Станки для шлифования и притирки клапанов и задвижек
Работаем по всей РФ и СНГ
Уважаемые партнёры! Будьте внимательны. Покупайте продукцию CLIMAX только у авторизованных поставщиков, данные о них есть на сайте CLIMAX – www.climaxportable.com/contact-us/
Представлены в трех конфигурациях, позволяют выполнять шлифовку и притирку гнезд запорных и обратных клапанов, а также восстанавливать поверхность в районе гнезд клапанов до стандартов производителя, и даже выше. Имеется регулятор для обеспечения быстрой и удобной регулировки усилия шлифования.
Мобильные станки для шлифовки и притирки клапанов VM1150, VM1200
- Диаметры седла клапана — 32-200 мм
- Глубина погружения — 450 мм
- Тип клапана — обратный клапан
- Тип привода — с электроприводом, пневматический
заказать
Мобильные станки для шлифовки и притирки клапанов VM1350, VM1500, VM1600
- Диаметры седла клапана — 40-600 мм
- Глубина погружения — 1000 мм
- Тип клапана — обратный клапан
- Тип привода — с электроприводом, пневматический
заказать
Мобильные станки для шлифовки и притирки клапанов VM1700, VM1900
- Диаметры седла клапана — 200-1000 мм
- Глубина погружения — 1400 мм
- Тип клапана — обратный клапан
- Тип привода — с электроприводом, пневматический
заказать
Мобильные станки для шлифовки и притирки Сферических/Предохранительных клапанов VM2050C, VM2100C, VM2150C, VM2350C
- Диаметры седла клапана — 10-305 мм
- Глубина погружения — 600 мм
- Тип клапана — регулирующий клапан (седло коническое)
- Тип привода — с электроприводом, пневматический
заказать
Мобильные станки для шлифовки и притирки Сферических /Предохранительных клапанов VM2050S, VM2150S
- Диаметры седла клапана — 10-150 мм
- Глубина погружения — 300 мм
- Тип клапана — регулирующий предохранительный клапан (седло плоское)
- Тип привода — с электроприводом, пневматический
заказать
Мобильные станки для шлифовки и притирки сёдел регулирующих клапанов VM2350, VM2500, VM2600
- Диаметры седла клапана — 80-600 мм
- Глубина погружения — 800 мм
- Тип клапана — регулирующий клапан (седло плоское)
- Тип привода — с электроприводом, пневматический
заказать
Станок для шлифования и притирки Стационарных Запорных / Сферических клапанов VM5800
- Диаметры седла клапана — 10-350 мм
- Глубина погружения — не имеется в наличии
- Тип клапана — запорно-регулирующий
- Тип привода — с электроприводом
заказать
Каталог «CLIMAX» 2020
заказать арендовать
Применение
Валы Фланцевые соединения Отверстия любого диаметра Металлические фундаменты,
Шлифовальный станок своими руками, самодельные тарельчатые и барабанные шлифстанки
Чтобы вы ни делали своими руками: домашнюю мебель, декоративные поделки из дерева и металла, рамки для фотографий или простые рукоятки для инструмента — всё это требует финишной обработки. А именно — шлифовки.
Поэтому в любой домашней мастерской обязательно должен быть шлифовальный станок.
Эти приспособления различаются по конструкции и размерам. Бывают универсальные и узкоспециализированные конструкции. Как показывает практика, дешевле и проще изготовить их самостоятельно.
В этой статье мы рассмотрим несколько бюджетных вариантов самодельных шлифовальных станков дискового и барабанного типа.
Для изготовления самодельных приспособлений вы можете использовать как покупные материалы, так и б/у — это уже на ваше усмотрение.
В качестве привода обычно используется электродвигатель (например, от стиралки). Также можно воспользоваться альтернативными вариантами — установить электродрель или болгарку.
Содержание
Самодельные шлифстанки дискового типа
Одним из наиболее популярных видов шлифовальных станков является конструкция тарельчатого типа. По сути, это обычный дисковый шлифстанок. Служит он для обработки небольших заготовок из дерева, фанеры, текстолита и металла.
Одной из-за характерных особенностей тарельчатой конструкции являются компактные размеры корпуса — станок не занимает много места на рабочем столе, и отлично подходит для работы в небольших помещениях.
Дисковый или тарельчатый шлифовальный станок может использоваться для полировки и выравнивания поверхностей, а также для заточки инструмента.
В большинстве случаев рабочая поверхность дискового станка находится в вертикальном положении. Однако встречаются самодельные конструкции, у которых рабочая поверхность (диск с наждачкой) может располагаться вертикально или даже под углом.
Шлифовальный станок из дрели
Это одна из самых простых самодельных конструкций шлифстанка, которую каждый может изготовить своими руками для работы в домашней мастерской.
Для изготовления самоделки нам потребуются деревянные бруски, фанера, металлический уголок, болты с барашковыми гайками.
Первым делом необходимо будет изготовить основание, на котором будут располагаться все остальные элементы конструкции.
Для этого будем использовать кусок фанеры толщиной 20 мм. Отрезаем заготовку требуемого размера с помощью лобзика или циркулярном станке.
На следующем этапе приступаем к изготовлению крепления для ручной электродрели, которая в данном случае будет выступать в качестве привода.
Отпиливаем два деревянных бруска подходящей длины. Соединяем их вместе с помощью струбцин, и в центральной части высверливаем отверстие под горловину корпуса дрели. После этого сверлим в брусках крепежные отверстия.
