ΡΠ΅Ρ Π½ΠΈΡΠ΅ΡΠΊΠΈΡ ΡΡΡΡΠΎΠΉΡΡΠ² ΠΈ ΡΠΈΡΡΠ΅ΠΌ β ΠΌΠ΅Ρ Π°Π½ΠΈΠ·ΠΌΠΎΠ², ΠΌΠ°ΡΠΈΠ½, Π°ΠΏΠΏΠ°ΡΠ°ΡΠΎΠ², ΡΠΈΡΡΠ΅ΠΌ Π°Π²ΡΠΎΠΌΠ°ΡΠΈΠΊΠΈ, ΡΡΠ°Π½ΠΊΠΎΠ², ΡΠ»Π΅ΠΊΡΡΠΎΠ½Π½ΠΎΠ³ΠΎ ΠΎΠ±ΠΎΡΡΠ΄ΠΎΠ²Π°Π½ΠΈΡ, Π³ΠΈΠ΄ΡΠ°Π²Π»ΠΈΡΠ΅ΡΠΊΠΎΠ³ΠΎ, ΠΏΠ½Π΅Π²ΠΌΠ°ΡΠΈΡΠ΅ΡΠΊΠΎΠ³ΠΎ ΠΈ ΡΠ»Π΅ΠΊΡΡΠΈΡΠ΅ΡΠΊΠΎΠ³ΠΎ ΠΏΡΠΈΠ²ΠΎΠ΄ΠΎΠ² ΠΌΠ°ΡΠΈΠ½ ΠΈ Ρ.Π΄. ΠΠ°Π΄Π΅ΠΆΠ½ΠΎΡΡΡ ΡΠ²Π»ΡΠ΅ΡΡΡ Π²Π°ΠΆΠ½Π΅ΠΉΡΠΈΠΌ ΡΠ΅Ρ Π½ΠΈΠΊΠΎ β ΡΠΊΠΎΠ½ΠΎΠΌΠΈΡΠ΅ΡΠΊΠΈΠΌ ΠΏΠΎΠΊΠ°Π·Π°ΡΠ΅Π»Π΅ΠΌ ΠΊΠ°ΡΠ΅ΡΡΠ²Π° Π»ΡΠ±ΠΎΠ³ΠΎ ΡΠ΅Ρ Π½ΠΈΡΠ΅ΡΠΊΠΎΠ³ΠΎ ΡΡΡΡΠΎΠΉΡΡΠ²Π° ΠΈΠ»ΠΈ ΡΠΈΡΡΠ΅ΠΌΡ. Π ΡΠ²ΡΠ·ΠΈ Ρ ΡΡΠΈΠΌ ΠΏΡΠΈ ΡΠΈΡΠΎΠΊΠΎΠΌ ΠΏΡΠΈΠΌΠ΅Π½Π΅Π½ΠΈΠΈ ΠΌΠ°ΡΠΈΠ½ ΠΈ ΠΈΡΠΏΠΎΠ»Π½ΠΈΡΠ΅Π»ΡΠ½ΡΡ ΠΌΠ΅Ρ Π°Π½ΠΈΠ·ΠΌΠΎΠ² Π² ΡΠΈΡΡΠ΅ΠΌΠ°Ρ ΡΠΏΡΠ°Π²Π»Π΅Π½ΠΈΡ ΠΏΡΠΎΠΈΠ·Π²ΠΎΠ΄ΡΡΠ²Π΅Π½Π½ΡΠΌΠΈ ΠΏΡΠΎΡΠ΅ΡΡΠ°ΠΌΠΈ ΡΠ΅Ρ Π½ΠΈΡΠ΅ΡΠΊΠΈΠΉ ΡΡΠΎΠ²Π΅Π½Ρ ΠΏΡΠΎΠΈΠ·Π²ΠΎΠ΄ΡΡΠ²Π° Π² Π±ΠΎΠ»ΡΡΠ΅ΠΉ ΡΡΠ΅ΠΏΠ΅Π½ΠΈ ΠΎΠΏΡΠ΅Π΄Π΅Π»ΡΠ΅ΡΡΡ Π½Π°Π΄Π΅ΠΆΠ½ΠΎΡΡΡΡ ΡΡΠΈΡ ΠΌΠ°ΡΠΈΠ½ ΠΈ ΡΠΈΡΡΠ΅ΠΌ. ΠΡΠΊΠ°Π·Ρ ΠΌΠ°ΡΠΈΠ½ ΠΈ ΡΠΈΡΡΠ΅ΠΌ Π² ΠΏΡΠΎΡΠ΅ΡΡΠ΅ ΡΠΊΡΠΏΠ»ΡΠ°ΡΠ°ΡΠΈΠΈ Π½Π°Π½ΠΎΡΡΡ Π·Π½Π°ΡΠΈΡΠ΅Π»ΡΠ½ΡΠΉ ΡΡΠ΅ΡΠ± ΠΏΡΠΎΠΌΡΡΠ»Π΅Π½Π½ΠΎΡΡΠΈ ΠΈ ΡΡΠ°Π½ΡΠΏΠΎΡΡΠ½ΠΎΠΌΡ ΡΡΡΠΎΠΈΡΠ΅Π»ΡΡΡΠ²Ρ.
Π Π½Π°ΡΡΠΎΡΡΠ΅Π΅ Π²ΡΠ΅ΠΌΡ Π±ΡΡΡΡΡΠΌΠΈ ΡΠ΅ΠΌΠΏΠ°ΠΌΠΈ ΡΠ°Π·Π²ΠΈΠ²Π°Π΅ΡΡΡ ΠΏΡΡΠ΅Π²Π°Ρ ΡΠ΅Ρ Π½ΠΈΠΊΠ°, ΡΠΎΠ·Π΄Π°ΡΡΡΡ Π½ΠΎΠ²ΡΠ΅ Π²ΡΡΠΎΠΊΠΎΠΏΡΠΎΠΈΠ·Π²ΠΎΠ΄ΠΈΡΠ΅Π»ΡΠ½ΡΠ΅ ΠΈ Π΄ΠΎΡΠΎΠ³ΠΎΡΡΠΎΡΡΠΈΠ΅ ΠΌΠ°ΡΠΈΠ½Ρ. Π Π°ΡΡΡΡ ΡΡΠ΅Π±ΠΎΠ²Π°Π½ΠΈΡ ΠΈ ΠΊ ΠΊΠ°ΡΠ΅ΡΡΠ²Ρ Π³ΡΡΠ·ΠΎΠΏΠΎΠ΄ΡΠ΅ΠΌΠ½ΡΡ , ΠΏΡΡΠ΅Π²ΡΡ , ΡΡΡΠΎΠΈΡΠ΅Π»ΡΠ½ΡΡ , Π΄ΠΎΡΠΎΠΆΠ½ΡΡ ΠΌΠ°ΡΠΈΠ½ ΠΈ ΠΎΠ±ΠΎΡΡΠ΄ΠΎΠ²Π°Π½ΠΈΡ (ΠΠ‘ΠΠ). ΠΠ°ΠΆΠ½Π΅ΠΉΡΠΈΠΌ ΠΏΠΎΠΊΠ°Π·Π°ΡΠ΅Π»Π΅ΠΌ ΠΊΠ°ΡΠ΅ΡΡΠ²Π° ΡΠ²Π»ΡΠ΅ΡΡΡ Π½Π°Π΄Π΅ΠΆΠ½ΠΎΡΡΡ ΠΌΠ°ΡΠΈΠ½, ΠΎΡ ΠΊΠΎΡΠΎΡΠΎΠΉ Π² Π·Π½Π°ΡΠΈΡΠ΅Π»ΡΠ½ΠΎΠΉ ΡΡΠ΅ΠΏΠ΅Π½ΠΈ Π·Π°Π²ΠΈΡΠΈΡ ΡΡΡΠ΅ΠΊΡΠΈΠ²Π½ΠΎΡΡΡ ΠΈΡΠΏΠΎΠ»ΡΠ·ΠΎΠ²Π°Π½ΠΈΡ ΠΠ‘ΠΠ.
Π‘ΠΎΠ²ΡΠ΅ΠΌΠ΅Π½Π½ΡΠ΅ ΠΌΠ°ΡΠΈΠ½Ρ ΠΈΡΠΏΠΎΠ»ΡΠ·ΡΡΡΡΡ Π² ΡΠ°Π·Π½ΠΎΠΎΠ±ΡΠ°Π·Π½ΡΡ ΠΊΠ»ΠΈΠΌΠ°ΡΠΈΡΠ΅ΡΠΊΠΈΡ ΡΡΠ»ΠΎΠ²ΠΈΡΡ . Π ΡΡΠΈΠΌ ΡΡΠ»ΠΎΠ²ΠΈΡΠΌ ΠΎΡΠ½ΠΎΡΡΡΡΡ: ΠΈΠ·ΠΌΠ΅Π½Π΅Π½ΠΈΠ΅ ΡΠ΅ΠΌΠΏΠ΅ΡΠ°ΡΡΡΡ ΠΈ Π΄Π°Π²Π»Π΅Π½ΠΈΠ΅ ΠΎΠΊΡΡΠΆΠ°ΡΡΠ΅Π³ΠΎ Π²ΠΎΠ·Π΄ΡΡ Π°, Π²ΡΡΠΎΠΊΠ°Ρ Π²Π»Π°ΠΆΠ½ΠΎΡΡΡ, ΡΠ°Π·Π»ΠΈΡΠ½ΡΠ΅ Π°Π³ΡΠ΅ΡΡΠΈΠ²Π½ΡΠ΅ ΡΡΠ΅Π΄Ρ, ΡΠ΄Π°ΡΡ ΠΈ Π²ΠΈΠ±ΡΠ°ΡΠΈΠΈ, Π²ΡΡΠΎΠΊΠΈΠ΅ ΠΌΠ΅Ρ Π°Π½ΠΈΡΠ΅ΡΠΊΠΈΠ΅ ΠΏΠ΅ΡΠ΅Π³ΡΡΠ·ΠΊΠΈ ΠΈ Ρ.Π΄. ΠΡΠ΅ ΡΡΠΈ ΡΠ°ΠΊΡΠΎΡΡ ΡΠΊΡΡΠ²Π°ΡΡ Π½Π΅Π±Π»Π°Π³ΠΎΠΏΡΠΈΡΡΠ½ΠΎΠ΅ Π²Π»ΠΈΡΠ½ΠΈΠ΅ Π½Π° Π½Π°Π΄Π΅ΠΆΠ½ΠΎΡΡΡ ΠΠ‘ΠΠ.
ΠΠ΅ΡΠΌΠΎΡΡΡ Π½Π° ΡΠ°Π·Π½ΠΎΠΎΠ±ΡΠ°Π·ΠΈΠ΅ ΠΌΠ°ΡΠΈΠ½ ΠΈ ΡΡΠ»ΠΎΠ²ΠΈΠΉ ΠΈΡ ΡΠ°Π±ΠΎΡΡ, ΡΠΎΡΠΌΠΈΡΠΎΠ²Π°Π½ΠΈΠ΅ ΠΏΠΎΠΊΠ°Π·Π°ΡΠ΅Π»Π΅ΠΉ Π½Π°Π΄Π΅ΠΆΠ½ΠΎΡΡΠΈ ΠΏΡΠΎΠΈΡΡ ΠΎΠ΄ΠΈΡ ΠΏΠΎ ΠΎΠ±ΡΠΈΠΌ Π·Π°ΠΊΠΎΠ½Π°ΠΌ, ΠΏΠΎΠ΄ΡΠΈΠ½ΡΠ΅ΡΡΡ Π΅Π΄ΠΈΠ½ΠΎΠΉ Π»ΠΎΠ³ΠΈΠΊΠ΅ ΡΠΎΠ±ΡΡΠΈΠΉ, ΠΈ ΡΠ°ΡΠΊΡΡΡΠΈΠ΅ ΡΡΠΈΡ ΡΠ²ΡΠ·Π΅ΠΉ ΡΠ²Π»ΡΠ΅ΡΡΡ ΠΎΡΠ½ΠΎΠ²ΠΎΠΉ Π΄Π»Ρ ΠΎΡΠ΅Π½ΠΊΠΈ, ΡΠ°ΡΡΠ΅ΡΠ° ΠΈ ΠΏΡΠΎΠ³Π½ΠΎΠ·ΠΈΡΠΎΠ²Π°Π½ΠΈΡ Π½Π°Π΄Π΅ΠΆΠ½ΠΎΡΡΠΈ, Π° ΡΠ°ΠΊΠΆΠ΅ Π΄Π»Ρ ΠΏΠΎΡΡΡΠΎΠ΅Π½ΠΈΡ ΡΠ°ΡΠΈΠΎΠ½Π°Π»ΡΠ½ΡΡ ΡΠΈΡΡΠ΅ΠΌ ΠΏΡΠΎΠΈΠ·Π²ΠΎΠ΄ΡΡΠ²Π°, ΠΈΡΠΏΡΡΠ°Π½ΠΈΡ ΠΈ ΡΠΊΡΠΏΠ»ΡΠ°ΡΠ°ΡΠΈΠΈ ΠΌΠ°ΡΠΈΠ½.
ΠΠ»Ρ Π²ΡΠΏΠΎΠ»Π½Π΅Π½ΠΈΡ ΡΡΠΎΠΉ Π·Π°Π΄Π°ΡΠΈ ΡΠ°Π·ΡΠ°Π±ΠΎΡΠ°Π½Π° ΡΠΈΡΡΠ΅ΠΌΠ° ΠΏΠΎΠ½ΡΡΠΈΠΉ ΠΈ Π²Π·Π³Π»ΡΠ΄ΠΎΠ², ΠΊΠΎΡΠΎΡΠ°Ρ ΠΏΠΎΠ·Π²ΠΎΠ»ΡΠ΅Ρ ΡΠ°Π·Π»ΠΈΡΠ½ΡΠ΅ ΡΡΠΎΡΠΎΠ½Ρ ΠΈ Π²Π·Π°ΠΈΠΌΠΎΡΠ²ΡΠ·ΠΈ ΡΡΠΎΠΉ ΠΏΡΠΎΠ±Π»Π΅ΠΌΡ ΠΎΠ±ΡΠ΅Π΄ΠΈΠ½ΠΈΡΡ Π² ΠΎΠ΄Π½ΠΎ ΡΠ΅Π»ΠΎΠ΅ ΠΈ ΡΡΡΠ°Π½ΠΎΠ²ΠΈΡΡ ΡΠΎΠ»Ρ, Π·Π½Π°ΡΠ΅Π½ΠΈΠ΅ ΠΈ ΠΏΡΠΎΠΏΠΎΡΡΠΈΠΈ Π²ΡΠ΅Ρ ΡΠΎΡΡΠ°Π²Π½ΡΡ ΡΠ°ΡΡΠ΅ΠΉ.
ΠΠ°Π΄Π΅ΠΆΠ½ΠΎΡΡΡ Π°ΠΊΠΊΡΠΌΡΠ»ΠΈΡΡΠ΅Ρ ΠΈ ΡΠΈΠ½ΡΠ΅Π·ΠΈΡΡΠ΅Ρ Π²ΡΠ΅ ΡΠΎ, ΡΡΠΎ ΡΠΏΠΎΡΠΎΠ±ΡΡΠ²ΡΠ΅Ρ ΠΏΠΎΠ²ΡΡΠ΅Π½ΠΈΡ ΡΠ°Π±ΠΎΡΠΎΡΠΏΠΎΡΠΎΠ±Π½ΠΎΡΡΠΈ ΠΠ‘ΠΠ ΠΈ ΠΈΡ ΡΠΎΡΡΠ°Π²Π½ΡΡ ΡΠ°ΡΡΠ΅ΠΉ, ΠΎΠ½Π° ΡΠ²Π»ΡΠ΅ΡΡΡ ΠΎΡΡΠ°ΠΆΠ΅Π½ΠΈΠ΅ΠΌ Π΄ΠΎΡΡΠΈΠΆΠ΅Π½ΠΈΠΉ Π² ΠΎΠ±Π»Π°ΡΡΠΈ ΠΏΡΠΎΠ΅ΠΊΡΠΈΡΠΎΠ²Π°Π½ΠΈΡ, ΡΠ΅Ρ Π½ΠΎΠ»ΠΎΠ³ΠΈΠΈ ΠΈ ΡΠΊΡΠΏΠ»ΡΠ°ΡΠ°ΡΠΈΠΈ ΠΌΠ°ΡΠΈΠ½.
Π‘Π»Π΅Π΄ΡΠ΅Ρ ΠΏΠΎΠ΄ΡΠ΅ΡΠΊΠ½ΡΡΡ, ΡΡΠΎ Π½Π°ΡΠΊΠ° ΠΎ Π½Π°Π΄Π΅ΠΆΠ½ΠΎΡΡΠΈ Π½Π΅ ΡΠ°ΡΡΠΌΠ°ΡΡΠΈΠ²Π°Π΅Ρ Π²ΠΎΠΏΡΠΎΡΠΎΠ² Π΄ΠΎΡΡΠΈΠΆΠ΅Π½ΠΈΡ ΠΎΠΏΡΠ΅Π΄Π΅Π»Π΅Π½Π½ΠΎΠ³ΠΎ ΡΡΠΎΠ²Π½Ρ ΠΏΠΎΠΊΠ°Π·Π°ΡΠ΅Π»Π΅ΠΉ ΠΊΠ°ΡΠ΅ΡΡΠ²Π° ΠΌΠ°ΡΠΈΠ½ β ΠΈΡ ΡΠΎΡΠ½ΠΎΡΡΠΈ, ΠΌΠΎΡΠ½ΠΎΡΡΠΈ, ΠΠΠ, ΠΏΡΠΎΠΈΠ·Π²ΠΎΠ΄ΠΈΡΠ΅Π»ΡΠ½ΠΎΡΡΠΈ β ΡΡΠΎ Π·Π°Π΄Π°ΡΠ° Π΄ΡΡΠ³ΠΈΡ Π½Π°ΡΠΊ, Π° ΡΠ°ΡΡΠΌΠ°ΡΡΠΈΠ²Π°Π΅Ρ ΠΏΡΠΎΡΠ΅ΡΡ ΠΈΠ·ΠΌΠ΅Π½Π΅Π½ΠΈΡ ΡΡΠΈΡ ΠΏΠΎΠΊΠ°Π·Π°ΡΠ΅Π»Π΅ΠΉ Ρ ΡΠ΅ΡΠ΅Π½ΠΈΠ΅ΠΌ Π²ΡΠ΅ΠΌΠ΅Π½ΠΈ.
ΠΠ°Π΄Π΅ΠΆΠ½ΠΎΡΡΡ β ΡΡΠΎ ΠΎΠ΄ΠΈΠ½ ΠΈΠ· ΠΎΡΠ½ΠΎΠ²Π½ΡΡ ΠΏΠΎΠΊΠ°Π·Π°ΡΠ΅Π»Π΅ΠΉ ΠΊΠ°ΡΠ΅ΡΡΠ²Π° ΠΈΠ·Π΄Π΅Π»ΠΈΠΉ, ΠΏΡΠΎΡΠ²Π»ΡΡΡΠΈΠΉΡΡ Π²ΠΎ Π²ΡΠ΅ΠΌΠ΅Π½ΠΈ ΠΈ ΠΎΡΡΠ°ΠΆΠ°ΡΡΠΈΠΉ ΠΈΠ·ΠΌΠ΅Π½Π΅Π½ΠΈΡ, ΠΏΡΠΎΠΈΡΡ ΠΎΠ΄ΡΡΠΈΠ΅ Π² ΠΌΠ°ΡΠΈΠ½Π΅ Π½Π° ΠΏΡΠΎΡΡΠΆΠ΅Π½ΠΈΠΈ Π²ΡΠ΅Π³ΠΎ Π²ΡΠ΅ΠΌΠ΅Π½ΠΈ Π΅Π΅ ΡΠΊΡΠΏΠ»ΡΠ°ΡΠ°ΡΠΈΠΈ. Π‘Π»Π΅Π΄ΠΎΠ²Π°ΡΠ΅Π»ΡΠ½ΠΎ, Π½Π°Π΄Π΅ΠΆΠ½ΠΎΡΡΡ ΠΌΠ°ΡΠΈΠ½Π½ΠΎΠΉ ΡΠΈΡΡΠ΅ΠΌΡ Ρ Π°ΡΠ°ΠΊΡΠ΅ΡΠΈΠ·ΡΠ΅ΡΡΡ Π²Π΅ΡΠΎΡΡΠ½ΠΎΡΡΡΡ Π±Π΅Π·ΠΎΡΠΊΠ°Π·Π½ΠΎΠΉ ΡΠ°Π±ΠΎΡΡ Π² ΡΠ΅ΡΠ΅Π½ΠΈΠ΅ Π·Π°Π΄Π°Π½Π½ΠΎΠ³ΠΎ ΠΏΡΠΎΠΌΠ΅ΠΆΡΡΠΊΠ° Π²ΡΠ΅ΠΌΠ΅Π½ΠΈ.
ΠΠΎΠ΄ ΠΎΡΠΊΠ°Π·ΠΎΠΌ Π² ΡΠ΅ΠΎΡΠΈΠΈ Π½Π°Π΄Π΅ΠΆΠ½ΠΎΡΡΠΈ ΠΏΠΎΠ½ΠΈΠΌΠ°Π΅ΡΡΡ ΡΠΎΠ±ΡΡΠΈΠ΅, ΠΏΠΎΡΠ»Π΅ Π²ΠΎΠ·Π½ΠΈΠΊΠ½ΠΎΠ²Π΅Π½ΠΈΡ ΠΊΠΎΡΠΎΡΠΎΠ³ΠΎ ΠΈΠ·Π΄Π΅Π»ΠΈΠ΅ ΡΡΡΠ°ΡΠΈΠ²Π°Π΅Ρ ΡΠ²ΠΎΡ ΡΠΏΠΎΡΠΎΠ±Π½ΠΎΡΡΡ Π²ΡΠΏΠΎΠ»Π½ΡΡΡ Π·Π°Π΄Π°Π½Π½ΡΠ΅ ΡΡΠ½ΠΊΡΠΈΠΈ. Π ΠΎΠ±ΡΠ΅ΠΌ ΡΠ»ΡΡΠ°Π΅ ΠΏΠΎΠ΄ ΠΎΡΠΊΠ°Π·ΠΎΠΌ ΡΠ»Π΅Π΄ΡΠ΅Ρ ΠΏΠΎΠ½ΠΈΠΌΠ°ΡΡ Π½Π΅ ΡΠΎΠ»ΡΠΊΠΎ Π½Π΅ΠΏΡΠ΅Π΄Π²ΠΈΠ΄Π΅Π½Π½ΡΡ ΠΎΡΡΠ°Π½ΠΎΠ²ΠΊΡ ΠΌΠ°ΡΠΈΠ½Ρ (ΡΠΈΡΡΠ΅ΠΌΡ) ΠΈΠ·βΠ·Π° ΡΠ»ΡΡΠ°ΠΉΠ½ΠΎΠΉ Π΅Π΅ Π½Π΅ΠΈΡΠΏΡΠ°Π²Π½ΠΎΡΡΠΈ, Π½ΠΎ ΡΠ°ΠΊΠΆΠ΅ ΠΈ Π²ΡΠ½ΡΠΆΠ΄Π΅Π½Π½ΠΎΠ΅ ΠΏΡΠ΅ΠΊΡΠ°ΡΠ΅Π½ΠΈΠ΅ Π΅Π΅ ΡΠ°Π±ΠΎΡΡ Π΄Π»Ρ Π²ΡΠΏΠΎΠ»Π½Π΅Π½ΠΈΡ Π½Π΅ΠΎΠ±Ρ ΠΎΠ΄ΠΈΠΌΠΎΠ³ΠΎ ΡΠ΅ΠΌΠΎΠ½ΡΠ° ΠΈ ΠΎΠ±ΡΠ»ΡΠΆΠΈΠ²Π°Π½ΠΈΡ. ΠΠΎΡΡΠΎΠΌΡ ΠΊ ΠΎΡΠΊΠ°Π·Ρ Π² ΡΠ°Π±ΠΎΡΠ΅ Π½ΡΠΆΠ½ΠΎ ΠΎΡΠ½ΠΎΡΠΈΡΡ Π²ΡΠ΅ Π²ΡΡ ΠΎΠ΄Ρ ΠΈΠ· ΡΠ°Π±ΠΎΡΠ΅Π³ΠΎ ΡΠΎΡΡΠΎΡΠ½ΠΈΡ.
Π‘ΡΠ°ΡΠΈΡΡΠΈΠΊΠ° ΠΎΡΠΊΠ°Π·ΠΎΠ², ΡΠ²Π»ΡΠ΅ΡΡΡ ΠΎΡΠ½ΠΎΠ²Π½ΡΠΌ ΠΈΡΡΠΎΡΠ½ΠΈΠΊΠΎΠΌ ΠΈΠ½ΡΠΎΡΠΌΠ°ΡΠΈΠΈ Π΄Π»Ρ ΡΡΠΆΠ΄Π΅Π½ΠΈΡ ΠΎ Π½Π°Π΄Π΅ΠΆΠ½ΠΎΡΡΠΈ ΠΈΠ·Π΄Π΅Π»ΠΈΡ, Π½ΠΎ ΡΡΠΎ Π»ΠΈΡΡ ΡΠΈΠ³Π½Π°Π» ΠΎΠ±ΡΠ°ΡΠ½ΠΎΠΉ ΡΠ²ΡΠ·ΠΈ, Π΄Π°ΡΡΠΈΠΉ ΠΏΡΠ΅Π΄ΡΡΠ°Π²Π»Π΅Π½ΠΈΠ΅ ΠΎ ΡΠΎΠΌ, Π½Π°ΡΠΊΠΎΠ»ΡΠΊΠΎ ΠΊΠΎΠ½ΡΡΡΡΠΊΡΠΈΡ, ΡΠ΅Ρ Π½ΠΎΠ»ΠΎΠ³ΠΈΡ ΠΈ ΡΡΠ»ΠΎΠ²ΠΈΡ ΡΠΊΡΠΏΠ»ΡΠ°ΡΠ°ΡΠΈΠΈ ΠΎΠ±Π΅ΡΠΏΠ΅ΡΠΈΠ»ΠΈ ΠΆΠ΅Π»Π°Π΅ΠΌΡΠ΅ ΠΏΠΎΠΊΠ°Π·Π°ΡΠ΅Π»ΠΈ Π½Π°Π΄Π΅ΠΆΠ½ΠΎΡΡΠΈ (ΠΊΠ°ΠΊ ΠΏΡΠ°Π²ΠΈΠ»ΠΎ, ΡΠ°ΠΊΠ°Ρ ΠΈΠ½ΡΠΎΡΠΌΠ°ΡΠΈΡ ΠΏΠΎΡΡΡΠΏΠ°Π΅Ρ Ρ Π±ΠΎΠ»ΡΡΠΈΠΌ ΠΎΠΏΠΎΠ·Π΄Π°Π½ΠΈΠ΅ΠΌ, ΠΊΠΎΠ³Π΄Π° ΡΠ΅ΡΠΈΡ ΠΌΠ°ΡΠΈΠ½ ΡΠΆΠ΅ Π·Π°ΠΏΡΡΠ΅Π½Π° Π² ΡΠΊΡΠΏΠ»ΡΠ°ΡΠ°ΡΠΈΡ). ΠΠΎΡΡΠΎΠΌΡ Π½Π΅ ΡΡΠ°ΡΠΈΡΡΠΈΡΠ΅ΡΠΊΠΈΠ΅ Π΄Π°Π½Π½ΡΠ΅, Π° ΡΠ°ΡΡΠ΅Ρ ΠΈ ΠΏΡΠΎΠ³Π½ΠΎΠ·ΠΈΡΠΎΠ²Π°Π½ΠΈΠ΅ Π²ΠΎΠ·ΠΌΠΎΠΆΠ½ΠΎΠ³ΠΎ ΠΏΠΎΠ²Π΅Π΄Π΅Π½ΠΈΡ ΠΌΠ°ΡΠΈΠ½Ρ Π² ΠΏΡΠ΅Π΄ΠΏΠΎΠ»Π°Π³Π°Π΅ΠΌΡΡ ΡΡΠ»ΠΎΠ²ΠΈΡΡ ΡΠΊΡΠΏΠ»ΡΠ°ΡΠ°ΡΠΈΠΈ, ΡΠ΅Ρ Π½ΠΎΠ»ΠΎΠ³ΠΈΡΠ΅ΡΠΊΠΎΠ΅ ΠΎΠ±Π΅ΡΠΏΠ΅ΡΠ΅Π½ΠΈΠ΅ Π·Π°Π΄Π°Π½Π½ΡΡ ΠΏΠΎΠΊΠ°Π·Π°ΡΠ΅Π»Π΅ΠΉ ΠΊΠ°ΡΠ΅ΡΡΠ²Π°, ΡΠΏΠ΅ΡΠΈΠ°Π»ΡΠ½ΡΠ΅ ΠΈΡΠΏΡΡΠ°Π½ΠΈΡ ΠΈ ΡΠ΅Π³Π»Π°ΠΌΠ΅Π½ΡΠ°ΡΠΈΡ ΡΡΠ»ΠΎΠ²ΠΈΠΉ ΡΠΊΡΠΏΠ»ΡΠ°ΡΠ°ΡΠΈΠΈ ΠΌΠ°ΡΠΈΠ½ ΡΠ²Π»ΡΡΡΡΡ ΠΎΡΠ½ΠΎΠ²ΠΎΠΉ Π΄Π»Ρ ΡΠΏΡΠ°Π²Π»Π΅Π½ΠΈΡ Π½Π°Π΄Π΅ΠΆΠ½ΠΎΡΡΡΡ ΠΈ ΠΎΠ±Π΅ΡΠΏΠ΅ΡΠ΅Π½ΠΈΡ Π΅Π΅ ΡΡΠ΅Π±ΡΠ΅ΠΌΠΎΠ³ΠΎ ΡΡΠΎΠ²Π½Ρ.
ΠΠ°Π΄Π΅ΠΆΠ½ΠΎΡΡΡ ΡΠ»ΠΎΠΆΠ½ΠΎΠΉ ΠΌΠ°ΡΠΈΠ½Ρ ΠΈΠ»ΠΈ ΠΎΠ±ΠΎΡΡΠ΄ΠΎΠ²Π°Π½ΠΈΡ Π·Π°Π²ΠΈΡΠΈΡ ΠΎΡ Π½Π°Π΄Π΅ΠΆΠ½ΠΎΡΡΠΈ ΡΠ°Π±ΠΎΡΡ Π²ΡΠ΅Ρ Π΅Π΅ ΡΠ»Π΅ΠΌΠ΅Π½ΡΠΎΠ². ΠΠ°ΠΏΡΠΈΠΌΠ΅Ρ, Π½Π°Π΄Π΅ΠΆΠ½ΠΎΡΡΡ Π΄Π²ΠΈΠ³Π°ΡΠ΅Π»Ρ Π²Π½ΡΡΡΠ΅Π½Π½Π΅Π³ΠΎ ΡΠ³ΠΎΡΠ°Π½ΠΈΡ, ΠΊΠ°ΠΊ ΡΠ»ΠΎΠΆΠ½ΠΎΠ³ΠΎ ΡΡΡΡΠΎΠΉΡΡΠ²Π°, Π·Π°Π²ΠΈΡΠΈΡ ΠΎΡ Π½Π°Π΄Π΅ΠΆΠ½ΠΎΡΡΠΈ ΡΠ°Π±ΠΎΡΡ Π΅Π΅ ΠΎΡΠ½ΠΎΠ²Π½ΡΡ ΡΠ°ΡΡΠ΅ΠΉ β ΡΠ°ΡΡΠ½Π½ΠΎ-ΠΏΠΎΡΡΠ½Π΅Π²ΠΎΠΉ Π³ΡΡΠΏΠΏΡ, Π³Π°Π·ΠΎΡΠ°ΡΠΏΡΠ΅Π΄Π΅Π»ΠΈΡΠ΅Π»ΡΠ½ΠΎΠ³ΠΎ ΠΌΠ΅Ρ Π°Π½ΠΈΠ·ΠΌΠ°, ΠΏΠΎΠ΄ΡΠΈΠΏΠ½ΠΈΠΊΠΎΠ², Π΄Π΅ΡΠ°Π»Π΅ΠΉ ΡΠΈΡΡΠ΅ΠΌΡ ΠΏΠΈΡΠ°Π½ΠΈΡ, ΡΠΈΡΡΠ΅ΠΌΡ ΡΠΌΠ°Π·ΠΊΠΈ ΠΈ ΠΎΡ Π»Π°ΠΆΠ΄Π΅Π½ΠΈΡ ΠΈ Π΄Ρ. Π’Π΅ΠΎΡΠΈΡ Π½Π°Π΄Π΅ΠΆΠ½ΠΎΡΡΠΈ ΡΠ°Π·Π»ΠΈΡΠ°Π΅Ρ ΡΡΠΈ Ρ Π°ΡΠ°ΠΊΡΠ΅ΡΠ½ΡΡ ΡΠΈΠΏΠ° ΠΎΡΠΊΠ°Π·ΠΎΠ², ΠΊΠΎΡΠΎΡΡΠ΅ Π²Π½ΡΡΡΠ΅Π½Π½Π΅ ΠΏΡΠΈΡΡΡΠΈ ΠΌΠ°ΡΠΈΠ½Π΅ ΠΈΠ»ΠΈ Π»ΡΠ±ΠΎΠΌΡ ΠΈΠ·Π΄Π΅Π»ΠΈΡ ΠΈ ΠΏΡΠΎΡΠ²Π»ΡΡΡΡΡ Π½Π΅Π·Π°Π²ΠΈΡΠΈΠΌΠΎ ΠΎΡ ΠΎΠ±ΡΠ»ΡΠΆΠΈΠ²Π°ΡΡΠ΅Π³ΠΎ ΠΏΠ΅ΡΡΠΎΠ½Π°Π»Π°. Π Π½ΠΈΠΌ ΠΎΡΠ½ΠΎΡΡΡΡΡ:
— ΠΏΡΠΈΡΠ°Π±ΠΎΡΠΎΡΠ½ΡΠ΅ ΠΎΡΠΊΠ°Π·Ρ, ΠΊΠΎΡΠΎΡΡΠ΅ Π²ΠΎΠ·Π½ΠΈΠΊΠ°ΡΡ Π½Π° ΡΠ°Π½Π½Π΅ΠΌ ΠΏΠ΅ΡΠΈΠΎΠ΄Π΅ ΡΠΊΡΠΏΠ»ΡΠ°ΡΠ°ΡΠΈΠΈ ΠΈ Π² Π±ΠΎΠ»ΡΡΠΈΠ½ΡΡΠ²Π΅ ΠΏΡΠΎΠΈΡΡ ΠΎΠ΄ΡΡ Π²ΡΠ»Π΅Π΄ΡΡΠ²ΠΈΠ΅ Π½Π΅Π΄ΠΎΡΡΠ°ΡΠΊΠΎΠ² ΡΠ΅Ρ Π½ΠΎΠ»ΠΎΠ³ΠΈΠΈ ΠΏΡΠΎΠΈΠ·Π²ΠΎΠ΄ΡΡΠ²Π° ΠΈ Π½Π΅Π΄ΠΎΡΡΠ°ΡΠΎΡΠ½ΠΎΠ³ΠΎ ΠΊΠ°ΡΠ΅ΡΡΠ²Π° ΠΊΠΎΠ½ΡΡΠΎΠ»Ρ Π΄Π΅ΡΠ°Π»Π΅ΠΉ ΠΏΡΠΈ ΠΈΡ ΠΈΠ·Π³ΠΎΡΠΎΠ²Π»Π΅Π½ΠΈΠΈ ΠΈ ΡΠ±ΠΎΡΠΊΠ΅;
— ΠΎΡΠΊΠ°Π·Ρ, Π²ΠΎΠ·Π½ΠΈΠΊΠ°ΡΡΠΈΠ΅ Π² ΠΌΠ°ΡΠΈΠ½Π°Ρ ΠΏΡΠΈ Π½Π΅ΠΏΡΠ°Π²ΠΈΠ»ΡΠ½ΠΎΠΉ ΠΈΡ ΡΠΊΡΠΏΠ»ΡΠ°ΡΠ°ΡΠΈΠΈ ΠΏΡΠΈ ΠΈΠ½ΡΠ΅Π½ΡΠΈΠ²Π½ΠΎΠΌ ΠΈΠ·Π½ΠΎΡΠ΅ ΠΎΡΠ΄Π΅Π»ΡΠ½ΡΡ Π΄Π΅ΡΠ°Π»Π΅ΠΉ. ΠΡΠΈ ΠΎΡΠΊΠ°Π·Ρ ΠΌΠΎΠ³ΡΡ Π±ΡΡΡ ΠΎΠ³ΡΠ°Π½ΠΈΡΠ΅Π½Ρ, Π·Π° ΡΡΠ΅Ρ ΡΠ²ΠΎΠ΅Π²ΡΠ΅ΠΌΠ΅Π½Π½ΠΎΠΉ Π·Π°ΠΌΠ΅Π½Ρ ΠΈΠ·Π½ΠΎΡΠ΅Π½Π½ΡΡ Π΄Π΅ΡΠ°Π»Π΅ΠΉ Π½ΠΎΠ²ΡΠΌΠΈ Π²ΠΎ Π²ΡΠ΅ΠΌΡ ΡΠ΅ΠΌΠΎΠ½ΡΠ°;
— Π²Π½Π΅Π·Π°ΠΏΠ½ΡΠ΅ ΠΎΡΠΊΠ°Π·Ρ Π² ΠΏΠ΅ΡΠΈΠΎΠ΄ Π½ΠΎΡΠΌΠ°Π»ΡΠ½ΠΎΠΉ ΡΠΊΡΠΏΠ»ΡΠ°ΡΠ°ΡΠΈΠΈ ΠΌΠ°ΡΠΈΠ½, ΠΊΠΎΡΠΎΡΡΠ΅ Π²ΠΎΠ·Π½ΠΈΠΊΠ°ΡΡ ΡΠ»ΡΡΠ°ΠΉΠ½ΠΎ ΠΈ Π½Π΅ ΠΌΠΎΠ³ΡΡ Π±ΡΡΡ ΡΡΡΡΠ°Π½Π΅Π½Ρ Π½ΠΈ Π½Π°Π»Π°Π΄ΠΊΠΎΠΉ, Π½ΠΈ Π±ΠΎΠ»Π΅Π΅ Π²ΡΡΠΎΠΊΠΈΠΌ ΠΊΠ°ΡΠ΅ΡΡΠ²ΠΎΠΌ ΠΎΠ±ΡΠ»ΡΠΆΠΈΠ²Π°Π½ΠΈΡ. Π’Π°ΠΊΠΈΠ΅ ΠΎΡΠΊΠ°Π·Ρ Π²ΠΎΠ·Π½ΠΈΠΊΠ°ΡΡ Π² ΡΠ΅Π·ΡΠ»ΡΡΠ°ΡΠ΅ ΡΠΊΠ°ΡΠΊΠΎΠΎΠ±ΡΠ°Π·Π½ΠΎΠ³ΠΎ ΠΈΠ·ΠΌΠ΅Π½Π΅Π½ΠΈΡ Ρ Π°ΡΠ°ΠΊΡΠ΅ΡΠΈΡΡΠΈΠΊ ΠΈΠ»ΠΈ ΠΏΠ°ΡΠ°ΠΌΠ΅ΡΡΠΎΠ² ΠΌΠ°ΡΠΈΠ½Ρ ΠΏΠΎΠ΄ Π²Π»ΠΈΡΠ½ΠΈΠ΅ΠΌ Π²Π½Π΅Π·Π°ΠΏΠ½ΡΡ ΠΏΠ΅ΡΠ΅Π³ΡΡΠ·ΠΎΠΊ ΠΈΠ»ΠΈ Π΄ΡΡΠ³ΠΈΡ ΡΠ°ΠΊΡΠΎΡΠΎΠ².
Π’Π΅ΠΎΡΠΈΡ Π½Π°Π΄Π΅ΠΆΠ½ΠΎΡΡΠΈ ΠΌΠ°ΡΠΈΠ½ Π½Π΅ ΠΌΠΎΠΆΠ΅Ρ ΠΏΡΠ΅ΡΠ΅Π½Π΄ΠΎΠ²Π°ΡΡ Π½Π° Π·Π°ΠΊΠΎΠ½ΡΠ΅Π½Π½ΠΎΡΡΡ, ΡΠ°ΠΊ ΠΊΠ°ΠΊ Π½Π΅ΠΊΠΎΡΠΎΡΡΠ΅ Π²ΠΎΠΏΡΠΎΡΡ ΡΡΠΎΠΉ ΡΠ΅ΠΎΡΠΈΠΈ Π΅ΡΠ΅ Π½Π΅Π΄ΠΎΡΡΠ°ΡΠΎΡΠ½ΠΎ ΡΠ°Π·ΡΠ°Π±ΠΎΡΠ°Π½Ρ ΠΈ Π½ΡΠΆΠ΄Π°ΡΡΡΡ Π² ΡΡΠΎΡΠ½Π΅Π½ΠΈΠΈ. ΠΠΌΠ΅ΡΡΠΈΠ΅ΡΡ ΠΎΠΏΡΠ±Π»ΠΈΠΊΠΎΠ²Π°Π½Π½ΡΠ΅ Π½Π΅ΠΏΠΎΠ»Π½ΡΠ΅ ΡΡΠ°ΡΠΈΡΡΠΈΡΠ΅ΡΠΊΠΈΠ΅ Π΄Π°Π½Π½ΡΠ΅ ΠΎΠ± ΡΡΠΎΠ²Π½Π΅ Π½Π°Π΄Π΅ΠΆΠ½ΠΎΡΡΠΈ ΡΠ°Π·Π»ΠΈΡΠ½ΡΡ ΡΠΈΠΏΠΎΠ² ΡΠΊΡΠΏΠ»ΡΠ°ΡΠΈΡΡΠ΅ΠΌΡΡ ΠΌΠ°ΡΠΈΠ½ Π² Π½Π°ΡΡΠΎΡΡΠ΅Π΅ Π²ΡΠ΅ΠΌΡ Π² ΡΠ²ΡΠ·ΠΈ Ρ ΠΈΠ½ΡΠ΅Π½ΡΠΈΠ²Π½ΡΠΌ ΡΠ°Π·Π²ΠΈΡΠΈΠ΅ΠΌ Π½ΠΎΠ²ΡΡ ΠΌΠ΅ΡΠΎΠ΄ΠΎΠ² ΠΏΡΠΎΠ΅ΠΊΡΠΈΡΠΎΠ²Π°Π½ΠΈΡ ΠΈ ΠΏΡΠΎΠΈΠ·Π²ΠΎΠ΄ΡΡΠ²Π° ΡΠΆΠ΅ Π½Π΅Π΄ΠΎΡΡΠ°ΡΠΎΡΠ½ΠΎ ΠΏΠΎΠ»Π½ΠΎ ΠΎΡΡΠ°ΠΆΠ°ΡΡ ΡΠ°ΠΊΡΠΈΡΠ΅ΡΠΊΠΎΠ΅ ΡΠΎΡΡΠΎΡΠ½ΠΈΠ΅ ΠΏΡΠΎΠ±Π»Π΅ΠΌΡ Π½Π°Π΄Π΅ΠΆΠ½ΠΎΡΡΠΈ, Π² ΠΎΡΠΎΠ±Π΅Π½Π½ΠΎΡΡΠΈ Π½Π° ΡΠΎΠ½Π΅ ΡΠΎΠ²Π΅ΡΡΠ΅Π½ΡΡΠ²ΠΎΠ²Π°Π½ΠΈΡ ΠΊΠΎΠ½ΡΡΡΡΠΊΡΠΈΠΉ, ΠΏΠΎΡΠ²Π»Π΅Π½ΠΈΡ Π½ΠΎΠ²ΡΡ ΠΌΠ°ΡΠ΅ΡΠΈΠ°Π»ΠΎΠ² Π΄Π»Ρ Π½ΠΈΡ ΠΈ Ρ.Π΄. Π’Π΅ΠΎΡΠΈΡ Π½Π°Π΄Π΅ΠΆΠ½ΠΎΡΡΠΈ ΠΌΠ°ΡΠΈΠ½ ΠΎΡ Π²Π°ΡΡΠ²Π°Π΅Ρ ΡΠΈΡΠΎΠΊΠΈΠΉ ΠΊΡΡΠ³ Π²ΠΎΠΏΡΠΎΡΠΎΠ², ΠΎΡΡΠ°ΠΆΠ°ΡΡΠΈΡ ΠΎΠ±ΡΡΡ ΡΠ΅ΠΎΡΠΈΡ Π½Π°Π΄Π΅ΠΆΠ½ΠΎΡΡΠΈ, Π²ΠΎΠΏΡΠΎΡΡ ΠΏΡΠΎΠ΅ΠΊΡΠΈΡΠΎΠ²Π°Π½ΠΈΡ, ΡΠ΅Ρ Π½ΠΎΠ»ΠΎΠ³ΠΈΠΈ ΠΏΡΠΎΠΈΠ·Π²ΠΎΠ΄ΡΡΠ²Π° ΠΈ ΡΠΊΡΠΏΠ»ΡΠ°ΡΠ°ΡΠΈΠΈ ΠΌΠ°ΡΠΈΠ½. Π ΡΠ²ΡΠ·ΠΈ Ρ ΡΡΠΈΠΌ ΠΎΠ·Π½Π°ΠΊΠΎΠΌΠ»Π΅Π½ΠΈΠ΅ Ρ ΡΡΠΎΠΉ ΠΏΡΠΎΠ±Π»Π΅ΠΌΠΎΠΉ ΡΡΠ΅Π±ΡΠ΅Ρ Π·Π½Π°Π½ΠΈΠΉ Π² ΠΎΠ±Π»Π°ΡΡΠΈ ΠΊΠΎΠ½ΠΊΡΠ΅ΡΠ½ΡΡ ΠΈΠ·Π΄Π΅Π»ΠΈΠΉ ΠΈ ΠΌΠ°ΡΠ΅ΠΌΠ°ΡΠΈΡΠ΅ΡΠΊΠΎΠΉ ΠΏΠΎΠ΄Π³ΠΎΡΠΎΠ²ΠΊΠΈ.
Π§Π΅ΡΡΡΠ΅ Π²Π΅Π΄ΡΡΠΈΡ ΠΏΠΎΠΊΠ°Π·Π°ΡΠ΅Π»Ρ ΠΎΠ±ΡΠ»ΡΠΆΠΈΠ²Π°Π½ΠΈΡ ΠΎΠ±ΠΎΡΡΠ΄ΠΎΠ²Π°Π½ΠΈΡ
Π‘ΠΏΡΠ°ΡΠΈΠ²Π°Π»ΠΈ Π»ΠΈ Π²Π°Ρ ΠΊΠΎΠ³Π΄Π°-Π½ΠΈΠ±ΡΠ΄Ρ: Β«Π‘ΠΊΠΎΠ»ΡΠΊΠΎ Π΅ΡΠ΅ ΠΎΠ½ Π±ΡΠ΄Π΅Ρ ΡΠ°Π±ΠΎΡΠ°ΡΡ?Β», Β«Π‘ΠΌΠΎΠΆΠ΅ΠΌ Π»ΠΈ ΠΌΡ ΡΠΎΡΡΠ°Π²ΠΈΡΡ Π½Π°Ρ ΠΏΡΠΎΠΈΠ·Π²ΠΎΠ΄ΡΡΠ²Π΅Π½Π½ΡΠΉ Π³ΡΠ°ΡΠΈΠΊ?Β» ΠΠ»ΠΈ Π΄ΡΡΠ³ΠΈΠ΅ Π²ΠΎΠΏΡΠΎΡΡ ΡΠΈΠΏΠ° Β«Ρ
ΡΡΡΡΠ°Π»ΡΠ½ΠΎΠ³ΠΎ ΡΠ°ΡΠ°Β»? ΠΠ° ΡΠ°ΠΊΠΈΠ΅ Π²ΠΎΠΏΡΠΎΡΡ ΠΌΠΎΠΆΠ΅Ρ Π±ΡΡΡ ΠΎΡΠ΅Π½Ρ ΡΠ»ΠΎΠΆΠ½ΠΎ ΠΈΠ»ΠΈ ΠΏΡΠ°ΠΊΡΠΈΡΠ΅ΡΠΊΠΈ Π½Π΅Π²ΠΎΠ·ΠΌΠΎΠΆΠ½ΠΎ ΠΎΡΠ²Π΅ΡΠΈΡΡ. ΠΠ½ΠΈ ΡΠ°ΡΡΠΎ ΡΡΠ°Π²ΡΡ ΡΠΏΠ΅ΡΠΈΠ°Π»ΠΈΡΡΠ° ΠΏΠΎ Π½Π°Π΄Π΅ΠΆΠ½ΠΎΡΡΠΈ Π² Π·Π°ΡΡΡΠ΄Π½ΠΈΡΠ΅Π»ΡΠ½ΠΎΠ΅ ΠΏΠΎΠ»ΠΎΠΆΠ΅Π½ΠΈΠ΅.
ΠΠ΅ΠΊΠΎΡΠΎΡΡΠ΅ Π±ΡΠ΄ΡΡΠΈΠ΅ ΠΈΠ½Π΄ΠΈΠΊΠ°ΡΠΎΡΡ Π΄ΠΎΡΡΡΠΏΠ½Ρ (ΠΈΠ»ΠΈ Π΄ΠΎΠ»ΠΆΠ½Ρ Π±ΡΡΡ) Π΄ΠΎΡΡΡΠΏΠ½Ρ Π²Π°ΡΠ΅ΠΉ ΠΎΡΠ³Π°Π½ΠΈΠ·Π°ΡΠΈΠΈ, ΠΊΠΎΡΠΎΡΡΠ΅ ΠΏΠΎΠΌΠΎΠ³ΡΡ Π²Π°ΠΌ ΠΎΡΠ²Π΅ΡΠΈΡΡ Π½Π° Π²ΡΡΠ΅ΡΠΊΠ°Π·Π°Π½Π½ΡΠ΅ Π²ΠΎΠΏΡΠΎΡΡ, ΠΊΠΎΠ³Π΄Π° ΠΈΡ
Π·Π°Π΄Π°Π΄ΡΡ.Π§Π΅ΡΡΡΠ΅ ΠΈΠ· ΡΡΠΈΡ
ΠΏΠΎΠΊΠ°Π·Π°ΡΠ΅Π»Π΅ΠΉ:
1. Π£ΡΠΎΠ²Π΅Π½Ρ Π·Π°Π²Π΅ΡΡΠ΅Π½ΠΈΡ ΠΏΡΠΎΡΠΈΠ»Π°ΠΊΡΠΈΡΠ΅ΡΠΊΠΎΠ³ΠΎ ΠΎΠ±ΡΠ»ΡΠΆΠΈΠ²Π°Π½ΠΈΡ (PM)
ΠΠΈΠ·ΠΊΠΈΠ΅ ΠΏΠΎΠΊΠ°Π·Π°ΡΠ΅Π»ΠΈ Π·Π°Π²Π΅ΡΡΠ΅Π½ΠΈΡ ΠΏΡΠΎΡΠΈΠ»Π°ΠΊΡΠΈΡΠ΅ΡΠΊΠΎΠ³ΠΎ ΠΎΠ±ΡΠ»ΡΠΆΠΈΠ²Π°Π½ΠΈΡ Π½Π°ΠΏΡΡΠΌΡΡ ΡΠ²ΡΠ·Π°Π½Ρ Ρ ΡΠ²Π΅Π»ΠΈΡΠ΅Π½ΠΈΠ΅ΠΌ ΠΎΠ±ΡΠ΅ΠΌΠ° ΡΠ°Π±ΠΎΡ ΠΏΠΎ ΡΠ΅Ρ
Π½ΠΈΡΠ΅ΡΠΊΠΎΠΌΡ ΠΎΠ±ΡΠ»ΡΠΆΠΈΠ²Π°Π½ΠΈΡ ΠΎΠ±ΠΎΡΡΠ΄ΠΎΠ²Π°Π½ΠΈΡ Π² Π±ΡΠ΄ΡΡΠ΅ΠΌ. ΠΡΡΠΎΠΊΠΈΠ΅ ΠΏΠΎΠΊΠ°Π·Π°ΡΠ΅Π»ΠΈ Π·Π°Π²Π΅ΡΡΠ΅Π½Π½ΠΎΡΡΠΈ PM ΠΎΠ·Π½Π°ΡΠ°ΡΡ, ΡΡΠΎ Π½Π΅ΠΎΠ±Ρ
ΠΎΠ΄ΠΈΠΌΠΎΠ΅ ΡΠ΅Ρ
Π½ΠΈΡΠ΅ΡΠΊΠΎΠ΅ ΠΎΠ±ΡΠ»ΡΠΆΠΈΠ²Π°Π½ΠΈΠ΅ ΠΎΠ±ΠΎΡΡΠ΄ΠΎΠ²Π°Π½ΠΈΡ ΡΠΆΠ΅ Π·Π°Π²Π΅ΡΡΠ΅Π½ΠΎ, ΠΈ ΠΏΡΠΎΠ±Π»Π΅ΠΌ Ρ ΡΠ΅Ρ
Π½ΠΈΡΠ΅ΡΠΊΠΈΠΌ ΠΎΠ±ΡΠ»ΡΠΆΠΈΠ²Π°Π½ΠΈΠ΅ΠΌ Π² Π±ΡΠ΄ΡΡΠ΅ΠΌ ΠΌΠΎΠΆΠ½ΠΎ ΠΈΠ·Π±Π΅ΠΆΠ°ΡΡ.
2. ΠΡΡΠ½Π°Π» Π³ΠΎΡΠΎΠ²Π½ΠΎΡΡΠΈ ΠΊ ΡΠ°Π±ΠΎΡΠ΅
ΠΡΠΎ ΠΏΠΎΠΊΠ°Π·Π°ΡΠ΅Π»Ρ Π³ΠΎΡΠΎΠ²Π½ΠΎΡΡΠΈ ΠΈ ΡΡΡΠ΅ΠΊΡΠΈΠ²Π½ΠΎΡΡΠΈ Π΄Π»Ρ Π·Π°Π²Π΅ΡΡΠ΅Π½ΠΈΡ ΡΠ°Π±ΠΎΡ ΠΏΠΎ ΡΠ΅Ρ
ΠΎΠ±ΡΠ»ΡΠΆΠΈΠ²Π°Π½ΠΈΡ.
3. Π‘ΠΎΠ±Π»ΡΠ΄Π΅Π½ΠΈΠ΅ Π³ΡΠ°ΡΠΈΠΊΠ° ΠΎΡΠΊΠ»ΡΡΠ΅Π½ΠΈΠΉ
ΠΡΠΎ ΠΎΡΠ΅Π½Ρ Π²Π°ΠΆΠ½Π°Ρ ΠΌΠ΅ΡΡΠΈΠΊΠ°, ΠΊΠΎΡΠΎΡΡΡ Π½ΡΠΆΠ½ΠΎ ΠΎΡΡΠ»Π΅ΠΆΠΈΠ²Π°ΡΡ, ΠΈ ΠΈΠ½Π΄ΠΈΠΊΠ°ΡΠΎΡ Π±ΡΠ΄ΡΡΠΈΡ
ΡΠ°Π±ΠΎΡ ΠΏΠΎ ΡΠ΅Ρ
Π½ΠΈΡΠ΅ΡΠΊΠΎΠΌΡ ΠΎΠ±ΡΠ»ΡΠΆΠΈΠ²Π°Π½ΠΈΡ.ΠΠ΅ΡΠΎΠ±Π»ΡΠ΄Π΅Π½ΠΈΠ΅ Π³ΡΠ°ΡΠΈΠΊΠΎΠ² ΠΏΡΠΎΡΡΠΎΠ΅Π² ΠΏΡΠΈΠ²ΠΎΠ΄ΠΈΡ ΠΊ ΠΎΡΡΡΠΎΡΠΊΠ΅ ΠΎΠ±ΡΠ»ΡΠΆΠΈΠ²Π°Π½ΠΈΡ ΠΎΠ±ΠΎΡΡΠ΄ΠΎΠ²Π°Π½ΠΈΡ. ΠΡΠΎ ΠΏΡΠΈΠ²ΠΎΠ΄ΠΈΡ ΠΊ ΡΠ²Π΅Π»ΠΈΡΠ΅Π½ΠΈΡ ΡΠΈΡΠΊΠΎΠ² ΠΈ Π²Π΅ΡΠΎΡΡΠ½ΠΎΡΡΠΈ ΡΠΎΠ³ΠΎ, ΡΡΠΎ ΠΏΡΠΎΠΈΠ·Π²ΠΎΠ΄ΠΈΡΠ΅Π»ΡΠ½ΠΎΡΡΡ ΠΎΠ±ΠΎΡΡΠ΄ΠΎΠ²Π°Π½ΠΈΡ Π² Π±ΡΠ΄ΡΡΠ΅ΠΌ ΡΠ½ΠΈΠ·ΠΈΡΡΡ, ΡΡΠΎ ΠΏΡΠΈΠ²Π΅Π΄Π΅Ρ ΠΊ ΡΠ½ΠΈΠΆΠ΅Π½ΠΈΡ Π΅ΠΌΠΊΠΎΡΡΠΈ, ΡΠ²Π΅Π»ΠΈΡΠ΅Π½ΠΈΡ Π²ΡΠ΅ΠΌΠ΅Π½ΠΈ ΠΏΡΠΎΡΡΠΎΡ ΠΈ ΡΠ²Π΅Π»ΠΈΡΠ΅Π½ΠΈΡ ΡΠ°ΡΡ
ΠΎΠ΄ΠΎΠ².
