IX. Виды дефектов и особенности
Намагничивания для разных
Уровней чувствительности
Виды дефектов, обнаруживаемых магнитопорошковым методом
По природе образования дефекты металла, выходящие на поверхность, подразделяются на возникающие из-за пороков основного металла типа расслоений, трещин, сульфидных включений, раковин, плен, закатов и др.; дефекты формирования: непровары, подрезы, прожоги, неравномерная ширина и высота шва, наплывы и др.; трещины, шлаковые и газовые включения, выплески, царапины.
Распространены дефекты, выявляемые магнитными методами, связанные с нарушением технологии сварки и термообработки: непровары, прожоги, выплески, шлаковые и газовые включения, трещины, подрезы, дефекты структуры и закалки.
Трещины — это разрывы металла шва либо основного металла, создающие резкую концентрацию внутренних напряжений. Они обычно недопустимы. Трещины разделяются по размерам (макро- и микроскопические), по расположению (продольные, поперечные) в шве, в зоне термического влияния и в основном металле, а также по происхождению (горячие, холодные и усталостные).
Горячие (кристаллизационные) трещины могут образовываться в период кристаллизации металла в интервале температур 1400…950°С для стали вследствие повышенной хрупкости металла в твердо-жидком состоянии и действия растягивающих напряжений.
Горячие трещины возникают при сварке в околошовной лоне, чему способствуют вредные примеси металла, высокая погонная тепловая энергия, малая глубина проплавления металла и т. д.
Особую группу составляют холодные трещины, возникающие при температуре 300…100°С и ниже, располагаясь по телу кристаллов металла. Появление их связано с образованием структур закалки, которые наблюдаются при сварке углеродистых, низко — и среднелегированных, а также некоторых высоколегированных сталей. Наиболее часто они располагаются в околошовной зоне. В отличие от горячих, холодные трещины имеют меньшую ширину раскрытия, что затрудняет выявление их внешним осмотром.
Усталостные трещины могут появиться в конструкциях, длительно работающих в условиях динамических и знакопеременных нагружений. На поверхности зоны, работающей со знакопеременными нагрузками, до появления усталостных трещин появляются поля, аналогичные полям рассеяния над дефектами. Кроме того, в сварных соединениях также могут иметь место различного рода сварочные дефекты. Приведем основные из них.
Дефекты структуры сварных соединений, выходящие на поверхность. Это разная зернистость, пережог металла, отклонение химического состава шва от установленных значений, наличие в металле сварного соединения структур закалки, фосфидных и нитридных включений.
Непровары образуются при недостаточном токе, чрезмерно большой скорости сварки, неточном направлении электродной проволоки или неправильной манипуляции электродом.
Отсутствие сплавления между основным металлом и металлом сварочной ванны по периметру разделки шва называют несплавлением. Этот дефект сопровождается подрезами на границе шва и увеличенным усилием валика сварного соединения. Подрезы в большинстве случаев заполнены шлаком.
Наплывы могут образовываться при малой скорости сварки или чрезмерной подаче электрода в случаях смещения электрода от осевой линии шва. Они могут быть при сварке «на подъем», в вертикальном положении или выполнении горизонтальных швов на вертикальной плоскости.
Углубления по поверхности шва, образующиеся благодаря вытеснению металла, называют кратерами. Наиболее глубокие и протяженные кратеры возникают при автоматической многодуговой сварке под флюсом. Кратеры часто имеет радиально расходящиеся трещины.
Часто на поверхность выходят поры — пустоты, возникающие при наличии в сварочной ванне газов, главным образом, водорода и азота. Растворимость водорода и азота, например, в низкоуглеродистой стали, резко падает при ее затвердении (азота в 4, водорода в 1,7 раза). При этом образовываются сквозные поры, пронизывающие всю толщину шва, поверхностные либо внутренние микроскопические или до нескольких миллиметров пустоты.
Наиболее эффективный метод борьбы с пористостью — устранение причин их вызывающих, и строгое соблюдение технологической дисциплины при выполнении подготовительных, сборочных и сварочных работ.
Шлаковые включения располагаются по границе сплавления основного металла с наплавленным, вызывая непровары и несплавления. Они могут пронизывать всю толщину шва.
При дуговой сварке возникают подрезы — выемки в основном металле вдоль краев шва, выплавляющиеся при сварке. Подрезы в угловых соединениях и в стыковых соединениях с разделкой кромок указывают на чрезмерную ширину провара ввиду повышенного тока и напряжения дуги.
По величине эффективного диаметра дефектов округлого сечения или ширине раскрытия щелевидных каналов сквозные дефекты можно подразделить на обыкновенные (>0,5), макро- (0,5…2*104 мм) и микрокапиллярные.
Опасны все перечисленные выше дефекты. Однако наиболее опасными из них являются трещины, особенно трещины усталости, ориентированные поперек детали. Трещины усталости легко можно отличить от других дефектов по месту характерного их расположения и по форме осевшего порошка. Как ранее упоминалось, они возникают преимущественно в характерных участках детали, имеют вид резкоочерченных плотных линий из осевшего порошка даже при слабом намагничивании детали.
Часто источником трещин усталости на сварных узлах и деталях являются: непровар, а также мелкие трещины на кратере и в конце сварного шва, не заваренные при изготовлении. Поэтому все сварные детали ответственного назначения подвергают при ремонте тщательному магнитопорошковому контролю.
Трещины на цементированных хромированных поверхностях. При эксплуатации деталей с азотированной и цементированной поверхностями иногда происходит растрескивание хрупкого поверхностного слоя. Трещины в основном бывают двух типов:
трещины, возникающие от ударов по детали, при правке деталей или при действии изгибающих нагрузок эксплуатации;
термические трещины, возникающие на поверхностях трения.
