Π’ΠΎΡΠΌΠΎΠ·Π½Π°Ρ ΡΠΈΡΡΠ΅ΠΌΠ° ΡΠΏΠ΅ΡΡΠ΅Ρ Π½ΠΈΠΊΠΈ: Π½Π°Π·Π½Π°ΡΠ΅Π½ΠΈΠ΅, Π½Π΅ΠΏΠΎΠ»Π°Π΄ΠΊΠΈ, ΡΠ΅ΠΌΠΎΠ½Ρ
Π’ΠΎΡΠΌΠΎΠ·Π½Π°Ρ ΡΠΈΡΡΠ΅ΠΌΠ° ΡΠΏΠ΅ΡΡΠ΅Ρ Π½ΠΈΠΊΠΈ ΠΎΡΠ²Π΅ΡΠ°Π΅Ρ Π·Π° ΠΏΡΠ΅Π΄ΡΠΊΠ°Π·ΡΠ΅ΠΌΡΠΉ, ΡΡΠ°Π±ΠΈΠ»ΡΠ½ΡΠΉ ΡΠΎΡΠΌΠΎΠ·Π½ΠΎΠΉ ΠΏΡΡΡ, ΡΡΠΎ ΡΠ²Π»ΡΠ΅ΡΡΡ Π·Π°Π»ΠΎΠ³ΠΎΠΌ Π±Π΅Π·ΠΎΠΏΠ°ΡΠ½ΠΎΡΡΠΈ Π΄Π»Ρ Π»ΡΠ΄Π΅ΠΉ ΠΈ ΡΠΎΡ ΡΠ°Π½Π½ΠΎΡΡΠΈ ΡΠ°ΠΌΠΎΠ³ΠΎ ΠΎΠ±ΠΎΡΡΠ΄ΠΎΠ²Π°Π½ΠΈΡ.
ΠΠΎΡΠΎΠΆΠ½ΠΎ-ΡΡΡΠΎΠΈΡΠ΅Π»ΡΠ½Π°Ρ ΡΠ΅Ρ Π½ΠΈΠΊΠ°, ΠΊΠ°ΠΊ ΠΈ ΠΊΠ°ΠΆΠ΄ΠΎΠ΅ ΡΡΠ°Π½ΡΠΏΠΎΡΡΠ½ΠΎΠ΅ ΡΡΠ΅Π΄ΡΡΠ²ΠΎ, Π΄ΠΎΠ»ΠΆΠ½Π° ΠΈΠΌΠ΅ΡΡ Π² Π½Π°Π»ΠΈΡΠΈΠΈ ΡΠ°Π±ΠΎΡΡΡ, Π·Π°ΠΏΠ°ΡΠ½ΡΡ ΠΈ ΡΡΠΎΡΠ½ΠΎΡΠ½ΡΡ ΡΠΎΡΠΌΠΎΠ·Π½ΡΠ΅ ΡΠΈΡΡΠ΅ΠΌΡ.
Π Π°Π±ΠΎΡΠ°Ρ ΡΠΎΡΠΌΠΎΠ·Π½Π°Ρ ΡΠΈΡΡΠ΅ΠΌΠ° ΠΏΡΠΈΠ·Π²Π°Π½Π° ΠΎΠ±Π΅ΡΠΏΠ΅ΡΠΈΠ²Π°ΡΡ Π² ΠΏΡΠΎΡΠ΅ΡΡΠ΅ Π΄Π²ΠΈΠΆΠ΅Π½ΠΈΡ Π½Π΅ΠΎΠ±Ρ ΠΎΠ΄ΠΈΠΌΠΎΠ΅ ΡΠ½ΠΈΠΆΠ΅Π½ΠΈΠ΅ ΡΠΊΠΎΡΠΎΡΡΠΈ ΠΈ ΠΎΡΡΠ°Π½ΠΎΠ²ΠΊΡ ΡΡΠ°Π½ΡΠΏΠΎΡΡΠ°. ΠΡΠ΅Π΄Π½Π°Π·Π½Π°ΡΠ΅Π½ΠΈΠ΅ Π·Π°ΠΏΠ°ΡΠ½ΠΎΠΉ ΡΠΎΡΠΌΠΎΠ·Π½ΠΎΠΉ ΡΠΈΡΡΠ΅ΠΌΡ β ΠΎΡΡΠ°Π½ΠΎΠ²ΠΊΠ° ΠΌΠ°ΡΠΈΠ½Ρ ΠΏΡΠΈ Π²ΡΡ ΠΎΠ΄Π΅ ΠΈΠ· ΡΡΡΠΎΡ ΡΠ°Π±ΠΎΡΠ΅ΠΉ ΡΠΎΡΠΌΠΎΠ·Π½ΠΎΠΉ ΡΠΈΡΡΠ΅ΠΌΡ. Π‘ΡΠΎΡΠ½ΠΎΡΠ½Π°Ρ ΡΠΎΡΠΌΠΎΠ·Π½Π°Ρ ΡΠΈΡΡΠ΅ΠΌΠ° ΠΏΠΎΠ·Π²ΠΎΠ»ΡΠ΅Ρ ΡΠ΄Π΅ΡΠΆΠΈΠ²Π°ΡΡ Π³ΡΡΠΆΠ΅Π½ΡΠ΅ Π°Π²ΡΠΎΠΌΠΎΠ±ΠΈΠ»ΠΈ ΠΈΠ»ΠΈ ΡΠ΅Ρ Π½ΠΈΠΊΡ, ΠΏΡΠ΅Π²ΡΡΠ°ΡΡΡΡ ΠΎΠΏΡΠ΅Π΄Π΅Π»Π΅Π½Π½ΡΠΉ Π²Π΅Ρ, Π½Π° ΡΠΏΡΡΠΊΠ΅ ΠΈΠ»ΠΈ ΠΏΠΎΠ΄ΡΠ΅ΠΌΠ΅, Π²Π½Π΅ Π·Π°Π²ΠΈΡΠΈΠΌΠΎΡΡΠΈ ΠΎΡ Π΄Π»ΠΈΡΠ΅Π»ΡΠ½ΠΎΡΡΠΈ ΠΎΡΡΠ°Π½ΠΎΠ²ΠΊΠΈ. ΠΠ± ΡΡΡΠ΅ΠΊΡΠΈΠ²Π½ΠΎΡΡΠΈ ΡΠ°Π±ΠΎΡΡ ΡΠΎΡΠΌΠΎΠ·Π½ΠΎΠΉ ΡΠΈΡΡΠ΅ΠΌΡ ΡΠ²ΠΈΠ΄Π΅ΡΠ΅Π»ΡΡΡΠ²ΡΠ΅Ρ ΡΠΎΡΠΌΠΎΠ·Π½ΠΎΠΉ ΠΏΡΡΡ.
Π’ΠΎΡΠΌΠΎΠ·Π½Π°Ρ ΡΠΈΡΡΠ΅ΠΌΠ° ΡΠΏΠ΅ΡΡΠ΅Ρ Π½ΠΈΠΊΠΈ ΡΠΎΡΡΠΎΠΈΡ ΠΈΠ· ΡΠ»Π΅Π΄ΡΡΡΠΈΡ ΡΠ»Π΅ΠΌΠ΅Π½ΡΠΎΠ²: ΡΠ°ΡΡΠΈΡΠΈΡΠ΅Π»ΡΠ½ΠΎΠΉ ΠΊΠ°ΠΌΠ΅ΡΡ, ΡΠΎΡΠΌΠΎΠ·Π½ΡΡ ΠΊΠΎΠ»ΠΎΠ΄ΠΎΠΊ, Π±Π°ΡΠ°Π±Π°Π½ΠΎΠ², ΡΡΠΏΠΏΠΎΡΡΠΎΠ², Π΄ΠΈΡΠΊΠΎΠ², Π½Π°ΡΠΎΡΠΎΠ² ΠΈ Π΄ΡΡΠ³ΠΈΡ Π΄Π΅ΡΠ°Π»Π΅ΠΉ.
ΠΠΈΠ°Π³Π½ΠΎΡΡΠΈΠΊΠ° ΡΠΎΡΠΌΠΎΠ·Π½ΠΎΠΉ ΡΠΈΡΡΠ΅ΠΌΡ β ΠΎΠ±ΡΠ·Π°ΡΠ΅Π»ΡΠ½ΡΠΉ ΠΏΡΠ½ΠΊΡ ΠΏΠ»Π°Π½ΠΎΠ²ΠΎΠ³ΠΎ ΡΠ΅Ρ Π½ΠΈΡΠ΅ΡΠΊΠΎΠ³ΠΎ ΠΎΠ±ΡΠ»ΡΠΆΠΈΠ²Π°Π½ΠΈΡ ΡΠΏΠ΅ΡΡΠ΅Ρ Π½ΠΈΠΊΠΈ. Π’ΠΎΡΠΌΠΎΠ·Π½Π°Ρ ΡΠΈΡΡΠ΅ΠΌΠ° Π΄ΠΎΠ»ΠΆΠ½Π° ΠΏΡΠΎΠ²Π΅ΡΡΡΡΡΡ ΡΡΡΠΎΠ³ΠΎ Π² ΡΠΎΠΎΡΠ²Π΅ΡΡΡΠ²ΠΈΠΈ Ρ ΡΠ΅Π³Π»Π°ΠΌΠ΅Π½ΡΠΎΠΌ, ΠΊΠΎΡΠΎΡΡΠΉ ΡΡΡΠ°Π½ΠΎΠ²Π»Π΅Π½ Π·Π°Π²ΠΎΠ΄ΠΎΠΌ ΠΈΠ·Π³ΠΎΡΠΎΠ²ΠΈΡΠ΅Π»Π΅ΠΌ. Π Π΅ΠΊΠΎΠΌΠ΅Π½Π΄ΡΠ΅ΡΡΡ ΠΏΡΠΎΠΈΠ·Π²ΠΎΠ΄ΠΈΡΡ ΠΏΡΠΎΠ²Π΅ΡΠΊΡ ΠΏΡΠΈ ΠΊΠ°ΠΆΠ΄ΠΎΠΌ Π’Π, Π½ΠΎ ΠΌΠΈΠ½ΠΈΠΌΡΠΌ ΡΠ°Π· Π² Π³ΠΎΠ΄.
ΠΠΎΠ·ΠΌΠΎΠΆΠ½ΡΠ΅ Π½Π΅ΠΈΡΠΏΡΠ°Π²Π½ΠΎΡΡΠΈ ΡΠΎΡΠΌΠΎΠ·Π½ΠΎΠΉ ΡΠΈΡΡΠ΅ΠΌΡ:
- Π‘ΠΊΡΠ΅ΠΆΠ΅Ρ, ΡΠΊΡΠΈΠΏ, ΠΏΠΎΡΡΠΎΡΠΎΠ½Π½ΠΈΠ΅ Π·Π²ΡΠΊΠΈ Π² ΠΌΠΎΠΌΠ΅Π½Ρ ΡΠΎΡΠΌΠΎΠΆΠ΅Π½ΠΈΡ;
- ΠΡΠΎΠ²Π°Π»ΠΈΠ²Π°Π½ΠΈΠ΅, Π·Π°Π΅Π΄Π°Π½ΠΈΠ΅, Π²ΠΈΠ±ΡΠ°ΡΠΈΡ, Π±ΠΎΠ»ΡΡΠΎΠΉ ΡΠ²ΠΎΠ±ΠΎΠ΄Π½ΡΠΉ Ρ ΠΎΠ΄ ΠΏΠ΅Π΄Π°Π»ΠΈ ΡΠΎΡΠΌΠΎΠ·Π°;
- Π£Π²Π΅Π»ΠΈΡΠ΅Π½ΠΈΠ΅ Π΄Π»ΠΈΠ½Ρ ΡΠΎΡΠΌΠΎΠ·Π½ΠΎΠ³ΠΎ ΠΏΡΡΠΈ;
- ΠΠ°Π³ΡΠ΅Π² Π±Π°ΡΠ°Π±Π°Π½ΠΎΠ² ΠΈ ΡΠΎΡΠΌΠΎΠ·Π½ΡΡ Π΄ΠΈΡΠΊΠΎΠ²;
- ΠΠ΅ΡΠ°Π²Π½ΠΎΠΌΠ΅ΡΠ½ΡΠΉ ΠΈΠ·Π½ΠΎΡ ΠΊΠΎΠ»ΠΎΠ΄ΠΎΠΊ;
- Π‘ΠΊΠ»ΠΎΠ½Π½ΠΎΡΡΡ ΠΌΠ°ΡΠΈΠ½Ρ ΠΊ Π·Π°Π½ΠΎΡΡ;
- ΠΠΈΠΊΡΠΎΡΡΠ΅ΡΠΈΠ½Ρ Π½Π° ΡΠ»Π°Π½Π³Π°Ρ Π²ΡΡΠΎΠΊΠΎΠ³ΠΎ Π΄Π°Π²Π»Π΅Π½ΠΈΡ;
- Π£ΡΠ΅ΡΠΊΠ° ΡΠΎΡΠΌΠΎΠ·Π½ΠΎΠΉ ΠΆΠΈΠ΄ΠΊΠΎΡΡΠΈ;
- Π£Π²ΠΎΠ΄ ΡΠ΅Ρ Π½ΠΈΠΊΠΈ ΠΏΡΠΈ ΡΠΎΡΠΌΠΎΠΆΠ΅Π½ΠΈΠΈ Π² ΡΡΠΎΡΠΎΠ½Ρ ΠΎΡ ΠΏΡΡΠΌΠΎΠ»ΠΈΠ½Π΅ΠΉΠ½ΠΎΠ³ΠΎ Π΄Π²ΠΈΠΆΠ΅Π½ΠΈΡ.
ΠΡΠΈΡΠΈΠ½Ρ Π½Π΅ΠΏΠΎΠ»Π°Π΄ΠΎΠΊ Π² ΡΠ°Π±ΠΎΡΠ΅ ΡΠΎΡΠΌΠΎΠ·Π½ΠΎΠΉ ΡΠΈΡΡΠ΅ΠΌΡ
ΠΡΡΠ΅ΠΊΡΠΈΠ²Π½Π°Ρ ΡΠ°Π±ΠΎΡΠ° ΡΠΎΡΠΌΠΎΠ·Π½ΠΎΠΉ ΡΠΈΡΡΠ΅ΠΌΡ ΠΌΠΎΠΆΠ΅Ρ Π½Π°ΡΡΡΠ°ΡΡΡΡ ΠΈΠ·-Π·Π° Π½Π΅ΠΈΡΠΏΡΠ°Π²Π½ΠΎΡΡΠΈ ΠΈΠ»ΠΈ ΠΈΠ·Π½ΠΎΡΠ° ΡΠΎΡΠΌΠΎΠ·Π½ΡΡ ΠΊΠΎΠ»ΠΎΠ΄ΠΎΠΊ ΠΈΠ»ΠΈ ΡΠΈΠ»ΠΈΠ½Π΄ΡΠΎΠ², Π·Π°Π³ΡΡΠ·Π½Π΅Π½ΠΈΡ ΠΌΠ΅Ρ Π°Π½ΠΈΠ·ΠΌΠΎΠ² ΡΠΎΡΠΌΠΎΠ·Π½ΠΎΠΉ ΡΠΈΡΡΠ΅ΠΌΡ, Π½Π°ΡΡΡΠ΅Π½ΠΈΡ ΡΠ΅Π³ΡΠ»ΠΈΡΠΎΠ²ΠΊΠΈ ΡΠΎΡΠΌΠΎΠ·ΠΎΠ², ΠΏΡΠΎΡΠ΅ΠΊΠ°Π½ΠΈΡ ΡΠΎΡΠΌΠΎΠ·Π½ΠΎΠΉ ΠΆΠΈΠ΄ΠΊΠΎΡΡΠΈ, ΠΈΠ·Π½ΠΎΡΠ° ΠΊΠΎΠ»ΠΎΠ΄ΠΎΠΊ ΠΈΠ»ΠΈ Π΄ΠΈΡΠΊΠΎΠ² ΠΈ ΡΡΠ΄Π° Π΄ΡΡΠ³ΠΈΡ ΠΏΡΠΈΡΠΈΠ½.
Π ΠΏΡΠΎΡΠ΅ΡΡΠ΅ ΡΠ΅ΠΌΠΎΠ½ΡΠ° ΡΠΎΡΠΌΠΎΠ·Π½ΠΎΠΉ ΡΠΈΡΡΠ΅ΠΌΡ ΠΌΠΎΠΆΠ΅Ρ ΠΎΡΡΡΠ΅ΡΡΠ²Π»ΡΡΡΡΡ Π·Π°ΠΌΠ΅Π½Π°:
- Π’ΠΎΡΠΌΠΎΠ·Π½ΡΡ ΠΊΠΎΠ»ΠΎΠ΄ΠΎΠΊ;
- Π’ΠΎΡΠΌΠΎΠ·Π½ΠΎΠ³ΠΎ Π±Π°ΡΠ°Π±Π°Π½Π°;
- ΠΠΎΠ»Π΅ΡΠ½ΡΡ ΡΠΎΡΠΌΠΎΠ·Π½ΡΡ ΡΠΈΠ»ΠΈΠ½Π΄ΡΠΎΠ²;
- ΠΠ΅Ρ Π°Π½ΠΈΠ·ΠΌΠ° Π°Π²ΡΠΎΠΌΠ°ΡΠΈΡΠ΅ΡΠΊΠΎΠΉ ΠΏΠΎΠ΄Π²ΠΎΠ΄ΠΊΠΈ ΡΠΎΡΠΌΠΎΠ·Π½ΡΡ ΠΊΠΎΠ»ΠΎΠ΄ΠΎΠΊ;
- ΠΠΏΠΎΡΠ½ΠΎΠ³ΠΎ Π΄ΠΈΡΠΊΠ° ΡΠΎΡΠΌΠΎΠ·Π½ΠΎΠΉ ΡΠΈΡΡΠ΅ΠΌΡ;
- Π‘ΡΡΠ³ΠΈΠ²Π°ΡΡΠΈΡ ΠΏΡΡΠΆΠΈΠ½.
ΠΠ°ΠΌΠ΅Π½Π° ΡΠ»Π΅ΠΌΠ΅Π½ΡΠΎΠ² ΡΠΎΡΠΌΠΎΠ·Π½ΠΎΠΉ ΡΠΈΡΡΠ΅ΠΌΡ ΡΠ΅ΡΡΠΈΡΠΈΡΠΈΡΠΎΠ²Π°Π½Π½ΡΠΌΠΈ Π½Π΅ΠΎΡΠΈΠ³ΠΈΠ½Π°Π»ΡΠ½ΡΠΌΠΈ Π΄Π΅ΡΠ°Π»ΡΠΌΠΈ ΠΊΠΎΠΌΠΏΠ°Π½ΠΈΠΈ Blumaq ΠΏΠΎΠ·Π²ΠΎΠ»ΠΈΡ Π² ΠΊΡΠ°ΡΡΠ°ΠΉΡΠΈΠ΅ ΡΡΠΎΠΊΠΈ ΠΈ ΠΏΠΎ Π΄ΠΎΡΡΡΠΏΠ½ΠΎΠΉ ΡΠ΅Π½Π΅ Π²Π΅ΡΠ½ΡΡΡ ΡΠ΅Ρ Π½ΠΈΠΊΡ Π² ΠΈΡΠΏΡΠ°Π²Π½ΠΎΠ΅ ΡΠΎΡΡΠΎΡΠ½ΠΈΠ΅, ΠΎΠ±Π΅ΡΠΏΠ΅ΡΠΈΠ² Π΅Π΅ ΡΡΡΠ΅ΠΊΡΠΈΠ²Π½ΡΡ ΠΈ Π±Π΅Π·ΠΎΠΏΠ°ΡΠ½ΡΡ ΡΠ°Π±ΠΎΡΡ.
blumaq.ru
Π Π΅ΠΌΠΎΠ½Ρ ΡΠΎΡΠΌΠΎΠ·Π½ΠΎΠΉ ΡΠΈΡΡΠ΅ΠΌΡ ΡΠΏΠ΅ΡΡΠ΅Ρ Π½ΠΈΠΊΠΈ
ΠΠΈΠ°Π³Π½ΠΎΡΡΠΈΠΊΠ° ΠΈ ΡΠ΅ΠΌΠΎΠ½Ρ ΡΠΎΡΠΌΠΎΠ·Π½ΠΎΠΉ ΡΠΈΡΡΠ΅ΠΌΡ ΡΠΊΡΠΊΠ°Π²Π°ΡΠΎΡΠ°-ΠΏΠΎΠ³ΡΡΠ·ΡΠΈΠΊΠ°, ΡΡΠΎΠ½ΡΠ°Π»ΡΠ½ΠΎΠ³ΠΎ ΠΏΠΎΠ³ΡΡΠ·ΡΠΈΠΊΠ°, ΡΠΊΡΠΊΠ°Π²Π°ΡΠΎΡΠ°, Π²ΠΈΠ»ΠΎΡΠ½ΠΎΠ³ΠΎ ΠΏΠΎΠ³ΡΡΠ·ΡΠΈΠΊΠ°, ΡΠ΅Π»Π΅ΡΠΊΠΎΠΏΠΈΡΠ΅ΡΠΊΠΎΠ³ΠΎ ΠΏΠΎΠ³ΡΡΠ·ΡΠΈΠΊΠ° ΠΈ Π΄ΡΡΠ³ΠΎΠΉ ΡΠΏΠ΅ΡΠΈΠ°Π»ΠΈΠ·ΠΈΡΠΎΠ²Π°Π½Π½ΠΎΠΉ ΡΠ΅Ρ Π½ΠΈΠΊΠΈ Π² Π‘Π°Π½ΠΊΡ-ΠΠ΅ΡΠ΅ΡΠ±ΡΡΠ³Π΅
Π’ΠΎΡΠΌΠΎΠ·Π½Π°Ρ ΡΠΈΡΡΠ΅ΠΌΠ° Π»ΡΠ±ΠΎΠ³ΠΎ ΡΡΠ°Π½ΡΠΏΠΎΡΡΠ½ΠΎΠ³ΠΎ ΡΡΠ΅Π΄ΡΡΠ²Π°, Π² ΡΠΎΠΌ ΡΠΈΡΠ»Π΅ ΠΈ ΡΠΏΠ΅ΡΠΈΠ°Π»ΠΈΠ·ΠΈΡΠΎΠ²Π°Π½Π½ΠΎΠΉ ΡΠ΅Ρ Π½ΠΈΠΊΠΈ, Π΄ΠΎΠ»ΠΆΠ½Π° ΠΎΠ±Π΅ΡΠΏΠ΅ΡΠΈΠ²Π°ΡΡ ΡΡΠ°Π±ΠΈΠ»ΡΠ½ΠΎΠ΅ ΠΈ ΠΏΡΠ΅Π΄ΡΠΊΠ°Π·ΡΠ΅ΠΌΠΎΠ΅ ΡΠΎΡΠΌΠΎΠΆΠ΅Π½ΠΈΠ΅, ΠΊΠ°ΠΊ Π²ΠΎ Π²ΡΠ΅ΠΌΡ Π΄Π²ΠΈΠΆΠ΅Π½ΠΈΡ, ΡΠ°ΠΊ ΠΈ Π²ΠΎ Π²ΡΠ΅ΠΌΡ Π΄Π»ΠΈΡΠ΅Π»ΡΠ½ΠΎΠΉ ΡΡΠΎΡΠ½ΠΊΠ΅ Π±Π΅Π· Π΄Π²ΠΈΠΆΠ΅Π½ΠΈΡ.
ΠΠ΅ Π·ΡΡ, Π² ΠΏΡΠ½ΠΊΡΠ΅ 2.3.1. ΠΠΠ ΠΏΠ΅ΡΠ²ΠΎΠΉ Π½Π΅ΠΈΡΠΏΡΠ°Π²Π½ΠΎΡΡΡΡ, ΠΏΡΠΈ ΠΊΠΎΡΠΎΡΠΎΠΉ Π·Π°ΠΏΡΠ΅ΡΠ°Π΅ΡΡΡ Π΄Π²ΠΈΠΆΠ΅Π½ΠΈΠ΅ ΡΡΠ°Π½ΡΠΏΠΎΡΡΠ½ΠΎΠ³ΠΎ ΡΡΠ΅Π΄ΡΡΠ²Π° ΡΠ²Π»ΡΠ΅ΡΡΡ Π½Π΅ΠΈΡΠΏΡΠ°Π²Π½ΠΎΡΡΡ ΡΠ°Π±ΠΎΡΠ΅ΠΉ ΡΠΎΡΠΌΠΎΠ·Π½ΠΎΠΉ ΡΠΈΡΡΠ΅ΠΌΡ.
ΠΠΎΠΌΠ½ΠΈΡΠ΅ ΠΎ ΡΠΎΠΌ, ΡΡΠΎ ΠΈΡΠΏΡΠ°Π²Π½Π°Ρ ΡΠΎΡΠΌΠΎΠ·Π½Π°Ρ ΡΠΈΡΡΠ΅ΠΌΠ° β ΡΡΠΎ Π½Π΅ ΡΠΎΠ»ΡΠΊΠΎ Π·Π°Π»ΠΎΠ³ Π±Π΅Π·ΠΎΠΏΠ°ΡΠ½ΠΎΡΡΠΈ Π΄Π»Ρ ΠΎΠΏΠ΅ΡΠ°ΡΠΎΡΠ°, ΠΎΠ±ΡΠ»ΡΠΆΠΈΠ²Π°ΡΡΠ΅Π³ΠΎ ΠΏΠ΅ΡΡΠΎΠ½Π°Π»Π°, ΡΡΠ°ΡΡΠ½ΠΈΠΊΠΎΠ² Π΄ΠΎΡΠΎΠΆΠ½ΠΎΠ³ΠΎ Π΄Π²ΠΈΠΆΠ΅Π½ΠΈΡ, ΡΡΡΠΎΠΈΡΠ΅Π»ΡΠ½ΡΡ ΡΠ°Π±ΠΎΡΠ½ΠΈΠΊΠΎΠ² ΠΈ Π΄ΡΡΠ³ΠΈΡ Π»ΡΠ΄Π΅ΠΉ Π½Π°Ρ ΠΎΠ΄ΡΡΠΈΡ ΡΡ Π² Π½Π΅ΠΏΠΎΡΡΠ΅Π΄ΡΡΠ²Π΅Π½Π½ΠΎΠΉ Π±Π»ΠΈΠ·ΠΎΡΡΠΈ ΠΎΡ ΠΌΠ°ΡΠΈΠ½Ρ, Π½ΠΎ ΠΈ Π³Π°ΡΠ°Π½Ρ ΡΠΎΡ ΡΠ°Π½Π½ΠΎΡΡΠΈ ΡΠ°ΠΌΠΎΠ³ΠΎ ΡΠ°Π±ΠΎΡΠ΅Π³ΠΎ ΠΎΠ±ΠΎΡΡΠ΄ΠΎΠ²Π°Π½ΠΈΡ.
Π’ΠΠΠΠΠ«Π Π‘ΠΠΠΠ’ΠΠΠ« ΠΠΠΠ‘ΠΠ ΠΠΠΠΠ‘Π’ΠΠ Π’ΠΠ ΠΠΠΠΠΠ Π‘ΠΠ‘Π’ΠΠΠ« ΠΠ Π‘ΠΠΠ¦Π’ΠΠ₯ΠΠΠΠ:
ΠΠΎΠ½ΠΈΠΆΠ°Π΅ΡΡΡ ΡΡΠΎΠ²Π΅Π½Ρ ΡΠΎΡΠΌΠΎΠ·Π½ΠΎΠΉ ΠΆΠΈΠ΄ΠΊΠΎΡΡΠΈ Π² ΡΠ°ΡΡΠΈΡΠΈΡΠ΅Π»ΡΠ½ΠΎΠΌ Π±Π°ΡΠΊΠ΅.
ΠΠ΅Π΄Π°Π»Ρ ΡΠΎΡΠΌΠΎΠ·Π° ΠΏΡΠΎΠ²Π°Π»ΠΈΠ»Π°ΡΡ, Π΄ΡΡΠ³ΠΈΠΌΠΈ ΡΠ»ΠΎΠ²Π°ΠΌΠΈ Π½Π°Ρ ΠΎΠ΄ΠΈΡΡΡ ΡΠ»ΠΈΡΠΊΠΎΠΌ Β«Π½ΠΈΠ·ΠΊΠΎΒ».
ΠΠ΅Π΄Π°Π»Ρ ΡΠΎΡΠΌΠΎΠ·Π° ΡΡΠ°Π»Π° ΡΠ»ΠΈΡΠΊΠΎΠΌ Β«ΠΌΡΠ³ΠΊΠΎΠΉΒ».
ΠΠ΅Π΄Π°Π»Ρ ΡΠΎΡΠΌΠΎΠ·Π° ΡΡΠ°Π»Π° ΠΈΠΌΠ΅ΡΡ ΡΠ»ΠΈΡΠΊΠΎΠΌ Π±ΠΎΠ»ΡΡΠΎΠΉ Ρ ΠΎΠ΄.
ΠΡΡΠ΅ΠΊΡΠΈΠ²Π½ΠΎΡΡΡ ΡΠ°Π±ΠΎΡΠ΅ΠΉ ΡΠΎΡΠΌΠΎΠ·Π½ΠΎΠΉ ΡΠΈΡΡΠ΅ΠΌΡ Π·Π°ΠΌΠ΅ΡΠ½ΠΎ ΡΠ½ΠΈΠ·ΠΈΠ»Π°ΡΡ.
ΠΡΠΈΡΡΡΡΡΠ²ΡΠ΅Ρ Ρ Π°ΡΠ°ΠΊΡΠ΅ΡΠ½ΡΠΉ ΡΠΊΡΠ΅ΠΆΠ΅Ρ ΠΏΡΠΈ Π°ΠΊΡΠΈΠ²ΠΈΡΠΎΠ²Π°Π½ΠΈΠΈ ΡΠΎΡΠΌΠΎΠ·Π½ΠΎΠΉ ΡΠΈΡΡΠ΅ΠΌΡ.
ΠΡΠΈΡΡΡΡΡΠ²ΡΠ΅Ρ ΡΠ²Π½ΡΠΉ ΡΠ²ΠΈΡΡ ΠΈΠ»ΠΈ Π²ΠΈΠ·Π³ ΠΏΡΠΈ ΡΠΎΡΠΌΠΎΠΆΠ΅Π½ΠΈΠΈ.
ΠΠ΅ΡΠ°Π²Π½ΠΎΠΌΠ΅ΡΠ½ΠΎΠ΅ ΠΈ Π½Π΅Π΄ΠΎΡΡΠ°ΡΠΎΡΠ½ΠΎ ΡΡΡΠ΅ΠΊΡΠΈΠ²Π½ΠΎΠ΅ ΡΠΎΡΠΌΠΎΠΆΠ΅Π½ΠΈΠ΅.
Π’ΠΎΡΠΌΠΎΠΆΠ΅Π½ΠΈΠ΅ ΠΏΡΠΎΠΈΡΡ ΠΎΠ΄ΠΈΡ Ρ ΠΏΡΠ»ΡΡΠ°ΡΠΈΠ΅ΠΉ.
ΠΠ°ΡΠΈΠ½Ρ Β«ΡΠ²ΠΎΠ΄ΠΈΡΒ» Π² ΠΊΠ°ΠΊΡΡ-Π»ΠΈΠ±ΠΎ ΠΈΠ· ΡΡΠΎΡΠΎΠ½ ΠΏΡΠΈ Π²ΡΠΏΠΎΠ»Π½Π΅Π½ΠΈΠΈ ΡΠΎΡΠΌΠΎΠΆΠ΅Π½ΠΈΡ.
ΠΠ΅ Π΄Π΅ΡΠΆΠΈΡ ΡΡΠΎΡΠ½ΠΎΡΠ½ΡΠΉ ΡΠΎΡΠΌΠΎΠ·.
Π§ΡΠ΅Π·ΠΌΠ΅ΡΠ½ΡΠΉ Π½Π°Π³ΡΠ΅Π² Π±Π°ΡΠ°Π±Π°Π½ΠΎΠ² ΠΈ ΡΠΎΡΠΌΠΎΠ·Π½ΡΡ Π΄ΠΈΡΠΊΠΎΠ²
ΠΈ Ρ.Π΄.
ΠΡΠ»ΠΈ ΠΡ ΡΡΠΎΠ»ΠΊΠ½ΡΠ»ΠΈΡΡ Ρ ΠΎΠ΄Π½ΠΎΠΉ ΠΈΠ· Π²ΡΡΠ΅ ΠΏΠ΅ΡΠ΅ΡΠΈΡΠ»Π΅Π½Π½ΡΡ Π½Π΅ΠΈΡΠΏΡΠ°Π²Π½ΠΎΡΡΠ΅ΠΉ, Π½Π° ΡΠ²ΠΎΠ΅ΠΌ ΡΠΊΡΠΊΠ°Π²Π°ΡΠΎΡΠ΅-ΠΏΠΎΠ³ΡΡΠ·ΡΠΈΠΊΠ΅ (ΡΠ΅ΠΌΠΎΠ½Ρ Terex, ΡΠ΅ΠΌΠΎΠ½Ρ ΡΠΊΡΠΊΠ°Π²Π°ΡΠΎΡΠ°-ΠΏΠΎΠ³ΡΡΠ·ΡΠΈΠΊΠ° TEREX, ΡΠ΅ΠΌΠΎΠ½Ρ FERMEC, ΡΠ΅ΠΌΠΎΠ½Ρ ΡΠΊΡΠΊΠ°Π²Π°ΡΠΎΡΠ°-ΠΏΠΎΠ³ΡΡΠ·ΡΠΈΠΊΠ° FERMEC, ΡΠ΅ΠΌΠΎΠ½Ρ JCB, ΡΠ΅ΠΌΠΎΠ½Ρ ΡΠΊΡΠΊΠ°Π²Π°ΡΠΎΡΠ°-ΠΏΠΎΠ³ΡΡΠ·ΡΠΈΠΊΠ° JCB, ΡΠ΅ΠΌΠΎΠ½Ρ HIDROMEK, ΡΠ΅ΠΌΠΎΠ½Ρ ΡΠΊΡΠΊΠ°Π²Π°ΡΠΎΡΠ°-ΠΏΠΎΠ³ΡΡΠ·ΡΠΈΠΊΠ° HIDROMEK, ΡΠ΅ΠΌΠΎΠ½Ρ CASE, ΡΠ΅ΠΌΠΎΠ½Ρ ΡΠΊΡΠΊΠ°Π²Π°ΡΠΎΡΠ°-ΠΏΠΎΠ³ΡΡΠ·ΡΠΈΠΊΠ° CASE, ΡΠ΅ΠΌΠΎΠ½Ρ CATERPILLAR, ΡΠ΅ΠΌΠΎΠ½Ρ ΡΠΊΡΠΊΠ°Π²Π°ΡΠΎΡΠ°-ΠΏΠΎΠ³ΡΡΠ·ΡΠΈΠΊΠ° CATERPILLAR, ΡΠ΅ΠΌΠΎΠ½Ρ NEW HOLLAND, ΡΠ΅ΠΌΠΎΠ½Ρ ΡΠΊΡΠΊΠ°Π²Π°ΡΠΎΡΠ°-ΠΏΠΎΠ³ΡΡΠ·ΡΠΈΠΊΠ° NEW HOLLAND, ΡΠ΅ΠΌΠΎΠ½Ρ KOMATSU, ΡΠ΅ΠΌΠΎΠ½Ρ ΡΠΊΡΠΊΠ°Π²Π°ΡΠΎΡΠ°-ΠΏΠΎΠ³ΡΡΠ·ΡΠΈΠΊΠ° KOMATSU, ΡΠ΅ΠΌΠΎΠ½Ρ HYUNDAI, ΡΠ΅ΠΌΠΎΠ½Ρ ΡΠΊΡΠΊΠ°Π²Π°ΡΠΎΡΠ°-ΠΏΠΎΠ³ΡΡΠ·ΡΠΈΠΊΠ° HYUNDAI, ΡΠ΅ΠΌΠΎΠ½Ρ FIAT Kobelco, ΡΠ΅ΠΌΠΎΠ½Ρ ΡΠΊΡΠΊΠ°Π²Π°ΡΠΎΡΠ°-ΠΏΠΎΠ³ΡΡΠ·ΡΠΈΠΊΠ° FIAT KOBELCO, ΡΠ΅ΠΌΠΎΠ½Ρ VOLVO, ΡΠ΅ΠΌΠΎΠ½Ρ ΡΠΊΡΠΊΠ°Π²Π°ΡΠΎΡΠ°-ΠΏΠΎΠ³ΡΡΠ·ΡΠΈΠΊΠ° VOLVO ΠΈ Π΄Ρ. ΡΠ΅Ρ Π½ΠΈΠΊΠΈ), ΠΊΠΎΠ»Π΅ΡΠ½ΠΎΠΌ ΡΠΊΡΠΊΠ°Π²Π°ΡΠΎΡΠ΅ (ΡΠ΅ΠΌΠΎΠ½Ρ ΡΠΊΡΠΊΠ°Π²Π°ΡΠΎΡΠ° TEREX), ΡΡΠΎΠ½ΡΠ°Π»ΡΠ½ΠΎΠΌ ΠΏΠΎΠ³ΡΡΠ·ΡΠΈΠΊΠ΅ (ΡΠ΅ΠΌΠΎΠ½Ρ ΡΡΠΎΠ½ΡΠ°Π»ΡΠ½ΠΎΠ³ΠΎ ΠΏΠΎΠ³ΡΡΠ·ΡΠΈΠΊΠ° TEREX), ΡΠ΅Π»Π΅ΡΠΊΠΎΠΏΠΈΡΠ΅ΡΠΊΠΎΠΌ ΠΏΠΎΠ³ΡΡΠ·ΡΠΈΠΊΠ΅ (ΡΠ΅ΠΌΠΎΠ½Ρ MANITOU, ΡΠ΅ΠΌΠΎΠ½Ρ GENIE, ΡΠ΅ΠΌΠΎΠ½Ρ ΡΠ΅Π»Π΅ΡΠΊΠΎΠΏΠΈΡΠ΅ΡΠΊΠΎΠ³ΠΎ ΠΏΠΎΠ³ΡΡΠ·ΡΠΈΠΊΠ° MANITOU, ΡΠ΅ΠΌΠΎΠ½Ρ ΡΠ΅Π»Π΅ΡΠΊΠΎΠΏΠΈΡΠ΅ΠΊΠΎΠ³ΠΎ ΠΏΠΎΠ³ΡΡΠ·ΡΠΈΠΊΠ° GENIE) ΠΈΠ»ΠΈ Π΄ΡΡΠ³ΠΎΠΉ ΡΠΏΠ΅ΡΠΈΠ°Π»ΠΈΠ·ΠΈΡΠΎΠ²Π°Π½Π½ΠΎΠΉ ΡΠ΅Ρ Π½ΠΈΠΊΠ΅, ΠΠ°ΠΌ Π² ΡΡΠΎΡΠ½ΠΎΠΌ ΠΏΠΎΡΡΠ΄ΠΊΠ΅ Π½Π΅ΠΎΠ±Ρ ΠΎΠ΄ΠΈΠΌΠ° Π΄ΠΈΠ°Π³Π½ΠΎΡΡΠΈΠΊΠ° ΠΊΠ²Π°Π»ΠΈΡΠΈΡΠΈΡΠΎΠ²Π°Π½Π½ΠΎΠ³ΠΎ ΡΠΏΠ΅ΡΠΈΠ°Π»ΠΈΡΡΠ°, Π° Π² ΡΠ»ΡΡΠ°Π΅ Π½Π΅ΠΎΠ±Ρ ΠΎΠ΄ΠΈΠΌΠΎΡΡΠΈ Π½Π΅Π·Π°ΠΌΠ΅Π΄Π»Π΅Π½Π½ΡΠΉ ΡΠ΅ΠΌΠΎΠ½Ρ ΠΈ ΡΡΡΡΠ°Π½Π΅Π½ΠΈΠ΅ ΠΈΠΌΠ΅ΡΡΠ΅ΠΉΡΡ Π½Π΅ΠΈΡΠΏΡΠ°Π²Π½ΠΎΡΡΠΈ ΡΠΎΡΠΌΠΎΠ·Π½ΠΎΠΉ ΡΠΈΡΡΠ΅ΠΌΡ.
ΠΠ»Ρ Π·Π°ΠΏΠΈΡΠΈ Π½Π° Π΄ΠΈΠ°Π³Π½ΠΎΡΡΠΈΠΊΡ ΠΈ ΡΠ΅ΠΌΠΎΠ½Ρ ΡΠΎΡΠΌΠΎΠ·Π½ΠΎΠΉ ΡΠΈΡΡΠ΅ΠΌΡ Π·Π²ΠΎΠ½ΠΈΡΠ΅ ΠΏΠΎ ΡΠ΅Π»Π΅ΡΠΎΠ½Π°ΠΌ:
+7 (921) 952-25-60, +7 (931) 225-28-98, +7 (812) 372-56-70
ΠΠ°Π΄Π°Π²Π°ΠΉΡΠ΅ Π²ΠΎΠΏΡΠΎΡΡ ΠΈ ΠΎΡΠΏΡΠ°Π²Π»ΡΠΉΡΠ΅ Π·Π°ΡΠ²ΠΊΠΈ ΠΏΠΎ ΡΠ»Π΅ΠΊΡΡΠΎΠ½Π½ΠΎΠΉ ΠΏΠΎΡΡΠ΅:
E-mail: [email protected]
ΠΠ΄ΡΠ΅Ρ ΡΡΠ°ΡΠΈΠΎΠ½Π°ΡΠ½ΠΎΠ³ΠΎ ΡΠ΅ΡΠ²ΠΈΡΠ½ΠΎΠ³ΠΎ ΡΠ΅Π½ΡΡΠ° ΠΠΠ Β«ΠΠΠΠ€ΠΠ Β»:
Π³. Π‘Π°Π½ΠΊΡ-ΠΠ΅ΡΠ΅ΡΠ±ΡΡΠ³, 3-ΠΠ΅ΡΡ Π½ΠΈΠΉ ΠΏΠ΅ΡΠ΅ΡΠ»ΠΎΠΊ, Π΄ΠΎΠΌ 3, ΠΊΠΎΡΠΏ. 4
(ΠΏΡΠΎΠΌΠ·ΠΎΠ½Π° «ΠΠ°ΡΠ½Π°Ρ»)
.
ΠΡΠ°ΡΠΈΠΊ ΡΠ°Π±ΠΎΡΡ: ΠΠ-ΠΠ’ Ρ 8.00 Π΄ΠΎ 17.00, Π‘Π, ΠΠ‘ Π²ΡΡ ΠΎΠ΄Π½ΡΠ΅ Π΄Π½ΠΈΠ‘ΠΏΠ΅ΡΠΈΠ°Π»ΠΈΡΡΡ ΡΠ΅ΡΠ²ΠΈΡΠ½ΠΎΠ³ΠΎ ΡΠ΅Π½ΡΡΠ° ΠΠΠ Β«ΠΠΠΠ€ΠΠ Β» ΠΏΡΠΎΠ²ΠΎΠ΄ΡΡ ΡΠΈΡΠΎΠΊΠΈΠΉ ΡΠΏΠ΅ΠΊΡΡ ΡΠ°Π±ΠΎΡ ΠΏΠΎ Π΄ΠΈΠ°Π³Π½ΠΎΡΡΠΈΠΊΠ΅, ΡΠ΅ΠΌΠΎΠ½ΡΡ ΠΈ ΠΎΠ±ΡΠ»ΡΠΆΠΈΠ²Π°Π½ΠΈΡ ΡΠΎΡΠΌΠΎΠ·Π½ΡΡ ΡΠΈΡΡΠ΅ΠΌ Π½Π° ΡΠΊΡΠΊΠ°Π²Π°ΡΠΎΡΠ°Ρ -ΠΏΠΎΠ³ΡΡΠ·ΡΠΈΠΊΠ°Ρ TEREX, ΡΡΠΎΠ½ΡΠ°Π»ΡΠ½ΡΡ ΠΏΠΎΠ³ΡΡΠ·ΡΠΈΠΊΠ°Ρ TEREX, ΡΠΊΡΠΊΠ°Π²Π°ΡΠΎΡΠ°Ρ -ΠΏΠΎΠ³ΡΡΠ·ΡΠΈΠΊΠ°Ρ HIDROMEK, ΡΠΊΡΠΊΠ°Π²Π°ΡΠΎΡΠ°Ρ -ΠΏΠΎΠ³ΡΡΠ·ΡΠΈΠΊΠ°Ρ JCB, ΡΠ΅Π»Π΅ΡΠΊΠΎΠΏΠΈΡΠ΅ΡΠΊΠΈΡ ΠΏΠΎΠ³ΡΡΠ·ΡΠΈΠΊΠ°Ρ GENIE, ΡΠ΅Π»Π΅ΡΠΊΠΎΠΏΠΈΡΠ΅ΡΠΊΠΈΡ ΠΏΠΎΠ³ΡΡΠ·ΡΠΈΠΊΠ°Ρ MANITOU, Π²ΠΈΠ»ΠΎΡΠ½ΡΡ ΠΏΠΎΠ³ΡΡΠ·ΡΠΈΠΊΠΎΠ² MANITOU, ΡΠΊΡΠΊΠ°Π²Π°ΡΠΎΡΠ°Ρ LIEBHERR, ΡΡΠΎΠ½ΡΠ°Π»ΡΠ½ΡΡ ΠΏΠΎΠ³ΡΡΠ·ΡΠΈΠΊΠ°Ρ LIEBHERR ΠΈ Π΄ΡΡΠ³ΠΎΠΉ ΡΠΏΠ΅ΡΠΈΠ°Π»ΠΈΠ·ΠΈΡΠΎΠ²Π°Π½Π½ΠΎΠΉ ΡΠ΅Ρ Π½ΠΈΠΊΠ΅, Π²ΠΊΠ»ΡΡΠ°ΡΡΠΈΡ Π² ΡΠ΅Π±Ρ:
1. ΠΡΠΎΠ²Π΅ΡΠΊΡ ΡΠΎΡΠΌΠΎΠ·Π½ΠΎΠΉ ΡΠΈΡΡΠ΅ΠΌΡ Π½Π° Π³Π΅ΡΠΌΠ΅ΡΠΈΡΠ½ΠΎΡΡΡ. Π£ΡΡΡΠ°Π½Π΅Π½ΠΈΠ΅ ΡΡΠ΅ΡΠ΅ΠΊ ΡΠΎΡΠΌΠΎΠ·Π½ΠΎΠΉ ΠΆΠΈΠ΄ΠΊΠΎΡΡΠΈ.
2. ΠΡΠΎΠΊΠ°ΡΠΊΡ ΡΠΎΡΠΌΠΎΠ·Π½ΠΎΠΉ ΡΠΈΡΡΠ΅ΠΌΡ, ΡΠ΄Π°Π»Π΅Π½ΠΈΠ΅ Π²ΠΎΠ·Π΄ΡΡ Π° ΠΈΠ· ΡΠΎΡΠΌΠΎΠ·Π½ΠΎΠΉ ΡΠΈΡΡΠ΅ΠΌΡ.
3. ΠΠ°ΠΌΠ΅Π½Ρ ΡΠΎΡΠΌΠΎΠ·Π½ΠΎΠΉ ΠΆΠΈΠ΄ΠΊΠΎΡΡΠΈ/ ΠΏΡΠΎΠΌΡΠ²ΠΊΡ ΡΠΎΡΠΌΠΎΠ·Π½ΠΎΠΉ ΡΠΈΡΡΠ΅ΠΌΡ.
4. ΠΠ°ΠΌΠ΅Π½Ρ ΡΠΎΡΠΌΠΎΠ·Π½ΡΡ ΠΊΠΎΠ»ΠΎΠ΄ΠΎΠΊ/ ΡΠΎΡΠΌΠΎΠ·Π½ΡΡ Π΄ΠΈΡΠΊΠΎΠ².
5. ΠΠ°ΠΌΠ΅Π½Π° ΡΠΎΡΠΌΠΎΠ·Π½ΠΎΠ³ΠΎ ΡΠΈΠ»ΠΈΠ½Π΄ΡΠ°, Π·Π°ΠΌΠ΅Π½Π° ΡΠΏΠ»ΠΎΡΠ½Π΅Π½ΠΈΠΉ ΡΠΎΡΠΌΠΎΠ·Π½ΠΎΠ³ΠΎ ΡΠΈΠ»ΠΈΠ½Π΄ΡΠ°.
6. ΠΠ°ΠΌΠ΅Π½Π° ΡΠΎΡΠΌΠΎΠ·Π½ΠΎΠ³ΠΎ ΡΡΠΏΠΏΠΎΡΡΠ°, ΠΏΠ΅ΡΠ΅Π±ΠΎΡΠΊΠ° ΠΈ ΠΎΡΠΈΡΡΠΊΠ° ΡΡΠΏΠΏΠΎΡΡΠ° ΠΎΡ Π³ΡΡΠ·ΠΈ.
7. Π Π΅Π³ΡΠ»ΠΈΡΠΎΠ²ΠΊΡ ΡΡΠΎΡΠ½ΠΎΡΠ½ΠΎΠ³ΠΎ ΡΠΎΡΠΌΠΎΠ·Π°.