4. ΠΡΡΠ΅ΡΠ½ΠΎΡΡΡ ΠΎ ΡΠΎΡΡΠΎΡΠ½ΠΈΠΈ Π°ΠΊΡΠΈΠ²ΠΎΠ² ΠΎΠ±ΠΎΡΡΠ΄ΠΎΠ²Π°Π½ΠΈΡ
ΠΠ°Π΄Π»Π΅ΠΆΠ°ΡΠ΅Π΅ ΠΈΡΠΏΠΎΠ»ΡΠ·ΠΎΠ²Π°Π½ΠΈΠ΅ ΡΠ΅Ρ
Π½ΠΎΠ»ΠΎΠ³ΠΈΠΉ ΠΌΠΎΠ½ΠΈΡΠΎΡΠΈΠ½Π³Π° ΡΠΎΡΡΠΎΡΠ½ΠΈΡ, ΡΠ°ΠΊΠΈΡ
ΠΊΠ°ΠΊ Π°Π½Π°Π»ΠΈΠ· Π²ΠΈΠ±ΡΠ°ΡΠΈΠΈ, ΠΈΠ½ΡΡΠ°ΠΊΡΠ°ΡΠ½Π°Ρ ΡΠ΅ΡΠΌΠΎΠ³ΡΠ°ΡΠΈΡ, Π°Π½Π°Π»ΠΈΠ· ΡΠΌΠ°Π·ΠΊΠΈ, ΡΠ»ΡΡΡΠ°Π·Π²ΡΠΊ ΠΈ Π΄ΡΡΠ³ΠΈΠ΅, ΡΠ²Π»ΡΠ΅ΡΡΡ ΡΠΏΡΠ΅ΠΆΠ΄Π°ΡΡΠ΅ΠΉ ΡΡΡΠ°ΡΠ΅Π³ΠΈΠ΅ΠΉ, Π³Π°ΡΠ°Π½ΡΠΈΡΡΡΡΠ΅ΠΉ, ΡΡΠΎ ΡΠΊΡΡΡΡΠ΅ ΠΎΡΠΊΠ°Π·Ρ ΡΡΠ°Π½ΡΡ ΠΈΠ·Π²Π΅ΡΡΠ½Ρ ΠΈ ΠΈΡΠΏΡΠ°Π²Π»Π΅Π½Ρ Π΄ΠΎ ΡΠΎΠ³ΠΎ, ΠΊΠ°ΠΊ ΠΎΠ½ΠΈ ΠΏΡΠΈΠ²Π΅Π΄ΡΡ ΠΊ ΠΏΡΠΎΡΡΠΎΡ ΠΎΠ±ΠΎΡΡΠ΄ΠΎΠ²Π°Π½ΠΈΡ ΠΈΠ»ΠΈ Π΄ΡΡΠ³ΠΈΠΌ Π½Π΅ΠΆΠ΅Π»Π°ΡΠ΅Π»ΡΠ½ΡΠΌ ΡΠ²Π»Π΅Π½ΠΈΡΠΌ. ΠΏΠΎΡΠ»Π΅Π΄ΡΡΠ²ΠΈΡ.Π‘ΠΎΠ²ΠΌΠ΅ΡΡΠ½ΠΎΠ΅ ΠΎΡΡΠ»Π΅ΠΆΠΈΠ²Π°Π½ΠΈΠ΅ ΡΡΠΈΡ
ΠΏΠΎΠΊΠ°Π·Π°ΡΠ΅Π»Π΅ΠΉ ΠΌΠΎΠΆΠ΅Ρ Π΄Π°ΡΡ ΠΏΡΠ΅Π΄ΡΡΠ°Π²Π»Π΅Π½ΠΈΠ΅ ΠΎ ΡΠΎΡΡΠΎΡΠ½ΠΈΠΈ Π°ΠΊΡΠΈΠ²ΠΎΠ² Π² Π±ΡΠ΄ΡΡΠ΅ΠΌ. ΠΠ½ΠΎΠΆΠ΅ΡΡΠ²ΠΎ Β«ΠΊΡΠ°ΡΠ½ΡΡ
Β» Π°ΠΊΡΠΈΠ²ΠΎΠ², ΡΠ²ΡΠ·Π°Π½Π½ΡΡ
Ρ ΡΡΠΈΠΌΠΈ ΡΠ΅Ρ
Π½ΠΎΠ»ΠΎΠ³ΠΈΡΠΌΠΈ, ΠΏΡΠΈΠ²Π΅Π΄ΡΡ ΠΊ Π½Π΅ΠΆΠ΅Π»Π°ΡΠ΅Π»ΡΠ½ΠΎΠΌΡ ΠΎΠ±ΡΠ»ΡΠΆΠΈΠ²Π°Π½ΠΈΡ ΠΎΠ±ΠΎΡΡΠ΄ΠΎΠ²Π°Π½ΠΈΡ Π² Π±ΡΠ΄ΡΡΠ΅ΠΌ ΠΈ Π½Π΅ΠΆΠ΅Π»Π°ΡΠ΅Π»ΡΠ½ΡΠΌ ΠΏΡΠΎΡΡΠΎΡΠΌ, Π΅ΡΠ»ΠΈ Π½Π΅ Π±ΡΠ΄ΡΡ ΠΏΡΠ΅Π΄ΠΏΡΠΈΠ½ΡΡΡ ΠΊΠΎΡΡΠ΅ΠΊΡΠΈΡΡΡΡΠΈΠ΅ Π΄Π΅ΠΉΡΡΠ²ΠΈΡ. ΠΡΠΎΠΌΠ΅ ΡΠΎΠ³ΠΎ, ΡΡΠΎ ΠΌΠΎΠΆΠ½ΠΎ ΠΈΡΠΏΠΎΠ»ΡΠ·ΠΎΠ²Π°ΡΡ Π΄Π»Ρ ΠΎΠΏΡΠ΅Π΄Π΅Π»Π΅Π½ΠΈΡ ΠΏΡΠΈΠΎΡΠΈΡΠ΅ΡΠΎΠ² ΠΏΡΠΈ ΡΠ΅Ρ
Π½ΠΈΡΠ΅ΡΠΊΠΎΠΌ ΠΎΠ±ΡΠ»ΡΠΆΠΈΠ²Π°Π½ΠΈΠΈ ΠΎΠ±ΠΎΡΡΠ΄ΠΎΠ²Π°Π½ΠΈΡ, Π΅ΡΠ»ΠΈ ΠΈΠΌΠ΅Π΅ΡΡΡ Ρ
ΠΎΡΠΎΡΠ°Ρ ΡΠΈΡΡΠ΅ΠΌΠ° ΡΠ°Π½ΠΆΠΈΡΠΎΠ²Π°Π½ΠΈΡ ΠΊΡΠΈΡΠΈΡΠ΅ΡΠΊΠΈ Π²Π°ΠΆΠ½ΠΎΠ³ΠΎ ΠΎΠ±ΠΎΡΡΠ΄ΠΎΠ²Π°Π½ΠΈΡ.
Π£Π·Π½Π°ΠΉΡΠ΅ ΠΎΠ± ΠΈΠ½ΡΡΡΡΠΌΠ΅Π½ΡΠ°Ρ ΠΌΠΎΠ½ΠΈΡΠΎΡΠΈΠ½Π³Π° Π²ΠΈΠ±ΡΠ°ΡΠΈΠΈ LUDECA
Π‘ΠΎΠ²Π΅Ρ ΠΏΡΠ΅Π΄ΠΎΡΡΠ°Π²ΠΈΠ»: LUDECA
ΠΡΠ±Π΅ΡΠΈΡΠ΅ ΠΏΡΠ°Π²ΠΈΠ»ΡΠ½ΡΠ΅ ΠΏΠΎΠΊΠ°Π·Π°ΡΠ΅Π»ΠΈ Π΄Π»Ρ ΡΠ»ΡΡΡΠ΅Π½ΠΈΡ ΠΎΠ±ΡΠ»ΡΠΆΠΈΠ²Π°Π½ΠΈΡ ΠΈ Π½Π°Π΄Π΅ΠΆΠ½ΠΎΡΡΠΈ
ΠΠΊΡΠΏΠ΅ΡΡΡ ΡΡ ΠΎΠ΄ΡΡΡΡ Π²ΠΎ ΠΌΠ½Π΅Π½ΠΈΠΈ, ΡΡΠΎ Π»ΡΡΡΠΈΠΉ ΡΠΏΠΎΡΠΎΠ± ΠΏΡΠ΅ΠΎΠ΄ΠΎΠ»Π΅ΡΡ ΠΊΠ°ΡΠ°ΡΡΡΠΎΡΠΈΡΠ΅ΡΠΊΠΈΠΉ ΠΎΡΠΊΠ°Π· ΠΌΠ°ΡΠΈΠ½Ρ — Π½Π΅ ΠΈΠΌΠ΅ΡΡ Π΅Π΅.ΠΠ΄Π½Π°ΠΊΠΎ ΡΠΏΠ΅ΡΠΈΠ°Π»ΠΈΡΡΡ ΠΏΠΎ ΡΠ΅Ρ Π½ΠΈΡΠ΅ΡΠΊΠΎΠΌΡ ΠΎΠ±ΡΠ»ΡΠΆΠΈΠ²Π°Π½ΠΈΡ ΠΏΠΎΠ½ΠΈΠΌΠ°ΡΡ, ΡΡΠΎ Π½Π°Π΄Π΅ΠΆΠ½ΠΎΡΡΡ ΠΌΠ°ΡΠΈΠ½Ρ ΠΈΠΌΠ΅Π΅Ρ ΡΠ²ΠΎΡ ΡΠ΅Π½Ρ.
ΠΠ΄ΠΈΠ½ ΡΠΎΠ»ΡΠΊΠΎ ΠΌΠΎΠ½ΠΈΡΠΎΡΠΈΠ½Π³ ΠΊΠ»ΡΡΠ΅Π²ΡΡ ΠΏΠΎΠΊΠ°Π·Π°ΡΠ΅Π»Π΅ΠΉ Π½Π°Π΄Π΅ΠΆΠ½ΠΎΡΡΠΈ ΠΌΠ°ΡΠΈΠ½Ρ ΠΌΠΎΠΆΠ΅Ρ Π½Π΅ ΠΏΠΎΠΌΠΎΡΡ Π² Π±ΠΎΡΡΠ±Π΅ Ρ ΡΠ°ΡΡΠΎΡΠΈΡΠ΅Π»ΡΠ½ΡΠΌΠΈ ΠΈ Π½Π΅ΡΡΡΠ΅ΠΊΡΠΈΠ²Π½ΡΠΌΠΈ ΡΠ°ΡΡ ΠΎΠ΄Π°ΠΌΠΈ, ΠΊΠΎΡΠΎΡΡΠ΅ Π±Π΅Π· ΠΎΡΠΎΠ±ΠΎΠ³ΠΎ ΡΠ½ΡΡΠ·ΠΈΠ°Π·ΠΌΠ° ΠΏΡΠ΅Π΄Π½Π°Π·Π½Π°ΡΠ°Π»ΠΈΡΡ Π΄Π»Ρ ΡΠΌΠ΅Π½ΡΡΠ΅Π½ΠΈΡ ΠΊΠΎΠ»ΠΈΡΠ΅ΡΡΠ²Π° ΠΎΡΠΊΠ°Π·ΠΎΠ² ΠΈ ΠΏΡΠΎΡΡΠΎΠ΅Π².
Π‘ Π΄ΡΡΠ³ΠΎΠΉ ΡΡΠΎΡΠΎΠ½Ρ, ΠΈΠ½ΠΈΡΠΈΠ°ΡΠΈΠ²Ρ, ΠΊΠΎΡΠΎΡΡΠ΅ ΡΠΎΠΊΡΠ°ΡΠ°ΡΡ ΡΠ΅ΠΊΡΡΠΈΠ΅ ΡΠ°ΡΡ ΠΎΠ΄Ρ Π½Π° ΡΠ΅Ρ Π½ΠΈΡΠ΅ΡΠΊΠΎΠ΅ ΠΎΠ±ΡΠ»ΡΠΆΠΈΠ²Π°Π½ΠΈΠ΅ Π±Π΅Π· ΡΡΠ΅ΡΠ° Π΄ΠΎΠ»Π³ΠΎΡΡΠΎΡΠ½ΡΡ ΠΏΠΎΡΠ»Π΅Π΄ΡΡΠ²ΠΈΠΉ Π΄Π»Ρ Π½Π°Π΄Π΅ΠΆΠ½ΠΎΡΡΠΈ, ΡΠ°ΡΡΠΎ ΠΎΠΊΠ°Π·ΡΠ²Π°ΡΡΡΡ Π½Π° ΠΊΠΎΠΏΠ΅ΠΉΠΊΡ ΠΈ Π½Π΅ΡΠ°Π·ΡΠΌΠ½Ρ.
ΠΠ»Ρ Π±ΠΎΠ»ΡΡΠΈΠ½ΡΡΠ²Π° ΠΊΠΎΠΌΠΏΠ°Π½ΠΈΠΉ Π²Ρ — ΡΡΠΎ ΡΠΎ, ΡΡΠΎ Π²Ρ ΠΈΠ·ΠΌΠ΅ΡΡΠ΅ΡΠ΅. ΠΠ΅ΡΡΠΈΠΊΠΈ ΡΠΎΡΠΌΠΈΡΡΡΡ ΠΈ ΠΎΠΏΡΠ΅Π΄Π΅Π»ΡΡΡ ΠΎΡΠ³Π°Π½ΠΈΠ·Π°ΡΠΈΡ. ΠΡΠ΅ ΠΌΡ Ρ Π΄Π΅ΡΡΡΠ²Π° ΠΏΠΎΠ΄Π²Π΅ΡΠ³Π°Π»ΠΈΡΡ ΡΠ°Π·Π»ΠΈΡΠ½ΡΠΌ ΠΈΠ·ΠΌΠ΅ΡΠ΅Π½ΠΈΡΠΌ.
ΠΡΠΎΡ ΡΠ°Π½Π½ΠΈΠΉ ΠΎΠΏΡΡ Π²Π°ΡΡΠΈΡΠΎΠ²Π°Π»ΡΡ ΠΎΡ ΠΏΠΎΠ±Π΅Π΄Π½ΠΎΠ³ΠΎ ΡΡΠ΅ΡΠ° Π² Π½Π°ΡΠ΅ΠΉ ΠΌΠ°Π»Π΅Π½ΡΠΊΠΎΠΉ Π±Π΅ΠΉΡΠ±ΠΎΠ»ΡΠ½ΠΎΠΉ Π»ΠΈΠ³Π΅ Π΄ΠΎ ΠΌΡΡΠΈΡΠ΅Π»ΡΠ½ΠΎ ΡΠ΅ΡΡΠ΅Π·Π½ΠΎΠ³ΠΎ Π΄Π½Ρ, ΠΊΠΎΠ³Π΄Π° ΠΌΡ ΠΏΡΠΈΠ½Π΅ΡΠ»ΠΈ Π΄ΠΎΠΌΠΎΠΉ Π½ΠΈΠ·ΠΊΡΡ ΠΎΡΠ΅Π½ΠΊΡ Π² ΡΠΊΠΎΠ»ΡΠ½ΠΎΠΉ ΡΠ°Π±Π΅Π»Π΅.
ΠΡ ΡΠ·Π½Π°Π»ΠΈ, ΡΡΠΎ Π²Π°ΠΆΠ½ΠΎ ΡΠΎ, ΡΡΠΎ ΠΈΠ·ΠΌΠ΅ΡΡΠ΅ΡΡΡ, Π° ΡΠ°ΠΊΠΆΠ΅ Π΅Π³ΠΎ Π»ΠΎΠ³ΠΈΡΠ΅ΡΠΊΠΎΠ΅ ΡΠ»Π΅Π΄ΡΡΠ²ΠΈΠ΅β¦ ΡΠΎ, ΡΡΠΎ ΠΈΠ·ΠΌΠ΅ΡΡΠ΅ΡΡΡ, Π΄Π΅Π»Π°Π΅ΡΡΡ.Π― Π·Π°Π²ΠΈΠ΄ΡΡ ΡΠ΅Π»ΠΎΠ²Π΅ΠΊΡ, ΠΊΠΎΡΠΎΡΡΠΉ ΠΏΠ΅ΡΠ²ΡΠΌ ΠΏΡΠΎΠΈΠ·Π½Π΅Ρ ΡΡΠΈ ΡΠ»ΠΎΠ²Π°.
ΠΠ½Π΅ Π²ΡΠ΅Π³Π΄Π° Π»ΡΠ±ΠΎΠΏΡΡΠ½ΠΎ ΡΠ²ΠΈΠ΄Π΅ΡΡ Π΄ΠΈΠ°Π³ΡΠ°ΠΌΠΌΡ ΠΈ Π³ΡΠ°ΡΠΈΠΊΠΈ, ΡΠ°Π·ΠΌΠ΅ΡΠ΅Π½Π½ΡΠ΅ Π½Π° Π΄ΠΎΡΠΊΠ΅ ΠΎΠ±ΡΡΠ²Π»Π΅Π½ΠΈΠΉ Π²ΠΎΠ·Π»Π΅ ΠΎΡΠΈΡΠ° ΡΡΠΊΠΎΠ²ΠΎΠ΄ΠΈΡΠ΅Π»Ρ. ΠΡΡΡΡΡΠΉ Π²Π·Π³Π»ΡΠ΄ Π½Π° ΡΡΠΈ ΠΏΠΎΠΊΠ°Π·Π°ΡΠ΅Π»ΠΈ Π² Π·Π½Π°ΡΠΈΡΠ΅Π»ΡΠ½ΠΎΠΉ ΡΡΠ΅ΠΏΠ΅Π½ΠΈ ΠΎΠΏΡΠ΅Π΄Π΅Π»ΡΠ΅Ρ ΡΠ΅Π»ΠΈ ΡΡΡΠ΅ΠΊΡΠΈΠ²Π½ΠΎΡΡΠΈ Π³ΡΡΠΏΠΏΡ, ΠΊΠΎΡΠΎΡΠΎΠΉ ΠΎΠ½ ΡΠΏΡΠ°Π²Π»ΡΠ΅Ρ.
ΠΡΠΎΠ½ΠΈΡΠ°ΡΠ΅Π»ΡΠ½ΡΠΉ ΠΌΠ΅Π½Π΅Π΄ΠΆΠ΅Ρ Π±ΡΠ΄Π΅Ρ ΡΡΠ°ΡΠ΅Π»ΡΠ½ΠΎ ΡΠΎΠ³Π»Π°ΡΠΎΠ²ΡΠ²Π°ΡΡ Π΄ΠΈΠ°Π³ΡΠ°ΠΌΠΌΡ ΠΈ Π³ΡΠ°ΡΠΈΠΊΠΈ Ρ ΡΠ΅ΠΌΠΈ ΠΏΠΎΠΊΠ°Π·Π°ΡΠ΅Π»ΡΠΌΠΈ, ΠΊΠΎΡΠΎΡΡΠ΅ ΠΎΠΏΡΠ΅Π΄Π΅Π»ΡΡΡ Π΅Π³ΠΎ Π³ΠΎΠ΄ΠΎΠ²ΠΎΠΉ Π±ΠΎΠ½ΡΡ ΠΈ ΡΠ²Π΅Π»ΠΈΡΠΈΠ²Π°ΡΡ Π΅Π³ΠΎ ΡΠ°Π½ΡΡ Π½Π° ΠΏΡΠΎΠ΄Π²ΠΈΠΆΠ΅Π½ΠΈΠ΅ ΠΏΠΎ ΡΠ»ΡΠΆΠ±Π΅. ΠΠ°ΠΆΠ΅ Π±ΠΎΠ»Π΅Π΅ ΠΌΡΠ΄ΡΡΠ΅ Π±ΠΈΠ·Π½Π΅Ρ-Π»ΠΈΠ΄Π΅ΡΡ ΡΠ°ΡΡΠΌΠ°ΡΡΠΈΠ²Π°ΡΡ Π΄ΠΎΠ»Π³ΠΎΡΡΠΎΡΠ½ΡΠ΅ Π±ΠΈΠ·Π½Π΅Ρ-Π²ΠΎΠ·ΠΌΠΎΠΆΠ½ΠΎΡΡΠΈ ΠΈ ΡΠ°Π·ΡΠ°Π±Π°ΡΡΠ²Π°ΡΡ ΡΡΡΠ°ΡΠ΅Π³ΠΈΡΠ΅ΡΠΊΠΈΠ΅ ΡΠ΅Π»ΠΈ ΠΈ ΠΏΠΎΠΊΠ°Π·Π°ΡΠ΅Π»ΠΈ Π΄Π»Ρ ΠΌΠ°ΠΊΡΠΈΠΌΠΈΠ·Π°ΡΠΈΠΈ Π°ΠΊΡΠΈΠΎΠ½Π΅ΡΠ½ΠΎΠΉ ΡΡΠΎΠΈΠΌΠΎΡΡΠΈ, ΠΌΠΎΡΠ°Π»ΡΠ½ΠΎΠ³ΠΎ Π΄ΡΡ Π° ΡΠΎΡΡΡΠ΄Π½ΠΈΠΊΠΎΠ² ΠΈ Π»ΠΎΡΠ»ΡΠ½ΠΎΡΡΠΈ ΠΊ Π±ΡΠ΅Π½Π΄Ρ.
Π‘ΠΎΠ²ΡΠ΅ΠΌΠ΅Π½Π½ΡΠ΅ ΡΡΡΠ°ΡΠ΅Π³ΠΈΠΈ ΠΎΠ±ΡΠ»ΡΠΆΠΈΠ²Π°Π½ΠΈΡ Π²ΠΊΠ»ΡΡΠ°ΡΡ ΡΠ°Π·Π²Π΅ΡΡΡΠ²Π°Π½ΠΈΠ΅ ΠΌΠ½ΠΎΠΆΠ΅ΡΡΠ²Π° ΠΏΠΎΠΊΠ°Π·Π°ΡΠ΅Π»Π΅ΠΉ ΠΏΡΠΎΠΈΠ·Π²ΠΎΠ΄ΠΈΡΠ΅Π»ΡΠ½ΠΎΡΡΠΈ, Π½Π°ΠΏΡΠ°Π²Π»Π΅Π½Π½ΡΡ Π½Π° ΠΎΠΏΡΠΈΠΌΠΈΠ·Π°ΡΠΈΡ (Π° Π½Π΅ Π½Π° ΠΌΠ°ΠΊΡΠΈΠΌΠΈΠ·Π°ΡΠΈΡ) Π½Π°Π΄Π΅ΠΆΠ½ΠΎΡΡΠΈ ΠΌΠ°ΡΠΈΠ½Ρ.
Π₯ΠΎΡΠΎΡΠΎ ΠΏΡΠΎΠ΄ΡΠΌΠ°Π½Π½Π°Ρ ΠΏΠ°Π½Π΅Π»Ρ ΠΌΠΎΠ½ΠΈΡΠΎΡΠΈΠ½Π³Π° ΡΠ΅Ρ Π½ΠΈΡΠ΅ΡΠΊΠΎΠ³ΠΎ ΠΎΠ±ΡΠ»ΡΠΆΠΈΠ²Π°Π½ΠΈΡ — ΡΡΠΎ ΠΊΠΎΠΌΠ°Π½Π΄Π½ΡΠΉ ΠΏΡΠ½ΠΊΡ ΠΊΠ»ΡΡΠ΅Π²ΡΡ ΠΏΠΎΠΊΠ°Π·Π°ΡΠ΅Π»Π΅ΠΉ ΡΡΡΠ΅ΠΊΡΠΈΠ²Π½ΠΎΡΡΠΈ, Π½Π΅ΠΊΠΎΡΠΎΡΡΡ ΠΎΠΏΠ΅ΡΠ΅ΠΆΠ°ΡΡΠΈΡ ΠΏΠΎΠΊΠ°Π·Π°ΡΠ΅Π»Π΅ΠΉ (ΡΡΠΎ Π΄ΠΎΠ»ΠΆΠ½ΠΎ ΠΏΡΠΎΠΈΠ·ΠΎΠΉΡΠΈ) ΠΈ Π½Π΅ΠΊΠΎΡΠΎΡΠΎΠ³ΠΎ Π·Π°ΠΏΠ°Π·Π΄ΡΠ²Π°Π½ΠΈΡ (ΡΡΠΎ ΠΏΡΠΎΠΈΠ·ΠΎΡΠ»ΠΎ ΠΈΠ»ΠΈ ΠΏΡΠΎΠΈΡΡ ΠΎΠ΄ΠΈΡ). ΠΠ½ ΡΡΠ°Π½ΡΠ»ΠΈΡΡΠ΅Ρ ΡΠ΅ ΠΌΠ΅ΡΡ, ΠΊΠΎΡΠΎΡΡΠ΅ ΡΠ²Π»ΡΡΡΡΡ Π½Π°ΠΈΠ±ΠΎΠ»Π΅Π΅ Π²Π°ΠΆΠ½ΡΠΌΠΈ Π½Π° ΠΌΠ°ΠΊΡΠΎΡΡΠΎΠ²Π½Π΅, Π½ΠΎ ΠΏΠΎΠ·Π²ΠΎΠ»ΡΠ΅Ρ ΠΏΠΎΠ»ΡΡΠΈΡΡ Π±ΠΎΠ»Π΅Π΅ ΠΏΠΎΠ΄ΡΠΎΠ±Π½ΡΡ ΠΈΠ½ΡΠΎΡΠΌΠ°ΡΠΈΡ ΠΈ ΠΊΠΎΠ½ΠΊΡΠ΅ΡΠΈΠ·Π°ΡΠΈΡ ΠΏΠΎ ΠΊΠΎΠΌΠ°Π½Π΄Π΅.
ΠΠΎΠΌΠ°Π½Π΄Π½ΡΠΉ ΠΏΡΠ½ΠΊΡ Π½Π°Π΄Π΅ΠΆΠ½ΠΎΡΡΠΈ Π΄ΠΎΠ»ΠΆΠ΅Π½ ΡΠΎΠΎΠ±ΡΠ°ΡΡ Ρ ΠΎΡΠΎΡΠΈΠ΅ ΠΈ ΠΏΠ»ΠΎΡ ΠΈΠ΅ Π½ΠΎΠ²ΠΎΡΡΠΈ Π² ΡΠ΅ΠΆΠΈΠΌΠ΅, Π±Π»ΠΈΠ·ΠΊΠΎΠΌ ΠΊ ΡΠ΅Π°Π»ΡΠ½ΠΎΠΌΡ Π²ΡΠ΅ΠΌΠ΅Π½ΠΈ, Π² Π·Π°Π²ΠΈΡΠΈΠΌΠΎΡΡΠΈ ΠΎΡ ΠΏΡΠΈΠΎΡΠΈΡΠ΅ΡΠ° (ΡΠΈΡΠΊ, ΠΊΡΠΈΡΠΈΡΠ½ΠΎΡΡΡ ΠΈ Ρ. Π.).). Π― Π²ΡΠ΅Π³Π΄Π° Π²Π΅ΡΠΈΠ» Π² ΡΠΎ, ΡΡΠΎ ΠΏΠ»ΠΎΡ ΠΈΠ΅ Π½ΠΎΠ²ΠΎΡΡΠΈ ΠΌΠΎΠΆΠ½ΠΎ ΡΠΎΠΎΠ±ΡΠ°ΡΡ Π±ΡΡΡΡΠΎ, ΠΏΠΎΠΊΠ° ΠΎΠ½ΠΈ Π΅ΡΠ΅ ΡΠΏΡΠ°Π²Π»ΡΠ΅ΠΌΡ.
ΠΠ°ΠΈΠ±ΠΎΠ»Π΅Π΅ ΡΠ΅ΡΡΠ΅Π·Π½ΡΠ΅ ΠΏΡΠ΅Π΄ΡΠΏΡΠ΅ΠΆΠ΄Π΅Π½ΠΈΡ Ρ Β«ΠΊΡΠ°ΡΠ½ΡΠΌ ΠΊΠΎΠ΄ΠΎΠΌΒ» Π΄ΠΎΠ»ΠΆΠ½Ρ Π±ΡΡΡ Π±ΡΡΡΡΠΎ ΡΠΎΠΎΠ±ΡΠ΅Π½Ρ ΠΏΠ»Π°Π½ΠΈΡΠΎΠ²ΡΠΈΠΊΠ°ΠΌ ΠΈ ΡΠΎΡΡΠ°Π²ΠΈΡΠ΅Π»ΡΠΌ Π³ΡΠ°ΡΠΈΠΊΠΎΠ², ΡΡΠΎΠ±Ρ ΠΎΠΏΠ΅ΡΠ°ΡΠΈΠ²Π½ΠΎΠ΅ Π²ΠΌΠ΅ΡΠ°ΡΠ΅Π»ΡΡΡΠ²ΠΎ ΠΌΠΎΠ³Π»ΠΎ Π±ΡΡΡ Π²ΡΠΏΠΎΠ»Π½Π΅Π½ΠΎ Π½Π° Π»Π΅ΡΡ. ΠΠΎΡΠ»Π΅ ΡΡΠΎΠ³ΠΎ Π²ΠΎΠ·ΡΠΌΠΈΡΠ΅ Π·Π° ΠΏΡΠΈΠ²ΡΡΠΊΡ Π²ΡΠΏΠΎΠ»Π½ΡΡΡ Π°Π½Π°Π»ΠΈΠ· ΠΎΡΠ½ΠΎΠ²Π½ΠΎΠΉ ΠΏΡΠΈΡΠΈΠ½Ρ ΠΎΡΠΊΠ°Π·Π°, ΡΡΠΎΠ±Ρ ΡΠ±Π΅Π΄ΠΈΡΡΡΡ, ΡΡΠΎ ΠΏΡΠΈΡΠΈΠ½Π° Π½Π°ΡΡΡΠ΅Π½ΠΈΡ Π½Π΅ Π΄ΠΎΠΏΡΡΠ΅Π½Π° ΠΊ Π²ΡΡ ΠΎΠ΄Ρ Π½Π° Π±ΠΈΡ.
Π’Π°ΠΊ ΡΡΠΎ Π΄Π»Ρ ΡΠ΅Ρ ΠΈΠ· Π²Π°Ρ, ΠΊΡΠΎ ΡΠ²Π»ΡΠ΅ΡΡΡ ΠΌΠ΅ΡΡΠΈΡΠ΅ΡΠΊΠΈΠΌ ΠΌΠ°Π½ΡΡΠΊΠΎΠΌ, Π±ΡΠ΄ΡΡΠ΅ ΠΎΡΡΠΎΡΠΎΠΆΠ½Ρ Ρ ΠΈΠ·ΠΌΠ΅ΡΠ΅Π½ΠΈΡΠΌΠΈ. ΠΠΎΠ»ΡΡΠΈΠ½ΡΡΠ²ΠΎ Π»ΡΠ΄Π΅ΠΉ Π·Π°ΠΏΡΠΎΠ³ΡΠ°ΠΌΠΌΠΈΡΠΎΠ²Π°Π½Ρ Π½Π° ΡΠ°Π±ΠΎΡΡ Ρ ΠΌΠ΅ΡΡΠΈΠΊΠΎΠΉ.ΠΡΠ±ΠΎΡ ΠΏΡΠ°Π²ΠΈΠ»ΡΠ½ΠΎΠ³ΠΎ ΡΠΎΡΠ΅ΡΠ°Π½ΠΈΡ ΠΏΠΎΠΊΠ°Π·Π°ΡΠ΅Π»Π΅ΠΉ ΠΌΠΎΠΆΠ΅Ρ ΠΎΠ±Π΅ΡΠΏΠ΅ΡΠΈΡΡ ΠΎΡΠ»ΠΈΡΠ½ΡΡ ΠΏΡΠΎΠΈΠ·Π²ΠΎΠ΄ΠΈΡΠ΅Π»ΡΠ½ΠΎΡΡΡ. ΠΠ΄Π½Π°ΠΊΠΎ, Π΅ΡΠ»ΠΈ Π²Ρ ΡΠ΄Π΅Π»Π°Π΅ΡΠ΅ ΠΌΠ΅ΡΡΠΈΡΠ΅ΡΠΊΠΈΠ΅ ΠΎΡΠΈΠ±ΠΊΠΈ, Π²Ρ, ΠΊ ΡΠΎΠΆΠ°Π»Π΅Π½ΠΈΡ, ΡΠΈΡΠΊΡΠ΅ΡΠ΅ Π½Π΅ΡΠ΅Π°Π»ΠΈΠ·ΠΎΠ²Π°Π½Π½ΡΠΌΠΈ ΡΠ΅Π»ΡΠΌΠΈ ΠΈΠ»ΠΈ Π΄Π°ΠΆΠ΅ ΠΊΠ°ΡΠ°ΡΡΡΠΎΡΠΎΠΉ.
ΠΠΎΠΊΠ°Π·Π°ΡΠ΅Π»ΠΈ Π½Π°Π΄Π΅ΠΆΠ½ΠΎΡΡΠΈ
ΠΠ°Π΄Π΅ΠΆΠ½ΠΎΡΡΡ ΠΈΠ³ΡΠ°Π΅Ρ ΠΊΠ»ΡΡΠ΅Π²ΡΡ ΡΠΎΠ»Ρ Π² ΡΠΊΠΎΠ½ΠΎΠΌΠΈΡΠ΅ΡΠΊΠΎΠΉ ΡΡΡΠ΅ΠΊΡΠΈΠ²Π½ΠΎΡΡΠΈ ΡΠΈΡΡΠ΅ΠΌ ΠΈ ΠΎΠΏΡΠ΅Π΄Π΅Π»ΡΠ΅ΡΡΡ Ρ ΡΠΎΡΠΊΠΈ Π·ΡΠ΅Π½ΠΈΡ Π²Π΅ΡΠΎΡΡΠ½ΠΎΡΡΠΈ ΠΈΠ»ΠΈ ΡΠ°ΡΡΠΎΡΡ Ρ ΠΏΠΎΠΌΠΎΡΡΡ Π½Π°Π±ΠΎΡΠ° ΡΡΠ°ΡΠΈΡΡΠΈΡΠ΅ΡΠΊΠΈΡ ΠΏΠΎΠΊΠ°Π·Π°ΡΠ΅Π»Π΅ΠΉ, ΠΊΠΎΡΠΎΡΡΠ΅ Π½Π΅Π»ΡΠ·Ρ ΠΈΠ³Π½ΠΎΡΠΈΡΠΎΠ²Π°ΡΡ.
Π ΠΈΠ½ΠΆΠ΅Π½Π΅ΡΠ½ΡΡ ΡΠΈΡΡΠ΅ΠΌΠ°Ρ ΠΈ ΡΠΈΡΡΠ΅ΠΌΠ°Ρ Π±Π΅Π·ΠΎΠΏΠ°ΡΠ½ΠΎΡΡΠΈ Π½Π°Π΄Π΅ΠΆΠ½ΠΎΡΡΡ ΠΎΠΏΡΠ΅Π΄Π΅Π»ΡΠ΅Ρ ΠΎΡΠ΅Π½ΠΊΡ, ΠΏΡΠ΅Π΄ΠΎΡΠ²ΡΠ°ΡΠ΅Π½ΠΈΠ΅ ΠΈ ΡΠΏΡΠ°Π²Π»Π΅Π½ΠΈΠ΅ Π΄ΠΎΠ»Π³ΠΎΠ²Π΅ΡΠ½ΠΎΡΡΡΡ, Π½Π΅ΠΎΠΏΡΠ΅Π΄Π΅Π»Π΅Π½Π½ΠΎΡΡΡΡ ΠΈ ΡΡΠΎΠ²Π½ΡΠΌΠΈ ΠΎΡΠΊΠ°Π·ΠΎΠ² ΠΌΠ°ΡΠΈΠ½Ρ ΠΈΠ»ΠΈ ΡΡΡΠ°Π½ΠΎΠ²ΠΊΠΈ. ΠΠΎΠΊΠ°Π·Π°ΡΠ΅Π»ΠΈ Π½Π°Π΄Π΅ΠΆΠ½ΠΎΡΡΠΈ ΡΠ²Π»ΡΡΡΡΡ ΡΡΠ°ΡΠΈΡΡΠΈΡΠ΅ΡΠΊΠΈΠΌΠΈ ΠΏΠΎ ΡΠ²ΠΎΠ΅ΠΉ ΠΏΡΠΈΡΠΎΠ΄Π΅ ΠΈ Π½Π΅ ΡΠ²Π»ΡΡΡΡΡ Π΅Π΄ΠΈΠ½ΡΠΌ ΠΊΠΎΠΌΠΏΠ»Π΅ΠΊΡΠ½ΡΠΌ ΠΈΠ½ΡΡΡΡΠΌΠ΅Π½ΡΠΎΠΌ Π΄Π»Ρ ΠΎΠΏΡΠ΅Π΄Π΅Π»Π΅Π½ΠΈΡ ΠΏΡΠΈΡΠΈΠ½Ρ ΡΠ±ΠΎΡ, ΠΈ ΠΈΡ Π½Π΅Π»ΡΠ·Ρ ΠΈΡΠΏΠΎΠ»ΡΠ·ΠΎΠ²Π°ΡΡ Π΄Π»Ρ ΠΏΡΠΎΠ³Π½ΠΎΠ·ΠΈΡΠΎΠ²Π°Π½ΠΈΡ Π½Π°Π΄Π΅ΠΆΠ½ΠΎΡΡΠΈ Ρ ΠΎΠΏΡΠ΅Π΄Π΅Π»Π΅Π½Π½ΠΎΡΡΡΡ ΠΈ ΡΠΎΡΠ½ΠΎΡΡΡΡ.
Π‘ Π΄ΡΡΠ³ΠΎΠΉ ΡΡΠΎΡΠΎΠ½Ρ, ΠΈΠ½ΠΆΠ΅Π½Π΅ΡΠΈΡ Π½Π°Π΄Π΅ΠΆΠ½ΠΎΡΡΠΈ ΠΈ ΠΌΠ΅ΡΠΎΠ΄Ρ Π±Π΅Π·ΠΎΠΏΠ°ΡΠ½ΠΎΡΡΠΈ ΡΠ΅ΡΠ½ΠΎ ΡΠ²ΡΠ·Π°Π½Ρ, ΠΏΠΎΡΠΎΠΌΡ ΡΡΠΎ Π² Π½ΠΈΡ ΠΈΡΠΏΠΎΠ»ΡΠ·ΡΡΡΡΡ ΠΎΠ±ΡΠΈΠ΅ ΠΌΠ΅ΡΠΎΠ΄Ρ Π°Π½Π°Π»ΠΈΠ·Π°.ΠΡΠΈ ΠΏΡΠΎΠ΅ΠΊΡΠΈΡΠΎΠ²Π°Π½ΠΈΠΈ Π½Π°Π΄Π΅ΠΆΠ½ΠΎΡΡΠΈ ΠΎΡΠ½ΠΎΠ²Π½ΠΎΠ΅ Π²Π½ΠΈΠΌΠ°Π½ΠΈΠ΅ ΡΠ΄Π΅Π»ΡΠ΅ΡΡΡ ΡΡΠΎΠΈΠΌΠΎΡΡΠΈ ΠΎΡΠΊΠ°Π·Π° ΠΈΠ·-Π·Π° ΠΏΡΠΎΡΡΠΎΡ ΡΠΈΡΡΠ΅ΠΌΡ, ΡΡΠΎΠΈΠΌΠΎΡΡΠΈ Π·Π°ΠΏΠ°ΡΠ½ΡΡ ΡΠ°ΡΡΠ΅ΠΉ, ΡΠ΅ΠΌΠΎΠ½ΡΠΈΡΡΠ΅ΠΌΠΎΠ³ΠΎ ΠΎΠ±ΠΎΡΡΠ΄ΠΎΠ²Π°Π½ΠΈΡ, ΠΏΠ΅ΡΡΠΎΠ½Π°Π»Ρ ΠΈ Π³Π°ΡΠ°Π½ΡΠΈΠΉΠ½ΡΠΌ ΠΏΡΠ°Π²Π°ΠΌ.
Π’Π΅Ρ Π½ΠΎΠ»ΠΎΠ³ΠΈΠΈ Π±Π΅Π·ΠΎΠΏΠ°ΡΠ½ΠΎΡΡΠΈ ΠΎΠ±ΡΡΠ½ΠΎ ΠΎΡΠΈΠ΅Π½ΡΠΈΡΠΎΠ²Π°Π½Ρ Π½Π° Π·Π°ΡΠΈΡΡ Π»ΡΠ΄Π΅ΠΉ. ΠΠ½ΠΈ ΠΈΠΌΠ΅ΡΡ Π΄Π΅Π»ΠΎ ΡΠΎΠ»ΡΠΊΠΎ Ρ ΠΎΡΠΎΠ±ΠΎ ΠΎΠΏΠ°ΡΠ½ΡΠΌΠΈ ΡΠ°ΠΊΡΠΎΡΠ°ΠΌΠΈ ΠΎΡΠΊΠ°Π·Π°. ΠΡΡΠΎΠΊΠ°Ρ Π½Π°Π΄Π΅ΠΆΠ½ΠΎΡΡΡ — ΡΡΠΎ ΡΠ°ΠΊΡΠΎΡ Π±Π΅Π·ΠΎΠΏΠ°ΡΠ½ΠΎΡΡΠΈ, ΡΠ΅Π·ΡΠ»ΡΡΠ°ΡΡ ΠΊΠΎΡΠΎΡΠΎΠ³ΠΎ ΡΠ°ΠΊΠΆΠ΅ Π·Π°Π²ΠΈΡΡΡ ΠΎΡ ΠΌΠ΅ΡΠΎΠ΄ΠΎΠ² ΠΏΡΠΎΠ΅ΠΊΡΠΈΡΠΎΠ²Π°Π½ΠΈΡ ΠΈ ΠΏΡΠΎΠΈΠ·Π²ΠΎΠ΄ΡΡΠ²Π°, Π° Π½Π΅ ΡΠΎΠ»ΡΠΊΠΎ ΠΎΡ ΡΡΠ°ΡΠΈΡΡΠΈΠΊΠΎ-ΠΌΠ°ΡΠ΅ΠΌΠ°ΡΠΈΡΠ΅ΡΠΊΠΈΡ ΠΏΠΎΠΊΠ°Π·Π°ΡΠ΅Π»Π΅ΠΉ ΠΈ ΠΌΠΎΠ΄Π΅Π»Π΅ΠΉ.
ΠΠΠ Π½Π°Π΄Π΅ΠΆΠ½ΠΎΡΡΠΈ
ΠΡΠΎΠΌΡΡΠ»Π΅Π½Π½Π°Ρ ΠΈ ΠΏΡΠΎΠΈΠ·Π²ΠΎΠ΄ΡΡΠ²Π΅Π½Π½Π°Ρ Π½Π°Π΄Π΅ΠΆΠ½ΠΎΡΡΡ ΠΎΡΠ½ΠΎΠ²ΡΠ²Π°Π΅ΡΡΡ Π½Π° ΠΊΠ»ΡΡΠ΅Π²ΡΡ ΠΏΠΎΠΊΠ°Π·Π°ΡΠ΅Π»ΡΡ ΡΡΡΠ΅ΠΊΡΠΈΠ²Π½ΠΎΡΡΠΈ, ΠΊΠΎΡΠΎΡΡΠ΅ ΠΏΠΎΠΌΠΎΠ³Π°ΡΡ ΠΎΡΡΠ»Π΅ΠΆΠΈΠ²Π°ΡΡ Π΄Π΅ΠΉΡΡΠ²ΠΈΡ ΠΏΠΎ ΡΠ΅Ρ Π½ΠΈΡΠ΅ΡΠΊΠΎΠΌΡ ΠΎΠ±ΡΠ»ΡΠΆΠΈΠ²Π°Π½ΠΈΡ Ρ ΡΠ΅ΡΠ΅Π½ΠΈΠ΅ΠΌ Π²ΡΠ΅ΠΌΠ΅Π½ΠΈ.ΠΡΠΈ ΠΈΠ½Π΄ΠΈΠΊΠ°ΡΠΎΡΡ ΠΏΠΎΠΊΠ°Π·ΡΠ²Π°ΡΡ, ΡΠ°Π±ΠΎΡΠ°Π΅Ρ Π»ΠΈ ΠΊΠΎΠΌΠΏΠ°Π½ΠΈΡ ΠΈΠ»ΠΈ ΠΏΠΎΠ΄ΡΠ°Π·Π΄Π΅Π»Π΅Π½ΠΈΠ΅ Π½Π° ΠΏΡΠΈΠ΅ΠΌΠ»Π΅ΠΌΠΎΠΌ ΡΡΠΎΠ²Π½Π΅. ΠΠ½ΠΈ Π½Π΅ ΡΠΎΠ»ΡΠΊΠΎ Π΄Π°ΡΡ ΠΏΡΠ΅Π΄ΡΡΠ°Π²Π»Π΅Π½ΠΈΠ΅ ΠΎ ΡΠ°Π±ΠΎΡΠ΅ ΠΎΡΠ΄Π΅Π»Π° ΡΠ΅Ρ Π½ΠΈΡΠ΅ΡΠΊΠΎΠ³ΠΎ ΠΎΠ±ΡΠ»ΡΠΆΠΈΠ²Π°Π½ΠΈΡ, Π½ΠΎ ΡΠ°ΠΊΠΆΠ΅ ΠΎΡΠΎΠ±ΡΠ°ΠΆΠ°ΡΡΡΡ Π½Π° ΠΈΠ½ΡΠΎΡΠΌΠ°ΡΠΈΠΎΠ½Π½ΡΡ ΠΏΠ°Π½Π΅Π»ΡΡ ΠΈΠ»ΠΈ Π΄ΡΡΠ³ΠΈΡ ΠΊΠΎΠΌΠΏΡΡΡΠ΅ΡΠ½ΡΡ Π½ΠΎΡΠΈΡΠ΅Π»ΡΡ , ΡΡΠΎ ΠΏΠΎΠ·Π²ΠΎΠ»ΡΠ΅Ρ ΠΊΠΎΠΌΠΏΠ°Π½ΠΈΠΈ ΠΏΡΠΈΠ½ΠΈΠΌΠ°ΡΡ ΡΠ΅ΡΠ΅Π½ΠΈΡ ΠΎ Π½Π°Π΄Π΅ΠΆΠ½ΠΎΡΡΠΈ Π°ΠΊΡΠΈΠ²ΠΎΠ², Π±ΡΠ΄ΠΆΠ΅ΡΠ΅ ΠΈ ΠΏΠ»Π°Π½ΠΈΡΠΎΠ²Π°Π½ΠΈΠΈ ΠΏΡΠΎΠΈΠ·Π²ΠΎΠ΄ΡΡΠ²Π°. ΠΠΎΡΠΌΠΎΡΡΠΈΠΌ Π½Π° ΠΎΡΠ½ΠΎΠ²Π½ΡΠ΅.
Π‘ΡΠ΅Π΄Π½ΡΡ Π½Π°ΡΠ°Π±ΠΎΡΠΊΠ° Π½Π° ΠΎΡΠΊΠ°Π·
ΠΠ½Π΄ΠΈΠΊΠ°ΡΠΎΡ MTBF (Π‘ΡΠ΅Π΄Π½Π΅Π΅ Π²ΡΠ΅ΠΌΡ Π½Π°ΡΠ°Π±ΠΎΡΠΊΠΈ Π½Π° ΠΎΡΠΊΠ°Π·) ΠΏΡΠ΅Π΄ΡΡΠ°Π²Π»ΡΠ΅Ρ ΡΠΎΠ±ΠΎΠΉ ΡΡΠ°ΡΠΈΡΡΠΈΡΠ΅ΡΠΊΠΎΠ΅ ΠΈΠ·ΠΌΠ΅ΡΠ΅Π½ΠΈΠ΅ ΠΎΠΆΠΈΠ΄Π°Π΅ΠΌΠΎΠ³ΠΎ ΡΡΠ΅Π΄Π½Π΅Π³ΠΎ Π²ΡΠ΅ΠΌΠ΅Π½ΠΈ Π½Π°ΡΠ°Π±ΠΎΡΠΊΠΈ Π½Π° ΠΎΡΠΊΠ°Π·.ΠΠ½ ΠΏΡΠ΅Π΄ΡΡΠ°Π²Π»ΡΠ΅Ρ ΡΠΎΠ±ΠΎΠΉ ΡΡΠ΅Π΄Π½Π΅Π΅ Π²ΡΠ΅ΠΌΡ ΠΌΠ΅ΠΆΠ΄Ρ Π²ΠΎΠ·Π½ΠΈΠΊΠ½ΠΎΠ²Π΅Π½ΠΈΠ΅ΠΌ ΠΎΠ΄Π½ΠΎΠΉ Π½Π΅ΠΈΡΠΏΡΠ°Π²Π½ΠΎΡΡΠΈ ΠΈ Π½Π°ΡΠ°Π»ΠΎΠΌ ΡΠ»Π΅Π΄ΡΡΡΠ΅ΠΉ. Π‘ΡΠ΅Π΄Π½Π΅Π΅ Π²ΡΠ΅ΠΌΡ Π±Π΅Π·ΠΎΡΠΊΠ°Π·Π½ΠΎΠΉ ΡΠ°Π±ΠΎΡΡ ΠΎΠ±ΡΡΠ½ΠΎ ΠΈΠ·ΠΌΠ΅ΡΡΠ΅ΡΡΡ ΡΠ°ΡΠ°ΠΌΠΈ. ΠΡΠΎ ΡΡΠ°ΡΠΈΡΡΠΈΡΠ΅ΡΠΊΠΈΠΉ ΠΏΠΎΠΊΠ°Π·Π°ΡΠ΅Π»Ρ, ΠΊΠΎΡΠΎΡΡΠΉ ΠΏΠΎΠΌΠΎΠ³Π°Π΅Ρ ΡΡΠΊΠΎΠ²ΠΎΠ΄ΠΈΡΠ΅Π»ΡΠΌ ΠΏΡΠ΅Π΄ΠΏΡΠΈΡΡΠΈΠΉ ΠΈΠ»ΠΈ ΠΌΠ΅Π½Π΅Π΄ΠΆΠ΅ΡΠΎΠ² ΠΏΠΎ ΡΠ΅Ρ Π½ΠΈΡΠ΅ΡΠΊΠΎΠΌΡ ΠΎΠ±ΡΠ»ΡΠΆΠΈΠ²Π°Π½ΠΈΡ ΠΏΠΎΠ½ΠΈΠΌΠ°ΡΡ ΠΈ ΠΏΡΠ΅Π΄ΠΎΡΠ²ΡΠ°ΡΠ°ΡΡ ΡΠ°Π±ΠΎΡΡ ΠΌΠ°ΡΠΈΠ½Ρ ΠΈΠ»ΠΈ Π²ΡΠ΅Π³ΠΎ ΠΏΡΠ΅Π΄ΠΏΡΠΈΡΡΠΈΡ.
ΠΠΎΡΠΊΠΎΠ»ΡΠΊΡ MTBF ΡΠΊΠ°Π·ΡΠ²Π°Π΅Ρ Π²ΡΠ΅ΠΌΡ ΡΠ°Π±ΠΎΡΡ Π°ΠΊΡΠΈΠ²Π°, ΡΡΠΎ ΠΏΠΎΠΊΠ°Π·Π°ΡΠ΅Π»Ρ, ΠΊΠΎΡΠΎΡΡΠΉ ΡΠ΅ΡΠ½ΠΎ ΡΠ²ΡΠ·Π°Π½ Ρ ΡΠ°ΡΡΠ΅ΡΠΎΠΌ Π½Π°Π΄Π΅ΠΆΠ½ΠΎΡΡΠΈ ΡΡΡΠ°Π½ΠΎΠ²ΠΎΠΊ ΠΈ ΠΎΠ±ΠΎΡΡΠ΄ΠΎΠ²Π°Π½ΠΈΡ, ΡΠ°ΠΊ ΠΆΠ΅ ΠΊΠ°ΠΊ ΠΈ ΠΏΠΎΠΊΠ°Π·Π°ΡΠ΅Π»ΠΈ, ΠΈΡΠΏΠΎΠ»ΡΠ·ΡΠ΅ΠΌΡΠ΅ Π΄Π»Ρ ΡΠ°ΡΡΠ΅ΡΠ° ΡΠΊΡΠΏΠ»ΡΠ°ΡΠ°ΡΠΈΠΎΠ½Π½ΠΎΠΉ Π³ΠΎΡΠΎΠ²Π½ΠΎΡΡΠΈ ΠΌΠ°ΡΠΈΠ½Ρ, Π² ΡΠ°ΡΡΠ½ΠΎΡΡΠΈ OEE (ΠΠ±ΡΠ΅Π΅ ΠΎΠ±ΠΎΡΡΠ΄ΠΎΠ²Π°Π½ΠΈΠ΅ ΠΡΡΠ΅ΠΊΡΠΈΠ²Π½ΠΎΡΡΡ).
ΠΡΠΈ ΠΎΡΠΎΠ±Π΅Π½Π½ΠΎΡΡΠΈ Π΄Π΅Π»Π°ΡΡ MTBF ΠΎΠ΄Π½ΠΈΠΌ ΠΈΠ· ΠΎΡΠ½ΠΎΠ²Π½ΡΡ ΠΠΠ, ΠΌΠΎΠ½ΠΈΡΠΎΡΠΈΠ½Π³ ΠΊΠΎΡΠΎΡΠΎΠ³ΠΎ ΡΠ²Π»ΡΠ΅ΡΡΡ ΠΎΠ΄Π½ΠΈΠΌ ΠΈΠ· ΠΊΠ»ΡΡΠ΅Π²ΡΡ ΡΠ°ΠΊΡΠΎΡΠΎΠ² ΠΏΠΎΠ²ΡΡΠ΅Π½ΠΈΡ ΠΏΡΠΎΠΈΠ·Π²ΠΎΠ΄ΠΈΡΠ΅Π»ΡΠ½ΠΎΡΡΠΈ ΠΏΡΠ΅Π΄ΠΏΡΠΈΡΡΠΈΡ ΠΈ ΠΈΠ·ΠΌΠ΅ΡΠ΅Π½ΠΈΡ Π½Π°Π΄Π΅ΠΆΠ½ΠΎΡΡΠΈ Π°ΠΊΡΠΈΠ²Π°.
