Как сделать колеса низкого давления своими руками, диски
Использование правильных шин – одно из главных условий хорошей проходимости для любого вездехода. Поскольку стоимость специализированного комплекта, почасту изготавливающегося мелкосерийно либо и вовсе на заказ, нельзя назвать гуманной, рассмотрим, как сделать колеса низкого давления своими руками. На видео продемонстрируем процесс преображение стандартных грузовых покрышек в ободрыши.
Целесообразность установки
Рассмотрим особенности, которые делают шины низкого давления настолько эффективными:
- небольшой вес, по сравнению с обычными внедорожными покрышками соизмеримых габаритов. Благодаря этому ДВС намного легче проворачивать колеса, что равнозначно увеличению крутящего момента без изменений в двигателе либо трансмиссии;
- увеличенная площадь контакта с дорожным полотном. Как известно из курса физики, чем больше площадь, на которую распределяется масса, тем меньше давление на поверхность в каждой точке.
Именно это обуславливает использование колес низкого давления на болото- и снегоходах. Аналогичный эффект используется и в сельскохозяйственной технике, где излишняя нагрузка на грунт вредна для культур. При определенном соотношении массы транспортного средства, вытесняющей площади и количества помещающегося в покрышку воздуха, автомобиль приобретает плавучесть.
Регулировать удельное давление на грунт, а следовательно, и проходимость можно изменение внутреннего давления покрышки. Транспортное средство реально оборудовать автоматической подкачкой шин, после чего изменять давление можно из салона.
Варианты конструкции
Поскольку в нашем случае нам интересен процесс изготовления покрышек повышенной проходимости своими руками, останавливаться на заводских вариантах конструкции мы не будем. Виды шин низкого давления, которые доступны для самостоятельного изготовления:
- в качестве базы используется камера из шины нужного размера.
Диск при этом можно полностью изготовить своими руками либо дооснастить необходимыми упорами и крепежами готовое колесо. Поскольку камера очень эластичная, ей необходим дополнительный подпор, который будет препятствовать заламыванию при боковых нагрузках. По периметру пятная контакта камера обвязывается кусками плотного материала или цепями, что необходимо не только для крепления камеры к диску, но и для создания эффекта грунтозацепов. Возможность цепляться важна не только на песке, рыхлом грунте либо снегу, но и на воде;
- ободрыши низкого давления. В качестве основы используются грузовые шины, из которых срезается часть протекторного и профильного слоя. В итоге покрышка становиться легче и приобретает дополнительную эластичность. Чтобы уменьшить риск разбортировать колеса при езде на низком давлении, как и в предыдущем случае, необходимо изготовить дополнительный боковой упор. Как сделать ободрыши, а также конструкцию диска рассмотрим далее на фото и видео.
Камерный вариант
В первую очередь вам необходимо подобрать или выточить самостоятельно диски, которые будут подходить под параметры ступиц вашего ТС. Как можно поступить, если необходимо подогнать ширину диска под камеру:
- разрезать диск, вырезав внутреннюю часть необходимого размера, затем опять сварив диски, если необходимо уменьшить посадочный размер;
- если ширину нужно увеличить, то между двумя разрезанными половинами вваривается часть другого диска. Сделать такие колеса вам могут на заказ, так как изготовление разварок – довольно распространенная услуга.
Для изготовления выбранного нами вида колес низкого давления потребуются металлические пруты (безопасная толщина зависит от размера камеры, а также частоты расположения перемычек). Боковые упоры привариваются к основе диска, к ним потом крепятся поперечные перемычки, которые и будут посадочным местом на диске для камеры. Для улучшенной боковой поддержки вся система укрепляется по внутреннему периметру профиля шины круговым прутом.
Некоторые изобретатели для перемычек, огибающих пятно контакта, используют цепи. Решение неплохое, поскольку позволяет получить дополнительные снего-, водо- и грунтозацепы. Также можно использовать буксировочные тросы, которые после обвязки будут покрывать долю камеры, препятствуя ее повреждению.
Скорее всего, лишним будет напоминание о том, что все крепежные элементы, обращенные к камере, должны быть довольно плоскими. Иначе при проезде неровностей есть большая вероятность пробить камеру.
Делаем ободрыши
Для самостоятельного изготовления шин низкого давления вам потребуются:
- б/у покрышки от грузовика (к примеру, от Газ-66 или шины ВИ-3, устанавливаемые на Краз 255). Если вы будете покупать шины специально под ободрыши, то выбирайте резину, не «пожеванную» внутри. Иначе после снятия верхнего слоя вы получите слабое место или и вовсе дыру, которую придется вулканизировать;
- строительный нож и комплект сменных лезвий, так как в конструкции шины используются достаточно прочные нити, которые быстро тупят лезвия;
- шаблон, который можно изготовить из плотного картона или тонколистовой стали.
Чтобы ободрыши были не только эффективными, но и смотрелись неплохо, протектор необходимо вырезать максимально ровно и симметрично. Также вам потребуется мелок либо маркер, которым вы будете обводить шаблон;
- прочные зажимы. Таковые часто используют рихтовщики для зажатия кузовных панелей при восстановлении битых автомобилей. Подойдет и обычная струбцина, но действовать в таком случае нужно аккуратней;
- ручная либо механическая лебедка, а также трос, которыми натягивается отрезаемый кусок протекторного слоя. Можно использовать ручной редуктор либо лебедку, установленную на автомобиле. Вручную создать усилие, чтобы сделать ободрыши, у вас не получится, так как слои резины очень плотно скреплены.
Самостоятельное изготовление
Чтобы изготовить ободырыши, первым делом необходимо вытащить боковой металлический корд. Для этого сделайте надрез, отступив от внутренней части покрышки примерно 10 мм. Подцепите корд отверткой, а затем, зацепив крюком, выдерните металлический обод с помощью лебедки.
По всему периметру колеса с помощью шаблона нанесите будущее очертание протектора. Некоторые ободрыши можно увидеть с оставленным по центру протектором. Именно по контуру очертаний необходимо сделать надрезы резины. Для этого лучше всего использовать строительный нож, так как вы сможете контролировать глубину пореза, выставив необходимую длину лезвия. Если вы уверены в своих силах, можете использовать болгарку. Чтобы не прорезать шину насквозь, ориентируйтесь по звуку. Как только вы прорежете резиновый слой и достанете до металлического корда шины, звук приобретет соответствующую окраску.
Надрежьте профиль покрышки по внутреннему периметру (где раньше было металлическое кольцо из проволоки). Именно за надрезанный отрезок необходимо зацепиться зажимом. С помощью лебедки создайте натяжения, а затем канцелярским ножом постепенно подрезайте отслаиваемый кусок. После обдирки всей шины вы получите ободрыши. Учтите, что при создании натяжения шина будет стремиться посунуться, поэтому необходимо реализовать упор.
При работе не стойте по направлению натяжения лебедки, чтобы зацеп не сорвался и не причинил вам травм. Разумеется, стоит подумать о сохранности вещей, находящихся в зоне поражения.
Диски
Диски для вездеходов своими руками — Пневмоход.ру
admin Статьи 0 комментариев
Умельцев, которые делают своими руками вездеходы, часто интересует вопрос — можно ли, и если можно, то как сделать диски самостоятельно. Вездеход – это такая машина, которая застрянет там, куда остальные не доедут, поэтому требования к дискам в данном случае самые жесткие.
Требования к дискам:
- Диски должны иметь высокие антикоррозийные характеристики.
Так как их эксплуатация сопряжена со сложными условиями, материал, из которого сделан диск, не должен покрываться ржавчиной или коррозией даже после продолжительного нахождения во влажных условиях.
- Небольшой вес. Внедорожники и вездеходы сами по себе обладают высоким весом, поэтому не стоит утяжелять автомобиль еще и слишком тяжелыми дисками.
- Возможность коррекции. Эксплуатация вездехода в сложных условиях приводит к тому, что диски могут погнуться, поэтому хорошие диски для вездехода должны иметь возможность починки.
- Хорошее соотношение цена-качество. Дешевые диски быстро ломаются, а кованные – слишком дороги. Поэтому для каждого конкретного случая должен быть индивидуальный подход.
Купить подходящие диски к вездеходам иногда бывает невозможно, поэтому стоит подумать о том, чтобы сделать их своими руками.
Как сделать диски для вездехода своими руками
Процесс работы над дисками можно разделить на этапы.
Этапы работы:
- В первую очередь следует сделать запорные кольца.
Они могут быть изготовлены из обортовки двухсотлитровой бочки. Если вам удалось найти такую бочку с металлическим ободом, то вам повезло. Если вы не смогли найти обод от такой бочки, можно попытаться загнуть кольца из уголков на 25 мм или из ленты железа 2 -3 мм.
- Подготавливаем кольцо так, чтобы оно плотно входило в посадочное место уже ободранной покрышки. Плотно – это значит так, чтобы его можно было заколотить внутрь молотком.
- Следующий этап – измерение внутренней длины окружности этого кольца. Это можно сделать с помощью плоской металлической ленты. Кусок такой ленты отрезают и используют как шаблон при изготовлении бочки, подгоняя ее под внутреннюю окружность.
- Когда запорные кольца готовы, можно приступать к изготовлению самой бочки дисков. Для этого потребуется цельный лист железа.
- Рисуем развертку со следующими размерами. Она будет прямоугольной формы, где длина равна внутренней длине окружности запорного кольца, а ширина — ширине диска.
- Вырезаем полученный прямоугольник.
- Из полученного железного прямоугольника сворачиваем бочку. Контрольной лентой ещё раз проверяем внешнюю длину окружности бочки, которая будет чуть больше из-за толщины листа металла.
- На следующем этапе нам надо срезать излишек. Допускается погрешность не более 1 мм.
- Шов на бочке герметично привариваем, после чего его надо отшлифовать от подтеков. Шлифовать надо с двух сторон – и снаружи, и внутри.
- Для того, чтобы изготовить конус для диска, измеряем внутреннюю длину окружности готовой бочки. Далее используем формулу: внешний радиус конуса «R» = «С»внут.б. / 2 пи = «С»внут.б. / 6,28.
- Свариваем элементы.
Таким образом, у вас будет сделана бочка для диска.
Как сделать своими руками конус для диска
Чтобы сделать конус, для начала надо рассчитать, начертить и вырезать его развёртку. Это можно делать как с целого куска металла, так и из частей. Чаще всего развертку делают из трёх частей, которые потом сваривают в единое целое на трафарете.
Вырезка развертки конуса из трех частей имеет большое преимущество – такой способ в два раза экономит металл.
В первую очередь выберем нужный угол конуса. Опыт показывает, что самый оптимальный вариант – это угол в 45 градусов. Можно сделать и более тупой угол, до 60-70 градусов, однако такой угол подойдет в том случае, если надо увеличить вынос диска.
Сектора следует обрезать строго по радиальной линии.
Важно: при работе над дисками есть одна проблема — во время эксплуатации сварочный шов может лопнуть.

Перед эксплуатацией диск следует покрасить. Можно использовать порошковую покраску автомобильных дисков от zahidcolor
И не забудьте проверить, не упирается ли шаровая опора во внутренний конус. Это распространенная проблема, когда диски хочется сделать своими руками. В результате приходится диск смещать к краю бочки, и внутренний конус получается практически прямым без наклона.
Tagged диски, диски для вездеходов, Диски для шин низкого давления, самодельные диски
Самодельные диски для шин низкого давления
- 1 Общая характеристика ШНД
- 2 Изготовление дисков и шин
- 3 Несколько полезных советов
- 4 Заключение по теме
Многие жители встречали на дорогах автомобили с установленными огромными колесами, поставленными на самодельные диски для шин низкого давления. Таких дисков нет в продаже. Их делают только на заказ. Колеса низкого давления пользуются спросом у таких категорий населения, как:
- военные различных родов войск;
- охотники и рыбаки, особенно зимой;
- фермеры;
- геологи;
- путешественники.
Общая характеристика ШНД
Шины низкого давления (ШНД), по сравнению с обычными моделями, имеют, исходя из названия, значительно меньшее давление. Они отличаются большими размерами и низким давлением на почву, что позволяет передвигаться по дорогам с любым покрытием. Не страшно этим шинам и полное бездорожье. Так как сцепление с дорогой довольно высокое, автомобиль может преодолеть:
- болотистую местность;
- разного рода бездорожье;
- пашню;
- лес.
Специалисты оценивают КПД таких колес на 20% больше, чем обычных, выпускаемых на заводах. Они имеют следующие преимущества:
- площадь соприкосновения с грунтом большая;
- удельное давление низкое.
Увеличенная площадь соприкосновения не дает возможности резине преждевременно изнашиваться. Низкий уровень удельного веса положительно сказывается на пашне. Но на таких колесах рекомендуется меньше ездить по шоссейным дорогам с твердым покрытием. Связано это с тем, что боковые их стороны довольно тонкие. Самодельные колеса можно купить, но заплатить за них придется почти 50% стоимости транспортной единицы. Именно это стало причиной того, что автолюбители сами все чаще берутся за их изготовление.
Изготовление дисков и шин
Изображение 2. Диски автомобиля ВАЗ.Диски для шин низкого давления и шины можно сделать самостоятельно. Для этого нужно знать некоторые их особенности. Самодельные колеса могут быть следующей формы:
- арочные;
- широкопрофильные;
- тороидальные;
- пневмокатки.
Арочные конструкции предназначены для передвижения по бездорожью. Их обычно ставят на ведущий привод автомашины. За основу такого колеса рекомендуется брать широкопрофильную резину толщиной до 700 мм. После обработки ее ширина может стать в несколько раз больше. Внешне колесо походит на бочку. Накачивать его следует до уровня 0,05 МПа.
Широкопрофильные имеют вид овала. Давление в них ниже стандартного в 2 раза. Применяются в автомобилях высокой грузоподъемности. Довольно устойчивы к качению.
Тороидальные ШНД изготавливаются как камерные, так и бескамерные. Особым спросом пользуются у военных, охотников и путешественников.
Пневмокатки имеют грунтозацепы, выполняющие функции ребер жесткости. Отличаются высокой износоустойчивостью. Хорошо работают на бездорожье.
Диски для шин низкого давления (изображение № 1) тоже самодельные. Простая конструкция — это пневматик и пара дисков. Сначала вытачивается ступица с гнездом для подшипников. На ней крепятся фланцы. Изготовление деталей может быть из листовой стали. Ее толщина — от 1 до 3 мм. Можно использовать алюминиевый сплав марки Д 16. Вместо Д 16 используют и марку АМГ.
Изображение 3. Резьбовой фиксатор.Если нет особого желания заниматься подобной работой, можно пойти по менее трудному пути. Для этого достаточно взять диски от автомобиля. Размер они должны иметь такой, какой вам нужен. Например, это могут быть диски автомобиля ВАЗ (изображение № 2). C лицевой стороны к ободу привариваются резьбовые фиксаторы (изображение № 3). Болты, закрученные в них, будут удерживать шину низкого давления от проворачивания. Дальнейший порядок работы такой:
- к дискам привариваются спицы;
- по кругу устанавливается трубка и закрепляется сваркой, образуя обруч;
- изготовленное ранее место крепежа с осью тоже приваривается к диску;
- после всех работ болгаркой следует удалить все острые детали, чтобы защитить от прокола камеру.
Для изготовления шин низкого давления своими руками нужны материалы и инструменты (изображение № 4):
- шины;
- маркер;
- острый нож;
- точило или брусок для заточки ножа;
- болты;
- перемычки из резины;
- лебедка, установленная на основание.

Нож желательно иметь с двухсторонней заточкой. Шину, которая выбрана в качестве заготовки, нужно хорошо промыть и высушить. Затем маркером она размечается и вырезается лишний материал. Для соединения с диском вырезаются небольшие окошки для болтов. Проволоку корда и лишнюю резину удаляют лебедкой, так как руками это сделать весьма сложно. Далее поверхность очищается шкуркой, шина надевается на диски и накачивается. Сделать это можно по-разному, в зависимости от размеров и форм диска.
Созданные колеса низкого давления своими руками:
- обладают небольшим весом;
- обладают высокой степенью эластичности;
- хорошо амортизируют неровности;
- способны преодолевать участки болотистой местности;
- имеют большой объем воздуха, который создает предпосылки для плавучести транспортного средства.
Несколько полезных советов
- Для придания транспортному средству большей плавучести все свободные места в дисках следует заполнить пенопластом или монтажной пеной.
- На место посадки основной камеры сначала нужно натянуть разрезанную старую.
- Самоделки низкого давления крепятся к дискам перемычками из резины, прикрепленными к болтам на ободе. Их обычно ставят не меньше 12 штук.
- Посредине перемычек рекомендуется установить продольную широкую полосу, заменяющую покрышку.
Заключение по теме
На современном автомобильном рынке можно сделать покупку любой комплектующей детали для транспортных средств. Продаются и шины для езды летом, для эксплуатации в зимних условиях, для движения по бездорожью. Многие владельцы транспорта стараются своими силами и средствами создавать колеса, имеющие пониженное давление. Цена этих самоделок гораздо ниже, чем у готовых изделий с рынка. Обычно шины низкого давления имеют довольно большие размеры, но при этом у них небольшой вес.
Проходимость транспорта, оснащенного подобными колесами, гораздо выше, чем у стандартного автомобиля или мотоцикла.
Не зря в народе их часто называют болотоходами. Большой дороги вашим большим колесам!