В последнем случае трещины по внешнему виду похожи на шлифовочные и наблюдаются, когда трущиеся детали работают при недостаточной смазке. В результате этого поверхность нагревается до высокой температуры и тогда происходит заедание или частичное разрушение одной детали, скользящей по поверхности другой.
В табл. 11 собрана информация об основных причинах образования трещин.
Шлифовочные трещины возникают из-за повышенного неравномерного местного нагрева шлифуемой поверхности детали. Наиболее склонны к образованию этих трещин цементированные, азотированные и закаленные детали из легированных и малоуглеродистых сталей. При неправильно подобранных режимах шлифования на поверхности хромированных деталей, как правило, появляются шлифовочные трещины.
Шлифовочные трещины легко отличить от трещин других видов: они тонкие, неглубокие (от десятитысячных до десятых долей миллиметра), располагаются на поверхности группами в виде сетки или тонких линии поперек направления шлифовки.
Они резко понижают усталостную прочность деталей, у оснований зубьев шестерен, шлицев, у отверстий, на поверхности галтелей, на обоймах подшипников, местах концентрации напряжений и т.д.
Закалочные трещины возникают при охлаждении деталей в результате действия внутренних напряжений. Они могут возникать и позже в деталях, длительное время не подвергавшихся отпуску, уменьшающему внутренние напряжения.
Высокие и неравномерные внутренние напряжения при недостаточной жесткости детали вызывают ее коробление. Если же в детали имеются ослабленные сечения, то могут возникнуть и трещины. Наиболее вероятные места зарождения закалочных трещин — это места с резким изменением сечения, острые углы и подрезы.
Причиной образования трещин могут служить и дефекты материала (волосовины, шлаковые включения, флокены), ковочные трещины или несоблюдение режимом термической обработки деталей.
Таблица 11. Причины образования трещин в сварных соединениях
Характеристика трещины | Возможные причины образования |
1. Кристаллизационные трещины «горячие» зарождаются в процессе кристаллизации, после охлаждения до 1100…1200°С. В переходной зоне от шва к основному материалу возникают извилистые, в изломе имеющие темный цвет, сильно окисленные но границам зерна, сквозные и песквозные трещины. 2. Трещины в шве профильные или поперечные, в изломе темного цвета — сильно окисленные или светлые с цветами побежалости 3. Трещины в кратере, который образуется в результате выдувания электрической дугой расплавленного металла 4. «Холодные» трещины возникают при остывании металла ниже 200о в околошовной зоне, в металле шва и развиваются вдоль или поперек шва. 5. Мелкие трещины в шве или надрывы в переходной зоне; микротрещипы 6. Трещины, возникающие в процессе термической обработки (закалки) могут иметь любое направление. 7. Трещины в сварных соединениях, возникающие при правке изделий; в изломе они светлые | Неправильная технология сварки и непрочная конструкция изделия Неправильно выбрана марка присадочного материала Неправильная техника сварки (неправильное окончание сварки) Повышенное содержание в металле кремния, водорода; неправильно выбранный присадочный материал; неправильная техника сварки Неудовлетворительное качество присадочного материала флюса, обмазки Неправильная технология термической обработки Неудачная технология правки изделия, коробление изделия |
Отличительным признаком закалочных трещин является неопределенность их направления. Они выявляются хорошо даже при слабом намагничивании, так как материал закаленных деталей имеет достаточно высокие значения остаточной индукции и коэрцитивной силы, а закалочные трещины имеют большие размеры и почти всегда выходят на поверхность детали.
Закалочные трещины дают интенсивное, плотное осаждение порошка в виде ломаных, извилистых линий, идущих в различных направлениях. Четкие и рельефные рисунки осажденного порошка, получающиеся над закалочными трещинами, позволяют отличить их от других дефектов.
Надрывы, возникающие в результате деформации металла. Надрывы — это неглубокие трещины, возникающие на деталях в результате деформации металла, например, при накатке резьбы, изготовлении пружин. При холодной штамповке деталей могут возникнуть трещины в местах резких перегибов, особенно когда материал имеет недостаточно высокие пластические свойства.
Ковочные трещины при металлографическом анализе на стальных деталях легко можно отличить от закалочных вследствие наблюдаемого обезуглероживания стали по их границе. Ковочные и штамповочные поверхностные трещины выявляются магнитным методом также хорошо, как и закалочные — в виде четких, рельефных линий, имеющих самые разнообразные направления на поверхности детали.
Флокены представляют собой мелкие трещины длиной от 20…30 мм разнообразного направления, залегающие преимущественно во внутренних, более глубоких зонах стальных поковок.
Флокены являются опасными дефектами. Присутствие их в стали резко отражается на ее механических свойствах, особенно если направление действия сил не совпадает с плоскостью залегания флокенов.
На деталях они могут быть обнаружены магнитным методом только в том случае, если они выходят на поверхность или залегают неглубоко под ней. При магнитопорошковом контроле флокены выявляются в виде отдельных прямолинейных или искривленных черточек длиной от 1 до 25…30 мм, расположенных в большинстве случаев группами и имеющих разнообразное направление. Флокены обычно сосредоточены в центральной части заготовки в виде семейства гонких и коротких трещинок. В периферийном слое флокены отсутствуют.
Неметаллические раскатанные шлаковые и другие включения представляют собой: продукты реакций раскисления, протекающих в ванне и в ковше при выплавке и разливке стали; шлаки, растворенные при высоких температурах в металле и выделяющиеся из него при понижении температуры в виде включений MnO; FeO; FeS и др.
Волосовины — это тонкие нити неметаллических включений или газовых пузырей, вытянутых вдоль волокон металла при его ковке, прокате или протяжке. Волосовины прямолинейные и вытянуты в направлении прокатки.
На некоторых деталях, работающих на растяжение или изгиб, допускается небольшое количество продольных волосовин и шлаковых включений. В местах концентрации напряжений (на галтелях, острых углах, у масляных отверстий) их не допускают.