8. Π Π΅ΠΌΠΎΠ½Ρ ΠΌΠΎΡΡΠΎΠ² DANA Spicer, ΡΠ΅ΠΌΠΎΠ½Ρ ΠΌΠΎΡΡΠΎΠ² CARRARO, ΡΠ΅ΠΌΠΎΠ½Ρ ΠΌΠΎΡΡΠΎΠ² ZF, ΡΠ΅ΠΌΠΎΠ½Ρ ΠΌΠΎΡΡΠΎΠ² Kessler ΠΈ Π΄Ρ. ΠΏΡΠΎΠΈΠ·Π²ΠΎΠ΄ΠΈΡΠ΅Π»Π΅ΠΉ, ΠΎΡΠ½Π°ΡΠ΅Π½Π½ΡΡ Π΄ΠΈΡΠΊΠΎΠ²ΡΠΌΠΈ ΡΠΎΡΠΌΠΎΠ·Π°ΠΌΠΈ, ΡΠ°Π±ΠΎΡΠ°ΡΡΠΈΠΌΠΈ Π² ΠΌΠ°ΡΠ»Π΅, ΡΠ°ΠΊ Π½Π°Π·ΡΠ²Π°Π΅ΠΌΡΠ΅ Β«ΠΌΠΎΠΊΡΡΠ΅Β» ΡΠΎΡΠΌΠΎΠ·Π°:
8.1. Π‘Π½ΡΡΠΈΠ΅ ΠΈ ΡΡΡΠ°Π½ΠΎΠ²ΠΊΠ° ΠΌΠΎΡΡΠ°;
8.2. Π Π°Π·Π±ΠΎΡΠΊΠ° ΠΈ ΡΠ±ΠΎΡΠΊΠ° ΠΌΠΎΡΡΠ°;
8.3. ΠΡΠΎΠΌΡΠ²ΠΊΠ° ΠΌΠΎΡΡΠ° ΠΎΡ ΠΏΡΠΎΠ΄ΡΠΊΡΠΎΠ² ΠΈΠ·Π½ΠΎΡΠ° ΠΈ ΡΡΠ°ΡΠΎΠ³ΠΎ ΠΌΠ°ΡΠ»Π°;
8.4. ΠΠ°ΠΌΠ΅Π½Π° ΡΡΠΈΠΊΡΠΈΠΎΠ½Π½ΡΡ ΡΠΎΡΠΌΠΎΠ·Π½ΡΡ Π΄ΠΈΡΠΊΠΎΠ² ΠΈ ΠΌΠ΅ΡΠ°Π»Π»ΠΈΡΠ΅ΡΠΊΠΈΡ ΡΠΎΡΠΌΠΎΠ·Π½ΡΡ Π΄ΠΈΡΠΊΠΎΠ²;
8.5. ΠΠ°ΠΌΠ΅Π½Π° ΡΠΏΠ»ΠΎΡΠ½ΠΈΡΠ΅Π»ΡΠ½ΡΡ ΠΊΠΎΠ»Π΅Ρ ΡΠΎΡΠΌΠΎΠ·Π½ΡΡ ΠΏΠΎΡΡΠ½Π΅ΠΉ.
9. ΠΠ°ΠΌΠ΅Π½Ρ ΡΠΎΡΠΌΠΎΠ·Π½ΡΡ Π±Π°ΡΠ°Π±Π°Π½ΠΎΠ².
10. ΠΡΠΎΠ²Π΅ΡΠΊΡ ΠΈ ΡΠ΅ΠΌΠΎΠ½Ρ ΡΠ»Π΅ΠΌΠ΅Π½ΡΠΎΠ² ΠΊΠΎΠ½ΡΡΠΎΠ»ΡΠ½ΠΎΠΉ ΠΈΠ½Π΄ΠΈΠΊΠ°ΡΠΈΠΈ ΡΠΎΡΠΌΠΎΠ·Π½ΠΎΠΉ ΡΠΈΡΡΠ΅ΠΌΡ.
11. ΠΠ°ΠΌΠ΅Π½Ρ ΡΠΎΡΠΌΠΎΠ·Π½ΡΡ ΡΠ»Π°Π½Π³ΠΎΠ² ΠΈ ΡΡΡΠ±ΠΎΠΏΡΠΎΠ²ΠΎΠ΄ΠΎΠ²
ΠΈ Π΄ΡΡΠ³ΠΈΠ΅ Π²ΠΈΠ΄Ρ ΡΠ°Π±ΠΎΡ.
ΠΠΠ¨Π ΠΠ ΠΠΠΠ£Π©ΠΠ‘Π’ΠΠ!
1. Π‘Π΅ΡΠ²ΠΈΡΠ½ΡΠΉ ΡΠ΅Π½ΡΡ ΠΠΠ Β«ΠΠΠΠ€ΠΠ Β» ΡΠΏΠ΅ΡΠΈΠ°Π»ΠΈΠ·ΠΈΡΡΠ΅ΡΡΡ Π½Π° ΠΊΠΎΠΌΠΏΠ»Π΅ΠΊΡΠ½ΠΎΠΌ ΡΠ΅ΠΌΠΎΠ½ΡΠ΅ ΡΠΏΠ΅ΡΡΠ΅Ρ Π½ΠΈΠΊΠΈ, ΠΏΠΎΡΡΠΎΠΌΡ ΠΎΠ±ΡΠ°ΡΠ°ΡΡΡ ΠΊ Π½Π°ΠΌ Π·Π° ΡΠ΅ΠΌΠΎΠ½ΡΠΎΠΌ ΡΠΎΡΠΌΠΎΠ·Π½ΠΎΠΉ ΡΠΈΡΡΠ΅ΠΌΡ ΠΈ ΡΠΎΡΡΠ°Π²Π½ΡΡ ΡΠ»Π΅ΠΌΠ΅Π½ΡΠΎΠ² ΡΠΎΡΠΌΠΎΠ·Π½ΠΎΠΉ ΡΠΈΡΡΠ΅ΠΌΡ, ΠΡ ΠΏΠΎΠ»ΡΡΠΈΡΠ΅ ΠΏΠΎΠ»ΠΎΠΆΠΈΡΠ΅Π»ΡΠ½ΡΠΉ ΡΠ΅Π·ΡΠ»ΡΡΠ°Ρ Π½Π΅ ΡΠΎΠ»ΡΠΊΠΎ ΠΏΠΎ ΡΠΎΡΠΌΠΎΠ·Π°ΠΌ, Π½ΠΎ ΠΈ ΠΈΠΌΠ΅Π΅ΡΠ΅ Π²ΠΎΠ·ΠΌΠΎΠΆΠ½ΠΎΡΡΡ ΠΏΠΎΠΏΡΡΠ½ΠΎ ΠΎΡΠ΅Π½ΠΈΡΡ ΡΠ°Π±ΠΎΡΠ΅Π΅ ΡΠΎΡΡΠΎΡΠ½ΠΈΠ΅ Π΄ΡΡΠ³ΠΈΡ Π½Π΅ ΠΌΠ΅Π½Π΅Π΅ Π²Π°ΠΆΠ½ΡΡ ΡΠ°Π±ΠΎΡΠΈΡ ΡΠΈΡΡΠ΅ΠΌ ΠΈ Π°Π³ΡΠ΅Π³Π°ΡΠΎΠ² ΡΠ²ΠΎΠ΅ΠΉ ΠΌΠ°ΡΠΈΠ½Ρ, Π²ΠΊΠ»ΡΡΠ°Ρ ΡΠ»Π΅ΠΊΡΡΠΈΡΠ΅ΡΠΊΡΡ ΠΈ Π³ΠΈΠ΄ΡΠ°Π²Π»ΠΈΡΠ΅ΡΠΊΡΡ.
2. ΠΠΈΠ°Π³Π½ΠΎΡΡΠΈΠΊΠ° ΠΈ ΡΠ΅ΠΌΠΎΠ½Ρ ΡΠΎΡΠΌΠΎΠ·Π½ΠΎΠΉ ΡΠΈΡΡΠ΅ΠΌΡ ΡΠΏΠ΅ΡΠΈΠ°Π»ΠΈΠ·ΠΈΡΠΎΠ²Π°Π½Π½ΠΎΠΉ ΡΠ΅Ρ Π½ΠΈΠΊΠΈ ΠΎΡΡΡΠ΅ΡΡΠ²Π»ΡΠ΅ΡΡΡ Π½Π° ΠΎΡΠ½ΠΎΠ²Π΅ ΠΈΠΌΠ΅ΡΡΠ΅ΠΉΡΡ Π² ΡΠ΅ΡΠ²ΠΈΡΠ½ΠΎΠΌ ΡΠ΅Π½ΡΡΠ΅ ΠΠΠ Β«ΠΠΠΠ€ΠΠ Β» Π·Π°Π²ΠΎΠ΄ΡΠΊΠΎΠΉ ΡΠ΅ΠΌΠΎΠ½ΡΠ½ΠΎ-ΡΠ΅Ρ Π½ΠΈΡΠ΅ΡΠΊΠΎΠΉ Π΄ΠΎΠΊΡΠΌΠ΅Π½ΡΠ°ΡΠΈΠΈ, Ρ ΠΈΡΠΏΠΎΠ»ΡΠ·ΠΎΠ²Π°Π½ΠΈΠ΅ΠΌ Π½Π΅ ΡΠΎΠ»ΡΠΊΠΎ ΡΠΈΠΏΠΎΠ²ΠΎΠ³ΠΎ ΡΠ»Π΅ΡΠ°ΡΠ½ΠΎΠ³ΠΎ ΠΈΠ½ΡΡΡΡΠΌΠ΅Π½ΡΠ°, Π½ΠΎ ΠΈ ΡΠΏΠ΅ΡΠΈΠ°Π»ΠΈΠ·ΠΈΡΠΎΠ²Π°Π½Π½ΠΎΠ³ΠΎ ΠΌΠ΅Ρ Π°Π½ΠΈΡΠ΅ΡΠΊΠΎΠ³ΠΎ, ΡΠ»Π΅ΠΊΡΡΠΈΡΠ΅ΡΠΊΠΎΠ³ΠΎ ΠΈ Π³ΠΈΠ΄ΡΠ°Π²Π»ΠΈΡΠ΅ΡΠΊΠΎΠ³ΠΎ.
3. ΠΠΎ Π²ΡΠ΅ΠΌΡ ΡΠ΅ΠΌΠΎΠ½ΡΠ° ΠΌΡ Π³ΠΎΡΠΎΠ²Ρ ΠΈΡΠΏΠΎΠ»ΡΠ·ΠΎΠ²Π°ΡΡ, ΠΊΠ°ΠΊ ΠΊΠΎΠΌΠΏΠ»Π΅ΠΊΡΡΡΡΠΈΠ΅ ΡΠ°ΠΌΠΈΡ Π·Π°ΠΊΠ°Π·ΡΠΈΠΊΠΎΠ², ΡΠ°ΠΊ ΠΈ ΠΏΠΎΠ΄ΠΎΠ±ΡΠ°Π½Π½ΡΠ΅ ΡΠΏΠ΅ΡΠΈΠ°Π»ΠΈΡΡΠ°ΠΌΠΈ ΠΠΠ Β«ΠΠΠΠ€ΠΠ Β» Ρ ΡΠΎΠ±ΡΡΠ²Π΅Π½Π½ΠΎΠ³ΠΎ ΡΠΊΠ»Π°Π΄Π°, Π° Π² ΡΠ»ΡΡΠ°Π΅ ΠΎΡΡΡΡΡΡΠ²ΠΈΡ, ΡΠΎ ΡΠΊΠ»Π°Π΄ΠΎΠ² Π½Π°ΡΠΈΡ ΠΏΠΎΡΡΠΎΡΠ½Π½ΡΡ ΠΈ ΠΏΡΠΎΠ²Π΅ΡΠ΅Π½Π½ΡΡ Π²ΡΠ΅ΠΌΠ΅Π½Π΅ΠΌ ΠΏΠΎΡΡΠ°Π²ΡΠΈΠΊΠΎΠ² ΠΈΠΌΠΏΠΎΡΡΠ½ΡΡ ΠΈ ΠΎΡΠ΅ΡΠ΅ΡΡΠ²Π΅Π½Π½ΡΡ Π΄Π΅ΡΠ°Π»Π΅ΠΉ.
4. ΠΠ»Ρ ΠΎΠΏΡΠΈΠΌΠΈΠ·Π°ΡΠΈΠΈ ΡΡΠΎΠΈΠΌΠΎΡΡΠΈ ΡΠ΅ΠΌΠΎΠ½ΡΠ½ΡΡ ΡΠ°Π±ΠΎΡ ΠΏΡΠ°ΠΊΡΠΈΠΊΡΠ΅ΠΌ Π½Π΅ ΡΠΎΠ»ΡΠΊΠΎ Π½Π°ΠΈΠ±ΠΎΠ»Π΅Π΅ ΡΠ΄ΠΎΠ±Π½ΡΠΉ Π°Π³ΡΠ΅Π³Π°ΡΠ½ΡΠΉ ΡΠ΅ΠΌΠΎΠ½Ρ, ΠΏΡΡΠ΅ΠΌ Π·Π°ΠΌΠ΅Π½Ρ Π²ΡΡΠ΅Π΄ΡΠ΅Π³ΠΎ ΠΈΠ· ΡΡΡΠΎΡ ΠΈΠ·Π΄Π΅Π»ΠΈΡ Π½Π° Π½ΠΎΠ²ΠΎΠ΅, Π½ΠΎ ΠΈ Π»ΠΎΠΊΠ°Π»ΡΠ½ΡΠΉ ΡΠ΅ΠΌΠΎΠ½Ρ ΠΎΡΠ΄Π΅Π»ΡΠ½ΡΡ ΠΏΠΎΠ΄Π³ΡΡΠΏΠΏ, ΠΈΠ·Π΄Π΅Π»ΠΈΠΉ ΠΈ Π°Π³ΡΠ΅Π³Π°ΡΠΎΠ². ΠΠ°ΠΏΡΠΈΠΌΠ΅Ρ: ΡΠ΅ΠΌΠΎΠ½Ρ ΠΏΠ΅Π΄Π°Π»ΠΈ ΡΠΎΡΠΌΠΎΠ·Π°, ΡΠ΅ΠΌΠΎΠ½Ρ ΠΌΠ΅Ρ Π°Π½ΠΈΠ·ΠΌΠ° ΡΡΡΠ½ΠΎΠ³ΠΎ ΡΠΎΡΠΌΠΎΠ·Π° ΠΈ Ρ.Π΄.
5. ΠΠ»Ρ ΡΡΠΊΠΎΡΠ΅Π½ΠΈΡ ΠΎΠ±ΡΠ»ΡΠΆΠΈΠ²Π°Π½ΠΈΡ, Π΄ΠΈΠ°Π³Π½ΠΎΡΡΠΈΠΊΠΈ ΠΈ ΠΌΠ΅Π»ΠΊΠΎΠ³ΠΎ ΡΠ΅ΠΌΠΎΠ½ΡΠ° Π½Π΅ΠΈΡΠΏΡΠ°Π²Π½ΠΎΡΡΠ΅ΠΉ ΡΠΎΡΠΌΠΎΠ·Π½ΠΎΠΉ ΡΠΈΡΡΠ΅ΠΌΡ ΡΠΏΠ΅ΡΡΠ΅Ρ Π½ΠΈΠΊΠΈ Π½Π΅ΠΏΠΎΡΡΠ΅Π΄ΡΡΠ²Π΅Π½Π½ΠΎ Π½Π° ΠΎΠ±ΡΠ΅ΠΊΡΠ΅ ΠΊΠ»ΠΈΠ΅Π½ΡΠ° Ρ ΡΠ΅ΡΠ²ΠΈΡΠ½ΠΎΠΉ ΡΠ»ΡΠΆΠ±Ρ ΠΠΠ «ΠΠΠΠ€ΠΠ » Π΅ΡΡΡ Π²ΡΠ΅Π·Π΄Π½ΡΠ΅ Π±ΡΠΈΠ³Π°Π΄Ρ. ΠΡΠ΅Π·Π΄ Π½Π° Π΄ΠΈΠ°Π³Π½ΠΎΡΡΠΈΠΊΡ ΠΈ ΠΌΠ΅Π»ΠΊΠΈΠΉ ΡΠ΅ΠΌΠΎΠ½Ρ ΡΠΎΡΠΌΠΎΠ·Π½ΠΎΠΉ ΡΠΈΡΡΠ΅ΠΌΡ ΠΊ ΠΊΠ»ΠΈΠ΅Π½ΡΡ ΠΏΡΠΎΠ²ΠΎΠ΄ΠΈΡΡΡ Π½Π° ΡΠΎΠ±ΡΡΠ²Π΅Π½Π½ΡΡ Π°Π²ΡΠΎΠΌΠΎΠ±ΠΈΠ»ΡΡ ΡΠ΅Ρ Π½ΠΈΡΠ΅ΡΠΊΠΎΠΉ ΡΠ»ΡΠΆΠ±Ρ ΠΠΠ Β«ΠΠΠΠ€ΠΠ Β».
Π Π΅ΠΌΠΎΠ½Ρ ΠΈ Π΄ΠΈΠ°Π³Π½ΠΎΡΡΠΈΠΊΡ ΡΠΎΡΠΌΠΎΠ·Π½ΠΎΠΉ ΡΠΈΡΡΠ΅ΠΌΡ, ΠΊΠΎΡΠΎΡΡΠ΅ ΠΏΠΎ ΡΠ΅Ρ Π½ΠΈΡΠ΅ΡΠΊΠΈΠΌ ΠΈ ΡΠ΅Ρ Π½ΠΎΠ»ΠΎΠ³ΠΈΡΠ΅ΡΠΊΠΈΠΌ ΡΠΎΠΎΠ±ΡΠ°ΠΆΠ΅Π½ΠΈΡΠΌ Π½Π΅Π²ΠΎΠ·ΠΌΠΎΠΆΠ½ΠΎ ΡΠ΄Π΅Π»Π°ΡΡ Π½Π° Π²ΡΠ΅Π·Π΄Π΅, ΠΌΡ ΠΏΡΠ΅Π΄Π»Π°Π³Π°Π΅ΠΌ Π²ΡΠΏΠΎΠ»Π½ΠΈΡΡ ΡΡΠ°ΡΠΈΠΎΠ½Π°ΡΠ½ΠΎ Π² ΡΠΎΠ±ΡΡΠ²Π΅Π½Π½ΠΎΠΌ ΡΠ΅ΡΠ²ΠΈΡΠ½ΠΎΠΌ ΡΠ΅Π½ΡΡΠ΅ Π² Π‘ΠΠ±.
7. Π‘ΠΎΠ²ΡΠ΅ΠΌΠ΅Π½Π½Π°Ρ ΡΠΎΡΠΌΠΎΠ·Π½Π°Ρ ΡΠΈΡΡΠ΅ΠΌΠ° Π½Π΅ ΡΠ°ΠΌΠ°Ρ ΡΠ»ΠΎΠΆΠ½Π°Ρ ΡΠΈΡΡΠ΅ΠΌΠ° ΡΠΏΠ΅ΡΠΌΠ°ΡΠΈΠ½Ρ, Π½ΠΎ Π΄ΠΎΡΡΠ°ΡΠΎΡΠ½ΠΎ Β«ΡΡΠ²ΡΡΠ²ΠΈΡΠ΅Π»ΡΠ½Π°ΡΒ» ΠΊ ΡΠ°Π·Π»ΠΈΡΠ½ΡΠΌ Π½Π΅Π°ΠΊΠΊΡΡΠ°ΡΠ½ΡΠΌ Π²ΠΌΠ΅ΡΠ°ΡΠ΅Π»ΡΡΡΠ²Π°ΠΌ ΠΈ Π½Π΅ΠΊΠΎΡΡΠ΅ΠΊΡΠ½ΡΠΌ Π΄Π΅ΠΉΡΡΠ²ΠΈΡΠΌ ΡΠΎ ΡΡΠΎΡΠΎΠ½Ρ ΠΎΠ±ΡΠ»ΡΠΆΠΈΠ²Π°ΡΡΠ΅Π³ΠΎ ΠΏΠ΅ΡΡΠΎΠ½Π°Π»Π°. ΠΡΠ΅ΠΊΡΠ°ΡΠ½ΠΎ ΠΎΡΠΎΠ·Π½Π°Π²Π°Ρ ΡΡΠΎ, Π° ΡΠ°ΠΊΠΆΠ΅ ΡΠΎ, ΡΡΠΎ Ρ ΠΊΠ°ΠΆΠ΄ΠΎΠ³ΠΎ ΠΏΡΠΎΠΈΠ·Π²ΠΎΠ΄ΠΈΡΠ΅Π»Ρ ΡΠΏΠ΅ΡΡΠ΅Ρ Π½ΠΈΠΊΠΈ Π΅ΡΡΡ ΡΠ²ΠΎΠΈ ΡΠΏΠ΅ΡΠΈΡΠΈΡΠ΅ΡΠΊΠΈΠ΅ ΠΎΡΠΎΠ±Π΅Π½Π½ΠΎΡΡΠΈ, ΠΊΠΎΡΠΎΡΡΡ ΡΠ»Π΅Π΄ΡΠ΅Ρ ΠΏΡΠΈΠ΄Π΅ΡΠΆΠΈΠ²Π°ΡΡΡΡ Π²ΠΎ Π²ΡΠ΅ΠΌΡ Π²ΡΠΏΠΎΠ»Π½Π΅Π½ΠΈΡ ΡΠ΅ΠΌΠΎΠ½ΡΠ½ΠΎ-Π΄ΠΈΠ°Π³Π½ΠΎΡΡΠΈΡΠ΅ΡΠΊΠΈΡ ΠΌΠ΅ΡΠΎΠΏΡΠΈΡΡΠΈΠΉ, ΠΌΡ Π½Π΅ ΡΡΠ°Π²ΠΈΠΌ ΠΏΠ΅ΡΠ΅Π΄ ΡΠΎΠ±ΠΎΠΉ ΡΠ΅Π»ΠΈ, ΡΠ΅ΠΌΠΎΠ½ΡΠΈΡΠΎΠ²Π°ΡΡ ΡΠΎΡΠΌΠΎΠ·Π½ΡΡ ΡΠΈΡΡΠ΅ΠΌΡ Π»ΡΠ±ΡΡ ΠΌΠ°ΡΠΈΠ½ ΠΊΠ»ΠΈΠ΅Π½ΡΠΎΠ², ΠΎΠ±ΡΠ°ΡΠΈΠ²ΡΠΈΡ ΡΡ Π² ΡΠ΅ΡΠ²ΠΈΡΠ½ΡΠΉ ΡΠ΅Π½ΡΡ ΠΠΠ Β«ΠΠΠΠ€ΠΠ Β».
ΠΡΠ½ΠΎΠ²Π½ΠΎΠΉ ΡΠΏΠΎΡ Π΄Π΅Π»Π°Π΅ΡΡΡ Π½Π° ΡΠ΅Ρ ΠΏΡΠΎΠΈΠ·Π²ΠΎΠ΄ΠΈΡΠ΅Π»Π΅ΠΉ ΡΠΏΠ΅ΡΡΠ΅Ρ Π½ΠΈΠΊΠΈ (ΡΠ΅ΠΌΠΎΠ½Ρ ΡΠΎΡΠΌΠΎΠ·Π½ΠΎΠΉ ΡΠΈΡΡΠ΅ΠΌΡ ΡΠΊΡΠΊΠ°Π²Π°ΡΠΎΡΠ°-ΠΏΠΎΠ³ΡΡΠ·ΡΠΈΠΊΠ° TEREX, ΡΠ΅ΠΌΠΎΠ½Ρ ΡΠΎΡΠΌΠΎΠ·Π½ΠΎΠΉ ΡΠΈΡΡΠ΅ΠΌΡ ΡΡΠΎΠ½ΡΠ°Π»ΡΠ½ΠΎΠ³ΠΎ ΠΏΠΎΠ³ΡΡΠ·ΡΠΈΠΊΠ° TEREX, ΡΠ΅ΠΌΠΎΠ½Ρ ΡΠΎΡΠΌΠΎΠ·Π½ΠΎΠΉ ΡΠΈΡΡΠ΅ΠΌΡ ΡΠΊΡΠΊΠ°Π²Π°ΡΠΎΡΠ°-ΠΏΠΎΠ³ΡΡΠ·ΡΠΈΠΊΠ° HIDROMEK, ΡΠ΅ΠΌΠΎΠ½Ρ ΡΠΎΡΠΌΠΎΠ·Π½ΠΎΠΉ ΡΠΈΡΡΠ΅ΠΌΡ ΡΠΊΡΠΊΠ°Π²Π°ΡΠΎΡΠ°-ΠΏΠΎΠ³ΡΡΠ·ΡΠΈΠΊΠ° JCB, ΡΠ΅ΠΌΠΎΠ½Ρ ΡΠΎΡΠΌΠΎΠ·Π½ΠΎΠΉ ΡΠΈΡΡΠ΅ΠΌΡ ΡΠ΅Π»Π΅ΡΠΊΠΎΠΏΠΈΡΠ΅ΡΠΊΠΎΠ³ΠΎ ΠΏΠΎΠ³ΡΡΠ·ΡΠΈΠΊΠ° MANITOU, ΡΠ΅ΠΌΠΎΠ½Ρ ΡΠΎΡΠΌΠΎΠ·Π½ΠΎΠΉ ΡΠΈΡΡΠ΅ΠΌΡ Π²ΠΈΠ»ΠΎΡΠ½ΠΎΠ³ΠΎ ΠΏΠΎΠ³ΡΡΠ·ΡΠΈΠΊΠ° MANITOU, ΡΠ΅ΠΌΠΎΠ½Ρ ΡΠΎΡΠΌΠΎΠ·Π½ΠΎΠΉ ΡΠΈΡΡΠ΅ΠΌΡ ΡΡΠΎΠ½ΡΠ°Π»ΡΠ½ΠΎΠ³ΠΎ ΠΏΠΎΠ³ΡΡΠ·ΡΠΈΠΊΠ° TEREX, ΡΠ΅ΠΌΠΎΠ½Ρ ΡΠΎΡΠΎΠΌΠ·Π½ΠΎΠΉ ΡΠΈΡΡΠ΅ΠΌΡ ΡΠΊΡΠΊΠ°Π²Π°ΡΠΎΡΠ°-ΠΏΠΎΠ³ΡΡΠ·ΡΠΈΠΊΠ° Hyundai, ΡΠ΅ΠΌΠΎΠ½Ρ ΡΠΎΡΠΌΠΎΠ·Π½ΠΎΠΉ ΡΠΈΡΡΠ΅ΠΌΡ ΡΠΊΡΠΊΠ°Π²Π°ΡΠΎΡΠ°-ΠΏΠΎΠ³ΡΡΠ·ΡΠΈΠΊΠ° John Deer, ΡΠ΅ΠΌΠΎΠ½Ρ ΡΠΎΡΠΌΠΎΠ·Π½ΠΎΠΉ ΡΠΈΡΡΠ΅ΠΌΡ ΡΠΊΡΠΊΠ°Π²Π°ΡΠΎΡΠ°-ΠΏΠΎΠ³ΡΡΠ·ΡΠΈΠΊΠ° Case, ΡΠ΅ΠΌΠΎΠ½Ρ ΡΠΎΡΠΌΠΎΠ·Π½ΠΎΠΉ ΡΠΈΡΡΠ΅ΠΌΡ ΡΠΊΡΠΊΠ°Π²Π°ΡΠΎΡΠ° HIDROMEK, ΡΠ΅ΠΌΠΎΠ½Ρ ΡΠΎΡΠΌΠΎΠ·Π½ΠΎΠΉ ΡΠΈΡΡΠ΅ΠΌΡ ΡΠΊΡΠΊΠ°Π²Π°ΡΠΎΡΠ°-ΠΏΠΎΠ³ΡΡΠ·ΡΠΈΠΊΠ° New Holland ΠΈ Π΄Ρ. ΡΠ΅Ρ Π½ΠΈΠΊΠΈ), Π΄Π»Ρ ΠΊΠΎΡΠΎΡΡΡ ΠΌΡ ΠΌΠΎΠΆΠ΅ΠΌ ΠΎΠ±Π΅ΡΠΏΠ΅ΡΠΈΡΡ Π²ΡΠ΅ ΡΡΠ»ΠΎΠ²ΠΈΡ ΠΏΡΠΎΠ²Π΅Π΄Π΅Π½ΠΈΡ Π²ΡΡΠΎΠΊΠΎΠΊΠ°ΡΠ΅ΡΡΠ²Π΅Π½Π½ΠΎΠ³ΠΎ ΠΈ ΠΎΠΏΠ΅ΡΠ°ΡΠΈΠ²Π½ΠΎΠ³ΠΎ ΡΠ΅ΠΌΠΎΠ½ΡΠ°.
8. ΠΡΠ»ΠΈ ΠΊΠ°ΠΊΠΈΠ΅-ΡΠΎ ΡΠΏΠ΅ΡΠΈΡΠΈΡΠ΅ΡΠΊΠΈΠ΅ ΡΠ°Π±ΠΎΡΡ Π½Π΅ ΠΌΠΎΠ³ΡΡ Π±ΡΡΡ Π²ΡΠΏΠΎΠ»Π½Π΅Π½Ρ ΡΠΈΠ»Π°ΠΌΠΈ Π½Π°ΡΠΈΡ ΡΠΏΠ΅ΡΠΈΠ°Π»ΠΈΡΡΠΎΠ², ΠΊΠ»ΠΈΠ΅Π½ΡΡ Π±ΡΠ΄Π΅Ρ Π²ΡΠ΅Π³Π΄Π° ΠΏΡΠ΅Π΄Π»ΠΎΠΆΠ΅Π½ΠΎ Π°Π»ΡΡΠ΅ΡΠ½Π°ΡΠΈΠ²Π½ΠΎΠ΅ ΠΎΠΏΡΠΈΠΌΠ°Π»ΡΠ½ΠΎΠ΅ ΡΠ΅ΡΠ΅Π½ΠΈΠ΅ ΠΈ Π°Π»Π³ΠΎΡΠΈΡΠΌ Π΄Π΅ΠΉΡΡΠ²ΠΈΠΉ ΠΏΠΎ Π²ΡΡ ΠΎΠ΄Ρ ΠΈΠ· ΡΠ»ΠΎΠΆΠΈΠ²ΡΠ΅ΠΉΡΡ ΡΠΈΡΡΠ°ΡΠΈΠΈ.
ΠΠΠ «ΠΠΠΠ€ΠΠ » ΠΎΡΡΡΠ΅ΡΡΠ²Π»ΡΠ΅Ρ ΡΠ΅ΠΌΠΎΠ½Ρ ΡΠΎΡΠΌΠΎΠ·Π½ΡΡ ΡΠΈΡΡΠ΅ΠΌ, ΠΏΠΎΠΌΠΈΠΌΠΎ Tere[ Construction, ΠΌΠ½ΠΎΠ³ΠΈΡ Π΄ΡΡΠ³ΠΈΡ Π²ΡΠ΅ΠΌΠΈΡΠΎΠ½ΠΎ ΠΈΠ·Π²Π΅ΡΡΠ½ΡΡ ΠΏΡΠΎΠΈΠ·Π²ΠΎΠ΄ΠΈΡΠ΅Π»Π΅ΠΉ ΡΠΏΠ΅ΡΡΠ΅Ρ Π½ΠΈΠΊΠΈ: FERMEC (ΡΠ΅ΠΌΠΎΠ½Ρ FERMEC, ΡΠ΅ΠΌΠΎΠ½Ρ ΡΠΊΡΠΊΠ°Π²Π°ΡΠΎΡΠ°-ΠΏΠΎΠ³ΡΡΠ·ΡΠΈΠΊΠ° FERMEC), JCB (ΡΠ΅ΠΌΠΎΠ½Ρ JCB, ΡΠ΅ΠΌΠΎΠ½Ρ ΡΠΊΡΠΊΠ°Π²Π°ΡΠΎΡΠ°-ΠΏΠΎΠ³ΡΡΠ·ΡΠΈΠΊΠ° JCB), HIDROMEK (ΡΠ΅ΠΌΠΎΠ½Ρ HIDROMEK, ΡΠ΅ΠΌΠΎΠ½Ρ ΡΠΊΡΠΊΠ°Π²Π°ΡΠΎΡΠ°-ΠΏΠΎΠ³ΡΡΠ·ΡΠΈΠΊΠ° HIDROMEK), CASE Construction (ΡΠ΅ΠΌΠΎΠ½Ρ CASE, ΡΠ΅ΠΌΠΎΠ½Ρ ΡΠΊΡΠΊΠ°Π²Π°ΡΠΎΡΠ°-ΠΏΠΎΠ³ΡΡΠ·ΡΠΈΠΊΠ° CASE), CATERPILLAR (ΡΠ΅ΠΌΠΎΠ½Ρ CATERPILLAR, ΡΠ΅ΠΌΠΎΠ½Ρ ΡΠΊΡΠΊΠ°Π²Π°ΡΠΎΡΠ°-ΠΏΠΎΠ³ΡΡΠ·ΡΠΈΠΊΠ° CATERPILLAR), NEW HOLLAND (ΡΠ΅ΠΌΠΎΠ½Ρ NEW HOLLAND, ΡΠ΅ΠΌΠΎΠ½Ρ ΡΠΊΡΠΊΠ°Π²Π°ΡΠΎΡΠ°-ΠΏΠΎΠ³ΡΡΠ·ΡΠΈΠΊΠ° NEW HOLLAND), KOMATSU (ΡΠ΅ΠΌΠΎΠ½Ρ KOMATSU, ΡΠ΅ΠΌΠΎΠ½Ρ ΡΠΊΡΠΊΠ°Π²Π°ΡΠΎΡΠ°-ΠΏΠΎΠ³ΡΡΠ·ΡΠΈΠΊΠ° KOMATSU), HYUNDAI (ΡΠ΅ΠΌΠΎΠ½Ρ HYUNDAI, ΡΠ΅ΠΌΠΎΠ½Ρ ΡΠΊΡΠΊΠ°Π²Π°ΡΠΎΡΠ°-ΠΏΠΎΠ³ΡΡΠ·ΡΠΈΠΊΠ° HYUNDAI), FIAT KOBELCO (ΡΠ΅ΠΌΠΎΠ½Ρ FIAT Kobelco, ΡΠ΅ΠΌΠΎΠ½Ρ ΡΠΊΡΠΊΠ°Π²Π°ΡΠΎΡΠ°-ΠΏΠΎΠ³ΡΡΠ·ΡΠΈΠΊΠ° FIAT KOBELCO), VOLVO (ΡΠ΅ΠΌΠΎΠ½Ρ VOLVO, ΡΠ΅ΠΌΠΎΠ½Ρ ΡΠΊΡΠΊΠ°Π²Π°ΡΠΎΡΠ°-ΠΏΠΎΠ³ΡΡΠ·ΡΠΈΠΊΠ° VOLVO) ΠΈ Π΄Ρ. ΠΏΡΠΎΠΈΠ·Π²ΠΎΠ΄ΠΈΡΠ΅Π»ΠΉ ΡΠΏΠ΅ΡΡΠ΅Ρ Π½ΠΈΠΊΠΈ.
ΠΠ΅ΠΏΠΎΠ»Π½ΡΠΉ ΠΏΠ΅ΡΠ΅ΡΠ΅Π½Ρ ΠΎΠΏΠ΅ΡΠ°ΡΠΈΠΉ, Π²ΡΠΏΠΎΠ»Π½ΡΠ΅ΠΌΡΡ ΡΠΏΠ΅ΡΠΈΠ°Π»ΠΈΡΡΠ°ΠΌΠΈ Π‘Π΅ΡΠ²ΠΈΡΠ½ΠΎΠ³ΠΎ ΡΠ΅Π½ΡΡΠ° ΠΠΠ Β«ΠΠΠΠ€ΠΠ Β», ΠΏΠΎ ΡΠ΅ΠΌΠΎΠ½ΡΡ ΠΈ Π΄ΠΈΠ°Π³Π½ΠΎΡΡΠΈΠΊΠ΅ ΡΠΎΡΠΌΠΎΠ·Π½ΠΎΠΉ ΡΠΈΡΡΠ΅ΠΌΡ ΡΠΏΠ΅ΡΡΠ΅Ρ Π½ΠΈΠΊΠΈ:
ΠΡΡΠ²Π΅ΡΠ»ΠΈΠ²Π°Π½ΠΈΠ΅ Π±ΠΎΠ»ΡΠ° ΡΠ»Π°Π½ΡΠ° ΡΡΡΠ½ΠΈΠΊΠ° Π½Π° ΡΠΊΡΠΊΠ°Π²Π°ΡΠΎΡΠ΅-ΠΏΠΎΠ³ΡΡΠ·ΡΠΈΠΊΠ΅ TEREX Π² Π‘Π°Π½ΠΊΡ-ΠΠ΅ΡΠ΅ΡΠ±ΡΡΠ³Π΅ (Π‘ΠΠ±)
ΠΠΈΠ°Π³Π½ΠΎΡΡΠΈΠΊΠ° ΡΠΎΡΠΌΠΎΠ·Π½ΠΎΠΉ ΡΠΈΡΡΠ΅ΠΌΡ Π½Π° ΡΠΊΡΠΊΠ°Π²Π°ΡΠΎΡΠ΅-ΠΏΠΎΠ³ΡΡΠ·ΡΠΈΠΊΠ΅ TEREX Π² Π‘Π°Π½ΠΊΡ-ΠΠ΅ΡΠ΅ΡΠ±ΡΡΠ³Π΅ (Π‘ΠΠ±)
ΠΠ°ΠΌΠ΅Π½Π° ΠΊΠΎΠ»ΠΎΠ΄ΠΎΠΊ ΡΡΡΠ½ΠΈΠΊΠ° Π½Π° ΡΠΊΡΠΊΠ°Π²Π°ΡΠΎΡΠ΅-ΠΏΠΎΠ³ΡΡΠ·ΡΠΈΠΊΠ΅ TEREX Π² Π‘Π°Π½ΠΊΡ-ΠΠ΅ΡΠ΅ΡΠ±ΡΡΠ³Π΅ (Π‘ΠΠ±)
ΠΠ°ΠΌΠ΅Π½Π° ΠΊΡΠΎΠ½ΡΡΠ΅ΠΉΠ½Π° ΡΠΎΡΠΌΠΎΠ·Π½ΠΎΠ³ΠΎ Π±ΠΎΡΠΊΠ° Π½Π° ΡΠΊΡΠΊΠ°Π²Π°ΡΠΎΡΠ΅-ΠΏΠΎΠ³ΡΡΠ·ΡΠΈΠΊΠ΅ TEREX Π² Π‘Π°Π½ΠΊΡ-ΠΠ΅ΡΠ΅ΡΠ±ΡΡΠ³Π΅ (Π‘ΠΠ±)
ΠΠ°ΠΌΠ΅Π½Π° ΡΠΎΡΠΌΠΎΠ·Π½ΠΎΠ³ΠΎ Π±Π°ΡΠΊΠ° Π½Π° ΡΠΊΡΠΊΠ°Π²Π°ΡΠΎΡΠ΅-ΠΏΠΎΠ³ΡΡΠ·ΡΠΈΠΊΠ΅ TEREX Π² Π‘Π°Π½ΠΊΡ-ΠΠ΅ΡΠ΅ΡΠ±ΡΡΠ³Π΅ (Π‘ΠΠ±)
ΠΠ°ΠΌΠ΅Π½Π° ΡΠΎΡΠΌΠΎΠ·Π½ΠΎΠ³ΠΎ ΠΌΠ°ΡΠ»Π° Π½Π° ΡΠΊΡΠΊΠ°Π²Π°ΡΠΎΡΠ΅-ΠΏΠΎΠ³ΡΡΠ·ΡΠΈΠΊΠ΅ TEREX Π² Π‘Π°Π½ΠΊΡ-ΠΠ΅ΡΠ΅ΡΠ±ΡΡΠ³Π΅ (Π‘ΠΠ±)
ΠΠ°ΠΌΠ΅Π½Π° ΡΠΎΡΠΌΠΎΠ·Π½ΠΎΠ³ΠΎ ΡΠΈΠ»ΠΈΠ½Π΄ΡΠ° Π½Π° ΡΠΊΡΠΊΠ°Π²Π°ΡΠΎΡΠ΅-ΠΏΠΎΠ³ΡΡΠ·ΡΠΈΠΊΠ΅ TEREX Π² Π‘Π°Π½ΠΊΡ-ΠΠ΅ΡΠ΅ΡΠ±ΡΡΠ³Π΅ (Π‘ΠΠ±)
ΠΠ°ΠΌΠ΅Π½Π° ΡΠΎΡΠΌΠΎΠ·Π½ΠΎΠ³ΠΎ ΡΠ»Π°Π½Π³Π° Π½Π° ΡΠΊΡΠΊΠ°Π²Π°ΡΠΎΡΠ΅-ΠΏΠΎΠ³ΡΡΠ·ΡΠΈΠΊΠ΅ TEREX Π² Π‘Π°Π½ΠΊΡ-ΠΠ΅ΡΠ΅ΡΠ±ΡΡΠ³Π΅ (Π‘ΠΠ±)
ΠΠ°ΠΌΠ΅Π½Π° ΡΡΠΎΡΠ° ΡΡΡΠ½ΠΎΠ³ΠΎ ΡΠΎΡΠΌΠΎΠ·Π° Π½Π° ΡΠΊΡΠΊΠ°Π²Π°ΡΠΎΡΠ΅-ΠΏΠΎΠ³ΡΡΠ·ΡΠΈΠΊΠ΅ TEREX Π² Π‘Π°Π½ΠΊΡ-ΠΠ΅ΡΠ΅ΡΠ±ΡΡΠ³Π΅ (Π‘ΠΠ±)
ΠΠ°ΠΌΠ΅Π½Π° ΡΠ»Π°Π½ΡΠ° ΡΡΡΠ½ΠΈΠΊΠ° Π½Π° ΡΠΊΡΠΊΠ°Π²Π°ΡΠΎΡΠ΅-ΠΏΠΎΠ³ΡΡΠ·ΡΠΈΠΊΠ΅ TEREX Π² Π‘Π°Π½ΠΊΡ-ΠΠ΅ΡΠ΅ΡΠ±ΡΡΠ³Π΅ (Π‘ΠΠ±)
ΠΠ°ΠΌΠ΅Π½Π° ΡΡΡΡΠ΅ΡΠΎΠ² ΡΠΎΡΠΌΠΎΠ·Π½ΠΎΠ³ΠΎ ΡΠΈΠ»ΠΈΠ½Π΄ΡΠΎΠ² Π½Π° ΡΠΊΡΠΊΠ°Π²Π°ΡΠΎΡΠ΅-ΠΏΠΎΠ³ΡΡΠ·ΡΠΈΠΊΠ΅ TEREX Π² Π‘Π°Π½ΠΊΡ-ΠΠ΅ΡΠ΅ΡΠ±ΡΡΠ³Π΅ (Π‘ΠΠ±)
ΠΡΠΎΠΊΠ°ΡΠΊΠ° ΡΠΎΡΠΌΠΎΠ·ΠΎΠ² Π½Π° ΡΠΊΡΠΊΠ°Π²Π°ΡΠΎΡΠ΅-ΠΏΠΎΠ³ΡΡΠ·ΡΠΈΠΊΠ΅ TEREX Π² Π‘Π°Π½ΠΊΡ-ΠΠ΅ΡΠ΅ΡΠ±ΡΡΠ³Π΅ (Π‘ΠΠ±)
Π Π΅Π³ΡΠ»ΠΈΡΠΎΠ²ΠΊΠ° Π³Π΅ΡΠΊΠΎΠ½Π° ΡΡΡΠ½ΠΈΠΊΠ° Π½Π° ΡΠΊΡΠΊΠ°Π²Π°ΡΠΎΡΠ΅-ΠΏΠΎΠ³ΡΡΠ·ΡΠΈΠΊΠ΅ TEREX Π² Π‘Π°Π½ΠΊΡ-ΠΠ΅ΡΠ΅ΡΠ±ΡΡΠ³Π΅ (Π‘ΠΠ±)
Π Π΅Π³ΡΠ»ΠΈΡΠΎΠ²ΠΊΠ° ΡΡΠΎΡΠ½ΠΎΡΠ½ΠΎΠ³ΠΎ ΡΠΎΡΠΌΠΎΠ·Π° Π½Π° ΡΠΊΡΠΊΠ°Π²Π°ΡΠΎΡΠ΅-ΠΏΠΎΠ³ΡΡΠ·ΡΠΈΠΊΠ΅ TEREX Π² Π‘Π°Π½ΠΊΡ-ΠΠ΅ΡΠ΅ΡΠ±ΡΡΠ³Π΅ (Π‘ΠΠ±)
Π Π΅ΠΌΠΎΠ½Ρ ΡΠΎΡΠΌΠΎΠ·Π½ΠΎΠ³ΠΎ ΡΠΈΠ»ΠΈΠ½Π΄ΡΠ° Π½Π° ΡΠΊΡΠΊΠ°Π²Π°ΡΠΎΡΠ΅-ΠΏΠΎΠ³ΡΡΠ·ΡΠΈΠΊΠ΅ TEREX Π² Π‘Π°Π½ΠΊΡ-ΠΠ΅ΡΠ΅ΡΠ±ΡΡΠ³Π΅ (Π‘ΠΠ±)
Π Π΅ΠΌΠΎΠ½Ρ ΡΠΎΡΠΌΠΎΠ·Π½ΠΎΠ³ΠΎ ΡΡΡΡΠ΅ΡΠ° ΡΡΡΠ±ΠΊΠΈ Ρ Π·Π°Π΄Π½Π΅Π³ΠΎ ΠΌΠΎΡΡΠ° Π½Π° ΡΠΊΡΠΊΠ°Π²Π°ΡΠΎΡΠ΅-ΠΏΠΎΠ³ΡΡΠ·ΡΠΈΠΊΠ΅ TEREX Π² Π‘Π°Π½ΠΊΡ-ΠΠ΅ΡΠ΅ΡΠ±ΡΡΠ³Π΅ (Π‘ΠΠ±)
Π‘/Π£ ΡΠ»Π°Π½ΡΠ° ΡΡΡΠ½ΠΈΠΊΠ° Π²ΠΎΡΡΡΠ°Π½ΠΎΠ²Π»Π΅Π½ΠΈΠ΅ ΠΏΠΎΡΠ°Π΄ΠΎΡΠ½ΠΎΠ³ΠΎ ΠΌΠ΅ΡΡΠ° ΠΊΡΠ΅ΡΡΠΎΠ²ΠΈΠ½Ρ Π½Π° ΡΠΊΡΠΊΠ°Π²Π°ΡΠΎΡΠ΅-ΠΏΠΎΠ³ΡΡΠ·ΡΠΈΠΊΠ΅ TEREX Π² Π‘Π°Π½ΠΊΡ-ΠΠ΅ΡΠ΅ΡΠ±ΡΡΠ³Π΅ (Π‘ΠΠ±)
ΠΠ΅ΠΌΠΎΠ½ΡΠ°ΠΆ-ΠΌΠΎΠ½ΡΠ°ΠΆ ΠΌΠ΅Ρ Π°Π½ΠΈΠ·ΠΌΠ° ΡΡΡΠ½ΠΈΠΊΠ° Π½Π° ΡΠΊΡΠΊΠ°Π²Π°ΡΠΎΡΠ΅-ΠΏΠΎΠ³ΡΡΠ·ΡΠΈΠΊΠ΅ TEREX Π² Π‘Π°Π½ΠΊΡ-ΠΠ΅ΡΠ΅ΡΠ±ΡΡΠ³Π΅ (Π‘ΠΠ±)
ΠΡΠΎΠΌΠ°Π·ΠΊΠ° ΠΏΠ΅Π΄Π°Π»Π΅ΠΉ ΡΠΎΡΠΌΠΎΠ·ΠΎΠ² Π½Π° ΡΠΊΡΠΊΠ°Π²Π°ΡΠΎΡΠ΅-ΠΏΠΎΠ³ΡΡΠ·ΡΠΈΠΊΠ΅ TEREX Π² Π‘Π°Π½ΠΊΡ-ΠΠ΅ΡΠ΅ΡΠ±ΡΡΠ³Π΅ (Π‘ΠΠ±)
Π‘Π½ΡΡΠΈΠ΅ ΠΈ ΡΡΡΠ°Π½ΠΎΠ²ΠΊΠ° ΡΠΎΡΠΌΠΎΠ·Π½ΠΎΠ³ΠΎ ΡΠΈΠ»ΠΈΠ½Π΄ΡΠ° Π½Π° ΡΠΊΡΠΊΠ°Π²Π°ΡΠΎΡΠ΅-ΠΏΠΎΠ³ΡΡΠ·ΡΠΈΠΊΠ΅ TEREX Π² Π‘Π°Π½ΠΊΡ-ΠΠ΅ΡΠ΅ΡΠ±ΡΡΠ³Π΅ (Π‘ΠΠ±)
Π£ΡΡΠ°Π½ΠΎΠ²ΠΊΠ° ΠΊΡΠΎΠ½ΡΡΠ΅ΠΉΠ½Π° ΡΠΎΡΠΌΠΎΠ·Π½ΠΎΠ³ΠΎ Π±ΠΎΡΠΊΠ° Π½Π° ΡΠΊΡΠΊΠ°Π²Π°ΡΠΎΡΠ΅-ΠΏΠΎΠ³ΡΡΠ·ΡΠΈΠΊΠ΅ TEREX Π² Π‘Π°Π½ΠΊΡ-ΠΠ΅ΡΠ΅ΡΠ±ΡΡΠ³Π΅ (Π‘ΠΠ±)
Π£ΡΡΠ°Π½ΠΎΠ²ΠΊΠ° ΠΏΡΡΠΆΠΈΠ½Ρ Π½Π° ΠΏΠ΅Π΄Π°Π»Ρ ΡΠΎΡΠΌΠΎΠ·Π° Π½Π° ΡΠΊΡΠΊΠ°Π²Π°ΡΠΎΡΠ΅-ΠΏΠΎΠ³ΡΡΠ·ΡΠΈΠΊΠ΅ TEREX Π² Π‘Π°Π½ΠΊΡ-ΠΠ΅ΡΠ΅ΡΠ±ΡΡΠ³Π΅ (Π‘ΠΠ±)
Π£ΡΡΠ°Π½ΠΎΠ²ΠΊΠ° ΡΠ΅ΡΠ²ΠΈΡΠ½ΠΎΠ³ΠΎ ΠΊΠΎΠΌΠΏΠ»Π΅ΠΊΡΠ° ΡΠΎΡΠΌΠΎΠ·Π½ΡΡ ΡΠΈΠ»ΠΈΠ½Π΄ΡΠΎΠ² Π½Π° ΡΠΊΡΠΊΠ°Π²Π°ΡΠΎΡΠ΅-ΠΏΠΎΠ³ΡΡΠ·ΡΠΈΠΊΠ΅ TEREX Π² Π‘Π°Π½ΠΊΡ-ΠΠ΅ΡΠ΅ΡΠ±ΡΡΠ³Π΅ (Π‘ΠΠ±)Π‘Π½ΡΡΠΈΠ΅ ΠΈ ΡΡΡΠ°Π½ΠΎΠ²ΠΊΠ° Π·Π°Π΄Π½Π΅Π³ΠΎ ΠΌΠΎΡΡΠ°
Π Π°Π·Π±ΠΎΡΠΊΠ° ΠΈ ΡΠ±ΠΎΡΠΊΠ° Π·Π°Π΄Π½Π΅Π³ΠΎ ΠΌΠΎΡΡΠ° Π½Π° ΡΠΊΡΠΊΠ°Π²Π°ΡΠΎΡΠ΅-ΠΏΠΎΠ³ΡΡΠ·ΡΠΈΠΊΠ΅ TEREX Π² Π‘Π°Π½ΠΊΡ-ΠΠ΅ΡΠ΅ΡΠ±ΡΡΠ³Π΅ (Π‘ΠΠ±)
ΠΠ°ΠΌΠ΅Π½Π° ΡΡΠΈΠΊΡΠΈΠΎΠ½ΠΎΠ² Π·Π°Π΄Π½Π΅Π³ΠΎ ΠΌΠΎΡΡΠ° Π½Π° ΡΠΊΡΠΊΠ°Π²Π°ΡΠΎΡΠ΅-ΠΏΠΎΠ³ΡΡΠ·ΡΠΈΠΊΠ΅ TEREX Π² Π‘Π°Π½ΠΊΡ-ΠΠ΅ΡΠ΅ΡΠ±ΡΡΠ³Π΅ (Π‘ΠΠ±)
ΠΡΠΎΠΌΡΠ²ΠΊΠ° Π·Π°Π΄Π½Π΅Π³ΠΎ ΠΌΠΎΡΡΠ° Π½Π° ΡΠΊΡΠΊΠ°Π²Π°ΡΠΎΡΠ΅-ΠΏΠΎΠ³ΡΡΠ·ΡΠΈΠΊΠ΅ TEREX Π² Π‘Π°Π½ΠΊΡ-ΠΠ΅ΡΠ΅ΡΠ±ΡΡΠ³Π΅ (Π‘ΠΠ±)
ΠΠ°ΠΌΠ΅Π½Π° ΠΌΠ°Π½ΠΆΠ΅Ρ ΡΠΎΡΠΌΠΎΠ·Π½ΡΡ ΠΏΠΎΡΡΠ½Π΅ΠΉ Π½Π° ΡΠΊΡΠΊΠ°Π²Π°ΡΠΎΡΠ΅-ΠΏΠΎΠ³ΡΡΠ·ΡΠΈΠΊΠ΅ TEREX Π² Π‘Π°Π½ΠΊΡ-ΠΠ΅ΡΠ΅ΡΠ±ΡΡΠ³Π΅ (Π‘ΠΠ±)
ΠΈ Π΄Ρ. Π²ΠΈΠ΄Ρ ΡΠ°Π±ΠΎΡ
.