Колеса низкого давления своими руками
Содержание:
- Недостатки шин низкого давления
- Шины низкого давления своими руками
- Пример изготовления облегченной покрышки по методу А. Кокшарова из Карелии
- Отличительные черты колес низкого давления
- Самостоятельное изготовление
- Делаем ободрыши
- Самостоятельное изготовление
- Диски
- Самодельный вездеход
Недостатки шин низкого давления
Вместе с перечисленными преимуществами, такие шины имеют ряд определенных недостатков. Прежде всего, рекомендуется их использовать только по рыхлым участкам дорожного покрытия, которыми являются снег, грязь или болото. Дело в том, что на обычной асфальтированной дороге, сцепление колес с дорожным покрытием становится намного хуже, что значительно повышает тормозной путь автомобиля. Кроме того, особую опасность представляет профиль таких шин. На поворотах, если двигаться слишком с большой скоростью, то многократно увеличивается шанс «разуться», а также появляется реальная возможность лопнуть колесо прямо на ходу, что делает шины очень опасными для езды по жесткому покрытию.
Совсем не желательно передвигаться на такой резине по острым камням или скалам. Причины вполне аналогичные асфальту.
Последний недостаток – это высокая стоимость таких шин. Если сравнивать цену с обычными колесами, то одна такая шина будет стоить чуть больше, чем комплект качественной зимней резины для обычного легкового автомобиля. Именно поэтому, не все водители могут позволить себе такое дорогое удовольствие и возможность отправиться на своем автомобиле куда угодно.
Шины низкого давления своими руками
Вездеход-самоделка на шинах низкого давления
Как и любое колесо, пневматик низкого давления конструктивно состоит из ступицы, монолитного или разъемного диска (или спиц) и шины. Давайте рассмотрим некоторые виды самодельных колес и способы их изготовления.
Самую простую конструкцию имеет пневматик с двумя дисками. Согласно заранее сделанных расчетов вытачивается ступица (если это ведущий элемент, то с посадочным местом под ось, если колесо не является ведущим, то делается посадочное место под подшипники). На ступице так же протачиваются фланцы для крепления дисков. Далее необходимо вырезать два диска из листового металла. Любители часто используют тонкую листовую сталь (1 – 3 мм), либо сплавы на основе алюминия (Д16-Т, АМГ) и им подобные.
Пример крепления диска колеса низкого давления
После закрепления дисков на ступице, следует соединить их между собой полосами металла, изогнутыми по диаметру поперечного сечения камеры. Число таких полос обычно делают не менее 12. Соединительные полосы делают из того же материала, что и диски. Все соединения деталей движителя делают либо заклепочными, либо болтовыми с элементами контровки.
После сборки основы, на нее одевается камера и крепится к ободу (диску) брезентовыми ремнями с помощью зацепов или винтов. Вместо брезентовых ремней некоторые “самоделкины” используют полосы из тонкой транспортерной ленты. При накачивании шины, камера несколько выпирает в промежутки между крепящими ремнями, образуя тем самым своеобразные грунтозацепы.
Так как “голая” камера подвержена повреждениям об острый лед, камни и другие препятствия, распространена такая мера повышения живучести: самодельные колеса низкого давления обувают в облегченные покрышки.
Для этого используют либо разрезанную камеру такого же размера, как и основной баллон, либо используют облегченные стандартные покрышки от различной техники.
Пример изготовления облегченной покрышки по методу А. Кокшарова из Карелии
В своей методике автор использует принцип надрезания лишних слоев резины на покрышке (с помощью болгарки с самодельным ограничителем) и их удаления. Попутно он нарезает новый рисунок протектора, такой, какой ему нужен. По его словам, переделке поддаются практически все покрышки, которые выпускаются отечественной промышленностью.
Автор отмечает, что применение данной технологии значительно повышает срок службы самодельных шин, а так же повышает проходимость вездеходов собственного производства.
http://gredx.ru
Отличительные черты колес низкого давления
Как разбортировать колесо своими руками Видеоинструкция ЗР
Чем же так приглянулись конструкторам каракатов сделанных своим руками шины такого типа? Пневматик обладает небольшим весом, очень высокой эластичностью и давлением на грунт в небольших пределах. Все эти характеристики вкупе с большим радиусом качения придают вездеходному аппарату потрясающую проходимость наряду с экономичностью.
Заводские колеса НД
Приличный объем камер придает конструкции с таким движителем достаточную плавучесть. Это можно назвать дополнительным бонусом к проходимости машины. Кроме того, заполнив внутреннее пространство диска пенопластом, можно придать вездеходу дополнительную устойчивость на воде и одновременно снизить налипание снега или грязи на внутренние поверхности колеса.
Простая конструкция этих элементов шасси и отсутствие проблем с поиском материалов для их изготовления позволяет смастерить пневмоход своими руками без особых материальных и трудовых затрат. Это сделало машины, построенные по такому принципу очень востребованными среди самодельщиков.
Конечно же, такие конструкции имеют и свои недостатки, в частности малый ресурс камер, но они преодолеваются введением в конструкцию дополнительных элементов.
Самостоятельное изготовление
Самодельные болотоходы своими руками особенности и советы
Наиболее востребованной основой для болотоходов являются подержанные колеса от авиатехники. Если нет возможности найти такую заготовку, то используют скаты от грузовиков. Предварительно колеса моются от различных загрязнений и сушатся. С наружной стороны наносится предварительный рисунок с помощью маркера.
При работе в первую очередь понадобится удалить проволочный корд. Надо прорезать окошко и перекусить ближайший виток. С помощью пассатижей или длинной отвертки поддеваем и тянем проволоку из всего диаметра.
В некоторых случаях используется лебедка для вытягивания проволоки. С ее помощью отслаиваем куски резины, подрезанные строительным ножом. Наружную поверхность получившегося ската потребуется отшлифовать. Делать это можно с помощью наждачной бумаги или механизированного приспособления. На это уходит немало времени, но процедура является обязательной.
Для изготовления диска понадобится стандартный диск, через который будет проходить монтаж, а также пара колец и 6-8 соединительных пластин. Их сваривают в конструкцию, а затем избавляются с помощью зачистки от острых краев, способных повредить подготовленную резину.
Диск понадобится прогрунтовать и покрыть несколькими слоями защитной краски. Обычно используют для этого молотковую краску, которая надежно уберегает от коррозии. После этого резину монтируют на диск. Первые испытания нужно проводить недалеко от ремонтных зон, чтобы при необходимости получилось исправить возможные монтажные или конструкционные недочеты.
Делаем ободрыши
Для самостоятельного изготовления шин низкого давления вам потребуются:
- б/у покрышки от грузовика (к примеру, от Газ-66 или шины ВИ-3, устанавливаемые на Краз 255). Если вы будете покупать шины специально под ободрыши, то выбирайте резину, не «пожеванную» внутри. Иначе после снятия верхнего слоя вы получите слабое место или и вовсе дыру, которую придется вулканизировать;
- строительный нож и комплект сменных лезвий, так как в конструкции шины используются достаточно прочные нити, которые быстро тупят лезвия;
- шаблон, который можно изготовить из плотного картона или тонколистовой стали. Чтобы ободрыши были не только эффективными, но и смотрелись неплохо, протектор необходимо вырезать максимально ровно и симметрично. Также вам потребуется мелок либо маркер, которым вы будете обводить шаблон;
- прочные зажимы.
Таковые часто используют рихтовщики для зажатия кузовных панелей при восстановлении битых автомобилей. Подойдет и обычная струбцина, но действовать в таком случае нужно аккуратней;
- ручная либо механическая лебедка, а также трос, которыми натягивается отрезаемый кусок протекторного слоя. Можно использовать ручной редуктор либо лебедку, установленную на автомобиле. Вручную создать усилие, чтобы сделать ободрыши, у вас не получится, так как слои резины очень плотно скреплены.
Самостоятельное изготовление
Чтобы изготовить ободырыши, первым делом необходимо вытащить боковой металлический корд. Для этого сделайте надрез, отступив от внутренней части покрышки примерно 10 мм. Подцепите корд отверткой, а затем, зацепив крюком, выдерните металлический обод с помощью лебедки.
По всему периметру колеса с помощью шаблона нанесите будущее очертание протектора. Некоторые ободрыши можно увидеть с оставленным по центру протектором. Именно по контуру очертаний необходимо сделать надрезы резины. Для этого лучше всего использовать строительный нож, так как вы сможете контролировать глубину пореза, выставив необходимую длину лезвия. Если вы уверены в своих силах, можете использовать болгарку. Чтобы не прорезать шину насквозь, ориентируйтесь по звуку. Как только вы прорежете резиновый слой и достанете до металлического корда шины, звук приобретет соответствующую окраску.
Надрежьте профиль покрышки по внутреннему периметру (где раньше было металлическое кольцо из проволоки). Именно за надрезанный отрезок необходимо зацепиться зажимом. С помощью лебедки создайте натяжения, а затем канцелярским ножом постепенно подрезайте отслаиваемый кусок. После обдирки всей шины вы получите ободрыши. Учтите, что при создании натяжения шина будет стремиться посунуться, поэтому необходимо реализовать упор.
Особое внимание этому пункту стоит уделить, если ободрыши вы делаете с помощью установленной на автомобиле лебедки. Для обдирки совсем необязательно создавать большое усилие
Для пущей безопасности положите на трос старую куртку, которая послужит своеобразным гасителем, если зажим все-таки сорвется.
Диски
На видео достаточно ясно показан процесс изготовления дисков своими руками. Поскольку шина после обдирки приобретает эластичность, необходимо позаботится о хорошем боков подпоре. Чтобы при уменьшении давления ободрыши не спускали и не стремились разбортироваться, при монтаже применяется специальный герметик. При выполнении всех рекомендаций самостоятельно сделанные шины низкого давления практически не уступают заводским аналогам.
Самодельный вездеход
При движении по пересеченной местности на автомобиле с ШНД автомобиль, кроме высокого клиренса, получает достаточное пятно контакта при сцеплении с грунтом. Это происходит за счет меньшего давления в резиновых полостях. При поездке по сельскохозяйственному полю осуществляется минимальное прессование почвы, что способствует снижению потери урожайности.
Такой процесс невозможно сделать без пониженного давления в шинах. Колесо во время проезда по препятствию практически обволакивает его своей поверхностью. Это обеспечивает легкость проезда. Однако, вождение данного транспорта требует определенных навыков, чтобы не повредить эти скаты
Особенно важно правильно совершать маневры, повороты и развороты
Наиболее уязвимыми в конструкции являются боковые поверхности. Они в большей мере подвергаются эксплуатационному воздействию и способны быстрее изнашиваться.
Шины низкого давления своими руками, как сделать правильно
Как сделать шины низкого давления своими руками. Общая информация, алгоритм и перечень мероприятий. Изготовление диска.
Использовать автомобиль для разных целей — мечта любого владельца. Помимо штатных передвижений в условиях городской местности, агрегат хочется применить и для поездки на рыбалку в отдаленную деревеньку, и доставки компании друзей на заимку с тем, чтобы вволю поохотится и наговориться. Стоимость покрышек специального назначения для «переобувки« легкового транспорта выше типовых конструкций 3—4 раза. Проблема как изготовить шины низкого давления своими руками давно и успешна решена семейством «самоделкиных», к многочисленному отряду которых читателям web-ресурса предлагается присоединиться.
Конструкция колеса состоит из покрышки, установленной поверх диска. Первым этапом работы является создание шины низкого давления, вторым — металлического основания, на которую она крепится, затем идет сборка.
Наиболее доступны покрышки от ГАЗ-66 или ЗИЛа 131. Стоит упомянуть о том, что лучшими исходниками для экспериментов являются колеса от авиационной техники. Они рассчитаны на значительную нагрузку. Их структура и свойства однозначны во всех направлениях.
Можно использовать шины, бывшие в употреблении.
Для того чтобы ознакомиться с фронтом работ, следует представить конструкцию покрышек. Многослойный «пирог», названный автомобильной шиной, представляет собой череду разного рода оболочек, составленных из металлизированных нитей, тканевой основы, несходных покровов резины.
Алгоритм процесса
Суть работы состоит в планомерном избавлении исходной покрышки от нескольких наслоений. Выполняется согласно заранее продуманной схеме.
Основную часть материала снимают с протектора и боковин. Демонтируют крепежные сердечники. Роль ребер жесткости в конструкции шин низкого давления играют выпуклые элементы узора, оставшиеся нетронутыми. Как правило, в качестве рапорта применяется «елочка» с узкой дорожкой — ребордой — посередине (или без нее).
Для первопроходцев этого дела, рекомендуют раздобыть не один комплект шин, а на одну-две больше. Перед тем как приступить к частичной обдирке слоев, первую покрышку нужно разрезать и внимательно ознакомиться с ее строением. Например, определиться с тем, на какой глубине расположен тот или иной слой. На второй запасной шине желательно отработать приемы работы, например, сделать вытяжку нитей корда или отсечь одинаковые куски резины по размеченной схеме.
Опытные водители предлагают приноровиться резать на глубине, где проходит границы самых прочных слоев. Так затрачивается меньше физических усилий. Работа получается более аккуратной и протекает быстрее.
Перечень мероприятий
1. Подготовка. Для процесса обдирки будущей шины низкого давления, она должна быть вычищена, вымыта и обсушена. Затем ее поверхность размечают с помощью маркера.
2. Прорезание контура. Более легко надрезать боковину, поэтому с этого места начинают работу. Делают надрез на глубину до первого слоя нитей корда шины. Через него с помощью кусачек перерезают проволоку. Одно за другим вытягивают металлические волокна.
Согласно эскизу делается более широкий надрез, проходящий через беговую дорожку и боковину. Используя кусачки, надсекают поверхность и отрывается часть обшивки. В случае если есть лебедка, натяжение троса постепенно увеличивают, пока не достигнут цели — полного отделения слоистого элемента резины, называемого клыком.
Таким способом обрабатывают всю поверхность. По завершении работы покрышку необходимо внимательно проконтролировать на предмет перерезания основания. Если такой казус случился, то время потрачено впустую, и надо брать в работу новую шину.
3. Конструкция подчищается наждачной шкуркой и слегка рихтуется молотком.
Изготовление диска и сборка конструкции
Для основания каркаса чаще всего берут готовую конструкцию. Как правило, ее разрезают вдоль и для расширения вставляют дополнительный лист-вкладыш из металла или создают жесткую конструкцию путем наваривания ряда шпилек (либо прутков).
Монтаж колеса осуществляют посредством ремней, обвернутых кольцами резины и диска. В качестве подсобных средств применяется пожарный шланг, тонкая лента от промышленного транспортёра, брезентовые полосы.
Иногда нарезают алюминий на ленты. Каждая из них крепится болтовыми соединениями или заклепками. Начинают монтаж с одной стороны диска, затем огибают резину и заканчивают у другого основания. Минимально число лент — 12.
Завершающим этапом работы является подкачка шин. Выпуклые места станут плоскостями, контактирующими с дорогой, а конструкция колеса будет более упругой.
На этом информация о том, как сделать своими руками шины для пневматиков или обычного агрегата заканчивается.
Рискуйте, экспериментируйте и выигрывайте шанс изведать новые ощущения от вождения своего транспортного средства.
Шины низкого давления своими руками, как сделать шины и диски для вездехода и болотохода видео
Использовать транспортное средство в различных условиях – вполне разумное желание любого автовладельца. Помимо стандартного использования транспортного средства не редко возникает необходимость передвижения по пересечённой местности, а следовательно потребуется солидное увеличение проходимости. Одним из наиболее эффективных и при этом доступных способов является использование специальных шин, предназначенных специально для преодоления сложных участков пересечённой местности. Колёса низкого давления можно не только купить, но и изготовить своими руками, сэкономив при этом колоссальное количество денег. В данной статье рассмотрим процесс изготовления такого типа шин своими силами из подручных средств.
Зачем необходимы колёса низкого давления?
Ответить на данный вопрос не так просто как кажется, ведь перечислять все преимущества, которые автолюбитель получает после установки такого типа шин можно достаточно долго. Стоит отметить наиболее важные моменты:
- Благодаря шинам низкого давления, можно значительно увеличить дорожный просвет (клиренс) автомобиля, а это в свою очередь даёт возможность легко преодолевать неровные участки дорог, ухабы, легко проезжать колею и т.д.
- Помимо прочего колёса подобного типа значительно увеличивают уровень проходимости транспортного средства. Достигается это за счёт большей площади соприкосновения с дорогой. Особенно это становится заметно на мягких почвах и болотистой местности. Шины низкого давления
При этом стоит отметить, что у шин низкого давления существует и ряд недостатков:
- Ощутимо снижается скорость автомобиля на любом покрытии
- Значительно изменяется клиренс транспортного средства и в связи с этим снижается устойчивость транспортного средства и увеличивается склонность к опрокидыванию
- Ну и нельзя не отметить повышенные нагрузки на узлы трансмиссии и подвеску, что приводит к преждевременному износу узлов и агрегатов.
Особенности и назначение
Отличительная особенность таких шин – низкий уровень давления. Это, в свою очередь, гарантирует большую площадь соприкосновения и лучшую проходимость.
Автомобиль как будто передвигается на четырех огромных подушках, которым не страшны никакие преграды и бездорожье на пути.
Грязь, болото, пересеченная местность – все это не проблема для колес с низким давлением, не зря многие их называют болотоходы. С момента появления такой резины было проведено множество исследований, и все они лишь подтверждали высокий уровень их КПД.
