Основные методы изготовления деталей из карбона
Качество деталей из карбона в первую очередь зависит от правильного выбора и качества смолы и углеродного полотна. При ошибках в выборе плотности полотна карбона и смолы для карбона вы не сможете аккуратно выложить заготовку в форме, плотно прижать и полностью удалить пузырьки воздуха.
Содержание
Основные методы изготовления деталей из карбонаК основным методам изготовления можно отнести:
- формование из препрегов, то есть полуфабрикатов,
- метод аппликации,
- формование непосредственно в форме с вакуумом,
- формование давлением (ручная прикатка).
Изготовление карбона дома не требует сложного оборудования, и при определенных навыках можно получить детали достойного качества. Поэтому сделать углепластик удовлетворительного качества самому вполне реально.
Карбон для автотюнингаВнимание! Так называемый 3D-карбон, автовинил или пленка «под карбон» никакого отношения к карбону не имеет, кроме отличной имитации поверхности карбона.
Это разноцветные виниловые и ПВХ-пленки с визуальными эффектами только для декоративной отделки поверхности, но не для упрочнения.
А вот для изготовления некоторых облегченных элементов, где требуется высокая прочность, например, для бамперов, капотов, мелких деталей кузова, может использоваться дорогостоящий настоящий карбон. Можно попробовать даже сделать обтяжку карбоном своими руками некрупных элементов.Но необходимо помнить, что этот материал очень чувствителен к точечным ударам и есть риск повреждения мелкими камнями и щебнем из-под колес.
И здесь определяющую роль играет мастерство автомастера, насколько совершенно он владеет навыками подбора полотна, смолы и толщины слоев. А ремонт карбоновых деталей — тоже дорогостоящий процесс.
Если же для вас главную роль играют эстетические параметры, а не облегчение веса автомобиля или мотоцикла, то присмотритесь к ПВХ-пленкам «под карбон», аква-печати или аэрографии.
Изготовление деталей из карбона методом препреговПромышленный процесс формования изделия из препрега (заготовок для формования) в автоклаве представляет собой одновременное протекание сложных процессов:
- полимеризацию компаунда,
- вакуумное удаление воздуха и излишков смолы,
- высокое давление ( до 20 атм) прижимает все слои к матрице, уплотняя и выравнивая их.
Это дорогостоящий процесс, поэтому для мелкосерийного тюнинга в домашних условиях малопригодный.
Но разделение этих процессов удешевляет и удлиняет всю процедуру самостоятельного получения карбона. Изменения при этом вносятся в технологию подготовки препрега, поэтому всегда нужно обращать внимание, для какой технологии предназначена заготовка.
В этом случае препрег готовится в виде сэндвича. После нанесения смолы заготовка с обеих сторон покрывается полиэтиленовой пленкой и пропускается между двух валов. При этом лишняя смола и нежелательный воздух удаляются.
Препрег вдавливается в матрицу пуансоном, и вся конструкция помещается в термошкаф. То есть в данном случае препрег представляет полностью готовую к формованию заготовку, с обжатыми слоями и удаленным воздухом.
Этот метод чаще всего и используют автомастерские, покупая заготовки карбона, а матрицы изготавливаются из алебастра или гипса, иногда вытачиваются из металла или в качестве модели используется сама деталь.
Углепластик своими руками проще всего сделать методом «обтяжки» или аппликации углеполотна на заготовку.
Метод аппликации (ручная оклейка)Сделать карбон своими руками можно методом оклейки, который включает пять основных этапов:
- Тщательная подготовка оклеиваемой поверхности: зашкуривание, обезжиривание, скругление углов.
- Нанесение адгезива.
- Приклеивание углеткани с пропитыванием эпоксидной смолой с отвердителем.
- Сушка.
- Покрытие защитным лаком или краской.
Наполнители для смолы используют как для придания декоративности, так и для предотвращения стекания смолы с вертикальных поверхностей.