ΠΠ»Ρ Π·Π°ΠΏΠΈΡΠΈ Π½Π° Π΄ΠΈΠ°Π³Π½ΠΎΡΡΠΈΠΊΠΊΡ ΠΈ ΡΠ΅ΠΌΠΎΠ½Ρ ΡΠΎΡΠΌΠΎΠ·Π½ΠΎΠΉ ΡΠΈΡΡΠ΅ΠΌΡ Π·Π²ΠΎΠ½ΠΈΡΠ΅ ΠΏΠΎ ΡΠ΅Π»Π΅ΡΠΎΠ½Π°ΠΌ:
+7 (921) 952-25-60, +7 (931) 225-28-98, +7 (812) 372-56-70
ΠΠ°Π΄Π°Π²Π°ΠΉΡΠ΅ Π²ΠΎΠΏΡΠΎΡΡ ΠΈ ΠΎΡΠΏΡΠ°Π²Π»ΡΠΉΡΠ΅ Π·Π°ΡΠ²ΠΊΠΈ ΠΏΠΎ ΡΠ»Π΅ΠΊΡΡΠΎΠ½Π½ΠΎΠΉ ΠΏΠΎΡΡΠ΅:
E-mail: [email protected]
ΠΠ΄ΡΠ΅Ρ ΡΠ΅ΡΠ²ΠΈΡΠ½ΠΎΠ³ΠΎ ΡΠ΅Π½ΡΡΠ° ΠΠΠ Β«ΠΠΠΠ€ΠΠ Β»:
Π³. Π‘Π°Π½ΠΊΡ-ΠΠ΅ΡΠ΅ΡΠ±ΡΡΠ³, 3-ΠΠ΅ΡΡ Π½ΠΈΠΉ ΠΏΠ΅ΡΠ΅ΡΠ»ΠΎΠΊ, Π΄ΠΎΠΌ 3, ΠΊΠΎΡΠΏ. 4
(ΠΏΡΠΎΠΌΠ·ΠΎΠ½Π° «ΠΠ°ΡΠ½Π°Ρ»)
.
ΠΡΠ°ΡΠΈΠΊ ΡΠ°Π±ΠΎΡΡ: ΠΠ-ΠΠ’ Ρ 8.00 Π΄ΠΎ 17.00, Π‘Π, ΠΠ‘ Π²ΡΡ ΠΎΠ΄Π½ΡΠ΅ Π΄Π½ΠΈ
www.benfer.ru
Π Π°Π±ΠΎΡΠΈΠΉ ΡΠΎΡΠΌΠΎΠ·Π½ΠΎΠΉ ΡΠΈΠ»ΠΈΠ½Π΄Ρ β Π·Π°ΠΌΠ΅Π½Π° ΠΈΠ»ΠΈ ΡΠ΅ΠΌΠΎΠ½Ρ?
ΠΡΠ»ΠΈ Π²ΡΡΠ°ΠΆΠ΅Π½ΠΈΠ΅ β Β«Π³Π»Π°Π²Π½ΠΎΠ΅ Π²ΠΎΠ²ΡΠ΅ΠΌΡ ΠΎΡΡΠ°Π½ΠΎΠ²ΠΈΡΡΡΡΒ» Π² ΠΏΠΎΠ²ΡΠ΅Π΄Π½Π΅Π²Π½ΠΎΠΌ ΠΎΠ±ΡΠ΅Π½ΠΈΠΈ ΠΊΠ°ΡΠ°Π΅ΡΡΡ ΠΌΠΎΡΠ°Π»ΡΠ½ΡΡ
ΠΏΡΠΈΠ½ΡΠΈΠΏΠΎΠ², ΡΠΎ Π² ΠΊΠΎΠ½ΡΠ΅ΠΊΡΡΠ΅ Π°Π²ΡΠΎΡΡΠ°Π½ΡΠΏΠΎΡΡΠ° ΡΡΠΎ Π²ΡΡΠ°ΠΆΠ΅Π½ΠΈΠ΅ ΠΌΠΎΠΆΠ΅Ρ Π·Π°ΡΡΠΎΠ½ΡΡΡ ΠΌΠ°ΡΠ΅ΡΠΈΠ°Π»ΡΠ½ΡΠΉ Π°ΡΠΏΠ΅ΠΊΡ ΠΆΠΈΠ·Π½ΠΈ ΠΈ Π·Π΄ΠΎΡΠΎΠ²ΡΠ΅ Π°Π²ΡΠΎΠΌΠΎΠ±ΠΈΠ»ΠΈΡΡΠ°.
Π ΡΡΡΡΠΎΠΉΡΡΠ²Π΅ Π°Π²ΡΠΎΠΌΠΎΠ±ΠΈΠ»Ρ Π½Π΅Ρ Π²ΡΠΎΡΠΎΡΡΠ΅ΠΏΠ΅Π½Π½ΡΡ Π°Π³ΡΠ΅Π³Π°ΡΠΎΠ², Π½ΠΎ ΡΠΎΡΠΌΠΎΠ·Π½Π°Ρ ΡΠΈΡΡΠ΅ΠΌΠ° Π΄ΠΎΠ»ΠΆΠ½Π° ΡΡΠ°ΡΡ ΠΏΡΠΈΠΎΡΠΈΡΠ΅ΡΠΎΠΌ Π² ΠΎΠ±ΡΠ»ΡΠΆΠΈΠ²Π°Π½ΠΈΠΈ ΠΈ ΡΠ΅ΠΌΠΎΠ½ΡΠ΅ ΠΌΠ°ΡΠΈΠ½Ρ. Π ΡΡ Π΅ΠΌΠ΅ ΡΠ°Π±ΠΎΡΡ Π³ΠΈΠ΄ΡΠ°Π²Π»ΠΈΡΠ΅ΡΠΊΠΈΡ ΡΠΎΡΠΌΠΎΠ·ΠΎΠ² ΠΎΡΠ½ΠΎΠ²Π½ΡΠΌΠΈ ΡΠ²Π»ΡΡΡΡΡ ΠΊΠ°ΠΊ Π³Π»Π°Π²Π½ΡΠΉ, ΡΠ°ΠΊ ΠΈ ΡΠ°Π±ΠΎΡΠΈΠΉ ΡΠΎΡΠΌΠΎΠ·Π½ΠΎΠΉ ΡΠΈΠ»ΠΈΠ½Π΄Ρ. ΠΠ°Π²Π°ΠΉΡΠ΅ ΡΠ°ΡΡΠΌΠΎΡΡΠΈΠΌ ΠΏΡΠΈΠ½ΡΠΈΠΏ ΡΠ°Π±ΠΎΡΡ, ΡΡΡΡΠΎΠΉΡΡΠ²ΠΎ, Π΄ΠΈΠ°Π³Π½ΠΎΡΡΠΈΠΊΡ, ΡΠ΅ΠΌΠΎΠ½Ρ ΠΈ Π·Π°ΠΌΠ΅Π½Ρ ΡΡΠΎΠ³ΠΎ ΡΠ·Π»Π° Π½Π° ΠΏΡΠΈΠΌΠ΅ΡΠ΅ ΡΠ°ΡΠΏΡΠΎΡΡΡΠ°Π½Π΅Π½Π½ΠΎΠ³ΠΎ Π°Π²ΡΠΎΠΌΠΎΠ±ΠΈΠ»Ρ ΠΌΠ°ΡΠΊΠΈ ΠΠΠ.
ΠΡΠΈΠ½ΡΠΈΠΏ ΡΠ°Π±ΠΎΡΡ
ΠΠΎΡΡΡΠΏΠ°ΡΡΠ°Ρ ΠΈΠ· Π³Π»Π°Π²Π½ΠΎΠ³ΠΎ, ΠΏΠΎΠ΄ Π΄Π°Π²Π»Π΅Π½ΠΈΠ΅ΠΌ, ΡΠΎΡΠΌΠΎΠ·Π½Π°Ρ ΠΆΠΈΠ΄ΠΊΠΎΡΡΡ Π²ΠΎΠ·Π΄Π΅ΠΉΡΡΠ²ΡΠ΅Ρ Π½Π° ΠΎΠ±Π° ΠΏΠΎΡΡΠ½Ρ Π² ΡΠ°Π±ΠΎΡΠ΅ΠΌ ΡΠΈΠ»ΠΈΠ½Π΄ΡΠ΅, ΡΠ΅, Π² ΡΠ²ΠΎΡ ΠΎΡΠ΅ΡΠ΅Π΄Ρ, ΡΠ΄Π°Π²Π»ΠΈΠ²Π°ΡΡ ΠΈΠ»ΠΈ ΡΠ°Π·ΠΆΠΈΠΌΠ°ΡΡ ΡΠΎΡΠΌΠΎΠ·Π½ΡΠ΅ ΠΊΠΎΠ»ΠΎΠ΄ΠΊΠΈ, ΡΡΠΎ ΠΏΡΠΈΠ²ΠΎΠ΄ΠΈΡ ΠΊ ΡΠΎΡΠΌΠΎΠΆΠ΅Π½ΠΈΡ. ΠΠ΅ΡΠ΅Π΄Π½ΠΈΠΉ ΠΊΠΎΠ½ΡΡΡ ΡΠΎΡΠΌΠΎΠ·ΠΎΠ² Π΄ΠΈΡΠΊΠΎΠ²ΡΠΉ, Π·Π°Π΄Π½ΠΈΠΉ Ρ ΠΌΠ½ΠΎΠ³ΠΈΡ Π°Π²ΡΠΎ β Π±Π°ΡΠ°Π±Π°Π½Π½ΠΎΠ³ΠΎ ΡΠΈΠΏΠ°.
- ΠΠ΅ΡΠ΅Π΄Π½ΠΈΠ΅ ΡΡΠΏΠΏΠΎΡΡΠ°.
- Π’ΡΡΠ±ΠΎΠΏΡΠΎΠ²ΠΎΠ΄, ΠΏΠΎΠ΄Π²ΠΎΠ΄ΡΡΠΈΠΉ Π³ΠΈΠ΄ΡΠ°Π²Π»ΠΈΡΠ΅ΡΠΊΡΡ ΠΆΠΈΠ΄ΠΊΠΎΡΡΡ ΠΊ ΠΏΠ΅ΡΠ΅Π΄Π½ΠΈΠΌ ΠΊΠΎΠ»Π΅ΡΠ°ΠΌ.
- ΠΠ°Π΄Π½ΠΈΠΉ ΡΡΡΠ±ΠΎΠΏΡΠΎΠ²ΠΎΠ΄.
- ΠΠ°Π»ΡΡΡ Π·Π°Π΄Π½ΠΈΡ ΠΊΠΎΠ»Π΅Ρ.
- ΠΠ°ΡΠΎΠΊ.
- ΠΠ»Π°Π²Π½ΡΠΉ Π²Π°Π»ΡΡ.
- ΠΠ΄ΠΈΠ½ ΠΈΠ· ΠΏΠΎΡΡΠ½Π΅ΠΉ.
- Π¨ΡΠΎΠΊ.
- ΠΠ΅Π΄Π°Π»Ρ.
Π£ΡΡΡΠΎΠΉΡΡΠ²ΠΎ
Π£ΡΡΡΠΎΠΉΡΡΠ²ΠΎΠΌ ΠΏΠ΅ΡΠ΅Π΄Π½ΠΈΠΉ ΡΡΠΏΠΏΠΎΡΡ ΠΈ Π·Π°Π΄Π½ΠΈΠΉ ΡΠΎΡΠΌΠΎΠ·Π½ΠΎΠΉ ΡΠΈΠ»ΠΈΠ½Π΄Ρ Π°Π²ΡΠΎΠΌΠΎΠ±ΠΈΠ»Ρ ΠΠΠ ΡΠ°Π·Π½ΡΡΡΡ Π²ΠΎ Π²Π½Π΅ΡΠ½Π΅ΠΌ Π²ΠΈΠ΄Π΅ ΠΊΠΎΡΠΏΡΡΠ° ΠΈ ΠΎΡΠ½ΠΎΠ²Π½ΡΡ
ΡΠ°ΡΡΠ΅ΠΉ.
Π£ΡΡΡΠΎΠΉΡΡΠ²ΠΎ Π΄ΠΈΡΠΊΠΎΠ²ΠΎΠ³ΠΎ ΡΠΎΡΠΌΠΎΠ·Π° ΡΠΎΡΡΠΎΠΈΡ ΠΈΠ· ΡΠ°ΠΊΠΈΡ
ΠΎΡΠ½ΠΎΠ²Π½ΡΡ
Π΄Π΅ΡΠ°Π»Π΅ΠΉ:
1 β ΠΠΎΡΡΠ΅Π½Ρ.
2 β ΠΡΠ»ΡΠ½ΠΈΠΊ.
3 β Π£ΠΏΠ»ΠΎΡΠ½ΠΈΡΠ΅Π»ΡΠ½Π°Ρ ΠΌΠ°Π½ΠΆΠ΅ΡΠ°.
4 β ΠΠΎΡΠΏΡΡ ΡΡΠΏΠΏΠΎΡΡΠ°.
6 β ΠΠΎΠ·Π΄ΡΡΠ½ΡΠΉ ΡΡΡΡΠ΅Ρ.
7 β ΠΡΡΠΆΠΈΠ½Ρ, ΠΏΡΠΈΠΆΠΈΠΌΠ°ΡΡΠΈΠ΅ ΠΊΠΎΠ»ΠΎΠ΄ΠΊΠΈ.
12 β ΠΠΎΠ»ΠΎΠ΄ΠΊΠΈ.
Π ΡΡΡΡΠΎΠΉΡΡΠ²Π΅ ΡΠΎΡΠΌΠΎΠ·Π° Π±Π°ΡΠ°Π±Π°Π½Π½ΠΎΠ³ΠΎ ΡΠΈΠΏΠ° ΠΏΡΠΈΠΌΠ΅Π½ΡΡΡΡΡ ΡΠ°ΠΊΠΈΠ΅ Π΄Π΅ΡΠ°Π»ΠΈ:
2 β Π¨ΡΡΡΠ΅Ρ ΠΏΡΠΎΠΊΠ°ΡΠΊΠΈ.
3, 11 β ΠΡΠ»ΡΠ½ΠΈΠΊ.
4, 10 β ΠΠΎΡΡΠ΅Π½Ρ.
6, 9 β Π£ΠΏΠ»ΠΎΡΠ½ΠΈΡΠ΅Π»ΡΠ½Π°Ρ ΠΌΠ°Π½ΠΆΠ΅ΡΠ° ΠΏΠΎΡΡΠ½Ρ.
7 β ΠΠΎΡΠΏΡΡ.
ΠΠΈΠ°Π³Π½ΠΎΡΡΠΈΠΊΠ°
Π ΡΠΎΠΌ, ΡΡΠΎ ΠΏΡΠΈΠ±Π»ΠΈΠΆΠ°Π΅ΡΡΡ ΡΠ΅ΠΌΠΎΠ½Ρ ΡΠ°Π±ΠΎΡΠ΅Π³ΠΎ ΡΠΎΡΠΌΠΎΠ·Π½ΠΎΠ³ΠΎ ΡΠΈΠ»ΠΈΠ½Π΄ΡΠ°, Π°Π²ΡΠΎΠΌΠΎΠ±ΠΈΠ»ΠΈΡΡΡ ΡΠ°ΡΡΠΊΠ°ΠΆΡΡ ΡΠ°ΠΊΠΈΠ΅ ΠΏΡΠΈΠ·Π½Π°ΠΊΠΈ:
- ΠΠ΅ΡΠ°Π²Π½ΠΎΠΌΠ΅ΡΠ½ΠΎΠ΅ ΡΡΠ°Π±Π°ΡΡΠ²Π°Π½ΠΈΠ΅ ΠΊΠΎΠ»Π΅Ρ ΠΏΡΠΈ ΡΠΎΡΠΌΠΎΠΆΠ΅Π½ΠΈΠΈ, ΡΠ»Π΅Π΄ΡΡΠ²ΠΈΠ΅ΠΌ ΡΠ΅Π³ΠΎ ΠΌΠΎΠΆΠ΅Ρ ΡΡΠ°ΡΡ Π·Π°Π½ΠΎΡ Π°Π²ΡΠΎ. ΠΡΠΎ ΠΏΡΠΈΠ·Π½Π°ΠΊ Π·Π°Π΅Π΄Π°Π½ΠΈΡ ΠΏΠΎΡΡΠ½Ρ, ΠΊΠΎΡΠΎΡΡΠΉ ΠΌΠΎΠΆΠ΅Ρ Π²ΡΠ·Π²Π°ΡΡ ΠΏΡΠΈΠΌΠ΅Π½Π΅Π½ΠΈΠ΅ Π½Π΅ΠΊΠ°ΡΠ΅ΡΡΠ²Π΅Π½Π½ΠΎΠΉ ΠΆΠΈΠ΄ΠΊΠΎΡΡΠΈ ΠΈΠ»ΠΈ ΠΏΠΎΠΏΠ°Π΄Π°Π½ΠΈΠ΅ Π² ΡΠΈΡΡΠ΅ΠΌΡ Π²ΠΎΠ·Π΄ΡΡ Π°.
- Π‘ΡΠ°Π±Π°ΡΡΠ²Π°Π½ΠΈΠ΅ ΠΈΠ½Π΄ΠΈΠΊΠ°ΡΠΎΡΠ½ΠΎΠΉ Π»Π°ΠΌΠΏΠΎΡΠΊΠΈ ΠΏΡΠΈ ΠΊΡΠΈΡΠΈΡΠ΅ΡΠΊΠΎΠΌ ΠΏΠΎΠ½ΠΈΠΆΠ΅Π½ΠΈΠΈ ΠΆΠΈΠ΄ΠΊΠΎΡΡΠΈ Π² Π±Π°ΡΠΊΠ΅, ΠΈΠ»ΠΈ ΠΎΠ±Π½Π°ΡΡΠΆΠ΅Π½ΠΈΠ΅ ΡΡΠΎΠ³ΠΎ ΠΏΡΠΈ Π²ΠΈΠ·ΡΠ°Π»ΡΠ½ΠΎΠΌ ΠΎΡΠΌΠΎΡΡΠ΅, ΡΡΠΎ Π³ΠΎΠ²ΠΎΡΠΈΡ ΠΎ Π²ΠΎΠ·ΠΌΠΎΠΆΠ½ΠΎΠΉ ΡΡΠ΅ΡΠΊΠ΅ Π³ΠΈΠ΄ΡΠ°Π²Π»ΠΈΡΠ΅ΡΠΊΠΎΠΉ ΠΆΠΈΠ΄ΠΊΠΎΡΡΠΈ ΠΈΠ· ΠΈΠ·Π½ΠΎΡΠΈΠ²ΡΠΈΡ ΡΡ ΠΌΠ°Π½ΠΆΠ΅Ρ ΠΈΠ»ΠΈ ΠΏΡΠΎΡ ΡΠ΄ΠΈΠ²ΡΠΈΡ ΡΡ ΠΏΠ°ΡΡΡΠ±ΠΊΠΎΠ².
- ΠΠ°ΠΆΠ°ΡΠΈΠ΅ ΠΏΠ΅Π΄Π°Π»ΠΈ Π΄Π°Π΅ΡΡΡ Ρ Π±ΠΎΠ»ΡΡΠΈΠΌ ΡΡΠΈΠ»ΠΈΠ΅ΠΌ, ΡΡΠΎ ΠΌΠΎΠΆΠ΅Ρ ΠΏΡΠΎΠΈΡΡ ΠΎΠ΄ΠΈΡΡ ΠΏΠΎ Π²ΡΠ΅ΠΌ Π²ΡΡΠ΅ΠΎΠΏΠΈΡΠ°Π½Π½ΡΠΌ ΠΏΡΠΈΡΠΈΠ½Π°ΠΌ.
ΠΠ°Π΅Π΄Π°ΡΡΠΈΠΉ ΠΏΠΎΡΡΠ΅Π½Ρ ΠΈ ΡΡΠ³Π°Ρ ΠΏΠ΅Π΄Π°Π»Ρ Π΅ΡΠ΅ Π½Π΅ ΠΏΠΎΠΊΠ°Π·Π°ΡΠ΅Π»Ρ Π΄Π»Ρ ΡΠ΅ΠΌΠΎΠ½ΡΠ° ΠΈ Π·Π°ΠΌΠ΅Π½Ρ ΡΠ°Π±ΠΎΡΠΈΡ ΡΠΈΠ»ΠΈΠ½Π΄ΡΠΎΠ². Π‘Π»Π΅Π΄ΡΠ΅Ρ ΠΎΠ±ΡΠ°ΡΠΈΡΡ Π²Π½ΠΈΠΌΠ°Π½ΠΈΠ΅ Π½Π° ΡΠΎΠ»ΡΠΈΠ½Ρ ΠΊΠΎΠ»ΠΎΠ΄ΠΎΠΊ, Π΅ΡΠ»ΠΈ ΠΈΡ ΠΈΠ·Π½ΠΎΡ Π΄ΠΎΡΡΠΈΠ³ ΠΌΠ°ΠΊΡΠΈΠΌΡΠΌΠ°, ΡΡΠΎ ΠΌΠΎΠΆΠ΅Ρ ΡΠΏΡΠΎΠ²ΠΎΡΠΈΡΠΎΠ²Π°ΡΡ Π·Π°ΠΊΠ»ΠΈΠ½ΠΈΠ²Π°Π½ΠΈΠ΅ ΠΏΠΎΡΡΠ½Π΅ΠΉ, ΡΠ°ΠΊ ΠΊΠ°ΠΊ ΠΎΠ½ΠΈ ΠΏΡΠ°ΠΊΡΠΈΡΠ΅ΡΠΊΠΈ Π½Π΅ ΡΠ°Π±ΠΎΡΠ°ΡΡ.
ΠΠ·Π½Π°ΡΠ°Π»ΡΠ½ΠΎ ΡΠ°ΠΊΠΆΠ΅ ΠΌΠΎΠΆΠ΅Ρ ΠΏΠΎΠΌΠΎΡΡ ΠΈΡΠΏΡΠ°Π²ΠΈΡΡ ΡΡΠΈ ΠΏΡΠΎΠ±Π»Π΅ΠΌΡ ΠΏΠΎΠ»Π½Π°Ρ Π·Π°ΠΌΠ΅Π½Π° Π³ΠΈΠ΄ΡΠ°Π²Π»ΠΈΡΠ΅ΡΠΊΠΎΠΉ ΠΆΠΈΠ΄ΠΊΠΎΡΡΠΈ ΠΈΠ»ΠΈ ΠΏΡΠΎΠΊΠ°ΡΠΊΠ° ΡΠΈΡΡΠ΅ΠΌΡ ΡΠΎΡΠΌΠΎΠ·ΠΎΠ². ΠΡΠ»ΠΈ ΡΡΠΈ Π΄Π΅ΠΉΡΡΠ²ΠΈΡ Π½Π΅ ΠΏΡΠΈΠ²Π΅Π»ΠΈ ΠΊ ΠΏΠΎΠ»ΠΎΠΆΠΈΡΠ΅Π»ΡΠ½ΠΎΠΌΡ ΡΠ΅Π·ΡΠ»ΡΡΠ°ΡΡ, ΡΡΠ΅Π±ΡΠ΅ΡΡΡ ΠΎΡΡΠ΅ΠΌΠΎΠ½ΡΠΈΡΠΎΠ²Π°ΡΡ ΡΠ°Π±ΠΎΡΠΈΠΉ ΡΠΎΡΠΌΠΎΠ·Π½ΠΎΠΉ ΡΠΈΠ»ΠΈΠ½Π΄Ρ, Π±Π»Π°Π³ΠΎ Π² ΠΏΡΠΎΠ΄Π°ΠΆΠ΅ Π΅ΡΡΡ ΡΠ΅ΠΌΠΊΠΎΠΏΠ»Π΅ΠΊΡ ΡΠ°Π±ΠΎΡΠ΅Π³ΠΎ ΡΠΎΡΠΌΠΎΠ·Π½ΠΎΠ³ΠΎ ΡΠΈΠ»ΠΈΠ½Π΄ΡΠ°, Π² Π½Π°Π±ΠΎΡ ΠΊΠΎΡΠΎΡΠΎΠ³ΠΎ, Π² Π·Π°Π²ΠΈΡΠΈΠΌΠΎΡΡΠΈ ΠΎΡ ΠΌΠ°ΡΠΊΠΈ Π°Π²ΡΠΎ, Π²Ρ ΠΎΠ΄ΡΡ: ΠΌΠ°Π½ΠΆΠ΅ΡΡ, ΠΏΠΎΡΡΠ΅Π½Ρ, ΠΏΡΠ»ΡΠ½ΠΈΠΊ ΠΈ ΠΏΡΠΎΡΠΈΠ΅ ΡΠΎΡΡΠ°Π²Π»ΡΡΡΠΈΠ΅.
Π Π΅ΠΌΠΎΠ½ΡΠ½ΡΠ΅ ΡΠ°Π±ΠΎΡΡ
Π Π°Π·Π±ΠΎΡΠΊΠ°, ΡΠ΅ΠΌΠΎΠ½Ρ ΠΈ Π·Π°ΠΌΠ΅Π½Π° ΡΠΎΡΠΌΠΎΠ·Π½ΠΎΠ³ΠΎ ΡΠΈΠ»ΠΈΠ½Π΄ΡΠ° Π°Π²ΡΠΎΠΌΠΎΠ±ΠΈΠ»Ρ ΠΠΠ Π½Π΅ ΠΏΡΠ΅Π΄ΡΡΠ°Π²Π»ΡΠ΅Ρ ΠΎΡΠΎΠ±ΠΎΠΉ ΡΠ»ΠΎΠΆΠ½ΠΎΡΡΠΈ. ΠΡΠΈΠΎΠ±ΡΠ΅ΡΡ Π½Π΅ΠΎΠ±Ρ ΠΎΠ΄ΠΈΠΌΡΠΉ ΡΠ΅ΠΌΠΊΠΎΠΌΠΏΠ»Π΅ΠΊΡ ΡΠ°Π±ΠΎΡΠ΅Π³ΠΎ ΡΠΎΡΠΌΠΎΠ·Π½ΠΎΠ³ΠΎ ΡΠΈΠ»ΠΈΠ½Π΄ΡΠ°, ΠΎΡΠΊΡΡΡΠΈΠ²Π°Π΅ΠΌ ΠΊΠΎΠ»Π΅ΡΠΎ ΠΈ, ΠΎΡΡΠΎΠ΅Π΄ΠΈΠ½ΠΈΠ² ΠΏΠ°ΡΡΡΠ±ΠΊΠΈ, ΡΠ½ΠΈΠΌΠ°Π΅ΠΌ Π½Π΅ΠΈΡΠΏΡΠ°Π²Π½ΡΠΉ ΡΠΈΠ»ΠΈΠ½Π΄Ρ (Π±ΠΎΠ»Π΅Π΅ ΠΏΠΎΠ΄ΡΠΎΠ±Π½ΠΎ ΡΡ Π΅ΠΌΠ° Π΄Π΅ΠΌΠΎΠ½ΡΠ°ΠΆΠ° Π±ΡΠ΄Π΅Ρ ΠΎΠΏΠΈΡΠ°Π½Π° Π½ΠΈΠΆΠ΅).
ΠΠ»Ρ ΡΠ΄ΠΎΠ±ΡΡΠ²Π°, Π·Π°ΠΆΠ°Π² ΠΊΠΎΡΠΏΡΡ Π² ΡΠΈΡΠΊΠ°Ρ ΠΈ ΡΠ½ΡΠ² ΠΏΡΠ»ΡΠ½ΠΈΠΊ, ΠΏΠΎΠ»ΡΡΠ°Π΅ΠΌ Π΄ΠΎΡΡΡΠΏ ΠΊ ΡΡΠΎΠΏΠΎΡΠ½ΠΎΠΌΡ ΠΊΠΎΠ»ΡΡΡ, ΡΠΈΠΊΡΠΈΡΡΡΡΠ΅ΠΌΡ ΠΏΠΎΡΡΠ΅Π½Ρ, ΠΏΠΎΡΠ»Π΅ ΡΠ½ΡΡΠΈΡ ΠΊΠΎΡΠΎΡΠΎΠ³ΠΎ, Π²ΡΠ½ΠΈΠΌΠ°Π΅ΠΌ Π²ΡΠ΅ ΡΠ°Π±ΠΎΡΠΈΠ΅ Π΄Π΅ΡΠ°Π»ΠΈ.
ΠΡΠΎΠΈΠ·Π²Π΅Π΄Ρ ΡΠ°Π·Π±ΠΎΡΠΊΡ ΠΊΠΎΡΠΏΡΡΠ° Π½ΡΠΆΠ½ΠΎ ΠΏΡΠΎΠΌΡΡΡ Π²ΡΡ ΡΠΎΡΠΌΠΎΠ·Π½ΠΎΠΉ ΠΆΠΈΠ΄ΠΊΠΎΡΡΡΡ ΠΈ ΠΎΡΠΌΠΎΡΡΠ΅ΡΡ Π·Π΅ΡΠΊΠ°Π»ΠΎ ΠΊΠΎΡΠΏΡΡΠ° Π½Π° ΠΏΡΠ΅Π΄ΠΌΠ΅Ρ ΠΌΠ΅Ρ Π°Π½ΠΈΡΠ΅ΡΠΊΠΈΡ ΠΏΠΎΠ²ΡΠ΅ΠΆΠ΄Π΅Π½ΠΈΠΉ.
ΠΡΠ»ΠΈ ΠΏΠΎΠ²ΡΠ΅ΠΆΠ΄Π΅Π½ΠΈΠΉ Π½Π΅ Π²ΡΡΠ²Π»Π΅Π½ΠΎ, ΡΠΎ, Π²ΡΠΊΡΡΠ² ΡΠ΅ΠΌΠΊΠΎΠΌΠΏΠ»Π΅ΠΊΡ ΡΠ°Π±ΠΎΡΠ΅Π³ΠΎ ΡΠΎΡΠΌΠΎΠ·Π½ΠΎΠ³ΠΎ ΡΠΈΠ»ΠΈΠ½Π΄ΡΠ°, ΠΏΡΠΎΠΈΠ·Π²Π΅ΡΡΠΈ Π·Π°ΠΌΠ΅Π½Ρ Π½Π΅ΠΈΡΠΏΡΠ°Π²Π½ΡΡ Π΄Π΅ΡΠ°Π»Π΅ΠΉ.
ΠΠ±ΡΠ·Π°ΡΠ΅Π»ΡΠ½ΡΠΌ ΡΡΠ»ΠΎΠ²ΠΈΠ΅ΠΌ, Π² Π½Π΅Π·Π°Π²ΠΈΡΠΈΠΌΠΎΡΡΠΈ ΠΎΡ ΠΈΡ ΡΠΎΡΡΠΎΡΠ½ΠΈΡ, ΡΠ²Π»ΡΠ΅ΡΡΡ Π·Π°ΠΌΠ΅Π½Π° Π²ΡΠ΅Ρ ΡΠ΅Π·ΠΈΠ½ΠΎΠ²ΡΡ Π΄Π΅ΡΠ°Π»Π΅ΠΉ Π²Ρ ΠΎΠ΄ΡΡΠΈΡ Π² ΡΠ΅ΠΌΠΊΠΎΠΌΠΏΠ»Π΅ΠΊΡ ΡΠ°Π±ΠΎΡΠ΅Π³ΠΎ ΡΠΎΡΠΌΠΎΠ·Π½ΠΎΠ³ΠΎ ΡΠΈΠ»ΠΈΠ½Π΄ΡΠ°. Π ΡΡΠΎΡ ΡΠΏΠΈΡΠΎΠΊ Π²Ρ ΠΎΠ΄ΡΡ: ΠΏΡΠ»ΡΠ½ΠΈΠΊ, ΠΌΠ°Π½ΠΆΠ΅ΡΠ° ΠΈ ΠΏΡΠΎΡΠ΅Π΅.
ΠΠ°ΠΌΠ΅Π½Π° Π½Π΅ΠΈΡΠΏΡΠ°Π²Π½ΠΎΠ³ΠΎ ΡΠΈΠ»ΠΈΠ½Π΄ΡΠ° ΡΠΎΡΠΌΠΎΠ·ΠΎΠ²
Π‘Ρ Π΅ΠΌΠ° Π·Π°ΠΌΠ΅Π½Ρ Π² ΡΠ΅ΠΌΠ΅ΠΉΡΡΠ²Π΅ ΠΠΠ ΠΏΡΠ°ΠΊΡΠΈΡΠ΅ΡΠΊΠΈ ΠΎΠ΄ΠΈΠ½Π°ΠΊΠΎΠ²Π° Π΄Π»Ρ ΡΠΈΠ»ΠΈΠ½Π΄ΡΠΎΠ² ΠΎΠ±ΠΎΠΈΡ ΠΊΠΎΠ½ΡΡΡΠΎΠ² Ρ ΠΌΠ΅Π»ΠΊΠΈΠΌΠΈ ΡΠ°Π·Π»ΠΈΡΠΈΡΠΌΠΈ.
ΠΠ·Π½Π°ΡΠ°Π»ΡΠ½ΠΎ Π½ΡΠΆΠ½ΠΎ ΠΏΡΠΈΠ³ΠΎΡΠΎΠ²ΠΈΡΡ Π½Π΅ΠΎΠ±Ρ ΠΎΠ΄ΠΈΠΌΡΠ΅ ΠΊΠ»ΡΡΠΈ ΠΈ ΠΏΠΎΠ΄Ρ ΠΎΠ΄ΡΡΠΈΠ΅ ΠΏΠΎ ΡΠ°Π·ΠΌΠ΅ΡΡ ΠΏΠ°ΡΡΡΠ±ΠΊΠΎΠ² Π·Π°Π³Π»ΡΡΠΊΠΈ. Π‘Π½ΡΠ² ΠΊΠΎΠ»Π΅ΡΠΎ ΠΈ ΠΎΡΠΊΡΡΡΠΈΠ² ΠΏΠ°ΡΡΡΠ±ΠΊΠΈ, Π΄Π»Ρ ΠΏΡΠ΅Π΄ΠΎΡΠ²ΡΠ°ΡΠ΅Π½ΠΈΡ ΡΡΠ΅ΡΠΊΠΈ ΠΆΠΈΠ΄ΠΊΠΎΡΡΠΈ Π½Π°Π΄Π΅Π²Π°Π΅ΠΌ Π½Π° Π½ΠΈΡ Π·Π°Π³Π»ΡΡΠΊΠΈ. ΠΡΠΊΡΡΡΠΈΠ² ΡΠΎΠΎΡΠ²Π΅ΡΡΡΠ²ΡΡΡΠΈΠ΅ Π³Π°ΠΉΠΊΠΈ, Π΄Π΅ΠΌΠΎΠ½ΡΠΈΡΡΠ΅ΠΌ ΡΡΠ°ΡΡΠΉ ΡΠΈΠ»ΠΈΠ½Π΄Ρ ΠΈ Π½Π° Π΅Π³ΠΎ ΠΌΠ΅ΡΡΠΎ ΡΡΠ°Π²ΠΈΠΌ Π½ΠΎΠ²ΡΠΉ, ΠΏΡΠΎΠΈΠ·Π²ΠΎΠ΄Ρ ΡΠ±ΠΎΡΠΊΡ Π² ΠΎΠ±ΡΠ°ΡΠ½ΠΎΠΌ ΠΏΠΎΡΡΠ΄ΠΊΠ΅. ΠΡΠ»ΠΈ ΠΏΠΎΡΠ»Π΅ Π·Π°ΠΌΠ΅Π½Ρ, ΡΠ±ΠΎΡΠΊΠ΅ ΠΊΠΎΠ»Π΅ΡΠ° ΠΌΠ΅ΡΠ°ΡΡ ΡΠ»ΠΈΡΠΊΠΎΠΌ ΡΠ°Π·Π²Π΅Π΄Π΅Π½Π½ΡΠ΅ ΠΊΠΎΠ»ΠΎΠ΄ΠΊΠΈ, ΠΌΠΎΠΆΠ½ΠΎ ΠΏΠΎΠ΄ΠΏΠΈΠ»ΠΈΡΡ ΠΊΠΎΠ½ΡΠΎΠ²ΠΊΠΈ ΠΊΠΎΠ»ΠΎΠ΄ΠΎΠΊ, ΡΠΎΠ»ΡΠΊΠΎ Π½Π΅ ΠΏΠ΅ΡΠ΅ΡΡΠ΅ΡΠ΄ΡΡΠ²ΡΠΉΡΠ΅, ΡΡΠΎ ΠΌΠΎΠΆΠ΅Ρ ΡΠΊΠ°Π·Π°ΡΡΡΡ Π½Π° ΡΠ°Π±ΠΎΡΠ΅ ΡΡΡΠ½ΠΎΠ³ΠΎ ΡΠΎΡΠΌΠΎΠ·Π°.
ΠΠΎΡΠ»Π΅ Π»ΡΠ±ΡΡ ΠΌΠ°Π½ΠΈΠΏΡΠ»ΡΡΠΈΠΉ Ρ ΡΠΈΡΡΠ΅ΠΌΠΎΠΉ ΡΠΎΡΠΌΠΎΠ·ΠΎΠ² ΡΡΠ΅Π±ΡΠ΅ΡΡΡ Π΅Π΅ ΠΏΡΠΎΠΊΠ°ΡΠΊΠ° ΡΠΎΠ³Π»Π°ΡΠ½ΠΎ ΡΡ Π΅ΠΌΠ΅.
ΠΡΠΎΠΊΠ°ΡΠΊΠ° ΡΠΈΡΡΠ΅ΠΌΡ ΡΠΎΡΠΌΠΎΠ·ΠΎΠ².
ΠΠ»Ρ ΠΏΡΠΎΠΊΠ°ΡΠΊΠΈ ΠΏΠΎΠ΄Π³ΠΎΡΠΎΠ²ΡΡΠ΅: ΠΆΠΈΠ΄ΠΊΠΎΡΡΡ, ΠΊΠ»ΡΡ ΠΏΠΎΠ΄Ρ ΠΎΠ΄ΡΡΠ΅Π³ΠΎ Π΄ΠΈΠ°ΠΌΠ΅ΡΡΠ° ΠΊ Π²ΠΎΠ·Π΄ΡΡΠ½ΠΎΠΌΡ ΡΡΡΡΠ΅ΡΡ, ΡΠ»Π°Π½Π³, ΠΏΠ»ΠΎΡΠ½ΠΎ ΠΎΠ΄Π΅Π²Π°ΡΡΠΈΠΉΡΡ Π½Π° ΡΡΡΡΠ΅Ρ ΠΈ Π»ΡΠ±ΡΡ Π΅ΠΌΠΊΠΎΡΡΡ. Π‘Ρ Π΅ΠΌΠ° ΠΏΡΠΎΠΊΠ°ΡΠΊΠΈ Π·Π°Π²ΠΈΡΠΈΡ ΠΎΡ ΡΠΎΠ³ΠΎ, ΠΊΠ°ΠΊ ΡΠ°ΡΠΏΠΎΠ»ΠΎΠΆΠ΅Π½Ρ ΠΊΠΎΠ½ΡΡΡΡ Π² ΠΊΠΎΠ½ΠΊΡΠ΅ΡΠ½ΠΎΠΉ ΠΌΠΎΠ΄Π΅Π»ΠΈ ΠΠΠ. Π£ΡΡΡΠΎΠΉΡΡΠ²ΠΎ ΡΠΎΡΠΌΠΎΠ·ΠΎΠ² Π½Π΅ΠΊΠΎΡΠΎΡΡΡ ΠΏΠΎΠ΄ΡΠ°Π·ΡΠΌΠ΅Π²Π°Π΅Ρ ΠΏΡΠΎΠΊΠ°ΡΠΊΡ ΠΎΡ Β«Π΄Π»ΠΈΠ½Π½ΠΎΠ³ΠΎ ΡΡΡΠ±ΠΎΠΏΡΠΎΠ²ΠΎΠ΄Π°Β», ΠΈΠΌΠ΅Π΅ΡΡΡ Π² Π²ΠΈΠ΄Ρ ΠΎΡ ΡΠ°ΠΌΠΎΠ³ΠΎ Π΄Π°Π»ΡΠ½Π΅Π³ΠΎ ΠΊΠΎΠ»Π΅ΡΠ° ΠΎΡΠ½ΠΎΡΠΈΡΠ΅Π»ΡΠ½ΠΎ Π³Π»Π°Π²Π½ΠΎΠ³ΠΎ ΡΠΈΠ»ΠΈΠ½Π΄ΡΠ°.
ΠΡΠ»ΠΈ ΠΊΠΎΠ½ΠΊΡΠ΅ΡΠ½Π΅Π΅ ΡΡΠΎ Π²ΡΠ³Π»ΡΠ΄ΠΈΡ ΡΠ°ΠΊ: Π² ΠΌΠ°ΡΠΈΠ½Π΅ Π³Π»Π°Π²Π½ΡΠΉ ΡΠΈΠ»ΠΈΠ½Π΄Ρ ΡΠ°Π·ΠΌΠ΅ΡΠ΅Π½ Π³Π»ΡΠ΄Ρ Π½Π° Π·Π°Π΄Π½ΠΈΠΉ Π±Π°ΠΌΠΏΠ΅Ρ, Π·Π½Π°ΡΠΈΡ ΠΏΠ΅ΡΠ²ΡΠΌ ΠΏΡΠΎΠΊΠ°ΡΠΈΠ²Π°Π΅ΡΡΡ Π·Π°Π΄Π½ΠΈΠΉ ΠΏΡΠ°Π²ΡΠΉ ΡΠΈΠ»ΠΈΠ½Π΄Ρ, Π·Π°ΡΠ΅ΠΌ Π·Π°Π΄Π½ΠΈΠΉ Π»Π΅Π²ΡΠΉ. Π‘Π»Π΅Π΄ΡΡΡΠΈΠΌ ΠΈΠ΄Π΅Ρ ΠΏΠ΅ΡΠ΅Π΄Π½ΠΈΠΉ Π»Π΅Π²ΡΠΉ, ΠΈ ΠΎΠΊΠ°Π½ΡΠΈΠ²Π°Π΅ΡΡΡ ΠΏΡΠΎΡΠ΅Π΄ΡΡΠ° ΠΏΡΠΎΠΊΠ°ΡΠΊΠΎΠΉ ΡΠΎΠ³ΠΎ ΠΊΠΎΠ»Π΅ΡΠ°, ΠΊΠΎΡΠΎΡΠΎΠ΅ Π½Π°Ρ ΠΎΠ΄ΠΈΡΡΡΡ Ρ ΠΏΡΠ°Π²ΠΎΠΉ ΡΡΠΎΡΠΎΠ½Ρ ΠΎΡ Π³Π»Π°Π²Π½ΠΎΠ³ΠΎ ΡΠΈΠ»ΠΈΠ½Π΄ΡΠ°. Π Π±ΠΎΠ»Π΅Π΅ ΠΏΠΎΠ·Π΄Π½ΠΈΡ ΠΌΠΎΠ΄Π΅Π»ΡΡ ΡΡ Π΅ΠΌΠ° ΠΏΠΎΠ΄ΡΠ°Π·ΡΠΌΠ΅Π²Π°Π΅Ρ ΠΏΡΠΎΠΊΠ°ΡΠΊΡ ΠΊΡΠ΅ΡΡ-Π½Π°ΠΊΡΠ΅ΡΡ Π³Π»ΡΠ΄Ρ Π½Π° ΠΌΠ°ΡΠΈΠ½Ρ ΡΠ·Π°Π΄ΠΈ:
- ΠΏΡΠ°Π²ΠΎΠ΅ Π·Π°Π΄Π½Π΅Π΅ ΠΊΠΎΠ»Π΅ΡΠΎ;
- Π»Π΅Π²ΠΎΠ΅ ΠΏΠ΅ΡΠ΅Π΄Π½Π΅Π΅ ΠΊΠΎΠ»Π΅ΡΠΎ;
- Π»Π΅Π²ΠΎΠ΅ Π·Π°Π΄Π½Π΅Π΅ ΠΊΠΎΠ»Π΅ΡΠΎ;
- ΠΏΡΠ°Π²ΠΎΠ΅ ΠΏΠ΅ΡΠ΅Π΄Π½Π΅Π΅ ΠΊΠΎΠ»Π΅ΡΠΎ.
Π Π»ΡΠ±ΠΎΠΌ ΡΠ»ΡΡΠ°Π΅ Π·Π°ΠΊΠ°Π½ΡΠΈΠ²Π°ΡΡ ΠΏΡΠΎΠΊΠ°ΡΠΊΡ ΡΠ»Π΅Π΄ΡΠ΅Ρ ΠΏΠ΅ΡΠ΅Π΄Π½ΠΈΠΌ ΠΏΡΠ°Π²ΡΠΌ ΠΊΠΎΠ»Π΅ΡΠΎΠΌ.
Π ΠΏΡΠΎΡΠ΅ΡΡΠ΅ ΡΡΠΎΠ³ΠΎ Π΄Π΅ΠΉΡΡΠ²ΠΈΡ Π½Π΅ Π·Π°Π±ΡΠ²Π°ΠΉΡΠ΅ ΡΠ»Π΅Π΄ΠΈΡΡ Π·Π° ΡΡΠΎΠ²Π½Π΅ΠΌ Π³ΠΈΠ΄ΡΠ°Π²Π»ΠΈΡΠ΅ΡΠΊΠΎΠΉ ΠΆΠΈΠ΄ΠΊΠΎΡΡΠΈ Π² Π±Π°ΡΠΊΠ΅, ΡΡΠΎΠ±Ρ Π²ΠΎΠ·Π΄ΡΡ ΠΎΠΏΡΡΡ Π½Π΅ ΠΏΠΎΠΏΠ°Π» Π² ΡΠΈΡΡΠ΅ΠΌΡ.
Π’Π°ΠΊΠΆΠ΅ ΡΠ΅ΠΊΠΎΠΌΠ΅Π½Π΄ΡΠ΅ΠΌ ΠΊ ΠΏΡΠΎΡΠΌΠΎΡΡΡ Π²ΠΈΠ΄Π΅ΠΎ ΠΏΠΎ ΡΠ΅ΠΌΠ΅:
autoremont2.ru
Π Π΅ΠΌΠΎΠ½Ρ Π³Π»Π°Π²Π½ΠΎΠ³ΠΎ ΡΠΎΡΠΌΠΎΠ·Π½ΠΎΠ³ΠΎ ΡΠΈΠ»ΠΈΠ½Π΄ΡΠ° ΡΠ²ΠΎΠΈΠΌΠΈ ΡΡΠΊΠ°ΠΌΠΈ Β» ΠΠ²ΡΠΎΠΠΎΠ²Π°ΡΠΎΡ
Π ΠΏΠ΅ΡΠ΅Π²ΠΎΠ΄Π΅ Ρ ΡΡΡΠΊΡΠΊΠΎΠ³ΠΎ ΡΠ·ΡΠΊΠ° ΡΠΎΡΠΌΠΎΠ· (turmaz) ΠΎΠ·Π½Π°ΡΠ°Π΅Ρ ΠΏΠΎΠ΄ΠΊΠ»Π°Π΄ΠΊΡ ΠΏΠΎΠ΄ ΠΊΠΎΠ»Π΅ΡΠ° Π°ΡΠ±Ρ. ΠΡ ΡΠΆΠ΅ ΠΏΡΠΎΡΠ»ΠΈ ΠΏΠΎ ΡΠ²ΠΎΠ»ΡΡΠΈΠΎΠ½Π½ΠΎΠΉ Π»ΠΈΠ½Π΅ΠΉΠΊΠ΅ ΡΠ°Π·Π²ΠΈΡΠΈΡ ΡΡΠ°Π½ΡΠΏΠΎΡΡΠ°, ΠΈ Π² ΡΠΎΠ²ΡΠ΅ΠΌΠ΅Π½Π½ΠΎΠΌ Π°Π²ΡΠΎΠΌΠΎΠ±ΠΈΠ»Π΅ ΡΠΎΡΠΌΠΎΠ·Π½Π°Ρ ΡΠΈΡΡΠ΅ΠΌΠ° Π½Π΅ ΠΎΠ³ΡΠ°Π½ΠΈΡΠΈΠ²Π°Π΅ΡΡΡ ΠΎΠ΄Π½ΠΎΠΉ ΡΠΎΠ»ΡΠΊΠΎ ΠΏΠΎΠ΄ΠΊΠ»Π°Π΄ΠΊΠΎΠΉ ΠΏΠΎΠ΄ ΠΊΠΎΠ»ΡΡΠ° Π°Π²ΡΠΎ.