В среднем пятно контакта покрышек низкого давления с поверхностью составляет около 1/3-1/4 всего диаметра колеса, что гарантирует отличные вездеходные качества.
В качестве отдельных помощников могут выступать специальные зацепы на колесах, которые буквально «въедаются» в поверхность почвы.
Что касается давления внутри, то здесь важно придерживаться следующего принципа — разница между низким и сверхнизким давлением должна составлять около 0,3 МПа.
Благодаря своим уникальным вездеходным свойствам шины низкого давления активно используются в сельском хозяйстве и при геологической разведке.
Кроме этого, они пользуются популярность у рыбаков, военных и путешественников.
Знают цену таких колес и охотники, тропы которых частенько пролегают по бездорожью. Устанавливаются шины низкого давления на болотоходах, тракторах, специальных вездеходах и авто с индивидуальной конструкцией.
Виды шин низкого давления
Условно можно разделить шины такого типа на два вида:
- Камерные. Отличительной особенностью такого типа является их повышенная устойчивость к механическим повреждениям и износу. Но при этом конструктивно они являются более тяжёлыми, громоздкими и менее комфортны.
- Бескамерные. Шины такого плана гораздо легче, безопаснее и комфортнее. Но при этом такого плана шины гораздо легче повредить или деформировать.
Так же колёса низкого давления можно разделить на следующие категории:
- Тороидные, могут быть изготовлены как в камерном, так и бескамерном варианте.
Конструкция подобного типа является наиболее распространённой.
- Арочные шины, имеют специальное предназначение для езды по бездорожью. Отличительной особенностью является то, что шины имеют очень широкий профиль, который может превышать ширину стандартного колеса в четыре раза.
- Пневмокатки. Эластичные бочкообразные колеса с характерным профилем. Протектор выполняется в виде жёстких грунтозацепов, которые помимо увеличения проходимости придают дополнительной прочности. Благодаря высокой эластичности и низкому давлению внедорожные свойства такого типа колёс выгодно выделяются на фоне аналогов.
По конструкции бывают
Арочными.
Основное назначение – поездки по бездорожью. Установка производится на ведущую ось.
Диски должны иметь специальную боковую поддержку. Ширина резины до 70 см. Профиль превышает стандартную величину в 2-4 раза.
Внешне арочные покрышки напоминают бочонки. Оптимальное давление внутри — на уровне от 0,05 до 0,14 Мпа.
Широкопрофильными.
Такая резина отличается овальным профилем, может работать с различным давлением (чаще всего данный параметр в 1,5-2 раза ниже, чем в обычных колесах).
Необходимые инструменты, необходимые для изготовления шин низкого давления.
Учитывая, что стоимость комплекта такого типа шин может в несколько раз превышать стоимость комплекта обычной резины, многие автовладельцы достаточно серьёзно подходят к вопросу их изготовления своими силами. Однако, перед тем, как начинать работу, потребуется произвести подготовку необходимого инструмента.
- В первую очередь потребуется найти подходящий исходный материал, из которого и будут изготовлены шины. Для этих целей отлично подходит вертолётная и самолётная резина, которая изначально заточена под повышенные нагрузки и тяжёлые условия. Однако, найти их не так просто, поэтому автолюбителями активно используются шины от грузовиков.
- Для резки протектора потребуется несколько остро заточенных двухсторонних ножей
- Точилка для ножей, т.
к. работа предстоит достаточно долгая и тяжёлая, а острый нож потребуется обязательно
- Острое шило, а ещё лучше – несколько, различного диаметра
- Молоток
- Несколько кусачек разного размера
- Пассатижи, отвёртка и возможно ручная лебёдка для вытягивания проволоки
Инструкция по созданию гусеничной модели
Схемы создания вездеходных транспортных средств, которые сооружают самостоятельно, в целом очень похожи. Однако создание гусеничной модели имеет собственную специфику. Основные её аспекты перечислены в следующей инструкции.
- Для того чтобы создать вездеход с гусеничной ходовой, необходимо начать с проведения монтажа кузова: он должен обладать высокой прочностью и водонепроницаемостью. Для создания жёсткой основы при его монтаже используются стальные трубы – они способны вынести большое напряжение.
- Затем нужно установить сами гусеницы. Для этого применяется листовая резина, из которой делают резину кольцевого типа. К её внешней стороне крепятся алюминиевые лопатки.
С обратной стороны монтируют ограничители: важно, чтобы ширина их шага была не более ширины шага колеса. Через отверстия в кузове выводят мосты, применяя для защиты специальные муфты из резины. Лента при этом прикрепляется так, чтобы как передние, так и задние колёса располагались между ограничителями.
- Для того чтобы поддерживать ленту, между основными колёсами устанавливаются дополнительные. Стоит заметить, что после завершения всей производимой работы нужно установить сверхпрочные стёкла, которые не дадут грязи попасть внутрь транспортного средства.
Во время создания последующих частей и элементов конструкции необходимо осуществлять проверку их работоспособности и прочности. Для того чтобы будущий вездеход был действительно надёжным, нужно, чтобы он обладал пятикратным запасом прочности, как минимум.
После тестирования всех частей вездехода и окончания работы стоит оценить то, как агрегат будет вести себя в реальных условиях, и лишь потом приступать к постоянному пользованию.
Пошаговая инструкция создания шин низкого давления своими руками
Процесс изготовления колёс низкого давления должен производиться в определённом порядке, для того что бы добиться максимально эффективного результата. Рассмотрим процесс более подробно:
- На первом этапе автолюбителю потребуется удалить и корда проволочное усиление, для этого производится надрез, и перекусывается один из витков, далее пассатижам производится вытягивание проволоки, иногда для этих целей целесообразно использовать ручную лебёдку или любой другой подобный инструмент. Как правило, на данный процесс уходит большое количество времени, однако избежать его не получится, да и сама процедура должна производиться максимально качественно.
- Достаточно важным аспектом является подбор протектора шин. В частности, для торфяников не целесообразно применять грубый и высокий протектор, при его применении будет происходить смещение верхнего слоя почвы, тем самым значительно снижать Шины своими руками
сцепление с дорогой.На песке и в снегу рекомендуется применять шины с редкими и крупными элементами протектора.
- Узор на самодельной шине вырезается самостоятельно, для этого потребуется произвести разметку протектора маркером. Вырезают его ножом, при этом желательно произвести финальную шлифовку наждачной бумагой, при этом можно произвести грубую рихтовку поверхности молотком.
- При вырезании протектора, стоит начать с боковых порезов, ориентируясь на разметку. Отогнув край резины нужно захватить её клещами или пассатижами и оторвать надрезанную полосу.
- После этого собирается специальный каркас, на который и одевается камера и шина.
- В завершении стоит тщательно осмотреть результат работы, особенно места, где осуществлялись порезы. Осмотр производится на предмет глубоких порезов и серьёзных дефектов. Отдельно стоит обратить внимание на внутреннюю поверхность, где сквозные порезы будут более заметны.
- Всё! Колёса можно устанавливать на транспортное средство и ехать покорять распутицу.
Выбор двигателя для вездехода
Чаще всего в качестве силового агрегата для самостоятельного изготовления вездехода используют двигатели следующего типа:
- Мотоциклетные.
- Автомобиля ЗАЗ.
- Мотоблока.
- Отечественных автомобилей.
Наличие в вездеходе определенного двигателя не имеет принципиальной разницы. Более важно учитывать такую особенность, как обеспечение его достаточного охлаждения, так как транспортное средство эксплуатируется круглый год в различных температурных условиях и при невысокой скорости движения.
Другим основным критерием выбора двигателя для будущей самоделки является его мощность.
Выбрав агрегат с запасом мощности, получают лучшую производительность, предупреждают перегрев и создают условия для максимально долгого срока эксплуатации.
Как сделать диски?
Естественно, что без дисков использовать шины будет невозможно. Следовательно, изготовить их потребуется самостоятельно. Рассмотрим данный процесс более детально:
- Наиболее распространённое явление – это изготовление диска из стандартного, при этом крайне важно правильно подкорректировать его параметры.
- Расширение диска принято производить при помощи дополнительной вставки в виде полосы.
- На легких вездеходах распространена установка дисков изготовленных из алюминиевых тазиков, но в тяжёлых условиях они, как показывает практика, не выдерживают нагрузку. Хотя именно на просторах Диски
интернета это, казалось бы, странное техническое решение получило достаточно высокую популярность - Крепление к диску производится при помощи ремней, в качестве которых применяют транспортную ленту или даже пожарные шланги, которые так же обладают достаточной прочностью. По большому счёту использовать можно всё что угодно, самое главное, что бы материал был достаточно прочным и эластичным.
- В целом, диск для шин низкого давления – достаточно индивидуальная конструкция, которая зависит от многих факторов.
Многие решения автовладельцев требуют тщательного испытания «в деле», при этом дорабатываются они в процессе эксплуатации. Весьма распространены решения, когда диск состоит из двух половинок и сваривается при помощи полосок металла или стягивается насквозь длинными металлическими шпильками.
Преимущества и недостатки
Планируя изготовить самодельные автомобильные колёса низкого давления, можно существенно сэкономить и получить при этом ряд преимуществ. Далеко не один завод выпускает готовые вездеходные покрышки, но их стоимость очень высокая.
К сильным сторонам самодельных ободрышей можно отнести:
- Низкая стоимость. Затраты минимальные, поскольку можно использовать любые старые покрышки.
- Превосходное сцепление. Для преодоления сложнейших участков это незаменимая вещь.
- Сравнительно небольшой вес. Даже если поставить колёса на обычную легковушку, мощности двигателя хватит для вращения этих шин.
- Способность преодолевать песок, мягкий грунт, снежные заносы.
- Возможность регулировать давление в зависимости от целей и условий эксплуатации.
- Никого вреда для грунта, что позволяет использовать ободрыши даже в условиях распаханного и засеянного грунта.
Но тут есть и свои недостатки, которые важно учитывать. Главные минусы здесь такие:
- эти шины непригодны для эксплуатации по асфальту и бетону, поскольку они быстро износятся;
- легковые машины заметно теряют устойчивость;
- ездить на скорости более 60 км/час нельзя и опасно;
- нельзя выполнять резкие развороты и манёвры;
- ободрыши нагружают подвеску, детали трансмиссии, быстрее их изнашивания;
- проколоть такие покрышки намного легче;
- требуется переоформление авто, поскольку теперь это вездеход.
Насколько эти недостатки существенные, каждый решает для себя сам.
Обдирка шин для вездехода
Итак, приступая к изготовлению камеры, определяемся с размерами и выбором покрышки (наиболее популярны от ГАЗ-66, ЗИЛ 131). Далее подготавливаем требуемый инструмент и рабочее место.
Инструменты
Наш инструмент будет не замысловат: ножи, желательно с двухсторонней режущей кромкой, точило для правки ножей, молоток, шило, кусачки и «дралка». С помощью «дралки» мы и будем снимать слои резины с грузовых шин.
Дралка — лебедка на основании
Сам механизм представляет собой закрепленную лебедку с электроприводом, кнопка включения которого выведена непосредственно к рабочему месту. Для удобства работы иногда делают ножной привод. Главное что бы обороты лебедки не были слишком высокими.
Простой каракат 4×4 «logza»
Данный каракат строился для поездок на рыбалку, охоту, а так же использования для хозяйственных нужд, вроде доставки дров. Вездеход рассчитан на двух человек, а так же может перевозить груз весом до 250 килограмм. Для постройки вездехода автор использовал следующие детали: 1) двигатель от мотоцикла ИЖ-Планета 5 2) мосты от автомобиля москвич 412 с передаточным числом 4. 22 3) редуктор СЗД 4) Камеры и покрышки от т-150 5) диски от газ-52 6) коробка переключения передач от Уаза 7) звезды на 20 зубьев и другие
цепи с шагом 19 и 25.4, а так же цепь от мотоцикла Иж
Рассмотрим более подробно основные этапы постройки вездехода и узлы его конструкций.
А еще интересно: Обзор вездеходов на шинах низкого давления: 5 отечественных и зарубежных моделей
Была сделана раздаточная коробка из редуктора инвалидки.
Переход ШРУСа во фланец сделан довольно просто: была выточена шайба, которая одета на обрезанный вал гранаты ШРУСа, а затем обварена с двух сторон.
Колеса вездехода сделаны из камер т 150 размером 530 на 610, покрышки от этого же трактора были облегчены. Диски были изготовлена на основе дисков газ 52 и трубы 12 дюйма.
Покрышка была облегчена, оставлены 4 слоя основного корда. Толщина покрышки по беговой дорожке и до половины боковины стала 6-7 мм. В месте крепления ремней оставлено утолщение. Вес покрышки составляет 36-37 килограмм. само же колесо в сборе, состоящее из камеры, диска, флиппера, покрышки весит примерно 70 килограмм.
Ниже представлены фотографии обдирки покрышек и нарезания протектора:
Эта покрышка была изготовлена из радиальной резины, отличие от диагональной только в долговечности. Сложность обработки примерно одинаковая у обоих типов резины. На фотографиях колес виден старый флиппер, в новой варианте он заходит под покрышку.
Стальной пучок был отрезан вместе с частью покрышки. Усилие на лебедке не большое. Лебедка необходима только, чтобы завернуть резину под 180 градусов, а дальше автор использовал сапожный нож и мыльную воду. При временных затратах по 3-4 часа в день, автор делал одну покрышку за неделю.
Ремешки , которыми крепится покрышка к диску были изготовлены из приводного ремня. Толщина одного ремешка составляет 6-8мм, ширина 5-6 сантиметров. Сами ремни крепятся на болты м6. Время замены камеры даже быстрее чем время замены колес трекол.
За долгое время эксплуатации вездехода, было всего два прокола камер, причем оба между диском и покрышкой. Ремешки же отлично выдерживают нагрузки и не рвались.
Вот так сделан узел перелома рам на вездеходе: До модернизации на каракате стояла раздаточная коробка реверс, которая была собрана из корпуса мотоколяски сзд и внутренностей самой сзд, а так же мотороллера муравей.
После была установлена вторая коробка от УАЗ 469. Благодаря такой модернизации максимальная скорость вездехода возросла с 40 километров в час до 60 километров в час по ровной поверхности.
На карданный вал установлена звезда от заднего колеса мотоцикла Иж-планета спорт. Она зажата между двумя фланцами кардана и хвостовика моста стандартными четырьмя болтами. Количество зубьев на звезде такое же как на стандартном иже. Уязвимыми местами трансмиссии является сильный вылет колесного диска. Перегруз вездехода так же отрицательно влияет на целостность полуосей.
При работе в паре с дополнительной коробкой переключения передач мощности двигателя от Ижа хватает полностью. Без дополнительной коробки было бы довольно сложно перевозить тяжелые грузы, особенно по болотистой местности. то есть без дополнительной коробки передач, автору бы не удалось выбираться за сбором ягод, что естественно его не устраивало и он установил коробку.
Другие фотографии конструкций вездехода:
Для коробки передач от Уаза было выточено два корпуса под дополнительные подшипники и сальники на первичный и вторичный валы. причем, на первичном и вторичном валах была нарезана резьба для закрепления ступиц звёздочек. Так же были изготовлены сами ступицы под звёзды. Плюс подобной конструкции для автора в том, что запчасти для Уаза найти в его местности довольно легко и по относительно дешевой цене.
Цепь с коробки на мост не тянется,прочности ижевской цепи хватает полностью. Цепи были использованы с шагом 19 и 25.4, хотя мотоциклетная цепь гораздо качественнее чем обычные колхозные. К тому же цепь для мотоцикла Иж продается практически в любом специализированном магазине. На коробке переключения передач установлены звезды по 20 зубьев.
Работы по обшивке вездехода:
Фотографии испытания машины:
Вездеход имеет несколько недостатков. Самым очевидным автор считает отсутствие пониженных передач. Вторым недостатком является не столь сильная надежность полуосей как хотелось бы, хотя если не превышать нагрузки в 250 килограмм, то полуоси вполне выдерживают. В остальном же вездеход доказал свою надежность и качество и за много лет эксплуатации трансмиссия вездехода не нуждалась в капитальном ремонте либо модернизации.
Автор вездехода: Виктор с ником «logza» из города Шенкурск Архангельской области.
Источник Доставка новых самоделок на почту
Получайте на почту подборку новых самоделок. Никакого спама, только полезные идеи!
*Заполняя форму вы соглашаетесь на обработку персональных данных
Становитесь автором сайта, публикуйте собственные статьи, описания самоделок с оплатой за текст. Подробнее здесь.
Самостоятельное изготовление
Чтобы изготовить ободырыши, первым делом необходимо вытащить боковой металлический корд. Для этого сделайте надрез, отступив от внутренней части покрышки примерно 10 мм. Подцепите корд отверткой, а затем, зацепив крюком, выдерните металлический обод с помощью лебедки.
По всему периметру колеса с помощью шаблона нанесите будущее очертание протектора. Некоторые ободрыши можно увидеть с оставленным по центру протектором. Именно по контуру очертаний необходимо сделать надрезы резины. Для этого лучше всего использовать строительный нож, так как вы сможете контролировать глубину пореза, выставив необходимую длину лезвия.
Надрежьте профиль покрышки по внутреннему периметру (где раньше было металлическое кольцо из проволоки). Именно за надрезанный отрезок необходимо зацепиться зажимом. С помощью лебедки создайте натяжения, а затем канцелярским ножом постепенно подрезайте отслаиваемый кусок.