Необходимые материалы
- Адгезив для фиксации углеткани на поверхности.
- Ткань из углеволокна, которую укладывают на смолу послойно, с прикатыванием твердым валиком.
- Эпоксидная смола средней вязкости с отвердителем (иногда она используется в качестве адгезива).
- Защитный лак. Лучше всего для защиты от царапин подходит полиуретановый. Нужно выбирать водостойкий и светостойкий. Он не помутнеет. Для высокого блеска в качестве финишного покрытия можно использовать акриловый лак.
Смолу наносят 2-3 раза с промежуточной сушкой и шлифовкой.
Этот метод отличается от традиционного изготовления карбоновых изделий по моделям нанесением адгезива, а не разделителя для легкого съема получившегося полуфабриката.
Компания 3М предлагает даже самоклеющееся углеполотно, но работа с ним требует хороших навыков.
И карбон остается на оклеиваемой детали, упрочняя ее. Такое производство карбона чаще всего используется для оклеивания бампера, приборной панели и пр.
Метод формования карбона в форме с вакуумомДля этого метода требуется специальное оборудование и хорошие навыки.
- Нанесение разделительного состава на поверхность модели.
Для матовых и полуглянцевых поверхностей обычно применяется разделительный воск, а для глянцевых поверхностей(пластик и металл) — разделитель типа WOLO и растворы для грунтования, которые используются при мелкосерийном призводстве.
- Выкладывание углеткани в матрицу, без морщин и пузырей.
- Пропитка углеткани смолой.
- Слоев может быть несколько. В некоторых случаях углеткань можно чередовать со стеклотканью.
- Наложение перфорированной пленки для отжима излишков смолы и выхода воздуха. Желательно укладывать внахлест.
- Прокладка впитывающего слоя.
- Установка вакуумной трубки и порта для подключения вакуумного насоса.
- Помещение всей конструкции в прочную вакуумную пленку, приклеивание герметизирующим жгутом к оснастке.
Вся процедура напоминает помещение какого-либо предмета в вакуумный пакет, которые продаются в магазинах для хранения вещей, с последующей откачкой из него воздуха. Можно поэкспериментировать с такими вакуумными пакетами. Они очень прочные и продаются разных размеров. А вакуумный насос для домашнего использования обойдется в среднем в 150-200$.
Еще один вариант вакуумной технологии — процесс формования включает в себя наложение слоев углеродного волокна на пресс-форму, упаковывание в мешки всей сборки и удаление лишнего воздуха с помощью вакуумной системы. Смоляная смесь затем подается с одного конца и затем всасывается в пакетированный узел под действием вакуума внутри. После периода охлаждения формованная деталь отделяется от пресс-формы, а избыток материала обрезается.
Метод формования карбона с помощью давления (ручная прикатка) Применяется для самостоятельного изготовления деталей из карбона и аналогичен методу формования вакуумом, но без использования дорогостоящей оснастки. Наборы включают кисти для нанесения смолы и валики для выдавливания воздуха и прикатки слоев.Для простого тюнинга автомобиля понадобятся:
- углеполотно плотностью 200-300 г/м,
- эпоксидная смола,
- отвердитель,
- жесткий валик и кисть.
На Alibaba.com углеполотно плотностью 200 г/м.кв. плетения twill предлагается по цене от 10 до 25 долларов за квадратный метр. Правда, и покупать нужно от 10 метров. Но можно договориться о получении образцов, которые позволят самостоятельно изготовить небольшие изделия из карбона.
В общих чертах процесс изготовления углепластика своими руками выглядит так:
- На поверхность формы наносится разделительный воск, гелькоат для формирования защитно-декоративного слоя на поверхности готового изделия.
- После его высыхания наносится тонкий слой смолы, на который прикатывается или прижимается углеткань, для выхода пузырьков воздуха.