Π£ΡΡΡΠΎΠΉΡΡΠ²ΠΎ Π³Π»Π°Π²Π½ΠΎΠ³ΠΎ ΡΠΎΡΠΌΠΎΠ·Π½ΠΎΠ³ΠΎ ΡΠΈΠ»ΠΈΠ½Π΄ΡΠ°
Π’ΠΎΡΠΌΠΎΠ·Π½Π°Ρ ΡΠΈΡΡΠ΅ΠΌΠ° Π°Π²ΡΠΎΠΌΠΎΠ±ΠΈΠ»Ρ ΡΠ΅Π³ΠΎΠ΄Π½Ρ β ΡΡΠΎ ΡΠ»ΠΎΠΆΠ½Π΅ΠΉΡΠ°Ρ ΡΠΈΡΡΠ΅ΠΌΠ° ΠΌΠ΅Ρ Π°Π½ΠΈΡΠ΅ΡΠΊΠΈΡ ΠΈ ΡΠ»Π΅ΠΊΡΡΠΎΠ½Π½ΡΡ ΡΠ·Π»ΠΎΠ² ΠΈ Π΄Π΅ΡΠ°Π»Π΅ΠΉ, ΠΊΠΎΡΠΎΡΡΠ΅ ΠΏΡΠ΅Π΄Π½Π°Π·Π½Π°ΡΠ΅Π½Ρ Π΄Π»Ρ Π·Π°ΠΌΠ΅Π΄Π»Π΅Π½ΠΈΡ Π΄Π²ΠΈΠΆΠ΅Π½ΠΈΡ ΠΈΠ»ΠΈ ΠΎΡΡΠ°Π½ΠΎΠ²ΠΊΠΈ ΡΡΠ°Π½ΡΠΏΠΎΡΡΠ½ΠΎΠ³ΠΎ ΡΡΠ΅Π΄ΡΡΠ²Π°. Π’ΠΎΡΠΌΠΎΠ·Π° β ΡΡΠΎ Π½Π°ΡΠ° Π±Π΅Π·ΠΎΠΏΠ°ΡΠ½ΠΎΡΡΡ, ΠΏΠΎΡΡΠΎΠΌΡ ΡΠ²ΠΎΠ΅Π²ΡΠ΅ΠΌΠ΅Π½Π½ΠΎΠ΅ ΠΎΠ±ΡΠ»ΡΠΆΠΈΠ²Π°Π½ΠΈΠ΅ ΠΈ ΡΠ΅ΠΌΠΎΠ½Ρ ΡΠΎΡΠΌΠΎΠ·Π½ΠΎΠΉ ΡΠΈΡΡΠ΅ΠΌΡ β ΠΏΠΎ ΡΠΌΠΎΠ»ΡΠ°Π½ΠΈΡ ΠΏΡΠΈΠΎΡΠΈΡΠ΅ΡΠ½ΠΎΠ΅ ΠΏΠΎΠ½ΡΡΠΈΠ΅.
ΠΡΠ½ΠΎΠ²Π½ΡΠΌ Π·Π²Π΅Π½ΠΎΠΌ Π² ΡΠΎΡΠΌΠΎΠ·Π½ΠΎΠΉ ΡΠΈΡΡΠ΅ΠΌΠ΅ ΡΠ²Π»ΡΠ΅ΡΡΡ Π³Π»Π°Π²Π½ΡΠΉ ΡΠΎΡΠΌΠΎΠ·Π½ΠΎΠΉ ΡΠΈΠ»ΠΈΠ½Π΄Ρ.
Π Π΅ΠΌΠΎΠ½Ρ Π³Π»Π°Π²Π½ΠΎΠ³ΠΎ ΡΠΎΡΠΌΠΎΠ·Π½ΠΎΠ³ΠΎ ΡΠΈΠ»ΠΈΠ½Π΄ΡΠ° Π΅ΡΡΠ΅ΡΡΠ²Π΅Π½Π½ΡΠΌ ΠΎΠ±ΡΠ°Π·ΠΎΠΌ ΠΏΠΎΠ΄ΡΠ°Π·ΡΠΌΠ΅Π²Π°Π΅Ρ Π·Π½Π°Π½ΠΈΠ΅ Π΅Π³ΠΎ ΡΡΡΡΠΎΠΉΡΡΠ²Π°. Π―Π²Π»ΡΡΡΡ Π³Π»Π°Π²Π½ΡΠΌ ΠΌΠ΅Ρ Π°Π½ΠΈΠ·ΠΌΠΎΠΌ, ΠΏΡΠΈΠ²ΠΎΠ΄ΡΡΠΈΠΌ Π² Π΄Π΅ΠΉΡΡΠ²ΠΈΠ΅ ΡΠΎΡΠΌΠΎΠ·Π°, Π³Π»Π°Π²Π½ΡΠΉ ΡΠΎΡΠΌΠΎΠ·Π½ΠΎΠΉ ΡΠΈΠ»ΠΈΠ½Π΄Ρ, ΠΏΠΎ ΡΡΡΠΈ, ΡΡΡΡΠΎΠ΅Π½ ΠΏΡΠΎΡΡΠΎ. ΠΠ°ΠΊ ΠΈ Π²ΡΡ Π³Π΅Π½ΠΈΠ°Π»ΡΠ½ΠΎΠ΅.
ΠΡΠ½ΠΎΠ²Π½ΡΠΌΠΈ ΠΊΠΎΠΌΠΏΠΎΠ½Π΅Π½ΡΠ°ΠΌΠΈ Π΅Π³ΠΎ ΡΠ²Π»ΡΡΡΡΡ: ΠΏΠΎΡΡΠ½ΠΈ, ΠΏΡΠΈΠ²ΠΎΠ΄ΡΡΠΈΠ΅ Π² Π΄Π΅ΠΉΡΡΠ²ΠΈΠ΅ ΠΊΠΎΠ½ΡΡΡΡ ΠΏΠ΅ΡΠ΅Π΄Π½ΠΈΡ ΠΈ Π·Π°Π΄Π½ΠΈΡ ΡΠΎΡΠΌΠΎΠ·ΠΎΠ², Π²ΠΎΠ·Π²ΡΠ°ΡΠ½ΡΠ΅ ΠΏΡΡΠΆΠΈΠ½Ρ ΠΈ ΡΠΏΠ»ΠΎΡΠ½ΠΈΡΠ΅Π»ΡΠ½ΡΠ΅ ΠΊΠΎΠ»ΡΡΠ°. ΠΠ»Π°Π²Π½ΡΠΉ ΡΠΎΡΠΌΠΎΠ·Π½ΠΎΠΉ ΡΠΈΠ»ΠΈΠ½Π΄Ρ ΡΠ°Π±ΠΎΡΠ°Π΅Ρ Π² ΠΏΠ°ΡΠ΅ Ρ Π²Π°ΠΊΡΡΠΌΠ½ΡΠΌ ΡΡΠΈΠ»ΠΈΡΠ΅Π»Π΅ΠΌ.
ΠΠ΅ΡΠ΅Π΄ ΡΠ΅ΠΌ, ΠΊΠ°ΠΊ Π½Π°ΡΠΈΠ½Π°ΡΡ ΡΠ΅ΠΌΠΎΠ½Ρ ΡΠΎΡΠΌΠΎΠ·Π½ΠΎΠ³ΠΎ ΡΠΈΠ»ΠΈΠ½Π΄ΡΠ°, Π½Π΅ΠΎΠ±Ρ
ΠΎΠ΄ΠΈΠΌΠΎ Π·Π½Π°ΡΡ, ΡΡΠΎ ΡΠ·Π»Ρ ΠΏΠ΅ΡΠ²ΠΈΡΠ½ΠΎΠ³ΠΎ ΠΈ Π²ΡΠΎΡΠΈΡΠ½ΠΎΠ³ΠΎ ΠΏΠΎΡΡΠ½Π΅ΠΉ Π½Π΅ ΡΠ°Π·Π±ΠΈΡΠ°ΡΡΡΡ, Π° ΠΌΠ΅Π½ΡΡΡΡΡ Π² ΡΠ±ΠΎΡΠ΅ Π½ΠΎΠ²ΡΠΌΠΈ.
ΠΠΈΠ°Π³Π½ΠΎΡΡΠΈΠΊΠ° Π³Π»Π°Π²Π½ΠΎΠ³ΠΎ ΡΠΎΡΠΌΠΎΠ·Π½ΠΎΠ³ΠΎ ΡΠΈΠ»ΠΈΠ½Π΄ΡΠ°
ΠΠ΅ΡΠ²ΡΠΌ ΠΏΡΠΈΠ·Π½Π°ΠΊΠΎΠΌ ΡΠΎΠ³ΠΎ, ΡΡΠΎ Π³Π»Π°Π²Π½ΡΠΉ ΡΠΈΠ»ΠΈΠ½Π΄Ρ Π½Π΅ Π² ΠΏΠΎΡΡΠ΄ΠΊΠ΅, ΡΠ²Π»ΡΠ΅ΡΡΡ Π½ΠΈΠ·ΠΊΠ°Ρ ΡΡΡΠ΅ΠΊΡΠΈΠ²Π½ΠΎΡΡΡ ΡΠΎΡΠΌΠΎΠΆΠ΅Π½ΠΈΡ Π»ΠΈΠ±ΠΎ ΡΠ»ΠΈΡΠΊΠΎΠΌ ΠΌΡΠ³ΠΊΠΈΠΉ Ρ ΠΎΠ΄ ΠΏΠ΅Π΄Π°Π»ΠΈ ΡΠΎΡΠΌΠΎΠ·Π°. ΠΠ½Π°ΡΠΈΡ, ΠΏΡΠΈΡΠ»Π° ΠΏΠΎΡΠ° ΠΏΡΠΎΠ²Π΅ΡΡΠΈ ΡΡΠ°ΡΠ΅Π»ΡΠ½ΡΡ Π΄ΠΈΠ°Π³Π½ΠΎΡΡΠΈΠΊΡ ΡΠΎΡΠΌΠΎΠ·Π½ΠΎΠΉ ΡΠΈΡΡΠ΅ΠΌΡ. Π Π½Π°ΡΠ°ΡΡ Π½ΡΠΆΠ½ΠΎ Ρ Π³Π»Π°Π²Π½ΠΎΠ³ΠΎ ΡΠΎΡΠΌΠΎΠ·Π½ΠΎΠ³ΠΎ ΡΠΈΠ»ΠΈΠ½Π΄ΡΠ°.
ΠΠ° Π½Π΅ΠΈΡΠΏΡΠ°Π²Π½ΠΎΡΡΠΈ ΡΠΎΡΠΌΠΎΠ·ΠΎΠ² Π²Π»ΠΈΡΡΡ ΠΌΠ½ΠΎΠ³ΠΈΠ΅ ΡΠ°ΠΊΡΠΎΡΡ, ΠΈ Π½Π΅ ΡΠ°ΠΊΡ, ΡΡΠΎ ΠΏΡΠΈΡΠΈΠ½Π° ΠΊΡΠΎΠ΅ΡΡΡ Π² Π³Π»Π°Π²Π½ΠΎΠΌ ΡΠΈΠ»ΠΈΠ½Π΄ΡΠ΅. ΠΠΈΠ°Π³Π½ΠΎΡΡΠΈΠΊΠ° ΡΠΎΡΠΌΠΎΠ·ΠΎΠ² ΠΌΠΎΠΆΠ΅Ρ ΠΏΠΎΠ΄Π²Π΅ΡΡΠΈ Π²Π°Ρ ΠΊ Π½Π΅ΠΎΠ±Ρ ΠΎΠ΄ΠΈΠΌΠΎΡΡΠΈ ΠΏΡΠΎΠ²ΠΎΠ΄ΠΈΡΡ ΡΠ΅ΠΌΠΎΠ½Ρ ΠΏΠ΅ΡΠ΅Π΄Π½Π΅Π³ΠΎ ΡΠΎΡΠΌΠΎΠ·Π½ΠΎΠ³ΠΎ ΡΠΈΠ»ΠΈΠ½Π΄ΡΠ° ΠΈΠ»ΠΈ ΡΠ΅ΠΌΠΎΠ½Ρ Π·Π°Π΄Π½Π΅Π³ΠΎ ΡΠΎΡΠΌΠΎΠ·Π½ΠΎΠ³ΠΎ ΡΠΈΠ»ΠΈΠ½Π΄ΡΠ°. ΠΠΎ, ΠΊΠ°ΠΊ Π³ΠΎΠ²ΠΎΡΠΈΡΡΡ, β Π²ΡΠΊΡΡΡΠΈΠ΅ ΠΏΠΎΠΊΠ°ΠΆΠ΅Ρ.
ΠΡΠΎΠ²Π΅ΡΡΠ΅ΠΌ Π³Π»Π°Π²Π½ΡΠΉ ΡΠΎΡΠΌΠΎΠ·Π½ΠΎΠΉ ΡΠΈΠ»ΠΈΠ½Π΄Ρ
ΠΡΠΎΠ²Π΅ΡΠΊΠ° Π½Π°ΡΠΈΠ½Π°Π΅ΡΡΡ Ρ ΠΊΠΎΡΠΏΡΡΠ°. Π ΠΏΠ΅ΡΠ²ΡΡ ΠΎΡΠ΅ΡΠ΅Π΄Ρ ΠΏΡΠΎΠ²Π΅ΡΡΠ΅ΠΌ ΡΠ»Π΅Π΄Ρ ΠΏΠΎΠ΄ΡΠ΅ΠΊΠ°Π½ΠΈΡ ΡΠΎΡΠΌΠΎΠ·Π½ΠΎΠΉ ΠΆΠΈΠ΄ΠΊΠΎΡΡΠΈ Π½Π° ΠΊΠΎΡΠΏΡΡΠ΅ ΡΠΈΠ»ΠΈΠ½Π΄ΡΠ°, Π·Π°ΡΠ΅ΠΌ Π½Π°Π»ΠΈΡΠΈΠ΅ ΡΡΠ΅ΡΠΈΠ½ ΡΠ°ΠΌΠΎΠ³ΠΎ ΠΊΠΎΡΠΏΡΡΠ°.
ΠΠ°ΡΠ΅ΠΌ ΠΏΠ΅ΡΠ΅Ρ ΠΎΠ΄ΠΈΠΌ ΠΊ ΠΏΡΠΎΠ²Π΅ΡΠΊΠ΅ ΡΠΎΡΡΠΎΡΠ½ΠΈΡ ΡΠΏΠ»ΠΎΡΠ½ΠΈΡΠ΅Π»ΡΠ½ΡΡ ΡΠ»Π΅ΠΌΠ΅Π½ΡΠΎΠ² ΡΠΈΠ»ΠΈΠ½Π΄ΡΠ°. Π£ΠΏΠ»ΠΎΡΠ½ΠΈΡΠ΅Π»ΠΈ ΡΠ°Π·Π±ΡΡ Π»ΠΈ, Π·Π½Π°ΡΠΈΡ ΠΏΡΠΈΡΡΡΠΏΠ°Π΅ΠΌ ΠΊ ΠΏΡΠΎΠΌΡΠ²ΠΊΠ΅ Π³Π»Π°Π²Π½ΠΎΠ³ΠΎ ΡΠΎΡΠΌΠΎΠ·Π½ΠΎΠ³ΠΎ ΡΠΈΠ»ΠΈΠ½Π΄ΡΠ°. ΠΡΠΎΠΌΡΠ²ΠΊΡ Π½ΡΠΆΠ½ΠΎ ΠΎΡΡΡΠ΅ΡΡΠ²Π»ΡΡΡ ΡΠΏΠΈΡΡΠΎΠΌ. ΠΠΈΠ½ΠΎΠΉ Π²ΡΠ΅ΠΌΡ ΡΠ²Π»ΡΠ΅ΡΡΡ, ΡΠΊΠΎΡΠ΅Π΅ Π²ΡΠ΅Π³ΠΎ, Π½Π΅ΠΏΠΎΠ΄Ρ ΠΎΠ΄ΡΡΠ°Ρ ΡΠΎΡΠΌΠΎΠ·Π½Π°Ρ ΠΆΠΈΠ΄ΠΊΠΎΡΡΡ. ΠΠΈΠ±ΠΎ Π΅Ρ ΡΠΈΠ»ΡΠ½ΠΎΠ΅ Π·Π°Π³ΡΡΠ·Π½Π΅Π½ΠΈΠ΅.
ΠΡΠ±ΠΎΠΉ ΡΠ΅ΠΌΠΎΠ½Ρ Π³Π»Π°Π²Π½ΠΎΠ³ΠΎ ΡΠΎΡΠΌΠΎΠ·Π½ΠΎΠ³ΠΎ ΡΠΈΠ»ΠΈΠ½Π΄ΡΠ° ΠΏΠΎΠ΄ΡΠ°Π·ΡΠΌΠ΅Π²Π°Π΅Ρ ΠΏΠΎΠ»Π½ΡΡ Π·Π°ΠΌΠ΅Π½Ρ ΡΠ΅Π·ΠΈΠ½ΠΎ-ΡΠ΅Ρ Π½ΠΈΡΠ΅ΡΠΊΠΈΡ ΠΈΠ·Π΄Π΅Π»ΠΈΠΉ.
ΠΠΎΡΠ»Π΅ ΠΏΡΠΎΠΌΡΠ²ΠΊΠΈ Π΄Π΅ΡΠ°Π»Π΅ΠΉ ΠΎΠ½ΠΈ Π΄ΠΎΠ»ΠΆΠ½Ρ Π±ΡΡΡ Π²ΡΡΡΡΠ΅Π½Ρ ΡΠΆΠ°ΡΡΠΌ Π²ΠΎΠ·Π΄ΡΡ ΠΎΠΌ. ΠΠ΅ΡΠΊΠ°Π»ΠΎ ΡΠ°ΠΌΠΎΠ³ΠΎ ΡΠΈΠ»ΠΈΠ½Π΄ΡΠ° ΠΈ ΠΏΠΎΡΡΠ½ΠΈ Π΄ΠΎΠ»ΠΆΠ½Ρ Π±ΡΡΡ ΡΠΈΡΡΡΠΌΠΈ, Π±Π΅Π· Π²ΠΈΠ·ΡΠ°Π»ΡΠ½ΠΎ Π²ΠΈΠ΄ΠΈΠΌΡΡ ΠΌΠ΅Ρ Π°Π½ΠΈΡΠ΅ΡΠΊΠΈΡ ΠΏΠΎΠ²ΡΠ΅ΠΆΠ΄Π΅Π½ΠΈΠΉ ΠΈ ΡΠΆΠ°Π²ΡΠΈΠ½Ρ.
ΠΠ΅ΡΠΌΠ΅ΡΠΈΡΠ½ΠΎΡΡΡ Π³Π»Π°Π²Π½ΠΎΠ³ΠΎ ΡΠΎΡΠΌΠΎΠ·Π½ΠΎΠ³ΠΎ ΡΠΈΠ»ΠΈΠ½Π΄ΡΠ° ΠΏΡΠΎΠ²Π΅ΡΡΠ΅ΡΡΡ Π½Π° ΡΡΠ΅Π½Π΄Π΅. ΠΠΎΡΡΠΎΠΌΡ Π² Π³Π°ΡΠ°ΠΆΠ½ΡΡ ΡΡΠ»ΠΎΠ²ΠΈΡΡ ΡΠ°ΠΊΠ°Ρ ΠΏΡΠΎΠ²Π΅ΡΠΊΠ° ΠΈΡΠΊΠ»ΡΡΠ΅Π½Π°. ΠΠ΅ Π΄ΠΎΠΏΡΡΠΊΠ°Π΅ΡΡΡ ΡΠ²Π΅Π»ΠΈΡΠ΅Π½Π½ΡΠΉ Π·Π°Π·ΠΎΡ ΠΌΠ΅ΠΆΠ΄Ρ ΠΏΠΎΡΡΠ½ΡΠΌΠΈ ΠΈ ΡΠΈΠ»ΠΈΠ½Π΄ΡΠΎΠΌ, ΠΏΡΠΎΠ²Π΅ΡΡΡΠ΅ Π΅Π³ΠΎ Π² ΡΠΎΠΎΡΠ²Π΅ΡΡΡΠ²ΠΈΠ΅ Ρ ΠΏΠ°ΡΠ°ΠΌΠ΅ΡΡΠ°ΠΌΠΈ ΠΌΠ°Π½ΡΠ°Π»Π°.
ΠΠΎΡΡΠ΄ΠΎΠΊ ΡΠ΅ΠΌΠΎΠ½ΡΠ° ΠΈΠ»ΠΈ Π·Π°ΠΌΠ΅Π½Ρ ΡΠ·Π»ΠΎΠ² ΠΈ ΠΌΠ΅Ρ Π°Π½ΠΈΠ·ΠΌΠΎΠ²
ΠΠΎΠΎΠ±ΡΠ΅-ΡΠΎ ΠΏΠΎ Π½Π°Π±Π»ΡΠ΄Π΅Π½ΠΈΡΠΌ ΠΈ ΠΎΡΠ΅Π½ΠΊΠ°ΠΌ ΡΠΏΠ΅ΡΠΈΠ°Π»ΠΈΡΡΠΎΠ², ΡΠ΅ΠΌΠΎΠ½Ρ Π³Π»Π°Π²Π½ΠΎΠ³ΠΎ ΡΠΎΡΠΌΠΎΠ·Π½ΠΎΠ³ΠΎ ΡΠΈΠ»ΠΈΠ½Π΄ΡΠ° Π² Π³Π°ΡΠ°ΠΆΠ½ΡΡ ΡΡΠ»ΠΎΠ²ΠΈΡΡ ΡΠ΅Π΄ΠΊΠΎ ΠΏΡΠΈΠ²ΠΎΠ΄ΠΈΡ ΠΊ ΠΆΠ΅Π»Π°Π΅ΠΌΠΎΠΌΡ ΡΠ΅Π·ΡΠ»ΡΡΠ°ΡΡ β ΠΏΠΎΠ²ΡΡΠ΅Π½ΠΈΠ΅ ΡΡΡΠ΅ΠΊΡΠΈΠ²Π½ΠΎΡΡΠΈ ΡΠΎΡΠΌΠΎΠ·ΠΎΠ².
Π Π΅ΠΊΠΎΠΌΠ΅Π½Π΄Π°ΡΠΈΡ ΠΏΡΠΎΡΡΠ° β ΠΏΡΠΎΡΠ΅ Π·Π°ΠΌΠ΅Π½ΠΈΡΡ Π³Π»Π°Π²Π½ΡΠΉ ΡΠΎΡΠΌΠΎΠ·Π½ΠΎΠΉ ΡΠΈΠ»ΠΈΠ½Π΄Ρ Π² ΡΠ±ΠΎΡΠ΅, Π΅ΡΠ»ΠΈ ΡΠ΅ΡΡ Π½Π΅ ΠΈΠ΄ΡΡ Π»ΠΈΡΡ ΠΎ Π·Π°ΠΌΠ΅Π½Π΅ ΡΠ΅Π·ΠΈΠ½ΠΎΠ²ΡΡ ΡΠΏΠ»ΠΎΡΠ½ΠΈΡΠ΅Π»Π΅ΠΉ.
ΠΡΠΈ Π·Π°ΠΌΠ΅Π½Π΅ Π±Π°ΡΠΊΠ° Π³Π»Π°Π²Π½ΠΎΠ³ΠΎ ΡΠΎΡΠΌΠΎΠ·Π½ΠΎΠ³ΠΎ ΡΠΈΠ»ΠΈΠ½Π΄ΡΠ° ΡΠ΅ΠΊΠΎΠΌΠ΅Π½Π΄ΡΠ΅ΡΡΡ ΠΌΠ΅Π½ΡΡΡ ΡΠΏΠ»ΠΎΡΠ½ΠΈΡΠ΅Π»ΡΠ½ΡΠ΅ ΠΏΡΠΎΠΊΠ»Π°Π΄ΠΊΠΈ, ΠΏΡΠ΅Π΄Π²Π°ΡΠΈΡΠ΅Π»ΡΠ½ΠΎ ΡΠ»Π΅Π³ΠΊΠ° ΡΠΌΠ°Π·Π°Π² ΠΈΡ ΡΠΎΡΠΌΠΎΠ·Π½ΠΎΠΉ ΠΆΠΈΠ΄ΠΊΠΎΡΡΡΡ.
ΠΡΠΈ ΠΏΠΎΠ»Π½ΠΎΠΉ Π·Π°ΠΌΠ΅Π½Π΅, ΠΈΠ»ΠΈ Π΄Π΅ΠΌΠΎΠ½ΡΠ°ΠΆΠ΅ Π΄Π»Ρ ΡΠ΅ΠΌΠΎΠ½ΡΠ° Π³Π»Π°Π²Π½ΠΎΠ³ΠΎ ΡΠΎΡΠΌΠΎΠ·Π½ΠΎΠ³ΠΎ ΡΠΈΠ»ΠΈΠ½Π΄ΡΠ°, ΠΏΡΠ΅Π΄Π²Π°ΡΠΈΡΠ΅Π»ΡΠ½ΠΎ ΠΎΡΠΊΠ°ΡΠ°ΠΉΡΠ΅ ΡΠΎΡΠΌΠΎΠ·Π½ΡΡ ΠΆΠΈΠ΄ΠΊΠΎΡΡΡ ΠΈΠ· Π±Π°ΡΠΊΠ° ΠΈ Π·Π°Π³Π»ΡΡΠΈΡΠ΅ ΡΡΡΠ±ΠΎΠΏΡΠΎΠ²ΠΎΠ΄Ρ.
ΠΠ°ΡΠ΅Π³ΠΎΡΠΈΡΠ΅ΡΠΊΠΈ Π·Π°ΠΏΡΠ΅ΡΠ°Π΅ΡΡΡ ΡΠ΅ΠΌΠΎΠ½ΡΠΈΡΠΎΠ²Π°ΡΡ ΡΠ΅Π³ΡΠ»ΡΡΠΎΡ Π΄Π°Π²Π»Π΅Π½ΠΈΡ Π³Π»Π°Π²Π½ΠΎΠ³ΠΎ ΡΠΎΡΠΌΠΎΠ·Π½ΠΎΠ³ΠΎ ΡΠΈΠ»ΠΈΠ½Π΄ΡΠ°. Π₯Π°ΡΠ°ΠΊΡΠ΅ΡΠΈΡΡΠΈΠΊΠΈ ΡΠ΅Π³ΡΠ»ΡΡΠΎΡΠ° ΡΡΡΠ°Π½ΠΎΠ²Π»Π΅Π½Ρ ΠΏΡΠΎΠΈΠ·Π²ΠΎΠ΄ΠΈΡΠ΅Π»Π΅ΠΌ ΠΏΡΠΈ ΠΈΠ·Π³ΠΎΡΠΎΠ²Π»Π΅Π½ΠΈΠΈ, ΠΏΠΎΡΡΠΎΠΌΡ ΡΠ΅Π³ΡΠ»ΡΡΠΎΡΡ Π΄Π°Π²Π»Π΅Π½ΠΈΡ ΠΌΠ΅Π½ΡΡΡΡΡ Π² ΠΊΠΎΠΌΠΏΠ»Π΅ΠΊΡΠ΅.
ΠΠΎΡΠ»Π΅ ΡΠ΅ΠΌΠΎΠ½ΡΠ° ΡΠΎΡΠΌΠΎΠ·Π½ΠΎΠ³ΠΎ ΡΠΈΠ»ΠΈΠ½Π΄ΡΠ° Π½Π΅ Π·Π°Π±ΡΠ΄ΡΡΠ΅ ΠΏΡΠΎΠ²Π΅ΡΡΠΈ ΠΏΡΠΎΠΊΠ°ΡΠΊΡ ΡΠΎΡΠΌΠΎΠ·Π½ΠΎΠΉ ΡΠΈΡΡΠ΅ΠΌΡ.
Π£Π΄Π°ΡΠΈ Π²Π°ΠΌ ΠΏΡΠΈ ΠΏΡΠΎΠ²Π΅Π΄Π΅Π½ΠΈΠΈ ΡΠ΅ΠΌΠΎΠ½ΡΠ° Π³Π»Π°Π²Π½ΠΎΠ³ΠΎ ΡΠΎΡΠΌΠΎΠ·Π½ΠΎΠ³ΠΎ ΡΠΈΠ»ΠΈΠ½Π΄ΡΠ°.
carnovato.ru
Π Π΅ΠΌΠΎΠ½Ρ ΡΠΎΡΠΌΠΎΠ·Π½ΠΎΠΉ ΡΠΈΡΡΠ΅ΠΌΡ Π°Π²ΡΠΎΠΌΠΎΠ±ΠΈΠ»Ρ Π£ΡΠ°Π»
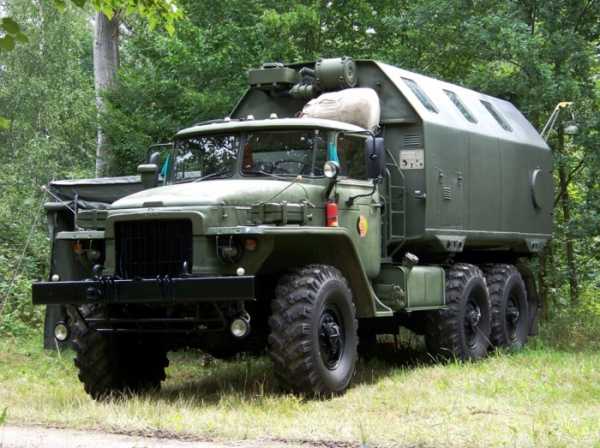
Π£ΡΠ°Π»
ΠΠ»Ρ ΡΠ΅ΠΌΠΎΠ½ΡΠ° ΠΏΡΠΈΠ±ΠΎΡΡ ΠΈ Π°Π³ΡΠ΅Π³Π°ΡΡ ΡΠΎΡΠΌΠΎΠ·Π½ΠΎΠΉ ΡΠΈΡΡΠ΅ΠΌΡ ΡΠ½ΡΡΡ Ρ Π°Π²ΡΠΎΠΌΠΎΠ±ΠΈΠ»Ρ, ΡΠ°Π·ΠΎΠ±ΡΠ°ΡΡ, ΠΏΡΠΎΠΌΡΡΡ Π΄Π΅ΡΠ°Π»ΠΈ, ΠΏΡΠΎΠ²Π΅ΡΠΈΡΡ ΠΈΡ ΡΠΎΡΡΠΎΡΠ½ΠΈΠ΅ ΠΈ ΠΎΠΏΡΠ΅Π΄Π΅Π»ΠΈΡΡ ΠΏΡΠΈΠ³ΠΎΠ΄Π½ΠΎΡΡΡ Π΄Π΅ΡΠ°Π»Π΅ΠΉ Π΄Π»Ρ Π΄Π°Π»ΡΠ½Π΅ΠΉΡΠ΅Π³ΠΎ ΠΈΡΠΏΠΎΠ»ΡΠ·ΠΎΠ²Π°Π½ΠΈΡ.
Π Π°Π·Π±ΠΎΡΠΊΠ°. Π Π°Π·Π±ΠΎΡΠΊΡ ΡΠ°Π±ΠΎΡΠΈΡ
ΡΠΎΡΠΌΠΎΠ·ΠΎΠ² Π²ΡΠΏΠΎΠ»Π½ΡΡΡ Π² ΡΠ»Π΅Π΄ΡΡΡΠ΅ΠΌ ΠΏΠΎΡΡΠ΄ΠΊΠ΅.
ΠΠΎΠ΄Π½ΡΡΡ ΠΌΠΎΡΡ Π΄ΠΎΠΌΠΊΡΠ°ΡΠΎΠΌ, ΡΠ½ΡΡΡ ΠΊΠΎΠ»Π΅ΡΠΎ ΠΈ ΠΊΡΡΡΠΊΡ ΡΡΡΠΏΠΈΡΡ, Π²ΡΠ²Π΅ΡΠ½ΡΡΡ ΡΠ³ΠΎΠ»ΡΠ½ΠΈΠΊ ΡΠ»Π°Π½Π³Π° ΠΏΠΎΠ΄ΠΊΠ°ΡΠΊΠΈ ΡΠΈΠ½ ΠΈ ΠΏΡΠΈ ΠΏΠΎΠΌΠΎΡΠΈ ΡΡΠ΅ΠΌΠ½ΠΈΠΊΠ° Π²ΡΠ½ΡΡΡ ΠΏΠΎΠ»ΡΠΎΡΡ.
ΠΡΠΎΠ³Π½ΡΡΡ ΡΡΠΎΠΏΠΎΡΠ½ΡΡ ΡΠ°ΠΉΠ±Ρ ΠΈ ΠΎΡΠ²Π΅ΡΠ½ΡΡΡ Π½Π°ΡΡΠΆΠ½ΡΡ Π³Π°ΠΉΠΊΡ ΠΊΡΠ΅ΠΏΠ»Π΅Π½ΠΈΡ ΠΏΠΎΠ΄ΡΠΈΠΏΠ½ΠΈΠΊΠΎΠ² ΡΡΡΠΏΠΈΡΡ, Π²ΡΠ½ΡΡΡ Π·Π°ΠΌΠΎΡΠ½ΡΡ ΡΠ°ΠΉΠ±Ρ ΠΈ ΠΎΡΠ²Π΅ΡΠ½ΡΡΡ Π²Π½ΡΡΡΠ΅Π½Π½ΡΡ Π³Π°ΠΉΠΊΡ.
Π‘Π½ΡΡΡ ΡΡΡΠΏΠΈΡΡ Ρ ΡΠΎΡΠΌΠΎΠ·Π½ΡΠΌ Π±Π°ΡΠ°Π±Π°Π½ΠΎΠΌ ΠΈ ΠΏΠΎΠ΄ΡΠΈΠΏΠ½ΠΈΠΊΠ°ΠΌΠΈ, ΡΡΡΠΆΠ½ΡΡ ΠΏΡΡΠΆΠΈΠ½Ρ ΠΊΠΎΠ»ΠΎΠ΄ΠΎΠΊ, ΡΡΠΎΠΏΠΎΡΠ½ΡΠ΅ ΡΠΊΠΎΠ±Ρ Π½Π° ΠΏΠ°Π»ΡΡΠ°Ρ
ΠΈ ΠΊΠΎΠ»ΠΎΠ΄ΠΊΠΈ, ΠΎΡΠΈΡΡΠΈΡΡ Π²ΡΡΠ»ΠΊΡ ΠΈ ΠΏΠ°Π»Π΅Ρ ΠΊΠΎΠ»ΠΎΠ΄ΠΊΠΈ.
ΠΡΠ²Π΅ΡΠ½ΡΡΡ ΡΡΡΠ±ΠΎΠΏΡΠΎΠ²ΠΎΠ΄ ΠΈ Π±ΠΎΠ»ΡΡ, ΡΠ½ΡΡΡ ΠΊΠΎΠ»Π΅ΡΠ½ΡΠΉ ΡΠΈΠ»ΠΈΠ½Π΄Ρ ΠΈ ΡΠ°Π·ΠΎΠ±ΡΠ°ΡΡ Π΅Π³ΠΎ, ΠΎΡΠ²Π΅ΡΠ½ΡΡΡ Π³Π°ΠΉΠΊΠΈ ΠΈ ΡΠ½ΡΡΡ ΠΎΠΏΠΎΡΠ½ΡΠ΅ ΠΏΠ°Π»ΡΡΡ ΠΊΠΎΠ»ΠΎΠ΄ΠΎΠΊ.
Π‘Π½ΡΡΡ ΡΠΈΡ ΡΠΎΡΠΌΠΎΠ·Π° ΠΈ Π²ΠΎΠΉΠ»ΠΎΡΠ½ΡΠΉ ΡΠ°Π»ΡΠ½ΠΈΠΊ.
Π Π°Π·Π±ΠΎΡΠΊΠ° ΠΏΠ½Π΅Π²ΠΌΠΎΡΡΠΈΠ»ΠΈΡΠ΅Π»Ρ, ΡΠΎΡΠΌΠΎΠ·Π½ΠΎΠ³ΠΎ ΡΠΈΠ»ΠΈΠ½Π΄ΡΠ°, ΡΠΎΡΠΌΠΎΠ·Π½ΠΎΠ³ΠΎ ΠΊΡΠ°Π½Π°, ΡΡΠΎΡΠ½ΠΎΡΠ½ΠΎΠ³ΠΎ ΡΠΎΡΠΌΠΎΠ·Π°, ΠΊΠΎΠΌΠΏΡΠ΅ΡΡΠΎΡΠ° ΡΡΡΠ΄Π½ΠΎΡΡΠ΅ΠΉ Π½Π΅ ΠΏΡΠ΅Π΄ΡΡΠ°Π²Π»ΡΠ΅Ρ. ΠΡΠΈ ΡΡΠΎΠΌ Π½Π΅ΠΎΠ±Ρ
ΠΎΠ΄ΠΈΠΌΠΎ ΠΎΠ±ΡΠ°ΡΠΈΡΡ Π²Π½ΠΈΠΌΠ°Π½ΠΈΠ΅ Π½Π° ΡΠ»Π΅Π΄ΡΡΡΠ΅Π΅.
ΠΡΠΈ ΡΠ°Π·Π±ΠΎΡΠΊΠ΅ Π³Π»Π°Π²Π½ΠΎΠ³ΠΎ ΡΠΎΡΠΌΠΎΠ·Π½ΠΎΠ³ΠΎ ΡΠΈΠ»ΠΈΠ½Π΄ΡΠ° Π½Π΅ ΡΠ΅ΠΊΠΎΠΌΠ΅Π½Π΄ΡΠ΅ΡΡΡ ΠΎΡΠ²Π΅ΡΡΡΠ²Π°ΡΡ ΠΏΡΠΎΠ±ΠΊΡ.
ΠΠΎΠ»ΠΎΠ²ΠΊΡ ΡΠΈΠ»ΠΈΠ½Π΄ΡΠ΅ ΠΊΠΎΠΌΠΏΡΠ΅ΡΡΠΎΡΠ° ΡΠ°Π·Π±ΠΈΡΠ°ΡΡ ΡΠΎΠ»ΡΠΊΠΎ ΠΏΡΠΈ Π½Π΅ΠΎΠ±Ρ
ΠΎΠ΄ΠΈΠΌΠΎΡΡΠΈ. ΠΠΎΡΠ»Π΅ ΡΠ½ΡΡ Π»Ρ Ρ ΠΏΠΎΠΌΠΎΡΡΡ ΠΏΠ»ΠΎΡΠΊΠΎΠ³ΡΠ±ΡΠ΅Π² Π½Π°ΠΏΡΠ°Π²Π»ΡΡΡΠΈΡ
Π²ΠΏΡΡΠΊΠ½ΡΡ
ΠΊΠ»Π°ΠΏΠ°Π½ΠΎΠ² Π²ΡΠΏΡΠ΅ΡΡΠΎΠ²Π°ΡΡ ΡΠ΅Π΄Π»Π° ΠΏΡΠΈ ΠΏΠΎΠΌΠΎΡΠΈ ΡΡΠ΅ΠΌΠ½ΠΈΠΊΠ°.
ΠΠΎΠ½ΡΡΠΎΠ»Ρ Π΄Π΅ΡΠ°Π»Π΅ΠΉ. ΠΠ°ΠΌΠ°ΡΠ»Π΅Π½Π½ΡΠ΅ Π½Π°ΠΊΠ»Π°Π΄ΠΊΠΈ ΠΏΡΠΎΠΌΡΡΡ Π² Π±Π΅Π½Π·ΠΈΠ½Π΅, ΠΏΡΠΎΡΡΡΠΈΡΡ, Π° Π·Π°ΡΠ΅ΠΌ ΠΎΡΠΈΡΡΠΈΡΡ ΡΠ°Π±ΠΎΡΠΈΠ΅ ΠΏΠΎΠ²Π΅ΡΡ
Π½ΠΎΡΡΠΈ ΠΌΠ΅ΡΠ°Π»Π»ΠΈΡΠ΅ΡΠΊΠΎΠΉ ΡΠ΅ΡΠΊΠΎΠΉ ΠΈΠ»ΠΈ Π½Π°ΠΆΠ΄Π°ΡΠ½ΠΎΠΉ Π±ΡΠΌΠ°Π³ΠΎΠΉ. ΠΡΠ»ΠΈ ΠΎΡ ΠΏΠΎΠ²Π΅ΡΡ
Π½ΠΎΡΡΠΈ Π½Π°ΠΊΠ»Π°Π΄ΠΎΠΊ Π΄ΠΎ Π³ΠΎΠ»ΠΎΠ²ΠΎΠΊ Π·Π°ΠΊΠ»Π΅ΠΏΠΎΠΊ ΠΎΡΡΠ°Π΅ΡΡΡ ΠΌΠ΅Π½Π΅Π΅ 0,5 ΠΌΠΌ, Π½Π°ΠΊΠ»Π°Π΄ΠΊΠΈ Π·Π°ΠΌΠ΅Π½ΠΈΡΡ Π½ΠΎΠ²ΡΠΌΠΈ.
ΠΠΎΠ»ΠΎΠ΄ΠΊΠΈ ΡΡΠΎΡΠ½ΠΎΡΠ½ΠΎΠ³ΠΎ ΡΠΎΡΠΌΠΎΠ·Π° ΠΎΠ±ΡΠ°Π±ΠΎΡΠ°ΡΡ ΡΠΎΠ²ΠΌΠ΅ΡΡΠ½ΠΎ Ρ ΡΠ°Π·ΠΆΠΈΠΌΠ½ΡΠΌ ΠΊΡΠ»Π°ΠΊΠΎΠΌ, ΡΡΡΠ°Π½ΠΎΠ²ΠΈΠ² ΠΌΠ΅ΠΆΠ΄Ρ ΡΡΡ
Π°ΡΡΠΌΠΈ ΠΊΠΎΠ»ΠΎΠ΄ΠΎΠΊ ΠΈ ΠΊΡΠ»Π°ΠΊΠΎΠΌ ΠΏΠ»Π°ΡΡΠΈΠ½Ρ ΡΠΎΠ»ΡΠΈΠ½ΠΎΠΉ 0,98-1,00 ΠΌΠΌ.
Π’ΠΎΡΠΌΠΎΠ·Π½ΡΠ΅ Π±Π°ΡΠ°Π±Π°Π½Ρ ΡΠ°Π±ΠΎΡΠ΅Π³ΠΎ ΡΠΎΡΠΌΠΎΠ·Π° Ρ ΠΊΠΎΠ»ΡΡΠ΅Π²ΡΠΌΠΈ ΠΊΠ°Π½Π°Π²ΠΊΠ°ΠΌΠΈ Π±ΠΎΠ»Π΅Π΅ 1 ΠΌΠΌ ΠΏΡΠΎΡΠΎΡΠΈΡΡ.
ΠΠΎΠ»Π΅ΡΠ½ΡΠ΅ ΡΠΈΠ»ΠΈΠ½Π΄ΡΡ Ρ ΡΠΈΡΠΊΠ°ΠΌΠΈ ΠΈ ΡΠ»Π΅Π΄Π°ΠΌΠΈ ΠΊΠΎΡΡΠΎΠ·ΠΈΠΈ Π½Π° ΡΠ°Π±ΠΎΡΠ΅ΠΉ ΠΏΠΎΠ²Π΅ΡΡ
Π½ΠΎΡΡΠΈ Π½Π΅ΠΎΠ±Ρ
ΠΎΠ΄ΠΈΠΌΠΎ Ρ
ΠΎΠ½ΠΈΠ½Π³ΠΎΠ²Π°ΡΡ. ΠΠΎΡΡΠ½ΠΈ ΠΈ ΡΠ΅Π·ΠΈΠ½ΠΎΠ²ΡΠ΅ ΠΌΠ°Π½ΠΆΠ΅ΡΡ ΠΏΡΠΈ Π½Π°Π»ΠΈΡΠΈΠΈ ΡΠΈΡΠΎΠΊ ΠΈΠ»ΠΈ Π·Π½Π°ΡΠΈΡΠ΅Π»ΡΠ½ΠΎΠΌ ΠΈΠ·Π½ΠΎΡΠ΅ ΡΠ°Π±ΠΎΡΠΈΡ
ΠΏΠΎΠ²Π΅ΡΡ
Π½ΠΎΡΡΠ΅ΠΉ Π·Π°ΠΌΠ΅Π½ΠΈΡΡ. ΠΡΠΎΠΌΡΡΡ ΠΈ ΡΡΠ°ΡΠ΅Π»ΡΠ½ΠΎ ΠΎΡΠΌΠΎΡΡΠ΅ΡΡ Π·Π°ΡΠΈΡΠ½ΡΠΉ ΡΠ΅Ρ
ΠΎΠ» ΠΊΠΎΠ»Π΅ΡΠ½ΠΎΠ³ΠΎ ΡΠΈΠ»ΠΈΠ½Π΄ΡΠ°, ΠΏΡΠΈ ΡΠΊΠ²ΠΎΠ·Π½ΡΡ
ΡΠ°Π·ΡΡΠ²Π°Ρ
β Π·Π°ΠΌΠ΅Π½ΠΈΡΡ, ΠΏΡΠΈΠΌΠ΅Π½ΡΡ ΠΏΡΠΈΡΠΏΠΎΡΠΎΠ±Π»Π΅Π½ΠΈΠ΅.
ΠΠ»Π°Π²Π½ΡΠΉ ΡΠΎΡΠΌΠΎΠ·Π½ΠΎΠΉ ΡΠΈΠ»ΠΈΠ½Π΄Ρ. ΠΡΠ»ΠΈ Π½Π° Π·Π΅ΡΠΊΠ°Π»Π΅ Π³Π»Π°Π²Π½ΠΎΠ³ΠΎ ΡΠΎΡΠΌΠΎΠ·Π½ΠΎΠ³ΠΎ ΡΠΈΠ»ΠΈΠ½Π΄ΡΠ° ΠΈΠΌΠ΅ΡΡΡΡ Π·Π°Π΄ΠΈΡΡ, ΡΠ»Π΅Π΄Ρ ΠΊΠΎΡΡΠΎΠ·ΠΈΠΈ, ΡΠΎ Π΅Π³ΠΎ ΡΠ»Π΅Π΄ΡΠ΅Ρ Π·Π°ΠΌΠ΅Π½ΠΈΡΡ ΠΈΠ»ΠΈ ΠΎΡΡ
ΠΎΠ½ΠΈΠ½Π³ΠΎΠ²Π°ΡΡ. ΠΡΠΈ ΡΡΠΎΠΌ ΡΠ΅ΠΊΠΎΠΌΠ΅Π½Π΄ΡΠ΅ΡΡΡ ΠΏΠΎΡΡΠ°Π²ΠΈΡΡ Π½ΠΎΠ²ΡΠ΅ ΠΌΠ°Π½ΠΆΠ΅ΡΡ.
ΠΡΠΈ ΠΈΠ·Π½ΠΎΡΠ΅ ΠΏΠΎΡΡΠ½Ρ Π³Π»Π°Π²Π½ΠΎΠ³ΠΎ ΡΠΈΠ»ΠΈΠ½Π΄ΡΠ°, Π½Π°Π»ΠΈΡΠΈΠΈ Π½Π° ΡΠ°Π±ΠΎΡΠ΅ΠΉ ΠΏΠΎΠ²Π΅ΡΡ
Π½ΠΎΡΡΠΈ ΠΎΠ±ΡΠ°ΡΠ½ΠΎΠ³ΠΎ ΠΊΠ»Π°ΠΏΠ°Π½Π° ΠΈ ΠΌΠ°Π½ΠΆΠ΅ΡΠΎΠ² Π³Π»Π°Π²Π½ΠΎΠ³ΠΎ ΡΠΈΠ»ΠΈΠ½Π΄ΡΠ° ΡΠ»Π΅Π΄ΠΎΠ² ΠΏΠΎΠ²ΡΠ΅ΠΆΠ΄Π΅Π½ΠΈΡ, ΡΠ°Π·Π±ΡΡ
Π°Π½ΠΈΡ ΠΈΡ
Π½Π΅ΠΎΠ±Ρ
ΠΎΠ΄ΠΈΠΌΠΎ Π·Π°ΠΌΠ΅Π½ΠΈΡΡ.
ΠΠ°Π»ΠΈΡΠΈΠ΅ ΡΠΎΡΠΌΠΎΠ·Π½ΠΎΠΉ ΠΆΠΈΠ΄ΠΊΠΎΡΡΠΈ Π² ΠΏΠ΅ΡΠ²ΠΎΠΌ ΡΠΈΠ»ΠΈΠ½Π΄ΡΠ΅ ΠΏΠ½Π΅Π²ΠΌΠΎΡΡΠΈΠ»ΠΈΡΠ΅Π»Ρ ΡΠΊΠ°Π·ΡΠ²Π°Π΅Ρ Π½Π° Π½Π΅ΠΎΠ±Ρ
ΠΎΠ΄ΠΈΠΌΠΎΡΡΡ Π·Π°ΠΌΠ΅Π½Ρ Π½Π°ΡΡΠΆΠ½ΠΎΠ³ΠΎ (ΠΊΠΎΠ»ΡΡΠ΅Π²ΠΎΠ³ΠΎ) ΠΌΠ°Π½ΠΆΠ΅ΡΠ° ΠΏΠΎΡΡΠ½Ρ Π³Π»Π°Π²Π½ΠΎΠ³ΠΎ ΡΠΈΠ»ΠΈΠ½Π΄ΡΠ° (ΠΎΡΠ»Π°Π±Π»Π΅Π½ΠΈΠ΅ ΠΏΠΎΡΠ°Π΄ΠΊΠΈ ΠΌΠ°Π½ΠΆΠ΅ΡΠ° Π½Π° ΠΏΠΎΡΡΠ½Π΅).