При работе не стойте по направлению натяжения лебедки, чтобы зацеп не сорвался и не причинил вам травм. Разумеется, стоит подумать о сохранности вещей, находящихся в зоне поражения.
Особое внимание этому пункту стоит уделить, если ободрыши вы делаете с помощью установленной на автомобиле лебедки. Для обдирки совсем необязательно создавать большое усилие. Для пущей безопасности положите на трос старую куртку, которая послужит своеобразным гасителем, если зажим все-таки сорвется.
Общая эффективность системы | СОЗУ
Ваш браузер не поддерживает все функции нашего веб-сайта. Для повышения удобства покупок мы рекомендуем вам использовать самые последние версии Google Chrome, Safari или Firefox.
Der neue 303 Firecrest ist der erste Radsatz, der für die Erreichung der Gesamtsystemeffizienz (TSE™) entwickelt wurde. Basierend auf der einfachen Prämisse «Effizienz = Geschwindigkeit» ist TSE ™ unsere Lösung für Geschwindigkeit in der realen Welt… einer Welt unvollkommener Straßen und sich ändernder Fahrbedingungen.
TOTAL SYSTEM EFFICIENCY™
Schnelleres Fahren auf oder neben der Straße bedeutet Effizienz — mehr Geschwindigkeit bei weniger Leistung. Die Kombination aus einem breiteren, schlauchlosen Reifen, einem niedrigeren Reifendruck, einem breiteren, für die Reifenschnittstelle optimierten Felgenprofil und einem neuen Felgenlaminat sorgt für ein effizienteres Fahrverhalten. Effizienz bedeutet bei der Anwendung auf Fahrräder weniger Aufwand bei der Überwindung von:
- Люфтвидерстенд
- Гравитация
- Роликовая стойка
- Вибрация
LUFTWIDERSTAND
Scheibenbremsen verbessern die Bremskraft, erhöhen aber auch deine Geschwindigkeit. Das Fehlen von Felgenbremssätteln ermöglicht ein breiteres Felgenprofil mit einer glatteren Schnittstelle zwischen Reifen und Felge für eine optimale Aerodynamik bei breiteren Reifen, die einen Nettogewinn an Effizienz erzielen.
Gravitation (Gewicht gegen Haltbarkeit)
Die Schwerkraft ist unerbittlich und leichte Komponenten sind seit langem ein Schwerpunkt für jeden Radfahrer. Sobald die Straße bergauf zeigt, wird das Gewicht ein wesentlicher Faktor für die Geschwindigkeit. Unsere beiden neuen 303 Modelle wurden einer deutlichen Gewichtsreduzierung unterzogen, die ausschließlich von der Felge ausgeht, wodurch die Räder extrem wendig werden. Wir haben uns darauf konzentriert, das Gewicht dieses Rads zu reduzieren, da wir verstanden haben, dass leichte Räder für den modernen Rennradfahrer eine Priorität sind. Der neue 303 Firecrest ist 300 грамм (20%) leichter als sein Vorgänger. In der Regel geht ein geringeres Gewicht zu Lasten der Haltbarkeit. Das Design und der Herstellungsprozess des 303 bieten jedoch eine robuste Haltbarkeit bei geringerem Gewicht.
ROLLWIDERSTAND
Vielleicht erinnerst du dich an den Physikunterricht: Druck = Kraft, die über einen Bereich verteilt ist. Oder einfach ausgedrückt: Fläche = Kraft/Druck. Beim Radfahren ist dies eine nützliche Gleichung. Der Bereich der Reifenkontaktfläche wird durch das Fahrergewicht und den Reifendruck bestimmt. Wenn du auf zwei verschiedene Fahrräder mit zwei Reifen unterschiedlicher Breite, aber gleichem Reifendruck steigen würdest, würde die Kontaktfläche der verschiedenen Reifen übereintimmen, da beide Reifen Dieselbe Last mit demselben Druck tragen. Der einzige Unterschied in diesen beiden Szenarien ist die FORM der Auflagefläche. Ein breiterer Reifen erzeugt im Vergleich zu einem schmalen Reifen eine breitere und kürzere Kontaktfläche.
Es gibt zwei Möglichkeiten, einen Reifen breiter zu machen: einen breiteren Reifen montieren oder eine Felge mit einem breiteren Reifenbett.
Breitere Felge + breiterer Reifen = breitere und kürzere Reifenaufstandsfläche. Dies fördert einen geringeren Durchhang des Reifens, wodurch der Reifen weniger verformt wird, был zu einem geringeren Energieverlust im rollenden Reifen führt. Ist der Rollwiderstand ein wichtiger Gesichtspunkt? Джа! Die Verbesserung des Rollwiderstands шляпа den gleichen Einfluss auf die Gesamteffizienz wie die Wahl der richtigen Felgenform.
СОПРОТИВЛЕНИЕ КАЧЕНИЮ
Наше решение: Возможно, вы помните это из урока физики: давление = сила, распределенная по площади. При езде на велосипеде площадь пятна контакта с шиной определяется весом гонщика и давлением в шинах. Если вы сядете на два разных велосипеда с двумя шинами разной ширины, но с одинаковым давлением в шинах на обоих велосипедах, пятно контакта разных шин будет совпадать, потому что обе шины выдерживают одинаковую нагрузку с одинаковым давлением. Единственная разница в этих двух сценариях заключается в ФОРМЕ пятна контакта. Более широкая шина дает более широкое и короткое пятно контакта по сравнению с узкой шиной.
Есть два способа сделать шину шире: купить шину большего размера или установить обод с более широкой платформой. Более широкий обод + более широкая шина = более широкое и короткое пятно контакта с шиной. Это способствует меньшему провисанию шины, в результате чего шина меньше деформируется, что приводит к меньшим потерям энергии при качении шины. Улучшение сопротивления качению оказывает такое же влияние на общую эффективность, как и выбор правильной формы обода.
ПОТЕРИ ОТ ВИБРАЦИИ
Наше решение: Используя новый ламинированный ободок, мы разработали универсальные колеса Zipp: на них можно ездить по традиционным дорогам, но они также способны преодолевать более твердую местность, включая неровные дороги, легкий гравий и — конечно — булыжники весенней классики. Мы разработали колеса с более широкими покрышками, которые можно использовать при более низком давлении в шинах, чтобы сгладить езду.
VIBRATIONSVERLUSTE
Moderne Rennräder sind vielseitig einsetzbar: Sie können auf Traditionalellen Straßen gefahren werden, sind aber auch in der Lage, schwierigeres Gelände wie unebene Straßen, leichten Schotter bebebene straßen sogar Kopfsteinpflaster. Wir mussten verstehen, был die schnellsten Räder unter so unterschiedlichen Bedingungen ausmacht.
Die vertikale Verschiebung entzieht dem System Energie und gelangt direct in den Körper des Fahrers. Schauen Sie sich die Arme in diesen beiden unterschiedlichen Einstellungen an: Dieser Muskel, der sich heftig hin und her bewegt, nimmt die Kraft aus dem System auf. Der menschliche Körper wirkt wie ein großes Dämpfersystem. Je weniger der Dämpfer vibriert, desto weniger Energie verlierst du durch Vibration.
Deine nächste Frage sollte lauten: «Na und?» Über wie viel Verlust sprechen wir? 1 Вт? 3 Вт?
ДРУК ПРОТИВ. LEISTUNG
Daten aus unseren RollingRoad -Tests zeigen, dass der Unterschied zwischen niedrigem und hohem Reifendruck auf unebener Straße zu einer Einsparung von 50 Watt führen kann. Diese Tests messen die Leistung, die erforderlich ist, um 32 km/h at the verschiedenen Untergründen zu fahren und erfassen die Verluste durch Reifenverformung, den Antriebsstrang und Ganzkörpervibrationen.
Die Größenordnung dieser Art von Verlusten verdient deine Aufmerksamkeit. Mit zunehmender Unebenheit solltest du breitere Reifen mit niedrigeren Drücken fahren. Wir empfehlen die Verwendung eines бескамерные установки, um alle Vorteile zu nutzen. Durchschläge bei niedrigem Druck sind mit tubeless deutlich unwahrscheinlicher. Zusätzliche Vorteile eines breiteren Reifens bei niedrigerem Druck sind besseres Handling und Kurvenverhalten. Dein Reifen springt nicht an kleinen Unebenheiten ab oder verliert in Kurven den Grip.
Empfehlungen sind ein Ausgangspunkt für Fahrer, um ihren оптимальный Reifendruck für das Fahren auf der Straße einzustellen. Der 303 Firecrest имеет максимальное давление до 5 бар (72,5 фунтов на кв. дюйм).
Zipp Laufräder MIT TSE
858 NSW
808 FireCrest
454 NSW
404 FireCrest
353 NSW
303 Firecrest
303 S303
0000 Обслуживание авиационных колес и шин Самолетные колеса и шины ОбслуживаниеКолесо и шина самолета Обслуживание
Небольшое количество обслуживающего персонала коммерческих самолетов получили серьезные травмы в результате взрывов колес/шин в сборе во время обслуживания. В каждом случае причиной взрыва была нерегулируемая подача азота или воздуха. Хотя многие колеса оснащены клапанами сброса давления при избыточном накачивании,
чтобы избежать образования избыточного давления в колесе/шине, при накачивании шин всегда следует использовать регулятор.
Ежедневно во всем мире во время планового технического обслуживания накачиваются тысячи авиашин. Иногда механик или другой сотрудник наземной службы был серьезно или смертельно ранен в результате взрыва, вызванного использованием нерегулируемого давления из баллона с воздухом или азотом. Последний зарегистрированный инцидент произошел в 1998 году, когда механик накачивал носовое колесо/шину в сборе на самолете 737. В общей сложности было зарегистрировано пять подобных инцидентов, которые привели к серьезным травмам или смерти обслуживающего персонала (таблица 1).
Эти виды травм можно предотвратить, если понять
- Причины взрыва колеса/шины в сборе.
- Профилактические меры.
Причины взрыва колеса/шины в сборе
Самолетное колесо/шина в сборе накачиваются до высокого давления (многие превышают 200 фунтов на квадратный дюйм). Кроме того, давление в баллоне или тележке для обслуживания шин может достигать 3000 фунтов на квадратный дюйм. В результате, когда баллон высокого давления подключается непосредственно к колесу без регулятора, колесо внезапно подвергается воздействию высокого давления, которое может превышать расчетные пределы для колеса и колесных стяжных болтов. Следовательно, колесо, стяжные болты колеса или и то, и другое испытывают взрывное разрушение и становятся снарядами.
В большинстве зарегистрированных случаев связанных травм взорвавшимся колесом и шиной было переднее колесо самолета меньшей конфигурации, такого как 737 или DC-9. Сообщается, что когда произошел взрыв, колеса накачивались из баллона высокого давления или тележки без регулятора.
Кроме того, колеса не были оборудованы системой избыточного давления. предохранительный (OPR) клапан. Клапан OPR представляет собой устройство, подобное показанному на рисунке 1.
Он включен во многие узлы колес для ограничения давления в сборе колесо/шина. Однако на некоторых старых колесах этот клапан отсутствует. Если давление в колесе превысит заданное значение, диск в клапане OPR сработает.
разрыв, позволяя газу выйти, тем самым снижая давление в колесе, прежде чем оно может сломаться. После разрыва диска газ в колесе выйдет через клапан OPR. Клапан устроен так, что при разрыве диска газ
выходит из колеса быстрее, чем его можно подать от источника давления.
Кроме того, компания Boeing получила сообщения о трех подтвержденных случаях и других предполагаемых случаях, когда колесо/шина в сборе взрывались, когда кислород в шинах, наполненных воздухом, смешивался с летучими газами, выделяемыми сильно перегретой шиной. В одном случае шина перегрелась в результате пробуксовки тормозов, и колесо/шина взорвались, когда достигли температуры самовоспламенения. В другом случае причиной катастрофической гибели одного самолета был взрыв в колесной нише во время полета. Аналогичный взрыв причинил серьезные повреждения еще двум.
В результате Федеральное авиационное управление США издало Директиву о летной годности 87-08-09, требующую, чтобы для накачки шин самолетов на колесах с тормозами использовался только азот. Однако в удаленных местах, где может отсутствовать азот, шины могут заполняться воздухом, если содержание кислорода в шинах не превышает 5 процентов по объему.
Предупреждающие меры
Для предотвращения несчастных случаев такого типа можно принять несколько мер предосторожности, в том числе
- Использование регулятора.
- Использование надувных клеток.
- Соблюдение установленных инструкций по техническому обслуживанию.
- Оснащение всего обслуживающего оборудования регуляторами.
- Накачка колес/шин только азотом.
Использование регулятора.
Обслуживающий персонал всегда должен использовать регулятор при накачивании любого колеса/шины в сборе. Как показано в таблице 1, во всех зарегистрированных авариях были задействованы носовые колеса. Это может быть связано с тем, что колеса не имели клапана OPR и что носовые колеса, как правило, имеют небольшие размеры, что означает, что они содержат меньший объем воздуха или азота. . Накачивание без регулятора быстро создаст давление в колесе, которое значительно превышает возможности колеса. В результате колесо или колесные болты раскалываются на куски, которые могут серьезно травмировать человека, обслуживающего шину, или повредить соседнее оборудование.
Использование надувных клеток.
Большинство шиномонтажных мастерских авиакомпаний или ремонтных станций оборудованы клетками для накачивания шин. Клетка для накачивания состоит из прочной стальной конструкции, которая окружает колесо/шину в сборе во время накачивания шины. Соответственно, когда колеса в сборе с шиной первоначально накачиваются баллонным азотом в шиномонтажном цехе, сборка колесо/шина помещается в клетку для защиты. от травм и повреждений в случае взрыва. Однако не всегда целесообразно использовать надувные клетки, если колесо/шина в сборе установлены на самолете.
Соблюдение установленных процедур руководства по техническому обслуживанию.
Для предотвращения несчастных случаев очень важно
чтобы обслуживающий персонал использовал следующие процедуры, предназначенные для снижения риска взрыва во время обслуживания шин:
Оснащение всего сервисного оборудования
регуляторы.
Операторы должны следить за тем, чтобы оборудование для обслуживания шин было надлежащим образом оснащено регуляторами для предотвращения избыточного давления.
Накачка колеса/шины только азотом.
Первоначально шины необходимо накачивать только азотом. Однако воздух можно использовать для накачки шины низкого давления, если
самолет находится в месте, где азот недоступен, при условии, что содержание кислорода не превышает
5 процентов по объему. Дополнительные процедуры для обеспечения того, чтобы содержание кислорода в шине не превышало 5 процентов, обычно изложены в главе 12 AMM. Эти процедуры включают в себя таблицу, в которой указано максимальное давление при заправке по сравнению с первоначальным давлением в шинах. Сумма всех давлений воздуха, добавленных к данной шине, не может превышать давление, указанное в таблице для соответствующего начального давления накачки.
Резюме
За последние 20 лет во время обслуживания шин произошло несколько несчастных случаев, когда колесо взорвалось из-за избыточного давления или высокого содержания кислорода, что привело к серьезным травмам или гибели обслуживающего персонала или повреждению оборудования. Строгое соблюдение установленных процедур в АММ и ШМ поможет обеспечить безопасность обслуживающего персонала при шиномонтаже. Кроме того, важно, чтобы оборудование для обслуживания шин было оснащено регулятором, чтобы предотвратить воздействие на шины избыточного давления, которое может привести к взрыву.
—————————————————————
Таблица 1 | ||
Самолет | Описание | Травмы/повреждения |
737 | После замены узла носового колеса/шины механик подсоединил шланг к тележке для обслуживания шин с баллонами с азотом, находящимися под давлением 3000 фунтов на квадратный дюйм.![]() | Колесо взорвалось, ударив присевшего возле руля механика, отрубив ему обе руки выше локтя и сильно повредив ногу. |
737 | Два механика накачивали шину передней стойки шасси с помощью нерегулируемого источника давления. | Колесо взорвалось, в результате чего один механик потерял обе руки, а второй механик потерял ногу. |
737 | При обслуживании узла носового колеса/шины, половин внутреннего и внешнего колеса сломан, а гайки стяжных болтов срезаны и разделены. | Механик погиб при ударе внешней половинкой колеса и осколками. |
ДС-9-32 | После замены шины левой передней стойки шасси колесо взорвалось при накачивании шины газовым баллоном высокого давления. | Погиб сотрудник наземной службы.![]() |
ДС-9 | При обслуживании узла носового колеса/шины с помощью баллона с сухим воздухом под высоким давлением колесо взорвалось. Регулятор не использовался. | Взрыв оторвал механику руку. |
————————————————————- —
Таблица 2: Информация об авариях в сборе колеса/шины | |||
Название | Номер | Дата | Источник |
Общее сообщение оператора: «Травма в результате избыточного давления в колесе» | М-7200-98-01293 | 9 апреля 1998 г. | Коммерческие самолеты Боинг |
Письмо всем эксплуатантам: «Отказ шины передней стойки шасси» | АОЛ 9-2274 | 21 июля 1992 г.![]() | Макдоннелл Дуглас |
Сервисное информационное письмо: «Меры предосторожности при накачивании колес и шин в сборе» | СИ 639 | 31 мая 1998 г. | Allied Signal Aerospace (Бендикс) |
Совет по техническому обслуживанию: «Меры предосторожности при обслуживании колес/шин» | 707 MT-32-001 727 MT-32-001 737 MT-32-005 747 MT-32-043 747-400 MT-32-020 757 MT-32-014 -736 024 777 МТ-32-018 | 20 октября 1998 г. | Коммерческие самолеты Боинг |
————————————————————— —
———————————————— —
Рис. 2:
Брайан Челиус
Главный инженер
707/727/737/757
Сервисная инженерия
Boeing Commercial
Самолеты
вернуться наверх | только текстовое содержимое AERO | Боинг Главная | Коммерческий номер
Copyright The Boeing Company. Все права защищены.