MTTR
Π‘ΡΠ΅Π΄Π½Π΅Π΅ Π²ΡΠ΅ΠΌΡ ΡΠ΅ΠΌΠΎΠ½ΡΠ° ΠΈΠ»ΠΈ MTTR — ΡΡΠΎ ΡΡΠ΅Π΄Π½Π΅Π΅ Π²ΡΠ΅ΠΌΡ, Π² ΡΠ΅ΡΠ΅Π½ΠΈΠ΅ ΠΊΠΎΡΠΎΡΠΎΠ³ΠΎ Π°ΠΊΡΠΈΠ² (ΠΈΠ½ΡΡΡΡΠΌΠ΅Π½Ρ, ΠΎΠ±ΠΎΡΡΠ΄ΠΎΠ²Π°Π½ΠΈΠ΅, Π·Π°Π²ΠΎΠ΄) Π΄ΠΎΠ»ΠΆΠ΅Π½ ΡΠ½ΠΎΠ²Π° Π½Π°ΡΠ°ΡΡ ΡΠ°Π±ΠΎΡΡ. Π ΠΏΡΠΎΡΡΠ΅ΠΉΡΠ΅ΠΉ ΡΠΎΡΠΌΡΠ»ΠΈΡΠΎΠ²ΠΊΠ΅ ΡΡΠΎ ΡΠΎΠΎΡΠ½ΠΎΡΠ΅Π½ΠΈΠ΅ ΠΌΠ΅ΠΆΠ΄Ρ ΠΎΠ±ΡΠΈΠΌ Π²ΡΠ΅ΠΌΠ΅Π½Π΅ΠΌ ΠΎΠ±ΡΠ»ΡΠΆΠΈΠ²Π°Π½ΠΈΡ ΠΈ ΠΊΠΎΠ»ΠΈΡΠ΅ΡΡΠ²ΠΎΠΌ ΡΠ΅ΠΌΠΎΠ½ΡΠΎΠ². ΠΡΠΎ ΡΡΠ½Π΄Π°ΠΌΠ΅Π½ΡΠ°Π»ΡΠ½ΡΠΉ ΠΏΠΎΠΊΠ°Π·Π°ΡΠ΅Π»Ρ ΡΠ΅ΠΌΠΎΠ½ΡΠΎΠΏΡΠΈΠ³ΠΎΠ΄Π½ΠΎΡΡΠΈ ΡΠ΅ΠΌΠΎΠ½ΡΠΈΡΡΠ΅ΠΌΡΡ ΡΠ»Π΅ΠΌΠ΅Π½ΡΠΎΠ².ΠΠ°ΡΠ΅ΠΌΠ°ΡΠΈΡΠ΅ΡΠΊΠΈ Π²ΡΡΠ°ΠΆΠ΅Π½Π½ΡΠ΅ Π·Π½Π°ΡΠ΅Π½ΠΈΠ΅ΠΌ, ΠΏΡΠ΅Π΄ΡΡΠ°Π²Π»ΡΡΡΠΈΠΌ ΡΡΠ΅Π΄Π½Π΅Π΅ Π²ΡΠ΅ΠΌΡ, Π½ΠΈΠ·ΠΊΠΈΠ΅ Π·Π½Π°ΡΠ΅Π½ΠΈΡ ΡΠΊΠ°Π·ΡΠ²Π°ΡΡ Π½Π° Π»ΡΡΡΠΈΠ΅ Ρ Π°ΡΠ°ΠΊΡΠ΅ΡΠΈΡΡΠΈΠΊΠΈ. Π¦Π΅Π»ΡΡ ΠΎΡΠ΄Π΅Π»Π° ΡΠ΅Ρ Π½ΠΈΡΠ΅ΡΠΊΠΎΠ³ΠΎ ΠΎΠ±ΡΠ»ΡΠΆΠΈΠ²Π°Π½ΠΈΡ ΡΠ²Π»ΡΠ΅ΡΡΡ ΠΏΠΎΠ΄Π΄Π΅ΡΠΆΠ°Π½ΠΈΠ΅ ΡΡΠ΅Π΄Π½Π΅Π³ΠΎ Π²ΡΠ΅ΠΌΠ΅Π½ΠΈ Π²ΠΎΡΡΡΠ°Π½ΠΎΠ²Π»Π΅Π½ΠΈΡ ΡΠ°Π±ΠΎΡΠΎΡΠΏΠΎΡΠΎΠ±Π½ΠΎΡΡΠΈ Π² ΠΏΡΠ΅Π΄Π΅Π»Π°Ρ Π΄ΠΎΠΏΡΡΡΠΈΠΌΡΡ Π·Π½Π°ΡΠ΅Π½ΠΈΠΉ, ΡΡΠΎΠ±Ρ ΡΠΌΠ΅Π½ΡΡΠΈΡΡ ΠΈΡ Π² ΠΌΠ°ΠΊΡΠΈΠΌΠ°Π»ΡΠ½ΠΎ Π²ΠΎΠ·ΠΌΠΎΠΆΠ½ΠΎΠΉ ΡΡΠ΅ΠΏΠ΅Π½ΠΈ. ΠΡΡΠ»Π΅ΠΆΠΈΠ²Π°Π½ΠΈΠ΅ ΠΈ ΠΌΠΎΠ½ΠΈΡΠΎΡΠΈΠ½Π³ MTTR ΠΌΠΎΠΆΠ΅Ρ ΠΏΠΎΠΌΠΎΡΡ ΡΠΎΠΊΡΠ°ΡΠΈΡΡ Π²ΡΠ΅ΠΌΡ ΡΠ΅ΠΌΠΎΠ½ΡΠ°, ΡΠ»ΡΡΡΠΈΡΡ ΡΠΏΡΠ°Π²Π»Π΅Π½ΠΈΠ΅ ΡΠΊΠ»Π°Π΄ΠΎΠΌ ΠΈ ΠΏΡΠΈΠ½ΡΡΡ ΠΎΠ±ΠΎΡΠ½ΠΎΠ²Π°Π½Π½ΡΠ΅ ΡΠ΅ΡΠ΅Π½ΠΈΡ ΠΎ ΡΡΡΠ°ΡΠ΅Π³ΠΈΡΡ ΠΎΠ±ΡΠ»ΡΠΆΠΈΠ²Π°Π½ΠΈΡ.
MTTF
Π ΡΠ°ΠΌΠΊΠ°Ρ ΡΠ΅Ρ ΠΆΠ΅ ΠΏΠ°ΡΠ°ΠΌΠ΅ΡΡΠΎΠ² ΠΌΡ ΡΠ°ΠΊΠΆΠ΅ Π½Π°Ρ ΠΎΠ΄ΠΈΠΌ MTTF (ΡΡΠ΅Π΄Π½Π΅Π΅ Π²ΡΠ΅ΠΌΡ Π΄ΠΎ ΠΎΡΠΊΠ°Π·Π°), ΠΊΠΎΡΠΎΡΠΎΠ΅ ΠΎΡΠ½ΠΎΡΠΈΡΡΡ ΠΊ ΡΡΠ΅Π΄Π½Π΅ΠΌΡ Π²ΡΠ΅ΠΌΠ΅Π½ΠΈ Π²ΠΎΠ·Π½ΠΈΠΊΠ½ΠΎΠ²Π΅Π½ΠΈΡ ΠΎΡΠΊΠ°Π·Π°.MTBF ΠΈ MTTF — ΡΡΠΎ ΡΡΠ°ΡΠΈΡΡΠΈΡΠ΅ΡΠΊΠΈΠ΅ ΠΏΠ°ΡΠ°ΠΌΠ΅ΡΡΡ, ΠΈΡΠΏΠΎΠ»ΡΠ·ΡΠ΅ΠΌΡΠ΅ Π΄Π»Ρ ΠΏΡΠ΅Π΄ΡΡΠ°Π²Π»Π΅Π½ΠΈΡ Π½Π°Π΄Π΅ΠΆΠ½ΠΎΡΡΠΈ ΠΊΠΎΠΌΠΏΠΎΠ½Π΅Π½ΡΠΎΠ², ΠΊΠΎΡΠΎΡΡΠ΅ Π½Π΅ ΡΠ»Π΅Π΄ΡΠ΅Ρ ΠΏΡΡΠ°ΡΡ ΡΠΎ ΡΡΠ΅Π΄Π½Π΅ΠΉ ΠΏΡΠΎΠ΄ΠΎΠ»ΠΆΠΈΡΠ΅Π»ΡΠ½ΠΎΡΡΡΡ ΠΎΠ±ΡΠ»ΡΠΆΠΈΠ²Π°Π½ΠΈΡ. ΠΠ½Π°ΡΠ΅Π½ΠΈΡ MTTF ΠΎΠ±ΡΡΠ½ΠΎ ΡΡΠΈΡΡΠ²Π°ΡΡΡΡ Π΄Π»Ρ ΠΏΡΠΈΠ±ΠΎΡΠΎΠ² ΠΈ Π΄Π°ΡΡΠΈΠΊΠΎΠ² ΠΈ ΠΎΠ±ΡΡΠ½ΠΎ Π·Π°ΠΌΠ΅Π½ΡΡΡΡΡ Π² ΡΠ»ΡΡΠ°Π΅ ΠΎΡΠΊΠ°Π·Π°. ΠΠ°ΠΆΠ½ΠΎ ΠΎΡΠΌΠ΅ΡΠΈΡΡ, ΡΡΠΎ MTBF — ΡΡΠΎ ΡΡΠΌΠΌΠ° MTTF ΠΈ MTTR. Π‘Π»Π΅Π΄ΠΎΠ²Π°ΡΠ΅Π»ΡΠ½ΠΎ, Π΅ΡΠ»ΠΈ ΠΎΡΠΊΠ°Π· ΠΏΡΠΎΠΈΡΡ ΠΎΠ΄ΠΈΡ Π² ΠΌΠΎΠΌΠ΅Π½Ρ Π²ΡΠ΅ΠΌΠ΅Π½ΠΈ t1, ΠΏΠΎΡΡΠ΅Π±ΡΠ΅ΡΡΡ Π²ΡΠ΅ΠΌΡ Π΄Π»Ρ Π·Π°Π²Π΅ΡΡΠ΅Π½ΠΈΡ ΡΠ΅ΠΌΠΎΠ½ΡΠ° ΠΈ Π²ΡΠ΅ΠΌΡ Π΄Π»Ρ ΡΠΎΠ³ΠΎ, ΡΡΠΎΠ±Ρ ΠΎΡΠΊΠ°Π· ΠΏΡΠΎΠΈΠ·ΠΎΡΠ΅Π» ΠΏΠΎΡΠ»Π΅ Π²ΡΠ΅ΠΌΠ΅Π½ΠΈ t2.
ΠΠΎ ΡΡΡΠΈ, MTBF = t2 — t1 = MTTF + MTTR.Π‘Π»Π΅Π΄ΡΠ΅Ρ ΠΏΡΠΎΡΠ²Π»ΡΡΡ ΠΎΡΡΠΎΡΠΎΠΆΠ½ΠΎΡΡΡ, ΡΡΠΎΠ±Ρ Π½Π΅ ΠΏΡΡΠ°ΡΡ Π·Π½Π°ΡΠ΅Π½ΠΈΠ΅ MTBF Ρ ΠΈΠ½ΡΠ΅Π½ΡΠΈΠ²Π½ΠΎΡΡΡΡ ΠΎΡΠΊΠ°Π·ΠΎΠ², ΠΊΠΎΡΠΎΡΠ°Ρ Π²ΠΌΠ΅ΡΡΠΎ ΡΡΠΎΠ³ΠΎ ΠΏΡΠ΅Π΄ΡΡΠ°Π²Π»ΡΠ΅Ρ ΠΊΠΎΠ»ΠΈΡΠ΅ΡΡΠ²ΠΎ Π°ΠΊΡΠΈΠ²ΠΎΠ², Π½Π΅ ΡΠ°Π±ΠΎΡΠ°ΡΡΠΈΡ ΠΏΠΎ ΠΏΡΠΎΡΠ΅ΡΡΠ²ΠΈΠΈ ΠΎΠΏΡΠ΅Π΄Π΅Π»Π΅Π½Π½ΠΎΠ³ΠΎ Π²ΡΠ΅ΠΌΠ΅Π½ΠΈ, ΡΡΠ΅Π΄ΠΈ ΠΎΠ±ΡΠ΅Π³ΠΎ ΡΠΈΡΠ»Π° ΠΎΡΡΠ»Π΅ΠΆΠΈΠ²Π°Π΅ΠΌΡΡ . Π ΡΡΠΎΠΌΡ Π°Π½Π°Π»ΠΈΠ·Ρ Π½Π΅ΠΎΠ±Ρ ΠΎΠ΄ΠΈΠΌΠΎ Π΄ΠΎΠ±Π°Π²ΠΈΡΡ ΡΠΎΡΠΌΡΠ»Ρ Π΄Π»Ρ Π½Π°Π΄Π΅ΠΆΠ½ΠΎΡΡΠΈ = MTBF / (MTBF + MTTR). ΠΡΠΎ ΡΡΠ°Π²Π½Π΅Π½ΠΈΠ΅ ΡΡΡΠ°Π½Π°Π²Π»ΠΈΠ²Π°Π΅Ρ Π²Π·Π°ΠΈΠΌΠΎΡΠ²ΡΠ·Ρ ΠΌΠ΅ΠΆΠ΄Ρ ΡΠ»ΡΡΡΠ΅Π½ΠΈΠ΅ΠΌ MTBF ΠΈ Π΄ΡΡΠ³ΠΈΠΌΠΈ ΠΏΠΎΠΊΠ°Π·Π°ΡΠ΅Π»ΡΠΌΠΈ, ΡΠ²ΡΠ·Π°Π½Π½ΡΠΌΠΈ Ρ ΠΏΡΠΎΠΈΠ·Π²ΠΎΠ΄ΠΈΡΠ΅Π»ΡΠ½ΠΎΡΡΡΡ ΠΏΡΠ΅Π΄ΠΏΡΠΈΡΡΠΈΡ.
AVA ΠΈ PMC
ΠΠ΅Π»ΡΠ·Ρ ΡΠΏΡΡΠΊΠ°ΡΡ ΠΈΠ· Π²ΠΈΠ΄ΡAVA (Π΄ΠΎΡΡΡΠΏΠ½ΠΎΡΡΡ) ΠΈ PMC (ΠΏΡΠΎΡΠ΅Π½Ρ ΠΏΠ»Π°Π½ΠΎΠ²ΠΎΠ³ΠΎ ΠΎΠ±ΡΠ»ΡΠΆΠΈΠ²Π°Π½ΠΈΡ).ΠΠ±Π° ΠΏΠΎΠΊΠ°Π·Π°ΡΠ΅Π»Ρ Π²ΡΡΠ°ΠΆΠ΅Π½Ρ Π² ΠΏΡΠΎΡΠ΅Π½ΡΠ°Ρ . AVA — ΡΡΠΎ ΠΏΠΎΠΊΠ°Π·Π°ΡΠ΅Π»Ρ ΠΏΡΠΎΠΈΠ·Π²ΠΎΠ΄ΠΈΡΠ΅Π»ΡΠ½ΠΎΡΡΠΈ Π°ΠΊΡΠΈΠ²Π° ΠΈ ΠΎΡΠ½ΠΎΠ²Π½ΠΎΠΉ ΠΊΠΎΠΌΠΏΠΎΠ½Π΅Π½Ρ OEE, ΠΊΠΎΡΠΎΡΡΠΉ ΠΈΠ·ΠΌΠ΅ΡΡΠ΅Ρ ΠΎΠ±ΡΡΡ ΡΡΡΠ΅ΠΊΡΠΈΠ²Π½ΠΎΡΡΡ Π°ΠΊΡΠΈΠ²Π° ΠΈ ΠΎΠ±ΠΎΠ±ΡΠ°Π΅Ρ Π΅Π³ΠΎ Π΄ΠΎΡΡΡΠΏΠ½ΠΎΡΡΡ, ΡΡΡΠ΅ΠΊΡΠΈΠ²Π½ΠΎΡΡΡ ΠΈ ΠΊΠ°ΡΠ΅ΡΡΠ²ΠΎ. PMC — ΡΡΠΎ ΠΏΡΠΎΡΠ΅Π½Ρ ΡΠ°ΡΠΎΠ² ΠΎΠ±ΡΠ»ΡΠΆΠΈΠ²Π°Π½ΠΈΡ, Π½Π΅ΠΎΠ±Ρ ΠΎΠ΄ΠΈΠΌΡΡ Π΄Π»Ρ ΠΏΠ»Π°Π½ΠΎΠ²ΠΎΠ³ΠΎ ΠΎΠ±ΡΠ»ΡΠΆΠΈΠ²Π°Π½ΠΈΡ, ΠΏΠΎ ΡΡΠ°Π²Π½Π΅Π½ΠΈΡ Ρ Π²Π½Π΅ΠΏΠ»Π°Π½ΠΎΠ²ΡΠΌ ΠΎΠ±ΡΠ»ΡΠΆΠΈΠ²Π°Π½ΠΈΠ΅ΠΌ. ΠΠ½ ΡΠ°ΡΡΡΠΈΡΡΠ²Π°Π΅ΡΡΡ ΠΏΡΡΠ΅ΠΌ Π΄Π΅Π»Π΅Π½ΠΈΡ Π·Π°ΠΏΠ»Π°Π½ΠΈΡΠΎΠ²Π°Π½Π½ΡΡ ΡΠ°ΡΠΎΠ² ΡΠ°Π±ΠΎΡΡ Π½Π° ΡΠ΅Ρ Π½ΠΈΡΠ΅ΡΠΊΠΎΠ΅ ΠΎΠ±ΡΠ»ΡΠΆΠΈΠ²Π°Π½ΠΈΠ΅ Π½Π° ΠΎΠ±ΡΠ΅Π΅ ΠΊΠΎΠ»ΠΈΡΠ΅ΡΡΠ²ΠΎ ΡΠ°ΡΠΎΠ² ΡΠ΅Ρ Π½ΠΈΡΠ΅ΡΠΊΠΎΠ³ΠΎ ΠΎΠ±ΡΠ»ΡΠΆΠΈΠ²Π°Π½ΠΈΡ Π·Π° ΠΊΠΎΠ½ΠΊΡΠ΅ΡΠ½ΡΠΉ ΠΏΠ΅ΡΠΈΠΎΠ΄ Π²ΡΠ΅ΠΌΠ΅Π½ΠΈ.
ΠΠΎΠΊΠ°Π·Π°ΡΠ΅Π»ΠΈ Π½Π°Π΄Π΅ΠΆΠ½ΠΎΡΡΠΈ Π² ΡΠΏΡΠ°Π²Π»Π΅Π½ΠΈΠΈ ΠΌΠ΅Π΄ΠΈΡΠΈΠ½ΡΠΊΠΈΠΌ ΠΎΠ±ΠΎΡΡΠ΄ΠΎΠ²Π°Π½ΠΈΠ΅ΠΌ
- R.Π‘. ΠΠ°ΠΌΠΈΠ»Π°
- Π. Π. Π£ΠΈΠ»ΡΡΠΌ
- Π€. Π Π΅Π½Π°Π½
- Π. Π Π΅Π½Π°ΡΠΎ
Π Π΅ΡΠ΅ΡΠ°Ρ
Π Π΄Π°Π½Π½ΠΎΠΉ ΡΡΠ°ΡΡΠ΅ ΠΏΡΠ΅Π΄ΡΡΠ°Π²Π»Π΅Π½ΠΎ ΠΈΡΡΠ»Π΅Π΄ΠΎΠ²Π°Π½ΠΈΠ΅, Π² ΠΊΠΎΡΠΎΡΠΎΠΌ ΠΈΡΠΏΠΎΠ»ΡΠ·ΡΡΡΡΡ ΠΏΠΎΠΊΠ°Π·Π°ΡΠ΅Π»ΠΈ Π½Π°Π΄Π΅ΠΆΠ½ΠΎΡΡΠΈ Π΄Π»Ρ ΡΠΏΡΠ°Π²Π»Π΅Π½ΠΈΡ ΠΌΠ΅Π΄ΠΈΡΠΈΠ½ΡΠΊΠΈΠΌ ΠΎΠ±ΠΎΡΡΠ΄ΠΎΠ²Π°Π½ΠΈΠ΅ΠΌ. ΠΠ»Ρ ΡΠ°ΡΡΠ΅ΡΠ° ΡΡΠ΅Π΄Π½Π΅ΠΉ Π½Π°ΡΠ°Π±ΠΎΡΠΊΠΈ Π½Π° ΠΎΡΠΊΠ°Π· ΠΈ ΡΡΠ΅Π΄Π½Π΅Π³ΠΎ Π²ΡΠ΅ΠΌΠ΅Π½ΠΈ Π΄ΠΎ ΡΠ΅ΠΌΠΎΠ½ΡΠ° ΡΡΠΈΡΡΠ²Π°ΡΡΡΡ Π·Π°ΠΏΠΈΡΠΈ ΠΎ ΠΊΠΎΡΡΠ΅ΠΊΡΠΈΡΡΡΡΠ΅ΠΌ ΠΈ ΠΏΡΠΎΡΠΈΠ»Π°ΠΊΡΠΈΡΠ΅ΡΠΊΠΎΠΌ ΠΎΠ±ΡΠ»ΡΠΆΠΈΠ²Π°Π½ΠΈΠΈ. ΠΡΠΈ ΠΏΡΠΈΠΌΠ΅Π½Π΅Π½ΠΈΠΈ ΡΡΠΎΠ³ΠΎ ΠΌΠ΅ΡΠΎΠ΄Π° ΡΠΎΠ±ΡΠ°Π½Π½ΡΠ΅ Π·Π°ΠΏΠΈΡΠΈ ΡΠ΅Ρ Π½ΠΈΡΠ΅ΡΠΊΠΎΠ³ΠΎ ΠΎΠ±ΡΠ»ΡΠΆΠΈΠ²Π°Π½ΠΈΡ ΠΎΡΠ½ΠΎΡΡΡΡΡ ΠΊ Π°Π½Π΅ΡΡΠ΅Π·ΠΈΠΎΠ»ΠΎΠ³ΠΈΡΠ΅ΡΠΊΠΎΠΌΡ ΠΎΠ±ΠΎΡΡΠ΄ΠΎΠ²Π°Π½ΠΈΡ, ΠΈΡΠΏΠΎΠ»ΡΠ·ΡΠ΅ΠΌΠΎΠΌΡ Π² ΠΎΠΏΠ΅ΡΠ°ΡΠΈΠΎΠ½Π½ΡΡ ΠΏΡΡΠΈ ΠΌΠ΅Π΄ΠΈΡΠΈΠ½ΡΠΊΠΈΡ ΡΡΡΠ΅ΠΆΠ΄Π΅Π½ΠΈΠΉ Π³ΠΎΡΡΠ΄Π°ΡΡΡΠ²Π΅Π½Π½ΠΎΠΉ ΡΠ΅ΡΠΈ ΡΡΠ°ΡΠ° Π‘Π°Π½ΡΠ°-ΠΠ°ΡΠ°ΡΠΈΠ½Π°, ΠΡΠ°Π·ΠΈΠ»ΠΈΡ.ΠΠ½Π°Π»ΠΈΠ· ΠΏΠΎΠΊΠ°Π·Π°ΡΠ΅Π»Π΅ΠΉ ΠΏΡΠΎΠΈΠ·Π²ΠΎΠ΄ΠΈΠ»ΡΡ ΠΏΠΎ ΠΌΠ°ΡΠΊΠ°ΠΌ ΠΈ Π΄Π°ΡΠ΅ ΡΡΡΠ°Π½ΠΎΠ²ΠΊΠΈ Π°Π½Π΅ΡΡΠ΅Π·ΠΈΠΎΠ»ΠΎΠ³ΠΈΡΠ΅ΡΠΊΠΎΠ³ΠΎ ΠΎΠ±ΠΎΡΡΠ΄ΠΎΠ²Π°Π½ΠΈΡ. Π‘ΡΠ΅Π΄Π½Π΅Π΅ Π²ΡΠ΅ΠΌΡ Π½Π°ΡΠ°Π±ΠΎΡΠΊΠΈ Π½Π° ΠΎΡΠΊΠ°Π· Π°Π½Π°Π»ΠΈΠ·ΠΈΡΡΠ΅ΠΌΠΎΠ³ΠΎ ΠΎΠ±ΠΎΡΡΠ΄ΠΎΠ²Π°Π½ΠΈΡ ΡΠ²Π»ΡΠ΅ΡΡΡ ΠΏΡΠΈΠ΅ΠΌΠ»Π΅ΠΌΡΠΌ ΠΈ ΡΠΎΡΡΠ°Π²Π»ΡΠ»ΠΎ 16 ΠΌΠ΅ΡΡΡΠ΅Π² Π΄Π»Ρ ΠΌΠ°ΡΠΊΠΈ A ΠΈ 10 ΠΌΠ΅ΡΡΡΠ΅Π² Π΄Π»Ρ ΠΌΠ°ΡΠΊΠΈ B. ΠΠ΄Π½Π°ΠΊΠΎ Π±ΡΠ»ΠΎ Π½Π΅Π²ΠΎΠ·ΠΌΠΎΠΆΠ½ΠΎ ΡΠ΄Π΅Π»Π°ΡΡ Π²ΡΠ²ΠΎΠ΄ ΠΎ ΡΠΎΠΌ, ΡΠ²Π»ΡΠ΅ΡΡΡ Π»ΠΈ ΠΏΠ΅ΡΠΈΠΎΠ΄ΠΈΡΠ½ΠΎΡΡΡ Π²ΡΠΏΠΎΠ»Π½Π΅Π½Π½ΠΎΠ³ΠΎ ΠΏΡΠΎΡΠΈΠ»Π°ΠΊΡΠΈΡΠ΅ΡΠΊΠΎΠ³ΠΎ ΠΎΠ±ΡΠ»ΡΠΆΠΈΠ²Π°Π½ΠΈΡ ΡΡΡΠ΅ΠΊΡΠΈΠ²Π½ΠΎΠΉ ΠΈΠ»ΠΈ Π½Π΅Ρ Π΄Π»Ρ Π»ΠΎΠΊΠ°Π»ΠΈΠ·Π°ΡΠΈΠΈ Π½Π΅ΡΠ΄Π°ΡΠΈ. Π‘Π΄Π΅Π»Π°Π½ Π²ΡΠ²ΠΎΠ΄ ΠΎ ΡΠΎΠΌ, ΡΡΠΎ Π°Π½Π°Π»ΠΈΠ· ΠΏΠΎΠΊΠ°Π·Π°ΡΠ΅Π»Π΅ΠΉ, Π΅ΡΠ»ΠΈ Π½Π΅ ΠΎΠΏΠΈΡΡΠ²Π°Π΅Ρ ΠΎΠΏΠ΅ΡΠ°ΡΠΈΠΎΠ½Π½ΡΠΉ ΠΊΠΎΠ½ΡΠ΅ΠΊΡΡ ΠΈΡΠΏΠΎΠ»ΡΠ·ΠΎΠ²Π°Π½ΠΈΡ, ΠΌΠΎΠΆΠ΅Ρ ΠΏΡΠΈΠ²Π΅ΡΡΠΈ ΠΊ Π²ΡΠ²ΠΎΠ΄Ρ ΠΎ Π½Π°Π΄Π΅ΠΆΠ½ΠΎΡΡΠΈ ΠΎΡΠ°ΠΆΠ΄Π΅Π½Π½ΡΡ Π±ΡΠ΅Π½Π΄ΠΎΠ², ΠΊΠΎΡΠΎΡΡΠ΅ Π½Π΅ ΡΠΎΠΎΡΠ²Π΅ΡΡΡΠ²ΡΡΡ Π΄Π΅ΠΉΡΡΠ²ΠΈΡΠ΅Π»ΡΠ½ΠΎΡΡΠΈ.
ΠΠ»ΡΡΠ΅Π²ΡΠ΅ ΡΠ»ΠΎΠ²Π°
ΠΠΎΠΊΠ°Π·Π°ΡΠ΅Π»ΠΈ Π½Π°Π΄Π΅ΠΆΠ½ΠΎΡΡΠΈ ΠΌΠ΅Π΄ΠΈΡΠΈΠ½ΡΠΊΠΎΠ³ΠΎ ΠΎΠ±ΠΎΡΡΠ΄ΠΎΠ²Π°Π½ΠΈΡ Clinical EngineeringΠΡΠΎ ΠΏΡΠ΅Π΄Π²Π°ΡΠΈΡΠ΅Π»ΡΠ½ΡΠΉ ΠΏΡΠΎΡΠΌΠΎΡΡ ΡΠΎΠ΄Π΅ΡΠΆΠΈΠΌΠΎΠ³ΠΎ ΠΏΠΎΠ΄ΠΏΠΈΡΠΊΠΈ,
Π²ΠΎΠΉΠ΄ΠΈΡΠ΅ Π² ΡΠΈΡΡΠ΅ΠΌΡ, ΡΡΠΎΠ±Ρ ΠΏΡΠΎΠ²Π΅ΡΠΈΡΡ Π΄ΠΎΡΡΡΠΏ.
ΠΡΠ΅Π΄Π²Π°ΡΠΈΡΠ΅Π»ΡΠ½ΡΠΉ ΠΏΡΠΎΡΠΌΠΎΡΡ
ΠΠ΅Π²ΠΎΠ·ΠΌΠΎΠΆΠ½ΠΎ ΠΎΡΠΎΠ±ΡΠ°Π·ΠΈΡΡ ΠΏΡΠ΅Π΄Π²Π°ΡΠΈΡΠ΅Π»ΡΠ½ΡΠΉ ΠΏΡΠΎΡΠΌΠΎΡΡ. Π‘ΠΊΠ°ΡΠ°ΡΡ ΠΏΡΠ΅Π²ΡΡ PDF.
ΠΠ½ΡΠΎΡΠΌΠ°ΡΠΈΡ ΠΎΠ± Π°Π²ΡΠΎΡΡΠΊΠΈΡ ΠΏΡΠ°Π²Π°Ρ
Β© Springer International Publishing Switzerland 2015
ΠΠ²ΡΠΎΡΡ ΠΈ Π°ΡΡΠΈΠ»ΠΈΡΠΎΠ²Π°Π½Π½ΡΠ΅ Π»ΠΈΡΠ°
- R. S. Camila
- C. A. William
- F. Renan
- G.Π Π΅Π½Π°ΡΠΎ
- 1. ΠΠ½ΡΡΠΈΡΡΡ Π±ΠΈΠΎΠΌΠ΅Π΄ΠΈΡΠΈΠ½ΡΠΊΠΎΠΉ ΠΈΠ½ΠΆΠ΅Π½Π΅ΡΠΈΠΈ / ΡΠ°ΠΊΡΠ»ΡΡΠ΅Ρ ΡΠ»Π΅ΠΊΡΡΠΎΡΠ΅Ρ Π½ΠΈΠΊΠΈ Π€Π΅Π΄Π΅ΡΠ°Π»ΡΠ½ΡΠΉ ΡΠ½ΠΈΠ²Π΅ΡΡΠΈΡΠ΅Ρ Π‘Π°Π½ΡΠ°-ΠΠ°ΡΠ°ΡΠΈΠ½Π° Π€Π»ΠΎΡΠΈΠ°Π½ΠΎΠΏΠΎΠ»ΠΈΡ, ΠΡΠ°Π·ΠΈΠ»ΠΈΡ
ΠΠ»ΡΡΠ΅Π²ΡΠ΅ ΠΏΠΎΠΊΠ°Π·Π°ΡΠ΅Π»ΠΈ ΡΡΡΠ΅ΠΊΡΠΈΠ²Π½ΠΎΡΡΠΈ Π΄Π»Ρ ΡΡΡΠ΅ΠΊΡΠΈΠ²Π½ΠΎΠ³ΠΎ ΡΠΏΡΠ°Π²Π»Π΅Π½ΠΈΡ β’ Infraspeak Blog
Π ΡΠ°Π·Π΄Π΅Π»Π΅ Β«Π’Π΅Ρ Π½ΠΈΡΠ΅ΡΠΊΠΎΠ΅ ΠΎΠ±ΡΠ»ΡΠΆΠΈΠ²Π°Π½ΠΈΠ΅Β» ΠΌΡ ΠΎΠΏΡΠ΅Π΄Π΅Π»ΡΠ΅ΠΌ ΠΊΠ»ΡΡΠ΅Π²ΡΠ΅ ΠΏΠΎΠΊΠ°Π·Π°ΡΠ΅Π»ΠΈ ΡΡΡΠ΅ΠΊΡΠΈΠ²Π½ΠΎΡΡΠΈ (Π±ΠΎΠ»Π΅Π΅ ΠΈΠ·Π²Π΅ΡΡΠ½ΡΠ΅ ΠΊΠ°ΠΊ KPI), ΡΡΠΎΠ±Ρ ΠΈΠ·ΠΌΠ΅ΡΠΈΡΡ ΠΏΡΠΎΠΈΠ·Π²ΠΎΠ΄ΠΈΡΠ΅Π»ΡΠ½ΠΎΡΡΡ Π΄Π°Π½Π½ΠΎΠΉ Π·Π°Π΄Π°ΡΠΈ. ΠΠ½ΠΈ ΠΌΠΎΠ³ΡΡ ΠΈΠ·ΠΌΠ΅ΡΠΈΡΡ Π²ΡΠ΅, ΡΡΠΎ ΡΠ³ΠΎΠ΄Π½ΠΎ, ΠΎΡ Π²ΡΠ΅ΠΌΠ΅Π½ΠΈ, ΠΏΡΠΎΡΠ΅Π΄ΡΠ΅Π³ΠΎ Π²ΠΎ Π²ΡΠ΅ΠΌΡ ΠΎΡΡΠ°Π½ΠΎΠ²Π° (Π½Π΅Π·Π°Π²ΠΈΡΠΈΠΌΠΎ ΠΎΡ ΡΠΎΠ³ΠΎ, Π²ΡΠ·Π²Π°Π½ΠΎ Π»ΠΈ ΡΡΠΎ ΠΏΠ»Π°Π½ΠΎΠ²ΡΠΌ ΠΎΠ±ΡΠ»ΡΠΆΠΈΠ²Π°Π½ΠΈΠ΅ΠΌ ΠΈΠ»ΠΈ Π½Π΅Ρ), Π΄ΠΎ ΡΠ²ΠΎΠ»ΡΡΠΈΠΈ ΠΏΡΠΎΠΈΠ·Π²ΠΎΠ΄ΡΡΠ²Π΅Π½Π½ΡΡ ΠΏΡΠΎΡΠ΅ΡΡΠΎΠ².
ΠΠ»ΡΡΠ΅Π²ΡΠ΅ ΠΏΠΎΠΊΠ°Π·Π°ΡΠ΅Π»ΠΈ ΡΡΡΠ΅ΠΊΡΠΈΠ²Π½ΠΎΡΡΠΈ ΠΎΠ±ΡΠ»ΡΠΆΠΈΠ²Π°Π½ΠΈΡ (KPI) ΡΠ°Π·Π»ΠΈΡΠ°ΡΡΡΡ Π² Π·Π°Π²ΠΈΡΠΈΠΌΠΎΡΡΠΈ ΠΎΡ ΠΊΠΎΠΌΠΏΠ°Π½ΠΈΠΈ, Π΅Π΅ ΡΠ΅Π»Π΅ΠΉ, ΡΡΡΠ°ΡΠ΅Π³ΠΈΠΉ ΠΈ ΠΏΠ»Π°Π½ΠΎΠ² Π΄Π΅ΠΉΡΡΠ²ΠΈΠΉ. ΠΠ΄Π½Π°ΠΊΠΎ Π΅ΡΡΡ Π½Π°Π±ΠΎΡ ΠΏΠΎΠΊΠ°Π·Π°ΡΠ΅Π»Π΅ΠΉ, ΠΊΠΎΡΠΎΡΡΠ΅ ΠΏΠΎΠ»ΡΠ·ΡΡΡΡΡ Π±ΠΎΠ»ΡΡΠΈΠΌ ΡΡΠΏΠ΅Ρ ΠΎΠΌ ΠΈ ΠΈΡΠΏΠΎΠ»ΡΠ·ΡΡΡΡΡ ΡΠ°ΡΠ΅. ΠΡΠ»ΠΈ Π²Ρ ΡΠ΅Ρ Π½ΠΈΡΠ΅ΡΠΊΠΈΠΉ ΡΠΏΠ΅ΡΠΈΠ°Π»ΠΈΡΡ ΠΈΠ»ΠΈ ΠΌΠ΅Π½Π΅Π΄ΠΆΠ΅Ρ ΠΏΠΎ ΡΠ΅Ρ Π½ΠΈΡΠ΅ΡΠΊΠΎΠΌΡ ΠΎΠ±ΡΠ»ΡΠΆΠΈΠ²Π°Π½ΠΈΡ, ΠΊΠΎΡΠΎΡΡΠΉ Π²ΡΠ΅ Π΅ΡΠ΅ ΡΠ΅ΡΠ°Π΅Ρ, ΠΊΠ°ΠΊΠΈΠΌΠΈ ΠΌΠΎΠ³ΡΡ Π±ΡΡΡ ΡΡΠΈ ΠΈΠ½Π΄ΠΈΠΊΠ°ΡΠΎΡΡ, ΠΈΡΠΏΠΎΠ»ΡΠ·ΡΠΉΡΠ΅ ΡΡΡΡΠΊΡΡΡΡ SMART: S pecific, M easurable, A ttainable, R ealistic ΠΈ T giverable.
ΠΡΡΠ³ΠΈΠΌΠΈ ΡΠ»ΠΎΠ²Π°ΠΌΠΈ, Π²Π°ΡΠ° ΡΡΡΠ°ΡΠ΅Π³ΠΈΡ Π΄ΠΎΠ»ΠΆΠ½Π° Π±ΡΡΡ ΠΊΠΎΠ½ΠΊΡΠ΅ΡΠ½ΠΎΠΉ , ΡΠΎ Π΅ΡΡΡ ΠΎΠ½Π° Π±ΡΠ΄Π΅Ρ ΠΎΡΠ΄Π°Π²Π°ΡΡ ΠΏΡΠΈΠΎΡΠΈΡΠ΅Ρ ΠΏΡΠΎΡΡΡΠΌ, Π½ΠΎ ΡΡΡΠ΅ΠΊΡΠΈΠ²Π½ΡΠΌ KPI, ΠΊΠΎΡΠΎΡΡΠ΅ ΠΌΠΎΠ³ΡΡ ΠΏΡΠ΅Π΄ΠΎΡΠ²ΡΠ°ΡΠΈΡΡ ΠΎΡΠΈΠ±ΠΊΠΈ, ΠΊΠΎΡΠΎΡΡΠ΅ Π²Ρ ΡΠΎΠ²Π΅ΡΡΠ°Π»ΠΈ Π² ΠΏΡΠΎΡΠ»ΠΎΠΌ; ΠΈΠ·ΠΌΠ΅ΡΠΈΠΌΡΠ΅ , , ΡΡΠΎΠ±Ρ Π²Ρ ΠΌΠΎΠ³Π»ΠΈ ΠΏΡΠΈΠΌΠ΅Π½ΡΡΡ ΠΊΠΎΠ»ΠΈΡΠ΅ΡΡΠ²Π΅Π½Π½ΡΠ΅ ΠΌΠ΅ΡΠΎΠ΄Ρ Π΄Π»Ρ ΡΠΎΠΏΠΎΡΡΠ°Π²Π»Π΅Π½ΠΈΡ Π΄ΠΎΡΡΠΈΠΆΠ΅Π½ΠΈΠΉ Ρ ΠΏΠ»Π°Π½ΠΎΠΌ; Π΄ΠΎΡΡΠΈΠΆΠΈΠΌΠΎ , ΠΏΠΎΡΠΎΠΌΡ ΡΡΠΎ ΡΡΠ°Π²ΠΈΡΡ ΡΠ΅Π»ΠΈ Π²ΡΡΠ΅ Π²ΠΎΠ·ΠΌΠΎΠΆΠ½ΠΎΡΡΠ΅ΠΉ Π²Π°ΡΠ΅ΠΉ ΠΊΠΎΠΌΠ°Π½Π΄Ρ Π±Π΅ΡΡΠΌΡΡΠ»Π΅Π½Π½ΠΎ; ΡΠ΅Π°Π»ΠΈΡΡΠΈΡΠ½ΠΎ , Ρ ΡΡΠ΅ΡΠΎΠΌ ΡΠ΅ΠΊΡΡΠΈΡ , Π° Π½Π΅ ΡΠΎΠ»ΡΠΊΠΎ ΠΆΠ΅Π»Π°Π΅ΠΌΡΡ ΡΡΠ»ΠΎΠ²ΠΈΠΉ; ΠΈ ΡΠ²ΠΎΠ΅Π²ΡΠ΅ΠΌΠ΅Π½Π½ΠΎ , ΡΡΠΎ ΡΡΠ΅Π±ΡΠ΅Ρ ΡΠ°Π·ΡΠΌΠ½ΡΡ ΡΡΠΎΠΊΠΎΠ².
ΠΠ°ΠΊΠΈΠ΅ ΠΊΠ»ΡΡΠ΅Π²ΡΠ΅ ΠΏΠΎΠΊΠ°Π·Π°ΡΠ΅Π»ΠΈ ΡΡΡΠ΅ΠΊΡΠΈΠ²Π½ΠΎΡΡΠΈ ΠΎΠ±ΡΠ»ΡΠΆΠΈΠ²Π°Π½ΠΈΡ ΡΠ²Π»ΡΡΡΡΡ Π»ΡΡΡΠΈΠΌΠΈ?
ΠΠ΅ΡΠΌΠΎΡΡΡ Π½Π° ΡΠΎ, ΡΡΠΎ ΠΊΠ»ΡΡΠ΅Π²ΡΠ΅ ΠΏΠΎΠΊΠ°Π·Π°ΡΠ΅Π»ΠΈ ΡΡΡΠ΅ΠΊΡΠΈΠ²Π½ΠΎΡΡΠΈ ΡΠ΅ΡΠ½ΠΎ ΡΠ²ΡΠ·Π°Π½Ρ Ρ ΡΡΠΎΠ²Π½Π΅ΠΌ ΠΏΡΠΎΠΈΠ·Π²ΠΎΠ΄ΠΈΡΠ΅Π»ΡΠ½ΠΎΡΡΠΈ, ΠΊΠΎΡΠΎΡΠΎΠ³ΠΎ Π²Ρ Ρ ΠΎΡΠΈΡΠ΅ Π΄ΠΎΡΡΠΈΡΡ, Π½Π΅ ΠΏΡΠΈΠ½ΠΈΠΌΠ°ΠΉΡΠ΅ ΠΈΡ Π·Π° ΡΠ΅Π»ΠΈ ΡΠ°ΠΌΠΈ ΠΏΠΎ ΡΠ΅Π±Π΅. ΠΠ΅ Π·Π°Π±ΡΠ²Π°ΠΉΡΠ΅, ΡΡΠΎ ΠΈΠ½Π΄ΠΈΠΊΠ°ΡΠΎΡ — ΡΡΠΎ Π²ΡΠ΅Π³ΠΎ Π»ΠΈΡΡ ΠΌΠ΅ΡΡΠΈΠΊΠ°, ΠΈΡΠΏΠΎΠ»ΡΠ·ΡΠ΅ΠΌΠ°Ρ Π² ΠΊΠ°ΡΠ΅ΡΡΠ²Π΅ ΠΊΠΎΠ»ΠΈΡΠ΅ΡΡΠ²Π΅Π½Π½ΠΎΠ³ΠΎ ΠΌΠ΅ΡΠΎΠ΄Π° Π΄Π»Ρ ΠΎΠΏΡΠ΅Π΄Π΅Π»Π΅Π½ΠΈΡ ΠΏΡΠΎΠΈΠ·Π²ΠΎΠ΄ΠΈΡΠ΅Π»ΡΠ½ΠΎΡΡΠΈ Π΄Π°Π½Π½ΠΎΠ³ΠΎ ΡΠ΅Ρ Π½ΠΈΡΠ΅ΡΠΊΠΎΠ³ΠΎ ΠΎΠ±ΡΠ»ΡΠΆΠΈΠ²Π°Π½ΠΈΡ, Π°ΠΊΡΠΈΠ²Π° ΠΈΠ»ΠΈ ΠΎΡΠ΄Π΅Π»Π°.
ΠΡΠΎΠΌΠ΅ ΡΠΎΠ³ΠΎ, ΠΈΠ½Π΄ΠΈΠΊΠ°ΡΠΎΡΡ ΠΌΠΎΠΆΠ½ΠΎ ΡΠ°Π·Π΄Π΅Π»ΠΈΡΡ Π½Π° Π΄Π²Π΅ ΠΊΠ°ΡΠ΅Π³ΠΎΡΠΈΠΈ: Π²ΠΎ-ΠΏΠ΅ΡΠ²ΡΡ , ΡΠ΅, ΠΊΠΎΡΠΎΡΡΠ΅ Π΄Π΅ΠΌΠΎΠ½ΡΡΡΠΈΡΡΡΡ Π²Π»ΠΈΡΠ½ΠΈΠ΅ Π½Π°Π΄Π»Π΅ΠΆΠ°ΡΠ΅Π³ΠΎ ΡΠΏΡΠ°Π²Π»Π΅Π½ΠΈΡ ΡΠ΅Ρ Π½ΠΈΡΠ΅ΡΠΊΠΈΠΌ ΠΎΠ±ΡΠ»ΡΠΆΠΈΠ²Π°Π½ΠΈΠ΅ΠΌ Π½Π° ΠΎΠ±ΡΡΡ ΡΡΡΠ΅ΠΊΡΠΈΠ²Π½ΠΎΡΡΡ Π±ΠΈΠ·Π½Π΅ΡΠ°; ΠΈ, Π²ΠΎ-Π²ΡΠΎΡΡΡ , ΡΠ΅, ΠΊΠΎΡΠΎΡΡΠ΅ ΠΊΠ°ΡΠ°ΡΡΡΡ Π½Π°Π΄Π΅ΠΆΠ½ΠΎΡΡΠΈ ΠΈ Π΄ΠΎΡΡΡΠΏΠ½ΠΎΡΡΠΈ Π°ΠΊΡΠΈΠ²ΠΎΠ².Π’Π°ΠΊΠΈΠΌ ΠΎΠ±ΡΠ°Π·ΠΎΠΌ, ΠΌΡ ΠΌΠΎΠΆΠ΅ΠΌ Π²ΡΠ΄Π΅Π»ΠΈΡΡ ΡΠ»Π΅Π΄ΡΡΡΠΈΠ΅ ΠΊΠ»ΡΡΠ΅Π²ΡΠ΅ ΠΏΠΎΠΊΠ°Π·Π°ΡΠ΅Π»ΠΈ ΡΡΡΠ΅ΠΊΡΠΈΠ²Π½ΠΎΡΡΠΈ Π΄Π»Ρ ΡΠΏΡΠ°Π²Π»Π΅Π½ΠΈΡ ΡΠ΅Ρ Π½ΠΈΡΠ΅ΡΠΊΠΈΠΌ ΠΎΠ±ΡΠ»ΡΠΆΠΈΠ²Π°Π½ΠΈΠ΅ΠΌ: Π²ΡΠ΅ΠΌΡ ΠΏΡΠΎΡΡΠΎΡ , Π½Π΅Π²ΡΠΏΠΎΠ»Π½Π΅Π½Π½Π°Ρ ΡΠ°Π±ΠΎΡΠ°, MTBF, MTTR, OEE, PMP ΠΈ ΡΠΎΠΎΡΠ²Π΅ΡΡΡΠ²ΠΈΠ΅ ΡΠ°ΡΠΏΠΈΡΠ°Π½ΠΈΡ . Π’Π΅ΠΏΠ΅ΡΡ ΠΌΡ ΡΠ°ΡΡΠΌΠΎΡΡΠΈΠΌ ΠΈΡ ΡΠΎΠΎΡΠ²Π΅ΡΡΡΠ²ΡΡΡΠ΅Π΅ ΠΈΡΠΏΠΎΠ»ΡΠ·ΠΎΠ²Π°Π½ΠΈΠ΅, ΠΏΡΠ΅ΠΈΠΌΡΡΠ΅ΡΡΠ²Π° ΠΈ ΡΡΠ΅Π΄Π½ΠΈΠ΅ Π·Π½Π°ΡΠ΅Π½ΠΈΡ.
1. ΠΡΠ΅ΠΌΡ ΠΏΡΠΎΡΡΠΎΡ
ΠΡΠΎΡ ΠΈΠ½Π΄ΠΈΠΊΠ°ΡΠΎΡ ΠΎΠ±ΡΠ»ΡΠΆΠΈΠ²Π°Π½ΠΈΡ ΠΎΡΡΠ»Π΅ΠΆΠΈΠ²Π°Π΅Ρ, ΠΊΠΎΠ½ΡΡΠΎΠ»ΠΈΡΡΠ΅Ρ ΠΈ ΠΎΡΠ΅Π½ΠΈΠ²Π°Π΅Ρ Π½Π°Π΄Π΅ΠΆΠ½ΠΎΡΡΡ Π°ΠΊΡΠΈΠ²Π°.
ΠΡΠ΅ΠΌΡ ΠΏΡΠΎΡΡΠΎΡ ΠΎΡΡΠ»Π΅ΠΆΠΈΠ²Π°Π΅Ρ ΠΎΠ±ΡΠ΅Π΅ Π²ΡΠ΅ΠΌΡ, Π² ΡΠ΅ΡΠ΅Π½ΠΈΠ΅ ΠΊΠΎΡΠΎΡΠΎΠ³ΠΎ ΠΎΠ±ΠΎΡΡΠ΄ΠΎΠ²Π°Π½ΠΈΠ΅ Π±ΡΠ»ΠΎ Π½Π΅Π΄ΠΎΡΡΡΠΏΠ½ΠΎ ΠΈΠ»ΠΈ ΠΎΡΠΊΠ»ΡΡΠ΅Π½ΠΎ , ΡΡΠΎ ΠΎΠ·Π½Π°ΡΠ°Π΅Ρ, ΡΡΠΎ ΠΏΡΠΎΠΈΠ·ΠΎΡΠ»ΠΎ Π½Π΅ΠΆΠ΅Π»Π°ΡΠ΅Π»ΡΠ½ΠΎΠ΅ ΡΠΎΠ±ΡΡΠΈΠ΅ ΠΈ ΠΏΠΎΡΡΠ΅Π±ΡΠ΅ΡΡΡ ΠΊΠ°ΠΊΠΎΠ΅-ΡΠΎ Π²ΠΌΠ΅ΡΠ°ΡΠ΅Π»ΡΡΡΠ²ΠΎ.ΠΡ ΠΌΠΎΠΆΠ΅ΡΠ΅ ΠΈΡΠΏΠΎΠ»ΡΠ·ΠΎΠ²Π°ΡΡ ΡΡΠΎΡ ΠΊΠ»ΡΡΠ΅Π²ΠΎΠΉ ΠΏΠΎΠΊΠ°Π·Π°ΡΠ΅Π»Ρ ΡΡΡΠ΅ΠΊΡΠΈΠ²Π½ΠΎΡΡΠΈ Π½Π΅Π·Π°Π²ΠΈΡΠΈΠΌΠΎ ΠΎΡ ΡΠΎΠ³ΠΎ, Π΅ΡΡΡ Π»ΠΈ Π΄Π»Ρ ΡΡΠΎΠ³ΠΎ Π°ΠΊΡΠΈΠ²Π° ΠΏΠ»Π°Π½ ΠΎΠ±ΡΠ»ΡΠΆΠΈΠ²Π°Π½ΠΈΡ ΠΈΠ»ΠΈ Π½Π΅Ρ. ΠΡΠΎ ΡΠ°ΠΊΠΆΠ΅ Π²Π°ΡΠΈΠ°Π½Ρ ΠΏΡΠΎΡΠ΅Π½ΡΠ° ΠΏΠ»Π°Π½ΠΎΠ²ΠΎΠ³ΠΎ ΠΎΠ±ΡΠ»ΡΠΆΠΈΠ²Π°Π½ΠΈΡ, ΠΎ ΠΊΠΎΡΠΎΡΠΎΠΌ ΠΌΡ ΡΠ°ΡΡΠΊΠ°ΠΆΠ΅ΠΌ Π½ΠΈΠΆΠ΅.
ΠΠ°ΡΠ° ΡΠ΅Π»Ρ ΠΏΠΎ ΡΡΠΎΠΌΡ ΠΊΠ»ΡΡΠ΅Π²ΠΎΠΌΡ ΠΏΠΎΠΊΠ°Π·Π°ΡΠ΅Π»Ρ ΡΡΡΠ΅ΠΊΡΠΈΠ²Π½ΠΎΡΡΠΈ Π΄ΠΎΠ»ΠΆΠ½Π° ΡΠΎΡΡΠ°Π²Π»ΡΡΡ 10%. ΠΡΠΎ ΠΎΠ·Π½Π°ΡΠ°Π΅Ρ, ΡΡΠΎ Π°ΠΊΡΠΈΠ² Π΄ΠΎΠ»ΠΆΠ΅Π½ Π±ΡΡΡ ΠΏΠΎΠ»Π½ΠΎΡΡΡΡ Π³ΠΎΡΠΎΠ² ΠΊ ΡΠ°Π±ΠΎΡΠ΅ (ΡΠ°ΠΊΠΆΠ΅ Π½Π°Π·ΡΠ²Π°Π΅ΠΌΡΠΉ Β«Π²ΡΠ΅ΠΌΡ Π±Π΅Π·ΠΎΡΠΊΠ°Π·Π½ΠΎΠΉ ΡΠ°Π±ΠΎΡΡΒ») ΠΎΠΊΠΎΠ»ΠΎ 90% Π²ΡΠ΅ΠΌΠ΅Π½ΠΈ, ΡΡΠΎΠ±Ρ ΠΏΡΠΎΠΈΠ·Π²ΠΎΠ΄ΡΡΠ²ΠΎ Π½Π΅ ΠΎΡΡΠ°Π½ΠΎΠ²ΠΈΠ»ΠΎΡΡ. ΠΡΡΡΡΡΡΠ²ΠΈΠ΅ ΠΈΠ½ΡΡΠ°ΡΡΡΡΠΊΡΡΡΡ, ΠΌΠΎΠ½ΠΈΡΠΎΡΠΈΠ½Π³Π° ΠΈ ΠΏΠ»Π°Π½ΠΈΡΠΎΠ²Π°Π½ΠΈΡ ΠΎΠ±ΡΡΠ½ΠΎ ΠΏΡΠΈΠ²ΠΎΠ΄ΠΈΡ ΠΊ ΡΠ²Π΅Π»ΠΈΡΠ΅Π½ΠΈΡ ΠΏΡΠΎΡΠ΅Π½ΡΠ° ΠΏΡΠΎΡΡΠΎΠ΅Π².
ΠΡΠΎΡ ΠΈΠ½Π΄ΠΈΠΊΠ°ΡΠΎΡ ΠΌΠΎΠΆΠ΅Ρ ΠΏΠΎΠΌΠΎΡΡ Π²Π°ΠΌ ΡΠ°Π·ΡΠ°Π±ΠΎΡΠ°ΡΡ ΡΡΡΠ°ΡΠ΅Π³ΠΈΡ ΠΏΡΠΎΡΠΈΠ»Π°ΠΊΡΠΈΡΠ΅ΡΠΊΠΎΠ³ΠΎ ΠΎΠ±ΡΠ»ΡΠΆΠΈΠ²Π°Π½ΠΈΡ Ρ ΡΠ΅Π»ΡΡ ΡΠΎΠΊΡΠ°ΡΠ΅Π½ΠΈΡ Π²ΡΠ΅ΠΌΠ΅Π½ΠΈ ΠΏΡΠΎΡΡΠΎΡ Π½Π° ΡΡΠΎΠ²Π½Π΅ Π½ΠΈΠΆΠ΅ ΡΡΠ΅Π΄Π½Π΅Π³ΠΎ, Π° ΡΠ°ΠΊΠΆΠ΅ ΠΌΠΈΠ½ΠΈΠΌΠΈΠ·Π°ΡΠΈΠΈ ΡΡΡΠ΅ΠΊΡΠ° Π½Π΅Π·Π°ΠΏΠ»Π°Π½ΠΈΡΠΎΠ²Π°Π½Π½ΡΡ ΠΎΡΡΠ°Π½ΠΎΠ²ΠΎΠ². ΠΠΎΠΌΠ½ΠΈΡΠ΅, ΡΡΠΎ ΠΊΠΎΠ³Π΄Π° Π°ΠΊΡΠΈΠ² Π½Π΅ ΡΠ°Π±ΠΎΡΠ°Π΅Ρ, Π½Π΅Ρ Π½ΠΈΠΊΠ°ΠΊΠΎΠΉ ΠΎΡΠ΄Π°ΡΠΈ, ΡΡΠΎ Π² ΠΊΠΎΠ½Π΅ΡΠ½ΠΎΠΌ ΠΈΡΠΎΠ³Π΅ ΠΏΡΠΈΠ²ΠΎΠ΄ΠΈΡ ΠΊ ΡΠ±ΡΡΠΊΠ°ΠΌ.