ΠΠ½Π΅Π²ΠΌΠΎΡΡΠΈΠ»ΠΈΡΠ΅Π»ΠΈ ΠΈ Π΄Π΅ΡΠ°Π»ΠΈ, Π²Ρ
ΠΎΠ΄ΡΡΠΈΠ΅ Π² Π½ΠΈΡ
, ΠΎΡΠΈΡΡΠΈΡΡ ΠΈ ΠΏΡΠΎΠΌΡΡΡ. Π‘Π»Π΅Π΄Ρ ΠΊΠΎΡΡΠΎΠ·ΠΈΠΈ ΠΈ ΡΠΈΡΠΊΠΈ Π½Π° ΡΠ°Π±ΠΎΡΠΈΡ
ΠΏΠΎΠ²Π΅ΡΡ
Π½ΠΎΡΡΡΡ
ΡΠΈΠ»ΠΈΠ½Π΄ΡΠΎΠ² ΡΠ΄Π°Π»ΠΈΡΡ Ρ ΠΏΠΎΠΌΠΎΡΡΡ ΠΌΠ΅Π»ΠΊΠΎΠΉ Π½Π°ΠΆΠ΄Π°ΡΠ½ΠΎΠΉ Π±ΡΠΌΠ°Π³ΠΈ.
ΠΡΠΈ Π½Π°Π»ΠΈΡΠΈΠΈ ΠΏΠΎΠ²ΡΠ΅ΠΆΠ΄Π΅Π½ΠΈΠΉ ΠΌΠ°Π½ΠΆΠ΅ΡΠΎΠ² ΠΈΡ
Π½Π΅ΠΎΠ±Ρ
ΠΎΠ΄ΠΈΠΌΠΎ Π·Π°ΠΌΠ΅Π½ΠΈΡΡ.
ΠΠΎΠΌΠΏΡΠ΅ΡΡΠΎΡ. ΠΠΎΡΠΏΡΡΠ½ΡΠ΅ Π΄Π΅ΡΠ°Π»ΠΈ Π½Π΅ Π΄ΠΎΠ»ΠΆΠ½Ρ ΠΈΠΌΠ΅ΡΡ ΡΡΠ΅ΡΠΈΠ½, ΡΠΊΠΎΠ»ΠΎΠ², Π° ΠΏΡΠΈΠ²Π°Π»ΠΎΡΠ½ΡΠ΅ ΠΏΠΎΠ²Π΅ΡΡ
Π½ΠΎΡΡΠΈ Π·Π°Π±ΠΎΠΈΠ½ ΠΈ ΠΊΠΎΡΠΎΠ±Π»Π΅Π½ΠΈΡ. ΠΠ½ΡΡΡΠ΅Π½Π½ΠΈΠ΅ ΠΏΠΎΠ»ΠΎΡΡΠΈ Π΄ΠΎΠ»ΠΆΠ½Ρ Π±ΡΡΡ ΠΎΡΠΈΡΠ΅Π½Ρ ΠΎΡ ΠΎΡΠ»ΠΎΠΆΠ΅Π½ΠΈΠΉ. ΠΠ΅ΠΏΠ»ΠΎΡΠΊΠΎΡΡΠ½ΠΎΡΡΡΒ ΠΏΡΠΈΠ²Π°Π»ΠΎΡΠ½ΡΡ
ΠΏΠΎΠ²Π΅ΡΡ
Π½ΠΎΡΡΠ΅ΠΉ ΠΊΠΎΡΠΏΡΡΠ½ΡΡ
Π΄Π΅ΡΠ°Π»Π΅ΠΉ Π΄ΠΎΠ»ΠΆΠ½Π° Π±ΡΡΡ 0,05 ΠΌΠΌ (Π½Π΅ Π±ΠΎΠ»Π΅Π΅). ΠΠ·Π½ΠΎΡ Π³Π½Π΅Π·Π΄ ΠΏΠΎΠ΄ ΠΏΠΎΠ΄ΡΠΈΠΏΠ½ΠΈΠΊΠΈ ΠΊΠΎΠ»Π΅Π½ΡΠ°ΡΠΎΠ³ΠΎΒ Π²Π°Π»Π° Π² ΠΊΠ°ΡΡΠ΅ΡΠ΅ ΠΊΠΎΠΌΠΏΡΠ΅ΡΡΠΎΡΠ° Π΄ΠΎΠΏΡΡΠΊΠ°Π΅ΡΡΡ Π΄ΠΎ Π΄ΠΈΠ°ΠΌΠ΅ΡΡΠ° 72,05 ΠΌΠΌ.
ΠΠ·Π½ΠΎΡ Π²ΠΏΡΡΠΊΠ½ΠΎΠ³ΠΎ ΠΊΠ»Π°ΠΏΠ°Π½Π° ΠΏΠΎ ΡΠΎΠ»ΡΠΈΠ½Π΅ Π΄ΠΎΠΏΡΡΠΊΠ°Π΅ΡΡΡ Π΄ΠΎ 0,8 ΠΌΠΌ, Π½Π΅ΠΏΠ»ΠΎΡΠΊΠΎΡΡΠ½ΠΎΡΡΡ ΠΊΠ»Π°ΠΏΠ°Π½ΠΎΠ² β 0,01 ΠΌΠΌ. Π ΡΠΊΡΠΏΠ»ΡΠ°ΡΠ°ΡΠΈΠΈ Π΄ΠΎΠΏΡΡΠΊΠ°Π΅ΡΡΡ ΠΏΠ»ΡΠ½ΠΆΠ΅Ρ ΡΠ°Π·Π³ΡΡΠ·ΠΎΡΠ½ΠΎΠ³ΠΎ ΡΡΡΡΠΎΠΉΡΡΠ²Π° Ρ ΡΠ°Π±ΠΎΡΠΈΠΌ Π΄ΠΈΠ°ΠΌΠ΅ΡΡΠΎΠΌ Π½Π΅ ΠΌΠ΅Π½Π΅Π΅ 9,9 ΠΌΠΌ, Π° Π²Π½ΡΡΡΠ΅Π½Π½ΠΈΠΉ Π΄ΠΈΠ°ΠΌΠ΅ΡΡ Π²ΡΡΠ»ΠΊΠΈ ΠΏΠ»ΡΠ½ΠΆΠ΅ΡΠ° -Π½Π΅ Π±ΠΎΠ»Π΅Π΅ 10,04 ΠΌΠΌ.
Π Π΅Π·ΠΈΠ½ΠΎΠ²ΡΠ΅ ΡΠΏΠ»ΠΎΡΠ½ΠΈΡΠ΅Π»ΡΠ½ΡΠ΅ ΠΊΠΎΠ»ΡΡΠ° ΠΏΠ»ΡΠ½ΠΆΠ΅ΡΠΎΠ² ΡΠ°Π·Π³ΡΡΠ·ΠΎΡΠ½ΠΎΠ³ΠΎ ΡΡΡΡΠΎΠΉΡΡΠ²Π° Π½Π΅ Π΄ΠΎΠ»ΠΆΠ½Ρ ΠΈΠΌΠ΅ΡΡ ΡΡΠ΅ΡΠΈΠ½, ΡΡΠ΅Π·ΠΌΠ΅ΡΠ½ΡΡ
ΠΈΠ·Π½ΠΎΡΠΎΠ² ΠΈ ΡΡΠ°ΡΠ΅Π½ΠΈΡ.
ΠΠ΅ΠΏΠ°ΡΠ°Π»Π»Π΅Π»ΡΠ½ΠΎΡΡΡ ΠΎΡΠ΅ΠΉ Π²Π΅ΡΡ
Π½Π΅ΠΉ ΠΈ Π½ΠΈΠΆΠ½Π΅ΠΉ Π³ΠΎΠ»ΠΎΠ²ΠΎΠΊ ΡΠ°ΡΡΠ½Π° Π΄ΠΎΠΏΡΡΠΊΠ°Π΅ΡΡΡ Π½Π΅ Π±ΠΎΠ»Π΅Π΅ 0,07 ΠΌΠΌ Π½Π° Π΄Π»ΠΈΠ½Π΅ 100 ΠΌΠΌ.
ΠΠ΅ΡΠ°Π»ΠΈ ΠΈ ΡΡΡΠ±ΠΎΠΏΡΠΎΠ²ΠΎΠ΄Ρ ΡΠΎΡΠΌΠΎΠ·Π½ΠΎΠ³ΠΎ ΠΏΡΠΈΠ²ΠΎΠ΄Π° ΠΎΡΠΈΡΡΠΈΡΡ, ΠΏΡΠΎΠΌΡΡΡ ΠΈ ΠΎΡΠΌΠΎΡΡΠ΅ΡΡ. ΠΡΠΈ Π½Π°Π»ΠΈΡΠΈΠΈ ΠΏΠΎΠ²ΡΠ΅ΠΆΠ΄Π΅Π½ΠΈΠΉ Π΄Π΅ΡΠ°Π»ΠΈ Π·Π°ΠΌΠ΅Π½ΠΈΡΡ.
ΠΡΠΎΠ±ΠΎΠ΅ Π²Π½ΠΈΠΌΠ°Π½ΠΈΠ΅ ΠΎΠ±ΡΠ°ΡΠΈΡΡ Π½Π° ΡΠΎΡΡΠΎΡΠ½ΠΈΠ΅ ΠΈ Π½Π°Π΄Π΅ΠΆΠ½ΠΎΡΡΡ ΠΊΡΠ΅ΠΏΠ»Π΅Π½ΠΈΡ ΡΡΡΠ±ΠΎΠΏΡΠΎΠ²ΠΎΠ΄ΠΎΠ² Π½Π° ΠΌΠΎΡΡΠ°Ρ
. ΠΠΈΠ±ΠΊΠΈΠ΅ ΡΠ»Π°Π½Π³ΠΈ Π½Π΅ Π΄ΠΎΠ»ΠΆΠ½Ρ ΠΈΠΌΠ΅ΡΡ ΡΡΠ΅ΡΠΈΠ½ ΠΈ ΠΏΠΎΡΠ΅ΡΡΠΎΡΡΠ΅ΠΉ.
Π‘Π±ΠΎΡΠΊΠ°. Π‘Π±ΠΎΡΠΊΡ Π³Π»Π°Π²Π½ΠΎΠ³ΠΎ ΠΈ ΠΊΠΎΠ»Π΅ΡΠ½ΡΡ
ΡΠΎΡΠΌΠΎΠ·Π½ΡΡ
ΡΠΈΠ»ΠΈΠ½Π΄ΡΠΎΠ², ΠΏΠ½Π΅Π²ΠΌΠΎΡΡΠΈΠ»ΠΈΡΠ΅Π»Ρ, ΡΡΠΎΡΠ½ΠΎΡΠ½ΠΎΠ³ΠΎ ΠΈ ΡΠ°Π±ΠΎΡΠ΅Π³ΠΎ ΡΠΎΡΠΌΠΎΠ·ΠΎΠ² Π²ΡΠΏΠΎΠ»Π½ΡΡΡ Π² ΠΏΠΎΡΡΠ΄ΠΊΠ΅, ΠΎΠ±ΡΠ°ΡΠ½ΠΎΠΌ ΡΠ°Π·Π±ΠΎΡΠΊΠ΅. ΠΡΠΈ ΡΡΠΎΠΌ Π½Π΅ΠΎΠ±Ρ
ΠΎΠ΄ΠΈΠΌΠΎ ΠΎΠ±ΡΠ°ΡΠΈΡΡ Π²Π½ΠΈΠΌΠ°Π½ΠΈΠ΅ Π½Π° ΡΠ»Π΅Π΄ΡΡΡΠ΅Π΅.
ΠΠ΅ΡΠ΅Π΄ ΡΠ±ΠΎΡΠΊΠΎΠΉ Π³Π»Π°Π²Π½ΠΎΠ³ΠΎ ΠΈ ΠΊΠΎΠ»Π΅ΡΠ½ΡΡ
ΡΠΈΠ»ΠΈΠ½Π΄ΡΠΎΠ² Π΄Π΅ΡΠ°Π»ΠΈ ΠΏΡΠΎΠΌΡΡΡ Π² ΡΠΏΠΈΡΡΠ΅. ΠΠΎΡΡΠ½ΠΈ, ΠΌΠ°Π½ΠΆΠ΅ΡΡ ΠΈ ΡΠ°Π±ΠΎΡΠΈΠ΅ ΠΏΠΎΠ²Π΅ΡΡ
Π½ΠΎΡΡΠΈ ΡΠΈΠ»ΠΈΠ½Π΄ΡΠΎΠ² ΡΠΌΠ°Π·Π°ΡΡ ΠΊΠ°ΡΡΠΎΡΠΎΠ²ΡΠΌ ΠΌΠ°ΡΠ»ΠΎΠΌ ΠΈΠ»ΠΈ ΡΠΌΠ°Π·ΠΊΠΎΠΉ ΠΠ’-1. ΠΠ° ΡΠ°Π±ΠΎΡΡΡ ΠΏΠΎΠ²Π΅ΡΡ
Π½ΠΎΡΡΡ ΠΏΠ½Π΅Π²ΠΌΠΎΡΠΈΠ»ΠΈΠ½Π΄ΡΠΎΠ², ΡΡΠΎΠΊΠ°, ΡΠ°Π»ΡΠ½ΠΈΠΊΠ° ΠΏΡΠΎΡΡΠ°Π²ΠΊΠΈ, ΠΌΠ°Π½ΠΆΠ΅ΡΠΎΠ² ΠΏΠΎΡΡΠ½Π΅ΠΉ ΠΏΠ½Π΅Π²ΠΌΠΎΡΡΠΈΠ»ΠΈΡΠ΅Π»Π΅ΠΉ ΠΈ Π²ΠΎΠΉΠ»ΠΎΡΠ½ΠΎΠ³ΠΎ ΠΊΠΎΠ»ΡΡΠ° Π½Π°Π½Π΅ΡΡΠΈ ΡΠΌΠ°Π·ΠΊΡ Π¦ΠΠΠ’ΠΠ-201. ΠΠΎΠ»ΡΡ ΠΊΡΠ΅ΠΏΠ»Π΅Π½ΠΈΡ Π³Π»Π°Π²Π½ΠΎΠ³ΠΎ ΡΠΎΡΠΌΠΎΠ·Π½ΠΎΠ³ΠΎ ΡΠΈΠ»ΠΈΠ½Π΄ΡΠ° ΠΏΠΎΡΡΠ°Π²ΠΈΡΡ Π½Π° ΡΠΏΠ»ΠΎΡΠ½ΠΈΡΠ΅Π»ΡΠ½ΡΡ ΠΏΠ°ΡΡΡ. ΠΠΎΡΡΠ½ΠΈ ΠΏΠ½Π΅Π²ΠΌΠΎΡΡΠΈΠ»ΠΈΡΠ΅Π»Π΅ΠΉ ΡΠΎΠ±ΠΈΡΠ°ΡΡ Π² Π³ΠΈΠ»ΡΠ·Π΅ Π΄ΠΈΠ°ΠΌΠ΅ΡΡΠΎΠΌ 150 ΠΌΠΌ; ΡΡΡΠ°Π½Π°Π²Π»ΠΈΠ²Π°ΡΡ ΠΈΡ
Π½Π° ΡΡΠΎΠΊΠ΅ Ρ ΠΏΠΎΠΌΠΎΡΡΡ Π³Π°Π΅ΠΊ ΡΠΎΠ³Π»Π°ΡΠ½ΠΎ ΡΠ°Π·ΠΌΠ΅ΡΠ°ΠΌ, ΠΏΡΠΈΠ²Π΅Π΄Π΅Π½Π½ΡΠΌ Π½Π° ΡΠΈΡ. 154. ΠΠ°ΠΉΠΊΠΈ ΡΡΡΠΆΠ½ΡΡ
Π±ΠΎΠ»ΡΠΎΠ² ΠΏΠ½Π΅Π²ΠΌΠΎΡΡΠΈΠ»ΠΈΡΠ΅Π»Π΅ΠΉ ΡΡΠ΅Π·ΠΌΠ΅ΡΠ½ΠΎ Π½Π΅ Π·Π°ΡΡΠ³ΠΈΠ²Π°ΡΡ.
ΠΠΎΡΠ»Π΅ ΡΠ±ΠΎΡΠΊΠΈ ΠΏΠ½Π΅Π²ΠΌΠΎΡΡΠΈΠ»ΠΈΡΠ΅Π»Ρ ΠΏΡΠΎΠ²Π΅ΡΠΈΡΡ Π½Π° Π³Π΅ΡΠΌΠ΅ΡΠΈΡΠ½ΠΎΡΡΡ Π΄Π°Π²Π»Π΅Π½ΠΈΠ΅ΠΌ Π²ΠΎΠ·Π΄ΡΡ
Π° 3,5-4 ΠΊΠ³Ρ/ΡΠΌ2, ΠΏΡΠΈ ΡΡΠΎΠΌ Π³Π»Π°Π²Π½ΡΠΉ ΡΠΈΠ»ΠΈΠ½Π΄Ρ Π΄ΠΎΠ»ΠΆΠ΅Π½ ΡΠΎΠ·Π΄Π°Π²Π°ΡΡ Π΄Π°Π²Π»Π΅Π½ΠΈΠ΅ ΠΆΠΈΠ΄ΠΊΠΎΡΡΠΈ 85-100 ΠΊΠ³Ρ/ΡΠΌ2. Π£ΡΠ΅ΡΠΊΠΈ Π²ΠΎΠ·Π΄ΡΡ
Π° ΠΈ ΠΆΠΈΠ΄ΠΊΠΎΡΡΠΈ Π½Π΅ Π΄ΠΎΠΏΡΡΠΊΠ°ΡΡΡΡ.
ΠΠΏΠΎΡΠ½ΡΠ΅ ΠΏΠ°Π»ΡΡΡ ΠΈ Π²ΡΡΠ»ΠΊΠΈ ΠΊΠΎΠ»ΠΎΠ΄ΠΎΠΊ ΡΠ°Π±ΠΎΡΠ΅Π³ΠΎ ΡΠΎΡΠΌΠΎΠ·Π° ΡΠΌΠ°Π·Π°ΡΡ Π³ΡΠ°ΡΠΈΡΠ½ΠΎΠΉ ΡΠΌΠ°Π·ΠΊΠΎΠΉ. ΠΠΎΡΠ»Π΅ ΡΠ±ΠΎΡΠΊΠΈ ΠΊΠΎΠ»Π΅ΡΠ½ΡΠΉ ΡΠΈΠ»ΠΈΠ½Π΄Ρ ΠΈΡΠΏΡΡΠ°ΡΡ Π½Π° Π³Π΅ΡΠΌΠ΅ΡΠΈΡΠ½ΠΎΡΡΡ Π΄Π°Π²Π»Π΅Π½ΠΈΠ΅ΠΌ Π²ΠΎΠ·Π΄ΡΡ
Π° 4-5 ΠΊΠ³Ρ/ΡΠΌ2 Ρ ΠΏΠΎΠ³ΡΡΠΆΠ΅Π½ΠΈΠ΅ΠΌ Π² ΡΠΏΠΈΡΡ. Π£ΡΠ΅ΡΠΊΠ° Π²ΠΎΠ·Π΄ΡΡ
Π° Π½Π΅Π΄ΠΎΠΏΡΡΡΠΈΠΌΠ°. ΠΡΠΈ ΠΈΡΠΏΡΡΠ°Π½ΠΈΠΈ Π΄ΠΎΠ»ΠΆΠ½ΠΎ Π±ΡΡΡ ΠΈΡΠΊΠ»ΡΡΠ΅Π½ΠΎ Π²ΡΠΏΠ°Π΄Π°Π½ΠΈΠ΅ ΠΏΠΎΡΡΠ½Π΅ΠΉ ΠΏΠΎΠ΄ Π΄Π°Π²Π»Π΅Π½ΠΈΠ΅ΠΌ Π²ΠΎΠ·Π΄ΡΡ
Π°.
ΠΠΎΡΠ»Π΅ ΡΠ±ΠΎΡΠΊΠΈ ΡΠ°Π±ΠΎΡΠ΅Π³ΠΎ ΡΠΎΡΠΌΠΎΠ·Π° ΠΏΡΠΈ ΠΏΠΎΠΌΠΎΡΠΈ ΠΎΠΏΠΎΡΠ½ΡΡ
ΠΏΠ°Π»ΡΡΠ΅Π² ΠΈ ΡΠ΅Π³ΡΠ»ΠΈΡΠΎΠ²ΠΎΡΠ½ΡΡ
ΡΠΊΡΡΠ΅Π½ΡΡΠΈΠΊΠΎΠ² ΠΎΡΡΠ΅Π³ΡΠ»ΠΈΡΠΎΠ²Π°ΡΡ Π·Π°Π·ΠΎΡ ΠΌΠ΅ΠΆΠ΄Ρ Π½Π°ΠΊΠ»Π°Π΄ΠΊΠΎΠΉ ΠΊΠΎΠ»ΠΎΠ΄ΠΊΠΈ ΠΈ Π±Π°ΡΠ°Π±Π°Π½ΠΎΠΌ. ΠΠ°Π·ΠΎΡ ΠΈΠ·ΠΌΠ΅ΡΡΡΡ ΡΠ΅ΡΠ΅Π· Π»ΡΠΊ Π² Π±Π°ΡΠ°Π±Π°Π½Π΅ ΡΡΠΏΠΎΠΌ Π΄Π»ΠΈΠ½ΠΎΠΉ 200 ΠΌΠΌ Π½Π° ΡΠ°ΡΡΡΠΎΡΠ½ΠΈΠΈ 30 ΠΌΠΌ ΠΎΡ ΡΠΎΡΡΠ° Π½Π°ΠΊΠ»Π°Π΄ΠΎΠΊ. ΠΠ°Π·ΠΎΡ Π΄ΠΎΠ»ΠΆΠ΅Π½ Π±ΡΡΡ 0,35 ΠΌΠΌ Π² Π²Π΅ΡΡ
Π½Π΅ΠΉ ΡΠ°ΡΡΠΈ, 0,2 ΠΌΠΌ Π² Π½ΠΈΠΆΠ½Π΅ΠΉ ΡΠ°ΡΡΠΈ.
ΠΡΠΈ ΡΠ±ΠΎΡΠΊΠ΅ ΡΡΠΎΡΠ½ΠΎΡΠ½ΠΎΠ³ΠΎ ΡΠΎΡΠΌΠΎΠ·Π° ΡΠ°Π·ΠΆΠΈΠΌΠ½ΡΠΉ ΠΊΡΠ»Π°ΠΊ, Π²ΡΡΠ»ΠΊΡ ΠΊΡΠ»Π°ΠΊΠ°, ΠΎΠΏΠΎΡΠ½ΡΠΉ ΠΏΠ°Π»Π΅Ρ ΠΊΠΎΠ»ΠΎΠ΄ΠΎΠΊ, Π° ΡΠ°ΠΊΠΆΠ΅ ΡΠ°ΡΠ½ΠΈΡΠ½ΡΠ΅ ΡΠΎΠ΅Π΄ΠΈΠ½Π΅Π½ΠΈΡ ΠΏΡΠΈΠ²ΠΎΠ΄Π° (ΠΎΡΠΈ, Π²ΡΡΠ»ΠΊΠΈ, ΠΏΠ°Π»ΡΡΡ) ΠΏΠΎΠΊΡΡΡΡ ΡΠ»ΠΎΠ΅ΠΌ ΡΠΌΠ°Π·ΠΊΠΈ Π¦ΠΠΠ’ΠΠ-201. ΠΡΠ΅ ΠΊΠΎΠ½ΠΈΡΠ΅ΡΠΊΠΈΠ΅ ΡΠ΅Π·ΡΠ±ΠΎΠ²ΡΠ΅ ΡΠΎΠ΅Π΄ΠΈΠ½Π΅Π½ΠΈΡ ΠΏΠ½Π΅Π²ΠΌΠΎΡΠΈΡΡΠ΅ΠΌΡ ΡΡΡΠ°Π½Π°Π²Π»ΠΈΠ²Π°ΡΡ Π½Π° ΡΠΏΠ»ΠΎΡΠ½ΠΈΡΠ΅Π»ΡΠ½ΡΡ ΠΏΠ°ΡΡΡ.
ΠΡΠΈ ΡΠ±ΠΎΡΠΊΠ΅ ΠΊΠΎΠΌΠΏΡΠ΅ΡΡΠΎΡΠ° Π³Π°ΠΉΠΊΠΈ ΠΊΡΠ΅ΠΏΠ»Π΅Π½ΠΈΡ Π³ΠΎΠ»ΠΎΠ²ΠΊΠΈ Π·Π°ΡΡΠ³ΠΈΠ²Π°ΡΡ ΠΏΠΎΠΏΠ°ΡΠ½ΠΎ, Π½Π°ΡΠΈΠ½Π°Ρ ΡΠΎ ΡΡΠ΅Π΄Π½Π΅ΠΉ Π΄ΠΈΠ°ΠΌΠ΅ΡΡΠ°Π»ΡΠ½ΠΎ ΡΠ°ΡΠΏΠΎΠ»ΠΎΠΆΠ΅Π½Π½ΠΎΠΉ ΠΏΠ°ΡΡ, Π² Π΄Π²Π° ΠΏΡΠΈΠ΅ΠΌΠ°. ΠΠΎΠΌΠ΅Π½Ρ Π·Π°ΡΡΠΆΠΊΠΈ 1,2-1,7 ΠΊΠ³Ρ-ΠΌ.
Π’Π΅Ρ
Π½ΠΈΡΠ΅ΡΠΊΠΎΠ΅ ΡΠΎΡΡΠΎΡΠ½ΠΈΠ΅ ΠΊΠΎΠΌΠΏΡΠ΅ΡΡΠΎΡΠ° ΠΏΡΠΎΠ²Π΅ΡΡΡΡ Π½Π° ΡΡΠ΅Π½Π΄Π΅ ΠΏΡΠΈ ΡΠ»Π΅Π΄ΡΡΡΠΈΡ
ΡΡΠ»ΠΎΠ²ΠΈΡΡ
: ΡΠ°ΡΡΠΎΡΠ° Π²ΡΠ°ΡΠ΅Π½ΠΈΡ ΠΊΠΎΠ»Π΅Π½ΡΠ°ΡΠΎΠ³ΠΎ Π²Π°Π»Π° ΠΊΠΎΠΌΠΏΡΠ΅ΡΡΠΎΡΠ° 1200-1500 ΠΎΠ±/ΠΌΠΈΠ½, Π΄Π°Π²Π»Π΅Π½ΠΈΠ΅ ΠΌΠ°ΡΠ»Π°, ΠΏΠΎΡΡΡΠΏΠ°ΡΡΠ΅Π³ΠΎ Π² ΠΊΠΎΠΌΠΏΡΠ΅ΡΡΠΎΡ,- 1,5-3,0 ΠΊΠ³Ρ/ΡΠΌ2 ΠΈ ΡΠ΅ΠΌΠΏΠ΅ΡΠ°ΡΡΡΠ° ΠΌΠ°ΡΠ»Π° Π½Π΅ Π½ΠΈΠΆΠ΅ 40Β° Π‘.
ΠΡΠΎΠΈΠ·Π²ΠΎΠ΄ΠΈΡΠ΅Π»ΡΠ½ΠΎΡΡΡ ΠΊΠΎΠΌΠΏΡΠ΅ΡΡΠΎΡΠ° Π΄ΠΎΠ»ΠΆΠ½Π° Π±ΡΡΡ 220 Π»/ΠΌΠΈΠ½ ΠΏΡΠΈ 2000 ΠΎΠ±/ΠΌΠΈΠ½ Π²Π°Π»Π° ΠΊΠΎΠΌΠΏΡΠ΅ΡΡΠΎΡΠ°; ΠΏΡΠΎΠ²Π΅ΡΡΠ΅ΡΡΡ ΠΏΡΠΈ ΡΠΎΠ΅Π΄ΠΈΠ½Π΅Π½ΠΈΠΈ Π±Π°Π»Π»ΠΎΠ½Π° Ρ Π°ΡΠΌΠΎΡΡΠ΅ΡΠΎΠΉ ΡΠ΅ΡΠ΅Π· ΠΊΠ°Π»ΠΈΠ±ΡΠΎΠ²Π°Π½Π½ΡΠΉ ΠΊΠ°Π½Π°Π» 0 1,6 ΠΌΠΌ Π΄Π»ΠΈΠ½ΠΎΠΉ 3 ΠΌΠΌ. ΠΠ°Π²Π»Π΅Π½ΠΈΠ΅ Π² Π±Π°Π»Π»ΠΎΠ½Π΅ Π΄ΠΎΠ»ΠΆΠ½ΠΎ Π±ΡΡΡ Π½Π΅ ΠΌΠ΅Π½Π΅Π΅ 6 ΠΊΠ³Ρ/ΡΠΌ2.
ΠΠ΄Π½ΠΎΠ²ΡΠ΅ΠΌΠ΅Π½Π½ΠΎ ΠΏΡΠΎΠ²Π΅ΡΡΡΡ ΠΌΠ°ΡΠ»ΠΎΠΏΡΠΎΠΏΡΡΠΊΠ½ΡΡ ΡΠΏΠΎΡΠΎΠ±Π½ΠΎΡΡΡ. ΠΠΎΠ»ΠΈΡΠ΅ΡΡΠ²ΠΎ ΠΌΠ°ΡΠ»Π°, Π²ΡΡΠ΅ΠΊΠ°ΡΡΠ΅Π³ΠΎ ΡΠ΅ΡΠ΅Π· ΡΠ»ΠΈΠ²Π½ΠΎΠ΅ ΠΎΡΠ²Π΅ΡΡΡΠΈΠ΅ Π² Π½ΠΈΠΆΠ½Π΅ΠΉ ΠΊΡΡΡΠΊΠ΅ ΠΊΠ°ΡΡΠ΅ΡΠ°, Π΄ΠΎΠ»ΠΆΠ½ΠΎ Π±ΡΡΡ Π½Π΅ Π±ΠΎΠ»Π΅Π΅ 500 Π³ Π·Π° 5 ΠΌΠΈΠ½.
ΠΡΡΡΡΡΡΠ²ΠΈΠ΅ ΡΠ΅ΡΠΈ ΠΌΠ°ΡΠ»Π°, ΠΏΠ΅ΡΠ΅Π³ΡΠ΅Π²Π° ΠΏΠΎΠ΄ΡΠΈΠΏΠ½ΠΈΠΊΠΎΠ², ΠΏΠΎΡΡΠΎΡΠΎΠ½Π½ΠΈΡ
ΡΡΡΠΊΠΎΠ² ΠΏΡΠΎΠ²Π΅ΡΡΡΡ ΠΏΡΠΈ ΡΠ°Π±ΠΎΡΠ΅ Π½Π° Ρ
ΠΎΠ»ΠΎΡΡΠΎΠΌ Ρ
ΠΎΠ΄Ρ, Ρ. Π΅. ΠΏΡΠΈ ΠΏΠΎΠ΄Π°ΡΠ΅ Π²ΠΎΠ·Π΄ΡΡ
Π° Π² Π°ΡΠΌΠΎΡΡΠ΅ΡΡ. ΠΡΠΎΠ΄ΠΎΠ»ΠΆΠΈΡΠ΅Π»ΡΠ½ΠΎΡΡΡ ΠΈΡΠΏΡΡΠ°Π½ΠΈΠΉ 5 ΠΌΠΈΠ½.
Π Π°Π±ΠΎΡΡ ΡΠ°Π·Π³ΡΡΠ·ΠΎΡΠ½ΠΎΠ³ΠΎ ΡΡΡΡΠΎΠΉΡΡΠ²Π° ΠΏΡΠΎΠ²Π΅ΡΡΡΡ ΠΏΡΠΈ ΠΏΠΎΠ΄Π°ΡΠ΅ Π² ΠΊΠ°Π½Π°Π» 28 (ΡΠΌ. ΡΠΈΡ. 150) ΡΠΆΠ°ΡΠΎΠ³ΠΎ Π²ΠΎΠ·Π΄ΡΡ
Π° ΠΏΠΎΠ΄ Π΄Π°Π²Π»Π΅Π½ΠΈΠ΅ΠΌ 5 ΠΊΠ³Ρ/ΡΠΌ2. ΠΡΠΈ ΡΡΠΎΠΌ ΠΏΠ»ΡΠ½ΠΆΠ΅ΡΡ Π΄ΠΎΠ»ΠΆΠ½Ρ ΠΏΠΎΠ΄Π½ΡΡΡΡΡ ΠΈ ΠΏΠΎΠ»Π½ΠΎΡΡΡΡ ΠΎΡΠΊΡΡΡΡ Π²ΠΏΡΡΠΊΠ½ΡΠ΅ ΠΊΠ»Π°ΠΏΠ°Π½Ρ. ΠΠ΄Π½ΠΎΠ²ΡΠ΅ΠΌΠ΅Π½Π½ΠΎ ΠΏΡΠΎΠ²Π΅ΡΡΡΡ Π³Π΅ΡΠΌΠ΅ΡΠΈΡΠ½ΠΎΡΡΡ ΡΠΏΠ»ΠΎΡΠ½Π΅Π½ΠΈΡ ΠΏΠ»ΡΠ½ΠΆΠ΅ΡΠΎΠ². ΠΠ°Π΄Π΅Π½ΠΈΠ΅ Π΄Π°Π²Π»Π΅Π½ΠΈΡ Π·Π° 1 ΠΌΠΈΠ½ Π½Π΅ Π΄ΠΎΠ»ΠΆΠ½ΠΎ ΠΏΡΠ΅Π²ΡΡΠ°ΡΡ 0,5 ΠΊΠ³Ρ/ΡΠΌ2.
ΠΡΠ±ΡΠΎΡ ΠΌΠ°ΡΠ»Π° ΠΏΡΠΎΠ²Π΅ΡΡΡΡ ΠΏΠΎ ΠΌΠ°ΡΠ»ΡΠ½ΠΎΠΌΡ ΠΏΡΡΠ½Ρ Π½Π° ΠΏΠ»Π°ΡΡΠΈΠ½Π΅, ΠΏΠΎΠΌΠ΅ΡΠ°Π΅ΠΌΠΎΠΉ Π½Π° ΡΠ°ΡΡΡΠΎΡΠ½ΠΈΠΈ 50 ΠΌΠΌ ΠΎΡ ΡΠΎΡΡΠ° Π²ΡΠΏΡΡΠΊΠ½ΠΎΠ³ΠΎ ΠΎΡΠ²Π΅ΡΡΡΠΈΡ. ΠΠΎΡΠ»Π΅ 10 Ρ ΡΠ°Π±ΠΎΡΡ ΠΊΠΎΠΌΠΏΡΠ΅ΡΡΠΎΡΠ° ΠΏΡΡΠ½ΠΎ Π΄ΠΎΠ»ΠΆΠ½ΠΎ ΡΠΌΠ΅ΡΠ°ΡΡΡΡ Π² ΠΊΡΡΠ³Π΅ Π΄ΠΈΠ°ΠΌΠ΅ΡΡΠΎΠΌ 20 ΠΌΠΌ.
ΠΠ΅ΡΠΌΠ΅ΡΠΈΡΠ½ΠΎΡΡΡ Π½Π°Π³Π½Π΅ΡΠ°ΡΠ΅Π»ΡΠ½ΡΡ
ΠΊΠ»Π°ΠΏΠ°Π½ΠΎΠ² ΠΏΡΠΎΠ²Π΅ΡΡΡΡ ΠΏΠΎ ΠΏΠ°Π΄Π΅Π½ΠΈΡ Π΄Π°Π²Π»Π΅Π½ΠΈΡ ΡΠΆΠ°ΡΠΎΠ³ΠΎ Π²ΠΎΠ·Π΄ΡΡ
Π° Π² Π±Π°Π»Π»ΠΎΠ½Π΅. ΠΠ°Π΄Π΅Π½ΠΈΠ΅ Π΄Π°Π²Π»Π΅Π½ΠΈΡ Π²ΠΎΠ·Π΄ΡΡ
Π° Π² Π±Π°Π»Π»ΠΎΠ½Π΅ Ρ 6-7 ΠΊΠ³Ρ/ΡΠΌ2 Π½Π΅ Π΄ΠΎΠ»ΠΆΠ½ΠΎ ΠΏΠ°Π΄Π°ΡΡ Π±ΠΎΠ»Π΅Π΅ ΡΠ΅ΠΌ Π½Π° 0,5 ΠΊΠ³Ρ/ΡΠΌ2 Π·Π° 1 ΠΌΠΈΠ½.
Π‘Π±ΠΎΡΠΊΡ ΠΈ ΡΠ΅Π³ΡΠ»ΠΈΡΠΎΠ²ΠΊΡ ΡΠΎΡΠΌΠΎΠ·Π½ΠΎΠ³ΠΎ ΠΊΡΠ°Π½Π° Π½Π΅ΠΎΠ±Ρ
ΠΎΠ΄ΠΈΠΌΠΎ Π²ΡΠΏΠΎΠ»Π½ΡΡΡ Π² ΡΠΏΠ΅ΡΠΈΠ°Π»ΠΈΠ·ΠΈΡΠΎΠ²Π°Π½Π½ΡΡ
ΠΌΠ°ΡΡΠ΅ΡΡΠΊΠΈΡ
.
www.dymz.ru
Π Π΅ΠΌΠΎΠ½Ρ ΠΈ Π·Π°ΠΌΠ΅Π½Π° ΡΠ°Π±ΠΎΡΠ΅Π³ΠΎ ΡΠΎΡΠΌΠΎΠ·Π½ΠΎΠ³ΠΎ ΡΠΈΠ»ΠΈΠ½Π΄ΡΠ° β ΠΠΠ’ΠΠΠΠ‘Π’ΠΠ Π‘ΠΠΠ―
Π ΡΡΡΡΠΎΠΉΡΡΠ²Π΅ Π°Π²ΡΠΎΠΌΠΎΠ±ΠΈΠ»Ρ Π½Π΅Ρ Π²ΡΠΎΡΠΎΡΡΠ΅ΠΏΠ΅Π½Π½ΡΡ Π°Π³ΡΠ΅Π³Π°ΡΠΎΠ², Π½ΠΎ ΡΠΎΡΠΌΠΎΠ·Π½Π°Ρ ΡΠΈΡΡΠ΅ΠΌΠ° Π΄ΠΎΠ»ΠΆΠ½Π° ΡΡΠ°ΡΡ ΠΏΡΠΈΠΎΡΠΈΡΠ΅ΡΠΎΠΌ Π² ΠΎΠ±ΡΠ»ΡΠΆΠΈΠ²Π°Π½ΠΈΠΈ ΠΈ ΡΠ΅ΠΌΠΎΠ½ΡΠ΅ ΠΌΠ°ΡΠΈΠ½Ρ. Π ΡΡ Π΅ΠΌΠ΅ ΡΠ°Π±ΠΎΡΡ Π³ΠΈΠ΄ΡΠ°Π²Π»ΠΈΡΠ΅ΡΠΊΠΈΡ ΡΠΎΡΠΌΠΎΠ·ΠΎΠ² ΠΎΡΠ½ΠΎΠ²Π½ΡΠΌΠΈ ΡΠ²Π»ΡΡΡΡΡ ΠΊΠ°ΠΊΒ Π³Π»Π°Π²Π½ΡΠΉ, ΡΠ°ΠΊ ΠΈ ΡΠ°Π±ΠΎΡΠΈΠΉ ΡΠΎΡΠΌΠΎΠ·Π½ΠΎΠΉ ΡΠΈΠ»ΠΈΠ½Π΄Ρ. ΠΠ°Π²Π°ΠΉΡΠ΅ ΡΠ°ΡΡΠΌΠΎΡΡΠΈΠΌ ΠΏΡΠΈΠ½ΡΠΈΠΏ ΡΠ°Π±ΠΎΡΡ, ΡΡΡΡΠΎΠΉΡΡΠ²ΠΎ, Π΄ΠΈΠ°Π³Π½ΠΎΡΡΠΈΠΊΡ, ΡΠ΅ΠΌΠΎΠ½Ρ ΠΈ Π·Π°ΠΌΠ΅Π½Ρ ΡΠ°Π±ΠΎΡΠ΅Π³ΠΎ ΡΠΎΡΠΌΠΎΠ·Π½ΠΎΠ³ΠΎ ΡΠΈΠ»ΠΈΠ½Π΄ΡΠ° Π½Π° ΠΏΡΠΈΠΌΠ΅ΡΠ΅ ΡΠ°ΡΠΏΡΠΎΡΡΡΠ°Π½Π΅Π½Π½ΠΎΠ³ΠΎ Π°Π²ΡΠΎΠΌΠΎΠ±ΠΈΠ»Ρ ΠΌΠ°ΡΠΊΠΈ ΠΠΠ.
ΠΡΠΈΠ½ΡΠΈΠΏ ΡΠ°Π±ΠΎΡΡΒ ΡΠ°Π±ΠΎΡΠ΅Π³ΠΎ ΡΠΎΡΠΌΠΎΠ·Π½ΠΎΠ³ΠΎ ΡΠΈΠ»ΠΈΠ½Π΄ΡΠ°
ΠΠΎΡΡΡΠΏΠ°ΡΡΠ°Ρ ΠΈΠ· Π³Π»Π°Π²Π½ΠΎΠ³ΠΎ, ΠΏΠΎΠ΄ Π΄Π°Π²Π»Π΅Π½ΠΈΠ΅ΠΌ, ΡΠΎΡΠΌΠΎΠ·Π½Π°Ρ ΠΆΠΈΠ΄ΠΊΠΎΡΡΡ Π²ΠΎΠ·Π΄Π΅ΠΉΡΡΠ²ΡΠ΅Ρ Π½Π° ΠΎΠ±Π° ΠΏΠΎΡΡΠ½Ρ Π² ΡΠ°Π±ΠΎΡΠ΅ΠΌ ΡΠΈΠ»ΠΈΠ½Π΄ΡΠ΅, ΡΠ΅, Π² ΡΠ²ΠΎΡ ΠΎΡΠ΅ΡΠ΅Π΄Ρ, ΡΠ΄Π°Π²Π»ΠΈΠ²Π°ΡΡ ΠΈΠ»ΠΈ ΡΠ°Π·ΠΆΠΈΠΌΠ°ΡΡ ΡΠΎΡΠΌΠΎΠ·Π½ΡΠ΅ ΠΊΠΎΠ»ΠΎΠ΄ΠΊΠΈ, ΡΡΠΎ ΠΏΡΠΈΠ²ΠΎΠ΄ΠΈΡ ΠΊ ΡΠΎΡΠΌΠΎΠΆΠ΅Π½ΠΈΡ. ΠΠ΅ΡΠ΅Π΄Π½ΠΈΠΉ ΠΊΠΎΠ½ΡΡΡ ΡΠΎΡΠΌΠΎΠ·ΠΎΠ² Π΄ΠΈΡΠΊΠΎΠ²ΡΠΉ, Π·Π°Π΄Π½ΠΈΠΉ Ρ ΠΌΠ½ΠΎΠ³ΠΈΡ Π°Π²ΡΠΎ β Π±Π°ΡΠ°Π±Π°Π½Π½ΠΎΠ³ΠΎ ΡΠΈΠΏΠ°.
- ΠΠ΅ΡΠ΅Π΄Π½ΠΈΠ΅ ΡΡΠΏΠΏΠΎΡΡΠ°.
- Π’ΡΡΠ±ΠΎΠΏΡΠΎΠ²ΠΎΠ΄, ΠΏΠΎΠ΄Π²ΠΎΠ΄ΡΡΠΈΠΉ Π³ΠΈΠ΄ΡΠ°Π²Π»ΠΈΡΠ΅ΡΠΊΡΡ ΠΆΠΈΠ΄ΠΊΠΎΡΡΡ ΠΊ ΠΏΠ΅ΡΠ΅Π΄Π½ΠΈΠΌ ΠΊΠΎΠ»Π΅ΡΠ°ΠΌ.
- ΠΠ°Π΄Π½ΠΈΠΉ ΡΡΡΠ±ΠΎΠΏΡΠΎΠ²ΠΎΠ΄.
- ΠΠ°Π»ΡΡΡ Π·Π°Π΄Π½ΠΈΡ ΠΊΠΎΠ»Π΅Ρ.
- ΠΠ°ΡΠΎΠΊ.
- ΠΠ»Π°Π²Π½ΡΠΉ Π²Π°Π»ΡΡ.
- ΠΠ΄ΠΈΠ½ ΠΈΠ· ΠΏΠΎΡΡΠ½Π΅ΠΉ.
- Π¨ΡΠΎΠΊ.
- ΠΠ΅Π΄Π°Π»Ρ.
Π£ΡΡΡΠΎΠΉΡΡΠ²ΠΎΒ ΡΠ°Π±ΠΎΡΠ΅Π³ΠΎ ΡΠΎΡΠΌΠΎΠ·Π½ΠΎΠ³ΠΎ ΡΠΈΠ»ΠΈΠ½Π΄ΡΠ°
Π£ΡΡΡΠΎΠΉΡΡΠ²ΠΎΠΌ ΠΏΠ΅ΡΠ΅Π΄Π½ΠΈΠΉ ΡΡΠΏΠΏΠΎΡΡ ΠΈ Π·Π°Π΄Π½ΠΈΠΉ ΡΠΎΡΠΌΠΎΠ·Π½ΠΎΠΉ ΡΠΈΠ»ΠΈΠ½Π΄Ρ Π°Π²ΡΠΎΠΌΠΎΠ±ΠΈΠ»Ρ ΠΠΠ ΡΠ°Π·Π½ΡΡΡΡ Π²ΠΎ Π²Π½Π΅ΡΠ½Π΅ΠΌ Π²ΠΈΠ΄Π΅ ΠΊΠΎΡΠΏΡΡΠ° ΠΈ ΠΎΡΠ½ΠΎΠ²Π½ΡΡ ΡΠ°ΡΡΠ΅ΠΉ. Π£ΡΡΡΠΎΠΉΡΡΠ²ΠΎ Π΄ΠΈΡΠΊΠΎΠ²ΠΎΠ³ΠΎ ΡΠΎΡΠΌΠΎΠ·Π° ΡΠΎΡΡΠΎΠΈΡ ΠΈΠ· ΡΠ°ΠΊΠΈΡ ΠΎΡΠ½ΠΎΠ²Π½ΡΡ Π΄Π΅ΡΠ°Π»Π΅ΠΉ: 1 β ΠΠΎΡΡΠ΅Π½Ρ. 2 β ΠΡΠ»ΡΠ½ΠΈΠΊ. 3 β Π£ΠΏΠ»ΠΎΡΠ½ΠΈΡΠ΅Π»ΡΠ½Π°Ρ ΠΌΠ°Π½ΠΆΠ΅ΡΠ°. 4 β ΠΠΎΡΠΏΡΡ ΡΡΠΏΠΏΠΎΡΡΠ°. 6 β ΠΠΎΠ·Π΄ΡΡΠ½ΡΠΉ ΡΡΡΡΠ΅Ρ. 7 β ΠΡΡΠΆΠΈΠ½Ρ, ΠΏΡΠΈΠΆΠΈΠΌΠ°ΡΡΠΈΠ΅ ΠΊΠΎΠ»ΠΎΠ΄ΠΊΠΈ. 12 β ΠΠΎΠ»ΠΎΠ΄ΠΊΠΈ.
Π ΡΡΡΡΠΎΠΉΡΡΠ²Π΅ ΡΠΎΡΠΌΠΎΠ·Π° Π±Π°ΡΠ°Π±Π°Π½Π½ΠΎΠ³ΠΎ ΡΠΈΠΏΠ° ΠΏΡΠΈΠΌΠ΅Π½ΡΡΡΡΡ ΡΠ°ΠΊΠΈΠ΅ Π΄Π΅ΡΠ°Π»ΠΈ: 2 β Π¨ΡΡΡΠ΅Ρ ΠΏΡΠΎΠΊΠ°ΡΠΊΠΈ. 3, 11 β ΠΡΠ»ΡΠ½ΠΈΠΊ. 4, 10 β ΠΠΎΡΡΠ΅Π½Ρ. 6, 9 β Π£ΠΏΠ»ΠΎΡΠ½ΠΈΡΠ΅Π»ΡΠ½Π°Ρ ΠΌΠ°Π½ΠΆΠ΅ΡΠ° ΠΏΠΎΡΡΠ½Ρ. 7 β ΠΠΎΡΠΏΡΡ.
ΠΠΈΠ°Π³Π½ΠΎΡΡΠΈΠΊΠ°Β ΡΠ°Π±ΠΎΡΠ΅Π³ΠΎ ΡΠΎΡΠΌΠΎΠ·Π½ΠΎΠ³ΠΎ ΡΠΈΠ»ΠΈΠ½Π΄ΡΠ°
Π ΡΠΎΠΌ, ΡΡΠΎ ΠΏΡΠΈΠ±Π»ΠΈΠΆΠ°Π΅ΡΡΡ ΡΠ΅ΠΌΠΎΠ½Ρ ΡΠ°Π±ΠΎΡΠ΅Π³ΠΎ ΡΠΎΡΠΌΠΎΠ·Π½ΠΎΠ³ΠΎ ΡΠΈΠ»ΠΈΠ½Π΄ΡΠ°, Π°Π²ΡΠΎΠΌΠΎΠ±ΠΈΠ»ΠΈΡΡΡ ΡΠ°ΡΡΠΊΠ°ΠΆΡΡ ΡΠ°ΠΊΠΈΠ΅ ΠΏΡΠΈΠ·Π½Π°ΠΊΠΈ:
- ΠΠ΅ΡΠ°Π²Π½ΠΎΠΌΠ΅ΡΠ½ΠΎΠ΅ ΡΡΠ°Π±Π°ΡΡΠ²Π°Π½ΠΈΠ΅ ΠΊΠΎΠ»Π΅Ρ ΠΏΡΠΈ ΡΠΎΡΠΌΠΎΠΆΠ΅Π½ΠΈΠΈ, ΡΠ»Π΅Π΄ΡΡΠ²ΠΈΠ΅ΠΌ ΡΠ΅Π³ΠΎ ΠΌΠΎΠΆΠ΅Ρ ΡΡΠ°ΡΡ Π·Π°Π½ΠΎΡ Π°Π²ΡΠΎ. ΠΡΠΎ ΠΏΡΠΈΠ·Π½Π°ΠΊ Π·Π°Π΅Π΄Π°Π½ΠΈΡ ΠΏΠΎΡΡΠ½Ρ, ΠΊΠΎΡΠΎΡΡΠΉ ΠΌΠΎΠΆΠ΅Ρ Π²ΡΠ·Π²Π°ΡΡ ΠΏΡΠΈΠΌΠ΅Π½Π΅Π½ΠΈΠ΅ Π½Π΅ΠΊΠ°ΡΠ΅ΡΡΠ²Π΅Π½Π½ΠΎΠΉ ΠΆΠΈΠ΄ΠΊΠΎΡΡΠΈ ΠΈΠ»ΠΈ ΠΏΠΎΠΏΠ°Π΄Π°Π½ΠΈΠ΅ Π² ΡΠΈΡΡΠ΅ΠΌΡ Π²ΠΎΠ·Π΄ΡΡ Π°.