Регулировка давления в шинах для уменьшения уплотнения почвы
Перейти к концу галереи изображений
Современные сельскохозяйственные шины рассчитаны на высокие нагрузки при низком давлении для максимальной эффективности и минимального уплотнения почвы. Изображение предоставлено: Энди Джексон (Skyblu Farms)
Перейти к началу галереи изображений
Знаете ли вы, что вы можете получить больше работы от своего трактора, потреблять меньше топлива и уменьшить уплотнение почвы, уменьшив давление в перекачанных шинах? Это связано с тем, что давление в шинах влияет на площадь контакта вашего оборудования с почвой и влияет на проскальзывание. Шины, накачанные до высокого давления, имеют небольшую площадь контакта с поверхностью, что приводит к высокому поверхностному напряжению, выраженному в фунтах на квадратный дюйм (psi), и сильному проскальзыванию. Гусеницы также имеют большую площадь контакта и, следовательно, меньшее уплотнение и проскальзывание. За прошедшие годы в шинную технологию было внесено множество усовершенствований, позволяющих эксплуатировать их при низком давлении. Переход от диагональных к радиальным шинам стал первым значительным улучшением — радиальные шины имеют гораздо более «квадратную» площадь контакта, что помогает увеличить площадь контакта шины с почвой и позволяет эксплуатировать их при более низком давлении в шинах. Дальнейшие улучшения были внесены в стандартные радиальные шины в виде технологии повышенной гибкости (IF) или очень высокой гибкости (VF). Шины «IF» могут выдерживать такую же нагрузку при снижении давления в шинах на 20% по сравнению с той же стандартной шиной, в то время как шины «VF» могут выдерживать ту же нагрузку при давлении в шинах на 40% ниже. Недавно мы объединились с местным фермером, специалистами Titan Tire и представителем Binkley and Hurst, чтобы продемонстрировать шины с низкими боковинами (LSW) в нашей полевой клинике Landisville Field Crop Clinic. Шины LSW имеют больший обод и меньшую боковину, что помогает справиться с скачками мощности и дорожным уклоном, которые иногда возникают у более высоких шин.
Шины LSW (за некоторыми исключениями) являются шинами VF. Эти шины доступны для тракторов, комбайнов, опрыскивателей и многого другого. Однако вам нужно отрегулировать давление в шинах до минимально возможного давления, чтобы воспользоваться их способностями. Я проиллюстрирую, как определить правильное давление в шинах комбайна, на примере Университета Титан, программы обучения, организованной Titan Tyres. В этом примере комбайн оснащен шинами LSW1250/35R46 на передней оси и шинами LSW850/55R30 на задней оси. Позвольте мне объяснить, что означают эти цифры для передних шин: LSW означает Low SideWall, 1250 — ширина шины в мм, 35 — отношение высоты шины к ширине; R обозначает радиальную шину; 46 — диаметр обода в дюймах. Эта номенклатура является стандартной для любой шины. Чтобы определить правильное давление в шинах, вам необходимо загрузить таблицу накачки шин и вес каждой шины. Вы можете взвесить свое оборудование, используя свои сельскохозяйственные весы, весы на местном зерновом заводе или переносные весы (некоторые продавцы семян используют их для полевых испытаний).
При взвешивании убедитесь, что оборудование находится на ровной поверхности. Наиболее важно взвешивать каждую ось отдельно, чтобы можно было определить нагрузку на отдельные колеса. В этом случае вес под каждой шиной определялся отдельно и отображался в таблице 1.
Таблица 1. Масса каждого колеса пустого комбайна (фунты), используемого в этом примере 23 960 7 400 Справа 21 000 7 500 Общая ось 44 960 14 900
Теперь нам нужно определить вес полного комбайна. Вместимость бункера этого комбайна составляет 350 бушелей. Предполагая, что 56 фунтов/бушель (для кукурузы) и разделение 70/30 между передней и задней частью, это добавит 350×56 = 19.600 фунтов, разделенных между передней (19 600 х 70% = 13 720 фунтов) и задней (19 600 х 30% = 5880 фунтов). В целях безопасности мы используем максимальную нагрузку на передние и задние шины. Общая нагрузка на переднее левое колесо при заполненном мусорном ведре составляет 23 960 фунтов. + (13 720/2) = 30 820 фунтов. Для задней правой шины это 7500 фунтов. + (5880/2) = 10 440 фунтов. (Обратите внимание, что вес контейнера был для каждой оси, поэтому его нужно было разделить на два, чтобы получить нагрузку на колесо). Теперь вы переходите к таблицам нагрузки на шины для каждой таблицы. Для этих шин имеется пять столбцов (см. рис. 1). Первый показывает давление в шинах. Вторая максимальная нагрузка в фунтах. со скоростью 43 мили в час, третий со скоростью 40 миль в час, а четвертый предназначен для «циклического обслуживания». Цикличность обслуживания актуальна для комбайнов, где нагрузка то увеличивается, то уменьшается по ходу уборки. Так как скорость комбайна при уборке не более 10 миль в час, мы можем использовать последний столбец и показать, что передние шины необходимо накачать до 29psi (берем первый ряд, где нагрузка превышает 30 820 фунтов), а задние шины до 12 psi (это самое низкое давление в шинах для данной шины).
Для перевозки по дорогам комбайн пуст, поэтому нагрузка на передние колеса составляет не более 23 960 фунтов. и рассчитан на скорость 40 миль в час (но не 43 мили в час). Задняя шина (7500 фунтов) рассчитана на скорость 43 мили в час.
Рис. 1. Таблицы нагрузок для передних и задних шин, использованные в приведенном выше примере.
Этот пример для комбайна, но он аналогичен для другого оборудования. Я бы порекомендовал вам отрегулировать давление в шинах ваших тракторов перед весенним и осенним сезоном, используя самый тяжелый вес дышла, который вы тянете в предстоящем сезоне. Если у вас есть какие-либо вопросы, обратитесь за советом к местному преподавателю или продавцу оборудования или свяжитесь со мной по адресу sduiker@psu.edu.
Уплотнение почвы | Расширение UMN
- Дом
- Растениеводство
- Почва и вода
- Управление почвой и здоровье
- уплотнение почвы
Краткие факты
В Миннесоте растет обеспокоенность по поводу уплотнения почвы, поскольку резко увеличились как годовые осадки, так и размер сельскохозяйственного оборудования.
Влажные почвы особенно подвержены уплотнению. Тяжелая техника и почвообрабатывающие орудия усиливают повреждение структуры почвы, уменьшая поровое пространство и еще больше ограничивая объем почвы и воды.
Улучшение структуры почвы — лучшая защита от ее уплотнения. Хорошо структурированная почва удерживает и проводит воду, питательные вещества и воздух, необходимые для здоровой корневой деятельности растений.
Что такое уплотнение?
Уплотнение почвы происходит, когда частицы почвы сжимаются вместе, уменьшая поровое пространство между ними (рис. 1). Сильно уплотненные грунты содержат мало крупных пор, меньший общий объем пор и, следовательно, большую плотность.
Уплотненная почва имеет пониженную скорость как инфильтрации воды, так и дренажа. Это происходит потому, что большие поры более эффективно перемещают воду вниз через почву, чем более мелкие поры.
Кроме того, в уплотненных грунтах замедляется газообмен, что повышает вероятность проблем, связанных с аэрацией. Наконец, в то время как уплотнение почвы увеличивает прочность почвы — способность почвы сопротивляться перемещению приложенной силы — уплотненная почва также означает, что корни должны прилагать большую силу, чтобы проникнуть в уплотненный слой.
Рис. 1: Влияние уплотнения на поровое пространство.
Уплотнение почвы изменяет размер пор, их распределение и прочность почвы. Одним из способов количественной оценки изменения является измерение объемной плотности. По мере уменьшения порового пространства в почве объемная плотность увеличивается. Почвы с более высоким процентным содержанием глины и ила, которые, естественно, имеют больше порового пространства, имеют более низкую объемную плотность, чем более песчаные почвы.
- Циклы замораживания-оттаивания уменьшают большую часть уплотнения почвы, создаваемого техникой.
- О каком бы уплотнении не позаботилась Мать-природа, глубокая обработка почвы или рыхление сделают это.
- Используйте прецизионную обработку для больших допусков и подгонки.
- Отборные высококачественные компоненты для изготовления ступиц.
- Легкий вес.
- Низкие эксплуатационные расходы.
- Низкое сопротивление качению.
- Долговечный.
- Простая работа с .
- Колеса для шоссейных велосипедов . Карбон является преобладающим материалом для колес среди гонщиков World Tour, профессионалов Continental и серьезных гонщиков-любителей, от критериумов до многодневных многодневных гонок. Их аэродинамические свойства и быстрое ускорение идеально подходят для постоянно меняющегося темпа шоссейных гонок.
- Колеса для велосипедов для триатлона — Триатлонисты часто первыми начинают пользоваться велосипедами, тем более что федерации триатлона менее строги в отношении технологических достижений, чем многие федерации шоссейного велоспорта.
Это относится к карбоновым колесам. Это, безусловно, колеса, которые вы увидите практически на любой гонке по триатлону.
- Велосипедные колеса для гонок на время . Как и в случае с триатлоном, участники гонок на время регулируются федерациями шоссейных гонок. Все федерации одобряют карбоновые диски с глубоким профилем или дисковые колеса. Вы редко увидите гонщика на время на любом другом типе колеса.
- Велосипедные колеса Ultra Cycling – Гонщики, участвующие в этих гонках продолжительностью от 12/24 часов до гонок RAAM на расстояние более 3000 миль, ценят комфорт и дополнительную скорость при снижении мощности карбоновых колесных пар.
- Колеса для гравийных велосипедов — Гравийные шлифовальные машины сейчас в моде благодаря тому, что водители могут ездить вдали от пробок и исследовать уникальные пейзажи. Углеродные колеса новее для гравийной дисциплины. FLO G700 и G650 являются ведущими соперниками на гравийном рынке, предлагая отличную аэродинамику, низкое сопротивление качению, уменьшенную вибрацию, лучшее сцепление, прочность и устойчивость на постоянно меняющемся покрытии, которым является гравий.
- 1/4″ = от 2,5 до 3,5 кубических футов в минуту
- 3/8″ = от 4,5 до 5 кубических футов в минуту
- 3/8″ = от 2,5 до 3,5 кубических футов в минуту
- 1/2″ = от 4 до 5 кубических футов в минуту
- 1″ = 10 кубических футов в минуту
Мифы об уплотнении почвы
Существует два широко распространенных мифа об уплотнении почвы:
|
Причины уплотнения
Существует несколько сил, естественных и техногенных, которые уплотняют почву (рис. 3). Эта сила может быть большой, например, от трактора, комбайна или почвообрабатывающего орудия, или она может исходить от чего-то такого маленького, как капля дождя. Ниже перечислены причины уплотнения почвы.
Рисунок 3: Уменьшение роста корней из-за уплотнения от ударов дождевых капель, обработки почвы и следов от колес. Это, безусловно, естественная причина уплотнения, и мы видим его в виде почвенной корки (обычно толщиной менее 1/2 дюйма на поверхности почвы), которая может препятствовать появлению всходов (рис. 4). Роторное рыхление часто может облегчить эту проблему.
Движение колес, без сомнения, является основной причиной уплотнения почвы (рис. 5). С увеличением размера фермы время для своевременного выполнения этих операций часто ограничено.
Масса тракторов увеличилась с менее чем трех тонн в 1940-х годах до примерно 20 тонн сегодня для больших полноприводных агрегатов. Это вызывает особую озабоченность, поскольку весенняя посадка часто проводится до того, как почва станет достаточно сухой, чтобы выдержать тяжелое посадочное оборудование.
Рисунок 5: Движение колес.Последствия уплотнения
|
Рисунок 7: Хорошо агрегированная почва.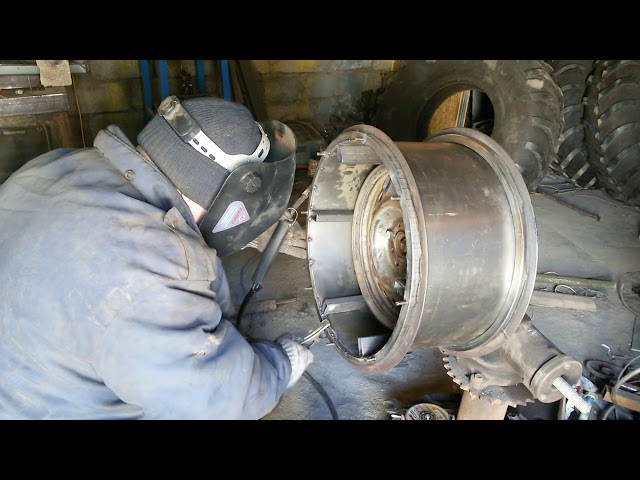
W структура кур и поры уменьшаются, в почве меньше воздуха и влаги. Это состояние отрицательно влияет на все фазы растениеводства, включая прорастание семян, появление всходов, рост корней, а также поглощение питательных веществ и воды (рис. 10).
Рисунок 10: Рост корней ограничен уплотненной почвой.Уплотнение почвы увеличивает ее плотность. Корни менее способны проникать в почву и, как правило, мелкие и деформированные.
Поскольку их рост ограничен, они менее способны использовать почву для получения питательных веществ и влаги. Дефицит азота и калия является наиболее распространенным явлением (рис. 11). Это приводит к дополнительной потребности в удобрениях и увеличивает производственные затраты.
Вы можете уменьшить неблагоприятные последствия уплотнения, применяя удобрения таким образом, чтобы улучшить доступ к корням растений. Это может включать раздельное внесение азота или групповое внесение фосфора и калия.
Таблица 1: Влияние уплотнения почвы на высоту кукурузы
Лечение | Высота растений кукурузы: через шесть недель после посева | Высота растений кукурузы: при сборе урожая |
---|---|---|
Без уплотнения | 28,8 дюйма (a) | 114,3 дюйма (ab) |
Ежегодное уплотнение шин флотации | 26,4 дюйма (ab) | 108,7 дюйма (abc) |
Ежегодное уплотнение дорожных шин | 22,5 дюйма (в) | 102,4 дюйма (в) |
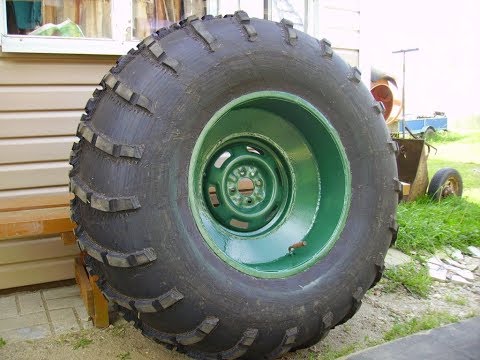
Как справиться с уплотнением почвы
Одним из наиболее важных факторов снижения способности почвы к уплотнению является держание подальше от почвы, когда она влажная. К сожалению, это не всегда возможно, так как часто ограничивает возможности выездной работы. Хотя уплотнение не может быть устранено, его следует контролировать.
|
Рисунок 20: Полевой охват обычными ежегодными полевыми операциями. Рис. 21: Полевое покрытие в условиях контролируемого движения.Таблица 2: Приблизительные нагрузки на ось для полевого оборудования
Полевое оборудование | Осевая нагрузка |
---|---|
Цистерна для навозной жижи (4200 галлонов) | 10-12 тонн на ось |
Цистерна для навозной жижи (7200 галлонов) | 17-18 тонн на ось |
Комбайн класса 9 (590 л.![]() | 20 тонн на ось |
Комбайн 12-рядный (полный с головкой) | 24 тонны на ось |
Тележка для зерна (720 бушелей, полная, 1 ось) | 22 тонны на ось |
Зерновоз (1200 бушелей, полный, 1 ось) | 35-40 тонн на ось |
Тележка для зерна (2000 бушелей, полная, 1 ось) | 70-76 тонн на ось |
Terra-Gator (задняя ось) | 12-18 тонн на ось |
Трактор 4WD (200 л.с., передний мост) | 7,5 т на ось |
Трактор 4WD (325 л.![]() | 13 тонн на ось |
Трактор 4WD (530 л.с., передний мост) | 18 тонн на ось |
Таблица 3: Влияние различных осевых нагрузок на износ дорожного покрытия
Тип | Оси | Количество проходов до отказа: 6 дюймов бетона на портландцементе (PCC) | Количество проходов до отказа: 7 дюймов PCC* |
---|---|---|---|
5-осный тягач-полуприцеп (80 000 фунтов) | 1 одинарный/2 тандема | 12 000 | 135 000 |
7-осный тягач-полуприцеп (96 000 фунтов) | 1 одинарный/2 тандема | 78 000 | 175 000 |
Зерновоз (875 бушелей, 57 000 фунтов, 20% на тягаче) | Одноместный | <10 | <30 |
Тележка для зерна (650 бушелей, 42 000 фунтов, 20% на тягаче) | Одноместный | <30 | 270 |
Комбайн: пустой (32 000 фунтов с кукурузной приставкой) | 2 одинарных (1 шина на асфальте): 26 000 спереди и 6 000 сзади | 887 000 | 1 980 000 |
Комбайн с 240 бушелями (46 000 фунтов с кукурузной приставкой) | 2 одинарных (1 шина на асфальте): 36 000 спереди и 10 000 сзади | 100 000 | 456 000 |
Малый пропашной трактор (18 000 фунтов) | 2 одинарных: 11 000 спереди и 7 000 сзади | 1 525 000 | 3 410 000 |
Резервуары для жидкого навоза (7 500 галлонов, 71 000 фунтов) | 2 тандема | <10 | <30 |
Джоди ДеДжонг-Хьюз, преподаватель дополнительного образования
Отзыв в 2018
Поделиться этой страницей:
Обзор страницы
Полное руководство для велосипедистов
Если вы когда-нибудь занимались велосипедным спортом, вы видели как профессиональных, так и любительских райдеров на дорогих велосипедах с колесами с глубоким ободом. Возможно, вы с завистью смотрели на их колесные пары, а может быть, у вас уже есть карбоновые колеса, и у вас просто есть вопросы или вы подумываете об обновлении. Мы создали это подробное руководство, чтобы ответить на часто задаваемые вопросы о карбоновых велосипедных колесах. Это руководство поможет вам принять мудрое решение, если вы решите обновить колеса своего велосипеда.
