Картография кузова — журнал «АБС-авто»
Зачем нужны карты?
Любая современная технология – это система. Сказанное полностью относится к антикоррозионной защите автомобиля. Разумеется, если говорить о полноценной профессиональной обработке.
Система антикоррозионной защиты включает многое: обучение персонала, технологию и методику работы, оборудование, материалы, контроль, гарантии. Словом, весь цикл обработки, основанный на единой концепции. Один из обязательных признаков системы – технологическая карта. Поговорим о ней подробнее.
Сотрудник концерна Dinol GmbH Свен Ларсен создает технологические карты для антикоррозионной обработки автомобилей. Он побывал и в нашей стране, продемонстрировав свое умение на российских моделяхВ России немало сервисов, где антикоррозионная обработка выполняется формально, лишь бы «замылить глаз» клиенту. Особенно этим грешат автосалоны, денно и нощно мечтающие о лишних строчках в заказ-наряде.
Вроде бы все правильно, клиент доволен, деньги получены. Но если спросить мастера: «А есть ли у вас технологическая карта для обработки данной конкретной машины?» – ответ будет примерно таким: «А зачем?». Мол, все автомобили одинаковы.
Такая реакция говорит лишь об одном: о недостаточной подготовке мастера. Настоящие профессионалы давно отказались от клише «все кузова одинаковы». Да, у всех автомобилей имеются пороги, стойки, двери, капоты и проч. Но тут-то сходство и заканчивается. В угоду обеспечения жесткости кузова при непрерывном снижении веса автомобиля в полостях делаются сложнейшие нахлесты, фигурные ребра, усилители и т.д.
Поэтому полости кузова современного автомобиля таят в себе хитрые переплетения металла. Пороги «японок» отличаются от «немецких», конденсат в полостях «американцев» скапливается не там, где у «французов», а расположение сварных швов у «корейцев» иное, чем у «шведов».
Как их делают?
Самостоятельно изучить особенности всех автомобильных «тел», конечно же, невозможно. Да и не нужно, поскольку сей труд взяли на себя производители антикоррозионных материалов. Как же они изучают кузова?
Во-первых, штудируя техническую документацию завода – изготовителя автомобиля. Во-вторых, при помощи бороскопов (технических видеоэндоскопов), позволяющих заглянуть в самые потаенные уголки скрытых полостей. В-третьих, разрезая кузова аварийных и утилизированных машин. В результате появляется статистика: где и в какие сроки возникают очаги коррозии у той или иной модели.
А потом на свет рождаются руководства к действию – технологические карты обработки кузова. Вспомним банальную истину: коррозия приходит изнутри. Поэтому надежная защита на 99% зависит от грамотной профессиональной обработки скрытых сечений. Иными словами, от действий мастера по алгоритму конкретной технологической карты. Только карта укажет, как дотянуться факелом материала до критических точек и проблемных участков, где просверлить дополнительное отверстие и когда поменять насадку.
Говоря формально, технологические карты – это составная часть информационного обеспечения профессиональной антикоррозионной защиты. Такая же как обучение персонала, описание технологий и методик работы, контроль, гарантии, работа с клиентурой.
Технологичекая карта российского автомобиля УАЗ Patriot, разработанная Свеном Ларсеном (фрагмент)Обратимся к опыту немецкого концерна Dinol GmbH. Именно он разработал систему антикоррозионной защиты на основе материалов Dinitrol. Наряду с описаниями препаратов, инструкциями, руководствами и прочими полезными вещами, фирменные сервисы получают технологические карты со схемами и рисунками. В них указана вся необходимая мастеру информация: в какой последовательности, какими материалами, каким инструментом, какие участки автомобильного кузова обрабатывать. Причем не какого-то абстрактного автомобиля, а конкретной марки, модели и года выпуска.
Давайте посмотрим на приведенные здесь карты Dinitrol. Они усеяны графическими значками. Это своеобразный язык, которому присущи однозначность, простота и доступность.
Не будем сейчас разъяснять всю символику этих карт – для их изучения предусмотрены специальные руководства, и дублировать их нет смысла. Но отдельные значки все же расшифруем.
Пустой кружок говорит о том, что материал закачивается в отверстие, выполненное заводом – изготовителем автомобиля. Кружок с закрашенной сердцевиной – это отверстие, также выполненное заводом-изготовителем, но заглушенное пробкой.
Кружок с незакрашенным треугольником говорит о том, что отверстие для закачки материала необходимо просверлить на станции антикоррозионной обработки.
Кружок с закрашенным треугольником – что отверстие необходимо просверлить и заглушить после обработки.
Наличие подробных технологических карт, безусловно, говорит о тщательности, скрупулезности фирменного подхода к антикоррозионной защите автомобиля. А строгое следование документации позволяет свести к минимуму человеческий фактор и избежать ошибок при обработке.
Русские «картежники»
Не следует думать, что технологические карты создаются исключительно за рубежом. Dinol GmbH потому и считается мировым производителем антикоров, что учитывает специфику различных регионов планеты. Например, зачем создавать технологическую карту для автомобиля УАЗ Patriot в Швеции, если основная масса этих внедорожников сосредоточена в России? Да и рассказать об особенностях этих машин могут только россияне.
Поэтому не так давно нашу страну посетил Свен Ларсен, сотрудник датского отделения Dinol GmbH. Свен – ас антикоррозионного ремесла. Достаточно сказать, что у себя в Дании он курирует и консультирует 67 антикоррозионных станций. А в Скандинавии к защите автомобилей относятся более чем серьезно – море, соленые ветра, перепады температур многому научили местных жителей.
Эскизы Свена Ларсена после обработки становятся полноценными технологическими картамиНо вернемся в Россию. Совместно со специалистами из компании ЮВК Свен отобрал следующие автомобили: УАЗ Hunter, УАЗ Patriot, Kia Rio, SsangYong Aсtyon, Lifan Solano, Lifan X60, Lifan Smily, Chery Tiggo, КАМАЗ, LADA Granta. Технологические карты решили разработать именно для этих марок и моделей. Логично: часть из них выпускается в нашей стране, другая же часть получила в России наиболее широкое распространение.
В чем заключалась работа Свена Ларсена? В принципе она описана в предыдущем разделе. Он изучал скрытые полости с помощью видеоэндоскопа, отслеживал, есть ли в конструкции кузова технологические заглушки для обработки полости, надо ли сверлить специальное отверстие и где можно его сверлить, чтобы не нанести вред автомобилю.
Кроме того, датчанин отмечал расположение электронных блоков, подушек безопасности, исполнительных механизмов и датчиков на каждом автомобиле. Все тщательно фотографировал и зарисовывал. Изучал моторный отсек, багажник, отмечал каждую конструктивную и технологическую особенность панелей.
Затем г-н Ларсен вернулся в Данию, чтобы вместе с другими специалистами Dinol GmbH создать фирменную технологическую карту обработки каждого из перечисленных автомобилей. Чтобы читатели оценили его титанический труд, мы публикуем фрагмент технологической карты для автомобиля УАЗ Patriot. Впечатляет, не правда ли?
А так выглядит карта для одного из популярных «иностранцев» (фрагмент)Карта плюс опыт
Директор компании ЮВК Юрий Климин и ведущий технический специалист той же компании Леонид Игнатьев рассказали редакции много интересного. Оказывается, карты год от года меняются. Это естественно, ведь меняются и сами автомобили, а карты всего лишь их отражение.
Например, в современных моделях уменьшилось число высверливаемых отверстий для закачки материала. Во-первых, автопроизводители увеличили число других отверстий – технологических, полученных еще на этапе изготовления кузова и закрытых заглушками. Причина новшества проста: автомобильные концерны работают в контакте с производителями антикоров и прислушиваются к их советам.
Во-вторых, появились новые «хитрые» распылительные насадки, способные дотянуться до участков, о защите которых без сверления раньше и мечтать не могли.
И наконец, в-третьих, антикоррозионные материалы непрерывно совершенствуются: расширяется ассортимент, появляются новые ингибиторы коррозии, увеличивается проникающая способность препаратов.
Многим клиентам нравится, что кузова их машин не сверлят. Но полностью устранить эту операцию пока не удается. Поэтому, уточняет Леонид Игнатьев, для получения отверстий необходимо использовать специальное сверло – коническое с пошаговым диаметром точно под резиновую или пластиковую заглушку. К тому же такое сверло не повредит пучок проводки, датчик или любое другое скрытое от глаз оборудование.
Увеличилось число пластиковых обтекателей и щитков на днище кузова. Естественно, при обработке их необходимо демонтировать, что увеличивает общее время обработки. К тому же встает проблема крепежа (клипсов). Зачастую они одноразовые и легко ломаются. К счастью, запастись крепежом на станции сегодня не проблема.
Символы и пиктограммы, обозначающие особенности работы с конкретным участком кузова. Тут и пояснений особых не надо – белый кружок, дрель перечеркнута, значит, это заводское отверстие без заглушки. Подробно – в тексте статьи. А в нижней части рисунка – типы насадок для пистолетов. Например, насадка К обеспечивает кольцевой распыл и применяется для защиты внутренних полостей
А сколько особенностей у конкретных автомобилей! Взять тот же УАЗ. На переднем и заднем мостах у него есть особые «подушки» высотой 6–7 см, сваренные из листов толщиной 4 мм. Они не прогрунтовываются и не прокрашиваются, поэтому обработка антикором здесь обязательна. Причем имеющим не просто хорошую, а отличную пенетрацию. И толстую пленку, выдерживающую 500 часов в камере соляного тумана, что эквивалентно пяти годам эксплуатации.
Проблемная зона любого автомобиля – место сварки заднего крыла и багажника. При погружении в катафорезную ванну на заводе шов защищается недостаточно и начинает ржаветь. При обработке на СТОА ему надо уделять особое внимание.
Кромки дверей. Вот уж где поиздевались над металлом, сетует Леонид. Согнули, завальцевали, грунтовка и краска в эти нахлесты не проходит, а влага поселяется мгновенно. Здесь тоже необходим материал с высокой пенетрацией.
Примеры можно продолжать едва ли не бесконечно. Так работает симбиоз технологической карты и опыта. Синергия науки и практики. А в результате автомобиль получает действительно надежную защиту от коррозии. В ближайшее время мы продолжим эту тему.
Документы, регламенты
Нормативные документы
При оказании услуг по антикоррозионной обработке автомобилей и других работ производимых нашей компанией, основной нормативной базой являются законы Российской федерации.
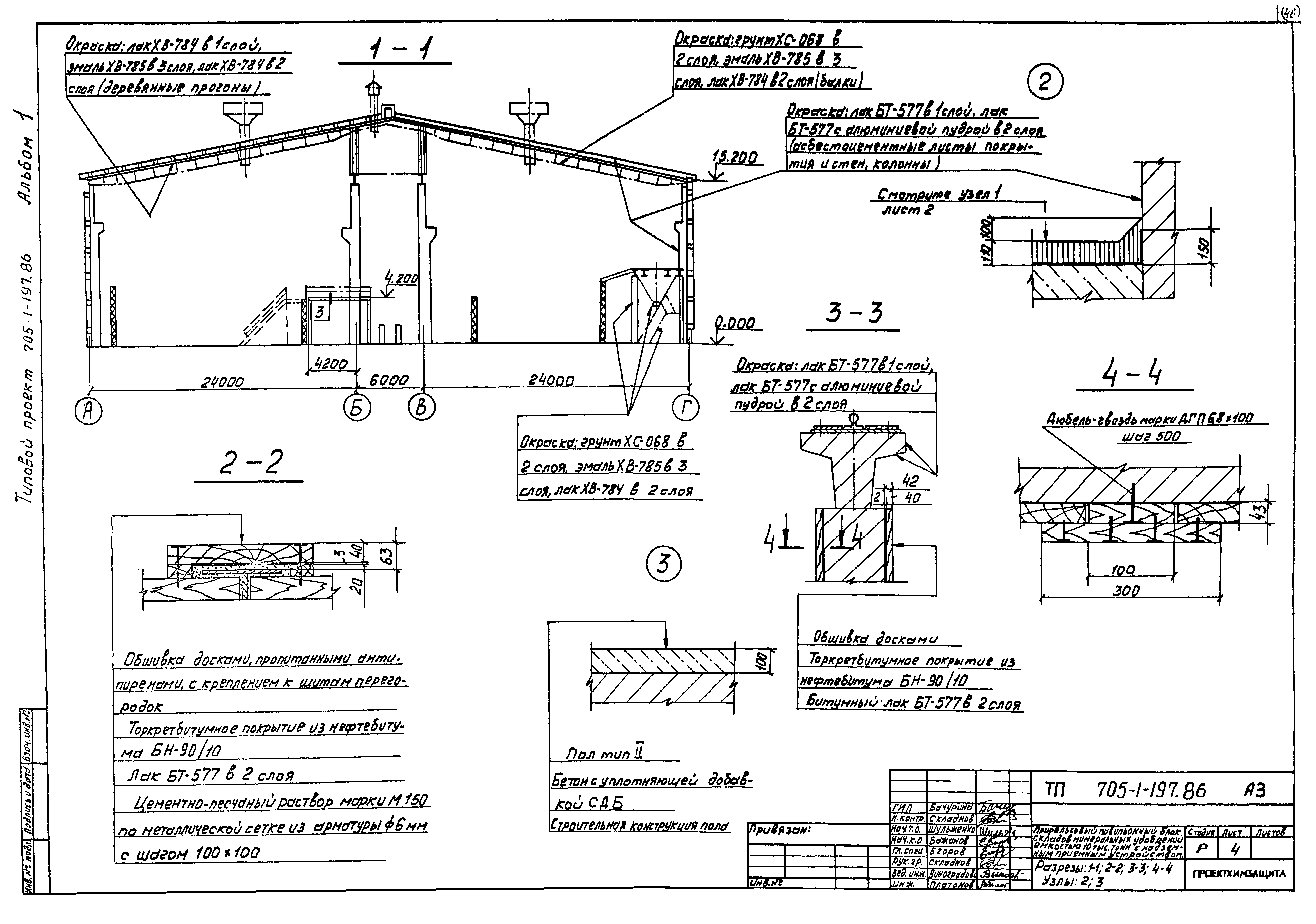
— Регламент антикоррозионной обработки
— Регламент ежегодного профилактического осмотра
— «Щадящий» режим эксплуатации после проведения работ по антикоррозионной обработке
Мы производим антикоррозионную обработку и шумоизоляцию автомобилей по следующим расценкам:
— Прейскурант на обработку автомобилей длиной до 4 м.