В основании также нужно будет просверлить два отверстия, в которые устанавливаем длинные болты. С нижней стороны основания надо сделать посадочные места под шляпки болтов, чтобы они были утоплены вровень с поверхностью.
На болты надеваем подготовленные деревянные бруски, между ними устанавливаем дрель, и фиксируем барашковыми гайками.
В патроне дрели зажимаем шлифовальную насадку тарельчатого типа. Также можно установить лепестковый круг для обработки металла.
Далее отрезаем два металлических уголка, и вырезаем в одной из полок продольные пазы. В другой полке сверлим отверстия, и прикручиваем уголки к основанию.
Отпиливаем три кусочка фанеры. Соединяем их между собой на саморезы буквой «П». В результате у нас получился рабочий столик. По бокам опорных частей столика сверлим отверстия и устанавливаем болты.
Далее крепим столик к направляющим уголкам. К верхней части столика прикручиваем лист металла толщиной 1,5-2 мм.
Видео
Во всех подробностях изготовление тарельчатого шлифовального станка своими руками показано на видео ниже. Идея самоделки принадлежит автору Mistry MakeTool.
Make A Drill Powered Sander Machine || Drill Hack || Drill HolderТакой станочек очень просто сделать, и при этом не потребуется практически никаких вложений. Подойдет для шлифования мягкой и твердой древесины.
Для крепления самодельной конструкции к верстаку лучше использовать струбцины — после шлифовки заготовок станок можно будет убрать на полку, чтобы не мешал.
Если же убирать со стола вы его не планируете, то тогда имеет смысл прикрепить основание с помощью болтового соединения.
Шлифовальный станок из болгарки
Необходимые материалы и комплектующие:
- УШМ;
- дисковая насадка с липучкой;
- наждачный круг;
- полоса металла;
- профильная труба;
- болты с гайками;
- листовой металл.
Для изготовления этого шлифовального станка нам потребуется маленькая болгарка. Устанавливаем на неё дисковую насадку с липучкой, и крепим к ней наждачку.
Далее отрезаем заготовки из металлической полосы, и изготавливаем из них крепление для болгарки. С помощью болтов прикручиваем крепление к корпусу редуктора УШМ.
Отрезаем кусок профильной трубы, сверлим в нём два отверстия, вставляем в них болты, и привариваем. Затем крепление с болгаркой надеваем на эти болты, фиксируем гайками.
В нижней пластине предварительно надо вырезать пазы.
На следующем этапе необходимо будет изготовить основание шлифовального станка. Отрезаем четыре кусочка профильной трубы, обрезаем углы под углом 45 град., и свариваем из них квадратную рамку.
Профильная труба с креплением для болгарки приваривается к основанию.
На противоположной стороне станины необходимо приварить крепление с регулируемой стойкой. К верхней части стойки будет крепиться опорный столик. Его мы изготовим из листового металла толщиной 3-4 мм.
В самом креплении сверлим отверстие и привариваем гайку. В неё вкручиваем рым-болт или обычный барашковый болт, с помощью которого стойка со столиком будет фиксироваться на необходимой высоте.
На последнем этапе останется только зачистить сварные швы и покрасить элементы конструкции. После этого приступаем к сборке.
Видео
Изготовление и сборку дискового шлифовального станка своими руками можно посмотреть на видео.
Шлифовальный станок из болгарки своими руками.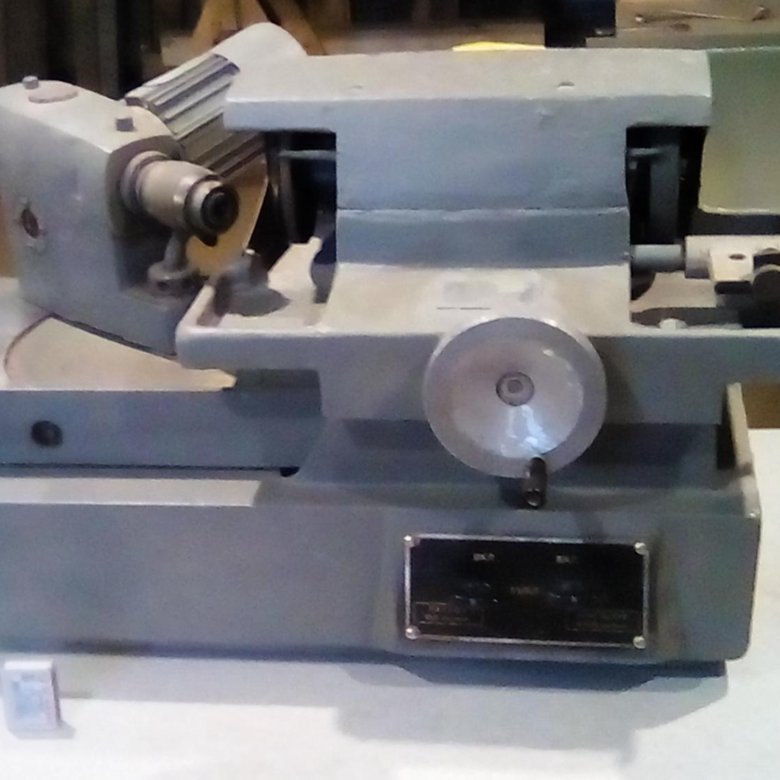
Такой самодельный шлифовальный станок отлично подойдёт для обработки заготовок из дерева, фанеры или металла. Желательно использовать болгарку с регулировкой оборотов.