- Затем наносится еще один слой смолы для пропитки. Можно нанести несколько слоев ткани и смолы, в зависимости от требуемых параметров изделия.
- Смола может полимеризироваться на воздухе. Это происходит обычно в течение 5 дней. Можно поместить заготовку в термошкаф, нагретый до температуры 140 – 180 ◦С, что значительно ускорит процесс полимеризации.
Затем изделие извлекаем из формы, шлифуем, полируем, покрываем лаком, гелькоутом или красим.
Каждый слой прокатывается валиком для удаления пузырьков воздуха и получения максимального сцепления.
При таком методе получается высокий расход смолы (в три раза выше плотности углеполотна), но зато именно таким способом можно изготовить любую деталь из карбона своими руками.
Автор Ирина Химич
Технология производства современного композитного материала – карбон.
Главная Полезно знать
Современные технологии требуют появления все новых и новых композитных материалов со специальными свойствами, находя им широкое применение в различной продукции. Одним из таких композитный материалов является – карбон.
Уникальные свойства карбона позволяют использовать его для производства и тюнинга различных транспортных средств, яхт и морских судов, в авиастроении и космической техники.
Свое рождение карбон начал с исследований Эдисона, именно он в 1880 году ведя поиск материала для спирали лампы накаливания исследовал уклеволокно являющееся основой карбона. Слабое развитие технического прогресса в то время не дало возможности полностью раскрыть свойства нового материала и найти ему достойное применение. Только выход человечества в космос и использование карбонового углеволокна при строительстве космических кораблей NASA раскрыло перед карбоном все двери.
Особенностью углепластика является разнонаправленность физических свойств поэтому для получения однородного композитного материала армирующие волокна переплетают, образуя специальную сетку именно она и придает привлекательный вид карбону.
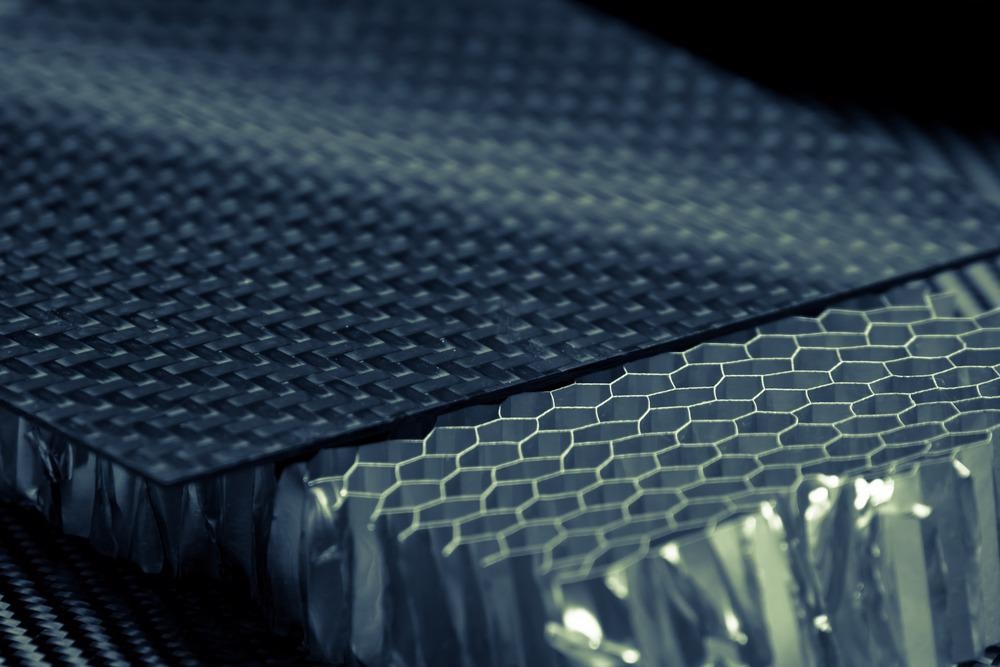
Технология получения непосредственно самих нитей углеволокна довольно сложна, можно получить органические волокна углепластика используя автоклав высокого давления методом химической осадкой углерода или выращивать кристаллы нити углепластика в световой дуге. Современный автоклав промышленный более производителен и метод автоклавного формирования углеволокна более технологичен.