— Прейскурант на обработку автомобилей длиной от 4 до 5 м.
— Прейскурант на обработку автомобилей длиной свыше 5 м.
— Прейскурант на обработку кроссоверов
— Прейскурант на обработку минивэнов
— Прейскурант на обработку внедорожников, пикапов
— Прейскурант на обработку минигрузовиков
— Прейскурант на обработку микроавтобусов
— Прейскурант на шумоизоляцию автомобилей
— Прейскурант на отдельные категории работ, не входящие в основной прейскурант
— Главный нормативный документ
При антикоррозийной обработке мы руководствуемся схемами обработки, полученными от поставщиков материалов и производителей автомобилей.

— Образец технологической карты
На все проведенные работы мы даем гарантии.
— Условия гарантии на антикоррозионную обработку
При проведении работ по антикоррозионной обработке и нанесению различных защитных покрытий, все наши специалисты обязаны строго соблюдать данные регламенты, а так же инструкции к материалами и защитным составам, согласно данным производителей материалов.
Ежегодно наши сервисы проходят сертификацию на соответствие российским стандартам предприятий автомобильной отрасли:
— Сертификат антикор-центра Варшавское ш., д. 125, стр. 20
— Сертификат антикор-центра Кронштадтский б-р, д. 35 Б
— Сертификат антикор-центра Высоковольтный пр-д. д. 9
— Сертификат антикор-центров 2014-2015 г.
— Сертификат антикор-центров 2015-2016 г.
— Сертификат на установку допоборудования 2015-2016 г.
— Cертификат антикор-центров 2016-2017 г.; Приложение к Сертификату 2016-2017 г.
— Сертификат антикор-центров 2017-2018 г.
— Приложение 2017-2018 (Кронштадтский б-р. д. 35 Б)
— Приложение 2017-2018 (Высоковольтный пр-д. д. 9)
— Приложение 2017-2018 (Варшавское ш. д. 125, стр. 20)
— Приложение 2017-2018 (Бережковская наб. 20, стр. 23)
— Сертификат антикор-центров 2018-2019 г.
— Приложение 2018-2019 (Кронштадтский б-р. д. 35 Б)
— Приложение 2018-2019 (Высоковольтный пр-д. д. 9)
— Приложение 2018-2019 (Варшавское ш. д. 125, стр. 20)
— Приложение 2018-2019 (Бережковская наб. 20, стр. 23)
— Приложение 2018-2019 (1 Измайловского зверинца, д. 8)
Технологическая карта антикоррозийной обработки geely mk
G eely МК / C ross. ПРОЧИСТКА ДРЕНАЖНЫХ ОТВЕРСТИЙ КУЗОВА
Во время эксплуатации в полостях порогов, дверей и крышке багажника скапливается влага, вызывающая коррозию. Для удаления влаги служат дренажные отверстия, расположенные снизу порогов, две-
рей и в крышке багажника. Они постоянно забиваются грязью, поэтому прочищайте их при каждом техническом обслуживании (через каждые 10 тыс. км пробега). При эксплуатации автомобиля на проселочных дорогах проводите эту операцию чаще.
Прочищайте дренажные отверстия перед мойкой автомобиля.
Вам потребуется отвертка или тонкая деревянная палочка.
1. Поддев отверткой.
2. . снимите заглушки.
3. . и прочистите дренажные отверстия в каждом пороге кузова.
Так расположены дренажные отверстия в порогах кузова.
4. Аналогично прочистите дренажные отверстия в передних и задних дверях.
5. Снимите заглушки и прочистите дренажные отверстия в крышке багажника.
6. Прочистите отверстия в лонжеронах кузова.
Зачем нужны карты?
Любая современная технология – это система. Сказанное полностью относится к антикоррозионной защите автомобиля. Разумеется, если говорить о полноценной профессиональной обработке.
Система антикоррозионной защиты включает многое: обучение персонала, технологию и методику работы, оборудование, материалы, контроль, гарантии. Словом, весь цикл обработки, основанный на единой концепции. Один из обязательных признаков системы – технологическая карта. Поговорим о ней подробнее.
Сотрудник концерна Dinol GmbH Свен Ларсен создает технологические карты для антикоррозионной обработки автомобилей. Он побывал и в нашей стране, продемонстрировав свое умение на российских моделях
В России немало сервисов, где антикоррозионная обработка выполняется формально, лишь бы «замылить глаз» клиенту. Особенно этим грешат автосалоны, денно и нощно мечтающие о лишних строчках в заказ-наряде. И тогда работа выглядит так. Помыли машину, побрызгали жидким материалом в полости дверей, стоек, капота и багажника. Потом подняли машину, опять же побрызгали в полости, доступные снизу, покрыли мастикой днище – и, пожалуйста, готово.
Вроде бы все правильно, клиент доволен, деньги получены. Но если спросить мастера: «А есть ли у вас технологическая карта для обработки данной конкретной машины?» – ответ будет примерно таким: «А зачем?». Мол, все автомобили одинаковы.
Такая реакция говорит лишь об одном: о недостаточной подготовке мастера. Настоящие профессионалы давно отказались от клише «все кузова одинаковы». Да, у всех автомобилей имеются пороги, стойки, двери, капоты и проч. Но тут-то сходство и заканчивается. В угоду обеспечения жесткости кузова при непрерывном снижении веса автомобиля в полостях делаются сложнейшие нахлесты, фигурные ребра, усилители и т.д.
Поэтому полости кузова современного автомобиля таят в себе хитрые переплетения металла. Пороги «японок» отличаются от «немецких», конденсат в полостях «американцев» скапливается не там, где у «французов», а расположение сварных швов у «корейцев» иное, чем у «шведов». И даже слияния концернов и общие платформы не спасают – унификации нет, и быть не может.
Как их делают?
Самостоятельно изучить особенности всех автомобильных «тел», конечно же, невозможно. Да и не нужно, поскольку сей труд взяли на себя производители антикоррозионных материалов. Как же они изучают кузова?
Во-первых, штудируя техническую документацию завода – изготовителя автомобиля. Во-вторых, при помощи бороскопов (технических видеоэндоскопов), позволяющих заглянуть в самые потаенные уголки скрытых полостей. В-третьих, разрезая кузова аварийных и утилизированных машин. В результате появляется статистика: где и в какие сроки возникают очаги коррозии у той или иной модели.
А потом на свет рождаются руководства к действию – технологические карты обработки кузова. Вспомним банальную истину: коррозия приходит изнутри. Поэтому надежная защита на 99% зависит от грамотной профессиональной обработки скрытых сечений. Иными словами, от действий мастера по алгоритму конкретной технологической карты. Только карта укажет, как дотянуться факелом материала до критических точек и проблемных участков, где просверлить дополнительное отверстие и когда поменять насадку.
Говоря формально, технологические карты – это составная часть информационного обеспечения профессиональной антикоррозионной защиты. Такая же как обучение персонала, описание технологий и методик работы, контроль, гарантии, работа с клиентурой.
Технологичекая карта российского автомобиля УАЗ Patriot, разработанная Свеном Ларсеном (фрагмент)
Обратимся к опыту немецкого концерна Dinol GmbH. Именно он разработал систему антикоррозионной защиты на основе материалов Dinitrol. Наряду с описаниями препаратов, инструкциями, руководствами и прочими полезными вещами, фирменные сервисы получают технологические карты со схемами и рисунками. В них указана вся необходимая мастеру информация: в какой последовательности, какими материалами, каким инструментом, какие участки автомобильного кузова обрабатывать. Причем не какого-то абстрактного автомобиля, а конкретной марки, модели и года выпуска.
Бороскоп (технический видеоэндоскоп) с камерой и встроенной подсветкой позволяет заглянуть в потаенные уголки кузова
Давайте посмотрим на приведенные здесь карты Dinitrol. Они усеяны графическими значками. Это своеобразный язык, которому присущи однозначность, простота и доступность.
Не будем сейчас разъяснять всю символику этих карт – для их изучения предусмотрены специальные руководства, и дублировать их нет смысла. Но отдельные значки все же расшифруем.
Пустой кружок говорит о том, что материал закачивается в отверстие, выполненное заводом – изготовителем автомобиля. Кружок с закрашенной сердцевиной – это отверстие, также выполненное заводом-изготовителем, но заглушенное пробкой.
Кружок с незакрашенным треугольником говорит о том, что отверстие для закачки материала необходимо просверлить на станции антикоррозионной обработки.
Кружок с закрашенным треугольником – что отверстие необходимо просверлить и заглушить после обработки.
Наличие подробных технологических карт, безусловно, говорит о тщательности, скрупулезности фирменного подхода к антикоррозионной защите автомобиля. А строгое следование документации позволяет свести к минимуму человеческий фактор и избежать ошибок при обработке.
Русские «картежники»
Не следует думать, что технологические карты создаются исключительно за рубежом. Dinol GmbH потому и считается мировым производителем антикоров, что учитывает специфику различных регионов планеты. Например, зачем создавать технологическую карту для автомобиля УАЗ Patriot в Швеции, если основная масса этих внедорожников сосредоточена в России? Да и рассказать об особенностях этих машин могут только россияне.
Поэтому не так давно нашу страну посетил Свен Ларсен, сотрудник датского отделения Dinol GmbH. Свен – ас антикоррозионного ремесла. Достаточно сказать, что у себя в Дании он курирует и консультирует 67 антикоррозионных станций. А в Скандинавии к защите автомобилей относятся более чем серьезно – море, соленые ветра, перепады температур многому научили местных жителей.
Эскизы Свена Ларсена после обработки становятся полноценными технологическими картами
Но вернемся в Россию. Совместно со специалистами из компании ЮВК Свен отобрал следующие автомобили: УАЗ Hunter, УАЗ Patriot, Kia Rio, SsangYong Aсtyon, Lifan Solano, Lifan X60, Lifan Smily, Chery Tiggo, КАМАЗ, LADA Granta. Технологические карты решили разработать именно для этих марок и моделей. Логично: часть из них выпускается в нашей стране, другая же часть получила в России наиболее широкое распространение.
В чем заключалась работа Свена Ларсена? В принципе она описана в предыдущем разделе. Он изучал скрытые полости с помощью видеоэндоскопа, отслеживал, есть ли в конструкции кузова технологические заглушки для обработки полости, надо ли сверлить специальное отверстие и где можно его сверлить, чтобы не нанести вред автомобилю.
Кроме того, датчанин отмечал расположение электронных блоков, подушек безопасности, исполнительных механизмов и датчиков на каждом автомобиле. Все тщательно фотографировал и зарисовывал. Изучал моторный отсек, багажник, отмечал каждую конструктивную и технологическую особенность панелей. И заранее прикидывал, каким именно составом Dinitrol предпочтительно обрабатывать те или иные области кузова.
Еще один фрагмент карты УАЗ Patriot. Работа с капотом и дверьми. Попробуйте догадаться, что означают эти значки. А расшифровку мы даем в тексте
Затем г-н Ларсен вернулся в Данию, чтобы вместе с другими специалистами Dinol GmbH создать фирменную технологическую карту обработки каждого из перечисленных автомобилей. Чтобы читатели оценили его титанический труд, мы публикуем фрагмент технологической карты для автомобиля УАЗ Patriot. Впечатляет, не правда ли?
А так выглядит карта для одного из популярных «иностранцев» (фрагмент)
Карта плюс опыт
Директор компании ЮВК Юрий Климин и ведущий технический специалист той же компании Леонид Игнатьев рассказали редакции много интересного. Оказывается, карты год от года меняются. Это естественно, ведь меняются и сами автомобили, а карты всего лишь их отражение.
Например, в современных моделях уменьшилось число высверливаемых отверстий для закачки материала. Во-первых, автопроизводители увеличили число других отверстий – технологических, полученных еще на этапе изготовления кузова и закрытых заглушками. Причина новшества проста: автомобильные концерны работают в контакте с производителями антикоров и прислушиваются к их советам.
Что характерно для технологических карт последнего поколения – они не содержат операций сверления. Или сводят их к минимуму
Во-вторых, появились новые «хитрые» распылительные насадки, способные дотянуться до участков, о защите которых без сверления раньше и мечтать не могли.
И наконец, в-третьих, антикоррозионные материалы непрерывно совершенствуются: расширяется ассортимент, появляются новые ингибиторы коррозии, увеличивается проникающая способность препаратов.
Многим клиентам нравится, что кузова их машин не сверлят. Но полностью устранить эту операцию пока не удается. Поэтому, уточняет Леонид Игнатьев, для получения отверстий необходимо использовать специальное сверло – коническое с пошаговым диаметром точно под резиновую или пластиковую заглушку. К тому же такое сверло не повредит пучок проводки, датчик или любое другое скрытое от глаз оборудование.
Увеличилось число пластиковых обтекателей и щитков на днище кузова. Естественно, при обработке их необходимо демонтировать, что увеличивает общее время обработки. К тому же встает проблема крепежа (клипсов). Зачастую они одноразовые и легко ломаются. К счастью, запастись крепежом на станции сегодня не проблема.