Конструкция получилась довольно компактной, благодаря чему она не будет занимать много места на рабочем столе.
При наличии сварочного аппарата и навыков работы со сваркой изготовить такую самоделку сможет абсолютно каждый.
Дисковый шлифовальный станок
За основу данной самоделки будет использоваться электродвигатель от старой советской стиральной машины. Его мощность составляет 180 Вт.
Конечно, такой мощности будет недостаточно для выполнения серьезных работ. Но для обработки небольших заготовок из дерева такой станочек вполне сгодится.
Своим личным опытом поделился автор YouTube канала GARAGE 100.
Первым делом необходимо изготовить основание. Оно должно быть достаточно массивным и прочными, чтобы выдержать вес электродвигателя. Для изготовления основания будем использовать фанеру толщиной 18-20 мм.
Основание шлифовального станка состоит из нескольких элементов:
- нижней части:
- двух боковин;
- верхней части.
Поскольку на верхней части будет находиться электродвигатель, то её необходимо сделать потолще. Для этого мы просто склеиваем два куска фанеры.
В нижней части корпуса электродвигателя имеются небольшие «ушки» с отверстиями. Вставляем в них шпильки, на концах которых закреплены мебельные металлические уголки.
И с помощью этих уголков крепим электродвигатель к верхней части основания. В качестве крепежа используются винты с гайками.
На следующем этапе из фанеры изготавливаем подвижные кронштейны, которые крепятся к передней части основания.
Затем надо будет изготовить опорный рабочий столик с регулируемым упором. Крепим его к верхней части кронштейнов.
К одной из боковых сторон основания прикручиваем одноклавишный выключатель, с помощью которого можно будет включать и отключать электродвигатель.
На вал двигателя надеваем дисковую насадку с липучкой, на которую крепим наждачку.
Видео
Как изготовить бюджетный шлифовальный станок по дереву своими руками, пошагово показано в авторском видеоролике. Советуем посмотреть.
Станок собраный на коленке ! А столько пользы от него !Главным плюсом данной самоделки является возможность быстрой смены наждачки и установки полировального круга.
Ещё один немаловажный плюс заключается в том, что изготовить данную конструкцию можно без использования сварочного аппарата. Для многих мастеров это имеет огромное значение.
Шлифстанки барабанные своими руками
Рабочим элементом данного вида шлифовального станка является цилиндр (или попросту — барабан), на который по всей длине намотана полоса наждачной бумаги (шлифовальной ленты).
Причем барабан может устанавливаться как вертикальном положении, так и горизонтально.
Наибольшее распространение получили шлифовальные станки с горизонтально установленным барабаном.
Они используются в основном для калибровки досок, реек, мебельных щитов и других деревянных заготовок.
Шлифовальные станки с вертикальным барабаном отлично подходят для шлифования радиусов и полукруглых выемок. Также на таких станках очень удобно обрабатывать внутренние стороны круглого отверстия.
Барабанный шлифовальный станок для деревянных щитов
Предлагаем вашему вниманию самодельную конструкцию барабанного шлифовального станка, в которой барабан установлен в горизонтальном положении. В качестве привода используется электродвигатель.
Как мы уже говорили ранее, такой шлифстанок отлично подойдет для калибровки досок и склеенных мебельных щитов.
Идеей данной самоделки поделился автор YouTube канала DIY Tools.
Необходимые материалы:
- фанера;
- деревянные бруски;
- корпусные подшипники;
- болты с гайками;
- резьбовая шпилька;
- шлифовальная лента.
Первым делом вырезаем две заготовки из фанеры толщиной 20 мм. Размеры листов могут быть разными — на ваше усмотрение.
Лист фанеры большего размера выступает в качестве основания конструкции, тогда как второй лист служит опорной площадкой шлифовального станка, по которой будут перемещаться обрабатываемые заготовки.
Соединяем обе заготовки из фанеры с помощью дверных петель, как показано на фото ниже.
Далее необходимо будет изготовить винтовой механизм для регулировки угла наклона опорной площадкой.
Для его изготовления мастера используют деревянные бруски, резьбовую шпильку, кусочки фанеры и корпусные подшипники.
По бокам основания необходимо прикрутить опоры, собранные из деревянных брусков. К верхней части крепятся корпусные подшипники. В них устанавливаем деревянный вал, который по сути являются барабаном.
Деревянный вал можно изготовить из обычного бруска, округлив его на токарном станке.
Располагается барабан над поверхностью опорной площадки. Таким образом, изменяя угол наклона опорной площадки, можно регулировать расстояние между её поверхностью и барабаном.
На следующем этапе на основании конструкции устанавливаем опорную площадку с электродвигателем. Соединяем вал мотора с барабаном. Наматываем на барабан шлифовальную ленту.
Если вы занимаетесь склейкой мебельных щитов, то данная самоделка обязательно вам пригодится.
На этом станке вы сможете без проблем откалибровать щит до нужного вам размера. Помимо этого, можно отшлифовать обычную доску или деревянную планку.
Барабанный шлифовальный станок из электродвигателя и фанеры
Рассмотрим ещё один бюджетный вариант самодельного шлифстанка для работы в домашней мастерской. Только в данном случае рабочий элемент будет установлен вертикально.
На таком станке удобно шлифовать полукруглые вырезы и изогнутые края на деревянных и металлических заготовках.
В качестве привода используется электродвигатель асинхронного типа. Можно использовать движок от стиральной машинки.
Идеей самоделки поделился автор YouTube канала «Алексей Чезганов».