2. ΠΠ°Π΄Π΅ΡΠΆΠ°Π½Π½ΡΠ΅ ΡΠ°Π±ΠΎΡΡ ΠΏΠΎ ΡΠ΅Ρ ΠΎΠ±ΡΠ»ΡΠΆΠΈΠ²Π°Π½ΠΈΡ
ΠΠ°Π΄Π΅ΡΠΆΠΊΠ° — ΡΡΠΎ ΠΈΠ½Π΄ΠΈΠΊΠ°ΡΠΎΡ Π²ΡΠ΅ΠΌΠ΅Π½ΠΈ, ΠΎΠ±ΠΎΠ·Π½Π°ΡΠ°ΡΡΠΈΠΉ Β« Π·Π°Π΄Π΅ΡΠΆΠ΅ΠΊ ΠΎΠ±ΡΠ»ΡΠΆΠΈΠ²Π°Π½ΠΈΡ Β». ΠΠ½ Π·Π°ΠΊΠ»ΡΡΠ°Π΅ΡΡΡ Π² Π½Π°ΡΠ°ΡΠΈΠ²Π°Π½ΠΈΠΈ Π½Π΅Π·Π°Π²Π΅ΡΡΠ΅Π½Π½ΡΡ ΠΈ Π·Π°ΠΏΠ»Π°Π½ΠΈΡΠΎΠ²Π°Π½Π½ΡΡ ΠΌΠ΅ΡΠΎΠΏΡΠΈΡΡΠΈΠΉ Π½Π° ΠΊΠ°ΠΆΠ΄ΠΎΠ³ΠΎ ΡΠ΅Ρ Π½ΠΈΡΠ΅ΡΠΊΠΎΠ³ΠΎ ΡΠΏΠ΅ΡΠΈΠ°Π»ΠΈΡΡΠ°, Π½Π΅Π·Π°Π²ΠΈΡΠΈΠΌΠΎ ΠΎΡ ΡΠΎΠ³ΠΎ, ΡΡΠΎ ΠΎΠ½ΠΈ ΡΠΆΠ΅ Π²ΡΠΏΠΎΠ»Π½ΡΡΡΡΡ.
ΠΡΡΠ³ΠΈΠΌΠΈ ΡΠ»ΠΎΠ²Π°ΠΌΠΈ, ΠΎΡΠ΅ΡΠ΅Π΄Ρ — ΡΡΠΎ Π²ΡΠ΅ΠΌΡ, Π½Π΅ΠΎΠ±Ρ ΠΎΠ΄ΠΈΠΌΠΎΠ΅ Π΄Π»Ρ Π²ΡΠΏΠΎΠ»Π½Π΅Π½ΠΈΡ ΡΠ΅Π°ΠΊΡΠΈΠ²Π½ΠΎΠ³ΠΎ , ΠΏΡΠ΅Π΄ΡΠΏΡΠ΅Π΄ΠΈΡΠ΅Π»ΡΠ½ΠΎΠ³ΠΎ ΠΈΠ»ΠΈ ΠΏΡΠΎΠ³Π½ΠΎΠ·ΠΈΡΡΡΡΠ΅Π³ΠΎ ΡΠ°Π±ΠΎΡΠ΅Π³ΠΎ Π·Π°Π΄Π°Π½ΠΈΡ; ΠΊΠΎΠ½ΡΡΠΎΠ»Ρ ΠΊΠ°ΡΠ΅ΡΡΠ²Π°; ΡΠ»ΡΡΡΠ΅Π½ΠΈΡ ΠΈΠ»ΠΈ Π»ΡΠ±ΡΠ΅ Π΄ΡΡΠ³ΠΈΠ΅ Π΄Π΅ΠΉΡΡΠ²ΠΈΡ, ΡΠΏΠΎΡΠΎΠ±ΡΡΠ²ΡΡΡΠΈΠ΅ ΠΆΠ΅Π»Π°Π΅ΠΌΠΎΠΉ ΠΏΡΠΎΠΈΠ·Π²ΠΎΠ΄ΠΈΡΠ΅Π»ΡΠ½ΠΎΡΡΠΈ Π°ΠΊΡΠΈΠ²Π°. Π§ΡΠΎΠ±Ρ ΡΠ°ΡΡΡΠΈΡΠ°ΡΡ ΡΡΡ ΠΌΠ΅ΡΡΠΈΠΊΡ, Π½Π΅ΠΎΠ±Ρ ΠΎΠ΄ΠΈΠΌΠΎ ΡΡΠΈΡΡΠ²Π°ΡΡ Π²Π΅ΡΡ ΡΠ°Π±ΠΎΡΠΈΠΉ ΠΏΡΠΎΡΠ΅ΡΡ ΠΏΡΠΈ ΠΏΠ»Π°Π½ΠΈΡΠΎΠ²Π°Π½ΠΈΠΈ ΠΈ ΠΊΠΎΠ½ΡΡΠΎΠ»Π΅ ΡΠ΅Ρ Π½ΠΈΡΠ΅ΡΠΊΠΎΠ³ΠΎ ΠΎΠ±ΡΠ»ΡΠΆΠΈΠ²Π°Π½ΠΈΡ.
ΠΠ½Π°ΡΠ΅Π½ΠΈΠ΅ ΡΠ°Π²Π½ΡΠ΅ΡΡΡ ΡΡΠΌΠΌΠ΅ Π·Π½Π°ΡΠ΅Π½ΠΈΠΉ ΡΠ΅Π»ΠΎΠ²Π΅ΠΊΠΎ-ΡΠ°ΡΠΎΠ² Π΄Π»Ρ Π·Π°ΠΏΠ»Π°Π½ΠΈΡΠΎΠ²Π°Π½Π½ΡΡ , ΠΎΠΆΠΈΠ΄Π°ΡΡΠΈΡ ΠΈ Π²ΡΠΏΠΎΠ»Π½Π΅Π½Π½ΡΡ Π·Π°ΠΊΠ°Π·ΠΎΠ² Π½Π° ΡΠ°Π±ΠΎΡΡ, ΡΠ°Π·Π΄Π΅Π»Π΅Π½Π½ΠΎΠΉ Π½Π° ΠΎΠ±ΡΠ΅Π΅ Π΄ΠΎΡΡΡΠΏΠ½ΠΎΠ΅ ΠΊΠΎΠ»ΠΈΡΠ΅ΡΡΠ²ΠΎ ΡΠ΅Π»ΠΎΠ²Π΅ΠΊΠΎ-ΡΠ°ΡΠΎΠ².Π£ΡΠΈΡΡΠ²Π°ΠΉΡΠ΅ ΡΠΎΠ»ΡΠΊΠΎ ΠΏΡΠΎΠ΄ΡΠΊΡΠΈΠ²Π½ΠΎΠ΅ Π²ΡΠ΅ΠΌΡ ΠΊΠ°ΠΆΠ΄ΠΎΠ³ΠΎ ΡΠ΅Ρ Π½ΠΈΠΊΠ°, ΠΏΠΎΡΠΊΠΎΠ»ΡΠΊΡ ΠΎΠ½ΠΈ Π½Π΅ Π²ΡΠΏΠΎΠ»Π½ΡΡΡ Π·Π°ΠΊΠ°Π·Ρ Π½Π° ΡΠ°Π±ΠΎΡΡ Π² 100% ΡΠ»ΡΡΠ°Π΅Π²!
ΠΠΎΡΠΊΠΎΠ»ΡΠΊΡ ΠΎΠ½ ΠΈΠ·ΠΌΠ΅ΡΡΠ΅Ρ Π²ΡΠ΅ΠΌΡ, ΡΠ΅Π·ΡΠ»ΡΡΠ°Ρ Π΄ΠΎΠ»ΠΆΠ΅Π½ Π±ΡΡΡ ΠΏΡΠ΅Π΄ΡΡΠ°Π²Π»Π΅Π½, Π½Π°ΠΏΡΠΈΠΌΠ΅Ρ, Π² ΡΠ°ΡΠ°Ρ , Π΄Π½ΡΡ , Π½Π΅Π΄Π΅Π»ΡΡ ΠΈΠ»ΠΈ ΠΌΠ΅ΡΡΡΠ°Ρ . Π‘ΡΠ°Π½Π΄Π°ΡΡΠ½ΠΎΠ΅ ΠΎΡΡΡΠ°Π²Π°Π½ΠΈΠ΅, ΠΈΠ·ΠΌΠ΅ΡΡΠ΅ΠΌΠΎΠ΅ Π² ΡΠ°Π±ΠΎΡΠΈΡ Π΄Π½ΡΡ , ΡΠΎΡΡΠ°Π²Π»ΡΠ΅Ρ 2 Π½Π΅Π΄Π΅Π»ΠΈ. ΠΠ»Ρ ΠΊΠΎΠΌΠΏΠ°Π½ΠΈΠΉ, ΠΊΠΎΡΠΎΡΡΠ΅ ΡΠ°Π±ΠΎΡΠ°ΡΡ ΠΊΡΡΠ³Π»ΠΎΡΡΡΠΎΡΠ½ΠΎ 7 Π΄Π½Π΅ΠΉ Π² Π½Π΅Π΄Π΅Π»Ρ, ΡΡΠΎ Π³Π΄Π΅-ΡΠΎ ΠΎΡ 3 Π΄ΠΎ 4 Π½Π΅Π΄Π΅Π»Ρ.
ΠΡΠ΅ΠΈΠΌΡΡΠ΅ΡΡΠ²ΠΎ ΡΡΠΎΠ³ΠΎ ΠΏΠΎΠΊΠ°Π·Π°ΡΠ΅Π»Ρ — ΠΎΡΠ΅Π½ΠΊΠ° ΠΏΡΠΎΠ΄ΡΠΊΡΠΈΠ²Π½ΠΎΡΡΠΈ ΠΊΠΎΠΌΠ°Π½Π΄Ρ, Π° ΡΠ°ΠΊΠΆΠ΅ ΠΎΠΏΡΠ΅Π΄Π΅Π»Π΅Π½ΠΈΠ΅ ΠΏΡΠΈΡΠΈΠ½, ΡΡΠΎΡΡΠΈΡ Π·Π° Π½Π΅ΠΉ (Π΅ΡΠ»ΠΈ ΠΎΠ½ΠΈ Π²ΠΎΠ·Π½ΠΈΠΊΠ°ΡΡ).Π‘ ΡΡΠΎΠ³ΠΎ ΠΌΠΎΠΌΠ΅Π½ΡΠ° ΠΌΡ ΡΠ΅ΠΊΠΎΠΌΠ΅Π½Π΄ΡΠ΅ΠΌ Π²Π°ΠΌ ΠΏΡΠΈΠΌΠ΅Π½ΡΡΡ ΡΡΡΠ°ΡΠ΅Π³ΠΈΠΈ Π΄Π»Ρ ΠΎΠΏΡΠΈΠΌΠΈΠ·Π°ΡΠΈΠΈ ΠΏΡΠΎΠΈΠ·Π²ΠΎΠ΄ΡΡΠ²Π°.
ΠΠΎΠΊΠ° Π²Ρ Π·Π΄Π΅ΡΡ, ΠΊΠ°ΠΊ Π½Π°ΡΡΠ΅Ρ ΡΠΎΠ³ΠΎ, ΡΡΠΎΠ±Ρ ΠΎΠ·Π½Π°ΠΊΠΎΠΌΠΈΡΡΡΡ Ρ Π½Π°ΡΠΈΠΌ ΠΏΠΎΠ»Π½ΡΠΌ ΡΡΠΊΠΎΠ²ΠΎΠ΄ΡΡΠ²ΠΎΠΌ ΠΏΠΎ ΡΡΡΠ΅ΠΊΡΠΈΠ²Π½ΠΎΡΡΠΈ ΡΠΏΡΠ°Π²Π»Π΅Π½ΠΈΡ ΡΠ΅Ρ Π½ΠΈΡΠ΅ΡΠΊΠΈΠΌ ΠΎΠ±ΡΠ»ΡΠΆΠΈΠ²Π°Π½ΠΈΠ΅ΠΌ?
ΠΡ ΡΠΎΠ±ΡΠ°Π»ΠΈ 50 Π΄Π΅ΠΉΡΡΠ²Π΅Π½Π½ΡΡ ΡΠΎΠ²Π΅ΡΠΎΠ² Π½Π° Π±ΠΎΠ»Π΅Π΅ ΡΠ΅ΠΌ 20 ΡΡΡΠ°Π½ΠΈΡΠ°Ρ ΠΏΠΎΠ΄ΡΠΎΠ±Π½ΠΎΠ³ΠΎ ΠΊΠΎΠ½ΡΠ΅Π½ΡΠ° ΠΎ ΡΠΎΠΌ, ΠΊΠ°ΠΊ ΠΏΠΎΠ²ΡΡΠΈΡΡ ΡΡΡΠ΅ΠΊΡΠΈΠ²Π½ΠΎΡΡΡ ΡΠ°Π±ΠΎΡΡ, Π°ΠΊΡΠΈΠ²ΠΎΠ² ΠΈ ΡΠ½Π΅ΡΠ³ΠΎΡΡΡΠ΅ΠΊΡΠΈΠ²Π½ΠΎΡΡΠΈ. ΠΠ°Π³ΡΡΠ·ΠΈΡΠ΅ Π΅Π³ΠΎ Π±Π΅ΡΠΏΠ»Π°ΡΠ½ΠΎ ΠΈ ΡΠ΄Π΅Π»Π°ΠΉΡΠ΅ ΡΠ²ΠΎΡ ΡΠ°Π±ΠΎΡΡ Π±ΠΎΠ»Π΅Π΅ ΡΡΡΠ΅ΠΊΡΠΈΠ²Π½ΠΎΠΉ ΡΠΆΠ΅ ΡΠ΅Π³ΠΎΠ΄Π½Ρ.
3. Π‘ΡΠ΅Π΄Π½Π΅Π΅ Π²ΡΠ΅ΠΌΡ Π±Π΅Π·ΠΎΡΠΊΠ°Π·Π½ΠΎΠΉ ΡΠ°Π±ΠΎΡΡ — ΡΡΠ΅Π΄Π½Π΅Π΅ Π²ΡΠ΅ΠΌΡ Π½Π°ΡΠ°Π±ΠΎΡΠΊΠΈ Π½Π° ΠΎΡΠΊΠ°Π·
ΠΡΠ΅ ΠΎΠ΄Π½ΠΈΠΌ ΠΎΠ±ΡΠ΅ΠΏΡΠΈΠ·Π½Π°Π½Π½ΡΠΌ ΠΊΠ»ΡΡΠ΅Π²ΡΠΌ ΠΏΠΎΠΊΠ°Π·Π°ΡΠ΅Π»Π΅ΠΌ ΡΡΡΠ΅ΠΊΡΠΈΠ²Π½ΠΎΡΡΠΈ ΡΠ²Π»ΡΠ΅ΡΡΡ MTBF, ΠΊΠΎΡΠΎΡΡΠΉ ΠΈΠ·ΠΌΠ΅ΡΡΠ΅Ρ Π½Π°Π΄Π΅ΠΆΠ½ΠΎΡΡΡ .ΠΠ½ ΡΡΠΈΡΡΠ²Π°Π΅Ρ ΡΠ»ΡΡΠ°ΠΉΠ½ΡΡ ΠΎΡΠΊΠ°Π·ΠΎΠ², (Π½Π΅Π·Π°ΠΏΠ»Π°Π½ΠΈΡΠΎΠ²Π°Π½Π½ΡΡ ), Π² ΡΠΎΠΌ ΡΠΈΡΠ»Π΅ Π²ΡΠ·Π²Π°Π½Π½ΡΡ ΡΠ±ΠΎΡΠΌΠΈ ΠΏΡΠΎΠ³ΡΠ°ΠΌΠΌΠ½ΠΎΠ³ΠΎ ΠΎΠ±Π΅ΡΠΏΠ΅ΡΠ΅Π½ΠΈΡ ΠΈ ΠΏΡΠΎΠΈΠ·Π²ΠΎΠ΄ΡΡΠ²Π΅Π½Π½ΡΠΌΠΈ Π΄Π΅ΡΠ΅ΠΊΡΠ°ΠΌΠΈ. Π‘Π±ΠΎΠΈ, Π½Π΅ Π²ΡΠ²ΠΎΠ΄ΡΡΠΈΠ΅ Π°ΠΊΡΠΈΠ² ΠΈΠ· ΡΠΊΡΠΏΠ»ΡΠ°ΡΠ°ΡΠΈΠΈ, Π½Π΅ ΡΡΠΈΡΡΠ²Π°ΡΡΡΡ.
ΠΠΎΡΠΊΠΎΠ»ΡΠΊΡ Π² ΡΠ΅Π·ΡΠ»ΡΡΠ°ΡΠ΅ ΡΡΠΈΡΡΠ²Π°Π΅ΡΡΡ Π²ΡΠ΅ΠΌΡ, ΠΏΡΠΎΡΠ΅Π΄ΡΠ΅Π΅ ΠΌΠ΅ΠΆΠ΄Ρ ΠΊΠ°ΠΆΠ΄ΡΠΌ ΠΎΡΠΊΠ°Π·ΠΎΠΌ, ΠΎΠ½ ΡΠ°ΠΊΠΆΠ΅ ΡΠΎΡΡΠ°Π²Π»ΡΠ΅Ρ , ΠΈΠ·ΠΌΠ΅ΡΠ΅Π½Π½ΡΠΉ Π²ΠΎ Π²ΡΠ΅ΠΌΠ΅Π½ΠΈ (ΡΠ°ΡΡ, Π΄Π½ΠΈ, Π½Π΅Π΄Π΅Π»ΠΈ ΠΈΠ»ΠΈ ΠΌΠ΅ΡΡΡΡ). Π§Π΅ΠΌ Π΄ΠΎΠ»ΡΡΠ΅ MTBF, ΡΠ΅ΠΌ Π½Π°Π΄Π΅ΠΆΠ½Π΅Π΅ Π°ΠΊΡΠΈΠ² — Π² ΠΎΡΠ»ΠΈΡΠΈΠ΅ ΠΎΡ MTTR, ΠΊΠΎΡΠΎΡΠΎΠ΅ Π΄ΠΎΠ»ΠΆΠ½ΠΎ Π±ΡΡΡ ΠΌΠΈΠ½ΠΈΠΌΠ°Π»ΡΠ½ΠΎ Π²ΠΎΠ·ΠΌΠΎΠΆΠ½ΡΠΌ.
ΠΠ»Ρ ΡΠ°ΡΡΠ΅ΡΠ° MTBF Π½Π΅ΠΎΠ±Ρ ΠΎΠ΄ΠΈΠΌΠΎ Π²ΡΡΠ΅ΡΡΡ ΠΎΠ±ΡΠ΅Π΅ Π²ΡΠ΅ΠΌΡ ΠΎΡΠΊΠ°Π·Π° ΠΈΠ· ΠΎΠ±ΡΠ΅Π³ΠΎ ΡΠ°Π±ΠΎΡΠ΅Π³ΠΎ Π²ΡΠ΅ΠΌΠ΅Π½ΠΈ; Π° ΠΏΠΎΡΠΎΠΌ ΠΏΠΎΠ΄Π΅Π»ΠΈΡΠ΅ Π½Π° ΠΊΠΎΠ»ΠΈΡΠ΅ΡΡΠ²ΠΎ ΠΏΠΎΠ»ΠΎΠΌΠΎΠΊ.ΠΠ±ΡΠ΅Π΅ ΡΠ°Π±ΠΎΡΠ΅Π΅ Π²ΡΠ΅ΠΌΡ ΠΌΠΎΠΆΠ΅Ρ ΡΠΎΡΡΠ°Π²Π»ΡΡΡ 24 ΡΠ°ΡΠ° ΠΈΠ»ΠΈ ΠΏΠ΅ΡΠΈΠΎΠ΄, Π² ΡΠ΅ΡΠ΅Π½ΠΈΠ΅ ΠΊΠΎΡΠΎΡΠΎΠ³ΠΎ ΡΠ°Π±ΠΎΡΠ°Π΅Ρ ΠΎΠ±ΠΎΡΡΠ΄ΠΎΠ²Π°Π½ΠΈΠ΅. ΠΠ±ΡΠ΅Π΅ Π²ΡΠ΅ΠΌΡ ΠΏΠΎΠ»ΠΎΠΌΠΊΠΈ Π²ΠΊΠ»ΡΡΠ°Π΅Ρ Π²ΡΠ΅ Π²ΡΠ΅ΠΌΡ, ΠΏΠΎΡΠ΅ΡΡΠ½Π½ΠΎΠ΅ Π΄ΠΎ ΡΠΎΠ³ΠΎ, ΠΊΠ°ΠΊ ΠΎΠ½ ΡΠ½ΠΎΠ²Π° Π·Π°ΡΠ°Π±ΠΎΡΠ°Π΅Ρ.
Π ΡΡΠΎΠΌ ΡΠ»ΡΡΠ°Π΅ Π³Π»ΠΎΠ±Π°Π»ΡΠ½ΠΎΠ΅ ΡΡΠ΅Π΄Π½Π΅Π΅ Π·Π½Π°ΡΠ΅Π½ΠΈΠ΅ Π²Π°ΡΡΠΈΡΡΠ΅ΡΡΡ Π² Π·Π°Π²ΠΈΡΠΈΠΌΠΎΡΡΠΈ ΠΎΡ ΡΠΈΠΏΠ° ΠΎΠ±ΠΎΡΡΠ΄ΠΎΠ²Π°Π½ΠΈΡ ΠΈΠ»ΠΈ Π±ΠΈΠ·Π½Π΅ΡΠ° . Π’Π΅ΠΌ Π½Π΅ ΠΌΠ΅Π½Π΅Π΅, ΠΎΠ½ Π΄ΠΎΠ»ΠΆΠ΅Π½ Π±ΡΡΡ ΠΌΠ°ΠΊΡΠΈΠΌΠ°Π»ΡΠ½ΠΎ Π²ΡΡΠΎΠΊΠΈΠΌ. ΠΠΎ ΠΏΡΠΎΡΠ΅ΡΡΠ²ΠΈΠΈ Π²ΡΠ΅ΠΌΠ΅Π½ΠΈ ΡΡΠ°Π²Π½ΠΈΡΠ΅ Π΅Π³ΠΎ Ρ ΠΏΡΠ΅Π΄ΡΠ΄ΡΡΠΈΠΌΠΈ ΡΠ΅Π·ΡΠ»ΡΡΠ°ΡΠ°ΠΌΠΈ, ΡΡΠΎΠ±Ρ ΡΠ²ΠΈΠ΄Π΅ΡΡ, ΡΠ²Π΅Π»ΠΈΡΠΈΠ²Π°Π΅ΡΡΡ Π»ΠΈ ΠΎΠ½.
4. MTTR — Π‘ΡΠ΅Π΄Π½Π΅Π΅ Π²ΡΠ΅ΠΌΡ ΡΠ΅ΠΌΠΎΠ½ΡΠ°
MTTR, ΠΎΠ±ΠΎΠ·Π½Π°ΡΠ°ΡΡΠ΅Π΅ ΡΡΠ΅Π΄Π½Π΅Π΅ Π²ΡΠ΅ΠΌΡ ΡΠ΅ΠΌΠΎΠ½ΡΠ° , — Π΅ΡΠ΅ ΠΎΠ΄ΠΈΠ½ ΠΎΠ±ΡΠΈΠΉ ΠΊΠ»ΡΡΠ΅Π²ΠΎΠΉ ΠΏΠΎΠΊΠ°Π·Π°ΡΠ΅Π»Ρ ΡΡΡΠ΅ΠΊΡΠΈΠ²Π½ΠΎΡΡΠΈ ΡΠ΅Ρ Π½ΠΈΡΠ΅ΡΠΊΠΎΠ³ΠΎ ΠΎΠ±ΡΠ»ΡΠΆΠΈΠ²Π°Π½ΠΈΡ.ΠΠ³ΠΎ ΠΌΠΎΠΆΠ½ΠΎ ΠΏΡΠΈΠΌΠ΅Π½ΠΈΡΡ ΠΊ Π°ΠΊΡΠΈΠ²Ρ, ΠΌΠ°ΡΠΈΠ½Π΅, ΠΎΡΠ΄Π΅Π»ΡΠ½ΠΎΠΌΡ ΠΊΠΎΠΌΠΏΠΎΠ½Π΅Π½ΡΡ ΠΈΠ»ΠΈ Π²ΡΠ΅ΠΉ ΡΠΈΡΡΠ΅ΠΌΠ΅. MTTR ΡΡΠΈΡΡΠ²Π°Π΅Ρ Π²ΡΠ΅ΠΌΡ, ΠΊΠΎΡΠΎΡΠΎΠ΅ ΡΡΠ΅Π±ΡΠ΅ΡΡΡ Π²Π°ΡΠ΅ΠΉ ΠΊΠΎΠΌΠ°Π½Π΄Π΅, ΡΡΠΎΠ±Ρ Π²ΠΌΠ΅ΡΠ°ΡΡΡΡ ΠΈΠ»ΠΈ Π²ΡΠΏΠΎΠ»Π½ΠΈΡΡ ΠΊΠΎΡΡΠ΅ΠΊΡΠΈΡΡΡΡΠ΅Π΅ ΠΎΠ±ΡΠ»ΡΠΆΠΈΠ²Π°Π½ΠΈΠ΅ ΠΏΠΎΡΠ»Π΅ ΡΠΎΠ³ΠΎ, ΠΊΠ°ΠΊ ΠΏΡΠΎΠΈΠ·ΠΎΡΠ΅Π» ΡΠ±ΠΎΠΉ.
Π ΠΎΡΠ»ΠΈΡΠΈΠ΅ ΠΎΡ MTBF, Π²Ρ Π΄ΠΎΠ»ΠΆΠ½Ρ ΡΡΡΠ΅ΠΌΠΈΡΡΡΡ ΠΊ ΠΌΠΈΠ½ΠΈΠΌΠ°Π»ΡΠ½ΠΎΠΌΡ Π·Π½Π°ΡΠ΅Π½ΠΈΡ MTBF ΠΈΠ· Π²ΠΎΠ·ΠΌΠΎΠΆΠ½ΡΡ . Π Π½Π΅ΠΊΠΎΡΠΎΡΠΎΠΌ ΡΠΌΡΡΠ»Π΅, ΡΡΠΎ ΡΠ°ΠΊΠΆΠ΅ ΡΠ°Π±ΠΎΡΠ°Π΅Ρ ΠΊΠ°ΠΊ ΡΠΏΡΡΠΊΠΎΠ²ΠΎΠΉ ΠΊΡΡΡΠΎΠΊ Π΄Π»Ρ ΠΏΡΠΈΠ½ΡΡΠΈΡ ΡΠ΅ΡΠ΅Π½ΠΈΠΉ, ΠΊΠΎΡΠΎΡΡΠ΅ ΠΏΡΠΈΠ²ΠΎΠ΄ΡΡ ΠΊ ΠΌΠ°ΠΊΡΠΈΠΌΠ°Π»ΡΠ½ΠΎΠΉ ΠΏΡΠΈΠ±ΡΠ»ΠΈ ΠΈ ΠΌΠΈΠ½ΠΈΠΌΠ°Π»ΡΠ½ΡΠΌ ΡΠΈΡΠΊΠ°ΠΌ.
ΠΠ»Ρ ΡΠ°ΡΡΠ΅ΡΠ° ΡΡΠ΅Π΄Π½Π΅Π³ΠΎ Π²ΡΠ΅ΠΌΠ΅Π½ΠΈ Π²ΠΎΡΡΡΠ°Π½ΠΎΠ²Π»Π΅Π½ΠΈΡ Π½Π΅ΠΎΠ±Ρ ΠΎΠ΄ΠΈΠΌΠΎ ΠΏΡΠΈΠ½ΡΡΡ Π²ΠΎ Π²Π½ΠΈΠΌΠ°Π½ΠΈΠ΅ ΠΎΠ±ΡΠ΅Π΅ Π²ΡΠ΅ΠΌΡ, Π·Π°ΡΡΠ°ΡΠΈΠ²Π°Π΅ΠΌΠΎΠ΅ Π½Π° ΡΠ΅ΠΌΠΎΠ½Ρ ΠΏΠΎΡΠ»Π΅ ΠΊΠ°ΠΆΠ΄ΠΎΠ³ΠΎ ΠΎΡΠΊΠ°Π·Π° Π² ΡΠ΅ΡΠ΅Π½ΠΈΠ΅ ΠΎΠΏΡΠ΅Π΄Π΅Π»Π΅Π½Π½ΠΎΠ³ΠΎ ΠΏΠ΅ΡΠΈΠΎΠ΄Π° Π²ΡΠ΅ΠΌΠ΅Π½ΠΈ.ΠΠΎΠ»ΡΡΠΈΠ² ΠΎΡΠ²Π΅Ρ, ΡΠ°Π·Π΄Π΅Π»ΠΈΡΠ΅ Π΅Π³ΠΎ Π½Π° ΠΊΠΎΠ»ΠΈΡΠ΅ΡΡΠ²ΠΎ ΡΠ±ΠΎΠ΅Π², Π·Π°ΡΠ΅Π³ΠΈΡΡΡΠΈΡΠΎΠ²Π°Π½Π½ΡΡ Π·Π° ΡΠΎΡ ΠΆΠ΅ ΠΏΠ΅ΡΠΈΠΎΠ΄ Π²ΡΠ΅ΠΌΠ΅Π½ΠΈ.
Π’Π°ΠΊΠΈΠΌ ΠΎΠ±ΡΠ°Π·ΠΎΠΌ, Π²Ρ ΠΌΠΎΠΆΠ΅ΡΠ΅ ΠΎΡΠ΅Π½ΠΈΡΡ ΠΊΠΎΠ»ΠΈΡΠ΅ΡΡΠ²ΠΎ Π²ΡΠ΅ΠΌΠ΅Π½ΠΈ (ΠΎΠΏΡΡΡ ΠΆΠ΅, Π² ΡΠ°ΡΠ°Ρ , Π΄Π½ΡΡ , Π½Π΅Π΄Π΅Π»ΡΡ ΠΈΠ»ΠΈ ΠΌΠ΅ΡΡΡΠ°Ρ ), Π² ΡΠ΅ΡΠ΅Π½ΠΈΠ΅ ΠΊΠΎΡΠΎΡΠΎΠ³ΠΎ Π΄Π°Π½Π½ΡΠΉ Π°ΠΊΡΠΈΠ² Π±ΡΠ» Π½Π΅Π΄ΠΎΡΡΡΠΏΠ΅Π½, Π° ΡΠ°ΠΊΠΆΠ΅ ΡΠΎ, ΡΡΠΎ Π²Ρ Π΄ΠΎΠ»ΠΆΠ½Ρ ΡΠ΄Π΅Π»Π°ΡΡ, ΡΡΠΎΠ±Ρ ΡΡΠΎ Π½Π΅ ΠΏΠΎΠ²ΡΠΎΡΠΈΠ»ΠΎΡΡ. ΠΠ°ΠΊ ΠΈ MTBF , Π½Π΅ ΡΡΡΠ΅ΡΡΠ²ΡΠ΅Ρ Π³Π»ΠΎΠ±Π°Π»ΡΠ½ΠΎΠ³ΠΎ ΡΡΠ°Π½Π΄Π°ΡΡΠ° , ΠΊΠΎΡΠΎΡΡΠΉ ΠΏΠΎΠ΄Ρ ΠΎΠ΄ΠΈΠ» Π±Ρ Π΄Π»Ρ Π»ΡΠ±ΠΎΠΉ ΠΎΡΡΠ°ΡΠ»ΠΈ ΠΈ Π»ΡΠ±ΠΎΠ³ΠΎ ΡΠΈΠΏΠ° ΠΎΠ±ΠΎΡΡΠ΄ΠΎΠ²Π°Π½ΠΈΡ. ΠΠ΄Π½Π°ΠΊΠΎ Π²Π°ΠΌ ΡΠ»Π΅Π΄ΡΠ΅Ρ ΠΏΠΎΡΠ°Π±ΠΎΡΠ°ΡΡ Π½Π°Π΄ ΡΠ΅ΠΌ, ΡΡΠΎΠ±Ρ Π΅Π³ΠΎ ΠΌΠ°ΠΊΡΠΈΠΌΠ°Π»ΡΠ½ΠΎ ΡΠ½ΠΈΠ·ΠΈΡΡ.
5. OEE — ΠΠ±ΡΠ°Ρ ΡΡΡΠ΅ΠΊΡΠΈΠ²Π½ΠΎΡΡΡ ΠΎΠ±ΠΎΡΡΠ΄ΠΎΠ²Π°Π½ΠΈΡ
OEE — ΠΎΠ΄ΠΈΠ½ ΠΈΠ· ΡΠ°ΠΌΡΡ Π²Π°ΠΆΠ½ΡΡ KPI ΠΏΡΠΈ ΡΠ΅Ρ Π½ΠΈΡΠ΅ΡΠΊΠΎΠΌ ΠΎΠ±ΡΠ»ΡΠΆΠΈΠ²Π°Π½ΠΈΠΈ. ΠΠ½ ΠΈΠ·ΠΌΠ΅ΡΡΠ΅Ρ ΠΎΠ±ΡΡΡ ΡΡΡΠ΅ΠΊΡΠΈΠ²Π½ΠΎΡΡΡ ΠΊΠΎΠΌΠΏΠ°Π½ΠΈΠΈ , ΡΡΠΎ ΠΏΠΎΠ·Π²ΠΎΠ»ΡΠ΅Ρ ΠΎΠΏΡΠ΅Π΄Π΅Π»ΠΈΡΡ, ΡΡΡΠ΅ΠΊΡΠΈΠ²Π½Ρ Π»ΠΈ ΠΏΡΠΎΡΠ΅ΡΡΡ, ΠΊΠΎΡΠΎΡΡΠ΅ Π²Ρ Π²Π½Π΅Π΄ΡΠΈΠ»ΠΈ, ΠΈΠ»ΠΈ Π½Π΅Ρ. ΠΠ°ΠΊ ΠΏΡΠ°Π²ΠΈΠ»ΠΎ, ΡΡΡΠ΅ΠΌΠΈΡΠ΅ΡΡ ΠΊ ΠΏΠΎΠΊΠ°Π·Π°ΡΠ΅Π»Ρ OEE Π½Π° ΡΡΠΎΠ²Π½Π΅ 77% ΠΈΠ»ΠΈ Π²ΡΡΠ΅.
ΠΠ΄Π½ΠΈΠΌ ΠΈΠ· ΠΌΠ½ΠΎΠ³ΠΈΡ ΠΏΡΠ΅ΠΈΠΌΡΡΠ΅ΡΡΠ² ΡΠ°ΡΡΠ΅ΡΠ° OEE ΡΠ²Π»ΡΠ΅ΡΡΡ ΠΎΠΏΡΠ΅Π΄Π΅Π»Π΅Π½ΠΈΠ΅ , ΠΊΠ°ΠΊ ΡΠ°ΡΡΠΎ Π°ΠΊΡΠΈΠ²Ρ Π΄ΠΎΡΡΡΠΏΠ½Ρ Π΄Π»Ρ ΡΠ°Π±ΠΎΡΡ .ΠΡ ΡΠ·Π½Π°Π΅ΡΠ΅, Π½Π°ΡΠΊΠΎΠ»ΡΠΊΠΎ Π±ΡΡΡΡΡΠΌ ΡΠ²Π»ΡΠ΅ΡΡΡ ΠΏΡΠΎΠΈΠ·Π²ΠΎΠ΄ΡΡΠ²Π΅Π½Π½ΡΠΉ ΠΏΡΠΎΡΠ΅ΡΡ ΠΈ, ΡΡΠΎ Π½Π΅ ΠΌΠ΅Π½Π΅Π΅ Π²Π°ΠΆΠ½ΠΎ, ΡΠΊΠΎΠ»ΡΠΊΠΎ ΠΏΡΠΎΠ΄ΡΠΊΡΠΎΠ² (ΠΈΠ»ΠΈ ΡΡΠ»ΡΠ³) ΠΏΡΠΎΠΈΠ·Π²ΠΎΠ΄ΠΈΡΡΡ (ΠΈΠ»ΠΈ Π²ΡΠΏΠΎΠ»Π½ΡΠ΅ΡΡΡ) Π±Π΅Π· ΠΊΠ°ΠΊΠΈΡ -Π»ΠΈΠ±ΠΎ ΡΠ±ΠΎΠ΅Π².
Π€ΠΎΡΠΌΡΠ»Π° Π΄ΠΎΠ²ΠΎΠ»ΡΠ½ΠΎ ΠΏΡΠΎΡΡΠ°. Π§ΡΠΎΠ±Ρ ΡΠ°ΡΡΡΠΈΡΠ°ΡΡ OEE, ΡΠΌΠ½ΠΎΠΆΡΡΠ΅ Π΄ΠΎΡΡΡΠΏΠ½ΠΎΡΡΡ, ΠΏΡΠΎΠΈΠ·Π²ΠΎΠ΄ΠΈΡΠ΅Π»ΡΠ½ΠΎΡΡΡ ΠΈ ΠΊΠ°ΡΠ΅ΡΡΠ²ΠΎ. ΠΡ ΠΎΠΏΡΠ΅Π΄Π΅Π»ΡΠ΅ΠΌ Π΄ΠΎΡΡΡΠΏΠ½ΠΎΡΡΡ ΠΏΠΎ Π²ΡΠ΅ΠΌΠ΅Π½ΠΈ ΠΏΡΠΎΡΡΠΎΡ ΠΈ Π±Π΅Π·ΠΎΡΠΊΠ°Π·Π½ΠΎΠΉ ΡΠ°Π±ΠΎΡΡ, ΠΊΠ°ΠΊ ΠΌΡ ΡΠΆΠ΅ Π³ΠΎΠ²ΠΎΡΠΈΠ»ΠΈ. ΠΡΠΎΠΈΠ·Π²ΠΎΠ΄ΠΈΡΠ΅Π»ΡΠ½ΠΎΡΡΡ ΡΠ°ΡΡΡΠΈΡΡΠ²Π°Π΅ΡΡΡ ΠΏΡΡΠ΅ΠΌ ΡΡΠ°Π²Π½Π΅Π½ΠΈΡ ΡΠ΅ΠΊΡΡΠ΅Π³ΠΎ ΠΏΡΠΎΠΈΠ·Π²ΠΎΠ΄ΡΡΠ²Π° Ρ ΠΏΡΠΎΠ³Π½ΠΎΠ·Π°ΠΌΠΈ. ΠΠ°ΠΊΠΎΠ½Π΅Ρ, ΠΊΠ°ΡΠ΅ΡΡΠ²ΠΎ ΠΎΠΏΡΠ΅Π΄Π΅Π»ΡΠ΅ΡΡΡ ΠΎΠ±ΡΠΈΠΌ ΠΎΠ±ΡΠ΅ΠΌΠΎΠΌ ΠΏΡΠΎΠΈΠ·Π²ΠΎΠ΄ΡΡΠ²Π° Π·Π° Π²ΡΡΠ΅ΡΠΎΠΌ Π±ΡΠ°ΠΊΠ° Π² Π΄Π°Π½Π½ΠΎΠΌ ΠΎΠ±ΡΠ°Π·ΡΠ΅.
Π₯ΠΎΡΡ Π³Π»ΠΎΠ±Π°Π»ΡΠ½ΠΎΠ΅ ΡΡΠ΅Π΄Π½Π΅Π΅ Π·Π½Π°ΡΠ΅Π½ΠΈΠ΅ ΡΠΎΡΡΠ°Π²Π»ΡΠ΅Ρ 77%, ΠΊΠΎΠΌΠΏΠ°Π½ΠΈΠΈ ΠΌΠΈΡΠΎΠ²ΠΎΠ³ΠΎ ΠΊΠ»Π°ΡΡΠ° ΡΠ²Π΅ΡΠ΅Π½Π½ΠΎ ΡΠΈΠ΄ΡΡ ΠΌΠ΅ΠΆΠ΄Ρ 85% ΠΈ 99%.
OEE ΡΠ΅ΡΠ½ΠΎ ΡΠ²ΡΠ·Π°Π½ Ρ Π΄Π²ΡΠΌΡ Π΄ΡΡΠ³ΠΈΠΌΠΈ KPIS, OOE ΠΈ TEEP. ΠΡΠΎΠΉΠ΄ΠΈΡΠ΅ ΠΏΠΎ ΡΡΠΎΠΉ Π΄ΠΎΡΠΎΠ³Π΅, ΡΡΠΎΠ±Ρ ΡΠ·Π½Π°ΡΡ Π²ΡΠ΅ ΠΎΠ± OOE, OEE ΠΈ TEEP.
6. PMP — ΠΡΠΎΡΠ΅Π½Ρ ΠΏΠ»Π°Π½ΠΎΠ²ΠΎΠ³ΠΎ ΡΠ΅Ρ ΠΎΠ±ΡΠ»ΡΠΆΠΈΠ²Π°Π½ΠΈΡ
ΠΡΠΎΡΠ΅Π½Ρ ΠΏΠ»Π°Π½ΠΎΠ²ΠΎΠ³ΠΎ ΠΎΠ±ΡΠ»ΡΠΆΠΈΠ²Π°Π½ΠΈΡ ΡΡΠΈΡΡΠ²Π°Π΅Ρ Π²ΡΠ΅ΠΌΡ, Π·Π°ΡΡΠ°ΡΠ΅Π½Π½ΠΎΠ΅ Π½Π° Π·Π°ΠΏΠ»Π°Π½ΠΈΡΠΎΠ²Π°Π½Π½ΡΠ΅ Π΄Π΅ΠΉΡΡΠ²ΠΈΡ (ΠΎΠ±ΡΠ»ΡΠΆΠΈΠ²Π°Π½ΠΈΠ΅, ΡΠ΅ΠΌΠΎΠ½Ρ ΠΈΠ»ΠΈ Π·Π°ΠΌΠ΅Π½Π°) Π°ΠΊΡΠΈΠ²Π°.ΠΡΠΎΡ ΠΊΠ»ΡΡΠ΅Π²ΠΎΠΉ ΠΏΠΎΠΊΠ°Π·Π°ΡΠ΅Π»Ρ ΡΡΡΠ΅ΠΊΡΠΈΠ²Π½ΠΎΡΡΠΈ ΠΎΠ±ΡΠ»ΡΠΆΠΈΠ²Π°Π½ΠΈΡ Π½Π°ΠΏΡΡΠΌΡΡ ΡΠ²ΡΠ·Π°Π½ Ρ ΠΏΠ»Π°Π½ΠΎΠΌ ΠΏΡΠΎΡΠΈΠ»Π°ΠΊΡΠΈΡΠ΅ΡΠΊΠΎΠ³ΠΎ ΠΎΠ±ΡΠ»ΡΠΆΠΈΠ²Π°Π½ΠΈΡ ΠΊΠΎΠΌΠΏΠ°Π½ΠΈΠΈ.
ΠΡ ΠΏΡΠΈΠ½ΠΈΠΌΠ°Π΅ΠΌ Π²ΠΎ Π²Π½ΠΈΠΌΠ°Π½ΠΈΠ΅ ΡΡΡΠ΅ΠΊΡΠΈΠ²Π½ΠΎΡΡΡ, ΡΠΎΠΎΡΠ²Π΅ΡΡΡΠ²ΠΈΠ΅ ΠΈ ΡΠΎ, ΠΊΠ°ΠΊ ΠΊΠ°ΠΆΠ΄ΠΎΠ΅ Π΄Π΅ΠΉΡΡΠ²ΠΈΠ΅ Π±ΡΠ»ΠΎ Π²ΡΠΏΠΎΠ»Π½Π΅Π½ΠΎ, Π° ΡΠ°ΠΊΠΆΠ΅ Π²ΡΠ΅ΠΌΡ, Π½Π΅ΠΎΠ±Ρ ΠΎΠ΄ΠΈΠΌΠΎΠ΅ Π΄Π»Ρ Π΅Π³ΠΎ Π²ΡΠΏΠΎΠ»Π½Π΅Π½ΠΈΡ. ΠΠ°ΡΠ΅ΠΌ ΠΏΡΠΎΡΡΠΎ ΡΠ°Π·Π΄Π΅Π»ΠΈΡΠ΅ ΠΎΠ±ΡΠ΅Π΅ ΠΊΠΎΠ»ΠΈΡΠ΅ΡΡΠ²ΠΎ ΡΠ°ΡΠΎΠ² Π·Π°ΠΏΠ»Π°Π½ΠΈΡΠΎΠ²Π°Π½Π½ΠΎΠ³ΠΎ ΠΎΠ±ΡΠ»ΡΠΆΠΈΠ²Π°Π½ΠΈΡ Π½Π° ΠΎΠ±ΡΠ΅Π΅ ΠΊΠΎΠ»ΠΈΡΠ΅ΡΡΠ²ΠΎ ΡΠ°ΡΠΎΠ² ΠΎΠ±ΡΠ»ΡΠΆΠΈΠ²Π°Π½ΠΈΡ. Π£ΠΌΠ½ΠΎΠΆΡΡΠ΅ ΡΠ΅Π·ΡΠ»ΡΡΠ°Ρ Π½Π° 100, ΡΡΠΎΠ±Ρ ΠΏΠΎΠ»ΡΡΠΈΡΡ ΠΏΡΠΎΡΠ΅Π½Ρ.
ΠΡΠΎΡ ΡΠ΅Π·ΡΠ»ΡΡΠ°Ρ ΠΏΠΎΠΊΠ°Π·ΡΠ²Π°Π΅Ρ ΡΡΠΎΠ²Π΅Π½Ρ ΡΡΡΠ΅ΠΊΡΠΈΠ²Π½ΠΎΡΡΠΈ ΠΊΠΎΠΌΠΏΠ°Π½ΠΈΠΈ , Π° ΡΠ°ΠΊΠΆΠ΅ Π΅Π΅ ΡΠ΅Π·ΡΠ»ΡΡΠ°ΡΠΈΠ²Π½ΠΎΡΡΡ ΠΈ ΡΡΠΏΠ΅Ρ Π² ΡΠ²ΠΎΠ΅ΠΌ ΡΠ΅ΠΊΡΠΎΡΠ΅.Π§ΡΠΎΠ±Ρ ΡΠΎΠΎΡΠ²Π΅ΡΡΡΠ²ΠΎΠ²Π°ΡΡ Π³Π»ΠΎΠ±Π°Π»ΡΠ½ΡΠΌ ΠΌΠ΅Π΄ΠΈΠ°Π½Π½ΡΠΌ Π·Π½Π°ΡΠ΅Π½ΠΈΡΠΌ, Π·Π½Π°ΡΠ΅Π½ΠΈΠ΅ PMP Π΄ΠΎΠ»ΠΆΠ½ΠΎ ΡΠΎΡΡΠ°Π²Π»ΡΡΡ ΠΎΠΊΠΎΠ»ΠΎ 85% ΠΈΠ»ΠΈ Π²ΡΡΠ΅.
ΠΡ ΠΌΠΎΠΆΠ΅ΡΠ΅ ΠΏΠΎΠΏΡΠΎΠ±ΠΎΠ²Π°ΡΡ CMMS, ΡΡΠΎΠ±Ρ ΡΠ»ΡΡΡΠΈΡΡ ΡΠ²ΠΎΠΈ ΡΠ΅Π·ΡΠ»ΡΡΠ°ΡΡ. ΠΡΠ»ΠΈ Π²Ρ Ρ ΠΎΡΠΈΡΠ΅ ΡΠ·Π½Π°ΡΡ Π±ΠΎΠ»ΡΡΠ΅, ΠΏΠΎΠ³ΠΎΠ²ΠΎΡΠΈΡΠ΅ Ρ ΠΎΠ΄Π½ΠΈΠΌ ΠΈΠ· Π½Π°ΡΠΈΡ ΡΠΏΠ΅ΡΠΈΠ°Π»ΠΈΡΡΠΎΠ² ΠΏΠΎ ΠΎΠ±ΡΠ»ΡΠΆΠΈΠ²Π°Π½ΠΈΡ ΠΏΡΠΎΠ³ΡΠ°ΠΌΠΌΠ½ΠΎΠ³ΠΎ ΠΎΠ±Π΅ΡΠΏΠ΅ΡΠ΅Π½ΠΈΡ, ΡΡΠΎΠ±Ρ Π·Π°ΠΏΠ»Π°Π½ΠΈΡΠΎΠ²Π°ΡΡ Π΄Π΅ΠΌΠΎΠ½ΡΡΡΠ°ΡΠΈΡ.
7. Π‘ΠΎΠ±Π»ΡΠ΄Π΅Π½ΠΈΠ΅ Π³ΡΠ°ΡΠΈΠΊΠ° / ΠΠ»Π°Π½ΠΎΠ²ΠΎΠ΅ ΡΠ΅Ρ Π½ΠΈΡΠ΅ΡΠΊΠΎΠ΅ ΠΎΠ±ΡΠ»ΡΠΆΠΈΠ²Π°Π½ΠΈΠ΅
ΠΡΠΎΡ ΠΊΠ»ΡΡΠ΅Π²ΠΎΠΉ ΠΏΠΎΠΊΠ°Π·Π°ΡΠ΅Π»Ρ ΡΡΡΠ΅ΠΊΡΠΈΠ²Π½ΠΎΡΡΠΈ Π½Π΅ ΠΌΠΎΠΆΠ΅Ρ Π±ΡΡΡ ΠΏΡΠΎΠΏΡΡΠ΅Π½ ΠΈΠ· ΡΠΏΠΈΡΠΊΠ° Π½Π°ΠΈΠ±ΠΎΠ»Π΅Π΅ Π²Π°ΠΆΠ½ΡΡ ΠΊΠ»ΡΡΠ΅Π²ΡΡ ΠΏΠΎΠΊΠ°Π·Π°ΡΠ΅Π»Π΅ΠΉ ΡΡΡΠ΅ΠΊΡΠΈΠ²Π½ΠΎΡΡΠΈ ΠΏΡΠΈ ΡΠ΅Ρ Π½ΠΈΡΠ΅ΡΠΊΠΎΠΌ ΠΎΠ±ΡΠ»ΡΠΆΠΈΠ²Π°Π½ΠΈΠΈ. ΠΠΎΡΠΎΡΠ΅ Π³ΠΎΠ²ΠΎΡΡ, ΠΎΠ½ Π°Π½Π°Π»ΠΈΠ·ΠΈΡΡΠ΅Ρ ΡΠΎΠΎΡΠ²Π΅ΡΡΡΠ²ΠΈΠ΅ ΡΡΡΠ°Π½ΠΎΠ²Π»Π΅Π½Π½ΠΎΠΌΡ Π²Π°ΠΌΠΈ ΠΏΠ»Π°Π½Ρ .
ΠΠ»ΠΈ, ΡΡΠΎ Π΅ΡΠ΅ Π»ΡΡΡΠ΅, ΡΡΡΠ΅ΠΊΡΠΈΠ²Π½ΠΎΡΡΡ ΠΈ ΠΏΡΠΈΠ²Π΅ΡΠΆΠ΅Π½Π½ΠΎΡΡΡ ΡΠ΅Ρ Π½ΠΈΠΊΠΎΠ² ΠΈ ΠΌΠ΅Π½Π΅Π΄ΠΆΠ΅ΡΠΎΠ², ΠΊΠΎΡΠΎΡΡΠ΅ ΠΏΡΠΎΠ΄Π΅ΠΌΠΎΠ½ΡΡΡΠΈΡΠΎΠ²Π°Π»ΠΈ ΠΏΡΠΈ Π²ΡΠΏΠΎΠ»Π½Π΅Π½ΠΈΠΈ ΡΠ²ΠΎΠΈΡ Π·Π°ΠΏΠ»Π°Π½ΠΈΡΠΎΠ²Π°Π½Π½ΡΡ Π·Π°Π΄Π°Ρ. Π‘ΠΎΠ±Π»ΡΠ΄Π΅Π½ΠΈΠ΅ Π³ΡΠ°ΡΠΈΠΊΠ° ΠΊΠ°ΠΊ ΠΊΠ»ΡΡΠ΅Π²ΠΎΠΉ ΠΏΠΎΠΊΠ°Π·Π°ΡΠ΅Π»Ρ ΡΡΡΠ΅ΠΊΡΠΈΠ²Π½ΠΎΡΡΠΈ ΠΎΠ±ΡΠ»ΡΠΆΠΈΠ²Π°Π½ΠΈΡ ΠΈΠ·ΠΌΠ΅ΡΡΠ΅Ρ ΠΏΡΠΎΠΈΠ·Π²ΠΎΠ΄ΠΈΡΠ΅Π»ΡΠ½ΠΎΡΡΡ Π²ΡΠ΅ΠΉ ΠΊΠΎΠΌΠ°Π½Π΄Ρ, ΠΎΡ Π»ΠΈΡ, ΠΏΡΠΈΠ½ΠΈΠΌΠ°ΡΡΠΈΡ ΡΠ΅ΡΠ΅Π½ΠΈΡ, Π΄ΠΎ Π»ΡΠ΄Π΅ΠΉ, ΠΊΠΎΡΠΎΡΡΠ΅ ΠΈΠ·ΠΎ Π΄Π½Ρ Π² Π΄Π΅Π½Ρ ΡΠΎΠ±Π»ΡΠ΄Π°ΡΡ ΠΏΠ»Π°Π½.
Π‘ΠΊΠΎΠ»ΡΠΊΠΎ ΠΌΠ΅ΡΠΎΠΏΡΠΈΡΡΠΈΠΉ Π±ΡΠ»ΠΎ Π²ΡΠΏΠΎΠ»Π½Π΅Π½ΠΎ Π² ΡΠΎΠΎΡΠ²Π΅ΡΡΡΠ²ΠΈΠΈ Ρ ΡΡΡΠ°Π½ΠΎΠ²Π»Π΅Π½Π½ΡΠΌΠΈ ΠΏΡΠ°Π²ΠΈΠ»Π°ΠΌΠΈ? ΠΠ°ΠΊ ΠΏΡΠ°Π²ΠΈΠ»ΠΎ, ΠΌΠ΅Π½Π΅Π΄ΠΆΠ΅ΡΡ ΠΎΡΠ΅Π½ΠΈΠ²Π°ΡΡ Π΄Π°ΡΡ, Π²ΡΠ΅ΠΌΡ, Π½Π΅ΠΎΠ±Ρ ΠΎΠ΄ΠΈΠΌΠΎΠ΅ Π΄Π»Ρ Π²ΡΠΏΠΎΠ»Π½Π΅Π½ΠΈΡ Π·Π°Π΄Π°ΡΠΈ, ΠΈ ΡΡΡΠ΅ΠΊΡΠΈΠ²Π½ΠΎΡΡΡ. Π‘ΠΎΠΎΡΠ²Π΅ΡΡΡΠ²ΠΈΠ΅ Π΄ΠΎΠ»ΠΆΠ½ΠΎ ΡΠΎΡΡΠ°Π²Π»ΡΡΡ 90% ΠΈΠ»ΠΈ Π±ΠΎΠ»Π΅Π΅.
ΠΡΠΏΠΎΠ»ΡΠ·ΠΎΠ²Π°Π½ΠΈΠ΅ ΡΡΠΎΠ³ΠΎ ΠΏΠΎΠΊΠ°Π·Π°ΡΠ΅Π»Ρ ΠΈ ΠΎΠ±Π΅ΡΠΏΠ΅ΡΠ΅Π½ΠΈΠ΅ Π΅Π³ΠΎ ΡΠΎΠΎΡΠ²Π΅ΡΡΡΠ²ΠΈΡ ΡΡΠ΅Π΄Π½Π΅ΠΌΡ (ΠΈΠ»ΠΈ Π±ΠΎΠ»Π΅Π΅ Π²ΡΡΠΎΠΊΠΎΠΌΡ) Π·Π½Π°ΡΠ΅Π½ΠΈΡ ΠΎΠ·Π½Π°ΡΠ°Π΅Ρ, ΡΡΠΎ ΠΏΡΠΎΠΈΠ·Π²ΠΎΠ΄ΠΈΡΠ΅Π»ΡΠ½ΠΎΡΡΡ Π²ΡΡΠΎΠΊΠ° Ρ ΠΌΠΈΠ½ΠΈΠΌΠ°Π»ΡΠ½ΡΠΌΠΈ ΡΠΈΡΠΊΠ°ΠΌΠΈ ΠΎΡΠΊΠ°Π·Π° ΠΈ ΠΏΠΎΡΠ΅ΡΡΠΌΠΈ.