Символы и пиктограммы, обозначающие особенности работы с конкретным участком кузова. Тут и пояснений особых не надо – белый кружок, дрель перечеркнута, значит, это заводское отверстие без заглушки. Подробно – в тексте статьи. А в нижней части рисунка – типы насадок для пистолетов. Например, насадка К обеспечивает кольцевой распыл и применяется для защиты внутренних полостей
Под пластиковыми щитками обнаруживается изрядное количество грязи – спекшийся конгломерат глины, песка, соли. До нескольких килограммов! Для наглядности мы приводим фотографии этого «бесценного груза». В холода он замерзает и начинает давить и на пластик, и на металл. И бывает, выдавливает обоих. Такое никакой технологической картой не предусмотришь.
Так выглядит специальное сверло. Благодаря конической форме инструмента стружка выбрасывается наружу, а края зенкуются. Зенкование решает две задачи: убирает заусенцы и формирует площадку под специальную заглушку (пробку-«грибок»)
А сколько особенностей у конкретных автомобилей! Взять тот же УАЗ. На переднем и заднем мостах у него есть особые «подушки» высотой 6–7 см, сваренные из листов толщиной 4 мм. Они не прогрунтовываются и не прокрашиваются, поэтому обработка антикором здесь обязательна. Причем имеющим не просто хорошую, а отличную пенетрацию. И толстую пленку, выдерживающую 500 часов в камере соляного тумана, что эквивалентно пяти годам эксплуатации.
Проблемная зона любого автомобиля – место сварки заднего крыла и багажника. При погружении в катафорезную ванну на заводе шов защищается недостаточно и начинает ржаветь. При обработке на СТОА ему надо уделять особое внимание.
Наш консультант ведущий технический специалист компании ЮВК Леонид Игнатьев При обработке этой «японки» демонтировали пластиковые кожухи, призванные защищать днище, и обнаружили… …в каждом из кожухов по 2–3 кг грязи из окаменевшей смеси песка, глины и соли. Так, казалось бы, совершенно неожиданно, создаются условия для образования коррозии
Кромки дверей. Вот уж где поиздевались над металлом, сетует Леонид. Согнули, завальцевали, грунтовка и краска в эти нахлесты не проходит, а влага поселяется мгновенно. Здесь тоже необходим материал с высокой пенетрацией.
Примеры можно продолжать едва ли не бесконечно. Так работает симбиоз технологической карты и опыта. Синергия науки и практики. А в результате автомобиль получает действительно надежную защиту от коррозии. В ближайшее время мы продолжим эту тему.
Процесс антикоррозийной обработки автомобиля
В этой статье вы поближе познакомитесь с процессом антикоррозионной обработки автомобиля.
Не секрет, что машины должны поддаваться ей на этапе производства. Но это не всегда так, а в связи с длительной эксплуатацией даже автомобили, которые проходили ее, теряют часть такой защиты.
Обработка проводится по трем направления: выполняется обработка колесных арок и днища кузова; скрытых полостей с использованием проникающих составов; нанесение защитного слоя антигравийного материала на лицевые панели.
Термодинамическая неустойчивость металла – это основная причина, по которой автомобиль поддается коррозии. Стремление перейти в более привычное окисленное состояние металлов и сплавов, которые являются частью автомобиля, приводит к возникновению коррозии.
Чтобы защитить машину от этого воздействия, приходится использовать специальные пленочные составы, разработанные на основе битумов, тонких масел, восков. Чтобы технология обработки принесла желаемый результат, она должна быть выполнена в определенной последовательности.
Перед непосредственной обработкой понадобится провести подготовку, которая даст возможность проводить основные работы.
Для начала нужно загнать автомобиль на пост антикоррозионной обработки, после чего он поднимается на подъемник. После этого снимаются колеса.
Далее машину нужно тщательно промыть горячей водой под давлением.
Промываются кузов, колесные арки, двигатель, днище.
Обязательно следует на всем процессе антикоррозионной обработки проводить уборку и поддерживать чистоту участка.
После этого выполняется сушка автомобиля, для чего применяется тепловая пушка. Длительность сушки составляет 1-1,5 часа.
Если антикоррозионная обработка будет выполнятся в помещение, следует обратить внимание, что оно должно иметь хорошую вентиляцию.
Используя технологическую карту из альбома, нужно снять заглушки с технических и дренажных отверстий. В случае необходимости, можно просверлить дополнительные отверстия. Для этого предназначено конусное сверло, с помощью которого можно сделать отверстия без стружки.
Автомобиль поднимается на подъемнике, при этом, можно визуально определить точки распыления ориентируясь на технологическую карту.
Затем, немного опустив машину, проверяется состояние кузова и возможные повреждения антикоррозионного покрытия корпуса автомобиля.
При наличии интерскопа можно выполнить более детальную проверку состояния скрытых полостей, проникновение во все технологические отверстия. Эта процедура даст возможность оценить внутренние дефекты металла и степень покрытия их ржавчиной. После ее проведения можно дать оценку состояния машины перед началом антикоррозионной обработки.
На следующем этапе понадобится закрыть узлы, которые не будут обрабатываться. На тормозные диски надеваются защитные покрытия. Подготовку к проведению обработки на этом можно считать законченной.
Для антикоррозионной обработки используются два пневматических насоса. Первый – насос высокого давления, который позволяет выполнить обработку способом безвоздушного нанесения на днище высоковязких составов. На выходе можно достичь давления примерно 150 атмосфер. Специальный шарнир предотвращает поворачивание шлангов. Регулировать подачу материала можно с помощью редуктора. При засорении используется насадка с поворотным флажком.
Что касается второго насоса – это поршневое приспособление низкого давления, c помощью которого производится обработка скрытых полостей аэрозольным методом. Распылитель соединяется с двумя шлангами, по одному из них поступает воздух с компрессора, по другому – материал. В распылителе проходит их смешивание. Через специальные насадки они наносятся на кузов.
Для обработки могут применятся другие типы насосов, которые способны создавать еще большее давление.
После ознакомления с оборудованием, можно перейти к обработке. Используем насос низкого давления, который даст возможность провести обработку скрытых полостей. Проводим воздушное распыливание материала в скрытой полости. Насадки могут быть длиной от 1,5 до 2 метров.
Чтобы обрабатывать пороги, лонжероны, усилители было наиболее удобно, автомобиль нужно поднять. На этом этапе нужно тщательно обработать все элементы, которые находятся под машиной.
Используемые в нашем случае материалы Noxudol не имеют в своем составе летучих растворителей, обработку можно выполнять без защитных масок. Данный МЛ состав покрывает внутренние поверхности кузовных деталей, дает возможность заполнить поры, сварные швы, а также вытесняет влагу из всех щелей и пор благодаря капилярному эффекту.
Тонкая пленка, которая образуется на скрытых полостях, защищает их на протяжении нескольких лет. Этот же состав позволяет выполнить грунтование швов или сложных профилей, если такие есть на днище автомобиля.
В этом МЛ составе есть специальные присадки, которые замедляют коррозию.
После этого, с помощью специального износоустойчивого состава, обрабатываются колесные арки. Наносится он шпателем или кистью вручную.
Переходим к обработке днища автомобиля.
Снова нужно поднять машину на подъемнике и выполнить грунтование участков со сложным профилем. Высоковязкий материал Noxudol 300 перед применением нужно разогреть до температуры 30 градусов, для чего используется электрический тен. После этого он наносится на кузов автомобиля безвоздушным методом.
В различных видах этот состав может быть обыкновенно черным или с добавлением алюминиевой пудры. Она позволяет армировать состав и образует плотную пленку. Воторой вариант применяется, если машина чаще эксплуатируется на дорогах с плохим покрытием.
Когда обработка будет закончена, автомобиль опускается и снимается защитная пленка с тормозных дисков. После этого устанавливаются колеса.
Ставим машину на пол и начинаем обработку скрытых полостей, для чего поднимаем капот, открываем багажник и двери.
Для работы используем насос низкого давления. Не обойтись и без специальных насадок. Добраться к скрытым полостям для их обработки можно через технологические отверстия автомобиля. МЛ состав наносится на боковые двери, усилители капота, багажника, стойки кузова. Перед обработкой боковых дверей на кресла нужно одеть защитные чехлы.
В процессе работы понадобится для различных технологических отверстий использовать различные насадки. После завершения обработки заглушки ставятся на свое место, устанавливаются подкрылки.
Устраняются остатки антикоррозионных материалов с помощью специальных растворов, которые удаляют жиры и масла
Автомобиль можно использовать сразу после обработки, однако для «жидких подкрылок» щадящий режим сушки составляет не менее суток.
Для удобства автомобилистов материал можно приобрести в аэрозольных баллонах. Noxudol 300 предназначен для обработки днища автомобиля; Noxudol 700 – проникающий антикор для внутренних поверхностей на основе масла МЛ; в линейке продукции компании есть также Noxudol 1100 – антигравийное покрытие, которое наносится на лицевые панели и пороги.
Применяется часто для автомобилей, которые не имеют на порогах специальных пластиковых накладок. Наносят его с помощью антигравийного пистолета. Специальный переходник пистолета дает возможность надеть его на специальный евробаллон и при подаче воздуха антигравийное покрытие можно наносить на поверхность.
Антикоррозийная обработка кузова автомобиля | Выбрать антикор для авто
Коллапс на валютном рынке показал, что в ближайшее время российские автолюбители будут массово отучаться от привычки менять автомобиль каждые 3 года. Очевидно, что многим из них станут интересны продукты, позволяющие существенно продлить срок жизни старого автомобиля. Поэтому некоторые автосервисы сегодня включают в свои услуги антикоррозийную обработку. Однако далеко не всегда этот вид работ выполняется правильно. Журнал «КУЗОВ» совместно со специалистами сети независимых СТО «Tuning-S» протестировали линейку защитных препаратов Dinitrol.
На протяжении двух десятилетий автопроизводители твердят, что современные автомобили не нуждаются в дополнительной антикоррозийной обработке. Одни концерны делают упор на оцинковку, другие используют гальванику и катафорез. Специалисты компании Dinitrol, ведущего производителя антикоррозийных защитных покрытий, путем лабораторных испытаний доказали, что соляной раствор при перепадах температур в кратчайшие сроки разъедает любой металл. Именно поэтому продукция компании востребована в авиастроении и даже используется при обработке железнодорожных составов.
Недостаточно постаринке «вымазать» днище машины гудроном. Современный автомобиль имеет огромное количество скрытых труднодоступных полостей, найти которые может только квалифицированный специалист при наличии технической карты автопроизводителя. Кроме того, для проведения качественной антикоррозийной обработки требуется специализированное оборудование, высококачественные составы и неукоснительное соблюдение предписаний поставщика химии.
Компания «ЮВК» не только реализует продукцию Dinitrol, но также оказывает консультативную и техническую поддержки своим клиентам. На тренингах специалисты независимых СТО получают наиболее полную информацию по необходимым инструментам и нормам использования расходных материалов бренда. Немецкое представительство компании-производителя DinolGmbh внимательно следит за появлением новых моделей автомобилей и в кратчайшие сроки предоставляет своим партнерам обновленные технологические карты, что гарантирует правильность и качество выполнения работ. Все продукты производятся на предприятиях в Германии и Швеции.
На примере автомобиля Mitsubishi L200 мы подробно рассмотрим весь процесс антикоррозийной обработки кузова автомобиля. В самом начале необходимо правильно подготовить поверхность. Машина загоняется на подъемник, где специалист снимает подкрылки и промывает днище мощным напором воды.
Влага высушивается тепловыми пушками, механически зачищаются очаги коррозии, и поверхность обезжиривается очистителем Dinitrol 7225 или 582.
Если автомобиль совсем новый, то обойтись можно лишь обезжириванием.
Теперь стоит определиться с видом антикора. Если клиента интересует дополнительная шумоизоляция, то ему подойдут «жидкие подкрылки» Dinitrol 479.
Наносится материал специальным пистолетом Dinitrol в два слоя (толщиной 1,5 мм каждый) с выдержкой в 15 минут при рабочем давлении от 6 до 10 атмосфер.
Высохшая поверхность покрывается шагренью, которая гасит потоки воздуха, поглощая шум от колес. В основе материала – синтетическая резина, которая позволяет надежно защитить поверхность от воздействия песка, камней и гравия.
Материал имеет 80% сухого остатка, поэтому при работе в прохладном помещении следует учесть, что емкости с продуктами предварительно нужно поставить на донный нагреватель и установить нагрев на уровне не выше 40 градусов.
На днище мы нанесли полуторамиллиметровый слой состава Dinitrol 4941 на восково-битумной основе, который противостоит коррозии и обеспечивает эффективную защиту от абразивных повреждений. Средний расход на автомобиль D класса – 4-5 литров.
Вышеупомянутые продукты можно заменить более прогрессивным, усиленным дисперсией алюминия восковым составом Dinitrol Metalliс, отличающимся высокой тиксотропией, лучшими антикоррозийными свойствами и хорошим шумопоглощающим эффектом. Материал также распространяется в 1, 5, 20, 60 и 208-литровых упаковках, покрывая потребности любого сервиса.
В каждом автомобиле сотни сварных швов и точек. Несмотря на оцинковку или гальванику, со временем металл в этих местах ослабевает, и кузов теряет прежнюю жесткость, что сказывается на безопасности. Предотвратить появление коррозии в скрытых полостях поможет Dinitrol 3641-А80. Но если «болезнь» уже запущена, то скрытые полости проливают Dinitrol Penetrant или Dinitrol ML. Эти влаговытесняющие составы, благодаря ингибиторам коррозии, обладают способностью проникать в ржавчину и консервировать химический процесс.
Для работы со скрытыми полостями потребуется комплект виниловых шлангов высокого давления с крюкообразными наконечниками. Трубка подсоединяется к оборудованию высокого давления воздушного режима работы, которое увеличивает рабочее давление распределения материалов в 3 раза. Антикоррозионный состав наносят методом распыления внутри труднодоступной полости при помощи насадок на 190° и 360° под давлением в 18 атмосфер. Стоит отметить, что при ежедневном использовании оборудование не нуждается в чистке, материалы просто не успевают засохнуть внутри», – рассказал Денис Кобюк, ведущий технический специалист компании «ЮВК».Следующим этапом работы является нанесение защитного антикоррозийного воска Dinitrol Korrotec 485 в местах, которые могут соприкасаться с кожей человека или одеждой. Обрабатываются крепления дверей и амортизаторов, водостоки, желоба и прочие стыки, а также соединения под капотом и в багажнике.