Первым делом необходимо будет приварить к валу мотора удлиненную гайку. В процессе сварки важно контролировать чтобы вал двигателя и удлиненная гайка были соосны друг другу.
Поэтому сначала необходимо зафиксировать свариваемые детали на прихватки, а потом уже, убедившись в том, что они располагаются правильно, обварить полностью.
После завершения сварочных работ обязательно нужно зачистить сварной шов с помощью болгарки и лепесткового круга.
На следующем этапе необходимо будет изготовить рабочий элемент конструкции — барабан.
Для этого из фанеры толщиной 20 мм с помощью кольцевой пилы по дереву вырезаем круглые заготовки подходящего диаметра. Затем эти заготовки склеиваем между собой.
Рабочий столик шлифовального станка изготавливаем из фанеры толщиной 20 мм.
Вырезаем заготовку требуемого размера, сверлим в ней крепежные отверстия, после чего с помощью болтов и гаек прикручиваем опорный стол к корпусу электродвигателя. Двигатель при этом должен быть установлен вертикально.
К торцевой части сделанного барабана необходимо будет прикрепить металлическую втулку, чтобы можно было насадить барабан на вал двигателя.
Далее отрезаем подходящей длины кусок наждачной бумаги, и приклеиваем его к барабану. После этого надеваем шлифовальный барабан на вал двигателя.
К опорному столику прикручиваем лист фанеры, который будет выступать в качестве рабочей поверхности для опирания заготовок.
Под опорной столешницей крепится блок с кнопкой для включения-выключения электродвигателя.
Видео
Пошаговый процесс изготовления шлифовального станка по дереву своими руками показан в авторском видеоролике.
Простая шлифовалка из куска фанеры и двигателяСобранная самодельная конструкция крепится к рабочему верстаку с помощью струбцин или болтового соединения. Второй вариант более надежный.
Шлифовальный станок из запчастей от стиральной машины
В данном обзоре рассмотрим опыт автора YouTube канала peChoO по изготовлению самодельного шлифовального станка. Для этого автор использует запчасти от стиралки.
От стиральной машины потребуется корпус, внутри которого находится барабан. Помимо этого, автор использует профильные трубы и листовой металл.
Барабан от стиралки в данном случае нам не потребуется. Извлекаем его аккуратно из металлического корпуса, и оставляем для следующих самоделок.
Берем болгарку с отрезным диском, и отрезаем от корпуса все лишнее.
Основные этапы работВозможно, вам интересно будет узнать, как изготовить ручной ленточно-шлифовальный станок из болгарки.
Из профильных труб необходимо изготовить станину шлифовального станка. Отрезаем по размеру заготовки и свариваем их вместе.
К нижней части основания станины привариваем поворотные колесики — для возможности легкого перемещения станка по мастерской.
Далее из МДФ (фанеры или ДСП) нужно вырезать круг подходящего диаметра. К нему прикручиваем крепление с валом от стиралки.
Устанавливаем круг внутрь корпуса. На вал надеваем шкив.
После этого необходимо будет прикрепить к корпусу электродвигатель (250W, 2800 об.). На вал мотора надеваем шкив. Соединяем оба шкива с помощью ремня.
Далее изготавливаем и крепим к корпусу рабочий столик (подручник). Из листового металла мастер делает защитный кожух для приводного ремня.
В рабочем столики высверливаем отверстие и привариваем патрубок, на который надеваем кусок шланга. Ко второму концу шланга подключаем пылесос.
Вырезаем круг из наждачной бумаги и приклеиваем его к кругу из МДФ, установленному внутри корпуса.
Видео
Подробно о том, как своими руками изготовить большой шлифовальный станок, можно посмотреть на видео ниже.
Washing machine Never Die!!! Awesome IDEA?Шлифовальный станочек из редуктора от маленькой УШМ
Друзья, если не выбрасывать в металлолом вышедший из строя электроинструмент (дрель, УШМ и др.), то из доставшихся на халяву запчастей можно сделать много чего полезного.
В данном обзоре расскажем, как из редуктора от маленькой болгарки изготовить настольный шлифовальный станочек.
Несмотря на компактные размеры, станок со своей задачей вполне справляется. В качестве абразива используется шлифовальный круг, который крепится к диску с липучкой.
Советуем также прочитать: как собрать настольный станок по металлу, используя тормозной диска автомобиля.
Размеры шлифовального станочка (ширина и длина) — 23х14 см, высота — 14 см. То есть конструкция действительно очень компактная. При этом весит весь станок всего 2,5 кг.
Особенности конструкции
Основным узлом шлифстанка является редуктор от сгоревшей болгарки. На вал редуктора крепится стандартная насадка с липучкой.
В качестве привода используется электромотор мощностью около 200 Вт. Рабочее напряжение — 24 V. Скорость вращения вала — 6000 об./мин.
Самодельный шлифовальный станочек предназначен для обработки заготовок и деталей (из дерева, пластика, металла) небольшого размера в условиях гаража и домашней мастерской.
Рабочий столик изготовлен из куска металлической пластины. Это самый простой столик, без регулировки угла наклона.
Конечно, скорость вращения шлифовального диска невысокая, однако в этом есть свой плюс — пыль в процессе шлифовки деревянных заготовок не разлетается по всей мастерской.
Процесс изготовления шлифстанка
Вал электромоторчика обрезаем. На оставшуюся часть вала надеваем переходник, на который надевается маленькая шестеренка.
Элементы станины можно изготовить из фанеры толщиной 18-20 мм. В основании сверлим отверстия для крепления двигателя и редуктора.