ΠΠΎΠΊΠ°Π·Π°ΡΠ΅Π»ΠΈ ΡΠ΅Ρ Π½ΠΈΡΠ΅ΡΠΊΠΎΠ³ΠΎ ΠΎΠ±ΡΠ»ΡΠΆΠΈΠ²Π°Π½ΠΈΡ Π΄Π»Ρ Π»ΡΡΡΠ΅Π³ΠΎ ΠΏΡΠΈΠ½ΡΡΠΈΡ ΡΠ΅ΡΠ΅Π½ΠΈΠΉ
ΠΠΎΠΆΠ°Π»ΡΠΉ, ΡΠ°ΠΌΡΠΌ Π±ΠΎΠ»ΡΡΠΈΠΌ ΠΏΡΠ΅ΠΈΠΌΡΡΠ΅ΡΡΠ²ΠΎΠΌ ΠΏΡΠΈ ΡΠ°ΡΡΠ΅ΡΠ΅ ΠΈ ΠΏΡΠΈΠΌΠ΅Π½Π΅Π½ΠΈΠΈ ΠΊΠ»ΡΡΠ΅Π²ΡΡ ΠΏΠΎΠΊΠ°Π·Π°ΡΠ΅Π»Π΅ΠΉ ΡΡΡΠ΅ΠΊΡΠΈΠ²Π½ΠΎΡΡΠΈ ΡΠ΅Ρ Π½ΠΈΡΠ΅ΡΠΊΠΎΠ³ΠΎ ΠΎΠ±ΡΠ»ΡΠΆΠΈΠ²Π°Π½ΠΈΡ ΡΠ²Π»ΡΠ΅ΡΡΡ Π³Π»ΡΠ±ΠΎΠΊΠΎΠ΅ ΠΏΠΎΠ½ΠΈΠΌΠ°Π½ΠΈΠ΅ Π²Π½ΡΡΡΠ΅Π½Π½ΠΈΡ ΠΏΡΠΎΡΠ΅ΡΡΠΎΠ² ΠΈ Π΄Π΅ΠΉΡΡΠ²ΠΈΠΉ. Π’Π°ΠΊΠΈΠΌ ΠΎΠ±ΡΠ°Π·ΠΎΠΌ, Π²Ρ ΠΌΠΎΠΆΠ΅ΡΠ΅ ΠΏΠΎΠ½ΡΡΡ, ΡΡΠΎ Π΄Π΅ΠΉΡΡΠ²ΠΈΡΠ΅Π»ΡΠ½ΠΎ ΡΠ°Π±ΠΎΡΠ°Π΅Ρ (Π° ΡΡΠΎ Π½Π΅Ρ) ΠΈ Π³Π΄Π΅ Π΅ΡΡΡ Π²ΠΎΠ·ΠΌΠΎΠΆΠ½ΠΎΡΡΠΈ Π΄Π»Ρ ΡΠ»ΡΡΡΠ΅Π½ΠΈΡ.
ΠΠΎΡΡΠ°Π½ΠΎΠ²ΠΊΠ°, Π΄ΠΎΡΡΠΈΠΆΠ΅Π½ΠΈΠ΅ ΠΈ ΠΈΠ·ΠΌΠ΅ΡΠ΅Π½ΠΈΠ΅ Π²Π°ΡΠΈΡ ΡΠ΅Π»Π΅ΠΉ Ρ ΠΏΠΎΠΌΠΎΡΡΡ ΠΊΠ»ΡΡΠ΅Π²ΡΡ ΠΏΠΎΠΊΠ°Π·Π°ΡΠ΅Π»Π΅ΠΉ ΡΡΡΠ΅ΠΊΡΠΈΠ²Π½ΠΎΡΡΠΈ ΠΎΠ±ΡΠ»ΡΠΆΠΈΠ²Π°Π½ΠΈΡ — ΡΡΠΎ Π½Π΅ ΡΠΎΠ»ΡΠΊΠΎ ΠΎΠ±Π΅ΡΠΏΠ΅ΡΠ΅Π½ΠΈΠ΅ ΠΏΡΠΎΠ΄ΡΠΊΡΠΈΠ²Π½ΠΎΡΡΠΈ ΠΊΠΎΠΌΠΏΠ°Π½ΠΈΠΈ , Π½ΠΎ ΡΠ°ΠΊΠΆΠ΅ ΠΈΠ³ΡΠ°Π΅Ρ Π·Π½Π°ΡΠΈΡΠ΅Π»ΡΠ½ΡΡ ΡΠΎΠ»Ρ Π² ΠΌΠΎΡΠΈΠ²Π°ΡΠΈΠΈ ΠΈ ΡΠΎΡΡΠ΅ ΠΊΠΎΠΌΠ°Π½Π΄Ρ. ΠΡΠΈΠ±ΡΠ»Ρ ΠΎΡΡΠ°Π½Π΅ΡΡΡ ΡΡΠ°Π±ΠΈΠ»ΡΠ½ΠΎΠΉ ΠΈ Π² ΡΠ°ΠΌΠΊΠ°Ρ ΠΏΡΠΎΠ³Π½ΠΎΠ·ΠΎΠ², Π±Π΅Π· ΠΏΠ°Π΄Π΅Π½ΠΈΠΉ ΠΈΠ»ΠΈ ΡΠ±ΡΡΠΊΠΎΠ². ΠΠΎΠΌΠΏΠ°Π½ΠΈΡ ΡΠ°ΠΊΠΆΠ΅ ΡΠ»ΡΡΡΠΈΡ ΡΠ²ΠΎΡ ΡΠ΅ΠΏΡΡΠ°ΡΠΈΡ , ΠΏΠΎΡΠΊΠΎΠ»ΡΠΊΡ Π½Π°Π΄Π΅ΠΆΠ½ΠΎΡΡΡ ΠΈΠΌΠ΅Π΅Ρ ΡΠ΅Π½Π΄Π΅Π½ΡΠΈΡ ΠΏΠΎΠ²ΡΡΠ°ΡΡΡΡ Ρ ΡΠΌΠ΅Π½ΡΡΠ΅Π½ΠΈΠ΅ΠΌ ΠΊΠ°ΠΊ ΡΠΈΡΠΊΠΎΠ², ΡΠ°ΠΊ ΠΈ Π²ΡΠ΅ΠΌΠ΅Π½ΠΈ ΠΏΡΠΎΡΡΠΎΡ.
ΠΠ°ΠΊΠΎΠ½Π΅Ρ, Π²Ρ ΠΌΠΎΠΆΠ΅ΡΠ΅ ΠΈΠ·Π±Π΅ΠΆΠ°ΡΡ ΠΆΠ°Π»ΠΎΠ± ΠΎΡ ΠΊΠ»ΠΈΠ΅Π½ΡΠΎΠ² , ΡΡΠΎ ΠΏΡΠ΅Π΄ΠΎΡΠ²ΡΠ°ΡΠ°Π΅Ρ ΠΏΠ΅ΡΠ΅Π³ΡΡΠ·ΠΊΡ ΠΎΠ±ΡΠ»ΡΠΆΠΈΠ²Π°Π½ΠΈΡ ΠΊΠ»ΠΈΠ΅Π½ΡΠΎΠ².
ΠΠΎΡΠ΅ΠΌΡ ΠΎΡΡΠ»Π΅ΠΆΠΈΠ²Π°Π½ΠΈΠ΅ ΠΊΠ»ΡΡΠ΅Π²ΡΡ ΠΏΠΎΠΊΠ°Π·Π°ΡΠ΅Π»Π΅ΠΉ ΡΡΡΠ΅ΠΊΡΠΈΠ²Π½ΠΎΡΡΠΈ ΡΠΏΠΎΡΠΎΠ±ΡΡΠ²ΡΠ΅Ρ Π±ΠΎΠ»Π΅Π΅ ΡΡΡΠ΅ΠΊΡΠΈΠ²Π½ΠΎΠΌΡ ΠΎΠ±ΡΠ»ΡΠΆΠΈΠ²Π°Π½ΠΈΡ — Accelix
ΠΠ»ΡΡΠ΅Π²ΡΠ΅ ΠΏΠΎΠΊΠ°Π·Π°ΡΠ΅Π»ΠΈ ΡΡΡΠ΅ΠΊΡΠΈΠ²Π½ΠΎΡΡΠΈ (KPI) — Π²Π°ΠΆΠ½ΡΠ΅ ΠΌΠ΅ΡΡΠΈΠΊΠΈ, ΠΈΡΠΏΠΎΠ»ΡΠ·ΡΠ΅ΠΌΡΠ΅ Π΄Π»Ρ ΠΏΡΠ΅Π΄ΠΎΡΡΠ°Π²Π»Π΅Π½ΠΈΡ ΡΠ°Π±ΠΎΡΠ½ΠΈΠΊΠ°ΠΌ ΠΈ ΠΌΠ΅Π½Π΅Π΄ΠΆΠ΅ΡΠ°ΠΌ ΡΠΎΡΠ½ΠΎΠΉ ΠΊΠ°ΡΡΠΈΠ½Ρ ΡΠΎΡΡΠΎΡΠ½ΠΈΡ ΠΈ ΠΏΡΠΎΠΈΠ·Π²ΠΎΠ΄ΠΈΡΠ΅Π»ΡΠ½ΠΎΡΡΠΈ Π²ΡΠ΅Ρ Π°ΡΠΏΠ΅ΠΊΡΠΎΠ² ΠΎΡΠ³Π°Π½ΠΈΠ·Π°ΡΠΈΠΈ. ΠΠ½ΠΈ ΠΈΠ·ΠΌΠ΅ΡΡΡΡ Π²ΡΠ΅, ΠΎΡ ΠΏΡΠΎΠ΄Π°ΠΆ ΠΈ ΠΏΡΠΎΠΈΠ·Π²ΠΎΠ΄ΠΈΡΠ΅Π»ΡΠ½ΠΎΡΡΠΈ Π΄ΠΎ ΠΊΠ°Π΄ΡΠΎΠ²ΠΎΠΉ ΡΡΠ°ΡΠΈΡΡΠΈΠΊΠΈ, Π° ΡΠ°ΠΊΠΆΠ΅ ΡΠΈΡΠΎΠΊΠΈΠΉ ΡΠΏΠ΅ΠΊΡΡ ΠΏΡΠΎΠΈΠ·Π²ΠΎΠ΄ΡΡΠ²Π΅Π½Π½ΡΡ ΠΏΠΎΠΊΠ°Π·Π°ΡΠ΅Π»Π΅ΠΉ ΠΈ ΠΏΠΎΠΊΠ°Π·Π°ΡΠ΅Π»Π΅ΠΉ ΡΡΡΠ΅ΠΊΡΠΈΠ²Π½ΠΎΡΡΠΈ ΡΠ΅Ρ Π½ΠΈΡΠ΅ΡΠΊΠΎΠ³ΠΎ ΠΎΠ±ΡΠ»ΡΠΆΠΈΠ²Π°Π½ΠΈΡ.
Π§ΡΠΎ ΠΊΠ°ΡΠ°Π΅ΡΡΡ ΠΎΠ±ΡΠ»ΡΠΆΠΈΠ²Π°Π½ΠΈΡ, ΡΠΎ ΡΠΎΡΡ ΡΠΈΡΠ»Π° ΠΏΠΎΠ΄ΠΊΠ»ΡΡΠ΅Π½Π½ΡΡ ΡΠΈΡΡΠ΅ΠΌ Π² ΡΠ°ΠΌΠΊΠ°Ρ ΠΏΡΠΎΠΌΡΡΠ»Π΅Π½Π½ΠΎΠ³ΠΎ ΠΠ½ΡΠ΅ΡΠ½Π΅ΡΠ° Π²Π΅ΡΠ΅ΠΉ (IIoT) ΠΏΠΎΠ·Π²ΠΎΠ»ΡΠ΅Ρ ΠΎΡΠ³Π°Π½ΠΈΠ·Π°ΡΠΈΡΠΌ ΠΎΡΡΡΠ΅ΡΡΠ²Π»ΡΡΡ Π±Π΅ΡΠΏΡΠΎΠ²ΠΎΠ΄Π½ΠΎΠΉ ΠΌΠΎΠ½ΠΈΡΠΎΡΠΈΠ½Π³ ΠΈ ΡΠ±ΠΎΡ Π΄Π°Π½Π½ΡΡ ΠΎ ΠΏΡΠΎΠΈΠ·Π²ΠΎΠ΄ΠΈΡΠ΅Π»ΡΠ½ΠΎΡΡΠΈ ΠΏΡΠ°ΠΊΡΠΈΡΠ΅ΡΠΊΠΈ Π»ΡΠ±ΠΎΠ³ΠΎ ΠΏΡΠΎΡΠ΅ΡΡΠ° ΠΈ ΠΏΡΠΎΠΈΠ·Π²ΠΎΠ΄ΡΡΠ²Π΅Π½Π½ΡΡ Π°ΠΊΡΠΈΠ²ΠΎΠ² Π²ΠΏΠ»ΠΎΡΡ Π΄ΠΎ ΡΡΠΎΠ²Π½Ρ ΠΊΠΎΠΌΠΏΠΎΠ½Π΅Π½ΡΠΎΠ².ΠΠΎΠ·ΠΌΠΎΠΆΠ½ΠΎΡΡΡ Π°Π²ΡΠΎΠΌΠ°ΡΠΈΡΠ΅ΡΠΊΠΎΠΉ ΠΏΠΎΡΠΎΠΊΠΎΠ²ΠΎΠΉ ΠΏΠ΅ΡΠ΅Π΄Π°ΡΠΈ ΡΡΠΈΡ Π΄Π°Π½Π½ΡΡ Π² ΠΊΠΎΠΌΠΏΡΡΡΠ΅ΡΠΈΠ·ΠΈΡΠΎΠ²Π°Π½Π½ΠΎΠ΅ ΠΏΡΠΎΠ³ΡΠ°ΠΌΠΌΠ½ΠΎΠ΅ ΠΎΠ±Π΅ΡΠΏΠ΅ΡΠ΅Π½ΠΈΠ΅ Π΄Π»Ρ ΡΠΏΡΠ°Π²Π»Π΅Π½ΠΈΡ ΡΠ΅Ρ Π½ΠΈΡΠ΅ΡΠΊΠΈΠΌ ΠΎΠ±ΡΠ»ΡΠΆΠΈΠ²Π°Π½ΠΈΠ΅ΠΌ (CMMS) ΡΠΏΡΠΎΡΠ°Π΅Ρ, ΡΠ΅ΠΌ ΠΊΠΎΠ³Π΄Π°-Π»ΠΈΠ±ΠΎ, ΠΎΡΡΠ»Π΅ΠΆΠΈΠ²Π°Π½ΠΈΠ΅ Π·Π½Π°ΡΠΈΠΌΡΡ KPI ΡΠ΅ΠΊΡΡΠΈΡ Π΄Π°Π½Π½ΡΡ Π² ΡΡΠ°Π²Π½Π΅Π½ΠΈΠΈ Ρ ΠΏΡΠΎΡΠ»ΡΠΌΠΈ ΠΏΠΎΠΊΠ°Π·Π°ΡΠ΅Π»ΡΠΌΠΈ, ΡΠ΅Π»ΡΠΌΠΈ ΠΊΠΎΠΌΠΏΠ°Π½ΠΈΠΈ ΠΈ ΠΏΠΎΠΊΠ°Π·Π°ΡΠ΅Π»ΡΠΌΠΈ Β«ΠΌΠΈΡΠΎΠ²ΠΎΠ³ΠΎ ΡΡΠΎΠ²Π½ΡΒ». Π Π΅Π·ΡΠ»ΡΡΠ°ΡΡ ΠΏΠΎΠΌΠΎΠ³Π°ΡΡ ΡΠΏΠ΅ΡΠΈΠ°Π»ΠΈΡΡΠ°ΠΌ ΠΏΠΎ ΡΠ΅Ρ Π½ΠΈΡΠ΅ΡΠΊΠΎΠΌΡ ΠΎΠ±ΡΠ»ΡΠΆΠΈΠ²Π°Π½ΠΈΡ ΡΠ°Π·ΡΠ°Π±Π°ΡΡΠ²Π°ΡΡ Π±ΠΎΠ»Π΅Π΅ Π°ΠΊΡΠΈΠ²Π½ΡΠ΅ ΠΈ ΡΡΡΠ΅ΠΊΡΠΈΠ²Π½ΡΠ΅ ΠΏΡΠΎΠ³ΡΠ°ΠΌΠΌΡ ΡΠ΅Ρ Π½ΠΈΡΠ΅ΡΠΊΠΎΠ³ΠΎ ΠΎΠ±ΡΠ»ΡΠΆΠΈΠ²Π°Π½ΠΈΡ, ΡΡΠΎ, Π² ΡΠ²ΠΎΡ ΠΎΡΠ΅ΡΠ΅Π΄Ρ, ΡΠ½ΠΈΠΆΠ°Π΅Ρ Π·Π°ΡΡΠ°ΡΡ ΠΈ ΡΠ»ΡΡΡΠ°Π΅Ρ ΠΎΠ±ΡΠ΅Π΅ ΡΠΎΡΡΠΎΡΠ½ΠΈΠ΅ ΠΈ ΠΏΡΠΎΠΈΠ·Π²ΠΎΠ΄ΠΈΡΠ΅Π»ΡΠ½ΠΎΡΡΡ ΠΈΡ ΠΏΡΠ΅Π΄ΠΏΡΠΈΡΡΠΈΡ.
ΠΡΡΠ»Π΅ΠΆΠΈΠ²Π°Ρ ΠΊΠ»ΡΡΠ΅Π²ΡΠ΅ ΠΏΠΎΠΊΠ°Π·Π°ΡΠ΅Π»ΠΈ ΡΡΡΠ΅ΠΊΡΠΈΠ²Π½ΠΎΡΡΠΈ ΠΎΠ±ΡΠ»ΡΠΆΠΈΠ²Π°Π½ΠΈΡ ΠΈ ΠΈΠ½Π΄ΠΈΠΊΠ°ΡΠΎΡΡ ΡΠΎΡΡΠΎΡΠ½ΠΈΡ ΠΎΠ±ΠΎΡΡΠ΄ΠΎΠ²Π°Π½ΠΈΡ Π½Π° ΠΌΠΎΠ±ΠΈΠ»ΡΠ½ΡΡ ΠΏΠ°Π½Π΅Π»ΡΡ ΠΌΠΎΠ½ΠΈΡΠΎΡΠΈΠ½Π³Π°, ΠΊΠΎΡΠΎΡΡΠ΅ Π΄ΠΎΡΡΡΠΏΠ½Ρ ΠΊΡΡΠ³Π»ΠΎΡΡΡΠΎΡΠ½ΠΎ ΠΈ Π±Π΅Π· Π²ΡΡ ΠΎΠ΄Π½ΡΡ , ΠΎΡΠ³Π°Π½ΠΈΠ·Π°ΡΠΈΠΈ ΠΌΠΎΠ³ΡΡ ΠΏΠΎΠ»ΡΡΠΈΡΡ ΠΏΡΠ΅Π΄ΡΡΠ°Π²Π»Π΅Π½ΠΈΠ΅ ΠΎ ΡΠΎΠΌ, ΠΊΠ°ΠΊ ΠΈΡ ΠΏΡΠΎΠΈΠ·Π²ΠΎΠ΄ΠΈΡΠ΅Π»ΡΠ½ΠΎΡΡΡ ΡΠΎΠΎΡΠ½ΠΎΡΠΈΡΡΡ Ρ ΠΈΡ ΡΠΎΠ±ΡΡΠ²Π΅Π½Π½ΡΠΌΠΈ ΡΠ΅Π»ΡΠΌΠΈ ΠΈ Ρ Π»ΡΡΡΠΈΠΌΠΈ ΠΏΡΠ°ΠΊΡΠΈΠΊΠ°ΠΌΠΈ Π΄ΡΡΠ³ΠΈΡ ΠΎΡΠ³Π°Π½ΠΈΠ·Π°ΡΠΈΠΉ, ΠΊΠΎΡΠΎΡΡΠ΅ Π² Π½Π°ΡΡΠΎΡΡΠ΅Π΅ Π²ΡΠ΅ΠΌΡ Π²ΡΠΏΠΎΠ»Π½ΡΡΡ Β«ΠΎΠ±ΡΠ»ΡΠΆΠΈΠ²Π°Π½ΠΈΠ΅ ΠΌΠΈΡΠΎΠ²ΠΎΠ³ΠΎ ΠΊΠ»Π°ΡΡΠ°Β». Β»ΠΠ°ΡΠ΅Π³ΠΎΡΠΈΡ.
ΠΠ°ΠΊΠΈΠ΅ ΠΊΠ»ΡΡΠ΅Π²ΡΠ΅ ΠΏΠΎΠΊΠ°Π·Π°ΡΠ΅Π»ΠΈ ΡΡΡΠ΅ΠΊΡΠΈΠ²Π½ΠΎΡΡΠΈ Π²Π°ΠΆΠ½Ρ?
ΠΠ»Ρ ΡΠ±ΠΎΡΠ° Π΄Π°Π½Π½ΡΡ ΠΎ ΡΠ΅Ρ Π½ΠΈΡΠ΅ΡΠΊΠΎΠΌ ΠΎΠ±ΡΠ»ΡΠΆΠΈΠ²Π°Π½ΠΈΠΈ ΠΈ ΡΠΎΡΡΠΎΡΠ½ΠΈΠΈ ΠΎΠ±ΠΎΡΡΠ΄ΠΎΠ²Π°Π½ΠΈΡ Π΄ΠΎΡΡΡΠΏΠ΅Π½ ΡΠΈΡΠΎΠΊΠΈΠΉ ΡΠΏΠ΅ΠΊΡΡ ΠΈΠ½ΡΡΡΡΠΌΠ΅Π½ΡΠΎΠ² ΠΈ Π΄Π°ΡΡΠΈΠΊΠΎΠ², Π° ΡΠ°ΠΊΠΆΠ΅ ΠΏΠΎΡΠ΅Π½ΡΠΈΠ°Π»ΡΠ½ΠΎ ΠΌΠΎΠΆΠ½ΠΎ ΡΠΎΠ±ΡΠ°ΡΡ ΡΠΎΡΠ½ΠΈ ΠΏΠΎΠΊΠ°Π·Π°ΡΠ΅Π»Π΅ΠΉ ΠΈ ΠΊΠΎΠ½ΡΡΠΎΠ»ΡΠ½ΡΡ ΠΏΠΎΠΊΠ°Π·Π°ΡΠ΅Π»Π΅ΠΉ. ΠΠ΅ΡΠ²Π°Ρ Π·Π°Π΄Π°ΡΠ° — ΠΎΠΏΡΠ΅Π΄Π΅Π»ΠΈΡΡ, ΠΊΠ°ΠΊΠΈΠ΅ ΠΈΠ· Π½ΠΈΡ Π½Π°ΠΈΠ±ΠΎΠ»Π΅Π΅ Π²Π°ΠΆΠ½ΠΎ ΠΎΡΡΠ»Π΅ΠΆΠΈΠ²Π°ΡΡ Π½Π° ΡΠ΅Π³ΡΠ»ΡΡΠ½ΠΎΠΉ ΠΎΡΠ½ΠΎΠ²Π΅. ΠΠ°ΡΠ΅ΠΌ Π²Ρ ΠΌΠΎΠΆΠ΅ΡΠ΅ Π»Π΅Π³ΠΊΠΎ ΡΠΎΠ·Π΄Π°Π²Π°ΡΡ ΠΈΠ½ΡΠΎΡΠΌΠ°ΡΠΈΠΎΠ½Π½ΡΠ΅ ΠΏΠ°Π½Π΅Π»ΠΈ ΠΈ ΠΎΡΡΠ΅ΡΡ Π² ΡΠ²ΠΎΠ΅ΠΉ ΡΠΈΡΡΠ΅ΠΌΠ΅ CMMS, ΡΡΠΎΠ±Ρ ΠΎΡΡΠ»Π΅ΠΆΠΈΠ²Π°ΡΡ ΠΊΠ»ΡΡΠ΅Π²ΡΠ΅ ΠΏΠΎΠΊΠ°Π·Π°ΡΠ΅Π»ΠΈ ΡΡΡΠ΅ΠΊΡΠΈΠ²Π½ΠΎΡΡΠΈ, ΠΎΡΠ½ΠΎΡΡΡΠΈΠ΅ΡΡ ΠΊ Π²Π°ΡΠ΅ΠΉ ΠΎΡΠ³Π°Π½ΠΈΠ·Π°ΡΠΈΠΈ, ΠΏΠΎ ΠΏΠΎΠΌΠ΅ΡΠ΅Π½ΠΈΡΠΌ, ΡΠΈΠΏΠ°ΠΌ ΠΎΠ±ΠΎΡΡΠ΄ΠΎΠ²Π°Π½ΠΈΡ, ΠΏΠΎΠ΄ΡΠ°Π·Π΄Π΅Π»Π΅Π½ΠΈΡΠΌ ΠΈΠ»ΠΈ Π² Π³Π»ΠΎΠ±Π°Π»ΡΠ½ΠΎΠΌ ΠΌΠ°ΡΡΡΠ°Π±Π΅ Π² ΠΌΠ°ΡΡΡΠ°Π±Π°Ρ Π²ΡΠ΅Π³ΠΎ ΠΏΡΠ΅Π΄ΠΏΡΠΈΡΡΠΈΡ.
ΠΠΎ-ΠΏΠ΅ΡΠ²ΡΡ , Π½Π΅ΠΎΠ±Ρ ΠΎΠ΄ΠΈΠΌΠΎ ΠΎΠΏΡΠ΅Π΄Π΅Π»ΠΈΡΡ, ΠΊΠ°ΠΊΠΈΠ΅ ΠΊΠ»ΡΡΠ΅Π²ΡΠ΅ ΠΏΠΎΠΊΠ°Π·Π°ΡΠ΅Π»ΠΈ ΡΡΡΠ΅ΠΊΡΠΈΠ²Π½ΠΎΡΡΠΈ ΡΠ΅Ρ Π½ΠΈΡΠ΅ΡΠΊΠΎΠ³ΠΎ ΠΎΠ±ΡΠ»ΡΠΆΠΈΠ²Π°Π½ΠΈΡ ΠΈ ΡΠΎΡΡΠΎΡΠ½ΠΈΡ ΠΎΠ±ΠΎΡΡΠ΄ΠΎΠ²Π°Π½ΠΈΡ ΡΠ»Π΅Π΄ΡΠ΅Ρ ΠΎΡΡΠ»Π΅ΠΆΠΈΠ²Π°ΡΡ.
ΠΠ±ΡΠΈΠ΅ ΠΠΠ ΠΎΠ±ΡΠ»ΡΠΆΠΈΠ²Π°Π½ΠΈΡ Π²ΠΊΠ»ΡΡΠ°ΡΡ:
- ΠΠ°Π΄Π΅ΡΠΆΠΊΠΈ ΠΏΠΎ ΡΠ΅Ρ ΠΎΠ±ΡΠ»ΡΠΆΠΈΠ²Π°Π½ΠΈΡ
- Π‘ΡΠ΅Π΄Π½Π΅Π΅ Π²ΡΠ΅ΠΌΡ ΡΠ΅ΠΌΠΎΠ½ΡΠ° (MTTR)
- Π‘ΡΠ΅Π΄Π½ΡΡ Π½Π°ΡΠ°Π±ΠΎΡΠΊΠ° Π½Π° ΠΎΡΠΊΠ°Π· (MTBF)
- ΠΠ±ΡΠ°Ρ ΡΡΡΠ΅ΠΊΡΠΈΠ²Π½ΠΎΡΡΡ ΠΎΠ±ΠΎΡΡΠ΄ΠΎΠ²Π°Π½ΠΈΡ (OEE)
- Π‘ΠΎΠΎΡΠ²Π΅ΡΡΡΠ²ΠΈΠ΅ ΠΏΡΠΎΡΠΈΠ»Π°ΠΊΡΠΈΡΠ΅ΡΠΊΠΎΠΌΡ ΠΎΠ±ΡΠ»ΡΠΆΠΈΠ²Π°Π½ΠΈΡ (PM)
- ΠΡΠΎΡΠ΅Π½Ρ ΠΏΠ»Π°Π½ΠΎΠ²ΠΎΠ³ΠΎ ΠΎΠ±ΡΠ»ΡΠΆΠΈΠ²Π°Π½ΠΈΡ
ΠΡΠΎΡ ΡΠΏΠΈΡΠΎΠΊ ΠΌΠΎΠΆΠ½ΠΎ ΡΠ°Π·Π΄Π΅Π»ΠΈΡΡ Π½Π° Β«ΠΎΠΏΠ΅ΡΠ΅ΠΆΠ°ΡΡΠΈΠ΅Β» ΠΈΠ½Π΄ΠΈΠΊΠ°ΡΠΎΡΡ, ΡΠΈΠ³Π½Π°Π»ΠΈΠ·ΠΈΡΡΡΡΠΈΠ΅ ΠΎ Π±ΡΠ΄ΡΡΠΈΡ ΡΠΎΠ±ΡΡΠΈΡΡ , ΠΈ Β«Π·Π°ΠΏΠ°Π·Π΄ΡΠ²Π°ΡΡΠΈΠ΅Β» ΠΈΠ½Π΄ΠΈΠΊΠ°ΡΠΎΡΡ, ΡΠ»Π΅Π΄ΡΡΡΠΈΠ΅ Π·Π° ΡΠΎΠ±ΡΡΠΈΡΠΌΠΈ.ΠΠ΅Π΄ΡΡΠΈΠ΅ ΠΈΠ½Π΄ΠΈΠΊΠ°ΡΠΎΡΡ Π²ΠΊΠ»ΡΡΠ°ΡΡ ΡΠ°ΠΊΠΈΠ΅ ΠΏΠΎΠΊΠ°Π·Π°ΡΠ΅Π»ΠΈ, ΠΊΠ°ΠΊ ΡΠΎΠΎΡΠ²Π΅ΡΡΡΠ²ΠΈΠ΅ ΡΡΠ΅Π±ΠΎΠ²Π°Π½ΠΈΡΠΌ PM ΠΈ ΡΠ°ΡΡΠ΅ΡΠ½Π°Ρ ΠΏΡΠΎΠΈΠ·Π²ΠΎΠ΄ΠΈΡΠ΅Π»ΡΠ½ΠΎΡΡΡ ΠΏΠΎ ΡΡΠ°Π²Π½Π΅Π½ΠΈΡ Ρ ΡΠ°ΠΊΡΠΈΡΠ΅ΡΠΊΠΎΠΉ ΠΏΡΠΎΠΈΠ·Π²ΠΎΠ΄ΠΈΡΠ΅Π»ΡΠ½ΠΎΡΡΡΡ. ΠΠ½ΠΈ ΠΏΠΎΠ»Π΅Π·Π½Ρ Π΄Π»Ρ ΠΏΠ»Π°Π½ΠΈΡΠΎΠ²Π°Π½ΠΈΡ ΠΎΠ±ΡΠ»ΡΠΆΠΈΠ²Π°Π½ΠΈΡ ΠΈ ΠΎΡΠ΅Π½ΠΊΠΈ ΠΏΠΎΡΡΠ΅Π±Π½ΠΎΡΡΠ΅ΠΉ Π² ΠΏΠ΅ΡΡΠΎΠ½Π°Π»Π΅. ΠΠ½Π΄ΠΈΠΊΠ°ΡΠΎΡΡ Π·Π°ΠΏΠ°Π·Π΄ΡΠ²Π°Π½ΠΈΡ Π²ΠΊΠ»ΡΡΠ°ΡΡ Π² ΡΠ΅Π±Ρ ΡΠ°ΠΊΠΈΠ΅ ΠΏΠΎΠΊΠ°Π·Π°ΡΠ΅Π»ΠΈ ΠΎΠ±ΡΠ»ΡΠΆΠΈΠ²Π°Π½ΠΈΡ, ΠΊΠ°ΠΊ MTBF ΠΈ MTTR, ΠΈ ΠΌΠΎΠ³ΡΡ ΠΏΠΎΠΌΠΎΡΡ Π² ΡΠ΅ΡΠ΅Π½ΠΈΠΈ ΠΏΡΠΎΠ±Π»Π΅ΠΌ ΠΎΠ±ΡΠ»ΡΠΆΠΈΠ²Π°Π½ΠΈΡ, ΠΊΠΎΡΠΎΡΡΠ΅ Ρ ΡΠΎΠ½ΠΈΡΠ΅ΡΠΊΠΈ Π½Π΅ Π΄ΠΎΡΡΠΈΠ³Π°ΡΡ ΡΠ΅Π»Π΅ΠΉ. ΠΠ°ΠΈΠ±ΠΎΠ»Π΅Π΅ ΠΏΠΎΠ»Π½ΡΠ΅ ΡΠΈΡΡΠ΅ΠΌΡ ΠΎΡΡΠ»Π΅ΠΆΠΈΠ²Π°Π½ΠΈΡ KPI CMMS Π²ΠΊΠ»ΡΡΠ°ΡΡ ΠΊΠΎΠΌΠ±ΠΈΠ½Π°ΡΠΈΡ ΠΎΠΏΠ΅ΡΠ΅ΠΆΠ°ΡΡΠΈΡ ΠΈ Π·Π°ΠΏΠ°Π·Π΄ΡΠ²Π°ΡΡΠΈΡ ΠΈΠ½Π΄ΠΈΠΊΠ°ΡΠΎΡΠΎΠ².
ΠΠΎΠΌΠΈΠΌΠΎ ΠΊΠ»ΡΡΠ΅Π²ΡΡ ΠΏΠΎΠΊΠ°Π·Π°ΡΠ΅Π»Π΅ΠΉ ΡΡΡΠ΅ΠΊΡΠΈΠ²Π½ΠΎΡΡΠΈ ΠΎΠ±ΡΠ»ΡΠΆΠΈΠ²Π°Π½ΠΈΡ, ΠΌΠΎΠΆΠ½ΠΎ ΡΠΎΠ±ΠΈΡΠ°ΡΡ ΠΈΠ½Π΄ΠΈΠΊΠ°ΡΠΎΡΡ ΡΠΎΡΡΠΎΡΠ½ΠΈΡ ΠΎΠ±ΠΎΡΡΠ΄ΠΎΠ²Π°Π½ΠΈΡ, ΡΡΠΎΠ±Ρ ΠΎΠ±Π΅ΡΠΏΠ΅ΡΠΈΡΡ ΡΠ΅ΠΊΡΡΠ΅Π΅ ΠΈ ΠΈΡΡΠΎΡΠΈΡΠ΅ΡΠΊΠΎΠ΅ ΠΏΡΠ΅Π΄ΡΡΠ°Π²Π»Π΅Π½ΠΈΠ΅ ΠΎ ΡΠΎΡΡΠΎΡΠ½ΠΈΠΈ ΠΎΠ±ΠΎΡΡΠ΄ΠΎΠ²Π°Π½ΠΈΡ.ΠΠ½ΠΈ ΡΠ°ΠΊΠΆΠ΅ ΠΌΠΎΠ³ΡΡ ΠΏΡΠ΅Π΄ΡΠΏΡΠ΅Π΄ΠΈΡΡ Π²Π°Ρ ΠΎ ΠΏΠΎΡΠ΅Π½ΡΠΈΠ°Π»ΡΠ½ΡΡ ΠΏΡΠΎΠ±Π»Π΅ΠΌΠ°Ρ Π½Π° ΡΠ°Π½Π½ΠΈΡ ΡΡΠ°Π΄ΠΈΡΡ .
ΠΠ±ΡΠΈΠ΅ ΠΈΠ½Π΄ΠΈΠΊΠ°ΡΠΎΡΡ ΡΠΎΡΡΠΎΡΠ½ΠΈΡ ΠΎΠ±ΠΎΡΡΠ΄ΠΎΠ²Π°Π½ΠΈΡ Π²ΠΊΠ»ΡΡΠ°ΡΡ:
Π‘ΠΏΠ΅ΡΠΈΠ°Π»ΠΈΡΡΡ ΠΏΠΎ ΠΎΠ±ΡΠ»ΡΠΆΠΈΠ²Π°Π½ΠΈΡ ΠΌΠΎΠ³ΡΡ ΡΠΎΠΎΡΠ½ΠΎΡΠΈΡΡ ΠΊΠ»ΡΡΠ΅Π²ΡΠ΅ ΠΏΠΎΠΊΠ°Π·Π°ΡΠ΅Π»ΠΈ ΡΡΡΠ΅ΠΊΡΠΈΠ²Π½ΠΎΡΡΠΈ ΠΎΠ±ΡΠ»ΡΠΆΠΈΠ²Π°Π½ΠΈΡ Ρ ΠΈΠ½Π΄ΠΈΠΊΠ°ΡΠΎΡΠ°ΠΌΠΈ ΡΠΎΡΡΠΎΡΠ½ΠΈΡ ΠΎΠ±ΠΎΡΡΠ΄ΠΎΠ²Π°Π½ΠΈΡ, ΡΡΠΎΠ±Ρ ΡΡΡΠ°Π½ΠΎΠ²ΠΈΡΡ ΠΏΡΠΎΡΠΎΠΊΠΎΠ»Ρ Π΄Π»Ρ ΠΎΠΏΡΠΈΠΌΠ°Π»ΡΠ½ΠΎΠ³ΠΎ Π²ΡΠ΅ΠΌΠ΅Π½ΠΈ Π΄Π»Ρ ΡΠ΅ΡΠ΅Π½ΠΈΡ ΠΏΠΎΡΠ΅Π½ΡΠΈΠ°Π»ΡΠ½ΡΡ ΠΏΡΠΎΠ±Π»Π΅ΠΌ ΠΈ ΠΏΡΠ΅Π΄ΠΎΡΠ²ΡΠ°ΡΠ΅Π½ΠΈΡ Π½Π΅ΠΆΠ΅Π»Π°ΡΠ΅Π»ΡΠ½ΡΡ ΠΏΡΠΎΡΡΠΎΠ΅Π² ΠΈ / ΠΈΠ»ΠΈ ΠΏΠΎΠ²ΡΠ΅ΠΆΠ΄Π΅Π½ΠΈΡ ΠΎΠ±ΠΎΡΡΠ΄ΠΎΠ²Π°Π½ΠΈΡ.
ΠΡΡΠ»Π΅ΠΆΠΈΠ²Π°Π½ΠΈΠ΅ ΡΡΠΈΡ Π΄Π°Π½Π½ΡΡ ΡΠΊΠ°Π·ΡΠ²Π°Π΅Ρ Π½Π° Π²ΠΎΠ·ΠΌΠΎΠΆΠ½ΠΎΡΡΠΈ Π΄Π»Ρ ΡΠ»ΡΡΡΠ΅Π½ΠΈΡ ΠΈ ΡΡΡΠ°Π½Π°Π²Π»ΠΈΠ²Π°Π΅Ρ Π±Π°Π·ΠΎΠ²ΡΠ΅ ΠΏΠ°ΡΠ°ΠΌΠ΅ΡΡΡ Π΄Π»Ρ ΠΎΠΏΡΠ΅Π΄Π΅Π»Π΅Π½ΠΈΡ ΡΠΎΠ³ΠΎ, Π½Π°ΡΠΊΠΎΠ»ΡΠΊΠΎ Ρ ΠΎΡΠΎΡΠΎ Π²Π°ΡΠ° ΠΎΡΠ³Π°Π½ΠΈΠ·Π°ΡΠΈΡ ΠΈ Π²Π°ΡΠ° CMMS ΠΏΠΎΠ΄Π΄Π΅ΡΠΆΠΈΠ²Π°ΡΡ ΠΏΠ΅ΡΠ΅Π΄ΠΎΠ²ΡΠ΅ ΠΌΠ΅ΡΠΎΠ΄Ρ.ΠΠ΅ΡΠ²ΡΠΌ ΡΠ°Π³ΠΎΠΌ ΡΠ²Π»ΡΠ΅ΡΡΡ ΠΎΠΏΡΠ΅Π΄Π΅Π»Π΅Π½ΠΈΠ΅ ΠΏΡΠΈΠΎΡΠΈΡΠ΅ΡΠ½ΠΎΡΡΠΈ Π±ΠΈΠ·Π½Π΅Ρ-ΡΠ΅Π»Π΅ΠΉ (Π½Π°ΠΏΡΠΈΠΌΠ΅Ρ, ΠΏΠ΅ΡΠ΅ΡΠΈΡΠ»Π΅Π½Π½ΡΡ Π½ΠΈΠΆΠ΅) ΠΈ ΠΎΠΏΡΠ΅Π΄Π΅Π»Π΅Π½ΠΈΠ΅ ΠΏΠΎΠΊΠ°Π·Π°ΡΠ΅Π»Π΅ΠΉ, ΠΊΠΎΡΠΎΡΡΠ΅ ΠΏΠΎΠΌΠΎΠ³ΡΡ Π²Π°ΠΌ Π΄ΠΎΡΡΠΈΡΡ ΡΡΠΈΡ ΡΠ΅Π»Π΅ΠΉ:
- Π‘Π½ΠΈΠΆΠ΅Π½ΠΈΠ΅ Π·Π°ΡΡΠ°Ρ
- Π‘Π½ΠΈΠΆΠ΅Π½ΠΈΠ΅ ΠΊΠΎΠ»ΠΈΡΠ΅ΡΡΠ²Π° ΠΎΡΠΊΠ°Π·ΠΎΠ²
- Π‘ΠΎΠΊΡΠ°ΡΠ΅Π½ΠΈΠ΅ Π²ΡΠ΅ΠΌΠ΅Π½ΠΈ ΠΏΡΠΎΡΡΠΎΡ
- Π£Π»ΡΡΡΠ΅Π½ΠΈΠ΅ ΠΈΠ΄Π΅Π½ΡΠΈΡΠΈΠΊΠ°ΡΠΈΠΈ ΡΠ°Π±ΠΎΡΡ
- Π£Π²Π΅Π»ΠΈΡΠ΅Π½ΠΈΠ΅ ΠΏΠ»Π°Π½ΠΈΡΠΎΠ²Π°Π½ΠΈΡ ΡΠ°Π±ΠΎΡ
- ΠΠΎΠ»Π΅Π΅ ΡΡΡΠ΅ΠΊΡΠΈΠ²Π½ΠΎΠ΅ ΠΏΠ»Π°Π½ΠΈΡΠΎΠ²Π°Π½ΠΈΠ΅ ΡΠ°Π±ΠΎΡΡ
- ΠΠΎΠ»Π΅Π΅ ΡΡΡΠ΅ΠΊΡΠΈΠ²Π½ΠΎΠ΅ Π²ΡΠΏΠΎΠ»Π½Π΅Π½ΠΈΠ΅ ΡΠ°Π±ΠΎΡΡ
ΠΠ±ΡΠΈΠ΅ ΠΊΠ»ΡΡΠ΅Π²ΡΠ΅ ΠΏΠΎΠΊΠ°Π·Π°ΡΠ΅Π»ΠΈ ΡΡΡΠ΅ΠΊΡΠΈΠ²Π½ΠΎΡΡΠΈ ΠΎΠ±ΡΠ»ΡΠΆΠΈΠ²Π°Π½ΠΈΡ Π΄Π»Ρ ΠΏΠΎΠ²ΡΡΠ΅Π½ΠΈΡ ΠΏΡΠΎΠΈΠ·Π²ΠΎΠ΄ΠΈΡΠ΅Π»ΡΠ½ΠΎΡΡΠΈ PM
Π₯ΠΎΡΡ ΡΠΏΠ΅ΡΠΈΠ°Π»ΠΈΡΡΡ ΠΏΠΎ ΠΎΠ±ΡΠ»ΡΠΆΠΈΠ²Π°Π½ΠΈΡ ΠΌΠΎΠ³ΡΡ ΡΡΡΠ°Π½ΠΎΠ²ΠΈΡΡ Π»ΡΠ±ΠΎΠ΅ ΠΊΠΎΠ»ΠΈΡΠ΅ΡΡΠ²ΠΎ KPI, ΡΡΠΎΠ±Ρ ΠΏΠΎΠΌΠΎΡΡ ΠΎΡΠ΅Π½ΠΈΡΡ ΠΊΠ°ΡΠ΅ΡΡΠ²ΠΎ ΡΠ²ΠΎΠ΅ΠΉ ΠΏΡΠΎΠ³ΡΠ°ΠΌΠΌΡ ΠΎΠ±ΡΠ»ΡΠΆΠΈΠ²Π°Π½ΠΈΡ, Π²ΠΎΡ Π½Π΅ΠΊΠΎΡΠΎΡΡΠ΅ ΠΎΠ±ΡΠΈΠ΅ KPI, ΠΊΠΎΡΠΎΡΡΠ΅ ΠΎΡΡΠ»Π΅ΠΆΠΈΠ²Π°Π΅Ρ Π±ΠΎΠ»ΡΡΠΈΠ½ΡΡΠ²ΠΎ ΠΎΡΠ³Π°Π½ΠΈΠ·Π°ΡΠΈΠΉ.
ΠΡΡΠ½Π°Π» ΠΎΠ±ΡΠ»ΡΠΆΠΈΠ²Π°Π½ΠΈΡ
ΠΠ°Π΄Π΅ΡΠΆΠΊΠ° ΠΏΠΎ ΠΎΠ±ΡΠ»ΡΠΆΠΈΠ²Π°Π½ΠΈΡ — ΡΡΠΎ Π½Π°ΠΊΠΎΠΏΠ»Π΅Π½ΠΈΠ΅ Π·Π°ΠΊΠ°Π·ΠΎΠ² Π½Π° ΡΠ΅ΠΌΠΎΠ½ΡΠ½ΡΠ΅ ΡΠ°Π±ΠΎΡΡ, ΡΡΠΎΠΊ Π²ΡΠΏΠΎΠ»Π½Π΅Π½ΠΈΡ ΠΊΠΎΡΠΎΡΡΡ ΠΈΡΡΠ΅ΠΊ. ΠΠ½ΠΈ ΠΈΠΌΠ΅ΡΡ ΠΏΡΠΈΠΎΡΠΈΡΠ΅Ρ Π² ΡΠΎΠΎΡΠ²Π΅ΡΡΡΠ²ΠΈΠΈ Ρ ΠΈΡ Π²Π»ΠΈΡΠ½ΠΈΠ΅ΠΌ Π½Π° Π±Π΅Π·ΠΎΠΏΠ°ΡΠ½ΠΎΡΡΡ ΠΈ Π½Π΅ΠΎΠ±Ρ ΠΎΠ΄ΠΈΠΌΠΎΡΡΡΡ ΠΏΡΠ΅Π΄ΠΎΡΠ²ΡΠ°ΡΠ΅Π½ΠΈΡ Π΄Π°Π»ΡΠ½Π΅ΠΉΡΠΈΡ ΠΏΠΎΠ»ΠΎΠΌΠΎΠΊ Π°ΠΊΡΠΈΠ²ΠΎΠ². ΠΡΠ΅Π½Π΅Π±ΡΠ΅ΠΆΠ΅Π½ΠΈΠ΅ ΠΎΡΡΠ»Π΅ΠΆΠΈΠ²Π°Π½ΠΈΠ΅ΠΌ ΡΡΠΎΠ³ΠΎ KPI ΡΡΠ°Π²ΠΈΡ ΠΎΡΠ³Π°Π½ΠΈΠ·Π°ΡΠΈΡ Π² ΡΡΠ·Π²ΠΈΠΌΠΎΠ΅ ΠΏΠΎΠ»ΠΎΠΆΠ΅Π½ΠΈΠ΅. ΠΠ΅Π· Π²ΠΈΠ΄ΠΈΠΌΠΎΡΡΠΈ ΠΊΠ»ΡΡΠ΅Π²ΡΡ ΠΏΡΠΎΠ΅ΠΊΡΠΎΠ² ΡΠ΅Ρ Π½ΠΈΡΠ΅ΡΠΊΠΎΠ³ΠΎ ΠΎΠ±ΡΠ»ΡΠΆΠΈΠ²Π°Π½ΠΈΡ, ΠΊΠΎΡΠΎΡΡΠ΅ Π½Π΅ Π²ΡΠΏΠΎΠ»Π½ΡΡΡΡΡ, ΠΏΡΠ°ΠΊΡΠΈΡΠ΅ΡΠΊΠΈ Π½Π΅Π²ΠΎΠ·ΠΌΠΎΠΆΠ½ΠΎ ΡΡΡΠ΅ΠΊΡΠΈΠ²Π½ΠΎ ΡΠ°ΡΡΡΠ°Π²ΠΈΡΡ ΠΏΡΠΈΠΎΡΠΈΡΠ΅ΡΡ Π΄Π»Ρ ΡΡΠΈΡ Π½Π΅Π²ΡΠΏΠΎΠ»Π½Π΅Π½Π½ΡΡ ΡΠ°Π±ΠΎΡ. ΠΠ°ΠΊ ΠΏΡΠ΅ΡΠ»ΠΎΠ²ΡΡΠΎΠ΅ Β«ΡΠΊΡΠΈΠΏΡΡΠ΅Π΅ ΠΊΠΎΠ»Π΅ΡΠΎΒ» ΡΠΌΠ°Π·ΡΠ²Π°Π΅ΡΡΡ, ΡΠ°ΠΊ ΡΠ°ΡΡΠΎ ΡΠ°ΠΌΡΠΉ Π³ΡΠΎΠΌΠΊΠΈΠΉ Π³ΠΎΠ»ΠΎΡ ΡΡΠ°Π·Ρ ΠΏΡΠΈΠ²Π»Π΅ΠΊΠ°Π΅Ρ Π²Π½ΠΈΠΌΠ°Π½ΠΈΠ΅.
ΠΠ΅Π· Π½Π°Π΄Π΅ΠΆΠ½ΡΡ Π΄Π°Π½Π½ΡΡ Π½Π΅Π²ΡΠΏΠΎΠ»Π½Π΅Π½Π½ΡΡ ΡΠ°Π±ΠΎΡ ΠΏΠΎ ΡΠ΅Ρ Π½ΠΈΡΠ΅ΡΠΊΠΎΠΌΡ ΠΎΠ±ΡΠ»ΡΠΆΠΈΠ²Π°Π½ΠΈΡ ΡΠΏΠ΅ΡΠΈΠ°Π»ΠΈΡΡΡ ΠΏΠΎ ΡΠ΅Ρ Π½ΠΈΡΠ΅ΡΠΊΠΎΠΌΡ ΠΎΠ±ΡΠ»ΡΠΆΠΈΠ²Π°Π½ΠΈΡ Π½Π΅ ΠΌΠΎΠ³ΡΡ ΡΠΎΡΠ½ΠΎ ΡΠ°ΡΡΡΠ°Π²ΠΈΡΡ ΠΏΡΠΈΠΎΡΠΈΡΠ΅ΡΡ Π΄Π»Ρ ΠΏΡΠΎΠ΅ΠΊΡΠΎΠ². Π ΡΠ΅Π·ΡΠ»ΡΡΠ°ΡΠ΅ Π°ΠΊΡΠΈΠ²Ρ ΠΌΠΎΠ³ΡΡ Π½Π΅ΠΎΠΆΠΈΠ΄Π°Π½Π½ΠΎ Π²ΡΠΉΡΠΈ ΠΈΠ· ΡΡΡΠΎΡ ΠΈ Π·Π°Π΄Π΅ΠΉΡΡΠ²ΠΎΠ²Π°ΡΡ Π±ΠΎΠ»ΡΡΡΡ ΡΠ°ΡΡΡ Π΄ΠΎΡΡΡΠΏΠ½ΡΡ ΡΠ΅ΡΡΡΡΠΎΠ² Π΄Π»Ρ ΡΡΡΠ΅Π½ΠΈΡ ΠΏΠΎΠΆΠ°ΡΠΎΠ², ΡΡΠΎ Π΅ΡΠ΅ Π±ΠΎΠ»ΡΡΠ΅ ΡΠ²Π΅Π»ΠΈΡΠΈΡ ΠΎΠ±ΡΠ΅ΠΌ Π½Π΅Π²ΡΠΏΠΎΠ»Π½Π΅Π½Π½ΡΡ ΡΠ°Π±ΠΎΡ ΠΏΠΎ ΡΠ΅Ρ Π½ΠΈΡΠ΅ΡΠΊΠΎΠΌΡ ΠΎΠ±ΡΠ»ΡΠΆΠΈΠ²Π°Π½ΠΈΡ. Π§Π΅ΠΌ Π΄ΠΎΠ»ΡΡΠ΅ ΠΎΡΠΊΠ»Π°Π΄ΡΠ²Π°ΡΡΡΡ ΡΠ°Π±ΠΎΡΡ ΠΏΠΎ ΡΠ΅Ρ Π½ΠΈΡΠ΅ΡΠΊΠΎΠΌΡ ΠΎΠ±ΡΠ»ΡΠΆΠΈΠ²Π°Π½ΠΈΡ, ΡΠ΅ΠΌ Π²ΡΡΠ΅ ΡΠΈΡΠΊ ΠΏΡΠΎΠ΄ΠΎΠ»ΠΆΠ°ΡΡΠΈΡ ΡΡ ΡΠ΅ΡΡΠ΅Π·Π½ΡΡ ΠΈ Π΄ΠΎΡΠΎΠ³ΠΎΡΡΠΎΡΡΠΈΡ ΠΎΡΠΊΠ°Π·ΠΎΠ², ΡΠΎΠ·Π΄Π°Π²Π°Ρ ΡΠ΅ΠΌ ΡΠ°ΠΌΡΠΌ ΠΏΠΎΡΠΎΡΠ½ΡΠΉ ΠΊΡΡΠ³ ΡΠ΅Π°ΠΊΡΠΈΠ²Π½ΠΎΠ³ΠΎ, Π° Π½Π΅ ΡΠΏΡΠ΅ΠΆΠ΄Π°ΡΡΠ΅Π³ΠΎ ΠΎΠ±ΡΠ»ΡΠΆΠΈΠ²Π°Π½ΠΈΡ.
ΠΡΡΠ»Π΅ΠΆΠΈΠ²Π°Ρ KPI Π½Π΅Π²ΡΠΏΠΎΠ»Π½Π΅Π½Π½ΡΡ ΡΠ°Π±ΠΎΡ ΠΏΠΎ ΡΠ΅Ρ Π½ΠΈΡΠ΅ΡΠΊΠΎΠΌΡ ΠΎΠ±ΡΠ»ΡΠΆΠΈΠ²Π°Π½ΠΈΡ Π² ΡΠΈΡΡΠ΅ΠΌΠ΅ CMMS, Π²Ρ ΠΌΠΎΠΆΠ΅ΡΠ΅ ΡΡΠ°Π·Ρ ΡΠ²ΠΈΠ΄Π΅ΡΡ, ΠΊΠ°ΠΊΠΈΠ΅ Π·Π°Π΄Π°ΡΠΈ Π΅ΡΠ΅ Π½Π΅ Π²ΡΠΏΠΎΠ»Π½Π΅Π½Ρ, ΠΈ ΠΏΡΠ΅Π΄ΠΏΡΠΈΠ½ΡΡΡ ΡΠ°Π³ΠΈ, ΡΡΠΎΠ±Ρ Π½Π°Π²Π΅ΡΡΡΠ°ΡΡ ΡΠΏΡΡΠ΅Π½Π½ΠΎΠ΅.ΠΡΠ»ΠΈ ΠΊΡΠΈΡΠΈΡΠ΅ΡΠΊΠΎΠ΅ ΠΎΠ±ΡΠ»ΡΠΆΠΈΠ²Π°Π½ΠΈΠ΅ Π½Π΅ Π²ΡΠΏΠΎΠ»Π½ΡΠ΅ΡΡΡ, Π²Ρ ΠΌΠΎΠΆΠ΅ΡΠ΅ ΠΏΠ΅ΡΠ΅Π½Π°Π·Π½Π°ΡΠΈΡΡ ΡΠ΅ΡΡΡΡΡ Ρ ΠΌΠ΅Π½Π΅Π΅ Π²Π°ΠΆΠ½ΠΎΠΉ ΡΠ°Π±ΠΎΡΡ Π΄ΠΎ ΡΠ΅Ρ ΠΏΠΎΡ, ΠΏΠΎΠΊΠ° ΡΠ°Π±ΠΎΡΠ° Π½Π΅ Π±ΡΠ΄Π΅Ρ Π·Π°Π²Π΅ΡΡΠ΅Π½Π°.