Некоторые клиенты предпочитают, чтобы на машине был виден антикор. В этом случае для обработки видимых частей порогов и бамперов подойдет Dinitrol 3641 бежевого оттенка.
В финальной части нашего мастер-класса специалист должен защитить двигатель и картер автомобиля составом Dinitrol Сorroheat 4010 или спреем Dinitrol Corrosion Prevention. «Этот состав специально разработан для использования на поверхностях, подверженных воздействию как высоких, так и низких температур. Наносится на предварительно помытый и высушенный двигатель, окружающий пластик, резинки, датчики и даже проводку. Состав обладает высокими теплопроводными функциями и очень тонкую поверхностную пленку, поэтому теплоудара можно не опасаться», – уверен Сергей Федоров, менеджер по продажам СТО «Trade-c». Консервант не только защищает агрегаты моторного отсека от коррозии, но также предотвращает их загрязнение и облегчает последующую мойку. Мы продемонстрировали максимальный комплекс услуг по консервации кузова. Как видно из статьи, оборудование зоны под антикоррозийную обработку не требует больших затрат. Вне зависимости от слесарной или кузовной специфики сервиса услуга позволяет существенно повысить стоимость среднего чека в кризисный год.Антикор кузова Lada Largus / Лада Ларгус
Скрытые полости для антикоррозийной обработки
Впрыск антикоррозийного состава производится в указанных на рисунках точках:
1, 2, 3 и 4 — для защиты соединения накладки нижней секции боковины кузова с усилителем нижней секции боковины кузова.
5, 6 и 7 — для защиты соединения пола с усилителем лонжерона.
8 — для защиты соединения пола с поперечиной крепления переднего сиденья.
12, 13 и 14 — для защиты соединения панели порога с усилителем панели порога.
Во все остальные точки также впрыскивается антикоррозийный состав. Все отверстия закрыты резиновыми заглушками. После обработки не забывайте устанавливать на место заглушки. Порвавшиеся, или отсутствующие заглушки замените новыми (каталожные номера см. здесь, здесь и в соседних с ними разделах.)
Антикоррозийная обработка скрытых полостей осущестляется с помощью удлиннительного шланга, который вставляется в полость на максимально возможную глубину, после чего производится впрыск состава с одновременным, постепенным извлечением шланга из полости.
О дополнительной антикоррозийной обработке
(Примечание: информация носит общепознавательный характер)
Во времена дикого накопления капитала, «ЛогоВАЗа» с господином Березовским и резкого снижения продаж отечественных автомобилей в связи с хлынувшим в Россию потоком подержанных иномарок стала необычайно актуальна тема защиты кузова от коррозии. Не то чтобы раньше это было неважно, просто в конце 90-х — начале 2000-х отечественные автозаводы перешли на очень облегченные, почти обходные технологии грунтовки и окраски.
Объяснялось это просто — прибыли падали, экономические связи трещали по швам, заводы обложили натуральным рэкетом — не до качественной покраски стало. В результате неубиваемые когда-то «Волги», «Жигули» и УАЗы уже через год начинали цвести, причем не только на стыках, но и по площадям, еще пара-тройка лет — и в кузове появлялись откровенные дыры. Гнило все — оперение, лонжероны, пороги, двери, что при такой технологии подготовки и окраски совершенно не удивляло.
Тогда-то по гаражам и мастерским появились спецы, вытравливающие ржу ортофосфорной кислотой, производящие локальную сварку и покрывающие затем все потенциально опасные зоны антикоррозийным покрытием, наивным, конечно, по нынешним временам — пушечным салом да отработкой, но все равно частично и это помогало.
Одновременно появились и фирменные центры по антикоррозионной обработке, использующие уже совсем другие, значительно более эффективные препараты импортного производства. Правилом хорошего тона на тот момент было после покупки автомобиля отогнать оный в подобный техцентр и произвести полную комплексную обработку дорогим, но зато действенным фирменным составом вроде «Тектил-цинка». Оно еще и выгоднее выходило — продать на вторичном рынке машину с нормальным кузовом было проще, а главное, автомобиль меньше терял в цене.
В нашем суровом климате гниению подвержено все — и отечественные машины, и «Мерседесы» S-класса, разнится лишь скорость взаимодействия с окружающей средой, поэтому центры антикоррозионной обработки работой были вполне загружены. Однако в каждом правиле есть свои исключения. Ими оказались автомобили из Ингольштадта. Марка Audi уже давно начала оцинковывать свои модели, причем не скупясь на цинк, видимо, маркетологи в те времена были людьми порядочными. Толщина покрытия 20-25 микрон давала полную уверенность в завтрашнем дне, да что там, Audi В2 до сих пор можно увидеть на улицах Москвы — где-то краска уже даже слезла сама но себе, виден голый металл, но чистый, без ржавчины.
Скорость окисления цинка в условиях гальванической пары цинк/железо — порядка пяти-шести микрон за семь-восемь лет, так что у старых Audi запас прочности будь здоров. Насмотревшись на удачливых конкурентов, очень многие автопроизводители также начали оцинковывать кузова, однако маркетологи уже поняли свою задачу, да и цинк надо экономить, так что покрытие новых авто стало не в пример тоньше — порядка 5-10 микрон, что, кстати, создает опасность механического повреждения и дальнейшей галопирующей коррозии в очаге этого повреждения. Сейчас оцинковывают даже Lada, но не полностью, к тому же сварные швы цинкуются достаточно сложно, бюджетные марки полноценного процесса позволить себе не могут, так и возникают дополнительные очаги коррозии, впрочем, в смысле маркетинга это неплохо — ведь автомобиль должен отходить лишь гарантийный срок, а дальше ему лучше бы развалиться и сгнить, дабы вам можно было впарить новый.
Потом, существует целый ряд проблем на российских предприятиях, кстати, в том же Черкесске, где варят и красят почти все автомобильные кузова для китайских марок. В общем, если потребители, то есть мы с вами, не согласны с волюнтаризмом маркетологов, приходится шевелиться самим, ведь «спасение утопающих — дело рук самих утопающих», верно?
В этой связи опять актуальной становится дополнительная антикоррозионная обработка даже нового «железного коня», поскольку в случае наступления гарантийного случая дилер быстрее всего откажет вам в ремонте, сославшись на «нарушение условий эксплуатации».
Кстати говоря, о дилерских услугах. Хотелось бы предупредить настоящего или потенциального владельца авто: дилерский техцентр — это последнее место, где стоит делать дополнительный антикор. Во-первых, они на нем не специализируются, во-вторых, вовсю применяют обходные технологии, заботясь лишь о внешнем виде машины. Доводилось видеть, как в ремзоне пластиковые подкрылки сажают на саморезы, прямо сквозь краску, грунтовку и металл. Что будет в месте крепления крыла и подкрылка? Правильно, сквозная ржавая дыра, причем уже через год-полтора.
Сейчас все работы лучше выполнять у профессионалов, хотя и за ними нужен глаз да глаз, так что советую раньше времени не расслабляться. А рекомендации очевидны: электрику делаем у электриков, моторы у мотористов, а антикор, соответственно, в специализированном центре.
Впервые антикоррозионную обработку в привычном для нас виде стали делать шведы в 50-х годах прошлого века, тогда-то и появился термин «ML-состав». Изначально это была высокотекучая смесь на масляной или восковой основе для обработки скрытых полостей автомобиля, но с 50-х прошло уже очень много времени, за которое химический состав ингредиентов ML-жидкостей весьма сильно изменился, и, естественно, в лучшую сторону. Сейчас в антикор-центрах обработка скрытых полостей ведется ML-составами уже пятого поколения, однако, по отзывам специалистов, уже третье поколение данных препаратов дает весьма приемлемый результат.
Так чем же они так хороши?
Дело в том, что в скрытые коробчатые полости частенько попадает влага, иногда проникая сквозь уплотнения, иногда в виде конденсата при скачке температуры наружного воздуха. В России климат резко континентальный, что как раз и обуславливает подобные скачки, соответственно, в коробах и скрытых полостях без дополнительной обработки постоянно повышена влажность, а контакт голого железа с водой и кислородом как раз и приводит к химической реакции окисления — коррозии. Поэтому обработка машины на специализированной станции выглядит так — удаляются все технологические заглушки, полости промываются водой под напором, а затем сушатся с помощью тепловых пушек. Занятие это долгое и муторное, посему за мастерами во время работы лучше проследить, дабы они сделали все но технологической карте.
Сама технологическая карта, которую разрабатывают производители соответствующей автохимии под каждый конкретный автомобиль, должна быть у техцентра в наличии; если ее нет, лучше поискать другую мастерскую, поскольку, если половину скрытых полостей пропустить при обработке, само нанесение покрытия в целом уже бессмысленно.
ML-составы, особенно последнего поколения, хороши тем, что вытесняют влагу и пропитывают уже образовавшуюся ржавчину, создавая на ней защитный слой и препятствуя дальнейшему разрушению металла. Но есть и другая сторона медали — если эти жидкости хорошо работают в скрытых полостях, то снаружи они живут недолго, со временем смываются водой и летящим из-под колес абразивом. В общем, снаружи автомобиль приходится дополнительно обрабатывать уже другими смесями с определенным набором свойств или производить комплексное покрытие: ML + битумная мастика. Покрытия, плохо поддающиеся механическим воздействиям, изготавливаются в основном на основе битума с резиновой крошкой или гальваническим наполнителем — тем же цинком или алюминием. Они разделяются по вязкости, химическому составу и, соответственно, применяемости. «Антигравий», «Жидкие подкрылки» — все эти термины хорошо известны автомобилистам. С «Антигравием», местами его нанесения и эффектом от применения более или менее ясно: если он защищает проблемные места машины от пескоструйки и бомбардировки мелкими камнями в процессе эксплуатации, то у «Жидких подкрылков» и мастики для днища уже и состав, и преследуемые цели немного другие. Объединяет их одно — высокая механическая стойкость, но мастика должна обладать дополнительным рядом свойств — являться ингибитором коррозии частично корродировал, необходимо выяснить степень коррозии, прежде чем покрывать днище. На начальной стадии, когда очаги поражения не фатальны и находятся лишь на поверхности, можно применить комплексную обработку: сначала ML-состав и лишь потом мастика. Если же коррозия проникла глубоко и ржавчина уже пластинчатая, перед нанесением мастики проблемные места необходимо полностью очистить от коррозии и лишь затем обрабатывать поверхность антикором. В случае если просто залить ржавое дно битумным составом, мастика просто отвалится вместе со ржавчиной, опять открыв доступ влаге и воздуху к металлу.
В общем, если вам хочется сохранить машину и, соответственно, свои инвестиции, несмотря на все старания маркетологов, за кузовом придется следить — именно он самая дорогая деталь автомобиля.
Владимир Кузьменно, Автокомпоненты
Видео
Антикоррозийная обработка — какую выбрать
«Хотелось бы сделать антикоррозийную обработку 5-летнему Mitsubishi ASX. По виду днища — пора, ржавчина уже есть! Какую обработку посоветуете и почему?»
Антикоррозийная обработка бывает полной и частичной, профессиональной и самостоятельной. Не увидев, как на самом деле обстоит ситуация с коррозией в конкретном автомобиле, невозможно аргументировано посоветовать, какую из них выбрать. В общем виде технологический процесс антикоррозийной обработки состоит из нескольких подготовительных и окончательных операций, но не все из них являются обязательными. Какие процедуры можно безболезненно исключить, а без каких не обойтись — это зависит от текущего состояния кузова, причем не только в плане развития на нем коррозии, но и в отношении имеющейся к настоящему времени штатной защиты.
В частности, сомнительно, что на днище 5-летнего автомобиля коррозия разгулялась настолько, что начинать борьбу с ней придется с пескоструйной очистки. Еще маловероятнее, что началу антикоррозийной обработки должны предшествовать сварочные работы.
Скорее всего, в рассматриваемой машине появившиеся очаги ржавления невелики, качественно удалить с них коррозию удастся вручную с помощью щетки, наждачной бумаги или соответствующей насадки на электродрель.
В таком случае бороться с коррозией можно самостоятельно, тем более что антикоррозийные препараты нетрудно купить в большинстве крупных автомагазинов и на рынках запчастей.
Исходите из того, что принцип работы любого препарата — изоляция защищаемой поверхности от влаги и кислорода. Качественная изоляция позволяет процесс коррозии если не приостановить, то существенно замедлить. При этом значение имеет не только то, насколько хорош применяемый препарат, но и технология обработки. Например, если при подготовке к нанесению препарата не будет уделено внимания удалению старой ржавчины, в ее рыхлом слое останется все необходимое, чтобы процесс коррозии продолжался и под свеженанесенным покрытием.
Технологический процесс полной обработки подразумевает демонтаж пластиковой защиты с мест, которые будут подвергаться нанесению антикора, их мойку и сушку, удаление ржавчины и потерявшего защитные свойства старого покрытия, сверление технологических отверстий, необходимых для обработки скрытых полостей, грунтование. Завершает работу нанесение основного покрытия на наружные поверхности и в закрытые полости, его сушка, удаление препарата, вытекшего из щелей, и обратный монтаж пластиковой защиты.
В некоторых случаях может понадобиться демонтаж задних фонарей, обшивки капота и крышки багажника, если без этого невозможно обработать изнутри задние крылья, капот и багажник.