Расслоения образуются при прокатке слитков, внутри которых имеются усадочные раковины, большие участки неметаллических включений или плены, т.е. окисленные слои металла. При прокатке включения, раковины, плены раскатываются и образуют расслоения.
studfiles.net
15. Классификация дефектов. Методы, средства и последовательность дефектации.
Дефект — это каждое отдельное несоответствие продукции требованиям нормативной документации. По последствиям дефекты подразделяют на критические, значительные и малозначительные.
Критический дефект — это дефект, при котором использование продукции по назначению практически невозможно или исключается в соответствии с требованиями техники безопасности.
Значительный дефект — это дефект, который существенно влияет на использование продукции по назначению и (или) на ее долговечность, но не является критическим.
Малозначительный дефект — это дефект, который не оказывает существенного влияния на использование продукции по назначению и на ее долговечность. По месту расположения все дефекты подразделяют на наружные и внутренние. Наружные дефекты, такие как деформация, поломки, изменение геометрической формы и размеров, легко выявляют визуально или в результате несложных измерений. Внутренние дефекты, такие как усталостные трещины, трещины термической усталости и т. п., выявляют различными методами структуроскопии деталей. К методам структуроскопии относят магнитодефектоскопию, рентгеноскопию, ультразвуковую дефектоскопию и другие методы. Таким образом, в процессе структуроскопии деталей выполняется комплекс работ, состоящий в выявлении и характеристике дефектов, имеющихся в деталях. Дефекты по возможности исправления классифицируют на исправимые и неисправимые.
Исправимые дефекты — это дефекты, устранение которых технически возможно и экономически целесообразно. К ним относят такие дефекты, как деформации, вмятины, обломы, износ поверхностей, задиры и другие дефекты, не ведущие к полной утрате работоспособности детали.
Неисправимые дефекты — это дефекты, устранение которых технически невозможно или экономически нецелесообразно. По причинам возникновения дефекты подразделяют на три класса: конструктивные, производственные, эксплуатационные.
Конструктивные дефекты — это дефекты, выражающиеся в несоответствий требованиям технологического задания или установленных правил разработки (модернизации) продукции. Причины таких дефектов могут быть весьма различны: ошибочный выбор материала изделия, неверное определение, размеров деталей, режима термической обработки и т. д. Эти дефекты являются следствием несовершенства конструкции и ошибок конструирования.
Производственные дефекты — это дефекты, выражающиеся в несоответствии требованиям нормативной документации на изготовление (ремонт) или поставку продукции. Такого рода дефекты возникают, в результате нарушения технологического процесса при изготовлении или восстановлении деталей. Производственные дефекты подразделяют на шесть групп:
Первая группа — дефекты плавления и литья. К ним относятся: отклонения химического состава от заданного, ликвация, газовые поры, земляные и шлаковые включения, усадочные раковины, спаи, горячие и холодные трещины и др.
Вторая группа — дефекты, возникающие при обработке давлением. К ним относятся: поверхностные и внутренние трещины, разрывы, риски, волосовины, закаты, плены, расслоения, флокены, зажимы и т. д.
Третья группа — дефекты термической, химикотермической и электрохимической обработки. В эту группу входят: термические трещины, обезуглероживание, науглероживание, водородные трещины, перегрев, пережог, трещины отслаивания и др.
Четвертая группа — дефекты механической обработки. К этой группе относятся: отделочные трещины, прижоги, шлифовочные трещины, нарушение герметических размеров.
Пятая группа — дефекты, возникающие при правке, монтаже и демонтаже. К ним относятся: рихтовочные и монтажные трещины, погнутость, обломы резьбы, нарушение посадок.
Шестая группа — дефекты соединения металлов сваркой и наплавкой. В эту группу входят: раковины, поры, шлаковые включения, перегрев, изменение размеров зерна, горячие и холодные трещины, непровар, неполное заполнение шва, нахлест, смещение кромок шва, непропаивание, непроклеивание, отслоение и др.
Эксплуатационные дефекты — это дефекты, которые возникают в результате износа, усталости, коррозии и неправильной эксплуатации. В процессе эксплуатации наибольший процент отказов возникает в результате изнашивания деталей.
Изнашивание — это процесс постепенного изменения размеров и формы тела при трении, проявляющийся в отделении с поверхности трения материала и в его остаточной деформации. Изнашивание деталей зависит от ряда факторов, в частности от условий трения. В зависимости от наличия между трущимися телами смазки различают сухое, граничное и жидкостное трение. Учитывая, что каждому классу деталей присущи конструктивные особенности и определенные условия эксплуатации, можно ориентировочно установить характерные дефекты деталей каждого класса.
Техническое состояние деталей определяют внешним осмотром, остукиванием, измерением размеров, проверкой с помощью универсальных инструментов, специальных шаблонов, приборов, приспособлений и стендов.
При осмотре выявляют наружные повреждения деталей, деформации, трещины, задиры, обломы, прогар, раковины, коррозию, негерметичность и др.
Остукиванием определяют состояние неподвижных соединений (ослабление посадок заклепок, штифтов, шпилек, колец), наличие трещин в корпусных деталях. При легком простукивании плотно сидящие и неподвижные детали издают звонкий металлический звук, а в случае наличия трещин или слабой посадки — дребезжащий, глухой.
С помощью универсальных измерительных средств определяют фактические размеры, отклонения от размеров, формы, взаимного расположения конструктивных элементов детали. В соединениях измеряют величину зазора. Для определения геометрических параметров деталей используют штангенциркули, микрометры, индикаторные нутромеры, штангензубомеры и др. Порядок измерения, применяемый инструмент, приспособления, место замеров указываются в соответствующих технологических картах.
С целью повышения производительности и упрощения контроля и сортировки деталей в специализированном ремонтном производстве применяют дефектовочные калибры (жесткий предельный инструмент) и шаблоны. Шаблоны изготавливают по принципу однопредельных скоб.