Предыстория и история карбоновых колес
Преимущества карбоновых велосипедных колес
Углеродные диски
Другие важные части карбонового колеса
Углеродные колесные пары и типы шин
Спицы на карбоновых колесах
Колесо из углеродного диска
Углеродные велосипедные колеса и безопасность
Использование дисциплины велоспорта и углерод
Покупка карбоновых колесных пар
Почему велосипедные колеса так важны? Колеса вашего велосипеда, вероятно, являются самой важной частью вашего велосипеда. Они постоянно вращаются и являются единственной точкой контакта с землей во время езды. Из-за этого они оказывают большое влияние на вашу езду на велосипеде, безопасность и комфорт.
Что такое углеродное волокно?
Углеродное волокно появилось в аэрокосмической промышленности. Он состоит из свободных волокон, состоящих из атомов углерода, которые затем суспендируются в смоле, образуя твердый материал. Углеродные волокна или углеродные волокна представляют собой волокна диаметром от 5 до 10 микрометров, состоящие в основном из атомов углерода. Углеродные волокна имеют ряд преимуществ, включая высокую жесткость, высокую прочность на растяжение, малый вес, высокую химическую стойкость, устойчивость к высоким температурам и низкое тепловое расширение.
Как изготавливается колесо из углеродного волокна?
Диски из углеродного волокна состоят из двух компонентов; углеродное волокно и эпоксидная смола. При формовании колеса из углеродного волокна куски препрега углеродного волокна закладываются в формы. Препрег — это необработанное углеродное волокно, пропитанное эпоксидной смолой. До изобретения препрега необработанное углеродное волокно укладывалось на место, а эпоксидная смола наносилась поверх углеродного волокна, что было грязным и сложным процессом. Препрег делает производственный процесс более чистым и удобным.
После того, как препрег-углерод уложен в форму, он помещается в печь, где проходит заданный цикл нагрева, известный как цикл линейного нагрева. Печь с формой запускается при низкой температуре, постепенно увеличивается до заданной температуры, а затем снижается до температуры на выходе. Каждый этап имеет заранее определенное время. Если бы вы построили график изменения температуры во времени, была бы создана форма линейного изменения, отсюда и название цикла линейного изменения.
Когда углеродное волокно выходит из формы, это твердая готовая деталь. Однако все эпоксидные смолы имеют так называемую «температуру стеклования», при которой затвердевшая эпоксидная смола снова превращается из стекла в жидкость. Когда это происходит, объект из углеродного волокна становится мягким и выходит из строя.
Дизайн и выбор эпоксидной смолы имеют решающее значение для ободьев из углеродного волокна. Большинство мифов, упомянутых в начале этой статьи, восходят к тому времени, когда впервые производились карбоновые диски в 90-х и начале 00-х годов. В то время эпоксидные смолы могли выдерживать высокие температуры, необходимые для нагрева тормозов, только если они делали деталь хрупкой. Вы не смогли найти смолу, которая производила бы прочный обод, который также выдерживал бы высокие температуры.
Сегодня эпоксидные смолы достигли значительных успехов, и мы можем производить диски, которые выдерживают высокие температуры и более долговечны, чем алюминий.
Когда был изготовлен первый клинчер из углеродного волокна?
Lew Composites представила первый полностью карбоновый клинчерный обод в 1998 году. Владелец компании Пол Лью, заядлый триатлонист, хотел такой же экономии веса и аэродинамики, которую могли предложить карбоновые трубы, но с легкостью и универсальностью клинчера.
Когда в гонке впервые использовали велосипедное карбоновое колесо?
В 1993 году Хайнц Обермайер и Рудольф Дирл разработали колесо со спицами из карбона, которое сразу же получило сертификат UCI для поддержки соревнований при его запуске в 1994.
Преимущества карбоновых велосипедных колес Являются ли карбоновые велосипедные колеса быстрее, чем легкосплавные? Если бы форма и вес легкосплавного и карбонового дисков были одинаковыми, аэродинамические преимущества были бы одинаковыми. Тем не менее, гораздо проще придать карбону необходимую форму, чем обод из цельного сплава. Колеса из углеродного волокна часто быстрее из-за используемых методов конструкции, особенно на полностью карбоновых ободах. Полностью карбоновые колеса не имеют соединения углерода и алюминия, а спицы соединены с ободом, тогда как в алюминиевых + карбоновых колесах карбоновые обтекатели имеют отверстия, через которые проходят спицы. Это может позволить конструкции колеса иметь уменьшенный Cda и, таким образом, они, как правило, быстрее.
Поскольку карбоновые колеса изготавливаются с помощью пресс-формы, они могут иметь более сложную форму, чем легкосплавные диски. Этот пошив позволяет улучшить аэродинамику. Хотя раньше вес был решающим фактором, более поздние исследования показывают, что аэродинамика играет более важную роль, чем вес, с точки зрения скорости, за исключением случаев постоянного подъема по крутым уклонам 12% или более. Если у вас есть только короткий участок с крутыми уклонами, аэродинамика выигрывает. Аэродинамика колеса важнее веса в соотношении 60:1.
Колеса из карбона удобнее? Углеродное волокно как материал поглощает вибрацию лучше, чем алюминиевые колеса. Кроме того, конструкция карбонового колеса создает эффект листовой пружины на боковых стенках карбонового обода. Это связано с тем, что спицы соединяются с внутренним диаметром обода. На ободе «алюминий + карбон» спицы проходят через обтекатель и соединяются с алюминиевым ободом. Это не позволяет использовать преимущества листовой рессоры.
В результате езда на карбоновых колесах более комфортна из-за более низкого уровня вибрации.
Карбоновые дискиПри обсуждении велосипедных колесных пар наибольшее внимание обычно уделяется ободам. Это связано с тем, что обод очень хорошо виден и оказывает наибольшее аэродинамическое и весовое влияние на характеристики карбонового колеса.
Обычно существует два типа карбоновых дисков. Полностью карбоновые диски и алюминиевые диски с карбоновым обтекателем.
Узнайте больше об ободах из карбона и обтекателях.
Есть ободья с крючками и без крючков.
Узнайте больше об ободах с крючком и без крючка.
Глубина карбонового обода измеряется в миллиметрах. Большинство карбоновых дисков со спицами имеют глубину от 30 до 90 мм. Производители часто называют свои колеса в соответствии с их глубиной. Zipp 808 имеет глубину 80 мм, FLO 77 AS имеет глубину 77 мм, а Enve SES 4. 5 имеет глубину 45 мм.
Более глубокие диски обычно соответствуют улучшенной аэродинамике. Это связано с тем, что глубокий обод создает большую боковую силу. Боковую силу можно рассматривать как подъемную силу на крыле самолета или как воздух взаимодействует с парусом на лодке. Сегодня мы узнали, что улучшения в аэродинамике — это баланс ширины и глубины вокруг определенного профиля шины. Поиск правильного сочетания ширины и глубины позволяет получить быстрое и стабильное колесо.
Глубина велосипедного обода FLO FLO предлагает колеса All Sport для шоссе и триатлона глубиной 64 мм и 77 мм. Мы предлагаем наши карбоново-алюминиевые колеса глубиной 60 мм и 90 мм. Некоторые люди спрашивали нас, почему мы перешли на новые размеры колес AS (например, почему у нас нет 90-го размера в модели AS). Ответ заключается в том, что наши продвинутые алгоритмы оптимизации научили нас тому, что быстрое колесо имеет правильную комбинацию ширины и глубины. Глубина — это только один из компонентов скорости колеса при ее оптимизации для конкретного профиля шины. Стабильность колеса также является важным фактором при проектировании колеса. Глубокое колесо, которое очень неустойчиво на ветру, производит более медленного спортсмена. Опять же, ключевым моментом является поиск правильного баланса ширины и глубины.
Одно из соображений, касающихся шоссейных велосипедов и велосипедов для триатлона, заключается в том, как они будут реагировать на боковой ветер. Прямой встречный или попутный ветер, хотя и влияет на скорость, мало влияет на управляемость мотоцикла. Боковой ветер — это совсем другая история. Это особенно верно, если они порывы. Глубина переднего обода является наиболее важным фактором, определяющим управляемость, поскольку он прикреплен к подвижной вилке и, в меньшей степени, поскольку меньший вес водителя приходится на переднее колесо. Поскольку на тело гонщика приходится большая часть сопротивления ветру, езда на колесе, которое требует, чтобы тело гонщика вышло из оптимального аэродинамического положения, тратит на гонщика больше времени, чем выигрывает аэродинамические преимущества колеса. При выборе карбонового колеса, особенно переднего, обязательно учитывайте вес своего тела, уверенность в управлении и типичные погодные условия.
Мы обнаружили, что почти все водители могут справиться с нашими передними колесами глубиной 64 мм, а большинство из них могут справиться с нашими передними колесами 77 мм. Например, у нас есть 190 фунтов. Гонщик FLO Factory Team, занявший подиум в 12-часовой гонке Ultra на переднем FLO 64 AS и заднем FLO 77 AS при боковом ветре в Техасе со скоростью 39 миль в час. Почти все гонщики могут справиться с нашими 77-миллиметровыми задними или дисковыми колесами, за исключением очень сильного бокового ветра. Единственным исключением из этого правила является очень маленький всадник (< 5 футов 2 дюймов и/или < 110 фунтов). В этой ситуации вы можете рассмотреть передний FLO 49AS, чтобы помочь с управлением велосипедом.
Форма обода Углеродные обода имеют параболическую форму для обеспечения максимальной аэродинамической эффективности и устойчивости при боковом ветре.
Большинство шоссейных и триатлонных ободов имеют ширину от 19 до 28 мм. До конца 2000-х годов считалось, что самые узкие диски — самые быстрые. Профи обычно ездили на узких колесах и шинах. Шины Rider шириной 21 мм годами использовались повсеместно в крупных турах. Но более глубокое понимание сопротивления качению в тандеме с аэродинамикой привело к тенденции использования более широких дисков с более широкими шинами с 2010 года. Более широкие диски также обеспечивают больший комфорт, поскольку более широкие диски и шины позволяют использовать более низкое давление воздуха. (См. раздел о шинах ниже).
Аэродинамика колес и обода FLO Компания FLO разработала передовые алгоритмы оптимизации, которые мы используем для создания быстрых и стабильных форм обода с точки зрения аэродинамики. Наша дорожная работа по изучению сопротивления качению позволила нам понять, что более широкие внутренние обода обеспечивают меньшее сопротивление качению. Мы использовали эти знания для разработки аэродинамических ободьев для широких шин и широкой внутренней ширины обода, чтобы снизить аэродинамическое сопротивление и сопротивление качению, создаваемые ободом.
Важным фактором успеха и безопасности в гонках является способность гонщика эффективно и рационально останавливать велосипед. Езда в пелотоне требует плавного торможения для тяги и резких остановок, чтобы избежать аварии впереди. Спуск предъявляет свои уникальные требования к торможению, так как самые быстрые спускники минимизируют скорость очистки, но когда им нужно, очень важно, чтобы их тормоза сработали, чтобы они не промахнулись за поворот. Даже триатлонистам и гонщикам на время требуется надежное торможение при крутых поворотах, дорожных препятствиях и других происшествиях.
Ободные тормоза Давняя проблема, связанная с колесами с полностью карбоновыми ободами, связана с их тормозной способностью. Когда ободные тормоза были основным типом тормозной системы на дорогих велосипедах, а дисковые тормоза были запрещены UCI, беспокойство было еще больше. Это связано с тем, что ободной тормоз работает за счет суппорта с колодками, которые прижимаются к поверхности обода.
Когда эта колодка соприкасается с углеродом, возникают опасения по поводу количества трения, необходимого для остановки, а также соответствующего износа и нагрева обода. Одним из вариантов является создание карбонового колеса с алюминиевым тормозом, чтобы обеспечить неуглеродную точку контакта колодки. Это предотвращает износ тормозной гусеницы, но не полностью снимает проблемы с нагревом. Однако последние разработки в области углеродных технологий позволяют использовать все карбоновые диски в сочетании с ободными тормозами, если тормозные колодки специально разработаны для карбоновых дисков. Этот новый углерод устойчив к износу и лучше справляется с нагревом. Некоторые гонщики, в том числе Крис Фрум и другие профессионалы, по-прежнему предпочитают ободные тормоза для быстрой смены колес во время соревнований и меньше проблем с истиранием дисковых тормозов из-за смещения. В качестве бонуса ободные тормоза, как правило, показали себя более аэродинамическими в испытаниях в аэродинамической трубе. Однако все больше и больше производителей велосипедов переходят на дисковые тормоза, а это означает, что производители колес должны последовать их примеру.
Новейшая тенденция в области торможения позволяет водителям останавливаться, не касаясь тормозной колодкой обода. Вместо этого дисковые тормоза имеют металлический ротор, который находится в центре колеса и соединен со ступицей.
Дисковые тормоза Давление поршня прикладывается к этому металлическому диску вместо поверхности обода, чтобы обеспечить тормозную мощность. Это снижает опасения по поводу износа обода и проблем с перегревом (дополнительную информацию о перегреве обода см. в разделе безопасности ниже). Они также останавливают водителя быстрее, чем ободные тормоза. Это особенно верно, когда условия влажные. UCI и другие руководящие органы теперь разрешают использование дисковых тормозов на соревнованиях. Дисковые тормоза обеспечивают большую тормозную способность, что может быть полезно на длинных спусках, и они обеспечивают более точное торможение, снижая вероятность блокировки колес. Также проще использовать более широкие шины с дисковыми тормозами, и единственным ограничителем является рама, а не возможности ширины тормозного суппорта.
Flo производит как полностью карбоновые, так и алюминиевые + карбоновые диски. Мы предлагаем как ободные, так и дисковые тормоза каждой из наших карбоновых моделей, чтобы удовлетворить самые разные потребности велосипедистов. Предпочитаете ли вы ободные или дисковые тормоза, у нас есть колесо, которое точно соответствует вашим потребностям. Мы предлагаем специальные тормозные колодки для использования с ободными тормозами с нашими карбоновыми колесами. Мы разработали эти колодки, чтобы работать в гармонии с нашим углеродом для оптимальной тормозной способности во влажных и сухих условиях с минимальным износом колеса. Каждое из наших колес для дисковых тормозов поставляется готовым к использованию с предпочитаемым вами ротором с центральным замком.
Ось фиксируется на месте, когда колесо соединено с рамой, а подшипники в ступице позволяют колесу свободно вращаться вокруг оси. Есть два типа осей.
Быстросъемная ось , , которая позволяет открывать рычаг для быстрого снятия колеса. Они были популярны в течение многих лет на велосипедных трассах.
Быстросъемная ось Совсем недавно, 9Сквозные оси 0354 стали популярными благодаря своей прочности и использованию с колесами с дисковыми тормозами. Ось через – проходит через ступицу и вкручивается прямо в раму велосипеда, что предотвращает отсоединение колеса. Сквозные оси обычно являются собственностью Framemaker, но могут использоваться с несколькими типами карбоновых колес.
Ступица — это центральная часть переднего и заднего колес велосипеда . Ступица позволяет колесу вращаться вокруг оси. Ступица содержит подшипники, которые позволяют колесо свободно вращаться на оси.
Передняя втулка (вверху) и задняя втулка (внизу) Передняя втулкаВтулка переднего колеса велосипеда свободно вращается в обоих направлениях. Это более простая конструкция, чем задняя ступица. Это позволяет переднему колесу одинаково свободно вращаться в обоих направлениях.
Задняя втулка Втулка позволяет велосипедисту двигаться вперед без вращения педалей с помощью храпового механизма (точно так же, как инструмент для установки торцевых головок). Ступица срабатывает, когда велосипедист нажимает на педаль, и продолжает вращать колесо, когда велосипедист перестает крутить педали. Втулки также содержат кассету зубчатых колес, также известную как шестерни. У старых велосипедов было 5 задних передач и две шестерни, прикрепленные к шатунам педалей. Именно здесь появилось название «10-скорость» как прозвище для шоссейного велосипеда. Сегодня задние кассеты имеют 10, 11 или даже 12 зубцов, что позволяет использовать широкий спектр вариантов передачи. Большинство шоссейных, горных и триатлонных велосипедов оснащены втулками.