Все это трудоемко, долго и, главное, индивидуально для каждой конкретной модели автомобиля. На некоторых СТО, профессионально занимающихся антикоррозийной обработкой, существуют технологические карты, которыми руководствуются при проведении работ. Если речь идет о полной обработке кузова, лучше обращаться на такие СТО. Самостоятельную обработку, о которой упоминалось выше, можно рекомендовать лишь для локальной защиты мест, на которых была обнаружена коррозия, а также в случаях, когда старому, но вполне работоспособному защитному покрытию потребовался ремонт из-за повреждений, появившихся, например, после движения в плохих дорожных условиях, когда днище могло контактировать с какими-то препятствиями.
Контрольный вопрос, который требуется задавать при выборе СТО, — какова гарантия на выполненную работу, какими документами она будет подкреплена? Нет смысла поручать заниматься автомобилем специалистам, гарантия которых основана лишь на устных заверениях в непревзойденном качестве использованных материалов и собственном мастерстве. Если же на вопрос о гарантии в ответ услышите пожелание для начала посмотреть автомобиль — это уже серьезно. Как и в случае аргументированного совета, какую обработку выбрать, ни одна ответственная СТО не рискнет давать письменную гарантию и оговаривать тот или иной срок действия обязательств, пока воочию не оценит коррозийное состояние машины.
Сергей БОЯРСКИХ
Фото автора
ABW.BY
У вас есть вопросы? У нас еcть ответы. Интересующие вас темы квалифицированно прокомментируют либо специалисты, либо наши авторы — результат вы увидите на сайте abw.by. Присылайте вопросы на адрес [email protected] и следите за сайтом
В каком сервисе сделать антикоррозийную обработку, выбирайте здесь!
Антикор скрытых полостей автомобиля – как сделать обработку, какие средства использовать
В данной статье мы рассмотрим, где находятся скрытые полости автомобиля, как обработать их от коррозии и какие средства для этого использовать. Вы узнаете, как сделать антикор скрытых полостей своими руками, либо на что обратить внимание при заказе услуги в автосервисе.
Почему возникает коррозия?
В процессе эксплуатации кузов автомобиля подвергается воздействию нескольких видов коррозии, наиболее опасной из которых является электрохимическая. Она возникает при взаимодействии влаги с металлом кузова. Различные виды загрязнений, присутствующие в атмосфере и на поверхности дорог, противогололедные реагенты в зимний период – все это превращает влагу в электролит, в котором протекают электрохимические процессы, приводящие к коррозии металла.
Наиболее уязвимы для коррозии скрытые полости кузова. Если на открытых поверхностях влага быстро высыхает, то в скрытых полостях она остается постоянно, постепенно разъедая металл. Поэтому при антикоррозийной обработке автомобиля необходимо тщательно обработать все скрытые полости, к которым относятся замкнутые элементы кузова:
- пороги;
- лонжероны;
- стойки кузова;
- поперечины и усилители днища;
- места под молдингами и накладками;
- усилители моторного отсека.
Кроме того, на автомобиле много полостей, закрытых обшивкой и накладками:
- усилители капота;
- усилители крышки багажника;
- пространство между арками колес и крыльями;
- карманы дверей;
- места установки фар.
У многих производителей автомобилей разработаны технологические карты обработки скрытых полостей, с указанием мест их нахождения и способов доступа.
Процесс антикоррозийной обработки
Антикоррозийная обработка скрытых полостей кузова автомобиля производится ML-методом с использованием специального оборудования – пистолета-распылителя с различными насадками.
Антикоррозийный препарат наносится через технологические или специально просверленные отверстия. Подающийся под давлением состав образует внутри обрабатываемой детали туман, который осаждается на стенках полости, образуя пленку. Обработку производят до тех пор, пока из отверстия не появятся несколько капель препарата.
При антикоррозийной обработке скрытых полостей кузова для каждого элемента используются наиболее подходящие насадки для пистолета-распылителя:
- круглые;
- с вращающейся головкой;
- щелевые.
Желательно не эксплуатировать автомобиль в первые сутки после антикоррозийной обработки, чтобы нанесенные препараты окончательно просохли и имели хорошее сцепление с металлом кузова.
Материалы для антикора скрытых полостей
Производителями антикоррозийных материалов разработаны различные ML-препараты на основе высокоочищенных масел с добавлением воска. Качественный антикор для скрытых полостей автомобиля может содержать до 200 различных компонентов, обеспечивающих полную защиту скрытых полостей от коррозии.
Если вы выбираете, чем лучше обработать скрытые полости автомобиля от коррозии, обратите внимание, что материалы должны обладать следующими свойствами:
- образовывать эластичную пленку на поверхности полости;
- содержать замедлители коррозии;
- высокую адгезию к металлу;
- обладать хорошей проникающей способностью в образовавшуюся ржавчину;
- иметь высокую проникающую способность в трещины и микрозазоры;
- вытеснять воду с поверхности металла;
- не иметь резкого устойчивого запаха.
Мы в техцентре RB Group используем для обработки скрытых полостей средства шведской фирмы Auson AB – Mercasol и Noxudol. Данные материалы разработаны для эксплуатации автомобиля в тяжелых условиях, прошли полный цикл лабораторных испытаний в солевом тумане в течение 2500 часов и показали высокую эффективность.
Препараты Mercasol
Легкие препараты Mercasol созданы на восковой основе с использованием органических растворителей, что делает их экологически безопасными. Обладают высокой проникающей способностью, полностью заполняют все микротрещины и возможные дефекты в сварных швах.
Наличие грамотно подобранных ингибиторов останавливает процесс коррозии (если она уже появилась), а высокая пластичность препаратов Mercasol позволяет полностью заполнить всю скрытую полость любой конфигурации.
Антикоррозийная обработка скрытых полостей автомобиля материалами Mercasol производится методом распыления под давлением, с использованием специального оборудования или аэрозолями в евробаллонах. Оптимальная толщина покрытия составляет 100 микрон.
Препараты Noxudol
Материалы Noxudol, как и Mercasol, имеют восковую основу, но выпускаются в двух вариантах – с применением органических растворителей и безрастворительные. Оба вида имеют в своем составе ингибиторы коррозии, но безрастворительные препараты Noxudol обладают более высокой текучестью, что позволяет более тщательно заполнить микротрещины и очагов начавшейся коррозии.
Предназначенные для антикоррозийной обработки скрытых полостей автомобиля материалы Noxudol содержат специальные антикатализаторы, препятствующими полному отвердеванию, поэтому препараты Noxudol остаются пластичными и хорошо держатся на стенках полостей в любых условиях эксплуатации автомобиля. Обработка автомобиля этими препаратами производится распылением под давлением с помощью специального оборудования. Предварительно безрастворительные материалы Noxudol необходимо подогреть до 30°С.
Препараты Mercasol и Noxudol для антикоррозийной обработки скрытых полостей автомобиля эффективно защищают поверхность от коррозии и при этом являются одними из самых экологичных материалов на сегодняшний день.
Заказать антикор на автомобиль в техцентре RB Group.
Anti-Corrosion — обзор | Темы ScienceDirect
22.1 Введение: роль лазерной сварки в железнодорожном машиностроении
Железнодорожные вагоны из нержавеющей стали обладают многими преимуществами, такими как легкая конструкция кузова, высокая степень защиты от коррозии, характеристики безопасности, хорошие экологические характеристики и т. Д. SUS301L является одним из самых широко применяемые материалы в конструкции автомобиля из нержавеющей стали на неокрашенных внешних панелях [1]. Из-за низкой теплопроводности и большого коэффициента линейного расширения нержавеющая сталь обычно собирается с помощью точечной контактной сварки (RSW).Но из-за ударной мощности и теплового ввода сопротивления электрода для точечной сварки на поверхности кузова автомобиля из нержавеющей стали останется видимое углубление диаметром 1 см, что влияет на качество внешнего вида и герметичность. Необходимо и срочно найти новый метод решения этих проблем.
В последнее время сварочные процессы с высокой плотностью мощности все чаще используются в промышленном производстве из-за их огромных преимуществ, таких как незначительные искажения формы, уменьшение размера зоны термического влияния (HAZ) и более высокая скорость сварки, связанная с большим проплавлением [ 2].В некоторых исследованиях [3,4] изучалась возможность применения лазерной технологии для замены точечной контактной сварки при сборке элементов жесткости на боковых панелях рельсового транспортного средства. Японская компания Kawasaki Heavy Industries изучила метод лазерной сварки внахлест нержавеющей стали SUS304 без видимых вмятин на внешней поверхности, о чем сообщалось в Ref. [3]. Автор также указал на проблемы, рассмотренные выше, и резюмировал соединение точечной контактной сварки как «точечные» соединения, а соединение лазерной сварки — как «линейные» соединения.Некоторые эксперименты [5,6] показали, что скорость сварки должна соответствовать мощности лазера, а именно, высокая скорость сварки должна соответствовать высокой мощности лазера, чтобы получить соединение без видимых вмятин на поверхности. Различные исследования показали, что скорость сварки может достигать 5 м / мин, что слишком велико для обычных лазеров [3,4].
Кроме того, технология лазерной сварки будет применена к поезду на магнитной подушке Siemens в Германии, высокоскоростному поезду уровня DMU IC4 в Дании, высокоскоростным пригородным поездам ETR500 в Италии и т. Д.
Сравнение 5 коррозионно-стойких металлических покрытий
Легкие металлы стали популярным выбором во многих отраслях промышленности. Такие металлы, как алюминий, титан и теперь даже магний, стали жизненно важными для автомобильной, аэрокосмической и многих других областей применения. Сочетание их изобилия, исключительного отношения прочности к весу и универсальности означает, что они являются предпочтительным выбором для инженеров по всему миру.
Некоторые легкие сплавы обеспечивают превосходную коррозионную стойкость даже в необработанном виде, но неизбежно потребуется обработка поверхности готового продукта для обеспечения рабочих характеристик, долговечности и качества.Магний известен своей плохой коррозионной стойкостью, но менее известно то, что некоторые алюминиевые сплавы, такие как 2xxx, 7xxx и другие высокопрочные семейства, содержащие медь или другие переходные металлы, также подвержены такой же чувствительности.
Выбор правильного метода защиты от коррозии важен для успешного проектирования и производства компонентов. Каждый метод имеет уникальный набор преимуществ и потенциальных проблем. Мы собрали это сравнение различных методов лечения, чтобы помочь вам найти наиболее подходящее решение для ваших нужд.
1. Анодирование
Анодирование — самый популярный метод улучшения коррозионной стойкости алюминия. Вообще говоря, он включает в себя четырехэтапный процесс для достижения защиты.
Первый этап включает погружение материала в ванну с проводящим раствором — обычно кислотную ванну с низким pH — и подключение сплава к аноду электрической цепи. При подаче электрического тока на поверхности металла происходит реакция окисления:
2Al (S) + 6OH — (водн.) — 6e — Al 2 O 3 (s) + 3H 2 O (l)
Это вызывает утолщение естественного оксида на поверхности металла, создавая защитный внешний слой оксида алюминия.Толщина покрытия может быть изменена за счет увеличения времени нанесения покрытия, что обеспечивает широкий спектр применения:
- При легком нанесении может обеспечить хорошую предварительную обработку под краску или
последующих покрытий - При окрашивании можно получить особые цветовые эффекты.
- При нанесении тонким слоем (обычно <20 мкм) он полупрозрачный, что
сохраняет металлический эстетический вид, при желании
Выбор толщины покрытия играет ключевую роль в определении коррозионной стойкости.В наружных условиях или при интенсивном внутреннем стрессе (например, при постоянном контакте с жидкостью) рекомендуется минимум 20 мкм. Если для слоев требуется толщина 10 мкм, более высокое напряжение может повредить материал, растрескивая защитный оксидный слой и становясь пористым.
Кроме того, механизм роста и столбчатая микроструктура вызывают растрескивание по всей толщине на углах, что ограничивает защиту кромок, обеспечиваемую слоями анодирования. Уплотнения с горячей водой могут использоваться для обеспечения более надежной защиты, но более эффективные уплотнения могут быть достигнуты за счет использования опасных химических растворов, таких как ацетат никеля или бихромат натрия.
В конечном счете, для материалов, требующих определенных эстетических качеств, при сохранении высокой устойчивости к коррозии при контакте с жидкостями, анодирование — не лучший метод повышения коррозионной стойкости.
2. ПЭО
Плазменное электролитическое окисление (ПЭО) включает использование плазменных разрядов для преобразования металлической поверхности легких металлов. Он образует твердый и плотный адгезионный оксидный слой.
Компоненты погружаются в ванну, и электрический ток используется для «выращивания» однородного слоя оксида на поверхности.ПЭО состоит из трех этапов:
- Окисление подложки (как происходит в процессе анодирования)
- Соосаждение элементов из электролита в покрытие
- Модификация полученного слоя плазменным разрядом
Хотите узнать больше о методологии PEO Keronite? Щелкните ниже, чтобы загрузить бесплатный информационный документ.
PEO образует твердые, плотные и износостойкие покрытия для легких металлов, таких как алюминий, титан и магний.По сравнению непосредственно с анодированными покрытиями, PEO образует покрытия с более высокой твердостью, химической пассивностью и выгодной нерегулярной структурой пор, которая обеспечивает высокую устойчивость к деформации и более прочную адгезию.
Помимо превосходных физических и химических характеристик, процесс ПЭО может быть проведен экологически безопасным методом благодаря доброкачественным электролитам, доступным для использования, и нетоксичным побочным продуктам процесса окисления. Электролиты не содержат кислот, аммиака, тяжелых металлов и хрома, а используемые щелочные растворы с низкой концентрацией не представляют опасности и легко утилизируются.
Это означает более экологичное решение, чем альтернативы, а также ряд других преимуществ.
3. Хроматное конверсионное покрытие
Усиление контроля над производственными процессами со стороны государственных органов и регулирующих органов привело к постепенному отказу от использования хроматных конверсионных покрытий как метода защиты от коррозии, хотя это один из наиболее эффективных методов.
