Упрочнение методом холодной пластической деформации
ЛЕКЦИЯ 5
СПОСОБЫ УПРОЧНЕНИЯ МАТЕРИАЛОВ
Ранее были рассмотрены механические свойства металлов и сплавов. Основным свойством для машиностроительных материалов является прочность. Однако, уровень прочности материалов в исходном состоянии не всегда соответствует требуемым значениям.
В этом случае необходимо повысить характеристики прочности для данного сплава, используя один из способов упрочнения.
К способам упрочнения относятся:
Холодная пластическая деформация (ХПД).
Термическая обработка.
Легирование (введение в состав сплава дополнительных химимческих элементов).
Химико-термическая обработка (упрочнение поверхностных слоев металла и деталей малых сечений).
Механо-термическая обработка (сочетание механической и термической обработки).
Рассмотренный ранее механизм пластической деформации, позволяет
сделать вывод, что процесс сдвига в кристаллах под действием внешних напряжений будет происходить тем легче, чем больше дислокаций будет в металле.
После пластической деформации дислокационная плотность увеличивается и достигает значении 108 ‑1010 см -2. При этом формируются дислокационные скопления: сплетения в виде клубков дислокаций. При увеличении степени деформации плотность дислокаций возрастает до 1011 – 1012 см -2.
Повышение прочности
с возрастанием плотности дислокаций
объясняется тем, что при этом возникают
не только параллельные друг другу
дислокации, но и дислокации в разных
кристаллографических плоскостях и
направлениях. Такие дислокации будут
мешать друг другу перемещаться и реальная
прочность металла повышается, так как
замедляется движение дислокаций и
уменьшается пластическая деформация.
Упрочнение металла под действием пластической деформации называется наклепом. С ростом степени деформации прочность и твердость повышаются, а способность к пластической деформации снижается (рис.5.1).
Рис.5.1. Изменение свойств металла с увеличением степени
деформации.
Степень предварительной деформации определяется по характеристике
ε = [(H — h) / H] ∙ 100%.
Рост числа дислокаций
и возникновение внутренних напряжений
в результате наклепа приводит к тому,
что свободная энергия металла растет,
и он переходит в неравновесное,
неустойчивое состояние. Нагрев металла
должен способствовать возврату металла
в более устойчивое исходное структурное
состояние.
Уже при небольшом нагреве происходит снятие искажений кристаллической решетки, уменьшение плотности дислокаций, снижение внутренних напряжений. При этом видимых изменений структуры не наблюдается и вытянутая форма зерен сохраняется. Этот процесс называется возвратом. При возврате прочность уменьшается незначительно (на 20 — 30%), а пластичность несколько увеличивается.
С ростом температуры нагрева подвижность атомов растет, и образуются новые зерна вместо ориентированной волокнистой структуры. Образование и рост новых равноосных зерен называется рекристаллизацией.
Рис.5.2. Схема процесса рекристаллизации в деформированном
металле при нагреве.
Процесс рекристаллизации протекает в две стадии:
Первая стадия — рекристаллизация
обработки — процесс образования новых зерен.
Вторая стадия — собирательная рекристаллизация — процесс роста вновь образованных рекристаллизованных зерен (рис.5.2).
Новые зерна возникают на границах старых зерен. Процесс первичной рекристаллизации термодинамически выгоден, так как при переходе деформированного металла в более устойчивое равновесное состояние сопровождается уменьшением свободной энергии.
Температура, при которой возникают новые зерна и изменяются механические свойства, называется температурой рекристаллизации (Тр).
Она зависит от температуры плавления.
Тр = а ∙ Тпл,
где а — коэффициент, зависящий от состава и структуры металла.
для чистых металлов: Тр = 0,3 — 0,4 ∙ Тпл;
для сплавов : Тр = 0,7 — 0,8 ∙ Тпл.
Изменение структуры
и свойств деформированного металла при
нагреве представлено на рис.
Рис. 5.3. Схема изменения структуры и свойств деформированного металла при нагреве:
1-2 – возврат; 2-3 – первичная кристаллизация; 3-4 – собирательная рекристаллизация
Таким образом, если необходимо снять наклеп, то следует провести нагрев деформированного металла при температуре выше, чем температура рекристаллизации.