- Π‘ΡΠ°Π±Π°ΡΡΠ²Π°Π½ΠΈΠ΅ ΠΈΠ½Π΄ΠΈΠΊΠ°ΡΠΎΡΠ½ΠΎΠΉ Π»Π°ΠΌΠΏΠΎΡΠΊΠΈ ΠΏΡΠΈ ΠΊΡΠΈΡΠΈΡΠ΅ΡΠΊΠΎΠΌ ΠΏΠΎΠ½ΠΈΠΆΠ΅Π½ΠΈΠΈ ΠΆΠΈΠ΄ΠΊΠΎΡΡΠΈ Π² Π±Π°ΡΠΊΠ΅, ΠΈΠ»ΠΈ ΠΎΠ±Π½Π°ΡΡΠΆΠ΅Π½ΠΈΠ΅ ΡΡΠΎΠ³ΠΎ ΠΏΡΠΈ Π²ΠΈΠ·ΡΠ°Π»ΡΠ½ΠΎΠΌ ΠΎΡΠΌΠΎΡΡΠ΅, ΡΡΠΎ Π³ΠΎΠ²ΠΎΡΠΈΡ ΠΎ Π²ΠΎΠ·ΠΌΠΎΠΆΠ½ΠΎΠΉ ΡΡΠ΅ΡΠΊΠ΅ Π³ΠΈΠ΄ΡΠ°Π²Π»ΠΈΡΠ΅ΡΠΊΠΎΠΉ ΠΆΠΈΠ΄ΠΊΠΎΡΡΠΈ ΠΈΠ· ΠΈΠ·Π½ΠΎΡΠΈΠ²ΡΠΈΡ ΡΡ ΠΌΠ°Π½ΠΆΠ΅Ρ ΠΈΠ»ΠΈ ΠΏΡΠΎΡ ΡΠ΄ΠΈΠ²ΡΠΈΡ ΡΡ ΠΏΠ°ΡΡΡΠ±ΠΊΠΎΠ².
- ΠΠ°ΠΆΠ°ΡΠΈΠ΅ ΠΏΠ΅Π΄Π°Π»ΠΈ Π΄Π°Π΅ΡΡΡ Ρ Π±ΠΎΠ»ΡΡΠΈΠΌ ΡΡΠΈΠ»ΠΈΠ΅ΠΌ, ΡΡΠΎ ΠΌΠΎΠΆΠ΅Ρ ΠΏΡΠΎΠΈΡΡ ΠΎΠ΄ΠΈΡΡ ΠΏΠΎ Π²ΡΠ΅ΠΌ Π²ΡΡΠ΅ΠΎΠΏΠΈΡΠ°Π½Π½ΡΠΌ ΠΏΡΠΈΡΠΈΠ½Π°ΠΌ.
ΠΠ°Π΅Π΄Π°ΡΡΠΈΠΉ ΠΏΠΎΡΡΠ΅Π½Ρ ΠΈ ΡΡΠ³Π°Ρ ΠΏΠ΅Π΄Π°Π»Ρ Π΅ΡΠ΅ Π½Π΅ ΠΏΠΎΠΊΠ°Π·Π°ΡΠ΅Π»Ρ Π΄Π»Ρ ΡΠ΅ΠΌΠΎΠ½ΡΠ° ΠΈ Π·Π°ΠΌΠ΅Π½Ρ ΡΠ°Π±ΠΎΡΠΈΡ ΡΠΈΠ»ΠΈΠ½Π΄ΡΠΎΠ². Π‘Π»Π΅Π΄ΡΠ΅Ρ ΠΎΠ±ΡΠ°ΡΠΈΡΡ Π²Π½ΠΈΠΌΠ°Π½ΠΈΠ΅ Π½Π° ΡΠΎΠ»ΡΠΈΠ½Ρ ΠΊΠΎΠ»ΠΎΠ΄ΠΎΠΊ, Π΅ΡΠ»ΠΈ ΠΈΡ ΠΈΠ·Π½ΠΎΡ Π΄ΠΎΡΡΠΈΠ³ ΠΌΠ°ΠΊΡΠΈΠΌΡΠΌΠ°, ΡΡΠΎ ΠΌΠΎΠΆΠ΅Ρ ΡΠΏΡΠΎΠ²ΠΎΡΠΈΡΠΎΠ²Π°ΡΡ Π·Π°ΠΊΠ»ΠΈΠ½ΠΈΠ²Π°Π½ΠΈΠ΅ ΠΏΠΎΡΡΠ½Π΅ΠΉ, ΡΠ°ΠΊ ΠΊΠ°ΠΊ ΠΎΠ½ΠΈ ΠΏΡΠ°ΠΊΡΠΈΡΠ΅ΡΠΊΠΈ Π½Π΅ ΡΠ°Π±ΠΎΡΠ°ΡΡ.
ΠΠ·Π½Π°ΡΠ°Π»ΡΠ½ΠΎ ΡΠ°ΠΊΠΆΠ΅ ΠΌΠΎΠΆΠ΅Ρ ΠΏΠΎΠΌΠΎΡΡ ΠΈΡΠΏΡΠ°Π²ΠΈΡΡ ΡΡΠΈ ΠΏΡΠΎΠ±Π»Π΅ΠΌΡ ΠΏΠΎΠ»Π½Π°Ρ Π·Π°ΠΌΠ΅Π½Π° Π³ΠΈΠ΄ΡΠ°Π²Π»ΠΈΡΠ΅ΡΠΊΠΎΠΉ ΠΆΠΈΠ΄ΠΊΠΎΡΡΠΈ ΠΈΠ»ΠΈ ΠΏΡΠΎΠΊΠ°ΡΠΊΠ° ΡΠΈΡΡΠ΅ΠΌΡ ΡΠΎΡΠΌΠΎΠ·ΠΎΠ². ΠΡΠ»ΠΈ ΡΡΠΈ Π΄Π΅ΠΉΡΡΠ²ΠΈΡ Π½Π΅ ΠΏΡΠΈΠ²Π΅Π»ΠΈ ΠΊ ΠΏΠΎΠ»ΠΎΠΆΠΈΡΠ΅Π»ΡΠ½ΠΎΠΌΡ ΡΠ΅Π·ΡΠ»ΡΡΠ°ΡΡ, ΡΡΠ΅Π±ΡΠ΅ΡΡΡ ΠΎΡΡΠ΅ΠΌΠΎΠ½ΡΠΈΡΠΎΠ²Π°ΡΡ ΡΠ°Π±ΠΎΡΠΈΠΉ ΡΠΎΡΠΌΠΎΠ·Π½ΠΎΠΉ ΡΠΈΠ»ΠΈΠ½Π΄Ρ, Π±Π»Π°Π³ΠΎ Π² ΠΏΡΠΎΠ΄Π°ΠΆΠ΅ Π΅ΡΡΡ ΡΠ΅ΠΌΠΊΠΎΠΏΠ»Π΅ΠΊΡ ΡΠ°Π±ΠΎΡΠ΅Π³ΠΎ ΡΠΎΡΠΌΠΎΠ·Π½ΠΎΠ³ΠΎ ΡΠΈΠ»ΠΈΠ½Π΄ΡΠ°, Π² Π½Π°Π±ΠΎΡ ΠΊΠΎΡΠΎΡΠΎΠ³ΠΎ, Π² Π·Π°Π²ΠΈΡΠΈΠΌΠΎΡΡΠΈ ΠΎΡ ΠΌΠ°ΡΠΊΠΈ Π°Π²ΡΠΎ, Π²Ρ ΠΎΠ΄ΡΡ: ΠΌΠ°Π½ΠΆΠ΅ΡΡ, ΠΏΠΎΡΡΠ΅Π½Ρ, ΠΏΡΠ»ΡΠ½ΠΈΠΊ ΠΈ ΠΏΡΠΎΡΠΈΠ΅ ΡΠΎΡΡΠ°Π²Π»ΡΡΡΠΈΠ΅.
Π Π΅ΠΌΠΎΠ½ΡΠ½ΡΠ΅ ΡΠ°Π±ΠΎΡΡ
Π Π°Π·Π±ΠΎΡΠΊΠ°, Π·Π°ΠΌΠ΅Π½Π° ΠΈΠ»ΠΈ ΡΠ΅ΠΌΠΎΠ½Ρ ΡΠΎΡΠΌΠΎΠ·Π½ΠΎΠ³ΠΎ ΡΠΈΠ»ΠΈΠ½Π΄ΡΠ° Π°Π²ΡΠΎΠΌΠΎΠ±ΠΈΠ»Ρ ΠΠΠ Π½Π΅ ΠΏΡΠ΅Π΄ΡΡΠ°Π²Π»ΡΠ΅Ρ ΠΎΡΠΎΠ±ΠΎΠΉ ΡΠ»ΠΎΠΆΠ½ΠΎΡΡΠΈ. ΠΡΠΈΠΎΠ±ΡΠ΅ΡΡ Π½Π΅ΠΎΠ±Ρ ΠΎΠ΄ΠΈΠΌΡΠΉ ΡΠ΅ΠΌΠΊΠΎΠΌΠΏΠ»Π΅ΠΊΡ ΡΠ°Π±ΠΎΡΠ΅Π³ΠΎ ΡΠΎΡΠΌΠΎΠ·Π½ΠΎΠ³ΠΎ ΡΠΈΠ»ΠΈΠ½Π΄ΡΠ°, ΠΎΡΠΊΡΡΡΠΈΠ²Π°Π΅ΠΌ ΠΊΠΎΠ»Π΅ΡΠΎ ΠΈ, ΠΎΡΡΠΎΠ΅Π΄ΠΈΠ½ΠΈΠ² ΠΏΠ°ΡΡΡΠ±ΠΊΠΈ, ΡΠ½ΠΈΠΌΠ°Π΅ΠΌ Π½Π΅ΠΈΡΠΏΡΠ°Π²Π½ΡΠΉ ΡΠΈΠ»ΠΈΠ½Π΄Ρ (Π±ΠΎΠ»Π΅Π΅ ΠΏΠΎΠ΄ΡΠΎΠ±Π½ΠΎ ΡΡ Π΅ΠΌΠ° Π΄Π΅ΠΌΠΎΠ½ΡΠ°ΠΆΠ° Π±ΡΠ΄Π΅Ρ ΠΎΠΏΠΈΡΠ°Π½Π° Π½ΠΈΠΆΠ΅). ΠΠ»Ρ ΡΠ΄ΠΎΠ±ΡΡΠ²Π°, Π·Π°ΠΆΠ°Π² ΠΊΠΎΡΠΏΡΡ Π² ΡΠΈΡΠΊΠ°Ρ ΠΈ ΡΠ½ΡΠ² ΠΏΡΠ»ΡΠ½ΠΈΠΊ, ΠΏΠΎΠ»ΡΡΠ°Π΅ΠΌ Π΄ΠΎΡΡΡΠΏ ΠΊ ΡΡΠΎΠΏΠΎΡΠ½ΠΎΠΌΡ ΠΊΠΎΠ»ΡΡΡ, ΡΠΈΠΊΡΠΈΡΡΡΡΠ΅ΠΌΡ ΠΏΠΎΡΡΠ΅Π½Ρ, ΠΏΠΎΡΠ»Π΅ ΡΠ½ΡΡΠΈΡ ΠΊΠΎΡΠΎΡΠΎΠ³ΠΎ, Π²ΡΠ½ΠΈΠΌΠ°Π΅ΠΌ Π²ΡΠ΅ ΡΠ°Π±ΠΎΡΠΈΠ΅ Π΄Π΅ΡΠ°Π»ΠΈ.
ΠΡΠΎΠΈΠ·Π²Π΅Π΄Ρ ΡΠ°Π·Π±ΠΎΡΠΊΡ ΠΊΠΎΡΠΏΡΡΠ° Π½ΡΠΆΠ½ΠΎ ΠΏΡΠΎΠΌΡΡΡ Π²ΡΡ ΡΠΎΡΠΌΠΎΠ·Π½ΠΎΠΉ ΠΆΠΈΠ΄ΠΊΠΎΡΡΡΡ ΠΈ ΠΎΡΠΌΠΎΡΡΠ΅ΡΡ Π·Π΅ΡΠΊΠ°Π»ΠΎ ΠΊΠΎΡΠΏΡΡΠ° Π½Π° ΠΏΡΠ΅Π΄ΠΌΠ΅Ρ ΠΌΠ΅Ρ
Π°Π½ΠΈΡΠ΅ΡΠΊΠΈΡ
ΠΏΠΎΠ²ΡΠ΅ΠΆΠ΄Π΅Π½ΠΈΠΉ.
ΠΡΠ»ΠΈ ΠΏΠΎΠ²ΡΠ΅ΠΆΠ΄Π΅Π½ΠΈΠΉ Π½Π΅ Π²ΡΡΠ²Π»Π΅Π½ΠΎ, ΡΠΎ, Π²ΡΠΊΡΡΠ² ΡΠ΅ΠΌΠΊΠΎΠΌΠΏΠ»Π΅ΠΊΡ ΡΠ°Π±ΠΎΡΠ΅Π³ΠΎ ΡΠΎΡΠΌΠΎΠ·Π½ΠΎΠ³ΠΎ ΡΠΈΠ»ΠΈΠ½Π΄ΡΠ°, ΠΏΡΠΎΠΈΠ·Π²Π΅ΡΡΠΈ Π·Π°ΠΌΠ΅Π½Ρ Π½Π΅ΠΈΡΠΏΡΠ°Π²Π½ΡΡ Π΄Π΅ΡΠ°Π»Π΅ΠΉ.
Β
ΠΠ±ΡΠ·Π°ΡΠ΅Π»ΡΠ½ΡΠΌ ΡΡΠ»ΠΎΠ²ΠΈΠ΅ΠΌ, Π² Π½Π΅Π·Π°Π²ΠΈΡΠΈΠΌΠΎΡΡΠΈ ΠΎΡ ΠΈΡ ΡΠΎΡΡΠΎΡΠ½ΠΈΡ, ΡΠ²Π»ΡΠ΅ΡΡΡ Π·Π°ΠΌΠ΅Π½Π° Π²ΡΠ΅Ρ ΡΠ΅Π·ΠΈΠ½ΠΎΠ²ΡΡ Π΄Π΅ΡΠ°Π»Π΅ΠΉ Π²Ρ ΠΎΠ΄ΡΡΠΈΡ Π² ΡΠ΅ΠΌΠΊΠΎΠΌΠΏΠ»Π΅ΠΊΡ ΡΠ°Π±ΠΎΡΠ΅Π³ΠΎ ΡΠΎΡΠΌΠΎΠ·Π½ΠΎΠ³ΠΎ ΡΠΈΠ»ΠΈΠ½Π΄ΡΠ°. Π ΡΡΠΎΡ ΡΠΏΠΈΡΠΎΠΊ Π²Ρ ΠΎΠ΄ΡΡ: ΠΏΡΠ»ΡΠ½ΠΈΠΊ, ΠΌΠ°Π½ΠΆΠ΅ΡΠ° ΠΈ ΠΏΡΠΎΡΠ΅Π΅.
ΠΠ°ΠΌΠ΅Π½Π° Π½Π΅ΠΈΡΠΏΡΠ°Π²Π½ΠΎΠ³ΠΎ ΡΠΈΠ»ΠΈΠ½Π΄ΡΠ° ΡΠΎΡΠΌΠΎΠ·ΠΎΠ²
Π‘Ρ Π΅ΠΌΠ° Π·Π°ΠΌΠ΅Π½Ρ Π² ΡΠ΅ΠΌΠ΅ΠΉΡΡΠ²Π΅ ΠΠΠ ΠΏΡΠ°ΠΊΡΠΈΡΠ΅ΡΠΊΠΈ ΠΎΠ΄ΠΈΠ½Π°ΠΊΠΎΠ²Π° Π΄Π»Ρ ΡΠΈΠ»ΠΈΠ½Π΄ΡΠΎΠ² ΠΎΠ±ΠΎΠΈΡ ΠΊΠΎΠ½ΡΡΡΠΎΠ² Ρ ΠΌΠ΅Π»ΠΊΠΈΠΌΠΈ ΡΠ°Π·Π»ΠΈΡΠΈΡΠΌΠΈ.
ΠΠ·Π½Π°ΡΠ°Π»ΡΠ½ΠΎ Π½ΡΠΆΠ½ΠΎ ΠΏΡΠΈΠ³ΠΎΡΠΎΠ²ΠΈΡΡ Π½Π΅ΠΎΠ±Ρ ΠΎΠ΄ΠΈΠΌΡΠ΅ ΠΊΠ»ΡΡΠΈ ΠΈ ΠΏΠΎΠ΄Ρ ΠΎΠ΄ΡΡΠΈΠ΅ ΠΏΠΎ ΡΠ°Π·ΠΌΠ΅ΡΡ ΠΏΠ°ΡΡΡΠ±ΠΊΠΎΠ² Π·Π°Π³Π»ΡΡΠΊΠΈ. Π‘Π½ΡΠ² ΠΊΠΎΠ»Π΅ΡΠΎ ΠΈ ΠΎΡΠΊΡΡΡΠΈΠ² ΠΏΠ°ΡΡΡΠ±ΠΊΠΈ, Π΄Π»Ρ ΠΏΡΠ΅Π΄ΠΎΡΠ²ΡΠ°ΡΠ΅Π½ΠΈΡ ΡΡΠ΅ΡΠΊΠΈ ΠΆΠΈΠ΄ΠΊΠΎΡΡΠΈ Π½Π°Π΄Π΅Π²Π°Π΅ΠΌ Π½Π° Π½ΠΈΡ Π·Π°Π³Π»ΡΡΠΊΠΈ. ΠΡΠΊΡΡΡΠΈΠ² ΡΠΎΠΎΡΠ²Π΅ΡΡΡΠ²ΡΡΡΠΈΠ΅ Π³Π°ΠΉΠΊΠΈ, Π΄Π΅ΠΌΠΎΠ½ΡΠΈΡΡΠ΅ΠΌ ΡΡΠ°ΡΡΠΉ ΡΠΈΠ»ΠΈΠ½Π΄Ρ ΠΈ Π½Π° Π΅Π³ΠΎ ΠΌΠ΅ΡΡΠΎ ΡΡΠ°Π²ΠΈΠΌ Π½ΠΎΠ²ΡΠΉ, ΠΏΡΠΎΠΈΠ·Π²ΠΎΠ΄Ρ ΡΠ±ΠΎΡΠΊΡ Π² ΠΎΠ±ΡΠ°ΡΠ½ΠΎΠΌ ΠΏΠΎΡΡΠ΄ΠΊΠ΅. ΠΡΠ»ΠΈ ΠΏΠΎΡΠ»Π΅ Π·Π°ΠΌΠ΅Π½Ρ, ΡΠ±ΠΎΡΠΊΠΈ ΠΊΠΎΠ»Π΅ΡΠ° ΠΌΠ΅ΡΠ°ΡΡ ΡΠ»ΠΈΡΠΊΠΎΠΌ ΡΠ°Π·Π²Π΅Π΄Π΅Π½Π½ΡΠ΅ ΠΊΠΎΠ»ΠΎΠ΄ΠΊΠΈ, ΠΌΠΎΠΆΠ½ΠΎ ΠΏΠΎΠ΄ΠΏΠΈΠ»ΠΈΡΡ ΠΊΠΎΠ½ΡΠΎΠ²ΠΊΠΈ ΠΊΠΎΠ»ΠΎΠ΄ΠΎΠΊ, ΡΠΎΠ»ΡΠΊΠΎ Π½Π΅ ΠΏΠ΅ΡΠ΅ΡΡΠ΅ΡΠ΄ΡΡΠ²ΡΠΉΡΠ΅, ΡΡΠΎ ΠΌΠΎΠΆΠ΅Ρ ΡΠΊΠ°Π·Π°ΡΡΡΡ Π½Π° ΡΠ°Π±ΠΎΡΠ΅ ΡΡΡΠ½ΠΎΠ³ΠΎ ΡΠΎΡΠΌΠΎΠ·Π°. ΠΠΎΡΠ»Π΅ Π»ΡΠ±ΡΡ ΠΌΠ°Π½ΠΈΠΏΡΠ»ΡΡΠΈΠΉ Ρ ΡΠΈΡΡΠ΅ΠΌΠΎΠΉ ΡΠΎΡΠΌΠΎΠ·ΠΎΠ² ΡΡΠ΅Π±ΡΠ΅ΡΡΡ Π΅Π΅ ΠΏΡΠΎΠΊΠ°ΡΠΊΠ° ΡΠΎΠ³Π»Π°ΡΠ½ΠΎ ΡΡ Π΅ΠΌΠ΅.
ΠΡΠΎΠΊΠ°ΡΠΊΠ° ΡΠΈΡΡΠ΅ΠΌΡ ΡΠΎΡΠΌΠΎΠ·ΠΎΠ²
ΠΠ»Ρ ΠΏΡΠΎΠΊΠ°ΡΠΊΠΈ ΠΏΠΎΠ΄Π³ΠΎΡΠΎΠ²ΡΡΠ΅: ΠΆΠΈΠ΄ΠΊΠΎΡΡΡ, ΠΊΠ»ΡΡ ΠΏΠΎΠ΄Ρ ΠΎΠ΄ΡΡΠ΅Π³ΠΎ Π΄ΠΈΠ°ΠΌΠ΅ΡΡΠ° ΠΊ Π²ΠΎΠ·Π΄ΡΡΠ½ΠΎΠΌΡ ΡΡΡΡΠ΅ΡΡ, ΡΠ»Π°Π½Π³, ΠΏΠ»ΠΎΡΠ½ΠΎ ΠΎΠ΄Π΅Π²Π°ΡΡΠΈΠΉΡΡ Π½Π° ΡΡΡΡΠ΅Ρ ΠΈ Π»ΡΠ±ΡΡ Π΅ΠΌΠΊΠΎΡΡΡ. Π‘Ρ Π΅ΠΌΠ° ΠΏΡΠΎΠΊΠ°ΡΠΊΠΈ Π·Π°Π²ΠΈΡΠΈΡ ΠΎΡ ΡΠΎΠ³ΠΎ, ΠΊΠ°ΠΊ ΡΠ°ΡΠΏΠΎΠ»ΠΎΠΆΠ΅Π½Ρ ΠΊΠΎΠ½ΡΡΡΡ Π² ΠΊΠΎΠ½ΠΊΡΠ΅ΡΠ½ΠΎΠΉ ΠΌΠΎΠ΄Π΅Π»ΠΈ ΠΠΠ. Π£ΡΡΡΠΎΠΉΡΡΠ²ΠΎ ΡΠΎΡΠΌΠΎΠ·ΠΎΠ² Π½Π΅ΠΊΠΎΡΠΎΡΡΡ ΠΏΠΎΠ΄ΡΠ°Π·ΡΠΌΠ΅Π²Π°Π΅Ρ ΠΏΡΠΎΠΊΠ°ΡΠΊΡ ΠΎΡ Β«Π΄Π»ΠΈΠ½Π½ΠΎΠ³ΠΎ ΡΡΡΠ±ΠΎΠΏΡΠΎΠ²ΠΎΠ΄Π°Β», ΠΈΠΌΠ΅Π΅ΡΡΡ Π² Π²ΠΈΠ΄Ρ ΠΎΡ ΡΠ°ΠΌΠΎΠ³ΠΎ Π΄Π°Π»ΡΠ½Π΅Π³ΠΎ ΠΊΠΎΠ»Π΅ΡΠ° ΠΎΡΠ½ΠΎΡΠΈΡΠ΅Π»ΡΠ½ΠΎ Π³Π»Π°Π²Π½ΠΎΠ³ΠΎ ΡΠΈΠ»ΠΈΠ½Π΄ΡΠ°.
ΠΡΠ»ΠΈ ΠΊΠΎΠ½ΠΊΡΠ΅ΡΠ½Π΅Π΅ ΡΡΠΎ Π²ΡΠ³Π»ΡΠ΄ΠΈΡ ΡΠ°ΠΊ: Π² ΠΌΠ°ΡΠΈΠ½Π΅ Π³Π»Π°Π²Π½ΡΠΉ ΡΠΈΠ»ΠΈΠ½Π΄Ρ ΡΠ°Π·ΠΌΠ΅ΡΠ΅Π½ Π³Π»ΡΠ΄Ρ Π½Π° Π·Π°Π΄Π½ΠΈΠΉ Π±Π°ΠΌΠΏΠ΅Ρ, Π·Π½Π°ΡΠΈΡ, ΠΏΠ΅ΡΠ²ΡΠΌ ΠΏΡΠΎΠΊΠ°ΡΠΈΠ²Π°Π΅ΡΡΡ Π·Π°Π΄Π½ΠΈΠΉ ΠΏΡΠ°Π²ΡΠΉ ΡΠΈΠ»ΠΈΠ½Π΄Ρ, Π·Π°ΡΠ΅ΠΌ Π·Π°Π΄Π½ΠΈΠΉ Π»Π΅Π²ΡΠΉ. Π‘Π»Π΅Π΄ΡΡΡΠΈΠΌ ΠΈΠ΄Π΅Ρ ΠΏΠ΅ΡΠ΅Π΄Π½ΠΈΠΉ Π»Π΅Π²ΡΠΉ, ΠΈ ΠΎΠΊΠ°Π½ΡΠΈΠ²Π°Π΅ΡΡΡ ΠΏΡΠΎΡΠ΅Π΄ΡΡΠ° ΠΏΡΠΎΠΊΠ°ΡΠΊΠΎΠΉ ΡΠΎΠ³ΠΎ ΠΊΠΎΠ»Π΅ΡΠ°, ΠΊΠΎΡΠΎΡΠΎΠ΅ Π½Π°Ρ ΠΎΠ΄ΠΈΡΡΡ Ρ ΠΏΡΠ°Π²ΠΎΠΉ ΡΡΠΎΡΠΎΠ½Ρ ΠΎΡ Π³Π»Π°Π²Π½ΠΎΠ³ΠΎ ΡΠΈΠ»ΠΈΠ½Π΄ΡΠ°. Π Π±ΠΎΠ»Π΅Π΅ ΠΏΠΎΠ·Π΄Π½ΠΈΡ ΠΌΠΎΠ΄Π΅Π»ΡΡ ΡΡ Π΅ΠΌΠ° ΠΏΠΎΠ΄ΡΠ°Π·ΡΠΌΠ΅Π²Π°Π΅Ρ ΠΏΡΠΎΠΊΠ°ΡΠΊΡ ΠΊΡΠ΅ΡΡ-Π½Π°ΠΊΡΠ΅ΡΡ Π³Π»ΡΠ΄Ρ Π½Π° ΠΌΠ°ΡΠΈΠ½Ρ ΡΠ·Π°Π΄ΠΈ:
- ΠΏΡΠ°Π²ΠΎΠ΅ Π·Π°Π΄Π½Π΅Π΅ ΠΊΠΎΠ»Π΅ΡΠΎ;
- Π»Π΅Π²ΠΎΠ΅ ΠΏΠ΅ΡΠ΅Π΄Π½Π΅Π΅ ΠΊΠΎΠ»Π΅ΡΠΎ;
- Π»Π΅Π²ΠΎΠ΅ Π·Π°Π΄Π½Π΅Π΅ ΠΊΠΎΠ»Π΅ΡΠΎ;
- ΠΏΡΠ°Π²ΠΎΠ΅ ΠΏΠ΅ΡΠ΅Π΄Π½Π΅Π΅ ΠΊΠΎΠ»Π΅ΡΠΎ.
Π Π»ΡΠ±ΠΎΠΌ ΡΠ»ΡΡΠ°Π΅ Π·Π°ΠΊΠ°Π½ΡΠΈΠ²Π°ΡΡ ΠΏΡΠΎΠΊΠ°ΡΠΊΡ ΡΠ»Π΅Π΄ΡΠ΅Ρ ΠΏΠ΅ΡΠ΅Π΄Π½ΠΈΠΌ ΠΏΡΠ°Π²ΡΠΌ ΠΊΠΎΠ»Π΅ΡΠΎΠΌ. Π ΠΏΡΠΎΡΠ΅ΡΡΠ΅ ΡΡΠΎΠ³ΠΎ Π΄Π΅ΠΉΡΡΠ²ΠΈΡ Π½Π΅ Π·Π°Π±ΡΠ²Π°ΠΉΡΠ΅ ΡΠ»Π΅Π΄ΠΈΡΡ Π·Π° ΡΡΠΎΠ²Π½Π΅ΠΌ Π³ΠΈΠ΄ΡΠ°Π²Π»ΠΈΡΠ΅ΡΠΊΠΎΠΉ ΠΆΠΈΠ΄ΠΊΠΎΡΡΠΈ Π² Π±Π°ΡΠΊΠ΅, ΡΡΠΎΠ±Ρ Π²ΠΎΠ·Π΄ΡΡ ΠΎΠΏΡΡΡ Π½Π΅ ΠΏΠΎΠΏΠ°Π» Π² ΡΠΈΡΡΠ΅ΠΌΡ.
Π’Π°ΠΊΠΆΠ΅ ΡΠ΅ΠΊΠΎΠΌΠ΅Π½Π΄ΡΠ΅ΠΌ ΠΊ ΠΏΡΠΎΡΠΌΠΎΡΡΡ Π²ΠΈΠ΄Π΅ΠΎ ΠΏΠΎ ΡΠ΅ΠΌΠ΅:
AutoRemont2.ru
avtodoc24.ru
26 Π’Π΅Ρ Π½ΠΈΡΠ΅ΡΠΊΠΈΠ΅ ΡΡΠ΅Π±ΠΎΠ²Π°Π½ΠΈΡ Π½Π° ΡΠ΅ΠΌΠΎΠ½Ρ ΡΠΎΡΠΌΠΎΠ·Π½ΡΡ ΡΠΈΠ»ΠΈΠ½Π΄ΡΠΎΠ² ΠΏΠ°ΡΡΠ°ΠΆΠΈΡΡΠΊΠΈΡ Π²Π°Π³ΠΎΠ½ΠΎΠ²
26.1. Π’ΠΎΡΠΌΠΎΠ·Π½ΡΠ΅ ΡΠΈΠ»ΠΈΠ½Π΄ΡΡ Π΄ΠΎ 16β (Π²ΠΊΠ»ΡΡΠΈΡΠ΅Π»ΡΠ½ΠΎ) ΡΠ΅ΠΌΠΎΠ½ΡΠΈΡΠΎΠ²Π°ΡΡ ΠΈ ΠΈΡΠΏΡΡΡΠ²Π°ΡΡ Π² ΡΠΎΠΎΡΠ²Π΅ΡΡΡΠ²ΠΈΠΈ Ρ ΡΠ°Π·Π΄Π΅Π»ΠΎΠΌ 8.
26.2 Π’ΠΎΡΠΌΠΎΠ·Π½ΠΎΠΉ ΡΠΈΠ»ΠΈΠ½Π΄Ρ ΡΠΎ Π²ΡΡΡΠΎΠ΅Π½Π½ΡΠΌ ΡΠ΅Π³ΡΠ»ΡΡΠΎΡΠΎΠΌ
26.2.1 ΠΠΎΡΡΡΠΏΠΈΠ²ΡΠΈΠ΅ Π² ΡΠ΅ΠΌΠΎΠ½Ρ ΡΠΎΡΠΌΠΎΠ·Π½ΡΠ΅ ΡΠΈΠ»ΠΈΠ½Π΄ΡΡ ΡΠΎ Π²ΡΡΡΠΎΠ΅Π½Π½ΡΠΌΠΈ ΡΠ΅Π³ΡΠ»ΡΡΠΎΡΠ°ΠΌΠΈ (Π΄Π°Π»Π΅Π΅ — Π’Π¦Π ) Π½Π΅ΠΎΠ±Ρ ΠΎΠ΄ΠΈΠΌΠΎ ΡΠ½Π°ΡΡΠΆΠΈ ΠΎΡΠΈΡΡΠΈΡΡ ΠΎΡ ΠΏΡΠ»ΠΈ ΠΈ Π·Π°Π³ΡΡΠ·Π½Π΅Π½ΠΈΠΉ, ΠΏΠΎΡΠ»Π΅ ΡΠ΅Π³ΠΎ ΡΠ°Π·ΠΎΠ±ΡΠ°ΡΡ.
ΠΠΎΡΠ»Π΅ Π½Π°ΡΡΠΆΠ½ΠΎΠΉ ΠΎΡΠΈΡΡΠΊΠΈ ΠΈ ΠΎΠ±ΠΌΡΠ²ΠΊΠΈ Π’Π¦Π ΡΠ°Π·Π±ΠΎΡΠΊΡ ΡΠ΅Π³ΡΠ»ΠΈΡΡΡΡΠ΅Π³ΠΎ ΠΌΠ΅Ρ Π°Π½ΠΈΠ·ΠΌΠ° ΠΏΡΠΎΠΈΠ·Π²ΠΎΠ΄ΠΈΡΡ Ρ ΠΏΡΠΈΠΌΠ΅Π½Π΅Π½ΠΈΠ΅ΠΌ ΡΠΏΠ΅ΡΠΈΠ°Π»ΡΠ½ΡΡ ΠΏΡΠΈΡΠΏΠΎΡΠΎΠ±Π»Π΅Π½ΠΈΠΉ.
ΠΠ΅ΡΠ°Π»ΠΈ Π’Π¦Π ΡΡΠ°ΡΠ΅Π»ΡΠ½ΠΎ ΠΎΡΠΈΡΡΠΈΡΡ, ΠΏΡΠΎΠΌΡΡΡ, Π½Π°ΡΡΡ ΠΎ Π²ΡΡΠ΅ΡΠ΅ΡΡ ΠΈ ΠΎΡΠΌΠΎΡΡΠ΅ΡΡ.
26.2.2 Π Π΅ΠΌΠΎΠ½Ρ ΡΠΎΡΠΌΠΎΠ·Π½ΠΎΠ³ΠΎ ΡΠΈΠ»ΠΈΠ½Π΄ΡΠ° Π½Π΅ΠΎΠ±Ρ ΠΎΠ΄ΠΈΠΌΠΎ ΠΏΡΠΎΠΈΠ·Π²ΠΎΠ΄ΠΈΡΡ Ρ ΡΠΎΠ±Π»ΡΠ΄Π΅Π½ΠΈΠ΅ΠΌ ΡΠ»Π΅Π΄ΡΡΡΠΈΡ ΡΡΠ΅Π±ΠΎΠ²Π°Π½ΠΈΠΉ:
— Ρ ΠΊΠΎΡΠΏΡΡΠ° ΡΠΎΡΠΌΠΎΠ·Π½ΠΎΠ³ΠΎ ΡΠΈΠ»ΠΈΠ½Π΄ΡΠ° ΠΈ Π΅Π³ΠΎ Π΄Π΅ΡΠ°Π»Π΅ΠΉ Π½Π΅ Π΄ΠΎΠΏΡΡΠΊΠ°ΡΡΡΡ ΡΡΠ΅ΡΠΈΠ½Ρ, ΠΎΡΠΊΠΎΠ»Ρ, ΠΈΠ·Π»ΠΎΠΌΡ ΠΈ ΡΡΡΠ² ΡΠ΅Π·ΡΠ±Ρ;
-ΠΌΡΡΡΡ ΠΈ ΠΊΠΎΡΠΏΡΡ ΡΠΎΡΠΌΠΎΠ·Π½ΠΎΠ³ΠΎ ΡΠΈΠ»ΠΈΠ½Π΄ΡΠ°, ΠΈΠΌΠ΅ΡΡΠΈΠ΅ ΡΡΠ΅ΡΠΈΠ½Ρ, Π·Π°ΠΌΠ΅Π½ΡΡΡΡΡ;
— Π·Π°Π΄ΠΈΡΡ Π½Π° ΡΠ°Π±ΠΎΡΠ΅ΠΉ ΠΏΠΎΠ²Π΅ΡΡ Π½ΠΎΡΡΠΈ ΠΊΠΎΡΠΏΡΡΠ° Π·Π°ΡΠΈΡΠ°ΡΡΡΡ;
— ΠΈΠ·Π½ΠΎΡΠ΅Π½Π½ΡΠ΅ ΠΊΠΎΡΠΏΡΡΠ½ΡΠ΅ ΠΏΠΎΠ²Π΅ΡΡ Π½ΠΎΡΡΠΈ ΠΎΠ³ΡΠ°Π½ΠΈΡΠΈΡΠ΅Π»Ρ ΠΈ Π³Π°Π΅ΠΊ Π±ΠΎΠ»Π΅Π΅ 0,6Β ΠΌΠΌ Π½Π°ΠΏΠ»Π°Π²Π»ΡΡΡΡΡ ΠΈ ΠΏΡΠΎΡΠ°ΡΠΈΠ²Π°ΡΡΡΡ Ρ ΡΠΎΡ ΡΠ°Π½Π΅Π½ΠΈΠ΅ΠΌ ΠΊΠΎΠ½ΡΡΠ½ΠΎΡΡΠΈ, ΠΏΡΠ΅Π΄ΡΡΠΌΠΎΡΡΠ΅Π½Π½ΠΎΠΉ ΡΠ΅ΡΡΠ΅ΠΆΠ°ΠΌΠΈ.
— ΡΠ΅Π·ΠΈΠ½ΠΎΠ²Π°Ρ ΠΌΠ°Π½ΠΆΠ΅ΡΠ° ΠΏΡΠΈ ΠΏΠΎΡΠ΅ΡΠ΅ ΡΠ»Π°ΡΡΠΈΡΠ½ΠΎΡΡΠΈ, ΡΠ°Π·Π±ΡΡ Π°Π½ΠΈΠΈ, ΡΠ°ΡΡΠ»ΠΎΠ΅Π½ΠΈΠΈ, ΡΠ°Π·ΡΡΠ²Π°Ρ , ΡΡΠ΅ΡΠΈΠ½Π°Ρ ΠΈΠ»ΠΈ ΠΏΡΠΎΡΡΠΎΡΠ΅Π½Π½ΠΎΠΌ ΡΡΠΎΠΊΠ΅ ΡΠ»ΡΠΆΠ±Ρ Π·Π°ΠΌΠ΅Π½ΡΠ΅ΡΡΡ Π½ΠΎΠ²ΠΎΠΉ.
— ΠΈΠ·Π³ΠΈΠ±, ΠΈΠ·Π½ΠΎΡ ΡΠ΅Π·ΡΠ±Ρ ΠΈ Π΄ΡΡΠ³ΠΈΠ΅ Π½Π΅ΠΈΡΠΏΡΠ°Π²Π½ΠΎΡΡΠΈ Π²ΠΈΠ½ΡΠ°, Π½Π°ΡΡΡΠ°ΡΡΠΈΠ΅ Π΅Π³ΠΎ ΡΡΠ½ΠΊΡΠΈΠΎΠ½ΠΈΡΠΎΠ²Π°Π½ΠΈΠ΅, Π½Π΅ Π΄ΠΎΠΏΡΡΠΊΠ°ΡΡΡΡ;
— ΠΈΠ·Π½ΠΎΡ ΡΠ΅Π·ΡΠ±Ρ Π²ΡΠΏΠΎΠΌΠΎΠ³Π°ΡΠ΅Π»ΡΠ½ΠΎΠΉ Π³Π°ΠΉΠΊΠΈ Π΄ΠΎΠΏΡΡΠΊΠ°Π΅ΡΡΡ Π΄ΠΎ 1Β ΠΌΠΌ, ΠΏΡΠΈ Π±ΠΎΠ»ΡΡΠ΅ΠΌ ΠΈΠ·Π½ΠΎΡΠ΅ Π³Π°ΠΉΠΊΠ° Π·Π°ΠΌΠ΅Π½ΡΠ΅ΡΡΡ;
— ΡΠ°ΡΠΈΠΊΠΎΠ²ΡΠΉ ΠΏΠΎΠ΄ΡΠΈΠΏΠ½ΠΈΠΊ Π·Π°ΠΌΠ΅Π½ΡΠ΅ΡΡΡ ΠΏΡΠΈ Π½Π°Π»ΠΈΡΠΈΠΈ ΡΡΠ΅ΡΠΈΠ½ Π½Π° Π½Π°ΡΡΠΆΠ½ΡΡ ΠΊΠΎΠ»ΡΡΠ°Ρ ΠΈ ΡΠ΅ΠΏΠ°ΡΠ°ΡΠΎΡΠ΅, ΡΠΆΠ°Π²ΡΠΈΠ½Ρ, Π·Π°ΡΡΠ΅Π½ΡΠ΅Π² ΠΈΠ»ΠΈ Π²ΡΠΊΡΠ°ΡΠΈΠ²Π°Π½ΠΈΡ ΠΌΠ΅ΡΠ°Π»Π»Π° Π½Π° Π±Π΅Π³ΠΎΠ²ΡΡ Π΄ΠΎΡΠΎΠΆΠΊΠ°Ρ Π²Π½ΡΡΡΠ΅Π½Π½ΠΈΡ ΠΈ Π½Π°ΡΡΠΆΠ½ΡΡ ΠΊΠΎΠ»Π΅Ρ;
— ΠΏΡΡΠΆΠΈΠ½Ρ ΠΏΡΠΈ Π½Π°Π»ΠΈΡΠΈΠΈ ΠΈΠ·Π»ΠΎΠΌΠΎΠ² ΠΈΠ»ΠΈ ΡΡΠ΅ΡΠΈΠ½ Π² Π²ΠΈΡΠΊΠ°Ρ , ΠΏΡΠΎΡΠ°Π΄ΠΊΠΈ Π±ΠΎΠ»Π΅Π΅ Π΄ΠΎΠΏΡΡΠΊΠ°Π΅ΠΌΠΎΠΉ Π·Π°ΠΌΠ΅Π½ΡΡΡΡΡ. ΠΡΠΎΠ³ΠΈΠ± ΠΏΡΡΠΆΠΈΠ½Ρ ΡΠΎΡΠΌΠΎΠ·Π½ΠΎΠ³ΠΎ ΡΠΈΠ»ΠΈΠ½Π΄ΡΠ° ΠΏΠΎΠ΄ Π½Π°Π³ΡΡΠ·ΠΊΠΎΠΉ (65Β±6,5)Β ΠΊΠ³Ρ Π΄ΠΎΠ»ΠΆΠ΅Π½ Π±ΡΡΡ 49Β ΠΌΠΌ, Π° ΠΏΡΠΎΠ³ΠΈΠ± ΠΏΡΡΠΆΠΈΠ½Ρ Π²ΡΡΡΠΎΠ΅Π½Π½ΠΎΠ³ΠΎ ΡΠ΅Π³ΡΠ»ΡΡΠΎΡΠ° ΠΏΠΎΠ΄ Π½Π°Π³ΡΡΠ·ΠΊΠΎΠΉ (15Β±1,5)Β ΠΊΠ³Ρ Π΄ΠΎΠ»ΠΆΠ΅Π½ Π±ΡΡΡ 14Β ΠΌΠΌ.
26.2.3 ΠΡΠΈ ΡΠ±ΠΎΡΠΊΠ΅ Π’Π¦Π ΡΡΡΡΠΈΠ΅ΡΡ ΠΏΠΎΠ²Π΅ΡΡ Π½ΠΎΡΡΠΈ Β«ΠΌΠ΅ΡΠ°Π»Π»-ΠΌΠ΅ΡΠ°Π»Π»Β» Π΄ΠΎΠ»ΠΆΠ½Ρ Π±ΡΡΡ ΡΠΌΠ°Π·Π°Π½Ρ ΡΠΌΠ°Π·ΠΊΠΎΠΉ Π¦ΠΠΠ’ΠΠ-201, Π° Β«ΠΌΠ΅ΡΠ°Π»Π»-ΡΠ΅Π·ΠΈΠ½Π°Β» β ΡΠΌΠ°Π·ΠΊΠΎΠΉ ΠΠ’-79Π.
26.2.4 ΠΠΎΡΠ»Π΅ ΡΠ±ΠΎΡΠΊΠΈ Π’Π¦Π Π½Π΅ΠΎΠ±Ρ ΠΎΠ΄ΠΈΠΌΠΎ ΠΈΡΠΏΡΡΠ°ΡΡ Π½Π° Π³Π΅ΡΠΌΠ΅ΡΠΈΡΠ½ΠΎΡΡΡ.
ΠΡΠΏΡΡΠ°Π½ΠΈΠ΅ Π½Π° ΡΡΠ΅Π½Π΄Π΅ ΡΠ½ΠΈΡΠΈΡΠΈΡΠΎΠ²Π°Π½Π½ΠΎΠΉ ΠΊΠΎΠ½ΡΡΡΡΠΊΡΠΈΠΈ Π½Π΅ΠΎΠ±Ρ ΠΎΠ΄ΠΈΠΌΠΎ ΠΏΡΠΎΠΈΠ·Π²ΠΎΠ΄ΠΈΡΡ Π² ΡΠΎΠΎΡΠ²Π΅ΡΡΡΠ²ΠΈΠΈ Ρ ΡΠ°Π·Π΄Π΅Π»ΠΎΠΌ 27.
ΠΡΠΏΡΡΠ°ΡΠ΅Π»ΡΠ½ΡΠΉ ΡΡΠ΅Π½Π΄, ΡΡ Π΅ΠΌΠ° ΠΊΠΎΡΠΎΡΠΎΠ³ΠΎ ΠΎΡΠ»ΠΈΡΠ°Π΅ΡΡΡ ΠΎΡ ΡΡ Π΅ΠΌΡ ΡΡΠ΅Π½Π΄Π° ΡΠ½ΠΈΡΠΈΡΠΈΡΠΎΠ²Π°Π½Π½ΠΎΠΉ ΠΊΠΎΠ½ΡΡΡΡΠΊΡΠΈΠΈ, Π΄ΠΎΠ»ΠΆΠ΅Π½ Π±ΡΡΡ Π΄ΠΎΠΏΡΡΠ΅Π½ ΠΊ ΠΏΡΠΈΠΌΠ΅Π½Π΅Π½ΠΈΡ Π² ΠΠΠ Π² ΡΡΡΠ°Π½ΠΎΠ²Π»Π΅Π½Π½ΠΎΠΌ ΠΏΠΎΡΡΠ΄ΠΊΠ΅, Π° ΠΈΡΠΏΡΡΠ°Π½ΠΈΠ΅ Π½Π° Π½Π΅ΠΌ Π½Π΅ΠΎΠ±Ρ ΠΎΠ΄ΠΈΠΌΠΎ ΠΏΡΠΎΠΈΠ·Π²ΠΎΠ΄ΠΈΡΡ Π² ΡΠΎΠΎΡΠ²Π΅ΡΡΡΠ²ΠΈΠΈ Ρ ΡΡΠΊΠΎΠ²ΠΎΠ΄ΡΡΠ²ΠΎΠΌ ΠΏΠΎ ΡΠΊΡΠΏΠ»ΡΠ°ΡΠ°ΡΠΈΠΈ ΡΡΠΎΠ³ΠΎ ΡΡΠ΅Π½Π΄Π°.
26.2.5 ΠΡΠΎΠ²Π΅Π΄Π΅Π½ΠΈΠ΅ ΠΈΡΠΏΡΡΠ°Π½ΠΈΠΉ Π½Π° ΡΡΠ΅Π½Π΄Π΅ Ρ ΡΠ΅Π³ΠΈΡΡΡΠ°ΡΠΈΠ΅ΠΉ ΠΏΠ°ΡΠ°ΠΌΠ΅ΡΡΠΎΠ² ΠΏΡΠΈ Π²ΡΠΊΠ»ΡΡΠ΅Π½Π½ΡΡ ΡΠ΅Π³ΠΈΡΡΡΠΈΡΡΡΡΠΈΡ ΡΡΡΡΠΎΠΉΡΡΠ²Π°Ρ Π·Π°ΠΏΡΠ΅ΡΠ°Π΅ΡΡΡ.
27 ΠΡΠΏΡΡΠ°Π½ΠΈΠ΅ ΡΠΎΡΠΌΠΎΠ·Π½ΡΡ ΡΠΈΠ»ΠΈΠ½Π΄ΡΠΎΠ² ΠΏΠ°ΡΡΠ°ΠΆΠΈΡΡΠΊΠΈΡ Π²Π°Π³ΠΎΠ½ΠΎΠ²
27.1. Π’ΠΎΡΠΌΠΎΠ·Π½ΡΠ΅ ΡΠΈΠ»ΠΈΠ½Π΄ΡΡ Π΄ΠΎ 16β (Π²ΠΊΠ»ΡΡΠΈΡΠ΅Π»ΡΠ½ΠΎ) ΠΈΡΠΏΡΡΡΠ²Π°ΡΡ Π² ΡΠΎΠΎΡΠ²Π΅ΡΡΡΠ²ΠΈΠΈ Ρ ΡΠ°Π·Π΄Π΅Π»ΠΎΠΌ 8.
27.2 ΠΡΠΏΡΡΠ°Π½ΠΈΠ΅ ΡΠΎΡΠΌΠΎΠ·Π½ΠΎΠ³ΠΎ ΡΠΈΠ»ΠΈΠ½Π΄ΡΠ° ΡΠΎ Π²ΡΡΡΠΎΠ΅Π½Π½ΡΠΌ ΡΠ΅Π³ΡΠ»ΡΡΠΎΡΠΎΠΌ
27.2.1 ΠΡΠΈΠ½ΡΠΈΠΏΠΈΠ°Π»ΡΠ½Π°Ρ ΠΏΠ½Π΅Π²ΠΌΠ°ΡΠΈΡΠ΅ΡΠΊΠ°Ρ ΡΡ Π΅ΠΌΠ° ΡΡΠ΅Π½Π΄Π° Π΄Π»Ρ ΠΈΡΠΏΡΡΠ°Π½ΠΈΡ ΡΠΎΡΠΌΠΎΠ·Π½ΠΎΠ³ΠΎ ΡΠΈΠ»ΠΈΠ½Π΄ΡΠ° ΡΠΎ Π²ΡΡΡΠΎΠ΅Π½Π½ΡΠΌ ΡΠ΅Π³ΡΠ»ΡΡΠΎΡΠΎΠΌ Π΄ΠΎΠ»ΠΆΠ½Π° ΡΠΎΠΎΡΠ²Π΅ΡΡΡΠ²ΠΎΠ²Π°ΡΡ ΡΡ Π΅ΠΌΠ΅, ΠΏΡΠΈΠ²Π΅Π΄Π΅Π½Π½ΠΎΠΉ Π½Π° ΡΠΈΡΡΠ½ΠΊΠ΅ 20.