Погнутость, скрученность, биение и коробление поверхностей деталей определяют при помощи специальных приспособлений и устройств. Для этой цели используют поверочные плиты; универсальные штативы с индикаторами часового типа, специальные призмы и центры, линейки, угольники, щупы.
Скрытые дефекты деталей (трещины, раковины и др.) выявляют пневматическим, гидравлическим, магнитным, капиллярным и ультразвуковым методами.
Пневматический метод применяют для проверки герметичности радиаторов, топливных баков, топливопроводов, резиновых камер и т. д. Деталь погружают в ванну с водой. Если она имеет больше одного отверстия, то остальные закрывают пробками, а в оставшиеся подают воздух. По пузырькам выходящего воздуха определяют место дефекта.
Гидравлическим методом на специальных стендах проверяют герметичность рубашек блоков, головок цилиндров, всасывающих труб двигателей и т. д. Деталь устанавливают на стенд, отверстия закрывают специальными заглушками с прокладками, внутреннюю полость заполняют водой и создают определенное давление. Подтекание воды укажет место трещины. Гидравлический метод применяют также при проверке плунжерных пар, нагнетательных клапанов топливных насосов высокого давления, форсунок и топливопроводов после ремонта.
Магнитную дефектоскопию применяют для обнаружения скрытых трещин, пор, шлаковых включений в деталях, изготовленных из ферромагнитных материалов. Метод основан на появлении магнитного поля рассеивания в зоне расположения дефекта при прохождении магнитно-силовых линий через деталь. Намагничивание производится пропусканием электрического тока через деталь. Перед намагничиванием деталь посыпают ферромагнитным порошком или поливают суспензией, состоящей из трансформаторного масла (40%), керосина (60%) с добавлением 50 г/л магнитного порошка. Частицы порошка концентрируются по краям дефекта, как у полюсов магнита, и указывают место его расположения и конфигурацию.
Капиллярные методы позволяют выявить нарушения сплошности (трещины, поры и т. п.) у деталей, изготовленных из ферромагнитных и немагнитных материалов. Они основаны на способности некоторых жидкостей проникать в мельчайшие поверхностные нарушения сплошности. К этим методам относится люминесцентная и цветная дефектоскопии.
Простейший из капиллярных методов — цветная дефектоскопия. Проникающую жидкость (керосин — 65%, трансформаторное масло — 30%, скипидар — 5%) окрашивают в красный цвет (добавляется судан, 10 г/л). Ее наносят на обезжиренную поверхность и через 5-10 мин деталь протирают. Для проявления трещины используют раствор масла, который наносят на проверяемую поверхность. По мере высыхания на белой поверхности появляется узор, показывающий расположение дефекта.
studfiles.net
Виды дефектов и их характеристика
Дефект — это отдельное несоответствие продукции установленным требованиям.
Повреждение — событие, заключающееся в нарушении исправного состояния объекта при сохранении работоспособного состояния.
По своим последствиям дефекты подразделяют на:
- критические
- значительные
- малозначительные
По месту расположения дефекты делят на:
- наружные
- внутренние
По возможности устранения выделяют:
- исправимые
- неисправимые
По отражению в нормативной документации выделяют:
- явные
- скрытые
Критический дефект такой, при наличии которого использование детали невозможно. Значительный дефект существенно влияет на использование детали и (или) на ее долговечность, а малозначительный — не оказывает такого влияния. Наружные дефекты выявляются осмотром или путем измерений. Внутренние дефекты выявляются способами структуроскопии или проникающими способами. Устранение исправимого дефекта технически возможно и экономически целесообразно, а неисправимого — невозможно или нецелесообразно. Если для выявления дефекта в технической документации предусмотрены соответствующие правила и средства, то дефект считается явным, в противном случае дефект признают скрытым.
В зависимости от того, какая стадия жизненного цикла автомобиля повлияла на возникновение дефектов, они бывают:
- конструктивные
- производственные
- эксплуатационные
Конструктивные дефекты возникают в результате ошибок и просчетов конструирования, производственные — в результате нарушения технологического процесса изготовления или восстановления деталей, а эксплуатационные — в результате использования автомобиля.
Состояние деталей определяется значениями параметров, в качестве которых применяют размеры (линейные и угловые) элементов детали, их форму и взаимное расположение, наличие трещин, размеры трещин и пробоин, расход пробного вещества (воды, воздуха) сквозь течи, механические характеристики. Эти значения могут быть допустимыми и предельными. Детали с допустимыми значениями параметров используют в дальнейшем без восстановительных работ, а с предельными — выбраковывают. Если значения параметров находятся в отрезке значений между допустимым и предельным, то деталь подлежит восстановлению. У деталей измеряют те параметры, которые изменяются при их использовании.
Техническое состояние деталей в основном определяется эксплуатационными дефектами в виде износов, усталостных изменений, деформаций, изломов, трещин, пробоин, коррозии и старения материала.
ustroistvo-avtomobilya.ru
Классификация дефектов продукции
Основная задача контроля качества состоит в выявлении дефектов продукции, к которым относится каждое отдельное несоответствие товара установленным требованиям. При этом, дефекты продукции могут быть обнаружены как при органолептическом, так и при измерительном контроле; а могут быть выявлены только в процессе эксплуатации.
Классификация дефектов может быть следующей.
В зависимости от возможности выявления дефекты могут быть явные и скрытые.
– Явный дефект – дефект, для обнаружения которого в нормативной документации, обязательной для данного вида контроля, существуют соответствующие правила, методы и средства. Многие явные дефекты обнаруживаются уже при визуальном контроле продукции.
– Скрытый дефект – дефект, для обнаружения которого в нормативной документации, обязательной для данного вида контроля, не предусмотрены соответствующие правила, методы и средства. Скрытые дефекты обнаруживаются при эксплуатации товара (изделия).
По происхождению дефекты могут быть производственные и непроизводственные.