В качестве исходного материала для получения нитей углеволокна берут волокна полиакрилонитрила, их окисляют при температуре 250°C в течение 24 часов в воздушной среде. Далее волокна помещают в автоклав горизонтальный с рабочим объемом, заполненным инертным газом, автоклав электрический
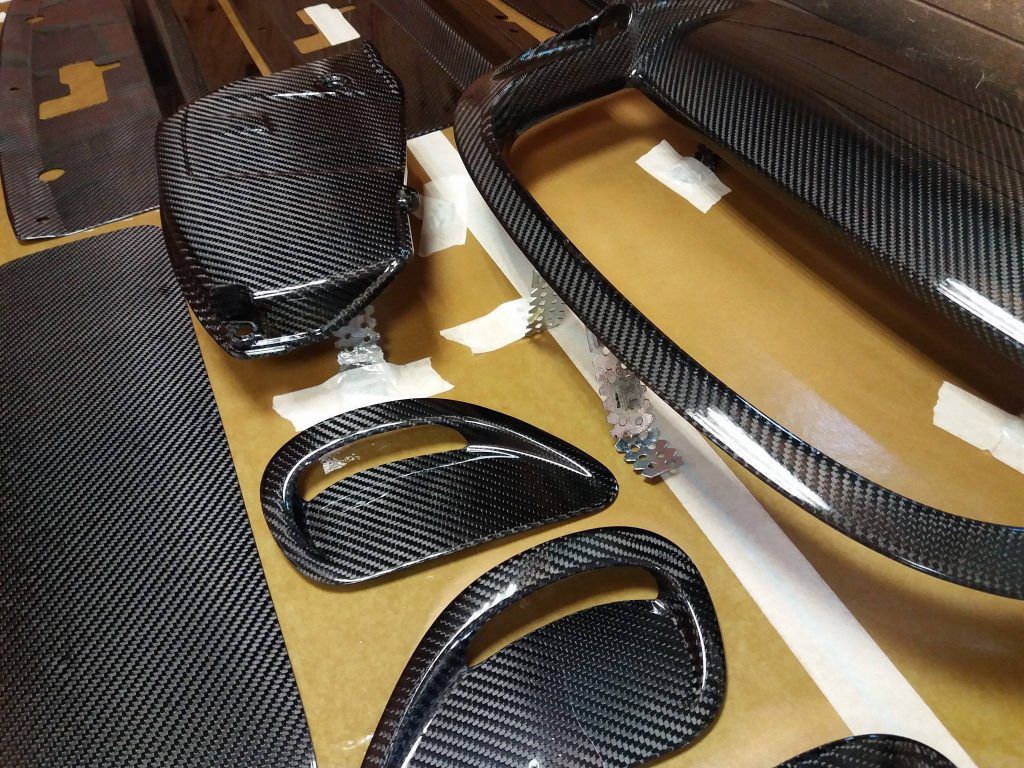
Собрать армирующие нити в готовое карбоновое полотно можно двумя способами сухим и мокрым
Мокрый способ WET — наиболее распространен. Сетка из армирующих волокон укладывается в специальную форму, пропитывается связывающим элементом — эпоксидными смолами. Современный автоклав высокого давления производит автоклавирование при давлении выше 10 атм производя отверждение материала и горячую полимеризацию при температурке150 °C.
При сухом способе DRY автоклав для карбона использует еще более высокое давление до 32 атм, подача вакуума в рабочую зону при температуре 200°С позволяет получить очень тонкий слой карбона около 0,5 мм и гарантирует высокую точность изделий.