После этого соединяем основание с подставкой, выдерживая прямой угол между деталями. После склейки покрываем фанеру слоем лака.
Отрезаем кусок профильной трубы. Один конец профиля нужно заглушить. Затем на другой стороне привариваем две втулки с резьбой — к ним крепится крышка с кнопкой и гнездом питания.
Профильная труба крепится к основанию и подставке с помощью винтов, и дает дополнительную жесткость вертикальной стойке. Когда все готово, приступаем к сборке станка.
Видео
Подробнее о том, как сделать шлифовальный станочек из редуктора от маленькой болгарки, можно посмотреть в авторском видеоролике. Этот обзор подготовлен на основе видео с YouTube канала «I.V. Мне интересно».
Простой шлифовальный дисковый станочек. (grinding disc machine)Полезная самоделка для мастерской из сломанной болгарки
Вместо того, чтобы оставлять вышедшие из строя электроинструменты пылиться в углу, можно подарить им «вторую жизнь».
По крайней мере, некоторые детали, которые находятся внутри корпуса, вполне можно использовать для изготовления разных самоделок.
Автор YouTube канала Ollari’s использовал старую сломанную болгарку, чтобы изготовить полезное приспособление для своей мастерской! Почему бы не последовать его примеру?
Основные этапы работСоветуем также прочитать статью-обзор: как сделать подъемный столик из профтрубы и домкрата.
Первым делом необходимо будет разобрать болгарку. Для изготовления самоделки нам понадобятся редуктор и ведущий вал с якорем.
Отпиливаем кусок фанеры толщиной 20 мм. Прикручиваем к нему редуктор болгарки с вставленным в него ведущим валом.
Далее отпиливаем еще три куска фанеры, и собираем корпус будущего приспособления.
После этого при помощи нейлера прибиваем к корпусу кусок фанеры с отверстием под шланг пылесоса. Изготавливаем подручник.
Из фанеры вырезаем круг подходящего диаметра. По центру прикручиваем на саморезы прижимную гайку от УШМ.
Накручиваем круг из фанеры на вал редуктора. Далее крепим к корпусу самодельный подручник.
На круг наклеиваем наждачку, а сам корпус необходимо будет покрасить. Устанавливаем его на рабочий стол сверлильного станка. Ведущий вал зажимаем в сверлильном патроне. Получился шлифовальный станок.
Видео
С пошаговым процессом сборки можно ознакомиться в авторском видеоролике ниже. Как вам такая идея?
Don’t throw away your broken tools! Angle Grinder HackВ этой статье мы подробно рассмотрели, как в условиях домашней мастерской собрать самодельные шлифовальные станки. Специально для вас постарались найти в интернете самые простые и бюджетные конструкции. Надеемся, что какая-нибудь из этих идей вас заинтересует.
Андрей Васильев
Задать вопрос
Самодельный станок для шлифовки клапанов Стоимость $0
JavaScript отключен. Для лучшего опыта, пожалуйста, включите JavaScript в вашем браузере, прежде чем продолжить.
- Автор темы Свомпратт
- Дата начала
Свомпратт
Снайпер
- #1
То, что у меня валялись вещи, не стоило мне ничего, кроме времени.
Я получил эти головки Vortec 906, и головки выглядят великолепно, но, поскольку в головках Vortec не используются вращатели клапанов, а двигатели обычно работают на низких оборотах большую часть своего срока службы, выпускные клапаны немного изнашиваются.
Бадди оставил здесь свою точилку для клапанов сиу, но уронил ее и погнул головку, и эта штука теперь бесполезна для притирки клапанов.
Я исследовал самодельные шлифовальные станки для клапанов, и какой-то чувак построил один. Мне понравилась концепция, и у меня были детали. Вот его видео.
Я взял очень изрытый клапан и заземлил его.. да, это заняло около 3 минут.
Затем, чтобы убедиться, что угол находится на деньгах, я притер клапан к седлу в головке 3-й рисунок. . Для меня достаточно. У меня пробег более 100000км намного хуже.
Немного фото.
deerwhacker444
Снайпер
- #2
Надеюсь, движения транспортира были точными..
Мне нравится…
Catt57
Gill-Gun Guru
- #3
Глупая идея, которая работает, не глупа. ..
Свомпратт
Снайпер
- #4
Я не измерял, я чертил линии на дереве, но это было бесполезно.
Я установил тефлоновый блок на деревянную доску с 1 винтом, чтобы я мог изменить угол, поворачивая его.
Я посмотрел на диск резака дремелем, выровнял на нем седло клапана и вставил еще один винт через тефлон в дерево, чтобы закрепить его.
Затем я взял пробный клапан и посмотрел, на деньгах ли он.
Теперь седло используемого клапана будет утоплено… и если вы посмотрите это видео выше и продвинетесь вперед на 1:30 секунды видео, вы увидите, где его клапан выходил на поверхность на внешнем крае и внутреннем крае седла. площадь одновременно.
Во время первого удара шлифовального круга.
Это поставило бы вас на деньги, чтобы быть в согласии с сиденьем. Или чертовски близко и достаточно близко, чтобы работать.
Так действовали мои клапаны, когда я начал шлифовать их на этом грубом инструменте.
Я заземлил их все и притер 2 клапана, и это выглядит великолепно.
Единственная проблема заключается в том, что диск малого диаметра позволит моему тефлоновому блоку работать только с клапанами на 1,5 дюйма или 1,60 дюйма в текущем завинченном положении. Впускные клапаны на 1,94 дюйма мне нужно будет переместить в блок и отрегулировать.