– Производственный дефект возникает в процессе производства товара, из-за нарушения технологического режима изготовления изделия.
– Непроизводственный дефект возникает после завершения процесса производства товара – при транспортировке, хранении, реализации, эксплуатации или . потреблении.
По возможности устранения дефекты делятся на устранимые и неустранимые.
– Устранимые дефекты – дефекты, устранение которых технически возможно и экономически целесообразно.
– Неустранимые дефекты – дефекты, устранение которых технически невозможно и (или) экономически нецелесообразно.
При изучении дефектов, необходимо определить его значимость — относительная величина, определяемая видом, размером, местонахождением дефекта и характеризуемая степенью его влияния на уровень качества товара по сравнению с другими дефектами.
В зависимости от степени влияния на качество дефекты могут быть: критические, значительные, малозначительные.
– Критический дефект – дефект, при существовании которого использование товара по назначению практически невозможно или недопустимо.
– Значительные дефекты продукции существенно влияют на возможность употребления товара по назначению, на его качество и длительность эксплуатации.
– Малозначительные (незначительные) дефекты существенно не влияют на использование изделия по назначению и на его долговечность.
В процессе сплошного или выборочного контроля качества продукции обнаруживается годная продукция и брак.
– Годная продукция – товар, соответствующий всем установленным требованиям.
– Брак – продукция, передача которой потребителю не допускается из-за наличия дефектов, недопускаемых нормативными документами.
Необходимо помнить, что для некоторых групп и видов продукции предусмотрено деление по сортам. Оно зависит от наличия дефектов и отклонений по некоторым показателям потребительных свойств.
Порядок установления сортов:
1) сорта устанавливают по балльной или ограничительной системе. Наиболее распространена балльная система, при которой нормативными документами для каждого из сортов ограничивают вид дефектов, их количество, размеры, местоположение на изделии;
2) при балльной системе отклонения от нормы стандарта по контролируемым показателям и параметрам дефектов оценивают в условных единицах – баллах;
3) путем сравнения суммы баллов, приобретенных изделием при контроле, с нормативными требованиями стандартов, предусматривающих для каждого сорта допустимую сумму баллов, товар относят к тому или иному сорту.
Но в последние годы наблюдается тенденция к уменьшению количества сортов или вообще к отказу деления товаров на сорта.
studfiles.net
Основные типы дефектов, образующихся при ионном легировании полупроводника
При ионном легировании характерными являются дефекты по Френкелю, представляющие собой совокупность выбитого из узла в междоузлие атома полупроводника и образовавшегося пустого узла — вакансии V. Вакансии мигрируют по кристаллу, при этом энергия их миграции в кремнии p-типа равна 0,33 эВ, а в кремнии n-типа — 0,18 эВ. Междоузельные атомы также подвижны: в кремнии p-типа их энергия миграции составляет 0,01 эВ, а в кремнии n-типа — 0,4 эВ.
Вакансии при своем движении по кристаллу могут объединяться в пары — дивакансии или более сложные комплексы — тривакансии, тетравакансии и даже гексавакансии. Эти дефекты устойчивы при комнатной температуре. Вакансии образуют также комплексы с атомами примесей: V + P, V + Sb, V + Al, V + О. При этом вакансия занимает узел, соседний с примесным атомом.
В результате объединения простых дефектов, например под действием механических напряжений, возникают линейные и плоскостные дефекты — дислокации, дефекты упаковки. Плотность дислокаций, подсчитанная по фигурам травления в кремнии при дозе ионов 31016 ион/см2, составляет 3105 см–2. В процессе отжига линейные дефекты могут изменять свою длину, форму и местоположение в кристалле.
Характер возникающих дефектов зависит от массы иона, полной дозы и температуры мишени. Простейшие дефекты, например дефекты по Френкелю, возникают в кремнии при внедрении легких и средних ионов малыми дозами при комнатной температуре. Условно легкими и средними считают ионы, с атомной массой M < 60, тяжелыми — с M > 60.
При внедрении тяжелых ионов малыми дозами при комнатной температуре в кристаллической решетке возникают разупорядоченные области, называемые кластерами. Кластер в кремнии представляет собой отдельную разупорядоченную область, которая состоит из центральной области нарушенной структуры диаметром, равным примерно 50 нм, окруженной областью объемного заряда, создаваемого благодаря захвату основных носителей дефектами центральной области.
При больших дозах ионов разупорядоченные области, т.е. кластеры, перекрываются, концентрация дефектов может превысить предельную. В этом случае происходит аморфизация полупроводника.
Таким образом, при малых дозах внедрения ионов области разупорядочения, прилегающие к отдельным трекам ионов, пространственно отделены друг от друга, при больших дозах внедрения ионов отдельные области разупорядочения перекрываются, образуя в кристалле сплошной аморфный слой.
Распределение дефектов по глубине кристалла, их концентрация зависят от числа и распределения первоначально смещенных атомов. При вычислении числа смещенных атомов обычно учитывают лишь упругие ядерные столкновения, так как они в основном приводят к разупорядочению решетки вблизи траектории иона и ответственны за эффекты радиационного повреждения. Зная энергию, теряемую ионами в ядерных столкновениях, можно оценить среднее число смещенных атомов, их усредненное пространственное распределение.
Число смещенных атомов Nd в твердом теле обычно находят по формуле, выведенной Кинчином и Пизом:
где E — энергия иона; Ed — эффективная пороговая (т.е. наименьшая) энергия смещения атома мишени из узла кристаллической решетки. При этом предполагается, что атомы при соударении ведут себя как твердые шары и все соударения упругие, т.е. на электронное возбуждение энергия не расходуется. Указанная формула выведена для случая равных масс иона и атома мишени, но и для слу-чая неравных масс это выражение удовлетворительно согласуется с экс-периментом.