Относительно температуры рекристаллизации различают холодную и горячую деформацию. Холодная деформация проводится при температурах ниже температуры рекристаллизации и является способом упрочнения металлов и сплавов. Горячая деформация проводится при температурах выше температуры рекристаллизации. Так, при механической обработке давлением имеют место два процесса: упрочнение за счет пластической деформации и последующее разупрочнение при рекристаллизации.
ЛЕКЦИЯ
6
ТЕОРИЯ СПЛАВОВ
Чистые металлы
обычно имеют низкую прочность и невысокие
технологические свойства. В машиностроении
обычно применяются сплавы. Сплавами называют
сложные вещества, полученные сплавлением
нескольких элементов.
Элементы, образующие сплав, называются компонентами. Компонентами металлических сплавов могут быть не только металлы, но и неметаллы. В зависимости от числа компонентов сплавы могут быть двойные, тройные и т.д.
В жидком состоянии компоненты сплава обычно неограниченно растворяются друг в друге, образуя жидкие растворы.
В твердом состоянии компоненты могут образовывать три типа сплава (типа взаимодействия между собой):
1. Механические смеси.
2. Химические соединения.3. Твердые растворы.
При рассмотрении типов взаимодействия компонентов в сплаве обозначим один компонент как А и второй компонент как В.
Твердые
растворы.
При образовании твердого раствора один компонент является растворителем, другой компонент – растворимый. Растворитель – тот компонент, кристаллическая решетка которого сохраняется.
Растворимый компонент – его атомы располагаются в кристаллической решетке растворителя.
В зависимости от расположения атомов в кристаллической решетке различают твердые растворы замещения и твердые растворы внедрения.
В твердом растворе замещения
В твердом растворе внедрения атомы растворимого компонента размещаются между атомами компонента – растворителя (рис.6.1, б).
а | б |
Рис. 6.1. Кристаллическая
решетка ГЦК твердого раствора замещения
(а) и твердого раствора внедрения (б)
Обозначение твердых растворов: А (В), где
А – растворитель, В – растворимый компонент
или буквами греческого алфавита: α, β, γ.В зависимости от концентрации компонентов в сплаве различают ограниченные и неограниченные твердые растворы.
Неограниченные твердые растворы образуются во всем интервале концентрации компонентов в сплаве.
Ограниченные твердые растворы образуются только в определенном интервале концентрации компонентов.
Твердые растворы в структуре имеют одинаковые однородные зерна, т.е. имеют одну фазу – фазу твердого раствора. Кристаллизация твердых растворов происходит в интервале температур.
Сплавы,
представляющие твердые растворы,
отличаются хорошими свойствами. Они
имеют более высокую твердость и прочность,
чем чистые компоненты, входящие в состав
этих сплавов. Твердые растворы обладают
хорошей пластичностью и технологичностью.
Такие сплавы хорошо обрабатываются.
4.2. Механизм пластической деформации. Материалы для ювелирных изделий
4.2. Механизм пластической деформации
Пластическая деформация осуществляется посредством сдвига внутри кристалла по определенным кристаллографическим плоскостям, которые называются плоскостями скольжения. Сдвиг в кристалле начинается при достижении внешним напряжением величины предела текучести. Так как зерна в образце ориентированы различно относительно внешнего напряжения, то пластическая деформация развивается в металле неоднородно. В первую очередь деформируются те зерна, которые ориентированы таким образом, что напряжение в их плоскости скольжения достигает величины напряжения сдвига. Форма зерна в результате многочисленных сдвигов изменяется. При этом, так как зерна взаимно связаны, происходит поворот соседних зерен, их ориентация относительно внешнего напряжения изменяется, и пластическая деформация распространяется на другие зерна. Постепенно все зерна металла деформируются, их форма изменяется, зерна вытягиваются в направлении приложенного напряжения. В кристаллической структуре металла возникают дефекты.
В результате пластической деформации изменяются механические свойства металла: прочность увеличивается, пластичность уменьшается. Это явление называется «наклеп».
Упрочнение металла при пластической деформации и уменьшение его пластичности ограничивает возможность дальнейшей деформации. Так, при волочении проволоки с уменьшением сечения при следующих проходах через фильеру возникают обрывы.