Но эти впускные клапаны не имеют ямок и будут притерты как есть
Притирка не требуется
Gunbuffer
Снайпер
- #5
Вместо этих отрезных кругов я бы использовал насадку для барабанного шлифования. Они плохо переносят боковое давление, как я уверен, вы знаете. они легко отклоняются и взрываются
пара советов; используйте HD-диски, они толще обычных и складывайте по 2-3 вместе, при условии, что на крепежном винте достаточно резьбы. это поможет укрепить его
Свомпратт
Снайпер
- #6
Вы правы. В итоге я их удвоил. Я мог видеть, что он едва прогибается с 1 диском, а затем я добавил еще один.
Я слегка надавил на диск, когда он вращался на высокой скорости, а моя дрель вращала клапан в другом направлении.
Поэтому Притирка клапана заняла 3 минуты, а не несколько секунд, как на видео.
Но мои клапаны были изъедены довольно глубоко.
Мой клапан соприкасался с диском в середине, а не на внешнем крае, так что там точно меньше прогибается.
доктор
Снайпер
- #7
Свомпратт сказал:
Ты прав. В итоге я их удвоил. Я мог видеть, что он едва прогибается с 1 диском, а затем я добавил еще один.
![]()
Я слегка надавил на диск, когда он вращался на высокой скорости, а моя дрель вращала клапан в другом направлении.
Поэтому Притирка клапана заняла 3 минуты, а не несколько секунд, как на видео.Но мои клапаны были сильно изъедены.
Мой клапан соприкасался с диском в середине, а не на внешнем крае, так что там точно меньше прогибается.Нажмите, чтобы развернуть…
Теперь используйте эту установку для работы с 3-угловым или 5-угловым клапаном, и я буду впечатлен! Просто шучу. Это на самом деле чертовски круто. Парень на видео выглядел так, будто у него за шлифовальным диском был какой-то покровитель, чтобы сделать его жестче.
Свомпратт
Снайпер
- #8
Да, я видел этого покровителя.. Диск на самом деле хорошо режет, так что большого давления не требуется.
С другой стороны, я взялся за работу с заводскими клапанами GM в небольшом блоке Chevy и с заводскими клапанами и просто притер их без обрезки клапана или седла, и пробежал середину 11 на 1/4 мили без добавления мощности.
Народная мастерская в Нормане сделала для меня 5 угловых клапанов на некоторых головках 601, это головки 305 HO.
Затем я портировал головки и удалял все углы, кроме двух, и запускал 11-е на насосе с октановым числом 91 с двигателями 355 дюймов. Никаких усилителей мощности.
Аллен делал для меня головки в то время. Головки 305 он сработал … все покупатели, которые пробовали
, возвращались за другими головками, потому что головки 305 не работали
Он хотел знать, что я сделал с ними после того, как они вышли из магазина
Однажды я пригласил его на обед и сказал ему. .. Я предупредил его, что ему не понравится то, что я собираюсь ему сказать.
он был полностью посвящен трубке Вентури на выпускном отверстии.. и, играя с расходомером, измеряющим различные параметры, вы обнаружите много воздуха в форме трубки Вентури.
Я сказал ему, что вынул трубку Вентури из выпускного отверстия и оставил 2 угла.
Он покачал головой, а затем сказал: Ну, конечно, получилось. Автомобиль разогнался до 117 миль в час на 1/4. Это был лучший MPH.
Неплохо для 355 дюймов в 78 Nova с 29Плоский толкатель 2H comp с полки.
Эти камеры 305HO начинались с 53,5 куб. см, а после снятия кожуха я получил 61,5 куб. Удаление большого количества металла.
Вы можете оставить его в районе 57 куб. см с заводскими клапанами 1,84-1,50.. в этот клапан были вставлены 1,94-дюймовые клапаны. двигатель видит
Вы должны прибегнуть к испытанию своих вещей в реальных условиях
Как мы знаем
Карбюраторы Edelbrock Carter AFB LS тюнинг.
- Свомпратт
- Редукторы
- Ответы
- 1
- просмотров
- 673
Свомпратт
Делиться:
Фейсбук Твиттер Реддит Пинтерест Тамблер WhatsApp Электронная почта Делиться Связь
Верх Низ
работа клапана своими руками | Только для тела Mopar Forum
273
Известный член
- #1
Я смотрел несколько видеороликов на YouTube о том, как самому делать клапаны и направляющие.
Мне было интересно проконсультировать по необходимому оборудованию, в основном для головок Magnum la 318/360.
Например, старый станок для шлифовки клапанов и/или ручные фрезы и т. д. ?
Мюррей
Золотой член FABO
- #2
Ничего подобного. Не заменит настоящие вещи.
гилберттитан08
Мексиканская деревенщина!!!
- #3
273 сказал:
Я смотрел несколько видеороликов на YouTube о том, как самому делать клапаны и направляющие.
Мне было интересно проконсультировать по необходимому оборудованию, в основном для головок Magnum la 318/360.
Например, старый станок для шлифовки клапанов и/или ручные фрезы и т. д. ?Нажмите, чтобы развернуть…
Я многому научился, работая своими руками. Возьмите его и сделайте это правильно.
273
Известный член
- #4
Может быть, я хочу учиться на собственном горьком опыте
Последнее редактирование:
джос51700
Зеленый Подшипник резьбы ценителя
- #5
Можете ли вы взять изношенный и освежить его за несколько миль?