Высокие давления требуют использовать наиболее надежное устройство автоклав с байонетным затвором, таким же высоким уровнем надежности отличается и автоклав для триплекса.
Сегодня карбон можно производить, используя автоклав Российского производства.
Как производить детали из углеродного волокна
Композитные материалы, такие как пластмассы, армированные углеродным волокном, являются универсальными и эффективными материалами, стимулирующими инновации на различных рынках от аэрокосмической промышленности до здравоохранения. Они превосходят традиционные материалы, такие как сталь, алюминий, дерево или пластик, и позволяют производить высокопроизводительные легкие изделия.
В этом руководстве изучите основы производства деталей из углеродного волокна, включая различные методы укладки, ламинирования и формования углеродного волокна, а также способы использования 3D-печати для изготовления форм из углеродного волокна для снижения затрат и экономии времени.
Информационный документ
Загрузите этот технический документ, содержащий рекомендации по проектированию пресс-форм для композитов и пошаговые руководства по методам препрега и ручного ламинирования для создания деталей из углеродного волокна.
Загрузить информационный документ
Композитный материал представляет собой комбинацию двух или более компонентов с характеристиками, отличными от характеристик этих отдельных компонентов. Инженерные свойства обычно улучшаются, такие как дополнительная прочность, эффективность или долговечность. Композиты состоят из армирующего материала — волокна или частиц, скрепленных матрицей (полимерной, металлической или керамической).
Полимеры, армированные волокном (FRP) доминируют на рынке и стимулируют рост новых применений в различных отраслях промышленности. Среди них углеродное волокно является широко используемым композитом, в частности, для самолетов, гоночных автомобилей и велосипедов, поскольку оно более чем в три раза прочнее и жестче, чем алюминий, но на 40% легче. Он образован армированным углеродным волокном, связанным с эпоксидной смолой.
Волокна могут иметь однонаправленное переплетение и стратегически выровнены для создания прочности относительно вектора. Переплетенные волокна могут использоваться для создания прочности в нескольких векторах, и они также отвечают за фирменный стеганый вид композитных деталей. Обычно детали изготавливаются с комбинацией обоих. Доступно несколько типов волокон, в том числе:
Fiberglass | Carbon fiber | Aramid fiber (Kevlar) |
---|---|---|
The most popular fiber Lightweight, moderate tensile and compressive strength Low cost and easy to work with | Highest strength and stiffness отношение массы к весу в промышленности (предельная прочность на растяжение, сжатие и изгиб) Дороже, чем другие волокна | Более высокая ударопрочность и стойкость к истиранию, чем у углеродного волокна Низкая прочность на сжатие Трудно резать или обрабатывать |
Смола используется для скрепления этих волокон и создания жесткого композита. В то время как сотни видов смол можно использовать, вот наиболее популярные из них:
Смола | Pros | Cons | Curring | ||
---|---|---|---|---|---|
Epoxy | 2 3333333332333233323332333233233332332332333233323323332332332333233233233233323323323332323333232332333232323332323332323233323233323232333232323332332. срок годности | Самый дорогой Чувствителен к соотношению компонентов смеси и колебаниям температуры | Использует специальный отвердитель (двухкомпонентная система) Некоторые эпоксидные смолы требуют нагрева | Низкая прочность и коррозионная стойкость | Отверждение с катализатором (МЭКП) |
Виниловый эфир | Сочетает характеристики эпоксидной смолы и стоимость полиэстера Лучшая коррозионная стойкость, термостойкость и удлинение | Меньшая прочность, чем у эпоксидной смолы, и более высокая стоимость, чем у полиэстера Ограниченный срок хранения | Отверждение с помощью катализатора (MEKP) |
Производство армированных волокном полимеров, таких как детали из углеродного волокна, является умелым и трудоемким процессом. используется как в единичном, так и в серийном производстве. Время цикла варьируется от одного часа до 150 часов в зависимости от размера и сложности детали. Как правило, при изготовлении FRP непрерывные прямые волокна соединяются в матрице, образуя отдельные слои, которые наслаиваются слой за слоем на конечную деталь.