Имеются теоретические расчеты распределений дефектов (смещенных атомов) по глубине при бомбарди-ровке неориентированных мишеней различными ионами. На рис.3.17 по-казано распределение концентрации бора N и дефектов Nd по глубине при бомбардировке Si ионами B+ (расчет методом Монте-Карло). Расчеты, выполненные по этому методу, показывают, что распределение вакансий соответствует распределению потерь энергии в процессе торможения.
Характерной особенностью распределения дефектов является смещение их максимума в сторону меньших глубин относительно максимума концентрации примесных атомов. Это объясняется тем, что слои, расположенные в районе максимума концентрации примесей, экранируются вышележащими слоями кремния и испытывают смещения от меньшего числа ионов по сравнению со слоями, расположенными ближе к поверхности. Действительно, прежде чем ион в процессе столкновений потеряет значительную часть своей кинетической энергии и прекратит перемещение внутри кристаллической решетки кремния, он создаст на пути своего движения область с высокой концентрацией радиационных дефектов. Это сильно разупорядоченная область оказывает экранирующее действие по отношению к лежащему ниже слою, задерживая часть ионов с энергией E Ed и уменьшая тем самым вероятность образования дефектов в этом слое.
Возникновение двух пространственно разделенных областей с высокой концентрацией радиационных дефектов и высокой концентрацией примеси может привести к тому, что сильно легированный слой полупроводника окажется отделенным от поверхности образца высокоомным аморфным слоем. Последующий отжиг полупроводника с такой структурой приведет к смещению профиля концентрации примеси ближе к поверхности из-за диффузии атомов примеси в область с наибольшей концентрацией вакансий. Концентрация радиационных дефектов для ионов одинаковой энергии увеличивается с ростом массы иона. Это происходит как за счет уменьшения толщины поврежденного слоя (сокращается длина пробега более тяжелого иона), так и вследствие роста доли энергии, затрачиваемой на упругие столкновения.
Число дефектов зависит также от дозы легирования. При дозах менее 1014 ион/см2 число дефектов линейно растет с увеличением концентрации внедренных ионов, причем максимум дефектов совпадает с областью торможения ионов. Дальнейшее увеличение дозы приводит к переходу кремния в аморфное состояние, при этом концентрация дефектов остается постоянной. Если пучок ионов ориентирован относительно кристаллографической оси, то при малых дозах (менее 1014 ион/см2) образуется в два-три раза меньше дефектов, чем при неориентированном пучке. С ростом дозы легирования это различие быстро уменьшается вследствие увеличения вероятности деканалирования на накапливающихся дефектах решетки.
studfiles.net
ГОСТ про дефекты
ГОСТ 15467-79
(СТ СЭВ 3519-81)
Группа Т00
ГОСУДАРСТВЕННЫЙ СТАНДАРТ СОЮЗА ССР
Управление качеством продукции
ОСНОВНЫЕ ПОНЯТИЯ
Термины и определения
Product-quality control.
Basic concepts. Terms and definitions
Дата введения 1979-07-01
УТВЕРЖДЕН И ВВЕДЕН В ДЕЙСТВИЕ Постановлением Государственного комитета СССР по стандартам от 26 января 1979 г. N 244
ВЗАМЕН ГОСТ 15467-70, ГОСТ 16431-70, ГОСТ 17341-71, ГОСТ 17102-71
ПЕРЕИЗДАНИЕ (июнь 1986 г.) с Изменением N 1, утвержденным в январе 1985 г. (ИУС 4-85)
Настоящий стандарт устанавливает применяемые в науке и технике термины и определения основных понятий в области управления качеством продукции.
Термины, установленные настоящим стандартом, обязательны для применения в документации всех видов, учебниках, учебных пособиях, технической и справочной литературе. В остальных случаях применение этих терминов рекомендуется.
Для каждого понятия установлен один стандартизованный термин.
Применение терминов-синонимов стандартизованного термина запрещается.
Установленные определения разрешается при необходимости изменять по форме изложения, не допуская нарушения границ понятий.
Допускается применение отраслевых терминов, не установленных настоящим стандартом, отражающих специфические особенности продукции отрасли.
В справочном приложении даны пояснения и примеры к ряду терминов.
В стандарте приведен алфавитный указатель содержащихся в нем терминов.
Стандарт полностью соответствует СТ СЭВ 3519-81.
38. Дефект | Каждое отдельное несоответствие продукции установленным требованиям |
41. Явный дефект | Дефект, для выявления которого в нормативной документации, обязательной для данного вида контроля, предусмотрены соответствующие правила, методы и средства |
42. Скрытый дефект | Дефект, для выявления которого в нормативной документации, обязательной для данного вида контроля, не предусмотрены соответствующие правила, методы и средства |
43. Критический дефект | Дефект, при наличии которого использование продукции по назначению практически невозможно или недопустимо |
44. Значительный дефект | Дефект, который существенно влияет на использование продукции по назначению и (или) на ее долговечность, но не является критическим |
45. Малозначительный дефект | Дефект, который существенно не влияет на использование продукции по назначению и ее долговечность |
46. Устранимый дефект | Дефект, устранение которого технически возможно и экономически целесообразно |
47. Неустранимый дефект | Дефект, устранение которого технически невозможно или экономически нецелесообразно |
К термину «Дефект» (п.38)
Если рассматриваемая единица продукции имеет дефект, то это означает, что по меньшей мере один из показателей ее качества или параметров вышел за предельное значение или не выполняется (не удовлетворяется) одно из требований нормативной документации к признакам продукции.
Несоответствие требованиям технического задания или установленным правилам разработки (модернизации) продукции относится к конструктивным дефектам.
Несоответствие требованиям нормативной документации на изготовление или поставку продукции относится к производственным дефектам.
Примерами дефектов могут быть: выход размера детали за пределы допуска, неправильная сборка или регулировка (настройка) аппарата (прибора), царапина на защитном покрытии изделия, недопустимо высокое содержание вредных примесей в продукте, наличие заусенцев на резьбе и т.д.