На рис. 4.2 показана зависимость прочности и пластичности латуни Л68 от степени пластической деформации. В качестве характеристики пластичности выбрано относительное удлинение, ?%, т. е. отношение прироста длины разрушенного образца к его первоначальной длине. Степень пластической деформации оценивается по отношению:
с. п.д. = (d20 – d2д / d20,
где с.п.д. – степень пластической деформации,
dQ – диаметр проволоки до волочения,
dд – диаметр проволоки после волочения.
Рис. 4.2. Влияние степени холодной пластической деформации на твердость (НВ), прочность (?в) и пластичность (?,%) латуни А68.
Упрочнение, вызванное предварительной пластической деформацией, можно снять нагревом деформированного металла. В процессе пластической деформации металл запасает энергию, и поэтому состояние его является неустойчивым. Однако при низких температурах диффузия в металле не происходит, так как подвижность атомов в твердом теле мала. При нагреве металла подвижность атомов увеличивается и, начиная с определенной температуры, возникают самопроизвольное зарождение новых, недеформированных зерен и их рост.
Этот процесс называется рекристаллизацей обработки или первичной рекристаллизацей. Температуру, при которой начинается этот процесс, называют температурой начала рекристаллизации Тнр. С повышением температуры выше температуры начала рекристаллизации образование и рост новых зерен продолжается вплоть до того, как будет достигнута температуры конца рекристаллизации Ткр. Температура начала рекристаллизации зависит от множества факторов. В первую очередь она связана с природой самого металла, для чистого металла ее можно приближенно оценить по температуре его плавления:
Тнр = 0,ЗТпл (К),
где Тпл – температура плавления металла,
Тнр – температура начала рекристаллизации.Коэффициент 0,3 приближенный и зависит от чистоты металла. Для особо чистых металлов он уменьшается до 0,25—0,15, для сплавов увеличивается до 0,6.
Температура начала рекристаллизации зависит также от степени пластической деформации и уменьшается с увеличением степени пластической деформации.
Образование новых недеформированных зерен и снижение внутренней энергии металла за счет уменьшения концентрации дефектов приводит к изменению механических свойств.
На рис. 4.3 показана зависимость прочности и пластичности холоднодеформированного железа от температуры отжига. Пластичность и вязкость металлов и сплавов существенно зависят от размера зерна. В свою очередь, размер зерна зависит от температуры рекристализационного отжига и степени предварительной пластической деформации. В процессе рекристаллизации обработки размер зерна обычно уменьшается по сравнению с исходным, так как происходит влияние температуры отжига на прочность и пластичность холоднодеформированного металла.
С увеличением температуры выше температуры конца рекристаллизации зерно продолжает расти. Особенно интенсивно это происходит в чистых металлах. На размер зерна оказывает влияние также степень предварительной холодной пластической деформации. Чем выше степень деформации, тем меньше размер рекристаллизованного зерна.
Температура рекристаллизации обработки является физической границей между холодной и горячей пластической деформацией.
Пластическая деформация ниже этой температуры является холодной. При этом возникает упрочнение металла – наклеп. Пластическая деформация при температурах выше температуры рекристаллизации называется горячей. При горячей пластической деформации наклеп непрерывно снимается процессом рекристаллизации. После горячей пластической деформации упрочнения металла не наблюдается.
Данный текст является ознакомительным фрагментом.
11.3. Механизм возникновения и развития пожаров
11.3. Механизм возникновения и развития пожаров Следует отличать пожар от возгорания.Пожар – это неконтролируемое горение, причиняющее материальный ущерб, вред жизни и здоровью граждан, интересам общества и государства. Горение под контролем человека не является
3.3. Механизм управления качеством
3. 3. Механизм управления качеством
Управление качеством происходит на государственном, региональном и отраслевом уровнях, а также на уровне фирмы (предприятия).Под управлением качеством продукции понимаются действия, осуществляемые при создании, эксплуатации или
ОДНОСПУСКОВОЙ МЕХАНИЗМ ФИРМЫ «ГОЛЛАНД-ГОЛЛАНД»
ОДНОСПУСКОВОЙ МЕХАНИЗМ ФИРМЫ «ГОЛЛАНД-ГОЛЛАНД» Односпусковой механизм для двуствольных ружей «Голланд-Голланд» имеет механическое переключение с постоянной последовательностью выстрелов. Замедление переключения достигается точным соотношением силы пружины и длины
5.1.3. Механизм воздействия
5.1.3. Механизм воздействия Сегодня существуют многочисленные теории, объясняющие механизм действия серебра на микроорганизмы. Наиболее распространенная – адсорбционная теория, в соответствии с которой клетка теряет жизнеспособность в результате взаимодействия
5.