Свойства композита определяются как материалами, так и процессом ламинирования: способ включения волокон сильно влияет на характеристики детали. Термореактивные смолы формуются вместе с арматурой в инструменте или форме и отверждаются для получения прочного продукта. Существуют различные методы ламинирования, которые можно разделить на три основных типа:
При мокром укладывании волокно разрезается и укладывается в форму, после чего смола наносится кистью, валиком или распылителем. Этот метод требует больших навыков для создания высококачественных деталей, но это также наименее затратный рабочий процесс с самыми низкими требованиями для начала изготовления деталей из углеродного волокна своими руками. Если вы новичок в производстве деталей из углеродного волокна и еще не экипированы, мы рекомендуем начать с ручного ламинирования методом влажной укладки.
Посмотрите видео, чтобы увидеть, как работает процесс влажной укладки углеродного волокна.
При ламинировании препрегом смола вливается в волокно впереди. Предварительно пропитанные листы хранят в холоде, чтобы замедлить отверждение. Затем слои отверждаются в форме под действием тепла и давления в автоклаве. Это более точный и воспроизводимый процесс, поскольку количество смолы контролируется, но это также и самый дорогой метод, который обычно используется в высокопроизводительных приложениях.
При формовании RTM сухое волокно помещается в форму, состоящую из двух частей. Форма закрывается зажимом перед закачиванием смолы в полость под высоким давлением. Обычно он автоматизирован и используется для производства больших объемов.
Информационный документ
Загрузите наш технический документ, чтобы узнать, как быстро создавать сложные формы с помощью 3D-печати, и узнать о советах и рекомендациях, которым вы должны следовать при подготовке деталей формы.
Загрузить информационный документ
Поскольку качество пресс-формы напрямую влияет на качество конечной детали, изготовление инструментов является критическим аспектом производства FRP. Большинство форм изготавливаются из воска, пенопласта, дерева, пластика или металла с помощью станков с ЧПУ или ручной работы. В то время как ручные методы очень трудоемки, обработка с ЧПУ по-прежнему требует сложного и трудоемкого рабочего процесса, особенно для сложных геометрических форм, а аутсорсинг обычно сопряжен с высокими затратами и длительным сроком выполнения. Оба варианта требуют квалифицированных рабочих и предлагают небольшую гибкость при проектировании и корректировке пресс-формы.
Аддитивное производство предлагает решение для быстрого изготовления пресс-форм и моделей при низких затратах для изготовления деталей из углеродного волокна. Использование полимерной оснастки в производственных процессах постоянно растет. Замена металлических инструментов пластиковыми деталями, напечатанными собственными силами, является мощным и экономичным средством сокращения времени производства при расширении гибкости конструкции. Инженеры уже работают с деталями, напечатанными на 3D-принтере из полимерной смолы, для изготовления приспособлений и приспособлений для поддержки таких методов, как намотка нити или автоматическое размещение волокна. Точно так же малотиражные печатные формы и штампы используются в литье под давлением, термоформовании или формовании листового металла для доставки небольших партий.
Настольная 3D-печать внутри компании требует ограниченного оборудования и упрощает рабочий процесс. Профессиональные настольные принтеры, такие как Form 3+, доступны по цене, просты в установке и могут быть быстро масштабированы в соответствии со спросом. Изготовление крупных инструментов и форм также возможно с помощью широкоформатных 3D-принтеров, таких как Form 3L.
Стереолитография (SLA) Технология 3D-печати позволяет создавать детали с очень гладкой поверхностью, что очень важно для пресс-форм для укладки углеродного волокна. Это позволяет создавать сложные геометрические фигуры с высокой точностью. Кроме того, в библиотеке полимеров Formlabs есть конструкционные материалы с механическими и термическими свойствами, которые хорошо сочетаются с изготовлением пресс-форм и моделей.