Химические составы конверсии хромата сильно различаются, но многие из них включают применение растворов хромовой кислоты, натрия, хромата или дихромата калия для очистки металлических поверхностей вместе с другими добавками.Использование таких добавок вызывает окислительно-восстановительные реакции на поверхности, оставляя на металле подложки пассивную пленку, содержащую оксид хрома (IV) и гидратированные соединения. Это обеспечивает высокую коррозионную стойкость и хорошо сохраняет последующие покрытия.
Высокая защита от коррозии обусловлена способностью соединений хрома (VI) восстанавливать защитную оксидную пленку на поврежденном участке покрытия, подвергающемся воздействию атмосферного кислорода. Это называется самовосстановлением. Аналогичный механизм используется для создания нержавеющей стали: хром, добавленный к сплаву, естественным образом образует очень тонкий пассивный слой оксида хрома на поверхности, предотвращая окисление железа.Он быстро восстанавливается, если поверхность повреждена, а подповерхностный хром подвергается воздействию атмосферы. Хромат также можно использовать в качестве добавки к краскам или в качестве герметика при анодировании, повышая их защиту от коррозии.
Однако в настоящее время известно, что соединения шестивалентного хрома, используемые при обработке с конверсией хромата, обладают повреждающими и канцерогенными свойствами. Побочные продукты хроматных конверсионных покрытий очень опасны, и поэтому неудивительно, что материалы, использующие этот процесс, занимают жесткую позицию.
Сегодня его использование запрещено во многих отраслях промышленности и строго регулируется. Он по-прежнему широко используется в аэрокосмической отрасли, не склонной к риску, но требует все большего изменения. К сожалению, он остается лучшим методом химической пассивации алюминия благодаря своим самовосстанавливающимся свойствам. Интенсивные исследования начались в 1980-х годах, чтобы найти альтернативы самовосстановлению без хрома, но они еще не соответствуют его общему уровню защиты. Инженеры ищут альтернативы, такие как анодирование или обработка на основе ПЭО, для повышения производительности в суровых условиях.
4. Краски
Растворы для поверхностных покрытий, такие как краски, грунтовки и другие полимерные системы, кажутся безграничными как по наличию, так и по разнообразию. Самым привлекательным преимуществом работы с красками является то, что их можно раскрашивать, обрабатывать или наносить разными способами.
Полимерные финишные покрытия также доступны с таким разнообразием и различными способами нанесения. Могут быть внесены альтернативные химические составы и добавки, которые обеспечивают такие свойства, как блеск, дополнительную твердость, смазывающую способность, определенные текстуры, температурную стабильность и химическую стойкость, и это лишь некоторые из них.
Краскипредставляют собой относительно недорогой метод повышения коррозионной стойкости. Однако задействованные процессы крайне неэффективны; Во время нанесения до 50% покрытия может испариться, а при отверждении в печи образуются вредные побочные продукты, которые опасны и дороги в утилизации в больших объемах.
Обладая превосходной химической и особенно коррозионной стойкостью, как и другие полимерные углеводороды, краски мягкие (их твердость определяется сравнением грифеля карандаша), что означает, что они легко царапаются и истираются.
5. Порошковые покрытия
Порошковые покрытия, как и краски, представляют собой еще один относительно недорогой вариант. Хотя преимущества порошковых покрытий во многом такие же, как и у красок, но более толстые защитные слои можно наносить более эффективно и быстрее.
Покрытия толстые, что добавляет объемные слои (обычно вверх до 80 мкм), которые существенно повышают коррозионную стойкость материала. Стоимость этой дополнительной защиты заключается в увеличении толщины, а также в том, что эстетические эффекты не столь привлекательны и неодинаковы для разных материалов.
Заключение
В этой статье мы попытались дать краткий обзор покрытий из легких материалов для улучшения коррозионной стойкости легких сплавов. На самом деле существуют сотни различных методов и процессов, доступных от разных поставщиков, каждый с небольшими вариациями в способах достижения результатов.
Выбор правильного покрытия жизненно важен, но непрост. Примите целостный взгляд на процесс нанесения покрытия, начиная с ранних этапов проектирования компонентов. Геометрия компонентов, обеспечение подходящего дренажа, предотвращение несовместимых комбинаций материалов и выбор сплава — все это решающие факторы.
Для достижения наилучших результатов выберите предварительную обработку, обеспечивающую хорошую адгезию к основанию и любой последующей обработке. Верхние покрытия следует выбирать с учетом их совместимости с предварительной обработкой и требуемых конечных / функциональных / эстетических свойств.
5 различных методов предотвращения коррозии
Мы в EonCoat понимаем важность предотвращения коррозии. Ржавчина и другие формы коррозии могут привести к проблемам с безопасностью и нарушить целостность вашего оборудования и расходных материалов.Даже плановое техническое обслуживание по удалению и устранению коррозии может привести к увеличению затрат. К счастью, есть ряд мер, которые можно предпринять, чтобы минимизировать коррозию. Здесь мы выделим четыре из этих методов с точки зрения затрат и эффективности.
1. Барьерные покрытия
Один из самых простых и дешевых способов предотвратить коррозию — использовать барьерные покрытия, такие как краска, пластик или порошок. Порошки, включая эпоксидную смолу, нейлон и уретан, нагреваются до металлической поверхности, образуя тонкую пленку. Пластик и воск часто распыляют на металлические поверхности.Краска действует как покрытие, защищающее металлическую поверхность от электрохимического заряда, исходящего от коррозионных соединений. Современные системы окраски на самом деле представляют собой комбинацию различных слоев краски, которые выполняют разные функции. Грунтовка действует как ингибитор, промежуточное покрытие увеличивает общую толщину краски, а завершающее покрытие обеспечивает устойчивость к факторам окружающей среды.
Самый большой недостаток покрытий заключается в том, что их часто нужно снимать и наносить повторно. Неправильно нанесенные покрытия могут быстро выйти из строя и привести к повышенному уровню коррозии.Покрытия также могут содержать летучие органические соединения, которые могут сделать их уязвимыми для коррозии.
Отказ барьерного покрытия
2. Горячее цинкование
Этот метод защиты от коррозии заключается в погружении стали в расплавленный цинк. Железо в стали вступает в реакцию с цинком, образуя прочное покрытие из сплава, которое служит защитой. Этот процесс существует уже более 250 лет и используется для защиты от коррозии таких вещей, как художественные скульптуры и игровое оборудование.По сравнению с другими методами защиты от коррозии гальванизация известна более низкими начальными затратами, устойчивостью и универсальностью.
К сожалению, цинкование невозможно провести на месте, а это означает, что компаниям приходится снимать оборудование с работы для обработки. Некоторое оборудование может быть просто слишком большим для процесса, что вынуждает компании вообще отказываться от этой идеи. Кроме того, если процесс не будет выполнен должным образом, цинк может отслоиться или отслоиться. А высокое воздействие элементов окружающей среды может ускорить процесс износа цинка, что приведет к увеличению количества проверок при техническом обслуживании.Наконец, пары цинка, выделяющиеся в процессе цинкования, токсичны.
3. Легированная сталь (нержавеющая)
Легированная сталь— один из наиболее эффективных методов защиты от коррозии, сочетающий в себе свойства различных металлов для обеспечения дополнительной прочности и устойчивости получаемого продукта. Коррозионно-стойкий никель, например, в сочетании с стойким к окислению хромом дает сплав, который можно использовать в окисленных и восстановленных химических средах. Различные сплавы обеспечивают устойчивость к различным условиям, что дает компаниям большую гибкость.
Несмотря на свою эффективность, легированная сталь очень дорога. Компаниям с ограниченными финансовыми ресурсами, вероятно, придется обратиться к другим методам. Контроль состояния поверхности имеет решающее значение, поскольку трещины или царапины могут привести к усилению коррозии. Компаниям также необходимо убедиться, что используемые при техническом обслуживании средства не обладают коррозионными свойствами.
Трубопровод с катодной защитой
4. Катодная защита
Катодная защита защищает от гальванической коррозии, которая возникает, когда два разных металла соединяются и подвергаются воздействию коррозионного электролита.Чтобы предотвратить это, активные центры на поверхности металла необходимо преобразовать в пассивные за счет подачи электронов из другого источника, обычно с гальваническими анодами, прикрепленными к поверхности или рядом с ней. Металлы, используемые для анодов, включают алюминий, магний или цинк.
Хотя катодная защита очень эффективна, аноды необходимо часто проверять, что может увеличить затраты на техническое обслуживание. Они также увеличивают вес прикрепляемой конструкции и не всегда эффективны в средах с высоким удельным сопротивлением.Наконец, аноды приводят к увеличению расхода воды на кораблях и другом подводном оборудовании.
EonCoat до (слева) и после 18 месяцев наказания соленой водой (справа). Без коррозии и пузырей.
5. EonCoat
Выбрать подходящую защиту от коррозии для вашего оборудования непросто. У каждого из вышеперечисленных методов есть свои плюсы и минусы, и здесь на помощь приходит EonCoat. По сравнению с рентабельностью, отсутствием обслуживания и возможностями EonCoat на месте другие методы не могут конкурировать.EonCoat не использует токсичных химикатов и является экологически чистым. Наша 30-летняя гарантия гарантирует, что ваше оборудование останется защищенным дольше. Мы сделали ставку на то, чтобы предоставить лучший метод защиты от коррозии, чтобы помочь компаниям, подобным вашей, двигаться вместе с минимальными хлопотами. Нет причин не воспользоваться преимуществами EonCoat сегодня.
Понимание коррозии и способы защиты от нее
Ежегодно корродированные машины, здания и оборудование обходятся американской промышленности примерно в 7 миллиардов долларов.Коррозия — дорогостоящая проблема. Но, понимая его коренные причины, можно предпринять эффективные шаги для предотвращения и борьбы с ним.
Существует несколько видов затрат на коррозию, которые необходимо учитывать рабочим завода:
• Прямая потеря или повреждение металлических конструкций из-за коррозии. Примером может служить резервуар для горячей воды, который подвергся коррозии и должен быть утилизирован.
• Затраты на техническое обслуживание, связанные с коррозией. Любая металлическая поверхность, которую необходимо красить каждые несколько лет для предотвращения коррозии, попадает в эту область.
• Косвенные потери в результате коррозии. Эти потери могут возникнуть в результате утечки и пожара. Взрывы, связанные с утечками, отключениями электроэнергии, остановкой оборудования и потерями рабочей силы, также косвенно являются результатом коррозии.
Первый шаг к контролю этих затрат требует понимания того, что такое коррозия и что ее вызывает.
Что такое ржавчина?
При коррозии железа или стали образуется оксид железа или то, что мы называем ржавчиной. Сталь в основном состоит из железной руды.В естественном состоянии железная руда очень похожа на ржавчину: темно-красная, мелкозернистая, со способностью удерживать влагу.
Железная руда является стабильным веществом до тех пор, пока не превратится в железо или сталь, естественно более слабые элементы. Когда сталь подвергается воздействию влаги и кислорода, она сразу же начинает возвращаться в свое естественное состояние. Несмотря на то, что были приняты защитные меры, большая часть стали, произведенной в этом столетии, уже превратилась в оксид в своем естественном состоянии.
Для существования коррозии необходимы три элемента: защищенный металл, корродированный металл и токопроводящая среда между ними.Когда два разнородных металла соприкасаются, один становится защищаемым металлом, а другой — корродированным. Операторы установки могут распознать экологические ситуации, способствующие коррозии.
Например:
• Если на стальных трубах используются оцинкованные фитинги, оцинкованные (цинковые) фитинги подвергаются коррозии, а сталь остается защищенной.
• Сталь или другие металлы, находящиеся под напряжением, подвергаются коррозии, в то время как ненапряженная сталь защищена от коррозии.Это причина того, что на стали появляются язвы ржавчины.
• Свежесрезанная сталь быстрее подвергается коррозии. Резьба, нарезанная на трубе, всегда сначала ржавеет.
Даже если кусок стали не соприкасается с другим металлом, не подвергается напряжению и не является свежепрезанным, он будет ржаветь под воздействием погодных условий. Это связано с тем, что сталь не совсем однородна по составу — небольшие изменения плотности и состава будут происходить внутри одного куска стали, что приводит к коррозии.
Третий ингредиент, необходимый для коррозии стали, — это электролит.Обычно это жидкое или водосодержащее вещество, которое проводит ток коррозии от защищаемого металла к корродированному металлу. Самым распространенным токопроводящим веществом является вода. Дождь, роса, влажность в воздухе и т. Д. Служат эффективными проводниками электричества. Сталь очень медленно подвергается коррозии в пустынном климате, где влажность низкая, а дожди редки. В условиях повышенной влажности и частых дождей защита стали имеет решающее значение. Операторы установки узнают некоторые из следующих сред, в которых используются электрические токи для ускорения процесса коррозии:
• Добавление соли в воду значительно увеличивает ее токопроводящую способность.Таким образом, сталь, подвергающаяся воздействию морской воды или солевого тумана, будет корродировать быстрее, чем сталь в пресной воде. Атмосферная коррозия сильнее в районах около океанов из-за воздействия соленого воздуха. Концентрированные солевые растворы, например, используемые в пищевой промышленности, вызывают сильную коррозию.
• Промышленный дым и пары содержат кислоты, щелочи и другие химические вещества, которые служат проводниками тока. Следовательно, атмосферная коррозия в промышленных районах более серьезна, чем в сельской местности.
• Почва, глина и земляные материалы также являются хорошими проводниками электричества. Трубопроводы и другая сталь, закопанная в землю, будут подвержены коррозии, если не будут защищены. Подобно тому, как почва значительно различается по составу, она также различается по своей электропроводности: одни почвы вызывают более сильную коррозию, чем другие.