Π‘ΡΠ΅Π΄Π½Π΅Π΅ Π²ΡΠ΅ΠΌΡ ΡΠ΅ΠΌΠΎΠ½ΡΠ° (MTTR)
Π‘ΡΠ΅Π΄Π½Π΅Π΅ Π²ΡΠ΅ΠΌΡ Π²ΠΎΡΡΡΠ°Π½ΠΎΠ²Π»Π΅Π½ΠΈΡ (MTTR) — ΡΡΠΎ ΡΡΠ΅Π΄Π½Π΅Π΅ Π²ΡΠ΅ΠΌΡ, Π½Π΅ΠΎΠ±Ρ ΠΎΠ΄ΠΈΠΌΠΎΠ΅ Π΄Π»Ρ ΡΡΡΡΠ°Π½Π΅Π½ΠΈΡ Π½Π΅ΠΈΡΠΏΡΠ°Π²Π½ΠΎΡΡΠΈ ΠΎΡΠΊΠ°Π·Π°Π²ΡΠ΅Π³ΠΎ ΡΠ»Π΅ΠΌΠ΅Π½ΡΠ° ΠΎΠ±ΠΎΡΡΠ΄ΠΎΠ²Π°Π½ΠΈΡ ΠΈ Π²ΠΎΠ·Π²ΡΠ°ΡΠ° Π΅Π³ΠΎ ΠΊ ΡΠ°Π±ΠΎΡΠ΅. Π§Π°ΡΡ ΠΎΡΡΡΠΈΡΡΠ²Π°ΡΡ Π²ΡΠ΅ΠΌΡ Ρ ΠΌΠΎΠΌΠ΅Π½ΡΠ° Π²ΠΎΠ·Π½ΠΈΠΊΠ½ΠΎΠ²Π΅Π½ΠΈΡ ΠΏΡΠΎΠ±Π»Π΅ΠΌΡ Π΄ΠΎ ΡΠ΅Ρ ΠΏΠΎΡ, ΠΏΠΎΠΊΠ° ΠΎΠ½ΠΈ Π½Π΅ Π²Π΅ΡΠ½ΡΡΡΡ ΠΊ ΠΏΠΎΠ»Π½ΠΎΠΉ ΠΏΡΠΎΠΈΠ·Π²ΠΎΠ΄ΡΡΠ²Π΅Π½Π½ΠΎΠΉ ΠΌΠΎΡΠ½ΠΎΡΡΠΈ. Π Π°ΡΡΡΠΈΡΡΠ²Π°Π΅ΡΡΡ ΠΊΠ°ΠΊ:
Π‘ΡΠ΅Π΄Π½Π΅Π΅ Π²ΡΠ΅ΠΌΡ Π²ΠΎΡΡΡΠ°Π½ΠΎΠ²Π»Π΅Π½ΠΈΡMTTR = ΠΠ±ΡΠ΅Π΅ Π²ΡΠ΅ΠΌΡ ΠΏΡΠΎΡΡΠΎΡ / ΠΊΠΎΠ»ΠΈΡΠ΅ΡΡΠ²ΠΎ ΠΎΡΠΊΠ°Π·ΠΎΠ²
ΠΌΠΎΠΆΠ΅Ρ ΠΈΠΌΠ΅ΡΡ Π·Π½Π°ΡΠΈΡΠ΅Π»ΡΠ½ΠΎΠ΅ Π²Π»ΠΈΡΠ½ΠΈΠ΅ Π½Π° ΡΠΈΡΡΡΡ ΠΏΡΠΈΠ±ΡΠ»Ρ, ΠΏΠΎΡΠΎΠΌΡ ΡΡΠΎ ΡΠ΅ΠΌ Π΄ΠΎΠ»ΡΡΠ΅ ΡΡΠ΅Π΄Π½Π΅Π΅ Π²ΡΠ΅ΠΌΡ Π²ΠΎΡΡΡΠ°Π½ΠΎΠ²Π»Π΅Π½ΠΈΡ, ΡΠ΅ΠΌ Π±ΠΎΠ»ΡΡΠ΅ Π²Π΅ΡΠΎΡΡΠ½ΠΎΡΡΡ ΡΠΎΠ³ΠΎ, ΡΡΠΎ ΡΡΠΎ ΠΏΡΠΈΠ²Π΅Π΄Π΅Ρ ΠΊ ΠΏΡΠΎΠΏΡΡΠ΅Π½Π½ΡΠΌ Π·Π°ΠΊΠ°Π·Π°ΠΌ, Π½Π΅Π²ΡΠΏΠΎΠ»Π½Π΅Π½Π½ΡΠΌ Π±ΠΈΠ·Π½Π΅Ρ-ΡΠ΅Π»ΡΠΌ ΠΈ Π½Π°Π½Π΅ΡΠ΅Π½ΠΈΡ ΡΡΠ΅ΡΠ±Π° ΡΠ΅ΠΏΡΡΠ°ΡΠΈΠΈ ΠΎΡΠ³Π°Π½ΠΈΠ·Π°ΡΠΈΠΈ.ΠΡΡΠ»Π΅ΠΆΠΈΠ²Π°Ρ ΠΈ ΠΎΡΡΠ»Π΅ΠΆΠΈΠ²Π°Ρ ΡΡΠΈ Π΄Π°Π½Π½ΡΠ΅, ΠΎΡΠ³Π°Π½ΠΈΠ·Π°ΡΠΈΠΈ ΠΌΠΎΠ³ΡΡ ΠΏΠΎΠ»ΡΡΠΈΡΡ Π»ΡΡΡΠ΅Π΅ ΠΏΡΠ΅Π΄ΡΡΠ°Π²Π»Π΅Π½ΠΈΠ΅ ΠΎ Π½Π΅ΠΎΠ±Ρ ΠΎΠ΄ΠΈΠΌΠΎΠΌ ΠΏΠ΅ΡΡΠΎΠ½Π°Π»Π΅, ΡΠΏΡΠ°Π²Π»Π΅Π½ΠΈΠΈ Π·Π°ΠΏΠ°ΡΠ°ΠΌΠΈ (ΡΠ±Π΅Π΄ΠΈΡΠ΅ΡΡ, ΡΡΠΎ Ρ Π½ΠΈΡ Π΅ΡΡΡ Π΄Π΅ΡΠ°Π»ΠΈ Π² ΠΊΡΠ°ΡΡΠ°ΠΉΡΠΈΠ΅ ΡΡΠΎΠΊΠΈ), Π° ΡΠ°ΠΊΠΆΠ΅ ΠΎ ΡΠΎΠΌ, ΠΊΠΎΠ³Π΄Π° ΡΠ΅ΠΌΠΎΠ½ΡΠΈΡΠΎΠ²Π°ΡΡ ΠΈ ΠΊΠΎΠ³Π΄Π° Π·Π°ΠΌΠ΅Π½ΡΡΡ Π½Π° ΠΎΡΠ½ΠΎΠ²Π΅ ΠΎΠ±ΡΠ΅ΠΊΡΠΈΠ²Π½ΡΡ Π΄Π°Π½Π½ΡΡ . ΠΡΠΎΡ KPI ΡΠ°ΠΊΠΆΠ΅ ΠΏΡΠ΅Π΄ΠΎΡΡΠ°Π²Π»ΡΠ΅Ρ ΠΎΡΠ³Π°Π½ΠΈΠ·Π°ΡΠΈΡΠΌ Π²Π°ΠΆΠ½ΡΠ΅ Π΄Π°Π½Π½ΡΠ΅, ΠΊΠΎΡΠΎΡΡΠ΅ ΠΎΠ½ΠΈ ΠΌΠΎΠ³ΡΡ ΠΈΡΠΏΠΎΠ»ΡΠ·ΠΎΠ²Π°ΡΡ Π΄Π»Ρ Π±ΠΎΠ»Π΅Π΅ ΡΡΡΠ΅ΠΊΡΠΈΠ²Π½ΠΎΠ³ΠΎ ΡΠ΅Π°Π³ΠΈΡΠΎΠ²Π°Π½ΠΈΡ Π½Π° ΠΏΡΠΎΠ±Π»Π΅ΠΌΡ Ρ ΠΎΠ±ΠΎΡΡΠ΄ΠΎΠ²Π°Π½ΠΈΠ΅ΠΌ ΠΈ Π·Π°ΠΊΠ»ΡΡΠ΅Π½ΠΈΡ ΡΠ΅Π°Π»ΠΈΡΡΠΈΡΠ½ΡΡ ΡΠΎΠ³Π»Π°ΡΠ΅Π½ΠΈΠΉ ΠΎΠ± ΡΡΠΎΠ²Π½Π΅ ΠΎΠ±ΡΠ»ΡΠΆΠΈΠ²Π°Π½ΠΈΡ.
Π‘ΡΠ΅Π΄Π½ΡΡ Π½Π°ΡΠ°Π±ΠΎΡΠΊΠ° Π½Π° ΠΎΡΠΊΠ°Π· (MTBF)
MTBF— Π²Π°ΠΆΠ½ΡΠΉ ΡΠΏΠΎΡΠΎΠ± ΠΊΠΎΠ»ΠΈΡΠ΅ΡΡΠ²Π΅Π½Π½ΠΎΠΉ ΠΎΡΠ΅Π½ΠΊΠΈ Π½Π°Π΄Π΅ΠΆΠ½ΠΎΡΡΠΈ Π°ΠΊΡΠΈΠ²Π° ΠΈ ΠΏΡΠΎΠ³Π½ΠΎΠ·ΠΈΡΠΎΠ²Π°Π½ΠΈΡ Π±ΡΠ΄ΡΡΠ΅ΠΉ ΠΏΡΠΎΠΈΠ·Π²ΠΎΠ΄ΠΈΡΠ΅Π»ΡΠ½ΠΎΡΡΠΈ.ΠΠ½ ΠΎΠΏΡΠ΅Π΄Π΅Π»ΡΠ΅ΡΡΡ ΠΊΠ°ΠΊ ΡΡΠ΅Π΄Π½Π΅Π΅ Π²ΡΠ΅ΠΌΡ, ΠΏΡΠΎΡΠ΅Π΄ΡΠ΅Π΅ ΠΌΠ΅ΠΆΠ΄Ρ ΠΎΡΠΊΠ°Π·Π°ΠΌΠΈ ΡΠΈΡΡΠ΅ΠΌΡ Π²ΠΎ Π²ΡΠ΅ΠΌΡ ΡΠ°Π±ΠΎΡΡ. ΠΡΠΎ Π²Π°ΠΆΠ½ΡΠΉ KPI Π΄Π»Ρ ΠΎΠΏΡΠ΅Π΄Π΅Π»Π΅Π½ΠΈΡ ΠΏΡΠΎΠΈΠ·Π²ΠΎΠ΄ΠΈΡΠ΅Π»ΡΠ½ΠΎΡΡΠΈ ΠΊΡΠΈΡΠΈΡΠ΅ΡΠΊΠΈ Π²Π°ΠΆΠ½ΡΡ ΡΠ»Π΅ΠΌΠ΅Π½ΡΠΎΠ² ΠΎΠ±ΠΎΡΡΠ΄ΠΎΠ²Π°Π½ΠΈΡ. Π Π°ΡΡΡΠΈΡΡΠ²Π°Π΅ΡΡΡ ΠΊΠ°ΠΊ:
Π‘ΡΠ΅Π΄Π½Π΅Π΅ Π²ΡΠ΅ΠΌΡ Π±Π΅Π·ΠΎΡΠΊΠ°Π·Π½ΠΎΠΉ ΡΠ°Π±ΠΎΡΡ = (Π½Π°ΡΠ°Π»ΠΎ ΠΏΡΠΎΡΡΠΎΡ — Π½Π°ΡΠ°Π»ΠΎ Π²ΡΠ΅ΠΌΠ΅Π½ΠΈ Π±Π΅Π·ΠΎΡΠΊΠ°Π·Π½ΠΎΠΉ ΡΠ°Π±ΠΎΡΡ) / ΠΊΠΎΠ»ΠΈΡΠ΅ΡΡΠ²ΠΎ ΠΎΡΠΊΠ°Π·ΠΎΠ²
ΠΠ±ΡΠ°Ρ ΡΡΡΠ΅ΠΊΡΠΈΠ²Π½ΠΎΡΡΡ ΠΎΠ±ΠΎΡΡΠ΄ΠΎΠ²Π°Π½ΠΈΡ (OEE)
OEE ΠΎΡΠ΅Π½ΠΈΠ²Π°Π΅Ρ, Π½Π°ΡΠΊΠΎΠ»ΡΠΊΠΎ Π΄ΠΎΡΡΡΠΏΠ½ΠΎ ΠΎΠ±ΠΎΡΡΠ΄ΠΎΠ²Π°Π½ΠΈΠ΅, ΠΊΠ°ΠΊ ΠΎΠ½ΠΎ ΡΠ°Π±ΠΎΡΠ°Π΅Ρ ΠΈ ΠΊΠ°ΠΊΠΎΠ΅ ΠΊΠ°ΡΠ΅ΡΡΠ²ΠΎ ΠΎΠ±Π΅ΡΠΏΠ΅ΡΠΈΠ²Π°Π΅Ρ, ΡΡΠΎΠ±Ρ ΠΏΡΠ΅Π΄ΠΎΡΡΠ°Π²ΠΈΡΡ Π²ΡΡΠΎΠΊΠΎΡΡΠΎΠ²Π½Π΅Π²ΡΡ ΠΊΠ°ΡΡΠΈΠ½Ρ ΡΡΡΠ΅ΠΊΡΠΈΠ²Π½ΠΎΡΡΠΈ ΠΎΠ±ΠΎΡΡΠ΄ΠΎΠ²Π°Π½ΠΈΡ Π½Π° ΠΎΡΠ½ΠΎΠ²Π΅ Π΄Π°Π½Π½ΡΡ .OEE — ΡΡΠΎ ΠΎΠ±ΡΠΈΠΉ KPI, ΠΏΠΎΠΌΠΎΠ³Π°ΡΡΠΈΠΉ ΠΎΡΠ³Π°Π½ΠΈΠ·Π°ΡΠΈΡΠΌ Π²ΠΎ Π²ΡΠ΅Ρ ΠΎΡΡΠ°ΡΠ»ΡΡ ΡΠ΅Π°Π»ΠΈΠ·ΠΎΠ²Π°ΡΡ ΠΈΠ½ΠΈΡΠΈΠ°ΡΠΈΠ²Ρ ΠΏΠΎ Π±Π΅ΡΠ΅ΠΆΠ»ΠΈΠ²ΠΎΠΌΡ ΠΏΡΠΎΠΈΠ·Π²ΠΎΠ΄ΡΡΠ²Ρ. Π‘ΡΠ°Π²Π½ΠΈΡΠ΅Π»ΡΠ½ΡΠΉ Π°Π½Π°Π»ΠΈΠ· OEE ΠΌΠΎΠΆΠ΅Ρ Π΄Π°ΡΡ ΠΏΡΠ΅Π΄ΡΡΠ°Π²Π»Π΅Π½ΠΈΠ΅ ΠΎΠ± ΡΡΠΏΠ΅Ρ Π°Ρ Π² ΠΎΠ±ΡΠ»ΡΠΆΠΈΠ²Π°Π½ΠΈΠΈ ΠΈ ΠΏΠΎΠΌΠΎΡΡ Π²ΡΡΠ²ΠΈΡΡ ΠΎΠ±Π»Π°ΡΡΠΈ, Π½ΡΠΆΠ΄Π°ΡΡΠΈΠ΅ΡΡ Π² ΡΠ»ΡΡΡΠ΅Π½ΠΈΠΈ. Π Π°ΡΡΠ΅Ρ OEE ΠΎΡΠ½ΠΎΠ²Π°Π½ Π½Π° ΡΡΠ΅Ρ Π½Π°Π±ΠΎΡΠ°Ρ ΡΠ°ΡΡΠ΅ΡΠΎΠ²:
- ΠΠΎΡΡΡΠΏΠ½ΠΎΡΡΡ = ΠΡΠ΅ΠΌΡ ΡΠ°Π±ΠΎΡΡ / ΠΠ»Π°Π½ΠΈΡΡΠ΅ΠΌΠΎΠ΅ Π²ΡΠ΅ΠΌΡ ΠΏΡΠΎΠΈΠ·Π²ΠΎΠ΄ΡΡΠ²Π°
- ΠΡΠΎΠΈΠ·Π²ΠΎΠ΄ΠΈΡΠ΅Π»ΡΠ½ΠΎΡΡΡ = (ΠΈΠ΄Π΅Π°Π»ΡΠ½ΠΎΠ΅ Π²ΡΠ΅ΠΌΡ ΡΠΈΠΊΠ»Π° Ρ ΠΎΠ±ΡΠ΅Π΅ ΠΊΠΎΠ»ΠΈΡΠ΅ΡΡΠ²ΠΎ) / Π²ΡΠ΅ΠΌΡ ΡΠ°Π±ΠΎΡΡ
- ΠΠ°ΡΠ΅ΡΡΠ²ΠΎ = Π₯ΠΎΡΠΎΡΠ΅Π΅ ΠΊΠΎΠ»ΠΈΡΠ΅ΡΡΠ²ΠΎ / ΠΠ±ΡΠ΅Π΅ ΠΊΠΎΠ»ΠΈΡΠ΅ΡΡΠ²ΠΎ
Π Π°ΡΡΠ΅Ρ ΠΎΠ±ΡΠ΅Π³ΠΎ OEE Π΄Π»Ρ ΠΊΠΎΠ½ΠΊΡΠ΅ΡΠ½ΠΎΠΉ Π΅Π΄ΠΈΠ½ΠΈΡΡ ΠΎΠ±ΠΎΡΡΠ΄ΠΎΠ²Π°Π½ΠΈΡ:
OEE = Π΄ΠΎΡΡΡΠΏΠ½ΠΎΡΡΡ X ΠΏΡΠΎΠΈΠ·Π²ΠΎΠ΄ΠΈΡΠ΅Π»ΡΠ½ΠΎΡΡΡ X ΠΊΠ°ΡΠ΅ΡΡΠ²ΠΎ
ΠΡ ΠΌΠΎΠΆΠ΅ΡΠ΅ ΠΈΡΠΏΠΎΠ»ΡΠ·ΠΎΠ²Π°ΡΡ OEE Π² ΠΊΠ°ΡΠ΅ΡΡΠ²Π΅ ΡΡΠ°Π»ΠΎΠ½Π° Π΄Π»Ρ ΡΡΠ°Π²Π½Π΅Π½ΠΈΡ ΠΏΡΠΎΠΈΠ·Π²ΠΎΠ΄ΠΈΡΠ΅Π»ΡΠ½ΠΎΡΡΠΈ Π°ΠΊΡΠΈΠ²Π° Ρ ΠΎΡΡΠ°ΡΠ»Π΅Π²ΡΠΌΠΈ ΡΡΠ°Π½Π΄Π°ΡΡΠ°ΠΌΠΈ ΠΈΠ»ΠΈ Ρ Π°Π½Π°Π»ΠΎΠ³ΠΈΡΠ½ΡΠΌΠΈ Π°ΠΊΡΠΈΠ²Π°ΠΌΠΈ Π½Π° Π²Π°ΡΠ΅ΠΌ ΠΏΡΠ΅Π΄ΠΏΡΠΈΡΡΠΈΠΈ.ΠΡ ΡΠ°ΠΊΠΆΠ΅ ΠΌΠΎΠΆΠ΅ΡΠ΅ ΠΈΡΠΏΠΎΠ»ΡΠ·ΠΎΠ²Π°ΡΡ OEE Π΄Π»Ρ ΠΈΠ·ΠΌΠ΅ΡΠ΅Π½ΠΈΡ ΠΏΡΠΎΠΈΠ·Π²ΠΎΠ΄ΠΈΡΠ΅Π»ΡΠ½ΠΎΡΡΠΈ Π°ΠΊΡΠΈΠ²Π° Π² ΡΠ°Π·Π½ΡΠ΅ ΡΠΌΠ΅Π½Ρ. ΠΡΠΎ ΠΏΠΎΠ·Π²ΠΎΠ»ΡΠ΅Ρ Π²Π°ΠΌ ΠΎΡΡΠ»Π΅ΠΆΠΈΠ²Π°ΡΡ ΡΠ»ΡΡΡΠ΅Π½ΠΈΡ Ρ ΡΠ΅ΡΠ΅Π½ΠΈΠ΅ΠΌ Π²ΡΠ΅ΠΌΠ΅Π½ΠΈ, ΡΡΠΎΠ±Ρ ΠΎΠΏΡΠ΅Π΄Π΅Π»ΠΈΡΡ ΡΡΡΠ΅ΠΊΡΠΈΠ²Π½ΠΎΡΡΡ Π²Π°ΡΠΈΡ ΠΏΡΠΎΡΠ΅ΡΡΠΎΠ² ΠΎΠ±ΡΠ»ΡΠΆΠΈΠ²Π°Π½ΠΈΡ.
PM Π‘ΠΎΠΎΡΠ²Π΅ΡΡΡΠ²ΠΈΠ΅
PM — ΡΡΠΎ ΡΠ΅Π³ΡΠ»ΡΡΠ½ΠΎΠ΅ ΠΏΠ»Π°Π½ΠΎΠ²ΠΎΠ΅ ΡΠ΅Ρ Π½ΠΈΡΠ΅ΡΠΊΠΎΠ΅ ΠΎΠ±ΡΠ»ΡΠΆΠΈΠ²Π°Π½ΠΈΠ΅ Π΅Π΄ΠΈΠ½ΠΈΡΡ ΠΎΠ±ΠΎΡΡΠ΄ΠΎΠ²Π°Π½ΠΈΡ Π΄Π»Ρ ΡΠ½ΠΈΠΆΠ΅Π½ΠΈΡ Π²Π΅ΡΠΎΡΡΠ½ΠΎΡΡΠΈ Π²ΡΡ ΠΎΠ΄Π° ΠΈΠ· ΡΡΡΠΎΡ. ΠΠ½ Π²ΡΠΏΠΎΠ»Π½ΡΠ΅ΡΡΡ, ΠΏΠΎΠΊΠ° ΠΎΠ±ΠΎΡΡΠ΄ΠΎΠ²Π°Π½ΠΈΠ΅ Π΅ΡΠ΅ Π½Π°Ρ ΠΎΠ΄ΠΈΡΡΡ Π² ΡΠ°Π±ΠΎΡΠ΅ΠΌ ΡΠΎΡΡΠΎΡΠ½ΠΈΠΈ, ΡΡΠΎΠ±Ρ ΠΈΠ·Π±Π΅ΠΆΠ°ΡΡ Π½Π΅ΠΎΠΆΠΈΠ΄Π°Π½Π½ΡΡ ΠΏΠΎΠ»ΠΎΠΌΠΎΠΊ. PM Compliance ΡΠΊΠ°Π·ΡΠ²Π°Π΅Ρ ΠΏΡΠΎΡΠ΅Π½Ρ Π·Π°ΠΏΠ»Π°Π½ΠΈΡΠΎΠ²Π°Π½Π½ΡΡ ΠΏΡΠΎΡΠΈΠ»Π°ΠΊΡΠΈΡΠ΅ΡΠΊΠΈΡ Π·Π°ΠΊΠ°Π·ΠΎΠ² Π½Π° ΡΠ°Π±ΠΎΡΡ, ΠΊΠΎΡΠΎΡΡΠ΅ Π²ΡΠΏΠΎΠ»Π½Π΅Π½Ρ Π² ΡΠΊΠ°Π·Π°Π½Π½ΡΠΉ ΠΏΠ΅ΡΠΈΠΎΠ΄ Π²ΡΠ΅ΠΌΠ΅Π½ΠΈ.ΠΡΠΎΡ KPI ΠΏΠΎΠΊΠ°Π·ΡΠ²Π°Π΅Ρ, Π½Π°ΡΠΊΠΎΠ»ΡΠΊΠΎ ΡΡΡΠ΅ΠΊΡΠΈΠ²Π½Π° Π²Π°ΡΠ° ΠΏΡΠΎΠ³ΡΠ°ΠΌΠΌΠ° ΡΠΏΡΠ°Π²Π»Π΅Π½ΠΈΡ ΠΏΡΠΎΠ΅ΠΊΡΠ°ΠΌΠΈ, ΠΈ ΠΌΠΎΠΆΠ΅Ρ ΠΏΠΎΠΌΠΎΡΡ Π²Π°ΠΌ ΠΎΠΏΡΠ΅Π΄Π΅Π»ΠΈΡΡ, ΠΊΠΎΠ³Π΄Π° Π²Π°ΠΌ ΠΌΠΎΠΆΠ΅Ρ ΠΏΠΎΡΡΠ΅Π±ΠΎΠ²Π°ΡΡΡΡ Π΄ΠΎΠ±Π°Π²ΠΈΡΡ ΠΈΠ»ΠΈ ΠΏΠ΅ΡΠ΅Π½Π°Π·Π½Π°ΡΠΈΡΡ ΡΠ΅ΡΡΡΡΡ ΠΎΠ±ΡΠ»ΡΠΆΠΈΠ²Π°Π½ΠΈΡ.
ΠΡΠΎΡ KPI Π½Π΅ ΡΠΎΠ»ΡΠΊΠΎ ΠΏΠΎΠΌΠΎΠ³Π°Π΅Ρ Π²Π°ΡΠ΅ΠΉ ΠΎΡΠ³Π°Π½ΠΈΠ·Π°ΡΠΈΠΈ ΠΏΠΎΠ΄Π΄Π΅ΡΠΆΠΈΠ²Π°ΡΡ ΡΡΡΠ΅ΠΊΡΠΈΠ²Π½ΡΠΉ Π³ΡΠ°ΡΠΈΠΊ PM; ΡΡΠΎ ΡΠ°ΠΊΠΆΠ΅ ΡΠΏΡΠΎΡΠ°Π΅Ρ Π΄ΠΎΠΊΡΠΌΠ΅Π½ΡΠΈΡΠΎΠ²Π°Π½ΠΈΠ΅ ΡΠΎΠ±Π»ΡΠ΄Π΅Π½ΠΈΡ ΡΡΠΎΠ³ΠΎ Π³ΡΠ°ΡΠΈΠΊΠ° ΠΈ ΠΎΠ±Π΅ΡΠΏΠ΅ΡΠΈΠ²Π°Π΅Ρ Π²ΠΈΠ΄ΠΈΠΌΠΎΡΡΡ ΠΏΡΠΎΠ±Π»Π΅ΠΌ, ΠΊΠΎΡΠΎΡΡΠ΅ ΠΏΡΠ΅ΠΏΡΡΡΡΠ²ΡΡΡ ΡΡΠΎΠΌΡ ΡΠΎΠ±Π»ΡΠ΄Π΅Π½ΠΈΡ.
ΠΡΠΎΡΠ΅Π½Ρ ΠΏΠ»Π°Π½ΠΎΠ²ΠΎΠ³ΠΎ ΡΠ΅Ρ ΠΎΠ±ΡΠ»ΡΠΆΠΈΠ²Π°Π½ΠΈΡ
ΠΡΠΎΡΠ΅Π½Ρ ΠΏΠ»Π°Π½ΠΎΠ²ΠΎΠ³ΠΎ ΠΎΠ±ΡΠ»ΡΠΆΠΈΠ²Π°Π½ΠΈΡ — ΡΡΠΎ ΠΏΡΠΎΡΠ΅Π½ΡΠ½ΠΎΠ΅ ΡΠΎΠΎΡΠ½ΠΎΡΠ΅Π½ΠΈΠ΅ ΡΠ°ΡΠΎΠ² ΠΎΠ±ΡΠ»ΡΠΆΠΈΠ²Π°Π½ΠΈΡ, ΠΏΠΎΡΡΠ°ΡΠ΅Π½Π½ΡΡ Π½Π° ΠΏΠ»Π°Π½ΠΎΠ²ΡΠ΅ (ΠΏΡΠΎΡΠΈΠ»Π°ΠΊΡΠΈΡΠ΅ΡΠΊΠΈΠ΅) ΠΌΠ΅ΡΠΎΠΏΡΠΈΡΡΠΈΡ ΠΏΠΎ ΠΎΠ±ΡΠ»ΡΠΆΠΈΠ²Π°Π½ΠΈΡ ΠΏΠΎ ΡΡΠ°Π²Π½Π΅Π½ΠΈΡ Ρ Π½Π΅Π·Π°ΠΏΠ»Π°Π½ΠΈΡΠΎΠ²Π°Π½Π½ΡΠΌΠΈ (ΡΠ΅Π°ΠΊΡΠΈΠ²Π½ΡΠΌΠΈ).ΠΡΠΎΡ ΠΏΡΠΎΡΠ΅Π½Ρ ΡΠ°ΡΡΡΠΈΡΡΠ²Π°Π΅ΡΡΡ ΠΏΡΡΠ΅ΠΌ Π΄Π΅Π»Π΅Π½ΠΈΡ ΡΠ°Π±ΠΎΡΠ΅Π³ΠΎ Π²ΡΠ΅ΠΌΠ΅Π½ΠΈ Π½Π° ΠΏΠ»Π°Π½ΠΎΠ²ΠΎΠ΅ ΡΠ΅Ρ Π½ΠΈΡΠ΅ΡΠΊΠΎΠ΅ ΠΎΠ±ΡΠ»ΡΠΆΠΈΠ²Π°Π½ΠΈΠ΅ Π½Π° ΠΎΠ±ΡΠ΅Π΅ ΠΊΠΎΠ»ΠΈΡΠ΅ΡΡΠ²ΠΎ ΡΠ°ΡΠΎΠ² ΡΠ΅Ρ Π½ΠΈΡΠ΅ΡΠΊΠΎΠ³ΠΎ ΠΎΠ±ΡΠ»ΡΠΆΠΈΠ²Π°Π½ΠΈΡ Π² ΡΠ΅ΡΠ΅Π½ΠΈΠ΅ ΠΎΠΏΡΠ΅Π΄Π΅Π»Π΅Π½Π½ΠΎΠ³ΠΎ ΠΏΠ΅ΡΠΈΠΎΠ΄Π° Π²ΡΠ΅ΠΌΠ΅Π½ΠΈ.
Π Π°Π½ΡΡΠ΅ Π±ΠΎΠ»ΡΡΠΈΠ½ΡΡΠ²ΠΎ ΠΎΡΠ³Π°Π½ΠΈΠ·Π°ΡΠΈΠΉ ΡΠ°Π±ΠΎΡΠ°Π»ΠΈ Π² ΡΠ΅ΠΆΠΈΠΌΠ΅ Β«Π½Π°ΡΠ°Π±ΠΎΡΠΊΠ° Π΄ΠΎ ΠΎΡΠΊΠ°Π·Π°Β» ΠΈΠ»ΠΈ Π² ΡΠ΅ΠΆΠΈΠΌΠ΅ ΡΠ΅Π°ΠΊΡΠΈΠ²Π½ΠΎΠ³ΠΎ ΠΎΠ±ΡΠ»ΡΠΆΠΈΠ²Π°Π½ΠΈΡ. ΠΠ½ΠΈ ΡΠ΅ΠΌΠΎΠ½ΡΠΈΡΠΎΠ²Π°Π»ΠΈ ΠΎΠ±ΠΎΡΡΠ΄ΠΎΠ²Π°Π½ΠΈΠ΅ ΠΏΠΎΡΠ»Π΅ ΡΠΎΠ³ΠΎ, ΠΊΠ°ΠΊ ΠΎΠ½ΠΎ Π²ΡΡΠ»ΠΎ ΠΈΠ· ΡΡΡΠΎΡ. ΠΠ° ΠΏΠ΅ΡΠ²ΡΠΉ Π²Π·Π³Π»ΡΠ΄ ΡΡΠΎ ΠΌΠΎΠΆΠ΅Ρ ΠΏΠΎΠΊΠ°Π·Π°ΡΡΡΡ ΠΌΠ΅Π½Π΅Π΅ Π·Π°ΡΡΠ°ΡΠ½ΡΠΌ, ΡΠ΅ΠΌ ΡΠΎΠ·Π΄Π°Π½ΠΈΠ΅ Π·Π°ΠΏΠ»Π°Π½ΠΈΡΠΎΠ²Π°Π½Π½ΠΎΠΉ ΠΏΡΠΎΠ³ΡΠ°ΠΌΠΌΡ PM. ΠΠ΄Π½Π°ΠΊΠΎ ΠΈΡΡΠ»Π΅Π΄ΠΎΠ²Π°Π½ΠΈΡ ΠΏΠΎΠΊΠ°Π·Π°Π»ΠΈ, ΡΡΠΎ ΡΠ°ΠΊΠΎΠΉ ΡΠ΅Π°ΠΊΡΠΈΠ²Π½ΡΠΉ ΠΏΠΎΠ΄Ρ ΠΎΠ΄ ΠΌΠΎΠΆΠ΅Ρ ΡΡΠΎΠΈΡΡ Π² ΠΏΡΡΡ-Π²ΠΎΡΠ΅ΠΌΡ ΡΠ°Π· Π΄ΠΎΡΠΎΠΆΠ΅, ΡΠ΅ΠΌ ΠΏΡΠΎΠ°ΠΊΡΠΈΠ²Π½ΡΠΉ ΠΏΠΎΠ΄Ρ ΠΎΠ΄ ΠΊ ΠΎΠ±ΡΠ»ΡΠΆΠΈΠ²Π°Π½ΠΈΡ.
Π Π΄Π΅ΠΉΡΡΠ²ΠΈΡΠ΅Π»ΡΠ½ΠΎΡΡΠΈ Π½Π΅ΠΎΠ±Ρ ΠΎΠ΄ΠΈΠΌΠΎΡΡΡ Π² ΡΠ΅Π°ΠΊΡΠΈΠ²Π½ΠΎΠΌ ΠΎΠ±ΡΠ»ΡΠΆΠΈΠ²Π°Π½ΠΈΠΈ Π±ΡΠ΄Π΅Ρ Π²ΡΠ΅Π³Π΄Π°, Π½ΠΎ ΠΏΡΠ°ΠΊΡΠΈΠΊΠ° ΠΎΠ±ΡΠ»ΡΠΆΠΈΠ²Π°Π½ΠΈΡ ΠΌΠΈΡΠΎΠ²ΠΎΠ³ΠΎ ΠΊΠ»Π°ΡΡΠ° ΠΏΡΠ΅Π΄ΠΏΠΎΠ»Π°Π³Π°Π΅Ρ, ΡΡΠΎ 90% ΠΎΠ±ΡΠ»ΡΠΆΠΈΠ²Π°Π½ΠΈΡ ΡΠ»Π΅Π΄ΡΠ΅Ρ ΠΏΠ»Π°Π½ΠΈΡΠΎΠ²Π°ΡΡ. ΠΠ°ΠΆΠ΅ ΡΠΎΠΎΡΠ½ΠΎΡΠ΅Π½ΠΈΠ΅ 80% Π·Π°ΠΏΠ»Π°Π½ΠΈΡΠΎΠ²Π°Π½Π½ΡΡ ΠΊ 20% Π½Π΅Π·Π°ΠΏΠ»Π°Π½ΠΈΡΠΎΠ²Π°Π½Π½ΡΡ ΡΡΠΈΡΠ°Π΅ΡΡΡ Π²ΡΠ³ΠΎΠ΄Π½ΡΠΌ, ΠΏΠΎ ΡΡΠ°Π²Π½Π΅Π½ΠΈΡ Ρ ΡΠΈΠΏΠΈΡΠ½ΡΠΌ ΡΡΠ΅Π΄Π½ΠΈΠΌ Π·Π½Π°ΡΠ΅Π½ΠΈΠ΅ΠΌ Π·Π°ΠΏΠ»Π°Π½ΠΈΡΠΎΠ²Π°Π½Π½ΠΎΠ³ΠΎ ΠΎΠ±ΡΠ»ΡΠΆΠΈΠ²Π°Π½ΠΈΡ 55% ΠΈΠ»ΠΈ ΠΌΠ΅Π½ΡΡΠ΅. ΠΡΠΎΡ ΠΏΡΠΎΡΠ΅Π½Ρ ΠΌΠΎΠΆΠ½ΠΎ Π»Π΅Π³ΠΊΠΎ ΠΎΡΡΠ»Π΅ΠΆΠΈΠ²Π°ΡΡ Ρ ΠΏΠΎΠΌΠΎΡΡΡ ΡΡΡΠ΅ΠΊΡΠΈΠ²Π½ΠΎΠΉ ΡΠΈΡΡΠ΅ΠΌΡ CMMS ΠΈ ΠΈΡΠΏΠΎΠ»ΡΠ·ΠΎΠ²Π°ΡΡ Π² ΡΠΎΡΠ΅ΡΠ°Π½ΠΈΠΈ Ρ Π΄ΡΡΠ³ΠΈΠΌΠΈ ΠΊΠ»ΡΡΠ΅Π²ΡΠΌΠΈ ΠΏΠΎΠΊΠ°Π·Π°ΡΠ΅Π»ΡΠΌΠΈ ΡΡΡΠ΅ΠΊΡΠΈΠ²Π½ΠΎΡΡΠΈ Π΄Π»Ρ ΡΠ²Π΅Π»ΠΈΡΠ΅Π½ΠΈΡ ΠΏΡΠΎΡΠ΅Π½ΡΠ° ΠΏΠ»Π°Π½ΠΎΠ²ΠΎΠ³ΠΎ ΠΈ ΡΠ΅Π°ΠΊΡΠΈΠ²Π½ΠΎΠ³ΠΎ ΠΎΠ±ΡΠ»ΡΠΆΠΈΠ²Π°Π½ΠΈΡ Ρ ΡΠ΅ΡΠ΅Π½ΠΈΠ΅ΠΌ Π²ΡΠ΅ΠΌΠ΅Π½ΠΈ.
ΠΠΎΠ½ΠΈΡΠΎΡΠΈΠ½Π³ ΡΠΎΡΡΠΎΡΠ½ΠΈΡ ΠΎΠ±ΠΎΡΡΠ΄ΠΎΠ²Π°Π½ΠΈΡ
Π Π΄ΠΎΠΏΠΎΠ»Π½Π΅Π½ΠΈΠ΅ ΠΊ ΠΌΠΎΠ½ΠΈΡΠΎΡΠΈΠ½Π³Ρ ΡΠ°Π·Π»ΠΈΡΠ½ΡΡ KPI PM, ΠΎΡΠ³Π°Π½ΠΈΠ·Π°ΡΠΈΠΈ ΠΌΠΎΠ³ΡΡ ΠΎΡΡΠ»Π΅ΠΆΠΈΠ²Π°ΡΡ ΡΡΠ΄ Π΄Π°Π½Π½ΡΡ ΠΎ ΡΠΎΡΡΠΎΡΠ½ΠΈΠΈ ΠΎΠ±ΠΎΡΡΠ΄ΠΎΠ²Π°Π½ΠΈΡ, ΡΠ°ΠΊΠΈΡ ΠΊΠ°ΠΊ ΡΠ»Π΅ΠΊΡΡΠΈΡΠ΅ΡΠΊΠΈΠ΅, ΡΠ΅ΠΌΠΏΠ΅ΡΠ°ΡΡΡΠ½ΡΠ΅ ΠΈ Π²ΠΈΠ±ΡΠ°ΡΠΈΠΎΠ½Π½ΡΠ΅ ΡΠ°ΠΊΡΠΎΡΡ, ΡΡΠΎΠ±Ρ ΡΡΡΠ°Π½Π°Π²Π»ΠΈΠ²Π°ΡΡ Π±ΠΎΠ»Π΅Π΅ ΡΡΡΠ΅ΠΊΡΠΈΠ²Π½ΡΠ΅ Π³ΡΠ°ΡΠΈΠΊΠΈ ΠΎΠ±ΡΠ»ΡΠΆΠΈΠ²Π°Π½ΠΈΡ ΠΈ Π²ΡΡΠ²Π»ΡΡΡ ΠΏΡΠΎΠ±Π»Π΅ΠΌΡ Ρ ΠΎΡΠ΄Π΅Π»ΡΠ½ΡΠΌΠΈ Π°ΠΊΡΠΈΠ²Π°ΠΌΠΈ Π΄ΠΎ ΡΠΎΠ³ΠΎ, ΠΊΠ°ΠΊ ΠΎΠ½ΠΈ ΠΏΡΠΈΠ²Π΅Π΄ΡΡ ΠΊ ΠΎΡΠΊΠ°Π·Ρ.Π ΡΡΠ΅Π΄Π΅ IIoT ΠΏΠΎΠ΄ΠΊΠ»ΡΡΠ΅Π½Π½ΠΎΠ΅ ΠΎΠ±ΠΎΡΡΠ΄ΠΎΠ²Π°Π½ΠΈΠ΅, ΠΈΠ½ΡΡΡΡΠΌΠ΅Π½ΡΡ ΡΠ΅ΡΡΠΈΡΠΎΠ²Π°Π½ΠΈΡ ΠΈ Π΄Π°ΡΡΠΈΠΊΠΈ ΠΌΠΎΠ³ΡΡ ΠΏΠ΅ΡΠ΅Π΄Π°Π²Π°ΡΡ Π΄Π°Π½Π½ΡΠ΅ ΠΎ ΡΠΎΡΡΠΎΡΠ½ΠΈΠΈ ΠΊΠΎΠΌΠΏΠΎΠ½Π΅Π½ΡΠΎΠ² Π² ΡΠΈΡΡΠ΅ΠΌΡ CMMS Π² ΡΠ΅Π°Π»ΡΠ½ΠΎΠΌ Π²ΡΠ΅ΠΌΠ΅Π½ΠΈ Π΄Π»Ρ ΠΏΠΎΡΡΡΠΎΠ΅Π½ΠΈΡ ΠΏΡΠΎΡΠΈΠ»Ρ ΠΏΡΠΎΠΈΠ·Π²ΠΎΠ΄ΠΈΡΠ΅Π»ΡΠ½ΠΎΡΡΠΈ ΠΎΠ±ΠΎΡΡΠ΄ΠΎΠ²Π°Π½ΠΈΡ Π΄ΠΎ, Π²ΠΎ Π²ΡΠ΅ΠΌΡ ΠΈ ΠΏΠΎΡΠ»Π΅ ΡΠΎΠ±ΡΡΠΈΡ. ΠΡΠΎ ΠΏΡΠ΅Π΄ΠΎΡΡΠ°Π²Π»ΡΠ΅Ρ Π±ΠΎΠ³Π°ΡΡΠΉ ΠΈΡΡΠΎΡΠ½ΠΈΠΊ ΠΈΠ½ΡΠΎΡΠΌΠ°ΡΠΈΠΈ Π΄Π»Ρ ΡΡΠΊΠΎΡΠ΅Π½ΠΈΡ ΠΏΠΎΠΈΡΠΊΠ° ΠΊΠΎΡΠ½Ρ ΠΏΡΠΎΠ±Π»Π΅ΠΌΡ ΠΈ ΡΠΏΡΠ΅ΠΆΠ΄Π°ΡΡΠ΅Π³ΠΎ ΠΎΠΏΡΠ΅Π΄Π΅Π»Π΅Π½ΠΈΡ ΡΡΠ»ΠΎΠ²ΠΈΠΉ, ΠΊΠΎΡΠΎΡΡΠ΅ ΠΌΠΎΠ³ΡΡ ΠΏΡΠΈΠ²Π΅ΡΡΠΈ ΠΊ ΠΏΠΎΡΠ΅Π½ΡΠΈΠ°Π»ΡΠ½ΡΠΌ ΡΠ±ΠΎΡΠΌ Π² ΡΠ°Π±ΠΎΡΠ΅ Π² Π±ΡΠ΄ΡΡΠ΅ΠΌ.
ΠΠΎΠ»Π΅Π΅ ΡΠΎΠ³ΠΎ, ΡΠΈΡΡΠ΅ΠΌΠ° CMMS ΠΏΡΠ΅ΠΎΠ±ΡΠ°Π·ΡΠ΅Ρ ΡΡΠΈ Π΄Π°Π½Π½ΡΠ΅ Π² Π·Π½Π°ΡΠΈΠΌΡΠ΅ ΠΈΠ½Π΄ΠΈΠΊΠ°ΡΠΎΡΡ ΡΠΎΡΡΠΎΡΠ½ΠΈΡ ΠΎΠ±ΠΎΡΡΠ΄ΠΎΠ²Π°Π½ΠΈΡ, ΠΊΠΎΡΠΎΡΡΠ΅ ΡΠΏΠ΅ΡΠΈΠ°Π»ΠΈΡΡΡ ΠΏΠΎ ΡΠ΅Ρ Π½ΠΈΡΠ΅ΡΠΊΠΎΠΌΡ ΠΎΠ±ΡΠ»ΡΠΆΠΈΠ²Π°Π½ΠΈΡ ΠΌΠΎΠ³ΡΡ ΠΎΡΡΠ»Π΅ΠΆΠΈΠ²Π°ΡΡ ΠΈΠ· Π»ΡΠ±ΠΎΠ³ΠΎ ΠΌΠ΅ΡΡΠ° Π½Π° ΠΌΠΎΠ±ΠΈΠ»ΡΠ½ΠΎΠΌ ΡΡΡΡΠΎΠΉΡΡΠ²Π΅ ΠΈΠ»ΠΈ ΠΠ Π² ΡΠ΅ΠΆΠΈΠΌΠ΅ ΡΠ΅Π°Π»ΡΠ½ΠΎΠ³ΠΎ Π²ΡΠ΅ΠΌΠ΅Π½ΠΈ ΠΈ ΠΏΠΎΠ»ΡΡΠ°ΡΡ ΠΏΡΠ΅Π΄ΡΠΏΡΠ΅ΠΆΠ΄Π΅Π½ΠΈΡ Π² ΡΠ΅Π°Π»ΡΠ½ΠΎΠΌ Π²ΡΠ΅ΠΌΠ΅Π½ΠΈ, Π΅ΡΠ»ΠΈ ΠΈΠ½Π΄ΠΈΠΊΠ°ΡΠΎΡΡ ΠΏΡΠ΅Π²ΡΡΠ°ΡΡ ΠΏΠΎΡΠΎΠ³ΠΎΠ²ΡΠ΅ Π·Π½Π°ΡΠ΅Π½ΠΈΡ.
ΠΠ±ΡΠΈΠ΅ ΠΈΠ·ΠΌΠ΅ΡΠ΅Π½ΠΈΡ ΡΠΎΡΡΠΎΡΠ½ΠΈΡ ΠΎΠ±ΠΎΡΡΠ΄ΠΎΠ²Π°Π½ΠΈΡ Π²ΠΊΠ»ΡΡΠ°ΡΡ:
- ΠΠΎΠ½ΠΈΡΠΎΡΠΈΠ½Π³ Π²ΠΈΠ±ΡΠ°ΡΠΈΠΈ: ΠΠΎΠ½ΠΈΡΠΎΡΠΈΠ½Π³ Π²ΠΈΠ±ΡΠ°ΡΠΈΠΈ ΠΏΠΎΠΌΠΎΠ³Π°Π΅Ρ ΠΎΠ±Π½Π°ΡΡΠΆΠΈΠ²Π°ΡΡ ΠΏΠΎΡΠ΅Π½ΡΠΈΠ°Π»ΡΠ½ΡΠ΅ ΠΏΡΠΎΠ±Π»Π΅ΠΌΡ Π½Π° ΠΎΡΠ΅Π½Ρ ΡΠ°Π½Π½Π΅ΠΉ ΡΡΠ°Π΄ΠΈΠΈ. ΠΠ°ΡΡΠΈΠΊΠΈ Π²ΠΈΠ±ΡΠ°ΡΠΈΠΈ ΠΈΠ΄Π΅Π½ΡΠΈΡΠΈΡΠΈΡΡΡΡ ΠΏΠΈΠΊΠΈ Π²ΠΈΠ±ΡΠ°ΡΠΈΠΈ ΠΊΠΎΠΌΠΏΠΎΠ½Π΅Π½ΡΠΎΠ² ΠΌΠ°ΡΠΈΠ½Ρ, ΡΡΠΎΠ±Ρ ΠΎΠ±Π½Π°ΡΡΠΆΠΈΡΡ Π½Π΅ΡΠΎΠΎΡΠ½ΠΎΡΡΡ, Π΄ΠΈΡΠ±Π°Π»Π°Π½Ρ ΠΈ ΠΎΡΠ»Π°Π±Π»Π΅Π½ΠΈΠ΅, Π° ΡΠ°ΠΊΠΆΠ΅ ΠΏΠΎΠ΄ΡΠΈΠΏΠ½ΠΈΠΊΠΈ, ΠΊΠΎΡΠΎΡΡΠ΅ ΠΌΠΎΠ³ΡΡ Π²ΡΠΉΡΠΈ ΠΈΠ· ΡΡΡΠΎΡ ΠΈΠ·-Π·Π° ΠΌΠ΅Ρ Π°Π½ΠΈΡΠ΅ΡΠΊΠΈΡ ΠΏΡΠΎΠ±Π»Π΅ΠΌ, ΠΏΡΠΎΠ±Π»Π΅ΠΌ ΡΠΎ ΡΠΌΠ°Π·ΠΊΠΎΠΉ ΠΈΠ»ΠΈ ΠΈΠ·Π½ΠΎΡΠΎΠΌ. Π‘ΡΠ°Π²Π½ΠΈΠ²Π°Ρ ΠΎΠ±ΡΠ°Π·ΡΡ ΠΏΠΈΠΊΠΎΠ² Π²ΠΈΠ±ΡΠ°ΡΠΈΠΈ Ρ Π΄Π°Π½Π½ΡΠΌΠΈ, Π½Π°ΠΉΠ΄Π΅Π½Π½ΡΠΌΠΈ Π² Π±Π°Π·Π΅ Π΄Π°Π½Π½ΡΡ Π΄Π»Ρ Π°Π½Π°Π»ΠΎΠ³ΠΈΡΠ½ΡΡ ΠΈΡΠΏΡΠ°Π²Π½ΡΡ ΠΌΠ°ΡΠΈΠ½, Π²Ρ ΠΌΠΎΠΆΠ΅ΡΠ΅ ΠΎΠΏΡΠ΅Π΄Π΅Π»ΠΈΡΡ ΡΠ΅ΡΡΠ΅Π·Π½ΠΎΡΡΡ Π½Π΅ΠΈΡΠΏΡΠ°Π²Π½ΠΎΡΡΠΈ ΠΌΠ°ΡΠΈΠ½Ρ ΠΈ ΠΏΠΎΡΠ΅ΠΊΠΎΠΌΠ΅Π½Π΄ΠΎΠ²Π°ΡΡ ΡΠ΅ΠΌΠΎΠ½Ρ.
- ΠΠ½ΡΡΠ°ΠΊΡΠ°ΡΠ½ΡΠΉ ΠΈ ΠΊΠΎΠ½ΡΠ°ΠΊΡΠ½ΡΠΉ ΠΊΠΎΠ½ΡΡΠΎΠ»Ρ ΡΠ΅ΠΌΠΏΠ΅ΡΠ°ΡΡΡΡ: ΠΠ΅ΡΠ΅Π³ΡΠ΅Π² ΡΠ²Π»ΡΠ΅ΡΡΡ ΠΎΡΠ½ΠΎΠ²Π½ΡΠΌ ΠΏΡΠ΅Π΄ΠΈΠΊΡΠΎΡΠΎΠΌ Π½Π°Π΄Π²ΠΈΠ³Π°ΡΡΠ΅Π³ΠΎΡΡ ΠΎΡΠΊΠ°Π·Π° ΠΊΠΎΠΌΠΏΠΎΠ½Π΅Π½ΡΠΎΠ² Π²ΡΠ°ΡΠ°ΡΡΠ΅Π³ΠΎΡΡ ΠΎΠ±ΠΎΡΡΠ΄ΠΎΠ²Π°Π½ΠΈΡ, ΡΠ°ΠΊΠΎΠ³ΠΎ ΠΊΠ°ΠΊ Π½Π°ΡΠΎΡΡ, Π΄Π²ΠΈΠ³Π°ΡΠ΅Π»ΠΈ, Π²Π΅Π½ΡΠΈΠ»ΡΡΠΎΡΡ ΠΈ ΠΊΠΎΠΌΠΏΡΠ΅ΡΡΠΎΡΡ, Π° ΡΠ°ΠΊΠΆΠ΅ ΡΠ»Π΅ΠΊΡΡΠΈΡΠ΅ΡΠΊΠΈΡ ΠΏΠ°Π½Π΅Π»Π΅ΠΉ. Π‘ΡΡΠ΅ΡΡΠ²ΡΠ΅Ρ Π΄Π²Π° ΠΌΠ΅ΡΠΎΠ΄Π° ΠΈΠ·ΠΌΠ΅ΡΠ΅Π½ΠΈΡ ΡΠ΅ΠΌΠΏΠ΅ΡΠ°ΡΡΡΡ: Π±Π΅ΡΠΊΠΎΠ½ΡΠ°ΠΊΡΠ½ΡΠΉ ΠΈ ΠΊΠΎΠ½ΡΠ°ΠΊΡΠ½ΡΠΉ.
- Π’Π΅ΠΏΠ»ΠΎΠ²ΠΈΠ·ΠΈΠΎΠ½Π½ΠΎΠ΅ / ΠΈΠ½ΡΡΠ°ΠΊΡΠ°ΡΠ½ΠΎΠ΅ ΠΈΠ·ΠΎΠ±ΡΠ°ΠΆΠ΅Π½ΠΈΠ΅ — ΠΎΡΠ»ΠΈΡΠ½ΡΠΉ ΠΈΠ½ΡΡΡΡΠΌΠ΅Π½Ρ Π΄Π»Ρ Π±Π΅ΡΠΊΠΎΠ½ΡΠ°ΠΊΡΠ½ΠΎΠ³ΠΎ ΠΈΠ·ΠΌΠ΅ΡΠ΅Π½ΠΈΡ ΡΠ΅ΠΌΠΏΠ΅ΡΠ°ΡΡΡΡ ΠΏΠ΅ΡΠ΅Π΄ΠΎΠ²ΡΡ ΠΊΠΎΠΌΠΏΠΎΠ½Π΅Π½ΡΠΎΠ² Π΄Π»Ρ ΠΌΠΎΠ½ΠΈΡΠΎΡΠΈΠ½Π³Π° ΠΊΠΎΠΌΠΏΠΎΠ½Π΅Π½ΡΠΎΠ², ΠΏΠΎΡΠΊΠΎΠ»ΡΠΊΡ ΡΠ΅Ρ Π½ΠΈΡΠ΅ΡΠΊΠΈΠΉ ΡΠΏΠ΅ΡΠΈΠ°Π»ΠΈΡΡ ΠΌΠΎΠΆΠ΅Ρ ΡΡΠΎΡΡΡ Π½Π° ΡΠ°ΡΡΡΠΎΡΠ½ΠΈΠΈ ΠΈ ΡΠΊΠ°Π½ΠΈΡΠΎΠ²Π°ΡΡ ΠΎΠ±ΠΎΡΡΠ΄ΠΎΠ²Π°Π½ΠΈΠ΅ Π²ΠΎ Π²ΡΠ΅ΠΌΡ Π΅Π³ΠΎ ΡΠ°Π±ΠΎΡΡ.ΠΡΠΏΠΎΠ»ΡΠ·ΡΡ ΠΏΠΎΡΡΠ°ΡΠΈΠ²Π½ΡΡ ΠΈΠ½ΡΡΠ°ΠΊΡΠ°ΡΠ½ΡΡ ΠΊΠ°ΠΌΠ΅ΡΡ (ΡΠ°ΠΊΠΆΠ΅ Π½Π°Π·ΡΠ²Π°Π΅ΠΌΡΡ ΡΠ΅ΠΏΠ»ΠΎΠ²ΠΈΠ·ΠΎΡΠΎΠΌ) ΠΈΠ»ΠΈ ΠΏΠΎΡΠΎΠΊΠΎΠ²ΡΠ΅ ΠΈΠ·ΠΌΠ΅ΡΠ΅Π½ΠΈΡ Ρ ΡΠ΅ΠΏΠ»ΠΎΠ²ΠΈΠ·ΠΈΠΎΠ½Π½ΠΎΠ³ΠΎ Π΄Π°ΡΡΠΈΠΊΠ°, ΡΠ΅Ρ Π½ΠΈΡΠ΅ΡΠΊΠΈΠ΅ ΡΠΏΠ΅ΡΠΈΠ°Π»ΠΈΡΡΡ ΠΌΠΎΠ³ΡΡ Π±ΡΡΡΡΠΎ ΠΎΠ±Π½Π°ΡΡΠΆΠΈΡΡ ΠΏΠ΅ΡΠ΅Π³ΡΠ΅ΡΡΠ΅ ΠΏΠΎΠ΄ΡΠΈΠΏΠ½ΠΈΠΊΠΈ ΠΈ ΠΌΡΡΡΡ, Π³ΠΎΡΡΡΠΈΠ΅ ΡΠΎΡΠΊΠΈ Π² ΠΊΠΎΡΠΏΡΡΠ΅ Π΄Π²ΠΈΠ³Π°ΡΠ΅Π»Ρ, Π½Π΅ΠΈΡΠΏΡΠ°Π²Π½ΡΠ΅ ΡΠΎΠ΅Π΄ΠΈΠ½Π΅Π½ΠΈΡ Π² ΡΠ»Π΅ΠΊΡΡΠΈΡΠ΅ΡΠΊΠΈΡ ΡΠ΅ΠΏΡΡ ΠΈ ΠΎΠ±ΠΎΡΡΠ΄ΠΎΠ²Π°Π½ΠΈΠΈ Π±ΠΎΠ»ΡΡΠΎΠΉ ΠΌΠΎΡΠ½ΠΎΡΡΠΈ, Π° ΡΠ°ΠΊΠΆΠ΅ ΠΏΠ΅ΡΠ΅Π³ΡΠ΅ΡΡΡ ΡΠ°ΡΠΏΡΠ΅Π΄Π΅Π»ΠΈΡΠ΅Π»ΡΠ½ΡΡ ΠΊΠΎΡΠΎΠ±ΠΊΡ. ΡΠ»ΡΡΠ°ΠΈ. Π’Π΅ΠΏΠ»ΠΎΠ²ΠΈΠ·ΠΈΠΎΠ½Π½ΠΎΠ΅ ΠΈΠ·ΠΎΠ±ΡΠ°ΠΆΠ΅Π½ΠΈΠ΅ ΡΠ°ΠΊΠΆΠ΅ ΠΌΠΎΠΆΠ½ΠΎ ΠΈΡΠΏΠΎΠ»ΡΠ·ΠΎΠ²Π°ΡΡ Π΄Π»Ρ ΠΎΠ±Π½Π°ΡΡΠΆΠ΅Π½ΠΈΡ ΡΡΠ΅ΡΠ΅ΠΊ ΠΈ ΠΎΡΠ΅Π½ΠΊΠΈ ΡΡΠΎΠ²Π½Π΅ΠΉ ΠΆΠΈΠ΄ΠΊΠΎΡΡΠΈ Π² Π·Π°ΠΊΡΡΡΡΡ ΡΠΎΡΡΠ΄Π°Ρ ΠΈ ΡΠ΅Π·Π΅ΡΠ²ΡΠ°ΡΠ°Ρ , ΠΊΠΎΠ½ΡΡΠΎΠ»Ρ Ρ Π°ΡΠ°ΠΊΡΠ΅ΡΠΈΡΡΠΈΠΊ ΠΈΠ·ΠΎΠ»ΡΡΠΈΠΈ ΡΠ΅Ρ Π½ΠΎΠ»ΠΎΠ³ΠΈΡΠ΅ΡΠΊΠΈΡ ΡΡΡΠ±ΠΎΠΏΡΠΎΠ²ΠΎΠ΄ΠΎΠ² ΠΈΠ»ΠΈ Π΄ΡΡΠ³ΠΈΡ ΠΈΠ·ΠΎΠ»ΠΈΡΠΎΠ²Π°Π½Π½ΡΡ ΠΏΡΠΎΡΠ΅ΡΡΠΎΠ² ΠΈ Π²ΡΡΠ²Π»Π΅Π½ΠΈΡ ΠΏΡΠΎΠ±Π»Π΅ΠΌ Π² ΡΠ»Π΅ΠΊΡΡΠΈΡΠ΅ΡΠΊΠΎΠΌ ΡΠ°ΡΠΏΡΠ΅Π΄Π΅Π»ΠΈΡΠ΅Π»ΡΠ½ΠΎΠΌ ΡΡΡΡΠΎΠΉΡΡΠ²Π΅.