Неподвижная ступица не позволяет велосипедисту двигаться накатом. Часто называемый фиксом, если велосипед движется вперед, педали поворачиваются в зависимости от скорости движения. Если вы когда-либо катались на Spin Bike ® в классе упражнений, то вы испытали, как ездит фиксированная втулка. Фиксированные задние ступицы имеют только одну передачу, а это означает, что гонщик должен определить передачу, выбрав размер передней шестерни кривошипа и одинарной задней шестерни. Для трековых гонок на велодромах требуются трековые велосипеды с фиксированной передачей. Есть фиксированные шоссейные гонки, называемые аллеями, критерий Red Hook и последний мужчина / женщина, выжившие Rad Races на закрытых картинговых дорожках. Фиксики, как известно, являются предпочтительным велосипедом для велокурьеров и городских гонщиков (они же хипстеры), поскольку у них меньше механических проблем, а уникальный стиль вождения предотвращает кражу.
Да. Любое трение при вращении ступицы снижает скорость колеса. В ступицах используются подшипники, состоящие из двух обойм и шарикоподшипников для уменьшения трения. Если грязь или грязь попадают через уплотнение ступицы в направляющую шарикоподшипника, трение увеличивается. Если подшипники ненастоящие (идеально круглые) или изношены, в ступице присутствует большее трение. Это замедляет велосипедиста.
Ступицы FLOВ колесах FLO используются наши запатентованные передовые втулки FLO Vortex.
Втулки FLO Vortex рассчитаны на длительный срок службы, низкие требования к техническому обслуживанию, легкость в работе и высокую скорость. Для производства концентраторов, отвечающих этим требованиям, мы сделали следующее.
В результате этих двух вещей наши втулки:
Шины, которые выбирает гонщик, имеют ключевое значение для характеристик колеса. Шины оказывают большое влияние на сопротивление качению, аэродинамические характеристики и плавность хода колеса. Времена, когда чем тоньше-ширина-шины, тем лучше, давно прошли. Очень важно, чтобы ширина шины соответствовала рекомендациям производителя. Тип выбранной шины также может повлиять на производительность. Вот типы шин, которые используют велосипедисты:
Раньше профессиональные велосипедисты предпочитали камерные шины. Трубчатые шины похожи на автономную камеру, приклеенную к ободу. Причина, по которой они нравились профессионалам, заключается в том, что если бы они были плоскими, они могли бы продолжать немного ездить на них, ожидая, пока машина их команды догонит их, не повредив обод. Замена спущенной шины на трубчатую без полной замены колеса занимает больше времени. Гонщик должен остановиться и приклеить новую трубку, а для отверждения обычного трубчатого клея требуется до 24 часов.
КлинчерыВ отличие от трубчатых шин, клинчеры не являются автономными камерами. Вместо этого они используют синтетический борт на обоих краях шины, которые цепляются за канавку на ободе, называемую клинчерным крюком. Клинчерные шины очень популярны благодаря своей доступности и простоте использования.
Существует два типа клинчерных шин:
камерные клинчерные шины камерные шины требуют камеры, в которой находится давление воздуха. Если камера проколота, шина спустится. Поскольку есть трубка, необходимо использовать более высокое давление, чтобы трубка не защемилась, что приведет к защемлению (также известному как укус змеи). Повышение давления в шине может привести к увеличению сопротивления качению из-за увеличения вибрации, прошедшей контрольную точку импеданса шины.
Для получения дополнительной информации о точке разрыва импеданса прочитайте эту статью.
Бескамерные клинчерные шины Бескамерные шины быстро набирают популярность. В случае бескамерной шины обод заклеивается лентой для обеспечения герметичности. Это означает, что трубка не нужна для удержания воздуха. Большинство пользователей бескамерных шин также используют небольшое количество жидкого герметика в шине. Если шина проколота, давление воздуха, выбрасываемое из прокола, выталкивает герметик в отверстие, и шина герметизируется. Из-за этого у бескамерных гонщиков меньше проколов, если со временем пополнять запас герметика.
Бескамерные шины можно эксплуатировать при более низком давлении, поскольку в них нет внутренней камеры, которую можно защемить. Это приводит к двум преимуществам: более комфортной езде, поскольку шина с меньшим давлением может привести к более низкому сопротивлению качению и улучшенному гашению вибрации. Это недавнее открытие в области колес. И хотя это немного нелогично, колесо с более низким давлением может обеспечить меньшее сопротивление ролика. (Подробнее о сопротивлении качению).
Рекомендации по шинам FLO Каждое колесо FLO Cycling разработано с учетом рекомендуемого диапазона дорожных шин + ширины и уровней давления воздуха, а также ширины и давления для гравийных шин, чтобы оптимизировать их аэродинамические преимущества и сопротивление качению. Каждая из наших моделей колес имеет руководство пользователя по оптимальной ширине и давлению в зависимости от веса гонщика и состояния дорожного покрытия, с соответствующей экономией мощности и времени, привязанной к каждому размеру колеса на дистанции 40 км, поездках Century и IRONMAN®.
Спицы на карбоновых колесах изготавливаются из стали, алюминия или иногда из более экзотических материалов, таких как углеродный композит или керамика. Они соединяют обод со ступицей. Спицы позволяют карбоновому колесу быть прочным, уменьшая при этом вес и затраты энергии на ускорение колеса. Колеса более высокого класса имеют спицы овальной формы (или лопастные), а не круглые для лучшей аэродинамики.
Спицы В велосипедных колесахиспользуются спицы различных моделей. У тангенциальных спиц спицы соединяются от ступицы к ободу не по прямой линии, а под углом. Они пересекаются друг с другом. Радиальные спицы соединяют обод со ступицей по прямой линии. Тангенциальные узоры прочнее радиальных, но радиальные узоры легче.
Тангенциальный рисунок спиц (слева) и радиальный рисунок спиц (справа) Карбоновые колеса выходят из строя? Если вы едете на велосипеде и замечаете, что колесо шатается, возможно, оно не соответствует действительности. Самая распространенная причина, по которой колеса выходят из строя: ослабленные спицы. Наладка карбонового обода осуществляется теми же способами, что и любого другого обода: вы или велосипедный механик регулируете натяжение спиц, чтобы обеспечить правильное вращение обода.
В колесах FLO со спицами используются овальные спицы Sapim CX-Ray. Sapim заявляет, что эти спицы имеют самые высокие показатели усталостных испытаний среди всех спиц на рынке. Его уникальная гибкость и прочность делают CX-Ray подходящим для большинства высококлассных велосипедных дисциплин, от гравия до шоссейных гонок и триатлона (и даже для катания на горных велосипедах). FLO использует 20-спицевый радиальный дизайн спиц на передних колесах и 24-спицевый сдвоенный тангенциальный рисунок на наших задних колесах. Это минимизирует вес, улучшает аэродинамику, создает динамично реагирующее колесо и увеличивает прочность там, где это больше всего необходимо.
Изобретение дискового колеса для повышения производительности на самом деле не было преднамеренным. Дирл и Обермайер основали компанию KDO GmbH. Они производили чехлы для дисков задних колес велосипедов, чтобы защитить детские ноги от спиц. Триатлонисты, видя возможность повышения производительности и не руководствуясь UCI, адаптировали покрытие в качестве аэродинамического помощника.
После принятия триатлетами первые дисковые колеса для гонок без массового старта, гонок на время, в гонках, санкционированных UCI, впервые появились в конце 1980-е годы. Первыми дисками, использовавшимися в гонках UCI, была колесная пара Мозера с часовым рекордом в 1984 году. к шине воздух может течь по диску без прерывания, которое создают спицы. Благодаря дополнительной форме колесо с аэродинамическим диском обеспечивает наиболее эффективное соотношение мощности и скорости для велосипедиста, поскольку сопротивление воздуха / возмущение меньше. Это улучшение наблюдается не только при встречном или попутном ветре, но даже при различных рысканиях (углах, под которыми ветер бьет по водителю/колесу). Диск может функционировать как парус при определенных углах рыскания, а колесо толкает водителя вперед.
Кто-то может сразу подумать: «Я должен использовать дисковые колеса спереди и сзади, чтобы быть как можно быстрее». Помимо использования на велодроме в помещении, это было бы неразумно, поскольку эффект паруса на переднем колесе может нанести ущерб управляемости велосипеда. Даже если рассматривать только задний диск, в большинстве гонок с массовым стартом, где гонщики драфтуют и едут в пелотоне, использование диска не допускается. Преобладающие типы езды на дисковых колесах — это гонки на время и триатлон / дуатлон. Это связано с тем, что в непосредственной близости от велосипедиста никого нет, если сильный ветер унесет его в бок. Тем не менее, даже некоторые из этих гонок, такие как знаменитая Kona IRONMAN, ограничивают использование задних дисков из-за нестабильного бокового ветра. Тем не менее, большинство ТТ и Три позволяют их.
Компания FLO производит четыре дисковых колеса. У нас есть конструкция «алюминий + карбон» и полностью карбоновая конструкция. Для каждого типа мы предлагаем вариант ободного и дискового тормоза. FLO DISC — это колеса со спицами и обтекателями из углеродного волокна. Это позволяет получить преимущества колеса со спицами, такие как отзывчивость и податливость, а также возможность придавать карбоновым обтекателям двояковыпуклую форму. Наша двояковыпуклая форма обеспечивает более быстрое колесо по сравнению с дисковым колесом с плоской поверхностью.
Карбоновые велосипедные колеса и безопасность Насколько прочнее карбоновые колеса по сравнению с легкосплавными? Углеродное волокно может быть более прочным, чем алюминий, при правильной укладке и использовании эпоксидных смол. Это означает, что карбоновые колеса могут быть прочнее алюминиевых. Во время ударных испытаний наши алюминиевые диски повреждаются раньше, чем карбоновые.
Большинство людей думают о том, что они видят, когда колесо повреждено. Алюминий обычно изгибается и выглядит незначительным по сравнению с тем, как углеродное волокно имеет тенденцию иметь вид чего-то, что взорвалось. Более серьезный вид повреждения углеродом отчасти привел к убеждению, что углерод не так прочен, как алюминий, но это не так.
Долговечны ли карбоновые колеса?Благодаря высокой прочности на растяжение и жесткости карбоновые колеса очень долговечны. Хотя некоторые люди оставляют пару колес для гонок, в этом нет необходимости. Вы можете использовать одни и те же колеса как для тренировок, так и для гонок.
Могут ли карбоновые колеса выйти из строя? Несмотря на то, что карбоновые колеса невероятно прочные, их единственной проблемой является нагрев. Тепло возникает в основном из-за разрывов обода, которые останавливают велосипед из-за трения, возникающего между тормозной колодкой и поверхностью обода. Резкое торможение на спуске приводит к повышению температуры обода.
Карбон в ободе скрепляется эпоксидной смолой. Если смола нагреется слишком сильно, она может расплавить обод. Это происходит только при очень высокой температуре (обычно 220ºC/430ºF). Причина этого в том, что углерод не рассеивает тепло, как алюминиевый сплав. Сегодня солидные колесные компании производят диски, не имеющие проблем с нагревом. Как правило, они сочетаются с тормозными колодками, специфичными для используемых систем эпоксидной смолы.
Эта реакция на тепло является одной из причин, по которой дисковые тормоза становятся настолько распространенными на карбоновых ободах. Тепло создается на поверхности металлического диска, а не на поверхности углеродного обода. Также увеличена останавливающая сила.
Колеса FLO, созданные на века Компания FLO использует эпоксидные смолы, которые позволяют производить прочные диски, способные выдерживать высокие температуры. Все наши колеса проходят испытания на соответствие или превышение стандартов безопасности ISO в отношении эффективности торможения. Мы также производим тормозные колодки, предназначенные для работы с нашими системами на основе эпоксидной смолы. Благодаря этому мы можем добиться того же уровня эффективности торможения, что и наши алюминиевые колеса.
Карбон используется во многих велосипедных дисциплинах, в том числе:
Приобретение карбоновых колесных пар
Сколько стоят карбоновые колеса?В первые годы существования карбоновых колес их цена делала их недоступными для многих велосипедистов. С более эффективными методами производства цены упали. Типичное колесо из углеродного волокна от известного производителя стоит от 599 до 3000 долларов за колесо.
Бренды через дистрибьюторов к розничным торговцамЭто классический способ продажи велосипедных колес. Бренд решил, что хочет сделать колесо. нашел производителя, а затем использовал продавца, чтобы убедить велосипедные магазины продавать этот продукт. Затем они создали логистические и дистрибьюторские сети, чтобы доставлять свою продукцию в каждый магазин велосипедов. Каждый из уровней добавляет уровень надбавки к цене, уплаченной конечным пользователем. Так по-прежнему работает большинство известных брендов.
Модель колесных пар напрямую потребителю Модель FLO Cycling отличается от модели дорогостоящей дистрибуции. Мы продаем через наш веб-сайт напрямую вам, потребителю. Это позволяет нам создавать продукт, который не уступает по производительности громким именам в отрасли, и при этом нам не нужно устанавливать ту же цену, что и они. В уравнении нет посредников, а это означает, что вы получаете колесо мирового класса без высокой цены мирового класса.
Карбоновая колесная пара — отличное решение для большинства велосипедистов. Преимущества включали большую скорость при меньшей мощности, меньший вес на глубине обода, лучшую управляемость, меньшую вибрацию, большую жесткость для лучшей передачи мощности и более комфортную езду. Имея множество доступных и доступных карбоновых вариантов, это должно быть одно из первых обновлений, которое велосипедист делает для своего велосипеда. Это особенно верно, если ваш велосипед является бюджетным или средним, поскольку большинство производителей велосипедов используют более дешевые легкосплавные диски, чтобы сэкономить на затратах.
Колеса FLO Cycling спроектированы так, чтобы обеспечить максимальную аэродинамическую эффективность при различных направлениях ветра (ветер YAW) и улучшенное сопротивление качению. Модель FLO, ориентированная непосредственно на потребителя, позволяет вам приобретать высокотехнологичные карбоновые колесные пары за небольшую часть цены на модели, предназначенные для розничной продажи. Мы обслуживаем велосипедистов в различных видах спорта, от триатлона до шоссейных гонок, гравия и велокросса. Мы считаем, что у нас есть продукт, который соответствует или превосходит характеристики наших конкурентов в каждой спортивной категории. Наш соучредитель, Джон Торнхэм, инженер-механик, занимается разработкой колесных технологий посредством уникальных и постоянных исследований в области аэродинамики, сопротивления качению и анализа вибрации. Клиенты могут заказать колеса на нашем сайте с доставкой в любую страну мира.
Наша заводская команда FLO состоит из более чем 650 гонщиков из 21 страны, которые полностью верят в наши колеса и неоднократно тестировали их в самых соревновательных ситуациях. Мы поддерживаем каждый из наших продуктов с нашей честностью и гарантией. Пожалуйста, не стесняйтесь задавать нам любые вопросы. Мы будем рады быть вам полезными.
Как определить необходимое давление воздуха для приложений
Воздушные компрессоры и пневматические инструменты позволяют за секунды выполнить то, на что вручную ушли бы часы. Когда дело доходит до резки твердых материалов и ослабления давно затянутых болтов, пневматический инструмент может мгновенно выполнить то, что в противном случае было бы невозможно. Однако важно знать требования к давлению воздуха для данного инструмента или приложения.
Связаться с нами Узнать больше Найти ближайшего к вам дилера
Давление воздуха по применению
Так как же узнать, какое давление воздуха необходимо для данного применения? Пневматические инструменты, предназначенные для общего использования с переносными воздушными компрессорами, обычно требуют от 0 до 5 кубических футов в минуту (куб. футов в минуту) при давлении от 70 до 90 фунтов на квадратный дюйм (фунт/кв. дюйм), тогда как для более крупных инструментов, подключенных к стационарным системам, требования обычно превышают 10 кубических футов в минуту при от 100 до 120 фунтов на квадратный дюйм.
При периодическом использовании инструменты стандартного размера для определенных применений имеют особые требования к давлению воздуха. Тем не менее, важно помнить, что различные уровни кубических футов в минуту должны быть умножены на четыре, когда в игру вступает непрерывное использование.
Вот некоторые из этих приложений, а также их соответствующие уровни кубических метров в минуту:
Угловое шлифование.
При обслуживании и ремонте автомобилей или при металлообработке угловая шлифовальная машина используется для резки, шлифовки и полировки. Углошлифовальную машину можно использовать даже для шлифования поверхностей и кромок определенных материалов, если инструмент оснащен подходящим диском. Угловыми шлифовальными машинами также можно управлять одной или двумя руками — на большинстве моделей есть боковая рукоятка, позволяющая работать двумя руками. Для общего применения стандартной 7-дюймовой ручной угловой шлифовальной машине требуется от 5 до 8 кубических футов в минуту при 90 фунтов на квадратный дюйм.
Бред прибивает.
В строительстве и ремонте дома этот инструмент используется для глубокого забивания гвоздей в стены и дверные проемы, а также в другие части дома или здания, где обычные гвозди визуально не будут заметны. Гвозди, названные в честь этого инструмента, представляют собой тонкие гвозди без шляпки, которые невооруженным глазом выглядят гораздо менее броскими, чем обычные гвозди с плоской головкой. Будучи относительно легким пневматическим инструментом, гвоздезабивной инструмент обычно требует всего 0,3 кубических фута в минуту при 90 фунтов на квадратный дюйм.
Долбление.