1βΠΈΡΠΏΡΡΡΠ΅ΠΌΡΠΉ Π’Π¦Π ΡΠΎ Π²ΡΡΡΠΎΠ΅Π½Π½ΡΠΌ ΡΠ΅Π³ΡΠ»ΡΡΠΎΡΠΎΠΌ; 2βΡΡΡΠ±ΠΎΠΏΡΠΎΠ²ΠΎΠ΄; 3, 4βΠΌΠ°Π½ΠΎΠΌΠ΅ΡΡ; 5- ΠΊΡΠ°Π½ ΡΠ°Π·ΠΎΠ±ΡΠΈΡΠ΅Π»ΡΠ½ΡΠΉ ; 6βΠΊΡΠ°Π½ ΠΌΠ°ΡΠΈΠ½ΠΈΡΡΠ° 326Π‘; 7βΡΠ΅Π»Π΅ Π΄Π°Π²Π»Π΅Π½ΠΈΡ 404; 8βΡΠ»Π΅ΠΊΡΡΠΎΠΏΠ½Π΅Π²ΠΌΠ°ΡΠΈΡΠ΅ΡΠΊΠΈΠΉ Π²Π΅Π½ΡΠΈΠ»Ρ; 9βΠ΄Π°ΡΡΠΈΠΊ Π΄Π°Π²Π»Π΅Π½ΠΈΡ; 10βΠ²ΡΠΊΠ»ΡΡΠ°ΡΠ΅Π»Ρ ΠΈΡΡΠΎΡΠ½ΠΈΠΊΠ° ΡΠΎΠΊΠ° Π½Π°ΠΏΡΡΠΆΠ΅Π½ΠΈΠ΅ΠΌ 50 Π; 11βΠΊΠ»Π°ΠΏΠ°Π½ Π²ΡΠΏΡΡΠΊΠ½ΠΎΠΉ ΠΎΠ΄ΠΈΠ½Π°ΡΠ½ΡΠΉ; 12βΡΡΡΡΠΎΠΉΡΡΠ²ΠΎ Π΄Π»Ρ ΡΠΈΠΊΡΠ°ΡΠΈΠΈ ΡΠΏΠΎΡΠ°.
Π ΠΈΡΡΠ½ΠΎΠΊ 20β ΠΡΠΈΠ½ΡΠΈΠΏΠΈΠ°Π»ΡΠ½Π°Ρ ΡΡ Π΅ΠΌΠ° ΡΡΠ΅Π½Π΄Π° Π΄Π»Ρ ΠΈΡΠΏΡΡΠ°Π½ΠΈΡ ΡΠΎΡΠΌΠΎΠ·Π½ΠΎΠ³ΠΎ ΡΠΈΠ»ΠΈΠ½Π΄ΡΠ° ΡΠΎ Π²ΡΡΡΠΎΠ΅Π½Π½ΡΠΌ ΡΠ΅Π³ΡΠ»ΡΡΠΎΡΠΎΠΌ.
Π‘ΡΠ΅Π½Π΄ Π΄ΠΎΠ»ΠΆΠ΅Π½ ΠΈΠΌΠ΅ΡΡ:
— ΡΡΡΠ±ΠΎΠΏΡΠΎΠ²ΠΎΠ΄Ρ ;
— ΠΌΠ°Π½ΠΎΠΌΠ΅ΡΡ 3 Ρ ΠΏΡΠ΅Π΄Π΅Π»ΠΎΠΌ ΠΈΠ·ΠΌΠ΅ΡΠ΅Π½ΠΈΡ 0,1Β ΠΠΠ° (1,0Β ΠΊΠ³Ρ/ΡΠΌ2) ΠΊΠ»Π°ΡΡΠ° ΡΠΎΡΠ½ΠΎΡΡΠΈ 1,5;
— ΠΌΠ°Π½ΠΎΠΌΠ΅ΡΡ 4 Ρ ΠΏΡΠ΅Π΄Π΅Π»ΠΎΠΌ ΠΈΠ·ΠΌΠ΅ΡΠ΅Π½ΠΈΡ 1,0Β ΠΠΠ° (10Β ΠΊΠ³Ρ/ΡΠΌ2) ΠΊΠ»Π°ΡΡΠ° ΡΠΎΡΠ½ΠΎΡΡΠΈ 0,6;
— ΠΊΡΠ°Π½Ρ ΡΠ°Π·ΠΎΠ±ΡΠΈΡΠ΅Π»ΡΠ½ΡΠ΅ ;
— ΠΊΡΠ°Π½ ΠΌΠ°ΡΠΈΠ½ΠΈΡΡΠ° 326Π‘ ;
— ΡΠ΅Π»Π΅ Π΄Π°Π²Π»Π΅Π½ΠΈΡ 404 ;
— ΡΠ»Π΅ΠΊΡΡΠΈΡΠ΅ΡΠΊΠΈΠΉ Π²Π΅Π½ΡΠΈΠ»Ρ;
— Π΄Π°ΡΡΠΈΠΊ Π΄Π°Π²Π»Π΅Π½ΠΈΡ ;
— Π²ΡΠΊΠ»ΡΡΠ°ΡΠ΅Π»Ρ ΠΈΡΡΠΎΡΠ½ΠΈΠΊΠ° ΡΠΎΠΊΠ° 50Π;
— Π±Π»ΠΎΠΊ ΡΠ»Π΅ΠΊΡΡΠΎΠΏΠΈΡΠ°Π½ΠΈΡ 50 Π;
— ΠΊΠ»Π°ΠΏΠ°Π½ Π²ΡΠΏΡΡΠΊΠ½ΠΎΠΉ ΠΎΠ΄ΠΈΠ½Π°ΡΠ½ΡΠΉ ΠΈ ΡΡΡΡΠΎΠΉΡΡΠ²ΠΎ Π΄Π»Ρ ΡΠΈΠΊΡΠ°ΡΠΈΠΈ ΡΠΏΠΎΡΠ°.
27.2.2 ΠΠ΅ΡΠΎΠ΄ΠΈΠΊΠ° ΠΈΡΠΏΡΡΠ°Π½ΠΈΡ.
ΠΡΠΎΠ²Π΅ΡΠΈΡΡ Π³Π΅ΡΠΌΠ΅ΡΠΈΡΠ½ΠΎΡΡΡ ΡΠΈΠ»ΠΈΠ½Π΄ΡΠ° Π’Π¦Π . ΠΡΠΎΠ²Π΅ΡΠΊΠ° Π³Π΅ΡΠΌΠ΅ΡΠΈΡΠ½ΠΎΡΡΠΈ ΡΠΈΠ»ΠΈΠ½Π΄ΡΠ° ΠΏΡΠΎΠΈΠ·Π²ΠΎΠ΄ΠΈΡΡΡ ΠΏΡΠΈ ΠΏΠΎΠ»Π½ΠΎΠΌ Π²ΡΡ ΠΎΠ΄Π΅ ΡΡΠΎΠΊΠ°.
ΠΡΠΈ Π½Π°Π»ΠΈΡΠΈΠΈ Ρ ΡΠΎΡΠΌΠΎΠ·Π½ΠΎΠ³ΠΎ ΡΠΈΠ»ΠΈΠ½Π΄ΡΠ° ΡΡΠΎΡΠ½ΠΎΡΠ½ΠΎΠ³ΠΎ ΡΠΎΡΠΌΠΎΠ·Π°, ΠΏΡΠΈΠ²ΠΎΠ΄ΠΈΠΌΠΎΠ³ΠΎ Π² Π΄Π΅ΠΉΡΡΠ²ΠΈΠ΅ Π²ΠΎΠ·Π΄ΡΡ ΠΎΠΌ, ΠΈΡΠΏΡΡΠ°Π½ΠΈΡ ΡΠΎΡΠΌΠΎΠ·Π½ΠΎΠ³ΠΎ ΡΠΈΠ»ΠΈΠ½Π΄ΡΠ° ΡΠΎ Π²ΡΡΡΠΎΠ΅Π½Π½ΡΠΌ ΡΠ΅Π³ΡΠ»ΡΡΠΎΡΠΎΠΌ ΠΏΡΠΎΠ²ΠΎΠ΄ΠΈΡΡ ΠΏΡΠΈ Π΄Π°Π²Π»Π΅Π½ΠΈΠΈ Π² ΠΏΠΎΠ»ΠΎΡΡΠΈ ΡΡΠΎΡΠ½ΠΎΡΠ½ΠΎΠ³ΠΎ ΡΠΎΡΠΌΠΎΠ·Π° Π½Π΅ ΠΌΠ΅Π½Π΅Π΅ (0,40+0,02)Β ΠΠΠ° [(4,0+0,2)Β ΠΊΠ³Ρ/ΡΠΌ2].
ΠΠΎΠ΄Π½ΡΡΡ Π΄Π°Π²Π»Π΅Π½ΠΈΠ΅ Π²ΠΎΠ·Π΄ΡΡ Π° Π² ΡΠΈΠ»ΠΈΠ½Π΄ΡΠ΅ Ρ Π½ΡΠ»Ρ Π΄ΠΎ (0,40+0,02)Β ΠΠΠ° [(4,0+0,2)Β ΠΊΠ³Ρ/ΡΠΌ2] ΠΈ ΠΎΡΠΊΠ»ΡΡΠΈΡΡ ΠΈΡΡΠΎΡΠ½ΠΈΠΊ ΠΏΠΈΡΠ°Π½ΠΈΡ. ΠΠ° 3 ΠΌΠΈΠ½ΡΡΡ Π΄Π°Π²Π»Π΅Π½ΠΈΠ΅ Π½Π΅ Π΄ΠΎΠ»ΠΆΠ½ΠΎ ΠΏΠΎΠ½ΠΈΠΆΠ°ΡΡΡΡ Π±ΠΎΠ»Π΅Π΅ ΡΠ΅ΠΌ Π½Π° 0,01Β ΠΠΠ° (0,1Β ΠΊΠ³Ρ/ΡΠΌ2), ΠΏΠΎΡΠ»Π΅ ΡΠ΅Π³ΠΎ ΡΠ½ΠΈΠ·ΠΈΡΡ Π΄Π°Π²Π»Π΅Π½ΠΈΠ΅ Π΄ΠΎ Π½ΡΠ»Ρ.
ΠΡΠΎΠ²Π΅ΡΠΊΡ Π³Π΅ΡΠΌΠ΅ΡΠΈΡΠ½ΠΎΡΡΠΈ ΠΏΠΎΠ»ΠΎΡΡΠΈ ΡΡΠΎΡΠ½ΠΎΡΠ½ΠΎΠ³ΠΎ ΡΠΎΡΠΌΠΎΠ·Π° ΡΠ»Π΅Π΄ΡΠ΅Ρ ΠΏΡΠΎΠΈΠ·Π²ΠΎΠ΄ΠΈΡΡ ΠΏΡΠΈ Π΄Π°Π²Π»Π΅Π½ΠΈΠΈ (0,40+0,02)Β ΠΠΠ° [(4,0+0,2)Β ΠΊΠ³Ρ/ΡΠΌ2]. ΠΠ° 3 ΠΌΠΈΠ½ΡΡΡ Π΄Π°Π²Π»Π΅Π½ΠΈΠ΅ Π½Π΅ Π΄ΠΎΠ»ΠΆΠ½ΠΎ ΠΏΠΎΠ½ΠΈΠΆΠ°ΡΡΡΡ Π±ΠΎΠ»Π΅Π΅ ΡΠ΅ΠΌ Π½Π° 0,01Β ΠΠΠ° (0,1Β ΠΊΠ³Ρ/ΡΠΌ2).
ΠΠΎΠ΄Π½ΡΡΡ Π΄Π°Π²Π»Π΅Π½ΠΈΠ΅ Π²ΠΎΠ·Π΄ΡΡ Π° Π² ΡΠΈΠ»ΠΈΠ½Π΄ΡΠ΅ Ρ Π½ΡΠ»Ρ Π΄ΠΎ (0,10+0,01)Β ΠΠΠ° [(1,0Β±0,1)Β ΠΊΠ³Ρ/ΡΠΌ2], ΠΎΡΠΊΠ»ΡΡΠΈΡΡ ΠΈΡΡΠΎΡΠ½ΠΈΠΊ ΠΏΠΈΡΠ°Π½ΠΈΡ. ΠΠ° 1 ΠΌΠΈΠ½ΡΡΡ Π΄Π°Π²Π»Π΅Π½ΠΈΠ΅ Π½Π΅ Π΄ΠΎΠ»ΠΆΠ½ΠΎ ΠΏΠΎΠ½ΠΈΠΆΠ°ΡΡΡΡ Π±ΠΎΠ»Π΅Π΅ ΡΠ΅ΠΌ Π½Π° 0,01 ΠΠΠ° (0,1Β ΠΊΠ³Ρ/ΡΠΌ2).
ΠΠΎΠ½ΡΡΠΎΠ»Ρ Π·Π° ΡΡΡΠ°Π½ΠΎΠ²ΠΈΠ²ΡΠΈΠΌΡΡ Π΄Π°Π²Π»Π΅Π½ΠΈΠ΅ΠΌ Π² ΡΠΈΠ»ΠΈΠ½Π΄ΡΠ΅ ΠΏΡΠΎΠΈΠ·Π²ΠΎΠ΄ΠΈΡΡ ΡΠ΅ΡΠ΅Π· 60-80Β Ρ ΠΏΠΎΡΠ»Π΅ Π΄ΠΎΡΡΠΈΠΆΠ΅Π½ΠΈΡ Π·Π°Π΄Π°Π½Π½ΠΎΠ³ΠΎ Π΄Π°Π²Π»Π΅Π½ΠΈΡ.
ΠΡΠΎΠ²Π΅ΡΠΈΡΡ Π²Π΅Π»ΠΈΡΠΈΠ½Ρ Π΄Π°Π²Π»Π΅Π½ΠΈΡ ΡΠΆΠ°ΡΠΎΠ³ΠΎ Π²ΠΎΠ·Π΄ΡΡ Π° Π² ΡΠΈΠ»ΠΈΠ½Π΄ΡΠ΅ ΠΏΡΠΈ Π½Π°ΡΠ°Π»Π΅ ΠΏΠ΅ΡΠ΅ΠΌΠ΅ΡΠ΅Π½ΠΈΡ ΠΏΠΎΡΡΠ½Ρ ΠΏΡΠΈ ΡΠΎΡΠΌΠΎΠΆΠ΅Π½ΠΈΠΈ, ΠΊΠΎΡΠΎΡΠ°Ρ Π΄ΠΎΠ»ΠΆΠ½Π° Π±ΡΡΡ Π½Π΅ Π±ΠΎΠ»Π΅Π΅ 0,03Β ΠΠΠ° (0,3Β ΠΊΠ³Ρ/ΡΠΌ2). ΠΡΠΎΠ²Π΅ΡΠΊΡ ΠΏΡΠΎΠΈΠ·Π²ΠΎΠ΄ΠΈΡΡ ΠΏΠΎΠ²ΡΡΠ΅Π½ΠΈΠ΅ΠΌ Π΄Π°Π²Π»Π΅Π½ΠΈΡ Π²ΠΎΠ·Π΄ΡΡ Π° Π² ΡΠΈΠ»ΠΈΠ½Π΄ΡΠ΅ ΠΈ ΡΠΈΠΊΡΠΈΡΠΎΠ²Π°ΡΡ Π²Π΅Π»ΠΈΡΠΈΠ½Ρ Π΄Π°Π²Π»Π΅Π½ΠΈΡ Π² ΠΌΠΎΠΌΠ΅Π½Ρ Π½Π°ΡΠ°Π»Π° ΠΏΠ΅ΡΠ΅ΠΌΠ΅ΡΠ΅Π½ΠΈΡ ΠΏΠΎΡΡΠ½Ρ.
ΠΡΠΎΠ²Π΅ΡΠΈΡΡ ΡΠ°Π±ΠΎΡΡ ΡΠ΅Π³ΡΠ»ΠΈΡΡΡΡΠ΅Π³ΠΎ ΠΌΠ΅Ρ Π°Π½ΠΈΠ·ΠΌΠ° Π²ΠΎ Π²ΡΠ΅ΠΌ Π΄ΠΈΠ°ΠΏΠ°Π·ΠΎΠ½Π΅ Π΅Π³ΠΎ ΡΠ°Π±ΠΎΡΡ. ΠΡΠΈ ΡΠ²Π΅Π»ΠΈΡΠ΅Π½ΠΈΠΈ Π·Π°Π·ΠΎΡΠ° ΠΌΠ΅ΠΆΠ΄Ρ ΡΠΎΡΠΌΠΎΠ·Π½ΡΠΌΠΈ Π½Π°ΠΊΠ»Π°Π΄ΠΊΠ°ΠΌΠΈ ΠΈ Π΄ΠΈΡΠΊΠΎΠΌ (ΠΈΠΌΠΈΡΠΈΡΠΎΠ²Π°Π½Π½ΠΎΠ³ΠΎ Π½Π° ΡΡΠ΅Π½Π΄Π΅) ΡΠ΅Π³ΡΠ»ΠΈΡΡΡΡΠΈΠΉ ΠΌΠ΅Ρ Π°Π½ΠΈΠ·ΠΌ Π΄ΠΎΠ»ΠΆΠ΅Π½ ΡΠΎΠΊΡΠ°ΡΠΈΡΡ Π·Π°Π·ΠΎΡ Π΄ΠΎ ΠΏΠ΅ΡΠ²ΠΎΠ½Π°ΡΠ°Π»ΡΠ½ΠΎΠΉ Π²Π΅Π»ΠΈΡΠΈΠ½Ρ ΠΏΠΎΡΠ»Π΅ ΡΠΎΡΠΌΠΎΠΆΠ΅Π½ΠΈΡ Π΄Π°Π²Π»Π΅Π½ΠΈΠ΅ΠΌ Π²ΠΎΠ·Π΄ΡΡ Π° (0,40+0,02)Β ΠΠΠ° [(4,0+0,2)Β ΠΊΠ³Ρ/ΡΠΌ2] ΠΈ ΠΎΡΠΏΡΡΠΊΠ°.
ΠΡΠΈ ΠΏΠΎΠ²ΡΠΎΡΠ½ΡΡ ΡΠΎΡΠΌΠΎΠΆΠ΅Π½ΠΈΡΡ Π΄Π°Π²Π»Π΅Π½ΠΈΠ΅ΠΌ Π²ΠΎΠ·Π΄ΡΡ Π° (0,40+0,02)Β ΠΠΠ° [(4,0+0,2)Β ΠΊΠ³Ρ/ΡΠΌ2] Π’Π¦Π Π΄ΠΎΠ»ΠΆΠ΅Π½ ΡΠΎΡ ΡΠ°Π½ΠΈΡΡ ΠΏΠΎΡΡΠΎΡΠ½Π½ΡΡ Π²Π΅Π»ΠΈΡΠΈΠ½Ρ Π²ΡΡ ΠΎΠ΄Π° ΡΡΠΎΠΊΠ°.
27.3 Π Π΅Π·ΡΠ»ΡΡΠ°ΡΡ ΠΈΡΠΏΡΡΠ°Π½ΠΈΡ Π’Π¦Π Π΄ΠΎΠ»ΠΆΠ½Ρ Π±ΡΡΡ ΠΎΡΡΠ°ΠΆΠ΅Π½Ρ Π² ΡΡΠ΅ΡΠ½ΠΎΠΉ ΠΊΠ½ΠΈΠ³Π΅ ΡΡΡΠ°Π½ΠΎΠ²Π»Π΅Π½Π½ΠΎΠΉ ΡΠΎΡΠΌΡ.
ΠΡΠΈ ΠΈΡΠΏΡΡΠ°Π½ΠΈΠΈ Π½Π° ΡΡΠ΅Π½Π΄Π΅ Ρ ΡΠ΅Π³ΠΈΡΡΡΠ°ΡΠΈΠ΅ΠΉ ΠΏΠ°ΡΠ°ΠΌΠ΅ΡΡΠΎΠ² ΡΠ΅Π·ΡΠ»ΡΡΠ°ΡΡ ΠΈΡΠΏΡΡΠ°Π½ΠΈΡ Π΄ΠΎΠ»ΠΆΠ½Ρ Π±ΡΡΡ ΡΠΎΡ ΡΠ°Π½Π΅Π½Ρ Π² ΠΏΠ°ΠΌΡΡΠΈ ΠΠΠΠ, Π° Π² ΡΡΠ΅ΡΠ½ΠΎΠΉ ΠΊΠ½ΠΈΠ³Π΅, ΡΡΡΠ°Π½ΠΎΠ²Π»Π΅Π½Π½ΠΎΠΉ ΡΠΎΡΠΌΡ, Π½Π΅ΠΎΠ±Ρ ΠΎΠ΄ΠΈΠΌΠΎ Π·Π°ΠΏΠΈΡΡΠ²Π°ΡΡ Π΄Π°ΡΡ ΠΈΡΠΏΡΡΠ°Π½ΠΈΡ, ΡΠΈΠΏ ΠΈ Π½ΠΎΠΌΠ΅Ρ ΠΏΡΠΈΠ½ΡΡΠΎΠ³ΠΎ Π’Π¦Π Ρ ΡΠΎΡΠΏΠΈΡΡΡ ΠΈΡΠΏΠΎΠ»Π½ΠΈΡΠ΅Π»Ρ ΡΠ΅ΠΌΠΎΠ½ΡΠ° ΠΈ ΡΡΠΊΠΎΠ²ΠΎΠ΄ΠΈΡΠ΅Π»Ρ ΡΠ΅ΠΌΠΎΠ½ΡΠ½ΠΎΠ³ΠΎ ΠΏΠΎΠ΄ΡΠ°Π·Π΄Π΅Π»Π΅Π½ΠΈΡ ΠΈΠ»ΠΈ Π΄ΡΡΠ³ΠΎΠ³ΠΎ Π΄ΠΎΠ»ΠΆΠ½ΠΎΡΡΠ½ΠΎΠ³ΠΎ Π»ΠΈΡΠ°, Π½Π° ΠΊΠΎΡΠΎΡΠΎΠ΅ Π² ΡΠΎΠΎΡΠ²Π΅ΡΡΡΠ²ΠΈΠΈ Ρ Π΄ΠΎΠ»ΠΆΠ½ΠΎΡΡΠ½ΠΎΠΉ ΠΈΠ½ΡΡΡΡΠΊΡΠΈΠ΅ΠΉ Π²ΠΎΠ·Π»ΠΎΠΆΠ΅Π½Ρ ΡΡΠΈ ΠΎΠ±ΡΠ·Π°Π½Π½ΠΎΡΡΠΈ.
27.4 ΠΠ° ΠΎΡΡΠ΅ΠΌΠΎΠ½ΡΠΈΡΠΎΠ²Π°Π½Π½ΠΎΠΌ ΠΈ ΠΏΡΠΈΠ½ΡΡΠΎΠΌ Π’Π¦Π Π΄ΠΎΠ»ΠΆΠ½Π° ΡΡΠΎΡΡΡ Π±ΠΈΡΠΊΠ°. ΠΠ° Π±ΠΈΡΠΊΠ΅ Π΄ΠΎΠ»ΠΆΠ½Ρ Π±ΡΡΡ Π½Π°Π½Π΅ΡΠ΅Π½Ρ ΠΊΠ»Π΅ΠΉΠΌΠΎ ΠΠΠ ΠΈ Π΄Π°ΡΠ° ΡΠ΅ΠΌΠΎΠ½ΡΠ° (ΡΠΈΡΠ»ΠΎ, ΠΌΠ΅ΡΡΡ ΠΈ Π΄Π²Π΅ ΠΏΠΎΡΠ»Π΅Π΄Π½ΠΈΠ΅ ΡΠΈΡΡΡ Π³ΠΎΠ΄Π°).
28 Π’Π΅Ρ Π½ΠΈΡΠ΅ΡΠΊΠΈΠ΅ ΡΡΠ΅Π±ΠΎΠ²Π°Π½ΠΈΡ Π½Π° ΡΠ΅ΠΌΠΎΠ½Ρ ΠΈ ΠΈΡΠΏΡΡΠ°Π½ΠΈΠ΅ ΠΊΡΠ°Π½ΠΎΠ² ΠΈ ΠΊΠ»Π°ΠΏΠ°Π½ΠΎΠ² ΠΏΠ°ΡΡΠ°ΠΆΠΈΡΡΠΊΠΈΡ Π²Π°Π³ΠΎΠ½ΠΎΠ²
28.1 ΠΠΎΠ½ΡΠ΅Π²ΡΠ΅ ΠΊΡΠ°Π½Ρ
28.1.1 ΠΠΎΠ½ΡΠ΅Π²ΡΠ΅ ΠΊΡΠ°Π½Ρ ΡΠ΅ΠΌΠΎΠ½ΡΠΈΡΠΎΠ²Π°ΡΡ ΠΈ ΠΈΡΠΏΡΡΡΠ²Π°ΡΡ Π² ΡΠΎΠΎΡΠ²Π΅ΡΡΡΠ²ΠΈΠΈ Ρ ΡΠ°Π·Π΄Π΅Π»ΠΎΠΌ 9.
28.2 Π Π°Π·ΠΎΠ±ΡΠΈΡΠ΅Π»ΡΠ½ΡΠΉ ΠΊΡΠ°Π½ ΠΏΡΠΎΠ±ΠΊΠΎΠ²ΠΎΠ³ΠΎ ΡΠΈΠΏΠ° (ΠΊΡΠ°Π½ 377)
28.2.1 ΠΠΎΡΡΡΠΏΠΈΠ²ΡΠΈΠ΅ Π² ΡΠ΅ΠΌΠΎΠ½Ρ ΡΠ°Π·ΠΎΠ±ΡΠΈΡΠ΅Π»ΡΠ½ΡΠ΅ ΠΊΡΠ°Π½Ρ ΠΏΡΠΎΠ±ΠΊΠΎΠ²ΠΎΠ³ΠΎ ΡΠΈΠΏΠ° Π½Π΅ΠΎΠ±Ρ ΠΎΠ΄ΠΈΠΌΠΎ ΡΠ°Π·ΠΎΠ±ΡΠ°ΡΡ, Π²ΡΠ΅ Π΄Π΅ΡΠ°Π»ΠΈ ΠΏΡΠΎΠΌΡΡΡ ΠΈ ΠΏΡΠΎΠ΄ΡΡΡ ΡΠΆΠ°ΡΡΠΌ Π²ΠΎΠ·Π΄ΡΡ ΠΎΠΌ.
28.2.2 ΠΡΠ΅ Π΄Π΅ΡΠ°Π»ΠΈ ΡΠ°Π·ΠΎΠ±ΡΠΈΡΠ΅Π»ΡΠ½ΠΎΠ³ΠΎ ΠΊΡΠ°Π½Π° ΡΠ»Π΅Π΄ΡΠ΅Ρ ΠΎΡΠΌΠΎΡΡΠ΅ΡΡ. ΠΠ΅ΡΠ°Π»ΠΈ Π΄ΠΎΠ»ΠΆΠ½Ρ Π±ΡΡΡ Π·Π°ΠΌΠ΅Π½Π΅Π½Ρ ΠΏΡΠΈ Π½Π°Π»ΠΈΡΠΈΠΈ ΡΠ»Π΅Π΄ΡΡΡΠΈΡ Π΄Π΅ΡΠ΅ΠΊΡΠΎΠ²:
— ΡΡΠ΅ΡΠΈΠ½ ΠΈ ΠΎΡΠΊΠΎΠ»ΠΎΠ² Π² ΠΊΠΎΡΠΏΡΡΠ΅;
— ΠΈΠ·Π»ΠΎΠΌΠΎΠ² ΠΈ Π΄Π΅ΡΠΎΡΠΌΠ°ΡΠΈΠΈ ΡΡΡΠΊΠΈ;
— Π΄Π΅ΡΠΎΡΠΌΠ°ΡΠΈΠΈ ΠΈ ΡΡΡΠ²Π° ΡΠ΅Π·ΡΠ±Ρ;
— Π΄Π΅ΡΠΎΡΠΌΠ°ΡΠΈΠΈ ΠΊΠ²Π°Π΄ΡΠ°ΡΠ° ΠΏΡΠΎΠ±ΠΊΠΈ.
ΠΡΡΠΎΡΠ° ΠΏΡΡΠΆΠΈΠ½Ρ Π² ΡΠ²ΠΎΠ±ΠΎΠ΄Π½ΠΎΠΌ ΡΠΎΡΡΠΎΡΠ½ΠΈΠΈ Π΄ΠΎΠ»ΠΆΠ½Π° Π±ΡΡΡ Π² ΠΏΡΠ΅Π΄Π΅Π»Π°Ρ ΠΎΡ 36 Π΄ΠΎ 40Β ΠΌΠΌ.
28.2.3 Π‘Π±ΠΎΡΠΊΡ ΡΠ°Π·ΠΎΠ±ΡΠΈΡΠ΅Π»ΡΠ½ΠΎΠ³ΠΎ ΠΊΡΠ°Π½Π° Π½Π΅ΠΎΠ±Ρ ΠΎΠ΄ΠΈΠΌΠΎ ΠΏΡΠΎΠΈΠ·Π²ΠΎΠ΄ΠΈΡΡ Ρ ΡΠΎΠ±Π»ΡΠ΄Π΅Π½ΠΈΠ΅ΠΌ ΡΠ»Π΅Π΄ΡΡΡΠΈΡ ΡΡΠ΅Π±ΠΎΠ²Π°Π½ΠΈΠΉ:
— Π½Π΅ΠΎΠ±Ρ ΠΎΠ΄ΠΈΠΌΠΎ ΠΏΡΠΎΠ²Π΅ΡΠΈΡΡ Π½Π°Π»ΠΈΡΠΈΠ΅ Π½Π° ΡΠΎΡΡΠ΅ ΠΊΠ²Π°Π΄ΡΠ°ΡΠ° ΠΏΡΠΎΠ±ΠΊΠΈ ΡΠ΅ΡΠΊΠΈΡ ΠΊΠΎΠ½ΡΡΠΎΠ»ΡΠ½ΡΡ ΡΠΈΡΠΎΠΊ;
— ΡΠ»Π΅Π΄ΡΠ΅Ρ ΠΏΡΠΎΠ²Π΅ΡΠΈΡΡ Π½Π°Π»ΠΈΡΠΈΠ΅ Π½Π° ΡΡΡΠΊΠ΅ ΠΎΠ³ΡΠ°Π½ΠΈΡΠΈΡΠ΅Π»Ρ Π΅Π΅ ΠΏΠΎΠ²ΠΎΡΠΎΡΠ°;
— ΠΏΡΠΎΠ±ΠΊΡ ΠΊΡΠ°Π½Π° Π½Π΅ΠΎΠ±Ρ ΠΎΠ΄ΠΈΠΌΠΎ ΠΏΡΠΈΡΠ΅ΡΠ΅ΡΡ ΠΊ ΠΊΠΎΡΠΏΡΡΡ, ΠΏΠΎΡΠ»Π΅ ΡΠ΅Π³ΠΎ ΠΏΡΠΎΡΠ΅ΡΠ΅ΡΡ ΠΈ ΡΠΌΠ°Π·Π°ΡΡ ΡΠΌΠ°Π·ΠΊΠΎΠΉ Π² ΡΠΎΠΎΡΠ²Π΅ΡΡΡΠ²ΠΈΠΈ Ρ ΡΠ°Π±Π»ΠΈΡΠ΅ΠΉ 3;
— Π·Π°Π³Π»ΡΡΠΊΠ° Π΄ΠΎΠ»ΠΆΠ½Π° Π±ΡΡΡ ΠΏΠΎΡΡΠ°Π²Π»Π΅Π½Π° Π½Π° ΡΠΌΠ°Π·ΠΊΡ ΠΠΠΠ ΠΠ-232 ΠΈ Π·Π°ΡΡΠ½ΡΡΠ° Π΄ΠΎ ΡΠΏΠΎΡΠ° Π² ΠΊΠΎΡΠΏΡΡ;
— ΡΡΡΠΊΠ° ΠΊΡΠ°Π½Π° Π΄ΠΎΠ»ΠΆΠ½Π° Π±ΡΡΡ ΠΏΡΠΎΡΠ½ΠΎ Π·Π°ΠΊΡΠ΅ΠΏΠ»Π΅Π½Π° Π½Π° ΠΊΠ²Π°Π΄ΡΠ°ΡΠ΅ ΠΏΡΠΎΠ±ΠΊΠΈ, Π΄ΠΎΠΏΡΡΠΊΠ°Π΅ΡΡΡ ΡΡΡΡΠ°Π½ΡΡΡ Π·Π°Π·ΠΎΡ ΠΌΠ΅ΠΆΠ΄Ρ ΠΊΠ²Π°Π΄ΡΠ°ΡΠΎΠΌ ΠΏΡΠΎΠ±ΠΊΠΈ ΠΈ ΠΊΠ²Π°Π΄ΡΠ°ΡΠΎΠΌ ΡΡΡΠΊΠΈ ΠΏΠΎΡΡΠ°Π½ΠΎΠ²ΠΊΠΎΠΉ ΠΌΠ΅ΡΠ°Π»Π»ΠΈΡΠ΅ΡΠΊΠΎΠΉ ΠΏΠ»Π°ΡΡΠΈΠ½Ρ ΡΠΎΠ»ΡΠΈΠ½ΠΎΠΉ Π½Π΅ Π±ΠΎΠ»Π΅Π΅ 1Β ΠΌΠΌ Ρ ΠΎΠ±ΡΠ·Π°ΡΠ΅Π»ΡΠ½ΠΎΠΉ ΡΠΈΠΊΡΠ°ΡΠΈΠ΅ΠΉ Π΅Π΅ ΡΡΠΈΡΡΠΎΠΌ, ΠΊΡΠ΅ΠΏΡΡΠΈΠΌ ΡΡΡΠΊΡ ΠΊΡΠ°Π½Π° Π½Π° ΠΊΠ²Π°Π΄ΡΠ°ΡΠ΅ ΠΏΡΠΎΠ±ΠΊΠΈ;
— Π² Π·Π°ΠΊΡΡΡΠΎΠΌ ΠΏΠΎΠ»ΠΎΠΆΠ΅Π½ΠΈΠΈ ΡΡΡΠΊΠ° ΠΊΡΠ°Π½Π° Π΄ΠΎΠ»ΠΆΠ½Π° ΡΠ°ΡΠΏΠΎΠ»Π°Π³Π°ΡΡΡΡ ΠΏΠ΅ΡΠΏΠ΅Π½Π΄ΠΈΠΊΡΠ»ΡΡΠ½ΠΎ ΠΊ ΠΏΡΠΎΠ΄ΠΎΠ»ΡΠ½ΠΎΠΉ ΠΎΡΠΈ Π΅Π³ΠΎ ΠΊΠΎΡΠΏΡΡΠ°.
28.2.4 ΠΠΎΡΠ»Π΅ ΡΠ±ΠΎΡΠΊΠΈ ΡΠ°Π·ΠΎΠ±ΡΠΈΡΠ΅Π»ΡΠ½ΡΠΉ ΠΊΡΠ°Π½ Π½Π΅ΠΎΠ±Ρ ΠΎΠ΄ΠΈΠΌΠΎ ΠΈΡΠΏΡΡΠ°ΡΡ Π½Π° ΠΏΠ»ΠΎΡΠ½ΠΎΡΡΡ ΡΠΆΠ°ΡΡΠΌ Π²ΠΎΠ·Π΄ΡΡ ΠΎΠΌ ΠΏΠΎΠ΄ Π΄Π°Π²Π»Π΅Π½ΠΈΠ΅ΠΌ (0,60+0,05)Β ΠΠΠ° [(6,0+0,5)Β ΠΊΠ³Ρ/ΡΠΌ2].
ΠΡΠΏΡΡΠ°Π½ΠΈΠ΅ ΠΏΡΠΎΠΈΠ·Π²ΠΎΠ΄ΠΈΡΡΡ ΠΏΡΠΈ Π΄Π²ΡΡ ΠΏΠΎΠ»ΠΎΠΆΠ΅Π½ΠΈΡΡ ΡΡΡΠΊΠΈ ΠΊΡΠ°Π½Π° — ΠΏΡΠΈ ΠΎΡΠΊΡΡΡΠΎΠΌ ΠΈ ΠΏΡΠΈ Π·Π°ΠΊΡΡΡΠΎΠΌ.
ΠΡΠΈ ΠΏΡΠΎΠ²Π΅Π΄Π΅Π½ΠΈΠΈ ΠΈΡΠΏΡΡΠ°Π½ΠΈΡ ΡΠ°Π·ΠΎΠ±ΡΠΈΡΠ΅Π»ΡΠ½ΠΎΠ³ΠΎ ΠΊΡΠ°Π½Π° ΡΠΆΠ°ΡΡΠΉ Π²ΠΎΠ·Π΄ΡΡ Π΄ΠΎΠ»ΠΆΠ΅Π½ ΠΏΠΎΠ΄Π°Π²Π°ΡΡΡΡ ΠΊ ΠΎΠ΄Π½ΠΎΠΉ ΠΈΠ· ΡΡΠΎΡΠΎΠ½ ΠΊΡΠ°Π½Π°, ΠΏΡΠΈ ΡΡΠΎΠΌ ΠΏΡΠΎΡΠΈΠ²ΠΎΠΏΠΎΠ»ΠΎΠΆΠ½Π°Ρ ΡΡΠΎΡΠΎΠ½Π° Π΄ΠΎΠ»ΠΆΠ½Π° Π±ΡΡΡ Π·Π°Π³Π»ΡΡΠ΅Π½Π°.
ΠΡΠΎΠ²Π΅ΡΠΊΠ° Π³Π΅ΡΠΌΠ΅ΡΠΈΡΠ½ΠΎΡΡΠΈ ΠΊΡΠ°Π½Π° ΠΏΡΠΎΠΈΠ·Π²ΠΎΠ΄ΠΈΡΡΡ ΠΎΠ΄Π½ΠΈΠΌ ΠΈΠ· ΡΠ»Π΅Π΄ΡΡΡΠΈΡ ΡΠΏΠΎΡΠΎΠ±ΠΎΠ²:
— ΠΏΠΎ Π½Π°Π»ΠΈΡΠΈΡ ΠΌΡΠ»ΡΠ½ΡΡ ΠΏΡΠ·ΡΡΠ΅ΠΉ;
— ΠΏΠΎ ΠΏΠ°Π΄Π΅Π½ΠΈΡ Π΄Π°Π²Π»Π΅Π½ΠΈΡ.
ΠΡΠΈ ΠΏΡΠΎΠ²Π΅ΡΠΊΠ΅ Π³Π΅ΡΠΌΠ΅ΡΠΈΡΠ½ΠΎΡΡΠΈ ΠΏΠΎ ΠΎΠ±ΡΠ°Π·ΠΎΠ²Π°Π½ΠΈΡ ΠΌΡΠ»ΡΠ½ΡΡ ΠΏΡΠ·ΡΡΠ΅ΠΉ ΠΎΠ±ΠΌΡΠ»ΠΈΠ²Π°ΡΡ Π½Π΅ΠΎΠ±Ρ ΠΎΠ΄ΠΈΠΌΠΎ Π²Π΅ΡΡ ΠΊΡΠ°Π½. ΠΡΠΈ ΡΡΠΎΠΌ ΠΏΠΎΡΠ²Π»Π΅Π½ΠΈΠ΅ ΠΏΡΠ·ΡΡΠ΅ΠΉ Π½Π΅ Π΄ΠΎΠΏΡΡΠΊΠ°Π΅ΡΡΡ.
ΠΡΠΎΠ²Π΅ΡΠΊΠ° Π³Π΅ΡΠΌΠ΅ΡΠΈΡΠ½ΠΎΡΡΠΈ ΠΏΠΎ ΠΏΠ°Π΄Π΅Π½ΠΈΡ Π΄Π°Π²Π»Π΅Π½ΠΈΡ ΠΏΡΠΎΠΈΠ·Π²ΠΎΠ΄ΠΈΡΡΡ Π½Π° ΠΈΡΠΏΡΡΠ°ΡΠ΅Π»ΡΠ½ΠΎΠΌ ΡΡΡΡΠΎΠΉΡΡΠ²Π΅, ΠΈΠΌΠ΅ΡΡΠ΅ΠΌ Π² ΡΠ²ΠΎΠ΅ΠΉ ΡΡ Π΅ΠΌΠ΅ ΠΊΠΎΠ½ΡΡΠΎΠ»ΡΠ½ΡΠΉ ΡΠ΅Π·Π΅ΡΠ²ΡΠ°Ρ ΠΎΠ±ΡΠ΅ΠΌΠΎΠΌ 5 Π»ΠΈΡΡΠΎΠ². ΠΡΠΈ ΡΡΠΎΠΌ ΠΏΠ°Π΄Π΅Π½ΠΈΠ΅ ΡΡΡΠ°Π½ΠΎΠ²ΠΈΠ²ΡΠ΅Π³ΠΎΡΡ Π΄Π°Π²Π»Π΅Π½ΠΈΡ Π² ΠΊΠΎΠ½ΡΡΠΎΠ»ΡΠ½ΠΎΠΌ ΡΠ΅Π·Π΅ΡΠ²ΡΠ°ΡΠ΅ Π±ΠΎΠ»Π΅Π΅ 0,01 ΠΠΠ° (0,1Β ΠΊΠ³Ρ/ΡΠΌ2) Π² ΡΠ΅ΡΠ΅Π½ΠΈΠ΅ 5 ΠΌΠΈΠ½ΡΡ Π½Π΅ Π΄ΠΎΠΏΡΡΠΊΠ°Π΅ΡΡΡ.
28.3 ΠΡΠ°Π½Ρ ΡΠ°ΡΠΎΠ²ΡΠ΅ ΡΠ°Π·ΠΎΠ±ΡΠΈΡΠ΅Π»ΡΠ½ΡΠ΅
28.3.1 Π Π΅ΠΌΠΎΠ½Ρ ΠΈ ΠΈΡΠΏΡΡΠ°Π½ΠΈΠ΅ ΡΠ°ΡΠΎΠ²ΡΡ ΡΠ°Π·ΠΎΠ±ΡΠΈΡΠ΅Π»ΡΠ½ΡΡ ΠΊΡΠ°Π½ΠΎΠ² Π½Π΅ΠΎΠ±Ρ ΠΎΠ΄ΠΈΠΌΠΎ ΠΏΡΠΎΠΈΠ·Π²ΠΎΠ΄ΠΈΡΡ Ρ ΡΠΎΠ±Π»ΡΠ΄Π΅Π½ΠΈΠ΅ΠΌ ΡΠ»Π΅Π΄ΡΡΡΠΈΡ ΡΡΠ΅Π±ΠΎΠ²Π°Π½ΠΈΠΉ:
— ΠΏΠΎΡΡΡΠΏΠΈΠ²ΡΠΈΠΉ Π² ΡΠ΅ΠΌΠΎΠ½Ρ ΡΠ°ΡΠΎΠ²ΠΎΠΉ ΡΠ°Π·ΠΎΠ±ΡΠΈΡΠ΅Π»ΡΠ½ΡΠΉ ΠΊΡΠ°Π½ Π΄ΠΎΠ»ΠΆΠ΅Π½ Π±ΡΡΡ ΡΠ½Π°ΡΡΠΆΠΈ ΠΎΡΠΈΡΠ΅Π½ ΠΎΡ ΠΏΡΠ»ΠΈ ΠΈ Π·Π°Π³ΡΡΠ·Π½Π΅Π½ΠΈΠΉ,
— Π½Π΅ΠΎΠ±Ρ ΠΎΠ΄ΠΈΠΌΠΎ ΠΏΡΠΎΠΊΠΎΠ½ΡΡΠΎΠ»ΠΈΡΠΎΠ²Π°ΡΡ ΡΠΎΡΡΠΎΡΠ½ΠΈΠ΅ ΠΏΡΠΈΡΠΎΠ΅Π΄ΠΈΠ½ΠΈΡΠ΅Π»ΡΠ½ΠΎΠΉ ΡΠ΅Π·ΡΠ±Ρ, ΠΏΠΎΡΠ»Π΅ ΠΈΡΠΏΡΡΠ°ΡΡ ΠΊΡΠ°Π½ Π½Π° Π³Π΅ΡΠΌΠ΅ΡΠΈΡΠ½ΠΎΡΡΡ;
— ΡΠ°Π·Π±ΠΈΡΠ°ΡΡ ΡΠ°ΡΠΎΠ²ΠΎΠΉ ΡΠ°Π·ΠΎΠ±ΡΠΈΡΠ΅Π»ΡΠ½ΡΠΉΠΊΡΠ°Π½ Π½Π΅ΠΎΠ±Ρ ΠΎΠ΄ΠΈΠΌΠΎ ΡΠΎΠ»ΡΠΊΠΎ Π² ΡΠ»ΡΡΠ°Π΅ Π½Π°Π»ΠΈΡΠΈΡ Π²Π½Π΅ΡΠ½ΠΈΡ Π΄Π΅ΡΠ΅ΠΊΡΠΎΠ², Π½Π°ΡΡΡΠ°ΡΡΠΈΡ Π΅Π³ΠΎ ΡΠ°Π±ΠΎΡΡ ΠΈ ΠΏΡΠΈ Π½Π΅ΡΠ΄ΠΎΠ²Π»Π΅ΡΠ²ΠΎΡΠΈΡΠ΅Π»ΡΠ½ΡΡ ΡΠ΅Π·ΡΠ»ΡΡΠ°ΡΠ°Ρ ΠΈΡΠΏΡΡΠ°Π½ΠΈΡ.
28.3.2 ΠΡΠΏΡΡΠ°Π½ΠΈΠ΅ ΠΊΡΠ°Π½Π° Π½Π° Π³Π΅ΡΠΌΠ΅ΡΠΈΡΠ½ΠΎΡΡΡ ΠΏΡΠΎΠΈΠ·Π²ΠΎΠ΄ΠΈΡΡΡ ΡΠΆΠ°ΡΡΠΌ Π²ΠΎΠ·Π΄ΡΡ ΠΎΠΌ Π΄Π°Π²Π»Π΅Π½ΠΈΠ΅ΠΌ (0,60+0,05)Β ΠΠΠ° [(6,0+0,5)Β ΠΊΠ³Ρ/ΡΠΌ2] ΠΏΡΠΈ Π΄Π²ΡΡ Π΅Π³ΠΎ ΠΏΠΎΠ»ΠΎΠΆΠ΅Π½ΠΈΡΡ β ΠΏΡΠΈ ΠΎΡΠΊΡΡΡΠΎΠΌ ΠΈ ΠΏΡΠΈ Π·Π°ΠΊΡΡΡΠΎΠΌ.
ΠΡΠΈ ΠΈΡΠΏΡΡΠ°Π½ΠΈΠΈ Π² Π·Π°ΠΊΡΡΡΠΎΠΌ ΠΏΠΎΠ»ΠΎΠΆΠ΅Π½ΠΈΠΈ ΡΠΆΠ°ΡΡΠΉ Π²ΠΎΠ·Π΄ΡΡ Π΄ΠΎΠ»ΠΆΠ΅Π½ ΠΏΠΎΠ΄Π°Π²Π°ΡΡΡΡ ΠΊ ΠΎΠ΄Π½ΠΎΠΉ ΠΈΠ· ΡΡΠΎΡΠΎΠ½ ΡΠ°ΡΠΎΠ²ΠΎΠ³ΠΎ ΡΠ°Π·ΠΎΠ±ΡΠΈΡΠ΅Π»ΡΠ½ΠΎΠ³ΠΎ ΠΊΡΠ°Π½Π°, ΠΏΡΠΈ ΡΡΠΎΠΌ Π½Π° ΠΏΡΠΎΡΠΈΠ²ΠΎΠΏΠΎΠ»ΠΎΠΆΠ½ΡΡ ΡΡΠΎΡΠΎΠ½Ρ Π΄ΠΎΠ»ΠΆΠ½Π° Π±ΡΡΡ Π½Π°Π΄Π΅ΡΠ° Π·Π°Π³Π»ΡΡΠΊΠ° Ρ Π°ΡΠΌΠΎΡΡΠ΅ΡΠ½ΡΠΌ ΠΎΡΠ²Π΅ΡΡΡΠΈΠ΅ΠΌ Π΄ΠΈΠ°ΠΌΠ΅ΡΡΠΎΠΌ 4 ΠΌΠΌ. Π¨Π°ΡΠΎΠ²ΠΎΠΉ ΡΠ°Π·ΠΎΠ±ΡΠΈΡΠ΅Π»ΡΠ½ΡΠΉ ΠΊΡΠ°Π½ Π² Π·Π°ΠΊΡΡΡΠΎΠΌ ΠΏΠΎΠ»ΠΎΠΆΠ΅Π½ΠΈΠΈ Π΄ΠΎΠ»ΠΆΠ΅Π½ Π±ΡΡΡ ΠΈΡΠΏΡΡΠ°Π½ Ρ Π΄Π²ΡΡ ΡΡΠΎΡΠΎΠ½. ΠΡΠΈ ΠΏΡΠΎΠ²Π΅ΡΠΊΠ΅ Π³Π΅ΡΠΌΠ΅ΡΠΈΡΠ½ΠΎΡΡΠΈ ΠΏΠΎ ΠΏΠ°Π΄Π΅Π½ΠΈΡ Π΄Π°Π²Π»Π΅Π½ΠΈΡ ΡΠΏΠ΅ΡΠΈΠ°Π»ΡΠ½ΡΡ Π·Π°Π³Π»ΡΡΠΊΡ Ρ Π°ΡΠΌΠΎΡΡΠ΅ΡΠ½ΡΠΌ ΠΎΡΠ²Π΅ΡΡΡΠΈΠ΅ ΠΌΠΎΠΆΠ½ΠΎ Π½Π΅ ΡΡΡΠ°Π½Π°Π²Π»ΠΈΠ²Π°ΡΡ.