- ΠΠ΅ΡΠΏΡΠΎΠ²ΠΎΠ΄Π½ΡΠ΅ ΠΊΠΎΠ½ΡΠ°ΠΊΡΠ½ΡΠ΅ Π΄Π°ΡΡΠΈΠΊΠΈ ΡΠ΅ΠΌΠΏΠ΅ΡΠ°ΡΡΡΡ ΠΌΠΎΠ³ΡΡ Π±ΡΡΡ ΠΏΡΠΈΠΊΡΠ΅ΠΏΠ»Π΅Π½Ρ Π²Π½ΡΡΡΠΈ ΡΠ»Π΅ΠΊΡΡΠΈΡΠ΅ΡΠΊΠΈΡ ΠΏΠ°Π½Π΅Π»Π΅ΠΉ ΠΈΠ»ΠΈ ΡΠ°Π±ΠΎΡΠ΅Π³ΠΎ ΠΎΠ±ΠΎΡΡΠ΄ΠΎΠ²Π°Π½ΠΈΡ Π΄Π»Ρ ΠΏΠΎΡΠΎΠΊΠΎΠ²ΠΎΠΉ ΠΏΠ΅ΡΠ΅Π΄Π°ΡΠΈ ΠΏΠΎΠΊΠ°Π·Π°Π½ΠΈΠΉ Π² ΡΠΈΡΡΠ΅ΠΌΡ CMMS. ΠΠ° ΡΠ΅Π·ΡΠ»ΡΡΠ°ΡΠ°ΠΌΠΈ ΠΌΠΎΠΆΠ½ΠΎ ΡΠ΄Π°Π»Π΅Π½Π½ΠΎ ΡΠ»Π΅Π΄ΠΈΡΡ Ρ ΠΌΠΎΠ±ΠΈΠ»ΡΠ½ΠΎΠ³ΠΎ ΡΡΡΡΠΎΠΉΡΡΠ²Π° ΠΈΠ»ΠΈ ΠΠ.
- ΠΠΎΠ½ΡΡΠΎΠ»Ρ ΠΌΠΎΡΠ½ΠΎΡΡΠΈ: ΠΡΠ»ΠΈ ΠΎΠ±ΠΎΡΡΠ΄ΠΎΠ²Π°Π½ΠΈΠ΅ Π½Π΅ΠΈΡΠΏΡΠ°Π²Π½ΠΎ ΠΈ ΠΏΡΠΎΠ±Π»Π΅ΠΌΠ° Π½Π΅ Π² ΠΌΠ΅Ρ Π°Π½ΠΈΡΠ΅ΡΠΊΠΎΠΉ ΠΈΠ»ΠΈ ΡΠ»Π΅ΠΊΡΡΠΈΡΠ΅ΡΠΊΠΎΠΉ ΡΠ°ΡΡΠΈ ΡΠ°ΠΌΠΎΠ³ΠΎ ΠΎΠ±ΠΎΡΡΠ΄ΠΎΠ²Π°Π½ΠΈΡ, Π²Π΅ΡΠΎΡΡΠ½ΠΎ, Π²ΠΈΠ½ΠΎΠ²Π°ΡΠΎ ΠΊΠ°ΡΠ΅ΡΡΠ²ΠΎ ΡΠ»Π΅ΠΊΡΡΠΎΡΠ½Π΅ΡΠ³ΠΈΠΈ. ΠΠΎΡΠΎΠΊΠΎΠ²Π°Ρ ΠΏΠ΅ΡΠ΅Π΄Π°ΡΠ° Π·Π°ΠΏΠΈΡΠ°Π½Π½ΡΡ Π΄Π°Π½Π½ΡΡ Ρ ΡΡΠ΅Ρ ΡΠ°Π·Π½ΠΎΠ³ΠΎ ΠΌΠΎΠ½ΠΈΡΠΎΡΠ° ΠΌΠΎΡΠ½ΠΎΡΡΠΈ ΠΏΠΎΠ·Π²ΠΎΠ»ΠΈΡ Π²Π°ΠΌ ΡΠ²ΠΈΠ΄Π΅ΡΡ ΡΠ΅Π½Π΄Π΅Π½ΡΠΈΠΈ ΠΈ ΠΊΠΎΠ»Π΅Π±Π°Π½ΠΈΡ, ΠΊΠΎΡΠΎΡΡΠ΅ ΠΌΠΎΠ³ΡΡ ΡΠΊΠ°Π·ΡΠ²Π°ΡΡ Π½Π° ΠΏΡΠΎΠ±Π»Π΅ΠΌΡ ΠΊΠ°ΡΠ΅ΡΡΠ²Π° ΡΠ»Π΅ΠΊΡΡΠΎΡΠ½Π΅ΡΠ³ΠΈΠΈ, ΡΠ°ΠΊΡΡ ββΠΊΠ°ΠΊ Π³Π°ΡΠΌΠΎΠ½ΠΈΠΊΠΈ, ΠΊΠΎΡΠΎΡΠΊΠΈΠ΅ Π·Π°ΠΌΡΠΊΠ°Π½ΠΈΡ ΠΈΠ»ΠΈ ΠΏΠ΅ΡΠ΅Ρ ΠΎΠ΄Π½ΡΠ΅ ΠΏΡΠΎΡΠ΅ΡΡΡ Π²ΡΡΠΎΠΊΠΎΠ³ΠΎ Π½Π°ΠΏΡΡΠΆΠ΅Π½ΠΈΡ ΠΎΡ ΠΌΠΎΠ»Π½ΠΈΠΈ.
- ΠΠΎΠ½ΠΈΡΠΎΡΠΈΠ½Π³ ΡΠΎΠΊΠ° ΠΈ Π½Π°ΠΏΡΡΠΆΠ΅Π½ΠΈΡ : ΠΠΎΠ½ΠΈΡΠΎΡΠΈΠ½Π³ ΡΠΎΠΊΠ° ΠΈ Π½Π°ΠΏΡΡΠΆΠ΅Π½ΠΈΡ ΠΏΡΠ΅Π΄ΠΎΡΡΠ°Π²Π»ΡΠ΅Ρ ΠΊΠ»ΡΡΠ΅Π²ΡΡ ΠΈΠ½ΡΠΎΡΠΌΠ°ΡΠΈΡ ΠΎ ΡΠΎΠΌ, ΠΊΠ°ΠΊ ΡΠ°Π±ΠΎΡΠ°Π΅Ρ ΠΎΠ±ΠΎΡΡΠ΄ΠΎΠ²Π°Π½ΠΈΠ΅, ΠΈ ΠΌΠΎΠΆΠ΅Ρ ΠΏΠΎΠΌΠΎΡΡ Π²ΡΡΠ²ΠΈΡΡ ΠΈ ΡΡΡΡΠ°Π½ΠΈΡΡ ΡΠΈΡΡΠ°ΡΠΈΠΈ, ΠΊΠΎΡΠΎΡΡΠ΅ ΠΌΠΎΠ³ΡΡ ΠΏΡΠΈΠ²Π΅ΡΡΠΈ ΠΊ ΠΎΡΡΠ°Π½ΠΎΠ²ΠΊΠ°ΠΌ, Π½Π°ΠΏΡΠΈΠΌΠ΅Ρ, ΠΊΠΎΠ³Π΄Π°:
- ΠΠ°Π·ΠΎΠ²ΡΠΉ ΡΠΎΠΊ ΠΈΠ»ΠΈ Π½Π°Π³ΡΡΠ·ΠΊΠ° Π½Π° ΠΊΡΠΈΡΠΈΡΠ΅ΡΠΊΠΎΠΌ Π½Π°ΡΠΎΡΠ΅ Π±Π»ΠΈΠ·ΠΊΠ° ΠΊ ΠΌΠ°ΠΊΡΠΈΠΌΠ°Π»ΡΠ½ΠΎΠΌΡ Π½ΠΎΠΌΠΈΠ½Π°Π»ΡΠ½ΠΎΠΌΡ ΡΠΎΠΊΡ Π΄Π²ΠΈΠ³Π°ΡΠ΅Π»Ρ.
- ΠΠ±ΡΠ°Ρ ΠΌΠΎΡΠ½ΠΎΡΡΡ ΠΈΠ½Π΄ΡΠΊΡΠΈΠΎΠ½Π½ΠΎΠΉ ΠΏΠ΅ΡΠΈ Π½Π΅Π½ΠΎΡΠΌΠ°Π»ΡΠ½ΠΎ ΠΊΠΎΠ»Π΅Π±Π»Π΅ΡΡΡ Π²ΠΎ Π²ΡΠ΅ΠΌΡ ΡΠΈΠΊΠ»Π° ΠΎΡΠ²Π΅ΡΠΆΠ΄Π΅Π½ΠΈΡ.
- ΠΠΎΠ³ΡΡΠΆΠ½ΠΎΠΉ ΠΈΠ»ΠΈ Π³ΠΈΠ΄ΡΠ°Π²Π»ΠΈΡΠ΅ΡΠΊΠΈΠΉ Π½Π°ΡΠΎΡ Π½Π΅ ΠΏΠΎΠ΄Π΄Π΅ΡΠΆΠΈΠ²Π°Π΅Ρ ΠΏΠΎΡΠΎΠΊ ΠΈΠ»ΠΈ Π΄Π°Π²Π»Π΅Π½ΠΈΠ΅.
ΠΠ·ΠΌΠ΅ΡΡΡ ΡΠΎΠΊ ΠΈ Π½Π°ΠΏΡΡΠΆΠ΅Π½ΠΈΠ΅ ΠΎΡ Π·Π°ΠΏΡΡΠΊΠ° Π΄ΠΎ Π½ΠΎΡΠΌΠ°Π»ΡΠ½ΠΎΠΉ ΡΠ°Π±ΠΎΡΡ, Π²Ρ ΠΌΠΎΠΆΠ΅ΡΠ΅ Π²ΡΡΠ²ΠΈΡΡ ΠΏΡΠΎΠ±Π»Π΅ΠΌΡ Ρ ΠΏΡΡΠΊΠΎΠ²ΡΠΌ ΡΠΎΠΊΠΎΠΌ, ΠΊΡΠ°ΡΠΊΠΎΠ²ΡΠ΅ΠΌΠ΅Π½Π½ΡΠΌΠΈ ΡΠΊΠ°ΡΠΊΠ°ΠΌΠΈ ΠΈ ΠΏΡΠΎΠ²Π°Π»Π°ΠΌΠΈ Π½Π°ΠΏΡΡΠΆΠ΅Π½ΠΈΡ ΠΈΠ»ΠΈ Π΄ΡΡΠ³ΠΈΠΌΠΈ ΡΡΠ»ΠΎΠ²ΠΈΡΠΌΠΈ, ΠΊΠΎΡΠΎΡΡΠ΅ ΠΌΠΎΠ³ΡΡ Π²ΡΠ·Π²Π°ΡΡ ΡΠ°Π·ΠΌΡΠΊΠ°Π½ΠΈΠ΅ ΡΠ΅ΠΏΠ΅ΠΉ ΠΈ Π½Π΅ΠΏΡΠ°Π²ΠΈΠ»ΡΠ½ΡΡ ΡΠ°Π±ΠΎΡΡ. ΠΡΠΈ ΠΈΠ·ΠΌΠ΅ΡΠ΅Π½ΠΈΡ ΡΠ°ΡΠ΅ Π²ΡΠ΅Π³ΠΎ ΡΠΈΠΊΡΠΈΡΡΡΡΡΡ Ρ ΠΏΠΎΠΌΠΎΡΡΡ ΡΠΈΡΡΠΎΠ²ΠΎΠ³ΠΎ ΠΌΡΠ»ΡΡΠΈΠΌΠ΅ΡΡΠ° (DMM), ΡΠΎΠΊΠΎΠΈΠ·ΠΌΠ΅ΡΠΈΡΠ΅Π»ΡΠ½ΡΡ ΠΊΠ»Π΅ΡΠ΅ΠΉ ΠΈΠ»ΠΈ ΠΏΠΎΠ»ΡΡΠΈΠΊΡΠΈΡΠΎΠ²Π°Π½Π½ΡΡ Π΄Π°ΡΡΠΈΠΊΠΎΠ² ΠΌΠΎΠ½ΠΈΡΠΎΡΠΈΠ½Π³Π° ΡΠΎΡΡΠΎΡΠ½ΠΈΡ.
ΠΠΎΠ½ΠΈΡΠΎΡΠΈΠ½Π³ ΠΎΠ±ΡΠ΅Π³ΠΎ ΠΎΠ±ΠΎΡΡΠ΄ΠΎΠ²Π°Π½ΠΈΡ ΠΠΠ
ΠΠ½ΠΎΠ³ΠΈΠ΅ ΠΈΠ· ΠΏΠ΅ΡΠ΅ΡΠΈΡΠ»Π΅Π½Π½ΡΡ Π²ΡΡΠ΅ ΠΏΠΎΠΊΠ°Π·Π°ΡΠ΅Π»Π΅ΠΉ ΠΏΡΠΈΠΌΠ΅Π½ΠΈΠΌΡ ΠΊ Π½Π΅ΡΠΊΠΎΠ»ΡΠΊΠΈΠΌ Π°ΠΊΡΠΈΠ²Π°ΠΌ Π½Π° ΠΏΡΠΎΠΈΠ·Π²ΠΎΠ΄ΡΡΠ²Π΅Π½Π½ΠΎΠΌ ΠΈΠ»ΠΈ ΠΏΠ΅ΡΠ΅ΡΠ°Π±Π°ΡΡΠ²Π°ΡΡΠ΅ΠΌ ΠΏΡΠ΅Π΄ΠΏΡΠΈΡΡΠΈΠΈ.ΠΠ»Ρ ΠΊΠ°ΠΆΠ΄ΠΎΠ³ΠΎ Π°ΠΊΡΠΈΠ²Π° ΠΌΠΎΠΆΠ΅Ρ ΠΏΠΎΡΡΠ΅Π±ΠΎΠ²Π°ΡΡΡΡ ΠΎΡΡΠ»Π΅ΠΆΠΈΠ²Π°Π½ΠΈΠ΅ Π½Π΅ΡΠΊΠΎΠ»ΡΠΊΠΈΡ ΠΈΠ· ΠΏΠ΅ΡΠ΅ΡΠΈΡΠ»Π΅Π½Π½ΡΡ Π²ΡΡΠ΅ ΠΏΠΎΠΊΠ°Π·Π°ΡΠ΅Π»Π΅ΠΉ. ΠΠΎΠΏΡΡΡΠΈΠΌΡΠ΅ Π·Π½Π°ΡΠ΅Π½ΠΈΡ Π±ΡΠ΄ΡΡ Π²Π°ΡΡΠΈΡΠΎΠ²Π°ΡΡΡΡ ΠΎΡ ΠΎΠ΄Π½ΠΎΠ³ΠΎ ΡΠΈΠΏΠ° Π°ΠΊΡΠΈΠ²Π° ΠΊ Π΄ΡΡΠ³ΠΎΠΌΡ. ΠΠΈΠΆΠ΅ ΠΏΡΠΈΠ²Π΅Π΄Π΅Π½Ρ Π½Π΅ΠΊΠΎΡΠΎΡΡΠ΅ ΡΠ΅ΠΊΠΎΠΌΠ΅Π½Π΄ΡΠ΅ΠΌΡΠ΅ ΠΈΠ½Π΄ΠΈΠΊΠ°ΡΠΎΡΡ, ΠΊΠΎΡΠΎΡΡΠ΅ ΠΌΠΎΠΆΠ½ΠΎ Π΄ΠΎΠ±Π°Π²ΠΈΡΡ Π½Π° ΠΏΠ°Π½Π΅Π»Ρ ΠΌΠΎΠ½ΠΈΡΠΎΡΠΈΠ½Π³Π° ΡΠΎΡΡΠΎΡΠ½ΠΈΡ ΠΎΠ±ΠΎΡΡΠ΄ΠΎΠ²Π°Π½ΠΈΡ.
ΠΠ°ΡΠΎΡΡ
ΠΠ°ΡΠΎΡΡ — ΠΎΠ΄Π½ΠΎ ΠΈΠ· ΡΠ°ΠΌΡΡ ΡΠ°ΡΠΏΡΠΎΡΡΡΠ°Π½Π΅Π½Π½ΡΡ Π°ΠΊΡΠΈΠ²ΠΎΠ² Π½Π° Π·Π°Π²ΠΎΠ΄Π΅. ΠΠ½ΠΈ ΡΠ²Π»ΡΡΡΡΡ Π½Π΅ΠΎΡΡΠ΅ΠΌΠ»Π΅ΠΌΠΎΠΉ ΡΠ°ΡΡΡΡ ΠΌΠ½ΠΎΠ³ΠΈΡ ΠΊΡΠΈΡΠΈΡΠ΅ΡΠΊΠΈ Π²Π°ΠΆΠ½ΡΡ ΡΠΈΡΡΠ΅ΠΌ, Π²ΠΊΠ»ΡΡΠ°Ρ HVAC, ΠΎΠ±ΡΠ°Π±ΠΎΡΠΊΡ, ΠΊΠΎΠ½ΡΡΠΎΠ»Ρ ΡΠ΅ΠΌΠΏΠ΅ΡΠ°ΡΡΡΡ ΠΈ Π±Π΅Π·ΠΎΠΏΠ°ΡΠ½ΠΎΡΡΡ. ΠΡΠΊΠ°Π· Π½Π°ΡΠΎΡΠ° ΠΌΠΎΠΆΠ΅Ρ Π²ΡΠ·Π²Π°ΡΡ ΠΎΡΡΠ°Π½ΠΎΠ²ΠΊΡ ΠΊΡΠΈΡΠΈΡΠ΅ΡΠΊΠΎΠ³ΠΎ ΠΏΡΠΎΡΠ΅ΡΡΠ° ΠΈΠ»ΠΈ ΡΡΠ°ΡΡΠΊΠ°, Π° ΡΠ°ΠΊΠΆΠ΅ ΠΏΡΠΎΠ±Π»Π΅ΠΌΡ Ρ Π±Π΅Π·ΠΎΠΏΠ°ΡΠ½ΠΎΡΡΡΡ.ΠΡΠ»Π°Π±Π»Π΅Π½Π½ΡΠ΅, ΡΠΌΠ΅ΡΠ΅Π½Π½ΡΠ΅ ΠΈΠ»ΠΈ Π½Π΅ΡΠ±Π°Π»Π°Π½ΡΠΈΡΠΎΠ²Π°Π½Π½ΡΠ΅ Π²Π°Π»Ρ Π½Π°ΡΠΎΡΠ° ΠΌΠΎΠ³ΡΡ ΡΡΠΊΠΎΡΠΈΡΡ ΠΈΠ·Π½ΠΎΡ ΠΏΠΎΠ΄ΡΠΈΠΏΠ½ΠΈΠΊΠΎΠ² ΠΈ ΡΠΏΠ»ΠΎΡΠ½Π΅Π½ΠΈΠΉ, ΡΡΠΎ ΠΏΡΠΈΠ²Π΅Π΄Π΅Ρ ΠΊ ΠΏΡΠ΅ΠΆΠ΄Π΅Π²ΡΠ΅ΠΌΠ΅Π½Π½ΠΎΠΌΡ Π²ΡΡ ΠΎΠ΄Ρ ΠΈΠ· ΡΡΡΠΎΡ. ΠΠ΅ΠΊΠΎΡΠΎΡΡΠ΅ ΠΈΠ· ΠΊΠ»ΡΡΠ΅Π²ΡΡ ΠΈΠ·ΠΌΠ΅ΡΠ΅Π½ΠΈΠΉ, ΡΠ²ΡΠ·Π°Π½Π½ΡΡ Ρ ΠΌΠΎΠ½ΠΈΡΠΎΡΠΈΠ½Π³ΠΎΠΌ Π½Π°ΡΠΎΡΠΎΠ², Π²ΠΊΠ»ΡΡΠ°ΡΡ:
- ΠΠΎΠ½ΡΡΠΎΠ»Ρ Π²ΠΈΠ±ΡΠ°ΡΠΈΠΈ
- Π‘ΡΠ΅Π΄Π½Π΅Π΅ Π²ΡΠ΅ΠΌΡ Π±Π΅Π·ΠΎΡΠΊΠ°Π·Π½ΠΎΠΉ ΡΠ°Π±ΠΎΡΡ
ΠΠ²ΠΈΠ³Π°ΡΠ΅Π»ΠΈ
ΠΠ²ΠΈΠ³Π°ΡΠ΅Π»ΠΈ ΠΈΠΌΠ΅ΡΡ ΡΠ΅ΡΠ°ΡΡΠ΅Π΅ Π·Π½Π°ΡΠ΅Π½ΠΈΠ΅ Π΄Π»Ρ ΠΌΠ½ΠΎΠ³ΠΈΡ Π°ΡΠΏΠ΅ΠΊΡΠΎΠ² ΠΏΡΠΎΠΈΠ·Π²ΠΎΠ΄ΡΡΠ²Π° Π½Π° ΠΏΡΠΎΠΈΠ·Π²ΠΎΠ΄ΡΡΠ²Π΅Π½Π½ΡΡ ΠΈ ΡΠ΅Ρ Π½ΠΎΠ»ΠΎΠ³ΠΈΡΠ΅ΡΠΊΠΈΡ ΠΏΡΠ΅Π΄ΠΏΡΠΈΡΡΠΈΡΡ . ΠΡ Π·Π°ΠΌΠ΅Π½Π° Π΄ΠΎΡΠΎΠ³ΠΎΡΡΠΎΡΡΠ°Ρ, ΠΏΠΎΡΡΠΎΠΌΡ PM ΠΈΠΌΠ΅Π΅Ρ ΡΠ΅ΡΠ°ΡΡΠ΅Π΅ Π·Π½Π°ΡΠ΅Π½ΠΈΠ΅ Π΄Π»Ρ ΠΏΠΎΠ΄Π΄Π΅ΡΠΆΠ°Π½ΠΈΡ ΠΈΡ Π² ΡΠ°Π±ΠΎΡΠ΅ΠΌ ΡΠΎΡΡΠΎΡΠ½ΠΈΠΈ ΠΈ ΠΏΡΠΎΠ΄Π»Π΅Π½ΠΈΡ ΡΡΠΎΠΊΠ° ΠΈΡ ΡΠ»ΡΠΆΠ±Ρ. ΠΡΠ»Π°Π±Π»Π΅Π½Π½ΡΠ΅, ΡΠΌΠ΅ΡΠ΅Π½Π½ΡΠ΅ ΠΈΠ»ΠΈ Π½Π΅ΡΠ±Π°Π»Π°Π½ΡΠΈΡΠΎΠ²Π°Π½Π½ΡΠ΅ Π²Π°Π»Ρ Π΄Π²ΠΈΠ³Π°ΡΠ΅Π»Ρ ΠΌΠΎΠ³ΡΡ ΠΏΡΠΈΠ²Π΅ΡΡΠΈ ΠΊ ΡΡΠΊΠΎΡΠ΅Π½Π½ΠΎΠΌΡ ΠΈΠ·Π½ΠΎΡΡ ΠΏΠΎΠ΄ΡΠΈΠΏΠ½ΠΈΠΊΠΎΠ², ΡΡΠΎ ΠΏΡΠΈΠ²Π΅Π΄Π΅Ρ ΠΊ ΠΏΡΠ΅ΠΆΠ΄Π΅Π²ΡΠ΅ΠΌΠ΅Π½Π½ΠΎΠΌΡ Π²ΡΡ ΠΎΠ΄Ρ Π΄Π²ΠΈΠ³Π°ΡΠ΅Π»Ρ ΠΈΠ· ΡΡΡΠΎΡ.ΠΡΠΎΠΌΠ΅ ΡΠΎΠ³ΠΎ, Π΄Π²ΠΈΠ³Π°ΡΠ΅Π»ΠΈ, Π½Π΅ ΡΠ°Π±ΠΎΡΠ°ΡΡΠΈΠ΅ Ρ ΠΎΠΏΡΠΈΠΌΠ°Π»ΡΠ½ΠΎΠΉ ΠΏΡΠΎΠΈΠ·Π²ΠΎΠ΄ΠΈΡΠ΅Π»ΡΠ½ΠΎΡΡΡΡ, ΠΏΠΎΡΡΠ΅Π±Π»ΡΡΡ Π½Π°ΠΌΠ½ΠΎΠ³ΠΎ Π±ΠΎΠ»ΡΡΠ΅ ΡΠ½Π΅ΡΠ³ΠΈΠΈ. ΠΠ΅ΡΠ΅Π³ΡΠ΅Π² — ΠΎΠ΄ΠΈΠ½ ΠΈΠ· ΡΠ°ΠΌΡΡ ΡΠ΅ΡΡΠ΅Π·Π½ΡΡ ΡΠ°ΠΊΡΠΎΡΠΎΠ², ΡΠΎΠΊΡΠ°ΡΠ°ΡΡΠΈΡ ΡΡΠΎΠΊ ΡΠ»ΡΠΆΠ±Ρ Π΄Π²ΠΈΠ³Π°ΡΠ΅Π»Ρ. ΠΠΊΡΠΏΠ»ΡΠ°ΡΠ°ΡΠΈΡ ΠΏΡΠΈ ΡΠ΅ΠΌΠΏΠ΅ΡΠ°ΡΡΡΠ΅, ΠΏΡΠ΅Π²ΡΡΠ°ΡΡΠ΅ΠΉ Π½ΠΎΠΌΠΈΠ½Π°Π»ΡΠ½ΠΎΠ΅ Π·Π½Π°ΡΠ΅Π½ΠΈΠ΅ Π½Π° ~ 10 Β°, ΡΠΎΠΊΡΠ°ΡΠ°Π΅Ρ ΡΡΠΎΠΊ ΡΠ»ΡΠΆΠ±Ρ Π΄Π²ΠΈΠ³Π°ΡΠ΅Π»Ρ Π²Π΄Π²ΠΎΠ΅.
ΠΠ²Π° ΠΊΠ»ΡΡΠ΅Π²ΡΡ ΠΏΠΎΠΊΠ°Π·Π°ΡΠ΅Π»Ρ, ΠΊΠΎΡΠΎΡΡΠ΅ Π½Π΅ΠΎΠ±Ρ ΠΎΠ΄ΠΈΠΌΠΎ ΠΎΡΡΠ»Π΅ΠΆΠΈΠ²Π°ΡΡ Π΄Π»Ρ ΡΠ°Π½Π½Π΅Π³ΠΎ Π²ΡΡΠ²Π»Π΅Π½ΠΈΡ ΠΏΠΎΡΠ΅Π½ΡΠΈΠ°Π»ΡΠ½ΡΡ ΠΏΡΠΎΠ±Π»Π΅ΠΌ Ρ Π΄Π²ΠΈΠ³Π°ΡΠ΅Π»Π΅ΠΌ:
- ΠΠΎΠ½ΠΈΡΠΎΡΠΈΠ½Π³ Π²ΠΈΠ±ΡΠ°ΡΠΈΠΈ Π΄Π»Ρ Π²ΡΡΠ²Π»Π΅Π½ΠΈΡ ΡΠ°ΠΊΠΈΡ ΠΏΡΠΎΠ±Π»Π΅ΠΌ, ΠΊΠ°ΠΊ ΠΏΠ΅ΡΠ΅ΠΊΠΎΡ, ΠΈΠ·Π½ΠΎΡ ΠΏΠΎΠ΄ΡΠΈΠΏΠ½ΠΈΠΊΠΎΠ² ΠΈΠ»ΠΈ Π½Π΅ΠΎΠ±Ρ ΠΎΠ΄ΠΈΠΌΠΎΡΡΡ ΡΠΌΠ°Π·ΠΊΠΈ
- Π’Π΅ΠΌΠΏΠ΅ΡΠ°ΡΡΡΠ½ΡΠΉ ΠΌΠΎΠ½ΠΈΡΠΎΡΠΈΠ½Π³ Π΄Π»Ρ ΠΊΠΎΠ½ΡΡΠΎΠ»Ρ ΡΠ΅ΠΌΠΏΠ΅ΡΠ°ΡΡΡΡ Π²ΠΎ Π²ΡΠ΅ΠΌΡ ΡΠ°Π±ΠΎΡΡ ΠΎΠ±ΠΎΡΡΠ΄ΠΎΠ²Π°Π½ΠΈΡ, ΡΡΠΎΠ±Ρ ΡΠ΅Ρ Π½ΠΈΡΠ΅ΡΠΊΠΈΠ΅ ΡΠΏΠ΅ΡΠΈΠ°Π»ΠΈΡΡΡ ΠΌΠΎΠ³Π»ΠΈ Π±ΡΡΡΡΠΎ ΠΎΠ±Π½Π°ΡΡΠΆΠΈΠ²Π°ΡΡ ΡΠΈΡΡΠ°ΡΠΈΠΈ, ΡΡΠ΅Π±ΡΡΡΠΈΠ΅ Π½Π΅ΠΌΠ΅Π΄Π»Π΅Π½Π½ΠΎΠ³ΠΎ Π²Π½ΠΈΠΌΠ°Π½ΠΈΡ, Π±Π΅Π· Π½Π΅ΠΎΠ±Ρ ΠΎΠ΄ΠΈΠΌΠΎΡΡΠΈ Π²ΡΠΊΠ»ΡΡΠ°ΡΡ ΡΠΈΡΡΠ΅ΠΌΡ.
Π‘ΠΈΡΡΠ΅ΠΌΡ ΠΎΡΠΎΠΏΠ»Π΅Π½ΠΈΡ, Π²Π΅Π½ΡΠΈΠ»ΡΡΠΈΠΈ ΠΈ ΠΊΠΎΠ½Π΄ΠΈΡΠΈΠΎΠ½ΠΈΡΠΎΠ²Π°Π½ΠΈΡ Π²ΠΎΠ·Π΄ΡΡ Π°
Π‘ΠΎΠ²ΡΠ΅ΠΌΠ΅Π½Π½ΡΠ΅ ΡΠΈΡΡΠ΅ΠΌΡ ΠΎΡΠΎΠΏΠ»Π΅Π½ΠΈΡ, Π²Π΅Π½ΡΠΈΠ»ΡΡΠΈΠΈ ΠΈ ΠΊΠΎΠ½Π΄ΠΈΡΠΈΠΎΠ½ΠΈΡΠΎΠ²Π°Π½ΠΈΡ Π²ΠΎΠ·Π΄ΡΡ Π° ΠΏΡΠ΅Π΄ΡΡΠ°Π²Π»ΡΡΡ ΡΠΎΠ±ΠΎΠΉ ΡΠ»ΠΎΠΆΠ½ΡΡ ΠΊΠΎΠΌΠ±ΠΈΠ½Π°ΡΠΈΡ Π½Π°ΡΠΎΡΠΎΠ², Π΄Π²ΠΈΠ³Π°ΡΠ΅Π»Π΅ΠΉ, Π²Π΅Π½ΡΠΈΠ»ΡΡΠΎΡΠΎΠ², ΠΊΠΎΠΌΠΏΡΠ΅ΡΡΠΎΡΠΎΠ², Π° ΡΠ°ΠΊΠΆΠ΅ ΡΠ»Π΅ΠΊΡΡΠΈΡΠ΅ΡΠΊΠΈΡ ΠΈ ΡΠ»Π΅ΠΊΡΡΠΎΠ½Π½ΡΡ ΠΊΠΎΠΌΠΏΠΎΠ½Π΅Π½ΡΠΎΠ². ΠΡΠ±ΠΎΠΉ ΠΈΠ· Π½ΠΈΡ ΠΌΠΎΠΆΠ΅Ρ Π²ΡΠΉΡΠΈ ΠΈΠ· ΡΡΡΠΎΡ Π² Π»ΡΠ±ΠΎΠΉ ΠΌΠΎΠΌΠ΅Π½Ρ. ΠΠ»Ρ ΠΎΠ±ΡΠ»ΡΠΆΠΈΠ²Π°Π½ΠΈΡ ΡΡΠΈΡ ΠΊΡΠΈΡΠΈΡΠ΅ΡΠΊΠΈ Π²Π°ΠΆΠ½ΡΡ ΡΠΈΡΡΠ΅ΠΌ ΡΡΠ΅Π±ΡΠ΅ΡΡΡ ΡΠΏΠΎΡΠΎΠ±Π½ΠΎΡΡΡ ΠΎΠ΄Π½ΠΎΠ²ΡΠ΅ΠΌΠ΅Π½Π½ΠΎ ΡΠΎΠ±ΠΈΡΠ°ΡΡ ΠΈ ΠΊΠΎΠ½ΡΡΠΎΠ»ΠΈΡΠΎΠ²Π°ΡΡ Π½Π΅ΡΠΊΠΎΠ»ΡΠΊΠΎ ΡΠΈΠΏΠΎΠ² ΠΈΠ·ΠΌΠ΅ΡΠ΅Π½ΠΈΠΉ, ΡΠ°ΠΊΠΈΡ ΠΊΠ°ΠΊ ΡΠ΅ΠΌΠΏΠ΅ΡΠ°ΡΡΡΠ½ΡΠ΅, ΡΠ»Π΅ΠΊΡΡΠΈΡΠ΅ΡΠΊΠΈΠ΅, ΡΠ»Π΅ΠΊΡΡΠΎΠ½Π½ΡΠ΅ ΠΈ Π²ΠΈΠ±ΡΠ°ΡΠΈΠΈ Ρ ΡΠ΅ΡΠ΅Π½ΠΈΠ΅ΠΌ Π²ΡΠ΅ΠΌΠ΅Π½ΠΈ.
ΠΠ»ΡΡΠ΅Π²ΡΠ΅ KPI, ΡΠ²ΡΠ·Π°Π½Π½ΡΠ΅ Ρ ΠΏΡΠΎΠΈΠ·Π²ΠΎΠ΄ΠΈΡΠ΅Π»ΡΠ½ΠΎΡΡΡΡ ΡΠΈΡΡΠ΅ΠΌΡ HVAC, Π²ΠΊΠ»ΡΡΠ°ΡΡ:
- ΠΠΎΠ½ΠΈΡΠΎΡΠΈΠ½Π³ ΡΠ΅ΠΌΠΏΠ΅ΡΠ°ΡΡΡΡ Π΄Π»Ρ ΠΎΠΏΡΠ΅Π΄Π΅Π»Π΅Π½ΠΈΡ ΡΠΈΠΏΠΎΠ»ΠΎΠ³ΠΈΠΈ HVAC, ΠΏΠΎΠΊΠ°Π·ΡΠ²Π°ΡΡΠΈΠΉ, ΠΊΠ°ΠΊ ΡΠ°ΡΠΏΡΠ΅Π΄Π΅Π»ΡΡΡΡΡ ΠΎΡΠΎΠΏΠ»Π΅Π½ΠΈΠ΅ ΠΈ ΠΎΡ Π»Π°ΠΆΠ΄Π΅Π½ΠΈΠ΅
- ΠΠΎΠ½ΠΈΡΠΎΡΠΈΠ½Π³ ΠΊΠ°ΡΠ΅ΡΡΠ²Π° ΡΠ»Π΅ΠΊΡΡΠΎΡΠ½Π΅ΡΠ³ΠΈΠΈ Π΄Π»Ρ ΠΎΠΏΡΠ΅Π΄Π΅Π»Π΅Π½ΠΈΡ ΡΡΠΎΠΈΠΌΠΎΡΡΠΈ PUD ΠΏΠΎ ΡΡΠ°Π²Π½Π΅Π½ΠΈΡ Ρ ΠΏΠΎΡΡΠ΅Π±Π»ΡΠ΅ΠΌΠΎΠΉ ΡΠ½Π΅ΡΠ³ΠΈΠ΅ΠΉ
ΠΠ΅Π½ΡΠΈΠ»ΡΡΠΎΡΡ ΠΈ Π½Π°Π³Π½Π΅ΡΠ°ΡΠ΅Π»ΠΈ
ΠΠ΅Π½ΡΠΈΠ»ΡΡΠΎΡΡ ΠΈ Π½Π°Π³Π½Π΅ΡΠ°ΡΠ΅Π»ΠΈ ΠΈΡΠΏΡΡΡΠ²Π°ΡΡ ΠΏΡΠΎΠ±Π»Π΅ΠΌΡ Ρ Π²ΠΈΠ±ΡΠ°ΡΠΈΠ΅ΠΉ ΠΏΠΎ ΠΌΠ½ΠΎΠ³ΠΈΠΌ ΠΏΡΠΈΡΠΈΠ½Π°ΠΌ, Π² ΡΠΎΠΌ ΡΠΈΡΠ»Π΅:
- Π’ΡΠ΅ΡΠΊΠ°Π½ΠΈΠ΅ Π»ΠΎΠΏΠ°ΡΡΠΈ Π²Π΅Π½ΡΠΈΠ»ΡΡΠΎΡΠ°
- ΠΠ΅ΡΠΎΠΎΡΠ½ΠΎΡΡΡ Π²Π°Π»Π° ΠΈ ΠΊΠΎΡΠΏΡΡΠ°
- ΠΠ΅ΡΡΠ°Π²Π½ΠΎΠ²Π΅ΡΠ΅Π½Π½ΠΎΡΡΡ Π²Π°Π»Π° ΠΈ Π»ΠΎΠΏΠ°ΡΡΠ΅ΠΉ Π²Π΅Π½ΡΠΈΠ»ΡΡΠΎΡΠ°
- ΠΠ°ΠΊΠΎΠΏΠ»Π΅Π½ΠΈΠ΅ ΠΏΡΠΎΠ΄ΡΠΊΡΠΎΠ² ΠΈΠ»ΠΈ ΡΡΠΎΠ·ΠΈΡ Π»ΠΎΠΏΠ°ΡΡΠ΅ΠΉ Π²Π΅Π½ΡΠΈΠ»ΡΡΠΎΡΠ°
ΠΠ΅Π· ΡΠ°Π½Π½Π΅Π³ΠΎ ΠΎΠ±Π½Π°ΡΡΠΆΠ΅Π½ΠΈΡ ΠΈ ΠΈΡΠΏΡΠ°Π²Π»Π΅Π½ΠΈΡ ΠΌΠΎΠ³ΡΡ Π²ΠΎΠ·Π½ΠΈΠΊΠ½ΡΡΡ Π΄ΡΡΠ³ΠΈΠ΅ Π½Π΅ΠΈΡΠΏΡΠ°Π²Π½ΠΎΡΡΠΈ, ΡΠ°ΠΊΠΈΠ΅ ΠΊΠ°ΠΊ Π½Π΅ΠΎΠ±ΡΠ°ΡΠΈΠΌΠ°Ρ Π΄Π΅ΡΠΎΡΠΌΠ°ΡΠΈΡ Π²Π°Π»Π°, ΠΈΠ·Π³ΠΈΠ± Π²Π°Π»Π° ΠΈ ΡΠΌΠ΅Π½ΡΡΠ΅Π½ΠΈΠ΅ Π·Π°Π·ΠΎΡΠΎΠ².ΠΡΠ»ΠΈ ΠΈΡ Π½Π΅ ΠΎΡΡΠ°Π½ΠΎΠ²ΠΈΡΡ, Π²ΡΠ΅ ΡΡΠΎ ΠΌΠΎΠΆΠ΅Ρ ΠΏΡΠΈΠ²Π΅ΡΡΠΈ ΠΊ ΡΠ½ΠΈΠΆΠ΅Π½ΠΈΡ ΡΡΡΠ΅ΠΊΡΠΈΠ²Π½ΠΎΡΡΠΈ ΠΈ, Π² ΠΊΠΎΠ½Π΅ΡΠ½ΠΎΠΌ ΠΈΡΠΎΠ³Π΅, ΠΊ ΡΠΎΠΊΡΠ°ΡΠ΅Π½ΠΈΡ ΡΡΠΎΠΊΠ° ΡΠ»ΡΠΆΠ±Ρ Π²Π΅Π½ΡΠΈΠ»ΡΡΠΎΡΠ° ΠΈΠ»ΠΈ Π½Π°Π³Π½Π΅ΡΠ°ΡΠ΅Π»Ρ.
ΠΠ»ΡΡΠ΅Π²ΠΎΠΉ ΠΏΠΎΠΊΠ°Π·Π°ΡΠ΅Π»Ρ, ΠΊΠΎΡΠΎΡΡΠΉ Π½Π΅ΠΎΠ±Ρ ΠΎΠ΄ΠΈΠΌΠΎ ΠΎΡΡΠ»Π΅ΠΆΠΈΠ²Π°ΡΡ Π΄Π»Ρ Π²Π΅Π½ΡΠΈΠ»ΡΡΠΎΡΠΎΠ² ΠΈ Π½Π°Π³Π½Π΅ΡΠ°ΡΠ΅Π»Π΅ΠΉ:
- ΠΠΎΠ½ΠΈΡΠΎΡΠΈΠ½Π³ Π²ΠΈΠ±ΡΠ°ΡΠΈΠΈ Π΄Π»Ρ ΠΎΠΏΡΠ΅Π΄Π΅Π»Π΅Π½ΠΈΡ ΠΏΠ΅ΡΠ΅ΠΊΠΎΡΠ° Π²Π°Π»Π° ΠΈ ΠΊΠΎΡΠΏΡΡΠ° ΠΈΠ»ΠΈ Π΄ΠΈΡΠ±Π°Π»Π°Π½ΡΠ° Π»ΠΎΠΏΠ°ΡΡΠ΅ΠΉ
- Π’Π΅ΠΌΠΏΠ΅ΡΠ°ΡΡΡΠ½ΡΠΉ ΠΌΠΎΠ½ΠΈΡΠΎΡΠΈΠ½Π³ Π΄Π»Ρ Π²ΡΡΠ²Π»Π΅Π½ΠΈΡ ΡΠΎΡΠ΅ΠΊ ΠΈΡΡΠΈΡΠ°Π½ΠΈΡ Π»ΠΎΠΏΠ°ΡΡΠ΅ΠΉ Π²Π΅Π½ΡΠΈΠ»ΡΡΠΎΡΠ° ΠΈ ΡΠΊΠΎΠΏΠ»Π΅Π½ΠΈΠΉ ΠΏΡΠΎΠ΄ΡΠΊΡΠ°, Π²ΡΠ·ΡΠ²Π°ΡΡΠΈΡ ΠΏΠ΅ΡΠ΅Π³ΡΠ΅Π².
ΠΡΠΏΠΎΠ»ΡΠ·ΠΎΠ²Π°Π½ΠΈΠ΅ CMMS Π΄Π»Ρ ΠΎΠΏΡΠΈΠΌΠΈΠ·Π°ΡΠΈΠΈ ΠΎΠ±ΡΠ»ΡΠΆΠΈΠ²Π°Π½ΠΈΡ
Π‘ΠΈΡΡΠ΅ΠΌΡCMMS ΠΏΠΎΠΌΠΎΠ³Π°ΡΡ ΠΎΡΠ³Π°Π½ΠΈΠ·Π°ΡΠΈΡΠΌ ΡΠΎΡΡΠ°Π²Π»ΡΡΡ Π³ΡΠ°ΡΠΈΠΊ, ΠΏΠ»Π°Π½ΠΈΡΠΎΠ²Π°ΡΡ, ΡΠΏΡΠ°Π²Π»ΡΡΡ ΠΈ ΠΎΡΡΠ»Π΅ΠΆΠΈΠ²Π°ΡΡ Π΄Π΅ΠΉΡΡΠ²ΠΈΡ ΠΏΠΎ ΡΠ΅Ρ Π½ΠΈΡΠ΅ΡΠΊΠΎΠΌΡ ΠΎΠ±ΡΠ»ΡΠΆΠΈΠ²Π°Π½ΠΈΡ ΠΎΠ±ΠΎΡΡΠ΄ΠΎΠ²Π°Π½ΠΈΡ, ΡΡΠ°Π½ΡΠΏΠΎΡΡΠ½ΡΡ ΡΡΠ΅Π΄ΡΡΠ² ΠΈΠ»ΠΈ ΠΎΠ±ΡΠ΅ΠΊΡΠΎΠ².ΠΠ°Π½Π½ΡΠ΅ ΠΌΠΎΠ³ΡΡ Π±ΡΡΡ ΡΠΎΠ±ΡΠ°Π½Ρ Ρ ΠΏΠΎΠ΄ΠΊΠ»ΡΡΠ΅Π½Π½ΡΡ ΠΏΠΎΡΡΠ°ΡΠΈΠ²Π½ΡΡ ΠΈΠ½ΡΡΡΡΠΌΠ΅Π½ΡΠΎΠ² ΡΠ΅ΡΡΠΈΡΠΎΠ²Π°Π½ΠΈΡ ΠΈ Π±Π΅ΡΠΏΡΠΎΠ²ΠΎΠ΄Π½ΡΡ Π΄Π°ΡΡΠΈΠΊΠΎΠ² ΠΈ ΠΎΡΠΏΡΠ°Π²Π»Π΅Π½Ρ Π½Π΅ΠΏΠΎΡΡΠ΅Π΄ΡΡΠ²Π΅Π½Π½ΠΎ Π² ΡΠΈΡΡΠ΅ΠΌΡ CMMS Π² ΠΎΠ±Π»Π°ΠΊΠ΅. Π‘ΠΈΡΡΠ΅ΠΌΠ° Ρ ΡΠ°Π½ΠΈΡ Π΄Π°Π½Π½ΡΠ΅ ΠΎΠ± Π°ΠΊΡΠΈΠ²Π°Ρ , Π²ΠΊΠ»ΡΡΠ°Ρ ΠΈΠ·ΠΌΠ΅ΡΠ΅Π½ΠΈΡ, ΠΈΠ·ΠΎΠ±ΡΠ°ΠΆΠ΅Π½ΠΈΡ, ΠΏΠΈΡΡΠΌΠ΅Π½Π½ΡΠ΅ ΠΈ ΡΡΡΠ½ΡΠ΅ Π·Π°ΠΌΠ΅ΡΠΊΠΈ, ΡΡΠΎΠ±Ρ ΠΈΡ ΠΌΠΎΠΆΠ½ΠΎ Π±ΡΠ»ΠΎ ΠΈΡΠΏΠΎΠ»ΡΠ·ΠΎΠ²Π°ΡΡ Π΄Π»Ρ Π΄Π°Π»ΡΠ½Π΅ΠΉΡΠ΅Π³ΠΎ ΠΈΡΠΏΠΎΠ»ΡΠ·ΠΎΠ²Π°Π½ΠΈΡ. ΠΠ° ΠΎΡΠ½ΠΎΠ²Π΅ ΡΡΠΈΡ Π΄Π°Π½Π½ΡΡ CMMS Π°Π²ΡΠΎΠΌΠ°ΡΠΈΡΠ΅ΡΠΊΠΈ Π³Π΅Π½Π΅ΡΠΈΡΡΠ΅Ρ ΡΠ°Π±ΠΎΡΠΈΠ΅ Π·Π°Π΄Π°Π½ΠΈΡ, ΡΠΎΡΡΠ°Π²Π»ΡΠ΅Ρ Π³ΡΠ°ΡΠΈΠΊ ΡΠ°Π±ΠΎΡ ΠΏΠΎ ΡΠ΅Ρ Π½ΠΈΡΠ΅ΡΠΊΠΎΠΌΡ ΠΎΠ±ΡΠ»ΡΠΆΠΈΠ²Π°Π½ΠΈΡ ΠΈ ΡΠ΅ΡΡΡΡΠ°ΠΌ, ΠΎΡΡΠ»Π΅ΠΆΠΈΠ²Π°Π΅Ρ ΡΡΠΎΠ²Π½ΠΈ Π·Π°ΠΏΠ°ΡΠΎΠ² ΠΈ ΠΏΡΠ΅Π΄ΠΎΡΡΠ°Π²Π»ΡΠ΅Ρ Π² ΡΠ΅Π°Π»ΡΠ½ΠΎΠΌ Π²ΡΠ΅ΠΌΠ΅Π½ΠΈ ΠΈΠ½ΡΠΎΡΠΌΠ°ΡΠΈΠΎΠ½Π½ΡΠ΅ ΠΏΠ°Π½Π΅Π»ΠΈ KPI ΠΈ ΠΎΡΡΠ΅ΡΡ, ΠΊ ΠΊΠΎΡΠΎΡΡΠΌ ΠΌΠΎΠΆΠ½ΠΎ ΠΏΠΎΠ»ΡΡΠΈΡΡ Π΄ΠΎΡΡΡΠΏ ΠΈΠ· Π»ΡΠ±ΠΎΠ³ΠΎ ΠΌΠ΅ΡΡΠ° Π½Π° ΠΌΠΎΠ±ΠΈΠ»ΡΠ½ΠΎΠΌ ΡΡΡΡΠΎΠΉΡΡΠ²Π΅ ΠΈΠ»ΠΈ ΠΠ Π΄Π»Ρ ΠΏΡΠΈΠ½ΡΡΠΈΡ ΡΠ΅ΡΠ΅Π½ΠΈΠΉ.
ΠΠΎΠ·ΠΌΠΎΠΆΠ½ΠΎΡΡΠΈ ΠΏΠΎΠΈΡΠΊΠ° Π² ΡΠΈΡΡΠ΅ΠΌΠ΅ CMMS:
- ΠΠ½ΡΠ΅Π³ΡΠΈΡΠΎΠ²Π°Π½Π½ΡΠΉ Ρ ΠΎΡΡΠΈΠ½Π³ Π΄ΠΎΠΊΡΠΌΠ΅Π½ΡΠΎΠ² , ΠΊΠΎΡΠΎΡΡΠΉ ΠΎΠ±Π΅ΡΠΏΠ΅ΡΠΈΠ²Π°Π΅Ρ Π½Π΅ΡΠΊΠΎΠ»ΡΠΊΠΎ ΠΌΠ΅ΡΡ Ρ Π΄ΠΎΡΡΡΠΏΠΎΠΌ ΠΊ ΠΎΠ΄Π½ΠΈΠΌ ΠΈ ΡΠ΅ΠΌ ΠΆΠ΅ Π΄Π°Π½Π½ΡΠΌ, ΡΠΎΡΠΎΠ³ΡΠ°ΡΠΈΡΠΌ, ΡΠ΅ΡΡΠ΅ΠΆΠ°ΠΌ, ΡΠΏΠΈΡΠΊΠ°ΠΌ Π΄Π΅ΡΠ°Π»Π΅ΠΉ ΠΈ ΠΏΠΎΠ΄ΡΠΎΠ±Π½ΡΠΌ ΠΈΠ½ΡΡΡΡΠΊΡΠΈΡΠΌ Π΄Π»Ρ ΠΏΠΎΠ²ΡΠΎΡΡΡΡΠΈΡ ΡΡ ΡΠ°Π±Π»ΠΎΠ½Π½ΡΡ PM Π½Π° ΠΎΠ±ΡΠ΅ΠΌ ΠΎΠ±ΠΎΡΡΠ΄ΠΎΠ²Π°Π½ΠΈΠΈ.
- ΠΠ°ΡΡΡΠ°ΠΈΠ²Π°Π΅ΠΌΡΠ΅ ΠΎΡΡΠ΅ΡΡ, , ΡΠ°ΠΊΠΈΠ΅ ΠΊΠ°ΠΊ Π΅ΠΆΠ΅Π΄Π½Π΅Π²Π½Π°Ρ Π΄Π΅ΡΡΠ΅Π»ΡΠ½ΠΎΡΡΡ Π³ΡΡΠΏΠΏ ΡΠ΅Ρ Π½ΠΈΡΠ΅ΡΠΊΠΎΠ³ΠΎ ΠΎΠ±ΡΠ»ΡΠΆΠΈΠ²Π°Π½ΠΈΡ, ΡΠ°Π±ΠΎΡΠΈΠ΅ ΡΠ°ΡΡ Π΄Π»Ρ ΠΎΡΠ΄Π΅Π»ΡΠ½ΡΡ ΡΠ°Π±ΠΎΡΠΈΡ Π·Π°Π΄Π°Π½ΠΈΠΉ, ΠΏΡΠΎΡΠ΅Π½Ρ ΠΏΡΠΎΡΡΠΎΠ΅Π² ΠΈ Π΄ΡΡΠ³ΠΈΠ΅ ΠΊΠ»ΡΡΠ΅Π²ΡΠ΅ ΠΏΠΎΠΊΠ°Π·Π°ΡΠ΅Π»ΠΈ ΡΡΡΠ΅ΠΊΡΠΈΠ²Π½ΠΎΡΡΠΈ.
- Π€ΡΠ½ΠΊΡΠΈΠΈ ΠΎΡΡΠ»Π΅ΠΆΠΈΠ²Π°Π½ΠΈΡ Π·Π°ΡΡΠ°Ρ , ΠΊΠΎΡΠΎΡΡΠ΅ Π½Π°ΡΠΈΡΠ»ΡΡΡ Π·Π°ΡΡΠ°ΡΡ Π½Π° Π·Π°ΠΊΠ°Π·Ρ Π½Π° ΡΠ°Π±ΠΎΡΡ, Π΄ΠΎΠΊΡΠΌΠ΅Π½ΡΠΈΡΡΡΡ ΡΠ½ΠΈΠΆΠ΅Π½ΠΈΠ΅ Π·Π°ΡΡΠ°Ρ ΠΈ ΠΏΠΎΠ΄Π΄Π΅ΡΠΆΠΈΠ²Π°ΡΡ ΡΠ°ΡΡΠ΅Ρ ΡΡΠΎΠΈΠΌΠΎΡΡΠΈ ΠΆΠΈΠ·Π½Π΅Π½Π½ΠΎΠ³ΠΎ ΡΠΈΠΊΠ»Π° Π°ΠΊΡΠΈΠ²ΠΎΠ².