Конечно.
Стоит ли это времени и денег?
Обычно нет.
Машинная работа не является делом рук, потому что иначе все бы этим занимались.
273
Известный член
- #6
Я ценю слова предупреждения, я хочу иметь возможность сделать это для себя, не тратя десятки тысяч долларов на оборудование, так что любой, кто там работает, работает головой с помощью скромных инструментов. Если бы вы могли перечислить, что вы польза и зачем и какие уловки.
Пожалуйста и спасибо.
гилберттитан08
Мексиканская деревенщина!!!
- #7
273 сказал:
Может быть, я хочу учиться на собственном горьком опыте.
Нажмите, чтобы развернуть…
А если это дорогая ошибка? Как мой дедушка всегда говорил моему отцу, и мой отец всегда говорил мне. «У вас есть деньги, чтобы сделать что-то дважды, но вы не хотите тратить деньги, чтобы сделать это правильно».
gdrill
Я ЕСМЬ
- #8
Жаль, что у меня нет старой машины Sioux с клапаном и седлом.
gdrill
Я ЕСМЬ
- #9
Теперь, когда я смотрю, они продаются везде!
Здесь их несколько:
Станок для шлифовки клапанов Sioux 680 — 750 долларов США (sierra viata)
318willrun
Канал Utube 318willrun
- #10
Я думаю, это здорово, что ты хочешь попробовать. Я много лет делал себе головы —
из них. У меня были годы службы у этих голов. Некоторые из этих головок до сих пор стоят на автомобилях спустя 20 лет. Я перечислю, что я делаю дома с помощью обычных инструментов…
- Разборка
- проверьте направляющие и осмотрите головки.
- Притирка клапанов и проверка на утечки
- перенос
- установить новые пружины, клапаны, если необходимо, и уплотнения клапанов
- в сборе
Что не могу сделать:
- установить новые сиденья или новые направляющие. Однако я уверен, что это можно сделать с помощью некоторых инструментов «сделай сам», предназначенных для этой цели.
- магнафлекс для трещин. Но, я могу присмотреться к трещинам в общих местах.
RustyRatRod
Я родился в понедельник. Не в прошлый понедельник.
- #11
Мысль о том, что машинный труд — это какой-то джин в бутылке, просто безумна. Вы, конечно, можете научиться делать это самостоятельно. Я сам много работаю над головкой блока цилиндров. Я никогда не публиковал это здесь и никогда не буду, потому что я использую методы старой школы, такие как камни и алмазные точилки. Те, кто сосет яйца Серди, будут смеяться надо мной, так что вы никогда не увидите меня в постах. Я думал о том, как сделать, но ни за что.
318willrun
Канал Utube 318willrun
- #12
РастиРатРод сказал:
Мысль о том, что машинный труд — это какой-то джин в бутылке, просто безумна. Вы, конечно, можете научиться делать это самостоятельно. Я сам много работаю над головкой блока цилиндров. Я никогда не публиковал это здесь и никогда не буду, потому что я использую методы старой школы, такие как камни и алмазные точилки.
Нажмите, чтобы развернуть…
Если работает, значит работает. Я разместил свои здесь, но если кто-то хочет их увидеть, они могут зайти на мой канал u-tube и посмотреть их. Я сделал низкие 318 долларов на этом сайте, и более 4 лет спустя они все еще терпят крах, и самое главное — я доволен ими! Расходы? новые выпускные клапаны, сальники клапанов и новые вихревые пружины, а также несколько камней для портирования и, возможно, 125 баксов в сумме.
RustyRatRod
Я родился в понедельник. Не в прошлый понедельник.
- №13
318willrun сказал:
Если работает, значит работает. Я разместил свои здесь, но если кто-то хочет их увидеть, они могут зайти на мой канал u-tube и посмотреть их. Я сделал низкие 318 долларов на этом сайте, и более 4 лет спустя они все еще терпят крах, и самое главное — я доволен ими! Расходы? новые выпускные клапаны, сальники клапанов и новые вихревые пружины, а также несколько камней для портирования и, возможно, 125 баксов в сумме.
Нажмите, чтобы развернуть…
Я посмотрела все ваши, и они мне нравятся.
fishmens67
FABO Gold Member
- №14
318willrun сказал:
Я думаю, это здорово, что ты хочешь попробовать. Я много лет делал себе головы —
некоторыеиз них. У меня были годы службы у этих голов. Некоторые из этих головок до сих пор стоят на автомобилях спустя 20 лет. Я перечислю, что я делаю дома с обычными инструментами.
..
- Разборка
- проверьте направляющие и осмотрите головки.
- Притирка клапанов и проверка на утечки
- перенос
- установить новые пружины, клапаны, если необходимо, и уплотнения клапанов
- в сборе
Что не могу сделать:
- установить новые сиденья или новые направляющие. Однако я уверен, что это можно сделать с помощью некоторых инструментов «сделай сам», предназначенных для этой цели.
- магнафлекс для трещин. Но, я могу присмотреться к трещинам в общих местах.
Нажмите, чтобы развернуть…
Ты уверен, что не был с нами в магазине 40 лет назад?
fishmens67
FABO Gold Member
- №15
РастиРатРод сказал:
Мысль о том, что машинный труд — это какой-то джин в бутылке, просто безумна. Вы, конечно, можете научиться делать это самостоятельно. Я сам много работаю над головкой блока цилиндров. Я никогда не публиковал это здесь и никогда не буду, потому что я использую методы старой школы, такие как камни и алмазные точилки. Те, кто сосет яйца Серди, будут смеяться надо мной, так что вы никогда не увидите меня в постах. Я думал о том, как сделать, но ни за что.