Π‘ΠΆΠ°ΡΡΠΉ Π²ΠΎΠ·Π΄ΡΡ ΠΏΡΠΈ ΠΈΡΠΏΡΡΠ°Π½ΠΈΠΈ Π² ΠΎΡΠΊΡΡΡΠΎΠΌ ΠΏΠΎΠ»ΠΎΠΆΠ΅Π½ΠΈΠΈ Π΄ΠΎΠ»ΠΆΠ΅Π½ ΠΏΠΎΠ΄Π°Π²Π°ΡΡΡΡ ΠΊ ΠΎΠ΄Π½ΠΎΠΉ ΠΈΠ· ΠΏΡΠΈΡΠΎΠ΅Π΄ΠΈΠ½ΠΈΡΠ΅Π»ΡΠ½ΡΡ ΡΡΠΎΡΠΎΠ½ ΡΠ°ΡΠΎΠ²ΠΎΠ³ΠΎ ΡΠ°Π·ΠΎΠ±ΡΠΈΡΠ΅Π»ΡΠ½ΠΎΠ³ΠΎ ΠΊΡΠ°Π½Π° ΠΏΡΠΈ Π·Π°Π³Π»ΡΡΠ΅Π½Π½ΠΎΠΉ Π΄ΡΡΠ³ΠΎΠΉ.
ΠΡΠΎΠ²Π΅ΡΠΊΠ° Π³Π΅ΡΠΌΠ΅ΡΠΈΡΠ½ΠΎΡΡΠΈ ΡΠ°ΡΠΎΠ²ΠΎΠ³ΠΎ ΡΠ°Π·ΠΎΠ±ΡΠΈΡΠ΅Π»ΡΠ½ΠΎΠ³ΠΎ ΠΊΡΠ°Π½Π° ΠΏΡΠΎΠΈΠ·Π²ΠΎΠ΄ΠΈΡΡΡ ΠΎΠ΄Π½ΠΈΠΌ ΠΈΠ· ΡΠ»Π΅Π΄ΡΡΡΠΈΡ ΡΠΏΠΎΡΠΎΠ±ΠΎΠ²:
— ΠΏΠΎ Π½Π°Π»ΠΈΡΠΈΡ ΠΌΡΠ»ΡΠ½ΡΡ ΠΏΡΠ·ΡΡΠ΅ΠΉ;
— ΠΏΠΎ ΠΏΠ°Π΄Π΅Π½ΠΈΡ Π΄Π°Π²Π»Π΅Π½ΠΈΡ.
ΠΡΠΈ ΠΏΡΠΎΠ²Π΅ΡΠΊΠ΅ Π³Π΅ΡΠΌΠ΅ΡΠΈΡΠ½ΠΎΡΡΠΈ ΠΏΠΎ Π½Π°Π»ΠΈΡΠΈΡ ΠΌΡΠ»ΡΠ½ΡΡ ΠΏΡΠ·ΡΡΠ΅ΠΉ ΠΎΠ±ΠΌΡΠ»ΠΈΠ²Π°ΡΡ Π½Π΅ΠΎΠ±Ρ ΠΎΠ΄ΠΈΠΌΠΎ Π²Π΅ΡΡ ΡΠ°ΡΠΎΠ²ΠΎΠΉ ΡΠ°Π·ΠΎΠ±ΡΠΈΡΠ΅Π»ΡΠ½ΡΠΉ ΠΊΡΠ°Π½. ΠΡΠΈ ΡΡΠΎΠΌ ΠΏΠΎΡΠ²Π»Π΅Π½ΠΈΠ΅ ΠΌΡΠ»ΡΠ½ΠΎΠ³ΠΎ ΠΏΡΠ·ΡΡΡ Π½Π΅ Π΄ΠΎΠΏΡΡΠΊΠ°Π΅ΡΡΡ.
ΠΡΠΎΠ²Π΅ΡΠΊΠ° Π³Π΅ΡΠΌΠ΅ΡΠΈΡΠ½ΠΎΡΡΠΈ ΠΏΠΎ ΠΏΠ°Π΄Π΅Π½ΠΈΡ Π΄Π°Π²Π»Π΅Π½ΠΈΡ ΠΏΡΠΎΠΈΠ·Π²ΠΎΠ΄ΠΈΡΡΡ Π½Π° ΠΈΡΠΏΡΡΠ°ΡΠ΅Π»ΡΠ½ΠΎΠΌ ΡΡΡΡΠΎΠΉΡΡΠ²Π΅, ΠΈΠΌΠ΅ΡΡΠ΅ΠΌ Π² ΡΠ²ΠΎΠ΅ΠΉ ΡΡ Π΅ΠΌΠ΅ ΠΊΠΎΠ½ΡΡΠΎΠ»ΡΠ½ΡΠΉ ΡΠ΅Π·Π΅ΡΠ²ΡΠ°Ρ ΠΎΠ±ΡΠ΅ΠΌΠΎΠΌ 5 Π»ΠΈΡΡΠΎΠ². ΠΡΠΈ ΡΡΠΎΠΌ ΠΏΠ°Π΄Π΅Π½ΠΈΠ΅ ΡΡΡΠ°Π½ΠΎΠ²ΠΈΠ²ΡΠ΅Π³ΠΎΡΡ Π΄Π°Π²Π»Π΅Π½ΠΈΡ ΡΠΆΠ°ΡΠΎΠ³ΠΎ Π²ΠΎΠ·Π΄ΡΡ Π° Π² ΠΊΠΎΠ½ΡΡΠΎΠ»ΡΠ½ΠΎΠΌ ΡΠ΅Π·Π΅ΡΠ²ΡΠ°ΡΠ΅ Π΄ΠΎΠΏΡΡΠΊΠ°Π΅ΡΡΡ Π½Π΅ Π±ΠΎΠ»Π΅Π΅ ΡΠ΅ΠΌ Π½Π° 0,01 ΠΠΠ° (0,1Β ΠΊΠ³Ρ/ΡΠΌ2) Π² ΡΠ΅ΡΠ΅Π½ΠΈΠ΅ 5 ΠΌΠΈΠ½ΡΡ.
28.4 Π‘ΡΠΎΠΏ-ΠΊΡΠ°Π½
28.4.1 ΠΠΎΡΡΡΠΏΠΈΠ²ΡΠΈΠΉ Π² ΡΠ΅ΠΌΠΎΠ½Ρ ΡΡΠΎΠΏ-ΠΊΡΠ°Π½ Π½Π΅ΠΎΠ±Ρ ΠΎΠ΄ΠΈΠΌΠΎ ΡΠ°Π·ΠΎΠ±ΡΠ°ΡΡ, Π΄Π΅ΡΠ°Π»ΠΈ ΡΡΠΎΠΏ- ΠΊΡΠ°Π½Π° ΠΏΡΠΎΡΠ΅ΡΠ΅ΡΡ ΠΈ ΠΎΡΠΌΠΎΡΡΠ΅ΡΡ.
28.4.2 Π Π΅ΠΌΠΎΠ½Ρ ΠΈ ΠΈΡΠΏΡΡΠ°Π½ΠΈΠ΅ ΡΡΠΎΠΏ-ΠΊΡΠ°Π½Π° Π½Π΅ΠΎΠ±Ρ ΠΎΠ΄ΠΈΠΌΠΎ ΠΏΡΠΎΠΈΠ·Π²ΠΎΠ΄ΠΈΡΡ Ρ ΡΠΎΠ±Π»ΡΠ΄Π΅Π½ΠΈΠ΅ΠΌ ΡΠ»Π΅Π΄ΡΡΡΠΈΡ ΡΡΠ΅Π±ΠΎΠ²Π°Π½ΠΈΠΉ:
— Π½Π°Π»ΠΈΡΠΈΠ΅ ΡΡΠ΅ΡΠΈΠ½ Π² ΠΊΠΎΡΠΏΡΡΠ΅, Π·Π°Π±ΠΎΠΈΠ½ ΠΈ ΠΏΠΎΠ²ΡΠ΅ΠΆΠ΄Π΅Π½ΠΈΠΉ Π½Π° ΡΠ΅Π·ΡΠ±Π΅ Π½Π΅ Π΄ΠΎΠΏΡΡΠΊΠ°Π΅ΡΡΡ;
— ΡΠ΅Π·ΠΈΠ½ΠΎΠ²ΡΠ΅ ΡΠΏΠ»ΠΎΡΠ½Π΅Π½ΠΈΡ Π½Π΅ΠΎΠ±Ρ ΠΎΠ΄ΠΈΠΌΠΎ Π·Π°ΠΌΠ΅Π½ΠΈΡΡ Π½ΠΎΠ²ΡΠΌΠΈ;
— ΡΠ΅Π΄Π»ΠΎ ΠΊΠ»Π°ΠΏΠ°Π½Π° Π½Π° ΡΡΡΡΠ΅ΡΠ΅ Π½Π΅ Π΄ΠΎΠ»ΠΆΠ½ΠΎ ΠΈΠΌΠ΅ΡΡ Π·Π°Π±ΠΎΠΈΠ½, Π²ΡΡΠ΅ΡΠ±ΠΈΠ½ ΠΈ Π΄ΡΡΠ³ΠΈΡ Π΄Π΅ΡΠ΅ΠΊΡΠΎΠ²;
— ΡΡΡΡΠ΅Ρ ΠΊΡΠ°Π½Π° ΡΠ»Π΅Π΄ΡΠ΅Ρ ΡΡΠ°Π²ΠΈΡΡ Π½Π° ΡΠΌΠ°Π·ΠΊΠ΅ ΠΠΠΠ ΠΠ-232 ΠΈ Π·Π°ΡΡΠ³ΠΈΠ²Π°ΡΡ Π½Π° ΡΠ΅Π·ΡΠ±Π΅ Π΄ΠΎ ΡΠΏΠΎΡΠ° Π² ΠΊΠΎΡΠΏΡΡ.
28.4.3 ΠΡΠΏΡΡΠ°Π½ΠΈΠ΅ ΡΡΠΎΠΏ-ΠΊΡΠ°Π½Π° ΠΏΡΠΎΠΈΠ·Π²ΠΎΠ΄ΠΈΡΡΡ ΡΠΎΠ»ΡΠΊΠΎ Π² Π·Π°ΠΊΡΡΡΠΎΠΌ ΠΏΠΎΠ»ΠΎΠΆΠ΅Π½ΠΈΠΈ ΠΏΡΠΈ Π΄Π°Π²Π»Π΅Π½ΠΈΠΈ (0,60+0,05)Β ΠΠΠ° [(6,0+0,5)Β ΠΊΠ³Ρ/ΡΠΌ2].
ΠΡΠΎΠ²Π΅ΡΠΊΠ° Π³Π΅ΡΠΌΠ΅ΡΠΈΡΠ½ΠΎΡΡΠΈ ΡΡΠΎΠΏ-ΠΊΡΠ°Π½Π° ΠΏΡΠΎΠΈΠ·Π²ΠΎΠ΄ΠΈΡΡΡ ΠΎΠ΄Π½ΠΈΠΌ ΠΈΠ· ΡΠ»Π΅Π΄ΡΡΡΠΈΡ ΡΠΏΠΎΡΠΎΠ±ΠΎΠ²:
— ΠΏΠΎ Π½Π°Π»ΠΈΡΠΈΡ ΠΌΡΠ»ΡΠ½ΡΡ ΠΏΡΠ·ΡΡΠ΅ΠΉ;
— ΠΏΠΎ ΠΏΠ°Π΄Π΅Π½ΠΈΡ Π΄Π°Π²Π»Π΅Π½ΠΈΡ.
ΠΡΠΈ ΠΏΡΠΎΠ²Π΅ΡΠΊΠ΅ Π³Π΅ΡΠΌΠ΅ΡΠΈΡΠ½ΠΎΡΡΠΈ ΠΏΠΎ Π½Π°Π»ΠΈΡΠΈΡ ΠΌΡΠ»ΡΠ½ΡΡ ΠΏΡΠ·ΡΡΠ΅ΠΉ ΠΎΠ±ΠΌΡΠ»ΠΈΠ²Π°ΡΡ Π½Π΅ΠΎΠ±Ρ ΠΎΠ΄ΠΈΠΌΠΎ Π²Π΅ΡΡ ΡΡΠΎΠΏ-ΠΊΡΠ°Π½. ΠΡΠΈ ΡΡΠΎΠΌ ΠΏΠΎΡΠ²Π»Π΅Π½ΠΈΠ΅ ΠΏΡΠ·ΡΡΠ΅ΠΉ Π½Π΅ Π΄ΠΎΠΏΡΡΠΊΠ°Π΅ΡΡΡ.
ΠΡΠΎΠ²Π΅ΡΠΊΠ° Π³Π΅ΡΠΌΠ΅ΡΠΈΡΠ½ΠΎΡΡΠΈ ΠΏΠΎ ΠΏΠ°Π΄Π΅Π½ΠΈΡ Π΄Π°Π²Π»Π΅Π½ΠΈΡ ΠΏΡΠΎΠΈΠ·Π²ΠΎΠ΄ΠΈΡΡΡ Π½Π° ΠΈΡΠΏΡΡΠ°ΡΠ΅Π»ΡΠ½ΠΎΠΌ ΡΡΡΡΠΎΠΉΡΡΠ²Π΅, ΠΈΠΌΠ΅ΡΡΠ΅ΠΌ Π² ΡΠ²ΠΎΠ΅ΠΉ ΡΡ Π΅ΠΌΠ΅ ΠΊΠΎΠ½ΡΡΠΎΠ»ΡΠ½ΡΠΉ ΡΠ΅Π·Π΅ΡΠ²ΡΠ°Ρ ΠΎΠ±ΡΠ΅ΠΌΠΎΠΌ 5 Π»ΠΈΡΡΠΎΠ². ΠΡΠΈ ΡΡΠΎΠΌ ΠΏΠ°Π΄Π΅Π½ΠΈΠ΅ ΡΡΡΠ°Π½ΠΎΠ²ΠΈΠ²ΡΠ΅Π³ΠΎΡΡ Π΄Π°Π²Π»Π΅Π½ΠΈΡ Π² ΠΊΠΎΠ½ΡΡΠΎΠ»ΡΠ½ΠΎΠΌ ΡΠ΅Π·Π΅ΡΠ²ΡΠ°ΡΠ΅ Π² ΡΠ΅ΡΠ΅Π½ΠΈΠ΅ 5 ΠΌΠΈΠ½ΡΡ Π½Π΅ Π΄ΠΎΠΏΡΡΠΊΠ°Π΅ΡΡΡ.
28.5 ΠΠ»Π°ΠΏΠ°Π½ Π²ΡΠΏΡΡΠΊΠ½ΠΎΠΉ 31Π
28.5.1 ΠΠΎΡΡΡΠΏΠΈΠ²ΡΠΈΠΉ Π² ΡΠ΅ΠΌΠΎΠ½Ρ Π²ΡΠΏΡΡΠΊΠ½ΠΎΠΉ ΠΊΠ»Π°ΠΏΠ°Π½ Π½Π΅ΠΎΠ±Ρ ΠΎΠ΄ΠΈΠΌΠΎ ΡΠ°Π·ΠΎΠ±ΡΠ°ΡΡ ΠΈ ΠΎΡΠΌΠΎΡΡΠ΅ΡΡ
28.5.2 Π Π΅ΠΌΠΎΠ½Ρ ΠΈ ΠΈΡΠΏΡΡΠ°Π½ΠΈΠ΅ Π²ΡΠΏΡΡΠΊΠ½ΠΎΠ³ΠΎ ΠΊΠ»Π°ΠΏΠ°Π½Π° Π½Π΅ΠΎΠ±Ρ ΠΎΠ΄ΠΈΠΌΠΎ ΠΏΡΠΎΠΈΠ·Π²ΠΎΠ΄ΠΈΡΡ Ρ ΡΠΎΠ±Π»ΡΠ΄Π΅Π½ΠΈΠ΅ΠΌ ΡΠ»Π΅Π΄ΡΡΡΠΈΡ ΡΡΠ΅Π±ΠΎΠ²Π°Π½ΠΈΠΉ:
— ΠΏΡΠΎΡΠ°Π΄ΠΊΠ° ΠΏΡΡΠΆΠΈΠ½Ρ Π±ΠΎΠ»Π΅Π΅ 3Β ΠΌΠΌ, Π·Π°Π±ΠΈΡΠ°Ρ ΠΈΠ»ΠΈ ΡΠΎΡΠ²Π°Π½Π½Π°Ρ ΡΠ΅Π·ΡΠ±Π° Π½Π΅ Π΄ΠΎΠΏΡΡΠΊΠ°ΡΡΡΡ;
— ΡΠ΅Π΄Π»ΠΎ ΠΊΠ»Π°ΠΏΠ°Π½Π° Π½Π΅ Π΄ΠΎΠ»ΠΆΠ½ΠΎ ΠΈΠΌΠ΅ΡΡ ΡΠ°ΠΊΠΎΠ²ΠΈΠ½ ΠΈ Π·Π°Π±ΠΎΠΈΠ½;
— ΡΠ΅Π·ΠΈΠ½ΠΎΠ²ΠΎΠ΅ ΡΠΏΠ»ΠΎΡΠ½Π΅Π½ΠΈΠ΅ ΠΊΠ»Π°ΠΏΠ°Π½Π° ΡΠ»Π΅Π΄ΡΠ΅Ρ Π·Π°ΠΌΠ΅Π½ΠΈΡΡ ΠΏΡΠΈ ΡΠΎΠ»ΡΠΈΠ½Π΅ ΡΠ΅Π·ΠΈΠ½ΠΎΠ²ΠΎΠ³ΠΎ ΡΠΏΠ»ΠΎΡΠ½Π΅Π½ΠΈΡ ΠΊΠ»Π°ΠΏΠ°Π½Π° ΠΌΠ΅Π½Π΅Π΅ 3Β ΠΌΠΌ ΠΈ (ΠΈΠ»ΠΈ) ΠΏΡΠΈ Π½Π°Π»ΠΈΡΠΈΠΈ ΠΏΡΠΎΡΠ°Π΄ΠΊΠΈ ΠΊΠ»Π°ΠΏΠ°Π½Π° Π±ΠΎΠ»Π΅Π΅ ΡΠ΅ΠΌ Π½Π° 0,5Β ΠΌΠΌ;
-ΠΏΠ΅ΡΠ΅Π΄ ΡΠ±ΠΎΡΠΊΠΎΠΉ ΠΏΡΡΠΆΠΈΠ½Ρ, Π²ΡΡΠ»ΠΊΡ ΠΊΠ»Π°ΠΏΠ°Π½Π° ΠΈ Π²ΡΠ΅ Π΄ΡΡΠ³ΠΈΠ΅ ΡΡΡΡΠΈΠ΅ΡΡ ΠΏΠΎΠ²Π΅ΡΡ Π½ΠΎΡΡΠΈ Π΄Π΅ΡΠ°Π»Π΅ΠΉ ΡΠ»Π΅Π΄ΡΠ΅Ρ ΡΠΌΠ°Π·Π°ΡΡ ΡΠΌΠ°Π·ΠΊΠΎΠΉ ΠΠ’-79Π. Π¨ΡΡΡΠ΅Ρ ΡΠ»Π΅Π΄ΡΠ΅Ρ ΡΡΠ°Π²ΠΈΡΡ Π½Π° ΡΠΌΠ°Π·ΠΊΠ΅ ΠΠΠΠ ΠΠ-232, Π²Π²ΠΈΠ½ΡΠΈΠ²Π°Ρ Π΄ΠΎ ΡΠΏΠΎΡΠ° Π² Π·Π°ΠΏΠ»Π΅ΡΠΈΠΊΠΈ ΠΊΠΎΡΠΏΡΡΠ° ΠΊΠ»Π°ΠΏΠ°Π½Π°.
28.5.3 ΠΡΠΏΡΡΠ°Π½ΠΈΠ΅ ΠΊΠ»Π°ΠΏΠ°Π½Π° Π½Π° ΠΏΠ»ΠΎΡΠ½ΠΎΡΡΡ ΠΏΡΠΎΠΈΠ·Π²ΠΎΠ΄ΠΈΡΡΡ Π΄Π°Π²Π»Π΅Π½ΠΈΠ΅ΠΌ ΡΠΆΠ°ΡΠΎΠ³ΠΎ Π²ΠΎΠ·Π΄ΡΡ Π° (0,60+0,05)Β ΠΠΠ° [(6,0+0,5)Β ΠΊΠ³Ρ/ΡΠΌ2].
ΠΡΠΎΠ²Π΅ΡΠΊΠ° ΠΏΠ»ΠΎΡΠ½ΠΎΡΡΠΈ ΠΊΠ»Π°ΠΏΠ°Π½Π° ΠΏΡΠΎΠΈΠ·Π²ΠΎΠ΄ΠΈΡΡΡ ΠΎΠ΄Π½ΠΈΠΌ ΠΈΠ· ΡΠ»Π΅Π΄ΡΡΡΠΈΡ ΡΠΏΠΎΡΠΎΠ±ΠΎΠ²:
— ΠΏΠΎ Π½Π°Π»ΠΈΡΠΈΡ ΠΌΡΠ»ΡΠ½ΡΡ ΠΏΡΠ·ΡΡΠ΅ΠΉ;
— ΠΏΠΎ ΠΏΠ°Π΄Π΅Π½ΠΈΡ Π΄Π°Π²Π»Π΅Π½ΠΈΡ.
ΠΡΠΈ ΠΏΡΠΎΠ²Π΅ΡΠΊΠ΅ ΠΏΠ»ΠΎΡΠ½ΠΎΡΡΠΈ ΠΏΠΎ Π½Π°Π»ΠΈΡΠΈΡ ΠΌΡΠ»ΡΠ½ΡΡ ΠΏΡΠ·ΡΡΠ΅ΠΉ ΠΎΠ±ΠΌΡΠ»ΠΈΠ²Π°ΡΡ Π½Π΅ΠΎΠ±Ρ ΠΎΠ΄ΠΈΠΌΠΎ Π²Π΅ΡΡ ΠΊΠ»Π°ΠΏΠ°Π½. ΠΡΠΈ ΡΡΠΎΠΌ ΠΏΠΎΡΠ²Π»Π΅Π½ΠΈΠ΅ ΠΏΡΠ·ΡΡΠ΅ΠΉ Π½Π΅ Π΄ΠΎΠΏΡΡΠΊΠ°Π΅ΡΡΡ.
ΠΡΠΎΠ²Π΅ΡΠΊΠ° ΠΏΠ»ΠΎΡΠ½ΠΎΡΡΠΈ ΠΏΠΎ ΠΏΠ°Π΄Π΅Π½ΠΈΡ Π΄Π°Π²Π»Π΅Π½ΠΈΡ ΠΏΡΠΎΠΈΠ·Π²ΠΎΠ΄ΠΈΡΡΡ Π½Π° ΠΈΡΠΏΡΡΠ°ΡΠ΅Π»ΡΠ½ΠΎΠΌ ΡΡΡΡΠΎΠΉΡΡΠ²Π΅, ΠΈΠΌΠ΅ΡΡΠ΅ΠΌ Π² ΡΠ²ΠΎΠ΅ΠΉ ΡΡ Π΅ΠΌΠ΅ ΠΊΠΎΠ½ΡΡΠΎΠ»ΡΠ½ΡΠΉ ΡΠ΅Π·Π΅ΡΠ²ΡΠ°Ρ ΠΎΠ±ΡΠ΅ΠΌΠΎΠΌ 5 Π»ΠΈΡΡΠΎΠ². ΠΡΠΈ ΡΡΠΎΠΌ ΠΏΠ°Π΄Π΅Π½ΠΈΠ΅ ΡΡΡΠ°Π½ΠΎΠ²ΠΈΠ²ΡΠ΅Π³ΠΎΡΡ Π΄Π°Π²Π»Π΅Π½ΠΈΡ Π² ΠΊΠΎΠ½ΡΡΠΎΠ»ΡΠ½ΠΎΠΌ ΡΠ΅Π·Π΅ΡΠ²ΡΠ°ΡΠ΅ Π² ΡΠ΅ΡΠ΅Π½ΠΈΠ΅ 5 ΠΌΠΈΠ½ΡΡ Π½Π΅ Π΄ΠΎΠΏΡΡΠΊΠ°Π΅ΡΡΡ.
28.6 ΠΠ»Π°ΠΏΠ°Π½ Π²ΡΠΏΡΡΠΊΠ½ΠΎΠΉ 4315
28.6.1 ΠΠΎΡΡΡΠΏΠΈΠ²ΡΠΈΠΉ Π² ΡΠ΅ΠΌΠΎΠ½Ρ Π²ΡΠΏΡΡΠΊΠ½ΠΎΠΉ ΠΊΠ»Π°ΠΏΠ°Π½ ΡΠ½Π°ΡΡΠΆΠΈ ΠΎΡΠΈΡΡΠΈΡΡ ΠΎΡ ΠΏΡΠ»ΠΈ, Π³ΡΡΠ·ΠΈ ΠΈ Π΄ΡΡΠ³ΠΈΡ Π·Π°Π³ΡΡΠ·Π½Π΅Π½ΠΈΠΉ, ΡΠ°Π·ΠΎΠ±ΡΠ°ΡΡ ΠΈ ΠΎΡΠΌΠΎΡΡΠ΅ΡΡ Π²ΡΠ΅ Π΄Π΅ΡΠ°Π»ΠΈ.
28.6.2 Π Π΅ΠΌΠΎΠ½Ρ ΠΈ ΠΈΡΠΏΡΡΠ°Π½ΠΈΠ΅ Π²ΡΠΏΡΡΠΊΠ½ΠΎΠ³ΠΎ ΠΊΠ»Π°ΠΏΠ°Π½Π° Π½Π΅ΠΎΠ±Ρ ΠΎΠ΄ΠΈΠΌΠΎ ΠΏΡΠΎΠΈΠ·Π²ΠΎΠ΄ΠΈΡΡ Ρ ΡΠΎΠ±Π»ΡΠ΄Π΅Π½ΠΈΠ΅ΠΌ ΡΠ»Π΅Π΄ΡΡΡΠΈΡ ΡΡΠ΅Π±ΠΎΠ²Π°Π½ΠΈΠΉ:
— ΠΏΡΡΠΆΠΈΠ½Ρ Ρ ΠΏΡΠΎΡΠ°Π΄ΠΊΠΎΠΉ Π΄ΠΎ Π²ΡΡΠΎΡΡ ΠΌΠ΅Π½Π΅Π΅ 27Β ΠΌΠΌ ΡΠ»Π΅Π΄ΡΠ΅Ρ Π·Π°ΠΌΠ΅Π½ΠΈΡΡ;
— Π·Π°Π±ΠΈΡΠ°Ρ ΠΈΠ»ΠΈ ΡΠΎΡΠ²Π°Π½Π½Π°Ρ ΡΠ΅Π·ΡΠ±Π° Ρ Π΄Π΅ΡΠ°Π»Π΅ΠΉ ΠΊΠ»Π°ΠΏΠ°Π½Π° Π½Π΅ Π΄ΠΎΠΏΡΡΠΊΠ°Π΅ΡΡΡ;
— ΠΊΠΎΡΠΏΡΡ Ρ Π·Π°Π±ΠΎΠΈΠ½Π°ΠΌΠΈ Π½Π° ΠΏΠΎΠ²Π΅ΡΡ Π½ΠΎΡΡΠΈ ΡΠ΅Π΄Π»Π° ΠΊΠ»Π°ΠΏΠ°Π½Π° Π½Π΅ΠΎΠ±Ρ ΠΎΠ΄ΠΈΠΌΠΎ Π·Π°ΠΌΠ΅Π½ΠΈΡΡ;
— ΡΠ΅Π·ΠΈΠ½ΠΎΠ²ΠΎΠ΅ ΡΠΏΠ»ΠΎΡΠ½Π΅Π½ΠΈΠ΅ ΠΊΠ»Π°ΠΏΠ°Π½Π° ΡΠ»Π΅Π΄ΡΠ΅Ρ Π·Π°ΠΌΠ΅Π½ΠΈΡΡ Π½Π° Π½ΠΎΠ²ΠΎΠ΅.
— ΠΏΠ΅ΡΠ΅Π΄ ΡΠ±ΠΎΡΠΊΠΎΠΉ Π²Π½ΡΡΡΠ΅Π½Π½ΠΈΠ΅ ΠΎΠ±ΡΠ°Π±ΠΎΡΠ°Π½Π½ΡΠ΅ ΠΏΠΎΠ²Π΅ΡΡ Π½ΠΎΡΡΠΈ ΠΊΠΎΡΠΏΡΡΠ° ΠΈ ΡΡΡΡΠ΅ΡΠ°, ΠΏΡΡΠΆΠΈΠ½Ρ ΡΠ»Π΅Π΄ΡΠ΅Ρ ΡΠΌΠ°Π·Π°ΡΡ ΡΠΎΠ½ΠΊΠΈΠΌ ΡΠ»ΠΎΠ΅ΠΌ ΡΠΌΠ°Π·ΠΊΠΈ ΠΠ’-79Π. Π¨ΡΡΡΠ΅Ρ ΡΠ»Π΅Π΄ΡΠ΅Ρ ΡΡΠ°Π²ΠΈΡΡ Π½Π° ΡΠΌΠ°Π·ΠΊΠ΅ ΠΠΠΠ ΠΠ-232, Π²Π²ΠΈΠ½ΡΠΈΠ²Π°Ρ Π΄ΠΎ ΡΠΏΠΎΡΠ° Π² Π·Π°ΠΏΠ»Π΅ΡΠΈΠΊΠΈ ΠΊΠΎΡΠΏΡΡΠ° ΠΊΠ»Π°ΠΏΠ°Π½Π°.
28.6.3 ΠΡΠΏΡΡΠ°Π½ΠΈΠ΅ Π½Π° ΠΏΠ»ΠΎΡΠ½ΠΎΡΡΡ ΠΏΡΠΎΠΈΠ·Π²ΠΎΠ΄ΠΈΡΡΡ Π΄Π°Π²Π»Π΅Π½ΠΈΠ΅ΠΌ ΡΠΆΠ°ΡΠΎΠ³ΠΎ Π²ΠΎΠ·Π΄ΡΡ Π° (0,25+0,05)Β ΠΠΠ° [(2,5+0,5)Β ΠΊΠ³Ρ/ΡΠΌ2] ΠΈ (0,60+0,05)Β ΠΠΠ° [(6,0+0,5)Β ΠΊΠ³Ρ/ΡΠΌ2].
ΠΡΠΎΠ²Π΅ΡΠΊΠ° ΠΏΠ»ΠΎΡΠ½ΠΎΡΡΠΈ ΠΊΠ»Π°ΠΏΠ°Π½Π° ΠΏΡΠΎΠΈΠ·Π²ΠΎΠ΄ΠΈΡΡΡ ΠΎΠ΄Π½ΠΈΠΌ ΠΈΠ· ΡΠ»Π΅Π΄ΡΡΡΠΈΡ ΡΠΏΠΎΡΠΎΠ±ΠΎΠ²:
ΠΏΠΎ Π½Π°Π»ΠΈΡΠΈΡ ΠΌΡΠ»ΡΠ½ΡΡ ΠΏΡΠ·ΡΡΠ΅ΠΉ;
ΠΏΠΎ ΠΏΠ°Π΄Π΅Π½ΠΈΡ Π΄Π°Π²Π»Π΅Π½ΠΈΡ.
ΠΡΠΈ ΠΏΡΠΎΠ²Π΅ΡΠΊΠ΅ ΠΏΠ»ΠΎΡΠ½ΠΎΡΡΠΈ ΠΏΠΎ Π½Π°Π»ΠΈΡΠΈΡ ΠΌΡΠ»ΡΠ½ΡΡ ΠΏΡΠ·ΡΡΠ΅ΠΉ ΠΎΠ±ΠΌΡΠ»ΠΈΠ²Π°ΡΡ Π½Π΅ΠΎΠ±Ρ ΠΎΠ΄ΠΈΠΌΠΎ Π²Π΅ΡΡ ΠΊΠ»Π°ΠΏΠ°Π½. ΠΡΠΈ ΡΡΠΎΠΌ ΠΏΠΎΡΠ²Π»Π΅Π½ΠΈΠ΅ ΠΏΡΠ·ΡΡΠ΅ΠΉ Π½Π΅ Π΄ΠΎΠΏΡΡΠΊΠ°Π΅ΡΡΡ.
ΠΡΠΎΠ²Π΅ΡΠΊΠ° ΠΏΠ»ΠΎΡΠ½ΠΎΡΡΠΈ ΠΏΠΎ ΠΏΠ°Π΄Π΅Π½ΠΈΡ Π΄Π°Π²Π»Π΅Π½ΠΈΡ ΠΏΡΠΎΠΈΠ·Π²ΠΎΠ΄ΠΈΡΡΡ Π½Π° ΠΈΡΠΏΡΡΠ°ΡΠ΅Π»ΡΠ½ΠΎΠΌ ΡΡΡΡΠΎΠΉΡΡΠ²Π΅, ΠΈΠΌΠ΅ΡΡΠ΅ΠΌ Π² ΡΠ²ΠΎΠ΅ΠΉ ΡΡ Π΅ΠΌΠ΅ ΠΊΠΎΠ½ΡΡΠΎΠ»ΡΠ½ΡΠΉ ΡΠ΅Π·Π΅ΡΠ²ΡΠ°Ρ ΠΎΠ±ΡΠ΅ΠΌΠΎΠΌ 5 Π»ΠΈΡΡΠΎΠ². ΠΡΠΈ ΡΡΠΎΠΌ ΠΏΠ°Π΄Π΅Π½ΠΈΠ΅ ΡΡΡΠ°Π½ΠΎΠ²ΠΈΠ²ΡΠ΅Π³ΠΎΡΡ Π΄Π°Π²Π»Π΅Π½ΠΈΡ Π² ΠΊΠΎΠ½ΡΡΠΎΠ»ΡΠ½ΠΎΠΌ ΡΠ΅Π·Π΅ΡΠ²ΡΠ°ΡΠ΅ Π² ΡΠ΅ΡΠ΅Π½ΠΈΠ΅ 5 ΠΌΠΈΠ½ΡΡ Π½Π΅ Π΄ΠΎΠΏΡΡΠΊΠ°Π΅ΡΡΡ.
28.7 ΠΠ»Π°ΠΏΠ°Π½ ΠΎΠ±ΡΠ°ΡΠ½ΡΠΉ 176
28.7.1 ΠΠΎΡΡΡΠΏΠΈΠ²ΡΠΈΠΉ Π² ΡΠ΅ΠΌΠΎΠ½Ρ ΠΎΠ±ΡΠ°ΡΠ½ΡΠΉ ΠΊΠ»Π°ΠΏΠ°Π½ ΡΠ½Π°ΡΡΠΆΠΈ ΠΎΡΠΈΡΡΠΈΡΡ ΠΎΡ ΠΏΡΠ»ΠΈ ΠΈ Π·Π°Π³ΡΡΠ·Π½Π΅Π½ΠΈΠΉ.
28.7.2 ΠΠΎΡΠ»Π΅ Π½Π°ΡΡΠΆΠ½ΠΎΠΉ ΠΎΡΠΈΡΡΠΊΠΈ ΠΈ ΠΎΠ±ΠΌΡΠ²ΠΊΠΈ ΠΎΠ±ΡΠ°ΡΠ½ΡΠΉ ΠΊΠ»Π°ΠΏΠ°Π½ ΡΠ°Π·ΠΎΠ±ΡΠ°ΡΡ, Π²ΡΠ΅ Π΄Π΅ΡΠ°Π»ΠΈ ΠΎΡΠΌΠΎΡΡΠ΅ΡΡ, Π½Π΅ΠΈΡΠΏΡΠ°Π²Π½ΡΠ΅ ΠΎΡΡΠ΅ΠΌΠΎΠ½ΡΠΈΡΠΎΠ²Π°ΡΡ ΠΈΠ»ΠΈ Π·Π°ΠΌΠ΅Π½ΠΈΡΡ.
28.7.3 Π Π΅ΠΌΠΎΠ½Ρ ΠΈ ΠΈΡΠΏΡΡΠ°Π½ΠΈΠ΅ ΠΎΠ±ΡΠ°ΡΠ½ΠΎΠ³ΠΎΠΊΠ»Π°ΠΏΠ°Π½Π° Π½Π΅ΠΎΠ±Ρ ΠΎΠ΄ΠΈΠΌΠΎ ΠΏΡΠΎΠΈΠ·Π²ΠΎΠ΄ΠΈΡΡ Ρ ΡΠΎΠ±Π»ΡΠ΄Π΅Π½ΠΈΠ΅ΠΌ ΡΠ»Π΅Π΄ΡΡΡΠΈΡ ΡΡΠ΅Π±ΠΎΠ²Π°Π½ΠΈΠΉ:
— ΡΠ΅Π΄Π»Π° ΠΊΠ»Π°ΠΏΠ°Π½Π° ΠΈ ΠΊΠ»Π°ΠΏΠ°Π½Ρ Π½Π΅ Π΄ΠΎΠ»ΠΆΠ½Ρ ΠΈΠΌΠ΅ΡΡ Π·Π°Π±ΠΎΠΈΠ½ ΠΈΠ»ΠΈ ΡΠΈΡΠΎΠΊ;
— ΠΏΡΠΎΠ²Π΅ΡΠΈΡΡ Π²ΡΡΠΎΡΡ ΠΏΡΡΠΆΠΈΠ½Ρ Π² ΡΠ²ΠΎΠ±ΠΎΠ΄Π½ΠΎΠΌ ΡΠΎΡΡΠΎΡΠ½ΠΈΠΈ. ΠΡΠΈ ΡΡΠΎΠΌ Π½ΠΎΠΌΠΈΠ½Π°Π»ΡΠ½Π°Ρ Π²ΡΡΠΎΡΠ° ΠΏΡΡΠΆΠΈΠ½Ρ ΠΎΠ±ΡΠ°ΡΠ½ΠΎΠ³ΠΎ ΠΊΠ»Π°ΠΏΠ°Π½Π° 176 ΡΠΎΡΡΠ°Π²Π»ΡΠ΅Ρ 22 ΠΌΠΌ, Π° ΠΏΠΎΠ΄ ΡΠ°Π±ΠΎΡΠ΅ΠΉ Π½Π°Π³ΡΡΠ·ΠΊΠΎΠΉ 0,74Β±0,07 ΠΊΠ³Ρ β 13 ΠΌΠΌ. ΠΡΠΎΡΠ΅Π²ΡΡΡ ΠΏΡΡΠΆΠΈΠ½Ρ ΠΈ ΠΏΡΡΠΆΠΈΠ½Ρ Ρ ΠΎΠ±Π»ΠΎΠΌΠ°Π½Π½ΡΠΌΠΈ Π²ΠΈΡΠΊΠ°ΠΌΠΈ Π·Π°ΠΌΠ΅Π½ΠΈΡΡ Π½ΠΎΠ²ΠΎΠΉ. Π Π°ΡΡΡΠ³ΠΈΠ²Π°Π½ΠΈΠ΅ ΠΈ Π·Π°Π΄Π΅Π»ΠΊΠ° ΠΏΡΡΠΆΠΈΠ½Ρ Π½Π΅ Π΄ΠΎΠΏΡΡΠΊΠ°Π΅ΡΡΡ;
-ΠΏΡΠΎΠΊΠ»Π°Π΄ΠΊΡ ΠΈ ΠΊΠΎΠ»ΡΡΠΎ, ΠΈΠΌΠ΅ΡΡΠΈΠ΅ Π½Π°Π΄ΡΡΠ²Ρ ΠΈ ΡΡΠ΅ΡΠΈΠ½Ρ, Π° ΡΠ°ΠΊΠΆΠ΅ Ρ ΠΈΡΡΠ΅ΠΊΡΠΈΠΌ ΡΡΠΎΠΊΠΎΠΌ ΡΠ»ΡΠΆΠ±Ρ, Π·Π°ΠΌΠ΅Π½ΠΈΡΡ Π½ΠΎΠ²ΡΠΌΠΈ. Π‘ΡΠΎΠΊ ΡΠ»ΡΠΆΠ±Ρ ΡΠ»Π΅Π΄ΡΠ΅Ρ ΠΎΠΏΡΠ΅Π΄Π΅Π»ΡΡΡ ΠΏΠΎ ΠΌΠ°ΡΠΊΠΈΡΠΎΠ²ΠΊΠ΅ Π½Π° ΡΠ΅Π·ΠΈΠ½ΠΎΠ²ΠΎΠΉ Π΄Π΅ΡΠ°Π»ΠΈ, ΠΈΡΠΊΠ»ΡΡΠ°Ρ Π³ΠΎΠ΄ Π΅Π΅ ΠΈΠ·Π³ΠΎΡΠΎΠ²Π»Π΅Π½ΠΈΡ ΠΏΠΎ Π΄Π°ΡΠ΅ ΠΈΠ·Π³ΠΎΡΠΎΠ²Π»Π΅Π½ΠΈΡ ΠΊΠ»Π°ΠΏΠ°Π½Π°, ΡΠΊΠ°Π·Π°Π½Π½ΠΎΠΉ Π½Π° ΠΊΠΎΡΠΏΡΡΠ΅;
— Π·Π°Π±ΠΈΡΡΡ ΠΈΠ»ΠΈ ΡΠΎΡΠ²Π°Π½Π½ΡΡ ΡΠ΅Π·ΡΠ±Ρ Π²ΠΎΡΡΡΠ°Π½ΠΎΠ²ΠΈΡΡ ΠΈΠ»ΠΈ Π·Π°ΠΌΠ΅Π½ΠΈΡΡ Π΄Π΅ΡΠ°Π»ΠΈ;
— ΠΏΡΠΈ ΡΠ±ΠΎΡΠΊΠ΅ ΠΎΠ±ΡΠ°ΡΠ½ΠΎΠ³ΠΎ ΠΊΠ»Π°ΠΏΠ°Π½Π° Π»Π΅Π³ΠΊΠΈΠΌ ΡΠ»ΠΎΠ΅ΠΌ ΡΠΌΠ°Π·Π°ΡΡ ΡΡΡΡΠΈΠ΅ΡΡ ΠΏΠΎΠ²Π΅ΡΡ Π½ΠΎΡΡΠΈ ΡΠΌΠ°Π·ΠΊΠΎΠΉ ΠΠ’-79Π.
28.7.4 ΠΡΠΏΡΡΠ°Π½ΠΈΡ ΠΏΡΠΎΠΈΠ·Π²ΠΎΠ΄ΠΈΡΡ Π½Π° ΡΡΠ΅Π½Π΄Π΅, ΡΡΡΠ°Π½ΠΎΠ²Π»Π΅Π½Π½ΠΎΠΌ Π² Π·Π°ΠΊΡΡΡΠΎΠΌ ΠΏΠΎΠΌΠ΅ΡΠ΅Π½ΠΈΠΈ ΠΈ ΠΏΠΎΠ΄ΠΊΠ»ΡΡΠ΅Π½Π½ΡΠΌ ΠΊ Π²ΠΎΠ·Π΄ΡΡ ΠΎΠΏΡΠΎΠ²ΠΎΠ΄Π½ΠΎΠΉ ΠΌΠ°Π³ΠΈΡΡΡΠ°Π»ΠΈ Ρ Π΄Π°Π²Π»Π΅Π½ΠΈΠ΅ΠΌ ΡΠΆΠ°ΡΠΎΠ³ΠΎ Π²ΠΎΠ·Π΄ΡΡ Π° Π½Π΅ Π½ΠΈΠΆΠ΅ 1,0 ΠΠΠ° (10,0 ΠΊΠ³Ρ/ΡΠΌ2) ΡΠ΅ΡΠ΅Π· Π²Π»Π°Π³ΠΎΠΎΡΠ΄Π΅Π»ΠΈΡΠ΅Π»Ρ Π»ΡΠ±ΠΎΠΉ ΠΊΠΎΠ½ΡΡΡΡΠΊΡΠΈΠΈ.
ΠΡΠΏΡΡΠ°Π½ΠΈΠ΅ ΠΊΠ»Π°ΠΏΠ°Π½Π° Π½Π° ΠΏΠ»ΠΎΡΠ½ΠΎΡΡΡ ΠΏΡΠΎΠΈΠ·Π²ΠΎΠ΄ΠΈΡΡ Π΄Π°Π²Π»Π΅Π½ΠΈΠ΅ΠΌ ΡΠΆΠ°ΡΠΎΠ³ΠΎ Π²ΠΎΠ·Π΄ΡΡ Π° (1,00+0,05)Β ΠΠΠ° [(10,0+0,5)Β ΠΊΠ³Ρ/ΡΠΌ2].
ΠΡΠΎΠ²Π΅ΡΠΊΠ° ΠΏΠ»ΠΎΡΠ½ΠΎΡΡΠΈ ΠΊΠ»Π°ΠΏΠ°Π½Π° ΠΏΡΠΎΠΈΠ·Π²ΠΎΠ΄ΠΈΡΡΡ ΠΎΠ΄Π½ΠΈΠΌ ΠΈΠ· ΡΠΏΠΎΡΠΎΠ±ΠΎΠ²:
— ΠΏΠΎ Π½Π°Π»ΠΈΡΠΈΡ ΠΌΡΠ»ΡΠ½ΡΡ ΠΏΡΠ·ΡΡΠ΅ΠΉ;
— ΠΏΠΎ ΠΏΠ°Π΄Π΅Π½ΠΈΡ Π΄Π°Π²Π»Π΅Π½ΠΈΡ.
ΠΡΠΈ ΠΏΡΠΎΠ²Π΅ΡΠΊΠ΅ ΠΏΠ»ΠΎΡΠ½ΠΎΡΡΠΈ ΠΏΠΎ Π½Π°Π»ΠΈΡΠΈΡ ΠΌΡΠ»ΡΠ½ΡΡ ΠΏΡΠ·ΡΡΠ΅ΠΉ ΠΏΡΠΈΡΠΎΠ΅Π΄ΠΈΠ½ΠΈΡΡ ΠΎΡΡΠΎΡΡΠΎΠΊ ΠΊΠΎΡΠΏΡΡΠ° ΠΊ Π²ΠΎΠ·Π΄ΡΡ ΠΎΠΏΡΠΎΠ²ΠΎΠ΄Ρ ΡΠ°ΠΊ, ΡΡΠΎΠ±Ρ Π²ΠΎΠ·Π΄ΡΡ ΠΏΠΎΡΡΡΠΏΠ°Π» Π² ΠΊΠΎΡΠΏΡΡ ΠΏΡΠΎΡΠΈΠ² ΡΡΡΠ΅Π»ΠΊΠΈ, ΡΠΊΠ°Π·Π°Π½Π½ΠΎΠΉ Π½Π° Π½Π΅ΠΌ (Π²ΠΎΠ·Π΄ΡΡ ΠΏΠΎΠ΄Π°Π΅ΡΡΡ Π² ΠΏΠΎΠ»ΠΎΡΡΡ ΠΏΠΎΠ΄ Π·Π°ΡΠ²ΠΎΡΠΎΠΌ). ΠΠ° Π΄ΡΡΠ³ΠΎΠΉ ΠΎΡΡΠΎΡΡΠΎΠΊ Π½Π°Π²Π΅ΡΡΡΠ²Π°Π΅ΡΡΡ Π³Π°ΠΉΠΊΠ° Ρ ΠΎΡΠ²Π΅ΡΡΡΠΈΠ΅ΠΌ Π΄ΠΈΠ°ΠΌΠ΅ΡΡΠΎΠΌ 10Β ΠΌΠΌ. ΠΡΠΈ ΠΈΡΠΏΡΡΠ°Π½ΠΈΠΈ Π½Π° ΠΎΠ±ΠΌΡΠ»Π΅Π½Π½ΡΡ ΠΏΠΎΠ²Π΅ΡΡ Π½ΠΎΡΡΡΡ (ΠΎΡΠ²Π΅ΡΡΡΠΈΠ΅ 10Β ΠΌΠΌ, ΠΌΠ΅ΡΡΠ° ΡΠΎΠ΅Π΄ΠΈΠ½Π΅Π½ΠΈΡ ΠΈ ΠΊΠΎΡΠΏΡΡ) Π² ΡΠ΅ΡΠ΅Π½ΠΈΠ΅ 1 ΠΌΠΈΠ½ Π½Π΅ Π΄ΠΎΠ»ΠΆΠ½Ρ ΠΎΠ±ΡΠ°Π·ΠΎΠ²ΡΠ²Π°ΡΡΡΡ ΠΌΡΠ»ΡΠ½ΡΠ΅ ΠΏΡΠ·ΡΡΠΈ.
ΠΡΠΈ ΠΏΡΠΎΠ²Π΅ΡΠΊΠ΅ ΠΏΠ»ΠΎΡΠ½ΠΎΡΡΠΈ ΠΏΠΎ ΠΏΠ°Π΄Π΅Π½ΠΈΡ Π΄Π°Π²Π»Π΅Π½ΠΈΡ ΠΏΡΠΎΠ²Π΅ΡΠΊΡ Π½Π΅ΠΎΠ±Ρ ΠΎΠ΄ΠΈΠΌΠΎ ΠΏΡΠΎΠΈΠ·Π²ΠΎΠ΄ΠΈΡΡ Π½Π° ΠΈΡΠΏΡΡΠ°ΡΠ΅Π»ΡΠ½ΠΎΠΌ ΡΡΡΡΠΎΠΉΡΡΠ²Π΅, ΠΈΠΌΠ΅ΡΡΠ΅ΠΌ Π² ΡΠ²ΠΎΠ΅ΠΉ ΡΡ Π΅ΠΌΠ΅ ΠΊΠΎΠ½ΡΡΠΎΠ»ΡΠ½ΡΠΉ ΡΠ΅Π·Π΅ΡΠ²ΡΠ°Ρ ΠΎΠ±ΡΠ΅ΠΌΠΎΠΌ 8Β Π»ΠΈΡΡΠΎΠ². ΠΡΠΈ ΡΡΠΎΠΌ ΠΏΠ°Π΄Π΅Π½ΠΈΠ΅ ΡΡΡΠ°Π½ΠΎΠ²ΠΈΠ²ΡΠ΅Π³ΠΎΡΡ Π΄Π°Π²Π»Π΅Π½ΠΈΡ Π² ΠΊΠΎΠ½ΡΡΠΎΠ»ΡΠ½ΠΎΠΌ ΡΠ΅Π·Π΅ΡΠ²ΡΠ°ΡΠ΅ Π² ΡΠ΅ΡΠ΅Π½ΠΈΠ΅ 5 ΠΌΠΈΠ½ Π½Π΅ Π΄ΠΎΠΏΡΡΠΊΠ°Π΅ΡΡΡ.
studfiles.net