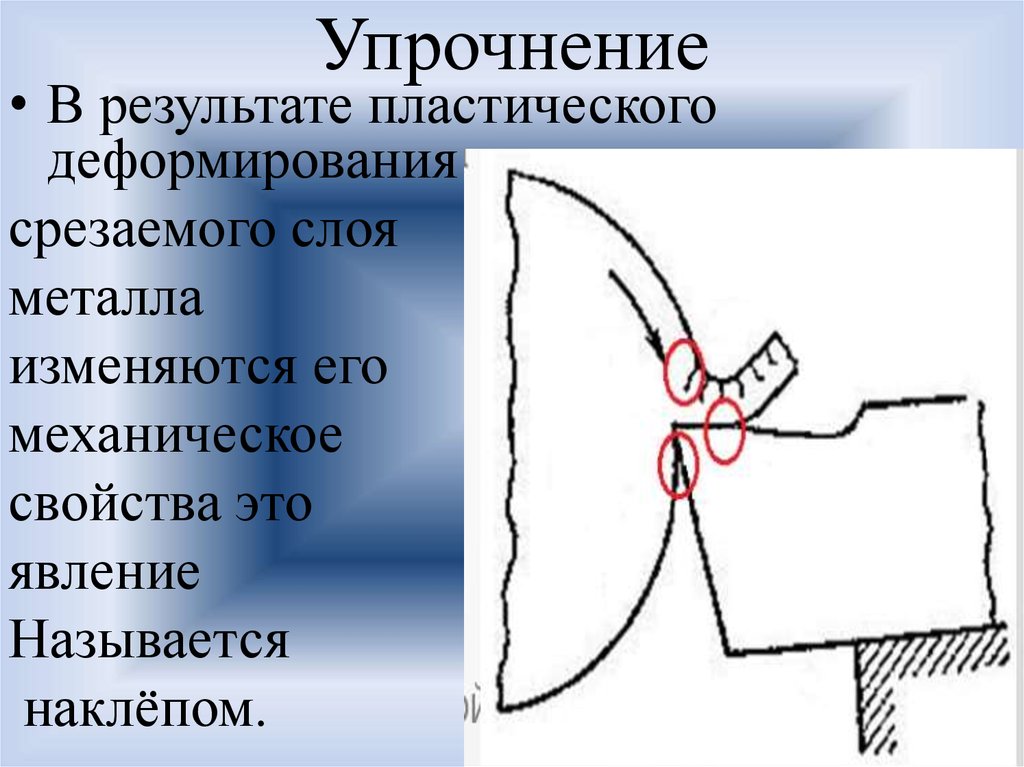
5.2.2. Механизм воздействия Исследования по выяснению механизма антибактериального действия меди проводили еще в давние времена. Например, в 1973 г. ученые из лаборатории «Колумбус Баттел» провели всесторонний научный и патентный поиск, в котором собрали всю историю
Рулевой механизм типа червяк – ролик
Рулевой механизм типа червяк – ролик Такой рулевой механизм применяют на некоторых грузовых автомобилях, имеющих механическое рулевое управление. Рис. Устройство рулевого управления автомобиля ГАЗ а – рулевой механизм типа червяк – ролик, б – рулевой привод, 1 –
Кривошипно – шатунный механизм
Кривошипно – шатунный механизм
Кривошипно-шатунный механизм служит для восприятия давления газов в такте рабочего хода и преобразования возвратно-поступательного движения поршней во вращательное движение коленчатого вала. Он состоит из блока цилиндров, гильз и
Холодная пластическая деформация — что это такое?