Контроль коррозии
Чтобы сделать использование стали и других металлов практичным в строительстве и производстве, необходимо применять некоторые методы защиты от коррозии.В противном случае срок службы стали и других металлов будет ограничен, что снизит эффективность и увеличит стоимость обслуживания. Есть несколько эффективных способов остановить коррозию:
1. Подаваемый ток. Используя подходящее генерирующее ток оборудование и средства управления, можно воспроизвести ток, равный по силе корродирующему току, но текущий в противоположном направлении. Этот тип защиты обычно ограничивается трубопроводами, заглубленными резервуарами и т. Д. И требует тщательного проектирования и компоновки.При неправильном использовании приложенный ток может вызвать коррозию.
2. Жертвенные металлы. Сталь может быть защищена путем размещения рядом с другим металлом. Например, если цинк или магний находятся в непосредственном контакте со сталью, они защищают сталь от коррозии. Здесь цинк и магний служат жертвенными металлами, которые не только защищают область непосредственного контакта, но и защищают за пределами металла во всех направлениях. Защита от ржавчины с помощью жертвенных металлов обычно используется в нескольких формах:
• Цинковые или магниевые блоки часто используются для защиты корпусов судов, внутренних поверхностей резервуаров для воды и других погруженных поверхностей.
• Часто выполняется полное покрытие стали жертвенным металлом. Например, оцинкованная сталь — это сталь, покрытая цинком. Цинк жертвенный и защитит стальную основу.
• Покрытия с высоким содержанием цинка могут наноситься на стальную поверхность для обеспечения катодной защиты. Покрытия с высоким содержанием цинка содержат от 85% до 95% металлического цинка в подходящем связующем. Частицы цинка, нанесенные при окраске, защищают сталь.
3. Грунтовки. Грунтовки и готовые покрытия защищают металлические поверхности, создавая барьер между сталью и корродирующими элементами.Они также предотвращают попадание влаги на поверхность стали. Пленка покрытия защищает нижележащие металлические подложки тремя способами:
• Покрытия могут замедлять скорость диффузии воды и кислорода из окружающей среды к металлической поверхности. Это замедляет процесс коррозии.
• Пленка краски может замедлить скорость диффузии продуктов коррозии с металлической поверхности через пленку краски. Это также замедляет процесс коррозии.
• Антикоррозионные пигменты, содержащиеся в качественных грунтовках, изменяют поверхностные свойства основного металла.В результате металл приобретает высокое электрическое сопротивление. Разные пигменты по-разному осуществляют эту реакцию. Грунтовки поглощают и связывают влагу, поэтому она не вступает в реакцию со сталью.
Как выбрать антикоррозийное покрытие
Рассмотрение следующих критериев может выявить наиболее эффективный тип антикоррозионного покрытия, необходимый для конкретного проекта.
Качество покрытия / нанесения — Какой уровень антикоррозийной краски требуется? Насколько важно, чтобы краска была устойчива к выцветанию и / или истиранию? Как часто вы планируете перекрашивать? Есть ли предпочтения по нанесению: кисть / валик или распылитель?
Эстетика — Какие материалы будут покрыты? Насколько важно, чтобы лакокрасочный слой выглядел привлекательно? Важно ли сохранять цвет?
Цена — Как правило, более качественная краска увеличивает цену.Учитываются ли заявки на подкрашивание при оценке затрат на техническое обслуживание? Какова стоимость выбранной краски? Как часто нужно будет перекрашивать?
Экологические нормы — Каковы местные экологические нормы для красок и покрытий? Соответствует ли краска этим стандартам? Как процесс покраски повлияет на близлежащее окружение? С июня 2002 года правительство США примет постановление о снижении количества загрязняющих веществ в краске для повышения защиты окружающей среды.Новые пределы содержания летучих органических соединений (ЛОС) упадут до 450 г / л краски. Более жесткие ограничения будут введены в Калифорнии, Аризоне, Нью-Йорке и Нью-Джерси, сведя к минимуму твердые объемы до уровня всего 340 г / л.
Покрытия
Существует три основных типа покрытий, используемых при ремонтной окраске. Исходя из требований к качеству, цене, применению и эстетике, операторы установки могут выбрать подходящее покрытие из следующего:
• Алкидные эмали — Алкидные эмали предназначены для внутренних и наружных поверхностей в умеренных и тяжелых условиях.Это покрытие обеспечивает надежную коррозионную стойкость на срок до 3-5 лет. Алкидные эмали обеспечивают глянцевый цвет, устойчивы к выцветанию и могут наноситься валиком или распылителем. • Эпоксидные покрытия — Эпоксидные покрытия используются для внутренних и наружных поверхностей в промышленных условиях, где сохранение цвета и блеск не важны. Качество покрытия будет лучше, чем у алкидной эмали, поскольку она выдерживает суровые промышленные условия. Эпоксидные покрытия лучше всего наносить распылением, но также можно использовать кисти и валики.
• Полиуретановые покрытия — Полиуретановое покрытие — это краска наилучшего качества из всех трех вариантов. Он выдерживает самые суровые условия окружающей среды и может прослужить до 10 лет. Он обеспечивает сильное сохранение цвета и блеска и устойчив к истиранию. Полиуретановые покрытия наносятся методом напыления.
Заключение
Краски работают, потому что они замедляют коррозию за счет уменьшения скорости протекания тока в процессе электрохимической коррозии. Понимая, что такое коррозия, операторы установок могут предсказать, где может возникнуть ржавчина, и определить факторы окружающей среды на своем предприятии, которые способствуют коррозии.Хорошая новость заключается в том, что, хотя коррозия может быть дорогостоящей, это не обязательно. Краски — это экономичное средство защиты от коррозии. Регулярное техническое обслуживание операторами установки может минимизировать появление и последствия коррозии.
Услуги по нанесению коррозионно-стойких покрытий | Praxair Inc.
Коррозионно-стойкие покрытия
Покрытия, устойчивые к коррозии, обычно требуются, поскольку они обеспечивают существенную защиту металлических компонентов и других предметов, которые вступают в контакт с потенциально опасными условиями.
Что такое коррозия?
Прежде чем разбираться в возможных решениях по нанесению покрытий, вы должны иметь представление о коррозии. Коррозия возникает, когда металл вступает в химическую или электрохимическую реакцию, в результате которой металл расходуется с образованием металлического соединения, такого как сульфид, гидроксид или оксид. Проще говоря, это когда контакт с окружающей средой приводит к ухудшению качества металла.
Что вызывает коррозию?
Металл корродирует в результате реакции, в которой обычно участвуют кислород, водород, хлор и / или сера из окружающей среды.Агрессивность коррозии может значительно возрасти в присутствии тепла, электрического тока или механического воздействия. Коррозионное растрескивание стали — хорошо известный пример коррозионного воздействия механического напряжения, которое приводит к взрывам котлов, разрывам газопроводов и обрушению мостов.
Какие бывают типы коррозии?
- Равномерная или общая коррозионная коррозия происходит равномерно по поверхности материала.
- Точечная коррозия локализована и возникает, если локальная точка превращается в очаг коррозии.
- Щелевая коррозия имеет место на материалах, где доступ к окружающей среде ограничен. Часто находится под прокладками и болтами или между фитингами .
- Межкристаллитная коррозия происходит на границах зерен металлического сплава. Эти границы имеют другой химический состав, чем массивный сплав, и более подвержены коррозии.
- Коррозия под напряжением Растрескивание — это рост трещин в коррозионной среде на определенных сплавах под действием механического напряжения.Без механического напряжения окружающая среда будет иметь небольшое коррозионное воздействие на основной материал, но под механическим воздействием основной материал может быстро и катастрофически корродировать.
- Гальваническая коррозия или биметаллическая коррозия — это когда разные металлы контактируют друг с другом и подвергаются воздействию агрессивной среды. Менее «благородный» металл будет подвергаться ускоренной коррозии, тогда как более «благородный» металл будет корродировать медленнее.
- Высокотемпературная коррозия — это химическое воздействие газов, твердых или расплавленных солей или расплавленных металлов, обычно при температурах выше 400 ° C (750 ° F).
- Высокотемпературное окисление — это один из процессов высокотемпературной коррозии, включающий реакцию между металлическими сплавами или песком покрытия и кислородом воздуха при повышенных температурах.
- Горячая коррозия — это ускоренное окисление металлических сплавов или покрытия, вызванное расплавленными солями в окислительной атмосфере при температуре обычно от 1200 ° F до 1700 ° F для металлов и сплавов.
Какие способы предотвращения коррозии?
Существует три основных категории антикоррозионных покрытий, обеспечивающих защиту.
- Барьеры непористые и защитные. Барьерный защитный слой наносится непосредственно поверх самого металла, образуя защитный слой, оставляющий металл не подверженным воздействию коррозионной среды. Покрытие, используемое для защиты основного материала, будет зависеть от типа металла, а также от типа повреждений, которых вы хотите избежать.
- Ингибирующие покрытия создают пассивный слой на подложке. Они часто встречаются в грунтовках, и со временем защита снижается.
- Жертвенные покрытия коррозируют преимущественно как способ защиты находящегося под ними материала. Если вы помните описание гальванической коррозии, временное покрытие создает преднамеренную гальваническую коррозию, когда корродирует менее благородное покрытие, а не более благородный материал под ним.
Возможные решения по покрытию для обеспечения коррозионной стойкости или защиты?
Фторполимеры
Среди органических материалов фторполимеры уникальны тем, что одновременно сочетают в себе разные свойства, которые обычно можно найти только по отдельности в разных и различных классах полимеров: среди других различных свойств они проявляют:
- универсальная химическая инертность (только очень ограниченное количество экзотических полностью фторированных химикатов может химически воздействовать на них при высокой температуре)
- высокая термостойкость, до 260 ° C
- полностью пластичное и прочное поведение в диапазоне температур между криогенными условиями и максимальной рабочей температурой
- Полная устойчивость к погодным условиям с выдающимися характеристиками во всех длительных испытаниях на открытом воздухе (испытания в Аризоне и Флориде, испытательные шкафы QUV и т. Д.).
- очень низкое и незначительное выщелачивание, поэтому можно гарантировать чистоту технологических жидкостей, контактирующих с фторполимерами.
По этой причине они широко используются в химической, фармацевтической, энергетической и полупроводниковой отраслях, где необходимо бороться с коррозией в суровых условиях.
В частности, фторполимерные покрытия стали играть важную роль в предоставлении инженерам-технологам, специалистам по техническому обслуживанию и производству единственного жизнеспособного решения и альтернативы сплавам с высоким содержанием никеля (Inconel 625, Hastelloy C и т. Д.) Для защиты их технологического оборудования (независимо от того, изготовлены из углеродистой стали), везде, где присутствуют сильные кислотные условия, в частности, выше 60 ° C (когда резиновая футеровка больше не обеспечивает раствор) или где присутствует комбинация растворителей и кислот, смешанных вместе, или когда чистота процесса жидкости из любого металлического катиона, даже на уровне частей на миллиард, должны быть предоставлены, как обычно требуется в фармацевтической или полупроводниковой промышленности.
Высокоэффективные покрытия для суспензии
Неорганическое металлокерамическое базовое покрытие состоит из водного неорганического связующего в сочетании с частицами алюминия, которые обеспечивают защиту от гальванической коррозии. Его распыляют на подготовленный материал основы с последующим процессом сушки, отверждения и полировки для образования защитного слоя. Связующее на основе хромата-фосфата, фосфата или силиката часто используется для обеспечения химического связывания с субстратом. Иногда поверх базового покрытия используется герметизация, чтобы создать дополнительный барьер от коррозии путем заполнения пор, повышения коррозионной стойкости и повышения эффективности работы в более агрессивных средах.Герметизирующее покрытие, иногда называемое верхним слоем, состоит либо из неорганических связующих, либо из систем органических связующих с пигментами или без них для усиления защиты от коррозии металлической основы с уже нанесенным покрытием.
Диффузионные покрытия
Диффузионные покрытия состоят из поверхностного слоя сплава подложки, обогащенного защитными оксидными отложениями Al, Cr, Si или их комбинацией на глубину от 15 до 100 мкм. Эти элементы в сочетании с первичными составляющими сплава подложки образуют новый химический состав со значительным высоким содержанием Al, Cr, Si или их комбинаций.Для разных областей применения были разработаны различные диффузионные покрытия. Для защиты от высокотемпературного окисления предпочтительным диффузионным покрытием являются алюминиды, которые образуют защитную окалину из оксида алюминия при воздействии высоких температур на воздухе. Для защиты от горячей коррозии более предпочтительны покрытия из алюминия, модифицированного платиной или хромом, а также хромирующее покрытие.
Диффузионное покрытие — это, по сути, вид обогащения поверхности путем химического осаждения из паровой фазы.Как правило, он может быть произведен с помощью процесса цементации насадки, процесса суспензии, процесса выше или ниже насадки и процесса «истинного» химического осаждения из паровой фазы.
Покрытия для термического напыления
- Металлик
- карбиды
- МАРКИРОВКА
- Керамика
Накладки для лазерной наплавки и сварки TIG с подогревом
Гальванические покрытия
Обработка от коррозии режущей кромки | D&D Coatings
Страдает ли ваша металлическая крыша от коррозии по краям?
если да, то мы можем помочь!
Давайте подробнее расскажем об этой серьезной постоянной проблеме в Великобритании!
Коррозия в середине листа до и после обработки.Что такое коррозия режущей кромки?
Коррозия порезанной кромки возникает на нахлестах и концах листов на профилированной металлической крыше. Готовые кровельные листы разрезаются по длине в соответствии с планировкой здания. Обычно разрезы подвергаются наиболее сильной коррозии.
Коррозия развивается преимущественно на крышах. Это случается, когда покрытие отслаивается и отслаивается от края листа. В первую очередь это связано с выветриванием. Если не лечить, открытая металлическая поверхность подвергнется коррозии и, в конечном итоге, проколется.В этой статье на Building.co.uk более подробно рассматривается проблема и рассматриваются научные причины.