Термин «дефект» связан с термином «неисправность», но не является его синонимом. Неисправность представляет собой определенное состояние изделия. Находясь в неисправном состоянии, изделие имеет один или несколько дефектов.
Термин «дефект» применяют при контроле качества продукции на стадии ее изготовления, а также при ее ремонте, например, при дефектации, составлении ведомостей дефектов и контроле качества отремонтированной продукции.
Термин «неисправность» применяют при использовании, хранении и транспортировании определенных изделий. Так, например, словосочетание «характер неисправности» означает конкретное недопустимое изменение в изделии, которое до его повреждения было исправным (находилось в исправном состоянии).
В отличие от термина «дефект» термин «неисправность» распространяется не на всякую продукцию, в том числе не на всякие изделия, например, не называют неисправностями недопустимые отклонения показателей качества материалов, топлива, химических продуктов, изделий пищевой промышленности и т.п.
Термин «дефект» следует отличать также от термина «отказ».
Отказом называется событие, заключающееся в нарушении работоспособности изделия, которое до возникновения отказа было работоспособным. Отказ может возникнуть в результате наличия в изделии одного или нескольких дефектов, но появление дефектов не всегда означает, что возник отказ, т.е. изделие стало неработоспособным.
К терминам «Явный дефект» и «Скрытый дефект» (пп.41, 42)
Деление дефектов на явные и скрытые обусловливается предусмотренными правилами, методами и средствами контроля качества продукции.
К правилам контроля относят его распорядок (регламент, график), к методам — технологию (способы, приемы, последовательность операций), объем (число контролируемых показателей или параметров) и точность.
К средствам контроля относят используемое оборудование (стенды, испытательные машины, оснастку позиций и площадок на полигонах и т.п.), измерительную и регистрирующую аппаратуру, а также инструменты и приборы.
Многие явные дефекты выявляются при внешнем осмотре (визуально). Однако, если нормативной документацией предусмотрена проверка отсутствия какого-либо дефекта инструментом, прибором или разборкой контролируемого изделия, то такой дефект относится к категории явных, несмотря на невозможность его визуального обнаружения.
Скрытые дефекты, как правило, выявляются после поступления продукции к потребителю или при дополнительных, ранее не предусмотренных проверках, в связи с обнаружением других (явных) дефектов.
К терминам «Критический дефект», «Значительный дефект» и
«Малозначительный дефект» (пп.43, 44, 45)
При разработке нормативной документации (главным образом, при установлении методов контроля изготовляемой или ремонтируемой продукции) все возможные дефекты могут подразделяться на критические, значительные и малозначительные. Такое разделение основано на оценке степени влияния каждого рассматриваемого дефекта на эффективность и безопасность использования продукции с учетом ее назначения, устройства, показателей ее качества, режимов и условий эксплуатации.
Указанное разделение дефектов производится для последующего выбора вида контроля качества продукции (выборочный или сплошной) и для назначения такой характеристики выборочного контроля, как риск потребителя (заказчика).
Чтобы не пропустить критический дефект, контроль продукции должен быть сплошным и в ряде случаев — неоднократным. Контроль отсутствия значительного дефекта допускается осуществлять выборочно только при достаточно низком значении риска потребителя. Отсутствие малозначительного дефекта может контролироваться выборочно при относительно высоком значении риска потребителя.
Для некоторых видов продукции определенные совокупности дефектов, каждый из которых при отдельном его рассмотрении является малозначительным, могут быть эквивалентны значительному или даже критическому дефекту и должны относиться к соответствующей категории. Совокупности же значительных или значительных с малозначительными дефектов аналогичным образом могут быть эквивалентны критическому дефекту и должны относиться к категории критических.
В отдельных отраслях промышленности может, при необходимости, производиться более детальная классификация дефектов по степени их влияния на эффективность использования продукции.
В соответствии с приведенной классификацией дефектов иногда по результатам контроля продукции различают следующие ее единицы (в частности, изделия) :
критически дефектные, т.е. имеющие хотя бы один критический дефект;
значительно дефектные, т.е. имеющие один или несколько значительных дефектов, но не имеющие критических дефектов;
малозначительно дефектные, т.е. имеющие один или несколько дефектов малозначительных по отдельности и в совокупности, но не имеющие значительных и критических дефектов.
К терминам «Устранимый дефект» и «Неустранимый дефект» (пп.46, 47)
Устранимость и неустранимость дефекта определяют применительно к рассматриваемым конкретным условиям производства и ремонта с учетом необходимых затрат и других факторов.
Один и тот же дефект может быть отнесен к устранимым или неустранимым в зависимости от того, обнаружен он на ранних или на заключительных этапах технологического процесса производства (ремонта).
Неустранимые дефекты могут переходить в категорию устранимых также в связи с усовершенствованием технологии производства (ремонта) продукции и снижением затрат на исправление брака.
studfiles.net
Дефекты сварных соединений | Учебные материалы
В сварочном производстве принято выделять следующие типы дефектов (рисунок 3.15):
- Дефекты подготовки и сборки изделий под сварку.
- Дефекты формы шва.
- Наружные и внутренние дефекты.
Дефекты подготовки и сборки
Характерными видами являются неправильный угол скоса кромок в швах с V–, X– и U–образной разделкой, слишком большое или малое притупление по длине стыкуемых кромок; непостоянство зазора между кромками; несовпадение стыкуемых плоскостей ведущих к смещению кромок, слишком большой зазор между кромками, расслоения и загрязнения кромок.
Форма и размеры сварных швов обычно задаются техническими условиями, указываются на чертежах и регламентируются стандартами: конструктивные элементы b – ширина шва, высота усиления С и глубина провара h.
Основные дефекты – неравномерная ширина и высота усиления, местные бугры и седловины. Эти виды дефектов наиболее характерны при ручной электродуговой сварке.
Такие дефекты снижают прочность соединения и косвенно указывают на возможность образования внутренних дефектов.