В качестве инструмента, который иногда используется для резки металла, пневматическое долото является одним из самых тяжелых ручных пневматических инструментов. Пневматическое долото с его плоской узкой режущей кромкой также можно использовать для обработки камня или дерева, что делает его полезным инструментом при строительстве и ремонте домов и зданий. Стамески особенно удобны для вырезания соединений типа «ласточкин хвост» и пазов при возведении примыкающих стен и панелей полок. В общем случае для пневматического долота требуется от 3 до 11 кубических футов в минуту при 90 фунтов на квадратный дюйм.
Резка.
Если и есть инструмент, требующий питания, то это отрезной инструмент, предназначенный для разрезания листов металла в ремесленных работах, домашнем или автомобильном обслуживании, а также в промышленности. Если вам нужно отрезать углы от металлических листов или панелей от металлических стен, отрезной инструмент с пневматическим приводом выполнит эту задачу за считанные секунды. В некотором смысле металл выглядит как бумага на вращающихся дисках этих инструментов, для которых требуется от 4 до 10 кубических футов в минуту при 90 фунтах на квадратный дюйм.
Бурение.
При работе с твердыми материалами воздушные компрессоры особенно полезны для бурения, которое считается трудной задачей среди дрожащих рук. Благодаря мощности и скорости пневматических дрелей сверла входят и выходят так быстро, что остается мало времени для неуклюжих движений рук и кистей, которые в противном случае могли бы отправлять предметы по диагонали, а не прямо. В то время как традиционные электрические дрели могут пробить только древесину, пневматические дрели могут также сверлить металл и камень. Будь то прямолинейная или реверсивная, пневматическая дрель требует от 3 до 6 кубических футов в минуту при 90 фунтов на квадратный дюйм.
Двойное шлифование.
До изобретения электроинструмента немногие работы были настолько изнурительными для ладони, запястья и локтя, как шлифование. В то время как большая часть тяжелого подъема и давления была сосредоточена на этапах пиления, резки и забивания гвоздей, требовалось больше реальных движений рук только для того, чтобы каждая необработанная поверхность была очищена до красивой гладкой поверхности.
К счастью, с тех пор интенсивный труд, связанный с шлифованием, был освобожден благодаря двойным шлифовальным машинам с пневматическим приводом, которые шлифуют и полируют за считанные секунды. Всего этого можно добиться, просто удерживая инструмент над поверхностью. Отлично подходит для обработки металла и дерева, двойные шлифовальные машины требуют от 11 до 13 кубических футов в минуту при 90 фунтов на квадратный дюйм.
Прибивание рамы.
При обрамлении интерьера дома можно вбить десятки гвоздей за несколько коротких минут. С каркасным гвоздезабивателем вам не нужно держать гвозди под рукой, потому что ленты для гвоздей загружаются в инструмент, как пули в пулемет. Пневматический гвоздезабиватель для каркаса позволяет скреплять доски десятками друг с другом всего лишь за долю времени, которое потребовалось бы при работе с молотком, независимо от того, работаете ли вы с каркасом стены или стропилами. Самое удивительное, что монтажному гвоздезабивателю требуется всего 2,2 кубических фута в минуту при 90 фунтов на квадратный дюйм.
Смазка.
Движущиеся части машин нуждаются в смазке, которая является единственным фактором, защищающим трущиеся металлические поверхности от износа при трении и последующего нагревания. В автомобилях, например, смазочные шприцы используются для смазывания дверных петель и деталей двигателя. Нанесение смазки вручную может быть грязной операцией, но пневматический смазочный шприц делает всю работу аккуратной и аккуратной. Смазочный шприц также является простым пневматическим инструментом с относительно низким давлением в эксплуатации, так как для него требуется всего 4 кубических фута в минуту при 90 фунтов на квадратный дюйм.
Выкусывание металла.
Люди часто с удивлением смотрят на мебель, светильники и произведения искусства, сделанные из резного и уникально вырезанного листового металла. Если вы видите металлическую настенную подвеску в виде силуэта солнца, луны, цветка или животного, скорее всего, она была сделана вручную с помощью канцелярского ножа. Подобно тому, как ножи X-Acto и ионные резаки вырезают формы из бумаги и картона, высечные ножи позволяют резать металл так же просто, как резать бумагу.
Кроме того, высечки хороши для обрезки дюймов с металлических поверхностей и контурирования углов острых металлических концов. При правильном ведении вдоль листового металла с минимальным давлением рычага воздушному высекателю требуется 4 кубических фута в минуту при 90 фунтов на квадратный дюйм.
Минишлифовка.
Даже самые маленькие металлические и деревянные предметы иногда нуждаются в уходе. Хотите ли вы отшлифовать и сгладить края на определенных лотках или отполировать и зашлифовать поверхность старой монеты, миниатюрная шлифовальная машина станет идеальным пневматическим инструментом. Миниатюрная шлифовальная машина также может использоваться для трафаретной печати по дереву с умеренным рельефом и других поделок. От шлифовальных наконечников до амортизирующих колес — инструмент имеет малый вес независимо от насадки. Для мини-шлифовальной машины требуется от 4 до 6 кубических футов в минуту при 90 фунтов на квадратный дюйм.
Масштабирование иглы.
Несмотря на то, что металлы являются самым прочным типом материала, они все же подвержены ржавчине, окалине и другим остаткам, возникающим в результате воздействия. Состоящие из множества дребезжащих стальных игл, воздушные игольчатые зачистные машины способны удалять сварочный шлак, ржавчину, краску и различные другие признаки износа с твердых поверхностей. Если вы видите сварные швы на металлическом кронштейне, их можно удалить, аккуратно проведя игольчатым скребком несколько раз по площади поверхности. Игольчатый скейлер позволяет вернуть металлическим поверхностям блестящую гладкость за секунды, и для этого требуется всего от 8 до 16 кубических футов в минуту при 90 фунтов на квадратный дюйм.
Орбитальное шлифование.
Трудно представить достаточно гладкие деревянные поверхности без изобретения орбитальной воздушной шлифовальной машины. Орбитальная шлифовальная машина, созданная для того, чтобы сделать часто утомительную задачу шлифования такой же простой, как движение рукой по поверхности, устраняет шероховатость деревянных панелей, прежде чем они наконец будут проданы в виде полок, столов и книжных шкафов.
Идеально подходит как для ремесленников, так и для промышленных столяров. Головка шлифовального станка с круглым диском перемещается по эллипсам по каждой поверхности, что обеспечивает гладкость, поскольку никогда не проходите одни и те же места дважды одним и тем же способом. При небольшом усилии руки для пневматической орбитальной шлифовальной машины требуется от 6 до 9кубических футов в минуту при 90 фунтов на квадратный дюйм.
Живопись.
Возможно, лучшим из всех пневматических инструментов является воздушная кисть, которая устраняет полосы, пятна и несоответствия, которые часто трудно предотвратить при покраске вручную. Как один из самых деликатных этапов на заключительных этапах сборки автомобиля, здания и мебели, поток краски должен быть свободен от грязи и влаги. Эти требования стали возможными благодаря пневматическому аэрографу, который позволяет наносить слои краски и глазури с идеальным качеством, которое никогда не было достигнуто с помощью валиков, кистей или аэрозольных баллончиков. Для некоторых из лучших цветов и покрытий аэрографу требуется от 3 до 11,3 кубических футов в минуту при 90 фунтов на квадратный дюйм.
Храповой механизм.
Затянутый болт может быть упрямым зверем, особенно если он был на месте с того дня, как рассматриваемые детали только что сошли с конвейера. Торцевой ключ (или трещотка) с короткой рукояткой и боковым домкратом позволяет смещать болты в тесных узких местах, до которых было бы трудно добраться с помощью более крупного перпендикулярного инструмента.
Например, если у вас возникли проблемы с автомобилем, пневматический храповик позволяет легко снять и заменить проблемные детали под капотом без необходимости отвозить автомобиль в сервис. При всех деньгах, которые домашние механики экономят с помощью этого удобного инструмента, требования к размеру 9Ударный гайковерт на 0 фунтов на кв. дюйм:
Клепка.
Некоторые считают, что с появлением сварки заклепки уступили место дронтам, однако постоянная застежка до сих пор используется во множестве промышленных применений. Например, заклепки предпочтительны в конструкциях, где крепление должно быть максимально прочным, но вес должен быть минимальным, например, в самолетах. Гидравлический заклепочник также можно использовать в домашнем строительстве, например, при креплении кровли из гофрированного металла. Гидравлический заклепочник, как один из наименее энергозатратных пневматических инструментов, требует 4 кубических фута в минуту при 90 фунтов на квадратный дюйм.
Пиление.
В некоторых металлических проектах все, что необходимо, — это чистый, простой срез или угловой срез, без металлических полосок конфетти, которые выпадают на обочину во время применения воздушной резки. Современные пневматические пилы производят в среднем 9000 ударов в минуту, что обеспечивает скорость и точность при резке слоев листового металла 16-го калибра, а также пластин и полос из алюминия, меди и пластика. От садовых украшений до искусства труб, пневматическая скоростная пила может служить жизненно важным инструментом в строительстве различных форм изделий из меди и металла, не говоря уже об автомобильном и промышленном применении. Для работы с оптимальной производительностью воздушной пиле требуется 5 кубических футов в минуту при 90 фунтов на квадратный дюйм.
Стрижка.
Когда дело доходит до тяжелой резки металла, вам понадобится нечто большее, чем просто высечные ножницы. С помощью пневматических ножниц вы можете нарезать, обрезать и обрезать листовые металлы для промышленных и ремесленных проектов. Сегодняшние версии пневматического инструмента, оснащенные ножницами с пистолетной рукояткой, могут выполнять примерно 2600 разрезов в минуту. Независимо от того, работаете ли вы с металлической мебелью или приспособлениями, стандартные пневматические ножницы могут разрезать холоднокатаную сталь толщиной до 20, а также листовой металл 16 и алюминий 14. Идеальный инструмент для металлообрабатывающих мастерских любой производительности, для пневматических ножниц требуется от 8 до 16 куб.0 фунтов на квадратный дюйм.
Отвинчивание.
Когда винт или болт кажется приваренным, истина где-то посередине. В то время как время и элементы могут сделать затянутый болт невозможным для откручивания вручную даже самым сильным человеком, ударный гайковерт выполнит эту работу за считанные секунды. Если в задней части вашего грузовика есть сцепное устройство для лодки или прицепа, которое вы больше не используете, это сцепное устройство можно легко открутить — независимо от того, сколько дождя и суровых температур оно выдержало — с помощью 1,5-дюймового ударного гайковерта.
Ударный гайковерт также можно использовать для установки или снятия колпаков, а также для сборки и разборки ограждений, настилов и наружных конструкций. Лучше всего то, что ударный гайковерт практически не требует усилия или напряжения со стороны пользователя, независимо от того, используется ли он для работы в обратном или прямом направлении. В зависимости от размера сопла требования к ударному гайковерту на 90 фунтов на кв. дюйм следующие:
Как рассчитать компрессор CFM
Ваши пневматические инструменты и воздушный компрессор рассчитаны на куб. футов в минуту. Этот рейтинг указывает объем воздуха, требуемый пневматическим инструментом или производимый компрессором при заданном уровне давления. Знание того, сколько фунтов на квадратный дюйм вам нужно для применения воздушного компрессора, поможет определить, сколько кубических футов в минуту требуется компрессору для эффективной работы ваших пневматических инструментов.
Требования к куб. футам в минуту вашего инструмента могут дать представление о том, сколько кубических футов в минуту требуется от вашего воздушного компрессора, но вам также необходимо учитывать уровни давления, необходимые для конкретной функции, которую будет выполнять этот инструмент. Простого сопоставления рейтинга вашего пневматического инструмента с рейтингом компрессора не всегда будет достаточно. Вот тут-то и пригодится это руководство и наша удобная диаграмма кубических футов в минуту для воздушных компрессоров.
Количество кубических футов в минуту, необходимое вашему воздушному компрессору, определяется несколькими факторами: типом и количеством инструментов, которые вам нужны для питания, а также тем, требуются ли ваши инструменты для непрерывного или периодического использования.
Тип инструментов
Учитывайте требования к куб. футам в минуту вашего конкретного пневматического инструмента или инструментов. Руководство производителя должно указывать эту информацию в инструкции к инструменту. Если вы используете один пневматический инструмент, будь то дрель на 1/2 дюйма или 90-фунтовый отбойный молоток, минимальная мощность вашего воздушного компрессора должна быть максимальной, указанной для этого инструмента.
Очень важно учитывать рабочий цикл при определении требований вашего воздушного компрессора к куб. футам в минуту. В этом случае рабочий цикл относится к проценту времени, в течение которого воздушный компрессор может работать, прежде чем потребуется перерыв, чтобы наверстать упущенное или остыть. Средний рейтинг кубических футов в минуту для пневматических инструментов обычно основан на рабочем цикле 25%. Из-за этого часто рекомендуется, чтобы рейтинг вашего компрессора в кубических футах в минуту был в 1,5 раза больше, чем у вашего пневматического инструмента. Эта регулировка предотвратит перегрузку вашего воздушного компрессора.
Если ваша команда должна использовать инструменты в течение длительного периода времени, учитывайте требования вашего компрессора в кубических футах в минуту при 100% рабочем цикле. Могут потребоваться дополнительные расчеты, поэтому очень важно оценить, какие инструменты вы используете и как вы их используете.
Количество инструментов
Использование нескольких инструментов одновременно повлияет на требования вашего компрессора в кубических футах в минуту. Такая ситуация распространена на фабриках и в мастерских, где два или более человека работают на одной работе или работах в тесной последовательности. Возможность запуска нескольких инструментов может значительно повысить эффективность вашей команды, поэтому очень важно предусмотреть эту возможность.
Если вы используете несколько инструментов от одного и того же воздушного компрессора, вам необходимо добавить индивидуальные рейтинги в кубических футах в минуту для каждого инструмента, чтобы определить общую потребность вашего компрессора в кубических футах в минуту. Например, команда, которая одновременно использует 2-дюймовую шлифовальную машину, для которой требуется 30 кубических футов в минуту, и 1-дюймовый ударный гайковерт, для которого требуется 60 кубических футов в минуту, будет иметь общую потребность в 90 кубических футов в минуту. Это означает, что у рабочих должен быть воздушный компрессор, который надежно производит 90 кубических футов воздуха в минуту для питания обоих устройств.
В этом примере характеристики пневматических инструментов в кубических футах в минуту уже рассчитаны для 100% рабочего цикла. Важно учитывать, будут ли ваши инструменты использоваться постоянно или с перерывами, особенно при одновременном использовании нескольких устройств. Если вы стремитесь к непрерывной работе более чем одного инструмента, вам может потребоваться умножить общее количество кубических футов в минуту на 4, если отдельные инструменты рассчитаны только на рабочий цикл 25%. При непрерывном использовании нескольких инструментов может потребоваться значительный объем воздуха.
Непрерывное и периодическое использование
Важно то, как вы используете свои инструменты. При определении потребностей вашего воздушного компрессора в кубических футах в минуту важно изучить, как вы и ваша команда работаете ежедневно. Вы работаете быстрыми очередями с короткими перерывами или должны использовать свои инструменты в течение длительного времени? Есть ли у воздушного компрессора достаточно времени между периодами использования, чтобы наверстать упущенное и охладиться?
Задав себе эти или подобные вопросы, вы убедитесь, что используете свои инструменты с учетом их предполагаемого использования. Если ваше приложение требует, чтобы вы использовали пневматические инструменты в течение длительного периода, вы должны рассчитать требования вашего воздушного компрессора в кубических футах в минуту для 100% рабочего цикла. Напротив, обычные пневматические инструменты, используемые для прерывистых импульсов, могут обойтись менее мощным, но более экономичным компрессором.
Воздушный компрессор Таблица CFM
Посмотрите, сколько кубических футов в минуту вам потребуется для работы с некоторыми из наиболее распространенных инструментов с максимальной производительностью. Эта диаграмма кубических футов в минуту для воздушного компрессора показывает давление воздуха, необходимое для конкретных применений.
Правильное давление воздуха для каждого применения
От шлифования, долбления и сверления до шлифования, покраски и смазывания крайне важно иметь воздушный компрессор, который может обеспечить нужное давление воздуха для каждого применения. Независимо от того, управляете ли вы автомастерской или мастерской по металлообработке, или просто выполняете работы по металлу или дереву в своем домашнем гараже, Quincy Compressor поставляет множество машин, которые соответствуют необходимым спецификациям для широкого спектра пневматических инструментов.
С 1920 года Quincy находится в авангарде всех последних инноваций в технологии воздушных компрессоров. В Соединенных Штатах и за рубежом наши машины и инструменты используются на фабриках, сборочных предприятиях, ремонтных мастерских и в частных мастерских. Воздушные компрессоры Quincy позволяют механикам, техникам и ремесленникам получать оптимальные результаты при работе на больших и малых предприятиях, используя правильное давление для каждого применения.
Компрессоры Quincy сэкономили деньги и время, сняв нагрузку и обеспечив оптимальные результаты для компаний, рабочих групп и частных пользователей, и наши продукты могут сделать то же самое для вас. Если ваш арсенал оборудования не дал вам блестящих результатов, и вам нужна система, которая обеспечивает сжатый воздух без влаги для различных инструментов, посетите страницу продуктов Quincy, чтобы узнать больше о наших предложениях. Затем свяжитесь с нашими торговыми представителями , которые помогут вам получить воздушный компрессор, который позволит вам легко выполнять необходимые задачи.