- ΠΠ½ΡΠΎΡΠΌΠ°ΡΠΈΠΎΠ½Π½ΡΠ΅ ΠΏΠ°Π½Π΅Π»ΠΈ Π² ΡΠ΅Π°Π»ΡΠ½ΠΎΠΌ Π²ΡΠ΅ΠΌΠ΅Π½ΠΈ , ΠΊΠΎΡΠΎΡΡΠ΅ ΠΏΡΠ΅Π΄ΡΡΠ°Π²Π»ΡΡΡ Π½Π°ΡΡΡΠ°ΠΈΠ²Π°Π΅ΠΌΡΠΉ Π½Π°Π±ΠΎΡ Π΄Π°Π½Π½ΡΡ ΠΈ KPI Π½Π° ΠΌΠΎΠ±ΠΈΠ»ΡΠ½ΠΎΠΌ ΡΡΡΡΠΎΠΉΡΡΠ²Π΅ ΠΈΠ»ΠΈ ΠΠ ΠΈ Π½Π΅ΠΌΠ΅Π΄Π»Π΅Π½Π½ΠΎ ΠΏΡΠ΅Π΄ΡΠΏΡΠ΅ΠΆΠ΄Π°ΡΡ ΠΎΠ±ΡΠ»ΡΠΆΠΈΠ²Π°ΡΡΠΈΠΉ ΠΏΠ΅ΡΡΠΎΠ½Π°Π» ΠΈ ΠΌΠ΅Π½Π΅Π΄ΠΆΠ΅ΡΠΎΠ² Π² ΡΠ»ΡΡΠ°Π΅ Π²ΠΎΠ·Π½ΠΈΠΊΠ½ΠΎΠ²Π΅Π½ΠΈΡ ΠΏΡΠΎΠ±Π»Π΅ΠΌΡ.
ΠΠ΄Π°ΠΏΡΠΈΡΡΠΉΡΠ΅ Π²Π°ΡΡ ΡΠΈΡΡΠ΅ΠΌΡ CMMS ΠΊ Π²Π°ΡΠ΅ΠΉ ΡΠ°Π±ΠΎΡΠ΅
Π Π½Π°ΡΡΡΠ°ΠΈΠ²Π°Π΅ΠΌΠΎΠΉ ΡΠΈΡΡΠ΅ΠΌΠ΅ CMMS Π²Ρ ΠΌΠΎΠΆΠ΅ΡΠ΅ Π½Π°ΡΡΡΠΎΠΈΡΡ KPI, ΠΊΠΎΡΠΎΡΡΠ΅ ΠΈΠΌΠ΅ΡΡ Π·Π½Π°ΡΠ΅Π½ΠΈΠ΅ Π΄Π»Ρ Π²Π°ΡΠ΅ΠΉ ΠΎΠΏΠ΅ΡΠ°ΡΠΈΠΈ ΠΎΠ±ΡΠ»ΡΠΆΠΈΠ²Π°Π½ΠΈΡ. ΠΡΡΠ»Π΅ΠΆΠΈΠ²Π°ΠΉΡΠ΅ Π²ΡΠ΅, ΠΎΡ ΡΡΠ΅Π΄Π½Π΅Π³ΠΎ Π²ΡΠ΅ΠΌΠ΅Π½ΠΈ Π²ΠΎΡΡΡΠ°Π½ΠΎΠ²Π»Π΅Π½ΠΈΡ Π΄ΠΎ OEE, ΠΏΡΠΎΡΠ΅Π½ΡΠ½ΠΎΠ΅ ΡΠΎΠΎΡΠ½ΠΎΡΠ΅Π½ΠΈΠ΅ ΠΏΠ»Π°Π½ΠΎΠ²ΠΎΠ³ΠΎ ΠΈ Π²Π½Π΅ΠΏΠ»Π°Π½ΠΎΠ²ΠΎΠ³ΠΎ ΠΎΠ±ΡΠ»ΡΠΆΠΈΠ²Π°Π½ΠΈΡ, Π° ΡΠ°ΠΊΠΆΠ΅ ΡΠ°Π·Π»ΠΈΡΠ½ΡΠ΅ Π΄Π°Π½Π½ΡΠ΅ ΠΎ ΡΠΎΡΡΠΎΡΠ½ΠΈΠΈ ΠΎΡΠ΄Π΅Π»ΡΠ½ΡΡ ΠΊΠΎΠΌΠΏΠΎΠ½Π΅Π½ΡΠΎΠ² ΠΎΠ±ΠΎΡΡΠ΄ΠΎΠ²Π°Π½ΠΈΡ.ΠΡΠΈ Π΄Π°Π½Π½ΡΠ΅ ΠΎΠΊΡΠΏΡΡΡΡ Π²:
- ΠΠΊΠΎΠ½ΠΎΠΌΠΈΡ Π²ΡΠ΅ΠΌΠ΅Π½ΠΈ Π±Π»Π°Π³ΠΎΠ΄Π°ΡΡ Π°Π²ΡΠΎΠΌΠ°ΡΠΈΡΠ΅ΡΠΊΠΎΠΌΡ ΡΠΎΠ·Π΄Π°Π½ΠΈΡ ΠΈ ΠΏΠ»Π°Π½ΠΈΡΠΎΠ²Π°Π½ΠΈΡ ΡΠ°Π±ΠΎΡΠΈΡ Π·Π°Π΄Π°Π½ΠΈΠΉ
- ΠΠΎΠ»Π΅Π΅ ΠΈΠ½ΡΠΎΡΠΌΠΈΡΠΎΠ²Π°Π½Π½ΡΠ΅ ΠΌΠ΅Π½Π΅Π΄ΠΆΠ΅ΡΡ Π·Π° ΡΡΠ΅Ρ ΡΠΏΡΠΎΡΠ΅Π½Π½ΠΎΠΉ ΠΎΡΡΠ΅ΡΠ½ΠΎΡΡΠΈ Π΄Π»Ρ ΡΠΎΠ±Π»ΡΠ΄Π΅Π½ΠΈΡ Π½ΠΎΡΠΌΠ°ΡΠΈΠ²Π½ΡΡ ΡΡΠ΅Π±ΠΎΠ²Π°Π½ΠΈΠΉ, ΡΠΎΡΡΠ°Π²Π»Π΅Π½ΠΈΡ Π±ΡΠ΄ΠΆΠ΅ΡΠ° ΠΈ ΡΠ°ΡΠΏΠΈΡΠ°Π½ΠΈΡ
- Π‘Π½ΠΈΠΆΠ΅Π½ΠΈΠ΅ Π·Π°ΡΡΠ°Ρ Π·Π° ΡΡΠ΅Ρ Π±ΠΎΠ»Π΅Π΅ Π΄Π»ΠΈΡΠ΅Π»ΡΠ½ΠΎΠ³ΠΎ ΡΡΠΎΠΊΠ° ΡΠ»ΡΠΆΠ±Ρ Π°ΠΊΡΠΈΠ²ΠΎΠ², Π±ΠΎΠ»Π΅Π΅ ΡΡΡΠ΅ΠΊΡΠΈΠ²Π½ΠΎΠ³ΠΎ ΠΏΠ»Π°Π½ΠΈΡΠΎΠ²Π°Π½ΠΈΡ ΠΈ ΠΌΠ΅Π½ΡΡΠ΅Π³ΠΎ ΠΊΠΎΠ»ΠΈΡΠ΅ΡΡΠ²Π° Π½Π΅Π½ΡΠΆΠ½ΠΎΠ³ΠΎ ΠΎΠ±ΡΠ»ΡΠΆΠΈΠ²Π°Π½ΠΈΡ
- ΠΠΎΠ²ΡΡΠ΅Π½ΠΈΠ΅ ΠΏΡΠΎΠΈΠ·Π²ΠΎΠ΄ΠΈΡΠ΅Π»ΡΠ½ΠΎΡΡΠΈ Π·Π° ΡΡΠ΅Ρ ΠΊΡΡΠ³Π»ΠΎΡΡΡΠΎΡΠ½ΠΎΠ³ΠΎ Π΄ΠΎΡΡΡΠΏΠ° ΠΊ Π΄Π°Π½Π½ΡΠΌ ΠΎ ΡΠΎΡΡΠΎΡΠ½ΠΈΠΈ ΠΎΠ±ΠΎΡΡΠ΄ΠΎΠ²Π°Π½ΠΈΡ Π² ΡΠ΅Π°Π»ΡΠ½ΠΎΠΌ Π²ΡΠ΅ΠΌΠ΅Π½ΠΈ ΠΈ ΠΈΡΡΠΎΡΠΈΡΠ΅ΡΠΊΠΈΠΌ Π΄Π°Π½Π½ΡΠΌ ΠΎ ΡΠΎΡΡΠΎΡΠ½ΠΈΠΈ ΠΎΠ±ΠΎΡΡΠ΄ΠΎΠ²Π°Π½ΠΈΡ
Π Π΅Π°Π»ΡΠ½ΡΠ΅ Π²ΡΠ³ΠΎΠ΄Ρ
ΠΡΡΠ΅ΠΊΡΠΈΠ²Π½ΠΎΠ΅ ΠΎΡΡΠ»Π΅ΠΆΠΈΠ²Π°Π½ΠΈΠ΅ ΠΏΠΎΠΊΠ°Π·Π°ΡΠ΅Π»Π΅ΠΉ ΡΠ΅Ρ Π½ΠΈΡΠ΅ΡΠΊΠΎΠ³ΠΎ ΠΎΠ±ΡΠ»ΡΠΆΠΈΠ²Π°Π½ΠΈΡ ΠΈ ΡΠΎΡΡΠΎΡΠ½ΠΈΡ ΠΎΠ±ΠΎΡΡΠ΄ΠΎΠ²Π°Π½ΠΈΡ Π΄Π°Π΅Ρ ΡΠ΅Π°Π»ΡΠ½ΡΠ΅ ΠΏΡΠ΅ΠΈΠΌΡΡΠ΅ΡΡΠ²Π° Π² ΡΠ΅Π°Π»ΡΠ½ΡΡ ΠΏΡΠΈΠ»ΠΎΠΆΠ΅Π½ΠΈΡΡ .ΠΠ°ΠΏΡΠΈΠΌΠ΅Ρ:
- ΠΡΡΠ»Π΅ΠΆΠΈΠ²Π°Π½ΠΈΠ΅ ΠΊΠ»ΡΡΠ΅Π²ΡΡ ΠΏΠΎΠΊΠ°Π·Π°ΡΠ΅Π»Π΅ΠΉ ΡΡΡΠ΅ΠΊΡΠΈΠ²Π½ΠΎΡΡΠΈ ΡΠ΅Ρ Π½ΠΈΡΠ΅ΡΠΊΠΎΠ³ΠΎ ΠΎΠ±ΡΠ»ΡΠΆΠΈΠ²Π°Π½ΠΈΡ ΠΏΠΎΠΌΠΎΠ³Π»ΠΎ ΠΏΡΠΎΠΈΠ·Π²ΠΎΠ΄ΠΈΡΠ΅Π»Ρ ΠΏΠΈΡΠ΅Π²ΡΡ ΠΏΡΠΎΠ΄ΡΠΊΡΠΎΠ² ΠΎΠΏΡΠ°Π²Π΄Π°ΡΡ ΡΠ²ΠΎΠΈ Π±ΡΠ΄ΠΆΠ΅ΡΠ½ΡΠ΅ Π·Π°ΠΏΡΠΎΡΡ Π½Π° ΡΠ΅Ρ Π½ΠΈΡΠ΅ΡΠΊΠΎΠ΅ ΠΎΠ±ΡΠ»ΡΠΆΠΈΠ²Π°Π½ΠΈΠ΅. ΠΠΎΠ½ΠΈΠΌΠ°Ρ, ΡΡΠΎ ΡΠ΅Ρ Π½ΠΈΡΠ΅ΡΠΊΠΈΠ΅ ΡΠΏΠ΅ΡΠΈΠ°Π»ΠΈΡΡΡ ΡΡΠ°ΡΠΈΠ»ΠΈ ΡΠ»ΠΈΡΠΊΠΎΠΌ ΠΌΠ½ΠΎΠ³ΠΎ Π²ΡΠ΅ΠΌΠ΅Π½ΠΈ Π½Π° ΠΎΡΠ²Π΅ΡΠ½ΡΠ΅ Π·Π°ΠΊΠ°Π·Ρ Π½Π° ΡΠ°Π±ΠΎΡΡ ΠΈ ΡΠ»ΠΈΡΠΊΠΎΠΌ ΠΌΠ°Π»ΠΎ Π²ΡΠ΅ΠΌΠ΅Π½ΠΈ Π½Π° Π·Π°ΠΊΠ°Π·Ρ Π½Π° ΠΏΡΠΎΡΠΈΠ»Π°ΠΊΡΠΈΡΠ΅ΡΠΊΠΈΠ΅ ΡΠ°Π±ΠΎΡΡ, ΠΊΠΎΠΌΠΏΠ°Π½ΠΈΡ ΡΠΌΠΎΠ³Π»Π° ΠΎΠΏΡΠ°Π²Π΄Π°ΡΡ ΠΏΠΎΡΡΠ΅Π±Π½ΠΎΡΡΡ Π² Π΄ΠΎΠΏΠΎΠ»Π½ΠΈΡΠ΅Π»ΡΠ½ΡΡ ΡΠ΅Ρ Π½ΠΈΡΠ΅ΡΠΊΠΈΡ ΡΠΏΠ΅ΡΠΈΠ°Π»ΠΈΡΡΠ°Ρ , Π° ΡΠ°ΠΊΠΆΠ΅ ΠΏΠΎΡΡΠ΅Π±Π½ΠΎΡΡΡ Π² Π½ΠΎΠ²ΠΎΠΌ ΠΎΠ±ΠΎΡΡΠ΄ΠΎΠ²Π°Π½ΠΈΠΈ.
- ΠΡΠΎΠΈΠ·Π²ΠΎΠ΄ΠΈΡΠ΅Π»Ρ ΠΏΡΠΈΡΠΎΠ΄Π½ΠΎΠ³ΠΎ Π³Π°Π·Π° Π·Π°ΠΌΠ΅Π½ΠΈΠ» ΡΠ²ΠΎΡ ΡΡΠΊΠΎΠΏΠΈΡΠ½ΡΡ ΡΠΈΡΡΠ΅ΠΌΡ ΡΠΏΡΠ°Π²Π»Π΅Π½ΠΈΡ ΡΠ΅Ρ Π½ΠΈΡΠ΅ΡΠΊΠΈΠΌ ΠΎΠ±ΡΠ»ΡΠΆΠΈΠ²Π°Π½ΠΈΠ΅ΠΌ ΡΠΈΡΡΠ΅ΠΌΠΎΠΉ CMMS. ΠΡΠΎ ΡΠ²Π΅Π»ΠΈΡΠΈΠ»ΠΎ ΠΊΠΎΠ»ΠΈΡΠ΅ΡΡΠ²ΠΎ Π·Π°Π²Π΅ΡΡΠ΅Π½Π½ΡΡ ΡΠ°Π±ΠΎΡ Ρ 70% Π΄ΠΎ 100% Π±Π΅Π· Π΄ΠΎΠΏΠΎΠ»Π½ΠΈΡΠ΅Π»ΡΠ½ΠΎΠ³ΠΎ ΠΏΠ΅ΡΡΠΎΠ½Π°Π»Π°.
- ΠΠΎΡΠ»Π΅ Π²Π½Π΅Π΄ΡΠ΅Π½ΠΈΡ ΡΠΈΡΡΠ΅ΠΌΡ CMMS ΠΏΡΠΎΠΈΠ·Π²ΠΎΠ΄ΠΈΡΠ΅Π»Ρ ΠΏΠ»Π°ΡΡΠΌΠ°ΡΡ ΡΠ²ΠΈΠ΄Π΅Π» ΡΠ²Π΅Π»ΠΈΡΠ΅Π½ΠΈΠ΅ OEE Π½Π° 20%, Π° ΡΠ°ΠΊΠΆΠ΅ ΡΠ»ΡΡΡΠ΅Π½ΠΈΠ΅ ΡΠΎΠ³Π»Π°ΡΠΎΠ²Π°Π½Π½ΠΎΡΡΠΈ, Π²Π·Π°ΠΈΠΌΠΎΠ΄Π΅ΠΉΡΡΠ²ΠΈΡ ΠΈ ΠΏΡΠΎΠΈΠ·Π²ΠΎΠ΄ΠΈΡΠ΅Π»ΡΠ½ΠΎΡΡΠΈ.
ΠΡΠΎ Π²ΡΠ΅Π³ΠΎ Π»ΠΈΡΡ Π½Π΅ΡΠΊΠΎΠ»ΡΠΊΠΎ ΠΏΡΠΈΠΌΠ΅ΡΠΎΠ² ΡΠΎΠ³ΠΎ, ΠΊΠ°ΠΊ ΠΈΡΠΏΠΎΠ»ΡΠ·ΠΎΠ²Π°Π½ΠΈΠ΅ ΡΠΈΡΡΠ΅ΠΌΡ CMMS Π΄Π»Ρ ΠΌΠΎΠ½ΠΈΡΠΎΡΠΈΠ½Π³Π° ΠΈ ΡΡΠ°Π²Π½Π΅Π½ΠΈΡ ΠΊΠ»ΡΡΠ΅Π²ΡΡ ΠΏΠΎΠΊΠ°Π·Π°ΡΠ΅Π»Π΅ΠΉ ΡΡΡΠ΅ΠΊΡΠΈΠ²Π½ΠΎΡΡΠΈ ΠΎΠ±ΡΠ»ΡΠΆΠΈΠ²Π°Π½ΠΈΡ ΠΌΠΎΠΆΠ΅Ρ ΠΎΠΊΡΠΏΠΈΡΡΡΡ ΠΏΠΎΠ²ΡΡΠ΅Π½ΠΈΠ΅ΠΌ ΡΡΡΠ΅ΠΊΡΠΈΠ²Π½ΠΎΡΡΠΈ, Π±Π΅Π·ΠΎΠΏΠ°ΡΠ½ΠΎΡΡΠΈ, ΡΠ²Π΅Π»ΠΈΡΠ΅Π½ΠΈΡ ΡΡΠΎΠΊΠ° ΡΠ»ΡΠΆΠ±Ρ ΠΎΠ±ΠΎΡΡΠ΄ΠΎΠ²Π°Π½ΠΈΡ ΠΈ ΠΏΡΠΈΠ±ΡΠ»ΡΠ½ΠΎΡΡΠΈ.
Maintenance KPI — Π»ΡΡΡΠΈΠΉ KPI Π΄Π»Ρ ΡΡΠΏΠ΅Ρ Π° ΠΎΡΠ΄Π΅Π»Π° ΡΠ΅Ρ Π½ΠΈΡΠ΅ΡΠΊΠΎΠ³ΠΎ ΠΎΠ±ΡΠ»ΡΠΆΠΈΠ²Π°Π½ΠΈΡ
KPI ΡΠ΅Ρ ΠΎΠ±ΡΠ»ΡΠΆΠΈΠ²Π°Π½ΠΈΡ Π½Π°ΠΈΠ±ΠΎΠ»Π΅Π΅ ΡΡΡΠ΅ΠΊΡΠΈΠ²Π½Ρ, ΠΊΠΎΠ³Π΄Π° ΠΎΠ½ΠΈ ΠΎΠΏΡΠ΅Π΄Π΅Π»ΡΡΡ ΠΏΠΎΠ²Π΅Π΄Π΅Π½ΠΈΠ΅ ΠΈ ΠΌΠ΅ΡΠΎΠ΄Ρ, ΠΊΠΎΡΠΎΡΡΠ΅ Π΄Π΅Π»Π°ΡΡ ΡΡΡΠ°Π½ΠΎΠ²ΠΊΠΈ ΠΈ ΠΎΠ±ΠΎΡΡΠ΄ΠΎΠ²Π°Π½ΠΈΠ΅ Π²ΡΡΠΎΠΊΠΎΠ½Π°Π΄Π΅ΠΆΠ½ΡΠΌΠΈ
KPI Π΄Π»Ρ ΠΎΡΠ΄Π΅Π»ΠΎΠ² ΡΠ΅Ρ Π½ΠΈΡΠ΅ΡΠΊΠΎΠ³ΠΎ ΠΎΠ±ΡΠ»ΡΠΆΠΈΠ²Π°Π½ΠΈΡ Π΄Π»Ρ Π΄ΠΎΡΡΠΈΠΆΠ΅Π½ΠΈΡ ΠΌΠ°ΠΊΡΠΈΠΌΠ°Π»ΡΠ½ΠΎΠ³ΠΎ ΡΡΠΏΠ΅Ρ Π° — ΡΡΠΎ ΠΎΠΏΠ΅ΡΠ΅ΠΆΠ°ΡΡΠΈΠ΅ ΠΈΠ½Π΄ΠΈΠΊΠ°ΡΠΎΡΡ.ΠΡΡΡΠ°ΡΡΠΈΠ΅ ΠΈΠ½Π΄ΠΈΠΊΠ°ΡΠΎΡΡ ΠΎΠ±ΡΠ»ΡΠΆΠΈΠ²Π°Π½ΠΈΡ ΠΈΠΌΠ΅ΡΡ Π½ΠΈΠ·ΠΊΡΡ ΡΠ΅Π½Π½ΠΎΡΡΡ ΠΏΠΎ ΡΡΠ°Π²Π½Π΅Π½ΠΈΡ Ρ ΠΈΡΠΏΠΎΠ»ΡΠ·ΠΎΠ²Π°Π½ΠΈΠ΅ΠΌ ΠΎΠΏΠ΅ΡΠ΅ΠΆΠ°ΡΡΠΈΡ ΠΈΠ½Π΄ΠΈΠΊΠ°ΡΠΎΡΠΎΠ² ΠΎΠ±ΡΠ»ΡΠΆΠΈΠ²Π°Π½ΠΈΡ Π² ΠΊΠ°ΡΠ΅ΡΡΠ²Π΅ ΠΊΠ»ΡΡΠ΅Π²ΠΎΠ³ΠΎ ΠΏΠΎΠΊΠ°Π·Π°ΡΠ΅Π»Ρ ΡΡΡΠ΅ΠΊΡΠΈΠ²Π½ΠΎΡΡΠΈ ΠΎΠ±ΡΠ»ΡΠΆΠΈΠ²Π°Π½ΠΈΡ
.KPI ΠΎΠ±ΡΠ»ΡΠΆΠΈΠ²Π°Π½ΠΈΡ Π½Π°ΠΈΠ±ΠΎΠ»Π΅Π΅ ΡΠ΅Π½Π½Ρ, ΠΊΠΎΠ³Π΄Π° ΠΎΠ½ΠΈ Π·Π°ΡΡΠ°Π²Π»ΡΡΡ ΠΎΡΠ³Π°Π½ΠΈΠ·Π°ΡΠΈΡ ΡΠΎΠΊΡΠ°ΡΠ°ΡΡ ΠΏΠΎΡΡΠ΅Π±Π½ΠΎΡΡΡ Π² ΠΎΠ±ΡΠ»ΡΠΆΠΈΠ²Π°Π½ΠΈΠΈ. ΠΠ°Π΄Π°ΡΠ° ΡΠ΅Ρ Π½ΠΈΡΠ΅ΡΠΊΠΎΠ³ΠΎ ΠΎΠ±ΡΠ»ΡΠΆΠΈΠ²Π°Π½ΠΈΡ KPI Π·Π°ΠΊΠ»ΡΡΠ°Π΅ΡΡΡ Π² ΡΡΡΡΠ°Π½Π΅Π½ΠΈΠΈ Π½Π΅ΠΎΠ±Ρ ΠΎΠ΄ΠΈΠΌΠΎΡΡΠΈ Π² ΠΎΠ±ΡΠ»ΡΠΆΠΈΠ²Π°Π½ΠΈΠΈ.
Π‘Π»Π΅Π΄ΡΡΡΠΈΠΉ Π·Π°ΠΏΡΠΎΡ ΠΎ ΠΊΠ»ΡΡΠ΅Π²ΡΡ ΠΏΠΎΠΊΠ°Π·Π°ΡΠ΅Π»ΡΡ ΡΡΡΠ΅ΠΊΡΠΈΠ²Π½ΠΎΡΡΠΈ ΡΠ΅Ρ Π½ΠΈΡΠ΅ΡΠΊΠΎΠ³ΠΎ ΠΎΠ±ΡΠ»ΡΠΆΠΈΠ²Π°Π½ΠΈΡ Π΄Π»Ρ ΠΎΡΠ΄Π΅Π»Π° ΡΠ΅Ρ Π½ΠΈΡΠ΅ΡΠΊΠΎΠ³ΠΎ ΠΎΠ±ΡΠ»ΡΠΆΠΈΠ²Π°Π½ΠΈΡ ΠΏΠΎΡΡΡΠΏΠΈΠ» Π² ΠΊΠΎΠ½ΡΠ΅ Π΄Π΅ΠΊΠ°Π±ΡΡ 2017 Π³ΠΎΠ΄Π°.
Π‘ΠΏΠ°ΡΠΈΠ±ΠΎ Π·Π° Π±Π΅ΡΠΏΠ»Π°ΡΠ½ΡΡ Π·Π°Π³ΡΡΠ·ΠΊΡ ΠΊΠ½ΠΈΠ³ΠΈ ΠΏΠΎ Π·Π΄ΠΎΡΠΎΠ²ΡΡ ΡΠ°ΡΡΠ΅Π½ΠΈΠΉ ΠΈ ΠΎΠ±ΠΎΡΡΠ΄ΠΎΠ²Π°Π½ΠΈΡ; ΠΎΡΠ΅Π½Ρ ΠΈΠ½ΡΠ΅ΡΠ΅ΡΠ½ΠΎΠ΅ ΡΡΠ΅Π½ΠΈΠ΅; ΠΏΡΠΈΠΌΠ΅ΡΠ½ΠΎ Π½Π° ΠΏΠΎΠ»ΠΏΡΡΠΈ.ΠΡΠ΅Π½Ρ Ρ ΠΎΡΠΎΡΠ΅Π΅ ΡΡΠ΅Π½ΠΈΠ΅, ΠΎΡΠΎΠ±Π΅Π½Π½ΠΎ Π² ΠΎΡΠ½ΠΎΡΠ΅Π½ΠΈΠΈ ΡΡΠ°Π½Π΄Π°ΡΡΠΎΠ² ΡΠ΅Ρ Π½ΠΈΡΠ΅ΡΠΊΠΎΠ³ΠΎ ΠΎΠ±ΡΠ»ΡΠΆΠΈΠ²Π°Π½ΠΈΡ ΠΏΠΎ ΡΠΌΠ°Π·ΠΊΠ΅, Π΄Π΅ΡΠΎΡΠΌΠ°ΡΠΈΠΈ ΠΈ Ρ. Π.
Π₯ΠΎΡΠ΅Π»ΠΈ ΡΠΏΡΠΎΡΠΈΡΡ, ΡΡΠΎ Π²Ρ Π΄ΡΠΌΠ°Π΅ΡΠ΅ ΠΎΠ± Π°Π²ΡΠΎΠ½ΠΎΠΌΠ½ΠΎΠΌ ΠΎΠ±ΡΠ»ΡΠΆΠΈΠ²Π°Π½ΠΈΠΈ Π² ΡΠ²ΡΠ·ΠΈ Ρ Π²Π°ΡΠ΅ΠΉ ΠΊΠ½ΠΈΠ³ΠΎΠΉ ΠΎ ΡΠΎΡΡΠΎΡΠ½ΠΈΠΈ Π·Π°Π²ΠΎΠ΄ΠΎΠ² ΠΈ ΠΎΠ±ΠΎΡΡΠ΄ΠΎΠ²Π°Π½ΠΈΡ? Π Π½Π°ΡΡΠΎΡΡΠ΅Π΅ Π²ΡΠ΅ΠΌΡ Ρ Π½Π°ΡΠΈΠ½Π°Ρ ΡΠ°Π±ΠΎΡΡ ΠΏΠΎ Π·Π°ΡΠΈΡΠ΅Π½Π½ΠΎΠΉ ΠΏΠ΅ΡΠ°ΡΠΈ; Π±ΠΎΠ»ΡΡΠ°Ρ ΡΠ°ΡΡΡ ΠΎΠ±ΠΎΡΡΠ΄ΠΎΠ²Π°Π½ΠΈΡ ΠΏΠΎΡΡΡΠΏΠ°Π΅Ρ ΠΈΠ· Π―ΠΏΠΎΠ½ΠΈΠΈ, ΠΏΠΎΡΡΠΎΠΌΡ Π΄ΠΈΠ·Π°ΠΉΠ½-Π°ΡΡ; Π’ΡΠΊ-ΠΊΠΎΠΊΠ΅ΡΠΊΡ ΠΎΡΠ΅Π½Ρ ΡΠ°ΡΡΠΎ ΠΈΡΠΏΠΎΠ»ΡΠ·ΡΡΡ.
Π’Π°ΠΊΠΆΠ΅ Ρ ΠΎΡΠ΅Π» Π±Ρ ΡΠΏΡΠΎΡΠΈΡΡ Π²Π°Ρ, ΡΡΠΎ Π²Ρ ΡΡΠΈΡΠ°Π΅ΡΠ΅ Π½Π°ΠΈΠ±ΠΎΠ»Π΅Π΅ Π²Π°ΠΆΠ½ΡΠΌ KPI Π΄Π»Ρ ΠΎΡΠ΄Π΅Π»Π° ΠΎΠ±ΡΠ»ΡΠΆΠΈΠ²Π°Π½ΠΈΡ, Π½Π°ΠΏΡΠΈΠΌΠ΅Ρ, MTBF; MTTR; ΠΏΠ»Π°Π½ΠΎΠ²ΠΎΠ΅ / Π²Π½Π΅ΠΏΠ»Π°Π½ΠΎΠ²ΠΎΠ΅ ΠΎΠ±ΡΠ»ΡΠΆΠΈΠ²Π°Π½ΠΈΠ΅ ΠΈ Ρ. Π΄.? Π Π²ΡΠΎΡΠΎΠΉ Π²ΠΎΠΏΡΠΎΡ: ΠΊΠ°ΠΊ Π»ΡΡΡΠ΅ Π²ΡΠ΅Π³ΠΎ ΡΠΎΠ±ΡΠ°ΡΡ ΡΡΠΈ Π΄Π°Π½Π½ΡΠ΅?
ΠΠ°ΡΠ°Π½Π΅Π΅ Π±Π»Π°Π³ΠΎΠ΄Π°ΡΠΈΠΌ Π·Π° ΡΠ΄Π΅Π»Π΅Π½Π½ΠΎΠ΅ Π²ΡΠ΅ΠΌΡ.
ΠΡΠΈΠ²Π΅Ρ, ΠΠΎΠ»,
Π Π°Π΄, ΡΡΠΎ Π²Π°ΠΌ ΠΏΠΎΠ½ΡΠ°Π²ΠΈΠ»Π°ΡΡ ΠΊΠ½ΠΈΠ³Π° Β«ΠΠ·Π΄ΠΎΡΠΎΠ²Π»Π΅Π½ΠΈΠ΅ Π·Π°Π²ΠΎΠ΄ΠΎΠ² ΠΈ ΠΎΠ±ΠΎΡΡΠ΄ΠΎΠ²Π°Π½ΠΈΡΒ». ΠΡΠΎΡΠ°Ρ ΠΊΠ½ΠΈΠ³Π°, Industrial and Manufacturing Wellness, ΠΎΠ±ΡΡΡΠ½ΡΠ΅Ρ ΠΏΠΎΠ»Π½ΡΡ ΠΌΠ΅ΡΠΎΠ΄ΠΎΠ»ΠΎΠ³ΠΈΡ ΠΆΠΈΠ·Π½Π΅Π½Π½ΠΎΠ³ΠΎ ΡΠΈΠΊΠ»Π° Plant Wellness Way EAM. ΠΠ΅ΡΠ²Π°Ρ ΠΊΠ½ΠΈΠ³Π°, Β«Plant and Equipment WellnessΒ», ΠΎΡ Π²Π°ΡΡΠ²Π°Π΅Ρ ΠΎΡΠ½ΠΎΠ²Π½ΡΠ΅ ΠΊΠΎΠ½ΡΠ΅ΠΏΡΠΈΠΈ Β«Plant Wellness WayΒ».
ΠΠ²ΡΠΎΠ½ΠΎΠΌΠ½ΠΎΠ΅ ΠΎΠ±ΡΠ»ΡΠΆΠΈΠ²Π°Π½ΠΈΠ΅ ΡΠ΅Π½Π½ΠΎ ΠΏΡΠΈ ΡΡΠ»ΠΎΠ²ΠΈΠΈ, ΡΡΠΎ ΠΎΠΏΠ΅ΡΠ°ΡΠΎΡ ΠΏΠΎΠ½ΠΈΠΌΠ°Π΅Ρ ΡΠ°Π±ΠΎΡΡ ΠΎΠ±ΠΎΡΡΠ΄ΠΎΠ²Π°Π½ΠΈΡ; ΠΏΠΎΠ»Π½ΠΎΡΡΡΡ ΠΊΠΎΠΌΠΏΠ΅ΡΠ΅Π½ΡΠ΅Π½ Π² Π·Π°Π΄Π°ΡΠ°Ρ ΠΎΠ±ΡΠ»ΡΠΆΠΈΠ²Π°Π½ΠΈΡ ΠΎΠ±ΠΎΡΡΠ΄ΠΎΠ²Π°Π½ΠΈΡ; ΠΈ Π²Π»Π°Π΄Π΅Π΅Ρ Π²ΡΠ΅ΠΌΠΈ Π½Π΅ΠΎΠ±Ρ ΠΎΠ΄ΠΈΠΌΡΠΌΠΈ ΠΈΠ½ΡΡΡΡΠΌΠ΅Π½ΡΠ°ΠΌΠΈ.(ΠΠΎΠΌΠΏΠ΅ΡΠ΅Π½ΡΠ½ΡΠΉ = ΠΎΠ±ΡΡΠ΅Π½Π½ΡΠΉ + ΠΊΠ²Π°Π»ΠΈΡΠΈΡΠΈΡΠΎΠ²Π°Π½Π½ΡΠΉ + ΠΎΠΏΡΡΠ½ΡΠΉ + Π·Π½Π°ΡΡΠΈΠΉ, ΡΡΠΎΠ±Ρ ΡΠ΅ΡΠ°ΡΡ ΠΏΡΠΎΠ±Π»Π΅ΠΌΡ, Π²ΠΎΠ·Π²ΡΠ°ΡΠ°ΡΡΡ ΠΊ ΡΡΠ΅Π±ΠΎΠ²Π°Π½ΠΈΡΠΌ ΠΏΡΠΎΠ΅ΠΊΡΠ° ΠΈΡΠΏΡΠ°Π²Π»Π΅Π½ΠΈΡ) Π ΠΏΡΠΎΡΠΈΠ²Π½ΠΎΠΌ ΡΠ»ΡΡΠ°Π΅ Π²Π°ΠΌ ΠΏΠΎΠ½Π°Π΄ΠΎΠ±ΠΈΡΡΡ ΠΊΠΎΠΌΠ°Π½Π΄Π° Π»ΡΠ΄Π΅ΠΉ, ΠΊΠΎΡΠΎΡΡΠ΅ Π² ΡΠΎΠ²ΠΎΠΊΡΠΏΠ½ΠΎΡΡΠΈ ΠΎΠ±Π΅ΡΠΏΠ΅ΡΠΈΠ²Π°ΡΡ ΠΊΠΎΠΌΠΏΠ΅ΡΠ΅Π½ΡΠ½ΠΎΠ΅ ΠΎΠ±ΡΠ»ΡΠΆΠΈΠ²Π°Π½ΠΈΠ΅.
ΠΡΠΎΠ΅ΠΊΡΠΈΡΠΎΠ²Π°Π½ΠΈΠ΅ ΠΈ Π·Π°ΡΠΈΡΠ° ΠΎΡ ΠΎΡΠΈΠ±ΠΎΠΊ Π½Π΅ ΠΎΠ·Π½Π°ΡΠ°Π΅Ρ, ΡΡΠΎ Π΄Π΅ΡΠ°Π»ΠΈ ΠΎΠ±ΠΎΡΡΠ΄ΠΎΠ²Π°Π½ΠΈΡ Π½Π΅ Π²ΡΠΉΠ΄ΡΡ ΠΈΠ· ΡΡΡΠΎΡ. Π― Ρ ΠΎΡΠ΅Π» Π±Ρ ΡΠ²ΠΈΠ΄Π΅ΡΡ ΡΡΠΊΠΎΠ²ΠΎΠ΄ΡΡΠ²Π° ΠΏΠΎ ΡΠΊΡΠΏΠ»ΡΠ°ΡΠ°ΡΠΈΠΈ ΠΈ ΡΠ΅Ρ Π½ΠΈΡΠ΅ΡΠΊΠΎΠΌΡ ΠΎΠ±ΡΠ»ΡΠΆΠΈΠ²Π°Π½ΠΈΡ ΠΎΡ ΠΏΡΠΎΠΈΠ·Π²ΠΎΠ΄ΠΈΡΠ΅Π»Π΅ΠΉ ΠΊΠΎΠΌΠΏΠ»Π΅ΠΊΡΠ½ΠΎΠ³ΠΎ ΠΎΠ±ΠΎΡΡΠ΄ΠΎΠ²Π°Π½ΠΈΡ, ΡΡΠΎΠ±Ρ ΡΠ·Π½Π°ΡΡ, ΠΊΠ°ΠΊΠΎΠ²Ρ ΠΈΡ ΡΠ΅ΠΊΠΎΠΌΠ΅Π½Π΄Π°ΡΠΈΠΈ ΠΏΠΎ ΡΠ΅Ρ Π½ΠΈΡΠ΅ΡΠΊΠΎΠΌΡ ΠΎΠ±ΡΠ»ΡΠΆΠΈΠ²Π°Π½ΠΈΡ.
ΠΠ°Ρ ΡΠΏΠΈΡΠΎΠΊ ΠΏΡΠΈΠΌΠ΅ΡΠΎΠ² KPI ΠΎΠ±ΡΠ»ΡΠΆΠΈΠ²Π°Π½ΠΈΡ ΠΏΡΠ΅Π΄ΡΡΠ°Π²Π»ΡΠ΅Ρ ΡΠΎΠ±ΠΎΠΉ Π·Π°ΠΏΠ°Π·Π΄ΡΠ²Π°ΡΡΠΈΠ΅ ΠΈΠ½Π΄ΠΈΠΊΠ°ΡΠΎΡΡ, ΡΡΠΎ ΠΎΠ·Π½Π°ΡΠ°Π΅Ρ, ΡΡΠΎ Π²Ρ ΠΈΠ·ΠΌΠ΅ΡΡΠ΅ΡΠ΅ ΡΠ²ΠΎΡ Π½Π°Π΄Π΅ΠΆΠ½ΠΎΡΡΡ ΠΈ ΠΏΡΠΎΠ±Π»Π΅ΠΌΡ Ρ ΠΎΠ±ΡΠ»ΡΠΆΠΈΠ²Π°Π½ΠΈΠ΅ΠΌ, ΡΡΠΎΠ±Ρ ΠΏΠΎΠ»ΡΡΠΈΡΡ ΠΈΡΡΠΎΡΠΈΡΠ΅ΡΠΊΡΡ ΠΈΠ½ΡΠΎΡΠΌΠ°ΡΠΈΡ, ΠΊΠΎΡΠΎΡΠ°Ρ ΡΠΎΠΎΠ±ΡΠΈΡ Π²Π°ΠΌ, ΡΡΠΎ Ρ Π²Π°Ρ Π±ΡΠ»ΠΈ ΠΏΡΠΎΠ±Π»Π΅ΠΌΡ Ρ Π½Π°Π΄Π΅ΠΆΠ½ΠΎΡΡΡΡ ΠΈ ΠΎΠ±ΡΠ»ΡΠΆΠΈΠ²Π°Π½ΠΈΠ΅ΠΌ.ΠΠ°ΠΊΠΎΠΉ Π±Π΅Π·ΡΠΌΠ½ΡΠΉ ΡΠΏΠΎΡΠΎΠ± Π²Π΅ΡΡΠΈ Π±ΠΈΠ·Π½Π΅Ρ! ΠΡΠ»ΠΈ Π²Π°ΠΌ Π½ΡΠΆΠ½Π° Π½Π΅ΠΏΡΠ΅Π²Π·ΠΎΠΉΠ΄Π΅Π½Π½Π°Ρ Π½Π°Π΄Π΅ΠΆΠ½ΠΎΡΡΡ ΡΡΡΠ°Π½ΠΎΠ²ΠΎΠΊ ΠΈ ΠΎΠ±ΠΎΡΡΠ΄ΠΎΠ²Π°Π½ΠΈΡ, Π²Π°ΠΌ Π½Π΅ΠΎΠ±Ρ ΠΎΠ΄ΠΈΠΌΠΎ ΠΏΡΠΎΡΠ²Π»ΡΡΡ ΠΈΠ½ΠΈΡΠΈΠ°ΡΠΈΠ²Ρ, ΡΡΠΎΠ±Ρ ΡΠ±Π΅Π΄ΠΈΡΡΡΡ, ΡΡΠΎ ΡΡΠΈΠ»ΠΈΡ Π²ΡΠ΅Ρ ΡΠΎΡΡΡΠ΄Π½ΠΈΠΊΠΎΠ² Π² ΡΠ°ΠΌΠΊΠ°Ρ Π²ΡΠ΅ΠΉ ΠΎΡΠ³Π°Π½ΠΈΠ·Π°ΡΠΈΠΈ ΠΈ Π΅Π΅ ΠΆΠΈΠ·Π½Π΅Π½Π½ΠΎΠ³ΠΎ ΡΠΈΠΊΠ»Π° ΡΠΎΠ·Π΄Π°ΡΡ Π½Π°Π΄Π΅ΠΆΠ½ΠΎΡΡΡ ΠΎΠΏΠ΅ΡΠ°ΡΠΈΠΎΠ½Π½ΡΡ Π°ΠΊΡΠΈΠ²ΠΎΠ² ΠΌΠΈΡΠΎΠ²ΠΎΠ³ΠΎ ΠΊΠ»Π°ΡΡΠ°.
ΠΠΎΠΊΠ°Π·Π°ΡΠ΅Π»ΠΈ Π½Π°Π΄Π΅ΠΆΠ½ΠΎΡΡΠΈ ΠΌΠΈΡΠΎΠ²ΠΎΠ³ΠΎ ΠΊΠ»Π°ΡΡΠ° ΡΡΠ΅Π±ΡΡΡ ΠΈΡΠΏΠΎΠ»ΡΠ·ΠΎΠ²Π°Π½ΠΈΡ ΠΎΠΏΠ΅ΡΠ΅ΠΆΠ°ΡΡΠΈΡ ΠΈΠ½Π΄ΠΈΠΊΠ°ΡΠΎΡΠΎΠ² Π΄Π»Ρ ΠΎΠ±ΡΠ»ΡΠΆΠΈΠ²Π°Π½ΠΈΡ KPI. ΠΡ Ρ ΠΎΡΠΈΡΠ΅, ΡΡΠΎΠ±Ρ KPI Π΄Π»Ρ ΠΎΡΠ΄Π΅Π»Π° ΠΎΠ±ΡΠ»ΡΠΆΠΈΠ²Π°Π½ΠΈΡ ΡΠΏΡΠ°Π²Π»ΡΠ» Π΄Π΅ΠΉΡΡΠ²ΠΈΡΠΌΠΈ ΠΈ ΠΏΠΎΠ²Π΅Π΄Π΅Π½ΠΈΠ΅ΠΌ, ΠΊΠΎΡΠΎΡΡΠ΅ ΡΠ½ΠΈΠΆΠ°ΡΡ ΠΏΠΎΡΡΠ΅Π±Π½ΠΎΡΡΡ Π² ΠΎΠ±ΡΠ»ΡΠΆΠΈΠ²Π°Π½ΠΈΠΈ. Π ΡΡΠΎΠΌ ΠΈΡΡΠΈΠ½Π½Π°Ρ Π±ΠΈΠ·Π½Π΅Ρ-ΡΠ΅Π»Ρ ΠΈ ΡΠ΅Π½Π½ΠΎΡΡΡ Π°Π²ΡΠΎΠ½ΠΎΠΌΠ½ΠΎΠ³ΠΎ ΠΎΠ±ΡΠ»ΡΠΆΠΈΠ²Π°Π½ΠΈΡ — ΠΎΠΏΠ΅ΡΠ΅ΠΆΠ°ΡΡ ΠΏΡΠΎΠ±Π»Π΅ΠΌΡ Π½Π°Π΄Π΅ΠΆΠ½ΠΎΡΡΠΈ ΠΈ ΠΏΡΠΎΠΈΠ·Π²ΠΎΠ΄ΡΡΠ²Π°, ΡΡΠΎΠ±Ρ ΠΎΠ½ΠΈ Π½Π΅ ΠΏΠ΅ΡΠ΅ΡΠ°ΡΡΠ°Π»ΠΈ Π² Π±ΠΎΠ»ΡΡΠΈΠ΅ Π·Π°ΡΡΠ°ΡΡ Π½Π° ΠΎΠ±ΡΠ»ΡΠΆΠΈΠ²Π°Π½ΠΈΠ΅.
ΠΠ΅Π΄ΡΡΠΈΠ΅ ΠΊΠ»ΡΡΠ΅Π²ΡΠ΅ ΠΏΠΎΠΊΠ°Π·Π°ΡΠ΅Π»ΠΈ ΡΡΡΠ΅ΠΊΡΠΈΠ²Π½ΠΎΡΡΠΈ ΡΠ΅Ρ Π½ΠΈΡΠ΅ΡΠΊΠΎΠ³ΠΎ ΠΎΠ±ΡΠ»ΡΠΆΠΈΠ²Π°Π½ΠΈΡ ΠΎΠΏΡΠ΅Π΄Π΅Π»ΡΡΡ, ΠΏΡΠ°Π²ΠΈΠ»ΡΠ½ΠΎ Π»ΠΈ Π²Ρ Π΄Π΅Π»Π°Π΅ΡΠ΅ Π² ΠΏΡΠΎΠΈΠ·Π²ΠΎΠ΄ΡΡΠ²Π΅, ΠΏΡΠΎΠ΅ΠΊΡΠΈΡΠΎΠ²Π°Π½ΠΈΠΈ, ΡΠ΅ΠΏΠΎΡΠΊΠ΅ ΠΏΠΎΡΡΠ°Π²ΠΎΠΊ ΠΈ ΠΎΠ±ΡΠ»ΡΠΆΠΈΠ²Π°Π½ΠΈΠΈ, ΡΡΠΎ ΠΎΠ±Π΅ΡΠΏΠ΅ΡΠΈΠ²Π°Π΅Ρ Π½Π°Π΄Π΅ΠΆΠ½ΠΎΡΡΡ ΠΌΠΈΡΠΎΠ²ΠΎΠ³ΠΎ ΠΊΠ»Π°ΡΡΠ° Π²ΠΎ Π²ΡΠ΅ΠΌΡ ΡΠ°Π±ΠΎΡΡ ΠΎΠ±ΠΎΡΡΠ΄ΠΎΠ²Π°Π½ΠΈΡ.
ΠΡ ΡΠ°Π±ΠΎΡΠ°Π΅ΡΠ΅ Π² ΡΠ΅Ρ Π΅ Π·Π°ΡΠΈΡΠ΅Π½Π½ΠΎΠΉ ΠΏΠ΅ΡΠ°ΡΠΈ, Π³Π΄Π΅ Π΄Π»Ρ ΠΈΠ·Π³ΠΎΡΠΎΠ²Π»Π΅Π½ΠΈΡ Π²Π°ΡΠ΅ΠΉ ΠΏΡΠΎΠ΄ΡΠΊΡΠΈΠΈ ΠΈΡΠΏΠΎΠ»ΡΠ·ΡΡΡΡΡ ΠΌΠ°ΡΠΈΠ½Ρ ΠΈ ΠΎΠ±ΠΎΡΡΠ΄ΠΎΠ²Π°Π½ΠΈΠ΅. ΠΡΠΈ ΡΠ»Π΅ΠΌΠ΅Π½ΡΡ ΡΡΡΠ°Π½ΠΎΠ²ΠΊΠΈ Π΄ΠΎΠ»ΠΆΠ½Ρ Π±ΡΡΡ ΠΎΡΠ΅Π½Ρ Π½Π°Π΄Π΅ΠΆΠ½ΡΠΌΠΈ, Π΅ΡΠ»ΠΈ Π²Ρ Ρ ΠΎΡΠΈΡΠ΅ ΠΌΠΈΠ½ΠΈΠΌΠΈΠ·ΠΈΡΠΎΠ²Π°ΡΡ ΡΠ²ΠΎΠΈ ΡΠΊΡΠΏΠ»ΡΠ°ΡΠ°ΡΠΈΠΎΠ½Π½ΡΠ΅ ΡΠ°ΡΡ ΠΎΠ΄Ρ ΠΈ Π·Π°ΡΡΠ°ΡΡ Π½Π° ΡΠ΅Ρ Π½ΠΈΡΠ΅ΡΠΊΠΎΠ΅ ΠΎΠ±ΡΠ»ΡΠΆΠΈΠ²Π°Π½ΠΈΠ΅. ΠΡΠΈΠΌΠ΅Π½ΡΠ΅ΠΌΡΠ΅ ΠΎΠΏΠ΅ΡΠ΅ΠΆΠ°ΡΡΠΈΠ΅ ΠΈΠ½Π΄ΠΈΠΊΠ°ΡΠΎΡΡ Π±ΡΠ΄ΡΡ ΠΎΠΏΡΠ΅Π΄Π΅Π»ΡΡΡ, ΡΠΏΠΎΡΠΎΠ±ΡΡΠ²ΡΠ΅Ρ Π»ΠΈ Π²Π°ΡΠ° ΠΎΠΏΠ΅ΡΠ°ΡΠΈΡ ΡΠΏΡΠ΅ΠΆΠ΄Π°ΡΡΠ΅ΠΌΡ ΠΏΠΎΠ²ΡΡΠ΅Π½ΠΈΡ Π½Π°Π΄Π΅ΠΆΠ½ΠΎΡΡΠΈ ΠΎΠ±ΠΎΡΡΠ΄ΠΎΠ²Π°Π½ΠΈΡ ΠΈ ΠΌΠΈΠ½ΠΈΠΌΠΈΠ·Π°ΡΠΈΠΈ Π·Π°ΡΡΠ°Ρ Π½Π° ΡΠ΅Ρ Π½ΠΈΡΠ΅ΡΠΊΠΎΠ΅ ΠΎΠ±ΡΠ»ΡΠΆΠΈΠ²Π°Π½ΠΈΠ΅.
ΠΡ Π²ΠΊΠ»ΡΡΠ°Π΅ΡΠ΅ ΡΠ±ΠΎΡ Π΄Π°Π½Π½ΡΡ Π΄Π»Ρ ΠΎΠΏΠ΅ΡΠ΅ΠΆΠ°ΡΡΠΈΡ ΠΈΠ½Π΄ΠΈΠΊΠ°ΡΠΎΡΠΎΠ² Π² ΠΏΡΠΎΡΠ΅Π΄ΡΡΡ, ΠΊΠΎΡΠΎΡΡΠ΅ Π²ΡΠΏΠΎΠ»Π½ΡΡΡ Π²Π°ΡΠΈ ΠΎΠΏΠ΅ΡΠ°ΡΠΎΡΡ ΠΈ ΠΎΠ±ΡΠ»ΡΠΆΠΈΠ²Π°ΡΡΠΈΠΉ ΠΏΠ΅ΡΡΠΎΠ½Π°Π», ΠΊΠΎΠ³Π΄Π° ΠΎΠ½ΠΈ Π²ΡΠΏΠΎΠ»Π½ΡΡΡ ΡΠ²ΠΎΡ ΡΠ°Π±ΠΎΡΡ.
ΠΠΎΡ ΡΠ΅ΠΊΠΎΠΌΠ΅Π½Π΄Π°ΡΠΈΡ ΠΏΡΠΈ ΡΠ°Π·ΡΠ°Π±ΠΎΡΠΊΠ΅ Π²Π΅Π΄ΡΡΠΈΡ KPI ΠΎΠ±ΡΠ»ΡΠΆΠΈΠ²Π°Π½ΠΈΡ ΡΠΎΡΡΠΎΠΈΡ Π² ΡΠΎΠΌ, ΡΡΠΎΠ±Ρ ΠΎΡΡΠ»Π΅ΠΆΠΈΠ²Π°ΡΡ ΠΈ ΠΈΠ·ΠΌΠ΅ΡΡΡΡ, ΡΡΠΎ Π²Π°ΡΠ° ΠΎΡΠ³Π°Π½ΠΈΠ·Π°ΡΠΈΡ ΠΏΡΠΎΠ°ΠΊΡΠΈΠ²Π½ΠΎ Π²ΡΠΏΠΎΠ»Π½ΡΠ΅Ρ Π²Π΅ΡΡ ΡΠΏΠΈΡΠΎΠΊ ΡΡΠ΅Π±ΠΎΠ²Π°Π½ΠΈΠΉ ΠΊ ΡΠΎΡΠ½ΠΎΠΌΡ ΠΎΠ±ΡΠ»ΡΠΆΠΈΠ²Π°Π½ΠΈΡ, ΡΠΊΠ°Π·Π°Π½Π½ΡΡ Π½Π° ΠΈΠ·ΠΎΠ±ΡΠ°ΠΆΠ΅Π½ΠΈΠΈ Π½ΠΈΠΆΠ΅.
ΠΡ ΠΌΠΎΠΆΠ΅ΡΠ΅ ΡΠ·Π½Π°ΡΡ Π±ΠΎΠ»ΡΡΠ΅ ΠΎ ΠΏΡΠ΅ΡΠΈΠ·ΠΈΠΎΠ½Π½ΠΎΠΌ ΠΎΠ±ΡΠ»ΡΠΆΠΈΠ²Π°Π½ΠΈΠΈ, ΡΠ΅Π»ΠΊΠ½ΡΠ² ΠΏΠΎ ΡΡΠΈΠΌ ΡΡΡΠ»ΠΊΠ°ΠΌ Π½Π° Π²Π΅Π±-ΡΡΡΠ°Π½ΠΈΡΡ Β«ΠΠ±ΡΡΡΠ½Π΅Π½ΠΈΠ΅ ΡΠΎΡΠ½ΠΎΠ³ΠΎ ΠΎΠ±ΡΠ»ΡΠΆΠΈΠ²Π°Π½ΠΈΡΒ» ΠΈ Π² PDF-Π΄ΠΎΠΊΡΠΌΠ΅Π½ΡΠ΅ ΠΡΠΏΠΎΠ»ΡΠ·ΠΎΠ²Π°Π½ΠΈΠ΅ ΠΈ Π²Π²Π΅Π΄Π΅Π½ΠΈΠ΅ Π² ΠΏΡΠ΅ΡΠΈΠ·ΠΈΠΎΠ½Π½ΠΎΠ΅ ΠΎΠ±ΡΠ»ΡΠΆΠΈΠ²Π°Π½ΠΈΠ΅
ΠΡΠ΅Π³ΠΎ Π½Π°ΠΈΠ»ΡΡΡΠ΅Π³ΠΎ,
ΠΠ°ΠΉΠΊ Π‘ΠΎΠ½Π΄Π°Π»ΠΈΠ½ΠΈ
Π Π΅ΡΠ΅Π½ΠΈΡ Π΄Π»Ρ ΠΎΠ±Π΅ΡΠΏΠ΅ΡΠ΅Π½ΠΈΡ Π½Π°Π΄Π΅ΠΆΠ½ΠΎΡΡΠΈ Π½Π° ΠΏΡΠΎΡΡΠΆΠ΅Π½ΠΈΠΈ Π²ΡΠ΅Π³ΠΎ ΡΡΠΎΠΊΠ° ΡΠ»ΡΠΆΠ±Ρ