Дефекты сварных соединений характеризуются как недопустимые, так и допустимые. Недопустимые дефекты вновь перевариваются.
Готовые сварные соединения прежде всего подвергаются внешнему осмотру на выявление внешних дефектов (трещины, ослабление шва, наплывы, подрезы, прожоги, местная ноздреватость, пористость и др.).
Трещины: горячие (технологические) и холодные. Горячие – в жестко закрепленных конструкциях легированных сталей (особенно при недостаточном качестве – Smax). Холодные – закалочная теория (Сmax) Сэкв=6,25 и водородная.
Наплывы образуются в результате стекания расплавленного металла на нерасплавленный металл.
Подрезы образуются по краям шва в основном металле (глубиной от десятых долей до нескольких мм). Прожоги – дефекты в виде сквозного отверстия в сварном шве (первый корневой слой или тонкий металл, или стекание через большой зазор).
Наличие скрытых внутренних дефектов в сварных соединениях контролируется различными физическими методами: просвечивание рентгеновскими лучами, просвечивание – лучами радиоактивных изотопов (кобальт – 60, цезий – 137), магнитографический метод, метод магнитного порошка и ультразвуковая дефектоскопия, контроль течеисканием.
Каждый из этих методов имеет свои специфические особенности, обуславливающие его чувствительность и область применения.

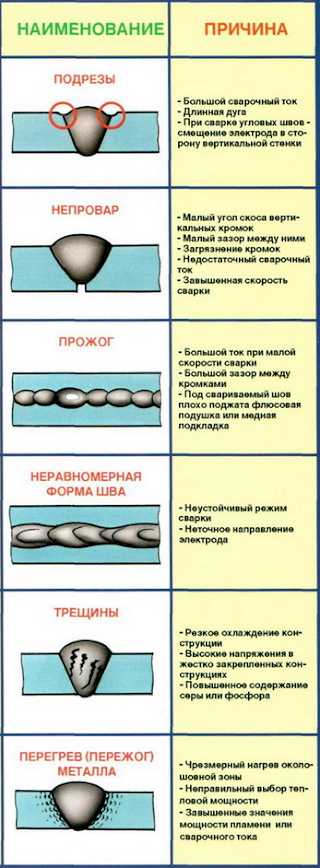
Рисунок 3.15 – Виды дефектов сварных швов и причины их возникновения
Испытание изделий на герметичность (ограничение проникновения жидкости или газа), или контроль течеисканием, выполняют применением легко проникающих сред (жидкостей или газов), хорошо различных визуально или с помощью приборов.
К внутренним дефектам относят поры, шлаковые включения, непровары, несплавления и трещины. Поры образуются вследствие загрязнений, влажности флюса или покрытия электродов, недостаточной защиты в среде защитного газа. Непровары из-за плохой зачистки кромок от окалины, ржавчины, шлака, блуждания дуги из-за магнитного дутья; неправильный выбор режима сварки (силы тока и напряжения дуги, скорости сварки) и т.п.
Кроме контроля качества внешним осмотром и с применением различных физических методов проверяется соответствие механических свойств и хим.состава сварных соединений требованиям технических условий и технологических инструкций по сварке на образцах – свидетелях.
Контроль качества исходных материалов, технологии и квалификации сварщиков
Для обеспечения высокого качества сварных соединений необходим контроль исходных материалов (основного металла, электродов, сварочной проволоки, флюсов, защитных газов и т.д.). Качество исходных материалов устанавливают на основании сертификатных данных, для чего определяют соответствие требованиям данного технологического процесса сварки изделий. При наличии внешних дефектов, а также при отсутствии сертификатов исходные материалы допускают только после проведения химического анализа, механических испытаний и испытаний на свариваемость.
При контроле основного металла особое внимание обращают на зоны, подлежащие к сварке – они должны быть очищены от грязи, масла, краски, ржавчины.
Прокат проверяют на наличие расслоений, окалины, равномерности толщины листа и т.д.
Электроды, сварочную проволоку проверяют выполняя пробную сварку для установления качества материалов по показателям характера плавления, легкость отделения шлака и качество формирования сварного шва. Они должны удовлетворять требованиям действующих ГОСТов.
Свариваемость – это свойство металла образовывать при установленной технологии сварки соединение, отвечающее требованиям, обусловленной конструкцией и условиями эксплуатации изделия. Свариваемость контролируют обычно в двух случаях: при выборе материалов и разработке технологии сварки, например, при стадии проекта или при технологической подготовке производства. Вторая проверка связана с возможными отклонениями показателей свойств основного металла, проволоки, партии электродов и флюсов от сертификатных значений.
Большое значение для обеспечения качества имеет контроль в процессе производства сварочных работ. Сюда относятся отмеченные выше методы контроля, включая контроль исправности сварочного оборудования и сварочных приспособлений и соблюдения установленных режимов сварки (по току, напряжению и скорости сварки). Такой контроль осуществляют технологи, мастера и другие инженерно–технические работники ответственные за работу данного участка, цеха, предприятия.
Тщательный планомерный контроль подготовки изделий под сварку и процесса сварки не будет эффективным без проверки уровня подготовленности сварщиков. Например, при сварке труб на монтаже более 70% брака возникает по вине сварщиков.
Для проверки квалификации сварщиков администрация предприятия организует квалификационную комиссию с участием инспектора Госгортехнадзора. Испытания должны проходить периодически. При этом проводят испытания по теории и практике сварочных работ с включением сварки образцов соответствующего изделия. Образцы сваривают в тех же условиях и пространственных положениях, что и реальное изделие (например, трубы – поворотные и неповоротные стыки). После внешнего осмотра сваренные образцы проверяют предусмотренными методами неразрушающего контроля, а также подвергают механическим испытаниям.
Количество образцов для испытаний регламентируются “Правилами аттестации сварщиков”.
dprm.ru