ОпубликованоХолодная пластическая деформация – Нержавеющие стали (в особенности аустенитные) имеют явную склонность к холодной штамповке. Кроме того, они подвергаются явлению деформационного упрочнения, то есть повышению механических свойств, таких как предел прочности при растяжении, предел текучести и поверхностная твердость.
Процесс формования: статическое давление или динамические воздействия.
Процесс формования представляет собой механическую обработку прессом или средствами динамического воздействия (горячего или холодного) для пластической деформации. Последние помещают материал на прессы или отбойный молоток . Это давление направлено на то, чтобы заставить материал заполнить углубление между двумя металлическими матрицами (обычно формой). В случае металлических материалов приступают к твердым элементам в виде стержней, заготовок, стержней или дисков.
Глубокое рисование: как это работает?
Глубокая вытяжка представляет собой процесс формовки листового металла, при котором заготовка из листового металла радиально втягивается в формующую матрицу под действием механического воздействия пуансона. Таким образом, это процесс преобразования формы с сохранением материала. Процесс считается «глубоким» волочением, когда глубина вычерчиваемой детали превышает ее диаметр. Глубокая вытяжка с прессом, удерживающим кромку листа заготовкой-держателем «б». А потом пресс штампом «с», пока он не окажется на дне формы «d».
Преимущество этого держателя заготовок :
- предотвращение втягивания листа внутрь формы до того, как он успеет принять окончательную форму
- предотвращает образование складок по краям.
Форма, штамп и заготовка-держатель вместе называются «формой». Процесс формования с использованием:
- механических прессов (когда требуется высокая скорость производства и малая/средняя глубина штамповки)
- прессы гидравлические (при значительной глубине штамповки)
Деформационное упрочнение, также известное как деформационное упрочнение или холодная обработка, представляет собой упрочнение металла путем пластической деформации. Это может быть желательным или нежелательным в зависимости от контекста:
- механические свойства :
- повысить твердость и прочность на растяжение
- уменьшение пластичности (как удлинение, так и сужение)
- снижение статической и динамической прочности конца (как сопротивление)
2. физические и химические свойства :
- увеличивают коэрцитивную напряженность поля, коэффициент теплового расширения и сжимаемость.
- уменьшают напряженность, электрическую проводимость, магнитную проницаемость и коррозионную стойкость .
Холодная пластическая деформация.
Найдите наши изделия из нержавеющей стали в интернет-магазине Inoxmare.
Щелкните здесь
Процесс холодной обработки и отжига
Добро пожаловать на образовательную веб-страницу по холодной обработке и отжигу!
Эта веб-страница была создана, чтобы предложить студентам колледжей краткое введение в процессы холодной обработки и отжига, которые часто используются в металлообрабатывающей промышленности. Часть содержимого этой веб-страницы может выходить за рамки материаловедческого образования читателя; на странице «Рекомендуемые тексты для дополнительного образования» перечислены два отличных источника для более глубокого ознакомления с материаловедением.
Одной из характеристик любого металла является предел текучести. Предел текучести металла – это напряжение, при котором этот металл начинает пластически деформироваться. Напряжения ниже предела текучести будут упруго деформировать материал. Если снять напряжение, металл после упругой деформации вернет свою первоначальную форму. Как правило, нагрузка на металл выше его предела текучести неблагоприятна; предотвращение предела текучести металла является основным соображением при проектировании. Тем не менее изучение изменения микроструктуры металла после деформации показало, что изменяются и механические свойства этого металла. В частности, испытания на растяжение показывают, что металлический образец, нагруженный сверх предела текучести, обычно упрочняется при деформации.
При пластической деформации металла внутри материала происходят дислокации атомов. В частности, дислокации возникают поперек или внутри зерен металла. Дислокации накладываются друг на друга, и плотность дислокаций в материале увеличивается. Увеличение перекрывающихся дислокаций затрудняет движение дальнейших дислокаций. Более того, предел текучести металла фактически увеличивается после его пластической деформации. Кроме того, эластичная область также увеличивается, и пластическая деформация требует нового, повышенного предела текучести. После деформационного упрочнения пластичность металла снижается, и металл становится более жестким. В силу вышеупомянутого упрочнения очевидно, что механическими свойствами металла можно управлять посредством деформационного упрочнения. Распространенный метод деформационного упрочнения известен как холодная обработка.