Нажмите, чтобы развернуть…
И этот парень прятался где-то в магазине. лол
Bodyperson
Педаль до металла
- №16
Вы можете притирать собственные сиденья и заменять уплотнения для зонтов. Вот об этом, насколько я могу видеть.
Наездник на драконах
Известный член
- # 17
вы можете использовать стержни осей и расширители, а также домашние направляющие
Бодиперсон
Педаль к металлу
- # 18
Драконий Всадник сказал:
вы можете использовать штоки os и развёртки и направляющие
Нажмите, чтобы развернуть…
???????? Не говорите код. ЛОЛ
Питтсбургрейсер
Золотой член FABO
- # 19
В этом посте много плохой информации. Я заплатил 400,00 за свой станок для шлифовки клапанов и почистил его много лет назад. У меня есть и я могу делать седла клапанов с камнями, но я редко делаю это больше. Я купил бывшие в употреблении резцы седла клапана Neway на Ebay и пилоты для каждого применения, для которого они мне нужны. Когда я перехожу к клапану большего размера, я могу это сделать, но это занимает очень много времени, поэтому я их разбираю и очищаю, а местный магазин берет с меня 80,00, чтобы открыть восемь впускных отверстий и выполнить работу клапана, необходимую для больших клапанов.
Наездник на драконах
Известный член
- #20
о. с.
стержни увеличенного размера вместо новых направляющих
, но вы должны купить развертку подходящего размера и щетку для бутылок
но
что только что сказал Питтсбург
Фрики
Известный член
- # 21
Создание мощных двигателей невозможно без современных станков с ЧПУ и твердосплавных фрез.
Вот так мы выиграли ВОВ! Как еще, по-вашему, США построили все эти массивные радиальные двигатели и двигатели V12 для нашей армейской авиации? Конечно, с невероятной инопланетной технологией ЧПУ. Без карбида и компьютеров, конечно, ничего примечательного не сделать.
Каттеры Neway, похоже, очень популярны среди любителей самоделок. Также много наборов для шлифовки. Шлифование — это приобретенный навык, который требует практики и сноровки, но ему можно научиться. Резчики могут болтать, но то же самое — их ловкость и техника могут иметь большое значение.
Если вы когда-либо управляли токарным станком или имели опыт работы с машинами, держу пари, кривая обучения не слишком крутая. Если нет… Что ж, ничему нельзя научиться, делая.
273
Известный член
- # 22
питтсбургрейсер сказал:
В этом посте много плохой информации. Я заплатил 400,00 за свой станок для шлифовки клапанов и почистил его много лет назад. У меня есть и я могу делать седла клапанов с камнями, но я редко делаю это больше. Я купил бывшие в употреблении резцы седла клапана Neway на Ebay и пилоты для каждого применения, для которого они мне нужны. Когда я перехожу к клапану большего размера, я могу это сделать, но это занимает очень много времени, поэтому я их разбираю и очищаю, а местный магазин берет с меня 80,00, чтобы открыть восемь впускных отверстий и выполнить работу клапана, необходимую для больших клапанов.
Нажмите, чтобы развернуть…
Это то, что я видел, как люди используют на Youtube. Спасибо
273
Известный член
- # 23
Фрикиш сказал:
Невозможно построить двигатели высокой мощности без современных шлифовальных станков с ЧПУ и твердосплавных фрез.
Вот так мы выиграли ВОВ! Как еще, по-вашему, США построили все эти массивные радиальные двигатели и двигатели V12 для нашей армейской авиации? Конечно, с невероятной инопланетной технологией ЧПУ. Без карбида и компьютеров, конечно, ничего примечательного не сделать.
Каттеры Neway, похоже, очень популярны среди любителей самоделок. Также много наборов для шлифовки. Шлифование — это приобретенный навык, который требует практики и сноровки, но ему можно научиться. Резчики могут болтать, но то же самое — их ловкость и техника могут иметь большое значение.
Если вы когда-либо управляли токарным станком или имели опыт работы с машинами, держу пари, кривая обучения не слишком крутая.
Если нет… Что ж, ничему нельзя научиться, делая.
Нажмите, чтобы развернуть…
В старших классах ходил в механический магазин, несколько лет назад, я уверен, что смогу понять это, лол
273
Известный член
- # 24
gilberttitan08 сказал:
А если это дорогая ошибка? Как мой дедушка всегда говорил моему отцу, и мой отец всегда говорил мне. «У вас есть деньги, чтобы сделать что-то дважды, но вы не хотите тратить деньги, чтобы сделать это правильно».
Нажмите, чтобы развернуть…
Это не имеет ничего общего с попыткой сэкономить доллар, я строю 5.9джип в качестве дрэг-трака, хочу немного заняться двигателестроением старой школы, не стремясь получить сумасшедшую мощность, хочу посмотреть, что я могу сделать со своим трудом, чтобы избавиться от в основном запасных частей.
Конечно, с точки зрения производительности я бы лучше купил что-то вроде трюковых потоков или чего-то подобного, меня это не интересует, чтобы легко зарабатывать энергию с помощью кредитной карты, с которой я хочу поиграть.
Фрики
Известный член
- # 25
273 сказал:
Чтобы легко получить власть в наши дни с помощью кредитной карты, я хочу поиграть.