3D-печатные формы для изготовления деталей из углеродного волокна могут снизить затраты и сократить время выполнения заказов.
Для мелкосерийного производства инженеры могут напрямую напечатать пресс-форму с низкими затратами и в течение нескольких часов, не вырезая ее вручную или не используя оборудование с ЧПУ; Программное обеспечение CAM, настройка станка, закрепление, оснастка и эвакуация стружки. Трудозатраты и время выполнения заказов на изготовление пресс-форм резко сокращаются, что позволяет быстро выполнять итерации проекта и настраивать детали. Они могут создавать сложные формы пресс-форм с мелкими деталями, которые было бы трудно изготовить традиционными методами.
Команда Formula Student Берлинского технического университета (FaSTTUBe) изготовила дюжину деталей из углеродного волокна для гоночных автомобилей. Инженеры в команде вручную ламинируют на пресс-форме, напечатанной с помощью смолы Formlabs Tough 1500 Resin. Эта смола характеризуется модулем растяжения 1,5 ГПа и удлинением при разрыве 51%. Он не только прочный и поддерживающий во время укладки, но и достаточно гибкий, чтобы отделить деталь от формы после отверждения.
Испытательный стенд FaSTTUBe с установкой для производства деталей из углеродного волокна.
Хотя этот метод не связан с интенсивными условиями отверждения, другие процессы ламинирования часто требуют более высоких давлений и температур. Компания DeltaWing Manufacturing использует High Temp Resin для создания компонентов воздушного потока в процессе препрега. Высокотемпературная смола имеет температуру теплового изгиба (HDT) 238°C при 0,45 МПа и способна выдерживать тепло и давление автоклава. DeltaWing Manufacturing напрямую печатает пресс-формы для производства серии из примерно 10 индивидуальных деталей.
Воздуховод крыла из углеродного волокна рядом с пресс-формой, состоящей из двух частей, напечатанной с помощью высокотемпературной смолы, производства DeltaWing Manufacturing.
Полимерные формы для прямой 3D-печати — отличный инструмент для оптимизации мелкосерийного производства. Однако их срок службы меньше, чем у традиционных пресс-форм, что делает их непригодными для крупносерийного производства.
Для увеличения производства компания DeltaWing Manufacturing печатает шаблоны форм из высокотемпературной смолы, а затем отливает их из смолы. Печать шаблона также является мощной альтернативой для процессов ламинирования, требующих интенсивных условий отверждения, которые не подходят для 3D-печатных форм. Производители могут печатать индивидуальные шаблоны по запросу и при этом исключить один шаг из своей технологии изготовления пресс-форм — изготовление шаблона.
Информационный документ
В этом техническом документе вы узнаете, как сочетать быструю оснастку с традиционными производственными процессами, такими как литье под давлением, термоформование или литье.
Загрузить информационный документ
Существует большой спрос на рабочие процессы, которые сочетают в себе прочность, долговечность и надежность традиционных деталей из углеродного волокна с гибкостью, геометрическими возможностями и воспроизводимостью 3D-печати. Поэтому неудивительно, что существует множество компаний, занимающихся 3D-печатью, которые предлагают 3D-печать углеродным волокном, при этом в настоящее время доступны два процесса: печать рублеными волокнами или непрерывными волокнами.
Используя измельченные углеродные волокна, Nylon 11 CF Powder для 3D-принтера Fuse 1+ 30 Вт с селективным лазерным спеканием (SLS) позволяет производителям создавать прочные, легкие и термостойкие детали, не полагаясь на традиционные методы наложения или механической обработки.
Порошок Formlabs Nylon 11 CF прочный, легкий и термостойкий, что делает его идеальным для автомобильной, аэрокосмической и производственной промышленности.