Изменения, внесенные в металл при холодной обработке, могут быть устранены путем воздействия на этот металл определенной температуры в течение определенного периода времени. Этот процесс известен как отжиг.
Холодная обработка пластически деформирует материал при температуре ниже его температуры рекристаллизации. Температура рекристаллизации материала – это температура, при которой новые зерна с низкой плотностью дислокаций начинают замещать зерна с высокой плотностью дислокаций.
Холодная обработка является полезным механизмом упрочнения благодаря деформационному упрочнению, но холодная обработка также полезна для придания формы материалам.
В этом эксперименте металлические образцы подвергались холодной прокатке, форма холодной обработки, при которой металлический образец продавливается через два валка с зазором между ними. Холодная прокатка часто используется в коммерческих целях для производства листового металла, пластин и прутков.
Когда металл подвергается холодной прокатке, он пластически деформируется, когда его продавливают между двумя валками. Металл сжимается валками и пластическая деформация идет в направлении прокатки. В отличие от испытания на растяжение, в металлическом образце не происходит образования шейки.
В этом эксперименте металлические образцы были подвергнуты холодной прокатке, чтобы можно было изучить влияние деформационного упрочнения.
Мера того, сколько холодной обработки необходимо подвергнуть материалу, если требуется исследование изменения механических свойств. Одним из средств измерения является изменение площади поперечного сечения металлического образца, подвергнутого холодной обработке. Это измерение изменения площади поперечного сечения известно как «процент холодной обработки». Уравнение 1 ниже иллюстрирует процент холодной обработки.
%CW = [ A 0 -A F ]/A 0 x 100%(1)
, где A 0 и A F. Finally и Finaly и Finally и Fination и Finaly и Finally и Finally и Fination и Finally Armater Ald и Fination и Fination и Fination и Fination и Fination и Finall и Final и Final и Final и Fination и Fination Antian6 F . -площадь сечения образца соответственно. В частности, для холодной прокатки уравнение 1 используется для толщины, а не для площади. Это измерение холодной прокатки известно как «процент обжатия в холодном состоянии». Уравнение 2 ниже иллюстрирует это выражение для холодной прокатки.
%CW = [T 0 -T F ] / T 0 x 100%(2)
, где T 0 и T FINTION и FILINAL и T FINTION и T FINTION и T F. толщина образца соответственно.
Холодная обработка увеличивает прочность материала, но снижает его пластичность и электропроводность. Кроме того, в материал вводятся остаточные напряжения из-за наложения и запутывания дислокаций.
Металлы подвергаются холодной обработке для изменения их формы. Материал теряет пластичность при холодной обработке или, тем более, при холодной прокатке. Если кто-то хочет частично или полностью восстановить первоначальные свойства холоднодеформированного материала, его можно отжечь. Отжиг осуществляется путем нагревания материала; в данном случае это металл. Существует три этапа отжига, и каждый этап дает разные результаты. Три стадии отжига: восстановление, рекристаллизация и рост зерна.
Восстановление
Стадия восстановления является первой стадией отжига. Эта стадия возникает, когда металл сначала подвергается нагреву. Эта стадия отжига мало влияет на плотность дислокаций и искажение зерен в материале. Однако стадия восстановления устраняет большую часть остаточных напряжений в материале. Можно думать об этом как о тепле, ослабляющем накопленное напряжение в материале. В материале также восстанавливается значительная электропроводность. Стадия восстановления позволяет дислокациям немного перемещаться и образовывать так называемую полигонизированную субзеренную структуру.
Рекристаллизация
Когда холоднодеформированный материал подвергается воздействию температуры, равной или превышающей его температуру рекристаллизации, новые зерна начинают зарождаться на границах ячеек, созданных полигонизированной субзеренной структурой. Это зародышеобразование устраняет большую часть дислокаций в обрабатываемом материале.
Рост зерен
По мере того, как температура повышается, зерна растут, и образуется тонкая рекристаллизованная зернистая структура. Более крупные и быстрорастущие зерна потребляют в процессе более мелкие зерна. На этом этапе устраняются все последствия холодной обработки. Рост зерен может ухудшить свойства материала и, как правило, может привести к шероховатости поверхности компонентов, изготовленных из листового металла.