На любой металлической крыше отслаивание покрытия неизбежно, если пренебречь им. Последующая коррозия обычно освобождается от гарантии производителя кровельного покрытия. Своевременное обнаружение и устранение отслаивания покрытия и коррозии режущей кромки имеет жизненно важное значение. Если его не обработать, замена кровельных листов будет единственным подходящим методом ремонта.
Начинает развиваться ранняя стадия коррозии кромок обрезных листов кровли.Сильная коррозия режущей кромки, отслоение краски и разрушение основания. Процесс обработки перекрытия кровельного листа, нанесение базового покрытия. Завершение антикоррозионной обработки кромки разреза, гарантия от 10 до 15 лет.Как мы лечим коррозию обрезной кромки
Ремонт после отслаивания и коррозии обрезанной кромки прост. После первоначального обследования участка, которое включает в себя тщательный осмотр обрабатываемых участков, мы посещаем предварительную встречу. На этой встрече мы обсуждаем объем работ, программирование основных дат и вопросы охраны труда и техники безопасности, относящиеся к работам.Как только дата установлена, мы готовы приступить к работе.
В отличие от многих других подрядчиков, мы начинаем с мойки локализованной территории. Это не только удаляет отслаивающиеся покрытия, но и очищает поверхность перед нанесением системы защиты обрезной кромки. Затем мы шлифуем вручную, чтобы удалить поверхностную коррозию и восстановить заводское покрытие. Это создает плотный край, который будет герметизирован системой обрезных краев.
Для нахлеста внахлест, сначала мы наносим герметик, который образует галтель на стыке внахлест, а затем — базовое покрытие.Затем на него наносится последний финишный слой цвета, подходящего к существующим кровельным листам. На края водостока наносим базовое покрытие, а затем верхнее покрытие. Для более высокого качества отделки, используя ленту, мы замаскируем внешние края перед нанесением верхнего покрытия. Это создает идеально прямую трамвайную линию, что придает более аккуратный вид.
Использование скотча для маскировки окрашиваемой области обеспечивает более профессиональную отделку. Стальные края конька крыши обработаны от коррозии.Пошаговый процесс обработки
- Осмотр и оценка для определения степени отслаивания покрытия и коррозии.
- Подготовка поверхности, включая промывку обрабатываемой области под высоким давлением.
- Удаление отслаивающейся краски и следов ржавчины ручным шлифованием и металлической щеткой.
- Нанесение мастики с помощью пистолета для герметизации нахлеста в середине листа.
- Повторное нанесение базового слоя с последующей нанесением верхнего покрытия кистью или валиком до указанной толщины.
Проиллюстрирован процесс коррозионной обработки обрезной кромки
Во всех случаях наши работы будут выполняться без нарушения нашего кодекса SafeContractor с соблюдением самых высоких стандартов безопасности и здоровья
Свяжитесь с нами сегодня по телефону
01606 554040 или 📧
, чтобы обсудить ваши требования к антикоррозионной обработке обрезной кромки
D&D Industrial Coatings Ltd является утвержденным подрядчиком для основных производителей красок в Великобритании
На наши ультрасовременные системы дается гарантия производителя от 10 до 15 лет.
Мы используем ленту во всех случаях, когда требуется маскировка.Мы считаем, что он обеспечивает более аккуратную и профессиональную отделку при обработке коньковых покрытий, потолочных светильников, перехлестов листов и торцов листов. Обработанные края водостока, на которых коррозия кромок может быть особенно заметной из-за постоянного воздействия и закрытия близость, вода и загрязняющие вещества. Постоянная обработка кромки коньковой заделки на участке большой крыши склада. Поделитесь этой страницей в социальных сетях:
Что такое питтинговая коррозия? Как обнаружить и лечить точечную коррозию?
Точечная коррозия поражает металлы и сплавы, такие как сталь, железо, алюминий и другие.Обычно это ограничивается определенными областями. Он проникает и атакует быстро, и его трудно обнаружить. Чаще всего это происходит, когда слой пассивного покрытия физически поврежден или подвергается химическому воздействию. Это создает слабое место, где вода или агрессивные растворы атакуют основание.
Соседние материалы часто выглядят незатронутыми. Если ее не остановить, точечная коррозия может иметь разрушительные последствия для кровельных систем или любых металлических конструкций. Это происходит быстро и легко не заметить, поэтому многие считают его самой опасной формой коррозии.
Объяснение питтинговой коррозии
Точечная коррозия — это полость, отверстие или ямка, образующаяся на небольшом участке или точке. Ямы или отверстия закрываются небольшим количеством продуктов коррозии (ржавчины) на поверхности. Когда катодная реакция на большой площади (покрытии) поддерживает анодную реакцию на небольшой площади (обнаженный металл), образуется яма, полость или небольшое отверстие. Окисление металла происходит даже при отсутствии кислорода.
Большая потребность в электронах со стороны большого катода накладывается на малый анод, что приводит к интенсивной точечной коррозии.Это будет незаметно и быстро с очень пагубными последствиями. На поверхности видно только небольшое пятно ржавчины, в то время как повреждение происходит глубоко в металлической конструкции внизу.
Диаграмма точечной коррозии, показывающая, как ржавчина образуется на небольшой анодной площади из-за высокой потребности в электронах большой катодной площадью, образующей яму внизу.
Что вызывает точечную коррозию?
Точечная коррозия возникает, когда катод (поврежденное покрытие) большой, а анод (открытый металл) маленький.Обычно поверхностный защитный слой или пленка становится катодом, когда он поврежден и растрескивается. Затем открывается небольшой участок металла, который становится анодным.
Язвенная коррозия является сильной, когда раствор на поверхности металла содержит ионы хлорида, гипохлорита или бромида. Другими вредными растворами являются те, которые содержат фториды и йодиды. Известно также, что сульфиды и вода усиливают процесс питтинга.
Наиболее частыми причинами точечной коррозии являются:
- Трещины в защитном покрытии
- Царапины, потертости и мелкие сколы
- Неравномерные напряжения
- Дефектная металлическая основа
- Турбулентный поток жидкости
- Неоднородное защитное покрытие
- Химическое воздействие на защитное покрытие
Металлы склонны к питтинговой коррозии;
- Нержавеющая сталь
- Хром
- Пассивное железо
- Ртуть
- Кобальт
- Алюминий
- Медь
- Сопутствующие сплавы
Другой пример точечной коррозии возникает, когда металл плохо обслуживается и подвергается воздействию капель воды и пыли частицы.Область под каплей недостаточно насыщена кислородом, в то время как окружающие области хорошо насыщены кислородом. Это приводит к дифференциальной аэрационной коррозии, когда окружающие области являются катодными, а небольшая область под каплями и частицами пыли становится анодной. Электроны проходят через металл и встречаются с водой и кислородом. Ионы образуются и вместе разряжаются, образуя ржавчину. По мере образования ржавчины в металле появляются ямки, трещины и щели.
Типы питтинговой коррозии
Точечная коррозия может проявляться в самых разных формах.Форма ямки во многом зависит от затронутого материала и направления волокон внутри этого материала. Чаще всего страдают пассивные металлы и сплавы, в том числе нержавеющая сталь и алюминий. Однако может пострадать практически любой металл или материал, подверженный коррозии.
Язвенная коррозия желоба
Форма ямки желоба обычно бывает полусферической, чашеобразной или неправильной формы. Точечная коррозия в желобах возникает, когда пассивная пленка (защитный слой) нарушается и металлическая стенка подвергается атаке с образованием узких и глубоких желобов.Их плоские стенки открывают кристаллическую структуру металла. Они могут быстро проколоть материал, например лист крыши, ферму или водосточный желоб.
Диаграмма вертикального поперечного сечения точечной коррозии в желобе с зернистостью
Диаграмма поперечного сечения точечной коррозии в узких и глубоких желобах.
Схема поперечного сечения точечной коррозии эллиптического желоба.
Диаграмма поперечного сечения мелкой и широкой канавки точечной коррозии.
Боковая питтинговая коррозия
Боковая ямка покрыта полупроницаемой мембраной из продуктов коррозии (ржавчины) и проявляется в виде горизонтального разрушения зерен, подрезов и подповерхностных форм.Боковая точечная коррозия может очень быстро проникнуть в металл. Это очень сложно обнаружить, потому что поверхность металла не будет повреждена и не подвержена коррозии. При наличии всего лишь нескольких небольших пятен ржавчины может показаться, что повреждение очень незначительное.
Диаграмма поперечного сечения точечной коррозии с горизонтальным воздействием зерна.
Схема поперечного сечения подповерхностной боковой точечной коррозии.
Схема поперечного сечения точечной коррозии поднутрения.
Как проверить питтинговую коррозию?
Визуальный осмотр корродированной металлической поверхности является первым и основным используемым методом.Подсчитайте количество ямок через окуляр микроскопа на определенной площади поверхности, например, 20 см 2 , чтобы определить приблизительный размер и распределение ямок. Количество ямок не обязательно является самым важным фактором. Глубина ямы — безусловно, самая большая опасность. Одна узкая глубокая яма может быть опаснее множества неглубоких ям. Металлографический разрез для измерения глубины ямок покажет интенсивность атаки.
Ультразвуковые испытания — это когда ультразвуковые импульсы звуковой энергии передаются через связующее вещество на масляной или водной основе на металлическую поверхность.Волны генерируются и отражают эхо, которое преобразуется в электрические сигналы. Эти сигналы можно интерпретировать, чтобы показать расположение ямок, щелей и трещин в металле. Этот тест имеет хорошую чувствительность и дает мгновенную информацию о глубине, ширине и местонахождении ямок и трещин.
Электромагнитное тестирование используется для обнаружения дефектов или неровностей в структуре электропроводящих материалов, таких как сталь и чугун. Материалы с дефектами будут создавать магнитное поле, отличное от поля эталонного материала без дефектов.
Электрохимические испытания для измерения точечной коррозии любого металла, такие как циклическая поляризация и потенциостатические испытания, также возможны. Это краткосрочные электрохимические тесты, дающие мгновенные результаты.
Другой вариант — испытание погружением или метод потери веса. Для выполнения этих тестов требуется больше времени. Они включают извлечение металлического образца и погружение в раствор. Через несколько дней его можно будет удалить, чтобы рассчитать скорость коррозии. Вы можете наблюдать ямы и глубину ям под микроскопом и производить необходимые расчеты.
Существует несколько стандартов, которые содержат рекомендации по электрохимическим испытаниям на точечную коррозию нержавеющих сталей, и самые популярные из них:
Как лечить точечную коррозию?
Рекомендуется использовать рекомендуемые процедуры очистки, чтобы полностью обнажить ямы и удалить продукты коррозии. Избегайте использования растворов, которые чрезмерно агрессивны к основному металлу. Желательно во время чистки периодически прощупывать ямы острым инструментом. Это позволит вам определить степень подрезов или подповерхностной коррозии.Тщательно очистив яму металлической щеткой, отверстия будут значительно увеличены. Удаление продуктов коррозии и подрезов металла поможет оценить степень повреждений.
Когда металлический материал будет чистым и свободным от мусора, проведите окончательную проверку на наличие повреждений. Если вы счастливы, что коррозия была обнаружена вовремя, вы можете приступить к нанесению основного грунтовочного покрытия, а затем еще одного или двух верхних слоев. Если повреждение серьезное, а компонент слишком слабый, его необходимо заменить.
Грунтовка фосфатом цинка — один из самых популярных методов покрытия для защиты от точечной коррозии. Специально разработанные грунтовки, такие как фосфат цинка, улучшают коррозионную стойкость.
Металлизация цинковым распылением — это очень эффективный метод защиты от коррозии. Он имеет гладкую поверхность, которая эстетически привлекательна и популярна. Он не обеспечивает такой же защиты, как горячее цинкование, но поскольку это холодный процесс, риск деформации металла отсутствует.Металлизация цинковым напылением идеально подходит для использования на декоративных металлических предметах, таких как художественные выставки, металлические перила и заборы.
Химическое покрытие использует электростатический заряд или сжатый воздух для нанесения порошкообразного материала специальной формулы на стальную поверхность. Затем он плавится, образуя гладкую защитную пленку. Обработанная таким образом сталь не только защищена от коррозии и ультрафиолетовых лучей, но и очень устойчива к отслаиванию, царапинам и растрескиванию.
Горячее погружение — это метод гальванического покрытия, который можно использовать на стали любых форм и размеров.Он заключается в погружении стали в ванну с расплавленным цинком при температуре до 450 ° C. Оцинкованная таким образом сталь является особенно популярным методом для труб, поскольку она хорошо защищена от коррозии, а также от экстремальных погодных условий.
Как предотвратить питтинговую коррозию и защитить от нее?
Факторы окружающей среды, вызывающие точечную коррозию, по возможности должны быть сведены к минимуму. Влажность, температура, уровень хлоридов и pH кислот и солей следует контролировать и минимизировать.
Для катодной защиты металл, подверженный риску, должен быть покрыт химически активным металлом, который легче корродирует. Это может быть оцинкованное цинковое покрытие или подобное. Реактивный металл будет действовать как анод и сначала коррозировать, предотвращая точечную коррозию в подложке.
Для защиты от химического воздействия лучше подходят коррозионно-стойкие металлы, такие как сплавы. Сплавы, содержащие титан, азот, хром и молибден, очень эффективны в средах с высоким содержанием хлорид-ионов.
Точечную коррозию можно контролировать с помощью:
- Использование покрытия, предотвращающего точечную коррозию на металлических поверхностях
- Использование более устойчивых к коррозии материалов
- Обеспечение регулярного вымывания жидкостей, контактирующих с материалом
- Использование катодных защита
- Предотвращение застойных зон
- Использование ингибиторов / контроль химического состава жидкости
- Сохранение защитной пленки материала
Дополнительная информация
Питтинговая коррозия — Википедия
Исследование и оценка точечной коррозии
Различные типы точечной коррозии
Взрыв канализации Гвадалахары из-за точечной коррозии