Образец детали
Убедитесь сами и убедитесь в качестве Formlabs. Мы отправим бесплатный образец детали в ваш офис.
Запросить бесплатный образец Деталь
Производство полимеров, армированных волокном, — увлекательный, но сложный и трудоемкий процесс. Использование 3D-печатных форм и шаблонов для изготовления деталей из углеродного волокна позволяет предприятиям упростить рабочий процесс, расширить гибкость и возможности проектирования, а также сократить затраты и время выполнения заказов.
На основе тематических исследований с TU Berlin и DeltaWing Manufacturing в нашем техническом документе представлены три рабочих процесса для использования 3D-печати в производстве композитов с быстрым изготовлением форм и моделей.
Загрузить информационный документ
Композитный материал | Технологии Тейджина | Исследования и разработки
- 日本語ページ
- 中文页面
Исследования и разработки
От поставщика материалов к поставщику уровня 1
До 2017 года компания Teijin поставляла автопроизводителям некоторые компоненты из армированного углеродным волокном пластика (CFRP) небольшими партиями. Однако компания была в первую очередь поставщиком материалов, особенно углеродного волокна, для поставщиков первого уровня. С приобретением Continental Structural Plastics (сейчас Teijin Automotive Technologies) компания Teijin закрепила за собой позицию поставщика первого уровня.
В настоящее время Тейджин занимается не только разработкой материалов, но и всем, от проектирования транспортных средств до массового производства прототипов и конечных автомобилей.
Первое коммерческое применение CFRTP
Компания Teijin разработала запатентованный термопласт, армированный углеродным волокном (CFRTP), который полностью пригоден для вторичной переработки. Этот материал, получивший название Sereebo®, используется General Motors в кузове пикапа GMC Sierra. По сравнению со сталью он на 40 процентов легче, обладает в 10 раз большей ударопрочностью и более устойчив к коррозии. Время формования Sereebo® составляет примерно одну минуту, что обеспечивает высокую массовую производительность, необходимую для автомобильных деталей. Это первое в мире использование CFRTP для конструкционных деталей серийного автомобиля.
Аккумуляторный ящик из нескольких материалов для электромобилей
Чтобы в будущем достичь углеродно-нейтрального уровня выбросов, автомобильная промышленность активно работает над переводом своих предложений с автомобилей с ДВС на электромобили. В то время как многие OEM-производители в настоящее время используют наши крышки аккумуляторных батарей из композитных материалов, мы предлагаем полный корпус аккумуляторной батареи, который включает в себя композитный лоток и крышку, а также металлическую раму. Крышка и лоток изготовлены из нашего фирменного огнестойкого листового литьевого компаунда (SMC), а рама изготовлена из металла. Оптимальная конструкция конструкции обеспечивает как снижение веса, так и безопасность.
Испытание на огнестойкость для SMC
«Стандарт GB» по огнестойкости — один из самых строгих мировых стандартов, которым должны соответствовать корпуса батарей. Этот стандарт предусматривает очень строгие испытания, чтобы пламя не проникло через крышку аккумуляторного отсека и не достигло салона автомобиля в течение 5 минут после начала возгорания, что дает пассажирам время покинуть автомобиль в случае пожара.
Подтверждено, что огнестойкий SMC Teijin не проникает даже при 10-минутном испытании на воздействие пламени, эквивалентном UL94-5VA.
Испытание на огнестойкость После испытания Огнестойкий SMC<Условия испытаний>
Снижение воздействия на окружающую среду
По мере того, как нормативы по снижению глобального потепления и защите окружающей среды становятся все более строгими, а цели по сокращению выбросов CO 2 ужесточаются, компания Teijin активно работает над снижением своего воздействия на окружающую среду. Помимо снижения веса автомобильных компонентов, мы работаем над снижением воздействия на окружающую среду за счет сокращения выбросов CO 2 выбросы в течение всего жизненного цикла компонентов — от производства до утилизации.